« FLYING START TO SANTOS CONTRACT
« MEET OUR NEW SEARCH AND RESCUE CADETS
« SUSTAINABILITY: NO FLY BY NIGHT PROGRAMME
« HELICOPTERS ARE ELEVATING OFFSHORE WIND
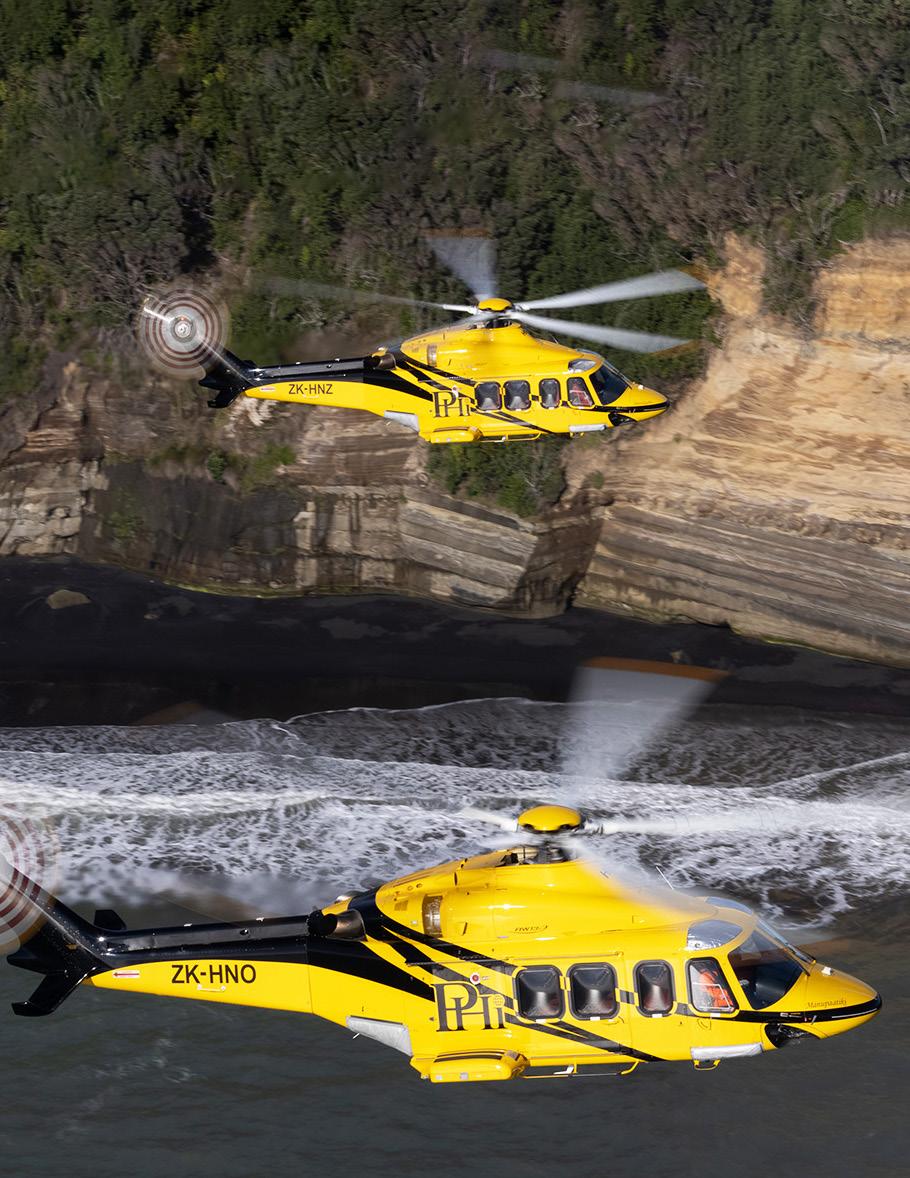
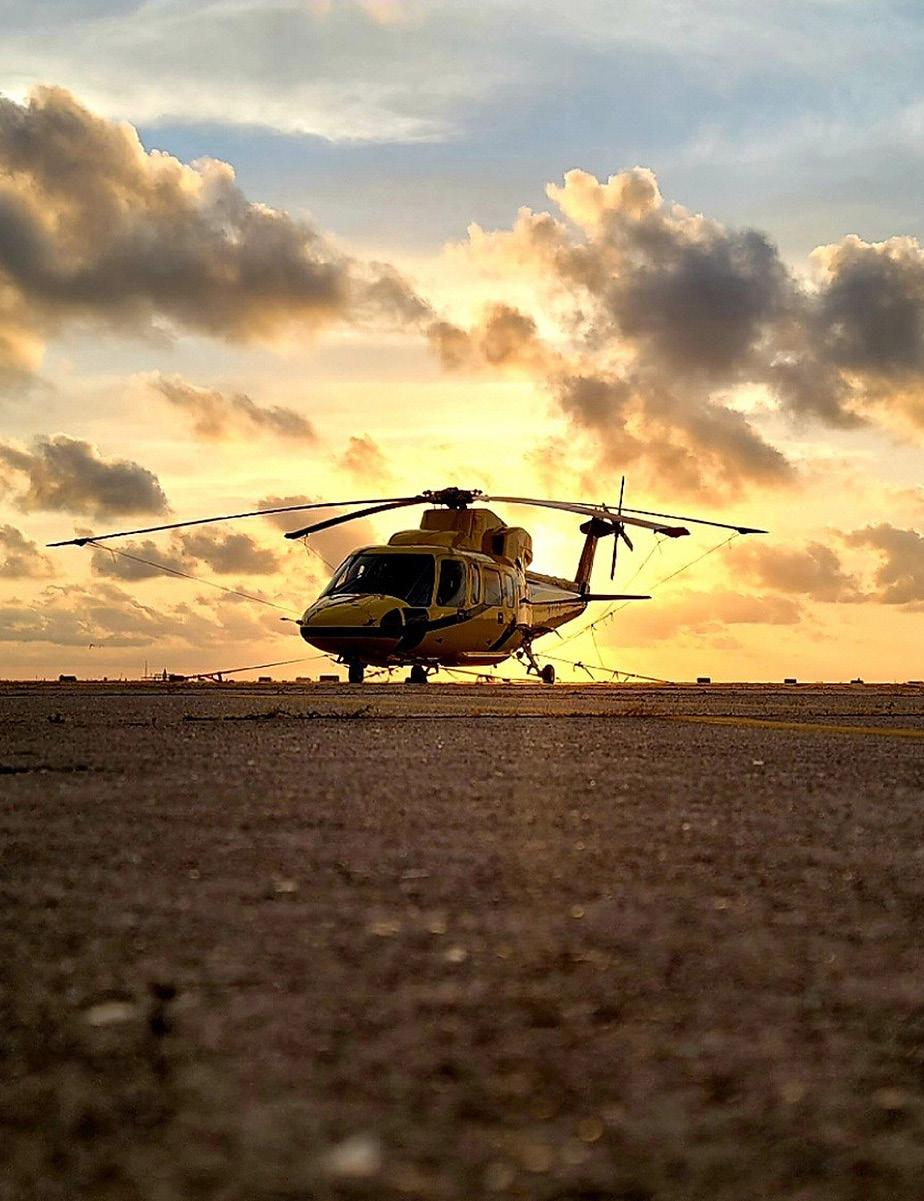
« FLYING START TO SANTOS CONTRACT
« MEET OUR NEW SEARCH AND RESCUE CADETS
« SUSTAINABILITY: NO FLY BY NIGHT PROGRAMME
« HELICOPTERS ARE ELEVATING OFFSHORE WIND
As we head into the third quarter of 2021, our business is in a strong position. We continue to be the partner of choice for many major offshore oil and gas operators, with several key long-term contracts successfully renewed. At the same time, we are building momentum with exploring new sectors as we continue to drive towards our strategic goal to diversify our business. In this issue, you’ll hear from Cory Latiolais, PHI Aviation Chief Commercial Officer, about how helicopters are a natural fit for renewable energy projects such as offshore wind, offering the safest, most efficient and sustainable mode of transport.
Safety continues to be a priority for us. With technology continually evolving to support safer air operations, we can lose sight of the fundamentals and the crucial role people play in creating the right climate for safety. Our Spotlight Interview this quarter is with PHI International Director of Strategic Safety Development Steve Walters, whose fascinating career in aviation spans 65 years. He discusses the importance of companies matching up personal behaviours around safety to published policies and shares his predictions on what will be the next frontier in safety.
One of our core strengths is mobilisation. Over decades we have honed our ability to set up operations and embrace communities in some of the most far-flung places in the world. Flick to page 24 for a glimpse behind the scenes of the setting up our newest base in the remote town of Onslow in Western Australia. Shortly after conducting our first flight from the base, we hosted an open day where we welcomed more than a quarter of the town’s population through our hangar doors to meet our team and learn more about what we do.
Our commitment to nurture the next generation of talent in our industry continues with our growing contingent of cadets and trainees across a spread of professions. Turn to page 16 to meet our new Search and Rescue Crew person cadets and a fresh face onto our co-pilot trainee programme; plus catch up with our other co-pilots on how they are tracking after joining the scheme at the height of the COVID-19 pandemic.
We’re also pleased to share an update on our progress with sustainability. After a successful phase of testing and developing our approach, we now have a roadmap for driving more sustainable practices across all of PHI Aviation. Read more on page 28
Thank you to everyone who contributed to this issue.
Enjoy HomeBase
Keith Mullett Managing Director – PHI AviationThere have been many firsts since PHI’s start in 1949— from making aviation history to celebrating company-wide achievements. When you look at all our success, it’s clear our company’s progress stems from our innovation and determination, but what sparks that spirit of innovation is even more impressive. Over the last 72 years, we’ve cultivated a team of passionate people who hold the key to our past, present and future.
Here at PHI, embracing new technologies and exploring innovative techniques isn’t just encouraged—it’s celebrated. In this industry, it’s easy to get stuck in the ‘we’ve-always-doneit-that-way’ mindset but doing what we’ve always done will only get the same results we’ve always gotten. So, to keep the pipeline of innovation going, we’re tapping in our teams, turning their ideas and challenges into positive and productive energy. After all, who better than our own employees to help solve our biggest problems and champion change?
It all starts with a culture of collaboration. We strive to create an environment where employees across all levels of the company feel empowered to advocate for what they need and then work together to develop solutions. Our team is introducing new ideas, suggesting better ways of doing business and bringing fresh energy to long-standing challenges. Together, we’re breaking down department silos and nurturing a pipeline of innovation that has allowed us to continue delivering safe, efficient, quality, service in a highly competitive and ever-changing environment.
Our Americas team is in the process of implementing the first-of-its-kind advanced tool control program. The program, slated to be fully implemented in 2022, has been a long time in the making—probably even longer than most people realize said Greg Edenfield, Senior Mechanic at our Lafayette base. The tool control program will automate the currently-manual tool inventories and audits, helping to assure the most accurate asset management and foreign object damage (FOD)/foreign material exclusion (FME) compliance.
“The system allows us to live and perform our core values at an even higher level,” said Greg. “By enhancing our tool control program, we’re improving the safety of our people and passengers, our quality level and our efficiency so we can better serve our customers.”
The new system keeps a rolling inventory, automatically detecting which tools have been removed or returned and making it easy to ensure every tool is accounted for. The toolboxes offer a real-time look at tool inventory with a one-touch listing of all tools out, who they’re issued to and where they’re being used.
“Right now, someone has to audit every personal toolbox in use at the beginning and end of each day— and that all takes time,” said Greg. “Our whole tool build is based on what our team says they need because, ultimately, this program is for their benefit.”
The program relies heavily on input from our mechanics. Greg, along with Lead Mechanic in Lafayette Harry Machno, worked with our front-line teams to identify exactly what goes into the base tool crib.
“We had one at Houma North, Houma East and Galveston,” said Harry. “We had a running list from our field mechanics of tools needed to be added, and from there, Greg and I worked to filter out duplicates. We were able to add everything they requested. We were actually pretty surprised—we didn’t realize just how much space the boxes have.”
With the implementation of the automated tool control program, PHI will be one of the first in our industry to shift from personal toolboxes to company-owned tools.
“The fact that you don’t have to worry about lugging your tools around is a huge plus,” said Harry. “You can go from working at Boothville to Galveston and all your tools are right there.”
There’s a lot happening at our Houma, Louisiana, North Ramp Heliport— a lot. Real Estate and Facility Operations Manager Chad Broussard, Base Infrastructure Manager Craig Matheny and Maintenance Manager Earl Johnson, had the scoop on the latest updates for some of our upcoming projects:
We’re considering expanding our S-92 parking ramp to increase the number of heavy-ship spots and accommodate future growth for our customers and aircraft.
The conceptual phase is well underway for our new hangar and parts warehouse. The project includes a new, S-92-capable three-bay hangar and a larger parts warehouse. The detached parts warehouse will feature on-site storage for high-usage parts and a parts counter for increased efficiency and security.
A committee that included Director of Maintenance John Ellyson, Director of Operations Pat Attaway, Chief Pilot James Maner, Base Infrastructure Manager Craig Matheny, Real Estate and Facility Operations Manager Chad Broussard, Program Directors and Mechanics met weekly to collaborate on the design and vision for the new hangar and warehouse.
“Our jobs were to go out and get input and ideas from employees on each schedule,” said Earl. “At the end of the day, the more minds—the better the end product.”
Together, they looked at ways to increase efficiencies and make improvements to our current base design— not just for PHI employees but for our customers and passengers, too. Leveraging their combined experience and input from our front-line employees, the team considered everything from handwashing stations and hydraulics to passenger arrival gates and parking lots.
“My role is bringing feedback from our team and our customers,” said Craig. “Help me understand how I can make your time at work better, safer and more productive.”
The first iteration of hangar and warehouse designs was scaled to produce a concept that was presented to the leadership team for feedback. We’re in the process of getting bids for the project and are hoping to begin construction at the end of this year.
“Collaboration needs to happen, no matter what the project is,” said Chad. “Just because you may not immediately see your contributions, it’s important to know that you’re being heard, and your ideas are being shared with the right people. Change doesn’t happen overnight but trust that we’re listening, and your ideas are being considered.”
Every step requires careful coordination between construction crews and our team to prevent interruption to operations.
We’re ahead of schedule on our rejected takeoff lane (RTOL) lighting project. Once completed, the project will allow PHI to maintain and maximize flight hours for our customers from the summer through winter seasons. The lighting package will enhance our pilots’ ability to identify the RTOL on approach during restricted visibility and pre-dawn takeoff, increasing safety for our crews and our customers. Craig, Base Infrastructure Manager, is working closely with construction crews and our team to ensure that the project is completed on schedule and to Federal Aviation Administration (FAA) standards—all without interruption to our daily flight operations or safety. On target for completion in August, our Houma North Ramp Heliport will be the only heliport in the Gulf with this lighting standard.
It’s a delicate dance between our pilots, mechanics and construction crews,” said Craig Matheny, Base Infrastructure Manager—PHI Americas. “I’m using my experience to make sure everything is done right and just as our teams need it.The RTOL lighting project at the end of May 2021, prior to cement being poured.
We’re in the process of upgrading onsite housing for our teams in Houma. A total of 22 new mobile home trailers are expected to be installed by the end of this year and additional trailers installed in 2022 with the goal of having enough updated onsite housing for all employees. But the project is more than simply replacing our current employee housing—the newly-installed trailers were designed to improve the quality of life for our teams while they’re at work. After all, they spend half their lives living here, and we want their living areas to be comfortable.
After considering leasing and even building apartments, we decided to redesign our mobile home trailers to better meet the wants and needs of our team. Chad and Craig spent time with pilots and mechanics in the old trailers to identify areas for improvement.
“I asked the team, ‘If you were king for a day, what would you add to the trailers?’” said Chad. “If leadership made decisions solely based on what we need or what we already have, then we’d never improve or move forward—we’d keep getting the same results. When we get feedback and work across departments, we can get as close as possible to what our teams want and need to do their jobs.”
Taking their feedback and requests into account, we partnered with a local vendor to help with the floorplan design. Although challenged by the sizing limitations of the trailers, we purchased two updated homes and put the initial design to the test. Once installed, Craig, Chad, senior leaders, line-level employees and cleaning crews spent several hours doing a walkthrough of the new mobile homes. Together, they assessed the layout and got additional feedback and recommendations to further improve the floorplan design.
The new mobile home trailers feature a four-bedroom, four-bath floorplan with each bedroom getting its own private bathroom—one of the most frequently requested upgrades. Other features include a washer and dryer, expanded kitchen and common areas, concrete patio and outdoor seating, covered porches, overhead AC vents for improved distribution and more. Some trailers also
include complete blackout window treatments for improved light control and better rest for our night-shift employees. Not only does better housing mean better health, rest and wellbeing for our employees, it also means better quality of living for the people who work hard to make PHI successful.
It’s an exciting time for PHI, and we’re proud to be on this journey together. The ability to innovate is central to our success as an organization, and the foundation for any innovation is collaboration across our teams. Leveraging the knowledge, creativity and experience of our team, PHI has an even greater opportunity to succeed in every way. No matter who you are or what your role is in the company, we want all our employees to feel empowered to share and think creatively. Your ideas drive the innovation and growth that keeps PHI at the forefront of our industry.
Seasoned aviation safety expert Steve Walters’ career took flight when he first set foot in a Cessna 172 aged 15. Originally from inner-city Birmingham in the United Kingdom, Steve was a young boy when his family upped sticks and immigrated to South Africa.
Armed with little more than a thick ‘Brummie’ accent and a burning passion to fly, he joined the South African Air Force as a school leaver, kicking off 23 years of service and the start of a remarkable career path that eventually landed him in the role he’s in today – Director of Strategic Safety Development for PHI International.
Steve spoke to HomeBase about a few of his experiences along the way, from flying a variety of jets to investigating aircraft accident sites, to a chance meeting with Nelson Mandela. And that only scratches the surface. Steve said: “I’m going on 70, which I think is the new 40 – it’s all been great fun – and continues to be – and I’d like another 20 years to see where it all goes!”
Director of Strategic Safety Development — PHI InternationalComplex technology breeds exotic failures.
You served 23 years with the South African Air Force as a line pilot – can you pinpoint a couple of experiences that stand out for you from your time serving – good and bad?
In one respect there’s no such thing as a good or bad experience, just experience and how its managed. That being said, I began aircraft accident investigation quite early in my career, with my final tour as Head of Flight Safety Investigations. So much of the bad came from standing in smoking holes (accident sites). As for the good, I loved my two tours as a flight instructor, the second being as Chief Instructor of the Air Force Central Flying School where it was great to have a hand in producing so many excellent pilots.
You’ve flown fast- and subsonic jets, a variety of pistons, singles, twins, variety of turboprop, airship, some helicopter – what’s your favourite aircraft to fly and why?
Undoubtedly it was the airship. I’ve had an obsession with airships since childhood, so when the opportunity arose to conduct initial trials on the then-only true, Zeppelin-like rigid airship on the planet, it was a dream come true. During one tethered flight at an Air Force base, an executive jet taxied in and a short while later I was informed President Nelson Mandela had noticed the airship and was coming to talk to us. We were using a rope ladder to access the cockpit, and in my haste to clamber down, I lost my hold and crunched onto the tarmac. I knew of the expression ‘Master Soul’ but I never thought I would meet one, especially from a horizontal position, and what a truly remarkable human being he was.
You spent three years in the prototype environment with South African company Denel Aviation (now Denel Aeronautics) supervising aspects on projects including the Red Hawk combat support helicopter, weapons systems and refurbished vintage aircraft. What was it like to be at the more experimental end of the spectrum?
In aviation, we are perpetual students, and this was one of the steepest learning curves I’ve ever experienced. For the first time, I was working primarily on the engineering side in system safety and was responsible for signing off the Certificates for Flight Trials issued for each experimental flight, stating that it was safe to proceed, so all quite nail-
biting. That side of the fence also taught me that the average aircraft engineer is probably the most abused component of the aviation system and that they need and deserve the same organisation protections as are given to aircrew.
You then moved into commercial aviation working with offshore helicopter operators, and presented training including Critical Decision Making to more than 2000 pilots, engineers and fire crew between 1990 and 2015. What – if any – are the common personality traits you noticed across the people who choose these kinds of professions?
Regardless of age, gender, culture and nationality, top aviation professionals share the same traits. As individuals, they relentlessly develop their own competencies, and in teams, they are equally effective as leaders or as followers. They communicate assertively and respectfully in an adultto-adult fashion, surrendering ego in focussing on the optimal solution for any particular problem.
When you worked for Shell as an Aviation Advisor responsible for SMS development and auditing of AOCs contracting globally, what were some of the more interesting places that took you and what are some of the interesting things you learned from your experiences?
Gosh, there’s so much. I enjoyed working with Russian pilots and engineers, they are a magnificent people, although during Crew Resource Management training there would be someone sitting at the back of the class. Whenever I asked a question, all heads would turn and the individual would imperceptibly nod or shake their head, and the crew would then answer or keep quiet as required. At the other end of the spectrum, I worked in Brazil for three years assisting local oil and gas company Petrobras and their contracted aircraft operators in developing an aviation advisory department. Often it was like trying to herd cats, but with their uninhibited communication style they formed the most amazingly synergistic teams I have ever encountered. Through all my travels, my observation is that to be truly effective we need the awareness to capitalise on our cultural strengths and compensate for our cultural weaknesses relative to the task in hand.
Then you joined PHI where your role has moved from Director Safety and Quality to Director Strategic Safety Development as the organisation grew globally. What drew you to the company?
At that stage, PHI (then HNZ) was a relatively small company, primarily operating single-engine helicopters. But they had a can-do, problem-solving, no-nonsense attitude that was matched with a solid approach to risk founded on operational and engineering excellence. All that the company required to emerge as worldclass was the development of the necessary corporate ‘systems’ e.g. for quality assurance, safety management and the like, and I was hired to assist in this. When Rob Cavers took over the Safety and Quality Department, this systematic development really took off, and what a wonderful success story it has been – there’s no doubting that PHI currently has world-class, industryleading safety and quality systems!
You studied an advanced degree in Industrial Psychology – what is that and how has it helped you in your career?
It’s the science of human factors – the fit between humans and their machines, teams organisations and operational environments. It’s where psychology, engineering and management science meet. Pure scientific theory is great, but it needs practical application and, to the best of my ability, I’ve endeavoured to interpret theory and apply its lessons to investigation, training and organisation development. For the past three years I’ve been focusing on resilience, the acceleration of expertise and the emerging science of complexity – the next great frontier.
What’s the most memorable moment of your career?
Like many pilots, it was my first solo flight, conducted off a grass airfield in an Air Force 1930’s T-6 Texan taildragger. Equally, was 20 years later in that my final air force flight was in the same aircraft at the same airfield, except I came within a hair’s breadth of ground looping and writing the aircraft off during landing! The lesson there is never get complacent, never let your guard down, the aircraft doesn’t care who or what you are, it just responds to your inputs good or bad.
There is no doubt that technology has transformed safety in the offshore helicopter world. In your view, what’s been the most significant change to benefit the industry?
It’s difficult to pinpoint a single piece of the jigsaw puzzle and complex technology breeds exotic failures. Aviation is a young profession – between my grandaddy being a Royal Flying Corps pilot, myself and the young
pilots of today, that pretty much encompasses heavier than air flight. That’s the blink of an eye. My grandad survived World War I but in the beginning, one in four landings was deadstick (a forced landing caused by engine failure), there were minimal procedures and no supporting theory of flight – just terribly hard-won experience. A hundred years later and we have ultra-reliable machines equipped with sophisticated digital protections, decades of refinement in regulation, proceduralisation and flight theory, a vigorous growth in human factors appreciation and a widespread systems approach to organisational management. But I believe the most significant change is still bubbling just under the surface. Safety statistic curves have flattened out and while the Newtonian approach to organisations as ‘mechanisms’ has been incredibly successful, I believe the next step-change will be for organisations to embrace and embed the principles of complexity and view themselves as a living organism rather than something that operates predictably and dependently, like clockwork. There is huge scope for this.
How do you think PHI fosters a safety-first company culture?
That’s multi-faceted, I believe. On the one hand, it’s through a rigorous selection and hiring process that brings only top-class professionals into the organisation but fundamentally, safety culture is defined by the actions of a company’s management. In PHI, Executive and Senior Management have created the climate for safety through matching their personal behaviours to their published policies. They walk the talk, for example, in their positive response to occurrences, through the provision of the top class equipment and for vigorously supporting the development of industry-leading Safety and Quality systems.
Helicopters are elevating the offshore wind sector and PHI is ready for take off
By Cory Latiolais Chief Commercial Officer — PHI AviationEnergy transition continues to be a major theme in 2021, with technology, political, social and economic factors driving the global transition. The world’s biggest companies and investors are lining up financing. In 2020, spending on wind and solar projects rose to nearly $220 billion, up from $135 billion six years earlier. As the demand for lower emissions and increased sustainability grows, interest in opportunities in offshore wind has never been greater. And PHI is no exception. As offshore wind projects become larger and further from shore, the importance of comprehensive planning to address infrastructure needs becomes even more critical, and we believe helicopters are a key part of the logistical equation.
Backed by our 70+ years of experience servicing the offshore oil and gas industry, we’ve narrowed down three key challenges that shape offshore energy operations: weather, time and safety. Over the last few years, extreme weather events have increased with predictions suggesting the upward trend will only continue. From record-breaking heat waves to rampant wildfires and, recently in the United States, the most active Atlantic hurricane season on record, planning for contingencies in the offshore environment is more important than ever to support the development of sustainable energy operations.
The challenge becomes mitigating adverse operational impacts with weather and sea state conditions in a safe and timely fashion—that’s where our helicopter operations come in.
Accessibility plays a huge factor in offshore energy operations, and we know that helicopters are uniquely equipped to handle the challenges of the often harsh and unpredictable offshore environments. With the ability to operate in sea state conditions with up to a six-meter wave height, helicopters can reduce or even eliminate the need for other traditional forms of transportation for offshore wind developments.
Helicopters provide the fastest form of transport to and from offshore assets. By spending less time traveling to and from shore, operators can streamline their service operations and logistics for a more efficient and effective use of resources. In fact, using helicopters as the primary form of travel approximately doubles onsite productive work time.
But the benefits don’t end there! Crew transportation by helicopters offers the lowest CO2 per passenger mile of any currently available offshore transportation option, producing half the amount of emissions on a per passenger basis. And with continued advancements in helicopter manufacturing and engine technology, we expect emissions to reduce even further in the coming years.
Most importantly, helicopters provide safe and reliable transportation to manage risks in the offshore environment. Recent studies show that occupational injuries are 170 percent higher when traveling to and from offshore wind farms in standard modes of transportation. Occupational safety is always a top priority as the safety of our employees and passengers is of the utmost importance.
Our team has the experience to mitigate risks throughout all phases of flight operations, and in the event of onsite injuries, we can evacuate people and deliver necessary assistance quickly and safely.
Analyzing the costs and benefits of transporting work crews offshore, helicopters make sense as the logical transportation partner for offshore wind, and diversification into the offshore wind environment is a natural progression of our services. PHI’s extensive experience in the offshore oil and gas industry sets us apart and demonstrates our ability to deliver services that meet and exceed the needs of the offshore wind industry—both in support of construction and ongoing maintenance of wind turbines.
As the offshore wind energy project development and operations pipeline grows, selecting a helicopter operator to support construction and ongoing operations will be key for success. Our business development and commercial teams across PHI Aviation know that collaboration and early engagement with partners is key to helping us unlock the most value in this complex environment, and we are already building relationships in the offshore wind sector. In May, I was honored to speak at US Offshore Wind 2021–the biggest offshore wind conference in the United States–about the natural fit between helicopters and offshore wind operators who need safe, efficient and reliable transport of people and materials to support their critical projects. It was great to connect directly with operators in the sector and to give them insight into how PHI can help continue to progress their projects. You can watch my presentation on PHI Aviation’s LinkedIn page or YouTube channel.
Over at International, the first tender for aviation services was submitted to support the construction of a wind farm off the coast of Taiwan, and the engagement between both parties has been positive. On both sides of our business, we anticipate many more tenders to support wind farms and other sustainable energy developments.
The demand for offshore wind energy has never been greater, and PHI has never been better positioned to capitalize on our deep understanding and experience in the offshore energy sector. Our flexibility, technology and dedication to safety—combined with our investments in aircraft, crews and facilities—makes us the best aviation services and logistics partner for the offshore wind industry. We can’t wait to see what’s on the horizon for offshore wind and PHI!
In the last HomeBase, we shared the story of our hunt for talent in Broome, Western Australia, to join our Search and Rescue Crewperson (SAR RCP) cadetship. The selection process was no easy feat, with candidates put through their paces in a week-long assessment involving fitness and medical tests, water confidence trials and teambuilding exercises. We are excited to introduce the fantastic four who made it through rigorous training and challenging interviews to earn a place on the programme. Meet our new SAR RCP cadets and discover what drew them to the SAR life.
Sonny never imagined being in a job where being winched out of a helicopter is just one of the many exhilarating tasks typical of his role.
Before taking the plunge and applying for a cadetship with PHI, Sonny was an education assistant for seven years..
“My brother saw the job ad in the paper and told me about it,” Sonny said. “I read the description, and essentially just bit the bullet to see what would happen.”
The whole process has been an entirely new experience for Sonny – right from taking a leap to apply to taking his first ride in a helicopter.
“I will admit it was a tough process, from applying and then flying to Perth, and then going through the training to see if we were fit and able.
“There were moments where I was thinking, far out, am I going to be able to complete this? We were given a lot of confidence by the team who ran the whole process, which was awesome. We were pushed through barriers, and I developed the mindset where I thought…maybe I can actually do this.”
The toughest moment for Sonny was the Helicopter Underwater Evacuation Training (HUET) where a simulator helicopter plunges into water and tips upside down.
“I think we were all afraid and anxious of what was going to happen, but getting through it gave us a new sense of confidence.”
Sonny said the experience has been life-changing, taking him in a completely different direction to his previous role in education. He has already attended call outs as part of the cadetship.
“Before the cadetship, I was quite afraid of heights, so to be up there in a helicopter for the first-time training was something I would never have dreamed of doing.
“I’m most looking forward to being the person who will be there to help people when they need it the most. I definitely feel a combination of nerves, anxiety and excitement waiting for that first job to come through.”
Sonny has been able to bring across valuable skills from his time as an education assistant. Something that stood out to him when going through the training was his ability to provide direct and clear instructions in any situation.
“I know with this role it’s important to provide firm direction in a friendly manner when its needed,” Sonny said. “I’ll be able to utilise this to help people keep calm and to control the situation as best I can.”
Sonny said before the cadetship he hadn’t heard of PHI and has enjoyed getting to know what we do.
“Having now got to know the team and seeing how the business works, it’s very exciting for me to be here and I’m looking forward to getting stuck in,” he said. “It’s great to be part of PHI, and the crew I’m working with have been so welcoming.”
Before joining PHI, Adam was a pearl diver. Working on a fortnightly schedule, he would spend up to 60-80 hours over one week underwater in the ocean – that’s right, underwater!
“Every dive there was always something different. The sea life and the things we saw were pretty incredible,” Adam said. “I knew this role would be an extension of the skills that I had previously learnt and used.”
Adam’s extensive underwater and commercial diving experience earnt him the title of marine industry expert, which has meant he is used to being in situations where a lot of things are out of human control, such as weather changes.
He told HomeBase he often worked overtime with his crew to build his understanding of these challenges and introduced safety systems and training for the team.
Safety is an integral part of the way everyone works at PHI, and Adam is confident he can bring these skills across to his new role, “In water and above water are definitely different, but I believe the knowledge will be transferrable,” he said. And even though he is now on the cadetship, he says he will continue to dive in his spare time as he loves it.
During the recruitment process for the cadetship, Adam observed some of the training exercises and was impressed with the level of professionalism PHI’s training crew demonstrated. “It showed me that the role is extremely serious, and you must be professional and confident in how you approach your work.
“Something that has been most surprising to me is the team’s ability to remain focused when at the edge of a helicopter ready to be winched out. To put all the adrenaline aside and realise it’s possible to stay focused on a task (instead of yahooing!) is quite incredible.”
When it came to what others found to be the toughest parts of the training – the HUET – Adam being no stranger to water-based training quite looked forward to it!
For him, the most difficult part was the line checks. “It wasn’t necessarily the scenario that made me nervous, but my desire to perform so that I didn’t let down all the people within PHI who had trained, helped and encouraged me along the way,” Adam said.
“Once we had all got through to the cadetship, I must say there was still quite a bit of internal pressure to want to get things right, and not wanting to let people down. I think we all found that a bit challenging, but it’s a great feeling to finally be here in the role.”
Adam has since mastered all his line checks and attended call outs. He said he feels inspired by how passionate the team is. “It’s exciting to be working with people who have been in the industry for more than a decade and still love what they do,” Adam said. “I hope I can follow in their footsteps.”
Micah had always known that she wanted to work in emergency services. When she applied for the SAR RCP Cadetship, she had recently landed back in Australia from Auckland, New Zealand, where she completed her first year of studying paramedicine.
Part of her studies included medical emergency simulations, which she said put her in the right mindset for many of the tests and activities in the selection process.
Micah has also previously completed technical courses in diving and kite surfing, which helped her to appreciate how important it is to have a strong focus on safety and safe equipment.
When asked what she found most difficult in the selection process, Micah said the interview was tougher than she expected.
“It was unlike anything I had ever experienced, but overall, I really enjoyed the whole process.” Micah said. “Another difficult part is having patience; I must admit it’s been a learning curve to be patient even when things don’t go how you expect or get cancelled or postponed.”
Micah said having made it through the whole training process, she felt humbled by how supportive and helpful the PHI team were and immediately wanted to put her skills to work.
She said: “It was above and beyond what I expected. I didn’t realise I would appreciate the personal and social aspect as much as I did. There were so many people to learn from, and it was so heart-warming to see how willing they are to help.”
“It’s great to see how well everyone gets along at PHI regardless of which department they’re from or their level of experience. I’m stoked to be here.”
She is also impressed with the strong focus on safety that PHI has. Her passion for helping people and background of paramedicine studies means this is something extremely important to her.
Micah plans to continue with her paramedicine degree next year part-time – knowing that these skills will continue to help her in the SAR role. She has now passed all her line checks – day and night – and attended call outs.
When asked what she will bring to the role Micah answered: “A lot of enthusiasm!”, which is what we like to hear at PHI!
Being on the frontline and working in high-pressure situations is something Jackie Carroll is well-versed at. Responding to emergency and non-emergency calls and working closely with the community, including elderly people and those struggling with mental health issues, was part and parcel of being a paramedic in the metro area of Perth, Australia. This was Jackie’s role for six years before spotting an ad for the SAR RCP cadetship.
“It sounded like the dream job for me” Jackie recalled. “The excitement of jumping out of helicopters and helping people is something I have always dreamt about.”
When Jackie saw the ad, she felt ready for a change and was looking for an opportunity to relocate more regionally. Talk about perfect timing!
Coming into the recruitment process, Jackie said she could tell from the outset that the comradery was strong and there was a lot of support.
“This is something I really value and was used to from the ambulance work,” Jackie said. “It makes you feel like you can go to work and have a good time with your mates.”
Jackie said the training process really put the group through their paces. “It’s completely different to what I’m used to, it was daunting and exciting at the same time. Swimming in a pool and jumping from heights isn’t ‘normal’ job stuff.”
“We were shown pretty quickly how we could push ourselves further than we thought, when you’re literally thrown in the deep end, you can achieve awesome things. I used to be afraid of heights before this!”
“The PHI team did an amazing job, the four of us are very excited to be here.”
Like her teammates, Jackie said she is most looking forward to is getting out there and completing her first call out successfully, as well as helping people on a whole other level to what she is used to. Jackie recently passed her day line check and is looking forward to ticking off her night line training. She also worked her first roster as part of the day crew, which she loved.
When asked what she will bring to the role from her past work experience, she said: “Having been exposed to high-stress situations in the past, it will be knowing I can go out there and keep a level-head.”
The trusting and supportive environment at PHI appealed to Jackie. “In a job like this, it’s important to have colleagues that have your back. When I saw how close everyone was I knew I wanted to be a part of the team.”
“It’s pretty special to be able to say that part of our job is hanging out of a helicopter and looking down onto the ocean, that’s a real privilege. Not many people get to be in this position.”
Alicia ‘Liss’ Earle and Cory Sutton were the first candidates onto PHI’s newly launched helicopter co-pilot training programme run out of its flagship New Zealand base in New Plymouth.
The opportunity was a dream come true for both, who had long-held aspirations to qualify as pilots and spent years driving towards their goal while balancing full time jobs in other professions.
But it wasn’t quite a smooth ride from there. Almost immediately after the pair were accepted onto the twoyear programme, the pandemic struck. It threw a spanner in the works with being able to get them on the base to gain hands-on experience.
Our New Plymouth team worked quickly to reshape the programme and had Cory and Liss focus on learning the theory online until they could join the team on the ground.
Since then, Cory and Liss have completed instrument rating training and begun flying the line as fully qualified co-pilots.
Liss said recently she has been remembering where she was this time last year, which was on a farm in a far-flung location in New Zealand studying ground school classes remotely.
At that point, she was yet to meet our New Plymouth team with a country-wide lockdown in force. “It’s amazing to think how much has changed since then,” said Liss.
“I’m so grateful to the team for the hard work they put into the programme and continued learning opportunities.”
“I’m now a fully trained signed off co-pilot. I’ve come through a lot of uncertainty to land my dream job.”
Cory said he is loving life as a qualified co-pilot and enjoys the challenge of applying his instrument training during poor weather.
“It’s an awesome job. I’m getting more comfortable with flying in the clouds. The instrument side of things is pretty cool.”
“Being in New Plymouth, you get quite a few days where the weather is bad so it keeps you on your toes.”
In their second year, the trainees will build up their hours and experience in the air. Liss and Cory have both been cleared to fly the line for day and night operations.
Liss will do this in New Plymouth while Cory will continue his development in Broome where he been transferred for six months to help out our team in Western Australia.
Liss says a highlight so far has been flying in parallel with another aircraft for a photoshoot for industry magazine HeliOps.
She said: “At the time my adrenalin was pumping – I didn’t really realise how much of a one-off it is until afterwards. We got to fly down the runway pretty fast and low.”
Liss said another highlight, despite the early starts, is catching beautiful sunrises. “The early bird catches the worm.
“Nothing gets you used to the super early starts but the sunrises make it worth it.”
Photograph by: Alicia Earle“My favourite place to visit in New Zealand – the Earnslaw Burn near Queenstown, which is only accessible by helicopter.”
Jared Fallaver is the latest co-pilot to join PHI’s trainee programme led out of PHI International’s flagship New Zealand base in New Plymouth. He joins Liss and Cory who kicked off their training in March last year.
Growing up in Palmerston North – a city in New Zealand’s North Island – much of Jared’s childhood was spent gazing up at pilots flying over his family’s farm in fixed wing and rotary agricultural aircraft and thinking: ‘that looks cool.’
His fascination with helicopters grew stronger with a local search and rescue helicopter based right next to his house. “The helicopter flight path went right over our house,” Jared said. “I used to watch them take off and think they were awesome while everyone else in my family hated it when they were flying all hours of the night.”
Before he learned to fly, Jared first spent several years working as a crop farmer operating heavy agricultural equipment including tractors, combine harvesters, fertiliser spreader trucks and excavators. Jared said: “I believe the machinery operating skills I have has helped me a lot when it comes to hands-on flying skill.”
He decided to enroll in a Diploma in Aviation for Helicopters and started flight training in his home city. He then transferred to Wanaka Helicopters in New Zealand’s South Island to complete his training. A popular tourist spot, Wanaka boasts snow-capped mountains, stunning lakes, nearby low flying training zones and a family atmosphereall of which proved to be the perfect blend to attract Jared to want to stay and make it his home.
Armed with a fresh commercial helicopter pilot license, he landed a casual/on-call job with Wanaka Helicopters carrying out frost protection, maintenance and ferry flights, while also working for an earthmoving contractor operating heavy machinery in the summer and pushing snow up on the ski fields in the winter to pay the bills. Within a year, opportunity knocked. Jared was sent to Port Moresby as a co-pilot flying Bell 212’s in Papua New Guinea for an operator that supplies helicopter services to the country’s defence force.
For the first two years, his role focused on moving defence force personnel around for border protection, natural disaster relief, soldier deployment into areas of civil unrest with a winch capable helicopter for search and rescue. During this time, he was able to witness the aftermath of two major earthquakes and watch a volcano violently erupt right in front of him while providing disaster relief.
Papua New Guinea’s mountainous and remote landscapes and dense rainforest up to 14,000ft means helicopters are the easiest way to transport people and materials around the country.
Jared said: “Papua New Guinea is such a unique country. I learned so much while working in some untouched and very remote places, flying in deep in the jungle and up in the mountains high, hot and heavy. It was an incredible start to my career.”
In his third year, the focus of Jared’s role turned to oil and gas operations with EXXON Mobil, undertaking pipeline survey, personnel transport, external load and medevac operations in a Bell 412 helicopter. His experience was the perfect prelude to where he would move onto next.
He spotted the advert to train as a co-pilot with PHI on a helicopter careers website, which answered a desire he had long harboured but until now, had not been able to pursue.
Jared said: “I had looked at training to become an Instrument Flight Rules (IFR) pilot myself before finding this opportunity with PHI, and to gain the required experience is a massive financial commitment – about $70,000 New Zealand dollars to start.
“The fact that PHI was giving people with low flying hours a paid opportunity to train as co-pilots, and with a company of its scale – it’s just awesome.”
Jared applied for the programme along with Liss and Cory and impressed the team, but just missed out at the final interview stage. He was offered a role in our New Plymouth dispatch office until a place on the programme came up after only a few months behind the desk.
“Coming from an agricultural background I never saw myself going down the IFR offshore route when I initially started flight training, but it was a new and different challenge that I’m excited to take head on.”
“I’m excited to work towards my captaincy and I would love to travel around all of PHI’s bases overseas. PHI is a great company to work for – there’s no better place I could be.”
The contract called for a new base to be set up in Western Australia, from which we could fly workers and freight in two Sikorsky S92s to the project site located approximately 65 nautical miles offshore.
Originally, Exmouth was earmarked as the location of PHI’s new base. But with COVID-19 restricting travel overseas, the small resort town had become a mecca for Western Australians looking for a beach getaway close by, and visitors had snapped up all the available accommodation.
Other options had to be explored. Onslow – a small coastal town with a population of about 850, only 61nm from the project site and with accommodation readily available – was to be the home of our new base.
Specifically Onslow airport was the location of our new base, situated a short 3km drive from the town centre. Before its recent makeover, the facility was little more than a large shed capable of housing two Sikorsky S92’s. Built five years ago by the Shire of Ashburton, the space was intended to house an offshore aviation company long-term but when that didn’t transpire, it sat empty and unused.
As soon as PHI was awarded the contract, our teams across Australia and New Zealand sprang into action, recruiting additional personnel and working closely with the Shire of Ashburton to establish a fully compliant operational hangar facility and base that met the high standard required for our operations in a month.
It was a massive achievement that all our teams should be proud of. Our client Santos has been very complimentary of our efforts, recognising the long hours and hard work we put in to complete the project.
Being a small town, Onslow is filled with friendly people who have been exceptionally welcoming, making it easy for our team to settle in and feel part of the community. By way of repaying their kindness, in June we opened our hangar doors and invited the local community to an open day where they had a chance to check out our new facility and get up close with one of our S92s, as well as enjoy a sausage sizzle and refreshments.
Our Onslow base may be PHI’s smallest in Australia with a team of only nine, but what we lack in numbers, we make up for in enthusiasm!
Our helicopter departs daily from Onslow flying west to Learmonth Airport, where Santos’ outbound passengers board the flight to the Valaris MS-1 on location some 52nm offshore. The aircraft then returns to Learmonth, unloading the inbound passengers, before flying back to base in Onslow.
Along with a passenger transfer helicopter, PHI also provides Santos a Limited Search and Rescue (LIMSAR) helicopter, covering day SAR and Medevac services, which is made ready for activation within 60 minutes’ notice during daylight hours.
Our contract commenced on the 10th of May 2021, with a first flight conducted for Santos on the same day.
Over the past 18 months, PHI has been on a mission to shape our approach to sustainability. Our vision is simple – to be a responsible partner in the industries we serve as the shift from fossil fuels to a renewable energy future progresses.
What started as a pilot project to measure carbon emissions at PHI International’s bases in New Plymouth, New Zealand and Mackay, Australia has flourished into a roadmap to achieve more sustainable business practices across all of PHI Aviation.
Using New Zealand as a test case, we enlisted the help of a local sustainability organisation with expertise in supporting global companies like PHI to make a start in minimising their impact on the environment.
With their support, we shaped the foundation of a strategy for implementing more sustainable business practices across our entire organisation focused on four key areas – our team, our community, our footprint and our business.
To ensure we were using consistent and comparable metrics that align with global environmental standards, we looked to the Future-Fit Benchmark Goals and KPIs to evaluate our existing sustainability practices and performance.
Future-Fit is linked to the United Nations Sustainable Development Goals and is widely considered to be among the ‘gold-standard’ of sustainability benchmarking, making it a good starting point for us to assess where our business currently sits on the sustainability scale, and how we move forward.
PHI Aviation Managing Director, Keith Mullet said, “The decisions we make today should not only preserve the longterm sustainability of our business, but also make a positive difference to the world we live in. This is important to us, our people, our clients and our stakeholders.
“We know we have a critical role to play, contributing to more sustainable business practices and helping to achieve better environmental, social and governance (ESG) outcomes for all.”
In April, PHI established a Sustainability Steering Group led by PHI Aviation’s Vice President of Health, Safety, Environmental and Quality (HSEQ), Robert Bouillion.
One of its first tasks is to find a sustainability consultant to support the implementation of the roadmap across the business.
A shortlist of potential partners is currently under review.
The decisions we make today should not only preserve the longterm sustainability of our business, but also make a positive difference to the world we live in. This is important to us, our people and our stakeholders.
Keith Mullett, Managing Director—PHI Aviation
Robert said, “Using an independent consultant with specific expertise will allow us to instil the right training, competencies and understanding in teams across our business of sustainability and ESG issues.
“By building our understanding and capability in-house, our people will be better equipped to navigate the complexities of implementing sustainability in our company.”
This approach has been tried tested with success in New Plymouth and Mackay, where teams have been trained to measure and report on carbon emissions.
As the initiative is rolled out to PHI’s other locations in the future, carbon emissions measurement is one of many practices that PHI’s people will learn more about to help drive progress towards our vision.
Keith said, “Sustainability is a big part of our plan going forward. In the past year and a half, we have really built up our understanding of what sustainability and ESG means.
“Due to climate change, we now see natural disasters such as major storms, floods or fires so often that they are starting to become normal occurrences, rather than extraordinary events.
“Even so, there is still confusion about what sustainability act ually is, and how sustainable practices can reduce our climate impact.
“It is much more than just recycling and electric vehicles. It flows through our entire operation – from the way we treat our people and our communities to our impact on the planet and the ethical practices by which we govern the business.
“It is the right way to run our business and it is what our customers expect of us.
“We are excited to be working to ensure the most responsible practices are in place in our industry – and that is something we want to be a part of for many years to come.”
Our goal is to be a responsible partner in the industry by actively participating in the eventual transition from oil and gas to renewable energy sources.
Employee wellness starts at home, and Facility Maintenance and Welding Supervisor John Reiners is no fish out of water.
We spend a large portion of our lives at work—upwards of 40 hours per week—so it’s no surprise that job satisfaction can dictate our mental and physical health. Although employee wellbeing was an increasingly popular topic even before COVID-19, the pandemic put more emphasis on mental wellbeing than ever before.
Gone are the days where the employee-employer relationship starts and ends with a paycheck. Nowadays, building a culture that encourages and promotes positive wellbeing is just as important as building and developing your brand. Employee health and wellbeing is more than just making your team happy at work—it’s about improving the holistic wellbeing of all employees both on and off the clock.
Work-life balance is an ever-evolving (and seemingly everelusive) concept that means different things to different people, but it’s ultimately about reaching a balance between business and personal life that’s right for YOU. In fact, recent findings suggest that a rewarding work-life balance is less of a one-time-achievement and more of an ongoing cycle that develops as our circumstances and priorities evolve.
For John Reiners, our Facility Maintenance and Welding Supervisor based in Lafayette, Louisiana, that balance has evolved with his wife and kids over the years. Fishing has long been John’s pastime of choice, and he happily indulges this hobby alongside his family.
Reiners and his life (and fishing) partner of 35 years, Nanette, have fished recreationally for many years—often with her making the first catch of the day.
“I pick at her if the fish aren’t biting,” he joked. “I’ll tell her to hurry up and catch one, so I can start catching!”
Together, they have three children, two sons and one daughter, and three grandsons. Over the years, John has placed and won tournaments with his sons but says that
having Nanette back at his side for their two most recent tournaments was the best.
In early April, John and Nanette finished second in an Acadiana Bass Club tournament. The tournament was a two-day event that they led after day one but ultimately finished second by less than a pound. John did come out first with the biggest bass of the tournament, weighing in at 5.63 pounds.
“That tournament was a tough one for us,” said Reiners. “We were dealing with strong winds and heavy fishing pressure from other large tournaments going on at the same time.
“I hate to even mention it because it’ll sound like ‘fishing stories’—but twice I hooked the keeper fish that would have won the tournament for us!”
The keeper fish may have gotten away then, but they managed to hook first place and the biggest bass of the tournament on Lake Sam Rayburn in March.
“She [Nanette] caught two nice keepers on the second day of that tournament and helped us overtake the lead to win.”
Here at PHI, we know that time spent away from work is just as important as work itself. Taking the time to refresh and reset is key to helping reduce stress and preventing burnout, but more than that, the time you take outside of work directly translates into how you live out our core values: safe, efficient, quality, service through your actions and decisions while on or—if you’re like John—off the clock.
“It’s funny,” he said “For me, tournaments are more like work.”
Like a day on the job, John plans ahead for tournaments so that he can maximize his efficiency in the boat and get the most out of the morning bite. With 40+ years at PHI, he’s no stranger to knowing what it takes to be efficient while maintaining top quality, but it’s more than just his competitive nature that bridges the gap between work and play.
“It’s our Life-Saving Behaviors, too. When I put my boat on the trailer, I don’t just tie it down and leave. I do a 360-degree walk-around—sometimes twice—to make sure everything is secure and that my lights are working properly.”
But when it comes to fishing for pleasure, John says that’s where the real rest starts.
“The good thing about Toledo Bend: the service is horrible,” he laughed.
“We leave early in the mornings and spend the whole day on the water—no rush, no distractions, no pressure. It’s an opportunity to forget about work and reconnect, and now that we’ve got grandkids, I can’t wait to get them in the boat, too.”
The health and wellbeing of our employees has always been a part of our agenda, but the COVID-19 pandemic exposed the need for additional support and targeted strategies. In August 2020, PHI International launched its Wellbeing Committee to encourage and promote positive wellbeing across our teams.
The Committee takes a proactive approach toward workplace health and wellbeing by focusing on five key areas of improvement: physical, mental and emotional, social, environmental and educational. Since its introduction, the Committee has led a series of initiatives designed to introduce tools and resources to help our workforce improve across each of these components that play a significant role in our personal and professional wellbeing.
PHI knows that employee wellbeing is more important than ever before. Not only is it beneficial for our teams, it also creates a working environment focused on safe, efficient, quality, service that benefits our business and customers.
PHI Americas’ Senior Benefits Analyst Jessie Romano says that, as a company, we continuously assess our benefits to make sure we’re offering the right balance of programs, resources and tools that support and promote the wellbeing of our employees.
“There are so many resources available to our teams, but a lot of our employees don’t use them simply because they don’t know what’s available. We’re always looking for more ways to improve the health and wellbeing of our employees.”
From improving job performance and productivity to fostering better relationships between leaders and line-level employees, the benefits of dedicated health and wellness strategies go far beyond bolstering our bottom line. Here at PHI, we’re committed to building a culture in which our employees and their families live happier, healthier lives.
As we work to expand our holistic wellbeing policies and programs, we look forward to continued success in supporting a more resilient workforce. Keep doing what makes you happy, PHI!
It runs in the family! John’s eldest son, Bradley, poses with his own eldest son, Wesley, and their catches. John and his daughter, Callie, making the most of a beautiful day on the water.