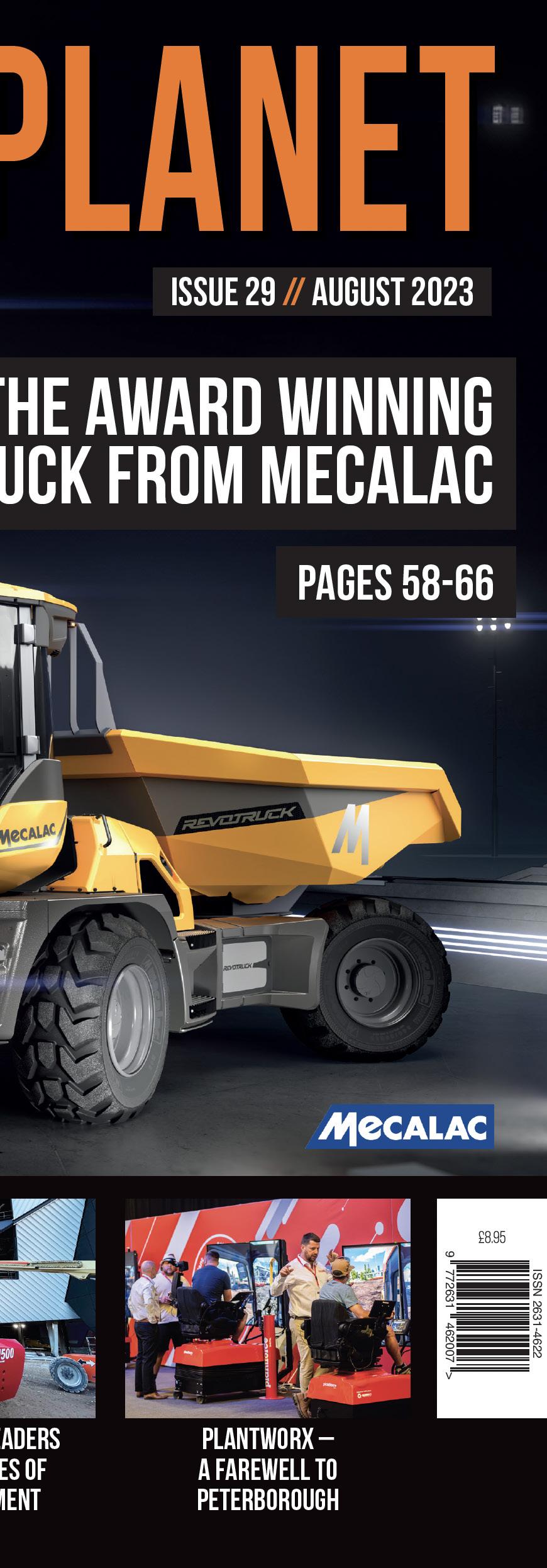
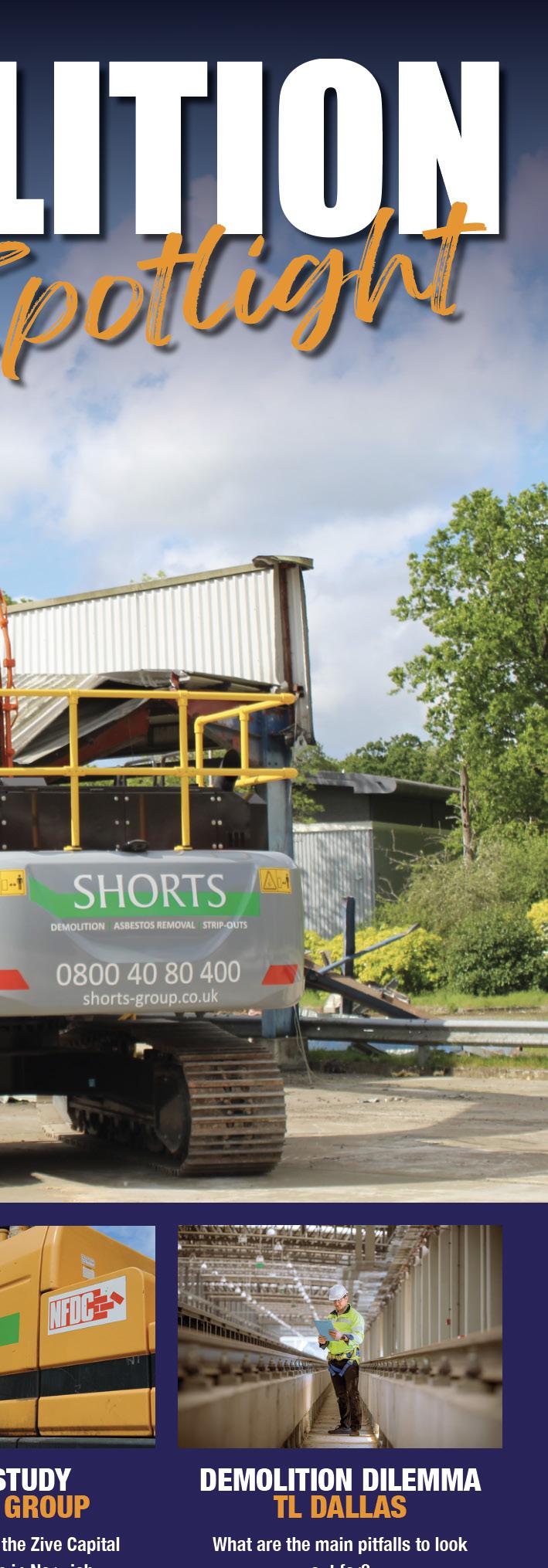
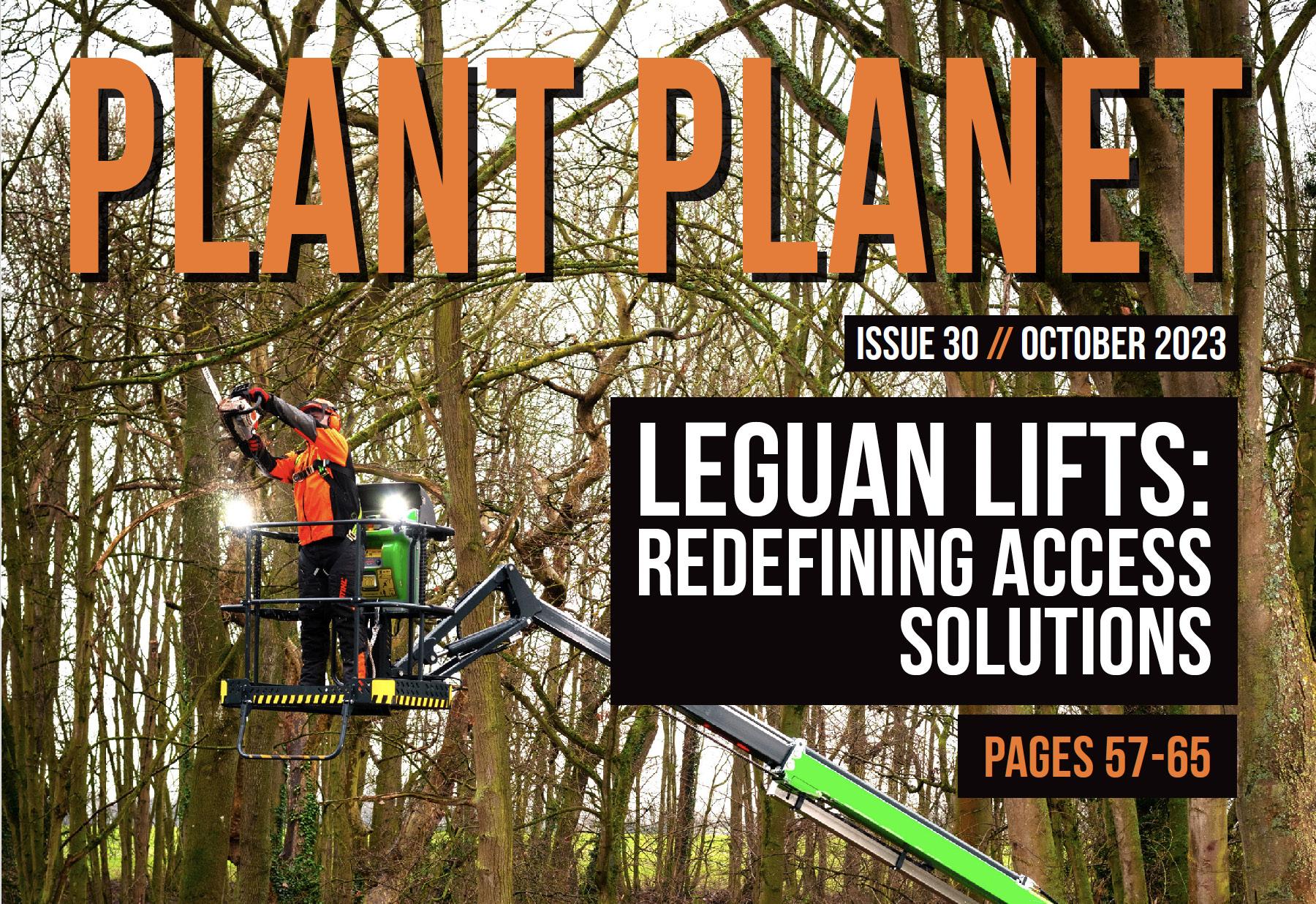
Breaking from the traditional yearbook format, we want to focus on what’s to come as opposed to what has been. We’ve gathered 3 of the biggest organisations in the construction bizz, along with a fantastic variety of renowned names to talk about what 2025 has in store for them.
And with that in mind, what exactly does 2025 hold for Plant Planet. Well, as always, we will be out and about in full force all throughout the year; shows, site visits, open days, we will be everywhere! Starting off the year we have the Executive Hire Show, the perfect kickstart to 2025. After the success of Intermat last year, Plant Planet is keeping things international and heading off to Bauma! In a first for our mag, we are thrilled to be exhibiting as part of the CEA stand at Europe’s biggest construction show. We are honoured as well to be returning to both of CPA’s major events, Stars of the Future and their annual conference, both of which play an integral role in the plant hire sector. Our autumn is looking very full, with not only UK Construction Week and Vertikal Days lined up, but we will also be returning to Plantworx, ready and raring to take the new location by storm!
What’s another exciting event we have coming up? Oh, I don’t know, maybe the launch of our BRAND NEW MAGAZINE! That’s right! After the success of Demolition Spotlight as a section of Plant Planet, we are delighted to announce that it will go into full mag format in March of this year! We have so many exciting interviews and site visits lined up already, as well as the return of the wonderful Paul Argent, who is signed on to continue working with us! We can’t divulge any more at this time… so don’t ask us you cheeky monkeys! But stay tuned into our socials where we will keep you updated with everything to come. This is but a little taster of our 2025. There will certainly be some very exciting announcements due imminently, so on behalf of myself and the team, all I can say is watch this space!
Rebecca Phillips Managing Editor
Kiwi Media and Promotions Ltd
2nd Floor, 41-42 Southgate, Chichester, West Sussex PO19 1ET +44 (0) 1243 345 323
Kiwi Media and Promotions Ltd. © 2025 all rights reserved. Reproduction in whole or part is prohibited except with permission in writing from the company.
Note to contributors: articles submitted to the Editor for consideration must be the original work of the author.
Where photographs are included that are not the property of the company or contributor, permission to reproduce them must have been received from the owner of the copyright. Any views or opinions expressed within this magazine are not necessarily those of the company.
ISSN: 2631-4622
Registered in England No: 09910499
All advertisements are accepted subject to the Kiwi Media & Promotions’ standard of insertion. For a copy of Advertising Terms & Conditions, please write to: Darren Shelton, 2nd Floor, 41-42 Southgate, Chichester, West Sussex, PO19 1ET
2024 was a pivotal year for the CEA, marked by key achievements, strengthened partnerships, and standout industry events. The year culminated in the CEA being shortlisted as a finalist in the Best Association Transformation category at the UK Trade Association Awards (winner to be announced in February 2025).
Viki Bell, the CEA’s Director of Operations, said, “2024 was a year of streamlining and strengthening for the CEA. In my first term as Director of Operations, we welcomed new team members, introduced a refreshed structure, and focused on ensuring the CEA operates smarter and more effectively for our members.
We also introduced a new website designed and built in-house by Beth Abbott, CEA’s Head of Marketing & Communications. This new platform made things clearer, easier, and more useful for our members and the wider industry. The new site, thecea.org.uk, is clean, simple to navigate, and mobile-friendly, so you can find everything you need –we are really proud of the new platform.”
The CEA also welcomed a record number of new members to the association, marking a significant milestone for the year. Another standout achievement was the success of the CEA Members’ Forums, which brought together industry leaders and stakeholders to tackle key challenges, share valuable insights, and explore opportunities for growth. These events provided a platform for new members to engage, with discussions focusing on decarbonisation, skills shortages, and market trends. One of the Forums, which was held on Budget Day, delivered a critical analysis by an industry-leading professor of economics of the UK Budget and challenges, keeping the conversation firmly aligned with current affairs and industry priorities.
Viki Bell, Dale Camsell, the CEA’s Senior Technical Advisor, and Charles Stephenson Director, JCB London Office, who is also a CEA Board Member, represented the association at the CECE (Committee for European Construction Equipment) event. They contributed to discussions on EU machinery regulations and autonomous equipment standards, underlining the CEA’s influence in shaping international policy frameworks. The CEA’s close alignment with European standards and practices remains vital for ensuring the UK industry’s competitiveness on the global stage, reinforcing its ability to navigate key regulatory and technological challenges.
Another key development in 2024 was the CEA’s partnership with Personal Group, launching innovative employee wellbeing initiatives through the Hapi platform. Known as WorkForce, this collaboration is helping members address recruitment challenges and improve workforce satisfaction.
For further details visit https://thecea.org.uk/workforce
“The partnership between CEA and Personal Group is a strategic move to enhance employee wellbeing and engagement, which is crucial for addressing the skills gap in the sector. By offering comprehensive benefits and support through the Hapi platform, this collaboration aims to create a happier, healthier, and more productive workforce for our members. This initiative is designed to positively impact employee retention and productivity, ultimately contributing to the sector’s growth and stability.” Viki explained.
The UK General Election provided the ideal platform to unveil the CEA’s firstever Manifesto. This comprehensive document highlighted key priorities for the
construction equipment industry, such as decarbonisation, digitalisation, skills development, and regulatory consistency. The manifesto called for an industrial strategy to address these priorities, reflecting the CEA’s commitment to tackling critical challenges and supporting the UK industry’s competitiveness and resilience. To learn more about how we work with the government on behalf of our members and the industry, visit our Get Involved page: thecea.org.uk/get-involved.
The CPA (Construction Plant-hire Association) Conference was another event highlight in the 2024 calendar. The CEA, alongside PlantWorx Construction Exhibition and Datatag— the delivery partner for the CEA’s CESAR Scheme—attended the event to showcase key initiatives. These included the CESAR Scheme and RAPID, demonstrating the organisation’s commitment to tackling equipment theft and improving industry security measures.
Viki Bell said: “What a year 2024 was for the CEA and my first in office. From being shortlisted in the Best Association Transformation category to welcoming a record number of new members, 2024 was a year of progress and collaboration. None of this would have been possible without the fantastic team behind the CEA—dedicated, hardworking, and always ready to tackle challenges head-on.
Our Members’ Forums, international contributions, and strategic partnerships reflect the collective drive to move our industry forward. I’m incredibly proud of what we’ve achieved together this year and the strong foundation we’ve built for 2025. Here’s to another year of growth, innovation, and delivering value for our members.”
The construction equipment sector faces ongoing challenges: a persistent skills shortage, ambitious sustainability goals, and increasingly complex regulations. Tackling these issues is key to ensuring long-term growth, competitiveness, and resilience for businesses across the industry.
The skills shortage remains one of the most pressing concerns, as the demand for STEM talent outpaces supply. Many businesses struggle to find workers with the technical expertise needed to operate, maintain, and contribute to the engineering, design, and manufacturing of increasingly advanced construction equipment. This challenge is further amplified by the industry’s rapid digitalisation, requiring a workforce equipped to work with technologies such as telematics, automation, and alternative power systems.
The CEA is taking a proactive approach to bridge this gap between education and the construction equipment sector. Recognising that a skilled workforce is the backbone of every business, we’ve developed The Education Landscape: A Guide for Employers in collaboration with the Department of Education and other academic organisations. This practical resource helps companies navigate the complexities of engaging with schools, colleges, and universities, highlighting opportunities to support education and the benefits of doing so.
Whether offering workplace experiences, supporting apprenticeships, or contributing to course design, businesses can play a vital role in developing the workforce of tomorrow. Collaboration is at the heart of this progress. The CEA is committed to connecting members with education providers, helping to shape skills development and ensuring the next generation has the tools it needs to thrive.
Alongside the skills gap, sustainability remains a significant challenge. With the UK construction industry facing stringent
decarbonisation targets, businesses must balance the transition to greener technologies with economic viability. Meeting these goals requires innovation and investment in alternative power solutions, such as electric machinery, hydrogen, and hybrid equipment. The changing regulatory landscape, particularly around EU emissions standards and domestic environmental policies, adds further complexity.
“We’re advocating for a comprehensive and inclusive approach to sustainability, as outlined in the CEA Manifesto,” said Viki. “This means supporting a full spectrum of innovations in alternative fuels and lowcarbon technologies, from hydrogen and battery solutions to biofuels and beyond. Our focus is on embracing all viable options rather than prioritising one over another, ensuring every pathway is explored and developed. By championing this approach, we aim to equip our members with the tools they need to meet evolving environmental demands, future-proof their businesses, and remain competitive in a rapidly changing industry.”
The CEA played a key role in shaping discussions around the UK Government’s Industrial Strategy Green Paper, providing detailed feedback and advocating for the construction equipment industry’s critical contributions to advanced manufacturing, clean energy, and sustainable growth. By highlighting the sector’s economic value, innovation, and role in meeting net-zero targets, the CEA ensured that industry priorities were firmly on the agenda.
In October 2024, the UK Government unveiled Invest 2035, a comprehensive Industrial Strategy aimed at driving sustainable economic growth across key sectors, including advanced manufacturing and clean energy.
The CEA welcomed this initiative and was pleased to have contributed to its development, recognising the potential it brings. However, as Viki noted: “We were pleased to see the Industrial Strategy align with our calls in the CEA manifesto. However, it’s disappointing that the construction equipment sector hasn’t been more prominently recognised, given its natural fit within advanced manufacturing and clean energy.
Our sector generates over £15 billion in revenue, supports over 44,000 jobs, and invests heavily in R&D— £250 million annually. We’re playing a leading role in advancing clean energy with sustainable innovations like battery storage and hydrogen fuel, which are critical to the transition.”
Viki added: “We look forward to continuing to work closely with our Government to ensure the sector’s role as a major contributor to the UK’s economic resilience is acknowledged.”
The path forward requires collaboration, innovation, and strategic planning. The CEA remains committed to driving practical solutions as we navigate the challenges of skills shortages, decarbonisation goals, and evolving regulations. Through initiatives like the Industrial Strategy and partnerships with education providers, we build stronger connections between industry, government, and technology to ensure businesses adapt and thrive.
“In 2025 and beyond, our focus will remain on equipping businesses with the tools, knowledge, and skilled workforce they need to address these challenges, embrace innovation, and secure a resilient and competitive future for the construction equipment sector.” Said Viki.
Before we get into everything else happening in 2025, let’s take a moment to talk about all things PlantWorx. Returning for its 6th edition from 23rd to 25th September at its new home, Newark Showground, PlantWorx will be the UK’s largest working construction equipment exhibition in 2025 and a cornerstone of the industry calendar. Owned and hosted by the CEA, this flagship event brings together cutting-edge machinery and pioneering technology. It’s a platform for innovation, collaboration, and discovery, showcasing the best the industry offers while reflecting the CEA’s commitment to driving progress.
“This will be my first PlantWorx as Director of Operations at the CEA, and I’m genuinely excited about the opportunities it will bring for our industry,” said Viki. “2025 is set to be a standout year for the construction and equipment sectors, with innovation, education, and partnerships leading the way. PlantWorx 2025 will once again set the standard as a must-attend event for professionals across the sector.
As the largest working construction show of the year, it will provide a platform to showcase new technologies and create opportunities for collaboration and growth. I’m incredibly proud to lead the CEA in delivering this flagship event, which continues to highlight the very best of our industry.”
As part of its commitment to driving innovation and inspiring the next generation, PlantWorx 2025 will host the inaugural Rethinking Futures initiative. Aimed at secondary school and college students aged 12 to 18, this programme offers a unique opportunity for young people to explore careers in construction engineering through hands-on experiences and industry engagement.
PlantWorx 2025 is set to be an unmissable event in the construction industry calendar —a showcase of cutting-edge machinery, pioneering technology, and opportunities for collaboration. With new housebuilding projects on the horizon, the demand for both equipment and a skilled workforce has never been greater. For exhibitors, PlantWorx offers the perfect platform to connect with key decision-makers and demonstrate the solutions the industry will need to meet these challenges head-on.
This focus on workforce and opportunity leads naturally to the next major announcement from the CEA for 2025—MyGlobalBridge. As the industry faces increasing demand for skilled workers, this innovative platform connects talent with opportunity, ensuring that young people and employers are equipped for the future.
Exclusive discounts to connected services including PlantWorx, bauma and the CESAR Scheme. Join the CEA now and benefit from:
Representation with UK & EU Governments
Technical & regulatory insights & advice
UK & global market insights
Promotional opportunities
Exclusive member events
Industry news & thought leadership
Workforce benefits & resources
MyGlobalBridge: revolutionising connections between students and employers with multimedia profiles and smart matching.
Looking ahead to 2025, the CEA is building momentum with MyGlobalBridge—a digital platform created to tackle the persistent skills shortage by transforming how young people and employers connect.
Viki explained, “Initially developed to bridge the gap between schools and businesses, the platform has been embraced as a tool to highlight the diversity of talent available, allowing young people to showcase their skills in ways that traditional CVs and grades can’t fully capture.
MyGlobalBridge enables students to create multimedia profiles that include projects, videos, and personal achievements, offering a richer and more dynamic perspective on their abilities. For employers, it’s a game-changer—providing a smart opportunity-matching system that connects them directly with candidates whose skills align with their needs.”
Beyond recruitment, the platform also delivers valuable data insights for schools, helping them refine their support programmes and better prepare students for the world of work.
This initiative is a step towards ensuring the long-term success of the construction equipment sector. By helping employers connect with diverse talent early, MyGlobalBridge is encouraging a fairer and more inclusive industry.
“For young people, it provides a unique opportunity to explore careers that might otherwise be overlooked, particularly in the construction equipment sector, where opportunities are plentiful but often under the radar.” Concluded Viki.
Exploring the future of construction with hydrogen-powered, batteryelectric, and hybrid machinery paving the way to sustainability.
“As we head into 2025, the CEA remains focused on progress and delivering value to our members and the wider industry. We are planning an exciting rebrand, and a key part of this is ensuring our image and messaging reflect our changing role. The rebranding is focused on modernising how we present ourselves, ensuring our communication reflects the changing needs of our members. It’s about staying relevant, practical, and effective in supporting the industry while maintaining our role as a trusted advocate for the construction equipment sector.
Education and skills development will continue to be a priority in the year ahead. We’re strengthening ties with schools, colleges, and universities to inspire the next generation of talent and tackle the skills challenges faced by the industry. By working closely with educators and businesses, we’re helping create pathways into rewarding construction equipment and engineering careers.
Looking further ahead, preparations are already underway for hosting the CECE Congress in 2026. Hosting this event is a significant milestone for the CEA and an opportunity to bring global leaders together to address the challenges and opportunities shaping the future of our industry.
As always, we’ll focus on delivering real, practical value to our members through forums, insights, and support that help them navigate the changing landscape. With a strong foundation and exciting plans ahead, we’re looking forward to a productive and impactful 2025.”
Viki Bell, Director of Operations, CEA (Construction Equipment Association)
2025 is packed with exciting events for the construction equipment industry, offering opportunities for networking, learning, and collaboration.
CEA Members’ Forum
17-18 March 2025 – ABAX, Peterborough 8-9 July 2025 – TBC 11-12 November 2025 – Caterpillar, Peterborough
CEA General Technical Committee
4 March 2025 – ABB, Daresbury 10-11 June 2025 – Terex, Northern Ireland
18 September 2025 – Cummins, Darlington 17-18 December 2025 – Staverton Park, Daventry
PlantWorx 2025
23-25 September 2025 – Newark Showground
With a diverse range of events and initiatives, 2025 promises to be a year of growth, innovation, and collaboration for the construction equipment sector.
Link to our events calendar: https://thecea.org.uk/events
Insights and comment exploring The UK Infrastructure in 2025 from one of the UK’s largest independent construction machinery part stockist.
The UK government’s infrastructure policy, funding, and delivery have shown a mix of progress and setbacks. Achieving the dual goals of net zero and regional growth while enhancing resilience and protecting the environment requires robust policies and implementation plans. The National Infrastructure Commission (NIC) has highlighted areas of progress, but significant gaps remain.
In order to service our customers to best effect, we are proactive in our tracking of challenges within the industries our businesses support and we have compiled a short update and overview for anyone who wishes to learn more about upcoming projects and expectations for the UK’s Infrastructure in 2025.
Recent progress includes advancements in digital networks, with gigabit-capable broadband on track for 85% coverage during 2025.
The government has revised National Policy Statements for energy, networks, and water resources and updated Ofgem’s duties to align with net-zero goals.
However, in other areas, progress has stalled or reversed. For instance, abrupt changes to heat policy have hindered the installation of heat pumps, jeopardising targets. Similarly, cancelling the northern leg of High Speed 2 (HS2) without clear alternatives undermines connectivity in the North and Midlands, threatening regional growth.
Policy stability and long-term commitments are crucial to addressing these challenges. Ambitious goals must be matched with scaled policies and actionable plans. Removing barriers to infrastructure delivery, increasing funding, and empowering local areas through devolution are vital steps.
The second National Infrastructure Assessment highlights a growing gap between current infrastructure and future needs. Issues such as inadequate transport investment in regional cities, stagnant recycling rates, and outdated water resources reflect this gap.
Closing it will require a sustained increase in public and private investment.
Public infrastructure spending, estimated to average £30 billion annually, needs to grow to meet NIC recommendations.
Beyond 2024-25, maintaining infrastructure funding in real terms is essential. Concurrently, private investment must rise, supported by policy stability, regulatory reforms, and streamlined planning processes.
Infrastructure investment aligns with the global push toward the UN’s Sustainable Development Goals (SDGs). These emphasise the need for safe, affordable transport, water, and energy systems while combating climate change. Research highlights opportunities for civil engineers to address SDGs but warns of potential trade-offs, such as increased emissions and biodiversity impacts.
Adopting innovative approaches like modern construction methods (MMC) and nature-based solutions is key. For example, Peruvian water engineers have leveraged indigenous practices to mitigate storm risks, offering lessons for integrating sustainability into UK projects. Standards like PAS 2080:2023 for carbon management provide frameworks for sustainable development.
The scrapping of HS2’s northern leg epitomises the political and financial unpredictability affecting transport infrastructure. High-profile projects such as Crossrail and smart motorways have faced delays and cost overruns, raising doubts about the sector’s ability to deliver efficiently. Nevertheless, decarbonising transport systems remains urgent.
Do you manage a fleet? See our Insight Whitepaper here: qrco.de/planthire
UK SMEs and sole traders are critical to the development of the UK’s infrastructure goals, acting as agile innovators and essential service providers within the supply chain. These businesses contribute specialised skills, local knowledge, and cost-effective solutions that bolster larger infrastructure projects.
Whether offering bespoke engineering services, or innovating in areas like renewable energy, digital networks, and sustainable construction, SMEs and sole traders help drive progress toward net-zero targets, regional growth, and resilience.
Their adaptability enables them to address specific challenges in transport, water resources, and energy transitions, making them indispensable partners in achieving the UK’s ambitious infrastructure objectives.
Since 1991, Plant Parts has been a cornerstone in the construction machinery industry, offering quality components and expert services to machine owners, dealers, and repairers across more than 100 countries.
Whether you need new, reconditioned, or bespoke solutions, our knowledgeable team is ready to help, providing the reliability and support you need to keep your machinery running efficiently.
Contact us for a quote or to learn more about the services we offer, extend the life of your machine or fleet!
1 2 & 1 3 F e b r u a r y 2 0 2 5
The Construction Plant-hire Association (CPA) is pleased to report that membership continued to grow in 2024 and as of January 2025, the CPA has 1933 members who supply over 85% of hired plant to the construction industry. Members range from owner operators with a single machine, right through to the largest companies in the industry, with hire fleets of thousands of machines.
2024 was a challenging time for CPA members and the plant-hire industry overall. The CPA has worked alongside key stakeholders and lobbied the Government on several issues directly affecting the sector, such as the need to extend the Full Expensing Allowance to the plant-hire sector; abnormal loads and embargo times; and concerns relating to the changes to inheritance tax, pensions, Business Property Relief (BPR) and the National Insurance contributions (NICs) increase.
A key CPA project carried out in 2024 was the completion of the first fully comprehensive study of the plant-hire sector in the UK. Carried out in conjunction with Oxford Economics, the report entitled ‘The Economic Impact of the UK Construction Plant-hire Sector’ shows the significance of plant-hire and its true value to the UK economy, both in GDP, productivity, and the number of jobs it supports.
Two flagship events were hosted by the CPA during 2024 - the Stars of the Future Awards in July and the CPA Conference in November. The Stars of the Future Awards identify some of the industry’s brightest up-and-coming talent and its future leaders across various occupations. A total of 80 nominations were received for the 2024 awards and almost 300 people attended the awards ceremony near Coventry.
From making work sites more sustainable to recruiting and retaining tomorrow’s workforce, the CPA’s 9th Annual Conference held in November 2024 discussed future trends and challenges facing hire firms. The Conference attracted a record number of participants with approximately 200 delegates and 26 sponsoring exhibitors.
Under the overall theme of ‘Shaping the Future: Insights for the Plant-Hire Sector’, five separate panel discussions brought industry experts together to share opinions and solutions, chaired by co-hosts Merryn Myatt, a former BBC news presenter, and construction industry journalist and vlogger Peter Haddock.
Other key developments at the CPA in 2024 were the appointment of Steve Mulholland as the association’s new Chief Executive Officer and the recruitment of Luis Bassett in the newly created role of Decarbonisation and Sustainability Manager. Steve has a long track record with the CPA and a great deal of experience in the planthire sector, having run his family business Mulholland Plant Services for many years. He was formerly the CPA Chair for six years and was a CPA Council Member for 10 years.
Luis joined the CPA team in October 2024 from the London Borough of Merton, where he worked for over eight years. He has extensive experience in low emission solutions for the construction plant sector, as Luis’s main role at London Borough of Merton was in the Cleaner Machinery Team, who implement the London NRMM Low Emission Zone on behalf of 32 London local authorities.
The appointment of Luis is the crucial next step in the development of the Association, as it helps the membership navigate the transition to Net Zero, whilst liaising closely with other industry stakeholders on future technologies and managing expectations within Government and local authorities on the timescales of what is possible in the short to medium term.
The CPA commissioned Oxford Economics to research and write a report into the size and scope of the plant-hire sector in the UK. It makes a compelling read for both those employed in the sector, but also for policymakers and stakeholders. It also helps put into perspective the breadth and scope of the sector and why it remains a key destination for highly skilled jobs and roles. Key findings of the CPA/Oxford Economics report entitled ‘The Economic Impact of the UK Construction Plant-hire Sector’ include:
• The construction plant-hire sector contributes £14 billion annually to the UK economy
• Construction plant-hire contributes 191,500 jobs to the UK economy
• For every £100 contributed to GDP directly by construction plant-hire, the sector supports a total of £218 around the economy
• Construction plant-hire workers are 25% more productive than the average UK worker, with a higher share being company managers or directors
• For every 100 people directly employed by construction plant-hire, the sector supports a total of 216 jobs around the economy
The construction sector is an important component of the UK economy, employing 7% of the UK workforce, and making activity in all other sectors of the economy possible through the infrastructure, offices, and factories that it builds. The construction plant-hire industry is an enabling sector that sits behind construction and allows it to function in an efficient way.
Steve Mulholland, CPA Chief Executive Officer commented:
“This research was carried out over many months and we were excited to share the findings for the first time at the CPA Conference. While the report is an opportunity to showcase the plant-hire sector, it also acts as a chance to review the progress made over recent years and the contribution CPA members make to the wider UK economy.
“Over the last few years, plant-hire businesses have had to adapt and evolve in order to survive. As we look to the future, it is one full of opportunities, growth, new technologies and innovations. Decarbonisation and the move to a Net Zero economy has been at the forefront of policymakers’ plansit is important that our sector plays its part in this process, as the move away from diesel and fossil fuels gathers pace. This, alongside the rise of AI and digitalisation, will all have a profound impact on plant-hire companies in the coming decades.
“The role of the CPA will also evolve as we meet these future challenges and opportunities, working hand in hand with our members in supporting them. This economic impact study helps set the foundations for moving forward for the CPA across every facet of our work and engagement and celebrating almost 85 years of supporting the UK’s construction plant-hire sector. It has only been possible because of the contribution our members have made to our continuing success,” he continued.
A digital copy of the CPA/Oxford Economics report can be downloaded from https://www.cpa.uk.net/news/cpa-oxfordeconomics-report-available-to-download. Hard copies are also available on request by emailing enquiries@cpa.uk.net
Construction plant-hire is an exceptionally difficult sector to decarbonise. It includes powerful machinery with challenging duty cycles operating on sites that have minimal existing infrastructure, if any. This is especially the case when those machines are building the infrastructure that the UK has to deliver at pace to achieve Net Zero.
Construction machinery is often designed to be a particular size, weight, reach or work in specific environments, such as on rail. For some tasks it is already challenging to get hold of a machine with the right specifications, even without restricting yourself to hybrid, Stage V, hydrogen or fully electric models. The design modifications required to decarbonise machines can compromise those desirable characteristics, with battery weight being a common stumbling block.
Commercial road fleets are moving towards electric, but there are challenges with public charging infrastructure. Fleet operators are being advised to focus on electrifying the shortest and most predictable routes first, and in the case of vans, considering whether employees are able to charge at home. This being the case, how far are we from charging infrastructure that works for HIABs and truck-mounted cranes, which not only need to travel to multiple sites, but carry out work once they get there?
For most types of equipment the only option is to bring the power to the machine. You can’t track a 100 Tonne electric crawler crane 14 miles down the road to the nearest charge point. Plant-hirers rarely have any control over the grid capacity on site, and sites often express frustrations in getting a connection. Even if you can get a sufficient grid connection, how green is the tariff?
Construction machinery is not cheap. Plant-hirers cannot always afford to invest in the latest kit, especially in cases where they do not qualify for full expensing. Residual value is another crucial consideration. How much a machine can be sold for determines how much money it needs to earn throughout ownership to be profitable, higher up-front investment and lower residual value makes it very difficult to keep rental prices down.
Although there are fuel savings to be had with new state-of-theart equipment, this does not always cancel out the difference in weekly hire cost. Passing the cost onto customers risks losing them, and regulation is not a silver bullet. If a company cannot afford a certain type of technology, forcing them to buy it does not increase demand, it just puts them out of business.
Electrification of smaller machines, hand-held items and stationary equipment suitable for tethering (concrete pumps for example) show a lot of promise, along with hydrogen combustion engines for the larger and mobile kit. However, the infrastructure will take time and government support to evolve, as will tackling the higher investment cost.
Drop in alternative fuels are commercially available and can reduce greenhouse gas (GHG) emissions by as much as 90%, as long as they are sufficiently high blend and sustainably sourced. This can be verified through the use of certified suppliers under the Renewable Fuels Assurance Scheme (RFAS), and the accompanying Renewable Fuel Declaration, which scores the fuel based on GHG savings compared to diesel.
HVO is the most well-known, though not yet manufactured in the UK. Diesel and petrol sold in forecourts in the UK already contains a small amount of biofuel, achieving modest GHG savings compared to 100% diesel. Higher blends of biofuel are available for greater GHG emission reductions, for example B20, B30, B100 and E85, but these may require modifications to the engine and/or fuel storage. Fuel additives that improve fuel efficiency are also commercially available.
Diesel-electric hybrid offers significant benefits through improved fuel efficiency, utilising battery power during periods of low demand. Being much less dependent on infrastructure, it is a more flexible, scalable and incremental solution, with opportunities to evolve towards predominantly plug-in models. External battery storage units are also widely available to hybridise diesel power generation on site as above, or enhance existing grid supplies by continuously trickle charging small amounts of power. This stored power can be delivered to site with more flexibility, acting as a buffer between the site and the grid and covering peak demand without the need for expensive infrastructure upgrades. There are also smaller transportable options available, designed to replace the traditional trolley generator.
Entries are now open for the Construction Plant-hire Association’s (CPA) Stars of the Future Awards 2025:
• Plant Mechanic of the Year (Level 2)
• Plant Technician of the Year (Level 3)
• Young Plant Operative of the Year
• Plant Operative of the Year
• Lifting Technician of the Year
• Hire Controller of the Year
• Plant Installer of the Year
• Technical Support Person of the Year Award for employers:
• Apprentice Mentor of the Year
Special awards are also available for all nominees
the nomination
from www.cpa.uk.net and make your nominations by 21st March 2025
General efficiencies like anti-idling practices, engineered solutions, eco-operator modes and power management (including renewable energy generation on site) can also reduce carbon emissions significantly, especially if used in conjunction with one another or alongside other stepping stone technologies.
Climate targets must recognise sector-specific challenges and allow scope for these approaches while the ‘zero’ technology gains momentum. Reductions in carbon emissions should not be vilified simply because they still contain a degree of fossil fuel use, a partial reduction is far better than no reduction at all, and far more likely in the short-medium term.
Less carbon tackled today, is more carbon to tackle tomorrow, and less time to do it in. Promising to support future technologies is welcome, but plant-hirers need an assurance that what they invest in today will also be supported, especially given that we don’t yet know what the future looks like for many of these powertrains.
This sector has proven time and time again that it will do what it can, when it can, but it cannot fund these transitions alone. Substantial visible progress in infrastructure and financial incentives like fuel rebates and full expense allowance will be required. These necessary financial incentives carry a hefty price tag, and what remains to be seen is how far the UK taxpayer can afford to run in this ‘race’ to Net Zero.
The CPA Stars of the Future Awards 2025 are now open for entries and employers across the industry are invited to recognise and reward their construction plant apprentices and trainees. The awards are free to enter and are open to both CPA members and non CPA members. Nominations are welcome from all employers including plant-hire companies, manufacturers, contractors, suppliers and others operating in the construction plant sector with apprentices and trainees in their workforce. Nominees need to be on an approved apprenticeship scheme or an employer in-house learning programme.
To make a nomination, employers can download a nomination form from the CPA website at https://www.cpa.uk.net/skillstraining/stars-of-the-future and complete and return it to the CPA by the nomination deadline of 21st March 2025
The winners will be announced at a prestigious awards ceremony at the Heart of England Conference and Events Centre in Fillongley, near Coventry, on 10th July 2025. The event will be hosted by construction industry journalist and vlogger Peter Haddock.
Awards will be made for the well-established categories of Plant Mechanic of the Year (Level 2), Plant Technician of the Year (Level 3), Young Plant Operative of the Year, Plant Operative of the Year, Plant Installer of the Year, Lifting Technician of the Year, Hire Controller of the Year, Apprentice Mentor of the Year and College of the Year. All nominees are also eligible for special awards including the Judges’ Special Award and the Best Personal Statement Award.
In recognition of the growth of the awards over the last 12 years, a new awards category has been added for 2025 for Technical Support Person of the Year. This award is for apprentices or trainees who are in a role that has a plant technical focus and who are supporting other plant-focused operations of their business such as data handling and supply, hiring activities, sales and marketing activities, parts and/or resources/equipment supply, machine/equipment systems programming/maintenance, site operational planning, supporting external customers, etc.
Steve Mulholland, CPA Chief Executive Officer said: “We urge employees - both small and large - to nominate apprentices and trainees who they see as being the industry’s future leaders, as it means the world to them to be nominated for an award. The awards are open to all employers across the industry, so nominating organisations needn’t be a CPA member to put someone forward.
“Stars of the Future is becoming more high profile every single year and last year’s winners received national recognition and won some fabulous prizes, including tool kits, machine training courses, iPads, an overseas trip to visit a Liebherr crane manufacturing plant in Germany, another overseas trip to one of Wolffkran’s manufacturing facilities in Luckau, Germany, and a VIP day courtesy of JCB. We know that many previous Stars of the Future winners have been fast-tracked to supervisory and management positions.
“At the CPA, one of our primary objectives is to encourage new blood into the construction plant sector, and Stars of the Future helps us to achieve this. The standard of entries gets higher every year and last year we received 80 nominations from across the industry. We anticipate even more this year,”
he added.
During 2025, the CPA will also be exhibiting at a number of trade shows. The first will be at the Executive Hire Show in Coventry in February, where the team can be found at stand
H20. In June the team will be at Rail Live at Long Marston Rail Innovation Centre and in September at Newark Showground for both Vertikal Days and PlantWorx.
Other developments in 2025 will include the introduction of a brand new CPA website. This is designed to be dynamic, engaging and content rich, serving CPA members well and also helping to attract new members to the association.
Following the October Budget and the announcement on changes to Business Property Relief and the impact on inheritance tax and family run businesses, plus the National Insurance contributions (NICs) increase, the CPA has been working with other trade associations and stakeholders in highlighting the impact of this short-sighted policy, and what it will mean for the plant-hire sector. This has included:
- CPA members taking part in a wide ranging economic impact survey in conjunction with Family Business UK and the CBI Economic Impact Analysis team, the results of which were widely reported in the national press.
- Producing a policy briefing which explains in more detail the unfairness of this move and the ramifications for both family run plant-hire firms and the wider plant-hire sector.
- Attending a meeting of the Business and Trade Select Committee research roundtable with senior MPs, and a meeting directly with James Murray, Exchequer Secretary to the Treasury, highlighting the issue.
- A call for CPA members to write directly to the Prime Minister with first-hand examples of how the change in policy towards Business Property Relief will impact their businesses.
- In addition, the CPA also wrote to the Prime Minister outlining our concerns, this was followed by an interview on Times Radio which Steve Mulholland took part in just before Christmas.
We are now working with a political consultancy and communications team to take this work forwards into 2025 to further outline on a high profile stage, the real concerns of
our members on what is a highly controversial move that will have real ramifications for family businesses in the plant-hire sector. At the very least, we are calling for a full consultation on the Treasury’s plans and what alternatives might be looked at. The announcement in the Budget came without warning and threatens to undermine confidence in the future viability of many long-established firms operating in our sector.
In addition, the CPA will be taking part in the Spending Review scheduled for later this year, as well as looking to work with the opposition and the newly elected Business and Trade Select Committee, and Treasury Select Committee to press our concerns further.
The CPA continues to work with colleagues as part of the Abnormal Loads Working Group, highlighting to policy makers, police constabularies and stakeholders on the need for consistency and flexibility in policing abnormal loads, as well as reform towards embargo times. It is over 18 months since we first received reports that the movement of construction equipment was being unfairly targeted by certain police forces. Since then, we have met with representatives from the police, including regional Police Chiefs, and Deputy Prime Minister Angela Raynor to highlight these concerns further, stressing the need for action and reform.
We have also written to the Secretary of State for Business and Trade, the Home Secretary and the Secretary of State for Transport. Following correspondence with the Business Secretary Jonathan Reynolds, the Department for Business agreed with our calls for a cross government approach with officials from both Business and Transport departments, working together on the abnormal loads issue. In addition, on behalf directly of affected members, we have written to MPs representing affected constituencies, calling directly for action and highlighting the issue.
Following this work, we are now waiting for the National Police Chiefs’ Council updated review into abnormal loads guidance to be published at some point in the first quarter of 2025. We are hopeful this leads to greater consistency and flexibility from constabularies that allows plant-hire equipment to be moved across the country, in line with previous protocols.
• 25 years’ experience with Volvo Dump-Trucks
• Selected-used or refurbished parts
• All models catered for
• Big savings • Engine and transmission rebuilds
• Maintenance and repairs
• Export enquiries welcome
• Your choice of Swedish quality SLP or genuine OEM
As we close the chapter on 2024, we can look back on another year of growth and impressive achievements across BTE Plant Sales. Our dedication to delivering excellence has allowed us to solidify our position as a trusted partner within the construction industry. From groundbreaking deals to supporting our customers’ goals, 2024 has been a year of new beginnings, growth and strengthened relationships.
We are committed to growing our departments to ensure we deliver the very best customer service. We have grown our Parts and Service departments and increased our numbers of engineers both on the road and in the workshop. We understand the importance of having a skilled team to our customers, ensuring machine downtime is kept to a minimum. Our partnerships with our manufacturers continue to grow and as we look ahead to 2025 we are excited to keep the momentum going to elevate our industry presence. From new product releases and expanding product ranges to innovative technologies, we work with the very best brands that keep us at the forefront of the industry. Working closely with Kubota,
Thwaites, Bomag, Atlas Copco and Eprioc is essential for keeping our customers up to date with all the latest.
The calendar for 2025 is already shaping up to be a busy one, with key appearances at major events including the Executive Hire Show, Plantworx, and the much-anticipated BAUMA in Munich. These events are not just an opportunity to showcase our manufacturers’ latest offerings but also a chance to engage directly with the people who power this industry. We’re looking forward to connecting, learning, and sharing ideas, working together to make great things happen.
As ever, our focus will remain on building upon our teams and delivering outstanding service. Whether through ensuring timely turnarounds and in-stock machines, offering expert advice, or introducing you to innovative solutions, we are here to support our customers every step of the way.
Here’s to another year of keeping your projects on track and your fleets in top condition. From all of us at BTE Plant Sales, thanks for trusting us with your heavy lifting in 2024. Let’s dig in and make 2025 even bigger and better, together.
Founded by David Short after his Army National Service, Shorts Group has grown from timber and land clearing into a leader in demolition, waste management, and complementary services. With over 68 years of expertise, we provide a comprehensive range of services, including Demolition Contracting, Waste Management, Skip and Plant Hire, Bagged Materials, and Agricultural Contracting. Guided by our family values and dedication to customer satisfaction, we deliver professional, sustainable solutions tailored to meet the unique needs of every client.
Our Demolition Contracting service stands out for its precision, safety, and innovation. From small-scale projects to large-site clearances, we provide reliable solutions customised to meet your requirements. Fully insured and accredited with industry-related schemes, we uphold the highest safety standards on every project.
A prime example is our Norwich demolition project, where our team combined advanced machinery with innovative solutions like demolition curtains and environmental monitoring stations. Maintaining effective communication with neighbours and recycling up to 98% of materials ensured minimal disruption and maximum sustainability.
Our innovative closed-loop business model integrates all services under one roof, fostering seamless collaboration and efficiency. By relying on in-house capabilities, we maintain strict quality control, reduce costs, and deliver eco-conscious solutions.
Supporting these core services, our Skip Hire and Plant Hire divisions ensure every project is equipped for success. Whether it’s compact skips and machinery for residential needs or heavy-duty equipment for industrial-scale operations, we provide the right resources for every job.
Sustainability is embedded in every aspect of our operations. Recycling is at the core of our approach, with a zerolandfill commitment ensuring waste is repurposed wherever possible. Our in-house Waste Management expertise enables the efficient handling of materials, focusing on repurposing, recycling, and recovering resources to minimise environmental impact.
Family values define our company culture and the way we work. We take the time to understand your needs, offering tailored advice and transparent communication at every step. For us, you’re not just another project—you’re a partner. Operating across Berkshire, Hampshire, Surrey, and surrounding counties, we combine this personalised approach with a strong commitment to sustainability, delivering exceptional results while contributing to a cleaner, greener future.
Ben Hirst, director and founder of Horizon Platforms, delivered a compelling presentation at IPAF’s Elevation UK event. In his talk, Hirst expressed his deep commitment to the powered access industry and emphasised the transformative potential of storytelling to improve safety and drive meaningful change.
Discussing his motivation to share his story, Hirst said: “I took inspiration from IPAF president Karel Huijser when, during his inaugural speech at the IPAF Summit in Copenhagen, he spoke about the power of storytelling. His message stuck with me.
“When we tell a story that’s rooted in a real-life event, we let listeners into that moment. We feel the atmosphere, we gain a deeper understanding of how things occurred.
“Stories truly create lasting memories, deliver valuable lessons, and, most importantly, spark change. That’s what we are hoping to achieve with the #ShareYourStory campaign.”
In his Elevation presentation, Hirst shared a personal and eye-opening account from his time leading Horizon Platforms. His story, now central to IPAF’s #ShareYourStory campaign, serves as a vivid reminder of how real-world experiences can enhance training, raise safety awareness, and ultimately save lives.
Hirst recounted an incident that occurred on a brisk morning at Horizon’s facility in West Yorkshire. At 5:15 a.m., a driver team was preparing a 26-tonne vehicle for delivery to Manchester. Despite following recognised good practices at the start of the job, a critical lapse occurred when a JLG Power Tower lift, weighing more than 340kg, was incorrectly loaded onto the vehicle.
The winch was detached prematurely, leaving the lift unsecured and relying solely on the pedestrian brake to hold it in place. However, the pedestrian brake failed to hold, causing the PAV to slide down the ramp and fall over, narrowly missing staff involved in the loading process.
Had the lift collided with anyone at the base of the ramp, the consequences could have been catastrophic. Thankfully, no one was injured, but the incident serves as a stark reminder of how easily accidents can happen when loading or unloading Mobile Elevating Work Platforms (MEWPs).
Hirst explained: “What we don’t see from the footage [of the incident] is that the platform was reloaded without proper inspection by a qualified engineer, and the driver headed off to site.
“It was only after another driver, who was feeling increasingly uncomfortable, reported his concerns to the transport manager that the delivery was thankfully stopped before the machine reached its destination. This prevented a potential chain reaction of negative events.”
While this incident did not result in a tragedy, Hirst highlighted the opportunity it presents for the industry: “I believe we can make a real shift in the culture of our industry – a shift towards transparency, storytelling, and learning from situations when things did not go so well.”
Hirst’s story is now part of an animated video analysis, created by IPAF, that illustrates what went wrong and what should have been done differently. The video breaks down the incident and demonstrates how storytelling can turn mistakes into valuable lessons for the entire industry.
Hirst hopes this approach will encourage a culture of shared learning and transparency, inspiring industry professionals to reflect on their own experiences and contribute to a growing knowledge base that prevents future accidents.
Hirst’s story is just one of many that could inspire safety improvements across the powered access industry.
IPAF’s #ShareYourStory campaign invites professionals to share their own experiences – whether incidents, near-misses, or lessons learned. By contributing, you play a crucial role in
Through storytelling, the powered access industry can promote greater transparency and collaboration.
creating impactful safety and training materials that resonate globally.
To share your story, visit IPAF’s #ShareYourStory page and provide details about your experience and the lessons learned. Your contribution could become the foundation for the next critical safety resource.
Alternatively, visit IPAF’s Accident Reporting Portal to anonymously report and monitor incidents involving powered access equipment, including MEWPs, MCWPs, and construction hoists (CHs).
Hirst’s message is clear: safety is not just about regulations and training; it is about culture, communication, and understanding the daily pressures workers face. Through storytelling, the powered access industry can promote greater transparency and collaboration.
Thank you to Horizon Platforms for sharing their incident and allowing others in the industry to learn from their experience.
Let’s work together to shape the future of our industry. By sharing your story, watching the incident breakdown video, and applying the lessons learned, we can prevent the accidents of tomorrow.
If you have a story that could help improve safety in the powered access industry, visit www.ipaf.org/ shareyourstory
Your story matters. Together, we can build a safer powered access industry for everyone. #ShareYourStory
The International Powered Access Federation (IPAF) has published its Global Safety Report, now available in a digitalonly format (Visit: ipaf.org/gsr2024). Designed to offer valuable insights into safety trends and practices within the powered access industry, the report is a key resource for professionals dedicated to improving workplace safety.
This comprehensive report is aimed at a wide range of industry professionals, including:
● Health and Safety Managers
● Construction Industry Professionals
● Equipment Manufacturers and Distributors
● Powered Access Equipment Operators
● Rental Companies
● Safety Consultants and Trainers
● Regulatory Authorities and Government Agencies
● Facility and Site Managers
The IPAF Global Safety Report provides a detailed analysis of incident data, offering valuable insights into industry sectors, machine categories, and incident trends. While the report highlights a decrease in overall Fatal and Major incident reports, it also underscores the need for continued vigilance in addressing persistent safety challenges, particularly in high-risk sectors such as construction.
The construction industry remains the most affected, accounting for a significant percentage of reported incidents. The data also highlights key geographical areas for incident reports, including the United States, the UK, and the Republic of Korea.
The IPAF Global Safety Report serves as a vital tool for driving improvement across the powered access industry. It reflects the collective effort of industry professionals, safety experts, and contributors who report incidents through the IPAF Accident Reporting Portal.
Alana Paterson, Chair of the IPAF International Safety Committee, noted: “Powered access remains one of the safest ways to work at height. However, serious incidents still occur, and it is vital that we learn from them. The insights shared in this report are invaluable for improving practices and preventing future accidents.”
Brian Parker, IPAF’s Head of Safety and Technical, added: “The move to a digitalonly format makes this important resource accessible to a wider audience while supporting sustainability goals. The insights in this report are a direct result of industry collaboration, and we encourage everyone to use this information to drive safety improvements.”
The IPAF Global Safety Report is a must-read for anyone working in or with the powered access industry. By engaging with the insights and trends detailed in the report, professionals can make informed decisions to enhance safety and reduce incidents across all sectors.
To access the IPAF Global Safety Report, visit:
ipaf.org/gsr2024
The shortlist for the 2025 International Awards for Powered Access (IAPAs) can be revealed following a meeting of the five expert judges last week.
With more than 140 entries for the 2025 edition, almost a record, The International Awards for Powered Access (IAPAs) has established itself as one of the world’s most anticipated access industry events.
Taking place in Dublin on 13 March, the IAPAs celebrate excellence and best practice in the access sector and are organised by IPAF and Access International.
There are 13 award categories ranging from new products and innovations to sustainability and safety, alongside equality and diversity in the workplace.
The IAPA ceremony takes place on the same day as the IPAF Summit, offering top level presentations and topical industry discussion, along with outstanding networking opportunities across both events.
The organisers would like to thank the independent judging panel of five longstanding industry experts for all their efforts in considering all the entries.
For more information about the awards and the IPAF Summit, visit: www.iapa-summit.info
Access Rental Company of the Year
GTAccess
KDM Hire
Mills
Sunbelt Rentals
Contribution to Safe Working at Height
Electroelsa - Integrated Bolts Presence Detector
Nationwide Platforms - Hinkley Point C
Niftylift - Safety technologies
Rapid Access - Stop Work Authority
Sunbelt Rentals - Safety initiatives
The Sustainability Award
Aver Asia - 3 pronged approach
Mills - B Corp certification
Tecnogera - Battery reuse
Dingli - Sustainable development strategy
Digital Development Award
AFI Rentals - Resource planner
Capja - CapjaDocs
PartnerLift - MIRA
Sunbelt Rentals - Apps
Equality, Diversity & Inclusion (EDI)
AMMEC Comercial
Dayim Equipment Rental
Mills
IAPA Innovative Technology Prize
Modern Access & Scaffolding - sMart Xensor
Niftylift - ClipOn
Ruthmann - T 1000 HF
Tecnogera - Batmov
Zoomlion - ZT51JEH
IPAF Training Centre of the Year
Mills
HSS Training
Industry Training Services
IPAF Training Instructor of the Year
Enda Geoghan - Lift Hire Ireland
Gonçalo Pereira - Transgrua
John McNeilly - HSS Training
Shaikha Mahfoudh - Dayim Equipment Rental
Product of the Year - Mast climbers/ Hoists
Electroelsa - PM-M56
Geda - ZZP F
Maber Hoist - MBC50
Product of the Year – Scissor Lifts & Vertical Masts
Easy Lift - EASYBB001
Haulotte - HS18 E MAX
MEC - 3232SE
Skyjack - SJ3219 Micro
Product of the Year – Self Propelled
Booms & Atrium Lifts
Dingli - BA44ERT
Haulotte - HA16 E (and E PRO)
Leguan Lifts - Leguan 265
Niftylift - HR22 SE (All-Electric Stickboom)
Skyjack - SJ60 AJE +
Product of the Year – Vehicle/trailer mounted
Aldercote - Jack-less Transit Conversion
Dinolift - Dino 120TLB
Ruthmann - T 380 XS
Ruthmann - T 1000 HF
Sinoboom - GKS32EL
IPAF/Access International Lifetime Achievement Award:
To be announced at the ceremony.
By extending the life of a Volvo L350F wheeled loader, Heidelberg Materials UK and SMT are demonstrating the power of collaboration and the circular economy in reducing carbon emissions and waste. Heidelberg Materials UK is one of the UK’s largest suppliers of building materials, including cement – a product responsible for approximately 7% of all global CO2 emissions. As a result, the company is keenly aware of the environmental impact of its operations and has set ambitious goals to reduce emissions by 15% from a 2019 baseline by 2030.
An ideal future fleet for Heidelberg Materials UK would consist entirely of zero-emission machines powered by electricity or hydrogen generated from renewable sources.
Elliot Wellbelove, carbon innovation manager at Heidelberg Materials UK
However, transitioning to these technologies requires the development of considerable supporting infrastructures. In addition, many of the company’s diesel machines are highly durable and have years of service life remaining.
To bridge the gap, Heidelberg Materials UK collaborated with Volvo dealer SMT to refurbish an older wheeled loader. This avoids the purchase of a new diesel machine that would run for many years to come, as well as the emissions and material consumption associated with its manufacture and transportation. Rebuilding older machines also offers faster delivery times and smoother operations due to the existing machine’s known history.
“Rebuilding existing machines is a sustainable practice,” says Dominie Carver, a strategic account manager at SMT. “Rebuilds can extend machine life, recycle major components and significantly reduce carbon emissions. Refurbishing a used engine for continued use, for example, can save around 56% in CO₂ emissions, and a transmission of about 60%.”
To explore the potential of equipment rebuilds, Heidelberg Materials UK and SMT selected a 14-year-old Volvo L350F wheeled loader used to load limestone into crushers at the Ribblesdale cement works in Clitheroe. Despite the 21,341 operating hours on the clock, the machine’s condition indicated that it could continue to operate reliably and productively with necessary repairs and upgrades.
The SMT rebuild process typically takes around 12 weeks, with machines selected based on national guidelines, service history, oil samples and component ageing. It also uses genuine Volvo parts, meaning that the machine is covered by a 24-month warranty on major components, offering Heidelberg Materials UK peace of mind with no additional costs for potential issues.
This collaboration underscores the importance of sustainability and innovation in the construction equipment industry and the successful rebuild of the L350F is a testament to the strides Heidelberg Materials UK and SMT are making towards decarbonisation, greater circularity, and improved operational efficiency.
“Collaboration with suppliers such as SMT is crucial for achieving Heidelberg Materials UK’s sustainability goals,” says Elliot Wellbelove, carbon innovation manager at Heidelberg Materials UK. “We can rely on SMT to provide emissions reduction data for rebuilt machines, which is essential for calculating environmental benefits and integrating them into our data systems.”
This regeneration effort is a crucial step in the transition toward a carbon-free industry and exemplifies how strategic collaboration can lead to impactful environmental benefits, without compromising productivity or quality.
SMT is constantly developing solutions that work to support our customers on their journey towards net
We believe in a sustainable future and we want to work together with our customers to explore new possibilities and technologies to drive change for a better tomorrow.
Start your journey towards net zero with SMT today.