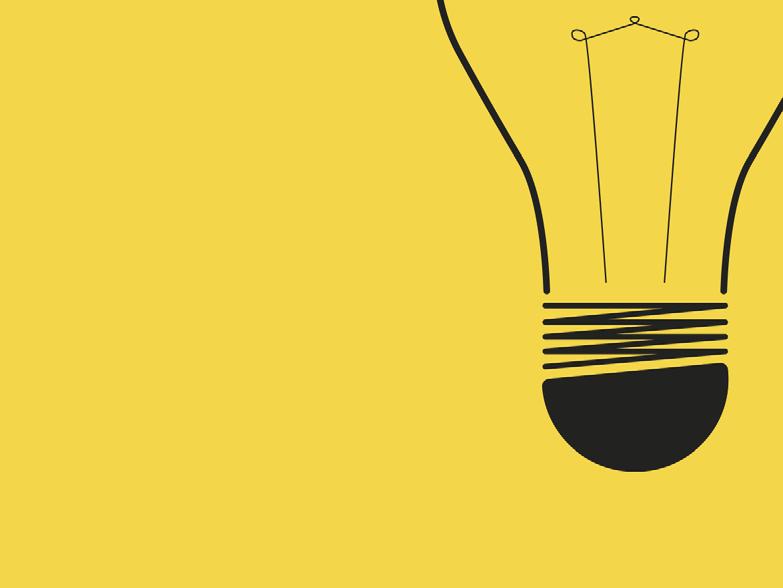
8 minute read
The case for controlling sulfur impurities
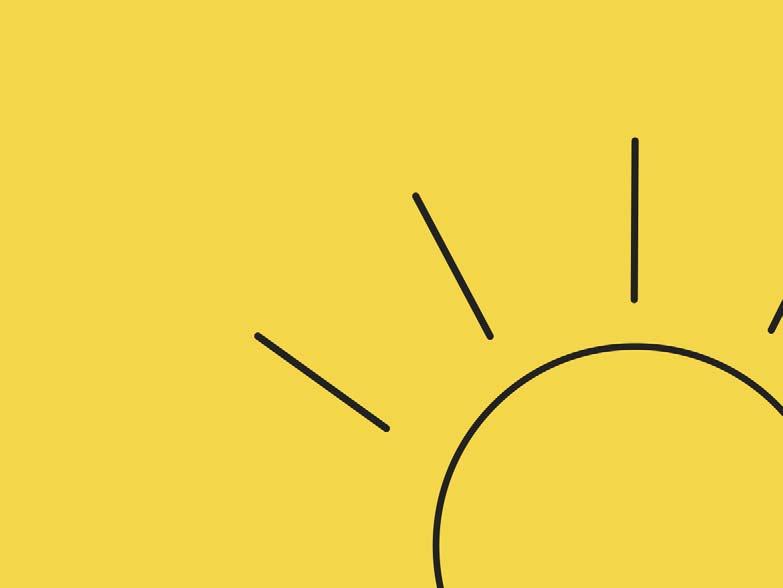
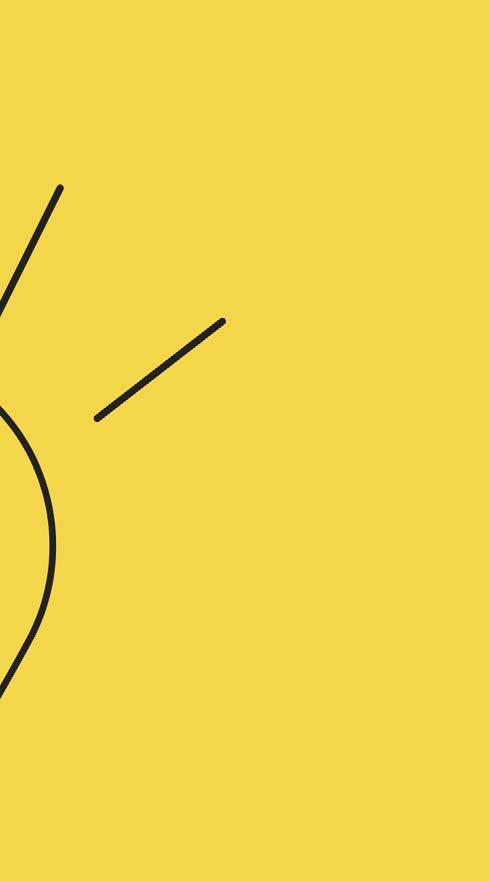
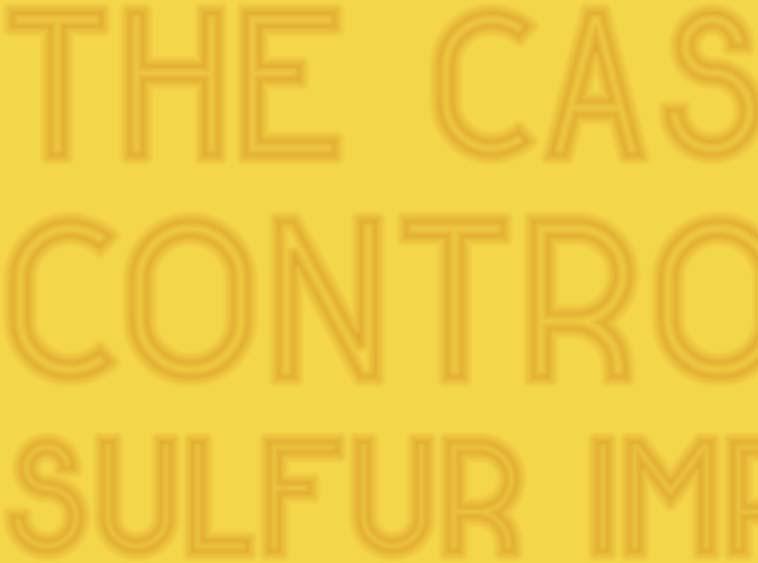
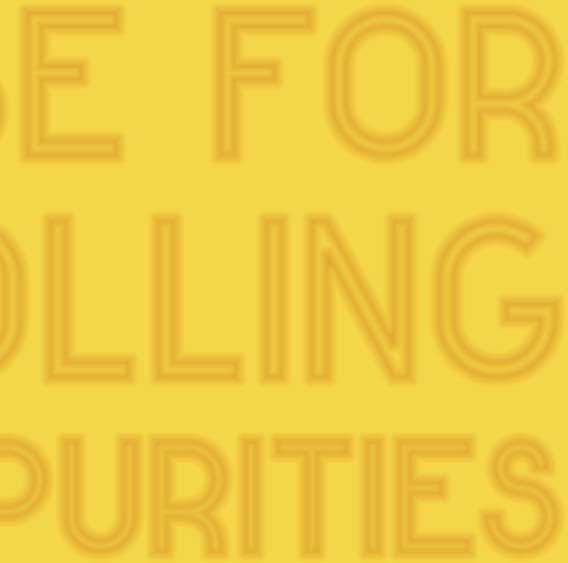
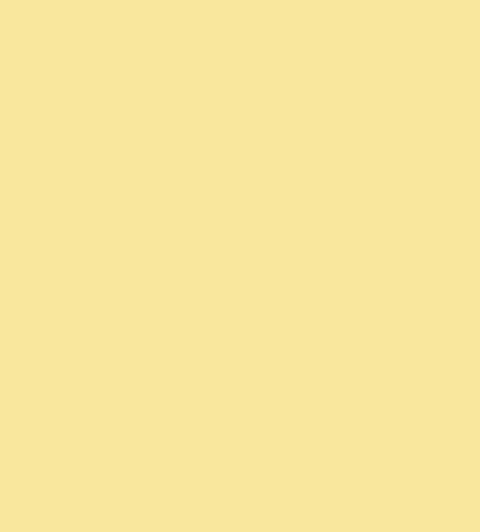
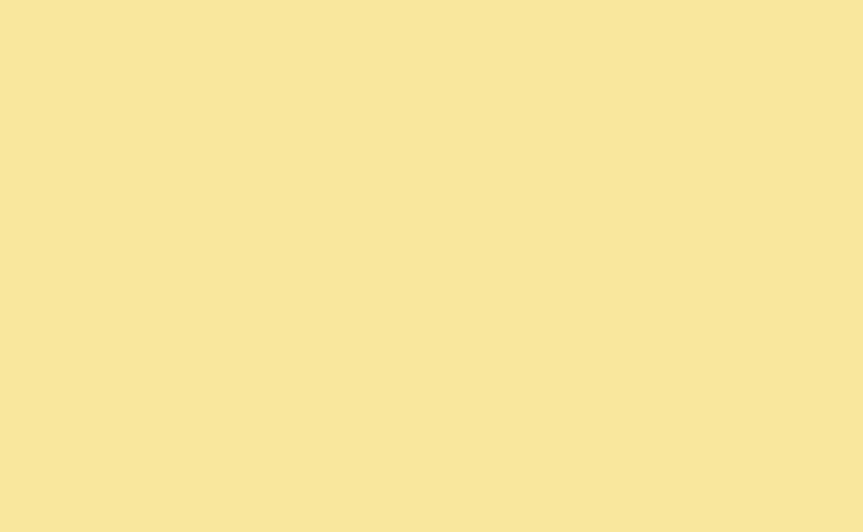

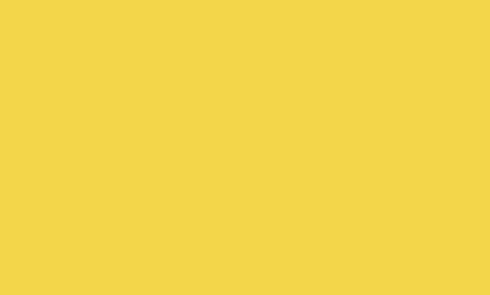
William K. Rouleau, Merichem Company, USA, discusses the need for controlling sulfur impurities in order to prevent contamination and to improve the efficiency of end user products.
Fossil fuels, formed from organic material over the course of millions of years, are the most widely used energy sources in the world. As an overall share of energy consumption, oil sits on top of the spectrum at 33% of all energy consumption.
Natural gas ranks third at 24%. In all, fossil fuels represent 82% of the world’s energy needs. Acidic in nature, sulfur is one of the most common and undesirable impurities present in crude oil. Sulfur compounds tend to deactivate some catalysts used in refi ning process units and can cause corrosion problems in pipeline, pumping, and refi ning equipment. Sulfur levels in automotive fuels also impairs the effectiveness of emission control systems which can lead to the sulfur oxide gases in the air. When those gases react with water in the atmosphere, they form sulfates and acid rain that can cause damage to buildings, destroy automotive paint fi nishes, acidify
soil, and ultimately lead to loss of forests and various other ecosystems. Sulfur emissions also cause respiratory illnesses, aggravate heart disease, trigger asthma, and contribute to the formation of atmospheric particulates.
The presence of sulfur is a critical issue that requires both conventional hydrodesulfurisation and alternative desulfurisation methods such as selective adsorption, oxidation/extraction (oxidative desulfurisation), etc. for removing refractory sulfur compounds from petroleum products. Research laboratories and refi neries are spending large amounts of money to fi nd viable and feasible solutions for reducing sulfur to a concentration of less than 10 mg/l.
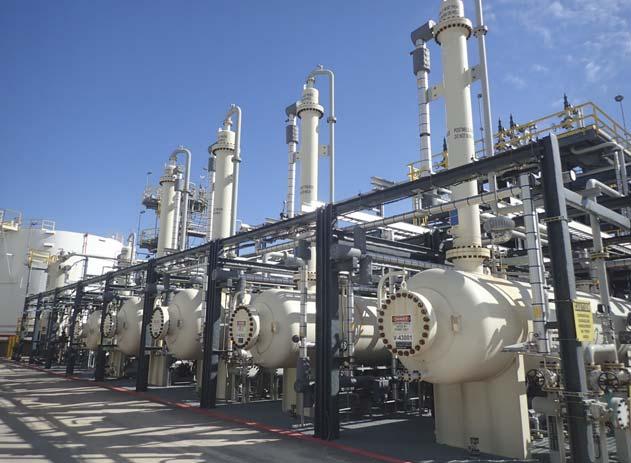
Figure 1. FIBER FILM treating units used in caustic treatment for removal of impurities from liquid hydrocarbon streams.
Figure 2. LO-CAT treating unit used with catalyst to reduce H2S concentrations to less than 1 ppm from gas streams.

Problem
There are many types of crude oil produced around the world that range in density and consistency, from very thin, light weight and volatile fl uidity to an extremely thick, semi-solid heavy weight oil. The market value of an individual crude stream is refl ected in its inherent characteristics. Sulfur content is one of the most important characteristics of crude oil that affects its market price.
The sulfur content of crude varies from less than 0.05 to more than 10 wt% but generally falls in the range of 1 – 4 wt%. Crude oil with less than 1 wt% sulfur is referred to as low sulfur or sweet, and that with more than 1 wt% sulfur is high sulfur or sour.
Crude oils contain sulfur heteroatoms in the form of elemental sulfur (S), dissolved hydrogen sulfi de (H2S), carbonyl sulfi de (COS), inorganic forms and most importantly organic forms, in which sulfur atoms are positioned within the organic hydrocarbon molecules. Sulfur containing constituents of crude oils vary from simple mercaptans, also known as thiols, to sulfi des and polycyclic sulfi des. Mercaptans are made of an alkyl chain with –SH group at the end (R–SH).
It is imperative that the impurities are removed to standards suitable for edible or industrial use.
The technical solutions
There are a range of hydrocarbon treating equipment, catalyst, and service solutions that remove sulfur and other impurities from hydrocarbon liquids and gases to the upstream, midstream, and downstream energy sectors.
CAC®-Products are a series of carbon-activated catalysts that have been designed for use within solid-bed hydrocarbon-treating technology. These products remove the heavy mercaptans found in jet fuel, kerosene and other middle distillate streams. CAC-Products are pre-impregnated with cobalt-based catalyst and will reduce mercaptan concentrations to less than 5 ppm.
JeSOL®-Products are a series of sulfur extraction catalysts that have been designed for use within hydrocarbon-treating technology without the need of solid-bed contacting. These products are utilised by refi ners and midstream processors to extract sulfur compounds from distillate, gasoline, and condensate streams and provide feedstock treating fl exibility across a wide range of COS, H2S and RSH concentrations. These products are supplied with a full life-cycle service which includes delivery of fresh catalyst and return of spent solution.
ARI®-100 Products are a series of concentrated cobalt catalysts that have been designed for use within regenerative caustic treating processes and are designed to accelerate the oxidation of mercaptans found in petroleum fractions. The products are offered in either a powdered form or a solids-free liquid form.
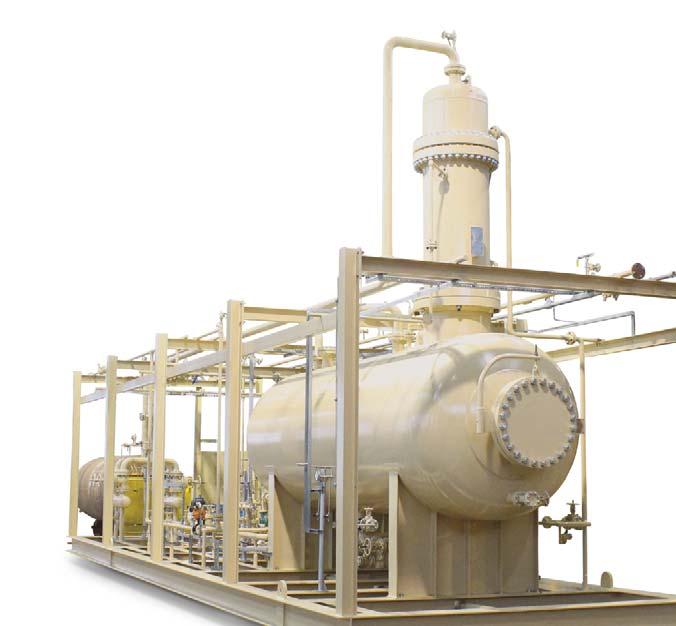


MC-500® Products are a series of catalysts that have been designed for use within the LO-CAT® iron-redox sulfur removal technology. The products will remove H2S from any type of gas stream and reduce the H2S concentrations to less than 1 ppm.
All catalysts mentioned are manufactured to be utilised within licensed treating processes.
The challenges
The conventional method of contacting two immiscible liquids – such as hydrocarbon and caustic or amine – is to disperse one liquid thoroughly into the other as small droplets. Impurities pass between the two phases at the surface of the droplet. Mass transfer can only be improved by creating more numerous and smaller droplets in order to increase surface area.
Even when the dispersion-based system provides adequate treatment, separating the two phases is usually extremely ineffi cient. The mixture must remain in the phase separator until the caustic droplets settle out by gravity, a process that may take hours. As the treating requirement becomes more diffi cult, mixing energy is increased to maximise interfacial surface area, leading to a greater dispersion of the aqueous phase which causes the separation time to become exponentially longer.
Stable emulsions can form in the mixing device, resulting in massive carryover out of the separator vessel. Due to excessive carryover, expensive equipment such as knockout vessels, sand fi lters, water wash units and electrostatic coalescers must be installed downstream to remove the dispersed aqueous phase from the treated product. Treatment is often interrupted if an emulsion develops.
Conventional dispersion and phase separation methods come with a host of problems, such as: lack of turndown capability, plugging, fl ooding, channelling, long settling times, aqueous phase carryover, plot space requirements, product contamination, and unpredictability. Caustic treating processes with dispersive mixing devices were once the only option available to the industry. Yet conventional dispersion and phase separation methods are subject to numerous shortcomings, such as lack of turndown capability, pluggage, fl ooding, channelling, unpredictable treating results, long settling times, aqueous phase carryover, generation of dilute aqueous wastes, lower service factor, hydrocarbon losses, larger plot space, product contamination, and additional processing steps and equipment needed to separate phases.
The treating processes
There is a technology on the market today with a unique design with a signifi cantly larger interfacial surface area, using minimum mixing energy, allowing for enhanced microscopic diffusion and a continuous renewal of the aqueous phase. Effi ciency of mass transfer is improved by an order of magnitude which reduces operating costs.
FIBER FILM® contactors are equipment for caustic removal of mercaptans, naphthenic acids and hydrogen sulfi de impurities from hydrocarbon streams. Mass transfer equipment creates an interfacial surface between hydrocarbon and caustic phases in a non-dispersive manner. It consists of a multitude of fi bres packed in a cylindrical column where the hydrocarbon and aqueous phases fl ow co-currently downward forming a thin fi lm on the fi bre surface. This eliminates problems associated with the principle of droplet formation and dispersion of one phase into the other, followed by conventional sulfur extraction/sweetening units.
Best case treating systems are custom designed to meet customer requirements, then engineered and fabricated to the customer’s specifications, whether the need is for a completely new facility, or a minimum retrofit to upgrade existing equipment.
Results
Petroleum refining is a unique and critical link in the petroleum supply chain, from the wellhead to the pump. Selecting the optimum treatment for removing impurities from hydrocarbon streams is a challenging task for any refiner. By providing the means to offer a series of proven liquid hydrocarbon treating technologies, oil companies can offer services that complement their own technology portfolios. Examples include: Turkish oil company Tüpraş treated a 22 000 bpd hydrocarbon stream at its Izmir refinery. The technologies help meet jet fuel specifications. In addition, its licensed caustic neutralisation technology treats up to 1.6 m3/h of spent caustic ahead of the existing wastewater treatment plant. Samsung Total Petrochemicals Co. Ltd required technologies for its heavy-ends by-product upgrade project. It treated 15 000 bpd of jet fuel in order to meet internationally accepted jet fuel specifications. Refineria de Cartagena SA (Reficar) selected technologies to treat hydrocarbons and spent caustic at its refinery in Cartagena, Colombia. It treated coker LPG and saturated LPG at the facility.
It added technologies, in conjunction with salt and clay beds, to treat kerosene and jet fuel streams. Shell Eastern Petroleum Pte Ltd used selective technologies for a revamp project at its refinery in
Pulau Bukom, Singapore. It treats propane/propylene, butane/butylene and light catalytically cracked gasoline streams to meet product specifications.
According to Global Market Insights, the global oil refining market will surpass US$7 trillion by 2024, but not all crude is created equal.1 The relative value for a crude is largely determined by its yields, which in turn is determined by its characteristics as it enters or leaves the refinery. The growing demand for lighter petroleum products coupled with the introduction of air borne emission regulations will continue to drive technological advancements in desulfurisation.
Reference
1. https://www.gminsights.com/pressrelease/oil-refining-market