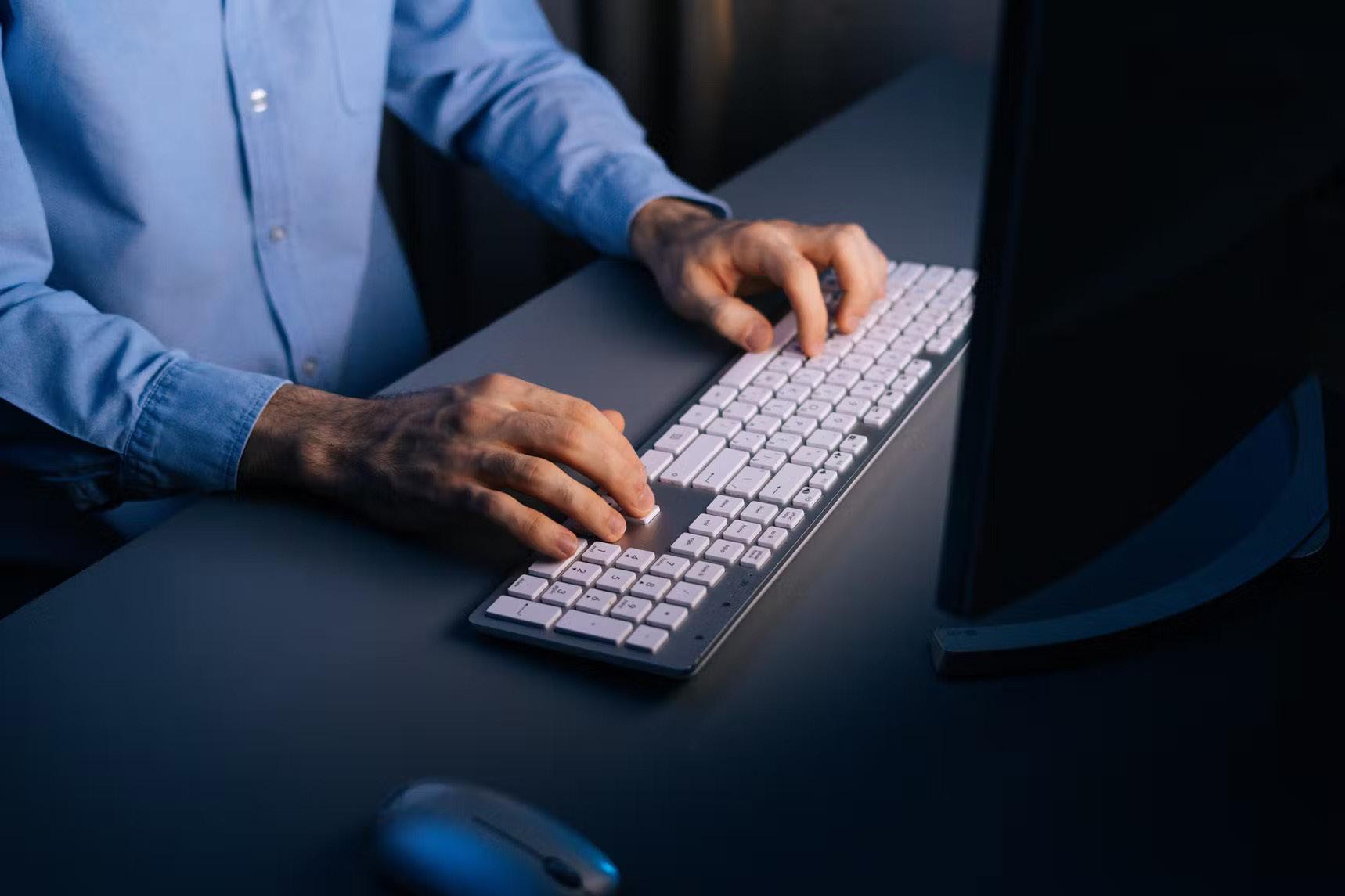
6 minute read
Collision repair estimation must change
from Auto Channel 45
by Via Media
The new way to estimate
Advertisement
Repair and replacement procedures have been around for as long as cars have been and in the past they could be relatively quick because the metals, tools, and techniques were similar. Replacing a rear body panel on almost all cars involved the same welder, tools, and thought process, as the materials were all mostly mild steel, and they were replaced similarly. But those days are over — if you do not research and implement following current procedures specific to that vehicle at that time, you have much catching up to do. Change needs to happen now! Switching to using ‘current procedures’ will also measure your processes and possibly expand them, while improving your accuracy.
WHY USE CURRENT REPAIR PROCEDURES
There are obvious reasons involving liability, and the improvement of efficiency, employee retention, and recruitment. In the past, workshops would assess the damage, even if just briefly, and hopefully retrieve the procedures for replacement.
For this discussion, let’s assume a vehicle was slowly backed into by a large flatbed truck in a parking lot, and the rear corner of the bed ripped into the quarter panel. Easy enough to repair — replace the quarter panel. Blend the rear door, boot lid, and rear bumper cover, and so on.
So you go on your trusty computer and pull up the quarter panel replacement procedures. At this point, you have already failed the test. This is not entirely wrong; you will need those specific procedures. The problem is the mindset. There should be a lot more research done before you get to that replacement procedure.
A ‘SIMPLE REPAIR’ IS ANYTHING BUT
In the recent past, we would mostly disassemble a vehicle and then look up procedures and documentation to support our repair plan, but perhaps there should not be a screw turned, or a clip removed, on that vehicle until the procedures are in hand,
You may consider you are doing research during and after disassembly, but you must at the very least first research/obtain some documentation even before disassembly begins. ADAS, construction/structural materials, and safety-related concerns such as batterydisconnect procedures should be sourced before touching the vehicle.
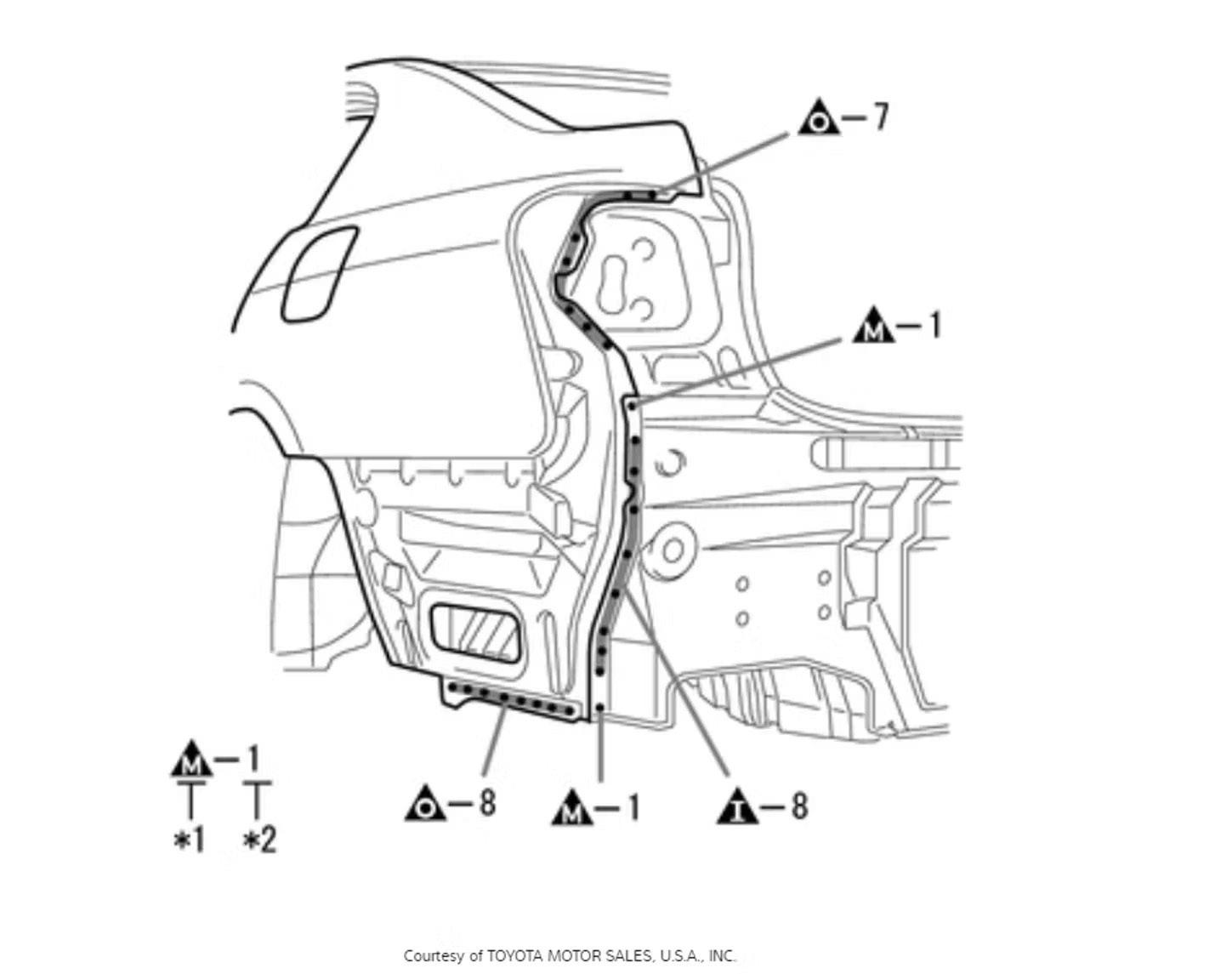
The days of the 10-minute estimate are over
PROCEDURES ARE ‘MOST CHANGED’
More vehicle manufacturers are doing a better job of providing the information needed to repair today’s vehicles. It’s in their interests to have their cars repaired properly, regardless of who is performing the repairs.
Aside from being more available, procedures are also in the top section of our industry’s ‘most changed’ list. We have so many changes in vehicle materials, construction methods, and added safety/comfort features. We also have different procedures for many aspects. Knowing how an ADAS function may be affected as the result of just removing a part/component for a related repair should drive the research component of repairplanning at the beginning phase.
HIGH-VOLTAGE HAZARDS
Check precautions on disabling or general handling for any vehicle with a high-voltage system, such as a hybrid or battery-electric. We should all know that orange is the typical colour used for high-voltage wiring and other components, but there are also vehicles built with a system above 12 volts that are not considered ‘high-voltage’. Those vehicles may use various colours for the wiring and components in those systems. Blue and yellow are common, but this is not standardised. Note these vehicles may not have much in the way of the helpful badging that BEV (Battery Electric Vehicle), HEV (Hybrid Electric Vehicle), FCEV (Fuel Cell Electric Vehicle), or PHEV (Plug-in Hybrid Electric Vehicle) vehicles typically display. The need to research before touching the vehicle is the important takeaway here. If you see large battery cable-size wiring that is not black or red, back away and do some research before proceeding.
ADDRESS SAFETY AND CALIBRATION REQUIREMENTS ON THE REPAIR PLAN
Once you have determined what systems the vehicle has, those safety and calibration requirements can be addressed on the initial estimate, or work order. It takes a lot longer to form a repair scenario than it ever has in days past. Hours, maybe even days, can be involved. Education is the key here. We cannot expect our industry to function as it did 20 years ago. There are far too many differences in these vehicles/ repair procedures, and the advancement of safety/ convenience features, to determine the proper collision repair process quickly, and proper research takes time.
REPAIR OR REPLACE?
Once we determine the vehicle is safe to approach and dismantle, the next question is, “What types of materials are we working with, and what is allowed?” We all know there are a lot of talented craftspeople in our industry who have the capability of repairing parts/panels. The problem with having the ability to do amazing things is that it can sometimes mean something is repaired when it should have been replaced. We must focus on subsequent collisions and the ‘whys’ behind a manufacturer’s procedures/guidelines.
The construction/structural material documentation and the general guidelines will determine if the repair or replace question is even valid. We already see less repairability when it comes to structural parts, meaning a replace-only description will be more common when it comes to damage to some advanced steels.
A BASIC CHECKLIST
Assuming the vehicle with the damaged quarter panel is not a hybrid/electric vehicle, or has anything above a standard 12-volt system, we need to assess the supplemental restraint system, enable/disable, repairs/inspections required after collision guidelines including seat belt inspections, etc.; battery disconnect procedures, and electronic components reset; construction/ structural materials diagram; material repairability matrix; welding guidelines/machine set up; body panel gap/tolerance guideline; welding symbols explanation, welding/bonding guideline; corrosion protection guidelines, body sealant procedures,
undercoating guidelines; body dimensions/opening measurements; soundproofing/insulation/foam guidelines or procedures; steering/alignment measurements/calibration; scanning pre/post, and ADAS inspections/calibrations (if applicable).
Now you can print those panel replacement procedures you’ve been after. You should have a book to place them in already. If you were researching any inner structure, uniside, frame rail, or such, expect that ‘book’ to be much thicker. It’s also important to note that even though there was no airbag deployment in our example, there may very well be specific and lengthy inspections of that system and related components.
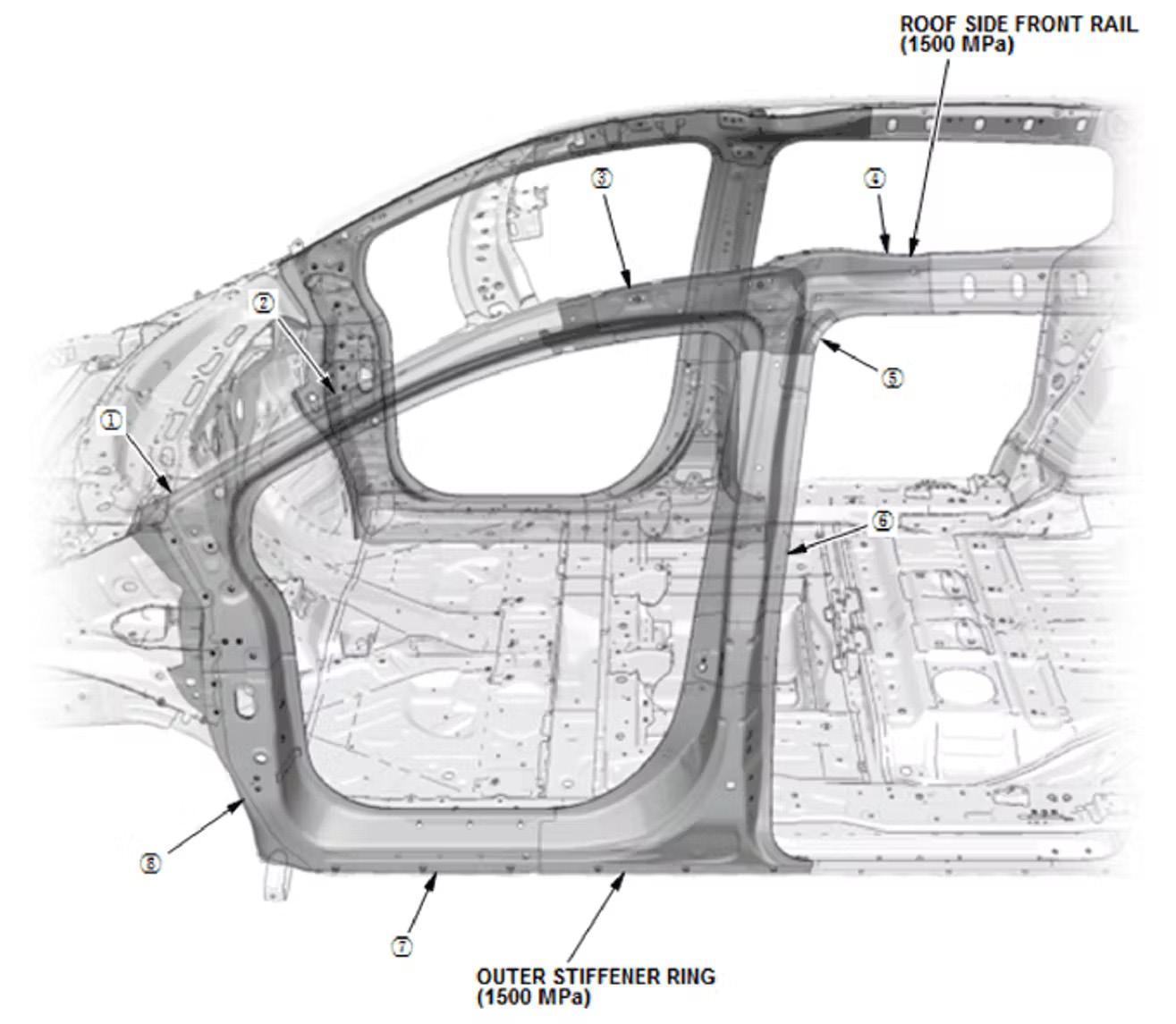
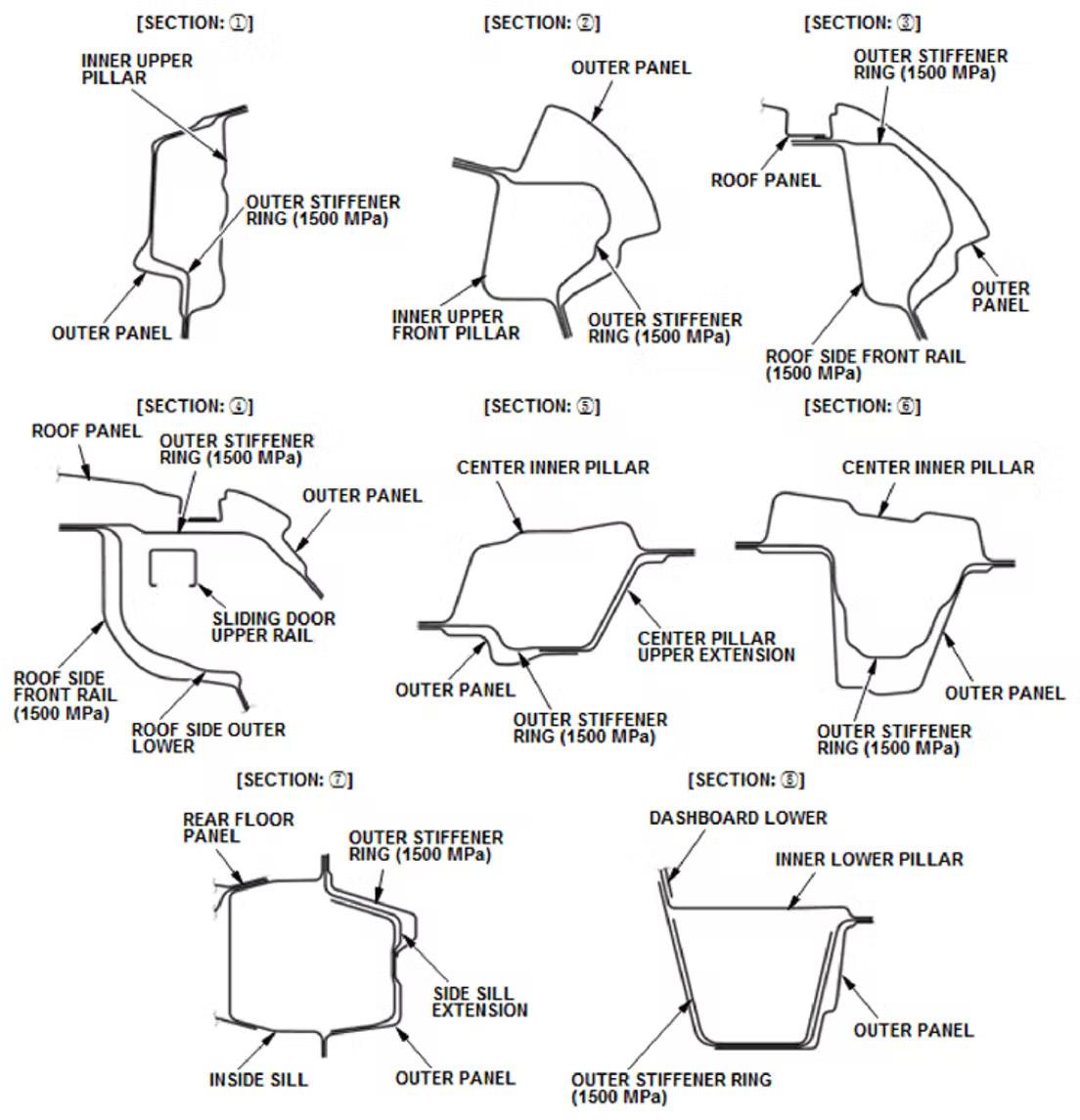

THE DISCOVERY PHASE
Before beginning any repairs, measurements of the body/frame and steering alignment diagnosis should be a part of the discovery phase. There is a lot of debate about why measurements and wheel alignment are necessary. Maybe you can look at a bonnet and tell if it’s damaged or not, but you cannot ‘look’ at a steering/suspension system or a structure and tell if it’s within specification.
The stack of procedures/guidelines must remain with the vehicle and be followed accordingly, but technicians often don’t take the time to read and understand what has been given to them. They need to understand that if administrative staff are doing procedure research, they are equipping that technician to do a safe and proper repair to that vehicle. The owner of that car, truck, or SUV deserves that commitment. If a third-party payer is involved, they also need to understand that this is needed for repairs to be performed properly, and there is a cost associated with this process. Most automakers have subscription capabilities for their repair manuals, which is not a cost of doing business. It is the best way to obtain current information. The time it takes to do research is another consideration.
IT’S A NEW WORLD
There is no more ‘one size fits all’. There is no more ‘I did that same repair last month’. There is no more ‘I’ve been doing this for XX years’. There will need to be sweeping changes in the expectations we deal with. It is the only way to provide a safe and quality repair that will endure the test of time and, more importantly, perform as designed in a subsequent collision.