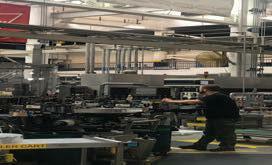
5 minute read
2022 Technology Excellence Awards
from OEM Winter 2022
Machine Builders Move in to Bridge the Skills Gap
With high employee turnover on the factory floor, manufacturers are asking OEMs to design easy-to-use equipment and provide ongoing training.
Stephanie Neil, Editor-in-Chief
The Anheuser-Busch facility in St. Louis serves as the hub of innovation for over 30 brands— the most popular being Budweiser and Michelob Ultra. Multiple lines are running at high speed on the packaging floor. As an example, one can line can package 1,950 12 ounce cans per minute and 1,650 16 ounce cans per minute.
With so much activity, operators have to be familiar with equipment and procedures. Unfortunately, the beverage manufacturer is not only dealing with the skills shortage that is impacting the entire industry, but it is also ready to lose about 40% of its workforce that is ready to retire. That means novice operators will be running machines and trying to interpret some of the antiquated HMIs that serve as the interface to equipment that has been in place for decades.
Fearful for what the future holds for the packaging floor, Ken VonderHaar, global director of the AnheuserBusch Can Division, has been going back to the drawing board in some cases, and asking OEMs to design machines that are much easier to learn and to use.
“Essentially, we’re asking for simplicity,” he says. “We would like for all of the complexity to be under the hood [of the machine], and we would like an operator interface that’s very simple, that’s easy to understand, and that enables our younger employees to interface with some type of video screen. We also look for set-up procedures that are built into the operator screen. And we’d love it if [OEMs] could help train our operators.”
Lisa Rathburn, vice president of engineering at food manufacturer T. Marzetti, agrees that training and easy interfaces can help close the skills gap. “We walk through the interfaces during design reviews to ensure that terminology matches what is used by our teams on the plant floor,” she says. “We are focused on standardizing where possible to simplify the diversity of knowledge needed. And we are also favoring changeover parts, rail adjustment, etc., that have clear indicators or push button operations to reduce human error and manual adjustments.”
OEMs are listening to customers’ requests and delivering intuitive HMIs, visual learning components, as well as offering augmented reality (AR), and remote management and diagnostic technologies in order to offload most of the maintenance issues.
The goal is to avoid a big problem when there’s an easy fix.
“We can solve 90% of the issues remotely and within an hour,” says Robert Mize, a technical support representative at Pearson Packaging Systems, a provider of end-of-line automated packaging systems.
Pearson’s remote service offering is free and available 24/7. They use several technologies to connect with customers and help them get back up and running quickly. The simplest form is Vuforia augmented reality technology from PTC, which allows the technician to make annotations on a shared screen. It’s a simple process that starts by sending a code to a phone with the Vuforia app and pulling up the software that allows operators and technicians to share the same screen. It does not require a remote connection to the machine and is especially useful when opera-
Workers monitor the packaging line at Anheuser-Busch’s St. Louis facility.
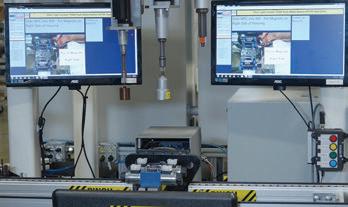
tors have language barriers or don’t know maintenance terminology. “It’s one of the first things we mobilize. We can see the machine and we can annotate in real time,” says Mize.
The next level of support is given via an Ewon router that connects to the PLC via a secure VPN tunnel. This router provides the technical support team the ability to see the state of the machine, including PLC and sensor data, as well as make corrections to the code if necessary. “Back in 2019, we made the decision that we were going to equip any plant or industrial network [our machines] are in with the ability to remote connect,” says Brian Patrick, Pearson’s vice president of engineering. “It’s allowed us to make further investments, not only just putting remote connection on machines, but also being able to send things out quickly from a support standpoint.”
In certain cases, Pearson also provides cameras that can be set up around the machine so that when a remote session takes place, technical support can see what the customer is seeing. This is especially helpful when a situation has to be assessed over a period of time.
Urgent calls
These types of services are proving to be vital given the current state of the workforce. For example, during a routine customer service call to Pearson tech support, Mize was answering questions about a machine while trying to gauge the operator’s familiarity with the technology. That’s when he learned that the caller had actually been a cashier at the warehouse retail site just an hour before being reassigned to the machine operator role.
“Even the tone of the callers is totally different than it was a few years ago,” Mize says. “There’s a sense of urgency. It’s like they’ve been dropped off in the middle of the ocean and they have to learn to swim for themselves.”
The urgency is heightened because every second counts. “Our customers make money when they get boxes out the door,” says Paul Wolf, director of customer service at R.A. Jones, a provider of primary and secondary packaging machinery. “So how do you get a new hire to operate a line in a day?” One solution, Wolf says, is a two minute training video.
The company has identified several of the most common faults on its machines and are now scripting out in a short, documentary-like form, videos on how to fix them. “A lot of documentation gets lost, but with a video of how to fix it, we can get an operator up to speed in record time,” Wolf says, noting they are also embedding videos in HMIs and online manuals, which can be customized to customer needs.
Other OEMs are aiding the untrained operator by developing somewhat self-sufficient machines.
At PACK EXPO International in October, BellatRx introduced a new labeling machine that includes a piece of equipment that takes the measurements of a bottle, which when entered into the HMI, automatically creates a recipe
A Bosch Rexroth system equipped with a camera and sensors confirm that operators move forward with the operation per the standard.
Pearson Packaging Systems uses PTC’s Vuforia augmented reality to connect operators and service technicians.
