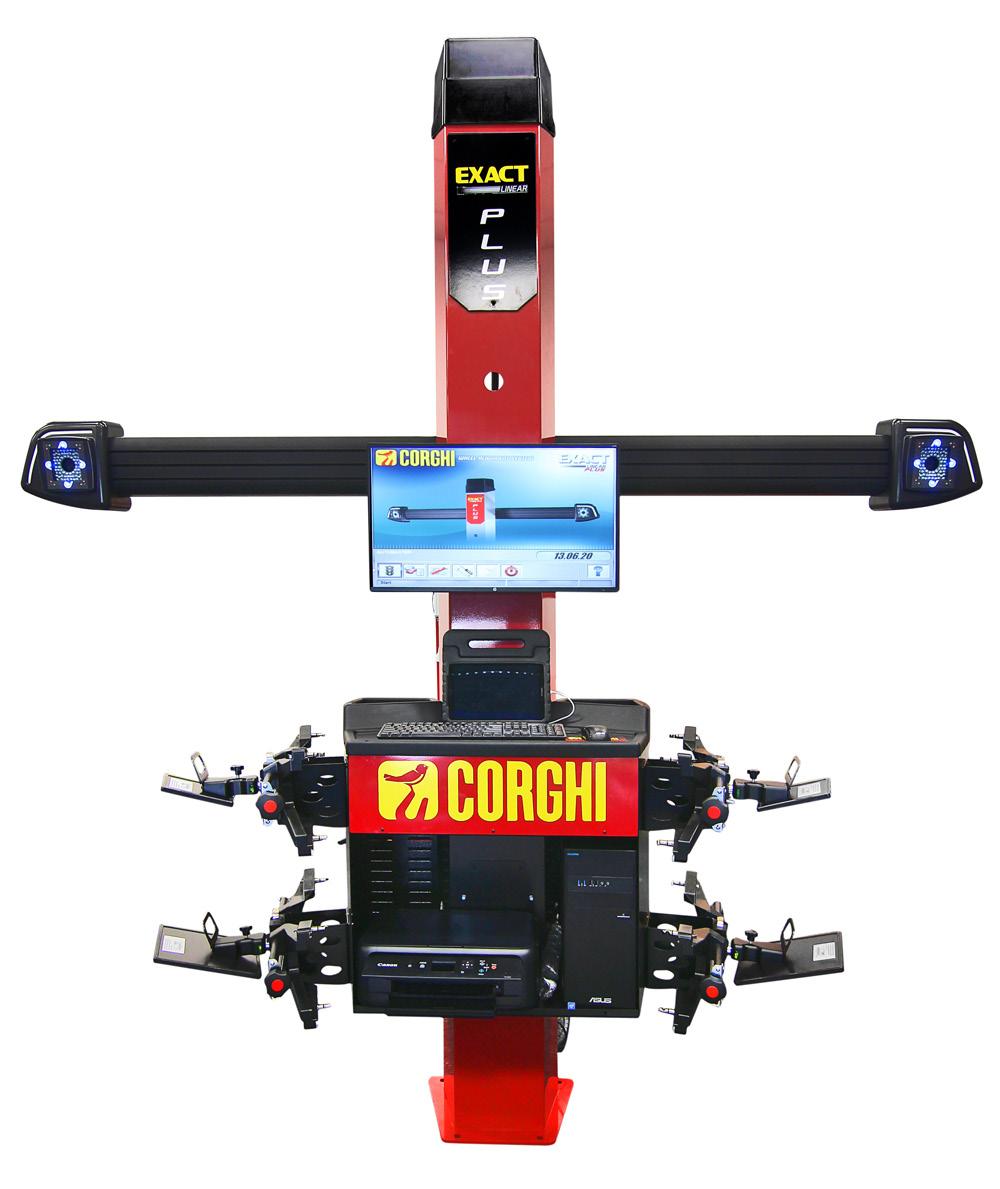
9 minute read
Product profiles
from Auto Channel 50
by Via Media
Products The latest automotive products
Exact aligner
Advertisement
The Corghi Exact Linear Plus 3D Aligner features two new high-resolution cameras with HI-Q artificial vision and integrated LPF filters that eliminate sunlight reflections. They target new compact high-resolution small and light targets. An automatic target tracking camera boom moves automatically with the lift. A new camera movement system uses a worm gear for better positioning accuracy. It allows the operator to work from pit level to over two metres. See automaster.co.nz, call 0800 214 604, or email info@automaster.co.nz.
Another cool profit centre
Summers are getting hotter, so air-con servicing becomes an increasingly valuable service to offer. Features of the Heshbon HR-371 air-con fluid recycler include automated recovery and recycling management, manual or automatic operation, and a dual operating mode: expert or beginner. It has a programmable vacuum phase automatic air-purge system and programmable maintenance. Options are available for all refrigerant types. RRP $5599 plus GST, delivered. For more information, contact sales@centurydistributors.co.nz, or call 04 567 1405.

Vinyl’s saviour
If it’s vinyl and has been worn down by the harsh New Zealand sun, Dirty Steve’s vinyl saviour is your ticket to restoring that silky satin finish. It’s a must-have in your detailing kit because of its versatility on all varieties of vinyl. It is non-oily, non-greasy, and has that new-vehicle smell we all enjoy, making it ideal for boaters and all areas of automotive trim and accessories. Simply spray the affected area and wipe it down with a microfiber cloth. Quick and efficient — the answer to all of your vinyl troubles. Available from all leading marine and automotive retailers.

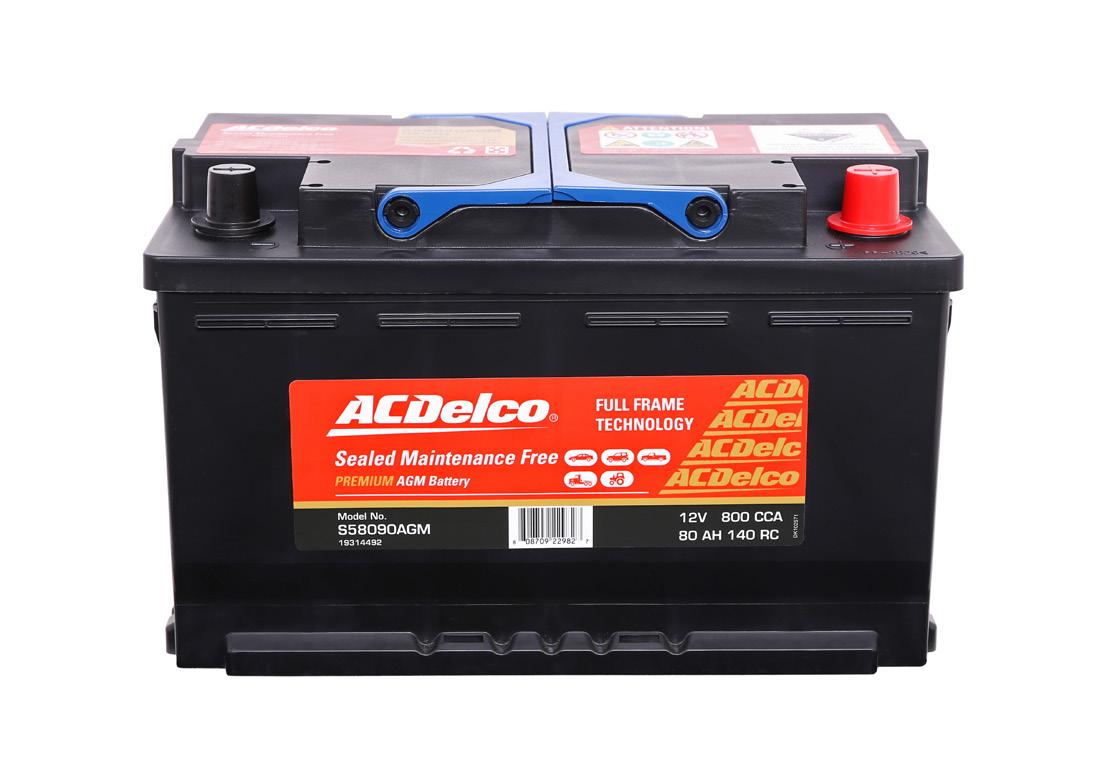
ACDelco does AGM
The ACDelco Absorbent Glass Mat (AGM) range is designed for highly developed cars and those with advanced fuel-saving technology, including stop-start and regenerative braking. AGM plate separators reduce internal resistance, improving performance, including increased cycling ability, faster recharge acceptance and improved cranking power in a partial state of charge. The AGM range is ideal for modern vehicles that have higher electrical accessory loads. For more information, or to become a stockist, call 0800 546 000, or visit www.rjbatt.co.nz.

Eco-friendly parts washing
CRC’s range of SmartWashers does away with workshop staff’s risk of exposure to volatile, flammable, and irritant solvent cleaners, and the need to buy, store and safely dispose of these chemicals. SmartWashers, which come in a range of sizes to suit different applications, use non-toxic emulsifying degreasers. The cleaning fluid is effectively self-cleaning, as selected bacteria in the SmartWasher breaks down oil and grease to oxygen and water leaving just dirt trapped in the filter for disposal. They drastically reduce compliance costs, clean just as effectively as solvent cleaners, and are much more pleasant and safer to use. The CRC Smartwasher range is available at NAPA Auto Parts. Visit napa.co.nz for your nearest branch, or call 0800 800 073, or login to PROLink.
Spark plug performance
Finding the right spark plug for the job can be a tricky process, with the wrong choice compromising precision engine output, reliability, and fuel efficiency. NGK Spark Plug Australia knows all too well spark plugs’ effect on performance and longevity and have taken the guessing game out of selecting and easily identifying spark plug issues by developing a series of short videos. NGK is the largest OE spark plug supplier in the world and they have tapped into their extensive experience to help mechanics and automotive technicians get it right the first time. To find out more visit ngk.com.au.
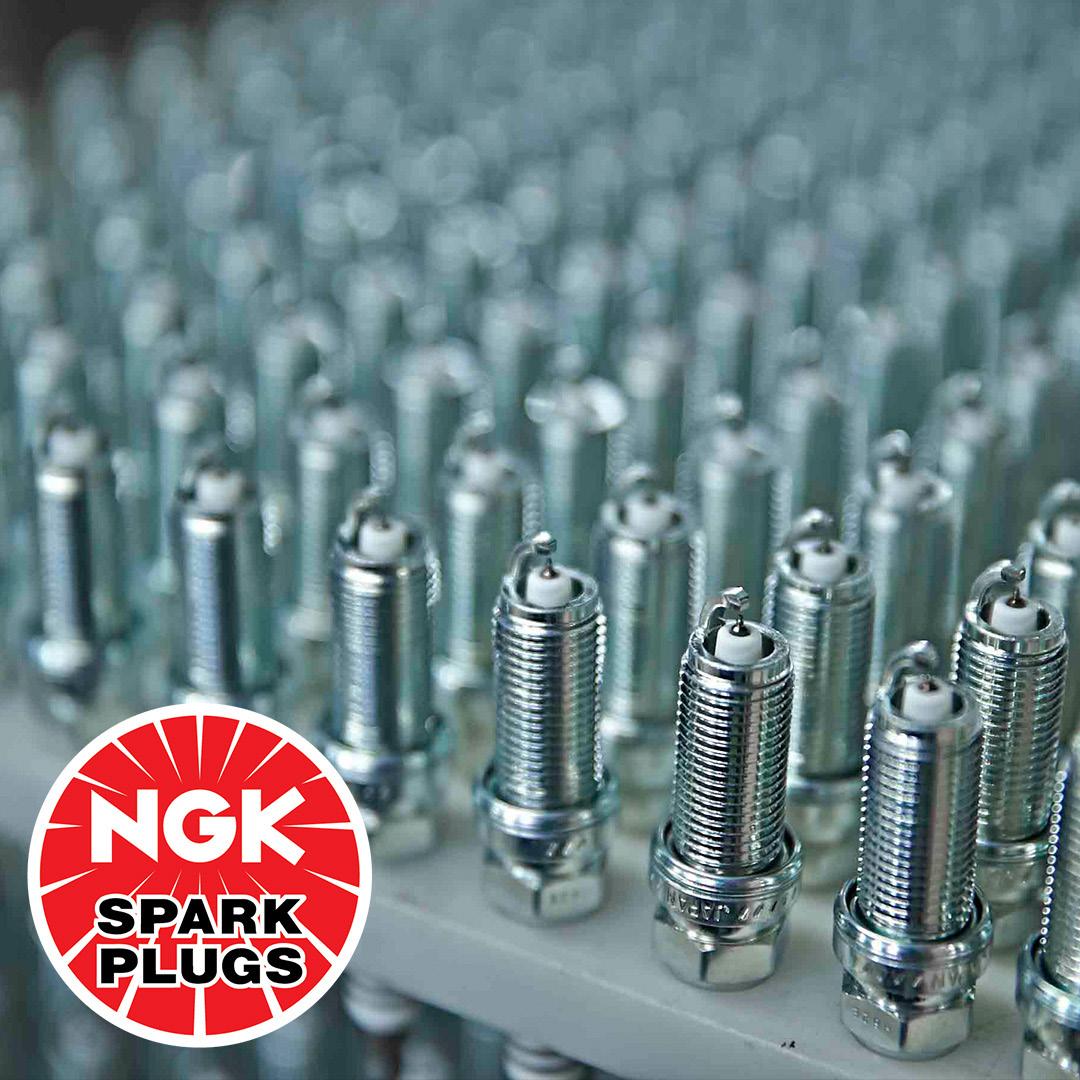
Convenient inspection lighting pack
OEX has taken lighting convenience to the next level with this pack which includes a wireless charging base that will also charge Qi compatible cellphones or other devices. Both inspection lights are dual output with a 70 lumen torch at the tip and a dimmable COB flood light on the side. The 250 lumen lamp has three hands-free mounting options: a 360-degree swivel hook, a magnetic back, and a magnetic pivoting base. The larger 300 lumen dimmable lamp is shaped for convenient handheld use. The lights can be charged by simply sitting them on the wireless charging base, or plugging them into it with the supplied USB cable. Available at NAPA Auto Parts. Visit napa.co.nz for your nearest branch, or login to PROLink.

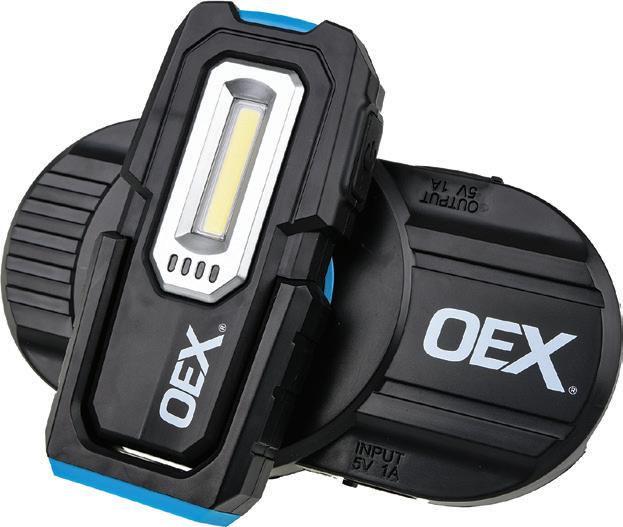
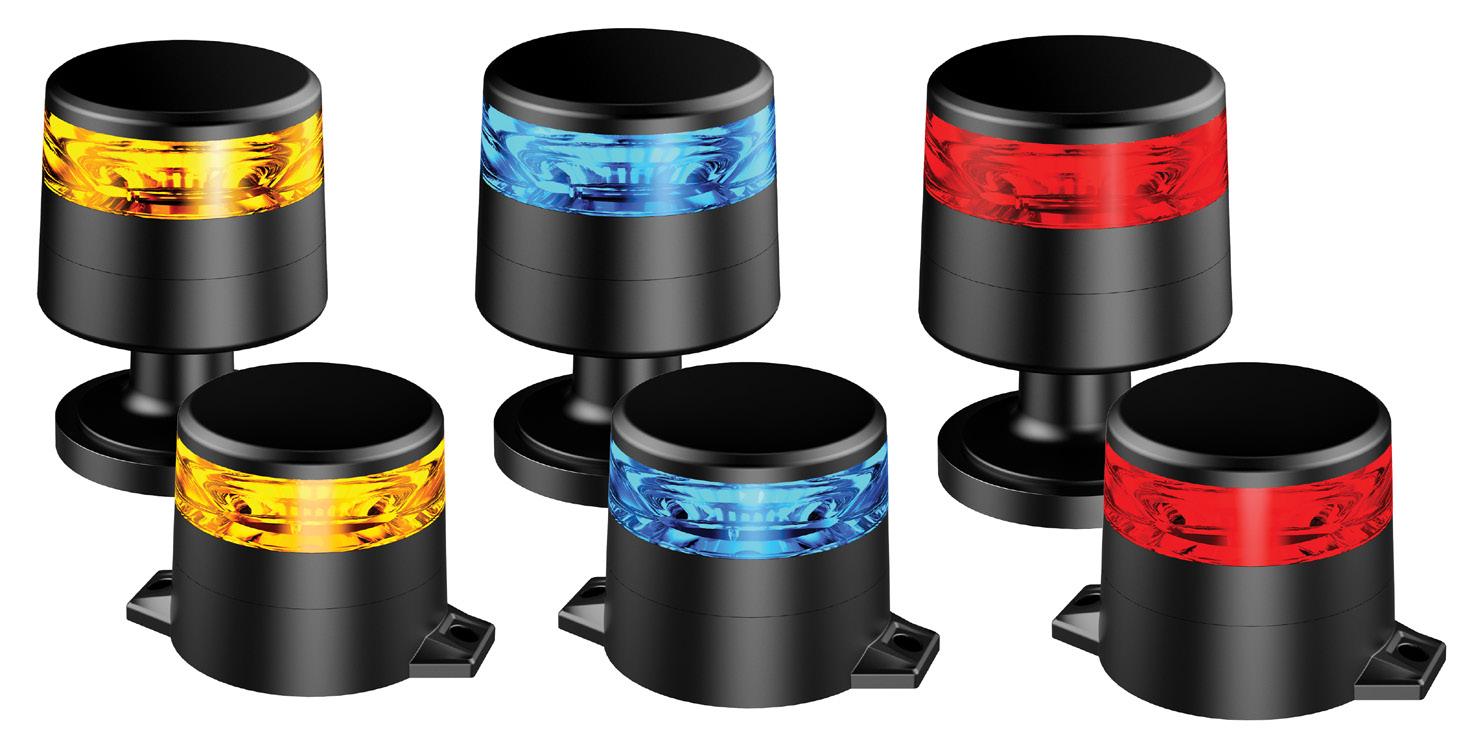
Ignite beacons
Ignite’s 10-80V LED Beacons offer 10x strobe and 2x rotating patterns with up to 100,000 hours LED lifespan. SAE J845 Class 1 and IP67 rated, the highquality beacons are available in amber, blue, or red with either a two-bolt metal mount, or magnet mount. Ignite LED Beacons have a low-profile black aluminium alloy powder-coated housing, a durable PMMA polycarbonate lens and come with a five-year warranty. Available from CoolDrive, or see cooldrive.co.nz.
Collision repair costing
GETTING ‘BLUEPRINTING’ TO WORK CAN MAXIMISE BODY SHOP PROFITABILITY
The point of blueprinting is discovering what once would have been hidden damage before the actual repairs begin, thereby building accuracy and efficiency and eliminating costly oversights.
STEP 1: UNDERSTANDING BLUEPRINTING
Workshops can differ widely in how they define and perform blueprinting. Some pull everything apart around the areas damaged or potentially damaged in a collision. Others focus only on areas of significant damage believing the margins in the extra work are not worthwhile, but those margins are still there.
Workshops should start by understanding the relationship between blueprinting and estimating. The estimate is the external business document intended for customers and insurers. It’s an appraisal but it should be as accurate as possible, so the people looking at it aren’t surprised later.
The blueprint is the internal document — the action plan for thoroughly repairing, painting, and preparing the vehicle for return to the customer.
More than that, the blueprint is the document that ties all parts of the workshop process together. As such, everyone should accept a part in creating and following the blueprint — estimators, the blueprinting person or team, techs, and painters.
It’s vital to get buy-in because proper blueprinting is essentially a culture change in the workshop. Workshops that try to adopt it without buy-in will generally conclude it doesn’t work.
STEP 2: DESIGN YOUR BLUEPRINTING MODEL

First discuss with staff how the blueprinting process would be conducted. Here again, understanding the basis of blueprinting is the guiding factor. Invite staff to think of looking at the vehicle holistically, working from the simple to the complex, and then in one organised motion from the front of the vehicle to the rear.
That starts with opening and closing all doors and the boot to ensure they operate correctly, performing a visual inspection of the vehicle, and then recording any damage. From here, the estimate takes a central role, as the blueprinting staff will use it to track further damage.
You’ll also want to run diagnostics, which may already have been performed as part of the estimate. Then, move in an orderly fashion from the front of the vehicle to the rear disassembling repair areas to look for further damage and noting it as such.
Once again, a good estimate is important here since you’ll want a complete understanding of manufacturer repairs to know exactly what work will need to be performed to repair the vehicle.
If you don’t understand the work, you can’t blueprint it, and already having that information in the estimate saves time.
Checking underneath is also vital. If you’re going to blueprint, you have to blueprint everything. Always check the tyres, suspension, exhaust system, and anything that might be hanging from the bottom that might cause issues on a test drive.
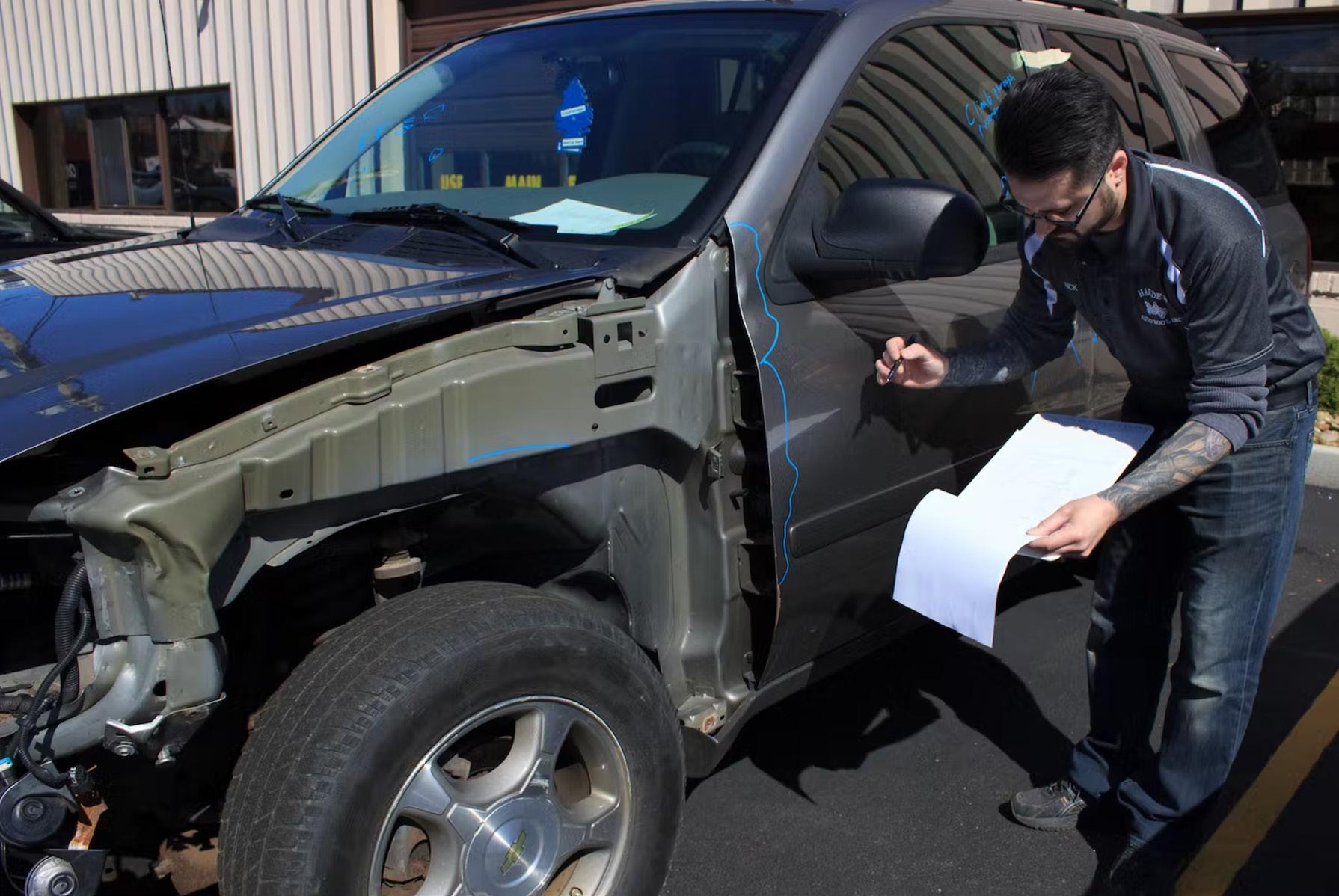
STEP 3: CREATE YOUR SOPS
You need to document how each step is conducted and when. The objective is to create a guide or standard operating procedures (SOPs) that will help you to repair vehicles consistently. This is work that will require input and some review by every member of your staff.
The challenge here is putting all of that into writing, a task many shops might find daunting. Writing clearly isn’t easy. Organising information isn’t easy. Rolling all of this together in a form that’s easy to read is even more difficult.
If you’re not comfortable doing this work, hire someone from outside to do it for you. Talk to hiring firms about bringing in an experienced technical writer who can take care of this work. Clear, concise writing makes a huge difference to how the blueprint is received and used. Work closely with your writer, so you can update it later as your blueprinting process evolves.
Again, make sure you involve your entire team in designing your blueprinting model so you can create the necessary business culture that supports this practice.
STEP 4: SEEK OUTSIDE GUIDANCE
A technical writer certainly isn’t the only external source you should leverage. Expert guidance can be the difference between a transformative blueprinting process and one that provides only modest results, or is later abandoned. Experience really counts here.
You can find consultants among your suppliers — for example, from your paint suppliers. Additional help can be found on the internet, where some of the brightest stars of the collision repair industry hold court.
Having help from an experienced guide who has seen this work in practice will also help to convince staff that blueprinting is a good move.
STEP 5: AUDIT YOUR WORK
External help can offer one other service — helping you crunch shop numbers to show the results of blueprinting. By looking at your pre-blueprinting KPIs (or pre- and post-change numbers for those of you looking to upgrade existing blueprinting strategies) and those collected afterwards, you can drive home to your staff the effect of this process and involve them in its refinement.
Look at cycle time, severity, and the average repair dollars per repair order (RO) and compare those to previous numbers. It’s imperative that management and staff compare their experiences before and after implementing blueprinting. Doing so helps work out any areas or issues hindering the process. This is aso a good time to address how well your employees are communicating and fix that as well.
In time, you should end up with a true-blue blueprinting operation that evolves as your business does. Though many details are involved in its development, those complexities ultimately improve your workflow and any actions that make your work easier and more profitable are well worthwhile.