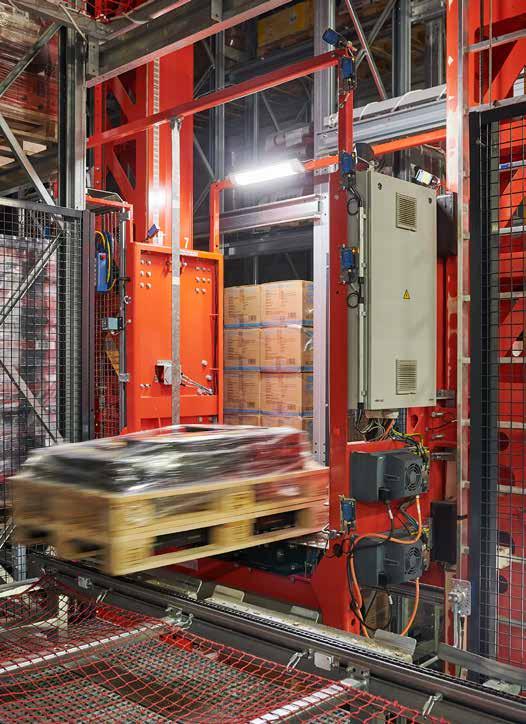
11 minute read
Der Lieferprozess Info
from Aroma 04/23
by Pistor AG
VORBEREITUNG
Waren einkaufen
Wareneingang kontrollieren
Umpacken von Palette auf Tray
Ware einlagern (ohne Frischware*)
Kundenbestellung annehmen
Ware kommissionieren
Wareneingang von Frischware* kontrollieren
Lieferung auf LkwTour verplanen
Lkw beladen
An Kunde liefern
* Frischfleisch, Gemüse, Früchte auf den globalen Warenfluss. Bei Pistor beträgt der Anteil ausländischer Lieferanten nur zehn Prozent, trotzdem sind heute noch gewisse Nachwirkungen spürbar.
Moritz gewährt mir einen Einblick in sein Tagesgeschäft: «Unser System kontrolliert viermal täglich die Mindestbestände. Entsprechend zeitnah handeln wir, wenn es knapp wird.» So weit kommt es normalerweise aber nicht. Das System prognostiziert aufgrund der Zahlen der vergangenen Monate, der Vorjahresperiode und der geplanten Aktionen den zu erwartenden Verbrauch. «Diese Zahlen beurteilen wir individuell und kaufen entsprechend ein.»
Von der Wareneingangskontrolle (oben) geht's zur Umpackstation (Mitte) und weiter ins Klein-Coli-Lager (unten).
Sorgfältige Eingangskontrolle
Bewegt sich der Lagerbestand von Artikel 6716 in Richtung Mindestmenge, wird er also nachbestellt. Treffen die getrockneten Tomaten in Rothenburg ein, heisst der erste Halt Wareneingangskontrolle. Hier im WUZ West, dem Umschlagzentrum für Normalware, werden pro Tag 800 bis 1200 Paletten angeliefert. Um Störungen auf der Anlage zu verhindern, wird jede Palette automatisch kontrolliert. Ist etwas nicht in Ordnung, wird sie aussortiert.
Ich treffe Jan Hiltbrunner, der die ankommende Ware gemäss internen Vorgaben prüft: Stimmen Temperatur, Menge und Qualität? Ist die Verpackung intakt? Bei Ware mit einem Label wie Bio, MSC/ ASC, IP SUISSE oder Fairtrade gilt es, weitere Kriterien zu prüfen. Entsprechen alle Faktoren den Vorgaben, bucht Jan die Artikel ins System ein. So auch den Artikel 6716, der mit 45 Tagen Haltbarkeit und 18 Grad Celsius Lagertemperatur ein klassischer Artikel für das Normalwarenlager ist.
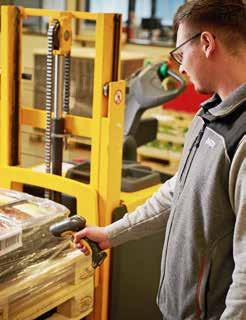
Die Palette mit den getrockneten Tomaten fährt anschliessend automatisch ins Hochregallager. Von dort geht ihre Reise weiter zur «Umpackstation», wo Antonio De Araujo Correira die 32 Stück «Tomate, getrocknet» von der Palette nimmt und je 16 Schalen in ein sogenanntes Tray umpackt. Dieses Umpacken von der Palette in Trays geschieht mit zahlreichen Artikeln. So findet jeder Artikel im Hochregallager seinen Platz.
Von frisch bis tiefgekühlt
Wären die Tomaten frisch, und nicht getrocknet, kämen sie ins WUZ Mitte, das Frischwaren-Umschlagzentrum. Auch hier packt Pistor die Artikel nach der Anlieferung von der Palette in Trays um. Doch dazu später mehr, denn morgen erklärt mir Matthias Fritschy, der Leiter dieses Bereichs, was hier im automatischen Kommissionierlager alles passiert. Und natürlich gibt es die Tomaten nicht nur frisch und getrocknet, sondern auch in vielen weiteren Formen wie zum Beispiel gewürfelt und tiefgekühlt. Diese Variante wird direkt ins Tiefkühllager, im WUZ Ost, angeliefert und eingelagert. Dort befinden sich aktuell rund 3000 verschiedene Artikel.

Es folgt: Sie bestellen.
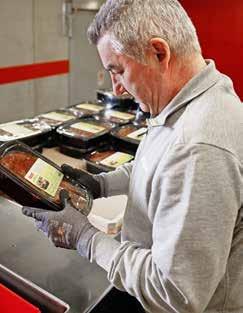
TAG A Wir erhalten die Bestellung
Im Pistor Eigenlager liegt er nun also, der Artikel 6716, die getrockneten Tomaten. Es ist Tag A und ich mache mich auf den Weg zu Jannik Schor im Verkaufsinnendienst (VID). Hier werden Bestellungen bearbeitet und Jannik erzählt mir vom VID-Alltag: «Vier von fünf Pistor Kunden und Kundinnen bestellen einfach und unkompliziert im Online-Shop. Diese Bestellart bietet ihnen die meisten Vorteile: Erstens endet der Bestellschluss nicht schon um 17 Uhr, sondern erst um Mitternacht. Zweitens kann der Kunde seine Bestellung vor Abschluss kontrollieren. Drittens erhält er bessere Konditionen, weil sein Auftrag automatisch durch das System rutscht und damit keine weiteren Klicks von uns nötig sind.»
Am Telefon
Ich höre bei Janniks Kundengesprächen zu. Der erste Anruf gehört zu den noch knapp acht Prozent an telefonischen Bestellungen. Die Bäckerin nennt Artikelnummer um Artikelnummer und Janniks Finger fliegen über die Tastatur. Zack. Fertig. «Das war gerade ein Musterbeispiel einer telefonischen Bestellung. Genau so soll es sein: Artikelnummer und Anzahl, so können wir die Bestellung ratzfatz eintippen.» Die Bestellung ist abgeschlossen und Jannik hat ein paar Minuten Zeit, um die Statusmeldungen zu prüfen. «Hier erscheinen jene Bestellungen, bei denen der Kunde online einen Hinweis eingetragen oder eine unüblich grosse Menge eines Artikels bestellt hat.» Jannik filtert die Liste nach seinen Kunden. Eine Kantine bestellt elfmal Salami Chorizo. Da Jannik letzte Woche mit dem Küchenchef über diesen Artikel gesprochen hat, weiss er, dass die Anzahl korrekt ist und winkt die Bestellung durch.
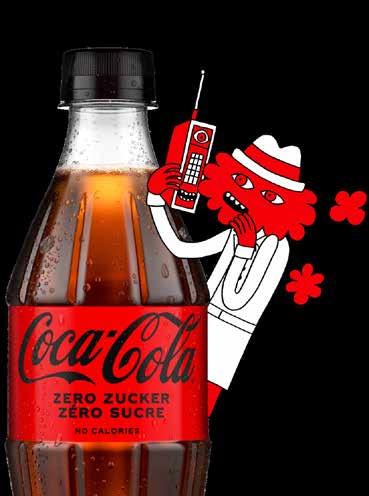
Ausnahmsweise nachbestellen
Bis Mitternacht kann der Kunde also online bestellen. Die Aufträge aus den anderen Kanälen müssen bis 17 Uhr im System sein. Und dann? «Enthalten die Bestellungen keine Statusmeldung, starten die Kollegen und Kolleginnen im WUZ bereits in der zweiten Nachthälfte von Tag B mit der Kommissionierung. Muss der Kunde ausnahmsweise etwas dazu bestellen, können wir dies noch bis elf Uhr erfassen und die Artikel werden zur bereits gerüsteten Lieferung dazugelegt.» Die Mitarbeitenden im VID sehen, wie viel Platz es für diese Lieferung im geplanten Lkw noch hat. Am Tag C, morgens um fünf Uhr, bricht dieser Lkw von Rothenburg in Richtung Kunde auf.
Passt die Nachbestellung also noch in den Lkw, kann Jannik die Nachbestellung freigeben. Ist der Lastwagen voll, wird es komplizierter. «Dann frage ich bei den Kollegen in der Dispo nach, ob es noch eine Möglichkeit gibt. Wenn nicht, informiere ich den Kunden. Es kann auch passieren, dass die Kollegen beim Rüsten feststellen, dass ein nachbestellter Artikel nicht verfügbar ist. Passiert dies nach 17 Uhr, können wir den Kunden nicht mehr informieren und ihm auch keine Alternative anbieten. Darum ist es so wichtig, dass die Bestellung rechtzeitig eintrifft.»
Abseits des Eigenlagers
«Speziell sind auch die sogenannten Crossdocking-Artikel», sagt Jannik. «Das sind jene Artikel, die wir nicht im Eigenlager führen, sondern aufgrund ihrer kurzen Haltbarkeit erst auf Kundenwunsch beim Lieferanten bestellen. Eine solche Bestellung leiten wir vor dem Mittag an den Lieferanten weiter. Dieser liefert uns die Ware am gleichen Nachmittag. Die Ware durchläuft das automatische Kommissionierlager und wird so der Gesamtbestellung des jeweiligen Kunden zugeordnet. Die Ware für Westschweizer Kunden müssen wir bis um 17.30 Uhr auf unsere eigenen Bahnwagen verladen. Hier holt sie die SBB ab und bringt sie auf nächtlicher Fahrt zur Verteilzentrale Chavornay.»
Zum Schluss teilt mir Jannik mit, dass die Bäckerei Müller heute drei Stück des Artikels 6716 bestellt hat. Diese drei Schalen werde ich also morgen zu Gesicht bekommen.
Zeitlicher Ablauf
Tag A / 24 Uhr
Ende Bestellung im Online-Shop

Tag B
Ware aus den verschiedenen Temperaturbereichen wird kommissioniert und auf eine Tour verplant.
Tag C / 5 Uhr
Lastwagen verlässt Rothenburg in Richtung Kundschaft
Es folgt: Wir kommissionieren.
Im hochmodernen automatischen Kommissionierlager laufen neben den gekühlten Produkten auch die Crossdocking-Artikel (Früchte, Gemüse, Frischfleisch) übers Band.
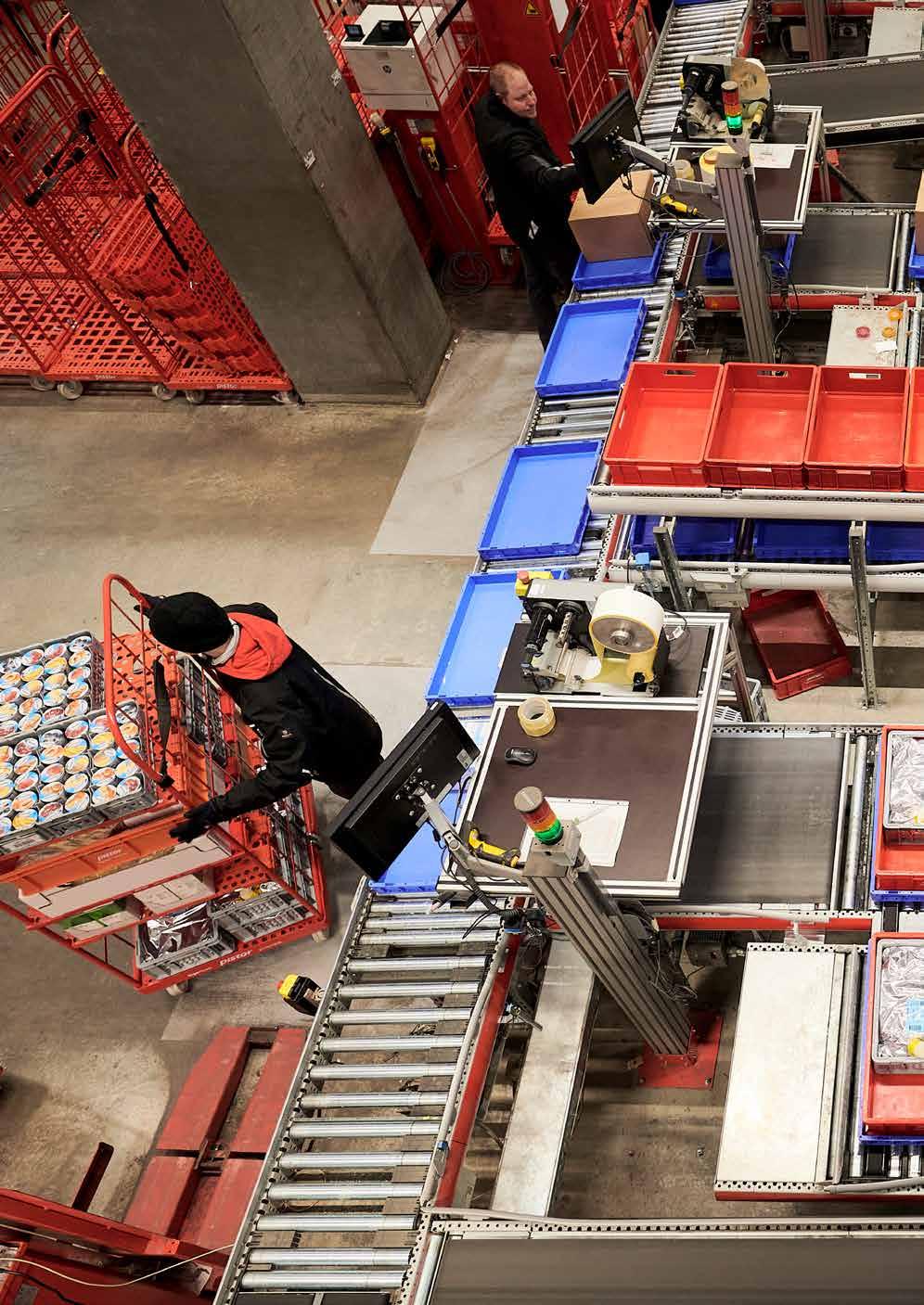

Oben: Besim fährt mit dem Rüstfahrzeug durch die Gänge des Normalwarenlagers. Unten: Wo die rote Lampe leuchtet, findet José den Artikel 6716.
Wir kommissionieren die Ware

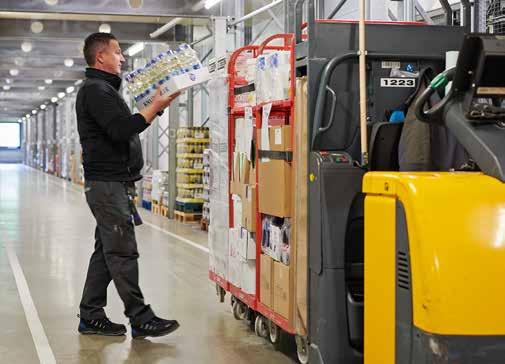
Nachdem die Bäckerei Müller die Schalen getrockneter Tomaten für ihr spezielles Caprese-Sandwich gestern bestellt hat, werden diese heute früh aus ihrem Lagerplatz geholt und in den vorgesehenen Kommissionierbereich gebracht. Die WUZ-West-Mitarbeitenden beginnen um fünf Uhr mit dem Kommissionieren der bestellten Ware. Ich lerne Besim Zeqiri kennen. Er kurvt mit seinem Rüstfahrzeug und drei Rollbehältern (RB) durch die Gänge des Hochregallagers. Hier belädt er die RB nach und nach mit jenen Artikeln, die ihm das Display seines Fahrzeuges anzeigt. «Wir beginnen hinten im Gang acht mit den schweren Artikeln und fahren bis nach vorne zu Gang eins, wo wir die eher leichten und heiklen Artikel zuladen», erklärt Besim das System.
Besim Zeqiri
Der Artikel 6716 wiegt weniger als fünf Kilo und liegt deshalb nebenan im KleinColi-Lager (KCL). Während Besim in den Gängen des WUZ West unterwegs ist, kommissioniert José Rodrigues im KCL die kleinen Artikel. Hier gibt es statische und dynamische Kommissionierplätze. Auf den statischen Plätzen liegen stets die gleichen Artikel. Auf den dynamischen Plätzen kommen immer jene Artikel zu liegen, die für die aktuellen Aufträge benötigt werden. Startet José einen Auftrag, leuchtet an dem Regal eine Lampe auf, wo er die benötigten Artikel findet. Die daneben aufleuchtende Ziffer zeigt ihm die Anzahl Artikel an, die er entnehmen muss. Blinkt die Lampe, weiss er, dass es sich um den letzten Artikel dieses Auftrags handelt. Er quittiert das Blinken und schliesst den Auftrag ab. Ich finde: Das ist ein ausgeklügeltes System, dessen Anweisungen José und seine Kollegen sorgfältig ausführen.
Gewickelt und gesichert
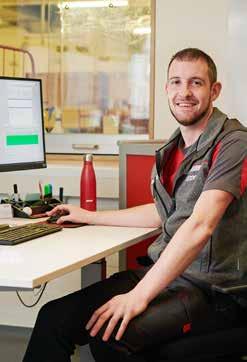
Hat Besim seine drei RB mit allen Artikeln aus dem Hochregallager beladen, «verdichtet» er sie. Verdichten bedeutet, dass die Ware aus verschiedenen Lagerbereichen auf dem für den Kunden vorgesehenen Rollbehälter zusammengepackt wird. Er scannt die Etikette des RBs, womit er die vorgängig von José kommissionierten Artikel aus dem Klein-Coli-Lager anfordert. Kurz darauf kommt der rote Behälter auf dem Rollband angefahren. Besim packt ihn auf den RB und schiebt diesen in die Wickelmaschine, die die Ware mit einer Folie für den Transport sichert.
Abläufe unter Kontrolle
Damit um fünf Uhr morgens mit dem Kommissionieren gestartet werden kann, werden die Bestellungen bereits um zwei Uhr nachts freigeschaltet. Dann fahren die Paletten und Trays in allen Bereichen des WUZ automatisch an den richtigen Ort. Es
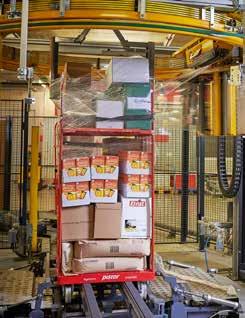
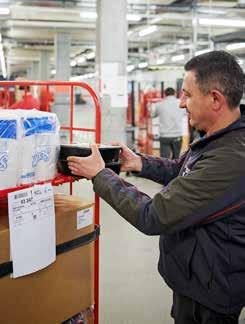
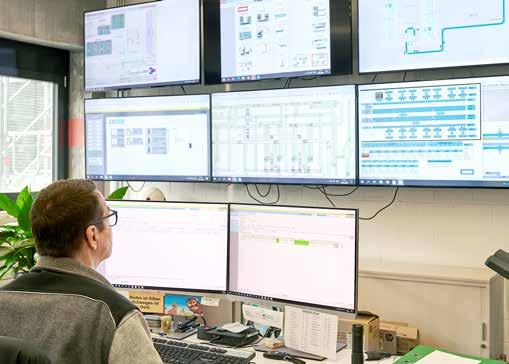
Im Leitstand laufen die Fäden des Warenumschlagzentrums zusammen. ist zehn Uhr und ich treffe Daniel Stierli im Leitstand. Er und seine Kollegen überwachen sämtliche Prozesse und Anlagen des Warenumschlagzentrums.
Auf einem der sechs grossen Bildschirme an der Wand sehe ich breite Striche, auf denen sich Vierecke bewegen. «Das sind die Paletten, Trays und Behälter, die durch die Anlage fahren», klärt mich Daniel auf und klickt auf ein Viereck. Die Information, die aufpoppt, nennt sämtliche Produktangaben zum Inhalt der angeklickten Palette.
Weiter informiert mich Daniel, dass nachts, wenn um zwei Uhr die Aufträge freigegeben werden, noch offen ist, welcher Kunde mit welchem Lastwagen beliefert wird. Wie ich später bei der Dispo erfahre, sind um ca. 13 Uhr die Touren und Lastwagen so weit verplant, dass die WUZ-Mitarbeiter die vollen RB nach und nach an den richtigen Rampenplatz verschieben können.
Weiter geht's: Wir kommissionieren.
Sämtliche Artikel werden automatisch in der richtigen Reihenfolge sortiert.
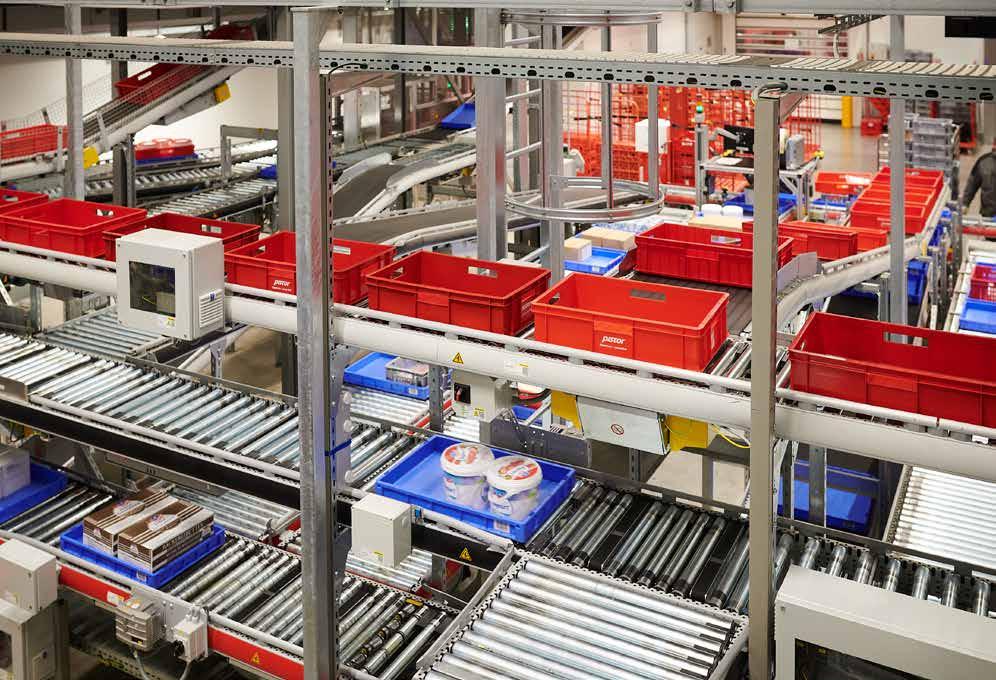

Im Frischelager
Am Nachmittag verabrede ich mich mit Matthias Fritschy, dem Leiter WUZ Mitte, der mir erklärt, was hier im Umschlagzentrum für Frischware vor sich geht. Wir betreten die Halle auf einer Höhe von etwa vier Metern. Unten sehe ich drei Rüstplätze, an denen meine Kollegen die Produkte aus den «anfahrenden» Trays nehmen und auf Rollbehälter packen.
«Natürlich beginnt die Arbeit hier nicht erst am Nachmittag, wenn die Crossdocking-Ware angeliefert wird», so Matthias. «Hier im gekühlten automatischen Kommissionierlager lagern rund 2000 Artikel, darunter Milch, Käse oder abgepacktes Fleisch. Diese Produkte werden am Vormittag bereits teilweise vorkommissioniert.»

Ware kommt herangefahren
Matthias erklärt mir den Ablauf anhand eines Beispiels: «Die Normalware, die der Kunde Arnold gestern bestellt hat, kommissionieren die Kollegen heute drüben im WUZ West. Nun bestellte der Kunde zusätzlich frische Tomaten, drei Pack Emmentaler und zehn Joghurts. Der Käse und die Joghurts sind bereits hier an Lager. An einem der vier Rüstplätze erscheint der Auftrag von Arnold auf dem Display. Der Mitarbeiter liest ‹drei Pack Emmentaler›, die Kiste mit dem Käse fährt heran, er nimmt drei Pack, quittiert und die Kiste fährt zurück ins Regal. Auf dem Display erscheint die nächste Position:
VIDEO Vom Feld auf den Teller
Frisch geerntet kommen Tomaten und Gurken in Rothenburg an. Verfolgen Sie deren Reise vom Feld bis zu Ihnen. link.pistor.ch/auf-teller zehn Joghurts. Diese fahren in der nächsten Kiste heran, er packt sie auf den Rollbehälter, quittiert, die leere Kiste fährt weg. Damit ist der erste Teil der Frischwarenbestellung abgeschlossen. Die Tomaten werden wie alle Cross-Docking-Artikel erst am Nachmittag angeliefert, umgepackt und ebenfalls hier ins automatische Kommissionierlager geschickt. Dadurch ist es möglich, auch die kurzfristig angelieferte Ware schnell und unkompliziert dem richtigen Empfänger zuzuordnen.»
Im Gegensatz zum Klein-Coli-Lager, wo José sich zum Tray mit dem jeweiligen Artikel bewegte, fährt hier sämtliche Ware zum Mitarbeiter. Zudem lässt sich der Rollbehälter stets auf die fürs Befüllen angenehme Höhe einstellen. «Dies ermöglicht unseren Mitarbeitenden ein ergonomisches Arbeiten», so Matthias abschliessend.
Bei den Tourenplanern
Während im gesamten Warenumschlagzentrum fleissig kommissioniert und verdichtet wird, planen die Kollegen in der Disposition die Touren. Da auch ich mich nicht zweiteilen kann, treffe ich den Disponenten Roger Bitzi an einem anderen Tag um acht Uhr.
Die Informationen aus den Systemen der anderen Abteilungen erscheinen bei Roger als spinnennetzartige Grafik auf dem Bildschirm. Sie zeigt die Schweizer Karte, auf der jede Tour in einer anderen Farbe abgebildet ist. Der Disponent erklärt: «Das System greift auf unsere Tourenvorlagen zurück und nimmt auf jeder Tour jene Kunden auf, die bis Mitternacht bestellt haben. Für den Tourenvorschlag zieht es die Details, welche zu den verfügbaren Fahrzeugen und Fahrern hinterlegt sind. Es errechnet die Tour anhand dreier Hauptfaktoren: die Distanz zwischen den einzelnen Abladeorten, die durchschnittliche Abladedauer, die in der Vergangenheit für den Ort nötig war, und das vom Kunden gewünschte Abladezeitfenster. Dazu kommen tourenspezifische Faktoren, wie Strassen oder Abladeplätze, die nur zu einer bestimmten Uhrzeit befahren werden dürfen.»
Bestmögliche Variante
Roger ergänzt, dass er und seine Kollegen aufgrund der Nachbestellungen, die bis elf Uhr eintreffen, 50 bis 60 Prozent der Abladeorte manuell einplanen. «Auch unsere Abläufe sind darauf ausgerichtet, dass die Bestellung am Tag A eintrifft und wir sie am Tag B auf die Touren von Tag C verplanen. Aufgrund der Nachbestellungen sind wir stets gefordert, die bestmögliche Tourvariante zu finden.» Dabei könne es vorkommen, dass sich ein Bäcker wundert, warum der Pistor Lastwagen zuerst vorbeifährt und erst später bei ihm ablädt. «Für einen solchen Fall gibt es zahlreiche Erklärungen: Eine davon ist das gewünschte Abladezeitfenster», sagt Roger. Inzwischen ist mir klar, warum die Dinge so laufen, wie sie laufen. Die Zeitfenster von der Bestellung übers Kommissionieren bis zum Verplanen der Route sind eng getaktet. Um diesen Fahrplan tagtäglich aufrechtzuerhalten, ist und bleibt der Zeitpunkt der Bestellung entscheidend.
Es folgt: Wir liefern.
C Wir liefern
Touren und Lagerplätze
LKW-TOUREN
Ab Rothenburg: 80 Morgen- und 6 Abendtouren plus 3 Touren für die Spitallogistik
Ab Verteilzentrum Chavornay: 15 Morgentouren
PLÄTZE HAT ES IM ...
... Normalwarenlager für 15 670 Paletten und 15 400 Tablar.
Im Herbst 2023 kommen mit der Erweiterung des WUZ West 6000 Paletten- und 9000 Tablarplätze dazu.
... Klein-Coli-Lager
15 500 Lagerplätze
... Frischelager
25 920 Tablarplätze
... Tiefkühlcenter
5100 Palettenplätze und
76 400 Behälterplätze
Im automatischen Kommissionierlager (Frischelager) lagern die 80 roten Shuttle pro Stunde 1600 Tablare ein und aus.

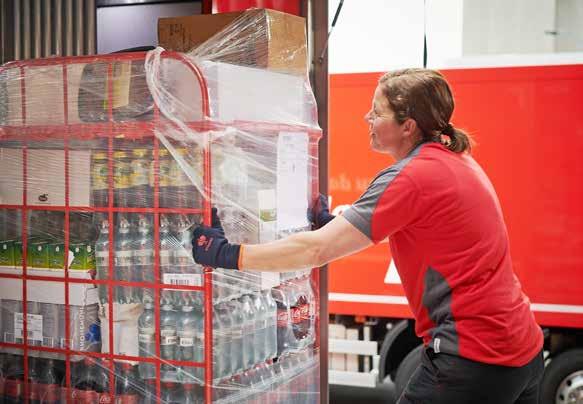
Zum Abschluss meiner Reise sehe ich den Artikel 6716, «Tomaten, getrocknet», sicher auf einem folierten RB verstaut. Es ist Tag C im Bestellprozess, der Tag der Lieferung. Um vier Uhr stehe ich verschlafen auf der Rampe, um Melanie Gautschi auf ihrer Tour in die Luzerner Innenstadt zu begleiten. Im Gegensatz zu mir ist sie putzmunter. Zum Glück, denn sie muss gedanklich bei der Sache sein und innert einer Stunde ihren Lkw beladen. Das tut sie nach einem Plan, der ihr alle Infos vermittelt, über die ich mit Roger in der Dispo gesprochen habe: Reihenfolge, Abladezeit, einkalkulierte Zeit fürs Abladen, gewünschtes Abladezeitfenster etc.
Die Normalware steht in der richtigen Reihenfolge an der Rampe. Melanie holt weitere RB aus dem Frischebereich und dem Tiefkühler. Die gekühlte Ware kommt sofort ins entsprechende Abteil des Lastwagens. Das Einhalten der Kühlkette hat bei der Lieferung von Lebensmitteln höchste Priorität. Nach einer Stunde ist der Lastwagen rappelvoll und sämtliche Ware sicher verstaut.
Auf dem Beifahrersitz
Um fünf Uhr fahren wir los und Melanie erzählt mir, wie viel Freude ihr der tägliche Kundenkontakt bereitet. Auf ihrem Handgerät quittiert sie fein säuberlich jede Ankunft und Weiterfahrt. Diese Informationen sind wichtig: Sie fliessen zurück ins System, das die Tourenplanung entsprechend optimiert. Beim fünften Stopp ist es so weit. Um 6.47 Uhr lädt Melanie den RB mit den getrockneten Tomaten bei der Bäckerei Müller aus. Nach ins- gesamt 18 Stopps kehrt sie nach Rothenburg zurück. Bei entfernteren Fahrten organisiert die Dispo jeweils die Abholung einer Lieferung, damit der Lastwagen nicht leer zurückfährt.
Eine lange Reise geht zu Ende; eine Reise voller neuer Eindrücke. Nun kenne ich unseren internen Warenfluss und bin beeindruckt. Hochmoderne Anlagen und Systeme unterstützen meine Kollegen und Kolleginnen dabei, dass jede Bestellung pünktlich am richtigen Ort ankommt. Gleichzeitig sind es ihre persönlichen Handgriffe, die dafür sorgen, dass jedes Zahnrädchen ins andere greift und die ganze Kette funktioniert. Mensch und Maschine arbeiten im Einklang.
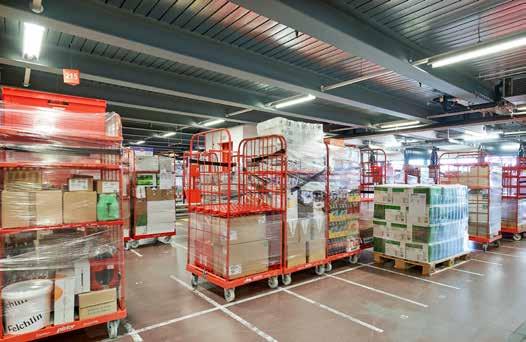
Ob die Tomaten schon heute oder erst morgen im Caprese-Sandwich landen, erfahre ich nicht mehr. Ich bin mir aber sicher, dass diese Sandwiches besonders gut schmecken. ▪
Bahnverlad
Der Kluge reist im Zuge – so machen es auch die Pistor Artikel, wenn wir sie von Rothenburg in die Verteilzentrale Chavornay liefern. Gegenüber dem Strassentransport spart das jährlich 337 Tonnen CO2 ein. Durch die geplante Verteilzentrale Ost in Sennwald SG werden wir in Zukunft auch bei der Belieferung unserer Ostschweizer Kundschaft CO2 einsparen. Lesen Sie hier, wie das Projekt voranschreitet: pistor.ch/vz-ost

Shop
Bestellen rund um die Uhr
Über 27 000 Foodund NonFoodProdukte stehen für Sie bereit. shop.pistor.ch