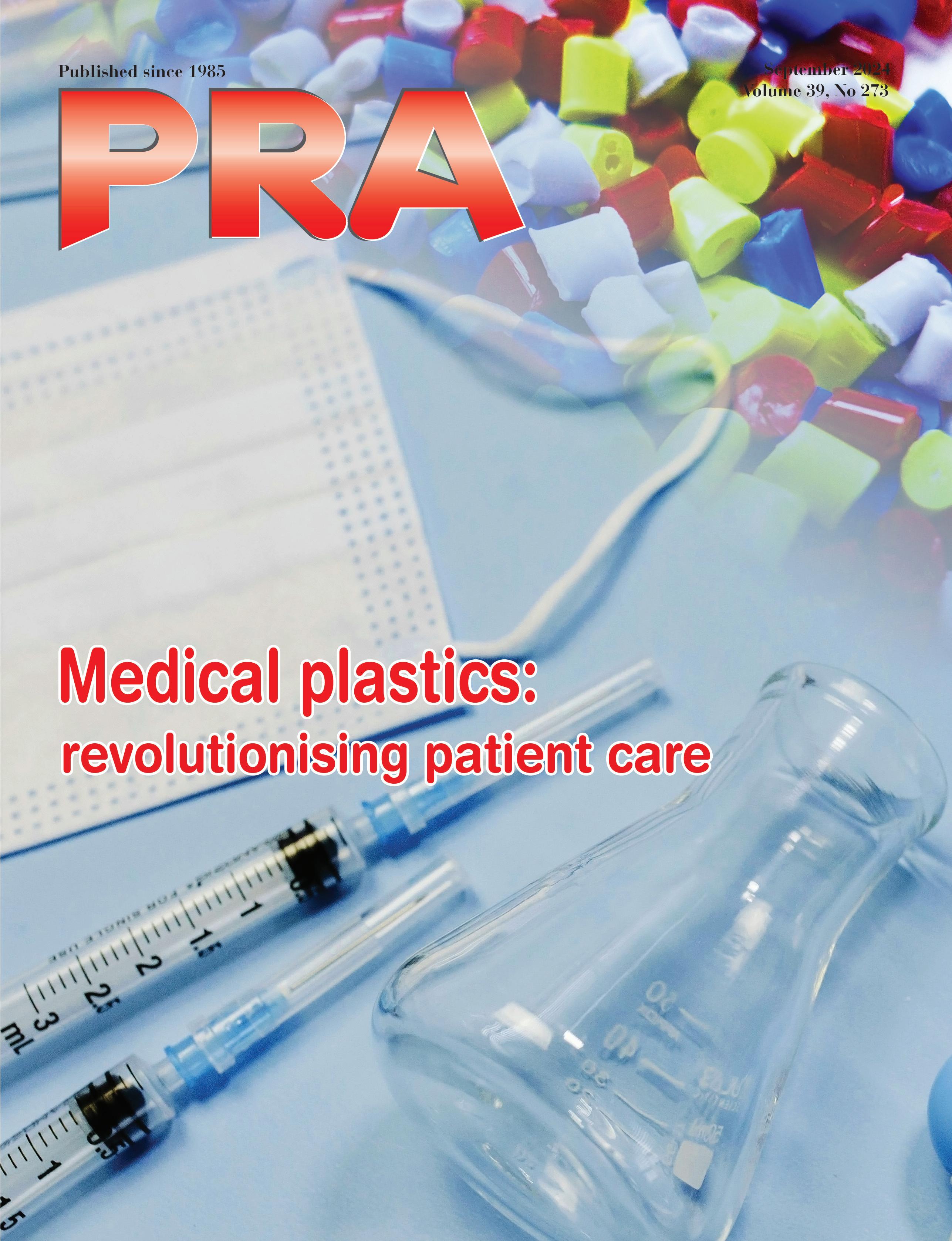
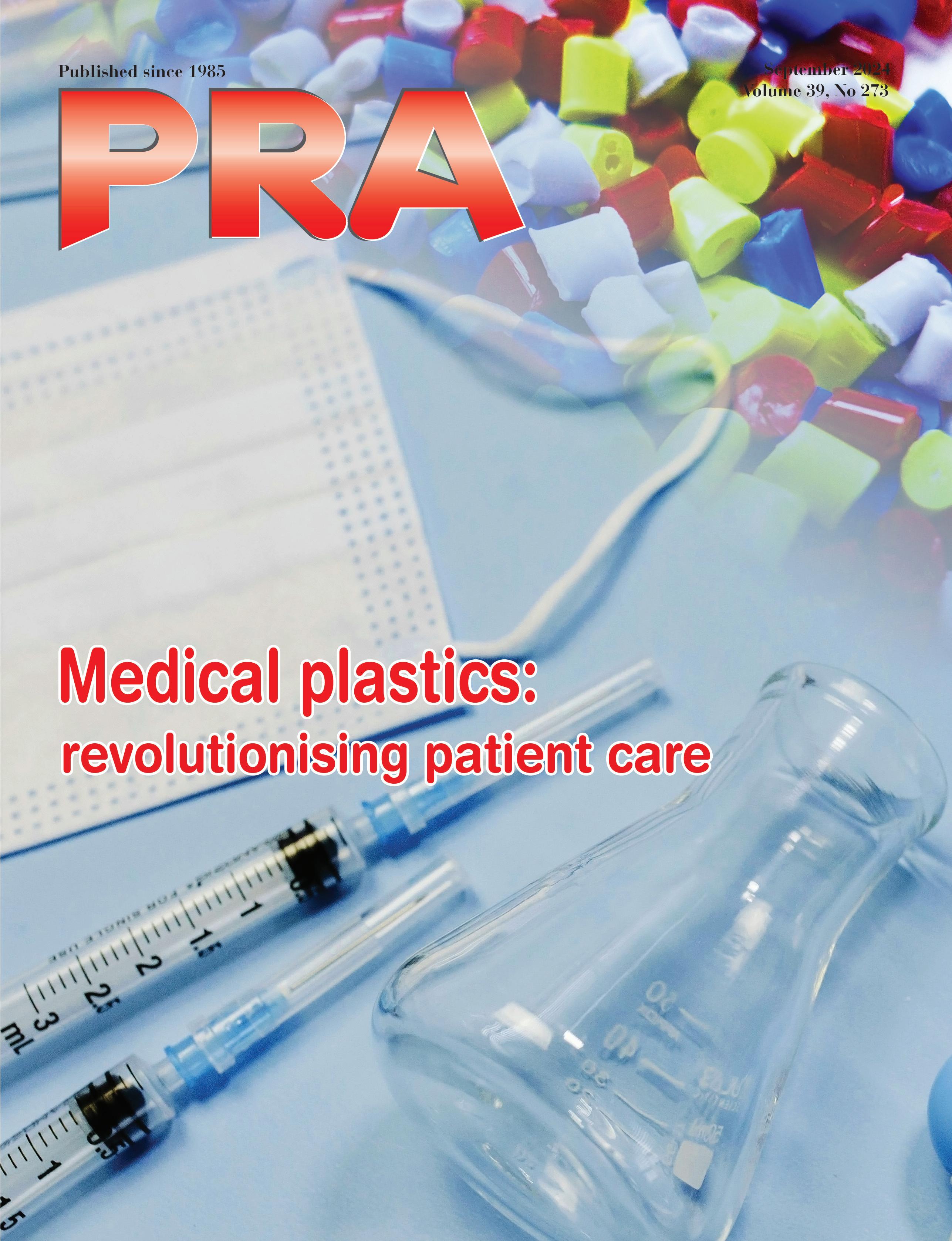
In this issue

Features
10 Advertorial – Discover excellence in PPE pharmaceutical and microbiological testing with Akron Rubber Development Laboratory (ARDL)
12 Renewables – The ASEAN region’s economic growth is fuelling an unprecedented demand for reliable and abundant energy, including fossil fuels and renewable sources, to support its expanding industries
16 Recycling – The Nanyang Technological University, Singapore (NTU Singapore), shares research on re-purposing e-waste plastics to grow “mini tumours” for laboratory testing in healthcare applications; converting hard-torecycle plastic waste into hydrogen and carbon additives for polymer foams used in cushioning and developing a method to break down plastics into valuable compounds using light.
18 Packaging – Highlights: ExxonMobil Chemical collaborated with value chain providers to develop high barrier MDO-PE/PE laminate for recyclable packaging; it also worked with Brazilian packaging converter Videplast for an ionomer-free VSP solution, reducing film thickness for food packaging applications. Meanwhile, Alpla and Zerooo have developed a standardised solution for reusable PET bottles for bathrooms and kitchens
Regulars
1 Industry News
4 Materials News supplements

country Focus: Taiwan is advancing sustainable energy and maintaining semiconductor industry leadership with clear strategies; this month the country will also host Taipeiplas 2024, from 24-28 September at Tainex, Taipei
Automotive: OEMs, vehicle makers and parts suppliers all have a vested interest in the sector, with sustainability-driven objectives. Asahi Kasei, Audi, LyondellBasell, Renault, and Antolin as well as BMW, Braskem and others are featured
Medical: Leading resin providers are offering advanced materials that improve the production of medical devices, promising to elevate patient care and enhance treatment outcomes
In this interview with Ellen Tan Go, President of PRIA (Philippine Rubber Industries Association Inc.), we find out how the Philippines rubber industry aims to produce competitive products by adopting technology, sustainability practices, and standards, and by connecting with local and global markets



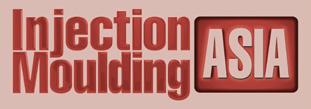
publisher/editor-in-chief
Arthur Schavemaker
Tel: +31 547 275005
Email: arthur@kenter.nl
Associate publisher/executive editor
Tej Fernandez
Tel: +6017 884 9102
Email: tej@plasticsandrubberasia.com
senior editor
Angelica Buan
Email: gel@plasticsandrubberasia.com
circulation
Stephanie Yuen
Email: stephanie@taramedia.com.my
layout/design
Prestige Trading
Email: prestige9a@gmail.com
permits
ISSN 1360-1245 is published 4 (four) times a year in English by Kenter & Co Publishers’ Representatives BV.
Whilst every effort is made to ensure that the information contained in this publication is correct, the publisher makes no warranty, expressed or implied, as to the nature or accuracy of such material to the extent permitted by applicable law.
© 2024 Kenter & Co Publishers’ Representatives BV No part of this publication may be reproduced, stored or used in any form, or by any means, without specific prior permission from the publisher.
PRA is a digital publication that is circulated free to trade readers in the plastics and rubber industry. Please view this link to subscribe/renew your free subscription: http://plasticsandrubberasia.com/register.html
www.plasticsandrubberasia.com www.rubberjournalasia.com www.injectionmouldingasia.com www.eog-asia.com
M&As/Tie-ups/ Investments
• Japan’s Denka Company Limited has invested in Carbon Fly, a start-up company developing carbon nanotubes, through a corporate venture capital (CVC) fund jointly managed with Pegasus Tech Ventures. Terms were not disclosed.
• US materials firm DuPont is acquiring Donatelle Plastics Incorporated, a medical device contract manufacturer specialising in the manufacture of medical components and devices. The transaction is expected to close in the third quarter 2024.
• US firm Dow is acquiring Circulus, a recycler of plastic waste. This transaction includes two facilities, one in Ardmore, Oklahoma, and another in Arab, Alabama, with a total capacity of 50,000 tonnes/year. It is
expected to close in the third quarter of 2024.
• Finnish sustainability fund UB Forest Industry Green Growth Fund (UB FIGG) and German specialty chemicals group Altana are investing in Finnish technology company Nordtreat. It specialises in the development and production of environmentally friendly flame retardants.
• South Korean energy/ chemical firms SK Innovation and SK E&S have merged, encompassing the value chain of both current energy sources (such as oil and LNG) and future energy sources (including renewable energy, hydrogen, and SMR), as well as electrification businesses like batteries and ESS.
• Technology firm Merck is selling its global Surface
Solutions business unit to Global New Material International Holdings Ltd (GNMI) for EUR665 million in cash. The transaction is expected to close in the course of 2025.
• Bangkok-based chemical producer Indorama Ventures has secured a new seven-year loan of US$200 million from the International Finance Corporation (IFC) to help fund the company’s sustainability programs in India, Thailand and Indonesia, and promote a circular economy.
• Additives firm Forward AM has acquired German chemical firm BASF’s additive manufacturing business, including Forward AM’s materials and solutions as well as its Sculpteo service business and leads to the creation of Forward AM Technologies
• Canadian recycling firm Polystyvert has closed
Plant Expansions/Plant Openings
• Australian recycling start-up Samsara Eco and Israelheadquartered nylon apparel maker Nilit are considering setting up a PA6.6 textile-to-textile recycled polymer production site in Southeast Asia, aiming to be operational by late 2026.
• India’s gas utility firm GAIL (India) and
US-based biofuel producer Petron Scientech Inc are exploring setting up of a 500 kilotonnes/year bio-ethylene plant in India.
• VTT Technical Research Centre of Finland and LUT University have opened a pilot plant in Espoo, Finland, to process captured
carbon dioxide into compounds that can replace fossil raw materials in plastic products and chemicals.
• Biotech firm Carbios and Zhink Group, specialising in PET and textiles, have tied up to build a 50 kiltonnes/ year PET recycling plant in China using Carbios’ technology.
the first tranche of a Series B funding for US$16 million, for the construction of its first commercial recycling plant in Montreal for PS waste, expected to start in 2026. Other companies supporting it include Infinity Recycling that led the round, followed by SWEN Blue Ocean, and Earth Foundry, an existing shareholder.
• The former Schenck Process Food and Performance Materials (FPM) group of companies have officially changed their name to Coperion. The transition follows the September 2023 acquisition of the companies by Hillenbrand, the parent company of Germanybased Coperion.
• Chemical firm LyondellBasell is acquiring full ownership of APK AG in Merseburg, Germany, which was under insolvency. Terms were not disclosed.
• Technology provider Lummus Technology and Eastern European oil/gas firm MOL Group are working on the first plastic recycling unit located at MOL’s facility in Tiszaújváro, Hungary. It will have a processing capacity of 40,000 tonnes/year of mixed waste plastics. As well, Lummus has licensed its PP technology to Petronet LNG for a
new US$2.4 billion, 500 kilotonnes/year plant in Dahej, Gujarat, India.
• India’s Bharat Petroleum Corporation has appointed Lummus to build a new ethylene plant in Bina, Madhya Pradesh state, India. Bharat has also selected tech firm Univation's Unipol PE process technology for two world-scale production lines to be located at its Bina Refinery site in Madhya Pradesh. The two units are designed to achieve a combined nameplate production capacity of 1 million tonnes/year of PE.
• Technology firm Wood has been awarded a $US40million engineering design contract by Japanese materials firm Kuraray to build a plant in Singapore to produce Kuraray’s Eval EVOH copolymer.
• A consortium comprising Abu Dhabi-based materials firm Borouge, Abu Dhabi National Oil Company (Adnoc) and Austrian chemical firm Borealis have tied up with China’s Wanhua Chemical and Wanrong New Materials, a subsidiary controlled by Wanhua Chemical Group, to study the feasibility of building a 1.6 million tonnes/year specialty polyolefins complex at Fuzhou, Fujian Province, China.
• Trelleborg Group is building a facility for engineered coated fabrics in Rutherfordton, North Carolina, US, to strengthen its positions in aircraft escape slides, water infrastructure, and advanced materials for healthcare and outdoor products. “
• India’s flexible packaging giant Jindal Poly Films Ltd, part of BC Jindal Group, is adding on a new BOPP line in Nashik, Maharashtra, by 2026 with a capacity of 60,000 tonnes/year.
• Germany’s BASF Catalysts India Private Limited (BCIL), a subsidiary of BASF Environmental Catalyst and Metal Solutions (ECMS), has inaugurated a new R&D lab at its site in Mahindra World City, Tamil Nadu, Chennai, for the development of emissions control catalysts tailored to the needs of the Indian automotive market.
• Chinese battery materials firm BTR New Material Group has opened its new lithium-ion battery anode materials plant in Indonesia. The project's first phase, which involved a US$478 million investment, has a capacity of 80,000 tonnes/year of anode materials. The second phase, scheduled to start in late 2024 with an additional
US$299 million investment, will expand the total capacity to 160,000 tonnes.
• Chemical firm Sabic is to build an engineering thermoplastics compounding plant in China’s Fujian Province. It will primarily produce pelletised Lexan PC and Cycoloy PC/ABS blends.
• Invista Nylon Chemicals (China) Co. has opened its US$240 million PA6.6 polymer expansion at the Shanghai Chemical Industry Park (SCIP). It has doubled the annual capacity of PA6.6 polymer to 400,000 tonnes. Elsewhere, Invista is investing US$17 million to restart its Hexamethylene Diamine (HMD) plant in Ontario, Canada, which was closed in 2009. HMD is a key ingredient in the production of PA6.6. The plant could start production in the first quarter of 2025.
• Trelleborg Sealing Solutions has inaugurated a new R&D facility providing local innovation backed by global expertise in Bangalore, India.
• Henkel Adhesives Technologies India Private Limited has completed Phase III of its Loctite facility in Kurkumbh, Maharashtra, to serve the adhesives, sealants, and surface treatment markets. Henkel has also
launched a second application centre in Thanh Hoa, north Vietnam, to expand its support for sports and fashion brands in AsiaPacific and China.
• US chemical firm Huntsman Corp. has opened a new innovation centre in Tienen, Belgium, for its PU business.
• Specialty materials provider Trinseo has opened a polymethyl methacrylate (PMMA) depolymerisation plant in Rho, Italy.
• Ineos Olefins & Polymers Europe has commissioned a new pilot line that it will use with customers to co-develop recyclable flexible packaging films. It has installed a multilayer, blown film line, supplied by Japanese machine maker Hosokawa Alpine, with Machine Direction Orientation (MDO) at its R&D centre in Brussels, Belgium.
• Japan’s Teijin Ltd has added on a production line for its PC resin Panlite sheet and film, located at its Matsuyama plant in Ehime Prefecture, with a capacity of 1,350 tonnes/year.
• China’s Changhua Chemical is constructing the country’s first manufacturing site for Carnol, a new
line of polycarbonate ether (PCE) polyols with 20-30% fewer greenhouse gases, in Lianyungang. It is targeting commercial volumes of about 80,000 tonnes in early 2025 and will scale to over 1 million tonnes in the coming years.
• Plastics processor Röchling Industrial is investing EUR10 million in setting up a sustainability centre in Germany to process more than 10,000 tonnes/year of plastic waste.
• Thailand-based chemical producer Indorama Ventures Public Company Limited, through its direct subsidiary – IVL Dhunseri Petrochem Industries Limited - and Dhunseri Ventures Limited have formed a joint venture with Varun Beverages Limited, PepsiCo's
second-largest bottling company globally outside the US, to establish two PET recycling facilities in India by 2025. One facility is in Kathua within the Jammu Division in Northern India, while the other is in Khurdha, Odisha. The aim is to reach 100 kilotonnes/year capacity of rPET across all the facilities when combined.
• India’s Reliance Industries Ltd (RIL) is setting up PVC and CPVC manufacturing facilities at its existing locations in Dahej and Nagothane with a total capacity of 1.5 million tonnes/ year, to commence commercial production in 2026-27. It is also expanding its polyester capacity by 1 million tonnes/ year and PTA capacity by 3 million tonnes/ year, also to be built by 2026–27.
Universally applicable –Optimised for your needs.
No matter if you are manufacturing metallised standard food and non-food packaging, easy-to-recycle stand-up pouches from MOPE film or technical products, SML's cast film lines are always optimised for your specific requirements.
Extrusion lines. Engineered to perform.
• Lummus Technology has been awarded a contract by Silleno LLP for an ethylene unit, which will be part of the first PE plant to be built in Kazakhstan, which will convert ethane from the Tengiz oil field into 1.3 million tonnes/year of ethylene.
• China’s Rongsheng Petrochemical has started trials at its polyolefin elastomer (POE) plant in Zhoushan, Zhejiang province. The alphaolefin pilot production facility has a capacity of 300 tonnes/ year of 1-octene or 1,000 tonnes/year of 1-hexene with alternative process conditions.
• BASF will end the production of adipic acid, cyclododecanone (CDon) and cyclopentanone (CPon) at its Ludwigshafen plant
in Germany. The production plant for CDon and CPon will be shut down in the first half of 2025 and the remaining adipic acid production in Ludwigshafen will be closed in the course of 2025, as part of the ongoing strategic review of its production set-up and to ensure competitiveness under changing market conditions.
• Russian petrochemical group Sibur is building a facility for piloting base polymer production technologies in Tobolsk at a cost of more than 6 billion rubles. The facility that will open end of 2024 will have a design capacity of up to 300 tonnes/ year, with possibility to test a broad range of grades of PE and PP to meet the demand for Russia.
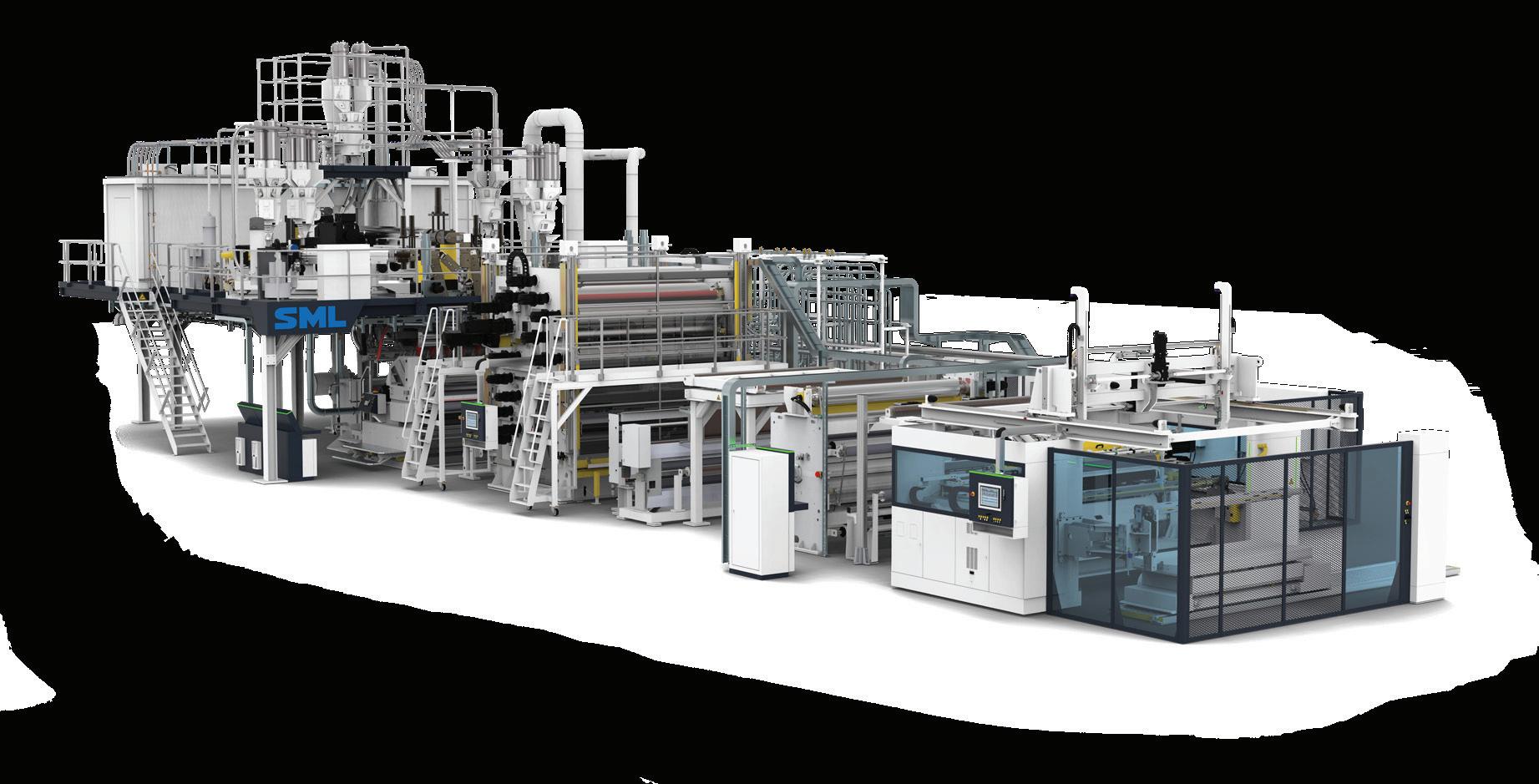
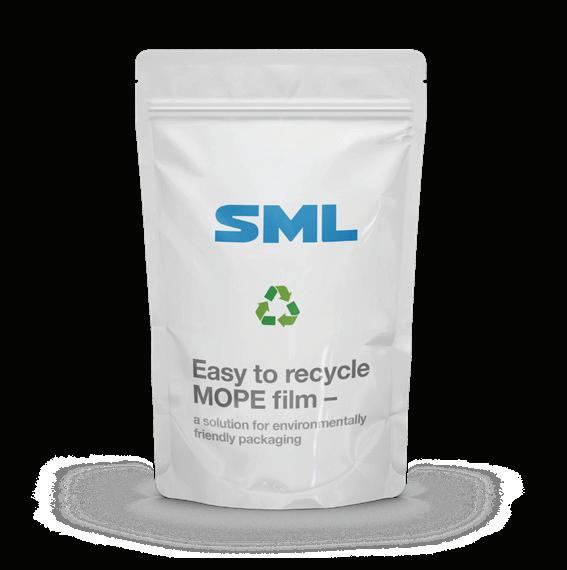
Learn more about SML's cast film lines.
Asia turns environmental challenges into sustainable opportunities
Asia's growing waste problem is driving a shift toward a circular economy by repurposing waste into high-value applications, says Angelica Buan in this report.
The global plastics waste problem has reached critical levels, with millions of tonnes generated each year, posing severe environmental and economic challenges. In Asia, the situation is particularly pressing. The World Bank 's report, What A Waste 2.0 - A Global Snapshot of Solid Waste Management to 2050 , projects that waste generation in the Asia-Pacific region will rise from approximately 802 million tonnes in 2016 to 1.1 trillion tonnes by 2030.
Similarly, waste volumes in Southeast Asia have surged since 2000, reaching around 150 million tonnes in 2016, with it to more than double by 2030, according to the United Nations Environment Programme (UNEP) summary report on Waste Management in ASEAN Countries.
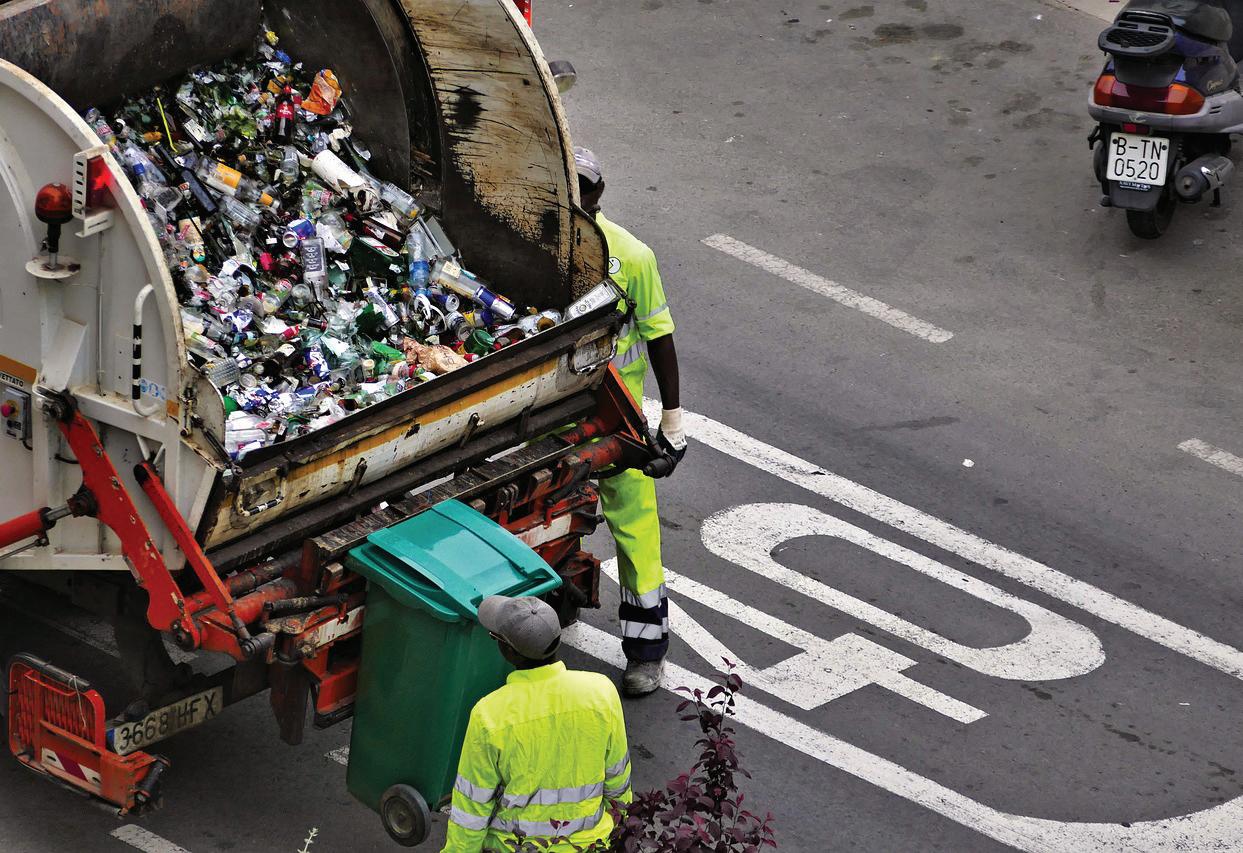
In response, Asia is emerging as a leader in innovative waste management, with various initiatives aimed at transforming waste into high-value materials. These efforts include converting plastics into versatile products, from packaging to industrial applications.
As such, these initiatives not only reduce environmental impact but also drive the circular economy, where materials are continually repurposed, minimising the need for new resources.
This shift is crucial for advancing sustainability, as it promotes efficient resource use, reduces waste, and fosters a more resilient, eco-friendly future.
Thailand: versatile bioplastics made from pineeapple waste
Thailand faces severe issues with unmanaged plastic waste, with 2.88 million tonnes of plastic not being recycled each year, resulting in an 87% loss of material value, according to a World Bank circularity analysis. Poor recycling systems, a lack of recycling design, and inadequate source segregation all contribute to low-quality recyclables and feedstock contamination.
Despite these hurdles, Thailand is leveraging its position as a regional bioplastics hub, owing to its strong raw material production and advanced technology across the bioplastics supply chain.
A recent collaborative effort by researchers from Thailand and Malaysia exemplifies this progress. They have developed a biodegradable film made from leftover pineapple stems, offering a sustainable alternative to traditional plastic films.
Led by Associate Professor Taweechai Amornsakchai from Mahidol University, the team created this film using high amylose starch from pineapple stems, combined with glycerol and citric acid to enhance flexibility. The film’s mechanical properties can be tailored by adjusting citric acid levels, making it suitable for various single-use applications where high strength is not required.

materials suitable for a variety of industries
Waste volumes in Southeast Asia could more than double by 2030, according to World Bank
Thai researchers have succeeded in creating biodegradable materials from pineapple leaf fibers, which can be transformed into durable, high-performance
The biodegradable film offers water resistance, heat-sealability, and fully disintegrates in soil within a month. This innovation is expected to reduce reliance on non-biodegradable materials by repurposing agricultural waste, marking a significant advancement in sustainable packaging solutions and promoting the circular economy.
Similarly, the Thai team of reseachers have also made significant strides in sustainable materials by upcycling waste HDPE milk bottles into high-stiffness composites reinforced with pineapple leaf fibres (PALF). This innovative approach has resulted in a 162% increase in flexural strength and a 204% increase in modulus, making the composites not only stronger but also environmentally friendly by sequestering carbon.
The process involves blending rHDPE with PALF and non-fibrous materials (NFM), which are then layered and compressed into composite sheets. The inclusion of PALF enhances the mechanical properties of the HDPE, particularly its heat distortion temperature (HDT), making it suitable for applications like automotive parts where durability under high temperatures is crucial.
The study highlights the potential of using agricultural waste for sustainable composite development, showing how waste can be transformed into durable, highperformance materials applicable across various industries, including the biomedical and automotive sectors, the researchers noted.
Bangladesh: practical farming solution with plastics
In recent years, Bangladesh has experienced a significant increase in plastic consumption. Data suggests that in 2020, the annual per capita plastic use in urban areas rose to 9 kg, tripling from 2005. This increase is largely attributed to the rise in the use of LDPE packaging materials, including plastic bags and wrappers.
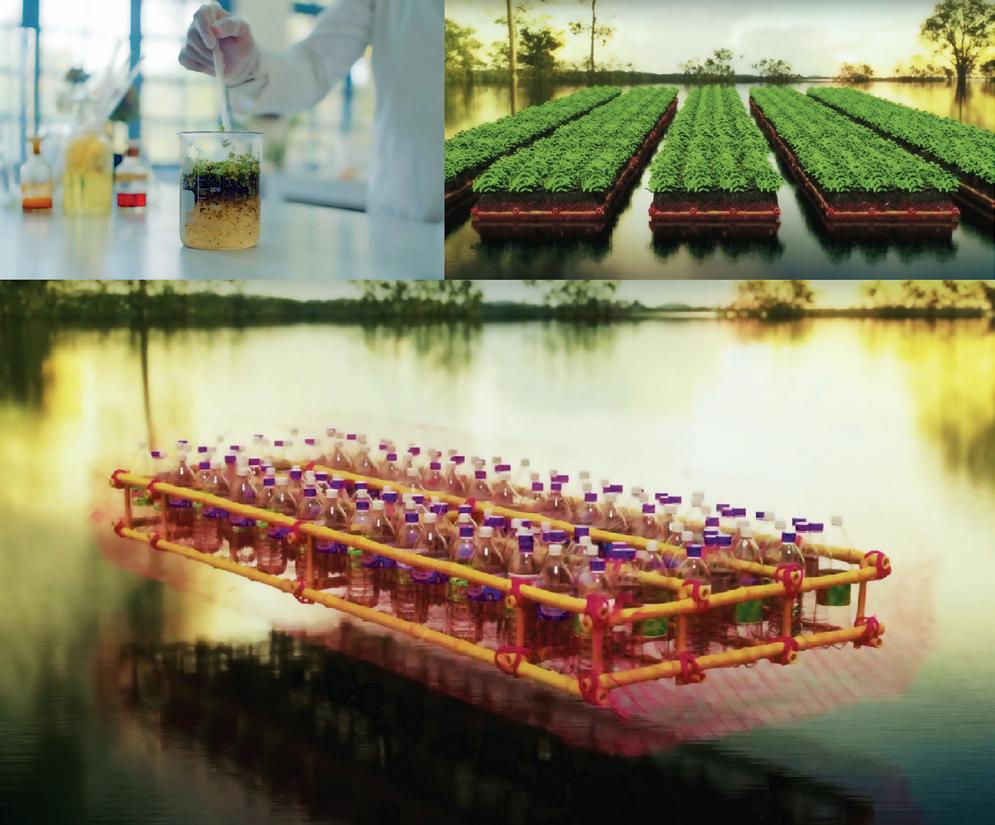
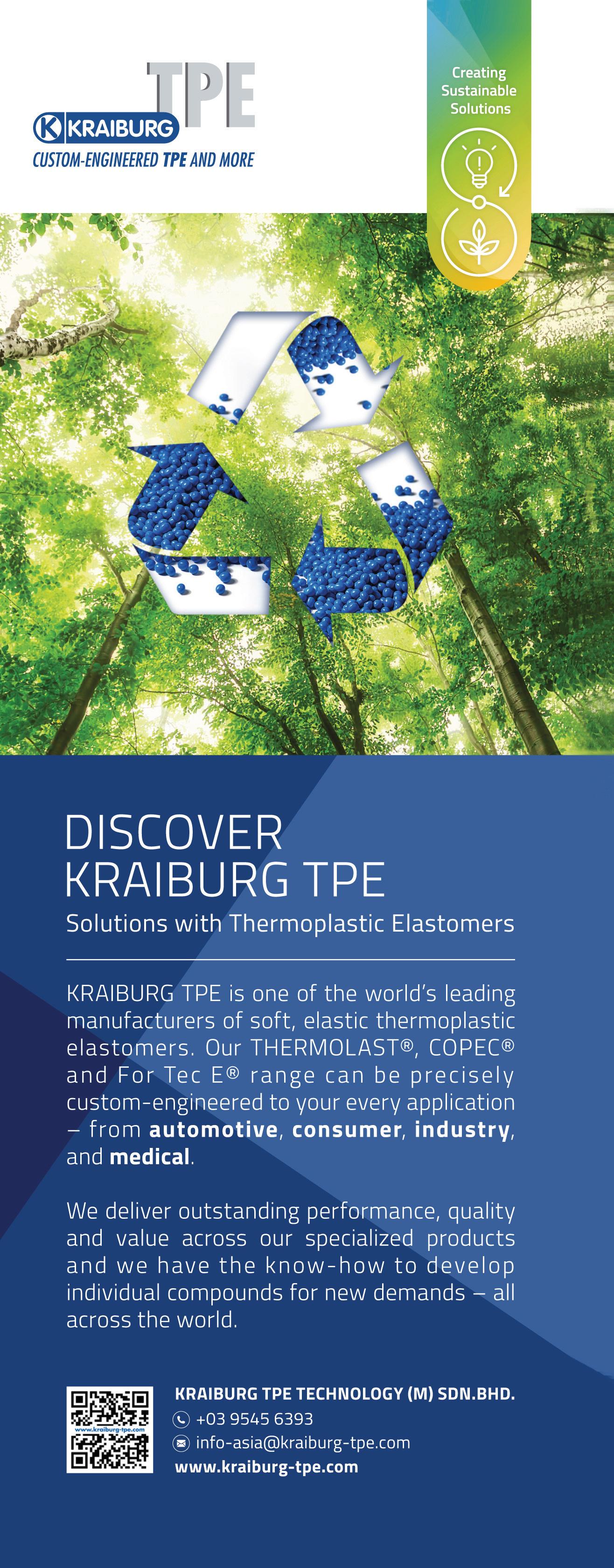
Bangladesh's plastic farming initiative, led by MGI, ingeniously utilises plastic bottles for floating farms, benefiting both farmers and the environment
Despite the soaring consumption, recycling efforts have lagged behind. In 2020, only 31% of the 977,000 tonnes of plastic used was recycled. The bulk of this waste consists of single-use plastics, such as shopping bags and wrappers, which have become a major source of pollution.
This mismanaged plastic waste has contributed to severe environmental issues, with pollution affecting urban areas, rural landscapes, and waterways including rivers and canals. It has also impacted the country’s agriculture sector because it is reportedly losing fertile land to rising sea levels and floods, and plastic across its rivers. It has adversely affected farmers’ livelihood and the nation’s food security.
Bangladesh is primarily an agricultural nation and it contributes nearly 14.8% to its GDP as well as employs about 41% of the labour force.
In response to environmental and agricultural challenges, an initiative, known as Plastic Farming, led by conglomerate Meghna Group of Industries ( MGI ), has garnered global praise. This project transforms plastic bottles into floating farms, benefiting both farmers and the environment.
MGI partnered with Bidyanondo Foundation , a local NGO that aids impoverished communities, to train landless farmers in this sustainable practice. They also collaborated with local authorities and farming communities to collect plastic waste from waterways as well as instruct communities on creating and using plastic floating beds for crop cultivation.
Implemented in the landless farming communities of Tungipara, Gopalganj, and Pirojpur districts, the floating farms are constructed using recycled plastic bottles arranged vertically in simple bamboo frames, covered with netting and topped with water hyacinth compost for planting. Crop seeds are planted in the compost. The plastic-based structure is expected to be durable enough for repeated use.
To address microplastic contamination, farmers can utilise water-based fungi, which are found effective in degrading microplastics and widely available in Bangladesh. After two years of R&D, agricultural scientists identified the water-based fungi as a key element in this hydroponic farming method.
Philippines: paving roads with "plastic sachets“
The Philippines is considered a significant contributor to marine plastic pollution, primarily due to its extensive use of single-use plastics, particularly multilayer sachets and pouches. This widespread consumption has earned the country the designation of a "sachet economy," with an estimated daily use of 163 million sachets, according to a 2021 World Bank report.
To address this issue, the government has developed an innovative approach by repurposing plastic waste for road construction. While plastic waste asphalt has been used in various Asian countries, it has also been tested in several locations within the Philippines.
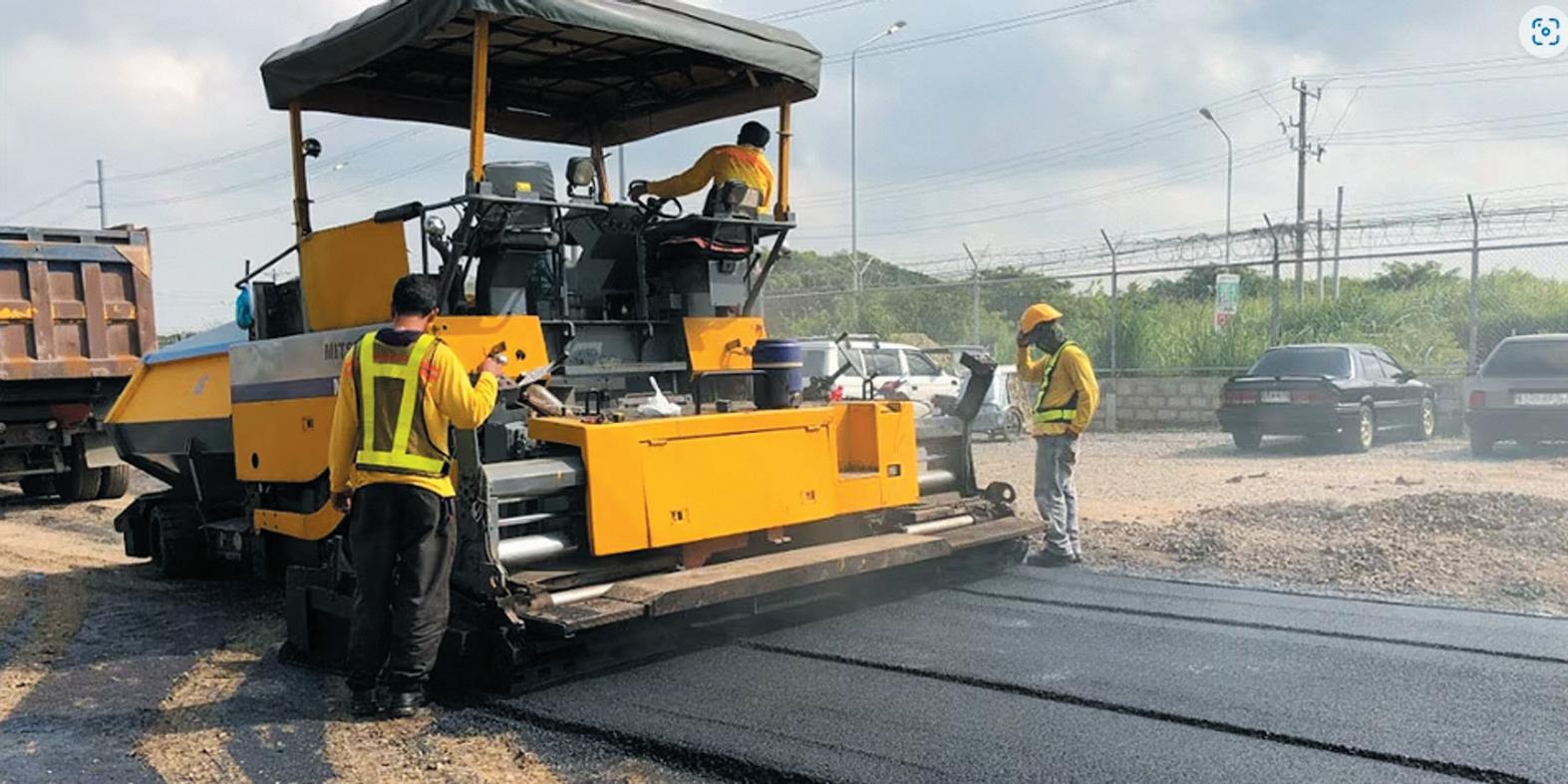
The Philippines' sachet economy takes a U-turn with plastic road plans; the country had its first recycled plastic road, with asphalt made from recycled plastics, through an SMCled initiative
Recently, the Department of Public Works and Highways (DPWH) approved a new initiative to integrate plastic waste into the construction of national roads. This strategy aims to alleviate the problem of unrecycled and hard-to-recycle plastics, including sachets.
DPWH Secretary Manuel Bonoan noted that incorporating waste plastics into road materials can enhance the durability of asphalt pavements.
DPWH has also set standards for incorporating recycled materials into road construction, such as the use of LDPE plastic bag waste in bituminous concrete. The policy promotes shredding LDPE waste and adding it to asphalt concrete to enhance durability and meet DPWH standards.
In 2019, multinational conglomerate San Miguel Corporation ( SMC ) introduced Philippines' first recycled plastics road. This pilot project involved laying asphalt made with recycled plastics on a 1,500-sq m test site at a new logistics centre in Cavite, south of Manila. The test site was selected due to its use as a marshaling area for heavy trucks and equipment.
For this project, approximately 900 kg of plastic waste, equivalent to around 180,000 sachets and plastic bags, were utilised.
SMC's technology partner, US materials company Dow, explained that recycled plastic waste is used as a binder in conjunction with bitumen to produce the asphalt. This method is expected to enhance the durability and longevity of roads compared to traditional asphalt. Pending further testing, SMC plans to use this technology for building roads at its facilities and for major infrastructure projects.
India: new spin on post-consumer recycled plastics with pails
India generates 15 million tonnes of plastic waste annually, but only a quarter of this is recycled due to an inadequate solid waste management system, according to the United Nations Development Programme (UNDP).
To tackle this, it has partnered with Hindustan CocaCola Beverages Private Limited ( HCCBPL ), Hindustan Unilever Limited ( HUL ), HDFC Bank , and the Coca-
Cola India Foundation ( CCIF ) to improve the collection, segregation, and recycling of all plastics. India is one of 12 countries, along with China, Russia, Brazil, Mexico, Vietnam, Iran, Indonesia, Egypt, Pakistan, the US and Turkey, that together account for 60% of the world’s mismanaged plastic waste, according to the Plastic Overshoot Day report by Swiss non-profit firm EA Earth Action.
While waste plastics are typically viewed as an environmental challenge, they are proving to be a valuable resource for companies like US materials firm ExxonMobil in achieving their sustainability goals.
ExxonMobil's new 20-l lubricant pails, launched in India in 2023, feature 50% post-consumer recycled (PCR) content, marking a first for lubricant packaging in the country. This initiative has recycled the equivalent of approximately 2.3 million plastic bottles, as well as jars, and battery casings, into these pails, which are also recyclable.
The company, working with plastic recyclers and compounders, has sourced 115 tonnes of recycled plastic for these pails. This effort aims to set a higher standard for PCR use in industrial-grade packaging.
ExxonMobil says it has conducted extensive tests at its Bengaluru R&D Technology Centre (BRDTC) to ensure that the PCR plastic does not affect the quality of the lubricating oils and that the pails meet quality-control standards for leakage, stacking, handling, and impact.
The company further that it continues to advance initiatives in India to enhance the recyclability of plastic packaging, including developing mono-material packaging solutions.
ExxonMobil's new 20-litre lubricant pails, launched in India in 2023, are the country's first to feature 50% post-consumer recycled content
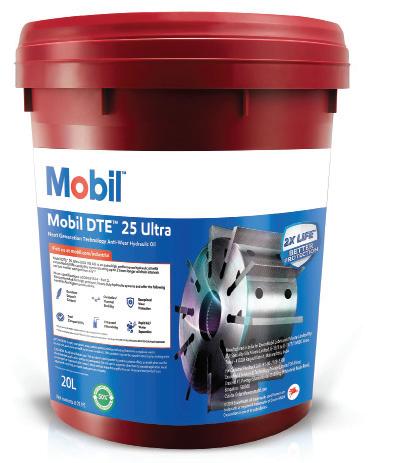
Recycling medical devices through the thermochemical method
Medical waste being overlooked
Disposable healthcare items are creating enormous amounts of waste, which is incinerated, but in many countries ends up in landfills. The Covid pandemic was an eye-opener to the mountain of medical waste and contributed to an avalanche-like increase in disposable items being used. Worldwide, used face masks alone were estimated to weigh around 2,641 tonnes/day in 2022.
In circular economy policies, medical waste is often overlooked since disposable healthcare items usually consist of several types of plastic that cannot be recycled with today's technology.
In addition, the items must be considered contaminated after use, and so, they must be handled so that risks of spreading potential infections are avoided. When it comes to the production of single-use healthcare items, it is also not possible to use recycled plastic, since the requirements for purity and quality are so high for materials intended for medical use.
Light at the end of tunnel for medical waste
Researchers at Chalmers University of Technology ,
in Sweden, have now shown how mixed waste from healthcare can be recycled in a safe and efficient way, using a technique where the material is heated and converted into chemical building blocks, which can then be used in the production of new plastic.
The technology is called thermochemical recycling and is based on a process called steam cracking. It breaks down the waste by mixing it with sand at temperatures up to 800°C. The plastic molecules are then broken apart and converted into a gas, which contains building blocks for new plastic.
Martin Seemann, Associate Professor at Chalmers' Division of Energy Technology, says the method “destroys bacteria and other microorganisms”.
"What are left are different types of carbon and hydrocarbon compounds. These can then be separated and used in the petrochemical industry, to replace fossil materials that are currently used in production."
Great potential for saving valuable chemicals
To test the technology in real life, the researchers have carried out two different projects in parallel in a test facility at Chalmers Power Central.

Researchers at Chalmers University of Technology, in Sweden, have now shown how mixed waste from healthcare can be recycled in a safe and efficient way, using a technique where the material is heated and converted into chemical building blocks, which can then be used in the production of new plastic
In the first project, a few different product types, such as face masks and plastic gloves, have gone through the process. In the second, a mixture was created that represents the average composition of hospital waste from the region's hospitals. The mixture contained about ten different plastic materials, as well as cellulose.
The results have been consistently positive in both projects, which shows the great potential that exists in the technology.
One of the projects was led by Judith González-Arias, now at the University of Seville in Spain, who says the method “facilitates the recovery of valuable carbon atoms”.
Furthermore, the researchers say this method is the “only” option available, given the strict regulations on medical use materials.
According to Seemann, "The same strict requirements for purity and quality actually also apply to food packaging. This is why the vast majority of plastic collected from packaging is incinerated today, or recycled into items where lower quality is allowed.”
The two projects build on previous Chalmers research, which has shown how mixed plastic waste can be converted into raw material for new plastic products of the highest possible quality.
The technology works well, but other factors also come into play
To scale up the method, new material flows and functioning business models need to be established, in collaboration between the healthcare and recycling sectors. Laws and regulations at different levels may also need to be changed in order for thermochemical recycling to be widely implemented in society.
Seemann adds, "For example, a requirement for carbon dioxide capture, when incinerating plastic, would create incentives to instead invest in more energy-efficient alternative technologies such as ours.”
Many countries have the technical prerequisites for recycling medical waste and other mixed plastic waste through steam cracking. However, regulations and structural conditions vary, which determines how players in waste management, the chemical industry and product manufacturing would need to work together to create functioning value chains in different places in the world.
Sweden lacks volume for thermochemical recycling
In Sweden, there is a great deal of interest in recycling, but single-use items from healthcare do not in themselves create large enough waste volumes for a functioning circular business model. Around 4,000 tonnes of such plastic were put on the market in the country in 2019.
"To build a plant of the size required for profitable thermochemical recycling, you would have to ensure a material flow of around 100,000 tonnes/year before startup," says González-Arias.
She says that new collaborations would therefore be needed between several different players for commercial thermochemical recycling, where healthcare waste could be part of the material flow.
The process would be optimised if a Swedish plant was built in an existing chemical cluster, such as the one in Stenungsund. The Chalmers researchers collaborated with Austrian polyolefins firm Borealis during the development of the technology since it has a steam cracker and related facilities there.
According to Seemann, “The technology is more energy-efficient than some other methods for recycling components in the plastic, such as carbon dioxide capture during incineration to use the carbon dioxide as a building block for new materials.”
The paper Steam gasification as a viable solution for converting single-use medical items into chemical building blocks with high yields for the plastic industry has been published in Resources, Conservation and Recycling.
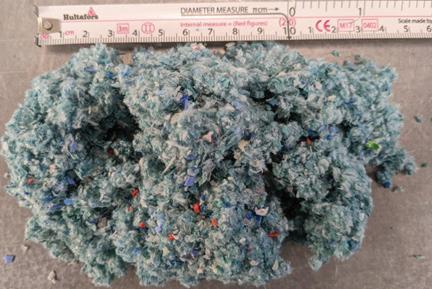
Ground healthcare items used in the experiments. The material mix includes gloves, surgical gowns, tubing and marker pens, among other things
TaipeiPLAS & ShoeTech Taipei 2024 kick off in September
TaipeiPLAS 2024 (Taipei International Plastics & Rubber Industry Show), a biennial event, will host 400 exhibitors across 1,800 booths, representing a 38% increase from the 2022 edition.
The event, scheduled for September 24-28 atTaipei Nangang Exhibition Centre, Hall 1, in conjunction with ShoeTechTaipei (Taipei International Shoe MakingTechnology Show), marks the return of international buyers after a six-year hiatus due to Covid-19. According to the show organiser, TAITRA, visitors from over 45 countries have registered, including delegation groups from India, Vietnam, Myanmar, and Algeria.
This year's TaipeiPlas will focus on main themes as "Innovative Materials," "Advanced Manufacturing," and "Circular Economy.” All-star exhibitors include Chen Hsong, Chumpower, CLF, Conair, CYKF, Diing Kuen, FCS, FKI, Formosa Chemicals & Fibre, Formosa Plastics, Huarong, igus, JSW, Lung Meng, Maguire, Moretto, Multiplas, Polystar, Siemens, Tenso, Victor Taichung, Wittmann, and YE I. The event will showcase the latest industry advancements, high-performance products for diverse
applications, and circular economy solutions with the addition of three new zones: “Bio, Recycled Plastics & Green Products,” “Composite Materials,” and “Adhesives & Glues.”
Chen Hsong will showcase its all-electric liquid silicone rubber (LSR) injection moulding machine, ideal for medical, electronic, optical, and consumer products. Igus will present its dry-tech bearings, designed to replace traditional metal bearings in extreme environments. Great Eastern Resins Industrial will feature its eco-friendly TPU resins, offering high toughness, strength, bio-compatibility, and a reduced environmental footprint compared to traditional materials.
TaipeiPLAS 2024 will also highlight the industry's sustainable and green supply chain. The “Visionary and Sustainable Development Summit,” held on September 25, will feature experts from BASF, Arburg, Wittmann, Remondis, Victor Taichung, Formosa Plastics, and Eternal Materials, who will share their experiences in low-carbon transformation. Register now at www.taipeiplas.com.tw. For more details, visit the website, follow on social media, or subscribe to the newsletter.
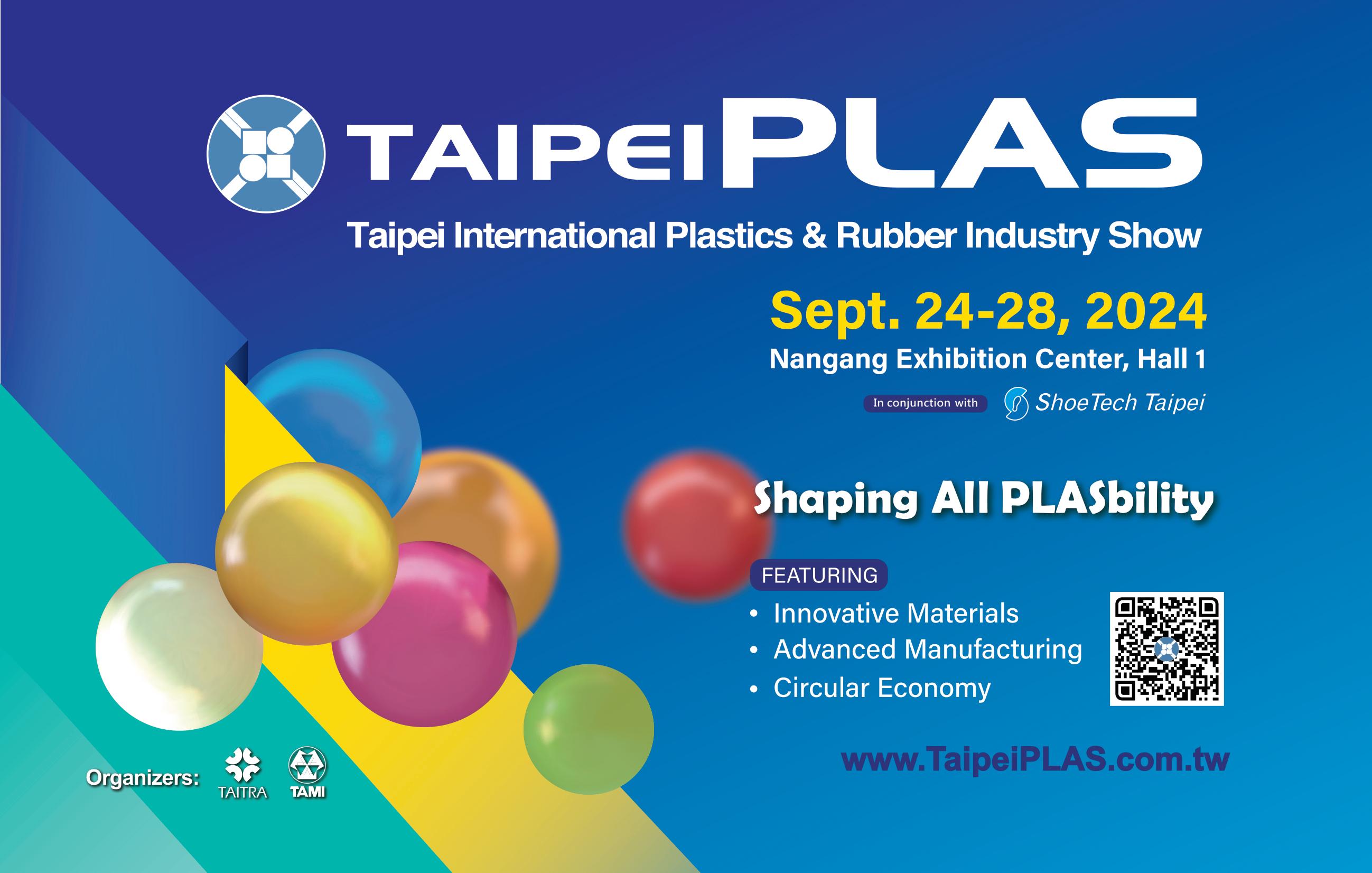
Discover Excellence in PPE Pharmaceutical and Microbiological Testing with ARDL
In the ever-evolving world of the medical and pharmaceutical industries, ensuring the safety, efficacy, and compliance of the Personal Protective Equipment products is paramount. Akron Rubber Development Laboratory, Inc. ( ARDL ) stands at the forefront of this mission, offering unparalleled testing services that set the gold standard in the industry. With decades of innovation, experience, state-of-theart facilities and a commitment to excellence, ARDL is your trusted partner for all your PPE testing needs.
At ARDL, quality is not just a promise, it is a guarantee. The laboratory is certified to the highest standards of quality management and laboratory competence. These certifications ensure that every test conducted meets rigorous international standards, providing you with reliable and accurate results.
ARDL’s Pharmaceutical and Microbiological Testing Services are certified under ISO 9001 (QMS Requirements), ISO 17025 (Testing and Calibration Laboratories QMS) and ISO 13485 (Medical Devices QMS).
ARDL’s data is recognized and accepted worldwide and used for regulatory compliance, compound development and troubleshooting, competitor analysis and supply chain assurance purposes. ARDL offers a wide array of testing services tailored to meet the diverse needs of the medical and pharmaceutical sectors.
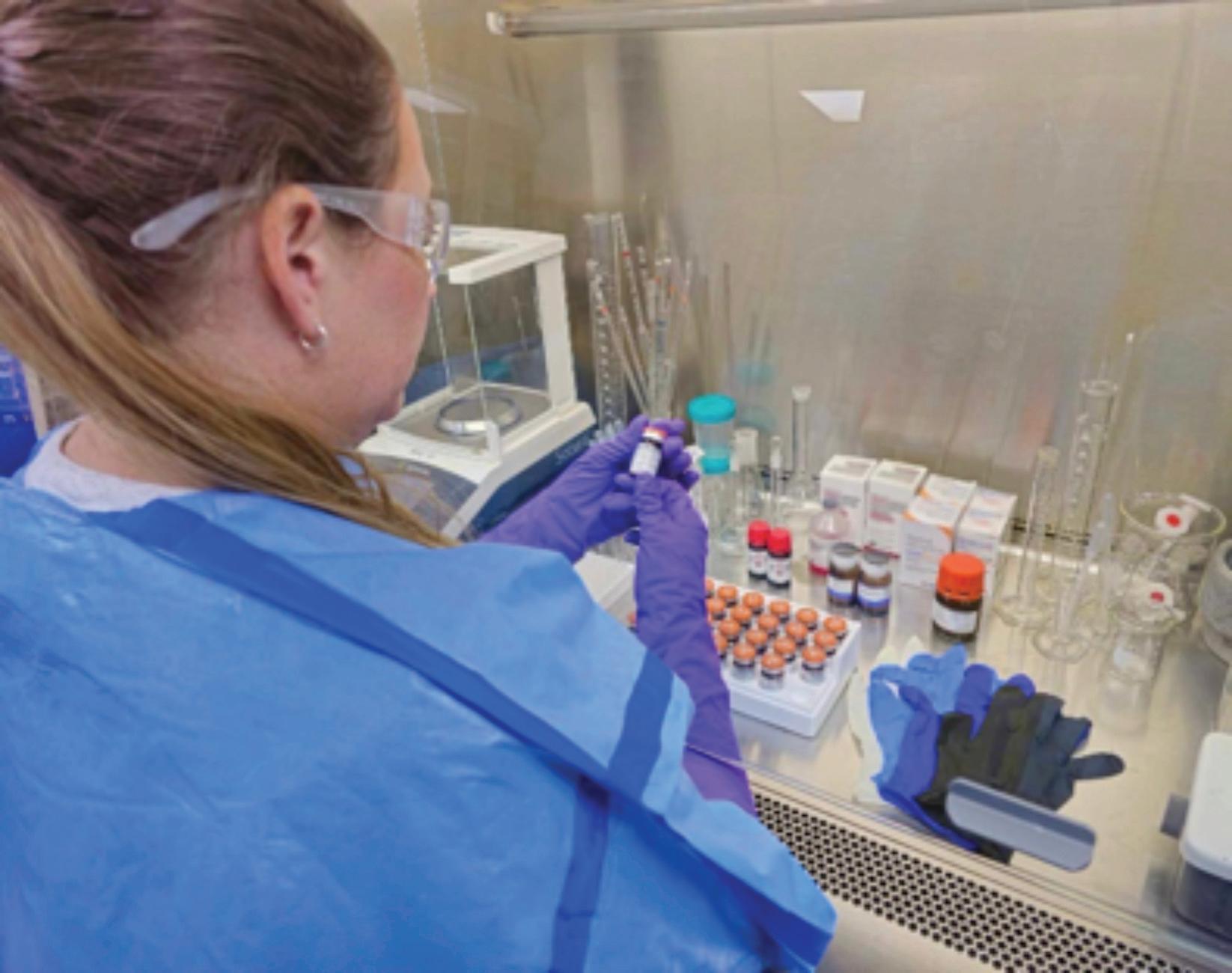
ARDL’s expertise includes : ASTM F3267-22 Standard Specification for Protective Clothing for Use Against Liquid Chemotherapy and Other Liquid Hazardous Drugs – Newly Added
ASTM D6978-05(2023) Standard Practice for Assessment of Resistance of Medical Gloves to Permeation by Chemotherapy Drugs
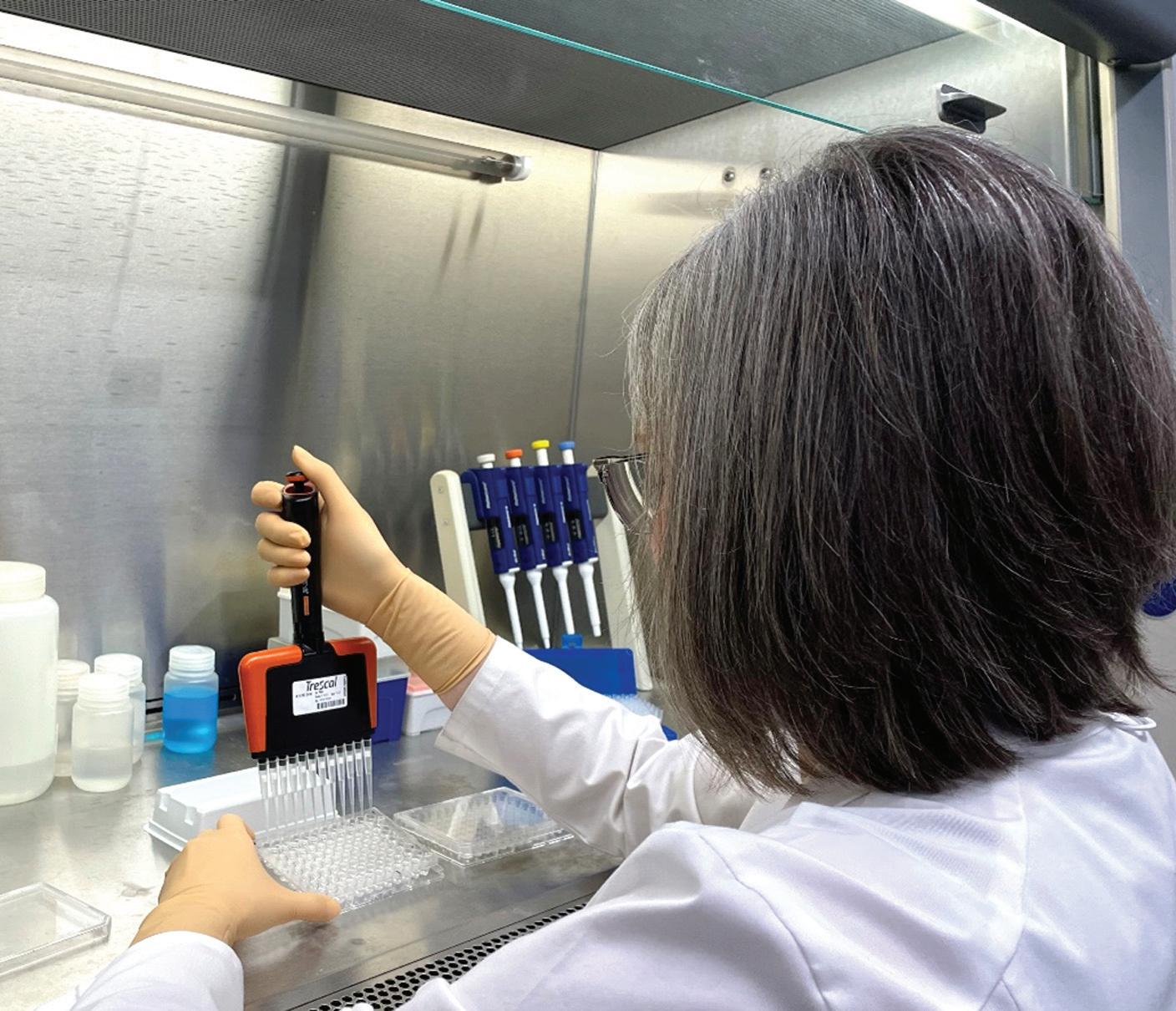
ASTM F1670/1670M-24 Standard Test Method for Resistance of Materials Used in Protective Clothing to Penetration by Synthetic Blood
ASTM F1671/1671M-22 Standard Test Method for Resistance of Materials Used in Protective Clothing to Penetration by Blood-Borne Pathogens Using Phi-X174 Bacteriophage Penetration as a Test System
ISO 16604:2004 Clothing for protection against contact with blood and body fluids — Determination of resistance of protective clothing materials to penetration by blood-borne pathogens — Test method using Phi-X 174 bacteriophage
ISO 10993-5:2009 Biological Evaluation of Medical Devices ( Tests for in vitro cytotoxicity )
ASTM F739-20 Standard Test Method for Permeation of Liquids and Gases Through Protective Clothing Materials Under Conditions of Continuous Contact
ASTM D5712-15(2020) Standard Test Method for Analysis of Aqueous Extractable Protein in Latex, Natural Rubber, and Elastomeric Products Using the Modified Lowry Method
ASTM D6499-24 Standard Test Method for Immunological Measurement of Antigenic Protein in Hevea Natural Rubber (HNR) and its Products
ANSI/AAMI PB70 Standard includes four standard tests to evaluate the barrier effectiveness of surgical gowns, isolation gowns, and surgical drapes (PPE-Info - Standard Details (cdc.gov))
AATCC 42 Impact Penetration2
AATCC 42 Impact Penetration
AATCC 127 Hydrostatic Pressure3
AATCC 42 Impact Penetration
AATCC 127 Hydrostatic Pressure
ASTM F1670 Synthetic Blood Penetration Test (for surgical drapes)
ASTM F1671 Viral Penetration Test (for surgical and isolation gowns)
1 In order of increasing protection
Bacteriophage Phi-X174
2 American Association of Textile Chemists and Colorists (AATCC) 42 Water resistance: impact penetration test determines the ability of a material to resist water penetration under spray impact [AATCC 2000]
3 AATCC 127 Water resistance: hydrostatic pressure test determines the ability of a material to resist water penetration under constant contact with increasing pressure [AATCC 1998]
Consulting and STAT services are available as well as Volume Discounts where applicable.
AdvertoriAl
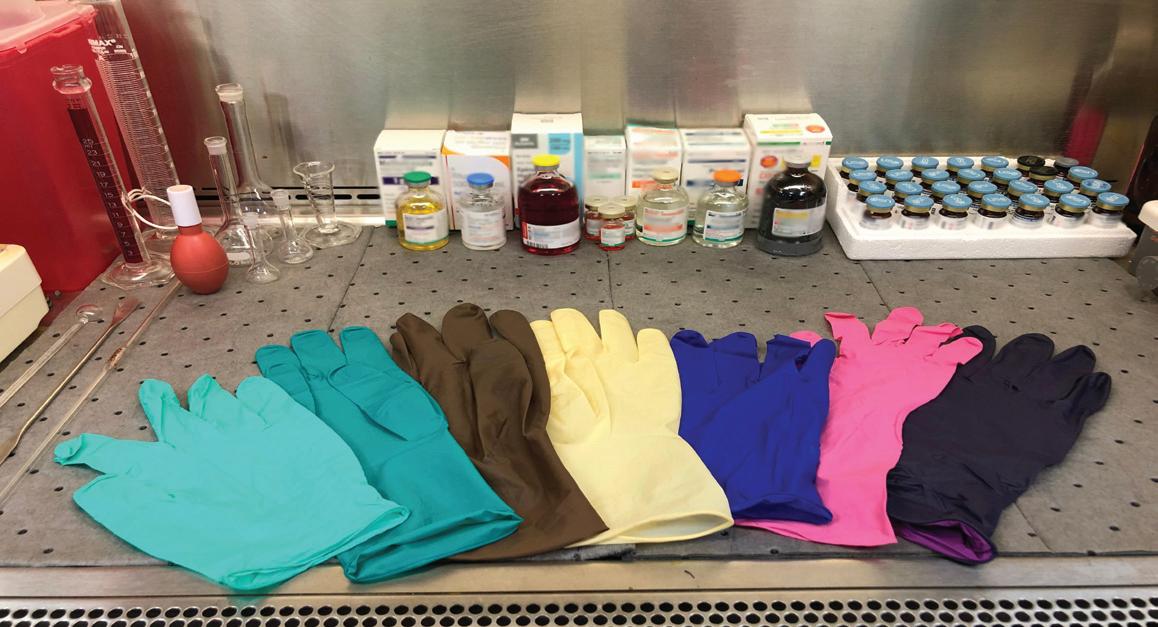
Expected Barrier Effectiveness
= 4.5 g = 1.0 g = 20 cm = 1.0 g = 50 cm
no penetration at 2 psi (13.8 kPa)
no penetration at 2 psi (13.8 kPa)
Minimal water resistance (some resistance to water spray)
Low water resistance (resistant to water spray and some resistance to water penetration under constant contact with increasing pressure)
Moderate water resistance (resistant to water spray and some resistance to water penetration under constant contact with increasing pressure)
Blood and viral penetration resistance (2 psi)
In a field where safety and compliance are paramount, ARDL stands out as a beacon of excellence. ARDL’s extensive certification, advanced testing methods, and customer-centric approach make it the ideal partner for all your pharmaceutical and microbiological testing needs. By choosing ARDL, you are not just selecting a testing laboratory, you are partnering with a team of experts dedicated to ensuring the safety and efficacy of your products.
Visit www.ardl.com or contact them directly at sales@ardl.com to learn more about how ARDL can support your testing needs. Experience the ARDL difference and discover why they are the trusted choice for leading companies in the PPE medical and pharmaceutical industries.
EnErgy SEctor
Renewable energy gains momentum in ASEAN countries
The region’s economic growth is fuelling an unprecedented demand for reliable and abundant energy to support its expanding industries, says Angelica Buan in this report.
As the Asia-Pacific region expands its economic footprint, securing reliable and abundant energy sources is vital. In ASEAN, rising energy demand is driven by population growth, urbanisation, and industrialisation. Rising industrial activity also intensifies the need to meet growing energy demands while balancing sustainability.
The International Renewable Energy Agency ( IRENA ) in its “Renewable Energy Outlook for ASEAN” report says that the region will experience a 4% annual growth in energy demand until 2025, resulting in a 50% increase from 2014 levels.
ASEAN aims to decarbonise emissionsintensive sectors like transport, industry, and energy, targeting 23% of primary energy from renewables by 2025, despite rising energy demand
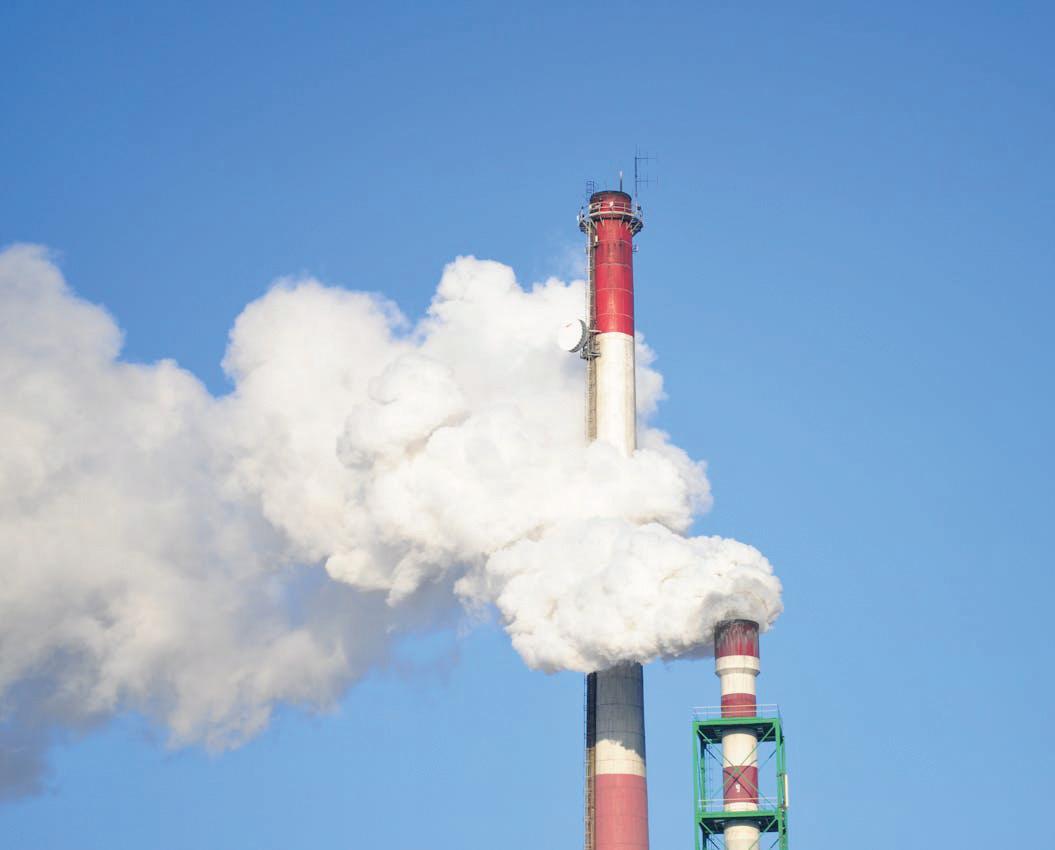
Electricity demand alone is projected to double between 2014-2025. To address this growing demand, ASEAN continues to rely on limited domestic fossil fuel resources, leading to a greater dependence on imported fossil fuels.
Rising demand for fossil fuels is also increasing carbon emissions, which contributes to air pollution. Energy-related emissions are projected to rise by 61%, reaching over 2.2 Gt/year by 2025.
To address this, ASEAN aims to decarbonise emissions-intensive sectors such as transport, industry, construction, manufacturing, and energy. The region is targeting to source 23% of its primary energy from modern, sustainable renewables by 2025, even as overall energy demand continues to grow significantly.
Despite the dominance of fossil fuels, transitioning to renewable energy sources is increasingly a priority among ASEAN nations. Key technologies such as green hydrogen, carbon capture utilisation and storage (CCUS), smart grids, offshore wind, and energy storage, along with expanded use of solar, wind, geothermal, and ocean energies, will be critical for achieving net-zero emissions.
Breaking free from coal use
Coal dominates the Asian energy mix, making up 57% of electricity generation due to rising demand.
The International Energy Agency ( IEA ) reports that China alone consumes 50% of the world's coal output and with India, Indonesia, Vietnam, and the Philippines, accounting for over 70% of global coal demand.
However, coal’s contribution to greenhouse gas emissions (GHG) compels countries to transition away from coal. Reducing coal use is imperative for limiting global warming to 1.5°C. Despite this urgency, completely abandoning coal remains a challenge.

Coal accounts for 57% of Asia's electricity generation, driven by rising demand
Reports indicate that while coal use is expected to peak and then decline, coal power plants continue to supply energy to factories, industries, and households due to their low cost and availability. On a brighter note, ASEAN nations are shifting away from coal in favour of cleaner energy alternatives. The region's commitment to reducing carbon emissions and addressing air pollution and climate change is driving this transition toward renewable energy and sustainable growth.
Indonesia: dominance in geothermal energy capability
According to the IEA, ASEAN’s coal demand surged by 13% to 413 million tonnes in 2022, with Indonesia accounting for nearly half of this total. Power generation consumed 71% of this coal. Demand is expected to increase to 528 million tonnes by 2026, largely driven by Indonesia's growing consumption, with a rise to 444 million tonnes projected for 2023.
In 2023, Indonesia became the fifth-largest coal generator globally, surpassing South Korea, according to Ember Climate data. Indonesia’s coal generation surged by 74% from 125 TWh in 2015 to 217 TWh in 2023, with a 7.1% annual growth rate. This growth has propelled Indonesia from eleventh to fifth place, overtaking powerhouse economies like Germany, Russia, Australia, and South Africa.
Indonesia's Batang Power Plant, with a capacity of 2 x 1,000 MW and utilising Ultra Super Critical (USC) technology, commenced commercial operations in 2022
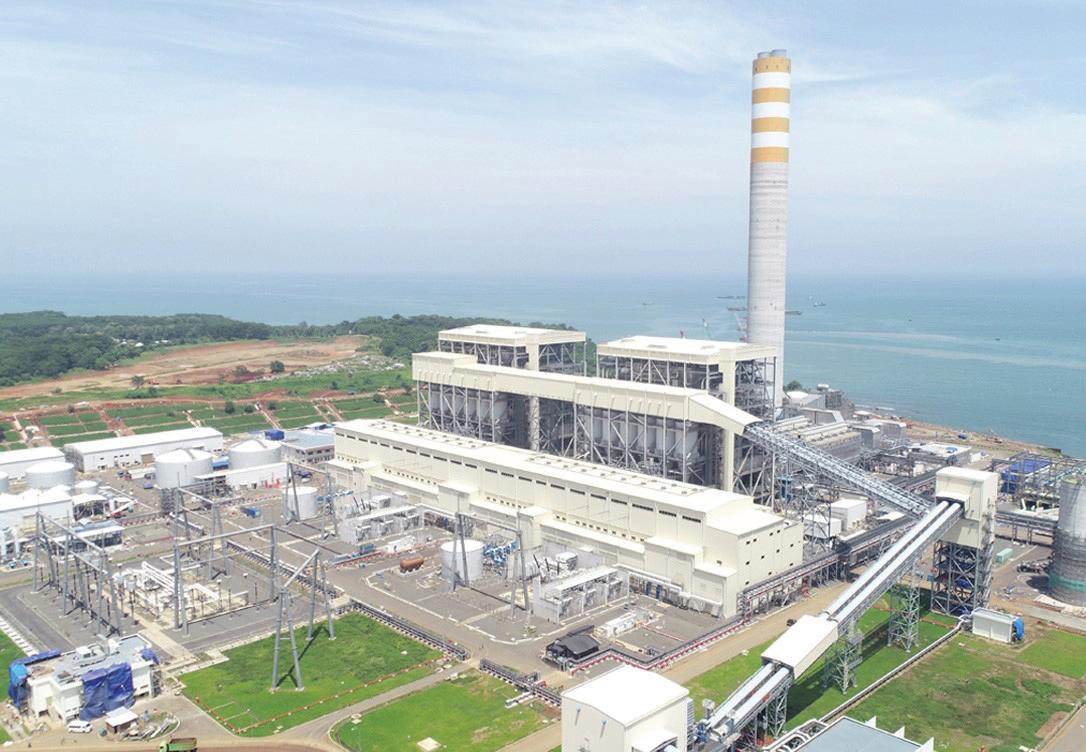
New coal-fired plants are focused on supporting nickel production, vital for electric vehicle batteries and steel. Indonesia, with 42% of the world's nickel reserves and substantial copper, gold, and tin, is investing in expanding nickel production to meet rising global demand. Regarding renewable energy, Indonesia aims for 23% of its energy mix by 2025 and 31% by 2050, as noted by the Minister of Energy and Mineral Resources at the 2022 IEA Clean Energy Transitions Summit.
According to Energy Tracker Asia , Indonesia ranks among the top five Asia-Pacific countries for renewable energy capacity, with 16 geothermal power plants operating across the country. These plants, with capacities ranging from 2.5 MW to 377 MW, are predominantly located in Java and Sumatra. Hydropower and geothermal plants currently contribute 8% and 5% to the country's energy mix, respectively.
The Asian Development Bank (ADB) has provided a boost to Indonesia to maximise its geothermal energy potential, estimated at 29 GW, and its second-largest installed capacity of 2.1 GW. ADB extended a US$300 million loan to PT Geo Dipa Energi (GDE), a state-owned geothermal developer, to expand geothermal power generation by 110 MW in Java. Additionally, ADB will oversee a US$35 million loan from the Clean Technology Fund for this project.
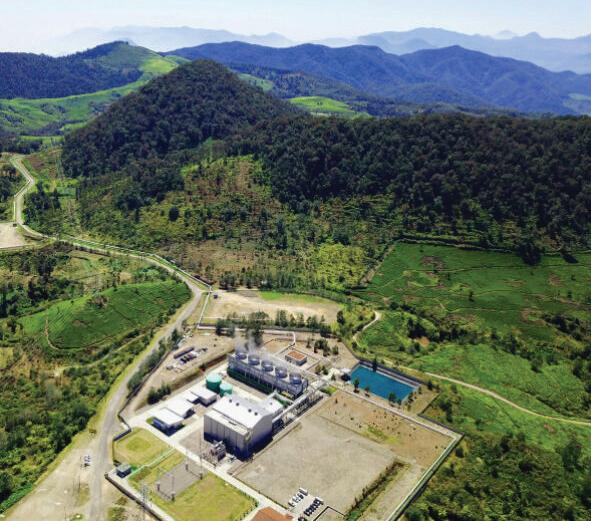
The geothermal power generation project will support the construction of two plants, including one in Patuha, West Java. This initiative aims to enhance GDE’s capabilities in planning and executing geothermal projects and conducting governmentsupported drilling, thereby attracting private sector investment to develop new geothermal sites.
Meanwhile, GDE recently secured a EUR825,000 grant from Germany’s Kreditanstalt für Wiederaufbau Bankengruppe ( KfW ), for drilling two temperature core holes in the Candi Umbul Telemoyo geothermal working area in Central Java, Indonesia.
Malaysia: roadmap for clean energy
The Malaysian government aims to achieve 31% of its total energy mix from renewable sources by 2025 and 70% by 2050, as part of its strategy to reach net-zero greenhouse gas emissions by 2050.
To support this transition, Malaysia has introduced three key policies to boost renewable energy, according to Global Data . These policies include the Renewable Energy Act, the National Renewable Energy Policy and Action Plan, and the Sustainable Energy Development Authority (SEDA) Act.
The Renewable Energy Act 2011 established a feed-in tariff (FiT) system with targets up to 2030 and guidelines for renewable energy tariffs. In 2021, the Ministry of Natural Resources, Environment and Climate Change (NRECC) set a renewable energy target for 2025, aligning with Malaysia's climate commitment to reduce carbon intensity by 2030.
The Malaysia Renewable Energy Roadmap (MyRER) includes assessing installed capacity and resources, setting technology-specific targets, and developing a strategic roadmap.
ADB supported renewable projects, including a geothermal power project to build two plants, one in Patuha, West Java

These efforts have positioned Malaysia as an attractive destination for expansion by major energy technology companies. For instance, Malaysia's largest clean energy firm, Solarvest Holdings Berhad , has secured a RM113 million EPCC contract with P Solar Sdn Bhd to develop a 45 MWp solar farm in Mukim Pekan, Pahang.
This project will generate 57,500 MWh/year of clean energy, offsetting around 36,800 tonnes of CO2 emissions. Scheduled for completion by the end of 2025, the farm is expected to produce nearly 60,000 Renewable Energy Certificates (RECs) to help companies meet sustainability goals.
The solar farm will be equipped with monsoonresistant designs and high-quality panels and inverters, with plans to integrate battery energy storage systems in future phases. Moreover, Solarvest is pursuing further opportunities to further advance Malaysia’s renewable energy capacity, targeting 40% by 2050.
Philippines: alliances to drive renewable energy goals
The Philippines is accelerating its shift to renewable energy, forging key partnerships to enhance its sustainable power efforts, to reduce the nation’s carbon footprint and bolster energy security.
In recent developments, wpd GmbH , a German company that develops and operates onshore and offshore wind farms and solar parks, and is actively engaged in 28 countries around the world, is set to invest over Php392 billion to set up offshore wind farms in the Philippines, in the provinces of Cavite, Negros Occidental, and Guimaras.
In 2023, it was reported that the company sought to register energy projects worth approximately Php55 billion with the Board of Investments (BOI). These projects, totalling a planned capacity of 565.6 MW, consist of onshore wind and solar photovoltaic (PV) power projects in Aklan, Ilocos Norte, Ilocos Sur, Abra, Antique, and Bulacan.
The Aklan project is an onshore wind farm with a total capacity of 75.6 MW. Triconti ECC Renewables Corporation , a German-Swiss-Filipino joint venture based in the Philippines, is collaborating on the planning and implementation of the project. It will comprise 18 Vestas V136 turbines with a capacity of 4.2 MW each, according to wpd. Currently, in the planning stage, commissioning is scheduled for the end of 2023.
The project is part of the "CNP Backbone Extension," a major grid reinforcement and expansion for Cebu, Negros, and Panay. The wind farm will connect to the grid through a new substation being built by wpd and Triconti and the partners are also negotiating a Power Purchase Agreement (PPA) to sell the electricity locally.
The Bremen-headquartered company has already implemented wind energy projects with approximately 2,400 turbines and a total output of 5,150 MW. It is planning additional projects with 12,300 MW onshore, 13,800 MW offshore, and 1,650 MWp solar energy.
Similarly, Acen , a major renewable energy company in the Philippines with a growing presence in Asia Pacific, is partnering with US-based BrightNight for the development of its 1 GWac renewable power portfolio in the country, with an estimated capital deployment of US$1.2 billion over the next five years.
This marks BrightNight and Acen’s second partnership. In 2023, Acen, through its subsidiary, Acen Renewables International ( ACRI ), established a 50-50 partnership with the Florida-headquartered company to develop a 1.2 GW large-scale hybrid wind/solar and round-the-clock renewable power projects in India.
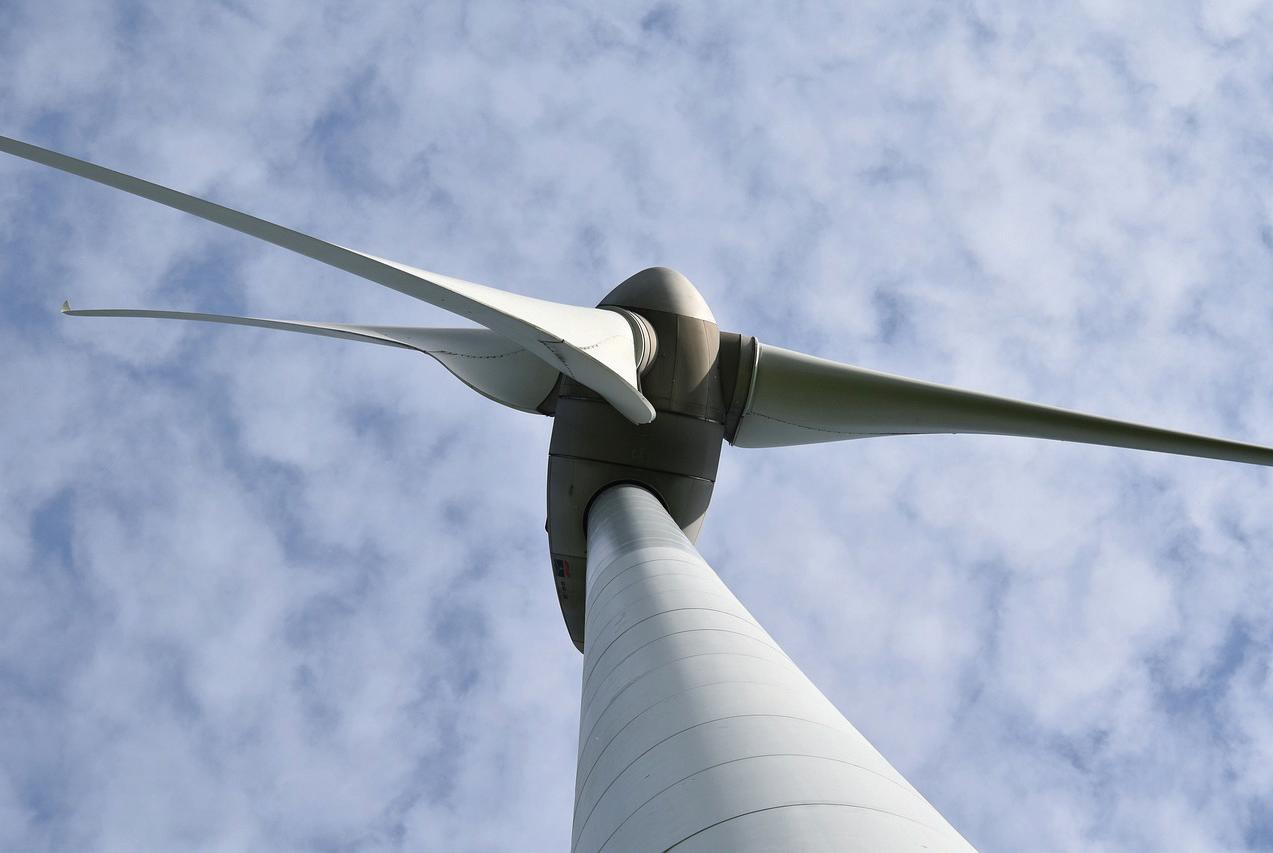
Solarvest's project in Malaysia, set to be completed by the end of 2025, will produce 57,500 MWh/year of clean energy and offset approximately 36,800 tonnes of CO2 emissions
The Philippines' Aklan project is an onshore wind farm with a total capacity of 75.6 MW
AI and interconnectivity propels SEA’s US$6 bn health market
Home to nearly 60% of the world’s population, the Asian region’s digital health market is expected to generate US$66.97 billion revenue in 2024 and reach a projected market value of US$99.57 billion by 2029, according to analysts Statista. The rapid digitisation of health services is leading industry sectors to experience significant growth.
As such, to be held alongside the Medical Fair Asia at Singapore’s Marina Bay Sands (11-12 September), GITEX Global, the world’s largest tech and start-up event, hosted in Dubai, has announced the creation of GITEX DIGI_ HEALTH 5.0 Conference, an AI and digital health expert gathering at the opportune inflection phase of the global healthcare evolution.
The inaugural conference, organised by Kaoun International, the international organising office of Dubai World Trade Centre (DWTC), will convene a premier line-up of international speakers including future health influencers and practitioners in Digital Health, Artificial Intelligence, Telemedicine, Consumer Health, and Patient Care.
Under the overarching theme of Implications of AI and Digitalisation in Disrupting Healthcare, the immersive two-day conference featuring global speakers from over 12 countries will highlight the integration of these technologies.
An expertise of public and private organisations in tech and healthcare will be joining the stage this year.
Headliners include Sutowo Wong, Director of Data Analytics at the Ministry of Health Singapore, Dr Pauline Erica Tay, Director of National Health Innovation Centre Singapore (NHIC), Dr Ossama ElHassan, Head of E-Health at the Dubai Health Authority from the United Arab Emirates, and Hanna Burkhardt, Head of UNICEF’s Venture Fund in Sweden.
Among the innovators, founders, and digital health leaders who will be attending are WeiWei Hong, Director of the healthcare network SingHealth, and Shravan Kumar, Co-Founder and CEO of the Healthcare solutions platform SpeedDoc from Singapore, Chwee Foon Lim, CEO for Asia- Pacific at the world’s largest exoskeleton company Ekso Bionics, headquartered in the United States, Dr Ramon Varughese, Chief Medical Officer of Qualitas Health from Malaysia, and many more.
Medical Fair Asia is organised by Messe Düsseldorf Asia. The showcase will feature 1,000 exhibitors from 62 countries and regions, with a Community Care dedicated area and a StartUp Park presenting highly innovative companies.
“We are delighted to see this co-location with GITEX DIGI_HEALTH 5.0 Conference in Singapore,” said Gernot Ringling, Managing Director of Messe Düsseldorf Asia. “This collaboration complements our event greatly, with Medical Fair Asia’s strengths as a regional sourcing and networking event and GITEX’s expertise as the world’s largest tech event brand.
He added, “With its leadership in biotech and health R&D, Singapore provides the ideal backdrop for this partnership in advancing healthcare and driving the future of digital health across Asia.”
The programme will explore opportunities in a hybrid healthcare future, where AI, IoT, predictive data analytics, and interoperability are transforming patient care systems. Talks and panel discussions will also cover the evolution of telemedicine, the integration of AI diagnostics, VR/AR consultations, and remote monitoring, and the impact of emerging technologies such as blockchain and Web3 on the healthcare sector.
Trixie LohMirmand, CEO of Kaoun International, organiser of GITEX worldwide, said: “Despite the broader worldwide downturn in funding, regional start-ups have attracted significant investments particularly in the digital future health sector where accessible and high accuracy diagnostic medical interventions and solutions are the priorities of future economies.”
To attend the conference from 11-12 September 2024 at the Marina Bay Sands in Singapore, visit the event’s website today and register for a free pass: www. gitexdigihealth.com.
As part of GITEX's expansion into the Asian region, GITEX ASIA — the most international cross sector tech and startup event in Asia—will make its debut in Singapore from 23-25 April 2025. This event strategically positions itself as the premier gateway to the Asian market, connecting the region with a global network of leading tech companies, unicorn founders, investors, AI pioneers, government leaders, and top-tier R&D institutions and academia. Learn more at www.gitexasia.com
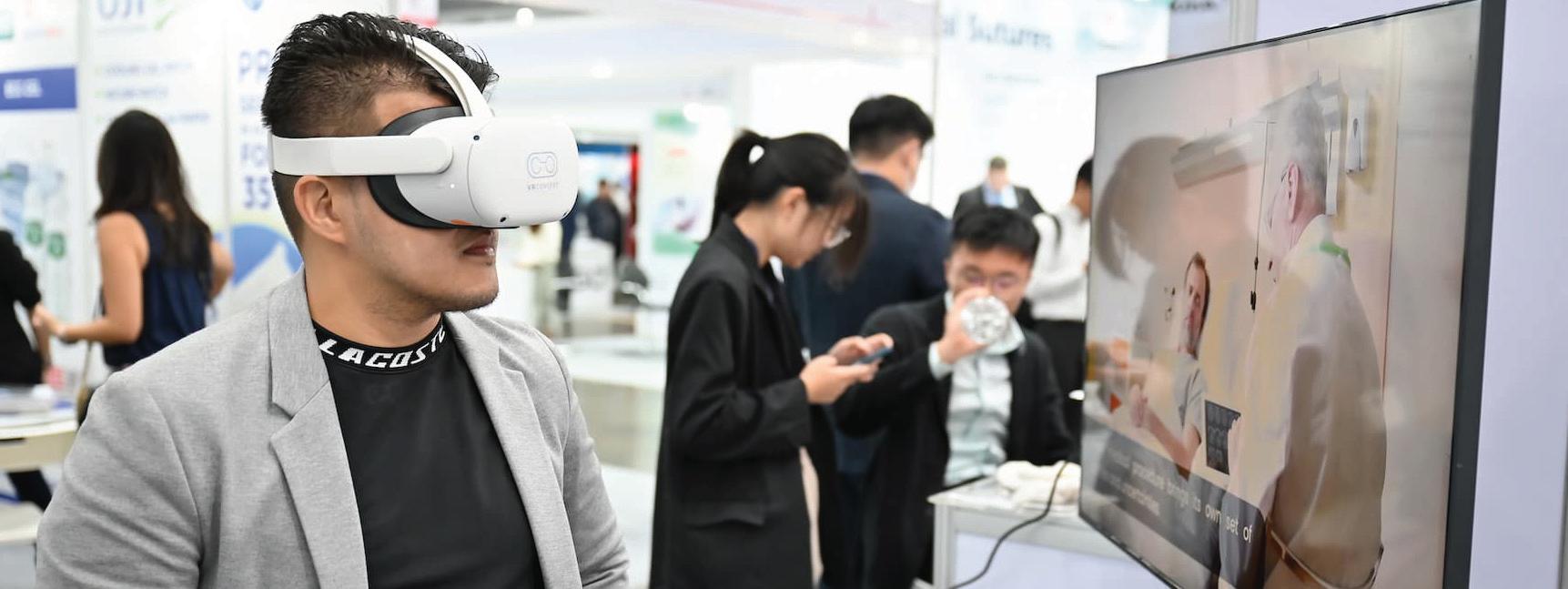
Recycling
Living in a plastic world: tackling the plastic pollution problem
With the growing onslaught of plastics pollution, the Nanyang Technological University, Singapore (NTU Singapore) is researching ways of recycling and reusing plastics, as well as addressing major bottlenecks faced when recycling plastics. Researchers have re-purposed e-waste plastics to grow “mini tumours” for laboratory testing in research and healthcare applications; converted hard-to-recycle plastic waste into hydrogen and carbon additives for polymer foams used in cushioning and developed a method to break down plastics into valuable compounds using light.
Plastic pollution has emerged as one of our most pressing environmental issues with the increasing use of disposable plastics. As they are nonbiodegradable, plastics accumulate in the environment, altering habitats and natural processes. Millions of wildlife are also trapped by plastic waste every year.
When plastics break down, they release toxic compounds that contaminate the environment. They also disintegrate into small pieces of plastic called microplastics.
Microplastics are now found all over the globe and are linked to severe health effects such as metabolic disorders and organ damage.
Recycling the way forward
Recycling plastics reduces the amount of plastic waste that would otherwise be discarded and conserves natural resources. However, only about 10% of plastic is currently recycled around the world. The figure is low in part because recycling some types of plastic, such as e-waste and marine plastic litter, is difficult. Chemical reactions that break down plastics into simpler components to be reused are also energy intensive.
From using e-waste plastics to culture cells to developing a greener method that breaks down plastics, researchers at NTU Singapore are solving some of the biggest challenges that stand in the way of recycling plastics and making strides in reducing plastic pollution.
Repurposing e-waste plastics to grow “mini tumours” for laboratory testing
Plastics comprise a large portion of electronic waste (e-waste), and rapid technological advances, and high consumer demand drives its growing use in electronics. According to a UN report, the generation of e-waste is rising five times faster than the official recycling rate figures show. In 2022, e-waste generated 17 million tonnes of plastic globally.
Single-use plastics are also widely used in research and healthcare applications such as cell culture.
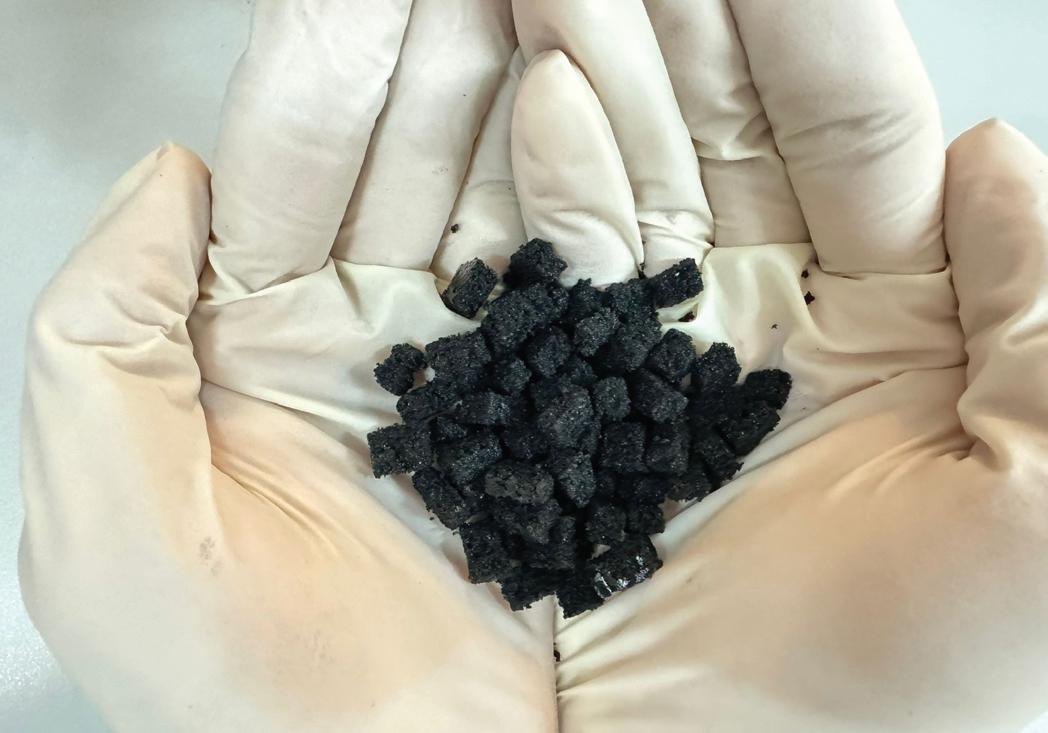
Acrylonitrile butadiene styrene (ABS) is an e-plastic commonly used in the housings of devices such as keyboards and laptops. Repurposing plastics such as ABS for high value biomedical applications could be an attractive waste-to-resource strategy for effectively reducing plastic waste.
NTU scientists have developed a synthetic matrix to culture cells using ABS from discarded keyboards. The matrix is porous like a sponge and functions as a support structure, providing a framework for cells to attach and grow.
The matrix can culture spherical clusters of cells, called cancer spheroids, whic resemble actual tumours. Due to their 3D shape, these “mini tumours” more accurately represent tumours than conventional cell cultures.
To fabricate the matrix, the scientists dissolved plastic scraps from discarded keyboards in an organic solvent, acetone and poured the solution into a mould.
The matrix supported the growth of breast, colorectal and bone cancer spheroids. The cancer spheroids had properties similar to those grown using commercially available matrices and may be used for biomedical applications such as drug testing.
ABS sponge
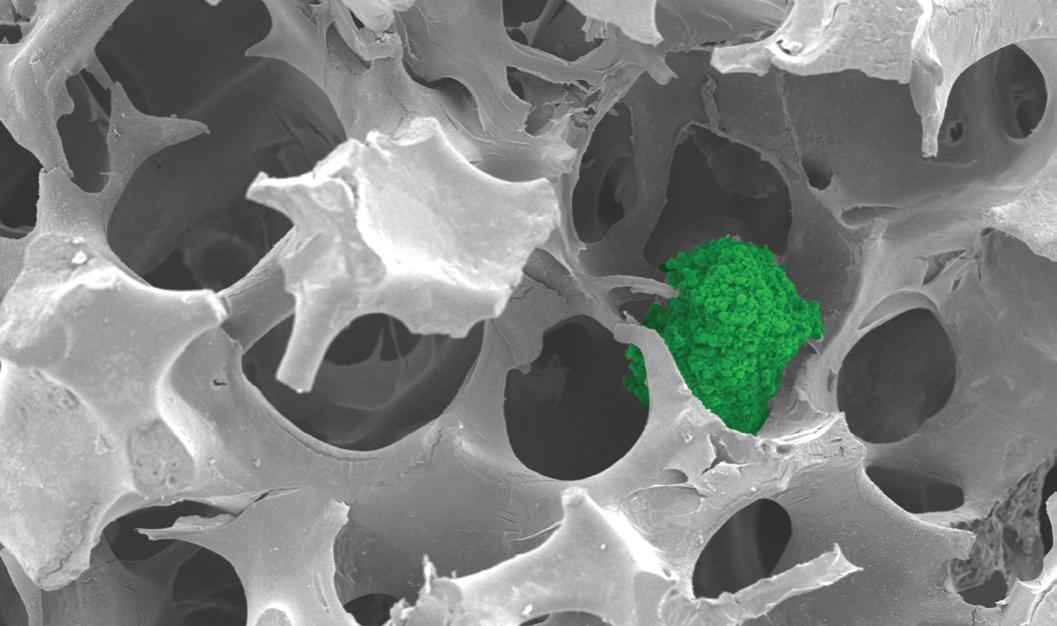
“Our innovation not only offers a practical means to reuse e-waste plastics but could also reduce the use of new plastics in the biomedical industry,” said Assoc Prof Dalton Tay of NTU’s School of Materials Science and Engineering, who led the research.
The research was reported in Resources, Conservation & Recycling in 2024.
Converting hard-to-recycle plastic waste into hydrogen and carbon additives for polymer foams
While some types of plastics can be repurposed into new products, it is not as easy to recycle other kinds of plastics. Household plastics, packaging waste and marine plastic litter recovered from the environment are all examples of plastic waste that are difficult to recycle. There are also limited economic benefits to treating mixed and contaminated plastics.
Researchers from NTU explored using difficult-torecycle plastics as a source of solid carbon material for application in polymer foams. The researchers first obtained gas and oil by heating different types of plastic waste at high temperatures (600°C) in the absence of oxygen. Then the gas and oil were heated at over 1000°C to break down the molecules into solid carbon and hydrogen.
The solid carbon can be added to polymer foam to increase its strength and resistance to abrasion for cushioning applications. The foam containing the synthesised solid carbon derived from plastic waste exhibited properties comparable to other carbon-based and conventional reinforcing materials available on the market.
At the same time, the hydrogen produced could be collected and used as fuel.
Published in the Journal of Hazardous Materials in 2024, the research is a milestone in finding a use for plastic waste that previously could not be recycled.
“We have developed a feasible approach to repurpose hard-to-recycle plastics, which is an important aspect of the circular economy,” said lead investigator Assoc Prof Grzegorz Lisak of NTU’s School of Civil and Environmental Engineering.
A bright way to break down plastics into valuable compounds
Although plastics can be broken down by heating them at high temperatures, such processes are energy intensive and generate greenhouse gases, contributing to global warming.
Addressing the need for greener methods of breaking down plastics, NTU scientists have developed a process that can upcycle most plastics into chemical compounds useful for energy storage. The reaction uses light-emitting diodes (LEDs) and a commercially available catalyst and occurs at room temperature. It can break down a wide range of plastics, including PP, PE and PS, all commonly used in packaging and discarded as plastic waste.
Compared to conventional plastic recycling methods, the process requires much less energy.
First, the plastics are dissolved in the organic solvent called dichloromethane, making the plastic polymer chains more accessible to the photocatalyst. The solution is then mixed with the catalyst and flowed through transparent tubes where LED light shines on it.
The light provides the initial energy to break the carbon-carbon bonds in a two-step process with the help of the vanadium catalyst. The plastics’ carbon-hydrogen bonds are oxidised, which makes them less stable and more reactive. After that, the carbon-carbon bonds are broken down.
The resulting end products are compounds such as formic acid and benzoic acid, which can be used to make other chemicals employed in fuel cells and liquid organic hydrogen carriers (LOHCs)–organic compounds that can absorb and release hydrogen through chemical reactions.

LOHCs are being explored by the energy sector as a storage media for hydrogen.
According to Assoc Prof Soo Han Sen of NTU’s School of Chemistry, Chemical Engineering, and Biotechnology, who led the study, the breakthrough not only provides a potential answer to the growing plastic waste problem but also reuses the carbon trapped in these plastics instead of releasing it into the atmosphere as greenhouse gases through incineration.
The method was reported in the journal Chem in 2023.
Recycling
Using light to break down plastics
Mini tumour from ABS sponge
Packaging
High barrier MDO-PE/PE laminate for recyclable packaging
To address the growing demand for recyclable packaging options, US materials firm ExxonMobil says it has successfully collaborated with Hosokawa Alpine , Henkel , Nordmeccanica Group and Univel to develop a high-barrier, recyclable MDO-PE//PE laminate. This advanced packaging solution is engineered to provide excellent barrier properties against oxygen and moisture, and targeted at a range of food products, ensuring optimal product freshness and protection.
The duplex MDO-PE//PE laminate was produced from a high-barrier PE sealant film and MDO-PE printing web. The MDO-PE printing web incorporated ExxonMobil HDPE HD7165L that was specifically designed to produce MDO-PE films. The MDO-PE film was produced on machine supplier Hosokawa Alpine’s five-layer blown film line with inline MDO.

ExxonMobil has developed a duplex high barrier MDOPE packaging solution
The blown PE sealant film was produced using ExxonMobil’s performance PE resins such as Exceed S, Enable and Exceed. Material supplier Evonik ’s TEGOMER 6810, an organo-modified siloxane, was used to help control the coefficient of friction (COF).
Two thin barrier coatings (BC) were then applied on the blown PE sealant film to help deliver outstanding barrier properties: the first layer contains vacuum-metallised aluminium, while the second layer contains 1 gsm of technology firm Henkel’s newly developed barrier coating Loctite LIOFOL BC 1582 RE.
Both functional layers were applied using Nordmeccanica Group's Vacuum & Coating machinery (Nordmet 12F Plus/Super Combi 5000). The MDO-PE film was printed by Univel.
The combination of metallisation and barrier coating to produce a very high PE-content laminate provides ultra-high oxygen barrier properties (similar to aluminium foil3) and excellent moisture barrier properties.
The oxygen-transmission rate (OTR) of the PE-based film was almost two magnitudes lower than the PETmet-based film when measured at 0% relative humidity at room temperature, whereas water vapour transmission rate (WVTR) of both structure was very similar.
The new solution not only meets the functional requirements for a wide range of food packaging applications, from dry goods to liquids, but also offers outstanding stiffness and clarity. This makes it a viable alternative to traditional materials such as PET and BOPP. Additionally, the solution addresses the challenge of maintaining barrier properties while ensuring ease of recyclability, often a limiting factor in conventional packaging materials.
Meanwhile, German machinery maker Reifenhäuser Blown Film has also showcased what it says is the “world’s first’ 18-micron MDO-PE film”. It claims to reduce the thickness of previous films by 25% and enable companies to transition into fully recyclable, low-carbon mono-material flexibles.
The film has been produced on Reifenhäuser EVO blown film lines using the patented EVO Ultra Stretch MDO technology and has been developed and tested for practical suitability in collaboration with raw material manufacturer LG Chem and printing specialist Bobst

The combination of suitable raw materials and Reifenhäuser’s MDO Ultra Stretch technology directly in the line's haul-off, where the film is stretched from the first heat, enables the production of the 18-micron film
Cost-effective solution as an alternative to ionomer vacuum skin packaging
Elsewhere, ExxonMobil has collaborated with Brazilian packaging converter Videplast to develop a vacuum skin packaging (VSP) solution to replace an existing resin that does not contain ionomers, thereby reducing film thickness for food packaging applications.
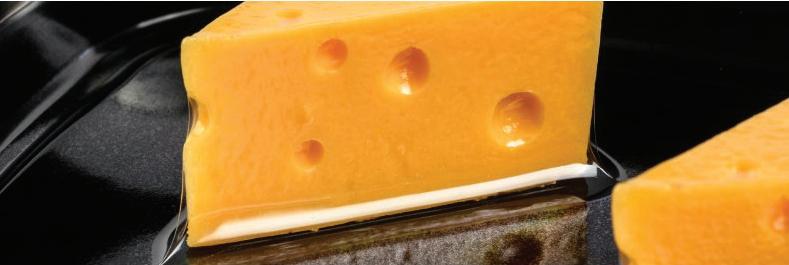
ExxonMobil has together with Videplast developed a cost-effective vacuum skin packaging (VSP) solution that does not contain ionomers
VSP is a type of packaging where a product is placed on a piece of tray (plastic or cardboard) and a thin barrier film is softened by heat and draped over the product on the tray. Vacuum is applied to ensure the film will cover the entire surface of a product/tray, removing as much air inside the package as possible.
Utilising ExxonMobil’s Exceed XP 7052ML performance PE, the new solution hopes to meet market demands for high-performance, cost-effective packaging that provides protection from food spoilage, leakage, and contamination and extends the shelf life of perishable goods by removing air and providing a tight seal.
The process involves ‘optimal thermoformability’ and a high oxygen barrier, aiming for effective vacuum sealing.
The solution is said to be ideal for packaging small portions of meat, cheese, fish, seafood, and other products requiring high-performance and visually appealing packaging solutions.
Reusable PET packaging for cosmetic brands
Together with packaging and recycling specialist Alpla , start-up Zerooo SEA ME has developed a standardised solution for cosmetics and care products and are now producing reusable PET packaging for bathrooms and kitchens.
From September, the first brands will be presenting shampoo, shower gel, detergent, body lotion and dental care products in 300-ml PET bottles. This reusable and fully recyclable plastic packaging is available
in three colours and is suitable for all caps. A laserengraved 2D data matrix code provides information on the contents of each bottle and its circulation.
Zerooo aims to create reusable packaging that fosters the circular economy in the cosmetics industry. The system from the German start-up SEA ME is said to offer brand manufacturers safe, affordable and sustainable PET bottles, in addition to glass bottles, for the first time. stands for reusable packaging that fosters the circular economy in the cosmetics industry.
The reusable PET bottle is available in clear, milky white and brown versions.
The company states it has created a fully recyclable solution in collaboration with Alpla and ten brand partners. It adds that the reusable PET bottle can be used as a shatterproof alternative for toiletries in the shower, and further formats are planned.
From September, the first manufacturers in Germany will present cosmetics and care products in PET containers from the Zerooo reusable system, with Austria following suit in October. In addition to SEA ME’s own brand, these include sodasan , i+m Naturkosmetik , Speick , Denttabs , 4 people who care and Aveo from Müller
Each Zerooo reusable PET bottle has a laserengraved 2D data matrix code – the zerooo ID – which provides information about the content and circulation history.
“The digital labelling enables transparency and ensures the quality of the bottles. By combining it with the information from the label, it can also be complemented with further product data,” explains Jörg Schwärzler, senior technology manager at Alpla. The reusable PET bottle is reportedly compatible with all automatic return systems, and at the end of their life cycle, the bottles and caps are sorted and recycled.
Alpla says it is promoting closed ‘bottle-to-bottle’ cycles with its own plants, and the Zerooo reusable PET bottle was developed with the SEA ME team at Alpla’s in-house design centre, at the company’s headquarters in Hard, Germany.

Alpla and Zerooo have developed reusable and fully recyclable PET bottles, available in three colours and suitable for all caps
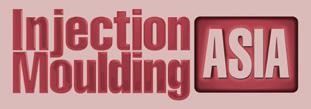
Injection Moulding Asia
Country Focus
Taiwan’s blueprint for a progressive carbon-neutral future
Taiwan is advancing sustainable energy and maintaining semiconductor industry leadership with clear strategies, adds Angelica Buan in this report.
Taiwan is rapidly emerging as a leader in sustainable innovation, combining its economic strengths with a strong commitment to a circular economy. As the 23-million-population East Asian nation advances its green energy initiatives, it is paving the way for its electric vehicle and semiconductor industries to thrive while leading in environmental responsibility, positioning the country as a global leader in both technology and sustainability.
Taiwan plays a crucial role in the global supply chain, leading in the integrated circuit (IC) industry and excelling in consumer goods such as footwear, as well as in textile R&D and production. However, its reliance on imported resources poses challenges to its economic development.
In response, Taiwan unveiled its “Pathway to Net-Zero Emissions in 2050” in 2022, a comprehensive plan focused on transforming energy, industry, lifestyle, and society. Supported by technological innovation and climate legislation, this plan includes 12 strategic initiatives to achieve net-zero emissions, featuring plans for energy transitions, industrial shifts, and green transportation.
Taiwan’s green energy push
Taiwan is making a strategic pivot towards renewable energy, which not only increases the use of wind, solar, and other green energy sources but also helps industries reduce greenhouse gas emissions (GHG), aligning economic growth with environmental responsibility.
According to Taiwan’s National Development Council ( NDC ) 2022 Phased Goals and Actions Toward Net-Zero Transition report, the country plans to boost the share of renewables in its energy mix from 2025 to 2050.
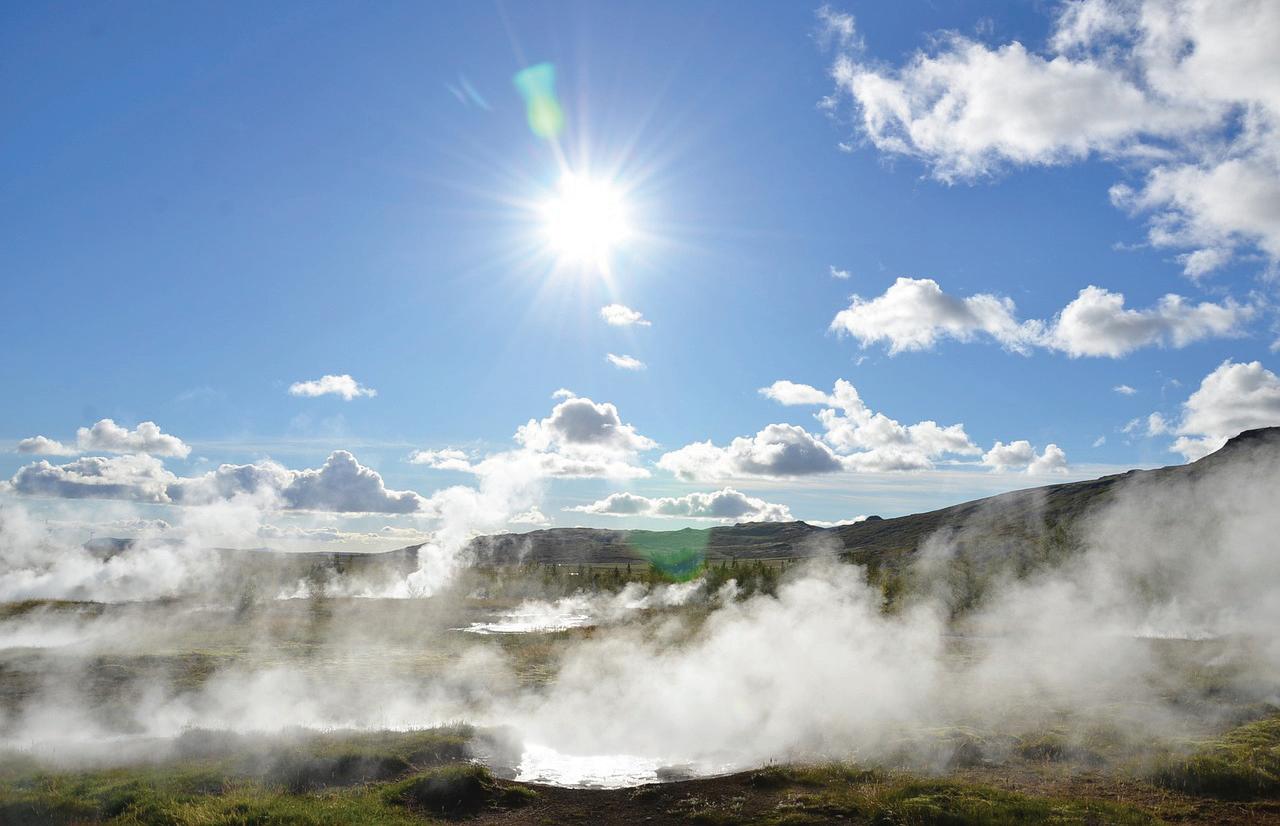
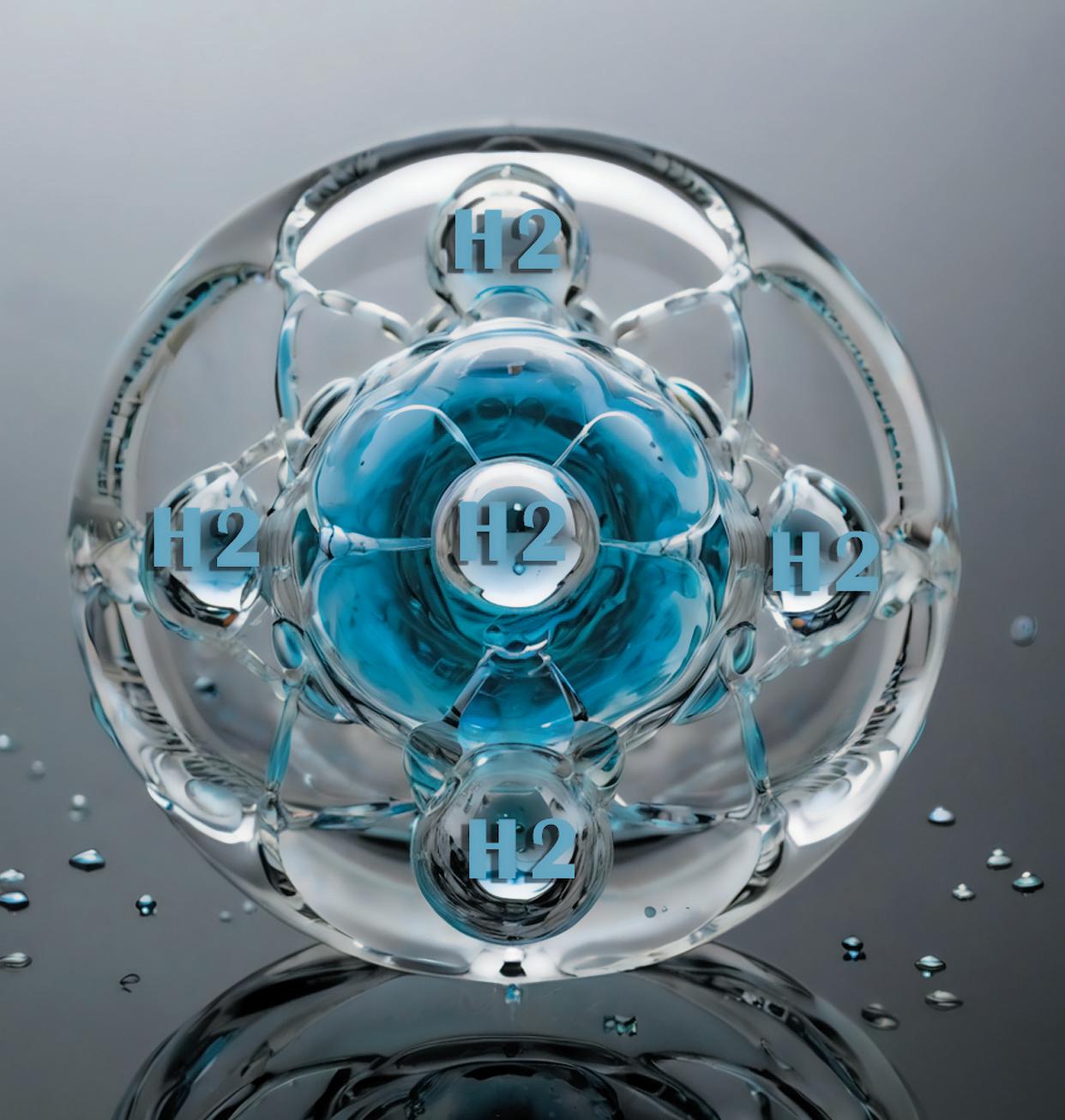
Specific targets include installing 91 MW of hydrogen capacity by 2025; 891 MW by 2030; and 7,300 MW by 2050, aiming for a reduction of 6,700 tonnes of GHG emissions by 2030 through hydrogen alone. To achieve these goals, Taiwan will collaborate with major hydrogen producers, expand hydrogen import sources, and build infrastructure for production, transportation, and storage, including international supply chains and liquid hydrogen stations.
Additionally, Taiwan is advancing blue hydrogen with CCSU testing and localised production technologies and plans to achieve 5% mixed combustion by 2030. The green energy roadmap also focuses on innovative sources such as geothermal, bioenergy, and ocean energy.
For wind and solar PV, the total installations targets by 2050 are 40 to 55 MW and 40 to 80 MW, respectively.
For geothermal energy, Taiwan is eying installations from 20 MW in 2025 to 6.2 GW by 2050, aiming to cut 180 to 620 kilotonnes of GHG emissions by 2030.
Bioenergy targets include 778 MW by 2025; 805 to 1,329 MW by 2030; and 1.4 to 1.8 GW by 2050, with expected reductions of 2.18 to 4 million tonnes of GHG emissions by 2030.
Ocean energy installations are projected to grow from 0 to 0.1 MW by 2025 to between 1.3 and 7.5 GW by 2050, aspires reductions of 0.13 to 1.3 kilotonnes of GHG emissions by 2030.
Taiwan targets a reduction of up to 620 kilotonnes of GHG emissions from geothermal energy by 2030
Taiwan is progressing blue hydrogen development with CCSU testing and aims for 5% mixed combustion by 2030
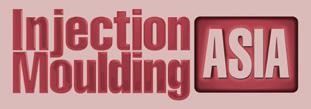
Injection Moulding Asia
Innovative energy strategies include developing a unified firing system with incentives for coal-to-biomass units, sourcing pellet biomass, and optimising conversion technologies while improving economic benefits through effective use of by-products like ash and biogas residue.
Authorities estimate that NT$4 trillion will be invested in the net-zero transition and zero-carbon technology deployment by 2030, which is expected to generate NT$5.9 trillion in production value and create over half a million jobs.
Journey to a net-zero transportation
Taiwan’s shift to clean energy and a circular economy is driving the growth of a robust electric vehicle ecosystem. By focusing on sustainability and reducing environmental impact, Taiwan aims to lead the global transition to sustainable transportation.
Vehicle efficiency is a major priority, with plans to offer subsidies for replacing old vehicles and promoting high-efficiency models. Regulations are being updated to align with global standards, improving fuel efficiency and optimising public transport.
The increased rollout of electric vehicles (EVs) is anticipated due to these carbon-free initiatives. According to the US International Trade Administration ( ITA ), passenger EVs made up 3.4% of total registrations in Taiwan in 2022, with EV sales soaring 128% from 7,064 units in 2021 to 16,106 units in 2022.
Taiwan aims to achieve 100% electric cars by 2030 and 100% electric motor vehicles and scooters by 2040.
In line with this, Foxconn (or Hon Hai Precision Industry Co Ltd ), a Taiwanese multinational electronics contract manufacturer, plans to deliver over 10,000 electric SUVs in 2024 through its joint venture with Taiwanese automaker, Yulon Motors , focusing on the Model C SUV. The Model B crossover will also be mass-produced for international markets.
Foxconn expects over 9,000 domestic orders, with total sales exceeding 10,000 units. Additionally, 1,555 units of the Luxgen n7 EV, developed with Yulon, were delivered in the first four months of the year.
Foxconn is also entering the commercial vehicle market, with a factory for electric buses in Kaohsiung set to start operations in 2025. The factory will initially produce 500 buses/year, ramping up to 1,000 by 2028.
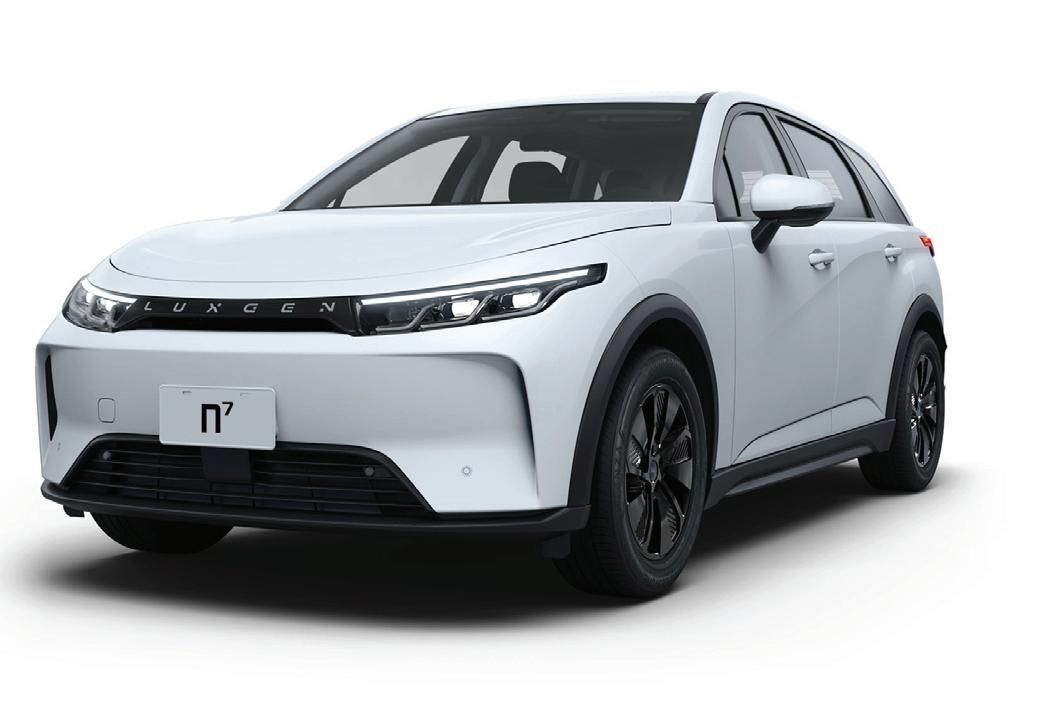
Expanding EV charging access
With this planned expansion for EV production and sales, Taiwan is rapidly scaling its charging network by establishing stations at highway service areas, transport hubs, tourist sites, and gas stations, as well as in industrial and science parks, exhibition centres, and other key locations.
Foxconn Interconnect Technology Ltd ( FIT Hon Teng ), a subsidiary of Hon Hai, is making notable advancements in the EV sector. Following its acquisition of German manufacturer of sensor, connectivity and automotive electrification solutions, Prettl SWH Group , in 2023 and the launch of the Voltaira brand, FIT Hon Teng has entered the EV charger market through a joint venture with Chinabased EV charging and energy storage systems specialist, XYPower Technology Co .
The new entity, Fxnwing New Energy Technology, merges XYPower’s expertise in EV charging and energy storage with FIT Hon Teng’s manufacturing capabilities. This collaboration aims to deliver high-quality charging and energy storage solutions globally, leveraging the growing EV market.
Under its One-FIT strategy, Fxnwing and Voltaira have introduced a new line of chargers, including the Voltaira Anoles AC charger, which offers 7kW and 22kW charging power. The Voltaira Royal Series, designed for the Middle East and North Africa (MENA) market, includes robust AC and DC chargers optimised for harsh climates, featuring intelligent power distribution and high efficiency.
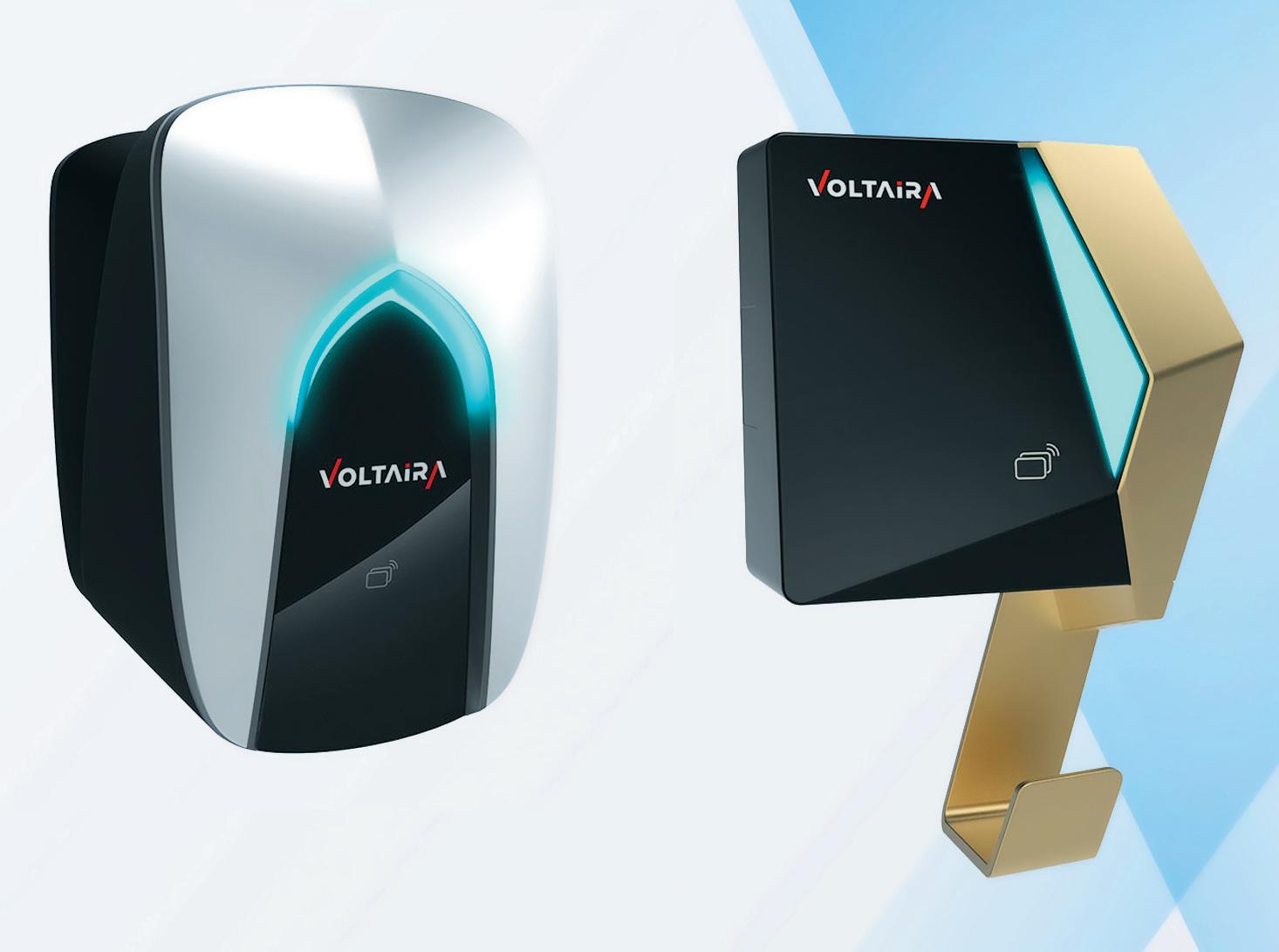
Fxnwing and Voltaira launched the Voltaira Royal Series for the MENA market, featuring robust AC and DC chargers optimized for harsh climates, with intelligent power distribution and high efficiency
is
In a similar vein, ProLogium , a Taiwanese lithium ceramic battery manufacturer, provides next-generation batteries with high energy density, fast charging, and enhanced safety features, avoiding the need for Cell to Pack (CTP) technology. These batteries are more compact and lighter, improving Life Cycle Assessment (LCA) performance and reducing carbon taxes, which results in lower initial costs for consumers and improved driving efficiency.
Foxconn
set to deliver over a thousand Luxgen n7 EVs, developed with Yulon, this year
Country Focus
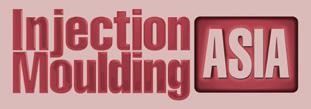
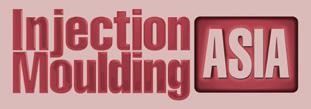
Injection Moulding Asia
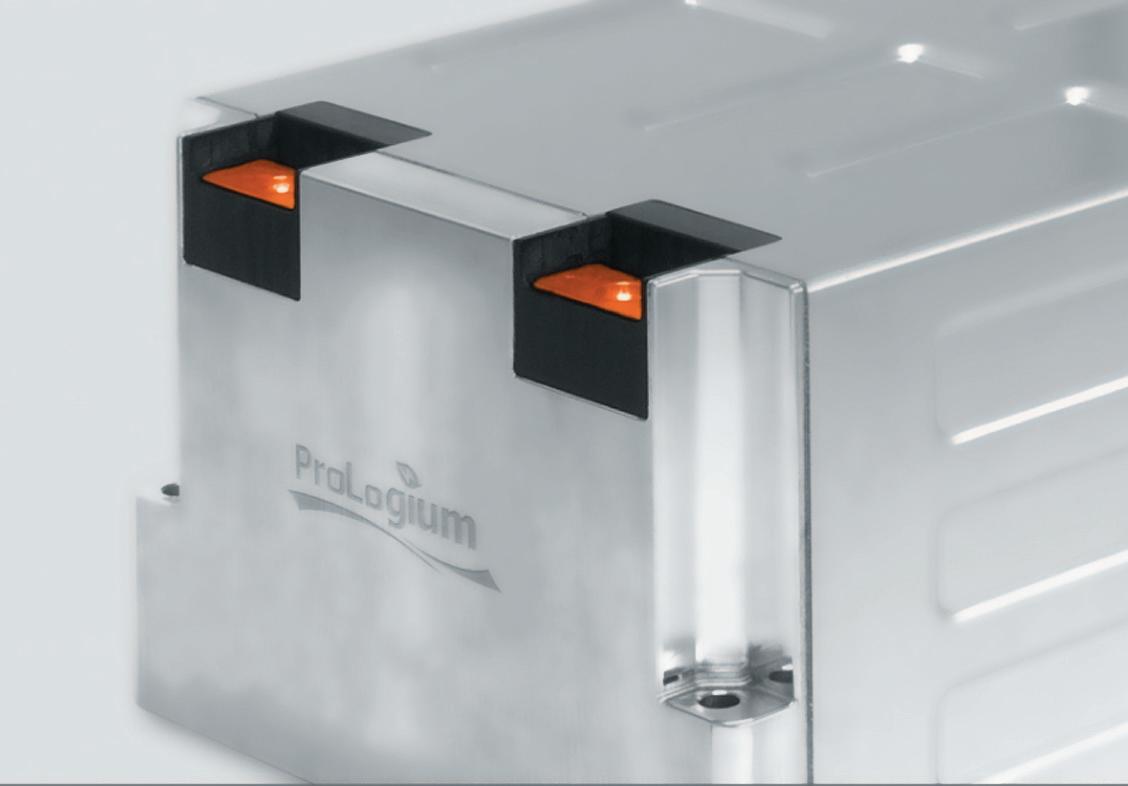
ProLogium’s modular battery pack designs also enable cell recycling and reuse, addressing concerns about the residual value of second-hand cars. Additionally, the batteries support ultra-fast charging, reaching 80% charge in just 8.5 minutes, which may drive the expansion of charging infrastructure due to the increased turnover rate at charging stations.
Securing semiconductor global footprint
As well, Taiwan’s semiconductor industry continues to be the country’s economic backbone, solidifying its position on the global market map. The industry is thriving, fueled by the government’s decarbonisation and net-zero strategies. With its strong market position, robust production values, and crucial role in global supply chains, the industry is poised for significant growth, supported by ongoing technological advancements and solid policy backing.
As a global leader in advanced chip manufacturing, Taiwan boasts impressive growth rates and plays a vital role in the global supply chain. The industry’s production value is expected to surpass NT$5 trillion in 2024, with key players like Taiwan Semiconductor Manufacturing Company ( TSMC ), United Microelectronics Corporation ( UMC ), MediaTek , and ASE Technology anchoring the sector.
However, some setbacks have occurred. In 2023, Taiwan’s integrated circuits (IC) industry, which includes design, manufacturing, packaging, and testing, reported NT$4.3 trillion in revenue, reflecting a 10% decline from 2022, according to the Taiwan Semiconductor Industry Association ( TSIA ).
Nevertheless, Taiwan remains the world’s second-largest player in the IC sector, following the US, and holds a 19.3% share of the global IC design market. This share is projected to rise to 20.1% by 2024, fuelled by increasing demand for emerging technologies like connected electronics, highperformance computing (HPC) devices, and artificial intelligence, alongside sturdy market demand.
Moving forward, data has shown that Taiwan has gained traction in the third-generation semiconductor market, particularly for its work with wide bandgap materials such as silicon carbide (SiC) and gallium nitride (GaN).
These “compound semiconductors” are essential for enhancing energy efficiency and supporting nextgeneration mobile communications. According to the Market Intelligence & Consulting Institute ( MIC ), Taiwan leads globally in the wafer foundry and packaging/testing sectors, with market shares exceeding 50% in each.
TSMC, the world’s largest semiconductor foundry, along with other major companies like Taiwanheadquartered semiconductor epitaxial wafers and silicon wafers OEM, Episil Technologies , has long been producing third-generation semiconductor components for international clients, including major US tech companies such as Apple and Nvidia
However, Taiwan’s development of end products in this field began gaining momentum only around late 2020. By 2024, Taiwan’s wafer foundry market is expected to capture an unprecedented 76.8% share globally, according to the TSIA.
In June, the Industrial Technology Research Institute ( ITRI ) projected Taiwan’s semiconductor output value to exceed NT$5 trillion in 2024. Leading the way in technological advancements, Taiwan is pioneering AI-enabled devices, high-performance computing, and next-generation manufacturing techniques such as extreme ultraviolet (EUV) lithography. This reinforces Taiwan’s role as a critical hub for semiconductor technology.
Concurrently, Taiwan’s commitment to net-zero emissions is reflected in its strategic progress across EVs, green energy, and semiconductor industries. Its policies are driving sustainable practices and boosting global competitiveness, positioning Taiwan as a key player in the low-carbon economy arena.
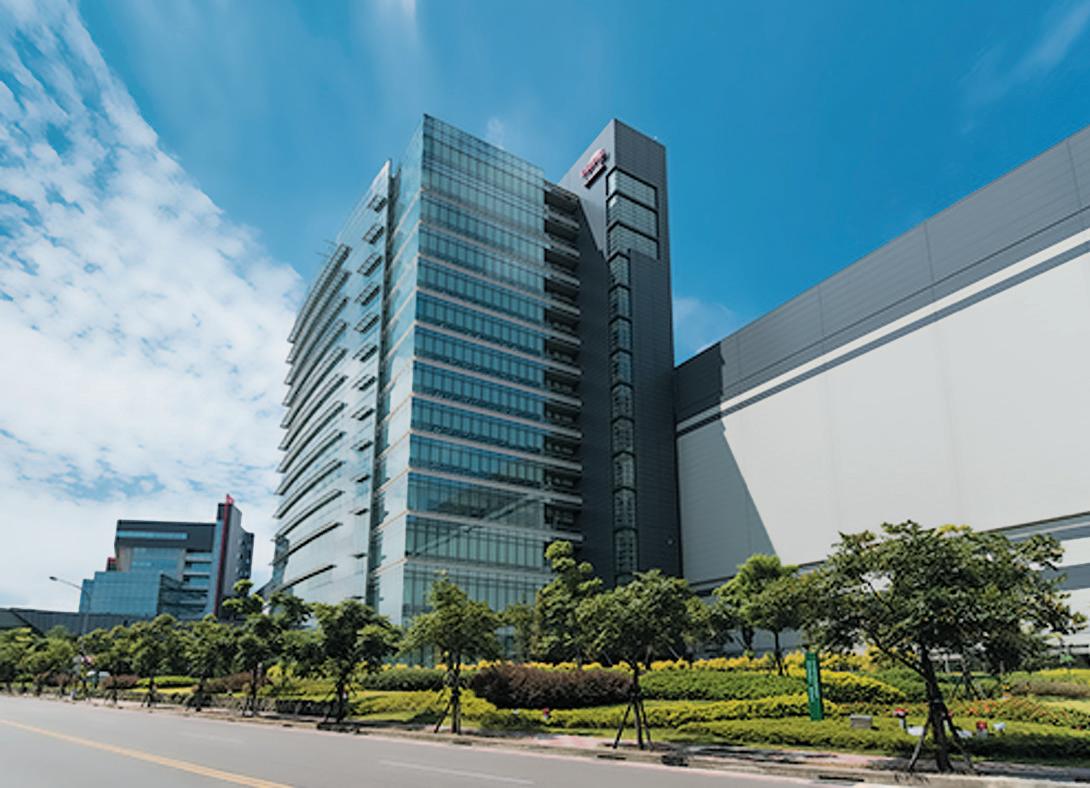
ProLogium’s modular battery pack designs also enable cell recycling and reuse, addressing concerns about the residual value of secondhand cars
Taiwan’s TSMC and other major companies have long produced third-generation semiconductor components for international clients, including Apple and Nvidia
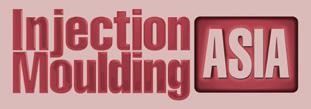
Injection Moulding Asia
Achieving sustainability-driven objectives
Improving recyclability of interior parts
Achieving a good balance between sustainability and functionality without sacrificing cost-competitiveness is a major issue for car manufacturers. To tackle this challenge, Japanese materials company Asahi Kasei says it is currently developing a tailor-designed thermoplastic styrene block copolymer (SEBS) grade for automotive interior surfaces, which require good haptics and soft touch.

Asahi Kasei will showcase at the upcoming Fakuma show a thermoplastic elastomer for improved recyclability of automotive interior parts
Whereas conventional approaches use different materials and production technologies for skin, foam, and core layers in automotive instrument panels, door panels, armrests or centre consoles, the new SEBS material is suitable for both skin and foam layers, which can be moulded in one step by utilising a core back injection moulding process.
The connection to the polypropylene (PP)-based core layer is possible in the same or separate injection moulding step. The strong chemical bonding between all layers eliminates the need for additional adhesive layers.
Asahi Kasei says its new SEBS contributes to reducing the total number of materials, simplifying the manufacturing process, and improving the recyclability of interior components.
Mass production of recycled-content radiator grilles
For the first time, car maker Audi says it is massproducing painted radiator grilles made from a blend of PC and PET recyclates for the new Audi A3 Sportback and Audi A3 Sedan. This achievement is the result of a collaboration between Mocom , a specialist in compounding and recycling, Winning Plastics , a plastics processor, and Audi.
The project was not without its challenges and the team had to take into effect the stringent technical requirements for mechanical properties in safety-critical components and the high purity needed for the material to be reused in painted parts.
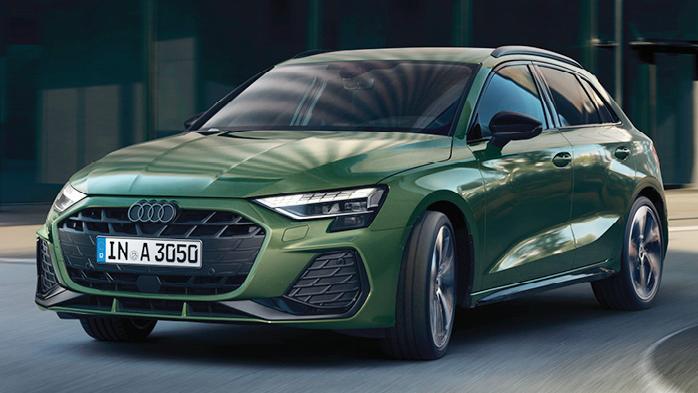
“Our objective is to systematically increase the use of recycled materials in Audi vehicles. With the A3 model update, the painted radiator grille contains a significant portion of secondary raw materials for the first time. As a key design element of Audi models, the grille must meet high standards in design, appearance, and quality, in addition to specific mechanical requirements,” explains Frank Fischer from Audi’s Materials Engineering department.
Werner Meschitz, Head of Innovations at Winning Plastics also said that suitable recyclates were not available off-theshelf, so together with its partner Mocom, the companies developed a recycled compound that partially incorporates painted scrap components from its own production.
“Standard recycling methods for scrap parts leave too many contaminants and paint residues, making it impossible to reuse the material in a new radiator grille. However, Mocom’s innovative process, particularly in paint removal, ensures the required purity of the recyclate, enabling a closed-loop recycling system,” he added.
The recycling process begins with scrap parts from production, known as post-industrial materials. In this case, these are painted radiator grilles with purely cosmetic defects, such as dust inclusions.
After the defective parts are shredded into approximately 30-mm pieces, they are processed in a hammer mill uniquely designed by Mocom. Here, the paint is removed primarily through friction, and the resulting debris is vacuumed away. The paint residue is discarded, while the de-painted PC+PET material is further processed into regranulate.
Next, during extrusion, the plastic mass undergoes fine melt filtration, where it is passed through special filters. The resulting PC+PET recyclate is then blended at a nominal 27% into the production of new radiator grilles for vehicle manufacturing. This process offers a cost-effective recycling solution with a lower carbon footprint compared to using new materials.
The firms say that the combined technologies enabled them to create a high-quality plastic compound with recycled content that meets the stringent requirements for manufacturing radiator grilles, and that the successful integration of recyclates in automotive plastic components opens up new opportunities for the entire automotive industry.
Audi has started mass production of radiator grilles with recycled content
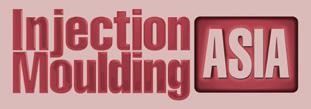
Injection Moulding Asia
Automotive Sector
LYB, Renault, and Antolin introduce low-emission foamed material
Chemical firm LyondellBasell ( LYB ), car maker Renault , and Antolin have announced the incorporation of LYB’s Hostacom TYC 2463F E2 foaming material in the interior design of the new Renault Rafale.
This PP compound is said to mark a significant leap forward in producing interior parts with elaborate designs, enhanced surface textures, scratch-resistance, and low emissions, through the deployment of advanced chemical foaming technology.
This foaming material is manufactured utilising LYB’s catalyst technology, enhancing the rheology of the PP polymer matrix.
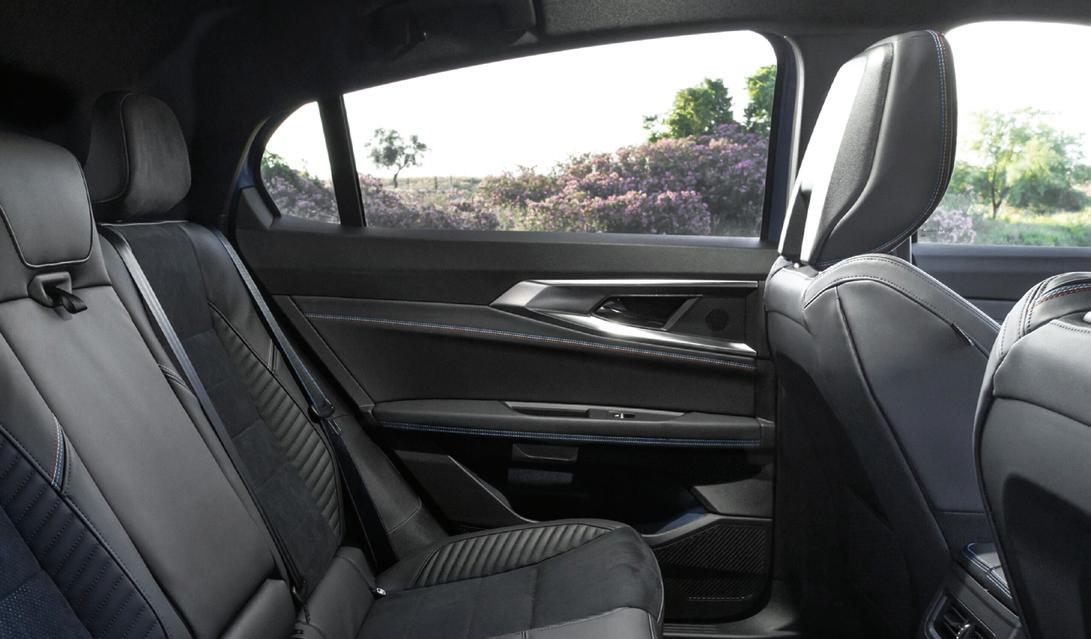
Key benefits include: high flowability, expanded processing window and melt strength to ensure optimal cell structure in foamed parts and significant weight savings using LYB PP compounds with a chemical blowing agent in core back technology. Meanwhile, the semi-ductile nature of the material broadens its use in various interior trim parts, offering a versatile and sustainable solution, the company adds.
Renault and Antolin, integral contributors to this innovation, affirm the successful culmination of years of concerted effort and collaboration, with the chemical foaming technology targeted at door panel applications.
The successful passing of standard specifications in this technology and its use for serial production signifies a significant achievement resulting from over five years of collaboration between LYB, Renault, and Antolin.
Lightweighting awarded: EV battery module; visionary car seat; lattice technology rebar
Automotive companies are treading the path towards lightweighting, especially in electric vehicle battery designs. In this regard, at the US-held 2024 Altair Enlighten Awards, in the Lightweighting Module, materials firm Syensqo won for General Motors ’ hybrid battery module structure that utilises Syensqo’s Amodel polyphthalamide (PPA).
The module stands out for its 37% weight reduction and 25% cost savings, achieved through part consolidation, which eliminates the need for compression limiters, films, and coatings found in conventional battery modules.
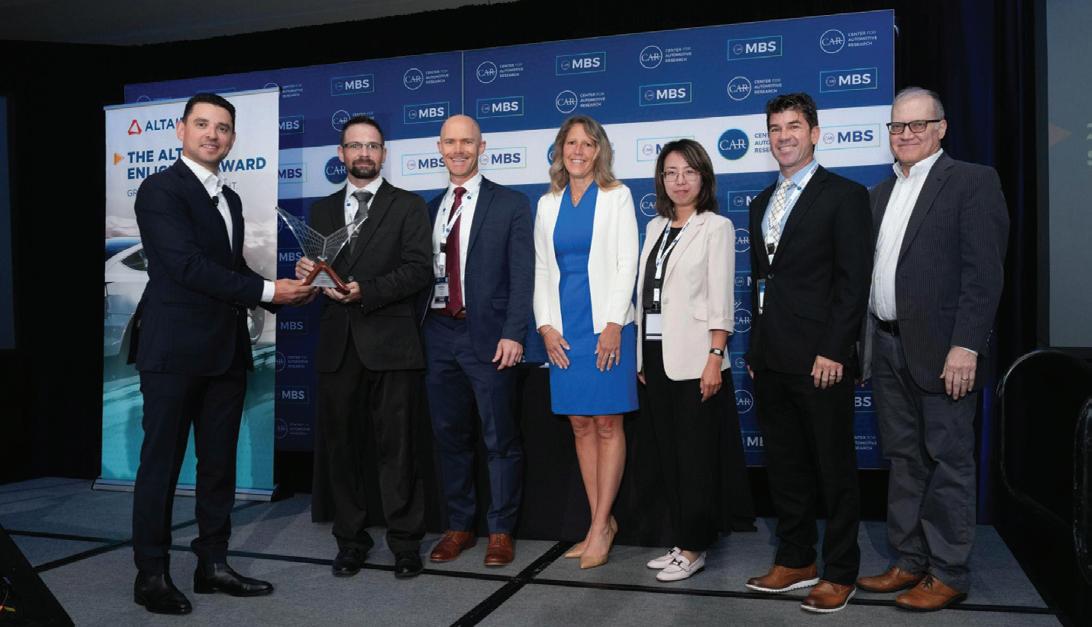
The recyclable Amodel HPP grade is fully commercialised and available globally, manufactured at the company’s Augusta, US.
Meanwhile, also at the Altair Enlighten Awards BMW Group received the award for its visionary car seat, since it features a monomaterial lightweight design that emphasises using sustainable, renewable materials such as recycled polyester textile, flaxfibre BioComposite, and biogene leather alternatives. As well, wherever possible, petrol-based raw materials through bio-based materials were made from algae and plant-based fillers – such as chalk and cork. The composite can be made from carbon, basalt, glass fibre, or natural fibres as needed.
In addition to BMW M GmbH as the project owner, BMW Group Designworks was responsible for the design, colour and material concept of the seat in collaboration with the BMW design team. The project was also realised in close cooperation with several partners: Automotive Management Consulting GmbH, Bcomp Ltd, Gradel Lightweight Sàrl and Lasso Ingenieurgesellschaft mbH
At the recent Altair Award, BMW was recognised for its visionary car seat that uses biomaterials
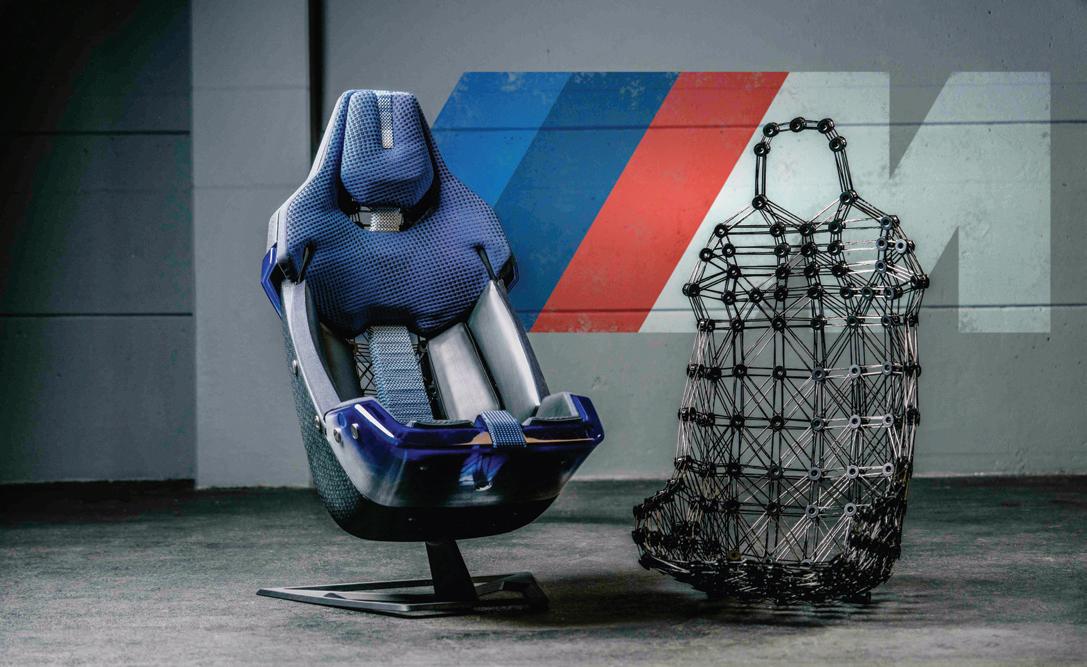
The firm says the seat’s CO 2 e footprint is 90% lower than a BMW M carbon bucket seat made today, thanks to the use of ultra-light, robotically-wound fibre composite seat support structures and materials of natural origin as well as the high recycling rate. In addition, lower module complexity and the use of materials grouped by type make it easier to recycle the seat at the end of its lifecycle.
LYB, Renault, and Antolin have introduce a foamed material for the Renault Rafale. The Hostacom solution will be shown during Fakuma, to be held in October
Syensqo and General Motors’ EV battery module was awarded for its lightweight design
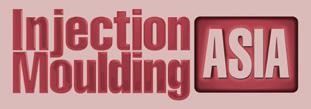
Injection Moulding Asia
BMW says the data obtained provides new insights, “for continuously improving sustainability and developing innovative solutions for forward-thinking mobility”.
Another notable product that won is a thermoplastic composite lattice technology in a tie-up between Brazilian polyolefins maker Braskem and composite materials start-up WEAV3D Inc . In partnership with the Clemson Composites Centre at Clemson University, the partners were named first place winners in recognition of a lightweight solution to enhance the performance of PP for structural automotive applications.
The combination of WEAV3D composite lattice reinforcement with Braskem PP enables lighter and less expensive thermoplastic solutions than conventional organosheet, unlocking new opportunities for the replacement of sheet metal structures with thermoplastics throughout the vehicle, the firms say.
Benefits include reduction of sheet blank weight by 50% and final part weight by 23%; reduction of costs by 50% with the increase of sheet yield from 25% to 45% by weight, resulting in a 62% reduction in trim waste.
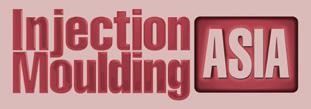
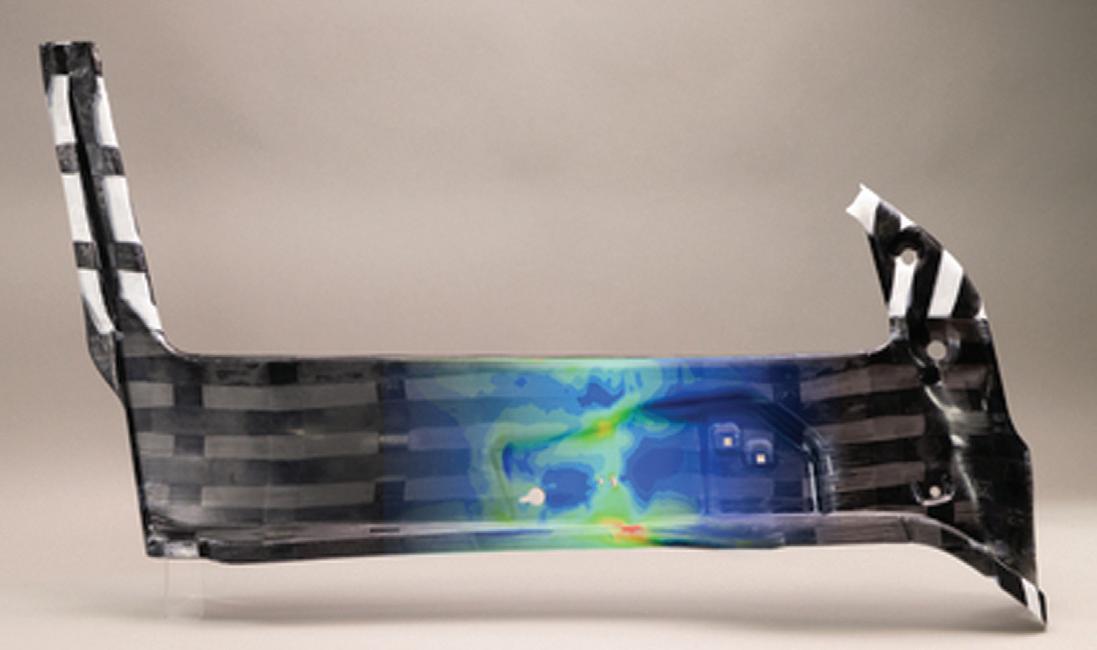
Also at Altair, Braskem in partnership with WEAV3D Inc. and the Clemson Composites Centre were named first place winners in recognition of a lightweight solution to enhance the performance of PP for structural automotive applications
“This is an industry-first high-rate structural automotive prototype that showcases WEAV3D’s tunable woven composite technology and Braskem’s cost-effective PP resin, leveraging our extensive experience in stampforming thermoplastic composites from the US Department of Energy’s Ultra-Lightweight Door programme,” said Sai Aditya Pradeep, former Manufacturing Applications Engineer and Project Lead for Clemson.
Injection Moulding Asia
Transforming patient care with next generation medical-grade plastics
Leading resin providers are offering advanced materials that improve the production of medical devices, promising to elevate patient care and enhance treatment outcomes, says Angelica Buan in this article.
lastics technology is a perennial force in modern healthcare, enhancing cost-effectiveness, safety, and hygiene while driving innovation. Commonly used yet essential medical devices such as syringes, IV bags, catheters, surgical tools, and prosthetics rely on plastics for their versatility, strength, and lightweight properties. These advanced plastics are engineered to offer enhanced functionality and performance, such as better biocompatibility and resistance to environmental stressors. Furthermore, the development of eco-friendly innovations, such as recyclable and biodegradable materials, helps mitigate the environmental impact of single-use items while maintaining high standards of patient care.
According to a recent report by Vantage Market Research , the global medical plastics market is projected to reach nearly US$51 billion in 2024 and US$86.4 billion by 2032, with a CAGR of 7.9% during the forecast period. This growth reflects the increasing importance of advanced plastics in healthcare technologies and their role in treatment success, ultimately enhancing patients’ quality of life.
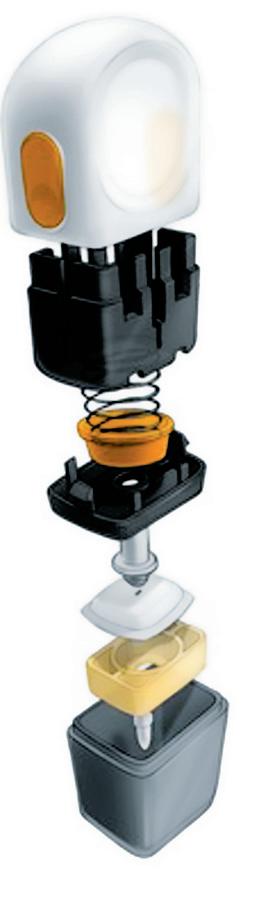
Resins for high precision, high performance components
Medical-grade resins are significantly improving the performance and reliability of high-precision medical devices. Chemicals firm Sabic has introduced a medical-grade PBT, Valor HX325HP, designed specifically for injection moulding components such as insulin delivery pens, insulin pumps, autoinjectors, and continuous glucose monitors.
Medical-grade PBT Valox HX325HP is designed for injection-moulded components like insulin pens, pumps, auto-injectors, and glucose monitors.
Medical Sector
Medical Sector
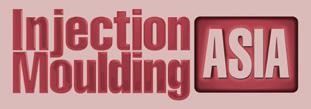
Injection Moulding Asia
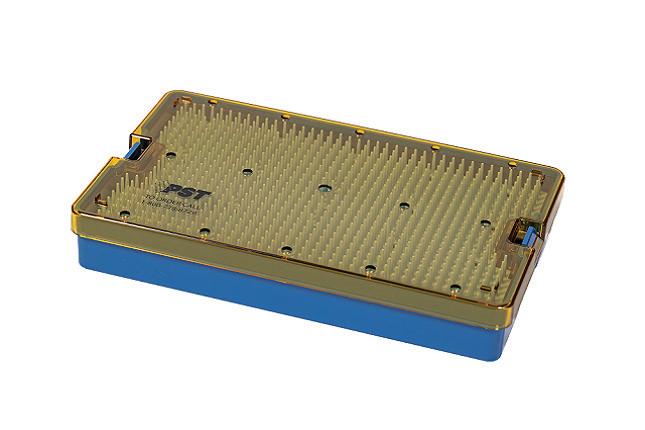
The new medical-grade PBT resin is said to have passed rigorous injection moulding trials, showing high flow even in complex designs and mould release properties with lower shrinkage variation, compared to competing engineering plastics. This resin also offers robust resistance to a wide range of chemicals, minimising environmental stress cracking (ESC), and is compatible with ethylene oxide (EtO), gamma irradiation, and steam sterilisation.
The resin also offers a formaldehyde-free alternative to polyoxymethylene (POM) materials. It is available as an unreinforced, neat material and in a limited range of standard colours, according to Sabic.
In a related development, Sabic showcased its Ultem HU resins at a US trade show earlier this year. These resins are designed to offer medical device manufacturers alternatives to EtO sterilisation.
Ultem HU resins are stable across various sterilisation methods, including vaporised hydrogen peroxide (VHP) gas plasma, steam autoclave, gamma radiation, electron beam, X-ray, and ultraviolet-C. They can endure multiple sterilisation cycles while maintaining high strength, dimensional stability, and aesthetic quality, potentially extending the lifespan of devices made from these materials.
The Ultem HU resins are available in different grades: Ultem HU1000, an unfilled polyetherimide (PEI) with mechanical and thermal properties, and Ultem HU1004, a PEI blend offering enhanced ductility and hydrostability. Both grades are biocompatible, chemically resistant, and inherently flame retardant.
The unreinforced Ultem HU resins’ strength and stiffness make them suitable for replacing metal in medical device components.
Silicone rubber for adhesive gel
Silicone rubber is increasingly used in adhesive gels, offering versatile solutions for a range of medical applications, from wound care to prosthetics.
Germany-based Wacker Chemical Corporation provides silicone products for the medical industry, and recently introduced a new gel, Silpuran 2124, designed for adhesion applications.
This gel is touted as Wacker’s strongest silicone adhesive gel to date, providing twice the peel strength of conventional gels, making it ideal for wearable
medical devices. Silpuran gels are said to ensure reliable adhesion to the skin with gentle, pain-free removal, leaving the skin intact. Wacker adds it also maintains FDA Device Master Files for certain silicone products used in healthcare applications.
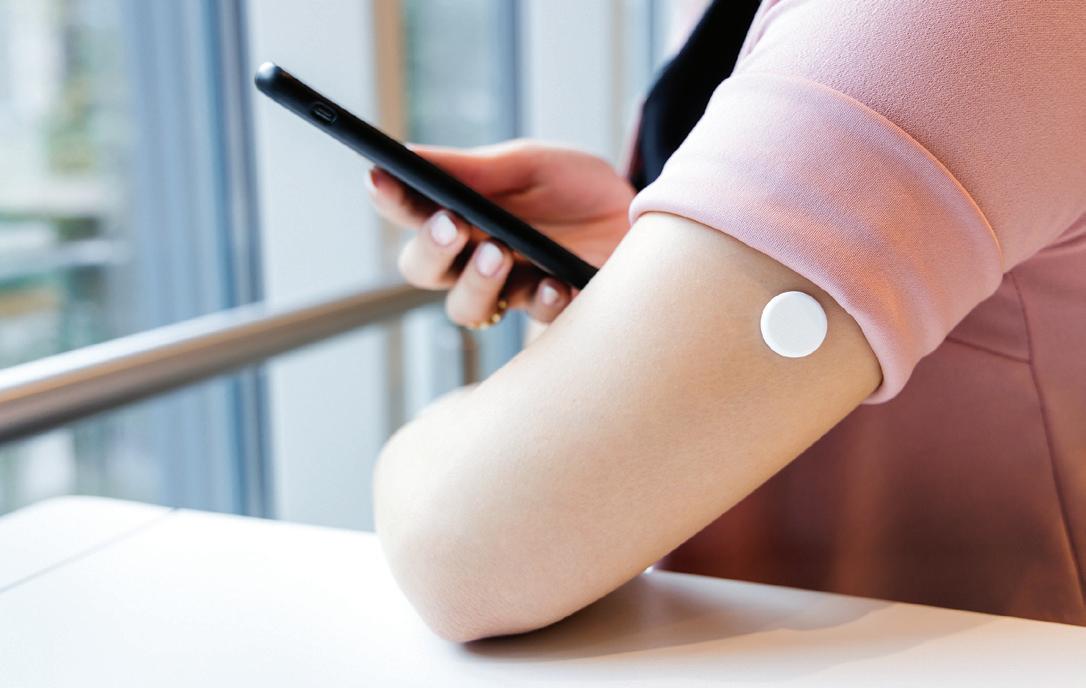
Medical-grade thermoplastic polyurethane (TPU) is advancing the development of cutting-edge medical instruments by offering exceptional durability and flexibility.
In this regard, ICP DAS – BM P, Asia’s first medicalgrade TPU supplier, showcased its extensive range of high-quality TPU products at a US trade show this year.
Based in Taiwan and ISO 13485-certified, ICP DAS –BMP presented its Alithane (ALP series), Durathane (ALC series), and Arothane (ARP series) products. Each TPU series features various hardness levels and radiopaque filler concentrations (tungsten/barium sulphate), enabling customers to select materials for their specific medical device requirements.
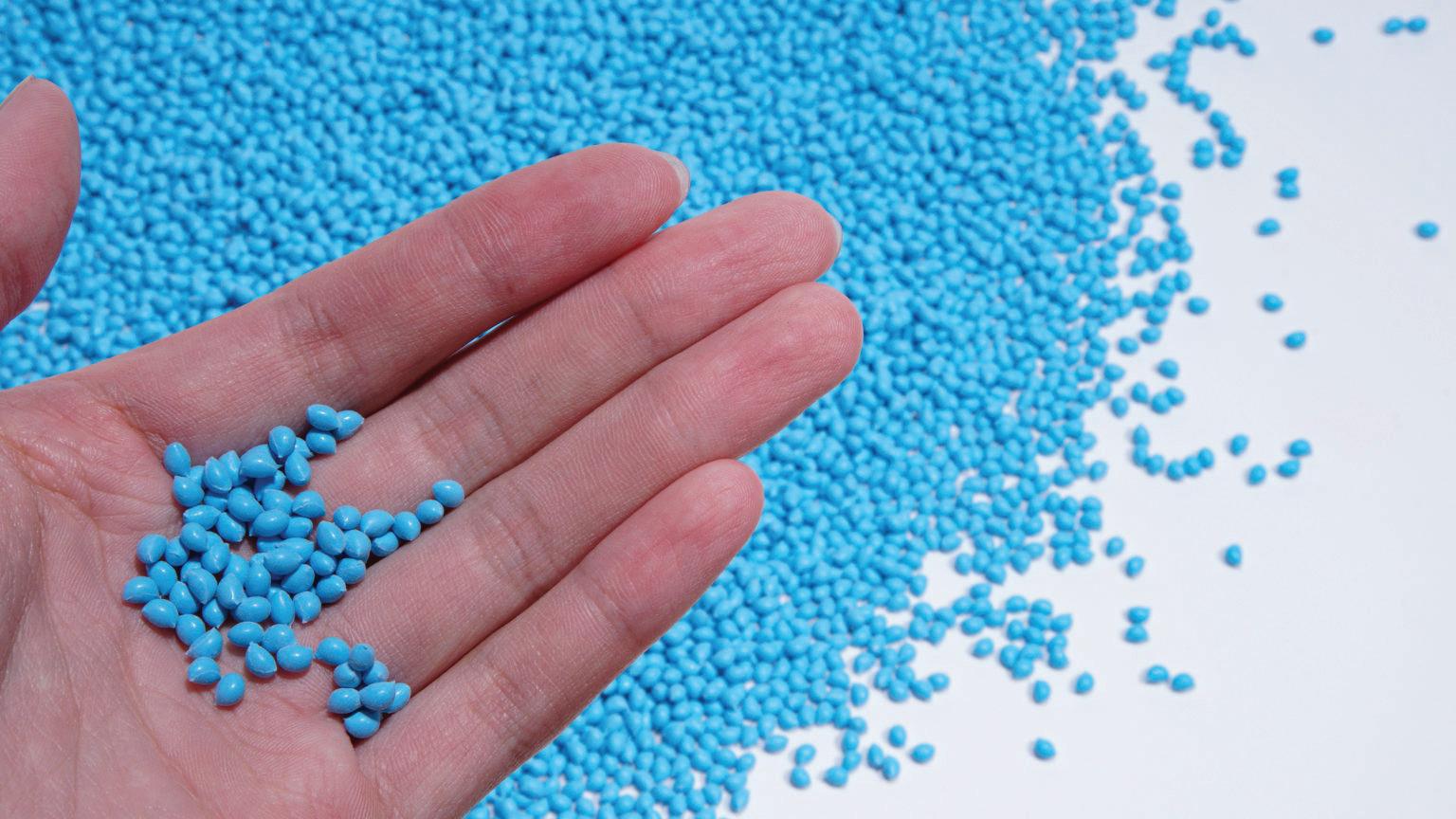
ICP DAS’s TPU pellets, containing 20% or 40% barium sulfate, are formulated through in situ polymerisation
For medical imaging, the company’s TPU pellets are available with 20% and 40% barium sulphate, formulated through in situ polymerisation, with the ALC series also offering 30% barium sulphate. The newly introduced ARP-W and ALP-W series feature 30-80% tungsten, designed for small-dimension or thinwall devices, providing imaging capabilities ideal for minimally invasive procedures.
Sabic’s Ultem HU resins are designed to offer medical device manufacturers alternatives to EtO sterilisation
Modern blood glucose monitors can be securely yet gently attached using Wacker’s Silpuran 2124 silicone adhesive
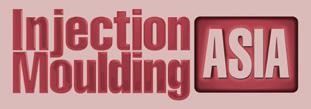
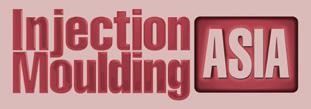
Injection Moulding Asia
The firm also launched the EARP and EALP series, known for their high hardness, heat resistance, and processability, for manufacturing various medical devices, including cardiovascular and gastrointestinal catheters, and other advanced medical instruments.
PEs and TPEs for recyclable packaging elements
Advanced plastics are driving innovation in recyclable packaging elements for the healthcare and medical sectors, improving sustainability while ensuring high performance.
In this context, TekniPlex ’s Consumer Products division, a US-based medical solutions provider, has introduced a new ePress Seal liner, said to be the first pressure-sensitive seal to use expanded polyethylene (EPE).
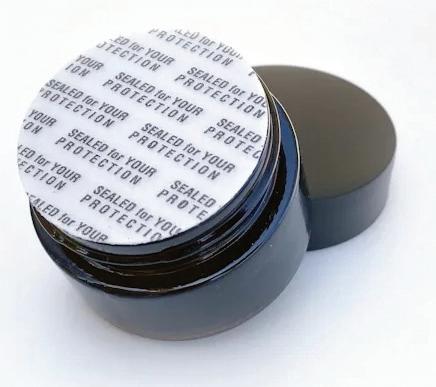
TekniPlex’s Consumer Products division has launched the ePress Seal liner, the first pressure-sensitive seal using expanded polyethylene
The ePress Seal is more flexible and resilient than polystyrene (PS) foam, offering improved compression resistance and maintaining its shape for longer-lasting gasketing properties. Lightweight and easy to remove, these liners are ideal for dry foods, herbs and spices, and nutritional supplements.
The ePress Seal, the latest addition to TekniPlex Consumer Products’ ProTecSeals liners portfolio and is recyclable in regions with PE recycling streams, making it more eco-friendly than conventional PS. This is particularly relevant as the European Union’s SingleUse Plastics (SUP) directive targets PS, with countries like France banning its use in packaging starting January 2025.
Designed for a variety of bottles and jars, most ProTecSeals solutions are perfect for packaging vitamins, supplements, protein powders, peanut butter, and other non-reactive, non-acidic dry products.
Similarly, TekniPlex’s Healthcare division has recently expanded its converting capabilities for US materials firm DuPont Tyvek healthcare styles to the Europe, Middle East, and Africa (EMEA) region. Tyvek, a 100% synthetic material made from high-density spunbound PE fibres, is known for its lightweight, durable, and breathable properties, as well as its resistance to water, abrasion, bacterial penetration, and ageing.
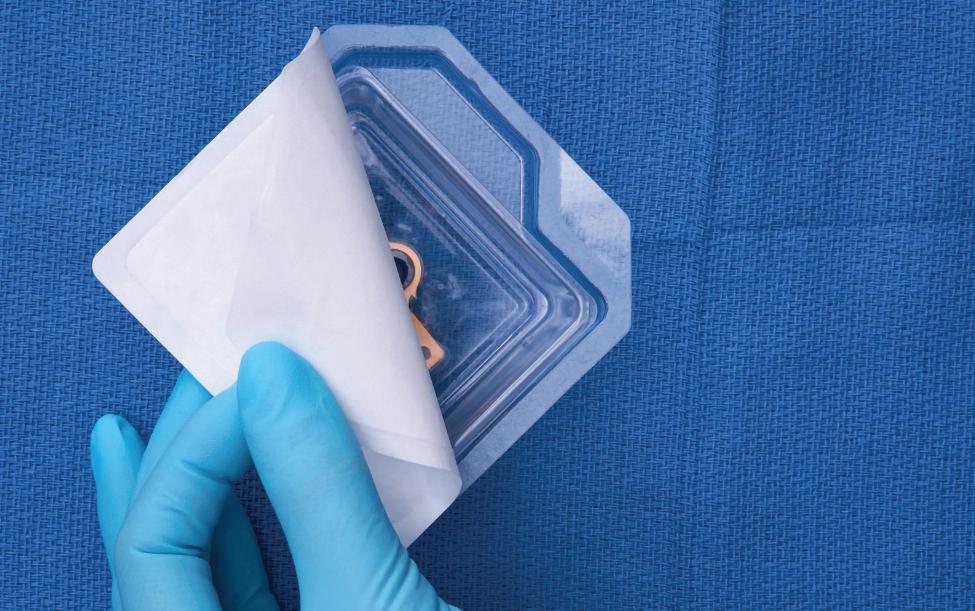
Initially offering Tyvek converting capabilities only in the US, TekniPlex Healthcare ’s recent expansion to the EMEA region will enable local sourcing and shorten lead times for market-leading coated solutions featuring Tyvek products.
These coated Tyvek solutions are utilised in various applications, including form-fill-seal and die-cut processes. The expanded capabilities will accelerate market access for existing customers and open new opportunities for increased market penetration across the EMEA region.
Meanwhile, Germany-based KRAIBURG TPE has launched TPE materials tailored for eye glass protectors, specifically for nose pads and ear hooks in the eyewear industry. These advanced materials are designed to offer protection, durability, and comfort, essential for the demanding safety prerequisites of medical professionals.
Eye glass protectors are crucial, as they promote clear vision and robust protection against potential hazards.
KRAIBURG TPE’s Thermolast H, HC/AP and HC/AD1/AP series, are tailored to meet the stringent requirements of the medical sector.
Advantages include adhesion to a wide range of materials such as PP, PE, PC, ABS, PC/ABS, ASA, SAN, PET, PETG, and PS. The materials can be processed via injection moulding and extrusion and offer optimised compression set. Besides being colourable, the materials are also sterilisable: compatible with autoclave (121°C) and EtO, to maintain hygiene standards.
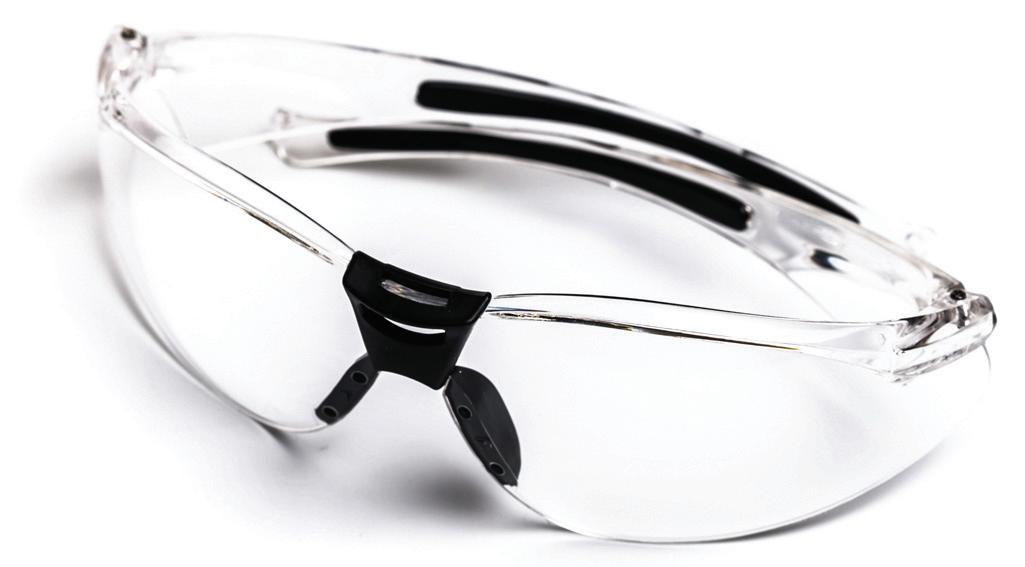
Tyvek, made from high-density spunbound PE fibres, is lightweight, durable, breathable, and resists water, abrasion, bacteria, and ageing
KRAIBURG TPE’s medical-grade Thermolast TPE series is being touted for eye glass protectors
Rubber Journal Asia
Philippine’s rubber sector roots for global competitiveness
The Philippine rubber industry aims to produce world-class, competitive products by adopting technology, sustainability practices, and standards, and by connecting with local and global markets, with the Philippine Rubber Industries Association Inc. ( PRIA ) at the helm, says Angelica Buan in this interview with Ellen Tan Go, President of PRIA.
PRIA: a unified voice for domestic rubber industry leaders
The Philippine rubber industry aims to become a key contributor to the country’s economic development by upgrading manufacturing skills, adopting technical and market standards, and strengthening connections with local and export markets.
Driven by economic growth and increasing demand for rubber products, the industry leverages its expertise in producing a wide array of products, technical capability, adaptability, and experienced labor to meet customer needs and fuel development.
The Philippine Rubber Industries Association Inc ( PRIA ), the main industry organisation, plays a crucial role in driving the sector’s growth and development. Established in 1979 from the merger of the Philippine Rubber Manufacturers Association ( PHIRMA ) and the Rubber Industries Association of the Philippines ( RIAP ), PRIA has brought together key figures in the rubber industry.

Today, PRIA has 46 member firms, including 26 direct industry players and several business development service providers, such as material suppliers and logistics companies.
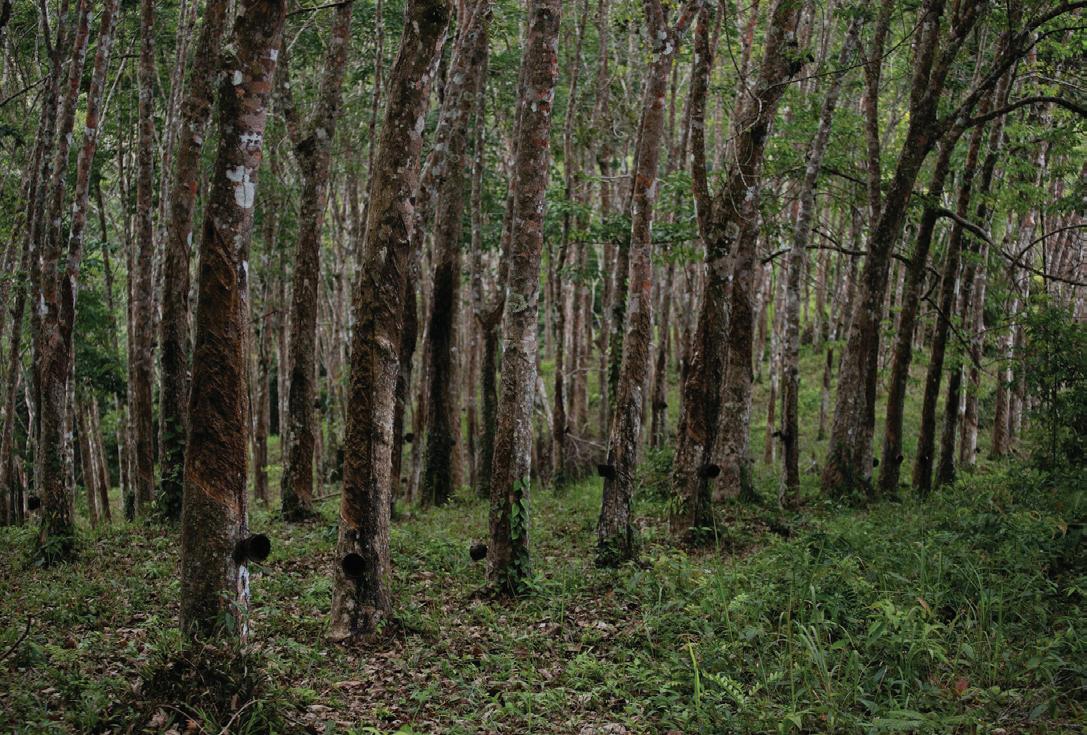
In an exclusive interview with Ellen Tan Go, President of PRIA, Rubber Journal Asia (RJA) explored the development goals, challenges, and successes of the Philippine rubber sector ahead of the upcoming 2024 Rubber Summit Conference, scheduled for 26-28 September in Davao.
RJA: Please provide an overview of PRIA and its main objectives.
Ellen Tan Go: PRIA has served as the unified voice of the country’s rubber industry. Its membership comprises companies from various sectors, including manufacturing, trading, planting, and rubber processing. PRIA’s mission is to a cost competitive quality driven, supply-reliable, product diversified value chain from farming to rubber products manufacturing under sustainable practices.
RJA: Are there any upcoming or future plans within the organization/industry that you would like to share with us?
Ellen Tan Go: PRIA will continue to be a leading organisation in the rubber industry with the goal to support the Philippines industry towards a brighter and sustainable future. As PRIA we will continue to improve the services we provide to our members as well as to increase and consolidate our membership base. This is the time to show leadership, vision and commitment. To secure growth and competitiveness, we need to convert ambitious ideas into measurable outcomes with lasting impact and to do so we need the support and contribution of every one that has at heart the future of the Philippines rubber economy.
PRIA’s Ellen Tan Go believes that enhancing cooperation among associations of rubber-producing and rubberconsuming countries will further grow the local rubber industry
The Philippine Rubber Industries Association, the main industry organisation in the country, plays a crucial role in driving the sector’s growth and development
Grace under pressure; coping with challenges
Rubber Journal Asia
The Philippines rubber industry, like many others both locally and globally, has faced numerous challenges in recent years due to market volatility and economic disruptions. These factors have impacted demand, production, and overall competitiveness.
According to a policy brief from the Department of Science and Technology - Philippine Council for Industry, Energy, and Emerging Technology Research and Development ( DOST-PCIEERD ), the industry must address several key issues: fluctuating supply and volatile prices, which have lowered the priority of testing services for producers and processors; a need for greater support for grassroots technology; and improvements in regulatory standards, access to rubber testing laboratories, and related areas.
Additionally, severe weather conditions, such as unseasonal rains and typhoons, have reduced production per hectare. These weather-related challenges disrupt supply chains and production schedules, exacerbating existing issues.
RJA enquired about the current situation on the ground.
RJA: What is the current situation of the country’s rubber industry and challenges? If there are any, how are these being addressed?
Ellen Tan Go: We live in a dynamic and ever-changing world. The development of new technologies, the need to mitigate and adapt to climate change risks, and the overarching goal of achieving a more sustainable society present both challenges and opportunities for the rubber industry.
Our priority should be to ensure growth and stability for our companies while also improving the quality of life for the millions of families working in both the upstream and downstream sectors of the rubber economy.
We need a human-centred approach that fosters people’s capabilities through new technologies, manages intergenerational social trends, and builds long-term competitive advantages by rethinking our business models.
These topics will be the focus of discussions at the three-day event organised by PRIA and Xida Communications, “Rubber: New Frontiers, New Markets,” which will be held in Davao city, Philippines.
RJA: Is government support for the industry adequate or lacking?
Ellen Tan Go: As I mentioned earlier, when we think about our industry, we need to adopt a human-centric approach. Providing better living conditions for workers, especially smallholders, must be a priority.
Close collaboration between the industry and national and local governments is key to achieving what we call “sustainability.” We need to define a rubber “sustainability” roadmap that addresses social, economic, and environmental aspects. Sustainable practices have the potential to reduce the carbon footprint of rubber production and use, making it more attractive to consumers and opening new markets and opportunities.
Growth and expansion prospects
The Philippines rubber industry is clearly experiencing rapid growth and expansion, driven by advancements in manufacturing and increasing demand for high-quality products. RJA inquired further about recent developments in the local rubber industry under PRIA’s oversight.
RJA: Can you provide an update on the latest expansion developments in the local rubber industry?
Ellen Tan Go: Head Sport , an Austrian-American sports equipment and apparel manufacturer that dominates the global tennis ball market, has opened a new plant facility in the Philippines.

This will be the largest tennis ball production facility in the world. Head Sport Philippines Inc . is located in the Anflo Industrial Estate in Davao del Norte. In addition to this development, we can see that several local motorcycle tyre manufacturers are also expanding their factories.
Head Sport, an Austrian-American sports equipment and tennis balls manufacturer, has opened a new plant facility in the Philippines
Rubber Journal Asia
Country Focus

RJA: Which are the major markets for Philippine rubber, and what applications are in demand?
Ellen Tan Go: Today, the downstream sector of the rubber industry in the Philippines is a dynamic and integral part of the overall value chain.
In the Philippines, as elsewhere, the major enduse market remains tyre manufacturing, though the market also includes producers of automotive parts, sports products, and footwear.
RJA: Do local tyre manufacturers/OEMs such as Dunlop, Yokohama, Westlake, Cooper, Aeolus, CST, Michelin, Agila, Leo, and Izumi, which have plants in the Philippines, utilise local rubber? Has their consumption of local rubber increased in the last five years?
Ellen Tan Go: Companies such as Yokohama are investing in new capabilities that will require increased domestic NR production. This is also true for other domestic tyre makers, as their local rubber consumption has significantly increased over the past five years.
The Filipino rubber manufacturing sector needs to attract investments to improve quality and ensure sustainable production. In this regard, a publicprivate partnership is key to moving from “strategy
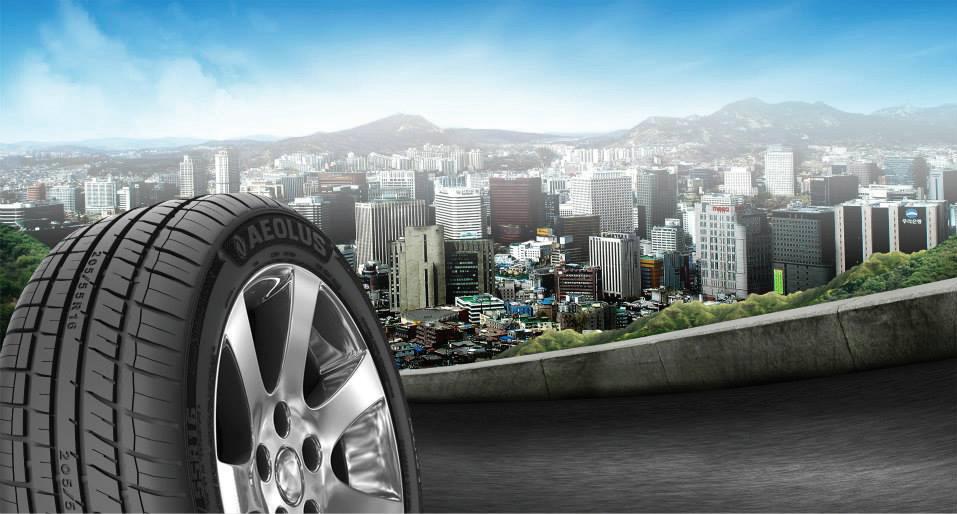
to action” and ensuring that the Philippines can harness its rubber production capabilities to boost economic development.
Cooperation to drive sector’s global edge Advancing technology and strengthening market connections are undoubtedly the secret sauce for boosting the industry’s global competitiveness and contributing to the Philippines’ economic development.
RJA: Are there any cooperations in the pipeline with other countries or markets that are targeted to drive growth?
Ellen Tan Go: The challenges we face are global, and the Philippine rubber industry needs to cooperate with other countries and organisations to identify priorities and provide solutions.
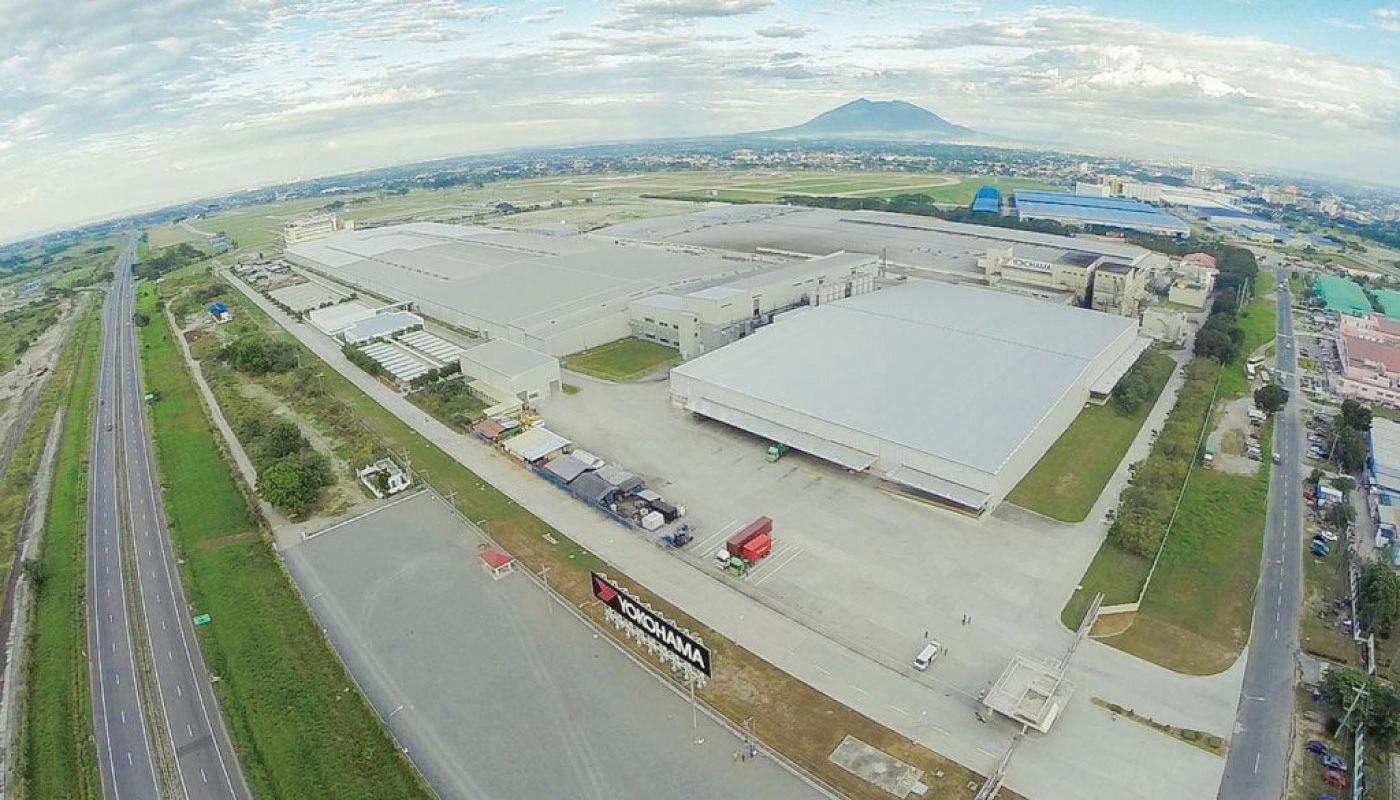
In this regard, PRIA collaborates locally with the Philippine Rubber Research Institute (PRRI) and the Department of Trade and Industry (DTI) to promote activities that strengthen the Philippines’ rubber supply chain.
This collaboration recognises the importance of smallholders and smallholders’ cooperatives, which are the backbone of the rubber economy in our country.
RJA: How can the local rubber industry be driven further for growth?
Ellen Tan Go: To enable further growth in the local rubber industry, we believe it is essential to enhance cooperation at an internal level, particularly among associations of rubber-producing and consuming countries.
We need to establish a platform that facilitates the exchange of experiences and best practices while improving mutual understanding of each other’s needs.
In the coming months, PRIA will lead efforts to promote such collaboration.
Anflo Industrial Estate in Davao del Norte is home to the largest tennis ball production hub
Aeolus Tyres, China’s largest OTR and all-steel truck radial tyre manufacturer, has expanded its regional footprint by opening an office/showroom in Cebu, located in the Central Visayas region
Tyre majors like Yokohama, is investing in new capabilities that will require increased domestic natural rubber production, says Ellen Tan Go
Events
18 – 21 SEPTEMBER
Vietnam PrintPack
Venue: SECC, Ho Chi Minh City, Vietnam
Tel: +886-2-26596000 Fax: +886-2-26597000
Email: exfdp@chanchao.com.tw
Website: www.chanchao.com.tw/VietnamPrintPack
24 – 28 SEPTEMBER
Taipeiplas | ShoeTech Taipei
Venue: Taipei Nangang Exhibition Center, Taipei, Taiwan
Tel: +886-2-2725-5200 Ext.2618
Email: cph@taitra.org.tw
Website: www.taipeiplas.com.tw
25 – 27 SEPTEMBER
Propak India
Venue: Bengaluru International Exhibition Centre, India
Tel: +91 9820209795
Email: mehraj.waghu@informa.com
Website: www.propakindia.com
2 – 4 OCTOBER
METALEX Vietnam
Venue: SECC, Ho Chi Minh City, Vietnam
Tel: +84 286 287 3355
Email: metalexvietnam@rxtradex.com
Website: www.metalexvietnam.com
2 – 4 OCTOBER
MTA Hanoi
Venue: ICE, Hanoi, Vietnam
Tel: +84 28 3622 2588 / 168
Email: Dung.Nguyen@informa.com
Website: www.mtahanoi.com
9 – 12 OCTOBER
AllPack Indonesia
Venue: JIExpo Kemayoran, Indonesia
Tel: +62 21 6345861
Email: info@kristamedia.com
Website: www.allpack-indonesia.com
10 – 12 OCTOBER
PackPrintPlas Philippines
Venue: SMX Convention Center Manila, Philippines
Tel: +63 917 706 8134
Email: info@packprintplasphilippines.com
Website: www.packprintplasphilippines.com
15 – 17 OCTOBER
Oman Plast
Venue: Oman Convention & Exhibition Centre, Muscat, Oman
Tel: ++968 24788804 Fax: +968 24788845
Email: info@omanplast.net
Website: www.omanplast.net
Check out the Advertisers' page on our website.
Information is categorised by the YEAR & DATE of publication for easy reference.
For further details, email us at: news@plasticsandrubberasia.com
15 – 19 OCTOBER
Fakuma
Venue: Friedrichshafen, Germany
Tel: +49 7025 9206 0
Email: info@schall-messen.de
Website: www.fakuma-messe.de
16 – 17 OCTOBER
International Trade Fair for Composite Materials, Technologies and Products - Kompozyt Expo
Venue: Krakow, Poland
Tel: + 48 12 644 59 32
Email: biuro@targi.krakow.pl Website: www.kompozyt-expo.pl
16 – 19 OCTOBER
VietnamPlas
Venue: Ho Chi Minh City, Vietnam
Tel: +886-2-2659-6000 Fax: +886-2-2659-7000
Email: exfdp@chanchao.com.tw
Website: www.vietnamplas.chanchao.com.tw
23 – 26 OCTOBER
Eurasia Packaging Istanbul
Venue: Istanbul, Turkey
Tel: +90 212 867 11 00 Fax: +90 212 886 67 48
Email: team@packagingfair.com
Website: www.packagingfair.com
30 – 31 OCTOBER
PEF World Congress
Venue: Düsseldorf, Germany
Tel: +49 2161 6884469
Email: mt@bioplasticsmagazine.com
Website: www.pef-world-congress.com
6 – 8 NOVEMBER
Film & Tape Expo
Venue: Shenzhen World Exhibition and Convention Center, China
Tel: +86 21 2231 7018
Email: edison.li@rxglobal.com
Website: www.film-expo.com
13 – 14 NOVEMBER
Plastics Recycling Show Asia (PRSA)
Venue: Marina Bay Sands, Singapore
Tel: + 44 (0)7739 302081
Email: mabarber@crain.com
Website: www.prseventasia.com
20 – 23 NOVEMBER
Plastics & Rubber Indonesia
Venue: Jakarta International Expo, Kemayoran, Indonesia
Tel: +62 21 2525 320
Email: faradiba@pamerindo.com
Website: www.plasticsandrubberindonesia.com
ADVERTISERS’ ENQUIRIES
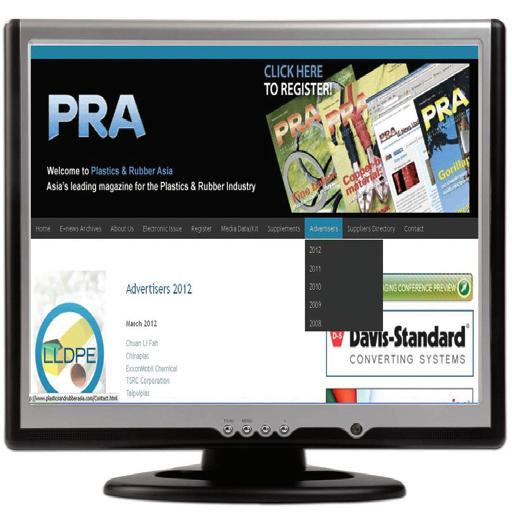
Publishing Office / Scandinavia, Benelux & France
Postbus 130, 7470 AC Goor, The Netherlands
Tel: +31 547 275005 Fax: +31 547 271831
Email: arthur@kenter.nl
Contact: Arthur Schavemaker
Regional Office
B6-11, Menara Indah, Jalan 9, Taman TAR 68000 Ampang, Selangor, Malaysia
Mobile: +6017-8849102
Email: tej@plasticsandrubberasia.com
Contact: Tej Fernandez
China & Hong Kong
Room 6B, Floor 6, Building HengLong, No. 50 Renming Zhong Road, Zhangjiagang, 215600 China
Tel: 0512-58919146
Fax: 0512-58919145
Mobile: +86-17751702720
Email: henry.xiao@matchexpo.com
Contact: Henry Xiao/Zhu Wei
Malaysia (Print, Web, Digital Advertising & Conferences)
Tara Media & Communications
Mobile: +6017 610 1270
E-mail: yokepeng@taramedia.com.my
Contact: Yoke Peng
Southeast Germany, Switzerland & Austria Verlagsbüro G. Fahr e.K
Breitenbergstrasse 17
D-87629 Füssen, Germany
Tel: +49 8362 5054990
Fax: +49 8362 5054992
Email: info@verlagsbuero-fahr.de
Contact: Simon Fahr
North-West Germany
JRM Medien+Verlag
Minkelsches Feld 39
D-46499 Hamminkeln, Germany
Tel: +49 2852 94180
Fax: +49 2852 94181
Email: info@jwmedien.de
Contact: Jürgen Wickenhöfer
Malaysia. India, Indonesia, Singapore, Thailand, Australia, New Zealand, Korea & Philippines
Tara Media & Communications
B6-11, Menara Indah, Jalan 9, Taman TAR 68000 Ampang, Selangor, Malaysia
Mobile: +6017-8849102
Email: tej@plasticsandrubberasia.com
Contact: Tej Fernandez
Italy, Spain & Portugal
MediaPoint & Communications Srl
Corte Lambruschini, Corso Buenos Aires, 8, Vo Piano - Interno 9, 16129 Genova, Italy
Tel: +39 010 570 4948 Fax: +39 010 553 0088
Email: info@mediapointsrl.it
Contact: Fabio Potesta
Taiwan 宗久實業有限公司
Worldwide Services
11F-B, No.540 Sec.1, Wen Hsin Rd., Taichung, Taiwan
Tel: +886 4 23251784 Fax: +886 4 23252967
Email: global@acw.com.tw
Contact: Robert Yu 游宗敏
USA & Canada
Plastics Media International P. O. Box 44, Greenlawn, New York 117430, USA
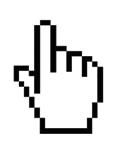
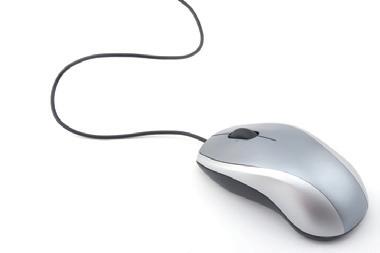
Tel/Fax: +1 631 673 0072
Email: mjm@4m-media.com
Contact: Michael J Mitchell
www.plasticsandrubberasia.com
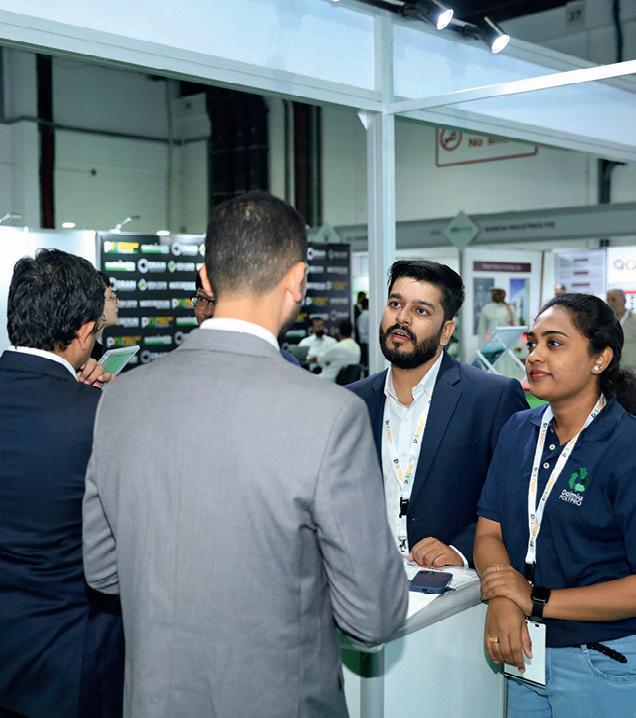
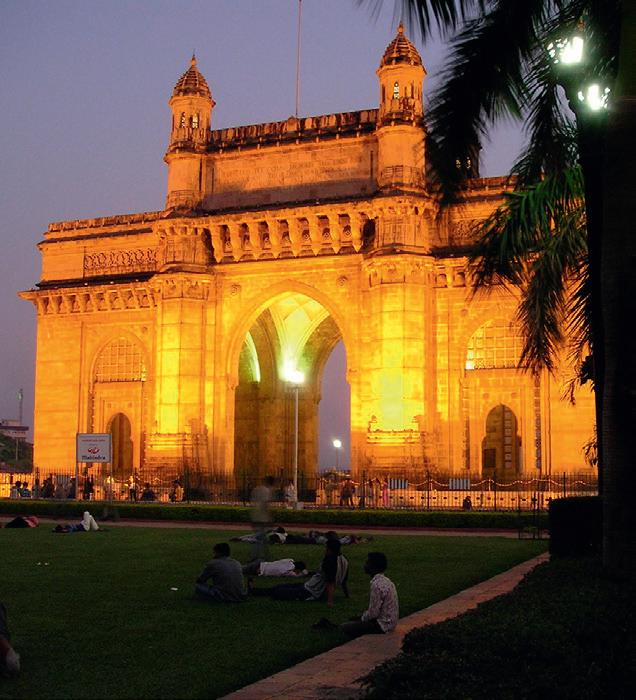
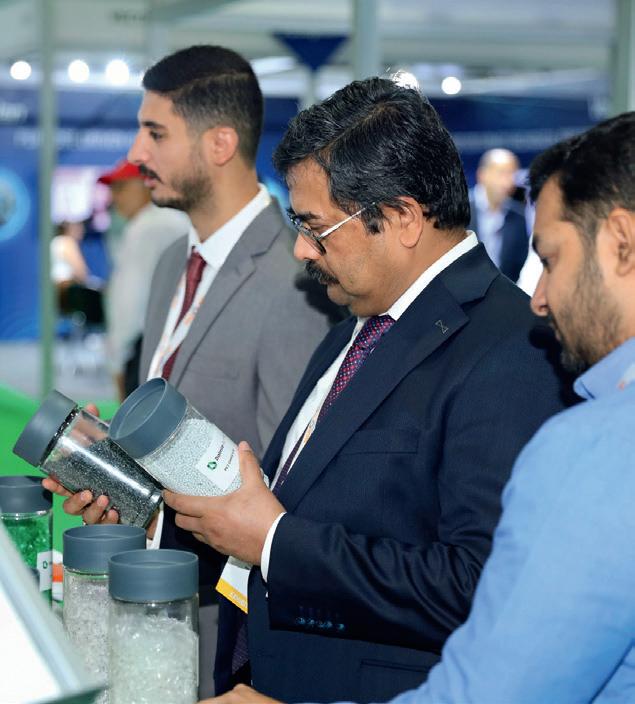
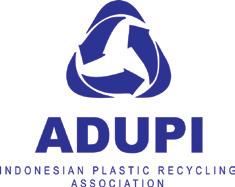
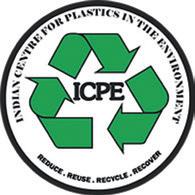
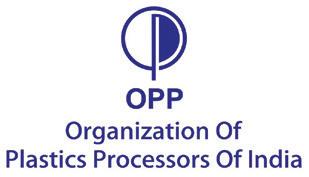
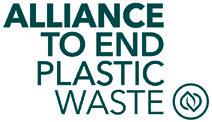
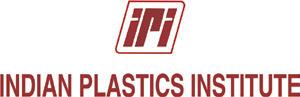
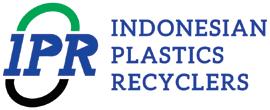