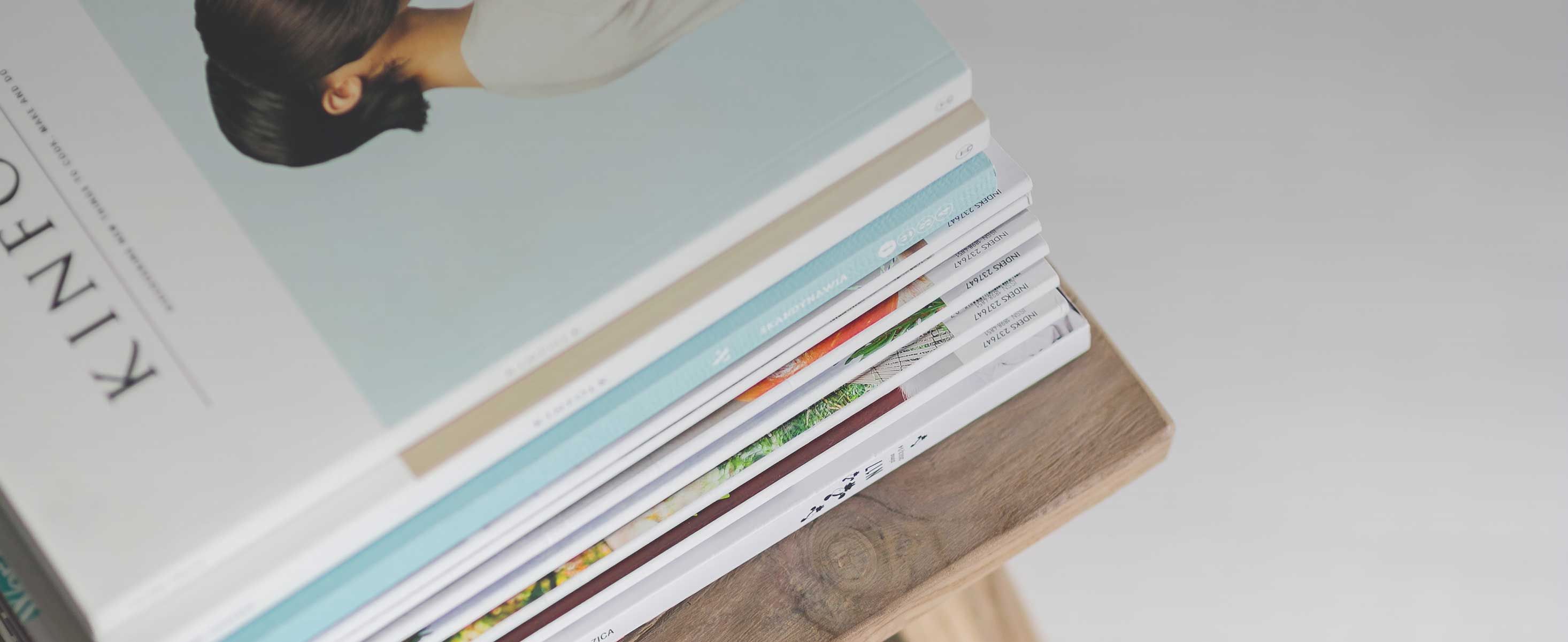
2 minute read
PRODUCTION PERSPECTIVES
Artificial Intelligence for Mobile Robot Fleet Management
By David Miller
dmiller@pmmimediagroup.com
Senior Technical Writer, Automation World
Autonomous mobile robots (AMRs) have seen growing adoption in recent years as increasingly diverse tooling options have improved their value proposition and business models such as robots-as-a-service (RaaS) have shrunk their upfront costs while also granting adopters more scalability. However, as AMRs have become a more ubiquitous presence in factories and warehouses, new challenges have emerged.
For one, safety has become a greater concern, particularly as higher payload AMRs begin to be integrated with robotic arms and other peripheral tooling that may affect their performance. In addition, as the size of AMR fleets grow, achieving effective coordination and interoperability could be a struggle. Currently, the issue of safety has begun to be addressed through new standards, and coordination concerns are slowly being improved via fleet management software. That said, new developments in artificial intelligence (AI) may provide a different set of answers to both problems. 634AI, a spin-out company of AI provider MusashiAI, was recently created to focus on the development of Maestro, an AI control tower which seeks to use a combination of computer vision and software intelligence to monitor and control the movements of various mobile assets on industrial plant floors. While AMR fleet management is one of Maestro’s primary functions, 634AI says it can be applied to a range of hardware, including forklifts, driven pallet jacks, and traditional automated guided vehicles (AGVs).
According to the company, many AMRs on the market today operate as stand-alone robots with sophisticated internal intelligence supported by expensive onboard hardware. As a result, configuring them to work in tandem with one another can be a complex task for integrators, particularly if AMRs from different vendors are being used within the same facility. In some cases, application programming interfaces (APIs) have enabled various AMRs to communicate with one another, but 634AI sees this approach increasing complexity.
In contrast, Maestro operates as a central controller which monitors the position of all AMRs on the plant floor via vision systems and issues commands based on their positions. Because all navigation instructions proceed from Maestro, the sophisticated software intelligence and supporting hardware inside each individual AMR can be removed. According to 634AI, this will not only drastically lower the costs of AMRs, but will provide more effective and interoperable fleet management capabilities.
“What has been happening in the AMR and the industrial floor automation industry over the last few years has been like spending millions on developing zero-gravity pens, when all we’ve needed has actually just been a pencil,” said Onn Fenig, CEO at 634AI. “Our motivation for creating Maestro was to give businesses a practical and affordable tool that will enable them to enjoy safer and smarter indoor mobility. We’re on a mission to make any indoor task autonomous and affordable.”
Watch this Take Five video to learn more about the artifi cal intelligence explosion in industrial automation at awgo.to/1195.