
31 minute read
PRZEMYSŁ 4.0
from Automatyka 12/2020
by Ł-PIAP


Advertisement



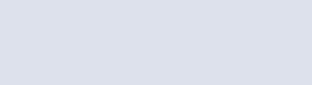



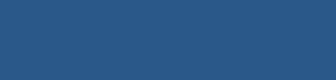

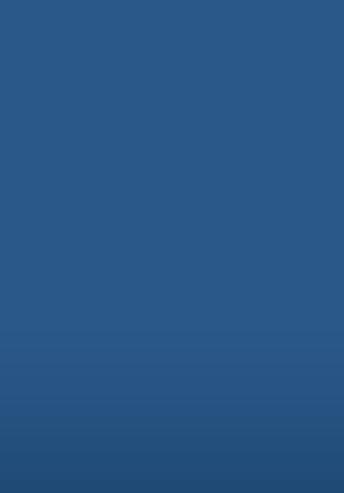
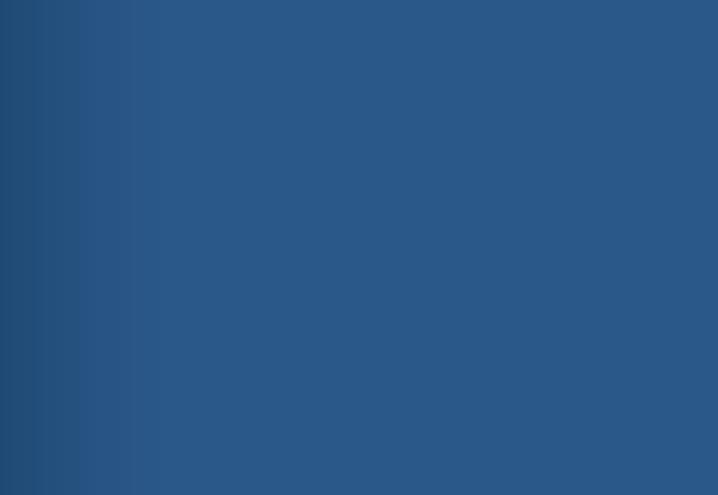
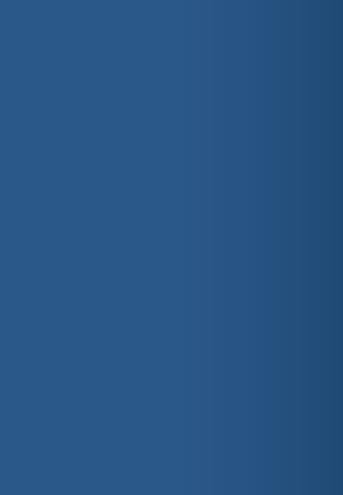
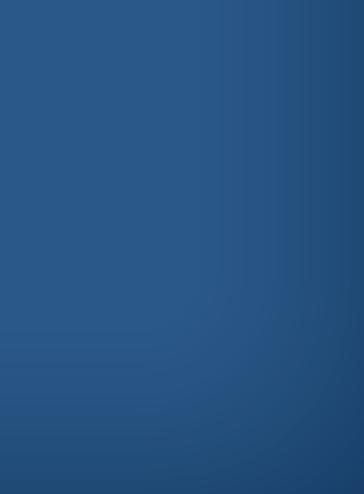


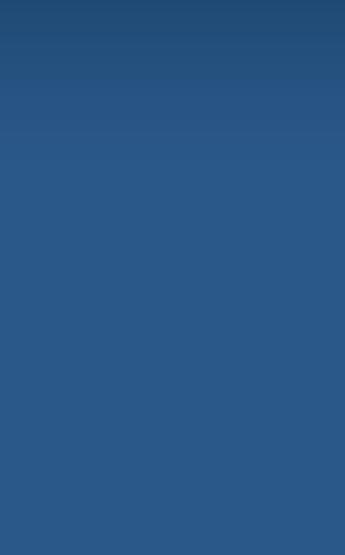


H
Hydraulika (ang. hydraulics, niem. Hydraulik) – dziedzina nauk technicznych, będąca działem inżynierii mechanicznej, zajmująca się problematyką budowy i aplikacji urządzeń i maszyn, w których przekazywanie energii i sterowanie realizowane jest za pomocą wody, oleju lub innej cieczy, powszechnie zaliczanych do płynu, o podobnych właściwościach, jako czynnika roboczego.
Słowo hydraulika (z języka greckiego zbitka słów woda (ὑδρω) i rura (ὐλικός), a więc ὑδραυλικός, hydraulikos) było używane dla opisywania ruchu wody, jej zachowań i wykorzystania, przy wykonywaniu niezliczonych prac człowieka długo wcześniej, zanim Blaise Pascal (1623–1662) i Daniel Bernoulli (1700–1782) sformułowali prawa, na których ten ruch i te zachowania cieczy się opierają.
Aktuatoryka hydrauliczna Część pierwsza eseju złożonego z dwóch artykułów: Aktuatoryka hydrauliczna i elektrohydrauliczna, Aktuatoryka hydrotroniczna.
Możliwości zastosowania układów hydraulicznych i elektrohydraulicznych nie są i nie będą w spodziewanej przyszłości już wyczerpane, bowiem niemal każdy dzień przynosi informacje o nowych ich zastosowaniach. Nie ma więc żadnej przesady w stwierdzeniu, że nowoczesna technika automatyzacji i robotyzacji nie istniałaby bez hydraulicznych napędów i elektrohydrauli-cznych układów sterowania i regulacji. Andrzej Pizoń (1995 r.)
Układy hydrauliczne (ang. hydraulic systems, niem. Hydrauliksysteme), w których energia jest przenoszona za pomocą różnego rodzaju cieczy, dzielą się na dwie grupy: • układy hydrostatyczne (ang. hydrostatic systems, niem. hydrostatische Systeme), których działanie polega na wykorzystaniu energii potencjalnej, czyli ciśnieniowej cieczy, • układy hydrokinetyczne (ang. hydrokinetic systems, niem. hydrokinetische Systeme), których działanie polega na wykorzystaniu energii kinetycznej, czyli przepływowej cieczy.
Podział ten nie jest ścisły, bowiem w układach hydrostatycznych istnieją także pewne przepływy cieczy, czyli istnieje także energia kinetyczna. W układach hydrostatycznych udział energii kinetycznej jest jednak bardzo mały i najczęściej w praktyce pomijany. Stąd też powszechnie, choć nie całkiem poprawnie, nazywa się układy hydrostatyczne –układami hydraulicznymi.
Aktuator (ang. actuator, niem. Aktor, Aktuator) – urządzenie wykonawcze produktów i środków ich produkcji, przede wszystkim maszyn i systemów technologicznych, w którym energia pomocnicza jest zamieniana na energię mechaniczną przemieszczeń liniowych, kątowych lub obrotowych, wykonywanych powtarzalnie, najczęściej z działaniem siłowym lub momentowym.
Synonimiczną nazwą aktuatora w potocznym języku inżynierskim jest napęd (ang. drive, niem. Antrieb), np. napęd liniowy, kątowy lub obrotowy, napęd hydrauliczny, napęd elektrohydrauliczny itp.
Aktuatory hydrauliczne (ang. hydraulic actuator, niem. hydraulische Aktoren) są specjalizowanymi układami hydraulicznymi, przeznaczonymi do wykonywania zadań ruchowych połączonych z działaniami siłowymi lub momentowymi.
Aktuator hydrauliczny (ang. hydraulic actuators, niem. hydraulischer Aktor) w swej klasycznej, konwencjonalnej wersji jest zbudowany z trzech zespołów: • napędu tłokowego (ang. piston drive, niem. Kolbenantrieb), zamieniającego energię ciśnienia cieczy na energię ruchu, w dwóch podstawowych rozwiązaniach: siłownika (ang. cylinder, linear motor, niem. Zylinder,
Zylinderantrieb, Linearantrieb), nazywanego potocznie cylindrem, realizującego ograniczone jego długością lub objętością przemieszczenia liniowe lub kątowe o obrocie nieprzekraczającym 360° lub silnika (ang. engine, rotary motor, niem. Stellmotor,
Drehantrieb) realizującego przemieszczenia obrotowe o dowolnie dużej drodze kątowej, • zaworu sterującego (ang. control valve, niem. Steuerventil) kierunkiem i natężeniem przepływu cieczy do komór napędu tłokowego oraz wartością jej ciśnienia, • hydraulicznej stacji zasilającej (ang. hydraulic power supply, niem. Hydraulikstation) złożonej w najbardziej ogólnym rozwiązaniu ze zbiornika (ang. tank, reservoir, niem. Behälter), pompy hydraulicznej (ang. hydraulic pump, niem. Hydraulikpumpe), silnika pompy hydraulicznej (ang. hydraulic pump motor, niem. Hydraulikpumpenmotor), filtra (ang. filter, niem. Filter), zaworu ciśnieniowego (ang. pressure relief valve, niem. Druck-Begrenzungsventil) oraz akumulatora hydraulicznego (ang. hydraulic accumulator, niem. Hydraulikspeicher).
Napęd tłokowy jest też nazywany przetwornikiem energii aktuatora (ang. energy converter, niem. Energiewandler), zawór sterujący – nastawnikiem energii (ang. energy controller, niem. Energieregler), traktując oba te połączone elementy jako obiekt sterowania lub regulacji w układzie hydraulicznym.
Pomijając koła wodne (ang. water wheels, niem. Wasseräder), znane już w II w. p.n.e., w Polsce od XII w. i do czasów nam współczesnych stosowane, jednak najczęściej w postaci turbin elektrowni wodnych, to w obszarze hydrauliki pierwsze rozwiązania techniczne pojawiły się dopiero w XVII w. Zapoczątkował te prace Johannes Kepler (1571–1632), który około 1600 r. wynalazł hydrauliczną pompę zębatą (ang. hydraulic gear pump, niem. hydraulische Zahnradpumpe), ale nie potrafił wtedy pokazać jej praktycznego wykorzystania.
Rys. 1.
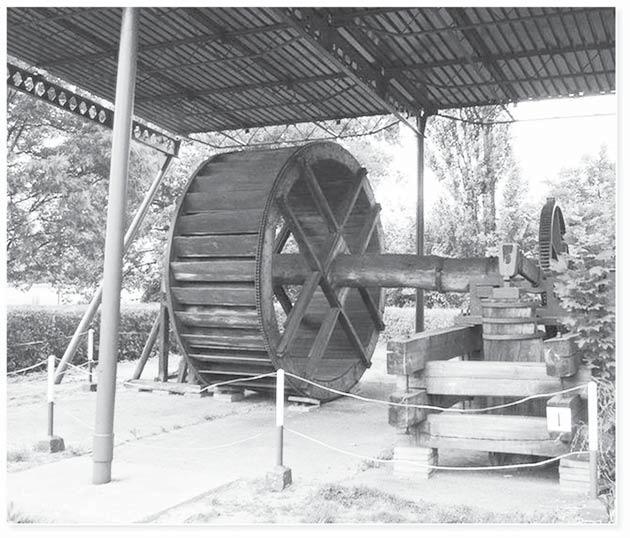
Bardziej istotne dla rozwoju hydrauliki okazały się prace dwóch wspomnianych już uczonych z XVII w.: Pascala, który w dziele Recit de la Grande Experience de l’Equilibre des Liquers sformułował trzy fundamentalne prawa hydrostatyki:
II. jeżeli na ciecz działają tylko siły powierzchniowe, to w każdym punkcie cieczy panuje jednakowe ciśnienie równe ciśnieniu zewnętrznemu,
III. ciśnienie w cieczy jest równe sile odniesionej do powierzchni jej działania na ciecz,
IIII. siła pochodząca od ciśnienia cieczy jest skierowana prostopadle do powierzchni ograniczających objętość tej cieczy
oraz wywiódł z tych praw koncepcję budowy prasy hydraulicznej oraz Bernoulliego, który w dziele Hydrodynamique podał równanie ruchu stacjonarnego cieczy idealnej (nazywane także równaniem ciągłości strumienia cieczy).
Pierwszą kompletną maszynę z napędem hydraulicznym buduje w Londynie w 1795 r. Joseph Bramah (1749–1814). Było to wykorzystanie podanej przez Pascala koncepcji przetworzenia ciśnienia w cieczy w siłę mechaniczną. Bramah stosował jako ciecz – wodę, ciśnienie w jej układzie wytwarzał początkowo za pomocą ręcznej pompy wodnej, w swojej pierwszej prasie korzystał jeszcze z drewnianej ramy konstrukcyjnej, ale wprowadził też jako pierwszy pierścienie uszczelniające między cylindrem, tłokiem lub nurnikiem prasy.
Pojawienie się silnika spalinowego (Benz, 1876 r.), upowszechnienie zastosowań silnika elektrycznego (Siemens, 1891 r.) oraz postępująca szybko rozbudowa elektrycznych sieci energetycznych zmniejszają zainteresowanie stosowania hydrauliki wodnej w napędach maszyn. Była to sytuacja identyczna jak w pneumatyce, która po euforii ogólnego, powszechnego zainteresowania jej wykorzystaniem w drugiej połowie XIX wieku, musiała znaleźć w pierwszej połowie XX wieku swoje nowe pola aplikacji, przestając być medium napędowym „do wszystkiego”.
W przypadku hydrauliki takim nowym, niezwykle ważnym, impulsem rozwojowym było wykorzystanie, zamiast wody, oleju mineralnego jako medium roboczego maszyn. Wodę jako medium robocze wprowadził Bramah i przez cały XIX w. była ona stosowana ze wszystkimi jej wadami, w tym przede wszystkim z objawami rdzewienia części stalowych, wydzielania się z niej powietrza, ograniczenia temperatury użytkowania i czasu eksploatacji tak napędzanych maszyn. Pierwsze udane próby z olejem mineralnym podjął Reynold Janney, budując przekładnię olejową dla nastawiania artylerii okrętowej na krążowniku USS Virginia w 1906 r.
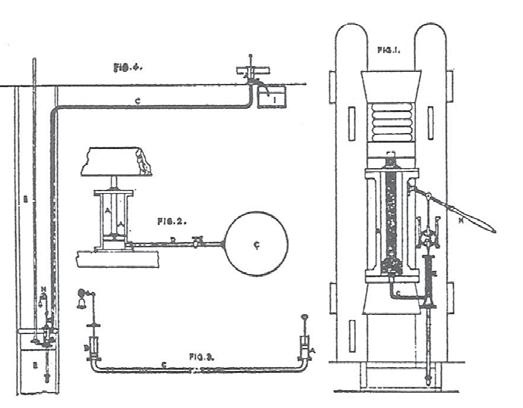

Rys. 3. Cooper & Hampton

W konstrukcji przekładni Janney korzystał z wcześniejszego, także bardzo istotnego dla rozwoju hydrauliki, opracowania efektywnych w działaniu hydraulicznych pomp osiowych. William Cooper patentuje mianowicie w 1893 r. i razem z George P. Hamptonem konstruuje w 1901 r. pierwszą tłokową, osiową pompę hydrauliczną.
Prawie równolegle do pojawienia się na przełomie stuleci rozwiązań osiowych maszyn hydraulicznych pracowano w latach 1901–1921 w szeregu amerykańskich i angielskich firm, m.in. Oil Gear Company, HPM, Vickers-Armstrong. Hele-Shaw, Thoma i Waterbury nad pompami, silnikami i przekładniami o budowie promieniowej, w tym już w powiązaniu z elektrycznym napędem silnikowym pomp, łącząc pompę, sterowanie zaworowe i cylindry hydrauliczne w zintegrowane jednostki napędowe.
W 1930 r. Benjamin Lassman wykorzystuje pomysł sterowania elektrycznego zaworami pneumatycznymi firmy Ross Operating Valve Company i uruchamia we współpracy z koncernem General Electric pierwszą w pełni zautomatyzowaną prasę elektrohydrauliczną z napędami przełączalnymi, stosując po raz pierwszy zawory elektrohydrauliczne. W 1936 r. Harry Vickers buduje pierwszy elektrohydrauliczny, dwustopniowy zawór ciśnieniowy.
Bezrobocie kryzysu lat 1929–1933, nazywanych Wielką Depresją Gospodarczą, nie wpłynęło na rozwój hydrauliki napędowej w tak katastrofalnym wymiarze, w jakim dotknęło to pneumatyki. Zaważyły na tej różnicy, między tymi dwoma technikami płynowymi, przygotowania do drugiej wojny światowej i produkcja ciężkiego sprzętu zbrojeniowego przed jej rozpoczęciem i w jej trakcie (pojazdy pancerne, artyleria, lotnictwo bojowe, okręty podwodne i nawodne), wymagające urządzeń i maszyn dysponujących nieosiągalnymi w pneumatyce i ówczesnej elektryce wydajnościami energetycznymi. Efektem był wyraźnie widoczny, także po zakończeniu wojny, postęp w rozwoju aktuatoryki hydraulicznej.
Rys. 4. Oil GearCompany)

Rys. 5.
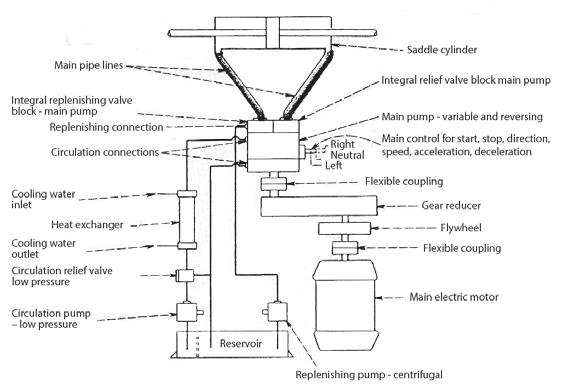
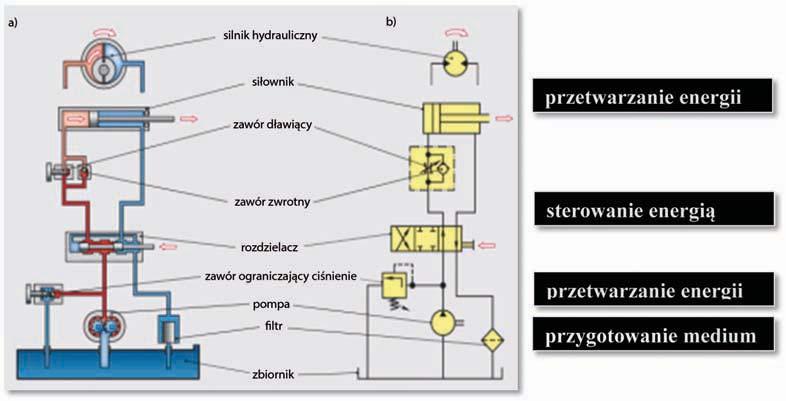
Rys. 6.
Problemem, z którym w bardzo różny sposób usiłowano się uporać w tych latach, był zapis projektów układów hydraulicznych i elektrohydraulicznych. W 1940 r. koncern General Motors Corporation sponsoruje Joint Industry Conference (JIC), która ustala symbolikę oznaczeń elementów hydrauliki, a potem we współpracy z American Society of Mechanical Engineers (ASME) i International Standards Organization (ISO) przenosi opracowaną symbolikę na elementy hydrauliczne i elektrohydrauliczne. Jednocześnie koncern Vickers rozpoczyna w swoich zakładach w Detroit kształcenie w dziedzinie hydrauliki, w 1945 r. zostaje uruchomiona pierwsza szkoła ze specjalnością aplikacji hydrauliki przemysłowej – Vickers Hydraulic School.
Kolejnym problemem, który pojawił się po wspomnianym wyżej, a wynikał z potrzeb unifikacji rozwiązań hydrauliki maszynowej, coraz powszechniej stosowanej w dwóch dekadach powojennego rozwoju gospodarczego, była standaryzacja podstawowych elementów hydrauliki. Było to żądanie przemysłu, który chciał wykorzystywać znane i oczywiście pojawiające się na rynku także nowe elementy pochodzące od różnych producentów, w budowie aktuatorów specjalizowanych na konkretne firmowe aplikacje maszynowe. Doskonałym świadectwem tych żądań były prezentowane na międzynarodowych targach przemysłowych w Chicago, w 1950 r., przełomowym wydarzeniu dla techniki maszynowej tych lat, liczne zastosowania pneumatyki i szczególnie hydrauliki w urządzeniach i maszynach produkcyjnych, roboczych, drogowych i budowlanych, komunikacyjnych, w tym samochodowych i lotniczych. Rozwiązania te były prawie bez wyjątku jednorodne konstrukcyjnie, było to specyfiką tych lat, bowiem, wobec braku sterowań elektrycznych, koniecznością było korzystanie dla realizacji złożonych zadań sterowania aktuatoryką z odpowiednio złożonych kombinacji zaworowych towarzyszących definicyjnemu siłownikowi i rozdzielaczowi.
Dobrym przykładem realizacji żądań przemysłu była standaryzacja w skali krajowej, a następnie normalizacja w skali europejskiej i międzynarodowej,konstrukcji podstawowego elementu aktuatoryki hydraulicznej, tzn. siłownika (cylindra) hydraulicznego. Objęła ona rozwiązania: tłokowe o ruchu liniowym, z dwustronnym i jednostronnym tłoczyskiem,
Rys. 7.

Rys. 8.
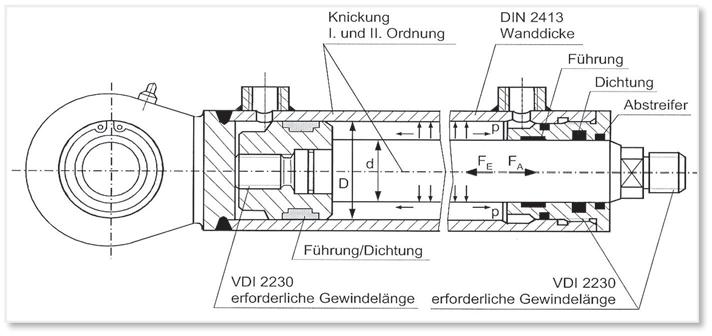
tłokowe o ruchu obrotowym (wahadłowym), nurnikowe, teleskopowe, wiążąc, w zależności od długości i smukłości (średnicy) cylindra siłownika i związanej z nimi średnicy tłoczyska, także od sposobu mocowania cylindra oraz zagrożenia wyboczeniem tłoczyska: • długość i średnicę cylindra i tłoczyska siłownika z obciążeniem siłowym tłoczyska oraz określając kształty konstrukcyjne cylindra i jego dwóch pokryw, tłoka i tłoczyska, otworów i gwintów mocujących i łączących, uszczelnień i prowadzeń elastycznych, także w zależności od obecności i rozwiązania zespołu amortyzacji dobiegu tłoka do pokryw.
Przełomową, i to w znaczeniu globalnym, innowacją w obszarze szeroko rozumianej techniki maszynowej, było opracowanie przez Billa Mooga w 1948 r. dwustopniowego serwozaworu elektrohydraulicznego, zamieniającego analogowy sygnał elektryczny w odpowiednio proporcjonalne przemieszczenie suwaka zaworu rozdzielającego przepływy do komór cylindra hydraulicznego. Moog połączył ten proces z dławieniem przepływów (ang. throttling of flows, niem. Strömungswiderstände) na krawędziach suwaka i otworów w tulejach korpusu zaworu, co pozwoliło na sterowanie prędkością ruchu tłoka i jego zatrzymanie, czyli pozycjonowanie, w dowolnym położeniu między pokrywami cylindra siłownika hydraulicznego. Pozwoliło to na produkcję i powszechność aplikacji elektrohydraulicznych aktuatorów serwomechanizmowych.
Następstwem tych działań staje się już w drugiej połowie lat 50. XX w. istotne poszerzenie obszaru aplikacji elektrohydraulicznej aktuatoryki serwomechanizmowej na większość rozwiązań oferowanych w szeroko rozumianym przemyśle maszynowym. Istotą tej innowacji było zmniejszenie kłopotliwie licznych sterowań zaworowych, koniecznych, jak już to wspomniano, w jednorodnych rozwiązaniach aktuatoryki hydraulicznej. Korzystają z tych nowych możliwości bezpośredniego wpływania przez kształtowanie przebiegu i wartości wejściowego sygnału elektrycznego serwozaworu, na zacho-

Rys. 9.
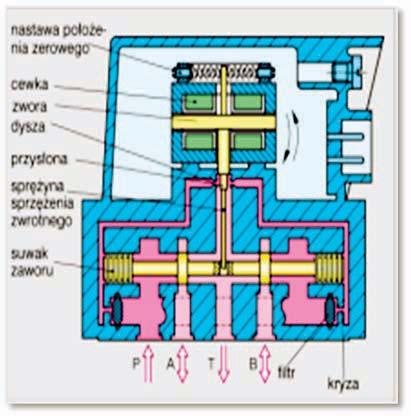
wanie pozycyjne i siłowe siłownika, jako pierwsze przemysły obrabiarkowe i lotnicze.
Szczególnie istotnym dla rozwoju aplikacji aktuatoryki elektrohydraulicznej był 1954 r. Były to dwa wydarzenia: uruchomienie w Stanach Zjednoczonych produkcji przemysłowej obrabiarek numerycznie sterowanych (NC) z elektrohydraulicznym napędem serwomechanizmowym.
Było to bezpośrednim następstwem dwóch wcześniejszych w stosunku do 1954 r. osiągnięć technicznych: wspomnianego już opracowania i uruchomienia przez
Mooga produkcji dwustopniowych serwozaworów rozdzielających, przetwarzających ciągłe sygnały elektryczne na pozycjonowany ruch tłoka cylindra hydraulicznego, jeszcze wcześniejszego, bo z 1927 r., opanowania przez
Pfleumera, zapisu sygnałów elektrycznych przez głowice magnetyzujące na taśmie magnetycznej.
Obrabiarki numeryczne znane już były od 1949 r., (MIT Cambridge Massachusetts), jednak jako maszyny z napędem elektrycznym, w praktyce wyłącznie z silnikami krokowymi (skokowymi), sterowanymi początkowo w pętli otwartej, o wydajności energetycznej 7,5–15,0 kg/kW, zdecydowanie poniżej wydajności energetycznej napędu hydraulicznego z tych lat, czyli 0,15–1,5 kg/kW, odnosząc wydajność do masy tych dwóch rodzajów napędów. W Europie obrabiarki NC z elektrohydraulicznym napędem serwomechanizmowym pojawiają się w 1961 r., w Polsce, prawie bez opóźnień do wymienionych regionów, także w pierwszej połowie lat 60. XX w. Upowszechniło to już w kolejnych dekadach lat rozwoju techniki maszynowej stosowanie napędu elektrohydraulicznego także w innych jej działach, obok maszyn obróbczych, głównie w wymagających bardzo dużych wydajności energetycznych maszynach roboczych, stacjonarnych i mobilnych;
Rys. 10. Sheffer Corporation opracowanie i opatentowanie przez George Devola programowalnej maszyny manipulacyjnej, nazwanej przez niego
Unimation(od nazwy firmy Universal Automation). Opracowanie jej było także bezpośrednim następstwem dwóch wspomnianych już wcześniejszych, w stosunku do 1954 r., osiągnięć technicznych, które skutkowały opracowaniem obrabiarek NC. Po kilku perypetiach finansowych i inwestycyjnych Devol odstąpił swój patent firmie kierowanej przez Josepha Engelbergera, który w Danbury (Connecticut) rozpoczyna przygotowanie tego projektu do zastosowań przemysłowych, ale pod inną nazwą – Unimate.
Pierwsze, technicznie nieudane zastosowanie robotów
Unimate ma miejsce w 1961 r. zakładach General Motors – do obsługi ciśnieniowej maszyny odlewniczej. Od 1962 r.
Engelberger próbuje zastosowań przemysłowych tych robotów, tym razem już udanych, m.in. również w zakładach General Motors – w 1968 r. udaje mu się umieścić w przemyśle po raz pierwszy 48 sztuk robotów.
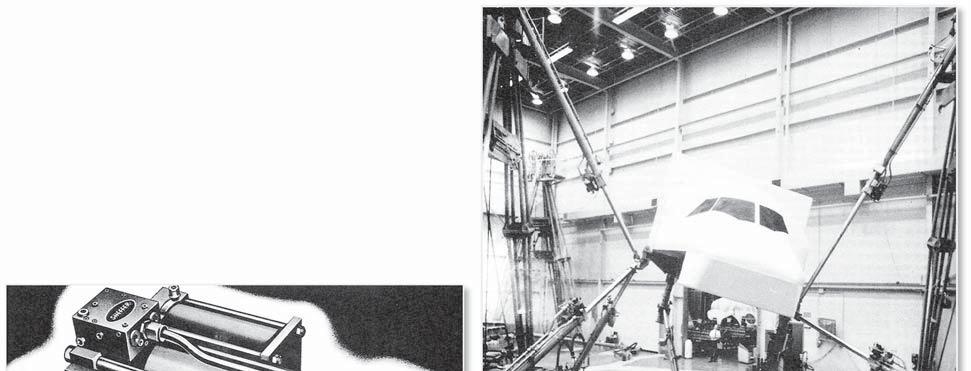
Trzydziestolecie lat 60.–80. XX w. to okres intensywnej optymalizacji już znanych i równie intensywnych poszukiwań nowych rozwiązań aktuatoryki elektrohydraulicznej, zdolnych konkurować z szybko wkraczającymi do techniki maszynowej elektrycznymi serwomechanizmami silnikowymi. Silniki te w połączeniu z różnymi przekładniami ruchu, głównie z przekładniami śrubowymi, doskonale imitowały hydrauliczne napędy siłownikowe i np. we współczesnej robotyce wyparły prawie całkowicie ich zastosowania.
Ośrodkiem, który wywarł największy wpływ na rozwój nowoczesnej aktuatoryki elektrohydraulicznej, nie tylko w skali europejskiej, ale także i światowej, był kierowany przez profesora Wolfganga Backé Institut für hydraulische und pneumatische Antriebe und Steuerungen der RWTH Aachen (Instytut Hydraulicznych i Pneumatycznych Napędów i Stero-
a)

a)
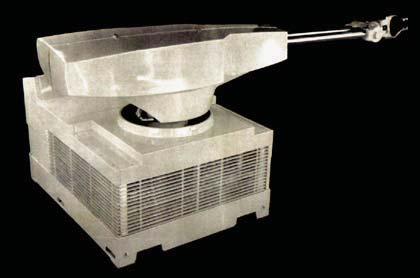

Rys. 11. Unimate Unimation Versatran Division of American Machine and Foundry Corporation Forda wania Reńsko-Westfalskiej Politechniki w Akwizgranie). Backé, nazywany ojcem niemieckiej techniki płynowej, od swojej rozprawy habilitacyjnej w 1962 r., razem ze swoimi przeszło trzydziestoma doktorantami, dokonał istotnego przełomu w podejściu do opisu zachowań dynamicznych elementów hydrauliki technicznej, potwierdzając zaawansowaną systematykę i teorię tego opisu licznymi eksperymentami w doskonale wyposażonym laboratorium i równie licznymi aplikacjami przemysłowymi nowych, także opracowanych i wykonanych w Instytucie rozwiązań. Tezy swoich zakończonych i proponowanych dokonań Backé zawarł w wydanej w 1974 r. monografii Systematik der hydraulischen Widerstandsschaltungen in Ventilen und Regelkreisen.
W latach przełomu XX i XXI wieku kierownictwo akwizgrańskiego Instytutu przejął jego wychowanek, Hubertus Murrenhoff, kładąc z kolei nacisk na cyfryzację i komputeryzację techniki płynowej, a na marginesie swej działalności wspierał, razem, z Backé, organizowane, w tym milenijnym okresie czasu, przez Instytut Automatyki i Robotyki Politechniki Warszawskiej Polsko-Niemieckie Seminaria „Innowacje i postęp w hydraulice i pneumatyce” (Deutsch-Polnische Seminare „Innovation und Fortschritt in der Fluidtechnik”).
Do głównych osiągnięć prac badawczych i rozwojowych wspomnianego już trzydziestolecia XX w. należy zaliczyć: opracowanie dwóch zasad budowy elektrohydraulicznych aktuatorów serwomechanizmowych, nazywanych inżyniersko: aktuatoryką dławieniową (ang. throttling actuatorics, niem. Widerstandsaktorik), polegająca na stosowaniu w stacji zasilającej pompy hydarulicznej wytwarzającej stałe natężenie przeplywu (nazywane wydajnością pompy) i nastawnika energii – elektrohydraulicznego
Rys. 12. R X A Unimate Unimation R R i lokalnych AL L R L


Rys. 13. T3 Cincinnati Milacron R L L L
serwozaworu umożliwiającego dławienie przepływu dostarczanego do komór przetwornika energii, silownika lub silnika hydraulicznego oraz aktuatoryką wyporową lub objętościową (ang. volumetric actuatorics, niem. Verdrängungs- lub Volumen- aktorik), polegająca na usunięciu z ukladu aktuatora elektrohydraulicznego zaworu dławiącego i zastąpieniu go sterowaną wydajnościowo pompą hydaruliczną, (ang. variable displacement pump, niem. Verstellpumpe), wytwarzającą zmienne, dostosowane do aktualnych potrzeb energetycznych aktuatora, natężenie przeplywu dostarczanego do komór przetwornika energii, siłownika lub silnika hydraulicznego, wprowadzenie jednostopniowego serwozaworu dławiącego, wykorzystując dla bezpośredniego sterowania ruchem suwaka zaworu elektryczne silniki liniowe lub obrotowe, pracujące w układzie regulacji jego położenia, zamiast silników momentowych wykorzystywanych jako przetworniki elektromechaniczne stopnia wejściowego serwozaworów konstruowanych według zasady podanej przez Mooga w 1948 r. Powodem były wysokie koszty tych serwozaworów, kłopoty eksploatacyjne związane z wymaganiami wysokiej czystości stosowanego medium (pierwszy stopień tych zaworów pracował w układzie kaskady hydraulicznej) oraz ich słaba dynamika wynikająca z dwustopniowości działania. Te

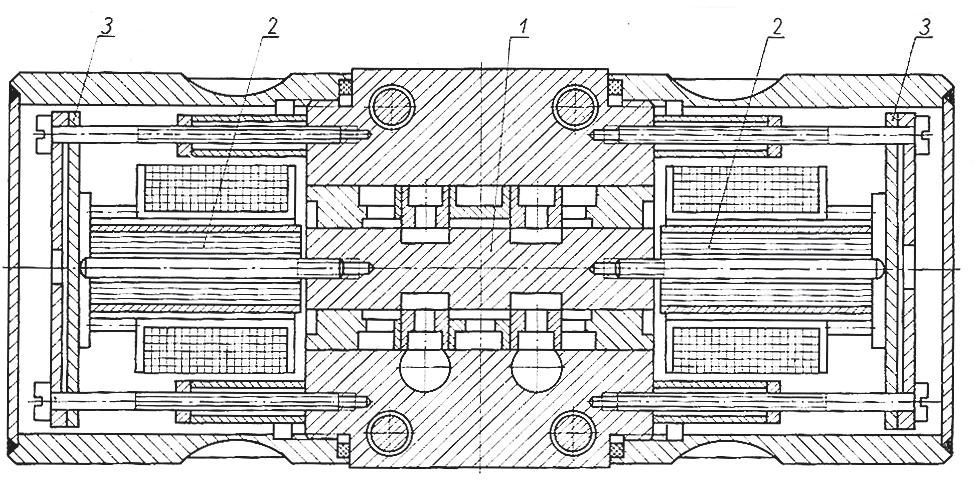
Rys. 15. Centralne Biuro Konstrukcji Obrabiarek w Pruszkowie,

nowe, jednostopniowe rozwiązania zaczęto nazywać od ich sterowania proporcjonalnymi zaworami rozdzielającymi, rozdzielaczami proporcjonalnymi lub serwozaworami proporcjonalnymi (ang. proportional valves, servovalves, niem. proportionale Wegeventile, direkte Servoventile). Zawory proporcjonalne, stały się szybko konkurencją dla serwozaworów dwustopniowych, pozwalając na budowanie nowych konstrukcji maszyn obróbczych i roboczych z napędem hydraulicznym. Warto tu przypomnieć jeszcze raz o pionierskości polskich rozwiązań zaworów proporcjonalnych, opracowanych już w pierwszej połowie lat 60. XX w., kolejnym nowym rozwiązaniem, istotnym na przełomie lat 70. i 80. XX w. (warto tu wspomnieć o światowym kryzysie energetycznym tych lat), stało się zaproponowane ze względu na możliwość oszczędności energii rozwiązanie tzw. Load-Sensing (pol. dopasowanie wydajności do obciążenia, niem. Load-Sensing). Istota tego rozwiązania polegała na sterowanym dopasowaniu wydajności pompy zasilającej kilka aktuatorów elektrohydraulicznych do aktuatora z najbardziej obciążonym serwonapędem dławieniowym. Warunkiem jest tu oczywiście zastosowanie pompy o sterowanej wydajności, przy czym w wymienionych latach nastawa wartości ciśnienia sterującego aktuatorem wydajności pompy musiała być realizowana przez szeregowe połączenie specjalizowanych hydraulicznych zaworów, nazywanych przełącznikami obiegu. Obecnie jest to oczywiście realizowane przez zastosowanie sensoryki i elektronicznego sterowania procesorowego,
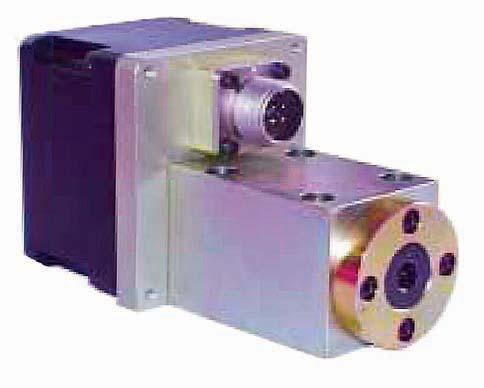
Rys. 16. Torque Schneider)
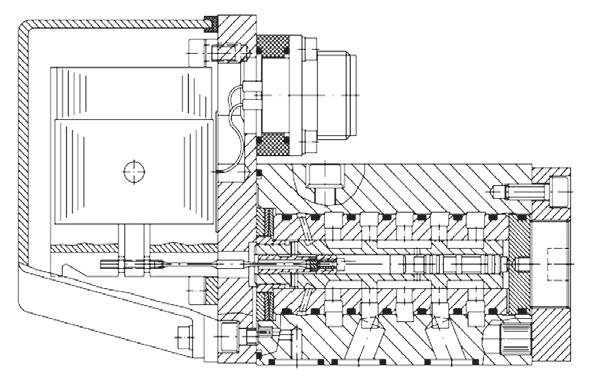
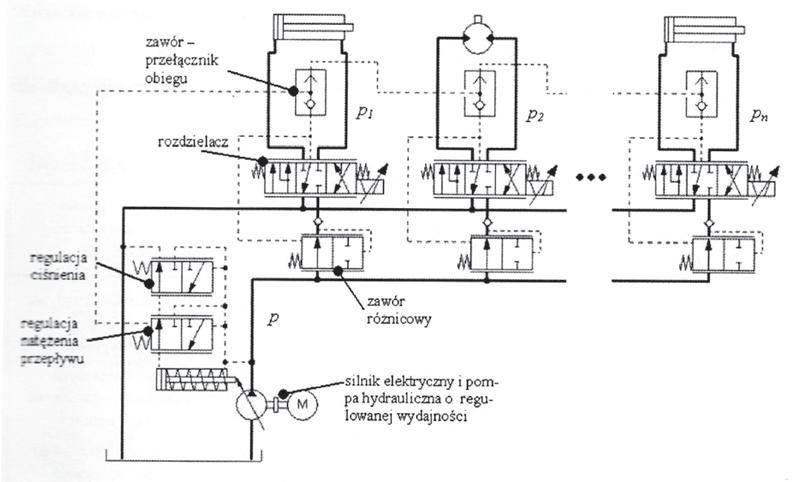
Rys. 17. Load-Sensing z lat
Rys. 18. Institut für hydraulische und pneumatische Antriebe und Steuerungen, der RWTH Aachen)
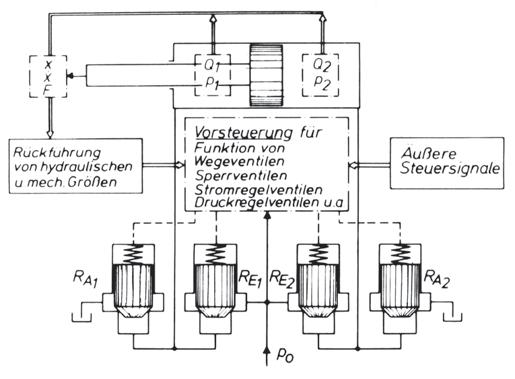
przełomowym w swym innowacyjnym znaczeniu dla całej techniki płynowej, ale niewykorzystanym jeszcze w praktyce hydrauliki przemysłowej omawianego okresu czasu, było opracowanie przez Wolfganga Backé podstaw budowy zaworów rozdzielających w układzie czwórnika mostkowego, z wykorzystaniem czterech zaworów dwudrogowych (w potocznym uproszczeniu inżynierskim nazywane w języku ang. cartridge, w niem. Kartridge, Patrone, także Cartridge). Ten mostkowy układ pozwalał bowiem na zastąpienie trudnej do wykonania, bardzo kosztownej, pary suwak i tuleja konwencjonalnego zaworu suwakowego, zaworem czwórnikowym, przy czym te zawory mogły pełnić zarówno funkcje rozdzielające – jako rozdzielacz, jak i funkcje dławiące – jako serwozawór. Dławienie przepływów (ang. throttling of flows, niem. Strömungswiderstände) na krawędziach suwaka i otworów w tulejach korpusu zaworu konwencjonalnego zostało po prostu zastąpione działaniem łatwych do wykonania
zaworów dwudrogowych, np. w wykonaniu gniazdowym, W porównaniu z zaworami suwakowymi, których głównymi wadami są wrażliwość na zanieczyszczenia cieczy roboczej oraz luzy promieniowe suwaka i tulei powodujące przecieki nawet w stanie zamknięcia, zawory gniazdowe są szczelne i praktycznie niewrażliwie na zanieczyszczenia cieczy roboczej, nie do pominięcia jest fakt podjęcia w omawianym trzydziestoleciu XX w. przez szereg ośrodków badawczych i przemysłowych, zajmujących się hydrauliką techniczną, problematyki sterowania pozycyjnego, nazywanego także sterowaniem położeniowym (ang. position control, niem. Lagesteuerung) w aktuatoryce hydraulicznej i elektrohydraulicznej – były to, i nadal są współcześnie stosowane, opisane niżej, rozwiązania tej problematyki przed 1948 r., tzn. przed opracowaniem przez Mooga serwozaworu elektrohydraulicznego i w następnym dziesięcioleciu jego upowszechnieniem, wykorzystywano wyłącznie sterowanie przestawne albo punktowe (ang. point control, niem. Punktsteuerung), polegające na doprowadzeniu tłoka siłownika aktuatora do pozycji żądanej i jego zatrzymaniu w tej pozycji, z dokładnością wynikająca z jakości przełączenia sensora położenia punktowego i opóźnienia w torze sterowania, przede wszystkim czasu przełączenia zaworu rozdzielającego, zastosowanie elektrohydraulicznych serwozaworów pozwoliło na przejście do zdecydowanie bardziej zaawansowanego sposobu sterowania, a w terminologii automatyki bardziej poprawnie, do regulacji pozycyjnej lub położeniowej (ang. (analog lub digital) position control, niem. Lageregelung), pozwalającej na stosowanie zarówno pozycjonowania przestawnego, jak i nadążnego, polegającego na realizacji przemieszczenia tłoka siłownika aktuatora według zadanej trajektorii zmian wielkości regulowanej, prędkości lub położenia w czasie tego procesu. Była to w praktyce najczęściej tzw. rampa, tzn. liniowy wzrost wartości tego parametru, utrzymania go przez pewien czas na stałej
a) c)
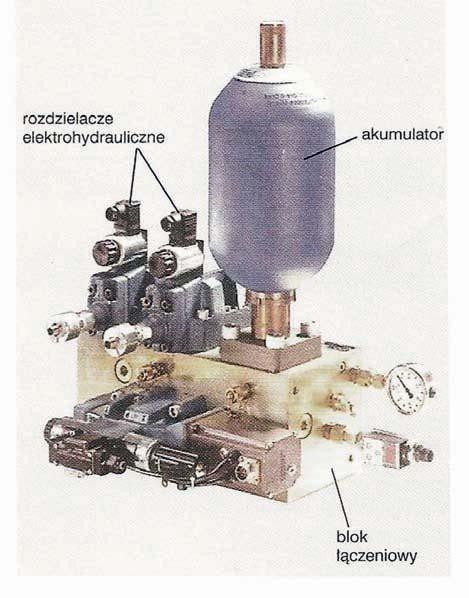
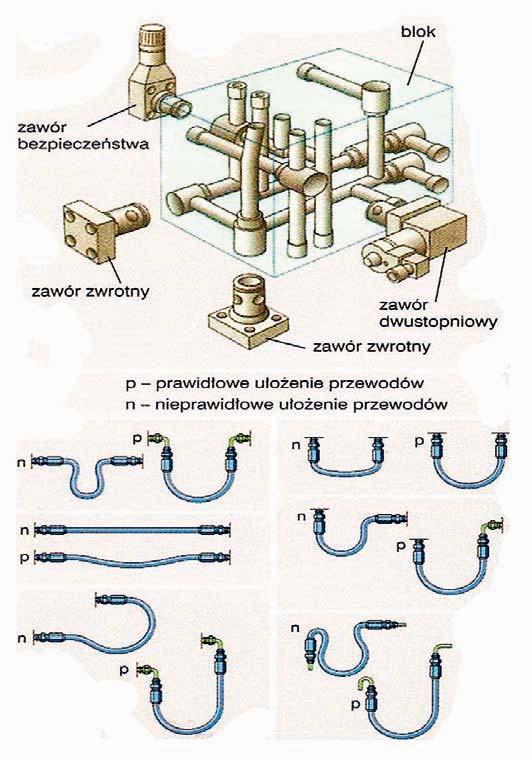
wartości i następnie liniowe zejście z tej wartości do zadanej pozycji. W początkowym okresie stosowania, w latach 60. XX w., korzystano z regulatorów proporcjonalnych (ang. proportional regulator lub P-controller, niem. Proportionalregler lub P-Regler). Ten typ regulatora zapewniał stabilną pracę aktuatora, jednak nie eliminował odchyłki statycznej, szczególnie dużej dla małych wartości wzmocnienia regulatora i słabo kompensował pojawiające się w czasie pracy aktuatorów hydraulicznych zakłócenia, powodowane zmianami wartości ciśnienia i temperatury medium roboczego oraz obciążeń masowych i siłowych aktuatora,
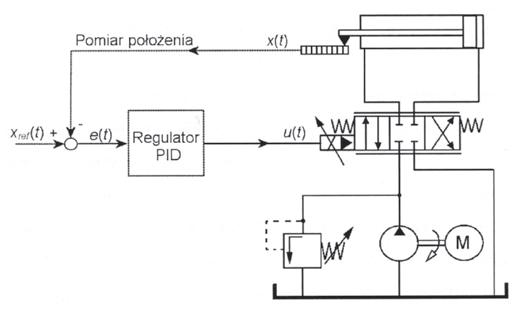
Rys. 19.
było to powodem zainteresowania, w latach 70. i 80.
XX w., wprowadzenia regulacji pozycyjnej typu PI lub
PD, ogólnie regulacji PID (ang. proportional-integral-derivative (action) control, niem. Proportional-Integral-Differential-Regelung). Pierwsza (PI) eliminuje odchyłkę statyczną, jednak w przypadku obiektu regulowanego o transmitancji zawierającej całkowanie, a jest to nieuniknione w przypadku napędów siłownikowych i silnikowych, skutkuje niestabilnością w postaci oscylacji wokół osiągniętej pozycji zadanej. Próbowano to wyeliminować przez wyłączanie całkowania w wybranej strefie wokół wartości zadanej, co eliminowało oscylacje, ale z kolei ustawiało odchyłkę na wybranej wartości tej strefy wyłączenia. Drugi typ regulacji, z różniczkowaniem (PD), zapewniał możliwość powiększenia wartości wzmocnienia proporcjonalnego, czyli pożądanego zmniejszenia odchyłki statycznej, był jednak obarczony ryzykiem wystąpienia nieakceptowanego, w przypadku większości zadań aktuatorów przemysłowych, przeregulowania.
Na przełomie lat 80. i 90. XX w. obszar aplikacji aktuatoryki hydraulicznej i elektrohydraulicznej objął zdecydowaną większość napędów maszyn mających związek z przemieszczeniami dużych i bardzo dużych mas (rzędu setek i tysięcy kg) i to mimo rosnącej szybko w tym czasie konkurencji nowoczesnych napędów elektrycznych i serwoelektrycznych.

Rys. 21.

Z jej właściwości korzystają m.in. przemysły: hutniczy, metalurgiczny, obrabiarkowy, maszynowy, stoczniowy, transportowy, zbrojeniowy, nawet lotniczy. Do tych szczególnie cenionych przez praktykę przemysłową właściwości zalicza się: kilkakrotnie większą w porównaniu z innych rodzajami napędów wydajność energetyczną odnosząc ją do masy i objętości aktuatorów – dla porównania ograniczając się do silników są to wartości: – silnik hydrauliczny 0,1–1,5 kg/kW, – silnik elektryczny 7,5–15,0 kg/kW, – silnik spalinowy benzynowy 1,0–3,0 kg/kW, – silnik spalinowy, olejowy, wysokoprężny 3,0–9,0 kg/kW, sterowanie przetwarzaniem energii: bezpośrednie w napędach hydraulicznych, przekładniowe w napędach elektromechanicznych i spalinowych, zarówno średniej, jak i dużej mocy, doskonałe właściwości dynamiczne wynikające z małych mas i momentów bezwładności elementów ruchomych, bezprzekładniowe sterowanie prędkością ruchu w bardzo szerokim zakresie jej wartości, możliwość dobrego, w porównaniu do napędów mechanicznych i elektromechanicznych, odprowadzania i doprowadzania ciepła przez medium cieczowe, doskonałą odporność na duże przeciążenia masowe, siło-


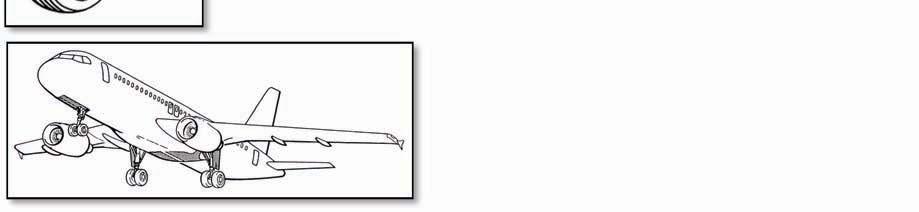
Rys. 23. sterowanie lotem

we i momentowe, w tym łatwy rozruch silnie obciążonych efektorów maszyn roboczych, zwłaszcza drogowych i budowlanych, możliwość wykorzystania cylindrów siłowników hydraulicznych jako wspomagających elementów konstrukcyjnych mechanizmów maszyn.
Kolejnym etapem ewolucji aktuatoryki hydraulicznej stała się na milenijnym przełomie lat jej intensywna mechatronizacja.
Rys. 24. W pierwszych dwóch dekadach XXI w. działania te objęły elektronizację, informatyzację i internetyzację rozwiązań hydraulicznych. Aktuatoryka elektrohydrauliczna stała się więc aktuatoryką hydrotroniczną i jednocześnie równouprawnioną, w stosunku do innych technik napędowych, składową procesu Transformacji Przemysłowej 4.0.
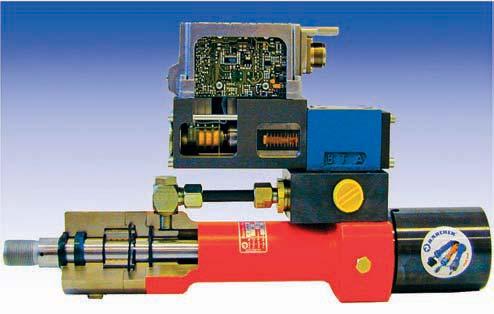
1. Backé W., Grundlagen der Őlhydraulik, RWTH Aachen,
Aachen 1972. 2. Backé W., Proportionaltechnik.. RWTH Aachen, Aachen 1993. 3. Backé W., Servohydraulik. RWTH Aachen, Aachen 1992. 4. Backé W., Systematik der hydraulischen Widerstandsschaltungen in Ventilen und Regelkreisen. Krausskopf-Verlag, Mainz 1974. 5. Backé W., Über die dynamische Stabiliaät hydraulischer Steuerungen unter Berücksichtigung der Strömungskräfte. Habilitationsschrift der RWTH Aachen, Aachen1962. 6. Banaś M., Stryczek J., Eine neue hydrostatische Anlaufkupplung.
Bauweise und Simulation des Anlaufes. Viertes Deutsch-Polnisches
Seminar Innovation und Fortschritt in der Fluidtechnik, TU Warschau, Fakultät für Mechatronik, Warszawa-Sopot 2001, 57–68. 7. Banaś M., Stryczek J., Hydrostatic Coupling as a Rotational
Speed Changer. Fünftes Deutsch-Polnisches Seminar Innovation und
Fortschritt in der Fluidtechnik, TU Warschau, Fakultät für Mechatro- nik, Warszawa 2003, 65–80.
8. Banaś M., Stryczek J., The Design and Modelling of the Drive System with Mulitifunctional Hydrostatic Machine. Proc. of the 5th International Fluid Power Conference, Shaker Verlag, Vol. 1, Aachen 2006, 399–408. 9. Dindorf R., Modelowanie i symulacja nieliniowych elementów i układów regulacji napędów płynowych. Wydawnictwo Politechniki Świętokrzyskiej, Kielce 2004. 10. Dindorf R., Napędy płynowe. Wydawnictwo Politechniki Świętokrzyskiej, Kielce 2009. 11. Guillon M., L’asservissement hydraulique et elektrohydraulique. V. I–II,
Paris 1972. 12. Helbig A., Kunstoff-Spritzgießmaschine mit drehzahlveränderbaren
Pumpen. Dissertation (Referent S. Helduser),vTechnische Universität
Dresden, Dresden 2005. 13. Helduser S., Antriebstechnik / Aktorik. Grundlagen der elektrohydraulischen Antriebstechnik. Technische Universität Dresden, Dresden 2009. 14. Helduser S., Fluidtechnische Antriebe und Steuerungen. Technische
Universität Dresden, Dresden 2004. 15. Helduser S., Mednis W., Olszewski M., Elementy i układy hydrauliczne. Oficyna Wydawnicza Politechniki Warszawskiej, Warszawa 2009. 16. Helduser S., Układy hydrauliczne. Oficyna Wydawnicza Politechniki warszawskiej. Warszawa 2000, 17. Mednis W., Hydrauliczne napędy i ich sterowanie. Oficyna Wydawnicza Politechniki Warszawskiej, Warszawa 1999. 18. Mierzejewski J., Serwomechanizmy obrabiarek sterowanych numerycznie. WNT, Warszawa 1977. 19. Neubert Th., Drehzahlveränderbarer Verstellpumpenantrieb in
Kunstoff-Spritzgießmaschinen. O+P „Őlhydraulik und Pneumatik”,4592001)10, 654-659. 20. Olszewski M., Cyfryzacja aktuatoryki pneumatycznej. Pneumatyka
Część I. „Automatyka”, 5–6(2020), 135–149. 21. Olszewski M., Elektryczne napędy i serwonapędy siłownikowe. „Automatyka”, 1–2(2018), 105–110. 22. Olszewski M., Helduser S. i in., Intelligent Control for High-Speed Injection Moulding Machine (ICON-HISIM). Raporty do Europejskego
Projektu STREP, 6. PR UE, 2004–2009. 23. Olszewski M., Hemer B., Model-following System – Developed Conception of Control for Weakly Damped Fluid Drives. 3rd Bath International Fluid Power Workshop, Research Studies Press, Oxford 1990, 192–197. 24. Olszewski M., Mechatronika. „Automatyka”, 1–2(2018), 97–99. 25. Olszewski M., Mechatronizacja produktu i produkcji – przemysł 4.0.
“Pomiary Automatyka Robotyka”, 3(20): 6–28, 2016. 26. Olszewski., Mednis W., Winnicki A., Wiśniewski P., Niektóre ograniczenia zastosowania przetwornic częstotliwości w napędach elektrohydraulicznych. Konferencja Automation 2006. Warszawa 2006, 432–438. 27. Olszewski., Mednis W., Wiśniewski P., Displacement and Throttle
Control of Electrohydraulic Servo Drive. 4. International Fluid Power
Conference, Dresden 2004, 83–90. 28. Olszewski M., Napędy pneumatyczne i hydrauliczne w budowie manipulatorów i robotów przemysłowych. I Krajowa Konferencja Robotyki,
Wrocław 1985. Zesz. Nauk. Polit. Wrocławskiej 67(1985), 89–108. 29. Olszewski M., Rozwój robotyki. Robotyka Część I. „Automatyka”, 3(2019), 159–168. 30. Olszewski M., Self-tuning & Model-following Control System for Weakly Damped Fluid Drives. Community’s Action for Coop. in Science and Technol. with Central and Eastern Europ. Countries, Project &
Report No CIPA3510PL923566, 1993. 31. Olszewski M., Winnicki A., Analiza sprawności hydraulicznych układów zasilających w stanach dynamicznych. Acta Hydraulica et Penumatica, 1(2005), 74–77. 32. Olszewski M., Winnicki A., Remarks about Stiffness of the Hydraulic
Actuators. Conference „Hydraulics and Pneumatics’2004”, Svit 2004, 181–185. 33. Olszewski M., Winnicki A., The Analysis of Efficiency of HydraulicSystem Electrical Motor-Pump in Dynamic States of Operation. Hydraulika a Pneumatika, 21(2006). 24–25. 34. Olszewski M., Współczesna robotyka. Robotyka Część III. „Automatyka”, 9(2019), 89–107. 35. Pachnick M., Analyse hydraulischer Regelkreise unter besonderer Berücksichtigung von Übertragungsfunktions-Nullstellen und
Poldominanzen. Dissertation (Referent W. Backé), RWTH Aachen,
Aachen 1994. 36. Piątek Z., Rynek kilku prędkości. Badanie krajowej branży dystrybucji elementów wykonawczych. „apa -Technika i Rynek Systemów
Automatyki”, 3(125): 154–166, 2017. 37. Pippenger J.J., Fluid Power – the Hidden Giant. Amalgam Publishing
Company, Jenks 1992. 38. Pizoń A., Elektrohydrauliczne analogowe i cyfrowe układy automatyki.
WNT, Warszawa 1995. 39. Rühlicke I., Elektrohydraulische Antriebssysteme mit drehzahlveränderbarer Pumpe. Dissertation (Referent S. Helduser), Technische
Universität Dresden, Dresden 1997. 40. Shearer J.L. et al., Fluid Power Control. Wiley, New York 1960. 41. Stryczek J., Fundamentals of Designing Hydraulic Gear Machines.
Wydawnictwo Naukowe PWN, Warszawa 2020. 42. Stryczek J., Podstawy projektowania hydraulicznych maszyn zębatych.
Wydawnictwo Naukowe PWN, Warszawa 2018. 43. Stryczek S., Napęd hydrostatyczny. WNT, Warszawa 2014. 44. Winnicki A., Odporne na zakłócenia ślizgowe sterowanie pozycyjne napędu elektrohydraulicznego. Rozprawa doktorska (promotor M.
Olszewski), Politechnika Warszawska, Warszawa 2013. 45. Winnicki A., Olszewski M., Focus on Safety Requirements in the Pneumatic and Hydraulic Machines. „Hydraulika a Pneumatika”, 27(2010), 57–61. 46. Winnicki A., Olszewski M., Sterowanie ślizgowe w zastosowaniu do serwonapędu elektrohydraulicznego. „Pomiary Automatyka Robotyka”, 11(2010), 116–119. 47. Winnicki A., Olszewski M., Rapid Control Prototyping of a Electro-hydraulic Drive System Using dSpace and Mathworks Simulink. “Hydraulika a Pneumatika”, 28(2011), 4–6. 48. Winnicki A., Olszewski M., Analysis of Energy Efficiency for Throttle and Dispacement Hydraulic Servo System, “Hydraulika a Pneumatika”, 28(2012), 19–21. 49. Wiśniewski P., Wnuk P., Winnicki A., Olszewski M., Lineárne riadenie vytlakového polonu na príklade modelu vstrekovacieho stroja. “Hydraulika a Pneumatika”, 25(2008), 36–38. 50. Wiśniewski P., Winnicki A., Olszewski M., Properties of Electrohydraulic Dispacement Drives. International Conference „Hydraulics and Pneumatics”, Terchová 2006; “Hydraulika a Pneumatika”, 22(2006), 34–36. 51. Wiśniewski P., Winnicki A., Wnuk P., Olszewski M., Linear Control of Electrohydraulic Injection Moulding Machine. “Pomiary
Automatyka Kontrola”, 55(2009), 178–182. 52. Wiśniewski P., Winnicki A., Wnuk P., Olszewski M., Experimental Tests of Linear Control of Electrohydraulic Injection Moulding
Machine. Hydraulika a Pneumatika, 26(2009), 47–50.
Technologie i ludzie
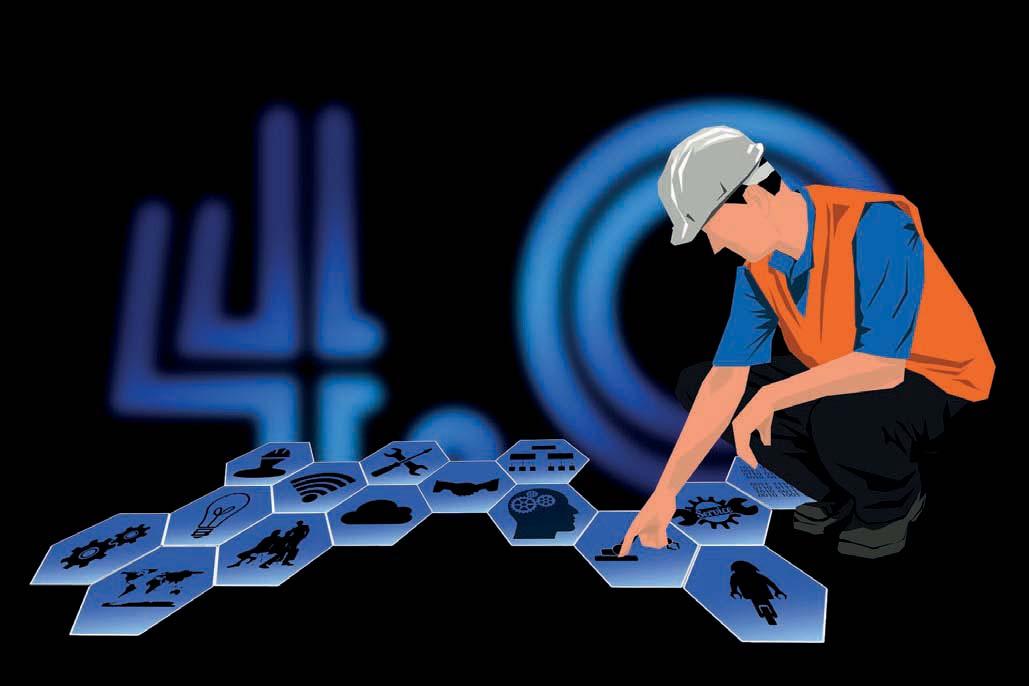
Urszula Chojnacka AUTOMATYKA
andemia COVID-19 przyspieszyła tylko to, co i tak było od dawna przesądzone – rozwój pracy zdalnej na masową skalę. Zmierzenie się z tym wyzwaniem było łatwiejsze dla tych, którzy są już za pan brat z nowoczesnymi technologiami. Zaawansowane, a jednocześnie często intuicyjne i łatwe w obsłudze narzędzia technologiczne umożliwiają wydajną i efektywną pracę zdalną, a pracownicy coraz częściej pracują i szkolą się w tym samym środowisku, korzystając z platform wirtualnej rzeczywistości. Teraz przyszedł czas, by spróbować odpowiedzieć na pytanie: co dalej? Sztuczna inteligencja Wyniki badania nie pozostawiają wątpliwości – w najbliższych latach będzie rządziła sztuczna inteligencja. Blisko 3/4 pracowników na różnych szczeblach uważa, że zapewni ona wyższe przychody niż praca człowieka, a 90% managerów ocenia, że inwestycje w rozwiązania oparte na sztucznej inteligencji będą w największym stopniu napędzały rozwój firmy. 63% ankietowanych uznało jednocześnie, że ta technologia może wyrównać szanse
między dużymi i mniejszymi graczami, dając tym ostatnim pierwsi przystosowują się do kooperacji z nowymi rozwiąznacznie lepsze możliwości rozwoju. zaniami technologicznymi, tym ten efekt może być lepszy. 91% specjalistów ocenia, że do 2035 r., na którym skupia 77% specjalistów uważa, że do 2035 r. sztuczna inteligencja się badanie ich firma wyda więcej na technologię i sztuczną znacznie przyspieszy ich proces decyzyjny, zwiększając tym inteligencję niż na pracowników, zaś 90% liderów biznesu samym ich produktywność, zaś 83% jest przekonana, że zauuważa, że inwestycje w technologię AI będą największym tomatyzuje większość powtarzalnych i mało wartościowych motorem wzrostu ich organizacji. 2028 to rok, który pro- zadań, dzięki czemu pracownicy będą mogli skupić się na fesjonaliści (w raporcie określono w ten sposób zbiorczo bardziej twórczej pracy. Jednak w tym ostatnim aspekcie liderów biznesu i pracowników) wyznaczyli jako punkt kry- badanie Work 2035 przyniosło też zaskakujące wnioski. tyczny, w którym technologia i sztuczna inteligencja zaczną Do tej pory o zastępowaniu człowieka przez technologie generować większe przychody dla ich organizacji niż ludzie. mówiło się najczęściej w odniesieniu do wykonywania lub to może się zmienić. Ponad połowa ankietowanych profetalent – tak sjonalistów uznała, że sztuczna inteligencja ma potencjał, Nowe technologie wciąż kojarzą się z bytem, który systema- aby podejmować większość decyzji biznesowych, eliminutycznie eliminuje człowieka z wykonywania różnych zadań, jąc potrzebę istnienia tradycyjnego zespołu kierowniczego a kolejka tych ostatnich jest coraz dłuższa. Jednak podczas wyższego szczebla. gdy maleje znaczenie fizycznej siły roboczej, a praca ludzi nadzorowania i koordynowania prac fizycznych. Teraz także stała się łatwiej „wymienna”, to rośnie waga personalnych zdolności i talentu. W dobie, kiedy automatyzacja zatacza Praca tymczasowa wielu osobom kojarzy się głównie z zajęcoraz szersze kręgi, a rola człowieka, który jest w nią zaan- ciami, które cechuje sezonowość. Jednak liczba pracowników gażowany coraz szybciej się zmienia, umiejętność dosto- tymczasowych szybko rośnie i dotyczy to wielu różnych zawosowania się i szybkiego przekwalifikowania coraz bardziej dów i branż. Wiele wskazuje na to, że proporcje liczebne między zyskują na znaczeniu. pracownikami stałymi i tymczasowymi będą nadal zmieniały
Udana integracja ludzi i technologii sprzyja zwiększeniu się na korzyść przyrostu liczby tych drugich. Zawdzięczamy to wydajności pracowników i działania firmy, a im lepiej ci technologii, faktowi, że dzięki niej granice geograficzne oraz lokalizacja pracy przestają mieć znaczenie, a także zmiaTabela nom potrzeb pracodawców. Liderzy Pracownicy Co ciekawe, o tym, że stała siła robocza zostanie w dużej 44% mierze zastąpiona przez pra cowników tymczasowych 76% bardziej przekonani są pra 68% cownicy niż liderzy biznesu design thinker ankietowani w badaniu Work 2035. Taki pogląd deklaruje jedynie 19% tych ostatnich i 60% pracowników. Liderzy Tabela 2. biznesu oceniają, że w 2035 r. Liderzy Pracownicy freelancerzy i „pracownicy na żądanie” będą stanowili samodoskonalenia 86% 48% około 1/5 ich kadry. Na ostateczny kształt sytuacji mogą 86% 47% wpłynąć także zmiany socjo 81% logiczne, społeczne i edukacyjne. Osoby reprezentujące (np. mikroczipy i inne elementy smart wbudowane najbardziej poszukiwane 44% zawody i mogące wykazać się najatrakcyjniejszym dla pracodawców wykształceniem 78% coraz chętniej zachowują niezależność pracowniczą. 39% liderów biznesu i 64% 64% pracowników spodziewa się, że takie osoby w 2035 r. będą głównie wolnymi strzelcami.
drogą, a to wiąże się z kosztami, zaś dla freelancerów poszujako „digital disconnect”, oceniając jednocześnie potencjal-
i człowieka będą coraz 14% 14% bardziej zacieśnione 12% i większość zauważa korzyści płynące z tego 10% stanu rzeczy, to jednak dość powszechne są 3% 5% 4% 3% 4% 7% 3% 6% 4% 6% także różnego rodzaju obawy. Pracownicy ankietowani w ramach 1% 2% badania Work 2035 boją się m.in. „okresu przejściowego” między 2020 2021 2022 2023 2024 2025 2026 2027 2028 2029 2030 2031 2032 2033 2034 2035 obecną formą pracy i przyszłą oraz tego, jak wypadną w zmierzeniu się z rywalem w posta-
Nowoczesna, bazująca na nowych technologiach infra- obawy są tym większe, że pandemia COVID-19 zachwiała struktura ułatwiła nie tylko organizację pracy zdalnej. Dziś wszystkimi rynkami, a więc pośrednio również rynkiem pracownicy po przeciwnych stronach globu mogą treno- pracy. wać i współpracować w tym samym środowisku, np. dzięki Przed pandemią zdalne wykonywanie obowiązków było platformom rzeczywistości wirtualnej, a kontakt następuje stosunkowo rzadką formą organizacji pracy. W ciągu niew czasie rzeczywistym. Sztuczna inteligencja może szybko spełna roku wdrożono je na masową skalę, a fakt, że był to lokalizować odpowiednie pliki i informacje oraz przesyłać je raczej przymus, a nie wybór postawił firmy w sytuacji nie do urządzenia pracownika, a co więcej, już niedługo będzie do pozazdroszczenia. Nauczone bolesnym doświadczeniem prawdopodobnie można wykorzystać do tego superszybką przyznają, że szukają nowych sposobów zwiększenia produksieć 6G. W tym nowym świecie jest też miejsce na technologie tywności pracowników i zabezpieczenia przed negatywnymi i kanały „śledzące” reputację i wartość zarówno pracownika, skutkami finansowymi. Tak deklaruje 71% liderów biznesu jak i pracodawcy, co już dziś częściowo realizują media spo- ankietowanych w Work 2035, a 68% zgadza się, że ze względu łecznościowe, jak np. LinkedIn. To wymagająca zmiana dla na zmianę sposobu pracy technologia, która śledzi wydajność obu stron – firmy nie mogą zaniedbać tworzenia wizerunku tą pracowników będzie miała coraz większe znaczenie. ci technologii. Obecnie kujących dobrych zarobków może to być kwestia być albo nie być. Czeka nas więc prawdopodobnie zaciekła i globalna Autorzy raportu sformułowali na bazie uzyskanych odpowiekonkurencja na tym polu. dzi kilka zasadniczych obszarów i działań, na które pracodawcy i pracownicy powinny położyć szczególny nacisk zanim staniemy oko w oko z rokiem 2035. Oto one: Informację, że pracodawca chce nam wszczepić chip potrak- – nie komplikuj organizacji pracy implementowaniem towalibyśmy dziś jako żart albo zamach na naszą prywatność nowych technologii za wszelką cenę i w przesadnym stopniu, i niezależność. Tymczasem w nie tak znowu odległej przyszło- – przygotuj się na wyjątkowo dynamicznie zmieniającą się ści taka praktyka może wejść w życie. Wszczepione urządze- sytuację i rosnącą konkurencję, nia mogą poprawić wydajność pracowników – tak stwierdziło – zadbaj o siłę roboczą, dostarczając pracownikom inspiruw badaniu Work 2035 77% liderów biznesu. Wśród samych jących doświadczeń, w których mogą łatwiej wykorzystać pracowników ten odsetek stanowi 43%. Dodatkowo 57% pra- inteligentne technologie, tak aby mogli rozwiązywać procowników byłoby gotowych pozwolić na wszczepienie im blemy w kreatywny sposób i szybciej podejmować decyzje. chipów czy czujników pod skórę, o ile byliby pewni, że jest to Tegoroczna pandemia i wywołane nią gospodarcze torbezpieczne, a ponadto przyniesie wymierne efekty w postaci nado dobitnie pokazały, że trudno jest przewidzieć, jak poprawy wydajności, jak również wyższych zarobków. Jed- ekosystem pracodawców i pracowników będzie wyglądał za nocześnie 66% pracowników i 54% liderów biznesu uważa, że parę tygodni, a co dopiero za kilkanaście lat. Istnieją jednak pracownicy z chipami będą uprzywilejowani na rynku pracy, przesłanki pozwalające z dużym prawdopodobieństwem co oznacza niższe notowania pozostałych. założyć, że określone zmiany i zjawiska zaistnieją. Do nich Organizacje, które dobrze się do tego przygotują, będą mogły Badanie Work 2035 zwraca także uwagę na aspekty określane działać spokojniej w oczekiwaniu na przyszłość. należy coraz większy udział technologii w systemie pracy. ny wpływ nowych technologii na zdrowie psychiczne. Cho- Urszula Chojnacka ciaż wszyscy zgadzają się co do tego, że związki technologii AUTOMATYKA