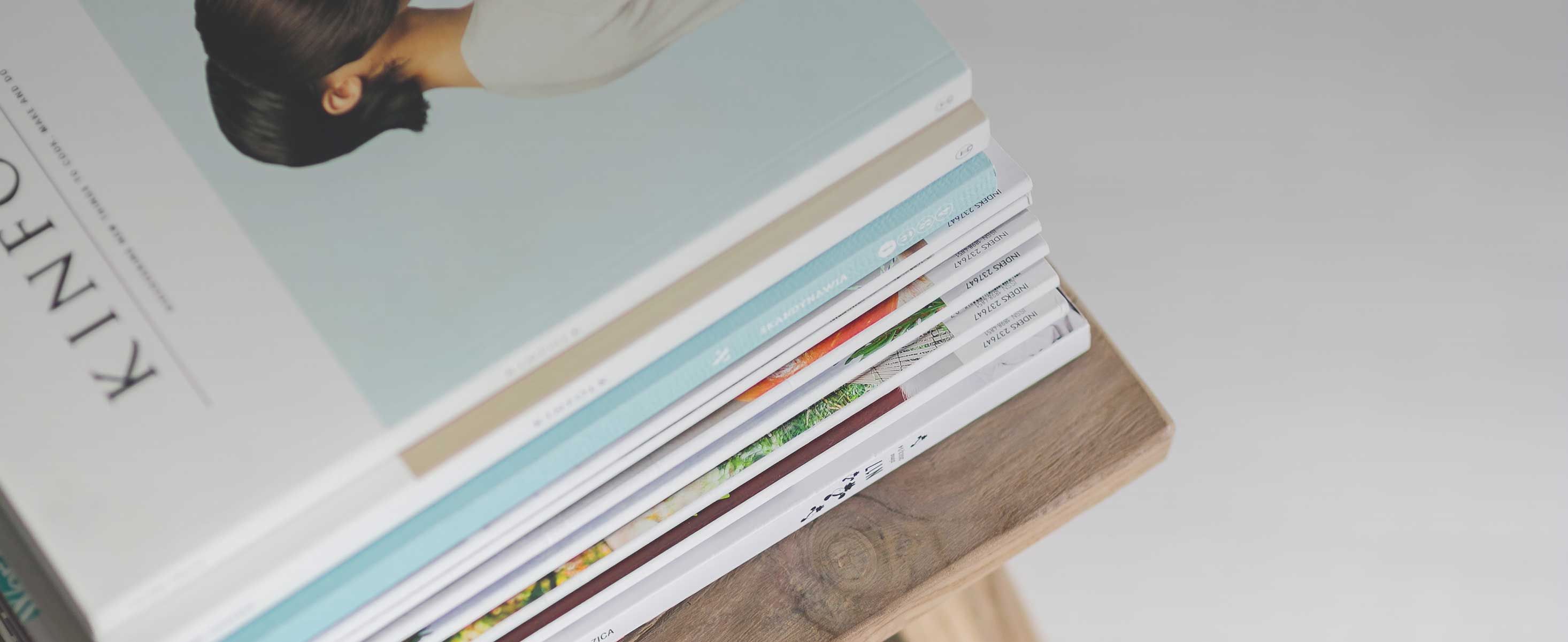
4 minute read
Cost Effectiveness
Balcony Mock-up: Thermal Performance
In addition to fenestrations in the building envelope, balconies are often one of the weakest areas in the residential buildings when it comes to thermal bridging. Depending on the type of structural connection, thermal performance of the balcony connection detail can have a sizable impact on the overall building performance. Conventional solutions, such as direct extension of floor structure in concrete or steel buildings, are known to be a less effective way of mitigating thermal bridging.
Advertisement
10 7
6
5
4 8
3 2
Understanding that Canada’s Earth Tower is designed to achieve a Passive House standard that has one of the most stringent energy targets, it requires an air-tight high-performance envelope system coupled with a unique approach to the balcony connection. While conventional industry standard methods do not lend themselves to achieving the stringent thermal performance required for the project, as part of the balcony mock-up the connection detail of the balcony to the building primary structure was custom designed to minimize thermal bridging, while keeping the overall design intent.
1
1. Interior CLT Floor w/Concrete Topping 2. Glulam Column Primary Structure
3. Balcony Lower Bracket (Built in Glulam Column Primary Structure) 4. Continuous Air & Vapor Barrier
5. Balcony Upper Bracket (Built-in Module Unitized Envelope System) 6. Sheet Metal Flashing
7. Module Unitized Envelope System
8. Fire Stopping
9. 165mm x 32mm Steel Plate
Figure 11: Balcony connection through a thermally broken detail to reduce heat transfer between interior and outdoor.
0
1:10 200 mm 400 mm 10. 165mm dia. Balcony Glulam Pole Strut
800 mm
1
3 2
4 6
5
7
Figure 12: Axonometric drawing showing a balcony customized steel connection with minimal connection points to reduce the thermal bridging.
1. Primary Structure
2. Module Unitized Envelope System
3. Balcony Connection Bracket (Built-in Glulam Column Primary Structure) 4. Balcony Connection Bracket (Built-in Module Unitized Envelope System) 5. 165mm x 32mm Structure Steel Side Plate
6. 165mm dia. Balcony Glulam Pole Strut
7. 165mm dia. Steel HSS Pipe
The size and number of the connection points back to the primary timber structure were reduced by the addition of timber strut compression elements. Although further thermal analysis would be helpful to quantify the relative reduction amount, as a rule of thumb this reduction in size and number of structural connections represents a significant reduction in thermal bridging at the balcony connection. While maintaining structural integrity, the performance of this connection can be further improved with the use of a thermally broken connector.
Balcony Mock-up: Constructability
As opposed to face-mounted prefabricated balconies, the conventional balcony construction approach through on-site concrete slab or floor structure extension has its merits and is still favored by many developers due to lower upfront construction cost and trade familiarity. However, it is increasingly scrutinized due to poor thermal performance as a result of thermal bridging. Off-site balcony fabrication with a discrete balcony connection detail provides efficiency in balcony construction and sequencing by allowing the completion of the building enclosure prior to installation of the prefabricated balconies.
While the erection process of the balcony mock-up benefited from a high degree of prefabrication, balcony steel brackets that provide intermittent connections between the balcony inner edge adjacent to the building cladding and the building structure, must be coordinated in the primary structural design and construction. In addition, the intermittent connections help reduce the extent of penetrations in the thermal enclosure, but additional waterproofing details must be considered at intermittent structural connections to maintain the continuity of air/vapour barriers and to further mitigate the risk of water ingress.
The balcony system can be prefabricated off-site, including the waterproofing membrane, which provides protection for the timber deck while allowing a highly controlled environment to make challenging detailing work easier to execute. In addition, balcony prefabrication allows for flexibility in the shape and design, superior quality assurance, control in balcony construction, acceleration of construction schedule, and minimizing construction waste.
Balcony Mock-up: Accessibility
The off-site prefabricated balcony approach may simplify the alignment of the interior floor structure with the exterior balcony structure to minimize the height of the door threshold for accessible dwelling units. The threshold requirements should be considered in detailing the thermally broken balcony connection, in conjunction with the structural support for the door openings. Dissociation of the interior floor structure from the balcony through the steel connection detail allows for the height of the balcony to be designed to minimize step-over height and accommodate accessibility (Figures 13 and 16). The accessibility requirement for the balcony mock-up dictated the final location of the balcony deck in relation to the interior floor surface. While the mock-up does not include actual windows or doors, the rough opening for the balcony access sliding door was detailed such that it would allow less than 13mm threshold condition while not compromising the thermal performance of the balcony connection (Figure 14). Special care should be given to the interface detailing to better sequence threshold door sill flashing and membrane termination. Also, structural steel connections and balcony detailing must accommodate differential floor-to-floor moment between the balcony and interior structure with regards to the membrane performance and differential thermal expansion and contraction.
Balcony Mock-up: Deck Construction
The balcony decks are prefabricated from a combination of a structural steel frame, exposed mass timber struts, dowel laminated timber (DLT), and cross-laminated timber (CLT) decks, that include a waterproofing membrane and finish decking material. The mock-up tested two different types of membrane—SBS and reinforced liquid applied PU, to assess how they would be compatible with the timber decking element. Guardrails are designed to be bolted on site in order to keep decks stackable and to facilitate transport. In the case of the mock-up, guardrails were not included for budgetary reasons, but design consideration around metal flashing and water-proofing membrane termination is of importance and dependent on how and where the guard support is attached to the balcony perimeter steel members.