OCTOBER 2022
« CELEBRATING 10 YEARS IN GHANA

« MEET OUR COO s
« OUR BROOME BASE TURNS FIVE
« PRINTING THE FUTURE
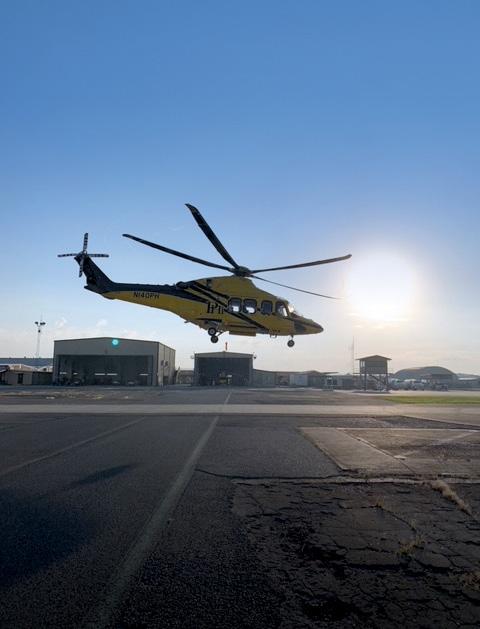
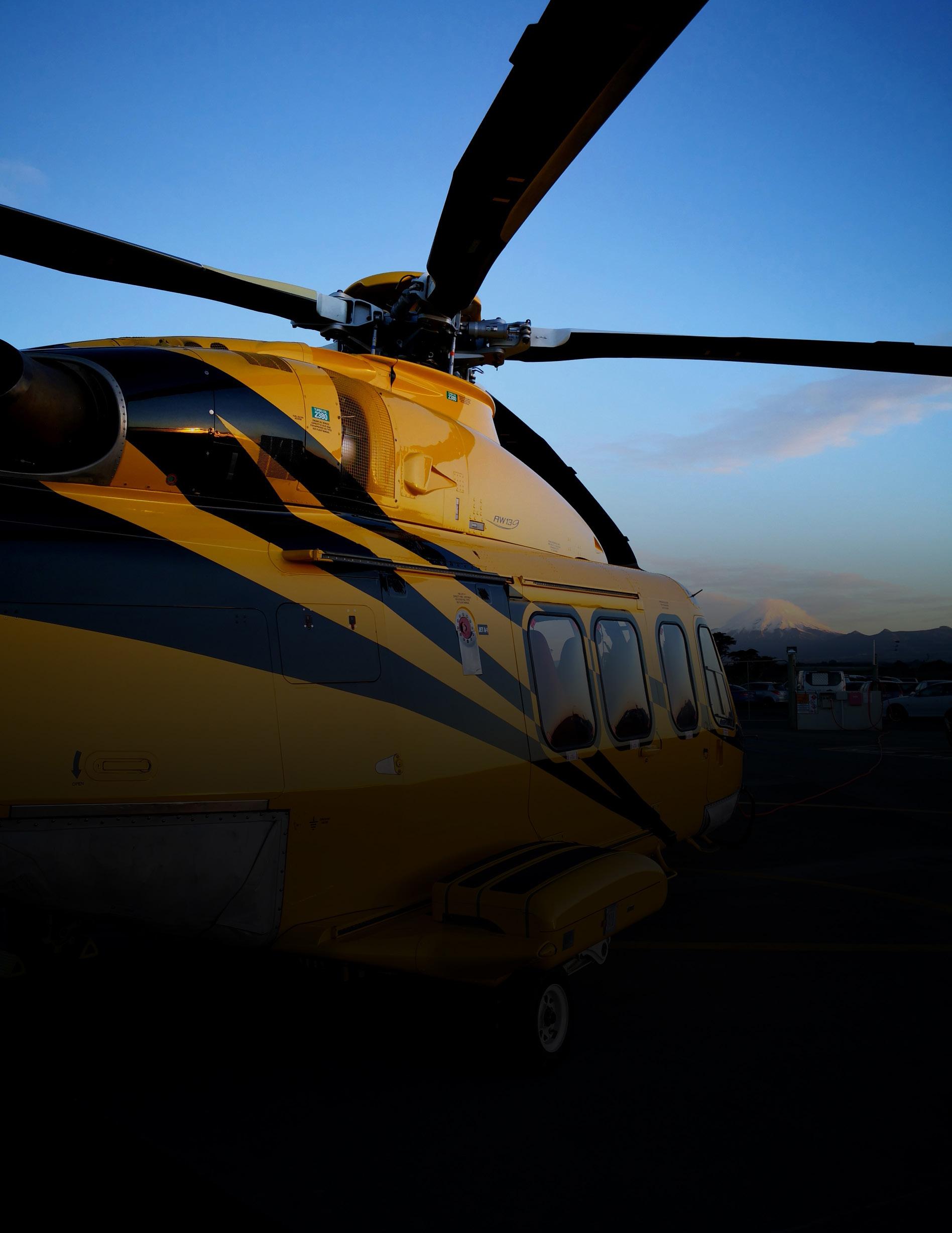
« CELEBRATING 10 YEARS IN GHANA
« MEET OUR COO s
« OUR BROOME BASE TURNS FIVE
« PRINTING THE FUTURE
Welcome to the latest issue of HomeBase – the first since we established our new global organization structure and leadership team on 1 June 2022.
It’s an exciting time for our business, with a number of new opportunities across different markets and locations. The changes we have made allow us to seize these opportunities and better align our organization and resources with our customers’ needs and our own strategic growth and diversification opportunities.
I’d like to thank all our employees for their hard work and continued commitment to our core values over the last few months.
Under the new structure, we have three geographically based operating units: PHI Americas (Americas), PHI Asia-Pacific (APAC) and PHI Europe, Middle East & Africa (EMEA). These business units are being supported by five global support functions in key best practice areas: Safety & Quality, Information Technology, Technical, Business Development and Sustainability, based out of our office in Lafayette, Louisiana, USA.
These geographic units are positioned to be responsive to our customer requirements and will better enable growth and diversification in all regions. Turn to pages 4 – 8 to read interviews with each of our three Chief Operating Officers – Jamie Hinch , Cory Latiolais and Jamie Mitchell
The organization restructure is complemented by a new leadership line-up that places decision-making and management closer to key markets, customers and growth opportunities. It is my belief that this is one of the deepest and most experienced teams in the sector.
We are one team – one PHI Aviation – operating globally and delivering locally.
Safety remains a core focus for everyone at PHI as we progress towards our goal of Destination Zero. You can find more about our refreshed safety initiatives on page 10, where we discuss our commitment to reinforce our core values; increase safety awareness for all employees; listen, connect and engage; continue to promote safety leaders; and grow as a team.
This quarter also marked five years of operation at our Broome base (story page 24) and ten years of PHI Century’s operations (story page 12) – congratulations to everyone who has made this possible.
We bring you spotlight interviews with Jon Rudy, Chief Commercial Officer – Business Development (page 22); Isabel Orran Padilla – our new Senior First Officer in Cyprus (page 18); Jenny Barclay, Commercial Manager – EMEA (page 34); a warm welcome to Mark Leighton with PHI Cares (page 16), and an in-depth look at our Avionics Engineer Trainee Program in Trinidad (page 30)
We have also included two sustainability stories – one looking at 3D printing (page 36) and another exploring a recent emissions reduction initiative that was undertaken at our New Plymouth base in New Zealand (page 20).
I hope you enjoy reading these stories as much as I do – HomeBase is a testament to our people and the great work that they do every day.
Thank you to everyone who contributed to this issue. Enjoy HomeBase
Keith Mullett, Managing Director – PHI Aviation“
Jamie Hinch is PHI Aviation’s COO for its Americas region.
HomeBase interviewed Jamie to find out more about who he is both in and outside PHI.
That’s the most rewarding part of any job—the positive impact you can have on the people as a leader.
“
What do you enjoy most about your role?
The challenge and the variety of it. Many people work through their entire careers in a single discipline or singular focus, and as a COO, I have the opportunity to be involved in every aspect of the business—not just one. Whether it’s HR, operations, customer relations, administration or finance, I like knowing that every day I’ve got something different to challenge me. But what I love most about working at PHI is the people. It’s every member of our team who shows up each day, who lives our core values and who’s committed to doing the best job they can—for our customers and for each other—it’s our people and our teams who really make all the difference.
What has been your career highlight at PHI to date?
I would say, successfully navigating the business through the height of the COVID-19 pandemic. In 2020, we saw the first ever negative oil price and parked 26 aircraft in one month, but despite all the challenges we faced, we ended the year with the best safety record performance in our 72-year history from a lagging indicator perspective and our first profitability since 2014. That success, in no small part, goes to each and every member of our team who continued to work together to deliver the safe, efficient, quality, service that our customers and the industry have come to expect from PHI.
How would you describe your leadership style?
I would describe my leadership style as collaborative—team first. I want our team to be successful and believe that our company’s success will follow. I would also say demanding and fair. I challenge myself and every member of our team to deliver on their commitments. That means saying what you’re gonna do and delivering on what you say — no matter how big or small the commitment.
What was your first job?
My first job was at a Feed & Farm Supply store at age 14, and I worked there for 11 years. I started as general labor earning $2.85 an hour, toting 50- and 100-pound sacks of grain. I worked there through part of middle school, high school and college, and was able to pay for my own way through university studies. When I left, I was the manager of one of the stores making $5.50 an hour. In the three years that I managed the store, I grew it by 400%. When I got my first job in HR and they said all I had to do was HR stuff, I thought ‘Man, that’s easy!’
Curiosity and learning. I believe that you’ve got to have a lot of varied experience, but not just the same experience—that’s what
hurts people in advancing their careers: having too much of the same experience over and over. I feel that people need multiple new experiences and challenges that build a strong foundational and balanced perspective. I’m 49 years old, but I’ve been working for 34 years. I’ve probably learned more from the worst bosses I’ve ever had than the good bosses because I learned all the things I didn’t want to do or how I didn’t want to treat people. You can always learn, and that’s the key to success in my opinion.
What’s one thing you’re learning now or learned recently?
I continue to learn every day. I learn more and more about aviation, aviation safety, risk mitigation and our people—the individuals who bring our mission and vision to life. It’s imperative to stay curious— you can’t think you know everything, and you can’t just accept what is. Be curious. Ask Questions. Learn it, understand it and find ways to make it better. I’m a firm believer that nothing stays the same, so if you stop learning or advancing, you fall behind.
What’s the biggest misconception people have about your position?
That’s a hard one. I don’t think people see my job as easy. I’d say one of the biggest things that people may struggle to understand is all the different areas to oversee and lead. Customer relations, employee matters, supply chain, safety, operations, maintenance, etc. The only thing that holds true across all disciplines is leadership. We must all be leaders of the company.
What keeps you busy outside of work?
My family; three boys and my wife of 23 years—that’s really all I do outside of work. A lot of outdoor activities together: boating, fishing, hunting, camping and four-wheeling.
A few things: First, always learn no matter what opportunity is presented—positive or negative—always learn from it and take that learning as your value. Second, always give or provide more than what’s asked for. And lastly, my father told me ‘Never forget that no matter how far you climb up the ladder of success, you have to come down,’ so it’s important to treat everyone fairly and with respect. In my opinion, that’s the most rewarding part of any job— the positive impact you can have on the people as a leader.
Most people don’t know that I had a rodeo scholarship to McNeese State University in Lake Charles, Louisiana. I roped calves, teamroped, worked cattle and trained horses for many years.
How would you describe your leadership style?
I believe leadership styles can, and often should, change depending on each situation, our strategy, our teams and our customer needs. Currently, we’re transitioning an entire regional office and I’m leading new team members, so my style is a mix of direct and ‘servant’ leadership.
I’m cognizant that there’s a fine balance between the need to take quick, decisive action toward a key business or team goal, and when it’s a value-add to seek team or individual input. With my background as both a certified maintenance technician and a certified safety professional, I’m accustomed to working across all levels to identify a solution that works for both our teams and our customers and that we are critically aligned with PHI’s core values.
I value critical thinking—the more we seek to understand how each department functions and how we impact each other, the more success we will have as a team and organization—and, more importantly, the more success each of our employees will have. My expectation is that all PHI employees—regardless of their job or title—view themselves as leaders of our organization.
What has been your career highlight at PHI to date?
The highlight of my career is the execution of our recent 10-year United States Gulf of Mexico (USGOM) contract. The long hours spent negotiating and countless time spent applying the multiple facets that I’ve learned in my tenure at PHI was a phenomenal experience—and well worth it for the sustainability of our business and the long-term relationships we have with our valued customers.
What keeps you grounded?
My upbringing keeps me grounded. My parents and grandparents worked very hard, and we were raised within our means. I can count on two hands how many days my dad missed work. He worked long hours with heavy machinery, and he never complained or quit.
I’m proud to say that I was the first generational college graduate on both sides of my family. I completed my college finance degree within 4 years while working full-time at PHI at the age of 39—paying for your own education is a humbling experience as well.
I am also grounded in my faith, but, above all, my mom is my inspiration—she’s tireless. She raised our family firmly but fairly and continues to be my inspiration and biggest advocate to this day.
What keeps you busy outside of work?
Outside of work I like to keep busy trying to stay in shape. I’ve always lifted weights but found CrossFit a few years ago. I am
not as consistent as I would like to be, but I enjoy the rigor of the program. I also enjoy cooking and have a passion for cars.
Do you have a favorite family recipe? What is it?
My favorite family recipe is seafood gumbo or Cajun jambalaya. During my high school and aviation school years, I worked in a large seafood restaurant. I also owned my own restaurant a few years back and continue to enjoy cooking for others.
What was your first job?
My first job was washing dishes every weekend at a local restaurant. This started at the age of 13 and I worked every weekend during my high school years. As the years progressed, so did my job responsibilities and weekly hours. I have a pretty good understating of the restaurant industry.
At PHI, my first job was working as a certified maintenance technician in our Lafayette Part 145 maintenance organization. There, we worked on many different model-type helicopters related to refurbishments and overhauls. It was a great place to learn the intricate details of different aircraft and the many aspects that go into each of these rebuild processes. I worked there for my first eight years and have fond memories with lots of lifelong friends.
When you were a kid, what did you want to be when you grew up?
I wanted to be an aircraft fighter pilot. After watching Top Gun in the 80s, how could you not want to be a fighter pilot? Although coming from a military family, I chose a different route and after graduating I went straight to aviation maintenance school, becoming certified at the age of 19.
Pineapple on pizza: yes or no?
I will eat it, but no—I do not request it.
Most of my days start very early, and I move quickly to the office or workplace—usually arriving at 5 am or 6 am. I grab a cup of coffee on my way and normally skip breakfast to maximize my time. It is always quiet first thing in the morning, which I find of tremendous value to me. In addition to starting meetings with my US counterparts, this time gives me an opportunity to catch up on emails and other outstanding items before diving into the busyness of the day ahead.
What’s one thing you wish you’d known when you started working at PHI?
That it’s okay to fail. I’ve had my fair share of disappointments, and I’m my own worst critic. Failing is an important step in learning—it helps you understand that by applying discipline and consistency, eventually your goals will be realized.
“ “
My expectation is that all PHI employees view themselves as leaders of our organization.
Cory Latiolais is PHI Aviation’s COO for its APAC region.
At HomeBase , we put some questions to Cory to better understand what makes him tick.
“
Jamie Mitchell is PHI Aviation’s COO for its EMEA region – covering Europe, the Middle East and Africa.
HomeBase sat down with Jamie to get to know him better.
PHI is all about its people. I have a fantastic team around me here.
“
What do you enjoy most about your job?
Working with great people. Everyone I meet has a story to tell, whether that be how they got to where they are today, what their aspirations for the future are, the pride they have in their work and—of course—their ideas for how we can continue to make PHI better. PHI is all about its people. I am very lucky in my job in that I now have a fantastic team around me in EMEA and I travel a lot, allowing me to meet many people from so many different parts of the world. We have a very diverse landscape at PHI, and I believe that truly adds value to the company.
How would you describe your job to a class of five-year-olds?
It was a lot easier when I was actively flying, and it was always a lot of fun to take a helicopter to a school and show the kids around. Now, I say I am helping others to fly and fix helicopters.
When you were a kid, what did you want to be when you grew up?
My father served his entire career as a submariner in the Royal Navy, so I spent a lot of my childhood surrounded by the wider military family. I was also fortunate to get a number of helicopter rides, so from about the age of about 12, I was hooked on being a military helicopter pilot.
Do you have a favourite family recipe?
During the Second World War, my grandmother used to bake a particular type of fruit cake using the ingredients she could find during rationing and would hand it out to local families who had been impacted by the blitz. My mother learned to bake the cake as a child and then through my childhood, it became a firm family favourite. The recipe continues to be passed down through the generations and my kids now love it too. It’s called Gargie cake as my grandmother was known as Gargie.
What has been your career highlight at PHI to date?
Being appointed to my current role as COO of EMEA is an amazing privilege and an opportunity to help shape the
future of the company. The EMEA business unit has huge potential, and we are at the very beginning of that growth.
I was lucky to be sponsored by the Royal Navy through University and then trained as a pilot, initially specialising in anti-submarine warfare—my dad wasn’t impressed! I spent 19 years in the military, doing a range of different operational flying roles. During the last 10 years of my time in the military, I specialised as a Search and Rescue commander and instructor.
I am a member of a local voluntary search and rescue organisation, Surrey Search and Rescue. We provide specialist assistance to the emergency services to find lost, missing or vulnerable people in our community. We also support them during emergency events such as flooding or wildfires. The team is equipped with drones, dogs and water teams to help, but we also spend a lot of time searching on foot. Volunteering in this capacity brings together a range of different skill sets, and I get to meet interesting people from other walks of life.
I also have a crazy two-year-old cocker spaniel, Billy. I hope to train him to be a search dog for the team, but it requires a lot of discipline and patience and right now he is a little too neurotic…and I’m a little too busy!
Without a doubt, my family. They have been amazing in supporting me through my career, particularly in the military with all the moves and challenges that military life brings. I have three sons and they are my fiercest supporters but also my biggest critics. My eldest is an active campaigner for the climate crisis and challenges me regularly on what PHI is doing to make a difference in this space. I also have twin sons currently at university—one is considering a life in the military too, although probably not as a pilot, and the other is a big rugby union fan. He plays for his university, and we are all off to watch the World Cup in France in 2023—Covid permitting!
Safety has always been integral to everything we do at PHI. It is the first of our four core values—safe, efficient, quality, service—and we recently introduced an internal campaign to further strengthen our commitment to our core values and to our vision of Destination Zero: zero flight accidents, zero personal injuries and zero preventable occurrences.
At PHI, safety is everybody’s responsibility, and we wanted to ensure that our people continue to be equipped with the skills and tools needed to be accountable for safety across everything they do.
Destination Zero and the Human Dimension of Safety were formally introduced in the PHI Americas operating units through training programs and sessions, and although no formal training took place in APAC or EMEA, our teams in these regions are aware of the initiatives and programs that exist.
Destination Zero has provided a clear vision around expectations, and our safety management systems in APAC/ EMEA have provided us with the tools necessary to be successful; however, we know that our safety culture still has plenty of opportunities for improvement across our entire PHI Aviation workforce. PHI believes that our people are the most critical aspect of our safety culture. More specifically, it’s our shared values, beliefs and patterns of behavior as a team that enable our success.
Although we are confident that PHI’s on-boarding process has set safety expectations and that our training programs have provided the knowledge for employees to be successful within our operational environment, we have a lot of people who were not with PHI at the time of the initial program roll-out. Those coming on board in the most recent years have not experienced the transformation or step changes in our safety management system, nor were they exposed to the drivers behind key safety initiatives supporting that transformation.
Instead of reinventing the wheel around safety management, PHI has chosen to circle back on critical elements of our safety management system that we believe have the greatest potential for taking our safety culture to the next level.
- Keith PHI Aviation Managing DirectorAt PHI, we know that it’s not enough to get the job done—it’s about getting the job done safely, every time.
“Our goal is to continue to strengthen our commitment to safety across PHI, to continue to be the industry leader and to extend our safety performance well into the future. We continue to design systems and processes to support the Human Dimension of Safety. Interaction, collaboration and teamwork will be critical to our success.”
Mullet,
Over the next few months, there will be a series of engagements designed to explore and strengthen our collective understanding of the key safety initiatives that are critical to maintaining our industry-leading safety performance.
PHI is strengthening our commitment to the key safety initiatives that have helped define our culture and solidify our position as an industry leader in safety. We are creating a series of videos and resources to:
§ Reinforce Our Core Values. Our core values of safe, efficient, quality, service are foundational to reaching our goals as an organization and are crucial to maintaining our place as an industry leader in aviation.
§ Increase Awareness for All Employees. We want to increase awareness for employees who may not have been at PHI during the initial rollout of our safety programs and offer an opportunity to refresh our seasoned teams on how they can promote and engage in a safe workplace.
§ Listen, Connect and Engage. We need your help to listen, connect and engage with your teams to ensure all PHI employees have a deep understanding of our safety philosophy, programs and goals.
§ Continue to Promote Safety Leaders. At PHI, we believe that leadership isn’t necessarily a position, but a set of actions. We empower our leaders to empower their teams to remain focused on our core values and continue working together to keep our people and our passengers safe.
§ Grow as a Team. Our safety programs and goals will continue to adapt and grow to meet the changing demands of our teams and organization. We will leverage the information and feedback gathered throughout this initiative to nurture and adjust our safety programs for the future.
This initiative will be implemented in several phases over the next few months, with phase one now complete. Phase one included an introductory video featuring key leaders from across our organization who set the tone and explained the goals for this initiative.
We recently celebrated PHI Century Limited’s 10th anniversary with an event held at Best Western Plus Atlantic Hotel in Takoradi, Ghana. PHI Century is a joint venture between PHI Aviation and the Ghanaian-owned Century Aviation Company Limited and was founded in 2011, commencing operations in 2012, to support the growing requirement for transportation to offshore drilling rigs and production platforms in West Africa.
PHI Century’s strength is derived from the combined expertise of each partner. PHI Aviation brings our depth of global experience, state-of-the-art fleet of helicopters, enhanced operational procedures and proprietary Safety Management Systems, while Century Aviation brings on board its vast experience and intricate knowledge of working in Ghana and West Africa’s aviation sector.
Well over 100 people attended the celebration, including the Western Region Manager for the Petroleum Commission, representatives from Ghana Civil Aviation Authority (GCAA), suppliers and customers. There was a live band, master of ceremonies, good food and even a cake in the shape of an S-92A.
Managing Director of PHI Century, Essie Anno Sackey and PHI Aviation COO – Europe, Middle East and Africa (EMEA), Jamie Mitchell, spoke at the event and discussed the strong partnership between PHI Century and PHI Aviation. A video was played highlighting the achievements of PHI Century over the last decade.
“We are the go-to provider of helicopter services for the West African oil and gas industry because we have a diverse offering, we go the extra mile to meet the needs of customers and we operate in a safe and efficient manner,” said Essie.
“Our team is able to easily and efficiently mobilize from our Takoradi base to serve our clients in Ghana and West Africa.”
PHI Century’s corporate office is in the Airport Residential Area in Accra, and its operational base is at Takoradi Airport, where it operates a fleet of Sikorsky S-92A helicopters. The operational base includes a parts building, a passenger lounge, a hangar for storing our aircraft, the maintenance office and a pilot office and lounge. More than 55 percent of the technical staff, including quality managers, pilots and aircraft engineers, are Ghanaians.
In its 10 years of operation, PHI Century has provided services for Hess Energy, Talisman B.V. (of Sierra Leone), Tullow Oil, Newmont Ghana Ltd., Aker Energy and Kosmos Energy Ltd.
“We are the go-to provider of helicopter services for the West African oil and gas industry because we have a diverse offering, we go the extra mile to meet the needs of customers and we operate in a safe and efficient manner”
- Essie Anno Sackey, Managing Director of PHI Century
Mark Leighton has joined our team as President of PHI Cares Direct to Consumer. Mark will oversee the Sales, Marketing and Expansion of PHI Health’s membership offering to millions of Americans who would benefit from this valuable program. Mark’s experience will lend itself to the significant scaling opportunity of the membership base.
Mark has over 30 years of leadership experience, 15 of which were focused in the healthcare space. Mark strongly believes that organizations working together are the key to delivering exceptional results and is extremely passionate about motivating and supporting his teams.
In Mark’s recent role as President of Medical Guardian, he oversaw Sales, Marketing and Operations reporting to the Founder and CEO. Under Mark’s leadership, the company grew significantly going from 60,000 customers to over 300,000 in 2022. Medical Guardian won numerous awards from, Inc. Magazine’s list of “Fastest Growing Private Companies in America” and as a “Fastest Growing Company” by The Philadelphia Business Journal and Philadelphia 100, as well as “Top Workplace Award Winner” by Philadelphia Inquirer.
Prior to Medical Guardian, Mark served as CEO of Medical Alert, a leading provider of personal emergency response devices. During his six years there, Mark significantly expanded the company’s Marketing and Sales capabilities, helping grow the business to the second-largest provider in North America. Other positions he held at Medical Alert included COO, CMO and Vice President of Sales.
Mark has three children, and he and his wife Cindy enjoy traveling, golfing and spending time with family.
We are very excited to welcome Mark to our team and look forward to the expansion of our PHI Cares footprint.
PHI Cares is a membership-based program that covers any out-of-pocket expenses for medically-necessary air transports aboard a PHI Air Medical or one of its cooperative service partners’ aircraft.
Membership with PHI Cares ensures you and your qualified household dependents are covered for emergency air transports. As a member, PHI Air Medical will work with your insurance provider to accept the insurance payment or other third-party payment as “payment in full” for any medically-necessary transport from one medical facility to another or from the scene of an emergency. PHI Air Medical has more than 60 flight bases across the United States with a helicopter service range of up to 200 nautical miles. PHI Cares membership plans start as low as $40 a year which is one of the most competitive in the industry and extends discounts to PHI employees, EMS workers and Veteran and Military personnel.
PHI Cares has two main channels for growth: Direct-to-consumer, led by Mark Leighton, and Municipality, which is led by Brian Coutts.
Brian has led the Municipality business for many years at PHI, and it is a program that focuses on PHI Cares memberships for cities, counties and managed groups where PHI Air Medical is the preferred provider when responding to a request for air medical transport.
To learn more about the PHI Cares Membership Program plans and eligibility, please visit phicares.com or call our membership department at 1 (888) 435-9744.
HomeBase spoke to Isabel Orran Padilla, Senior First Officer at our Cyprus base, about her career as a helicopter pilot, her experience as a woman in the aviation industry and what it’s like being based in sunny Cyprus.
Isabel’s interest in flying started at a young age, with her father’s passion for flying fueling her curiosity in a career as a pilot.
“Being a pilot was always the goal, but I had put it to the back of my mind because I couldn’t see an obvious route into training school. I was incredibly lucky when an opportunity presented itself,” says Isabel.
Isabel was preparing to go to university when she was awarded a financial grant to support her to pursue her dream and go to pilot school. She studied for two years to get her commercial license, which combined a lot of practical training, as well as time in the classroom studying aviation theory.
Isabel entered the workforce in 2010 and has had an exciting and varied career since then, working across emergency response services, the oil and gas industry and passenger transportation services.
She first worked as a firefighting copilot with Faasa Aviation where she was flying Bell 412 and Russian Kamov Ka32 as a fully type-rated first officer. The Ka32 is one of the biggest firefighting helicopters flying in Europe with almost 13,000 kg maximum take-off weight (AW139 is 7,000kg) and 5,000 liters of water in the Bambi bucket. She then took on a role with Babcock (formerly INAER), flying non-type-rated Agusta 109 and Eurocopter EC 135 helicopters as a copilot. During this time, she undertook 10 firefighting campaigns—nine in Spain and one in Chile, which Isabel describes as being both exciting and challenging.
“Working as a pilot, fighting fires and attending emergencies is incredibly rewarding. Flying towards a large fire, you get goosebumps and you can really see the progress as you tackle the fire. It’s a great feeling to be able to make a difference, saving homes and saving lives in challenging conditions and often racing against the clock to limit the spread and extinguish the fire.”
Isabel then served as Senior First Officer with Helity, a passenger transportation services provider in Europe, before working for the NHV Group as First Officer where she served the offshore oil and gas industry in the Northern Sea.
“I heard Cyprus was a great place to live, and when I saw the role advertised, I put my name forward. I was also encouraged by colleagues who had worked for PHI previously. I had never actually been to Cyprus before, but the role and the lifestyle in Cyprus motivated me to apply.”
“So far it’s been great! I have time to enjoy the island and live just 200 metres from the beach. Between the mountains and the beach, there’s a lot to enjoy, and there seems to be a good worklife balance.”
For those who are interested in a career in aviation, Isabel encourages patience.
“It’s a combination of learning on the job through getting your flying hours in as well as studying. It can be intense and demanding and requires a lot of commitment.”
Being a woman in a traditionally male-dominated industry has presented some challenges but significant progress has been made, says Isabel.
“I think the industry has come a long way in the last few years and while there’s more that can still be done, it’s a great industry to be a part of, with a lot of opportunities—whether that be aerial firefighting, flying as part of emergency response or servicing offshore industries. I’d recommend it as a career to anyone.”
“I USED TO WATCH MY DAD FLY LIGHT AIRCRAFT, AND I WAS DETERMINED THAT I WANTED TO HAVE THE SAME EXPERIENCE. I DISTINCTLY REMEMBER AT A YOUNG AGE WANTING TO BE A PILOT.”
Across the business, we are looking at ways to partner with our customers, stakeholders and the wider aviation industry to develop innovative solutions and services to support the transition to renewable resources.
As part of this approach, we are looking at what changes we can make internally to reduce our overall carbon footprint. Our New Plymouth Base was recently involved in a project to investigate the potential for fuel reductions outside of using SAF, without compromising PHI’s values—safe, efficient, quality, service.
HomeBase spoke to Russell Pirihi, PHI’s Chief Pilot – New Zealand, and Roger Duncan, PHI’s Base and Contract Manager – New Plymouth, about the program they have been championing, and what it could mean for the rest of PHI Aviation.
Roger – We wanted to pursue avenues that would make an impact and had the potential for genuine GHG savings — which is why we looked at aviation fuel burn, as it’s the biggest contributor to PHI’s carbon footprint. The project was set up to explore the potential options we had available to reduce fuel emissions from our operations. Russell is a long-time Captain here and knows the aircraft we operate really well. We began the project by holding a brainstorming session amongst a few key people here.
Roger – The project team explored a few different ideas, firstly whether we could operate the aircraft more efficiently via shortening flight routes—because anything that saves time in-flight will significantly cut down on fuel usage. However, routing changes didn’t bring up any obvious benefits. The routes in place were already as efficient as they could be for the landscape. Flight altitude was also examined— although flying higher typically burns less fuel than flying lower, aircraft burn more fuel to reach higher altitudes.
Russell – What we tried after this was flying at a more efficient cruise speed of 130 kts down from the standard 140 kts—quite a small difference in overall performance, but this has shown between 3-5% reductions in fuel burn, so cruise speed was a big finding in this project. To put that into perspective, that 3% figure is approximately 25 tons of jet fuel a year—it’s not big on the global scale, but it’s big for New Zealand and so is worthy of pursuing. We are also continuing to work with our clients, where possible, to find further efficiencies.
Roger – There are a number of factors that are left to explore, and sustainable aviation fuel (SAF) is definitely one of those. There has been some work done in this area but it’s early days yet. Sustainable aviation fuel is very expensive so bringing it to New Zealand in conjunction with other aviation operators in New Zealand would be a good start. For now, we need the SAF supply chain to be more advanced in New Zealand.
Roger – I’m not a pilot by trade but felt it was important that I made sure that nothing we were looking at would compromise operations, cut corners or compromise on safety. None of the project’s framework could jeopardize how we operate our aircraft or reduce the quality of service we provide. My approach to sustainability at the start of this project was to reduce our wastage and ensure that we were not wasting any resources—fuel or time. Rather than cutting corners, it’s more about reducing wastage and inefficiencies—while keeping the standard high.
Russell – Safety was one of our key considerations. There are safety margins built into fuel reserves already—so in theory if you carry less fuel you can save a little bit, but there was no suggestion we were going to go down that route—and it was key that we retained the way we operate the helicopter. We worked with air traffic control too but never looked for unreasonable shortcuts from them, just suggestions for any potential savings in changes to flight routes. It was actually a good result for us that we went into this project and came out the other side without any huge findings for improvements. This gave us reassurance that, in theory, we were already operating as efficiently as we could be, save for some small potential emissions savings in adjusting cruise speed, which was a great finding.
Russell – Our ideas for selecting the most efficient ways of operating the aircraft may have implications further afield, but more change is needed to generate more return on some of these efficiencies. We can certainly now share the data we’ve gathered from this project with our other geographical business units, although they will all have different constraints that they operate under, so some of our findings may not be applicable to them. Some considerations for the future for us and for the rest of PHI include exploring the use of different aircraft fuels and different aircraft types.
Roger – Wider adoption also depends to some extent on the approach our clients have and any constraints they have. We don’t have a golden answer yet, but we’ve made a start here in New Plymouth.
OUR CHIEF COMMERCIAL OFFICER - BUSINESS
Jon Rudy joined PHI earlier this year. Based out of Lafayette, Jon has taken on the role of Chief Commercial Officer – Business Development for PHI Aviation.
Jon and his family reside in Conroe, Texas. Jon and his wife Julie are proud parents to 16-year-old twins Jackson and Alison and 13-year-old Kate.
“
“
PHI’s reputation for safety, integrity and service is unmatched in this industry.
By way of background, Jon has spent two decades in the Aerospace and Defense sector. He is a former United States Marine and graduate of Texas A&M University.
We spoke to Jon about the different roles in his career so far and his role at PHI.
Fresh out of the Marine Corps, I joined Bell Helicopters in 1999 in an entry-level marketing position. Over my time at Bell, I had the opportunity to acquire a pilot’s license and serve in roles that included Regional Sales Manager, Director of UAV Programs and Director of Asia Pacific Commercial Sales. In 2008, I left Bell to take a position at General Dynamics where I led global sales of MRAP combat vehicles to allies around the world supporting Iraq and Afghanistan. In 2014, I joined Sikorsky where I served as the company point of contact for international oil and gas customers and later as the Director of Asia Pacific sales for commercial and military aircraft.
I’ve always had a great deal of respect for PHI. PHI’s reputation for safety, integrity and service is unmatched in this industry. When the opportunity came up, I jumped at the chance to join the PHI team.
I’ve joined as the Chief Commercial Officer. In this role, I work with the COOs and their business development resources to develop a broader global strategy for growth and diversification. I work with a great team; this is an exciting time for PHI, with our newly established headquarters in Perth and London which will bring us closer to our key markets and our focus on diversification.
Short answer—excellent. I’ve been here a couple of months now and have been on multiple international trips, meeting with a number of our customers and PHI team members.
After a challenging couple of years, the market has rebounded, and it’s been great to get out and foster new connections. The overwhelming message I’ve received from our customers is that they trust PHI because of our safety culture and commitment to excellence. This sets us apart from our competitors.
What areas of opportunity do you see in the near future?
There are significant opportunities for PHI, especially with our focus on diversification into new markets. We have opportunities to grow our traditional core business into new regions as well as adjacent markets including MRO, SAR, UAV operations, wind energy and government contracts.
What are you most proud of in your career?
At this point in my career, my greatest accomplishment is being offered a position at PHI. This position is a great honor with no shortage of responsibility. I take this role very seriously, and I look forward to the adventure ahead.
PHI’s Broome Base in Western Australia recently celebrated five years of successful operations. The base has come a long way since a small team set up the operations in March 2017, with the first offshore flight for INPEX conducted in April of that year.
Initially, there were 41 employees and two aircraft at the base, which has now grown to 95 employees and seven aircraft.
19 flights were completed during the first month and it was a busy time with many hurdles to overcome. Fortunately, we had a great team of people on the ground. Together they had a wealth of experience, coming from a variety of backgrounds and locations across the world.
In June 2017, our Broome base then transitioned to support the full INPEX contract, and the flying rate increased to roughly 17 flights per week. This has now increased to more than 70 flights per month.
In November 2017, PHI won the Search and Rescue (SAR) and Medevac services contract to support INPEX and Shell in the Browse Basin.
Initially, limited SAR services were provided, but 24/7 full SAR capabilities followed shortly after, with the full all-weather search and rescue aircraft arriving in April 2018.
Since the start of the SAR contract, the base has not only provided ongoing coverage for INPEX and Shell but has also provided search and rescue assistance to the local community with the Australian Maritime Safety Authority (AMSA).
The base has assisted AMSA in rescue operations for overturned vessels, beacon activation searches, sinking vessels and even a light aircraft engine shutdown, just to name a few.
To support the growing operation, in April 2020, the base repositioned from several smaller hangars and a standby house, into a second large hangar.
The relocation project took a considerable amount of planning and effort from everybody involved, but it allowed for the continuous growth of PHI’s operations.
As a result of Covid-19, in April 2020, INPEX requested the passenger transfer operations temporarily relocate to Truscott, a small airfield located in the remote Kimberley.
Story continues on Page 26.
The base has assisted the Australian Maritime Safety Authority (AMSA) in rescue operations for overturned vessels, beacon activation searches, sinking vessels and even a light aircraft engine shutdown, just to name a few.
In September 2020, the base welcomed a new aircraft type, the Leonardo AW139. This was the first AW139 for PHI operations in Australia and its mobilisation was only possible thanks to the hard work and many hours that the team put in.
Despite the many challenges that needed to be overcome, such as no road access or phone service, the base relocated in just 12 days. Operations successfully continued for 10 months, before heading back to Broome.
In September 2020, the base welcomed a new aircraft type, the Leonardo AW139. This was the first AW139 for PHI operations in Australia and its mobilisation was only possible thanks to the hard work and many hours that the team put in.
The aircraft was brought into the Broome operations in support of INPEX, but it has also provided a number of flights to assist the local community—including the delivery of supplies to remote areas after flooding and assisting with the distribution of Covid-19 vaccinations to communities.
90,885
BROOME BASE’S HISTORY AT A GLANCE:
NOVEMBER 2017
JUNE 2017
Transition to support full INPEX contract
APRIL 2018
Full all-weather search and rescue aircraft arrived at the base
APRIL 2020
Base relocation from several small hangars into a large hangar
SEPTEMBER 2021
SAR operation moved from sub-contract arrangement to a full complement of in-house crew
SEPTEMBER 2020
Arrival of the Leonardo AW139, the first for PHI’s operations in Australia, which was also used to assist with the distribution of Covid-19 vaccinations to remote communities
SEPTEMBER 2021
Introduction of SAR Cadetship
TRINIDAD
PHI has partnered with the University of Trinidad and Tobago (UTT) to facilitate practical aviation maintenance training for six final-year students annually during their sixweek summer vacation.
It’s their hard work and unwavering commitment to safe, efficient, quality, service that keeps us positioned as a global leader, and it’s why ‘Our Team’ is the first of our four pillars of Sustainability.
The Our Team pillar outlined in our global Sustainability Plan is not only our commitment to investing in our people through professional development and career advancement programs—it’s our pledge to recruiting a talented and diverse workforce and promoting a culture that nurtures their full potential. We are proud to celebrate and highlight our teams’ achievements within the PHI family.
Since 2017, PHI has partnered with the University of Trinidad and Tobago (UTT) to facilitate practical aviation maintenance training for six final-year students annually during their six-week summer vacation. Recognizing the talent and potential of the students coming out of the UTT Bachelor of Science in Aeronautical and Airworthiness Engineering program and the deficit of trained and qualified aircraft maintenance engineers in the region, we elected to hire two graduates from the class of 2019 as training engineers.
Arun Roopnarine was one of the trainees hired in October 2020. After joining the PHI team, Arun received on-the-job training under our approved maintenance training program with periodic performance reviews from our Director of Maintenance Kevon Ramtahal and lead engineers in Trinidad.
Arun quickly excelled in his role, and during his second year in our Maintenance Training Program, Arun applied for his Aircraft Maintenance Engineer’s license from the Trinidad and Tobago Civil Aviation Authority (TTCAA). On June 3, 2022, Arun successfully received his license as a certified Aircraft Maintenance Engineer with a focus in electrics.
Congratulations, Arun! Arun is scheduled to continue his training through the AW139 Avionics Field Maintenance course with Leonardo Helicopters in late 2023.
Stories like these are truly inspiring, and we look forward to welcoming the next group of students from the University of Trinidad and Tobago.
As an organization, we depend on the collective knowledge of our employees and their years of service in the industry to continue delivering the safe, efficient, quality, service that PHI is known for. To maintain our competitive advantage and our high-quality service, it is vital that our skills and knowledge are passed on to new and junior employees to ensure a sustainable business.
As part of our global Sustainability Plan, we are committed to developing career advancement programs and building long-term industry partnerships to help mentor the next generation of aviation professionals. We are proud to continue building our relationship with the University of Trinidad and Tobago and our other university and industry partners across the globe.
Sustainability is a core focus of these programs as we encourage our teams to share their knowledge and ideas, help pass on learned process efficiencies, minimize resource use and explore new ways of doing things.
AT PHI, WE BELIEVE OUR EMPLOYEES ARE OUR GREATEST ASSET, BUT MORE THAN THAT, WE BELIEVE THEY ARE THE FOUNDATION OF OUR BUSINESS AND THE KEY TO A SUCCESSFUL FUTURE FOR PHI.
Our team based in Western Australia has been kept busy over the past few months, undertaking a number of rescues in support of the Australian Maritime Safety Authority (AMSA). Our search and rescue (SAR) work and support for AMSA is a critical part of our community contribution in Western Australia and undoubtedly has saved many lives over the years.
No two days—or rescues—are the same for the crew. Our SAR work operates 24/7 and spans both offshore and inland emergencies. We are called in to undertake emergency rescues, respond to health emergencies and provide transportation to hospitals and undertake search operations in the instance of overturned or missing vessels.
The crew has recently undertaken two critical lifts from cruise ships off the coast of Broome, Western Australia. On both occasions, the patients were airlifted and transported to Broome Hospital.
The team was also called on to provide support to a multi-agency response to an incident at Horizontal Falls in Talbot Bay, in the Buccaneer Archipelago. The helicopter routed from Broome to recover personnel from a floating pontoon, where they were being treated, following a serious boating incident.
The rescues are carried out on Sikorsky S-92 search and rescue helicopters, which are operated by PHI Aviation from its Broome Airport Base, and which provide 24/7 SAR and aeromedical evacuation services in support of our clients.
“It’s great to have the continued support of our Broome-base clients, to be able to deploy our Broome SAR helicopter to respond to the request for support from AMSA. There is no doubt that this service saves lives.”
- Gordon Watt, Commercial and Business Development Director - APAC
“It’s great to have the continued support of our Broome-base clients, to be able to deploy our Broome SAR helicopter to respond to the request for support from AMSA. There is no doubt that this service saves lives.” - Gordon Watt, PHI’s Commercial Director
An intensive training program ensures our SAR crew is always rescue-ready. Becoming one of the SAR crew requires dedication, determination and a good level of physical fitness.
Those wanting to join one of our SAR crews need to go through rigorous training, which includes fitness tests, medical assessments, water confidence trials, interviews, team building activities, ground school lessons and simulated winch training.
Our crews also undertake Offshore Safety Induction and Emergency Training (TBOSIET).
This course involves a series of offshore safety elements, including Helicopter Underwater Escape Training (HUET), firefighting, smoke/zero visibility ship escape and Underwater Emergency Breathing System (UEBS) training.
The learning never stops with the crew also undertaking training in the operation of the forwardlooking infrared (FLIR) camera and night vision goggles (NVG), along with medical training, crew resource management training, aeronautical radio operations, SAR observer and aircraft voice-marshalling training also involved as part of SAR training.
Saving lives and giving back to the community are all part of a day’s work for our SAR crew.
Jenny Barclay joined PHI Aviation earlier this year, based in the UK and taking on the role of Commercial Manager for our Europe, Middle East and Africa (EMEA) region. She’s had an interesting and varied career in both the aviation and energy sectors.
Prior to joining PHI, Jenny was the Principal Consultant for aviation at Equinor (formerly Statoil) and before that, with CHC Helicopters. HomeBase spoke to her about her career to date and what she’s most looking forward to in her new role at PHI.
I joined the oil and gas industry in 1990, working for Occidental on the Piper Bravo project. I took the challenge of working offshore during the lengthy hook-up and commissioning phase. This was closely followed by other projects—Saltire, Scott and Dunbar—but having children put a stop to this and, after a short break, my onshore career started in earnest. In parallel, I studied part-time for a degree in International Marketing at Robert Gordon’s University in Aberdeen.
It can be a volatile industry but I’ve really enjoyed working with and for major energy and service companies. It’s full of characters and there’s never been a dull moment!
Whilst it does remain a male-dominated industry, it has changed significantly over the years. When I started working offshore, on a vessel of 800 people, I was one of only two women. However, I only ever experienced respect from the workforce.
The profile of the industry looks much different these days with many more women in key management and leadership roles. There’s a big cultural shift throughout the industry which is great to see. The industry has come a long way.
I’ve taken on the role of Commercial Manager but the remit of my role is quite wide-ranging as we’re building a new business unit within the bigger PHI group. Along with the small EMEA team, we’ll be looking to grow the business in what is a significantly large—and challenging— geographical area. In many ways, it feels like a ‘start-up’ and my first challenge was to find an office!
With the establishment of the new PHI headquarters in the United Kingdom, we have a greater presence in
the market and are looking to expand our footprint. We’ve got a big job to do and it’s exciting to be involved.
Quite simply, it was time for a change and a desire to return to the area of my career I loved the most—helicopters and finding solutions for customers.
The opportunity to be involved at the start in establishing the EMEA business unit drew me in. This, combined with the opportunity to work under the structure of a global organization with a significant market share, motivated me to apply.
I’m really proud of some of the new business wins and retention of contracts I’ve been involved with, in very competitive environments.
More recently, I’m grateful to have been involved in the energy industry’s response to the COVID pandemic. It was a hugely challenging time for everyone and through collaboration, the industry—with support from OEUK—kept going despite many travel restrictions and worldwide lockdowns.
In a nutshell, helping develop our region and working with a fantastic PHI team. Focus will be on developing relationships internally and across our customer base, finding solutions that match expectations. There’s a vast amount of potential opportunities across the EMEA region and I’m excited as to what comes next.
PHI’S ENGINEERING TEAM IS
HomeBase spoke to members of the engineering team Ken Boyer, Stewart Trahan, Mike Melton and Ryan Guillot to find out how 3D printing is increasing our efficiency.
At PHI, we’re always looking for ways to be more efficient—and more effective—with our time, resources and energy. Whether that’s investing in the latest and greatest technology or implementing ideas from our team, we strive to live each day by our core values of safe, efficient, quality, service. One way our engineering team is doing this is by incorporating 3D printing technology into their existing processes—and with great success so far!
Traditional fabrication is a time-consuming process that often limits designs. With high tooling costs and production limitations, initial designs, tooling and prototyping can take days, weeks or even months to complete— and not to mention requires a significant investment from our teams.
3D printing offers a flexible solution that can greatly reduce the number of components and enable on-the-fly innovation that’s not possible in traditional fabrication and manufacturing chains. Its impact on turnaround time, customization possibilities and design freedom, opens a world of exciting potential applications for our teams.
Traditional R&D fabrication requires a lot of trial and error, but with 3D printing, designs can go straight from sketch to production-ready using an AutoCAD file. Reducing and eliminating molds and the costs and time associated with tooling allows our teams to test multiple design variations before ever sending them to the sheet metal or machine shop for fabrication. With the ability to create fully-functional prototypes, the engineering team can print and test numerous variances—usually within a couple of hours—to quickly determine the final design.
Although plastic is the primary material used in 3D printing, there are a variety of advanced mediums available in a wide range of colors including those infused with nylon or carbon fiber. Traditional mediums like plastic offer an inexpensive, durable and lightweight material that makes it easy to transport printed tools and components for customer review or feedback.
Not only does 3D printing help save time throughout the fabrication process, but it can also help to save on material and labor costs. 3D printing allows for more efficient and effective collaboration between project teams. The engineering team can focus on testing and adjusting the product design before looping in the machine shop or sheet metal teams for the final design, making better use of everyone’s time and increasing team-wide productivity. In addition, the 3D printer only uses the amount of plastic required for the job itself with little to no wastage, and any adjustments to the design can be easily fulfilled at a nominal cost as compared to traditional fabrication methods.
Prototyping is a key part of our engineering design process—ideas are developed, and designs are refined based on the project scope and requirements. To help speed up and sharpen that process, our engineering team purchased a Fusion3 F410 3D printer for in-house use. The printer uses fused filament fabrication to produce large parts—or a large number of smaller parts in one print job—in as little as a few hours.
So when the team began working on a new tool to support control rod alignment, the 3D printer played a key role. After printing and examining the initial prototype, the team discovered that the rod assembly was too difficult to install and remove as an assembly. They were able to make minor adjustments to the technical design and print a second iteration of the prototype to validate their changes. From there, the design was altered again before arriving at the final design. What took about an hour to print would have taken days of back-and-forth with the machine shop to manufacture a successful unit. Instead, the engineering team was able to vet the assembly tool as it was intended, making adjustments to improve its ergonomics, before it was ever sent to the machine shop for fabrication.
Since then, the 3D printer has also been used to create scaled replicas of our maintenance stands for PHI Health. Similar to the assembly tool, the team was able to easily identify a crucial design flaw, make the design change and reprint the models in a matter of hours. Thanks to their light weight, the 3D-printed stands were easily shipped for final review by the customer.
3D printing allows our teams to explore more fabrication and manufacturing possibilities than ever before, and we’ve already seen improvements in our traditional R&D process. Whether the goal is quicker production, flexible design, customization or increased efficiency, 3D printing may be the next big thing in PHI’s long list of innovative solutions.
For more information about our 3D printing capabilities or for project requests, please contact Mike Melton.