Feed Production Machinery, Pelleting & Extruding
CFE GROUP
CFE have acquired Sevale Engineering in Gloucester and Turner Grain in Dublin in the past two years. Both companies provide valuable engineers and supply chain solutions for our Group. CFE have been partnering key customers in the past number of years in facilitating the optimisation of energy efficient quality throughout. Our value creation strategy at CFE Group is focusing on our core business, where we serve our current market positions in the compound feed industry. In maintenance, we refurbish pellet mills, flakers and grinders at our Haydock facility and our team of eight engineers, across the UK and Ireland, concentrates on contract maintenance for customer equipment. We are maintenance and service specialists, competent, highly experienced, and fully up to date with the technology and operating systems of the different brands of manufacturing equipment supplied to the feed and bio-mass markets.
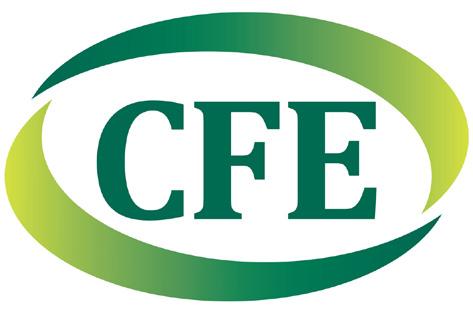
We are also growing our market share by increasing the footprint of CPM in the compound feed business. In the past year we have sold two new CPM Roskamp Grinders, 12 CPM Conditioners, 10 CPM Pellet Machines (7932/ & 7936/12) and supported all the CPM equipment in UK & Ireland We have a strong pipeline for the next two years, where we plan to continue this growth. CPM’s Double Pelleting system is by far the preferred production practice for ruminant feed. While expanders and high friction conditioners can give customers the edge for specific formulations, the Ruminant feed business has clearly opted for double pelleting ahead of all other processing systems, it gives consistent quality, maximum throughput and an energy efficient pellet. It’s important to match horsepower as closely as possible on the top and primary presses and the working width of dies must be in the range of 20%, i.e. the primary press being no more than 20% more open than the pre-pellet machine. Direct drive motors on a Double Pelleting stand reduce the installed motors from 4 to 2 and direct drives give more energy efficiency and torque required to keep the press running across a range of formulations.
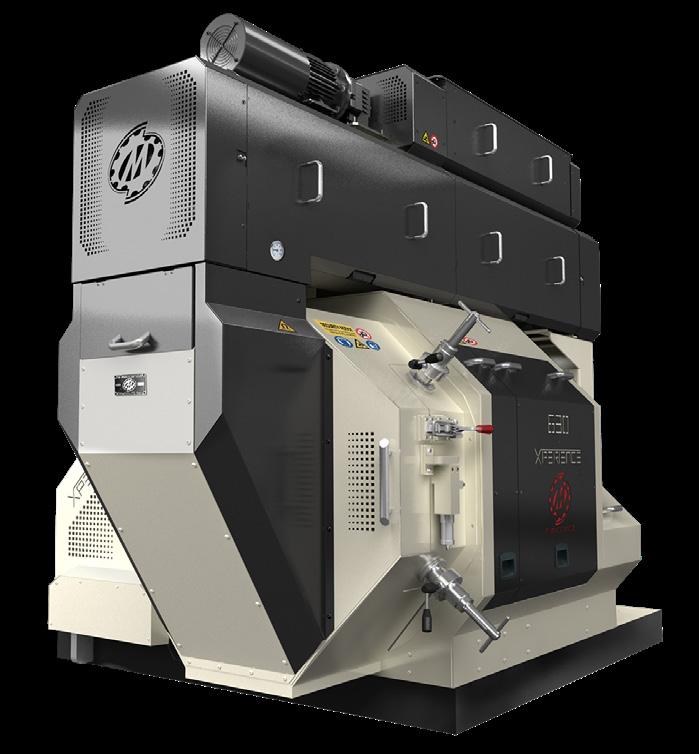
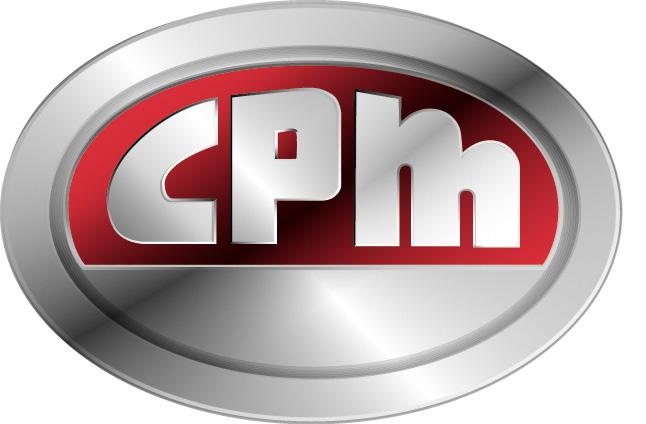
CFE’s Cost per Tonne (CPT) is an inclusive service for maintenance, pelleting consumable supply and engineering support, that offers feed compounders an insurance policy, guaranteed supply chain and working partnership. The CPT is a 3-year contract that cost matches against tonnes produced and invoices issued monthly; eliminating the peaks and troughs that can impact feed milling. The customer advises CFE of its tonnage on the final day of each month and the invoice is based on the actual tonnage figure. We are proud to continue working alongside our
compound feed partners as we all strive to grow and support our most important indigenous industry.
www.cfegroup.com
CONDEX (UK) LTD
La Meccanica Pellet Mills since 1986
La Meccanica pellet mills come with a 5 year, no major service guarantee. This means that as long as the machines are maintained and greased in accordance with the manufacturer’s guidelines, there will be no major servicing costs for the first five years; no seals, no bearings and most importantly no down-time.
With the large diameter, two roller design providing the optimum angle of nip and the main rotor having a high inertia, the La Meccanica pellet mills are one of the most efficient machines on the market, outperforming larger machines as a result of the design and main motor being utilised to its full potential.
No gearbox so no oil leaks around the pellet mill or more significantly into the feed; a major consideration now that UFAS directive states that food safe lubricants need to be used.
Condex also supply an extensive range of mixing, grinding, conditioning and ancillary equipment, including being an official agent for Geelen Counterflow coolers. Ensuring our clients are able to meet the high demands of the industry with equipment designed and manufactured to the same high standards as our pellet mills.
Our in-house design and installation services enable us to tailor equipment and process lines bespoke to a client’s requirements. This gives our clients the confidence of knowing all aspects of the process are taken into consideration, whether this is upgrading a single machine or a complete production line. With a single point of contact the end user can be reassured there are no surprises, no hidden costs and no delays as a result of miscommunication between contractors.
Customer satisfaction is our number one priority; we achieve this with UK based stock and service engineers, around-the-clock aftersales support and a die and roll refurbishment service second to none. Peace of mind at competitive prices.
Condex (UK) Ltd, White Cross, Lancaster, Lancashire, LA1 4XQ
Tel: 01524 61601, Fax: 01524 381515, Email: info@condex.co.uk, Web: www.condex.co.uk / www.pelletmills.com
DSL / DATASTOR SYSTEMS

Imperium4Feed is the new mill control system offered by DSL Systems and Datastor Systems combining their wealth of knowledge and experience to provide leading-edge process control, planning (MES) and information software for mills of all sizes.


increased throughput by 15%”
For further information or to arrange a demonstration, please contact:
Matthew Swallow
T: + 44 (0)1159 813700
E: matthewswallow@dsl-systems.com
Web: dsl-systems.com
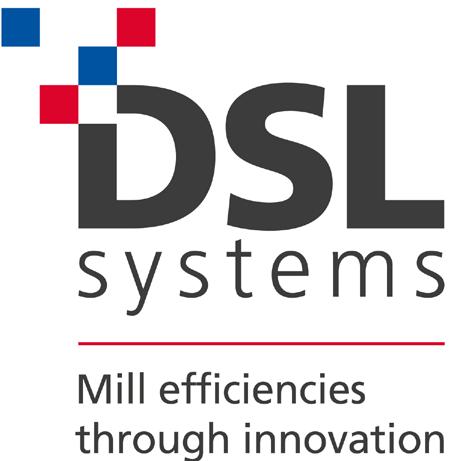
Bill Wright – T: +44 (0) 1260 277025, E: billwright@datastorsystems.com
Web datastorsystems.com
FUCHS LUBRICANTS (UK) PLC
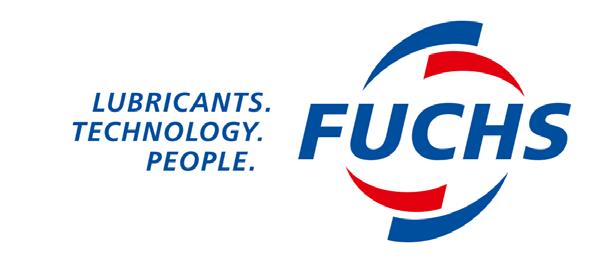
food grade lubricants
In the animal feed industry, the use of food-safe machine lubricants can mean the difference between a good name and no name at all. The production of animal feed puts the strictest requirements on the lubricants used in the manufacturing process.
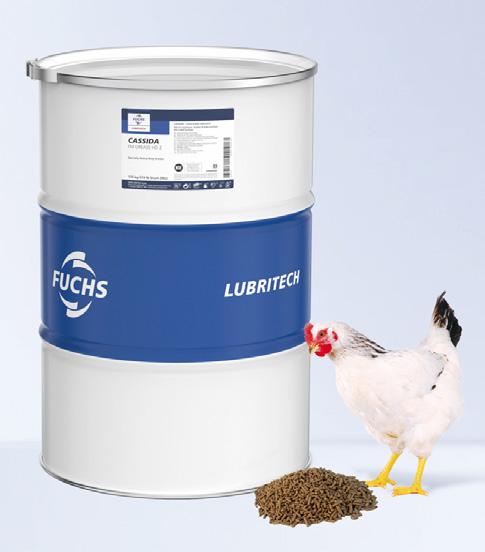
Consumer protection is absolutely essential. Incidental oil contamination at any point in the process needs to be avoided by animal feed manufacturers, who process millions of kilograms of animal feed for global markets every year. In addition, ensuring that the production process runs smoothly and is highly effective (meaning longer component lifetimes and extended maintenance intervals) is our number one priority.
Imperium4Feed’s pellet press and extruder control modules are designed to optimise quality, improve throughput and eliminate blockages. Imperium4Feed has a number of features to optimise pellet press control including automatic start-ups, flying bin-swaps, cooler fan speed optimisation, cold start-ups, anti-blockage detection, layered change overs and automatic flushing
All configurations of pellet mills, extruders and expanders are catered for, including: -
• Single pellet mill, Double side by side, Double in line, 3 pellet mills per line
• Up to 8 pre-pellet press bins per production line
• Hot start conditioner, long term conditioner, expander, HFC and BOA
• Kettle or Ripener
• Extruder
• Cooler control
• Fats spray at the die
• Downstream Fats Coater (PPLA)
• In-line pellet tester
“Changing control of our pellet presses to Imperium4Feed has
Our customers benefit from the excellent quality of the CASSIDA portfolio, which has been confirmed by numerous OEM approvals given by well-known manufacturers of production and manufacturing equipment.
Today, major animal feed manufacturers are taking the risk out of their processes by using CASSIDA food grade lubricants as the safe alternative for all lubrication points in their production plants.
Our support package
As well as providing you with high-performance food grade lubricants, FUCHS is able to offer expert technical advice and support. FUCHS can assist with oil condition monitoring, failure analysis and diagnosis, Lubrication Critical Control Point (LCCP) surveys, and much more.
Performance and safety
The CASSIDA range is NSF H1 registered, as well as being the first food grade lubricant range to receive ISO 21469 certification. Certified for Halal and Kosher production, the CASSIDA range provides a total solution for the animal feed industry.

Julian Potts, FUCHS UK
Email: Julian.Potts@Fuchs.com
Web: www.Fuchs.com/uk