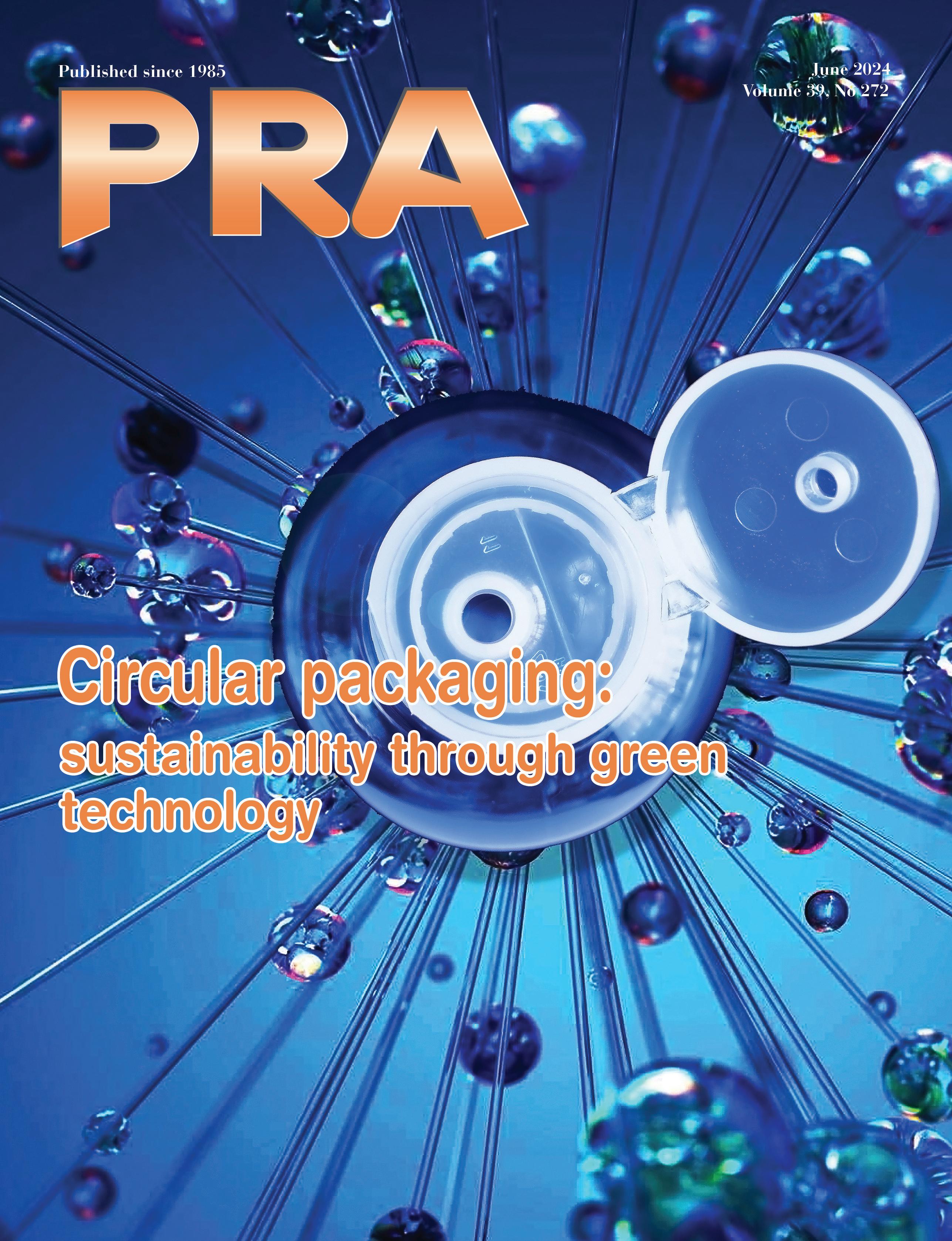
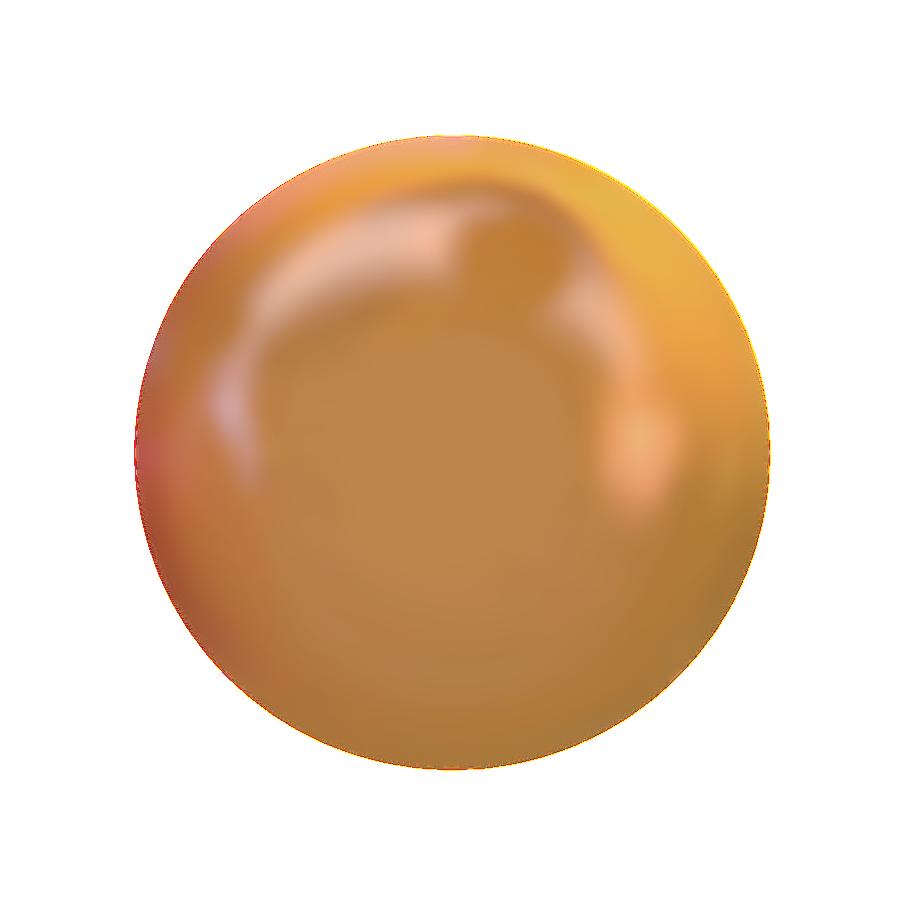
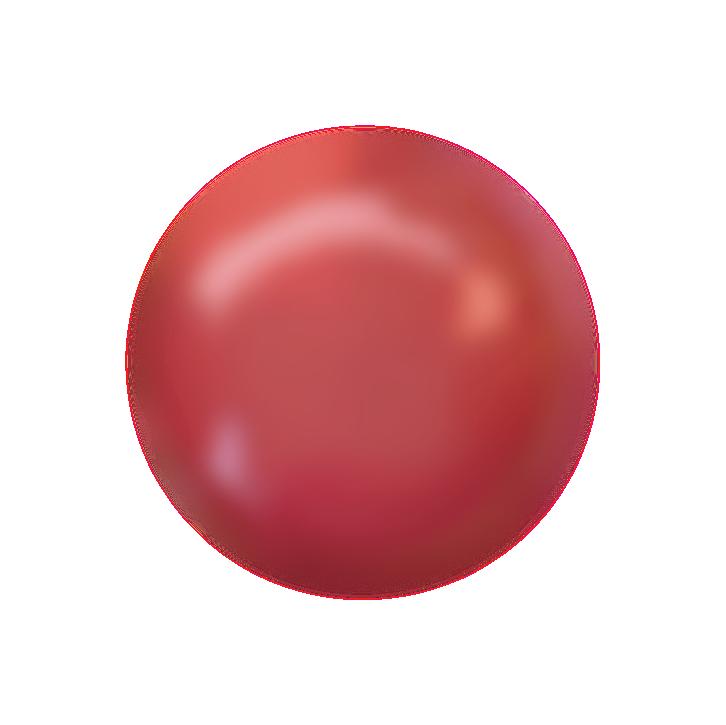
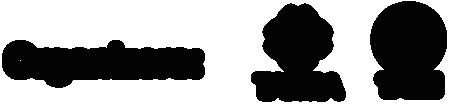
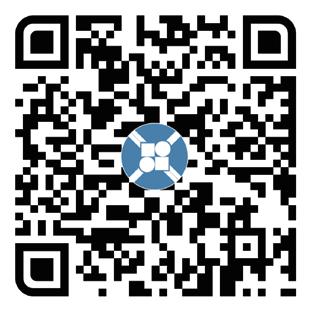
Evolving standards for plastic products, focusing on performance, application, quality, material guideline compliance and sustainability are driving advancements in additives, highlighting their critical role in modern manufacturing.
Materials firm Dow’s 35th Packaging Innovation Awards (PIA) seek packaging that meets sustainability and innovation criteria, says Angelica Buan, who joined a fireside chat with the jury of the awards to find out more on the power of packaging innovation for human progress
From an emerging economy, Thailand is now striving to claim global economic prominence through its commitment to the bioplastics sector and a circular economy as well as the fostering of partnerships.
2 Industry News
5 Machinery News
7 Materials News supplements
Additive Manufacturing: A round-up of the 3D printing sector highlighting AIM3D and its Voxefill process; how biobased resins could offer a recyclable future for 3D printing and china’s journey to attaining uS$8 billion in 3D printing hardware sales by 2032
Machinery News: husky Technologies application spotlight: transforming the cutlery market with sustainable innovation
Machinery News: husky Technologies application spotlight: GPS’s BPI-certified compostable coffee capsule
Tyres: Disruptive technologies in tyre manufacturing now focus on reducing the impact on the environment with materials featuring recycled content, says Angelica Buan in this report
Green technology is on the rise with companies searching for improved plastics materials, to foster a circular economy, where products are reused, recycled, and kept in circulation for as long as possible.
publisher/editor-in-chief
Arthur Schavemaker
Tel: +31 547 275005
Email: arthur@kenter.nl
Associate publisher/executive editor
Tej Fernandez
Tel: +6017 884 9102
Email: tej@plasticsandrubberasia.com
senior editor
Angelica Buan
Email: gel@plasticsandrubberasia.com
circulation
Stephanie Yuen
Email: stephanie@taramedia.com.my
layout/design
Prestige Trading
Email: prestige9a@gmail.com
permits
ISSN 1360-1245 is published 4 (four) times a year in English by Kenter & co Publishers’ representatives BV.
Whilst every effort is made to ensure that the information contained in this publication is correct, the publisher makes no warranty, expressed or implied, as to the nature or accuracy of such material to the extent permitted by applicable law.
© 2024 Kenter & co Publishers’ representatives BV No part of this publication may be reproduced, stored or used in any form, or by any means, without specific prior permission from the publisher.
PrA is a digital publication that is circulated free to trade readers in the plastics and rubber industry. Please view this link to subscribe/renew your free subscription: http://plasticsandrubberasia.com/register.html
www.plasticsandrubberasia.com www.rubberjournalasia.com www.injectionmouldingasia.com www.eog-asia.com
• South Korea ’s Hyosung TNC is investing US$1 billion to build multiple bio-textile materials plants in Vietnam’s Ba RiaVung Tau province. It will start off with a 50,000 tonnes/ year bio-BDO plant slated for start-up in 2026, upping to 200,000 tonnes/ year eventually.
• State-owned energy firm Saudi Aramco is acquiring a 10% stake in Hengli Group ’s Hengli Petrochemical , subject to required regulatory clearances. No financial details or timeline were provided.
• Suzano Ventures , the corporate venture capital arm of Suzano , the world’s largest pulp producer, is funding US$5 million for Canadian startup Bioform Technologies , which offers sustainable plastics alternatives developed at the University of British Columbia .
• National oil firm KazMunayGas ( KMG , a subsidiary of Samruk Kazyna ) has sold a 20% share in Silleno , a joint venture
developing a US$7.7 billion PE project, which is also being developed by chemical firms Sibur and Sinopec , in the Atyrau region, with a capacity of 1.25 million tonnes.
• Italy’s NextChem Tech , part of the Maire Group , has acquired an additional 34% stake in recycling firms MyReplast Industries and MyReplast from an existing stakeholder, increasing its interest to 85%, with the remaining 15% held by a local entrepreneur.
• Chemical firm Ineos has completed the acquisition of TotalEnergies ’ 50% share of Naphtachimie (720 kilotonnes/ year steam cracker), Appryl (300 kilotonnes/year PP business), Gexaro (270 kilotonnes/year aromatics business) and 3TC (naphtha storage) announced last year.
• Austrian materials firm Borealis has acquired a 100% stake in Integra Plastics AD , a mechanical recycling player based in Bulgaria, which has a
20,000 tonnes/year recycling plant.
• Italy’s Sacmi Group has sold its Beverage Business Unit to Omnia Technologies , a global group with Italian roots that provides automation technology in the food, beverage and pharmaceutical sectors. Terms were not disclosed.
• Loop Industries , that makes rPET, is forming a 50/50 India joint venture with Indian polyester films firm Ester Industries to build a US$165 million manufacturing facility for recycled dimethyl terephthalate, recycled monoethylene glycol and specialty polymers in India, using the Infinite Loop technology.
• Growth capital platform Infinity Recycling ( IRC ) has closed its Circular Plastics Fund I SCSp (CPF), securing EUR175 million in committed capital. Investors include Dutch insurance group ASR , Danish philanthropic association Realdania , ING Sustainable Investments ,
the sustainable Investment arm of ING , Danish investment and holding company KIRKBI , and the impact investment initiative of Swiss company Aprèsdemain
• Manufacturer of polylactic acid (PLA) NatureWorks , has secured financial support of US$350 million from Krungthai Bank PCL to optimise the capital structure for the new fullyintegrated Ingeo PLA manufacturing facility in Thailand.
• LyondellBasell ( LYB ) has completed the sale of its Ethylene Oxide & Derivatives (EO&D) business and facilities located in Texas, US, to ethylene/ propylene producer Ineos Oxide The business purchased for US$700 million has around 1 million tonnes/year of EO/derivatives nameplate capacity. In other news, LYB has completed the acquisition of a 35% interest in Saudi Arabia’s National Petrochemical Industrial Company ( NATPET ) from Alujain Corporation . The joint venture is enabled by LYB’s Spheripol PP technology.
• Chemovator , the business incubator and early-stage investor of German chemicals firm BASF , has invested in Heartland , a US-based startup involved in the production of natural fibre plastic additives.
• French firm Arkema is acquiring US materials firm Dow 's flexible packaging laminating adhesives business, generating annual sales of around US$250 million.
• Oil producer Abu Dhabi National Oil Co ( Adnoc ) has dropped
its bid to buy a stake in Brazilian petrochemicals firm Braskem Adnoc had made a non-binding US$2.1 billion offer to Novonor SA , Braskem's main shareholder, and proposed sharing control with Brazil's Petrobras , similar to Novonor's current arrangement. However, issues like valuation had derailed the deal.
• German chemical company Wacker is acquiring production facilities and know-how from US coater Bio Med Sciences Inc. to expand its expertise and business with silicone-coated healthcare products.
• UK recycling firm DeepTech Recycling , which has developed chemical recycling technology for different types of plastic waste, has secured a new tranche of £0.8 million in funding, led by deep tech venture capital firm EMV Capital , a wholly owned subsidiary of NetScientific Plc . The fundraising follows a first closing of £1.3 million that was completed in December 2023, bringing the total amount raised to £2.1 million.
• German materials firm Covestro has become a strategic partner in BioBTX , to enable the construction of a demo plant for the BioBTX ICCPTechnology in the Netherlands, scheduled to go online early 2027. The technology is able to produce chemicals such as benzene, toluene and xylene from organic and mixed plastic waste.
• Tech firm KBR has been awarded a contract by Sabic Fujian Petrochemicals
to license KBR's technology in China, for a 250 kilotonnes phenol plant. The final investment decision for this project was announced in January 2024 with expected completion in 2026.
• Borealis is co-investing with Adnoc in a 100,000 tonnes capacity expansion at materials firm Borouge ’s XLPE compounding facility in Ruwais, Abu Dhabi, for growing demand for wire and cable compounds in Asia
• Process technology provider Lummus Technology has taken a lead investor position in RWDC Industries ' convertible bond round, further strengthening the partnership between the two companies to bring polyhydroxyalkanoates (PHA) to the global market.
• Germany’s Biesterfeld Group has acquired Aerontec , a South African supplier and distributor of advanced composite materials and related technology. The closing was completed today.
and the Middle East. The project will be up by 2025.
Elsewhere, Borealis has installed a demo recyclatebased polyolefins (rPO) compounding line in Beringen, Belgium. To be fully operational by 2025, it will use Borealis' proprietary Borcycle M technology to transform mechanically recycled post-consumer waste into PP and PE materials.
• LyondellBasell (LYB) has set up a plastics recycling joint venture in Zhaoqing,
in Southern China, with China’s Genox Recycling that will use mechanical recycling technology to recycle plastic waste and produce new polymers, adding to the LYB‘s CirculenRecover portfolio.
• Vinyl maker I neos Inovyn has launched two PVC pilot plants at its site in Belgium, where its main R&D centre is located, to accelerate recycling PVC which is not mechanically recyclable. It aims to commission a unit with a 40 kilotonnes recyclable capacity by 2030.
• BASF India Limited will increase the production capacity by 40% of its Ultramid PA and Ultradur PBT compounding plants in Panoli, Gujarat, and Thane, Maharashtra, India, by 2025.
• A US$1.2million investment through a partnership between Coca-Cola Beverages Africa ( CCBA ) in Namibia and Plastic Packaging has culminated in the opening of a new PET flaking plant in Okahandja which will double the capacity of the only mechanical recycler of plastic waste in the country. The completion of this recycling facility will enable Namibia Polymer Recyclers ( NPR ), a subsidiary of Plastic Packaging, to recycle up to 500 tonnes/month.
• Chemical firm Syensqo has broken ground on its new battery-grade polyvinylidene fluoride (PVDF) facility in Augusta, Georgia, US. When completed, the site will be the largest PVDF production facility in North America.
• Engineering materials supplier Domo Chemicals has inaugurated a Technyl PA plant in Haiyan, Zhejiang, China. The EUR14
million plant will increase the current capacity of 25,000 to 35,000 tonnes and eventually 50,000 tonnes in the long term.
• The world’s largest PTA project by singleunit production capacity by Sinopec Yizheng Chemical Fiber has started up operation Jiangsu Province, China. The production capacity of 3 million tonnes/ year will come from two new plants added on to two existing lines at Yizheng.
• Belgian chemical firm Solvay has opened its production unit for Alve-One chemical blowing agent, ecodesigned to transform the thermoplastic foaming industry, in Rosignano, Italy.
• Speciality chemicals firm Orion has broken ground on a plant in Texas, US, that will be the only facility in the country producing acetylenebased conductive additives for lithiumion batteries.
• Toyo Ink India , part of Japanbased Artience Group (formerly Toyo Ink Group ), is expanding its production capacity for solvent-based adhesives at its site in Gujarat, India. It will start up in 2026 and boost the site’s adhesive capacity
by 3.5 times its current output.
• Speciality lubricants firm Klüber Lubrication , a part of German Freudenberg Chemical Specialities , is expanding its operations facility in Mysore, India, by 2027.
• Japan’s Shin-Etsu Chemical Co will construct a new silicone products plant in China in Pinghu City, Zhejiang Province.
• Specialty materials firm Celanese Corporation has opened two new Indian facilities: a technical centre in Silvassa and a shared service centre in Hyderabad, for application development, testing and analytics capabilities.
• BASF has inaugurated its second polymer dispersions production line at the Daya Bay site in Huizhou, China.
BASF is also investing in the expansion of its advanced additives plant at its Nanjing site. The new line is planned to start up by the end of 2025.
• Freepoint EcoSystems Belgium NV , an affiliate of Freepoint Commodities , is developing an 80,000
tonne/year-advanced recycling facility for plastics in Europe. It will be situated in Belgium, within the North Sea Port.
• Trillium Renewable Chemicals is using Ineos Nitriles ’ Green Lake facility in Texas, US, for a demo plant for converting plant-based glycerol into acrylonitrile, by 2026. Trillium has developed a technology for producing sustainable acrylonitrile, while Ineos is the developer of the AN process.
• To further strengthen the market position of its specialty moulding compounds globally, German materials firm Röhm has expanded its production capacity at the Wallingford plant in Connecticut (US).
• Manufacturer of thermoplastics, composites and seals, Greene Tweed has completed its manufacturing facility in Chungcheongbukdo, South Korea.
• Japan’s Zeon Corporation is constructing a cyclo olefin polymers (COP) plant in Japan to boost its combined capacity for COP to 54,000 tonnes/year, including the existing COP capacity of 42,000 tonnes/year at the Mizushima plant. It will be completed in 2028.
For Indian preform and plastic packaging manufacturer Magpet Polymer Pvt Ltd , machine makers Coperion and Herbold Meckesheim are collaborating technologies in construction of an entire plant for bottle-to-bottle recycling from a single source. In addition to mechanical processing of used PET bottles, the recycling system encompasses all process steps leading up to extrusion with a ZSK twin screw extruder, including pelletising and an SSP (Solid State Polycondensation) reactor.
This PET bottle recycling system is designed for a throughput of 5,500 kg/hour. It will deliver PET recyclate that is approved by the European Food Safety Administration (EFSA) and the US Food and Drug Administration (FDA) for direct contact with food. Moreover, the PET pellets manufactured on this bottle-to-bottle line are brand owner approved.
Magpet awarded the contract for the entire system to Coperion and Herbold Meckesheim, operating companies of Hillenbrand, as they have optimally coordinated their technologies and realised efficient plastic recycling solutions, according to Coperion.
Coperion’s and Herbold Meckesheim’s bottle-tobottle plants enable all recyclates to be processed together, even if they exhibit different IV (Intrinsic Viscosity) values or fluctuating bulk densities. What is more, the Coperion-Herbold solution saves
on operating costs, logistics costs, and energy consumption in comparison to conventional PET recycling processes.
The bottle-to-bottle recycling system first processes the PET bottles into flakes. For this purpose, Herbold uses granulators with forced feeding and washing system technologies that gently process the PET to minimise material loss due to fines formation and thus maximise yield.
This preprocessing is followed by conveying and feeding into the ZSK recycling twin screw extruder. There, the PET regrind is gently melted, intensively dispersed, and processed into a homogeneous mass. The ZSK’s twin screw technology efficiently transfers the energy into the melt. Thanks to the twin screw extruder’s high 18 Nm/cm³ torque, the PET’s residence time in the extruder is short. Processing takes place at low temperatures, polymer chain degradation is minimal, and the product quality achieved is high. Volatile components such as monomers, oligomers and water are removed from the melt and purged.
Following discharge from the ZSK recycling extruder, the still-warm material stream is transferred via a gear pump to an underwater granulator and an SSP reactor, where it is then condensed and decontaminated.
German extrusion machinery maker Reifenhäuser Blown Film has produced what it says is the world's first MDO-PE film with a thickness of 18 microns, said to meet or exceed all previous market standards in terms of mechanical properties, appearance, and further processing. It also saves on the amount of material used by 25%.
The film has been produced on Reifenhäuser EVO blown film lines using the patented EVO Ultra Stretch MDO technology and has been developed and tested for practical suitability in collaboration with raw material manufacturer LG Chem and printing specialist Bobst
The new 18-micron film reduces the amount of material used by around 25% compared to previous film thicknesses of 25 microns. This makes the production of fully recyclable mono-material structures significantly more economical, it adds.
Christoph Lettowsky, Senior Product Manager at Reifenhäuser Blown Film, explains: "Machine builders and manufacturers have been pursuing the same goal for some time: not to use more material in fully recyclable all-PE solutions than in conventional PETPE laminates. Technically, this is achieved due to the different densities of PET film and MDO-PE film by replacing the 12 micon PET film with a 16 to 17 micron MDO-PE film. With the reduction to 18 micron, we have taken a significant step in this direction - with further downgauging potential for the future."
The firm adds that this leap in development was made possible by the combination of MDO Ultra Stretch technology with suitable raw materials. Thanks to the patented position of the Ultra Stretch unit directly in the system's haul-off, the film is stretched from the first heat.
This makes the process particularly reliable: Reifenhäuser has produced the 18-micron MDO-PE film stably and reproducibly over many hours in the test runs, it adds.
Despite the low film thickness, producers do not have to make any compromises when it comes to optical and mechanical properties. With a modulus of elasticity MD exceeding 1,400 MPa and a modulus of elasticity TD exceeding 1,100 MPa, the 18-micron MDO-PE film achieves the current market standard for stretched PE films.
With a haze of less than 5%, the 18-micron MDO-PE film performs even better in terms of optical properties than the market standard, which is 6 to 7%.
The 18-micron MDO-PE film also performed in the converting process and exceeded all expectations of printing specialist Bobst.
Davide Rossello, Head of Competence Centre and Process Manager Gravure at Bobst says: "The way this extra-thin 18-micron MDO-PE blown film behaves on our printing machines is unique on the market. We have printed the film at high speeds of up to 500 m/minute with excellent results in terms of printing quality and register performances. But even more impressively, we were able to demonstrate the quality of our machine when printing in the Bobst oneECG process, achieving excellent print results at 300 m/minute (and above)."
Post-consumer plastics offer value to various industries, such as the packaging, automotive and furniture sectors, as they unravel their sustainability agendas, aided by new technologies, says Angelica Buan in this article.
The market for post-consumer recycled materials (PCR) continues to grow as adoption increases, thanks to policies that promote the use of PCR and increase its use across industries. Based on a study by Towards Packaging released this year, the global PCR plastic packaging market size is expected to reach US$64 billion by 2030, climbing to nearly US$73 billion by 2032—a 60% increase from the projected US$44.6 billion in 2024.
In line with the United Nations ( UN ) 2023 global commitment report, there is a call to action to raise the target percentage of PCR material across all plastic packaging used, with a goal of 26% by 2025. Sourcing may, however, become difficult when considering that these targets will probably increase even further in the upcoming years.
The UN seeks to raise the target percentage of PCR material used in all plastic packaging, aiming for 26% by 2025
Austrian chemical company OMV and polyolefins provider Borealis have entered into long-term feedstock supply agreement for their recycling facilities with Tomra Feedstock , a subsidiary of sorting technology producer
Tomra
Furthermore, according to a World Economic Forum ( WEF ) article on responsible sourcing of PCR, the lack of data and transparency surrounding PCR plastic and other materials leads to irresponsible sourcing. Notably, sourcing is impacted by inadequate collection, transparency of sources, limited waste management infrastructure, and the labour conditions of informal waste pickers.
New technologies are being developed to help industries meet global PCR content targets. These innovations focus on improving the efficiency and quality of recycling processes and recycled materials, enabling the use of more recycled materials in manufacturing.
Tomra has pioneered a process that transforms presorted mixed plastic waste into clean, specific polymer types, which can then be further processed in mechanical/ chemical recycling plants.
OMV will process feedstock supplied from Tomra plants in its ReOil facility in Schwechat, Austria, while Borealis will process feedstock produced by Tomra at its mechanical recycling operation in Europe. The feedstock will be produced from mixed PCR material at a first-of-itskind sorting facility currently being developed by Tomra in Germany.
OMV is also constructing a new ReOil plant at the same site with a capacity of 16,000 tonnes/year, while Tomra is building a sorting plant in Germany with a capacity of 80,000 tonnes/year, expected to be operational by the end of 2025.
Packaging redefined with biobased materials
Packaging design is changing as a result of the use of wasteand renewable-based materials, especially when considering sustainability. A noticeable trend in the packaging industry is the use of renewable resources like organic waste and biomass in the development of packaging solutions, as environmental responsibility becomes more and more important. Players in the materials business are driving this shift by making investments in cutting-edge technology to produce packaging that not only satisfies functional needs but also has a minimal environmental impact.
German chemical firm BASF is offering the packaging industry a pathway to increase the use of renewable feedstocks, by having expanded its portfolio of certified compostable biopolymers to include a biomass-balanced (BMB) ecoflex, a polybutylene adipate terephthalate (PBAT) commonly used in biopolymer compounding. For the new ecoflex F Blend C1200 BMB, fossil raw materials typically used in production are replaced with renewable feedstock at the beginning of the value chain.
BASF's biomass-balanced (BMB) ecoflex cuts fossil resource dependence and achieves a 60% lower Product Carbon Footprint (PCF) than standard ecoflex F Blend C1200
The biomass-balanced ecoflex not only reduces reliance on fossil resources but also achieves a 60% lower Product Carbon Footprint (PCF) compared to standard ecoflex F Blend C1200, adds BASF.
PCR use from packaging to furniture and automotive sectors
Apart from packaging, plastic products across various industries are increasingly applying PCR plastics into their manufacturing processes, from automotive components to household goods and electronics.
For instance, Borealis has introduced its Borcycle GD3600SY, a glass fibre-reinforced PP compound with 65% PCR polymer content. It will first be used in automotive interiors in a landmark project delivered in partnership with Plastivaloire, a thermoplastic injection specialist and Tier 1 supplier to the automotive sector, and Stellantis , an OEM and the owner of 14 automotive brands.
The material contains 30% glass fibre, meaning that almost the entire polymer fraction of the product is made from PCR PP. It will initially be used in centre console carriers for the new Peugeot 3008, marking the first instance of a compound with 65% PCR PP being used in series production for large automotive interior applications.
This development proactively addresses the expected requirements of the forthcoming European Commission’s end-of-life vehicles (ELVs) regulation, which stipulates that by 2030 25% of plastics used in new vehicles must come from PCR materials. Of that, 25% must be from circular or closed-loop streams within the automotive industry.
Given that PP accounts for about one-third of the plastic in cars, compounds like Borcycle GD3600SY will play a critical role in achieving these circularity goals, says Borealis.
Meanwhile, also in line with the European Commission’s ELV directives, materials firm Avient Corporation , has announced the extension of its reSound REC recycled content thermoplastic elastomers (TPEs) portfolio with new AF 7210 grades specifically developed for automotive interior applications such as mats, grips, and console trays.
Avient’s new TPE grades are suitable for use in interior automotive applications such as phone charging and cup holder mats, HVAC flaps, and pedal covers
Overall, the new reSound REC AF 7210 TPE grades from Avient contain 51-59% recycled content, with a minimum of 37% from PCR sources, including closed-loop feedstock. They offer an 8-18% reduction in product carbon footprint (PCF) compared to virgin TPE grades, adds Avient.
Avient’s new reSound REC AF 7210 TPE grades are available in hardnesses ranging from 43 - 90 Shore A and can be used for overmoulding onto PP substrates. They have good UV stability and meet standards for volatile organic compounds (VOCs) and fogging, making them acceptable for use in interior automotive applications.
Elsewhere, Netherlands-headquartered chemicals company LyondellBasell forged a cooperation with a German OEM and a specialised recycling company with expertise in mechanically recycling plastic waste.
LyondellBasell's value chain alliance converts waste fishing nets into innovative plastics for injection moulding. The CirculenRecover PPC TRC 2179N grade, a blend of the recycled material and virgin compounds, offers a sustainable solution
According to LyondellBasell, the automotive industry traditionally used recycled maritime plastic solely in fibre form for new vehicle components. However, the introduction of its CirculenRecover PPC TRC 2179N now allows this recyclate to be used for the first time in injection moulding, opening up new possibilities for recycled plastics applications.
In this collaboration, end-of-life fishing nets are collected and carefully sorted by type, then processed to create high-quality plastic recyclate. LyondellBasell compounds this recyclate with virgin materials to produce the CirculenRecover PPC TRC 2179N grade.
The injection-moulded components made from CirculenRecover PPC TRC 2179N are trim parts used in visible areas for the interior of various car models. This development is said to enable enhanced sustainability and environmental responsibility in the automotive industry.
Michael Büdinger, Business Development Manager at LyondellBasell, stated that the maritime gear will support OEMs in achieving the circularity goal of using up to 25% of PCR plastic waste in vehicles.
Similarly, Dutch-based modular furniture manufacturer Ahrend has developed an eco-friendly office chair using recycle-based polyamide Akulon RePurposed from German engineering materials company Envalior.
Ahrend’s Remode, a sustainable office chair, features structural seat components, a backrest mechanism, and a star base manufactured from Akulon RePurposed. The polyamide is made from recycled discarded fishing nets, also known as ghost fishing nets.
The new Remode office chair from Ahrend weighs just 15 kg, with more than two-thirds of its weight attributed to Envalior’s 30% glass fibre-reinforced recyclate Akulon RePurposed RE30, which is said to offer a superior mechanical property profile. The material contains a minimum of 62% recycled content, consisting of 50% ocean-bound plastic and 12% PCR content, according to Envalior.
Ahrend's sustainable office chair, Remode, uses Akulon RePurposed for its seat, backrest, and base, made from recycled ghost fishing nets.
The materials' extreme stiffness, strength, and toughness allow it to be utilised in the construction of structural parts of the seat, backrest mechanism, and star base—all of which are subjected to high static and dynamic loads, thus lightening the chair's weight.
Envalior, working closely with local partners, has collected and recycled over 3,000 tonnes of PA6 ghost fishing nets found in Indian coastal regions. These nets undergo cleaning, sorting, shredding, and are then mixed with post-industrial waste before being extruded into Akulon RePurposed regranulate.
Evolving standards for plastic products, focusing on performance, application, quality, and material guideline compliance, are driving advancements in additives, highlighting their critical role in modern manufacturing, adds Angelica Buan in this report.
Sustainable additives in a growth mode
Innovative additive technologies are fast emerging, with the potential to disrupt the polymer sector. Meanwhile, sustainable additives are gaining a significant market share.
According to a Lucintel report, the global green polymer additive market is set to grow along with the rising demand in packaging, injection moulding, automotive, and biopolymers. Growth is projected at a CAGR of 6-8% from 2022-2027, fuelled by a preference for biobased plastics, stringent environmental regulations, and cost-effective green polymers.
The packaging segment is expected to lead the market, with Asia Pacific experiencing the highest growth due to demand for sustainable packaging films and an expanding plastics industry in countries like China, Japan, India, South Korea, and Malaysia.
Stabilisers and coatings for recycled materials
South Korean additives manufacturer Songwon Industrial Co has developed a re-stabilisation technology, Songnox binary antioxidant blends, for materials containing mechanically recycled PCR content. These innovations allow recyclers to offer materials with improved melt flow, durable mechanical properties, and enhanced cost-efficiency.
Meanwhile, Songwon has also formulated a coating stabilisers range, which enhances durability and protect surfaces, adhesives, and sealants from the detrimental effects of light and heat.The latter includes a liquid hydroxyphenyl triazine (HPT) UV absorber, which is tailored to maximise performance, efficiency, and sustainability across various substrates.
Elsewhere, Greenmantra Technologies, a Canadian molecular recycling company, offers its solutions for transforming hardto-recycle plastics into specialty polymer additives through a high-yield process that uses low heat and pressure.
Its Ceranovus specialty PP and PE additives act as melt flow modifiers in plastic applications, enhancing operational efficiency and productivity while using less energy. They also enable the incorporation of higher recycled content in plastic parts. Target applications include agricultural drainage pipes, conduits, plastic lumber and decking, as well as crates and pallets.
Greenmantra employs various molecular recycling methods, such as depolymerisation, methanolysis, hydrolysis, and pyrolysis, to create sustainable products.This approach involves a patented process focused on mid-size polymer molecules,
like synthetic waxes, used as polymer additives.This strategy has successfully enabled Greenmantra to scale up production to commercial levels. Its target markets are for asphalt, plastic pipes, construction, and automotive parts sectors.
Along the same vein, German speciality chemicals firm Lanxess’s Adiprene Green line features polyether-based PU systems with renewable raw materials, expanding into adhesives, sealants, and one-component foam applications. These prepolymers are designed for safe handling with low free monomeric MDI content and comply with EU regulations, reducing environmental impact.
In adhesive, sealant, and OCF applications, Lanxess develops prepolymer grades with high NCO levels and low viscosity, underlining safety and compliance. Its Stabaxol stabilisers provide crucial hydrolysis protection in footwear and polyester-based cellular PU elastomers, enhancing product longevity under wet conditions.
Lanxess’s Adiprene Green line offers polyether-based PU systems with renewable raw materials, designed for safe handling with low free monomeric MDI content and compliance with EU regulations, reducing environmental impact
Meanwhile, the firm’s Modulast range optimises physical properties and reduces material costs in TPU and CASE (Coatings, Adhesives, Sealants, Elastomer) applications, with products like Modulast PU meeting industry standards for colouration, odour, and elasticity.
Green opportunity with colourants
The plastic colourant market, encompassing compounds such as masterbatches, pigments, dyes, and additives, was valued at US$42 million in 2023 and is projected to reach nearly US$ 87 million by 2030. This represents a growth rate of 10% CAGR from 2024-2030, according to Verified Market Reports. Industry leaders like Milliken & Company, D&L Industries, and others are driving colourant innovations in the current year.
US-based Milliken is focused on enhancing PP and PE formulations to optimise the reusability, recyclability, and efficiency of plastics without compromising performance. Thus, it has introduced two new solutions: UltraGuard 2.0 and Hyperform HPN 58ei.
UltraGuard 2.0 builds on the established line of tailored PE masterbatches, significantly boosting barrier performance in HDPE and LLDPE by up to 70%. This advancement supports expanded options for mono-material packaging and facilitates material downgauging. Hyperform HPN 58ei enhances performance for PP sheets and thermoformed parts, delivering improved optical properties, isotropic shrinkage, and regrind quality, and is FDA-approved for food packaging.
Milliken's UltraGuard Solutions enhance barrier properties by up to 70% in various markets, slowing oxygen and moisture transmission to increase shelf life, reduce costs and food waste, and enable more recyclable packaging
Additionally, Milliken’s Millad NX 8000 platform, a PP clarifying agent, reduces energy consumption and cycle times during injection moulding with UL-certified energy savings of up to 10%. Meanwhile, its viscosity modifiers enhance the performance of recycled polypropylene (rPP) by improving melt flow rates, thereby broadening application possibilities for both pre- and post-consumer rPP materials.
In the Philippines, D&L Industries is advancing the circular economy through its subsidiaries First in Colours Incorporated (FIC) and D&L Polymer & Colours (DLPC). With over six decades of experience in the plastics industry, D&L specialises in manufacturing colourants and additives that enhance the physical and chemical properties of plastics
across diverse sectors such as food and healthcare. The firm is responsible for pioneering technologies like Plastibond, Polyguard, and Deomate that enable plastic upcycling and customisation for specific applications.
President Lester Lao of FIC and DLPC conveyed the company's commitment to sustainable innovation, green chemistry promotion and assisting businesses in achieving sustainability objectives, including compliance with the country’s Extended Producer Responsibility (EPR) law.
Likewise, Swiss chemical firm Clariant has launched its AddWorks PPA product range for the polyolefin film extrusion market, aiming to enhance processability and optimise optical film qualities by addressing issues like sharkskin and dye build-up.
These additives, which maintain film tensile, mechanical, and sealing properties, while offering high thermal stability, low or no migration and low let down ratios, are free from inorganic content and silicone components, ensuring consistent high performance and compliance with PFAS regulations according to Miao Zhigang, Head of Clariant’s Polymer Solutions business.
Additionally, Clariant’s AddWorks PKG 158 serve as an efficient antioxidant that protects colour and reduces thermal oxidative degradation during polymer conversion processes.
Clariant's AddWorks PPA enhances polyolefin film extrusion by improving processability and optical quality, addressing sharkskin and dye build-up
Eliandro Felipe, Head of Sales Americas for Additives Polymer Solutions, highlighted the benefits in enhancing processability and preparing resins for recycling, providing stability at high temperatures and minimising discolouration and plate-out.
Hot trend for flame retardants
Lucintel's flame retardants (FRs) additives market report indicates bright prospects for FRs within the global plastic additive market, fuelled by rising demand from the electrical & electronics industry, increased adoption of thermoplastics to curb carbon emissions, and stringent government regulations aimed at improving fire safety standards. Strategic opportunities are anticipated across several industries including aerospace & defence, electrical & electronics, wires & cables, pipes & tanks, transportation, building & construction, and marine sectors. By 2028, the market for FRs in plastics is projected to reach about US$11 billion, growing at a CAGR of 5.7% from 2023-2028.
A prominent player in this segment, US specialty material solutions provider Trinseo, unveiled new FR grades of PC
and PC/ABS resins at the recent Chinaplas 2024 show. These resins are manufactured without PFAS (per and polyfluoroalkyl substances) or halogenated additives and offer options with recycled content. They address the rising demand and regulatory pressures to reduce PFAS use, particularly in consumer electronics & electrical industries.
Trinseo’s line-up includes Emerge PC 8600PV and 8600PR resins, along with Emerge PC/ABS 7360E65 resins. These products maintain critical performance attributes such as heat, oil, stain, grease, and water resistance while meeting sustainability demands. Initially launched in the AsiaPacific market, they cater to applications in IT equipment, electronics, battery chargers, and voltage stabilisers.
Trinseo has introduced new PFAS- and halogen-free FR grades of PC and PC/ABS resins, including options with recycled content
Trinseo's Senior Vice President and Chief Technology Officer, Han Hendriks, affirmed the company’s direction to developing sustainable solutions by eliminating PFAS and halogenated additives from their products. Both Emerge 8600PR and Emerge 7360E65 utilise PCR substrates, maintaining performance comparable to virgin materials. This approach not only reduces waste but also lowers carbon footprint and promotes recycling in the consumer electronics sector.
According to Trinseo, it prioritises non-halogenated additives in manufacturing, ensuring UL94 V0 rating (1.5 mm) across all colours with high-temperature resistance and options for glossy or matte finishes. Emerge 8600PR, which includes recycled content, is said to offer excellent dimensional stability, impact resistance, a wide processing window, and UV resistance.
Meanwhile, Trinseo's Emerge PC/ABS 7360E65 FR products achieve UL94 V2 rating (0.5 mm) across all colours, boasting high flow properties ideal for thinwall applications. These products also deliver thermal stability, incorporate 65% recycled content, and ensure dimensional stability along with a wide processing window and UV resistance.
Similarly, Lanxess offers phosphorus-based Levagard and Disflamoll FR brands, as well as the reactive brominecontaining PHT4 diol. Levagard products are ideal for both rigid and flexible PU foams, offering solutions that enhance performance in rigid foam applications. Disflamoll phosphates provide effective flame retardancy and plasticising properties across various PU applications, according to Lanxess.
17-19 July
17-19 July 2024
Shanghai World Expo Exhibition & Convention Center, Shanghai, China
The leading event for the Chinese Polyurethanes Industry.
Innovation in packaging involves collaboration to create sustainable solutions that serve their purpose and resonate with users. Materials firm Dow’s 35th Packaging Innovation Awards (PIA) seek packaging that meets sustainability and innovation criteria, says Angelica Buan, who joined a fireside chat with the jury of the awards to find out more on the power of packaging innovation for human progress.
Creativity meets technology
In the search for better packaging, the idea of a circular economy, where products are reused, recycled, and kept in circulation as long as possible, has become a key focus. Now, thanks to new green technologies, what once seemed impossible is becoming possible. Innovative solutions are now helping create packaging that meets the high standards of circularity, changing how we view waste as a potential resource.
As such, Dow’s 35th Packaging Innovation Awards (PIA) showcase the latest innovative designs that address challenges across the packaging value chain.
PIA’s criteria are stringent, with the jurors evaluating the entries based on three categories: technological advancement, sustainable/responsible packaging, which embodies the principles of the circular economy, and lastly, enhanced user experience.
Providing solutions to a myriad of challenges in the packaging segment is no easy task. However, collective efforts, ingenuity, and R&D that build upon existing solutions enable continued innovation in packaging.
Daniella Souza Miranda, Global Marketing Director, Dow
“Innovation is the only way to bring progress to the packaging industry,” according to Daniella Souza Miranda, Global Marketing Director of Dow, and a panelist during the fireside chat session on the topic titled “Unleashing the Potential of Progress through Innovative Packaging,” held recently in Thailand.
Currently, sustainability is the innovation model for various industries, especially for plastic packaging and packaging in general, which account for a significant share of generated waste, said the panelists.
Collaboration is key
Collaboration is advancing packaging and the supply chain by pooling diverse expertise and resources. By integrating stakeholders from manufacturing to retail, collaborative efforts streamline operations, improve product safety, and reduce environmental impact.
For instance, Dow's Pack Studio fosters collaboration by providing space for designing recyclable products and developing/testing packaging solutions aimed at waste reduction.
“Dow’s Pack Studios are a big hub for collaboration. Those are our centres of innovations and we have several across the globe. One thing that we developed recently is that you don't need to be physically present at Pack Studios to innovate,” Daniella said.
According to Dow, the connected platform is accessible from anywhere, featuring a combination of facilities offering equipment, labs, and testing capabilities paired with a network of packaging experts.
Pack Studios locations around the world offer pilot-scale production capabilities: from nine-layer blown film lines to vertical form fill seal packaging lines and more. The studios boast technology that enables quick development and testing of concepts, preparing them for use so users can keep their commercial lines running.
Meanwhile, Gautam Bhattacharjee, Senior Director of R&D Packaging at P&G opined that the innovation cannot be handled singly. “The value chain is increasingly critical in the innovation process because nowadays, innovation cannot occur in isolation. Instead, it necessitates partnerships and collaboration across different stages. It's about fostering relationships and leveraging expertise across the value chain, from raw materials to the end consumer,” he explained, implying that this holistic approach not only enhances the quality and efficiency of innovation but also ensures that solutions are well-integrated and impactful in the market.
He furthered: "For example, suppose a brand owner manufactures a shampoo and detergent but does not manufacture packaging. Without the packaging converter and the material supplier that enables the packaging converter to convert the materials into packaging, one cannot innovate the optimal packaging solution.”
KRAIBURG TPE, the global TPE manufacturer production site in Malaysia, has recently obtained the Global Recycled Standard (GRS) certification for selected thermoplastic elastomer (TPE) solutions. This milestone caters to various industries including personal care, household appliances, wearables, and consumer electronics.
In response to the growing demand for more sustainable solutions in the plastics industry, KRAIBURG TPE has taken proactive steps to provide customers with alternatives. The GRS certification ensures that these alternatives meet stringent social and environmental criteria throughout the production process, including the use of GRS-certified raw materials and seamless traceability in the supply chain.
Utilising GRS-certified recycling based TPE compounds offers numerous benefits for both customers and KRAIBURG TPE. The certification complies with international environmental and social standards. This supports sustainability initiatives and aligns with global climate targets.
The GRS certification for KRAIBURG TPE recycling based materials confirms:
• The chemicals used comply with international regulations and standards to ensure product safety.
• Externally verified recycling content.
• Complete traceability in the supply chain, enhancing transparency and accountability.
• Transition from fossil-based to more sustainable raw materials, consequently reducing the carbon footprint.
As part of its commitment to sustainability, KRAIBURG TPE will gradually increase the use of recycled materials in its products, further reducing its carbon footprint compared to its counterparts produced using virgin materials.
The company ensures that all necessary measures are taken to maintain product quality and processing equipment, ensuring a simplified transition for customers.
The GRS-certified recycling based TPE compounds are tailored to industries where the benefits of more sustainable materials are most significant, including personal care, household appliances, wearables, and consumer electronics.
KRAIBURG TPE is dedicated to supporting its partners and customers on their sustainability journey, driving an improved environmental and social impact while delivering high-quality solutions.
With the GRS certification, KRAIBURG TPE reaffirms its commitment to innovation and more sustainability, empowering customers with choices for their sustainability application.
Currently, the GRS certification is valid for recycling content products produced from KRAIBURG TPE’s production site in Malaysia.
Further information is available at: https://www.kraiburg-tpe.com/en/grs-certification
Asia increases participation; leads in convenient packaging Asia is at the centre of innovation, according to Daniella. “It is home to nearly half or 48% of the world’s manufacturing output, and from a supply perspective, offers tremendous opportunity for innovation, with rising middle class and urbanisation,” she said, adding that at this year’s PIA 40% of the submissions were from Asia.
The panelists agreed that the Asian region has driven the demand for convenient packaging and leads in flexible packaging formats, especially Japan, where up to 80% of products are sold in pouches or refill packs. Asia excels in small pack formats like sachets, ensuring diverse, sustainable packaging options, without compromising consumer experience, according to the panelists.
Gautam Bhattacharjee, Senior Director of R&D Packaging, P&G
Daniella also shared that in Asia Pacific, trends closely mirror those observed globally, emphasising the rapid growth driven by an expanding middle class and urbanisation. This region stands out for its accelerated demand for convenience, which is surpassing more mature markets.
With half of global manufacturing located in Asia, there is a significant opportunity to innovate in packaging materials and production methods. Collaborative efforts with customers, brands, and upstream partners are crucial in achieving impactful innovations quickly. By leveraging these partnerships and shared expertise, Asia Pacific aims to capitalise on its dynamic market growth effectively.
Gautam added that Asia offers the best in class in flexible packaging. “Across the region, there's a shift towards sustainable materials, transitioning from multi-layer laminates to mono-materials that can be recycled. However, the challenge lies in ensuring these recyclable materials are collected effectively. “
He also stressed that collaborative efforts along the value chain in Asia, involving brand owners, recyclers, and companies like Dow, are crucial. These partnerships aim to increase collection volumes of lightweight flexible packaging, which traditionally garners less interest from recyclers compared to heavier materials like bottles.
This collaborative approach has positioned Asia as a dynamic hub for flexible packaging innovation, where technological advancements and consumer habits are gradually driving industry-wide shifts over time.
Sustainability with PCR, advanced materials
Sustainability is currently central to all packaging design, integrated from the very start, according to the panelists.
Along the same vein, recent advancements in monomaterials have enhanced consumer experience and disposal ease, as highlighted by panelists. These materials, now utilised in various industries, are driving increased interest in collection, reprocessing, and production of post-consumer recycled (PCR) packaging.
Gautam commented: “One thing we have experienced in the industry is that you cannot simply sell sustainability to consumers. Therefore, we need to start designing products with sustainability in mind from the outset. What we are seeing now is a holistic approach to the consumer experience, where every aspect of design considers sustainability. For instance, we previously dealt with packaging made from composite or multilayer materials that were difficult to recycle. Despite this, we still need to deliver a seamless consumer experience, from opening the pouch to disposing of it after use. While we have seen a shift from multimaterial to monomaterial packaging, some monomaterials initially had performance issues, forcing consumers to compromise. This time, we have pushed the boundaries by enhancing single-material performance and adding additional features, maintaining or even improving the consumer experience while ensuring recyclability.”
Laura Buen Abad, Vice President of Technology and Marketing, Sonoco
Meanwhile, Laura Buen Abad, Technology Director/Global/ Rigid and Flexible Packaging at US-based packaging firm Sonoco , stated, "When discussing the transition from packaging that uses multiple materials to achieving circularity, our goal is to focus on specific streams such as polyethylene, paper, or metal. Essentially, we aim for a single material to exhibit the properties, behaviour, and processability of these previously combined materials. This approach enables us to advance material circularity effectively.”
AI and user connectivity
The adoption of Artificial Intelligence (AI) technologies in the plastics industry encourages data-driven innovations by enhancing production performance, cutting maintenance costs, optimising processes, and reducing waste.
David Luttenberger, Global Packaging Director at US-based research firm Mintel and moderator of the fireside chat session, shared about utilisation of connective technologies even in packaging.
David Luttenberger, Global Packaging Director, Mintel
“We're seeing a significant increase in the use of QR codes, RFID, NFC, and AI. In particular, AI is poised to revolutionise the entire world by taking evolutionary steps forward. (It is transforming) the entire packaging supply chain, from design and sourcing to production, trace and track, safety, and consumer engagement. AI will engage consumers on a greater level, sometimes in ways that may seem ‘scary’, but also very entertaining and informative. It will move us from mere fun to enhanced functionality, adding value to our lives by providing information and entertainment in new and more meaningful ways.”
Daniella expounded: “With AI and enhanced access to data, the need to protect your data diminishes. Since data is readily available, why not join forces across the value chain and even the entire industry to innovate and advance together? This collaborative approach can lead to finding answers before the questions are even asked. AI allows us to stay ahead of ourselves, which is a significant shift. This change was evident in the Packaging Innovation Awards and is transforming the way we approach future innovations.”
The panelists also added that AI significantly enhances the efficiency of industrial designers, allowing them to generate more ideas quickly. They agreed that it improves content creation, enabling precise communication on consumer labels and adding valuable information to packaging, as AI excels at analysing vast amounts of market and consumer insights, concisely summarising data, and driving efficiency in a company’s packaging innovation process.
“We need to understand how the packaging and product work together in harmony from the user’s perspective,” according to David from Mintel, adding that “packaging is a way to build an emotional connection to drive purchasing decision.”
But in the end, the use of emerging and advanced technologies like AI aims to drive packaging trends towards sustainability and improved customer experiences. Equally important to consider is the understated value of innovative packaging, which lies in its ability to establish a meaningful connection with the consumer, said the panelists.
From an emerging economy, Thailand is now striving to claim global economic prominence through its commitment to the bioplastics sector and a circular economy as well as the fostering of sustainable partnerships, says Angelica Buan in this report.
Thailand to contribute to regional growth
Economic prospects have fallen short of expectations, with slower-than-anticipated growth. The latest World Bank global economic report estimates global growth will stay at 2.6% in 2024 and 2025, rising slightly to 2.7% in 2025-26, despite geopolitical tensions and high interest rates.
Meanwhile, regional growth in Asia is projected to decline to 4.8% in 2024, as China's slowdown offsets faster growth in other large economies.
Regional trading partnerships and transformational government policies, particularly in emerging markets and middle-income economies like Thailand, could, however, support growth.
Taking strides with trading blocs integration
Thailand, with GDP growth projected at 2.6% in 2024 and 3% in 2025 by the Asian Development Bank's Asian Development Outlook (ADB-ADO) 2024, remains a significant pillar of the ASEAN bloc, which had a GDP of about US$3.6 trillion in 2022, making it the third-largest economy in Asia and the fifth-largest globally.
Meanwhile, Thailand is ambitiously aiming to join BRICS, a partnership founded by Brazil, Russia, India, China, and South Africa. As of 2024, Egypt, Ethiopia, Iran, and the United Arab Emirates have joined BRICS, with Thailand reportedly following suit, to advance its national interests and strengthen its strategic position in global politics.
According to Kungsri Research’s Thailand Industry Outlook for 2024-2026, Thai goods have become more competitive globally through participation in trade blocs and bilateral and multilateral free trade agreements (FTAs). Thailand is engaged in 14 FTAs with 18 countries, including the Regional Comprehensive Economic Partnership (RCEP), which bolsters its trade relationship with China.
A robust plastics manufacturing sector: Thailand's ccompetitive edge
Thailand's vibrant manufacturing sectors and diverse industries make it a natural fit for participation in global trade organisations. As a key player in sectors such as automotive, electronics, and agriculture, which rely on plastics, Thailand has established itself as a competitive economic force.
Krungsri Research anticipates global demand for plastic products to grow by 2-3% annually from 2024 to 2026. The report highlights that packaging, electrical appliances, automotive parts, construction materials, and medical devices will constitute nearly 80% of the total sales value of plastic products. It also forecasts that domestic demand for plastic products will increase by 2-3% per year, with exports rising at a similar rate.
The upward trend is corroborated by GII Research’s Plastic Market in Thailand 2024-2028 report, forecasting Thailand’s plastic market to reach nearly US$11 billion from 2023 to 2028, growing at a CAGR of 5.18% during the forecast period.
One of the key drivers supporting the country’s plastic market growth is the increasing demand for packaging materials, medical devices, automotive, electronics, consumer goods, and other plastic products.
Economic model for bioplastics
Additionally, advancements in plastic technology have led to the development of bioplastics, which align with current sustainability trends. Thailand has emerged as a global leader in bioplastic production, ranking second worldwide after the US.
Leveraging abundant raw materials like sugarcane and tapioca, Thailand currently produces 95,000 tonnes/year of bioplastic and plans to boost this capacity by an additional
75,000 tonnes/year. This surge in production not only enhances the value of Thailand's agricultural sector but also significantly reduces carbon dioxide emissions, offering a sustainable alternative to traditional plastics.
With up to 90% of Thailand’s bioplastic output exported, the country has a pivotal role in the global market. Domestically, bioplastics are replacing conventional plastics, conforming with Thailand’s bio-circular-green (BCG) economy model.
Thailand, concurrently, has achieved significant success in curbing the use of single-use plastic bags. A report from the Pollution Control Department reveals a 43% reduction, equivalent to 148,000 tonnes, over three years, attributed to strategic government policies that advocate for the transition to eco-friendly alternatives to achieve 100% plastic waste recycling by 2027.
As well, public participation has been crucial in Thailand’s drive towards sustainability. Campaigns such as “Everyday Say No to Plastic Bags” have garnered widespread support across communities, shopping centres, and convenience stores. From 2020 to 2022, this campaign alone prevented the use of over 14 billion single-use plastic bags, amounting to 81,531 tonnes of plastic waste reduction.
Striking a balance with high packaging demand and sustainability
In Thailand's plastics market, the primary challenges lie in managing plastic waste and curbing environmental pollution. The extensive use of plastics has resulted in substantial generation of plastic waste, posing significant threats to ecosystems, marine life, and human health.
Addressing these issues needs the implementation of effective recycling and waste management systems, as well as initiatives to reduce single-use plastics and promote sustainable alternatives.
Plastic bags and bottles dominate Thailand's plastic packaging waste, together constituting approximately 60% of total packaging waste. Despite the higher volume of plastic bag waste compared to bottles, very few bags are collected for recycling due to their lightweight nature and contamination issues.
The 2020 report by WWF Thailand and Dutch sustainability consulting firm, Metabolic, highlighted the potential for improving recycling rates through household waste separation. The report also underscored Thailand's struggle with inadequate waste infrastructure, notwithstanding that collection and contamination have been challenging.
Alliances for a circular economy
Nevertheless, Thailand is actively pursuing strategies. Apart from its agenda to ban plastic waste imports by 2025, Thailand is also actively advancing its circular economy through initiatives like the development of its first Circular Industrial Estate, underlining efficient resource utilisation, recycling, and sustainable practices to enhance global competitiveness.
The IEAT has signed an agreement with the EEC Policy Committee to develop Thailand's first Circular Industrial Estate
In view of this development, the Industrial Estate Authority of Thailand (IEAT) has signed an agreement with the Eastern Economic Corridor (EEC) Policy Committee to develop Thailand's first Circular Industrial Estate.
IEAT Governor Veeris Ammarapala highlighted that the partnership will combine IEAT's expertise in developing industrial estates with the EEC's strategic land resources. The project will enhance Thailand's global competitiveness by promoting investments in target industries. IEAT will study the feasibility of the project and manage its development, while the EEC Policy Committee will secure land and collaborate on project publicity.
Environmental accountability with recycling Thailand has forged partnerships aimed at recycling plastic materials into high-value products. Amongst the notable collaborations is one between SCG Chemicals and Israeli startup Plastic Back, which developed a superoxide process to recycle PVC waste into naphtha fuel. Supported by Thailand’s National Innovation Agency (NIA) and Israel Innovation Authority (IIA), this initiative marks a significant milestone since their 2018 collaboration agreement.
Similarly, US materials firm Dow and SCG Chemicals (SCGC) signed an MOU to transform 200 kilotonnes/ year of plastic waste into circular products by 2030, focusing on advanced and mechanical recycling, across Southeast Asia. This collaboration aligns with Dow's goal to commercialise 3 million tonnes/year of circular solutions by 2030 and SCGC's commitment to carbon neutrality by 2050.
Earlier this year, Corsair Bangkok Company partnered with Shell Singapore to supply pyrolysis oil derived from mixed plastic waste, supporting Shell's production of sustainable circular chemicals.
These various collaborations among industry majors significantly support Thailand's pivotal role in the global economy, positioning it to collaborate effectively within leading global trade organisations.
AIM3D makes a comeback; optimises Voxefill process ,After a consolidation phase and reorganisation of its shareholder structure, after a management buyout, 3D printer manufacturer AIM3D is back in the game, it adds.
Germany-based AIM3D says it has also succeeded in optimising its patented Voxelfill process, for overcoming inhomogeneous strengths in 3D-printed components. The firm adds that Voxelfill achieves a high level of process stability comparable to injection moulding thanks to material-friendly extrusion and cross-layer material filling. Tensile tests with materials firm Sabic ’s Ultem PEI 9085 resin confirm the homogeneous properties.
Variations of the Voxelfill strategy enable hybrid multi-material solutions with different Voxelfill materials and different materials, including within the same component. In this way, the material properties can be ‘customised’. Defined component weight, damping properties, elasticity or changes to the centre volume chambers (selective densities), component properties could be influenced in a targeted manner on the basis of FE simulations.
Clemens Lieberwirth, CTO at AIM3D, commented, “Of course, the Voxelfill process is particularly suitable for 3D printing of plastics and fibre-filled plastics, but it is also suitable for 3D printing of metal and ceramic components using the CEM process. In general, there are advantages due to the higher build speed and cross-layer filling.”
Meanwhile, AIM3D is cooperating with Denmarkbased software development company Create it Real on software optimisation and Germany’s Replique for Ultem applications, which is extensively used in aerospace and industrial applications. The amorphous material has high temperature resistance, is flame retardant, and has good strength and chemical
resistance. Although expensive, it meets many requirements for manufacturing components for industrial and aerospace applications.
However, for serial production, printing needs to be improved and material costs need to be decreased. If AIM3D can achieve this, it can move into producing high-value components with Replique, with whom it has collaborated on a panel for Alstom
In its tie-up with Create it Real it hopes to improve slicing in its slicing software, SlicEx, which it white labels from Create it Real. The company is hopeful it can enhance properties while printing at 150 cm³/ hour and is aiming for a single machine to produce 1-4 tonnes of parts.
As well, AIM3D’s ExAM 510 system is predestined for use in industrial production. The system, which was launched in 2022, currently operates at a maximum build rate of 150 cm³/hour, and it is aiming to up it to 300-600 cm³/hour.
offer recyclable future for 3D printing
A new type of recyclable resin, made from biosourced materials, has been designed for use in 3D printing applications.
In a study, published in Nature, researchers from the University of Birmingham , UK, showed that highresolution, 3D printed structures can be manufactured from an entirely bio-sourced feedstock.
Once they have reached the end of their useful life, the products can be recycled within an almost fully closed-loop system.
Photopolymer resins, which harden – or cure – on exposure to light, are commonly used in the manufacture of bespoke 3D printed parts. However, while technologies to improve the resolution of 3D printing and its speed of manufacture have advanced considerably, the resins themselves have changed very little since the process first emerged in the 1980s.
The basic materials – usually epoxies or acrylics – come mostly from petrochemical feedstocks. Although some progress has been made in the use of more sustainable resins derived from biomass, the recyclability of these is still limited, because they rely on irreversible bonds being created when the resin hardens. To break these bonds, additional chemicals have to be added at each stage, resulting in a ‘snowballing effect’, in which the only way to recycle the material is to make more of it.
In contrast, the Birmingham-led team has, for the first time, succeeded in producing a photopolymer resin that can be printed at high resolution but can then be
broken back down to its constituent parts, recycled and reprinted, with the addition of just a small amount of photoinitiator to maintain the material’s curable properties.
The feedstock for the process is made from lipoic acid, a naturally occurring fatty acid molecule that is commonly sold as a dietary supplement. The team made a combination of two monomers from the lipoic acid from which they were able to make a resin that could be recycled either back into the monomers, or right back to the original molecule for recycling.
In the study, the researchers completed two ‘recycles’, but anticipate that further recycles would be possible.
Uses for the material could include industries where rapid prototyping is used to test products before moving to mass production. Although currently the material is more flexible than might be commonly used in industry, future applications could include automotive parts, medical and dental components, and even jewellery design.
University of Birmingham Enterprise has filed a patent application covering the resin and its use in 3D printing.
China slated for US$8 billion in 3D printing hardware sales by 2032
China’s additive manufacturing (AM) market is expected to reach US$8 billion a year in hardware sales by 2032, according to a new Market Opportunity Brief by Additive Manufacturing ( AM ) Research
The report titled “The State of Chinese Additive Manufacturing” analyses the state and outlook for the additive manufacturing (AM) industry in China and considers such formative topics such as standards development, regional and governmental support, and foreign AM companies operating in China, as they shape Chinese 3D printing landscape today. Chinese AM markets are detailed for both the metal 3D printing and polymer 3D printing markets, and sectors analysed include Aerospace & Defense, Automotive, Medical & Dental, Energy, General Industry & Tooling, and Services Bureaus.
Analyst for AM Research Molitch-Hou, attributes the growth in part to “government stimulus”. However, he adds that it can be tough to validate claims from the outside. For instance, in 2023, one of the country’s leading makers of metal 3D printers, Xi’an Bright Laser Technologies ( BLT ) announced nearly 60% revenue growth from the prior year. This figure, combined with the increasing number of lasers that can be configured on Chinese metal 3D printers, should more than pique the interest of manufacturers globally.
In fact, evidence coming out of the Chinese AM industry suggests that country is catching up to and, in many ways, surpassing the US and Europe in terms of 3D printing adoption and manufacturing.
From 2015 to 2022, China’s AM sector grew at a rate of about 30%. This has significance both inside and outside of China, as well as inside and outside of the 3D printing industry.
He adds that much of the growth that’s taking place is remaining within the country. While AM professionals are now well aware of a handful of prominent Chinese players, there are many more that they have never heard of and, despite this fact, some of those lesser-known businesses are advancing at a pace similar to their more recognised competitors, according to Molitch-Hou.
Overview
PlantSwitch, an ambitious startup based out of the US that was aiming to replace petroleum-based single-use plastic with plant-based alternatives, contacted machine maker Husky Technologies in 2022 to learn more about injection moulding options for a line of innovative bio-plastic cutlery.
The challenge lay in overcoming a lack of experience in both the market and injection moulding techniques and processes, as moulding with bioresin typically requires vast processing knowledge to successfully produce a high-quality part.
Developing a winning business case
PlantSwitch understood that working with a proven and experienced injection moulding equipment solutions provider would be a key component in enabling their vision to be a leading bioresin based cutlery manufacturer and supplier.
Collaborating closely with PlantSwitch leadership, Husky worked with their team to develop a plan that included lab trials along with a number of business cases that helped PlantSwitch to understand the full scope of the investment that would be required for this project.
“Understanding that the market is shifting due to various legislative requirements around single use plastic, along with a consumer shift towards a more environmentally friendly solution, we saw an opportunity to leverage our bioresin technology and focus our efforts on providing the highest-quality home compostable resin. Utilising this resin, we developed a project in collaboration with Husky to produce industry-leading compostable cutlery,” said Dillon Baxter, CEO and Co-founder of PlantSwitch.
To ensure the effectiveness of their new, plant-based resin, PlantSwitch worked with Husky on testing to better understand how this material behaves in an injection process. Following robust lab and analysis trials, the resin showed extremely promising results using Husky hot runner technology. Coupled with a growing consumer market for environmentally friendly home-compostable products, the outcomes prompted a revival of the original cutlery production concept and the development of new cutlery designs.
The Husky team was able to build a new business case, define the necessary cavitation, and recommend an integrated solution best suited for the application: a Husky Hylectric packaging moulding system with a specialised mould utilising UltraMelt, Husky’s innovative hot runner technology for bioresin melt delivery.
A sustainable future
Armed with the Husky Hylectric system and UltraMelt hot runner, PlantSwitch soon secured a significant order from a leading American supermarket chain for a line of innovative, plant-based cutlery, positioning the company as a vertically integrated producer.
But PlantSwitch’s potential does not stop there. The company is now exploring the production of compostable coffee pods, showcasing their commitment to sustainable and environmentally friendly packaging alternatives.
“PlantSwitch stands at the forefront of the eco-conscious movement, and our collaboration with Husky has paved the way for a transformative impact, proving that when done right it’s possible for sustainability and economic viability to go hand-in-hand. Together, we’re not just creating products; we’re shaping a greener, more resilient future,” Baxter said.
Husky’s holistic approach to injection moulding Husky is a dedicated single-source provider, seamlessly integrating world-class injection moulding systems with a wealth of expertise, comprehensive guidance, and a holistic perspective to ensure customers’ success.
It provides:
• Comprehensive guidance throughout every phase from concept to completion
• Strategic application planning and consulting
• Expert engineering and design assistance
• Turnkey advisory services and project management
• In-depth materials expertise
• Advanced simulations covering mechanical, thermal, and rheological aspects
• Prototyping, meticulous testing, and efficient scale-up solutions
• Continuous 24/7/365 production monitoring through Advantage+Elite
• A global and responsive sales, parts, and service network
Husky’s Hylectric systems
To handle the sensitivity of injection moulding bioresins, Husky systems are adapted to meet the melt preparation needs and requirements of this specific raw material. The machine extruder and respective melt stream delivery components are modified to enable high part quality and a wide process window.
In addition, Hylectric systems are designed to support aggressive cycle times for a wide range of applications and are equipped with Husky’s distinctive three-platen clamping
unit. The Reflex platen is designed to enable uniform clamping force distribution across the entire molding surface, for part-topart consistency and quality.
Superior tonnage distribution helps to reduce clamping force and mould wear, as well as ensuring high part quality on long term runs. This, combined with wide tie-bar spacing, large platens and a stiff clamp base, make Hylectric ideally equipped to run heavy, high cavitation moulds at aggressive cycle times –making it the perfect fit to cutlery moulding.
The latest generation Hylectric systems also include all of the standard features and configurations of previous generations, with capabilities to enhance connectivity, control, energy management, and streamline operator experience. The result offers superior levels of productivity, versatility, and ease of use.
To meet growing demands for performance flexibility, Husky offers Hylectric systems from 120-1,200 tonnes with a broad selection of injection units. Longer versions of the clamping unit are available for large shut-height tools.
Husky’s UltraMelt technology is a premium melt-delivery approach for applications requiring excellent process and thermal control with minimal effect on resin chemistry.
Utilising dozens of different test manifolds, UltraMelt was designed to help users produce small parts with materials more sensitive to temperature and chemical reaction. UltraMelt features specifically designed components made from aerospace grade materials to preserve the sensitive chemistry of bioresin and minimise corrosion and other challenges. Configurations are available with a variety of gate methods, nozzle sizes, and actuation styles for low and high cavitation molds.
The hot runner manifold was designed for balanced melt supply to each mould cavity with careful consideration to both pressure and melt volume. A valve gate nozzle was used to maintain best-in-class gate quality and extended mould life. In addition, all components were designed with cost of ownership in mind, as well as extended maintenance intervals enabling maximum service life for years to come.
For further information contact: https://www.husky.co/en/contact/
Green Packaging Solutions ( GPS ), a commercially compostable coffee capsule producer, is aiming to be a leading provider of sustainable solutions in the coffee capsule industry. The company identified a growing demand for sustainable solutions in the market – fuelled by increasingly stringent global environmental legislation and continued demand from consumers for sustainable packaging and products – but found a lack of viable options.
Sustainable solutions drive the market
“Sustainable solutions are driving market demand, and consumers in the US are voting with their wallet. They’re saying to their favorite brands, coffee brands, ice cream brands, please give me sustainable packaging; GPS aims to be the leader on this compostable capsule solution,” said Miguel Gonzalez Jr., Chief Commercial Officer at GPS.
The first challenge was developing a capsule that would address the coffee capsule market’s significant environmental impact.
“Looking at the current capsule business in the US, there are currently 33 million households with a single-serve coffee brewer. If you consider an average of two and a half persons per household, you get a sense of the scale of the environmental impact – we’re talking about millions of coffee pods ending up in landfills,” Gonzalez Jr. said.
The second challenge was in bringing to market a high-quality product that would also be compatible with widely available coffee brewers.
“The vision of GPS is to provide a capsule that can be largely used worldwide, while also providing a level of compostability that can protect the world we’re living in,” said Oscar Chow, Co-Founder of GPS.
To achieve the necessary balance between quality, sustainability, and compatibility, GPS reached out to Husky for its extensive packaging experience, its multilayer technology, and the HyperSync system, which was designed to produce high-quality thinwall food and industrial packaging and medical applications.
Husky’s multi-layer technology
Multi-layer technology played a pivotal role for the company, enabling GPS to create barriers against oxygen and moisture that safeguard product freshness throughout its lifecycle.
“A multi-layer capsule is the only way to deliver perfect barriers for oxygen, humidity, and moisture, ensuring we secure the freshness of the product,” Roberto Stefanoni, Co-Founder and CEO at GPS, adding that with the HyperSync system, the company was able to harness the full potential of its proprietary formulation of compostable materials, resulting in a capsule that has far exceeded commercial composting standards.
“When you combine our proprietary formulation with Husky’s industry-leading co-injection systems and multi-layer technology, it’s a true competitive advantage. We are now the only coffee capsule with a PVOH barrier that decomposes in a commercial facility in 90 days,” Stefanoni said, explaining that this success is just the first step for GPS’ innovative coffee capsules.
“Husky’s expertise and technology will enable us to go from zero to 200 million capsules in year one, and in year two, we’re looking at another 200 million.”
Husky’s sustainable multi-layer technology
Husky’s multi-layer thinwall packaging solutions harness the capabilities of the HyperSync injection moulding machines, featuring a seamlessly integrated second injection unit. This integration enables synchronised actuation of the two injection units and the hot runner through advanced machine controls.
Husky’s proprietary algorithms then further streamline the control of the intricate co-injection process, providing unparalleled ease and intuitive operation.
By employing a functional barrier component sandwiched between two skin layers, Husky says it can provide an enhanced barrier capability that keeps products safe and fresh longer.
Husky adds that its accurate layer control offers unmatched freedom in selecting the amount, thickness, and placement of the functional material, enabling sustainable packaging with tailored aesthetics and superior performance.
For further information contact: https://www.husky.co/en/contact/
Disruptive technologies in tyre manufacturing now focus on reducing environmental impact through materials with recycled content, says Angelica Buan in this report.
Putting the brakes on waste rubber pollution
End-of-life tyres (ELTs) pose a significant environmental challenge by contributing to pollution akin to microplastics as rubber fragments enter the environment. The threat is clear, shown by recent studies revealing how much harm waste rubber can cause.
Recently, researchers from the University of Vienna in Austria and The Hebrew University of Jerusalem in Israel discovered traces of tyre additives in leafy vegetables. These chemicals, used to deter tyre ageing and corrosion, were found in vegetables from Swiss supermarkets and Israeli farms, highlighting the pervasive nature of tyre rubber particles in the environment.
Published in Frontiers in Environmental Science, the study tested leafy vegetables from Switzerland, Spain, and Italy, along with crops directly harvested from Israeli fields. Researchers identified tyre ingredients in 11 of 15 supermarket samples from Switzerland and nine of 13 samples from Israel. Notably, the additive 6PPD, used to prevent tyre cracking but known to be harmful to wildlife like coho salmon, was among the chemicals detected.
Scientists suspect these tyre additives enter the food chain through various pathways, including irrigation with treated wastewater and the use of sewage sludge as fertiliser. Airborne particles settling on soil may also contribute to contamination, albeit, at relatively low concentrations. Despite these findings, the study emphasises the potential risk of consuming additives present in food.
Amidst efforts to manage and reduce waste, tyre producers are increasingly focused on sustainable solutions, including reclaiming rubber from discarded tyres. By converting old tyres into valuable resources, the industry not only reduces its environmental impact but also sets new benchmarks for efficiency and waste reduction.
The global sustainable tyre materials market is projected to exceed US$530 million by 2032, growing at a CAGR of 32.88% from 2023 to 2032, according to Bis Research This rapid growth is driven by increasing demand for ecofriendly tyres and the adoption of sustainable materials in both passenger and commercial vehicle manufacturing. Despite challenges such as stringent regulations and environmental concerns, tyre manufacturers are leveraging advanced technology to turn these obstacles into opportunities.
Partnerships extend life cycle of materials
Finnish oil refining firm Neste , Austrian-headquartered polyolefin solutions provider Borealis , and German materials maker Covestro have teamed up to upend the use of discarded automotive materials.
By recycling old tyres into high-quality plastics, the partners aim to enhance sustainability and resource efficiency. The process begins with Neste liquefying old tyres through chemical recycling. Borealis then processes these liquefied materials into base chemicals such as phenol and acetone, which are supplied to Covestro. Covestro utilises these chemicals to manufacture high-purity polycarbonates for various automotive applications, ranging from headlamps to radiator grilles.
The partners’ stress the importance of collaboration in achieving circularity and supports sustainable polymer applications and the recycling of low-quality waste into high-quality plastics, benefiting both industries and the environment.
The first products resulting from this cooperation are already available, showcasing the successful integration of recycled content into high-performance automotive materials. With the potential for scalability, this project is anticipated to influence future EU regulations, such as the End of Life Vehicles Regulation.
As millions of tyres reach the end of their lifecycle annually, major industry players are stepping up to lead the charge in sustainable practices. These companies are investing heavily in the establishment of advanced infrastructure and recycling plants, which are essential for transforming waste tyres into valuable materials and products.
Forming strategic partnerships to develop cutting-edge recycling technologies, companies like French tyremaker Michelin have joined forces with international private equity firm Antin Infrastructure and Scandinavian Enviro Systems to build Europe’s first ELT recycling facility. This groundbreaking project utilises Enviro Systems’ pyrolysis technology to extract valuable raw materials from used tyres.
Enviro Systems’ patented, module-based recycling technology recovers materials such as carbon black and oil from used tyres. By replacing fossil-based materials with these recovered resources, the process offers substantial environmental benefits, including a significant reduction in carbon dioxide emissions.
The joint venture has finalised its investment plan for constructing a tyre recycling plant in Uddevalla, Sweden. Antin Infrastructure, the majority shareholder, is leading the venture, with Michelin as a minority shareholder and Enviro Systems holding an option for a significant minority stake.
Michelin, IFPEN, and Axens have launched the first industrial-scale plant producing bio-based butadiene from bioethanol as part of the BioButterfly project, supported by ADEME, to develop and commercialise a biomass-derived alternative to petrochemical-based butadiene
Construction of the Uddevalla plant is underway, with all necessary permits acquired. Expected to begin operations by 2025, it will process 35,000 tonnes/year of used tyres and create up to 40 green jobs. The joint venture plans to replicate this success with additional facilities across Europe.
According to the partners, the joint venture has secured multi-year contracts for a steady supply of ELTs. The primary outputs, recovered carbon black and pyrolysis oil, will replace virgin materials, significantly reducing emissions and environmental impact.
For its part, Michelin has already signed agreements for the supply of carbon black and pyrolysis oil. Looking ahead, the joint venture, which plans to expand its operations throughout Europe, expects a collective recycling capacity of 1 million tonnes/year of used tyres.
According to Zion Market Research , the global demand for the synthetic rubber market is projected to generate revenue of around US$41.7 billion by the end of 2026, with a compound annual growth rate (CAGR) of approximately 4.25% from 2020 to 2026. This growing demand increases the need for raw materials and compounds essential for producing synthetic rubber, widely used in tyres, industrial goods, medical equipment, footwear, and other applications. Thus, collaborations are vital for developing advanced technologies and efficient processes to ensure a consistent supply of these materials.
Michelin’s partnership with IFP Energies Nouvelles ( IFPEN ), a public research organisation in France; and Axens , a France-headquartered solutions provider for conversion of oil and biomass, has resulted in the launch of the first industrial-scale demonstrator plant producing bio-based butadiene from bioethanol. Located at Michelin’s site in Bassens near Bordeaux, France, it represents a significant advancement in the bio-based butadiene sector.
Butadiene, currently derived from petroleum, is a key compound used in synthetic rubber production and has global usage of over 12 million tonnes/year, with 40% allocated for tyre manufacturing.
The demonstrator, part of the BioButterfly project involving the three partners and supported by ADEME ( French Agency for Environment and Energy Management ), aims to develop and commercialise butadiene from biomass-derived ethanol, replacing the petrochemical-based alternative. This initiative offers potential applications beyond tyres, including varnish, resin, ABS plastic, nylon, textiles, and construction materials.
Since its launch in 2023, the industrial-scale demonstrator has been validating each stage of the bio-based butadiene manufacturing process, proving its technological and economic viability with an initial production capacity of 20-30 tonnes/year, paving the way for widespread industrial adoption.
Meanwhile, Axens’ role in commercialising this technology will ensure significant volumes of renewable butadiene.
According to Eric-Philippe Vinesse, EVP Research & Development and member of the Group’s Executive Committee, Michelin currently relies on petroleumderived butadiene for its synthetic rubbers, making this technology pivotal in achieving its goal of using 100% renewable or recycled materials in tyres by 2050.
Catherine Rivière, Assistant General Manager at IFPEN intoned that the demonstrator represents a significant breakthrough after more than a decade of research and innovation, while Jean Sentenac, CEO of Axens, echoed how the partnership and demonstrator empower industry players seeking renewable materials like biobased butadiene.
Goodyear has introduced a demonstration tyre made from 90% sustainable materials, including carbon black from methane, CO2, and plant-based oils, soybean oil for rubber flexibility and reduced petroleum use, among other ingredients
The BioButterfly project, with over EUR80 million in total investment, including EUR14.7 million from ADEME under the Investments for the Future Program, has garnered support from the Nouvelle Aquitaine region and the Bordeaux Urban Community, creating approximately 20 jobs at Michelin’s Bassens site.
From nature to tyre tread material
Today’s eco-conscious market shows a growing preference for sustainable products and it extends to tyres, where consumers are increasingly drawn to products made from waste materials sourced from plants and compounds derived from plant-based sources.
In a groundbreaking move towards sustainability, The Goodyear Tire & Rubber Company has introduced a demonstration tyre composed of 90% sustainable materials. This tyre has successfully passed rigorous regulatory and internal testing, showcasing lower rolling resistance compared to conventional models. The reduction in rolling resistance promises enhanced fuel efficiency and decreased carbon emissions, marking a significant leap forward in eco-friendly automotive technology.
Goodyear intends to manufacture a fully sustainable tyre, composed entirely of sustainable materials, by 2030. Building upon the introduction of a tyre featuring 70% sustainable materials in 2022, the company has unveiled a prototype soybean oil-based tyre with 90% sustainable materials, intending to roll it out at commercial scale.
The tyre blends 17 sustainable ingredients across 12 components, emphasising both sustainability and performance. It leverages carbon black derived from methane, CO2, plant-based oil, and pyrolysis oil to minimise emissions. Soybean oil enhances rubber pliability while reducing dependence on petroleum. Silica sourced from rice husk ash improves grip and fuel efficiency, and recycled polyester from post-consumer bottles reinforces tyre cords. Bio-renewable pine tree resins enhance traction, and high-recycled-content steel reinforces the tyre structure. Additionally, ISCC-certified polymers from bio and biocircular feedstocks contribute further to the tyre’s sustainability.
Goodyear’s transition to sustainable materials is already apparent in several current product lines, with eight lines and select racing tyres incorporating soybean oil. As well, Goodyear says it has more than doubled its utilisation of rice husk ash silica.
Meanwhile, Goodyear has forged a partnership with Visolis, a US-based biomanufacturing company, to produce isoprene through the upcycling of biobased materials. Isoprene, an important precursor for certain types of synthetic rubber, is commonly produced as a hydrocarbon by-product during crude oil refining.
Thus, the introduction of sustainable materials in tyre production is gaining traction as the sector veers toward sustainability.
2 – 5 JULY
MTA Vietnam
Venue: Ho Chi Minh, Vietnam
Tel: +84 28 3622 2588
Email: mtavietnam@informa.com
Website: www. mtavietnam.com
17 – 19 JULY
UTECH Asia | PU China
Venue: Shanghai, China
Tel: +44 (0)7739 302081
Email: mabarber@crain.com
Website: www.puchina.eu
17 – 20 JULY
Packaging Plastics, Mould & Die Machinery Surabaya
Venue: Grand City Convention & Exhibition Ctr, Surabaya, Indonesia
Tel: +62 21 2525 320
Email: faradiba@pamerindo.com
Website: www.manufacturingsurabaya.com
28 – 30 AUGUST
30th Vietnam International Industrial Fair (VIIF)
Venue: ICE, Hanoi, Vietnam
Tel: +84 24 3834 5655
Email: viif@vefac.vn
Website: www.viif.vn
28 – 30 AUGUST
Asiamold Select – Guangzhou
Venue: Guangzhou, China
Tel: +86 20 3825 1558 Fax: +86 20 3825 1400
Email: asiamold@china.messefrankfurt.com
Website: www.asiamold-china.cn.messefrankfurt.com
3 – 5 SEPTEMBER
Interfoam China
Venue: SNIEC, Shanghai, China
Tel: +86 21 63232733 Fax: +86 21 63232733
Email: katelyn.xue@interfoam.cn
Website: www.interfoam.cn
5 – 7 SEPTEMBER
3P Pakistan
Venue: Expo Centre, Pakistan
Tel: +92 21 35810637-39
Email: enquiry@plasprintpack.com
Website: www.plasprintpack.com
10 – 12 SEPTEMBER
Labelexpo Americas
Venue: Donald E. Stephen Convention Center, USA
Tel: +1 (262) 754-6931
Email: tventimiglia@labelexpo.com
Website: www.labelexpo-americas.com
Check out the Advertisers' page on our website.
Information is categorised by the YEAR & DATE of publication for easy reference.
For further details, email us at: news@plasticsandrubberasia.com
11 – 13 SEPTEMBER
Medical Manufacturing Asia
Venue: Marina Bay Sands, Singapore
Tel: +65 6332 9620
Email: mma@mda.com.sg
Website: www.medmanufacturing-asia.com
11 – 13 SEPTEMBER
NEPCON Vietnam
Venue: I.C.E. Hanoi, Vietnam
Tel: +84 286 287 3355
Email: nepconvietnam@rxtradex.com
Website: www.nepconvietnam.com
18 – 21 SEPTEMBER
Vietnam PrintPack
Venue: SECC, Ho Chi Minh City, Vietnam
Tel: +886-2-26596000 Fax: +886-2-26597000
Email: exfdp@chanchao.com.tw
Website: www.chanchao.com.tw/VietnamPrintPack
24 – 28 SEPTEMBER
Taipeiplas | ShoeTech Taipei
Venue: Taipei Nangang Exhibition Center, Taipei, Taiwan
Tel: +886-2-2725-5200 Ext.2618
Email: cph@taitra.org.tw Website: www.taipeiplas.com.tw
25 – 27 SEPTEMBER
Propak India
Venue: Bengaluru International Exhibition Centre, India
Tel: +91 9820209795
Email: mehraj.waghu@informa.com
Website: www.propakindia.com
2 – 4 OCTOBER
METALEX Vietnam
Venue: SECC, Ho Chi Minh City, Vietnam
Tel: +84 286 287 3355
Email: metalexvietnam@rxtradex.com
Website: www.metalexvietnam.com
2 – 4 OCTOBER
MTA Hanoi
Venue: ICE, Hanoi, Vietnam
Tel: +84 28 3622 2588 / 168
Email: Dung.Nguyen@informa.com
Website: www.mtahanoi.com
9 – 12 OCTOBER
AllPack Indonesia
Venue: JIExpo Kemayoran, Indonesia
Tel: +62 21 6345861
Email: info@kristamedia.com
Website: www.allpack-indonesia.com
Publishing Office / Scandinavia, Benelux & France
Postbus 130, 7470 AC Goor, The Netherlands
Tel: +31 547 275005 Fax: +31 547 271831
Email: arthur@kenter.nl
Contact: Arthur Schavemaker
Regional Office
B6-11, Menara Indah, Jalan 9, Taman TAR 68000 Ampang, Selangor, Malaysia
Mobile: +6017-8849102
Email: tej@plasticsandrubberasia.com
Contact: Tej Fernandez
China & Hong Kong
Room 6B, Floor 6, Building HengLong, No. 50 Renming Zhong Road, Zhangjiagang, 215600 China
Tel: 0512-58919146
Fax: 0512-58919145
Mobile: +86-17751702720
Email: henry.xiao@matchexpo.com
Contact: Henry Xiao/Zhu Wei
Malaysia (Print, Web, Digital Advertising & Conferences)
Tara Media & Communications
Mobile: +6017 610 1270
E-mail: yokepeng@taramedia.com.my
Contact: Yoke Peng
Southeast Germany, Switzerland & Austria Verlagsbüro G. Fahr e.K
Breitenbergstrasse 17
D-87629 Füssen, Germany
Tel: +49 8362 5054990
Fax: +49 8362 5054992
Email: info@verlagsbuero-fahr.de
Contact: Simon Fahr
North-West Germany
JRM Medien+Verlag
Minkelsches Feld 39
D-46499 Hamminkeln, Germany
Tel: +49 2852 94180
Fax: +49 2852 94181
Email: info@jwmedien.de
Contact: Jürgen Wickenhöfer
Malaysia. India, Indonesia, Singapore, Thailand, Australia, New Zealand, Korea & Philippines
Tara Media & Communications
B6-11, Menara Indah, Jalan 9, Taman TAR 68000 Ampang, Selangor, Malaysia
Mobile: +6017-8849102
Email: tej@plasticsandrubberasia.com
Contact: Tej Fernandez
Italy, Spain & Portugal
MediaPoint & Communications Srl Corte Lambruschini, Corso Buenos Aires, 8, Vo Piano - Interno 9, 16129 Genova, Italy
Tel: +39 010 570 4948 Fax: +39 010 553 0088
Email: info@mediapointsrl.it
Contact: Fabio Potesta
Taiwan 宗久實業有限公司
Worldwide Services
11F-B, No.540 Sec.1, Wen Hsin Rd., Taichung, Taiwan
Tel: +886 4 23251784 Fax: +886 4 23252967
Email: global@acw.com.tw
Contact: Robert Yu 游宗敏
USA & Canada
Plastics Media International
P. O. Box 44, Greenlawn, New York 117430, USA
Tel/Fax: +1 631 673 0072
Email: mjm@4m-media.com
Contact: Michael J Mitchell
www.plasticsandrubberasia.com