
19 minute read
Reaping The Rewards



Paul Iverson, SABIA, outlines the optimisation techniques set to enable cement producers to get the most value out of their PGNAA systems and realise the benefits of bulk material analysis technology.
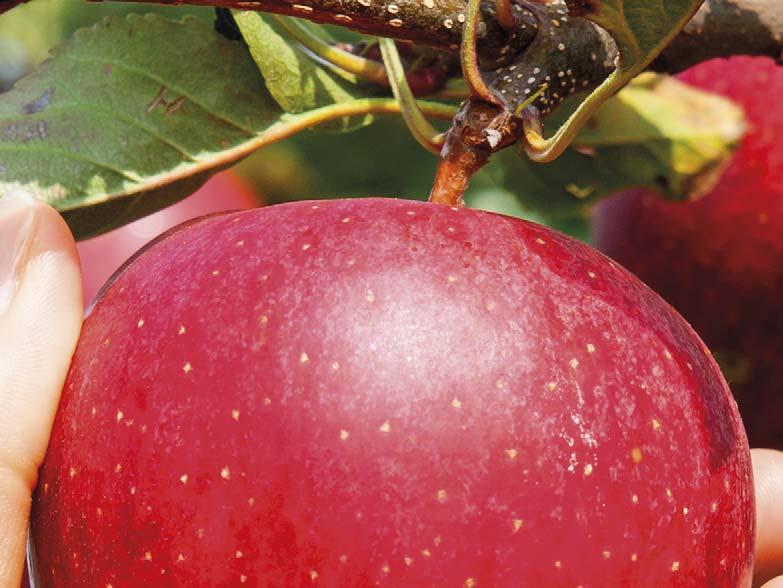
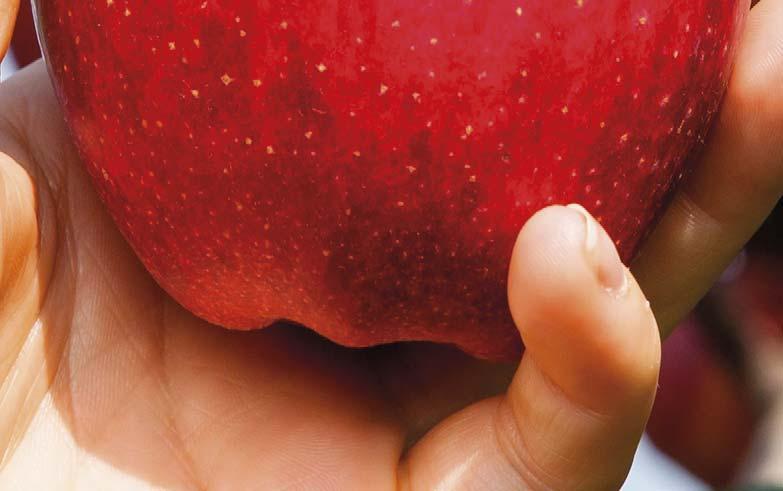
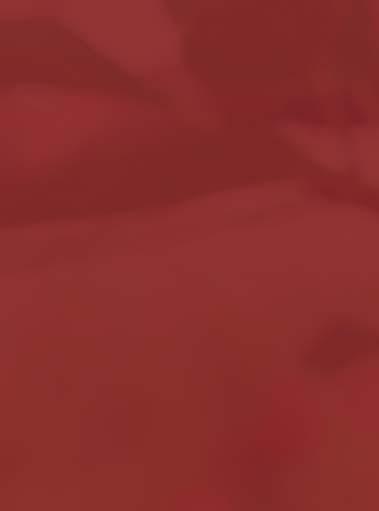

Prompt Gamma Neutron Activation Analysis (PGNAA) is a powerful analytical technology that has been used at cement plants worldwide to substantially improve quality control.
Continuous improvements of PGNAA equipment have enabled better compensation for highly variable manufacturing processes than ever before. However, it is important to remember that PGNAA remains bound by the laws of physics and is not a ‘plug-and-play’ technology. The following guidelines help optimise the performance of PGNAA in a cement process but are all not necessarily required to realise the benefi ts of this bulk material analysis technology.
PGNAA optimisation in general
Analyser confi guration
Cement producers should ensure a proper equipment configuration to meet their site-specific performance needs. PGNAA performance is largely determined by the quantity/size/type of gamma-ray detectors, the neutron source strength, the mass flow through the analyser, and the calibrated oxide ranges. When procuring a PGNAA analyser, cement producers should make sure the specifications for the analyser are appropriate for the application. In a cement raw mix control application where good precision is required, producers should not use a single detector analyser with only 20 micrograms of californium-252 (Cf-252) neutron source loading. A two-detector analyser configuration with at least 40 micrograms of Cf-252 should be used.
Neutron source
The cross-belt PGNAA industry-standard neutron source is californium-252; it is the safest neutron source for PGNAA due to the relatively low average energy of the Cf-252 neutrons. Low energy neutrons are readily shielded so adjacent periodic maintenance can be performed without safety concerns, with no need for a secure standoff zone or other complex mechanical radiation safety protection protocols. Californium-252 source also has no risk of failure or unscheduled downtime due to a predictable 2.645-year source half-life.
Analyser location
Selecting where to locate the analyser is critical, as the stream of percent-composition data the analyser continuously outputs must be actionable for the process control decisions made. An analyser installed before a stockpile will output material composition data that can be used to optimally segregate, stack and pre-blend sections the stockpile while also making quarry grade decisions, whereas an analyser located after a stockpile will output data only after pile reclamation, far too late in the process to be actionable with quarry, blending and stacking decisions.
Belt composition
The conveyor belt should not contain steel cords or chlorine. Because PGNAA measures iron and chlorine with great sensitivity, when present in the belt, these elements produce high background counts that must be compensated for with on-site analyser calibration. Large conveyor belts used in quarry and stockpile applications frequently contain steel cord reinforcements. Conveyor belts with fire-resistant coatings typically contain chlorine. Gamma signals from these elements produce noise that must be calibrated out.
Belt loading
It is important to keep the mass flow passing through the analyser as constant as possible. The variation of the depth of material on the belt should be minimised, with the aim of maintaining around 12 to 13 cm (about 5 in.) of material depth; if possible, avoid belt loading below 40 kg/m. 100 kg/m belt loading is typically considered optimal. While modern PGNAA systems utilise various methods to compensate for low belt loading and mass-flow variations, maintaining a consistent material flow with minimal bed-depth variation will produce the most stable PGNAA results.
Top size
While PGNAA is not affected by the size of rocks on the conveyor belt, it is not desirable to have only large chunks of material without smaller pieces to fill in empty spaces on the belt. As much as possible, cement producers should avoid belt loading with large voids in the material flow. It should be ensured that crushers are operating properly, and locating the analyser after a secondary crusher should be considered.
Layering
PGNAA continuously sees all bulk material passing through the analyser and results are optimised if bulk material layers are mixed before the analyser. This is straightforward to achieve at most sites by locating the

SABIA X1-LiNX analyser for pre-blend stockpile management.
analyser after a conveyor transfer point. It is typical for analysers used for raw mix control to see layered materials on the belt, but PGNAA will always achieve the best results when material layering is minimised.
Weight input
Ideally the belt-loading weight input to the analyser comes from a well-calibrated belt scale measuring a mass flow (t/hr) representative of the analyser location. Alternatively, feed rates for materials added on the belt can be summed together for a representative mass flow of the analyser location. When starting a PGNAA project, the type of weight signal to be provided for the analyser should be considered and planned for accordingly. Will the weight signal be from an analogue 4-20 mA cable, a digital output from a programmable logic controller, or summed feed rate values from a distributed control system?
Calibration ranges
The most accurate PGNAA results can be achieved using narrow ranges of analyte concentrations for calibration, but it is important to calibrate for the full typical operating range of analyte concentrations the analyser will see. For some applications it is desirable to use multiple narrow-range analyser calibrations to cover a wide concentration range for a single analyte. Working with a PGNAA supplier on the site-specific calibration plan is recommended.
Representative sampling
Dynamic tuning and performance verification of the PGNAA system is best when comparative sampling is coordinated with the PGNAA data points to ensure lab samples are representative of what has passed through the analyser. For optimal dynamic tuning, use an automated mechanical sampler to gather high-frequency samples and build composite samples for lab analysis. In quarry/stockpile applications, cement producers can back-calculate from mill samples to derive representative pile compositions. Working with the PGNAA supplier on a site-specific calibration plan in advance of installation is recommended.
Buy-in
A successful PGNAA installation requires buy-in, communication, and coordination by many parties. Be sure at the outset that plant operators, owners, and PGNAA suppliers share the same expectations. An ‘Analyser Champion’ who will ensure operational success should be assigned. A management sponsor for resource needs should also be established and IT staff should be prepared early on for system integrations. It is additionally a good idea for lab managers to be taught how the PGNAA system works in conjunction with the lab, and for a unified control strategy to be coordinated with operations to meet clearly defined process goals. A site with buy-in from everyone involved is well positioned to optimise PGNAA performance.
Software
Online bulk material measurements with PGNAA produce a great deal of useful information. Appropriate software should be used to get the most out of PGNAA data. Stockpile monitoring software can tag composition data by layer, time, and tonnage as a pile is built, including automated alerts when a deviation from quality targets is detected. An entire pile is represented by a tag group for reclamation. Raw mix control software uses PGNAA and lab results to automate raw material feeders to maintain preset quality targets with minimal variations. PGNAA specifi c software should be used to maximise the value of data.
PGNAA optimisation for raw mix control automation
Analyser location
The analyser is installed just before the raw mill and outputs continuous analysis data used to make rapid automated feeder adjustments. If instead the analyser is located after the raw mill, then the control loop will be less effective as all feeder adjustments will be delayed by the material residence time in the mill. When selecting where to install a raw mix control analyser it is important to minimise closed-loop control delays.
Belt loading
Using a conveyor transfer point, raw material layers can be mixed before the analyser. The material depth on the conveyor can be kept consistent using a variable frequency drive (VFD). If needed, consider reducing the belt speed to produce a minimum 40 kg/m belt loading for a strong PGNAA signal. It is common for raw mix analysers to see layered material with frequent bed depth variations or less than 40 kg/m on smaller belts, but these conditions are not optimal.
Uniform layering
If a process does not allow for a transfer point to mix layers before analysis, then it is key that each feeder adds material at a consistent rate, spread evenly across the conveyor belt. Perform routine feeder maintenance to prevent
clumping and plugging feeders. Designate the order of feeders to avoid two separate layers of wet clay on the belt. Even if there is a transfer point to mix materials, efforts should be made to spread additives evenly across the belt by using deflection plates where necessary.
Quarry quality
A consistent limestone feed allows for tighter calibrated ranges and relatively small feeder adjustments to meet quality targets. Pre-blending minimises limestone variations. It is important to plan in advance for times when a raw mix automation system will see significant changes in limestone quality. Consider using multiple calibrations or multiple product profiles for different limestone seams.
Additive consistency
Every raw mix automation system is configured for the site-specific additives in the raw mix. The more consistent raw material additives are, the greater the success that can be achieved in meeting quality targets with PGNAA. Additive compositions should not be changed without making corresponding changes to the PGNAA software. If additive qualities often vary greatly, consider establishing multiple product profiles to switch between depending on the quality of additives at any given time.
Oxide isolation
To the extent that it is possible, cement producers should try to utilise raw materials so that there is a single material source for each major oxide in the raw mix. Doing so will make quality control easier than trying to maintain consistent oxide targets using multiple material sources for a given oxide.
Avoid rogue materials
No additional materials should be added between the Raw Mix Analyser and the downstream mechanical sampling point after the raw mill. Care should be taken to ensure that composite samples for lab analysis are representative of the same material seen by the PGNAA analyser before the mill.
Kiln dust
It is best to recycle kiln dust back into the homogenisation silo when possible. Avoid adding kiln dust into the middle of the control circuit as it will not be detected by the PGNAA system. Additionally, kiln dust should not be added back into the kiln as this can make clinker samples less representative of the control circuit.
Sample collection
Fine tune the PGNAA calibration dynamically by collecting high-frequently mechanical samples to build one-hour composites that are highly representative of the bulk material flowing through the analyser. Care should be taken to synchronise lab XRF data and online PGNAA data so they represent the same time periods. Factor in mill residence times for synchronisation.
XRF accuracy
Ensure lab XRF results are accurate by using fused beads, avoiding sample contamination, and by taking great care to synchronise the timing of gathered samples and online bulk material analysis. Perform calibration checks and routine maintenance on lab XRF equipment per the advice of a selected XRF service provider.
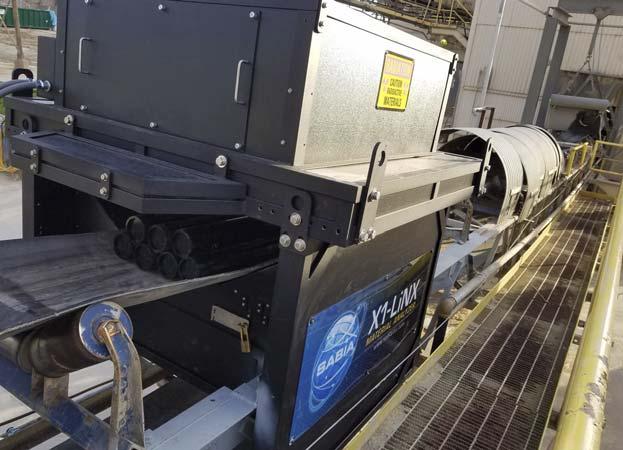
SABIA X1-LiNX analyser for raw mix control, during initial static calibrations with reference standards on an empty belt. Conclusions
The optimisation topics mentioned in this article will allow cement producers to get the most value out of their PGNAA systems. While some plants do not have the ability to apply all PGNAA optimisation techniques, they should implement as many as possible to maximise process quality control.
About the author
Paul Iverson has spent the past 8+ years focused on PGNAA solutions for the cement industry and is Director of Operations at SABIA Inc. He works closely with the founder of Gamma Metrics which first commercialised PGNAA in the 1980s. This PGNAA focus has instilled a robust understanding of the nuances associated with online bulk material analysis also including coal, gold, iron, nickel, phosphate, and other bulk materials.

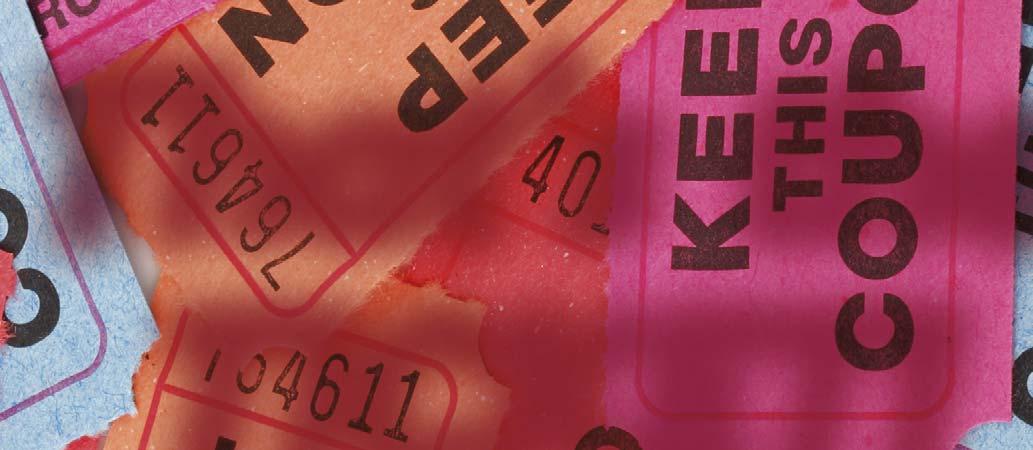
That’s the That’s the That’s the That’s the TICKET TICKET!TICKET TICKET!
Scott Dugan, Command Alkon, explains how companies can streamline business processes and the operational tasks necessary to ticket and scale cement, enabling drivers to check-in, load, and ticket trucks without interruption.
Digital innovations and intelligent networks offer tremendous opportunity to supercharge effi ciencies in the cement industry. New technologies have the strength to create powerful connections between physical and digital systems. Many cement players know the benefi ts of implementing digital solutions, but few have seen its full power or taken advantage of its full potential.
Cement operations can realise incredible results through digital technologies that enable employees to manage the business from quote through to collection – enabling dispatchers, fi eld workers, and customers to communicate directly with each other, while adding accountability and tracking that can be seen from the offi ce. Apex from Command Alkon streamlines business processes and operational tasks necessary to ticket and scale cement, enabling drivers to check-in, load, and ticket trucks without interruption.
Rush hour to rapid fl ow
Apex can expedite the ticketing process by ensuring all information about an order is in the system from the start, so that the truck driver knows exactly what is being picked up and where it needs to go as soon as they pull on-site. These point-of-sale modules interface directly with the sale, dispatch, transportation management, and back-offi ce modules for quoting, invoicing, receivables, inventory, reporting, and business intelligence. When order information is entered into the system from the get-go, that data fl ows through the entire ticketing process and throughout the entire enterprise so that everyone is in the loop.
Seeing as cement is such a pricey product, accurate loading is crucial. Site-automation technologies work in tandem with Apex to deliver improvements in loading accuracy, speed, effi ciency, and safety, and integrating Apex directly with the site PLCs and loading system can ensure that the right material is in the right truck and reduce the risk of lost loads.
Utilising Apex point-of-sale and back offi ce modules in conjunction with site-automation technologies typically presents the opportunity to cut down 35% of time in the yard. The system cuts down verbal communication once the truck pulls on to a site because the loads are already in the system and a truck is already assigned to those loads. Automating the process keeps the driver in the safety of the cab of the truck the entire time they are in the yard, promoting safety while streamlining throughput. The system also has the ability to interface with the loading system and receive feedback that permits them to prevent the truck from being loaded unless certain safety measures are in place.
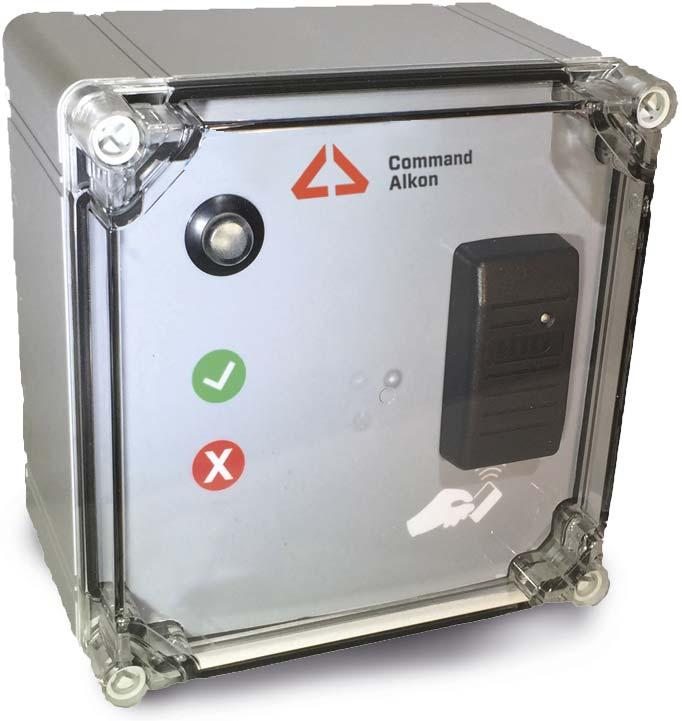
The Apex Express Reader works in conjunction with the Auto ID module to automate the ticketing process with this ‘swipe only’ device for vehicle identifi cation.
The All-Terrain Kiosk provides a touch screen interface for load assignment, driver selection, and load confi rmation. Boosting speed and effi ciency

Apex’s Auto ID module uses Radio Frequency (RF) devices or License Plate Recognition for vehicle identifi cation and assignments. The Apex Express Reader works in conjunction with the Auto ID module to automate the ticketing process with a ‘swipe only’ device for vehicle identifi cation. The Apex All-Terrain Kiosk (ATK) supports the Auto ID module to further automate the driver check-in process. The ATK provides a touch screen interface for load assignment, driver selection, and load confi rmation. This automation piece is intended to increase the speed and accuracy of the load processing without the addition of scale personnel. The Automated License Plate Recognition (ALPR) uses a combination of camera and Auto ID technology to identify and process a vehicle entering the site and/or scale in seconds.
Scale Watcher is the next generation of hardware and software to provide photo and video verifi cation of a truck’s weighing process. This is an integrated photo verifi cation tool that overlays ticket information onto a photo of a truck on the scale. This image is then saved in a PDF, HTML or other image-friendly format by ticket number. The ticket number provides easy retrieval of the image to email to customers. The tool also provides proof of vehicle pickup without signatures.
With Scale Watcher, an optional gate/valve anti-theft module alerts authorised personnel of potential theft of materials. The anti-theft module sends an email alert to one or more designated addresses whenever the gate/valve is opened and closed on a loading system and a ticket is not printed. The gate/valve anti-theft module is not reliant upon the scale or software to function and will work after hours when the plant is shut down. The scale sensing feature will also send an alert if: A truck has left the scale, but no ticket was generated. The tare weight is above the set threshold. The gross weight from the scale does not match that printed on the ticket. The weight on the scale exceeds the truck GVW (Gross Vehicle Weight). The ticketing system loses connection with the scale indicator.
New functionality also supports bagged cement, providing the ability to cross-check that the load
is accurate. If a certain number of bags are ordered and the truck comes over the scale, the system has the ability to check that the right number of bags are loaded based on a certain confi gurable threshold. If the truck comes over the scale and weighs more than the given threshold, the system can fl ag that load and the truck will not be allowed to receive a ticket unless someone manually overrides it.
Finally, the Remote Printer Enclosure enables drivers to pick up their scale ticket after weighing without getting out of the truck. Combined with a movable swing arm option, the enclosure is installed at cab height immediately following the outbound scale and rotates easily out of the way if bumped.
Apex can also integrate with TrackIt, Command Alkon’s truck tracking and telematics system. Utilising a telematics system provides full visibility of the truck throughout the entire delivery process. The system can provide statuses for when the truck arrives at the plant to be loaded and when the truck is in the loading area so that it is easy to determine the difference in the time during check-in to loading, when the truck leaves the loading area, when the truck is ticketed, and then all the way to the delivery site. The result is the ability to improve customer service by improving insight into what is really going on.
Site automation in action
The back offi ce is an integral part of any organisation, and a signifi cant percentage of customer dissatisfaction can be traced to back offi ce ineffi ciencies, which has the potential to greatly impact the operation’s profi tability. The lack of insight into back-offi ce activities costs many companies signifi cant amounts of money each year. Not having a system in place to manage and optimise productivity can present some serious implications on customer service and business reputation.
One of Command Alkon’s Apex customers built a custom application for their back-offi ce processes in 2001. In 2018, the company decided to add the Apex sales and back offi ce modules for quoting, invoicing, receivables, inventory, reporting, and business intelligence because it had expanded its services and had undergone some substantial growth. The company’s in-house system no longer had the power to handle its volume of work.
The company’s employees responded positively to the addition of the back-offi ce modules because the interface is familiar, and it is very similar to the way that their custom application works. The system is also highly customisable, so the company was able to easily tailor the solution to work the way that made the most sense for the business and for its people.
Because this particular company had been an Apex user for more than two decades prior to adding back offi ce modules, they already had a fi rm relationship with Command Alkon. This helped in making the implementation process as seamless as possible. The implementation caused no interruption in the company’s operations, and Apex has allowed it to universalise its process across the entire enterprise and have better insight into what is happening in real time from all parts of the organisation.
Now that the company has the back-offi ce modules in place with the loadout and scale ticketing, it is using the Apex system with each local plant to manage orders. The system has helped them go from a 15-day close at the end of the month to a three-day close because all the invoices are contained within one platform.
The company is now able to manage demand and keep trucks moving, and since implementation, it has maintained a record-setting year. The company also claims that Apex’s modularity is a big factor in this success.
Conclusion
Having one point of reference for information on the product from the time it is ordered, out the door, and billed, and streamlining check in and loadout processes, eliminates tedious manual tasks and allows companies to handle the orders that customers need each day.
About the author
Scott Dugan joined Command Alkon in 2005. He has performed roles in customer support, implementations, project management, product management, technical sales, and is currently the Director of Operations for Bulk Materials Products. His degree in management information systems and prior experience in information technology brings technical expertise to the Bulk Materials industry.
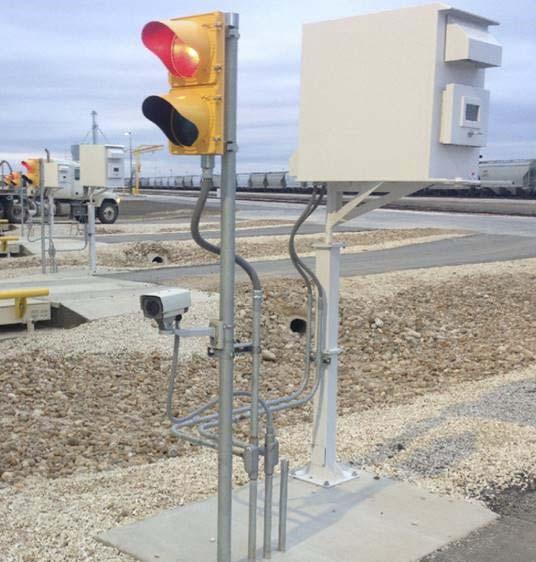
Apex’s rugged Remote Printer Enclosure keeps drivers in the cab, out of harm’s way, and gets vehicles on the road quicker.
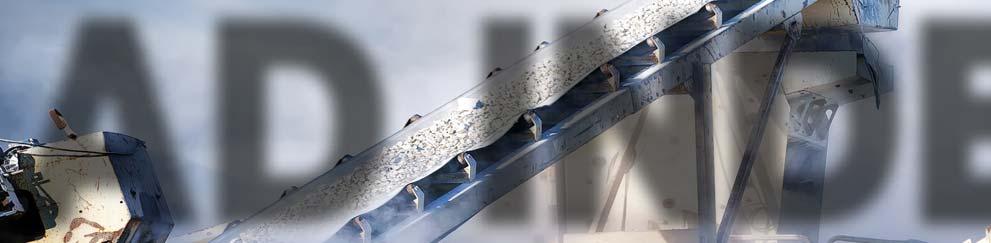
AD INDEX AD INDEX

ABC www.abc.org.uk
AXIANS IAS www.axians-ias.com
38
KIMA Process Control www.kima-process.de
OFC, 31
KINGSBLUE www.kingsblue.com
25
IFC
Brokk & Bricking Solutions www.brokk.com www.brickingsolutions.com
Dynamis www.dynamis-br.com
GCP Applied Technologies www.gcpat.com
HEKO www.heko.com
16 – 17
37
04
02
HGH Infrared Systems www.hgh-infrared.com
63
IEEE-IAS/PCA Cement Conference www.cementconference.org
59
Intercem www.intercem.de
49
Maerz www.maerz.com
IBC
Parker www.parker.com
Refratechnik www.refra.com
09
51, 55
RHI Magnesita www.rhimagnesita.com
Starlinger www.starlinger.com
OBC
13
Taiheiyo Engineering www.taiheiyo-eng.co.jp/en/
07
thyssenkrupp Industrial Solutions www.thyssenkrupp-industrial-solutions.com
21
KettenWulf www.kettenwulf.com