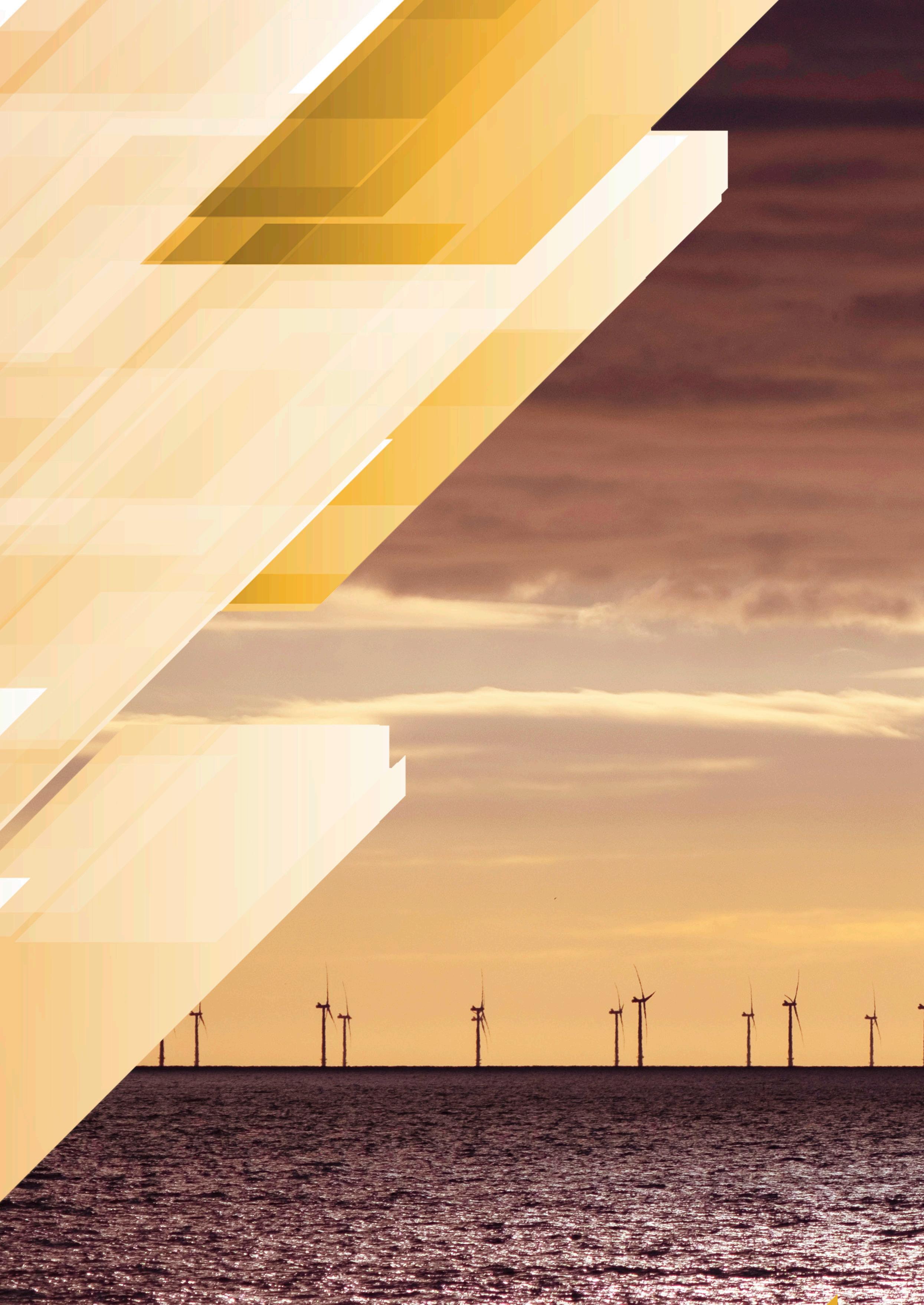
7 minute read
Digital solutions to improve safety at sea
Gaby Amiel, Sennen, UK, explores how developing rigorous systems for digitised operations will be essential in tackling the complexities of a growing industry.
The offshore wind industry is poised for impressive growth over the next five years. Research from the Offshore Wind Industry Council (OWIC), published earlier this year, states that direct and indirect jobs in the sector will almost treble from 26 000 in 2021 to approximately 70 000 by 2026. The stage looks set for a remarkable chapter in the sector’s history books, but how can the industry grow without compromising on safety? Developing rigorous systems will be essential in tackling the complexities of a growing industry.
Historically, the offshore wind industry has not faired badly when it comes to health and safety. Thankfully, it has not had any fatalities in recent years – but its safety record still lags behind oil and gas. In 2019, the Lost Time Injury
Figure 1. Rampion wind farm, Sussex, UK. Image courtesy of Zoltan Tasi.
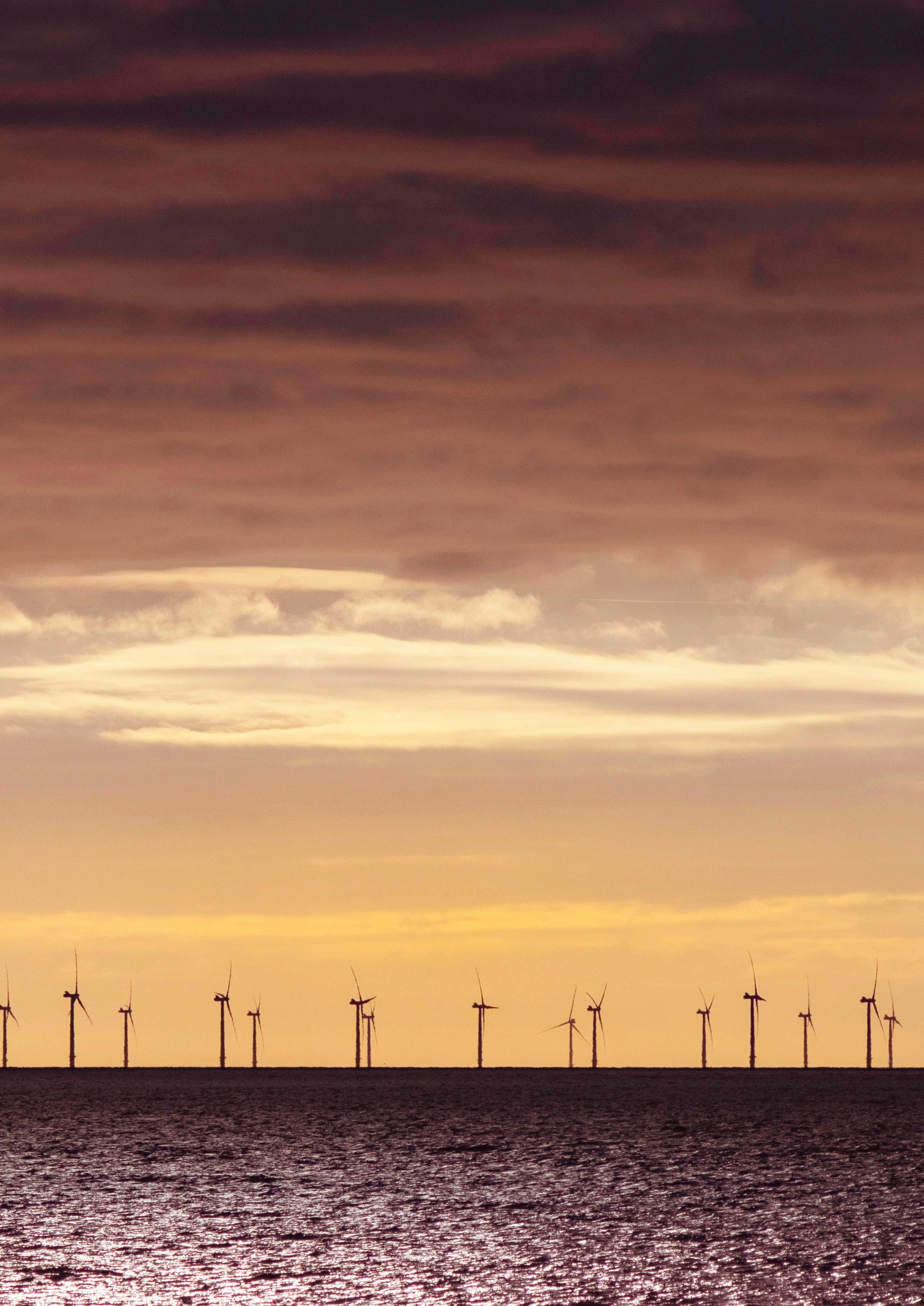
frequency rate for the European offshore wind industry was three times higher than offshore oil and gas.
Technology for growth
Creating systems and technology that enable the sector not only to maintain its safety record but improve on it, must be an integral part of the growth strategy. RenewableUK has said itself that there needs to be the right training and support in place in the transition towards clean energy, and that is absolutely right.
This is especially true considering that each new offshore auction brings a lower cost of energy, putting the squeeze on overheads and requiring more efficient service delivery. Also, more and more projects are being built further out at sea which adds to the complexity. Leading operators are introducing sophisticated automation to improve safety compliance and protect project returns. Here are some of the key areas where technology can improve safety and efficiency:

Figure 2. Sennen screenshot showing HSE KPIs.
Restrictions and alerts
If there is a problem on site, a restriction is raised. This could be anything from a lift that is overdue for inspection, or an electrical fault. When a restriction occurs, workers must be alerted. Sometimes a notification is all that is needed but, in other cases, only those with specific skills and equipment can proceed.
Proper restriction management requires painstaking administration work. Operators report that failure to notify restrictions in a timely way regularly causes interruptions to daily activity, wasting hundreds of thousands of pounds each year. Worse still, missing a restriction can put workers in danger and may have far greater financial ramifications.
However, when equipment service plans are stored centrally, restrictions can be automatically created, issued, and acknowledged. An integrated work planning system will alert users automatically, preventing disruption or cancellation of work.
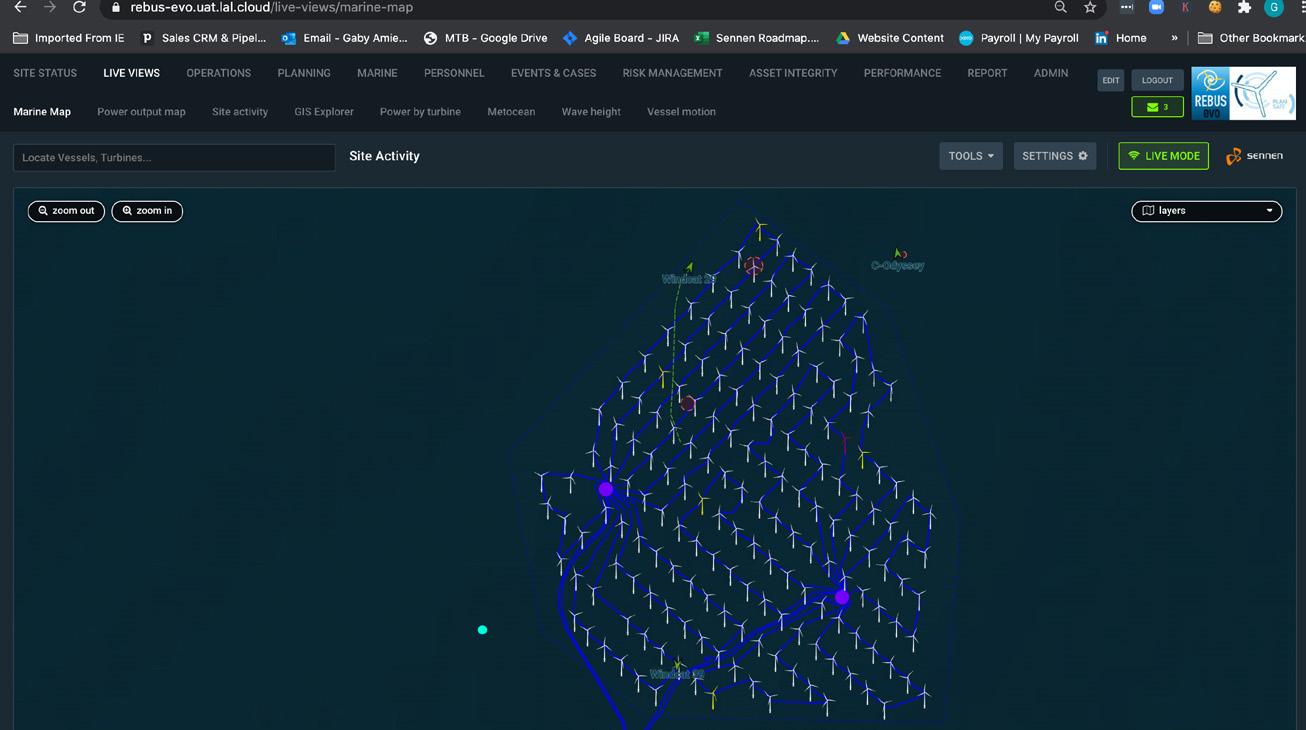
Figure 3. Screenshot of marine map showing cable overlay and vessel movements.
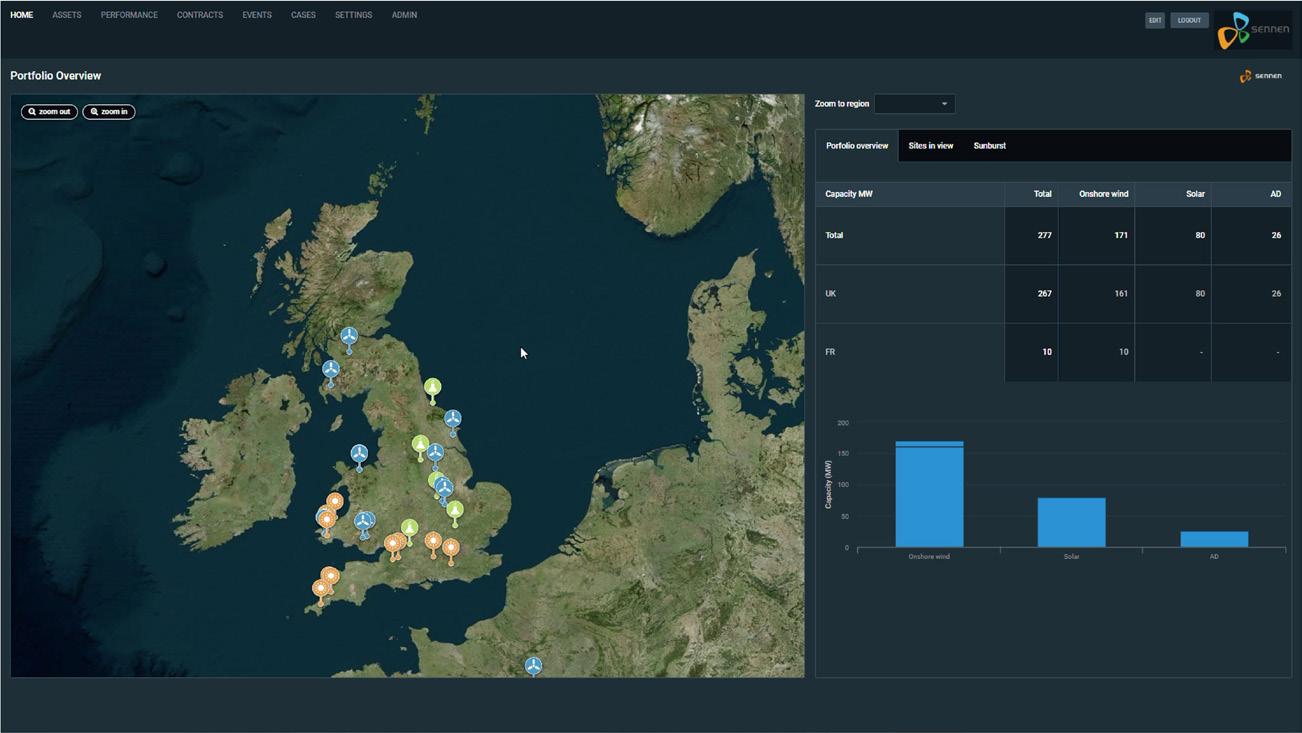
Figure 4. Portfolio overview.
Safe systems of work
Safe systems of work (such as wind turbine safety rules or high voltage safety rules) ensure that dangerous works are carefully controlled and managed. They are effective but highly cumbersome.
Through careful automation, a digital system can track the expiry of qualifications and competency levels, control the start and end of works, and ensure all key checkpoints are observed. Moreover, it can do so with much enhanced speed and rigour.
Hazards and incidents
Reporting health and safety incidents to the HSE is a legal requirement. Every injury, hazard, and near miss must be logged, categorised, and processed. This can be stressful for health and safety managers
as they struggle to keep up with multiple or overlapping incidents.
The reporting and investigation process is fertile ground for digitisation. If an HSE system is working well, incidents and actions on the ground are handled swiftly with a clear auditable record.
For instance, one operator has reported an immediate 33% uplift in hazard reporting after roll-out of Sennen’s specialised HSE system.
Risk monitoring
Every offshore site has a risk management system. Traditionally, a ‘risk register’ is compiled by scoring risks according to the danger they pose. This is stored in a spreadsheet and updated from time to time. It is labour intensive and prone to error. Digitising the risk register allows it to be updated quickly and easily.
Risk should be viewed as a dynamic and evolving metric rather than a static, absolute measure. This is achieved by recording a baseline risk score and recording the impact of mitigations and aggravating incidents.
With a timeline of risk, managers can observe trends, set targets, measure the effectiveness of actions taken, and motivate the team to implement safety improvements.
Weather planning
Earth’s weather systems are unpredictable at the best of times, so offshore maintenance always requires careful planning. With the next generation of wind farms being built further offshore, there is an even greater need for more accurate predictions of weather windows.
Intelligent technology can really help here. The right system will give access to live metocean conditions visualised in different formats and it can automate predicted safe working windows, individual vessel characteristics, and safety considerations – such as speed of the current for diving conditions.
O&M becomes more efficient and safer with fewer project interruptions as conditions can be predicted with greater accuracy.
Tomorrow’s needs
As the industry enters a new phase of growth, it needs to be open to new ways of working using technology that will flex to tomorrow’s needs. Systems that reflect the reality of what is happening on the ground rather than static, outdated recording tools are going to be a crucial in delivering safe and successful growth.
This approach is delivering for London Array which has adopted Sennen’s system to act as a control room to direct all work happening on-site. Safety and planning are key features. London Array is on top of hazard alerts and is able to respond instantly to emergencies. Potential issues are sorted at the planning phase and not once out at sea.
Sennen develops cloud-based software that digitises and centralises every element of managing and operating renewable energy assets. Its goal is to enable operators to maximise asset value while ensuring safe working.
The gains presented by technology go beyond the offshore wind industry. All renewable technologies have their own unique set of health and safety risks and, as each of those industries mature, they will need to examine their processes and discover smarter ways of working. This is an exciting opportunity to set the gold standard in digitised operations.
Ship shape at London Array
London Array is one of the world’s largest offshore wind farms. Its sheer size and make-up brings significant challenges, and ensuring the safety of the many contractors is mission critical. Sennen has created a system that acts as a control room to direct work happening on-site.
Mike Young, Operations Manager at London Array, said: “I have a responsibility across vessels, turbines, and technicians. There are multiple teams, often performing highly specialist work and doing so in confined spaces. Being able to run all of this from the control room, or even remotely from home, is key.”
At any one moment, there are regularly more than 100 people deployed and, at peak times, this figure can be more than 250. Effective co-ordination is thus crucial.
Many of the turbines are in shallow water and this means operational constraints are that bit tougher. The control room needs to direct the work so that the wind farm produces as much energy as possible, safely.
With Sennen, London Array can co-ordinate vessels and manpower so that they know exactly where they are at any point and are ready to respond to anything including turbine issues, changes in weather, vessel breakdowns, and emergencies. Personnel are only deployed if they have the correct qualifications.
Safety and planning have also been greatly improved. London Array is on top of hazard alerts and able to respond instantly to any emergencies. Potential issues are sorted at the planning phase and not once out at sea.
In 2020, while navigating the response to COVID-19, Sennen has once again proved invaluable. London Array has been able to stagger teams and maintain small groups in separate bubbles to minimise contact risk but keep the work on track.
Mike added: “Knowing that the personal qualifications are correct, and that a given vessel can get to a given location, or that there is enough room on that vessel for all of the team – knowing all this without having to check and re-check spreadsheets gives us a significant advantage when planning operations.”