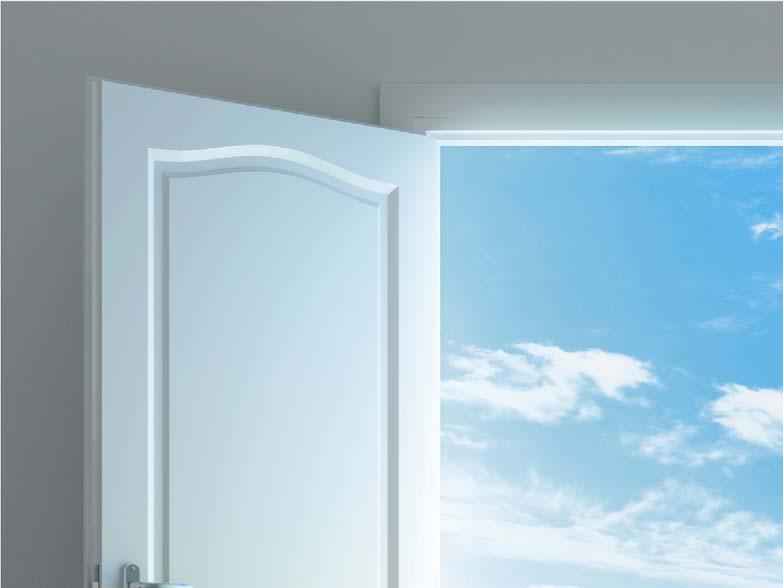
9 minute read
Thriving in the new reality
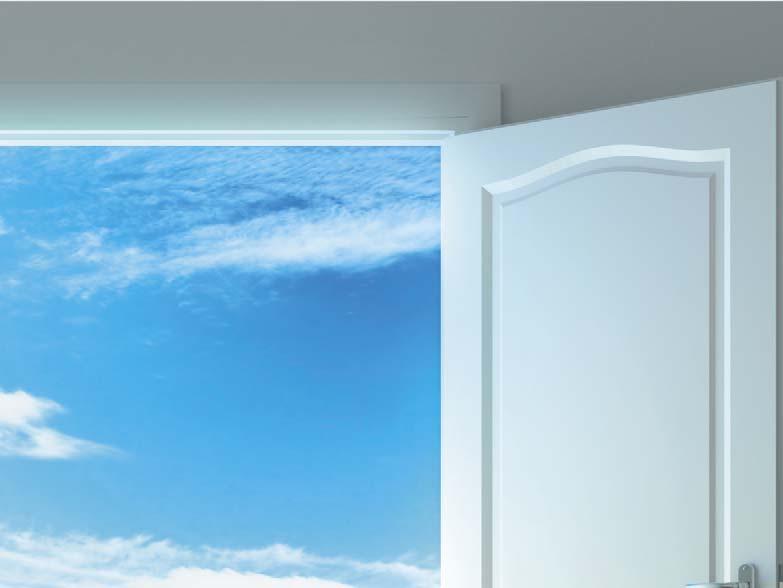
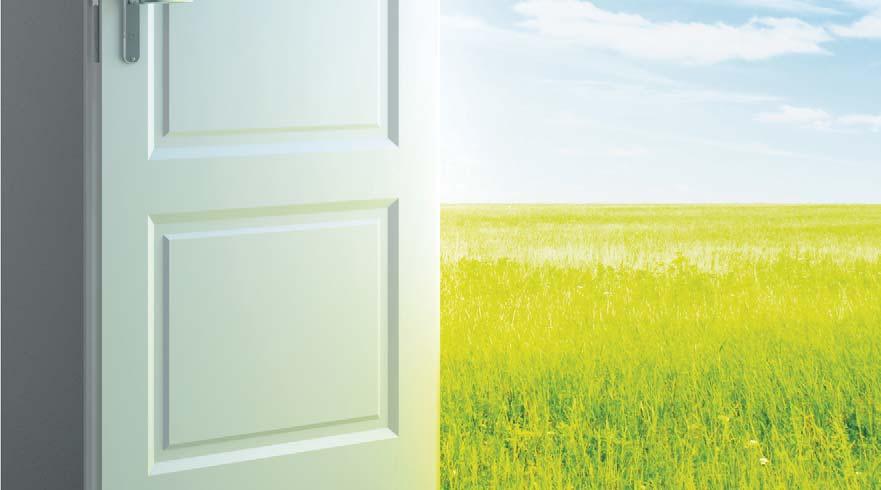
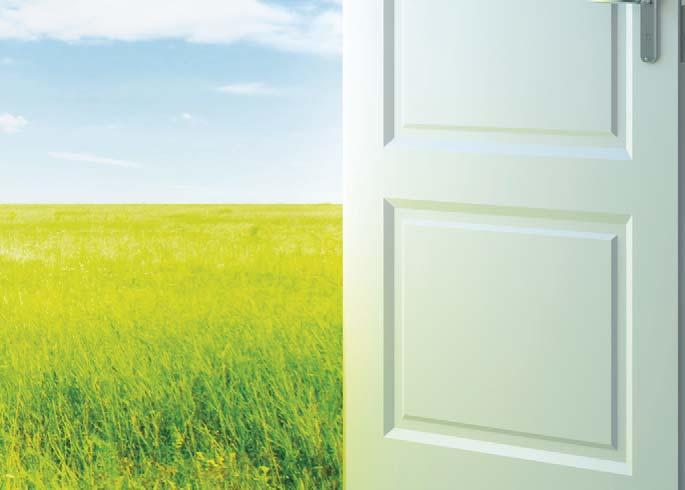
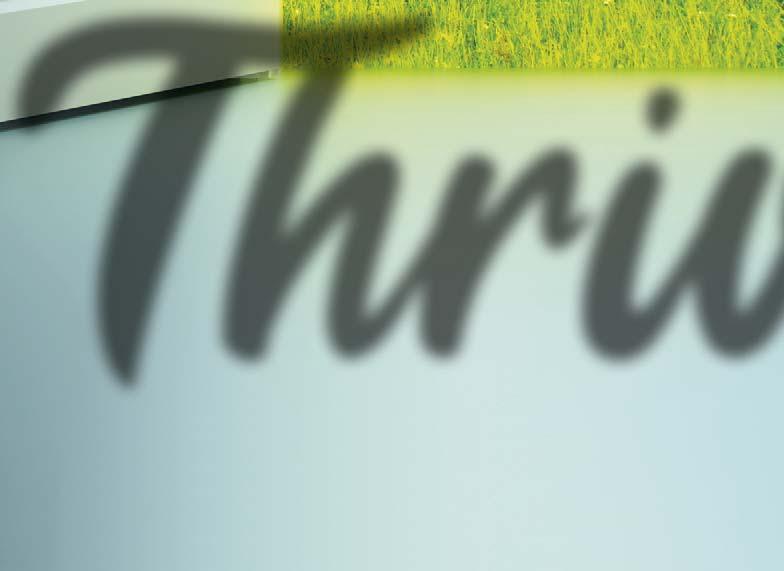
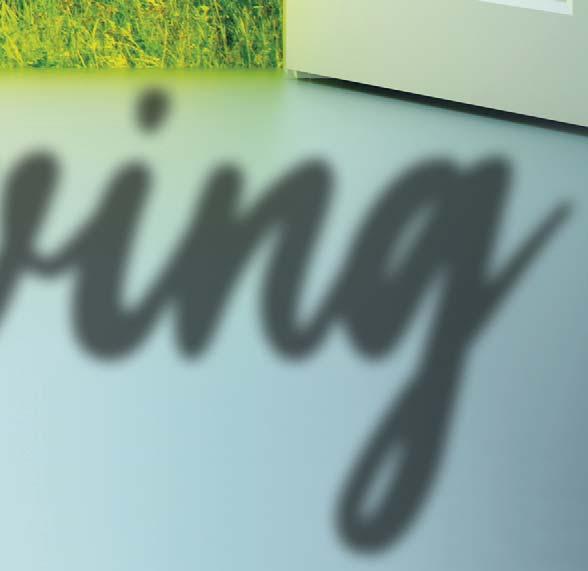
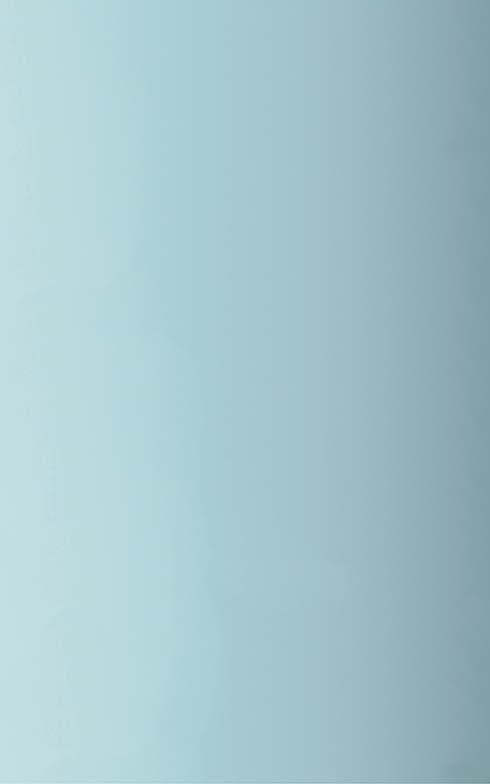
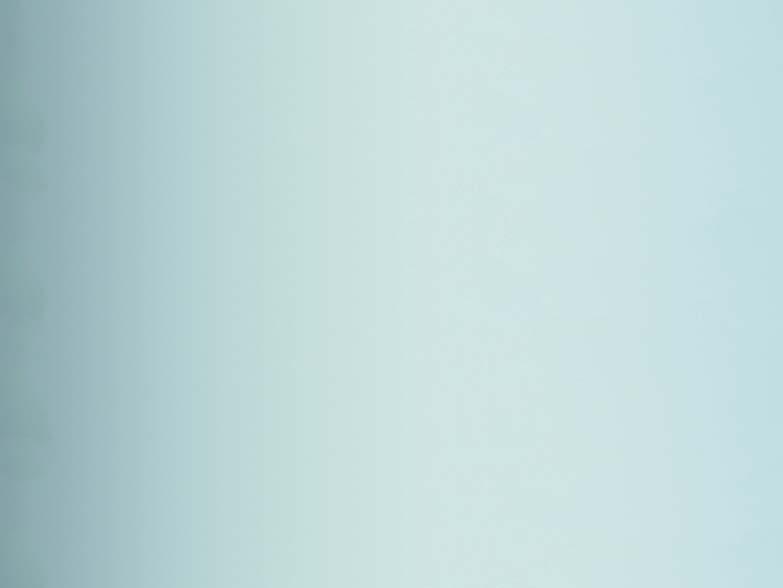
Nick Flinn, Shell Catalysts &
Technologies, UK, explains how the uncertainty of the COVID-19 pandemic offers opportunities for refineries.
The COVID-19 pandemic prompted a dramatic fall in product demand and skewed product slates. This has presented refiners with the challenge of needing to increase margins and profit. In addition, there is also accelerating activity around the energy transition and the need to reduce carbon emissions which will have an effect on product slates as well.
With the combination of these two challenges, the reality is that there will likely be a prolonged recovery and

long-lasting consequences that will require refiners to modernise their facilities. However, many refiners will have to adopt a conservative approach to capital investment with a goal of continuous improvement designed to maintain competitiveness. While all of this is challenging, there are low-capital revamp opportunities that can deliver high returns quickly and help refiners seize opportunities in the new business reality.
This article will provide an overview of current challenges and information on revamp scenarios for refineries that require low capital expenditures and offer high return on investment. These are intended to help refiners with ways to remain competitive. Considerations include increasing regulations, carbon reduction, market changes due to the pandemic and other forces, and technology equipment solutions. In this article, five possible revamps will be covered along with insights for each one.
Distillate hydrotreating
Revamping a diesel hydrotreater is a relatively low-cost response to several issues that can bring strong financial
returns on investment. This is important as more stringent emissions regulations are enacted and as other market changes occur, and different products may be required to meet growing demand for winter diesel and biofuels. A revamp can help resolve operational issues caused by the pandemic having disrupted global economic activity on a large scale, resulting in many refiners having to operate well below their normal throughputs, running their equipment far differently from their design points or delaying their turnarounds. This has often exposed or caused operational problems such as radial maldistribution, channeling of liquid flow or pressure-drop limitations that have led to suboptimal unit performance. As more countries and regions continue to adopt regulations requiring ultra-low sulfur levels in automotive gas oil, refineries need to react by increasing the operating severity of their diesel hydrotreating units. In some instances, this can be successfully managed by changing to a modern high-activity catalyst system, such as one from Shell Catalysts & Technologies, often in combination with upgrading the reactor internals. If Figure 1. Five key value-adding design differentiators of Shell’s deepflash technology. these improvements are insufficient or additional capacity is required, then revamping an existing unit is often a more cost-effective option than building a new grass-roots unit. Some areas are seeing a change in the demand split from heating oil to automotive diesel, which generally has much stricter specifications for properties such as sulfur, density, cetane and boiling range. Refineries affected by this will need severe hydrotreating of a higher proportion of distillates, including more difficult cracked components, so they can be blended into the automotive diesel pool. For some refiners, there is an economic incentive to meet additional, more stringent specifications such as low aromatic diesel or to meet severe cold flow properties. A reduction in product cloud point is achievable by including dewaxing technology into an existing diesel hydrotreater. There is also a growing world energy demand and incentive for biofuel production. The two most common types of biofuel are bioethanol and biodiesel. The two routes for producing biodiesel are the transesterification of vegetable oils or animal fats to make fatty acid methyl esters (FAME) or the hydrotreating of vegetable oils or animal fats to make paraffins in the diesel boiling range (hydrotreated vegetable oil or HVO).
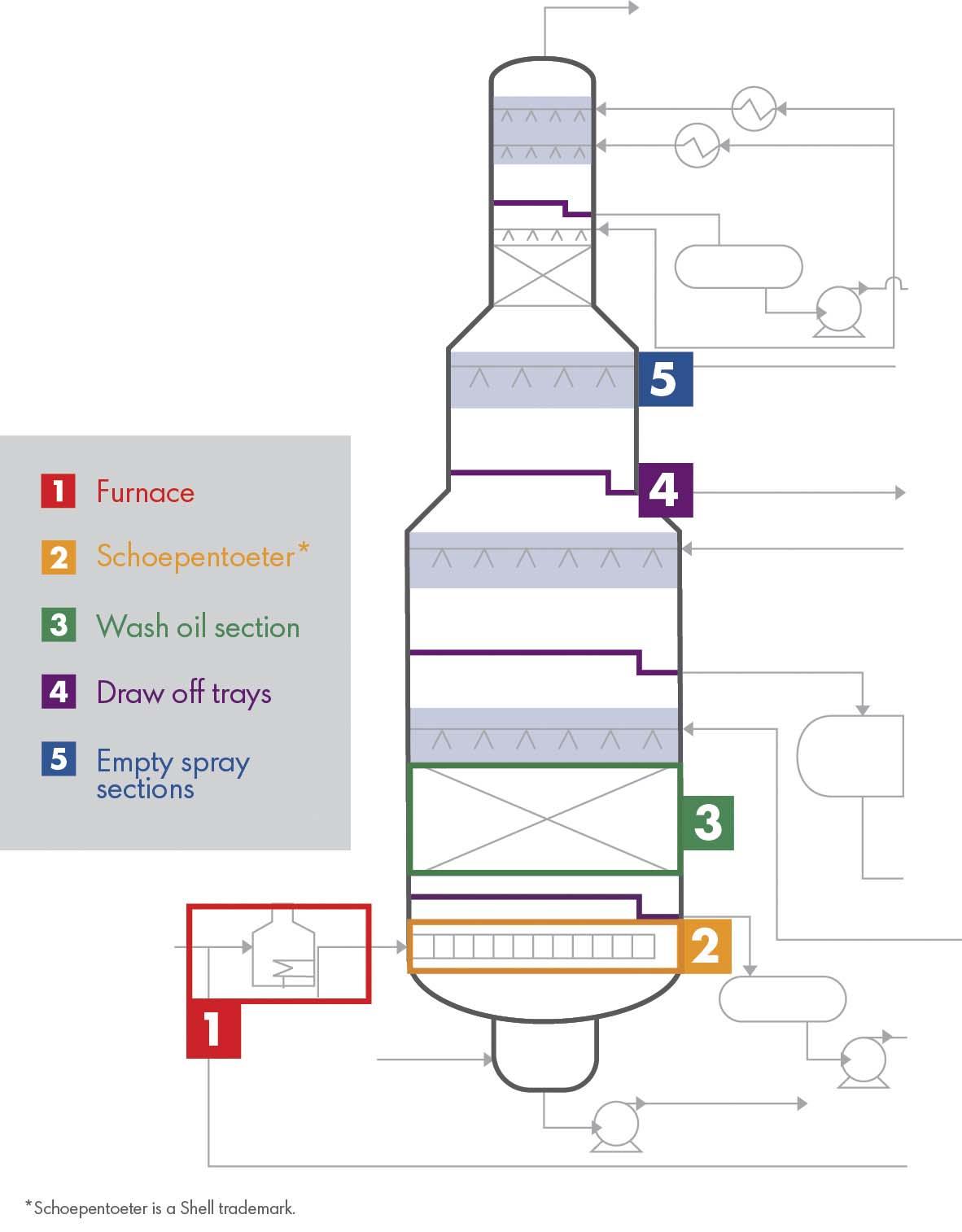
FCC-PT/FCC
Shell Catalysts & Technologies recommends that refiners should take an integrated approach to the fluidised catalytic cracking pretreatment (FCC-PT) and FCC units. This is even more important in today’s environment when yield shift flexibility and low-cost operations can be key to competitiveness.
The rationale for considering an integrated approach to the FCC-PT and FCC units is straightforward. Even though the two units have very different operating modes, constraints, and objectives, together they have complex interactions that cover feed quality effects, constraint-driven limitations and turnaround timings. The performance and limitations of each unit strongly influence the other, so substantial value is at risk if refiners do not consider the two units as an integrated operation.
For example, when considering upgrading an FCC-PT unit with the latest catalysts and technologies, remembering the FCC unit constraints will help in capturing the full potential margins from the synergy between both units. Similarly, by considering the units in isolation, a refiner could fail to identify the projects that would deliver the biggest returns.
Applying the best-available technology does not have to mean highly capital-intensive projects with extended implementation downtimes. With an experienced technical team assessing, developing, and implementing integrated solutions, many upgrades in capability are achievable with minor impacts on shutdown scopes and budgets, thereby providing a net return.
Hydrocracking
Refiners seeking to adapt their assets can take advantage of the inherent flexibility of a hydrocracker in several ways. This includes shifting to petrochemicals, improving residue conversion, moving to higher margin lubricant base oil feed and the processing of lower-priced crudes.
With industry commentators asserting that demand growth for gasoline and diesel is set to weaken in the long-term, some refiners are evaluating how they can repurpose their facilities. Though most hydrocrackers commissioned in the past 15 years have traditionally been designed as diesel-producing machines, they are now increasingly being reconfigured towards naphtha. Many refiners are pulling naphtha out of gasoline and then redirecting light naphtha to the ethylene cracker and sending heavy naphtha through additional processing units to produce paraxylene. If desired, it is also possible to continue to produce jet fuel, for which long-term demand is expected to remain strong.
The need to respond to the IMO 2020 fuel-sulfur cap and invest in residue conversion projects remains strong for many. By revamping a hydrocracker, repurposing it and integrating it with another fuel conversion technology such as solvent deasphalting, delayed coking or thermal cracking, refiners can cost-effectively reduce their exposure to high-sulfur fuel oil.
There is also a global trend away from Group I products based on solvent technology towards Group II and Group III lubricant base oils produced using catalytic dewaxing and hydrofinishing technology. In some regions, lubricant base oil feed can command a higher margin than middle distillates, so refiners are revamping their hydrocrackers to enable the right feed quality. The hydrocracker’s catalyst system and configuration are key, as they have major influences on the yield and quality of the final base oil products.
Another popular revamp objective is to facilitate the processing of lower-priced opportunity crudes such as West African, Mexican, Colombian, and Venezuelan, and non-standard feeds such as heavy coker gas oil and deasphalted oil (DAO).
Global petrochemical industry struggling with challenges and low operating rates
These are unprecedented times for the global petrochemical industry, and some products and value chains, including ethylene oxide (EO), are suffering from exceptionally challenging market conditions and low operating rates.
This environment forces EO producers to re-examine their operating and investment plans. When margins were good, the whole focus was on maximising production and minimising downtime, but now it is important to realise that there are other ways to improve profi tability.
Some of the options to consider include: Debottlenecking to run harder and reduce unit production costs. Adding or increasing high-purity EO (HPEO) capacity to improve margins and diversify the product portfolio. Lowering the carbon dioxide level to allow catalysts to run longer and at higher selectivity. Operating at lower rates to maximise selectivity and lifetime from the catalysts. Increasing energy efficiency.
The right choice depends on the local market environment and the drivers of each producer and each site. The position in terms of ethylene availability and the depth of the local market for HPEO can have a major infl uence on the choice of strategy.
For some, the optimum solution will involve adding or increasing HPEO, increasing work rate and changing to a latest-generation catalyst. But for others, it might mean bringing down operating costs by running at lower rates or by looking for opportunities to improve effi ciency.
Reactor internals
The pandemic has disrupted global economic activity on an unprecedented scale, so many refi ners have been operating well below normal throughputs, running equipment far away from design points or delaying turnarounds. Unfortunately, this has often exposed or caused operational problems such as radial
maldistribution, channeling of liquid fl ow or pressure-drop limitations that have led to suboptimal performance.
Meanwhile, as the need to increase margins and profi tability has arguably never been greater, other refi ners are exploring processing lower-cost crudes, more severe feedstocks or renewable feed components such as used cooking oil or tallow. However, such changes exacerbate the risk of fouling and can constrain performance.
Because they are designed to prevent fouling and increase catalyst volume and utilisation, Shell Catalyst & Technologies’ latest-generation reactor internals provide one of the most compelling response options available to refiners today. Furthermore, they offer a quick profit return for relatively low capital expenditure – payback can be in a few months.
Vacuum distillation
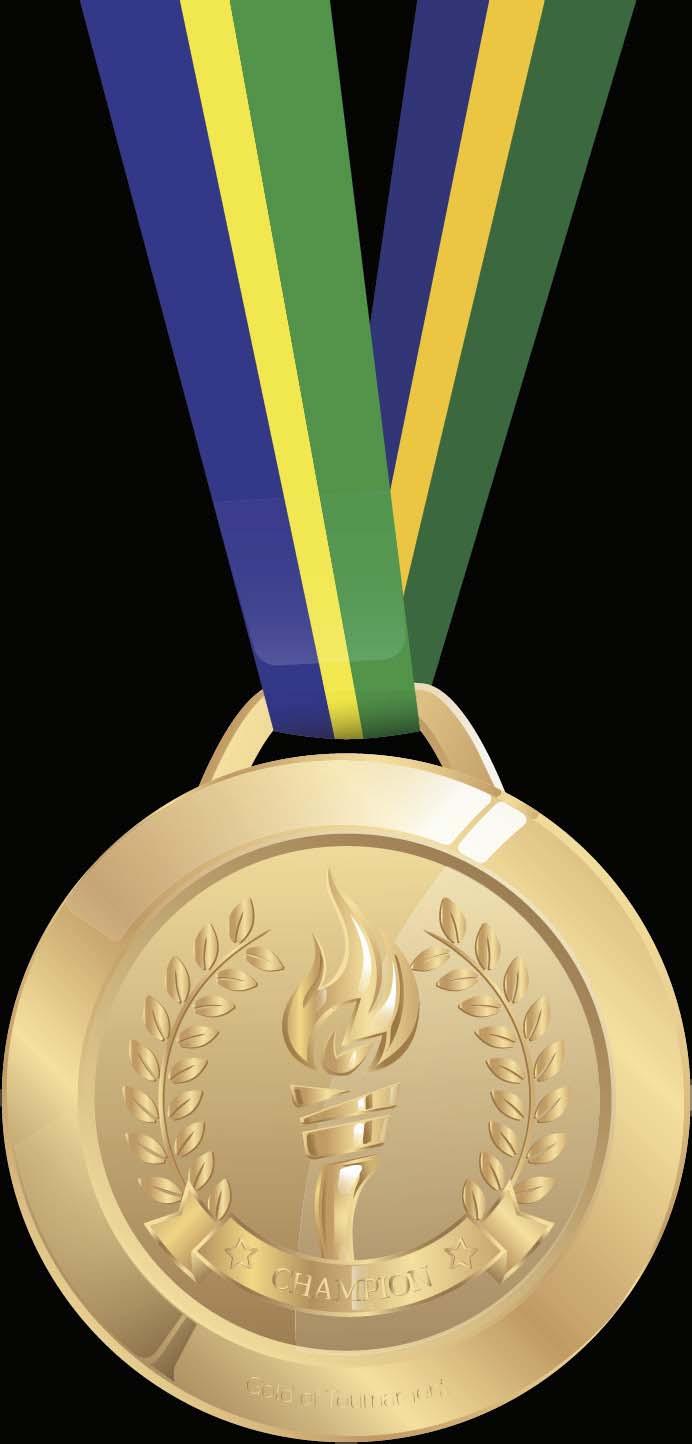
The performance of a vacuum distillation unit (VDU) can have a major bearing on a refinery’s margins. Not only is this the last opportunity to remove valuable distillates from crude and, therefore, to minimise refinery fuel oil make, it also improves the feed quality for the downstream conversion units (hydrocracking or fluidised catalytic cracking units) and is a major determinant of their cycle lengths.
Consequently, a VDU revamp offers refiners a major margin-improvement opportunity. Revamping these units using Shell Catalyst & Technologies’ deep-flash, high-vacuum technology can often be a low-cost way to unlock downstream assets, as it can help to increase vacuum gas oil (VGO) yield, enhance unit throughput, and improve unit reliability while also ensuring that contaminant levels remain within the conversion units’ acceptability limits.
Such projects can generate substantial value, as the capital cost is usually relatively low and payback times are short, typically a year or less. In addition, hardware changes can often be implemented within an existing refinery turnaround window.
Such technology has been developed through extensive research on mass transfer and separation equipment, including five key design features that can be tailored to meet specific revamp requirements. They include a proprietary furnace coil design, Schoepentoeter1 inlet device, wash-oil section design, insulated, low pressure drop, draw-off trays and direct contact condensation sections.
Conclusion
Existing global economic challenges combined with the pandemic have presented refiners with a dilemma – how to make smart investments while preserving cash in order to maintain their competitive position. These scenarios provide opportunities for a focused investment through revamps that can keep a refinery competitive and achieve high returns.
Note
1. Schoepentoete is a Shell trademark.