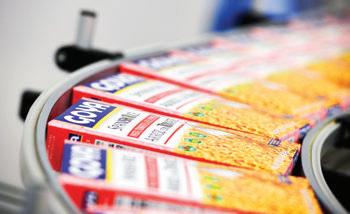
5 minute read
Case Study: Goya Foods
AARON HAND | EXECUTIVE EDITOR
Automated Bulk Bag Dischargers Help Keep Pace With High-Speed Packaging
A new distribution center not only provided four times the space to help relieve previous bottlenecks in rice, bean, and flour lines, but also needed more e cient bulk handling equipment to keep up with other high-speed functions.
AS THE LARGEST HISPANIC-OWNED food company in the U.S., Goya Foods was bursting at the seams. Though continuing to invest in its distribution center in Secaucus, N.J., it was time to open a new larger site as well. “We had run out of capacity for rice mixtures at our previous site,” says Luis Valencia, plant engineer for Goya’s new headquarters and distribution center in Jersey City, N.J. “In fact, all of the existing lines, including the bean and flour lines, were over-utilized. We were overdue for a change.”
Goya imports ingredients from around the world to create more than 2,500 food products of Latin cuisine traditional to Mexico, Spain, Central and South America, and the Caribbean. The new site, opened in 2015, provided four times the space of its previous facility—relieving several long-standing bottlenecks, Valencia says.
Not only did the company want more space, but it wanted higher-capacity equipment to fill that space. It outfitted the new site with a high-speed pouch filling line for its rice, along with more e cient bulk handling and packaging equipment, including 16 bulk bag and rigid tote IBC discharger systems from Flexicon.
“We had Flexicon equipment here already, so we knew they were reliable systems,” Valencia says.
E ciency is a key focus for these operations, Valencia notes. “The processes are relatively uncomplicated, so the simpler the process, the higher our e ciency must be,” he explains. “We’re always looking to increase quality, safety, and e ciency.”
Bringing in the materials
Goya receives rice, beans, dry vegetables, and flour in 2,200-lb bulk bags, and puts spice mixtures in rigid 1,100-lb totes. Ingredients are batched to the packaging machines by gain-in-weight control.
The handling of these bulk bags was one bottleneck that needed to be improved to increase productivity. The solution came in the form of Bulk-Out BFC bulk bag dischargers, which load bags quickly by means of a cantilevered I-beam, hoist, and trolley.
They provide more e ciency as well. The fast-loading units allow just two forklift drivers to serve all 16 of the site’s bulk bag dischargers, Valencia says. A single operator can load and discharge bulk bags across several product lines. After a forklift places a palletized bulk bag in front of the discharger, the operator connects the bag loops to Z-Clip bag strap holders on the lifting frame and, using a pendant, hoists the bag into the discharger.
PHOTO COURTESY OF GOYA FOODS
Goya Foods packages beans, rice mixes, corn meal, and other dry products at its new facility in Secaucus, N.J. Pictured here, filled and sealed packages of Spanish rice proceed to a cartoning line.
Fine-tuning bean and our lines
PHOTO COURTESY OF GOYA FOODS
Flexible screw conveyors transfer ingredients from bulk bag dischargers, through a wall, to feed packaging machines in the next room. The screws prevent product contact with seals or bearings.
A cantilevered I-beam with hoist and trolley allows bags to be raised and rolled into a discharger using a pendant.
Matching high-speed packaging
totes, which are hoisted above a Model BFHC-X half frame discharger mounted on a hopper with a 2,500-lb capacity. From the hopper outlet, a 25-ft-long flexible screw conveyor, also from Flexicon, is inclined at 32 degrees, moving the spices to a weigh hopper that discharges to the pouch filler. The flexible screw, which rotates inside a polymer outer tube, is the only moving part contacting material—keeping the material from contacting seals or bearings. “The conveyor is sanitized daily by disconnecting the flexible screw from the drive shaft and removing the screw for cleaning,” Valencia notes. Bean and flour lines are not only operating at higher capacity now with BFC bulk bag dischargers, but upgraded electronics are also enabling those lines to operate more precisely. The bean line uses six bulk bag dischargers—mounted over 5,000-lb capacity floor hoppers and arranged in three pairs. A bucket conveyor feeds a weigh hopper that then discharges into a pillow-bag packaging machine. The flour line uses three bulk bag dischargers, each with Flow-Flexer bag activator plates that increasingly raise and lower opposite bottom PHOTO COURTESY OF GOYA FOODS edges of the bag on timed cycles to promote total discharge. To match the production capacity of a new high- Goya Secaucus packages 50 di erent bean speed pouch filler for rice mixes, Goya also installed a varieties and 30 di erent flours—each with slightly gain-in-weight batching system for the rice, vegeta- di erent flow characteristics. “We changeover conble, and spice components, automating and expedit- stantly, and when you change a bean or a flour or a ing a process that previously required manual verifi- rice mix, there’s a lot of fine-tuning,” Valencia says. cation that batches reach the pouch filler. Fine flours are among the tougher products. “It’s
For rice, fork trucks deliver palletized bulk bags a challenge to dial it in; the higher the speed, the to side-by-side BFC bulk bag dischargers that more precision is required,” Valencia says, noting unload into two large 5,000-lb capacity floor hop- that Flexicon helped the facility upgrade its elecpers. The hoppers feed a common 20-ft-long buck- tronics to help with that precision. “They made sure et conveyor leading to a weigh hopper, which emp- the dischargers were feeding correctly and the ties into the pouch filler. Each discharger unloads a controls were reading the hopper levels correctly. 2,200-lb bulk bag of rice in 4 minutes. Dry vegeta- We control the weights better now and avoid probles move from bulk bag discharger to pouch filler cess loss.” in much the same way. Flexicon
Spices for the rice mixes are supplied in rigid www.flexicon.com
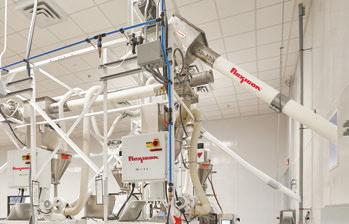