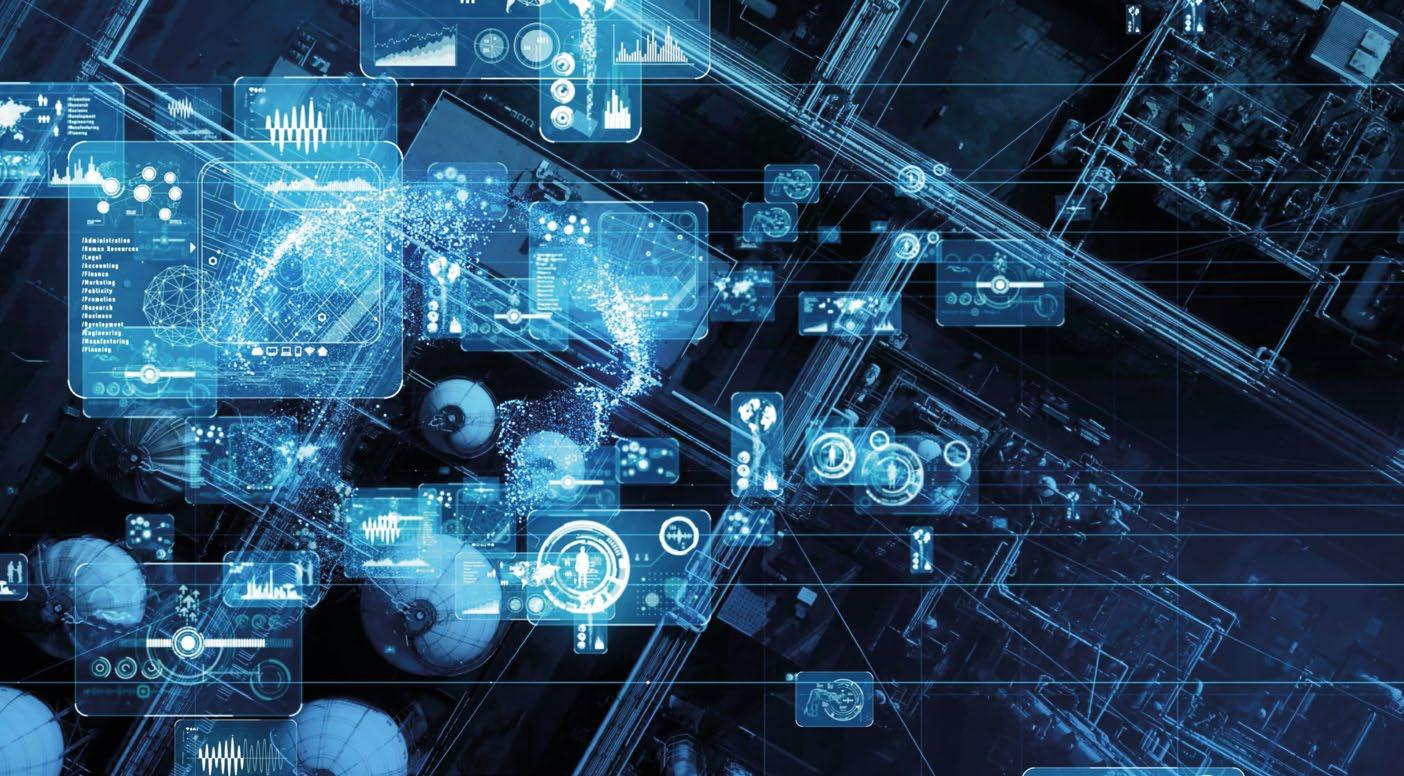
7 minute read
What does ‘digital transformation’ really mean for the packaging industry?
The phrases ‘digital transformation’, ‘digitalization’, ‘smart factories’ – we’ve heard them all so much the past few years that in some ways it can be hard to pin down their meaning. Like another ubiquitous word, ‘sustainability’, they can mean different things to different people. What we should really be interested in is how these words can translate to practical change in the industry, and this was the crux of Victoria Hattersley‘s recent conversation with Malte Schlüter, Global Director Food & Beverage/Life Science at Mitsubishi Electric Europe B.V. Factory Automation.
“First, we have to acknowledge that for some digitalization has become a buzzword,” begins Malte. “There are lots of different levels to this concept but in general I would say that digitalization on the production floor (OT) itself is still lower than it could be. Production machines are generating huge amounts of data, however in many cases the full potential of the intelligence that can be gained by analyzing this data has not yet been fully identified or realized.”
So, taking this into consideration, how can companies turn data into actionable insights to improve efficiency and productivity? Some would say they should all be processed in the Cloud but this, says Malte, should be deliberately and cautiously rethought when pursuing a digital transformation strategy. To demonstrate why, Mitsubishi Electric carried out a simple experiment. The company took a basic flow wrapping machine for cookies as a test case and worked out what it would cost to store all the data it produced in the Cloud for one year. The result was around 10,000 euros for just one machine, which means that with the amount of data generated by an entire factory, the potential costs can become millions of euros.
“To minimize the amount of remote storage needed and create highly responsive production systems, we suggest to our clients that they should implement edge computing technologies alongside Cloud solutions. These can provide local real-time data analysis capabilities that can lead to improved efficiencies while also reducing the amount of data that needs to be processed in the Cloud. Thinking ahead to the next stages of production optimization, the implementation of vision systems, 3D technology etc., can also be simplified as the effective collection and analysis of this data is already ensured.”
Case study: ‘Smart cocoa’ and the power of data
One example Malte gives to highlight the transformative role of data is Mitsubishi Electric’s recent collaboration with a global cocoa producer. The company collects data on several variables that could affect its product, from cocoa bean farmers – weather, for instance – which can influence the end quality. All this information is then factored in when implementing milling settings on the factory floor to achieve the desired product characteristics. The result: ‘Smart cocoa’.

Malte Schlüter, Global Director Food & Beverage/Life Science at Mitsubishi Electric Europe
To increase efficiency and productivity even further, it would be necessary to combine this ‘smarter’ use of data with more advanced technologies on the factory floor itself.
“Manual quality control can be time-consuming. To speed up this process and free up operators for other value-adding tasks, a vision system with deep learning technology could be used for checking the product and predicting the quality of the cocoa powder. Based on this data, the parameters for the milling process can be regularly and automatically updated. At the same time, another connected vision system can measure the output. The result is a constant closed loop system that guarantees consistent quality and even reduced production times.”
All the data generated by these vision systems can be analyzed and the results applied to additional production units, helping to optimize entire manufacturing lines. To benefit even further from this technology, vision systems could be used for a wide range of applications, such as inspecting packaging quality or sealing quality. These systems can also enable producers to drastically reduce waste.
Looking at this development from the consumer perspective, the next phase of this evolution could see each bar of chocolate with a QR code on it to offer increased traceability. This will allow the people to see where it was produced, where the cocoa was milled and what kind of cocoa was used in the mixture. “You would even be able to see a picture of the farmer and their family, enabling true personalization all the way along the value chain. It would mean the consumer has full transparency about what they are eating, if it is fair trade etc. This is still in the trial stage but it is what the future of fast-moving consumer goods (FMCG) will look like.”
From robots to cobots
Moving away from this single case study on data analytics, what does increased automation mean for the packaging industry as a whole? It is fair to say that the industry – or large parts of it – are shifting from sequential production to a different paradigm based on high levels of customization.
“There is demand for many different stock-keeping units (SKUs) and sequential flow strategies cannot efficiently support this, as machines carry out a single task and it can take weeks to change a line,” explains Malte. “In a smart factory, incoming pallets with QR codes, for example, can be scanned and help setup the manufacturing line, deciding which machine the product will be moved to or whether there is an in-between step. Today, modern and flexible robotic production lines can also be easily adjusted and repurposed to quickly conduct different tasks, support various packaging formats and SKUs.”
In addition to this, smart robots can be equipped with cameras and use vision technology, coupled with AI, to recognize what they are handling. Thus, the production model itself can be thought of as a series of ‘working cells’. The product flows through these cells until the final package is complete.
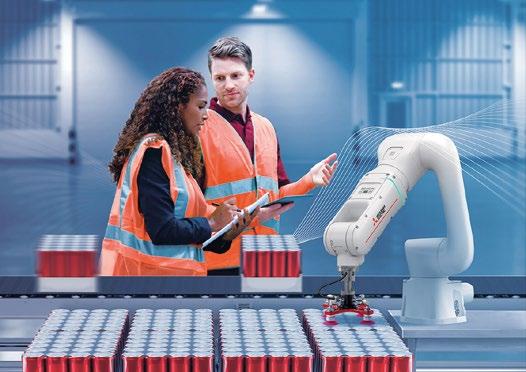
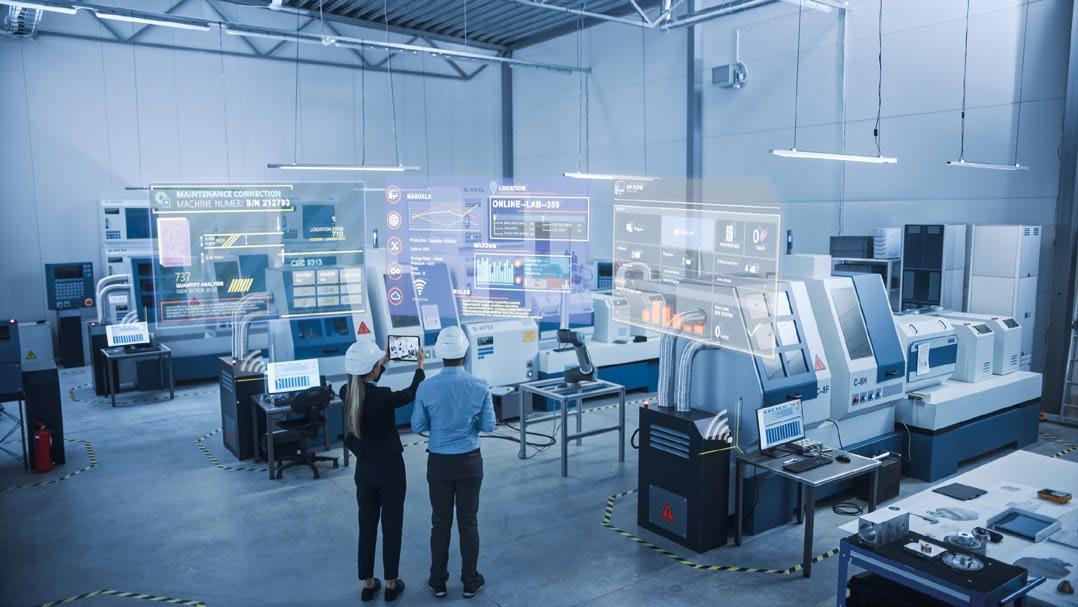
While the adoption of AI-equipped industrial robots on the factory floor is playing a central role in boosting the flexibility of manufacturing, Malte would like to discuss the future importance and added benefits of cobots. Unlike industrial robots, which are enclosed by physical barriers, collaborative robots can work safely alongside and with humans on the factory floor. However, he says, most of the ones that are currently available are only able to operate at low speed.
There are applications that may benefit from a hybrid industrial-collaborative approach enabling both high levels of customization as well as mass production. Supporting both strategies, Mitsubishi Electric’s MELFA ASSISTA is designed to work alongside humans without physical barriers, while also supporting high-speed operations when they are not present.
Malte explains: “By equipping MELFA ASSISTA with proximity sensors, the cobot can adapt its operations based on what is happening in its surroundings. It can run at high speed when its workspace is not shared with humans. When a person or object enters defined zones, it will then slow down and switch to collaborative mode, so that workers can safely interact with the machine. If the cobot makes contact with an object that it has not been programmed to interact with, it slowly retracts to a safe position. These characteristics are both particularly important in facilities where space may be limited.”
To enable quick deployment, MELFA ASSISTA is easy to set up and program, he adds: “When installing traditional industrial robots, skilled programming expertise is needed to define motion paths and operating parameters. Designed to simplify this process, our cobot offers a direct teaching feature as well as drag and drop functions for pick and place applications. As a result, even non-expert staff can make adjustments to MELFA ASSISTA’s programming with ease, speeding up its installation and redeployment.”
Combined, the benefits of hybrid industrial-collaborative robots and advanced data analytics are quickly eroding the barrier to a more widespread adoption of automation in the workplace. At the same time, the productivity improvements achieved prove these technologies to be cost-effective solutions. The reluctance of companies to invest in new technology is also disappearing, and in part, says Malte, it comes down to changed perceptions as a result of the Covid-19 pandemic.
“People have realized in how many situations we are relying on humans to do very basic, repetitive tasks that could be automated. Technology has the potential to free up operators to take on more complex, value adding tasks. We are already seeing large businesses moving in this direction, as well as smaller industry players, and we expect an increasing number of manufacturers will follow.” n

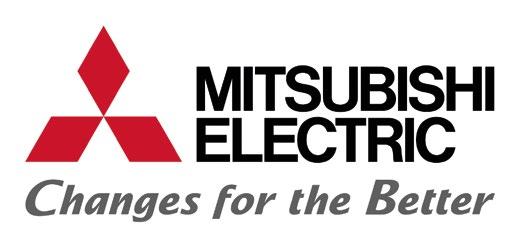