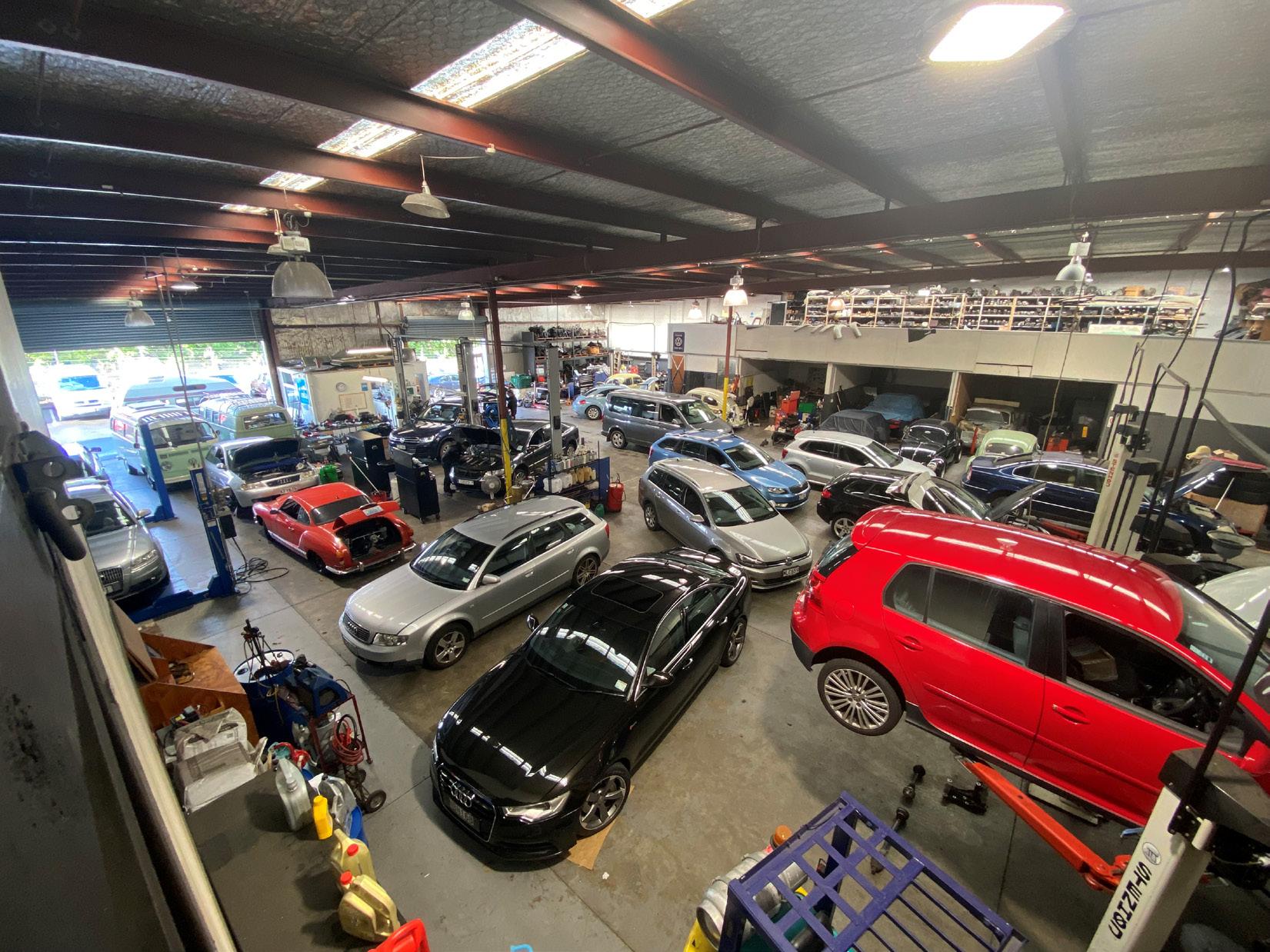
14 minute read
Qualitat European celebrates 50 years
from Auto Channel 50
by Via Media
Qualitat European Motors — 50 years young
QUALITAT EUROPEAN MOTORS, THE LARGEST INDEPENDENT VOLKSWAGEN-AUDI GROUP VEHICLE SERVICING CENTRE IN NEW ZEALAND, IS CELEBRATING 50 YEARS IN BUSINESS THIS MONTH
Advertisement
Director of the family-owned business Vagn Dyson says if the founders of the business in Penrose walked in today they’d find much that was familiar.
The business began in 1972 when the air-cooled Beetles and Campers were the mainstay of VW’s range, and to this day keeping those cars on the road is still an important part of the business.
Today, the workshop and car park offers an interesting mix of the latest autobahn-eating Audis and GTIs and the much more folksy air-cooled flat fours, and everything in between.
The left-hand side of the workshop specialises in air-cooled engines. They have an array of factory tooling, jigs, and presses, and the team’s decades of experience with these engines means they really know their way around a rebuild. They work with stock engines and with performance parts that can take the 1600 engine out to 2300cc and double its rather modest 65 horsepower output.
While most of the workshop is geared to servicing modern VAG vehicles, Vagn says the classic or air-cooled section “is still a very important part of our business”.
Vagn got his start in the air-cooled department some 30 years ago, and from time to time he has been known to get back on the tools when required, mainly due to Covid.
If the original staff came back, they wouldn’t really struggle to find the place either, as it is just 200m further along Station Road in Penrose. It moved to its current, larger premises about 17 years ago.
In fact, Vagn has been looking up old employees, long-standing customers and other people who have been important to the business to invite them to a 50th anniversary event next month — but it won’t be at the workshop. That’s full of cars, keeping seven technicians busy on modern VWs, Audis, and Skodas, as well as the two technicians working on the air-cooled Dubs.
Among the 20 staff in Auckland there’s one parts technician dedicated to the workshop, two service advisors, six parts interpreters, one of whom is the parts manager, and “super-administrator” Holly, who Vagn says has been with Qualitat almost as long as he has.
The parts business is the other big growth area for Qualitat, which now runs the largest independent inventory of VAG parts in New Zealand, with around 40,000 stock items at hand, both genuine VW and from respected aftermarket parts suppliers such as Febi Bilstein and Hans Pries Topran.
Qualitat also has customers for parts in the South Island, so to speed up service to them Qualitat opened its first additional branch at 210B Hazeldean Rd, Christchurch. Vagn says that you can buy parts there over the counter, as it functions as a retail and trade parts store.
Qualitat has also recently upgraded its website along with a complete overhaul of the on-line shopping experience, which was a well needed change to make the experience more user friendly. They are continuing to add more and more products to the site for air and watercooled vehicles.
While the modern vehicle parts business is straightforward, VW doesn’t manufacture parts for its legacy vehicles so the team at Qualitat is pleased when they can help a customer out with hardto-find parts. Vagn says an international network of suppliers of new and ‘new old stock’ that the company has built up over the years has proven an invaluable resource.
As increases in technology allow vehicle manufacturers to lock themselves ever closer into dealer relationships there is another aspect to the Qualitat business, and that is their ability to access full security and key coding. That’s a service you would normally only get from main agents but which this independent garage can also offer.
“Electronic and digital tooling is always increasing so we always take care to keep on top of the technology,” says Vagn.
To find out more see qualitat.co.nz, or call 09 579 3710.

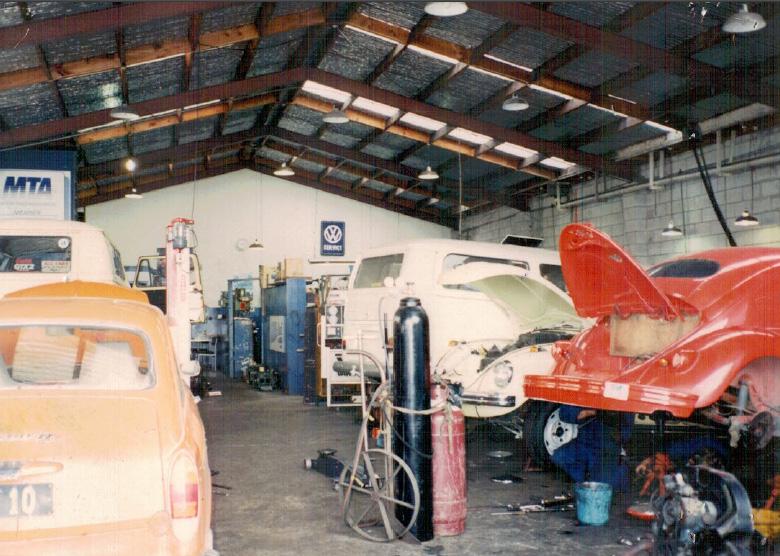
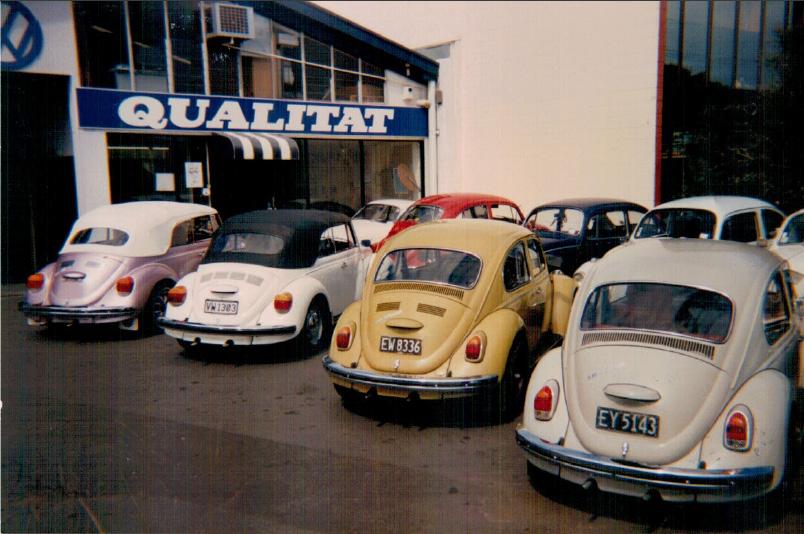
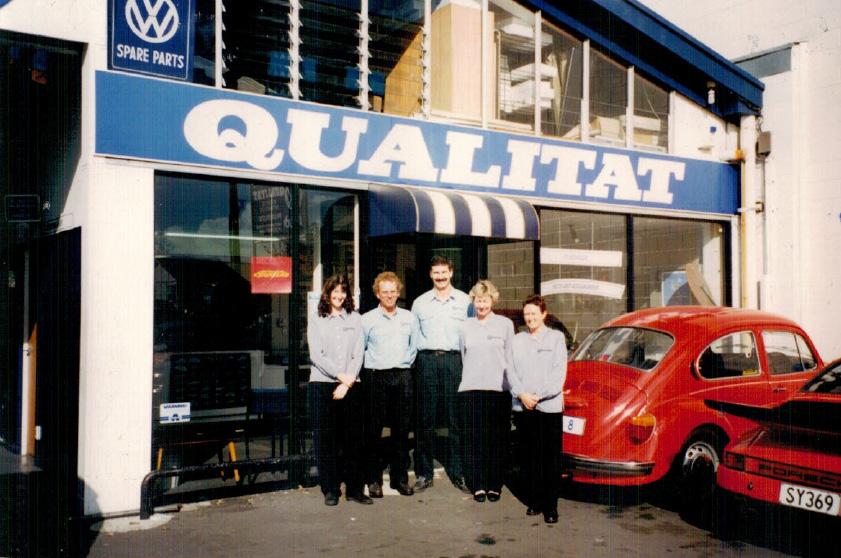
Top 5 brake complaints
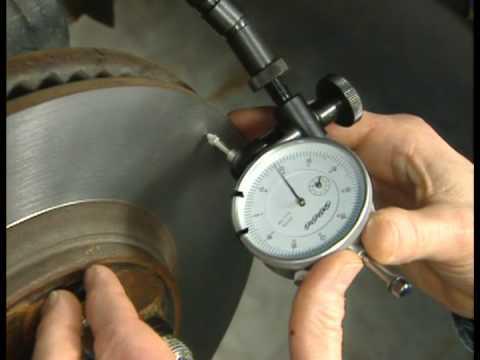
IT’S ALWAYS WORTH DOING THE JOB RIGHT AS MOST ISSUES IN MODERN BRAKES NOW RELATE TO POORLY PERFORMED SERVICING
The most common brake complaints involve noise, unusual or premature wear, and dusting. Other common concerns involve pulsations and stopping performance.
1/ NOISE
Brake noise, or squealing, is the most obvious problem. Unwanted, audible brake component movement causes it. Solutions are keeping brake components in place per factory specs and properly preparing surfaces during servicing.
Today’s brake systems are very sensitive to rust and corrosion and should receive a thorough cleaning in preparation for fresh lubricant, hardware, and friction material. Residual rust or corrosion left in critical areas can begin to cause brake issues almost immediately.
In addition to normal inspections for binding, corrosion, lack of lubrication, and worn or damaged components, calipers must be cleaned and special attention paid to lubricating areas of contact. Proper servicing of components that retain the pads is vital so that they are clean and free of corrosion.
Great gains in noise reduction also have been made on the manufacturing side. These advances in friction technology have greatly reduced problems with brake noise.
The introduction of ceramic brake pads in the 1980s paved the way for this. This new friction technology originally was engineered for popular Asian models, as noise was more evident in these small and quiet cars, but the solution was progressively adopted worldwide.
2/ PULSATION
If a customer has a brake pulsation, you know you have variation, so rotors will have to be resurfaced or replaced.
Measuring rotor thickness variation requires extremely accurate measurements every few inches around the rotor, with limits as low as 0.001-inch. Measuring rotor thickness to that degree is hard to do accurately in a workshop, and the pulsation tells you all you need to know. But you can check for run-out. Standard procedure for measuring lateral run-out is to measure it while simulating actual conditions by mounting the rotor to the hub with lug nuts and properly torquing them into place (you are using a torque wrench, right?). But what if there is corrosion between the rotor and hub? Would this not cause increased run-out?
As rust and corrosion grow between the rotor and hub, they can separate the two, pushing the rotor out and creating run-out, uneven wear, and pedal pulsation. Proper inspection and a clean mounting surface between hub and rotor are key to eliminating pulsation.
So, let’s say you have properly cleaned, inspected, and measured. What do you do if all else fails and there is still a pulsation? If all the rotor measurements are within specifications, the ‘pulsations’ the customer feels could be speed related. Checking tyre and wheel assemblies on equipment designed to measure and locating loaded radial-force variations could help pinpoint problems not caused by the brake system.
3/ DUST
When braking force is applied, a small amount of material is gradually worn off the brake pads. This ‘brake dust’ usually deposits itself on the braking system and the surrounding wheel.
The proper friction choice can affect dusting. Different brake pad formulations create different amounts of dust, and some formulations — particularly metallic brake pads — create more dust than others. Ceramic brake pads contain fewer metal particles, and therefore produce less corrosion of surrounding metal parts.
Addressing worn or corroded parts and proper cleaning and lubrication when performing a service are the best ammunition for eliminating brake dust complaints.
Taking care of a brake dust issue can eliminate other problems and help prevent or solve customer complaints. Using a combined effort of proper servicing and proper components should yield the best results. This is important because dust on wheels can be more than just a visual nuisance. If the acidic brake dust is left to accumulate, it can badly damage the finish of most wheels, so it pays to address it from the start.
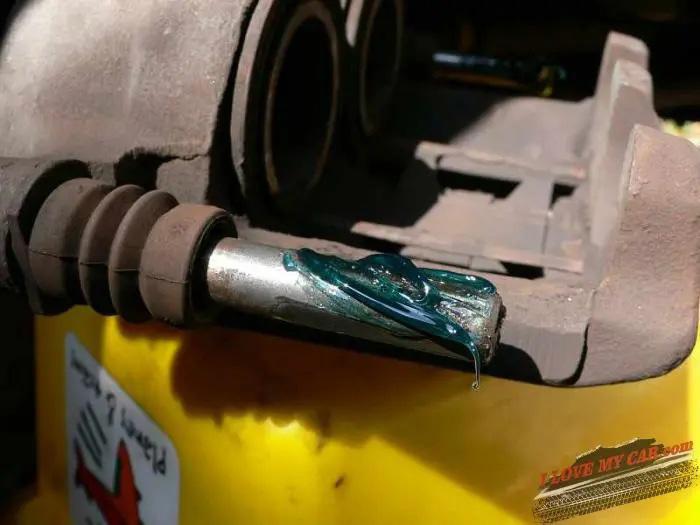
4/ WEAR
Increased power and performance of vehicles in response to customer demand, coupled with pressure to reduce weight for emissions and fuel economy, has placed even more emphasis on brake performance. A move by manufacturers toward larger rotors, increased service area of pads, and overall more aggressive braking systems creates an environment for increased component wear that must be serviced properly.
Given the extreme conditions under which modern brake systems operate, premature or irregular wear likely both result from a failure to fully and properly restore the brake system to its proper operating condition.
Proper restoration usually takes more than a quick pad change. Replacing all appropriate hardware, refinishing or replacing rotors as per manufacturer specs, and cleaning and lubricating sliding surfaces and pins as appropriate will allow the system to function properly under the most severe loads. But driving patterns also play a part.
5/ PERFORMANCE
Proper break-in period and technique can greatly affect the performance of new braking components. Yet not all OE manufacturers require break in and the different friction and adherent brake technologies require different approaches. As always, it is best to follow the individual component manufacturer’s recommendations.
Another cause of performance issues is old or inadequate brake fluid. The importance of always using a high-quality fluid with a high dry boiling point rating cannot be underestimated. As the brake system operates, heat is generated and transferred into the hydraulic system as it passes through various components.
In addition, over time moisture from the environment enters the system, contaminates the fluid, and decreases the boiling point. By flushing fluid at the manufacturer’s recommended interval, moisture contamination is removed and the proper boiling temperature is restored.
Improvements in engineering and manufacturing techniques as well as materials have eliminated some of the problems technicians used to see. In conclusion, modern vehicles are simply more detail oriented when it comes to servicing. Technicians must follow prescribed service recommendations precisely, without fail. Inspecting and servicing braking systems thoroughly will ensure customers have no cause for complaint.
Brake system checklist
WHILE TECHNICIANS BUILD UP THEIR OWN ROUTINES WHEN CHECKING SYSTEMS LIKE BRAKES, A CHECKLIST CAN PROVIDE A QUICK REFRESHER
When a customer visits a workshop because they hear noise when the brakes are applied, feel vibration, see the brake service light is on, or even smell a chemical/burning odour when braking, it’s time to inspect the braking system to diagnose the problem.
Regardless of what the customer may think is wrong, technicians know the importance of performing a full brake system inspection to ensure that they complete the right service for the vehicle.
The following checklist covers some of the most important areas to review when performing a brake system inspection: • Test drive the car. Check for any noises, vibration, or abnormal smells when applying the brakes. • Inspect the tyres. Make sure there are no punctures or damage to the tyres or rims that could be causing the symptoms your customer is experiencing. • Check the vehicle’s suspension system. Again, this
could be the cause of wobbles or vibration that your customer is feeling. • Look for leaking, cracked, or damaged hoses. Fluid leaks can cause major problems, so make sure everything is sealed and in good working order. • If needed, replace any leaking or damaged steel lines. • Replace any leaking or damaged calipers.
Preferably use an OE quality, ultra-premium caliper that is new, and not remanufactured. • Check the brake master cylinder for leaks. Leaks can be a common cause for repair. • Test the brake pedal. Make sure movement is smooth and completely depresses. • Inspect rotors and drums for damage. Low-quality rotors can wear unevenly, causing pulsation when the brakes are applied, and then uneven pad wear.
This can lead to more problems. Ultra-premium, high carbon rotors should always be used to help prevent these issues. • Replace the brake pads. Pads should be
thoroughly examined for wear. Remember, brake pads and brake rotors should always be serviced and replaced at the same time, using OE-quality brake pads. • Service wheel bearings if needed. • Lubricate caliper slides and shoe pads. • Check the brake fluid and flush if necessary. Often, neglected old brake fluid can cause problems if it’s not serviced regularly. The fluid should be light in colour. If it’s very dark, it’s time to swap it out for fresh brake fluid. • Adjust the vehicle’s parking brake, if applicable. • Check and replace any faulty sensors.
Once you’ve completed a thorough review of all braking system components and performed the necessary maintenance, it may be useful to remind your customer of the factors that contribute to excessive wear on their braking system: • Too much load from carrying more weight in the vehicle than it is rated for. • Heavy or aggressive braking, especially from high speeds, can add additional and unnecessary wear on the system. • Frequent driving in wet or extreme weather can create the need to brake more quickly to prevent slipping or skidding, again placing additional wear on the system.
Discussing with customers that their braking system is a major safety component in the vehicle should help them see repairs as an investment. By keeping a checklist handy, you can inspect brake systems quickly and accurately, confident you are making the correct repairs.
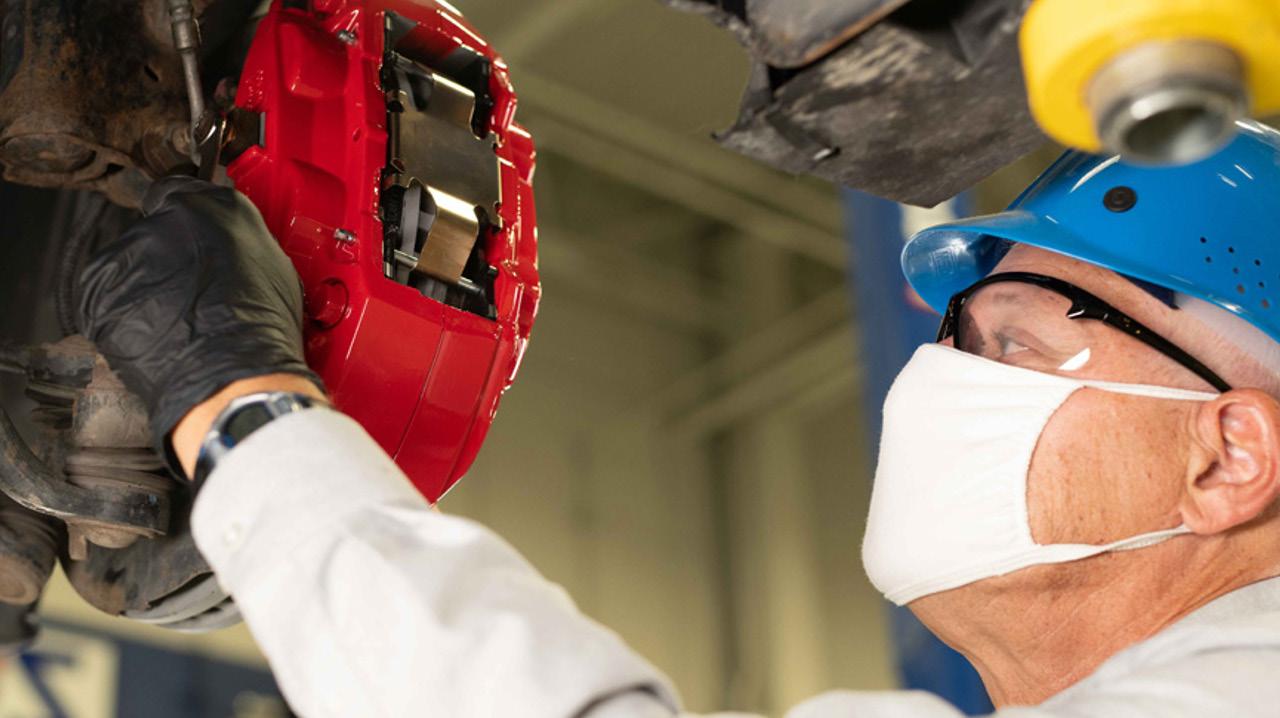
Walking the torque
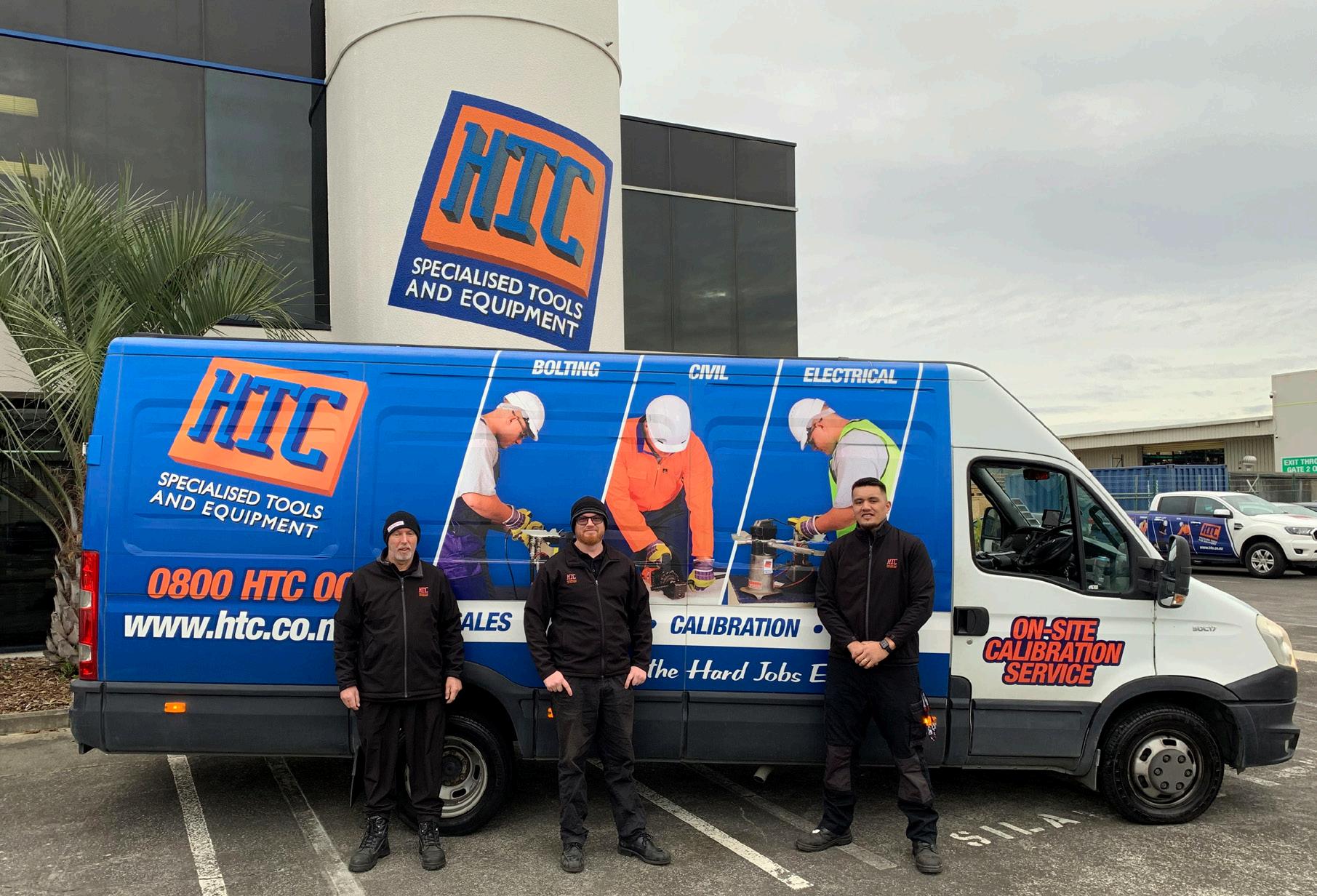
NZ’S LARGEST SUPPLIER OF TORQUE WRENCH TOOLS, HTC, GIVES US THE LOWDOWN ON WHY CALIBRATING YOUR EQUIPMENT IS SO IMPORTANT FOR OPERATOR SAFETY.
The whole point of torque wrenches is that they measure force and indicate when the required force is met. Yet, according to HTC Ltd, if they are not calibrated correctly, they can create dangerous and unnecessary risks for the equipment being worked on and for the operator’s safety.
“Most of us have used a torque wrench at one time or another for tightening fasteners. For some of us it’s an everyday thing,” says HTC Ltd’s General Manager, Daniel Brice.
Most people would also be aware that many road vehicles and many multimillion-dollar pieces of machinery depend on correctly tightened fasteners to avoid damage, downtime or most serious of all, injury. “Using torque wrenches helps ensure correct fastening,” says Daniel Brice “but the torque tool has to remain accurate within tolerances, and that means it also needs a maintenance plan.”
HTC has more than 40 years experience in dealing with high force engineering challenges and that’s why, more than 20 years ago it got into onsite calibration. Its services include certifying tooling but, in particular, helping companies evolve systems that limit their exposure to risk by confirming their tools’ integrity.
Daniel says that over the years, HTC has distilled the following principles into a successful formula that they use to create and develop torque systems and procedures for its customers:
Training: Correct bolting procedures should be established and regulated at management level with floor staff given practical training. In many cases failures occur when procedures are not clearly defined, being both documented and visible. This enables staff members to miss steps if tools are not checked regularly for wear and tear accuracy.
Calibration: In most New Zealand industries, local law and foreign auditing bodies are increasingly enforcing testing and calibration of equipment. Manufacturers of torque tools generally recommend annual calibrations but, in high use situations, shorter service or calibration intervals may be warranted.
Traceability: It is imperative that each tool has a unique serial number and that calibration certificates are kept for three to five years.
Care: Torque wrenches are ‘measuring devices’ and need to be cared for accordingly. Nine times out of ten, when wrenches become inaccurate, it is due to lack of care. Good quality torque tools are expensive, so it makes sense to keep them in service for as long as possible.
In the next edition we will cover what’s happening when we apply torque and what we are attempting to achieve.
HTC Ltd is New Zealand’s leading supplier of torque wrench tools and calibration, servicing and repair services. To book a calibration service for your torque tools visit www.htc.co.nz/calibrationand-testing/ and scroll down to the ‘Booking Form’. To contact the team directly, call 0800 48 2000.
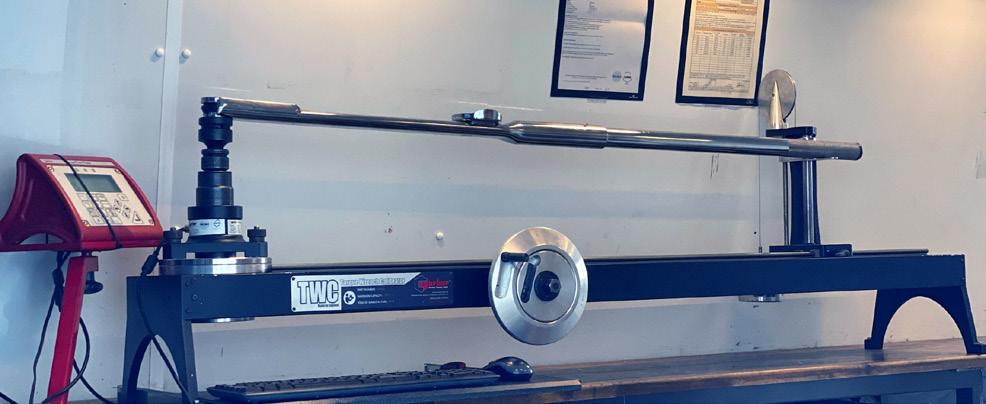
The HTC Calibration Vans can visit your worksite to service your torque wrenches, reducing down-time and courier costs
HTC calibration vans are fitted with the Norbar Torque Wrench Calibration wrench, to ensure accuracy