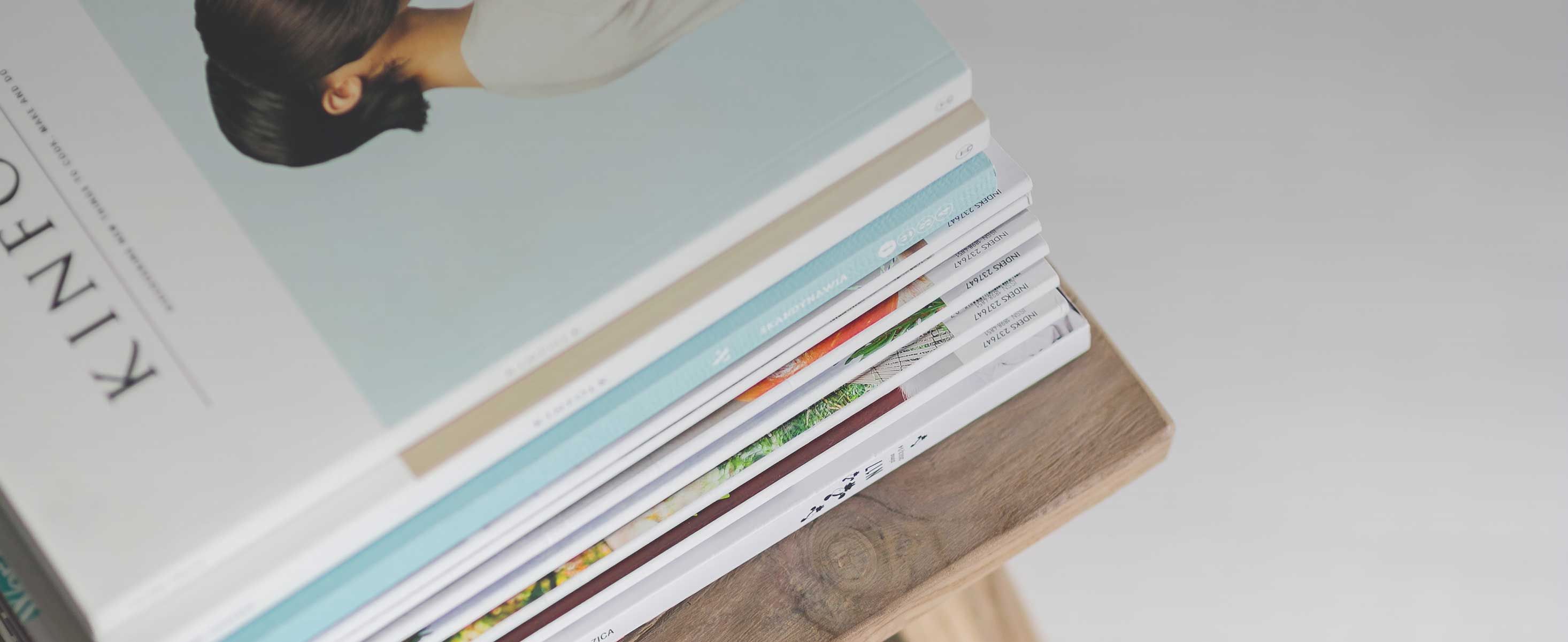
2 minute read
Minking K. Chyu, PhD
Professor Leighton and Mary Orr Chair Professor Distinguished Service Professor
Associate Dean, International Initiatives
626 Benedum Hall | 3700 O’Hara Street | Pittsburgh, PA 15261 P: 412-624-9784 C: 412-656-1020
mkchyu@pitt.edu http://www.engineering.pitt.edu/MinkingChyu
The Chyu Group’s focuses are energy technology, gas turbine engines, heat and mass transfer, manufacturing and thermoelectrics. Current research efforts are investigating high efficient cooling systems for high temperature applications, including advanced jet impingement heat transfer, transpiration/lattice cooling and application of additive manufacturing to turbine airfoils.
Introduction
Gas turbine engine is one of the most important components in modern power generation and propulsion. As a result, increase in engine efficiency and reduction in emission have a wide-reaching impact. One way to achieve these is by improving the aero-thermal performance of the gas turbine blades. This requires development of new cooling technologies and protective materials, which is the primary focus of this group.
Advanced Cooling Technologies
Since gas turbine blades are subject to environment with temperatures much above the melting point of the material, both internal and external cooling technologies are needed to ensure safe operation. The Chyu group focuses on both these fronts. Some examples of the recent research efforts include development of novel cooling technologies which utilize inline wall jets, swirling coolant flows, lattice networks, and transpiration microchannels to augment cooling in the gas turbine airfoil. These cooling technologies seek at complex 3D manipulation of the flow field to achieve favorable coolant redistribution to eliminate hotspots and reduce coolant consumption. The main experimental techniques include transient liquid crystal technology, PIV and IR imagery. A significant amount of computational simulation is also carried out to visualize and quantify the otherwise invisible flow behavior inside these channels.
Additively Manufactured ODS Coating and Cooling Structures
Collaborating with the Department of Energy and West Virginia University, the Chyu group became one of the first who implemented Additive Manufacturing to fabricate protective coating/cooling structures for turbine airfoils using oxide dispersion strengthened (ODS) alloy. ODS alloy has high oxidation resistance and excellent high-temperature creep strength, but is not amenable to conventional manufacturing. The capability of metallic additive manufacturing makes the integration of the ODS alloy and the advanced cooling technology possible. The cooling technology utilizes cool air coming from the compressor to cool down hot components. The coolant flow inside the cooling passages actively removes the heat from turbine blades and then effuses to hot stream outside through transpiration holes to form a thin coolant film above the outer surface of blades as an insulation layer. The objective of the research work aimed to design, fabricate and optimize the transpiration/lattice structures to improve cooling efficiency by more than 50% compared to conventional film and internal cooling.