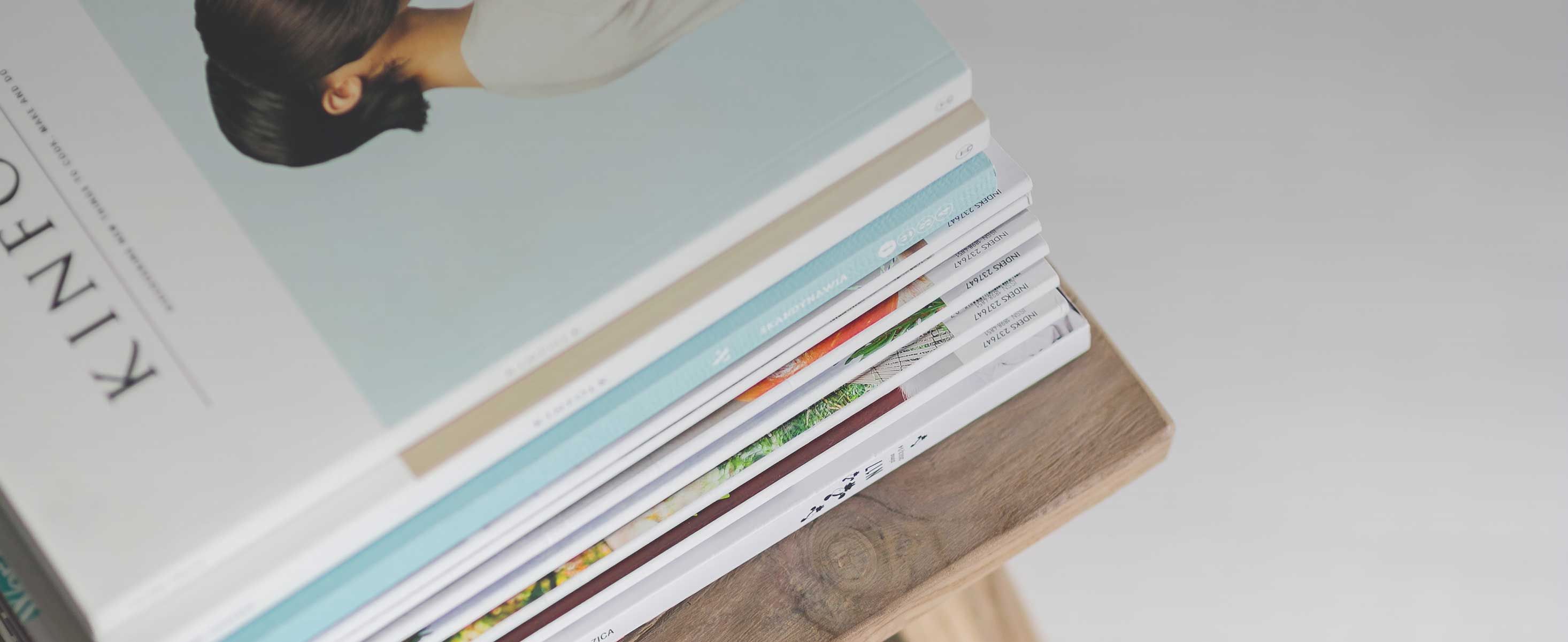
3 minute read
INDUSTRY VIEW
How Advances in Artifi cial Intelligence and 3D Printing Are Changing Manufacturing
By Dick Slansky
Senior Analyst, ARC Advisory Group
Top technology investment areas for aerospace manufacturing include advanced analytics, cloud computing, modeling and simulation, IoT platforms, optimization of production processes, and predictive analytics. Artificial intelligence (AI) and subsets of AI like machine learning (ML) will drive much of this technology in actual implementation.
Earlier research into AI and cognitive computing has resulted in real solutions being applied to real-world processes. In addition to robotics, additive manufacturing, and other disruptive technologies, the aerospace and defense (A&D) industries were relatively quick to recognize the potential of AI and readily embraced the science and technology it has spawned. Both industries have developed and implemented their respective roadmaps for digital transformation.
Automated systems have historically been an important element of the A&D industry from the cockpit to the factory floor. We’ve seen a steady progression from the first use of autopilots and other automated systems toward future autonomous avionics systems. Automated factory production systems have evolved from programmed control systems to machines and production systems based on predictive, prescriptive, and even autonomous self-healing systems enabled by AI/ ML algorithms.
In the factory production areas, ML is helping to improve and optimize the production process in several ways. These include reduced occurrence of equipment failures to keep the production rate humming and reduce expensive downtime. ML-based algorithms can access and analyze large volumes of data from vibration sensors in machines to detect and predict machine anomalies and failures. Moreover, ML can be prescriptive to determine how to best fix and prevent problems. Ultimately, ML algorithms can orchestrate a complete self-healing autonomous production environment of machines and assembly lines.
AI and ML are being used to determine the optimal production processes in aerospace manufacturing. Prescriptive analytics combine big data, mathematical statistics, logic, and ML to reveal the origins of the most complex production problems empirically and then suggest decision options to solve them. ML-based production intelligence systems use pattern recognition technology to analyze existing production data for both product and process and identify patterns of what works (best practices) and what does not (risk situations). These patterns are translated into a form of human-readable rules that are then applied to manufacturing operations for best practices. Aerospace manufacturers are using this method to optimize advanced composite manufacturing processes.
The rise of additive manufacturing
Today, the A&D industry is the largest user of additive manufacturing (AM) produced parts. From the commercial duopoly of Boeing and Airbus to defense OEMs like Lockheed Martin, thousands of AM “fly away” parts are used in the manufacturing of aircraft. For example, Boeing’s latest windbody model, the 777X, has more than 600 printed parts in the aircraft, with more than 300 printed parts in the huge GE9X engines. It is billed as the most powerful and efficient engine for a twinjet wide body aircraft today. The Boeing 777X is competing with the Airbus A350 XWB in terms of size, performance, and number of AM parts. The A350 already features more than 1,000 printed parts.
Boeing has made a major push into AM and has filed for patents related to the 3D printing of replacement aircraft parts, which could have serious implications to the company’s operations going forward. They want to create a parts library to store AM part definition files, including a database and a parts management system instead of storing parts at their various distribution hubs, or requiring parts to be shipped to them, causing extensive delays.
Instead, the company can just pull up a specific AM file for a part that is needed and have it fabricated within minutes or hours, wherever they have a printer available. Currently, the company has more than 350 AM standard parts spanning 10 different aircraft production programs with around 20,000 printed parts currently being used on their aircraft.
The other area of A&D manufacturing where AM is making a significant impact is in the tooling used to support production line assembly and installation. Using a new generation of big area additive manufacturing (BAAM) printers, large tooling fixtures and jigs can be fabricated as single large parts in reduced time, eliminating multiple part assemblies.
Currently, AI is an integral part of the design process for AM in aerospace. In designing parts for aircraft, achieving the optimal weight-to-strength ratio is a primary objective, since reducing weight is an important factor in air-frame structures design. Today’s PLM solutions offer function-driven generative design using AI-based algorithms to capture the functional specifications and generate and validate conceptual shapes best suited for AM fabrication. Using this generative functional design method produces the optimal lightweight design within the functional specifications.