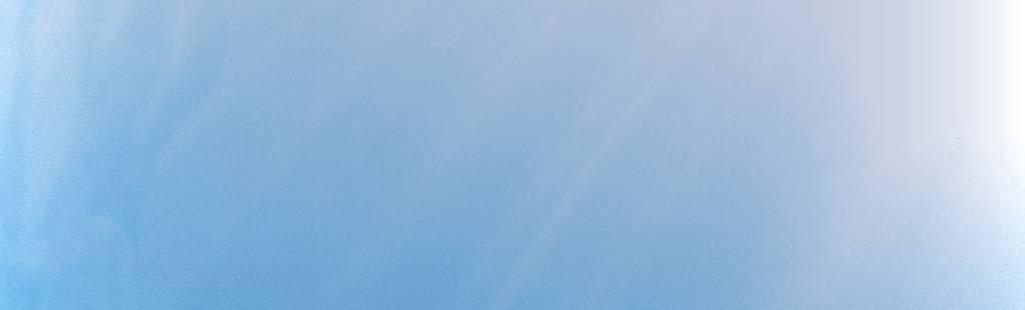
12 minute read
Optimising The Sustainability Of Wastewater Treatment
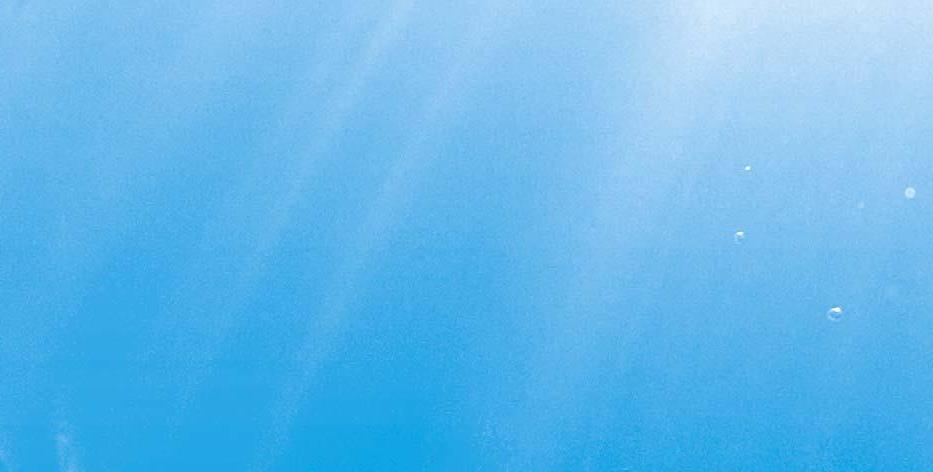
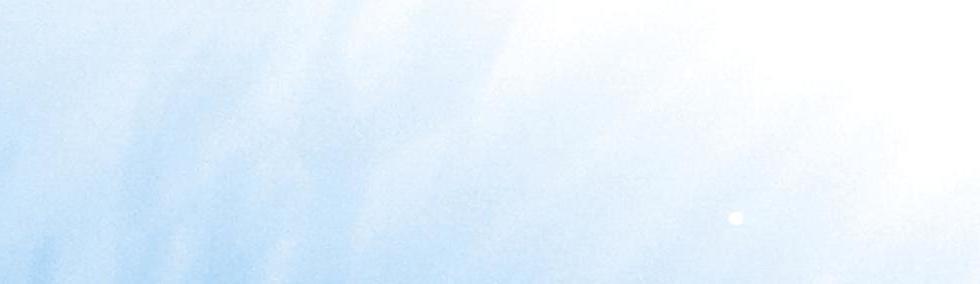
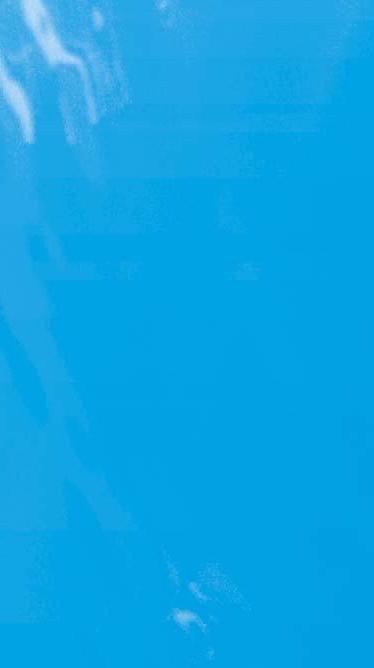
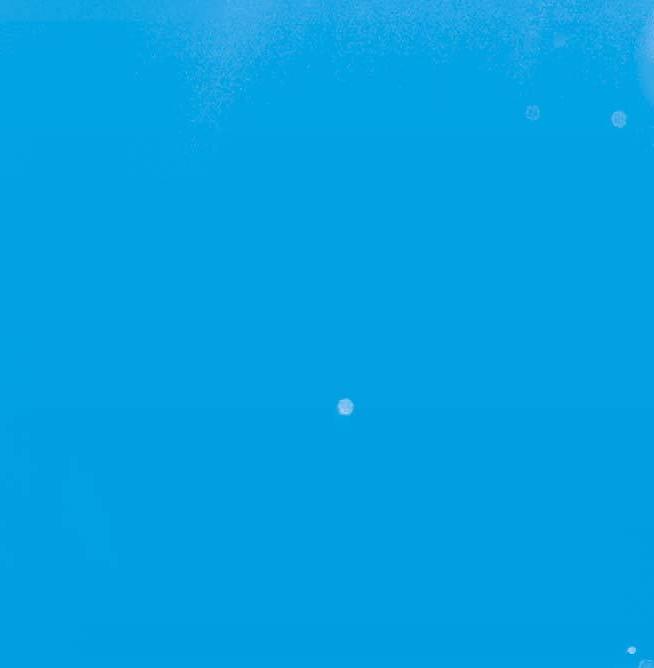

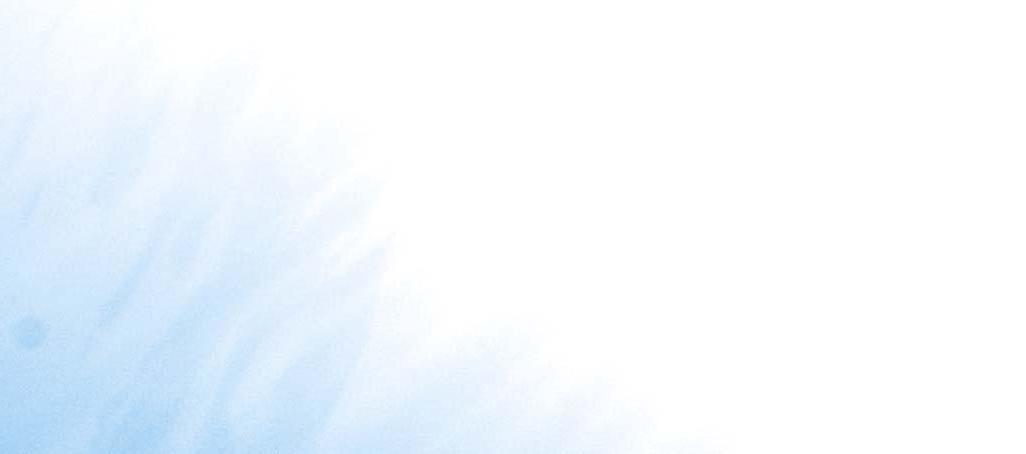

OPTIMISING THE
SUSTAINABILITY OF wastewater treatment
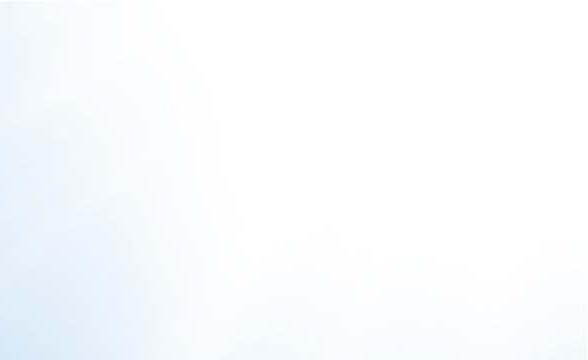
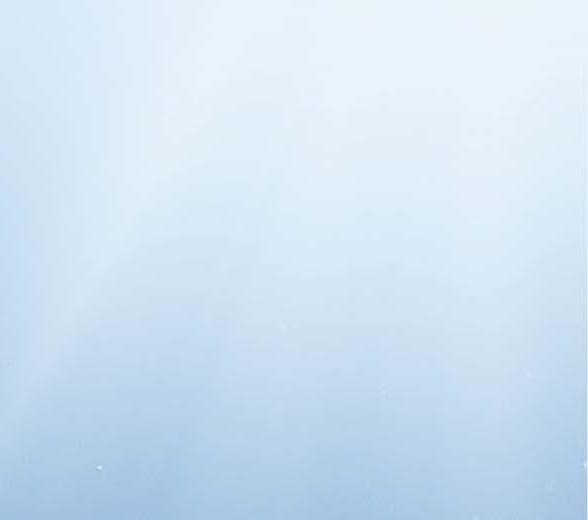
Alissa Pallagrosi, Andrea Carotti, David Lehmann and Joseph Lehmann, Saipem, look at the development of electrochemical technology designed to remove ammonia and urea contaminants from fertilizer plant process wastewater.
The abatement of emissions and implementation of sustainable processes are key targets in redefi ning the world economy, and are signifi cant drivers of continuous innovation. Wastewater generated at large-scale complexes should ideally be recycled and re-used or, when that is not feasible, treated so that it has a near-zero environmental impact.
One area of particular concern is wastewater that is rich in nitrogen eluates. This is typical of effl uent from many industrial and municipal plants, with nitrogenous fertilizer plants being a prime example. Such wastewater is associated with severe environmental impacts, including eutrophication of surface waters, toxic phenomena and decline in biodiversity. Ammonia is the main contaminant of concern, being extremely widespread and toxic at even low concentrations. The treatment technologies that are currently available are complex, costly and unreliable; as a result nitrogen-rich wastewater remains a major ‘pain point’ of the fertilizer and similar industries.
In response to the sustainability challenge and to the increasingly urgent need for effective and economically feasible solutions, Saipem S.p.A. sought to fi nd a solution to the issue of nitrogen-rich wastewater. Particular attention was paid to novel electrochemical technologies, in line with the ‘Emerging wastewater treatment techniques’ defi ned in the 2016 BAT review.1 In 2017, following a rigorous evaluation process, the company established a collaboration with Purammon Ltd., a technology start-up specialising in electrochemical technologies and processes, to commercialise a new electrochemical technology for the combined removal of ammonia and urea contaminants from process wastewater: SPELL. The technology quickly and cost-effectively transforms ammonia and/or urea into their harmless elemental components (e.g. gaseous nitrogen) with no sludge or other byproducts.
The technology has been commercially implemented (Figure 1) and further engineered up to a full-scale package application, capable of satisfying all applicable international industrial standards and the most stringent environmental requirements. It is simple, modular, robust and stable under volatile operating conditions.
The SPELL technology is based on an electrolytic reactor packed with electrodes coated with special catalysts that selectively react with nitrogen molecules when an electrical current is applied. These reactions continuously remove the contaminants as the wastewater fl ows through the reactor.
An illustration of a typical application of the system for direct removal of ammonia from the wastewater of fertilizer plants is presented in Figure 2.

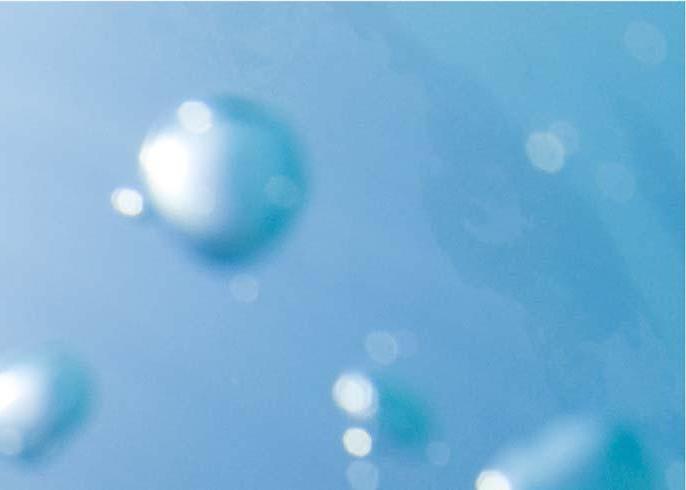

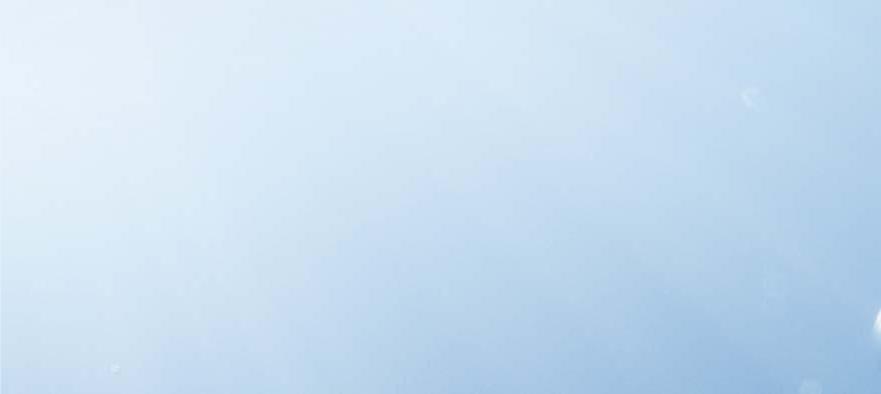

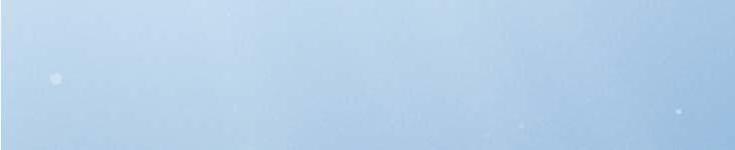


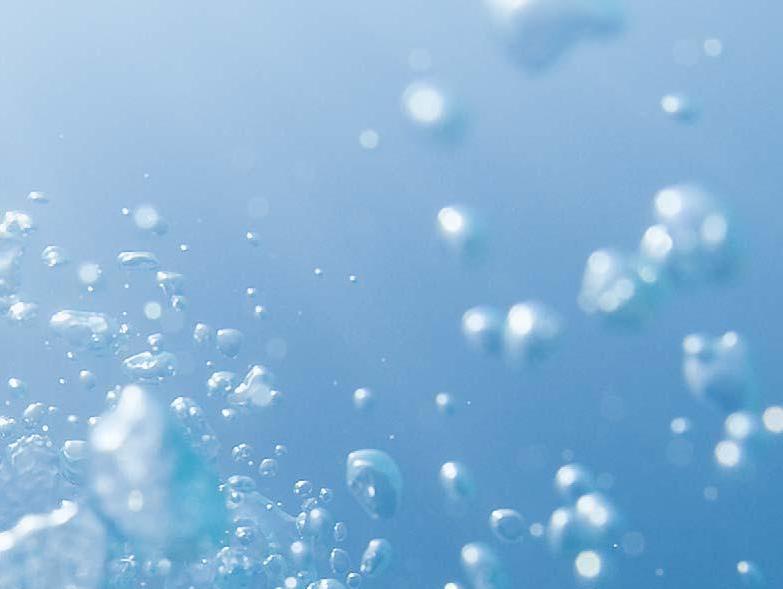
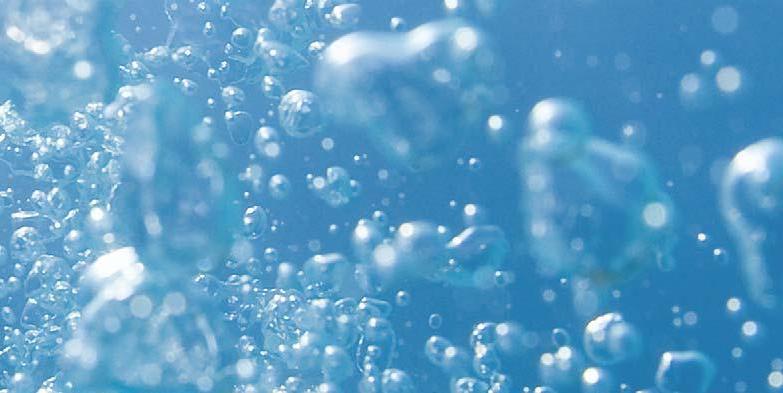
The treatment unit consists of the reactor and a degassing tank for separation and discharge of generated gases, complete with blower unit and pumps. A fi ltration unit can be installed upstream, if required, to reduce suspended solids. Chemical dosing packages can be included, if necessary, to balance water conductivity and alkalinity. Figure 3 represents a typical process scheme for the technology deployment. The untreated wastewater coming from the production process feeds the electrochemical reactor, where ammonia and urea contaminants are oxidised into inert nitrogen, carbon dioxide and hydrogen (Equations 1 and 2); these can be safely emitted into the atmosphere according to the following formula:
2 NH4 + → N2 + 4H2 (Equation 1) CO(NH2)2 + H2O → N2 + 3H2 + CO2 (Equation 2)
Since the exposure of the wastewater to the electrolytic cells is controllable in a precise manner, the process results in effl uent values that are within the pollution limits imposed by environmental regulations.
The following sections provide a short comparison of the electrochemical system, in terms of effi ciency, operations and costs, with currently available technologies.
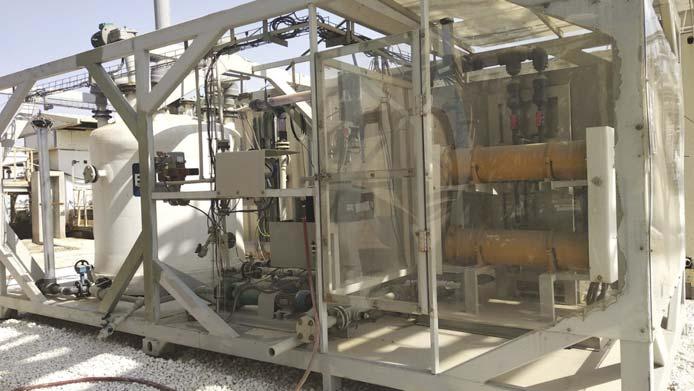
Effi ciency
The most commonly used treatment technology today is biological treatment. This has been used in wastewater recovery for many years and is generally accepted as covering the widest variety of application cases and combining reasonable effi ciency and deployment costs. However, biological treatments are prone to the intrinsic weakness of bacteria-based processes: occasional failures due to toxic shocks, low/high temperatures, fl uctuation in infl ow nitrogen concentrations that inhibit bacteria, high operational complexity, potential formation of the dangerous greenhouse gas nitrous oxide and demand for higher quality of the effl uent.
Biological treatment is inherently ineffi cient, as it oxidises ammonia in two complex and sensitive steps, namely nitrifi cation and denitrifi cation. The fi rst step, ammoniacal nitrogen nitrifi cation, is performed by autotrophic specifi c microorganisms, which extract energy (for their life functions) from ammonia oxidation (i.e. from inorganic compounds) and not from organic pollutants. They use carbon dioxide as their source for carbon instead of organic compounds. Nitrifi cation is an aerobic process (Equation 3).
Figure 1. Installed module on industrial scale. NH4 + → NO3 - / 8e- per N (Equation 3)
The second step, denitrifi cation, is performed by heterotrophic common microorganisms (e.g. Pseudomonas, Micrococcus, Archromobacter, Bacillus, Spirillum) that are often present in activated sludges and operate in anoxic conditions (i.e. with low dissolved oxygen concentration <0.4 mg/l). They can use nitrate instead of oxygen for a catabolic reaction, which produces free nitrogen as a gaseous product instead of CO2 and H2O (Equation 4).
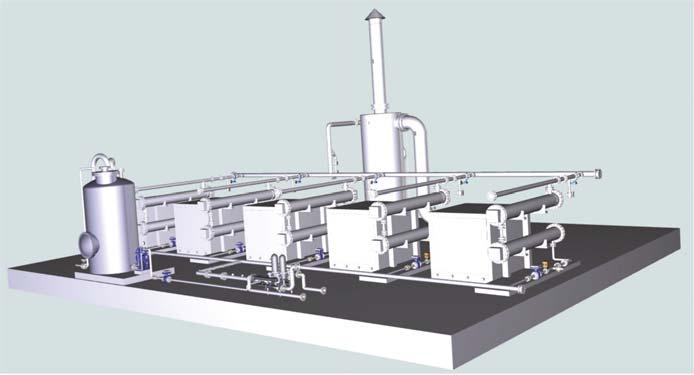
2NO3 → N2 / 5e- per N (Equation 4)
In both industrial and municipal wastewater treatment plants (WWTPs) the eight electrons needed for nitrifi cation (nitrogen oxidation state goes from -3 to +5) come from aeration (Equation 3), which requires energy (electricity) for its operation. The case is different for the fi ve electrons needed for denitrifi cation (nitrogen oxidation state goes from +5 to 0: Equation 4). While these electrons are available in municipal water that is rich with carbon, in the case of an inorganic industrial stream there is no such carbon source, and a supplement dosage is required (e.g. acetic acid or methanol) to maintain a balanced ratio between carbon and nitrogen. This is especially the case in fertilizer WWTPs, where additional carbonic compounds increase costs: for example, the acetic acid requirement for denitrifi cation is usually higher than 3.5 kg/kgN and may produce additional pollutants that, in turn, require additional treatment steps.
Figure 2. 15(m)X16(m) 3D plant model for a fl ow of wastewater of 40 m3/hr and effl uent ammonia of below 1.5 mg/L, based on new electrochemical technology.
Figure 3. Process scheme.

By contrast, the distinctive characteristic of the SPELL technology is its simple one step reaction, which is more effi cient than the standard biological treatment (Figure 4). This can be observed through comparison of the oxidation reactions occurring within the electrochemical and biological treatments respectively, as follows.
The electrochemical process directly oxidises ammonia through the reaction (Equation 5), which consumes three electrons per one atom of nitrogen:
2NH4 + → N2 / 3e- per N (Equation 5)
The driving force is electrical current and, consequently, the energy consumption and associated cost is directly proportional to the contaminant load. The system does not use bacteria and therefore there is no need for external carbon inputs and no production of sludge. The ammonia and the urea are removed through a zero-order reaction that is insensitive to the ammonia and urea concentrations, including their potential fl uctuations in the incoming wastewater.
The reactor selectively promotes only the intended reaction. This extreme selectivity is a key differentiation of Saipem’s electrochemical technology and is achieved by the composition of the catalyst with which the electrodes are coated. The selectivity results in a high effi ciency process and, by excluding unwanted reactions, avoids both unnecessary power consumption and the inadvertent generation of potentially hazardous or costly byproducts.
While space does not allow for a detailed comparison with the various non-biological technologies that are available today – such as breakpoint chlorination, ion exchange, air stripping and adsorption process using activated carbon – they are also complex and the inherent effi ciency advantages of the new technology over these alternatives are quite similar.
Operations
In addition to the effi ciency advantages described, the electrochemical system is also more stable and reliable than the biological treatment systems currently in use. Biological nitrifi cation/denitrifi cation occasionally fails due to toxic shocks, high organic loads or temperatures outside the range tolerable by the bacteria. By contrast, the electrochemical system is not affected by any of these issues and therefore has no associated risk of disruption.
The system can treat a wide range of contaminants and concentrations, from tens to hundreds and thousands ppm of specifi c/nitrogenous contaminants, and can be designed for the different thresholds required for different production processes and applications (Table 1).
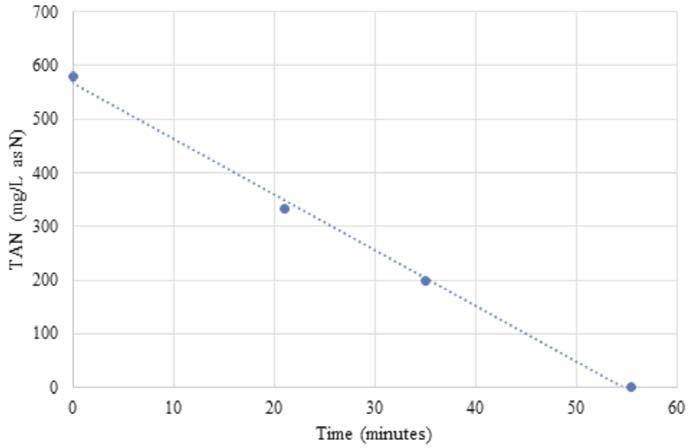
Figure 4. Total ammonium nitrogen removal in a fertilizer application.
Table 1. Wastewater parameters required at electrochemical reactor inlet Parameter Unit Design basis Maximum recommended Maximum allowable
Total suspended solids mg/l <30 ≤50 ≤80
Particle size micron <100 ≤150 ≤200 Biological oxygen demand (soluble) mg(O2)/l <50 ≤100 Hardness mg/l as CaCO3 <2000 ≤5000 -
Oil and grease mg/l <0.5 ≤1 ≤2
pH - ≥7 ≥6 ≥6 Temperature ˚C 10 – 45 10 – 50 70 Feed pressure bar(g) 0.5 – 3 0.5 – 6 -
LeadersinMoistureMeasurement&Control
noncontact.instant.accurate.
Withvaryingmoisturecontent,on-lineNear-Infrared measurementisakeytooltoensuringoptimum efficiencyandqualitycontrol.Theabilitytomeasure moistureandmakeprocessadjustmentsduringthe productioncycleiskey. Measuringthemoisturebeforeandafterthedryer willyieldsignificantimprovementstothefinished product. ProperMoistureControlCan: MinimizeWaste ReduceCost IncreaseProductQuality MaximizePlantEfficiency

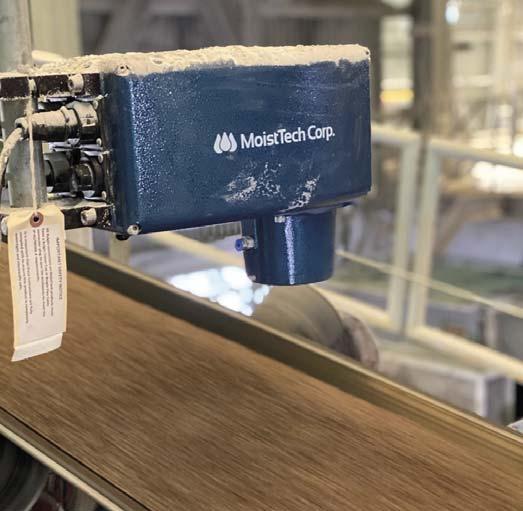
Additionally, the system can accommodate virtually any level of pollutant load and is fl exible in the face of pollutant load fl uctuations. It automatically recirculates the effl uent through the electrochemical reactor until the target outlet concentration is achieved.
The electrochemical process is controllable to a precise degree, and can be automated and integrated with the production facility’s other control systems and procedures.
Moreover, the system has a modular structure that can be extended to cover additional nitrogen load and/or volumetric fl ow to meet different plant capacities.
The system has few components, meaning the footprint is typically small and minimal site preparation is required. Importantly, it can be directly integrated within industrial process trains, rather than requiring a separate post-process discharge and treatment area. It requires control of few parameters and ensures stable and constant effl uent quality.
Costs
As an electrochemical process, the operational expenses are primarily derived from the consumption of electricity. This is directly proportional to the actual amount of ammonia and urea present in the wastewater. The system’s typical consumption is, on average, approximately 17 kWh/kg of total contaminating nitrogen.
The economics of biological and other conventional technologies are also undermined by the costs of disposing of the resulting sludge and other byproducts. By contrast, the electrochemical process is zero-discharge – it generates no sludge or other liquid or solid byproducts and therefore has no associated disposal costs.
In addition, whereas biological systems require specialised operation and maintenance personnel, the electrochemical process does not. Its operation is automatable and readily integrated into the duties of general process management resources.
As a result, the overall operational cost of the electrochemical process is 40 – 70% lower than alternative solutions. Cost savings may be even higher in scenarios where signifi cant load fl uctuations or other abrupt shifts in operating conditions (e.g. after paved road drainage) would often require rebalancing with other technologies but would not have any impact on the electrochemical process.
In addition to its OPEX advantages, the new technology can have major cost advantages when it comes to commissioning. It is constructed off-site and delivered turnkey within shipping containers. It is typically operating on-site within a few days of delivery, avoiding the civil engineering, permitting and extensive construction timetables typically associated with conventional systems.
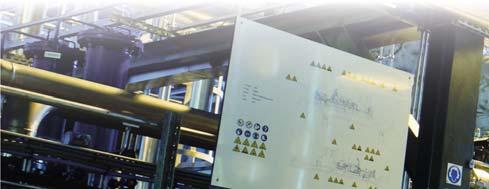
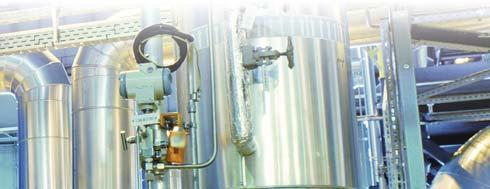
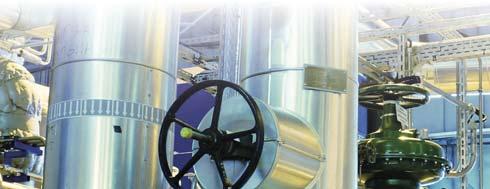
17 | 65th Annual Safety in Ammonia Plants & ..Related Facilities Symposium
IBC | Ammonia 2021
Conclusion
In summary, the new SPELL technology is well-suited to treating the wastewater of fertilizer plants. It is fl exible with a wide variety of design constraints and implementation confi gurations, and can serve as either the main treatment or as polishing treatment for ammonia removal, or for removal of ammonia and urea for both greenfi eld and brownfi eld applications.
From the second half of 2021 a 40 ft transportable plug-and-play unit will be available from stock for customers to test, experience and use the system at their premises.
Applying electrochemical technology is an important step within the overall objective of zero industrial pollution.
Reference
1. BRINKMANN, T., GINER SANTONJA, G., YÜKSELER, H., ROUDIER, S., and DELGADO SANCHO, L., ‘Best Available Techniques (BAT)
Reference Document for Common Waste Water and Waste
Gas Treatment/Management Systems in the Chemical Sector’, https://publications.jrc.ec.europa.eu/repository/handle/JRC103096 (2016).
AD INDEX
47 | MoistTech
IFC | Neelam Aqua & Speciality Chem(P) Ltd.
04 | Argus Media
OBC | Central Maintenance & Welding 07 | Prayon Technologies
OFC + 13 | REXA, Inc.
37 | DSH Systems
14 | EMT/Doyle Equipment Manufacturing
02 | Eurotecnica 09 | Stamicarbon
27 | Sulphur + Sulphuric Acid 2021
41 | Sustainable Fertilizer Production ...Technology Forum 2021
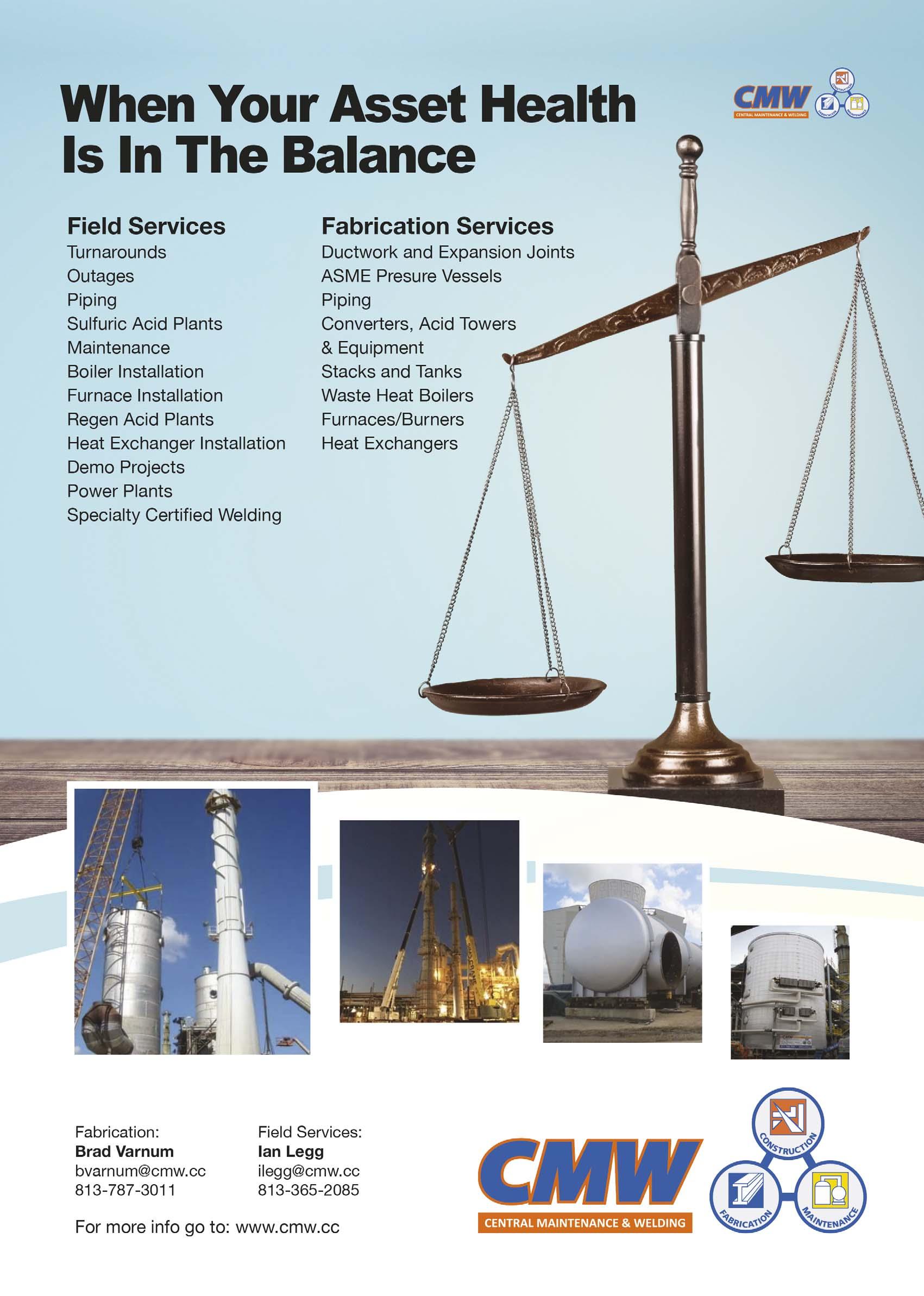