NOVEMBER 2022
A Quarterly Supplement of
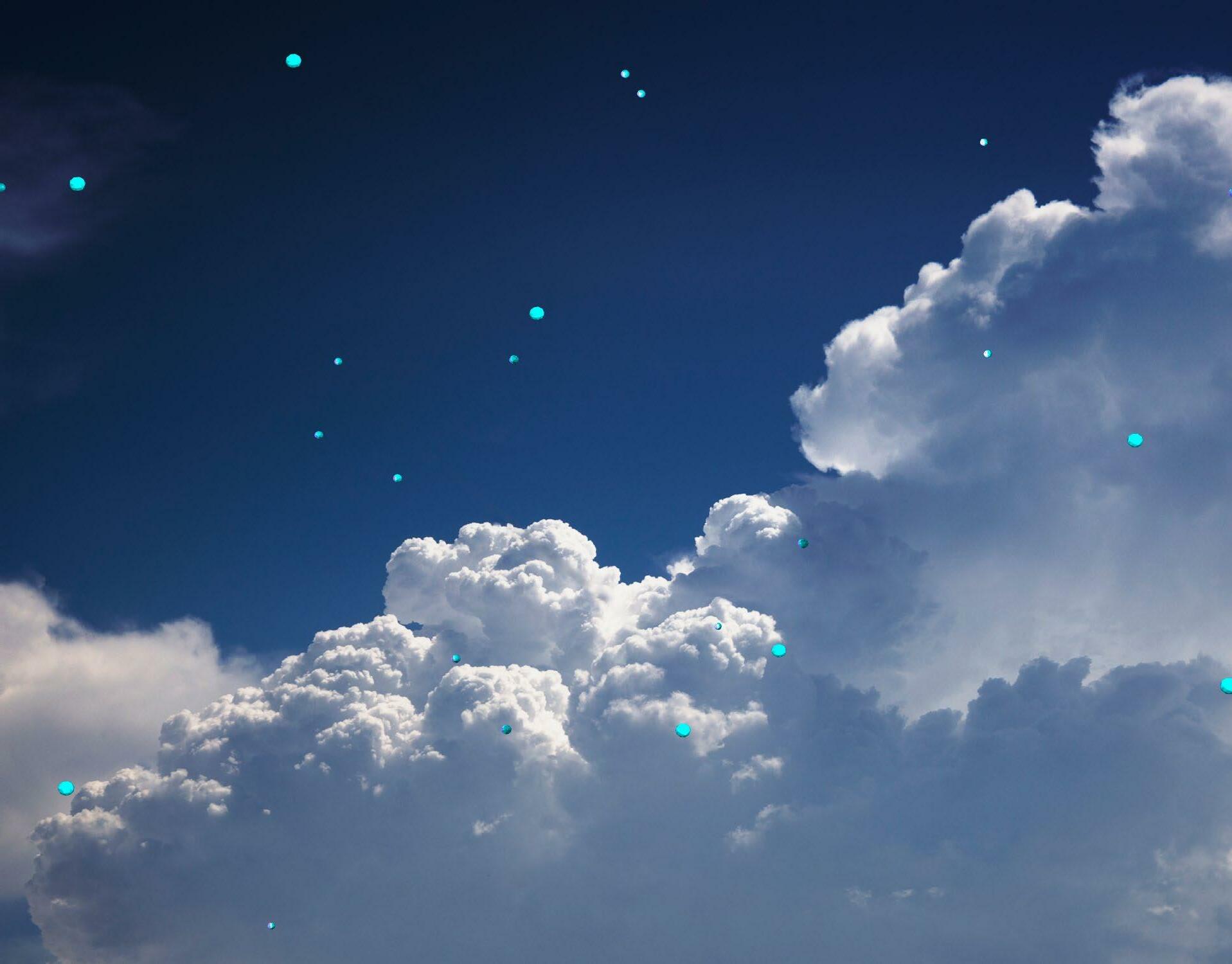
Chip, One Driver, All Protocols
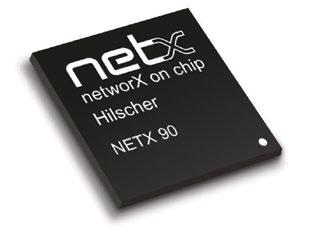
Improving asset health monitoring and maintenance is key to operations resiliency, agility, and efficiency. But how do you determine the best place to begin these improvements?
By Petra Nieuwenhuizen, senior product marketing manager, asset performance management, AvevaAmid overlapping global crises and countless mar ketplace upheavals, companies from every sector are looking to shore up their operations against future disruptions. Industry insiders have long seen improv
ing asset health monitoring and maintenance as a winning strategy to achieve resilience, agility, and efficiency.
However, it can be hard to identify which digital tools will deliver the maximum impact, and harder still to convince diverse groups of stakeholders that they should prioritize a given project over another. After all, what department wouldn’t benefit from additional resources? In the end, a solid business case for prioritizing spending on asset health and predictive maintenance comes down to demonstrating fast return on investment (ROI).
As with any aspect of digital transformation, scalability is key. Preventative maintenance, enabled by artificial intelligence (AI) and machine learning, needs an easy-to-scale solution that maximizes ROI up-front and continues to build returns as an organization further refines its digital capabilities. But how do executives determine the most cost-effective place to start?
Many organizations already use real-time data to conduct condition-based maintenance of their assets. Given recent supply chain disruptions, however, insight into spare part delivery time becomes much more important. Risk-based maintenance integrates aspects of reactive, preventative, condition-based, and predictive maintenance techniques, as
well as spare parts inventorying to improve asset availability and build resilience.
No matter where your organization is in its digital transfor mation, identifying where to invest for maximum returns is pivotal. Enterprises should look not only for discrete soft ware but scalable digital solutions that are part of a robust portfolio. Aveva Asset Strategy Optimization, for example, lays the foundation for higher-level capabilities. With Aveva Asset Strategy Optimization, organizations can assess asset criticality, which they can use to prioritize the assets they will focus on with predictive analytics.
predictive maintenance program. In reality, an algorithm only accounts for a small fraction of the comprehensive solution needed to deploy a holistic predictive maintenance strategy.
Aveva Predictive Analytics is one such scalable, comprehensive solution. It incorporates AI models that provide early asset performance anomaly detection and extensive diagnos tics to create the right insight from all data sources. The solution’s asset libraries provide reliability data that describes the best remediating actions in the event of a failure, allowing you to minimize downtime and act quickly to address equipment health and performance problems enterprise wide.
Aveva Asset Strategy Optimization gives a clear overview of all your assets, helping you pinpoint preventative main tenance investments with ROI in mind. It lets you tailor strategies to your company’s unique position. For example, if leadership is looking to further a sustainability initiative, Aveva Asset Strategy Optimization will show you which asset strategy will best achieve that goal.
The use of AI has become commonplace for detecting asset performance irregularities. The belief persists among some, however, that algorithms are the most important part of any
To achieve maximum ROI, any complete predictive maintenance solution must be easy-to-scale and operationalize for all stakeholders, not just data scientists and software programmers.
Solutions like Aveva Predictive Analytics can be easily scaled to encompass a single asset in one plant to all your assets worldwide.
The insight into asset criticality Aveva Asset Strategy Optimization provides, coupled with the easy-to-scale benefits Aveva Predictive Analytics delivers, demonstrates that Ave
va’s solutions represent the most comprehensive predictive analytics portfolio in the market, ensuring maximum ROI.
Operating a reliability centered maintenance (RCM) program can be a resource-intensive process. Because
Aveva Asset Strategy Optimization enables collabora tion between experts and non-experts, you can mini mize the time it takes to collect and verify information. Users can input data directly into a web-based interface, which is then easily accessible to reliability engineers at any time, anywhere. Using this method, teams have cut the time it takes for an RCM study by half. Aveva Asset Strategy Optimization accelerates RCM from study to deployment by bringing together people and data. With Aveva’s Asset Strategy Library, deployment time of asset strategies can be sped by up to 90%.
scriptive actions, coupled with integrated fault diagnostics,
speed up asset remediation. No-code architecture allows a wide range of users to quickly implement model manage ment strategies using templates. The solution also shows users an asset’s remaining lifespan.
When deployed in tandem, Aveva Asset Strategy Opti mization and Aveva Predictive Analytics create an easily scalable, comprehensive preventative maintenance toolkit, ensuring maximum ROI and allowing you to achieve your predictive maintenance goals.
Through native integration to the Aveva PI System, the solution is highly scalable. You can monitor a sin gle asset, plant, or a whole host of remote assets across multiple sites, allowing you to scale continuously with a minimal IT footprint.
Aveva Predictive Analytics makes it easy for users to train proven algorithms quickly and operationalize them. Pre
A look back at the key technology developments that delivered Industry 4.0 gives us a good indication of where industry is headed.
By Benson Hougland, vice president of marketing and product strategy, Opto 22As we enter the so-called fourth industrial revolu tion, which aims to finally close the gap between distributed automation systems and business sys tems, let’s take a quick look back at some of the develop ments that got us here and where they point for the future.
The PC revolution of the 1990s led to the popularity of the Microsoft Windows operating system (OS) and broad interest in using its graphical interface to see what was happening on the plant floor. But the automation industry had expanded rapidly in the preceding decades, introducing many new protocols and devices. To use Windows, early SCADA and HMI developers had to create a suite of pro prietary software drivers to communicate with every device the system might encounter. It was a time-consuming and expensive process and, in the race to expand the available
portfolio of supported devices, it generally led to very lim ited driver functionality. In response, Microsoft and a small group of automation vendors—including Opto 22—developed OLE for Process Control using Microsoft’s Object Linking and Embedding (OLE) technology. Now called Open Platform Communi cations, OPC defined a common specification based on a client-server model that allowed Windows-based SCADA/ HMI software to communicate indirectly with plant floor hardware by means of an OPC server, which housed all the drivers needed to communicate with those devices. With OPC, vendors could more easily develop software for industrial systems and the quantity and diversity of data that could be extracted improved.
But challenges remained. Taking advantage of OPC required a Windows-based computer or server to exchange operational data from plant floor devices with the software that needed this data. OPC Unified Architecture (OPC UA) was developed to meet this challenge by making it possible to run OPC at the edge of networks, directly embed ded into industrial processors and devices.
At the same time, we saw much greater interest in closing the gap between automation and business networks. As a result, automation manufacturers began introducing edge-oriented controllers and I/O systems. These devices offer state-ofthe-art, powerful CPUs that combine traditional real-time control and sensing functions with the communication, storage, security, and data processing functions previ ously found only in higher-level systems.
Internet of Things (IIoT) and Industry 4.0. We can clearly see the value and significance of open-source protocols and software. We can work on long-neglected capabilities like cybersecurity for industrial systems. We can again draw on innovations in IT to outfit control systems for the tasks we need them to perform.
Our history points clearly to the future, where edge computing capabilities and powerful software running on these plat forms are ushering in new levels of industrial communications. As automation professionals working on digital transformation, we can see how edge devices and interoperability stan dards are paving the way for companies to flourish.
Together, OPC UA and these new edge control lers and I/O systems significantly simplify the task of communicating operational data between plant floor systems and the software systems businesses rely on every day.
This combination has brought us to where we are today, with modern concepts like the industrial
The productivity and efficiency of your manufacturing operations depends on a constant cycle of collecting and analyzing IIoT data. Fortunately, Mitsubishi Electric has the hardware, software, and expertise to help you automate the process.
• Reduce energy
• Reduce downtime
• Increase productivity through data analysis
• Reduce startup costs with Digital Twin
The
of
is
Automation engineers and integrators who recognize the value of a smart MQTT broker will be in a good position to meet those demands and to develop increasingly sophisticated industrial IoT scenarios.
By Xavier Mesrobian, vice president of sales & marketing, Skkynet Cloud Systems Inc.One of the most popular industrial IoT (IIoT) pro tocols for data communications is MQTT. Originally developed for the oil and gas sector, it is efficient, quick, and secure, making it ideal for connecting field devices to a central SCADA system and passing data between them. With the advent of IIoT and Industrie 4.0, many automation professionals have turned to MQTT as a useful protocol for connecting devices to the cloud. But MQTT has its drawbacks. For example, it does not have a standardized data format to define how data is sent and received, causing interoperability issues.
To address this problem, Sparkplug B was created. Sparkplug B provides a topic namespace, state management, and payload definition for MQTT. It classifies MQTT clients as either edge of network (EoN) devices
that produce data, or as applications that consume data. Each Sparkplug B device produces messages of various kinds, like a “birth” message to show it has come online, “data” messages for sending data, and a “death” message when it goes offline. Any Sparkplug B application that is online receives these messages and is kept informed of which data is coming from which device.
The Sparkplug B specification makes MQTT a better choice for a range of IIoT applications. And yet even more can be done by enabling an MQTT broker to parse messages. By design, MQTT is a transport protocol. The broker that connects the clients acts like a postal service, passing along let ters but not knowing the contents. An MQTT broker that can
parse and act on the content of the messages as they stream through becomes a smart broker. A smart MQTT broker that also supports Sparkplug B provides some unique capabilities beyond what a normal Sparkplug B broker can offer.
For example, it can: Synchronize all applications. Because it is aware of all con nections, a smart broker can synthesize a “birth” (startup) message for each connected device whenever a new appli cation comes online. This allows that application to receive “data” messages from all currently connected devices, eliminating issues related to start-up order.
Respond to errors. In addition to its ability to identify outof-order or lost MQTT messages, a smart broker can also automatically disconnect a Sparkplug B device when these kinds of errors occur and allow it to reconnect. This causes the device to re-send its “birth” message, which resynchronizes all receiving applications, thus maintaining a single ver sion of the truth.
Resolve failed writes to devices. Another useful feature is the ability to check all write requests from applications to devices, to ensure the specified data value was written on the device. If the smart broker detects that the value on the device did not change, it forces the device to disconnect, causing it to retransmit its “birth” message. This resynchro
nizes all applications listening to that device and is another way to maintain a single version of the truth. Add data quality information. For systems that need to convert Sparkplug B data to other protocols, a smart broker can add quality information. For example, when converting
Sparkplug B data to OPC, it adds OPC data quality. “Birth” or “data” messages are assigned the OPC data quality of Good, while “death” (shutdown) messages can take a Not Connected quality.
Profibus & Profinet International works to make technologies like TimeSensitive Networking easy for end users, but we also help automation companies build TSN-capable products and ease industry-wide adoption.
By Michael Bowne, executive director, PI North AmericaTo help automation device vendors adopt Time-Sen sitive Networking (TSN), Profibus & Profinet International (PI) has released the Profinet Com munity [software] Stack. This portable software stack pro vides core functions required by Profinet-enabled devices. These core functions can then be adapted to the specific hardware upon which the stack is being implemented, and to the application software that will utilize it. From the outset, the Profinet Community Stack has been developed and released with TSN integration in mind.
software stacks that make it easy for device vendors to add Profinet to their products. They are the experts in helping add Profinet to a device and can be consulted at any point during the integration process.
Available to PI members, the stack can be downloaded for free from the PI website (www.profibus.com). It is intended primarily for Profinet solution providers or technology partners, and secondarily for the device vendors. It gives our technology partners a foundation upon which to build their
Every Profinet-enabled device is required to pass confor mance testing and certification before it can be released on the market. The same test tool used by PI test labs to put devices through their paces is available for download and use by device vendors. It is an automated tester that steps through test cases and gives clear results with each test case performed. Because TSN requires clock synchronization, hardware support is needed in the devices via TSN-capable Ethernet chips. This means the hardware employed by the test tool must also have such hardware support.
To ease the TSN integration process, the latest version of the Profinet test tool has been developed to use a widely available, commercial-off-the-shelf (COTS) development kit for the TSN functionality. The test tool runs on any lap top and initiates the test cases via the connected TSN dev kit. This ensures that device vendors can eas ily run through test cases themselves via this COTS hardware.
Automation component makers should focus their efforts on build ing out the features and functionality of their devices. Meanwhile, integration of a communication interface should be as painless as possible. With the Profinet Community Stack and COTS hardware for
automated TSN testing, PI is helping device vendors do just that. We want to enable adoption of TSN by end users by easing its integration for device vendors.
High-end machine performance is often delivered via a controller that also communicates with other machines in real-time and provides live production data for use by higher level systems to support OEE frameworks and manage artificial intelligence-enabled maintenance systems.
By Christian Nomine, strategic product manager visualization & analytics, Mitsubishi Electric Factory Automation EMEAThe requirement to multi-task while maintaining precise control over a machine (or multiple machines) means a modular PLC construction is more important than
ever. The latest IoT (Internet of Things) Gateway available for Mitsubishi Electric’s advanced iQ-R Series PLC is a perfect example. It makes use of the OPC UA standard designed to provide a direct exchange from smart OT (operations technology) devices to cloud-based systems.
In combination with an Iconics SCADA suite, the IoT Gateway can be used to access real-time-data from multiple robot controllers (and other automation devices) and make them available for easy on-screen monitoring and management via on-premises or cloud-based systems. This allows companies to benefit from predictive maintenance functionality built-in
to the robots which uses AI (artificial intelligence) to predict requirements ahead of time and make suggestions for servic ing or parts replacements. The flexibility to see this informa tion and act upon it from anywhere in the world empowers plant operations personnel to work remotely and take advan tage of their smart factory capabilities.
A plant-wide automation system can also be driven by the machine controller and its communication modules. An IoT Gateway and iQ-R modular PLC can be used as a hub to drive a simplified IIoT (Industrial Internet of Things)-enabled control and management environment. It effectively makes the most of the controller’s capability while creating transparency within the IT systems.
From a manufacturing perspective, introducing a time-sen sitive network such as CC-Link IE TSN can increase the speed and synchronicity of a production line significantly.
Micro-delays and bottlenecks can be effectively eliminated by ensuring that everything from in-feed machinery to CNC machines tools, conveyors, assembly systems, testing, marking, robot loading systems, packing and palletizing is synchronized in real time.
But this ecosystem doesn’t work in isolation. It relies on OPC UA, MQTT, and the likes of Azure IoT Hub to link ERP and MES layers to the PLC at the heart of the system via the IoT gateway. This allows personnel—from production to senior management—to pull reports and plan factory output based on demand and availability.
Mitsubishi Electric’s solution for edge computing, the MELIPC, captures data seamlessly from the PLC and can process, filter, and provide initial analysis locally. The most relevant results can be acted upon locally, while data need ing more advanced analytics can be sent to the cloud. The MELIPC addresses the need for processing as close as pos sible to the control system, while also using the same proto cols as the IoT Gateway, such as OPC UA and MQTT.
The MELIPC also uses machine learning to analyze collected data and generate a model of the machine’s operational state. This model can then be used to detect variations in the machine’s performance in real time to provide feedback to other IT-based systems to provide early warnings and advice that can impact quality, efficiency, and output volumes.
The role of the machine controller in an IIoT environment also helps integrate with edge and cloud processing platforms to deliver data analytics benefits. Edge computing is increasingly used for data analytics because it offers a low-latency solution for interpretation of targeted trends data rather than mass storage. Meanwhile, cloud computing is increasingly being used for complex, but less time-sensitive, analysis on larger data sets required for deep learning models.
Easy on-screen monitoring and management of multiple robot controllers is available both on-premises or in a cloud environment thanks to the Iconics SCADA suite. Source: Mitsubishi Electric Europe B.V.
Hardy’s HI 6200 features EtherNet/IP, ModBus, Ethernet TCP/ IP, and Profinet communication to support the widest range of international standards and IoT trends such as remote monitoring.
Weighing company Hardy Process Solutions has added Profinet communications to its HI 6200 single-channel weight controller/indicator. The decision to implement Profinet came about because of growing local market demand, and the fact that Hardy is increasingly supporting world markets where Profinet has achieved significant market penetration. Hardy is also pursuing the growing trend of IoT (Internet of Things) adoption, which is easily supported by netX.
We strongly believe that our customers should be free to use whatever communications protocol they prefer.”
The HI 6200 has been available with EtherNet/IP, Mod Bus, and Ethernet TCP/IP communications since launch.
“We’ve always been protocol agnostic,” says Tim Norman, Hardy product manager. “For example, back in the days of the fieldbus wars, we were one of the first North American companies to introduce Profinet into our products, to complement the protocols used here in North America.
The decision in 2020 to add Profinet came about because a significant amount of product sales now come from European, Asian, and South American markets. Norman says there’s a clear need to support the widest range of international standards. “The increasing trend towards deploying IoT, particularly remote monitoring, means that our products must have the latest technologies available,” says Norman. “That requires ever more and better con nectivity. We see Profinet as key in those global markets.”
The HI 6200 is an ultra-compact, DIN rail-mounted
device measuring just two inches wide and three-anda-quarter inches high. It allows for high-density panel designs compared with traditional weighing instrumen tation, reducing both machine costs and control cabinet footprints. It has a 32-bit ARM core for processing which, along with Hardy’s proprietary WaveSaver technology and a single-button-press calibration method, delivers accu rate, stable, and fast weight readings in the type of adverse conditions that plague process control.
The HI 6200 supports proactive maintenance strategies while delivering the benefits of IIoT device-level connec tivity though built-in web servers or directly via the UDP transport layer. It can also be used as a co-processer for a control system such as a PLC, DCS, or PAC, delivering 100 updates per second of processed weight data at reso lutions exceeding 1:10,000.
Integrating Profinet proved to be a bigger challenge than expected, mainly because the ultra-compact design meant there were limited resources available on the motherboard.
Norman says, “We initially purchased a Profinet software stack to reside on our existing Ethernet platform. How ever, the stack required an extensive rework and optimi
“The increasing trend towards deploying IoT, particularly remote monitoring, means that our products must have the latest technologies available.”
zation, and after many months of engineering effort it still wouldn’t pass Profinet certification. As we were in a hurry to get the product released, we decided to stop that approach and look for an integrated hardware and firm ware solution.”
tocol after manufacture to meet a customer’s particular requirements. Hilscher provides starter kits for developers and offers full engineering support.
Hardy evaluated several possible options and chose to use the netX 52 chip from Hilscher. “Our engineering staff already had experience with this chip from an earlier prod uct upgrade to our HI 4050+ single-scale weight con troller,” says Norman. “That’s quite an old product but we were able to add Profinet using the netX 52. So, it made sense to use the same chip when upgrading the HI 6200.”
Part of Hilscher’s netX family of network interfaces, the netX 52 is a Profinet node device. The netX range is unique in that it supports all popular industrial networking protocols by deploying appropriate firmware. The netX 52 supports up to 14 industrial networking protocols. Fully certified stacks are available for all supported protocols and simply loaded into a chip as needed.
Engineers from Hardy Process Solutions visited Hilscher North America in Chicago to receive local engineering training and guidance. With the netX 52, it took Hardy less than six months to achieve a certified Profinet weighing solution for the upgraded HI 6200.
Now the company is looking to use the netX 52 a third time, in a future flagship product designed to meet the growing demand for a weight controller that can support IoT-compliant systems and strategies.
Using netX devices enables an OEM to create a single hardware platform and install the communications pro
The most reliable and complete online directory of packaging and processing technology suppliers in North America – designed from the buyer’s perspective.
Features include:
• Plain-language filters so it’s easy to find what you need.
• Type-ahead keyword search.
• Visual navigation by machine or desired package type.
• Packaging-specific filters that are tailored to each product category.
Are you looking for packaging or processing solutions and you don’t know where to start?
When it comes to connecting IT and operations technology, the wide range of requirements from operations, marketing, finance, and maintenance mean that preplanning is a requirement. Here’s how to approach it.
By Charlie Norz, senior Automation Product Manager for WAGO Corp.Industrial manufacturers have recognized the many benefits of plant floor digitalization. Leaders in both IT and OT (operations technology) must work together to decide on the degree of information that needs to be collected as well as what type of analytics are required. Due to the wide range of requirements from other departments, such as operations, marketing, finance, and maintenance, pre-planning is the key for any IIoT (Industrial Internet of Things) application.
New consumers of industrial data want immediate opportunities to improve efficiency, profitability or pre vent downtime in ways that were not possible before. Cloud services and scalable storage are certainly drivers of this trend. Many controllers, for example, support the mainstream protocols commonly deployed in factories,
but also add new messaging schemes like MQTT and REST APIs to support these new applications.
There are challenges with these approaches, for sure. For example, cloud providers have their own set of APIs and services unique to their solution. Customers who are looking to adopt a cloud platform need to consider how portable their data is and how easily they can tie into existing systems within their organization. A controller that allows for open development, especially those that are Linux-based, will generally support more platforms than a closed system. Cloud platforms commonly use MQTT for secure IIoT communications, leaving the integrator to determine
how the JSON payload is structured; this adds flexibility but can also create interoperability challenges. Specifications like SparkPlug B help by defining the name space to address this challenge. But while Sparkplug B is supported, relatively few cloud platforms have formally adopted it yet. Cloud platforms are constantly evolving. For example, if you are using AWS Greengrass on a PLC and AWS releases a new machine learning service, a customer can easily adopt this new feature. A new driver or update used to mean installing and licensing new software on multiple servers, hoping there are no conflicts. Fortunately, this labor-intensive task might soon be a thing of the past.
Data collection, storage and retrieval is the first step in digital transformation. Many cloud agents can orches trate and manage your assets in a centralized way, allow ing changes to be scheduled and rolled back as necessary. It is also possible to remotely deploy code to a group of edge devices for non-real-time tasks. This is a fundamental change in the way controllers can be programmed and managed, potentially making a significant impact on our industry.
Central to the IIoT approach is edge computing—col lecting and processing data where it is generated. There is a lot happening in the edge of network space. This is an enabling technology that greatly simplifies soft ware development and testing, which is more in line with mainstream software development.
Adopting an open and easy approach to industrial controls and supporting IIoT is accomplished by designing controllers that support established protocols and programming speci fications, while at the same time extending support for new solutions or hybrid control schemes. This approach gives controls engineers flexibility to deploy the software applica tions that best meet their design goals.
Using an IP router with LAN and WAN capabilities means that a machine can be connected to the facility’s internal and external networks, enabling address changes on the machine to comply with the plant’s IP requirements.
By Harpartap Parmar, senior product manager, Contemporary ControlsMany manufacturing facilities are executing asset dig itization projects to incorporate Industrial Internet of Things (IIoT) connectivity between devices. In many instances, plant-wide and machine-to-machine commu nication using an Ethernet-based protocol is the norm.
Machines are utilizing Ethernet for internal communication between components as well. With more and more manufacturers depending on internet-connected machinery, the plant engineer now needs to follow the policies of the IT department in addition to usual operational technology (OT) requirements. Using an IP router can resolve network con flicts between the IT department and OT, allowing machines to be more easily integrated into an IIoT environment.
Modern machines are comprised of various complex sub
systems that communicate via the Internet Protocol (IP)— the backbone of the Internet. The machine builder pre-defines each subsystem IP address and the range of addresses devoted to each machine. This addressing convention may conflict with the customer’s addressing policies, which increases the installation time and introduces unnecessary complications. An IP router can quickly and effectively inte grate these machines to the customer’s existing IP infrastructure, benefiting both customer and machine builder alike. The various IP components of the machine are assigned IP addresses and the application controlling these various subsystems is programmed to communicate to these sub system devices using their IP addresses. A machine builder then ships this tested machine to his customer, but the IP addresses used at the customer’s site are probably differ
ent than what was tested at the machine builder’s factory. Changing the IP addresses on the machine and modifying the control program to communicate with revised IP addresses to comply with the customer’s IP address require ments adds significant time to the commissioning process and hinders the ability to bring the machine on-line quickly.
The use of an IP router allows the machine’s IP addresses to remain unchanged. The IP router consists of two networks, one internal network called LAN and one external network called WAN. The machine is connected to the internal network and the external network is connected to the plant which can be easily changed to comply with the plant’s IP requirements. The various machine subsystems are presented as one device to the plant network but can be easily accessed individually by using various features of the IP router like port forwarding, port range forwarding and NAT (network address translation).
For example, consider a machine builder tasked with the installation and network configuration of automated guided vehicles (AGVs). The project requires a method that sim plifies the Ethernet network within the AGV system and allows technicians to have dependable external access to the devices without IP address conflicts.
In this case, the AGV system consists of a programmable logic controller (PLC), a human machine interface (HMI), and a barcode reader that form an internal network with a built-in 4-port switch connected to the LAN side of a Contemporary Controls EIGR IP router. Using the port forwarding feature of the IP router, the different IP ports from the external WAN IP address are mapped to different internal LAN devices in the AGV. This setup is then easily uploaded to multiple routers for use in different AGVs allowing for the same configuration across all the devices. The time is takes to test the AGV while it is being built at the factory is reduced, and installation at the site is simplified by requiring just the WAN IP address to be config ured either via static IP or DHCP. No other IP settings for the devices or the applications need to be modified at the install site.
Using this set-up, there is direct access to the PLC through the IP router, allowing the customer to easily monitor and program the PLC. The HMI and the bar code reader can also be accessed through the router. The multicast traffic is kept within the AGV network and doesn’t impact the customer’s IT network. The IP router’s built-in firewall prevents direct unauthorized access to the LAN side devices from the WAN side, making the AGV system a secure and effective addition to the IIoT facility.