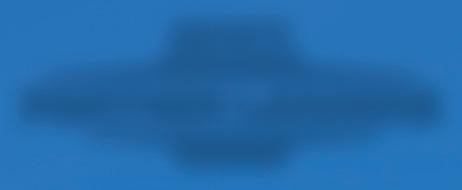



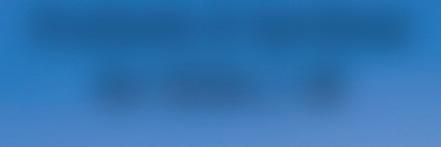



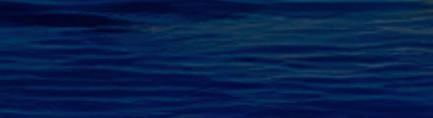
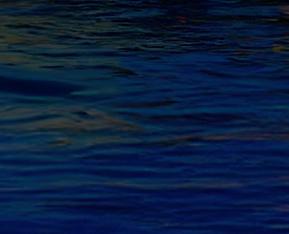

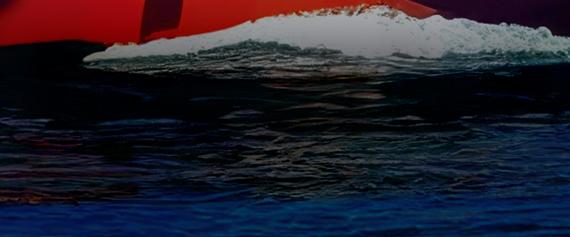


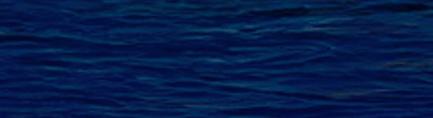

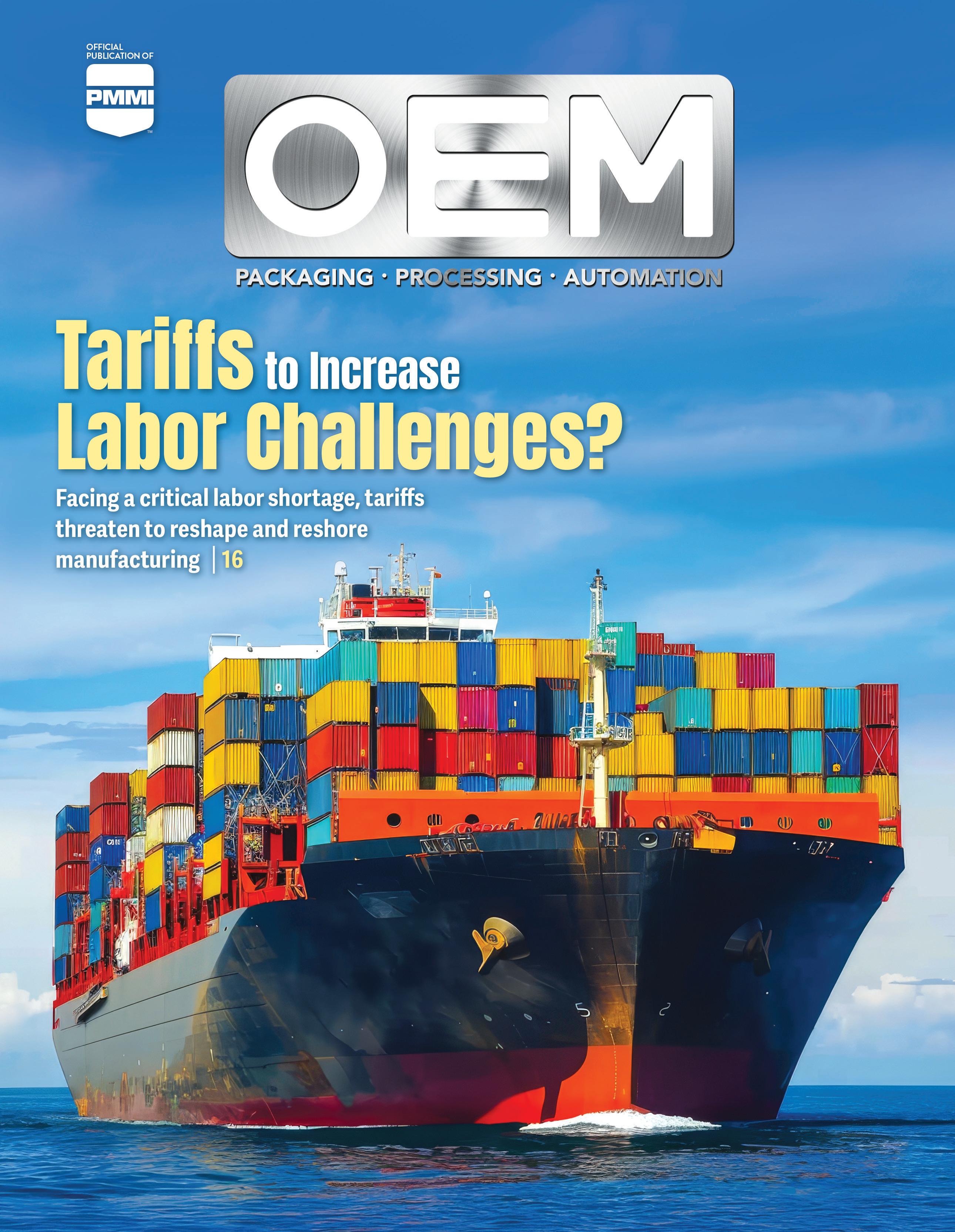
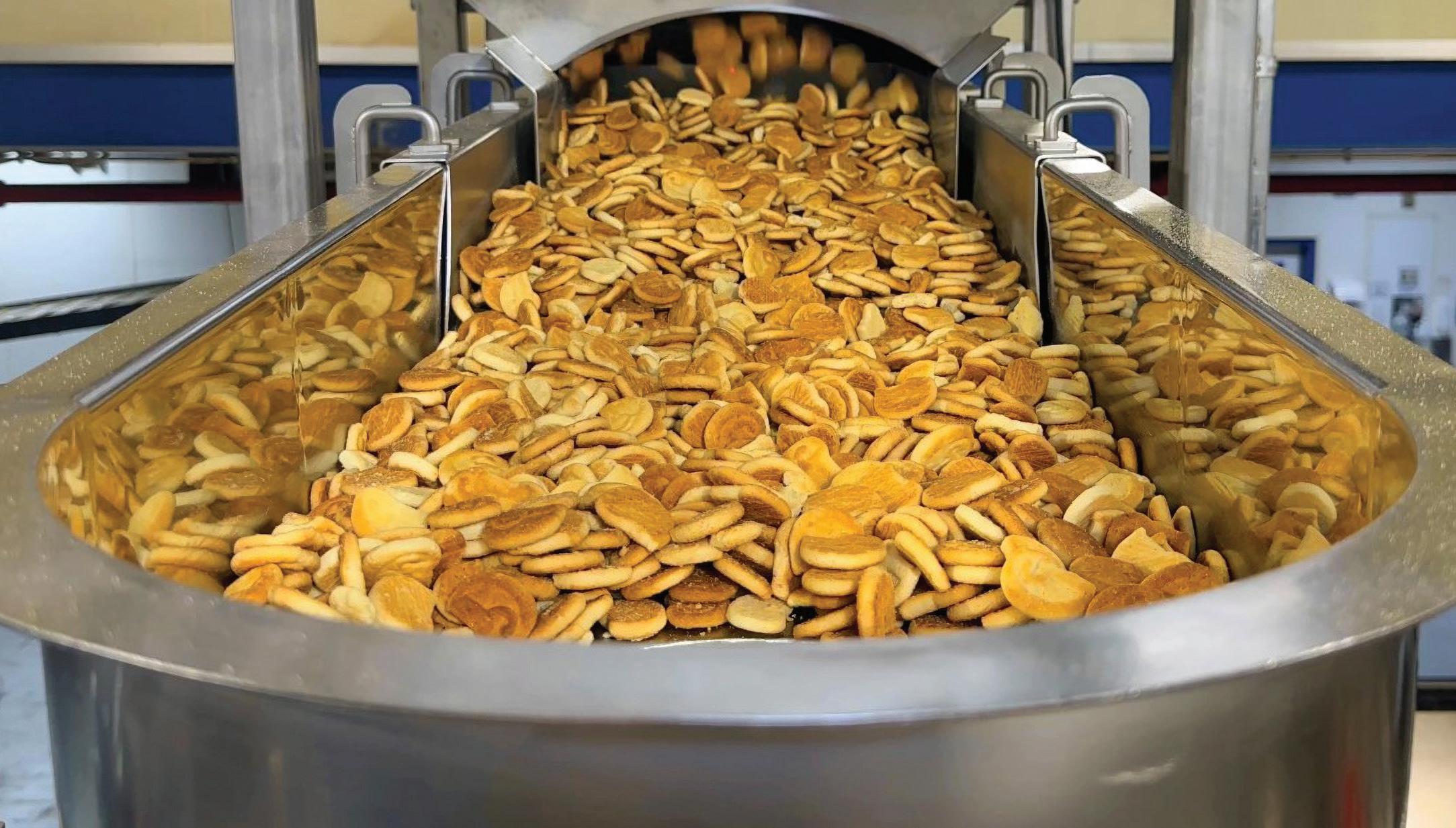
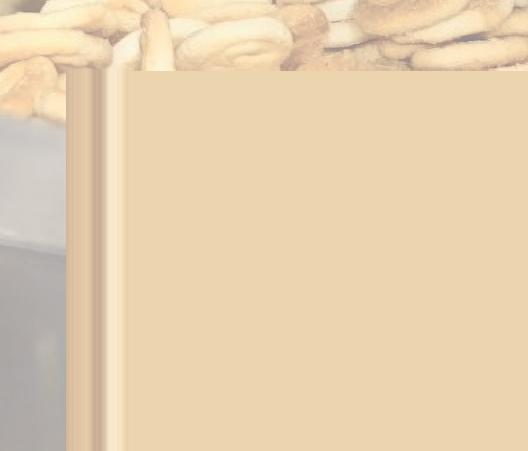
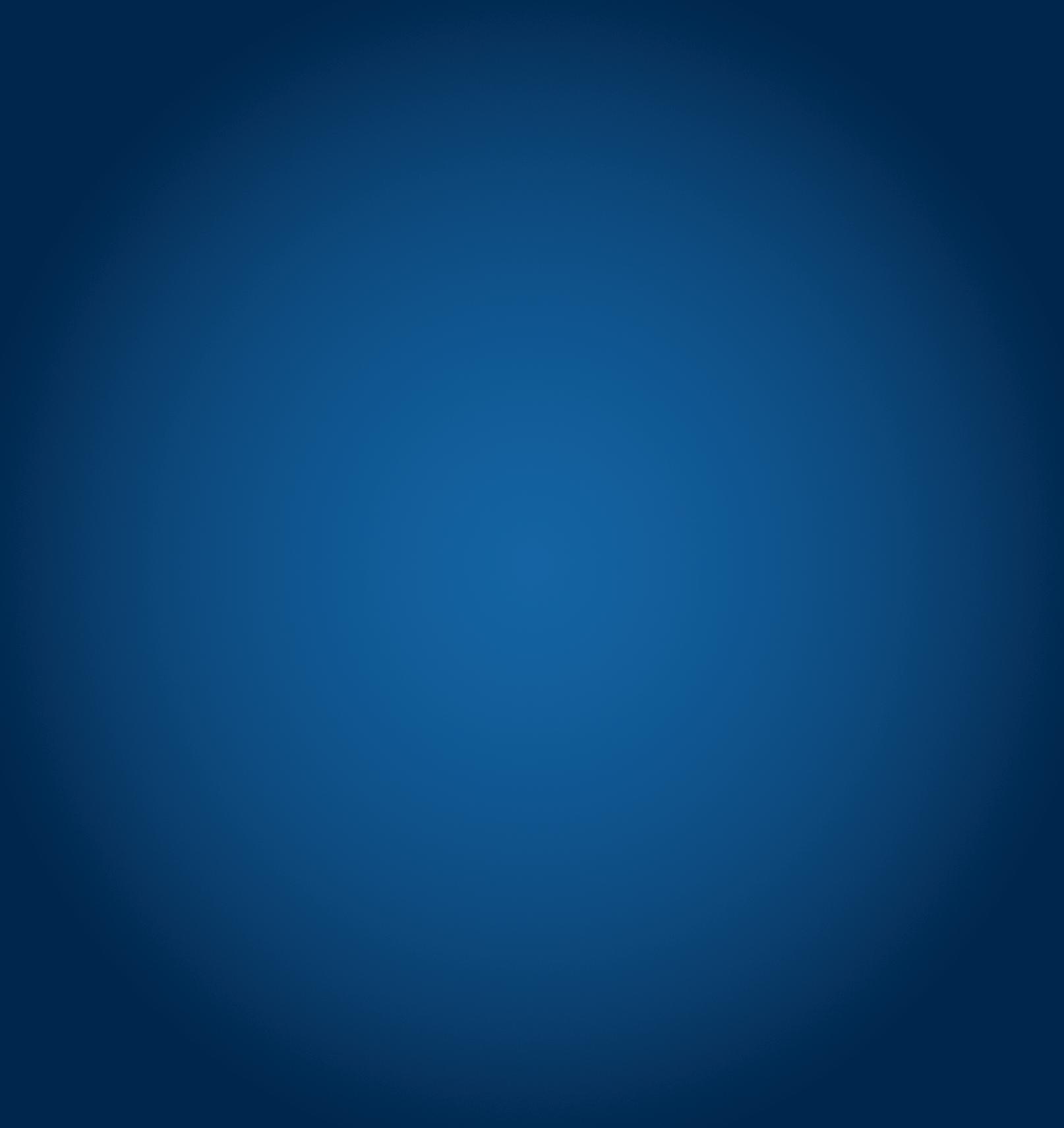
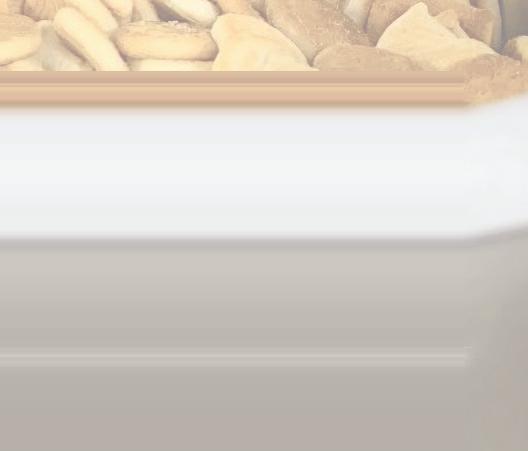
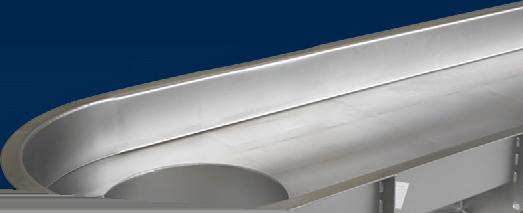
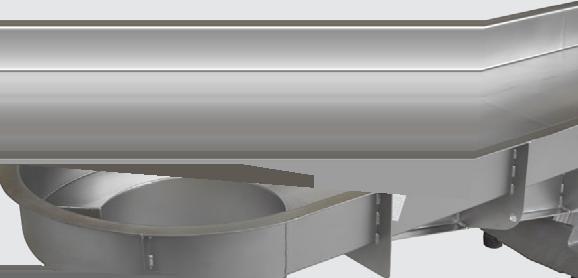

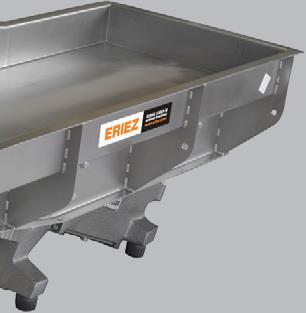
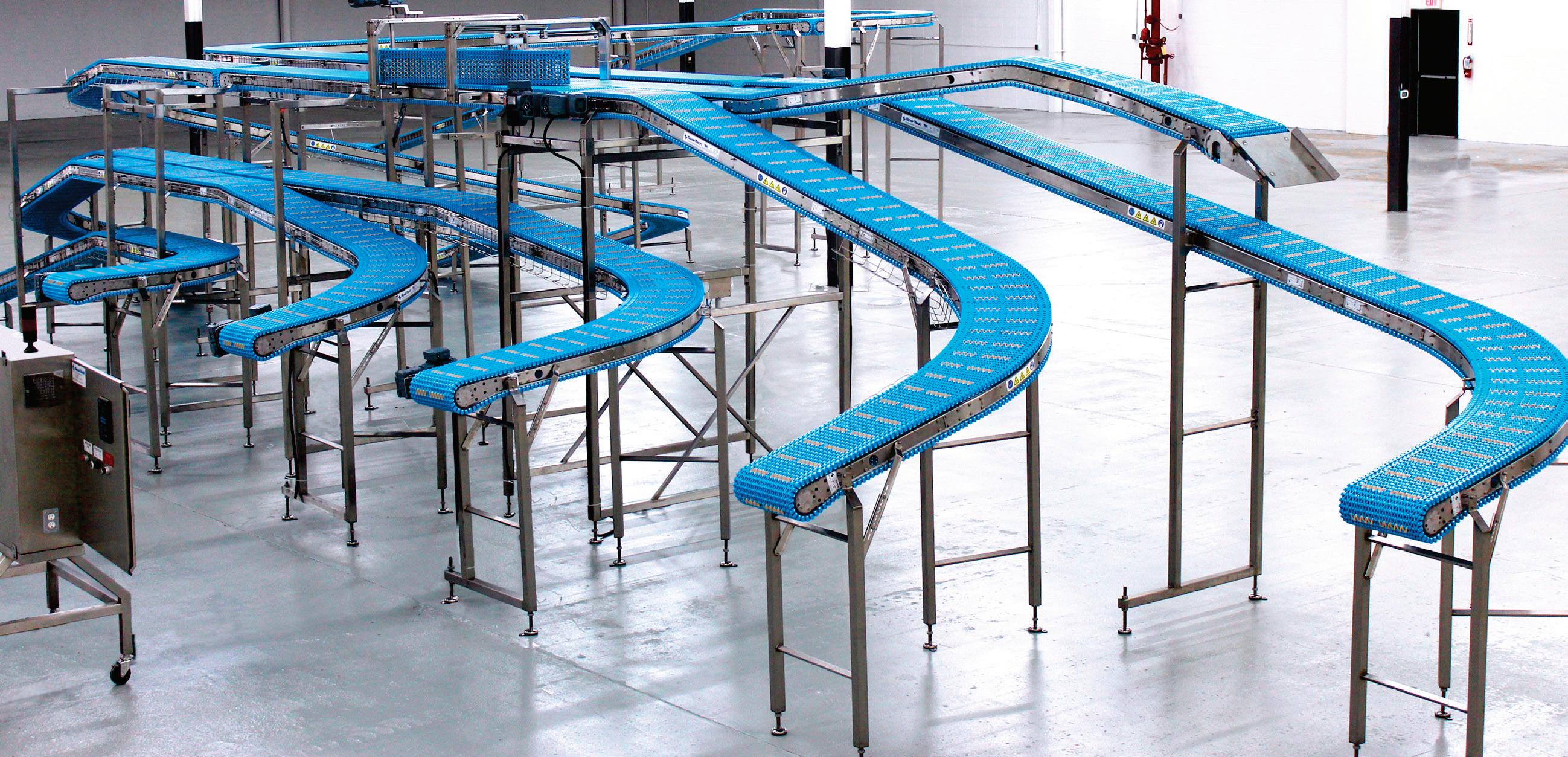

Our conveyor systems seamlessly integrate into your existing setup, streamlining your production processes and reducing manual labor. Trust Span Tech to be your long-term partner in success.
• Tailored Solutions: Our team of experts understands the unique challenges of OEMs. We customize conveyor systems to perfectly fit your manufacturing processes, ensuring optimal performance.
• Advanced Technology: Stay ahead in the industry with our state-of-the-art conveyor technology. From automated sorting to precision handling, our solutions integrate the latest innovations to enhance your production lines.
• Robust and Reliable: Downtime is not an option. Our conveyor systems are built to withstand the toughest conditions, guaranteeing a continuous and reliable workflow for your operations.
• Proven Track Record: Trusted by leading OEMs, we have a proven track record of delivering excellence. Join the ranks of satisfied clients who have experienced unparalleled success with our conveyor solutions.
and Utilization
PMMI white paper on Vision 2030 results
12 Transforming Sales Conversations
Do you know your clients as well as your products?
“ I would say that emotional intelligence is a lifelong journey.”
— Jan Tharp, president and CEO, Infinium Spirits
38 PMMI Member Round-Up Coach K headlines upcoming ELC
42 Emotional Intelligence Embracing and understanding EI
46 Exhibitor Education On the Go Podcasts, webinars, and more to accentuate PACK EXPO
charity had a remarkable 2024
ENSURE PERFORMANCE & RELIABILITY
The official publication of PMMI OEMMAGAZINE.ORG
Sean Riley Editor-in-Chief sriley@pmmimediagroup.com | 571 266 4419
Casey Flanagan Associate Editor
Kim Overstreet Director of Content
Norman Smith Art Director
David Bacho Creative Director
sales@pmmimediagroup.com
Courtney Nichols Director, Client Success & Development cnichols@pmmimediagroup.com
Lara Krieger Senior Manager, Print Operations lkrieger@pmmimediagroup.com
Janet Fabiano Financial Services Manager
jfabiano@pmmimediagroup.com
PMMI Media Group
500 W Madison, Suite 1000, Chicago, IL 60661 www.pmmimediagroup.com
David Newcorn President
Elizabeth Kachoris Vice President, Digital
Kelly Greeby Senior Director, Media Operations
Trey Smith Senior Director, Events
Jen Krepelka Director, Digital Media
Amber Miller Director of Marketing
Joan Jacinto Director, Ad Tech and Search
PMMI, The Association for Packaging and Processing Technologies 12930 Worldgate Dr., Suite 200, Herndon VA, 20170 Phone: 571 612 3200 | Fax: 703 243 8556 www.pmmi.org
Jim Pittas President and CEO
Joe Angel Executive VP, Industry Outreach, PMMI
Glen Long Senior VP
Tracy Stout VP, Marketing and Communications
Laura Thompson VP, Trade Shows
Andrew Dougherty VP, Member Services
SUBSCRIPTIONS
To subscribe to OEM visit: www.OEMmagazine.org/subscribe
To change or modify a subscription, please contact circulation@OEMmagazine.org
OEM EDITORIAL ADVISORY BOARD
Paul Irvine Executive Chairman & Owner, Plexpack
Greg Berguig President, PAC Machinery
Rick Fox III Vice President, Fox IV Technology
Zack Lynch Director of Sales, Nelson Integrated
Colin Warnes Director Sales Engineering & Project Management, ADCO Manufacturing
Stacy Johnson VP Business Development, Hoosier Feeder Company
Individually sele table: 256 color
Measure ent in progress
Sensor swit hing Pro ess alfun tion
By Sean Riley, Editor-in-Chief
I’ll be the first to admit I didn’t grow up pining to be a packaging and processing writer. I knew nothing about packaging and even less about processing. As my career in this industry unfolded over two decades, I think I got the hang of writing about it and sit here now typing away as your humble editor of OEM.
Well, two recent developments impacting our industry make me feel like I did 20 years ago when I didn’t know a case packager from an auger filler. Artificial Intelligence was the first recent headliner that made me feel I was back at square one. Its explosion into everything, including our industry, has been overwhelming, to say the least. Fortunately, PMMI Media Group President Dave Newcorn has been on the A.I. beat from day one and provides an incredible resource for readers on the burgeoning technology. He predicted almost from its widespread release that there would be ramifications for packaging and pro -
cessing, and the data accrued from our survey in our sister publication Packaging World (AI Chat-enabled Packaging Machines to the Rescue? p. 28) reveals that CPGs are already clamoring for it to be embedded in their packaging and processing equipment.
The second development that had my head spinning was tariffs. Writing about it feels like a political landmine, not to mention genuinely understanding the ins and outs of its impact on our industry. I did land on one initial thought, however. With a goal of reshoring, who would work these new jobs when we are already facing a crisis in manufacturing due to hundreds of thousands of unfilled positions? I attempted to paint that picture with our cover story Proposed Tariffs Could Increase Labor Challenges on p. 16. I hope you will give it and our whole issue a good read. As always, if you have any story ideas or any comments, good or bad, please don’t hesitate to reach out at sriley@pmmimediagroup.com. ■
PMMI Business Intelligence’s White Paper “Data Acquisition, Sharing, and Utilization” explores the obstacles and benefits of integrating digital connectivity and data utilization into manufacturing operations to enhance operational efficiency.
By Sean Riley, Editor-in-Chief
PMMI Business Intelligence’s White Paper “Data Acquisition, Sharing, and Utilization” reveals the results of the Vision 2030 panel session at PACK EXPO International. It highlighted the significance of Overall Equipment Effectiveness (OEE) as a key metric for tracking efficiency and data utilization in manufacturing operations. OEE, which focuses on availability, performance, and quality, is often the starting point for companies integrating data capture into their processes. The panelists emphasized the importance of real-time data collection for predictive maintenance and efficiency improvements while acknowledging the challenges posed by legacy equipment and cost constraints.
The collection of real-time data can guide predictive maintenance, as well as yield management and efficiency improvements. Quality data plays a crucial role in OEE, especially for end users; however, legacy equipment, cost constraints, and variable data sources often complicate scaling, making collaboration with OEMs essential for seamless data capture and interoperability. Panelists underscored the need for gradual implementation, ensuring projects secure manage-
“ Data is the new oil.”
ment buy-in and focus on capturing quality data that genuinely influences performance.
They also highlighted the importance of stakeholder support to ensure the most effective use of data, citing the provision of suitable modern PLCs to legacy machinery as an example. “Data is the new oil,” said one participant. A data-centric mindset must flow from the top down to effect change and encourage the use of analytics. All stakeholders must understand the significance of the data they receive and record. Measuring output was seen as the most effective data capture process, as it provides information that can be extracted from most machines, even older models. It is also a necessary step before implementing data processes such as predictive or prescriptive maintenance.
One speaker recommended cultivating a culture of Statistical Process Control (SPC) at both the macro and micro level, explaining: “At the end of the day, operators are going to know what’s going on, but using technology, specifically SPC, at that micro level to engage leadership to say, ‘Hey, there’s something going on in this area. Go look at it.’ And then at the macro level, again, using SPC on top of a data set to say this is noise or this is actually something that we need to pay attention to.”
At the micro level, operators should be able to assess data and alert managers to any issues. Analyzing a data set using an SPC method allows tactical leadership and management to identify issues, enhancing maintenance and efficiency. Panelists stated that dedicated teams should be created for data capture and analysis, where possible.
A key topic among participants in the panel and roundtable sessions was how to enhance data capture processes across more extensive areas of
Configurable CO2 laser Integrator Packages enable OEMs to choose the best combination of laser power, wavelength, and working distance to fit specific application and machine needs.
Factory pre-aligned CO2 laser sub-system include laser source, scan head, controller, software, and mounting hardware ordered as a single part number with harmonized shipping.
Discover
their operations. A representative from a large FMCG (fast-moving consumer goods) multinational shared how they executed a 31-plant rollout for a new data capture process within a year. The company will now roll out 17 additional factories over the next eight months. By employing a gradual implementation process, where they refined their OEE platform
in close collaboration with their SaaS (Software as a Service) provider, they leveraged the experience gained from the initial deployment to replicate the same process through parallel workstreams at various plants. The end user emphasized that in-person deployment leads to improved results, greater engagement with tools, and more effective user-developed applications for the OEE platform. Standardization was recognized as crucial for gathering data from diverse sources (including multiple vendors or OEMs in the end user’s situation) and facilitating solutions’ scalability.
For CPGs, it was seen as imperative that they standardize software programs on different equipment, using systems such as SCADA (Supervisory Control and Data Acquisition) or MES (Manufacturing Execution Systems) to ensure that technology is interoperable. Some participants also flagged the need for OEMs to allow end users access to machine-generated data as a key issue. Following the first roundtable discussion on how to scale digital technologies, participants were asked to vote on which of the suggested solutions they would most likely implement when looking to scale digital technologies across multiple lines, plants, and regions. The most popular solutions were
“ A key theme in the discussion was the need to simplify data capture while ensuring data accuracy.”
‘translating data into understandable information’ (46%) and ‘creating standards and using data to improve [operations]’ (41%) - demonstrating a clear desire for data literacy and effective utilization. The third most popular solution was the ‘gradual rollout of technology’ (26%).
A major barrier to achieving standardization discussed during the roundtable session was the difficulty of integrating legacy equipment into data connectivity networks and data capture processes. Challenges regarding non-standardization are more prevalent with older machines, particularly concerning compatibility with cybersecurity systems or platforms. However, it was suggested that legacy machines could be outfitted with devices that would connect them to digital connectivity networks. A key theme in the discussion was the need to simplify data capture while ensuring data accuracy. Recommendations included installing low-cost sensors and maintaining flexibility in data systems to accommodate diverse protocols from various equipment types. The importance of fostering a cultural shift by engaging employees and clearly demonstrating why data is being collected through actionable insights was emphasized.
Although integrating legacy machinery into digital networks was identified as an obstacle to effective data use, it was also noted that most packaging machinery is easier and cheaper to upgrade than commonly perceived. Participants voted on the results after presenting ideas from the roundtable discussion about the digital integration of legacy equipment into operations. The top three solutions were to implement only what’s necessary to get the job done (47%), upgrade existing automation (42%), and use low-cost sensors (28%).
The white paper highlights the critical need to embrace digital transformation and encourage collaboration across the packaging and processing industries to optimize operational performance. Companies can improve efficiency and minimize machine downtime by standardizing and scaling data processes. Success lies in implementing advanced technologies and fostering a companywide culture that values data as a strategic asset and understands how it is captured and used a strategic asset and understands how it is being captured and utilized. ■
From Vendor to partner: Do you know your clients as well as you know your products?
By Matthew Neuberger, President, Neuberger & Company, Inc.
If you ask most packaging equipment sales teams what they need to improve, you’ll hear the same response over and over: “I just need more product training.”
But here’s the real question:
• Do you know your clients as well as you know your products?
• Do you understand their challenges, priorities, and buying process as thoroughly as you understand your machine’s features and benefits?
As I work with sales teams, I rarely hear someone say, “I need to understand my customer at a higher level.” Yet, this is exactly what separates a trusted partner from just another vendor.
The most successful salespeople know their customers’ work, pressures, and decision-making process so well that they can anticipate challenges before the customer expresses them. When you focus on the right conversations instead of just your product specs, you move from pitching equipment to helping customers solve problems.
This column will show you how to do just that—by asking the right questions to transition from vendor to partner.
Understanding your buyer
Before we dive into partner-level questions, let’s clarify who we are selling to:
Name: Sarah Mitchell
Title: Director of Packaging Operations
Industry: Mid-Sized Food & Beverage Manufacturer
Measured by:
• Overall Equipment Effectiveness (OEE) – Uptime, throughput, and quality
• Cost Per Unit Packaged – Material and labor efficiency
• Waste Reduction – Minimizing product loss due to inefficiencies
• Compliance & Safety Metrics – Meeting industry regulations
What Sarah cares about:
• Production Efficiency – Every minute of downtime costs money. She needs packaging equipment that runs consistently with minimal disruption.
• Cost Justification & ROI – Every capital expense must be justified with clear financial impact—improved uptime, reduced labor, or increased throughput.
“ I need to understand my customer at a higher level.”
• Serviceability & Support – Post-sale support matters just as much as the initial purchase. If the machine goes down, she needs fast solutions.
• Automation & Workforce Challenges – With labor shortages, Sarah needs solutions that require less manual intervention while keeping her team productive.
• Ease of Integration – If equipment is too difficult to implement, it won’t work for her facility. The transition must be seamless.
• Sustainability & Compliance – Increasing industry and government pressure to reduce packaging waste means she needs solutions that support both efficiency and ESG goals.
The questions that transition you from vendor to Partner
Most salespeople start by discussing features. A partner starts by understanding how decisions are made, what pressures exist, and what risks the customer is facing.
• “What are your top three priorities for your packaging lines this year?”
• “What internal pressures are shaping your capital investment decisions?”
• “What’s the biggest frustration your team experiences with your current equipment?”
A great approach here is to play the curious outsider. Act as if you don’t already know the answers, even if you do. This encourages the customer to open up, rather than assume you already have a solution.
“ Do you know your clients as well as you know your products?”
Problem-focused questions: uncovering pain & opportunity
• “What’s your biggest bottleneck today, and what is that costing you in lost production?”
• “What happens when one of your packaging lines goes down? How does that impact your overall operation?”
• “How do you track OEE, and where are you seeing the biggest losses?”
A strategy that works well here is to reverse the conversation. Instead of pushing them toward admitting they need help, gently challenge them in the opposite direction:
• “Sounds like this isn’t a major issue for you right now?”
• “Maybe downtime isn’t having as big an impact as I assumed?”
If they push back and defend the problem, they’ll open up more about its impact.
Financial justification questions: Helping Sarah build an internal business case
• “What does a 1% increase in uptime mean in dollars for your operation?”
• “How does your leadership team typically evaluate capital investments? What’s most important to them?”
• “Would it be helpful if we modeled out the cost savings potential of upgrading your system?”
Instead of telling the customer they need to justify ROI, share an example:
• “I was just working with another plant manager who thought his costs were in line, but when we mapped out the downtime impact, he realized he was losing over $500,000 a year in missed production. Could that be something worth looking into here?”
Stories remove sales pressure and allow customers to see their own issues through someone else’s experience.
Competitive differentiation questions: Standing out from other vendors
• “What is something you’ve always wanted packaging equipment suppliers to do?”
• “What has your experience been with implementation—have past upgrades gone smoothly?”
• “If you could redesign your packaging process from scratch, what would you do differently?”
• “What is one thing you wish packaging equipment suppliers would start or stop doing to make your life easier?”
Don’t jump to the solution immediately when a customer shares a complaint about a past experience. Instead, keep them talking:
• “That sounds frustrating—what did that cost you?”
• “What did you end up doing to work around it?”
This helps them fully process the pain of their previous supplier’s failure and makes them more open to a better alternative.
• “What is the ROI and time frame that would make this worth exploring further?”
• “Would it make sense to set up a site visit to evaluate how our solution fits within your operations?”
• “What would need to happen internally for this project to move forward?”
A strong approach here is to set clear expectations before the close:
• “If we put together a solution that addresses your concerns and meets your ROI targets, what would happen next?”
If they hesitate, you’ve identified an obstacle before the official close.
Most salespeople know their products inside and out. But if you don’t know your customer’s business, challenges, and decision-making process, you’ll always be treated like a vendor instead of a partner.
The best salespeople in 2025 will:
• Speak their customer’s language—efficiency, ROI, compliance, automation.
• Anticipate challenges before the customer even verbalizes them.
• Use questioning strategies to guide conversations, uncover real needs, and create urgency.
Selling packaging equipment isn’t about pitching features—it’s about helping customers make better business decisions. And when you do that, you won’t just win a sale—you’ll earn long-term partnerships that drive repeat business. ■
The U.S. already faces a critical labor shortage, with tari s threatening to reshape and reshore manufacturing.
By Sean Riley, Editor-in-Chief
As the Spring issue of OEM Magazine went to print, President Donald Trump tasked his administration with establishing new global tariff levels for imported goods. A 25% duty on imports from Canada and Mexico was suspended following agreements with both countries to strengthen border and crime enforcement efforts. New tariffs with China remained and China announced a series of countermeasures, including additional tariffs on American imports. Mexico and Canada also threatened tariffs on U.S. imports if the U.S. tariff pause was lifted.
Because of these numerous uncertainties, the landscape of American manufacturing—including the packaging and processing sector—finds itself at the mercy of a complex interplay of trade policies and labor dynamics. President Trump’s ambitious plan to impose sweeping tariffs on imports to revitalize domestic production is at the core of this. However, this approach encounters a significant challenge well-known to those in packaging and processing: a shortage of skilled labor to meet what could be a surge in factory jobs.
Trump’s proposed tariffs aim to make foreign goods more expensive, thus encouraging companies to move production back to the U.S. The National Association of Manufacturers (NAM) has expressed apprehension about the potential impact on supply
chains and manufacturing costs. Jay Timmons, NAM President and CEO, emphasized the importance of maintaining the benefits derived from the United States-Mexico-Canada Agreement (USMCA), strengthening regional supply chains and economic ties.
“Protecting manufacturing gains that have come from our strong North American partnership is vital. The success of President Trump’s landmark trade agreement, the United States-Mexico-Canada Agreement, has strengthened North American supply chains and bolstered economic power across the region, boosting jobs, wages and investments here in the United States,” Timmons said, referencing the USMCA from the president’s first term. “Thanks to this agreement, one-third of critical U.S. manufacturing inputs now come from Canada or Mexico, rather than from competitors like China that often engage in unfair trade practices.
Timmons highlighted the risk these tariffs pose to manufacturing competitiveness, particularly for small and medium-sized enterprises that may struggle to adapt to the increased costs and supply chain disruptions.
An overlooked aspect of the administration’s vision to reshore most manufacturing is complicated by the reality that many manufacturing positions remain un-
Get way ahead with adaptive automation
Levitating planar movers
Scalable payload kg
Individual product transport
6D motion
Velocities up to 2 m/s
Free system layout
Elevate your automation game with XPlanar. Developed in-house by Beckhoff, this mechatronic system makes your production literally fly with magnetically levitating movers and base tiles that you can arrange to fit your unique applications – assembly and packaging, pharma and food, entertainment and beyond. So, what will you do with XPlanar?
Processing with up to 6 degrees of freedom
Transport and processing in one system
Wear-free, hygienic and easy to clean
Multi-mover control enables parallel and individual product handling
Fully integrated into the powerful and standardized PC-based Beckhoff control system
(TwinCAT, PLC IEC 61131, Motion, Measurement, Machine Learning, Vision, Communication, HMI)
filled. Recent data shows that around 450,000 manufacturing jobs are unfilled, underscoring the ongoing labor gap that has reached epidemic levels.
NAM emphasizes that 60% of its members consider hiring and retaining employees their top concern, even before the proposed tariffs. This issue is set to escalate, with forecasts predicting a need for an additional 3.8 million workers in the coming years. Factors such as an aging workforce, increased industrial demand, and new government-backed semiconductors and green energy initiatives contribute to this impending need.
Additionally, with reshoring and the potential effects of Trump’s immigration policies—which target the deportation of undocumented workers and restrictions on legal immigration—these measures could further diminish the available workforce, worsening the challenges packaging and processing manufacturers encounter.
Efforts to address the labor gap have included initiatives by manufacturing businesses and trade
groups to attract younger workers through paid training programs. These programs offer high school students the opportunity to earn journeyman’s certificates, equipping them with valuable skills and often leading to employment. Despite these efforts, the perception of manufacturing jobs as undesirable persists, with many young people deterred by the demanding schedules and the allure of more flexible work arrangements in other sectors.
The educational system’s role in addressing the labor shortage cannot be overlooked. There is a growing call for educational institutions to align more closely with industry needs, emphasizing vocational training and STEM education. For example, PMMI’s PMMI U elevates the talent level within the entire industry through cost-effective, convenient training and development opportunities and by connecting employers to the next-generation workforce. By fostering partnerships between schools and manufacturers, PMMI sees the potential to create a pipeline of skilled workers ready to meet the demands of modern manufacturing. PMMI’s Career Toolkit provides resources to help manufacturers address the critical shortage of skilled employees and help promote awareness of careers in the packaging and processing industry. A nation-
We help OEMs to focus on and optimize the other critical aspects of their application and machine, while we handle the containers. With over 25 engineers on the team, we offer a wide range of solutions that pair well with your equipment to make it run more efficiently and give you an edge up on your competition.
PMMI’S RECENT WHITEPAPER “2024 Technology & Workforce: Using Smart Technologies to Bridge the Skills Gap” highlights how technology can help address not only the labor shortage, but high turnover and the widening skills gap.
Download it at pmmi.org/businessintelligence/industry-reports.
wide approach throughout manufacturing could help dispel outdated perceptions of factory work and highlight the opportunities for innovation and advancement within the sector.
The potential for automation to address some labor shortages is being explored. While automation can boost efficiency and decrease reliance on human labor in specific areas, it also necessitates a skilled workforce operating and maintaining advanced machinery. This transition calls for training programs that provide workers with the technical skills essential for success in increasingly automated environments. Companies investing in automation must balance these innovations with retaining a human workforce capable of overseeing and complementing automated systems.
As manufacturing prepares for the potential impact of new tariffs, some companies are exploring strategies to ease what they anticipate as a financial burden. Some are renegotiating supplier contracts, reorganizing supply chains, and advocating for tariff exemptions. However, the long-term effects of these trade policies remain uncertain, particularly for those heavily reliant on imported materials.
The technology sector, for example, is subject to tariffs based on the foreign content and minerals in its products. Manufacturers reliant on imported metals, such as aluminum, zinc, and nickel, are especially vulnerable, given the limited domestic production of these materials.
The ripple effects of these tariffs reach beyond their immediate financial implications. They also pose a strategic challenge for companies that now need to reevaluate their global supply chains. Businesses are increasingly considering nearshoring options, which involve relocating production to neighboring countries like Mexico, potentially striking a balance between cost efficiency and reduced tariff exposure. This shift could redefine regional trade dynamics and alter the competitive landscape for U.S. manufacturers. ■
The World Packaging Organization’s first corporate partner provides packaging permeability and reliability testing instruments and services to a global customer base.
By Sean Riley, Editor-in-Chief
Labthink International came from humble beginnings when it began testing packaging and packaging materials in a discarded garage in 1989. Over the next 35-plus years, the new PMMI Member has filed nearly 100 patents as its portfolio grew to include all aspects of packaging testing, from gas permeability testers, oxygen/water and vapor transmission systems to thickness, tensile strength analyzers.
OEM Magazine sat down with Labthink International to share its story and offerings with fellow PMMI Members.
OEM: Can you provide a brief history of your company? Labthink Instruments was established in 1989 and quickly became involved in establishing test and measurement standards required for a packaging market that needs consistent test and quality assurance procedures. Labthink International was formed in 2012 and opened its offices in the Greater Boston area in Medford, Massachusetts.
In 2020, our European subsidiary, Labthink GmbH, was established in Frankfurt, Germany, with a multilingual international staff. More recently, in 2024, the company opened a Middle East office in Dubai and an Asian Regional office in Malaysia.
Since its establishment in 1989, Labthink has filed almost 100 international patents, approximately 50% of which relate to measuring permeation and classifying barrier materials. Labthink is the first corporate member of the World Packaging Organization, and representatives serve on ASTM standards development committees.
OEM: What sets your company apart in the industry—what makes it shine? We are fanatical about customer service. Priorities change, but values stay the same.
OEM: What drove our decision to join PMMI? PMMI is a great organization with excellent resources
Labthink’s C406H Oxygen /Water Vapor Transmission Rate Test System tests oxygen and water vapor transmission rates in the same unit. It allows for six package samples to be tested with independent data.
for manufacturers. It is a fantastic way to engage with our target audience and help them solve their test and measurement challenges. We admire PMMI and stand for its values.
OEM: Have you participated in any PMMI programs since becoming a member or have plans to in the future? We have exhibited at PACK EXPO International and PACK EXPO Las Vegas.
OEM: What’s your approach to new product development? How do you generate ideas for new machines and market-test them? We invest heavily in R&D and are keen to receive customer feedback. We also regularly undertake custom-engineered projects, which often result in developing a standard product for niche markets.
OEM: How has your product line broadened over the years? The Labthink product line is constantly evolving. Last year we introduced the first dual-sensor combination of WVTR (water vapor transmission rate) and OTR (oxygen transmission rate) analyzer. We now have the widest range of permeation analyzers available anywhere in the world and an extensive range of mechanical properties testers.
OEM: How do you balance standardized machine configurations with those requiring customization? Most of our equipment is standard, but many pieces feature a wide range of options, which permits customization. We are also happy to pursue
The quality of Yaskawa products is second to none, but Yaskawa Quality goes beyond that. It’s the total experience of purchasing Yaskawa products and working with people.
custom-engineered products if we can help solve a customer’s challenge. We then look out for other customers who may benefit from the same or similar solution.
OEM: Where do you find most of your employees? What sort of background or specific talents/skills do you look for? We look for well-qualified engineers; over 80% of our worldwide employees have formal engineering qualifications. Above all, we look for experienced employees with exceptional customer service.
OEM: Why do employees love working for your company? Labthink employees love working for Labthink because of the variety they encounter, the
“one company” philosophy we engender, and the approachable management team.
OEM: What’s your process for handling a customer’s initial inquiry and needs assessment? We like to arrange a face-to-face meeting, either in person or via video conference, to make certain that we understand the customer’s requirements. During this meeting, we can draw upon our experience in similar situations to provide the most appropriate solution for the customer, which will address not only their current challenges but hopefully help them anticipate future events.
OEM: Once a customer issues a P.O., what happens next? What can they expect? Once a PO is received, the customer will receive an order acknowledgment with an updated delivery schedule. The customer is introduced to our aftermarket team, with whom order updates are communicated. Near the delivery time, the customer will be contacted to arrange a startup and training appointment with one of our service teams. Lastly, once a startup has been accomplished, we survey all customers with a satisfaction survey. Our aftermarket team follows up on anything less than a perfect score to determine what we can do better.
As an OEM, designing and building conveyors to integrate with your primary product comes with many hidden expenses...
When established: 1989
Range of products: So flexible material testing instruments to ASTM, ISO and TAPPI standards.
Executive team: Haimo Jiang, Craig Primiani
International Headquarters: Medford, Massachuse s
Number of employees: 200+
Number of field service personnel: 40 plus worldwide
Facility square footage: 150,000+ square feet globally; all facilities
Geographic sales and support areas: Worldwide Company website: labthinkinternational.com
OEM: What influences a new machine’s turnaround/delivery time, and what happens during this process? Each piece of equipment has a standard delivery time. Some of the more popular units are kept in stock in small quantities. The current manufacturing schedule influences delivery time. Whenever possible, we seek a non-binding “agreement to purchase” from the customer to provisionally allocate space in our production schedules.
OEM: How do you handle field service and training? Do you have dedicated training personnel, or do Service Technicians typically conduct training? Service technicians conduct startup and training. Customers also receive unlimited free of charge video training and troubleshooting.
OEM: Do you have any plans for facility expansion or new operations? We are always considering our growth strategy. In the last five years, we have opened direct company sales and service centers in Europe, Asia, and the Middle East, in addition to our existing operations in the U.S. and China. We recently opened a new testing as a service laboratory in our U.S. head office as well as another in Frankfurt, Germany.
OEM: What challenges do you foresee affecting your firm and all companies in this industry? The biggest challenges come from keeping pace with the development of new and/or sustainable packaging materials, many of which present their own test and measurement challenges. ■
configure and reconfigure exact encoder
No need to change wheel diameter or size, TRP fits into your system parameters
Reliable and precise output
Fast installation for mounting on any surface and in any orientation
Reduce cost and inventory for a simplified system design
A dedication to innovation and a history of employee longevity shapes its response to evolving industry challenges.
By Sean Riley, Editor-in-Chief
In 1962, Jim Shuttleworth embarked on a packaging machinery journey with Shuttleworth, Inc., Huntington, Indiana, which focused on high-speed hydraulic case packers for bottles and cans. After a successful first decade, Shuttleworth found its niche with developing the SlipTorque® conveyor. This innovation represented a turning point in 1972, providing gentle handling and customizable features that distinguished the company in a competitive landscape.
The Slip-Torque conveyor's ability to prevent product crushing and overfeeding resonated with industries worldwide, leading to the establishment of a facility in Zulte, Belgium in 1979 to meet European demand. Over the years, Shuttleworth continued to evolve, introducing the Slip-Trak® conveyor frame in 1990, designed for clean room, electrostatic discharge (ESD) and harsh environment applications. This adaptability was further demonstrated by opening offices in Kuala Lumpur, Malaysia, in 1996, highlighting the company's commitment to expanding its global presence.
The development of the Low Profile conveyor for better operator ergonomics, Zone Control conveyor for electronic and silicon wafer handling, and stainlesssteel caustic designed Easy Clean conveyor for food and healthcare markets between 1997 and 2002 showcased Shuttleworth's dedication to industry-specific solutions.
Under the leadership of Jim’s wife Carol Shuttleworth, who became President and CEO in 2003 following the passing of the founder, the company continued to originate and its acquisition by ProMach in 2011 further solidified its position as a leader in the market.
Shuttleworth's involvement with PMMI is crucial in staying ahead of the competition. Jim and Carol Shuttleworth, and Bret Ranc were each part of the decision to join PMMI and Shuttleworth has been an active member. Carol was instrumental in creating the Packaging and Processing Women’s Leadership Network (PPWLN). Shuttleworth has sent team members to the Leadership Development Program, has members on PMMI’s Global Marketing and Trade Show committees, and sends representatives yearly to PMMI’s Annual meetings. This engagement benefits Shuttleworth and contributes to the broader industry dialogue on best practices and innovation.
Shuttleworth's product line has expanded significantly over the years, moving beyond the transportation of product to include machines for accumulation, stacking, rotating, and more. This diversification allows the company to serve nine different industries, each with unique requirements. The company embraces 6S lean to keep everything organized and help with throughput, only working on what needs to be worked on, focusing on the next task to keep less on the floor and having it flow through manufacturing more smoothly. They also do root cause analysis and corrective actions for quality issues and have done Value Stream Mapping for each department.
Project management at Shuttleworth operates like a well-oiled machine, with projects assigned according to their
“ Many [employees] have been with the company for decades— including some up to 40 years...”
complexity and resource availability. The process starts with a discovery meeting to assess customer needs, followed by onsite visits and testing to ensure that specifications are met. After a purchase order is issued, a comprehensive process involving design reviews, engineering, and customer updates guarantees a seamless transition from order to delivery. As the project nears completion, internal Factory Acceptance Tests (FATs) occur, and customer FATs (virtual or inperson) are conducted as needed. Once the system is shipped, the project team hands off the project
to its aftermarket department. Should a challenge arise in the field, Shuttleworth employs dedicated Service Technicians and Mechatronic Technicians, but will provide additional support from its controls department if needed.
Shuttleworth's workforce is central to its 63 years of success. It is characterized by long-tenured employees whose dedication and expertise are invaluable. Many have been with the company for decades—including some up to 40 years–contributing to a culture of tribal knowledge and pride in one’s work. This commitment is reflected in the company's approach to product development, which involves partnering with other OEMs to enhance their offerings
and meet diverse industry needs.
The company's focus on cultivating talent through partnerships with local universities like Purdue University and the Rose-Hulman Institute of Technology and a strong summer internship program further strengthens its position. By investing in the next generation of engineers and technicians, Shuttleworth ensures a steady flood of fresh ideas and skills. This approach not only addresses the industry's ongoing challenge of finding qualified personnel but also reinforces the company's commitment to fostering a culture of continuous improvement.
In addition to its technical prowess, Shuttleworth’s emphasis on customer relationships is a cornerstone of its operations. The company prioritizes understanding each client's unique needs,
tailoring solutions that meet and exceed expectations. By fostering strong client partnerships, Shuttleworth builds trust and loyalty, ensuring long-term collaboration and mutual success.
A recent expansion of over 55,000 square feet at its Indiana headquarters highlights Shuttleworth’s readiness to meet future demands. With sustainability at the forefront of every CPG’s approach in 2025, Shuttleworth is proactive in developing solutions that align with eco-friendly practices. As companies seek to transition from plastic to paper, Shuttleworth conveyors' compatibility with paperboard canisters and containers offers clients options that reduce environmental impact without compromising performance. ■
When established: 1962
Range of products: Accumulation/Bu ering Solutions, Machine Feeders, Laners, Stackers, Rotating/Orienting Solutions, Sorting, Custom conveyor and Product handling solutions
Executive team: VP – General Manager: Dan Nasato, North America Sales Director: Todd Eckert, Director of Engineering: Connor Hartford, Production/shipping volume per year: 100+ Systems & Solutions/year
Headquarters / manufacturing location(s):
Headquarters & N. American Manufacturing – Huntington, IN European Manufacturing – Zulte, Belgium
Number of employees: 93
Number of field service personnel: 3
Facility square footage: 100k+ sq (manufacturing)
Geographic sales and support areas: North America, Europe, Southeast Asia
Company website: www.shu leworth.com
Annual revenues: 20 to 50 million
New research from PMMI Media Group shows an appetite among CPGs for changing the way operators and technicians interact with machines on the plant floor. Is it time for packaging and processing equipment to come with a ChatGPT-style interface?
By Dave Newcorn, President, PMMI Media Group
It’s no secret that CPGs are suffering from a workforce problem. According to our Annual Outlook Report, about 80% of Packaging World readers are having trouble finding and retaining packaging line labor. It’s hard to find operators and technicians, and costs associated with training them becomes burdensome with high turnover that is increasingly common in the industry.
Can AI help? Now that we’ve all had a chance to experience generative AI in the form of a chatbot, flaws and all, it’s not hard to see where this is headed. It’s already being implemented. But what if all operators and technicians could chat with their machines directly?
Whether that means getting the right answers for a changeover procedure or trouble-shooting a root
cause of downtime, a natural-language interaction with the equipment could be more intuitive than operating an HMI. That could reduce the burden of skill required to operate and maintain the machine using today’s HMIs. And that’s where AI could become a useful answer for the workforce issues that CPGs and food processors are experiencing.
At a PMMI event last year, Danone’s Director of Innovation & Packaging Engineering Shawn French asked the audience, “Do you remember your iPhone training?” It was a tongue-in-cheek reference to the fact that the groundbreaking user interface, which today we all take for granted, was so intuitive at the time that no training was needed to operate what is essentially a highly sophisticated, pocket-size com-
What if the AI chat on the machine could respond with links to short videos based on the question being answered, e.g., how to do this or that on the machine?
puter with a novel interface.
It’s true that packaging machines are not cell phones; with technical data, warnings, or parameters that are difficult to simplify, along with diverse, complex operational states, safety considerations, and even regulatory constraints, HMIs are necessarily more complex than a phone and require skill to operate. Nor are we suggesting that HMIs will go away.
But what if AI-powered chat were built into every machine? Could that help simplify operation and address the worker quality and quantity problem?
We put the question to readers like you, who work at CPGs. The survey was conducted via email to Packaging World’s CPG and brand owner audience in December 2024 and reflects the views of 95 total respondents.
As the charts show, most respondents indicated a high degree of interest in integrating AI chat into packaging and processing equipment (see top chart, page 70). As one respondent wrote, “Anything that creates a venue for maintenance or operators to get quick ‘how-to’ answers is a no-brainer.”
Another wrote, “Using an AI chat that was fully capable of accessing the equipment manuals and repair/ setup aspects could be much easier and faster than searching either on paper on even electronically.”
Others have started to use AI elsewhere and concur on the potential: “We are finding AI helpful in so many areas now. Writing job postings, communicating with employees in different languages. It would be helpful to get immediate answers to the issues we face during production.”
Another wrote, “It could help the next generation of operators to understand and troubleshoot the equipment.”
However, there were skeptics.
“Details, details, details,” one respondent cautioned. “Need to understand the scope of the tool and
Would it be useful if operators and technicians could use “push-to-talk” functionality to speak their question to the machine (or to a phone or tablet), instead of typing out the question on a keyboard?
AI chat not needed at all, with or without voice inputs No, typing is good enough
but
Yes, this would be ver y helpful
interaction(s) with HMI on the shop floor. Would need to understand how the AI tool interfaces with nonOEM plant or company specific process(es) to avoid conflicting instructions.”
Another said, “Our industry would function more safely with well-defined logic. AI at this point isn’t transparent enough in its decision making.”
A third respondent suggested that AI chat doesn’t go nearly far enough. “AI interactions will not be helpful. What will be helpful is when AI can make decisions during a run without interacting with operators. For example, if print registration starts to slip, AI makes micro-adjustments to maintain registration on its own, no operator involvement. Having the equipment interacting with the operators will cause more headaches than it’s worth.”
Now that you’ve taken the sur vey, has your answer to the rst question changed? Would adding AI chat capability to your equipment be useful?
No, today’s HMIs are good enough Nice
Yes, this would be ver y helpful
The reality is that this kind of truly autonomous operation remains years in the future for a host of reasons related to safety, regulatory, liability, and technology-readiness issues. Also, it’s engineering of a different magnitude from the OEM’s perspective: true autonomy requires changes in control logic, sensor data, and the addition of robust machine learning models that go well beyond what a chatbot interface requires. The AI chat described in this survey is an operator and technician support tool and communication channel, not dynamic or autonomous machine operation.
Recognizing that no technology is perfect, another countered not to let the perfect get in the way of the good. “Instant response is better than no response or searching for a manager.”
And another said, “More intuitive HMIs would be higher on my priority list.” Another dismissed any issues with HMIs, saying “Operators generally learn how to operate the equipment and become familiar with the machine setting screen info.”
The survey was designed to expose different po -
When it comes to generative AI chatbots that we’ve all tried online, sometimes the answers provided are flat-out wrong, even as they are wrapped in self-assured language. Particularly notable in the early days of AI chat, this effect is charmingly referred to by experts as a “hallucination.” The rest of us would call it “Making #### up.” There are many reasons why this is, and the AI companies are working hard to reduce this. (And many believe that the problem has gotten better since ChatGPT 3.5 was released two years ago.)
However, the most significant way to greatly reduce risk associated with providing incorrect answers is by training AI chatbot only on manuals, drawings, videos and other material directly from the manufacturer. This technique is known as retrieval-augmented generation (RAG), which is where generative AI is directed to pull information exclusively from carefully curated sources and documentation rather than relying on generic pre-trained data or web knowledge. This approach greatly reduces the risk of hallucinations, as the AI generates answers based only on the trusted sources it’s given. And can be explicitly instructed to say “I don’t know” in cases where it’s less than 100%, or some other specified threshold percentage, confident in its answer.
Obviously, the answers are only as good as the data that’s fed in. If machine manuals aren’t up to date, or aren’t in digital form, that needs to be addressed first. Also, plants may have SOPs that vary from what the OEM specifies (and those SOPs may vary from plant to plant). All such variations would need to be either accounted for or standardized before being fed into the model. (This also means putting into place a serious process in place to ensure that manuals, SOPs, and other documents are up to date at all times. That speaks to robust content management practices and strict version control methodologies.)
Another serious concern is security. There’s no way most CPG IT departments would allow machines to
be connected to the internet to access a cloud-based AI. That’s why there’s so much buzz right now in the AI community about self-contained language models that are designed to run on a local machine, which some have taken to calling small language models (SLMs). No internet connection required.
Also, SLMs can run on any PC-based control or PC-based HMI without an internet connection. That’s because they are a fraction of the size of current large language models, require a fraction of the computing power, and can yield performance coming close to or even exceeding that of large language models, depending on the application. They also eliminate any latency associated with round-trip communications to the cloud. Most experts now believe that the future of AI in the plant revolves around self-contained AI based on highly tuned and purpose-built SLMs that operate locally within the machine or plant.
A huge issue is trust. For people to trust answers from AI chat, it must be configured to cite sources for any answers it provides (“Based on the OEM manual, section 2.3…”). This helps dispel the “black box” perception that many have regarding AI.
Finally, the ability to tap into error histories, “last modified by” records, or maintenance schedules presumes a level of integration with not only the machine’s PLC, but any external Manufacturing Execution System (MES) or Computerized Maintenance Management System (CMMS). The reality is that these systems may be running different versions, not integrated, or only partly digitized. (It also presumes a maturity level in “Industry 4.0” that is simply not present at many plants.) A phased approach starting with static manuals or information from a fixed repository is a good starting point before one tries to enable the integration of advanced diagnostics that require real-time data from sensors and control systems.
For
For TECHNICIANS, which of the following scenarios would be useful regarding an AI chat interface? Check all that apply.
tential features and capabilities to CPG professionals involved in buying and supporting equipment, including the ability for AI to:
• Respond to operators in a chat with links to short videos
• Operate in multiple languages
• Offer “push-to-talk” functionality bypassing the need to type
A majority of respondents said these features would be “very helpful” on their packaging and processing equipment. “Shortcuts to helpful videos, speaking to equipment on info needs/changes instead of just typing info in would be very helpful additions related to AI capabilities,” wrote one respondent.
Of course, plants can be loud, and factory-specific tuning of the audio or special microphones may be required for push-to-talk functionality.
The survey then went on to ask respondents to score a handful of use cases for both operators and technicians. (See charts)
The survey was also a bit of a trojan horse, designed to educate respondents about all the possibilities. That’s why we tacked on a question at the end, asking respondents whether their initial answer (about whether AI chat embedded into equipment would be useful) has changed once they went through the survey and saw all the potential use cases. Those answering “very useful” jumped from 59% to 70%.
Finally, we asked whether AI chat functionality would be more useful in packaging equipment or processing equipment. The clear majority said it’s equally useful in both, though there were a fair number that leaned more toward wanting to see it on packaging equipment.
The tools available to both OEMs and CPGs for incorporating AI are rapidly evolving. Several of the large automation suppliers including Rockwell Automation, Siemens, Schneider Electric, Beckhoff, and B&R have released “copilot” style functionality for writing PLC code, and some are already experimenting with AI chat style functionality. There are also several third-party tools available today that bear exploring. It’s early days still, but the appetite does appear to be there for exploring how AI and AI chat could support the operation of packaging and processing equipment while reducing the potential burden around training and support, leading to more uptime.
While a natural language interface can reduce friction, it should be clear that operators and technicians will still need fundamental training to interpret machine feedback safely and efficiently. At the end of the day, packaging equipment is mission-critical, and AI chat is not a substitute for thorough instruction and understanding of how equipment operates. A poorly trained operator can make mistakes even with top-notch AI chat. Nor, as indicated earlier, is AI chat a replacement for the HMI. Sometimes it’s just faster to press a button.
But incorporating some sort of AI chat seems sensible and, perhaps, inevitable. The first step would be a pilot project with a cooperative OEM and newer/lessexperienced operators who might benefit the most. ■
Don’t miss these upcoming training and development opportunities!
Technicians are the face of your organization. Learn the customer service skills to become a trusted advisor to customers.
APRIL 29-30, 2025
PMMI; Herndon, VA
JUNE 17-18, 2025
Enercon; Milwaukee, WI
SEPTEMBER 29-30, 2025
PACK EXPO Las Vegas; Las Vegas, NV
PMMI MEMBERS ONLY
Enhance your leadership skills to be recognized as an influential leader in the packaging and processing industry through interactive learning, self-awareness tools, and networking strategies.
MAY 14-15, 2025
PMMI; Herndon, VA
OCTOBER 21-22, 2025
PMMI Media Group; Chicago, IL
Maximize sales at PACK EXPO through preshow preparation, effective selling strategies, and post-show follow-up techniques.
JUNE 26-27, 2025
The Ritz-Carlton Dallas; Dallas, TX
AUGUST 26-27, 2025
PMMI Media Group; Chicago, IL
Learn systematic consultative selling techniques to become trusted advisors to customers purchasing packaging, processing, and automation equipment.
APRIL 22-23, 2025
PMMI; Herndon, VA
NOVEMBER 13-14, 2025
JW Marriott Nashville; Nashville, TN
PMMI MEMBERS ONLY
Learn the most effective strategies and techniques for delivering exceptional training across all employee skill levels with this industry-specific train-the-trainer program.
MAY 1-2, 2025
PMMI; Herndon, VA
JUNE 19-20, 2025
Enercon; Milwaukee, WI
SEPTEMBER 29-30, 2025
PACK EXPO Las Vegas; Las Vegas, NV
Identify and mitigate potential health and safety hazards, ensuring compliance with industry standards and regulations.
SEPTEMBER 27-28, 2025
PACK EXPO Las Vegas; Las Vegas, NV
For more information or to register for our upcoming workshops, visit pmmiu.org
According to a Packaging World Survey, CPGs are paradoxically either adding or not adding automation and robotics for very similar, predictable reasons.
By Sean Riley, Editor-in-Chief
The results of a Packaging World reader survey of CPGs on automation and robotics contained a running theme that it could have been a survey on workforce.
First things first, however, according to those surveyed, companies are very interested in adding automation and robotics. Almost two-thirds of respondents (65%) indicated they would add automation equipment, cobots, or robotics to their packaging operations in the coming year. Two of the strongest reasons cited for adding the new technology center around labor issues.
In fact, the number one reason in favor of adding automation equipment, as cited by 61% of respondents, was reducing the cost of labor/good ROI case. Automation and robotics have evolved to the point where operations can justify to the C-suite that it is more cost-effective over the long term to add automation vs. the high cost of labor or, as 34% indicated, the difficulty in finding labor to start with. In a workforce crisis that has reached epidemic levels, automation is being highlighted by CPGs as a leading solution.
Rick Rice, controls engineer/project manager for Crest Foods, evaluated the survey data and was not
shocked by the correlation between adding automation and robotics and workforce issues.
“I’m not at all surprised by the results,” Rice says. “The workforce simply did not come back after the pandemic. The diminished labor pool seems to be the justification needed to make [adding automation and robotics] happen.”
A survey respondent from Territorial Seed Company echoed Rice’s sentiments when he completed the survey, adding that the increase in innovation in automation and robotics, coupled with labor shortages, makes their addition all but inevitable.
We would be remiss if we didn’t add that speed/ throughput/volume was the second most cited reason for adding automation, coming in at 35%. Still, we feel, and we may be editorializing too much here, that is more of a typical response, as we have found through decades of covering the packaging industry that most capital equipment purchases are made with an aim toward improving output.
“Reducing cost and adding speed to a production line has always been a good thing,” Rice says.
The next two most common survey responses, at 27% and 26% respectively, provide more insight into the workforce tie-in. The former indicates a desire to add automation equipment to improve repeatability, accuracy, and precision. The latter concerns improving safety, highlighting ergonomics and risk assessment.
“When we had a large labor pool, it was easy to throw people at [endof-line palletizing, for example], but a smaller workforce means we have to
keep the skilled folks on the primary packaging end of the line,” says Rice.
A survey respondent from Coca-Cola also highlighted palletizing in particular as an area where planned automation will increase worker safety by eliminating the need for them to do those repetitive, heavy-lifting tasks. A fellow survey respondent from pet brand Whisker also saw potential in added automation by expanding how it could reallocate current labor by taking it off end-of-line operations.
These responses align with the “three Ds” often associated as critical factors in implementing robotics and automation: Dull, Dirty, and Dangerous. Operators in a packaging facility are human. By automating these tasks, the worker is physically and mentally preserved while allowing companies to move the labor to more inviting jobs that stimulate the mind. It’s not a giant leap to determine that a more engaged worker is likelier to enjoy the job, improving retention rates.
As a senior engineer at Procter & Gamble, Ervin Hardee has seen automation enter the packaging sphere and improve exponentially over the past two decades. In his opinion, these improvements are major contributors to the survey results.
“Robotics have come a long way in just the last 5 to 10 years,” he says. “Safety, ease of operation/programming, skills needed, cost, and flexibility, to name a few of the reasons [how they have improved.]”
cartoning (28%), case/tray packing (25%), case erecting/sealing (25%), labeling (25%), and palletizing/ depalletizing (19%) as the leading areas where they plan automation and robotics. It’s often the case that primary packaging is where automation happens first, since it tends to require the most speed and precision. Afterward, the bottleneck of slower and less repeatable human labor travels downstream on the line. So, results indicate some level of packaging automation sophistication already in place among respondents’ organizations—bound to be the case with the likes of Coca-Cola and P&G responding. But as Rice mentioned, it seems that downstream tasks are increasingly being automated to pinch hit for a dwindling workforce.
Survey respondents noted nearly the same lead answer regarding both the biggest internal ally in procuring automation and robotics and the most significant internal hurdle to adding the technologies: plant operations. Hardee summed it up succinctly, “Operations would be the biggest customer, so it has to benefit them, or it’s a hard sell.”
“ The workforce simply did not come back a er the pandemic.”
Based on the survey respondents’ comments, it is no coincidence that when it came to adding robotics, 38% specified end-of-line (palletizing, etc.), followed by secondary packaging at 32% and primary packaging at 25%.
Randy Quick, director of global engineering and maintenance for Spectrum Brands, can relate with the results, citing many of the listed options and reasons for adding automation.
“Most of [our] planned automation is in direct packaging, inspection, specific manual operations, and palletizing that is not currently automated,” Quick said. He further specified an example involved replacing a taxing manual operation with robotics to alleviate the need for temp employees.
“One example is a gallon bottle that has a trigger attached to the handle for the consumer to use if needed in the bottle,” he says. “Currently, these are attached manually by temp employees, but in the future, this will be a custom-built robotic application for this specific task.”
When it came specifically to automation, respondents named secondary and end-of-line tasks like
Sure enough, 57% of survey respondents listed operations as their biggest ally, followed by engineering at 50%, plant maintenance at 24%, and the C-suite at 20%. No other perceived ally broke 20%, with third-party integrators (18%), robotics manufacturers (17%), packaging machinery OEMs (15%), supply chain leadership (12%), and procurement (11%) all breaking double digits. Rice felt these aligned perfectly with how his company has found automation and robotics implementation.
“Getting operations, engineering, and maintenance on board was the first step, but now that we are well down the road on this, we have some solid vendors who are equally invested in the process, and we have developed some great relationships to make it happen,” says Rice “It is important to note that we didn’t put all our eggs in one [vendor] basket and that is helping to encourage innovation.”
As for the biggest internal obstacles in adding automation or robots, procurement barely nosed out plant operations, 38% to 34%. Plant maintenance was also the third biggest hurdle—just as it was the third largest ally—registering 28% of the vote, followed by the C-suite at 27% and supply chain leaders at 20%. Engineering (13%), third-party integrators (12%),
they perceive as even more complex new automation and robotics? The fourth most frequently mentioned response at 27% was the inflexibility of equipment and frequently changing packaging designs and materials. Right behind that at number five, 24% cite the biggest hurdle as the complexity of programming controls or the inability for unskilled workers to operate.
All told, our data represent quite a unique situation. For both sides—those who are embracing automation, and those who aren’t—a running theme of workforce issues is listed as their reasoning, and
as the most significant criteria for their responses and potential decision-making. Those who are adding automation believe it can help offset the rising cost of labor, perhaps lead to worker retention by eliminating repetitive tasks, and offset the inability to find labor in general. Those who won’t be incorporating automation cite the inability to find labor as well. But they also fear the technology is too complex for the workers they are able to find. Or it requires too skilled (read: expensive) of workers to maintain overtime. Quite the quandary. ■
Industrial Magnetics Mid-Tube Housings incorporate 2 inch diameter Rare Earth magnetic tubes on 4 inch centers into our proven Drawer-In-Housing configuration for optimum ferrous metal separation for difficult flowing products in high-flow rate applications.
Key Industries: Food & Grain, Bulk Powder, Plastics, Petrochem, & Pharmaceuticals
By Sean Riley, Editor-in-Chief
LOOK BACK on PMMI’s many successes in 2024 by reviewing our 2024 Highlights, dynamic, digital annual report at pmmi-highlights-2024.webflow.io.
• Review the 2024 programs that impacted your business.
• Experience the success of our record-breaking trade shows and meetings.
• Learn how we connected the industry.
In his session, Victory Through Teamwork and Leadership, Coach K will share the strategies behind his unprecedented success:
• Building trust and communication within high-performing teams
• Inspiring individuals to achieve beyond expectations
• Crafting a winning culture through powerful leadership.
This is your chance to hear from a Hall of Fame leader whose impact transcends sports. His insights are tailored for business executives seeking to level up their organizations and drive extraordinary results.
“This year has been pivotal for PMMI, marked by initiatives that have amplified our influence and created new opportunities. From industry-defining trade shows to expanded workforce development programs and advanced business intelligence, we are more dedicated than ever to empowering our members.”
Patricia Andersen
Vice President of Human Resources & Aftermarket Services, Delkor Systems, Inc.
Chairwoman of the Board, PMMI
Don’t miss this opportunity to learn from a true legend while networking with your peers. At the meeting you will:
• Engage with top executives shaping the industry.
• Gain actionable economic insights tailored to manufacturing & packaging.
• Leverage networking to fuel your business growth.
Register at www.pmmi.org/executive-leadershipconference/home to secure your spot at the Executive Leadership Conference!
GET READY for a game-changing experience at PMMI’s Executive Leadership Conference (April 6–9, 2025; The Cloister, Sea Island, Georgia)! We’re thrilled to announce Coach Mike Krzyzewski, the legendary coach of Duke University men’s basketball and a five-time NCAA champion, as our closing keynote speaker.
Known as Coach K, he’s more than just a coach — he’s a master motivator and leadership expert, guiding Team USA to three Olympic gold medals and leading organizations to victories both on and off the court.
ALL WHO ATTENDED PACK EXPO International last October felt the energy and optimism across the show floor! That same momentum can be felt in the newly released Q4 How’s Business report. This latest industry report reveals positive shifts in key market trends, including new orders, quotations, backlog, and supply chain disruptions. Download the full report now to uncover the insights shaping the future of packaging and processing.
Find Inside:
• 2025- 2026 is expected to bring industrial sector growth, with retail and wholesale trade already rising.
• Only 17% of members reported disruptions in Q4, the lowest since April 2020.
• The New Orders Index hit 55.0 in Q4 2024, up 5.6 points, marking the first expansion since March 2023.
Download the report at www.pmmi.org/report/ q4-2024-how-s-business
The Current and Future State of the Snack Food Market Infographic seen at right provides a look at the evolving landscape of snack food production, highlighting key investment trends, supplier considerations, and the driving forces behind machinery purchases. With 88% of companies planning to acquire new machinery—a 12% increase from previous years—industry leaders are focusing on automation, innovation, and efficiency to meet rising consumer demand. Additionally, more than 50% of companies are investing over $1 million in new equipment, with major factors like speed, customization, and reliability, guiding purchasing decisions. As snack food producers expand their product lines, sustainability, convenience, and packaging innovation remain priorities.
Explore the full insights and future outlook by diving into the Snack Foods Packaging Trends white paper at pmmi.org/report/2024-snack-foods-packaging-trends.
THE DATE
PMMI’S ROADSHOW is hitting the road again June 24–25 at The Ritz-Carlton
Dallas, Las Colinas, in Dallas, Texas—bringing industry insights, networking opportunities, and expert-led discussions straight to you! This two-day event connects packaging and processing professionals with key trends, business intelligence, and best practices to drive success.
New for 2025: Join us for an exclusive plant tour at Tetra Pak, offering a behind-the-scenes look at cutting-edge packaging and processing innovations.
Stay tuned for more details on the agenda and registration. You won’t want to miss this opportunity to engage with industry peers and gain valuable takeaways for your business.
Learn more at pmmi.org/roadshow.
The Young Professionals Conference (YPC) will be held on Monday, June 23, at the Ritz-Carlton in Dallas, Texas, the day before the PMMI Roadshow. Brought to you by the Young Professionals Network, the YPC will feature an executive panel, keynote sessions, and plenty of networking for emerging leaders in packaging and processing. To view the agenda and register, visit pmmi.org/young-professionals/ events.
Military to Manufacturing Fort Riley Career Fair –April 10; Fort Riley, Kansas
PMMI has partnered with the Manufacturing Institute in the Heroes MAKE America program initiative to help connect the military and veteran community with PMMI member companies who are hiring. Join us at Fort Riley on April 10, from 11 a.m. to 2 p.m., to meet qualified talent with diverse skill sets, a strong work ethic, and leadership experience. Learn more at pmmi.org/heroesmakeamerica.
Sales Success Starts with the Right Tools and Training
Packaging and Processing
Selling in Today’s Market – April 22-23; PMMI, Herndon, Virginia
Sharpen your sales team’s skills and deliver results in today’s competitive marketplace with our upcoming workshop, Packaging and Processing Selling in Today’s Market. This two-day in-person program, customized for the packaging and processing industry and exclusive to PMMI members, will help capital equipment sales professionals and their managers learn systematic consultative selling techniques to become trusted advisors to customers purchasing packaging, processing, and automation equipment.
April 29–30; PMMI, Herndon, Virginia
Field service technicians are the face of your organization. They spend more time with your customers than anyone from your operation. This two-day workshop explores the non-technical knowledge and skills needed to be a great technician.
May 1–2; PMMI, Herndon, Virginia
This workshop gives your company the strategies and tactics to become an effective and successful trainer across all employee skill levels. Participants will learn to perform a training needs assessment, develop a training plan, create documentation and job aids, and practice training techniques that enhance learning retention.
SheLeads: Navigating Leadership for Women – May 14-15; PMMI, Herndon, Virginia
This transformative two-day course is designed to inspire, equip, and advance the careers of women leaders in the manufacturing industry. Participants will learn how to overcome workplace challenges, foster collaboration, and lead with confidence. SheLeads offers actionable insights, valuable tools, and a network of peers to help women take their leadership skills to the next level.
WHAT BEGAN as a group golf chat between several PMMI: The Association for Packaging and Processing Technologies members and committee members morphed into a PMMI Fantasy Football League and an opportunity to give back. First things first, the league included the following members: Andy Stamp, Hamilton Casting, Andrew Karel, Valco Melton, Brian Hunnicutt, ProMach, John Bialecki, LAKO, Jordan Hamrick, Hamrick Packaging Systems, Mike Odom, Pacteon Group, Mike Brewster, Pacteon Group, Dustin Lee, Morrison Container Handling Solutions, Mark Lovelace, Dyco Inc., Frank Skerl, Hamrick Packaging Systems, Mark Navin, Spee-Dee Packaging Machinery, Inc., and John Partin, Schneider Electric. Also pictured are PMMI President and CEO Jim Pittas and Executive Vice President - Industry Outreach Joe Angel on behalf of PMMI.
The group started a tradition and generously donated all the winnings ($1000) from the league winners to the PMMI Foundation for educational initiatives. The league was a lot of fun, and they hope to have everyone back next year with a new belt ceremony at the 2026 Joint Committee Meeting.
“The inspiration to donate the winnings to the Foundation was primarily out of a sense of gratitude to PMMI for bringing all of us together, but for PMMI, I probably don’t even know most of the guys in our league and these are now some of my closest friends – highquality good people that I am grateful to be associated with. It’s a win-win all the way around from my perspective,” said league winner Bialecki. ■
The next Packaging and Processing Women’s Leadership Network Learning webinar, Learning Circle, is scheduled for June 12 at 2 p.m. EST and will dive into Navigating the Trade Show Experience for Women in Manufacturing. ■
By Sean Riley, Editor-in-Chief WOMEN’S
As a part of its ongoing Learning Circle Webinar series, the Packaging and Processing Women’s Leadership Network completed a deep dive into emotional intelligence, including misconceptions about what it is and how important it can be to career and relationship success. PMMI Media Group Senior Marketing Manager Rebecca Welsby moderated the discussion with PPWLN leader Jan Tharp, Infinium Spirits President and CEO, and Dr. Cranla Warren, Organizational Psychologist. The following are a few exchanges from the Webinar, which can be found at pmmi.org/womens-leadershipnetwork. The Q&A has been edited for clarity and space.
Rebecca Welsby: How is emotional intelligence defined?
Dr. Cranla Warren: Emotional intelligence, also often referred to as EI, is the ability to recognize, understand, and manage our own emotions while also tuning into the emotions of others. I’d say there are two sides to EI. There’s looking at the intra-personal experience. There’s this internal dialogue we have with ourselves.
allows us to communicate our needs assertively and read nonverbal cues better.
Jan Tharp: It’s a balancing act; you’re in a situation, and you’re really collecting data. Does the guy across the room have his arms crossed? Are they listening? Do they have a scowl on their face? You’re taking in body language, people’s tone, and how you feel; they’re all data points. EI is the ability to take all those data points and figure out, okay, what’s my next step? How will I use this data to move this discussion forward constructively?
“ I would say that emotional intelligence is a lifelong journey.”
Then there are interpersonal skills. Those are social skills. Emotions drive our behavior, so we feel and then we act. So one aspect of EI is the experience that I have within myself. The other is my experience in how I engage with people.
Rebecca Welsby: How does cultivating EI benefit us as women in the workforce?
Dr. Cranla Warren: Emotional intelligence can be a strategic advantage for women in the workforce. It can help us navigate unique challenges like balancing empathy with authority and overcoming stereotypes and biases around emotional expression. When we have high EI, we can communicate our needs, advocate for ourselves, and advocate for our team members with confidence and clarity. It also
Dr. Cranla Warren: Another thing that popped to mind about EI and benefiting women in the workforce is that so many of them feel pressured to do it all. They’re managing family, children, and work. EI can help us to recognize and set personal boundaries. To your point about data points, we’re taking in all these data points so we can recognize what’s coming in and set up our personal boundaries. By understanding and managing our emotions, we become role models for each other. That’s another thing I’ve been trying to set up in the workplace regarding peer role modeling and advocating for a balanced and healthy work culture. So I think there’s a lot here for women to dig into about what it is here for you: developing, honing, practicing, and being in lifelong practice with EI skills.
Jan Tharp: To your point, emotions drive behavior and are just the culmination of everything that’s happened to you. So, if you’ve had a bad morning and you sat in traffic, and everything was wrong and then you go into a meeting, and you haven’t taken the time to decompress and level set your head, then you’re bringing all that baggage into the meeting. And that could absolutely drive your emotions, which will then dictate the outcome. So you mentioned it, it’s self-regulation, understanding how your body talks to you and what those trigger points are so that
you could pause and say, “Okay, I’m going to take five seconds before I answer that question.” Instead of saying something that you might regret because you’re just saying whatever comes to your head.
Rebecca Welsby: Have that one moment for your brain to scream and then say, “Okay, we’re done. Put that away now.”
Elesa is a single-source manufacturer with a wide range of innovative, award-winning products available in inch and metric sizes.
Dr. Cranla Warren: When looking at emotional intelligence and the competencies, the first thing is a pause, and you’ve talked about that already, Jan. And the second is breathing or oxygenating. We need to get oxygen to the brain because otherwise, we’re shutting it off.
Rebecca Welsby: What do you think are some things we can do as leaders to help those around us develop their emotional intelligence and ways we can encourage that growth in those people who look to us for guidance?
Dr. Cranla Warren: One of the most powerful ways we can foster EI in others is by modeling it ourselves. Practicing active listening, managing emotions and reactions, showing empathy, and creating environments where the foundation is helping people to feel seen, heard, acknowledged, valued, and appreciated. It’s about creating safe spaces where curiosity about emotions and open communication are valued, tested, and played with. For instance, if a team member makes a mistake, a leader might handle it with understanding rather than anger or frustration and talk about this mishap to encourage growth and learning. What am I learning? How am I moving forward?
Rebecca Welsby: Is there a way to determine where we’re at in our emotional intelligence journey, discover our strengths and what we need to work on, and find some of those resources?
Dr. Cranla Warren: There are lots of tools online that can help us assess our emotional intelligence. I used to work at the Institute for Health and Human Potential, and they still offer a free EI quiz online. Assessments like this can really highlight strengths and areas for improvement. For example, if you score high in self-awareness and lower in self-management, you might focus on techniques for managing stress or reactivity and self-regulation of how you respond under pressure.
They’re a great starting point and can help guide where we want to invest our time and our energy for our own growth.
Jan Tharp: Whether you are in a leadership position or wherever you are in your career, have a personal board. The people who are on my personal board don’t even know they’re on my personal board. But they are people who I know will tell me, “You know what? You were wrong there.” Or, “You know what? You probably shouldn’t wear that again.” It’s a mirror, and it’s not the people who always tell you, “Oh yeah, that’s great. That’s perfect.” You want the people who will give you the feedback and tell you when you’re out of line because, trust me, we are all out of line. We’re humans and thank God that we are not perfect because it would be boring if everybody was perfect.
Rebecca Welsby: What would you say is one takeaway everyone should have from our discussion today?
Jan Tharp: I would say that emotional intelligence is a lifelong journey. And celebrating that journey is a pretty incredible experience because you’re growing as a person.
Dr. Cranla Warren: So well said. I guess for me, emotional intelligence is an essential skill and strength. It’s foundational to how we behave and react. It is worth putting the time into exploring what that can look like for you, cultivating and growing your EI skills. ■
The new initiative includes podcasts, webinars, and more to accentuate the PACK EXPO experience.
By Katie Young, Sr Coordinator, Exhibitor Services, PMMI
PACK EXPO is rolling out innovative new ways for exhibitors to get ahead and stay informed with “Exhibitor Education: Learning on the Go!” The program aims to make it easier than ever for exhibitors to access essential information —anytime and anywhere!
The new PACK EXPO Unpacked - Exhibitor Edition podcast is the perfect companion for busy exhibitors seeking quick, actionable insights. This four-part series delivers practical advice and tips on maximizing your booth’s impact, strategies for engaging attendees and making the most of your time at the show. Hosted by industry experts, the podcast provides real-world examples and expert commentary in bite-sized episodes that can be easily integrated into your daily schedule. Be sure to tune in for fresh content and updates on everything you need to know to succeed as an exhibitor.
Podcast Release Schedule:
• Episode #1: Available on Wednesday, May 14, 2025
• Episode #2: Available on Wednesday, June 4, 2025
• Episode #3: Available on Wednesday, July 2, 2025
• Episode #4: Available on Wednesday, July 30, 2025
To ensure you’re always in the loop, follow PACK EXPO on its official social media platforms: Instagram, Facebook, X (formerly Twitter), LinkedIn, TikTok, and YouTube.
Expect a variety of content, including:
• Education Reels: Short, dynamic videos packed with helpful tips and strategies.
• Exhibitor Announcements: Stay up to date with all the latest news and updates.
• Exclusive Content: Gain access to insider tips, tricks, and behind-the-scenes content that will help you maximize your experience as an exhibitor.
By following along, you’ll always have access to valuable information that will help you stay on top of your game— before, during, and after the show.
Looking for more in-depth insights? These live sessions will help exhibitors prepare for the event and improve their show presence. If you’re unable to attend a live session, don’t worry — all webinars will be posted on the Exhibitor Education page after each event, and you’ll be able to:
• Watch the presentation at your convenience
• Share the webinar with your team
• Access all the valuable content for free!
Be sure to sign up beforehand and ask questions in the session to make the most of these expert-led webinars. Whether you’re just starting your preparations or fine-tuning your strategy, these webinars offer essential advice and are a great way to boost your exhibitor experience. Be sure to mark your calendar for the upcoming Live Webinar series:
• Webinar #1: Thursday, May 15 at 2:00 PM EST
• Webinar #2: Thursday, June 19, at 2:00 PM EST
• Webinar #3: Thursday, July 10 at 2:00 PM EST
• Webinar #4: Thursday, August 7 at 2:00 PM EST
With these exciting new educational resources, exhibitors now have more ways than ever to stay ahead of the game. Whether you’re tuning into the PACK EXPO Unpacked Podcast, catching up on social media updates, or joining a live webinar, these tools are designed to help you succeed at every stage of the show cycle.
Take full advantage of Exhibitor Education: Learning on the Go!—and ensure that you’re fully prepared to make the most out of your PACK EXPO experience.
The best way to stay prepared, stay connected, and keep learning is right at your fingertips—whenever, wherever you need it. ■
October 18-21, 2026 Chicago, Illinois, USA
Engage with 48,000 packaging and processing professionals at PACK EXPO International 2026. Be the brand that delivers bold ideas and game-changing solutions, driving the innovations the industry demands.
Apply by June 2 to participate in priority space selection
66% OF ATTENDEES make or influence purchasing decisions
76% OF ATTENDEES say they’re likely to make a purchase as a result of visiting the show
The following section, Partner Leaders, features profiles of leading packaging and processing automation suppliers that stand to deliver value to you, the OEM. These companies specialize in bringing you the innovative products and services that you need, such as controls, components, integration, and more. Plus, you’ll find a companion Partner Leaders box prominently featured on the homepage of OEM (scan the QR code above or go to www.oemmagazine.org), with a drop-down menu of the participating companies listed by product category.
AMCI’s products are designed for superior performance, offering specialty I/O solutions that expand functionality and introduce capabilities like position sensing, motion control, stamping press automation, and packaging control. Whether linear or rotary, our PLC-based interface products provide user-friendly operation and set new industry standards.
AMCI also offers a full range of heavy-duty rotary shaft sensors for demanding applications. Our resolver transducers include single-turn, multi-turn, and redundant versions for precise absolute position sensing in harsh environments. Additionally, our stepper and servo motion control products feature optional network connectivity or seamless integration into existing systems, enhancing performance and reliability.
Warranty/Guarantee: AMCI guarantees our products to be free from defects in materials and workmanship for 18 months from the shipment date. We will repair or replace any defective product within this period, free of charge.
Service, Support & Spare Parts: Our commitment doesn’t end with a sale. AMCI is trusted across industries, and our 24/7 Technical Support team ensures maximum performance for every customer. Our resource library is available at no cost on our website.
Training: AMCI’s Sales Department offers virtual and in-person training to help customers and distributors maximize product use. We provide demo products at cost and promotional materials for better understanding. Our customer service team is dedicated to helping you find the best solutions for your application.
AMCI is committed to delivering high-quality automation solutions with a focus on customer satisfaction. Our goal is to provide seamless, reliable solutions for your industrial automation needs.
At Beckhoff, automation is our calling. We empower engineers to succeed as industry leaders across all aspects of packaging and processing. We help you differentiate by harnessing new technologies, embracing open standards and solving the world’s most complex problems.
Founded and led by engineers, we organically create advanced controls, communication, IoT and motion technologies that become unique tools for your one-of-a-kind challenges in an age of digital transformation. As a global partner with U.S. headquarters in Minneapolis, we remain committed to sustainability, inclusivity, and support for the people behind the automation.
So whether you’re harvesting data from V/F/F/S machines with integrated cloud connectivity, saving valuable plant floor space with cabinet-free control systems, optimizing traceability in pharma applications, or ensuring food safety in protein processing with integrated vision tech – you can reach new heights for your business, industry, and humankind.
439-8272
Powered by 75 years of relentless problem-solving and steadfast reliability, Bishop-Wisecarver® (BW) delivers innovative motion solutions around the world that thrive in harsh and extreme conditions. Our linear and rotary motion solutions, custom complex assemblies, and mechatronic solutions lead the manufacturing industry, and they are backed by our Signature Experience™ promise of expert guidance, confidence, and 100% customer satisfaction.
We create solutions for tough mechanical engineering challenges in a variety of industries, including Food Processing and Packaging. We continue to make high-quality products that provide durability, long life, and reliable functionality for even the most complex designs operating under strict rules and procedures. From dirty and corrosive conditions to cleanroom and washdown settings, our products come in many sizes, lengths, material types, and customizations no matter how few or many you order.
BW guides and actuators provide high speed, high acceleration, and high durability. As the original inventor of DualVee Motion Technology®, we offer a high-quality vee bearing guide wheel technology that is excellent for smooth motion, low noise, and long lengths. Our self-cleaning vee guide wheel technology wipes away dust and debris – well-suited for cutting, cartoning, and operations requiring reliable uptime.
Wisecarver Automation is a new division of Bishop-Wisecarver®. This new division combines expertise in mechanical, electrical, controls, and software engineering to offer comprehensive automation system design, custom-engineered solutions, enduring quality, multidisciplinary guidance, and advanced control system integration, solidifying Bishop-Wisecarver as a single-source supplier for innovative automation systems.
Whether you need straight, back-and-forth motion or a curved track solution with custom bends and turns, we have the technologies and resources to fit your needs to a vee.
Carleton Helical Technologies (CHT) serves both domestic and international customers with custom packaging machinery. Our product range includes Ionized Air Rinsers, Timing Screws & Timing Screw Drives, Inverting Solutions, Denesters, Belt Drive Units, Craft Beer Systems, and more. These products are designed to manipulate containers such as cans, bottles, and jars, preparing them for subsequent processes along the production line. Our equipment can seamlessly integrate into existing lines or function as standalone units.
CHT has proudly served the packaging industry for over 40 years. Our deep expertise and extensive knowledge of container handling along the production line are invaluable to our customers. As a family-owned and operated business, we are able to offer consistently competitive pricing. We continuously update our engineering and manufacturing processes to ensure that our customers receive the most reliable and efficient machinery in the industry.
CHT offers custom-designed Ionized Air Rinsers tailored to clean containers using ionized air, cleaning solutions, or water before downstream applications. Our Timing Screws and Drives handle a range of tasks including combining, dividing, and metering, with Feedscrews designed for precision using state-of-the-art CAD/CAM software. Our Invertors efficiently invert containers within a compact footprint, easily integrating into existing conveyor systems with color coding and quick changeover options. Common applications include inspection, coding, and product mixing. Helical Denesters separate stacked products like cups and trays, improving efficiency by securely handling manual or automatic loading, and streamlining the production process for faster processing.
We look forward to the opportunity to collaborate with your company in the near future.
800/280-3245
www.cyklop.com
Cyklop is On Your Side, By Your Side™. As your comprehensive packaging and coding partner, we work with you to customize a solution you can count on. Working with Cyklop means you’ll no longer need to rely on fragmented systems and multiple vendors, which can leave you exposed to supply chain hang-ups and logistical meltdowns. Our hands-on support and seamless integration give you the smooth efficiency you need to stay in motion.
Since 1912, Cyklop has been at the very forefront of packaging innovation. We’ve laid claim to more than 600 patents in that time — demonstrating our drive and commitment to push the boundaries of packaging possibilities. Every day, we work with customers large and small, across every possible industry. Whether a business has a tactical, specific request or it needs a custom, comprehensive solution, we’re there to innovate and find the best course of action.
While our best-in-class machines and tools are critical for success, it’s our human touch that customers value most. Our service department provides guidance and support from the moment a product is delivered — assisting with any needs regarding installation, technical support, user advice, necessary maintenance and the supply of spare parts. Should something go wrong, it’s our professional duty to respond quickly. As we expand our operations in the United States, we’re eager to prove how valuable it is to have Cyklop service in your corner at all times.
So whether you’re in need of a couple dependable strapping tools, a cutting-edge packaging operation with the latest and greatest automation, or anywhere in between — Cyklop is here to deliver on your needs, with a smile. We look forward to showing you how efficient and headache-free a Cyklop packaging system can be. Learn more about the partner who’s On Your Side, By Your Side™ today at Cyklop.com
278-8107
CELEBRATING OVER 75 YEARS IN THE INDUSTRY!
With tool and die shop heritage our highly experienced workforce, great engineering expertise and commitment to quality materials provides the best solution for OEMs.
PROVEN “OUT OF THE BOX” DEPENDABILITY
— Timing screws
— Bottom code and inspection diverters (unique with CSS)
— Quick change parts
— Drive units
— Side grip belt units
— Vacuum reject systems
We are committed to providing the most cost-effective engineered solutions using quality materials to ensure long-term reliability. We customize our equipment and materials to suit line conditions. We test components prior to shipment to assure hassle-free installation as well as follow-up with our customers to guarantee satisfaction.
With over 75 years of experience you can be confident of the long term reliability of our products.
To learn more about our products, visit www.cssintl.com.
To place an order, contact sales@cssintl.com or call (800) 278-8107 www.cssintl.com
At Dorner, our unwavering commitment is to revolutionize Conveyor Automation by delivering cutting-edge solutions with unparalleled support. This dedication, coupled with a storied history of proven excellence, has firmly established the Dorner Brand as a recognized leader in product handling for over 55 years. Our comprehensive range of customizable sanitary, industrial, pallet, and flexible chain automation solutions position Dorner as the go-to provider for conveyor applications.
Dorner’s conveyors are meticulously crafted to facilitate the seamless movement of products to precise locations at the right time and in the exact position required for the subsequent phase of the production line. Boasting industry-best product transfers and in-house belting capabilities, Dorner stands at the forefront of precision conveyance, facilitating the integration of conveyors with robots, personnel, and equipment with remarkable accuracy.
For more custom projects, Dorner’s Engineered Solutions Group (ESG) is transforming product handling with innovative solutions that are custom designed to solve customers’ unique needs. This full service team can provide systems for applications such as accumulation, indexing, positioning, product flow and much more.
Additional Dorner benefits:
• After sales support through services such as installation, maintenance, replacement part audits, and preventative maintenance programs.
• Industry best lead times with conveyors shipping in as few as three business days.
• Online Configurator (D-Tools) allows users to design conveyors and download 3D CAD assemblies for instant validation of fit.
At Elesa, we are more than a supplier—we are your strategic partner in optimizing packaging and processing equipment. Our mission is to provide the highest-quality standard machine parts to support your engineering, procurement, and maintenance needs, ensuring operational excellence in even the most demanding industrial environments.
With a commitment to innovation, efficiency, and long-term performance, Elesa offers an extensive product range that enhances machine reliability while minimizing downtime and maintenance costs. Our components are engineered to withstand the rigors of modern packaging operations, where precision, durability, and streamlined performance are critical to success. Elesa’s broad portfolio includes ergonomic handles, control levers, position indicators, leveling feet, hinges, and clamping components—designed to meet the exacting standards of packaging, processing, and automation industries. By integrating Elesa’s precision-engineered components into your equipment, you gain:
Superior Quality & Performance – Rigorously tested materials ensure durability and reliability in high-speed, high-demand applications.
Optimized Efficiency – Streamlined designs improve workflow, reduce downtime, and extend machinery lifespan.
Engineering Versatility – A wide selection of standard parts provides flexible solutions for diverse machinery and application needs.
Cost-Effective Solutions – Standardization reduces development time and costs while ensuring consistent quality.
Backed by over 80 years of expertise, Elesa has built a global reputation for innovation, quality, and ergonomic design. With 50+ industrial awards and more than 300 patented designs, our components continue to set industry benchmarks—helping engineers and manufacturers achieve superior performance, efficiency, and reliability in packaging and processing applications.
At Encoder Products Company, we strive to serve you with expert service, quality products, and fast delivery. EPC specializes in encoders for motion feedback in industrial automation applications such as packaging, printing, labeling, vision systems, food and beverage, motor feedback, and more.
We understand that each industrial automation application is different, and that you need encoders that fit the requirements of your applications. That’s why our encoders are highly configurable, offering a wide array of shaft or bore sizes, output types, connector types, mounting options, and resolutions up to 65,536 CPR. You’ll also get an industry-leading warranty, and fast delivery from Idaho, USA.
We offer:
•Our newest field programmable, high resolution linear measurement encoder, the TRP Tru-TracPro™ – an integrated encoder, measuring wheel, and pivot arm in one compact unit
•Draw wire units with wire lengths up to 42.5 meters
•The original Accu-CoderPro® programmable encoders
•Magnetic multi-turn absolute encoders that operate in the absence of power without gear trains or batteries
•Robust mechanical housings for harsh operating environments, with stainless steel and corrosion-resistant options
•Magnetic encoder modules with sealing to IP69K
•Temperature ranges from -40° C to 120° C
•Competitor cross referencing and drop-in ready Direct Replacement encoders
•Custom engineering services for your custom motion feedback needs
EPC is ISO 9001:2015 certified, and we design, manufacture, and assemble most of our encoders and accessories at our corporate headquarters in Idaho, USA. When you call EPC, you’ll talk to engineers and encoder experts who can help you find the right motion feedback for your application, and you’ll speak to them in under a minute! We look forward to your call today!
814/835-6000
www.eriez.com
Eriez Vibratory Feeders, Magnetic Separators, and Metal Detectors
Eriez® partners with OEMs to deliver high-performance vibratory feeders, metal detectors, and magnetic separators that enhance operational efficiency, product purity, and quality.
Vibratory Feeders
Eriez electromagnetic feeders offer precise material flow control, from micro-dosing to high-speed, high-volume applications. High Deflection (HD) and High Speed (HS) models provide exceptional packaging, weighing, and filling accuracy. Featuring energy-efficient electromagnetic drives, these feeders deliver high throughput and require minimal maintenance. With customizable tray configurations and variable speed controls, Eriez feeders can be tailored to tackle any processing challenge.
Magnetic Separators
Eriez magnetic separators effectively remove ferrous contaminants, safeguard downstream equipment, and preserve product integrity. These robust, state-of-the-art magnetic separation units are available in a wide variety of configurations and magnetic strengths to meet diverse application needs.
Metal Detectors
Eriez metal detectors seamlessly integrate into existing systems to detect metal contaminants in bulk materials, packaged goods, and liquids. These highly sensitive detectors meet stringent safety standards while reducing false rejections, upholding quality without compromising productivity.
Exor America stands at the forefront of innovation industrial automation and HMI solutions since over 30 years.
We reinforce our presence and enhance our capability to deliver cuttingedge technology and customized services to machine builders worldwide, adapting and advancing our offerings to meet the unique challenges of the American market.
At the core of our offerings is the X Platform, a holistic industrial automation suite that offers a robust framework for our hardware and software solutions and third parties technology, ensuring our clients have access to the most advanced, reliable, and efficient tools to propel their operations forward with a great impact also in transforming the service departments from cost to profit centers.
Coupled with JMobile for unparalleled interface flexibility and CORVINA for secure and scalable cloud connectivity, X Platform underscores our dedication to empowering clients with the tools necessary for both current and future success.
Exor America INC. is a strategic branch and a critical component of our global strategy, bringing Exor International’s innovative spirit and technological leadership to the American industrial market. Through the X Platform and our tailored solutions, we meet the current demands of our clients anticipating and shaping the future of industrial automation. www.exorint.com
847-827-2270
www.hiwin.com
marketing@hiwin.us
HIWIN Corporation established itself in the North American market with advanced ballscrew technology developed in Taiwan. HIWIN has grown into an industry leader in linear, rotary and multi-access motion by offering a robust selection of products that are at the core of the automation process for businesses across multiple industries. The Hiwin brand is recognized across the industrial space for precision, durability, reliability as well as engineering and mechatronic expertise. HIWIN Corporation North American headquarters is located in Huntley, Illinois.
Industrial Magnetics is a leading force in the magnetics industry, known for its strong emphasis on customized craftsmanship, quality, and performance.
Explore industrial magnet solutions: IMI T-Traps ensure the smooth operation of your processing line, safeguarding your valuable equipment and keeping production running. The Plate Style T-Trap is ideal for viscous products, allowing your product to flow through the housing without bridging. The Tube Style T-Trap is best for heavy-duty flow. Whether it’s thick, chunky slurries or liquids with a water consistency, we engineer magnets to integrate into your process seamlessly.
The Drawer-In-Housing contain rows of magnetic tubes assembled into drawers within a housing. IMI’s Large Tube Housing® design incorporates 3” diameter rare earth tubes into our Drawer-In-Housing configuration. The Ox® handles magnetic separation in difficult processing conditions, such as humidity, bridging, abrasion, corrosion, or galling. IMI Magnetic Grates separate ferrous tramp metal in bins, chutes, drawers, and more.
The Exposed Pole Tube protects your pneumatic line machinery before reaching processing equipment and bulk load out. The Bullet® Magnet is a pneumatic line option that maintains uniform velocity in line flow, allowing it to be used anywhere in your system.
When it comes to making things better, Industrial Magnetics is the industry leader. www.magnetics.com
JAX develops high-performance industrial and food-grade lubricants engineered for equipment reliability and efficiency.
A pioneer in food-grade lubrication, JAX has formulated hundreds of NSF-registered H1 and 3H lubricants to combat the rigorous demands of bakeries, meat processing, beverage bottling, and other key food and beverage operations. Beyond food processing, JAX serves a wide range of industrial sectors, including marine, metal forming, and container manufacturing, where specialized lubrication solutions are essential for performance and reliability.
At JAX, technical expertise drives everything we do. Our team of chemists and lubrication engineers provides hands-on support, in-plant training, and real-time problem-solving to keep your equipment running at peak performance. The JAX RPM Innovation Center leads the way in research and development, crafting advanced lubrication solutions and offering in-house used oil analysis to help eliminate downtime and maximize equipment longevity. Our commitment to safety and quality is backed by ISO 9001 and ISO 21469 certifications, ensuring the highest industry standards.
Did you know we also provide private label and filling services? OEMs choose to private label a lubricant to expand portfolio offerings and bring more products to their customers. This provides enhanced revenue potential by growing their business through aftermarket sales, and ensures performance and reliability by providing a solution that is formulated specifically for their equipment.
Innovation is at our core. Whether you’re facing a lubrication challenge or looking to optimize performance, JAX delivers tailored solutions built for your needs. Contact us today to discover the right lubricant for your operation.
Back in 1870, Lubriplate’s founders set out to make the highest quality, best performing lubricants available. In doing so, they helped pioneer the use of anti-wear additives that significantly increased lubricant performance through the years. Today, that innovative tradition continues with their complete line of ultra high-performance, 100% Synthetic, NSF H1 Registered, Food Grade Lubricants.
Manufactured under strict NSF/ ISO 21469 Certified and ISO 9001 Registered quality control standards, these lubricants are formulated to deliver a number of significant, cost effective advantages, including; extended lube and fluid change intervals, multiple application capability, lubricant inventory consolidation and improved performance. Clean, safe and non-toxic, their use can eliminate lubrication as a critical control point in HACCP programs.
All Lubriplate Lubricants come with Lubriplate’s ESP Extra Services Package at no additional charge. Services include; a complimentary plant lubrication survey by a factory direct representative, color coded lubrication charts and machinery tags, a toll free technical support hotline and email, and follow-up lubricant analysis.
All Lubriplate Lubricants come with Lubriplate’s ESP Extra Services Package at no additional charge. Services include; a complimentary plant lubrication survey by a factory direct representative, color coded lubrication charts and machinery tags, a toll free technical support hotline and email, and follow-up lubricant analysis.
For more information contact: Lubriplate Lubricants Company Newark, NJ 07105 / Toledo, OH 43605 Phone: 800-733-4755
E-Mail: LubeXpert@lubriplate.com www.lubriplate.com
708/756-6660
Innovation in the pursuit of greater line efficiencies has kept Morrison Container Handling Solutions the leading manufacturer of automated container handling equipment for over 54 years. In addition to being the leading manufacturer of timing screws in North America for OEMs, we design a variety of automated equipment that address many productivityrelated items for other OEM equipment.
We offer a wide range of solutions that pair well with your equipment to make it run more efficiently to give you an edge on the competition when it comes to product control. Whether it be to increase speed, automate container presentation, or a variety of other things, our products work with yours to present your customer with the best solution possible when it comes to packaging equipment.
With over 25 engineers on staff, OEMs often leverage our team to solve simple to complex challenges. Our standard product lines include timing screws, drive units [metering, feeding, turning, grouping], change parts, combiners, dividers, twist blocks, down bottle rejects, can openers, denesters, collating, stacking, multi-packing, orienting, and inverting systems. And when standard solutions won’t work, we provide some of the most robust, flexible custom equipment in the business.
Working with us, you receive expert-backed Support Built In® --- our industry renowned customer service program. It’s our promise to be there for you when it counts, so you can be there for your customers.
If your customer’s product needs to be in a certain position for your equipment to function effectively, we can help! From single timing screws to full machines that meter, turn, group, index, combine, divide, invert, or orient product, Morrison is your final destination for container handling equipment that will wow your customer.
We help you own more of the project by providing these pieces to the container handling puzzle. Leverage our container handling expertise in your next project!
Renowned as a custom conveyor manufacturer, Multi-Conveyor’s products are multiple and unique. We’ve built some of the most complicated OEM conveyor requests ever imagined. Yet, we provide simplistic, standard conveyor solutions on a regular basis as well. We’re committed to providing a more technologically advanced conveyor, designed to meet or exceed the project requirements.
Technical: Multi-Conveyor’s upfront technical support is what sets us apart. Hands down. We work with OEMs to provide the technical conveyor strategic advantage needed to move product from process to case packer -and every step in between.
Concept/Design: Multi-Conveyor’s designers and mechanical engineers factor in productivity, ease of use, reduced overall footprint, safety, sanitation (as required), maintenance, longevity and future growth. We use quality components that match or surpass your conveyor project scope.
Engineering/Electrical: Our engineers make sure your systems “talk”. We integrate technology driven operator-to-controls communications. HMI interface and servos provide faster, more efficient changeovers. Adaptability to various shapes, weights and sizes allows flexibility to match our solutions to your products for increased throughput and future expansion.
Project Management: Concise approval drawings clarify functionality of equipment prior to fabrication. We facilitate the entire project from start to finish, often times adapting unforeseen equipment changes mid-stream. Ending with OEM or customer approved performance FATs prior to shipment.
Chances are, we’ve already built a system that’s similar to the project you’re working on right now - or made one pretty dang close. Let’s do this.
The use of advanced laser technology in manufacturing and production environments continues to revolutionize many industries. From the latest additive manufacturing and micromachining processes, to advanced packaging and material converting, lasers are changing the face of next generation manufacturing beyond recognition. Advance laser processing systems bring unprecedented levels of precision, production efficiency, and mass customization to these applications.
Novanta holds a unique capability in this field, being a manufacturer of both the laser source AND the beam steering technology. This enables us to develop products that are specifically engineered to work in perfect harmony, deep within complex manufacturing environments. During our 50 years of heritage in developing laser-based manufacturing technologies, we’ve built up expertise that is the envy of the industry — from our unique ultra-high performance laser mirror technology and advanced beam steering solutions, all the way to our much-revered high reliability CO2 laser technologies.
Paxton Products manufactures high efficiency centrifugal air blowers and custom-engineered pneumatic air delivery devices and systems that are used for drying, air rinsing, and blow-off, in order to improve the quality of labeling, tamper branding, date coding, and other packaging processes.
The new Control Panel from Paxton Products offers manufacturers a simplified solution to manage Paxton’s Centrifugal Blowers in a turnkey manner. Designed for easy installation and scalability, Paxton’s Control Panel is ideal for simply controlling your Paxton Blower System while upholding safety standards and ensuring the highest of quality during operation.
Paxton’s Ionizing Rinsing Systems are designed to dissipate the static charges that cause dirt and debris to adhere to surfaces, and then blast the contaminants away using ultra-efficient, blower-driven air. Using a specially designed Air Knife or Nozzle Manifold, Paxton’s Ionizing Systems are available for can or bottle rinsing and eliminate the need for compressed air or water rinsing.
Paxton’s own PX-Series line of high efficiency centrifugal blowers use state-of-the-art impellers and scroll designs to achieve efficiencies as high as 80%, to generate 33% more air flow than a standard centrifugal blower.
Pepperl+Fuchs’ precision sensors and explosion protection enhance efficiency, reliability, sustainability, and safety in packaging for food, pharmaceuticals, and cosmetics.
In 1945, Walter Pepperl and Ludwig Fuchs founded a small radio workshop in Mannheim, Germany, based on the principles of inventiveness, entrepreneurial foresight, and self-reliance. The experience they acquired was transformed into new ideas, and they continued to enjoy developing products for customers. The eventual result was the invention of the proximity switch. This innovation represented the starting point of the company’s success story. Today, Pepperl+Fuchs is known by customers around the world as a pioneer and an innovator in electrical explosion protection and sensor technology.
From filling and capping to handling, sterilization, labeling, and coding, our sensor technology ensures seamless packaging processes. As pioneers of inductive sensor technology, we offer industry-leading Background Suppression and Clear Object Detection photoelectric sensors. We continue to lead globally in ultrasonic sensing while also providing advanced magnetic, vibration, encoding, capacitive, and positioning sensors. Our Factory Automation portfolio is further strengthened by industrial communication, RFID, and vision solutions. www.pepperl-fuchs.com
www.seweurodrive.com
Nearly 100 years of driving the world. Since 1931, SEW-EURODRIVE has designed and engineered the world’s finest machine automation products and systems. SEW-EURODRIVE has built its global reputation as a leader in motion control and automation by consistently delivering innovative solutions that empower industries worldwide. For over 90 years, SEW has remained at the forefront of engineering excellence, crafting products that combine reliability, precision, and energy efficiency. We create drive. We move business.
As a leader in driving the food and beverage industry, SEW-EURODRIVE’s line of hygienic drive solutions leads the pack. This line includes a full range of stainless steel gear units, servo motors, and other food processing rated drives and controls.
There’s nothing basic about our core gear units. SEW-EURODRIVE’s classic gearmotors stand out for their robust design, reliable performance, and versatility across various applications.
In addition, advanced products like the MOVI-C® automation platform offer true end-to-end solutions. MOVI-C integrates software, controllers, inverters, and drive components into a seamless, scalable system that meets the demands of modern manufacturing.
There are no hazard conditions, only robust components. SEWEURODRIVE engineers everything for the long haul. we use premium-grade materials like robust alloys and heat-treated metals to ensure resistance to wear, corrosion, and heavy mechanical stress, regardless of the environment.
To solve and to serve. While SEW-EURODRIVE engineers the finest industrial automation systems in the world, it is our drive to solve problems and serve customers - which distinguishes SEW-EURODRIVE around the world. First build relationships, then solutions. Let’s get to work.
SC Wellford
508/854-0799
Slideways was founded in 1994 as a manufacturer of superior quality machined plastic components for the conveying, packaging and processing industries. OEMs appreciate our 2D/2W service standard. Customers receive quotes on custom parts in 1-2 days and finished parts in 2-3 weeks. OEMs rely on this standard to keep them on schedule.
Our core products are used in food and beverage, pharmaceutical, bakery, and conveyor applications.
Solutions that increase productivity and reduce cost.
• Engineering and Design Assistance
• Chain and Belt Guides
• Custom Machined Plastics
• Guide Rails
• Extruded Wear Strips
• Guide Rail Brackets and Accessories
• Levelers (Foot Pads)
• Bearings and Bushings
Service levels are supported by CNC equipment and ample inventory.
Slideways works with a wide array of machinable plastics offering the most advanced friction reducing, wear reducing, corrosion resistance and broad temperature range materials to suit most environments. We offer long and short run production with quick turnaround.
Span Tech leads the industry as an innovative material handling company. We are known throughout the world for our quality, reliability, and excellent customer service. Today we are recognized as a global leader in developing unique and customizable solutions for conveying applications.
Our customized solutions ensure that your products get where they need to be when they need to be there and with countless number of chain configurations the possibilities are endless. From changing elevation while curving to transferring, our conveyor solutions have been proven effective time and time again.
Need to integrate? No problem. Span Tech conveyors can be designed to integrate with almost any type of machinery, work station, or robotics. We do not shy away from your challenges, we embrace them. If solutions do not exist yet, we create them.
Our Core Industries Include:
Food & Beverage Production, Pharmaceuticals, Packaging, Manufacturing, Warehousing, Distribution, E-Commerce, Cosmetics
Through product evolution and innovation, we provide our customers with the lowest total cost of ownership, as well as the longest service life available.
Contact us and let us show you how together we can Outlast, Outperform and Outdeliver. We are committed to building the best conveyor systems possible. It’s more than a goal. –It’s how we do business.
Founded in 1961, Technical Adhesives specializes in customized adhesive solutions. With an in-house lab, we collaborate with package manufacturers to create eco-friendly, effective packaging adhesives tailored to your needs. Our diverse product range addresses complex end of- line packaging challenges for any application.
Since our inception, we have taken pride in our support team. Our staff are knowledgeable, intuitive, and ready to collaborate on solutions tailored to your packaging needs. Our team will evaluate your parameters to provide the perfect adhesive solution that meets all your requirements and more.
With strategic locations across North America, our sales team offers industry-leading support. Whether you are running a trial, need to troubleshoot your application process, or need a general audit, Technical Adhesives is committed to supporting you in the best way possible.
We are thrilled to announce the opening of our new state-of-the-art facility located in Bastrop, Texas which will make it easier than ever to serve our customers south of the border.
Success comes from extensive communication with our trusted vendors. Our product development team boasts decades of collective experience in the adhesive industry. Our chemists are directly involved in sourcing innovative raw materials to ensure our formulas run clean and efficiently through your equipment, regardless of the application, or temperature requirements.
While our formula portfolio is extensive, our team works closely with every customer to optimize adhesive performance and provide the best solution for your packaging process. Custom formulas tailored to your specific requirements are always available.
Tempco Electric Heater Corp. | Proudly Made in the USA | Since 1972
Welcome to Tempco - Your Trusted Partner for Custom Heating Solutions
Tempco, an ISO 9001:2015 Certified manufacturer, specializes in custom electric heating elements, temperature sensors, & temperature control products. With over 50 years of experience, we provide high-quality, reliable solutions for OEMs across many industries. Our products, made in the USA, enhance heating systems & manufacturing processes.
Our Expertise & Capabilities
Tempco offers over 30 types of heating elements & temperature sensors with custom design options. We support many industries with tailored solutions. Our advanced manufacturing capabilities include CNC machining, casting, sheet metal fabrication, & certified control panels, ensuring the highest quality in every product.
Industries Served
• Plastics & Rubber Processing
• Medical & Laboratory Equipment
• Packaging & Food Service
• Energy & Power Generation
• Additive Manufacturing & 3D Printing
Custom Solutions for Every Need
• Immersion Heating & Fluidized Beds
• Kilns & Ovens
• Plastic Injection Molding & Extrusion
• Medical & Surgical Equipment
Why Choose Tempco?
• ISO 9001:2015 Certified
• Custom Solutions with full engineering support
• 50+ Years of Industry Expertise
• Made in the USA
• Global Re ach
VDG is the leader in the design and manufacturing of high-quality, premium-efficiency drum motors for all types of belt conveyor applications. Manufacturing in-house in the USA and Canada since 1985, using cuttingedge production technology and automation, VDG ensures product quality, short lead times, and after-sales service.
The VDG Drum Motor is a one-component conveyor drive that has all drive components, including the premium-efficiency electric motor, gear reducer, and bearings, enclosed inside the drive drum, increasing mechanical and electrical efficiency, optimizing space, and promoting operator safety. Designed for 80,000 hours of continuous operation before maintenance, VDG Drum Motors reduce maintenance and operational costs and increase productivity.
VDG’s patented IronGrip™ lagging increases the durability and lifespan of the lagging and the conveyor belt. IronGrip™ lagging consists of symmetrically welded steel bars on the outside of the drum with vulcanized rubber lagging inserts between the steel bars. IronGrip™ lagging eliminates uneven belt wear, improves belt tracking, increases belt traction by 40%, and has 5 times longer service life compared to standard lagging.
For food processing and handling belt conveyor applications, the SSV Series Drum Motor drives modular conveyor belts without using sprockets. The belt profile is either machined directly on the drive drum, or onto an exchangeable profiled sleeve (SSV-XP). All SSV Series Drum Motors feature an IP69K-rated sealing system, withstand up to 3,000 psi washdown pressure, and eliminate crevices that trap food by-products and bacterial harborage, reducing washdown time and water usage by 50%.
The IntelliDrive™ Drum Motor features new synchronous permanent magnet motor technology, delivering 40% increased electrical efficiency, a wider range of belt speeds without loss of torque, and an increase in electric motor lifespan compared to a traditional conveyor drive. It enables onsite diagnostics, full motor indexing speed control, and communications with other automated plant equipment.
513-272-0131
www.vega.com
For over 70 years, VEGA Americas, Inc. has been a leader in level, pressure, and density measurement solutions. VEGA provides OEMs globally with innovative, high-quality measurement solutions that enhance efficiency, safety, and accuracy in their systems. With a comprehensive product line and innovative technology, we offer industry-leading measurement solutions. Our goal is to provide easy-to-install, reliable, and safe measurement technology. As pioneers in radar level measurement, we introduced the first two-wire radar in 1997 and continue to innovate, with recent releases like VEGAPULS 6X, a versatile sensor designed for any application. Headquartered in Cincinnati, Ohio, VEGA Americas is part of VEGA Grieshaber KG in Germany, a family-owned company employing over 2,700 people globally. We prioritize investing in our community and employees, ensuring success for both our team and our customers.
VEGA manufactures hygienic pressure sensors and point level devices with a brilliant advantage. The VEGABAR pressure sensors and VEGAPOINT level switches use a universal hygienic adapter system, which provides the flexibility to keep installation effort and parts inventory to a minimum. Process fittings can be selected as needed to meet application-specific requirements. The VEGAPULS C 21 wired radar sensor is the ideal sensor for non-contact level measurement in simple applications where a high degree of protection is required.
The VEGAPOINT 21 compact capacitive limit switch and VEGABAR 38 pressure sensor with switching function comes standard with a 360° switching status display, which can easily be seen from any direction. The color of the illuminated ring can be customized with one of 256 different colors, all of which remain clearly visible, even in daylight. At a glance, users can see when the process is running, if the sensor is switching, or if the sensor requires maintenance.
Standard IO-Link protocol is built into every pressure sensor and point level switch, ensuring universal, simple communication. This gives these instruments a standardized communication platform, enabling seamless data transfer and simple system integration.
678/344-8300
www.wipotec.com/us
Wipotec North America – weighing technology at its best. Wipotec North America is a subsidiary of the German weighing technology specialist Wipotec GmbH based in Kaiserslautern, Germany. Wipotec is a technology leader in the production of weighing and inspection systems. The company has a worldwide staff of over 1,000 employees, and subsidiaries in Europe, Asia, and the United States.
The core business of Wipotec is the development, production, and integration of ultra-fast precision weigh cells and high-tech weighing systems for high-speed applications.
Wipotec weigh cells are used in a wide range of industrial production processes. Application examples include checkweighing, product filling, dosing, price labeling systems, and integration into packaging machines. Furthermore, highly specific solutions, customized to customer needs, are implemented for the pharmaceutical industry in order to weigh capsules, tablets, syringes, and vials in dry or wet food processing and packaging.
Wipotec weigh cells work according to the principle of Electro Magnetic Force Restoration (EMFR). They are based on the monoblock technology which makes them extremely precise and fast and enables them to render accurate weighing results even at the highest speeds and under the most adverse conditions. Vibrations can be actively compensated within the weigh cell. The product range includes models which can weigh a mere microgram and others which can deal with loads up to 120 kg.
The heart of all Wipotec weigh cells is the monoblock, and it is manufactured in our in-house machining center using state-of-the art CNC milling machines. The in-house development and project engineering departments enable the company to support unique customer requirements. For example, numerous combinations of infeed, outfeed, and weighing conveyors are available for use with our weigh cells to provide complete weighing kits designed to easily integrate into OEM machines.
Certified to DIN EN ISO 9001.
Wire Belt Company is a global leader in manufacturing top-quality stainless steel conveyor belts. With over 100 years of expertise, we design and deliver solutions that meet the highest standards of performance.
Wire Belt Company has a global presence, operating manufacturing plants in the USA, UK, and Germany. This ensures reliable delivery wherever you are.
Our conveyor belts support food processing applications such as:
• Baking
• Coating
• Cooling
• Frying
• Breading
• Dusting
• and more
Customer Service Excellence - When you contact Wire Belt, you’ll speak directly with a knowledgeable representative. Our technical engineers are also available to help optimize your application and select the right conveyor belt.
Comprehensive Solutions - We offer a wide range of conveyor belts tailored to improve process efficiency—from simple designs to specialized solutions.
Global Distribution - Our customer service and worldwide presence ensure seamless distribution to keep your operations running smoothly.
Call us if you need help with an efficient conveyor belt system for your process.
847/887/7457
www.yaskawa.com
You know the daily struggle with limited resources and tight deadlines. You can’t afford to settle for less than the right automation products and services to solve urgent problems with consistency and reliability you can trust. At Yaskawa, we help you explore what’s possible, and open new doors to opportunity. Rather than accepting the status quo, we invite you to wonder, “What if …?” And then we make it possible. That dedication to engineering and innovation is what makes us different.
Yaskawa’s global expertise in AC drive, motion control, and robotic technology is unmatched, with over 100 years of manufacturing excellence, locations in 30 countries, and $4.5 billion in global sales per year. Since 1915, Yaskawa has produced 25 million servo motors, 35 million variable frequency drives, and 600,000 robots. We provide both standard products and tailor-made solutions, all backed by proven quality and reliability.
Yaskawa AC servo systems come to a precise position with speed and consistency that is unmatched in the automation industry. Connect our rotary, linear, and direct drive motors to an advanced Yaskawa iC9200 machine controller to manage motion, logic, kinematics, safety, security, and more from a single EtherCAT-based controller utilizing our iCube Control™ platform.
Yaskawa AC drives support every application in the industrial plant, offering size and performance options from fractional HP to 16,000 HP. Our latest variable frequency drives provide simple motor setup with highly flexible network communications, embedded functional safety, no-power programming, and easy-to-use tools featuring mobile device connectivity with our Drive Wizard mobile app.
With 150+ models to choose from and the strength of decades of application expertise, Yaskawa robots increase efficiency, provide consistent quality, and boost productivity to deliver outstanding ROI. Our robotic portfolio ranges from 4 to 15-axis industrial robots with load capacities of 2 to 800 kg to special machines, devices, and turnkey robotic systems.
The era of cabinet-free packaging machines is here.
The MX-System from Beckhoff is a space-saving and intelligent automation hardware platform that can completely replace conventional control cabinets. This opens up exciting new possibilities to reduce equipment footprint, installation time, and maintenance efforts in today’s packaging operations.
Precision Timing Screws for Seamless Container Control
Our precision timing screws are designed to provide reliable and efficient control for containers. Perfectly engineered for seamless performance, they ensure smooth operations in any system requiring container management. www.Feedscrew.com
Our versatile, portable side grip belts are customized using various motors and tilt positioning. All of our belts are completely portable, height/width adjustable, can be set for left or right-hand feeding, and easily mounted to conveyors using floor levelers making side grip conveying applications.
Cyklop Carton Erecting Machine & Fully Automatic Case Sealer
These two machines can work independently or together in a packaging line to ensure reliable, precise folding and sealing of nearly any size carton. Find your custom solution with Cyklop, the partner who’s On Your Side, By Your Side™.
Field Programmable Motion Feedback with the NEW TRP Tru-TracPro™
Announcing our newest all-in-one programmable encoder for precision motion feedback! This compact, wheeled encoder for linear measurement is perfect for use in packaging, printing, labeling, coding, marking, vision systems and more!
Eriez Electromagnetic Vibratory Feeders
Eriez offers the broadest range of feeders in the world, and the experience needed to customize a reliable solution for your equipment. Electromagnetic Vibratory Feeders from Eriez offer precise control over material flows, ideal for conveying materials, feeding weigh scales, and metering ingredients.
Struggling with fragmented protocols, missing connectivity, and complex integrations? You need a gateway that simplifies it all—secure remote access, seamless device communication, and effortless cloud integration. No OS headaches, no security worries—just reliable data, exactly where you need it.
OEMs build it, Frain buys it, End users rent it. Frain buys another one. Frain offers short-term gap solutions by renting brand-new, state-of-the-art packaging and processing machinery, helping clients overcome challenges such as: lead time constraints, new product launches, proof-of-concept testing.
Choose from HIWIN individual hi-quality components or complete systems including multi-axis stages, articulated or scara robots.
Private label a quality lubricant for a more comprehensive portfolio
Enhance revenue potential and grow your business through aftermarket sales. Ensure performance and reliability by providing a solution formulated specifically for your equipment.
Lubriplate offers a full line of quality lubricants to meet your needs.
Lubriplate’s High-Performance NSF H1 Registered Food Grade Lubricants include; High-Performance Synthetic Gear Oils, Air Compressor Fluids, Hydraulic Fluids, MultiPurpose Greases, High-Temperature Chain Lubricants, Spray Lubricants and Specialty Lubricants.
As supplier of container handling products and machines, we help position the products upstream, within, and downstream of your equipment so you can provide a robust solution and own more of the project for your customer. Explore our feed screws, drive units, custom machines and more to enhance projects.
Novanta CO2 Laser Integrator Packages are configurable laser processing sub-systems that let OEMs choose the power level, wavelength, scan head, and working distance. These highperformance components are factory configured into a single part number for fast, easy integration.
The new Paxton Products Control Panel can be used with any size Paxton Blower System to effectively and simply manage blowers in a turnkey manner so you can ensure that your drying and blow-off systems are operating at the highest of standards.
Simple Housing Concept, Advanced Optical Features.
Known as the “problem solver,” the ML100 sensor combines all advanced photoelectric functional principles in a simple, miniature housing design to solve demanding automation tasks. The rugged ML100 series can easily withstand cold-storage applications with temperatures down to −30 °C.
Goodbye complex automation. Hello MOVI-C.
Enhance operations with SEW’s MOVI-C Automation System. Achieve seamless integration and cost efficiency through simplified engineering and plug-and-play features. This system supports essential functions from safety to robotics, ensuring easy operation and monitoring - all from one reliable source.
A more cost effective and sleeker design version of our original Outrunner Spiral. Engineered for optimal efficiency, this new design enhances your workflow with a compact footprint, reducing space requirements and maintenance costs. Lets talk about your next spiral application. 270-651-9166
Hot melt, water-based, and custom adhesives for the packaging industry
Founded in 1961, Technical Adhesives specializes in customized adhesive solutions. With an in-house lab, we collaborate with package manufacturers to create eco-friendly, effective packaging adhesives tailored to your needs.
Maintenance-free for 80,000 hours of continuous operation, the premium-efficiency VDG Drum Motor delivers a safe, efficient, and reliable conveyor belt drive solution. All components are designed and made in USA, ensuring product quality, short lead times, and after-sales service.
Standard IO-Link protocol is built into every pressure sensor and point level switch, ensuring universal, simple communication. This gives these instruments a standardized communication platform, enabling seamless data transfer and simple system integration. VEGA provides OEMs globally with innovative measurement solutions.
Wipotec weigh cells are used in all production processes. In addition to integration in checkweighers and filling/dosing lines, they are also installed in packaging machines of all kinds. Our weigh cells are superior due to maximum accuracy and longterm stability.
The Worldwide Leader in Stainless-Steel Conveyor Belt Manufacturing
Wire Belt Company offers many styles & specifications of conveyor belts to fit your application. After 8 decades, Wire Belt remains the source of quality conveyor belts that provide long life, ease-of-use, and easy sanitation. (603)644-2500 | sales@wirebelt.com | www.wirebelt.com
iCube Control™ with the iC9200 Machine Controller
Yaskawa’s iCube Control™ platform offers open system design, modular system integration, and advanced functional safety. iCube Control is centered around the iC9200 machine controller, a single controller for motion, logic, kinematics, safety, security, and more, ready for any challenge you’ll face.
Optimal Engineering Systems’ YPR-45-45100 Series of Pitch, Roll, and Yaw Three-axis Stages are the integration of two +/- 45 degrees Goniometers for lower (pitch) and middle (roll) axes, and a large upper, 100 mm diameter, Rotary Stage (yaw axis). The integration of goniometers and rotary stage enables the identification of crystals, estimating hyperspectral bidirectional reflectance, measurements of radiation pa erns of LEDs, manufacturing of quartz oscillator plates using quartz cu ing X-rays, examining cu ing edges of medical instruments, gloss measurements, laser machining and drilling, aligning mirrors, tracking and scanning.
This series of three-axes stages features four options. The 01 option (pictured) is Stepper Motor driven, the -02 option is Three-Phase Brushless Servo Motor driven with Quadrature Optical Encoders, the -03 is Brushed DC Servo Motor Driven with Quadrature Optical Encoders, and the -04 option is Stepper Motor Driven with Quadrature Optical Encoders for position verification.
Optimal Engineering Systems, www.oesincorp.com
Dynamic Conveyor highlights its advanced DynaClean® Conveyor System. Highly versatile, the DynaClean system features a patented design that allows for complete toolless disassembly of the conveyor and removal of the belt in minutes, significantly reducing cleaning time and improving operational e ciency. This innovative approach has set a sanitary standard in the industry since its introduction to the food processing and packaging sector in 2013.
The DynaClean conveyor system includes a full washdown design compliant with NSF, FDA, USDA, and BISCC standards, with an optional 3-A sanitary design. It utilizes corrosion-resistant materials, including HDPE, VHMW, and UHMW construction, ensuring durability in harsh cleaning environments. The system features tensionless belts that eliminate tracking issues and reduce maintenance needs, as well as standard high-e ciency motors for reduced energy consumption. Customizable belting options suit various applications and plug & play drives and controls allow for easy integration of additional equipment and accessories. Dynamic Conveyor, www.dynamicconveyor.com
Bosch Rexroth is expanding its comprehensive VarioFlow conveyor system to include the new VarioFlow belt conveyor variant, which features a fine-meshed chain surface. It ensures that Consumer Packaged Goods (CPG) are transported gently and e ciently. The VarioFlow belt product line fits seamlessly into the VarioFlow system portfolio, reducing engineering times and enabling customized material flow.
The new VarioFlow belt conveyor is a stand-alone conveyor system for flexible CPG products, delicate products and diverse items. The modular belt chain has a very fine-meshed, almost closed and flat surface. This makes it suitable for the mass transport of unstable or bulk, film-packed products such as small sealed-edge bags. However, the VarioFlow belt conveyor can also be used to convey large or wide products, such as packs of paper towel or toilet paper. Inherently stable products can even protrude sideways in horizontal sections. Unlike conventional chain conveyor systems, VarioFlow modular belts are also suitable for directly transporting deep-drawn plastic trays, which usually have a delicate contact surface.
Bosch Rexroth, www.boschrexroth.com
ProSys Fill, highlights the HL-60, a compact yet fully automated labeling system designed to streamline the production of industry-standard cosmetic and product sticks, from lip balm to body care products.
Designed and manufactured by ProSys’ exclusive partner Pendergraph Machines, the HL-60 brings together precision, flexibility, and e ciency in a compact machine, reducing floor space while automating key processes such as feeding, labeling, and counting. With the capacity to handle high production speeds and multiple stick sizes, this versatile system is ideal for co-packers and small manufacturers looking for a solution with entry-level pricing, American-made value, and stellar service.
The HL-60 optimizes production environments by feeding, labeling, and counting sticks into totes, all in one compact machine. This makes the system particularly well-suited for tight production areas, allowing manufacturers to maximize their space e ciency without compromising productivity. Additionally, the HL-60 features an automated stick feeding system, allowing the machine to load sticks at high speeds, reducing manual intervention and operator errors. This results in faster production times compared to manually loaded systems, a significant improvement for operators seeking to enhance throughput.
ProSys Fill, www.prosysfill.com
Certain applications, such as in jig construction, automation systems or testing systems, require moving elements supported by exact bearings. The JW Winco GN 7580 precision hinges offer the long service life and adjustability, to keep your project running smoothly.
The GN 7580 family comprises three size variants, each with four inner and outer leaf types. The leaves differ in turn by the type of mounting, which can be tangential or radial and make use of countersunk cylindrical bores or integrated threaded bushings of stainless steel. Plus, JW Winco put thought into ensuring simple and positionally accurate mounting - the fitting bores ensure exact positioning of the hinges during installation.
The four-leaf types are designed to be mutually compatible and can be used together as needed in any combination – to cover a wide range of applications.
To ensure lasting precision, the hinges can be re-adjusted at any time. The axial adjusting screws allow the hinge to be adjusted for smooth or stiff motion.
JW Winco, www.jwwinco.com
The EXAIR Varistat® Benchtop Ionizer is a powerful fan-driven static eliminator engineered to neutralize static charges on surfaces in demanding industrial environments. This Ionizer delivers a consistent stream of ionized airflow, effectively eliminating static and particulates without the need for compressed air. The Varistat is available in 230 volts to meet the needs of industrial locations. Easily mounted on benchtops or machines, this static eliminator is manually adjustable and perfect for processes needing comprehensive coverage.
The new 230-volt Varistat sets itself apart from other fan-driven static eliminators by offering highly adjustable features and allowing for versatility. Features like selectable voltage 115VAC/230VAC, variable fan speed, and adjustable polarity make the Varistat a comprehensive solution for eliminating static in a variety of processes and facilities. Once plugged in, the Varistat provides rapid static decay capable of reducing 1000V to 100V in .8 seconds. This product features two replaceable ion emitter points and two 30 PPI foam filters to ensure optimal performance over extended periods, as well as LED lights to signify proper function. EXAIR, www.exair.com
Emerson has launched its new Energy Manager solution, a preengineered hardware and so ware o ering designed to simplify industrial electricity monitoring with quick setup and intuitive operation. Ready out of the box, the Energy Manager solution monitors asset energy use in real time, allowing manufacturers to gain deeper insight into energy consumption and operating costs, lowering carbon dioxide (CO2) emissions and maximize energy and operational e ciency.
Most manufacturers, including original equipment and industrial manufacturers, consumer packaged goods companies and food and beverage producers, face pressure to increase productivity while reducing energy use and environmental impact. Yet industrial machinery is energy-intensive, consuming high power even when idle. To be er meet e ciency and sustainability goals, operators need the best possible visibility into their facilities’ energy use to address waste and ine ciencies.
Emerson, www.emerson.com
With the AM8300 servomotor series, Beckho expands its drive technology portfolio to include modular motors with integrated water cooling. Compared to conventional convectioncooled motors, these devices support higher speed requirements and boost standstill torque by a factor of three.
The AM8300 technology is based on the tried-and-tested AM8000 servomotor series and its modular system approach with numerous options and consistent availability. The new servomotors o er maximum dynamics with dependable performance: the increased speed and torque do not a ect the rotor moment of inertia. The servos come in five flange codes that each have three length options – with standstill torques from 5.1 to 274 Nm. As such, the AM8300 series covers an extremely wide range of motion control applications.
The AM8300 motors also o er options for a backlash-free permanent magnet holding brake, sha seal, and keyway. Depending on the size, they support numerous feedback systems such as resolvers or ba ery-less single and multiturn encoders with One Cable Technology (OCT) or Hiperface. Beckho Automation, www.beckho .com
Wipotec Technology‘s new MMS 2 is an ideal weigh cell for production lines in a variety of settings, including quality control scenerios for vial and syringe filling. The MMS2 offers IP65 protection for safe guarding of components against dust, foreign materials, water, and other environmental factors.
Flexiv, a provider in general-purpose robotics solutions, announces the launch of Elements Series 3, the latest evolution of the adaptive robot control system that makes programming faster, easier, and more capable than ever before.
Designed to simplify the complex, Flexiv’s engineers have reimagined the user experience focusing on human-centered design and advanced, semi-automated features.
With a combination of new rugged IP65 hardware, and intuitive easy to use so ware, be they in the o ce or the production line floor, robotic programmers of any skill level can easily create and manage robotic applications.
This ability to create programs from scratch is further enabled by the Elements Studio’s robotic simulation capability. This powerful 3D simulation tool allows users to design, test, and refine their applications before deploying them in the real-world. Fully compatible across PCs, the Teach Pendant, and all Flexiv robots, Elements Studio reduces deployment time and minimizes risk by allowing thorough testing in a virtual se ing.
As part of the newly released Elements hardware, the Motion Bar has also been redesigned to put complete control at an operator’s fingertips. Flexiv, www.flexiv.com
Our show truck will come to you. Scan here to make an appointment.
Advanced Micro Controls, Inc.
Beckhoff Automation
www.amci.com 26, 49
www.beckhoff.com 17, 50, 80
Bishop-Wisecarver Corporation www.bwc.com 19, 51
Carleton Helical Technologies
Cyklop
CSS International
Dorner Mfg. Corp.
Elesa U.S.A. Corporation
Encoder Products Company
Eriez Magnetics
www.feedscrew.com 6, 52, 80
www.cyklop.com 53. 80
www.cssintl.com 54, 80
www.dornerconveyors.com 22, 55
www.elesausa.com 44, 56
www.encoder.com 23, 57, 80
www.eriez.com IFC, 58, 80
Exor America www.exorint.com 25, 59, 81
Frain Industries
Hiwin Corporation
Industrial Magnetics, Inc.
JAX, Inc.
Lubriplate Lubricants
Morrison Container Handling Solutions
Multi-Conveyor
Novanta
Paxton Products
Pepperl + Fuchs
PMMI
Seifert Systems
SEW Eurodrive, Inc.
Slideways, Inc.
Span Tech LLC
www.fraingroup.com 15, 81
www.hiwin.com 10, 60, 81
www.magnetics.com 37, 61
www.jax.com 3, 62, 81
www.lubriplate.com 13, 64, 81
www.morrison-chs.com 18, 65, 81
www.multi-conveyor.com 4, 66
www. novantaphotonics.com 9, 67, 82
www.paxtonproducts.com 41, 68, 82
www.pepperl-fuchs.com 69, 82
www.pmmi.org 31, 33, 43, 47, 63, IBC
www.seifertsystems.com 14
www.seweurodrive.com 70, 82, OBC
www.slideways.com 45, 71
www.spantechconveyors.com 1, 72, 82
Technical Adhesives Limited www.technicaladhesives.com 36, 73. 82
Tempco Electric Heater Corporation www.tempco.com 27, 74
VDG (Van der Graaf)
VEGA Americas
Wipotec
www.vandergraaf.com 75, 83
www.vega.com 5, 76, 83
www.wipotec.com 77, 83, 86
Wire Belt Company of America www.wirebelt.com 7, 78, 83
Yaskawa America, Inc.
www.yaskawa.com 21, 79, 83
OEM Magazine (ISSN# 2377-293X) is a trademark application of PMMI, The Association for Packaging and Processing Technologies. OEM Magazine is published four times annually by PMMI with its publishing office, PMMI Media Group, located at 500 W. Madison, Suite 1000, Chicago, IL 60661; 312.222.1010. Periodicals postage paid at Chicago, IL, and additional mailing offices. Copyright 2025 by PMMI. All rights reserved. Materials in this publication must not be reproduced in any form without written permission of the publisher. Applications for a free subscription may be made online at www.oemmagazine.org/ subscribe. To subscribe or manage your subscription to OEM Magazine, visit www.oemmagazine.org/subscribe. Free digital edition available to qualified individuals outside the United States. POSTMASTER; Send address changes to OEM Magazine, 500 W. Madison, Suite 1000, Chicago, IL 60661. PRINTED IN USA by Quad. The opinions expressed in articles are those of the authors and not necessarily those of PMMI. Comments, questions and letters to the editor are welcome and can be sent to: support@oemmagazine.org. Mailing List: We make a portion of our mailing list available to reputable firms. If you would prefer that we don’t include your name, please write us at the Chicago, IL address. Volume 8 • Number 1
PMMI’s charity had a remarkable 2024 as it supported funding for the future packaging and processing workforce.
By Jim Pittas, President & CEO, PMMI
As we kick off 2025, I want to highlight the remarkable work of the PMMI Foundation for the packaging and processing industry and its ongoing achievements. Our progress this year is inspiring and reflects our commitment to building a strong, innovative workforce for the future. As the charitable arm of PMMI, the PMMI Foundation contributed over $800,000 in 2024 to support the future workforce, benefiting tens of thousands of students nationwide through partnerships, scholarships, and workforce development programs.
I’ll begin with one of my favorite initiatives from the foundation, the PMMI U Skills Fund for the Future Workforce. I’m leading with this because the program has already distributed $100,000 in 2025 alone as I write this column in mid-February. This follows nearly $478,000 in matching funds from the PMMI U Skills Fund in 2024. For those who need a refresher, the PMMI Skills Fund helps members support local and regional colleges, universities, technical schools, and high schools by matching contributions of up to $50,000 annually from your company.
to promote STEM education and sustainable packaging practices, and assisted PMMI member companies in bringing their interns to PACK EXPO through its Internship Reimbursement Program.
Applications for PMMI Scholarships opened on Jan. 1, following nearly $200,000 in scholarships awarded in 2024. This helped over 30 students pursuing degrees in packaging, engineering, mechatronics, and related fields. I’d be remiss not to highlight a scholarship available to immediate family members of employees at PMMI companies: the PMMI Family Member Scholarship. These $5,000 scholarships are awarded to the top 15 applicants pursuing degrees in packaging, processing, or related fields. Don’t miss this opportunity to make education more affordable and accessible for your loved ones.
...[ PMMI U Skills Fund ] has already distributed $100,000 in 2025 alone...
Further efforts by the Foundation supported over 17,000 students at the SkillsUSA National Leadership and Skills Conference, 11,576 students participating in FIRST Robotics Competitions — backed by $294,000 in contributions to help them develop STEM skills and explore engineering careers — and 1,710 students engaged in PACK EXPO International student events.
Speaking of PACK EXPO International, the PMMI Foundation made career exploration in the industry accessible to students at the show. A $75,000 travel fund enabled student groups to attend, while engaging competitions on the show floor, such as the Amazing Packaging Race, awarded $9,000 in prize money, and the PACK Challenge distributed $20,000. Additionally, the Foundation raised $41,000 through a Silent Auction, contributed $25,000 to sponsor 40 Girl Scouts
Entering its fourth year, the PMMI Foundation has partnered with SparkForce™, the Foundation of the Fabricators & Manufacturers Association, Intl. (FMA), to support summer manufacturing camps for kids ages 12-16. Last year, this program supported 35 camps, introducing 479 students to hands-on manufacturing experiences. Twenty-five camps are planned for 2025 and will be listed on the Foundation’s website in mid-April at www.pmmifoundation.org/summer-camps. These camps aim to narrow the growing skills gap by educating and inspiring the future manufacturing workforce to explore career opportunities in packaging and processing.
As we look forward to another impactful year with the PMMI Foundation, PMMI is grateful for the unwavering support of our sponsors and partners. Their contributions are not just investments in programs, but in the lives and futures of thousands of students. These partnerships form the cornerstone of our mission to inspire and prepare the next generation of leaders in our industry. ■
Jim Pittas is the President & CEO of PMMI. He may be reached at jpittas@pmmi.org or at linkedin.com/in/jimpittas.