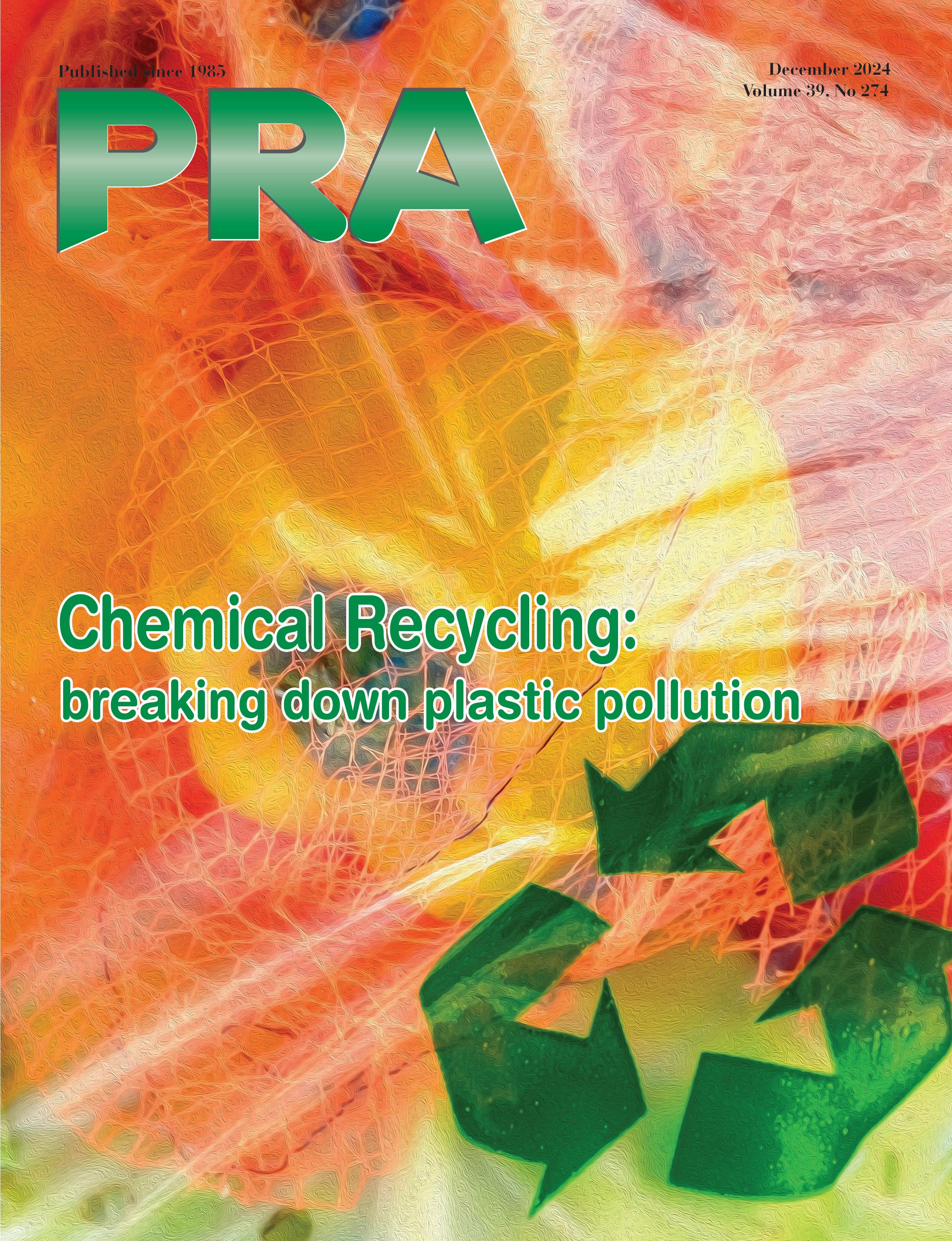
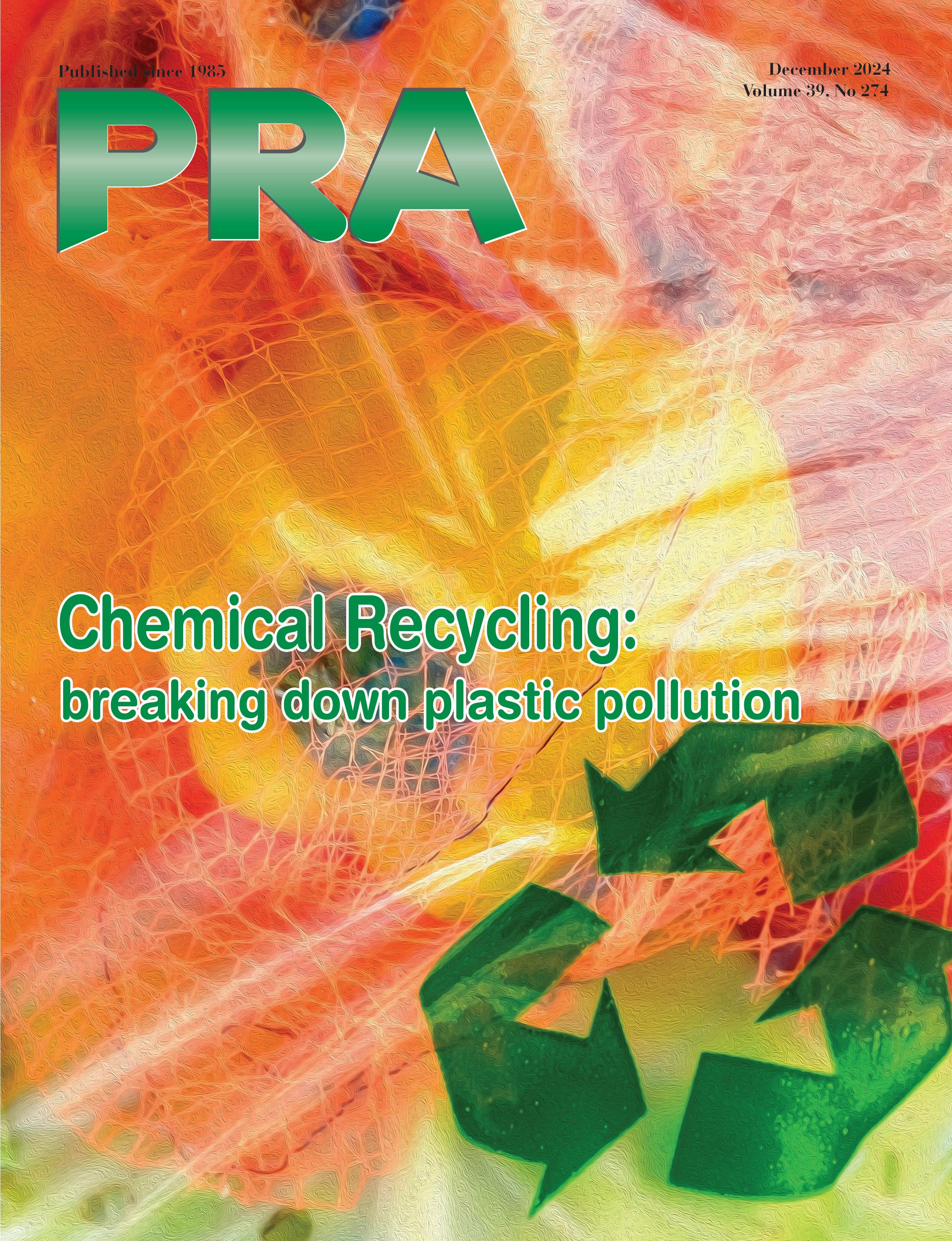
In this issue

Features
9 Chemicals Sector – The momentum is building up in the zero-tolow carbon chemicals and plastics space with many different pathways for production that will allow for the reduction of carbon footprints, says Joseph Chang, Global Editor, ICIS Chemical Business.
11 Recycling – Though chemical recycling is still a work-in-progress solution for plastic waste, with its environmental and economic viability largely debatable, there is growing market interest and innovations are being introduced.
14 Packaging – ExxonMobil has collaborated with key partners to develop fully recyclable thermoformed packaging featuring 95% PE content; and also with Chinese converter Huangshan Novel to produce stand-up-pouches made of MDO PE//PE laminate film, for easy recyclability.
15 Packaging – It has been found that food waste contributes to carbon emissions; thus sustainable packaging solutions appear to be an effective way to reduce this environmental impact.
Regulars
1 Industry News 6 Materials News supplements

Taiwan country Focus: Taiwan is emerging as Asia's catalyst for manufacturing innovation, especially in the plastics sector, as concluded from the recent Taipeiplas show, held in Taipei in September.
Tyre: With environmental issues increasing over rising carbon emissions, the rubber/tyre sector is stepping up speed in the tyre recycling arena and roll out of sustainable materials/ compounds for rubber.
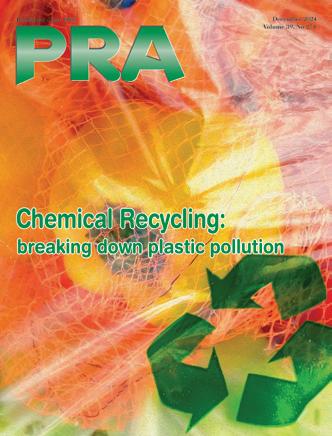


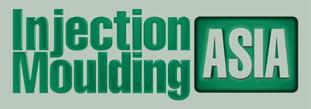
publisher/editor-in-chief
Arthur Schavemaker
Tel: +31 547 275005
Email: arthur@kenter.nl
Associate publisher/executive editor
Tej Fernandez
Tel: +6017 884 9102
Email: tej@plasticsandrubberasia.com
senior editor
Angelica Buan
Email: gel@plasticsandrubberasia.com
circulation
Stephanie Yuen
Email: stephanie@taramedia.com.my
layout/design
Prestige Trading
Email: prestige9a@gmail.com
permits
ISSN 1360-1245
is published 4 (four) times a year in English by Kenter & Co Publishers’ representatives BV.
Whilst every effort is made to ensure that the information contained in this publication is correct, the publisher makes no warranty, expressed or implied, as to the nature or accuracy of such material to the extent permitted by applicable law.
© 2024 Kenter & Co Publishers’ representatives BV No part of this publication may be reproduced, stored or used in any form, or by any means, without specific prior permission from the publisher.
PrA is a digital publication that is circulated free to trade readers in the plastics and rubber industry. Please view this link to subscribe/renew your free subscription: http://plasticsandrubberasia.com/register.html
www.plasticsandrubberasia.com www.rubberjournalasia.com www.injectionmouldingasia.com www.eog-asia.com
M&As/Tie-ups/ Investments
• German materials firm Covestro’s management and supervisory boards support Abu Dhabi National Oil Company (Adnoc)’s US$16.3 billion takeover offer. Closing of the transaction not expected before second half of 2025. Meanwhile, Covestro is investing around EUR100 million in its global R&D infrastructure and assets, over a timeframe of three years until 2025.
• Swedish materials firm Hexpol has acquired 80% shares in Piedmont Resin Supply, a US-based nylon compounder for US$86 million, funded by a combination of bank facilities and cash.
• Specialty chemicals company Lanxess is selling its Urethane Systems business to Japanese firm Ube Corporation with expected proceeds of around EUR500 million. The business comprises five manufacturing sites globally as well as application laboratories in the US, Europe and China; 400 employees and sales of around EUR250 million the last 12 months June 2024.
• Investment company AP Moller Holding
has launched a new company Vioneo that will manufacture fossil-free PE/ PP in Belgium, using proprietary technology that uses methanol as a feedstock. Commercial production could start in 2028, subject to offtake agreements, EU regulatory changes and lower energy costs.
• India’s Sudarshan Chemical Industries Limited (SCIL) has tied up with Germany-based Heubach Group, on its acquisition in a combination of an asset and share deal, to create a global pigments company. Terms were not disclosed.
• German chemical firm Evonik is reorganising two business lines: Coating & Adhesive Resins and Health Care with the remaining businesses outside these cores to be sold off or incorporated into partnerships, or discontinued Businesses affected by these changes generate sales of EUR350 million. In March, Evonik had announced up to 2,000 job cuts, mainly in Germany, by 2026 to reduce costs by EUR400
million annually. Coating & Adhesive Resins will focus on liquid polybutadienes as additives for
Plant Closures
• US material firm Dow is conducting a strategic review of European PU assets and intends to shut down a 550,000tonne/year propylene oxide (PO) unit at Freeport, Texas, in 2025, about 20% of the industry's capacity in North America.
• Italian energy firm Eni plans to shutter two ethylene crackers, in Brindisi and Priolo Gargallo, as part of an overhaul of its struggling Versalis chemical business. The business has lost US$3.2 billion over the past five years. The Brindisi cracker has 440,000 tonnes/ year of ethylene capacity; Priolo has 530,000 tonnes/year.
• Styrenics maker Ineos Styrolution will not restart its styrene monomer production site in Sarnia, Ontario, which has been shut down since April 2024, due to orders from regulatory authorities that forced the site to declare force majeure.
• Chemical firm Ineos is permanently closing its ABS production site in Ohio, US, due to overseas competition, by the
adhesives and sealants or tyres, and specialty acrylics for the medical and packaging industry.
second quarter of 2025.
• US-based additives firm SI Group is closing its alkylphenol manufacturing facility on Jurong Island in Singapore in the second half of 2025, due to high costs.
• Belgian chemical firm Solvay will cease the production of trifluoroacetic acid (TFA) and its fluorinated derivatives at its Salindres site in France. Both are organic compounds classified as PFAS according to the OECD definition.
• Japan’s Sumitomo Chemical Co has closed two of the three production lines for methyl methacrylate (MMA) monomer and polymethyl methacrylate (PMMA) at its whollyowned subsidiary Sumitomo Chemical Asia Pte Ltd in Singapore. This will result in 80% reduction in MMA monomer production capacity and 70% reduction in PMMA production capacity at the location.
Plant Expansions/Openings
• Speciality chemical firm Lygos is partnering with fermentation and biotechnology firm CJ Bio to build a facility in Fort Dodge, Iowa, US, that will produce 40,000 tonnes/year of biodegradable polyaspartates and biobased malonates from aspartic acid and malonic acid.
• Chemical firm LyondellBasell ( LYB ) is investing in a new closed-loop preparation centre in Lich, Germany, transforming plastic waste into feedstock.
• Canadian injection moulding solutions provider StackTeck Systems Ltd has made “significant” investment in its North American PET preform testing capabilities, having installed a Swiss Netstal PET-LINE 5000 system, integrated with a dryer from Italian auxiliary firm Piovan
• Japan’s Mitsui Chemicals ’ South Korean affiliate Kumho Mitsui Chemicals Inc . has commenced operations at additional production facilities for MDI, producing 200,000 tonnes/year, increasing the total capacity to 610,000 tonnes/year.
• Stahl , a supplier of speciality coatings for flexible materials, has opened a new facility for the manufacturing of polyurethane dispersions (PUD) in Singapore.
• Sumitomo Bakelite Co ’s group company in China has completed the construction of a US$40 million plant for epoxy resin moulding compounds for encapsulation of semiconductor devices.
• China Energy Group Ningxia Coal Industry Co has selected LyondellBasell’s Hostalen Advanced Cascade Process (Hostalen ACP) technology for a 300 kilotonnes/year HDPE plant in Yinchuan City, Ningxia Hui Autonomous region, China.
• German/Malaysian joint venture firm BASF PETRONAS Chemicals has inaugurated its second 2-ethylhexanoic acid (2-EHAcid) production line at the integrated site in Kuantan, Malaysia, doubling the annual production capacity to 60,000 tonnes. In other news, BASF is expanding its Neopor
insulation materials production capacity at its Ludwigshafen, Germany, site by 50,000 tonnes/year by 2027.
BASF also inaugurated a new world-scale alkyl ethanolamines production plant in Antwerp, Belgium, upping capacity by nearly 30% to over 140,000 tonnes/year.
• Packaging/recycling firm Alpla is opening a EUR60 million plant in Ballito, South Africa, to produce up to 35,000 tonnes/year of rPET.
• US-headquartered PP process technology provider WR Grace & Co ( Grace ) partnered with Nayara Energy Limited for a 450 kilotonnes/year Unipol PP plant in Vadinar, Gujarat, India. This facility uses Grace’s nonphthalate Consista catalysts to produce PP grades suited for applications in the pharmaceutical, health, and hygiene sectors.
• Covestro is constructing a new Thermoplastic Polyurethanes (TPU) APAC application development centre in Guangzhou, South China; it is the second investment for TPU in China with the company already building its largest TPU plant in Zhuhai.
• Italian firm Nextchem , through its subsidiary Conser , has been awarded by Al Baleed Petrochemical Company ( ABP ) the technology licensing, process design package and catalyst supply for a maleic anhydride plant to be located in the Salalah Free Zone, in Oman. The plant is part of a chemical park that ABP is developing for the value chain of LPG, methanol and ammonia and will have a capacity of 50,000 tonnes/year of maleic anhydride, an intermediate used for the production of biodegradable plastics.
• UK-based ECI Group has signed a licensing agreement with Shaanxi Yanchang China Coal Yulin Energy & Chemical Co ( YECC ) to deliver a 150 kilotonnes/ year copolymer plant project, using ECI’s proprietary hybrid reactor technology. The plant will be located in Yangqiaopan, Shaanxi Province.
• Engineering firm Wood has been awarded a threeyear contract to operate and maintain the Freepoint EcoSystems plant in Ohio, US. The pyrolysis-based facility is slated to begin operations by
end of 2024. The flagship facility spans 25 acres, utilising a 260,000 sq ft warehouse, making it one of the largest advanced recycling facilities in the world. This facility will apply advanced pyrolysis recycling technology to convert approximately 90,000 tonnes of end-of-life plastics into a petrochemical feedstock, pyrolysis oil, through a depolymerisation process.
• Indonesia’s PT
Inti Karya Persada Tehnik ( IKPT ), a subsidiary of Toyo Engineering Corp , has been awarded an EPC contract by PT. Nippon Shokubai Indonesia , a subsidiary of Nippon Shokubai Ltd. (Tokyo) to expand its Super Absorbent Polymer (SAP) production plant located in Cilegon, West Java. The SAP production facility will be upgraded with a capacity of 50,000 tonnes/year (totalling 140,000 tonnes/year when combined with the existing capacity of 90,000 tonnes/year).
• Indian PET recycler Srichakra Polyplast has commissioned two new Austrianmade Starlinger plastic recycling lines at its facility
in Hyderabad city, tripling its rPET production capacity to 42,000 tonnes/ year.
• US-based materials firm Blue Polymers ; recycler Republic Services ; and the City of Buckeye in Arizona recently broke ground on Blue Polymers’ latest rPE production facility, which will support sustainable packaging manufacturing throughout the Western US.
• Germany-based optics and speciality materials supplier Schott has completed its new production facility in Kulim, in the state of Kedah, Malaysia. This new site will significantly enhance Schott’s production capacity, complementing the existing facility in Penang, Malaysia, where it has been producing specialty glass for consumer electronics, semiconductors, diagnostics, and other high-tech sectors for 50 years.
• China Petroleum and Chemical Corporation or Sinopec has started up a new ethylene complex inTianjin, northern China. Sinopec began operating a 1.2 million tonnes/year ethylene plant that is
designed to provide 4 million tonnes/year of high-end chemical feedstocks. It brings the total ethylene capacity at Sinopec Tianjin subsidiary to 2.5 million tonnes/ year.
As well, Sinopec, together with Aramco and Fujian Petrochemical Company Limited ( FPCL ), has also broken ground on a new integrated refining and petrochemical complex in Gulei, Fujian, scheduled to start up in 2030. It is planned to have a 16 million tonnes/ year oil refining unit (320,000 barrels per day), a 1.5 million tonnes/year ethylene unit, a 2 million tonnes paraxylene and downstream derivatives capacity, and a 300,000 tonnes crude oil terminal.
• German chemicals firm Evonik has broken ground on its plant expansion for specialty amines in Nanjing, China, catering to the development of the polyurethane and epoxy curing agent markets.
• Speciality materials supplier Trinseo will supply a PC technology license as well as all proprietary PC production equipment in Stade, Germany, to a wholly owned subsidiary of Deepak
Nitrite Limited for use in India. The total value of the combined agreements is US$52.5 million.
• Germany-based PET recycling firm Revalyu Resources , which is owned by German technology group Heraeus , has commissioned its second PET recycling plant at its site in Nashik, India, to recycle over 20 million/day used PET bottles into 350,000 pounds/day of PET chips and PET polymer.
• US specialty chemicals firm Lubrizol and fluid conveyance system firm Polyhose are to set up a medical tubing site in Tamil Nadu, India, to increase Lubrizol’s local volume five-fold. Groundbreaking is expected in 2025 with operations going live in 2026.
• Chemical firm Sabic has launched its new US$170 million Ultem resin manufacturing facility in Singapore, marking the company’s first specialty chemical facility in the region. Though it did not specify the capacity, the firm says it will support its goal of increasing global Ultem production by more than 50%.
Reasons Why You Shouldn’t Miss CHINAPLAS’s Return to the Greater Bay Area: A Treasure Trove of Business Opportunities
CHINAPLAS 2024, which concluded successfully in Shanghai in April 2024, wrote a brilliant chapter of boundless innovation. The show will set sail once again towards the vibrant Guangdong-Hong Kong-Macao Greater Bay Area (GBA), where it is full of business opportunities. CHINAPLAS 2025 is scheduled to take place on April 15-18, 2025, at the Shenzhen World Exhibition and Convention Center (Bao'an), Shenzhen, PR China, with a total exhibition area of over 380,000 sqm. It is ready to receive more than 3,900 exhibitors from around the world.
"We have set 'Transformation, Collaboration, Sustainability' as the theme of CHINAPLAS 2025," said Ms. Ada Leung, General Manager of Adsale Exhibition Services Ltd., the organiser of CHINAPLAS. "Given the current complex international situation and the uncertainty in the global economy, industrial transformation is accelerating and evolving. As the leading high-tech platform for plastics and rubber industries in Asia, CHINAPLAS spares no efforts to gather the tremendous strength of the industries, promote enhanced communication and collaboration along the upstream and downstream industry chains, drive the industry's transformation and upgrading towards highend, intelligent, and green development, and jointly create a bright blueprint for the sustainable development of the industry."
Capture the unique value of CHINAPLAS. An industry feast in the GBA not to be missed.
As a high-tech platform covering the entire supply chain, CHINAPLAS spans every aspect of different application industries and product lifecycles. It actively presents comprehensive solutions in the field of plastics and rubber. Thousands of machines will be simultaneously showcased and demonstrated on-site, showcasing “New Productive Forces” and highlighting the show's unique value and leading
position in the industry. High-quality buyers and exhibitors will engage in face-to-face discussions on innovative technologies, explore collaborations and sign contracts, experiencing the surge of business opportunities and regaining confidence in development. The mega annual event alternates between Shenzhen and Shanghai every year. This time, returning to the GBA will bring together industrial elites and international visitors, promising an industry feast that should not be missed.
With the effectiveness of exhibiting at CHINAPLAS, booth reservations are in high demand.
According to a survey conducted by the organiser, 97% of exhibitors expressed satisfaction ranging from good to excellent with their participation at CHINAPLAS 2024. From the exhibitors' perspective, the top three benefits derived from the exhibition were: successful exploration of potential customers, the opportunity to meet buyers in person, and successful establishment of company/product image. Currently, booth reservations are in high demand, demonstrating a more enthusiastic response compared to previous years, with exhibitors swiftly confirming their booths. This not only indicates the strong market demand and the extraordinary appeal of CHINAPLAS but also reflects the vast confidence of participating companies in the Chinese market and the global plastics and rubber industries.
The Asian economy continues its moderate recovery trend, releasing the goodwill of the Regional Comprehensive Economic Partnership (RCEP).
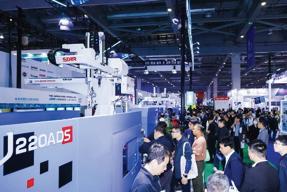
In June 2024, the Purchasing Managers' Index (PMI) for the Asian manufacturing sector stood at 51.1%, unchanged from the previous month. It has remained above 51% for four consecutive months, indicating a sustained moderate recovery trend in the Asian economy. Asia continues to act as the locomotive and power source of global economic growth. Meanwhile, China's foreign trade performance has exceeded expectations. In the first half of 2024, the total value of China's goods trade imports and exports reached RMB 21.17 trillion (up 6.1% by year). The RCEP celebrated its one-year anniversary of full implementation, marking a new milestone in regional open cooperation. In 2023, China's total imports and exports with the other 14 signatories
amounted to RMB 12.6 trillion, representing a 5.3% growth compared to the year before the agreement took effect in 2021. The liberalisation brought about by the RCEP is anticipated to fuel even greater growth in the coming decade, opening up vast opportunities for the plastics and rubber industries.
Emerging sectors are flourishing to unleash new business opportunities.
The surging data undoubtedly provides the strongest evidence. In the first quarter of 2024, China's newly installed capacity of renewable energy reached 63.67 gigawatts, a year-on-year increase of 34%, accounting for 92% of the newly installed capacity. From January to May, the installed capacity of solar power reached approximately 690 million kilowatts, a year-on-year increase of 52.2%, while the installed capacity of wind power reached approximately 460 million kilowatts, a year-on-year increase of 20.5%. New energy vehicles have also continued to grow rapidly, with a year-on-year increase of 30.1% and 32% in production and sales respectively in the first half of 2024. 2024 is said to be the "first year of low-altitude economy" in China. Under the vast blue sky, the "lowaltitude economy" is quietly rising and becoming a "new growth engine" for high-quality economic development. Additionally, new opportunities are continuously emerging in fields such as artificial intelligence and humanoid robots, injecting new vitality into economic development.
Vigorously developing "20+8" industrial clusters, the momentum of the plastics and rubber industries in Shenzhen is thriving.
Shenzhen, known as the no. 1 industrial city of China, is fully committed to the growth of 20 strategic emerging industries and 8 future industries, with advanced manufacturing as the main focus. Among them, the industry clusters closely related to polymer materials are particularly noteworthy. These include sectors such as ultra-high-definition video displays, smart terminals, intelligent sensors, new energy, low-altitude economy and aerospace, high-end medical devices, and high-performance materials. The development in these fields is thriving. CHINAPLAS 2025 returns to Shenzhen, the land of innovation with the anticipation of witnessing the vibrant growth of advanced manufacturing in the GBA together with the industries.
Global visitors’ promotion is in full swing to grab the strong demand from overseas buyers for procurement! CHINAPLAS 2024 welcomed a total of 321,879 visitors from 171 countries and regions, including 73,204 visitors from Hong Kong, Macao, Taiwan regions, and overseas, accounting for 22.74% of the total. This proportion has returned to the normal level of CHINAPLAS. At the annual event, overseas buyers arrived with clear procurement plans and specific objectives, praising China's plastics and rubber machinery and materials and demonstrating strong purchasing demand. With the start of the new edition of the show, international buyer promotion work has been fully launched. The global buyer team of the show organiser has
visited various countries and regions, met with chambers of commerce, associations and buyers, engaged in oneon-one in-depth communication and invitations, attended important local events, and actively connected with more overseas visitors through advertising campaigns and roadshows. The exhibition continues to join hands with the CPS+ eMarketplace to promote both online and offline sourcing channels, facilitating continuous supply and demand connection between buyers and suppliers throughout the year, ensuring uninterrupted business matching opportunities. It helps the exhibition accumulate a rich global buyer network and generate substantial sourcing demands.
A 144-hour transit visa exemption covers 54 countries offering favorable conditions for attracting overseas buyers. China continues to embrace the world. Starting from July 1, 2024, China has expanded its "circle of friends" by implementing visa-free policies for ordinary passport holders from three countries: New Zealand, Australia, and Poland. As of now, China has established visa-exemption agreements with 158 countries, covering different types of passports, and achieved comprehensive visa exemption with 24 countries. Furthermore, the scope of the 72/144-hour transit visa exemption policy has expanded to 54 countries, creating more favorable conditions for inviting international visitors to CHINAPLAS 2025.
Shenzhen Airport connects with more international destinations. On May 11, 2024, the direct passenger flight route from Shenzhen to Mexico City was officially launched, setting a new record for the longest direct international passenger flight in Chinese civil aviation. It is also currently the only direct passenger route from Mainland China, Hong Kong, Macao, and Taiwan regions to Mexico, and even to the entire Latin America. Since the beginning of this year, Shenzhen Airport has resumed expansion of international passenger routes to destinations such as Cairo (Egypt), Sapporo (Japan), Nagoya (Japan), Nha Trang (Vietnam), Jeju (South Korea), Mexico City (Mexico), Vienna (Austria), and Riyadh (Saudi Arabia). It continues to increase flight frequencies to countries and regions including Japan, South Korea, and ASEAN. It is believed that CHINAPLAS 2025 will have a wider reach and deeper impact.
"Thanks to the superior business environment and thriving industries in the GBA, along with strong market demand, we have full confidence in CHINAPLAS 2025’s return to Shenzhen. Whether its exhibits, innovative technologies, concurrent events, or on-site services, we believe they will bring unprecedented experiences and value to the industries. You definitely shouldn't miss next year's exhibition!" said Ms. Ada Leung.
The online pre-registration for CHINAPLAS 2025 has started. Go to https://adlnk.cn/edVl9aD to pre-register now for an admission ticket at RMB 50 or US$ 7.5. Pre-registered visitors shall receive their Visitor eBadges (for local visitors) or eConfirmation Letters (for overseas visitors) upon completion of pre-registration.
For more information or enquiries about the show, please visit www.ChinaplasOnline.com or contact Chinaplas.pr@adsale.com.hk.
From waste to resource: global rise of biopolymers
Amongst the emerging materials becoming commercially available, biopolymers offer appealing solutions, providing clear environmental benefits over traditional plastics, according to Angelica Buan in this report.
Industries are increasingly adopting sustainable, biobased materials in response to environmental pressures and strategic business goals. Rising consumer demand for eco-friendly products and stricter plastic waste regulations compel companies to reduce their environmental impact and integrate sustainable practices into their brands.
Biopolymers offer advantages over traditional plastics, such as biodegradability, reduced plastic waste, lower carbon footprint, and improved resource efficiency.
The biopolymers market is growing rapidly, fuelled by demand for alternatives to conventional plastics. It is projected to yield a market size that will grow at a CAGR of 10.4% from 2024, reaching nearly US$39 billion by 2030, according to Grandview Research ’s Biopolymers Market Report. Similarly, estimates from Precedence Research suggest the market could even breach US$90 billion by 2032.
Asian forays into PLA, biopolymers
Global demand for polylactic acid (PLA) materials is rising as efforts to reduce carbon emissions intensify. According to Grandview Research, the global PLA market is projected to grow at a CAGR of 21.4%, reaching nearly US$2.8 billion by 2030. Similarly, Expert Market Research anticipates a CAGR of 15.2% for the APAC region from 2024-2032.
The Asia-Pacific region is witnessing rapid growth in the biopolymer/PLA market, driven by rising consumer awareness, supportive regulations and access to agricultural resources for feedstock.
Key players in the biopolymer industry include Indiaheadquartered Praj Industries that has launched the country’s first demonstration facility for biopolymers, showcasing its proprietary PLA technology.
Praj’s facility represents a bold step for India in bioplastics, emphasising its commitment to biorefineries and sustainable technologies. This facility, part of Praj’s Bio-Prism portfolio, is the first in a series of biopolymer innovations and showcases an advanced production setup across three acres, with capacities of 100 tonnes/year for lactic acid, 60 tonnes/ year for lactide, and 55 tonnes/year for PLA. Equipped with sections for fermentation, chemical synthesis, separation, and purification, it integrates the complete PLA production process.
Aligning with India’s new BioE3 (Biotechnology for Economy, Environment, and Employment) Policy to support a Net Zero carbon economy, Praj’s PLA technology offers

applications in sectors including food, personal care, agriculture, and pharmaceuticals, providing both flexible and rigid product options.
Along the same vein, US-based NatureWorks has gained backing from Thailand’s Krungthai Bank PCL to optimise the capital structure for its new fully-integrated Ingeo brand PLA manufacturing facility in Thailand. The firm is jointly owned by Thailand’s largest integrated petrochemical/refining company PTT Public Company and US-based conglomerate Cargill . The financing from Krungthai Bank, the country’s third largest bank, amounting to US$350 million, is one of the singular largest loans in the bank’s decades-long history.
Erik Ripple, President/CEO of NatureWorks said that the funding will enable NatureWorks to expand its international customer access to fully biobased, low-carbon biomaterials that feature unique performance attributes valued by global downstream packaging and fibre markets.
NatureWorks' second facility will be located at the Nakhon Sawan Biocomplex, which provides access to local feedstock like sugarcane and established infrastructure for processing it into sugar for fermentation. The site also offers the necessary utilities for the plant's operation.
The new 75,000-tonne/year facility will produce the full range of Ingeo biopolymer grades to support rapid
Praj Industries' first biopolymer demonstration facility showcases its proprietary PLA technology, with capacities of 100 tonnes/year for lactic acid, 60 tonnes/year for lactide, and 55 tonnes/year for PLA

NatureWorks has secured US$350 million support from Krungthai Bank to optimise the capital structure for its new 75,000-tonne/ year fully integrated Ingeo brand PLA manufacturing facility in Thailand
growth in AsiaPacific markets, including 3D printing, hygiene nonwovens, compostable coffee capsules, flexible packaging, and food serviceware. Construction is on track and full production is slated for 2025.
Innovation drivers: from materials to machinery
Developing sustainable alternatives opens new market opportunities while future-proofing industries against resource scarcity and rising costs.
German blown film machinery manufacturer Reifenhäuser Blown Film has unveiled the world's first 18-micron MDO PE film, which meets or exceeds all previous market standards for mechanical properties, appearance, and processing. This film has been produced on Reifenhäuser’s EVO blown film lines using patented EVO Ultra Stretch MDO technology and developed in collaboration with South Korean chemical company LG Chem and Swiss machinery supplier Bobst

Reifenhäuser Blown Film has unveiled the world's first 18-micron MDO PE film, produced in collaboration with LG Chem and Bobst
The new film reduces material usage by approximately 25% compared to previous film thicknesses of 25 microns, making the production of fully recyclable mono-material structures significantly more economical.
Christoph Lettowsky, Senior Product Manager at Reifenhäuser Blown Film, stated that machine builders and manufacturers are exploring material usage in fully
recyclable all-PE solutions compared to conventional PET/ PE laminates. By replacing 12 micron PET film with 16–17 micron MDO-PE film, the company says it has achieved a notable reduction, with further potential for downgauging.
Lettowsky added that producers do not have to compromise on optical and mechanical properties despite the reduced thickness. This film achieves a machine-direction modulus of elasticity exceeding 1,400 MPa and a transverse direction modulus exceeding 1,100 MPa, meeting current market standards for stretched PE films. With a haze of less than 5%, it is said to outperform the market standard of 6-7% in optical properties.
In a related development, US-based biotechnology company Danimer Scientific together with Chinese disposable tableware producer Ningbo Homelink EcoiTech Co Ltd have initiated the commercial launch of home compostable extrusion coating biopolymers made with Danimer’s signature Nodax polyhydroxyalkanoate (PHA).
Homelink’s cups are coated with Nodax PHA, which is designed to replace PE and is used as a liquid barrier coating for paper cups.
According to Danimer Scientific’s CEO, Stephen Croskrey, Nodax PHA has been certified as both home and industrial compostable by TÜV Austria and commercially compostable by the Biodegradable Products Institute (BPI).
Thus, the biopolymer can be used to formulate grades that replace a variety of traditional plastic products, particularly those that cannot be or are difficult to recycle.
In 2018, Danimer introduced the first fully biodegradable plastic straw made with Nodax PHA. A study by the University of Georgia assessed the biodegradation of Nodax PHA in comparison to cellulose powder, food waste, plastic pellets, and other materials under both aerobic and anaerobic conditions. The results showed that in suitable waste management environments, Nodax PHA biodegrades at a rate comparable to that of cellulose powder or wood pulp, according the University.
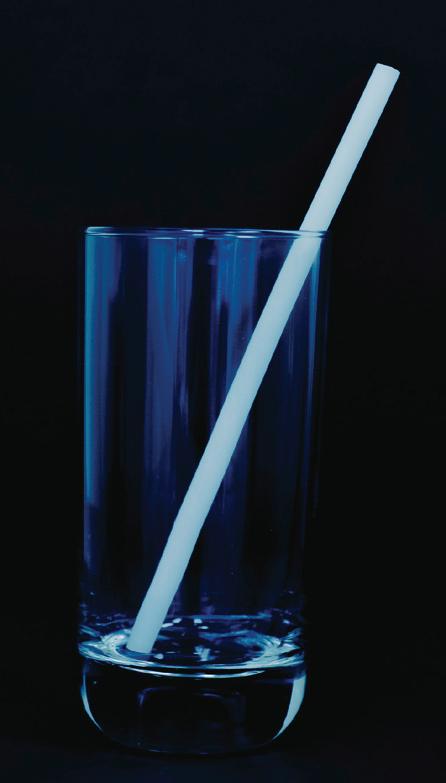
Danimer Scientific's Nodax PHA has been used in Ningbo Homelink Eco-iTech's cups and in the first fully biodegradable plastic straw introduced by Danimer in 2018
Additionally, the study found that Nodax PHA can be processed alongside food and organic waste in landfills. Researchers also observed that Nodax PHA begins to biodegrade within six months in ocean water, while traditional plastics remain unchanged in similar conditions.
PBT and PP: cooking up plastics with discarded oil
The automotive and electronics industries are the largest consumers of polybutylene terephthalate (PBT) compounds.
Asia’s consumer base for PBT is expanding, with Mordor Intelligence forecasting the market to grow from US$3.3 billion in 2024 to US$4.5 billion by 2029, at a CAGR of approximately 6.5%.
China leads in PBT demand, propelled by its automotive sector's push for lightweight materials to improve fuel efficiency and meet environmental standards. Japan and South Korea are also expanding their use of PBT compounds, especially in electronics and semiconductor applications, where lightweight, durable, and heat-resistant materials are critical.
India, home to one of the world’s largest electronics markets, is also set to benefit from advancements in the PBT sector. According to Prismane Consulting’s 2024 PBT market analysis, India’s electronics production, projected to reach US$300 billion by 2026, will further drive PBT demand.
Two prominent advanced materials producers are pushing forward in advancing PBT by repurposing an unlikely ingredient—used cooking oil.
For example, German engineering materials company Envalior offers ISCC Plus-certified Pocan X-MB series of new PBT compounds that utilise bio-circular 1.4-butanediol (BDO), derived from used cooking oil (UCO) as a secondgeneration feedstock, thus avoiding competition with food resources. UCO-derived BDO is chemically and physically identical to fossil-based BDO, says the firm, plus exhibit the same quality, meet identical technical specifications, and comply with certification standards.
Marc Marbach, Global Business Director for PBT at Envalior, stated that these new compounds provide alternatives based on bio-based and/or recycled materials across Envalior’s product portfolio. Besides used cooking oil, other sustainable raw materials are under consideration, such as post-consumer recycled (PCR) materials. Marbach noted that these innovations hold significant potential in standard PBT applications, including connectors, housings, and various structural and functional components.
The base resin of Pocan X-MB contains 26% sustainable materials, with the potential to increase this percentage by combining rPET and recycled glass fibres alongside sustainable BDO. For example, Pocan T3230 RC X-MB achieves a sustainable content of approximately 71%. These new compounds also feature a carbon footprint more than 30% lower than that of comparable standard materials.
Meanwhile, used cooking oil is also a key ingredient in Braskem America's bio-circular PP, used across various applications, including food packaging, flexible films, and consumer goods. The UCO-derived certified bio-circular ISCC Plus mass-balanced PP is marketed under the brand name Wenew. Notably, Braskem says its bio-circular PP equals the properties and performance of traditional PP.
Bill Diebold, Vice President, Braskem America Polyolefins, stated that the bio-circular PP is currently being supplied to various converters, which support the Quick Service Restaurant (QSR) industry. Ideal users include QSR chains, retail food suppliers, traditional restaurants, and snack food companies especially those seeking to enhance circularity from their cooking oil usage.
PHA: biodegradable material from algae
Algae-based biopolymers, sourced from microalgae and macroalgae, include alginate, carrageenan, and agar. Valued for their biodegradability, versatility, and renewability, these materials attract industries seeking sustainable options.
Based on Future Market Insight’s latest audit on algaebased biopolymers market, revenue generated by algaebased bioplastics in 2023 was pegged at US$105 million. Global sales of algae-based bioplastics are anticipated to reach a value of nearly US$176 million by 2034, and sales are projected to rise at a CAGR of 4.8% over the forecast period between 2024 and 2034.
On the other hand, algae-based PE, known for its flexibility and durability, is expected to exceed US$45 million in 2024 and reach US$71 million by the end of 2034. Despite challenges related to costs, scalability, and technical limitations, innovations in algae are expanding applications across packaging, pharmaceuticals, and agricultural films.
Recent studies also suggest that algal biopolymers can be used in energy applications, including separators and polymer electrolytes for batteries and fuel cells, along with microalgal biofuel.
Poised to meet industrial demand for algae-based polymers, the Waste2Plastic project at Umeå University , Sweden’s public research university, has strengthened its capability to produce biodegradable PHA using microalgae. The project received about US$1.4 million from the Swedish Energy Agency and its industrial partners to produce the algal plastic material. The algae are grown in wastewater in Umeå and convert carbon dioxide from flue gases into biomass.
Christiane Funk, Project Manager at the Department of Chemistry, explained that the Waste2Plastic project aims to reduce carbon footprints by using local strains of Nordic microalgae to produce biodegradable plastics. The project involves cultivating algae in industrial and municipal wastewater in Umeå, in collaboration with waste management company Vakin and energy company Umeå Energi.
Funk shared that the project's industrial partners will design lamps and packaging materials from this novel PHA material, and a company in Sundsvall will test its biodegradability.
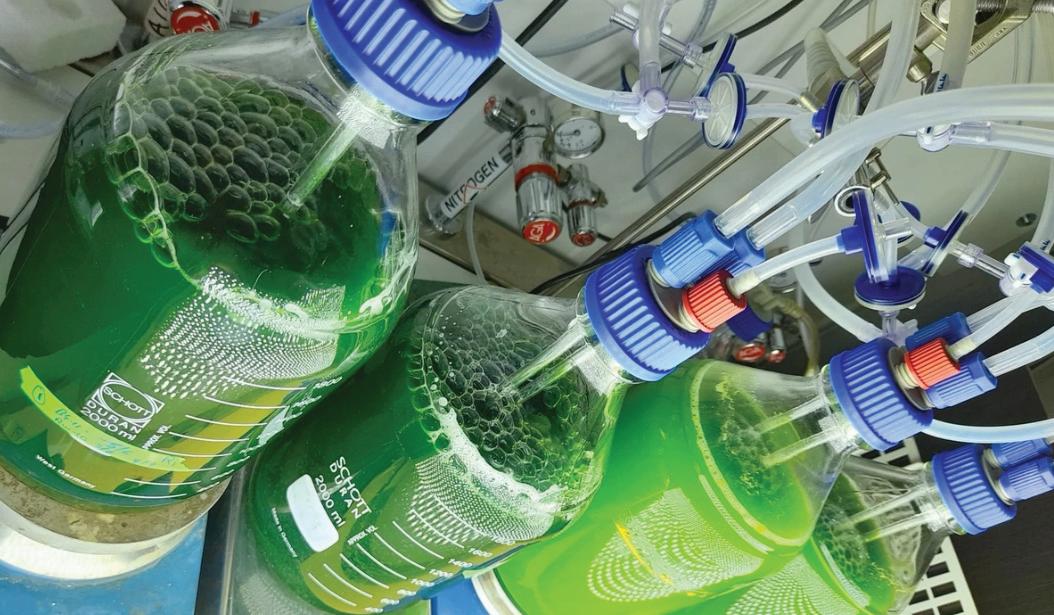
The Waste2Plastic project involves cultivating algae in industrial and municipal wastewater in Umeå, in collaboration with Vakin and Umeå Energi
Decarbonised chemicals, plastics gain momentum with multiple production pathways
by Joseph Chang, Global Editor, ICIS Chemical Business
Momentum is building in the zero-to-low carbon chemicals and plastics space with many different pathways to production that will give customers more options to reduce their carbon footprint.
There’s more than one way to skin a cat, as the English phrase goes. And so for the global decarbonisation challenge, all technologies and processes are on the table – carbon capture and storage (CCS), carbon capture and utilisation (CCU), biogenic CO2, green hydrogen, green methanol, e-naphtha and one day, direct air capture (DAC).
For now, we exclude recycled and bio-based plastics as these processes are already a bit more established.
For many new projects, offtake agreements will be critical, as decarbonisation is neither easy, nor cheap, as US materials firm Dow’s CEO Jim Fitterling has said.
With higher costs, the resulting decarbonised products would have to sell at a premium to conventional material –perhaps a considerable one early on – or be supported by government incentives. Or both.
Launch of Vioneo: fossil-free PP/PE
The latest splash in the pool comes from an industry ‘outsider’ - AP Moller, the parent company of shipping giant Maersk, as it launches Vioneo to “pioneer fossil-free plastics production”.
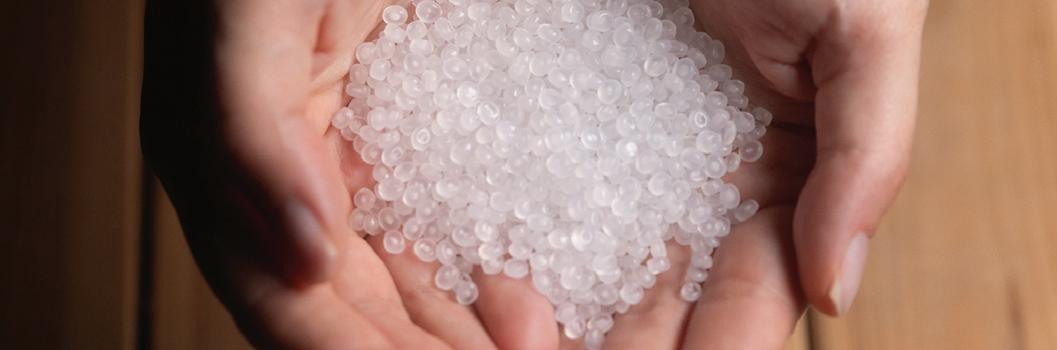
The new company has designed a production process using what it calls an “innovative and proven technology” to produce fossil-free PP and PE at scale, using green methanol as a feedstock.
The EUR1.5 billion project in Antwerp, Belgium, would have capacity of around 300,000 tonnes/year of PP and PE, and could start commercial operations by 2028. Vioneo will start front-end engineering and design (FEED) in Q4 2024 with a potential final investment decision (FID) in 2025.
To make green methanol, Vioneo would use biogenic CO2 and presumably green hydrogen from an electrolyser. Then presumably again, methanol-to-olefins (MTO) would yield propylene and ethylene, which would be polymerised to PP and PE.
The company claims its technology ensures a fully segregated and traceable supply chain, avoiding the mixing of non-certified and certified feedstocks. Production will also be powered by renewable electricity, significantly reducing greenhouse gas (GHG) emissions.
Vioneo said its PP and PP will save up to 6 kg of CO2 per kg of plastic and will be drop-in, virgin quality, suitable for applications across all sectors including medical appliances, home goods, automotive and packaging.
For the planned project to become reality, there are a set of conditions. The equity and debt funding will “depend on broad stakeholder support, including updated regulatory frameworks and policies supporting a competitive environment for fossil-free plastics, as well as better conditions for the European chemicals industry such as lower energy costs”, according to Vioneo.
“Furthermore, the success of the venture requires long-term offtake agreements of its customers,” it added.
The newly launched company said is in advanced discussions with several major global brands, including those in healthcare, automotive, fast moving consumer goods (FMCG), beauty and home products.
Borealis, Infinium to use e-naptha for PPE/PE
Another way to go is using green hydrogen and captured waste CO2 to produce e-naphtha which then can be fed into a conventional naphtha cracker to produce ethylene and propylene, and then PE and PP.
Austria’s Borealis earlier this year announced a partnership to source eNaphtha from eFuels producer Infinium to produce “ultra-low carbon footprint” PE and PP. It already started buying eNaphtha feedstock in Q2 and plans to offer commercial quantities of lowcarbon PE and PP starting in 2025.
Infinium is producing ISCC Plus-certified eNaphtha at its Project Pathfinder facility in Corpus Christi, Texas, US, and commercial eNaphtha volumes are being shipped to Borealis' facility in Porvoo, Finland.
AP Moller has launched Vioneo to pioneer fossil-free production of PP/PE
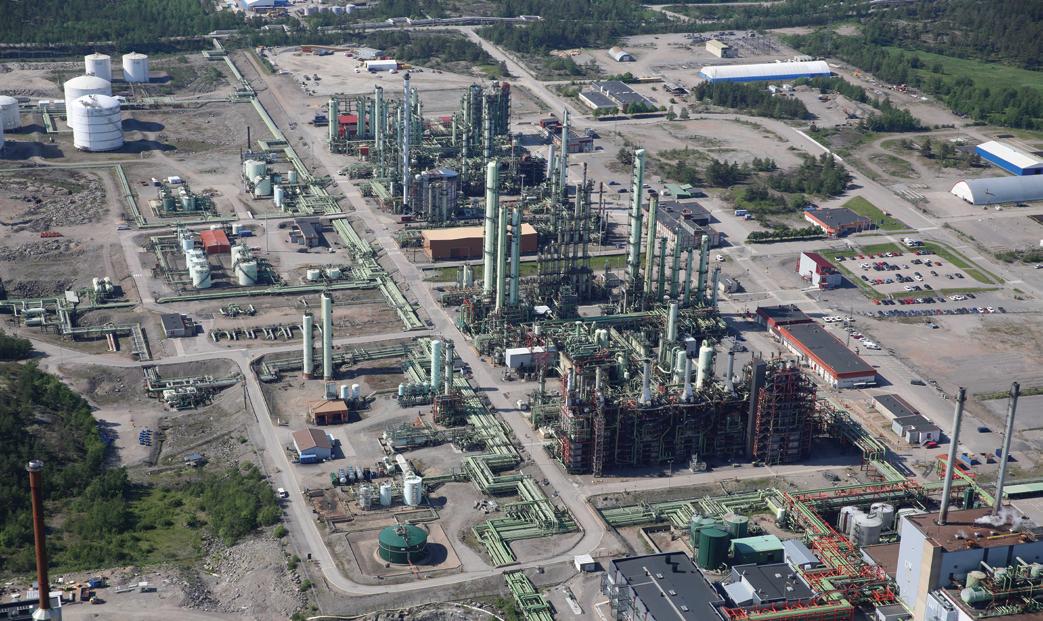
Borealis’ Porvoo cracker has ethylene capacity of 400,000 tonnes/year, and downstream capacities include 102,000 tonnes/year of HDPE, 150,000 tonnes of LDPE, 153,000 tonnes/year of LLDPE and 220,000 tonnes/year of PP.
Infinium’s eNaphtha is made from captured waste CO2 and green hydrogen produced from renewable power. It is said to contain no sulphur and is produced without process emissions, according to the company.
Celanese CCU methanol
Meanwhile, US chemicals firm Celanese is already selling commercial volumes of low-carbon methanol and derivatives in its acetyls chain.
In January 2024, the company announced it started running a carbon capture and utilisation (CCU) project at its Clear Lake, Texas, site as part of its Fairway Methanol joint venture with Mitsui & Co.
The project is expected to capture 180,000 tonnes/ year of CO2 industrial emissions and produce 130,000 tonnes/year of low-carbon methanol.
This low-carbon methanol can then be used to produce vinyl acetate monomer (VAM), vinyl acetate ethylene (VAE) emulsions and other downstream products, she added.
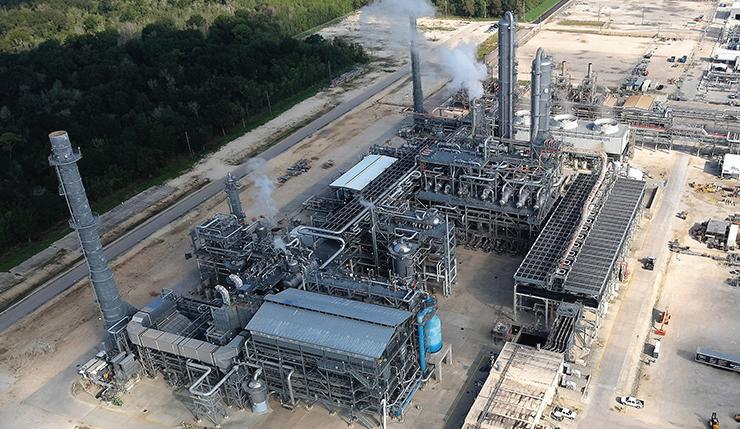
The CCU unit takes CO2 emissions that were otherwise being vented into the atmosphere from both Celanese and from third parties to use as a feedstock.
In March 2024, Celanese announced tha its low carbon CCU methanol has been certified under the ISCC Carbon Footprint Certification (CFC) system.
Low carbon CCU methanol demonstrated a greater than 70% reduction in carbon footprint relative to a global average benchmark for fossil-based methanol production, as included in EU legislation, according to Celanese.
Dow zero carbon cracker: takes the cake
Dow’s net zero carbon cracker project is the granddaddy of them all when it comes to scale.
Already under construction, Phase 1 of its Path2Zero project in Alberta, Canada, is expected to add around 1.3 million tonnes/year of ethylene and PE capacity by 2027. Then Phase 2 adds another 600,000 tonnes/year of net zero ethylene and PE capacity by 2029.
Yet this represents less than 2% of the likely market demand for low-carbon chemicals and plastics, executives said at Dow’s Investor Day in May.
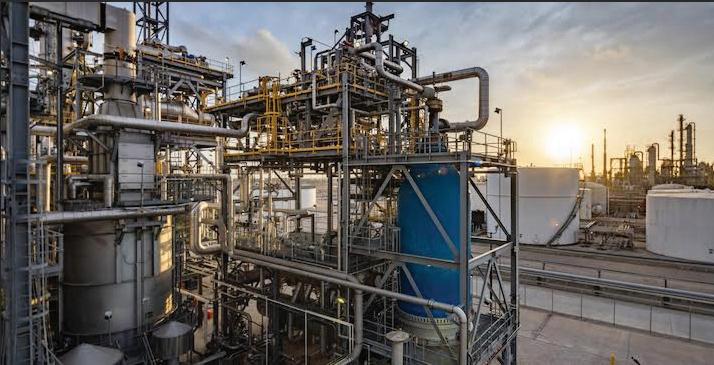
Dow's Path2Zero expansion project in Canada will create what is said to be the world's first net-zero emissions integrated ethylene cracker and derivatives site
At Dow’s Investor Day slides on Low-Emissions Market Opportunities and Supply/Demand Dynamics, the top end of the demand range is around 200 million tonnes by 2030, while the top end of the supply range appears to be around 75 million tonnes by 2030.
“One of the key outcomes has to be the emergence of new markets with their own supply/demand dynamics [and thus pricing] for our products that are analogues to the existing ones we sell – analogues with low-emission footprints,” said Dan Futter, chief commercial officer of Dow, at Dow’s Investor Day.
It’s a brave new world of decarbonised chemicals and plastics. Meaningful quantities will take time to develop but if there is demand, the volumes will come.
Celanese’s Sustainable Solutions portfolio, which includes low-carbon methanol and derivatives along with recycled and bio-based products, represents just around 5% of sales today but is growing double digits on a percentage basis every year, said its CEO.
Chemi C al Se C tor
Infinium and Borealis have partnered to produce low-carbon plastics from waste CO2. Commercial eNaphtha shipments are already underway to Borealis' Porvoo facility in Finland
Early this year, the 50-50 joint venture between Celanese/ Mitsui & Co started production of methanol from CO2 emitted from plants surrounding the facility
Chemical recycling: another formula for a circular economy
Though chemical recycling is still a work-in-progress solution for plastic waste, with its environmental and economic viability largely debatable, there is growing market interest and innovations being undertaken.
Pros and cons of chemical recycling
Chemical recycling, or advanced recycling, is gaining traction for its ability to process mixed and hard-torecycle plastics that are often unsuitable for mechanical recycling. Unlike traditional methods, it breaks down plastics into basic building blocks to create new products or raw materials. Additionally, the process can produce high-quality outputs comparable to virgin plastics, making it suitable for applications with stringent standards, such as food and medical packaging.
Despite these advantages, the effectiveness of chemical recycling has been questioned. A report by the International Pollutants Elimination Network (IPEN) and Beyond Plastics, two environmental NGOs, critiques the industry's claims. They argue that chemical recycling remains largely unproven, with evidence suggesting it could exacerbate pollution and contribute to climate change.
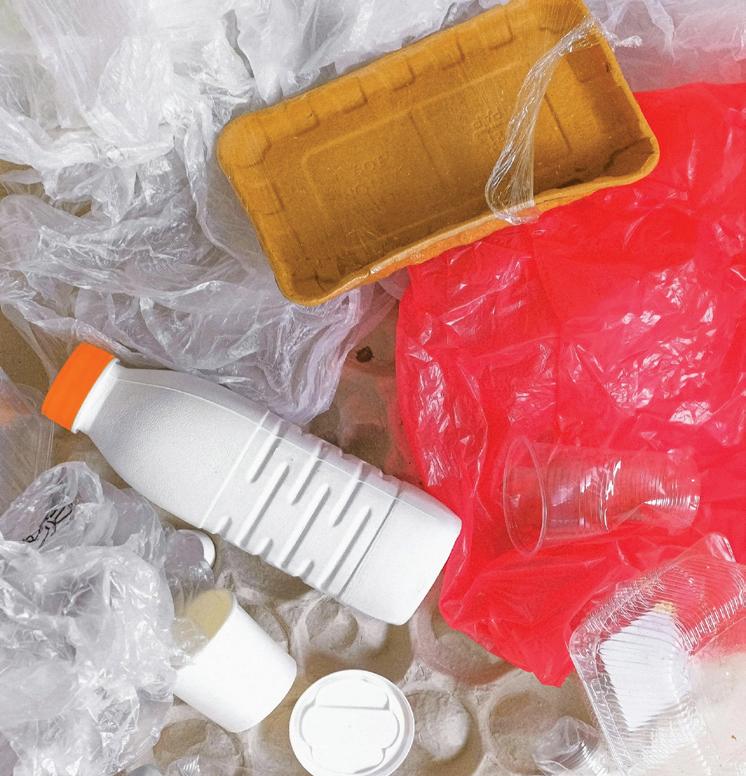
Chemical recycling has sparked debate about whether it genuinely offers a solution for managing waste pollution from hard-to-recycle plastics
The report examined 11 US-based chemical recycling facilities, assessing their output, financial backing, and environmental impact, and found that the process may generate significant toxic waste and emissions, raising concerns about its overall environmental benefits. Moreover, chemical recycling tends to be significantly more expensive than mechanical methods due to the sophisticated technology and high energy requirements. The economic viability of this process depends heavily on achieving large-scale operations, yet many existing facilities struggle with underutilisation.
Market growth: albeit slower than mechanical
Nevertheless, the market for chemical recycling continues to gain traction. It is projected to expand, growing at a CAGR of 9.4% from 2024-2030, according to a report by Grandview Research. Likewise, a report by UK-based intellectual property law firm Appleyard Lees shows a surge in patent filings for chemical recycling technologies. Pyrolysis, the most common chemical recycling method, leads in patent filings, far surpassing other methods like gasification and hydrothermal treatment.
However, according to research firm ICIS, the chemical recycling and dissolution sector remains in a state of relative infancy, with around 130 plants operational or at the final investment decision stage of approval, compared to around 2,500 mechanical recycling plants.
Industry installed plastic waste processing capacity (pyrolysis-based technologies, chemical depolymerisation and dissolution) in Europe in 2024 stood at 150,000 tonnes/ year, or 510,000 tonnes/year if including facilities in the construction and commissioning phase, but the current pre-FID project pipeline could add 3 million tonnes by 2029, according to ICIS.
However, ICIS adds that several anticipated startups were delayed in 2023-24 due to a combination of factors, including permitting delays, access to feedstock, unfavourable macroeconomics and extended commissioning.
Mechanical vs chemical recycling
Meanwhile, mechanically recycled polymers' share of the total market is set to increase in the coming decades but penetration, defined as domestic recycling production versus total polymer demand, is likely to remain limited through to 2050, says Tom Brown, Chief News Correspondent at ICIS. He adds that mechanical recycling domestic production is likely to represent 17% of total PE consumption in Europe, and 19% of PP by 2050, based on analysis of ICIS supply and demand data.
Rates in northern America and northeast Asia are likely to be similarly muted, according to ICIS analytics EMEA team lead for plastics recycling Egor Dementev.
Take-up of bottle grade mechanically recycled PET is likely to be stronger, at 49% in northern America and Europe, but technological issues limit the odds of greater market dominance for other polymers.
Recycling Secto R
“The penetration rates still stay quite limited, as lots of plastics applications such as polymer flexibles and textiles are intrinsically difficult to recycle mechanically,” Dementev said.
The projected 2050 rates are minor uptick compared to 2023 mechanically recycled PE market penetration rates of 12% in North American and Europe and 4% in northeast Asia.
ICIS says in future, chemical recycling could fill in some of the gaps left by mechanical recycling.
“Chemical recycling could be a complementary solution,” Dementev said. “Without chemical recycling, we are probably not going to leapfrog,” he added.
The relatively small number of operational or approved plants, which are largely small-scale units, obscures the scale of potential capacity in the pre-approval phase at present, Dementev added. As for FIDs postponements, they are largely policy driven, according to Dementev.
Chemically recycled plastics: strong contenders for sustainability
Chemically recycled plastics are widely used across various industries, for example in the consumer goods sector, specifically in retail packaging for cosmetics, household items, and food packaging, rHDPE and rPET are used in containers, bottles, and films.
In the automotive industry, recycled plastics are used in interior and exterior parts, reducing weight and improving efficiency. In construction, they are used for insulation, roofing, and plumbing, offering durability and a lower environmental impact. The textile and fashion industries incorporate rPET fibres in clothing, accessories, and home textiles. Electronics manufacturers use recycled plastics in device casings and components, ensuring technical compliance.
In a pivotal collaboration, Brazilian petchem firm Braskem and Georg Utz AG, a Swiss company specialising in reusable transport packaging, have introduced chemically recycled ISCC Plus-certified PP to the food transport packaging market. Braskem says this is its first closed-loop project with Georg Utz, in a “collaboration that demonstrates the power of joint efforts in the value chain to create solutions that not only meet the highest standards for food transport packaging.”
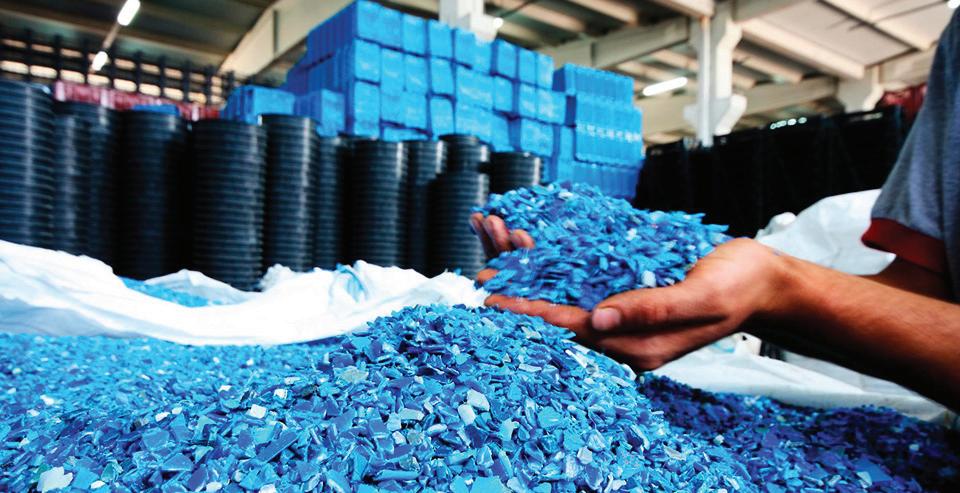
Scaling up pyrolysis and liquefaction solutions
Chemical recycling plants and plastics derived from this process are making significant strides in recycling hardto-recycle plastics, expediting the move toward a circular economy.
Netherlands-based Shell Chemicals Park Moerdijk started up a new unit that has a Market Development Upgrader (MDU) to process circular raw materials at scale. Pyrolysis oil is obtained by heating plastic waste to about 450°C until it melts and all oxygen is removed. The MDU purifies this oil so that it can serve as feedstock for the cracking plant at Moerdijk.
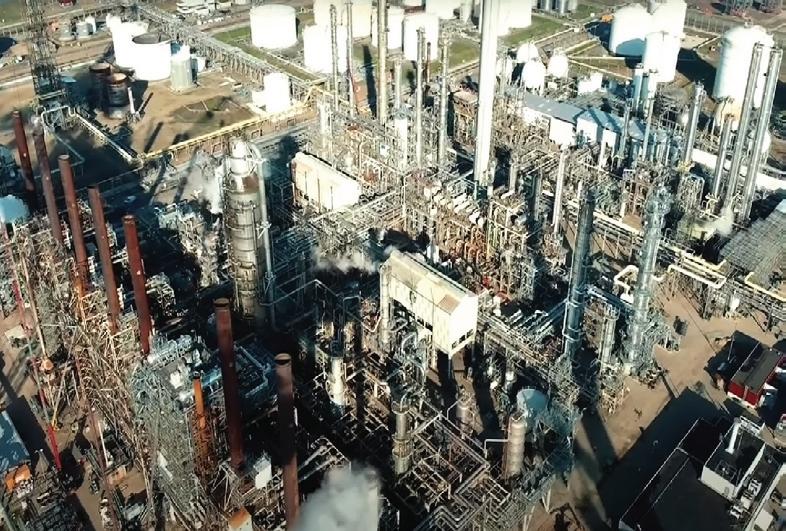
Shell Chemicals Park Moerdijk has launched a Market Development Upgrader unit to process circular raw materials at scale
This cracker breaks and separates larger and smaller molecular chains, producing the base chemicals for everyday products. Eventually, the MDU will be scaled up to full capacity and will handle up to 50 kilotonnes/year of pyrolysis oil, says Shell.
Meanwhile, French engineering firm Technip Energies, Alterra Energy, a US-based company that developed a proprietary thermochemical solution, and Finnish petchem firm Neste have tied up to offer a standardised modular solution globally, based on Alterra’s technology, to parties interested in building capacity for chemical recycling.
This solution will come in the form of readily designed and engineered liquefaction plant modules, which will lower pre-investment costs, accelerate implementation, improve project economics predictability, and reduce overall capital costs, say the firms.
Alterra’s thermochemical liquefaction process converts hard-to-recycle plastics into a liquid hydrocarbon product. This liquid intermediate product can then be further refined into high-quality raw materials for new plastics and chemicals.
As of today, Neste alone has processed more than 6,000 tonnes of plastic-derived feeds, including ISCC Plus- certified oil from Alterra’s Akron industrial-scale site.
Research-led innovations using water
Two heads are better than one, and this has never been truer as collaborations between technology firms and leading researchers advance recycling processes, particularly in the chemical recycling sector.
As such, UK-based recycler Mura Technology has teamed up with Ghent University's Laboratory for Chemical Technology (LCT) for a five-year research collaboration.
Braskem has supplied its Wenew chemically recycled PP to Georg Utz to create a circular food contact-approved packaging for transport
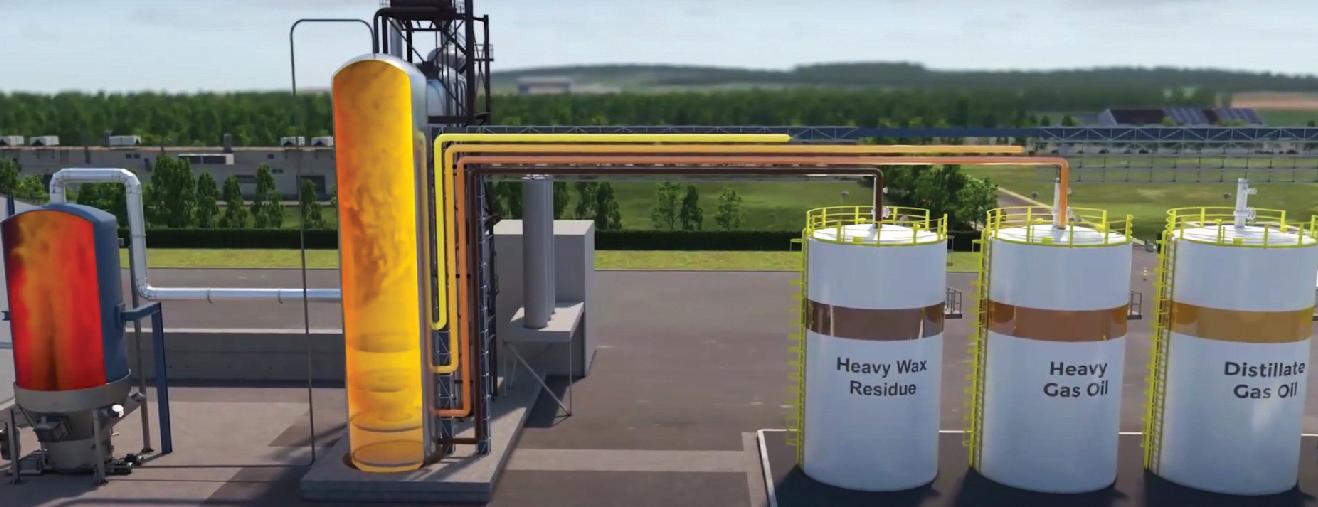
Mura’s Hydro-PRT process uses supercritical water - heated to extreme temperatures and pressures, behaving like both liquid and gas, allowing unlimited recycling cycles
The partnership will involve building a pilot-scale continuous flow testing facility to evaluate hard-to-recycle polymers, including complex composites.
Mura’s Hydrothermal Plastic Recycling (Hydro)-PRT process uses “supercritical water”, which is water that is heated to very high temperatures and pressures, making it behave like both a liquid and a gas. It also supports unlimited recycling cycles.
Unlike pyrolysis, Hydro-PRT, a cost-competitive alternative to incinerating waste plastic, enables the recycling of diverse plastics like post-consumer packaging, yielding high-quality recycled hydrocarbons for virgin-grade plastic production, according to Mura.
Hydro-PRT, which complements traditional mechanical recycling, is cited in the European Commission’s 2023 report as best-in-class with a 50% lower carbon footprint compared to pyrolysis.
To further develop Hydro-PRT’s sustainability, Mura teamed up with Warwick Manufacturing Group (WMG) at the University of Warwick and Innovate UK (IUK) in a two-year partnership. WMG will create operational sustainability models, identify improvement opportunities, and conduct Life Cycle Assessments (LCAs) to transparently demonstrate Hydro-PRT's environmental benefits.
Mura aims for over 1.5 million tonnes of recycling capacity globally by 2032 and its first commercial-scale plant at Wilton, Teesside, is set to be the world's largest advanced recycling facility, with additional plants in South Korea and Japan by this year-end.
Mura has also worked with Neste that allowed Neste to convert ISCC Plus-certified products from Mura’s Teesside plant into feedstock for the production of new plastics.
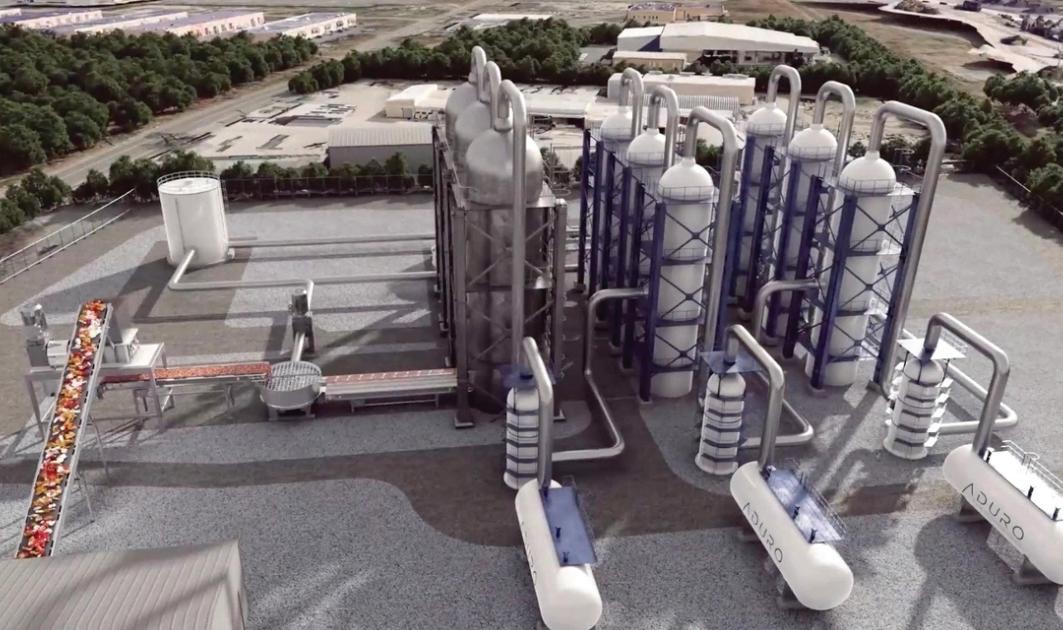
Similarly, Canadian clean technology company Aduro Clean Technologies Inc offers the Hydrochemolytic (HCT) process, a low-energy, high-tolerance technology for recycling mixed plastics. Unlike conventional methods, which are energy-intensive and costly, HCT operates without molecular hydrogen, reducing both environmental impact and operational costs, says the company.
HCT is particularly effective for recycling PE, PP, and PS, producing feedstocks for naphtha crackers that generate chemicals and new plastics. Its regenerative chemistry and lower operating temperatures lead to higher purity and yield, especially for difficult-to-recycle plastics like foam cups and food packaging.
Additionally, HCT’s scalability means it can be deployed in smaller, remote locations with low plastic waste volumes, making it an economically viable solution, adds Aduro.
The patented water-based technology also has applications in other sectors, including converting heavy crude into lighter oil and transforming renewable oils into higher-value fuels and chemicals.
From PCR plastic to high quality rPET
Hard-to-recycle plastics have created opportunities to develop more efficient and cost-effective methods for recycling waste materials.
In response, US materials giant Dow and consumer products firm Procter & Gamble (P&G) have tied up to create a new recycling technology that converts packaging into rPET of near-virgin quality with a low greenhouse gas emissions footprint, the firms add.
The technology will focus on recycling a broad range of plastic materials, particularly PE and post-household plastic waste like rigid, flexible, and multi-layer packaging. The aim is to deliver high-quality PCR polymer, enabling P&G to use it in packaging. The partnership combines Dow's and P&G's expertise in materials science, manufacturing, and supply chain management.
Aduro's Hydrochemolytic process, a low-energy, hightolerance recycling technology, operates without molecular hydrogen
In a similar effort towards PET recycling via depolymerisation, a research team led by Professor Kotohiro Nomura from Tokyo Metropolitan University has developed a method for breaking down PET using ethanol and an inexpensive iron catalyst (FeCl3 or FeBr3). This process allows for the selective chemical recycling of PET from both textile and plastic waste mixtures, without the need for harsh acids or bases, making it simpler, cost-effective, and environmentally friendly.
The method operates at moderate temperatures (160–180ºC) and achieves high selectivity (98–99%), converting PET into raw materials such as diethyl terephthalate (DET) and ethylene glycol (EG). Notably, it works well with mixed waste, including textiles made from PET and cotton, effectively recovering PET and 75% of the cotton content.The process also shows promise for selectively recycling PET from plastic waste, including PE.
These recent breakthroughs in chemical recycling demonstrate the untapped potential of the process, revealing its ability to evolve and drive progress in advancing the circular economy.
Packaging
ExxonMobil develops thermoformed packaging with 95% PE content
US materials firm ExxonMobil, working with key partners, has developed a fully recyclable thermoformed packaging featuring 95% polyethylene (PE) content.
Targeted at hot fill and aseptic applications in the food and beverage sectors, the new packaging design is said to offer a high oxygen barrier, excellent optics and enhanced puncture resistance while maintaining optimised formability.
The packaging comprises a thermoformed bottom web and machine direction oriented (MDO) PE lid film, both engineered with the company’s premium resins such as Exceed XP, Enable and Exact plastomers, along with Eval Evoh resins for barrier properties.
The barrier lines were developed by Germany-based machinery firm Hosokawa Alpine Group for the production of these films, delivering what ExxonMobil calls a “durable and recyclable solution that meets modern packaging requirements for sustainability without sacrificing performance.”
To further enhance the packaging’s environmental credentials, ExxonMobil says its design minimises material usage while still offering superior protection and sealing properties. By reducing the overall weight and maximising recyclability, the company says its new solution not only supports sustainability goals but also helps converters and brand owners meet increasingly stringent regulations on plastic packaging scrap and recycling targets.
The new packaging was successfully tested on Germany-based Multivac’s R245 machine, ExxonMobil says, achieving “excellent” machinability with high line speeds and ensuring the integrity of the package even under rigorous conditions.
“This innovation aligns with the industry’s shift toward more sustainable, circular packaging solutions that reduce environmental impact while ensuring product protection,” the company says.
Packaging with recycling potential in China Elsewhere, in China, ExxonMobil worked with Chinese converter Huangshan Novel Co Ltd to develop a solution that would help address the problem of recycling multimaterial flexible packaging waste.
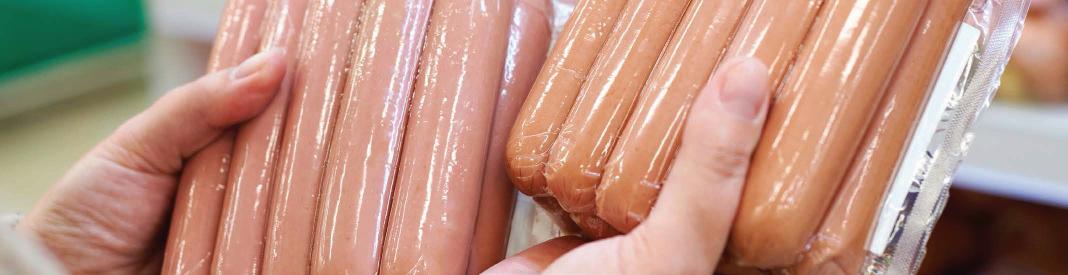
While improving potential for recycling, Huangshan Novel needed to make sure that packaging performance is maintained or even boosted.
ExxonMobil worked with Huangshan Novel to test formulations of stand-up-pouches (SUP) made of MDO PE//PE laminate film including ExxonMobil’s Exceed XP and Exceed 2012 performance PE.
The films showed high stiffness and good optical performance, as well as “outstanding” bag drop and package integrity, satisfying end users’ needs for packaging performance, while helping them deliver sustainability benefits due to the mono-material structure that can improve recyclability.
Compared to conventional laminated films, the MDO PE//PE show equivalent optics vs. BOPP//PE film, and similar stiffness to BOPP//PE and BOPA//PE films.
During the bag drop test from 1.5 m height, better performance than that of BOPET//PE film and equivalent to BOPA//PE film is demonstrated, says ExxonMobil.
“Exceed XP performance PE’s extreme performance, such as tensile strength, is critical for smooth MDO production. Together with medium density Enable 4009, the substrate film made using the MDO process can provide excellent stiffness and optical properties for shelf appeal; while the sealant film based on Exceed 2012 provides low SIT and high seal strength for package integrity. The performance of MDO PE//PE SUP is well-proven on packaging lines and in transportation tests,” said Wang Changchun, Deputy General Manager of Huangshan Novel.
The full PE solution has been commercialised and the Chinese company says it is receiving “positive market feedback with interest from more and more brand owners”.
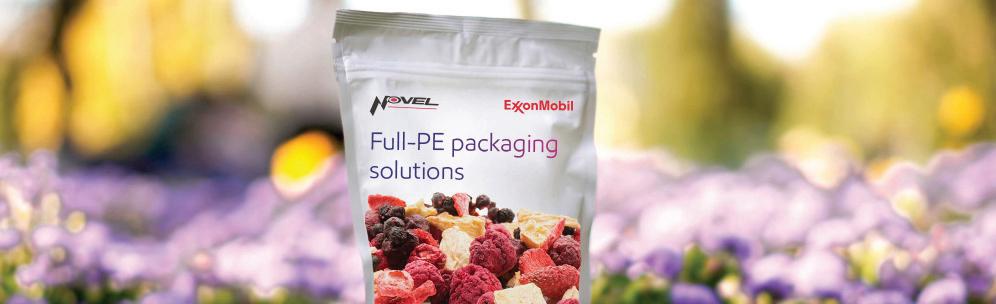
Wang added, “Due to the increasing global demand for packaging that can be recycled, for example the strong regulatory drive for ‘design for recyclability’ in Europe, we believe it has great potential in flexible packaging for food, dairy, pet food and personal daily care products, and will significantly help improve our competitiveness in both domestic and export business.”
Curbing food wastes and cutting carbon emissions
Data shows that food waste contributes to carbon emissions, and sustainable packaging solutions appear to be an effective way to reduce this environmental impact, says Angelica Buan in this report.
Environment in a pickle with food wastes
Mouldy food in the fridge, unsold bags of spoiled produce from supermarkets, or fast-food wrappers and leftovers discarded on the curb, ready to be collected and sent to landfills: these are just some of the ways how food waste is generated and disposed of daily.
Now, imagine the daily volume of food waste sent to landfills, along with packaging, much of it contaminated, that cannot be recycled.
The World Wide Fund ( WWF ) reports that an estimated one-third of all food produced globally, ie 1.3 billion tonnes of fruits, vegetables, meat, dairy, seafood, and grains, is wasted. This food either remains on farms, is spoiled in distribution, or is discarded by businesses and households.
Food waste creates a double burden by contributing to both food insecurity and carbon emissions. The United Nations ( UN ) stated that nearly 1 billion tonnes of food, 17% of all food available to consumers, is discarded annually.
Producing, transporting, and allowing this food to rot contributes over 8% of global greenhouse gas emissions, particularly through methane production,
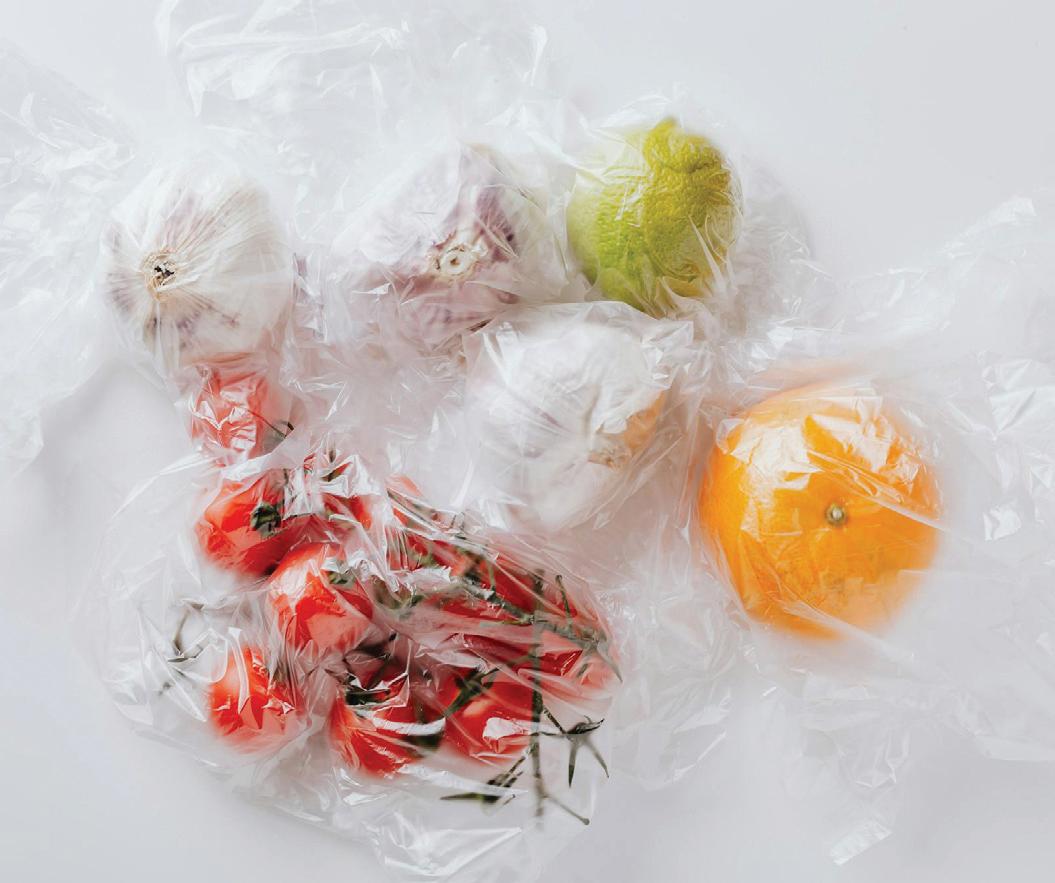
A UN report states that producing, transporting, and wasting this food contribute over 8% of global greenhouse gas emissions, reinforcing the need for effective packaging systems
according to UN’s “Food and Climate Change: Healthy diets for a healthier planet” report. When food waste is sent to landfills, it decomposes without oxygen, a process known as anaerobic decomposition, which produces methane: a greenhouse gas far more potent than carbon dioxide. In fact, methane accounts for about 58% of emissions from landfilled food waste, intensifying the impact on the climate.
Tackling food waste requires a variety of approaches, and one key strategy is adopting durable, biodegradable/compostable packaging, which resists damage and provides effective barriers as well as breaks down naturally, helping to reduce waste. Furthermore, other low-carbon-impact options are reusable or minimal-material packaging.
Using more packaging than necessary creates waste throughout the entire production process, from increased raw material use and energy consumption to more waste generation. While advocates for less packaging or even no packaging at all argue for reduced waste, this approach can pose risks to both consumers and the environment, especially in terms of carbon emissions.
The report also highlights that underpackaging can strain the system, resulting in food waste caused by spoilage or damage due to insufficient protection. The ideal solution is packaging that offers adequate protection, with innovations in biodegradable/ recyclable packaging continuing to grow.
Efficient barriers for longer shelf life
Efficient barriers in food packaging contribute to maintaining product quality, safety, and extending shelf life, to protect food from environmental factors such as moisture, oxygen, light, and microbial contamination. The significance of barrier properties cannot be overstated, as they directly influence the freshness, taste, and overall longevity of food products.
Advancing barrier innovations is the collaboration between US adhesives producer Henkel Adhesive Technologies and Indonesian manufacturer of CPP and LLDPE film, PT Panverta Cakrakencana ( Panverta ), to develop a sustainable solution for dry food packaging by improving the oxygen barrier properties of packaging films.
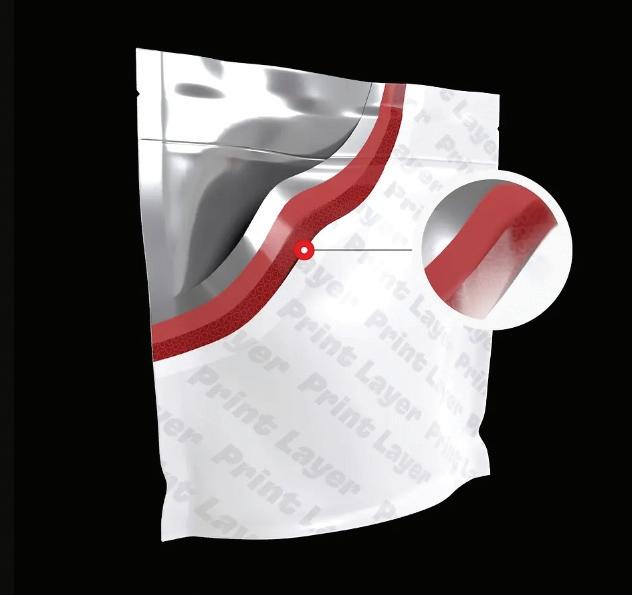
Henkel's certified recyclable Loctite Liofol oxygen barrier coating enables mono-material packaging while maintaining essential food preservation
Packaging for products like flour, rice, and pasta typically uses multiple layers for protection, but these are hard to recycle. The collaboration aims to reduce the number of layers, cutting waste while still ensuring quality food protection.
The joint innovation between Henkel and Panverta, which advances mono-material PP packaging for easier recycling, focuses on optimising metallised CPP and aluminium oxide-coated (AIOx) films. These films achieve oxygen barrier performances of less than 0.5 cc/ sq m/day and 8 cc/sq m/day, respectively.
Henkel says its certified recyclable Loctite Liofol oxygen barrier coating enables mono-material packaging designs without sacrificing the essential oxygen barrier needed to preserve food.
Stretching to nylon as a lightweight material Polyamide (PA)/nylon packaging is a strong, durable material with excellent barrier properties, ideal for food packaging. It protects against moisture, gases, and contaminants, helping extend food shelf life. Common uses include packaging for bakery items, meat, poultry, and dry goods.
According to MarketsandMarkets , the PA food packaging market was valued at US$49.8 billion in 2021 and is projected to exceed US$72 billion by 2027, growing at a CAGR of 6.4% from 2022-2027, driven by the increasing demand for ready-to-eat and convenience foods that require effective packaging solutions.
In response to this market growth, non-profit Advanced Packaging Association ( APA ) AISBL was established in 2023. Founded by companies in the
plastics sector such as Grupa Azoty ATT Polymers, BASF, Ube, Envalior, and Domo Chemicals, APA aims to highlight the key role of PA as a high-performance material for recyclable packaging applications by 2027, backed by scientific data.
StePac's Xgo packaging for fresh produce uses BASF's Ultramid Ccycled, a chemically recycled PA6
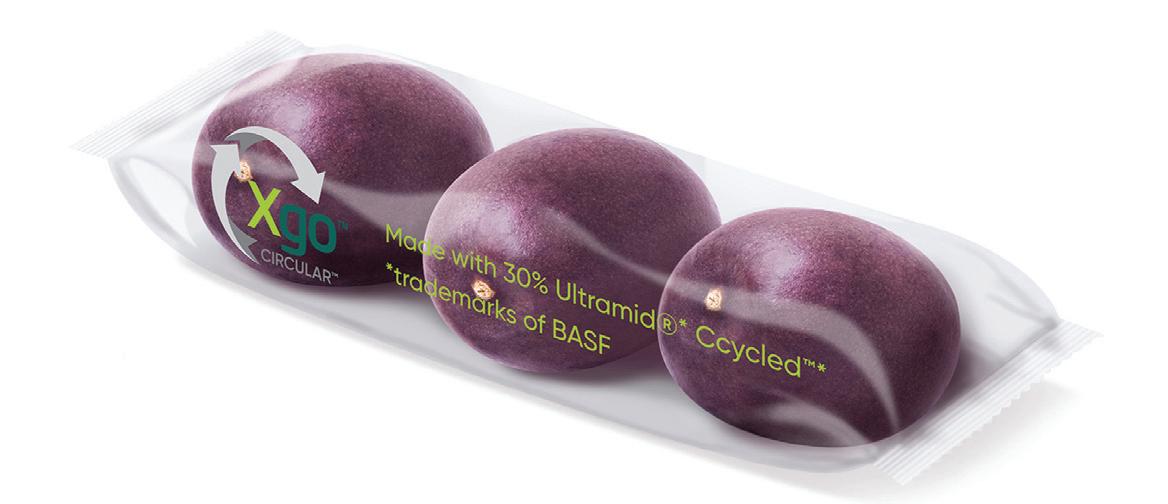
In this context, German chemical producer BASF and Israel's packaging specialist StePac have collaborated to develop sustainable packaging for the fresh produce sector. BASF provides StePac with Ultramid Ccycled, a chemically recycled PA6, enhancing the flexibility of StePac’s contact-sensitive packaging and elevating its sustainability within the circular economy. With REDcert2 certification, StePac incorporates recycled PA6 into its flexible, modified atmosphere packaging (MAP) products. The company’s brands, Xgo and Xtend, utilise MAP technology to control humidity, slow respiration, delay ageing, inhibit microbial decay, and preserve the produce's quality during storage and long shipments. Ultramid Ccycled makes up 30% of the packaging, with potential for higher integration.
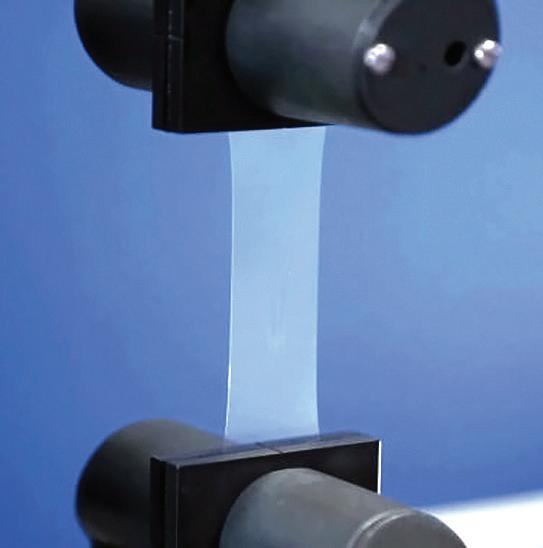
The non-profit APA aims to showcase polyamide's role as a high-performance material for recyclable packaging by 2027, backed by scientific data
Colombian passionfruit exporter Jardin Exotics is the first to use StePac’s Xgo packaging, which with MAP properties allow for slow ripening and preserve fruit quality during the long sea voyage from Colombia to Europe. By packing the fruit directly in retail packaging, repacking after arrival is eliminated.
Meanwhile, French resin manufacturer SK Functional Polymer ( SKFP ) offers Lotader recycling agents, which improve the environmental friendliness of plastics. Lotader is used to compatibilise plastic blends and enhance their mechanical properties.
Recycled PA feedstocks are often contaminated with small amounts of PE, which can negatively affect the mechanical performance of the recycled compound, even at low contamination levels (10% or less). This leads to degraded performance, making it inferior to virgin PA.
To address this issue, Lotader 3410 was evaluated for improving the performance of PA/PE blends with 25% PE content. Lotader 3410, a terpolymer of ethylene, butyl acrylate, and maleic anhydride, has a high ethylene and maleic anhydride (MAH) content, making it an effective compatibiliser for PE in PA.
Its unique composition enables a fine dispersion of PE within the PA6 matrix, which is essential for maintaining strong mechanical properties. It can be added to PA6, PA66, or PA12 at concentrations between 2.5-10% to significantly improve impact resistance and PE compatibility.
Recyclable packaging for coffee/nuts in a nutshell It is undeniable that packaging with the lowest carbon footprint is gaining consumer favour. Thus, innovations in this area must be recognised to foster further improvements in food packaging using new materials.
For example, Kenyan sustainable packaging manufacturer, Packaging Industries Limited ( PIL ), won a silver award at the recent Dow Packaging Innovation Awards for its BarrierFlex NutVault, a packaging bag for nuts. This fully recyclable, high-barrier ethylene-vinyl alcohol copolymer (EVOH) bag represents an innovation in bulk packaging for Kenya's cashew and macadamia nut exporters. It offers a sustainable alternative to traditional non-recyclable materials like PET/AL foil/PE, (biaxially oriented polyamide) BOPA/PE, and metallised polyester (METPET)/PE.
By eliminating the need for aluminium foil and metallised PET, the BarrierFlex NutVault not only extends the shelf life of nuts but also enhances product protection and reduces repacking costs.
The packaging is designed to work seamlessly with existing pouching machines, eliminating the need for lamination and further reducing production costs. Additionally, its
metal-free structure enhances safety by allowing metal detection, a feature not possible with aluminium or metallised PET, thereby improving quality control measures.
This 110-micron PE pouch further reduces dependency on imported films and laminates, supporting sustainability and resource efficiency.
Sharing in Dow’s recognition is packaging firm Amcor ’s AmPrima PE Plus for Coffee, a special awardee that replaces a complex three-layer structure with a mono-PE solution, reducing carbon emissions by 68% and ensuring recyclability within European PE streams.
Australia-headquartered Amcor, in collaboration with Norway’s Kjeldsberg , has developed this innovative coffee packaging to prioritise recyclability and reduce environmental impact.
Coffee packaging has traditionally used a threelayer structure of PET, aluminium, and PE. While effective at blocking oxygen and moisture, this design does not comply with recycling guidelines.
Relatedly, it can be recalled that in 2022, Amcor signed a five-year agreement with ExxonMobil to purchase certified-circular PE material, supporting its goal of incorporating 30% recycled material across its portfolio by 2030. The material volume will increase gradually each year, reaching an expected 100,000 tonnes/year by the end of the five-year period.
Amcor is focused to make all products recyclable, reusable or compostable by 2025, with 74% of total production by weight already designed to be recycled.
This reflects the entire packaging industry's direction, offering valuable food for thought on how to lower the carbon impact.
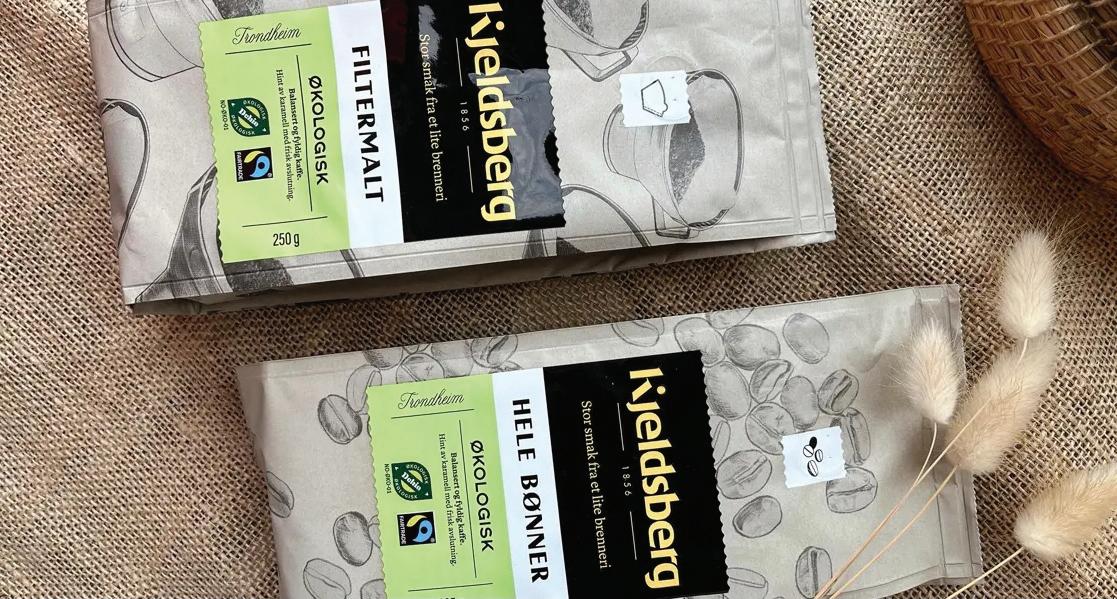
Amcor’s innovative coffee packaging for Kjeldsberg replaces a complex three-layer structure with a mono-PE solution
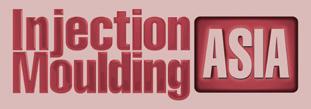
Injection Moulding Asia
Taiwan: Asia’s catalyst for manufacturing innovation
Taiwan’s technological assets establish the country as a vital player in the region’s sustainability transition, says Angelica Buan in this report based on the recently concluded Taipeiplas show in Taiwan in September.
Taiwan, often referred to as the “Silicon Valley of Asia”, produces 90% of the world’s most advanced chips, powering industries globally—from consumer electronics to automotive. But Taiwan is not stopping at technology; it is also emerging as a hub for sustainable manufacturing, with ambitious goals for netzero emissions and greener solutions.
The Asia Silicon Vall ey Development Plan aims to transform Taiwan from a traditional manufacturing base into an innovative startup destination. This initiative encourages achieving net-zero carbon emissions by 2050.
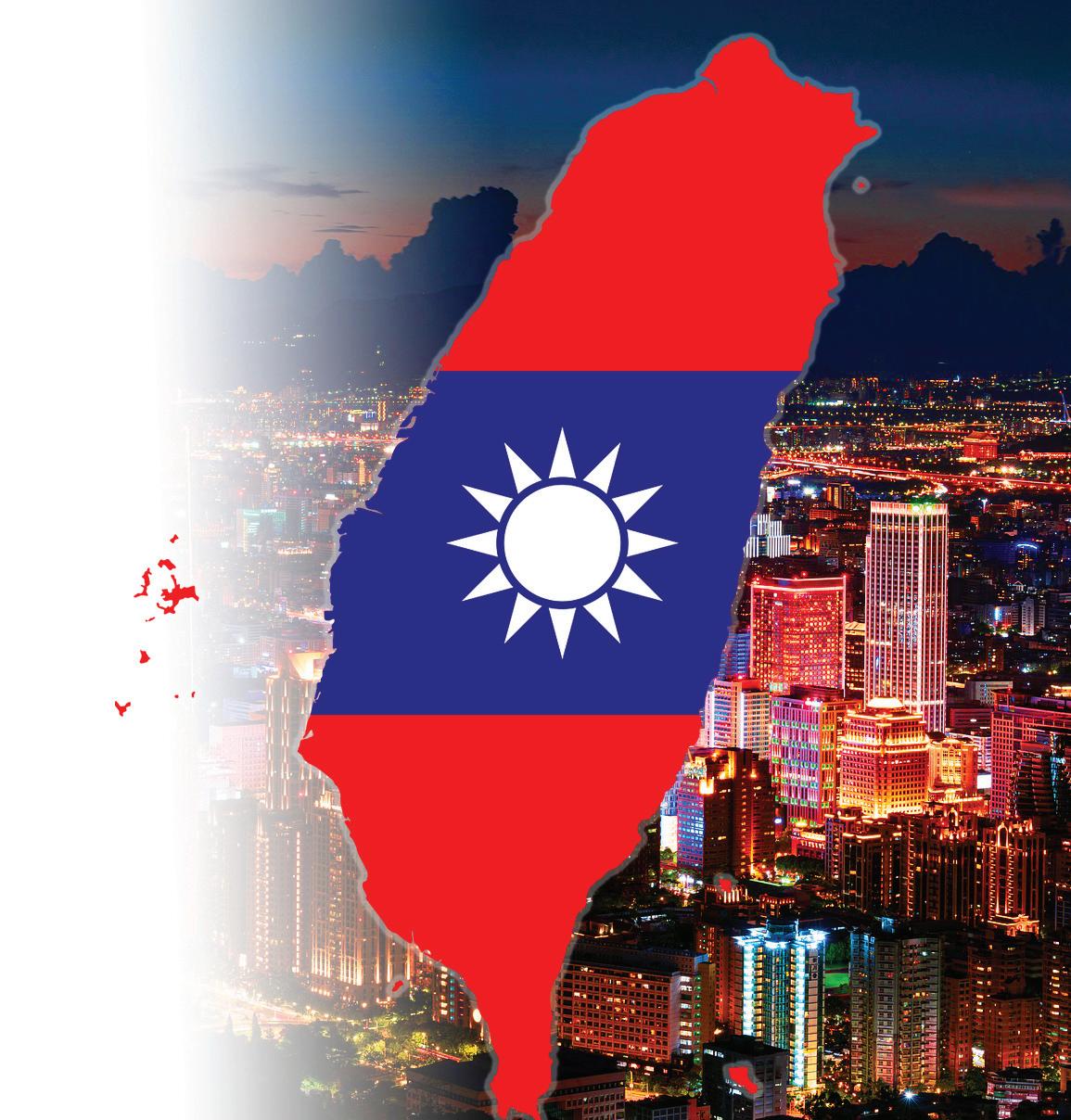
Taiwan, Asia’s “Silicon Valley” harnesses its technological prowess to advance sustainable manufacturing
Taiwan harnesses its technological prowess to advance eco-friendly manufacturing. Companies are adopting energyefficient processes, cutting emissions, and producing smart machinery, thereby setting a new standard for industrial growth. Along the same vein, machinery makers are taking the lead. Several Taiwanese companies are already deeply invested in sustainable practices, with long-term strategies in place.
PRA recently interviewed three major players in Taiwan’s machinery sector, all of whom are offering global customers advanced, sustainable, and cost-effective solutions to meet the growing demand for environmentally compliant technologies. These homegrown companies are ready to take the global market by storm.
Yi Tzung: A legacy of continuing innovation in rubber machinery
Weilin Liu, the fourth-generation head of Yi Tzung Precision Machinery Corp, is a Certified Machinery Safety Expert (CSME) and Executive Assistant to the President. Liu drives the company’s innovative direction.
Established in 1946, Yi Tzung has deep roots in the manufacturing of rubber and plastics machinery, with Liu noting that it is Taiwan’s oldest rubber machinery brand.

Yi Tzung’s array of machines is suited for applications ranging from automotive and bicycle tyres to shoe soles, silicone rubber products, medical items, and industrial rubber goods
Highlighting the durability of the machines, Liu shared an anecdote about a customer who inherited Yi Tzung machines from his grandparent, and that are still in mint condition.
“Stories like this prove that Yi Tzung machines can last for decades. It is not uncommon for our machines to be in use for 20 years or more!” Liu remarked.
Yi Tzung specialises in major mechanical processes, including rubber and EVA (ethylene-vinyl acetate) material from mixing, kneading, calendaring, coating, sheeting, and cooling, with applications ranging from automotive and bicycle tyres to shoe soles, silicone rubber products, medical items, and industrial rubber goods. The diverse product line includes over 20 different machines, and the company’s global sales network. Yi Tzung also operates its own casting factory.
Best in class solutions
At the exhibition, Liu highlighted that one of Yi Tzung’s best sellers is the intensive mixer, specifically designed for mixing compounds and various plastics. The machine features a robust structure, including a main air cylinder, floating weight, feeding door, mixing chamber, rotors, and discharge device.
At Taipeiplas, Yi Tzung showcased its intensive mixer, specifically designed for mixing compounds and various plastics

A key feature is its method of mixing: during compounding, materials and ingredients are simultaneously fed into the mixing chamber, where they are repeatedly sheared and squeezed by the rotors. This process facilitates a series of chemical interactions, enabling the material to coalesce into a paste-like mass. Mixing operations are conducted according to preset temperature and conditions.
This specially designed mixing machine provides efficient mixing and refining for a wide range of raw materials, including raw rubber, resins, asphalt, cellulose, PVC, and EVA.
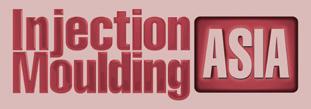
Injection Moulding Asia
It offers several advantages, such as a short mixing time, high efficiency, ease of operation, an advanced cooling system, mixing performance, effective dispersion, and no material leakage, ensuring a clean working environment.
Other technologies offered by Yi Tzung include the HD dispersion kneader, designed for processing single or multiple raw materials, such as natural rubber, synthetic rubber, plastic, and more. This model boasts a sturdy construction, large mixing capacity and high speed, complemented by fully automated temperature control, a simplified operating process, labour savings, and stable product quality.
The rear input and front output design facilitate smooth production flow, while the back window allows for easy observation of mixing conditions. Its sealed mixing chamber ensures safe operation and addresses environmental pollution concerns.
Additionally, the mixing chamber features a 135-degree dumping inclination, simplifying the removal and replacement of colouring ingredients.
The machine is easy to install and is characterised by its durability, low failure rate, and straightforward maintenance.
Another top-tier offering from Yi Tzung is the intermesh dispersion kneader mixer for rubber and plastic, which features a unique engage-type rotor designed for mixing and kneading compounds with varying characteristics. Notable features include a rapid mixing time of 3 to 8 minutes per batch (depending on material characteristics, feeding time, and cleaning time), an accurate temperature control system, and an efficient cooling system. Its sturdy construction eliminates shaking during the mixing process, and the pressure lid, driven by an oil hydraulic system, can be adjusted to reduce energy consumption, making it suitable for various composite materials.
These machines serve as a cornerstone for a myriad of industries such as tyres, footwear and more that benefit the company’s customers in Southeast Asia, which Liu described as “our largest market,” along with India, Romania, Germany, and over 62 other countries.
Most importantly, these machines are homegrown. “They are locally made in Taiwan, and Yi Tzung has its own casting factory. Over 70% of the machinery is produced in-house, while only certain critical components are outsourced to ensure quality,” Liu added.
Liu intoned that major brands in tyres—ranging from automotive and bicycle brands to sportswear, footwear, medical devices, and electronics—are among Yi Tzung’s customers.
Smart manufacturing
One of Yi Tzung’s pivotal focuses is advancing small-scale manufacturing by transitioning to smart systems. Liu provided an example, explaining that in traditional rubber manufacturing, such as tyre production, equipment used to require manual recording of processing status and product quality checks.
“This process was time-consuming and demanded the presence of an on-site technician or engineer,” he said. Today, however, machinery can be integrated with sensors and linked to industrial computers, creating an API (application programming interface) system. This shift reflects the growing importance of data-driven technology, allowing customers to collect and
organise data into actionable information for better analysis of settings like rotor speed, temperature, and pressure.
The system provides standardised data for quality checks and remote monitoring. “The future is moving toward smart manufacturing, incorporating automated functions for more efficient production processes,” Liu added.
Circularity
of carbon fibre materials
Yi Tzung is also making strides in sustainability by recycling materials that are typically hard to recycle, including carbon fibre.
Carbon fibre, used in industries such as wind turbines, becomes challenging to recycle after a certain period of use. However, through Yi Tzung’s partnership with a Taiwanese company, it is able to recycle the material. Their system removes unwanted substances like epoxy, allowing the purified carbon fibre to be re-compounded for future use.
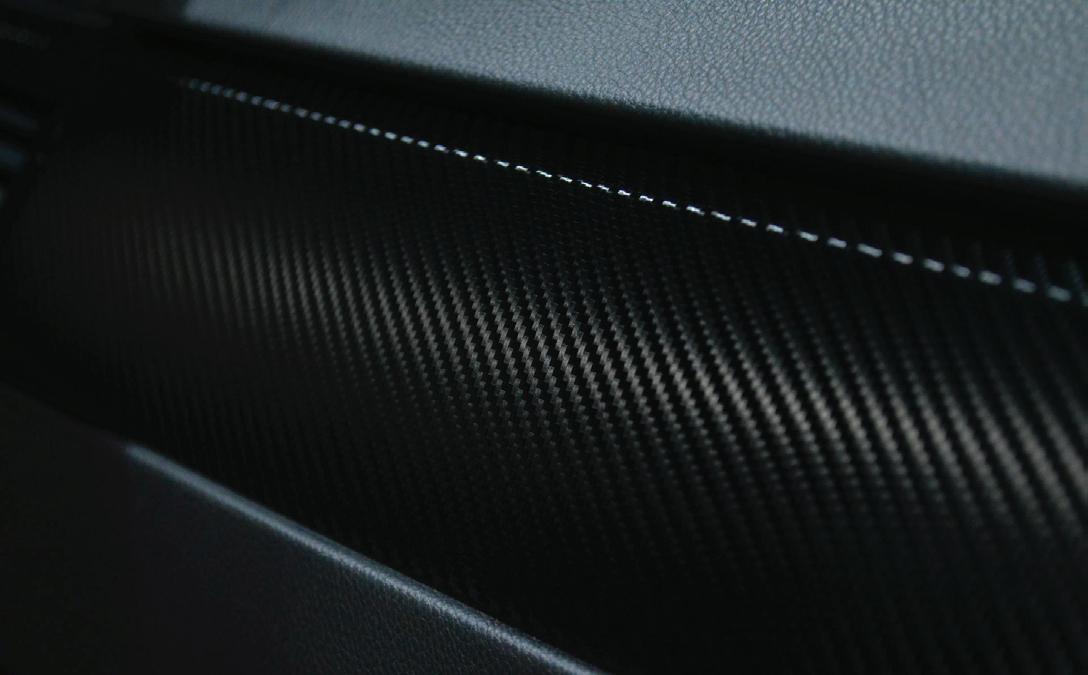
Yi Tzung claims its machinery is the only one in Taiwan capable of reaching temperatures up to 350°C, whereas most systems struggle to exceed 200°C. The high temperature is essential for efficient recycling of carbon fibre materials.
Recycled carbon fibre can be used in consumer products such as laptop casings and various electronic and industrial elements, serving as a replacement for PA66. Its tensile strength is significantly higher than that of PA materials, plus it allows for reduced weight and thickness without sacrificing strength.
CLF: Value-driven injection moulding solutions within reach of Asian customers
Taiwan’s strategic location in East Asia, near major markets like Japan and China, strengthens its role as a technology and manufacturing nexus. Its well-developed infrastructure, including international airports and industrial parks, ensures efficient global connectivity.
Additionally, Taiwan is considered a “safe” haven for countries that favour friend-shoring to mitigate geopolitical risks. This shift strengthens supply chain security by relocating operations to stable, economically aligned countries, confronting vulnerabilities from global crises like pandemics and political conflicts.
This strategic advantage also bodes well for Chuan Lih Fa Machinery Works Co Ltd, also known as CLF
Yi Tzung advances sustainability by recycling hard-to-recycle materials, including carbon fibre
Country Focus
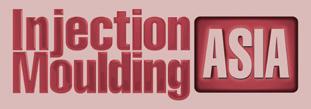
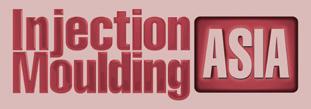
Injection Moulding Asia
The 60-year old manufacturer of injection moulding turnkey solutions has established a strong presence in markets across Asia, Africa, Europe, the Middle East, North and South America, and Oceania.
Established in 1966, the Tainan cityheadquartered company has service offices in China, Vietnam, and Thailand, providing convenient and timely after-sales support.

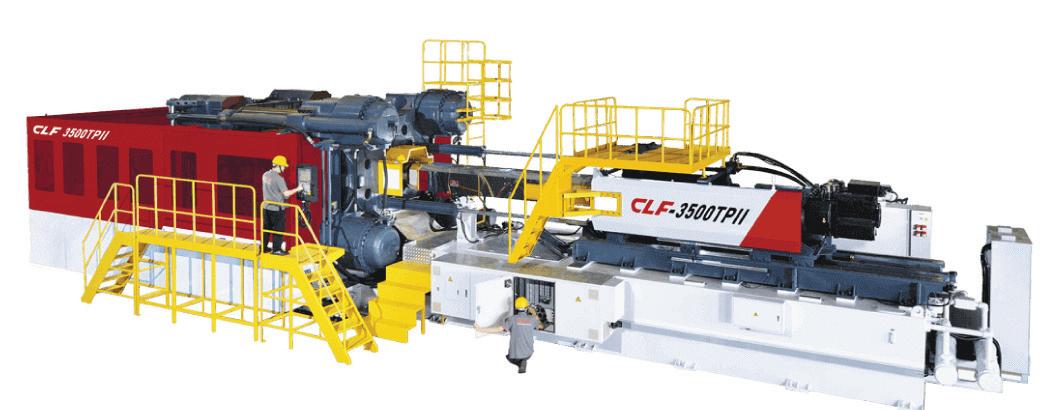
CLF’s injection moulding machines serve various applications, from pallets and PET preforms to automotive parts and medical devices
CLF’s injection moulding machines cater to a diverse range of applications, including plastic pallets, PET preforms, car bumpers, automotive parts, medical devices, and more.
Jenny Lin, Head of Marketing at CLF, introduced the company’s all-electric machine offerings at the recent Taipeiplas.
“Our customers span the globe and include major industries such as automotive parts, medical devices, electronics, and household goods. Currently, our largest market is Southeast Asia,” Lin shared.
She noted that Southeast Asian customers, who are increasingly seeking investment-worthy, technologically advanced machines, also view Taiwan’s proximity to the region as an advantage.
Capturing the market
CLF’s recent innovations include a two-platen machine that meets the demand for plastic pallets, recycled materials, and lighter weight solutions. It features tailored screw designs that enhance performance while minimising environmental impact, while the automation system features robotic pallet removal and transport, along with automated mixing and feeding.
With a direct hydraulic locking mechanism, and the capacity for larger moulds or multiple cavities, the space-efficient twoplaten machines are ideal for factories with limited space and smaller teams. Plus, the improved stability during moulding results in better product quality, dimensional accuracy.
CLF’s two-platen TPII Series features a clamping force range of 600 to 5,000 tonnes. Key benefits include a high-rigidity machine wall and a high-performance clamping cylinder, with structural strength confirmed through stress analysis, minimising mould deformation. Friction-free pillars eliminate surface wear, ensuring the mould remains unaffected by pillar deformation while maintaining precision. Additionally, the pillars require no lubrication, keeping the mould area and finished products clean.
CLF’s latest innovations feature a two-platen machine designed for plastic pallets, recycled materials, and lightweight solutions
The line’s space-efficient design reduces length by 15%, enhancing factory utilisation, saving energy, reducing carbon emissions, and lowering operating costs. Its ultra-long support base ensures smooth and stable mould opening and closing, maintaining precise parallelism and preventing tilting.
Lin noted that the platen design offers high customisation flexibility, compared to toggle-structured injection machines, and can incorporate a rotary table to fulfill multi-colour and multigroup injection requirements, adding value to finished products.
Meeting all-electric market demands
“These days, the all-electric machine market is very competitive,” mused Lin. However, CLF, leveraging its innovative capabilities, is on par with its competitors, in terms of technological advancements and price point, while complying with sustainability standards in manufacturing, according to Lin.
“Compared to Japanese machines, CLF assures quality, and when compared to China-made machines, CLF offers costeffective solutions,” she added, noting that CLF positions itself in the “middle-range” market.
To meet customer demands, especially for high-quality machines at affordable prices, Lin stressed, “We make design adjustments to highlight that all our products are made in Taiwan. Being Taiwan-made and assuring quality set us apart in the market.”
Lin also assured that CLF stands by its branding of “high quality, flexibility, excellent service, and strong after-sales support.”
Polystar: Material circularity with recycling made easy Asia’s recycling industry is growing, driven by rising environmental awareness, stricter government policies, and technological innovation. While challenges such as inadequate infrastructure and low recycling rates remain, countries across the region are adopting new strategies and technologies to boost recycling efforts and transition toward a circular economy.
Recycling machinery maker Polystar aims at simplifying recycling by focusing on user-friendly solutions that promote sustainability.
Since 1988, the company has been offering a range of recycling products, including the plastic film recycling machine, which provides a direct, one-step process for recycling PE/ PP film scraps with ease of operation and stable performance; the Repro-Flex Plus two-stage recycling machine , designed for heavily printed materials and post-consumer plastic waste; the shredder integrated recycling machine that offers a one-step solution for PP raffia, woven materials, and PE/PP film waste.
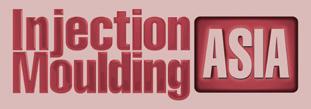
Injection Moulding Asia
For both hard and soft plastics, the hard plastic recycling machine delivers flexible recycling with stable hopper feeding. Additionally, the small plastic recycling machine caters to PE film and bag producers, while the squeezer drying machine efficiently dries washed films with up to 40% moisture content, a common challenge for post-consumer recyclers.
“The recycling industry faces the challenge of processing diverse materials, including post-industrial recycling (PIR) and post-consumer recycling (PCR). To address this, we are focusing on higher automation and implementing advanced filtration systems. This is particularly important for PCR materials, which often contain moisture, contaminants, dust, and paper labels that need to be effectively managed during recycling,” said David Lo, Chief Marketing Officer at Polystar.
At Taipeiplas, Lo flexed Polystar’s Repro-Flex one-step plastic recycling machine designed for reprocessing PE, HDPE, LDPE, LLDPE and PP flexible packaging materials, both printed and non-printed. This cutter-integrated pelletising system eliminates the need for pre-cutting, saving space and energy while producing high-quality plastic pellets efficiently.

Polystar’s Repro-Flex processes materials such as post-industrial film waste, washed flakes, and regrind from rigid plastic waste
The Repro-Flex can handle various materials, including post-industrial film waste, washed flakes, and regrind from rigid plastic waste. It is ideal for producers of commercial bags, garbage bags, agricultural films, food packaging, and PP woven bags, among others. Additionally, it can process PS sheets, PE and PS foam, PE nets, EVA, and PP mixed with PU (polyurethane).
The machine produces pellets that can be directly reused in blown film or pipe extrusion processes. It is also capable of processing washed post-consumer and agricultural films, with its cutter compactor generating frictional heat to dry and remove moisture from washed film flakes. The recycled pellets can be used 100% in extrusion processes or mixed to reduce raw material costs, and their quality can be enhanced with masterbatch and additives.
The Repro-Flex integrates cutting, extrusion, and pelletising in one compact system, eliminating the need for a separate crusher and addressing inconsistent feeding issues. Waste material enters via a belt conveyor or a nip roll feeder, with optional silo tank to store and feed pre-washed flakes. The cutter compactor prepares the material for extrusion by cutting, drying, and compacting it into a semi-molten state before feeding it directly into the extruder screw.
This integrated design results in higher output capacity, faster and more stable feeding, and uniform plastic pellets optimal for extrusion processes. Additional advantages include lower investment costs, reduced energy consumption, and quick machine delivery and installation.
Tackling growing market, evolving policies
Polystar’s market presence, particularly in Asia, is expanding in response to the increasing demand for sustainability through material circularity and sustainable manufacturing practices.
“We have distributed our machines to over 110 countries worldwide. Southeast Asia, especially Vietnam, Indonesia, and Thailand, is a rapidly growing market for Polystar,” says Lo.
When asked about plans for international expansion, Lo emphasised that Taiwan currently serves their business well. “At the moment, we do not see the need to invest in an overseas branch, as business is strong here. Taiwan provides us with a stable supply chain,” he stated.
Polystar utilises its core strengths of design, technical expertise from its engineering teams, and a global sales and marketing network to expand its installations. To date, the company has installed 1,500 recycling machines and 3,500 blown film extrusion machines worldwide.
“Recycling is a massive development trend,” says Lo, noting the emergence of recycling and recyclability regulations in major markets like Europe and the US.
The European Union (EU) has implemented policies to promote recycled materials as part of its waste management and sustainability strategies, focusing on stricter recycling targets, phasing out non-recyclable products, and ensuring that all packaging is recyclable by 2030.
In contrast, the US is implementing regulatory mechanisms and incentives to enhance recycling rates, including recycled content requirements and Extended Producer Responsibility (EPR), which holds producers accountable for the end-of-life management of their products.
These regulations will undoubtedly impact plastic producers worldwide. However, Lo assured that Polystar’s customers are well-prepared to comply with these evolving policies.
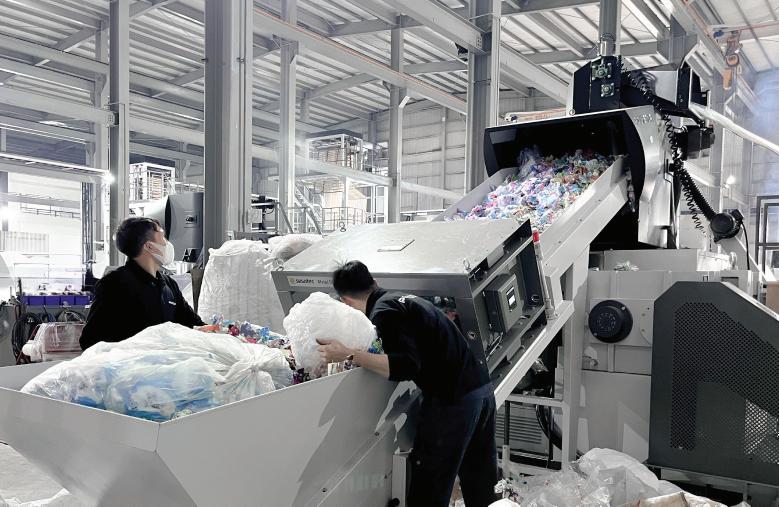
To date, Polystar has installed 1,500 recycling machines and 3,500 blown film extrusion machines worldwide
Rubber Journal Asia
Speeding up towards sustainability
Amid environmental issues over rising carbon emissions, the rubber/tyre sector is stepping up speed, fully committing to sustainability and making bold moves to ensure it achieves this goal, adds Angelica Buan in this article.
Market in a high gear
The global tyre industry is on track for significant growth, with projections showing its value rising from around US$164.9 billion in 2023 to approximately US$256.8 billion by 2032. This represents a CAGR of 4.9% during the forecast period, according to Imarc Group’s tyre market projection for 2032. Similarly, Precedence Research’s recent analysis anticipates growth for the automotive tyre market from nearly US$144 billion in 2024 to over US$232 billion by 2034, suggesting steady growth.
Likewise, Smithers projects the market’s value will rise fuelled by sectors like motorcycles and high-performance vehicles.
Tyre sector’s growth faces disruptions, prompting the adoption of innovative technologies and sustainability to secure its future
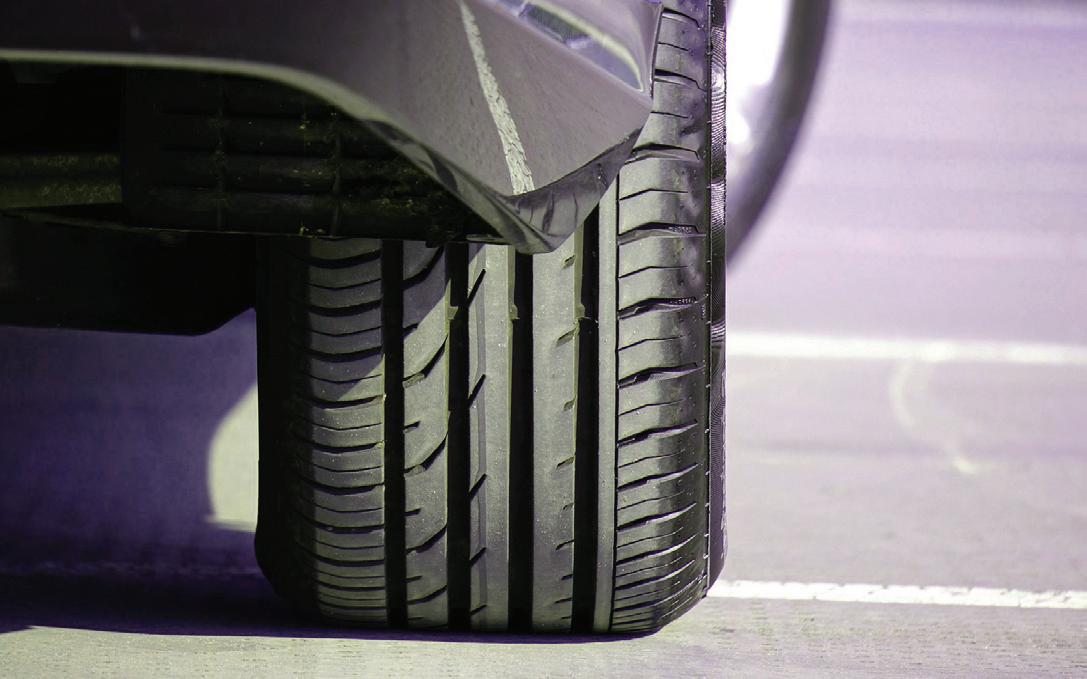
Despite these optimistic figures, the sector faces road bumps, such as supply chain disruptions, rising raw material costs, and a strict regulatory environment, catalysing the adoption of innovative technologies and sustainable practices to secure the industry’s future.
Asia steering tyre market growth/recycling Asia, a market front-runner and home to several global tyre majors, is seeing significant market growth. For example, Precedence Research reports that the Asia-Pacific tyre market is expected to reach US$95.3 billion by 2034, up from an estimated US$56.2 billion in 2023, growing at a CAGR of 5% from 2024-2034. This growth is driven by factors like rising disposable income, urbanisation, and increased demand for passenger vehicles.
However, the growing consumption of tyres brings with it an alarming increase in end-of-life tyres (ELTs), with around 1 billion tyres disposed of globally each year. Recycling tyres, as a primary method of disposal, is challenging due to their complex mix of rubber, steel, and synthetic fibres, which complicates efficient separation and processing. Without proper management, ELTs can lead to environmental and health hazards, such as harmful chemical runoff contaminating soil and water.
As such, the Asia-Pacific (APAC) region leads in tyre recycling, driven by its vast automotive industry and tightening environmental regulations, among other factors, according to a report by MarketsandMarkets
Major vehicle producers/consumers like China, India, Japan, and South Korea generate an immense volume of ELTs yearly and with several APAC countries introducing stricter environmental laws and Extended Producer Responsibility (EPR) regulations, tyre manufacturers are driving greater investment in sustainable recycling initiatives.
Investments, expansions in the fast lane Asia’s tyre sector is seeing a boost in investments and expansions, with manufacturers increasing production and capacity, and new plants opening to meet rising demand.
For example, German manufacturer Continental is investing EUR300 million to expand its tyre plant in Rayong, Thailand, increasing production capacity by an additional 3 million tyres/year. The expansion is backed by Thailand’s Board of Investment (BOI) as part of its Economic Recovery Scheme.
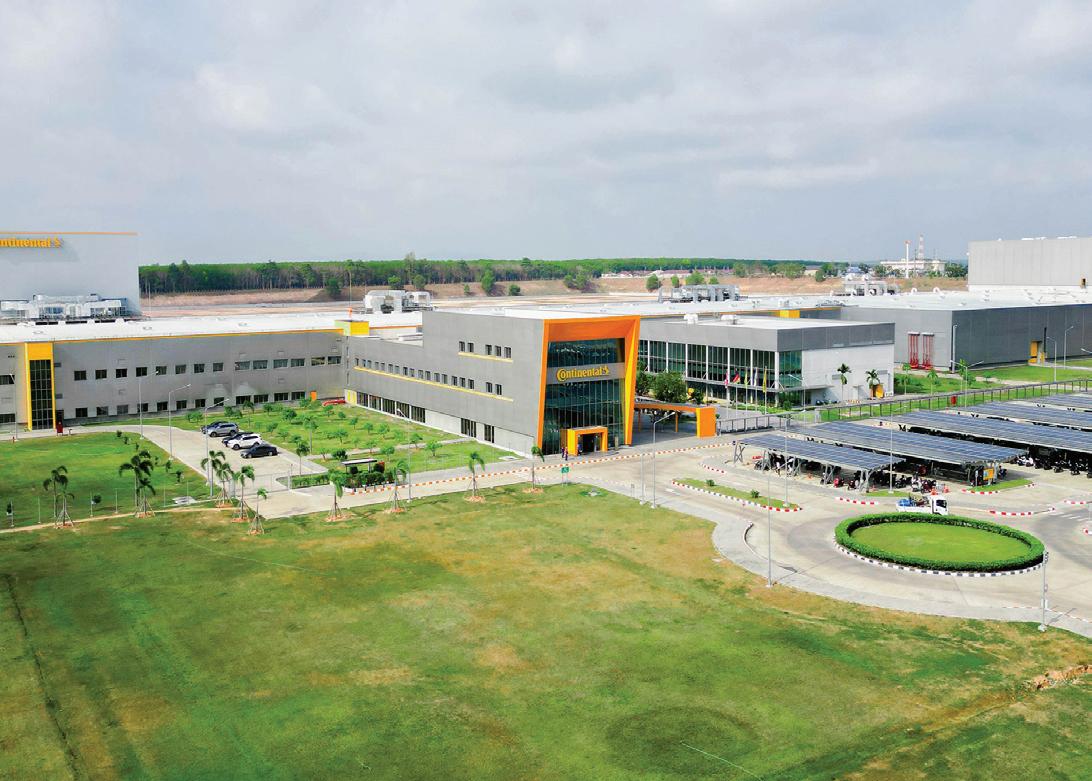
The Rayong plant, one of Continental’s largest production sites for motorcycle tyres, currently supplies both vehicle manufacturers and the replacement market, including specialised tyres for electric vehicles (EVs) and premium models like the MaxContact MC7. In 2023, the facility supplied OEM tyres for top EV manufacturers in the APAC region.
Continental’s Rayong plant has supplied OEM tyres for top EV manufacturers in the APAC region
Rubber Journal Asia
Continental says its Rayong plant uses advanced machinery and automated logistics systems, with a 6.7-MW capacity photovoltaic (PV) set-up, covering 13% of its annual electricity needs.
Similarly, expanding in Indonesia PT Matahari Tyre Indonesia (MTI), the new Indonesian subsidiary of China’s largest tyre manufacturer, Zhongce Rubber Group Co Ltd (ZC Rubber), has successfully produced its first all-steel radial tyre at its 500,000 sq m-factory located in Kendal Industrial Park, Semarang.
The production of MTI’s first all-steel radial tyre is just the beginning. With Phase II construction work already underway, ZC Rubber plans to boost production capacity.
On a similar growth track in India, where tyre demand is increasing, Bridgestone India Private Ltd, a subsidiary of Bridgestone Corporation, is investing US$85 million to expand its tyre production capacity at its operations at the Pune and Indore plants. By 2029, production at the Pune plant is expected to increase by 1.1 million tyres/year, while the Indore plant will focus on producing high-quality, premium tyres.
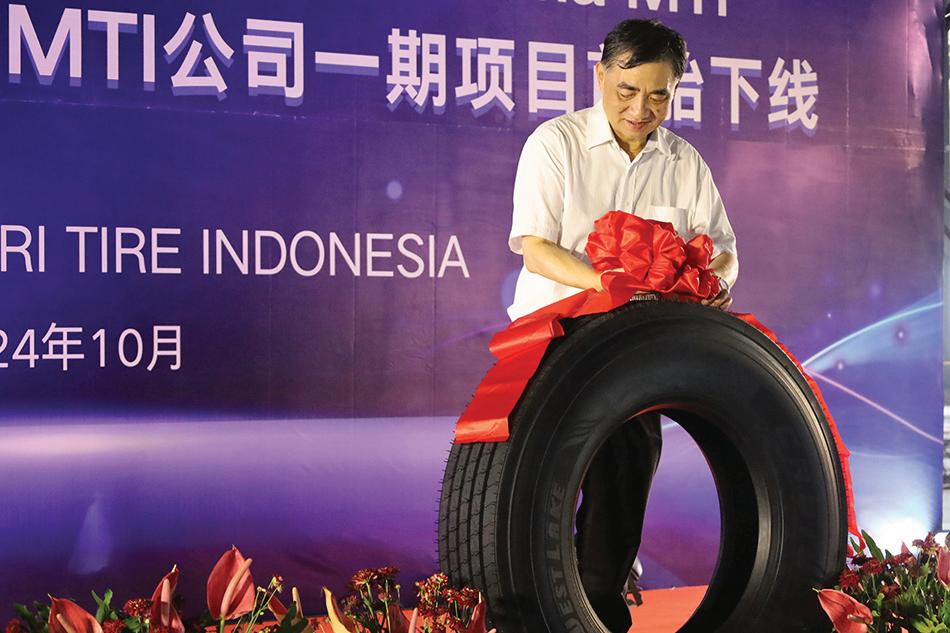
ZC Rubber’s Indonesian subsidiary, MTI, has rolled out its first all-steel radial tyre from its plant in Semarang
Additionally, a satellite technology centre will be built at the Pune plant in 2025 to develop products using Enliten technology, which uses proprietary lightweight materials to reduce rolling resistance, leading to lower fuel consumption, improved wear, and more durable tyres, says Bridgestone.
Meanwhile, Indian tyremaker Ceat has inaugurated a truck/bus radial (TBR) production line at its Chennai plant, with a capacity of 1,500 tyres/day. Located in Sriperumbudur across 160 acres, the plant is a key hub in Ceat’s global operations.
This expansion, which complements Ceat’s production of 20,000 passenger car radial (PCR) and 3,000 motorcycle radial (MCR/MCS) tyres/day, to meet the growing demands of both domestic and international markets, it adds.
De-fossilised tyres to be rolled out Amid environmental concerns and regulatory pressures on fossil-based material usage, tyre producers are now developing new technologies and biobased materials.
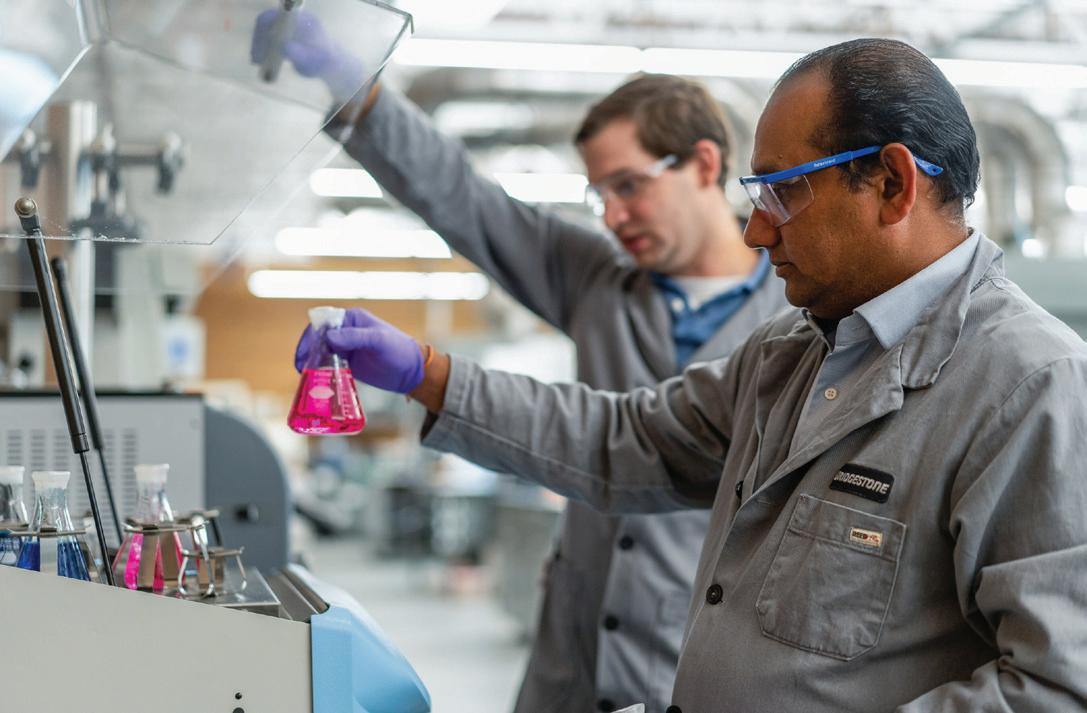
US-based Bridgestone Americas, flexing its sustainability goals in advancing towards using 100% sustainable materials in its tyres by 2050, has received a grant from the US Department of Energy (DOE) to develop a pilot plant for producing bio-butadiene, a key ingredient in synthetic rubber.
The project, which is expected to take three years to complete, starting with design and construction in Akron, Ohio, will test converting ethanol into butadiene, with the goal of reducing GHG emissions and potentially producing bio-based or recycled alternatives for butadiene. Bridgestone, in partnership with Pacific Northwest National Laboratory (PNNL), will use a proprietary catalyst system to scale the process.
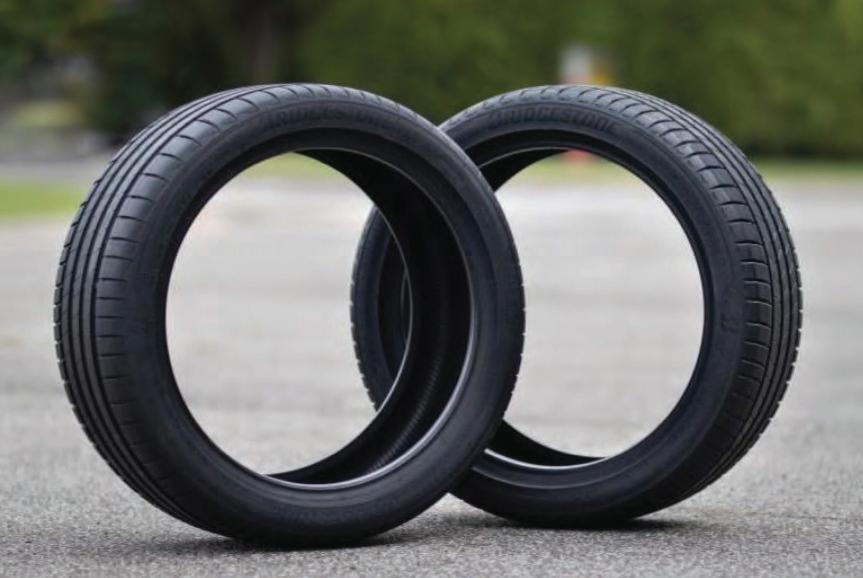
Meanwhile, carbon black from pyrolysis oil derived from used tyres is among the latest developments from Hankook Tire & Technology, which says it has begun mass production of tyres using three types of ISCC PLUS-certified carbon black derived from ELT pyrolysis oil.
By 2025, Bridgestone will use Enliten technology to create tyres with reduced rolling resistance, improving fuel efficiency and durability
Bridgestone Americas is developing a bio-butadiene pilot plant with a US DOE grant, partnering with PNNL to scale the process using a proprietary catalyst system
Tyre
has started mass production of tyres using ISCC Plus-certified carbon black
Rubber Journal Asia
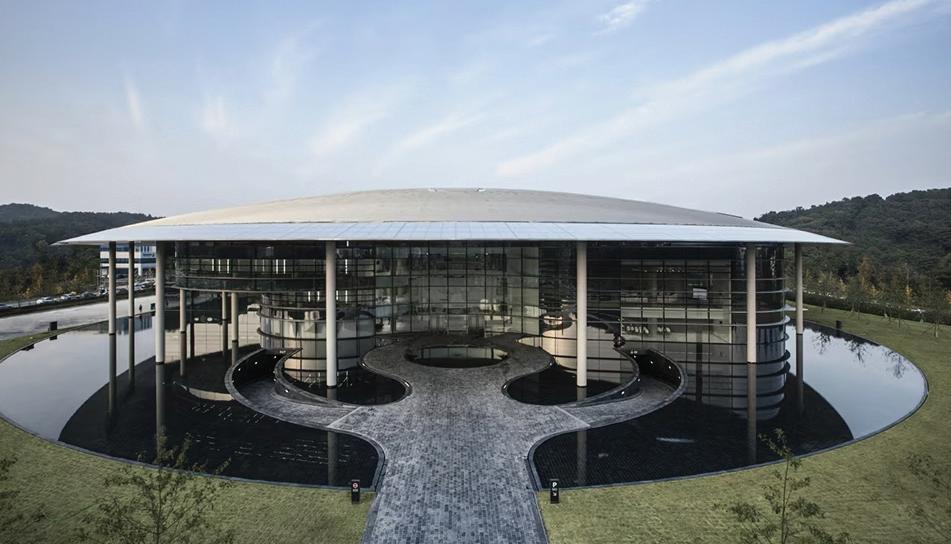
This follows the launch of the South Korean tyre maker’s circular economy model consortium, in collaboration with oil refining firm HD Hyundai Oilbank and HD Hyundai OCI, the country’ carbon black manufacturing joint venture between Hyundai Oilbank and OCI, the country’s largest carbon black company,
Hankook developed these certified materials using a mass balance approach, thus reducing reliance on petrochemicals. Hankook plans to use these sustainable materials in its products, aiming for 100% sustainability by 2050.
Over in Japan, Hiratsuka-based manufacturing company Yokohama Rubber joins in pushing for the development of sustainable materials and new biomass businesses. Most of the natural rubber, which is extensively used in tyre manufacturing, comes from the sap of the Para rubber tree. However, the seeds are mostly discarded. With this project, these discarded seed will be utilised, offering a carbonneutral resource while providing economic opportunities for agricultural communities.
The project, led by Tokyo University of Agriculture and Technology’s Associate Professor Shinji Kanehashi, is being conducted jointly by industry and Thailand, the world’s largest producer of natural rubber. Yokohama Rubber had already been involved in preliminary research through its Thai natural rubber processing subsidiary YT Rubber Co Ltd (YTRC).
Leveraging sustainable materials in Europe, too The European tyre value chain is also increasingly involved in global efforts to introduce more eco-friendly tyres to the market.
For example, Finnish tyre maker Nokian Tyres, recently signed a development agreement with Swedish biomaterials company Reselo AB, to further enhance the use of Reselo Rubber as a potential raw material in tyres. Reselo Rubber is a completely renewable material made from birch bark sourced from the residue of the global pulp, paper and plywood industry.
According to Reselo, a single mill produces an average of 100,000 tonnes of birch bark residue each year.
The forest industries in Finland and Sweden alone generate enough raw material to produce 200,000 tonnes of Reselo’s material. Reselo’s biorefinery concept is designed to reduce the environmental impact of its material.
In line with its sustainability goals, Nokian Tyres aims to have 50% of its raw materials be renewable or recycled by 2030 and in 2020, became the first tyre company to have its GHG reduction targets approved by the SBTi.
Also in line with this, the company has introduced its concept tyre, Nokian Tyres Green Step Ligna, featuring materials firm UPM Biochemical’s BioMotion renewable functional fillers (RFF). UPM uses a patent-protected process to produce BioMotion RFF, which has been developed together with partners for more than ten years. The process uses wood from sustainably managed forests and side streams from sawmill operations to produce the RFFs, according to UPM.
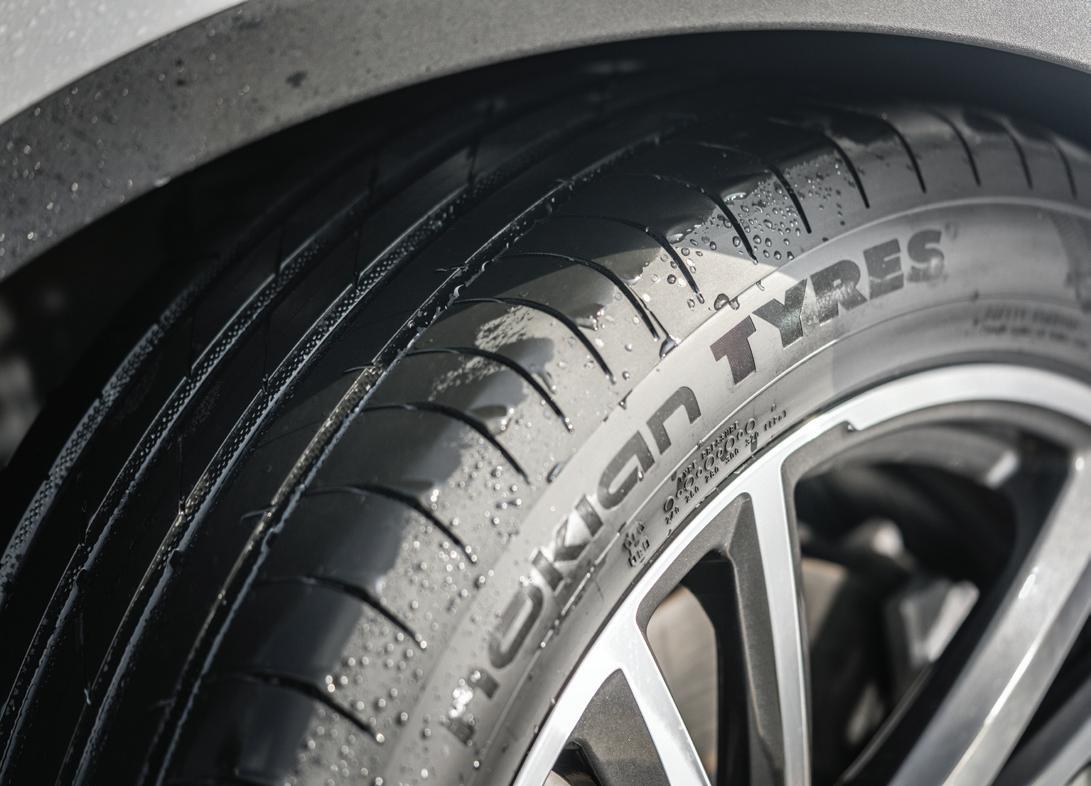
Along the same vein, in order to meet the sustainability targets of tyre manufacturers – namely, to produce completely “green” tyres by 2050, German specialty chemicals company Lanxess is offering the first sustainable variant of the TMQ antidegradant for rubber compounds, made with over 50% sustainable raw materials.
Antidegradants are chemicals that protect vulcanisates from harmful external influences, counteracting degradation caused by oxygen and heat. These processes can alter the properties of vulcanisates, leading to issues such as depolymerisation, fatigue, embrittlement, cracking, and even decomposition, which can ultimately damage the tyre.
Lanxess adds that in the case of TMQ, ISCC Plus certification demonstrates that the criteria for reliable balancing are met and correctly applied. Its facility at the production plant in Brunsbuettel, where Lanxess produces the antidegradant, will be certified this year.
This means that tyre manufacturers can use the sustainable TMQ variant, which is fully equivalent to its conventional counterpart in terms of its properties, without the need for fresh approval, it states.
Hankook
Nokian Tyres has tied up with Reselo to add renewable material made from residue birch bark to tyres
Events
4 – 6 DECEMBER
Plastics Recycling Show India (PRSI)
Venue: Mumbai, India
Tel: +44 0 7739 302081
Email: mabarber@crain.com
Website: www.prseventindia.com
4 – 7 DECEMBER
Plast Eurasia Istanbul
Venue: Tuyap Fair Convention and Congress Center, istanbul, Turkey
Tel: +90-212-867-11-00
Email: info@plasteurasia.com
Website: www.plasteurasia.com
2025
7 – 9 JANUARY
ArabPlast
Venue: Dubai, UAE
Tel: +971 50 557 4066
Email: sanjay@alfajer.net
Website: www.arabplast.info
12 – 14 FEBRUARY
ProPak Philippines
Venue: World Trade Center Metro Manila, Pasay City, Philippines
Tel: +63 2 8581 1930
Email: jessa.gonowon@informa.com
Website: www.propakphilippines.com
12 – 15 FEBRUARY
IPF Bangladesh
Venue: ICCB, Dhaka, Bangladesh
Tel: + 886-2-2659-6000
Email: exfdp@chanchao.com.tw
Website: www.chanchao.com.tw/ipf
18 – 20 FEBRUARY
plast alger
Venue: Palais des Expositions d'Alger - Safex, Algeria
Tel: +49-6221-4565-19
Email: f.detjen@fairtrade-messe.de
Website: www.plastalger.com
25 – 27 FEBRUARY
Asiamold Select - Guangzhou
Venue: Guangzhou, China
Tel: +86 20 3825 1558 Fax: +86 20 3825 1400
Email: asiamold@china.messefrankfurt.com
Website: www. asiamold-china.cn.messefrankfurt.com
11 – 14 March
Plastimagen Mexico
Venue: Centro Citibanamex, Mexico
Tel: +52 55-2919-5991
Email: oscar.sanchez@informa.com Website:www.plastimagen.com.mx
Check out the Advertisers' page on our website.
Information is categorised by the YEAR & DATE of publication for easy reference.
For further details, email us at: news@plasticsandrubberasia.com
14 – 15 MARCH
Koplas
Venue: Kintex, Korea
Tel: +82(2) 551-0102 Fax: +82(2) 551-0103
Email: koplas@koplas.com
Website: www.koplas.com
18 – 20 MARCH
ProPak Vietnam
Venue: SECC, HCMC, Vietnam
Tel: +84 28 3622 2588 (ext 167) Fax: +84 28 3622 2527
Email: propakvietnam@informa.com
Website: www.propakvietnam.com
18 – 20 MARCH
Plastics & Rubber Vietnam
Venue: Ho Chi Minh, Vietnam
Tel: +84 28 3622 2588
Email: plasticsvietnam@informa.com
Website: www.plasticsvietnam.com
15 – 18 April
Chinaplas
Venue: National Exhibition and Convention Center (Shanghai), China
Tel: +852 2516 3316
Email: Chinaplas.pr@adsale.com.hk. Website: www.chinaplasonline.com
9 – 12 May
Plastasia
Venue: Bangalore International Exhibition Centre, India
Tel: +91-98450 89641
Email: info@plastasia.in Website: www.plastasia.in
14 – 17 May
Metaltech & Automex
Venue: MITEC, Malaysia
Tel: +603 9771 2688 Fax: +603 9771 2799
Email: boonwye.yap@informa.com Website: www.metaltech.com.my
14 – 17 May
Plastic & Rubber Thailand
Venue: BITEC Bangkok, Thailand
Tel: +66 (0) 2036 0500
Email:plasticrubber-th@informa.com Website: www.intermachshow.com
14 – 17 May
Intermach and MTA Asia
Venue: BITEC Bangkok, Thailand
Tel: +66 (0) 2036 0500 Ext.216
Email:Intermach-th@informa.com Website: www.intermachshow.com
27 – 30 May
Greenplast
Venue: Fiera Milano, Italy
Tel: +39 02 8228371 Fax: +39 02 57512490
Email:info@greenplast.org Website: www.greenplast.orgI
www.plasticsandrubberasia.com
Publishing Office / Scandinavia, Benelux & France
Postbus 130, 7470 AC Goor, The Netherlands
Tel: +31 547 275005 Fax: +31 547 271831
Email: arthur@kenter.nl
Contact: Arthur Schavemaker
Regional Office
B6-11, Menara Indah, Jalan 9, Taman TAR 68000 Ampang, Selangor, Malaysia
Mobile: +6017-8849102
Email: tej@plasticsandrubberasia.com
Contact: Tej Fernandez
China & Hong Kong
Room 6B, Floor 6, Building HengLong, No. 50 Renming Zhong Road, Zhangjiagang, 215600 China
Tel: 0512-58919146
Fax: 0512-58919145
Mobile: +86-17751702720
Email: henry.xiao@matchexpo.com
Contact: Henry Xiao/Zhu Wei
Malaysia (Print, Web, Digital Advertising & Conferences)
Tara Media & Communications
Mobile: +6017 610 1270
E-mail: yokepeng@taramedia.com.my
Contact: Yoke Peng
Southeast Germany, Switzerland & Austria Verlagsbüro G. Fahr e.K
Breitenbergstrasse 17
D-87629 Füssen, Germany
Tel: +49 8362 5054990
Fax: +49 8362 5054992
Email: info@verlagsbuero-fahr.de
Contact: Simon Fahr
North-West Germany
JRM Medien+Verlag
Minkelsches Feld 39
D-46499 Hamminkeln, Germany
Tel: +49 2852 94180
Fax: +49 2852 94181
Email: info@jwmedien.de
Contact: Jürgen Wickenhöfer
Malaysia. India, Indonesia, Singapore, Thailand, Australia, New Zealand, Korea & Philippines
Tara Media & Communications
B6-11, Menara Indah, Jalan 9, Taman TAR 68000 Ampang, Selangor, Malaysia
Mobile: +6017-8849102
Email: tej@plasticsandrubberasia.com
Contact: Tej Fernandez
Italy, Spain & Portugal
MediaPoint & Communications Srl Corte Lambruschini, Corso Buenos Aires, 8, Vo Piano - Interno 9, 16129 Genova, Italy
Tel: +39 010 570 4948 Fax: +39 010 553 0088
Email: info@mediapointsrl.it
Contact: Fabio Potesta
Taiwan 宗久實業有限公司
Worldwide Services 11F-B, No.540 Sec.1, Wen Hsin Rd., Taichung, Taiwan
ENQUIRIES
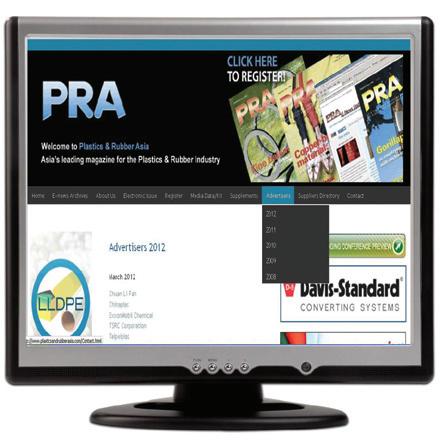
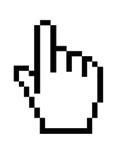

Tel: +886 4 23251784 Fax: +886 4 23252967
Email: global@acw.com.tw
Contact: Robert Yu 游宗敏
USA & Canada
Plastics Media International P. O. Box 44, Greenlawn, New York 117430, USA
Tel/Fax: +1 631 673 0072
Email: mjm@4m-media.com
Contact: Michael J Mitchell
www.plasticsandrubberasia.com
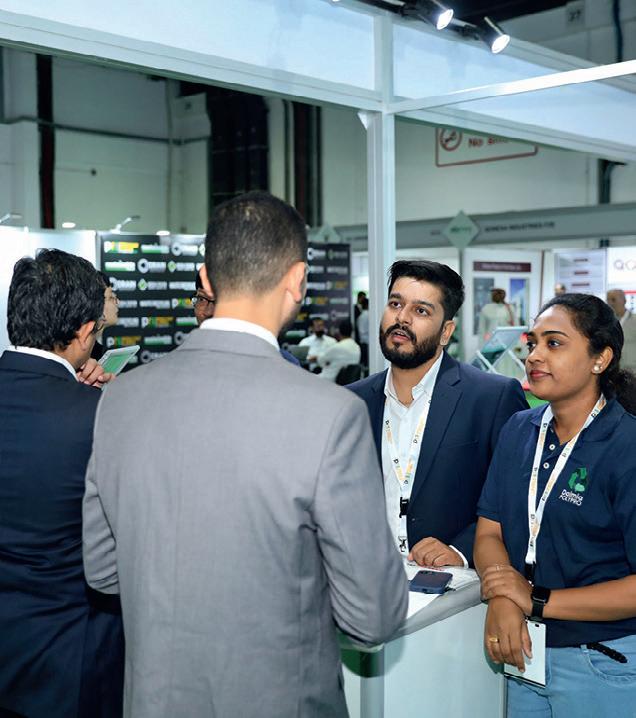

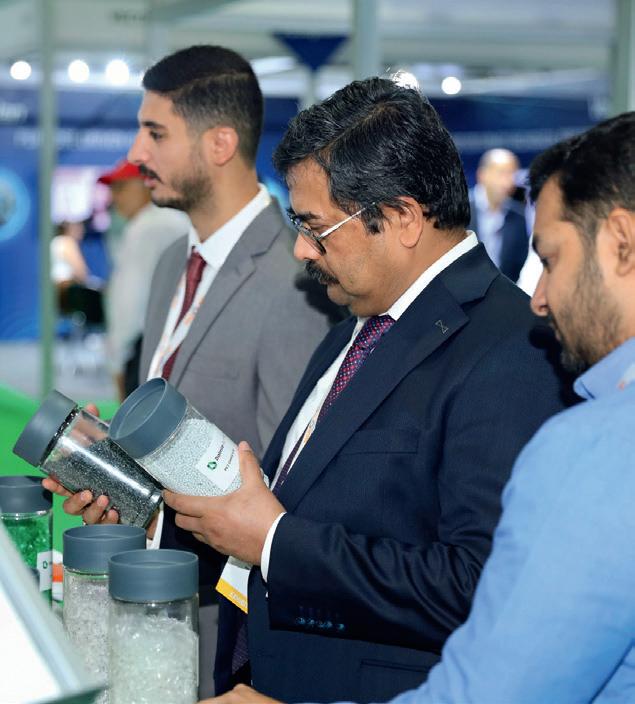
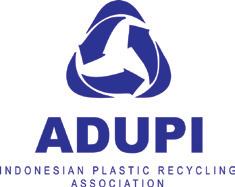
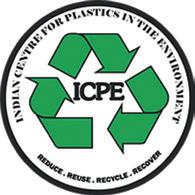
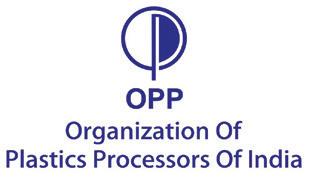
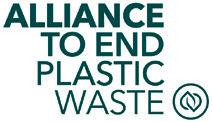
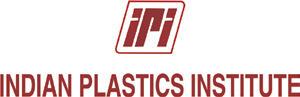
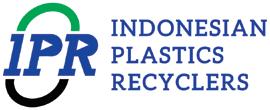