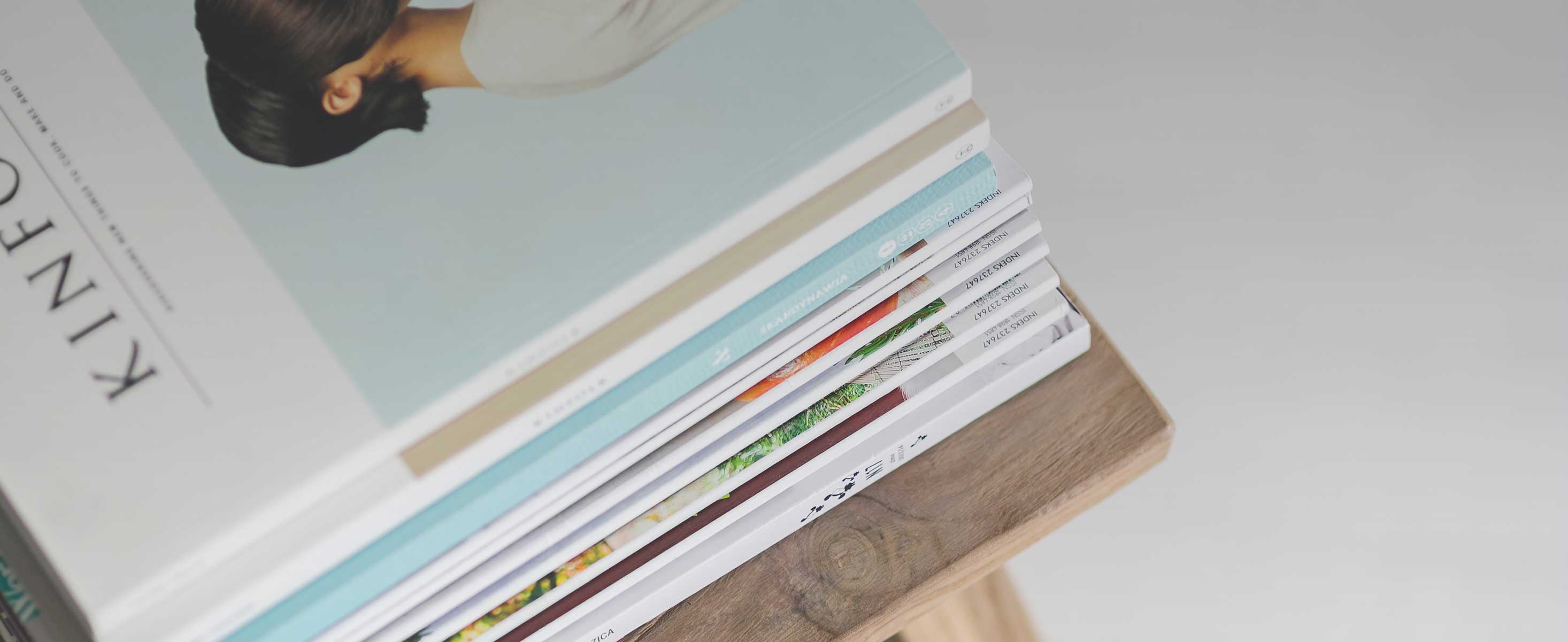
11 minute read
OEM Winter 2022
from OEM Winter 2022
The Race to Save the Planet
Fassl, Editor at Large, ProFood World
Sustainability is the new watchword for a huge and growing band of consumers, according to a June 2022 report from PMMI titled “Achieving Packaging Sustainability.” The ongoing green movement presents an opportunity for businesses facing increasing competitive and economic pressures to gain value in competitive advantage as they respond to environmental concerns and the pressures of resource scarcity, population growth, and higher and more varied consumer expectations.
Perhaps unfairly, the packaging industry is seen as one of the worst environmental offenders, the PMMI report states. At a recent Top to Top event held in Florida, PMMI hosted roundtables with participants from across the packaging value chain. Participants indicated that it’s not just CPGs that should be implementing sustainability strategies. OEMs also have a crucial part to play in energy savings. In fact, a current hot topic in Europe is a carbon footprint rating for each new machine.
Download the 2022 report, “Achieving Packaging Sustainability,” from PMMI. h ps://www.pmmi.org/report/2022-achievingpackaging-sustainability
Overall, the message from participants at the Top to Top meeting is that it’s all about the collaboration between CPGs, material suppliers, and OEMs as they plan ahead for the next generation of packaging materials.
However, while consumers continue to seek sustainable products, they may not be willing to pay the price, according to a recent report from market research firm AMC Global and OpinionRoute, a company that provides insights into process management. These survey results say that many consumers want sustainably produced and sourced products, but price remains the top consideration when making purchasing decisions. According to AMC Global, consumers believe these products are more expensive than their mainstream counterparts, and recent inflation and price increases are making affordability a key concern. In addition, a high percentage of respondents say it is hard to tell which brands are sustainable and which are not.
While 43% of people believe it is worth it to pay more for sustainable products, 66% say they can’t afford to do so due to recent price increases across the board.
While consumers often look to retailers and product packaging to guide them on sustainability, the winners
of ProFood World’s annual Sustainability Excellence in Manufacturing Awards are focused on reducing greenhouse gas emissions, electricity, and water, as well as food waste and materials management. Following are the six 2021 Program and Project Category winners.
first place | program category
No-cost project yields $1 million payback for Conagra Brands
The Oakdale, Calif., Conagra Brands facility makes Hunt’s and Ro-Tel brands, and other food products. Over the past year, the facility’s cross-functional team made excellent progress in reducing food waste. The team implemented a comprehensive plan and problem-solving program throughout 2021 to eliminate ingredient loss points for both jalapeños and tomatoes. The program addressed three causes of jalapeño waste (spoiled ingredients, batch planning, and fill controls) and two processes for tomato waste (peelers and fillers). As a result, the plant utilized 650,000 lb of jalapeño and 13.8 million lb of tomato raw ingredients compared to 2020, which reduced the site’s solid waste footprint by about 10%.
“By manufacturing food ingredients more efficiently, we are using utilities more efficiently,” says Kate Pitschka, director of supply chain sustainability, pointing to Scope 1 and 2 greenhouse gas (GHG) emissions. “We are also moving a significant portion of the site’s food waste up in the recovery hierarchy from animal feed and compost.”
The plant is located in a high water-risk region, and eliminating some of the organic load being sent to wastewater operations is reducing some stress on the region’s water cycle. By eliminating food waste, the facility is reducing the amount of Scope 3 GHG emissions (EPA WARM and Biogenic) that the food waste would create downstream.
Teams were established during March to May 2021, project scopes were defined within one to two months, and specific projects were implemented between July and October 2021, resulting in a 4% jalapeño yield improvement and a 1.8% tomato yield improvement.
“Savings were strictly through better use of available equipment resources and process improvements, with limited costs,” explains Pitschka.
The Oakdale cross-functional team delivered a $471,000 jalapeño yield loss reduction (spoiled ingredients, under net weight rejections, and overfill) and a $730,000 tomato yield loss reduction. These calculations do not include the energy cost savings associated with treating the food waste going to wastewater, nor the hauling costs of the solid waste.
second place | program category
Bob’s Red Mill focuses on wasted food rescue and materials management
Committed to creating a sustainable future while inspiring joy with wholesome foods, Bob’s Red Mill Natural Products fosters nourishing a healthy planet. One of the company’s main goals is reducing food loss from farm to fork through wasted food rescue. “By rescuing unavoidable scrap, we are avoiding climate emissions that would occur downstream,” says Julia Person, sustainability manager for Bob’s Red Mill. “We donate food to local non-profits, as well as send inedible product to animal feed. Another way we are furthering this work is by joining the Pacific Coast Food Waste Commitment to collectively work with other food businesses to cut food waste in half by 2030.”
The Milwaukie, Ore.-based company’s materials management focus extends beyond food waste to refuse, reduce, reuse, and recycle the maximum possible material flow at the plant, with a goal to reach zero waste. At Bob’s Red Mill, wasted food rescue and materials management programs have helped reduce operations costs for the employee-owned company and have a positive impact, both environmentally and socially, in the local community.
“In 2021, we kept over 385,000 lb of edible food from going to waste, upcycled 2,293 tons as animal feed instead of landfill or compost waste, and recycled more than 1,600 tons of materials such as cardboard, plastic, metal, and wood,” states Person. “Our food donations help provide healthy, wholesome food to those in need in our surrounding community.” Through donations to the Oregon Food Bank network, Bob’s Red Mill provided 161,521 meals to those experiencing hunger in 2021. It donated rescued food to four main organizations in the Portland, Ore., metro area—Oregon Food Bank, The Canby Center, Sunshine Division, and Gleaners of Clackamas County.
third place | program category
Pizza yield improvement project at Conagra Brands comes with no cost
Conagra Brands’ Troy, Ohio, team implemented a comprehensive continuous improvement program on the site’s bakery line when running pizza, and have set up new
process and operating standards, organization, and line planning. Ongoing efforts are expected to deliver more than $325,000 in cost savings by reducing yield loss by 13.4% and eliminating 267,000 lb of meat, cheese, and breading waste.
“Every opportunity to manufacture food more efficiently will allow us to use water and energy resources [Scope 1 and 2 GHG] more efficiently,” says Kate Pitschka, director of supply chain sustainability. “However, they are not directly quantified in this submission. Also, by eliminating food waste, we reduce the amount of Scope 3 GHG emissions [EPA WARM] that the food waste would create downstream.”
Meat toppings process and planning analysis took six months and concluded in August 2021; cheese process and planning improvements took five months and concluded in November 2021; extra toppings and cheese reuse took one month to implement in September 2021; and over a two-month period, employees’ continuous improvement skills were developed, beginning in November 2021.
The reduction of the weight average per case is forecasted to deliver annualized savings of more than $325,000.
first place | project category
The main objective of the project at Conagra Brands’ Irapuato, Mexico, plant was the reduction of water consumption. In this project, two specific situations were considered:
• Identification of water leaks and improvements in the sweet corn process and canning process equipment.
• Completing sanitation more efficiently on various lines to reduce the consumption of cleaning chemicals, resulting in greater production line availability. Also, some of the sweet corn equipment required a redesign to eliminate or make more efficient use of water.
Reducing water consumption is a benefit for the entire community since the plant is located in an area with limited water availability. By improving the operating conditions of its wastewater treatment facility and discharge parameters, the water can be reused for farmland irrigation.
“The corn/cannery production improvements were completed over seven months, finishing in September 2022, and the sanitation improvements were completed from April 2021 to May 2021,” says Fernando Alcántar Gómez, EHS manager. “Both projects resulted in an 8% reduction in water use per production year over
year, with ROI in less than a month.”
The project returned more than 10 times its cost, saved nearly 9 million gallons of water, and reduced chemical usage by 2,680 gal.
second place | project category
Switch to plastic combos at Smithfield Foods is an environmental winner
Early in 2021, Smithfield Foods’ Milan, Mo., plant started sending out hams for further processing, transporting them in cardboard combos. The facility quickly realized it could save money and reduce cardboard usage by using reusable plastic combos.
Less than 30 days into the project, the plant ordered 720 plastic reusable combos. On average, the Milan facility ships 100 combos of hams per day. “Although 720 plastic combos are not enough to replace every cardboard combo we ship, it will reward us with a 50% reduction in cardboard usage,” says Wes Maulsby, wastewater operator at the Milan facility.
The combo project’s goal included:
• Reducing GHG emissions—Cardboard savings can be directly related to the release of methane, a GHG, as it breaks down in a landfill. Per ton released, methane will contribute to global warming at a pace more than that of carbon dioxide.
• Reducing water usage—Using less cardboard creates less demand and reduces manufacturing water usage.
• Reducing energy—Fuel sources to manufacture cardboard are no longer needed.
• Reducing global warming—Deforestation is a huge contributor to global warming. The facility can save 17 trees per ton of corrugated cardboard savings, and every eight pallets saved will yield one saved tree.
• Reducing landfill—For every ton of cardboard savings, landfill area can be cut by 9 yd3.
The project was completed in the first quarter of 2021, when the Milan plant shipped the first hams for further processing. In February 2021, the facility received its first load of plastic reusable combos and, in March 2021, shipped the first load of hams in reusable combos. third place | project category
Conagra Brands’ blast cell air optimization project reaches ROI in less
Degradation of freezer blast cells was resulting in improper airflow and inefficiency of the blast cell function at Conagra Brands’ Marshall, Mo., facility. Repairs were made to air segregation, and baffle design was changed to reduce
potential damage from the forklift loading process.
“Baffles were added at the back of each rack column in the blast cells to force the airflow through the product pallets to improve the heat transfer of the freezer,” explains Scottie McKenzie, plant engineering manager. “This reduces the freeze time, lowers electricity consumption, and increases plant capacity.”
The project will reduce the plant’s electricity consumption by 5.7% and reduce the plant’s Scope 2 GHG footprint by almost 1,300 metric tons. “Efficiency projects like this will be an important piece of the entire company’s sciencebased target,” he adds.
In September 2021, a freezer evaluation uncovered inefficiencies in the blast cells. Contractors installed baffles inside the blast cells in November 2021, and performance monitoring occurred in December 2021. The project paid for itself in less than one year.
At the Marshall facility, product requiring freezing is estimated at 500,000 lb/day. Now the plant has seen a 10% reduction in freeze time, a 5.7% total site electricity reduction, and an overall reduction in kWh/lb usage. The result is a yearly savings of more than $200,000.
Easily share the full story with your peers: oemgo.to/sustainabilityawards2022
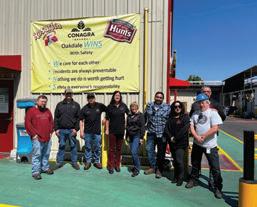
Conagra Brands — Oakdale, CA
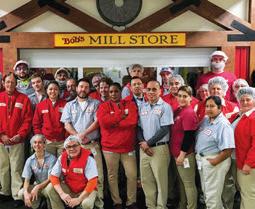
Bob’s Red Mill
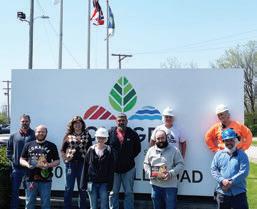
Conagra Brands - Troy, Ohio