
18 minute read
A Lifetime Achievement
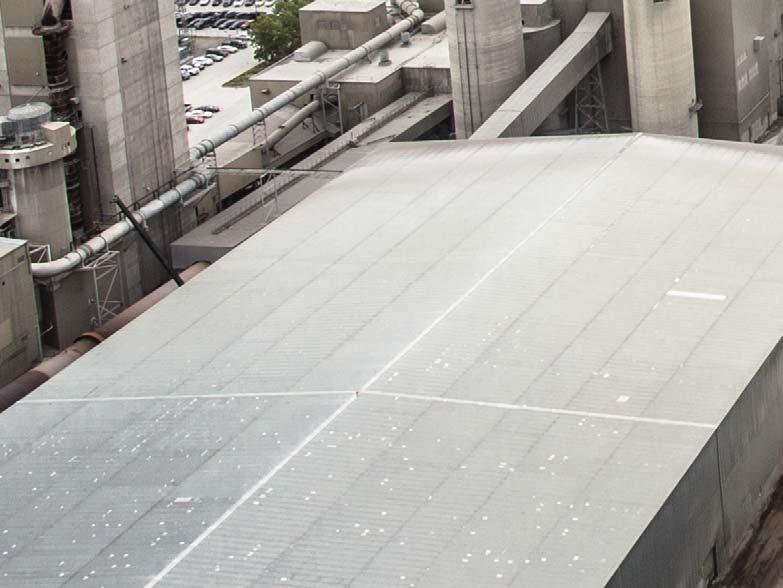
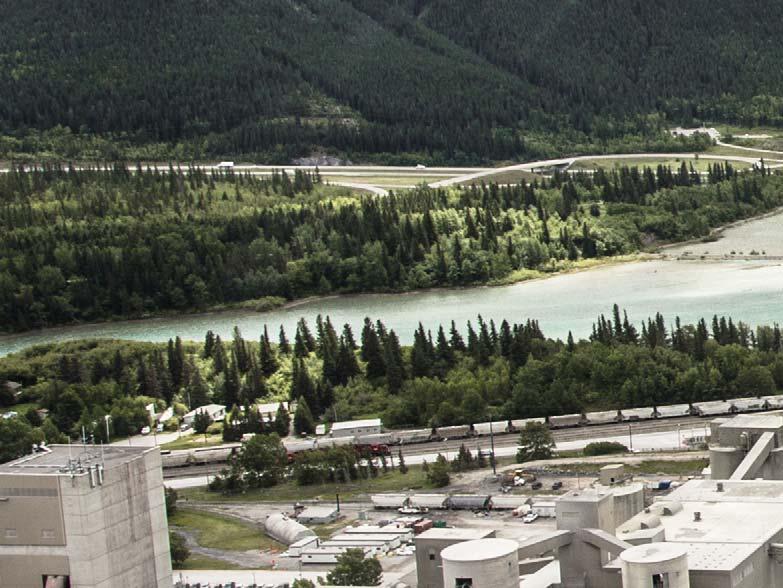
Daniel Hansted-Martin, HASLE Refractories, explains how Lafarge Canada’s Exshaw Cement Plant has reduced abrasion and chemical challenges and tripled the lifetime of the refractory lining in the facility’s Riser Duct using a precast Modular Lining.
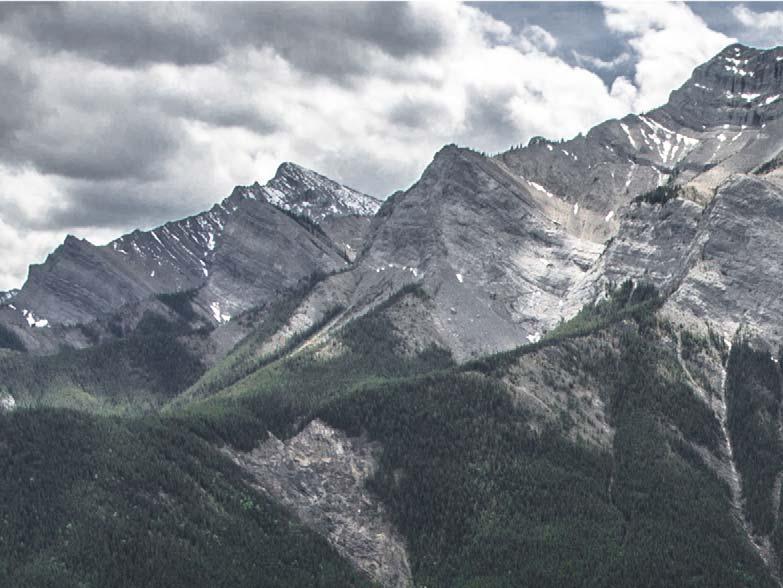
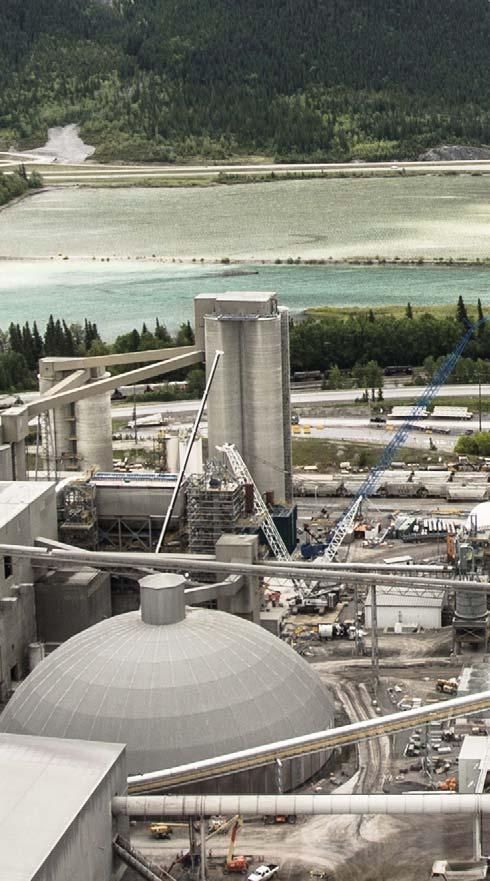

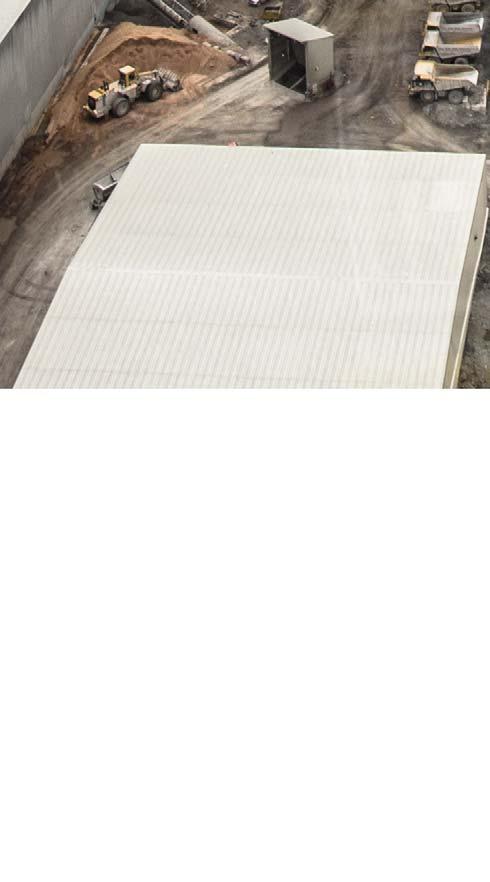
Set in pristine surroundings at the foot of the Canadian Rocky Mountains, Lafarge’s modernised cement plant showcases environmental and economic effi ciency. Built in 1906, as ‘the Western Canadian Cement & Coal Company’, the Lafarge Exshaw Cement Plant is Canada’s biggest cement factory with a capacity of 2.4 million tpy. Over the years, the plant has had six lines in operation, however, today only line K#5 and K#6 are being operated. Each has a production capacity of 2200 tpd and 4200 tpd, respectively. Lafarge Exshaw operates on 100% natural gas and is working towards using low carbon alternative fuels in the future. Its updated facilities operate the latest cement production technology. As a member of LafargeHolcim, the plant is continually seeking solutions to operate more effi ciently and sustainably.
Solving short lining lifetime in the Riser Duct
Responding to Western Canada’s signifi cant cement demands, Lafarge Exshaw seeks to increase capacity and minimise stoppages. However, in 2017, the plant faced abrasion and chemical challenges in its refractory lining in Riser Duct K#6. The lifetime of the company’s
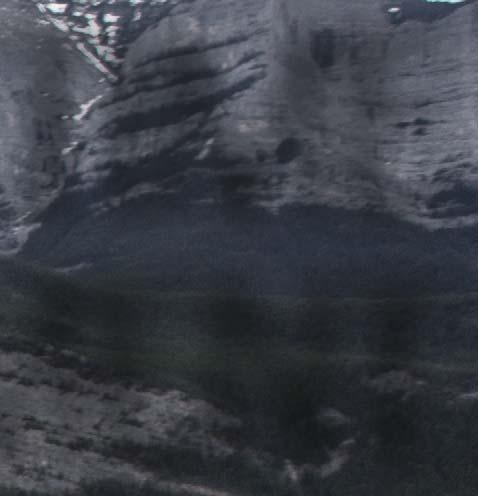
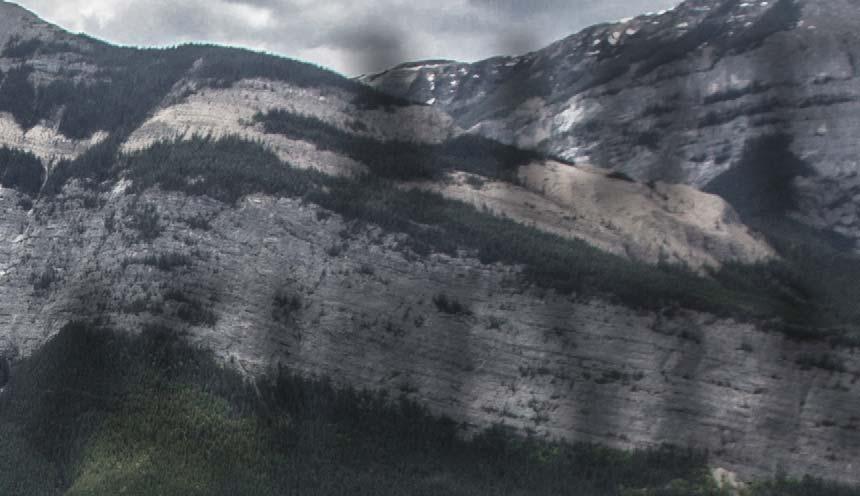
A LIFETIME A LIFETIME A LIFETIME ACHIEVEMENTACHIEVEMENT ACHIEVEMENT



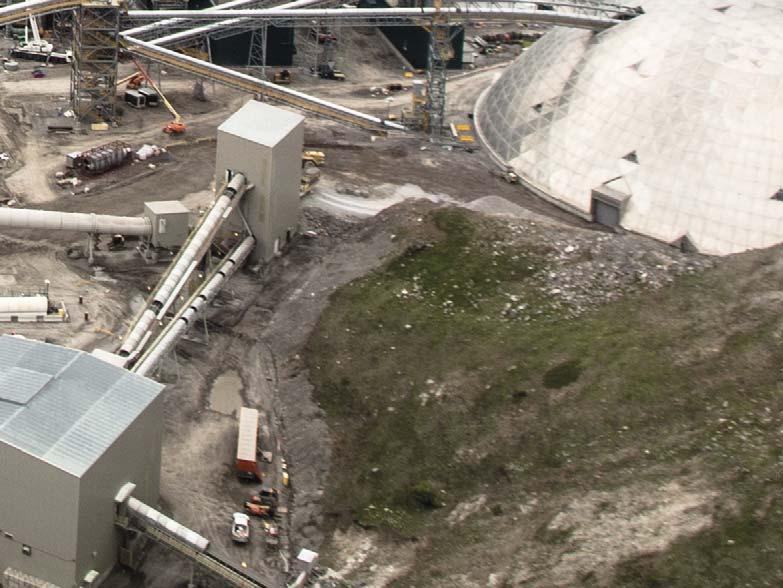
existing refractory lining was no more than six to 12 months. Needing a long-life, sustainable alternative, Plant Manager, Kate Strachan, contacted HASLE Refractories with a recommendation from another cement plant within the LafargeHolcim Group, which was already using HASLE’s precast Modular Lining. “We needed to achieve a signifi cantly longer lifetime”, said Kate. “When the Modular Lining was already showing excellent performance at another plant within the group, we didn’t hesitate to install it here at our Canadian plant.”
Upon receiving the technical drawings from Lafarge Exshaw, HASLE’s team of engineers designed a tailor-made solution for line K#6, based on the standard precast element design. Detailed drawings of all 138 m2 of the riser duct were made, and once they were approved by Lafarge Exshaw, the installation was scheduled for mid-March to mid-April 2018. To ensure that the optimal installation technique is used, a team of HASLE supervisors always participates on site whenever the precast Modular Lining is installed – in this case, they had the pleasure of cooperating with the Canadian installation company, Alliance, who undertook the installation at Lafarge Exshaw.

A worthwhile recommendation
By September of 2020, the precast Modular Lining installation had been in operation for more than two and a half years. The Lafarge Exshaw Cement Plant has achieved an excellent lining lifetime in its riser duct, with no re-linings or repairs needed to keep it running. This has lowered its use of natural resources per produced unit and resulted in an overall more stable production. When Lafarge Exshaw implements the use of low carbon alternative fuels in the future, the precast Modular Lining will remain a benefi cial lining choice for the riser duct, as its low, open porosity and smooth impact surface makes it highly resistant to alkali attack and build-up – even in extremely hostile environments.
“Currently, the precast Modular Lining has achieved a lifetime of +30 months”, said Plant Manager, Kate Strachan, and adds, “We estimate it will have an additional lifetime of up to 24 months, so we are very satisfi ed with it. It certainly proved to be a worthwhile recommendation.”
Although HASLE’s pre-cast Modular Lining has been installed at more than 100 plants worldwide, this instance was the fi rst in which the company supplied the lining to a Canadian company; the future might hold more precast Modular Lining installations for the North American country, whose cement industry in the year of the installation generated around CA$10.5 billion in revenue.
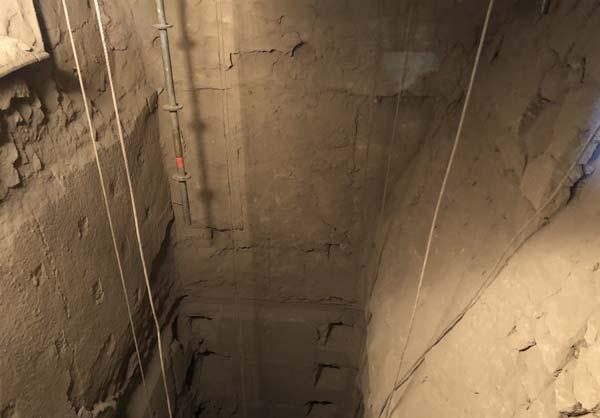
Earlier refractory lining in K#6 riser duct with a lifetime of only 6 – 12 months.
Steel rails are welded onto the casing and HASLE’s console lining is installed with mortar between the elements. It is now ready for installation of the precast Modular Lining elements. The design
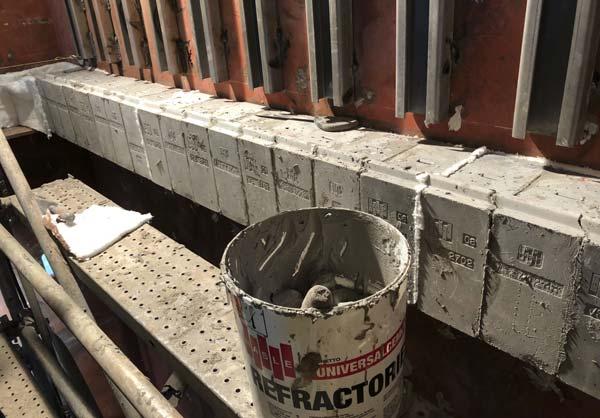
The HASLE precast Modular Lining was designed almost 20 years ago. The goal was to create a hot face refractory lining for the critical areas of high temperature industries, which was durable and resistant to abrasion, chemical attack and coating, resulting in a signifi cantly longer lifetime than the existing alternatives on the market. Since its creation, it has stood the test of time and can last twice or even three times as long as a traditional cast lining, and sometimes even longer.
Whereas traditional in-situ cast solutions typically have an open porosity of 18 – 20% or more, HASLE’s precast Modular Lining was designed to have a low open porosity of only 8 – 10%. This quality is achieved through a combination of selecting raw materials with an optimal corn distribution curve and adding only a very small amount of water (as little as 4.5%) when mixing the castable. The result is a refractory lining which has a longer lifetime, is abrasion- and alkali-resistant, and even when installed in plants operating on 100% RDFs, build-up is almost eliminated.
With the precast Modular Lining, it is also possible to achieve a lining thickness as low as 185 mm. This is often less than the thickness of a traditional cast lining, and presents two options; the plant can either decide to go for a reduction in heat loss by applying more back-up lining, or it can decide to increase the cross sectional volume, which will give additional space in the given area. In many cases, an increased production capacity has been achieved by removing a process bottle neck though the installation of the precast Modular Lining, thus increasing the volume of the given area.
In order to secure the highest quality of the Modular Lining elements, all elements are cast and pre-fi red under strictly controlled conditions in HASLE’s plant in Denmark. Casting the elements at the plant using specialised equipment such as vibration tables, special moulds and dry-out ovens and employing skilled workers secures a strong focus on each step of the casting process and ensures a consistent optimal quality. The process includes dry mixing for 60 seconds, adding water, wet mixing for 4 – 5 minutes., casting it into the moulds and covering the elements in plastic immediately after. The elements are then left to cure for 24 hours and are subsequently pre-fi red for fi ve days up to a peak temperature of 500ºC. All these steps are carefully monitored in order to secure the highest possible consistent quality of all pre-cast elements. However, even in this carefully monitored production environment, small deviations in quality can occur, and therefore each
element is both visually inspected and subjected to a strict quality control procedure prior to leaving the production facility.
Installation
Installing the precast Modular Lining is both fast and easy. Due to a smart element design combining steel anchors with a tongue-and-groove system, the installation of the pre-cast Modular Lining often takes about 50% less time than the installation of a traditional in-situ cast solution. Once preparations are completed, the time required for a typical lining is 80 min/m2, depending on the condition of the area to be lined i.e. number of air blasters, inspection holes, manholes etc. After the welding of the rails and steel plates holding the elements, the console elements are easily installed. Upon these, the square modular elements (250 x 250 mm) with a tongue and grove system are installed. The precast elements weigh only about 15 – 16 kg each, so no special lifting equipment is required.
All elements are pre-fi red at HASLE’s production facility in Denmark, so no dry out of the lining is required, which allows for a faster restart of production. To ensure the successful completion of each individual installation project, HASLE Refractories always supplies approximately 5% more elements than needed, and if a surplus of elements remains after completed installation, these can be stored and kept for many years as there is no limited shelf life. Compared to the limited shelf life of castables, this is another valuable advantage.

Precast elements are installed on the steel rails, on top of the console elements, with vermiculite back-up insulation between the rails. Ceramic fi bres are installed between every four elements (every 1 m) to allow thermal expansion. Now, the system is only missing the pouring of the insulating castable behind the pre-cast lining.
After 1.5 years of operation, HASLE’s logo embedded on the elements is still visible. Applications
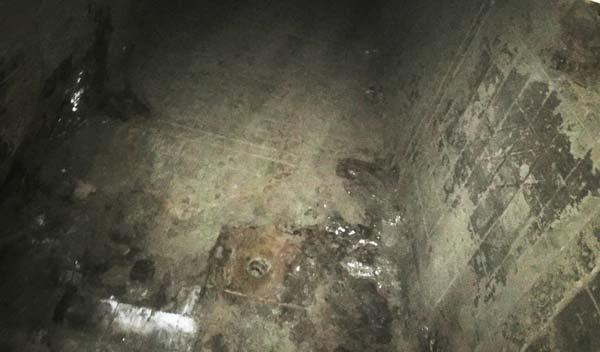
Now, the precast Modular Lining at Lafarge Exshaw has been in operation for +36 months, and the cement plant is looking into the possibilities of the use of the precast Modular Lining in other areas of their production.
Depending on the lifetime achieved from traditional castable or brick linings, there are many other areas in which the precast Modular Lining could be applied. HASLE’s Modular Lining has shown good performance when installed in a variety of applications throughout the world, i.e. feed pipes, coolers, cooler bull noses, smoke chambers, cyclone roofs as well as cyclone bull noses. All areas are lined with the same type of elements and can also be adapted for curved and cylindrical structures.
As long as there is a steel casing the rails can be welded to, the precast Modular Lining can be applied, and has even been installed in a number of boilers and incineration plants.
A sustainability perspective
Driven by climate policies and a desire to run a sustainable production, more and more cement plants are implementing sustainability goals. To reach these goals, effi ciency improvements are necessary and using HASLE’s precast Modular Lining could be a step towards running a more sustainable operation.
Not only does it require less material per installation to create a HASLE precast Modular Lining compared to an in-situ castable solution, but the Modular Lining also has the potential to last longer. Consequently, plants can lower their use of natural resources per produced unit, as using the Modular Lining reduces the number of re-linings and repairs needed. Contrary to a stocked monolithic castable, which can become unfi t for use over time, HASLE’s precast Modular Lining has an unlimited shelf-life, thus reducing material waste.
The lining offers tangible effi ciency improvements that companies in high temperature industries can make on their journey to becoming more sustainable.
About the author
Daniel Hansted-Martin is Regional Sales Manager at HASLE Refractories. Daniel holds a Bachelor’s Degree in International Management and services the European and North American cement markets. He has extensive theoretical and practical experience from on-site installations, and an in-depth understanding of refractory challenges and solutions.
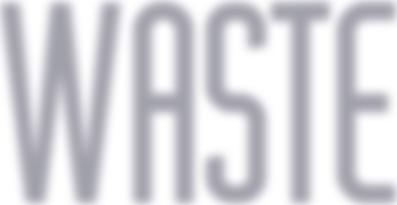
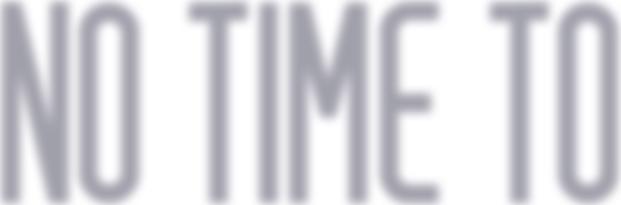
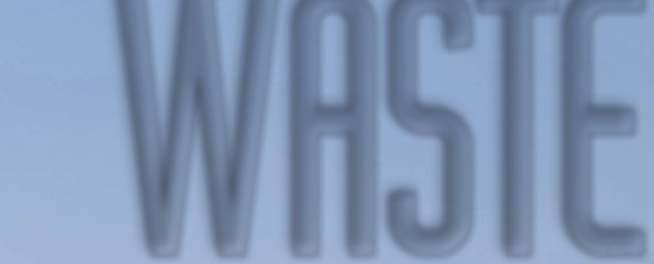

NO TIME TO Sabrina Santarossa, Turboden, explains how waste heat recovery technology could help cement plants to reach their sustainability goals, while increasing efficiency and reducing production costs. u e u g o rboden, at recovery cement stainability efficiency n costs. WASTE
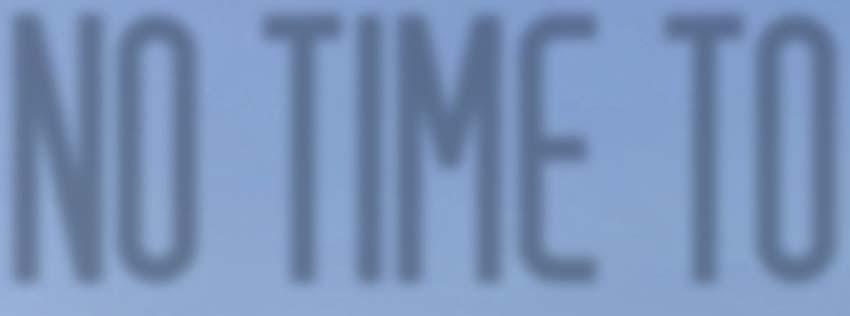



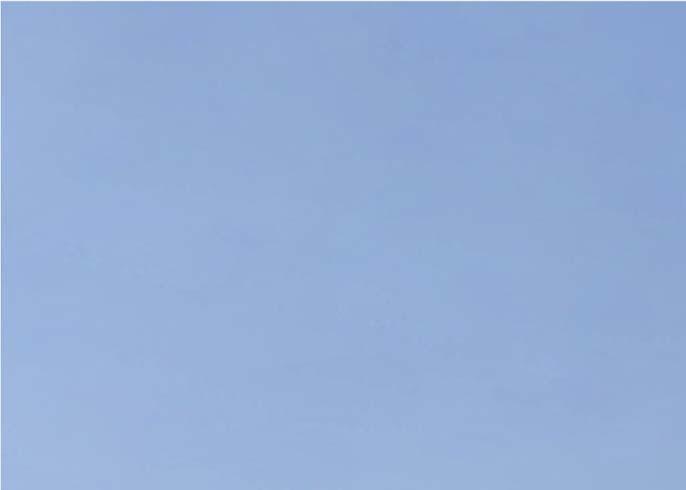
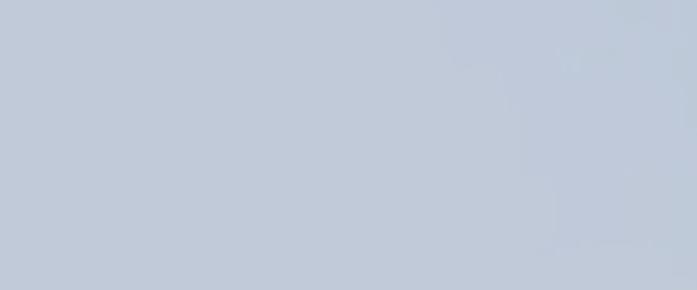
Waste heat recovery (WHR) is a proven and widely used technology for boosting the overall effi ciency of the cement sector with minimal impact on existing facilities. It allows profi t to be generated by valorising a waste heat source, and reducing the specifi c production cost by decreasing energy demand, thereby improving sustainability. Furthermore, the Levelised Cost Of Energy (LCOE) can reach very low values using waste heat recovery, assuring a low cost and constant source of green energy for at least 25 years.
The cement industry is being called upon to make its processes more environmentally-friendly. With the goal of reaching carbon neutrality by 2050, Europe is setting an ambitious target and encouraging the move towards a more sustainable industry.
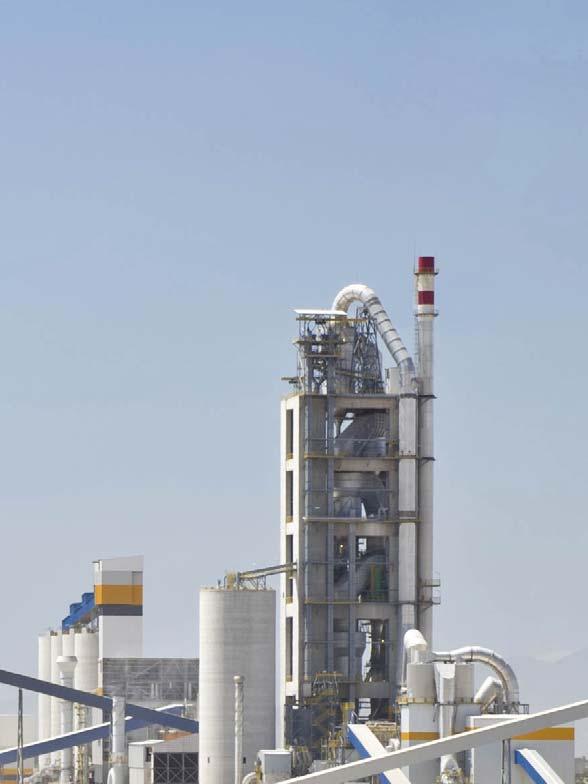


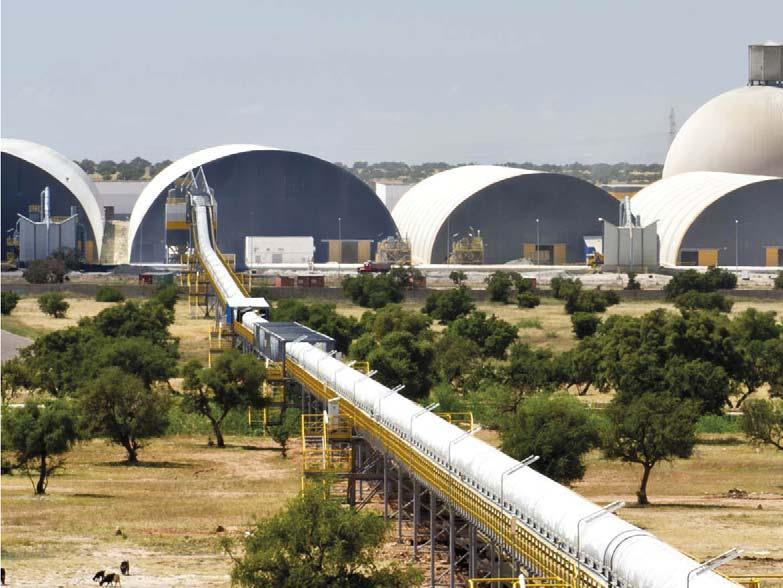
For the cement sector, generating 7 – 8% of global greenhouse gas emissions, the pressure to become carbon neutral is even greater. In addition, as the COVID-19 outbreak has slowed construction in many countries, cement companies that prioritise sustainability even during this diffi cult period are likely to emerge as the winners in the next cycle.
The conversion of waste heat into useful power represents a viable and profi table solution to hit these targets. In this framework, Organic Rankine Cycle (ORC) technology represents a feasible option for recovering the heat still available in the hot gases of the pre-heater and clinker cooler and to turn them into clean power.
Turboden is an ORC supplier with 40 years’ experience in different fi elds of applications, with 400 ORC units sold worldwide for a total installed capacity of about 700 MWe. ORC has several advantages compared to steam technology, in particular for electric power less than 15 – 20 MWe. With its high level of automation, good partial load behaviour, and low operation and maintenance costs, ORC is highly suitable for WHR plants, as it allows cement producers to focus on their core business while helping to reduce production costs. Additionally, ORC does not consume any water, thus offering a sustainable option for countries in which it is a scarce resource.
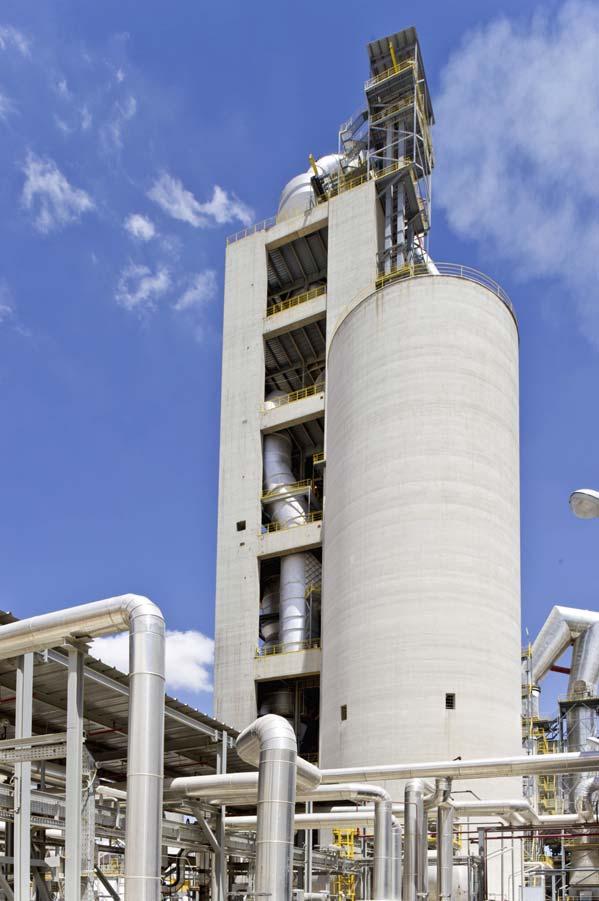
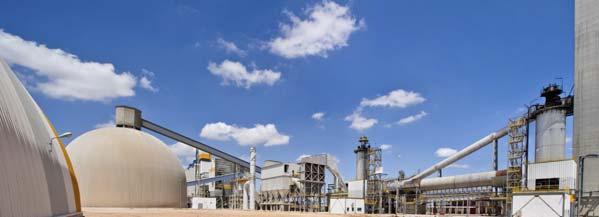
ORC technology recovers the heat available in the hot gases of the pre-heater and clinker cooler and turns them into clean electric power.
ORC is highly digitalised and self-operating; remote monitoring control has been an important feature during the COVID-19 pandemic. Heat recovery systems in the cement process
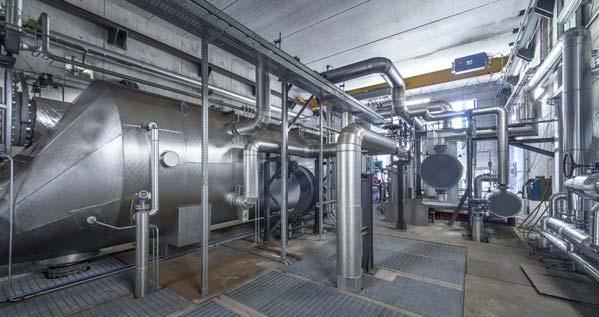
In the cement production process, there are two main hot gas streams where sensible heat can be recovered and transformed into electricity that usually is consumed by the plant itself.
The heat contained in the clinker cooler and pre-heater gas hot streams is transferred to the ORC unit through an intermediate fl uid or directly to the organic fl uid. Technical features of the two heat recovery exchangers are different due to the different characteristics of the exhaust gas, in particular the high dust content (20 – 100 g/Nm3) and the type of dust (abrasive on clinker cooler gas and soft and sticky on pre-heater gas). The heat recovery exchangers are installed in bypass mode to the main gas duct line to prevent the heat recovery plant having any infl uence on the main production process. In the ORC, the organic fl uid is heated up and vaporised in the pre-heater and evaporator due to the external heat source (gas or thermal oil). Organic vapour expands into the turbine connected to an electric generator producing electric power. After the expansion in the turbine, organic vapour is fi rstly cooled down in the regenerator and is then condensed in the air condenser. Once again in the liquid form, the organic fl uid is pumped into the regenerator and then into the pre-heater, thus closing the thermodynamic cycle.
One of the main advantages of ORC compared to steam is its low OPEX during the lifetime of the WHR plant. ORC does not require any major overhaul, or dedicated personnel, nor does it consume any water or require water treatment or related chemicals. In addition, ORC has shown good effi ciency, even at partial load, and
WHR system availability higher than 98% assures that electricity produced over the year is maximised. ORC is highly digitalised and self-operating, and remote monitoring control has been an important feature during COVID-19 times. In many cement plants, environmental benefi ts are not limited to the electricity produced by the WHR plant which translates into several tons of CO2 emissions avoided per year. There are further benefi ts related to electricity savings on the fans of air to air cooling systems often installed on clinker cooler gas lines before a bag fi lter, as these may not be used when the WHR plant is working. Additionally, the use of the quenching tower to cool pre-heater gas (if any) will not be necessary and the water normally consumed in it will be saved, thus contributing to a greener cement production.
Turboden has been installing ORCs for the cement industry since 2010. The fi rst plant was for Italcementi in Morocco, then other international groups such as LafargeHolcim in Romania and Switzerland, CRH in Slovakia and Switzerland, HeidelbergCement in Romania and Cementi Rossi in Italy, followed. WHR size was in the range of 2 to 5 MWe. In recent years, Turboden has installed one 7 MWe ORC and one 8 MWe ORC in Turkey (Çimko and Sonmez cement plants) and despite the COVID-19 outbreak, a new contract for a 7 MWe ORC for Secil group, Portugal, was signed in 2020, underlining the importance of becoming more effi cient in these diffi cult times.
The economic feasibility of a WHR system, since there is no cost of fuel, is mainly related to: Cost of electricity: With a cost above €60/MWh (US$70 /MWh) the economic feasibility of WHR systems is appealing. Investment cost (CAPEX): this depends on specifi c site conditions such as the size of the plant, standards to be followed, type of cooling system, cost of the local workforce, etc.
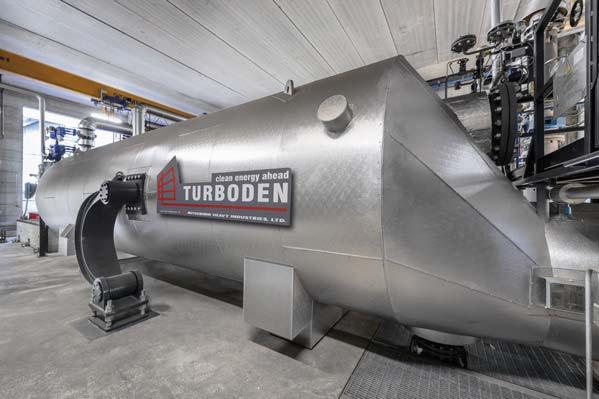
Despite the COVID-19 outbreak, a new contract for a 7 MWe ORC for Secil Group, Portugal, was signed in 2020, underlining the importance of becoming more effi cient in these diffi cult times.
Your PARTNER in Industrial Thermography
Monitor 24/7 Thermal Combustion with Field-Proven IR Scanners & Cameras
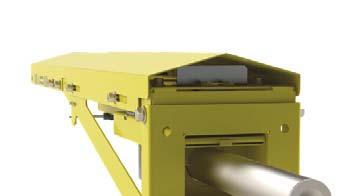

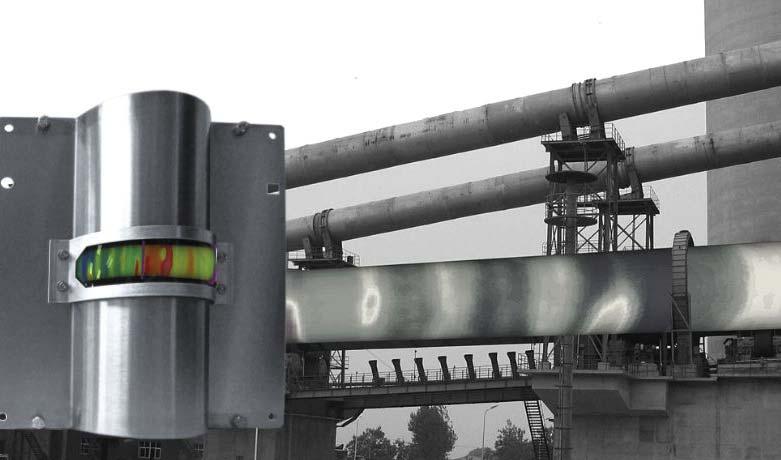
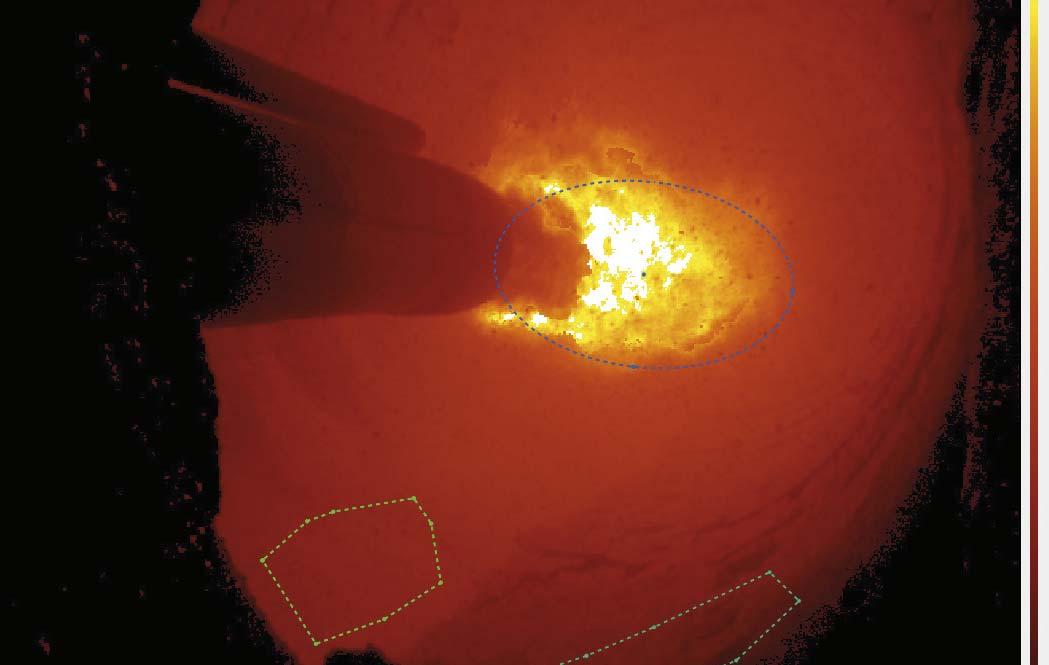
NEW§
NEW Improved ergonomics with unlimited temperature zones and replay mode with export of RAW images
Typical values range from about €1500/MW installed up to €2500 – 3000/MW. Operating and maintenance costs (OPEX):
This is mainly related to the specifi c site workforce cost, however when dealing with
ORC, OPEX is very low, about 1% of CAPEX per year. Kiln working hours per year: To reach a good level of economic feasibility, the kiln should work for at least 6000 hrs/year.
With 60/MWh and 7500 hrs/year, IRR (10 years) is above 17 – 26%, which is much higher than the typical cement industry WACC (Weighted Average Cost of Capital).
WHR potential is still huge and remains widely untapped. Some studies identify a potential of more than 2000 MWe to be installed in WHR at cement plants, which corresponds to more than 7 million t of CO2 emissions avoided per year. Sometimes barriers that are slowing down the implementation of WHR plants, even in regions with medium-high price of electricity, are related to restrictions in CAPEX, need for off-balance sheet investments and other fi nancing or investing limitations. Cement producers are encouraged to stay fi nancially focused on their core production process through the different fi nancial and investing solutions that allow them to benefi t from the advantages of a lower electricity bill obtained with a WHR system. Different alternatives are also available from a fi nancial point of view: BOT, BOO scheme; low cost fi nancing form International institutions like IFC – International Financing Corporation (World Bank group) and EBRD – European Bank for Reconstruction and Development; and the export credit scheme supported by Italian ECA.
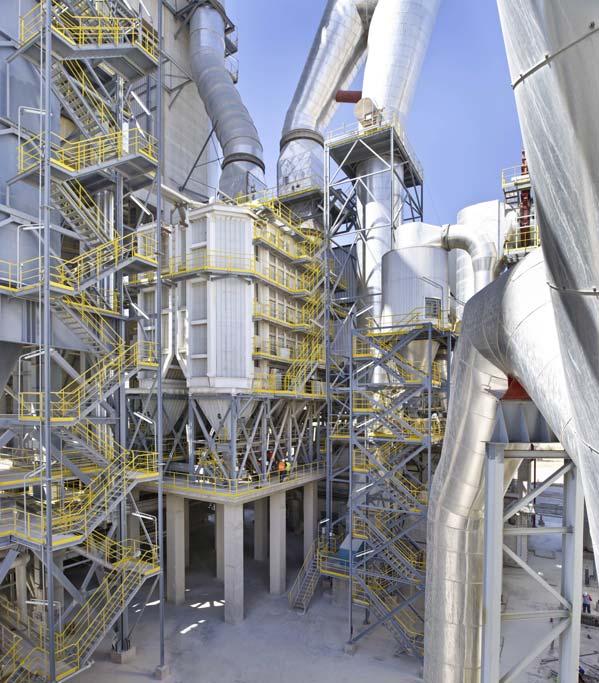
Several tons of CO2 emissions can be avoided per year thanks to a WHR system.

ORC technology is a well-proven solution to boost the overall effi ciency of the cement sector. Conclusion
Waste heat recovery is a great opportunity for cement plants to reach their goals to be more sustainable while increasing effi ciency and reducing production costs. ORC technology is a well-proven solution suitable for industrial customers and companies interested in investing in these projects. Good economic feasibility can be achieved whilst moving towards a greener industry.
About the author
Sabrina Santarossa is a Chemical Engineer with international experience in sales and business development in energy effi ciency and renewable energy. Sabrina has worked at Turboden since 2008. She is now a Sales Manager for Industrial Heat Recovery with focus on sustainable projects in the cement, glass and steel production process.
She supports potential customers to fi nd the optimised confi guration for each project with a consistent attitude to delivering high value customised solutions supported by a solid academic background.
In her free time she enjoys reading, sport and travelling.