
11 minute read
GPC builds next generation supply chain Cover
from Auto Channel 50
by Via Media
AUTO CHANNEL IS DISTRIBUTED TO 11,306 NEW ZEALAND BUSINESSES ONLINE autochannel.co.nz EMAIL editor@autochannel.co.nz MAIL PO Box 46,020, Herne Bay, Auckland 1147
EDITOR Ian Parkes, editor@autochannel.co.nz DESIGNER Day Barnes MEDIA SALES Mike White, michael.white@parkside.co.nz ADVERTISING COORDINATOR Kealy Mathews
Advertisement
AUTO CHANNEL IS PUBLISHED BY
PUBLISHER Greg Vincent, greg.vincent@parkside.co.nz BUSINESS DIRECTOR Michael White, michael.white@parkside.co.nz GENERAL MANAGER Simon Holloway, simon.holloway@parkside.co.nz WORKFLOW MANAGER Emily Khov PRINTING Ovato
NOTICE TO ADVERTISERS
Parkside Media uses due care and diligence in the preparation of this magazine, but is not responsible or liable for any mistakes, misprints, omissions, or typographical errors. Parkside Media prints advertisements provided to the publisher but gives no warranty and makes no representation to the truth, accuracy, or sufficiency of any description, photograph, or statement. Parkside Media accepts no liability for any loss which may be suffered by any person who relies either wholly or in part upon any description, photograph, or statement contained herein. Parkside Media reserves the right to refuse any advertisement for any reason. The views expressed in this magazine are not necessarily those of Parkside Media, the publisher, or editor. All material published, gathered, or created for Auto Channel is copyright 2022 Parkside Media Limited. All rights reserved in all media. No part of this magazine may be reproduced in any form without the express written permission of the publisher.
Auto Channel is the best way to reach the wider automotive industry. The publication is direct mailed to 11,298 New Zealand businesses in the following automotive sectors:
Automotive workshops, parts importers and distributors, transmission specialists, automotive recyclers, towing operators, panel beaters and painters, crash repairers, tyre dealers, suspension and underbody repairers, steering specialists, towing operators, auto-electrical repairers, new- and used-car dealers, air-conditioning repairers, heavy-machinery dealers, trucking and transport

Future-proofing
“The new distribution centre will be the most technically advanced, not just in New Zealand, but in the southern hemisphere,” Jonathon says. “It will ramp up our service delivery but it also demonstrates our commitment to the future of the automotive and industrial aftermarket in New Zealand. It provides a platform for future growth.
“We see great potential here to elevate performance standards to levels not seen here before, and that level of support will improve the automotive service industry’s own efficiency and performance.
“We have the scale now not just to improve our own business but to be a partner in improving efficiency and performance across the sector, which in turn has flow-on benefits to New Zealand Inc.”
The new distribution centre will support GPC’s 120-branch network of its retail arm Repco and trade Napa stores, as well as Motion New Zealand — its industrial supply business — across New Zealand.
Streamlining stock control
Behind the scenes, GPC has been rationalising the support networks of several wholly-owned subsidiaries at the same time as building up the relatively new Napa Auto Parts division. Moving to a common stock management system, for example, simplifies processes, reduces cost, and increases the visibility of SKUs across the network.
It’s also a key component in consolidating several distribution centres into one at the new location. Five local distribution centres will effectively move into the new building over the next two years.
While the move will reduce duplication of systems, Jonathon says all 100 of the current staff will have the opportunity to relocate.
“There will be no redundancies as a result of this development. It’s a measure of the growth we believe this investment will deliver that we fully expect it will lead to more employment opportunities in the future.”
The first staff to move into the new premises will be the GPC New Zealand industrial division — the teams from SAECOWilson, HCD Flow Technology, Seal Innovations and Conveyor & Transmission.
The building project started in February 2021. Completing the physical construction marks a significant milestone in the three-year project. Full capability of the site is due to be achieved in November 2023.
Jonathon paid tribute to contractors Calder Stewart who have managed to deliver the building on time and under budget, despite the much publicised supply chain disruption, materials supply issues, staffing and inflationary pressures of the past 10 months.
The next big step will be the installation of the ‘next generation’ automated Schaeffer racking and stacking system, planned to take place over the next six months.
Jonathon says the automation system designed for 70,000 SKUs is designed for maximum efficiency, which involves ‘auto organising’ overnight to enable optimal picking availability the next day.
The chauffeur system being installed will be the first of its kind in the Southern Hemisphere.
The Schaefer systems to be installed include small load container systems, shelf retrieval machines and shuttle systems designed for rapid access. They are modular systems that can be expanded as required.
Other Schaefer technologies include the Logimat vertical lift modules which are, effectively, oversized drawer cabinets, a chain-driven carousel that pulls out relevant trays from a vertical stack and delivers them to the operator at ground level.
Other technologies include the Navette automated miniload system which runs on rails at the front of racking units. Each Navette can
access up to eight storage levels and they can be arranged to access heights of up to 24m. Another solution is the Schaefer miniload crane (SMC) which automates retrieval of container cartons and trays from conventional racks, permitting higher density stacking than is possible with conventional forklifts.
Jonathon says another key driver of the project was to improve safety for staff in the distribution centre.
The level of automation being introduced will significantly reduce the physical effort needed compared with more manual systems.
It will also allow more staff to operate at a safe distance from the equipment stacking and retrieving stock at height.
While forklifts will be used in parts of the warehouse, they will be electric, reducing exhaust fumes and the hazards of fuel handling.
The new distribution system has also been designed to improve sustainability over the warehousing it replaces.
It is expected to deliver a 35 per cent water saving by recycling rainwater captured onsite. Solar panels and advanced energy control systems will also ensure energy savings, and electric fork lifts will be used..
Ultimately the new distribution centre is expected to hold 140,000 stock lines at completion.
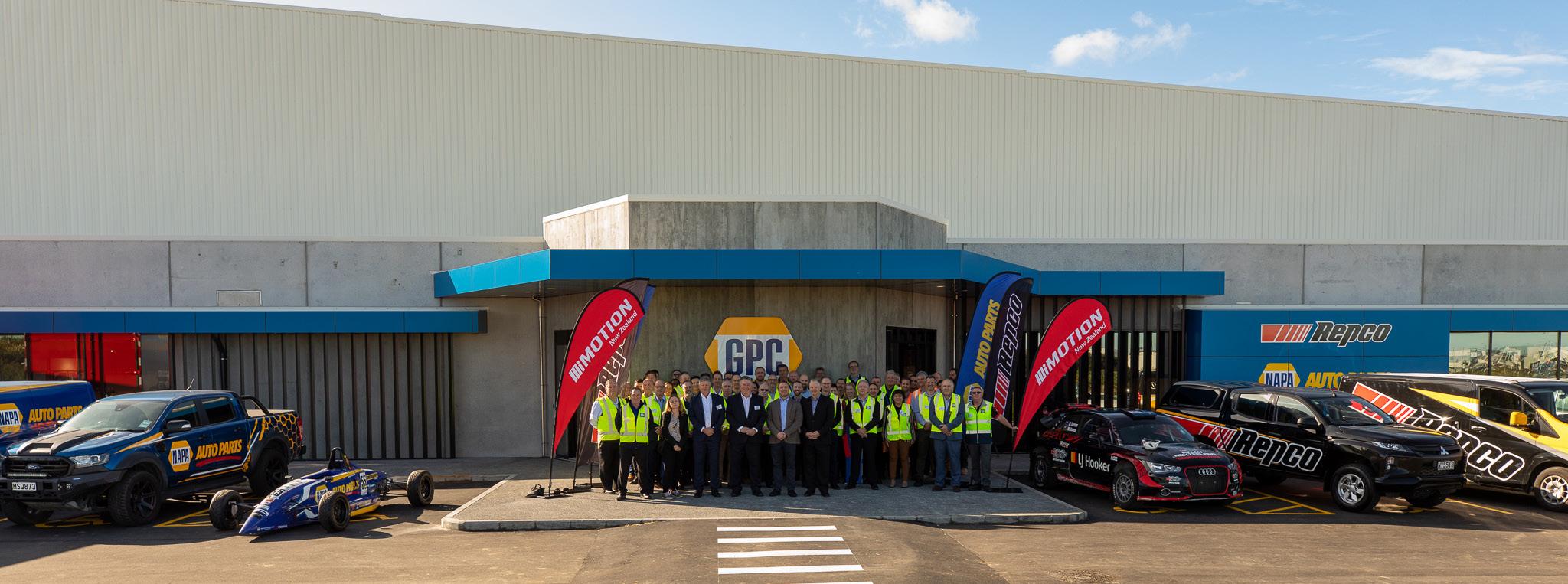
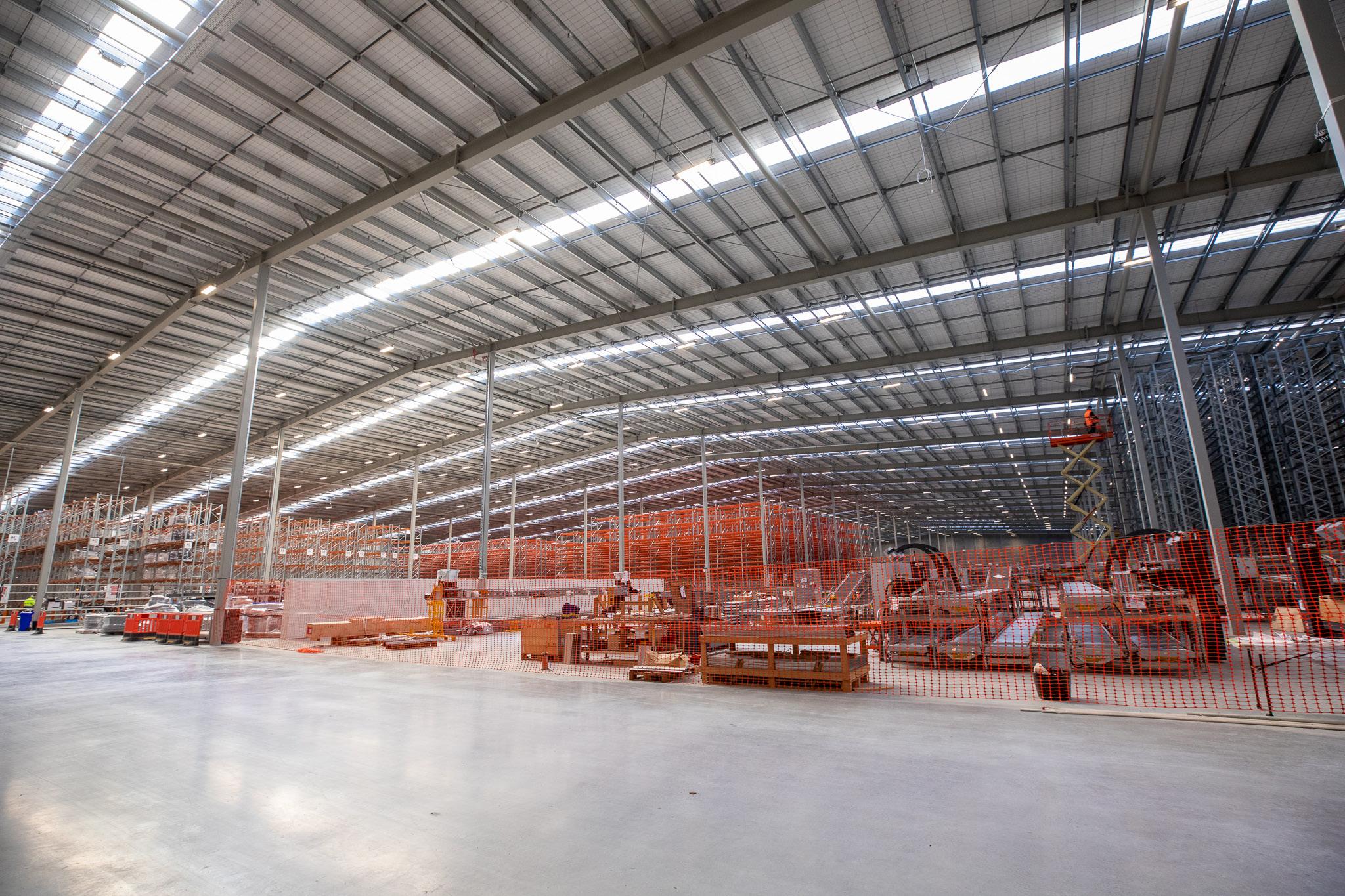

GPC (Repco, NAPA and Motion Industries) Auckland Distribution Centre: The Building is Complete!
PRESS RELEASE (BUSINESS) BRIEFING POINTS:
KEY MESSAGES 1. Building is complete on new GPC Distribution Centre (final completion of project 2023) 2. GPC makes significant investment in Auto and
Industrial aftermarket supply for New Zealand (our commitment to the future of the market in NZ) 3. New DC will be the most technologically advanced in southern hemisphere 4. Facility will power the future of GPC supply chain, empowering market leading enhancements in our speed to customer and supply chain accuracy. We know customers want faster and we have built this to deliver 5. Clear focus on safety and sustainability for our team
ABOUT PROJECT: • Distribution Centre will service GPC Automotive and
Industrial, supporting 120 branch network of NAPA and Repco and the Motion New Zealand industrial supply business • Started in Feb 2021, the DC building completion marks a milestone in this three year project • On time and under budget delivery from Calder
Stewart despite the unique challenges of supply chain disruption, supply scarcity and covid impacts on build time and team • Build of Schaeffer automation system has commenced and will take a further six months. • Full capability of the site will be in use at completion of this large capital project due in November 2023 • Five local DCs will move into the building in the next two years. No redundancies – all 100 staff relocating and anticipate further opportunities • First to move into the new facility is the GPC NZ
Industrial team – Motion New Zealand — comprising the SAECOWilson, HCD Flow Technology, Seal
Innovations and Conveyor and Transmission businesses
TECHNOLOGY INFO: • Schaeffer Systems first of its kind in Southern
Hemisphere • ‘Next generation’ technology • Automation stacks make it faster, safer and highly accurate for staff leading to better speed to customers and a positive environment for staff • Built for 70,000 SKUs the automation system will ensure maximum efficiency, auto organising overnight for optimal pick availability
BUILD INFO: • Site is 28,000 sqm, 5.8 hectare (eight rugby fields), greenfield. • Puaki Drive, Wiri • 7,500 cubic metres of concrete poured, 245 precast panels and 31,800sqm of roofing steel • 21 roller doors and 650 sqm of office and staff amenities • Designed for the future of aftermarket parts in NZ the building will hold 140,000 different stock lines at completion
SUSTAINABILITY: • 35 % annual water saving with recycling rainwater for toilet system • Solar panels and advanced energy control systems ensure energy savings • Electric forklifts will be in use
KYB moves into steering components aftermarket
OE SUSPENSION MANUFACTURER KYB HAS LAUNCHED A RANGE OF ‘IN-DEMAND’ REPLACEMENT STEERING COMPONENTS TO THE AUTOMOTIVE AFTERMARKET
KYB has been designing and manufacturing steering components for OE customers for more than 50 years and this extensive experience has been applied to the development and quality of the KYB aftermarket range.
NGK will initially stock five KYB steering product groups. These are ball joints, tie rod ends, steering rack ends, stabiliser links and control arms
“These components are crucial parts of a vehicle’s steering and suspension system and must be in excellent working condition, as they have great influence over a driver’s ability to maintain vehicle control and comfort,” says KYB group product manager, Larry Coulthard.
Steering and suspension components have a long-standing partnership given both product groups are generally integrated to work cohesively with each other.
As KYB is the brand of choice for suspension products within the Australasian aftermarket, KYB’s move into the design and manufacture of its own brand premium steering components is a smart approach, Larry says.
According to him, KYB is well regarded for its attention to detail — its ‘vehicle specificity,’ making each part ideal for its particular make and model.
“Just as it is with our suspension components, our process rings true for KYB steering components,” says Larry. “Perfect fit, first time, every time. KYB has been steering you in the right direction for more than 50 years.”
Established in 1919, KYB began as Kayaba Research Centre in Japan. Today KYB has become a world leader in the development and application of hydraulics technology. The company also supplies the automotive industry with components such as air suspensions, power steering systems, hydraulic pumps, motors, cylinders, and valves. Likewise, it specialises in hydraulics and aeronautical technology.
To view the full listing of products please visit www.kyb.com.au.
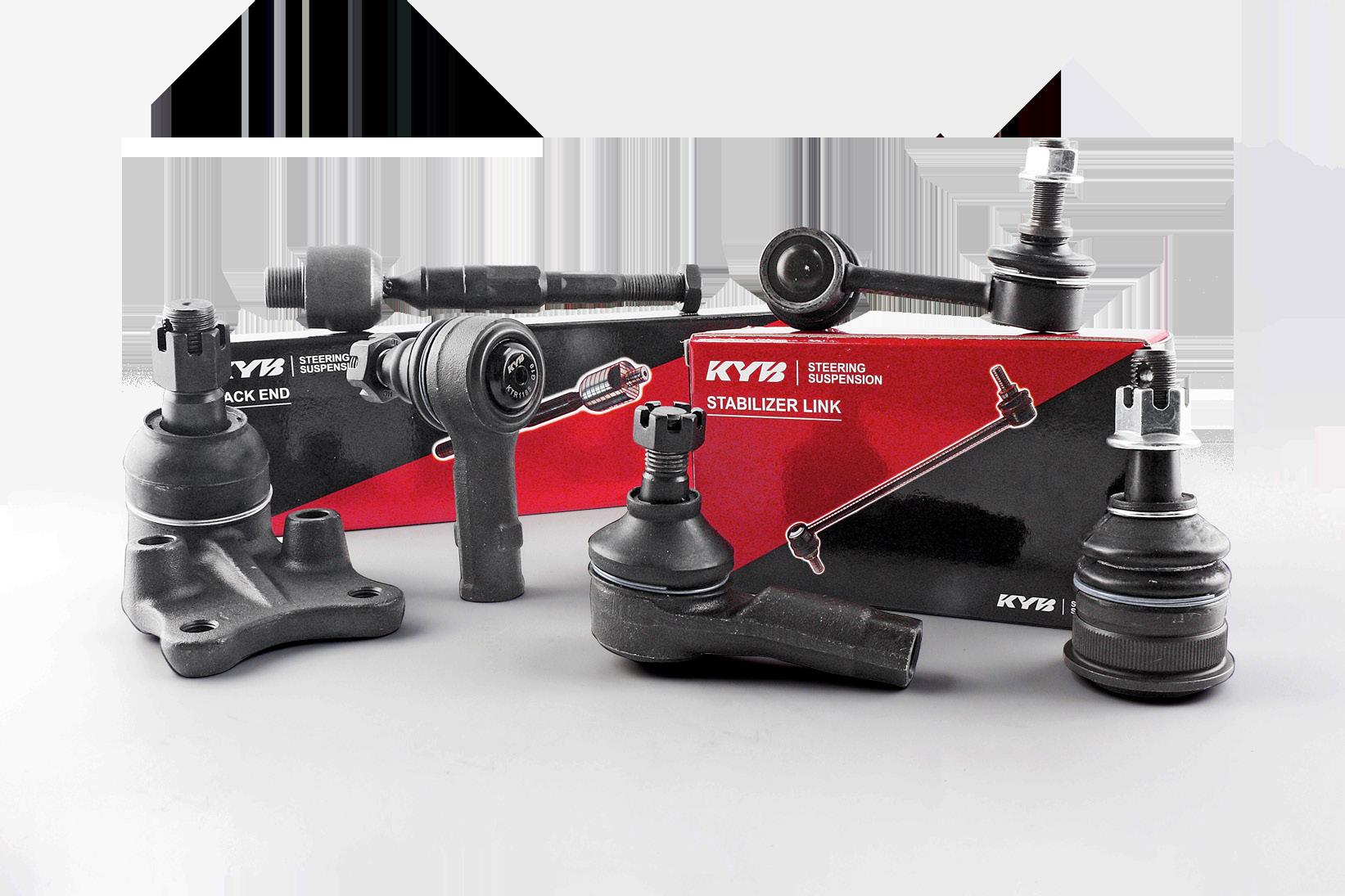
One size spark plug does not fit all
NGK HAS TAKEN THE EFFORT OUT OF FINDING THE CORRECT SPARK PLUG FOR YOUR CUSTOMER’S VEHICLE
Many spark plug suppliers recommend a single part number for a variety of vehicles, but NGK knows this ‘one size fits all’ approach compromises performance.
When spark plugs are generic, important attributes are often compromised and this can have a big effect on performance and longevity.
“Our research has found that installing a spark plug that is not specifically designed for the engine in which it is being installed can result in some pretty serious side effects, the biggest of which is the heat range,” explains James Filshie, general manager of the product division at NGK Spark Plug Australia.
“If the spark plug is too cold then carbon fouling can become a problem, while if the spark plug is too hot, pre-ignition can occur that can cause serious engine damage,” says James.
“Any manufacturer who still believes they can produce a spark plug to suit multiple applications is living in the dark ages. This old-school type of thinking disregards advancements in modern engine evolution and can compromise precision engine output, reliability, and fuel efficiency.”
Engine manufacturers spend many years researching and developing a new engine design. During this complex process, every engine component, including the spark plug, is engineered and tailored to perfectly match the make and model.
“Being the largest OE spark plug supplier in the world means that we work hand-in-hand with vehicle manufacturers during the development of each new engine configuration,” says James. “We engineer spark plugs specifically designed to suit each engine’s individual requirements to ensure optimum performance.”
In addition to heat range, there are a number of attributes which can impact the vehicle when a spark plug is commonised. These include the centre electrode projection length, number of ground electrodes, ground electrode design, and double fine electrode (DFE) design.
“To assist mechanics and automotive technicians to quickly and easily identify common spark plug issues, we have developed a series of short videos that you can check out on our website,” says James.
“At NGK Spark Plugs Australia, we are engine ignition specialists,” James says. “We partner with OE engine manufacturers to ensure all NGK Spark Plugs meet exacting engine-specific requirements.”
He recommends choosing the spark plug engineered for your engine and choosing NGK.
To find out more visit ngk.com.au.
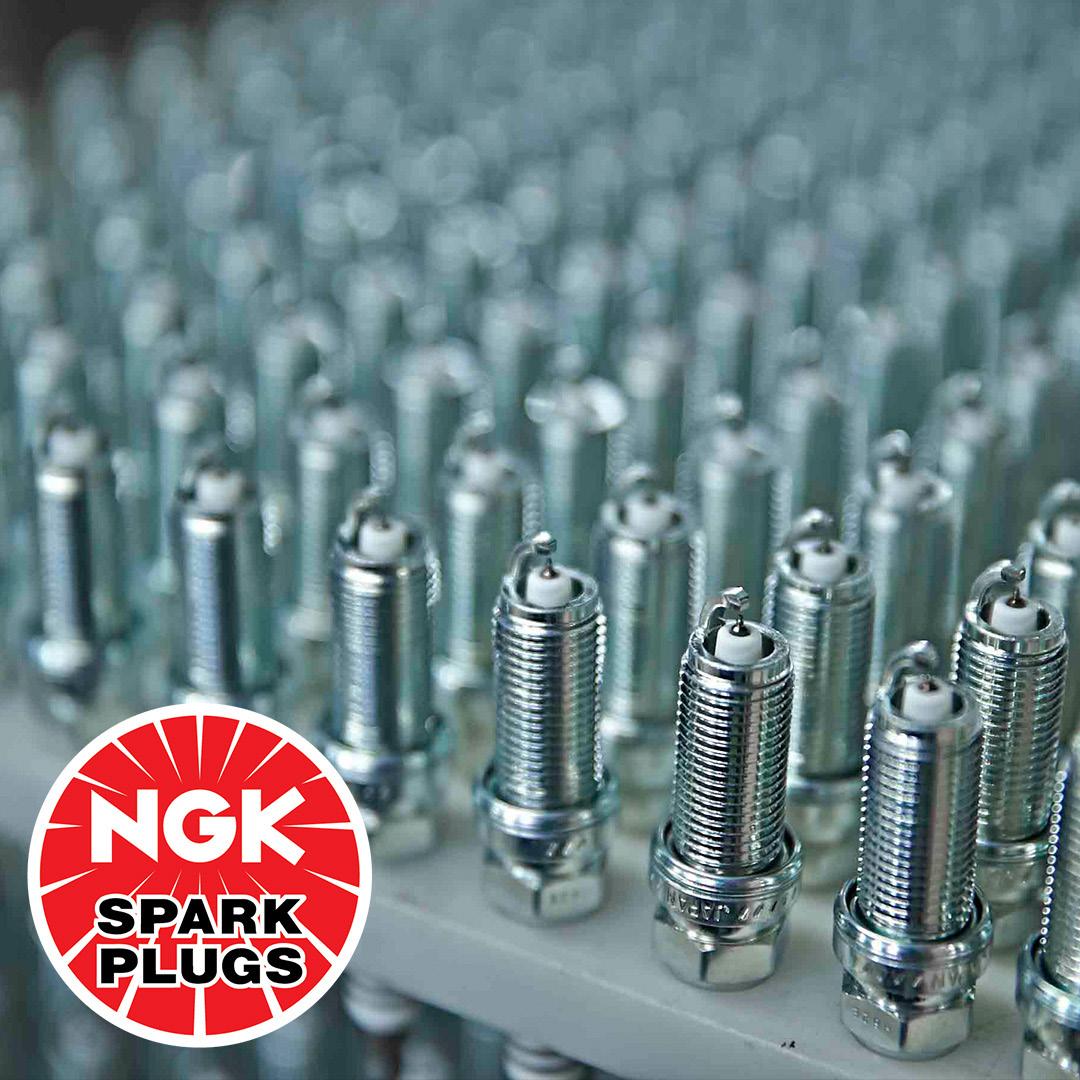