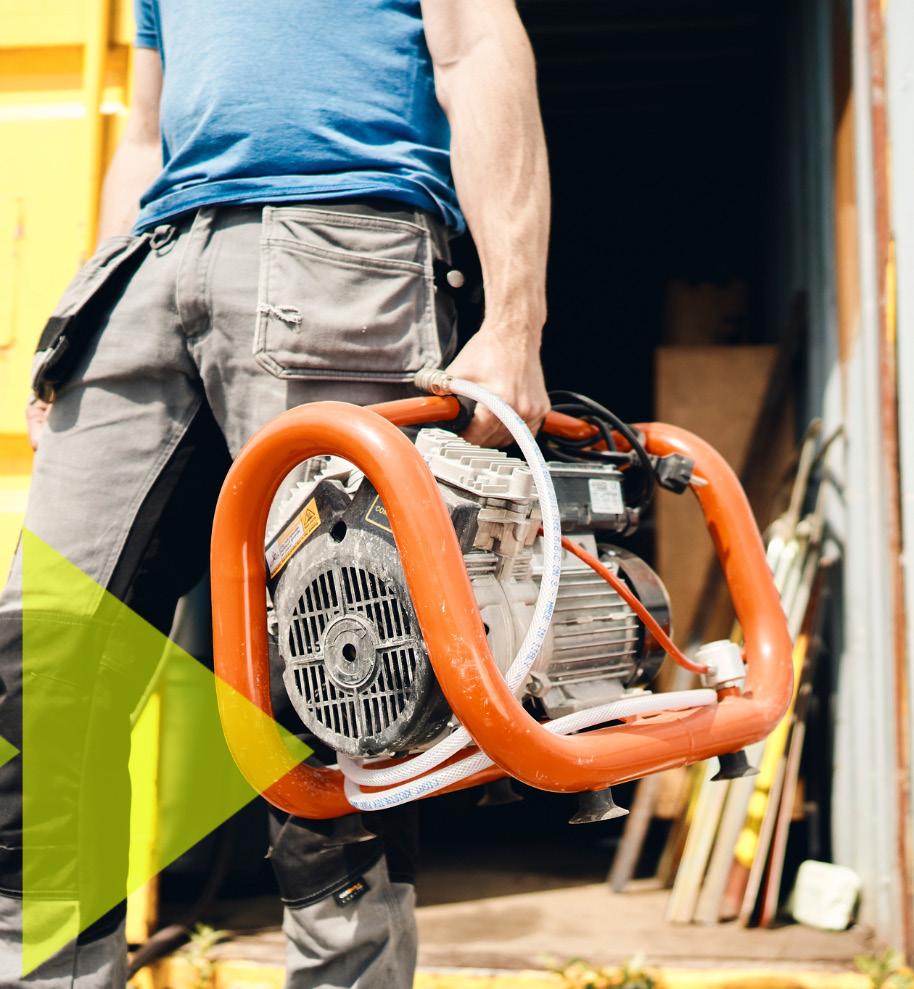
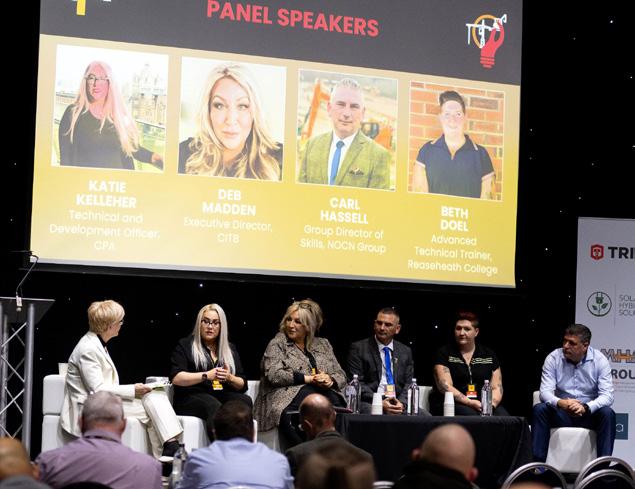
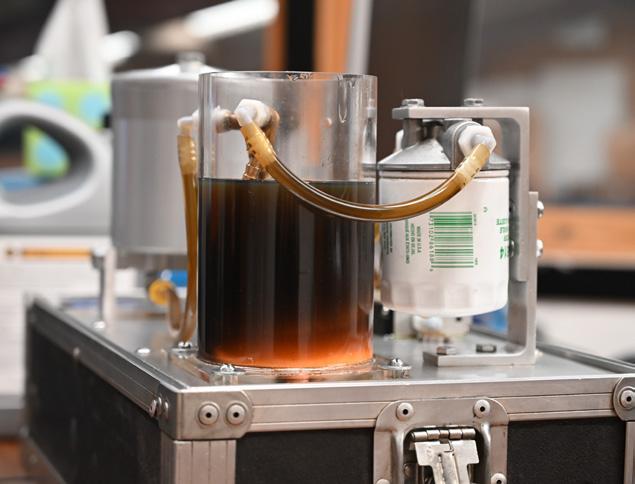
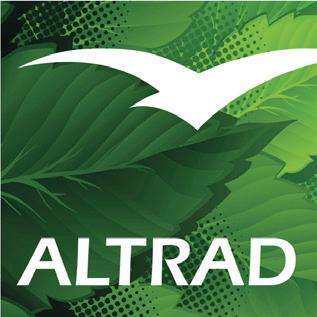











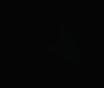










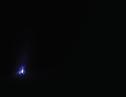








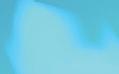



















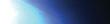






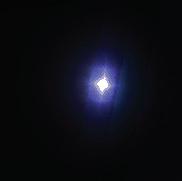








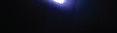


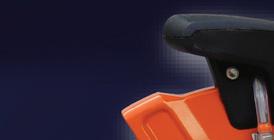
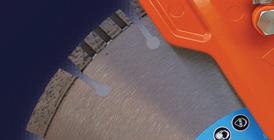
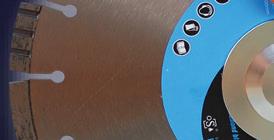
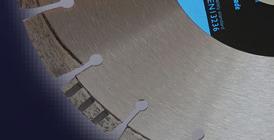
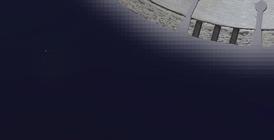





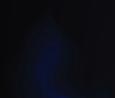









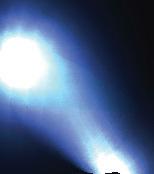
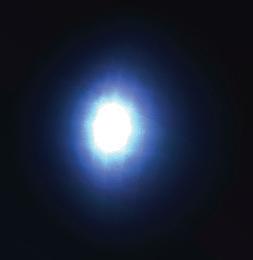









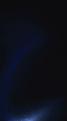





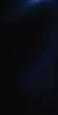


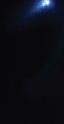

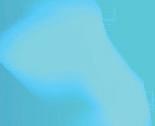

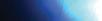
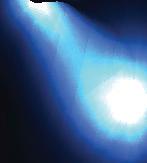
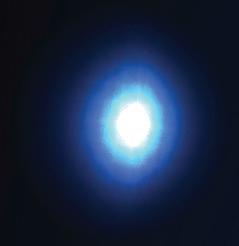

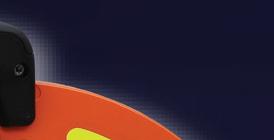
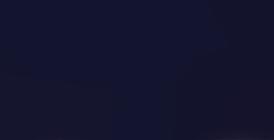
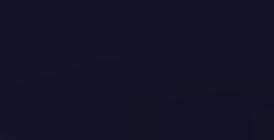
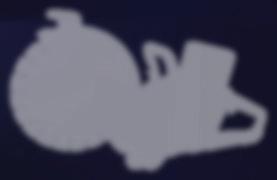
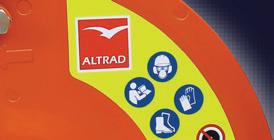
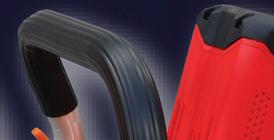
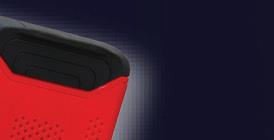
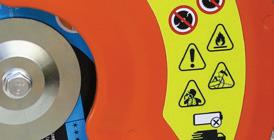
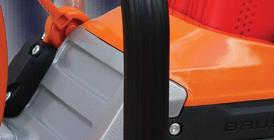
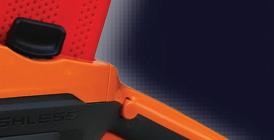
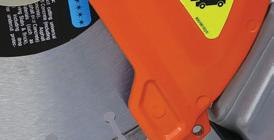

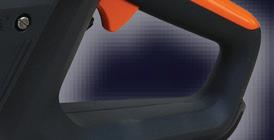
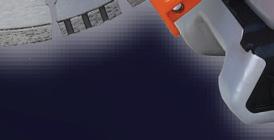

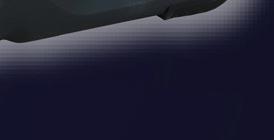



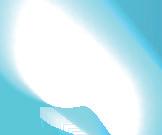
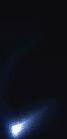

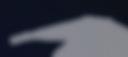

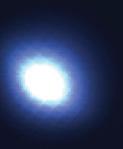


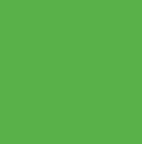





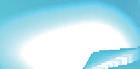

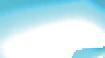



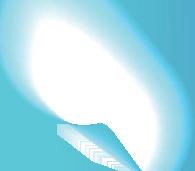











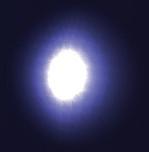
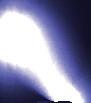

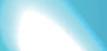
































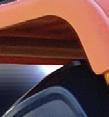
















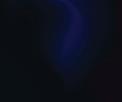

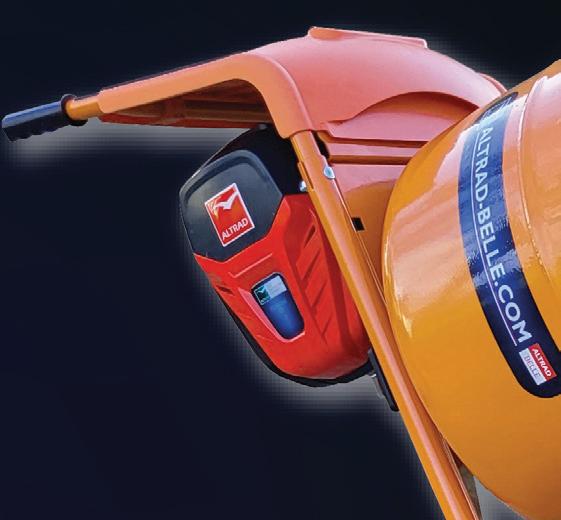

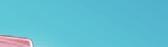
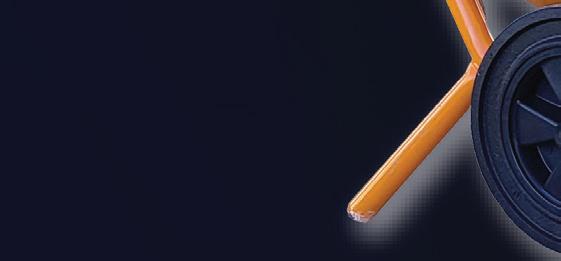
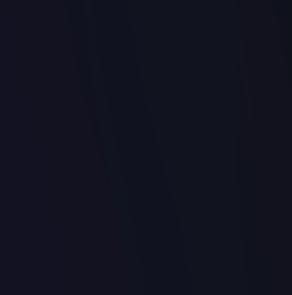
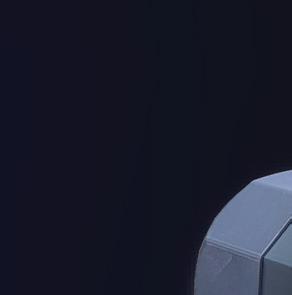



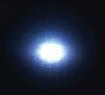







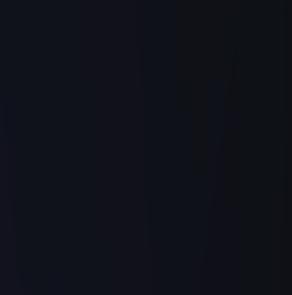
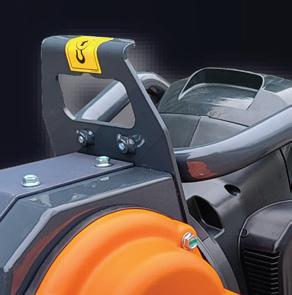




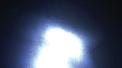

















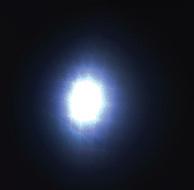


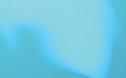














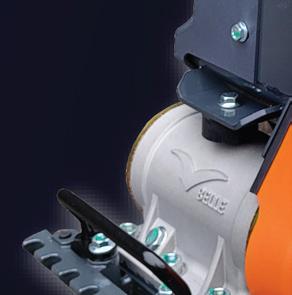

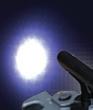






























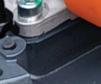


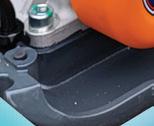



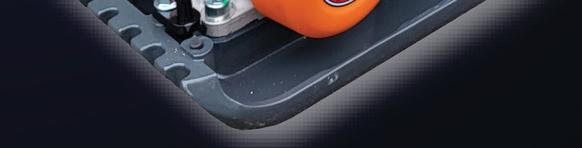








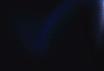
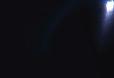





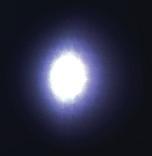
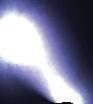

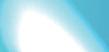




















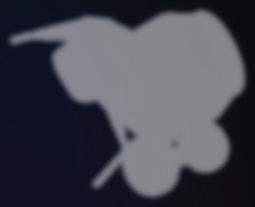

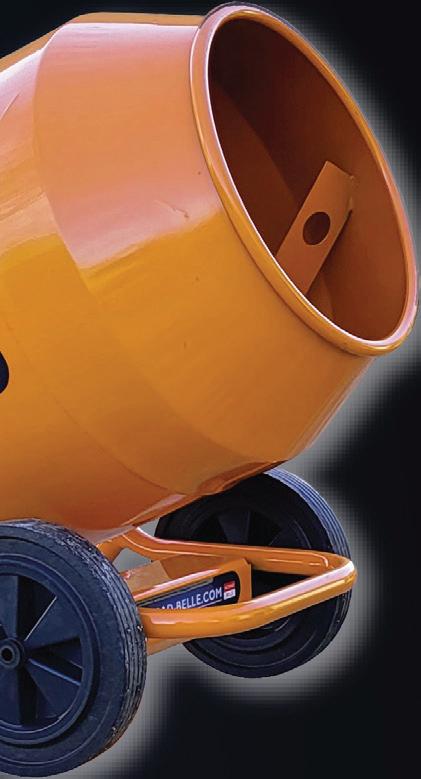













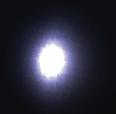





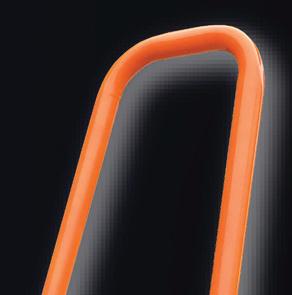
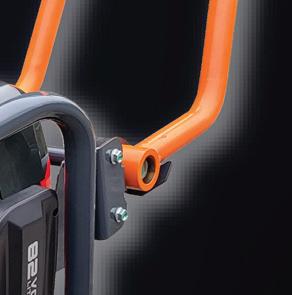
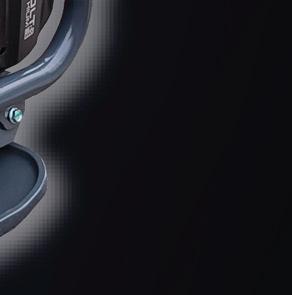
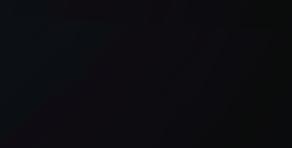









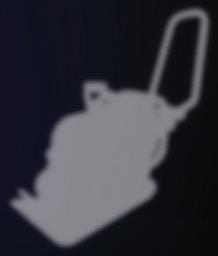








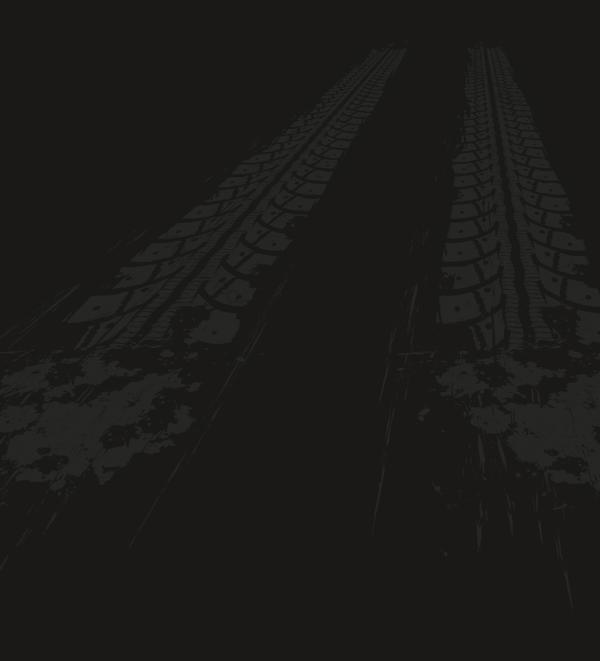
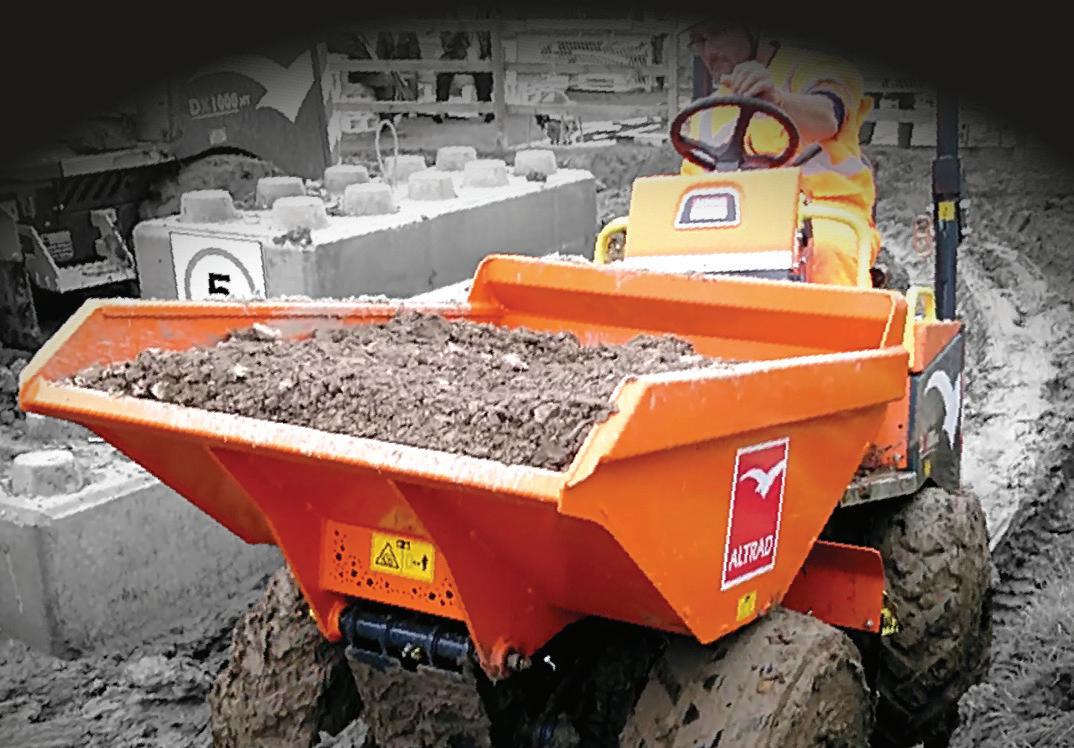

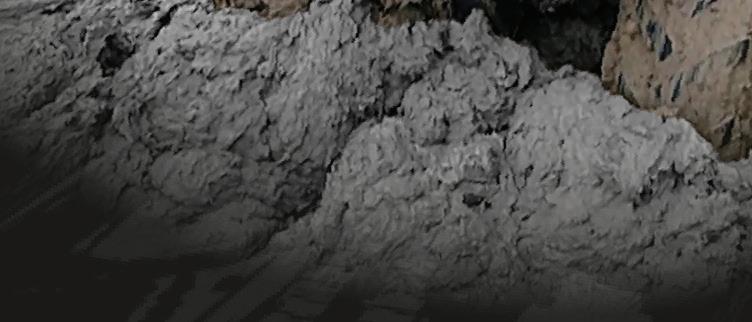
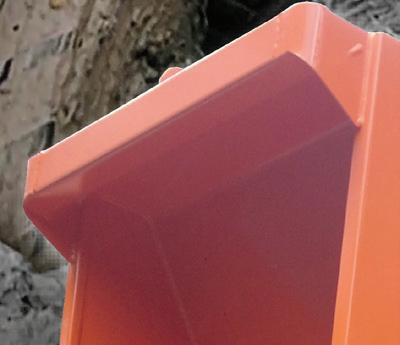

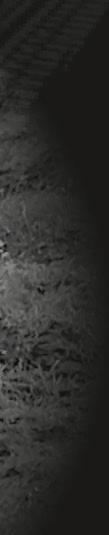
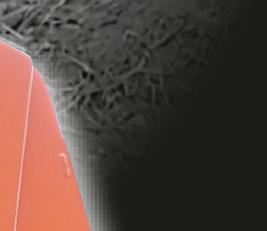
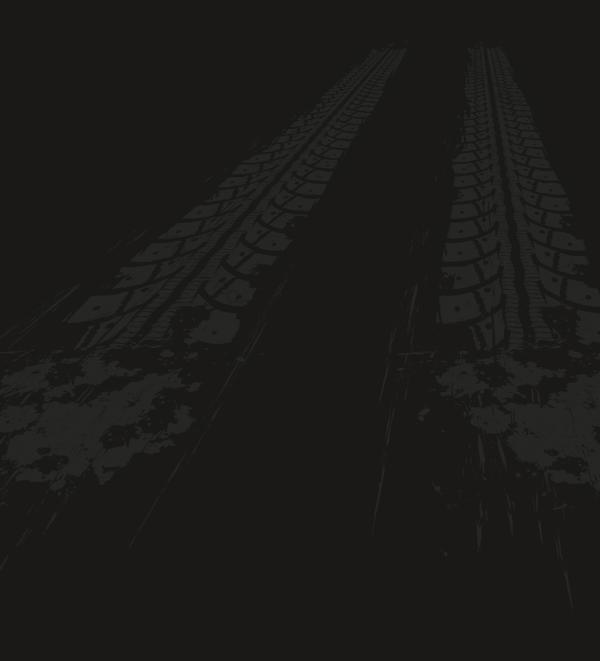

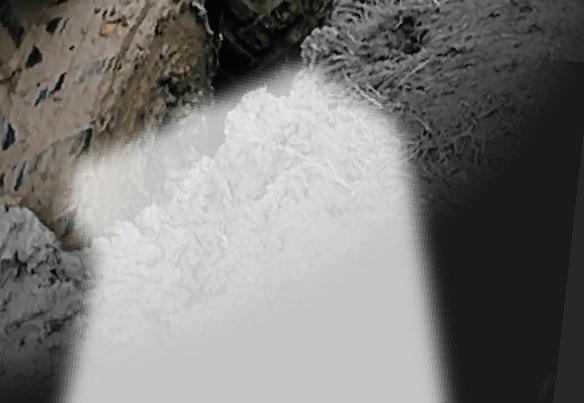
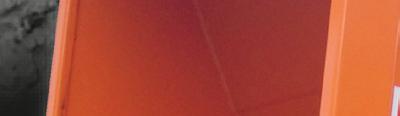
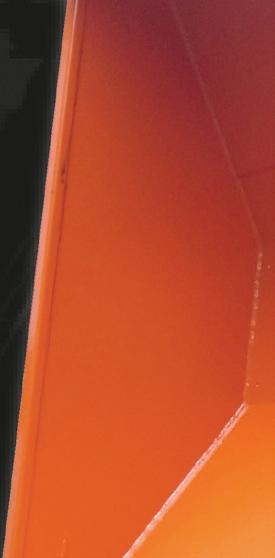
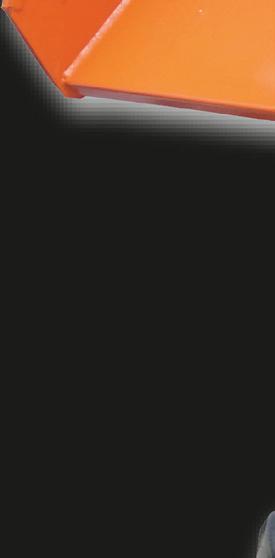
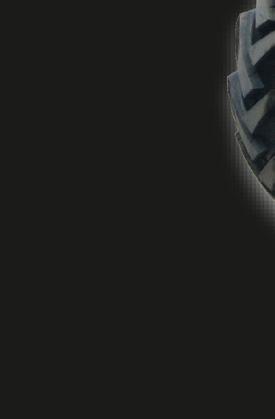
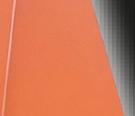
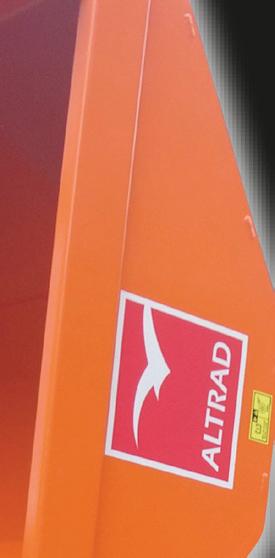
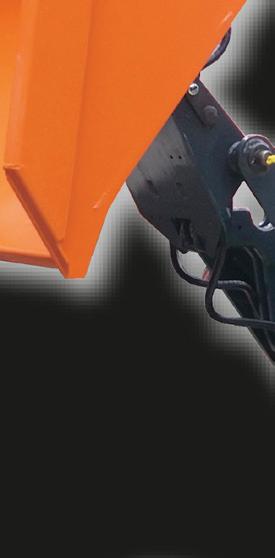
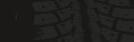
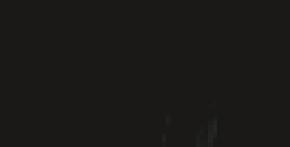
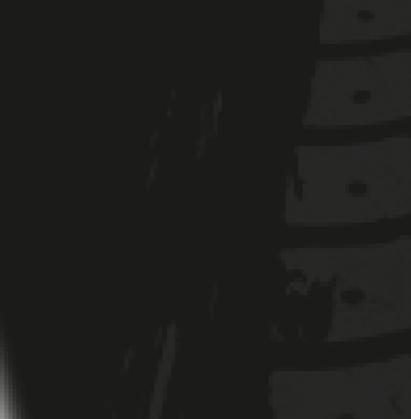
‘Best in Class’
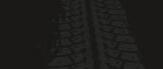

‘Best in Class’
Well, that’s a (Christmas )wrap on this year, lovely readers, and we can’t think of a better time to help you stretch those all-important pennies than this festive season. This issue is all about getting the most for your money, whether that be new long-term investments or a good saving on regular use items. Whatever your need, Plant Planet has you covered. It’s been quite the monumental year for us here at Plant Planet. Not only have we been to more shows than ever before, but we have also been invited to all sorts of incredible open days and site visits. Being out on the road was not always possible for us, but this is the start of a fantastic new chapter for the PP team. And speaking of new chapters, we launched Demolition Spotlight, which is taking the demolition world by storm!
We’ve also had one whole year of working with the incredible Lana Edwards, who has welcomed us into her world and taken us on an amazing journey. Of course, Lana is not the only familiar face, with the CPA still working closely with us to help deliver the best news and updates about the plant hire sector.
This is our long way of saying a big thank you to everyone, but most of all you, the reader. We wouldn’t be here without you, and we are so eternally grateful for your continued support.
Merry Christmas and a Happy New Year!
Rebecca Phillips Managing Editor
Plant Planet is published by Kiwi Media and Promotions Ltd 2nd Floor, 41-42 Southgate, Chichester, West Sussex PO19 1ET +44 (0) 1243 345 323
Kiwi Media and Promotions Ltd. © 2024 all rights reserved.
Reproduction in whole or part is prohibited except with permission in writing from the company.
Note to contributors: articles submitted to the Editor for consideration must be the original work of the author.
Where photographs are included that are not the property of the company or contributor, permission to reproduce them must have been received from the owner of the copyright. Any views or opinions expressed within this magazine are not necessarily those of the company.
ISSN: 2631-4622
Registered in England No: 09910499
All advertisements are accepted subject to the Kiwi Media & Promotions’ standard of insertion. For a copy of Advertising Terms & Conditions, please write to: Darren Shelton, 2nd Floor, 41-42 Southgate, Chichester, West Sussex, PO19 1ET
Protecting Our Planet
investment in sustainable equipment ,400+ solar & hybrid lighting solutions
Leave the how to us.
DARREN SHELTON BUSINESS MANAGER
REBECCA PHILLIPS MANAGING EDITOR
MARTINA TONELLI MARKETING MANAGER
PHIL EVERY SENIOR SALES EXECUTIVE
LORNA COWLIN CONTENT CREATOR
Submit your articles: editor@plant-planet.co.uk contributors
CHARLOTTE WALSH BRAND MANAGER
STEVE WILSON DESIGN MANAGER
ANNA EDWARDS ABAX
LISA COLLINS CPA
CHRIS BASSET AVANT TECNO AND LEGUAN LIFTS
KARL SERNEBERG STEELWRIST
FAITH COBINE IPAF
BRIAN JONES HEAD OF CONSTRUCTION PLANT-HIRE ASSOCIATION (CPA)
Brian Jones is President of the CPA, the largest trade association for the plant-hire sector in the UK with circa 1,900 members. He has worked in plant-hire for over 50 years. Brian was elected to the CPA Council over 30 years ago and has been CPA President since 2017.
RACHEL LAMBERT @KINGSTON PR
Rachel Lambert is a PR consultant and the founder of Kingston PR, a business she started over 30 years ago. A former magazine editor, she is also a freelance writer covering a range of sectors.
LANA EDWARDS @TRACKLASS1
Working with plant machinery since she was 8 years old, Lana Edwards is one of the most well known and respected inluencers in the construction industry. She is the Number One Woman in Construction for Wales as well as a Top 100 Women in Construction for the UK.
VIO33-7 & VIO38-7
Compact and robust, the ViO33-7 and ViO38-7 deliver outstanding efficiency on all types of worksites. Compact yet powerful, these models ensure optimal working comfort and productivity, even in the tightest spaces.
The ViO38-7 and ViO33-7 mark the latest advancements to Yanmar CE’s iconic zero-tail swing excavator range. Replacing the existing ViO38-6 and ViO33-6, these next-generation models boast improved performance, efficiency and operator comfort – all wrapped in a sleek and compact ‘Premium Red’ package.
The ViO38-7 and ViO33-7 offer substantial upgrades over their predecessors. The ViO38-7, with an Operating Weight (OW) of 3,585 kg, delivers a bucket digging force of 32.8 kN at 2,200 rpm. The lighter ViO33-7, at 3,265 kg OW, provides 30.69 kN of digging force, meaning that both of these highly compact units can handle demanding tasks in tight spots with ease. Both machines also benefit from hydraulic system improvements and an 18.5 kW Yanmar engine, resulting in smoother, faster operations and a 7% improvement in excavation efficiency compared to their previous counterparts.
The boom swing angle has been improved to the left side of the machine, with an effect on the turning radius of both units; resulting in a reduction of 115 mm compared to previous models, and providing operators with greater versatility and a wider working range.
The ViO33-7’s narrow width of 1,550 mm makes it perfectly suited to meet the dynamic needs of our modern, congested landscape, as does the ViO38-7’s width of 1,740 mm. Both models are also highly transportable, with transport weights of 3,210 kg (cabin) and 3.090 kg (canopy) for the ViO33-7, and 3,530 kg (cabin) and 3,405 kg (canopy) for the ViO387. Improvements to the travel motor and hydraulic pump also enhance the efficiency of earth removal work. Combined, these updates allow the excavators to travel faster on slopes, reducing overall travel time. The ViO33-7 now offers a maximum speed of 4.8 km/h – a 7% increase in speed on level ground – and a 25% improvement in speed
under load. Additionally, the standard automatic speed deceleration function contributes to more efficient operation, ensuring that every second on the jobsite is used effectively.
Operator-centric design with modern, sleek features
Operator comfort and modern luxury have all been a key focus in the development of the ViO38-7 and ViO33-7. Responding to direct customer feedback, both new units introduce a bold new design that merges Yanmar’s signature zero-tail swing functionality with a sleek, modern aesthetic. These models offer a striking appearance finished in Yanmar’s staple ‘Premium Red’ paint, while also delivering ease and practicality to the operator, including enhanced visibility, better transportability, and improved safety features.
The ergonomically redesigned cabins provide a more spacious and quieter environment, boosting both safety and comfort during long working hours. Meanwhile, a new 4.3-inch color display adds a modern touch to the inside of the cabin, while key updates like optimized air conditioning vents and accessible storage options further refine the operator experience. These thoughtful enhancements make the ViO38-7 and ViO33-7 ideal for operators seeking both functionality and comfort across a wide range of job sites.
Sunbelt Rentals were challenged with delivering a full range of sustainable equipment and solutions for the most ambitious road infrastructure project in Wales.
The A465 Heads of the Valleys road upgrade, spanning from 2021 to 2025, will transform the route to make it a safer, more efficient and accessible route for the region.
Extending over 17 kilometres, the project came with geographical and environmental challenge as it passes through two valleys, creating a tricky terrain for construction. In addition, certain sections were located near residential areas, schools and businesses, requiring expertise in reducing noise pollution and the environmental impact.
Future Valleys Construction, who were awarded the design and construction contract for sections 5 and 6, worked with Sunbelt Rentals to ensure the implementation of innovative and greener equipment solutions. These solutions not only helped them to meet the project’s environmental goals but also minimised disruption to the surrounding environment.
“The variety of kit Sunbelt Rentals offer from a small power drill up to a 13-tonne excavator is a massive advantage to us.”
Jonathan Lewis - Procurement Manager, FCC.
To make this project as sustainable as possible, Sunbelt Rentals supplied a range of stage V compliant equipment to reduce the environmental footprint. Alongside plant machinery, they provided powered access, mobile welfare units, eco-friendly lighting and solar-powered noise monitoring equipment. These innovative solutions helped to monitor the environmental impact and ensure compliance with regulations, all while maintaining efficiency. Onboard telemetry played an important role in managing the large-scale operation. It allowed for real-time monitoring of equipment performance, ensuring optimal usage and safety standards were met. Alerts for seatbelt use, driving speed and potential equipment theft provided an extra layer of security and control.
Over and above the supply of equipment, Sunbelt Rentals contributed to the local community projects with teammates volunteering their time and equipment for initiatives such as building a sensory garden for a local
school, supporting children with special educational needs and hosting a local school ‘girls into construction day’, aimed at inspiring the next generation of female professionals in the industry.
“We are delighted to provide a huge range of equipment across our complete range for the largest road infrastructure project ever carried out in Wales. It’s a brilliant example of how customers can leave the ‘How to Us’.” Toni Walters, Business Development Manager - UK, Sunbelt Rentals.
This project is set to have a lasting impact on the region, improving the infrastructure and quality of life for those living and working in the area. With Sunbelt Rentals as a key partner, the project is an example of how the construction industry can drive positive change through innovation and environmental solutions.
To learn more about Sunbelt Rentals, please visit: www.sunbeltrentals.co.uk
In an exciting first, 2024 marks a significant year for Merlo in Ireland, as the company embarks on a fresh chapter with the appointment of three new dealers. Previously operating through a distributor model, Merlo has shifted to a dealer network strategy, a move that reflects its commitment to strengthening its presence and customer relationships in Ireland.
This dealer-centric model, already successful in other regions, places customer service and aftersales support at the core of the business, ensuring that Merlo not only continues to grow its market share but also enhances the customer experience.
Merlo’s decision to transition to a dealer network in Ireland is part of a broader strategy aimed at positioning the company as a key player in the Irish telescopic handler market. Both the construction and agricultural sectors within the Republic of Ireland represent a growth area for Merlo. With new dealer partnerships in place, Merlo is confident that its customers will benefit from improved access to parts, service, and the latest product offerings.
The new model also aligns with
Merlo’s global strategy of expanding its reach by working closely with local partners. By transitioning to this dealer network model, Merlo aims to provide more localised after-sales support. As the Irish market for telescopic handlers continues to grow, Merlo is committed to strengthening its brand presence and building lasting relationships with its customers throughout the island of Ireland. On the construction side, D A Forgie have been a Merlo dealer in Northern Ireland for over ten years.
Paolo Merlo, CEO and President of Merlo Group, emphasised the importance of the Irish market in the company’s global expansion plans. “The Irish telescopic handler market continues to grow year on year, which is very encouraging.” He continued “As a familyowned and progressive business, we are committed to increasing our presence globally, and Ireland is a key part of our future plans.”
This sentiment is echoed by Shaun Groom, General Manager of Merlo UK and Ireland. Groom expressed his confidence in the new dealer partnerships and the positive impact they will have on customers. “Our goal is to provide Merlo customers with exceptional support and service,” Groom explained. “By partnering with FJS Plant Ltd,
Jim Power Agri Sales Ltd, and Nunan Farm Machinery, we are confident that Merlo owners will experience enhanced accessibility to parts, service, as well as to the latest product offerings.”
These new partnerships represent a major step forward for Merlo in Ireland. By working with local dealers who understand the needs of the Irish construction and agricultural markets, Merlo is not only positioning itself to grow its market share but also ensuring that its customers receive the best possible service.
In the coming months, Merlo Ireland is set to complete on a head office, which will include an all-important dedicated parts department. This new facility will serve as the central hub for the company’s Irish operations, streamlining support services and ensuring faster delivery of parts to customers across the country. By establishing a local headquarters, Merlo demonstrates its long-term commitment to the Irish market.
To learn more about Merlo, please visit: www.merlo.com/gbr/en/ FOR
100% electric, 100% performance
Komatsu builds machines to answer the needs of society. They boast a wide range of utility products which benefit from the same knowledge and expertise as their industry leading larger machines. With over a century of experience, you can be sure the same quality and innovation is interwoven into all their Utility products.
Distributed, serviced and supported in the United Kingdom solely by MarubeniKomatsu Ltd since 1972 – Komatsu continues to stay true to its brand promise of: Creating value together.
Expanding local reach and presence, Marubeni-Komatsu has recently appointed two specific Utility dealers - Johnsons of Cheadle who are covering the Staffordshire area and The Attachment Company who are covering the Lothians and Borders areas, with more local utility dealers to be announced soon.
Remarkably versatile, Komatsu’s miniexcavators are compact, light, and powerful. Starting with the PC09-1 at 1 ton, up to the PC58MR-5 at 5.6ton and a host of machines in between, they can work anywhere, particularly in tight spaces. Perfectly suited to both end-users and rental companies, these machines offer first-class comfort and controllability to the experienced and the novice operator alike. Powered by stateof-the-art battery technology the new electric mini-excavator PC33E-6 leaves zero local emissions in its wake, making it a game-changer for workers nearby and the surrounding environment.
Komatsu created midi-excavators as the perfect compromise between the compactness and manoeuvrability of mini-excavators and the power of larger earthmoving machines. Komatsu’s crawler and wheeled midi-excavators are specifically designed to work in tight spaces and hard-to-reach areas. With special features and options, these multipurpose machines are equipped with a swing offset boom and can be supplied in customised configurations. The Midi excavator range starts with the crawler PC80MR-5 at 8 tons all the way up to the wheeled PW138MR-11 at 13 tons.
Just jump in any Komatsu skid steer loader – and enjoy the ride. With a standard joystick and simple controls
at your fingertips, you will find these machines as easy to operate as your own car. Powerful, efficient, and userfriendly, Komatsu skid steer loaders display an impressive digging force and lifting capacity, and are perfectly suited for a large variety of jobs. Their Komatsu engine ensures low fuel consumption and exhausts emissions, with an easy access for maintenance. There are 3 Skid Steers available with payloads from 680kg up to 950kg
A broad choice of attachments, a comfortable seat and a great view. You’ll enjoy working at the controls of a Komatsu compact wheel loader, and feel at home on any job site. Easy to work with, for any operator, Komatsu compact wheel loaders fully meet customers’ needs. User-friendly, they are at home in confined spaces, are handy for moving material on construction and excavation sites, and are equally at ease with road work. Two models are available – the WA70M-8 at 5 tons and the WA80M-8 with a 6 ton operating weight.
To learn more about Komatsu, please visit: www.marubeni-komatsu.co.uk
With a demand for innovative tech on the rise, MCS Rental Software has put together 5 of its most popular solutions that have taken 2024 by storm already. From MyTimeTracker managing rental company timesheets, to eScan, its new QR Code scanning functionality for equipment, rental companies using MCS have access to the latest tech in the industry.
eScan
This powerful new feature allows MCS customers to place a unique QR code on any piece of equipment. By simply scanning this code, rental customers gain instant access to a wealth of information, such as user manuals, certificates, and other useful data. This provides them with an enhanced user experience, placing crucial information right at their fingertips.
iOS compatible app
The MCS Resource Mobile app gives engineers and drivers out on the road the ability to complete their tasks all via a mobile app, giving instant feedback to rental controllers in the back office. The new app has been revamped giving MCS users better traceability of where resources are during the day. Rental controllers now not only know when a job has been started, but can also keep track of job progress including when their resources are actively driving, or when they have arrived on site.
Capturing your employee timesheets has never been easier. The new MyTimeTracker app, means your employees can log their hours worked and complete their timesheets wherever they are.
MCS has now enhanced its comprehensive telematics offering with two industry-leading providers, Geoforce and Samsara. This development strengthens MCS’ commitment to providing cutting-edge solutions for rental businesses around the globe.
Geoforce is renowned for its advanced asset tracking solutions and brings a wealth of expertise to MCS Rental Software users, allowing them to precisely monitor the location, condition, and utilisation of their assets.
Samsara offers an innovative approach to fleet management, providing users
operations. With real-time GPS data, full vehicle tracking, integrated route optimisation, and custom route analysis, Samsara is a pioneer in telematics technology.
Rental companies can now automate price adjustments, confirm promotional rate periods, and introduce dynamic pricing mechanisms based on peak usage times. The result is a more streamlined, efficient, and proactive approach to pricing management that aligns with business needs and market demands.
The CEA (Construction Equipment Association) is proud to announce that it has been shortlisted for the “Best Association Transformation” category at the UK Trade Association Awards 2025.
The British Metals Recycling AOrganised by the Trade Association Forum (TAF), the awards recognise excellence among UK trade associations. This year’s entries were of a very high standard, making the CEA’s shortlisting a strong achievement. The recognition reflects the association’s efforts to transform its services, improve communication, and provide real value to its members.
Over the past year, the CEA has delivered a series of significant initiatives that have redefined how it supports its members and engages with the sector. Regular Members’ Forum meetings have been revitalised, featuring expert-led sessions on compliance guidance, market insights, and economic updates. These forums have become invaluable for networking, staying informed on legislative changes, and sharing industry knowledge.
The association has also enhanced its communications, introducing comprehensive newsletters that deliver timely updates, a refreshed website that improves accessibility, and practical resources such as the new member brochure and manifesto.
In addition, the CEA has strengthened its advocacy efforts, becoming one of the first to respond to key government announcements and ensuring the construction equipment sector’s voice is heard. The refocused resource on market intelligence has been instrumental in supporting member decision-making and long-term planning.
These transformative steps reflect the CEA’s commitment to driving progress, improving member engagement, and maintaining its leadership within the construction equipment industry.
Nathan Cook, Global Business Leader at CEA member company ABB Harnessflex, commented: “The CEA’s innovation in delivering smart, accessible data and sustaining member engagement has been transformative. Its future-focused approach and energy truly stand out.”
Managing Director of CEA member company Con Mech Engineers, David Waine added: “The CEA has reinvented itself. Its member engagement and services are now essential for staying informed on key industry developments and navigating legislative changes. The association is often among the first to react to government announcements, ensuring our industry’s voice is heard.”
Viki Bell, CEA Director of Operations, said: “This shortlisting is a testament to the dedication of the entire CEA team. Over the past year, we’ve focused on delivering real value to our members and ensuring the association is positioned to lead the construction equipment sector effectively. It’s fantastic to see our work recognised at this level.”
The winners will be announced on Thursday, 27th February 2025, at the De Vere Grand Connaught Rooms in London, where leading trade associations will come together to celebrate excellence in their fields.
To view the shortlist and find out more about the UK Trade Association Awards, visit tafawards.org/2025-shortlist/
MB Crusher has proven that reaching new heights is not just for climbers. Their innovative equipment has literally soared above the Alps, transported by helicopter, to demonstrate that working smarter, not harder, is more than a motto – it’s a reality.
When mountain logistics become a challenge, MB Crusher provides a solution: reduce effort, maximize results, and protect the environment. Here are three inspiring examples:
• Grands Montets, Mont Blanc (France) – At 3,300 meters, Pugnat TP used the MB BF90.3 S4 crusher bucket, flown in pieces by helicopter and reassembled on-site. Attached to a CAT 330 excavator, it crushed granite for the foundations of Renzo Piano’s new cable car station – saving time, money, and environmental impact.
• Dürrnbachhorn (Austria) – In the Chiemgau Alps at 1,776 meters, an MB-L140 crusher bucket mounted on a Kaiser spider excavator handled boulders during cable-laying. This reduced pollution and boosted efficiency in challenging terrain.
• Drogo’s Valley (Italy) – An MB-G500 selector grab reshaped riverbeds and embankments with precision. Helicopter transport ensured safe and effective deployment in steep, remote conditions.
From crushing granite to stabilizing riverbeds, MB Crusher equipment turns mountain challenges into triumphs – proving that smart solutions can truly take work to new heights.
With the country now well into what is termed the ‘Lighting Season’ rental specialists, Events Crew, are already ably prepared for a very busy period. They have invested in twenty-four X-ECO LED lighting towers manufactured by the leading lighting tower supplier Trime.
Events Crew currently have a fleet of forty Trime X-ECO LED and X-CHAIN lighting towers, all ideally suited to provide bright, safe lighting for a variety of applications. They also manage over two hundred Trime lighting towers on behalf of a leading UK rental organisation.
The X-ECO LED has many environmental qualities and safety aspects. The set is fitted with the AMOSS safety system,
which automatically lowers the mast if the lighting set is moved whilst the mast is still erected. The complete unit features an external emergency stop button, a fully bunded fuel tank, four height-adjustable stabilisers and site levels for guidance during deployment. The X-ECO LED is fitted with power-saving and long-lasting light-emitting diode(LED) lamps.
Events Crew selected the Trime units citing their excellent design, ease of set-up, and compact dimensions which means they can be loaded sideways on a lorry. Events Crew also value the long run times, and how simple it is to tow multiple units to the site. They also appreciate the telemetry system which allows Events Crew to remotely manage the lights from a web browser, desktop PC or mobile device.
Leading powertrain solutions provider, Lancereal, has announced a new chapter in its 37-year history, following a management buyout (MBO) and significant investment in growth and development.
The MBO comes alongside a rebrand, the launch of a new company website, increased marketing efforts, and the expansion of its workforce.
Laura Hampson and Rob Yorke, who have been part of the business for many years, are taking on new leadership roles as Managing Directors. Laura will focus on Sales & Business Development, while Rob will oversee Engineering & Operations. The MBO aims to build on the strong foundations laid by founder Nick Hampson, who has been at the helm of the company since its establishment in 1988.
In addition to the leadership transition, Lancereal has made strides to modernise its brand and operations as the sector moves towards electrification. A new company website has been launched as part of an upscaled marketing drive to enhance visibility and better communicate the company’s offerings
to current and potential customers. The rebrand aims to reflect the company’s long-term vision and its goal to become a global leader in integrated drive transmission solutions.
The business has also expanded its team, bringing on new hires across various departments to bolster its expertise and customer support capabilities as part of a broader strategy to stay competitive and adapt to the evolving demands of the industry.
Laura and Rob both underline their shared goal of sustainable growth and innovation. While their roles may have changed, the company’s core mission remains the same: to design, integrate, and source complete drive packages tailored to customer needs.
The new Managing Directors are keen to emphasise continuity for customers, suppliers, and employees during this transition. Laura Hampson, who is stepping into her father’s role, shared that the MBO is a natural progression for Lancereal, retaining the company’s established values while paving the way for future development.
She said: “Rob and I have been deeply involved in the commercial and
operational direction of the business for several years. This step will provide continuity and stability, ensuring our customers and suppliers continue to experience the same level of service, integrity, and support that Lancereal has provided for decades.”
Rob Yorke, who has worked at the company for over ten years, said: “The MBO is not just about ownership change but about maintaining the passion and ethos that have been the backbone of Lancereal since the beginning. We are committed to upholding the customerfirst approach and ensuring strong, trusted partnerships as we move forward.”
The MBO and accompanying initiatives represent a new phase in Lancereal’s history, maintaining its legacy while positioning the company for future opportunities and sustainable growth.
Connell Brothers Ltd Demolition is a demolition company in Manchester that work across the UK. Since getting OilQuick, jobs that used to require three machines now can be done with one machine.
“OilQuick is a very good system. It has increased the productivity of our machines. Safety-wise it is also great as the lads don’t have to leave the cab to switch attachments. This means less risk of injuries, and no knocking pins out or spilling hot oils,” says Neil Docherty who is the site manager at Connell Brothers Ltd Demolition.
Connell Brothers specialise in floorby-floor demolition on 12-story block of flats. The machine park ranges from 1.5-tonnes mini diggers up to 70- to 80-tonnes machines.
“We have a lot of machines, of which about 95 percent are equipped with OilQuick. We even have OilQuick on the mini diggers that work on top of the roofs,” he tells.
“For Connell Brothers the implementation of OilQuick’s automatic quick coupler system has resulted in a different way of working.”
“With OilQuick it takes 20 seconds to switch attachments and that’s it. This means that jobs that used to take three machines have been narrowed down to one machine. We can put a breaker on for five minutes, take the breaker off, put the grab on for a minute, switch to the steel magnet, and so on. It is a brilliant system in that way. It is so quick,” he says.
“Another advantage is that the expenses from replacing hoses have been
reduced to nearly zero and, moreover, work has become more convenient for the operators.”
“Back in the days when we had to switch hydraulic hoses manually, this was something that our lads weren’t looking forward to, especially not when it was rainy and bad weather. With OilQuick there is none of that. It’s straight on, straight off with a few button pushes.”
FULLY AUTOMATIC QUICK COUPLER SYSTEMS FOR MAXIMUM PERFORMANCE!
•Lightning fast change of hydraulic, electrical and mechanical attachments from inside the cab.
•Always the right attachment for the job.
•Distributes oil, grease, water and electricity.
• No staff around the machine during tool changes.
•Meets and exceeds safety standards globally.
•Improved safety.
•Reduces the number of machines on the site.
•Reduced transport costs.
•Increased productivity.
• Increased profitability.
•Eliminates oil spills.
•Protected hose run.
•Less dirt in the cab. eased eased
OQ
FULLY AUTOMATIC QUICK COUPLERS FOR EXCAVATORS FROM 1 TO 120 TONNES
TVH, a leading specialist in parts for material handling, agricultural, construction and industrial offroad machines, announces today the launch of the PK-TS Fork Positioner, the latest addition to its CAM attachments range. Designed for precision and safety in material handling, the PK-TS offers features tailored for operators of material handling machines like forklift trucks and telehandlers.
CAM attachments, subsidiary of TVH, specializes in manufacturing attachments for off-road equipment. Today they introduce the PK-TS Fork Positioner. This new attachment allows drivers to adjust fork spacing hydraulically from the cabin, eliminating the need for manual adjustments. This reduces the risk of injuries and operator fatigue, leading to a safer and more efficient work environment. Additionally, the sideshift function enables precise lateral
movement of loads, cutting down on cycle times and enhancing productivity.
Kobe Naert, Chief Product & Procurement at TVH, states: “Thanks to their numerous benefits fork positioners are increasingly becoming a standard upgrade feature on material handling equipment. By enabling precise adjustments of fork spacing, they enhance safety and efficiency in various operations. Operators can handle a wider range of loads with greater comfort, reducing strain and the risk of accidents. Additionally, the robust design of these positioners ensures durability, making them a reliable choice for diverse industrial applications.”
PK-TS
The body is designed from 2 C-Profiles for precise guiding of the fork carriers. Equal arm movement is guaranteed by choosing cylinders according to the hydraulic principle of communicating
vessels, instead of applying flow divider valves or throttles on the cylinders.
The PK-TS also features a reinforced frame and a scratch-resistant powder coating, the connections between piston rods and fork carriers are made of stainless steel extensions which feature ball eye rod ends. This helps absorb deflections between cylinder, body and carrier which happen in dynamic loadhandling processes, especially when moving loads over uneven grounds or under other tough conditions.
Its compact design and low over-height improve visibility and maneuverability in confined spaces, making it deployable for a variety of applications. This model comes as a hook-on version with carriers to install standard forks (ISO 2328:2011).
Other models of PK-Series can include fork arms and come either integrated, with or without a sideshift function, or in various combinations of these features.
TVH is a leading parts specialist for industrial off-road machines in the following markets: Material Handling, Industrial, Construction and Agricultural equipment. With a stock of over 1,120,000 different references, and a database of over 49,500,000 item numbers, TVH supplies to customers from 180 countries.
In addition, TVH’s technical experts offer a wide range of services, from
Europe’s largest fully-fledged electronics remanufacturing department, over TVH University to a unique remanufacturing division.
TVH is a global player with its headquarters in Waregem (Belgium) and a regional main office located in Kansas (US) serving the American market. In total, TVH operates from 90 branches across all continents. The company was founded in 1969 and employs more than 5,000 people worldwide.
In 2021, TVH joined forces with D’Ieteren Group, which acquired 40% of the shares. The other 60% remains in the hands of the Thermote family.
Construction’s top networking event of the year broke all fundraising records for the charity as supporters raised almost £290,000, a staggering amount for the construction community.
Friday 6th December at the Westminster Park Plaza and despite travel disruptions on the rail network, over 950 guests arrived to a warm welcome at the drinks reception in anticipation of an afternoon of top class entertainment.
Once again, rugby presenter and commentator David Flatman, ‘Flats,’ along with Ellie Costello, Weekend Breakfast presenter and journalist opened up proceedings with a hint of the sporting guests to come.
Edward Naylor and Lyndsey Gallagher, Co-Chairs of the Trustees formally opened the proceedings and paid tribute to two industry stalwarts Des O’Rourke and John Carey who had passed away earlier in the year, prompting a respectful standing ovation from the room. Former CEO Bill Hill was also presented with a commemorative Lighthouse pin and bottle of whiskey in recognition of his service to the charity.
Sarah Bolton, CEO of the Lighthouse Charity delivered an update on the charitable services delivered, highlighting a record number of families helped, financial support and sites visited.
This year saw MACL net the coveted Peter Capel’ Cup which is awarded each year in recognition of outstanding achievements from organisations supporting the charity. MACL’s annual fishathon has raised more than £60,000 since its inception four years ago. Ron “Rocket” Sant, Senior Site Manager said, “We are incredibly proud to be awarded the Peter Capel Cup and truly cannot think of a better charity to raise money for. Each year we are staggered by the amount of money we raise through the fishathons, but for us, it goes
beyond that, it’s an opportunity to raise awareness around wellbeing within the construction industry, helping to support those in need.”
Auctioneer Addison Gelpey took control of the room as he mastered some deft battles of bidding for top live auction lots including holidays, sporting memorabilia, concert tickets and unique sporting experiences.
VIP guests from the sporting arena were then welcomed to the stage and kicking off proceedings was former Liverpool and England International footballer, John Barnes, along with former England rugby centre Mike Tindall and Savannah Marshall, British Professional Boxer and MMA fighter. John shared his experiences playing with the infamous Gazza and the behind the scenes banter of the Italia 90 World Cup.
Next under the spotlight was Mike Tindall with tales of rugby antics and hilarious insights into his introduction to royal family protocols and his ‘baptism of fire’ at the royal dining table.
Savannah continued to keep the audience in stitches with her confession of “really not liking” one of her opponents and how that helped her to “punch really hard!”
The dynamics between the guests was clear, finding common ground in the challenges of performing at your peak and representing your country at world class level. Inevitably, that led to talk of John Barne’s infamous ‘World in Motion’ rap and he built up the crowd’s expectations as he shared the context of his star role on the song. The music started and Barnsey delivered a word perfect rap to the huge delight of the audience who joined in for the finale.
No one wanted the show to finish, especially as the audience were given live updates on how much was being raised and knew that they part of a record breaking fundraising event.
Sarah Bolton, Lighthouse Charity CEO expressed her extreme gratitude to everyone that supported the event, “This is our opportunity to reflect on our charity’s achievements throughout the year: the services we’ve delivered and the people we have helped. But most of all it’s to celebrate the successes of our fantastic supporters.
“Whether you are helping us to spread the message of support, organising fundraising, committing to be an annual company supporter or attending one of our events, you are helping us to make a life changing and lifesaving impact for our construction community.”
I am completely amazed at the amount of money raised, we’ve surpassing all previous fundraising events. Guests were hugely generous with their support of the live and silent auction, raffle entries and donations on the day. We know how tough it is out there at the moment which makes it all the more meaningful. A huge thank you goes out to everyone that supported us, whether it was volunteering behind the scenes, booking tables, sponsoring the event or donating auction items, thank you so much.”
The event culminated in a rousing rendition of opera favourites from tenor Martin Toal and violinist Rosie Judge, with guests waving napkins and swaying to the music. The festivities continued well into the evening with guests embracing the Christmas spirit and making the most of the networking opportunities.
If you or anyone you know is struggling, reach out for 24/7 free & confidential support; 24/7 helplines; 0345 605 1956, (UK) 1800 939 122 (ROI)
Live chat www.lighthouseclub.org Text HARDHAT to 85258
Find out more at www.lighthouseclub.org
Randstad UK and Ireland continues to shine a light on mental health issues faced within the construction industry by signing up to be a company supporter of the Lighthouse Charity in 2024-25.
The Lighthouse Charity is uniquely positioned as the only charity dedicated to providing emotional, physical and financial wellbeing support to the construction community and their families.
They offer a free and confidential 24/7 helpline, live web chat service and text facility which provides a range of information, guidance and support on a huge variety of wellbeing issues. These services are complemented by their free self-support app, along with their Lighthouse Beacons who provide a safe space for people to share concerns.
Randstad’s Construction, Property and Engineering (CP&E) team places more than 2,500 temporary workers every week - and more than 2,400 permanent employees in the last 18 months - into a wide range of permanent and contractor roles within the construction industry across the UK and Ireland.
For many years Randstad has lent its financial support to the charity by taking part in fundraising activities (with £6,000 raised already this year) and making an annual donation by signing up to be a continuing company supporter and promoter of the organisation.
In 2025, to further promote mental wellbeing, Randstad will feature the charity’s helpline number on desk calendars and annual wall planners
distributed across over 3,500 construction sites nationwide. This initiative aims to ensure that workers have easy access to crucial resources and support services and also highlights the charity’s key awareness campaigns.
Recognising the severity of mental ill health, Randstad CPE published concerning statistics following a survey of 3,400 construction workers in 2017. The report revealed that more than a third (34%) said that they had experienced a mental health condition within the previous 12 months, and that their mental health was prompting them to consider changing careers.
Randstad’s 2024 Workmonitor construction data revealed that 46% of workers would reject a job that negatively impacts their work-life balance, while 50% would quit if it hindered their enjoyment of life.
Additionally, mental health support ranks as a critical factor for 88% of employees when considering current or future employment opportunities. These findings highlight the urgent need for increased awareness and resources dedicated to mental health in the workplace.
Tessa Hollingworth, Managing Director of Randstad CPE, said: “With construction workers three times more likely to take their own life than the wider population it’s vital we encourage people to open up about mental health issues, which affect one in four people in the UK.
“We’re honoured to help those in need of expert advice through our continued support of the Lighthouse Charity.
It’s heartwarming to know that our contribution to the charity will assist the recovery of construction workers dealing with a variety of poor wellbeing issues.”
Sarah Bolton, CEO of the Lighthouse Charity, said: “I’d like to say a huge thank you to the Randstad team for their continued support as a company supporter and for the fantastic fundraising efforts. In addition to this, their proactive stance in promoting our charitable services continues to open conversations around positive wellbeing and helps to create a supportive working environment for everyone in our industry.”
With almost three quarters of construction workers (73%) feeling that their employers do not recognise early signs of mental health deterioration Randstad CPE ensures that employees have access to the help and support they need via Lighthouse’s 24-hour helpline.
So far this year, the Lighthouse Charity has supported over 4,200 families with a variety of emotional, physical and financial wellbeing issues, including emergency food shops, help will bill payments, free counselling and help with injuries and illnesses to name but a few.
If you or anyone you know is struggling, reach out for 24/7 free and confidential support now:
• 24/7 helplines; 0345 605 1956 (UK) / 1800 939 122 (ROI)
• Live chat www.lighthouseclub.org
• Text HARDHAT to 85258 www.lighthouseclub.org
Celebrating 25 years in the UK this year, Avant Tecno has established itself as a pioneer and market leader in the compact loader industry. Originally founded in Finland, Avant Tecno’s commitment to research, development, and innovation has led to the creation of high-quality loaders that have transformed construction and a variety of industries. The company introduced the world’s first compact loader, and ever since, it has consistently delivered versatile, durable machines that excel in power and performance despite their compact size.
In construction, where tight spaces, challenging landscapes, and varied tasks are part of daily life, Avant’s compact loaders have proven to be ideal. Models like the 400, 500, and 600 series stand out as highly versatile, all-terrain machines that can handle everything from demolition to material handling. With over 200 attachments, Avant loaders can be adapted to meet the demands of nearly any task on site. Their compact, manoeuvrable design combined with industry-leading power makes them a smart investment for contractors seeking an all-inone solution.
“Avant has been a leader in compact loader technology for 25 years in the UK. Our loaders bring together power, precision, and versatility in a way that few can rival,” says Raimo Ala-Korpi, Managing Director of Avant Tecno UK. “We’re proud to offer machines that are perfect for construction sites of all sizes, with attachments and features to meet a wide range of needs.”
In the construction industry, site restrictions and cramped working conditions are common challenges. Large machinery can be difficult to navigate in tight spaces, and transporting such equipment from one site to another can be costly and time-consuming. This is where Avant’s compact loaders have proven invaluable. Their small footprint allows them to be transported easily, manoeuvre through obstacles, and operate in confined spaces where larger machines cannot.
The 400, 500, and 600 series are excellent examples of Avant’s expertise in compact design. These loaders are not only easy to transport but also perform remarkably on-site. With advanced steering systems and intuitive controls, they’re highly manoeuvrable, allowing contractors to work efficiently in areas that would otherwise be hard to reach.
The 600 series, in particular, stands out for its power and lifting capabilities. With a lift capacity of up to 1,100 kg, the 600 series loaders are ideal for moving heavy construction materials like concrete, bricks, and steel. Contractors benefit from the loader’s compact size and surprising strength, a combination that enables the machine to work in restricted areas without sacrificing performance.
One of the hallmarks of Avant loaders is their incredible versatility. With more than 200 attachments available, Avant loaders can be transformed to handle nearly any task on a construction site. The attachments, specifically designed for construction, can be switched in a matter of minutes, saving time and maximising productivity.
For construction and demolition tasks, Avant offers attachments such as:
• Hydraulic breakers – Ideal for demolishing concrete and rock in confined spaces.
• Grapples – For securely lifting, carrying, and placing large rocks and debris.
• Concrete mixers – Efficient for preparing and transporting concrete onsite.
• Augers – Useful for precise digging and drilling.
• Pallet forks – Ideal for lifting and transporting materials like pallets and bricks.
Switching between attachments is fast and straightforward, thanks to Avant’s quick-attach system. This ease of attachment changeover makes the loaders incredibly adaptable, meaning a single machine can carry out multiple roles on-site.
“Construction sites are busy, fastmoving places. Avant’s quick-change attachment system allows contractors to switch tools in minutes, so they can stay productive and adapt to whatever task is at hand,” says Raimo.
Contractors benefit from the loader’s compact size and surprising strength
The all-electric e-series stands as the epitome of versatility in compact loaders, ideal for construction sites where noise and emissions must be minimised. Choose from our wide array of over 200 attachments and enjoy uninterrupted productivity with a single charge.
In line with the industry’s shift toward sustainable construction, Avant’s E-Series loaders bring all the benefits of electric machinery. With zero emissions and quiet operation, the E-Series is perfect for indoor demolition and working in urban or residential areas where noise and air pollution are concerns.
The E-Series loaders maintain all the strength and versatility of their diesel counterparts, and they come equipped with a powerful lithium-ion battery. This allows the loaders to run for extended periods on a single charge. Since there are no fumes, they are especially well-suited for indoor demolition work, where health and safety regulations are stringent.
Using electric loaders reduces both environmental impact and operating costs. With no need for diesel fuel and lower maintenance demands (electric motors require fewer repairs and servicing), contractors can enjoy significant
cost savings over time. Additionally, the quiet nature of the E-Series reduces noise pollution, allowing for work to be completed without disturbing surrounding areas.
“Our E-Series loaders are a fantastic solution for contractors looking to reduce their environmental footprint without compromising on power and performance,” says Raimo. “They’re perfect for indoor and residential work, where noise and emissions matter.”
Each of Avant’s loader series has unique features that make them ideal for specific construction tasks:
The 400 Series: Known for its small size and agility, the 400 series is perfect for light construction tasks. With a lift capacity of 550 kg and compact dimensions, this series is a great choice for navigating tight spaces and doing light material handling.
The 500 Series: This mid-sized option is highly versatile and suitable for a wide range of construction applications. It offers more power than the 400 series with a lift capacity of up to 800 kg. The 500 series is an excellent all-around option for contractors who need more lifting power without sacrificing mobility.
The 600 Series: With a lift capacity of 1,100 kg, the 600 series is ideal for handling heavy materials typically found on construction sites. It’s powerful enough to handle substantial loads yet compact enough to work in confined spaces. The 600 series represents the perfect blend of size and strength, making it a popular choice for demanding construction projects.
Avant’s newest addition, the 855i loader, combines the power of the 800 series with a more affordable price point. Equipped with the same high-performance Kohler KDI engine, the 855i offers impressive lifting capabilities with a lift height of 3.5 metres and a lift capacity of 1,900 kg. Unlike the twospeed 860i model, the 855i features singlespeed Poclain MSE05 drive motors, allowing Avant to offer this model at a significantly reduced cost.
The 855i is designed for jobs where speed over long distances is less critical, but powerful lifting and manoeuvring capabilities are essential. With this model, Avant enables contractors to invest in a top-tier loader with more funds available to allocate toward attachments and accessories.
“The 855i loader is an exciting addition to our lineup,” says Raimo Ala-Korpi. “It combines the power and lift height of our top models with an affordable price, giving contractors greater flexibility to invest in tools that will increase their work efficiency.”
Labour shortages have become a persistent challenge in the construction industry. Avant loaders address this issue by offering machines that are easy to operate and capable of performing multiple tasks with one operator. Their intuitive controls and ergonomic designs ensure that even operators with limited experience can quickly learn to handle these machines effectively.
By investing in Avant loaders, contractors can reduce the need for multiple specialised machines, which often require more training and expertise. Instead, a single Avant loader, equipped with the right attachments, can perform the work of several machines.
“Avant loaders are designed with ease of use in mind. Their versatility means that one machine can take on multiple tasks, helping contractors adapt to the industry’s labour shortages,” says Raimo.
With a 0% finance offer available until the end of December 2024 on all Avant models, contractors have an excellent opportunity to add these versatile machines to their fleets at an affordable rate. This finance option makes it easier for companies to invest in the equipment they need now without stretching their budgets.
Avant Tecno has long set the standard for compact loader innovation, and its 25th anniversary in the UK is a testament to its commitment to excellence. Avant’s compact loaders deliver powerful, versatile, and cost-effective solutions for the construction industry. Whether you’re tackling demolition tasks, moving materials, or working in confined spaces, Avant loaders are designed to meet the industry’s unique demands.
With a vast selection of over 200 attachments, the E-Series’ eco-friendly performance, and the newly launched 855i’s affordability, Avant loaders represent the ideal all-in-one solution for contractors navigating today’s challenges. Their compact nature, combined with impressive power and user-friendly operation, makes them a wise investment for any construction project.
“Avant’s loaders are transforming construction sites across the UK by offering compact, powerful, and sustainable solutions. We’re proud to be at the forefront of this industry, continuously innovating to meet the changing needs of our customers,” concludes Raimo. With that in mind, the Avant range of compact loaders continues to be game-changing in the construction industry.
Managing Editor, Becks, attends the Construction Plant-hire Association’s 2024 Conference. Back in full force, the 9th annual event was a resounding success!
It was fantastic to once again be back at the annual CPA conference on 7th November 2024 held, as always, at the Heart of England Conference and Events Centre. This year attracted a record number of attendees, with over 200 company delegates. Not only that, but there were 26 sponsoring exhibitors, a significant increase in comparison to last year’s 20.
The Headline Conference Sponsor was MHM Group, providing energy solutions to reduce costs and environmental impact. The list of other exhibitors included: ACOP Group, Acrow Bridge, CESAR Powered by Datatag, CITB, Capja, Conquip, Explore Plant and Transport Solutions, GGR Group, Groundhog, NOCN Group, Parksafe Group, Plant Parts, Plant Planet (us!), Plantworx, Point of Rental Software, Prolectric Services, Record360, Rouse Services, Scottish Qualifications Authority (SQA), Spartan Digital Operations, Supply Chain Sustainability School, Thomas Group, Tranzaura, VUE Group and WOLFF Onsite.
No stone was left unturned as the five different panels were put through their paces by presenters Merryn Myatt and newcomer, Peter Haddock. They played off one another so well, demonstrating the perfect balance between the softly spoken, measured professional and enthusiastic newcomer.
This year’s focus was very much about ‘shaping the future’, and the five panels tackled this overall theme with gusto. Even the power suddenly going out didn’t dampen anyone’s spirits. The chats continued unabashed as everyone blindly found their seats, enjoying the irony of the comeback song ‘I’ve got the power’.
After intros from Merryn and Peter, we had a welcome address from Steven Mulholland. He stressed a need for community, looking to future generations to keep up the good work, and talked about his extensive tenure, and why he is so passionate about the plant hire sector and all it entails. His speech was perfectly summed up in one quote by the man himself: “Collaboration. A great word. And that’s what we do here at the CPA.” Steve also stressed the importance of new technologies to aid everyone in the difficult journey towards Net Zero, alongside a definite change in attitude from everyone involved. It was a game of tortoise and hare, with Steve explaining that rash policy changes with no proper guidance helped no one achieve in the end. And with that, the show began.
The Plant-hire Sector in 2024 - Where the Industry Currently Sits in the Wider Economic and Political Context Panellists Chris Cassley, CPA Policy Manager, and Jamie Charles, Lead Economist with Oxford Economics began discussions by examining the justpublished report commissioned by the CPA into the size and significance of the industry, a report that provided many fascinating statistics and insights into the plant-hire sector. Not only was the plant-hire sector’s contribution to the UK economy an estimated £14 billion, but they are also responsible for 191,500 jobs. On top of this, construction plant-hire workers are known to be around 16% more productive than the average worker! Both panellists agreed on the importance of the report and how instrumental the information was for all of the delegates there that day.
The Innovative Plant-hire Company - Insights into Current and Future Developments and Innovations in the Sector
The second panel brought together the minds of four brilliant panellists: Brian Jones, CPA President, Asif Latief, Chief Commercial Officer with Speedy Hire, Kathryn Adams, Commercial Director at Prolectric Services and Mat Llewellyn, MD of MHM Group. Peter Haddock kicked off discussions with: “Two of my favourite letters will be spoken aboutAI.” And he wasn’t wrong! Everyone agreed that Artificial Intelligence was starting to be used more readily, and being able to access real-time data via telematics and energy management systems was essential in this day and age. There was a pertinent question from the crowd from a small business owner: “Why should I invest in green technology given the price pressures?” A relevant question if there ever was one, and it was met with equal fervour and debate. Ultimately, it was agreed that although it was an initial high cost, it was a solid investment that would show return over time.
Another four panellists ascended the stage for round three: Katie Kelleher, CPA Technical and Development Officer; Deb Madden, Executive Director with CITB; Carl Hassell, Chief Operating Officer at training standards organisation NOCN Group and Beth Doel, Advanced Technical Trainer at Reaseheath College. It was certainly the most spirited of the topics, with crowd questions such as: “How do we get kids the necessary experience so that they’re able to get a proper start in the industry?” The main topic of debate was how to encourage a wide range of people into construction amidst the problem of worker retention, with a particular focus on women. They wanted not only to identify the problems were, but provide a viable solution to overcome it. A particularly heated moment looked at women’s treatment and potential harassment, where personal experiences of the panellists were used to highlight the risks and issues. Merryn summed it up well: “an uncomfortable discussion but a valuable one.” Panellists looked at the ‘CITB Women in Construction Awards’ and why it’s not the awards that are important, but the community that it generates, as well as highlighting how incredible the journey for women has been and how they’ve fought for what they have. An issue very dear to my own heart, I must say.
One of the best things about the CPA Conference is the incredible sense of community. Every break time sparked intrigue and discussion; there hasn’t been a single CPA event I’ve gone to where I haven’t come away with many new LinkedIn connections. One in particular was Plant Parts, who were excited to share their critical takeaways from the conference: Growth amidst uncertainty, commitment to sustainability, embracing technology (particularly in fleet management and resource optimisation) and workforce development.
It was also an excellent time to catch-up with some of our favourites. Datatag were ready and raring to show off their incredible theft prevention technology, with Capja and Vue also standing strong in the technology corner. It was lovely to catchup with Genquip and Rouse, both who have graced the pages of our magazine numerous times.
And who could mention lunch without the announcement of the winner of the Lego Excavator! Kunal Kamor had the winning guess and took home the coveted prize (that I’m not at all sour about, no siree).
Speakers included David Graham and Chris Harvey, two Co-Founders and Directors of The Hire Exchange, set up to connect buyers and sellers of hire companies, Dani Saveker, Global CEO and Founder of the GLAS Group consultancy which supports entrepreneurs, and Ian McMillan, Head of Business Development at Thomas Group.
The panellists tell their stories and how they got into their line of work. Whether it was a family business or from the ground up, there was a wonderful mix of methods; stories and outcomes to help teach others how to pave their own path in the industry, with succession planning taking up much of the debate. David and Chris talked thoroughly about building a business through partnership, whereas Ian looked at the strategies required for taking over a business and how they grew from something small to look at a national expansion programme that caters to tier one contractors.
This final, and incredibly pertinent panel, comprised Steve Kerslake, Trustee and Founder of Construction Sport; Gary Higgerson, a Charity Advocate with the Lighthouse construction charity and Matt Hartill, Head of Wellbeing and Mental Health Support at Lyndon SGB.
Steve explained to the audience about construction sport and the support it provides to the community, giving people a safe space to be amongst likeminded people. Matt was incredibly candid as he spoke about his own struggles with mental health and how he was close to suicide. It was incredibly emotional but thoroughly enlightening. He brought up the age-old industry issue of “why don’t you talk to anyone? Because you’re a bloke.” Certainly, something to look at given that a large percentage of the construction cohort is male. Lucky then, that Gary’s charity, Lighthouse, is a cornerstone for mental health in the industry, and gives people that safe space to reach out to, saving countless lives of those who are struggling.
It’s good to see that, not only is the CPA tackling practical issues, but also social. It’s important to look at what’s affecting people in the industry as plant is powered by people. The panel subjects were an excellent balance of all faculties and gave the audience plenty of time to ask questions about the issues. Usually, I’m the only one making furious and copious notes at these events, but there were so many people scribbling away. The investment from the audience is paramount and this one had it in spades.
A thoroughly interesting event. Bring on 2025!
It’s crazy to think we’ve had a year of the lovely Lana in our magazine. What started out as a simple interview for a piece about Women in Construction (which we will be revisiting in our 2025 February issue) has blossomed into something truly incredible.
This charming, uncommonly kind and talented woman has allowed us a little glimpse into her world so that we are able to show the truth of the industry to you, our readers. The good, the bad, the highs, the lows, we have covered so much in this first year alone. And it won’t stop there. 2025 will bring a wealth of new adventures, fresh topics and life updates about one of the sectors most respected contractors.
So then, what did Lana get up to this year? And what has she taught me along the way?
(Spoiler alert: She’s taught me far too much to cover in a simple article, but I’ll do my best!)
It’s no surprise that the very first issue we covered was women in construction. My interest (dare I say obsession? Is that appropriate?) in Lana began when I was finishing up my Plantworx 2023 review, and I went into an internet rabbit hole watching videos of Awesome Earthmover’s Operator Challenge from the show. I had just started with Plant Planet, was plunged headfirst into the busy world of construction, and was thoroughly determined to find my footing and stake my writing claim on the sector. And there she was. Lana. Or Tracklass1 as I knew her then. I wanted to talk to the woman who talked the talk and walked the walk better than anyone else (and as I found out later, was the artist behind the ‘Plantworx’ carved into the showground with an excavator).
Always an advocate for women’s struggles, I was keen to talk to Lana about her experiences as someone who worked in construction in a time where a woman on site drew whispers and gasps. To me, a story riddled with such adversity would be inspiring for other young women who had joined construction, and perhaps also educational for those who work alongside them. And although Lana shared her story happily, she was quite insistent that she was not an influencer and was in fact just a person.
“I’ve had many people comment on my posts saying that I’m an inspiration for women in construction. Honestly, I’m not. I don’t see myself that way. I’m just doing the job I love, I’m just me doing my job to the best of my ability. I have absolutely nothing to prove anything to anyone.”
Humility remains Lana’s constant companion, and honestly even a year on, I don’t think I’ve convinced Lana how exceptional she is, and how vital she is to the industry. I’m still met with a shrug and a “well I’m just being myself.”
I will convince you one day Lana, mark my words!
I will say, it’s not just me that desperately wants Lana to understand just how astounding she is. A month or so later, I got the opportunity to see Lana in action for myself. Boots plunged into the thick mud of the worksite (quite literally, I got very stuck), me and my camera followed Lana as she went about a day’s work. The finesse, the poise, the casual expected shrug, it was an incredible eye opener to the world of Lana Edwards. I loved chatting to Lana’s on-site work team, as they were all just as much in awe of her as I was. Not just for her talent but for her shining personality and kindness she showed the world.
It’s especially brilliant given that Lana has experienced the harsh reality of some truly *INSERT NAUGHTY WORD I’M NOT ALLOWED TO PUBLISH* on site and suffered shocking treatment over the years from her work fellows. Lana has never let that stop her though, and instead of being bogged down by it, has pushed forward to be the kind of team player we all want to work alongside.
No wonder her entire team showed up to the CITB Women in Construction awards, suited and booted, to champion her to the fullest extent.
Wherever I’ve been with Lana, there has been a trail of respect and fondness. At Hillhead 2024, everyone we spoke to made a point of telling me ‘Lana is the best of the best’ and remind me how lucky I was to be hanging out with her. Believe me everyone, I know. I loved watching people get a little giddy to talk to her and steal her snippets of wisdom, both at Hillhead and at the KH Plant Training Day we went to in August. Her softly spoken talk about her experiences had the training room in complete silence, the audience hanging on her every word. I couldn’t stop smiling, quite honestly. That was my friend up there, getting the admiration she deserved.
Now I’m about to get mushy, my dear readers. And honestly, I won’t apologise for it.
Lana has always told me that the people you meet along the way can make all the difference to the job you do. It can truly be make or break for a career, and as always, she’s absolutely right.
Not only have I learned so much about construction from Lana, but I’ve learned what kind of writer I want to be; what kind of person I want to be. I’m not mechanically talented to say the least. I can’t inspire people with my incredible plant operating skills (unless you want to learn how to crash a forklift into a warehouse door, because if so, I’m your gal.) What I can do though, is offer a platform to those marginalised voices that need to be heard. I can show kindness and understanding where people have been left bereft. And I can continue to learn and listen to those in the know. A friend like Lana is invaluable for so many reasons, not least of all because she is literal sunshine in an otherwise dreary world. Sometimes my mind drifts back to this summer, when Lana and I were sat nestled on a hill near her home, looking out over the sea and the fluffy cloud formation over Snowdon. I don’t think I’ve ever felt so at peace or content, and as we chatted about everything and nothing, wiling away the time, I wonder if I’ll look back in many years and see that as a pivotal moment in my life. When the world was quiet and at rest, and two new friends chinwagged as though they had known one another for years.
I don’t know about you readers, but I can’t wait for all that next year brings. So, let’s get to it, shall we?
Komatsu’s Utility equipment is designed, manufactured and supported to meet the same industry-leading standards as our construction and mining industry machines. Versatile and easy to transport, with precision controls and simple maintenance features, our Utility performers are the right choice whenever you need flexible and reliable compact earthmoving equipment.
By Lorna Cowlin
In this industry, our machines are the most vital part of getting any job done, and you certainly want the right tools for the job! We take pride in our machines, show them off any chance given and look after them with the utmost care. So, when it comes to choosing attachments for it, you really need the right one…
As with anything, the basics are the best place to start. If you don’t know what attachments are out there, how are you ever going to pick? Don’t worry, we’ve got you covered!
- Buckets: Buckets are one of the most common attachments and come in various shapes and sizes. They range from simple general-purpose, all the way to heavy-duty. Making sure you choose the right bucket means you won’t overburden the machine it’s attached to!
- Augers: Augers are the best attachment when drilling or digging, specifically for tasks involving foundations, fence posts etc… Like the buckets, augers also come in different sizes to best suit the job at hand.
- Breakers: Very aptly named, as breakers do just that! They can be used to break through concrete, rock or asphalt. They are best used in demolition projects as they deliver high impact. They make the tough jobs look easy!
- Grapples: Grapples are much like the hands of the machine. They can handle materials like logs, debris, scrap and other heavy items, carrying them with extreme precision.
- Compactors: Compactor by name, compactor by nature; these guys are used when compacting materials such as soil, gravel or asphalt. Compactors are the attachments to use when your project involves any such earthmoving, creating a solid and stable foundation base. If the right attachment is chosen, the outcome will lead to reduced costs and greater efficiencies for all projects.
If the right attachment is chosen, the outcome will lead to reduced costs and greater efficiencies
However, not only do you need to make sure the attachment is correct, but also where you’re getting it from. But no need to stress! There are many great companies out there with high customer satisfaction and a wide berth of knowledge in this realm.
- BPH Attachments: BPH is a family-run company, and the UK’s leading excavator attachment specialist. Its extensive knowledge is the main reason why BPH’s customer satisfaction is so high, with the company enjoying an established reputation in the attachments industry.
- Invicta: As the largest and most established manufacturer of forklift forks and attachments based in the UK, Invicta’s expertise knows no bounds. The company provides both standard and bespoke solutions to fit all needs, and supplies a speedy, flexible service.
- Albutt Attachments: Founded over 50 years ago, long-established Albutt is widely respected for its high specification attachments for industries based in agriculture, waste, construction and forestry. Albutt builds to quality, not price, to make sure its attachments are precisely what their customers need.
In addition to the attachment specialists, there is one brand who is looking to be more innovative in their approach to drive simplicity and compatibility in the construction equipment industry. As a joint initiative between Rototilt and Steelwrist, the independent organisation Open-S Alliance was founded in 2020. Their main aim was to create a coupler standard for excavators: one universal approach. Likening it to the universal USB-C connection, the approach Open-S promotes an open interface. The wondrous ‘one fits all’ comes to construction!
I mean, if you’ve already spent thousands of pounds on good machines, why not invest in good attachments too?
The symmetrical standard (S standard) for couplers has been around since the mid 1980’s and what Open-S does is to define the position of the hydraulic couplings within this standard. Instead of locking customers into a closed proprietary interface, Open-S allows contractors around the world to be able to combine products from different brands. The machines on construction and demolition sites certainly aren’t cheap, so a high utilisation is critical. Therefore, there is a growing demand for automatic couplers allowing the operator to change hydraulic attachments in seconds, making sure you get the most out of each machine. With Open-S compliant products you can avoid adding additional machines to the job site as you can quickly switch between the attachments available allowing you to do different tasks with the same machine. This is an expansion on the concept of ‘one fits all’, and it’s so great that we’re seeing more of this in the construction industry!
The last 12 months have shown such immense growth for Open-S! The alliance is expanding with new members from North America and Asia this year, which shows that they’re not just growing nationally, but now globally. The members of Open-S are all customer focused, and honouring warranty when using attachments from different brands compliant with the standard is a high priority. More and more customers are seeing the benefits, and joining forces, which is nothing short of amazing news for Rototilt and Steelwrist.
The efforts made by the alliance are also being put into the members’ social media and marketing to further spread the word. After being initiated by Steelwrist and Rototilt the alliance now consists of the following members:
- Construction Equipment Group (Norway)
- Craig Manufacturing (Canada)
- Daedong Engineering (South Korea)
- KH-Maskin (Sweden)
- Pacific JCB (USA)
- Rotar (Netherlands)
- Rototilt (Sweden)
- Kinshofer Group (Germany)
- SMP Parts (Sweden)
- Steelwrist (Sweden)
- TP Manutention (France)
- Volvo Construction Equipment (Sweden)
- Wacker Neuson (Germany)
Speaking with Karl Serneberg, VP Marketing & OEM Sales, and Marianne Johansson, Marketing coordinator, at Steelwrist, it was clear to see their passion for this
project, and rightfully so! It was fascinating hearing about their venture, leaving it difficult not to feel inspired by this movement. It also left me thinking; why hadn’t this been thought of before? How innovative and insightful of a business move to create something that will only give contractors more ease on site with their machines. If a job can be made easier, then why not!
“Open-S is about the benefit for the contractors and machine operators. The idea with the standard is to make it possible for them to freely choose between, and mix, different brands of products, without losing any functionality or safety features of the products, and not be locked into a proprietary solution that limits their options. This idea made us take the initiative to start the work to build an international and open industry standard four years ago. It is fantastic to see that we are growing internationally, with new members in Asia and North America,” says Stefan Stockhaus, CEO of Steelwrist AB and Board Member of the Open-S Alliance.
I can’t wait to see how much further the Open-S Alliance can go, boosting an open standard for automatic couplers. It’s beyond fascinating, and it’ll be a wonderful day when we see it globally on every construction and demolition site possible!
Higher durability means fewer replacements and repairs, which is therefore more cost effective in the long run.
Construction sites can be incredibly harsh environments with abrasive materials and heavy loads. Therefore, the attachments have to be designed and built specifically to withstand such conditions. Attachments are the most used part of any machine, so they must be durable. High quality steel is known for its strength and resilience, and is an essential part of construction attachments. Common types of steel used are:
- Carbon Steel: This type of steel is hardy and immensely strong, and is the most popular material used when making construction attachments.
- Alloy Steel: Protecting machines from corrosion, this steel includes extra elements, such as chromium and nickel.
- Stainless Steel: Highly resistant to rust and corrosion, this steel is ideal for the harsher weathers and tougher environments.
The performance of the attachments is reliant on the materials used, and is critical for maintaining the longevity and efficiency of the equipment. This also avoids degradation of the machines, ensuring a longer life and enhancing functionality. Higher durability means fewer replacements and repairs, which is therefore more cost effective in the long run. And, all together, this promotes a more trustworthy health and safety value, leaving you safe in the knowledge that the equipment you’re buying is high level, giving you more bang for your buck!
So, choosing the right attachment really does help!
Yes, it sure does! As anything, the correct research goes a long way, and hopefully this article has done the hard work for you. Quality attachments support machine longevity and are the best investment one can make for machines, and for productivity. So, go on, treat yourself!
Wouldn’t it be good if we worked together?
Open-S is the open standard for automatic couplers for excavators. The goal is to give machine operators and contractors around the world the freedom to combine quick couplers, tiltrotators and work tools from manufacturers that are in compliance with the standard, and to promote continued technological development.
The future is open! Read more at opens.org
Executive Hire Show 2025: sold out the hire industry’s unmissable event
The countdown is on: the Executive Hire Show 2025 is officially sold out, and the buzz is electric. On Wednesday 12th and Thursday 13th February 2025, the CBS Arena in Coventry will transform into the centre of the tools, plant, and equipment hire industry. With every one of the 145 stands booked, the event promises two unmissable days of inspiration, innovation, and connection.
This year’s show, the 18th annual event, continues a tradition that has defined the hire sector for decades. It brings together the UK’s most passionate hirers and the suppliers shaping its future. Since launching in 2007, the Executive Hire Show has brought the hire industry together to discover innovations, connect with peers, and support the sector’s growth.
The Executive Hire Show 2025 tackles challenges head-on as the industry focuses on sustainability and efficiency. Expect to see the latest innovations in electric and hybrid machinery, alternative powertrains, and sustainable site solutions—all designed to help hire companies future-proof their operations. From tools that transform fleets to software solutions that streamline operations, this showcases what’s possible when initiative meets opportunity.
The Executive Hire Show is the heartbeat of the hire industry. It’s where major players and independents share ideas, spark partnerships, and shape the future. At last year’s show, independent hirers made up an impressive 86% of attendees, highlighting the event’s appeal across the breadth of the sector. Whether running a national operation or an ambitious start-up, this platform is the platform to learn, grow, and connect.
The final exhibitors to secure their places at the now sold-out Executive Hire Show highlight this year’s impressive range of expertise. Dantherm Group Ltd will bring its experience in climate control solutions, helping businesses maintain efficiency and comfort in demanding environments. At the same time, ABAX UK offers innovative telematics to improve fleet management and optimise operations. Ronda Enviro-Vac specialises in industrial vacuum systems designed for effective site maintenance, and PreTec will demonstrate its precision-engineered construction tools that enhance on-site productivity.
SANY UK & Ireland and Doosan Bobcat – both renowned for their excavators – will showcase machinery built for performance and reliability. Bobcat will also highlight its versatile attachments for a wide range of applications. ASKA International UK Ltd brings advanced safety solutions to ensure work sites meet the highest standards, while Filtertechnik offers filtration systems that maximise equipment longevity and efficiency.
Vendo Digital introduces cutting-edge digital display technology to enhance marketing efforts, and OMC Trailers provides robust and reliable transport solutions designed for heavy-duty use. These exhibitors highlight the innovation and diversity that make this event a must-attend for the hire industry.
Chris Moore, Executive Hire Show Director, commented: “The Executive Hire Show has become an essential event for our industry – a place where deals are struck, new ideas are explored, and the direction of hire is shaped. Being completely sold out highlights the value this event delivers to exhibitors and visitors.
“This year, we’re offering more than ever. Many exhibitors will have exclusive show-only deals, making it the perfect opportunity to upgrade fleets or secure new equipment. The event also goes beyond the exhibition floor. Day one concludes with the Networking After Party which incorporates the Executive Hire Show Passionate Hire Awards – an ideal chance to celebrate the industry’s achievements, connect with peers, and build relationships in a more relaxed setting. We’re looking forward to welcoming everyone in February for what promises to be a fantastic two days.”
Every stand at the 2025 show showcases the innovation and expertise driving the hiring industry forward. From household names like Thwaites, Niftylift, Mecalac, JCB, MHM, Altrad Belle, Husqvarna UK, Makita, The CPA (Construction Plant Hire Association), Groundhog, Ammann, Toro and many more to the energy of 45 first-time exhibitors, the diversity on display ensures something to inspire every visitor. While innovation is front and centre, the show also provides a space for real conversations about the challenges and opportunities facing the hiring sector today. With sustainability and decarbonisation dominating discussions, visitors will discover practical, actionable insights to take their businesses to the next level.
Exploring the exhibition floor is an opportunity to discover the latest innovations, engage with industry leaders, and experience live demonstrations that inspire new ideas and practical solutions.
Coventry is the only place to be this February if you’re serious about what’s new in hire. With over 145 exhibitors, countless networking opportunities, and a laser focus on the future, the Executive Hire Show 2025 promises to deliver insights and connections that could define your year.
Chris concluded “The EHS is about leaving with fresh ideas, valuable connections, updates for your fleet, and a clearer vision for the future of your business – too good to miss!”
Don’t miss your chance to be part of the energy, innovation, and inspiration at the Executive Hire Show 2025. This February, be there to experience the event where passion meets progress – and the hiring industry comes alive.
Registration and attendance are free – Visit the Executive Hire Show website now to register for fast-track entry and start planning your visit, with the online floor plan Executive Hire Show 2025 Registration. With just two days to experience the best in hire, early registration guarantees visitors more time on the show floor to secure the best in ‘show deals’.
www.executivehireshow.co.uk
7-9 MAY 2025 EXCEL, LONDON
THE BRAND NEW SHOW FOR:
THE LATEST TOOLS
COMPACT PLANT EQUIPMENT
SOLAR & HYBRID SYSTEMS
ZERO-EMISSION FUEL PRODUCTS
Co-located with
In the construction industry, tradespeople face numerous challenges daily. Among these, one issue often overlooked yet profoundly impactful is not having tools readily available. This seemingly minor problem can quickly trigger a chain reaction, disrupting productivity, safety, deadlines, and increasing costs. These disruptions ripple through entire projects, impacting everyone involved and threatening the overall success of the work.
Construction is built on the expertise of skilled tradespeople – electricians, plumbers, carpenters, bricklayers, and HVAC technicians, to name a few. Each trade brings unique skills that are essential for the successful completion of a project. However, even the most skilled workers are limited without their tools. Tools are not just accessories; they are the foundation of every task, and when they are missing, the entire project suffers.
“Fleet managers often underestimate the impact of misplaced tools. It’s not just about replacing them; it’s about the ripple effect on productivity and profitability when workers can’t complete jobs efficiently,” says Craig Allan, Director of Specialised Sales at ABAX.
Each trade has its own set of tools tailored to specific tasks. These tools are not only designed to facilitate work but also to ensure safety and compliance with building codes. When tradespeople are without their tools, they face significant obstacles:
• Delays in Project Timelines: Without the necessary tools, tasks cannot be completed on schedule. This delay can lead to a domino effect, impacting subsequent trades and extending the overall project timeline.
• Increased Costs: Delays often result in increased labour costs and can lead to penalties from clients for late deliveries. Furthermore, the cost of renting tools or purchasing replacements can strain project budgets.
• Safety Risks: Many tasks require specific tools for safety reasons. For instance, using improper tools can lead to accidents or injuries, putting both the worker and the project at risk.
• Increase Theft risk: When Tools aren’t where they should be, they are often ‘left’ somewhere and this significantly increases the opportunity for theft
The absence of tools doesn’t just cause inconvenience – it triggers a ripple effect that destabilises every aspect of a project.
1. Productivity
Construction projects operate on tight schedules, and even minor delays can cascade into significant disruptions. For example, if a plumber arrives onsite without essential tools, they might waste hours retrieving them or finding alternatives. This not only delays their work but also holds up other trades waiting to proceed.
The result? Increased costs, lost time, and unnecessary environmental impacts due to additional travel.
Workers spend up to 38 hours annually searching for misplaced tools, equivalent to almost an entire workweek. This inefficiency significantly contributes to delayed projects and inflated operational costs.
Source: ABAX Blog - Did You Know Construction Workers Spend 38 Hours Annually Looking for Their Tools?
2. Compromised Quality of Work
Quality is paramount in construction, and using the right tools is vital to achieving high standards. When tradespeople are forced to improvise or use inadequate tools, the quality of work can suffer. This not only affects the immediate project but can also lead to longterm issues, requiring costly repairs or adjustments down the line.
We’ll send you an alert when you leave site without your tools.
Tradespeople take pride in their craft, and lacking the right tools can lead to stress, frustration, and dissatisfaction. In an industry already grappling with labour shortages, maintaining worker morale is crucial.
“The construction sector loses an average of £7,000 annually per company due to tool loss and misplacement,” according to a recent productivity report by Hilti Group (Hilti Group Report).
Clients expect projects to be completed on time and within budget. Delays caused by tool-related issues can erode trust, damage reputations, and jeopardise future business opportunities.
EDS, a contractor with 40 employees across Merseyside and the West Midlands, faced challenges with wage overclaims and inefficient tool management. Implementing ABAX’s vehicle and tool tracking systems enabled monthly audits by crossreferencing timesheets with vehicle location data, saving approximately £200 monthly in overclaimed wages. The live map feature improved customer service by dispatching the nearest vehicles promptly. Additionally, tracking expensive equipment streamlined inventory processes, enhancing overall efficiency.
1. Tool Management Systems
A structured tool management system is essential for ensuring tools are available when needed. Key elements include:
• Tracking: Knowing where tools are and keeping a comprehensive inventory.
• Regular Maintenance Checks: Ensuring tools are functional and ready to use.
• Centralised Storage: Simplifying access to tools and reducing the risk of loss.
2. Training and Education
Training is essential not only for skill development but also for instilling a culture of responsibility regarding tools. By educating tradespeople on the importance of tool maintenance and management, firms can reduce the likelihood of tools being left behind or neglected.
For smaller or short-term projects, hiring tools can be a cost-effective solution. This approach ensures access to the right tools without the burden of ownership or maintenance.
4. Mobile Tool Kits
Providing tradespeople with mobile tool kits tailored to their specific needs can help mitigate the risk of tool unavailability. These kits should be designed to be portable and easily transportable, allowing professionals to carry their essential tools wherever they go.
5. Encouraging Accountability
Establishing clear policies and incentives can encourage workers to take responsibility for tools. Companies can integrate practices such as endof-shift tool check-ins or team competitions for maintaining tool inventories.
ABAX Locator and ABAX Worksite are designed to transform the way tools and assets are managed:
1. Bluetooth Tags: Attach these tags to tools and equipment for tracking and inventory management.
2. Lost & Found Functionality: Locate misplaced tools via the ABAX platform.
3. Geofencing: With ABAX Worksite, set up geofenced zones to monitor tool movement In and out of the predefined area. Alerts are triggered if equipment leaves the designated area.
4. Process Automation: Eliminate manual inventory management with automated reports and tracking systems.
5. Optimisation: Use insights from the ABAX platform to automate service schedules, reduce fuel consumption, optimise inventory, and lower emissions.
Charlie Wright-Roberts: “I have used ABAX for all of our plant equipment, and it has saved us from a £45,000 theft. I can see where all our equipment is in real time and the hours it has been used. I recommend it to all operators of plant equipment.” Via Trustpilot.
After implementing ABAX tracking systems, JMC Construction observed a notable increase in productivity. Plant Manager Jo McGarvie stated, “Since having the trackers on our vehicles and plant, productivity has increased during the day.”
The UK’s business-oriented tool market represents significant economic value, offering opportunities across various segments:
• Tool Manufacturing Industry: Generates £1.3 billion in revenue annually (IBISWorld).
• Power Tools Market: Expected to grow from £950 million in 2023 to £1.35 billion by 2032, with a CAGR of 3.95% (IMARC Group).
• Tool Distribution Market: Valued at £1.31 billion in 2022, projected to exceed £1.48 billion by 2028 (AMA Research).
• Hand Tools Market: Achieving a CAGR of over 6%, with growth of £120 million between 2020 and 2025 (AMA Research).
These figures reflect the immense reliance on tools in construction and beyond. To harness this value, tool management systems are indispensable. Here’s why:
1. Boost Productivity: Minimise time lost searching for tools.
2. Reduce Costs: Lower tool replacement and fuel expenses.
3. Monitor Usage: Use geofencing and alerts to locate tools and equipment.
4. Enhance Accountability: Foster responsibility among workers.
5. Optimise Resources: Streamline inventory and reduce waste.
In construction, tools are more than just equipment – they are the key to doing the job right. When tools aren’t available, the chain reaction of delays, safety risks, and cost increases can disrupt an entire project. These issues cause a ripple effect that impacts productivity, worker satisfaction, and client relationships. By adopting proper tool management systems, providing portable kits, and encouraging workers to take responsibility, companies can avoid these problems. As the construction industry evolves, ensuring tradespeople have the tools they need will remain essential to delivering projects on time, on budget, and to a high standard.
With the right tools and systems in place, the construction industry can continue to build efficiently, safely, and professionally.
In 2025 Steelwrist celebrates 20 years in business. Founded in Sweden back in 2005 manufacturing tiltrotators, quick couplers and work tools for excavators, the company has grown significantly since then, quickly becoming the global player it is today, represented in over 19 countries. The goal back then was the same as it is today, to be the “best in the world at developing, manufacturing and selling equipment to increase the efficiency of excavators.”
The tiltrotator is the centre-piece in the company’s offer. The concept has proven to be the key that truly unlocks the efficiency of an excavator. With 360 degrees rotation and 45 degrees tilt in both directions, the tiltrotator allows the operator to do more types of jobs, be faster and work with greater precision. Operators also say it makes the job more fun!
The company’s head office is located in Rosersberg, Sweden, close to Stockholm’s Arlanda airport. The move there in 2018 more than doubled the production area and saw a new automated machining centre installed, significantly increasing production capacity. The facility is located at the heart of the world’s most advanced excavator markets. The tiltrotator concept has been well established in the Nordic region for decades now, with operators and contractors keen to adapt and invest in new products and technology. This drive for innovation makes these markets among the most discerning and challenging customers in the world, which in turn spurs product development and healthy competition within the tiltrotator manufacturers, to the benefit of customers globally.
Steelwrist always strives to be responsive to customer feedback through continuously developing its product offerings. It was a proud moment when the company launched its third generation of tiltrotators in March 2024, the all new XTR range of tiltrotators. The XTR models have several new and innovative features, including a completely new state-ofthe-art, sensor based, system for enhancing safety on quick couplers and tiltrotators, known as LockSense, along with a number of other new and exclusive features.
If you ask excavator operators their opinion on using the tiltrotator they will tell you that they would never go back to being without one. In fact, during Steelwrist’s 20-year history there has never been a customer, to their knowledge, who started to utilise the tiltrotator concept and then went back to work without. The increase in worksite efficiency and safety comes from transforming the excavator into a true tool carrier, with reduced costs and more tasks being easily completed from the cab, therefore requiring less ground personnel, is very compelling. When you can reduce the number of machine movements to complete a task, you will be saving time, fuel and machine wear, also increasing safety.
But how big is the increase in efficiency really? How big are the fuel savings? By how much is the wear and tear on the excavator reduced? What tasks can you do that would not be possible without a tiltrotator? Unfortunately there is no one definitive answer, it can depend on a multitude of factors, including the size of the excavator, the type of work being carried out, right down to the mindset of the operator or contractor. However, independent studies in Japan show that when comparing the same task with the same excavator both with and then without a tiltrotator, both the efficiency increase and fuel saving was just above 40 percent. Although this might not be the case for all situations, it is quite safe to say that any five-day job could be completed in four or less with a tiltrotator.
Continuous product development has been at Steelwrists’ very core from day one. An important milestone was when Steelwrist introduced their patented Front Pin Lock (FPL) safety system back in 2012. Steelwrist were first in the industry to have a safety solution on both tiltrotators and quick couplers to reduce the risk of dropping a bucket. The system securely retained work tools in the event that the operator had made a mistake. The new patented LockSense technology takes this commitment to safety innovation even further by eliminating the mistake itself before it happens rather than simply preventing a mistake from becoming a mishap.
Steelwrist launched the third generation tiltrotators in March of 2024. The new tiltrotators share the common features from which the success of Steelwrist tiltrotators has been built; a low build height, high angle of tilt and
the unbeatable relationship between strength and weight associated with using steel cast components. The XTR20 is the first model in the new generation to have been released, designed for use on 15-20 tonne excavators, it demonstrates several innovative features both from a hardware and software perspective. The XTR20 uses cast steel components for all its major bodyparts including the upper coupler, main gearbox, as well as the attachment coupler below.
Despite its compact nature, with an overall reduction in both height and weight compared to its predecessors, the XTR20 still maintains a tilt angle of 45 degrees in both directions. The overall tilt geometry has been greatly improved on the XTR range. Redesigned, off-centre mounting brackets allow the tilt cylinder to not only become physically shorter than before, but also are key in minimising cylinder spread, all the while gaining an overall increase in tilting torque throughout the tilt cycle; this ensures consistent smooth operation at any angle. The refined position of the tilt cylinders, along with the reduction in spread, helps to prevent interference with the excavators’ bucket linkages, enhancing functionality, ease of use and of course installation.
The XTR tiltrotator range is the first to feature Steelwrist’s patented LockSense technology, a completely new, state-ofthe-art, sensor based system for indicating whether or not the work tool is securely locked while in operation, specifically
including during coupling and decoupling. The wireless design eliminates the need for cables and connectors to be exposed to the harsh environments found at the business end of an excavator. LockSense is a machine independent system that can be installed on all excavators to monitor the safety status of both the machine quick coupler and/or the tiltrotator’s attachment coupler. The system constantly monitors the locking status and does not interfere with the locking procedure of the coupler. It provides real-time status indication in the form of visual and auditory warnings to the operator, to prevent mishaps before they can occur. This innovation is in line with the direction that the latest ISO regulations are heading, ensuring compliance long into the future.
Tiltrotator maintenance and lubrication have been made considerably easier with the introduction of OptiLube, a built-in onboard lubrication system for the tiltrotator’s main gearbox. Also the number of lubrication points on XTR has been greatly reduced compared to the older models through the introduction of triple-sealed lubrication-free bearings in key positions on the XTR series, this will greatly reduce the amount of time the operator has to spend on daily checks and maintenance. OptiLube is integrated into the tiltrotator control system and takes care of lubrication automatically, ensuring consistent and optimal performance.
Steelwrist’s third generation tiltrotators takes efficiency for excavators to the next level. Best in class tilt geometry, LockSense - a new patented safety solution for work tool locking and OptiLube - an onboard lubrication system, are just some of the technical developments of the third generation high performance Steelwrist tiltrotators.
Easy installation with the InstallMate app
Lubrication free triple sealed bearings
Modular design for upgrade to SQ/Open-S
For 15-20 ton excavators
Also new, Steelwrist InstallMate, an intuitive app-based guide with step-by-step instructions that will simplify the Steelwrist installation process, making the setup straightforward and user-friendly for dealers and service partners wherever they are on the globe in their local language.
The XTR tiltrotator range is available with interfaces following the symmetrical standard (‘S-Type’). Thanks to the modular design it is possible to upgrade the tiltrotator from a standard ‘S-type’ to Steelwrist’s ‘SQ-type’ (high performance automatic quick coupler system). All Steelwrist ‘S’ and ‘SQ’ products comply with the Open-S standard for excavator quick couplers and attachments.
Building an open industry standard for automatic couplers
Wouldn’t it be good if contractors and machine operators could be free to choose between and mix different brands of products, without losing any functionality? This idea is what set off the creation of an open industry standard for automatic couplers. Based on the Symmetrical ‘S’ standard, it is today the fastest growing standard internationally. The open interface for automatic couplers is defined to ensure that using a combination of products from different manufacturers will not interfere with or alter the safety of the individual product.
Founded initially by Steelwrist and Rototilt, the Open-S standard was launched in October of 2020. The standard is managed by an independent organisation known as the Open-S Alliance. Since its inception a number of companies and manufacturers have become alliance members. During 2024 Open-S has welcomed several new members including, for the first time, companies from both North America and Asia. The idea of creating an open industry standard for automatic couplers continues to win over supporters and is gaining more and more attention in the trade press and industry forums across the globe.
Steelwrist automatic coupler system compliant with the Open-S standard
Automatic quick couplers on excavators are increasingly popular in the demolition and construction sectors thanks to the increased productivity, safety, and comfort benefits that they offer. For some applications, certainly in demolition, there is a need for frequent and fast work tool changes. With automatic couplers, there is no need to leave the cab when changing between hydraulic or mechanical work tools. This can mean the saving of a lot of time over the working life of a machine and also helps ensure the utilisation of the correct tool for the job in hand, not to mention the obvious safety
benefits of reducing personnel’s time spent out of the cab. Steelwrist has developed its own range of automatic couplers, known as SQ, with high performing automatic oil connection technology that allows a high flow capacity with minimal back-pressure, suitable for even the most demanding hydraulic work tools and applications in the industry. The SQ quick coupler range is complemented by a full range of adapters and brackets that can be made to fit most excavator work tools, Steelwrist has, to date, designed over 1000 patterns in all shapes and sizes.
Additional coupler sizes have been added over the years, most recently, the largest SQ quick coupler to date, the SQ90 for demolition contractors operating excavators in the 40-70 tonnes range, and the smaller SQ50 for midsized excavators between 7 and 12 tonnes.
Steelwrist’s belief in open interfaces is reflected in its continued work within the Open-S Alliance to establish and maintain an open standard for automatic couplers. All SQ products are designed to be able to connect to other brands who follow the Open-S standard.
If you dig into social media looking for tiltrotators and excavators you will find yourself richly rewarded! Excavator operators all over the world are often keen to share videos of their machines. The tiltrotator used with a variety of different work tools is a spectacle well worth watching! The efficiency and benefits can be immediately understood from watching them working in the hands of a skilled operator. Steelwrist has over 40 official ambassadors who post photos and videos spreading the word on the tiltrotator concept. In UK there is a group of talented operators who contribute (instagram accounts): Leigh Reynolds on leigh_digs, James Covell on kingslynnconstructionltd, Paul Bradshaw on bradpave, Jamie Inglis on jamieinglis1989, Harry Twigg on twiggsplantworks, James Harper on highwayharper and Johnpaul Napthine on johnpaulnapthine.
Amy Underwood, known as “The Digger Girl” on social media, recently partnered with Steelwrist in connection with getting a Steelwrist X12 tiltrotator fitted to her brand new Kubota KX085-5 excavator. With more than 800,000 cross-platform followers to her social media channels, Amy will help spread the word about Steelwrist tiltrotators and excavator efficiency to all who follow her digging projects in Scotland.
“It’s so great to be a part of a tiltrotator brand that alignes with my values and can support me to add even more value to the social media presence for our industry. I love the product and I am so excited to be able to document my journey of putting it through its paces during 2025,” says Amy Underwood.
If you are working at Steelwrist, or spend time anywhere near members of Steelwrist’s global team, you will surely notice the unique company culture. Steelwrist’s core values are ‘Responsiveness’, ‘Simplicity’ and ‘Speed’. An open, communicative and transparent environment pervades throughout the team, taking care to maintain a collective understanding of where the company is heading, and why. Employees are encouraged to engage actively and are entrusted to do so. The 20 year anniversary will soon be celebrated, after which Steelwrist is looking forward to the next 20 years of innovating and improving global excavator efficiency.
Steelwrist first entered the UK market back in 2009, and has since then been building the brand across the UK and Ireland to reach where it is today. Steelwrist UK Ltd’s offices are currently located in Banbury in the heart of England, with a growing team of professionals led by Joe Westman and a warehouse of product stock to enable fast delivery times across the region.
“The growth I have seen in my seven years so far at Steelwrist has been simply phenomenal!” says Joe Westman, Country Manager, Steelwrist UK. “I am proud to be part of such an incredible team of great people all around the globe and look forward to seeing how far we can go. I truly believe that tiltrotators are the future for excavators across the world.”
Tiltrotator technology is now established and proving to be successful in many of the world’s excavator markets, albeit with wildly different levels of penetration to date. Therefore the growth potential for Steelwrist as a global company, along with the tiltrotator concept as a whole remains extremely high. Steelwrist today has representation through employed team members in 19 countries so far, supported by a network of dealers and service partners all of whom are dedicated to ensuring the brand will continue to grow from strength to strength in its goal to increase jobsite safety and efficiency across the globe.
“I am extremely proud of what we’ve accomplished since Steelwrist was founded nearly 20 years ago. Excavator operators and contractors around the world are increasingly realizing the efficiency gains they get by equipping their excavator with a tiltrotator. It is with confidence that I look forward into the future as we launch our third-generation tiltrotators and continue to grow globally,” says Stefan Stockhaus, CEO and co-founder of Steelwrist. www.steelwrist.com
Remove DIRT & WATER in the same mobile application
Affordable and easy to change out replacement cartridges
Kind to the planet – as a natural, sustainable product
Save waste costs, replacement value and labour
Simple ‘plug and play’ application
Site permanently on a problematic machine or on a rotational cleanse across your fleet
Whether it be to tackle one off contamination issues, or as a permanent fix to heavy use equipment to protect pumps, valves & cylinders etc.. or as a rotational cleanse on off-hire equipment.
KLEENOIL offer a completely free trial at your site ; with before and after independent oil analysis.
Editor, Rebecca Phillips, travels to KLEENOIL headquarters in
Leeds, to learn in depth what a huge difference they make to the construction sector.
If there is one truly underrated faction of the construction industry, in fact ANY industry, it’s oil.
Let’s face it, without oil, the plant sector would come to a complete standstill. Literally nothing would work and yet sadly it is a ridiculously undervalued product. It is often the first place that people cut cost down; at least at first. Over time, poor quality oil will do more damage the good and cost far more in the long run.
But what if there was a product out there that meant you only had to invest in good oil once? What if there was a filtration system that made the reuse of oila product that, let’s face it, isn’t infinite- and industry standard?
That’s where KLEENOIL comes in.
My visit to the KLEENOIL HQ was truly eye opening and inspiring. Not simply because the company dog Yaz was such an excellent tour guide, but also learning in depth what their product really does and how they got started.
Established in 1976, KLEENOIL was originally adopted from a Japanese innovation and marketed as a by-pass filter, based on the need for an oil change every 6000 miles. This meant that for most transport companies, there would always be monthly downtime and expense; something that in any industry can amount to a big problem over time.
However, installation of KLEENOIL meant that there was no need for a change, and companies would be able to maintain the oil as clean as new. The only change necessary was a simple monthly 5 minute cartridge as opposed to the timely and messy full oil and filter schedule. Quite the difference right off the bat!
Now, for well over 45 years, KLEENOIL remains the market leader in By-Pass cellulose depth filtration. But what exactly is it?
By-pass filtration, which can be known as ‘kidney filtration’ or ‘polishing filters’, is typically used as a secondary filter with the purpose of eliminating nearly all contaminants from the oil.
A standard full flow filtration technique does not have the restriction capacity to stop finer particulate from passing through, even when using highly efficient medias. Unfortunately, this ends up rendering it ineffective. In comparison, By-pass filtration will take a ‘partial flow’ approach. This allows the flow to pass steadily through a dense media that permits entrapment of all particles down to 3 microns in size! As the media is absorptive, it will duly retain any moisture. By continually using a multi-pass method, a small amount of highly cleansed fluid goes back to the tank, eventually meaning the full system is cleaned. With permanent installation this will ensure a constantly cleansed, dry system. Not only that, but the ISO levels are better than that of new oil!
As KLEENOIL Cellulose Depth filters use a natural porous filtration medium, they retain particles throughout, rather than just on the surface, which means that KLEENOIL can retain a large mass of particles before becoming clogged or channelling, which is relative in comparison to other filters of that ilk. Depth filtration is generally typified by multiple porous layers which, at depth, are used to capture the solid contaminants from the liquid phase. Depth filters pose the added advantage that they can attain a high quantity of particles without compromising the separation efficiency.
This was a process I got to see before my very eyes!
Through our entire conversation, the filtration process had been running in a smaller format set up on the desk in front of us. The difference it made in that short amount of time was utterly incredible and showed the sheer power of the product to perfection. But don’t simply take my word for it, check it out on our socials page!
One of the best aspects of KLEENOIL is that they have many different styles of filter to suit the client’s needs. The following case study is for one of their mobile units, which was used for cleaning fuel tanks that were returned after rental for Will Power.
Filter carts can be used to clean any mineral oil and also diesel fuel. Will Power of Yorkshire trialled a unit to clean out a fuel bowser after rental. It was a great success, and they immediately purchased a KLEENFUEL MS4 bundled workstation. Now they clean every tank in transfer as it comes off rental to ensure the tanks haven’t been compromised.
Know your oil type: The type of oil inside your machine plays a significant role in determining which oil filter cart you should buy. If you were to pump viscous oil quickly, you’ll encounter air bubbles forming inside the machine which could damage pumps and oxidize oil. Cellulose depth works on cleaning oil slowly and continuously and so can be more effective as a constant permanent install.
Flow rate: You will generally want to know how much oil will be cleansed per hour; the rule of thumb on off-line filtration is to pass it through seven times to achieve the best level of a temporary install or rotational cleanse. When you use a filter cart, oil cleanliness is diluted by the dirty oil in the sump, since you’re taking oil from the dirty sump, filtering it and returning it to the same. To combat this dilution, the amount of oil in the tank must pass through the filter seven times to get the same cleanliness you would get from single-pass filtration. As an example, a Twin set Cellulose filtration set-up with the appropriate progressive cavity pumps on standard 32 or 46 sec hydraulic oils at 40 degree temperature will run approximately 500 lph. So a two hour cleanse would be more than adequate. Some sites will use a filter cart to transfer the cleanse out to an IBC, (allowing for a scrub of the tank) and then transfer cleanse back to the tank. But in doing this, never forget that sediment will be in pipes and cylinders so as a machine starts up this sediment will push back to the tank and re-pollute the cleansed oil. So, in a transfer cleanse it would be advised to leave the filtration on to tackle this remaining contaminant.
Robust Simplicity: Keeping a filter cart robust and simple is key. These machines are moved around in often harsh environments with heavy handling and challenging applications. So, a Filter Cart purchase is a worthy investment in any location where oil cleanliness is key to efficient operation. The use of secondary filtration can save a lot of wasted time, frustration, and resources. The application not only allows for higher efficiency and better utilization of time and productivity but also has an impact on lowering operating costs by reclaiming and extending the useful life of the oil and components and lowering yearly waste oil handling.
Summary
• The benefits of cellulose depth filtration as a cart: Removes dirt and water in the one same application. A finer level of filtration to remove particulate down to 3 microns. Removes water — emulsified or free.
• Affordable and easy to change out replacement cartridges.
• Kind to the planet — as a natural, sustainable product.
• Use of filter tops as a visual test.
• Can be used as a transfer unit.
• Simple “plug and play” application.
• Situates easily next to the sump/tank to be cleaned— either permanently or on a rotational cleanse.
It is easy to talk the talk, but KLEENOIL truly walk the walk, as is evidenced by glowing client reviews: I have used KLEENOIL filters for in excess of 30 years and still do, I have has them fitted to all my trucks, mobile and static plant for cleaning both engine and hydraulic oil.
My previous business (M&B Waste Management and Transport Logistics) ran a fleet of over 45 trucks with a mix of tractor units, skip trucks, rolonofs, we also had 10 JCB Tel handlers as well as material handlers, all had KLEENOIL filters fitted. Our generators, a mixture of Harris, BOA and Exel twin ram balers all had KLEENOIL filters fitted. The benefits were:
We only changed the engine oil annually on the trucks, which resulted in significant cost benefit without any compromise on component wear; regular sampling ensured we knew our oil was always on spec as well as our engines been reliable; we had some DAF trucks covering 500k kilometres per annum, as well as our local rolonofs working very hard with KLEENOIL filters on both engines and hydraulics
Our hard worked JCBs and cranes had both engine and hydraulic filters fitted to very good effect. We fitted some KLEENOIL filters on a Harris 3 ram baler with vane pumps which was needing new pumps every 9 months, after which we only changed a pump after 8 years hard work and went from changing 1200 gallons of oil annually to never, with frequent sampling to ensure our oils was in best condition throughout.
I use KLEENOIL filters to this day on all our balers and compactors with KLEENOIL monitoring the oil condition of each machine; based on my experience it is a very simple cost-effective solution to optimise oil life and reduce wear on moving parts as it is constantly cleaning the oils every hour they are working.
I have no hesitation recommending KLEENOIL filter products based on personal experience, with added bonus of ticking all the environmental box’s as well as the obvious cost savings.
Clive Hoyland, MCIWM MCILT AMSOE AMIRTE WRPS Ltd Material Recycling & Waste Management Specialists
KLEENOIL have a truly revolutionary product that truly stunned me. In a world with finite resources, it is fantastic to see that there is a solution that doesn’t simply recycle oil but keeps it in tip top order indefinitely.
This is not where our story ends though. Tune in next year where we step out on site with KLEENOIL to see their units in action for ourselves, and see not only how transformative this is for clients, but also witness KLEENOIL quiet professionalism in action!
Manufacturers/OEMs looking for new ways to connect to your Dealer Network?
Rental Companies looking to offer their products online?
Sales Companies looking to offer their products online?
Rent Pay Go is your strategic ally crafted to amplify your sales, optimise profits, increase visibility, and streamline operations.
• Share and market your products effortlessly to a wider audience online
• Reduce idle inventory and turn into revenue
• Reach new customers and provide a gateway for your existing customers to order more
• Build and connect your networks
By: Lorna Cowlin
IPAF’s premier annual Elevation Event returned for another year, hosted at the Hilton Birmingham Metropole, bringing people together from far and wide. And for my first conference, I felt fully immersed in the surrounding companies and people, all there
to do one thing: inspire.
As we arrived at the NEC, it felt like I was returning to a second home. Even though I’m still new, just a small girl in a big world of construction and plant-hire, I’m settling in very nicely with the familiarity of places and events. It was wonderful to meet so many new faces – so many of whom I had seen on LinkedIn, and have now met in the flesh; it was like meeting celebrities!
Everyone was so wonderfully welcoming. My biggest shoutout goes to Marketing and Membership Manager, Faith Cobaine, who made sure little ole’ me didn’t feel like too much of a lost puppy throughout the day!
Not only did this event host its usual afternoon conference, but this year it incorporated the Women in Powered Access networking event, bringing it back for a second run. Once it was 11am, we all huddled together for the presentation.
HR Business Partner for IPAF, Lisa Bailey, introduced us to the talk, mentioning the Women in Powered Access LinkedIn group, a mentoring scheme for women within this industry, as well as providing support with breast cancer and menopause policies. She further emphasised how IPAF is “all for women” and does all it can to raise awareness for equality and inclusivity.
The main section of the talk was led by Versalift’s Marketing Manager, Tara-Chelsie Fosbrook. She began by saying construction is stereotypically a male-dominated industry; but that doesn’t mean us girls don’t belong! We are constantly seeing a change; a positive, feminine shift that is proof that women can belong in a maledominated sector. Despite construction not being regarded as glamorous, we still all take extreme pride in what we do. The heavy machinery and construction technologies are simply a different kind of glamour. I couldn’t agree more with this. I’ve mentioned before that there’s a lot to learn in this field of work, and I can admit not everything is of peak interest to me. That said, I certainly do admire the immense pride and dedication I see day in and day out whenever I go to events or site visits. Tara is right! It is a different kind of glamour, but one we all adhere to.
Every woman in this industry is just as powerful as her male colleagues, supporters and rivals. Tara compared us to an army; we hold the same strength and driving force needed to keep everything working smoothly. Together, we all make the construction industry as successful as it is today, and we’re slowly seeing the shift from maledominated to equal.
As Tara beautifully said to sum up: “every job, every reach, every lift, we are keeping the world running.”
It would’ve been impossible to walk away from this talk without feeling inspired, seen or heard. Thank you IPAF for shedding more light on the smaller stories within!
I certainly felt like a bougie business girl attending all these networking talks and panel conferences! And up next was the IPAF Elevation Conference, hosted by Richard Whiting, UK Market General Manager for IPAF. First was none other than IPAF’s CEO and Managing Director, Peter Douglas. To begin, he celebrated the success of IPAF by sharing its global events programme, showing how widespread IPAF is. It’s immense, and it’s amazing to see how it promotes the safe and effective use of powered access equipment worldwide. He also shared the UK Membership and Training stats, further celebrating the success of IPAF in the last year.
Members YTD: 542 (5% increase)
Licences YTD: 113,240 (4% increase)
Physical/Digital: 65% digital
(These stats show 30th September 2024 vs 30th September 2023).
It’s clear to see that IPAF is continuously heading in the right direction with its mission to promote safety, and is always making a conscious effort in how it can keep influencing safety initiatives.
Next was Steve O’Brien, MEWP Compliance Team for Laing O’Rouke. His talk surrounded one main question: ‘why do we need MEWP Compliance?’
To put it simply: because it’s the law! However, it runs a lot deeper than just legislation, of course. As Steve put it: “if only it were that simple”. Meaning “mobile elevating work platform”, a lot of safety practice has to go into this, and Steve’s main point was that every journey starts with a single step in terms of prevention and protection. A lot of laws are needed when using MEWPs, such as Work at Heights Regs 2005, PPE Regs (amended) 2022, and HaSaW (etc) 1974, but like all laws, it’s a further extension of one overall mission: health and safety.
Toolbox Talk was then created, applying to all individuals using MEWPs which can then spot trends within accidents, incidents and near misses. With technology always advancing, Steve explained how it’s crucial to keep up to date with the latest new tech and telematics to adhere to health and safety laws. This also then avoids scams with fake PAL+ cards, and even fake Operator Training certificates!
Steve’s final point claimed that this industry will always keep elevating to the highest levels (excuse the pun) because of the immense community driving it forward. Every journey begins with a single step, and “the best thing about a journey is travelling with friends, because we can’t do this alone.”
Before we broke for an all-important tea and coffee break, Executive Chairman and Chief Legal Officer for SIMS (Serious Industrial Motion Simulators) Jim Colvin took to the stage. He discussed the importance of machinery simulation, a key factor that gives someone the practice before getting into a real machine. Not only do they provide simulation training, but they also provide Virtual Reality (VR) training too, aligning perfectly with PAL+. They had even brought VR headsets for people to try! Before anyone asks, no I did not try. I am simply a writer and social media girl; I’ll leave that to the experts!
Jim compared VR training to the terminator, claiming that “it knows where you are at all times. It’s coming for you.”
Whilst that sounds slightly terrifying (thanks for the nightmares, Jim), it’s clear that the eagle-eyed VR is training you to be the best of the best, eliminating any possibility for accidents. VR sees every action and infraction, giving extremely reliable results.
SIMS’ main aim is “take your MEWP training and safety to new heights with SIMS MEWP VR Simulator”, and their results support that massively. After only 45 minutes of simulator training, improvements can already be seen. VR training is vital, because it allows mistakes to be made without any severe consequences, and provides hours of practice before one can even go to a real life site. This is pivotal to prevention of extreme mishaps, further emphasising that the first thing on any contractor’s mind is always safety and efficiency. Jim finished with a closing image of proficiency, stating that SIMS “moves behind compliance to focus on safety, readiness, and risk reduction,” creating a safer, smoother operating industry.
The positivity from the conference flowed right through to the evening Gala. With wonderful food and great company, along with evening entertainment from Scott Bennett, and continued networking discussions, this was undoubtedly a very successful and positive event with an inspiring atmosphere. It felt like the perfect way to end the day! (Not to mention how incredible the cheese and pickle tart starter was - that dish alone deserves its own shoutout!)
Like last year, we were incredibly grateful to be invited to such an esteemed event, and even more delighted to have been the Official Media Partner for the second year in a row. The entire day had been a wonderful mix of constructive influencing, inspirational stories, lots of laughs, casual chats with friends and connecting with like-minded people in this positive, pragmatic industry.
IPAF, the honour was all ours. See you in Dublin next year!
Protect your pro tability with the proven results of ltration science. The right lters from Fleetguard on your equipment can help prolong engine life by removing contaminants that cause premature wear on critical components. You’ll get healthier engines, fewer breakdowns, lower repair costs and longer duty cycles.
As the construction industry continues to evolve, the need for reliable, innovative, and adaptable equipment becomes increasingly important. One brand leading the charge in providing advanced lifting solutions is Leguan Lifts, distributed exclusively across the UK and Ireland by Avant Tecno UK.
With a reputation for building robust, versatile, and efficient spider lifts, Leguan Lifts are becoming an indispensable tool on job sites. Through Avant’s extensive dealer network, Leguan Lifts are available to contractors, builders, and service professionals in every corner of the UK and Ireland.
Founded in Finland in 1990, Leguan Lifts has spent over three decades perfecting the design and functionality of its self-propelled spider lifts. The company’s core philosophy revolves around creating lifts that combine reliability, advanced technology, and ease of use. As pioneers in the field, Leguan Lifts was one of the first companies to introduce a self-propelled spider lift designed for outdoor use, revolutionising access to elevated work areas on challenging terrain.
“Leguan Lifts has built a strong reputation over the years by delivering high-quality, rugged, and versatile lifts,” says Raimo Ala-Korpi, Managing Director of Avant Tecno UK. “By partnering with Leguan, we’re able to offer our customers an unparalleled range of lifting solutions tailored to the needs of the construction industry.”
Leguan’s commitment to continuous innovation has led to the development of cutting-edge models that offer excellent safety features, user-friendly operation, and superior performance. From compact, easy-to-transport models to powerful machines capable of reaching significant heights, Leguan Lifts provides a diverse range of options to meet the unique demands of construction sites.
Leguan Lifts has built a strong reputation over the years by delivering high-quality, rugged, and versatile lifts
Leguan’s commitment to continuous innovation has led to the development of cutting-edge models that offer excellent safety features, user-friendly operation, and superior performance.
The NEW Leguan 195 is the latest evolution in spider lift technology, designed to set new standards in safety, efficiency, and versatility. Combining intuitive joystick controls, advanced boom engineering, and robust all-terrain capability, the Leguan 195 is the ultimate solution for professionals requiring a reliable and powerful lifting platform.
• Maximum Working Height: 19.7 metres.
• Maximum Outreach: 9.9 metres with 120 kg load; 9.0 metres with 250 kg load.
• Maximum Lift Capacity: 250 kg, suitable for two operators and their tools.
• Ergonomic Joystick Controls: Seamlessly manage boom movements and the track base with intuitive, precise controls.
• Fast Setup: Operate directly from the platform without manual track adjustments or lifting the jib boom, enabling rapid deployment on-site.
• Robust Design: Built for durability, with protection against external impacts and falling debris, making it ideal for challenging work environments.
• Large Working Envelope: A side reach of up to 9.9 metres ensures access to hard-to-reach areas, with exceptional up-and-over reach exceeding 7 metres.
• Advanced Safety Features: Automatic levelling of outriggers, proportional outreach monitoring, and a battery-powered emergency lowering system for enhanced operator security.
The Leguan 195 incorporates features tailored for ease of use and efficiency:
• Service Display: Integrated into the lower control panel, it provides real-time machine status, streamlining troubleshooting and enabling remote technical support.
• Platform Convenience: Equipped with 230V and USB outlets for powering tools and devices at height.
• Rapid Boom Movements: The Leguan 195 boasts the fastest boom movements in its class, significantly improving productivity on job sites.
For maximum portability, the Leguan 195 can be paired with a custom-designed trailer. The trailer enables the use of outriggers while the lift remains onboard, simplifying attachment and detachment with built-in cargo straps and chains.
Meet the Leguan 225
Get ready for the next generation of spider lifts. With faster boom hydraulics, greater working height, unrivalled up-and-over reach, and groud-breaking joystick controls the Leguan 225 is our most advanced spider lift to date. User friendly design, improved driving features and a steel-reinforced chassis guarantee premium performance even in the roughest terrains.
Leguan Lifts offers several models, each with distinct features designed to handle different tasks and site conditions.
Their versatility makes them invaluable for tasks such as high-level installations, facade work, tree trimming, and structural inspections.
To cater to the diverse needs of the construction industry, Leguan Lifts offers several models, each with distinct features designed to handle different tasks and site conditions. Below is an overview of the models available through Avant Tecno UK:
• Compact and manoeuvrable: Ideal for smaller job sites where space is limited.
• Working height: 13.4 metres, with a maximum outreach of 6.1 metres.
• User-friendly: Features an intuitive joystick control system and automatic levelling.
• Target users: Perfect for indoor and residential projects, as well as smaller construction tasks.
• Benefits: Lightweight design and easy transport make it suitable for operators who frequently move between sites.
• Heavy-duty performance: The 225 is designed for larger projects requiring significant reach and load capacity.
• Working height: 22.5 metres, with an outreach of 11.2 metres.
• Advanced safety and control: Equipped with an automatic levelling system and remote operation capabilities.
• Target users: Ideal for large-scale construction, high-rise maintenance, and industrial projects.
• Benefits: Its robust design and powerful hydraulic systems allow for seamless operation on challenging terrain.
“Leguan’s range of models means there’s a solution for every type of construction site, from compact residential areas to major commercial projects,” explains Raimo. “Having the right equipment on-site can significantly impact productivity, and Leguan’s lifts deliver on that promise.”
Leguan Lifts cater to a variety of professionals within the construction industry, including general contractors, maintenance teams, electricians, painters, and roofers. Their versatility makes them invaluable for tasks such as highlevel installations, facade work, tree trimming, and structural inspections.
benefits of using Leguan Lifts on construction sites include:
• Increased efficiency: Automatic levelling systems and intuitive controls allow operators to quickly set up and start working, minimising downtime.
• Safety first: Leguan Lifts are built with advanced safety mechanisms to ensure the wellbeing of operators, including harness attachment points and automatic safety checks.
• Adaptable power options: Models with dual power sources enable operators to switch between diesel and electric operation, offering flexibility for both indoor and outdoor use.
• Manoeuvrability: Compact models like the Leguan 135 NEO can navigate through tight spaces and be easily transported between sites.
• Reduced labour demands: One operator can effectively manage most Leguan models, which helps address the ongoing labour shortages in the construction industry.
Selecting the appropriate Leguan model for a construction project can make all the difference in terms of productivity and safety. For smaller, intricate projects, the Leguan 135 NEO offers an excellent balance of manoeuvrability and reach. For larger, more complex tasks, the Leguan 225 provides unmatched height and outreach capabilities.
When choosing a Leguan lift, contractors should consider factors such as:
• Height requirements: How high does the work need to reach?
• Space constraints: Will the lift need to navigate tight or indoor spaces?
• Power sources: Is there a need for electric operation to meet environmental or indoor regulations?
• Terrain: Does the job site have uneven or difficult ground?
Leguan Lifts’ commitment to continuous improvement is evident in their dedication to integrating the latest technology
and enhancing safety features across their product range. Whether it’s the automatic levelling system that speeds up setup or the ability to run on electric power to reduce emissions, Leguan’s innovations are designed with real-world construction needs in mind.
Avant Tecno UK’s extensive dealer network ensures that Leguan Lifts are accessible throughout the UK and Ireland. Contractors and construction professionals can rely on local support for maintenance, training, and service, making the investment in Leguan Lifts not just a purchase but a partnership.
Leguan Lifts, distributed by Avant Tecno UK, have set a high standard for construction equipment. With models like the 135 NEO, 195, and 225, Leguan provides solutions that cater to various construction needs, from compact indoor jobs to large-scale outdoor projects. Their innovative designs, powerful features, and focus on operator safety make Leguan Lifts a top choice for professionals looking for reliable, efficient, and versatile lifting solutions.
“Our partnership with Leguan Lifts has allowed us to bring world-class lifting solutions to the UK and Ireland,” says Raimo. “With these machines, construction professionals can work smarter, safer, and more.”
Avant Tecno UK has officially unveiled its new multimillion-pound headquarters in Bury St Edmunds, marking a significant milestone in the company’s growth and commitment to its UK operations.
Designed to facilitate Avant’s continued expansion, the 32,200 sq. ft purpose-built facility was crafted by local firm SEH French, with project management by Churchmanor Estates.
The grand opening of the headquarters was celebrated with an event welcoming trade and local media, partners, and esteemed guests, including the Ambassador of Finland to the United Kingdom, Jukka Siukosaari.
“This is a momentous occasion for Avant Tecno UK and our incredible team,” said Raimo Ala-Korpi, Managing Director of Avant Tecno UK. “The new headquarters is not only a symbol of our growth but also a stepping stone for our future aspirations. It’s a proud day for everyone involved and a testament to our commitment to delivering the best for our dealers, customers, and the community.”
Since establishing its presence in the UK in 1999, Avant Tecno UK has witnessed consistent growth. Previously operating near Thetford, the company identified the need for a larger, modern facility to support its operations and meet increasing demand. The new Bury St Edmunds headquarters reflects Avant’s forward-thinking vision, incorporating features that enhance efficiency, innovation, and sustainability. The facility includes:
• Modern office spaces to accommodate the growing team.
• A showroom to display Avant’s renowned compact loaders, attachments and Leguan access platforms.
• Dedicated training facilities to provide hands-on learning for dealers and end-users.
• A warehouse with automated technologies to improve logistics and inventory management.
• A technical workshop designed for hand-on training events, and equipment arrival checks.
The launch event began with a keynote address from Raimo, who highlighted the strategic importance of the new headquarters and its role in enhancing Avant Tecno UK’s operational efficiency and customer service.
“This investment demonstrates our long-term commitment to the UK market,” Raimo said. “It’s an opportunity to strengthen our dealer network, provide world-class training end-users, dealers and staff, and continue delivering cutting-edge solutions to our customers.”
Other speakers at the launch event included representatives from project partners Churchmanor Estates, LSI Architects, and SEH French, who detailed the project’s journey from conception to completion. They discussed the collaborative efforts and innovative techniques used to ensure the building met Avant’s high standards for quality and sustainability.
Ambassador Jukka Siukosaari, representing Finland at the event, praised Avant Tecno as an example of Finnish innovation and global excellence. During his speech, the Ambassador
emphasised the importance of government support in helping Finnish companies like Avant expand internationally.
Guests at the event were treated to a guided tour of the new facility, offering a first-hand look at its innovative features. From the spacious training rooms to the automated warehouse systems, the headquarters highlights Avant Tecno UK’s focus on innovation, efficiency, and sustainability.
Following the tour, attendees gathered for a networking lunch, further strengthening the connections between Avant, its partners, and the local community.
As Avant Tecno UK settles into its new home, the company remains focused on its core mission: delivering high-quality, innovative solutions that empower its customers. The new headquarters in Bury St Edmunds is more than just a building—it is foundation for a new centre of excellence for multi-functional compact machinery.
For more information, please visit www.avant.co.uk
Every hour your excavator is not working, you’re losing income. Whether it’s due to maintenance, repairs, or waiting on parts, downtime can severely affect your profits. Unexpected downtime is an inconvenience that impacts nearly every construction project, often throwing timelines off course. But how do you predict when it will happen and more importantly, how can you prevent it?
If you’ve experienced downtime recently, you already know how damaging it can be. Unexpected breakdowns can lead to several serious issues for your business, including:
• A tarnished reputation with clients
• Loss of productivity and efficiency
• Loss of revenue and tighter profit margins
• Project delays that affect future work
• A growing backlog of projects
• Increased overtime costs to catch up
• And much more
Downtime can be caused by many factors – usual wear and tear, unexpected weather conditions, or even human error from improper machine maintenance. So, what can be done to minimize these disruptions?
Regular Maintenance and Service Intervals Scheduling regular maintenance is crucial for extending the life of your machine and minimising the risk of sudden failure. Routine service can help identify potential issues before they become major problems, ensuring that your equipment runs smoothly and avoids delays.
Understanding Common Causes Knowing what typically leads to
downtime – whether it’s mechanical wear, weather, or operational mistakes – can help you better manage response times and prevent these issues from recurring. Training your team on proper equipment care and keeping a close eye on frequently overlooked maintenance tasks are key strategies in downtime prevention.
Have a Backup Plan In the event that your machine does fail unexpectedly, having a Plan B in place is essential. This could mean partnering with a trusted plant rental company or securing a reliable support service, like us, to ensure your project continues with minimal disruption.
Being prepared with these strategies will help you reduce the unexpected costs of downtime, keeping your projects on schedule and your business running smoothly.
To learn more about Plant Parts, please visit: www.plant-parts.eu FOR FURTHER INFORMATION
Managing machine hours, tracking fuel usage, and monitoring load capacities no longer rely on manual processes or on-site checks. PVS Data (Plant and Vehicle Services Ltd) has transformed fleet management for plant and construction companies worldwide, encompassing brands from all OEMs.
With the installation of the new D2 unit, businesses can access over 300 real-time data parameters, including live engine reports, precise machine locations through the w3w (What 3 Words) app integration, and safety metrics, including height, slew, and RCI (Rated Capacity Indicator) data from Xwatch Safety Solutions.
Xwatch Safety Solutions, part of the Hexagon Group, is redefining on-site and in-cab safety standards. Operators can now set precise height, slew, and RCI limitations directly from their excavator’s cab, providing a new level of control and assurance. Safety has always been a cornerstone of the construction industry, and Xwatch builds on this legacy with advanced in-app telematics across its product range. This innovation enables live, global visibility of key safety data, ensuring the highest levels of protection for operators, machines, and ground personnel.
Dan Leaney, Xwatch Safety Solutions, Sales Director, commented on the new technology, saying: “The telematics system for the D2 units from PVS, branded as XW-Insite by Xwatch, represents our most advanced safety and telematics solution to date. Currently being trialled with a leading plant hire firm, a tier-one contractor, and through PVS’s own trials, this system integrates Xwatch’s precise height, slew, and RCI data with PVS Data’s cloud-based platform. It delivers seamless telematics access across fleets, covering all major equipment brands. Operators can configure and monitor critical safety parameters directly from the cab, while managers gain real-time visibility into machine performance and safety metrics, whether on-site or working remotely. This innovation is designed to prevent accidents, reduce downtime, and enable smarter, data-driven decisions. At Xwatch, we are proud to collaborate with PVS to lead the industry in making construction sites safer and more efficient, and we look forward to seeing comparable data emerge from these trials in the coming months.”
This collaboration between PVS Data and Xwatch Safety Solutions brings powerful functionality to fleet management. PVS Data’s cloud-based computing and live reporting provide seamless access to telematics across an entire fleet, covering all major brands, including JCB, Sany, Hitachi and Takeuchi to name a few. Site managers gain a clear visual overview of their machinery equipped with Xwatch Safety Solutions. They can monitor height and slew settings, view the exact weight on the hook, confirm whether stop and creep controls are active, and analyse overall capacity utilisation – all in realtime.
Combine this safety information with real-time data such as fuel usage, engine performance, fault reporting, idle and productive hours, and carbon dioxide emissions. The result is a construction site that operates more efficiently, ensures greater safety for ground personnel, meets zero-emissions goals, reduces costs and downtime, extends machinery life, and encourages smarter machine operation.
Scott McCabe, Owner and Director of PVS Data, commented on the partnership: “Heightened safety on site has been at the heart of the industry for decades. Our partnerships with innovators like Xwatch make the platform the logical all-in-one solution for fleet health and safety. We’re excited to see where our current trials take us, advancing the platform to show a greater
number of meaningful data parameters, and growing our partnership with the Xwatch team”.
Hitachi Construction Machinery UK has been at the forefront of this partnership by delivering connected technology to their customers when purchasing new machines. Their custom-branded platform, created by PVS Data, is CTFleet Link®, and it’s changed the way their customers all over the country see their fleets of mixed-brand machinery.
Stephen Creaser, Director of Product Support for HCMUK, shared his thoughts on the intuitive platform and its capabilities: “At Hitachi UK, we’ve always been proud to take the first step to a more connected industry, a safer industry for operators and ground personnel, and a wider network of opportunities by innovative organisations. PVS, the D2 units and their platform showcasing Xwatch’s safety solutions are the logical solution for fleets worldwide, connecting OEMs in a single sign-on solution. Giving users on and off-site the ability to check on machine status and driver controls for designated safety equipment is logical and works. We’ve seen no end of evidence that the more eyes on what’s going on in the operator’s cab, the safer the construction site becomes”.
A safer site has more eyes on the machines and the controls their operators are using. A more efficient site is wellconnected, with pools of analysed data readily available to support decisions about an organisation’s economic growth
and future investments. Construction sites can unlock significant potential by embracing the expertise, knowledge, and safety improvements offered by Xwatch Safety Solutions and PVS Data.
To learn more about XWatch, please visit: www.xwatch.co.uk
Two Irish companies are taking construction equipment manufacturer Sunward to new heights. No-one could accuse Irish equipment hire solutions supplier Global Hire of hanging around!
For just a couple of months after being introduced to the Sunward brand of construction machinery, the County Laois company has purchased a total of more than 70 machines from the republic’s Sunward dealer Rushall Plant Services, who is also based in Laois.
The Sunward machines include an incredible 69 scissor lifts, including 23 SWSL 0607DCs, 17 SWSL 0807DCs (pictured), 13 SWSL 1412DCs, 11 SWSL 1212DCs, and five SWSL 1008DCs.
In addition to the scissor lifts, they purchased two SWTL 4538 compact tracked loaders, which have an operating capacity of 1.2 tonnes and a machine weight of 4.4 tonnes, and a couple of mini-excavators, including the SWE 25UF and the SWE 08B. These were all purchased through Sunward Financial, the manufacturer’s finance packages.
They are being used typically by electricians, fabrication companies, property management, air conditioning and carpentry, for tasks such as light fixture installations and pulling cables, and air ducts and ceiling works, in clean room environments such as data centres and pharmaceutical premises.
Global Hire, who specialise in providing top-tier equipment hire solutions to meet the needs of tradespeople, consumers and wind farm operators across Ireland, travelled with Rushall Plant Services’ MD Kevin Flanagan to Sunward’s factory in Belgium in July… and have not looked back since.
Their senior hire manager Keith Kenna said: “We haven’t had any problems. Despite this, the service we are getting from the dealer is second to none. He is always on the end of the phone or email to help us out.”
Kevin Flanagan, who became a Sunward dealer in 2019 after meeting the manufacturer at the Bauma show in Germany, said: “I had previously heard of Sunward and was interested in the machines.
“I had worked in construction all over Ireland, on the new M7 motorway at the time, so my customers now are old customers from those days and new customers. Many of them are repeat
customers, from people using the machines for their own personal use, to farmers, utilities and civil engineering and construction, even grave diggers! And how a hire company.
“I still have men employed on construction sites and they use the excavators daily and I also hire out Sunward excavators. They are good, sturdy, compatible and reliable machines, and very easy to work on. Parts are easily sourced if required but they seldom are.”
And of his record-breaking deal with
Global Hire, he said: “It’s great to get the deal with Global Hire. They are an up and coming company and we are hoping to do another deal in the near future.”
To learn more about Sunward, please visit: www.sunwardexcavators.com
In the construction industry, equipment reliability is crucial. Downtime means delays, increased costs, and missed opportunities. That’s why choosing the right filtration partner is essential. With over 100 years of filtration expertise, Donaldson is your go-to OEM filtration supplier, dedicated to keeping your machinery running smoothly, even in the toughest conditions. As a leader in filtration technology, we provide solutions that meet or exceed original specifications, ensuring optimal performance and extended equipment life.
Why Choose Donaldson?
• Proven Expertise in Construction: With over a century of innovation in filtration technology, Donaldson has the knowledge and experience to address the unique challenges faced by construction equipment. From heavyduty excavators to compact loaders, our solutions are engineered to protect your machinery in the most demanding environments.
• Reliable Performance, Anywhere: Construction sites are unpredictable, with harsh conditions like dust, dirt, and debris constantly threatening your equipment. Donaldson’s advanced filtration systems deliver superior durability and reliability, ensuring your machinery operates at peak efficiency, no matter where the job takes you.
• Extended Warranty for Peace of Mind: We back our filters with an extended warranty, giving you the confidence that our products not only meet but exceed OEM standards. This commitment to quality helps you avoid unexpected maintenance costs and minimizes downtime, keeping your projects on track.
Our Commitment to Construction Excellence At Donaldson Mobile Solutions Aftermarket, we are dedicated to enhancing the performance and longevity of your construction machinery. Our filtration products are specifically designed to withstand the harshest conditions, ensuring your equipment
remains protected and productive. From reducing engine wear to optimizing fuel efficiency, our solutions are crafted to support the unique needs of the construction industry.
Choose Donaldson Aftermarket –the partner that understands your business and is committed to delivering unmatched filtration performance. Partner with us and experience the difference that comes with over 100 years of expertise, innovation, and dedication to keeping your construction equipment moving forward.
Contact us today to learn more about how Donaldson can help you achieve higher productivity and lower operating costs. Visit the website to discover how our filtration solutions can make a difference in your construction projects.
ANGLIAN DEMOLITION
Transforming offices for state-of-the-art CamLIFE project
City Demoltion’s Dan Highfield gives us the ins and outs of his journey through demolition
Becks travels back to Norwich to see how their project has progressed
Can you believe that the first year of Demolition Spotlight has come to an end? No? Well, we can’t either. And honestly what an incredible year it has been. We have worked with some truly incredible people, been to some awesome places, and experienced things we only dreamed were possible in mini mag form. But now the time has come to put on our big boy boots and gear up for our full mag launch in March 2025. That’s right, this is our final mini mag!
What’s in store you ask? Oh, nothing much. Just 3 fantastic case studies from City Demolition, Anglian Demolition and Shorts Group! Plus an exclusive interview with Dan Highfield of City Demolition. On top of all this we have two incredible articles from the lovely Paul Argent as well as the latest news from some industry favs. This edition is more stuffed than the Christmas turkey!
Happy Reading, and a very merry Christmas!
Rebecca Phillips Managing Editor
DARREN SHELTON BUSINESS MANAGER
MARTINA TONELLI MARKETING CO-ORDINATOR
REBECCA PHILLIPS MANAGING EDITOR
LORNA COWLIN CONTENT CREATOR
CHARLOTTE WALSH SENIOR SALES EXECUTIVE
STEVE WILSON DESIGN MANAGER
contributors
PAUL ARGENT RPA MEDIA SERVICES
DAN HIGHFIELD CITY DEMOLITION
LOUISE DOYLE CITY DEMOLTION
CLAIRE MCGILL ANGLIAN DEMOLITION
BRYONY MORTON-SHORT SHORTS GROUP
ANDREW HOPE SHORTS GROUP
MADISON DUNN R COLLARD
For all content related queries, contact editor@demolitionspotlight.co.uk
For all sales related queries, contact charlotte@demolitionspotlight.co.uk
Liebherr’s range of high-reach demolition excavators equips customers with everything they need for a successful project. The full line-up is now available in a choice of configurations that allow you to work at even greater heights and with greater precision. Anywhere.
At Collard Group, we understand that a successful project requires diligent preparation, our services are designed to pave the way for smooth project execution while addressing critical preparatory tasks that set the stage for your main construction phase.
Because Collard Group are able to offer an end-to-end solution to our customers through our circular economy model, we find that the financial stability of the group allows us to leverage opportunities outside the capacity of regular demolition companies. This model also means we are able to be incredibly self sufficient due to little need to subcontract out works as the group can complete a project from start to finish independently. When it comes to reshaping landscapes, managing complex demolitions, and paving the way for developments, the Collard Group has built a reputation as a trusted partner in the construction industry. Offering a
seamless, end-to-end service across the UK, Collards brings unmatched expertise to every phase of development, from consultancy and site investigations to full-scale structural demolition and land remediation. We ensure sites are “shovel ready” for the next phase of development.
Collards’ comprehensive capabilities are showcased in projects currently underway across the country. In Reading, the team is well under way with the soil remediation phase of the Vastern Road project. Over in Basildon, the Essex Waste site is buzzing with activity as groundworks progress, including the meticulous filling of the main tipping halls pit. Meanwhile, at Pangbourne’s BP site, sheet piling and sewer diversions have now been successfully completed.
Collards’ work at Harvest Hill in Maidenhead is equally impressive, with 30,000 cubic meters of material
already imported to prepare the site for future housing developments. And at Spelthorne Leisure Centre, we are undertaking the preparatory groundworks. Notably, at a London hospital, the group’s in-house asbestos team, Amiante STR, has been tackling licensed and non-licensed asbestos removal across five floors, skilfully managing 23 enclosures while navigating the challenges of a multi-contractor site.
Behind Collards’ success lies a highly skilled team that thrives on collaboration and technical transformation. From operations managers and quantity surveyors to an in-house HSQE team, every project benefits from thorough oversight. The HSQE specialists ensure rigorous adherence to bespoke safety systems, creating environments where efficiency meets uncompromising safety standards.
Our efforts at the early tender stage often set the tone for the entire project. It’s about building trust and demonstrating our commitment to excellence from day one.
For those curious to see the faces behind the work, Collards invites you to “Meet the Team” on our website, where the expertise driving the company’s operations is displayed.
Asbestos management is a critical component of Collards’ service offering, and our expertise in this area is second to none. The acquisition of Amiante STR, a specialist asbestos firm, has bolstered our capacity to deliver safe, compliant removal and disposal solutions. From initial surveys and HSE notifications to the final removal of hazardous materials, Collards manages the entire process with precision.
Our group ethos is all about offering clients a single-source solution. This comprehensive approach has seen Collards successfully navigate asbestos challenges in a wide array of settings, including homes, businesses, schools, and hospitals. With extensive resources and management systems, we ensure that no detail is overlooked.
Our Earthworks & Civils division is at the forefront of landscape transformation, specialising in brownfield site remediation, soil stabilisation, and terrain reshaping. Whether constructing largescale embankments, dams, or levees, or tackling intricate load calculations and structural design, the division delivers innovative, client-focused solutions.
Our commitment to excellence extends to civil engineering projects, where we blend functionality with compliance
to meet local regulations and industry standards. By leveraging our fleet of modern excavators, bulldozers, and haulage lorries, Collards ensures every project is managed with efficiency, strict quality control, and timely completion.
A key differentiator for Collards is our embrace of the circular economy model. By integrating sustainability into our operations, the group remains financially robust while maintaining self-sufficiency. This model minimises the need for subcontractors, allowing Collards to independently oversee projects from concept to completion.
Our ability to deliver projects in-house means we maintain complete control over quality and timelines. It’s a game-changer for our clients, who can rely on us to deliver seamless, cost-effective solutions.
At Collards, preparation isn’t just a phase. Every detail, from the initial groundwork to the final touches, is meticulously planned and executed to set the stage for success. With a focus on innovation, collaboration, and sustainability, the Collard Group continues to explore what’s possible in the industry.
To learn more about our projects and meet the team that makes it happen, visit our website today.
On Friday 15 November in Birmingham, the only organisation in the World for demolition engineers, The Institute of Demolition Engineers, held it’s AGM and appointed a Birmingham born engineer as the new President.
Adrian McLean, Operations Manager at Armac Group, takes over the role from Past President Vernon Watson, who had steered the Institute through a sticky two years when revenue was low and internal changes needed to be made.
Adrian started his maiden speech as President by stating “I feel very honoured to be standing here before you today as the incoming President of the Institute of Demolition Engineers.”
He added: “It is my intention to work tirelessly for the further development of the IDE and its members. We work best when we collaborate, so your support on this journey will be much appreciated.”
There are key priorities that Adrian will drive during his presidency, but his focus will be to increase membership on a global level. “As President, I will be seeking to increase membership across the UK and the world,” he said. “I want to achieve this whilst also maintaining
our high standards of excellence – we are the only organisation in the world that champions demolition engineering”.
The IDE knows that there are hundreds of demolition professionals around the World who would benefit by becoming IDE members so he will spearhead the roll out of the new international member category within the IDE which allows those professionals from far off shores to become members via a new IDE education route which will hopefully lead to members in Europe, the Far East, Australia, New Zealand and USA.
Under Adrian’s direction, the IDE will also increase its focus on professional development initiatives. This will include exams, interviews, and the regional meetings that are so loved by existing IDE members. Regional meetings will be free to attend, held after work and will be both educational and enjoyable. Meetings are already in the diary for The Midlands and the North West.
The President will also promote the IDE educational partnerships—particularly with the University of Wolverhampton to promote degrees in demolition engineering.
Despite the successful 2017 launch of the UK’s first-ever demolition degree courses, which was done in partnership with the University of Wolverhampton, the most recent intake for the IDE Foundation Degree in Demolition Management was postponed due to a drop in applicants. The lack of interest in the courses may stem from the long-standing negative perception the public has of demolition industry work, something the new IDE President is keen to see change.
Another priority for Adrian is for the IDE to deepen its relationship with the Health and Safety Executive (HSE), by actively participating in its roadshows currently hosted by the NFDC, to strengthen the IDE’s industry links and to actively encourage more dialogue with HSE going forward.
The IDE is changing and that change will be fast and focused.
Open-S Alliance, the independent organization behind the initiative to create an open standard for automatic couplers for excavators, welcomes ACDE Europe AG as a member. ACDE Europe AG specializes in demolition and recycling attachments, providing a range of equipment for both dealers and OEM customers on the European market. With this addition to the list of members, the Open-S standard continues its international growth.
ACDE Europe AG, with headquarters in Wilen, Switzerland, was established in 1994 and is today present with distribution sales and service of Beilite® hydraulic hammers (80-13 000 kg) through a network of dealers in Europe. The company is a manufacturer of ACDE® Europe hydraulic grapples, pulverisers, shears and a wide range of demolition, forestry and quarry attachments. Deliveries of products and parts are handled through their logistics center in
the Netherlands, enabling short delivery times throughout Europe. ACDE Europe AG joins the Open-S Alliance as an Associate member.
“Joining the Open-S Alliance aligns perfectly with ACDE Europe’s commitment to innovation and quality in the demolition and recycling sectors. By collaborating with industry leaders, we can drive the development of standardized solutions that benefit our customers and the entire industry. This partnership allows us to continue offering cutting-edge products that meet the evolving needs of our clients”, says Karel Glaaser, CEO of ACDE Europe AG.
The Open-S standard builds on the established symmetrical standard for quick couplers, which is the fastest growing standard internationally. Open-S Alliance is an independent industry organization with the sole purpose of developing the Open-S standard for automatic couplers further. Not least is this a relevant development for the
demolition industry, where many and fast work tool changes are common. With an open standard the utilization increases and profitability improves on all types of job sites, as work tools can be shared easiliy between different excavators.
“We are glad to see the number of members and the support for the standard growing internationally. With ACDE Europe we have yet another quality supplier and manufacturer of excavator work tools joining the organization”, says Anders Jonsson, Chairman of the Board of Open-S Alliance.
For more information contact: Anders Jonsson, Chairman of the Board of Open-S Alliance AB anders.jonsson@opens.org, +46 70 590 09 49
Stefan Stockhaus, Board member of Open-S Alliance AB stefan.stockhaus@opens.org, +46 70 998 13 21
Joining the Open-S Alliance aligns perfectly with ACDE Europe’s commitment to innovation and quality in the demolition and recycling sectors.
Managing Editor Rebecca Phillips travels to Bromsgrove in Worcestershire to visit one of City Demolition’s latest projects.
A pleasant drive brought us from City Demolition’s headquarters in Birmingham to the active site in Bromsgrove, the site not far from the main high street. It’s always fascinating to visit a site in such a built up, active location and see how each company tackles the issues that presents, and the Bromsgrove site was a particularly interesting project to visit.
At our point of arrival, 2 of the 3 buildings were already demolished, the site beautifully tidy and still in working order. The project had been active for 14 weeks, with site manager Darren giving an estimated 1 month to bring down the final building and another 1 for clean-up. All in all, and from an outsiders’ perspective, things seemed to be relatively simple. However, a little probing gave us some deliciously interesting problems that had needed fixing.
Lucky then, that Darren was leading the way.
Location: Bromsgrove
Client: Unnamed
Time Spent: 14 Weeks to date
Time Remaining: Estimated 8 weeks
On Site Person: Darren Grainger
Machines Used:
400 Kobelco - Kobelco SK400DLC-10
300 Kobelco - Kobelco SK300LC-10E
Crusher - Terex Finlay J-1170 Crusher
Loading Shovel - Hyundai Loading Shovel HL960A
Volvo 380 - Volvo EC380EL
All machines are equipped with Oil-Quick coupler systems.
Having been in demolition for many years, and worked for City Demolition for over 14 years, Darren has seen an enormous variety of projects. He is regarded as one of the top and most respected site managers and meeting him proved why. He has a calm, relaxed countenance, with a quiet confidence in everything he does. As someone who is technically minded with a wealth of demotion knowledge, he is often brought into figure out the best method to bring the building down. For Darren, this is certainly something he enjoys. “I like the challenge a problem brings. Get the mind going.” That was certainly the case for this particular site, as there were more than a few niggly challenges to overcome.
As an example, the first building at the end of the site was only 1m away from the building next door, which gave very little room to begin the deconstruction process using machines. Any wrong footing (or driving) would have proved incredibly problematic and potentially destructive to the entirely wrong building.
Two machines had to be used to do so, in order for it to be conducted safely, and working in perfect conjunction, they were able to munch down the building without issue.
This is something that will also e considered with take down of the third building, as despite there being a tad more room on that side (an entire extra meter in fact!) it was still not enough to drive circles around the building.
“It’s a relatively easy fix,” Darren assured us. “We’ll chat to the neighbours and warn them when the work starts. And if we need access to their car park in order to get a better vantage point, we’ll ensure that’s all sorted before we begin. There’s always a fix.” At least with this final building though, the plan seemed relatively simple. With a good vantage point, Darren plans to munch it down and let gravity ‘do its thing’.
Another particularly fascinating aspect was the recycling side. Demolition, despite its seemingly bad rep, can actually be one of the greenest industries around as so much of the material is recycled for other projects, and City Demolition ensure that this is the case. Darren explained that only a few weeks ago, the site was covered in the neat, relevant piles of different materials ready to be whisked away. What proved to be a problem, was actually down to the previous occupation of the fallen building.
As it was an old fire station, there were actually contaminants in some of the materials. PFOS (or forever chemicals for the layman) were present in much of the brick as they are particularly present in the suppressants used by the fire service. As forever chemicals stick around, well… forever, they need to be kept away from people as they can cause health problems.
Happily, City Demolition have the right people on the job.
The relevant material was tested and segregated from the recyclables, with the contaminated material cordoned off to make doubly sure it wasn’t touched prior to removal. This also included putting in precautions to warn the neighbours, as just behind the site was a school. As with all of their projects, City Demolition approached the issue with the utmost care a diligence, making a potentially catastrophic problem an easy fix.
This is also important to note, as with many demolition sites, ‘urban explorers’ like to break onto site and explore the derelict buildings. The Bromsgrove site, with its tantalising history, was sadly no exception. It goes without saying that anyone who decides to walk into an empty building is taking their own life in their hands, but with the general process of demolition not being well understood, they are placing themselves far more at risk than they might first realise. Demolition is far more like deconstruction than it is about simply demolishing something.
In such a built up area, there will be no explosions, implosions, or historic wrecking balls. The process involves working backwards to take the building apart in the opposite order to its construction. So, there will often be supports that are no longer in place that those not in the know will not be aware of. Thankfully, City Demolition places security and safety as a top priority. High fences, warning signs and a stringent PPE policy means that a City Demolition site is a safe site. In fact, it perfectly embodies their slogan ‘Think Safety, Work Safely’
There have certainly been many highlights to this project as well, and not just in the form of a problem expertly overcome. For instance, the soft strip went easily without hitch, with all the disconnections made in a timely fashion. The wet weather, while often terrible for many outdoor jobs, has actually been good for dust suppression, meaning work could continue even when many other hardy outdoorsmen had retreated.
It’s also good to note how productivity is at the fore front of City Demo’s minds. For example, their use of Oil Quick couplers allows the change of attachments without having to leave the machine. It plays into the safety aspect of their work ethic but is also a huge time saver as there is less down time. This is also aided by such a tidy work site, as their job is not impeded by having to manoeuvre between random debris. “I won’t work in an untidy site,” says Darren.
From start to finish, this project has been fantastically managed. Whether from a contract’s perspective to an on site presence, all parties involved have worked seamlessly to keep this project in tip top shape. The professionalism was evident at every turn: sustainability, safety, security, you name it, City Demolition had it covered.
Our unique capability to repurpose virtually all construction and demolition waste from site helps our public sector, local authority, commercial and residential clients achieve zero-to-landfill targets.
Demolition
Structural alterations
Site clearance
Soft strip
Asbestos management
Remediation
Earthworks & civils
Temporary works
Demolition & Enabling Works Waste Management Aggregates & Concrete
By Paul Argent
2024 saw the muchanticipated release of Volvo’s new F series range of excavators replacing the market leading E series.
Unlike many manufacturers, Volvo’s launch of the standard F series models was almost immediately followed by an announcement of a demolition specific event held at the company’s development centre in Eskilstuna, Sweden.
The event began with a fanfare of fireworks and music revealing not one, but two new models in the manufacturer’s line up, an EC400 and EC500, both of which have taken the new F series excavator’s standard machine and transformed it into state of the art high reach machines, both of which have the capability of working with numerous boom configurations.
Both excavators use a hydraulically widening undercarriage, similar in design to the outgoing EC380E and EC480E models which provides additional width on the ground increasing the machine’s stability and working radius. The tracks are now fitted with heavy-duty rebar benders ensuring the longevity of the upper structure which can now be fitted with an improved SIPS system designed to not only protect the body, but to keep the overall width down allowing ease of transport in certain EU countries.
The slew ring is suitably protected from damage as is the underside of the upper structure. The F series range has been improved over the E series in several ways with the upgrading of the panelling around the machine, again, this has been done to reduce the cost from potential damage. Both models are also fitted with active personnel detection which alerts the operator should anyone stray into the working zone of the machine. A pair of sensors built into the rear counterweight and a third on the offside handrail can disseminate between an object or human and relays the information through Volvo’s new Co-Pilot system into the cab.
The event began with a fanfare of fireworks and music revealing not one, but two new models
With many operators saying the previous generation’s cab was the best, Volvo’s design team have taken that a step further on the F series
With many operators saying the previous generation’s cab was the best, Volvo’s design team have taken that a step further on the F series. A premium, heated and cooled seat awaits the operator with Volvo’s clean and easy to use interface upgraded for the new machine. Electro-hydraulic joysticks provide a greater degree of precision for the operator and along with the new CoPilot touch screen, allows for a vast array of machine information to be accessed with a simple touch.
Joining the Co-Pilot screen is Volvo’s all new Demolition Co-Pilot screen which is situated at the top of the front screen to the operator’s right hand side. This screen shows the information in real time gathered by the sensors mounted to the boom, intermediate boom and stick showing the exact position of the machine. The information gathered by the sensors is translated into showing the operator what the machine is doing, the duties it can achieve and through a series of traffic lights, allows them to see just where the limitations of the machine are.
‘We have developed this system to be user friendly and not too complicated.’ Sunghoon Shin, one of the demolition machine developers commented. ‘We wanted a system that can show the machine in real time allowing the operator to make informed decisions on what is shown on the screen.’ The cab has also been modified with the moving of the wiper motors away from the operator’s main field of vision to give them a wider expanse of glass to see through. To aid upward vision further, the cab also tilts back to a full 30°.
Looking at model specifics, the EC400 uses a 342hp D13J engine whilst the larger EC500’s D13J develops 423hp. Both engines have been calibrated with the pump system to provide ample hydraulic flow and pressures to the end of the stick enabling seamless attachment operation.
The new boom options on both models allow for an operating height of just over 23m on the EC400 with the pin height on the EC500 reaching a little over 28.5m. Both standard heights can be increased by a further 4m with the fitment of an additional boom extension between the boom foot and main boom section. Both the high reach boom, extension piece and digging equipment have been designed with new, low profile cradles allowing operators to easily access the hydraulic and water quick couplers mounted to the side of each section.
A full suite of hydraulic services allow a wide range of attachments to be used as well as the almost standard hydraulic
couplers now seen on most demolition machines. The level of detail put into the design of the boom is outstanding with the dust suppression pipework now terminated on the tipping link allowing it to follow the attachment wherever it goes. A simple turn of a nut on the side of the pipework allows the operator to change the spray pattern and volume of water being ejected from the pipe ensuring minimum issues from dust. For thos operators who want a clearer view of the worksite at up to 32m, a side mounted and underside of stick mounted camera have been fitted.
Like all of the sensitive equipment such as the positional sensors, these components have been suitable protected to reduce damage and operational costs. ‘We looked at the existing boom sections and have revised the hydraulic pipe runs reducing their width and keeping them inside the overall width of the boom. ‘This reduces the risk of damage when the boom is lifted using the dedicated lifting points.’ Martijn Donkersloot, Volvo’s Special Application Solutions Manager commented. ‘We have made 56 changes both large and small to the new generation of demolition machines following
extensive conversations with owners and operators of the previous generation to make the F series what we think is the best in its class.’
When utilising the digging equipment, the operator can choose either a straight or bent configuration and this is mirrored with the use of the boom extension allowing a myriad of combinations to be used. Tool carrying weights for both new models have increased with the EC400 maxing out at 3.3 tonnes with the larger machine capable of carrying up to 3.5 tonnes.
The new range has also been bolstered with the new EC400 straight boom. Carrying all the class leading characteristics of the standard EC400, the straight boom machine uses the same boom and stick system found on the outgoing EC380E model.
The rapid launch of these new machines is testament to Volvo’s desire to continue their elevated position within the demolition sector on the F series machines. Such was the glowing feedback from operators and owners at the event that the first EC400 model was ordered within a few hours of its launch!
following extensive conversations with owners and operators of the previous generation we think the F series is the best in its class
DISMANTLING
SOFT-STRIP/REFURBISHMENTS
FACADE RETENTION
SITE CLEARANCE/BULK EXCAVATION
Over this past year, it has been truly fascinating to meet such an extensive range of people with a wealth of knowledge. And this interview with Dan Highfield was no exception.
Sat with a cup of coffee, I genuinely wish this chat could have gone on forever. A bright, funny character who put everyone at ease, Dan took me through his entire career journey in what was a truly riveting conversation. I really appreciated getting to learn the ins and outs of how Dan got where he is today. It’s easy enough to Google the specifics oof a job role, but how someone got to it? Less so. And those pivotal choices are the topic of this interview.
Editing it down to just the highlights was no easy task, but just as Dan, my new favourite motivational speaker says: Nothing worth doing is without effort.
So best place to start off, how did you get into demolition? Has it all been with City Demo?
I actually started off as a qualified carpenter, and I did that for a good five years. But when work started to dry up, I had a couple of friends that worked here at City, and they got me an interview. And that was it really. The short story; I came in as a labourer, and progressed from there.
So how long ago was that? 11-12 years ago now.
And what kept you here? Because it was quite the career change in many ways…
It was all down to being offered the opportunity to do the apprenticeship really. I was clearly doing something right because I was one of the youngest people at the company, when Mark asked if I wanted to do an NFDC apprenticeship. And with that you basically came out of the course as a top man, so I went for it. I completed that and then was also a part of the first group to complete the new NFDC charge hand course. After this there was the opportunity to complete the supervisor’s card as well. So, I did that too. I never actually made it up to the gold card, because by the time I as in a position to complete the NVQ, I was already working in office at that point, I was now on a different path in my career. After a while of being in the office Mark offered me another opportunity to go to university to pursue a career in Quantity Surveying. This came as quite a shock as it’s something I would never have seen my self doing.
Now, as you’ve done both, as in theory and practical, would you say one is more vital than the other? Or do you need both?
Practical. All the way. It’s not to say you can’t learn anything from a book, but the knowledge will be limited to a more basic overview. When you’re out on site, you come up against all sorts of problems that you have to navigate, so you learn the ins and outs of the trade much better. That, and you’ve got the guys around you who have been doing the job for a long time and will give you practical advice a book wouldn’t know.
Do you think theory narrows people’s field of knowledge?
Only if you’re not open to learning on the job. And then you’re probably not the right person for the role. This is something you’ll come to see a lot of the time in both construction and demolition. Either people stay in it for a really short time, and they leave, or it’s forever. So, you can really learn if you put your mind to it. I wouldn’t leave this type of industry now.
Do you think you’ve hit your stride now? Is this where your future is?
Absolutely. It’s all about working for the right company and having a clear pathway. It might not always be straight, but you’ve just got to roll with it. I got to a high standard on site as a supervisor, so I made the switch to the office, where I came in and started at the bottom. So, I’ve worked my way up to where I am now, and there is still another level of achievement I’m aiming for. This comes with time and commitment from myself and the backing of the company to allow me to progress further.
That must be helpful for you when you’re doing your project valuations or any costings, as you’ve lived and breathed a work site.
I think so. I’ve got a pretty wellrounded view, but I certainly don’t know everything. But I like to learn, and I think as long as you are open to it, there is something new to take away from every day. It also helps with communicating with the lads on site and valuing their views and opinions.
Every day is a school day, as they say. 100%. It’s just strange to me as I honestly never thought I would be that way, let alone go to university. School was just something I went to; it never really held my attention. But with this industry I’m a bit of a nerd. I like to learn as much as I can all the time. My biggest fear when it came to university was never the knowledge though, it was the application of putting it on paper and doing the dissertation. English isn’t my strong point, but I ended up never dropping below a 1st with any of my submissions and coming out with 1st Class Honours.
That’s ridiculously impressive! It was clearly what I was meant to be doing. When I did the NFDC apprenticeship, I won apprentice of the year in 2016, which was insane because I honestly never thought I’d win it given that I was up against candidates who all worked in London. I was the first ever winner of this category, as it hadn’t existed up until then!
You’re right, you are a nerd. And proud.
What’s the next step for you then?
Well, I’m a Quantity Surveyor now, so the next pathway for me is really Commercial Manager. But I have more to do before I reach that level, so I’m working up to it. I like to earn my place, and it’s a discussion that me and the MD (Mark) have had. I’m certainly excited for what lies ahead.
Do you have any advice for up and commers who want to follow in your footsteps?
Well, I’m not one for motivational quotes, if I’m honest.
Not a motivational speaker then? Absolutely not, it’s all rubbish. I never needed anyone to motivate me, I always had my own drive, but what does motivate me is seeing someone physically working hard and getting rewarded for it I’m not saying it’s easy, but my main advice would be you definitely have to put in the work, and sometimes that’s actually going out and
looking for opportunities and when they do come take them It’s not about chasing praise, but you have to earn your position and not expect it to be handed to you. This is way the demolition industry really is such a rewarding job.
Is that what you’d say to yourself 10 years ago?
Just keep your head down, but you have to put the effort in or there is no point at all.
Definitely making that into a motivational quote, I’m afraid.
*Sighs*
What is truly inspiring about City Demolition, is the investment they make into their personnel. When it comes to people, their goal always seems to be to help them excel. It would explain why, in a sector where worker retention is so low, they have people working for them for tens of years. A company that cares is always one that will succeed, which is why City Demolition has the glowing reputation it does.
Norfolk-based demolition company Anglian, has undertaken a redevelopment project to help transform existing office buildings in Cambridge into a state-of-the-art 42-acre parkland science campus. The project has created premises which have reduced carbon emissions by 40% compared to a new build.
The three-month project at CamLIFE (Cambridge Lab and Innovation Focused Environment) in the location formerly known as Capital Park, was undertaken for Longfellow Real Estate Partners – the largest privately held investor and developer of life science buildings in the US. Anglian acted as main contractor for building and property maintenance firm Wates.
Employing a team of 30, Anglian carried out works including partial demolition, internal demolition, alterations and soft strip within three office buildings which were built in 2013. Once fully complete, CamLIFE will deliver approximately 170,000 square feet of best-in-class fitted lab and office space.
The aim of the redevelopment project was to utilise the existing properties and follow an adaptive redesign approach to achieve the lowest environmental impact. This has resulted in a 40% whole-life embodied carbon reduction compared to a newbuild net-zero equivalent. With a long-standing commitment to sustainable development, Longfellow is targeting BREEAM Excellent and EPC A during this project.
With many different materials within the buildings which all needed to be removed, Anglian utilised its expertise to complete each stage of the demolition process. This included carefully removing large panes of glass and metal spiral staircases, as well as saving 3000 bricks to be reused in the next construction phase.
As with every Anglian demolition job, all waste created was transported back to Anglian’s 10-acre facility in Attleborough to be processed. As much material as possible was reclaimed for recycling or looped back into the circular economy, including 87 tonnes of metal, seven tonnes of glass and 11.5 tonnes of rubble.
Andy Elvin, Senior Contracts Manager at Anglian Demolition & Asbestos, said: “We were delighted to undertake this latest project for Wates on behalf of Longfellow. This was a significant project for us which utilised the many skills we have within the team here at Anglian. As a business, we are committed to reducing the impact of demolition jobs on the environment by segregating and processing our waste as standard. This approach complemented perfectly the aims of Longfellow to create stateof-the-art premises with minimal environmental impact and the highest standards.”
Originally established as a demolition and asbestos services company, Anglian has always had firm foundations in the construction industry. The business was founded by Lee Storer, who began his career in the building trade at his father’s roofing supply company, before going on to start his own skip business.
Having gone into licensed asbestos removal services with business partner and former asbestos training lecturer John Fowler, Lee and John formally set up Anglian Demolition & Asbestos in 2007. Joining the Institute of Demolition Engineers and taking their existing qualifications and expertise with them, the company quickly began to pick up work with local leading contractors. Over the past 17 years, the company has expanded to offer additional specialist divisions for scaffolding, earthworks and waste recycling.
Managing Director, Lee Storer, says: “Although our business was started in demolition and asbestos services, we quickly spotted the opportunity to add on extra divisions which would support our core operations and also offer individual services in their own right. There is a natural synergy between all divisions at Anglian and as a result, the expertise we have across the business is second to none.”
The additional divisions not only enabled Anglian to go for larger, more complex demolition projects, offering a full turnkey operation, it also meant the business could provide clients with the full range of services for every project as required. The company has earned preferred supplier status among a host of Tier 1 contractors.
Based on a 10-acre licensed site in Norfolk just off the A11, today Anglian is the region’s fastest growing waste management company and metal recycling facility. As well as providing skips and ROROs for commercial and domestic customers, the scrap arm of Anglian’s operation processes and sends out hundreds of tonnes of ferrous and non-ferrous metal each month for recycling.
Waste from every demolition job (including the Wates project in Cambridge which you can read about in this issue) is segregated as much as possible on-site to allow Anglian to recover maximum materials for recycling or looping back into the circular economy. The business also provides a trusted pair of hands for other contractors, removing and processing waste from a wide range of third-party demolition sites.
Lee sums up: “Anglian is founded on a wealth of skill, experience and passion which runs throughout every division. We are extremely proud to be experts in our field, holding a raft of top industry accreditations. With a host of significant projects lined up for 2025, we are looking forward to what the new year brings.”
By Paul Argent
In just over 14 years, Putnam Construction has grown from a one-man operation into a nationwide, multi-disciplined contractor serving a long list of repeat, blue-chip clients.
Headed by Jake Putnam, Putnam Construction delivers a wide range of services from tipper and grab hire through to earthworks and demolition services. Based near High Wycombe, the company has built up their reputation across the region picking up clients who are now demanding their services across the country thanks to their constant drive to deliver a high-quality, reliable service.
As the company has grown, so has their investment in plant and equipment allowing them to increase their productivity and services for the clients. While the investment in equipment is one thing, having the right, likeminded people also play a major role in the growth of the company.
With an increase in their demolition order book and with the projects increasing in size, Jake looked to the market for a new high reach machine capable of taking the company literally to the next level. “Whilst we have several high reach machines in the fleet, but these were all too small for the projects we were pricing.” He commented. “For the projects we had in the order books, we needed something to give us more reach and whilst we could have hired a machine in, we like to invest in our company and looked to add one to our fleet. With lead times for new machines being over 12 months, we looked to the market for a good, used example and quickly found a CAT 349E which both suited our needs and was available to fit in with our program of works.”
The base 50t excavator had been sent to Ipswich based specialists Kocurek to undergo their typical conversion into a telescopic high reach machine. The 349E left the Hadleigh Road factory sporting a tilting cab, lengthened and hydraulically widening undercarriage, additional counterweight and Kocurek’s hook and pin boom system giving the machine a pin height of around 37m.
One of the first projects tackled by the new arrival was the completion of the demolition of one of Liverpool’s iconic landmarks. The Giro was a 12 storey steel and concrete office block in Bootle and when it shut, was one of banking giant Santander’s regional offices. Opened in 1968 the building was originally home to Girobank, part of the Post Office and was the first bank in Europe to offer interest on client’s current accounts and was also the first bank in Europe to offer a telephone banking service.
Nicknamed The Giro after its main task of sending out weekly giro cheques, the steady change of ownership along with changes in the way many banks did business, eventually saw the demise of banking at The Giro with it closing in 2021. Eventually sold to a private developer, the plan from the new owners includes the creation of a highly sustainable employment location.
As one of Putnam’s regular clients, the developer tasked Jake and his team with the safe demolition and land clearance ahead of the site’s redevelopment. The smaller buildings on the site, once soft stripped, were cleared very quickly leaving just the 12-storey block. Delays with service disconnection and the removal of a telecoms mast delayed the demolition of the building until mid-way through 2024. As the soft strip work had already been completed, the structural demolition works could commence immediately once the power was disconnected.
Whilst Jake’s fleet of modern demolition equipment and attachments capably removed some of the smaller buildings on site, the main office building standing at over 40m in height gave the company something to think about. “Even with the CAT on the fleet, we still needed a ramp to allow the machine to safely reach the top of the plant room located on the South side of the building.” Jake explains. “This meant we had to program the works to allow us to get sufficient quantities of material on the ground to build the ramp as the rest of the building was being dropped.”
Highly experienced operator Matt Thackray has recently joined the company following almost 10 years as an owner operator. “I wanted to get back onto the high reach work which I love.” He commented. “When Jake offered me a seat, I jumped at the chance. The company isn’t as established as other big names in the industry, but to be involved with such an up and coming business was one I relished. Jake is great to work for and is always willing to listen.”
With the company’s Volvo EC380E taking care of the lower parts of the Giro along with a Hitachi ZX210 on processing work, Matt started work on the 10-storeys to the North side of the building.
Already having a range of attachments for his existing fleet, Jake was keen to add a bespoke attachment for the new CAT high reach to ensure the reinforced concrete and steel structure could be taken down without any fuss. “We have been dealing with the team at Worsley Plant for several years and have several of their Rotar demolition attachments in the fleet.” He commented. “I’ve found the Rotar kit to be very reliable and capable of withstanding the punishment they get on site. I know that if anything was to go wrong with them, Worsley have the team capable of backing them up and quickly getting us working again.”
The latest addition to the Putnam Construction fleet is a Rotar RDC25S Combi Shear. The RDC25S boasts a maximum 900mm opening at its widest point and yet measures just 720mm in width allowing it to get into the tightest of spots with ease. Boasting over 100 tonnes of cutting force, the RDC25S is fitted with a set of removable tips and shear blades which can be quickly swapped over as and when required.
Fitted with a Lehnhoff Variolock automatic coupler, the combi crusher joins a range of other products sold and serviced through Worsley including several Rotar RG selector grabs and a range of Montabert hydraulic breakers. “I have been impressed with the Montabert breakers since their arrival onto the fleet.” Jake commented. “Pound for pound they are one of the most productive on the market.”
“The CAT and Rotar has been performing very well since it arrived.” Matt comments. “I’ve used several Rotar attachments over the years, and they have always been a great attachment. This is the first RDC I’ve used, and it must rank as one of the best combi tools I’ve been able to put to work. The cycle times are very impressive, and it has plenty of power to deal with some of the tougher concrete columns. Whilst this job doesn’t require the tool to be changed too often, having the Lehnhoff hitch has also made very appreciative of the technology allowing the tool to be swapped very quickly. Jake adds, “We have both OilQuick and Lehnhoff systems on our kit and find they improve our productivity massively. There is a significant cost in adding them to the fleet, but this can be recouped relatively quickly under the right conditions.”
With a wide variety of attachments on the fleet, the arrival of the new Rotar RDC cements the company’s relationship with Worsley Plant. “We have been dealing with the Worsley team for several years and find their customer service excellent.” Jake comments. “They have an excellent knowledge of their brands and what their customers need, the equipment is first class and to put it simply, we like dealing with them.”
Location: Norwich
Client: Working in partnership with Zive Capital On Site Person: Andrew Hope MCIOB, MIDE and Aaron Malin
Machines Used:
• High reach Kobelco SK550DLC High Reach fitted with various attachments cracker, Shear, Grab
• 52 ton Hyundai HY520 – with Pulveriser, Breaker etc
• 35 ton Hitachi ZX350 fitted with steel wrist and various attachments cracker, Pulveriser, Grab
• 30 ton Hitachi ZX300 fitted with steel wrist and various attachments cracker, Pulveriser, Grab
• 2 x 210 ton (1 x Hitachi ZX210 1 x Kobelco SK210 fitted with steel wrist and various attachments, both fitted with Steelwrist couplers to allow easy movement for the attachments)
• Sandvik QJ341 crusher 341 - 53 TON (Dehaco dust boss and moto fog for dust suppression) (Lowing shovel 100-ton crane also previously used)
It was a perfect end to the year getting to return to the Shorts Group demolition site in Norwich. Not only was it fantastic to see the progress made in the months since we had been away, but it was also the very first case study conducted for Demolition Spotlight! So then, the big question… what has Shorts Group been up to since last time?
We first visited the site right at the beginning of the project, with the disconnection of services and asbestos removal having been completed and the early stages of the soft strip having started. The main structure of the building was still intact, with machines arriving to site ready to begin the main demolition process. There was a little bit of apprehension from the neighbours about what the project might entail, though Andrew was on the case of how to ease their worries. And on top of that, there was a big focus on sustainability, not just from the client, Zive Capital, but as always from Shorts themselves. At only 6 weeks in, a lot had certainly happened.
By our visit in November, demolition was well underway, though not without difficulty as explained by both Andrew and Aaron. Before the actual process of deconstruction could start, an ecological survey was carried out which found seagull chicks on the two wing roofs, which immediately brought everything to a standstill as all species of gulls are protected under the Wildlife and Countryside Act 1981. This makes it illegal to intentionally or recklessly injure or kill any gull or damage or destroy an active nest or its contents. Initially, it was thought the delay would be six weeks.
Luckily, Andrew and the team came up with an innovative and creative solution. Rather than sticking to the original plan, they changed the sequence and began working from the top down on a different section as that was all handdemolition. They could then continue with the project within the allotted time frame, but it also allowed them access to monitor the chicks’ development. Thankfully, the hatchlings had fledged within five weeks, so they were able to keep the main work on track.
The gulls were not the only innovative solution used at the Norwich site. Shorts also employed the use of a demolition curtain, a relatively uncommon practice in the demolition world and one that is not aways readily used. Essentially, this giant curtain, that is suspended from a crane, is used to prevent the bounce back of debris into the surrounding area. Huge bins are then utilised to act as a barrier that will fully contain any bounce back. The choice of where they began the top down demolition meant enough space could be formed to create the 40 yard skip barrier and protect the live buildings as they munched their way through all 8 stories of this site.
Or even more importantly, the neighbours.
Given the close proximity of the site to surrounding buildings, this approach certainly plays into Shorts Group’s tactic to remain in constant contact with their neighbours and address any concerns they might have. Indeed, this has even led to a WhatsApp group being set up where locals are notified of progress, warned about any particularly loud or potentially intrusive works happening on a daily basis, and given a platform to speak about their worries surrounding the project. So, on top of aspects like the Demolition Curtain, they also installed environmental monitoring stations to maintain constant vigilance dust, noise and vibration, enabling Andrew, Aaron and team to be able to measure exactly what’s happening and then explain not only the practice to residents, but also assure them of their safety. Shorts Group are known for their diligence and commitment to best practice, and instances like this certainly prove that tenfold.
Alongside that, there is their continued dedication to sustainability. Andrew touched on this last time we visited, so there was already prior understanding of Shorts Group’s methodology. Now, we could see results. This even starts with the client themselves, who did a full life cycle analysis on the site, looking at its current carbon footprint, from the demolition to the carbon footprint of the new proposed design, so everything would be off set and end up more efficient in the end. So even if the general public were to start arguing that the original building could have been reused, there is evidence that proves longevity of the project, aided of course, by Shorts’ commitment to being fully sustainable.
For those in the know, the demolition process is really more of a deconstruction. It’s not a simple case of smashing down a building and going about the day. That means with the proper investment into recycling, so much of the raw material can be saved. The majority of demolition contractors regularly recycle up to 98% of their materials, as even if materials such as brick can’t be saved as is, they can be ground down and used as an aggregate. What Shorts ensure is that nothing that can be recycled goes to landfill, and that waste is segregated on site and sent to the relevant depot. This process is a balancing act between using the machines to do the heavy work and the workmen on site to assure proper practice, versus the time it takes to do that. For Shorts Group though, this presents no problem as this process is factored into every proposal they create, aided by the fact that everything can be recycled by Shorts Group themselves, so every project they set their hand to is sustainably minded. It’s incredibly forward thinking as more and more sustainability becomes a vital part of any plan. Andrew explained that while publicising the sustainable work they do with brick across all social media platforms, there were responses about only wanting the building to come down and not caring about the ‘green’ aspect. A short-sighted view, if there ever was one, and not one that Shorts Group would pay heed to.
And speaking of time constraints, as expected, this level of dedication goes further still. Their investment into their machinery is staggering, with over £3million worth of equipment being used on this site alone. Whether it’s universal couplers to pair with hard wearing attachments, or multiple excavators used to most efficiently bring the building down, Shorts Group have ensured it is covered. Proper machinery prevents irrelevant downtime, meaning speed, best practice and safety all play a keen role in, not just the Norwich site, but every Shorts Group project.
So, what’s the next step?
There is one final corner to take down whilst making use of the demo curtain and with that completed, they will be able to start cutting into the building, and then work back towards the core, which is left until last as that is where the reinforcement is. Then the building comes down, crushing foundations and finalising processing. Not long left to go at all - it will be wonderful to check back in a final time right at the end, and see a reflection of how the project went.
www.shorts-group.co.uk
There’s only one place you’ll find the heavy hitters of concrete and masonry this January: Vegas, baby — at World of Concrete 2025, the largest and only annual international event dedicated to your business. Be here to mix with industry giants. Get your hands on the latest technologies revolutionizing safety, performance and speed. And learn what it takes to not only claim a piece of our industry’s massive projected growth but dominate the field. Join the power players of concrete and masonry.
EXHIBITS: JANUARY 21-23, 2025
EDUCATION: JANUARY 20-23
LAS VEGAS CONVENTION CENTER