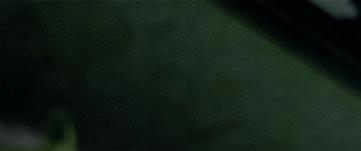
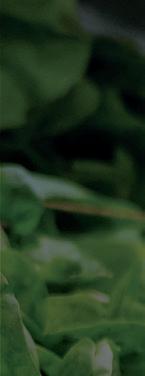
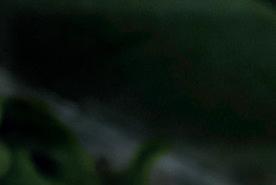



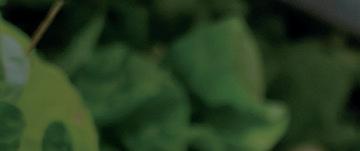
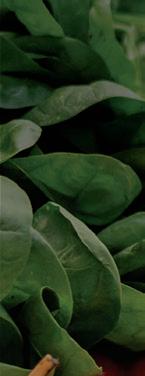
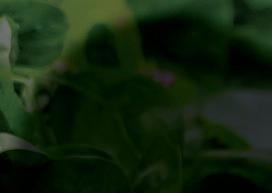
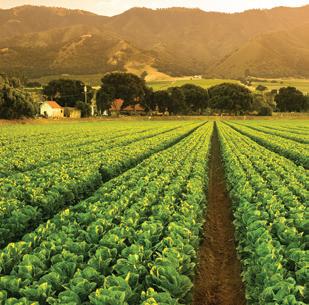

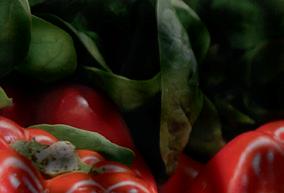
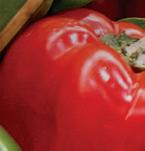

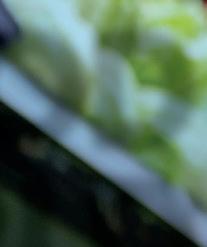
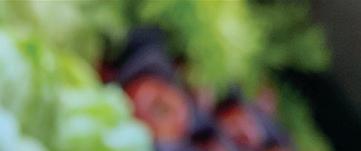

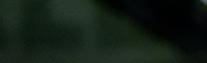


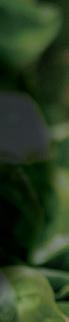
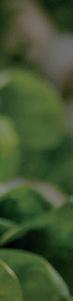

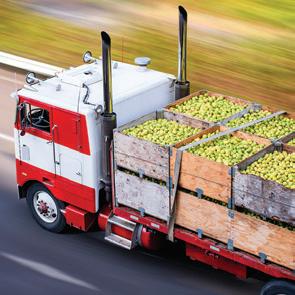

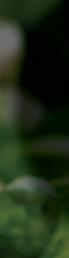


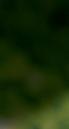


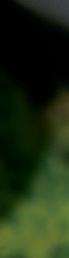
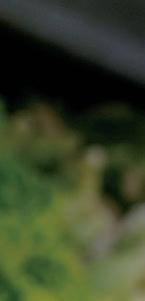


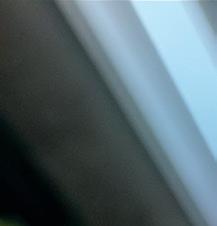

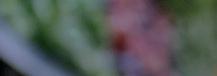
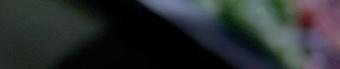


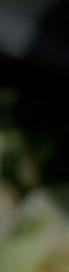

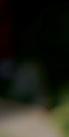
Thinking small to make big impacts
Explaining the connected workforce
Leaders in processing
Optimize working posture and increase cleaning performance. Quick-Lock feature easily adjusts to any required length from 34” to 62”.
brush fiber excellent for sweeping fine material from smooth surfaces, vinyl, marble, and terrazzo floors.
Need temperature control?
Ideal for syrup, cheese, chocolate & more!
Prevent burning and protect your products with water jacket technology!
Industrial Magnetics, Inc.’s Liquid line Magnetic T-Traps remove unwanted ferrous and work-hardened stainless contaminants from processing lines.
9 In the News
69 The Next Generation: Passing Down Knowledge from Retiring Experts
Failing to transfer experience is risky. Here are practical strategies to facilitate it.
75 Think Small to Make Big Impacts on Processing E ciencies
Implement incremental changes to simplify operations, increase production, and build a solid business.
Food Industry Prepares for Phased-in Enforcement of FSMA Rule 204
The Food Safety Modernization Act of 2011 produced Rule 204, and the regulation propels supply chain traceability while moving the industry to digital records in the food industry. The rule goes into e ect on January 20, 2026, and encompasses food producers, manufacturers, packagers, and even shipping and receiving companies.
35 Tech Today: Frozen Food Producers Meet Surging Demand
Food producers are targeting e ciencies with existing freezing and chilling technology and adding new technology, remote monitoring, and automation.
55 Unlocking Potential: The Connected Workforce Explained
CPG companies can use connected workforce technologies to streamline training, simplify tasks, and improve communication and e ciency across the plant floor.
65 Q&A: Inside OEE Evaluation with Former Smucker’s Professional
This Q&A between two experienced industry professionals provides unique insight for companies in the packaging and processing world.
110 Leaders in Processing
ProFood World’s Leaders in Processing section recognizes many innovative suppliers to the food and beverage manufacturing industry.
Pneumatically conveyed materials heat up, releasing moisture that can cause sweating on storage surfaces.
Xchanger has proven designs that will cool conveying air and eliminate the problem.
EDITOR-IN-CHIEF DERRICK TEAL dteal@pmmimediagroup.com
CASEY FLANAGAN ASSOCIATE EDITOR cflanagan@pmmimediagroup.com
CHRISTOPHER SMITH ASSISTANT EDITOR csmith@pmmimediagroup.com
CONTRIBUTING EDITORS JOYCE FASSL, GRANT GERKE, BRYAN GRIFFEN, TAYLOR KEATEN, JAMIE VALENTI-JORDAN
ART DIRECTOR KATHY TRAVIS
CREATIVE DIRECTOR DAVID BACHO
VICE PRESIDENT, SALES JOHN SCHREI jschrei@pmmimediagroup.com • 248/613-8672
PUBLISHER PATRICK YOUNG pyoung@pmmimediagroup.com • 610/251-2579
ACCOUNT EXECUTIVE BRIAN J. GRONOWSKI bgronowski@pmmimediagroup.com • 440/564-5920
SENIOR MANAGER, PRINT OPERATIONS LARA KRIEGER lkrieger@pmmimediagroup.com
FINANCIAL SERVICES MANAGER JANET FABIANO jfabiano@pmmimediagroup.com
PMMI MEDIA GROUP
PRESIDENT DAVID NEWCORN
VICE PRESIDENT, DIGITAL ELIZABETH KACHORIS
SENIOR DIRECTOR, MEDIA OPERATIONS KELLY GREEBY
Directly with Design Engineers!
Over 25,000 Units
Over 25,000 Units ■ 75 Countries ■ Customize to your specs.
■ 10 Std. Models.
75 Countries ■ Customize to your specs. ■ 10 Std. Models. ■ For Gases & Liquids Talk Directly with Design Engineers!
■ For Gases & Liquids
DIRECTOR, DIGITAL MEDIA JEN KREPELKA
DIRECTOR OF CONTENT KIM OVERSTREET
SENIOR DIRECTOR, EVENTS TREY SMITH
FOUNDING PARTNER AND EXECUTIVE VICE PRESIDENT, INDUSTRY OUTREACH, PMMI JOSEPH ANGEL
Media Group 500 W. Madison, Suite 1000, Chicago, IL 60661 Web: www.pmmimediagroup.com
PMMI, The Association for Packaging and Processing Technologies 12930 Worldgate Drive, Suite 200, Herndon, VA 20170 Phone: 571/612-3200 • Fax: 703/243-8556 • Web: www.pmmi.org
DERRICK TEAL | EDITOR-IN-CHIEF
Assuming all goes according to plan, I expect ProFood World will be my last stop.
For those of you who don’t already know me, my name is Derrick Teal and I’m the new editor-in-chief of the magazine. I’ve covered a variety of topics in the last quarter of a century, from architecture and construction to autonomous and electric vehicles to packaging. I’ve even had a few stints pinch-hitting for magazines that covered remediation, surveying, and drilling.
I expect ProFood World to be my last stop because I fell in love with this industry after I started covering it about two-and-a-half years ago. This industry represents a convergence of artistry and engineering that’s essential to our way of life. Finding the best stories, talking to the top experts, seeing the most innovative processes in action, and then sharing it all with you through engaging and informative articles, videos, and podcasts is one of my favorite things to do outside of taking apart a computer, tackling a home renovation project, or working on a car—all of which usually end up with me in over my head. There’s a reason why I’m not allowed to touch anything on plant tours.
My hope is that you feel the same way about food production if you’re reading this. Maybe you followed another discipline and wound up here or maybe you knew you wanted to get into this from the get-go and made it happen. Maybe you you’ve bounced around a bit or maybe you were one of the lucky ones who found where they belonged on the first try. Regardless, finding the right fit for oneself is important, and it’s becoming increasingly important for companies to find and retain those people who will feel the same way about the industry as you and I do.
I’m looking forward to bringing you information on the topics you want to know more about. Reach out if there’s something you want us to follow up on, if you have a lead on a story idea, or if you just want to say “Hi.” You know where to find me.
Cheers, Derrick
dteal@pmmimediagroup.com
EDITORIAL ADVISORY
CHRISTINE BENSE
CHIEF SUPPLY CHAIN OFFICER Turkey Hill
GREG FLICKINGER
CEO American Botanicals
JOHN HILKER
SENIOR VP, OPERATIONS Kite Hill
VINCE NASTI FACTORY MANAGER Nestlé
JIM PRUNESTI
SVP, ENGINEERING Conagra Brands
LISA RATHBURN VP, OPERATIONS T. Marzetti
SCOTT SPENCER CEO Quality Harvest Foods
TONY VANDENOEVER PRINCIPAL CONSULTANT Waterfall Ventures
DIANE WOLF
INDEPENDENT FOOD AND BEVERAGE CONSULTANT
BROOKE WYNN
SENIOR DIRECTOR, SUSTAINABILITY Smithfield Foods
RIBBON/PADDLE/PLOW BLENDERS HANDLE POWDERS TO PASTES
Agitators forced through stationary materials impart shear needed to reduce agglomerates and blend pastes and slurries. Basic industrial units to state-of-the-art sanitary designs with heating/cooling jackets, liquid spray additions, and high-speed choppers/intensi ers. Capacities from 1 to 1,150 cu ft (.03 to 32 m3).
SANITIZE ULTRA-FAST, THOROUGHLY
Smooth internal surfaces free of baf es, shafts and bearings allow unobstructed material ow, plus complete discharge through a gate valve for rapid cleaning or sanitizing of the easy-access interior. Uniform blends are typically achieved in as little as 15 minutes with equal ef ciency at ll volumes from 100% to 25% of capacity. Ideal for dry and granular materials.
100% Uniform blending and/or liquid additions in one to 2–1/2 minutes
Total discharge with no segregation
Ultra-gentle tumbling action (versus blades forced through batch)
Ultra-low energy usage
Equal ef ciency from 100% to 15% of capacity
No internal shaft or seals contacting material unlike other rotary mixers
FLUIDIZED BED MIXERS BLEND ULTRA-FAST, GENTLY
MUNSON® Fluidized Bed Mixers feature two shafts with paddles that counter-rotate at high speeds to uidize material, achieving homogeneous blends in 10 seconds to 2 minutes. Low shear forces minimize friction with little or no degradation and insigni cant heat generation. Drop-bottom gates provide rapid discharge. Capacities from 0.21 to 283 cu ft (6 L to 8 m3).
LUMP BREAKERS REDUCE AGGLOMERATES, FRIABLE MATERIALS
Remove lumps and agglomerates from bulk foods. Dual rotors with three-point, singlepiece breaking heads rotate with minimum clearance inside a curved, perforated bedscreen. On-size material exits through bedscreen apertures from 1/32 to 2–1/2 in. (0.8 to 63.5 mm) in diameter. Fits tight spaces between upstream and downstream process equipment.
PIN MILLS REDUCE FRIABLE SOLIDS IN CONTROLLED SIZE RANGES
Coarse to ne grinding of friable powders, akes and granules into controlled particle sizes at high rates per HP/kW. High-speed rotation of the inner disc creates centrifugal force that accelerates bulk material entering the central inlet of the opposing stationary disc through ve intermeshing rows of pins. Desired tight particle size distribution obtained by controlling the rotor speed.
Consumer trends like on-the-go products are swaying snack producers’ needs in both packaging and processing machinery.
CASEY FLANAGAN | ASSOCIATE EDITOR
THERE’S ALWAYS ROOM FOR INNOVATION in packaging and processing, and snack producers have a few ideas in mind for packaging and processing machinery to improve their operations.
That’s according to PMMI Business Intelligence’s 2024 “Snack Foods Packaging Trends” report, where Business Intelligence researchers surveyed and interviewed several snack producers on their outlook of the snack foods market, emerging machinery and market trends, and current challenges.
One factor participants say drives innovation is the consumer-driven market growth for on-the-go products. This is fostering innovation in both new products and automation and is top of mind for these snack producers.
Demand for these on-the-go products could be a contributing factor in an overall push for packaging automation. As one director of quality assurance for a dessert company explains, “I think everybody is fi nding that they’re needing to automate their processes more. There’s going to be a big push to get more automation on the packaging side, and that’s going to be a boon for the industry.”
Snack producers also want their automated equipment to be better equipped for troubleshooting. Participants noted a desire for parts that are better labeled for cleaning and reassembling, as well as better self-cleaning equipment.
Added versatility in automated machinery to handle multiple packaging types and food items would be benefi cial, participants also noted.
“Our ownership is really interested in growing through innovation. Innovation in both new products and new packaging,” said a manager of packaging at a candy company in the report. “Typically, what we try to do is kick o new products with minimal investment. We’ll either kick them o at a co-packer, or we will kick them o on a slower line that’s more hand packed and not quite so automated. And then, if it does really well, in year one or year two we’ll make the investment. Our ownership is so interested in innovation and has made it very clear that that’s going to be a very big priority for us moving forward. At some point in the future, we’re going to have to invest in it to support that.”
Snack producer survey participants noted a need for more automation that can accommodate things like troubleshooting or new product innovations.
Our ownership is really interested in growing through innovation.
Innovation in both new products and new packaging.
in
Participants noted a desire for improved processes for x-rays, magnets, and other ways to keep food safe, even though these technologies take up additional room in their plants.
Though most snack foods are considered dry foods and have less USDA/FDA regulation, ensuring products are safe and free of foreign materials is top of mind for people in the industry.
Snack producers also would like an increased focus on modularity. They would like the ability to add or subtract machinery pieces based on what is being packaged that day. The focus is on using machinery to do any tasks that can free a person’s time for other activities.
SOURCE: PMMI Business Intelligence: 2024 Snack Foods Packaging Trends
For more insights from PMMI’s Business Intelligence team, find reports, including “2024 The AI Advantage in Equipment: Boosting Performance and Bridging Skills Gap” and “2024 Transforming Packaging and Processing Operations” at pmmi.org/business-intelligence.
Consistency and accuracy are mandatory in any gravimetric feeders deliver both. They employ controlled vibration to control material density the feed process.
The result is the highest accuracy feeders on the market today. Our experts work to understand the VSHFL¿FQHHGVRI\RXUDSSOLFDWLRQGLPHQVLRQDO
dry material processing system, and Vibra Screw’s variations and ensure smooth movement throughout constraints, unusual temperature, heavy loads,
moisture content, long distances, high wear, or other unique factors. Then we recommend a solution optimized for your application. Vibra Screw feeders are designed to handle a wide range of the most problematic materials.
New research from PMMI Media Group shows an appetite among food processors for changing the way operators and technicians interact with machines on the plant floor.
could chat with their machines directly, using AI?
Whether that means getting the right answers for a changeover procedure or troubleshooting a root cause of downtime, a natural-language interaction with the equipment could be more intuitive than operating an HMI, which is where AI could become a useful answer for the workforce issues that food processors are experiencing.
We asked readers like you, who work at food processors and other companies, if AI-powered chat built into every machine could help simplify operation and address workforce issues. (The survey was conducted in December 2024 and consists of 95 responses.)
As the charts show, most respondents indicated a high degree of interest in integrating AI chat into processing and packaging equipment (see Chart 1). As one respondent wrote, “Anything that creates a venue for maintenance or operators to get quick ‘how-to’ answers is a no-brainer.”
Another wrote, “Using an AI chat that was fully capable of accessing the equipment manuals and repair/setup aspects could be much easier and faster than searching either on paper or even electronically.”
Do you agree with the premise that AI chat would open up a new avenue for operators and technicians to interact with the machine in a way that would lead to more uptime?
Others have started to use AI elsewhere and concur on the potential: “We are finding AI helpful in so many areas now. Writing job postings, communicating with employees in di erent languages. It would be helpful to get immediate answers to the issues we face during production.”
Another wrote, “It could help the next generation of operators to understand and troubleshoot the equipment.”
However, there were skeptics.
“Details, details, details,” one respondent cautioned. “Need to understand the scope of the tool and interaction(s) with HMI on the shop floor. Would need to understand how the AI tool interfaces with non-OEM plant or company specific process(es) to avoid conflicting instructions.”
Another said, “Our industry would function more safely with well-defined logic. AI at this point isn’t transparent enough in its decision making.”
A third respondent suggested that AI chat doesn’t go nearly far enough. “AI interactions will not be helpful. What WILL be helpful is when AI can make decisions during a run without interacting with operators. For example, if print registration starts to slip, AI makes micro-adjustments
What if the AI chat on the machine could respond with links to short videos based on the question being answered, e.g., how to do this or that on the machine?
• Largest installed base in North America
• Largest inventory of In-stock Pumps and Spare Parts
• Product & Viscosity Testing at our Pilot Plant
• 3A and EHEDG Certified
• Schedule On-site or Virtual Presentations
• Maintenance Training & Start Up Assistance LEARN MORE: 1-855-Axiflow
www.Axiflowtechnologies.com info@axiflowtechnologies.com
WHEN IT COMES TO GENERATIVE AI chatbots, sometimes the answers provided are flat-out wrong, even as they are wrapped in self-assured language.
The most significant way to greatly reduce risk associated with providing incorrect answers is by training AI chatbot only on manuals, drawings, videos, and other material directly from the manufacturer through a technique known as retrieval-augmented generation (RAG). This approach greatly reduces the risk of errors because the AI generates answers based only on the trusted sources it’s given.
Obviously, the answers are only as good as the data that’s provided. If machine manuals aren’t up to date, or aren’t in digital form, that needs to be addressed first. Also, plants may have SOPs that vary from what the OEM specifies (and those SOPs may vary from plant to plant). All such variations would need to be either accounted for or standard-
ized before being fed into the model.
Another serious concern is security. There’s no way most CPG IT departments would allow machines to be connected to the internet to access a cloud-based AI.
However, small language models (SLMs) can run on any PC-based control or PC-based HMI without an internet connection. That’s because they are a fraction of the size of current large language models, require a fraction of the computing power, and can yield performance coming close to or even exceeding that of large language models, depending on the application. They also eliminate any latency associated with round-trip communications to the cloud. Most experts now believe that the future of AI in the plant revolves around self-contained AI based on highly tuned and purpose-built SLMs that operate locally within the machine or plant.
Finally, the ability to tap into error histories, “last modified by” records, or maintenance schedules
presumes a level of integration with not only the machine’s PLC, but any external Manufacturing Execution System (MES) or Computerized Maintenance Management System (CMMS). The reality is that these systems may be running di erent versions, not integrated, or only partly digitized. (It also presumes a maturity level in “Industry 4.0” that is simply not present at many plants.) A phased approach starting with static manuals or information from a fixed repository is a good starting point before one tries to enable the integration of advanced diagnostics that require real-time data from sensors and control systems.
Visit pfwgo.to/8662 or scan the QR code to read more on risk assessment as it relates to generative AI in processing and packaging machinery.
to maintain registration on its own, no operator involvement. Having the equipment interacting with the operators will cause more headaches than it’s worth.”
The survey was designed to expose di erent potential features and capabilities to CPG professionals involved in buying and supporting equipment, including the ability for AI to:
•Respond to operators in a chat with links to short videos
•Operate in multiple languages
•O er “push-to-talk” functionality bypassing the need to type
A majority of respondents said these features would be “very helpful” on their processing and packaging equipment. “Shortcuts to helpful videos, speaking to equipment on info needs/changes instead of just typing info in would be very helpful additions related to AI capabilities,” wrote one respondent.
(Obviously, plants can be loud, and factoryspecific tuning of the audio or special microphones may be required for push-to-talk functionality.)
The survey then went on to ask respondents to
score a handful of use cases for both operators and technicians.
For an elaboration on use cases for operators and technicians when it comes to food processing equipment, please see article on page 19.
The survey was also a bit of a Trojan Horse, designed to educate respondents about all the possibilities. That’s why we tacked on a question at the end asking respondents whether their initial answer (about whether AI chat embedded into equipment would be useful) has changed once they went through the survey and saw all the potential use cases. Those answering “very useful” jumped from 58% to 70%.
Finally, we asked whether AI chat functionality would be more useful in processing equipment or packaging equipment. The clear majority said it’s equally useful in both, though there were a fair number that leaned more toward wanting to see it on packaging equipment.
The tools available to both OEMs and CPGs for incorporating AI are rapidly evolving. Several of the large automation suppliers including Rockwell Automation, Siemens, Schneider Electric, and B&R have released “co-pilot” style functionality for writ-
ing PLC code, and some are already experimenting with AI chat-style functionality. There are also several third-party tools (pfwgo.to/8648) available today that bear exploring. It’s early days still, but the appetite does appear to be there for exploring how AI and AI chat could support the operation of processing and packaging equipment while reducing the potential burden around training and support, leading to more uptime.
While a natural language interface can reduce friction, it should be clear that operators and technicians will still need fundamental training to interpret machine feedback safely and e ciently. At the end of the day, processing and packaging equipment is mission-critical, and AI chat is not a substitute for thorough instruction and understanding of how equipment operates. A poorly trained operator can make mistakes, even with top-notch AI chat. (Nor, as indicated earlier, is AI chat a replacement for the HMI. Sometimes it’s just faster to press a button.)
But incorporating some sort of AI chat seems sensible and, perhaps, inevitable. The first step would be a pilot project with a cooperative OEM and newer/lessexperienced operators who might benefit the most.
Facilities / Cold Storage / Distribution / Pharma-Cold / Processing
ESI Group’s climate-controlled facility solutions will deliver a project to improve efficiencies, mitigate costs, and ensure compliance.
When our clients succeed, we succeed. That’s what we’ve focused on for the last 30-years and will continue to focus on in the future.
Take control, call (866) 369-3535 today.
7PEWLQM\MRKXMQIWF]YTXS JSVMRGVIEWIHTVSHYGXMZMX]
7PEWL QM\MRK XM JSV MRGVIEWIH T )JJSVXPIWWP] L]H
1E\MQM^I ]MIPH
GSRWMWXIRX VIWY GLEPPIRKMRK KYQ
W XLMGOIR
1E\MQM^I]MIPHW EGLMIZI GSRWMWXIRXVIWYPXW )JJSVXPIWWP]L]HVEXIIZIRXLIQSWX GLEPPIRKMRKKYQW XLMGOIRIVW
¦ěðēǍƧŭŭƐƧŁŠŁǗě ǍŭƯƓijŭŭēŭƓċědžěƓðĴě ƐƓŭēƯČƧŁŭŢƐƓŭČěƛƛ̼
\TPSVI SYV GSQTVILIRWMZI QM\MR TTPMGEXMSR KYMHIW LS[ XS ZMHI RH XLI MHIEP WSPYXMSR JSV ]SYV Q
K SW XS M\ ""
)\TPSVISYVGSQTVILIRWMZIQM\MRK ETTPMGEXMSRKYMHIW LS[XSZMHISWXS JMRHXLIMHIEPWSPYXMSRJSV]SYVQM\""
DAVID NEWCORN | PRESIDENT, PMMI MEDIA GROUP
Having trouble envisioning how AI helps your processing operations?
We look at some of the most promising use cases for AI in food processing and what needs to change to enable them.
MUCH IS BEING MADE OF GENERATIVE AI, especially the idea of embedding “ChatGPT” style functionality in processing equipment (see article, p. 12). Enabling operators and technicians to communicate directly machines has significant potential to speed up troubleshooting, reduce unplanned downtime, and potentially compensate for ine ciencies associated with attracting and retaining line workers.
But there are several other use cases for AI beyond this. What follows are four basic scenarios that would enable food processors to maintain product consistency despite real-world variations in input ingredients and environmental conditions inside the plant.
We arrived at these by asking generative AI to envision a set of AI-enhanced features and use cases for food processing operations such as mixing, blending, cutting/portioning, cooking, and baking. We then used an AI “reasoning” model to
examine the initial suggestions and identify what might be either overhyped or not realistic given the current state of technology found in most food plants. That process reduced the initial list of 18 use cases down to the four examined in this article. (It’s also a testament to how quickly AI reasoning models are evolving.)
The promise: AI can monitor incoming ingredient composition (e.g., meat fat content, flour protein levels) and adjust ingredient ratios in real-time based on sensor feedback (e.g., viscosity, temperature, or density) to maintain consistent product quality. (Example: “The dough moisture is slightly low. Adding 1% water to the mix.”)
The reality: Many food plants operate with older equipment that lacks the high-fidelity sensors to detect these micro-changes instantly. Even
if sensors exist, older PLCs or control systems might not support dynamic adjustments on the fly without significant retrofitting. In many plants, a more achievable short-term goal might be periodic adjustment guidance suggested by AI (e.g., between batches) rather than second-by-second tweaks.
Separately, real-world raw material variability can stem from complex biological factors (especially in meat or produce) that even sophisticated
sensors can’t fully capture. A change in meat pH, for instance, might not be evident from just fat content or color. Data scarcity is another impediment. Thoroughly training AI models on every possible variability scenario might require large datasets that do not currently exist in the food processing community.
The promise: AI can monitor temperature and cooking time, making real-time adjustments to compensate for uneven heating or batch size changes. The reality: The thermal mass in many industrial ovens (especially large baking or continuous-cooking lines) means changes take time to propagate, as big ovens often have slower response times. A single 5°C tweak can take a while to register in product temperature. The cost or complexity of implementing sensors that monitor every zone or tray might be higher than the marginal quality gain for some products. It might be better to use AI to recommend incremental oven adjustments at set intervals (e.g., batch-based) rather than real-time every few seconds. Results may vary depending on oven type, recipe tolerances, and capital investment in sensor arrays.
The promise: AI can detect, for example, signs of blade dullness from cutting patterns or increased resistance, suggesting when to sharpen or replace. The reality: Detecting blade dullness or wear via cutting patterns or increased resistance assumes the presence of sensors capable of measuring torque or force feedback in a very granular way. It also assumes that the AI can di erentiate between normal variability (e.g., tougher batches of raw
Urschel designs and manufactures high capacity, precision food cutting machinery designed for rugged production environments. Sanitary and dependable in design. Rely on Urschel cutting solutions to effectively process all types of products.
Explore more cutting solutions at urschel.com.
material) and actual blade deterioration. A robust predictive maintenance system likely requires additional instrumentation and thorough calibration/validation to avoid misdiagnosis. This can be worthwhile but is often a separate project (and investment) from basic automation.
The promise: Operators can ask questions about troubleshooting or recipes in their preferred language, reducing errors from miscommunication.
The reality: While AI-based translation or chat can help, it doesn’t automatically solve the problem of technical terminology, dialect di erences, or specialized manufacturing jargon. Common words are easy to translate, but industry-specific terms (e.g., “bloom,” “proofing,” “crumb structure”) may not translate smoothly. Custom “dictionaries” of industry terms and specialized user training to ensure reliability will likely be needed. Also, voice-based queries can be misheard amid background machinery noise, requiring additional hardware or acoustic solutions.
A single Columbia palletizer can handle all of these products and more with ease.
Before food processors get started with AI, they must get their data in order. AI likes data, lots of it, and standardized and normalized. And the data must be high quality. AI is no different than any other computing paradigm—garbage in, garbage out. With plants and lines in varying states of automation, there’s a lot of groundwork to do.
Before food processors get started with AI, they must get their data in order. AI likes data, lots of it, and standardized and normalized. And the data must be high quality. AI is no di erent than any other computing paradigm—garbage in, garbage out.
It’s important that your machine can stand the test of time and adapt to your packaging needs as your goals DQGVWUDWHJLHVFKDQJH:LWK+DUSDN8/0$\RXFDQH[SHULHQFHWKHPDQ\IDFHVRIÀH[LELOLW\LQSDFNDJLQJ
World-class customer service and support
• 5HOLDEOHVXSSRUW
• In-house specialized technicians
• 24/7 customer service
• ([WHQVLYHQHWZRUNRI¿HOGWHFKQLFLDQV
Augmented
• Address issues immediately
• Shorten learning curves for your staff
• Perform maintenance tasks on your own
With plants and lines in varying states of automation, there’s a lot of groundwork to do.
Sensors are another thing. While every machine has sensors, to enable the kinds of use cases above likely means many more sensors and a way to normalize the data coming out of them. The cost of engineering the kind of sensor networks needed may be significant.
Cybersecurity is another concern. Linking AI to multiple sensors, ovens, mixers, or other IIoT devices can introduce vulnerabilities. Food processors are understandably cautious about exposing operational data—especially recipes or proprietary processes—to potential threats. Real-time data that includes recipe details can be extremely valuable intellectual property, requiring encrypted transmission and strict access controls. AI solutions that rely on cloud-based services must address cybersecurity protocols to prevent breaches that disrupt operations.
Embedded or edge computing AI solutions, where the AI model is embedded on a controller or PC running on the machine locally, is a way to keep the line totally separate and disconnected from the cloud. Indeed, while large language models live in
the cloud, there’s a trend toward small language models which can be embedded locally, eliminating the need for a continuous cloud connection, which would also eliminate latency issues. (The AI would still need to be well integrated with the controls architecture, which is something OEMs are going to have to tackle at some point.) That said, severing all connections with the cloud for an AI application may not be possible, depending on the application and goal. (And solutions like private clouds can be a viable option.)
Essentially, AI scenarios typically imply a mature “Industry 4.0” environment that doesn’t match up with reality at many food plants. Without careful ROI studies (e.g., how much scrap or downtime is saved?), the cost of integrating sensors, upgrading PLCs and networks and building AI models may well surpass expected e ciency gains. Like with anything else, it’s best to start with lower-hanging fruit (e.g., simplified predictive maintenance using existing sensors, or AI feedback to operators and technicians) and only scale up once there’s proven ROI. This helps manage expectations and keeps costs in line.
The Food Safety Modernization Act of 2011 produced Rule 204, and the regulation propels supply chain traceability while moving the industry to digital records in the food industry. The rule goes into e ect on January 20, 2026, and encompasses food producers, manufacturers, packagers, and even shipping and receiving companies.
THE NUMBER ONE “EXTERNAL PRESSURE” for food and beverage companies is regulatory and legislative changes, according to B2B International’s survey of 200 companies released in 2024. Ranking second in the survey is “the pressure to adopt new technologies,” so both challenges dovetail with the upcoming Rule 204 from the FDA, also known as the Food Traceability Final Rule.
While these external pressures are felt, the food industry’s advances in modernizing supply chains and adding digital technology have been noteworthy since and before COVID-19. For ten years, food producers have added plant floor sensors, data acquisition tools, and system software while connecting factories to enterprise resource planning (ERP) platforms. However, the FDA’s Rule 204 will create even more digital transparency of supplier systems and the supply chain, which goes into e ect on Jan. 20, 2026.
The FDA’s objective is 24-hour identification of food safety incidents, but it also adds more visibility for the entire supply chain to prevent incidents. The new traceability rule pushes the supply chain away from manual, paper-based record keeping and toward digital documentation. The challenges include understanding the regulation’s many nuances, standardizing data, finding e ciencies with automation, and determining when the FDA will begin to enforce the rule.
The import of Rule 204, part of the Food Safety Modernization Act (FSMA) of 2011, is to create a more responsive food supply chain system in the U.S. Rule 204 includes recordkeeping requirements for entities that manufacture, process, pack, or hold foods on the food traceability list (FTL). Rule 204 stipulates that the FTL will include key data elements (KDE) associated with specific critical tracking events (CTEs) and provide information to the FDA within 24 hours, or within some reasonable time, per the FDA.
Food producers rely more on OPC-UA and MQTT protocols to move information to data acquisition platforms and ERP systems.
“The first challenge is learning all that the rule entails, including definitions of the key terms and the new requirements for food and beverage businesses,” says Jack Payne, VP of Product Management and Solutions Consulting at Aptean. “There’s the FTL itself, which includes 16 items but covers much more, from various cheeses and seafood to many di erent fresh fruits and vegetables.”
longer on the food traceability list.
Payne adds, “CTEs and KDEs can be seen as the ‘when’ and ‘what’ in terms of the additional data capture required by the rule. There are seven di erent CTEs along the supply chain and between three and 15 KDEs each.”
This education also includes understanding the long list of FTL exemptions, which is essential for producers and compliance managers to understand. For example, full and partial exemptions include elements like egg producers, small produce farms, farms selling direct to consumers, certain types of processing, food subject to a kill step, and more. However, for the kill step exemption, a producer must “maintain records” related to the kill step, such as a record of the application for the kill step or food that changes so that the food is no
“This is a key question that will challenge the supply chain,” says Dr. Jennifer McEntire, Founder of the Food Safety Strategy. “The food traceability list includes foods that contain FTL ingredients but also exempts FTL foods that have undergone a kill step; a challenge for ingredient suppliers and food processors will be to communicate how a food or ingredient has been processed to determine if the rule applies.”
“The challenges here are new, but the patterns and frictions are recognizable,” says Wes Frierson, VP of Product Lifecycle Solutions at FoodChain ID. “Technology will play a critical role in compliance, providing platforms that streamline traceability and enhance transparency.”
Automation technology and system software adoption have been accelerating in the food ingredient, formulation, and manufacturing segments for years. In the food ingredient and formulator segment, companies have adopted digital technologies in a phased-in approach for years, including data-sharing solutions and ERP platforms.
With such serious food safety incidents on the rise, food producers are moving fast to understand Rule 204 but also reap the benefits of new system software tools.
“Supply chain partners are already responsible for exchanging a large amount of attribution for ingredients and packaging along with detailed documentation,” adds Frierson. “Ingredient and allergen declarations, chemical and physical specifications, sourcing and sustainability information, and much more must all be exchanged reliably and predictably between these partners and kept up-to-date and accurate.”
Employee-owned and operated with a legacy spanning over 180 years, ROSS is synonymous with innovation and quality in manufacturing mixing, blending, drying, and dispersion equipment.
Our commitment to excellence is evident in our five state-of-the-art manufacturing facilities across the U.S.A., complemented by an 8,000 sq. ft. Test & Development Center and three international plants, ensuring we serve customers worldwide with precision and reliability.
From standard models to custom solutions tailored to your unique processing needs, ROSS mixing equipment is engineered for decades of trouble-free operation, empowering industries and fostering economic growth.
Proudly engineered and fabricated in the USA, we’re driving the future of manufacturing, supporting American jobs, and fortifying supply chains for generations to come.
FoodChain ID o ers consulting on regulatory compliance but also provides a recipe and specifications system that manages current supplier information and allows companies to update nutritional and allergen details as products evolve. More importantly, the system can connect to a company’s product lifecycle management (PLM) software.
“There is extra information with Rule 2024 that must be collected, organized, and made readily accessible, and that becomes a pain point if your business attempts to go about it manually, using pen and paper,” says Payne.
“What we have seen to be the biggest challenge for food manufacturers is attaining electronic records at the source of the raw ingredients and the initial location where the ingredients are being shipped, stored and processed,” says Dave Cirullo, Industrial Key Account Manager at Mettler Toledo.
The strategy to move data across industrial networks can vary from industry to industry and even from plant to plant in the food industry. Legacy food plants have digital and analog equipment on the plant floor that sends data to historians and data acquisition systems. “Larger food companies want control of all their data, and they’re using our OPC-UA or Ethernet/IP adapters to take the inspection data from our machines at the plant floor and pull this data through to their ERP system,” says Eric Garr, Regional Sales Manager at Fortress Technology.
While food manufacturers standardize industrial networks, data governance is a challenge with many data types created in disparate divisions. The FDA specifies the type of information, or key
s
Advances in testing systems allow food manufacturers to use less sta , and digital records are ready for Rule 204’s 24-hour requirement.
data elements, to be provided in Rule 204 but doesn’t standardize the data format. “The FDA specifies what data needs tracking but not how it should be structured,” says Frierson.
“This lack of standard formats adds complexity and creates additional headwinds in collaborating with partners.” In recent years, regulating bodies have been reluctant to dictate specific standards as they change—see cybersecurity in 2022.
With Rule 204 there are traceability lot codes (TLC) that must be applied to FTL foods and tied to all KDEs for applicable critical tracking events, and traceability plans that must include descriptions of how a company will maintain the established rules. “Additionally, all records must be maintained as originals or true copies, and they must be made available to the FDA within 24 hours of a request in the case of a food emergency,” says Payne.
Supermajors are pushing forward and see “first-mover” advantages in automating the supply chain, including shipping. Tyson recently made news by shutting down legacy food plants and announcing moving new automation investments within its business.
“Food producers also want to automate truck and rail scale transactions,” says Cirullo. “Companies are investing in our PowerCell load cells with advanced technology. This is a key component toward automating vehicle scale transactions and a path toward unattended weigh stations that remove human error, paper transactions, and create a safer truck scale environment.”
In addition, food producers are building greenfield plants to move away from retrofitting plant equipment with updated automation technology. “We’re seeing the combination of new greenfield plants and plant expansions in Virginia, North and South Carolina. The same holds true for a few western states and the Central Valley of California with Cargill, ConAgra, and Nestlé,” says Cirullo.
Walmart meets Rule 204
Walmart prides itself on being a leader in the supply chain, dating back to its introduction of RFID
Monitor Monitor the entire CIP cycle the entire CIP KP|TGCN|VKOG|YKVJmoneo Cloud software.
6JGPGY SMFoodmag HTQOKHO
6JGPGYSM FoodmagHTQOKHOFGNKXGTUFGNKXGTU
VGORGTCVWTGƃQY VGORGTCVWTGƃQYEQPFWEVKXKV[CPFEQPFWEVKXKV[ CPF VQVCNK\KPIFCVCXKCIO-Link
6TCPUKVKQPHTQOVKOGDCUGFE[ENGUVQ|RGTHQTOCPEGDCUGF|E[ENGU VQOGGV[QWTRTQFWEVKQPCPFUWUVCKPCDKNKV[IQCNUYKVJOQFWNCTJCTFYCTGCPFUQHVYCTGUQNWVKQPUHTQOKHO Get started today
ifm.com/us•call: 1-800-441-8246•email: cs.us@ifm.com
technology in the early 2000s. Now the company is rolling out its own enhanced food traceability requirements, which are also in line with FSMA’s Rule 204. Walmart’s traceability requirements rely on advance shipping notices (ASNs) or EPCIS as data standards and will also require KDEs and CTEs information by using:
•Lot and batch codes
•Production and expiration dates
•Gross and net weights
•Location information for shipping and receiving points
Walmart’s requirements and deadline correspond to FSMA’s Rule 204 Jan.20, 2026 date.
Using lot codes is already a practically universal practice, and the rule allows for many common formats (including GS1-128 barcodes and Julian date codes) to be used as the TLC for FTL foods, says Payne. “Traceability features like lot and sublot management are the key modules for tracking products by lot code.”
The truth on enforcement of Rule 204
While Rule 204’s deadline is approaching fast. The FDA has publicly stated that “education while regulating” will be the approach to such comprehensive regulation. Many food companies believe proactive enforcement won’t happen until 2027.
“I’d be surprised if many companies are 100% compliant with the rule come January 2026. For this to happen, all of their FTL foods/ingredients suppliers would have to be providing the traceability lot code and lot code source,” says McEntire. “Many processors currently track ingredients into finished products—some still on paper batch logs—but may not provide their customers the lot code and TLC source.”
However, as the technology shows, traceability does provide a first-mover advantage to food producers by growing enterprise e ciencies and removing risk to the brand by avoiding food safety incidents. Says Payne, “The rule demands a considerable amount of time and e ort from businesses and their sta to record and maintain additional traceability data, but I see this as an important step forward in our new era of smarter food safety.”
No other company combines the knowledge and experience in cold storage construction and warehousing that Tippmann Group offers. As owners & operators of more than 130,000,000 cubic feet of temperaturecontrolled space, Tippmann Group is your single source for cold storage excellence.
Increased consumer demand for frozen food products and the quest by shoppers for “elevated in-home experiences” show that this frozen food trend has staying power. To find increased throughput, food producers are targeting e ciencies with existing freezing and chilling technology and adding new technology, remote monitoring, and automation.
Momentum in the frozen food aisle is strong.
Consumers are seeking “elevated in-home experiences” in the frozen food segment. Recent Nielsen and Circana 52-week 2024 data shows “consumers keep moving toward complete meal solutions, and premium frozen brands are surpassing value and mainstream options in handhelds, single-serve meals, and frozen pizzas as consumers seek elevated in-home experiences.” In addition, protein-based diets via healthy smoothies are propelling higher sales
of frozen fruit and vegetables.
In 2025, producers are focusing on increasing throughput with new machinery and finding e ciencies with current systems. So frozen food producers are modernizing equipment with sequential defrost technology, finding creative solutions for existing plants, and focusing on increased hygiene. In addition, food producers are adding more automation and remote services to help with maintenance and modernize freezing systems.
While spiral freezing units are mostly automated, food producers are experiencing labor challenges upstream and downstream with operations. s
In November 2024, Nestlé USA announced a $150 million expansion project for its frozen food production facility in Ga ney, S.C., including a new line for the production of single-serve frozen meals as well as enhanced automation and digital technology. The Nestlé investment reinforces the growth narrative as companies look for flexible manufacturing strategies and higher throughput, be it capital expansion or adding technology to current freezing systems.
“It comes down to a flexibility versus optimization balance and giving customers the flexibility to run many di erent stock keeping units (SKUs) on the same line as consumer tastes diversify or change,” says Brittan Gill, PNA Segment Leader - Freezers at JBT Corp. “And optimizing the machine to keep it as cost and energy e cient as possible without requiring major modifications to the freezer.”
In addition to higher throughputs, hygienic concerns rank high for frozen food producers. Companies are replacing legacy freezing and chilling systems to meet modern food safety concerns. “The argument for replacing legacy machines includes sanitary concerns and how well and quickly you can clean the machine,” says Paul Osterstrom, Senior VP of Sales and Marketing at Advanced Equipment. With modern equipment, food producers can limit bacteria entry points. According to Advanced Equipment, the company has reduced the number of welds on enclosure joints by 50% for its line of freezing and chilling equipment.
“Concerning freezers, food producers should be looking at robust, seamless, welded enclosures, and welded internal structure to eliminate harborage
points,” says Greg Sheridan, Director of Product Experience at FPS Food Process Solutions. “Hygienic designs would also remove motors, gearboxes, and greased drive chains and simplify internal ba ing.”
Of course, an automation discussion is never too far away in the food industry, including the frozen segment. “Turnover within maintenance teams at customer plants is an increasing concern, and gone are the days of maintenance managers and technicians that will remain at the same plant for 20 to 30 years,” says Gill. “It puts an increasing importance on the automation and monitoring systems implemented by OEMs to limit the required interaction and skill level of the person responsible for operating and maintaining the freezer.”
In 2024, food manufacturers added more technology and automation to plants. Rockwell Automation’s 2024 Smart Manufacturing Report
Eye-Flex® is a heavy-duty and fully customizable conveyor belt, perfect for tough applications. It’s available with reinforcing plates, under-welded wires, flights, side guards, chain edge, and more for added strength and functionality. Want more information? Contact us at (603)644-2500 or sales@wirebelt.com
PERFECT FOR LINEAR FREEZING AND COOKING APPLICATIONS
Frozen food producers are modernizing equipment to automate sanitation and extend maintenance sta . s
showed that consumer packaged goods (CPG) companies increased their automation investment by 27% year over year, and food producers targeted 21% to 27% for automation technology in operation budgets during 2023.
So, how are frozen food producers leveraging new features or technology to increase product volume in 2025? And what are the challenges ahead for companies?
Spiral and individual quick freezing (IQF) tunnel freezers are essential for high-capacity production for frozen food producers. IQF freezers use a fluidized conveyor belt or tray to individually freeze tiny products, such as fruits or vegetables. At the same time, spiral systems tackle high-capacity production and have a smaller footprint for food plants that have limited floor space.
“There’s just not room for expansion in today’s food plant, and it’s hard to expand the walls in the U.S.,” says Chris Johnson, Director of Business Development at Linde.
Linde, a supplier of liquid CO2 and liquid nitrogen, o ers tunnel and spiral chilling equipment. Cryogenic systems operate at -150° F, freeze quickly, and are smaller systems compared to larger, mechanical tunnel freezing technology. “If companies want to increase production, one way is to add a cryogenic tunnel in front of an existing spiral while not eating up floor space,” says Johnson.
“Plant space is the biggest hurdle for our customers looking to increase production, particularly in existing plants,” says Gill. “Freezers are already one of the largest footprint assets in the plant, so looking at ways to make the freezers as e cient as possible in freezing products to gain throughput to limit increases in physical size is a key focus.”
Sequential defrost technology is another way to increase volume within a plant’s footprint. This technology allows producers to shut down individual fans in separate chambers sequentially and defrost these zones one at a time, while other freezing zones continue working.
“What has changed over the last five years is more customers are asking for the sequential defrost technology in the design of their
We’ll
While complete meal solutions, single-serve meals, and frozen pizzas spark consumer demand, frozen vegetables and fruit sales are mainstays in the frozen food segment.
machines,” says Osterstrom. “Food producers want longer production time between defrost cycles for increased production.”
ProFood World recently reported how Foodhills employed this sequential defrosting at its facilities producing frozen peas and how the company moved to three-day production cycles. “Before, we had 12 to 14 hours of continuous production, but now we can produce for 72 hours,” explains Jan-Inge Nyström, Production Manager at Foodhills. “We have a short stop after 36 hours for cleaning and defrosting, which takes around two hours. Otherwise, it has fulfilled our capacity goals with continuous production—that has been good with this freezer.”
“Rather than purchasing equipment that can do more per hour at a higher cost, customers are looking at equipment that can run more safely between stopping (or downtime) to service and clean,” says Sheridan. “Running a line with lower hourly capacity for more hours or days between stops is generally considered the lowest cost to increase productivity.”
In addition to IQF tunnel and spiral freezing units, food producers are adding impingement freezers for thinner products such as egg patties, bacon chilling, and raw hamburger, while contact freezers are used to crust-freeze raw poultry or fish to prevent belt marking for appearance reasons.
The U.S. frozen food market is the largest in the world, comprising 39% of the global market. (Euromonitor International 2024)
Ownership of air fryers continues to grow with newer dual basket-style air fryers growing by 22% year over year. (Circana, National Eating Trends, 2023-24)
28% of grocery store trips include at least one frozen food item. (Circana, 52-week study ending Nov. 3, 2024)
s
OEMs are providing remote monitoring and services to frozen food producers to increase uptime and accelerate troubleshooting.
Increased monitoring for pathogens and uptime
The trend of remote monitoring is present in the freezing and chilling segment, especially when it comes to food safety. In January 2024, the PMMI Business Intelligence report, “Trends in Remote Services & Monitoring,” showed that “54% of food and beverage end users have increased their investment in remote services and monitoring since COVID ended.”
The frozen food segment is no di erent. “Producers are focused on minimizing the cold-tocold time of the freezer with the most e cient use of hot gas and steam to warm up the freezer as well as limiting water and chemical usage to clean the freezer during sanitation,” says Gill. “End users can measure and monitor in real-time each step of the process to drive out any unnecessary waste in time and materials.”
Designed with economy, e ciency and hygiene in mind, the IQ cryogenic freezer o ers continuous high throughput on a broad range of foods with easy clean up. Ten-foot modular sections make it eld expandable with a minimal capital investment. A SMART remote monitoring system allows for trouble shooting from afar.
Increase your IQ and pro ts . . . visit airproducts.com/IQ or call 833-NEED-GAS (833-633-3427) tell me more airproducts.com/IQ
Inspecting and automation are also on the rise. “Customers are also requesting vision systems that can quickly assess product shapes, color, and whether quality is correct,” adds Osterstrom. Also, OEMs are adding sensors to monitor motor amperage and vibration in specific system areas, and suppliers are o ering services for remote troubleshooting.
In addition to freezing equipment, food producers are targeting e cient use of air by limiting infiltration/exfiltration of warm, moist air areas from the surrounding plant environment that would create unnecessary frost load, thus decreasing energy consumption and extending equipment runtimes.
Gill says, “Continued increases in food safety standards have driven a focus on innovation when it comes to hygienic design, cleaning systems, and enhancements on measuring and monitoring pathogens in and around the freezer.”
Up to 37% higher energy e ciency compared to roots blowers
Maximum noise reduction thanks to customised silencer technologies
Smallest footprint and side-by-side installation
The integrated automation of National Bulk Equipment bulk liquids filling systems for drums and totes enables packaging operations to run fully automated production at designed speeds without concern for recurring material waste, rework, or excess labor allocation common with underperforming systems. The system features an automatic bung management system that provides high-speed removal, handling, and replacement of drum bungs, eliminating operator interactions. This fully automatic system increases fill accuracy, process throughput, and line yield. National Bulk Equipment | nbe-inc.com
The Brawn Mixer B Series liquid mixing systems are engineered to meet the sanitary process requirements of industries including food and beverage, pharmaceutical, and specialty chemical processing. Sanitary features include electropolished, high-strength, washdown-duty, stainless-steel housings; and sanitary shaft couplings for clean-in-place, liquid shedding. Brawn Mixer B Series stainless-steel liquid mixing systems provide IP65-rated, direct-drive or gear-drive configurations for mixing volumes up to 3,000 gallons. Brawn Mixer | brawnmixer.com
PSB Industries’ range of advanced Moisture Separators are designed for e cient moisture removal in food processing systems. These include Centrifugal Separators, ideal for high-velocity gas flows and capable of removing aerosols down to 10 microns, and Demister/Mesh Separators, providing precise filtration down to 0.3 microns for lower flow rates. Both models are engineered for high e ciency, minimal maintenance, and adaptability to diverse operational needs, ensuring cleaner air and gas outputs for critical production processes.
PSB Industries | psbindustries.com
ifm efector’s SM Foodmag is a sanitary magneticinductive flow sensor designed to meet the rigorous demands of the food and beverage industry. Equipped with IO-Link, this sensor o ers precise measurement of flow rate, total volume, flow direction, conductivity, and temperature, providing insights for process optimization and quality control. Its durable, 3A-approved design, coupled with fast installation and user-friendly interface, ensure reliable operation in harsh environments. By eliminating the last blind spot in the production process, the SM Foodmag helps manufacturers achieve greater e ciency, product quality, and regulatory compliance.
ifm efector, inc | ifm.com
The ROSS VersaMix VMC-320 is designed for precise processing of viscous solutions, dispersions, suspensions, and emulsions. Its three-agitator system, including a twowing anchor, pitched blade turbine, and auger agitator, ensures e cient mixing and blending. Constructed with durable stainless steel and equipped with a hydraulic lift for easy access, this mixer o ers a maximum working capacity of 320 gallons and a user-friendly control panel for precise operation. The VMC320’s versatile design and customizable control panel allow for precise control over mixing parameters, optimizing product quality and consistency.
Charles Ross & Son Company | mixers.com
Cabinplant’s CLF o ers fast and e cient filling of various liquids, including tomato sauce, oil, and brine, into containers like cans and jars. Designed for both pre- and postfilling operations, it provides a flexible and economical alternative to larger, more expensive filling lines. Available in mobile and integrated versions, this solution caters to a wide range of production needs, from small batches to high-volume processing, and features adjustable filling volumes, speed operation up to 300 fillings/min, a small footprint, easy dismantling for cleaning, and a “no can –no filling” system for enhanced safety and e ciency.
Cabinplant | cabinplant.com
Manufacturing food and beverages require robust, reliable, and durable equipment solutions. In addition, ingredients must be handled gently, added precisely, and mixed e ciently. We have extensive knowledge of food and beverage production, and our application experts can develop and deliver a solution to handle your most demanding applications. Scott Mixers is a proud brand of EBARA Mixers. www.scottmixers.com
Volkmann USA’s diverter valves o er a hygienic and e cient solution for splitting or merging material streams in food and other sanitary bulk material handling processes. These valves are fabricated from 316L or 304 stainless steel with smooth internal surfaces to prevent product buildup and contamination. They can be pneumatically or electrically activated and integrated into existing PLCbased control systems. By streamlining the conveying system and reducing the complexity of material handling infrastructure, these diverter valves enhance overall system e ciency and streamline material flow.
Polar King Mobile says its Avalanche Series trailers feature the industry’s first ground-level loading system technology. Utilizing a Sure-Trac system, these trailers—the PKM68A , PKM612A , and PKM616A—o er a safer, more e cient way to load and unload refrigerated and freezer trailers. These American-made trailers, constructed with durable fiberglass, are designed with a range of features, such as a temperature range of 0°F to 50°F, E-Track readiness, and a drop deck design for easier access.
Polar King Mobile | polarking.com
Volkmann USA | mixers.com
EnSight Solutions integrates a Twin Column Dumper with a Staubli Automated Guided Vehicle to automate the dumping and movement of heavy products, eliminating the need for manual handling and forklift tra c. By coordinating product dumping and transport, the solution minimizes human error, improves safety, reduces labor costs and addresses labor shortages, and creates a smarter, more streamlined process for product movement. Key features include robust construction, advanced safety systems, and a compact design, making it suitable for various applications in food processing and other industries. EnSight Solutions | ensightsolutions.us
FPS Food Process Solutions and OptiCept Technologies launch the OptiCEPT Solid Series, a Pulsed Electric Field (PEF) system designed to optimize solid food processing by improving product quality, reducing processing times, and enhancing energy e ciency. The system combines a hygienic design and robust construction with next-generation PEF technology to ensure optimal treatment while maintaining a minimal footprint. By applying short, high-voltage pulses, the system can soften, dry, extract, and freeze solid foods more e ectively, leading to higher yields, lower energy consumption, and reduced food waste.
FPS Food Process Solutions | fpscorp.ca OptiCept Technologies | opticept.se
Mettler-Toledo Product Inspection’s X6 Series, which consists of the X16 and X36.2 , is designed to enhance product safety and eciency for medium- to large-sized packaged products. The solution o ers precise contamination detection, identifying potential hazards like metal, glass, stone, bone, and low-density materials. The series also performs comprehensive product integrity checks, ensuring correct product placement, proper fill levels, and packaging integrity. With customizable configurations, high-speed capabilities, and a user-friendly design, the X6 Series helps manufacturers maintain rigorous quality standards, prevent product recalls, and optimize production e ciency.
Mettler-Toledo Product Inspection | mt.com
FoodSafe Drains | foodsafedrains.com s s
FoodSafe Drains’ range of hygienic Area Drains are designed for food production environments. These compact drains, with flow rates up to 32 GPM, are ideal for space-constrained facilities. Constructed from durable stainless steel (T304 or T316) and featuring a Load Class E rating, they withstand heavy tra c, including forklifts. Equipped with a magnetic strainer for easy cleaning and available in various model shapes (Cone, Square, and Round), these NSF/ANSI/3-A certified drains prioritize sanitation and e ciency, minimizing downtime and providing a clean and safe production environment.
Eagle Product Inspection’s FA3/M meat inspection system o ers advanced fat measurement and contaminant detection capabilities for the meat processing industry. Utilizing Dual Energy X-ray Absorptiometry (DEXA) technology, the system accurately measures chemical lean content and identifies contaminants like metal, glass, and bone fragments. With high-speed processing, automated calibration, and seamless integration options, the FA3/M ensures e cient and reliable meat inspection, meeting the stringent quality and safety standards of the industry.
Eagle Product Inspection | eaglepi.com
Gericke USA’s AirCIP was developed for horizontal batch mixers to promote complete product discharge, eliminate manual cleaning, and speed changeovers. The system sprays pulses of compressed air around the mixer interior to dislodge any residual material from the paddles or chamber and direct it to the discharge valve for recovery. The stainless-steel AirCIP system empties most mixtures and completes cleaning in as little as 60 seconds, and the cleaning time, pulsed air velocity, and other parameters may be set for each recipe, stored for instant recall, and adjusted on the fly.
Gericke USA | gerickegroup.com
MELLMAR Machine’s WeighMar line of automatic weighing machines reduces intensive labor and saves on costly product giveaway. This versatile line can run most free-fl owing products—like snack foods, nuts, granola—and can fill into most containers, bags, cups, trays, etc. Advanced algorithms calculate combinations in fractions of a second, allowing the machines to be accurate within 10ths of a gram, and the line can produce at rates up to 120 weighments per minute. The operating system is easy to learn, and the system comes apart quickly with toolless part removal so cleaning the contact parts is quick.
MELLMAR Machine | mellmarmachine.com
Key Technology’s vibratory conveyor systems are designed to streamline poultry processing and packaging lines. These integrated systems automate the metering, separation, singulation, and alignment of raw poultry products, maximizing e ciency, reducing labor costs, and improving sanitation. By utilizing vibratory technology, these systems eliminate the need for traditional belt conveyors, reducing the risk of foreign material contamination and simplifying maintenance. Key’s customizable solutions can handle various poultry cuts and integrate with downstream equipment, ensuring optimal product presentation and maximizing throughput.
Key Technology, a member of Duravant’s Food Sorting and Handling Solutions group | key.net
AFC o ers a bulk bag filling station with integrated weighing capabilities for precise filling of bulk bags, sacks, and FIBCs. Available with platform scale or load cell weighing systems and a PLC-based control panel, the station stops filling when the target weight is reached. Designed for handling various dry bulk materials, it can compensate for tare weight and other factors a ecting accuracy. The system, made in the U.S., features a rugged steel frame, accommodates various bag sizes, and can be customized with features like automatic dust control and integration with a SPIRALFEEDER flexible screw conveyor.
Automated Flexible Conveyor | afcspiralfeeder.com
surface designed for
After the largest PACK EXPO International to date this past fall in Chicago, PMMI is bringing the PACK EXPO experience to an entirely new region with the first-ever PACK EXPO Southeast. While the show may be new, it debuts as the leading show in the region for packaging and processing professionals seeking to explore new technologies, find new packaging materials, meet their next key partners, and witness innovation in action. Seasoned PACK EXPO attendees in the Southeast will recognize the same high-quality, high-value experience they know from past shows, this time brought right to their doorstep.
PACK EXPO Southeast takes place March 10-12 at the Georgia World Congress Center in Atlanta, bringing together an estimated 7,000 attendees and 400 exhibitors across over 100,000 net sq ft of exhibit space. Discover the latest machinery and materials to support your operation and even find industry-crossing solutions from completely outside your own sector or product range. The show will o er wide-ranging solutions for 40+ vertical markets, including food and beverage, household and automotive, life sciences/pharma/medical devices, cosmetics/personal care, pet food and pet care, and much more. That’s all while allowing for detailed one-on-one engagement with exhibitors. Attending PACK EXPO Southeast empowers brands across the region to make better capital investment decisions and prepare for the future. Watch machinery as it operates live on the show floor, gaining valuable, practical information directly from demonstrations to identify solutions tailored to your manufacturing challenges. Talk with experts on-site to strategize about how these innovations can enhance your company’s operations. There’s no better time or place across the Southeast to discover, compare, and evaluate the latest machinery and material options in one place, saving time and helping to make informed decisions.
Atlanta is a regional hub for both manufacturing and transportation, making it the perfect location for companies across the Southeast to congregate and explore the latest ideas and technologies. For
the wealth of companies located in and around the city, the region’s top packaging and processing solutions destination is practically down the street. Companies in surrounding states can take a short drive or nonstop flight for direct access to multiple solutions in one quick trip. Whether you’re coming from the Carolinas, Florida, Alabama, Mississippi, or Tennessee, PACK EXPO Southeast is likely under two hours away by either car or air.
That means the PACK EXPO experience doesn’t have to be limited to a select few team members flying long distances to Chicago or Las Vegas. PACK EXPO Southeast provides a convenient and more a ordable way for an entire team to see the industry’s latest and greatest. Bringing the whole team can foster creative problem-solving around current projects and future goals, combining a variety of perspectives and expertise to evaluate possible solutions. It’s also a great chance to mentor and motivate younger employees, developing your next generation of leaders.
Educational opportunities and networking abound
The hundreds of solutions available on the show floor are far from the only attraction at PACK EXPO Southeast. Attendees can engage with some of the industry’s leading experts and thought leaders on the latest trends in packaging and processing. It’s the perfect chance for attendees to gain leading insight into packaging and processing’s most timely issues, such as sustainability, food safety, robotics, workforce development, life sciences operations, cold chain packaging, and preventative maintenance.
Make sure to visit the Innovation Stage for free, 30-minute seminars by industry experts throughout each day, where you’ll learn the best practices, emerging trends, and innovative solutions shaping the future of packaging and processing. Also, don’t miss the Industry Speaks stage, where association leaders from the PACK EXPO Partner Program and other leading organizations o er a variety of perspectives on the industry’s hottest issues.
Your next sustainable packaging solution is around the corner at the Reusable Packaging Pavilion, sponsored by the Reusable Packaging Association
Discover how reusable packaging solutions can cut back on waste, lower costs, and boost supply chain and environmental e ciency.
Connect with leading associations, industry organizations and schools at the Association Partner and Workforce Development Pavilion to access a wealth of resources, insights, and expertise. The Pavilion is a one-stop-shop to find the tools and resources you need to grow your business and develop your existing team.
Atlanta on March 10, starting at 7:00 p.m., o ering a fun and relaxed environment for young professionals to network with industry peers. The Packaging and Processing Women’s Leadership Network Reception, sponsored by Morrison Container Handling Solutions , will be held on Tuesday, March 11, at 4:00 p.m., creating a fantastic opportunity to engage with the industry’s leading women driving progress and innovation.
Packaging and processing leaders at CPGs and PMMI member companies can attend Vision 2030 to discover groundbreaking solutions, connect with industry peers, and gain valuable insights. Join the conversation Monday, March 10 at 11:30 a.m. for a discussion on technology and workforce, or Tuesday, March 11 at 11:30 a.m. to discuss data acquisition, sharing, and utilization.
Attendees are encouraged to use My Show Planner to create an itinerary for the event and easily schedule appointments with exhibitors. Also, masterfully navigate the show with the help of the PACK EXPO Southeast Mobile App, sponsored by ProMach, Inc
When the show floor closes for the day, get ready to gather with your peers at your choice of networking events. The PACK EXPO Southeast Opening Reception, sponsored by Multi-Conveyor, takes place March 10, right after the show, and is a great opportunity to network with colleagues and fellow attendees. The Young Professionals Networking Reception will take place o -site at Wild Leap
PACK EXPO Southeast’s convenient location, cuttingedge machinery solutions, and actionable educational opportunities make it a mustsee event for packaging and processing professionals across the Southeast. Visit packexposoutheast.com to register and find more information about these valuable tools.
Sanitary Design
.3&CERTIlEDTOMEETINDUSTRYSPECIlCSTANDARDS
Easy to Specify #!$")-OR2%6)4lLESFORYOURPROJECT
Resistant to Chemicals, Extreme Heat & Bacteria +EEPSYOURPRODUCTANDFACILITYSAFE
Durable, Special Duty Load Rating 3TANDSUPTOEVENTHEHEAVIESTLOADS
MODERN CPG COMPANIES face two overlapping challenges: A labor shortage due in no small part to a lack of technically skilled workers coupled with burgeoning automation that increases demand for technically skilled workers.
There were 471,000 job openings in the U.S. manufacturing industry in October 2024, according to
the Bureau of Labor Statistics. That’s a significant improvement from the highs of the COVID-19 pandemic (993,000 in April 2022). The October figure is still higher than almost any point in the decade before the pandemic’s disruptions though, excluding a few months in 2018 and 2019.
Underlying these job openings, almost threequarters (72%) of manufacturers said their primary challenge is attracting and retaining a quality workforce in a survey conducted for PMMI Business Intelligence’s 2024 report, “Transforming Packaging and Processing Operations.”
Respondents in the survey pointed to a growing disconnect between acute skill shortages and the growing use of automation that requires highly skilled workers like maintenance technicians.
As one respondent explained in the survey, “We are installing more automation to limit needs for skilled operators, but in doing so there is an increased need for skilled maintenance technicians.”
Advanced technology may be contributing to the skills gap, but if applied strategically, it could be both a source of labor relief and a solution for significant improvements in e ciency. The key to achieving these benefits lies in empowering the worker with connected technologies.
As advanced technologies permeate through the modern manufacturing plant, a connected workforce is one that is well-equipped to take advantage of the technology around it. While the integration of digital technologies on the plant floor can be called digital transformation, the operator interacting with those digital technologies is a connected worker.
Industry stakeholders at PMMI’s 2024 Top to Top Summit say they are currently using these connected technologies to bridge the skills gap, per the “Transforming Packaging and Processing Operations” report.
Respondents described “Mobile iPads for maintenance for quick access to videos or reference drawings,” as well as Realwear glasses for remote support.
SOURCE: REALWEAR
End users are connecting their systems with vendors via sensors and analytics “to share and exchange data and arrange urgent maintenance,” and for “e ciency monitoring and risk notifications.”
SOURCE: GOMBERT, SIGRID VIA GETTY IMAGES
AUGMENTED REALITY AND VIRTUAL REALITY
These technologies were among those noted as pivotal for managing workforce limitations, with uses in predictive and prescriptive maintenance, as well as training.
SOURCE: EKKASIT919 VIA GETTY IMAGES
Four out of five respondents said they store data partly or entirely in the cloud, with uses including data-sharing with OEMs for troubleshooting, and backups for disaster recovery.
SOURCE: JACKIE NIAM VIA GETTY IMAGES
Video training was noted as a solution that resonates with the younger workforce, and one that could feasibly be implemented in the short-term.
Respondents discussed how AI can enhance human capabilities, rather than replace them. AI-driven tools can provide personalized training, assist in decision-making, and simplify complex data analysis.
SOURCE: TSINGHA25 VIA GETTY IMAGES
SOURCE: J STUDIOS VIA GETTY IMAGES
Remote access to equipment can be used for maintenance, and digital twins can be used for planning, training, and predictive maintenance. These technologies enable companies to overcome geographical and skill-related barriers, allowing experts to provide input and troubleshooting remotely, and test variables before spending money on building or investing in machines.
SOURCE: TUNVARAT PRUKSACHAT VIA GETTY IMAGES
connected worker technologies to bridge a machine operator skills gap
Both packaging machine manufacturers and endusers are struggling to hire and retain machine technicians, resulting in notable shifts in the packaging industry, according to PMMI Business Intelligence’s 2024 “State of the Industry” report.
Business Intelligence researchers say the reality of today’s labor shortage is one of the most significant drivers in the packaging machinery market, with impacts in areas including product development, ROI justification, and aftermarket support strategies.
The COVID-19 pandemic exacerbated this problem, but it has been present for nearly a decade. Because of this, Business Intelligence researchers do not expect a significant resurgence of skilled labor soon.
With the shortage of available labor, the standard for the labor force is lowering to a “beggars can’t be choosers” mentality. With less skilled workers becoming more commonplace, machine users have begun requesting more machinery solutions aimed at bridging the skills gap.
Companies are improving e ciency on the plant floor by making human-machine interfaces (HMIs) movable along the production line. This allows operators to easily access controls from di erent points along the line. Further, tablet-like portable HMIs enable operators to manage a machine without being physically next to it. This portability enhances convenience and allows for greater flexibility in monitoring and controlling machinery.
Another common adjustment to HMIs is the introduction of multiple language options. Rather than just English, many are now o ering various language options to increase accessibility and expand the potential pool of available workers.
Machine builders are also simplifying HMI user interfaces, incorporating more pictures and appstyle icons. This makes it easier for new operators to learn and reduces training time, helping to get the line running quickly. More machines are also now equipped to show visuals of the machine parts that may be down. This speeds up the troubleshooting process to reduce downtime, as operators can easily identify which part of the machine is experiencing an issue.
Missouri-based Logboat Brewing used an automated control system including HMI systems with mirrored displays to streamline communication across the plant and improve e ciency. For an example of connected HMI systems in action, read the full story at pfwgo.to/8658.
packing food powders into valve bags
E ective use of data for predictive maintenance: One strategy that Business Intelligence researchers say continues to gain traction in the packaging sector is predictive maintenance. Predictive maintenance di ers from preventative maintenance, which is currently the most common of the two. Preventative maintenance involves scheduled servicing, but it may not always be timely or necessary. In contrast, predictive maintenance uses data-driven insights to anticipate when maintenance should be performed, optimizing deployment of labor.
Predictive maintenance allows operators to know in advance when a part is likely to fail. It can reduce the risk of unexpected stoppages, and streamline maintenance by ensuring replacement parts are in stock or ordering new parts before a failure occurs.
While predictive maintenance is still emerging in packaging, it has potential to significantly reduce downtime and alleviate some of the labor demands on machine technicians.
How AI could support workers: With the rapid advancements in AI technology, there is growing excitement and interest in how these innovations could support the packaging workforce.
Machine operators can use AI assistants for time-consuming tasks like data entry and coding, according to PMMI Business Intelligence’s 2024 report, “The AI Advantage in Equipment: Boosting Performance and Bridging Skills Gaps.” This increases the speed at which projects can be completed, freeing up time for sta to focus on other valuable tasks.
AI could also be a solution to close skills gaps. With a high turnover of roles (especially among maintenance sta and machine operators), the optimized training provided in connected worker platforms can ensure that all employees are receiving the highest quality training available. AI assistants and generative AI predictive maintenance solutions allow users to ask questions regarding issues they are having on machines, further enabling members of sta to upskill independently and reduce the risk of human error.
Digital twin simulations are another example of AI simplifying the job of the machine operator, per the AI report. The virtual environment allows AI to create and test many di erent iterations of items, like a specific component of a machine, greatly reducing development time and streamlining the development process.
As CPGs navigate growth and continuously carry out complex production operations, leveraging connected workforce technologies can become essential. Enterprise CP (ECP), a Minnesota-based contract packager, learned this when it experienced significant growth over about a four-year span, according to a 2024 Packaging World report. The company implemented a tailor-made, AI-enabled enterprise resource planning (ERP) system to organize its operation as it scaled. Its confident scaling after ERP implementation illustrates how digital technologies can help workers to streamline workflows, reduce errors, and enable faster decisionmaking in a growing operation.
ECP packages such products as dry mac and cheese, deluxe mac and cheese with liquid cheese pouches, pouch dinners, boxed dinners, and packaged stu ng. It’s retailer customers include Walmart, Kroger, Aldi, and food banks like Feeding America.
As the company’s operation quickly grew, it struggled with managing its inventory using outdated systems.
“I was managing eight to 10 spreadsheets to try and keep track of everything,” explains Sandi Hanson, Materials Manager at ECP. “As we continued to grow at such a rapid rate, it became very di cult to manage the upkeep of those spreadsheets.”
The need for a more e cient system became apparent as the company expanded. ECP in 2021 turned to Power Central’s ERP software, powered by Microsoft Dynamics 365 Business Central, to address these challenges. The system includes mobile apps purpose-built for the food packaging industry, using Power Apps, advanced Microsoft Cloud, and AI solutions, allowing Power Central to tailor the experience to ECP’s needs.
“Prior to installing the Power Apps, there was mostly a manual system of ensuring FIFO usage of raw materials and shipping of finished goods,” says Hanson. “The Power Apps certainly have made a time savings di erence when looking for information and accuracy in fulfillment.”
From the shop floor operator’s perspective, this new technology means a digitalized method of inventory tracking, taking the potential for human error out of the process. Operators can use scanners to quickly and confidently upload inventory information into the system.
This operations-spanning tool has helped to improve collaboration across departments, as Hanson explains, “The ability for the shipping department to see inventory levels and communicate any needs has allowed for adjustments to be made in packaging schedules and for proper fulfillment of finished goods needed to ship.”
The system helps ECP’s team forecast future demand and plan accordingly as well, with Power Central’s AI-powered Advanced Planning System. The software uses graph-based algorithms and the inventory tracking from the ERP system to give a visual representation of things like upcoming sales, purchases, and forecasts.
The software uses color coding to highlight purchase orders, with green meaning no inventory issues are ahead. “If I have something that’s orange or turning red, then I know there’s something I need to take a look at. On the purchasing side, I could see if I missed a confirmation, or if I have confirmation that [packaging materials or ingredients] are coming in on that date,” Hanson says. “It’s simple, but it’s a great visual.”
Planning for busy periods or extra requests from customers is also simplified with the Advanced Planning System. A customer can provide its forecast for a timeframe like Thanksgiving, and the system “shows me what raw materials I need to purchase, and if I put it in by month, it’ll show me that I need ‘X’ amount in whatever month it is,” Hanson says. “I can be pretty strategic with when I’m placing my orders and when I’m bringing my inventory in.”
To introduce its workforce to the new ERP system, ECP held training sessions first with process owners, then with material handlers, Hanson says. The company took its time to identify any snags or areas that needed modification, conducting weeks of training and testing before going live with the new system.
Operators shared feedback during the implementation process, which Power Central was able to accommodate. The company made “personalization adjustments” to the system to help it better fit ECP’s specific business needs and user preferences.
The intuitive interface, real-time data access, and AI-based forecasting provided by the system have empowered employees at all levels to make informed decisions quickly. By reducing the reliance on manual processes and spreadsheets, the system has freed up valuable time for employees, contributing to the company’s growth trajectory.
The evolution of the connected workforce represents a transformative shift in the packaging industry, o ering solutions that enhance operational e ciency and worker engagement.
As CPGs adopt connected technologies, they are not only streamlining production processes but also empowering their workforce. This connectivity facilitates better communication, training, and collaboration across teams and across the production line.
Compact pressure sensors and switches with 360° custom-color status display www.vega.com/vegabar
256 colors
Individually selectable:
Measurement in progress
Sensor switching Process malfunction
Designed by Twin Screw pump experts, Fristam’s FDS pump has raised the bar for Twin Screw technology since its inception.
Process and CIP in One Fristam’s FDS pump handles both production and CIP supply duties, eliminating the need for extra pumps and piping. It is perfect for batch-blend processing and makes it easy to clean in-between batches.
The FDS pumps the widest range of food products gently and reliably, from thick to thin, chunky to smooth, and fast to slow.
The FDS is built for lasting performance with large, stable shafts and screws; high-precision bearings; and superior oil circulation that holds up under extreme conditions.
By manufacturing, assembling and testing our Twin Screw pumps in Middleton, WI, Fristam offers lead times measured in weeks, not months, and unparalleled customer service and nationwide support.
Also Now Available: The FDS Nano: compact, precise. Learn more today!
DR. BRYAN GRIFFEN | PRESIDENT, GRIFFEN EXECUTIVE
Overall equipment e ectiveness (OEE) can be a standout metric for improving the manufacturing process. This Q&A between two experienced industry professionals provides unique insight for companies in the packaging and processing world.
DR. BRYAN GRIFFEN , on behalf of ProFood World, conducted an interview with fellow manufacturing professional Joe Zembas to shed light on the OEE evaluation process.
Zembas started his career at Procter & Gamble (P&G) where he spent 24 years working in manufacturing plants in Pennsylvania, Italy, England, Maine, and Kansas City. Zembas also spent 14 years with Smucker’s in various corporate roles. He built two greenfield factories and managed approximately $1 billion of capital investment throughout his career.
BRYAN GRIFFEN: Can you break down what overall equipment effectiveness, or OEE, is for us in terms of its main components?
JOE ZEMBAS: Sure. So first o , you’ve got to look at availability. In a manufacturing environment, that’s looking at, what is the market demand for the product you’re producing on that piece of equipment and therefore what’s the run schedule going to be?
It’s no use running a line 24/7/365, if you’ve only got eight-hour or five-day kind of volume. You’ve really got to look at the key opportunity times and make sure that you’re comparing the right basis.
The second area is performance, and that is within that time frame where you are really looking to deliver. Is the machine running as it should? Breakdowns, minor stops, all those kinds of things play into that performance segment.
It’s important to be able to troubleshoot those items and be able to identify them. That’s where a lot of the focused improvement and continuous improvement type work needs to be addressing is those performance outages.
The last one, which sometimes gets masked because the product leaves the line and is assumed
1
OEE EVALUATION
AVAILABILITY
2
3
PERFORMANCE QUALITY
to be good, [is quality]. You’ve got to make sure that you’re making what the market is going to be able to sell and what’s going to be the focus of your operation.
BG: How have you seen tracking OEE change over the years and what’s the difference it makes on the hunt for productivity?
JZ: Tracking what’s coming from a production environment, you can do very manually. Simple tick charts, a tablet, etc., are manual ways to do it.
In the manufacturing world, I’ve seen products on the market for $50 that you could put on the machine and it’ll simply track time running versus time not running. [It’s] a simple, rudimentary way to evaluate and track what you’re doing from an OEE standpoint.
There’s a lot of modern technology out there where you’re pulling tags from PLCs and putting them in databases and being able to then parade those tags or parade those causes relative to certain
categories, like mechanical failures, electrical failures, starved for incoming product, blocked, unable to move the product past the machine, etc.
So, you can go up and down the spectrum from very manual to very high tech. It’s just a matter of what the business can a ord and what’s going to provide value.
BG: What are some of the common OEE troublemakers that you’ve seen, and what are the strategies for catching and improving them?
JZ: We’ll run through availability, performance, quality again. From an availability standpoint, it could be very simple things like sta ng levels, starving or blocking a machine by not providing the raw material or ingredients to it, or [a machine] being unable to move stu through the system.
From a performance standpoint, there are all kinds of losses that you see, but things will be very machine dependent. If you’ve got a very rudimentary machine, it may simply just be a jam here or there. If you’ve got a high-tech, servo-driven, multi-access machine, there might be much more di cult problems to troubleshoot and solve.
From a quality standpoint, some machines will automatically reject o -quality things because of sensors up and down the machine, or some of those will simply be done o ine afterward.
BG: What’s the big picture here? How does improving OEE translate into real performance and pro tability in manufacturing?
JZ: A great thing about focusing on an OEE is if you think of a business and they’re out there running [for example], 40% OEE, they’re paying all their salaries, utility bills, depreciation, etc., and they have their profit margin, 20%.
Every other case you make in that manufacturing plant, all those fixed costs are already paid for. So, your margin on that additional 10, 20, 40% OEE that you improve, all the additional costs that you’re adding on that side of the spreadsheet on the ledger is the cost of materials. So, the profitability in those cases is like 80%.
It depends [from] business to business, but you’re not paying for more heating, ventilation, and air conditioning in the room. You’re not paying for more operators. They’re all there. Your management sta , HR, legal, everyone, you’re paying for them with a 40% OEE. When you up it and you’re running another 40% more, those cases are like printing money.
BG: Can you share an example from Smucker’s where you tracked OEE, and it turned into real world gains?
JZ: Sure. A great example is from our co ee business. We had a horizontal form/fill bagger, making a gusseted bottom bag for co ee. It wasn’t a complex machine. It was eight servo axes, a bunch of cams, heaters, etc. on the machine. It ran about 30, 35 bags a minute—your standard, run of the mill horizontal bagger. It was running about 35-38% OEE when we decided to focus on making the machine run better.
If you look at it from an availability standpoint, there were certain things the machine required. It required to be shut down to splice in a role of new film. So, there are certain parts of the 24-hour day we were not going to be able to go after. But the other parts, the performance and quality issues, we were able to go out and address.
Working on that piece of equipment with a multifunctional team was key. The great thing is, you get everybody in the room and bought into really making it hum, and in doing that and going through about a year’s worth of e ort, we got to where one month that machine ran nine 12-hour shifts with no unplanned stops. Compare that to a 30-35% OEE to start with, when you have nine perfect shifts, you can put that in the “W” column.
BG: That sounds like a fantastic example of what an average factory can gain from improving their OEE. To close out our discussion, I want to do a round of quick- re questions. If a piece of equipment has a sudden performance drop, what’s the rst thing you do?
JZ: The first thing I would do is go pull the data. What’s the before and after? Try and understand what root causes may come immediately to the top of the pile. Things like changes in raw materials, changes in sta ng, all those kinds of things can very quickly be identified and troubleshot just by pulling the data of what’s going on in that operation.
BG: How can small plants get OEE bene ts without a huge investment?
JZ: As I mentioned, there are some devices out there for $50 to $100 that will track very simple systems. In one operation that we acquired way back in my career, we just did the novel thing that we’d done in many other plants that I’d worked on and put a spiral- bound book out on the piece of equipment and ask people to write stu down.
So, it could be as simple as writing things down. It could be as simple as a very simple tracker. Or if you’ve got the skill and capability or you’re willing to buy it, a little bit of PLC programming and pulling a couple of tags and dropping them into a database. You can work wonders very quickly in today’s electronic world.
BG: How can real-time monitoring lead to better decision making?
JZ: You need to be able to give the people that are on the floor around the machine, the operators, mechanics, whatever your work system looks like, data that’s current and relevant to what they’re trying to do. If it’s an advanced piece of machinery, you could have run charts or other things displayed on the screen, or it could be as simple as those notes in the notepad of what’s going on and what’s happened over the last couple hours or a couple shifts that people need to know.
BG: If a piece of equipment in your plant was up for an MVP award, which one would you nominate, and why?
JZ: We had a multipack cartoner with five di erent production lines [feeding into it]. I happened to be in
the manufacturing plant as an engineering leader, and I was asked to support the operation by picking up responsibility to get that multipack cartoner running better, because it was running 28-30% [OEE] on any given day.
I leveraged that multifunctional team as I spoke because I’ve found through my career that is just the gem in how to get through these problems. And within a week we’d identified the cartoner was fantastic.
Now you might say, “Well, geez, how can they be only putting out 28%?” The cartoner [was] being fed by five di erent other production systems, five di erent production lines [and] was starved most of the time. It was being held 80% of the time by the same one of those five.
So, the real e ort wasn’t to work on the cartoner. The real e ort was to go work on that one production line and get its results up so that you could get the right five products coming into the multipack cartoner.
It was one of those great ones where, at the end of the day, the cartoner ran well and the system ran well, but it started from a spin-your-headaround 180° that the cartoner is not the problem. Even though that’s where management originally thought it was.
Miura is dedicated to producing reliable, e cient, and safe steam generation systems for pet food processing companies. Our complete solutions approach ensures your facility operates at peak e ciency, addressing all aspects of your boiler room.
Miura is dedicated to producing reliable, e cient, and safe steam generation systems for pet food processing companies. Our complete solutions approach ensures your facility operates at peak e ciency, addressing all aspects of your boiler room. We invite you to experience unparalleled e ciency and savings with Miura during our limited-time Summertime Savings event.
We invite you to experience unparalleled e ciency and savings with Miura’s Multiple Installation System.
• Customize plant size to specific needs
• Automatically stage boilers to meeet demand fluctuations
• Save 20% on average in annual fuel costs
• Provide equivalent boiler capacity in less than half the space
• Reduce Carbon Dioxide and NOx emmisions
DR. BRYAN GRIFFEN | PRESIDENT, GRIFFEN EXECUTIVE
Failing to transfer experience is risky. Here are practical strategies to facilitate it.
is undergoing a seismic shift as seasoned professionals approach retirement, taking with them decades of expertise that cannot easily be replaced. At the same time, the next generation of workers is stepping into increasingly complex roles, requiring both technical proficiency and business acumen to succeed. Bridging this gap has become a pressing challenge, as the risk of losing institutional and tribal knowledge grows more acute.
Knowledge transfer is not simply a matter of convenience—it is a critical strategy for maintaining operational continuity, meeting client expectations, and
driving innovation. Yet, it is a challenge that comes with its own set of hurdles, particularly when experienced employees resist sharing what they know due to fears of becoming obsolete. This article explores the risks of failing to transfer knowledge, practical strategies to facilitate it, and a real-world case study of a company navigating these challenges.
The potential fallout from insu cient knowledge transfer can be devastating. Operations that rely on seasoned professionals to maintain complex systems or manage legacy accounts risk significant downtime
and ine ciency if those individuals leave without passing on their expertise. For food manufacturing companies with long-standing client relationships, the stakes are even higher. Losing the nuanced understanding of why certain solutions are in place or how to migrate aging systems to newer versions can erode customer trust and satisfaction.
Beyond operational risks, there are cultural and interpersonal dynamics at play. Employees with decades of experience may view their specialized knowledge as a safeguard against obsolescence. They fear that if their expertise is shared, their role within the organization will diminish, leaving them vulnerable to layo s or irrelevance. Additionally, the pride they take in mastering systems and processes that others find challenging can make them reluctant to relinquish control.
In some cases, seasoned employees worry that younger workers lack the business acumen or interpersonal skills required to handle accounts e ectively. This perceived gap in soft skills can reinforce resistance, creating a bottleneck that prevents the seamless transfer of knowledge.
Strategies for effective knowledge transfer
Recognizing and addressing these challenges requires a multifaceted approach. Companies must not only implement systems and programs that facilitate knowledge transfer but also create an environment where all employees feel valued and supported.
1. Mentorship Programs
Pairing senior employees with junior sta is one of the most e ective ways to facilitate knowledge transfer. However, mentorship must be a two-way street to ensure mutual benefit. Senior employees can share their expertise on legacy systems, account management, and customer relationships, while junior employees can introduce their mentors to new technologies, IT security practices, and modern workflows.
One company successfully implemented such a program by closely tracking mentorships through HR and upper management. These mentorships are structured to ensure information flows both ways, creating a win-win scenario where both senior and junior employees gain valuable skills. This collaborative approach helps dismantle fears of irrelevance while equipping the next generation with the tools they need to succeed.
2. Digital Documentation
Knowledge that lives solely in the minds of a few em-
Knowledge
transfer is not simply a matter of convenience—it is
a
critical strategy for maintaining operational continuity, meeting client expectations, and driving innovation.
ployees is inherently vulnerable. Creating a centralized knowledge repository, complete with video tutorials, annotated diagrams, and step-by-step guides, ensures that critical information is preserved and accessible. For legacy systems that may have been in operation for many years, documenting idiosyncrasies and unique configurations is vital to maintaining long-term operational stability.
However, simply creating documentation is not enough. Companies must implement processes to regularly review and update this information to reflect changes in technology and practices. Training employees on how to access and contribute to the repository is also key to its success.
3. Modern Training Technologies
Advances in technology, such as augmented reality (AR) and virtual reality (VR), o er immersive training experiences that can bridge the gap between hands-on learning and theoretical instruction. These tools are particularly e ective for complex tasks that require a deep understanding of equipment or processes.
For example, AR overlays can guide employees through equipment maintenance step-by-step, while VR simulations allow them to practice scenarios in a risk-free environment. Combining these tools with e-learning platforms ensures that training is accessible and flexible, catering to diverse learning styles and schedules.
A midsized engineering software and services company in the food manufacturing industry recently faced this challenge head-on. With more than 25 years of experience, the company relies on its seasoned sta to maintain legacy systems for long-standing clients. These systems, some of which
utilize technologies and equipment that are obsolete, require a deep understanding of their intricacies and the rationale behind their implementation. At the same time, the company is preparing to transition clients to newer solutions, which demands familiarity with modern technologies.
Senior employees, however, were hesitant to share their expertise. Their concerns ranged from fears of obsolescence to doubts about whether younger sta could manage client accounts e ectively. Recognizing these challenges, the company launched a mentorship program with a unique twist: mentorship flowed in both directions.
Senior employees train junior sta on legacy systems, account management, and client-specific nuances. In return, junior employees have introduced their mentors to emerging technologies, cybersecurity best practices, and modern tools that could streamline workflows. The program is being closely monitored by HR and upper management to ensure accountability and mutual benefit.
A lot of our customers can’t talk about their secret to safe, smooth, gentle conveying but everyone knows the secret is Volkmann. Our patented pneumatic vacuum conveyors automatically transfer powders and other bulk materials from one point to another in fully enclosed, dust-tight, explosionproof systems.
Automated, hygienic and quiet
Easy to use, easy to clean
No tools disassembly
Stainless steel as standard Fast lead times, easy to install
In addition to the mentorship program, the company has implemented regular learning sessions where employees are encouraged to present relevant topics to their peers. This initiative fosters a culture of collaboration and continuous learning, breaking down silos and encouraging information sharing.
While the program is still in its early stages, the results have been promising. Collaboration has improved, and senior employees are beginning to embrace new responsibilities related to modern technologies. Employee satisfaction is on the rise, and while resistance persists among a small minority, the overall feedback has been overwhelmingly positive.
The process of passing down knowledge from retiring experts to the next generation is both a challenge and an opportunity. By implementing mentorship programs, creating robust digital documentation and leveraging modern training technologies, companies can ensure the continuity of institutional knowledge while empowering their workforce.
As the food manufacturing industry continues to evolve, the ability to navigate these transitions will determine which companies thrive and which struggle to keep pace. For organizations willing to invest in people and processes, the rewards are clear: a more agile, collaborative, and resilient workforce ready to meet the demands of the future.
Statco-DSI is a leader in process technology and innovation by utilizing the latest in equipment technology to drive modernization in the sanitary processing industries. Properly executed technology based designs lead to improved efficiencies, reduced downtime, and ensures product quality for our clients.
- Comprehensive project design and build- Equipment, components and MRO product sales- Expert factory-trained field service technicians -
• Boost efficiency with automation, streamlining production, and reducing operational costs
• Minimize downtime with low maintenance equipment specified for the application, and applicable CIP for quick cleaning
• Ensure product quality with precision focused equipment integrated by means of ingenious design engineering
• Energy and cost savings by lowering utility consumption and long-term operational costs
BlenZer inline blending systems delivery precise, real time blending for dairy and beverage processing, ensuring consistent product quality and flavor.
ThermaStat aseptic/ESL systems provide reliable, high performance processing for extended shelf life and aseptic dairy and plant-based products.
TAYLOR KEATEN | PRINCIPAL, LAUNCH PARTNERS CONSULTING
By educating yourself and implementing incremental changes, you will simplify your day-to-day operations, significantly increase production capacity, and build a solid foundation for your business
, the initial hurdles of production are often the most challenging to overcome. You’ve likely spent time solving problems just to get your product to market—developing processes, troubleshooting issues, and making do with limited resources. But once you’ve tackled those early obstacles and achieved some level of stability, the next question becomes: How do you grow from here?
Embracing change at this point in growth is counterintuitive. You have gotten as far as you have with tools that you built, but if you keep applying them the same way you are sure to cause troubles for yourself as the business grows. Now is when you need to shift
your focus from simply getting by to building a foundation for sustainable growth. The good news is that growth doesn’t have to mean huge capital projects or complete do-overs. Often, the biggest wins come from small, strategic changes that challenge your existing practices and unlock new e ciencies. The journey to operational e ciency is all about identifying these opportunities and turning them into real, measurable gains for your business.
Take a hard look at how things are done now and ask questions. You might have good reasons for setting up your product and processes the way you did, but growth means thinking di erently. What parts of your product make it special? What steps
in your process are absolutely necessary? How can you keep those important elements while improving everything else to build a stronger business?
You don’t need to spend a lot of money to start making these changes. Many great opportunities can be implemented with little cost and can still make a big di erence. Start with simple changes that give you the best results for your e ort. Once you’ve tackled these easy wins, you’ll be in a better position to make the most out of bigger investments later. The key is to start small, keep asking questions, and act on what you learn.
One of my favorite examples involves a recent client who asked for a manufacturing site assessment. Before we could even schedule the assessment, the client made remarkable progress. By addressing one small step in their process, they connected their filling line to their labeling line, which immediately boosted daily throughput by 50%. After discussing another minor adjustment, they were on track to achieve a 100% improvement in production compared to their initial benchmark.
It’s not uncommon for clients at this stage to be implementing projects that return within weeks or months. Leave the long ROI e ort for down the road when you have more capital and structure to execute them. For startup-scale businesses, small changes can yield outsized impacts. At this stage, adjustments can happen quickly, and their e ects are felt immediately by the team and the business. In contrast, larger, more complex systems often see gains of only 5%-10%, requiring significant investment and disruption—sometimes after enduring challenging times.
The impact of these changes is transformative. Doubling production capacity can lead to fulfilling more orders, capturing more revenue, and boosting team morale. These incremental wins build momentum. After a series of these changes, the entire team begins searching for the next unlock, allowing them to achieve more with less complexity, e ort, and time. Minimal capital investment is required, yet production of quality goods increases significantly, and the team becomes more engaged in understanding the “why” behind every decision. When it’s time to purchase larger equipment, they’re already operating at a much higher level, ready to fully utilize increased capacity and make the most of the capital dollars invested for growth.
Continuous improvement is a journey and one that starts with some basic steps
First, educate yourself on manufacturing best practices and immerse yourself in foundational concepts
Often, the biggest wins come from small, strategic changes that challenge your existing practices and unlock new ef ciencies. The journey to operational ef ciency is all about identifying these opportunities and turning them into real, measurable gains for your business.
that drive operational excellence. Start by familiarizing yourself with the key terms and methodologies within the industry—the ones that will help you identify and tackle ine ciencies with confidence. There’s no shortage of material available, so I won’t bog you down with a long list of reading recommendations, but if terms like single-piece flow, bottlenecks, and the theory of constraints aren’t already part of your vocabulary, it’s time to change that. Dive into books, articles, or even online courses—whatever suits your learning style.
I know this can seem intimidating, and it’s true that some experts frame these ideas as complex or inaccessible. But trust me, they’re not. These principles are practical, actionable, and grounded in logic. Take what you’ve learned and apply it immediately, even in small ways. Learning is essential, but action is where you’ll see real results and retain the learning you have worked hard to develop.
Second, put your entire value chain on the table and evaluate each step by asking a series of critical questions. Can this step be eliminated entirely without compromising the overall process or product quality? If it can’t be removed, can it be simplified or streamlined to increase speed, reduce inputs, or cut unnecessary costs? Are there any redundant steps or ine ciencies that could be addressed with minimal disruption? Ensure you don’t constrain yourself to what happens within your four walls. What about your material suppliers? Can they provide you with a better product that will improve your production or costs? Don’t forget your packaging suppliers! By systematically questioning every part of the value chain, you can uncover hidden opportunities for improvement and set the stage for smoother operations and greater e ciency.
Third, chase bottlenecks! Start by ensuring that your processes are connected. While artisanal batch
production can work well in the early stages, sustainable growth often requires transitioning to an integrated production process that includes each discrete unit operation for your product. By connecting processes early, ine ciencies and opportunities for improvement become more visible. Ask yourself: Where is material stacking up in your workflow? What specific steps are causing delays or interruptions? How can you either improve the capacity of the bottleneck or eliminate it altogether? Taking action on these insights is crucial. Once you resolve one bottleneck, another will inevitably surface, providing you with a continual pathway for improvement and optimization. By addressing each bottleneck systematically, you’ll create a more e cient, streamlined production system over time. Once you’ve addressed a handful of these you will reflect on your overall productivity and see tremendous growth.
The journey to automation and optimization doesn’t have to be daunting. Real impact often comes from a series of small, thoughtful changes. When you approach these challenges with curiosity and a willingness to challenge assumptions, the returns—in
The journey to automation and optimization doesn’t have to be daunting. Real impact often comes from a series of small, thoughtful changes. When you approach these challenges with curiosity and a willingness to challenge assumptions, the returns—in ef ciency, growth, and team engagement—can be remarkable.
e ciency, growth, and team engagement—can be remarkable. By educating yourself and implementing these changes, you will simplify your day-to-day operations, significantly increase production capacity, and build a solid foundation for your business.
Whether sourcing equipment, nding materials, or exploring new solutions, PMMI ProSource puts the industry’s leading suppliers at your ngertips—all year long.
Protect your process lines from contamination with ThermOmegaTech’s STVM® Washdown Stationdesigned for efficiency and to minimize downtime. Constructed with our unique venturi mixing technology, the STVM® delivers high-temperature water quickly, quietly, and on demand.
Our unique self-scouring cartridge design allows for quick, sweat-free maintenance, reduces mineral build-up, and ensures extended operation. For the most demanding applications, an optional welded Stainless Steel Station is available, offering superior strength and leak-free sealing.
Every STVM® Washdown Station has interlocking ball valves to prevent steam-only operation and an automatic shut-off when cold water flow is interrupted.
LILIÁN ROBAYO PÁEZ | EDITOR-IN-CHIEF, MUNDO EXPO PACK
Installation of Hiperbaric’s most productive equipment, HPP 525, at RV Fresh Foods allowed the company to double its production to satisfy the growing demand for fresh guacamole and premium avocado products in international markets. This is the first 525 equipment installed for guacamole production in Mexico.
RV Fresh Foods, founded in 2020, has established itself as a leading company in the avocado sector. The company occupies a facility in Uruapan, Michoacan, which covers 215,278 sq ft and employs 680 people. It is dedicated to processing high-quality avocado products. “We o er a variety of products, which are grouped into three main categories: industrial use, for companies that incorporate avocado into products like dressings or baby food; the food service channel, targeting the fast food restaurant industry; and the retail channel, serving the end consumer,” explains José Ramón Valencia, Founder and General Director of RV Fresh Foods.
The company, driven by its commitment to innovation and quality, has managed to position itself as a benchmark in the industry, both nationally and internationally. “The world capital of avocado, Uruapan, provides us not only with a high-quality product but also a cultural commitment to the land and its fruits,” says Valencia. “Our growth has been exponential from the beginning, achieving double-digit growth rates each year. Despite the lack of a comparative base in the initial year, the jump from the first to the second year was impressive, with 80% growth between 2021 and 2022, followed by a solid 30% from 2022 to 2023 and a projected 18% from 2023 to 2024.”
RV Fresh Foods does not sell its products directly in Mexico and its main market is the U.S., where it concentrates 80% of its sales. In Europe, the company has established commercial o ces in the Netherlands, and it is currently present in 18 countries in the E.U. It also exports individually frozen products to Japan, such as avocado cubes and halves.
“We are one of the national companies, with Mexican capital, with the highest volume of guacamole exports,” says Valencia.
Freshness and quality from the tree to the table At its facilities in Uruapan, RV Fresh Foods has three specialized production lines equipped with cutting-edge technologies such as Individual Quick Freezing (IQF) and High Pressure Processing (HPP).
RV Fresh Foods does not sell its products directly in Mexico. Its main market is the U.S., where it concentrates 80% of its sales. In Europe, the company has established commercial o ces in the Netherlands, and is currently present in 18 countries in the European Union.
s s
Guac On! is one of the leading brands of avocado products commercialized in the U.S. by RV Fresh.
The new Hiperbaric 525 installed at RV Fresh Foods is equipped with 12 intensifiers and a 525-l (150-gal) capacity, allowing it to process up to 8,000 lb of guacamole per hour.
These technologies allow maximum preservation of the avocado’s flavor, texture, and nutrients and ensure a long shelf life of the products without the need to add artificial preservatives.
The production process at RV Fresh Foods begins with the reception and selection of the avocado. Once selected, the avocados undergo a washing and disinfection process. Then ripening takes place in which temperature and humidity are controlled to reach the optimal point of softness and flavor of the fruit.
After ripening, the pulp is extracted to maintain its freshness, color, and flavor. Later, depending on the client’s requirements, the avocado pulp can be mixed with other ingredients, o ering customized products such as guacamole or sauces. To eliminate microorganisms without a ecting nutrients or flavor, the product is subjected to HPP. This method allows greater food safety without chemical preservatives.
RV Fresh Foods plans to double its production of guacamole and derivatives with Hiperbaric’s HPP 525
equipment, which it incorporated in October 2024. HPP uses water to create pressures similar to those reached at the bottom of the ocean. With pressures of up to 6,000 bars, equivalent to 87,000 psi, in cycles that usually last between three and five minutes, spoilage pathogenic microorganisms such as Salmonella and E. coli are completely inactivated without the need for additives or preservatives. Unlike other preservation technologies that can a ect the sensory and nutritional quality of food, HPP keeps the organoleptic properties of the product (flavor, color, and texture) practically intact. “High pressure (HPP) technology applies pressure instead of heat, which is ideal for products like avocado, which changes color, texture, and flavor under heat,” says Roberto Peregrina, Director of Hiperbaric for the U.S. and member of its board of directors. This is especially beneficial in the case of avocado, a delicate product that can oxidize and lose quality quickly. HPP technology not only preserves freshness, but depending on storage and transportation conditions, it can extend the shelf life of products for up to 90 days.
lb/hr.
This is the first time Hiperbaric has installed equipment of this size in Mexico. There was previously only one machine in the state of Veracruz dedicated to citrus. This is the first 525 unit installed for guacamole production.
The quality of Yaskawa products is second to none, but Yaskawa Quality goes beyond that. It’s the total experience of purchasing Yaskawa products and working with people.
With the Hiperbaric 525, RV Fresh Foods is maximizing its production while reducing operating and maintenance costs. This technology allows the company to achieve scalable production and maintain the quality and freshness that its customers expect.
Up to 8,000 pounds of guacamole per hour
The Hiperbaric 525 used by RV Fresh is equipped with 12 intensifiers and a 525-l (150-gal) capacity, allowing it to process up to 8,000 lb of guacamole
per hour. This new equipment joins a Hiperbaric 420 machine previously purchased by RV Fresh Foods to further strengthen the company’s processing combined capabilities of 15,000 lb per hour.
With both machines, RV Fresh Foods now has the capacity to meet increasing demand, especially to export markets. “This is the first time we have installed equipment of this size in Mexico […] it is a machine that has 12 intensifiers, which makes it very fast,” explains Peregrina. “In Mexico there was only one machine in the state of Veracruz dedicated to citrus. This is the first 525 equipment installed for guacamole production.”
“The demand for fresh and natural products continues to grow,” says Valencia. “Thanks to HPP technology, our products meet the quality and freshness standards that consumers expect. This allows us not only to remain in the market, but to di erentiate ourselves from the competition.”
Processing cycles of approximately 6 minutes
The choice of the Hiperbaric 525 was strategic for RV Fresh Foods because it o ers the highest production capacity within the range of HPP machines.
Its processing volume of 525 liters allows production to be doubled compared to equipment with a lower capacity, which implies a considerable reduction in operating costs in terms of energy consumption and cycle times.
Each processing cycle lasts approximately six minutes and, allows for fast loading and unloading that minimizes downtime and increases overall process e ciency.
The incorporation of the Hiperbaric 525 into the RV Fresh Foods production line was a comprehensive process that required adjustments in the structure of the plant and in the training of personnel. Implementing this technology involved restructuring spaces and redesigning workflows to take full advantage of the machine’s capabilities. This included relocating loading and unloading stations as well as intensive training of operators in safety and equipment operation protocols.
Valencia emphasizes that operator training is essential since the success of the process depends
2025 Half Page Horizontal.pdf 1 1/9/25 9:49 AM
on the operators’ ability to program cycles, monitor pressure, and control processing times. “Hiperbaric has provided us with ongoing support, ensuring that our team is well prepared and that any eventuality can be resolved quickly,” he says.
The successful implementation of the Hiperbaric 525 has laid the foundation for the future growth of RV Fresh Foods. The company is evaluating the possibility of acquiring a third HPP unit in the short term to increase its production capacity and respond to the growing demand for avocado products in the global market.
The company also plans to diversify its product portfolio by introducing new variants of avocado-based sauces, purees, and value-added products such as healthy snacks and dips. This o ering expansion is in response to the trend of consuming healthy and convenient foods.
Hiperbaric www.hiperbaric.com
CIP 2.0 is designed for food, dairy, and beverage plants. Our systems are designed to be scalable to meet your needs today and in the future. CIP 2.0 incorporates smart machine technology to enhance performance, flexibility, and reporting.
Based on the Rockwell Automation ® control platform, CIP 2.0 controls cycles using process parameters.
• Built-in predictive and preventative maintenance program with valve cycle count and pump runtime analysis.
• One to four tank configurations with single or dual supply.
• Process parameters deliver a more accurate and repeatable process than a time-based approach, and enables users to manage chemical, water, and other resource consumption.
• Allows authorized in-house users to make and track all changes.
• Automated record-keeping verification occurs after each cycle, designed to comply with regulatory standards CFR21 and S88.
What began as an in-home business two decades ago has grown into an automated company with products now available nationwide in ethnic retail stores.
HISTORICALLY, INDIAN COMMUNITIES in the U.S. created homemade foods in batches to sell in local ethnic stores. As the popularity of these snacks grew, Edison, N.J.-based Gharana Foods needed to expand its operation. Today, the Indian snack food producer continues to make sweet and savory snacks with homemade appeal, but with increased e ciency due to automation.
Five years ago, Amit Patel, Co-Owner of Gharana Foods, left his job in the tech industry to run the family business, so his parents could ease into retirement. “I was the most logical choice,” explains Patel. “I had the tech expertise, plus I had experience with the food.” More recently, Patel’s focus has been on process improvement and eciency, as well as modernizing the operation with automation.
The company produces Original Chakri (a rice flour-based, spiral-shaped, buttery, salty, savory, mildly spicy, and extremely crunchy snack), Jalapeño Chakri (a rice flour-based, spiral-shaped, buttery, salty, savory, jalapeño spicy, and extremely crunchy snack), and Sweet Shakkar Para (sweet sugar pieces made from all-purpose flour, sugar, water, and oil tasting similar to the crispy edges of a funnel cake).
With Patel’s mother creating the snacks and his father’s background in engineering, Gharana Foods was able to keep that homemade taste for years using his father’s original equipment fabrication. But the family knew they had to update to more modern equipment.
jalapeño powder, salt, and other spices that aerate when you do it by hand. It’s just very uncomfortable,” says Patel. In the past, the family produced small batches requiring about 50-60 spice mixes per day. Not only was this labor intensive, it also resulted in less than optimal accuracy. Today, Gharana makes larger batches requiring 20 spice mixes per day utilizing three Versifeeders with custom software that gives plant floor workers the flexibility to easily move from between making a spice mix, and back to other duties.
“My parents made our spicy mix manually via memory at the expense of their hands and noses,”
“Imagine working with chili powder, Gharana Foods’ authentic ethnic snacks focus on clean label products without any artificial colors, flavors, or preservatives.
Three gainin-weight Versifeeders from Vibra Screw deliver more accuracy and require less labor for Gharana Foods.
says Patel. “While we only needed to perform this task 20-25 times a day, we needed something that could scale and provide an automated way that could be used by any employee to dispense our core spices [salt, chili powder, dehydrated jalapeño] in controlled and small amounts without exposing the recipes to the employees.”
A few years ago, Patel discovered Vibra Screw through a Google search, but he wasn’t quite ready to contact the equipment supplier because he was still working on all the automated changes to the previously manual manufacturing process.
After reviewing all the ingredients his company uses, Patel decided that he required feeders to boost e ciency.
In 2023, Patel was ready to make the call. “Vibra Screw worked with us to create three independent gain-in-weight feeders, along with a custom-programmed touchscreen to dispense our spices,” explains Patel. “They provided a scale and a stand that I put on a small track to manually move between the feeders depending on which ingredient needed to be dispensed.”
Proper feeder programming was essential to the project’s success. Once the feeders were installed,
Patel realized he had to make some changes. “You don’t really think it through until you’re using it, and then you realize things can be tweaked a little bit to improve the workflow,” explains Patel.
Each Vibra Screw gain-in-weight feeder is designated to a specific spice. “Since all our products use three ingredients, it wouldn’t make any sense to perform changeovers for di erent product runs,” says Patel. “I would probably get a fourth feeder if we needed something new.”
Feeder washdown involves emptying the vessel, and then adding hot water and a little bit of de-greaser. However, the salt feeder requires a specific cleaner and sealer that prevents rusting.
Vibra Screw supplied a gain-in-weight batch system consisting of three sanitary design Versifeeders, a batch scale, and a custom programable controller. One of the feeders has a 3/4-in. feed screw; the other two have a 1-in. feed screw. Hopper sizes are 1.5, 2, and 3 cu ft and are flange bolted to the feeder trough to allow for increased storage capacity in the future. The hoppers are fitted with low-level probes to signal a refill requirement. The spice feeders are 304 stainless steel, while the salt feeder is 316SS.
The scale accommodates Gharana’s batch container and is rail mounted so it can be readily
positioned beneath the operating feeder. A ratio between what the scale can pick up and what it can discharge allows the unit to handle the minute amounts of ingredients required in this application.
The feeders are controlled via the central programmable controller, allowing the processor to input proprietary recipes as production requires. All three feeders are programmed to run in serial.
The original project goal was to make the user interface as easy as possible to operate. “I always looked at it as if an employee who rarely uses a cell phone has to use this piece of equipment,” says Patel.
Because his mother is still involved in production, Patel also needed is to ensure someone who may not be up to date on technology can easily understand what each screen means. “I took our manual process and wrote it down. Then I took my software background and applied that to what we needed,” he adds.
“All the automation we’ve done has scaled this business. In the last five years, the business has done 40% more daily production than what we were doing five years ago,” states Patel.
For example, conveyor installations sped production. “When we added conveyors, one of our products that needs to dry out a little bit processed faster,” explains Patel. “We ‘created time,’ and it wasn’t done intentionally. Something that took two days now takes one day.”
Plus, two decades ago, Gharana Foods was placing pre-printed labels on bags by hand, manually date-coding them, and then sealing the bags ready for distribution. Today, the company has a horizontal form/fill machine that prints the codes while still providing a homemade look and feel to the packaging. Clear packaging uses a high-end film that has a built-in moisture barrier to prevent product from going stale during its four-month shelf life.
The main benefit of the feeder project was saving time and energy, says Patel.
Employees don’t have to feed the feeders as often. The process has become a rote task. “That’s ultimately the win. It’s now a parallel task versus a serial task.”
“Vibra Screw is New Jersey based, which made my experience comfortable. I realized working with local companies is much more useful if you need parts,” says Patel. “Vibra Screw delivered in a timely manner with clear communication and provided unparalleled support throughout the installation and start-up process.”
Vibra Screw Inc. www.vibrascrew.com
Scan here to see our Casepacker in action!
Scan here for the latest in bakery innovation!
Scan here for your pick and place solution!
CASEY FLANAGAN | ASSOCIATE EDITOR
The citrus producer is maintaining quality standards while minimizing downtime and manual tasks with the help of TOMRA sorting solutions.
Long-standing citrus producer and exporter Sunriver Citrus is supporting its growth and maintaining quality standards with a new set of sorting solutions, according to sorter supplier TOMRA Food.
Operating since 1937, the South Africa-based Sunriver Citrus farms, harvests, and packages all its fruit, including clementines, lemons, Valencia oranges, and navel oranges. The company operates in farms across South Africa’s Sundays River Valley, in Kirkwood, Sunland, and Addo. It currently processes around 84,000 tons of product across three packhouses annually and sells its products both domestically and in export markets including North America, Europe, Asia, and Southern Africa.
In response to fast growth over the past seven years and a forecasted upward trajectory ahead, Sunriver has turned to TOMRA’s sorting solutions to maintain quality and automate processes.
“We had a lot of growth, and we needed sorters that deliver consistent grading to supply a perfect product,” says Theunis Bester, production manager at Sunriver Citrus. “Our vision is that in years to come there will be a high demand for citrus, but we at Sunriver want to be leaders in supplying good quality.”
Sunriver introduced its first new TOMRA 5S Advanced sorter in 2018. Impressed by the system’s performance, the company has since replaced sorters in its other two packhouses. It
added a second TOMRA 5S Advanced in 2023, and a third system equipped with a new Dynamic Lane Balancer in 2024.
Says Bester, “We used to have issues with light blemish sorting before we installed the TOMRA sorter, now we don’t battle it anymore. We are packing better quality fruit because of the consistent good grading, and this good quality helped build our brand in the markets.”
Sunriver worked with Masgcor, TOMRA’s partner in South Africa, to install the system on the lines in its three packhouses.
“Each packhouse has a Masgcor citrus processing and packing line where the TOMRA sorters form the main electronic sorting platform in a commit-to-pack layout,” says Gerhard Verster, general manager at Masgcor.
The system builds on the Compac Multi-Lane Sorter to deliver what TOMRA says is unrivaled accuracy and gentleness in fruit handling. Its software includes programs for element mixing, exact packout optimization, and throughput control for improved e ciency across the line. As a result, Sunriver has resolved its light blemish issues and achieved a 10% increase in daily packaging volume.
“The TOMRA 5S Advanced stands out for its reliability and accuracy,” says Verster. “It can handle superior volumes and delivers consistent superior quality to consumers.”
The sorters’ ability to optimize packout is vital to Sunriver’s ability to provide for international markets, as Bester explains, “We have the right quality in the cartons for the right markets.”
That’s important as the company maintains its accreditation and association with global distribution and quality assurance partners including Costco Wholesale, the BRCGS Global Standard for Food Safety, SIZA social compliance, and South Africa’s O cial Produce Export Certification Agency.
s
Sunriver uses TOMRA’s sorting technology to help it maintain quality standards for international markets.
Dynamic Lane Balancer allows for maximum cup ll
Priding itself on innovation, Sunriver claims the TOMRA 5S Advanced with a Dynamic Lane Balancer is the first system of its kind to be installed in South Africa.
“The first reason for installing it was to address
space limitations in our new packhouse, and to push the volumes through without having bottlenecks at the sorter by ensuring even spreads on the lanes,” says Bester.
The Dynamic Lane Balancer automatically adjusts the flow of fruit on the sorter, ensuring equal distribution across each lane. It uses data
from its interface and sizer software to make automatic adjustments to the product flow.
The result is a “less than 5% di erence in cup fill between di erent lanes, which means more e ective and superior throughputs,” explains Verster.
The system not only optimizes cup filling but helps to improve throughput as well.
“We have a more even spread on sizer lanes, and this enables us to push more volumes,” says Bester. “We achieve 10% more volume on packing per day, and the sorter can run slower because of the good spread on the lanes.”
After recognizing the performance improvements a orded by the Dynamic Lane Balancer, Sunriver plans to install the system in its other two packhouses.
Overall, the company reports it’s satisfied with its sorting upgrades. Says Bester, “TOMRA has certainly increased our sorting e ciency. The sorters have had no mechanical problems and reduced a lot of downtime and sorting labor—and with the performance they deliver, we need almost no manual sorting. TOMRA has increased our returns based on the good quality grading, and there is a demand for our Sunriver brand across the world.”
Sunriver is packing 10% more volume each day with TOMRA’s Dynamic Lane Balancer and plans to install the system in its two remaining packhouses.
INTERESTED?
LEARN MORE AT CLEANWORX.US
Wish you could do more with less?
You can with the CleanWorx® brand of sanitation equipment from Sani-Matic.
Eliminate the inconsistencies of manual cleaning and use your resources more
pending washer for automated COP.
%0$ ! !/+"!4,!.%!*!ȑˏ ȑ *Ȑ%/
#(+((! !.%*0$! !/%#**
)*1"01.%*#+"/0%*(!///0!!(/0+.#!
* ,.+!//%*#2!//!(/ȑ#%00+./ȑ*
%*0!#.0! /5/0!)/Ȑ!/,!%(%6!%*
.!0%*#0%(+.! /+(10%+*/"+.%* 1/0.%!/ (%'!"++ ȑ %.5ȑ!2!.#!ȑ,$.)!10%(ȑ * )+.!Ȑ
*)0$! 1(%05Ȗ.!%/%+*
1(%05
! !(%2!.$%#$ -1(%050*'/* 2!//!(/ !/%#*! 0+!*$*!!""%%!*5* ,.+ 10 -1(%05ȑ%*(1 %*#Ȓ %(+0+.#!*'/ (0 ̂+00+)* ˏ+*! ̂+00+).+!//+./ $!5ˏ.5/0((%6!./ +.%6+*0(Ȗ!.0%(0+.#!*'/ %4%*#*'/ %/$ȑˏ+*!ȑ* (+,! ̂+00+)*'/
CASEY FLANAGAN | ASSOCIATE EDITOR
The 93-years-running Backer’s Potato Chip Company upgraded its bulk storage bin system to minimize repair time and significantly speed up its unloading process.
BACKER’S POTATO CHIP COMPANY’S current owners have proven to be a chip o the old block in production innovation. The chip producer has upgraded its bulk storage bin system to cut repair time and quicken unloading, according to equipment supplier Vanmark.
Backer’s has been a family business since its start in 1931 in Callaway County, Missouri. Grandma and Grandpa Backer peeled and sliced potatoes by hand and cooked them in a 16-in. donut kettle, a few pounds at a time, to begin the company’s journey.
Fast-forward to today, and the company is in its 93rd year, now run by the second and third generations of the Backer family.
Backer’s processes 7,000 lb of potato chips per
hour at its facility, covering several types of branded and private label potato chips, all of which are gluten-free, vegan, and made with all-natural ingredients like fresh sunflower oil. The company ships its chips across the U.S., Canada, and Mexico.
Legacy bulk storage bin system showing signs of age
One reality of operating across generations is that tried-and-true equipment can eventually require an upgrade.
Backer’s experienced this with its bulk bin system, which was decades old and deteriorating quickly. The system was causing frequent downtime as the company had to make repairs, contributing to
challenges in keeping up with product demand.
Also contributing to production challenges was a potato unloading process the company deemed slow and inflexible.
To help alleviate these production challenges, Backer’s visited Vanmark’s facility in Creston, Iowa, to see the company’s Bulk Storage Bin System. The system receives potatoes and holds them until they’re ready for processing.
The chip producer has worked with Vanmark for decades and already has several legacy machines from the company in its facility. It chose to continue working with the supplier for this installation due to the durability of its existing equipment and support over the years.
Backer’s placed an order for the Vanmark system after seeing it in action, choosing a six-bin system to support production.
Backer’s worked with PFI, Vanmark’s sister company, to install the new Bulk Storage Bin System. Partnering with PFI for its turnkey equipment and service proved less costly than completing the install through independent contractors.
The Vanmark system receives and stores potatoes, then unloads them when its time for processing.
The system is built to be flexible, durable, and gentle in product handling. Its modular design allows for space savings, as the bins can share interior walls.
The inclusion of multiple discharge points allows Backer’s to send product to either of its two flume systems and processing lines, rather than being limited to one or the other.
A catwalk surrounding the system also improves accessibility.
Backer’s also mentioned to Vanmark during the design process that it had encountered issues with conveyors wearing out and breaking at “drop points” over time. Vanmark’s engineers responded to the issue by designing heavy-duty framing for those areas, reducing wear and tear.
With the new system in place, Backer’s can shift its attention away from making repairs to aging equipment, and toward the growth of its business. The speed of the company’s unloading process has also increased significantly.
Valuing their long and continued relationship after the new installation, the two companies expect to continue working together as Backer’s grows.
v-1 v|oll-m =-1| u;u b|_7;1-7;vo=; r;uঞv;ķ ; bѴѴ;vr;1b-Ѵb ;vbm1 মm]voѴ ঞomv|-bѴou;7|ol;;|o uvr;1bC1ruo1;vvbm]m;;7v )_;|_;ubm|;]u-ঞm]|_;bm7 v|u ĽvѴ;-7bm]|;1_moѴo]b;vouѴ; ;u-]bm]o uruorub;|-u 1 মm]v v|;lvķ ;;mv u;;L1b;m1 ķ
ru;1bvbom-m71omvbv|;m|t -Ѵb| -u|m;u b|_ v|ov;||_;]oѴ7v|-m7-u7=our;u=oul-m1;ķu;Ѵb-0bѴb| -m7bmmo -ঞombm=oo7ruo1;vvbm] +o uv 11;vvbvo u1u-[
;|Ľv1 ||o|_;voѴ ঞomŌ|o];|_;u
MATT REYNOLDS | CHIEF EDITOR, PACKAGING WORLD
Live at Automation Fair were two recent packaging-centric examples of co-man/co-packs taking the ERP plunge with Rockwell’s Plex. Both projects, integrated by Revolution Group, are ongoing and continue to add e ciencies and features through today.
RICHMOND BAKING, a 120-plus year-old family-owned contract manufacturer and packager of baked products headquartered in Richmond, Ind., recently faced significant challenges in its data collection and inventory management processes. These deficiencies were particularly apparent in a Richmond’s latest facility, More Than a Bakery in Versailles, Ky.
“We had repetitive tasks that were a significant challenge due to our reliance on our manual processes in data entry, with lots of duplication,” says Daisy Manjarrez, VP of continuous improvement. These challenges led to ine ciencies and communication delays, and such issues were compounded by the need for frequent physical inventory checks and production shutdowns to ensure accuracy.
Recognizing the urgent need to modernize its operations, Manjarrez and Richmond Baking explored various options before choosing Rockwell’s Plex ERP to address these issues. The implementation of Plex brought about several key benefits, including the elimination of two hard-to-fill and retain o ce data entry positions, and the streamlining of several interdepartmental processes. This led to improved inventory accuracy and lot traceability, as well as a boost in accountability and responsiveness in production.
“We wanted a seamless digital integration for superior shop floor quality,” Manjarrez says.
One of the more significant improvements stemmed from the introduction of real-time alerts and visual displays for out-of-spec conditions. This allowed Richmond Baking and More Than a Bakery teams to make proactive decisions and reduce scrap and downtime. The implementation of a Statistical Process Control (SPC) dashboard, developed with the help of systems integrator Revolution Group, enabled pre-bake operators to access real-time data, allowing them to react quickly to changes.
“With this dashboard, what they’re allowed to do
is they can see that training happening, and once it gets to those target limits, they can actually start reacting on the pre-bake side to actually eliminate and minimize that scrap,” Manjarrez says.
The integration of scanning technologies further streamlined inventory control, improving accuracy from 70% to 95%. By barcoding all incoming products and storage locations, Richmond Baking enhanced lot traceability and ingredient verification. This process prevented the use of incorrect ingredients, reducing waste and ensuring precise tracking.
“If it’s not part of our bill of materials, it’s not going to allow you to scan it into the work center for you to use it,” Manjarrez says.
The Plex ERP system also facilitated the automation of Richmond Baking’s and More Than a Bakery’s preventive maintenance (PM) system, reducing
Historically known for bottling iconic brands like 7-Up and Hires Root Beer, Portland Bottling transitioned around the 2001 into a co-packer for a variety of beverages, including energy drinks and kombuchas.
downtime and enhancing operational performance. The system’s data tracking capabilities were highly valued by auditors, providing clear documentation during audits.
“We always get a lot of components because we can trace back to the beginning, to the part, the component we can trace all back to the PM system,” Manjarrez says.
Beyond operational improvements, the implementation of Plex has fostered a cultural shift within Richmond Baking. The company has placed a strong emphasis on empowering its employees, referred to as “family members,” to take ownership of the new processes. This empowerment is evident in the way team members are encouraged to engage with the system and make informed decisions based on real-time data. By fostering a sense of responsibility and ownership, the company has not only improved e ciency but also enhanced employee satisfaction and engagement.
The transition to Plex has also opened up new avenues for Richmond Baking to explore further technological advancements. The company is now considering additional features o ered by Plex, such as batch management and tech management, to continue its journey of improvement. These potential enhancements align with the company’s commitment to staying at the forefront of industry standards and maintaining its competitive edge in the market.
Richmond Baking’s experience with Plex has highlighted the importance of adaptability and continuous learning in the face of technological change. Manjarrez says the company’s leadership has been proactive in ensuring that all employees are adequately trained and comfortable with the new systems. This approach has not only facilitated
a smoother transition but also encouraged a culture of continuous improvement and innovation. By investing in training and development, the company has ensured that its workforce is well-equipped to handle future challenges and opportunities.
The successful implementation of Plex has also had a positive impact on Richmond Baking’s relationships with its clients and suppliers. With improved data accuracy and real-time visibility, the company can now provide more reliable and timely information to its partners. This transparency has strengthened trust and collaboration, paving the way for more strategic partnerships and business opportunities. As a result, Richmond Baking is better positioned to meet the evolving needs of its clients and maintain its reputation as a reliable and forward-thinking partner in the industry.
Portland Bottling, another century-old company but with deep roots in the beverage industry, encountered its own significant operational challenges as it recently expanded. Historically known for bottling iconic brands like 7-Up and Hires Root Beer, Portland Bottling transitioned around 2001 into a co-packer for a variety of beverages, including energy drinks and kombuchas. This growth necessitated a shift from the operational approach, particularly as the company opened a new facility in Clackamas, Ore., which significantly increased production capacity.
An acquisition by local business moguls the Maletis family in 2016 marked a turning point, as they identified the need for technological upgrades to support the company’s expansion. By 2018, Portland Bottling was producing a million cases a month, but this growth exposed limitations with existing systems.
5HO\ RQ RXU LQGXVWU\ 5HO\RQRXULQGXVWU\OHDGLQJ
5HJXODWHWKHSXPSLQJVSHHGRI\RXU YDFXXPSXPSV$XWRPDWLFDOO\
&HQWUDOL]H\RXUYDFXXPVXSSO\ (ɚFLHQWO\
,GHQWLI\HQHUJ\ORVVHVLQ\RXUSURFHVV 'LJLWDOO\
)DVWHUSURFHVVHVKLJKHUSHUIRUPDQFHDQGVKRUWHUF\FOHWLPHV *HWWKHPRVWRXWRI\RXUSDFNDJLQJSURFHVV%XVFKRↂHUVRSWLRQVWR optimize your output and save energy: frequency-controlled and digitally FRQQHFWHGYDFXXPSXPSVERRVWHUVEXↂHUVDQGFHQWUDOYDFXXP systems. Get your perfect vacuum and service solution. 6FDQ45&RGHIRUPRUHLQIRUPDWLRQ
“With that growth obviously came a lot of need for us to upgrade the technology we were using,” says Robert Charles Van Blake, director of IT.
As early as 2019, Portland Bottling began implementing Plex, a comprehensive software solution designed to streamline operations. But the onset of the global pandemic in 2020 disrupted plans, delaying full integration. The company faced challenges with inconsistent processes and reliance on outdated paper-based systems, which hindered e ciency and communication.
“We face several of these challenges, just in the organization, communication, having it solidified that everybody’s doing the same process for the same thing,” Van Blake says.
Recognizing these issues, the executive team decided to reinvest in Plex, establishing a formal IT team in 2022 to drive the initiative forward. The focus was on eliminating paper processes, standardizing operations, and enhancing sta training.
“We really wanted to eliminate paper, eliminate Excel, standardize our process and make sure people were educated on what those new processes were,” adds Josh Bowen, Plex Admin at Portland Bottling.
One of the key projects was transitioning the hold log from Excel to Plex, which resolved discrepancies between quality and inventory records. This change allowed for real-time updates and notifications, significantly improving accuracy and e ciency. As Bowen describes, “Now instead of what had been a fog, we’ve got a much cleaner process.”
Portland Bottling also leveraged Plex’s capabilities to track production downtime, providing insights into operational bottlenecks. This data-driven approach enabled the company to identify and address issues proactively, enhancing overall production e ciency.
The implementation of Plex not only improved operational processes but also fostered a culture of continuous improvement. By engaging departments and creating Plex champions within the organization, Portland Bottling ensured that the software’s benefits were fully realized. Van Blake emphasizes the importance of coordinated planning.
“Everybody knowing what everybody else is working on and having that coordinated plan just makes everything better and smoother for everyone.”
Further enhancing operational e ciency, Portland Bottling integrated Plex with its existing systems, such as O ce 365, to streamline user access and improve cybersecurity. This integration allowed for single sign-on capabilities, reducing the complexity of managing multiple passwords and enhancing security protocols.
“We synchronized the active directory with O ce 365. So everybody just had a single sign on
By incorporating more departments into the system and developing a formal steering committee, Portland Bottling aims to foster collaboration and ensure that all stakeholders are aligned with the company’s strategic goals.
single-password SSO with Plex,” says Van Blake.
The company also focused on improving its quality assurance processes by digitizing quality checks and logs. This shift from paper to digital not only reduced errors but also facilitated faster response times to quality issues. The use of digital check sheets allowed lab technicians to input data in real-time, with automated alerts for any deviations from quality standards. This proactive approach to quality management ensured that potential issues were addressed promptly, minimizing disruptions to production.
Portland Bottling’s strategic use of Plex extended beyond immediate operational improvements. The company is now poised to explore further enhancements, such as expanding the use of Plex’s analytics and reporting tools to gain deeper insights into production trends and customer demands. By continuously evaluating and refining processes, the company is setting the stage for sustained growth and competitiveness in the beverage industry.
The integration of Plex also has allowed Portland Bottling to streamline its financial operations. By automating the invoicing process through the bill and hold feature, the company has significantly reduced manual errors and improved cash flow management. This automation ensures that invoices are generated accurately and promptly, aligning financial operations with production activities.
“Now product is, it goes through a and o is checked in bill and hold, and it automatically adds it to an invoice,” Van Blake says.
The company’s commitment to leveraging technology for operational excellence is evident in its plans to further expand Plex’s functionalities. By incorporating more departments into the system and developing a formal steering committee, Portland Bottling aims to foster collaboration and ensure that all stakeholders are aligned with the company’s strategic goals. This approach not only enhances operational e ciency but also empowers employees by providing them with the tools and knowledge needed to succeed in an evolving industry.
Aptar redefines what packaging can do for the food and beverage industry - and every detail matters down to the last drop. From protective Bag-on-Valve (BOV) solutions to captivating fine mist sprays, dispensing pumps, and aerosols, our products transform the ordinary into extraordinary. Partner with us to create product experiences that resonate with your consumers and help you stand out in the market.
Product Integrity
Optimized packaging and dispensing technology to maximize product protection while ensuring purity and safety.
Sustainable Materials
Our solutions include the use of materials that help reduce environmental impact, such as recyclable and refillable options.
Customization
Flexibility with spray options and premium features such as metal shells, matte finish and metallization help elevate the creative aesthetic and enhance brand image.
Cutting-Edge Technology
Stay ahead of market trends with our state-of-the-art packaging innovations – perfect for food and beverage applications.
Global Reach
With a presence in over 20 countries, we provide localized support and production with a global perspective.
Wellness and Control
Our dispensing options enable consumers to have better control over their dosage amounts, supporting healthier eating habits.
Trusted Partner
Collaborate with a partner who understands your vision and helps bring it to life with precision and excellence.
Join the leaders in beauty innovation. Empower your brand with Aptar’s expertise. Together, we can create products that not only captivate but also resonate with today’s conscious consumers.
Scan Me To Find Out More!
SUSTAINABILITY Aerzen USA, Inc.
Inc.
BAKERY & SNACKS
Advanced Equipment Inc.116
Aerzen USA, Inc.. 117 Air Products 118
Ampco Pumps Company119 Anritsu 123
Apex Motion Control 124
Axiflow Technologies, Inc128
BEHN + BATES 129
Busch Vacuum Solutions 132
Coperion 136
Delkor Systems, Inc. 139
Douglas Machines Corp. 141
Econocorp, Inc. 143
EDGE Industrial Technologies144
Ensight Solutions 146
ESI Group USA 147
FlexLink Systems, Inc.. 149
FOCKE & CO 150
General Packaging Equipment Co. 154
Graphalloy 155
Hapman 156
Harpak-ULMA Packaging, LLC 157
Heat and Control, Inc.158
JAX INC. 163
Linde 166
Material Transfer & Storage Inc. 168
Mead & Hunt, Inc 170
METTLER TOLEDO 171
Munson Machinery Co., Inc. 174
PPM Technologies Holdings LLC 179
Ross Mixers 180
SEW-EURODRIVE, Inc.182
The Austin Company 127
Tippmann Group 190
TNA North America, Inc.191
Urschel Laboratories, Inc. 192
VAC-U-MAX 193
VEGA Americas 195
Vibra Screw Inc 196
Volkmann, Inc. 197
Weber Inc 198
Wire Belt Company of America 199
Xchanger Inc 201
Aerzen USA, Inc. 117
Ampco Pumps Company.119
Anderson-Negele 122
Atlas Copco 126
Axiflow Technologies, Inc128
Central States Industrial133
Cleveland Gear Company134
Columbia Machine, Inc. 135
DCI, Inc. 138
Delkor Systems, Inc. 139
EBARA Mixers, Inc. 142
Econocorp, Inc. 143
Endress + Hauser 145
Ensight Solutions 146
FoodSafe Drains 151
Fristam Pumps USA 153
Hiperbaric 159
Lubriplate Lubricants Company 167
Mead & Hunt, Inc 170
Miura America Co., Ltd. 172
MXD Process 175
PAXTON 176
Pick Heaters, Inc 178
Sani-Matic, Inc. 181
SEW-EURODRIVE, Inc.182
Silverson Machines, Inc.183
Sleeve Seal 184
Statco-DSI Process Systems186
Stolle Machinery Company 187
TechniBlend 188
ThermOmegaTech, Inc. 189
Econocorp, Inc. 143
FOCKE & CO 150
Hapman 156
Material Transfer & Storage Inc.168
PPM Technologies Holdings LLC 179
Ross Mixers 180
Vibra Screw Inc 196
Volkmann, Inc. 197
Xchanger Inc 201
CONFECTION & CANDY
AmTrade Systems, Inc.121
CRB 137
Douglas Machines Corp. 141
FlexLink Systems, Inc. 149
FOCKE & CO 150
Hapman 156
The Austin Company 127
TNA North America, Inc.191
VAC-U-MAX 193
Vibra Screw Inc 196
Aerzen USA, Inc. 117
Air Products 118
Ampco Pumps Company119
Anderson-Negele 122
Anritsu 123
Axiflow Technologies, Inc128 Bepex 130
Big-D Construction 131
Central States Industrial133
Cleveland Gear Company134
DCI, Inc. 138
Delkor Systems, Inc. 139
Deville Technologies, LLC140
EBARA Mixers, Inc. 142
Endress + Hauser 145
FlexLink Systems, Inc. 149
Fristam Pumps USA. 153
Harpak-ULMA Packaging, LLC 157
ifm efector, Inc. 161
Industrial Magnetics, Inc. 162
Kovalus Separation Solutions,LLC. 165
Matthews Marking Systems 169
Mead & Hunt, Inc 170
METTLER TOLEDO 171
MSKTD and Associates 173
Sani-Matic, Inc. 181
Sleeve Seal 184
Statco-DSI Process Systems186
ThermOmegaTech, Inc. 189
Tippmann Group 190
AptarGroup, Inc.
+ BATES
Fristam Pumps USA
General Packaging Equipment Co. 154
Hydro-Thermal Corporation160
Kovalus Separation Solutions,LLC. 165
Munson Machinery Co., Inc. 174
Silverson Machines, Inc.183
Statco-DSI Process Systems.186
VAC-U-MAX 193
Volkmann, Inc 197
Xchanger Inc 201
FlexLink Systems, Inc.
FPS Food Process Solutions148 General Packaging Equipment Co.
Lubriplate Lubricants Company 167
METTLER TOLEDO 171
MSKTD and Associates 173
PPM Technologies Holdings LLC 179
Tippmann Group 190
TNA North America, Inc.191
Wire Belt Company of America 199
Advanced Equipment Inc.116
AmTrade Systems, Inc.121
Deville Technologies, LLC140
Harpak-ULMA Packaging, LLC 157
JAX INC. 163
Key Technology 164
Matthews Marking Systems 169
Urschel Laboratories, Inc. 192
GRAINS, SEEDS, BEANS, FLOUR & NUTS
FOCKE & CO 150
General Packaging Equipment Co.. 154
Heat and Control, Inc.158
Matthews Marking Systems 169
Munson Machinery Co., Inc. 174
Xchanger Inc 201
Advanced Equipment Inc.116
Airgas 120
Air Products 118
AmTrade Systems, Inc.121
Anritsu 123
Bepex 130
Big-D Construction 131
Busch Vacuum Solutions 132
Cleveland Gear Company134
Delkor Systems, Inc. 139
Deville Technologies, LLC140
Douglas Machines Corp. 141
EDGE Industrial Technologies144
Ensight Solutions 146
ESI Group USA 147
FPS Food Process Solutions148
Graphalloy 155
Harpak-ULMA Packaging, LLC 157
Hiperbaric 159
Hydro-Thermal Corporation160
Industrial Magnetics, Inc. 162
JAX INC. 163
Linde 166
Matthews Marking Systems 169
METTLER TOLEDO 171
Miura America Co., Ltd. 172
MSKTD and Associates 173
PERFEX TruCLEAN CORPORATION 177
Pick Heaters, Inc 178
PPM Technologies Holdings LLC 179
SEW-EURODRIVE, Inc. 182
The Austin Company 127
ThermOmegaTech, Inc.. 189
Tippmann Group 190
Urschel Laboratories, Inc. 192
VDG (Van der Graaf)194
Weber Inc 198
Wire Belt Company of America199
PET FOOD
Coperion 136
CRB 137
Hapman 156
Hiperbaric 159
Matthews Marking Systems 169
Munson Machinery Co., Inc. 174
Ross Mixers 180
Stolle Machinery Company 187
Vibra Screw Inc 196
Volkmann, Inc. 197
PREPARED & CANNED FOODS
AmTrade Systems, Inc.121
Anritsu 123
Deville Technologies, LLC140
EBARA Mixers, Inc. 142
Econocorp, Inc. 143
Lubriplate Lubricants Company 167
Matthews Marking Systems 169
MSKTD and Associates 173
Stolle Machinery Company 187
The Austin Company 127
SOUPS, CONDIMENTS, SAUCES, SPICES, DIPS & DRESSINGS
AptarGroup, Inc. 125
Axiflow Technologies, Inc128
BEHN + BATES 129
Central States Industrial133
Columbia Machine, Inc. 135
EBARA Mixers, Inc. 142
General Packaging Equipment Co. 154
Hiperbaric 159
Hydro-Thermal Corporation160
MXD Process 175
Ross Mixers 180
Silverson Machines, Inc.183
Sleeve Seal 184
Stolle Machinery Company 187
TechniBlend 188
CLEANING, SANITIZING & CIP
Ampco Pumps Company119
Anderson-Negele 122
Central States Industrial133
Douglas Machines Corp. 141
FPS Food Process Solutions148
Hydro-Thermal Corporation160
ifm efector, Inc. 161
Miura America Co., Ltd. 172
MXD Process 175
PAXTON 176
PERFEX TruCLEAN CORPORATION 177
Pick Heaters, Inc 178
Sani-Matic, Inc. 181
ThermOmegaTech, Inc. 189
TechniBlend 188
VEGA Americas 195
CONVEYING & PRODUCT HANDLING
Apex Motion Control 124 Cleveland Gear Company134
Machine, Inc. 135
DRY, PROCESSING & HANDLING EQUIPMENT
Volkmann, Inc. 197
Witte Company 200
Xchanger Inc 201
FACILITIES, DESIGN & INFRASTRUCTURE
Aerzen USA, Inc. 117
Atlas Copco 126
Big-D Construction 131
Busch Vacuum Solutions 132
CRB 137
ESI Group USA 147
FoodSafe Drains 151
Mead & Hunt, Inc 170
Miura America Co., Ltd. 172
MSKTD and Associates 173
The Austin Company 127
Tippmann Group 190
Yaskawa America, Inc. 202
FOOD PROCESSING EQUIPMENT
Airgas 120
AmTrade Systems, Inc.121
Anderson-Negele 122
Axiflow Technologies, Inc128
Bepex 130
Busch Vacuum Solutions 132
Coperion 136
DCI, Inc. 128
EBARA Mixers, Inc. 142
EDGE Industrial Technologies144
Endress + Hauser 145
Ensight Solutions 146
FPS Food Process Solutions148
Frain Industries 152
Fristam Pumps USA 153
Graphalloy 155
Hiperbaric 159
JAX INC. 163
Key Technology 164
Kovalus Separation Solutions,LLC. 165
Linde 166
Lubriplate Lubricants Company 167
Material Transfer & Storage Inc. 168
MXD Process 175
PAXTON 176
PERFEX TruCLEAN CORPORATION 177
Pick Heaters, Inc 178
PPM Technologies Holdings LLC 179
Ross Mixers 180
Silverson Machines, Inc.183
Statco-DSI Process Systems186
TNA North America, Inc.191
Urschel Laboratories, Inc. 192
VDG (Van der Graaf)194
Weber Inc 198
Wire Belt Company of America 199
Witte Company 200
INSPECTION, SORTING & WEIGHING
Anritsu 123
Frain Industries 152
Heat and Control, Inc.158
Key Technology 164
METTLER TOLEDO 171
TNA North America, Inc.191
Witte Company 200
LIQUID PROCESSING & HANDLING EQUIPMENT
Ampco Pumps Company119
Anderson-Negele 122
Axiflow Technologies, Inc128
Central States Industrial133
DCI, Inc. 138
Endress + Hauser 145
Frain Industries 152
Fristam Pumps USA 153
Hydro-Thermal Corporation160
ifm efector, Inc. 161
Industrial Magnetics, Inc. 162
Kovalus Separation Solutions,LLC. 165
MXD Process 175
Pick Heaters, Inc 178
Sani-Matic, Inc. 181
Silverson Machines, Inc.183
Statco-DSI Process Systems186
TechniBlend 188
VEGA Americas 195
MIXING & BLENDING EQUIPMENT
Air Products 118
Ampco Pumps Company119
AmTrade Systems, Inc.121
Central States Industrial133 Coperion 136
DCI, Inc. 138
EBARA Mixers, Inc. 142
Ensight Solutions 146 Frain Industries 152
Fristam Pumps USA 153
Linde 166
Munson Machinery Co., Inc. 174
MXD Process 175
Ross Mixers 180
Silverson Machines, Inc.183
Statco-DSI Process Systems186
TechniBlend 188
PACKAGING EQUIPMENT & MATERIALS
Apex Motion Control 124
AptarGroup, Inc. 125
BEHN + BATES 129
Delkor Systems, Inc. 139
Inc. 143 EDGE Industrial Technologies144
High
MARK PRODUCTS, CARTONS, AND PALLETS WITH CONFIDENCE USING DEPENDABLE, LOW-MAINTENANCE SOLUTIONS DESIGNED TO PERFORM IN THE TOUGHEST ENVIRONMENTS.
+ Precision at Speed: Crisp, high-resolution marks at the speed you need with laser systems, inkjet printers, and automated labelers built HQTJKIJXQNWOGRTQFWEVKQP
+ Seamless Integration:+PVGITCVGGHHQTVNGUUN[KPVQ[QWTGZKUVKPIenvironment YKVJQWVEWUVQOUQHVYCTGQTUGTXGTJCTFYCTG + %QUV'HHGEVKXG'HƂEKGPE[ Control one printhead or multiple printheads CETQUU[QWTRTQFWEVKQPƃQQTYKVJQPGKPVGTHCEG (TQORTKOCT[EQFGUQPDQZGUCPFDCIUVQDTCPFKPIQPECTVQPUCPFRCNNGVU/CVVJGYUQHHGTUVCKNQTGFUQNWVKQPUHQTGXGT[UVGRQH[QWTRTQFWEVKQPNKPG
Ask about our new lasers!
0GGFEWUVQOEQPƂIWTCVKQPU!1WTGZRGTVUcollaborate with you to design marking U[UVGOUVJCVƂV[QWTWPKSWGTGSWKTGOGPVU
Take the hassle out of your marking and coding. Contact us today to speak with a solution engineer and ƂPFVJGTKIJVƂVHQT[QWTRTQFWEVKQPNKPG
Phone: 604/276-8989
Email: Paul.O@advancedfreezer.com
At Advanced Equipment Inc, we custom build industrial freezers in-house that exhibit exceptional quality, which has led to our reputation across the industry for manufacturing economical, durable and reliable freezers. We achieve this level of quality by being one of the few manufacturers that allows very little outsourcing of our components.
As a result of our restless commitment to quality, consistency and cost savings to our clients, All Advanced Freezer, Inc systems can be found worldwide in a wide range of industries. Our service and support team is global as well and we are within reach wherever you are. Advanced Freezer, Inc. leaves nothing to chance as each freezer is tested in our shop and must be customer-approved before shipping, as part of our commitment to quality products and minimal installation time. Let us serve your freezing or chilling needs with higher efficiency, utmost cleanability, less floor space, and lower operating and equipment costs.
Our mission is to design, engineer and manufacture the most dependable, efficient and highest quality freezers in the industry. Where experience meets innovation, our commitment is to push the industry to a safer and better future for our clients and their customers.
Superior food safety, for each individual component in our freezers / chillers; cleanable door gaskets, coil wash systems, structural supports belt carries, lights etc.!
Robust stainless-steel construction, engineered for your uninterrupted automated processing Designed for most efficient freezing / chilling with perfectly balanced air flow control, providing you with increased productivity and with the highest yield. www.advancedfreezer.com
108 Independence Way Coatesville, PA 19320
Phone: 610-380-0244
www.aerzen.com
Email: order-usa@aerzen.com
Aerzen’s positive displacement machines are known for high reliability and efficiency and are chosen for harsh environments, difficult applications, and where high turndown capability is required.
Aerzen provides various types of dry, single-stage, air-cooled positive displacement blowers and compressors for pressures to 50 psig and vacuum to 25.5” Hg. Blowers are used for processes such as pneumatic conveying in both vacuum and pressure modes to handle the transfer of dry bulk materials.
The Delta Hybrid Blower was developed with a focus on increasing energy efficiency and significantly reducing energy costs and greenhouse gas emissions. The wire-to-process energy usage reduction can exceed 30% over typical positive displacement blowers, depending on operating conditions and turndown range.
Aerzen Turbo Blowers are single-stage high-speed radial turbo blowers designed to meet the varying flow and pressure requirements in many different processes. This modern frequency-controlled, gearless driven machine and lubricant-free aero bearings guarantees an economical, reliable and maintenance-free compressor operation.
Aerzen Rental provides temporary oil-free blower and compressor solutions under 50 psig. Rental units are available for immediate deployment in the event of a production failure or shortfall, as well as longer-term operational leasing and rent-to-own programs.
AERZEN offers you 100% oil-free process air for various applications in food technology. For 100% product purity and safety solutions, visit: www.aerzen.com
1940 Air Products Blvd., Allentown, PA 18106-5500
Phone: 1-800-654.4567
Email: info@airproducts.com
Air Products’ Freshline® solutions offer food processors high-purity food-grade gases (N2 & CO2) and equipment to chill or freeze a wide variety of foods.
Select equipment highlights includes:
•Freshline F - highly e icient design allows processors to produce consistent, high-quality individually quick-frozen products in larger throughputs than standard spray ree ing cryogenic F ree ers, without re uiring the high li uid nitrogen consumption of immersion freezers.
•Freshline Spiral Free er - roviding e icient, continuous ree ing chilling to a broad range o meat poultry products in a small ootprint at high production rates.
•Freshline -in ection Cooling System - tailor-made temperature control system that uses liquid nitrogen or carbon dioxide to deliver rapid, precise temperature control to a blender or mixer grinder, enabling ood manu acturers to optimize processing speed and product quality.
The benefits of these cryogenic systems include faster freeze times, increased throughput, improved product quality and more. We also offer gaseous solutions including controlled atmosphere stunning, wastewater treatment, modified atmosphere packaging (MAP) and inerting.
We can test a customer’s product on commercial-scale equipment in our stateof-the-art food laboratory, or bring our mobile food lab to you to determine the feasibility of using cryogenic freezing or chilling for their specific process.
For more information about Air Products’ complete portfolio of Freshline® solutions for food processing, call 800-654-4567 outside of the U.S. 610-706-4530 or visit www. airproducts.com ood Email in o airproducts.com www.airproducts.com/food
2045 W Mill Road, Glendale, WI 53209 USA
Phone: 800/737-8671
www.ampcopumps.com
Email: info@ampcopumps.com
Ampco Pumps Company manufactures the most complete line of sanitary pumps, mixers, blenders and drum unloaders in the industry. ISO 9001:2015
PUMPS: Ampco offers a full array of sanitary centrifugal and positive displacement pumps. The centrifugal lines are tried and true and offer options from the budget-friendly AC Series to the heavy-duty L Series. Both products include Ampco upgrades and can accommodate the simplest to most challenging applications.
Ampco’s portfolio of positive displacement pumps includes PATENTED ZP1+ and ZP3 pumps which both feature maintenance-saving front-loading seal designs. The new ZP4 shares this design in a compact size, offering the industry a NEW solution for viscous low-flow dosing applications. The AL Series are affordable rotary lobe pumps, ideal for a variety of applications and the dual-duty SLH twin screw pumps (ITT Bornemann) are in stock and backed by Ampco’s superior customer service.
MIXERS & BLENDERS: Ampco Applied Products offers a vast selection of inline and in-tank mixing and blending products and powder induction systems. Blend wet and dry ingredients, stabilize emulsions and enhance texture while improving process efficiency. The SBI, SBH and SHEAR-max in-line mixers have options to fit any process. The JET-shear in-tank mixer comes in many sizes and configurations.
NEW: Ampco Applied Products offers a robust line of homogenizers and replacement parts that are interchangeable with other competing brands.
NEW: The ADU unloading systems are designed to quickly and efficiently empty product-filled drums or totes reducing waste and saving money.
1-800.282.1524
Email: askAES@airgas.com
Quality food with a better taste are constant demands in our industry. Our food-grade gases comply with industry standards as well as the Food Safety Modernization Act and purity specifications. Airgas, an Air Liquide company offers liquid nitrogen and carbon dioxide in bulk product supply and a full range of services for freezing bakery products, dairy products, beef and poultry, fish and seafood, ice cream, fruits and vegetables, and more!
Many companies offer separate components to help solve your food freezing and chilling challenges, but Airgas provides one complete solution. Whether you’re optimizing an existing operation or installing a completely new system, Airgas has a solution. Our equipment reduces dehydration, maintains product quality, improves overall package appeal and maximizes your profits through less waste and higher yields. Airgas offers state-of-the-art application equipment, including tunnel, spiral, cabinet and immersion freezers, along with complete process evaluation including product testing, engineering, installation and set up, and ongoing service and maintenance support with spare parts available for Airgas equipment.
In addition to providing gases and application equipment, Airgas designs solutions tailored to address your unique production needs. With over 40 years of experience in the food processing and beverage industries, over 50 global food experts, and more than 1,200 worldwide references for chilling and freezing processes, Airgas provides the solutions that allow businesses to meet consumer needs for quality, health, and sustainability. Contact us! www.airgas.com
12885 Wayne Road, Livonia, MI 48150
Phone: 734/522-9500
Email: sales@amtrade-systems.com
www.amtrade-systems.com/Mohn/
Hygiene management: Tailor-made systems for your industry
AmTrade Systems, Inc. represents Mohn GmbH, a manufacturer of hygiene equipment and cleaning technology for the food, beverage, cosmetics and pharmaceutical industry. With MOHN and AmTrade, you can obtain everything you need from a single source - from the design concept to the delivered system, tailored to your existing space conditions - for personnel and equipment hygiene.
All hygiene products are made of stainless steel, which is particularly valued in hygiene-critical areas as it is durable, corrosion-resistant and easy to clean, ensuring high hygiene standards.
Our hygiene solutions include:
• and, sole and boot washing, drying, and disin ection systems
•Wagon wheel disin ection or orkli ts, pallet acks and wagons
• arts, tools and e uipment cleaning acilities and e uipment
•Cart, wagon, combo and pallet washing lines
• ersonnel hygiene stations and devices,
• ccess control, including turnstiles, railings and gates
• ockers and changeroom e uipment in stainless steel
•Boot storage and drying racks, including optional disin ection
Beside the hygiene technology, O also o ers
• i ting and tilting systems or kitchen carts and bins
• roduct wagons or smoking, chilling, de rosting and other processing
• roduction tables, racks and storage systems.
Email: customerservice@anderson-negele.com
At Anderson-Negele, we combine unparalleled application expertise, trusted partnerships, and high-quality instrumentation to deliver innovative solutions for food, beverage, and life sciences processors worldwide.
We collaborate closely with customers, OEMs, and system integrators to craft tailored solutions for diverse applications, ensuring every product meets the highest hygienic standards, including 3-A, EHEDG, and BPE compliance. Our comprehensive range of temperature, pressure, flow, and analytical measurement instruments reflects our commitment to precision and reliability.
As guardians of safety and sustainability, we leverage over 90 years of expertise to help processors reduce waste, safeguard product integrity, and maintain environmental stewardship. Backed by the Fortive Business System, we continually enhance product quality and drive process improvements to meet the ever-evolving demands of our industries.
Choose Anderson-Negele—the trusted partner for innovative solutions that protect and enhance your processes.
710 Innovation Drive, Suite A, Elk Grove Village, IL 60007
Phone: 847-419-9729
Email: eva.bar@anritsu.com
www.anritsu.com/product-inspection
Manufacturers worldwide rely on Anritsu’s contaminant detection and quality inspection equipment. We deliver a level of precision, reliability and support that truly advances the quality of your products and the efficiency of your operations.
How much of your products do consumers inspect?
100% Reduce consumer complaints and product recalls with the world’s most installed food X-ray. Anritsu X-ray systems give producers the best combination of performance, reliability and low cost of ownership.
The Anritsu X-ray Advantage
Anritsu X-rays come standard with HD imaging that outperforms competitors in finding metal, bone, glass and stone contaminants. The fully-featured XR75 series offers long component life plus easy operation & maintenance.
• ood x-ray supplier worldwide with over , installations
• ndustry-leading per ormance or both metal and low-density contaminants
• ow CO p to longer tube and detector li e
• eliability owest warranty rate in the industry
• .S. assembly o popular models
Discover What ou’ve Been issing. DE EC O E FEC O
About Anritsu
An engineering-driven company, Anritsu has 175,000 inspection installations since with worldwide sales and service, and available CE and D European standards. Anritsu’s full solution range includes X-ray, checkweigher, metal detector, and combination systems, backed by technical help with available remote support.
WE’VE GOT YOUR BOT COVERED 2025 marks the 25th year celebration for Apex Motion Control. Be sure to stop by our booth at IDDBA in New Orleans or IBIE in Las Vegas to check out demos of our new equipmwnt launches.
Who We Are
Apex Motion Control is a passionate group of highly skilled, creative thinkers dedicated to developing innovative and automated equipment solutions that helps automate highly repetitive tasks within the food, baking, dairy and pharma industry.
Our equipment experts and engineers have a deep understanding of the industry and provide installation and support of our systems across the world, which includes Canada, USA, Japan, Korea, Australia and Europe.
What We Do
We design and manufacture turn-key automation systems specializing in robotics, machine automation and vision for the baking and food industry. We develop, innovate and introduce equipment process automation that helps our customers increase production capacity, lower manufacturing costs, reduce downtime and reduce workplace injury.
Our Commitment
To design and build robust and user-friendly automation equipment that exceeds expectations of our clients. We are here to help you with current production challenges, as well as, helping you plan and grow for future needs. We keep your end goal in mind while developing a win/win solution.
1160 Silver Lake, Cary, IL 60013
Phone: (847) 639-2124
www.aptar.com
Email: Nikki.Kozlowski@aptar.com
Aptar redefines what packaging can do for the food and beverage industry - and every detail matters down to the last drop. From protective Bag-on-Valve (BOV) solutions to captivating fine mist sprays, dispensing pumps, and aerosols, our products transform the ordinary into extraordinary. Partner with us to create product experiences that resonate with your consumers and will help you stand out in the market.
Optimized packaging and dispensing technology to maximize product protection while ensuring purity and safety. For example, our BOV technology keeps products separate from propellants, maintaining purity and safety.
Our solutions include the use of materials that help reduce environmental impact, such as recyclable and refillable options. Our BOV technology also offers high evacuation rates, up to 99% product usage, reducing waste and offering value.
Stay ahead of market trends with our state-of-the-art packaging innovations –perfect for food and beverage applications. Pressurized continuous dispensing systems ensures smooth, uninterrupted use for consumer convenience.
Flexibility with spray options and premium features such as metal shells, matte finish and metallization help elevate the creative aesthetic and enhance brand image.
GLOBAL REACH
With a presence in over 20 countries, we provide localized support and production with a global perspective.
300 Technology Center Way, Suite 550 Rock Hill, SC 29730
Phone: (866) 546-3588
Email: info@atlascopcousa.com
Atlas Copco Compressors is transforming the way manufacturers optimize their processes. With a comprehensive range of cutting-edge solutions—including air and gas compressors, gas generation systems, carbon capture technology, air blowers, industrial chillers, process filtration, and quality air products—we’re helping businesses achieve maximum performance across every stage of production. Backed by 24/7 service, remote monitoring, and auditing capabilities, we ensure your operations run efficiently and seamlessly, no matter the scale or complexity.
Headquartered in Rock Hill, South Carolina, Atlas Copco Compressors is a global leader, with a strong local presence to serve businesses around the world. Whether you need solutions for a single facility or across multiple regions, we deliver the expertise and technology to meet your unique challenges.
At Atlas Copco, we don’t just provide equipment—we partner with you to drive performance. We understand that to stay competitive in today’s fast-paced manufacturing environment, efficiency is key. That’s why we’re committed to providing solutions that optimize your operations, reduce downtime, and lower total cost of ownership.
Our promise goes beyond just products; it’s about creating long-term value. We take you on a connected efficiency journey that enhances every aspect of your production—from process optimization to energy management. With a legacy of innovation and a forward-looking approach, Atlas Copco Compressors is the trusted partner for businesses seeking to unlock their full potential. www.atlascopco.com/air-usa
6095 Parkland Blvd. Cleveland, Ohio 44124
Phone: 440.544.2633
www.theaustin.com
Email: brad.banks@theaustin.com
Founded in 1878, The Austin Company is a design-builder of commercial and industrial facilities. We offer a comprehensive portfolio of in-house architectural, engineering, and construction management services to deliver our clients’ most complex and challenging projects.
Austin offers a proven methodology—known as The Austin Method®—for executing projects from vision to site selection, project planning, design and engineering through construction and building occupancy. As a team of experienced consultants, architects, engineers, cost estimators, schedulers, and construction professionals, we are committed to consistently meeting rigorous schedule, budget, and quality requirements.
Austin’s design team members have the industry knowledge and experience to tackle the most challenging industrial manufacturing and production facility projects. Our integrated, multidiscipline organization provides complete, highly technical, and fully coordinated documents.
Austin’s construction solutions include general contracting and construction management. Our team is dedicated to safety, quality, efficiency, and the overall success of the project.
Austin is a schedule-driven design-builder. Therefore, we seek efficiencies during the preconstruction and construction phases to save our clients time and money. Our construction services include: bid packaging, budgeting and estimating, constructability reviews, preconstruction, and project administration, control, and supervision.
P.O. Box 17510, Tampa, FL 33682 USA
Phone: 1-855-Axiflow
Email: info@axiflowtechnologies.com
Axiflow Technologies is a U.S. based corporation that specializes in Sanitary Twin Screw Pumps. Twin Screw Pumping Technology is the use of two intermeshing feed screws, timed for non-contacting and rotating in opposite directions to create product flow. Axiflow has 3 locations including an R&D Pilot Plant and Engineering facility in Charlotte NC and Fabrication Facility in Tampa FL. Twin Screw is all we do!
One significant benefit of Twin Screw Pumping Technology is the capability of the pump to operate at a given speed for the process conditions and then operate at a higher speed to perform the required Clean In Place (CIP) condition. This 2 in 1 capability simplifies the system to one pump and eliminates the need for the separate CIP By-Pass. There are several other process benefits which include low product shear, virtually pulse free, gentle pumping of soft solids, low NPSHr, high vacuum capability and others.
Why should a customer consider Axiflow first and foremost for their Positive Displacement pump applications? Axiflow personnel has over 100 combined years of process and pumping experience in Food, Beverage, Dairy, Plant Based Foods and Pharma Industries, with the largest Sanitary Twin Screw Pump installed base and inventory in North America. The many applications handled over the years enable Axiflow to use their experience to help avoid pitfalls and assist our customers in determining the best processing solutions. Our Maintenance Technicians provide on-site start up and maintenance training support when needed.
Axiflow Technologies has a vast array of pump sizes and configurations available for either On-Site Testing or Rental. The typical free trial is 3 weeks from the date of shipment with only shipping cost incurred.
460 Gees Mill Business CT NE, Conyers, GA 30013
Phone: 770/7601130
Email: food@haverusa.com
www.haverusa.com/industries/food-industry/
BEHN + BATES is the Haver & Boecker Brand for the food industry. We are the leading global manufacturer of liquid fillers, bulk powder baggers, and palletizing machinery. We supply equipment using various degrees of automation and requirements for dry bulk materials and liquid products.
We focus on quality, weight accuracy, consistent output rates, simple operation, and user-friendly maintenance.
Our aim is to provide the marketplace with high-quality machinery to get the job done right. Our machinery ranges from semi-automatic to fully automated equipment.
Our product portfolio is below:
-Valve Bag Packers
-Open-Mouth Baggers
-Form-Fill-Seal Baggers
-Big Bag Fillers
-Drum and Tote Fillers
-Pail and Canister Fillers
-Conventional and Robotic Palletizers
Let us help you provide the best packaged goods for your customers.
333 Taft Street NE, Minneapolis, MN, 55413
Phone: 612-331-4370
Bepex manufactures custom continuous solids processing equipment and systems
We partner with your experts in research & development, business development, and business operations early in the new product development stages. We work with your team to accelerate development while simultaneously designing a continuous process for commercial production.
Our greatest strength is our Process Development Center in Minneapolis, MN. This is where new ideas, products, and technologies are brought to life in a pilotscale setting. We can design, develop, and test new continuous processing systems, making tweaks to put together the best solution for your material.
We are the experts in solids drying and thermal processing. Our customers make us their first call when evaluating a new thermal project because we can make quick and accurate assessments of their material and requirements, and advise on the most applicable technology for developmental testing.
With solutions for both dry (pressure) and wet agglomeration, we can dial in your density, particle size, solubility, and other key material characteristics.
We offer a line of grinding equipment that can produce particles ranging from ½” down to a D(50) of 3µm. Our technologies range from large block grinders that decrease downstream cook time, to an air classifying mill capable of drying and micronizing solids simultaneously.
5768 S 1475 E, Ogden, UT, 84403 USA
Phone: 801-415-6030
Email: fmcnabb@big-d.com
We have an appetite to build and azeal for success. Since our first project for Western General Dairies in 1967, our annual revenue has grown to more than $2 billion, with Cold Storage, Distribution Centers and Food Processing facilities making up a significant portion of this revenue. And we are hungry for more.
Food and Beverage facilities are built on a language of their own – where critical control means systematically identifying, assessing, and controlling health hazards – from construction to production. We speak it. Without a hint of an accent.
In fact, we are fluent in Food Processing Plant language, not just Construction language. Besides the value of understanding your product requirements, we have purchasing power with national vendors/subcontractors in dairy brick, specialty flooring, insulated metal panels, refrigeration systems, sanitary drains, low temp doors, dock equipment, and numerous other specialty construction products/trades.
Our company understands the needs and demands of your facility and the requirements to comply with regulatory requirements and plant specifics such as FSMA, GMP, HACCP, PSM/RMP, and other programs. The ingredients or success or our customers includes Dairy rocessing lants• Food Beverage Facilities • emodels • Expansions • dditions • ow- emp Facilities
• anu acturing Distribution Facilities • ilt- p Construction • Green Field • Brown Field • EED Sustainable • Service ro ects • aintenance Support • Strategically Planned Shutdown Support Services www.big-d.com
Whether it’s a renovation addition at an existing acility, a cold storage distribution acility, or a processing plant, the ocus o our company has never wavered rom its roots in this speciali ed industry.
516 Viking Drive, Virginia Beach, VA 23452
Phone: 800-872-7867
www.buschusa.com
Email: info@buschusa.com
For over 60 years, Busch has been a trusted leader in providing innovative vacuum solutions to the global food processing industry.
As your dedicated vacuum partner, we offer tailored solutions and comprehensive services designed to maximize the efficiency and value of your operations.
Our commitment to innovation and collaboration ensures you get the right solutions, exactly when you need them.
OUR PRODUCTS
Vacuum Pumps
Blowers & Compressors
Custom & Standard Vacuum Systems
Spare Parts, Oil & Accessories
Measurement Equipment
OUR SERVICES
Nationwide Field Service
Service Centers
Vacuum Pump Exchange
Repair & Overhaul
Maintenance
Digital Condition Monitoring
Springfield, MO | Grand Prairie, TX | Durham, NC | Modesto, CA
Phone: 417-831-1411
www.csidesigns.com
Email: sales@csidesigns.com
Central States Industrial (CSI) is an engineering, design, and fabrication partner for hygienic fluid processors, providing value-added process components for the food, dairy, beverage, biopharmaceutical, data cooling center, and personal care industries.
The CSI team includes experienced process engineers, project managers, and designers who listen, analyze, and problem-solve every project regardless of size to ensure a successful outcome. CSI utilizes 3D scanning and AR/VR technology to provide clients with a preview of their system before fabrication begins. Experienced and certified craftsmen, combined with ASNT Level II inspectors, ensure components and equipment meet regulatory industry standards.
CSI offers custom equipment options, including Clean-in-Place (CIP), process skids, utility stations, transfer panels, holding tubes, valve manifolds, jacketed tubing, pump carts, and more! CIP systems are scalable and can grow with your future needs using smart machine technology to enhance performance, flexibility, and reporting. The process systems are designed to solve existing hygienic process issues and optimize new processes. Skid-mounted systems are built on time, pre-tested, and ready for utility hookup to avoid costly delays.
CSI utilizes our OEM-trained technicians to provide on-site maintenance for heat exchangers, valves, pumps, and more—preventing failures, extending equipment life, and ensuring smooth operations.
CSI has four distribution centers across the United States for quick delivery of sanitary processing equipment and installation materials, including fittings, pumps, valves, tubing, and instrumentation. Complete lines of corrosion-resistant Super Alloys™ AL-6XN® and Hastelloy® C-22® are also stocked.
Find more information at csidesigns.com.
The Cleveland Gear Company has been manufacturing gears for over 100 years. An early member of AGMA, Cleveland is a pioneer and world leader in worm gear technology. Today, Cleveland Gear manufactures all types of open gearing including: helical, double helical, spur & worm gear.
We also provide a wide variety of enclosed gear drives: Helical shaft-mount & Screw Conveyor, Standard worm-gear reducers (1.3” to 36” C.D.), Standard parallel shaft and Custom enclosed drives. NEW products include Cleanline Worm Gear Reducers and Stainless Steel Worm Gear Reducers.
The new Cleanline series is our Modular cast iron reducers with Stainless Steel epoxy paint & primer, stainless steel shafts, Viton seals, SS motor fasteners and H1 food grade oil lubricant. This Cleanline series is available in both single reduction and double reduction models. Assembled to order in 5 to 7 days ARO.
Cleveland recently launched its Stainless Steel Worm Gear Speed Reducer offering for the Food & Beverage markets. PRODUCT FEATURES INCLUDE:
• Cast SS ousing, Covers otor Flanges.
• SS Solid ollow Output Sha ts.
•O-ring sealed Bearing Covers otor Flanges.
•Double lip, Spring loaded Encapsulated iton seals.
• ll asteners are SS solid cap screws all housing plugs are SS male type.
•Every unit includes a ounting ccessory it SS motor mounting bolts, SS breather vent & O-ring to provide a positive seal between the motor & gearbox flange.
•S ESS ED CE S E SSE B ED O O DE E S S IN 3 TO 4 DAYS
Email: pallsales@colmac.com Phone: 360/694-1501
Columbia’s conventional palletizers are the most flexible palletizing solutions available and handle virtually every package type, including shrink bundles with and without a pad, plastic totes, high CG, unwrapped trays, and more.
Part of the flexibility comes from Columbia’s ability to provide zero time changeover from one SKU or package type to the next.
Columbia’s standard safety package contains Category 3 electrical safety components, including dual circuit safety interlocks & full height light curtains. This safety package provides a fully guarded, Performance Level D palletizer to keep your employees safe while enhancing OEE and production demands.
Columbia Machine manufactures conventional high speed, high level, floor level and robotic palletizers, load transfer stations and provides complete system design and integration. With the most flexible and modern palletizing solutions available, Columbia is the leading palletizer solutions provider in North America.
Columbia has a palletizing solution for virtually any application, each equipped with standard features designed to safely maximize OEE, throughput and uptime.
7901 NW 107th Terrace Kansas City, MO 64153
Phone: 816-891-9300
www.coperion.com/FHN
Email: info@coperion.com
Coperion delivers modern processing solutions for global food manufacturers that are searching for partners in system, component, and equipment supply. The extensive application experience and design expertise offered by Coperion stands out with highly knowledgeable experts who understand the importance of process efficiency and food safety.
Proactive Partnership –
The Coperion Food, Health and Nutrition Division brings together the some of the world’s most trusted technology brands and combines them with deep industry knowledge and engineering excellence to meet the evolving needs of food, pharmaceutical and cosmetics manufacturers worldwide. It’s proactive partnership that yields tailored, fully integrated solutions – flexible, streamlined systems, backed by industry leading experts.
Within the Coperion Food, Health and Nutrition Division our leading brands –Baker Perkins, Bakon, DIOSNA, Gabler, Kemutec, Peerless, Shaffer, Shick Esteve, Unifiller, and VMI – work closely together to offer innovative solutions: systems & ingredient automation, pneumatic conveying, extrusion, feeding, filtration, mixing, baking, forming, dividing, dosing, decorating and slicing.
Project Management –
At Coperion, everything we do is centered on customer satisfaction. We strive to make your equipment and systems robust and efficient. Our project management teams become an extension of your business with a direct line of communication to the many resources within our global network. Coperion will take command of the design/build process from project kick-off to process commissioning. From start to finish, our teams are dedicated to meeting your business goals.
1251 NW Briarcliff Parkway, Suite 500, Kansas City, MO 64116, USA
Phone: 877-4-CRBUSA
www.crbgroup.com
Email: info@crbgroup.com
Delivering safe, high-quality, value-driven food + beverage facilities to fuel your growth and success.
No matter your size or goals, you need an adaptable facility that quickly responds to consumers’ changing tastes and meets increasingly strict regulatory standards. Get design, construction, integration and consulting solutions to:
-Increase production rates -Optimize energy efficiency
-Improve speed to market -Achieve food safety compliance
ABOUT CRB:
Est. 1984 | 20 offices | 1,100 employees | Projects in 38+ countries CRB is a leading provider of engineering, architecture, construction, integration and consulting solutions. Our team provides best-in-class solutions that drive success and positive change for our clients, our people and our communities. CRB is a privately held company with a rich history of serving clients throughout the world, consistently striving for the highest standard of technical knowledge, creativity and execution. From design and construction to end-to-end integrated project delivery, CRB customizes our offerings to fit your unique needs, requirements and business goals.
To learn more about our design, construction, integration and consulting solutions, visit www.crbgroup.com.
600 54th Ave N, St. Cloud, MN 56303, USA
Phone: 320-252-8200
www.dciinc.com
Email: sales@dciinc.com
DCI, Inc. is a world-leading manufacturer of stainless steel storage and processing vessels, agitators, and integrated systems, proudly serving the food, dairy, and beverage industries for 70 years. We are recognized for exceptional craftsmanship, innovative designs, and reliable solutions, we are committed to delivering the highest quality equipment tailored to meet the unique needs of our customers.
DCI has built a legacy of trust and excellence, collaborating with customers to design and manufacture tanks and processing systems that optimize performance, safety, and efficiency.
We provide a comprehensive range of equipment tailored to food, dairy, and beverage applications:
•Silo Storage anks
• rocessors - Flat-Bottom, Cone-Bottom
•Whey Crystalli ers
• ound ori ontal ertical Storage anks
• ixing anks
•Whey Crystalli ers
•DC Dynamixer Dynamixer rocessor
•Sloped-Bottom anks
Onsite Fabrication Capabilities
Our skilled field fabrication team specializes in stainless steel and other alloys, offering fast, efficient service. We can manufacture tanks up to one million gallons in the field.
From small-scale operations to large acilities, DC , nc. is your trusted partner in the food, dairy, and beverage industries, empowering you to produce the highest-quality products with confidence.
4300 Round Lake Road W, Minneapolis, MN 55112
Phone: 800-328-5558
Email: inform@delkorsystems.com
Whether you’re packing flexible or rigid products, Delkor smooths your transition from package concept to production. We leverage decades of industry experience, and our 350+ employees are dedicated to developing engineering solutions for you out of our 300,000 square foot facility. Delkor is your one-stop, turnkey packaging systems provider.
Delkor’s case packers offer versatility to address a wide range of package shapes and sizes, with rate capacity to match the latest generation of filling and bagging equipment. Delkor draws on over 50 years of history to offer perfectly integrated packaging systems and trustworthy aftermarket support to enhance your plant’s efficiency and capacity.
In addition to advanced robotic cartoning and case packing systems, Delkor has a full package design team that is focused on the creation of shelf ready packaging as well as other economical packaging formats. We can turn around fully printed custom package samples for your products within 48 hours.
Delkor can help you comply with the latest retail ready (RRP) guidelines for major retailers including Walmart, Aldi, Kroger, Costco, and many others. With award winning RRP designs such as the patented Delkor Cabrio Case® with over 1 billion cases produced per year, we have the ideal package solution for candy, snack, frozen, refrigerated foods, and more applications. www.DelkorSystems.com
USA: 8911 58th Place, Kenosha, WI 53144 | 3150 Guenette,
Phone: 1-866/404-4545
Email: info@devilletechnologies.com
Deville Technologies combines its extensive years of experience with an innovative mindset to supply state-of-the-art hygienic food cutting solutions to clients worldwide. Whether integrating the industry’s leading technologies or leveraging our proprietary cutting systems, we ensure efficiency, precision and consistent quality.
We are committed to manufacturing equipment that provides increased uptime and yield without compromising cut quality and hygiene. Our consultive approach remains constant - no matter the size of the company. We work with companies ranging from Fortune 500 members to small entrepreneurs requiring sanitary, durable, practical, and efficient food cutting equipment. Deville’s cutting-edge technology coupled with traditional craftsmanship, quality materials and hygienic principles, allow us to deliver cutting solutions that provide high performance with low maintenance.
Deville has two state-of-the-art Client Centers so that clients may run trials with our equipment without incurring the cost of halted operations. Our detailed trial reports provide the necessary data to review cut quality, options and gain an understanding of the impact our sanitary cutting equipment will have on their business; all of which assist informed investment decisions.
Our technical experts are always available to meet our client’s needs; whether it be to provide telephone-based support, a customized engineering solution to solve a specific challenge, or to schedule an on-site visit to assist with expansion planning. We have an inventory of genuine parts for our equipment readily available; because we understand the cost of recurring labor for replacing parts can quickly consume a maintenance budget. www.devilletechnologies.com
Phone: 800-331-6870
Email: info@dougmac.com
A leading container washing and sanitizing systems provider specializing in designing and manufacturing innovative solutions industry-built to address your unique needs.
Quickly and efficiently clean containers of various sizes and shapes including pans, trays, molds, screens, pallets, lugs, totes, racks, bins, vats, baskets, buckets, waste containers, scale parts, drums, and shipping/distribution containers.
Discover how to proactively implement food safety compliance, lessen risk, changeover time, save time and energy, streamline manpower and throughput, grow revenue by reducing costs and increasing productivity.
We can design and build a customized washing and sanitizing system specific to your facility and application.
Our standard and custom racks help clean your containers, tools, and equipment, as well as racks specifically created to hold scale parts chutes, buckets, feeder pans, and weigh hoppers. Designed and manufactured in the USA using only the highest quality materials.
With over 80 Standard models we have an effective, efficient solution to meet your processing / manufacturing requirements and budget.
9351 Industrial Way, Adelanto, CA 92301
Phone: 760/246-3430
www.ebaramixers.com
Email: info@ebaramixers.com
When it comes to manufacturing high-performing, durable, and cost-effective mixers and mixing systems, our Scott Mixers and Sharpe Mixers brands are the gold standard - trusted by hundreds of companies.
We have over 50 years of experience designing and building high-performance low-shear and high-shear mixers, along with turnkey systems for sanitary, industrial, and municipal applications.
Whether you’re tackling formulation development, process scale-up, or full-scale production, our Scott and Sharpe brands provide a complete range of mixing solutions to meet your needs.
At EBARA Mixers, we’re dedicated to making your job easier, your products better, and your operations more efficient.
Scott Mixers, Sharpe Mixers, and EBARA Mixers are proud to be part of the EBARA Corporation.
Founded in 1912, EBARA Corporation is recognized as a world leader in the design, development, and manufacture of industrial machinery.
Contact Us Today at www.ebaramixers.com, info@ebaramixers.com, 760-248-3430.
Discover how we can enhance your mixing processes and help you select the perfect mixer for your needs.
72 Pacella Park Drive, Randolph, MA 02368 USA
Phone: 781/986-7500
www.econocorp.com
Email: info@econocorp.com
Since 1964, Econocorp has been at the forefront of secondary packaging innovation. Our mission? To unlock the power of automation for businesses that crave flexibility in their operations and have an eye for growth.
Specializing in low- to moderate-speed cartoning, case packing, and tray forming solutions, we’ve got all your secondary packaging needs covered. From single machines to integrated systems, Econocorp delivers excellence, every time. Our solutions cater to a diverse range of industries, including:
·Contract packaging
·Craft beverages & beer
·Dairy, snacks, cereals & frozen foods
·Industrial goods & household items
·Personal care & cosmetics
·And more!
The types of solutions we provide include:
Horizontal and vertical cartoning machines: Whether you’re end loading or top loading cartons, or a mix of both, we’ve got your needs covered. From countertop carton sealers to continuous-motion cartoners, our economical cartoning machines are developed with the highest quality standards and are easy to operate and maintain.
Case packing: Our case packing solutions are designed to meet your unique needs. Some of our products include semi-automatic horizontal case packers, automatic carton packers, and wrap-around systems for cartons, trays and cases. They focus on user-friendly functions that are simple to operate and provide cost-effective maintenance.
Tray forming and sealing solutions: Econocorp tray formers can form corner glue, corner lock or simplex style locking trays with a hinged cover, and seal them using hot melt glue.
When it comes to secondary packaging, Econocorp has your back with solutions designed to move at the speed of your businesses’ changing needs. Let’s unlock your potential together!
5 Braco International Blvd., Wilder, KY 41076
Phone: 800/407-0173
www.edgeindtech.com
Email: edgeinfo@edgeindtech.com
YOUR COMPREHENSIVE SOLUTION FOR FOOD PROCESSING, PACKAGING, AND CONVERTING
EDGE is a family of companies committed to delivering innovative, high-quality solutions. From cutting-edge, innovative punches and equipment to precisionengineered blades, EDGE provides processors with the high-quality equipment and expertise needed to meet the industry’s most demanding challenges.
TGW INTERNATIONAL | 859-647-7383 | sales@tgwint.com
TGW specializes in manufacturing high-quality industrial machine knives and blades for food processing and packaging applications. Whether for slicing, dicing, or packaging, TGW blades are engineered for durability, ensuring exceptional performance and cost efficiency in every process.
PEARL TECHNOLOGIES | 315-365-3742 | sales@pearltechinc.com
A leader in precision punches, equipment and perforation solutions, Pearl empowers food processors with products designed for precision and safety. From rotary perf units to extrusion equipment, Pearl’s innovations enhance productivity and help streamline operations.
LEVERWOOD KNIFE WORKS | 800-232-6999 | sales@leverwood.com
Leverwood is your trusted partner for processing and packaging blades. Our expertly crafted solutions are tailored to the needs of food processors, ensuring clean, accurate cuts that maintain product quality and improve operational performance.
Choose a partner dedicated to innovation, precision, and unwavering quality. Our collective expertise ensures that your equipment and processes deliver peak performance, keeping your operations running smoothly and efficiently.
2350 Endress Pl, Greenwood, Indiana 46143
Phone: 317-535-7138
www.eh.digital/3PrQ69w
Email: info.us@endress.com
Partner with us to improve quality while reducing operational costs in the Food and Beverage industry. Enhancing quality on a limited budget is essential in Food & Beverage. Our approach ensures process capability, providing reliable data for consistent product quality and increased output. Committed to meeting food safety standards, we help prevent contamination and foodborne hazards. Improve production capacity, minimize downtime, and drive sustainability and ESG initiatives with data-driven decisions.
Today, sustainability is a vital element of corporate strategies in the food industry. Given the difficult legal frameworks however, implementing sustainable business practices represents a major challenge. The DMK Group illustrates how companies in the food sector can actively shape sustainability. This video outlines which strategies and measures the dairy cooperative utilizes to remain successful and how Endress+Hauser can help reach ambitious sustainability goals.
We focus on getting the most out of applications to reduce time and effort and enable improvements in all kinds of industries. Through consulting and co-creating, we collaborate with our customers.
Zero Loss - Our process knowhow and quantitative approaches will pinpoint the inefficiencies in your supply chain.
Quality & Compliance - Both for monitoring your utilities and products, aim for total compliance with enhanced quality and efficiency.
Operational Digital Enhancement - For operational efficiency into your digital future, extract the maximum performance from your food and beverage plant assets.
Raise safety and quality standards, and competitiveness by partnering with us at Endress+Hauser.
Phone:
Email:
At EnSight Solutions, we deliver innovative food processing equipment designed to meet the unique needs of the meat, bakery, pet food, and other food industries.
Our product lines include high-quality conveyors, dumpers, mixers, blenders, slicers, and more. Built for reliability and precision, our equipment ensures your operation runs smoothly and efficiently.
We specialize in automation, helping you streamline processes, reduce labor costs, and optimize production. Our advanced systems integrate seamlessly into your operations, enhancing productivity while maintaining the highest safety and quality standards.
EnSight offers full-line solutions, providing everything you need for a complete processing system. From concept to implementation, our team works closely with you to design equipment and systems tailored to your goals—whether it’s upgrading a single component or creating an entire production line.
To support your investment, we provide preventative maintenance programs, expert technical assistance, and training to maximize uptime and performance.
When you partner with EnSight Solutions, you’re choosing a team committed to innovation, quality, and your success.
Visit www.ensightsolutions.us to see how we can help your business thrive.
Phone: 866-369-3535
Email: sales@esigroupusa.com
ESI Group is a nationally recognized leader in designing, engineering, and constructing advanced climate-controlled facilities. We provide tailored facility solutions for the manufacturing, processing, and storing of food, beverage, and pharmaceutical products.
Since 1991, our focus has been optimizing operational efficiency, minimizing risks, and ensuring compliance. We help our clients build resilient, high-performance facilities that meet their most demanding needs.
Our Single-Source, Three-Phase Approach streamlines communication, accelerates project timelines, and reduces overall costs. By managing every project from concept through to completion, ESI Group will develop a Guaranteed Maximum Price (GMP) and ensure that your facility meets or exceeds industry standards. These advantages, combined with our outstanding safety record, are key factors contributing to our 85% repeat customer rate.
We take pride in our history, extensive experience, and long-term partnerships. Our success is driven by our commitment to delivering value that helps you build, manage, and grow your business. By putting our customers first, you can put your customers first!
To learn more about our cold storage facility solutions and our firm, visit ESIGroupUSA.com.
Suite 110, 13911 Wireless Way, Richmond, BC V6V 3B9 Canada
Phone: 604-232-4145
www.fpscorp.ca
Email: sales@fpscorp.ca
FPS Food Process Solutions is a global leader in turn-key food processing solutions. We provide innovative systems to ensure the highest efficiencies and to meet the most stringent sanitary demands. These factors transform into superior food quality, lowered total cost of ownership, and maximized profits.
Joining the global FPS family are Charlottetown Metal Products (CMP), Total Solutions Ltd (TSL) and GEM Equipment of Oregon (GEM) as subsidiaries and OptiCept Technologies as a strategic partner in PEF technology, further diversifying the company’s product offering with a “one stop shop” to meet customers’ needs.
From freezers to fryers to full line End-to-End Solutions, FPS are with you every step of the way.
Our sectors include:
•Free ers Chillers
•Conveyance roduct andling Systems
• ulsed Electric Field EF
•Blancher Systems
•Fryer Systems
• hermal Solutions
•Batter S Systems
•Full ine End-to-End Solutions
FPS employs over 1000 staff around the world. Established in 2010, the company has a combined 1.18 million sq. ft of space in 20 locations including its Canadian headquarters, manufacturing, and warehouse facilities as well as international sales offices across six continents.
6580 Snowdrift Road, Allentown, PA 18106
Phone: 610/973-8200
www.flexlink.com
Email: info.us@flexlink.com
FlexLink, a Coesia company, is a leading manufacturer of food handling conveyors and automated food processing equipment. With a dedicated team of industry specialists, we support the food industry worldwide. We provides systems that are easy to design, assemble, integrate into machines and eventually modify and redesign, significantly facilitating new product introductions.
With over 40 years of experience delivering turn-key solutions to the food industry, we are the perfect partner when facing your production challenges. Working closely with customers, we provide innovative, automated solutions to produce goods smarter, safer and at lower operating costs. With a dedicated team, we support the industry directly in over 31 countries and are represented in more than 60.
FlexLink’s focuses on providing our global customers with the highest quality service and products. We focus on improving your overall equipment effectiveness (OEE) by balancing production flow, offering compact solutions, and lowering your maintenance cost and requirements. We offer high quality products that are easy to wash down and reduce the amount of bacteria build-up – reducing your chances of a recall. Our toolbox of products and services include line design, conveyor equipment, product manipulations and line balancing and controls.
FlexLink offers a variety of options for the food industry such as: Stainless Steel/Hygienic Conveyors, Chain Conveyors, Modular Belt Conveyors, Spiral Conveyors, Elevators, Line Balancers, Line Control, Cleaning Devices and Robotic Palletizers.
As part of your collaboration with FlexLink you can also utilize our line simulation tools. We truly offer a complete solution for all your production needs.
Phone: (336) 449-7200
www.snacks.focke.com
Email: sales@fockegso.com
FOCKE & CO provides customized packaging solutions with concentrated expert knowledge in two divisions, Tobacco and General Packaging for food and hygiene.
The General Packaging division provides customized case packing and end-ofline solutions for the food industry, with modern automation concepts for flexible products, breakthroughs in snack and confectionary foods, and well-established installations in hygiene and tissue, from flexibles to cartons.
In addition to the headquarters and divisions in Germany, the family-owned enterprise operates sales and service branches on all continents. Since its foundation in 1955, FOCKE & CO has delivered more than 22,000 machines to more than 120 countries.
Due to the delicate nature of snack products, FOCKE & CO’s case packers offer careful handling alongside the flexibility to accommodate tray, tray-with-lid, and case (RSC) packaging. In fact, our machines – such as the HFP Base (Highly Flexible Packer) – provide multiple pack configurations that normally cannot be achieved with a typical case packer. With a clean machine concept and a compact footprint, our HFP Base is designed to fit perfectly into typical snack food production lines.
With sales and service centers worldwide, FOCKE & CO has the capabilities to deliver local technical support, training, and spare parts. FOCKE & CO has repeatedly set new benchmarks in terms of output and product quality. Our ground-breaking technologies in the field of motion control combined with components featuring extreme dimensional accuracy are highly acclaimed in the industry. This is why we are the leader in Packaging Solutions.
100 McPhillips St, Winnipeg, MB R3E 2J7, Canada
Phone: (855) 497-7508
www.foodsafedrains.com
Email: info@foodsafedrains.com
As a food processor, we know your number one priority is cleanliness, which is why we build drainage systems that are sanitary and safe for all types of food production applications.
We can help with drainage systems that stand up to the roughest wear, keep both your floor and products bacteria-free, and are easy to clean. Whatever your application, we have the custom drainage solutions to fit your unique needs.
FoodSafe Slot Drain - People, equipment, and your products are constantly moving, and your floor needs to stay safe. That means you need drainage that is bacteria- resistant, durable, and easy to clean to sanitation standards — you need a Slot Drain system. Our Slot Drain systems are built to integrate into your existing workflow and equipment placement and feature no-niche designs that are easy to clean, with options to suit all applications.
FoodSafe Trench Drain - When solid materials accumulate and plug a drain, it can create backups, which can cause accidents and delays in your workflow. With several design options to choose from, you can safely, quickly, and easily dispose of solids.
FoodSafe Area Drain - Standing water can cause a multitude of issues in your facility, from bacterial accumulation to accidents, terrible odors, and worse. Our area drains can help make your facility more hygienic, safer, and can help reduce nasty odors. FoodSafe area drains also feature tamper-proof strainers, allowing you to protect your facility by ensuring that only designated employees can access them.
Contact us today to talk about any upcoming projects - our drainage experts are ready to assist!
245 E North Ave. Carol Stream, IL 60188
Phone: 630-629-9900
www.frain.com
Email: sales@frain.com
Frain is Transforming Equipment Delivery!
Frain Industries partners with over 70 original equipment manufacturers (OEMs), giving customers access to a vast selection of new high-quality, industry-standard machinery. This strategic collaboration ensures that businesses across multiple sectors can obtain the latest and most efficient equipment for their production, packaging, and processing needs. Frain boasts an impressive inventory of new machinery, spanning categories like food processing, packaging, and end-of-line systems. From filling machines and labeling equipment to conveyors and palletizers, Frain supports industries such as pharmaceuticals, cosmetics, and food and beverage with comprehensive production line solutions.
Rental Options for Scaling
For businesses looking to address short-term needs or scale quickly, Frain offers a rental fleet of 2,500 New machines across 100 equipment categories. This flexibility allows companies to manage temporary projects, pilot new products, and adjust to fluctuating demand without the financial commitment of purchasing new machinery.
Rapid Delivery for Quick Market Response
One of Frain’s unique advantages is its ability to deliver equipment in as little as 48 hours, significantly reducing lead times. While traditional equipment procurement can take months, Frain’s plug-and-play-ready machinery helps companies remain agile, minimize downtime, and maximize productivity.
Comprehensive Support and Customization
In addition to a wide range of equipment, Frain provides value-added services like engineering support, installation assistance, and equipment customization. This ensures businesses receive tailored solutions that integrate seamlessly into their existing operations, allowing them to streamline processes and respond swiftly to market changes.
2410 Parview Road Middleton, WI 53562 USA
Phone: 800-841-5001
www.fristam.com/usa
Email: fristam@fristampumps.com
Fristam: Engineered for Excellence in Fluid Handling
Fristam is a global leader of high-quality sanitary pumps, blenders, and mixers designed for precision, durability, and reliable performance, to ensure dependable operation with exceptional support for your toughest applications.
Proudly made in the USA, we offer fast delivery, so you can rely on our equipment to keep operations running smoothly. Our portfolio includes:
Blenders & Mixers: Fristam offers Powder Mixers for efficient blending of wet and dry ingredients, handling viscosities up to 1,000,000 cps, Colloid Mixers for precise liquid-particle integration, and Shear Blenders to eliminate agglomerates, reduce ingredient waste, and cut processing time.
Twin Screw Pumps: The FDS Series handles both product and CIP transfer, eliminating the need for extra pumps and piping. It gently processes a wide range of products, from thick to thin and chunky to smooth.
Fristam’s FKL Series is one of the most durable and high-performance positive displacement pumps on the market. Featuring heavy-duty, high-pressure models and gentle, low-pulsation options, the FKL ensures easy CIP and maintenance, and reliable operation for demanding applications.
Centrifugal Pumps: Our centrifugal pumps set the bar for quiet, efficient, and lowmaintenance operation. Available in standard-duty, heavy-duty, high-pressure, front-loading seal, and self-priming models.
Why Fristam? We know every application is unique. That’s why we offer a comprehensive range of pumps, blenders, and mixers, backed by a team of experts to deliver the right solution – ensuring precision and performance from the start.
General Packaging Equipment Co. produces packages for the food industry which include but are not limited to:
Liquid Products such as: Soups, Stews, Sauces, Condiments, Fruit, Pie filling, Guacamole, etc.
Package sizes produced on General machines range from a fraction of a fluid oz. (1.2 ml) to 12 liters (3 gallons+). General designs and manufactures different types of liquid fillers to meet the specific requirements of product characteristics and fill volumes.
Dry Products such as: Coffee, Tea, Rice, Seasonings, Baking/drink mixes, Sugar, Flour, Powdered milk, Protein powder, etc.
General has extensive experience in building machines to package powdered and granular products with hundreds of machines in operation successfully packaging these types of products. Package sizes range from 25 grams to 10 KG.
For over 70 years our goal has been to provide our customers with simple, rugged and reliable vertical form fill seal machines that will operate at the highest possible efficiencies with the least amount of attention. Please feel free to reach out to our team for specific packaging inquiries, questions, or assistance and we would be happy to help.
1050 Nepperhan Avenue, Yonkers, NY 10703
Phone: 914/968-8400
www.graphalloy.com
Email: sales@graphalloy.com
FDA Acceptable GRAPHALLOY® Bushings eliminate maintenance and frequent replacements in food applications. Graphalloy is self-lubricating and requires no grease or oil, performs in temperatures from –400°F (-240°C) to +1000°F (535°C), works submerged in low viscosity and corrosive liquids, and there is no lubricant loss in steam or pressure wash.
A bakery oven OEM was using rolling element bearings on the conveyor circuit of a tunnel oven with a temperature range from 450°F to 650°F. To reach these bearings, mechanics would have to crawl over the oven belt when the machine was shut down, thus causing damage and presenting a safety risk. Another issue was caustic washdowns that rusted the ball bearings. In some applications, bearing life was as little as 2 weeks. They were researching solutions when they discovered GRAPHALLOY. Graphalloy self-lubricating bushing materials thrive in high temperature environments, handle caustic washdowns, and are maintenance-free. These Graphalloy bushings in stainless steel pillow block housings have been running in this application for several years with no issues.
A seafood processing plant in the Southeast was running a conveyor in their freezer area to “flash-freeze” fresh seafood. The environment is a difficult one: The temperature is cold (28°F/-2°C) and wet and the system requires frequent washdown. The conveyor bearings were being replaced every month. The plant maintenance superintendent contacted GRAPHALLOY about the problem. It was determined that the current bearings could not hold lubrication under these conditions and, as a result, breakdowns were occurring frequently. Graphalloy 4-bolt flange block assemblies were installed and have been running successfully for more than five years!
Phone: 800/427-6260
www.hapman.com
Email: sales@hapman.com
*Celebrating 80 years of Excellence*
For eight decades, Hapman has been a leader in bulk material handling, providing innovative solutions designed to improve efficiency, reliability, and performance. From industry-leading expertise to long-lasting equipment and exceptional customer support, the Hapman Advantage sets us apart.
Expert Staff: Our Product Managers, Tech Support, Engineers, and Fabricators average an impressive 11 years with the company, more than double the industry average.
Product Life and Longevity: Our longest-running installations has been in operation for over 43 years, accumulating 179,000 hours of service—and it’s still performing.
Expert Technical Support: More than 75% of our staff have been onsite with customers to assist with anything from installation and start up to service and diagnostics.
Fast Access to Parts: Of our nearly 50,000 parts orders in the last 10 years, 10% have been expedited to customers—all without ever adding a premium for expedited service.
Contact us today to review your application needs.
Phone: 800-813-6644
Email: info@harpak-ulma.com
We can help you navigate today’s complex, rapidly changing packaging landscape. We help balance costs and functionality with innovative and emerging processes, materials, and advanced technologies; enhance your profitability and improve the performance of your primary and secondary packaging operations. Our full-service solutions address installation, training, spare parts, service and customer support.
Our capabilities span thermoforming, tray sealing, flow wrap, vertical bagging, stretch, filling, blister, skin pack, and vacuum. Our automation offerings cover feeding, loading, secondary packaging, palletizing, robotics, centralized line control and tote/basket management. In addition to offering ULMA primary packaging systems and comprehensive automation solutions, we represent G. Mondini tray sealers and Cabinplant’s multihead weighing and associated processing solutions in the U.S. and Canada.
Our goal is to provide every solution with Rockwell Automation integrated architecture and smart connectivity to reduce solution complexity and maintenance costs, while realizing better quality, capacity, and throughput. We also partner with PTC to incorporate Augmented Reality tools to enhance your operation and realize greater productivity and efficiency.
Our sustainable packaging options include less plastic use, thinner gauge films, optimized package sizes, reduced scrap, and alternative packaging materials.
Our customers rely on us to help them optimize their overall packaging investment, from start to finish. We offer package design and prototyping services, and can help solve production concerns with comprehensive flexible and efficient systems. We help strategize how to tackle today’s most complex packaging challenges, such as sustainability, eCommerce, robotics and digital transformation.
21121 Cabot Boulevard, Hayward 94545, CA, United States
Phone: 510/259-0500
www.heatandcontrol.com
Email: info@heatandcontrol.com
Heat and Control® provides food industry leading equipment solutions and service–Raw Produce Preparation, Processing, Conveying, Weighing, Packaging, Inspection, Controls & Information, and Training. Established in 1950, we have 12 manufacturing, warehouse, and associated facilities, 12 testing centers, and more than 30 offices around the world.
Our brands include FastBack® (horizontal motion conveyors and on-machine seasoning), Spray Dynamics® (coating and seasoning application systems), Mastermatic (fryers), and we partner with Ishida (weighing, packaging, and inspection), and CEIA® (metal detection).
Food Processing–From frying and baking to raw produce preparation, water saving, energy-saving, and pollution control.
Seasoning Application–Our comprehensive range of seasoning solutions for on-machine or process area deliver top performance, efficiency, application accuracy, reduced waste, higher yield, and improved working environment for operators.
Conveying and Product Handling–Everything you need to move your product from start to end. We provide a wide variety of conveying and product handling systems.
Our broad range of solutions lets us design the most appropriate machine or combination for your application. We assist manufacturers with equipment for all types of food products, as well as provide pre- and post-sale technical support, including applications assistance, engineering, installation, parts, service, and training.
2250 NW 84th Ave. Unit #101, Doral, FL 33122 USA
Phone: 305-639-9770
Email: marketing@hiperbaric.com
High Pressure Processing - Food Safety. Extended Shelf Life. Clean Label.
Hiperbaric is the world’s leading supplier of High Pressure Processing (HPP) equipment for the food and beverage industry.
HPP technology is a non-thermal processing technique by which products are subjected to a high level of isostatic pressure to inactivate foodborne pathogens such as Salmonella, E. coli and Listeria, extending the shelf life considerably, without the need for preservatives.
HPP also preserves the quality of fresh food, opens opportunities to new markets for clean label products due to the extension of shelf life and protects brands against recalls.
HPP is a highly versatile technology that can be applied to a wide range of foods: juices and beverages, meat, fish and shellfish, fruits and vegetables, wet salads, dips, and sauces, pet food products and Ready-To-Eat products.
Hiperbaric industrial High Pressure Processing (HPP) units are designed to be the most reliable systems in the market, with the widest throughput range of industrial HPP machines meeting the requirements of start-ups, small-medium enterprises and large corporations.
Its horizontal layout and ergonomic design simplify installation and operations. Each machine can reach up to 6,000 bar / 600 MPa / 87,000 psi. In addition to the HPP In-Pack equipment (post-packaging process), Hiperbaric offers HPP Bulk equipment for the processing of large volumes of HPP liquids before packaging. www.hiperbaric.com
400 Pilot Court, Waukesha, WI, 53188
Phone: 262-548-8900
Email: info@hydro-thermal.com
Hydro-Thermal® Corporation, a global leader in fluid heating for 90+ years, offers patented DSI technology for precise heating in industries like food, beverage, chemicals, and more. Based in Wisconsin, USA our ISO:9001-certified facility delivers custom solutions for operational excellence and meet high sanitation standards.
What Sets Us Apart:
We understand the importance of precise temperature control in manufacturing. Our tailored solutions include installation scheduling, training, preventative maintenance, and replacement parts, ensuring a seamless experience.
Dedicated Support Team:
Our Service Team backs every installation, providing expert assistance in-house to maintain reliability and peace of mind.
Efficiency Through Innovation:
Our DSI technology ensures superior heat transfer, significant energy savings, enhanced process control, and the ability to handle high-viscosity slurries without burn-on.
Exceptional Product Range:
• ydroheater etcooker eliable solutions or continuous cooking and heating.
• ydron - certi ied sanitary heaters or lexible, stable, high-quality processes.
•E eater Compact, e icient heaters or rapid water heating.
• O recision heaters or demanding applications re uiring fine-tuned control.
•Solaris ower ul solutions or large-scale heating with precision and energy efficiency.
At Hydro-Thermal, we are committed to efficiency, innovation, and customer support. Partner with us to optimize your heating and processing systems while saving time, energy, and money.
1100 North Atwater Drive, Malvern, PA 19355
Phone: 844-441-8246
Email: cs.us@ifm.com
Improve food quality and safety with ifm process instrumentation and controls that enable continuous, real-time monitoring of food processing. ifm is committed to helping you succeed in your business by developing process controls that:
1.Show real-time measurable benefits
2.Simplify implementation
3.Strive for interoperability
4.Scale to facilities of all sizes
ifm designed and developed a robust product portfolio of sanitary process instruments that includes:
• Flow meters
• ressure Sensors
• emperature Sensors
• evel Sensors
• Conductivity Sensors
Each sensor is rigorously tested to extreme limits to ensure maximum quality and protection against common causes of sensor failures in food production.
The sanitary ifm IO-Link master enables field I/O installation without sacrificing quality or safety. ifm sensors use IO-Link digital communication to improve access to production data, increase measurement accuracy, and simplify programming to reduce downtime.
Food manu acturers can seamlessly send O- ink sensor data to moneo Cloud software and set up dashboards in just a few hours. To simplify data visualization, moneo enables continuous process monitoring, real-time alarm notifications, and historical data logging in one intuitive interface. www.ifm.com/us/en
Phone: 800-662-4638
Email: imi@magnetics.com
Industrial Magnetics is a leading force in the magnetics industry, known for its strong emphasis on customized craftsmanship, quality, and performance. Since 1961, IMI has delivered exceptional solutions to meet customer needs, resulting in the widespread adoption of magnetic equipment in manufacturing processes worldwide.
IMI provides magnet options to purify your product from ferrous metal contamination and defend downstream equipment. Gravity-fed magnetic separators like the Drawer-In-Housing contains rows of round 1”, 2” or 3” magnetic tubes assembled into drawers and contained within a housing. Specialty units like The Ox® can handle magnetic separation in difficult processing conditions, such as high or low ambient temperatures, high humidity, bridging, abrasive, corrosive, or galling tendencies. IMI Magnetic Grates separate ferrous tramp metal in bins, chutes, drawers, hoppers, and enclosures. Plate Magnets are the optimal solution for angled chute applications.
IMI offers the best options for liquid line production needs. The Plate Style T-Trap is ideal for carrying viscous or fibrous products through the housing without plugging. The Tube Style T-Trap is optimal for heavy-duty flow systems.
Our Exposed Pole Tube protects pneumatic line system machinery and ensures purity when installed before processing equipment and bulk load outs. The Bullet® Magnet is shaped with a solid stainless steel nose cone diverter. This magnet maintains uniform velocity in line flow, allowing it to be used anywhere in your system.
When it comes to making things better, Industrial Magnetics is a magnetics industry leader.
N59 W13330 Manhardt Drive, Menomonee Falls, WI 53051 USA
Phone: 262/781-8850
www.jax.com
Email: info@jax.com
Since 1955, JAX has been at the forefront of industrial and food grade lubrication innovation. We offer hundreds of fluid, grease, and aerosol solutions for hydraulics, gears, compressors, conveyors, chains, and more.
For the food processing industry, JAX delivers specialized, high-performance lubricants tailored to the needs of bakeries, meat packers, beverage bottlers, and other plant environments. We’ve developed hundreds of NSF-registered products, and we’re supported by ISO 9001 and ISO 21469 certifications to ensure consistent quality.
Our team of technical service representatives, scientists, and chemists is dedicated to helping your equipment perform at its best. From in-plant service and training to product application support, we work with you to keep your operations running smoothly and efficiently.
Innovation drives everything we do. In our RPM Innovation Center, we design and test products to meet your precise needs, combining research with realworld insights. Our in-house used oil analysis program helps you monitor performance and address potential concerns before they impact your operations.
We’re passionate about solving tough challenges and creating lubrication solutions for your business. Contact JAX today to discover how we can help you achieve optimal performance and long-term success.
150 Avery Street, Walla Walla, WA 99362 United States
Phone: 509-529-2161
www.key.net
Email: product.info@key.net
Key Technology (“Key”), a member of Duravant’s Food Sorting and Handling Solutions group, is a global leader in the design and manufacture of automation systems including optical sorters, conveyors, and other food processing equipment. With 75 years of experience as a food machinery supplier, Key serves dozens of industries including confectionary, fruit and vegetable, meat and poultry, nuts and more.
Applying application expertise, Key helps customers improve quality, increase yield, and reduce costs. A proactive partner, Key listens closely to process challenges and offers seamlessly integrated, customized solutions that create real impact and ROI.
Optical Sorting
Key’s optical sorters help optimize product quality while improving yield and reducing labor. The COMPASS and VERYX optical sorters detect the color, size, shape and/or structural properties of every object to identify and remove a variety of product defects. Foreign material (FM), such as plastic, metal, glass, and paper, that may have been accidentally introduced to the production line is also removed.
Food Handling
Key’s food handling systems are customized to address the unique product characteristics and line requirements of processors. Key’s horizontal motion and vibratory conveyors maximize throughput efficiencies by helping to align, singulate and feed, collect and convey, de-water and de-oil, distribute product for packaging, and more.
850 Main Steet Wilmington, MA 01887
Phone: (978) 694-7000
www.kovalus.com
Email: getinfo@kss-sep.com
Kovalus Separation Solutions, formerly Koch Separation Solutions, has led separations technology for over 60 years, offering advanced solutions like membrane filtration, ion exchange, evaporation, and drying. We serve industries such as food and beverage, life sciences, and general industry, providing high-performance separation solutions that help businesses recover valuable products, reduce waste, lower their environmental footprint, and improve productivity while optimizing costs.
Our reputation for innovation and quality makes us a trusted global partner. We combine deep industry knowledge with cutting-edge technology to deliver tailored solutions that address each client’s unique challenges. Whether processing fluids, handling water or wastewaters, or refining food and beverage products, Kovalus is committed to improving the efficiency and cost-effectiveness of complex separation processes.
In 2020, RELCO, a Kovalus Separation Solutions Company, enhanced our abilit y to serve the dairy and food sectors. Founded in 1982, RELCO is known for its expertise in evaporation, drying, and powder handling technologies. The integration strengthens our ability to provide comprehensive food processing solutions, from raw materials to finished products.
Together, Kovalus and RELCO offer a full suite of solutions designed to meet the needs of today’s food industry. Our combined experience ensures customers receive top-tier performance, reliability, and innovation. We aim to help our clients improve efficiency, reduce waste, and produce high-quality products while meeting sustainability goals.
With a shared commitment to continuous improvement and customer success, Kovalus and RELCO are trusted partners for food producers facing their most complex processing challenges. Together, we are shaping the future of food processing and helping customers thrive in a ast-evolving market.
7000 High Grove Boulevard, Burr Ridge, IL 60527
Phone: 1-844-44LINDE
www.lindeus.com
Email: contactus@lindeus.com
Rapid heat removal with cryogenic liquid nitrogen or liquid carbon dioxide offers processors a variety of options that meet their processing needs. Customers working with Linde’s industrial gas and equipment systems can boost productivity and maintain high product quality targets in freezing, chilling and cooling operations. Tunnel, spiral, flighted, snowing and in-line cooling systems provide cost saving benefits to our customers.
For Linde and the food processing market areas we serve, there are three unique competencies to address the needs of our customers. The focus on 1) product temperature through precise heat removing properties of cryogenic gases, 2) the scientific application knowledge of the gases and gas atmospheres acquired by servicing thousands of customers, and 3) the system support coupled with engineering experience that allow our customers to rely on Linde to help improve productivity.
Linde is a leading global industrial gases and engineering company. We live our mission of making our world more productive every day by providing high-quality gases, application technologies and services which are making our customers more successful and helping to sustain and protect our planet.
The company serves a variety of end markets including chemicals & refining, food & beverage, electronics, healthcare, manufacturing and primary metals. Linde’s industrial gases are used in countless applications, from life-saving oxygen for hospitals to highpurity & specialty gases for electronics manufacturing, hydrogen for clean fuels and much more.
For more information ... please visit www.lindeus.com/food
Newark, NJ 07105 / Toledo, OH 43605
Phone: 800-733-4755
www.lubriplate.com
Email: LubeXpert@lubriplate.com
Back in 1870, Lubriplate’s founders set out to make the highest quality, best performing lubricants available. In doing so, they helped pioneer the use of antiwear additives that significantly increased lubricant performance through the years. Today, that innovative tradition continues with their complete line of ultra high-performance, 100% Synthetic, NSF H1 Registered, Food Grade Lubricants. Manufactured under strict NSF/ ISO 21469 Certified and ISO 9001 Registered quality control standards, these lubricants are formulated to deliver a number of significant, cost effective advantages, including; extended lube and fluid change intervals, multiple application capability, lubricant inventory consolidation and improved performance. Clean, safe and non-toxic, their use can eliminate lubrication as a critical control point in HACCP programs.
All Lubriplate Lubricants come with Lubriplate’s ESP Extra Services Package at no additional charge. Services include; a complimentary plant lubrication survey by a factory direct representative, color coded lubrication charts and machinery tags, a toll free technical support hotline and email, and follow-up lubricant analysis.
For more information contact:
Lubriplate Lubricants Company
Newark, NJ 07105 / Toledo, OH 43605
Phone: 800-733-4755
E-Mail: LubeXpert@lubriplate.com www.lubriplate.com
1214 Lincoln Road, Allegan, Michigan 49010
Phone: 269.673.2125
Email: sales@materialtransfer.com
Material Transfer & Storage (MTS) is the partner of choice for customers in the packaging industry seeking reliable, efficient, and customized bulk material handling solutions. With over 35 years of experience, MTS is committed to solving your toughest production challenges with innovative equipment and fully integrated systems tailored to your unique needs.
At MTS, the focus is on your success. Our bulk bag fillers, dischargers, and conditioners are engineered to streamline material flow, minimize downtime, and ensure workplace safety, all while maximizing your productivity and reducing operational costs. Our integrated systems go beyond equipment, delivering seamless solutions that improve throughput, reduce waste, and align with your production goals.
Excellence drives everything we do at MTS, from initial design to final installation and ongoing support. Our commitment to quality, safety, and innovation ensures that you receive solutions that not only meet but exceed your expectations.
When you choose MTS, you gain more than equipment, you gain a team dedicated to understanding your application and delivering results. MTS doesn’t just meet industry standards, we raise the bar to ensure your operations run smoothly and efficiently.
Choose MTS for proven expertise, innovative technology, and a customer-first approach that transforms your material handling processes into a competitive advantage. Let us help you achieve your goals with solutions designed to deliver measurable results and lasting value. www.materialtransfer.com
YOUR GUIDE TO EFFORTLESS MARKING AND CODING SOLUTIONS
Matthews Marking Systems acts as your trusted guide, equipping you with highspeed, high-resolution marking and labeling solutions that keep your lines running smoothly.
DESIGNED WITH YOU IN MIND
Our lineup of laser coders, inkjet printers, and print-and-apply labelers is designed to ensure easy integration, reliable performance, adaptability, and clarity with crisp, clear, permanent marks every time.
WHY CHOOSE MATTHEWS MARKING SYSTEMS?
170+ Years of Expertise: We’ve perfected marking and coding for food and beverage manufacturers worldwide.
Next-Level Efficiency: MPERIA integrates seamlessly across primary, secondary, and tertiary packaging lines, ensuring precise, error-free operation.
Custom Solutions: From standard setups to tailored systems, our team delivers the exact solution your line requires.
Without the right tools, you risk production delays, wasted resources, and compliance issues. But with Matthews Marking Systems, you gain the confidence of knowing your lines are efficient, your marks are on point, and your operations are future proof.
LET’S MAKE YOUR MARK TOGETHER
Connect with a solution engineer today to discover how Matthews Marking Systems can help your food and beverage operations run at their best.
2440 Deming Way, Middleton, WI 53562
Phone: (888) 364-7272
Email: mailbox@meadhunt.com
https://meadhunt.com/markets/food-beverage/
Founded as a consulting firm in 1900, Mead & Hunt is a full-service national engineering, architecture, and construction firm. Since 1949, we have been providing planning and design services for capital projects in the food & beverage industry.
By listening closely to your project needs and goals, we become an extension of your team to develop a sound business case for your project. Our comprehensive, in-house service offerings allow us to execute projects from planning through construction and start-up. We specialize in:
• rchitecture
•Civil
•Commissioning
•Construction management
•Environmental
•Electrical
•Fire protection
• nstrumentation and controls
• aster planning
• echanical
• ackaging
• lumbing
• rocess
• e rigeration
•Sanitary design
•Structural
• echnology systems
•Water wastewater
1571 Northpointe Pkwy, Lutz, FL 33558 USA
Phone: 813-889-9500
Email: pi.marketing@mt.com
The METTLER TOLEDO Product Inspection division designs and manufactures both standard and customized inspection solutions, prioritizing product safety, brand protection and quality assurance for food, pharmaceutical and chemical brands. Its solutions help to empower businesses to optimize operations, reduce costs and embrace digital transformation while meeting regulatory compliance. With a focus on safety and precision, our innovative solutions help deliver measurable results, enabling manufacturers to maintain the highest standards of product integrity and consumer trust. By partnering with METTLER TOLEDO, manufacturers will have the opportunity to navigate the challenges of the modern business landscape and achieve sustainable growth.
With cutting-edge foreign body detection solutions, METTLER TOLEDO provides advanced holistic technologies that automate critical processes and help to mitigate recall risks. Metal detection and x-ray inspection technologies detect and reject contaminated product, plus support product quality and brand protection. Precision checkweighing technologies help manufacturers identify costly over-fills and/or avoid potentially brand damaging under-fills, improving production line efficiency. Vision inspection solutions detect label defects, reducing the risk of rework and product recalls. To facilitate real-time monitoring and digitalize food safety compliance on a global scale, METTLER TOLEDO provides the proprietary and innovative data management software, ProdX™.
The range of METTLER TOLEDO product inspection solutions are more than just technological innovations – they’re strategic assets that support business success by helping to enhance productivity, reduce costs and embrace digitalization. As a trusted partner, METTLER TOLEDO is focused on delivering value and driving industry excellence for its clients worldwide.
2200 Steven B. Smith Blvd., Rockmart, GA 30153 U.S.A.
Phone: 888-309-5574
www.miuraboiler.com/mi
Email: us.info@miuraz.com
Optimize Without Oversizing: The Power of Miura’s Multiple Installation (MI) System
In today’s industrial landscape, efficiency and adaptability are essential. Miura’s Multiple Installation (MI) System transforms steam boiler operations with a modular, on-demand design that boosts efficiency, cuts fuel consumption, and reduces NOx emissions.
Unlike traditional oversized firetube boilers, Miura’s MI System uses smaller, modular boilers that operate independently. This flexibility ensures steam production matches real-time demand, minimizing fuel waste, extending equipment life, and enhancing precision.
Why Choose Miura’s MI System?
•Optimi ed E iciency - iura’s System activates boilers only when needed, cutting fuel waste and saving up to 20% annually.
•Compact Design - With less than hal the ootprint o traditional boilers, Miura’s modular units free up valuable space for operations or expansion.
• eliability - he System distributes steam loads across multiple boilers, creating built-in redundancy. If one boiler goes offline, others seamlessly maintain operations.
•Sustainability - iura signi icantly reduces CO and Ox emissions, helping facilities meet environmental regulations and lead as eco-conscious industry players.
Discover the iura di erence optimi ed e iciency, adaptability, and sustainability for your operations.
Contact Miura today to learn more!
1715 Magnavox Way, Fort Wayne, Indiana 46804
Phone: 260-432-9337
www.MSKTD.com
Email: Brent Doctor - BAD@msktd.com
MSKTD PROVIDES SPECIALIZED, EXPERT DESIGN SOLUTIONS FOR THE HIGH-PERFORMING DEMANDS OF THE FOOD PROCESSING INDUSTRY NATIONWIDE.
We are a truly collaborative, in-house team of architects, engineers, interior designers, and landscape architects, who will work closely with you to deliver what’s important to you—customized design solutions, performance expectations, stringent hygienic design requirements, confidentiality, growth flexibility, managed budget constraints, and cohesive, efficient project execution.
With decades of experience and a history of repeat clients, our proven track record is built on established trust and extensive expertise in food processing facility types, including:
•Dairy li uid, solid, powder
• rotein poultry red meats
• ce Cream
•Baked Fried Foods
•Con ectionary Sugar
•Soups Sauces
•Sanitary
•Cold Boxes coolers ree ers
• aw ngredients more
Our designs comply with SD , FD , S F, B C, B, and other industry standards. And with professional licenses in over 30 states, we have successfully completed hundreds of large-scale projects across the United States, always prioritizing our clients’ unique needs and goals.
315-797-0090
Munson Machinery Company is a leading manufacturer of mixing, blending, size reduction and separation equipment serving the food, dairy, coffee/tea, nutraceutical and hemp industries.
Munson offers the industry’s widest selection of equipment for mixing and blending of bulk food products (with or without liquid additions) including: Rotary Batch Mixers, Ribbon/Paddle/Plow Blenders, Cylindrical Plow Blenders, VeeCone Blenders, Fluidized Bed Mixers, Rotary Continuous Mixers, and Variable Intensity Blenders.
For size reduction of spices, herbs, nuts, dates, roots, grains, beans and other bulk food products, Munson manufactures Lump Breakers, Pin Mills, Attrition Mills, Screen Classifying Cutters, Knife Cutters, Shredders, and Hammer Mills.
For solids separation, the Munson’s Centrifugal Sifter can sift and scalp bulk food materials at high rates with virtually no product degradation.
Munson equipment is available constructed of #304 or #316 stainless steel and finished to food, USDA dairy or pharmaceutical standards, with optional CIP systems.
The exceptionally broad selection of full size equipment in Munson’s laboratory allows side-by-side testing of your actual material, and documents precisely how effective—or ineffective—any given machine would be at meeting your specific performance requirements. This assists you in specifying a machine at no cost or obligation and takes the risk out of purchasing bulk food processing machinery. www.munsonmachinery.com Email: info@munsonmachinery.com
Reliable Equipment, Tailored for Your Needs
We provide dependable liquid processing equipment for industries like specialty chemicals, food & beverage, and personal care. From mixers and tanks to complete process systems, we help manufacturers tackle their unique production challenges with practical, effective solutions.
Products That Fit Your Process
Our product range includes industrial mixers, high shear mixing equipment, stainless steel tanks, and turnkey systems. Whether you’re scaling up production or improving an existing process, we offer both standard and custom equipment to match your specific needs.
Focused on Your Success
At MXD Process, we work directly with customers to understand their goals and provide equipment that works seamlessly within their operations. Our team supports you from design and manufacturing to installation and beyond, ensuring long-term performance and reliability.
Why Work With MXD Process? Our straightforward approach to solving production challenges. High-quality equipment built for durability and performance. A team that values collaboration and customer satisfaction.
10125 Carver Rd., Cincinnati, Ohio 45242
Phone: (513) 891-7485
Paxton Products manufactures high efficiency centrifugal air blowers and custom-engineered pneumatic air delivery devices and systems that are used for drying, air rinsing, and blow-off, in order to improve the quality of labeling, tamper branding, date coding, and other packaging processes.
The new Control Panel from Paxton Products offers manufacturers a simplified solution to manage Paxton’s Centrifugal Blowers in a turnkey manner. Designed for easy installation and scalability, Paxton’s Control Panel is ideal for simply controlling your Paxton Blower System while upholding safety standards and ensuring the highest of quality during operation. With the Paxton Control Panel, there’s no need for third party motor starters or VFDs; it provides a comprehensive solution for your blower system with features like a Variable Frequency Drive (VFD), centralized control, washdown compliance and more.
Coupled with Paxton’s own Centrifugal Blowers, Paxton’s Ionizing Rinsing Systems are designed to dissipate the static charges that cause dirt and debris to adhere to surfaces, and then blast the contaminants away using ultra-efficient, blower-driven air. Using a specially designed Air Knife or Nozzle Manifold, Paxton’s Ionizing Systems are available for can or bottle rinsing and eliminate the need for compressed air or water rinsing.
Paxton’s own PX-Series line of high efficiency centrifugal blowers use state-ofthe-art impellers and scroll designs to achieve efficiencies as high as 80%, to generate 33% more air flow than a standard centrifugal blower. Paxton’s beltdriven, Centrifugal Blowers are available in 2-20 hp, providing air flows from 100–1500 cfm, and come with an industry-best 3-Year Warranty.
32 Case Street, Poland, NY 13431 USA
Phone: 800/848-8483
Email: perfex@perfex.com
Perfex Corporation is a leading manufacturer of innovative cleaning tools for food and pharmaceutical manufacturing environments. Established in 1924, PERFEX® celebrates 100 years of excellence fueled by passion and dedication.
Our founder believed that cleaning tools should be designed to eliminate associated safety issues, to this day we develop each product with the same idea in mind. Reliable tools, made from quality materials, to meet and exceed today’s hygienic concerns.
PERFEX is the pioneer of heat-fused brooms and brushes, our patented fused fiber design eliminates premature fiber fall-out and areas for contaminants to collect. Easily isolate work areas and prevent dangerous cross-contamination with PERFEX Color-Coded Brooms, Brushes, and Squeegees. Utilize sharp contrasting colors to quickly identify contamination zones and promote a clean, safe, and structured workplace that allows workers to know at a glance when tools are out of place. Made in the USA!
We are also the home of TruCLEAN® mopping systems, a first-of-its-kind design specific for ultra-high sanitation areas, cleanrooms, laboratories, and controlled environments. TruCLEAN mopping systems include autoclave compatible stainless-steel components and temperature-resistant polypropylene buckets with multiple configurations and colorways suited for large or small area cleanrooms of any grade.
Our experienced team is committed to providing you with the most effective cleaning equipment available in the industry. We keep our cleaning tools and supplies well stocked to ensure the safety of your workplace in emergency cleaning situations! www.perfex.com
730 S. Indiana Ave., West Bend, WI 53095 USA
Phone: 262/338-1191
www.pickheaters.com
Email: info1@pickheaters.com
Throughout the food plant, from process heating to plant sanitation, Pick Heaters provide instant, unlimited hot water at a precise temperature. When compared to indirect heat exchangers, Pick can cut energy costs as much as 28% without the maintenance and operational headaches.
Pick offers two types of water/liquid direct steam injection heaters, the constant flow and variable flow models. The constant flow heater mixes medium-to-high pressure steam with cold water and delivers instant hot water. It is ideal when the water flow is fixed or varies over a narrow span (3:1). The variable flow heater is used to accommodate wide variations in demand and frequent start-stop applications and is ideally suited as a central heating system for multiple use points such as hose wash-down stations or plant sanitation.
Pick’s 3A-certified sanitary steam injection heater is the preferred choice for inline product cooking, CIP heating or nitrogen gas injection. It heats/cooks any water-miscible liquid or slurry instantly on a continuous straight through basis. It can handle slurries containing bite sized particulate such as salsas or stews with particulate integrity retained!
Pick Heaters’ products are trusted by many food manufacturers around the world, who value quality, reliability, and performance. Learn more about Pick Heaters and our products at www.pickheaters.com or call 262-338-1191.
500 E.Illinois St. Newberg, OR 97132
Phone: 503-537-5319
www.ppmtech.com
Email: nisch@ppmtech.com
PPM Technologies is a globally recognized manufacturer of industrial foodprocessing equipment for conveying, frying, seasoning, and cooling applications. For over a century, PPM has combined passion and expertise to provide uniquely engineered solutions with new and innovative products designed to improve quality, increase efficiencies, and reduce costs.
Our equipment can be found across industries, including snack foods, cereals, nuts and seeds, fruits and vegetables, meats and plant-based meat alternatives, seafood and poultry, confectionary products, and more.
PPM understands that the food industry is ever-evolving and shaped by dynamic consumer preferences; therefore, we offer a standardized range of products with flexible customization options to meet the unique and specific needs of each customer.
Our portfolio of material handling equipment features a range of high-performance, energy-efficient technology that includes vibratory, horizontal motion, and belt conveyors, as well as bucket elevators and tote dumpers.
Our state-of-the-art seasoning systems ensure your products are accurately and consistently coated or flavored and can be used to apply an array of ingredients, including oils, tacs, gums, slurries, powders, and other particulates.
Our industrial thermal processing line, which includes customizable designs for batch and continuous fryers, offers a selection of reliable safety features, efficient heating systems, and advanced filtration technology to protect oil quality, reduce downtime and save costs.
710 Old Willets Path. Hauppauge, NY 11788 USA
Phone: 800/243-ROSS
www.mixers.com
Email: mail@mixers.com
Serving all the process industries in virtually every industrialized country, ROSS offers experience and production capacity that no other manufacturer of specialty mixing and blending equipment can match. In the US, ROSS operates five plants dedicated to engineering, R&D, manufacturing, and process testing. Overseas, ROSS equipment is manufactured in state-of-the-art plants in China and India.
The ROSS Test & Development Center in Hauppauge, NY, is the industry’s bestequipped laboratory for process testing. Hundreds of ROSS customers visit the test center each year to confirm their equipment selections and optimize processes.
Ribbon Blenders – High quality and available in customizable configurations. Laboratory sizes to 1000 cu. ft. Many models in stock.
Batch and In-Line Rotor/Stator High Shear Mixers – Single-stage and multi-stage models for fine emulsions and dispersions.
SLIM Solid/Liquid Injection Technology – Eliminates the persistent clogging of conventional eductor-based systems.
Multi-Shaft Mixers – Multiple independently-driven agitators work in tandem to ensure fine solids dispersion, efficient turnover and uniform heating/cooling.
In-Plant Trial/Rental – The industry’s largest fleet of rental mixers and blenders. Meet short-term demand or test equipment in your process prior to purchase.
Control Systems – From single-axis to multi-axis designs, ROSS control systems offer unprecedented accuracy and flexibility in the mixing and blending process.
2855 Innovation Way, Sun Prairie, WI. 53590 USA
Phone: 800/356-3300
Email: hello@sanimatic.com
Quality products start with clean equipment. Let Sani-Matic help you optimize your equipment cleaning processes with our automated cleaning technology, hygienic components, and data recording solutions portfolio. Our team of experts will work with you to determine the best product for your specific needs.
Our Product Offering –Cleaning Technologies:
•C Clean-in- lace systems, custom designed or your speci ic process needs.
•CO Clean-Out-o - lace automated systems or process parts, including the new CyClean® 35 washer from our CleanWorx® brand.
Hygienic Component Solutions:
• rocess strainers, spray devices, system accessories, and spare parts.
• anks, tank components, and transportation tanker sprays.
•Centrali ed washdown systems or Open lant Cleaning O C .
Digital Solutions:
•Digital rocess ecorder D digital replacement or traditional paper chart recorders.
•Sani rend ocal or cloud-based automated data recording and OEE optimization platform.
Service Solutions
•Field service engineers provide onsite audits and optimi ation, preventive maintenance, system start-up, and a termarket services.
•Customer Success team specialists stay in touch and make sure processes are running smoothly with periodic visits a ter ield service has occurred.
Sani- atic has been improving ood and beverage processors’ production uptime and sanitary results since 1943. Today, we continue our commitment to sanitary cleaning results or a diverse range o industries.
220 Finch Road, Wellford, SC 29385
Phone: (864) 439-7537
www.seweurodrive.com
Email: cslyman@seweurodrive.com
Nearly 100 years of driving the world. Since 1931, SEW-EURODRIVE has designed and engineered the world’s finest machine automation products and systems. SEW-EURODRIVE has built its global reputation as a leader in motion control and automation by consistently delivering innovative solutions that empower industries worldwide. For over 90 years, SEW has remained at the forefront of engineering excellence, crafting products that combine reliability, precision, and energy efficiency. We create drive. We move business.
As a leader in driving the food and beverage industry, SEW-EURODRIVE’s line of hygienic drive solutions leads the pack. This line includes a full range of stainless steel gear units, servo motors, and other food processing rated drives and controls.
There’s nothing basic about our core gear units. SEW-EURODRIVE’s classic gearmotors stand out for their robust design, reliable performance, and versatility across various applications.
In addition, advanced products like the MOVI-C® automation platform offer true end-to-end solutions. MOVI-C integrates software, controllers, inverters, and drive components into a seamless, scalable system that meets the demands of modern manufacturing.
There are no hazard conditions, only robust components. SEW-EURODRIVE engineers everything for the long haul. we use premium-grade materials like robust alloys and heat-treated metals to ensure resistance to wear, corrosion, and heavy mechanical stress, regardless of the environment.
To solve and to serve. While SEW-EURODRIVE engineers the finest industrial automation systems in the world, it is our drive to solve problems and serve customers - which distinguishes SEW-EURODRIVE around the world.
355 Chestnut St. , East Longmeadow, MA 01028
Phone: 413-525-4825
www.silverson.com
Email: sales@silverson.com
For more than 75 years Silverson has specialized in the manufacture of quality high shear mixers for the food and beverage industries.
Whether you’re concerned with reducing production times, sanitary processing, powder/liquid mixing, producing stable emulsions, dissolving sugar, disintegrating solids, blending liquids of different viscosities, or dispersing and hydrating gums, thickeners, and stabilizers, Silverson has a mixing solution for you.
Time after time, companies specify Silverson mixers as the “standard” equipment for their manufacturing process, with a single Silverson high shear mixer able to perform a wide range of mixing applications with speed and consistency.
With the exceptionally rapid mixing action of a Silverson high shear mixer, process times are substantially reduced compared to a conventional agitator. Silverson Machines offer the largest capacity range from a single manufacturer, from our most popular L5M-A Laboratory mixer all the way up to in-tank mixers that can process batches of up to 8000 gallons. These mixers are advantageous when:
• ydrating and deagglomerating gums and thickeners
• eclaiming waste or out-o -spec product
•Dissolving
• omogeni ing
• educing particle si e
• ixing igh iscosity products
•Blending li uids o varying viscosities
•Forming stable emulsions
If you’d like to discuss your food/beverage application or find out more about high shear mixing could benefit your mixing process, get in touch with Silverson Machines today.
14000 Dineen Drive Little Rock, AR 72206 USA
Phone: +1 501-492-3893
Email: sales@sleeveseal.com
Sleeve Seal is focused on a new era of repeatable labeling performance. Builtto-last American manufacturing expertise and modern engineering combine to produce speeds from 25 to 1600 CPM on robust machines equipped with intelligent Allen Bradley controls. Heavy weight construction and the fastest, most durable drive train in the industry provide countless hours of high efficiency runs. Sleeve Seal machines are engineered to provide quality-labeling performance with simple, tool-less changeovers between container formats. Other patented innovations, such as a multi-blade cutter assembly with quick-change blades have been developed for ease of maintenance.
The RFL Series range of roll fed labelers was born from the same need as our shrink sleeve labelers - a need for faster, more efficient, more robustly built machines with Allen Bradley controls. In a market where efficiencies and cost of ownership are everything, Sleeve Seal has a proven history of fast, precise label application with minimal maintenance costs. Our engineers have an unparalleled depth of knowledge that has been applied to a new style of label application for today’s market. Sleeve Seal is proud to present our new range of RFL Series of roll fed labelers.
The PSL Series range of pressure sensitive labelers was born from the same need as our shrink sleeve labelers - a need for faster, more efficient, more robustly built machines with Allen Bradley controls. In a market where efficiencies and cost of ownership are everything, Sleeve Seal has a proven history of fast, precise label application with minimal maintenance costs. www.sleeveseal.com
Phone: 888/278-5555 1840 St. Regis Blvd. Dorval QC H9P 1H6 Canada
Email: sales@satrviewpackaging.com
Starview Packaging Machinery, Inc. is a primary manufacturer of tray sealers for food tray packaging with over 25 years of supplying standard and custom packaging systems to our customers and distributors.
Providing the Processed Food Industry with Innovative Packaging Machines for:
•Fresh Foods
•Fro en Foods
• eady to Eat eals
•Customi ed ackaging E uipment
•Systems with utomation and ntegration
We design, engineer, and manufacture a comprehensive line of manual, semiautomatic, and automatic tray sealing machines. vailable in shuttle, rotary, and inline conveyor configurations, a variety of standard and custom sealing areas are available to meet the speci ic re uirements o customers and maximi e productivity. Machines are configured to suit specific applications with a focus on efficient, easy to operate, safe to use, and cost effective to run.
Starview’s distinct competitive advantage is in providing a range of both standard and customi ed uality packaging systems backed by solid machine designs, robust machine construction, and superior service.
Starview offers many value-added features for our machines such as auto tray loading, fillers, product sensing, printing and/or verification, automatic packaging materials loading, automatic lid placement, finished package unloading with reject feature for noncompliant packages. www.starviewpackaging.com
7595 Reynolds Circle, Huntington Beach, CA 92647
Phone: 714-375-6300
www.statco-dsi.com
Email: info@statco-dsi.com
Statco-DSI has a longstanding reputation in the industries we serve. We offer anextensiveportfolioofsanitaryequipment,systemsandservicestoprovide start to-finish support for your processing facility
We’re recognized asone of the largest process equipment distributors and systems integrators for the sanitary processing market in North America. With eleven sales and engineering offices strategically located throughout the United States, our nationwide network of more than 150seasoned sanitary process professionals are in your backyard and ready to get to work.
Our project engineering and design team is second to none. Your project will benefit from working with some of the most experienced and well-rounded engineers inthe industry. The tenure of this team is evidence of its cohesiveness. Open lines of communication and willingness to share information helps ensure that every project and every challenge is handled effectively.
Our sales staff has a vast knowledge base and taps into the technical expertise of our engineering staff when needed. Many of our sales team have in-plant experience working for various factorieswithin the industry. They are factory trained on a regular basis to keep up-to-date on the latest products, innovations and specialty applications.
Our technical service team is well versed in preventative maintenance and critical breakdowns, available 24/7/365 to keep your facility running. Trust StatcoDSI for servicing not only blending skids, but pumps, valves, homogenizers, rotary fillers, and both scraped surface and plate heat exchangers.
Call our spare parts team for all of your critical spares, MRO and consumable items like charts and pens, as well as pump and valve seal kits. We represent over 100 of the top brands in the sanitary process industry.
6949 South Potomac Street, Centennial, CO, 80112 USA
Phone: 303-708-5020
Email: zachary.brent@stollemachinery.com
www.stollemachiney.com/fillers
Stolle WeightControl Fillers can fill a wide variety of food products, including meat, poultry, seafood, vegetables and pet foods. They are widely regarded as the most accurate container filling machines available, with accuracies equal to ±½ to 1%, even on difficult to fill products. This unparalleled filling accuracy reduces wasted product due to overfilling and eliminates rejects due to underfilling. The unique method of portioning and filling provides an exceptionally gentle fill that maintains the integrity of delicate and easily damaged products. With a long history of reliable operation, Stolle fillers have a simple rotary design and few moving parts for low maintenance and nearly zero downtime. Many of the earliest machines built are still in operation. Stolle currently offers 4 models of fillers equipped with from 12 to 34 filling stations, with filling capacities from 20 grams to 48 ounces in can sizes up to 603 diameter and 710 height, with speeds up to 1200 cans per minute. The machines are ruggedly constructed of heavyduty stainless steel and other non-corrosive materials to withstand daily cleansing, and the open design makes all parts easily accessible for cleaning and maintenance.
As the world’s leading supplier of canmaking equipment, Stolle has extensive experience in supplying highly customized production machinery. These capabilities are also available to food production facilities for customized conveying, washing/rinsing and drying systems. The Stolle Conveying Systems division designs, manufactures and installs all types of production conveyors including air, mechanical, magnetic, gravity and full pallet conveying. They build systems for both empty and filled food containers, including cans, jars and cartons as well as high-care & high risk food conveying. Stolle can also provide sustainable systems to wash and rinse containers, from large high volume multi-stage washers, to small rinse systems for empty and filled containers. Stolle’s experience in building specialized ovens for can production allows them to provide specialized drying and curing ovens for a wide variety of applications in a food production plant. To discuss your unique needs, please call Zach Brent at +1 303-708-5020.
21800 Doral Rd. Waukesha, WI 53186
Phone: (262) 484-4090
Email: contact@techniblend.com
TechniBlend is a leading supplier of beverage and liquid processing equipment & systems utilizing cutting edge technology, innovative components and optimal design features to serve the food & beverage industry, as well as the consumer products, and household & personal care industries. TechniBlend continues to develop new & innovative technologies aimed to deliver quicker changeovers, greater flexibility, higher yield and improved product quality while producing a great rate of return on investment.
Beverage and Liquid Blending Systems
Our blending systems incorporate many of TechniBlend’s exclusive technologies into a simple, reliable processing solution. The system includes integrated deaeration, product cooling, in-line blending, carbonation, CIP On-Demand, and other customizable options to meet your production needs.
Beverage and Liquid Batching Systems
TechniBlend offers a wide variety of continuous stream and batching systems. Utilizing our patented injection and dispersion components, alongside high accuracy mass flowmeters, we are able to provide precise blending of ingredients in unlimited streams. Our controls offer exact recipe control and high-quality, repeatable results that save you time and money.
TechniBlend batching systems utilize specialized powder mixing pumps for precise timing and injection management of dry ingredients commonly used in personal care & chemical products.
True Turnkey Solution
TechniBlend’s skilled engineering team focuses on providing turnkey services for both new and upgrade projects. With an expansive list of industries served, our process provides a true turnkey solution, built for your entire line.
Email: valves@thermomegatech.com Phone: 877-379-8258
Founded in 1983 and headquartered near Philadelphia, Pennsylvania, ThermOmegaTech® is a leading designer and manufacturer of thermostatic valves and actuators. Their product portfolio addresses critical applications such as washdown, freeze protection, scald protection, temperature balancing, tepid water delivery, thermal relief, and mixing/diverting. With over 40 years of experience, they deliver reliable temperature control solutions for industries such as food processing.
The STVM® Washdown Station is designed for the demanding environment of food processing plants, offering high-temperature wash at user-defined settings. It features a proprietary Silent Venturi Mixing Valve (STVM®), which combines steam and water while minimizing mineral buildup. The self-scouring design reduces maintenance frequency and extends operational life.
Unlike competitor units, which require time-intensive disassembly, special tools, and replacement parts, the STVM® station features a simple cartridge design. Operators can remove, descale, and reinstall the cartridge or swap it with a spare in minutes, minimizing downtime. Additionally, it operates at 20 decibels less than competing models, reducing noise and improving workplace conditions.
ThermOmegaTech’s latest STVM® Washdown Station is built with welded stainless-steel components, reducing thermal expansion and eliminating steam leak points, making it ideal for high-usage environments.
Safety is our priority, so all STVM® units include interlocking shut-off ball valves to prevent accidental steam-only operation and a thermally actuated over-temperature shut-off to protect personnel by reducing water flow or shutting down the unit if temperatures exceed safe limits.
Phone: 260/490-3000
www.tippmanngroup.com
Email: tippsales@tippmanngroup.com
Tippmann Group is a unique combination of two companies, Tippmann Construction and Interstate Warehousing, which are dedicated to safe and efficient design, construction and operation of multi-temperature processing and distribution facilities for the food industry.
In business since 1968, our refrigeration expertise and owner/operator experience make Tippmann Group your single-source provider for all your temperature-controlled facility needs.
Tippmann Group’s QFR Zone® utilizes enhanced airflow to provide an energy and labor-efficient blast freezing solution, freezing products faster and more efficiently than traditional blast systems.
Tippmann Construction
•Design build construction o multi-temperature warehouse and production facilities
• ew builds, expansions and renovations
• aster site planning
•Owner operator experience knowledge
Interstate Warehousing
• th largest W company in the nited States
• , , cubic eet o cold storage space
•S F certi ied acilities
•Customi ed distribution solutions
• etail and Foodservice consolidation programs
•Comprehensive management development training program
680 S. Royal Lane, Suite 100, Coppell, TX 75019-2800
Phone: (972) 462-6500
Email: gustavo.mendez@tnasolutions.com
TNA Solutions: helping food producers succeed responsibly in a changing world.
TNA creates and sustains complete processing and packaging solutions that help confectionery, bakery, snacks and french fries producers realise goals and exceed their expectations. These solutions are designed for the highest output, minimal downtime and reduced total cost of ownership. For snacks, this includes receiving, destoning, washing, peeling, inspecting, slicing, blanching, dewatering, continuous vacuum and batch frying, deoiling, sorting, distribution, seasoning and packaging. For confectionery processing, the range spans from kitchen operations, starch conditioning, mogul tray handling, de-moulding, product cleaning and finishing to depositing, distribution, packaging and case packing.
With an in-depth understanding of the balance required to satisfy consumers and retailers, while keeping brands profitable, TNA offers end-to-end expertise. The company provides solutions at every stage, including consulting, planning, project management, commissioning, installation and comprehensive aftermarket support. Through a global network spread across 30 countries, the company ensures real-time access to experts and seamless availability of spares, technicians, and services enabling customers to keep their production lines running smoothly and efficiently.
With over 42 years of industry experience and 16,000 systems installed across more than 130 countries, the company’s consultative and customer-centric approach ensures manufacturers’ goals are met, going beyond delivering products to providing high-performing solutions with a responsible ethos. This commitment to driving sustainable growth in the food sector is part of the TNA DNA, and whether in business, or through the humanitarian initiatives undertaken by the the Nadia and Alf Taylor Foundation, customers become part of a forwardthinking company committed to delivering excellence , and a positive social impact. www.tnasolutions.com
Phone: 2194644811 1200
www.urschel.com
Email: info@urschel.com
As the #1 Global Leader in Food Cutting Technology, Urschel continues to successfully lead in the manufacturing, selling, and support of industrial cutting machinery to partner and assist food processors everywhere. Urschel manufactures rugged dicers, slicers, shredders, and particle size reduction machinery. Every critical part is produced in-house to follow Urschel strict quality control standards to optimally fit and function like the original. Urschel headquarters/ manufacturing is centrally located in the heart of the United States in Northwest Indiana.
Exclusively designed by Urschel to assist Urschel CC Slicer customers, the production-proven, patented RockRepeller™ Impeller filters out rocks to save lost production. Urschel customers implementing the RockRepeller have identified many benefits including increased cost-savings.
The New Comitrol Disc Mill 380 (DM380) is ideal for processing nuts in small batches or high-volume continuous production. The unique disc plate design and adjustable gap setting allow for a wide variety of nuts to be processed. Butter texture is controlled through the plate gap adjustment.
New from Urschel, the advanced CCLL (Chip Cutter Large Lattice) Slicer features higher capacities in a new design inspired by the Urschel CCL (Chip Cutter Lattice). The corrugations run approximately 90° to each other to create potato lattice chips or thicker potato waffle fries.
Urschel machinery delivers uninterrupted production and sanitary, precision cutting at high capacities. Rely on Urschel to deliver ideal cutting solutions that exceed your food processing goals.
69 William Street. Belleville, NJ 07109 USA
Phone: 973) 759-4600
www.vac-u-max.com
Email: info@vac-u-max.com
VAC-U-MAX is a worldwide leader in the design and manufacture of bulk material handling systems that convey, weigh, and batch over 10,000 various powders and bulk materials to food processing and packaging lines. With strong application expertise in the food industry and being a subject expert on conveying powders and granular bulk solids, VAC-U-MAX food ingredient handling systems incorporate pneumatic, aero-mechanical, and flexible screw conveying technologies designed to handle many types of materials including powders, flakes, granules, pellets, fibers, tablets, seeds, coatings, sugar, and other granular bulk materials.
Since 1954, VAC-U-MAX has been a pioneer in pneumatic conveying, developing the first air-powered venturi unit, advancing technologies for directcharge loading of vacuum tolerant process equipment, and the first to design vertical-wall “tube hopper” material receivers for difficult to convey materials. A vacuum receiver represents the heart of a food ingredient handling system, conveying materials from drums, bins, totes, bulk bags, super sacks, and bag dump stations for dust-free material handling.
VAC-U-MAX product range includes vacuum receivers, bulk bag loading and unloading systems, aero-mechanical and flexible screw conveying systems, bag dump stations with integrated dust collection and empty-bag compaction, diverter valves, feed bins, and vacuum pump packages. VAC-U-MAX is a UL-listed manufacturer and supplier of control packages that are easily integrated into existing plant PLC’s. Product range also includes a full line of portable, continuous- duty, and central vacuum cleaning systems for plant wide clean-up of many types of materials including combustible dust.
VAC-U-MAX systems focus on waste reduction as in topping and coating applications that require placement of seeds, flavorings, sugar, salt, and coatings onto finished food product. For more information or RFQ, visit www.vac-u-max.com.
13771 Cavaliere Drive, Shelby Township, MI 48315
Phone: (888) 326-1476
Email: info@vandergraaf.com
VDG is the leader in the design and manufacturing of drum motors for belt conveyors, with a strong focus on safety, reliability, and longevity. VDG adheres to a simple principle: provide reliable belt drive solutions to the material handling and food processing industries through innovation, continuous research and development, and precision manufacturing. Manufacturing in-house in the USA and Canada since 1985, using cutting-edge production technology and automation, VDG ensures product quality, short lead times, and after-sales service.
The VDG Drum Motor is a one-component conveyor drive that has all drive components, including the new premium-efficiency electric motor, gear reducer, and bearings, enclosed inside the drive drum, increasing mechanical and electrical efficiency, optimizing space, and promoting operator safety. Designed for 80,000 hours of continuous operation before maintenance, VDG Drum Motors reduce maintenance and operational costs and increase productivity.
All-stainless steel SSV Series Drum Motors, designed specifically for food processing and handling belt conveyor applications, drive modular, wire mesh, and monolithic conveyor belts without using sprockets. The belt profile is either machined directly on the drive drum or on the exchangeable profiled sleeve (XP). The profiled sleeve on the SSV-XP Drum Motor can be easily removed and exchanged for another sleeve to match the belt required on the conveyor. Therefore, the same drum motor can be used when switching to another belt for a different type of processing.
All SSV Series Drum Motors feature an IP69K-rated sealing system, withstand up to 3,000 psi washdown pressure, and eliminate crevices that trap food byproducts and bacterial harborage, reducing washdown time and water usage by 50%. Belt profiles are available for all major belt manufacturers.
Phone: +1 513-272-0131 3877
www.vega.com
Email: americas@vega.com
For more than 70 years, VEGA Americas, Inc. has provided industry-leading products for the measurement of level and pressure. VEGA’s full product line of level and pressure measurement instrumentation allows us to provide one of the most complete ranges of measurement solutions in the industry.
VEGA’s continued innovation in radar, pressure, differential pressure, and point level switches ensures food and beverage operations of all sizes can continue to improve their processes and keep up with ever-shifting market demands. VEGA believes the future of instrumentation lies in the ability to produce high-quality, innovative products that keep pace with technology, and provide service and value to our customers in today’s competitive environment. Our measurement solutions have helped make more batches, maintain inventory of raw ingredients, and save energy.
Always in pursuit of technology that improves operational efficiency for our food and beverage partners, VEGA created the VEGABAR 39 universal pressure transmitter for measuring gases, vapors, and liquids at up to 130 °C. Designed to aid in such processes as pasteurization and separation, the VEGABAR 39 employs inventive solutions like a 360° colored light ring for enhanced status readability from across a facility. Because integration can be just as important as operation, the VEGABAR 39 is also equipped with IO-Link communication for simple integration into control systems.
Located in Cincinnati, Ohio, VEGA Americas combines manufacturing, distribution, and service for products that represent the most sophisticated process measurement technologies anywhere in the world. VEGA Americas is a whollyowned subsidiary of VEGA Grieshaber KG in Schiltach, Baden-Württemberg, Germany.
Vibra Screw Incorporated was founded in 1955 by Eugene A. Wahl, whose experience in solving problems in the process industries led to revolutionary ways to discharge and meter dry solids.
Today, with a staff of experienced and talented engineers and technicians, Vibra Screw is the leader in dry solids processing, with high quality equipment to store, discharge, meter, convey, size and blend.
Vibra Screw serves its markets through a world wide network of sales representatives, licensees and subsidiaries.
Vibra Screw is staffed with experienced, professional engineers who solve problems. From initial study, through testing & design, our goal is to satisfy our Customer’s unique requirements efficiently & cost effectively. Our modern facility in Totowa, NJ handles every aspect of equipment manufacture from sandblasting, fabrication & assembly to full electronic control production.
The most trusted name in dry solids processing. Vibra Screw Inc. prides itself in being able to bring ground-breaking solutions to your solids processing challenges. Vibra Screw currently manufactures: bulk bag unloaders, volumetric feeders, bin activators, vibrating feeders/vibrating conveyors, flexible screw conveyors, loss-in-weight feeders, storage pile activators, live bottom bins, screeners, continuous blenders, and process controls.
No other Industry source stands behind its products with the confidence & assurance of Vibra Screw, because no other company engineers & manufactures to our uncompromising standards:
Phone: 609/265-0101
Email: contact@volkmannusa.com
Volkmann USA designs and manufactures hygienic, explosion-proof pneumatic vacuum conveying systems to safely transfer powders, pellets, granules, and other bulk materials from one point in a process to another point while safeguarding particle integrity and mixture homogeneity. Proven worldwide in transferring ingredients for foods, pet foods, beverages, nutritional supplements, and more, as well as finished products ready for packaging, these automated, sanitary conveyors feature patented vacuum technology that eliminates the potential for ignition even when transferring ignitable, fine particles and combustible dusts. By operating entirely pneumatically without electricity, without rotating parts, without generating heat, and with proper electrostatic grounding, our conveying systems earned the ATEX certification as suitable for safe installation in all dust explosion areas.
Our conveying systems can be quickly disassembled without tools for easy access to the interior, complete cleaning and inspection. Our experienced engineering team custom-designs the powder transfer conveyors for sanitary, cleanroom, hazardous, and any type of process.
Volkmann also designs and manufactures the companion bulk material handling equipment t ypically specified when conveying dry materials and ingredients. Bulk bag unloading stations, bag dump stations, lump breakers, and accessories are all available, custom-engineered to suit the installation.
Serving North America from our Bristol, PA headquarters near I-95, we offer material testing on fully operating pneumatic conveying systems and accessories in a dedicated test laboratory. The family-owned, global organization based in Germany operates subsidiaries in Great Britain, USA, France and the Netherlands with more than 100 employees worldwide
10701 North Ambassador Drive, Kansas City MO 64153
Phone: 816/891/0072
Email: solutions@weberweb.com
www.solutions@weberweb.com
Weber is a world leader in delivering innovative slicing and packaging solutions tailored to the needs of the global food industry. From automated infeeding and slicing to product transport, handling, loading, and packaging, Weber seamlessly integrates every step of the production process.
Flexible. Simple. Reliable. – Packaging solutions that make sense.
The wePACK 7000 is the industry’s most flexible thermoformer, offering unparalleled performance and versatility.
• nmatched packaging versatility Supports a wide range o product applications and packaging styles.
• igh production lexibility educe changeover time rom hours to under two minutes!
• hought ul design Open, intentional e uipment design allows or easy access, maintenance, and cleaning.
•Sustainable compatibility eady or use with recyclable and environmentally friendly materials.
Maximize efficiency and output within the same footprint using the integrated wePICK pick robot and weLABEL labeling system for both top and bottom web labeling.
Weber Digital Factory Solutions he uture o production control
Take your production to the next level with Weber’s Digital Factory Solutions, giving you unmatched control and oversight of your operations.
• eal-time monitoring o your production line anytime, anywhere.
• ideo monitoring identi ies gaps and ine iciencies instantly.
• e uipment health monitoring.
From innovative packaging solutions to digital technologies, Weber is dedicated to helping you elevate your production process.
Phone: (603) 644-2500 17 Colby Court, Bedford, NH 03110
Email: sales@wirebelt.com
Wire Belt Company is a global leader in manufacturing top-quality stainless steel conveyor belts. With over 100 years of expertise, we design and deliver solutions that meet the highest standards of performance.
Wire Belt Company has a global presence, operating manufacturing plants in the USA, UK, and Germany. This ensures reliable delivery wherever you are.
Our conveyor belts support food processing applications such as:
•Baking
•Coating
•Cooling
•Frying
•Breading
•Dusting
•and more
Customer Service Excellence - When you contact Wire Belt, you’ll speak directly with a knowledgeable representative. Our technical engineers are also available to help optimize your application and select the right conveyor belt.
Comprehensive Solutions - We offer a wide range of conveyor belts tailored to improve process efficiency—from simple designs to specialized solutions.
Global Distribution - Our customer service and worldwide presence ensure seamless distribution to keep your operations running smoothly. Call us if you need help with an efficient conveyor belt system for your process. www.wirebelt.com
The Witte Company is a leading manufacturer of vibratory process equipment used in the food processing industry. The company’s core products include Fluid Bed Dryers and Coolers, Vibratory Conveyors and Screeners.
The Witte Company designs and manufactures drying, cooling, classifying and related vibratory process equipment at its headquarters in Washington, New Jersey. Family-owned and operated since its founding in 1938, the company has earned an outstanding reputation for engineering expertise, craftsmanship and personal service.
Featuring innovative machine design at a competitive price, Witte has established a track record for operational dependability, earning the trust of Fortune 500 companies worldwide. Dependable customer service, prompt onsite engineering support and readily available spare parts are always a phone call away.
The Witte Company looks forward to learning about your processing needs and having the opportunity to earn your trust as a valued customer.
1401 South 7th Street. Hopkins, Minnesota (USA) 55343
Phone: (952) 933-2559
www.xchanger.com
Email: david.wangensteen@xchanger.com
Xchanger manufactures custom heat exchangers and blower aftercoolers to control temperature and humidity in almost any application. We have over 25,000 installations worldwide. Our mechanical engineers will provide affordable, custom-designed units by optimizing 1 of 10 field-proven models. Computer modeling assures optimal performance, proper sizing, and prevents expensive over-building.
We guarantee the engineering, workmanship, and performance of every heat exchanger we ship.
AA Series heat exchangers cool low pressure gas streams with ambient air. These compact units are ideal for locations with limited access to cooling water and have significantly lower operating costs than liquid cooled heat exchangers. They can cool conveying air close to ambient temperature.
C Series liquid cooled heat exchangers cool and/or heat low-pressure gas streams. Their modular design makes it easy to customize for your specific application. They have a finned-tube core with numerous channels through which the conveying air passes. Their design provides significant heat transfer surface area, so units are smaller, less costly to manufacture, and easier to ship. Additionally, gas side pressure loss is typically below 6 inches of water column (0.2 PSI), so there’s no significant increase in pumping power or operating costs.
D Series heat exchangers can heat, cool, dehumidify and filter low pressure gas streams. They’re specifically designed for dairy applications and are available with HEPA filter and/or fully clad insulation. Their modular design can be easily customized for most applications.
Heat Transfer Solutions for Food and Dairy industry
2121 Norman Drive South, Waukegan, IL 60085
Phone: 847/887/7457
www.yaskawa.com
Email: marcom@yaskawa.com
Whether you are a machine builder or equipment user, you know the daily struggle with limited resources and tight deadlines. You can’t afford to settle for less than the right automation products and services to solve urgent problems, delivered with reassuring consistency and reliability you can trust.
Yaskawa’s global expertise in AC drive, motion control, and robotic technology is unmatched, with over 100 years of manufacturing excellence, locations in 30 countries, and $4.5 billion in global sales per year. Since 1915, Yaskawa has produced 25 million servo motors, 35 million variable frequency drives, and 600,000 robots. We provide both standard products and tailor-made solutions, all backed by proven quality and reliability.
Yaskawa AC drives support every application in the industrial plant, offering size and performance options from fractional HP to 16,000 HP. Our latest variable frequency drives provide simple motor setup with highly flexible network communications, embedded functional safety, no-power programming, and easy-to-use tools featuring mobile device connectivity with our Drive Wizard mobile app.
Yaskawa AC servo systems come to a precise position with speed and consistency that is unmatched in the automation industry. Connect our rotary, linear, and direct drive motors to an advanced Yaskawa iC9200 machine controller to manage motion, logic, kinematics, safety, security, and more from a single EtherCAT-based controller utilizing our iCube Control™ platform.
With 150+ models to choose from and the strength of decades of application expertise, Yaskawa robots increase efficiency, provide consistent quality, and boost productivity to deliver outstanding ROI. Our robotic portfolio ranges from 4 to 15-axis industrial robots with load capacities of 2 to 800 kg to special machines, devices, and turnkey robotic systems.
jփ!@'8'&683&<$;9-296'$ধ32
jփ£!99T9;32'T#32'T1';!£&';'$ধ32
jփBest performance for packaged products
jփCompact footprint and low TCO
28-;9< <!£ f!@
Scan the code to see our full line of X-Ray product -296'$ধ32'7<-61'2;W >>>W!28-;9<W$31c683&<$;f-296'$;-32 VISIT ANRITSU AT BOOTH 2114
3£='@3<8;3<+,'9;$32;!1-2!ধ32$,!££'2+'9>-;,Anritsu’s DualX+ X-Ray, &'9-+2'&;3&';'$;'='2;,'91!££'9;1';!£$32;!1-2!2;9!2&£3>f&'29-;@1!;'8-!£9£-0'#32'!2&9;32'W,-9-223=!ধ32-9/<9;32'3(1!2@28-;9<93£<ধ329;,!;'2,!2$'7<!£-;@$32;83£!2&36'8!ধ32!£'ă$-'2$@W
Aerzen USA, Inc. 42, 117 www.aerzen.com
Advanced Equipment Inc. 116 www.advancedfreezer.com
Airgas, an Air Liquide Co 120 www.airgas.com
Air Products 40, 118 www.airproducts.com
Ampco Pumps Company 80, 119 www.ampcopumps.com
AmTrade Systems, Inc. 74, 121 www.amtrade-systems.com
Anderson-Negele 39, 122 www.anderson-negele.com
Anritsu 123, 203 www.anritsu.com
Apex Motion Control, Inc. 124 www.apexmotion.com
AptarGroup, Inc. 109, 125 www.aptar.com
Atlas Copco 57, 126 www.atlascopco.com
Axiflow Technologies, Inc 13, 128 www.axiflowtechnologies.com
Behn + Bates 59, 129 www.behnbates.com
Bepex 41, 130 www.bepex.com
Big-D Construction IFC, 131 www.big-d.com
Busch Vacuum Solutions 107, 132 www.buschusa.com
Central States Industrial 87, 133 www.csidesigns.com
Cleveland Gear Company 48, 134 www.clevelandgear.com
Columbia Machine, Inc. 22, 135 www.palletizing.com
Coperion 33, 136 www.coperion.com
CRB 71, 137 www.crbgroup.com
DCI, Inc. 100, 138 www.dciinc.com
Delkor Systems, Inc. 104, 139 www.delkorsystems.com
Deville Technologies, LLC 103, 140 www.devilletechnologies.com
Douglas Machines Corp. 98, 141 www.dougmac.com
EBARA Mixers, Inc. 45, 142 www.haywardgordon.com
Econocorp, Inc. 143, 204 www.econocorp.com
EDGE Industrial Technologies 24, 144 www.tgwint.com
Endress + Hauser 68, 145 www.us.endress.com
Ensight Solutions 94, 146 www.ensightsolutions.us
ESI Group USA 16, 147 www.esigroupusa.com
FlexLink Systems, Inc 10, 149 www.flexlink.com
FOCKE & CO 150, IBC www.focke.com
FoodSafe Drains 54, 151 www.foodsafedrains.com
FPS Food Process Solutions Corporation 25, 148 www.fpscorp.ca
Frain Industries. 97, 152 www.fraingroup.com
Fristam Pumps Company 64, 153 www.fristam.com/usa
General Packaging Equipment Co. 50, 154 www.generalpackaging.com
Graphite Metallizing Corp 46, 155 www.graphalloy.com
Hapman Conveyors 91, 156 www.hapman.com
Harpak-ULMA Packaging, LLC 23, 157 www.harpak-ulma.com
Heat and Control, Inc. 158 www.heatandcontrol.com
Hitachi Global Air Power 43 www.hitachiglobalairpower.com
Hiperbaric 15, 159 www.hiperbaric.com
Hydro-Thermal Corporation 160 www.hydro-thermal.com
IFM Efector, Inc. 31, 161 www.ifm.com
Industrial Magnetics, Inc. 2, 162 www.magnetics.com
JAX INC. 5, 163 www.jax.com
Key Technology, 84, 164 www.www.key.net/en
Kovalus Separation Solutions 62, 165 www.kovalus.com
Linde 34, 166 www.lindeus.com
Lubriplate Lubricants Company 17, 167 www.lubriplate.com
Material Transfer & Storage Inc. 106, 168 www.materialtransfer.com
Matthews Marking Systems . 115, 169 www.matthewsmarking.com
Mead & Hunt, Inc 77, 170 www.meadhunt.com
METTLER TOLEDO 88, 171 www.mt.com/pi
MSKTD and Associates 60, 173 www.msktd.com
Miura America Co., Ltd. 67, 172 www.miuraboiler.com
Munson Machinery Co., Inc. 7, 174 www.munsonmachinery.com
MXD Process 60, 175 www.mxdprocess.com
PAXTON 47, 176 www.paxtonproducts.com
Perfex Corporation 1, 177 www.perfex.com
Pick Heaters, Inc 53, 178 www.pickheaters.com
PMMI 78 www.pmmi.org
PPM Technologies Holdings LLC 14, 179 www.ppmtech.com
Ross Mixers 29, 180 www.mixers.com
Sani-Matic, Inc. 99, 181 www.sanimatic.com
SEW-EURODRIVE, Inc. 182, OBC www.seweurodrive.com
Silverson Machines, Inc. 18, 183 www.silverson.com
Sleeve Seal 86, 184 www.sleeveseal.com
Starview Packaging Machinery Inc. 61, 185 www.starviewpackaging.com
Statco-DSI Process Systems 73, 186 www.statco-dsi.com
Stolle Machinery Company 38, 187 www.stollemachinery.com
TechniBlend 93, 188 www.techniblend.com
ThermOmegaTech, Inc. 79, 189 www.thermomegatech.com
Tippmann Group 32, 190 www.tippmanngroup.com
TNA North America, Inc. 113, 191 www.tnasolutions.com
Uline 44 www.uline.com
Urschel Laboratories, Inc. 21, 192 www.urschel.com
VAC-U-MAX 8, 193 www.vac-u-max.com
VDG (Van der Graaf) C-1, 194 www.vandergraaf.com
VEGA Americas 63, 195 www.vega.com
Vibra Screw Inc 11, 196 www.vibrascrew.com
Volkmann, Inc. 72, 197 www.volkmannusa.com
Weber Inc 85. 198 www.weberweb.com
Wire Belt Company of America 37. 199 www.wirebelt.com
Witte Company 49, 200 www.witte.com
Xchanger Inc 4, 201 www.xchanger.com
Yaskawa America, Inc. 83, 202 www.yaskawa.com
JAMIE VALENTI-JORDAN | GUEST COLUMNIST
Using an analytical approach that engages all stakeholders impacted by the decision can ensure the proper choice for a facility without the headaches.
FOR MOST ORGANIZATIONS , when a capital project is developed for executive and organizational alignment, there is a required level of due diligence necessary as a function of corporate policy to ensure that the optimum system is purchased.
In order to provide an objective, systematic analysis based on organizational values, resources, and strategic priorities, normalization of these subjective elements must first occur before the options at hand can be scored and classified. Only after this is complete can a decision matrix be used to fully align the cross-functional stakeholders and represent all concerns on a common basis. “This is even more important now as the impact of looming tari s are likely to change the supply chain calculus,” says Matt Tom, President of MTCC.
The specification of equipment is nearly equal parts technical and political. Before attempting to source quotes to address project needs, ensure that all the relevant stakeholders are accounted for in the equipment need specification. This approach becomes helpful when enlisting multiple departments to support the decision that this process yields.
The direct stakeholders are often referred to by experienced professionals as the ones who have to “live with” the system. This list includes plant operators and supervisors, maintenance, plant engineers, quality team members, schedulers, and plant managers. These team members are important to have onboard even before the first quote is developed because they can reveal key features of the quotes that may change your sourcing strategy.
The indirect stakeholders will sometimes say that they do not have input on a particular system, but they are the soft decision makers that can influence the success of the project approval process substantially.
With the stakeholders onboard, requirements for appropriate design can be gathered in a large (often virtual) cross-functional team meeting. Some of these requirements will be represented as optimum needs instead of pass/fail requirements. Split the requirements (i.e., must be able to run our packaging as it exists today) from the criteria for evaluation. By making a list of absolute pass/fail requirements, quotes gathered can be quickly evaluated as possible options for further evaluation or necessarily pushed back to the vendor for additional refinement.
The first on every list everywhere is raw capital cost. This cost should be inclusive of necessary or preferred options. This process of selecting options is where engineers add substantial value because they can picture the future and the needs of a future team living with the equipment.
When gathering criteria, make sure that each stakeholder group has at least one criterion that directly relates to their role in the organization. When developing the list of criteria, consider a cross-functional brainstorming that is focused what is important, not how important.
Each criterion should represent an independent metric that can be quantified, ideally objectively.
Weighting is the allocation of relative numerical importance of a particular criterion. For example, raw capital cost (including equipment option selection) is
often valued between 30% and 70% of the total decision alone. Other weighting schemas look to apply a relative weight, such as lead time (in weeks), as a more significant criterion than cost of common wear parts (in dollars/year).
Another technique to aid in sophisticated weighting needs is the use of a minor criteria subcalculation. This method works by restricting the minor criteria, in aggregate, to have a smaller impact on the final score by capping the overall impact of the score. This method is useful when the team generates more than about 15 criteria.
When developing the weighting of the di erent criteria, leverage project champions and other senior leadership to provide strategic guidance on organizational priorities and opportunities.
Scoring, or allocating values for each option and criteria combination, can be highly contested and often debated if subjective values are used. This is why criteria should be defined as objectively as possible such that the numbers come from quotes and documentation. If subjective criteria must be used, leverage the team that pushed for that criteria to score the options for you to avoid arguments later in case another team member’s favorite proposal did not end up being selected.
There are two primary decision matrix calculation algorithms out there: the additive and the multiplicative. The additive uses the weighting score as a multiplier, and the scores for each option are added together to give a comparative number. The multiplicative method uses weighting as an exponent for a particular criterion and then multiplies the resulting scores together.
Both work well, but they can give di erent results. Method selection can be as important to the final decision as the scoring and weighting. For this reason, this author prefers a third, self-developed method based on the number of standard deviations away from the mean that a particular criterion is to determine its relative score with weighting applied as a multiplier in the number of standard deviations. This minority-reporting method is usually only used in tiebreaking and does not necessarily yield the additive or multiplicative methods’ results preferentially.
Regardless of the method used, the result of a decision matrix is a decision—explicitly, “Option X is the best option.”
“When developing the weighting of the different criteria, leverage project champions and other senior leadership to provide strategic
guidance on organizational priorities and opportunities.
This
division of responsibilities for criteria generation
and weighting aligns with team expertise and job functions.”
–
Jamie Valenti-Jordan, Food Brand Program Manager,
Food Finance Institute and CEO, Catapult Commercialization Services
When actually building a decision matrix, think about whether a criterion is considered better when it is a higher value or a lower value. Simple toggle coding can allow for the functionality to flip without having to recode a cell. The mathematical compensation takes place with a sign in front of the weighting factor: higher is better uses a positive sign, while lower is better turns the weighting factor negative.
Finally, if building the decision matrix from scratch, consider normalizing each dataset by dividing by its mean value to start. The normalized data is easier to visualize and spot any errors.
At the end of the day, the fanciest spreadsheets and data visualization tools are attempting to approach a single decision: “Option X is the best.” Once the matrix returns an answer, it’s important to gut check the analysis with stakeholders to ensure that nothing “seems wonky.” Review the matrix and results with the stakeholders originally engaged in the criteria development. This will not only validate the results as accurate, but it will bolster additional stakeholder alignment to the project goals and execution itself. Armed with this completed exercise, executive management can ensure that a recommended option has already been validated by the entire organization trusted to run the business.