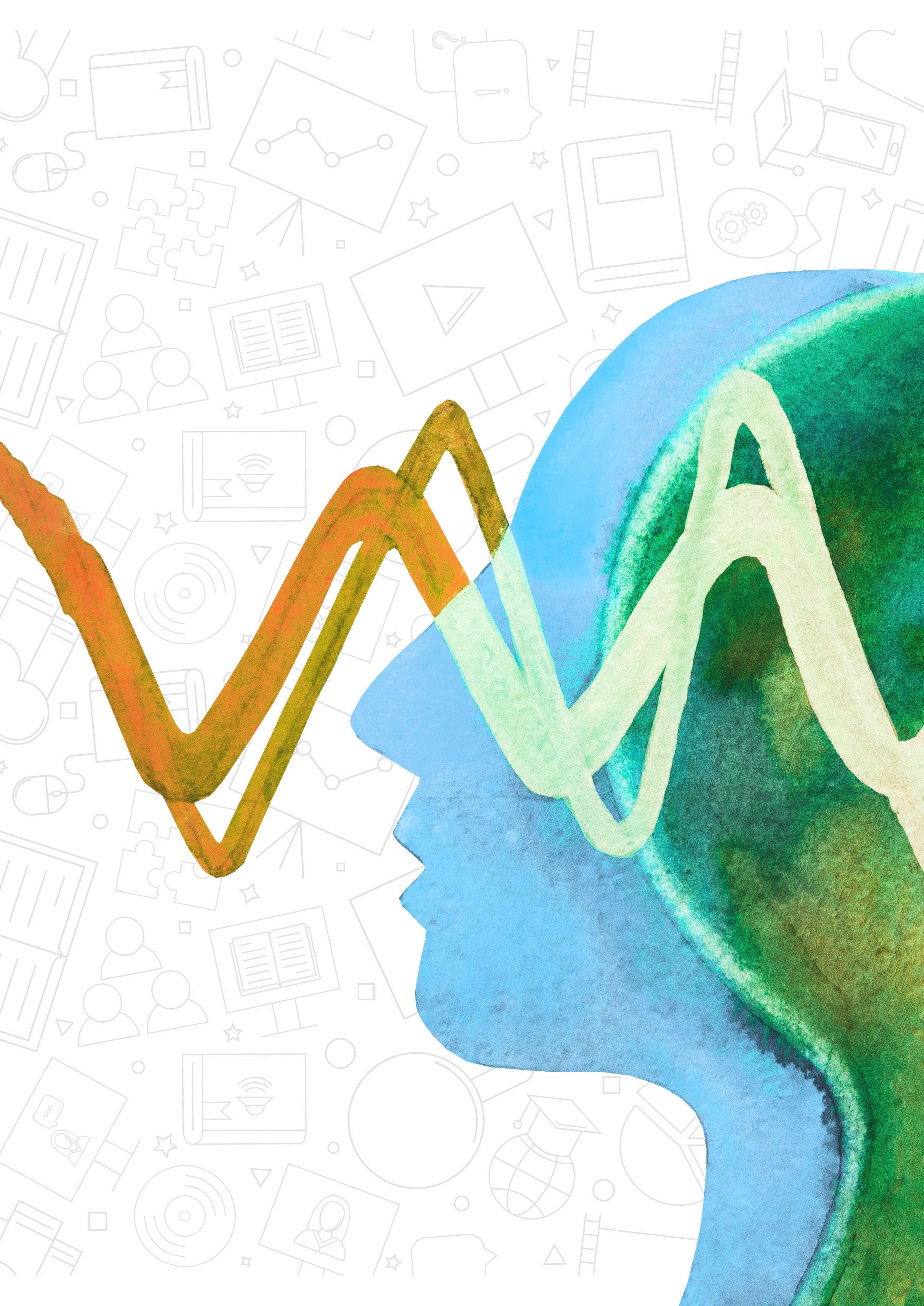
8 minute read
The transfer of knowledge
Chum Wai Hoe, Welltec,
Denmark, outlines how oil and gas expertise can be leveraged to plot geothermal’s hot future and manage challenges in geothermal systems.
At the end of 2020, total global installed geothermal capacity reached 15 608 MW. According to the International Energy Agency (IEA), an average 500 MW was added each year between 2014 and 2019, but only an additional 202 MW came online in 2020. That modest growth falls considerably short of the target set in the IEA’s Sustainable Development Scenario (SDS), where it called upon the geothermal sector to accomplish a 10% increase over the next decade. The IEA’s SDS outlines a major transformation of the global energy
system, showing how the world can change course to simultaneously deliver on the three main energy-related UN Sustainable Development Goals (SDGs). Policies tackling challenges associated with pre-development risks are needed to increase the deployment of geothermal resources for power generation.
With increased development efforts, there clearly has been a faster growth in geothermal capacity over the last 10 years than several preceding decades combined. While
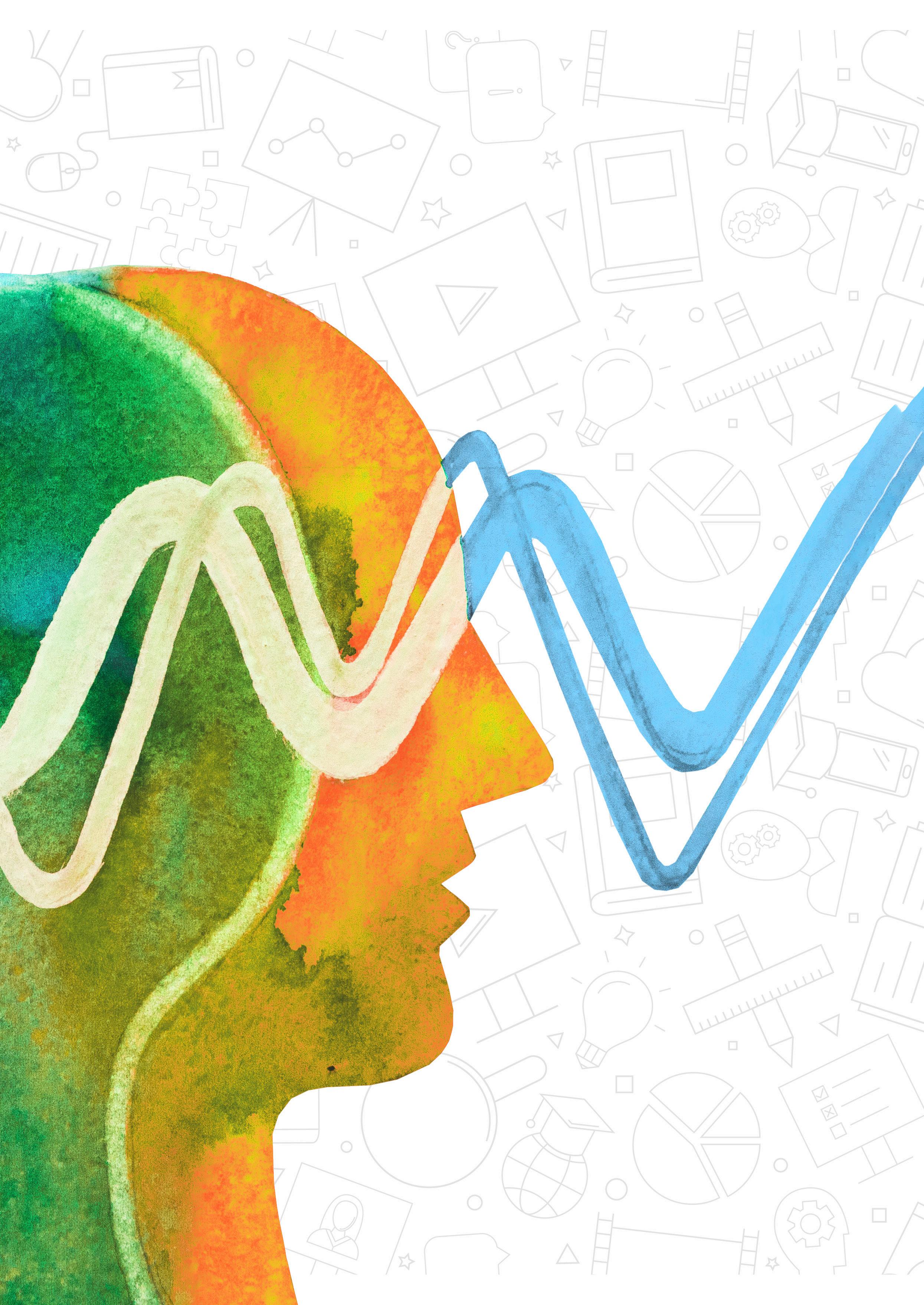
the COVID-19 pandemic delayed the start of new plants last year, construction efforts are progressing, and it is expected that there will be new capacity additions of up to 1500 MW in the next two to three years. ThinkGeoEnergy estimates that by 2026, the overall increase can reach up to 4000 MW in additional power generation capacity.
According to Alexander Richter – Founder and Principal of ThinkGeoEnergy – the geothermal sector is seeing an increased interest as part of renewable energy efforts worldwide. With a demand for non-intermittent sources of renewable energy, geothermal is receiving growing attention as a baseload source of energy to help stabilise electricity supply when paired with wind and solar markets.
With decarbonisation efforts high on the agenda in the heating and cooling sector, Richter sees an even more promising picture with regards to the development of geothermal projects.
“We have seen an increasing interest in geothermal energy for heating purposes, particularly in Europe and China. With the lower temperatures required in the context of use for heating, geothermal energy can be tapped across a much wider geographical area than for power generation. But we also see wider attention on geothermal capability for electricity generation beyond the hot regions of the world. So, all in all, there is a certain momentum that will see a faster growth in geothermal development worldwide than in the past.”
Furthermore, the use of geothermal heat in large scale greenhouses and related operations – as seen in the Netherlands and Turkey – is pushing geothermal energy to the forefront of the discussion.
“Quantifying the expected growth is difficult, but we believe that drilling activities will pick up at unprecedented rates and we expect more development for heating projects than power projects in Europe and beyond,” Richter adds.
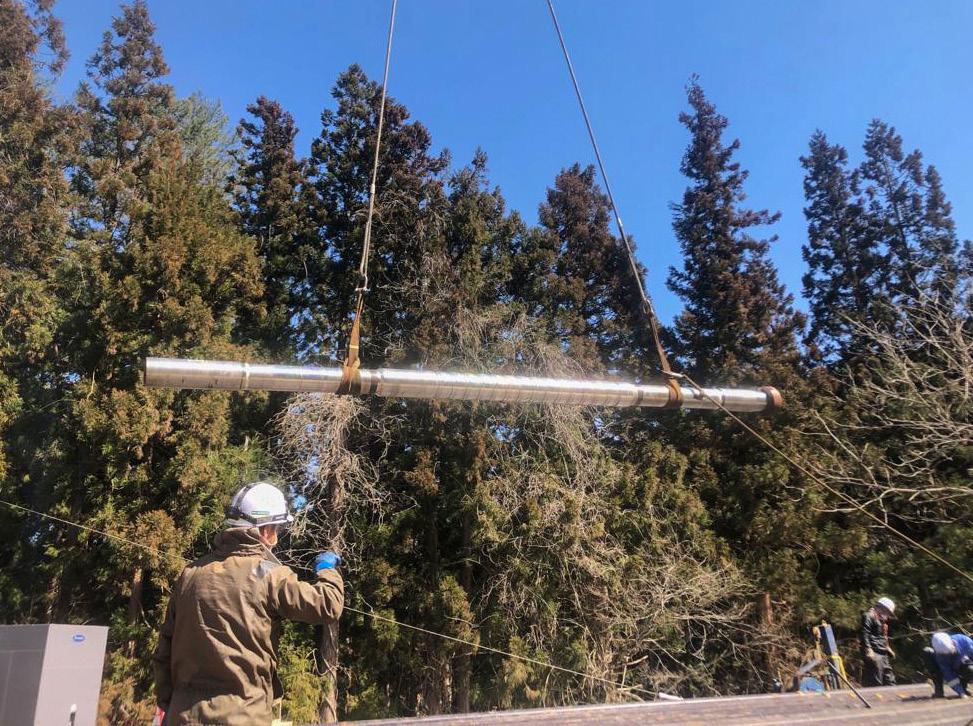
Figure 1. An all-metal Welltec Annular Barrier (WAB®) arrives on site in Japan.

Figure 2. Geothermal deployment in Japan.
The geothermal well
There are of course some key differences between a geothermal well and a petroleum well, such as the temperature and flowrate that needs to be endured, both of which are higher in a geothermal well.
Temperatures for an oil well are considered ‘hot’ between 150˚C and 175˚C, while in a geothermal setting the same would be said in the range of 150˚C to 350˚C. The flow for a geothermal well is up to 10 times higher than that of an oil well, and this requires a larger diameter. Furthermore, geothermal operations are normally set up for beyond 20 years of use, which naturally influences design. In addition to the higher temperature, there are often higher pressures experienced at the wellhead requiring specific considerations to valve designs.
As more progress is made along the energy transition journey, there are numerous companies in the renewable energy sector looking to utilise the experience and technology of the oil and gas industry. Despite any unique challenges in geothermal wells, skills and knowledge built up over many years are largely transferable, and Richter explained how this can be applied to drilling.
“With the increased development of geothermal projects where there is limited space on the surface, comes an increased demand for directional drilling efforts – this can be the case for heating projects in urban areas or as an increased effort for enhanced geothermal systems (EGS). Experience and technologies [drilling] from the oil and gas industry can make a huge impact. At the same time, efforts to speed-up drilling and decrease drilling costs will continue to be key elements going forward. The geothermal sector requires larger investment in order to grow the market and increase the demand for sub-surface experience and services of oil and gas service providers. Oil and gas industry experience can
also be applied in terms of funding exploration, engaging with stakeholders, and paired with investment across the value chain of geothermal.”
The case for technology transfer
Technology transfer is already taking place and can be seen in geothermal well construction. However, Richter believes that we will see more going forward, particularly in directional drilling and drilling related technologies.
“This transfer of know-how, experience, and technology will require further collaboration and co-operation between the two sectors. Increased interest in the geothermal sector (from oil and gas) creates a momentum that sees strong exchange and will create opportunities for both. The scale will be dependent on the long-term commitment made by the oil and gas sector, as well as the economic and political environment.”
Applying hydrocarbon expertise
As geothermal technology continues to develop, oil and gas completion solutions can offer the growing geothermal market the option to not only revive existing shut-in wells, but also develop new geothermal wells with a prolonged and reliable lifespan. Welltec has been adapting its expertise from the hydrocarbon sector and applying it to geothermal energy, enabling operators to optimise well design while minimising the risks and challenges associated with formation uncertainties and high temperatures.
Oil wells can be extremely deep – to date, the deepest is at BP’s Tiber Field in the Gulf of Mexico at 10 668 m vertical depth. When considering vertical and horizontal drilling (directional drilling), the Sakhalin well in Russia comes in at a lengthy 14 900 m.
The depth of geothermal wells varies dramatically depending on their region. In the Philippines and Iceland, the wells tend to be relatively shallow, often approximately 2 km, which is not very deep. When looking at places with no volcanic activity, such as Finland – where the hot rocks are nowhere near the surface – drilling can be required as deep as 6 km to reach sufficient heat.
Geothermal wells employ both vertical and directional drilling. The primary requirement for a vertical geothermal well is a hydrothermal system with sufficient water or steam trapped in a permeable formation.
In a country like Iceland, with its abundance of water and vigorous volcanic activity, drilling is undertaken vertically. However, with a vertical well there is less contact with the rocks. In some of the recent geothermal activities in North America, the heat from the rocks has been at the lower end of the required threshold, so a deviated well is needed to maintain contact – these wells have a lot in common with oil and gas operations. The optimal solution in these situations would be a horizontal well, but despite the obvious advantages and numerous efforts, horizontal wells have yet to become widely established in the geothermal setting.
However, as geothermal energy looks to become more widespread, using deeper and more solid formations will likely come into play.
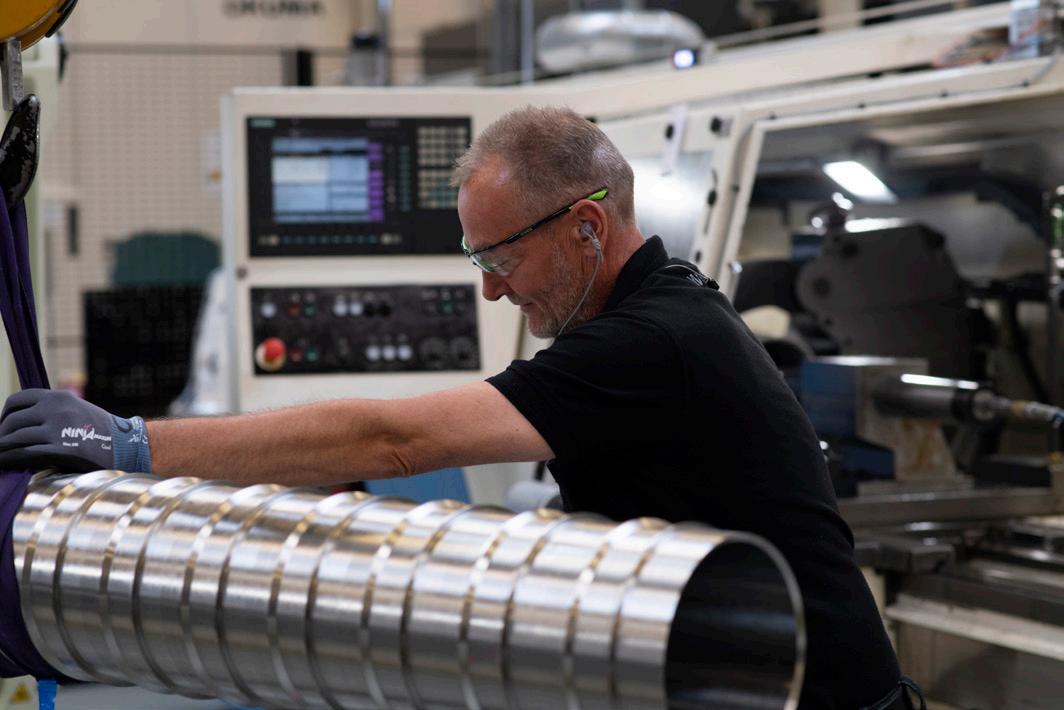
Figure 3. WAB – qualified and tested to the highest industry standards.
Going deeper for better results
To fully utilise the capacity of geothermal energy, the use of improved systems at greater depths is required, as conventional geothermal systems are limited to a few geographical hotspots around the world. This has been contemplated for years in the form of hot rock or EGS.
This is where completions experience from the oil and gas industry can play a pivotal role in the creation of horizontal systems with zonal isolation, and help fully take advantage of formation heat conductivity.
It is not just in the technology arena that companies such as Welltec can share their expertise. The oil and gas industry has been highly regulated since its inception, and this is a trend that geothermal operators are now having to address.
Despite differences between regions, the global experience of the oil and gas industry can help prevent undesired migration of fluids or gases through the lithosphere in a geothermal context; this is generally not permitted as a consequence of operations. A solution developed over many years in oil and gas wells is the ‘packer’. When relining a well, a packer is installed inside the casing and provides a base for cement to cover the previous casing that is damaged. These packers are specifically modified for geothermal application, first because it is vital that there be no trapped fluid, steam, or gas during relining, and second to mitigate for extreme thermal cycling over the life of a well.
Another role for these packers – that conventional geothermal wells are already benefitting from – is cement assurance. This is when a packer is installed to isolate a loss zone or cold feed zone, again providing a base for the cement. This essentially creates a strata system at the point of the relevant zone to guarantee the integrity of the casing.
With many similarities to the oil and gas industry, it is possible to draw on decades of experience to help manage these challenges in geothermal systems.
Much like with oil and gas, geothermal wells require drilling in open hole, as well as a certain degree of cementing in order to achieve casing integrity, and that is where Welltec has earned its reputation in completions over the past decade.