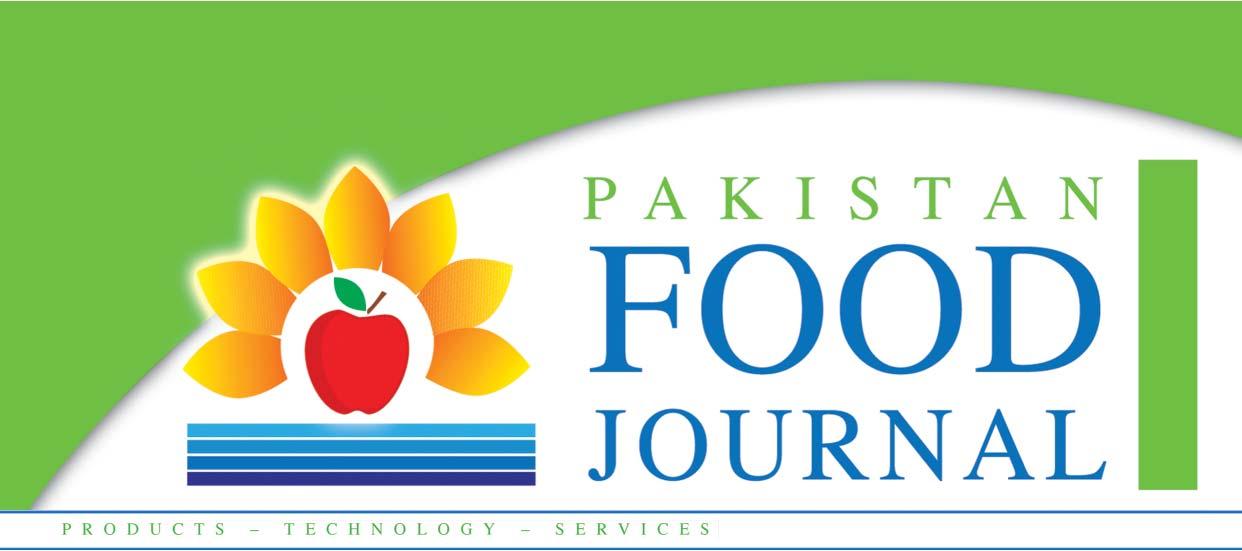
September - October 2024
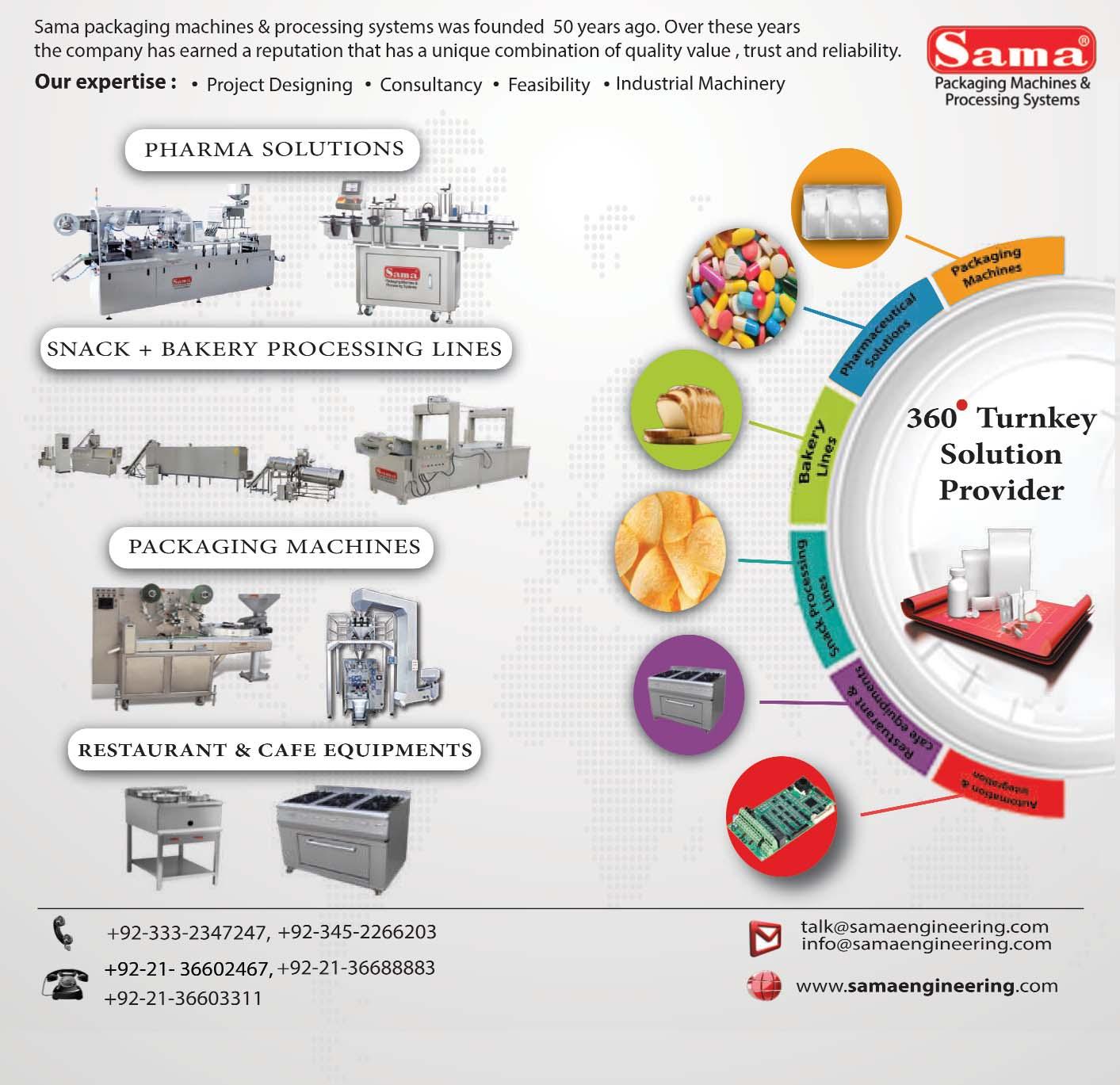
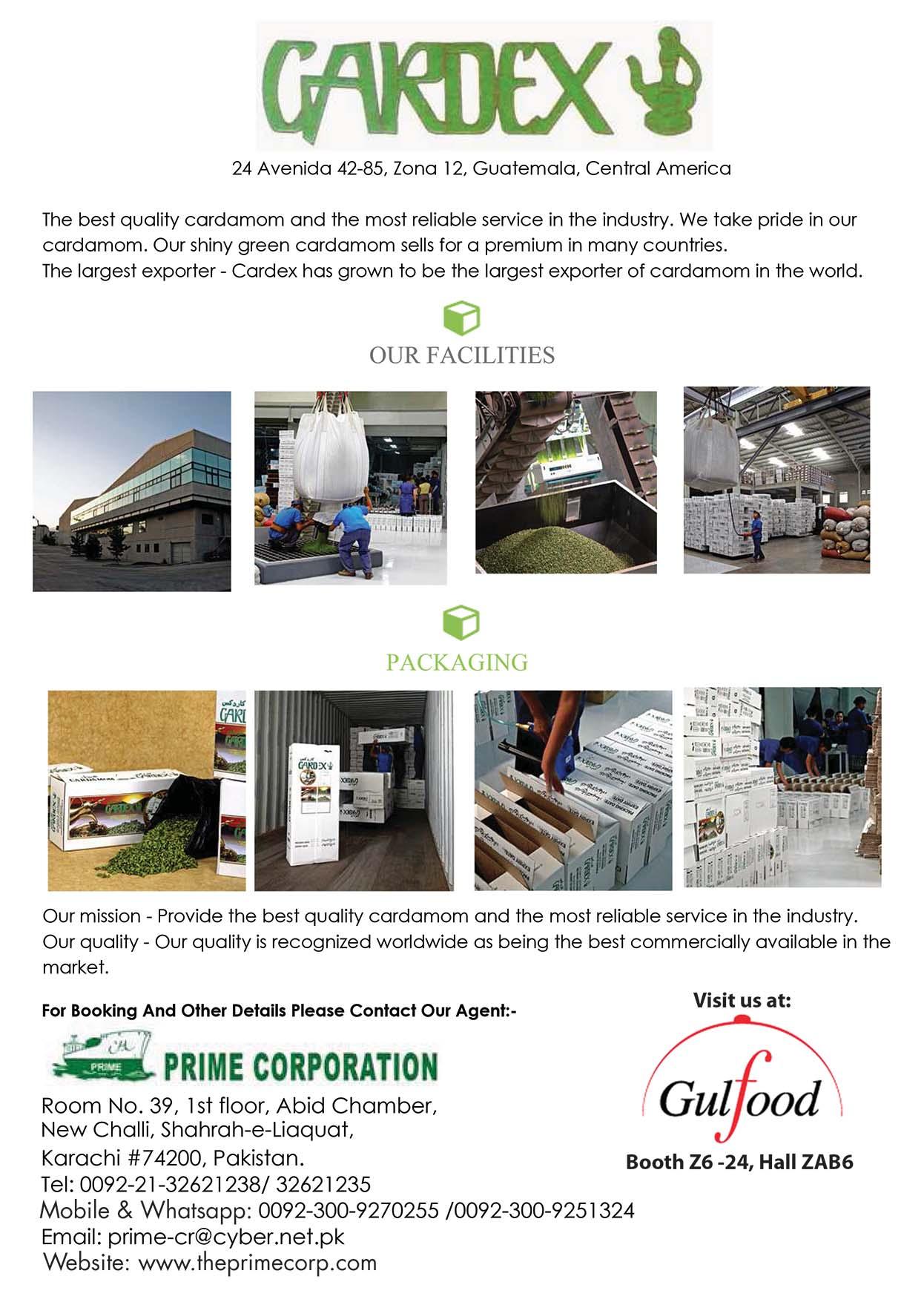

September - October 2024
Date: 5 to 7, November 2024.
Venue: Dubai World Trade Centre.
EIMA International 2024
Date: 6 to 10, November 2024.
Venue: International Agricultural and Gardening Machinery Exhibition, Bologna, Italy.
Dates: 11 to 13, November 2024.
Venue: Riyadh International Convention & Exhibition Center, Riyadh, Saudi Arabia
International Green Week
Date: 17 to 26, January 2025.
Venue: Berlin, Germany.
Fruit Logistica 2025
Date: 5 to 7, February 2025.
Venue: Messe Berlin, Germany.
Dates: 17 to 21, February 2025.
Venue: Dubai World Trade Centre, Dubai
Date: 29 to 31, May 2025.
Venue: Lahore Expo Centre.
Date: 02 to 04, June 2025.
Venue: Atlanta, Georgia, USA
Date: 11 to 13, June 2025.
Venue: Shanghai New International Expo Center ( No.2345 Longyang Road, Pudong New District, Shanghai, China)
Date: 3 to 5, September 2025.
Venue: Queen Sirikit National Convention Center, Bangkok, Thailand.
Date: 4 to 8, October 2025.
Venue: Cologne, Germany.
Dates: 23 to 26, March 2027
Venue: Cologne, Germany.
Dear readers,
In our September-October 2024 edition, the editorial board of Pakistan Food Journal is focusing on the current exhibitions related to the food industry that are held worldwide in the coming months. Pakistan’s record-breaking MoUs worth $ 434 million signed at FoodAg 2024 mark a significant step towards a promising future. With a target of $ 60 billion in exports in the next few years, Pakistan is set to usher in a new era of development and progress. Under the leadership of Minister Jam Kamal Khan, the Ministry of Commerce has outlined a plan to expand the production capacity and economy of farmers in Pakistan, ensuring food security in the country and surplus quantity for global export.
The 2024 EIMA event is offering a wideranging and highly topical program of conferences and events as part of the agricultural machinery trade fair being held at the Bologna exhibition center from 6 to 10 November. The five days of the exhibition will include over 150 meetings - in the form of conferences, talk shows, workshops and appointments outside the show - dedicated to important topics related to agriculture and agro-mechanics.
Gulfood Manufacturing 2024 represents the pinnacle of the global food and beverage manufacturing industry evolution, offering a decisive destination for those seeking to accelerate the adoption of technology, and improve efficiencies and productivity to meet new challenges it offers a comprehensive showcase of solutions for industry professionals seeking to stay at the forefront of the industry and presents a prime opportunity to network, form new global partnerships, announce new innovative products, deals, collaborations and signings.
Amina Baqai Editor in Chief
Hony. Editor Shahzad Umer Sama
Marketing Executive Layout & Design Mazhar Ali
Printed at Color Plus,
Pakistan Food Journal, September - October 2024
On2Cook: The World’s Fastest Cooking Device Storms B2B Cooking Space in India, Over 500 Units Successfully Deployed Across 35+ Brands . . . .14
GEA successfully deploys CF 8000 decanter at European wheat
.15 Krones AG 2024: Vegan burger patty made from brewer’s grains
.16
Renewable electricity agreement reduces carbon footprint of Tate & Lyle’s sucralose by 20%
Personalia
ADM appoints Monish Patolawala as executive vice president
.20 Shan Foods welcomes Tahir Malik as its first Global CEO
Exclusive Articles
MULTIVAC wins the German Packaging Award with Cooling@Packing . .22 German Packaging Award 2024 in the packaging machine category and Gold Award Less food wastage thanks to sustainable packaging and labelling concepts for fruit and vegetables
.23
MULTIVAC: site in Buchenau: Center of Excellence for slicing solutions . . .26 Tate & Lyle launches pioneering new automated lab in Singapore for mouthfeel solutions
Sidel capitalises on over 40 years’ experience in PET container production to launch Eco-Audit, a service for optimising the environmental
Gulfood 2025: The GCC is becoming a top culinary tourism destination. So, what’s cooking?
IFTECH Pakistan
IFTECH Pakistan - 20th International exhibition of food & beverage processing packaging technologies
ISM: Expanded to provide global perspective and connections to sweets and snacks sector
BIOFACH
.46
BIOFACH Congress 2025: Yes, we do! – How to effect change in the organic food segment
Pakistan's food exports saw impressive growth, with a 42% increase during July-August 2024 compared to the same period last year. This surge was driven by key products like Basmati rice, vegetables, and sugar. Basmati rice exports alone skyrocketed by 104%, while sugar exports jumped by 149%, showcasing the effectiveness of the country's improved trade strategies and efforts to enhance agricultural productivity.
Pakistan is projected to exceed $7 billion in food exports by the end of the fiscal year 2024, a significant achievement reflecting the country's growing global competitiveness. Major contributors to this growth include rice, fruits, vegetables, and meat products, which have found increasing demand across Asia, Europe, and the Middle East.
The Punjab Food Authority (PFA) marked World Food Day 2024 by hosting a seminar titled “Prevent Food Wastage from Farm to Fork” in Lahore, with Provincial Minister Bilal Yasin presiding over the event.
This gathering aimed to raise awareness about food security, global hunger, and sustainable practices, drawing attention to the theme of this year’s celebration: "The Right to Food for a Better Life and a Better Future."
Pakistan's fruit and juice exports to China have shown remarkable growth in the first seven months of 2024, reflecting increased demand and successful trade collaborations between the two nations. According to data from the General Administration of Customs of China (GACC), there has been a significant uptick in exports of frozen orange juice, marking a milestone for the country's agriculture sector.
The Pakistan Development Update report released in October 2024 emphasized the need for comprehensive regulatory reforms to facilitate smoother food exports. The report identified key areas for improvement, including sanitary and phytosanitary (SPS) standards, which have often been a bottleneck for exporters trying to enter new markets. Aligning local regulations
Australian almond sales have soared to unprecedented levels, with the Almond Board of Australia (ABA) reporting a remarkable 35% increase in exports for July compared to the previous year. The ABA's latest Position Report revealed that 22,450 tons were sold in July, surpassing the previous record of 17,547 tons set in July 2017 by 28%.
China's forest food production has exceeded 200 million metric tons annually, equating to approximately 140 kilograms per person, positioning it as the nation's thirdlargest agricultural product after grains and vegetables. This significant achievement was announced by the National Forestry and Grassland Administration earlier this month.
The European Commission has announced its decision to challenge China's anti-subsidy investigation into EU dairy imports at the World
Trade Organization (WTO). The move marks the first time Brussels has contested an investigation at its initiation stage.
The New Zealand government has announced a significant investment of NZ$9.6 million (USD 5.95 million) into a five-year program to develop cultivated fish products.
The initiative, part of the Endeavour Fund, aims to position New Zealand at the forefront of sustainable seafood production by supporting research into fish cell cultivation.
A new report from the Policy Exchange think tank is urging UK ministers to develop a national food security strategy that encompasses the entire food system, extending beyond agriculture to include manufacturing, logistics, and retail.
The report, titled Strengthening the UK’s Food Security: Innovation and Investment in the Food Manufacturing Sector, highlights the importance of prioritizing food
with international standards is seen as a critical step toward reducing trade barriers and enhancing competitiveness.
In a recent evaluation, Pakistan has been recognized as the lowest-risk country for food safety standards for the fiscal year 2023-24. According to the Rice Exporters Association of Pakistan (REAP), only 74 rapid alerts regarding issues such as pesticide residues and contamination were issued against Pakistani rice exporters last year. In comparison, India faced 264 alerts, highlighting a significant disparity in compliance and food safety measures between the two nations.
Pakistan's agricultural sector is currently facing significant challenges, primarily driven by a notable decline in urea offtakes, which have dropped by approximately 35% year-on-year. This downturn is attributed to rising fertilizer prices and a series of agricultural crises that threaten food production and security.
security as a core element of economic growth in the UK.
The US food and beverage sector is experiencing a critical labor shortage, as highlighted in a recent report by Expert Market, which was sponsored by the hospitality platform Toast. The findings reveal a stark reality: approximately 82 percent of businesses in this industry are actively seeking employees, yet many struggle to fill essential positions, indicating a significant gap in the workforce.
Potential cooperation between Vietnam and Malaysia, especially in the food industry, was highlighted at the ongoing Selangor International Business Summit (SBIS) 2024. Việt Nam's Commercial Counsellor in Malaysia, Lê Phú Cường, emphasized the impressive growth and potential of Vietnam’s food sector during the event.
Pakistan's food exports saw impressive growth, with a 42% increase during July-August 2024 compared to the same period last year. This surge was driven by key products like Basmati rice, vegetables, and sugar. Basmati rice exports alone skyrocketed by 104%, while sugar exports jumped by 149%, showcasing the effectiveness of the country's improved trade strategies and efforts to enhance agricultural productivity.
Several factors have contributed to this growth. Pakistan has been actively expanding its trade agreements, especially with countries where there is a high demand for quality food products. Enhanced production techniques, better infrastructure, and improved supply chain logistics have ensured that exports meet international standards, making Pakistani products more competitive globally. Additionally, government support through subsidies and incentives has been pivotal, enabling farmers and exporters to scale operations, thus boosting the sector’s overall output.
Despite these gains, industry experts emphasize the importance of continued investment in technology and logistics. Efficient supply chains, modern farming practices, and increased investment in research and development are crucial for sustaining growth and ensuring Pakistan's
food products remain competitive on the world stage. By focusing on quality control and expanding into new markets, Pakistan can further solidify its position as a major player in the global food trade.
Pakistan is projected to exceed $7 billion in food exports by the end of the fiscal year 2024, a significant achievement reflecting the country's growing global competitiveness. Major contributors to this growth include rice, fruits, vegetables, and meat products, which have found increasing demand across Asia, Europe, and the Middle East.
This milestone highlights the country’s strategic focus on diversifying its export portfolio. While rice has been a staple export, the country is now making signifi-
cant inroads into processed foods, dairy products, and beverages. This diversification helps reduce dependency on a few key products, ensuring a stable revenue stream even when market conditions fluctuate. The expansion into processed and value-added food products is especially important, as it taps into higher-margin segments of the global food market, offering new opportunities for revenue growth.
To maintain this success, industry stakeholders are looking to expand their reach into organic and specialty food products, which are in growing demand in Europe and North America. The government’s support for export-oriented growth, coupled with regulatory reforms, has also been instrumental. By creating a more business-friendly environment, Pakistan is making it easier for local companies to export and for foreign investors to engage with the country's food sector.
Further investments in marketing and trade facilitation will be essential to capitalize on this momentum and reach new markets around the world.
The Punjab Food Authority (PFA) marked World Food Day 2024 by hosting a seminar titled “Prevent Food Wastage from Farm to Fork” in Lahore, with Provincial Minister Bilal Yasin presiding over the event. This gathering aimed to raise awareness about food security, global hunger, and sustainable practices, drawing attention to the theme of this year’s celebration: "The Right to Food for a Better Life and a Better Future."
The event saw participation from key figures, including the Minister for Primary and Secondary Healthcare Imran Nazir, Punjab Secretary for Environment and Climate Change Raja Jahangir Anwar, PFA Director General Muhammad Asim Javaid, and experts from various sectors. They were joined by journalists, civil service members, and nutrition specialists who engaged in discussions on the critical issue of food waste and its impact on society.
In his address, Minister Bilal Yasin acknowledged the initial challenges faced by the PFA and highlighted its success in improving food standards across Punjab. He emphasized that the event aimed to raise awareness about issues like food production, distribution, and wastage
while promoting sustainable systems. Minister Yasin also mentioned the directives from Chief Minister Maryam Nawaz Sharif to intensify inspections and impose fines, which led to better food quality across several key sectors, including oil, poultry, and milk.
The PFA Director General, Muhammad Asim Javaid, spoke on the significant improvements achieved in food safety, attributing these advances to stricter regulations and awareness campaigns. He underscored the importance of combating food adulteration and encouraged healthier eating habits to ensure a healthier future generation.
Additionally, speakers like Shahzad Alam, former chairman of the PCSIR, stressed the need to increase food production and reduce waste as essential measures to tackle food shortages and malnutrition. He urged a collective commitment to halving food waste by 2025.
Civil Services Academy DG Farhan Aziz Khawaja highlighted the importance of
raising awareness at the grassroots level, noting that 40% of the population remains below the poverty line, while food waste continues to be a major issue.
Health Minister Khawaja Imran Nazir announced plans to expand the scope of the Punjab Chief Minister’s nutrition campaign, including the launch of mobile hospitals and job opportunities for nutritionists. He emphasized the role of proper nutrition in fostering future champions, making a reference to athletes like Arshad Nadeem as examples of the benefits of good health practices.
The seminar reflected the PFA's ongoing commitment to fostering a culture of sustainable food consumption, raising awareness, and working towards a foodsecure Punjab.
Pakistan's fruit and juice exports to China have shown remarkable growth in the first seven months of 2024, reflecting increased demand and successful trade collaborations between the two nations. According to data from the General Administration of Customs of China (GACC), there has been a significant uptick in exports of frozen orange juice, marking a milestone for the country's agriculture sector.
Ghulam Qadir, the Commercial Counsellor at the Pakistan Embassy, emphasized the benefits brought by the China-Pakistan Free Trade Agreement (FTA). The trade agreement, alongside
the efforts of the Pakistani government and exporters, has helped to diversify and expand Pakistan's reach in international markets. Qadir noted, "From January to July 2024, the export of fruit juices and related products to China exceeded $1.546 million, a 226% increase compared to the same period last year." The bulk of this success was due to frozen orange juice, which alone contributed over $1.54 million in exports.
The increase in exports can be attributed to China's growing demand for high-quality, nutritious fruits and juices. Pakistani mangoes, in particular, have gained popularity, with 4,214 kilograms of fresh mangoes imported by Chinese enterprises during the same period. This popularity was boosted by a gesture from Pakistan's Prime Minister, who gifted mangoes to Chinese leaders and enterprises, fostering goodwill and promoting the country's produce.
Wei Ling Chen, Regional Director of Direct Access, a Chinese enterprise, shared her company's experience with importing Pakistani mangoes, stating that they brought in three to five tons this year. Her company collaborated with topquality mango orchards in Pakistan, focusing on varieties like Sindhri and Chaunsa, known for their exceptional flavor and quality. Despite the non-uniform size and lack of bright, glossy skin, Pakistani mangoes are celebrated for their authentic, pure taste.
The surge in exports and growing demand signify potential opportunities for further collaboration between Pakistan and China, particularly in the agriculture sector. As both countries continue to strengthen trade ties, the future appears bright for Pakistani farmers and exporters seeking to tap into new markets.
The Pakistan Development Update report released in October 2024 emphasized the need for comprehensive regulatory reforms to facilitate smoother food exports. The report identified key areas for improvement, including sanitary and
phytosanitary (SPS) standards, which have often been a bottleneck for exporters trying to enter new markets. Aligning local regulations with international standards is seen as a critical step toward reducing trade barriers and enhancing competitiveness.
In response, the government has been actively working on simplifying export procedures and ensuring that compliance requirements do not become overly burdensome for exporters. By improving the efficiency of regulatory bodies and increasing transparency, the government aims to create a more business-friendly environment that can attract both local and international investors. This involves not only streamlining paperwork and approvals but also implementing better quality control measures to ensure that exports meet the stringent requirements of markets like the European Union and North America.
Moreover, these reforms are essential for building trust with international buyers, who demand consistency and strict adherence to quality standards. Efforts to streamline regulations and reduce bureaucratic red tape will enable Pakistan’s food sector to tap into highvalue markets, thus boosting exports. The introduction of digital tools and platforms to facilitate faster processing of export documents is also expected to improve efficiency, further supporting the sector’s growth.
The October 2024 Pakistan Development Update highlighted various initiatives aimed at improving food security and stabilizing domestic food prices.
Rising inflation has been a persistent issue, exacerbated by global supply chain disruptions and domestic production challenges. The government has implemented measures to boost local production, control imports, and manage inflation, ensuring that essential food items remain accessible and affordable for the population.
One of the key strategies has been encouraging sustainable farming practices, which not only improve productivity but also reduce the environmental impact of agriculture. Investments in technology, such as drip irrigation, soil health monitoring, and precision farming, have been promoted to increase crop yields and ensure better resource management. These initiatives are aimed at making the agricultural sector more resilient to climate change, which has been an increasing concern for farmers across the country.
Additionally, the government has provided subsidies to small and mediumsized farmers to help them cope with rising input costs. These subsidies, combined with training programs on modern farming techniques, are designed to create a resilient agricultural sector capable of meeting both local and international demands. Support for farmers has also included access to better financing options, which enable them to invest in modern equipment and improve their productivity.
The government’s focus on food security is also tied to its broader economic stability goals. By addressing the root causes of inflation and focusing on
long-term sustainability, these policies are expected to stabilize prices and ensure a steady supply of essential goods. The development of local food processing industries is another area where the government is focusing its efforts, with the aim of adding value to raw agricultural products and creating more jobs in rural areas.
In a recent evaluation, Pakistan has been recognized as the lowest-risk country for food safety standards for the fiscal year 2023-24. According to the Rice Exporters Association of Pakistan (REAP), only 74 rapid alerts regarding issues such as pesticide residues and contamination were issued against Pakistani rice exporters last year. In comparison, India faced 264 alerts, highlighting a significant disparity in compliance and food safety measures between the two nations.
This achievement underscores the effectiveness of Pakistan's food safety protocols and the continuous efforts made by both the government and the agricultural sector to enhance quality control. The REAP chairman remarked that this recognition is crucial for bolstering the country's reputation in the international market, especially as global consumers become increasingly concerned about food safety and quality
The announcement comes at a pivotal time for Pakistan's rice export sector. With India recently lifting its rice export ban, competition has intensified, making it essential for Pakistani exporters to uphold their food safety standards. The Pakistani government has taken proactive measures by removing the minimum
export price for rice, which is aimed at improving competitiveness, particularly in the European market. This adjustment is expected to facilitate increased exports and expand market share
Furthermore, maintaining stringent food safety practices will be vital for sustaining access to lucrative international markets. The REAP has called for continued investment in research, technology, and infrastructure to uphold these standards. As global food markets continue to evolve, ensuring compliance with international food safety regulations will not only protect consumer health but also enhance Pakistan's standing as a reliable supplier in the global rice market
Pakistan's agricultural sector is currently facing significant challenges, primarily driven by a notable decline in urea offtakes, which have dropped by approximately 35% year-on-year. This downturn is attributed to rising fertilizer prices and a series of agricultural crises that threaten food production and security.
Experts and industry stakeholders are
urging the government to implement immediate interventions aimed at stabilizing the supply of fertilizers. Access to affordable fertilizers is crucial for farmers to maintain crop yields, especially in a country where agriculture plays a vital role in the economy and employment.
The current situation has prompted widespread concern among farmers, who are experiencing difficulties in acquiring essential nutrients for their crops. High fertilizer prices, compounded by logistical challenges and economic constraints, are threatening agricultural output at a time when food security is of utmost importance. Pakistan, which is already facing economic pressures, must prioritize agricultural stability to ensure that food production can meet the growing demands of its population.
To address these challenges, the government is urged to consider implementing subsidies or financial assistance programs for farmers to ease the burden of rising fertilizer costs. Additionally, increasing domestic production of fertilizers could alleviate supply shortages and enhance self-sufficiency in agricultural inputs.
In the long term, fostering partnerships with private sector players to improve distribution networks and developing more sustainable farming practices could help mitigate future crises. Emphasizing research into alternative fertilizers and innovative agricultural techniques will also be crucial in enhancing resilience within the sector. By ensuring that farmers have reliable access to fertilizers, Pakistan can safeguard its agricultural productivity and food security, ultimately bolstering its position in both domestic and international markets.
Australian Almond Exports Reach Record Highs
Australian almond sales have soared to unprecedented levels, with the Almond Board of Australia (ABA) reporting a remarkable 35% increase in exports for July compared to the previous year. The ABA's latest Position Report revealed that 22,450 tons were sold in July, surpassing the previous record of 17,547 tons set in July 2017 by 28%.
Season-to-date figures show that total almond exports have reached 60,803 tons over the past five months, with overall sales nearing 71,000 tons. Factors driving this growth include a dry season and heightened demand from China, pushing sales beyond levels not seen in the last decade.
A significant contributor to this surge is the export of inshell almonds, with over 27,000 tons shipped this season compared to just over 12,000 tons last year. Exports to China have increased by 105%, now making up more than 55% of total almond exports, aided by favorable pricing from the free trade agreement.
Domestic sales have also shown improvement, rising by 22% compared to July 2023 and up 1% for the season, marking a positive turnaround following a decline over the last 18 months.
However, the ABA has revised its 2024-25 crop estimate from 164,700
China’s Forest Food Production Surpasses 200 million Metric Tons Annually
China's forest food production has exceeded 200 million metric tons annually, equating to approximately 140 kilograms per person, positioning it as the nation's third-largest agricultural product after grains and vegetables. This significant achievement was announced by the National Forestry and Grassland Administration on Friday.
According to Wang Junzhong, director of the administration's reform and development department, the increase in production capacity is supported by 46.7 million hectares of economic forest plantations and over 40 million hectares of forest land dedicated to understory industries. "This enhances the stability of China's food supply and provides a strong foundation for food security," Wang stated.
Forest food products encompass a variety of items, including edible oils, red dates, pine nuts, mushrooms, and ginseng. More than 2,400 of China's 2,800 counties have established economic forests, with their annual output value surpassing 2 trillion yuan (approximately $281.6 billion). Understory activities, such as mushroom cultivation, contribute an additional 1 trillion yuan to the economy, benefitting millions of forest farmers.
In the Xinjiang Uygur autonomous region, the production of forest fruits thrives due to ample sunlight, with 1.4 million hectares yielding 14 million tons annually, primarily in red dates. This year, Xinjiang set up 16 red date demonstration gardens, achieving yields of up to 12 tons per hectare and generating incomes exceeding 44,700 yuan per hectare.
Meanwhile, Jilin province is experiencing a boom in its ginseng industry, with 77,000 hectares dedicated to cultivation, producing over 780 tons annually and valued at nearly 10 billion yuan. Li
Dongyou, deputy director of the Jilin Provincial Forestry and Grassland Bureau, highlighted the high recognition of Changbai Mountain ginseng and the development of over 1,000 ginsengrelated products in the province.
The European Commission has announced its decision to challenge China's anti-subsidy investigation into EU dairy imports at the World Trade Organization (WTO). The move marks the first time Brussels has contested an investigation at its initiation stage.
The Commission stated that this action reflects its commitment to defending the interests of the EU dairy industry and protecting the integrity of the Common Agricultural Policy (CAP) against what it calls "abusive proceedings." The decision comes after China launched an investigation last month into subsidies linked to certain EU dairy products, including liquid milk, cream, and various cheeses. The probe, seen as a titfor-tat response to EU levies on Chinese electric vehicle imports, has raised concerns over escalating trade tensions.
Valdis Dombrovskis, Executive VicePresident and Commissioner for Trade, said, "The Commission is doing everything it takes to defend EU dairy producers and the Common Agricultural Policy
from the abuse of trade defense instruments. The Chinese investigation on EU dairy is based on questionable allegations and insufficient evidence, therefore we will continue to challenge it vigorously in all available venues."
The investigation targets dairy subsidies under the CAP, as well as certain national and regional programmes. China's Dairy Association and the China Dairy Industry Association requested the probe, claiming the subsidies harm local industries. The period under review covers from April 1, 2023, to March 31, 2024, with an examination of potential industry damages dating back to January 2020.
The consultation requested by the EU represents the initial step in the WTO's
dispute settlement process. Should consultations fail to yield a resolution, the EU could escalate the matter by requesting a panel to determine the outcome of the investigation. China accounts for approximately 9.5% of total EU dairy exports, underscoring the importance of this market for European producers.
As trade tensions continue, the outcome of this dispute could have significant implications for the future of EU-China trade relations.
New Zealand Government Invests USD 5.95 m in Cultivated Seafood Research
The New Zealand government has announced a significant investment of NZ$9.6 million (USD 5.95 million) into a five-year program to develop cultivated fish products. The initiative, part of the Endeavour Fund, aims to position New Zealand at the forefront of sustainable seafood production by supporting research into fish cell cultivation.
The program will be managed by Plant & Food Research, a state-owned research agency focused on advancing sustainable practices in agriculture and aquaculture. The research will explore new systems for cultivating fish cells, targeting applications like lab-grown fish products and cell-based collagen, which could potentially reduce the environmental impact of traditional fishing practices.
Dr. Georgina Dowd, who leads the cellular aquaculture research at Plant & Food Research, highlighted the need for innovation in cultivated seafood, noting the current limitations of existing technologies. She expressed hope that this funding would drive the development of healthier and more sustainable fish cell cultures.
The project will also consider social and cultural aspects, engaging with local communities, including M ori, to address concerns related to the cultivation of taonga species, which hold cultural significance.
The New Zealand seafood sector aims to quadruple its sales by 2035, but it faces challenges such as climate change and overfishing. Experts believe that cultivating fish cells could offer a more sustainable alternative, helping to secure the future of the country's aquaculture industry.
The funding is part of a broader strategy by the Ministry of Business, Innovation and Employment, which has allocated NZ$236 million across various research initiatives this year, further supporting New Zealand’s goal of promoting sustainable food systems.
A new report from the Policy Exchange think tank is urging UK ministers to develop a national food security strategy that encompasses the entire food system, extending beyond agriculture to include manufacturing, logistics, and retail. The report, titled Strengthening the UK’s Food Security: Innovation and Investment in the Food Manufacturing Sector, highlights the importance of prioritizing food security as a core element of economic growth in the UK.
The report notes that previous initiatives have focused too narrowly on agriculture, which is inadequate given the challenges posed by high food price inflation and disruptions in supply chains due to the pandemic, the war in Ukraine, and climate change impacts.
Polling conducted for the think tank
revealed that over half of food and drink manufacturers (53 percent) consider mitigating supply chain risks a significant concern. To address these risks, businesses are diversifying suppliers (68 percent), adapting supply chains (50 percent), and investing in product innovation (38 percent).
The report argues that effective food security plans must encompass all areas of the food ecosystem, including food manufacturing, logistics, and retail. Currently, the food and drink sector is the UK's largest manufacturing industry, boasting an estimated turnover of £142 billion and exports valued at over £24 billion. However, investment in this sector has fallen by 30 percent since 2019, underscoring the need for renewed focus and support.
The report outlines several recommendations for improving food security, including: Establishing a new food security transformation fund focused on technology investment, implementing a fast-track approval process by the Food Standards Agency for products already certified by trusted regulatory bodies in other countries, introducing a contingency framework to facilitate adjustments by food suppliers during geopolitical disruptions and enhancing the Foreign Office's focus on strengthening global food security within the UK’s development expenditures.
Industry leaders, including George Weston, Chief Executive of Associated British Foods plc, and Dame Fiona
Kendrick DBE, former Chair and CEO of Nestlé UK and Ireland, support the report’s recommendations, emphasizing the need for a collaborative approach to create a more secure and resilient food system.
If implemented, these recommendations could significantly bolster the future of the UK's food supply amidst increasing global challenges.
The US food and beverage sector is experiencing a critical labor shortage, as highlighted in a recent report by Expert Market, which was sponsored by the hospitality platform Toast. The findings reveal a stark reality: approximately 82 percent of businesses in this industry are actively seeking employees, yet many struggle to fill essential positions, indicating a significant gap in the workforce.
The report emphasizes that the shortage is most acute in the kitchen, where roles like chefs and cooks are highly sought after but difficult to recruit. These positions constitute around 30 percent of all job vacancies, reflecting a troubling gap in culinary staffing. Dishwashers and cashiers are also in short supply, making up 12 percent and 7 percent of open roles, respectively. The shortage of these key positions is impacting the industry's ability to operate efficiently and meet
consumer demands.
However, recruitment is not the only challenge faced by the industry. Retention of staff has become equally problematic, as the report mentions that nearly 30 percent of current employees are at risk of leaving within the next two years, according to a 2023 study by Toast. This high turnover rate exacerbates the labor shortage, creating a scenario where businesses are not only struggling to bring in new talent but are also fighting to keep existing staff from leaving.
Looking forward, the outlook for the industry remains challenging. More than a quarter (26 percent) of businesses anticipate that the staffing situation will deteriorate further over the next year.
In response to these issues, Expert Market has suggested several strategies for businesses to strengthen their recruitment efforts. These include offering competitive pay packages, creating a positive and supportive workplace culture, and leveraging technology to simplify and expedite the hiring process.
Chris Maillard, Editor at Expert Market, stressed the importance of a proactive approach, stating, “The Food & Beverage industry continues to be a complex landscape to navigate in 2024. Our survey findings show that while hospitality is very much a people-centered business, looking after staff as much as
customers should be a high priority for business owners in this sector.”
Maillard also pointed out the benefits of using technological tools to streamline operations, such as software for managing time, payroll, and inventory. Promoting a healthy work-life balance and acknowledging staff contributions are also seen as crucial elements in improving job satisfaction and increasing loyalty among employees.
As the US food and beverage industry grapples with these labor challenges, innovative staffing strategies will be essential for businesses to navigate the road ahead. With an emphasis on improved recruitment and retention practices, companies may be able to overcome the ongoing labor shortages and stabilize their workforce in the coming years.
Vietnam and Malaysia Explore Food Industry Cooperation at SBIS 2024
Potential cooperation between Vietnam and Malaysia, especially in the food industry, was highlighted at the ongoing Selangor International Business Summit (SBIS) 2024. Vietnam's Commercial Counsellor in Malaysia, Lê Phú Cường, emphasized the impressive growth and potential of Vietnam’s food sector during the event.
With a population nearing 100 million and a youthful workforce, Vietnam has successfully
implemented its agricultural export strategies, focusing on key products such as rice, coffee, and high-quality fresh fruits. In 2023, Vietnam's agricultural export value reached $26.4 billion, marking a 17% increase from the previous year. While imports of Vietnamese goods decreased in Europe and the Americas, the Asian market saw a 6.8% rise in agroforestry-aquatic product imports.
Key Vietnamese staples exported to Malaysia include tea, coffee, pepper, and rice, with rice exports alone exceeding $345 million last year. Notably, Malaysia imported as much rice from Vietnam in the first eight months of this year as it did throughout 2023. Additionally, various Vietnamese fruits like longan, lychee, passion fruit, and red-fleshed dragon fruit have gained traction in the Malaysian market.
Cường expressed enthusiasm about the increasing collaboration between Vietnamese businesses and the Vietnam Trade Office to showcase their products in Malaysia. He reaffirmed the trade office's commitment to assisting businesses in finding partners and facilitating their entry into the Malaysian market.
The Selangor International Business Summit is a highly anticipated annual event that promotes cross-border trade, fosters connections, and expands business networks across the ASEAN region. The event generated potential transaction values of up to $4 billion last year.
Running from October 16-19, this year’s summit features over 650 food and beverage exhibition booths and workshops focusing on halal standards, smart cities, and the digital economy, expecting to attract around 12,000 visitors from 18 countries and territories.
On2Cook, the world’s fastest cooking device launched recently in India, is already creating a storm in the B2B cooking space. Within months of its foray into the Indian and Middle East markets, more than 500 units of the revolutionary AI-integrated combination cooking device have been deployed across 35+ F&B brands, including cloud kitchens, cafeterias, restaurants, hospitality chains etc.
The inventor of the landmark cooking invention, Sanandan Sudhir, has further declared that the company has additionally received Letter of Intent for over 4000 units, which are slated to be deployed in commercial kitchens across different geographies. The early adopters of On2Cook include Grabs Kitchen, Carasid Café Goa, Hocco Eatery, Venky Residency and Salad Time, among others.“On2Cook is the future of cooking and we are elated to see its widespread adoption in the B2B F&B space.
The patented technology-based device has widespread implications for the commercial kitchens, such as eliminating gas-based cooking, replacing precooked meals with freshly cooked food, drastic saving on oil usage and the cumulative impact on enhancing the ROI. If we take a mid-sized kitchen serving around 100 plates per day for example, over Rs 16,000 can be saved monthly solely on oil consumption. Besides, its advantages are significant across all cooking verticals –restaurants, cloud kitchens, baking industry, casual dining, as well as Quick Service Restaurant (QSR) chains,” said On2Cook inventor Sanandan Sudhir.
Sharing his experience, Sunil Shrivastav, the owner of Carasid Café Goa, one of the early adopters of On2Cook, said, “We have been using On2Cook for the past few months. What
we found that other than the fact that it’s a very quick and efficient machine, it is extremely helpful for our fillings, which usually happens in batches of few kilos. Most important in our business is consistency in colour, quality, texture etc. And there is no doubt on the results obtained from On2Cook because once you use this machine for filling purposes, it can give you consistent quality, and the icing on the cake is it doen’t need any monitoring. There is no human intervention. I am really happy with the performance and intend to add up to hundred units soon across our chain of cafes.”
On2Cook, patented across India, US, UK and Russia, cooks any meal in onethird the usual time, saves over upto40% on power bills and around 50% on oil consumption, all while preparing healthier and more nutritious meals compared to any other known cooking method. The
device further reduces the number of cooks required in a commercial kitchen while improving the overall consistency and quality of food cooked. Equipped with an app and IoT capabilities, it automates order processing as well as cooking with over 300 predefined recipes.Currently, there is no existing methodology that can match On2Cook in terms of time as well as saving energy and oil.
Unveiled first during the Grand Finale of Shark Tank India Season 1, On2Cook grabbed the attention of industry stalwarts, including the likes of Anand Mahindra, even prior to its launch. Vegetables and meats cooked in On2Cook retain water-soluble nutrients, minerals, structure, texture as well as color, thereby preserving all elements that are often lost in boiled or blanched food.
The increasing importance of starch derived from various raw materials for the food and other industries requires innovative solutions for efficient processing. With the starchMaster CF 8000 decanter, GEA is responding to the growing global market for starch and starch products. According to Euromonitor, this market is expected to reach a volume of over 129 billion US dollars by 2030. The new decanter has been specially optimized for high-throughput starch extraction and gluten separation and is already being used successfully by European users following convincing tests. The high-performance starchMaster CF 8000 can be used for both 2-phase and 3-phase processes and offers a capacity of 15-20 tons of wheat flour equivalents per hour.
The CF 8000 decanter comes standard with the GEA summationdrive, whose frequency-controlled motors automatically and seamlessly adjust the differential speed according to the solid load. Since the intensive starch processing is often associated with high differential speeds and torques of the decanter and thus with considerable gearbox loads, the starchMaster CF 8000 has been proactively equipped with a cooling system. This ensures reliable gear operation even under the most extreme conditions.
Efficiency improvement with Active Torque Control and varipond C
Additionally, the CF 8000 decanter offers an optional Active Torque Control (ATC) system. This GEA solution provides precise, automatic adjustment of the dif-
ferential speed through active torque control to maintain the optimal operating point while avoiding stick-slip. This not only maximizes solid yield but also minimizes energy costs for thermal drying. ATC also significantly reduces the risk of machine damage from stick-slip, contributing to more efficient and sustainable production.
The starchMaster CF 8000 also features the new GEA varipond® C system, allowing flexible adjustment of the separation zone within the decanter. This system is suitable for both 2-phase and 3phase processes and enables quick response to changing feed conditions. With varipond®, users can adjust the running decanter to changing requirements at any time, ensuring optimal separation results and stable solid discharge through variable pond depth.
The new GEA X Control and extensive condition monitoring capabilities for the starchMaster CF 8000 complete the
package for this new decanter. By integrating the decanter into the cloud, operational data can be monitored in real time. Through customized Service Level Agreements (SLAs), GEA provides proactive service and maintenance with trained personnel to ensure maximum uptime and efficiency of the machines.
The stick-slip phenomenon is a detrimental effect that can occur in industrial machines like decanter centrifuges – irrespective of manufacturer and design –when the static friction between the solid bodies moving against each other is greater than the dynamic friction. If the slipping speed of the solid body becomes too slow, it gets stuck and needs additional energy to start slipping again. The stick-slip effect cannot be detected from the outside and leads to increased fatigue and wear to machine components such as the bowl, scroll, gearbox, shafts and coupling. Stick-slip increases the risk of unplanned, expensive downtimes with costly repairs.
What do burgers and beer have in common? As far as culinary pleasure goes, plenty of people will doubtlessly agree they are a perfect match. But for flexitarians, vegetarians and vegans who eat meat substitutes, beer and vegan burgers go equally well together. And for some time now, that has proved true not only at the table but also already during production. You see, the start-up Circular Food Solutions Switzerland has adopted a revolutionary approach based on upcycling brewer’s grains, so that they can be used to produce meat substitutes.
“Usually, that type of vegan product consists of protein sources such as peas, beans or soy. What a lot of people don’t know is that, in Europe, it is not mandatory to declare the ingredients’ origins. Therefore, many consumers do not realise that the basic ingredients often are not produced locally but imported from Asia and then processed here in Europe. I don’t consider that very sustainable,” says Christoph Nyfeler, managing director at Circular Food Solutions Switzerland AG. And it’s precisely this situation that the start-up team is addressing: They want to make meat substitutes more sustainable, starting by drastically changing their choice of raw materials. “We use an existing protein source that we purchase locally and adapt to our own vegan product range,” explains Christoph Nyfeler. And that takes us back to this article’s starting question: The protein source
locally comes directly from the Chopfab Boxer craft brewery based in Winterthur.
Anyone who has taken an in-depth look at the brewing process knows that one of its by-products is brewer’s grains, a material that is often underappreciated. It is mostly not used further even though it contains plenty of valuable proteins, which render it ideal for food production, as Christoph Nyfeler tells us: “In some cases, spent grains are sold to bakeries or the baked-goods industry. But most breweries don’t tap into that great potential and merely sell them to livestock farmers as animal feed. But brewer’s grains do in fact offer so much more.” And Circular Food Solutions not only
reveals that hidden potential but also makes full use of it.
One of a kind worldwide
The start-up’s team set to work in precisely the place where brewer’s grains are produced: the brewhouse. Once the mash has been separated, the spent grains are passed from the lauter tun directly into a further vessel, the disperser, with two mills linked up to the latter. “We’ve joined forces with Steinecker to develop a dedicated recirculating system, which serves to pass the spent grains repeatedly through the disperser and the mills, thus grinding them to an ever finer structure.” That’s how Christoph Nyfeler describes the process, and Matthias Pohl
from Steinecker’s sales team adds: “Our Phoenix BMC project has enabled us to gain valuable experience with brewer’s grains, and how they can be upcycled in this first important step. Of course, these insights have been put to good use in our job for Circular Food Solutions and successfully translated into shopfloor reality.”
Once the targeted fineness has been reached, the ground grains are first temporarily stored in buffer tanks (likewise supplied by Steinecker) and then extruded. “This wet-extruded material produced from brewer’s grains is one of a kind worldwide,” says Christoph Nyfeler with a distinct note of pride. “It’s the basis for any conceivable form of meat substitutes.”
To this end, Circular Food Solutions prepares the extruded material for further processing in line with the customer’s wishes and recipe by mixing the spent grains with another protein concentrate, water, aroma compounds or salts for example. Once this base material has been turned into the final product, it is dispatched chilled to the customer who then uses it to make not only burger patties but also strips or mince – all of it plant-based, of course. “Circular Food Solutions is a purely B2B operation. Our sole focus is on developing products and on the technology needed for making them,” explains Nyfeler. “Turning our base material into the food that consumers will find in the supermarkets’
refrigerated display cabinets, that’s our customers’ job.”
Steinecker is taking yet another approach to upcycling brewer’s grains with its Phoenix BMC concept, which comprises various modules for upcycling residual materials from the brewing process and using them for energy recovery. To give an example: Proteins are extracted from the spent grains and then likewise used in the food industry.
But why did the start-up’s team decide to set up its production process
directly in the brewhouse? For a number of reasons, first and foremost because microbiological safety is of vital importance, as Matthias Pohl explains: “You see, the company’s concept uses spent grains as a natural raw material for food, for which the hygienic requirements are significantly higher than for animal feed. For this reason alone, it is best to process the brewer’s grains with the requisite rigour directly in the brewery. It is, of course, also conceivable for the start-up to build its own processing plants. But that would entail elaborate logistics and intricate cold chains in order to ensure the requisite level of microbiological safety which is absolutely vital.” It is not only the advantages on the logistics side, though, that are cogent arguments in favour of integrating the production process into a brewery’s operation, as Matthias Pohl points out: “You see, all of the peripherals required for media supply and CIP cleaning are already in place here and can of course be easily modified, so that they can also be used for the spentgrains upcycling process.”
That is why the scope of Steinecker’s order for this holistically conceived concept subsumed not only part of the systems technology but also the line’s integration into the Botec F1 brewingprocess control system already in place at the Chopfab Boxer brewery. “The benefits for us here at Circular Food Solutions are that we can fine-tune the brewing and upcycling processes for a perfect
match because thanks to Botec we know exactly when a brew is finished and fresh spent grains are available. That enables us to combine our production sequences to optimum effect,” says Christoph Nyfeler. This planning reliability is important because it is imperative that the spent grains are processed as promptly as possible after lautering in order to guarantee food safety. What’s more, Botec F1 provides the requisite transparency to ensure complete traceability of each production batch.
Circular Food Solutions made its first products in early 2024. “I must admit that we had some ambitious goals and a comparatively tight timeframe for a process that didn’t even exist. Bearing that in mind, I can tell you this: We’re very satisfied with this system set-up,” says Christoph Nyfeler. “Needless to say that everything looks somewhat different on paper than it does on the shopfloor. And to make sure the system actually yields the results you had in mind when you started, you will have to fine-tune and optimise it at one point or another during ongoing operation. But that’s why we’ve brought partners on board who can draw upon experience in both systems engineering and in the brewing and food industries.”
The “ambitious goals” mentioned above also become manifest when you look at the system set-up installed. Even though Circular Food Solutions has only been active in its chosen market for a few short months, its list of customers already includes one of Switzerland’s leading private-label manufacturers. “That has validated our approach and confirms we’re on the right track,” says Christoph Nyfeler. “And we’re confident that it offers much, much more potential. It was for this reason that we invested in a largecapacity production line with a high degree of automation right from the start.”
And even though Circular Food Solutions is currently serving solely the food industry, the managing director has a lot more ideas. “The showcase line we’ve developed here in Winterthur can just as well be translated into shopfloor reality in other breweries,” he says. “Of course, some basic prerequisites will have to be met there as well, like a certain amount of spent grains, for example, to make sure that such an upcycling system can be run continuously, for optimum cost-effectiveness.”
And because the decision-makers at Circular Food Solutions had identified that opportunity at an early stage, they already set great store by designing a multipliable solution when the concept and technology for the new process were developed. To this end, the footprint of the system itself was kept as small as possible, so that the set-up can also be implemented in breweries where space is at a premium. That is because Christoph Nyfeler has a clear vision: to further increase the number of vegan meat-substitute variants on offer. “Demand for meat substitutes is soaring. And in our view, spent grains are one of the most sustainable basic ingredients, ideally suited for increasing regional sourcing of ingredients for vegan products, thus improving their sustainability.”
Agreement with Alabama Power means 100% of sucralose facility’s purchased electricity in McIntosh, US, will come from renewable sources and the carbon footprint of its sucralose ingredient will be reduced by more than 20%
Tate & Lyle PLC (Tate & Lyle), a world leader in ingredient solutions for healthier food and beverages, announces that it has signed an agreement with Alabama Power for the provision of renewable electricity, representing the next step towards meeting Tate & Lyle’s target of 100% of the electricity purchased for its operations coming from renewable sources by 2030.
Under the agreement, through its Renewable Energy Certificates (REC) programme, Alabama Power will provide Tate & Lyle with RECs and electricity each year to provide all the power needed for its sucralose production facility in McIntosh, Alabama. The RECs will be
sourced through Alabama Power from wind farms operating in Kansas and Oklahoma, and will reduce the McIntosh facility’s Scope 2 greenhouse gas emissions to zero. It will also increase Tate & Lyle’s total purchased electricity from renewable sources globally to more than 30%, and reduce the carbon footprint of its sucralose ingredient by more than 20%.
Nick Hampton, Chief Executive, Tate & Lyle said: “Climate change is the biggest threat to the world’s long-term future and so it’s vital that companies accelerate the transition to renewable energy. We have set ourselves ambitious science-based targets to significantly reduce our carbon footprint by 2028 and this agreement with Alabama Power is another clear demonstration of our commitment to meet our targets.”
George Parten, Sucralose Plant Manager, McIntosh, Alabama, US said:
“We are delighted to enhance our partnership with Alabama Power by purchasing renewable electricity. We will work together with them to help reduce the carbon footprint of our ingredient sucralose and our site, and to support the transition to cleaner energy. We are committed to minimizing our environmental impact and to helping build a more sustainable future for our business, our customers and our local community.”
This agreement is part of Tate & Lyle’s broader sustainability programme which includes initiatives to reduce energy consumption, increase the use of renewable electricity and support sustainable agriculture. Tate & Lyle’s climate targets are in line with a 1.5°C trajectory and have been approved by the Science Based Targets initiative. For more information on Tate & Lyle’s approach to climate action and its performance, visit https://www.tateandlyle.com/purpose.
ADM announced the appointment of Monish Patolawala as executive vice president and chief financial officer, effective 1 August 2024, succeeding Ismael Roig, who has been serving as ADM’s Interim CFO since January 2024.
Patolawala brings to ADM more than 25 years of experience overseeing global finance and technology teams across leading industrial and healthcare companies, most recently including 3M. As EVP and CFO of ADM, Mr. Patolawala will be responsible for overseeing Global Finance and Accounting, Global Business Services, Global Technology and Enterprise Strategy.
Chair of the Board and CEO Juan Luciano said, “We are thrilled to have an executive of Monish’s caliber joining ADM as we focus our enterprise on productivity, innovation and delivering with excellence. Monish has extensive experience and an impressive track record leading global, sophisticated finance and technology organizations and delivering
strong results. With more than 25 years overseeing innovation and sustainability focused teams across leading industrial and healthcare companies, we are confident that Monish is a strong fit for ADM’s continually evolving organization. Today’s announcement is the culmination of the Board’s thorough and thoughtful process to identify a proven leader to oversee our finance team as we execute with excellence across our strategic and operational priorities.”
Patolawala said, “It is an honor to join ADM as CFO at an important point in the Company’s trajectory. As a child growing up in India, I witnessed severe poverty and hunger firsthand, and that’s what makes me so passionate about the important work that ADM is doing to feed the world through its purpose of unlocking the power of nature to enrich the quality of life. As a member of the executive team, I look forward to drawing upon my experience to advance ADM’s operational excellence and discipline, as we deliver for
our stakeholders and drive shareholder value.”
Luciano continued, “On behalf of the Board, I would like to acknowledge and thank Ismael for stepping up to lead as Interim CFO and supporting a seamless transition. We will continue to benefit from his extensive expertise as President of EMEA and President of Animal Nutrition.”
Patolawala most recently served as President and CFO of 3M Company where he led finance, country prioritization and country governance, information technology, enterprise strategy and global service centers. Prior to joining 3M, Patolawala spent more than two decades at GE in various finance roles, including as CFO of $20 billion GE Healthcare from 2015 to 2020 and also as head of operational transformation for all of GE from 2019 to 2020. Mr. Patolawala also currently serves on the Board of Directors of biotechnology leader Biogen.
Shan Foods appoints Mr Tahir Malik as their first Global Chief Executive Officer, consolidating the company’s global operations, spread across more than 70+ countries, under a unified leadership structure.
Shan Foods is a leading global player in food industry with on ground operations in North America, Europe Africa & Middle East, Asia and Australia, and a global manufacturing footprint. It commands market leadership in key markets in the core categories the company operates in.
The incoming Global CEO, Tahir Malik, brings with him over 30 years of international experience in two blue chip consumer goods companies – Procter & Gamble and Reckitt. He has worked in global leadership roles across Europe, Asia, Latin America, Middle East and Africa and has extensive knowledge of leading Developing as well as Developed Markets across the globe. In the past ten years of his career, Tahir served as Regional President of Latin America, Asia and most recently Africa Middle East.
Chairman of the Board Mr. Sikandar Sultan commented “We are delighted to welcome Tahir as our Global Chief Executive after an extensive global search process. Tahir is a true visionary leader with extensive international experience across the globe, an excellent track record of driving transformations, fostering innovation, building world class organisations and delivering breakthrough results. Inshallah the Board looks forward to Tahir unleashing the full global potential of Shan Foods as we transform this business for the next +50 years”.
Commenting on his appointment, Tahir Malik remarked “I am excited to have been appointed to globally lead Shan Foods, at a time when the company is looking at major transformations to win globally in a big way. It is a business with an impressive global footprint, a strong
Mr.Tahir Malik; Chief Executive Officer
brand portfolio deeply rooted in providing superior product solutions, and an enviable position in the hearts and minds of consumers with its unmatched brand equity. This role is very close to my heart as it will allow me to truly put a Pakistani
rooted company to become a truly Global Multinational. I am thrilled to lead Shan Foods in its next chapter, up our ambition and deliver a step up in performance, delighting more and more consumers across the globe, every day!”
Greater freshness and longer shelf life, savings in energy costs and space requirements, as well as increased production capacity. These are the features of the new Cooling@Packing System from MULTIVAC. An innovation for cooling bakery products in a packaging machine, which has now been given the German Packaging Award. The solution was also honoured with a Gold Award, which is presented for outstanding innovations from among all the Packaging Award winners. On the Tuesday of FACHPACK the German Packaging Institute (Deutsche Verpackungsinstitut e. V.) selected the 41 winners of the German Packaging Awards in ten different categories. The award is the biggest prize in Europe for innovation in the packaging sector.
“It is a great honour for us to receive this award for our product innovation Cooling@Packing. A big thank you goes to the entire team for the great cooperation,” said Dr Tobias Richter, group president (CSO) of the MULTIVAC Group.
“The solution also reduces energy costs and space requirements – and the recognition by the jury is confirmation of our ongoing commitment to develop groundbreaking new technology, which helps our customers to produce more efficiently and sustainably.“
The MULTIVAC Cooling@Packing System is a vacuum application for cooling bakery products, which integrates the cooling process into the thermoforming packaging machine. This enables the bakery products to be packed immediately after baking, so that a longer product shelf life and greater freshness can be achieved.
Bakery products are traditionally cooled by means of cooling spirals at ambient temperature, or alternatively by passing through cooling tunnels. Both procedures require a lot of space in the production area, as well as a high level of investment. There is also the risk of product contamination during slow cooling processes.
The MULTIVAC Cooling@Packing System enables bakery products (e.g. baguettes, breads or biscuits) to be loaded directly from the oven, using loading robots to hygienically place the products into the open packs at the loading station of the thermoforming packaging machine. The bakery products are cooled down within a few seconds from 95°C to approx. 30°C in the packaging machine, using an evacuation process in the chambers. The cooling effect is produced by the vaporisation energy, which is released by the evaporation of the bakery product's own moisture during the evacuation process.
The MULTIVAC Cooling@Packing System not only offers space savings in production areas, but also savings in energy consumption for product cooling. The production capacity can also be increased thanks to shorter baking times, without the product quality suffering. The new solution can be integrated into MULTIVAC thermoforming packaging machines in the high-output range.
Particularly when it comes to natural food products such as fruit and vegetables, it is innovative, recyclable and resource-saving packaging and labelling solutions, which are stealing the show over conventional concepts. MULTIVAC adjusted to this trend at an early stage: Its solutions not only meet the sustainability requirements of customers, they also protect the packaged product perfectly, as well as reducing food wastage and appealing to retailers and consumers alike with their attractive design.
But completely environmentallyfriendly packaging with a lot of space for information? And also with the plus of product protection and pack security? And the whole package offering maximum efficiency and cost-effectiveness in the production process? Is that really possible? “Yes, it's possible! But only however with fresh ideas and practical concepts,” believes Christian Zimmermann, Project Manager for
Market Intelligence & Applications at MULTIVAC. His motto: "Thinking outside the box".
In the face of shocking figures...
A rethink is urgently required in terms of food wastage: According to estimates by the FAO (United Nations Food and Agriculture Organization), around 1.3 billion tons of food are lost every year for different reasons, and this equates to about a third of the entire food production.
The emissions from food products, which are not consumed, add up to around six percent of all emissions. With an unenviable share of this figure of 42 percent (550 million tons), the fruit and vegetable sector is the lonely frontrunner in food wastage, followed by cereals, root crops, tubers, dairy products, meat, fish and crustaceans. Another fact: Around a fifth of all fruit and vegetables is lost even before harvesting, and therefore not
processed or reaching the retail chain.
So how can we put a stop to food losses and the consequent waste of costly resources? And above all: What role does packaging play here?
The CO2 balance of food and packaging
Is rightly in the spotlight of public discussion about climate change and environmental protection. More than 190 countries worldwide have agreed on a strategy to halve food losses per head by 2030 at retail and consumer level in the "UN Agenda 2030 for Sustainable Development". In parallel with this, efforts will be made to significantly reduce losses throughout the process chain.
According to current studies, the ecological footprint of a packaged food product, when taking into account the cultivation, production, processing and logistics, is around 30 times higher than the footprint of the pack itself. Only
about three to four percent of the environmentally harmful effects can on average be assigned to the packs themselves. The influence of packaging, and in particular plastic packs, on the world's climate is therefore relatively small, but it is considerably overestimated by most consumers. However: Every gram of packaging material that can be saved does help. And every item of food produced, which does not perish prematurely or is not wasted unnecessarily thanks to the perfect packaging concept, improves the eco balance sustainably.
The fact is: Food packaging protects
The product throughout the entire logistics chain. It extends the product's shelf life. It prevents the loss of aroma and nutrition. It preserves the shape, colour, feel and substance - and therefore also the appetising appearance of the product. An intelligent packaging design also makes a significant contribution to a smaller pack volume. If a greater number of lighter packs can be stacked, stored and transported, this reduces the energy requirement for transport and chilling, and it also makes additional journeys unnecessary.
“Packs, which are perfectly matched to the product, are almost always associated with ecological benefits. Because the benefit in terms of avoidable food wastage is nearly always greater than the effort involved in producing and disposing of the packs,” underlines Christian Zimmermann. For example, fresh and crispy cucumbers can generally be enjoyed for about six days, when unpackaged and kept at the optimum storage temperature, whereas they can be consumed for up to 23 days if packaged. Despite the presence of plastic film, their eco balance is significantly better than that of the unpackaged product. It is a similar story with meat, ham and sausage products.
Where the best-before date is six days, the wastage rate in retail amounts to around six percent. If the best-before date can be doubled through the use of suitable packaging concepts, the food wastage is reduced by 40 percent overall. If one assumes that around 30 percent of
greenhouse gas emissions are associated with food, the eco footprint can be reduced overall by up to eight percent through the prevention of food wastagean enormous value.
More eco benefits when packaging fresh produce - solutions in tune with the times
MULTIVAC has been actively engaged for years in this area, and it sets the benchmark when it comes to sustainable machine solutions and packaging concepts. For the marketing of fruit and vegetables in particular, the packaging and processing specialists at MULTIVAC are increasingly focusing on plastic-free and recyclable packs. One particularly sustainable solution is available for every product and packaging applicationMULTIVAC PaperBoard, ranging from trays or cardboard backing material made from 100 percent paper-fibre, right up to solutions with a small proportion of around 10 percent plastic.
When it comes to labelling as well, the way is pointing directly towards sustainability. In addition to the classic full wrap labelling, which has already become firmly established in the market, and where a label is applied over all four sides of the pack, there are now two more sustainable solutions for the labelling and closure sealing of fresh produce trays: Top Wrap and Top Close labelling.
With Top Wrap labelling ...
The label makes sure, that the content can not fall out of the tray or be removed by the customer. “Thanks to a combination of cardboard trays and self-adhesive labels made of paper or renewable materials, this produces a plastic-free pack, which can for example be used for mushrooms, berries, lemons or small avocados, and which can be easily and perfectly recycled,” adds Ronald Helmel, Business Development Manager at MULTIVAC Marking & Inspection.
In addition to this, it is also possible to use film labels made of polypropylene. They offer the benefit, that the product is visible thanks to a transparent viewing window on the top of the tray. “The proportion of plastic in such a pack is under 10 % depending on the label material
used,” explains Ronald Helmel. “The label can also be easily removed, making it simple for the consumer to separate the materials into the different recycling channels.”
With Top Close
Plastic or cardboard trays with a wide flange or even round trays can be sealed closed simply and securely on the top and labelled at the same time. The label only adheres to the flanges of the tray. Thanks to an adhesive-free zone or retention of the backing material in the middle of the label, the product does not come into contact with the adhesive. The label can also be printed on the labeller itself with a best-before date for example, and it is even possible to inspect the print on the label. With an output of up to 200 products per minute, a labeller with Top Close has a particularly high output.
Both labelling solutions are very impressive thanks to their attractive label and recyclable pack. The self-adhesive labels on a backing material not only offer a large area for customer information and marketing purposes, they also open up a wide range of possibilities for product presentation in terms of material thickness and label shape. It is possible for example to have cut-outs in the label, as well as adhesive-free zones, so that contact with the product is prevented. Perforations serve as opening aids and make the handling of the packs easy for the consumer.
onveyor belt labellers - efficient, reliable and precise
The high-performance L 310 Top Close and L 310 Top Wrap conveyor belt labellers provide the solution. In the case of both models, the trays are automatically labelled on the run, and they are either fed in manually or transferred automatically from an upstream module. This provides tangible cost savings in personnel and very efficient processes, when compared with time-consuming, manual packaging solutions.
The output is on average up to 200 packs per minute. Labels with a width of up to 300 mm and a material grade of up to 170 g/m² can be run. If required, an additional label can also be applied very precisely to the base of the pack in the same operation.
And if a MULTIVAC splice table is used, the required change of label rolls can be performed in significantly less than one minute. The result is that downtime is reduced considerably and productivity increased. This positive effect can be topped still further with the so-called "Zero Downtime" version of the L 310: Here a second label dispenser automatically takes over the labelling, when a change of label material is due. “A flying label change like this makes it possible to have uninterrupted operation, and this provides a further boost to productivity,” adds Ronald Helmel.
The two compact models from MULTIVAC can be integrated seamlessly into existing lines, or they can be used as a stand-alone solution with manual product infeed.
MULTIVAC officially opened its new Center of Excellence for slicing solutions in Buchenau (Dautphetal) after a construction period of around two years. The investment amounted to approx. 15 million euros. Group presidents, Bernd Höpner (CTO) and Dr Tobias Richter (CSO), together with Jochen Ertl, Senior Director Slicing and Buchenau Site Director, greeted the guests at the inauguration ceremony.
The MULTIVAC Group has been developing and designing high-performance slicers for the food industry at its Buchenau site since 2017. Following strong growth since then in its Slicing Business Unit, the new building will now expand the current capacity. Built over a surface area of around 4,700 square metres, the new building complex comprises a Customer and Application Center, as well as production areas and warehouse facilities. The new building creates a second Application Center, in addition to that at the company's headquarters in Wolfertschwenden, and this new facility
offers even greater opportunities for customer tests and demonstrations at the Buchenau site. As part of the building's sustainable infrastructure, a number of measures have been taken to reduce greenhouse gases: The heating for the building is provided by air-heat exchangers combined with a photovoltaic system, and this is assisted by the waste heat from the air compressors, so that no fossil-fuel energy is used.
“We have built up a range of MULTIVAC slicing equipment in record time, and this comprehensive range includes all output categories. Thanks to the new Buchenau site, we can now react even more flexibly to our customers' requirements, as well as providing yet more complete lines as tailored solutions for food processing and packaging,” said Dr Tobias Richter, Director and CSO of the MULTIVAC Group. “And with the additional Application Center in particular, we can now offer our customers an even better and more accessible consultancy serv-
ice in that wider region.”
Bernd Höpner, Director and CTO of the MULTIVAC Group, added: “The investment is an important milestone in our growth strategy, and it is a clear recognition by the company's owners of their long-term commitment to the Marburg-Biedenkopf area. Thanks to the expanded development and production capacity, we now have the best conditions for continuing to develop the Slicing Business Unit successfully and sustainably.“
The new building also creates additional jobs at the Buchenau site. “With this first expansion phase up to 150 staff members will be working in the state-ofthe-art building complex,” said Jochen Ertl, Site Director at Buchenau. “We are offering interesting and future-proof jobs – and we are a highly attractive employer in the region. A further increase in the number of staff is planned for the coming years.”
Tate & Lyle PLC (Tate & Lyle or the Company), a world leader in ingredient solutions for healthier food and beverages, is pleased to announce the launch of its new ‘Automated Laboratory for Ingredient Experimentation’, known as ‘ALFIE’, at its Customer Collaboration and Innovation Centre in Singapore. Through the pioneering use of automated robotics, ALFIE represents a revolution in the delivery of mouthfeel solutions for customers, providing faster and more accurate ingredient design and accelerating speed-tomarket for new products.
ALFIE, which represents a multi-million pound investment in innovation by Tate & Lyle, has the ability to run characterisation tests at around 10 times the current rate, and provides enhanced predictive modelling. It comprises two robotic systems with complete connectivity and seamless data flow for fast ingre-
dient and solution design. By accelerating sample production, characterisation and modelling, the company will be able to trial new ingredients more efficiently and create new solutions for customers at greater pace.
This major investment makes the Singapore lab Tate & Lyle’s Asia Pacific hub for mouthfeel R&D and customer solutions. While ALFIE will be operated by Tate & Lyle’s on-site scientists in Singapore, it is also connected to Tate & Lyle’s Customer Collaboration and Innovation Centre in Hoffman Estates, near Chicago, US, where scientists will be able to operate ALFIE virtually.
Nick Hampton, Chief Executive, Tate & Lyle said:
“With this multi–million pound investment we are transforming the new product development process for our mouthfeel solutions, empowering our sci-
Nick Hampton, Chief Executive Officer
entists to accelerate experiment design, analysis, and delivery of innovative solutions for customers.
“Our goal was to create a revolutionary tool that will better predict product performance in food manufacturing,
allowing us to create faster and improved solutions to customer challenges. ALFIE’s cutting-edge technology will enable us to push the boundaries of food innovation, speed up our customers’ innovation cycles, improve consumer choice for healthier food and beverages, and help shape the future of the food industry.”
Andrew Taylor, President, Asia, Middle East, Africa and Latin America, Tate & Lyle said:
“ALFIE is a groundbreaking lab which we believe will redefine research and development in our industry. With automation and advanced data analytics at its core, ALFIE will accelerate innovation, enabling us to provide tailored solutions for our customers’ most complex needs. ALFIE’s unique system will offer
hour flight of Singapore, the location for ALFIE places Tate & Lyle very much at the centre of the future of food globally.”
Marcus Dass, Senior Vice President, Global Enterprises, Singapore Economic Development Board (EDB) said:
“The opening of Tate & Lyle’s new Automated Laboratory for Ingredient Experimentation (ALFIE) reflects Singapore’s position as a trusted hub for the region and for cutting-edge innovation in the food and nutrition space. We look forward to the lab accelerating
ingredient solution discoveries and enriching Asia’s food innovation ecosystem.”
Supported by our 160-year history of ingredient innovation, we partner with customers to provide consumers with healthier and tastier choices when they eat and drink. We are proud that millions of people around the world consume products containing our ingredients every day.
our customers access to technology and insights they didn’t have before.
The launch of ALFIE positions our Singapore Customer Innovation and Collaboration Centre as a leading food innovation hub globally. It also aligns with Singapore’s Food Manufacturing Industry Transformation Map (ITM) 2025 which charts the development of Singapore into a leading food and nutrition hub in Asia.
“If you consider that about 60% of the world’s population lives within a five-
Through our expertise in sweetening, fortification, and texture, we develop ingredient solutions which reduce sugar, calories, and fat, add fibre and protein, and provide texture and stability in categories including beverages, dairy, bakery, snacks, soups, sauces, and dressings.
We have more than 3,300 employees working in around 58 locations in 39 countries, serving customers across 121 countries. Science, Solutions, Society is our brand promise and how we will achieve our purpose of Transforming Lives Through the Science of Food. By living our purpose we believe we can successfully grow our business and have a positive impact on society. We live our purpose in three ways, by supporting healthy living, building thriving communities and caring for our planet.
Givaudan, a global leader in Taste & Wellbeing, announced the groundbreaking of its new, state-of-the-art production facility in Cikarang, Indonesia, reinforcing its commitment to the Southeast Asia region. The new site, which will complement our existing facility in Indonesia, represents an initial investment of CHF 50 million and will span 24,000 square metres within a total reserved land area of 50,000 square metres to accommodate future expansion plans. It will focus on producing a wide range of savoury, sweet, and snack powders, as well as infant nutrition solutions.
“The new facility in Cikarang marks a significant investment in Indonesia, reinforcing our commitment to expanding Givaudan’s manufacturing footprint in the Southeast Asia region. As market leaders, this expansion also enables us to seize growth opportunities through closer collaboration with our customers.” says, Louie D’Amico, President Taste & Wellbeing.
Set for substantial growth, the site is positioned to significantly expand in size over time, as Givaudan continues to invest in cutting-edge technologies and production processes. This strategic facil-
ity will enhance Givaudan’s presence in the region, bringing production closer to its customers and providing innovative solutions to meet the increasing demand while contributing to local economic development.
The new production facility will create around 60 jobs across diverse skill sets and drive a health-focused community programme, highlighting Givaudan’s commitment to fostering local talent and the sustainable growth of Indonesia’s economy.
Christina Yeo, the Head of Operations APAC, commenting at the opening ceremony, said: “At Givaudan, we are dedicated to purposeful growth. This groundbreaking ceremony represents a significant milestone, strengthening our production capabilities to co-create exceptional food experiences with our customers. By expanding our manufacturing footprint and enriching the communities we operate in, we continue to thrive on all fronts.”
Aligned with Givaudan’s sustainability goals, the new facility is designed with future-proofing in mind, allowing for the integration of sustainable technologies and features, including the utilisation of solar power, recycled water systems, enhanced natural and LED lighting with sensors, purchase of electricity from certified green energy partners, and rainwater harvesting systems. These efforts will minimise the environmental impact and ensure long-term operational efficiency and resilience.
Construction has started and is expected to be completed within 18 months, with operations scheduled to begin in the first half of 2026.
At a time when ecological issues have become a daily reality for manufacturers, Sidel is now helping its clients maximise their environmental performance thanks to Eco-Audit, a comprehensive approach to improve their PET container production processes. This service will soon apply to other equipment in Sidel’s portfolio.
The service, which can be broken down into several phases, begins with an in-depth audit of the container production process to accurately assess its true environmental impact, then offers expert support to significantly and rapidly reduce
the consumption associated with PET containers and blow moulding.
Against the backdrop of the current ecological crisis, environmental regulations are becoming increasingly stringent for manufacturers. At the same time, consumers are increasingly aware of the carbon footprint of the products they purchase. For manufacturers, this duty to be sustainable, when considered as a means of improvement, represents a genuine competitive factor. Reducing material or energy consumption often translates into a significant drop in operating costs, and
actively contributes to the creation of an enhanced brand image.
The carbon footprint of primary packaging is particularly significant. This is particularly true for manufacturers who package their products in PET. Indeed, although this material is convenient for consumers and is recyclable, the production of PET containers nevertheless represents at least 50% of the environmental impact and total cost of ownership of a packaging line, when considering both the preform material and the entire blowmoulding process. PET packaging and its production are therefore one of the first production parameters to be addressed
when it comes to reducing carbon footprint and production costs.
The value of manufacturer expertise
Determining the factors on which to work to reduce the environmental impact of PET bottle production often requires advanced knowledge of the plastics industry. Mathieu Druon, Eco-Audit Product Manager, explains: “The production process for PET containers is complex. Many factors come into play: the quantity of material and the design of the preform, heating and blowing technologies, and the technical configuration and operation of the machine, from production to maintenance. What’s more, these factors vary greatly from one manufacturer to the next, depending in particular on their economic and strategic choices, their mastery of the blowing process, their knowledge of the latest technological innovations, and the compatibility of these innovations with each machine model”.
This observation led Sidel to launch its Eco-Audit service. Mathieu Druon sums up: “Sidel is a pioneer in the development of stretch blow moulding technology, and in over 40 years of designing blowmoulding machines, we have developed proven expertise in all aspects of PET container production. So it was only natural that Sidel developed the Eco-Audit to help owners of Sidel blow-moulding machines better control and reduce their machines’ consumption”.
A comprehensive audit
The service offer developed by Sidel can be broken down into three phases to suit the exact needs and expectations of each manufacturer.
The first phase, called Eco-Assessment, is a comprehensive, in-depth audit of the production process and associated consumption, from the characteristics of the preform, to the machine’s technical configuration and operating parameters. Once this thorough diagnosis is completed, a full report is given to the client, detailing actual consumption, its ecological and economic impact, and all potential avenues for further reductions.
The second phase of the offer, called Eco-Value, aims to implement all the simple adjustments needed to achieve quick savings in materials and energy. All
aspects of the process are taken into account: recipe management, machine settings, from oven heating to the use of air in blowing and dedusting modules, or the detection and correction of potential air leaks.
Finally, the third phase, called EcoPartner and based on the analysis of the Eco-Assessment and the results of the Eco-Value, consists of fully supporting the client in transforming their production facilities to fundamentally improve the energy performance of their PET container production. This work can take the form of installing custom parts or options to enable the machine to benefit from the latest technological innovations developed by Sidel. Depending on the case, Sidel experts can also recommend improvements to the container (neck, preform or bottle design) in order to reduce the quantity of material and blowing pressure, and assist clients in the subsequent modification of their line. The Eco-Partner then concludes with another complete audit of the line, along with a quantified report on the savings achieved and forecasts for future gains.
Regarding the potential savings from the Eco-Audit of PET blow-moulding machines, Mathieu Druon states: “It’s hard to quantify because every industrial case is different. That’s why our intervention always begins with a detailed audit under real conditions: it enables us to evaluate precisely and factually the savings we can generate for the client. And this is precisely what enables us to deliver the results we announce when we work
on our clients’ lines to implement our recommendations.
Nevertheless, I can mention the results of two test audits we carried out with clients: in one case, we achieved annual reductions in carbon footprint of 7 tonnes of CO2 equivalent for over 80,000 Euro in savings, and in the second case, no less than 157 tonnes and over 180,000 Euro! And in both cases, the return on investment was barely a few months”.
An offer poised for growth
To make its clients aware of the savings that can be made in PET container production, Sidel will be distributing an informative brochure in early October, via its social networks and website, outlining solutions for improving the energy performance of their blow-moulding machines. And to deploy its Eco-Audit offer worldwide, Sidel has an international network of experts in packaging and blow moulding. They will also be able to rely on Sidel’s Evo-ON Eco, when installed on the line: this digital application, the result of Sidel’s dual expertise in packaging and digital technology, enables detailed, real-time monitoring of the line’s various consumption levels.
As for the other equipment in Sidel’s portfolio, Mathieu Druon explains that “Sidel intends to broaden the scope of the Eco-Audit to its other equipment in the near future, starting with bottle washers and pasteurisers. Our long-term ambition is to enable our clients to have the most cost-effective production throughout their packaging line”.
Travelers, talented chefs, and restaurateurs from around the world are increasingly visiting the countries for its unique culinary offerings. Travel is undergoing a unique metamorphosis. While luxury experiences and picturesque destinations remain alluring, a discerning new breed of traveler is emerging—the adventurous gourmand. This segment of travelers seeks captivating landscapes, cultural immersion, and a profound exploration of a destination’s culinary identity.
This burgeoning trend, aptly termed gastro-tourism, is finding plenty of unique experiences in the Gulf Cooperation Council (GCC) countries.
With a strategic blend of traditional cuisines and modern dining experiences, the GCC is attracting a growing number of food enthusiasts.
Culinary tourism stems from socioeconomic factors. First, the region has witnessed a surge in residents with disposable income, fostering a burgeoning middle class with a growing appetite for novel experiences. Second, GCC governments have embarked on a concerted effort to diversify their economies, with tourism as a central pillar of this strategy.
At the Michelin Guide Awards for Dubai in July, Gwendal Poullennec, International Director of the Michelin Guides, said: “What a pleasure to witness the blossoming of Dubai as an international gastronomic destination, developing itself year after year. Its appeal isn’t just with international travelers or local gourmets; talented chefs and restaurateurs from around the world are now also attracted by its vibrant dining scene.”
The hospitality sector within the GCC is aware of the culinary trend and adapting to it. Many hotel chain launches involve specific food and beverage (F&B) offerings. Partnerships with celebrity chefs and renowned restaurateurs are helping to create destination dining experiences.
Furthermore, the cultural richness of the GCC countries provides a unique selling point. Food is an integral part of Arabian hospitality, and visitors are often treated to immersive experiences, such as Bedouin-style dinners in the desert, traditional cooking classes, and visits to bustling local souks.
“One of the ways a hotel can create a compelling tourism experience is by working with a celebrity chef to launch a
restaurant and grow their portfolio within a popular culinary destination,” says Heiko Roeder, Vice President of Food & Beverage at Atlantis, The Palm. “Dubai’s reputation as one of the greatest cultural melting pots makes it ideally suited for celebrity chef restaurants, and this is something that guests are looking for when they travel to the region.”
“Our affiliation with celebrity chefs began at the iconic Atlantis, The Palm, since its opening. The idea is that guests can dine and enjoy cuisine from Peru, Spain, the UK, and beyond without needing to leave the resort,” adds Roeder.
The GCC’s gastro-tourism appeal lies in blending tradition with modernity while welcoming industry-leading third-culture restaurants, supporting locally developed concepts, and attracting other international culinary talent. For example, the globally recognized Michelin Guide will soon launch in Doha, and there is a collection of food festivals and conferences across the region, including the annual Gulfood and the InFlavour Expo in Riyadh.
While dining at restaurants is one way to experience culinary tourism, curated food tours take guests on an immersive journey. These tours allow guests to taste the food and understand the cultural and historical context that shapes it.
“The Middle East is evolving, so you see more all-encompassing tours,” says Arva Ahmed, co-founder and CEO of Frying Pan Adventures. “Travelers are now actively seeking food tours. The market is growing, driven by word of mouth, food shows, and YouTube. People want to eat like locals and avoid the same old, same old.”
“The corporate market for food tours is also expanding. HR teams and senior leaders seem to opt for a more culturally immersive experience around a city rather than the stock hotel buffet,” adds Ahmed.
The governments and private sectors are investing significantly in gastro-
tourism. For example, Saudi Arabia’s Vision 2030 plan includes substantial allocations for tourism infrastructure, focusing on cultural and culinary tourism. The UAE continues to bolster its reputation as a global food hub through events like the Dubai Food Festival and Abu Dhabi Culinary Season, which attract worldrenowned chefs and food connoisseurs.
Strategic partnerships are also pivotal. Collaborations with international culinary schools like Ecole Ducasse in Abu Dhabi, celebrity chef collaborations, and global food brands are helping to elevate the region’s gastronomic profile.
Despite its burgeoning growth, the gastro-tourism market faces challenges. In addition to competition in other, more well-developed, or recognized culinary destinations, the region’s extreme climate can be a deterrent, particularly during summer. Additionally, the high cost of dining in some of the more upscale venues might limit accessibility for a broader range of tourists.
However, various initiatives are addressing these challenges. The introduction of air-conditioned food markets and the development of more affordable yet high-quality dining options make the region’s culinary experiences more accessible. Restaurant weeks and food festivals offer chances for guests and locals to sample signature dishes without committing to a full meal.
“Culinary tourism plays a significant role in enhancing guest experiences and promoting cultural heritage. Our approach to developing partnerships with
chefs, restaurants, and food producers is integral to creating memorable culinary experiences for our guests,” says Yasser Younis, Director of F&B at Fairmont Hotel Riyadh.
Its most notable initiatives include collaborating with Michelin-experienced Chef Nicolas Isnard, who brought the House of Grill project to life, and Afternoon Tea collaboration with Jo Malone London, which blends the sensory elements of taste and scent.
“Working with renowned chefs and luxury brands, we tap into a wealth of expertise and creativity, ensuring our menus remain dynamic. This approach attracts culinary tourists and enhances Riyadh’s reputation as a vibrant culinary hub,” adds Younis.
The future of gastro-tourism in the GCC looks promising. As the region continues to invest in its culinary infrastructure and develop innovative experiences, Michelin-starred restaurants have already been drawn to its unique culinary landscape, establishing unique outposts, some for the first time outside of a home country.
By capitalising on its rich culinary traditions, strategic investments, and global partnerships, the GCC is becoming a leading destination for the discerning gourmand.
The agricultural mechanics exhibition this year also includes a full schedule of meetings on important topics. Innovative technologies for the great challenges of agriculture, development of markets and cooperation, applications of robotics and artificial intelligence are the main topics being considered.
The 2024 EIMA event is offering a wide-ranging and highly topical program of conferences and events as part of the agricultural machinery trade fair being held at the Bologna exhibition center from 6 to 10 November. The five days of the exhibition will include over 150 meetings - in the form of conferences, talk shows, workshops and appointments outside the show - dedicated to important topics related to agriculture and agromechanics.
The calendar of numerous events sponsored by institutional bodies, specialist publications, professional organizations, and associations active in the agricultural and agro-industrial supply chains, offers opportunities to stay up to date and in the know on issues such as the common agricultural policy, the market of machinery and services for agriculture and green care, international cooperation, safety at work, employment prospects in the sector and new technological frontiers. The program developed by the 11 Universities present in the EIMA Campus area is also extremely extensive, and together with the Italian Association of Agricultural Engineering will include lessons and training activities for students as part of the exposition.
This year's trade fair is taking place precisely at the moment when the politi-
cal discussion on eco-sustainable agriculture models is in full swing – explains FederUnacoma, the Italian federation of manufacturers that is the organizer of the event - on the new geography of markets, on the development of the African continent, on the system of incentives and on the needs for professional training or agriculture and agro-mechanics, and this makes the political- and economicthemed meetings to be held as part of the event particularly interesting. The first discussion scheduled as part of the program is of a purely political nature and will be held immediately after the inauguration ceremony. It is entitled: “Technologies for the agromechanical industry, professional skills and markets: new challenges for agricultural businesses”. In the afternoon of the same day, there will be a conference on "African Continental Free Trade
Area, agriculture and mechanization: a window on the future", promoted by Africa e Affari and FederUnacoma, that will focus on the development prospects of the continent in light of the establishment of the free trade area. The meetings that will take place during the visits planned by delegations of MEPs and Italian parliamentarians from the agriculture and environment committees are dedicated to political strategies, while an in-depth analysis of the role of Made in Italy products in the sector will be offered during the meeting on "Innovation and mechanization: the future of agricultural machines", organized by the Quotidiano Nazionale newspaper with the participation of the representatives of the sector associations that make up FederUnacoma.
Great space will be given to digital and robotic technologies, and to Artificial intelligence applications to agricultural processes and management of primary companies, thanks to a well-structured program sponsored by FederUnacoma in
collaboration with the international association of agricultural digital experts AEF. Among these meetings, the following are especially noteworthy: "Agricultural Robotics: The Future is Now", "AEF, ISOBUS and the Importance of certifica-
tion", "The new AEF trends: Autonomous machines, high speed AgIN and ISOBUS", and that on "Data, Cybersecurity, AI and more in the new European legislative program", which will also include participation by the European
manufacturers' committee CEMA.
Conferences dedicated to advanced electronic technologies include will one on "Artificial Intelligence: an industry perspective", also organized in partnership with CEMA, and one on "Transition 5.0" in agriculture"", while there will also be a space for official presentations of European research and training projects such as the one entitled "Agri Digital Growth" promoted by a partnership that also involves CREA as well as entities from
9 European countries. Sustainable health defense, agrivoltaics, traditional and electric motors, safety in agricultural work, financing and procedures for purchasing agricultural machinery are just some of the topics that will be covered by specialized publishing houses, as well as by institutions such as INAIL. The program of seminars and workshops on bioenergy and the circular economy promoted by ITABIA as part of the EIMA Green Show is also very sizeable. The EIMA 2024 event
will also dedicate special attention to young farmers and students, with a structured program, sponsored by AGIA-CIA, which will include events such as the conference entitled "Agrimage: the creativity of young people at the service of agromechanics", during which the prizes for the "Agrimage" contest will be awarded.
The multiple events to be held as part of Mech@grijobs, a program that advertises employment opportunities in the agromechanical supply chain promoted by Federacma in collaboration with FederUnacoma, are specifically dedicated to the youth audience. Other prestigious events that have become a regular part of the EIMA event program include the Tractor of the Year awards, sponsored by Trattori magazine, and the Contractor of the Year, sponsored by the Edagricole publishing group, to which is added the awards ceremony of the new EIMA Social Awards competition. Discussions on trends in agricultural mechanics will be held at all levels during the five-day event, which is also hosting the assembly of the Club of Bologna and the Agrievolution meeting.
$434 million
during two days at FoodAg
Pakistan’s record-breaking MoUs worth $ 434 million signed at FoodAg 2024 mark a significant step towards a promising future. With a target of $ 60 billion in exports in the next few years, Pakistan is set to usher in a new era of development and progress.
Under the leadership of Minister Jam Kamal Khan, the Ministry of Commerce has outlined a plan to expand the production capacity and economy of farmers in Pakistan, ensuring food security in the country and surplus quantity for global export.
Speaking to the media, Minister Jam Kamal Khan lauded FoodAG for managing an extremely well-orchestrated platform that brings together the business community, traders, and manufacturers from Pakistan and beyond. He proudly noted the participation of approximately 800 delegates, 350 Pakistani companies engaged, and approximately 450 stalls offering small business holders from the region, calling it a major achievement for
Pakistan. The 75 countries participating in this generous trade event signify Trust’s success in the Pakistani trade sector.
“Agriculture is a sector that forms the backbone of our country, yet it remains to be explored to its extensive potential. The event catered for small to medium business owners from far-flung areas and the
interiors of the country, ranging from Musakhel to Panjgur. This Agro-food festivity is not only a means to expand the trade capacity of Pakistan but also enables the commoner to become selfsufficient and independent financially through engaging in home-based/ small businesses that can easily be taken up
while adding greatly to the overall growth of Pakistan.”
“Trade is the backbone of our country, and this three-day event has demonstrated that Pakistan has a significant capacity for value addition.” The Minister praised the exhibition’s pivotal role in fostering connections between foreign delegates, media, and regulators from 55 countries with Pakistan’s exporters. These connections have led to the formation of beneficial ideas and long-term partnerships aimed at transforming the global food landscape.
“World-renowned chefs visiting this exceedingly successful event also depict how food and agriculture are gaining momentum and encouraging international chefs to direct their interest towards Pakistani cuisine and to take it back with them. This will assist in creating an international demand and thus a global market for Pakistani food products and cuisine,” the minister stated.
On a query related to the trade deficit and lack of trust of foreign investors, Minister Jam Kamal Khan clarified that this event at the biggest stage of business delegate’s attendees signifies the major role being played by companies and their willingness to attend. This reinforces the betterment of the trust deficit created in the previous years due to several concerns- including security and political stability. He further noted that Pakistan has experienced a remarkable surge in exports during the financial year 202324, attributing this success to collaborative efforts by the government and the business community. There is a scope for
many markets to be tapped and those existing to multiply. Despite the challenges faced by Pakistan, The Ministry of Commerce and TDAP have been able to pull a gigantic leap in the trade market from $5 Billion to $ 8.5 Billion.
“Pakistan traders have the capacity not only to expand but tap into new areas of trade generation. TDAP and our traders have worked tirelessly to ensure that the existing potential doesn’t go to waste. Trade relies heavily on the grower and is not entirely based on the willing-
ness of traders; this becomes an intertwined web of dealings that the Ministry of Commerce is undertaking.” He stated as he addressed a query.
Circling back to the event, he expressed his gratitude at its success: “$107 million worth of MOUs have been realised so far, while $434 million worth of MOUs were signed over the first day of the event. This has just resulted from a two-day response to this successful event, which shows that trade and commerce in Pakistan is up and running, unlike the general perception of mistrust rumoured to have pervaded.”
“Today’s event is a testament to the international interest in Pakistan as a trading partner. Foreign delegations are eager to explore opportunities and build stronger trade ties with Pakistan,” he concluded, instilling a sense of pride and confidence in the audience about Pakistan’s global standing.
Chief Executive of TDAP, Mr Muhammad Zubair Motiwala, also spoke occasionally and briefly discussed the fear of some of the MoUs signed between foreign buyers and local exporters.
20th International Exhibition of Food & Beverage Processing Packaging Technology. 29-31 May 2025 expo Lahore Show Highlights 2025 . Meat & Poultry Fruits and Vegetables Rice and Flour Milling.
At IFTECH, The Organizers take immense pride in being the pioneers of the International Food and Beverage Processing Packaging Technology exhibition in Pakistan.
The show invites local or international importers, distributors, retailers and food service professionals to meet and connect with food manufacturers from around the world to find new business partners and shape the future of the Pakistan food and hospitality market.
It is an international trade exhibition that serves as a business and networking platform for companies and industry stakeholders to promote the latest products and services in the food and beverage industries. It serves as an avenue to showcase the growth and development of the food and hospitality industries, which is seen to contribute largely to country's GDP.
To the trade visitor this expo serves as a
perfect platform for sourcing, updating on the latest innovations & brand recall as they interact & engage with the exhibitors.
The event is organized in Karachi and is scheduled to take place in Lahore Expo Center between 29th – 31st May 2025.
IFTECH has been the choice of world’s leading technology suppliers to approach and engage with Pakistan’s food and beverage producers and brand owners. Technologies displayed at IFTECH have added commercial significance to the manufacturing value chains of numerous food and beverage producers of the country. The
resplendent effect of this modernization of processing and packaging techniques paced well with the changing consumer trends and many new variants of food and beverages have made forays into the buying list of consumers.
Exhibit Profile
Rice & Flour milling
Fruits & Vegetables
Packaging
Meat & Poultry
Beverages
Dairy and Dairy Products
Flavors & Ingredients
Snacks & confectionery
Bakery.
500+ industry powerhouses participating, from 50+ countries
Exhibition space doubles in size
Inaugural ISM Expert Stage and Festive Showcase added to reformatted show
ISM Middle East 2024, the region's sole and most awaited sweets and snacks trade event, will be taking place in a larger event space than ever before this year. Meeting increasing industry demand in the region, particularly ahead of the busy end of year holiday season, ISM Middle East cements its place on the regional industry calendar by moving to September, offering a larger, more dynamic platform for the sweets and snacks sector. This year’s event, taking place at Dubai World Trade Centre from September 24-26, not only boasts a bigger exhibition footprint, but also an
unprecedented amount of content, activations and networking opportunities.
ISM Middle East 2024 will showcase over 50,000 trending and in-demand confectionery products and innovative snack foods, from the broadest-ever cross-section of the manufacturing indus-
try. Sectors represented include chocolate products, confectionery, snack foods, biscuits and cakes, ice cream & desserts, and more, with an impressive line-up of over 500 exhibitors from more than 50 countries covering double the exhibition space of previous years.
Trixie LohMirmand, Executive Vice President, Dubai World Trade Centre commented: "ISM Middle East continues to solidify its position as the premier platform for the global sweets and snacks industry, especially in the rapidly-growing MENA region. The significant expansion of our exhibition space and introduction of new features like the ISM Expert Stage reflect our commitment to fostering innovation and providing unmatched opportunities for networking and knowledge sharing. We are excited to welcome both returning and first-time exhibitors, and we look forward to seeing the groundbreaking products and insights that will shape the future of this vibrant industry."
Reflecting ISM Middle East’s everincreasing global reach, 16 countries –including Indonesia, France, Vietnam, Ukraine and Colombia - will be represented at ISM Middle East for the first time, with new and returning exhibitors including Zar Group, Wawel, Gumlink, Guatemalan Candies, Eastern Sweets, Confiteca, Confiserie Seidel, Farolin, SIAFA, Alreem Chocolate and Chocolake.
ISM Middle East is a joint venture between Dubai World Trade Centre and Koelnmesse GmbH.
Gerald Boese, President and Chief Executive Officer of Koelnmesse GmbH, commented: “As we continue our longstanding and successful collaboration with Dubai World Trade Centre, ISM Middle East has become a crucial hub for the sweets and snacks sector in the MENA region. This year’s event sees a significant step change in scale, with an expanded footprint, a diverse range of exhibitors, and the launch of new features that cater to the evolving needs of the industry. Our commitment to excellence in trade fair management ensures that ISM Middle East remains at the forefront of industry trends, offering unparalleled opportunities for businesses to connect, innovate, and thrive in a dynamic market”.
For the first time ever, the ISM Middle East Expert Stage will convene thought leaders and representatives of leading brands in the sweets and snacks industry to discuss over 120 emerging global industry trends, such as how AI is disrupting the FMCG industry, mindful and green snacking, vegan certification, preci-
sion fermentation and potent fats in chocolate production, and vegan and gluten-free snacking, as well as provide insights in how to enter into and grow in MENA markets.
Expert speakers will include Cagdas Kardes, Chief Commercial OfficerMENA, Haribo; Balki Radhakrishnan, Vice President and Managing Director - Global Emerging Markets, General Mills; Yasser Hejazi, Director of Private Label, B2B and Global Sourcing, Panda Retail Company –Savola Group; Mitri Haddad, Managing Director – MEA, Bahlsen Group; Milad Rouhana, Managing Director - Middle East, Africa and Pakistan, Perfetti van Melle; and Burcu Yazici, Senior Director, Cereal – MENAT & SSA, Kellanova.
With over 30,000 wholesalers, distributors, importers, retailers, and foodservice professionals from across the MENA region expected to attend, this premier event offers unparalleled opportunities for sourcing the best sweets and snacks in the MENA region. These buyers, and sweets and snacks manufacturers from around the world, will also have multiple opportunities to establish new professional connections and strengthen existing ones through the ISM Middle East Meetings Programme, which is designed to connect exhibitors directly with relevant and hand-picked buyers on the show floor. The programme offers personalised connections with key figures in the industry, initiating an anticipated 2,000+ quality meetings and creating business networking opportunities.
The second day of ISM Middle East will also witness a celebration of those exhibitors pioneering innovation and
product development, across eight categories including new categories Best Brand Story, Best Organic Product, Best Traditional Product, Best Healthy Snack, and Best Packaging.
For influential buyers looking for the next big festive gift trends, ISM Middle East’s Festive Showcase will be a showcase of the most creative and innovative confectionery products, as well as another chance to network with suppliers from some of the largest brands in the world.
Tetiana Gurnevych, International Sales Director at Wawel S.A. commented: "As one of the leading Polish confectionery brands with a strong commitment to quality, innovation, and customer satisfaction, Wawel views this exhibition as a crucial platform to strengthen its presence in the Middle East market. As a brand we are already recognizable on some markets in this area. We see great potential to connect with new partners, distributors, and consumers. This event not only allows us to showcase and promote our beloved products but also to stay at the forefront of market trends and continue offering innovative, high-quality confections that align with the tastes and preferences of local consumers."
ISM Middle East is co-located with Gulfood Green - the definitive platform for global leaders in the food industry to drive sustainable innovation; and Private Label Middle East convening global food suppliers, private labels, and contract manufacturers from 40+ countries from September 24-26 at Dubai World Trade Centre.
Three key levers for a secure food supply: sustainability as determining factor in the financial landscape, public sector as a driver for more organic food and using compelling stories to market organic food.
The global food supply is under significant pressure due to environmental destruction and economic uncertainty. The congress at the forthcoming BIOFACH 2025, which takes place in Nuremberg from 11 to 14 February, will highlight the solutions offered by the organic food industry and the approaches that could potentially drive the sector forward.
Under the banner “Yes, we do!”, the congress theme of BIOFACH 2025 underscores the fact that the organic sector is a pioneer in the food industry not just in theory, but in day-to-day practice – and with complete dedication and conviction. The congress is also inviting all interested parties to submit proposed topics for the event via the “Call for Ideas”. The discussion about the impact of food on the
environment is highly topical. In its “Consumer Monitor Sustainability 2024”, the German Retail Federation (HDE) revealed that a third of respondents were not aware of the correlation.
As Ravi R. Prasad, Executive Director of IFOAM Organics International, emphasises: “Amidst the urgency of global challenges like the climate crisis
and food security, the organic sector is presenting workable solutions. Ecological practices not only offer an alternative, but also a proven route to resilience and sustainability worldwide.”
Tina Andres, Chair of the German Federation of Organic Food Producers (BÖLW), adds: “Organic practices have an immense potential for sovereign, sus-
tainable and future-proof food systems, which are currently facing enormous challenges. All players in the ecological value chain must adapt, reinforce and clarify their responses and demands to the community and policymakers. The congress theme for 2025 is an invitation to work together on effective policies for change. In this context, green finance, institutional catering and communication are the key levers.”
Invest in the future – not the past: Strengthening ecological transformation through financial and tax systems
Investments in ecological practices tap into new opportunities for innovation, long-term profitability, and climate protection. The financial sector has already recognised that massive sums need to be mobilised to transform the global food system and is developing guidelines for sustainable investments and directing resources into them. In this way, investors are actively helping to shape the future of sustainable food and agriculture systems. This congress stream will provide a detailed snapshot to help the industry formulate policy requirements.
Levelling the playing field: The public sector as pioneer in institutional catering
Catering in schools, old people’s homes, hospitals or canteens can make a considerable contribution to healthy
nutrition for the wider population. In this context, the public sector could be a pioneer for genuine change on the principle “organic first”. Sustainable and fairer food systems call for an understanding of the hidden costs of food. Conventional
farming often results in long-term ecological damage and increased costs for public health.
Stories that make sense: compelling storytelling
How can good stories, clear communication and targeted marketing help ensure that – even in times of crisis –long-term sustainability takes precedence over short-term savings? How can we convince even more people of the benefits of organic food – at a societal and individual level? These questions are at the heart of the congress stream: Stories that make sense!
Submit your topics now and help shape a sustainable future
The “Call for Ideas” is online. This is where you can submit your proposals for topics for the congress theme and all the forums at the BIOFACH Congress 2025 –for the traditional panels and for formats like workshops.
Asia’s premier fresh produce trade show will again host Meet Ups across key markets, kicking off with the ‘Summit in Chile’ in Santiago on 22 October 2024.
ASIA FRUIT LOGISTICA is launching its 2025 roadshow of Meet Ups to showcase industry innovation, deepen its connections in key markets, and build even
greater momentum for the trade show’s return to Hong Kong on 3-5 September 2025.
ASIA FRUIT LOGISTICA’s roadshow of Meet Ups kicks off with the Summit in Chile on 22 October 2024 in Santiago.
The regional event is organised by FRUIT LOGISTICA, ASIA FRUIT LOGISTICA, the
Chilean-German Chamber of Commerce and Industry, and Fruitnet, with the support of ProChile.
The Summit in Chile brings together key players for a day of networking and knowledge-sharing. The informationpacked content programme provides expert insight into export opportunities, the outlook for the Chilean cherry industry, logistics and supply chain enhancements, and new technologies and sustainable approaches to production.
Speakers include Natalia Cortés, Head of Asia and Oceanía Department of ProChile; Claudio Salas, General Manager of Joy Wing Mau Chile; Gonzalo Matamala Ortiz, General Manager for Asia Pacific and China at Giddings Fruit; and Gonzalo Salinas, Senior Analyst of Fresh Produce at Rabobank.
The Summit in Chile attracts industry leaders from Chile’s growing global network and presents first-rate opportunities for networking and business development. Registration is open for attendees looking to connect with us in Chile: https://www.asiafruitlogistica.com/meetups-2025-chile/
In 2025, the roadshow of Meet Ups gets under way with Fresh Produce India on 3-4 April in Mumbai. Organised by Fruitnet together with official partner ASIA FRUIT LOGISTICA, Fresh Produce India is the premier annual event for India’s fresh fruit and vegetable business, attracting more than 300 key decision makers.
Ho Chi Minh City is the next stop, with the first edition of Fresh Produce Vietnam on 13-14 May. The brand-new event, organised by Fruitnet, features a full-day content programme alongside a bustling B2B expo and study tours showcasing food retailing and fresh produce distribution in this fast-growing market.
ASIA FRUIT LOGISTICA’s Bangkok Meet Up in Thailand follows on 25 June. Rounding out the series, the China Meet Up heads to Guangzhou on 8-9 September directly after ASIA FRUIT LOGISTICA in Hong Kong.
ASIA FRUIT LOGISTICA Meet Ups bring together existing and future part-
ners to learn from industry experts and connect with regional players in key markets, creating even more opportunities and value for ASIA FRUIT LOGISTICA visitors and exhibitors.
Industry professionals across the entire supply chain are invited to join the regional ASIA FRUIT LOGISTICA Meet Ups on the road to Asia’s biggest gathering of the global fresh produce business at ASIA FRUIT LOGISTICA on 3-5 September 2025.
For more information on ASIA FRUIT LOGISTICA Meet Ups, go here: https://www.asiafruitlogistica.com/meetups-2025/
ASIA FRUIT LOGISTICA is the leading international trade show for Asia’s fresh produce business. The 18th edition of ASIA FRUIT LOGISTICA takes place on 35 September 2025 at AsiaWorld-Expo in Hong Kong. ASIAFRUIT KNOWLEDGE CENTRE is the brand-new content hub at ASIA FRUIT LOGISTICA powered by Asiafruit Magazine, ASIA FRUIT LOGISTICA’s exclusive Knowledge Partner. ASIAFRUIT KNOWLEDGE CENTRE is headlined by ASIAFRUIT CONGRESS, together with ASIAFRUIT BUSINESS FORUM and ASIAFRUIT SHOWCASE.
Strong interest among exhibitors, in particular from Asia, has prompted the world’s leading fresh produce trade show to consider further expansion.
Demand for exhibition space at FRUIT LOGISTICA 2025 is so strong, its organiser is considering further expansion into new halls at the Messe Berlin fair ground.
The world’s leading fruit and vegetable trade show returns to the German capital from 5 to 7 February 2025. And as the 31 July deadline to book exhibition space approaches, growth in reservations is especially big among exhibitors based in Asia.
“It’s such a joy to see so much interest in FRUIT LOGISTICA,” says event director Kai Mangelberger. “We can really feel the excitement.”
China is set to play a prominent role and is expected to top this year’s 2,400 square metres, which was its recordlargest participation in FRUIT LOGISTICA.
A high-ranking delegation from the country plans to visit the show, an encouraging sign for many in the industry after Germany’s apple exporters were granted access to the Chinese market this year.
The cost of exhibiting at FRUIT LOGISTICA remains in line with the 2024 edition, while trade visitor prices have stayed the same since 2022. That’s great news for the event’s three target segments: fresh produce, machinery and technology, and logistics.
“We’ve had so much interest,” Mangelberger continues, “it’s possible we might have to open new halls to accom-
modate everyone. We always have some late bookings, which does make it harder for those companies to get their desired position. So my advice is, book in plenty of time!”
That means the next meeting is likely to welcome even more than the 2,750 exhibitors from 94 countries who took part in FRUIT LOGISTICA last February.
And those Eurasian connections will also be strengthened at ASIA FRUIT LOGISTICA, which will take place in Hong Kong this September.
Exhibitors are invited to register for FRUIT LOGISTICA 2025 by 31 July 2024 latest. Full details on how to register for a stand can be found on the website of FRUIT LOGISTICA. The team of FRUIT LOGISTICA in Berlin or one of Messe Berlin’s 150 local international representatives around the world will be glad to assist.
FRUIT LOGISTICA is the leading trade show for the globalfresh produce business and and represents the entire value added chain of the fruit and vegetable sector, from producer to the point of sale. At FRUIT LOGISTICA 2024 more than 2,770 exhibitors from 94 countries displayed their products, services and technical solutions. Some 66,000 buyers and trade visitors from 145 countries took part in the event. The next FRUIT LOGISTICA will take place from 5 to 7 February 2025 in Berlin.
Berlin has been a trade fair destination for 200 years, and has been one of the most important such hubs for many decades. Messe Berlin – the state’s own trade fair company –conceives, markets and organises hundreds of live events every year. It strives to be an outstanding host for visitors at all events, generate optimal business stimuli, and provide fair conditions for everyone. This concept is reflected in the company slogan: Messe Berlin –Hosting the World.
Gulfood Manufacturing represents the pinnacle of the global food and beverage manufacturing industry evolution, offering a decisive destination for those seeking to accelerate the adoption of technology, and improve efficiencies and productivity to meet new challenges it offers a comprehensive showcase of solutions for industry professionals seeking to stay at the forefront of the industry and presents a prime opportunity to network, form new global partnerships, announce new innovative products, deals, collaborations and signings.
Over 100 of the industry’s most dynamic and engaging speakers will convene at the FoodTech Summit to discuss a powerful agenda ranging from food engineering innovations, metaverse factories of the future, food safety, circular ecosystems, sustainability-linked finance models, and much more.
Industry Excellence Awards
Bestowed to the industry’s revolutionary pioneers in recognition of innovative products and technologies that have made outstanding contributions to the industry, encouraging more companies to
invest in technological innovation to improve productivity, provide users with increased convenience and achieving sustainable development.
Visitors to the event will also be able to take part in curated Innovation Tours, giving visitors the opportunity to see the latest industry innovations, up close and personal, on the show floor.
Hall of Fame
For the very first time at Gulfood Manufacturing, experience the pinnacle of innovation and excellence at the Hall of Fame: A dedicated space at the Pavilion hall where you can bring your
groundbreaking technologies or innovations to life, through our dynamic screens. Highlight any of your innovations in ingredients, processing and packaging from the past decade that were a gamechanger in the industry and significantly transformed the manufacturing production process in the region.
Owning a screen space at the Hall of Fame gives you the advantage to capti-
vate the attention of a vast Gulfood Manufacturing audience of potential clients and partners who want to see the best in the business. As an exhibitor, seize the opportunity to gain unparalleled visibility, elevate your brand’s prestige, and solidify your reputation as the F&B industry’s market leader.
This is an exclusive opportunity and screen spaces are limited, so secure your
screen time now and be part of this extraordinary event.
Email gfm@dwtc.com for more information or to reserve a space.
Join us from 5 – 7 November 2024 at Dubai World Trade Centre for the most significant gathering of its kind in the MEASA region.
On-stand, Hall 3, Booth A3-4, Sidel will be showcasing world-class aseptic packaging solutions and complete line innovations at Gulfood Manufacturing at the Dubai World Trade Centre from 5 - 7 November 2024.
Gulfood Manufacturing is the leading platform for the food and beverage industry in the Middle East and Africa (MEA) region bringing together industry professionals to embrace the next era of food manufacturing, digital adoption and breakthrough innovations.
With five decades of packaging and processing expertise, Sidel will spotlight its industry-leading Aseptic Combi Predis technology on-stand, as well as highlighting its Super Combi advanced technology solution for high-speed water and carbonated soft drinks.
As well as showcasing its award-winning bottle designs, Sidel will offer insights into how customers can maximise data intelligence and artificial intelligence (AI) to achieve their ESG goals.
Sidel will be highlighting on-stand the Aseptic Combi Predis, an integrated blow-fill-cap solution for PET bottles that incorporates Predis™ dry preform sterilisation.
Sidel’s Aseptic Combi Predis was selected by China’s leading food brand renowned for coconut milk, Hainan Chunguang Foodstaff Co., Ltd. Bottled in Sidel’s premium PET design in a 350ml format, Hainan Chunguang’s installation can run 28,000 bottles-per-hour (bph) and the ability to utilise dry technology over traditional wet aseptic solutions helped the customer meet economic and environmental sustainability targets.
New innovations in high-speed water and carbonated soft drinks
With water and carbonated soft drinks (CSD) remaining two of the world’s most valuable beverage categories, Sidel will demonstrate its next-generation Super Combi technology to on-stand visitors.
The Super Combi integrates five process steps - preform feeder, blower, labeller, filler/capper and cap feeder - into an all-in-one smart system. To deliver this self-optimising performance and increased long-term value, it combines intelligent automation with innovative technologies to advance production and maintenance services.
Utilising the Super Combi solution, Sidel installed the fastest PET complete bottling water line in the Middle East, Africa and Asia for Mai Dubai, helping the UAE-based company take the next step towards becoming the region’s number one water brand.
Through a film demonstration, visitors to the stand can witness how the line fills 86,000 bottles per hour (bph) in three different formats (200ml, 330ml and 500ml), with the optimal use of space, high consistent quality, and efficiency with flexibility.
Digitalisation, AI and ESG goals
“As well as seeing Sidel’s latest products and packaging innovations first-
hand, visitors to our stand can also take the opportunity to discuss wider industry issues, challenges and solutions with our experts,” comments Bassam Oussaifi, VP Sales, Middle East and Africa, Sidel.
“This could include how to maximise and integrate data intelligence to achieve peak performance through Sidel’s unique Evo-ON® cloud suite; how the switch to recycled PET can help meet sustainability targets; or how production solutions can help manufacturers stay ahead of changing packaging waste regulations.”
Sidel’s Evo-ON® is an AI-driven solution allowing real-time data analysis, predictive insights, and smarter decision-making in production environments.
Award-winning innovative packaging bottle design
Visitors can also examine StarLITE®R, Sidel’s ultra-efficient 100% rPET bottle for carbonated soft drinks which addresses the challenges associated with working with recycled content.
With over 45 years of experience in PET packaging, Sidel has developed a deep understanding of recycled PET resin characteristics and its impact on bottle production. As a result, StarLITE®R allows CSD producers to switch to rPET bottle production with ease and efficiency, while
significantly reducing the impact on product quality or packaging integrity.
Sidel is a leading provider of equipment and services solutions for packaging beverage, food, home and personal care products in PET, can, glass and other materials.
With over 40,000 machines installed in more than 190 countries, we have nearly 170 years of proven experience, with a strong focus on the factory of tomorrow with advanced systems, line engineering and innovation. Our 5,500+
employees worldwide are passionate about providing solutions that fulfil customer needs and boost the performance of their lines, products and businesses.
Delivering this level of performance requires that we stay flexible. We continuously ensure we understand our customers’ changing challenges and commit to meeting their unique performance and sustainability goals. We do this through dialogue and by understanding the needs of their markets, production and value chains. In turn, we apply our solid technical knowledge and smart data analytics to ensure lifetime productivity reaches its full potential.
Visit Cama Group at Gulfood Manufacturing, Sheikh Saeed Hall 2 – S2-B3
Becoming a best-in-class supplier for the MENA region. This is the goal of Cama Group at Gulfood Manufacturing 2024. The new Chief Sales Officer for the Middle East and North Africa, Ahmed Mohamed, will be attending the event. On showcase, the IF315 packaging machine.
Cama Group prepares to make a grand entrance at Gulfood Manufacturing 2024. The Italian packaging company – a longtime exhibitor at the Dubai trade show – will occupy a 112-square-meter stand this year, where the IF315 packaging machine will be showcased in a demo mode for the very first time. But it doesn’t end up here: from November 5 to 7, visitors will be guided through Cama’s latest technologies by Alessandro Bernini, Area Manager for the Indian market, and Lorenzo Birro, Key Account Manager for bakery & confectionery. Joining them, in his first official appearance in the role, will be Ahmed Mohammed, Cama’s new Chief Sales Officer for the Middle East.
The goal is clear: to become a strategic supplier of packaging technologies for the region’s food industry and also to showcase the key advantage of our offering; the ability to provide fully customizable, turn-key production systems, from processing operations to palletizing.
In the Middle East and North Africa, we have several installations, primarily in the bakery & confectionery sector. The IF 315 packaging machine, specifically designed for this segment, is a monobloc unit consisting of a single compact island. The
Ahmed Mohamed; Vice president of Sales
monobloc integrates multiple functions into a single frame, making it an extremely compact and versatile machine. It is capable of forming boxes, which are then loaded by two in-house delta-type robots, sealed, and sent to the next production stage.
The machine, which will be showcased in a demo mode at the Dubai exhibition, can process up to 40 boxes per minute with a maximum input of 400 products. It is equipped with Cama’s most advanced BTG (BreakThrough) Generation engineering and, thanks to its quick format change capability, can adapt to a variety of product types: from bakery and confectionery to coffee, as well as other food and non-food sectors. This machine will allow visitors at Gulfood Manufacturing to experience firsthand what Cama’s top technology can offer and to personally test our quality, with the on-site support of three highly qualified Cama experts. Launched in 2017, Cama’s BT Generation is now in its second release, featuring a refined design and even more efficient robotics. Additionally, augmented reality packages have become “a company’s signature. Over the years, we’ve worked on fully digitizing all aspects that contribute to
efficiency and productivity, from format changes to maintenance operations. These functions have been integrated into a tablet that serves as a user interface, which we will also be pleased to showcase at the Dubai exhibition
Among future business developments is the idea of creating a branch company exclusively to providing integrated lines, with dedicated purchasing and management logics. One of the latest solutions presented in this regard is the MTL Monoblock: a true revolution in adaptive production, made possible through a partnership with B&R, an expert in industrial automation and mechatronics. The MTL Monoblock is capable of handling 2,000 products per minute. This is thanks to the innovative ACOPOStrak track system with independent magnetic shuttles developed with B&R, which allows maximum flexibility in managing different kinds of packaging containing up to three different types of products.The machine, built for a major client in the United States, will be on display at Pack Expo, in Chicago from November 3 to 6 at the Cama Group stand.
Join us to explore the complete range of solutions for the food industry!
IMA is excited to announce its participation in Gulfood Manufacturing 2024, where we will showcase our latest processing, filling, dosing, and packaging solutions for the food market. Visit us at Hall S3 – Booth D36 and let our specialists guide you through our offerings.
IMA serves the international food market with top-tier platforms designed to meet a variety of industry needs. We offer a comprehensive array of processing, filling, and packaging technologies across key sectors, including tea and herbs, coffee, confectionery, stock cubes, dairy and baby food, bakery, protein, produce, and more. Leveraging synergies and integrations with Group companies, IMA provides fully engineered turnkey solutions that deliver highly efficient packaging lines.
Gulfood Manufacturing will allow us to present a range of specific solutions and innovations for the tea and coffee market, building on our world-leading position in the tea business and the renowned expertise of the IMA Coffee Hub in processing and packaging solutions.
Companies within the IMA FLX HUB (IMA Ilapak, IMA Eurosicma, and IMA Record) will showcase innovative horizontal and vertical solutions for flow wrapping food products. Additionally, IMA Gima’s experts will highlight new developments in packaging technologies dedicated to the confectionery industry.
Our specialists from IMA Benhil and IMA Corazza will unveil processing and packaging solutions for butter, margarine, cheese, and stock cubes, while IMA Erca, IMA Fillshape, IMA Gasti, and IMA Hassia will showcase their most innovative fill & seal solutions for pre-formed cups, as well as form, fill & seal solutions for the beverage, baby food, dressings, and sauces markets.
No line would be complete without the essential technologies to finalize the packaging process. The IMA END OF LINE hub (IMA BFB, IMA Ciemme, IMA Mespic, IMA Phoenix) will demonstrate
technologies designed to preserve contents and containers while providing a variety of packaging solutions, from display boxes to wrap around cases, trays with internal or external lids, RSC cases.
IMA Ilapak
Vegatronic 2000 ML
The most innovative intermittent vertical bagging machine, offering high flexibility in pack formats with an open frame structure that ensures easy accessibility for cleaning and maintenance.
The Vegatronic 2000 ML is capable of switching between heat sealing films and LDPE, as well as between pillow packs and stand-up pouches, featuring easy, tool-free changeovers. This machine is designed for producers seeking a high level of flexibility and includes a straightforward film path, installed tutorial videos for operational procedures, and the ability to retrofit the screen onto a remote portable device.
The PDP24 is the latest in a long line of IMA Corazza solutions for the food industry. Like any cube, there are six sides to the story and the PDP24 boasts as many reasons for making it the number one choice. Equipped with just 24 punches, the PDP24 processes up to 4000 ppm, ensuring consistent quality and cube weight thanks to separate preand final compression stations. With a minimal footprint, it also guarantees excellent hygiene standards, keeping the production area segregated from the mechanical housing. Through a more efficient design, maintenance costs and requirements are much lower and
punches and dies can be easily replaced. Able to adapt reliably to different powder types, the press allows for fast format changeovers between 4 and 13 grams as well as non-standard sizes.
IMA OpenLab is the IMA Group’s network of technological laboratories and testing areas focused on research in sustainable materials, technologies, and production optimization processes. OpenLab aims to create partnerships, discover new sustainable materials, share expertise, and foster synergy with packaging manufacturers and customers. The Lab is dedicated to maximizing equipment efficiency, reducing waste while maintaining pack presentation and seal integrity, and testing new, more sustainable packaging materials.
IMA ZERO is the evolution of the IMA commitment to Sustainable Development. Its ultimate goal is minimizing environmental impact in industrial manufacturing and promoting a working habitat that always puts people at the center. During Gulfood Manufacturing 2023, the focus will be on IMA NOP (No Plastic program) and on the sustainable packaging solutions developed for the food industry.
GNT will showcase its plant-based EXBERRY® color rainbow with an array of eye-catching food and drink concepts at Gulfood Manufacturing 2024 (5-7 November 2024, Dubai World Trade Centre).
EXBERRY® colors are made from nonGMO fruit, vegetables, and plants and can be used to achieve vibrant shades from across the whole spectrum. They are halal-certified and can provide an effective replacement for artificial colors and carmine in almost any application, including confectionery, baked goods, and dairy products.
At Gulfood Manufacturing, GNT (hall 6, stand B6-48) will give visitors the chance to sample popcorn, potato chip, and beverage concepts featuring a range of EXBERRY® colors.
Santhosh Thankappan, Sales Director at GNT Middle East, said: “Our vibrant rainbow of EXBERRY® coloring solutions can deliver spectacular results in food and drink while supporting natural ingredient lists. We’re excited to give Gulfood
Manufacturing visitors the chance to experience the power of plant-based colors through our innovative concepts.”
GNT offers full support to manufacturers when making the switch to EXBERRY® to simplify the product development process. The company’s experts will be available throughout Gulfood Manufacturing to discuss technical issues and beyond for specific project requirements.
Santhosh Thankappan added: “We’re committed to helping food and beverage brands succeed by delivering the vibrant, high-performing, and cost-effective coloring solutions they need. We pride ourselves on delivering exceptional service every step of the way, from color matching and stability testing through to regulatory matters and quality documentation.”
TNA Solutions, a global leader in complete processing and packaging solutions, will showcase its innovative offerings at this year’s Gulfood Manufacturing. From 5–7 November, visitors to Hall 4, Stand A4-A will discover how their advanced systems can help snack and confectionery producers to optimise output, decrease downtime and enhance production efficiency.
The stand will exhibit key highlights from TNA’s extensive portfolio. The company’s flagship tna robag® 3e vertical form fill and seal (VFFS) packaging system will be on display, allowing visitors to see the high-performance system in action. The tna robag® 3e delivers the fastest speeds in the industry, capable of producing up to 250 bags per minute with a high degree of accuracy that lowers product waste levels to 0.1%.
The tna intelli-flav® OMS 5.1 onmachine seasoning system will also be showcased. It offers snack manufacturers comprehensive control over the seasoning of their products, with a mass-based gravimetric spraying and dry seasoning control method to apply precise measures of seasoning or oil based on a pre-defined recipe. This, coupled with intelligent control and monitoring software, enables
manufacturers to efficiently adapt seasoning to specific products — all while offering high speeds and load capacity. Moreover, the tna intelli-flav® OMS 5.1 offers both powder flavouring and liquid oil in a single drum, allowing brands to effortlessly adapt to changing consumer demands.
These two systems, representing distinct stages of the snack production process, offer a snapshot into TNA’s unique ability as the ability to partner complete solutions for food manufacturers.
“There is a constant need for manufacturers to innovate to stay ahead of changes in the market,” explained Palani Karai, General Manager – TNA MENA. “We’re seeing significant advancements in snack production coming from the Middle East, with brands preferring to partner with global end-to-end solution providers, to reduce total cost of ownership, stay ahead of market trends and support future expansion plans.”
TNA’s recent success in the region was a partnership with the Egyptian National Services Projects Organisation (NSPO) Ministry of Defence last year to implement two innovative lines for potato products. The first line designed for hash browns and rosti, can produce 2 metric tonnes an hour and, the second line for french fries and wedges, produces up to 10 metric tonnes per hour, for the Egyptian Army. TNA supports every step of the production process, from washing and de-stoning to final product packaging.
It is this end-to-end expertise that the brand aims share with visitors at Gulfood Manufacturing 2024.
Ams Flavours & Fragrances Pvt Ltd
A leading manufacturing of flavors, food colours and fragrances. AMS is dedicated to The Pursuit of Excellence in every area of our business to provide our customers with superior consumer understanding and the highest quality products and service. The company was first established in 1880 by Sheikh Hoosainbhoy Bandukwala who first established contacts with BUSH during a Royal Entourage to attend the Coronation of King George VI and thus opened up W J Bush network in what it was then North India. An extensive network of traders from Karachi across to Delhi Since partition of the Indian Sub continent this retail network continues to efficiently work in Pakistan The retail trade. our main activities……. Blending/compounding vast range of flavours, food colours & fragrances. Our distribution and marketing comprise of these products along with Essential oils, aroma chemicals, food ingredients. We have built up over past few years with International associations.
Barkat Frisian
Pasteurized Egg Company (Pvt) Ltd
Barkat Frisian
Pasteurized Egg Company (Pvt) Ltd is a Pakistani - Dutch Joint Venture company producing high quality EU grade egg products in Pakistan. The company is the largest pasteurized egg products manufacturer in Pakistan. We produce whole egg, egg yolk and egg white in liquid/fresh and frozen categories. Our products can be used in any food application where eggs are used such as breakfast, biscuits, cookies, cakes, mayonnaise, sauces, ice-cream. We are certified for HALAL, FSSC 22000, ISO 9001, Sadex Currently exporting our products all over
GCC countries and looking for distributors for Asian and African markets
In 1967, Rainbow Chemicals embarked on pioneering efforts to establish indigenous food color production. This endeavor evolved into a blending house where food colors were meticulously crafted and packaged under the brand names foocal and raincol.
MATERIAL HANDLING SYSTEM & ROLE
OF CHERRY Any industrial activity cannot be imagined without Material handling. With the growing emphasis on productivity, profitability, product consistency and quality, energy conservation, eco-preservation and efficient deployment of financial and human resources, Material handling has come to play a crucial role in every industry & organization.
East Rice Company is the one stop solution to all your rice import requirements. Our diverse and coherent milling & processing facilities and our expertise in the rice sector are our strongest assets. East Rice Company is one of the largest, well organized and fastest growing rice export houses in the Pakistan but success does not came overnight, it is the result of decades of hard work and commitment. Rice business has been in the family for four generation it all started with Muhammad Din Narang well before the partition of Subcontinent, with the passage of time East Rice Company has grown into a mammoth group in the rice sector. At East Rice Company we do not resist change. We are always adopting new innovations to stay ahead of the competition. Our milling facilities are equipped with
modern, state of art paddy drying, parboiling and steam rice units.
Fazlee Sons, established in 1948, is a leading printing, packaging, and converting company in Pakistan. Originally a traditional printer and binder, it has evolved into a pioneer in flexible packaging. By introducing technologies like Flexo Printing in the 1980s and installing Pakistan's first Box Pouch machine in 2013, Fazlee has paved the way for others in the industry. The company offers high-quality packaging materials to FMCG, corporate, and multinational companies. With a combination of proven experience and innovative solutions, Fazlee provides complete packaging services from concept to delivery. We have helped Pakistani exporters compete globally by offering competitive packaging solutions. Today, Fazlee exports its products to Europe, Africa, and the Middle East, maintaining a competitive edge with cutting-edge technology and unmatched industry experience.
We are FrieslandCampina, nourishing by nature. To fulfill our purpose to create better nutrition for the world. Our organisation has branch offices in 29 countries and employs 20,928 people. And our products find their way to more than 100 countries. We supply consumer products, such as milk, evaporated milk, cream, yogurt, cheese, infant nutrition and desserts, products for the professional market, such as cream and butter products, ingredients such as AMF and semifinished products. We have branches in 29 countries and export to more than 100 countries worldwide.
Founded in the 1970s, General Machines has been a pioneer in the manufacturing of horizontal flow pack
machines. Starting with mechanicallyoperated systems, we have continuously evolved with the latest advancements in technology, introducing our first electronic machines in 2013. Our cuttingedge solutions have revolutionized the packaging industry in Pakistan, offering unparalleled precision, efficiency, and reliability. In addition to our established product range, we have expanded into automated feeding systems, including state-of-the-art aligner conveyors, providing a complete packaging solution for diverse industries. At General Machines, innovation is at the heart of everything we do, and we remain committed to advancing Pakistan’s manufacturing capabilities with our high-quality, technologically advanced machinery.
H.I. Pvt. Ltd.
Founded in the 1970s, General Machines has been a pioneer in the manufacturing of horizontal flow pack machines. Starting with mechanicallyoperated systems, we have continuously evolved with the latest advancements in technology, introducing our first electronic machines in 2013. Our cuttingedge solutions have revolutionized the packaging industry in Pakistan, offering unparalleled precision, efficiency, and reliability. In addition to our established product range, we have expanded into automated feeding systems, including state-of-the-art aligner conveyors, providing a complete packaging solution for diverse industries. At General Machines, innovation is at the heart of everything we do, and we remain committed to advancing Pakistan’s manufacturing capabilities with our high-quality, technologically advanced machinery.
Halal Gelatin Pvt. Ltd.
Founded in 2002, HALAL GELATIN is Pakistan’s leading manufacturer of highquality Halal Edible Gelatin, known for its innovative production from hides and bones. We proudly meet the highest standards set by the Gelatin Manufacturers Institute of America (GMIA), Gelatin Manufacturers of Europe (GME), and the Islamic Food and Nutrition Council of
America (IFANCA). With cutting-edge research and development, HALAL GELATIN is the only company in Pakistan to achieve a 300 bloom quality from hides. Our products, certified by the FDA, BRC, ISO 9001:2015, FSSC 22000: V6, GMP, HACCP, QMS, and various Halal authorities, are exported worldwide, including the USA, UK, Europe, China, and the Middle East. Expanding our operations to the USA and Dubai allows us to serve a global clientele, consistently delivering unparalleled quality, reliability, and customer satisfaction. HALAL GELATIN continues to set the benchmark for Halal Gelatin production, meeting the evolving needs of diverse industries.
Iftekhar Ahmed & Co.
Over six decades, we’ve grown from a small family business into one of Pakistan’s largest exporters of fruits and vegetables. Our commitment to quality is evident in every stage of our production process. We cultivate premium fruits like Kinnows (Mandarins) and Mangoes, and vegetables such as Onions and Potatoes. Beyond our own crops, we source top-quality fruits to produce pulps, concentrates, juices, nectars, fruit drinks, and sauces. Our fruit beverages, available in both Tetra Pack and PET bottles, are enjoyed globally, ensuring freshness and superior quality with every sip. These products serve renowned food and beverage companies and meet the needs of everyday consumers. From farm to table, we uphold the highest standards to deliver exceptional products that satisfy both industry clients and individual preferences.
IGLOO PAKISTAN is one of the pioneer in producing ice-cream, frozen flat bread and industrial chocolate. At Pakistan Dairy Products we understand the importance of offering premium quality frozen and Industrial chocolate products that not only meet but exceed the expectations of our clients. With our state-of-the-art facilities and a team of experienced professionals, we ensure that our products maintain their freshness,
flavor, and nutritional value throughout process. Our product range includes an extensive range of Paratha’s that is Plain paratha, wheat paratha, Aalo paratha ,chocolate paratha and we have added range of chocolate for B2B which include Dark chocolate slab, milky chocolate slab, chocolate coating(Magic shell) , premium coating & chocolate chips.
Irfan Yaqoob (Motiza)
Life is like a precious pearl. [Moti] Pearl (Za] Life; Here at Motiza, we believe i t is of utmost important for an individual to make valuable lifestyle choic- e s tobuild the ground base for a happier and a healthier self.
Belongingfrom the roots of herbal trading since over 40 years, Motiza has b e e n branched out in 2019. Situating our focus around sourcing the finest r a wingredients and the assembling of essential oils, Bakhoor's and, herbal care products for body &hair allows us to manufacture end-con- sumer products under highquality control and fulfil the needs of our cus- tomers. Committing to deliver expertise, our team strives to become the leading voice of our customers' requirements in order to empower the im- portance of a wholesome lifestyle.
In 1957, Kamil & Sons was established to fulfill the growing demands of paper and board in the newly born state of Pakistan. In the next few years, the company started to expand the business and production capacity by integrating skilled manpower and machinery. And it emerged as a trusted name in the industry having an extended clientele. After years of delivering quality paper and board products, the founders planned to extend the operation in more sectors. Hence, the vision of Kamil Packaging (Pvt) Ltd was ascertained.
Lautier Flavours & Ingredients (Pvt) Ltd
Lautier Flavours is a distinguished leader in the creation and production of premium flavors for the food and beverage industry. Driven by a passion for innovation and a dedication to excellence,
we offer a wide array of flavor profiles designed to elevate culinary experiences. Our team of expert flavorists and food scientists blends artistry with scientific precision to craft unique and high-quality flavors. Committed to staying at the forefront of emerging trends and consumer preferences, Lautier Flavours ensures that our offerings are both delightful and aligned with market demands. We pride ourselves on delivering exceptional, tailored solutions that meet the evolving needs of our clients, making us a trusted partner in flavor development.
Lunwa Biz Packaging is a pioneering manufacturer of Cardboard Edge Protectors in Pakistan, offering efficient and durable solutions for safeguarding goods during storage and transportation. As our flagship product, our cardboard edge protectors provide superior strength and stability, ensuring that products remain secure and undamaged, even under heavy load conditions. We proudly export to the UAE, Sri Lanka, Afghanistan, and other countries. In addition to Cardboard Edge Protectors, Lunwa Biz Packaging is also a key intermediary for sourcing and distributing a wide range of packaging machinery and materials. Our range of products includes, * Dunnage Air Bags * Press Wood Pallets * Self Adhesive Tape * Stretch Wrap Film * Semi & Fully Auto Strapping Machines * Carton Sealers * Automatic Filling Machines & Packing Lines * Shrink Wrap Machines * Pallet Wrapping Machines * Automatic Bag Sealing Machines * Auto Bottle Labelers * Label Applicators.
Matco Foods Limited
Matco Foods – is a leading producer of Organic and Conventional Rice Syrups, Brown Rice Syrup, Rice Proteins, Tapioca Syrup, Sweeteners, Corn Starch, Maltodextrin, Dextrose Monohydrate, Basmati Rice, Himalayan Pink Salt, Seasoning, Spices, Gluten-free Flours and functional ingredients predominantly. Our Products are Non-GMO and contain no artificial ingredients. We are Certified in Organic by the Control Union, USDA &
EU, and also certified by KOSHER, HACCP, BRC, & ISO. Our Products Include: • Organic Rice Syrups • Rice Syrup • Brown Rice Syrup • Rice Protein • Sweeteners • Tapioca Syrup • Corn Starch • Tapioca Starch • Maltodextrin • Dextrose Monohydrate • Basmati Rice • Long Grain Rice • Seasoning • Pink Salt • Spices • Recipe Mixes • Ginger & Garlic Powder & Pastes.
For over 60 years, Metatex has developed custom flexible packaging for businesses small and large, across the globe. Our varied manufacturing capabilities enable us to offer end-to-end innovative flexible packaging solutions to a range of industries and for a variety of applications, including confectionery, food & beverages, pharmaceuticals, cosmetics, agro-textiles and others. We offer premium-quality high-impact packaging & printing at competitive prices, with a strict adherence to international standards.
MFTC gums / Guar Gum manufacturers
Global Leader in Rice Exports and Specialty Food Ingredients Meskay & Femtee Trading Co. (Pvt) Ltd’s diversified porfolio includes: 1. Rice Processing and Export: We are largest exporters of an extensive range of rice varieties to over 100 destinations. 2. Guar Gum Production: Our state-of-the-art facilities manufacture premium Food Grade Guar Gum Powder, 3000 to 5000 cps. 3. Sesame Seeds Export: We process and export high-quality Sesame Seeds. 4. Wheat & Corn Trading: Our expertise extends to trading and export of Wheat and Corn. - FSSC 22000 - ISO 9001 - HACCP - KosherHalal - Sedex Infrastructure and Capabilities: - 8 processing and manufacturing facilities in southern and central Pakistan. - Over 200,000 square feet of storage warehouses in addition to 25 silos - Advanced quality control laboratoriesStrong logistics and supply chain management - Network of offices and representatives in Europe, China and other strategic destinations.
Private Limited, Based in Lahore Pakistan, having 16 years Production experiance in manufacturing of Food Essences, Flavoring Emulsions, Flavoring Compounds, Taste Essentials, Sugar Alternative Sweeteners, Seasonings Top Notes & Beverage Premixes. We are the biggest exporter from Pakistan in our field, as well as serving the local industry.
In 2002, Roshan Packages Limited installed the first of its kind corrugated box plant in Lahore. Our founders who were exporting fresh fruits and vegetables through Roshan Enterprises, observed that fruit was being wasted and damaged in the supply chain due to unhygienic wooden packaging. RPL continued its journey of excellence by offering international standard packaging and continued to innovate and expand to become one of the leading packaging solution providers in Pakistan. Roshan’s Corrugation Packaging Plant is the one of the only facility in the SAARC region to use European technology and machinery to produce high quality plain and printed cartons according to our clients’ needs. The Flexible Packaging Plant utilizes an Eight Color Rotogravure Printing Machine, a Solvent Less Laminator, Solvent Base Laminator and Slitting Machine to create customized wrappers, sachets and pouches. The plant is based on German standards to offer a host of immaculate packaging solutions.
Saga international is the leading association representing the international Packaging/ Printing community. Our goal is advance Industry growth through standards professional Competence time and cost saving solutions. In order to enhance efficiency of industries, Saga international has introduced specialized packaging/printing
Machine and packaging materials dedicated to major areas within the industries.
SAMA Packaging Machines & Processing Systems: Your Trusted Partner
SAMA Packaging Machines & Processing Systems, founded by Mr. Muhammad Umer Sama, has over 40 years of experience delivering turnkey packaging solutions. Since 1978, the company has grown from a small enterprise to a leader in the packaging industry, expanding into various sectors. SAMA specializes in custom solutions for the FMCG, Pharmaceuticals, Snacks, and confectionery industries. Its commitment to innovation and quality has driven global expansion across Asia, Africa, the Middle East, and Europe. With modern manufacturing facilities and a strong client-centric focus, SAMA delivers high-quality, costeffective packaging machinery. The company is dedicated to sustainable growth, offering custom design, manufacturing, and after-sales support. SAMA continues to thrive by maintaining its core values of professionalism, dedication, and excellence, ensuring its position as a global leader in packaging solutions.
Speciality
Printers is known as one of the pioneers of Flexible Packaging material running uninterruptedly since 1970. Our facility expanding over 30,000 sqm in the heart of Karachi. We are ISO 9001, 22000 from SGS & Halal Sanha certified company. We are catering to MNC. FMCGS, Export and domestic based clients. Our production line includes following: Rotogravure Printing Machine, CI Flexo, Solvent less/Dry/ Water base lamination, 5 layer blown film line for PE, Polyolefin Shrink, PE Shrink, Stretch, BOPA, films, Bag making facility includes all types of pouches including box pouch, state of the art lab includes GC, OTR & WVTR ana-
lyzer. Our wide range of products and speciality includes, Laminates, bubble and toffee paper, barrier films application, pouches, liquid pouches, meat packaging, dry fruit and food packaging, pet food and other various application. In 2024 we installed 1 MW of solar for clean energy to achieve carbon footprint goals.
Leading Pakistani Food Flavoring & Fragrance Manufacturer We are SMC –leading Pakistani food flavour & fragrance manufacturer, committed to developing high-quality flavours & fragrances with more than 100 years of experience in the industry. Tracing its roots to Pre-Partition India, SMC has been combining the experience passed down from one generation to another with modern technologies to deliver the best sensorial experience. In Standard Manufacturing Company, Our commitment to excellence is backed by our love for food that tastes great and fragrances that leave a signature impact.
The Trade Development Authority of Pakistan (TDAP) develops and promote exports via focus, synergy, and the collective wisdom and counsel of its stakeholders. In addition to aggressive, innovative, and proactive marketing and promotional efforts, it achieves the objective of rapid export growth through interaction and coordination with respective public and private-sector stakeholders, and enhancing the value of products and services by broadening the export base of the products; improving the capability and capacity of the supply base of goods and services; fostering supportive export
culture and facilitation; and encouraging export oriented foreign investment and joint venture,
Vibgyor - A Brand of Far Eastern Impex
Vibgyor - A brand of Far Eastern Impex has been a trusted name in Pakistan’s food industry for over 65 years. We provide high-quality ingredients to food manufacturers globally, ensuring compliance with ISO 9001, ISO 22000, FSSC, and Halal certifications. Our stateof-the-art facilities and dedicated R&D team, comprising expert food technologists, innovate to meet the evolving needs of the food industry. We offer a diverse portfolio, including food colors, flavors, syrups, emulsifiers, stabilizers, and seasonings, tailored to the specific needs of confectionery, bakery, dairy, snacks, meat & poultry, processed foods, and pharmaceuticals. Serving both local and international markets, Vibgyor’s products are used by leading brands in Pakistan and exported to countries like the USA, Kenya, UAE, Sri Lanka, and Ethiopia. With a legacy of quality and commitment to innovation, Vibgyor continues to be a reliable partner for food manufacturers worldwide.
Wiztec food solution is Pakistan’s biggest dehydration plant, which is equipped with a state-of-the-art manufacturing Plant. Our production unit is situated at Dera Ismail Khan. We are specialized in herbs, spices, and vegetable dehydration and provide in various forms i.e flakes, coarse and fine powder. It is available in different packaging and customized packaging as well.