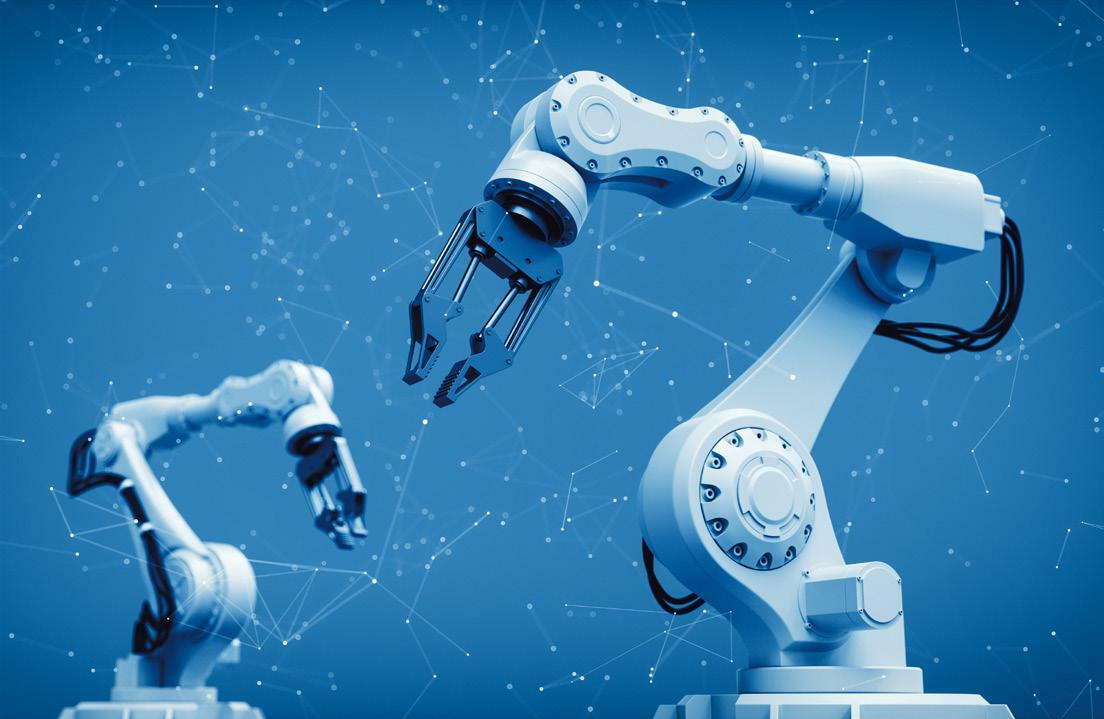
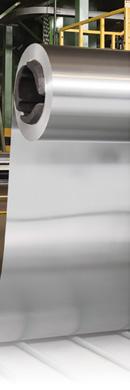
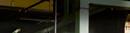
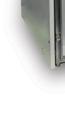



















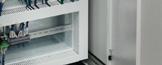






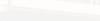
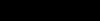





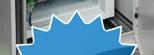
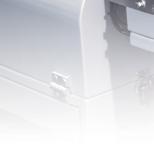
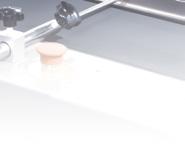
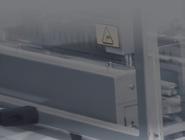
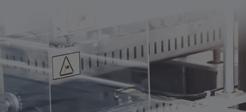


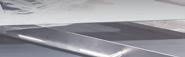
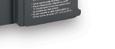






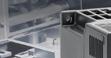
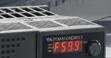













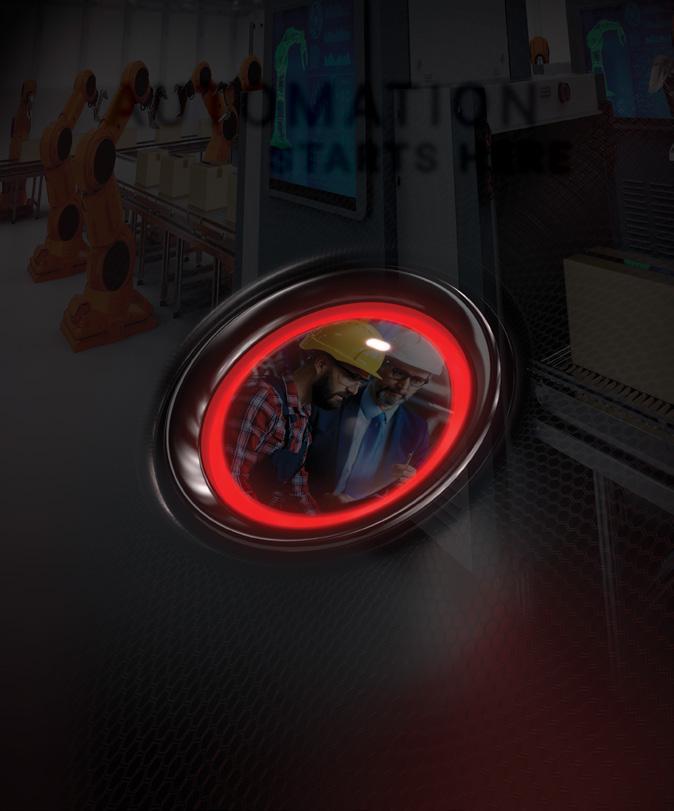






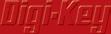
Michael De Boer automation manager, Interstates
Duane Grob principal engineer and business unit director, Avanceon
Benson Hougland vice president of marketing, Opto 22
Adam Jongewaard systems analyst, Interstates
Brent Kooiman senior project engineer, Interstates
David Smit systems analyst, Interstates
Mark Sobkow vice president of manufacturing solutions, RedViking
With manufacturing plants reacting to current market and sup ply chain issues by either embracing or eschewing just-in-time ordering and production processes, the integration of business sys tems with plant floor automation has proven to be an effective way to maintain their competitive stance.
Let's look at the business problems faced by many manufacturers today.
Supply Chains. In 2021, we all saw how shipping strains impacted global supply chains. Production can be negatively affected if you don’t know what inventory you have or how long it will take to secure your vital mate rials or ingredients. Integrating plant automation systems with your busi ness systems gives you a big picture look at your entire business and how it’s performing, helping you make smarter decisions about ordering and production schedules. Integration also provides better insight to the whole business unit—from workers on the plant floor to the sales team.
On a related note, keeping the right quantity of raw materials on hand can be difficult when you’re utilizing just-in-time manufacturing methods.
Instead of filling warehouses with raw materials and hoping the product will sell, businesses are having to focus on time-to-market, material arrival
times, and supply chain logistics. Analyzing sales cycles and understanding how your production operations actually work are both crucial to forecasting material needs. Integration links these aspects and makes it easier for plant managers to keep the right amount of materials on hand.
Consistency and Traceability. By linking business and plant floor com ponents, you create a traceable path from production orders coming in, to live production information, and back to business systems. This closed-loop process allows for improved quality control and maximum traceability.
Every business is feeling the impact of these challenges, but there are straightforward ways to weather the storm. The following tips can be used to get the most out of system integration projects at your plants.
• Find the experts. Companies that have found success have internal ex perts who understand technology (at both the operations technology and IT levels) and how each component ties together. If they don’t have such experts in-house, they find a third-party expert who can help navigate integration for them. Qualified consultants or systems
integrators can be knowledgeable partners.
• Know what you have. To integrate your processes and equipment, you need to map out what you already have in place. Quite often, systems integrators will uncover different systems and tools in a plant that its managers and operators didn't know existed. Performing an internal needs assessment beforehand can make the process of integrating much easier. This can be facilitated by a consultant or automation technology supplier partner.
• Have a tangible goal and stick to its scope. Start with a realistic goal. Like the old saying about eating a whole elephant one bite at a time, pick something you can undertake easily, complete one step, and then move on to the next. Too often, data initiatives associated with plant
floor to enterprise systems integration involve too many people and get clogged up with competing interests pursuing conflicting direc tions. Suddenly what could have been a $50,000 investment to get a proof of concept becomes a $1 million project in which 20 people are trying to make decisions. Keeping a tight rein on the scope will make your integration goals more achievable.
• Be ready to adjust. Understand that what you thought was going to be the answer might not be in reality. Often, manufacturers uncover sev eral hidden problems and inefficiencies through the process of plant floor to enterprise systems integration. You must be willing to accept the realities of what you find and be flexible to keep you on track and moving forward.
Larger companies with multiple production sites or facilities will likely find the most benefit from integration, as they’re typically able to lever age efficiencies at one plant to improve processes at all of them.
If you’re ready to get started, find integration experts versed in your technology platforms. Many companies are using SAP enterprise re source planning or even Microsoft software, which is a good place to start. You should also connect with the people already handling your plant floor automation. There are also many industry user groups that can help; in fact, there are so many resources for integration that choosing one can be daunting. Finding a system integrator with expertise in your industry vertical—and one that you trust—is a great first step.
When access to the internet goes out, can you still access your data? And will your HMI/SCADA still communicate with your PLCs?
Whether your access to the internet is dis rupted due to ISP outages, cyberattacks, or other causes, will you still be able to access your data in the cloud? As more industrial companies store large amounts of their data in the cloud, this is a serious concern.
When your internet access is disrupted, there is no straightforward “do this” or “deploy that” fix. Howev er, one way to ensure connection is to have dual ISPs supporting your access. This helps ensure that if there is disruption from one ISP, the other is on standby.
Taking this step is critical for operations with largescale cloud deployments that contain a site SCADA, historian, and other critical systems.
With the threat of an internet outage always being a concern, using edge devices for local data buffering is
a good strategy. This allows critical data to be collected so that when the internet connection is restored, the buffered data can be sent to the cloud data historian or archive. Most well-known SCADA platforms can be deployed in a way that allows local control to be performed using data buffered in edge devices when connection to the cloud is lost.
Having this kind of backup in place can also provide for a seamless transition to local control without dis ruption. That’s why many industrial companies choose to have an on-premises data historian that reports to a cloud-based enterprise level historian.
With a well-designed, on-site data buffering method ology, your data is safe on local, non-volatile memory.
As noted above, a well-designed cloud deployment should include some form of on-premises gateway
Using edge devices for local data buffering allows critical data to be collected so that when the internet connection is restored, the buffered data can be sent to the cloud data historian.
or lightweight software application running locally—either on an edge device, virtual machine, or computer. This locally running application allows your data historian to continuously collect data without a connection to the cloud. It also allows operators and engineers to continue interacting with the local equipment for control. There might be a disruption for people connecting remotely, but the priority is to maintain normal operations on-premises.
The key take-away here is that, when designed correctly, cloud-based SCADA and historian deployments can be viable, resilient, and reliable. Be sure to think through your local and cloud connection design, system allocation, and data buffering approach early in a deployment by keeping the potential for in ternet connection outages and disruptions in mind.
Do you have a perimeter firewall connecting your business to the public internet?
If so, here’s how to protect the industrial control system software on your network.
With the growing adoption of industrial Internet of Things (IIoT) and digital transformation efforts, the number of devices below firewalls connected to the internet is increasing at an alarming pace. The frightening fact is that this device count increase often doesn’t include systems with vulnerabilities that affect standard computer operating systems running industrial control systems (ICS) software on your plant floor network.
Understanding your firewall options—standard and edge—will help you determine how best to secure your ICS environment, including utilizing hardware, software and your internal ICS network policies.
A firewall’s purpose is to keep malicious traffic outside your environment and keep your highly secured data and workflow process information inside.
There is a new market for “hardened” firewalls in ICS environments that are often delivered in industrial PC form factors. These firewalls may be fanless or have specific temperature and dust ratings, but they operate the same way as any IT firewall. It’s important to note that some may not be hardened for harsh industrial environments or
compact enough to fit inside a control panel, and others may not have some of the specific data-handling features for manufacturing proto cols such as EtherNet/IP or Modbus. However, the critical thing they offer is a way to filter inbound and outbound traffic to and from your ICS network and your standard office network.
Similar in function to core ICS firewalls, edge firewalls are made to secure your industrial networks even further. Unlike ICS firewalls, however, edge firewalls are a relatively new concept in ICS environments. Edge firewalls are designed to be closer to your individual equipment, allowing you to configure micro-segmentation in your network and further isolate devices and layer 2 traffic.
Edge firewalls are typically placed near the top of a line or piece of equipment. This placement allows you to implement IEC 62443 concepts such as defense-in-depth and secure zones and conduits.
Once you’ve determined the type of firewall best suited to your application,
• Never place end user, third-party contractor, smart, or non-industrial IoT devices on the ICS network unless they are approved or have a specific task that your ICS network policy allows.
• Devices on the ICS network typically do not need to access the public internet. If you can’t control where they are getting their data, it is far
• The most important rule to follow is to restrict any unnecessary traffic from crossing the firewall. This restriction requires you to fully under stand and interpret the traffic you see within your environment.
The productivity and efficiency of your manufacturing operations depends on a constant cycle of collecting and analyzing IIoT data. Fortunately, Mitsubishi Electric has the hardware, software, and expertise to help you automate the process.
• Reduce energy
• Reduce downtime
• Increase productivity through data analysis
• Reduce startup costs with Digital Twin
The future of manufacturing is smart.
How edge device computing capabilities can be used for enterprise computing applications such as sending data to the cloud or serving as a central corporate server for analytics.
Acritical component of industry’s digital transformation is the connection of plant floor and enterprise-level systems. And while much of the focus on edge computing has centered on its ability to perform analysis of the machine or system to which it is directly connected, edge computing is also key to connecting the plant floor to the enterprise.
The principal element for this kind of connection is the establishment of edge-to-cloud communication, including hardware and software data processing capabilities, IT /OT (operations technology) compatibility (in cluding industrial hardening), and cybersecurity. An added, but not su perfluous component, is future-proofing this edge-to-cloud connection through the use of scalable, efficient communication protocols.
A key function of edge computing is to offload data processing and net working demand from central computing resources, simultaneously serv ing local process needs and communicating data to higher-level systems.
Therefore, processing capabilities should include multi-core or multi-processor hardware and general-purpose operating systems that permit parallel execution of real-time automation logic and software for data pre-processing and communications with enterprise systems.
Many edge computing devices designed for enterprise operation sup port IT communication features like DHCP, DNS, REST APIs, SNMP, VPN, and Ethernet or Wi-Fi network interfaces. However, for effective operation in industrial applications, edge computers should also provide a high degree of interoperability with industrial automation systems. In teroperability may come through direct I/O signal processing, support for traditional communication protocols like Modbus/TCP, support for interoperable standards like OPC, or even all three. Since many industrial systems reside in hazardous environments or require continuous uptime, industrial edge computing systems may require environmental approvals, resistance to temperature or other shocks, and hardware and software fault-tolerance features.
For data transmission to cloud systems and off-site data centers, cyber security is of even greater concern than for strictly on-premises commu nications. Since edge computing architectures are distributed by nature, each device in the system needs to support software security features like user authentication, data encryption, certificate management, and inter nal firewall configuration. Secure remote access through an embedded VPN client can be important, as well, since edge devices may be located off site. Additionally, hardware features such as independent network in terfaces may be required to appropriately segment trusted and untrusted traffic.
A key recommendation from many technology suppliers is for users to consider edge technologies that support the MQTT communication protocol, given that its design around device-originating connections and network anonymity inherently improves security.
MQTT is also highly recommended for its efficiency at reducing band width consumption, as it reportedly reduces bandwidth by 80%-95% compared to traditional protocols. And, when combined with support for the Sparkplug B payload specification, MQTT supports a scalable IIoT (in dustrial Internet of Things) architecture for mission-critical applications.
Users planning to implement edge computers only for on-premises appli cations might think they won’t need all the same capabilities as edge com
puting users who are connecting to the cloud. But the differences are less than one might think. While risks and costs increase by an order of magni tude when transmitting data over public internet or cellular versus private wired Ethernet, an edge computing device operating purely on-premises still needs data processing capability, IT/OT compatibility, industrial pack aging, and security features to be effective and reliable.
The edge computer must still process data and still connect easily to both IT and OT systems to provide data to business applications. Even on premises, some equipment may be in hazardous areas or difficult to reach. And because security threats can come from inside a facility, either pur posefully or accidentally, security features are still necessary. Traditional industrial control systems using proprietary networks have been assumed to be secure, but if they are opened to exchange data with company IT networks, they need the same safeguards in place.
Most industrial IoT applications require a complex hierarchy of hard ware, middleware, and software to acquire data, process it, and send it to on-premises or cloud-based targets. The promise of edge computing de vices is to reduce this complexity by providing greater processing capabili ties in the field or on the plant floor. Much of the traditional infrastructure for communication (middleware systems) and security (firewalls, network gateways) can be assimilated by edge computing devices.
Many edge devices also provide network switching or segmentation
Realize your vision with Festo‘s approach to smart automation for electronics manufacturing. Partner with Festo today.
Industry Leadership
Global Training & Support
www.festo.us
and access point features that can replace or complement the usual network switch/router infrastructure to some degree. Edge of net work access to intranet or public internet is still a must, however. A facility with an MQTT broker on-premises, on an intranet, or in the cloud will find edge data distribution much easier.
Integration with existing systems is also easier if edge computing devices provide sup port for traditional communication protocols like Modbus/TCP as well as support for in teroperable standards like OPC. If the edge computing device supports I/O processing itself, that provides a third option for parallel processing with existing automation or for in tegrating hardwired equipment.
For OT data management, the Sparkplug B specification for MQTT goes a long way to wards making data discoverable because it standardizes topic and payload formats. A network client with a connection to the net
work MQTT broker can browse available data providers and their tags without knowing the details of the end device’s address, protocol, etc.
For management of actual edge devices, many have secure, embedded web servers providing configuration and programming in terfaces that can be accessed from any web browser. Some devices support SNMP, a standard protocol used in IT systems to mon itor and manage network devices and applica tions, but its presence in OT networks is lim ited (programmable automation controllers being a notable exception) and OT specialists are often not familiar with the tools that sup port it.
Manufacturing plants typically lose 30% of compressed air due to pneumatic system leakages. This impacts energy efficiency and environmental sustainability goals. Emerson’s Industrial Internet of Things (IIoT) solutions and analytics software provide actionable insights to reduce waste and optimize the energy consumption of your machines.
Discover how digitally transforming your operations can help meet your sustainability goals:
Will fieldbus networks continue to be important amid industry’s digital transformation? The answer depends on the application, even though Ethernet is clearly winning out.
At this point, it’s obvious that Ethernet is fast replacing the fieldbus networks that have dominated industry for decades. A clear case in point comes from Michael Bowne, executive director at PI North Ameri ca, which promotes the Profibus (fieldbus) and Profinet (Ethernet) indus trial communications protocols. According to Bowne, four Profinet nodes are currently being sold for every Profibus node sold. This represents a 180-degree change from a decade ago.
Despite this change, plenty of fieldbus networks remain in place across global industrial sites; and some sites continue to purchase and install field bus, as evidenced by Bowne’s comment. However, an increasing number of integrators note that they rarely see requests for anything other than Ethernet.
A major factor driving the expansion of Ethernet in industry is the emergence of industrial grade hubs, switches, and routers that make Eth ernet communications more robust, predictable, and less prone to drop data. Plus, there are many already-ported fieldbuses that most people are familiar with, like Modbus, EtherNet/IP and Profinet, which were field
buses that had the protocols converted to Ethernet. This created a larger development community working on Ethernet evolution than on any spe cific fieldbus. And that community continues its work.
With all the major field device manufacturers offering an Ethernet op tion—and often supporting multiple protocols over Ethernet—the fact is that engineers, developers, and electrical support personnel understand this technology and generally have a fair amount of Ethernet already in place in the industrial landscape. Numerous manufacturers have been using SCADA, HMI, and PLCs with Ethernet for many years. So, the knowledge base within the operations technology environment and within the plant maintenance groups is widespread.
The stickiness of fieldbus amid industry’s growing use of Ethernet is largely due to the fact that replacing fieldbus with Ethernet is generally not the primary reason most manufacturers take on an Ethernet installa tion project. Typically, if manufacturers move from fieldbus to Ethernet, it’s because they're looking for a way to replace or add devices, and/or they're looking for things that will give them better information, such as
better diagnostics. Ethernet is an inexpensive addition for smart devices that can be added to instrumentation. For most device manufacturers, it's the preferred connection for its ability to help see problems arising and provide a diagnosis before a problem is able to take a process down.
Despite fewer end users requesting fieldbus connectivity today, a market still remains for the technology. Some discrete I/O fieldbuses, such as ASI and CANbus, are still used because they have more consistent response times. Plus, they're simple to use and implement. ASI and CANbus also offer an inexpensive digital I/O bus, which makes them attractive for ap plications like building maintenance or conveyor systems.
An important caveat that all users should investigate when considering
using Ethernet is the limited use of some types in classified areas where intrinsic safety is required. In such cases, users may want to favor field bus because there are some fieldbuses made specifically for those types of hazardous environments. Even though Ethernet can be used in these environments—a major factor driving single-pair Ethernet use—be sure you're using the proper tools if you do opt to do so.
The stickiness of fieldbus amid industry’s growing use of Ethernet is largely due to the fact that replacing fieldbus with Ethernet is generally not the primary reason most manufacturers take on an Ethernet installation project.
While robots have become much easier to program, the same can’t be said for their integration into existing production operations. Answering these four questions will help ensure you’re prepared.
Industrial robots can fill many different roles in the manufacturing en vironment, including welding, painting, assembly, pick and place, pack aging and labeling, palletizing, product inspection, and testing. As robotic systems become increasingly affordable and flexible, more factories are integrating robotics into their current processes.
Nearly any repetitive task is a candidate for robotic replacement, but how do you know the best time to take the plunge into robotic systems?
Answering the following four questions can help guide you and your team through the process.
Many companies believe that the initial investment in automating their processes will be too expensive. However, the return on investment over the life of the robotic system is also high. The best way to evaluate this concept is by conducting a cost benefit analysis—examining the pros and cons for all process options. Forecast the cost 5, 15, or even 25 years from now. This will help identify whether the upfront cost will be recognized within the first few years or if the forecasted return on investment is far ther down the road.
One of the costs of integrating a new robotic system into your manufac turing facility is time. Do you have the time and personnel needed to implement and test this new system? A solid integration plan is an essential component of a new robotic system. It is necessary to bring multiple sub systems or components together into one operation system. This requires a broad range of expertise in software, automation hardware, and controls methodology. A reputable systems integrator is often worth the expense to expedite the new system’s implementation. This also helps free up your key personnel so that all their time will not be consumed for the entirety of the project. Remember, the longer it takes to implement your new sys tem, the longer it will take to realize the return on your investment.
A project champion is the person within the organization commit ted to the project’s success. There are two key traits need in a proj ect champion: knowledge of the existing process and a commitment to implement a new process. The champion takes responsibility for
identifying a need, sourcing a solution, and im plementing the new automation process. Being familiar with the old and new process, a champion can identify potential issues before they happen. They can also follow through to assure that the system can be safely and efficiently used. For ex ample, ensuring that each team member required is properly trained and has complete cooperation from engineering and other departments within the organization.
Implementing an entirely new sys tem and process into your factory is a huge change. Does your legacy system have the capability to com municate with your new robotic system? Do your key personnel have the time and/or training to integrate these systems? If not, a reputable system integration team can handle both vertical and hori
zontal integration, making certain that each area of the facility can talk to each other, leaving less likelihood of equipment isolation.
Pick parameters that meet your application needs!
Customized products at competitive prices!
Minimum order quantityone!
Assessing the factors that come into play when deciding between general purpose and inverter duty-rated motors for industrial applications.
While software and other advanced technologies often capture the automation technology spotlight, the fact remains that not much happens in the manufacturing or processing industries without motors. From simple applications like powering conveyors, fans, and pumps to more complex systems, motors are central to countless production operations.
And though all motors deliver similar functions, there are many differ ent types available. Plus, the increasing use of drives for higher level motor control and energy efficiency purposes provides another facet of consid eration when selecting motors for a specific task.
The key difference between general purpose and inverter duty motors is that inverter duty motors are specifically built to be operated by a variable frequency drive (VFD). A VFD allows that motor to be run at different speeds, whereas a typical motor starter on a general-purpose motor is only going to operate the motor at full speed.
An important consideration when selecting between motor types is that, since the motor isn't always operating at full speed, the cooling of
the motor is critical. Most motors are cooled by a fan connected directly to the motor shaft. If the fan is spinning at a slower speed than the motor, less air is moving across the motor and the motor won't cool as well. This is especially important in classified areas (e.g., Class 1, Div. 2) where the temperature of the motor needs to be kept below the ignition point of the classified area. Inverter duty rated motors often will have more cooling capacity to make sure that that motor doesn't overheat.
VFDs can have high-frequency spikes in the drive’s electrical system caused by the switching of the transistors in the drive to adjust the mo tor’s speed. This is why inverter duty rated motors have thicker insulation on the motor’s windings so they can hold up to these spikes longer over time. This is also why inverter duty rated motors tend to have a longer lifetime when running on a VFD.
You can run a standard motor on a VFD, but you should be aware that doing so could overheat the motor, since standard-duty motors won’t fea ture the extra insulation. Over time, the lifetime of a standard duty motor will be shortened by operating it on a VFD.
Revolutions per minute (RPM) is, of course, a significant motor charac teristic that comes into play for specific applications. Both inverter duty and standard duty motors are available in many different RPM configura tions. When you have a VFD, the difference is that you can operate that motor from zero to 100% of that RPM.
The duty cycle of a motor relates to how often a motor is starting and stopping and how much of the time the motors are running. This is often defined as the number of times per hour that the motor starts and stops. With most applications, users will opt for a continuous duty rated motor, as that motor is often going to be running for multiple hours at a time. Both standard and inverter duty rated motors will have continuous duty ratings, whereas a duty cycle motor would be one that's only running for short periods of time.
Given the inverter duty motor’s higher insulation and flexible design, these motors tend to be about 15% more expensive than a standard duty motor of similar horsepower.
It’s common when selecting a motor to focus primarily on the motor’s capability as well as the drive (if using an inverter duty rated motor). But don’t overlook the cabling.
Using a good quality VFD cable to connect the VFD to the motor is
essential to making sure that the system will perform as intended. It helps minimize harmonics that can leak into the rest of the electrical system and affect instrumentation and other sensitive electronics.
Grounding is another element to factor in. Most issues with VFDs and their motors are related to improper grounding of that motor, the VFD, and the cable. If the system is installed as designed, then the harmonics are mitigated through the VFD and you won't see as many issues with overheating in the motor or causing interference with the electronics and instrumentation.
You can run a standard motor on a VFD, but you should be aware that doing so could overheat the motor, since standard-duty motors won’t feature the extra insulation.
Quality, efficiency and productivity are critical for every factory function regarding profitable manufacturing. In nearly every industry, innovative automated vision inspection technology is helping factories improve in those three areas.
The benefits of vision inspection systems are becoming increasingly known. When properly integrated, these systems keep production flow ing seamlessly with high-speed digital precision. The ability of machines, robots and autonomous systems to view, detect and interpret images is called machine vision. This enables automated product quality inspection on the production line, in the warehouse and at the distribution center. Quickly identifying flawed parts throughout production results in greater throughput and a better finished product. Quality-control processes are no longer a cumbersome offline task at the end of the line.
Manufacturers implement machine vision systems to:
• Reduce customer complaints and returns.
• Inspect every part, every time.
• Decrease labor costs.
• Eliminate bottlenecks.
• Increase machine throughput and uptime.
• Receive valuable data for process improvement and control.
Machine vision’s assembly of systems is responsible for processing and assessing the images taken. Comprising computer hardware, software algorithms and electronic components, these systems offer operational guidance by generating data that one can use to control and inspect a product or material.
Machine vision entails the following four processes: identification, mea surement, position and guidance, and quality inspection.
Machine vision identification systems play a crucial role in part and prod uct identification by detecting unique patterns, direct part marks, bar codes and data codes on labels, packages and parts based on their shape, color or size. The unique marking carries data on the product’s name, date code, manufacturer, expiration date and lot number.
Barcode Reading. A barcode is encoded information printed on a part,
label, or directly marked on a package or part of a product with a ma chine-readable visual pattern. Manufacturers can use barcode reading to track and identify items either from the start to the end of an assembly line or from a logistics facility to its final destination.
Artificial Intelligence (AI). Deep learning and AI technologies teach vi sion systems, machines and robots to simulate what humans can do to identify images and perform various roles in a production line.
Pattern Recognition and Matching. Pattern matching and pattern recognition extract information from a video or image to provide motion analysis, detect errors, measure objects, count, or compare an image’s unique color, size, pattern and shape with a target image.
Optical Character Verification (OCV). Optical character verification measures the similarity between a text character and an image. Text qual ity inspection identifies text errors by comparing it against the expected text string for the field.
Optical Character Recognition (OCR). Optical character recognition converts images and reads the text within the image.
Dimension measurement is a subset of vision inspection. It is critical in determining whether products or components have been assembled per manufacturing specifications. A vision system for measurement calcu lates the ranges between at least two points on a product and identifies whether the measurements meet the required specifications. If they do
SPONSOR SUPPLIED CONTENTnot, the system will send a fail message to the controller, activating a re ject process that will eject the item from the queue.
Equipment inspection for predictive maintenance and process control may also be incorporated into this type of machine vision application. In practice, a camera (fixed mount) takes images of components as they pass into view. System software then calculates distances between image points. Measuring via image processing aids in overcoming the challenges associated with traditional jig-based measurement approaches.
Image processing provides the following advantages:
• Measuring different section dimensions is easy.
• Costs are reduced while ensuring product quality.
• Data is stored for information quality management.
• Quick inspections increase output.
Measuring component and product dimensions in-line may reduce inspection time significantly. Systems for image processing accelerate screening and increase productivity. Machine vision and automation make it possible to inspect every product, every time.
Guidance helps manufacturers create more than one product using the same production line. As a result, manufacturers avoid manually position ing parts, saving time and money.
Machine vision guidance determines a part’s position and orientation
in 2D or 3D space, ensuring the part is at the correct angle. The robot or machine controller can quickly locate the part or machine and align it with the required specifications.
Fast and precise, vision positioning ensures that all workpieces function accurately, leading to proper factory automation. Applications for ma chine vision positioning as part of manufacturing processes include glass substrate positioning, measuring and correcting misalignments of bar codes or labels, checking for misaligned lids (especially on food containers) and controlling the position of vision-guided robots.
For many manufacturers, position and guidance applications are espe cially helpful in repetitive tasks or high-risk manufacturing spaces.
Quality inspections are essential in a highly competitive market. Customer happiness, loyalty, future contracts, and revenue will all suffer from subpar or variable product quality.
But finding efficient ways to check quality can be difficult. Manual in spections take a lot of time and frequently only cover a tiny portion of a run. Inspectors might not always carry out their checks regularly.
Often, people are asked to do the impossible task of inspecting product moving quickly down a manufacturing line. Studies show that humans are less than 87% effective at this task, whereas machine vision solutions can easily keep up and provide 99% or better inspection results.
Linescan image formation mockup for factory acceptance testing of an OEM inspection solution build. Image courtesy of Motion Ai.
Machine vision is crucial to any factory. With these accurate systems in place, businesses can avoid incurring expenses associated with manual monitoring. Ma chine vision ensures optimum factory operations and aims to achieve core func tions on the manufacturing floor.
Whether inspecting barcodes, small parts or intricate products, machine vision solutions can increase uptime, quality and ROI. Choosing a qualified machine vi sion specialist for your inspection application is vital to the proper design, product selection, installation and training needed to keep your manufacturing line running efficiently while improving product quality.
Steven Dehlin is the National Sales Director for Integro Technologies, the Machine Vi sion Division of Motion Ai. He has spent his career advising customers on how to solve their unique challenges using machine vision and automation technologies. Steven has a vast knowledge of existing technologies and stays up to date with the latest technolo gies to provide customers with the best solutions possible that fit their ROI and budget. He has a bachelor’s degree in Industrial Engineering from West Virginia University.
Tara Van Geons is the Marketing Manager for Motion Ai, a business group of Motion. She has over a decade of marketing experience in the automation industry. Tara re ceived her bachelor’s degree from Pfeiffer University and her master’s degree from the University of North Carolina at Charlotte.
For more information, visit ai.motion.com.