SHOW DAILY
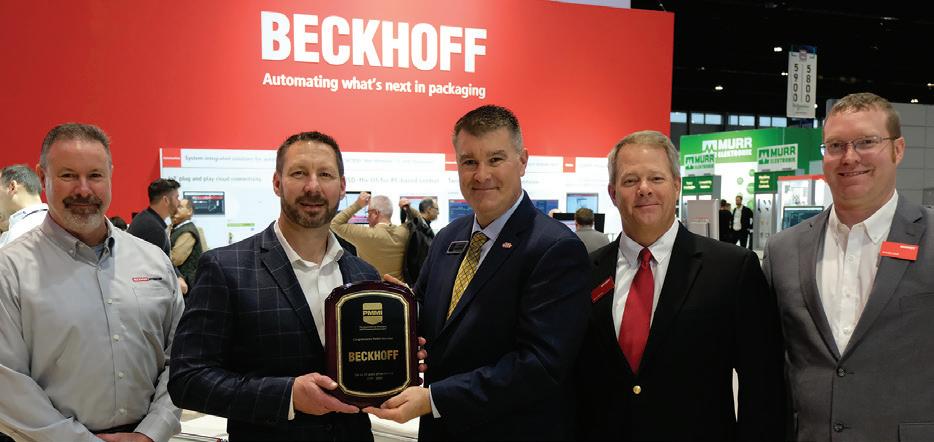
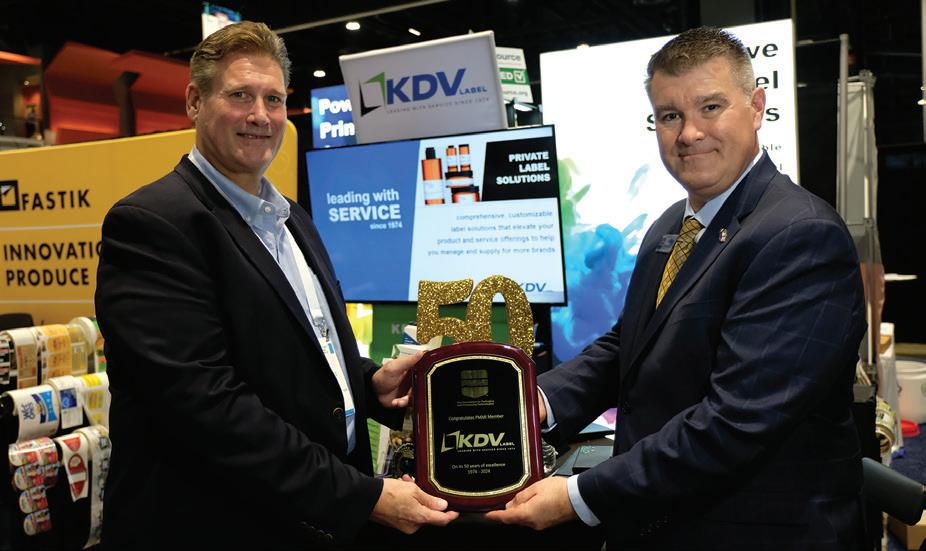

Registration Open for Inaugural PACK EXPO Southeast
New PACK EXPO debuts in Atlanta to serve the fast-growing southeast manufacturing hub.
As PACK EXPO International 2024 comes to a close today as the largest packaging and processing trade show this year, the PACK EXPO portfolio of trade shows doesn’t rest on its laurels, with registration open for the inaugural edition of PACK EXPO Southeast (March 10-12, 2025; Georgia World Congress Center, Atlanta). Produced by PMMI, e Association for Packaging and Processing Technologies, PACK EXPO Southeast will be the region’s most comprehensive packaging and processing show.
PMMI forecasts a convergence of 7,000 attendees
Sun Inspires at
PPWLN Breakfast
GRAVITAS founder and CEO
Lisa Sun, founder and CEO of retail brand and lifestyle company GRAVITAS, gave entrepreneurial insights, experiences, and valuable life lessons to an over ow crowd yesterday at e Packaging & Processing Women’s Leadership Network (PPWLN) Breakfast.

Sun seamlessly blended stories from her life’s work with data and experiencedriven insights from her 11 years at McKinsey & Company into how she founded GRAVITAS in 2012.
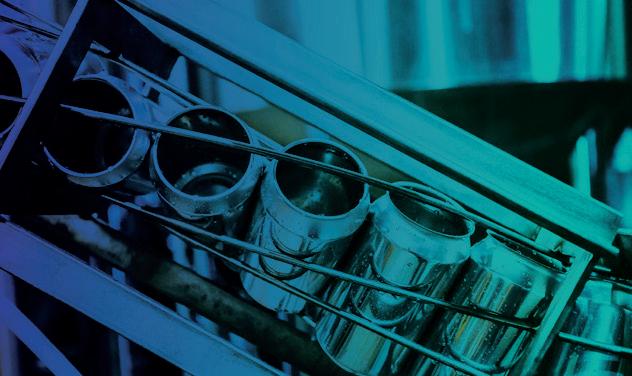
to Atlanta from consumer packaged goods and life sciences companies based in the Southeast to witness innovation in action, learn about the latest industry trends and topics, and network for brand and professional growth. PACK EXPO Southeast will feature 400 exhibitors displaying the latest solutions and technologies for 40+ vertical markets over
on page 6
Lots of Laughs at PACK Gives Back
Nate Bargatze cracks up the crowd.
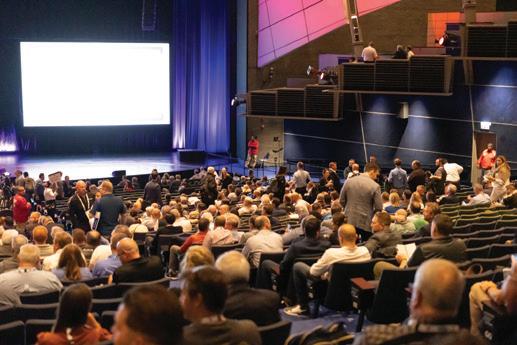
Award-winning comedian Nate Bargatze le a sold-out audience in stitches with his clean humor and relatable storytelling at Monday’s PACK gives BACK™ event, sponsored by Rockwell Automation (Booth S-1544). e annual bene t provided a fun- lled night of entertainment, networking, and philanthropy, with proceeds bene ting the PMMI Foundation, supporting the future packaging and processing workforce.
on page 2

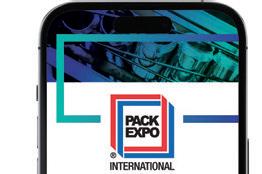
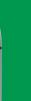
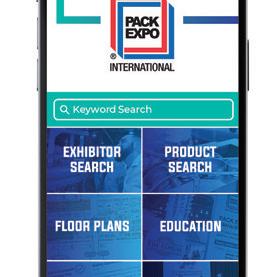
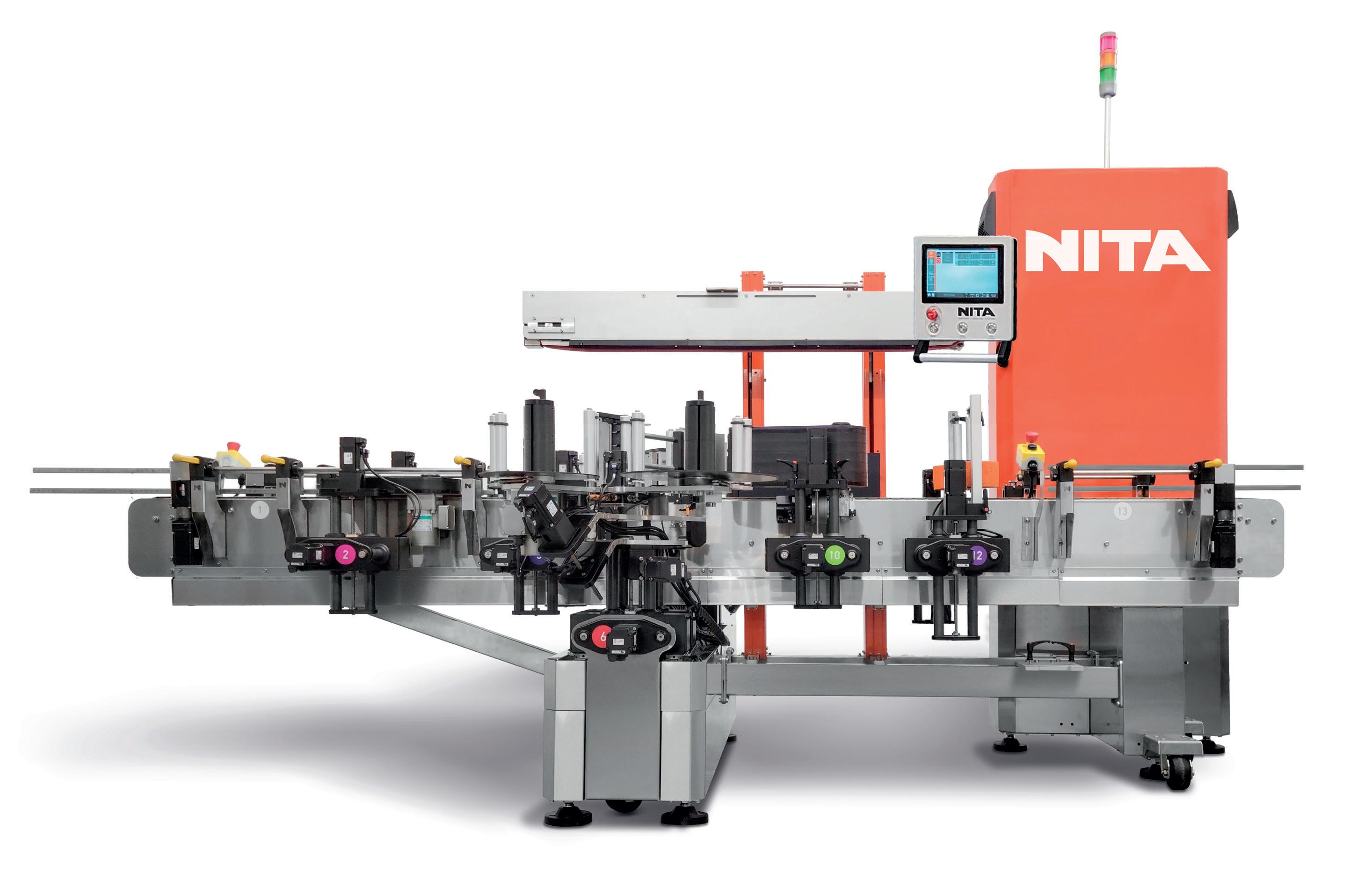


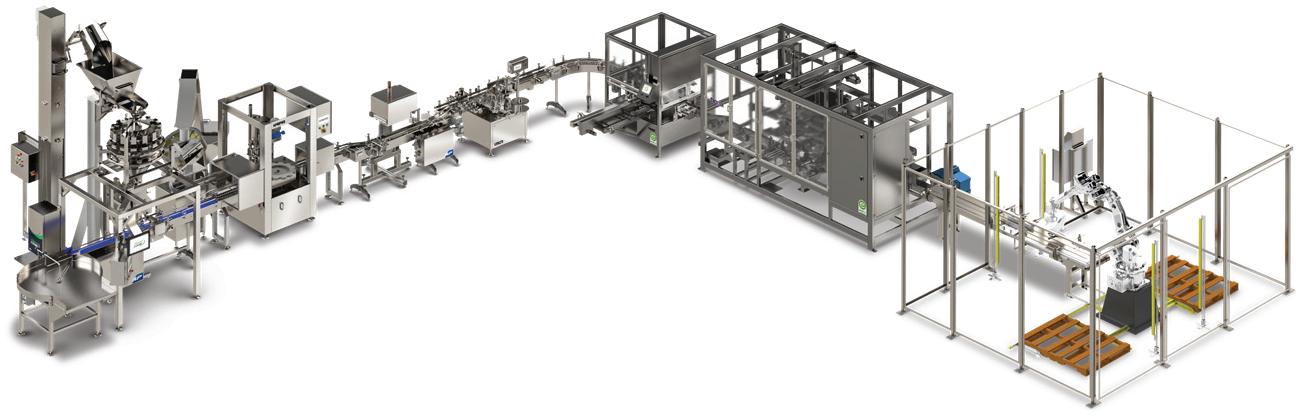
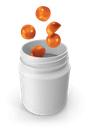

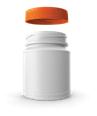

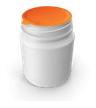


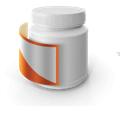

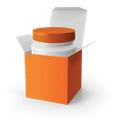

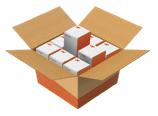

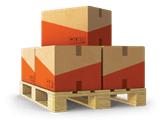



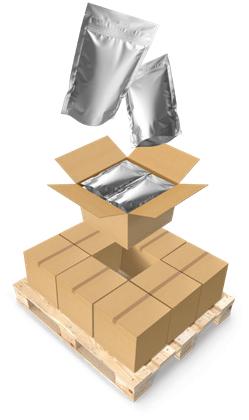

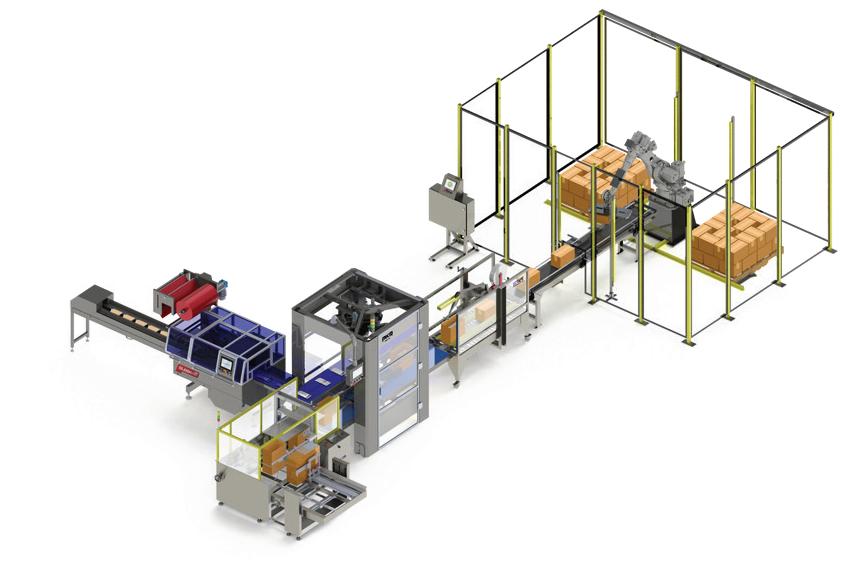
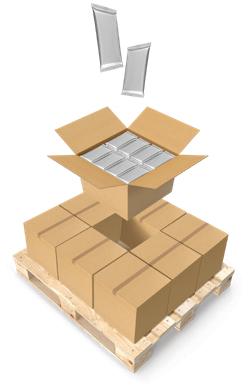

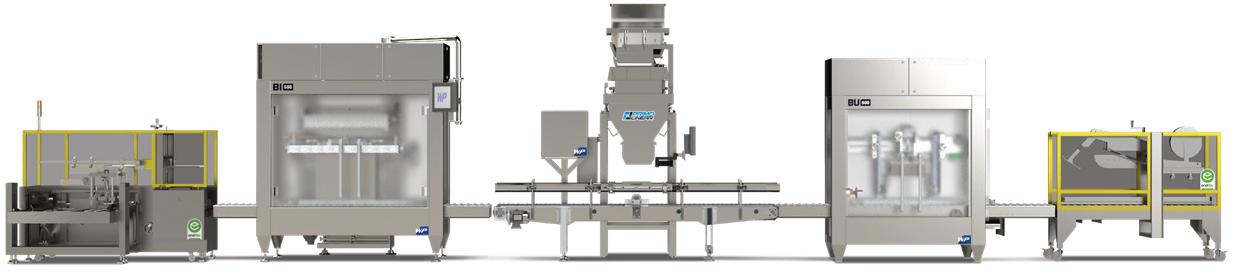
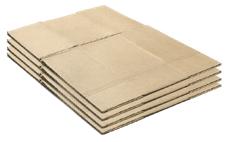

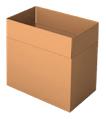
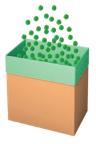


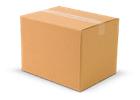
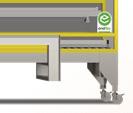
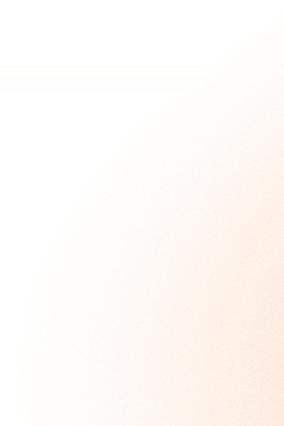




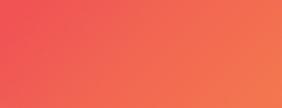
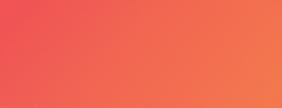
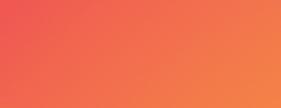
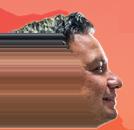


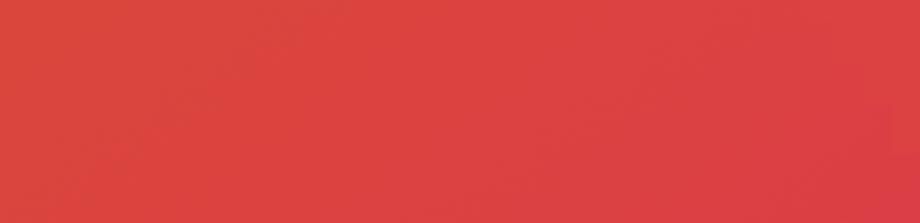



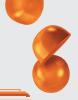



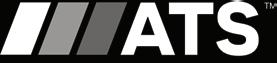
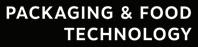

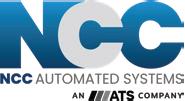

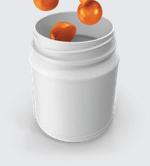


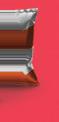
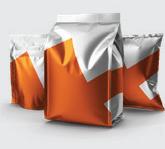

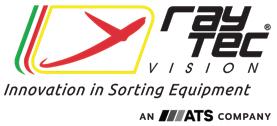
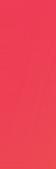


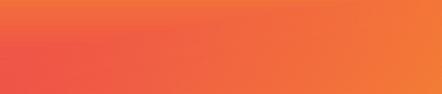
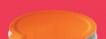
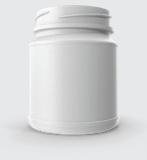
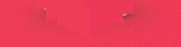
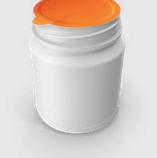
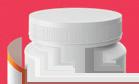




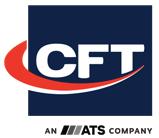



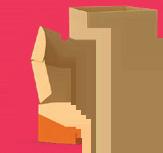
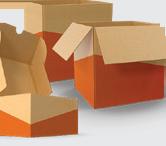
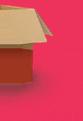
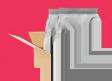

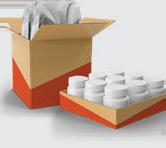

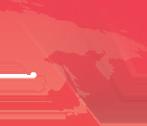

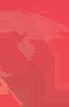
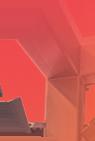
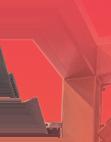
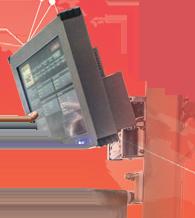
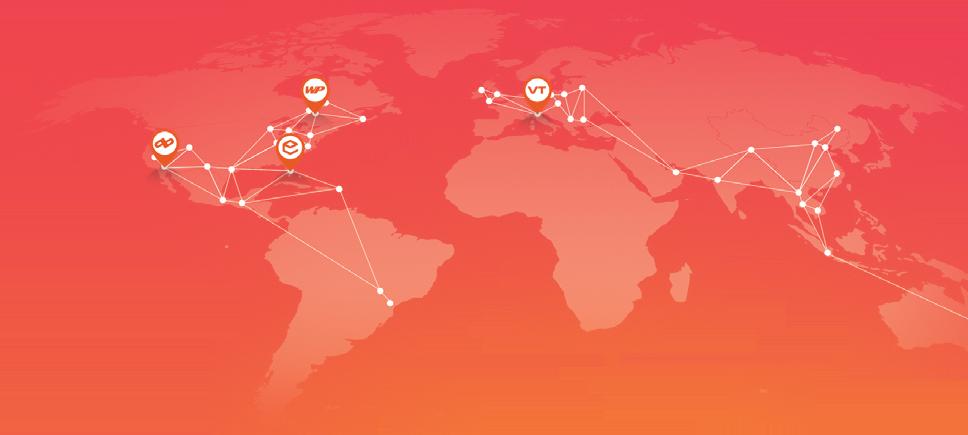
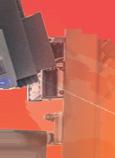
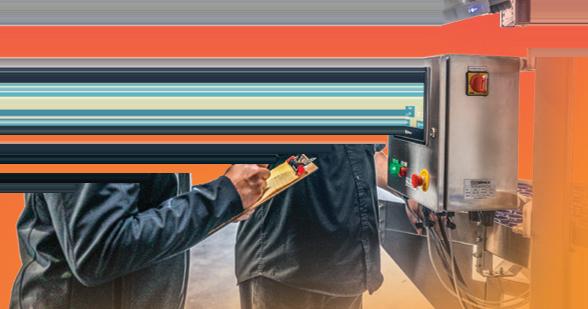
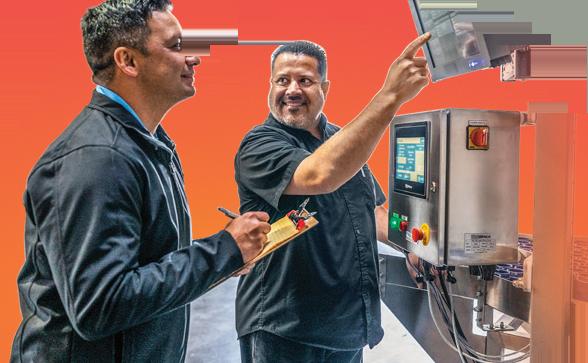
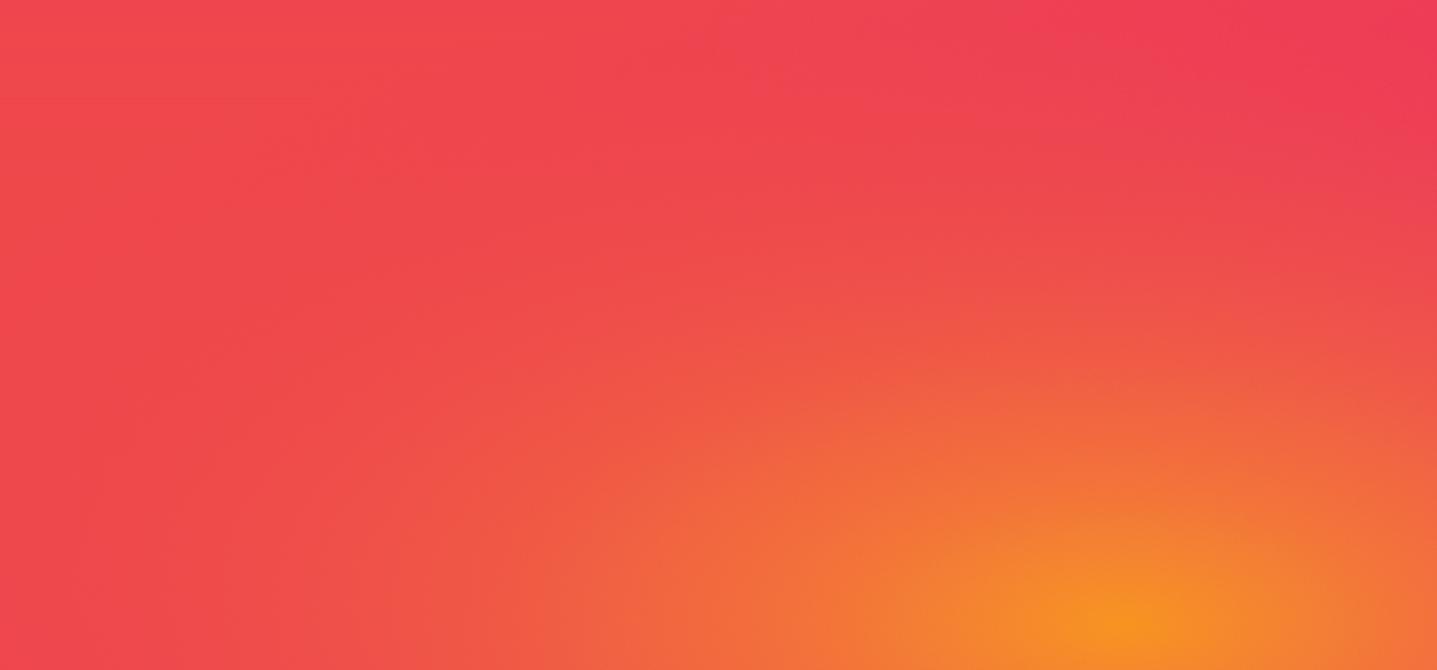




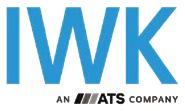
NEWS BRIEF
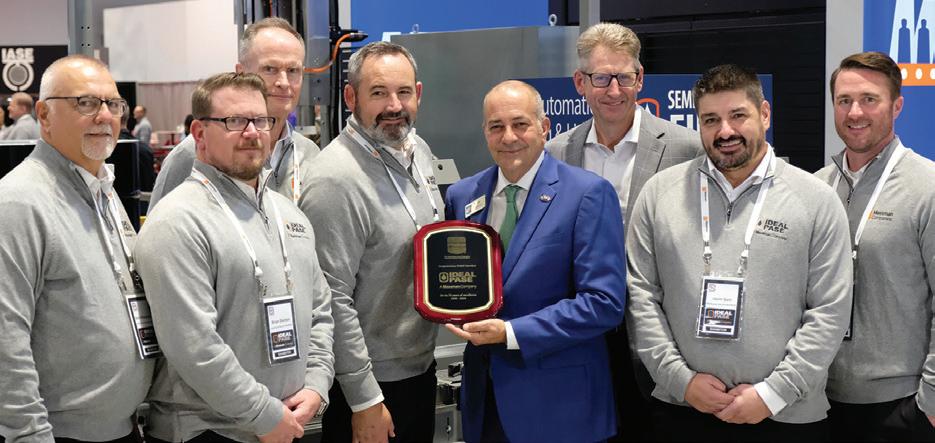
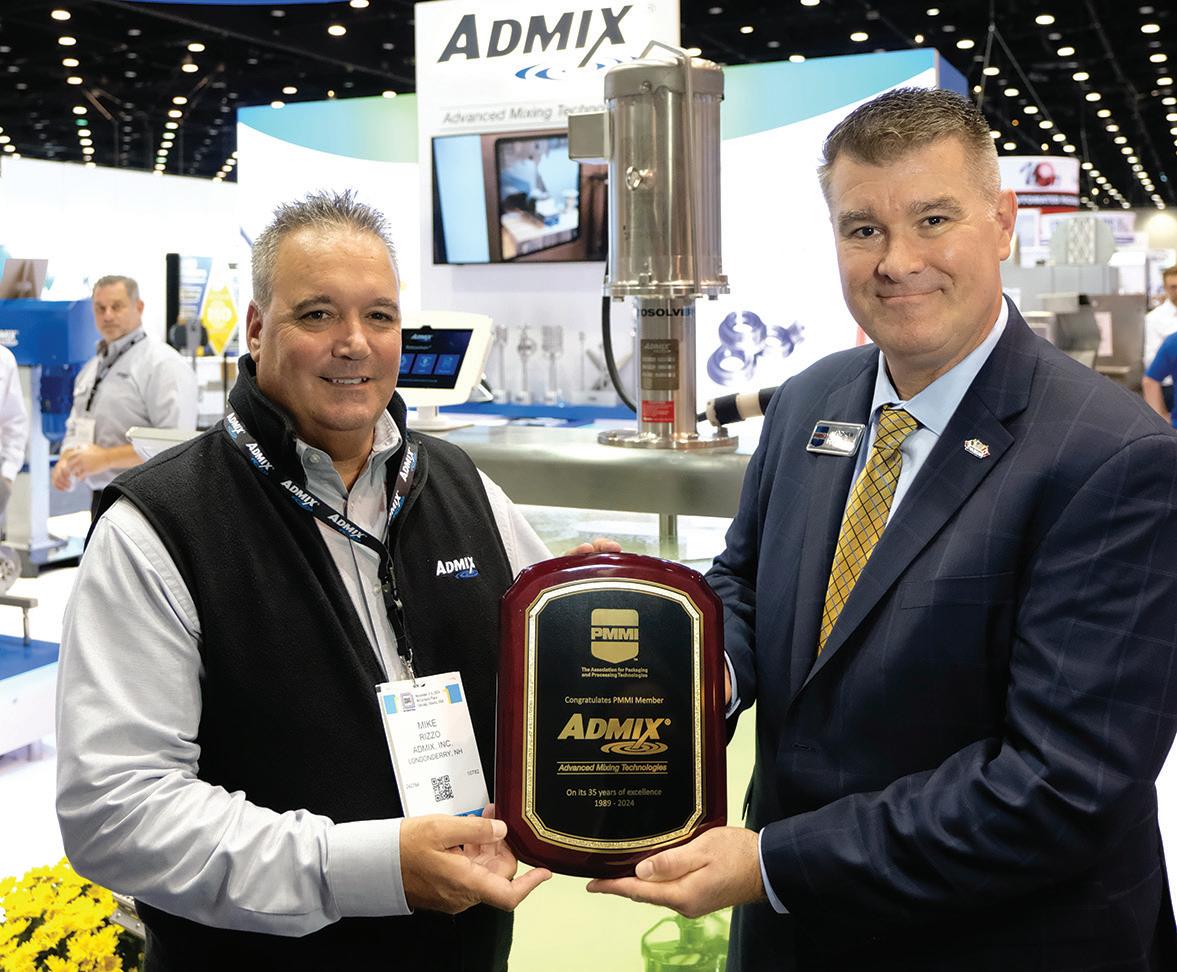
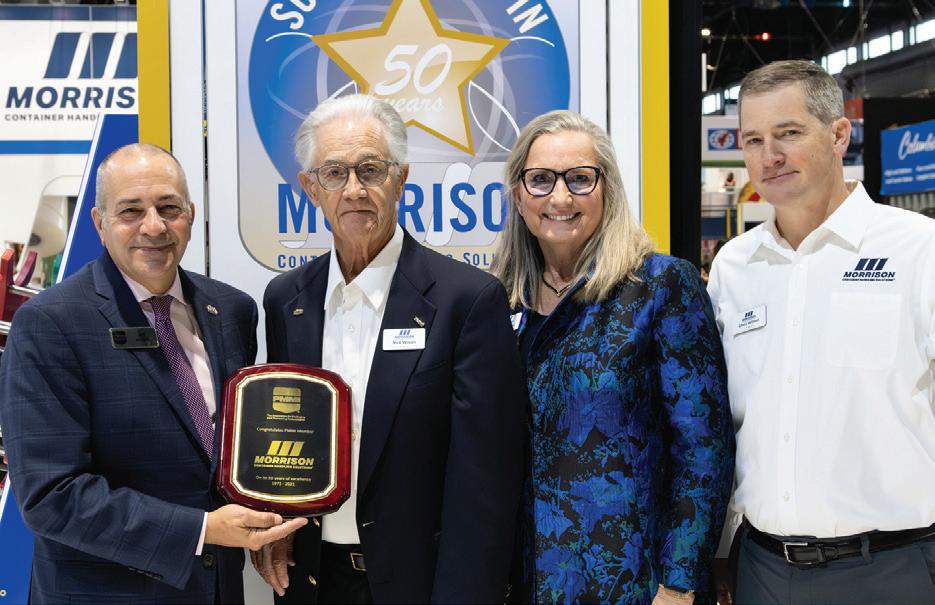
Sonoco Celebrates 125th Anniversary
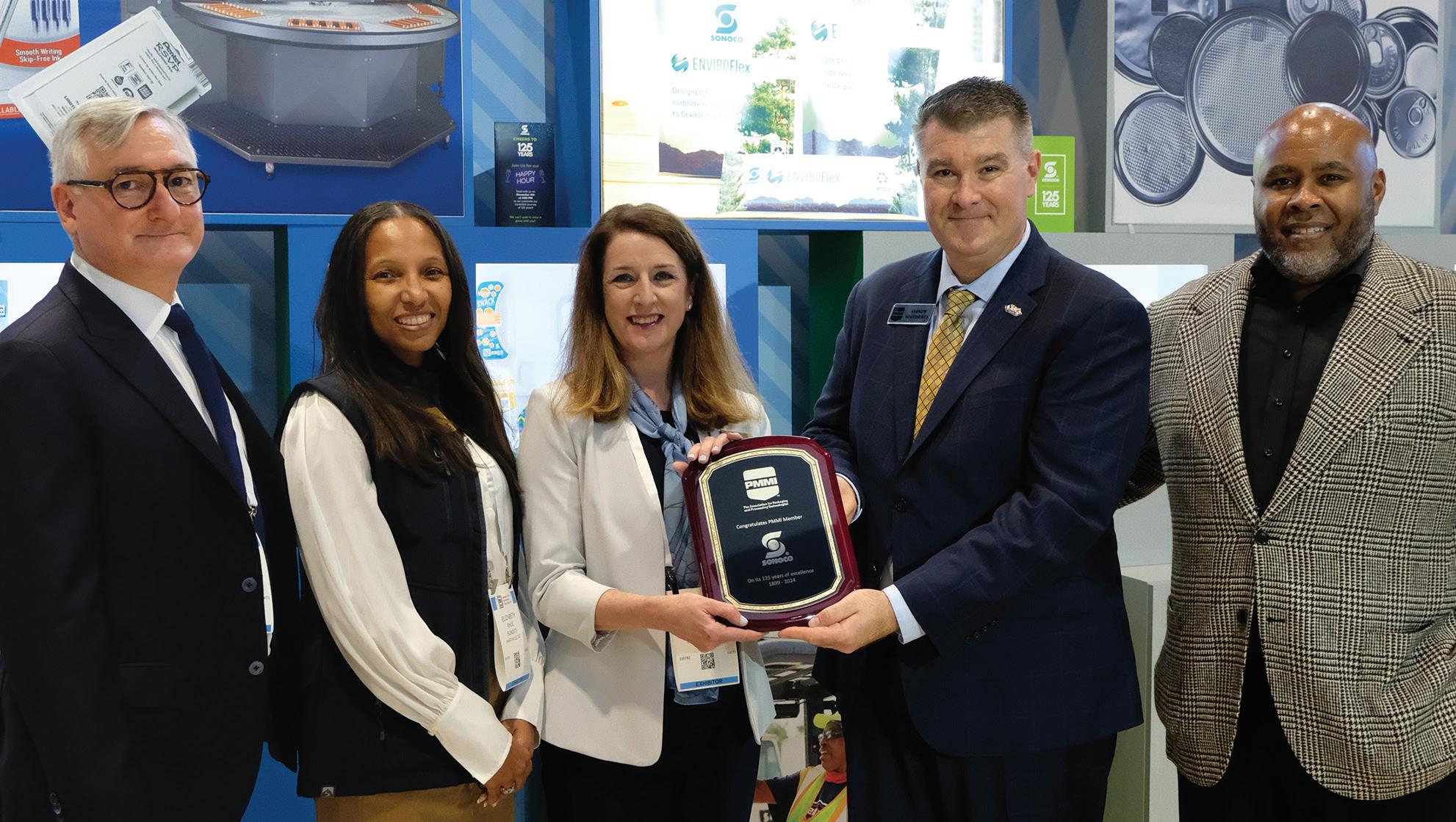
She regaled the audience with how she named her company. She was told at her first professional review, that she “comes across as young and overly enthusiastic at times,” that she “lacked gravitas,” and “should go buy a new dress, big jewelry, and great shoes.” With those words in mind, an understanding of the transformative power of clothing, and a determination to create a game-changing company, Sun filed for a global patent to build shapewear directly into dresses. She launched GRAVITAS as a company with a mission to catalyze confidence. GRAVITAS offers innovative size-inclusive apparel, styling solutions, and content designed to makeover women from the inside out.
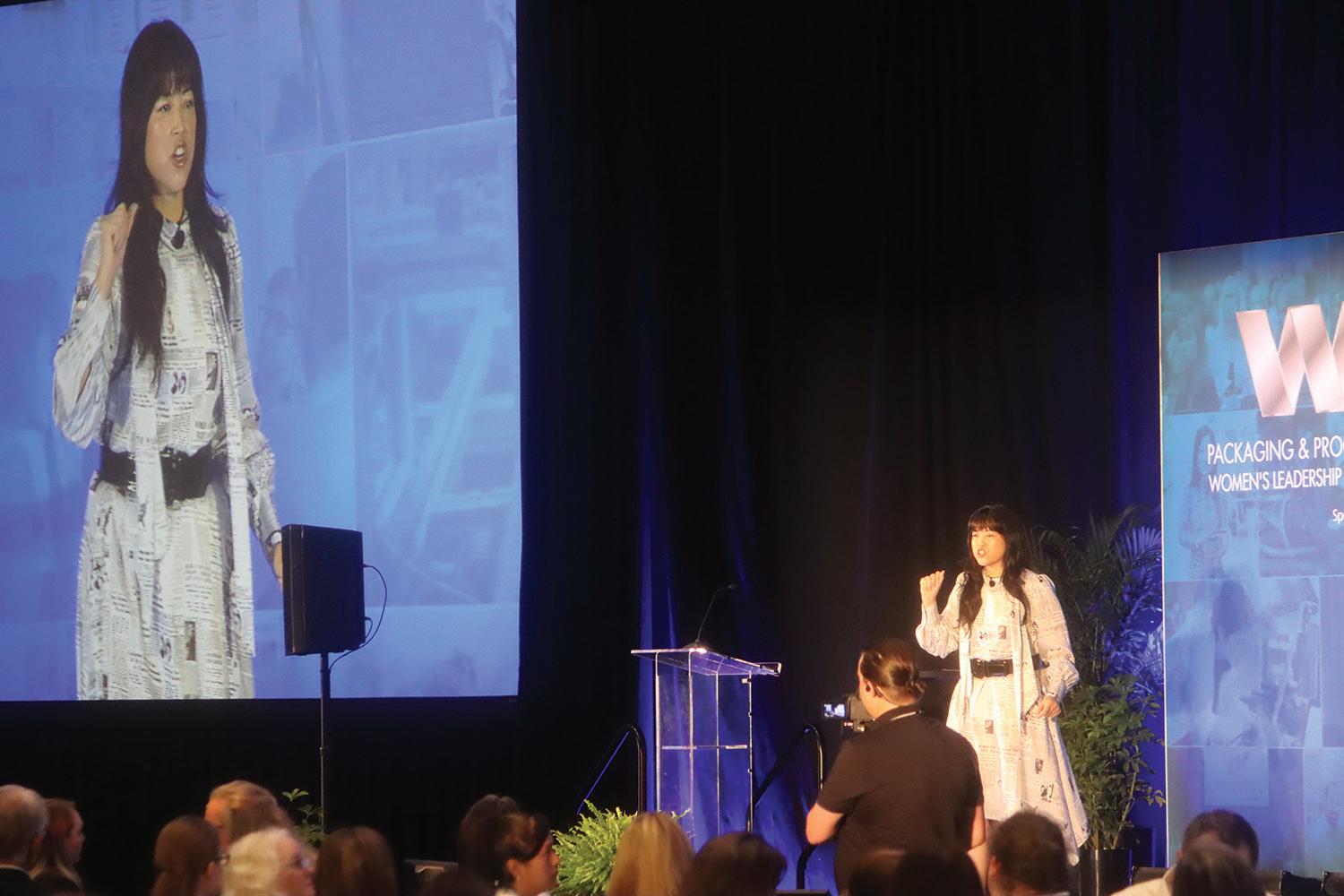
and reached number one on the Amazon bestseller list for its genre.
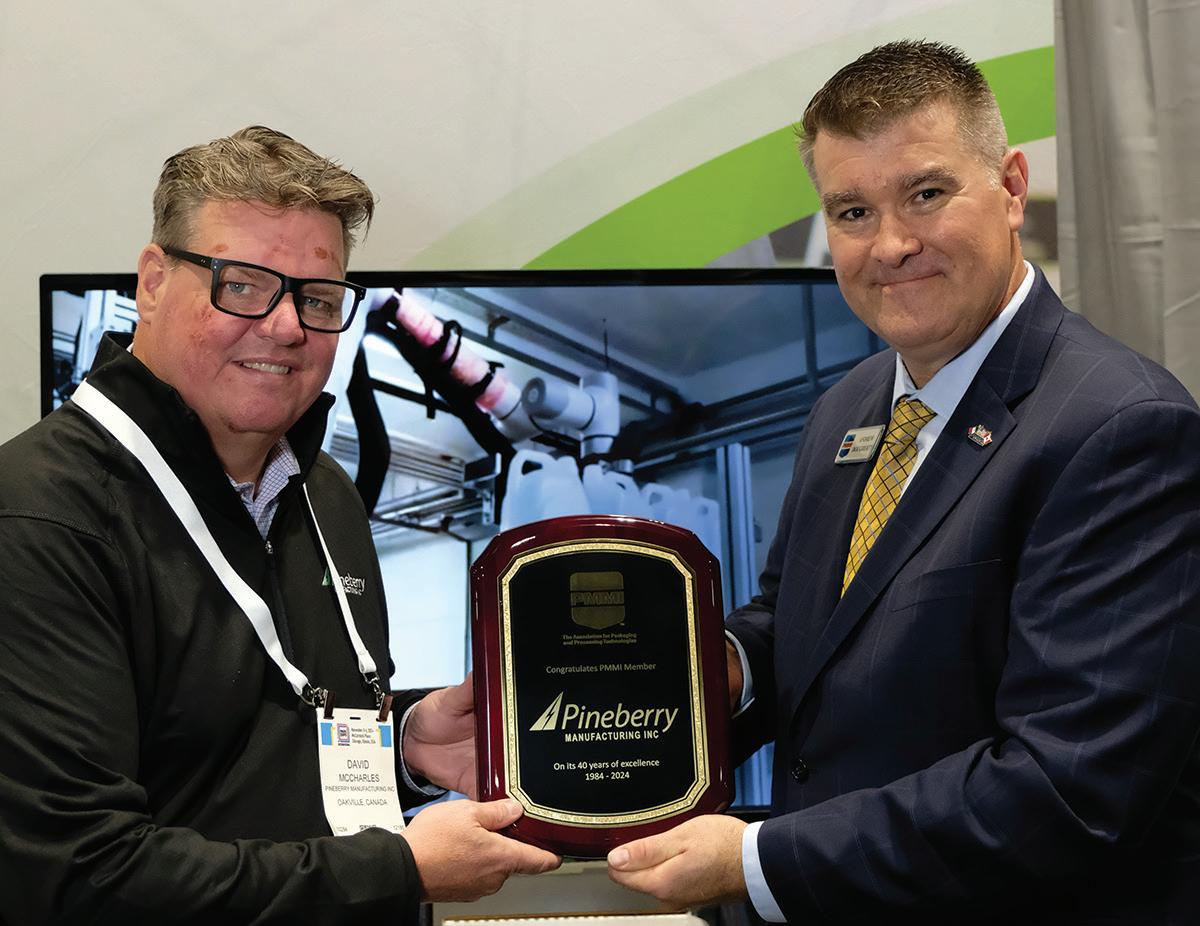
In addition to being a changemaker and entrepreneur, Sun is the national bestselling author of GRAVITAS: The 8 Strengths that Redefine Confidence. In the book, she shares her journey and the superpowers that anyone can call upon to be confident and successful. It is a USA Today bestseller
—PACK Gives BACK continued from page 1
Before the show, attendees enjoyed an exclusive networking opportunity with industry professionals while indulging in refreshments and appetizers, relaxing, unwinding, and connecting with peers in a casual, fun environment.
Since its inception in 1998, the PMMI Foundation has been a cornerstone of support for educational initiatives across the U.S. and
This year’s event sponsors were BW Packaging (Booth S-2100), Emerson (Booth N-5345), ID Technology (Booth S-3539), Morrison Container Handling Solutions (Booth N-4906), Plexpack Corp. (Booth S-2002), Schneider Electric (Booth S-3300, W-16041), Septimatech Group Inc. (Booth N-5136), and Syntegon Processing and Packaging (Booth S-2914). ■
Canada. To date, the foundation has awarded more than $3.8 million to programs to foster the next generation of packaging and processing professionals. By attending PACK gives BACK™, attendees directly contribute to this vital mission, helping students gain the education and skills they need to succeed in the ever-evolving world of packaging and processing. ■
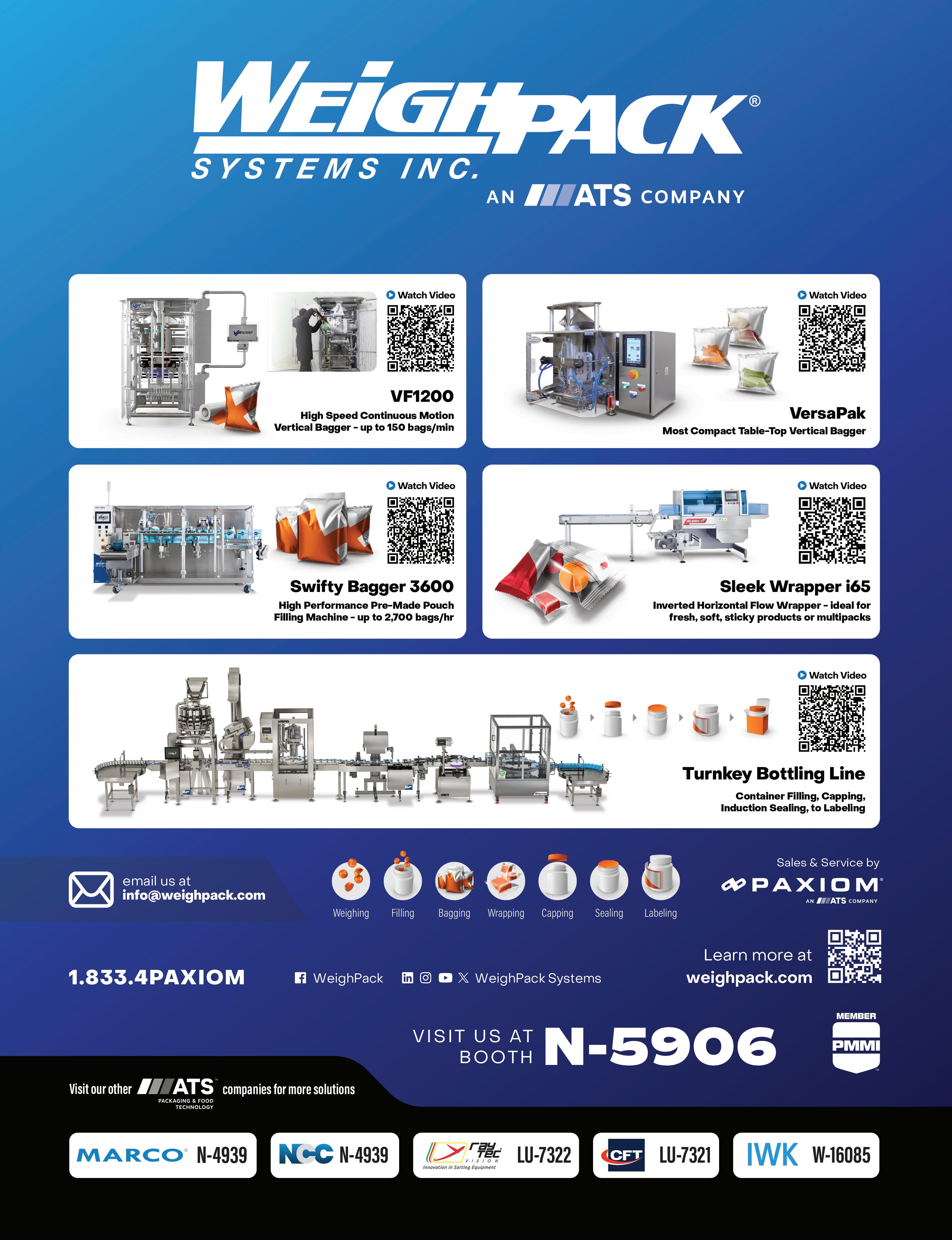
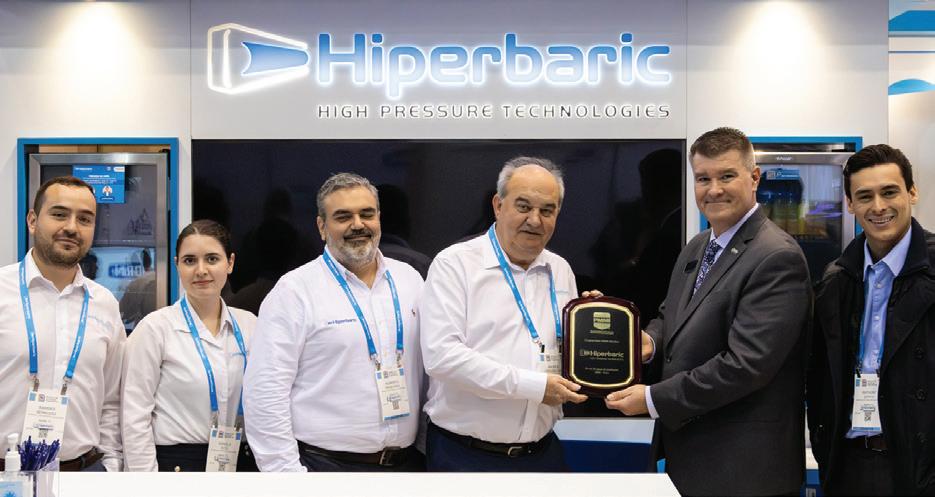
Andrew
Vice President, Member Services (second from right), congratulates Hiperbaric - High-Pressure Technologies (Booth LU-7765) on its 25th anniversary. ■

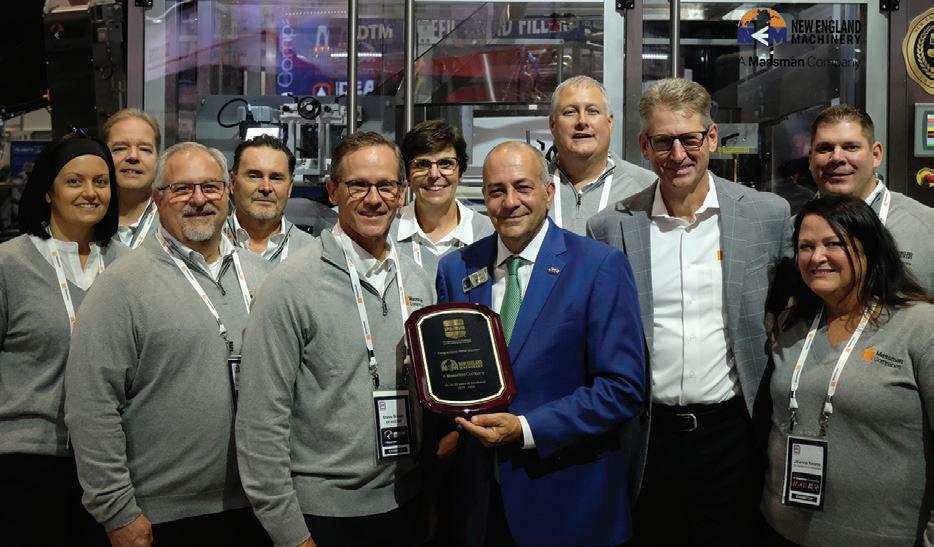
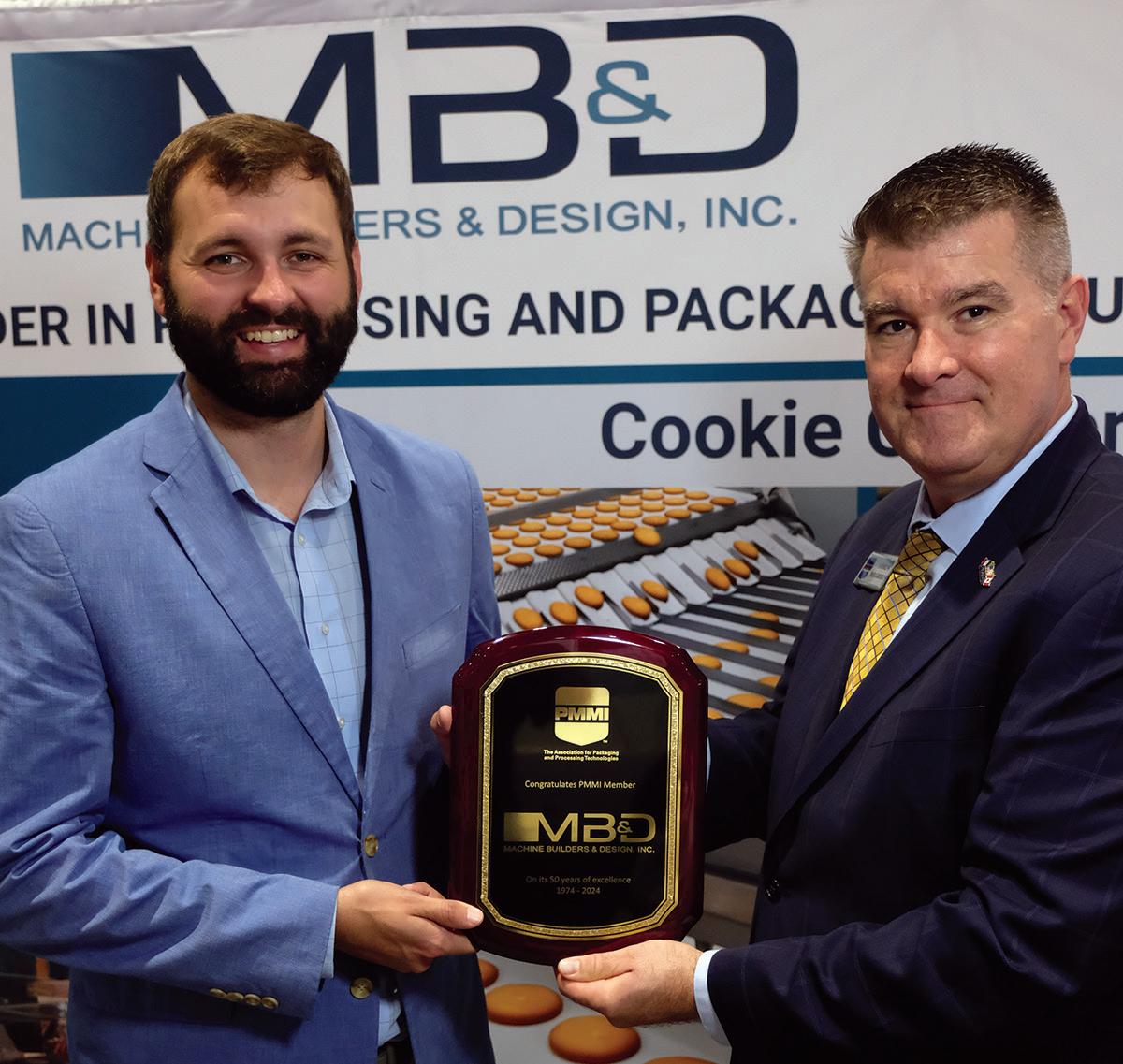
Four Winners Named in Technology Excellence Awards
Voting closed at noon yesterday for the Technology Excellence Award (TEA) competition, which honors technology never seen before at a PACK EXPO. Voters narrowed the eld of 12 nalists down to four winners, one in each category. Congratulations to the winners!
Food/Beverage
Food Radar
Technology: Detecting the invisible - e only proven detection technology for so plastic Booth: LU-7464
General Packaging & Processing
Fogg Filler Company
Technology: Fogg’s PF Series Pressure Filler Booth: S-3614
Personal Care/Pharma
Pace Packaging, LLC
Technology: Omni-IR Booth: S-3506
Sustainability
Plastipak Packaging, Inc.
Technology: PPK Natura: World’s First PET Resin Made from Waste Carbon Booth: W-24100
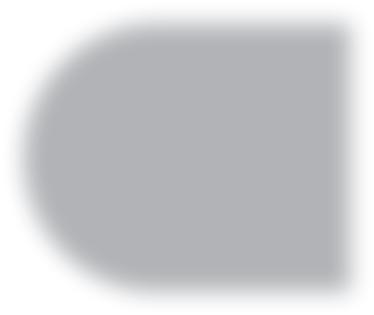
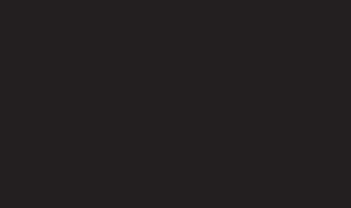
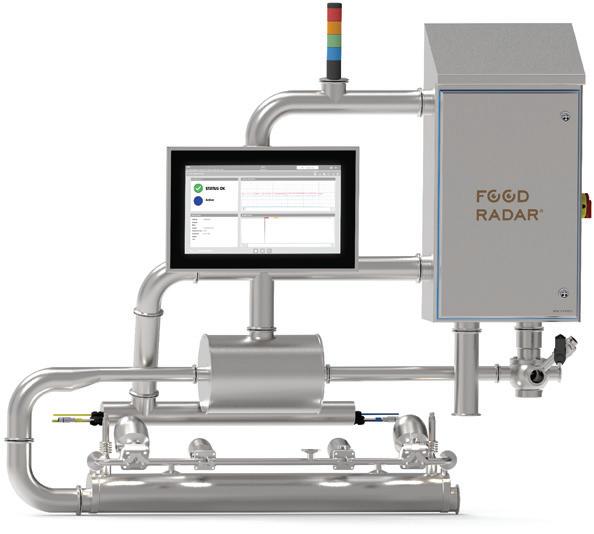
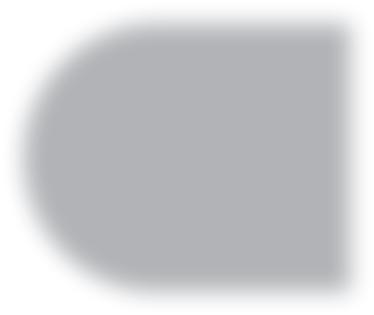
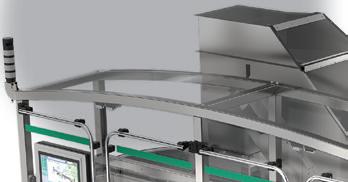

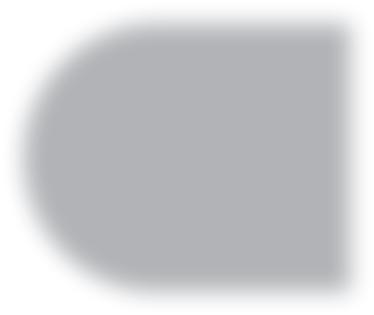
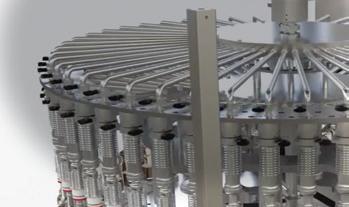
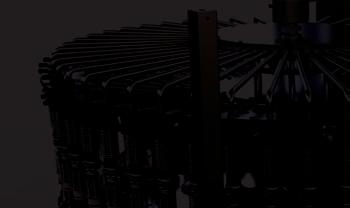
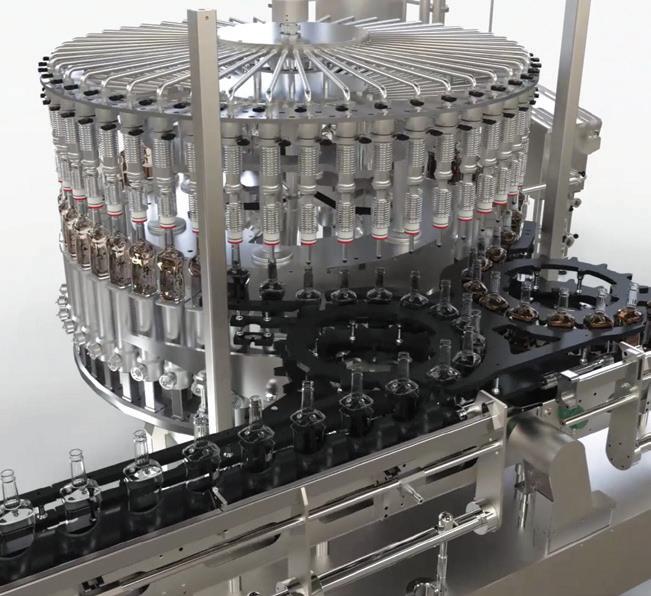
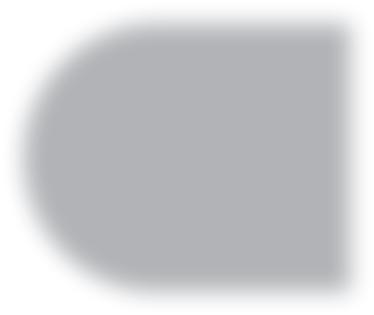
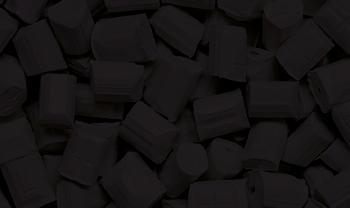




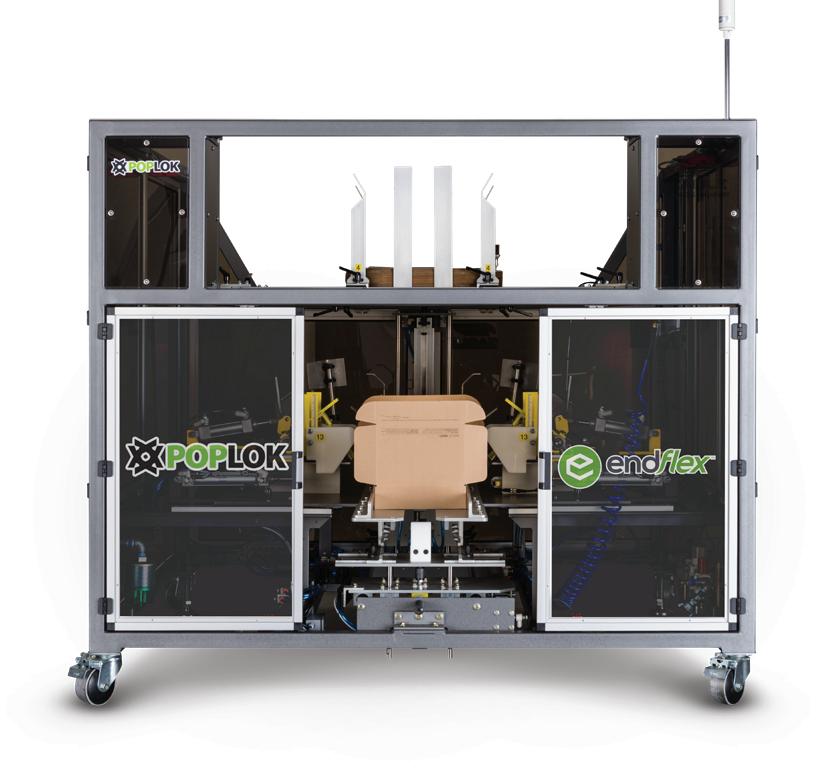
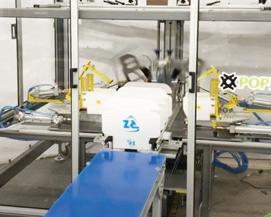
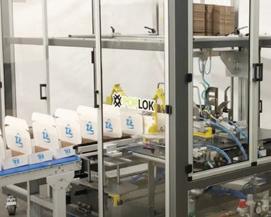
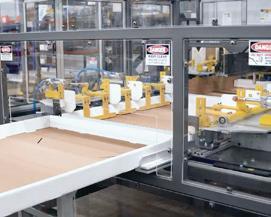

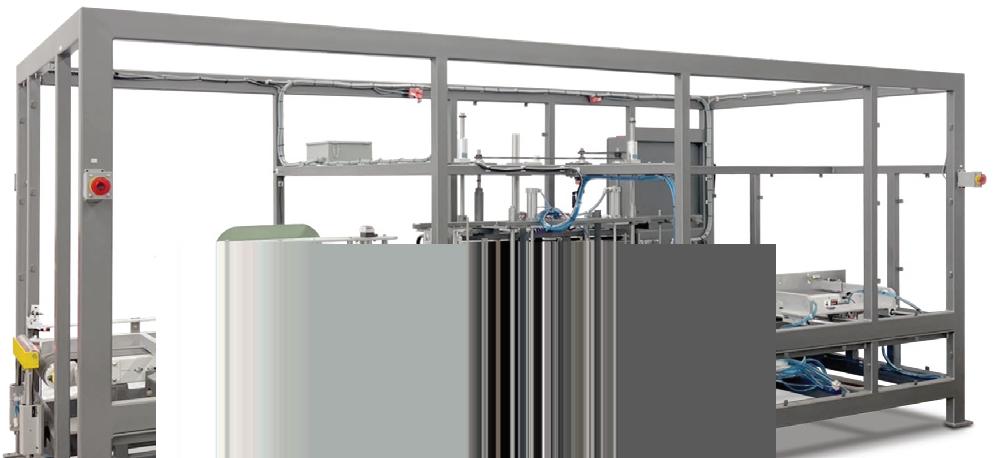
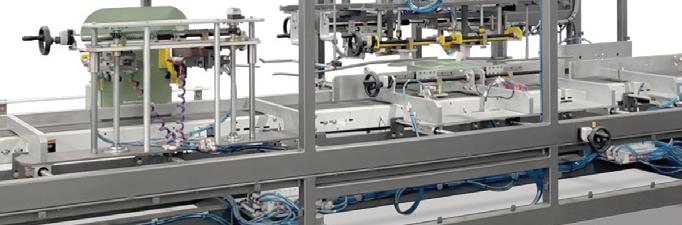

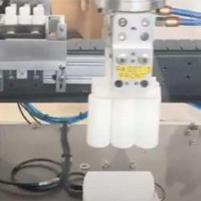

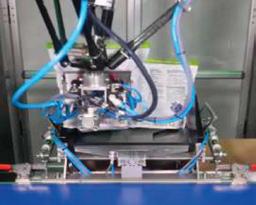
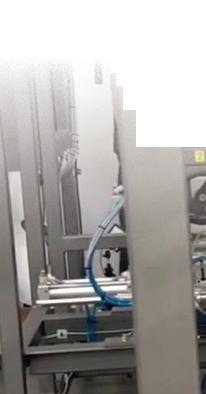
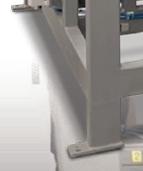
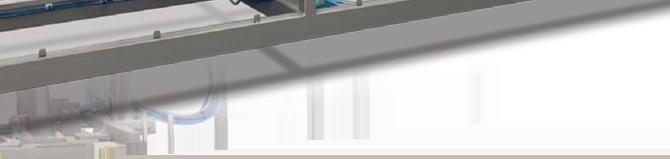
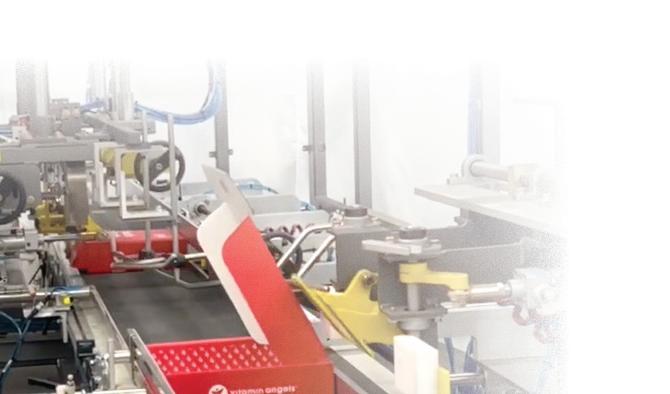



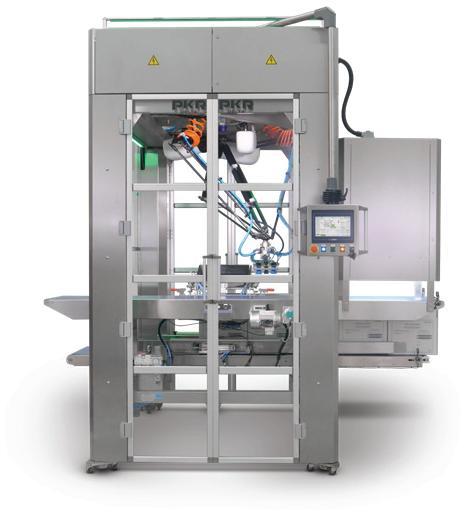
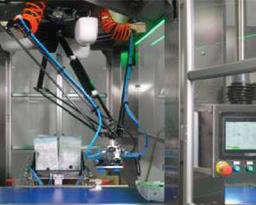
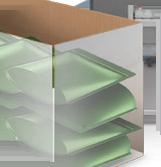
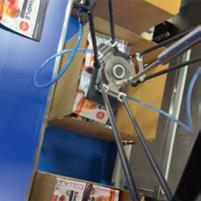
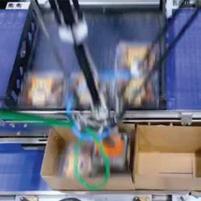

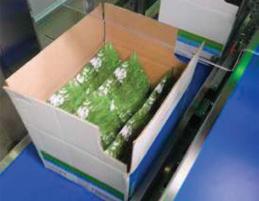
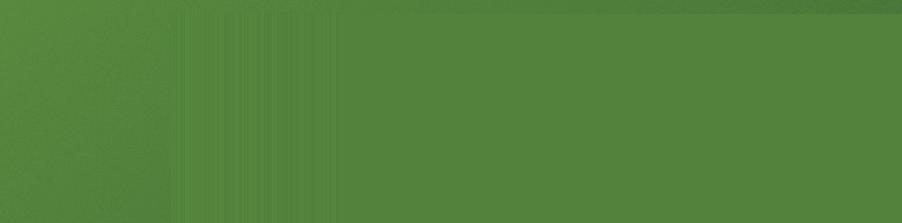

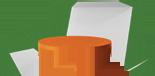
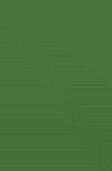
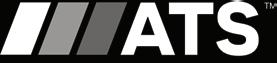
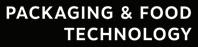

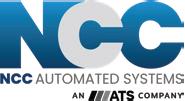


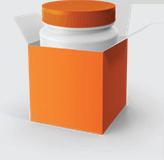
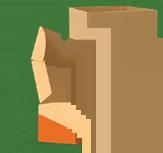
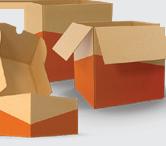
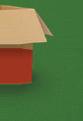
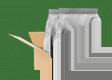

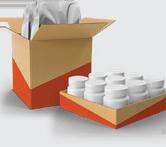

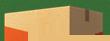

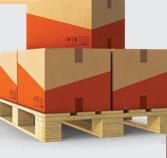
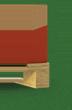


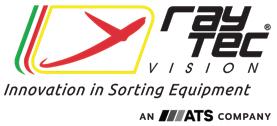
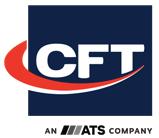
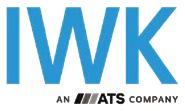




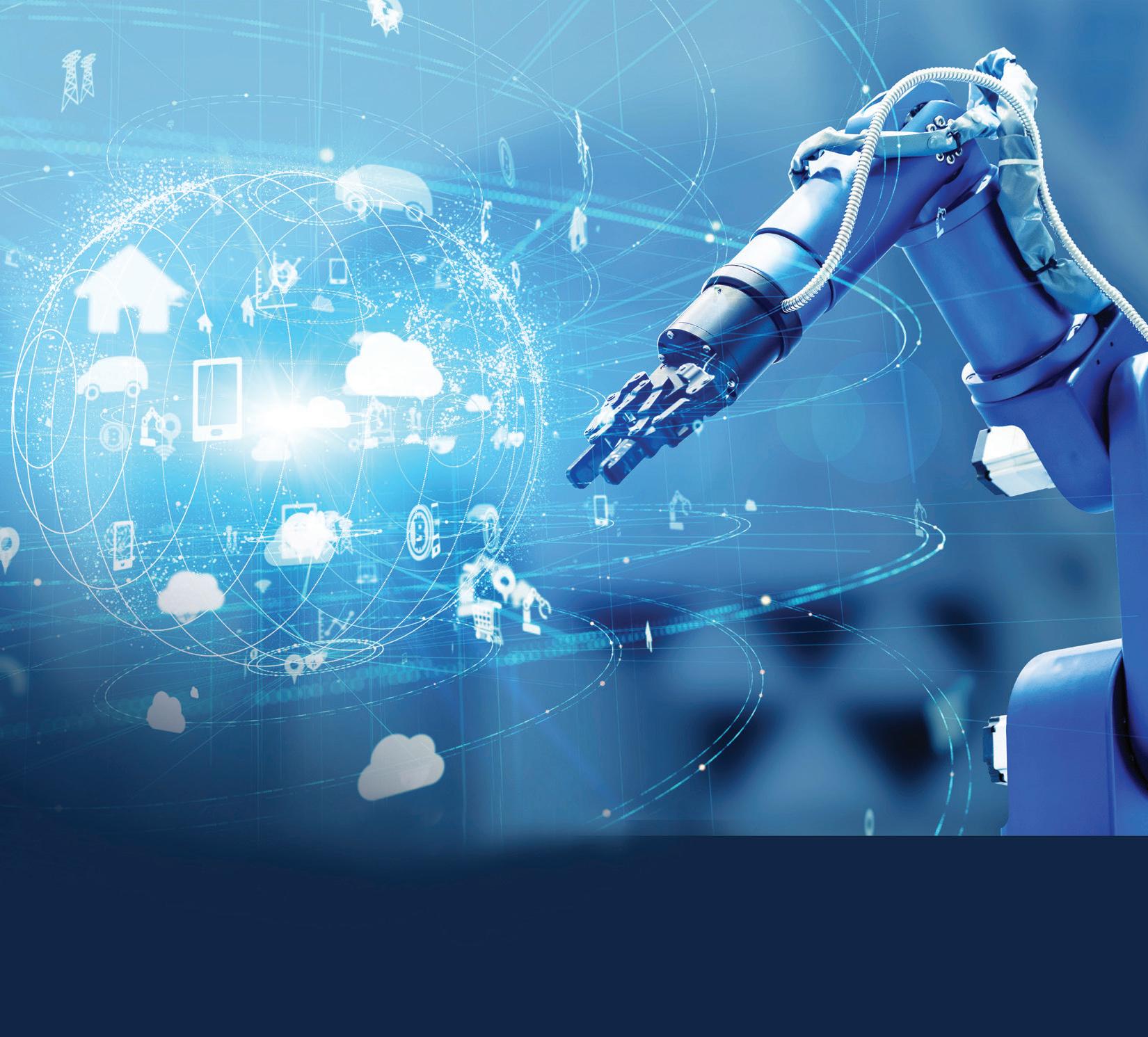
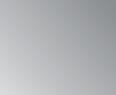

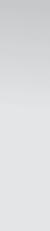
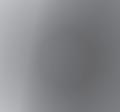

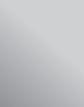
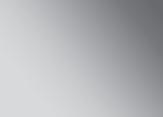

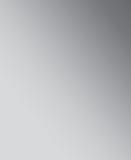

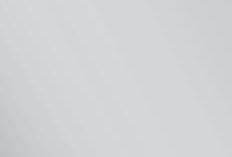


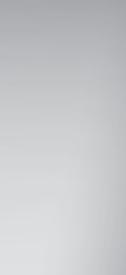
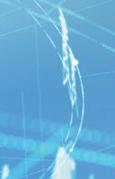

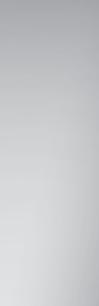



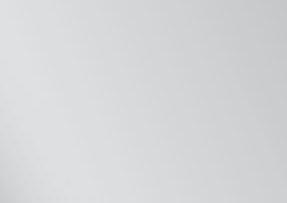
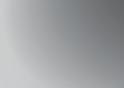





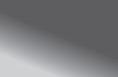
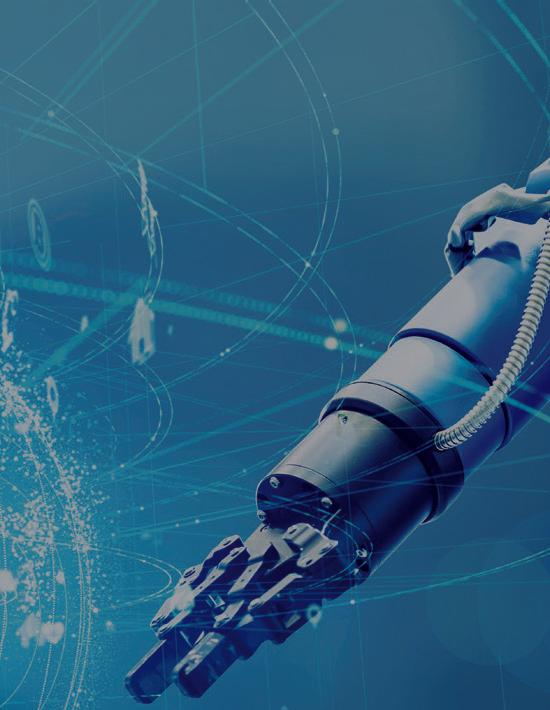


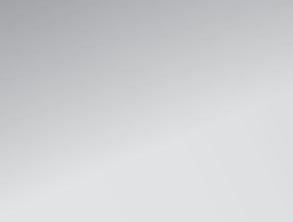
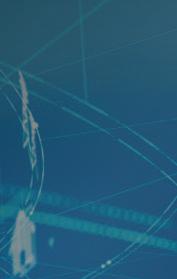
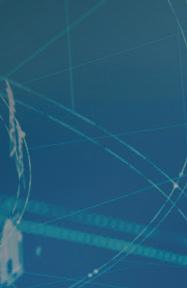
SHOWCASE Future Innovators
100,000 net square feet of space. It is a perfectly sized show for attendees to explore many solutions yet have a personalized experience and meaningful interactions to address their speci c needs.
e three-day event comes on the heels of another successful PACK EXPO International. e show’s success is due to the resilience of the packaging machinery industry in the face of global economic pressures. According to the newly released State of the Industry: US Packaging Machinery report, produced PMMI, the U.S. packaging machinery market is projected to reach $11.1 billion in 2024, driven by automation and sustainability. Industry growth is expected to peak in 2027, with a continued focus on innovative solutions to meet evolving consumer and regulatory demands.
“ e industry’s growth shows how important it is for manufacturers to nd innovative, tailored solutions,” says Jim Pittas, president and CEO, PMMI. “Whether it’s pushing for sustainability, embracing automation, or integrating AI, businesses are looking for a place to discover new ideas, keep up with the latest trends, and make meaningful connections.”
Paired with PMMI’s reputation as a world-class show producer, PACK EXPO Southeast is a must-attend event for packaging and processing professionals looking to see the latest innovations, address business needs, and keep pace with the latest trends.
“PACK EXPO Southeast is the only show in the region o ering attendees access to crossover innovations from other industries to address key packaging and processing challenges,” says Laura ompson, vice president, trade shows, PMMI.
THE ‘BOTS ARE TAKING OVER PACK EXPO International!
Come see high school students from across the country.
Interact with the bright minds of the future and ask questions about their innovative robot designs.
Located in the West Hall in Booth W21054
Sunday - Tuesday | 9:00 am - 5:00 pm Wednesday | 9:00 am - 3:00 pm
For more information about supporting student programs, visit the PMMI U booth at W20022.
Produced by:
“ e show’s Atlanta location is a regional hotspot for manufacturing that is easy to access and convenient to much of the southeastern United States. Teams can attend together to spark discussion, collaboration, and problem-solving around current projects and set future goals,” ompson continued.
PACK EXPO Southeast will o er dynamic show features to meet the needs of attendees and the industry at large, including the Reusable Packaging Pavilion, sponsored by the Reusable Packaging Association (RPA). e pavilion will present sustainable packaging solutions to help reduce waste, cut costs, and gain supply chain e ciency. Attendees can explore reusable transport packaging products and services and see innovative reuse solutions.
Education on the Show Floor
PACK EXPO Southeast is an opportunity for attendees to gain leading insight into packaging and processing’s most timely issues, such as sustainability, workforce development, life sciences operations, cold chain packaging, food safety, robotics, and preventative maintenance.
Dozens of educational sessions will occur right on the show oor, o ering convenient opportunities to learn about the latest topics and trends in packaging and processing.
In the center of the action, the Innovation Stage o ers ample opportunity for professional enrichment at PACK EXPO Southeast. Exhibitors present free, 30-minute seminars throughout the day, and attendees can learn about breakthrough technologies, innovative applications, and proven approaches from the experts.
At Industry Speaks, hear experts from the PACK EXPO Partner Program, covering multiple industry verticals, address the latest hot topics and industry trends. Previously covered topics include sustainability, remote access, supply chain solutions, augmented reality, and operational e ciency.
Networking and Special Events
PACK EXPO Southeast o ers quality connections through specialized networking events from the Opening Reception and the Young Professionals Networking Reception to the Packaging & Processing Women’s Leadership Network Reception.
Student Opportunities
PACK EXPO Southeast o ers additional programs and activities aimed at exciting students about careers in packaging and processing. Past activities from PACK EXPO shows have included student competitions, receptions, and tours.
Stay tuned for more details on each of these events.
To learn more and to register, visit packexposoutheast.com ■

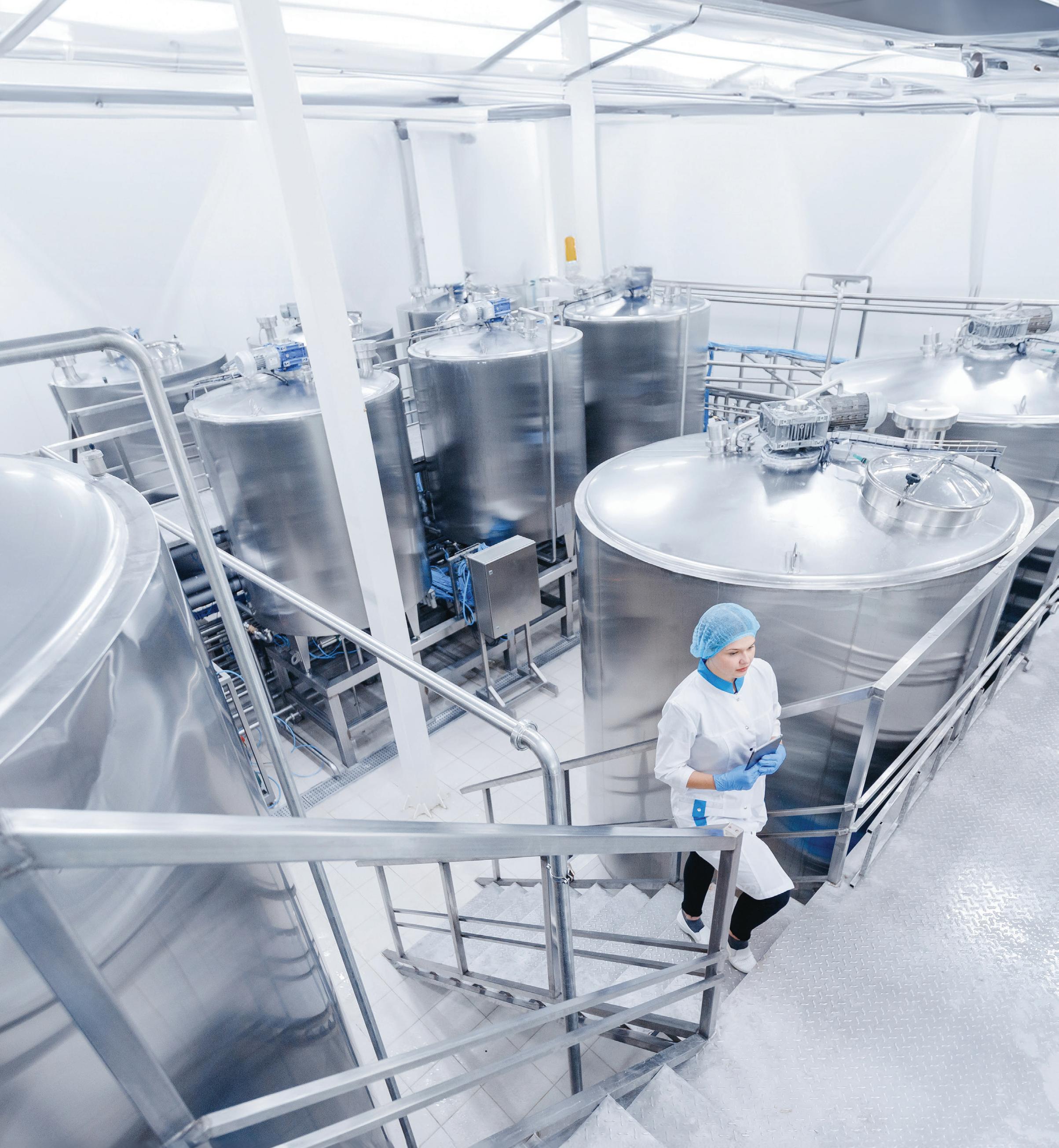
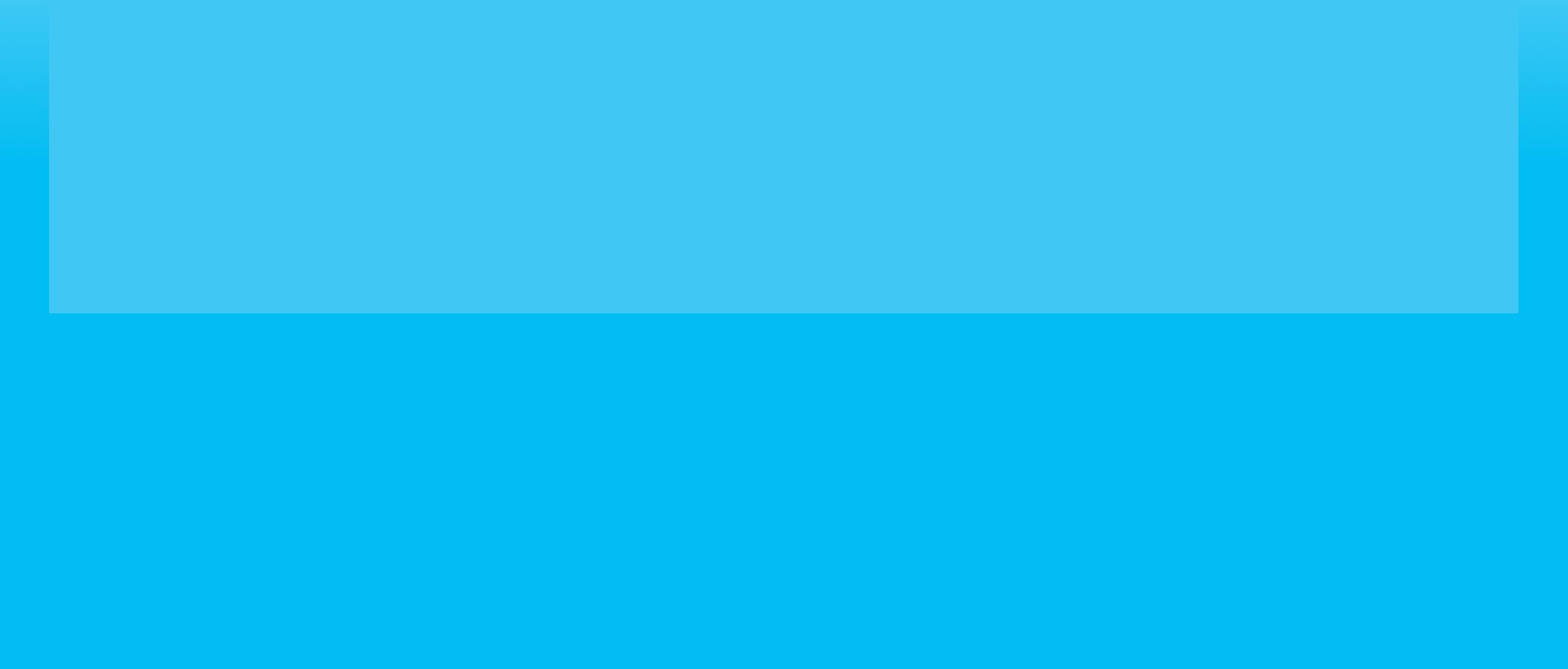
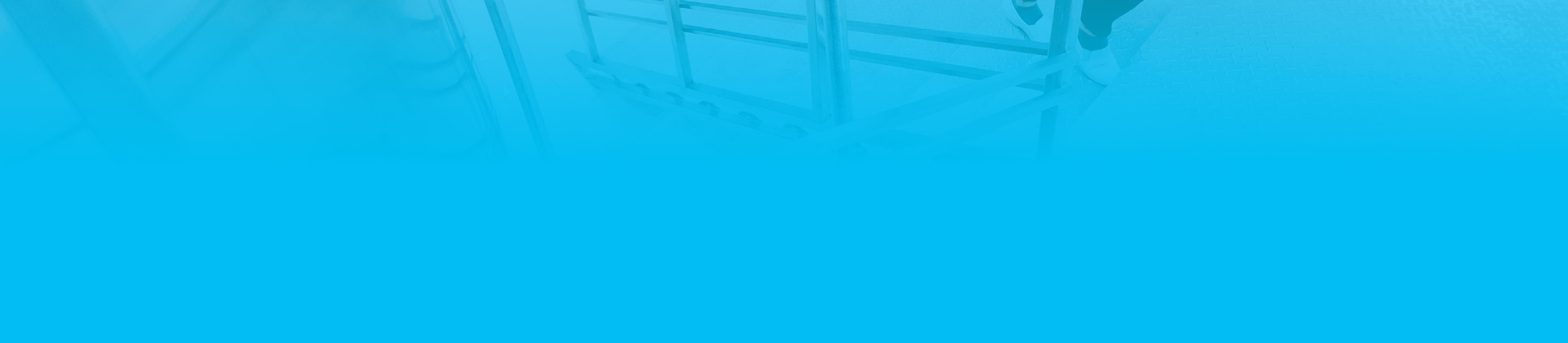
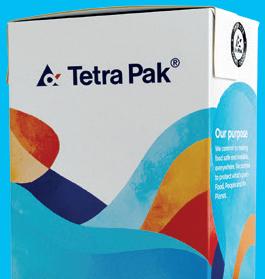
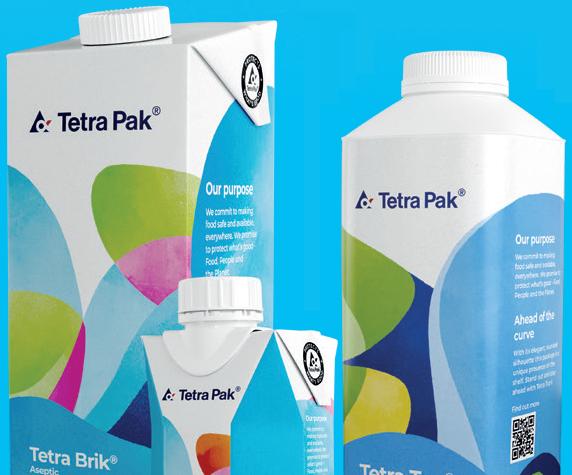
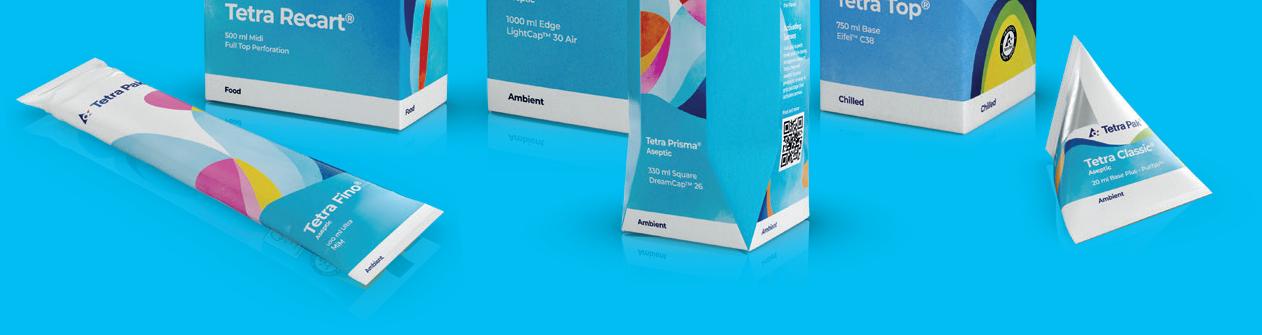
KUKA Highlights Four Innovative Robotics Cells
The live demonstrations will include an AMR, palletizing/depalletizing and more.
KUKA Robotics features four innovative robotics cells in Booth N-5414, highlighting speed, versatility, and flexibility for the packaging and processing industry. The live cell demonstrations will include autonomous mobile robot (AMR) solutions for intralogistics, robotic palletizing/depalletizing, a robotic bottle capping operation and a food handling system.
System integrator Stac Material Handling will use a KMP 1500P AMR and KR CYBERTECH , a compact palletizing cell that simulates a palletizing process for cardboard boxes in the food industry. The KMP 1500P is KUKA’s latest generation of AMRs for Logistics 4.0 and features intelligence,

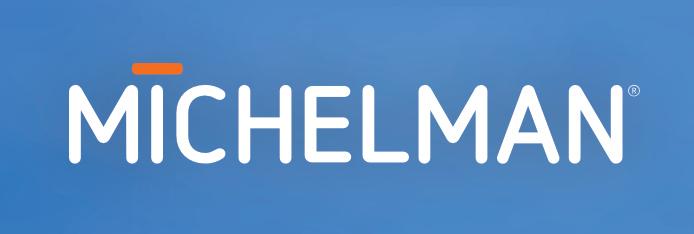
safety, and easy commissioning to navigate complex, dynamic environments with the SLAM (Simultaneous Localization and Mapping) navigation method. The AMR platform automatically identifies loads with QR code readers, and 3-D cameras detect obstacles in three-dimensional space.
Automation solution provider Technica International will use a KR IONTEC in the booth to demonstrate depalletizing open-top cardboard can trays. The cell’s KR 70 R2100 IONTEC has a maximum reach of 2,101 mm and a rated payload of 70 kg that can subsequently be adjusted even after mounting. KR IONTEC provides users with the highest output with a low total cost of ownership and high life cycle efficiency.
KUKA’s IONTEC family of robots is an extremely versatile six-axis medium payload robot that can be floor, wall, ceiling, or angle mounted, and its optimized design is well-suited to compact cells with a small footprint. Boasting a best-in-class work envelope and equipped with waterproof and dustproof in-line wrist and protected motors, IONTEC is suitable for virtually any application. The HO variant uses food-compatible H1 oil in all
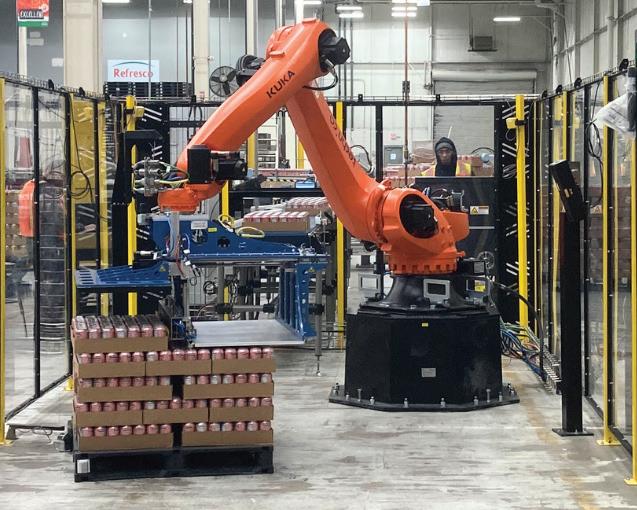
axes to eliminate the potential for contamination in the food processing and manufacturing sectors. Refrigerated and freezer packing applications can also be accomplished with KUKA’s QUANTEC PA Arctic, which does not require a cover or heater while working in temperatures down to -30 F.
Additionally, PACK EXPO International attendees will experience the speed and precision of KUKA’s high-performance SCARA robot family in a bottle—Continued on page 10


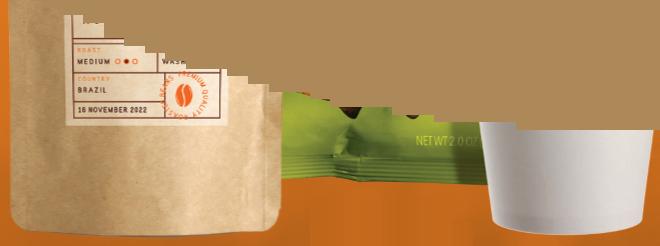
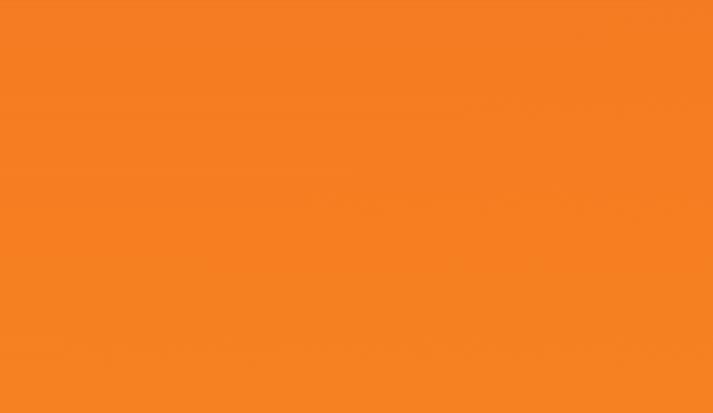
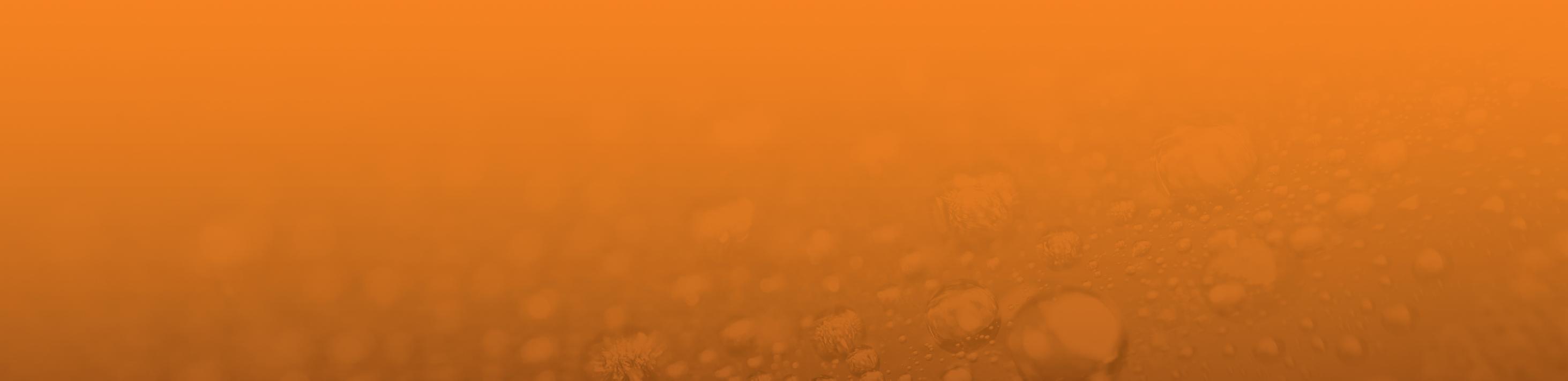
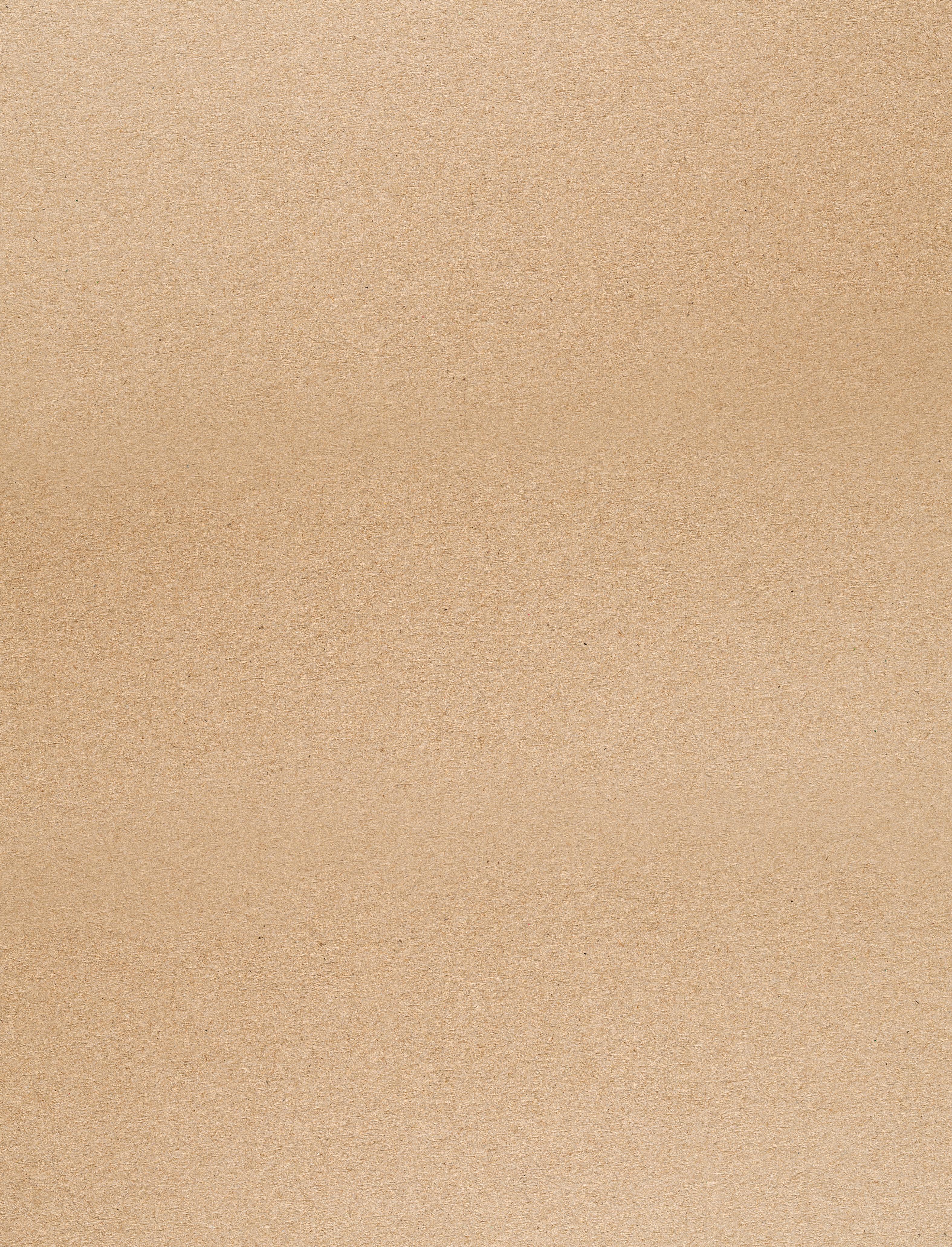

capping cell. The ultra-compact KR 6 R500 Z200-2 SCARA will cap small spray bottles with a cycle time of less than 0.36 seconds. With a maximum payload of 6 kg and a 500 mm reach, the four-axis KR 6 R500 Z200-2 has a serial mechanism with rotational joints in the first two axes, and the remaining axes are combined to allow rotation and linear movement in the Z-axis. The KR SCARA industrial robots are available in a variety of payloads, reaches and Z-axis strokes and are also available in an HO variant for safe food and beverage applications.
To demonstrate how KUKA automation provides food-processing companies with increased production control while avoiding failures and reducing costs, KUKA will highlight a primary
food handling solution using a KR DELTA HM hygienic robot. The KR DELTA hygienic robot provides outstanding performance and value for pick-and-place applications in the food, packaging, electronics and pharmaceutical industries. The KR DELTA combines precise grip, corrosion resistance and minimal maintenance requirements to excel in sensitive high-speed production applications. This ceiling-mounted robot offers a reach of 1200 mm, a maximum payload capacity of 3 kg and cycle times as low as 0.5 seconds.
The robot is made entirely from corrosion-resistant stainless-steel that protects against dust and moisture.
The design accepts alkaline or acidic high-pressure cleaning and disinfection up to 100 kPa for simplified upkeep and shorter downtimes. Food-sector certified for material safety, the entire robot carries IP 67 high-protection certification, with IP 69K for axis 4 that is also ISO 3 rated for cleanroom applications. The KR DELTA is equipped with KUKA’s new KR C5 microrobot controller that reduces full load power consumption by 35%.
All KUKA solutions are backed by the company’s expert service and support for training, complete system engineering and simulation, readily available spare parts, robot refurbishment, and more. ■
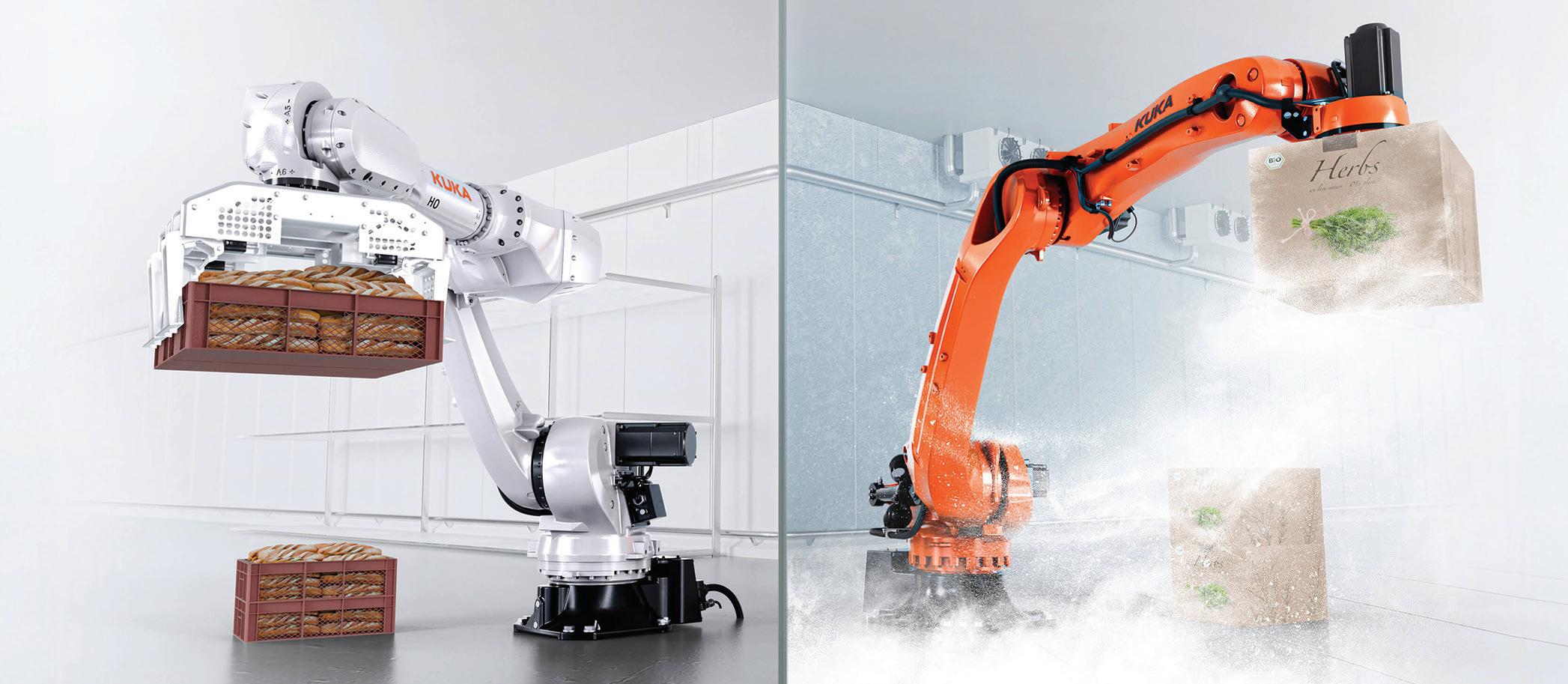
Feeders & Conveyors


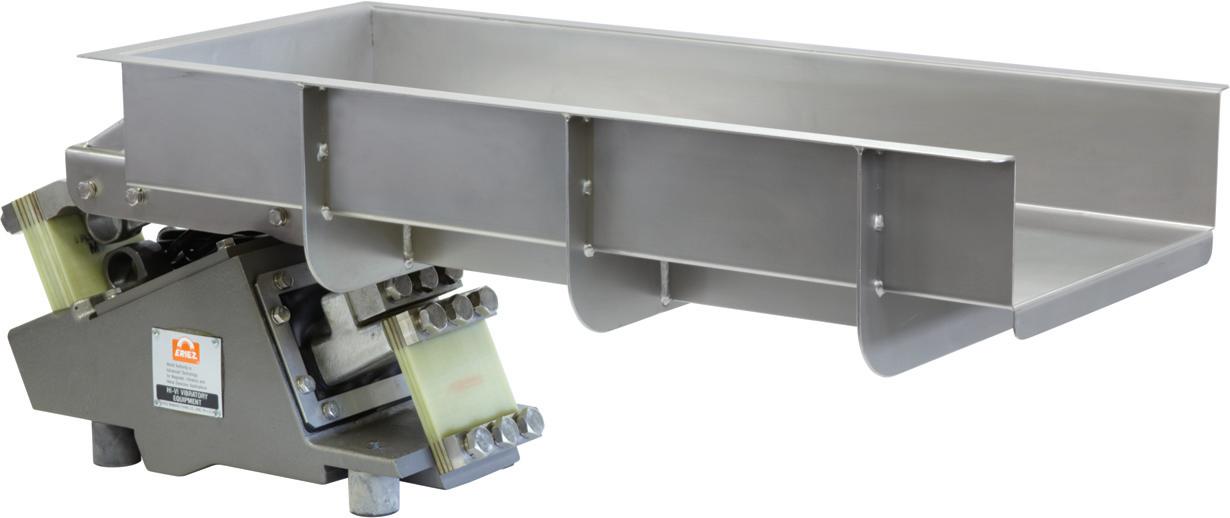

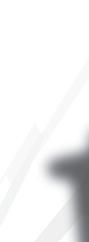

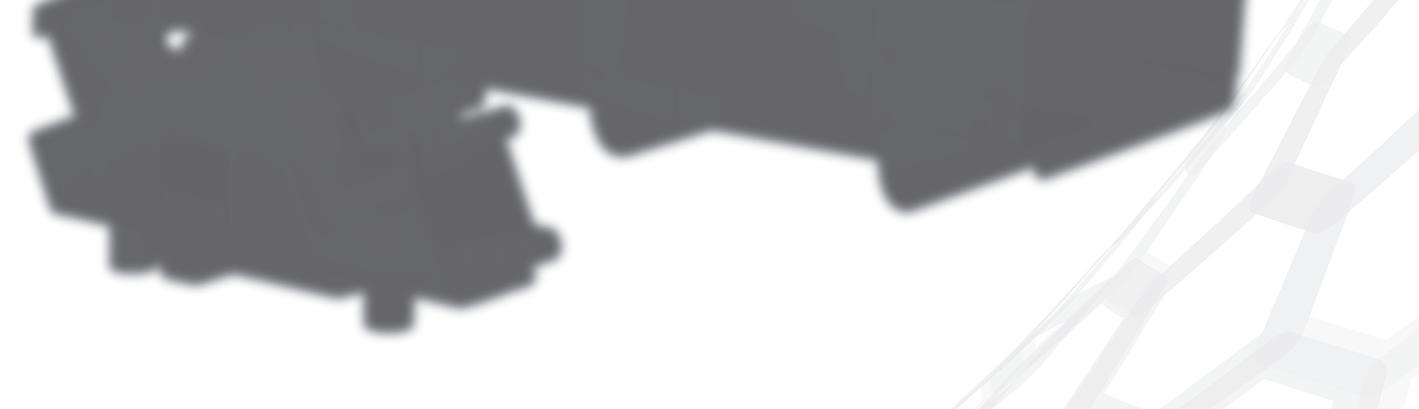
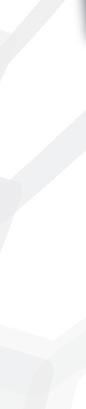
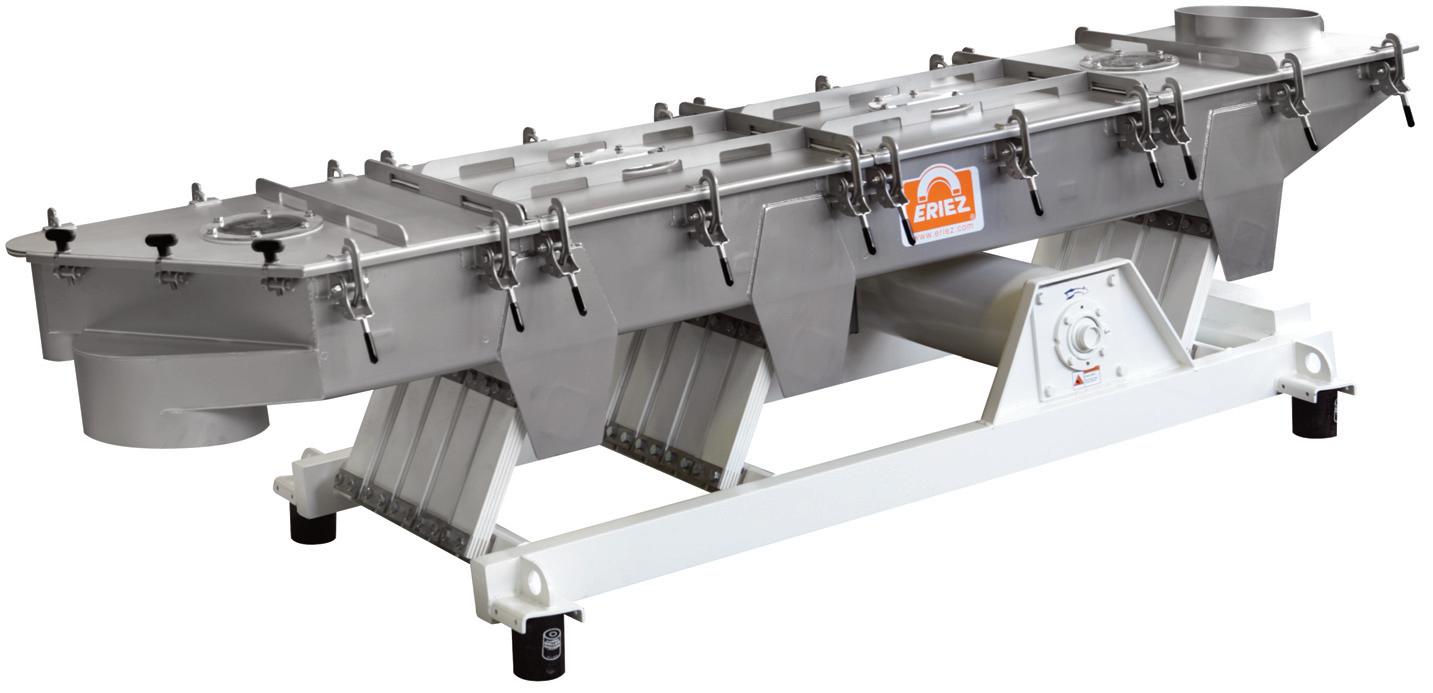

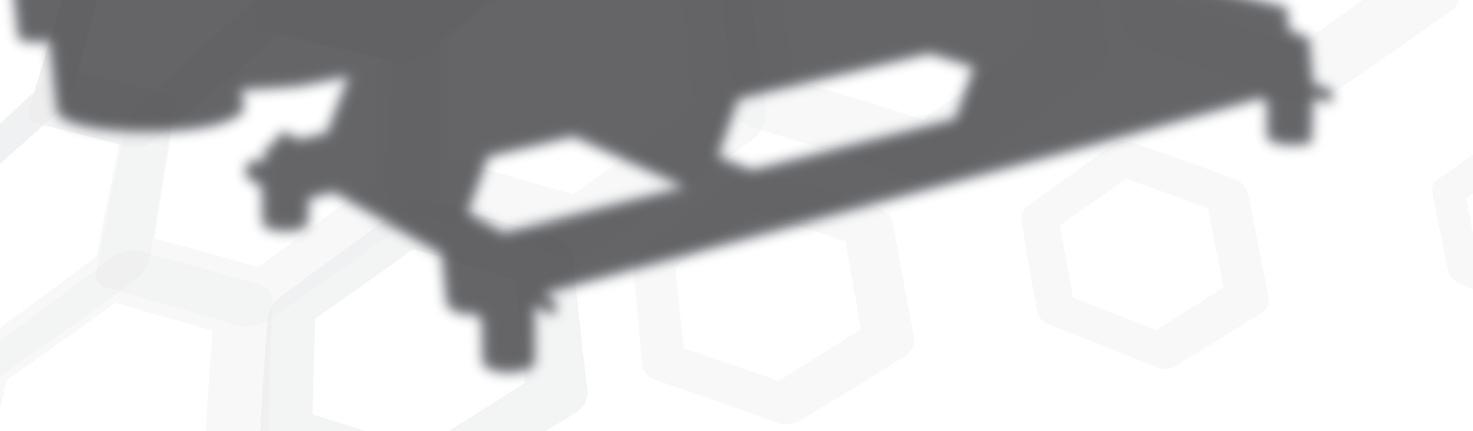
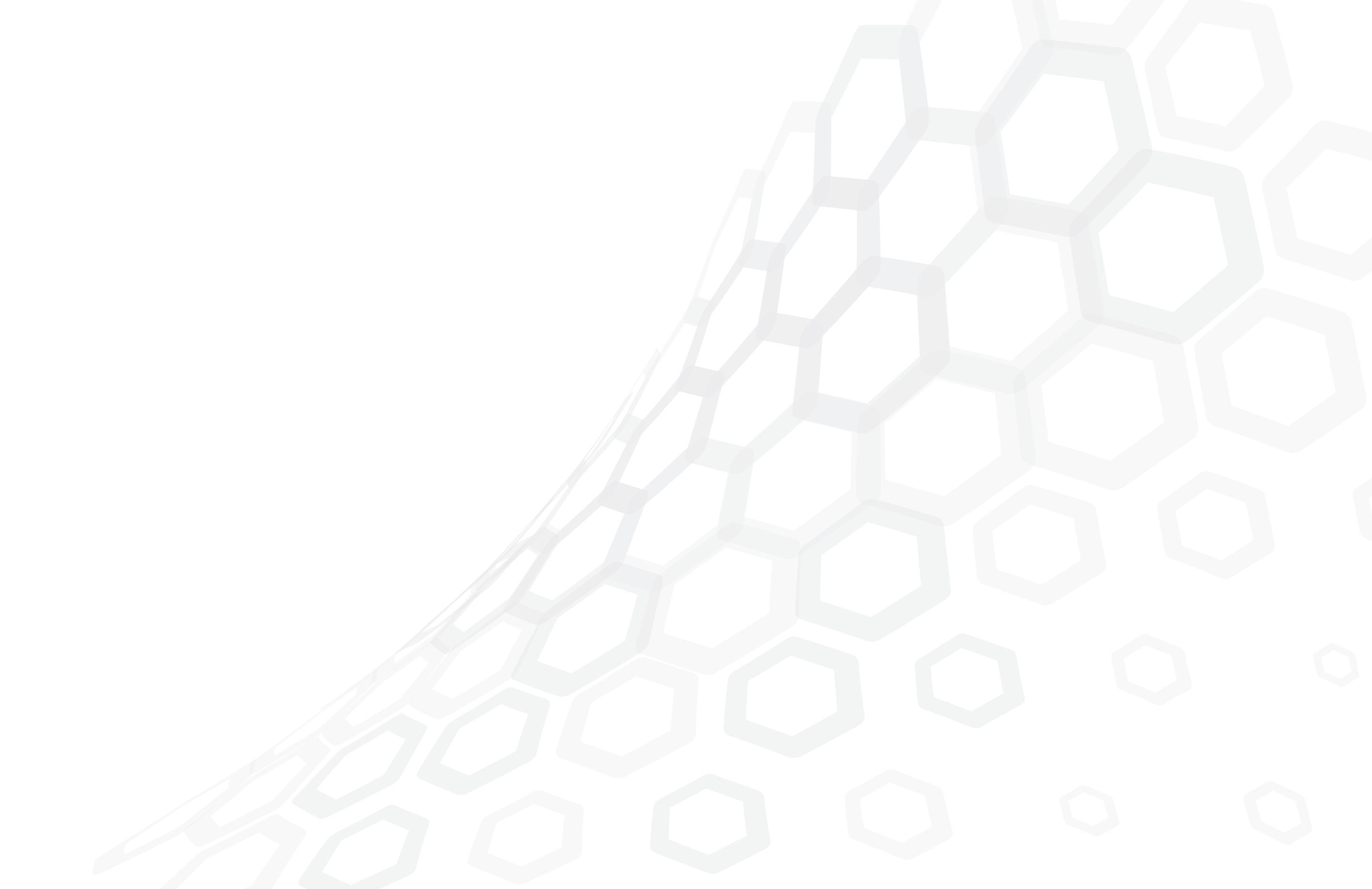
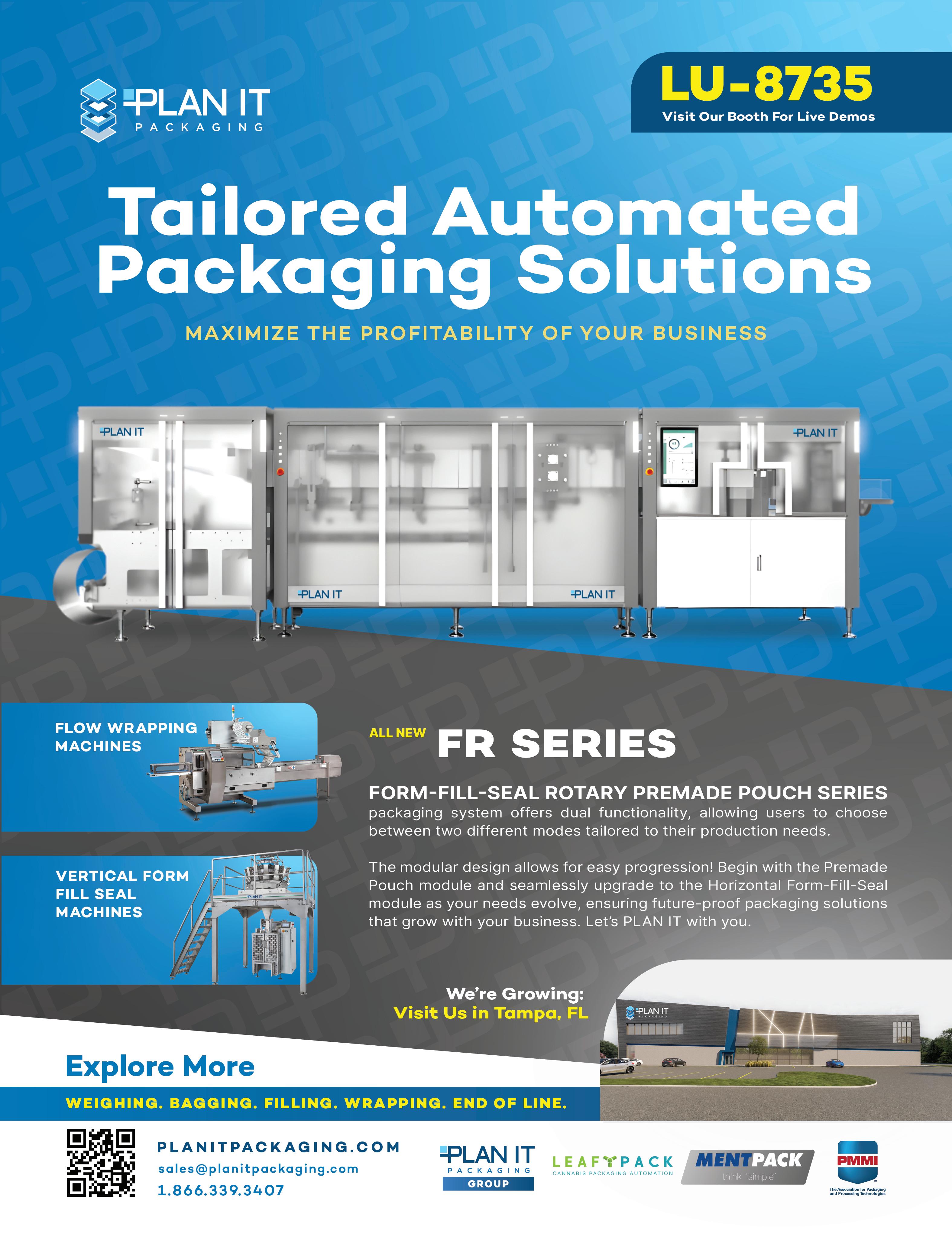
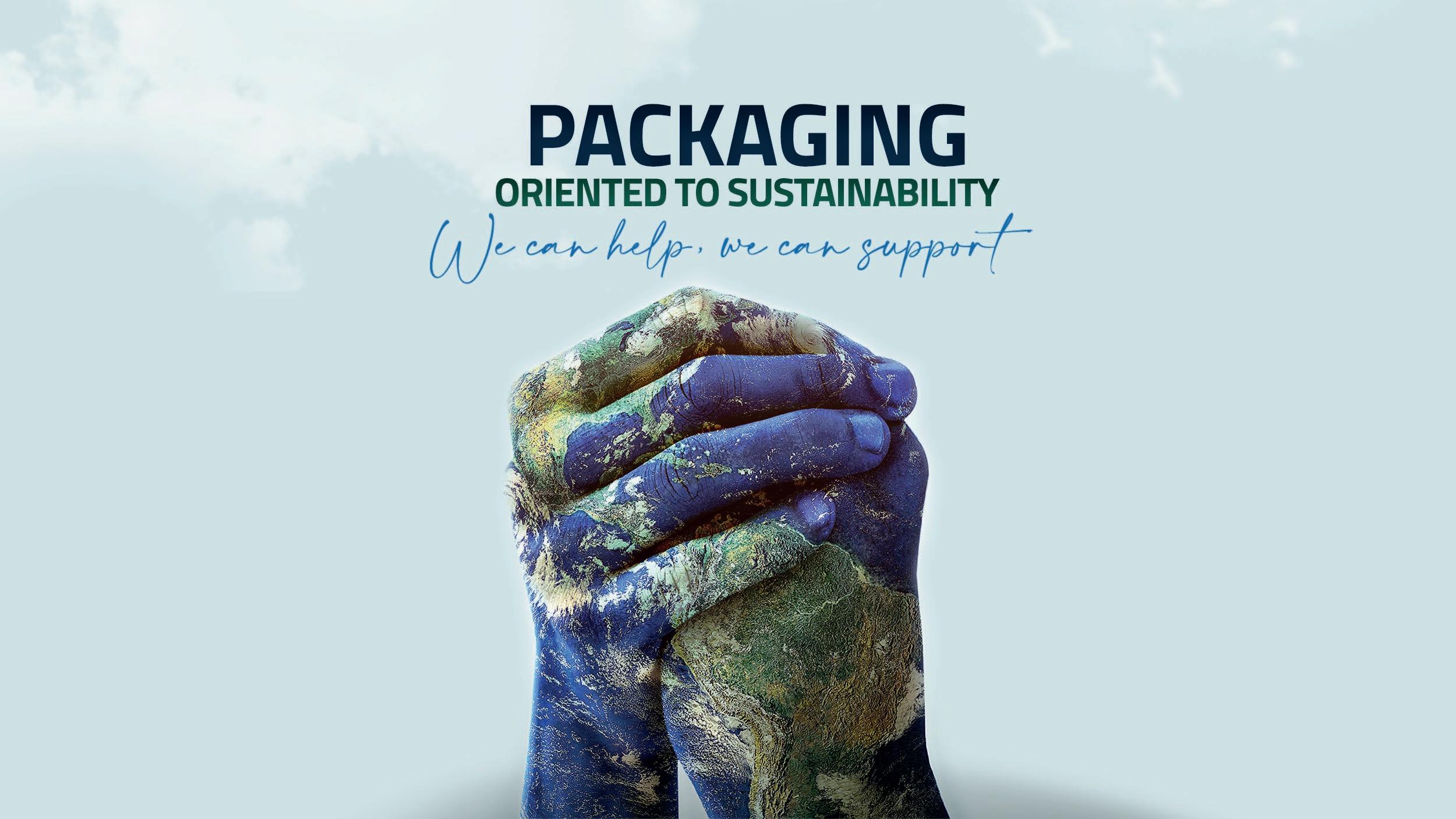
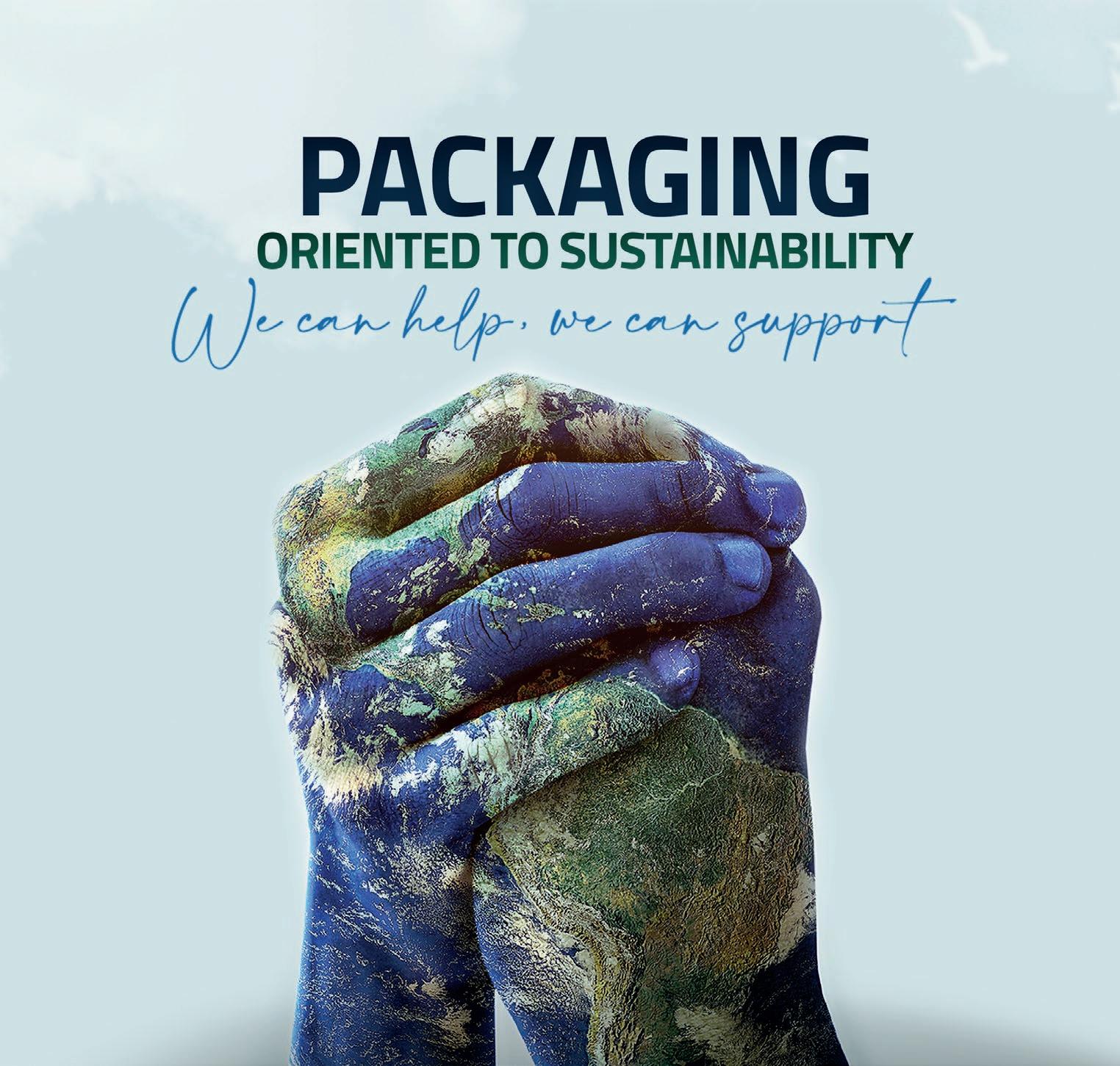
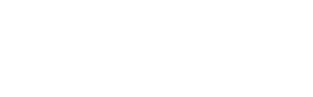
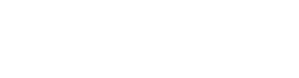
WEDNESDAY SHOW DAILY NOVEMBER 6, 2024
Foundation Awards
Nearly $200,000 in Academic Scholarships
Next generation of packaging and processing professionals get a financial boost for their education.
The PMMI Foundation, the charitable arm of PMMI, The Association for Packaging and Processing Technologies, awarded nearly $200,000 in educational scholarships to students pursuing careers in the packaging and processing industry.
“The PMMI Foundation’s commitment to supporting education is a cornerstone of our mission. We are pleased to empower these talented students who represent the future of our industry,” says Kate Fiorianti, PMMI director of workforce development. “Our scholarships not only reward academic excellence but also encourage the innovative spirit and dedication necessary for the packaging and processing sector to thrive.”
Each year, the PMMI Foundation provides academic scholarships to students studying packaging, food processing, engineering, and mechatronics. These scholarships underscore PMMI’s commitment to the future of the packaging and processing industry.
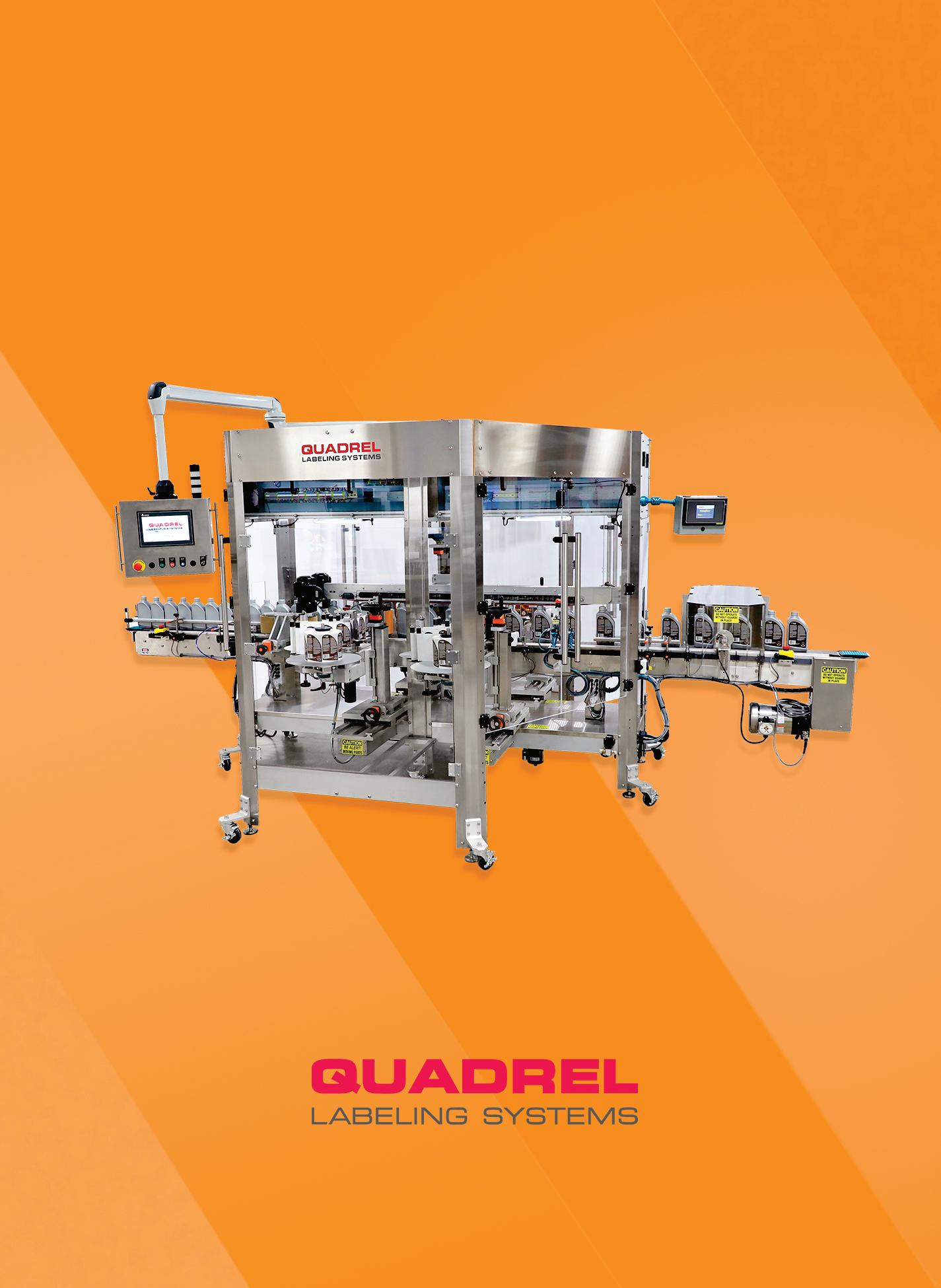
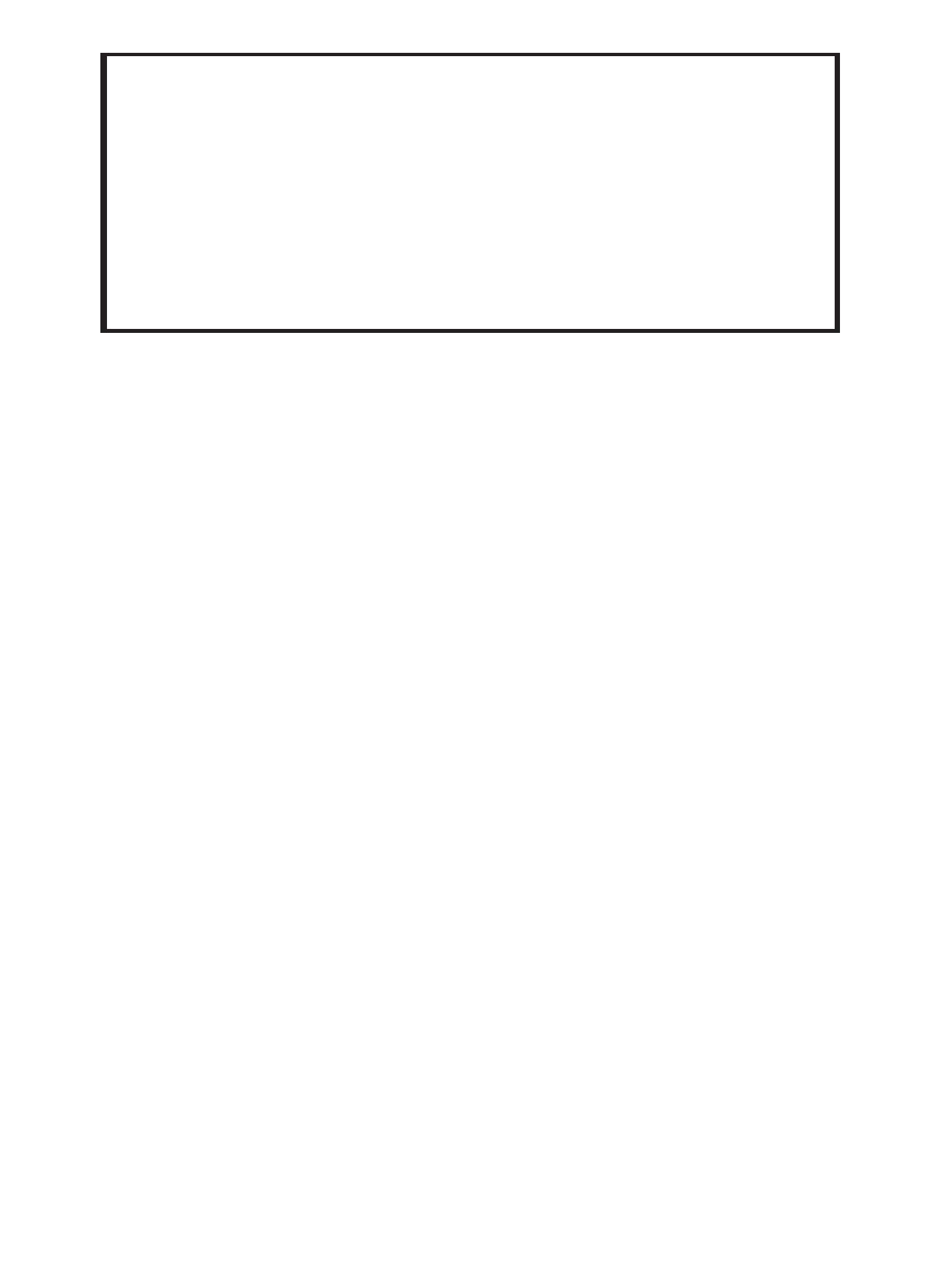
This year’s scholarship recipients represent a diverse group of talented individuals who have demonstrated exceptional dedication and potential in their respective fields of study. Among the scholarships awarded are:
PMMI Member Family Scholarship: $75,000 awarded. This scholarship supports immediate family members of PMMI member company employees interested in packaging and processing as a career choice. Fifteen outstanding applicants were selected to receive $5,000 scholarships annually. The recipients of the Member Family Scholarships for this year are:
Wyatt Cook, Widener University, Robotics Engineering
Makenzie Dick, Iowa State University, Chemical Engineering
Christian Hall, Milwaukee Area Technical College, Business Management
Ian Hohn, Colorado State University, Computer Engineering
Caroline Keeley, Xavier University, Undeclared
Ruby Levy, Tulane University, Digital Media Studies
Esteban Martinez, Michigan State University, Packaging Engineering
Molly McKee, Drexel University, Product Design
Ryan Monroe, University North Carolina-Charlotte, Electrical Engineering
Jarod Parsons, University of Wisconsin-Madison, Chemical Engineering
Jamie Stensgard, Hennepin Technical College, Automation Robotics Engineering Technology
Alexa Stierwalt, Marian University, Graphic Design and Marketing
Lucas Stierwalt, Marian University/Purdue University Indianapolis, Graphic Design and Mechanical Engineering
Natasha Vibhakar, University of South Florida, Supply Chain Management
Robert Wall, Purdue University, Mechanical Engineering
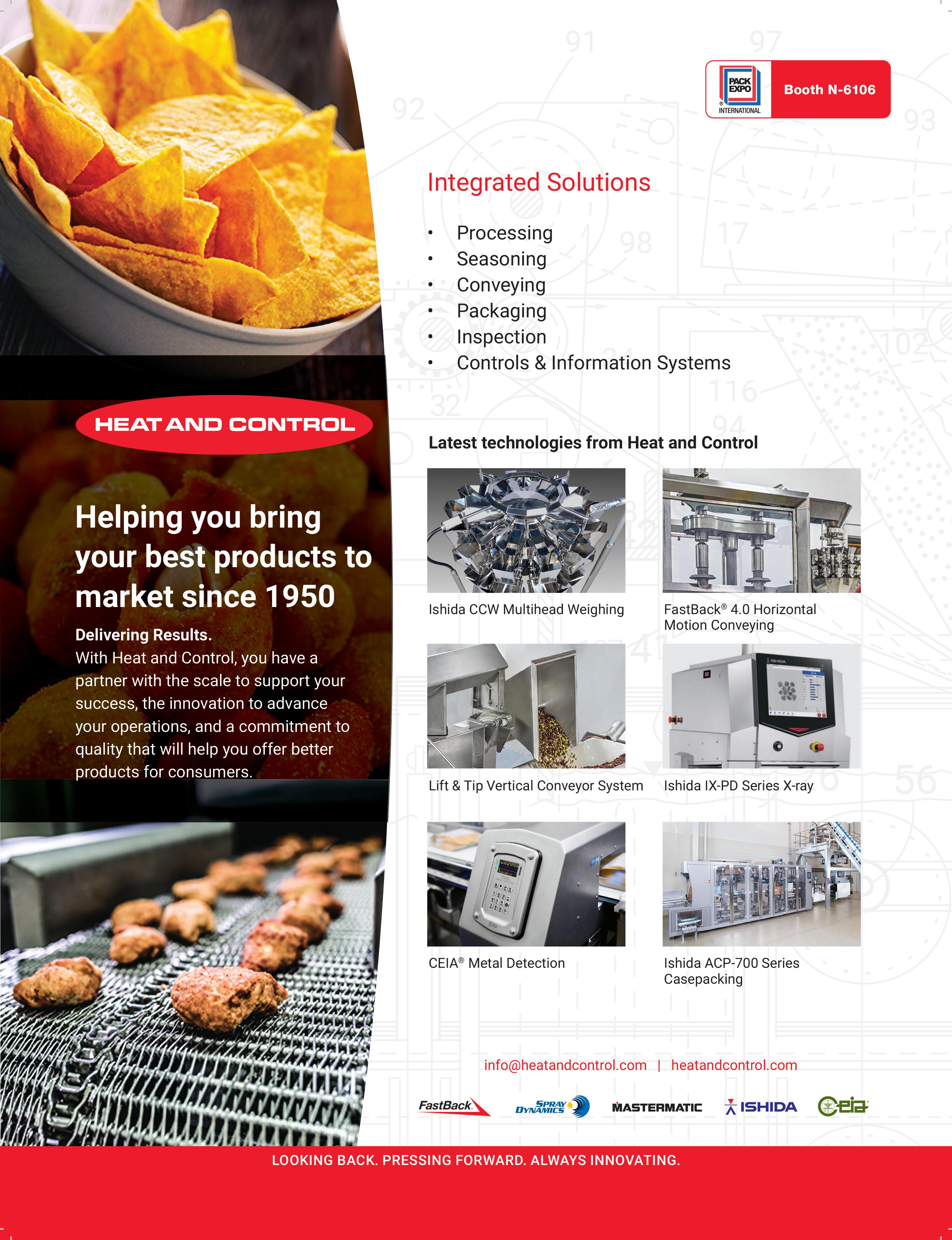
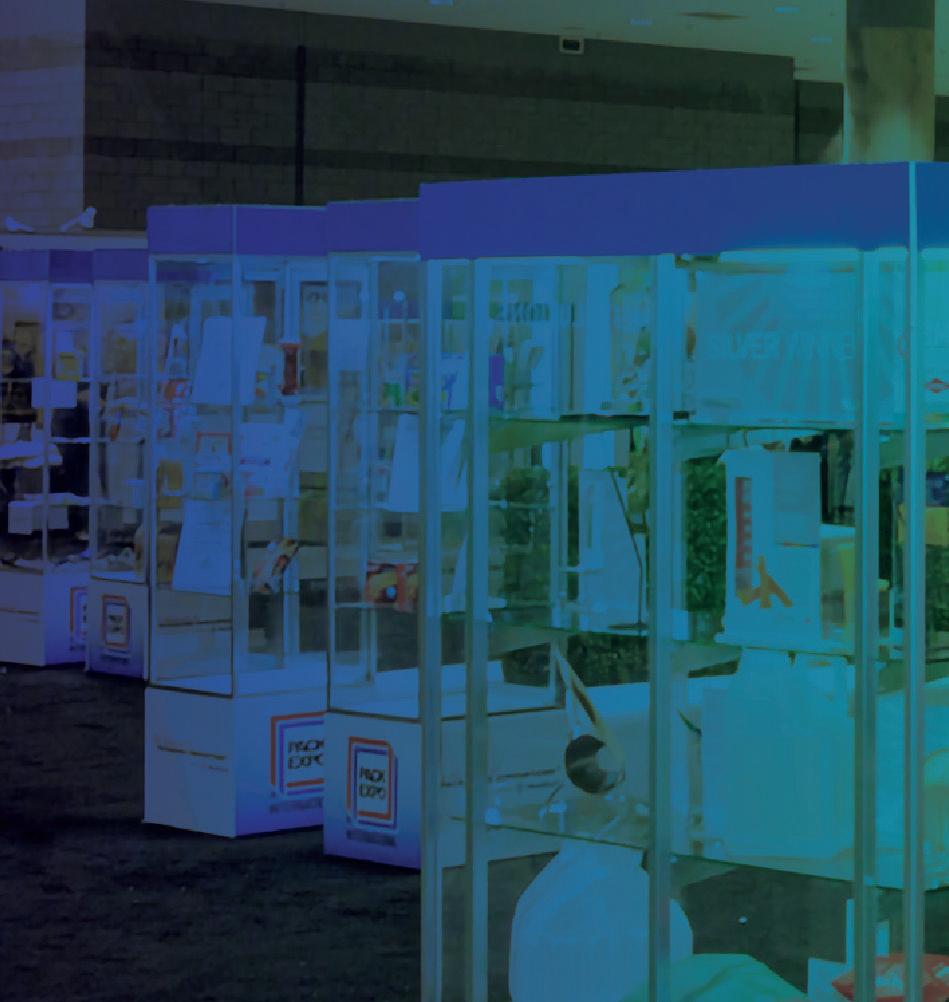
EXPLORE AWARD-WINNING PACKAGING
Get inspired by the world’s best packaging designs and spark your brand’s next big idea!

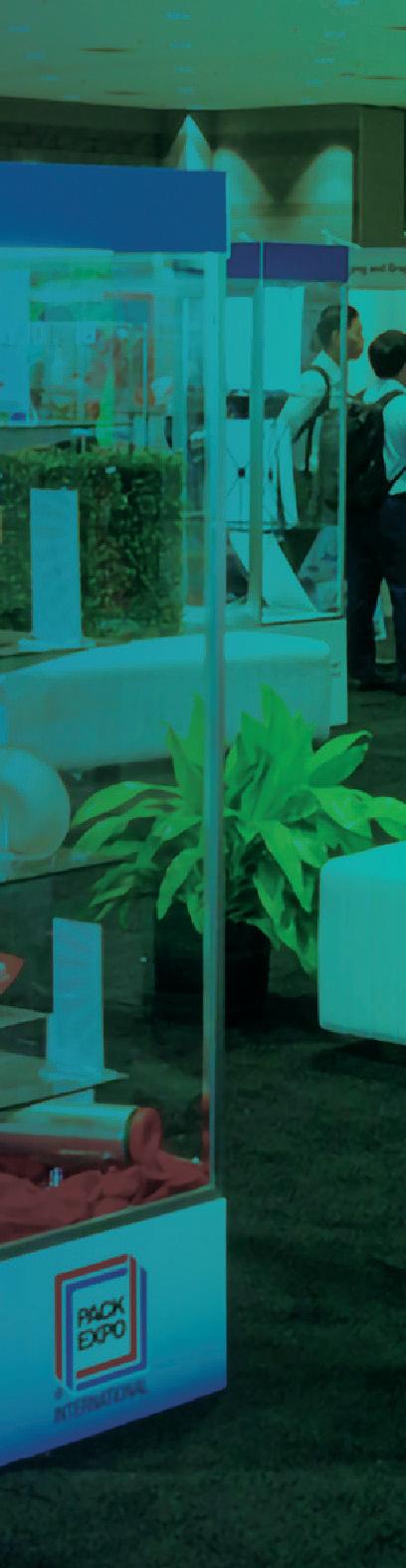
WEST HALL | Booth W21030
In the Containers and Materials Pavilion
FEATURING ENTRIES FROM:
⁌ ABRE – Brazilian Packaging Association
⁌ ARC – Association for Roll-to-Roll Converters
⁌ DOW – Packaging Innovation Awards
⁌ FPA – Flexible Packaging Association
⁌ FSEA – Foil and Specialty Effects Association
⁌ IMDA – In-Mold Decorating Association
⁌ IOPP – Institute of Packaging Professionals
⁌ RPA – Reusable Packaging Association
⁌ Smurfit Westrock
WEDNESDAY SHOW
NOVEMBER 6, 2024
—Continued from page 12
PMMI Memorial Scholarship in honor of Claude S. Breeden, Glenn Davis, and Art Schaefer: $20,000 awarded. Established to honor these industry leaders, this scholarship provides nancial assistance to North American technical college students. Each recipient received a $4,000 scholarship. Recipients of PMMI Memorial Scholarships are:
Daniel Chow, Columbus State Community College, Electromechanical Engineering Technology
Declan Couch, Manhattan College, Electrical/Computer Engineering
Moses Gbetuwa, Hennepin Technical College, Mechatronics
Pheng Lee, Hennepin Technical College, Automation Robotics Engineering Technology
Joseph Phillips, Hennepin Technical College, Mechatronics
PACK EXPO Scholarship: $30,000 awarded. This scholarship is the bene ciary of PMMI’s PACK gives BACK™ events at PACK EXPO International and PACK EXPO Las Vegas. Each year, six $5,000 scholarships are awarded to students attending a North American college or university. 2023’s recipients of PACK EXPO Scholarships are:
Morgan Bartholomew, Pennsylvania College of Technology, Polymer & Plastics Engineering
Amy Foo, California Polytechnic State University, San Luis Obispo, Industrial Technology and Packaging
Matthias Fowler, Hennepin Technical College, Mechatronics
Madison Roberts, Michigan State University, Packaging Science
Ethan Sawyer, Tennessee Technological University, Mechanical Engineering
Blake Strickland, Cape Fear Community College, Industrial Engineering Technology
Electrical Engineering Scholarship: $5,000 awarded Marcos Delgado from Worcester Polytechnic Institute will receive this scholarship, which is awarded to one student attending a North American four-year college or university with a focus on electrical and computer engineering.
Packaging & Processing Women’s Leadership Network (PPWLN) Scholarship: $5,000 awarded. The PPWLN scholarship aims to support women’s careers in the packaging and processing industry. This year’s recipient is Lia Grammer from Rochester Institute of Technology, who is studying packaging science.
Mechanical Engineer Scholarship: $5,000 awarded. Gavin Coley from East Carolina University, pursuing Mechanical Engineering.
Processing Scholarship: $5,000 awarded: Elen Huang, a University of Illinois at Urbana-Champaign student studying Food Science.
Chuck Yuska Scholarship: $5,000 awarded. Named in honor of PMMI’s former president & CEO of 28 years, this scholarship is awarded to a student representing innovation in the packaging industry. This year’s recipient is Timothy Oeser from Clemson University, who is studying Packaging Science.
e PMMI Foundation extends its warmest congratulations to all the scholarship recipients and wishes them continued success in their academic and professional endeavors. ese scholarships serve as a testament to the association’s commitment to nurturing the next generation of leaders and fostering excellence in the packaging and processing eld. For more information about the PMMI Foundation and its scholarship programs, visit pmmifoundation.org/scholarships ■

Next-level cosmetics fillin osin
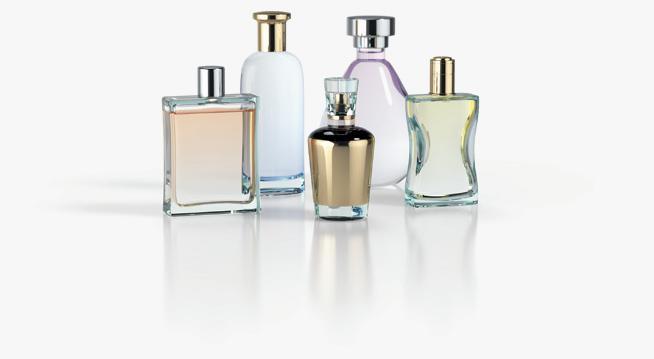
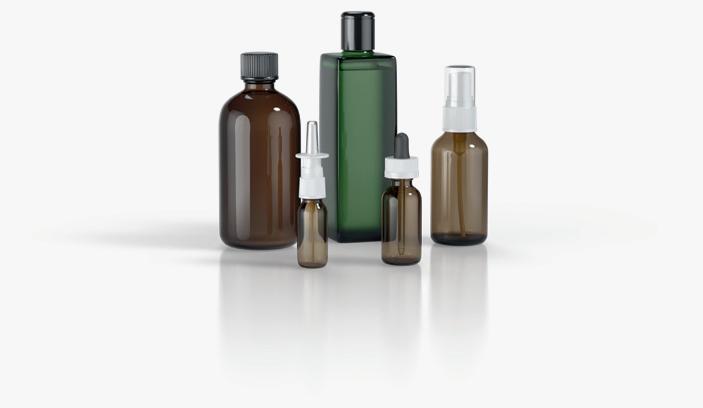
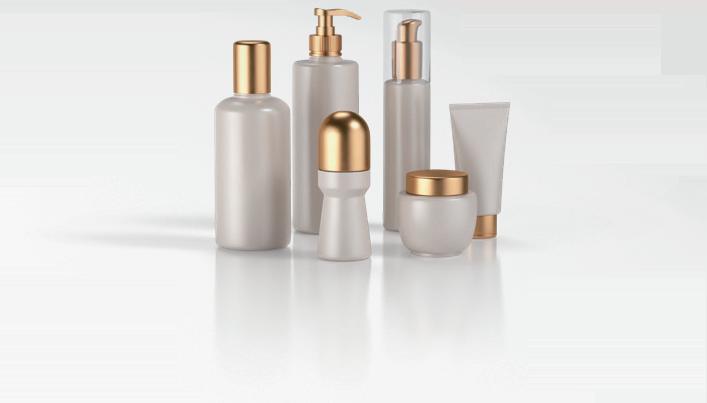
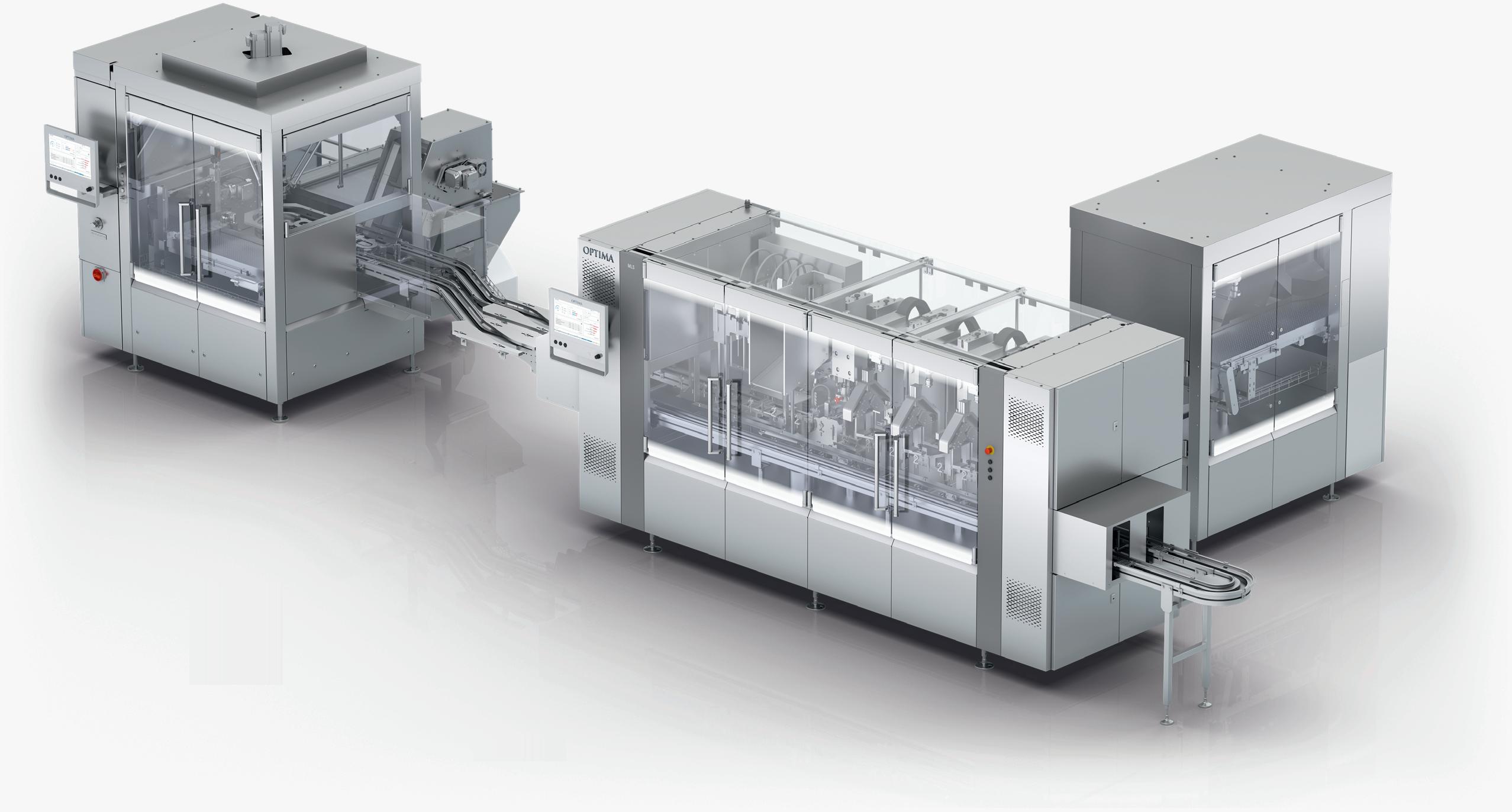
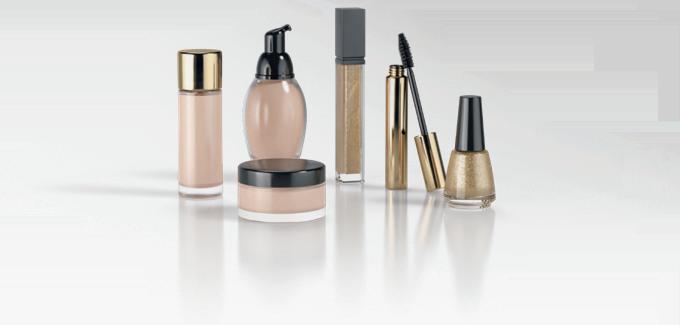

Your benefits
Reduced footprint

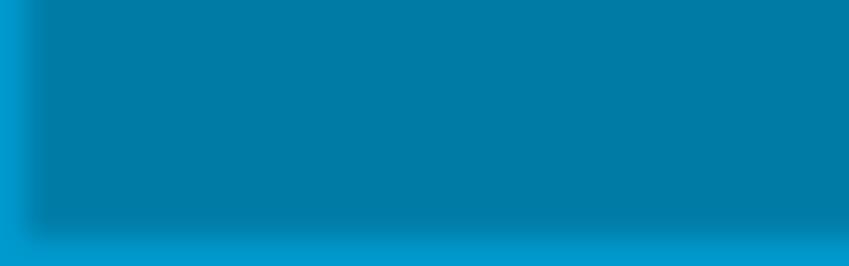
⚪ Up to >50% savings compared to linear competition
Reduced time-to-market
⚪ Maximum flexibility in containers
⚪ Reduction of the format costs of the
Linear machine concept
⚪ Reduction of format changeover
by >50%
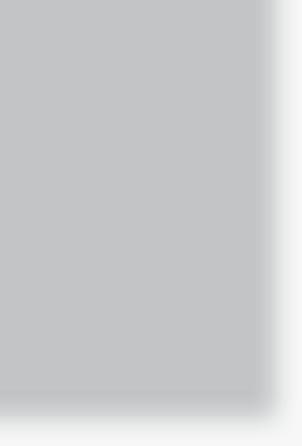
WEDNESDAY SHOW DAILY
Automating Snack Bag Line Cuts Labor Costs by 40%
Machinery from seven PACK EXPO International exhibitors enabled Darlington Snacks to double production while cutting labor costs.
Darlington Snacks is a thriving family-owned snack manufacturing and packaging facility located in the vibrant city of Joplin, Mo. Established in 1982, the company has grown from a small local operation to a respected national player in the snack industry. Darlington Snacks prides itself on producing highquality, innovative, and delicious snack products that cater to a diverse range of consumer tastes.
Serving daycares, schools, and the healthcare industry, Darlington Snacks is committed to sourcing the finest ingredients for their products. They partner with local farmers and suppliers whenever possible, supporting the local economy while ensuring that the freshest and highest-quality ingredients go into their snacks. This dedication to quality has earned the company a reputation for producing some of the tastiest and healthiest snacks in the nation.
Not long ago, management at the snack food company recognized that they faced significant challenges where staffing was concerned. Located as they are in an area dense with food manufacturing plants, they faced tough competition when it came to finding talented workers. With many open manufacturing jobs, they were scrambling to fill positions and overstressing current employees when trying to keep up with demand.
Also challenging was delivering packaging accuracy and being able to meet customers’ product handling requests. Being in the foodservice business for schools and healthcare institutions, the firm faced increased demand for snacks in single-serve containers that weren’t going to be handled by multiple parties, especially during the COVID pandemic.
At PACK EXPO Las Vegas, representatives from Darlington Snacks saw the impressive speed of the Viking Masek (Booth S-3971) Velocity vertical form/fill/seal packaging machine filling singleserve pouches. Brad Schweiss, vice president of manufacturing at Darlington Snacks, was already familiar with Viking Masek’s packaging equipment.
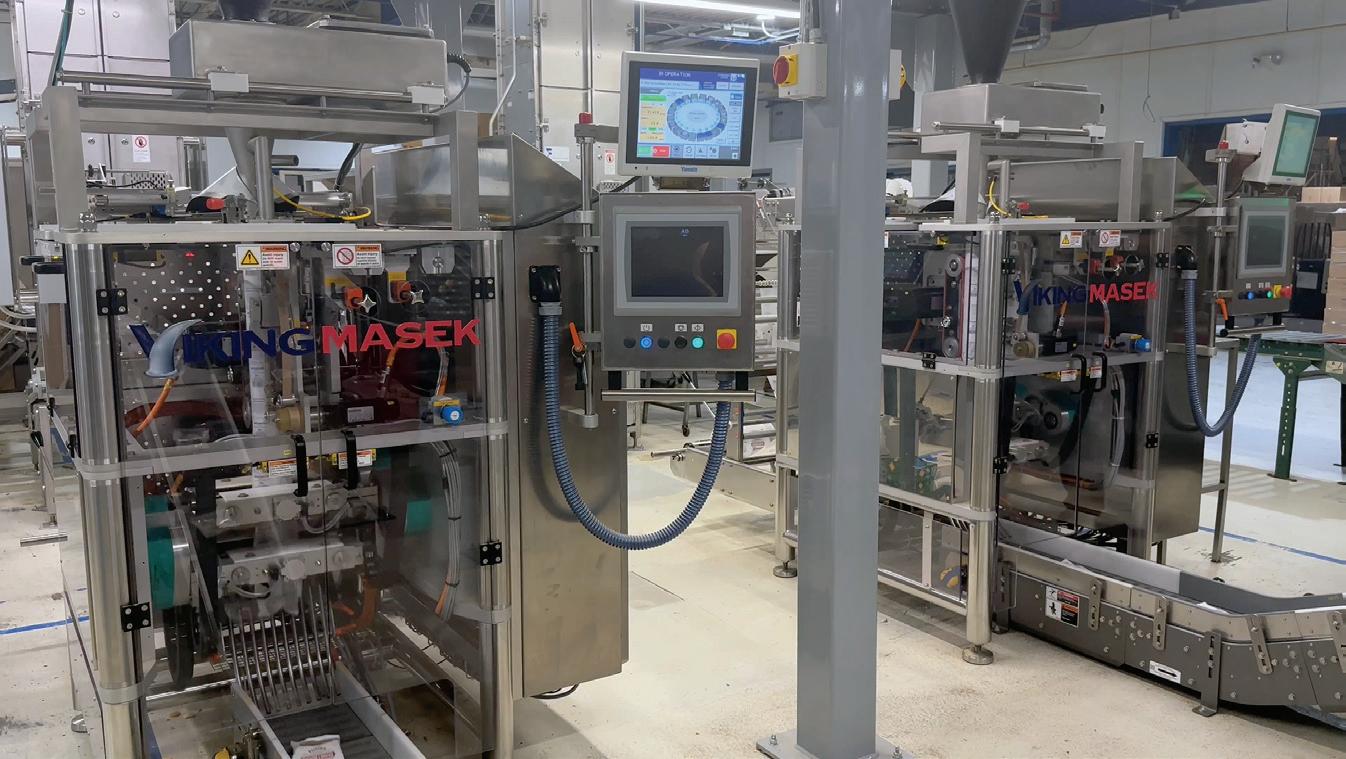
Vibratory infeed
Snack products first make their entrance into the automated packaging system through a vibratory infeed hopper from Eriez (Booth N-5121) and then are fed to a Whiz Lifter Model C bucket elevator from Frazier & Son (Booth N-4935). It conveys the snacks vertically to an Eriez feeder that delivers the product to an ADW-0-0120F 20-bucket combination scale from Yamato (Booth S-3195) where it is quickly and precisely weighed. Next, the snacks are gently dropped into bags that have been formed on the v/f/f/s Velocity packaging machine at a rate of 150 bags/minute on each machine (300 bags/min for both bagging lines
Two high-speed vf/f/s machines are at the heart of the new line, and each runs at 150/min. Shown below are the continuousmotion sealing jaws closing on the flexible film.
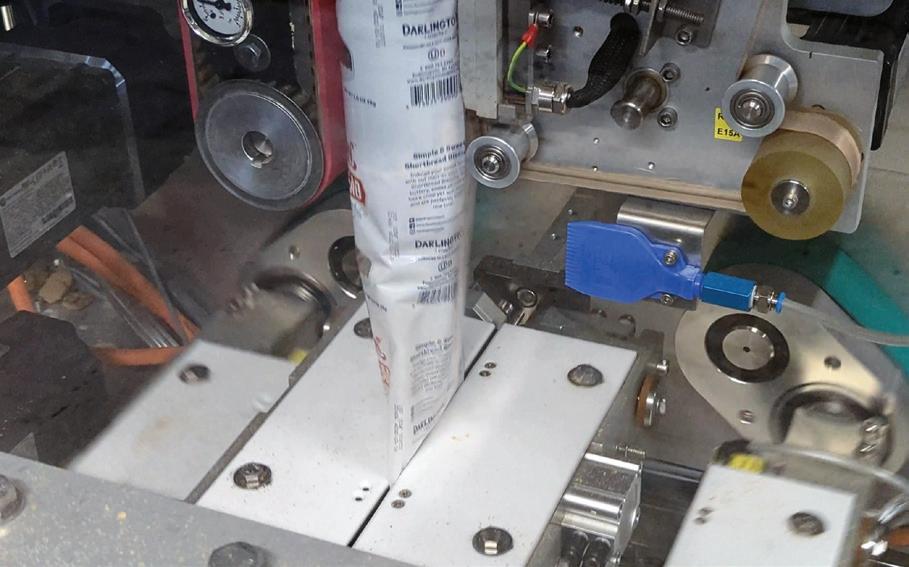
firm produces bag sizes ranging from 4.25 x 5.5 in. to 8 x 10 in.
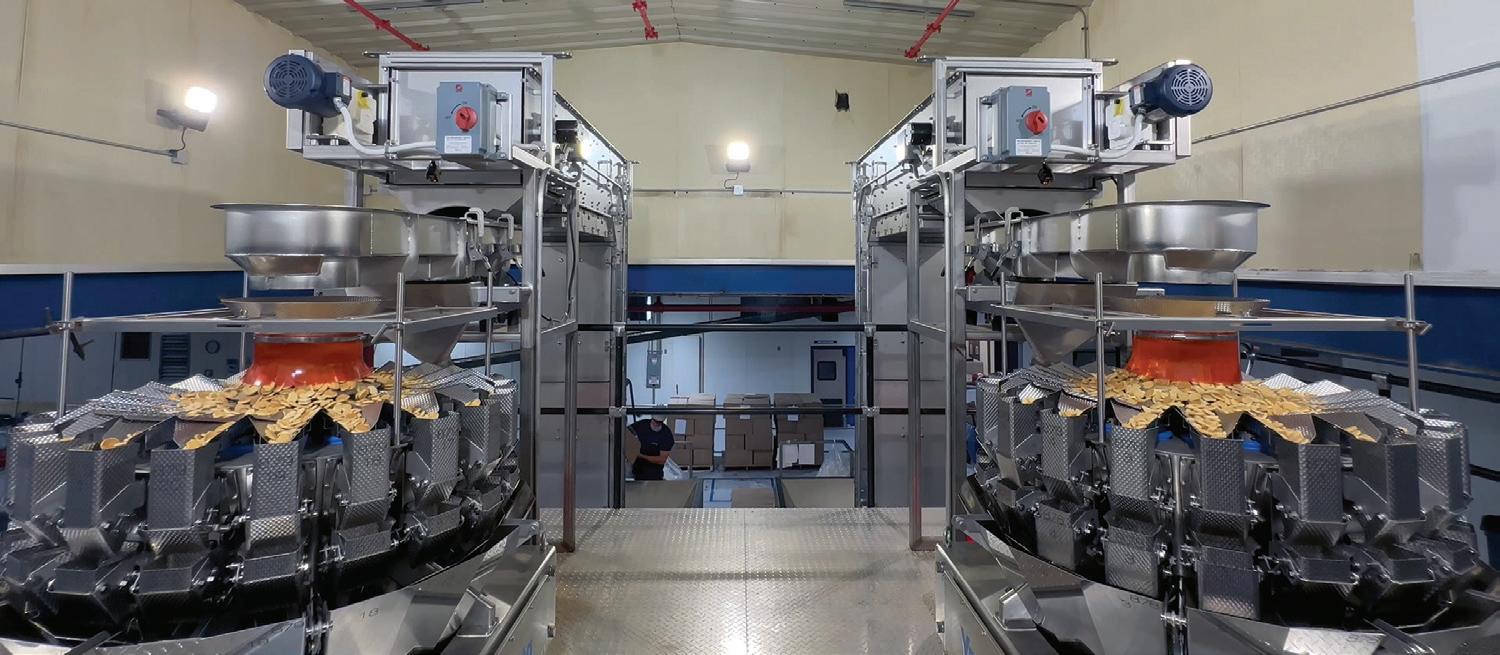
Above the baggers are two combination scales fed by vibratory conveyors.
“I’d been with Darlington for six years but in the industry for more than 30,” explains Schweiss. “So I was familiar with Viking Masek and what their services and capabilities were.”
After collaborating with Viking Masek’s team of snack packaging experts, Darlington Snacks purchased an entire snack packaging system consisting of two bagging lines that merge into a single case packing line. On each bagging line, the process looks like this.
Featuring controls from Rockwell (Booth S-1544) and patented servo-driven dual-jaw technology, Viking Masek calls the Velocity the “Fastest VFFS Packaging Machine in the World.” It’s capable of production speeds to 300 bags/min. The unique center-mounted filling tube and naturally counterbalanced sealing profile are designed to provide vibration-free, extremely smooth operation at all speeds. The machine is also versatile, producing packages as small as 60 x 90 mm (0.66 x 3.54 in.) or as large as 300 x 1000 mm (11.8 x 39.37 in.). Its versatility was appealing in Darlington’s case as the
Integrated into the Velocity bagger is a continuous ink-jet coder from Linx that marks each bag with date code information. The bags are sealed shut and drop onto a Z-shaped takeaway conveyor supplied by Multi-Conveyor (Booth S-1507). The finished bags pass over a Yamato CSJ22L-00/CE31 checkweigher to ensure accuracy before dropping from the Z-shaped Multi-Conveyor and through the basket of a batch gate from AS&E right into a waiting case below the gate. Inside the basket is a light curtain, so each time a bag drops through that curtain it gets counted. When the correct number of bags has been counted, a signal is sent to the controller of the Velocity bagger and that controller sends a signal to the batch gate to close long enough for the filled case to be conveyed away and for a fresh case to be conveyed in. With the fresh case in place, the batch gate opens and bags continue dropping into the basket for the next batch.
One minor feature worth mentioning is that when a case is being filled, a pair of vacuum cups attached to pneumatic devices attach themselves to the bottom sidewall of one side of the case and stroke constantly in and out. This bit of agitation ensures that the pouches are spread evenly across the case rather than grouping all in one part of the case.
As for case erection, it takes place not far from where the two AS&E batch gates are located. A Lantech (Booth N-5106) C-400 erects corrugated cases from flat blanks. It puts them on a roller conveyor that leads to two right angle conveyor spurs.
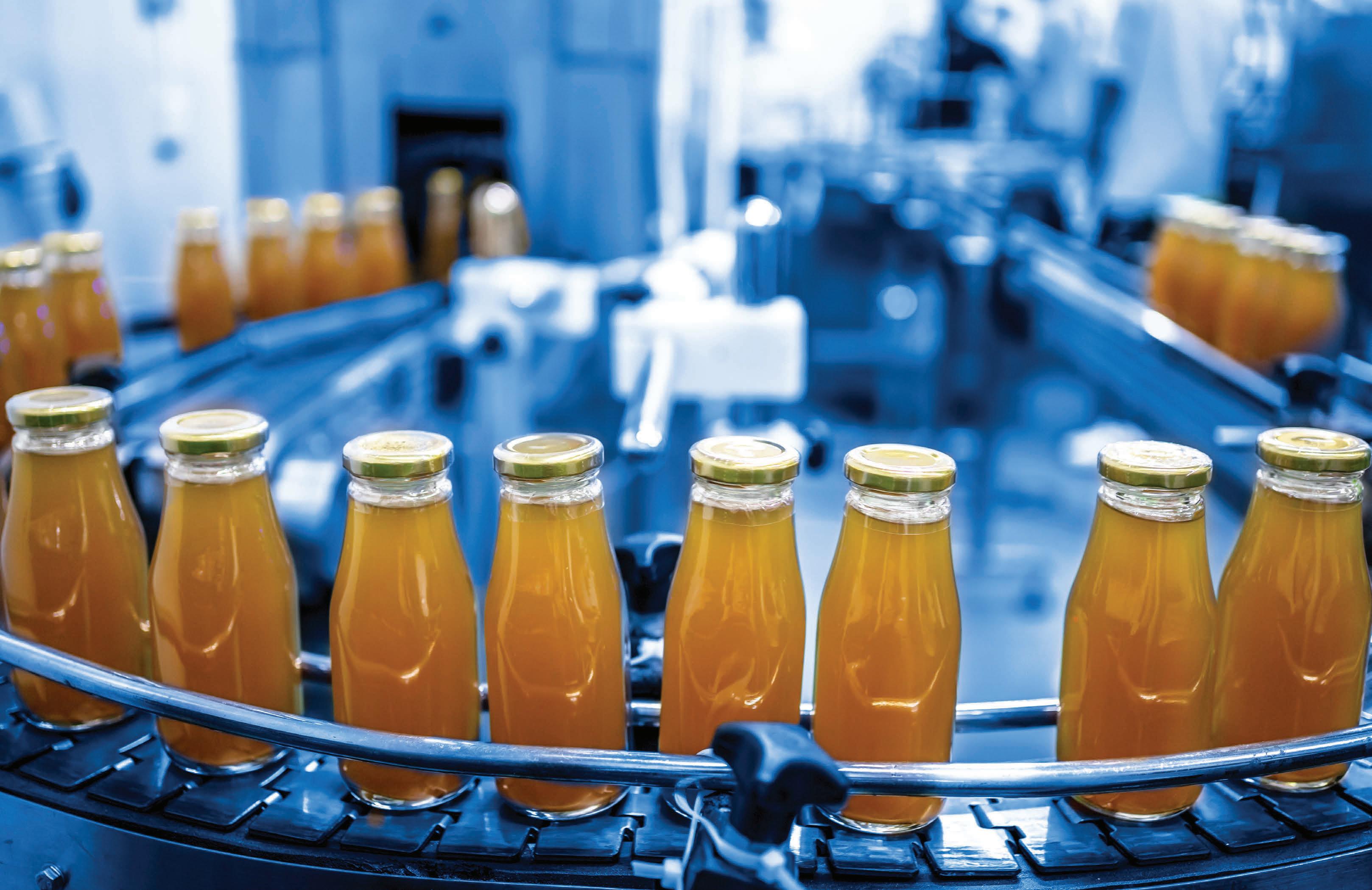
Automation Solutions from Washdown to Warehousing
Let Turck tackle whatever packaging automation challenges you are facing. Our wide range of reliable automation solutions – including sensors, industrial cordsets, distributed I/O products, and RFID stand up to the toughest packaging environments. From improving high-speed cap and can detection to cost-effective machine control with a combined HMI/PLC, or more rugged washdown-rated cables, Turck has a solution. Optimize your packaging machines and lines with Turck.
Visit us in booth N-5719
—Continued from page 16
Each of these spurs leads to an AS&E batch gate, and cases move into these gates based on demand.
Once a case has received its batch of bags from a batch gate, it’s carried away at another right angle on a roller conveyor that takes cases in a single file to a Veritiv Lantech CS-300 case taper.
As finished cases reach the end of the line, they are stacked manually onto pallets, and the pallets are then moved to a storage area where they await their journey to schools, daycares, and health care facilities across the country.
This entire snack packaging line was set up, tested,
and perfected at Viking Masek’s US headquarters in Oostburg, Wis., before it was even loaded on a delivery truck.
Trial run
“Before delivery of our automation, I took my plant engineer to Viking Masek to see the system’s capabilities, slow-motion videos for assessment, and a trial run of the line before it shipped with everything labeled the way we needed it to be,” explains Schweiss, who adds that he was quite impressed with Viking Masek’s comprehensive testing and checkout process.
Unlock New Packaging & Processing Innovations For EVERY Industry
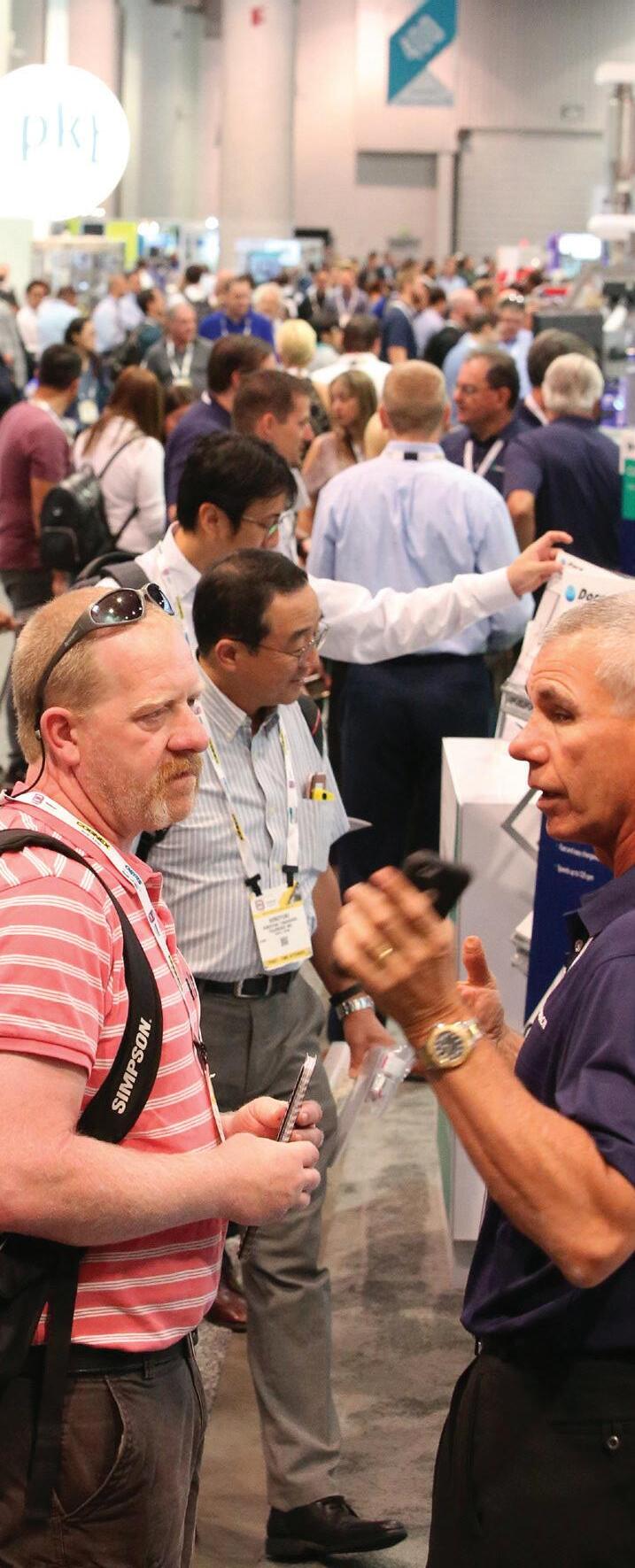
Discover solutions you won’t see anywhere else in the Southeast. The exciting new PACK EXPO Southeast 2025 unites all vertical markets in one dynamic hub, generating more innovative answers to your production challenges. Don’t miss this extraordinary opportunity for your business!
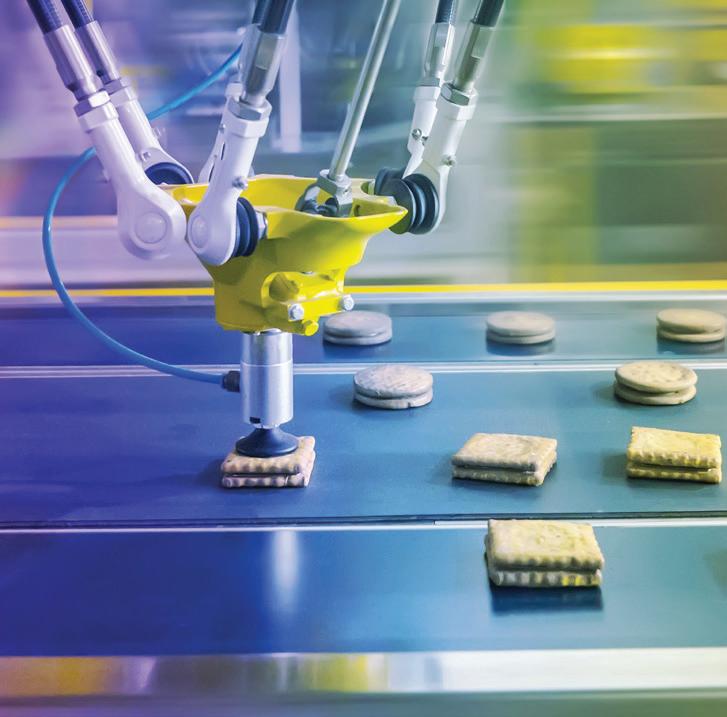
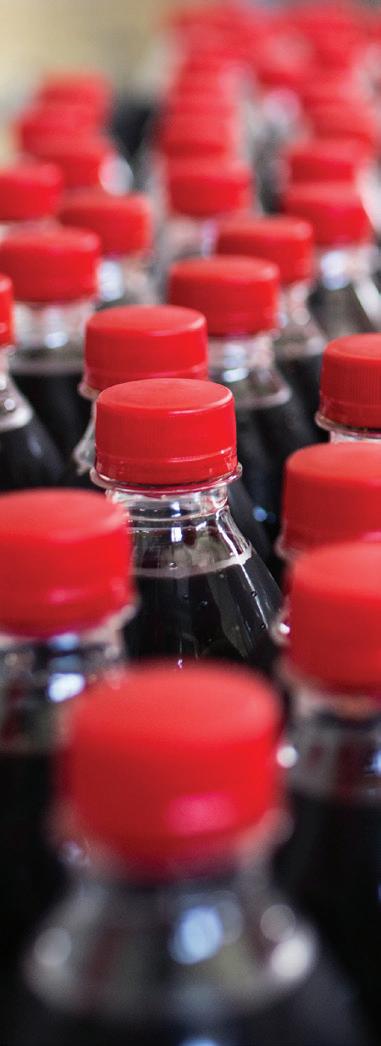
Viking Masek assembled the entire system onsite at Darlington Snack’s plant. The new snack packaging lines fit seamlessly into their packaging configuration, resulting in precisely the solution their customers were asking for.
“We didn’t have to worry about integration because Viking already took care of that for us,” comments Schweiss. “We bought it as a complete system and it’s functioned perfectly since.” Darlington Snack’s biggest victory with the automated packaging system is the accuracy of the batch gate—they report it’s consistently spot on.
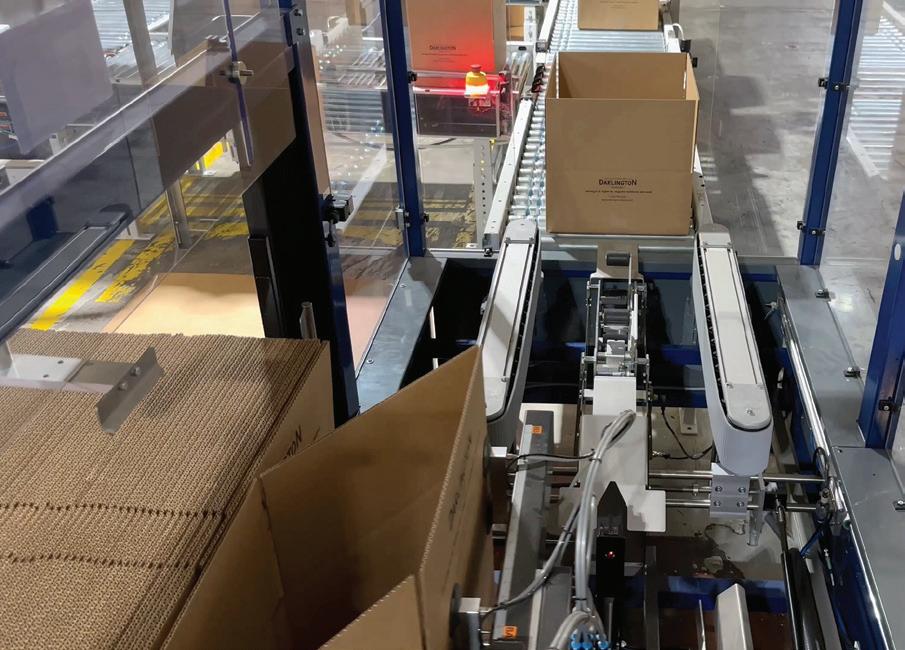
Corrugated cases are erected on this system (above) and sent on a roller conveyor that brings them to one of two right angle conveyor spurs, each leading to a batch gate that counts bags into cases. Shown below is one of the two conveyor infeeds leading to the batch gate counter.
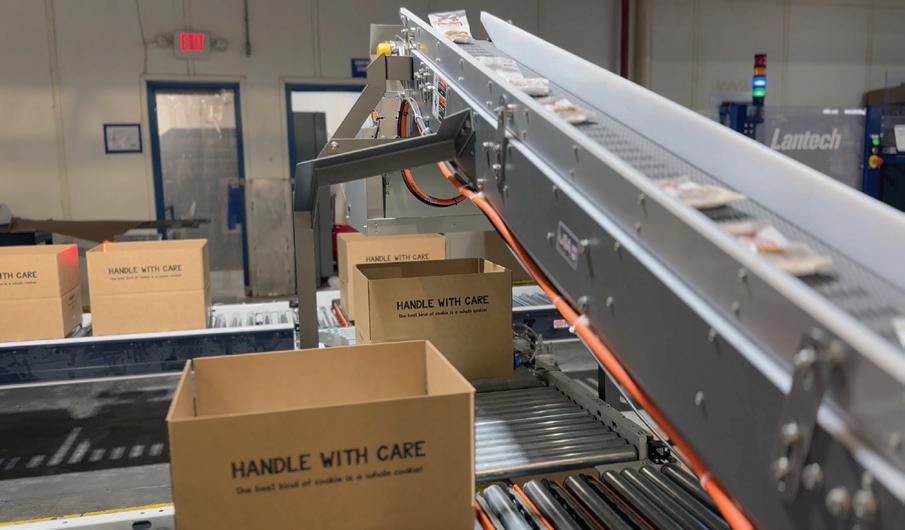
“The real trick for me was the downstream stuff to be able to make the counters work right,” explains Schweiss of the accuracy of their packaging line. “We had to be able to get the cases erected and into the two stations in the right sequences at the right time, and then on out to the palletizing operation. It has worked seamlessly.”
Today, Darlington’s packing operation, case conveyance, and case closing are all automated. Staff members who formerly were required to conduct such operations have been relocated to other areas of the facility. Since embracing automation, Darlington Snacks has seen substantial improvements with the throughput and labor-related challenges they were facing.
“Automation has cut down on our waste, overpacking, and amount of giveaway,” reports Schweiss. “It has made our customers’ experience better because we’re not coming up short on products. And I’m pleased to report we’ve doubled production with about 40 percent less labor on the line.” ■
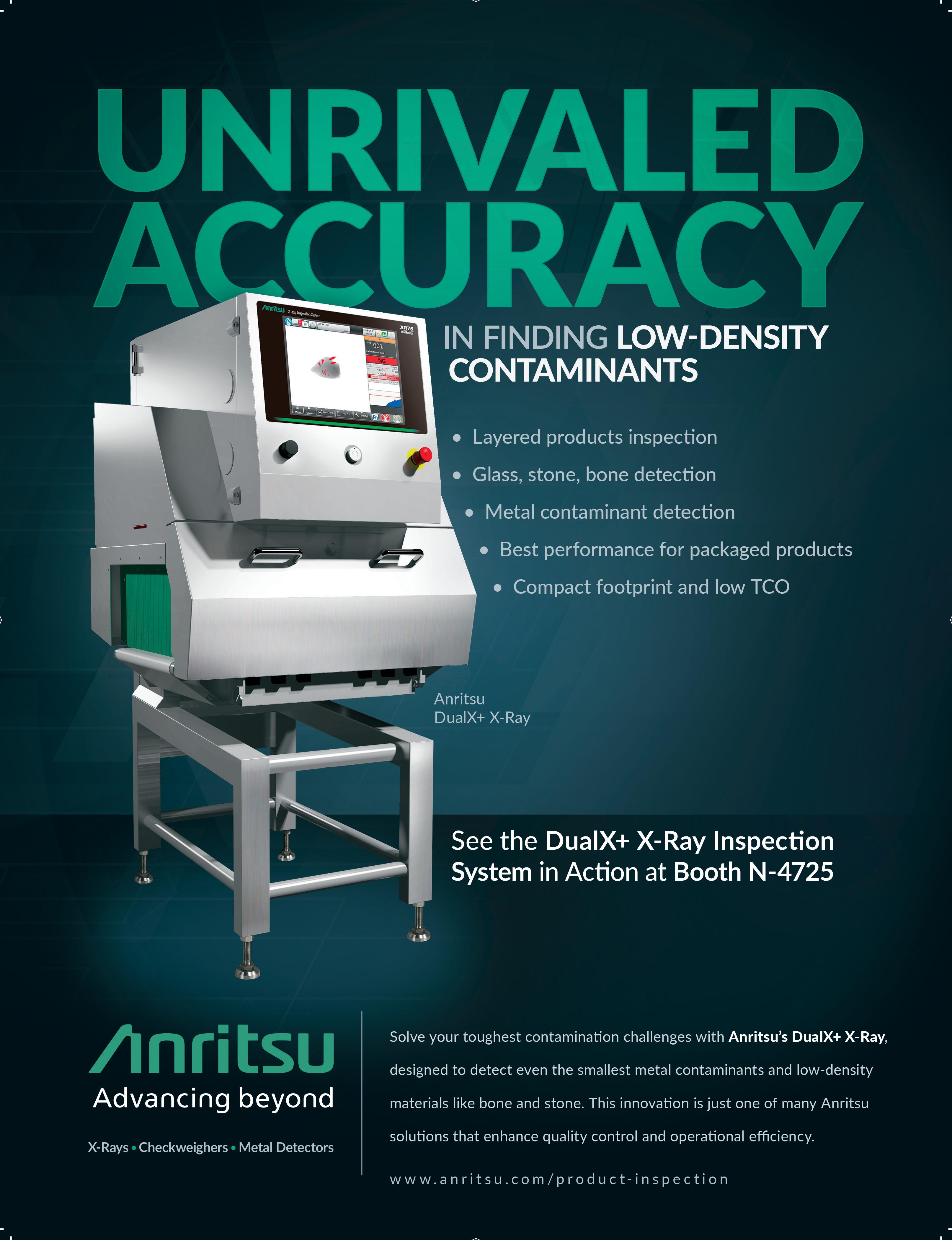
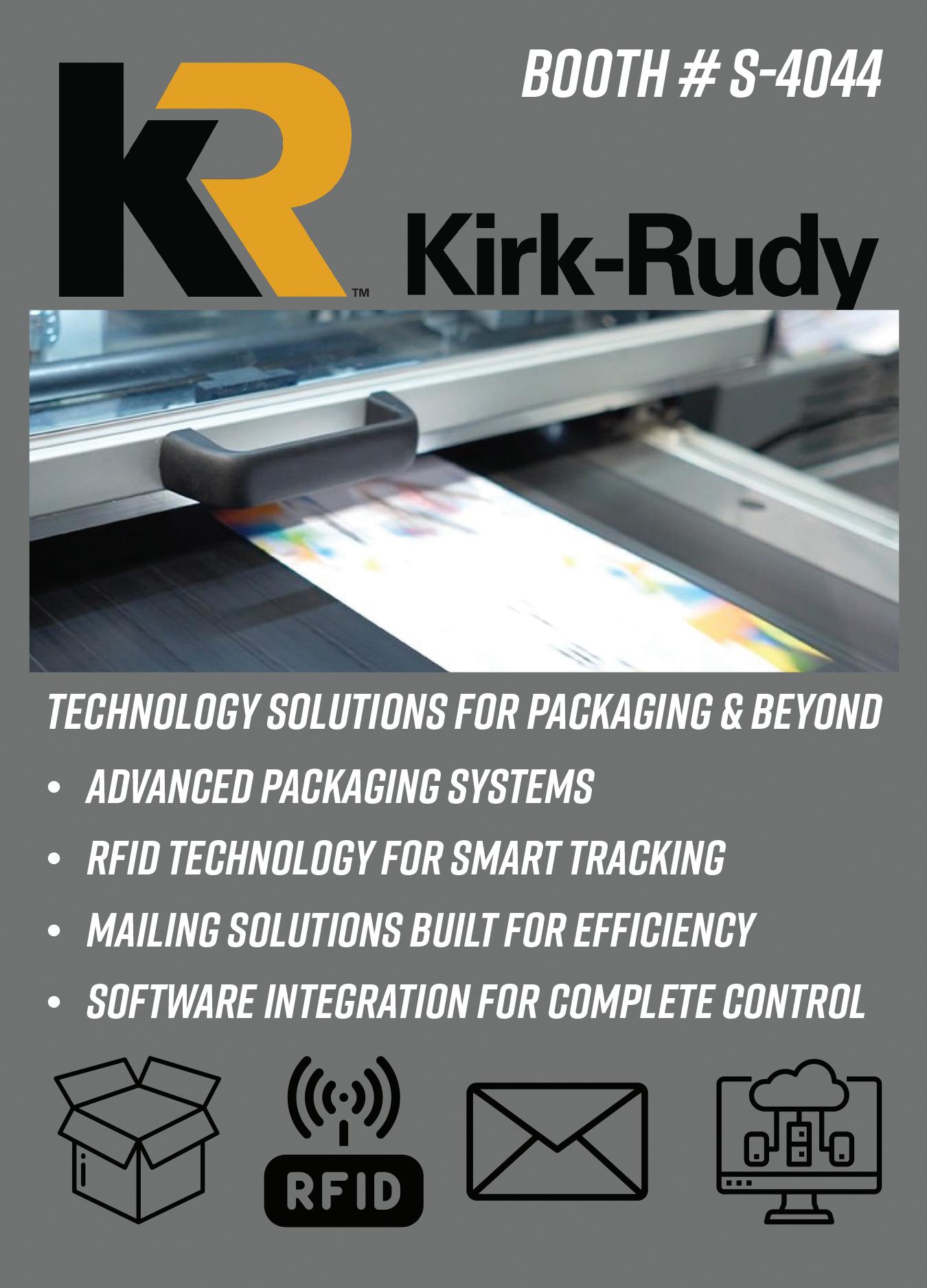

WEDNESDAY
Emerging Brands Accelerate Growth at PACK EXPO International
New show feature, Emerging Brands Central, offers free educational sessions and one-on-one consultations for businesses looking to scale up.
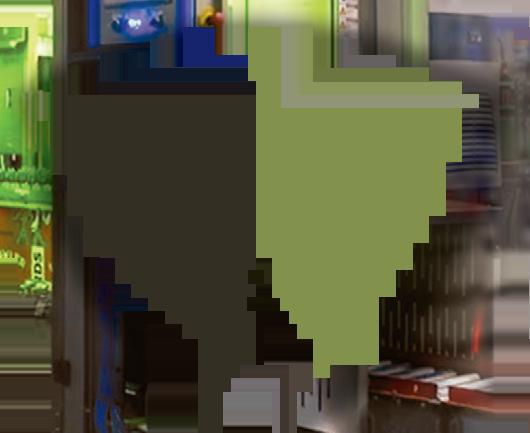
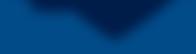
Growing brands seeking to scale up and expand operations can find valuable information and resources at the new Emerging Brands Central at PACK EXPO International 2024.
Emerging Brands Central, located in Booth W-20049, features free educational sessions with industry experts designed for brands growing their manufacturing operations. The free 30-minute sessions will cover topics such as:
• Brand Growth Strategies: How companies can effectively scale operations through value engineering and incremental automation.
• Sustainability and Innovation: Focused discussions on sustainable packaging, materials, and processes, plus utilizing innovations in manufacturing and packaging.
• Navigating Market Challenges: Insights into market trends, overcoming entry barriers and supply chain challenges for new brands.
A complete list of sessions can be found under the Education tab in Map Your Show or at www.packexpointernational.com/education/emerging-brands-central.
Expert advisors also will be available for complimentary one-on-one consultations on-site during the show. The advisors have decades of combined consumer packaged goods experience with companies like PepsiCo, Dannon, General Mills, Del Monte, Nestlé, and Kraft. Meet the advisors and schedule appointments at www.packexpointernational.com/education/emerging-brands-central
“The addition of Emerging Brands Central to PACK EXPO International shows that companies of all sizes and backgrounds have a place at the largest packaging and processing event in the manufacturing industry,” says Laura Thompson, vice president of trade shows, PMMI. “Growing brands seeking to expand can use this time to learn, get expert advice, and network with their peers. The possibilities of the types of connections that can be made are endless.”
Emerging brands can also take advantage of being introduced to thousands of manufacturing solutions located within seven specialty pavilions that can help them scale up and expand operations. In addition, there are 150+ educational sessions available at the show featuring topics such as sustainability, AI, automation, robotics, food safety, production, and more. Brands also have ample opportunity to connect with other businesses at the many networking and special events.
Emerging Brands Central is sponsored by Accredo Packaging Inc. (Booth W-24049), Bizerba USA, Inc. (Booth S-2066), Esko (Booth W-13051), Formic (Booth N-5069), Matthews Marking Systems (Booth S-2272), Oxipital AI (Booth LU-7243), Patterson Fan Co. (Booth LU-7127), PMMI ProSource (Booth N-4550), ProSys Fill LLC (Booth S-3656), Selig Group (N-5881), Sonoco (Booth S-2666), and Smurfit Westrock (Booth S-2830)
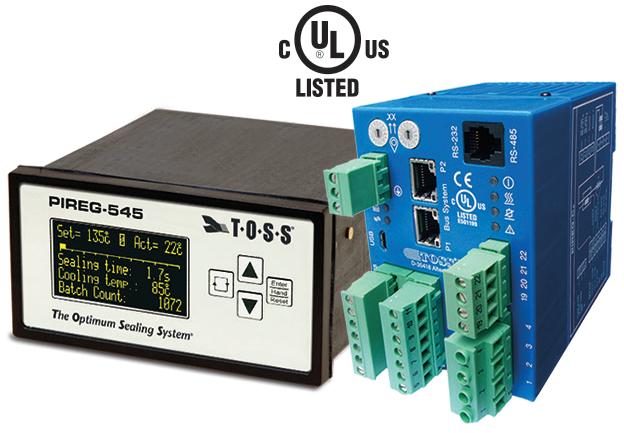

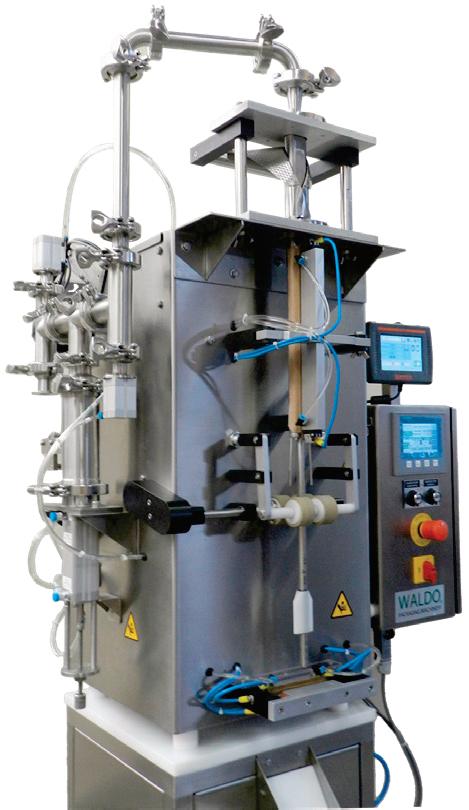
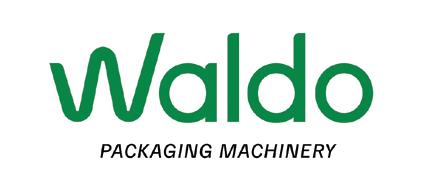
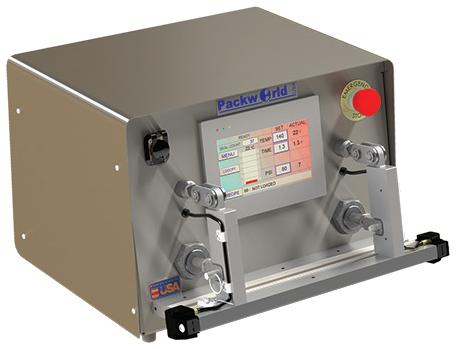


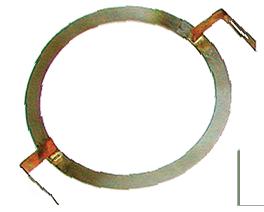
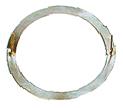

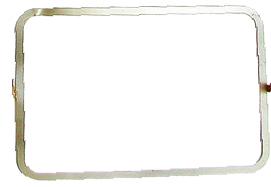
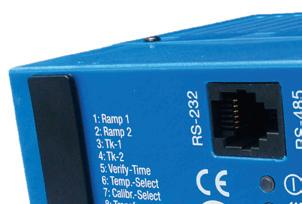
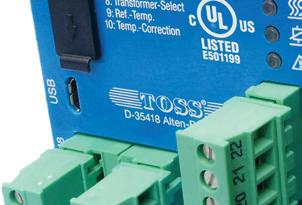
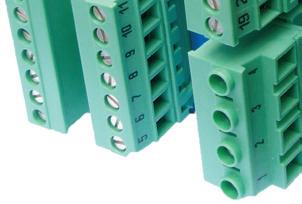
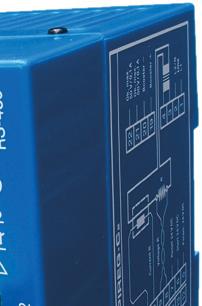


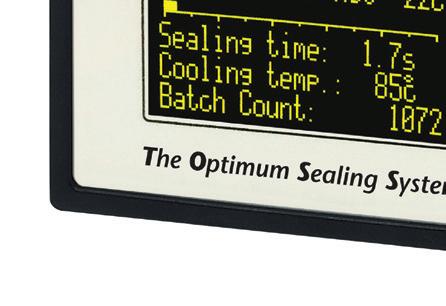
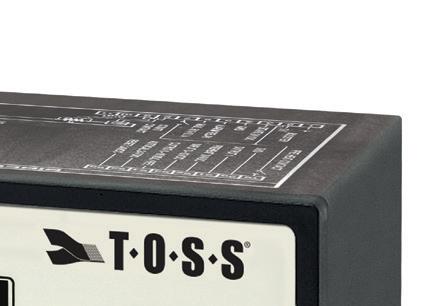
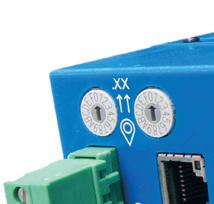
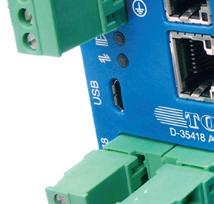
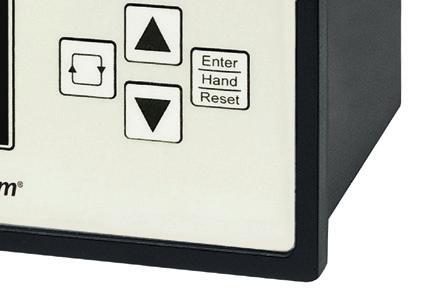
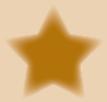
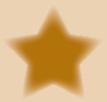

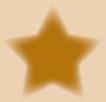
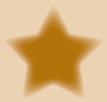
5 Star Rating
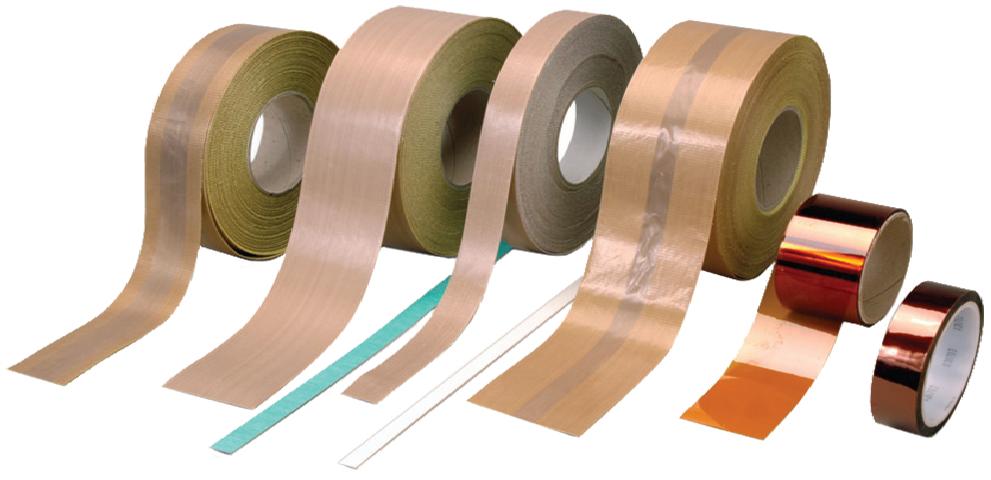
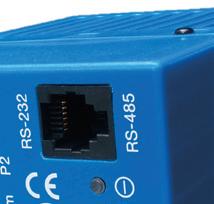
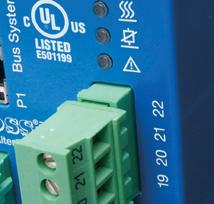
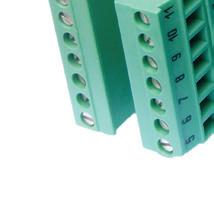
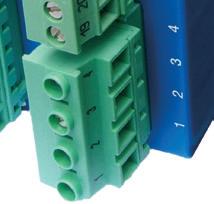
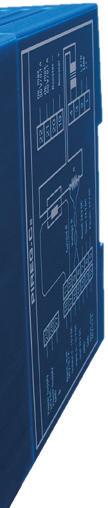
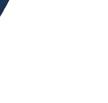
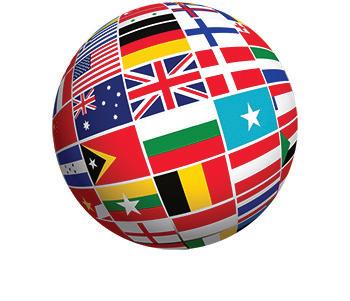
Truly are the EXPERTS AT IMPULSE HEAT SEALING!
15 minutes with a TOSS engineer and I learned more about impulse heat sealing than I have in my 30 years of designing V/F/F/S machines... THANKS TOSS!!
Technology is simply Fantastic.
The PIREG® Temperature Controller controls the time and temperature of the impulse heat seal band flawlessly on every cycle. TOSS Technology truly performs as advertised…
Alloy-20 ® Impulse Heat Seal Bands are far Superior. TOSS designed custom impulse heat seal bands for me to replace my current NiChrome bands. Now I’m getting longer life and cleaner seals. I’m a true believer! Only GENUINE TOSS Alloy-20 ® impulse heat seal bands from now on.
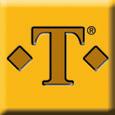
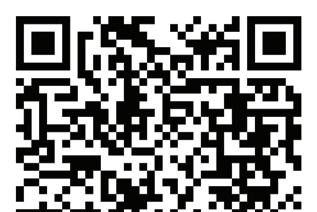
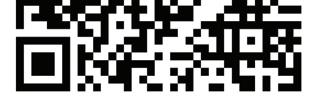

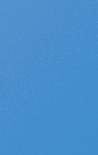
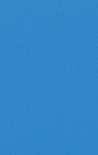
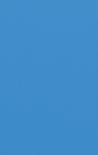
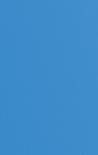

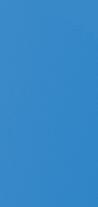


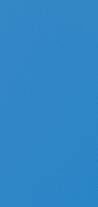
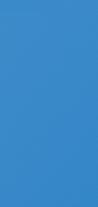
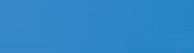

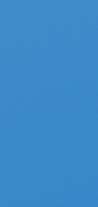

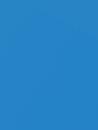

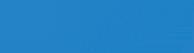
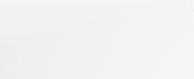

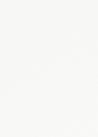
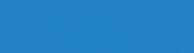
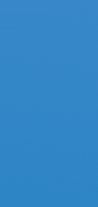
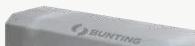
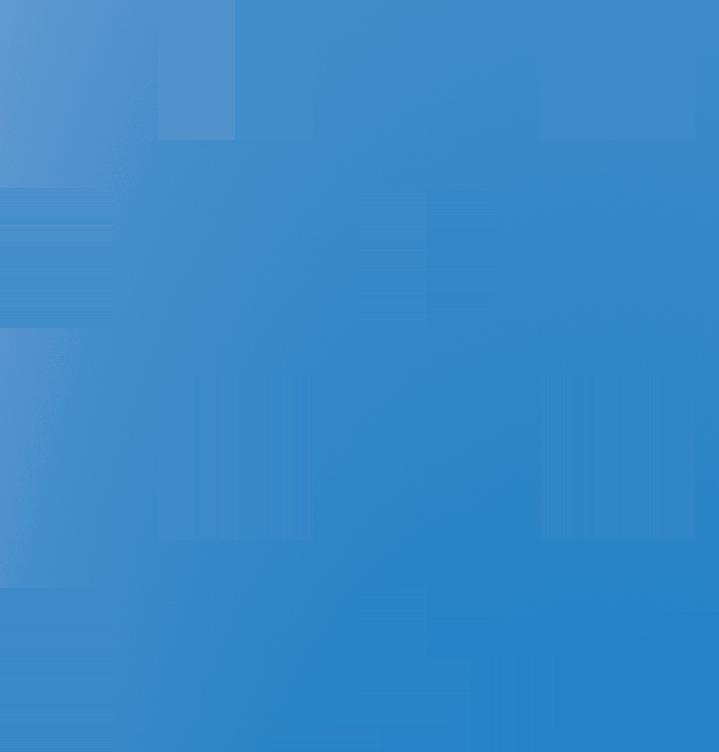
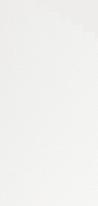

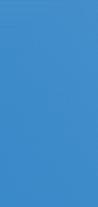
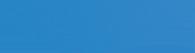
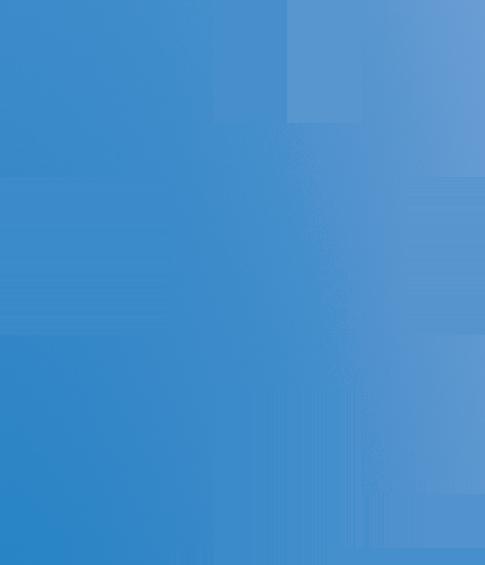
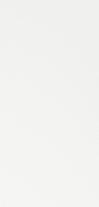

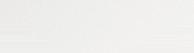
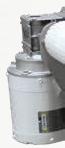
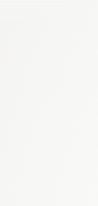
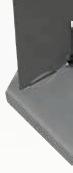
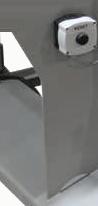


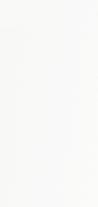


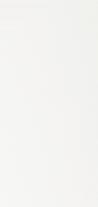
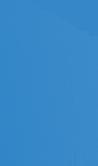
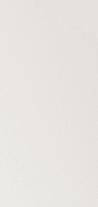
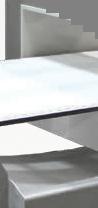

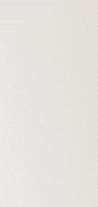
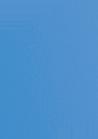


Blending Technology With Milling Tradition
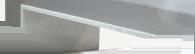
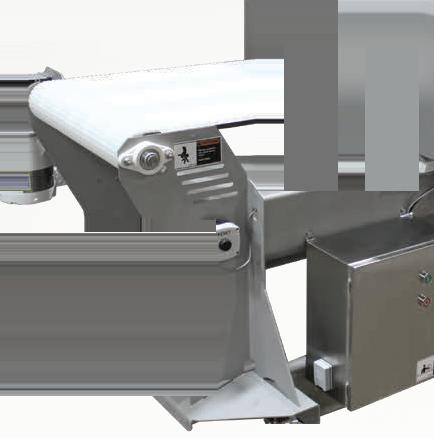
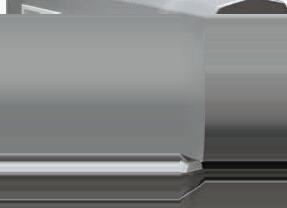
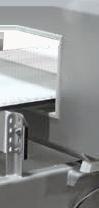
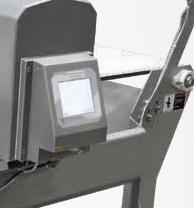
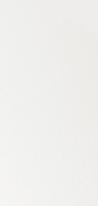
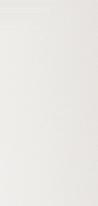
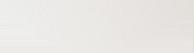

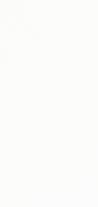
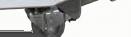
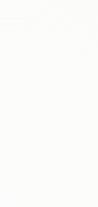
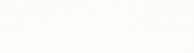
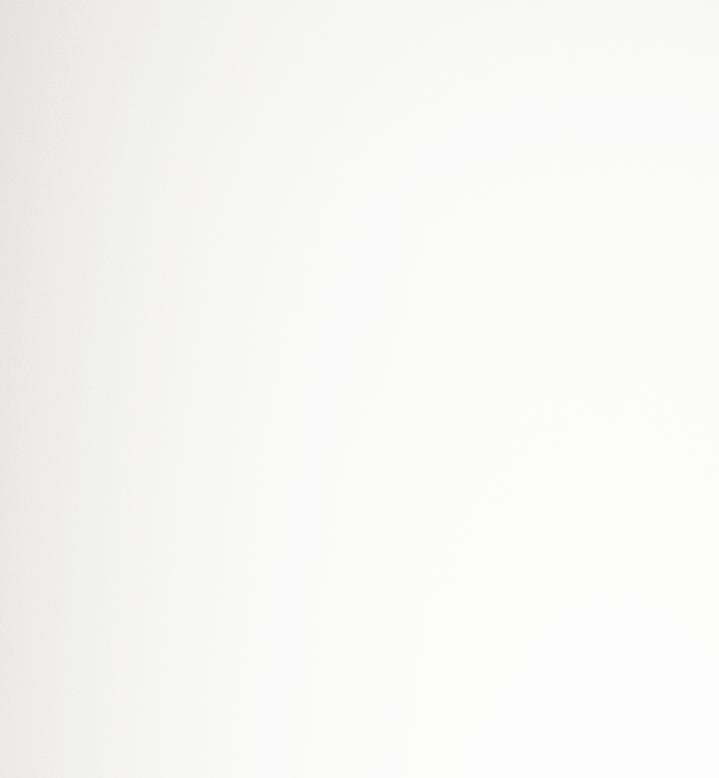
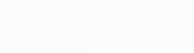
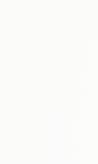
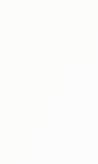
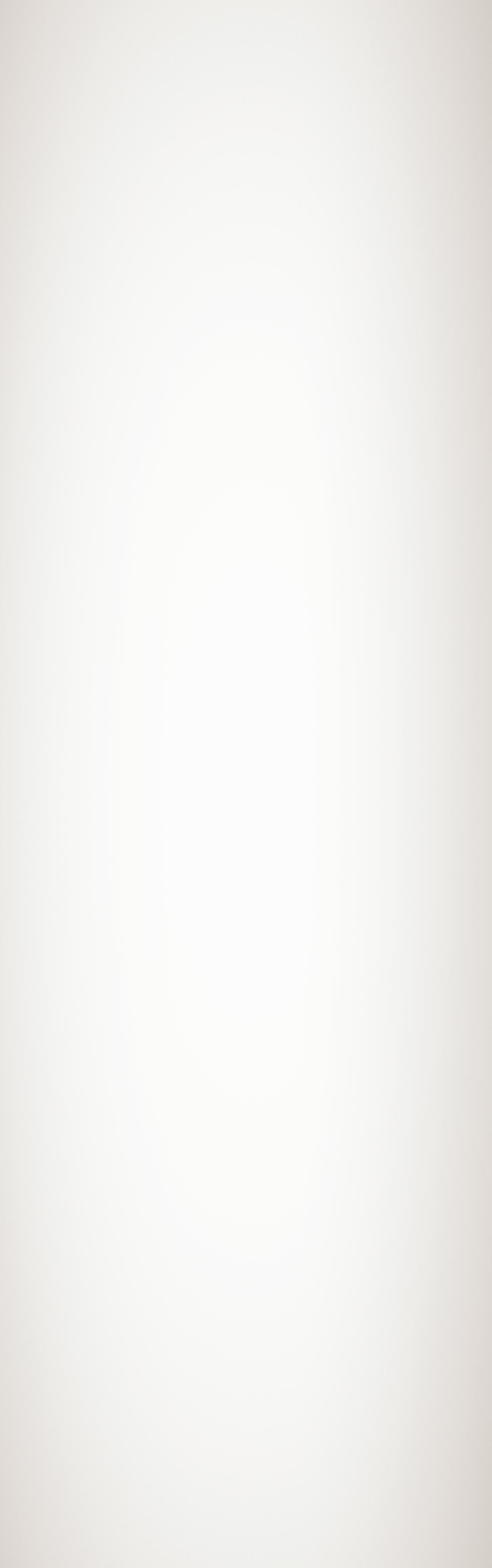
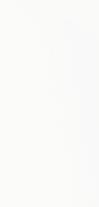
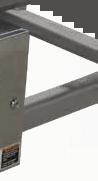


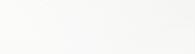

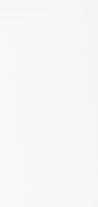

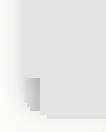
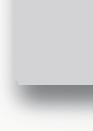
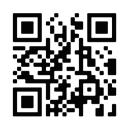
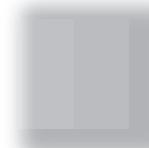
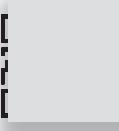




Metal Detector with Conveyor
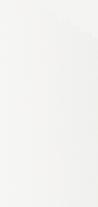

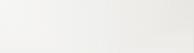
Flour milling and ingredient company Ardent Mills continues to elevate food and workforce safety by embracing the newest digital technologies.
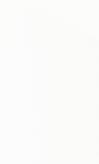

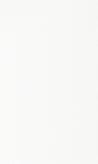
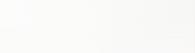
•Custom-designed conveyor belt system with tunnel style metal detector.
•Variety of reject options.
•Designed to match your production speed with fixed or variable speed drives.
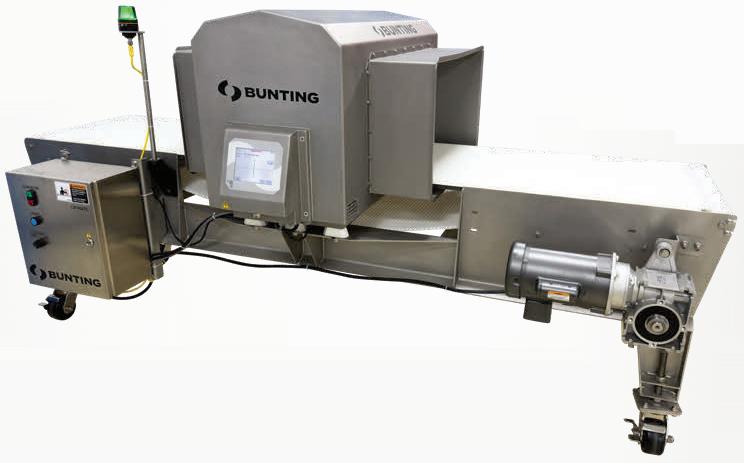
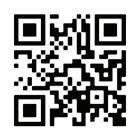
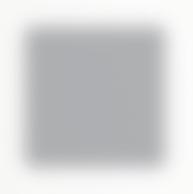
Tunnel Style Metal Detector with Bulk Sense Kit
•Accurately detects metal in 50 - 100 lb bags of dry product.
•Detects ferrous and non-ferrous metal as small as 1.5 mm.
•Detects 316 stainless steel as small as 2.0 mm.
A long-term advocate of Fortress Technology (Booth S-1758) metal detectors, three of Ardent’s 40+ mills are now fully embracing Halo Automatic Testing on packaging lines, as well as utilizing Contact 4.0 reporting software for enhanced quality control and networked traceability. Activating the technologies pre-installed on existing Fortress metal detectors has proven to be an efficiency and safety game-changer for many of Ardent Mills’ quality managers, said Packaging Engineer Manvine Bharj.
Ardent implements an end-of-line HACCP testing point just before palletizing at the mills that ship packed products directly to retailers and commercial bakeries. “We intentionally test our inspection equipment more often than our customers’ conformance requirements stipulate, as it provides extra quality assurance and fills us with confidence that our products are the safest they can be,” said Bharj.
Rather than relying on operators to perform, document and submit inspection tests, the Fortress Halo Automatic Testing solution independently tests all three metals in the exact geometric center of the
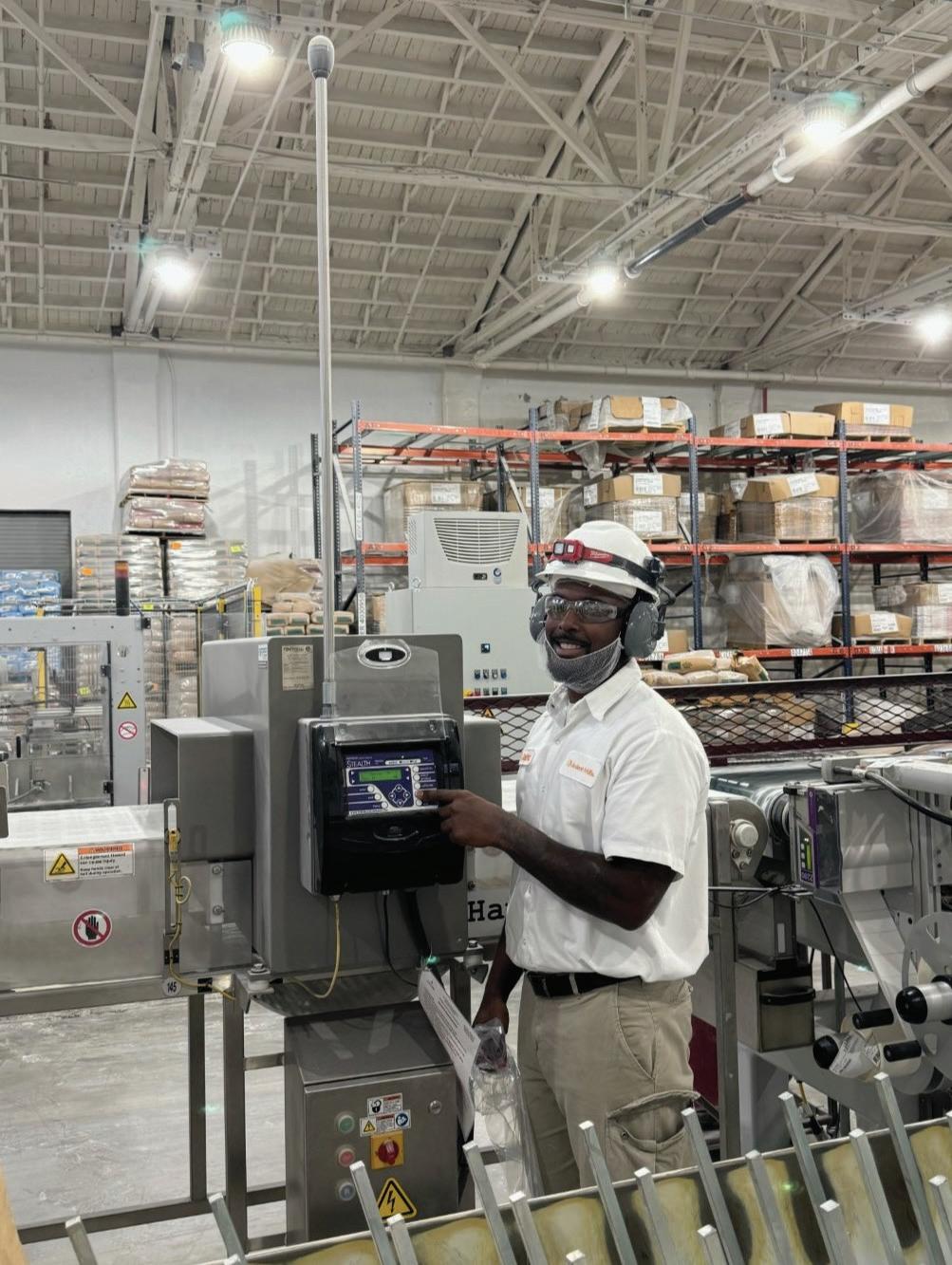
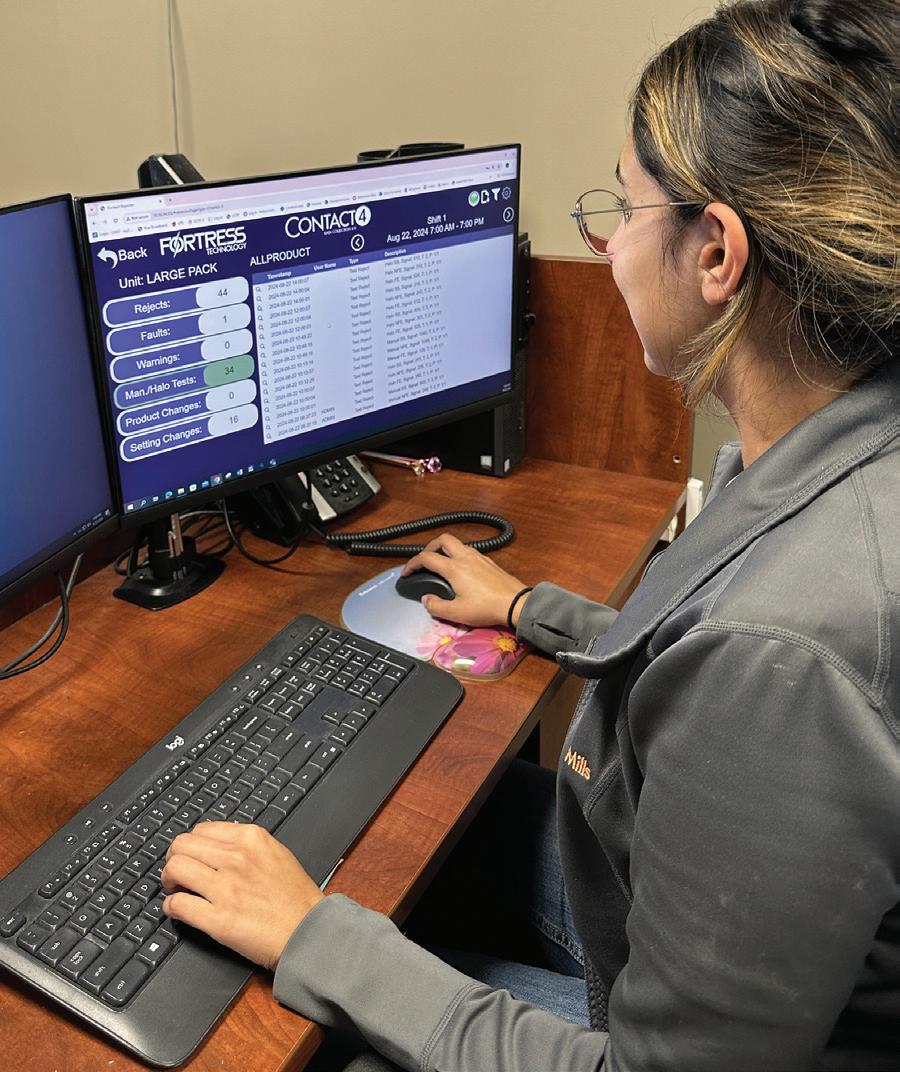
Stealth metal detector apertures. Replicating this test manually would require placing a test sample in the exact middle of each grain bag, passing this through the metal detector, removing it from the line, opening the packaging, removing the test sample, and inspecting it again.
To solve this issue, Halo Automatic Testing mimics the disturbance caused by a test contaminant calibrated to the precise size, metal type and speed that product bags pass through the metal detector aperture. A blue light system alerts operators when a test is running. “Without this blue light we would potentially have to sift and rework every 50lb test sack assuming it was contaminated or reject and waste it. That could have added up to re-inspecting 12 sacks, 600lbs of flour, per line, every shift,” said Bharj.
The resulting operational savings have been rapid. Bharj estimates the ROI on the original Stealth Metal Detector investment has been achieved in six months or less.
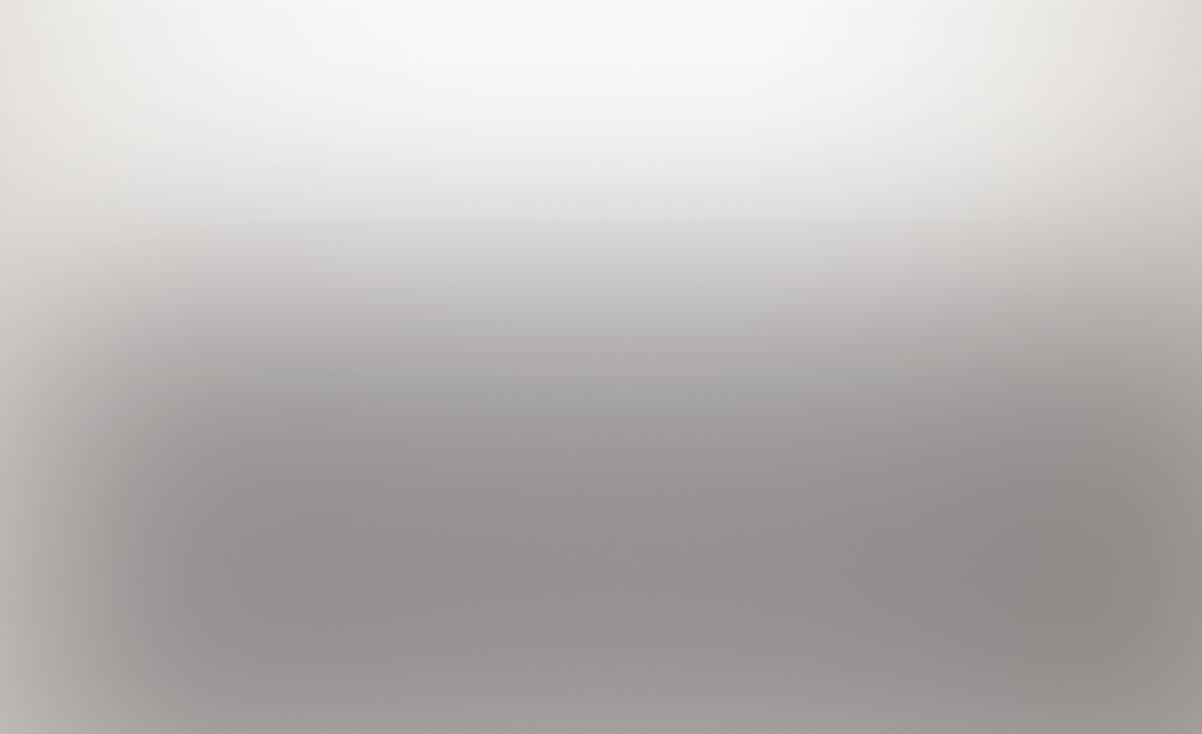
The three Ardent Mills sites have also deployed Fortress Technology’s Contact 4.0 networked data capture package. Rather than documenting everything on paper, Contact 4.0 automates the entire data-logging process. This streamlines traceability for quality assurance managers and helps to remove the risk of human error. Additionally, it prompts operators to test inspection equipment.
“As a networked system, it’s so easy for our quality managers to go into the centralized browser, select and email shift reports and view when tests were performed. Having this complete oversight allows them to immediately address issues and ensure the inspection process doesn’t cause a bottleneck,” said Bharj. ■
As a key player in the packaging industry, RYCHIGER Canada formerly known as Nuspark Inc. is excited to see you at PackExpo in Chicago. We specialize in delivering complete packaging lines, standalone machines, and customized solutions for primary, secondary, and tertiary equipment. To continue setting industry benchmarks, we will be showcasing our new innovative Tray Packer with our new nesting solution, smart linear track tray handling system, our small footprint vertical cartoner, and a collaborative robot palletizer.
Come by our Booth #S-2153 on November 3rd – 6th for a chance to WIN some amazing prizes by participating in our “pronunciation” challenge and discuss firsthand the power of our state-of-the-art packaging automation solutions. We are eager to connect with you and discuss opportunities, share insights and experience in the packaging industry.
www.rychiger.com/packexpo

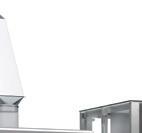


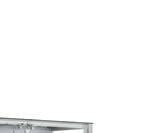
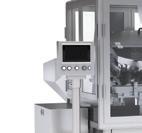
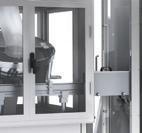


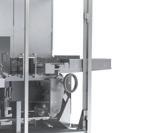
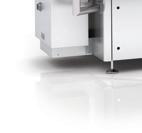
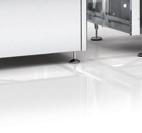

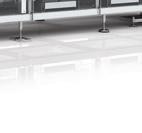

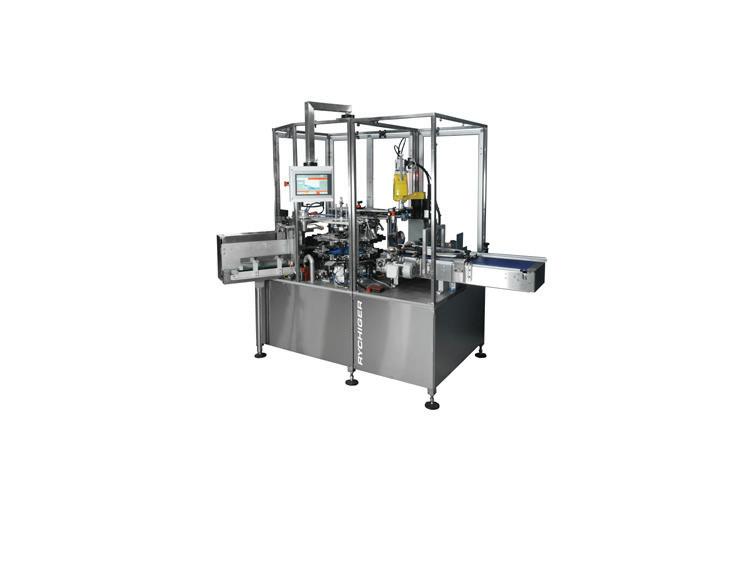
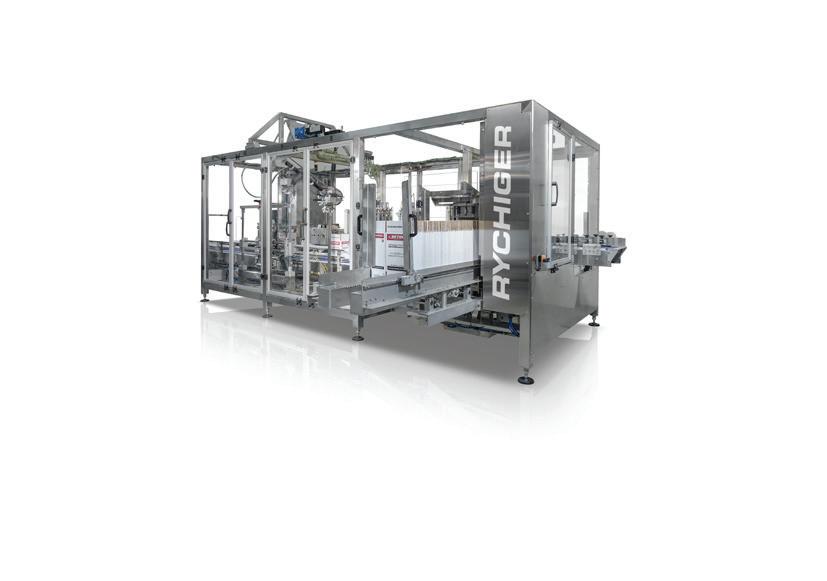
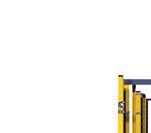

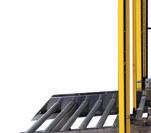

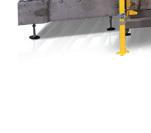
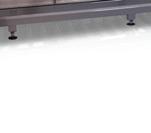
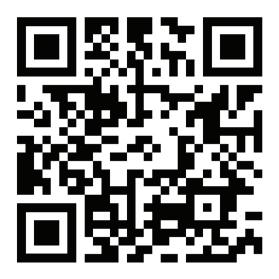
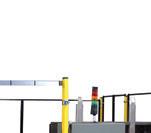
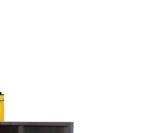
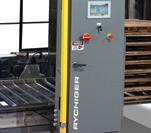
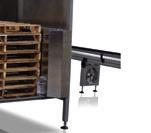
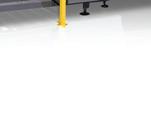

Boundless Educational Opportunities Available at PACK EXPO International 2024
Attendees can explore over 150 free educational sessions, engage with industry experts, and experience new show features that offer the latest strategies and innovations shaping the future of packaging and processing.
PACK EXPO International 2024 is proud to host unmatched educational opportunities designed to empower industry professionals from around the world. With over 150 free educational sessions available, attendees will have access to a wealth of knowledge, insights, and resources essential for navigating today’s rapidly evolving manufacturing landscape.
This year, two exciting new show features— Emerging Brands Central and Sustainability Central—will take center stage, offering attendees cutting-edge insights and strategies to propel their businesses forward.
Emerging Brands Central
Located in the West Hall at Booth W-20049, Emerging Brands Central is a must-visit destination for rising brands looking to scale their operations and expand their reach. This educational hub, an evolution
of the Emerging Brands Summit, will host 30-minute sessions led by industry experts.
These sessions will cover a range of topics including packaging machinery and innovation and scaling strategies, providing actionable advice for brands eager
Sustainability Central
to grow. Attendees will be uniquely able to engage with thought leaders and gain the practical knowledge needed to overcome growth challenges. Brands can also take advantage of an opportunity to meet industry expert advisors one-on-one at Emerging Brands Central. Advisors are available for complimentary oneon-one private consultations to provide personalized advice for each brand’s specific need.
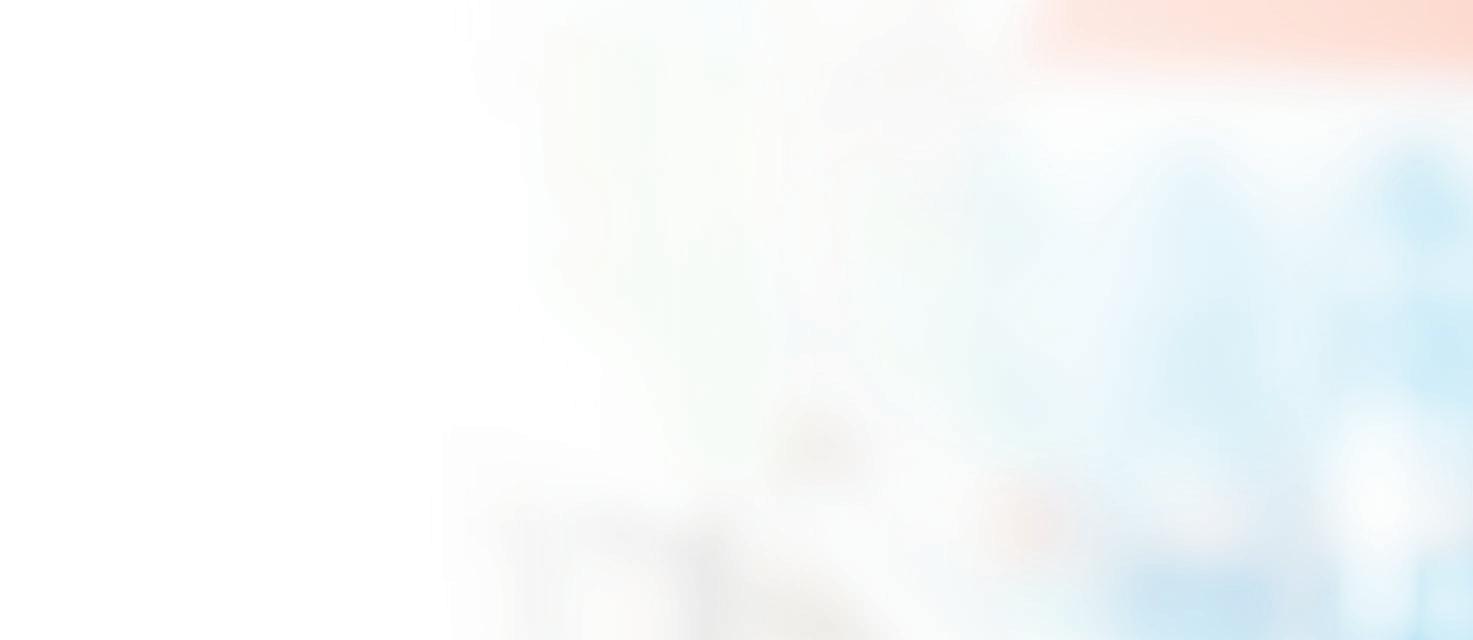
Packaging Solutions That Work!
ADCO’s innovative packaging solutions are perfect for food & beverage, pharmaceutical, consumer & household products and much more!
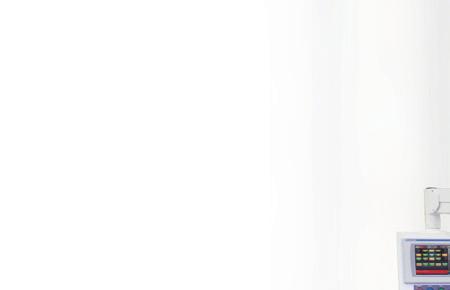
Making its debut at PACK EXPO International 2024, Sustainability Central is set to become the epicenter of sustainable packaging innovation. Located in the West Hall at Booth W-21020, this new feature provides a comprehensive look at what sustainability means for brands today. Industry experts will lead discussions on a wide array of topics, including sustainable packaging, design, EPR, and circularity. Attendees will walk away with actionable insights on enhancing their sustainability initiatives, making their brands more eco-friendly and competitive in an increasingly environmentally
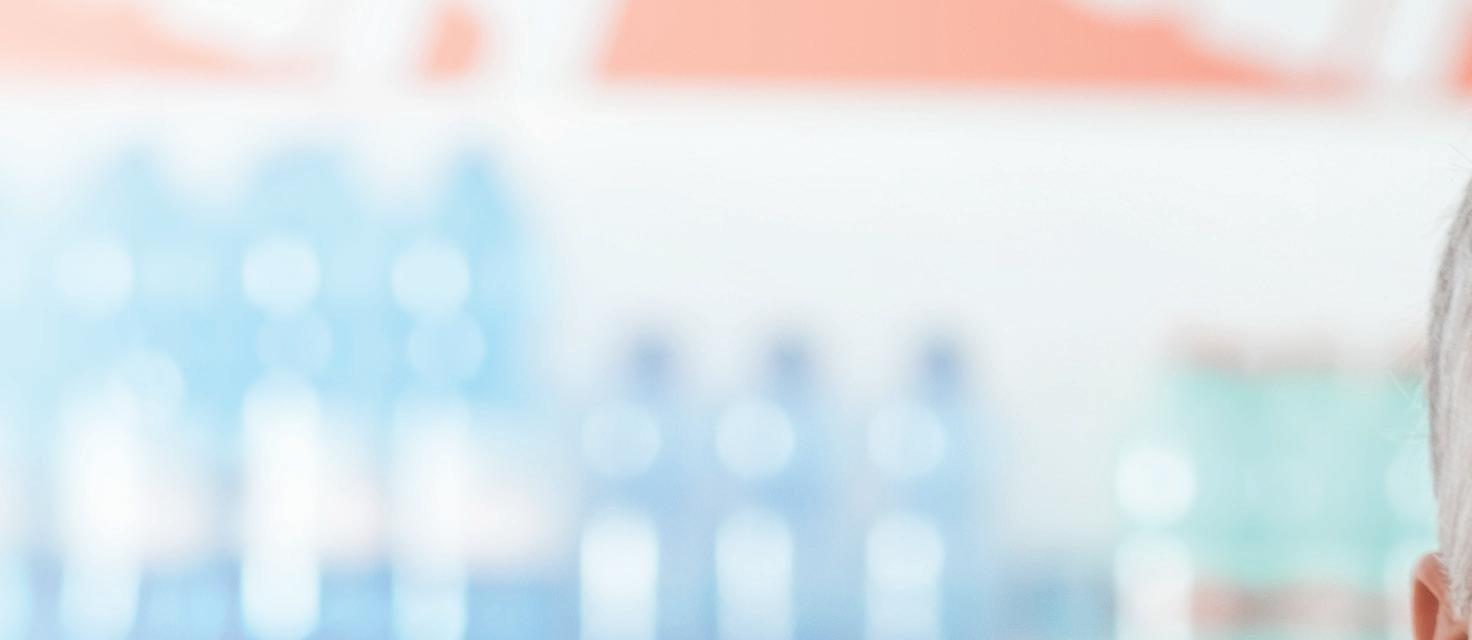
Explore the full line of ADCO packaging machinery at adcomfg.com.
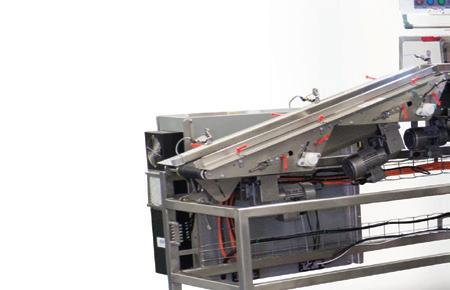
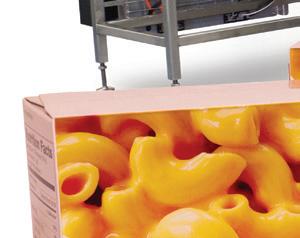
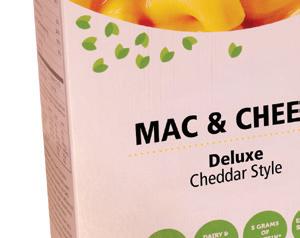

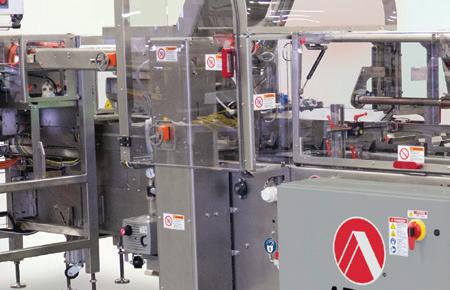
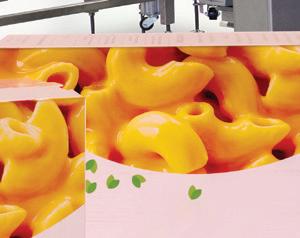

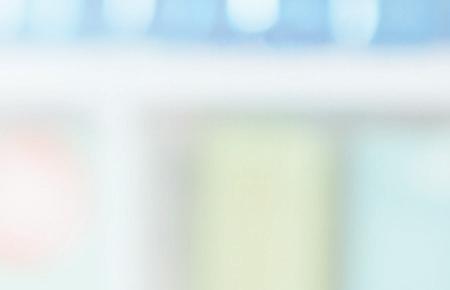
Don’t miss your chance to connect with us at BOOTH #S-2450!
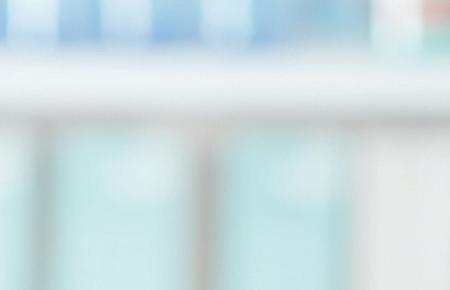
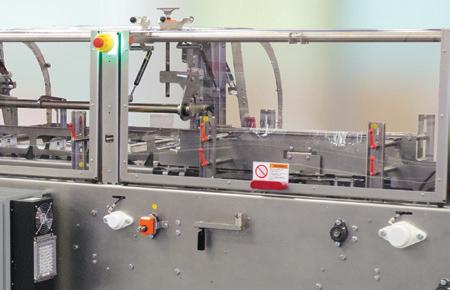
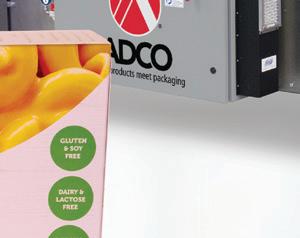
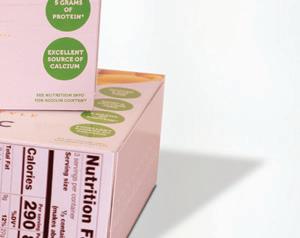
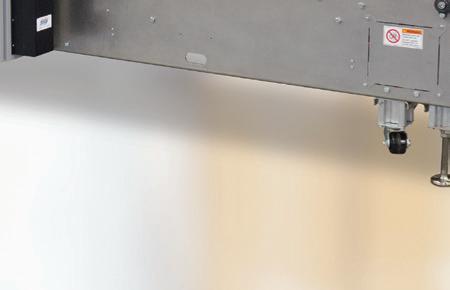
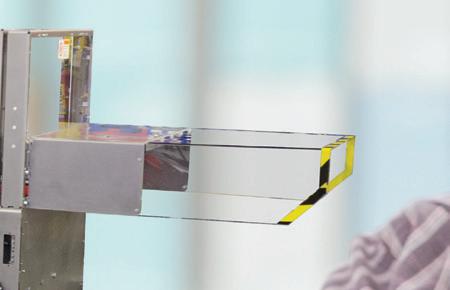


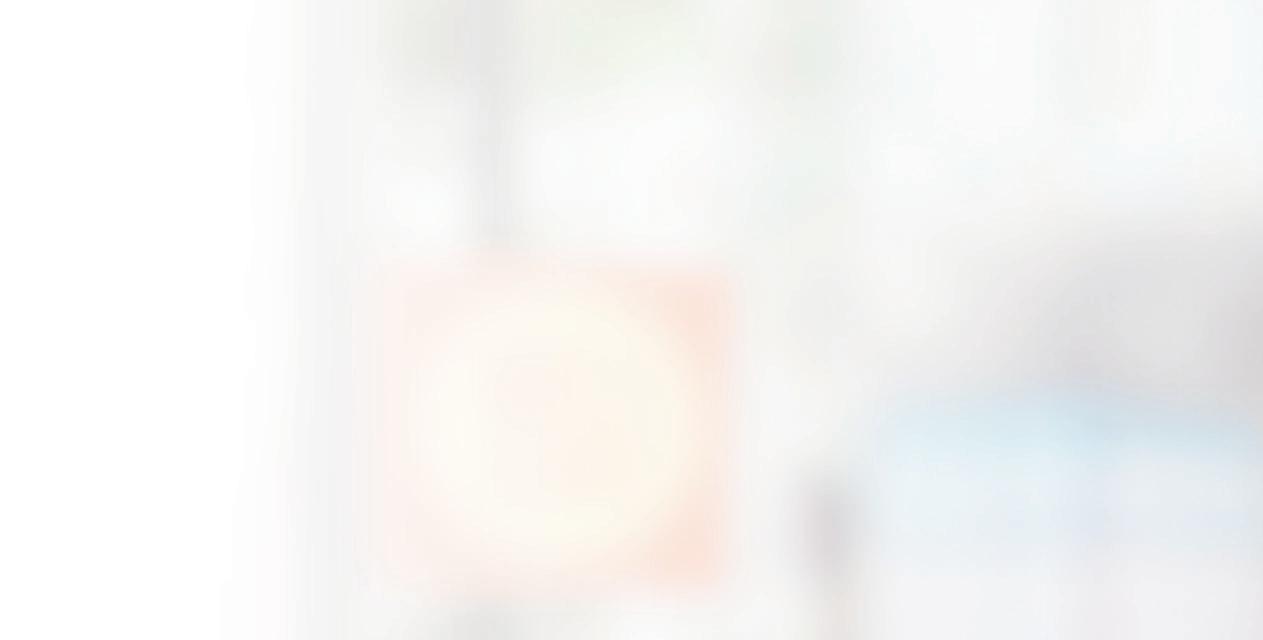
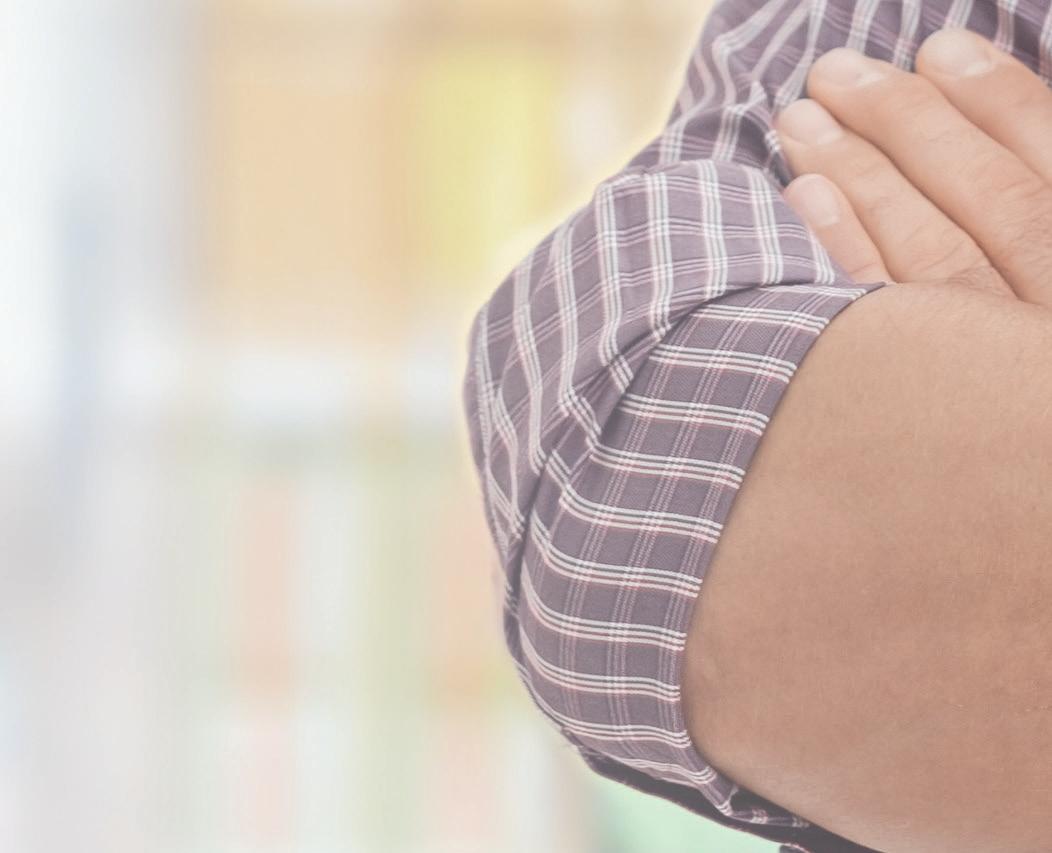

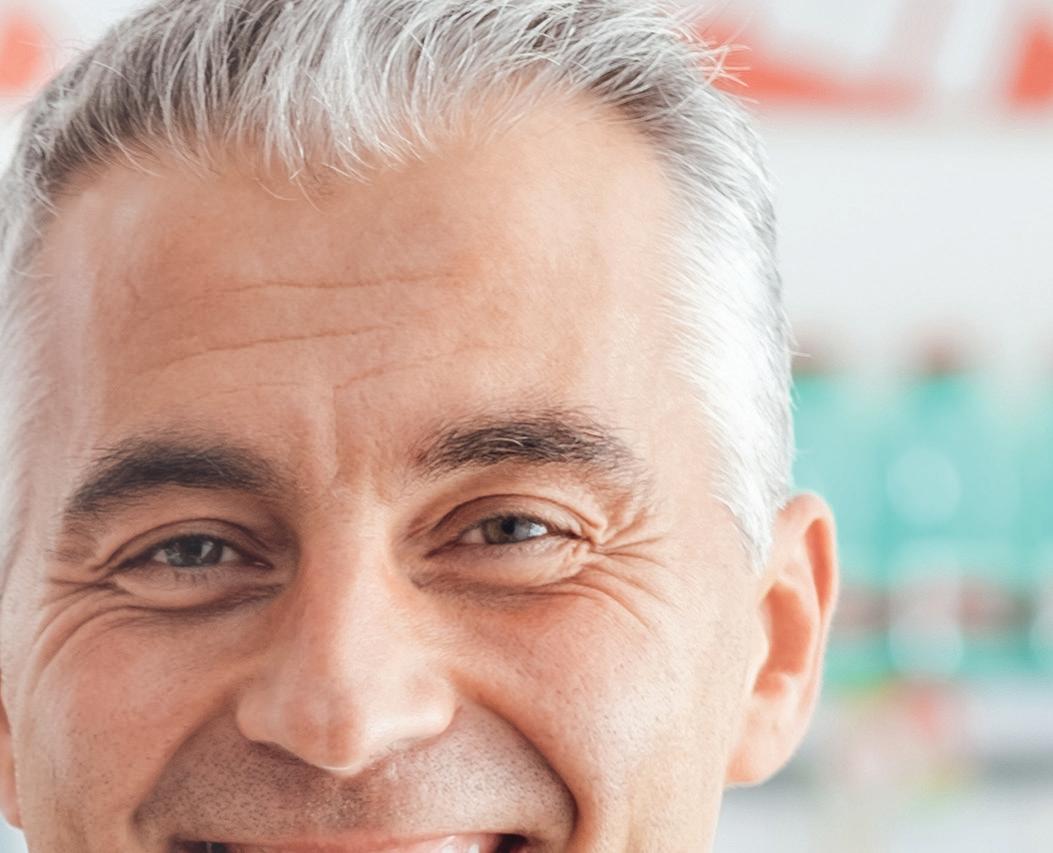
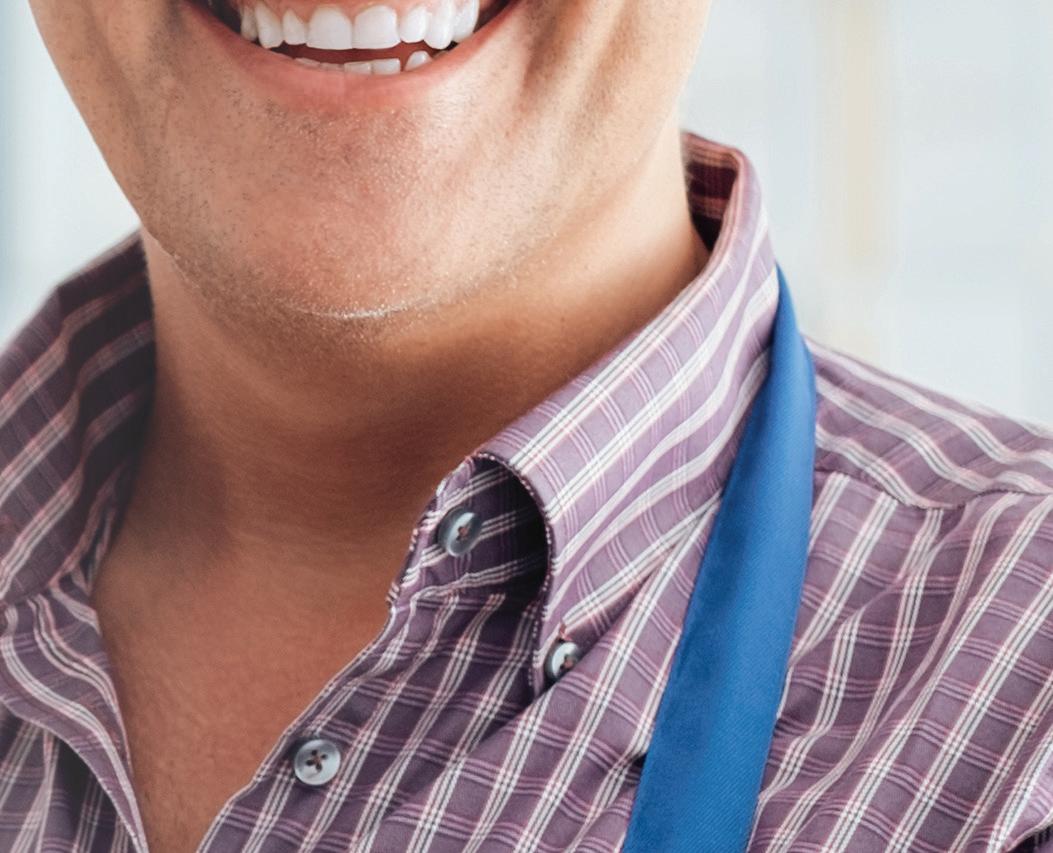
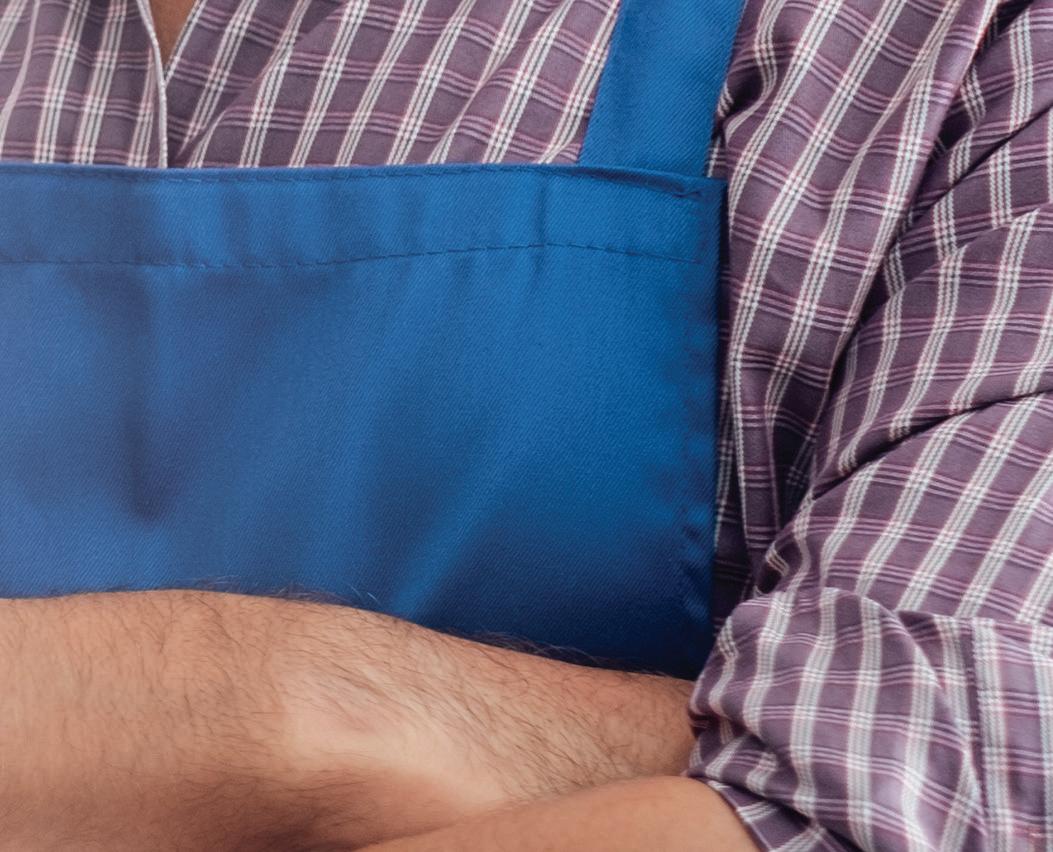
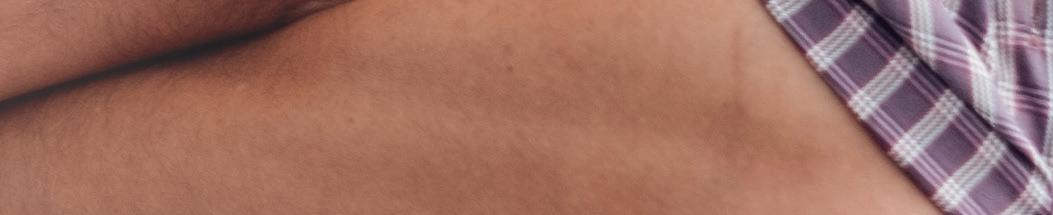
conscious marketplace. In addition, the latest research and best practices in sustainable packaging from leading colleges and universities, PMMI Business Intelligence, and AMERIPEN will be on display.
“PACK EXPO International 2024 is not just an exhibition; it’s a global hub for innovation and education,” says Laura Thompson, vice president, trade shows, PMMI. “With the introduction of Emerging Brands Central and Sustainability Central, we’re providing attendees with unparalleled access to cuttingedge strategies and solutions that are shaping the future of our industry. This is the place where ideas become reality and where professionals come to expand their knowledge and drive their businesses forward.”
A World of Learning at Your Fingertips
In addition to these new features, PACK EXPO International hosts a multitude of educational stages and pavilions where attendees can dive into specialized topics and learn from global industry leaders. Highlights include:
Reusable Packaging Learning Center: Sponsored by the Reusable Packaging Association, the Reusable Packaging Learning Center (Booth LU-6737) offers insights into how reusable packaging systems can
drive efficiency and sustainability in the supply chain and cover topics such as logistics, improving material handling performance, and value assessment.
PACK EXPO International 2024 is more than just a trade show—it’s a dynamic educational experience that equips packaging and processing professionals with the knowledge and skills needed to excel in today’s competitive environment.
Whether you are a seasoned expert or an emerging brand, the opportunities for growth and learning at this year’s event are unparalleled. ■

Precision Lab Mixing with High Shear
Obtain rapid results with the Silverson multipurpose L5M-A
Achieve effortless incorporation of even the toughest-to-mix ingredients
Innovation Stages: On three stages in the North Hall (Booths N-4560, N-4580, N-4585) exhibitors and subject matter experts present free 30-minute seminars on breakthrough technologies and solutions such as AI, robotics, design, and sustainability.
Processing Innovation Stage: Focused on food and beverage processing advancements, experts on this stage cover topics such as food safety and sustainability in 30-minute sessions at Lakeside Upper Hall, Booth LU-7147.
Scale from lab to production with consistent, reproducible results
Over 40+ Interchangeable workheads and assemblies available for increased versatility
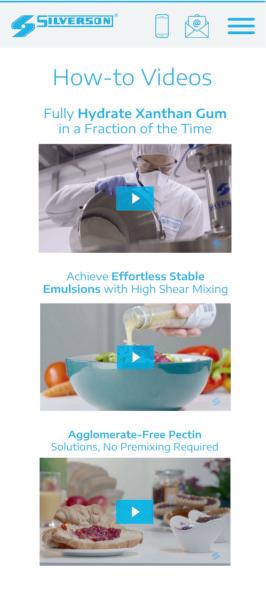
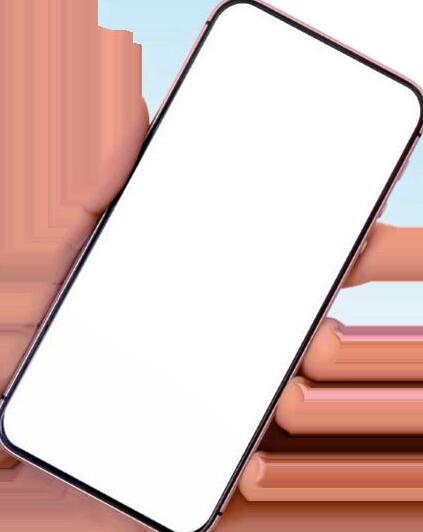
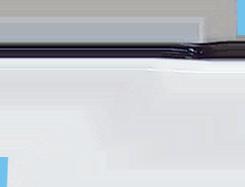
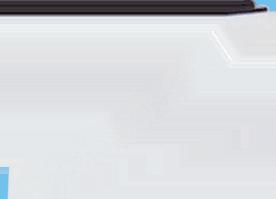
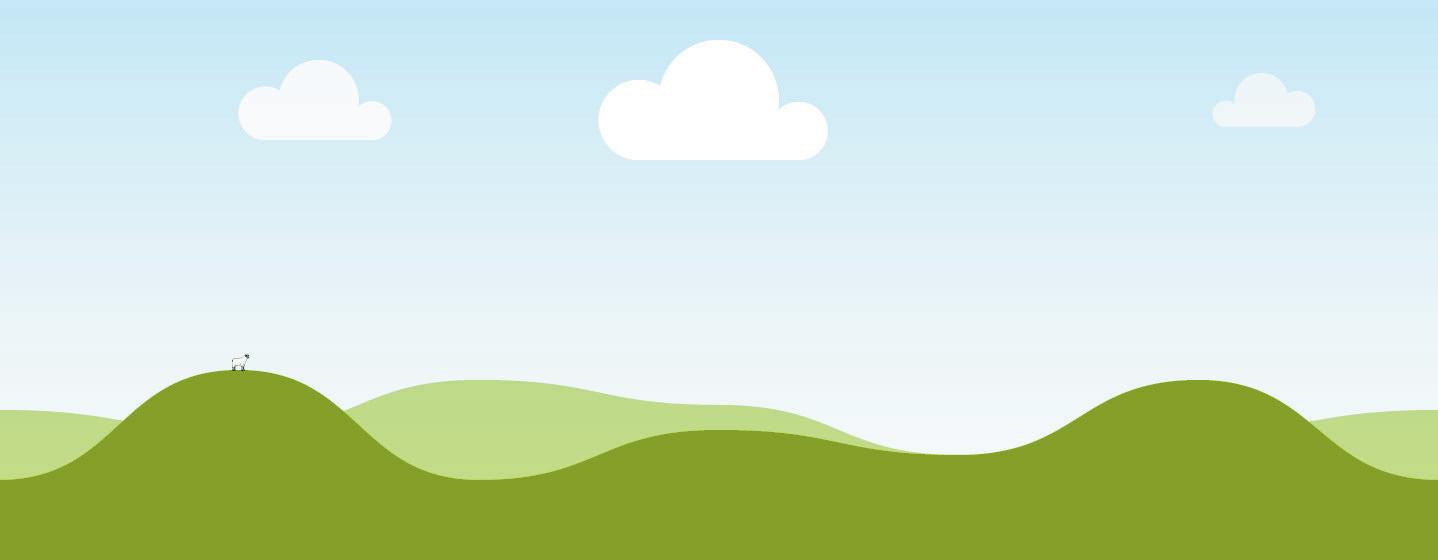
Industry Speaks: Experts from the PACK EXPO International Partner Program, covering multiple industry verticals, address the latest hot topics and industry trends such as sustainability, safety, AI, automation, design, and robotics. Located at Booth N-4544 in the North Hall.
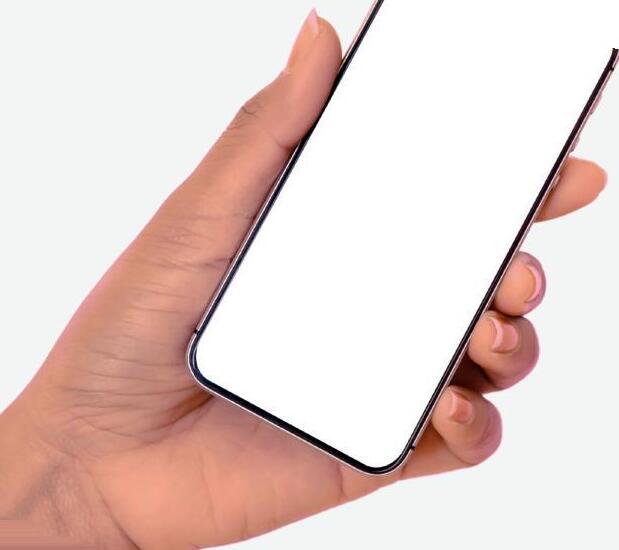
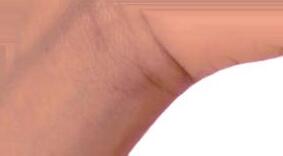
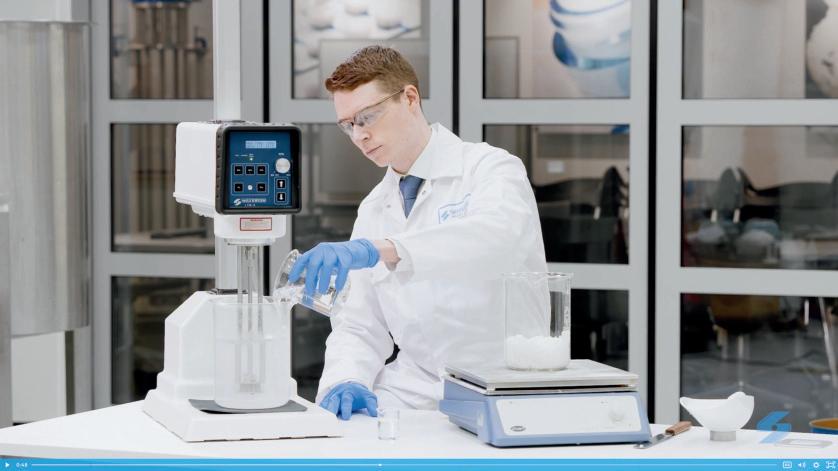
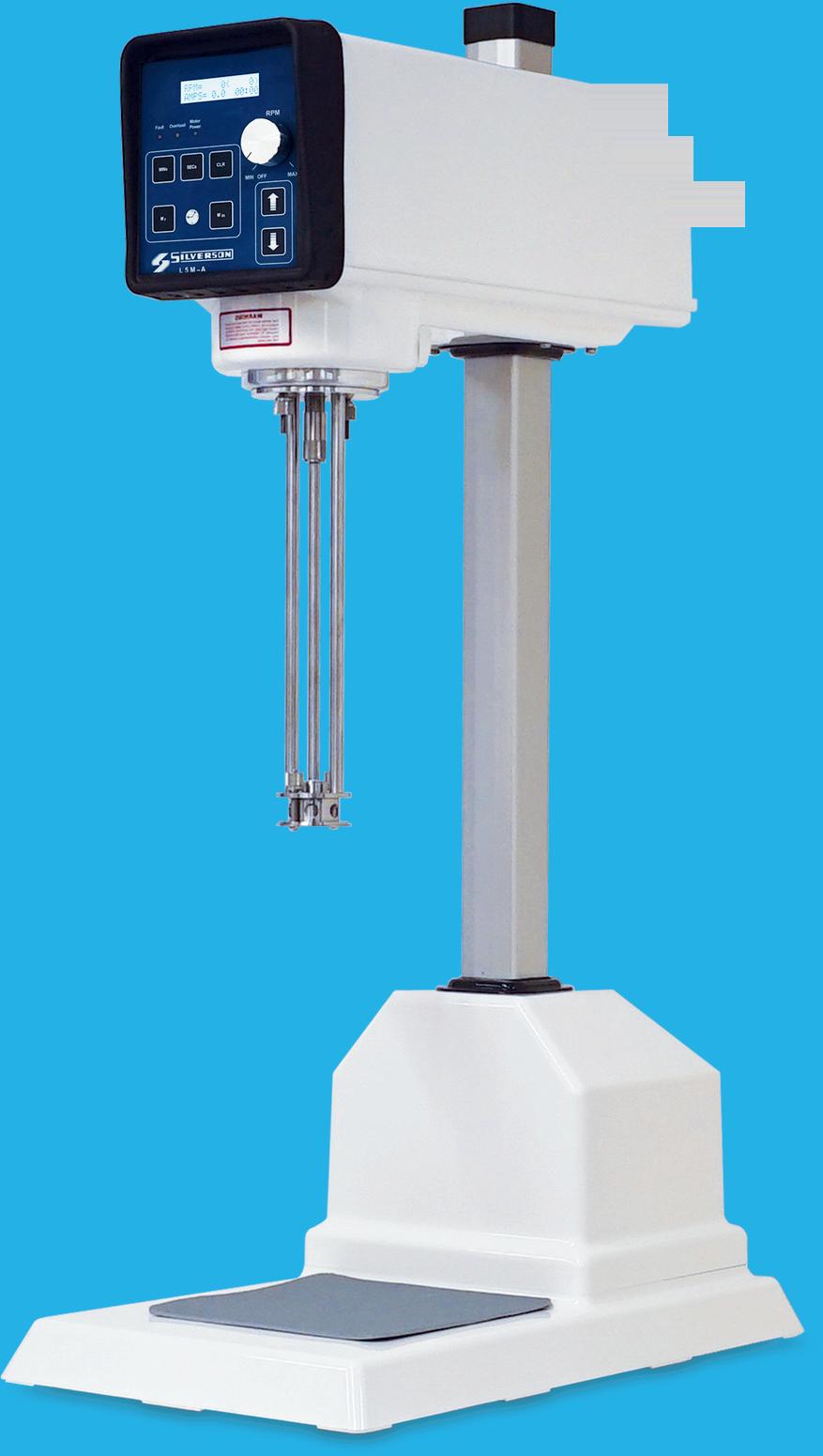
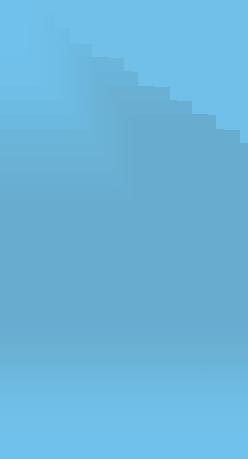
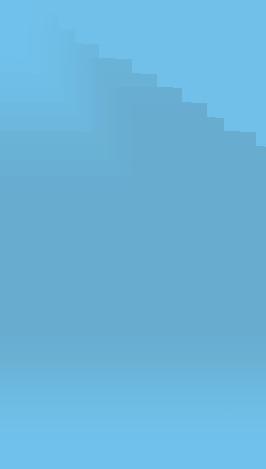

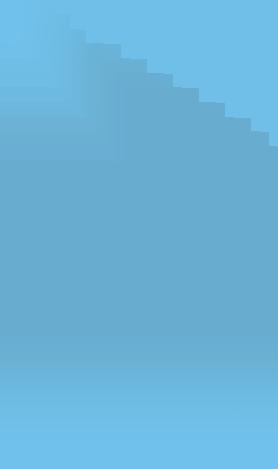
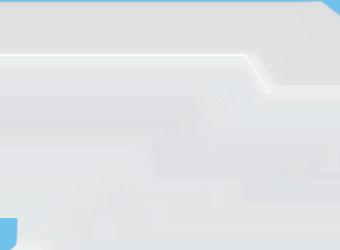
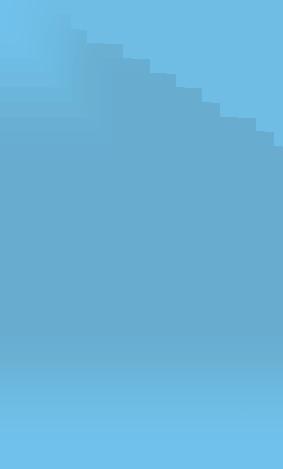
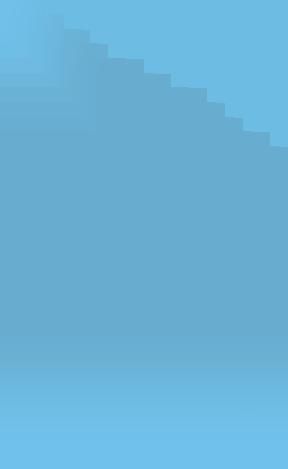
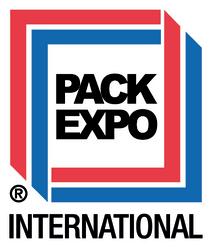
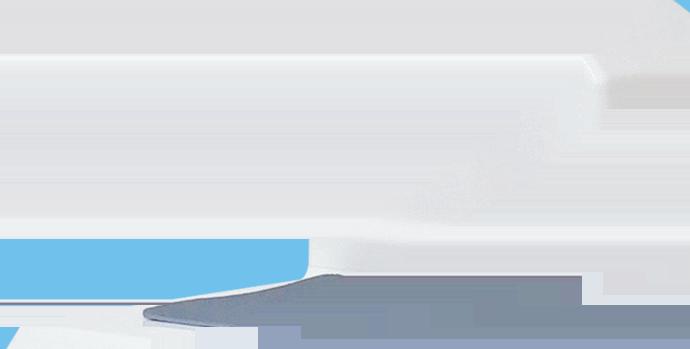

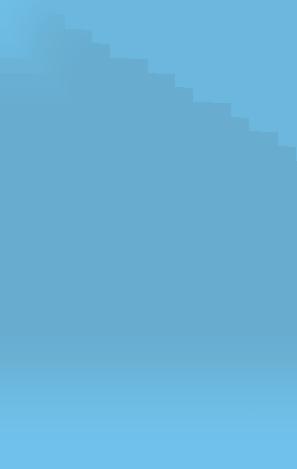
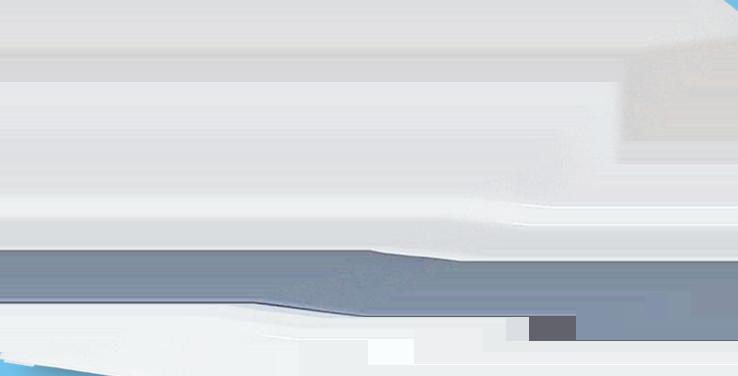
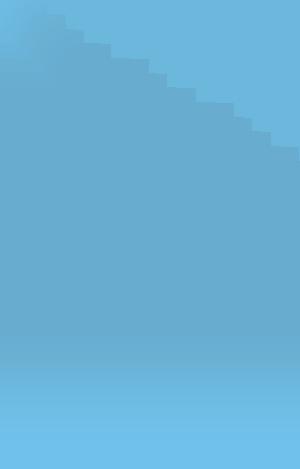
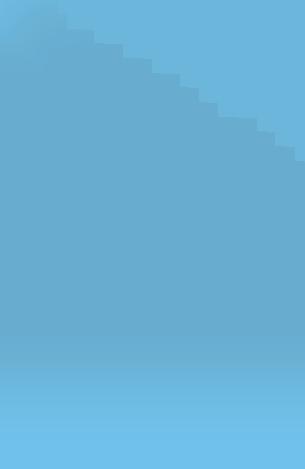

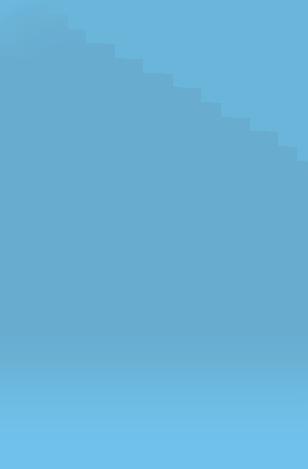



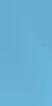
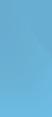
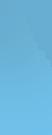
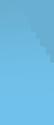

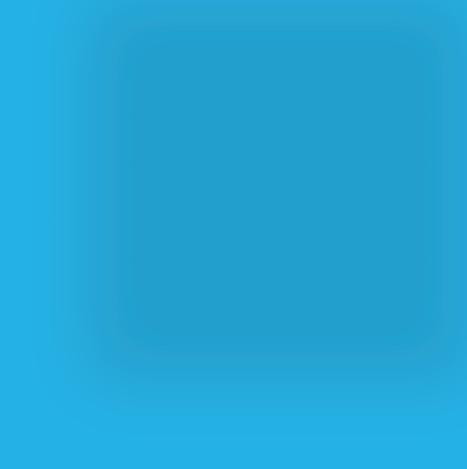
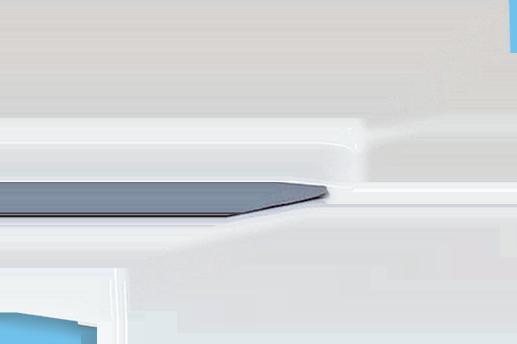

Ready to optimize your food or beverage production process?
Explore our comprehensive mixing application guides & how-to videos to find the ideal solution for your mix >>
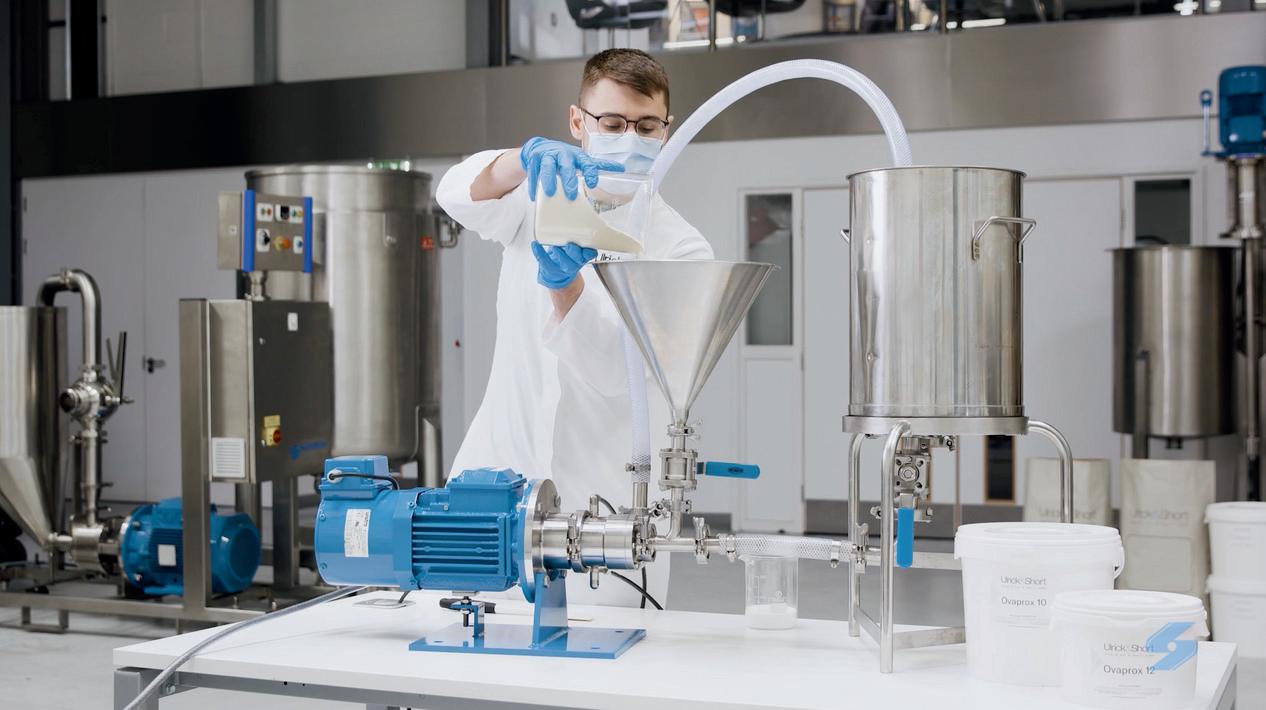
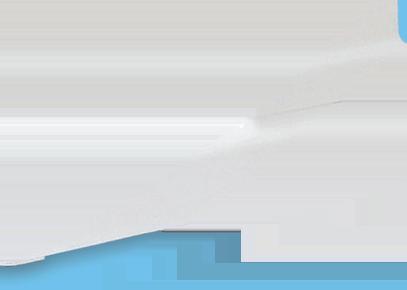
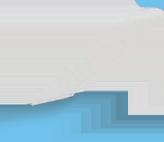
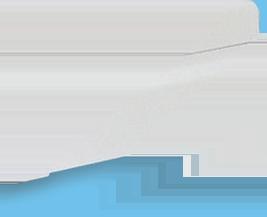


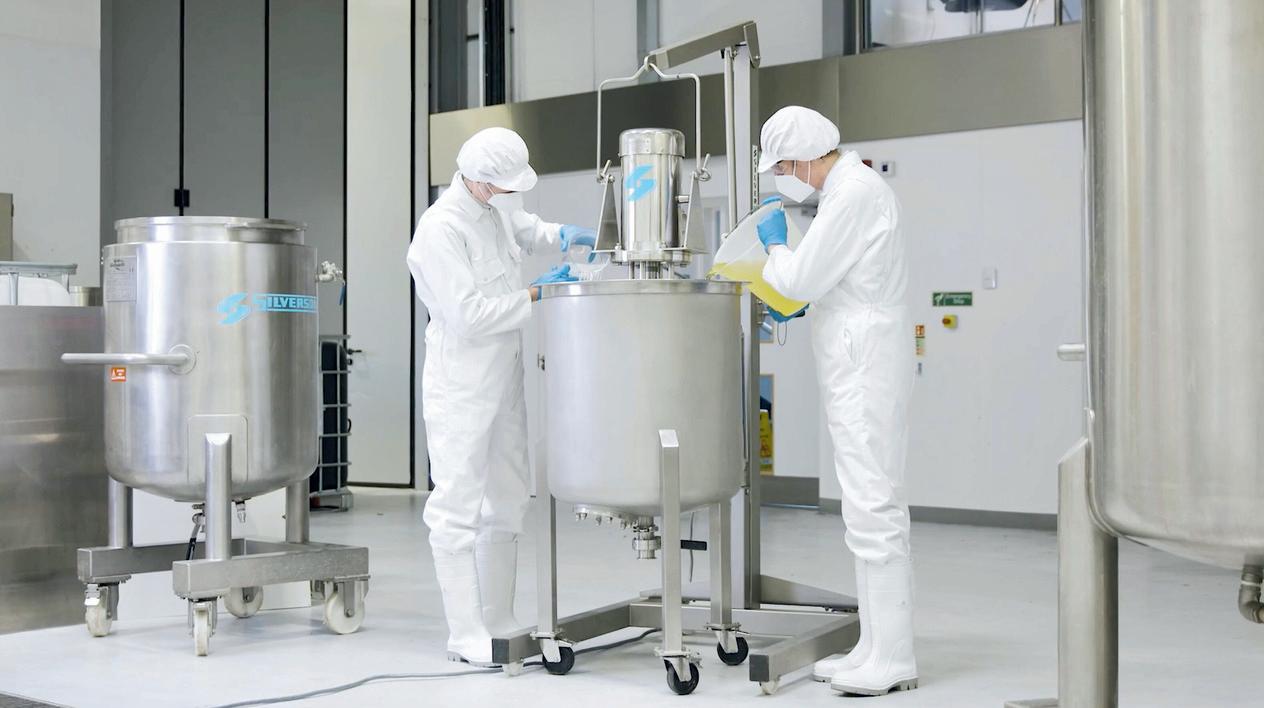
For more information please visit: Silverson.com sales@silverson.com • (413) 525-4825
Syntegon to Showcase Innovations and Complete Packaging System Solutions
Visit Booth S-2914 to explore seamless processes, innovative technologies, and sustainable solutions for the food industry, including the FGCT high-speed count feeder.
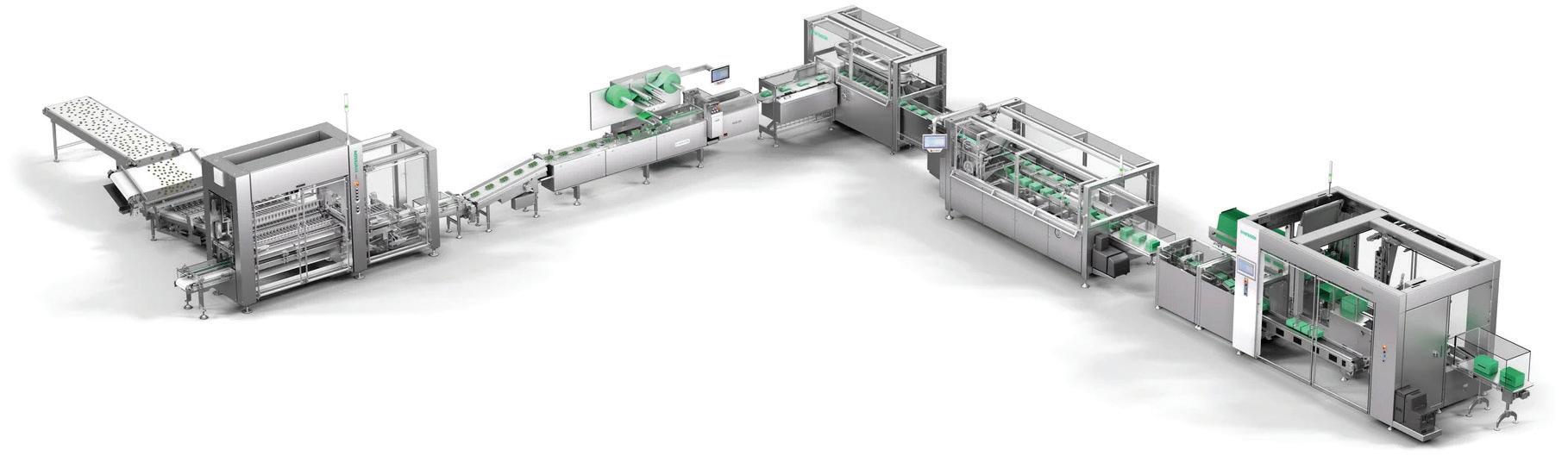
Syntegon, a provider of food packaging solutions and process technology, will highlight its latest innovations and comprehensive system solutions at PACK EXPO International 2024 at Booth S-2914 Experience highly automated systems for cookies, as well as fresh, chilled, and frozen food, along with the debut of the SVX Compact, part of Syntegon’s VFFS SVX series, for snacks.
“Syntegon is a one-stop supplier for seamless solutions with high levels of automation and efficiency,” says Brad Baker, Senior Sales Director North America at Syntegon. “Whether food manufacturers are looking for stand-alone primary, secondary or case packing equipment—or fully integrated turnkey systems—we provide sustainable and flexible solutions as well as comprehensive support services to future-proof their investment while maintaining impressive levels of operational efficiency.”
System Solution for Sandwich Cookies
Syntegon’s system solution for sandwich cookies offers a highly automated packaging line that prioritizes speed, flexibility, and efficiency. Central to this solution is the all-new FGCT high-speed count feeder (pictured above), which efficiently groups cookies and loads them into trays, minimizing damage and waste. This aligns with Syntegon’s commitment to sustainability. The FIT linear motor infeed and Pack 202 flow wrapper provide a compact solution for overwrapping trays. The Pack 202 is a versatile flow wrapping machine, that handles various formats at different speeds. Following the primary packaging process, the new MagTRAC collating unit, which uses linear motor technology for quick format changes, is seamlessly integrated into the compact BEC endload cartoner. This setup enhances flexibility and reduces changeover times. The BEC endload cartoner supports
high-speed operation and flexible format handling, minimizing downtime and resource consumption. The Elematic 1001 side load case packer optimizes floor space with its compact design and user-friendly interface, integrating smoothly into existing lines. This system solution for sandwich cookies addresses industry challenges like labor shortages and cost pressures. Syntegon also offers Service Agreements, including remote support and Synexio software for data analysis, helping optimize production efficiency.
System Solution for Fresh, Chilled, and Frozen Food
Syntegon’s solution for fresh, chilled, and frozen food features new wash-down RPP pick-and-place
—Continued on page 28

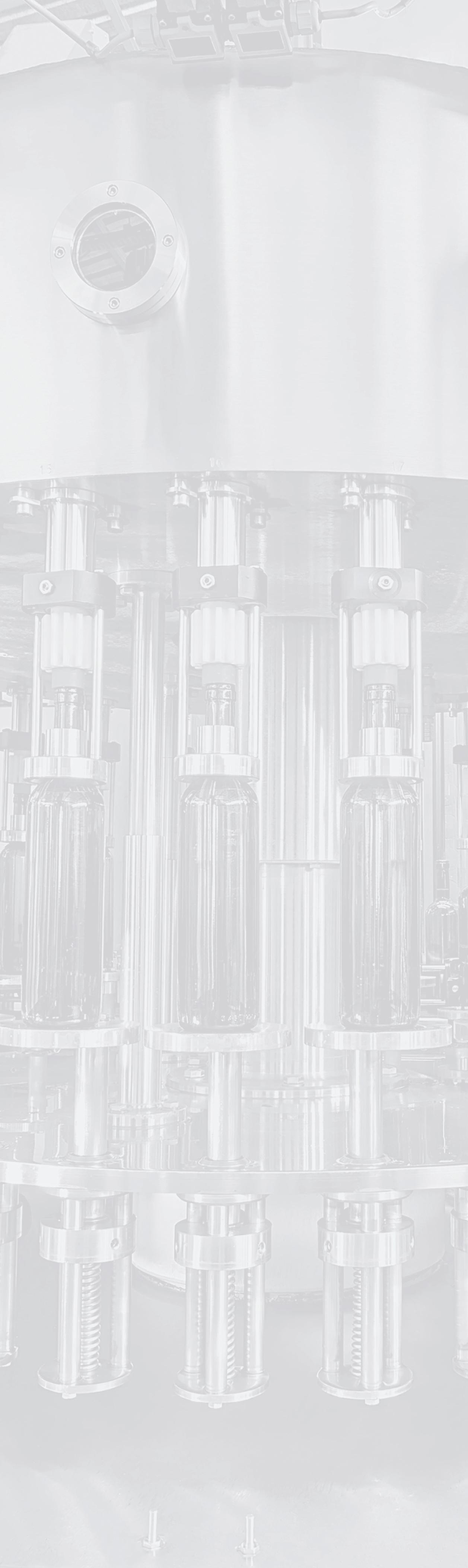
ATLANTA, USA
March 10-12, 2025
GUADALAJARA, MEXICO
June 10-12, 2025
LAS VEGAS, USA
Sept. 29-Oct. 1, 2025
PACK EXPO Premier Packaging and Processing Events
PHILADELPHIA, USA
Feb. 17-19, 2026
Wherever you are and whatever your industry, there’s a PACK EXPO event to provide solutions you need today and the inspiration for tomorrow.
MEXICO CITY, MEXICO
June 2-5, 2026
CHICAGO, USA
October 18-21, 2026
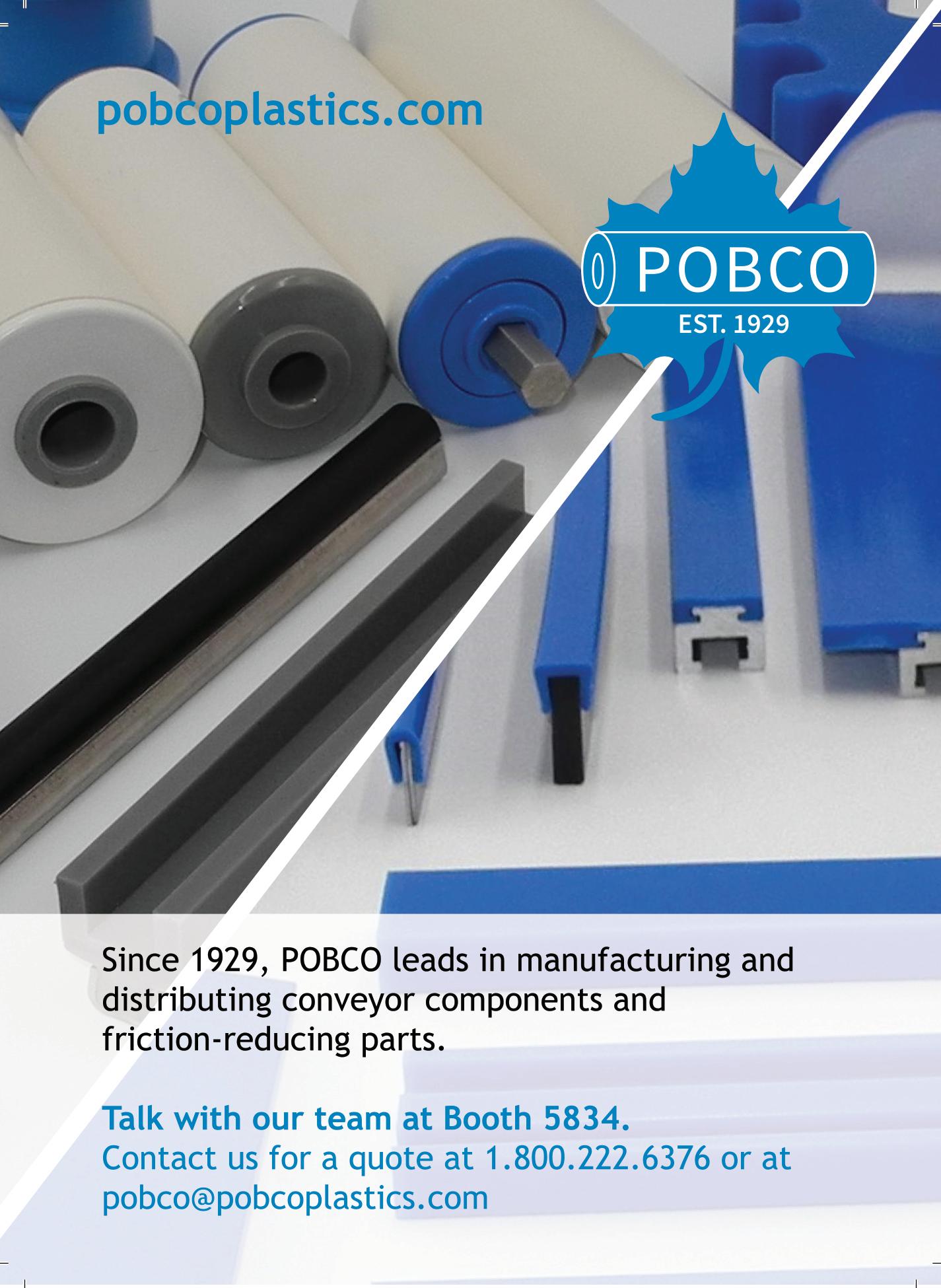
—Continued from page 26
robots integrated with a Pack 403 HE flow wrapper, designed for harsh environments with essential cleaning capabilities for food safety. The stainless-steel frames and motors of the RPP meet NEMA4X standards for durability. RPP robots efficiently load products into the flow wrapper infeed chain. In addition to the primary packaging process, the system includes a Kliklok ACE carton erector and a second RPP cell for loading the flow wrapped products into cartons. Kliklok ACE allows quick transitions between carton sizes, reducing downtime and enhancing flexibility. Its ergonomic design improves operator efficiency and safety. This solution showcases Syntegon’s dedication to innovative and seamless packaging processes. By integrating advanced technologies, Syntegon offers manufacturers a robust system that meets demanding hygiene and efficiency standards while future-proofing operations. The system’s hygienic design, with stainless-steel construction and wash-down capabilities, ensures high food safety standards and increased automation.
SVX Compact
The SVX Compact by Syntegon revolutionizes the snack industry with its innovative design, offering the fastest cycle times for snack manufacturers, achieving up to 300 cycles per minute. The drive system is positioned on the sealing mechanism, reducing frame size, making the machine ultra compact and a perfect fit for this industry. Modular design and quick format changes accommodate various product types and packaging styles enhancing future-proof flexibility and production output. The SVX Compact features a patent-pending cross-seal drive for reliable seals that enhance product integrity and extend shelf life. It supports the use of sustainable packaging materials. The hygienic design enables easy cleaning and compliance with food safety standards. Digital real-time monitoring boosts efficiency through data analysis. Remote service capabilities enable proactive maintenance, minimizing downtime. ■
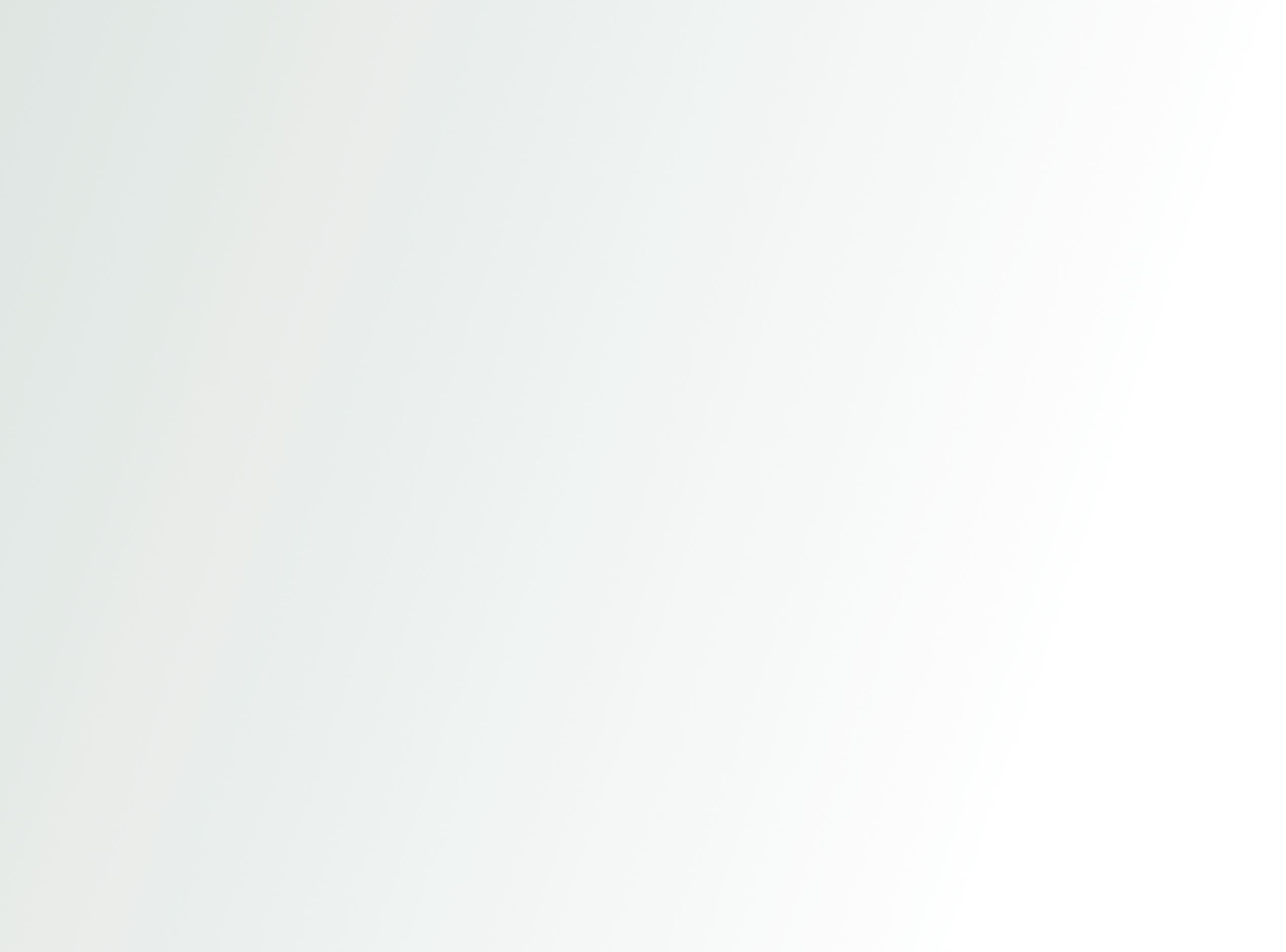






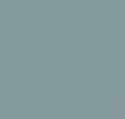
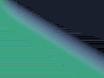


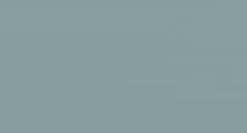






















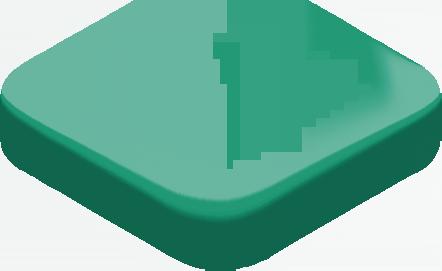




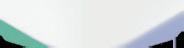




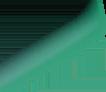
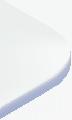
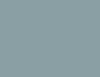





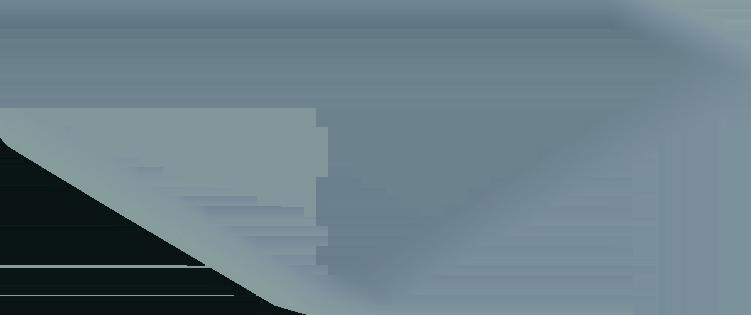





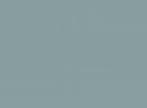

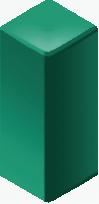
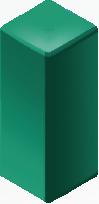
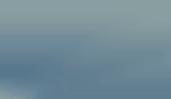
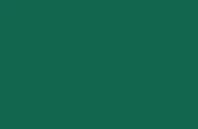
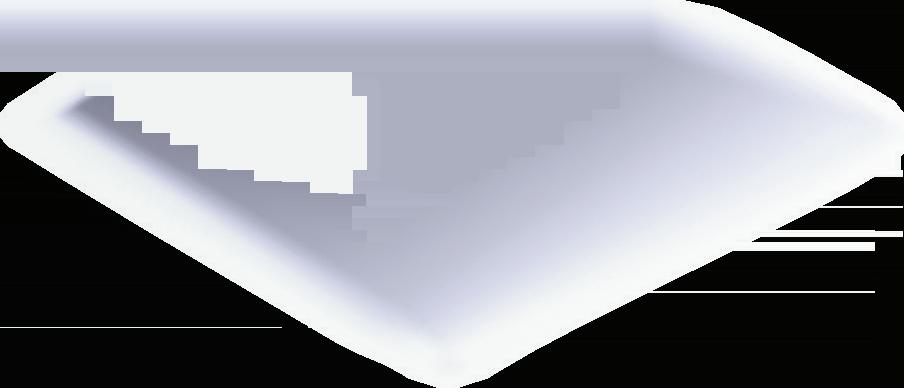



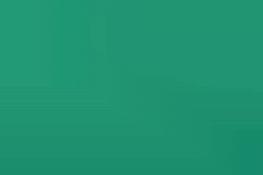



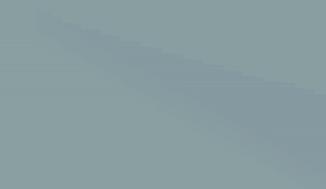














































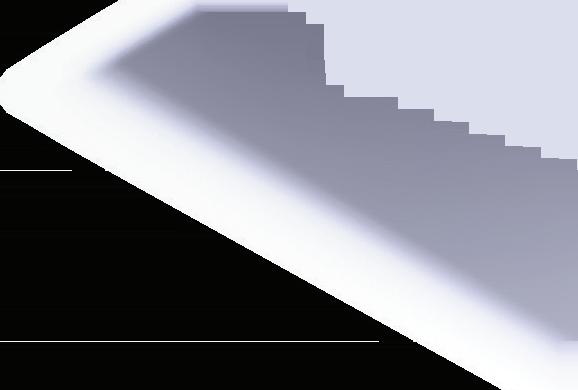
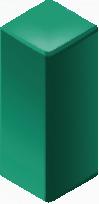

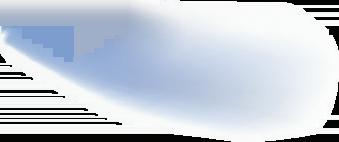

















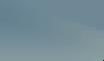
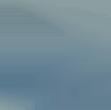
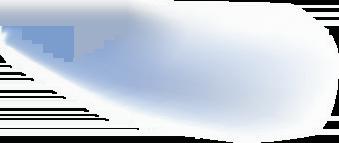
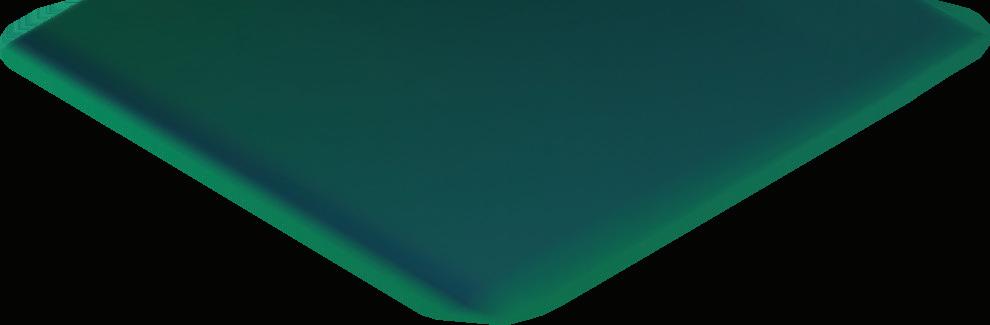



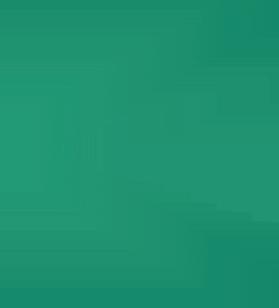


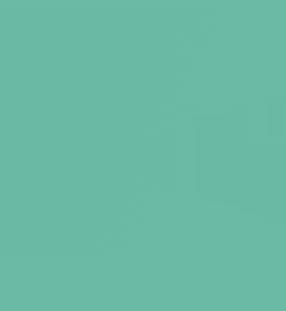

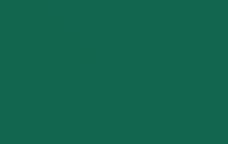

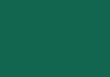



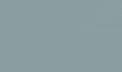
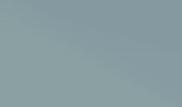


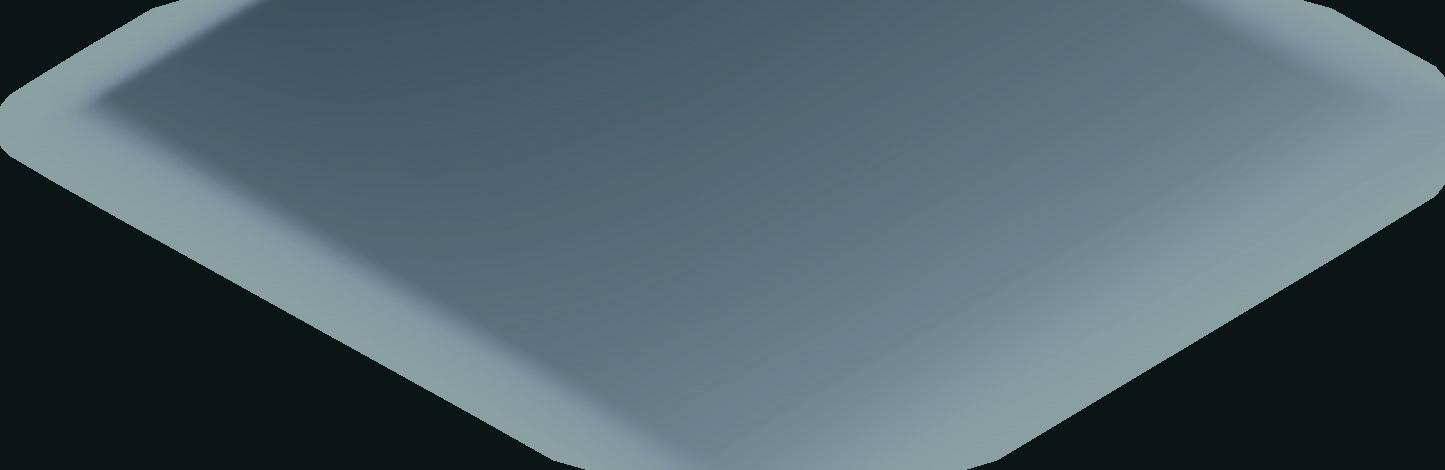
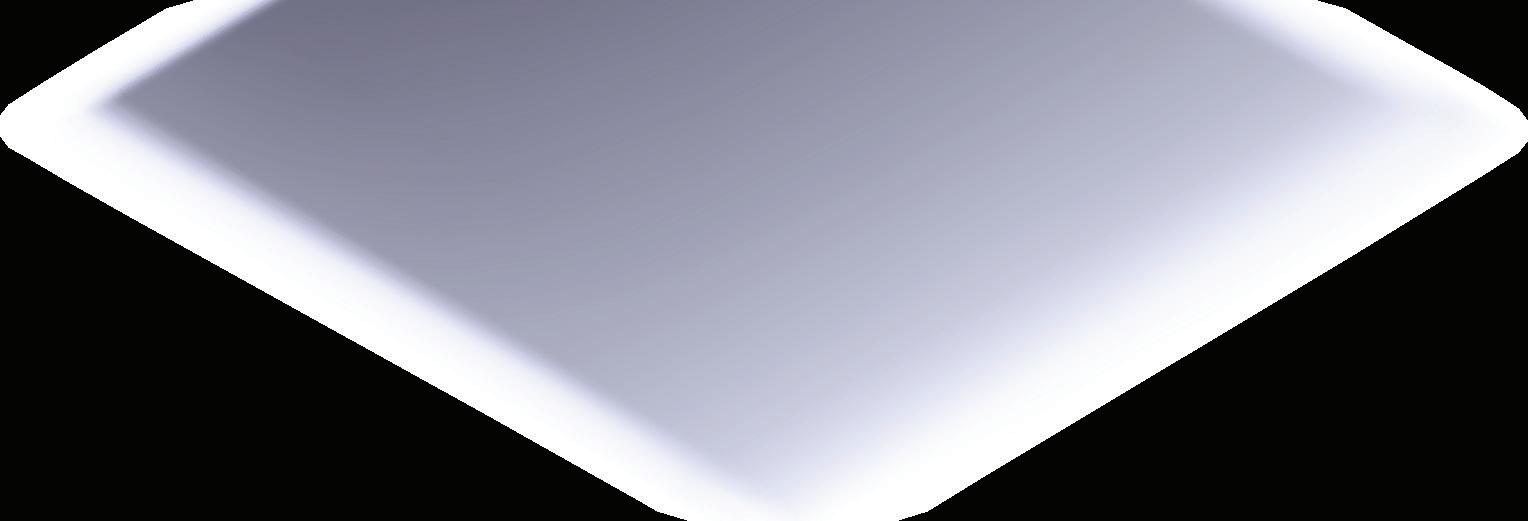
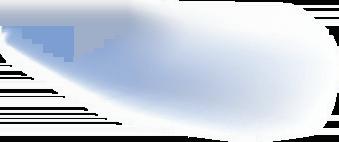
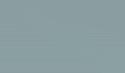

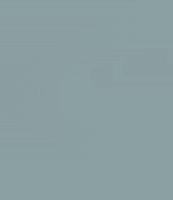


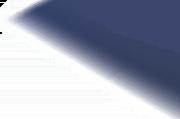

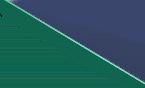
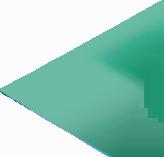
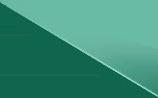
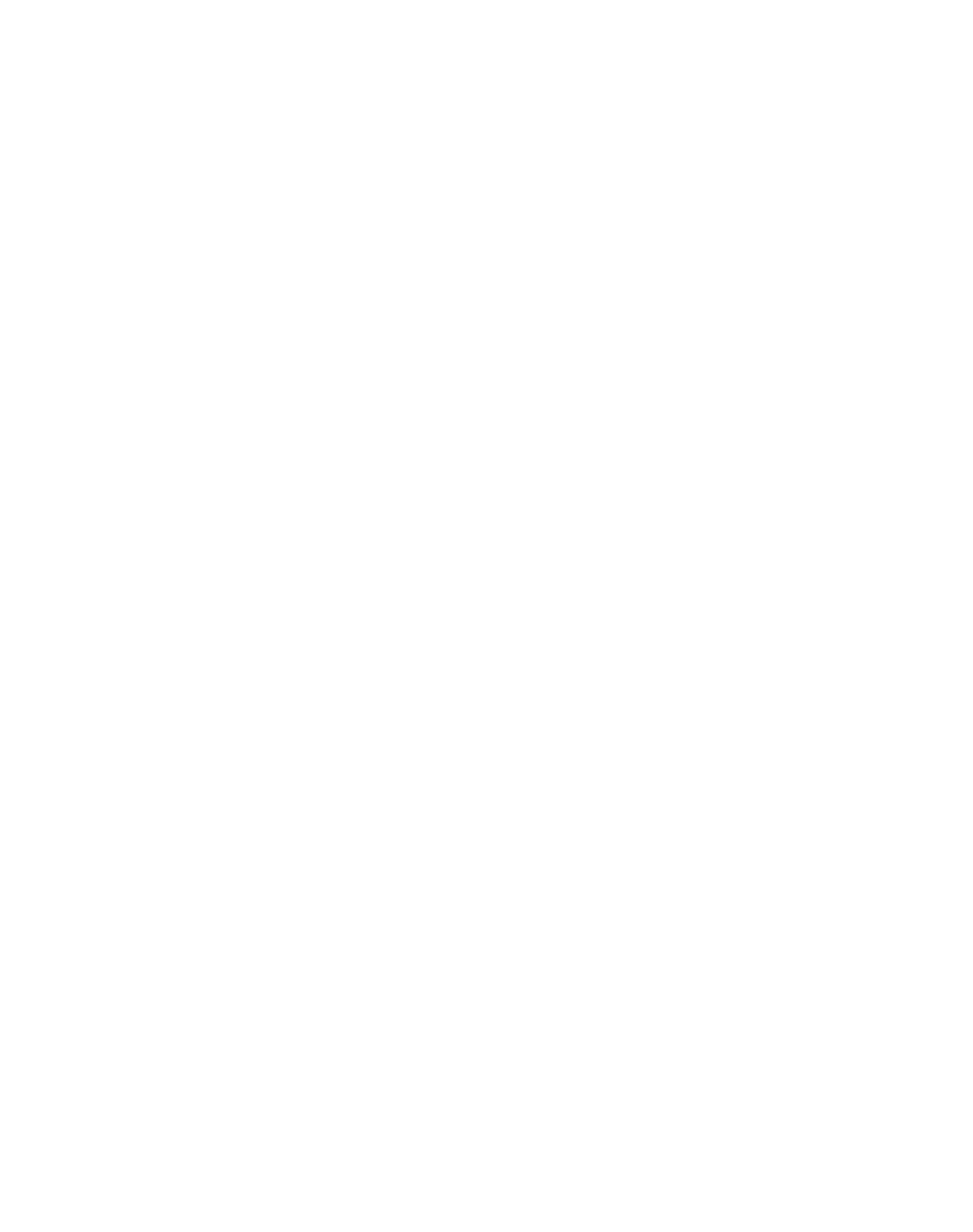
The World’s Largest Packaging and Processing Classroom
PACK EXPO International features programs designed to engage and inspire the next generation of talent in the packaging and processing sectors.
As the manufacturing industry faces a critical skills shortage, with the U.S. Bureau of Labor Statistics projecting the addition of 3.1 million jobs in maintenance and repair occupations by 2031, PACK EXPO International 2024 plays a pivotal role in addressing this challenge. The event features comprehensive programs designed to engage and inspire the next generation of talent in the packaging and processing sectors.
Student-Focused Initiatives
Recognizing the acute need to attract and retain a skilled workforce, PACK EXPO International, produced by PMMI, The Association for Packaging and Processing Technologies, prioritizes educational outreach to students.
“PACK EXPO International’s student activities are a bridge that connects today’s students to tomorrow’s workforce, empowering them with the skills, knowledge, and experiences needed to thrive in an ever-evolving world,” said Kate Fioranti, director,
workforce development, PMMI
The event features a variety of activities aimed at introducing high school and college students to opportunities within the industry:
Girl Scout Event: New to the show, local Chicago Girl Scout Troops will receive credit for their Sustainable Packaging Patch. Scouts will meet in the Student Lounge on Sunday, Nov. 3, at 11:00 a.m. for a hands-on project focusing on sustainability. Lunch will be provided, followed by a panel and show floor tour from industry professionals.
Silent Auction - Foundation Fundraiser: Also new to the show, the Silent Auction will take place Sunday through Wednesday. Notable items up for bid include accommodations at premier Chicagoarea hotels, including the Langham, Sheraton Grand Riverwalk, LondonHouse, Loews, and the InterContinental Magnificent Mile. In addition, premium wine and spirits, gift cards, and more are available. All bidding will occur virtually, and items will be displayed on the Grand Concourse, Level 2.5.
Proceeds will benefit the PMMI Foundation.
PACK Challenge: Returning for its second year, the PACK Challenge, sponsored by PepsiCo, invites five high school teams to participate in a machine-building competition. Competitors will demonstrate their skills by constructing full-scale material-handling machines capable of denesting
and orientating paper coffee cups. Participating schools are Argo Community High School, Elk Grove High School, Legacy Academy/Becker High School Coalition, Rich Township High School, and Waterford Union High School. This event will take place in the West Hall Lobby at Booth W-16005 Students PACK the EXPO: On Nov. 4 and 5,
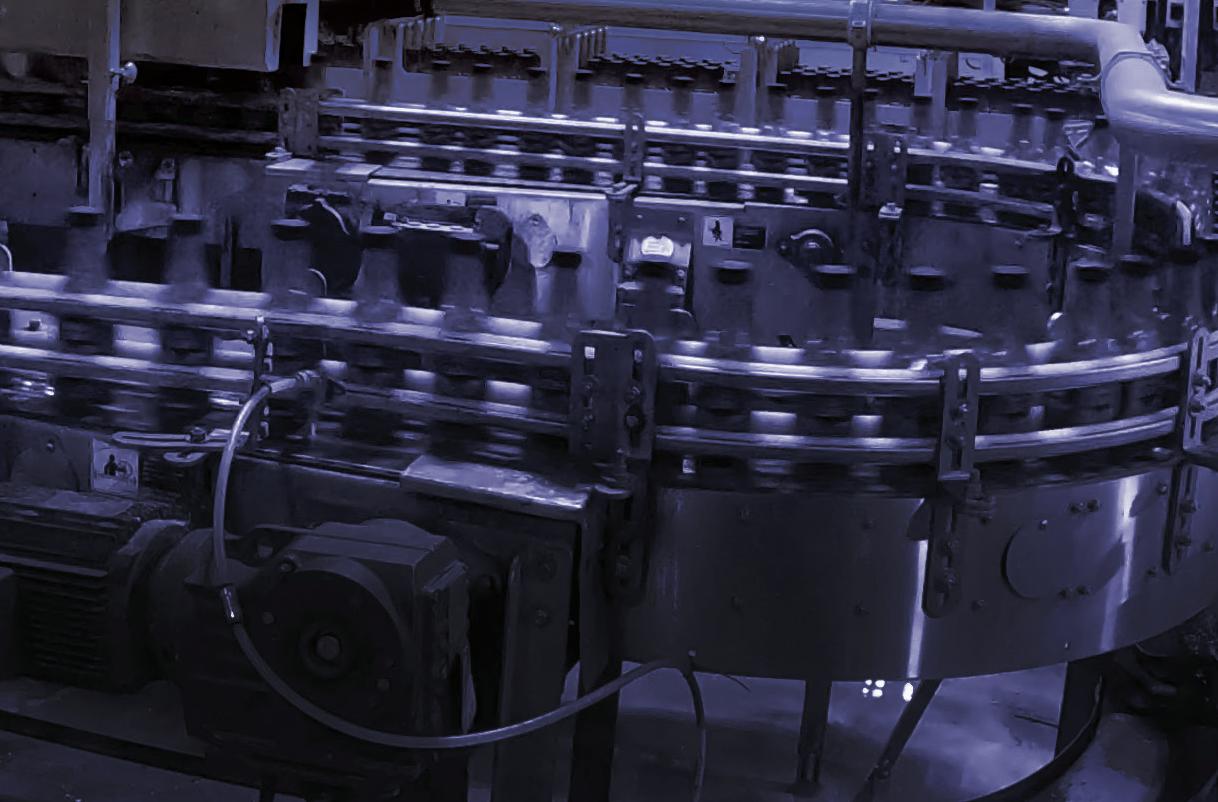

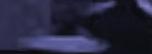
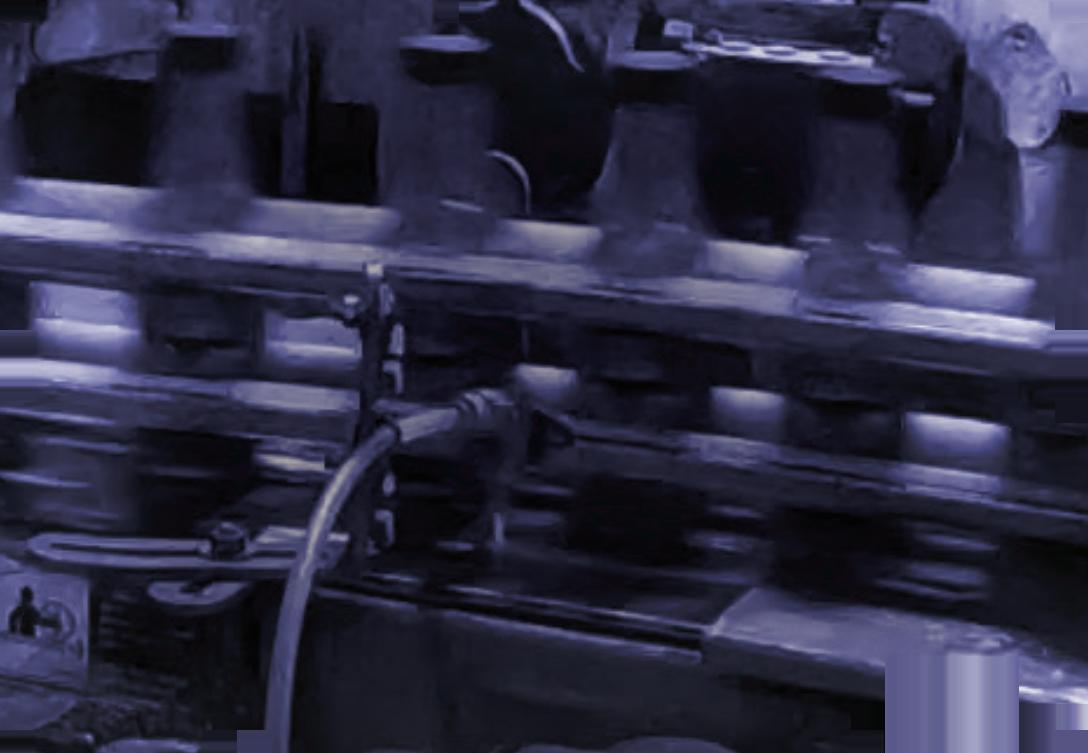
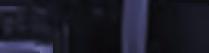
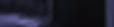
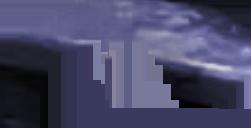
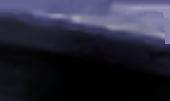
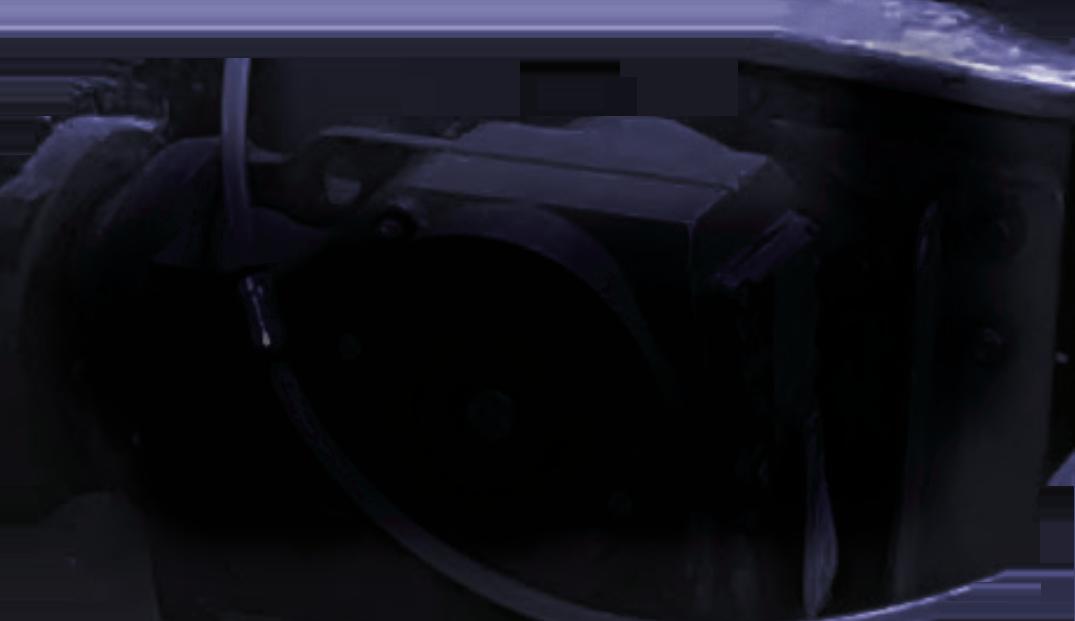

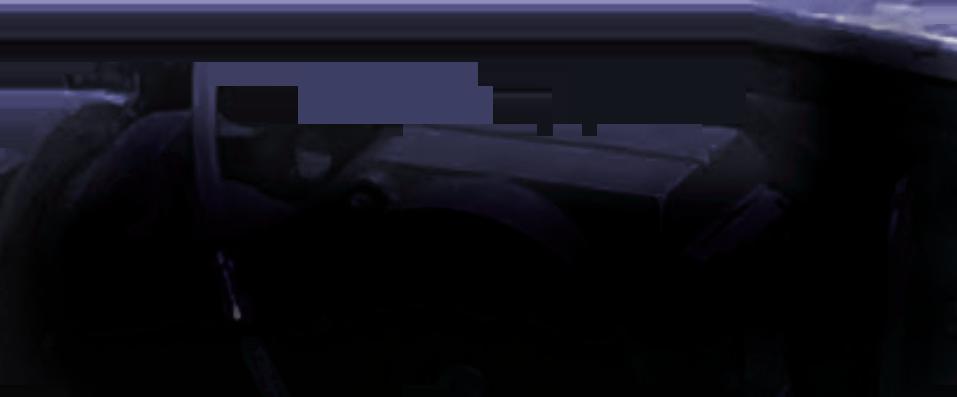




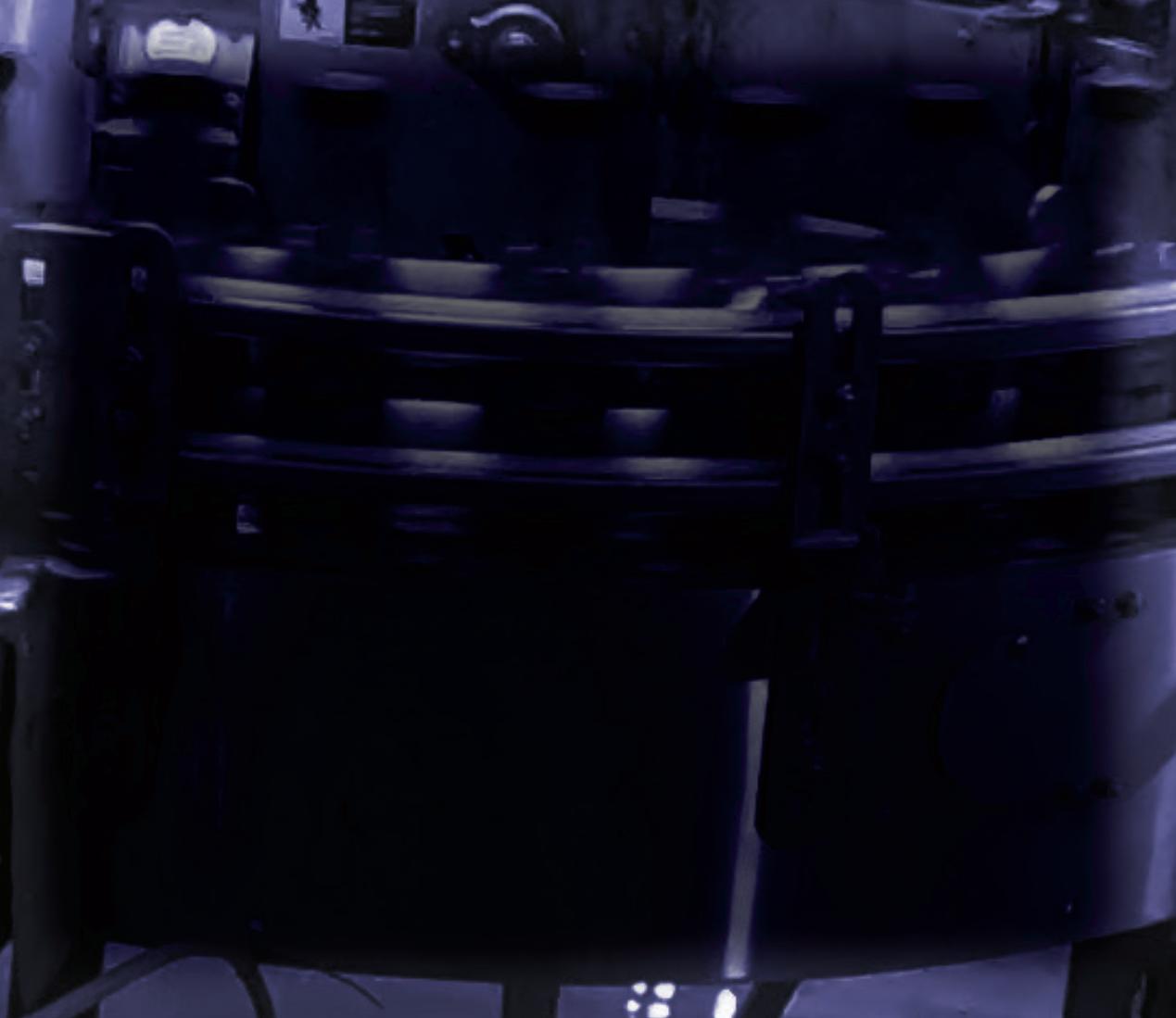
PMMI will host local area students from Indiana, Illinois, and Wisconsin for a comprehensive expo experience. Activities will include PACK Quest, student tours, and a lunch-and-learn session to deepen their understanding of the industry.
• Rochester Institute of Technology
• Rutgers University
• San Jose State University
• Toronto Metropolitan University
• Tuskegee University
• University of Florida
• University of Wisconsin – Stout
• Virginia Tech
Student Lounge (Room W-470b): PMMI HR professionals will conduct workshops focused on interview best practices and resume writing, equipping
students with essential tools to enter the workforce.
“These initiatives reflect our commitment to bridging the skills gap in the packaging and processing industries,” says Laura Thompson, vice president, trade shows, PMMI. “By connecting students with industry leaders and exposing them to real-world challenges and solutions, we are addressing immediate workforce needs and also investing in the future.”
For complete details on student activities at the show, visit packexpointernational.com/education/ student-opportunities ■
Amazing Packaging Race: Sponsored by Emerson Discrete Automation Group (Booth N-5345), this dynamic competition involves college and university students from across North America who will navigate the expo floor, engaging in tasks set by participating exhibitors. This event highlights student creativity and fosters teamwork and practical industry engagement.







Future Innovators Robotics Showcase: In this event, sponsored by Schneider Electric (Booth N-6030), attendees will be able to witness cuttingedge robotics from high school teams across the country. These students will showcase their design, engineering, and troubleshooting prowess in the West Hall at Booth W-21054.
Student Tours: PMMI staff will conduct tours of the show floor daily at 10:00 a.m. and 2:00 p.m. Tours start at the PMMI U/PMMI Foundation Booth at W-20022 (West Hall). Interested students should meet at the PMMI U Booth 10 minutes prior to the starting time. No pre-registration is required.
Professional Development
Further enhancing the student experience, PACK EXPO International will offer dedicated spaces for networking and professional development:
PMMI U/Workforce Development Pavilion: PACK EXPO International serves as the ultimate resource hub for strengthening the existing workforce and nurturing the future workforce. Colleges and universities will showcase their mechatronics and packaging and processing programs in the West Hall, while companies will have the opportunity to engage with students interested in pursuing careers in the industry. The list of participating schools include:
• California Polytechnic State University
• Clemson University
• Hennepin Technical College
• Illinois Institute of Technology
• Indiana State University
• Michigan State University
• Northwood Technical College
• Purdue University
RE Packaging-Filling Machines
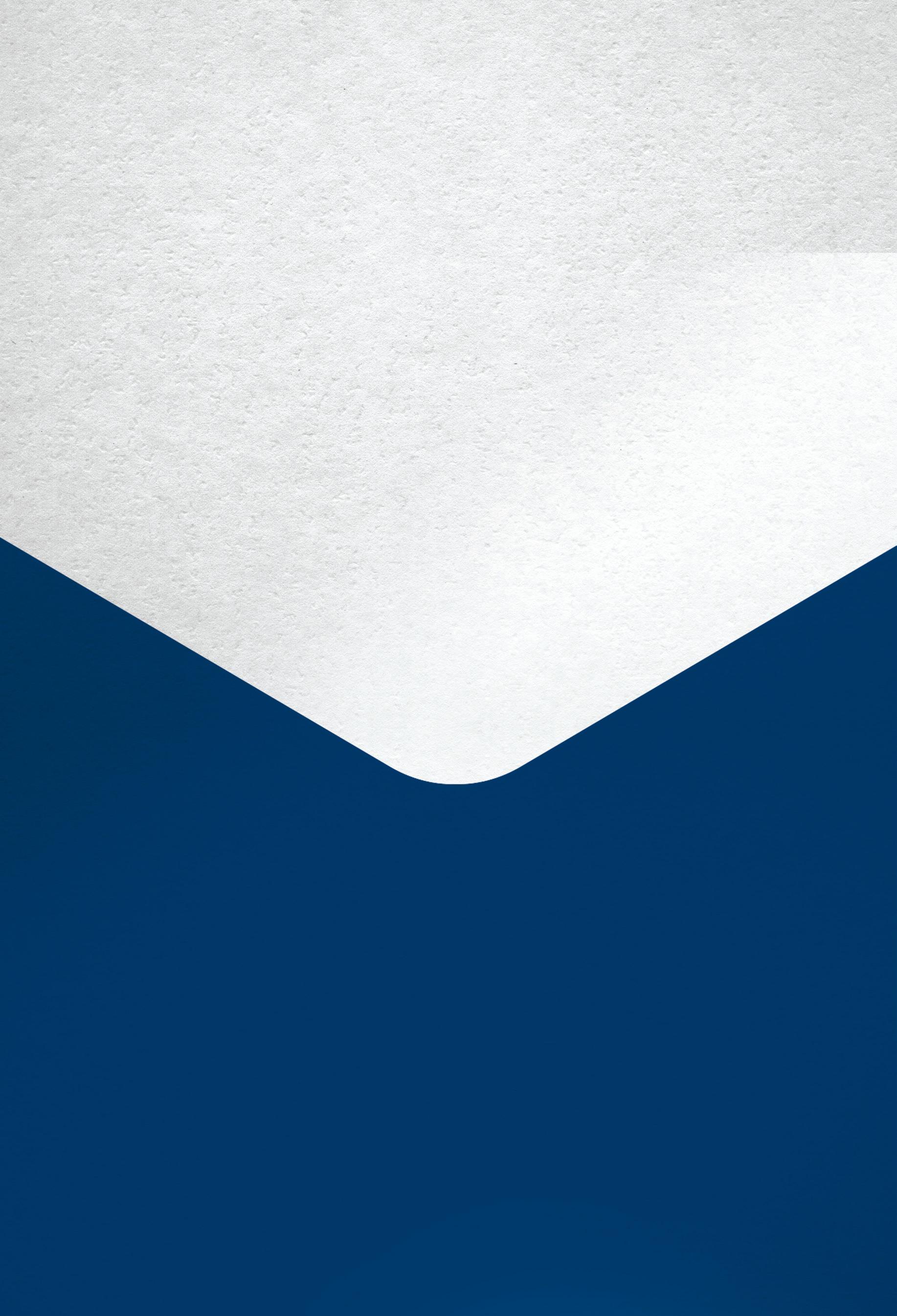
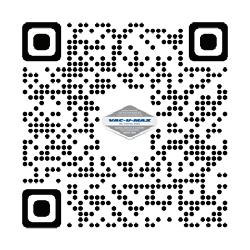

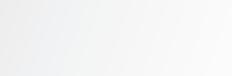
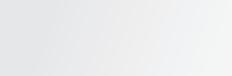
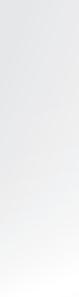
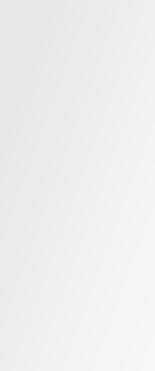
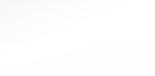

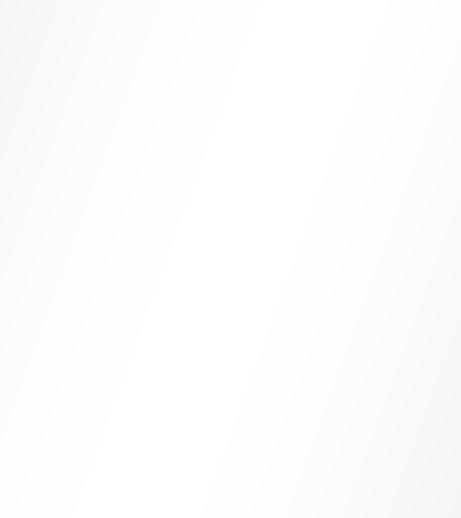

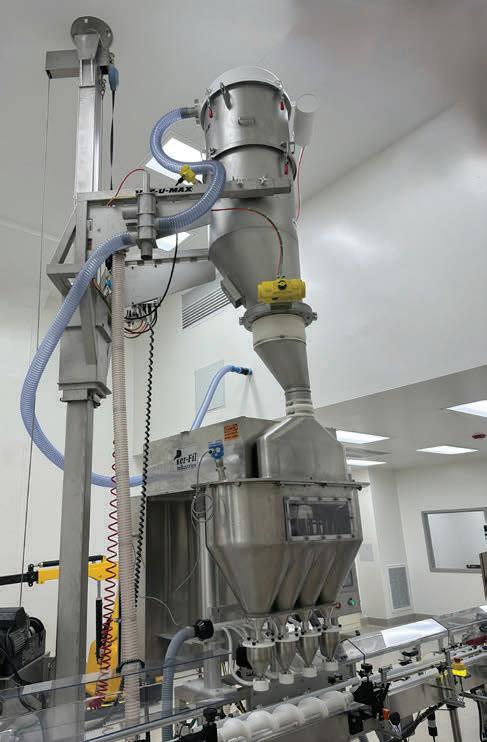



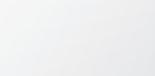
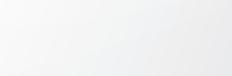



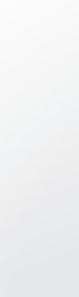

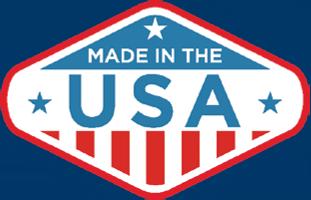
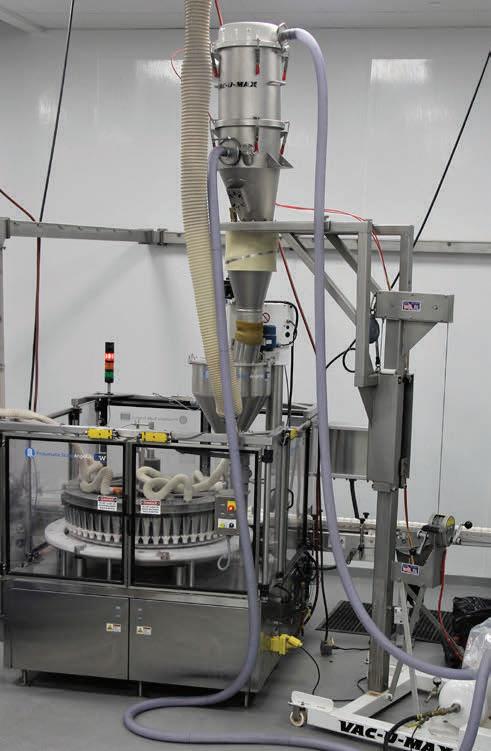

FIND TARGETED SOLUTIONS
LAKESIDE UPPER HALL
The Processing Zone
Find front-of-the-line solutions for food and beverage processing and discover ways to increase safety, improve efficiency, and achieve total system integration.
The Reusable Packaging Pavilion
Discover reusable assets that reduce waste, provide more reliable protection for your production, and can be part of a smart supply chain.
Sponsored by:
NORTH HALL
The Logistics Pavilion
Find supply chain solutions that include equipment and systems for warehousing and material handling, dock and warehouse, inventory management and control, distribution logistics services and transportation providers.
SOUTH HALL
The Confectionery Pavilion
Uncover specialized equipment and integrated systems for your candy, chocolate, mints, and gum production lines.
Sponsored by:
PACKage Printing Pavilion
Explore technology that makes customization, promotions, small runs, on-demand production, and smart packaging cost-effective.
WEST HALL
The Containers and Materials Pavilion
Find new sustainable materials, flexible packaging, printable films, and more. Also, see award-winning packages at:
Unlocking Optimized Beverage Line Performance with Regal Rexnord Powertrain Solutions
A
large
brewing company lowered energy, maintenance and service costs from ine cient processes and MRO.
Traditional beverage lines can be ine cient and use excessive water, lubricant, and energy — resulting in high operating and maintenance costs. is can cause manufacturers to retro t existing lines to meet increasing production needs and/or improve system e ciency, risking premature failures and lower functionality. e Regal Rexnord (Booth LL-10014) Powertrain Solutions team has decades of expertise and experience designing innovative custom solutions and partners with customers to minimize the risk associated with beverage line optimization.
The Challenge
One of the world’s largest brewing companies experienced high energy, maintenance, and service costs due to ine cient processes and MRO. is resulted in hundreds of thousands of dollars in lost maintenance and operating costs.
Most breweries use water and lubrication to ensure cans and bottles do not get damaged during processing. However, using water and lubrication is costly, ine cient and causes a strain on the environment. At this facility, an estimated 100,000 cases each year were damaged due to wet cans warping the packaging.

Approximately 30% of the electric motors on the facility’s can line needed to be replaced yearly due to unplanned and sporadic failures. Additionally, most of the motors were oversized, resulting in excessive energy usage, which became costly over time. Mechanical power transmission components, like bearings, require manual auditing every few months—which is both costly to perform and an inaccurate method of predicting imminent failures.
—Continued on page 34
The Healthcare Packaging Pavilion
Visit your one-stop shop for solutions targeted to pharmaceuticals, biologics, nutraceuticals, medical devices and more.
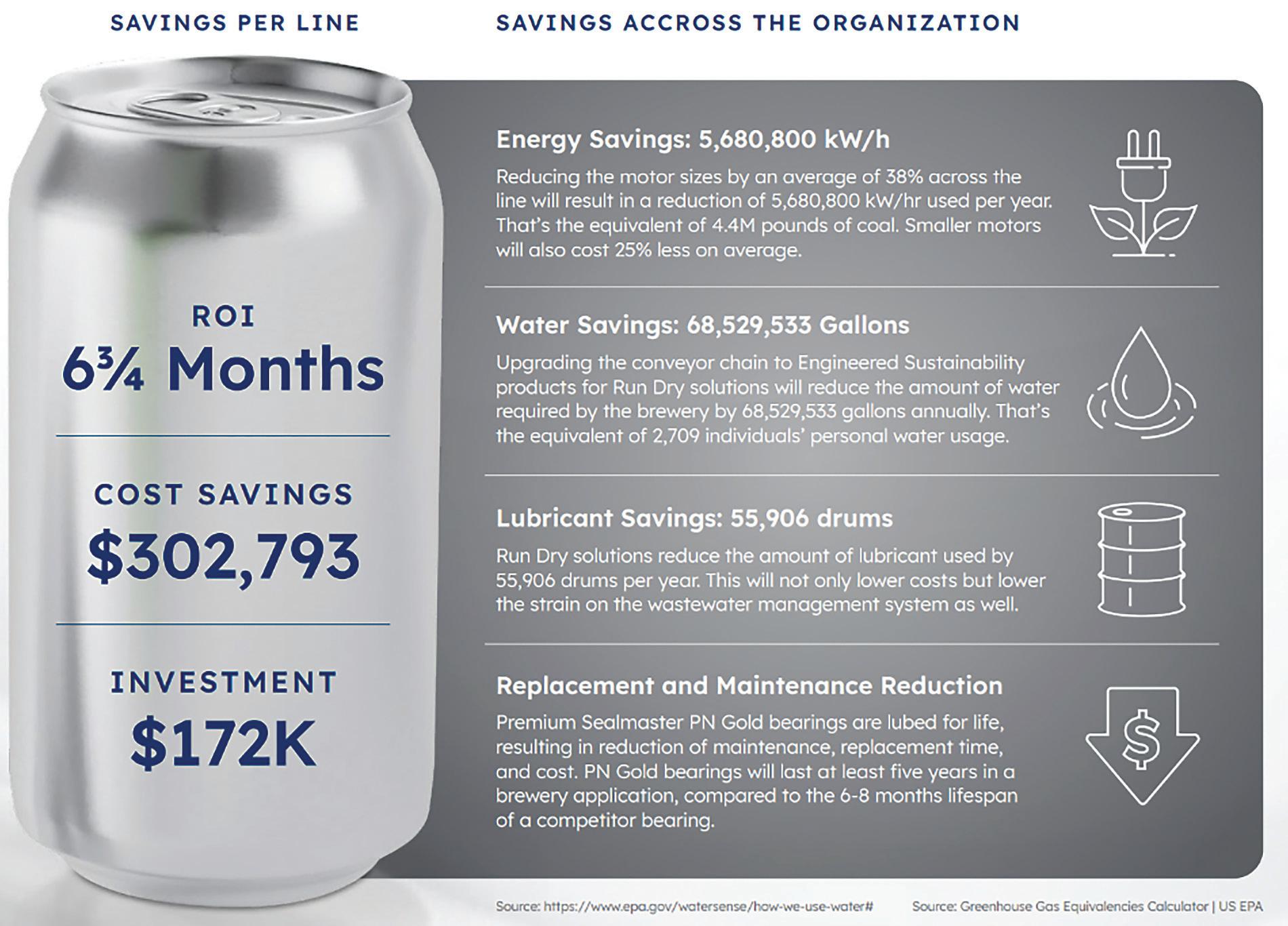
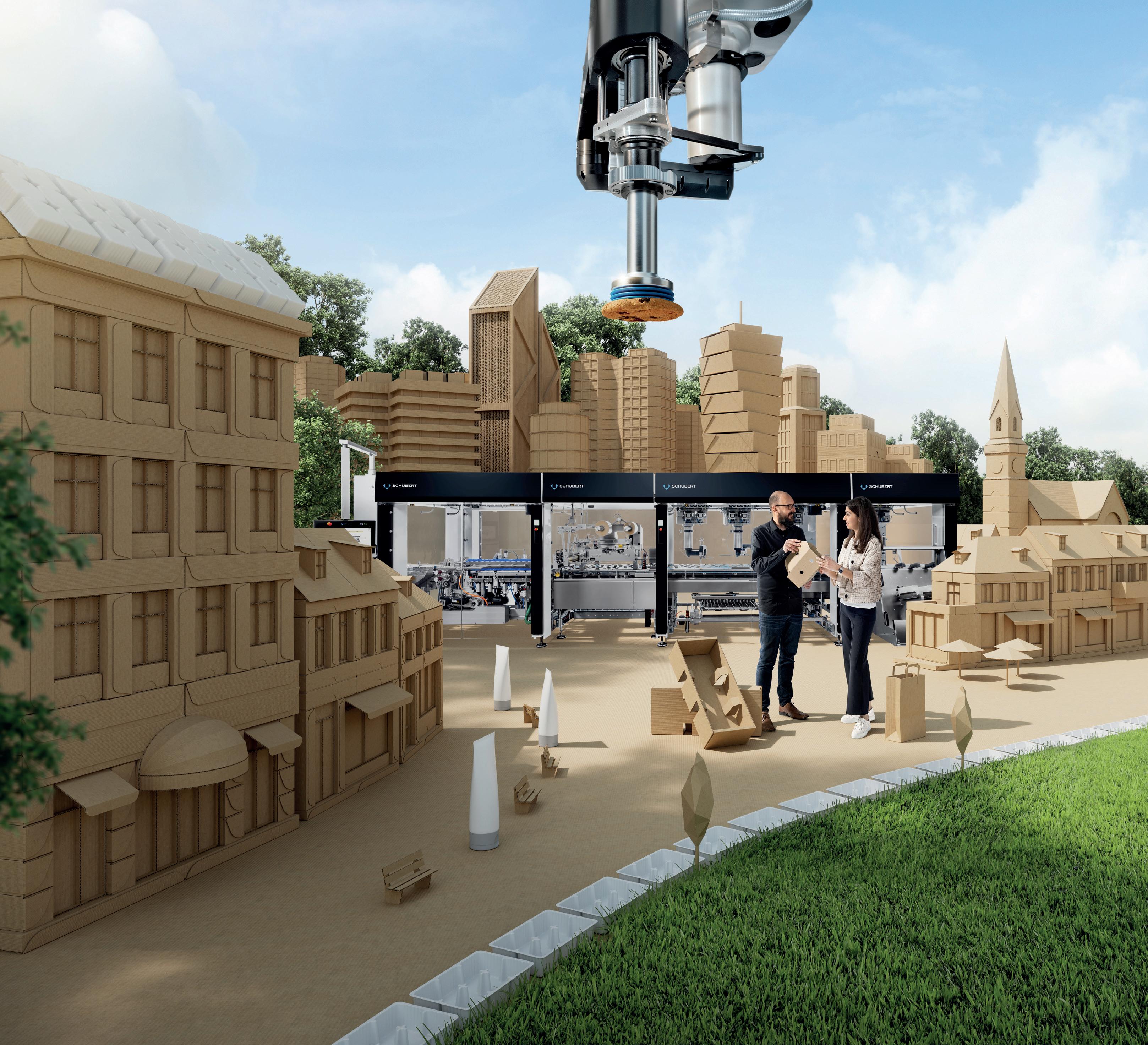
How can packaging be both environmentally friendly and cost-efficient? With our TLM packaging machines. They enable you to use the thinnest materials possible, cutting them to size to reduce consumption and dramatically decrease your use of resources. It’s great for the planet and you benefit from a real competitive edge. We call it Mission Blue and we promise: The mission goes on. www.mission-blue.com
—Continued from page 32
All of these ine ciencies resulted in an annual cost of $302,793 per year per line in both MRO and operating cost losses.
Considering the above, the brewery identi ed the following key objectives:
• Increase line e ciency
• Standardize inventory
• Improve ease of maintenance by standardizing products and decreasing monthly tasks
• Reduce energy usage
• Minimize water and lubrication usage
• Reduce yearly replacement costs
Achieving uptime and e ciency with one powertrain solution
Powertrain Solutions sent a survey team to perform an audit and inspection of the most problematic can line. at survey collected all necessary information to optimize and redesign both the electrical and mechanical power transmission components. e scope of the work included bearings, motors, gearboxes, and conveying chain/ components, as well as recommendations for digital monitoring solutions and services.
Following the survey, the Powertrain Solutions
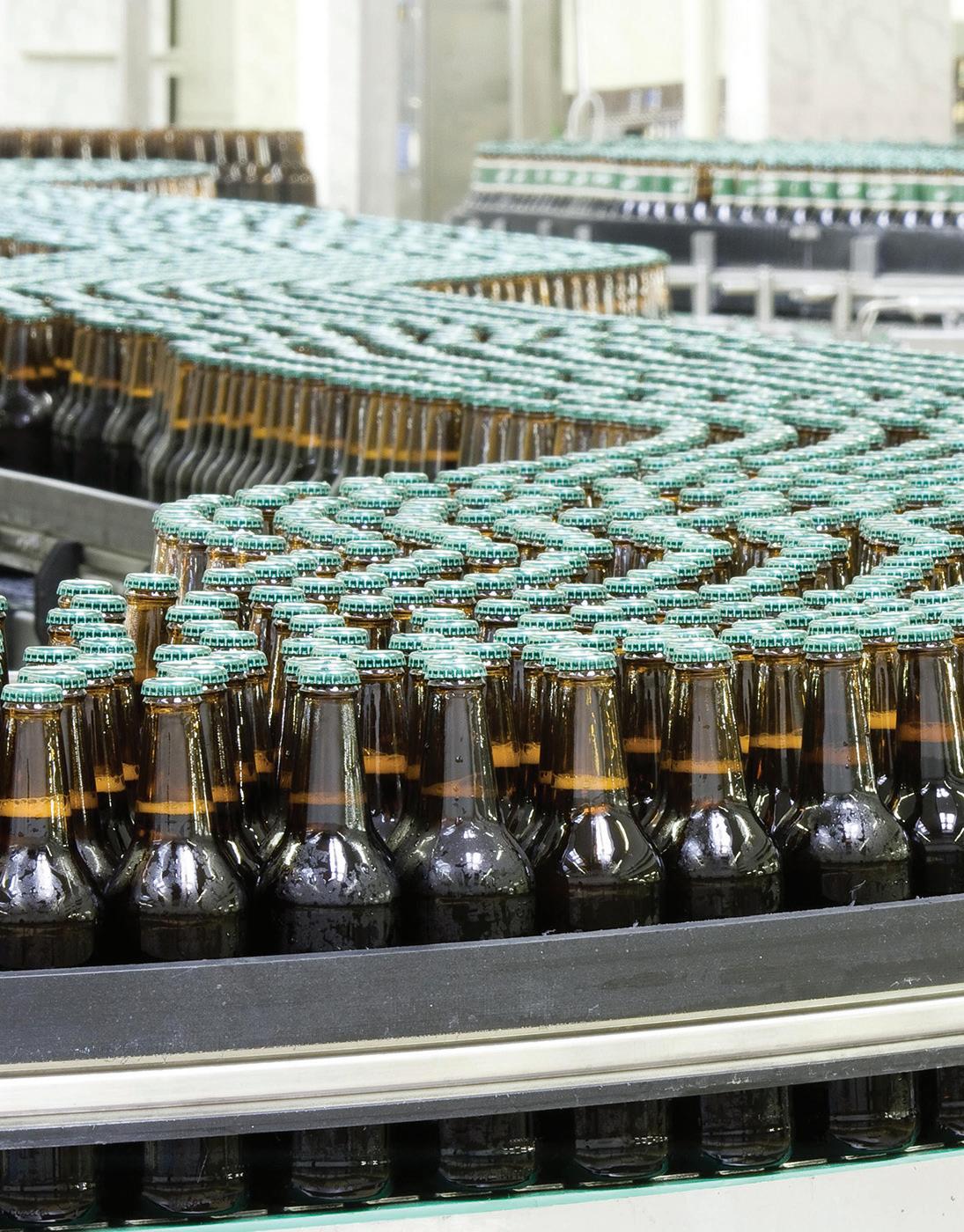
team made product and process improvement recommendations. e team recommended Rexnord® MatTop® PSX® Run Dry conveyor chain, which reduced the need for lubricant by 97.1% and decreased the need for water by 29%. e PSX chain also has double the life span of the existing chain. Decreasing water and lubrication usage reduced the risk of injury from wet oors in the plant and the potential for warped and damaged packaging. Installing serpentine returns and bi-material rollers eliminated scalloping and uneven wear of chain to maintain atness and smooth transfers, resulting in at least a 25% reduction in downtime.
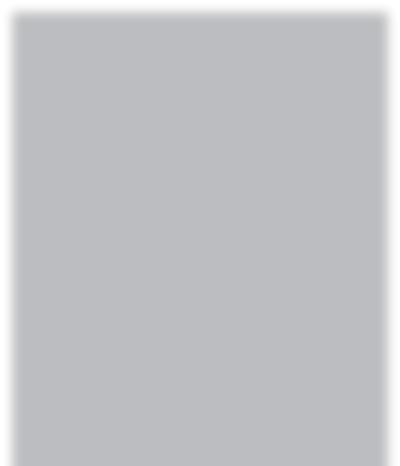
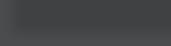


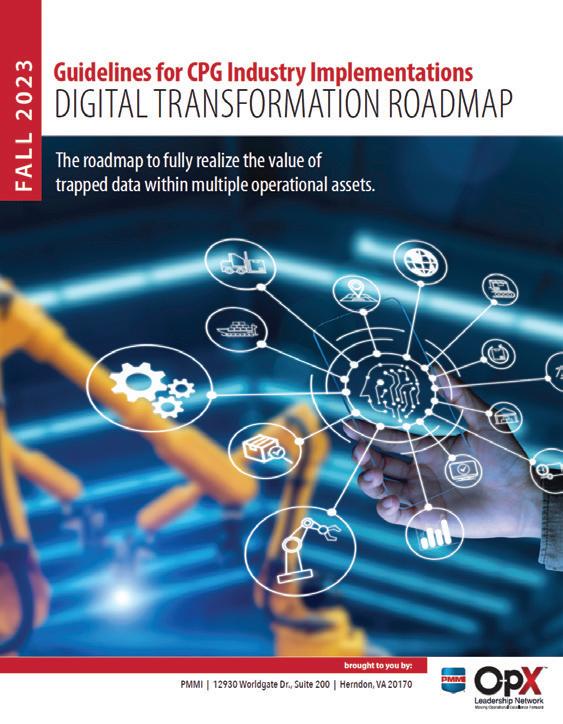
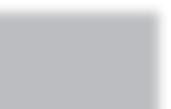
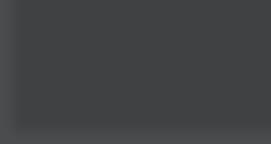
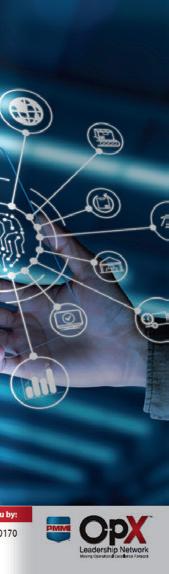
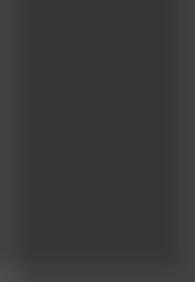
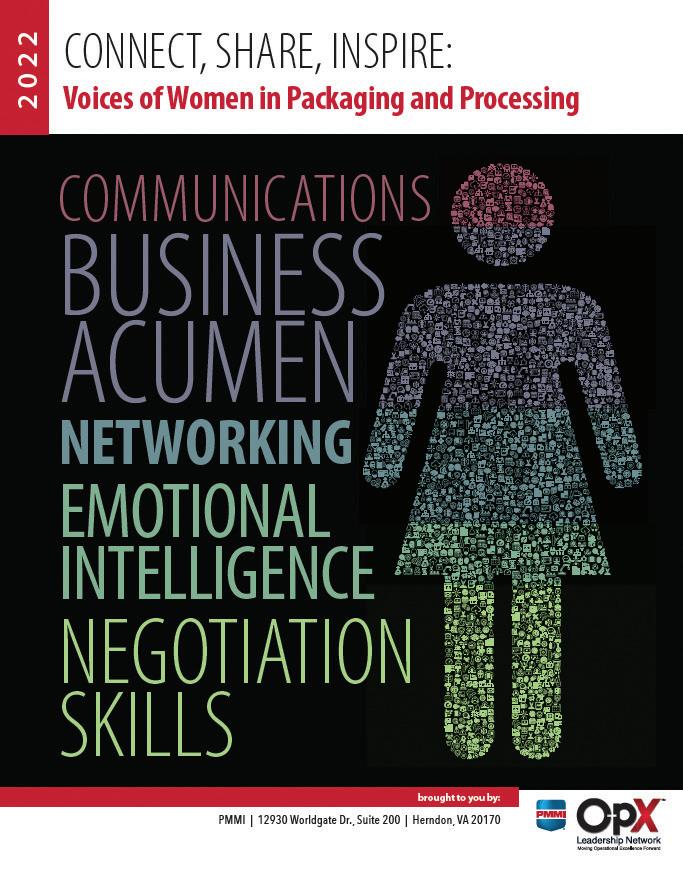

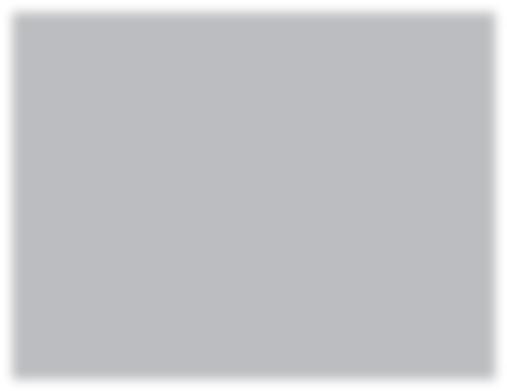

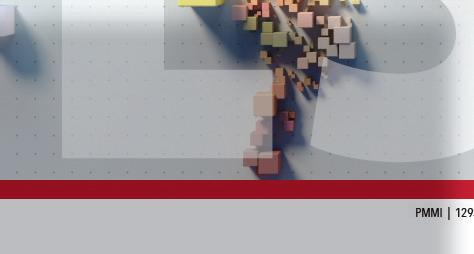


Powertrain Solutions also recommended downsizing the motors and gearboxes by an average of 38%, reducing the electrical energy consumption and lowering the cost of the components by 25%. e motor and gearbox con guration selected was LEESON®—the industry-leading e cient (>85%) washdown motor—paired with stainless steel HERA® (>90%) gearboxes. Both the motors and gearboxes feature IP55 and IP69 ingress protection, respectively. e products work seamlessly together to maximize life and have the capability to withstand frequent exposure to high-pressure washdown and harsh cleaning chemicals—for reliable, trouble-free operation.
Lastly, the Powertrain Solutions team selected Sealmaster® PN Gold™ Mounted Ball Bearings, as they do not require frequent relubrication, which leads to a 50% reduction of MRO labor. Powertrain Solutions also proposed on-site application engineering support for maintenance training and the start-up of upgraded lines and maintenance SOP recommendations. By analyzing and optimizing their entire powertrain system, the Powertrain Solutions team helped the brewing company increase e ciency, reduce energy costs, and improve Total Cost of Ownership (TCO). Additionally, cutting water and lubrication usage can help facilities meet their sustainability goals.
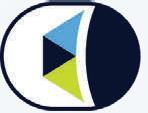


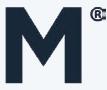
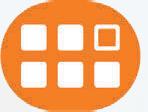









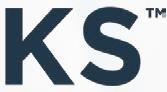
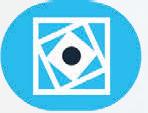





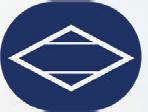
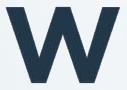
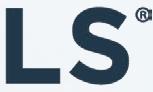
ProMach Pharma Solutions is four brands, within one company, that collaborate as your single source for total pharma packaging solutions.
Capabilities:
• Complete Turnkey Integrated Lines
• Aseptic Fill Finish Equipment
• Oral Solid Dose — Bottle or Blister Packaging
• Labelers, Label Printers & Coders
• Secondary Packaging including Cartoning, Case Packing & Palletizing
• Processing — Washing, Sterilization & Decontamination Solutions
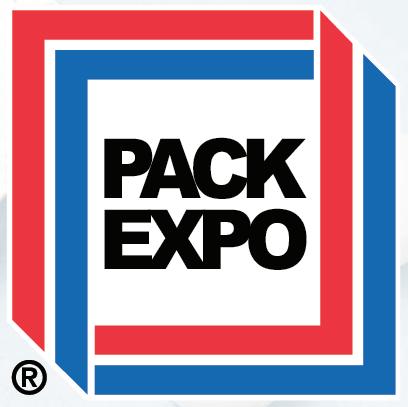
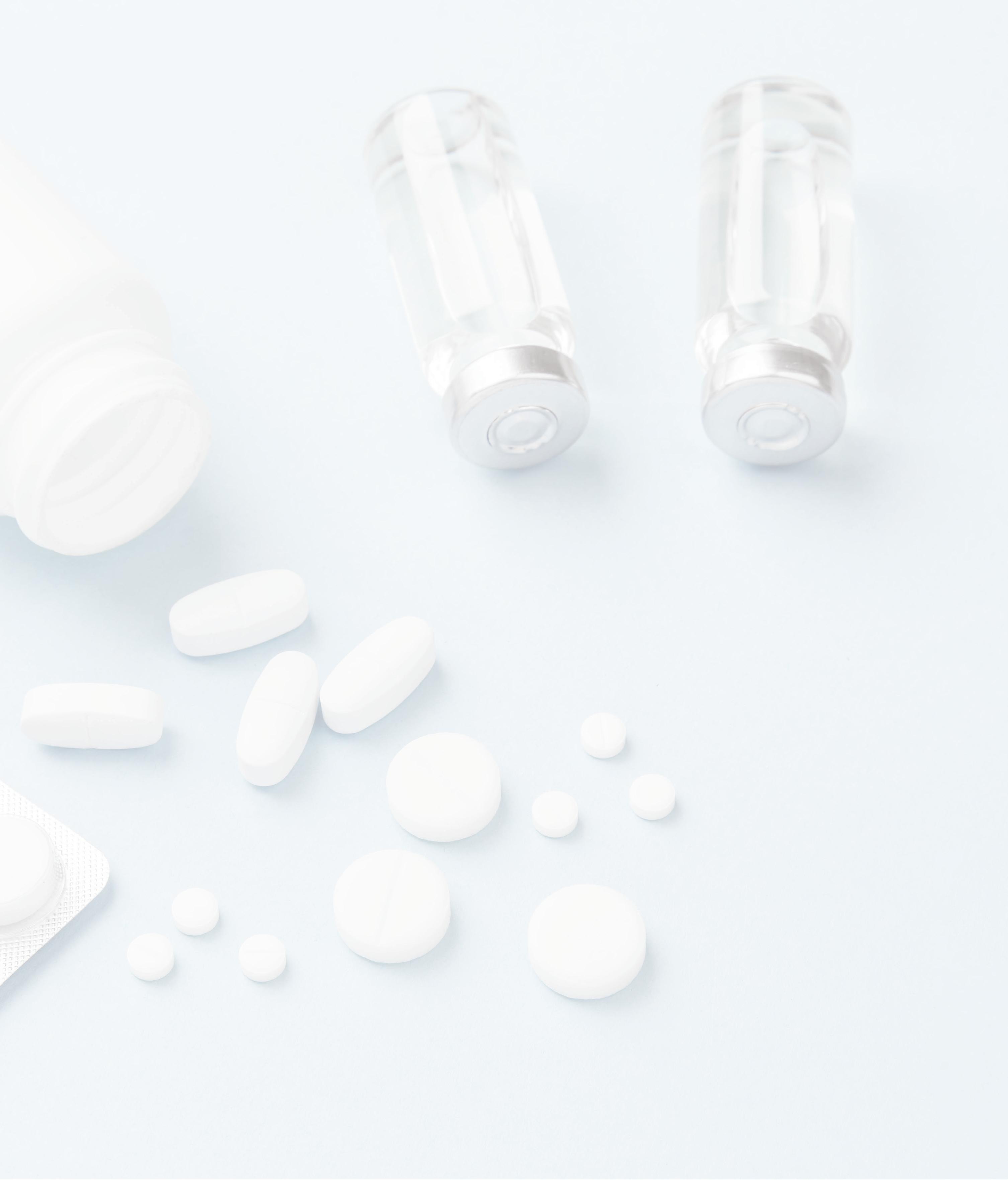
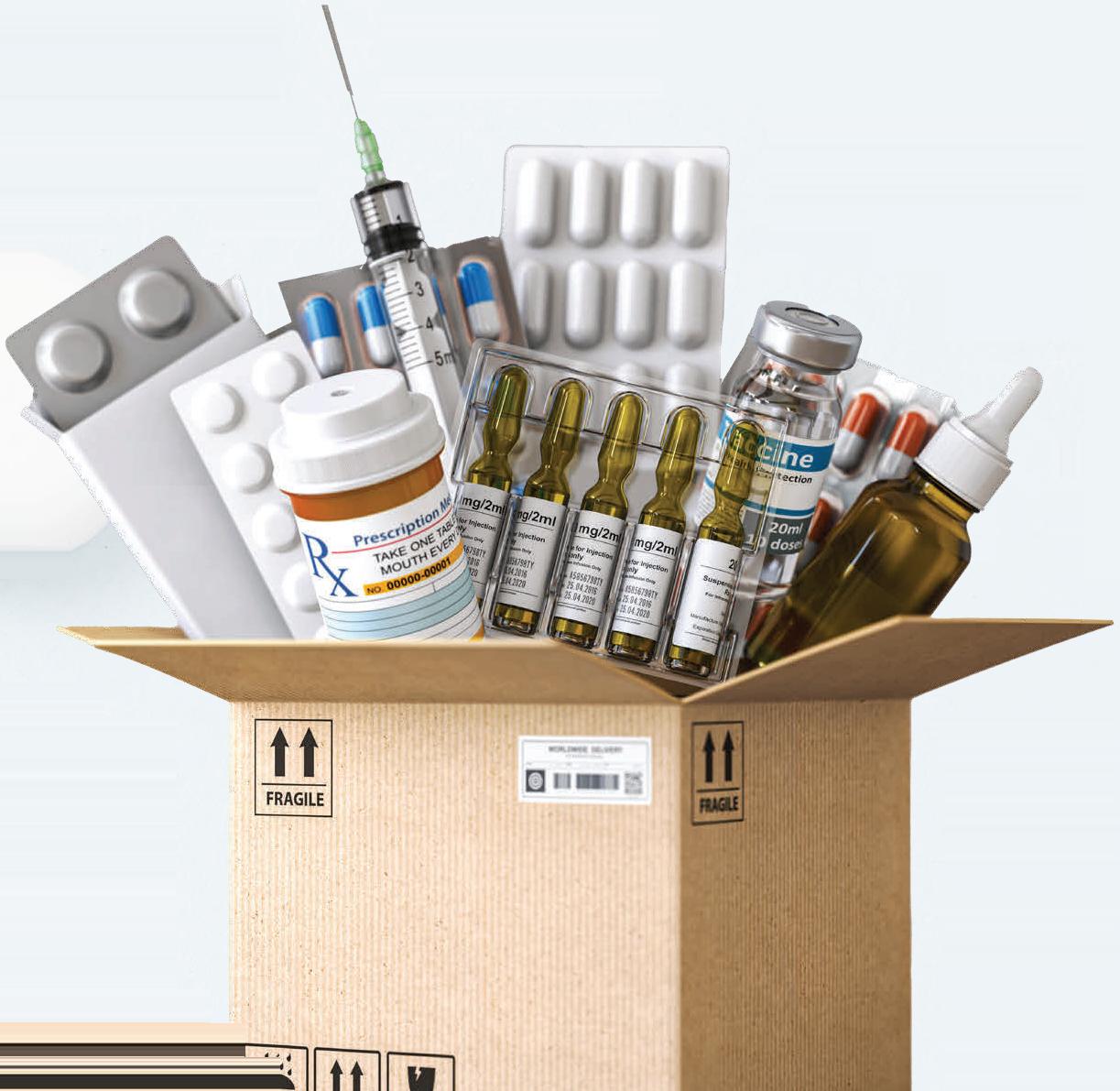
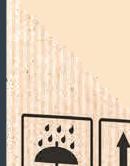

OpX Work Product: Transitioning to Flexible Materials
The latest work product from the OpX Leadership Network helps CPGs ensure a smooth transition when altering pack ops.
e OpX Leadership Network is pleased to introduce its latest work product, Best Practice Transitioning Flexible Materials. While this document is primarily focused on transitioning exible materials, it o ers broader insights into managing changes in capital
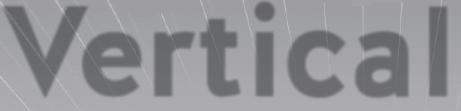
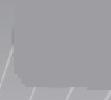
equipment. Flexible materials serve as the framework for this document, but its principles can be applied to various projects involving alterations to capital assets, such as material changes, speed increases, size adjustments, product modi cations, and more. In

Small
Vertical Conveying. Simplified.

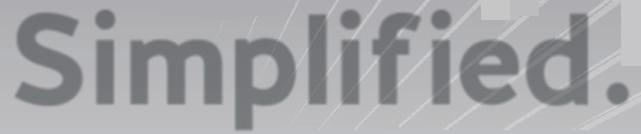


Footprint. Low
Maintenance.
Reliable Conveying... Ryson is the smart Vertical Conveying Solution.
Whether you are handling cases, trays and packs or bottles and cans in mass or a single file we can help. Ryson Spirals need less floor space than conventional conveyors and are faster and more reliable than any elevator or lift.
Each spiral is built to exact customer specifications, and can even be field modified if needed - thanks to our proprietary modular design. We also make a full line of Bucket Elevators for your bulk material conveying needs.
All Ryson equipment is modular and built to order. No matter the application, the Ryson team is up to the challenge of finding solutions for your conveying needs. For application assistance or more information, give us a call or visit www.ryson.com
See our equipment run at Booth N-5945. Ask us to see a maintenance demonstration.

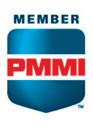
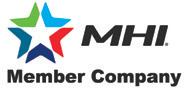
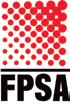
www.ryson.com (757) 898-1530

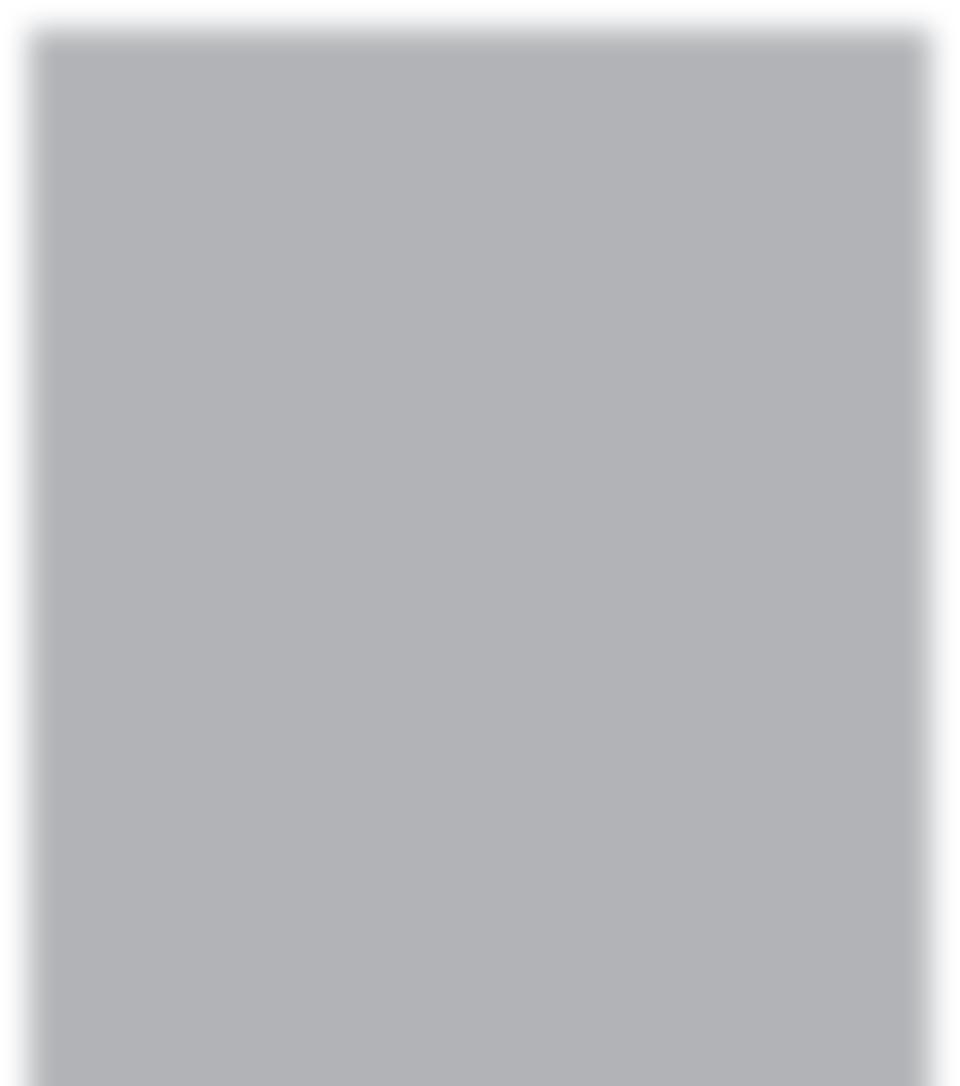

essence, it serves as a blueprint for e ective project management execution of engineering change orders. is exible guide results from a collaborative e ort that draws input from a diverse group of stakeholders. e expert solutions group is comprised of consumer packaged goods (CPG) companies, material suppliers/converters, and OEMs from the Flexible Packaging Association (FPA), PMMI, and the OpX Leadership Network.
Transitioning exible materials within CPG operations encompasses various processes, including modifying packaging materials, design changes, and equipment adjustments. is document is designed to assist brand manufacturers in ensuring the smooth and successful transition of exible materials in packaging operations by engaging relevant stakeholders at the right stages of the process.
Key highlights of the Best Practice include: Information on CPG materials usage and frequency of change: Understanding the dynamics of material usage is crucial for e ective transitions.
Flow chart detailing the order of tasks required for transitioning exible lms on packaging lines: A visual guide to streamline the transition process.
A RACI matrix depicting the level of responsibility for each group involved: Clarifying roles and responsibilities in the transition process.
Detailed information on each stage and task for transitioning exible lms in CPG operations: Indepth insights into every aspect of the transition.
Download the Best Practice Transitioning Flexible Materials work product and learn more about the OpX Leadership Network by visiting OpXLeadershipNetwork.org ■

How Robotics is Helping Leonard’s Syrup Thrive
Schneider Packaging Equipment’s custom robotic palletizer helped expand capacity.
Leonard’s Syrups is a successful family-owned company in Detroit. Today, Leonard Jr. serves as CEO; his son Leonard III is President, and his daughter Sherri Iskra is Vice President, where she is involved in project management, IT, operations, and finances. A son, Steve, who was the technologist in the family, passed away about 10 years ago. Several members of the fam-
ily’s fourth generation now work at the company.
Leonard’s has consistently grown based on its assortment of great products, outstanding service, and entrepreneurial attitude. On a typical day, Leonard’s 120 employees in three locations would produce 700 boxes of soda concentrate syrup packaged in a “bagin-box.” Further growth required increased capacity,
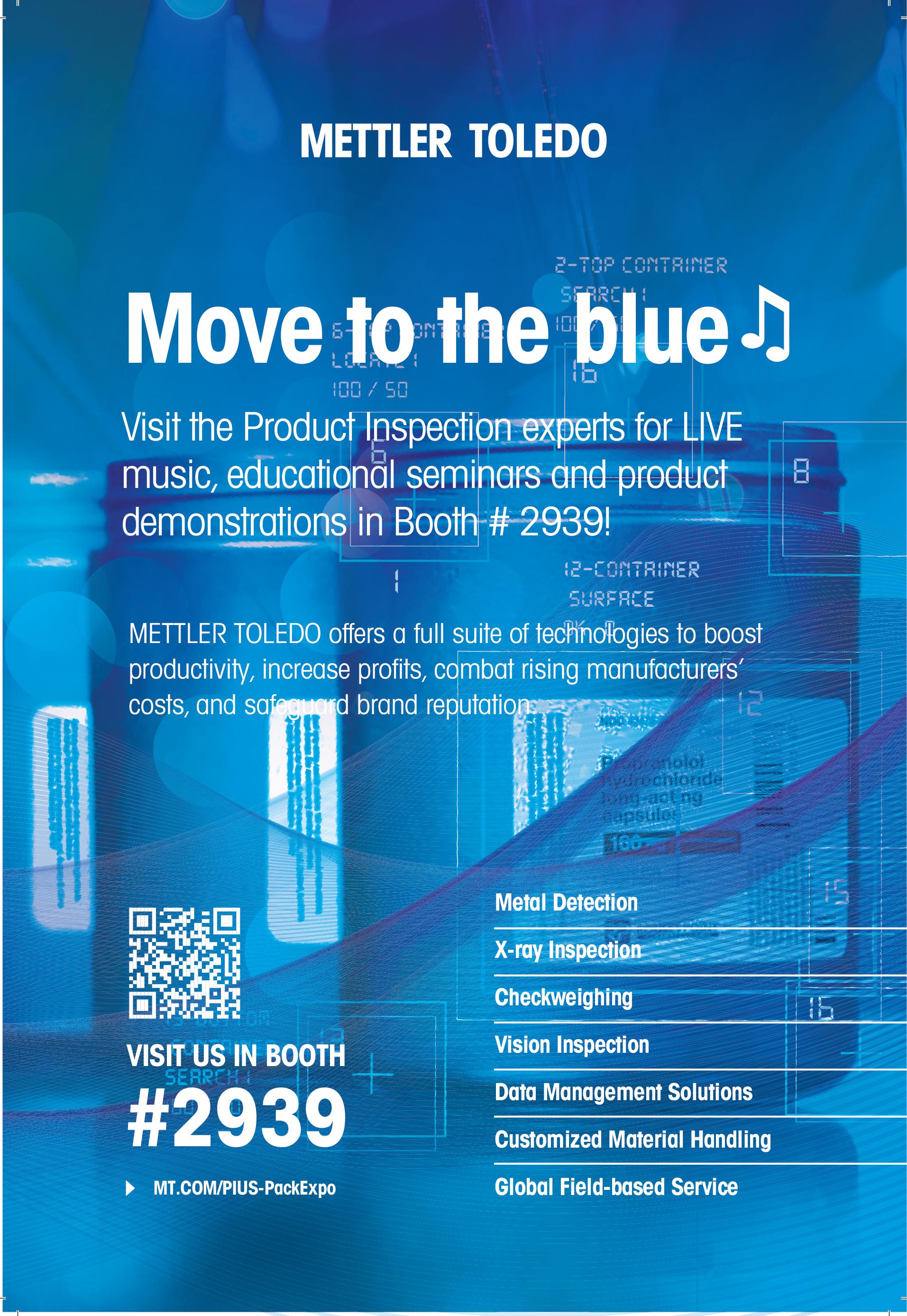
and adding more people wasn’t an option. The solution: automation and robotics.
The company needed to expand capacity and produce more boxes to automate production. “We had to increase our speed if we wanted to grow,” said Iskra, who noted that the company would be unable to add more customers or distributors unless they increased their production throughput.
Each box of the soda concentrate syrup weighs about 55 pounds. The manual manufacturing process required the production crew to lift each box off the line and place it on a pallet. At 700 boxes per day, Leonard’s aging workforce found this repetitive lifting physically strenuous.
Iskra concluded that the company could not continue to operate in the same old way. A change was necessary to grow and ease the burden on employees. After asking, “What could solve both of these problems?” Iskra found the answer in automation.
Finding an Automation and Robotics Partner
While Iskra loves technology (though not as much as her techie brother Steve did) and taking on projects to advance the company, the idea of automating their manual process intimidated her. To proceed down this path, Iskra started with semi-automation. As an initial step, Leonard’s purchased a vacuum lifter. This semi-automated solution removed the physical strain of lifting the 55-pound boxes from the workers. As she developed criteria for full automation, Iskra knew the footprint had to be compact to fit within Leonard’s production facility. The solution had to meet the 55-pound payload requirement of the boxes, a challenge for smaller robotic arms. It also had to be reliable and fit within Leonard’s budget.
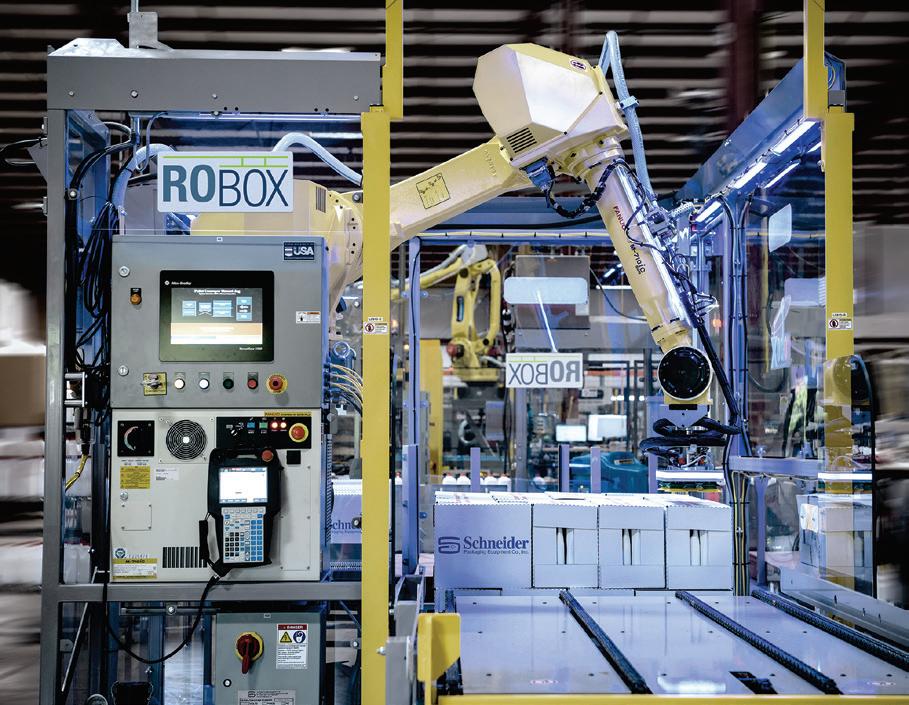
Schneider’s Robox.
Schneider’s Solution
Based on multiple recommendations, Iskra looked into Schneider Packaging Equipment (Booths S-3300, W-16041) and learned about the company’s modular robotic palletizer—the Robox, which comes
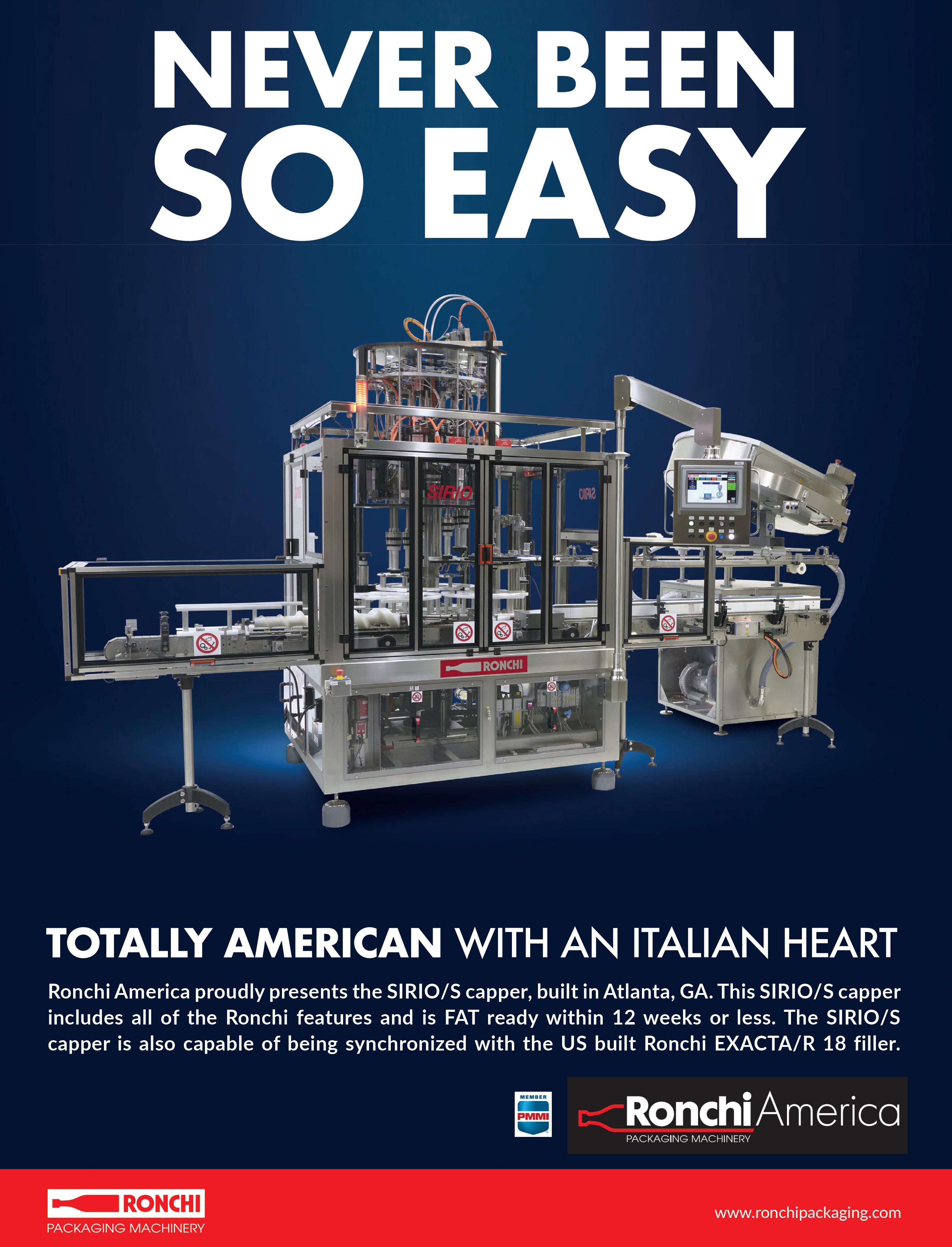
—Continued from page 38 pre-assembled and pre-con gured. She thought this might be an ideal solution. While the Robox would not meet her application, Iskra shared with Schneider Leonard’s situation and needs. Schneider engineers developed the perfect solution for Leonard’s and tested its performance at Schneider’s facility in Brewerton, New York. e system shipped to Leonard’s facility in Detroit, where it was commissioned in just a few days. Iskra commented, “ e implementation process was the smoothest of any project I’ve been in charge of in my 35 years at Leonard’s.”
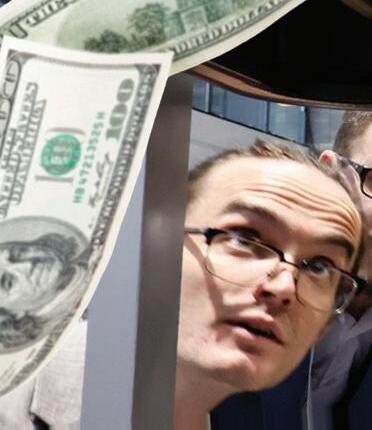
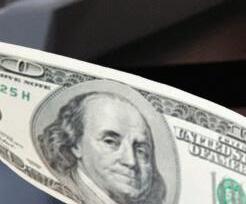
As an unexpected touch, Schneider named the robot “Steve” to honor Iskra’s deceased techie brother, who would have loved having a robot at Leonard’s.
Results: Steve Has Tripled Leonard’s Capacity—and More
Steve went live in May 2023. Leonard’s immediately began to produce and palletize over 2,000 boxes of cra soda per day, nearly triple the capacity. “It means we now have the opportunity to grow,” said Iskra.
While employees were initially nervous about the


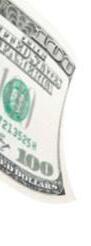
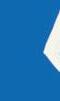
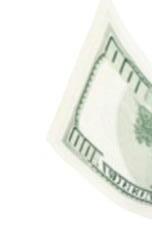
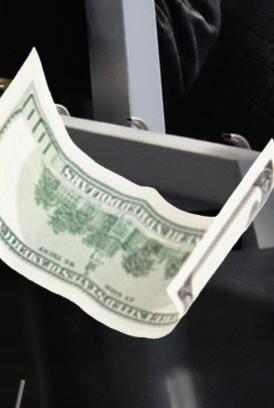
Scavenger Hunt & WIN BIG!
How to Play:
1. Download the PACK EXPO Mobile App –Select “Scavenger Hunt” for a listing of all required destinations. You must be logged into your My Show Planner to participate.
2. Visit Each Location – Enter the unique code located on signs at each destination stop.
3. Win Prizes – Complete all stops to enter the drawing for one of three $1,000 Gift Cards. Winners will be announced via email the week of November 11.
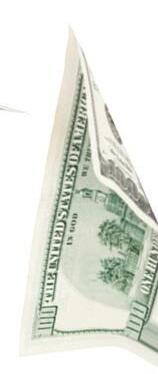


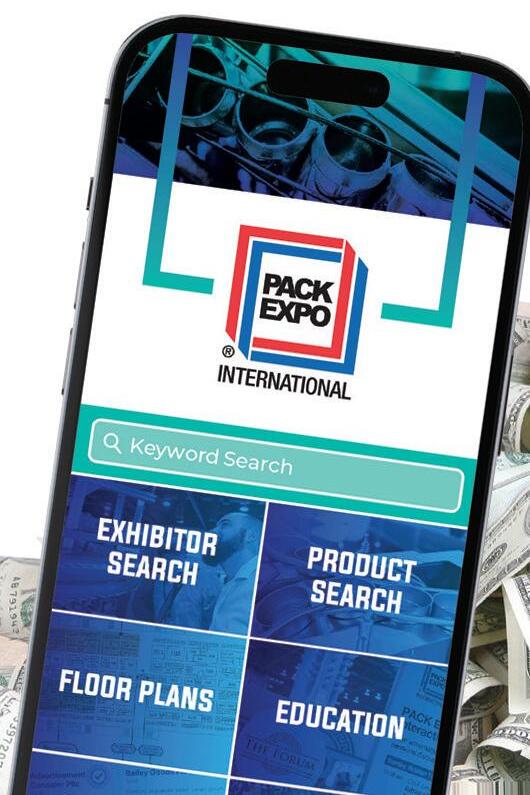
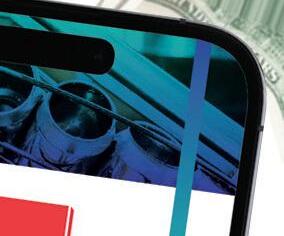
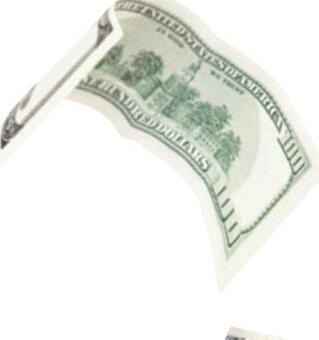
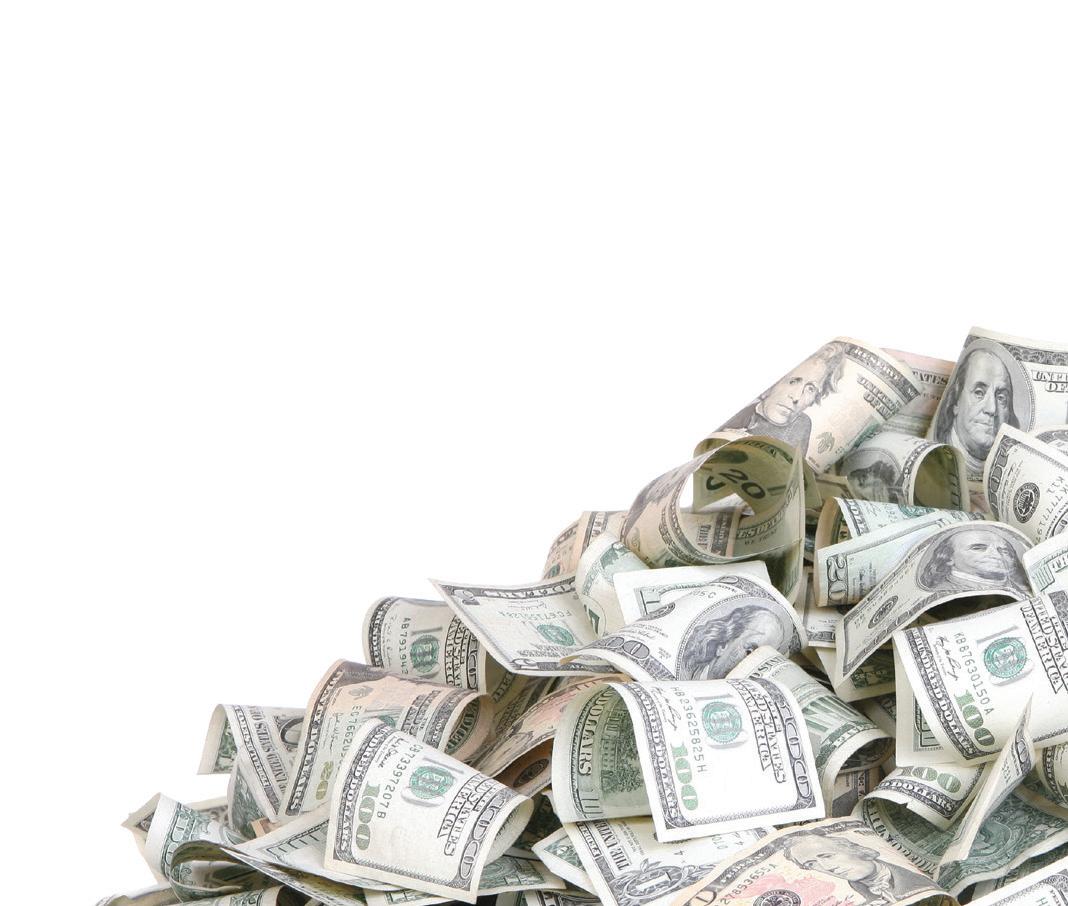

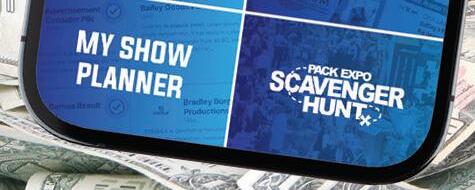
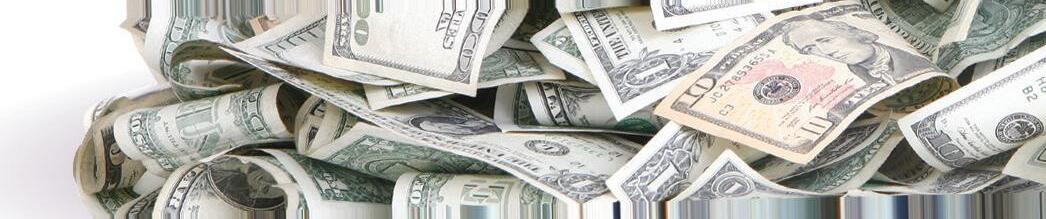
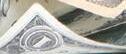

Join the Scavenger Hunt today and make your PACK EXPO experience unforgettable.
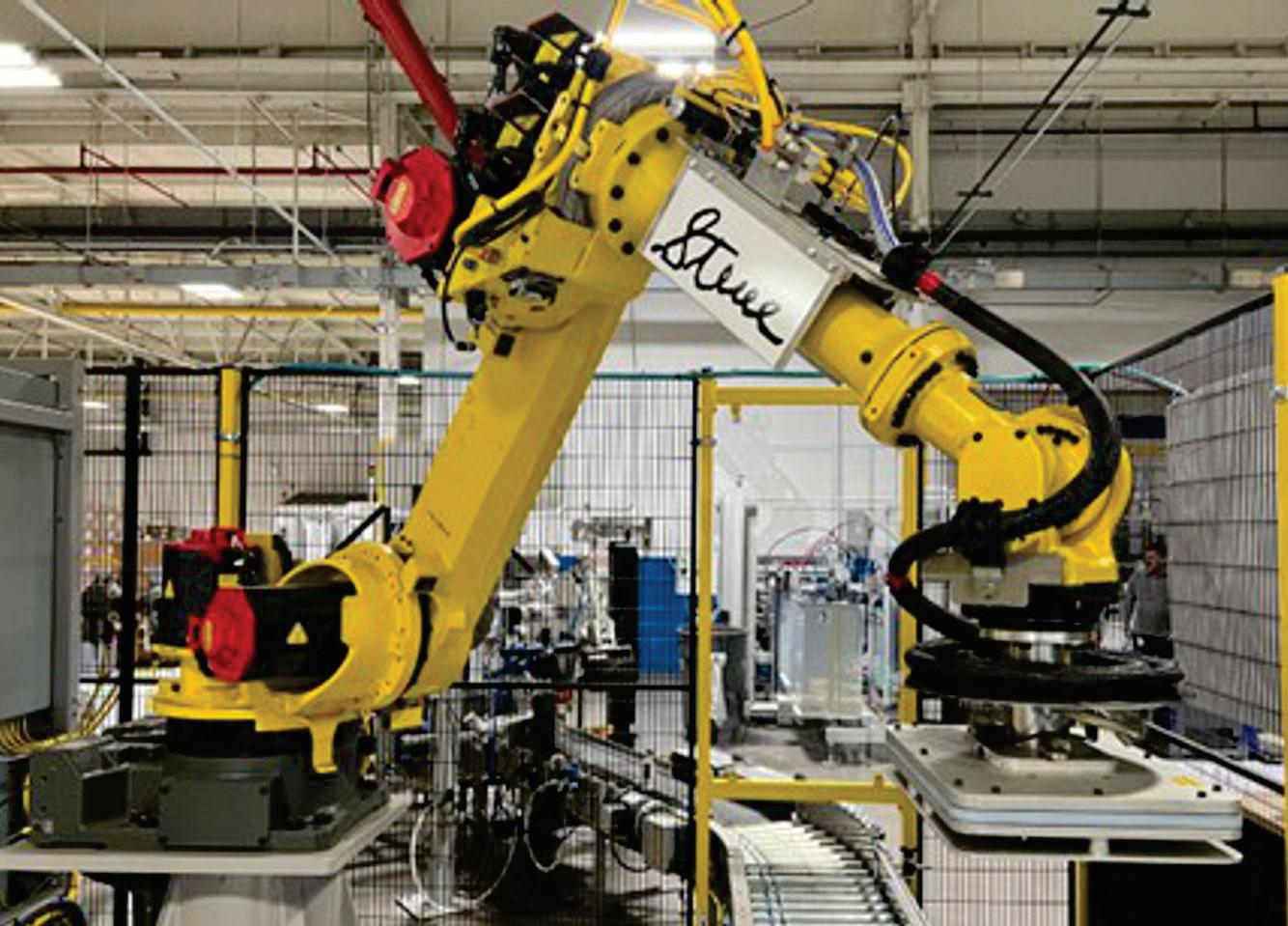
robot replacing them, they quickly saw that Leonard’s had no plan to remove their valuable human workers. Instead, Steve allowed Leonard’s production crew to focus on quality control, improve the end product, and spend more time deep cleaning the facility and organizing the warehouse.
In addition, Steve the robot increased productivity, created a safer work environment, and reduced waste and damage to the product. Leonard’s overhead also bene ted from the robotic arm’s energy e ciency.
Lessons Learned
In re ecting on this experience, Iskra o ered the following observations to other smaller businesses that might be considering automation and/or robotics:
Get started now. In retrospect, Iskra wishes she hadn’t waited so long to pursue automation. She had feared the cost would be too high and the bene ts would be too low. But the opposite has occurred: the bene ts have been enormous in just the rst six months, and the costs are less than she thought. “You won’t regret it if you just jump in,” she said.
Even smaller companies can do this. Leonard’s experience showed that robotics o er an a ordable automation solution for smaller companies. To her surprise and delight, it also showed Iskra that Schneider would devise custom solutions for smaller companies.
Success requires the right partner. e advice Iskra received to contact Schneider proved to be great advice. Her expectations were exceeded every step of the way—in communicating her situation and challenges, in devising the right solution, during implementation, and more. “ ey made me feel part of the process every step of the way,” she said.
Leonard’s experience with automation and robotics has helped transform this family-owned business. With Steve the robot, Leonard’s now has almost three times as much bag-in-box capacity and has increased employee productivity while easing the physical burden on workers. e work environment is safer, there is less damage to the end product, the company is using less energy, and it is well positioned for future growth.
“My experience was 100% positive, and I attribute that to Schneider,” Iskra said.
Leonard’s has embraced technology and robotics to improve the company’s operations—and is thriving. ■
DATA-DRIVEN DECISION MAKING TO MEASURE CARBON IMPACT
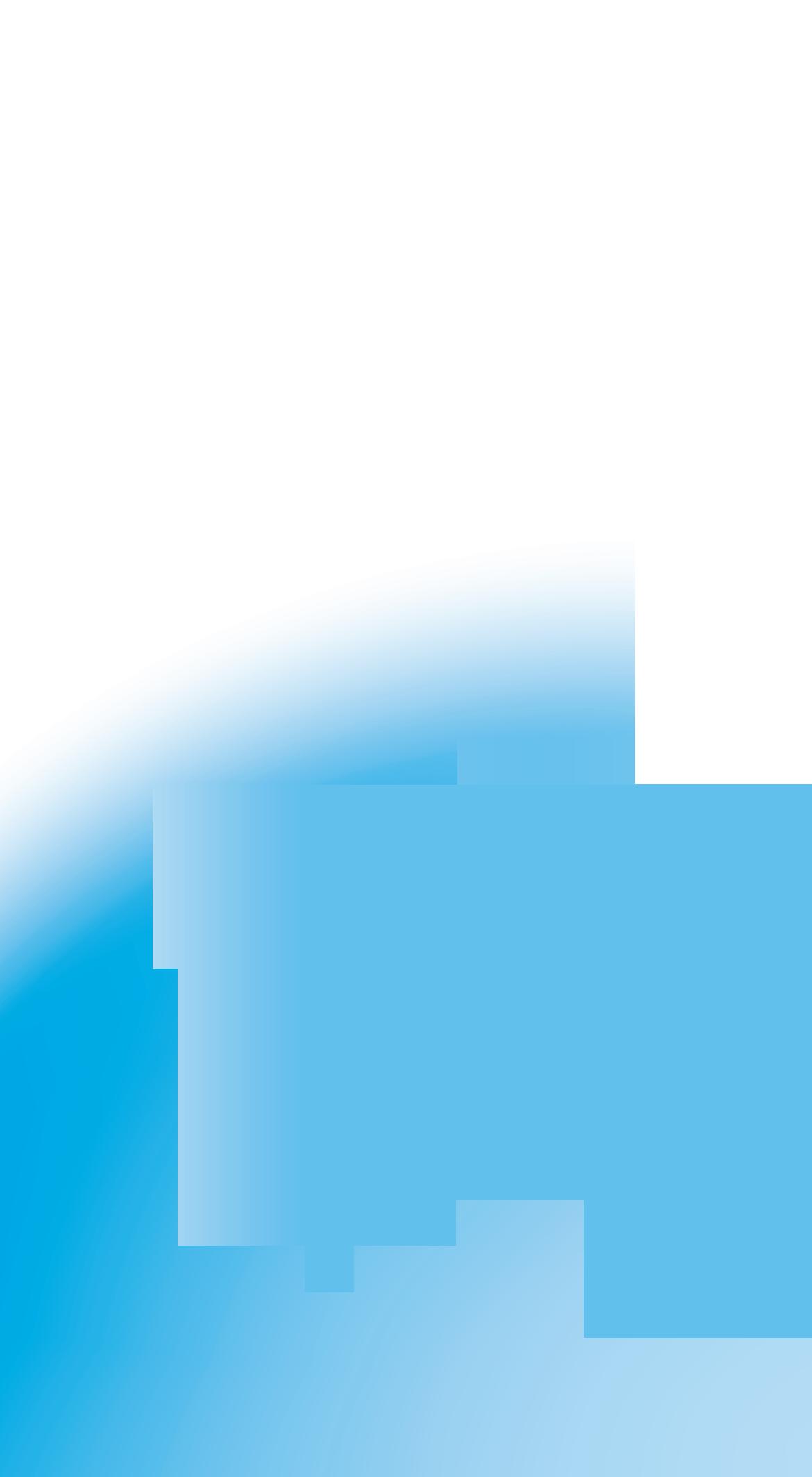
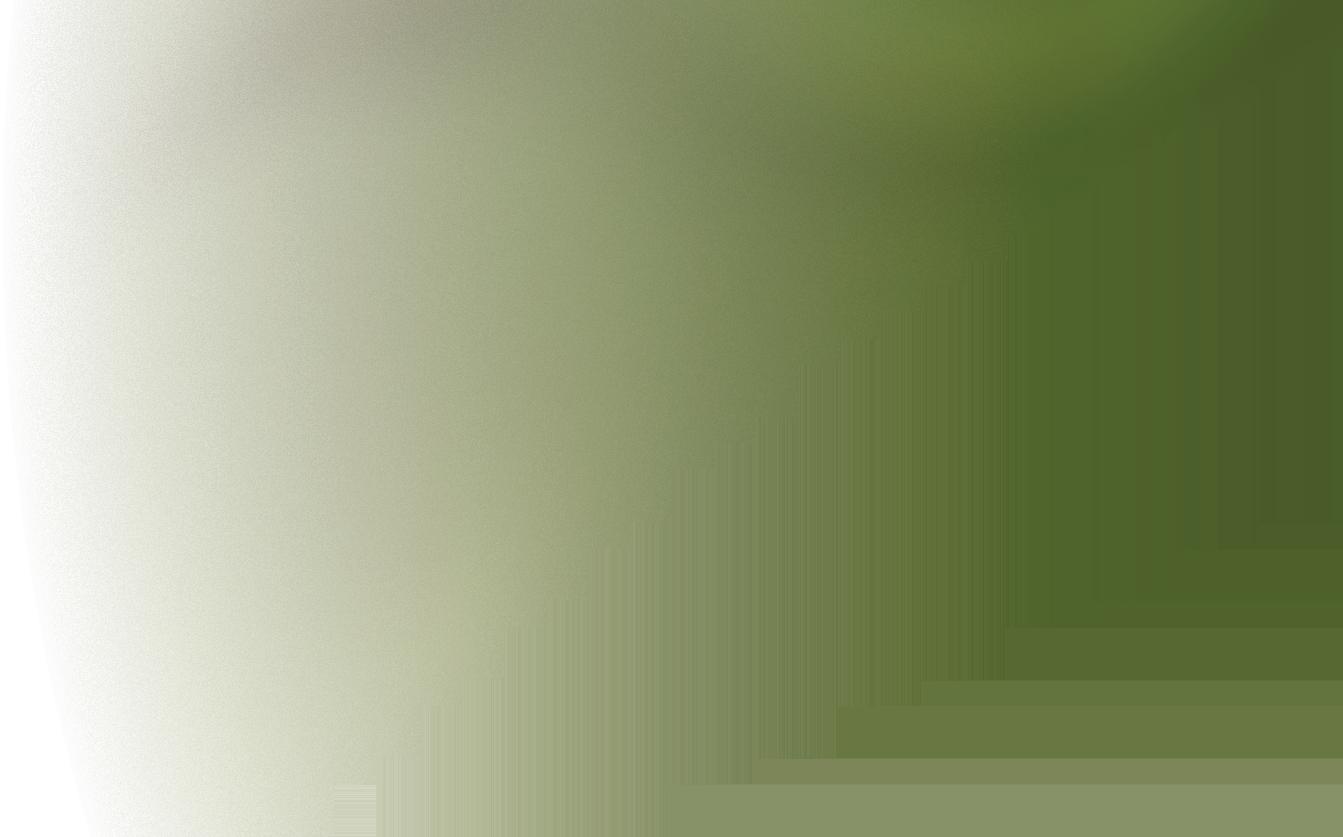
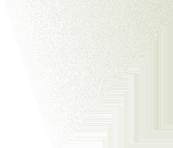



PACKAGING140MORESUSTAINABLE COMPARISONSATYOURFINGERTIPS
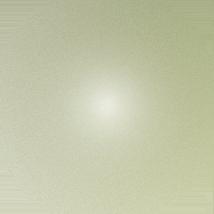
ASSET™ is Amcor’s third-party certified life cycle assessment program that measures carbon footprint at every stage of a product’s life cycle.
Rely on fact-based comparisons of different packaging to enable data-driven decisions for more responsible packaging materials.
Responsible packaging for a brilliant future.
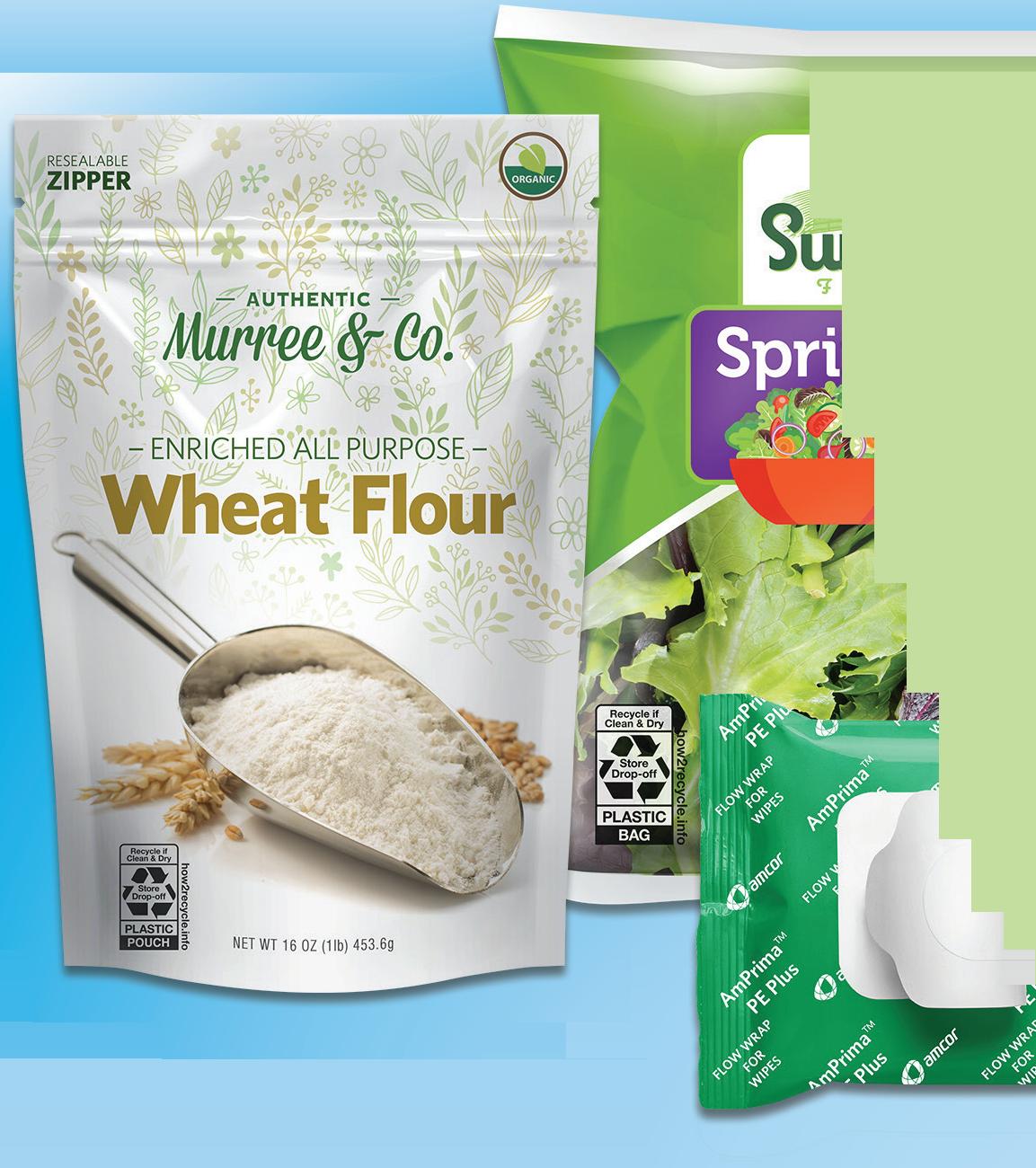

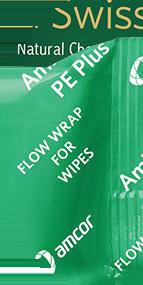

amcor.com/pack-expo

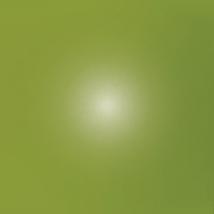
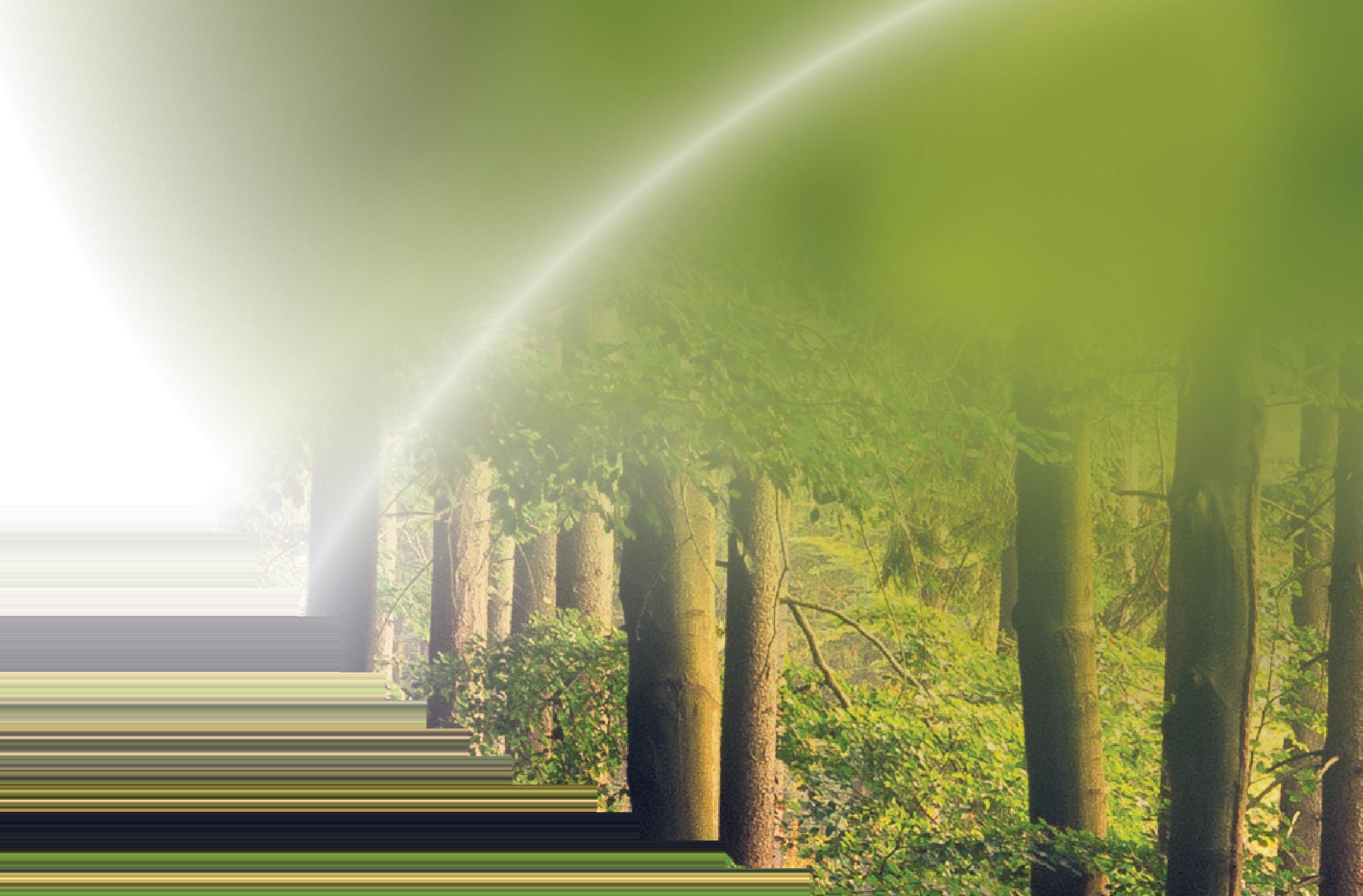
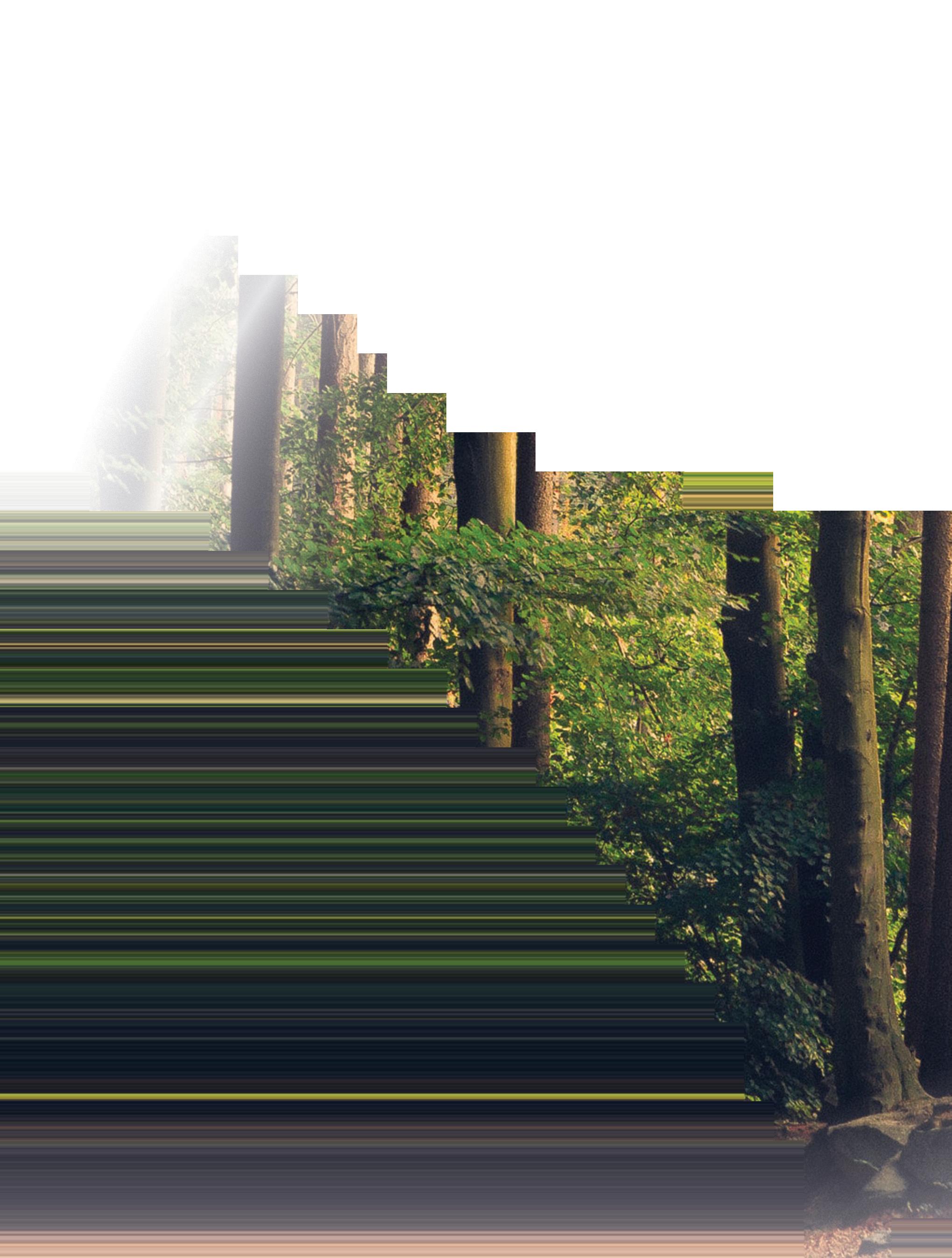
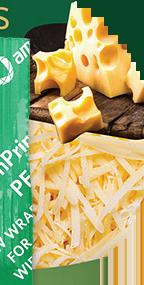
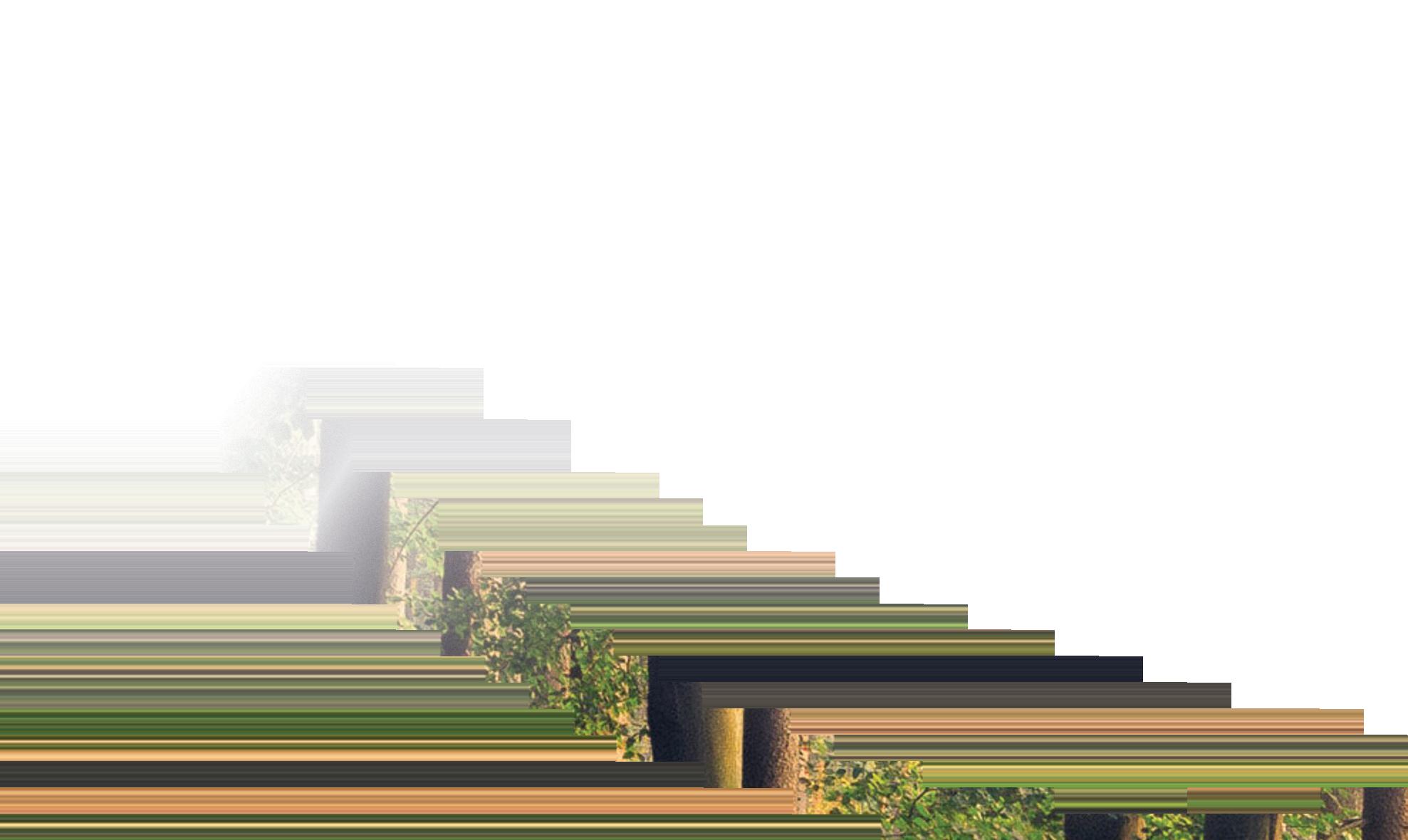
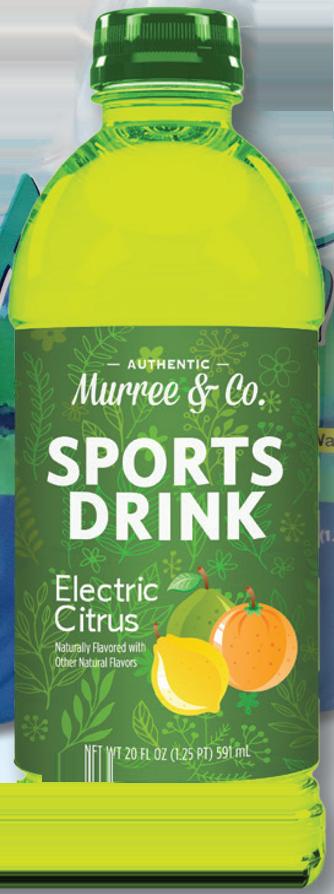

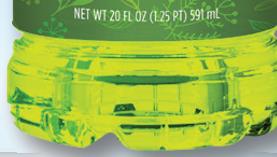
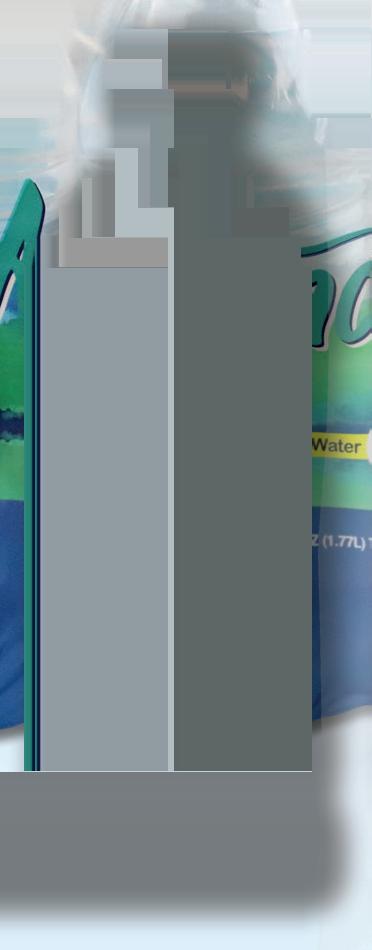
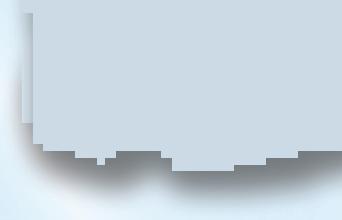
Explore the most responsible solutions, in real-time, with our sustainability experts at booth S-3705.
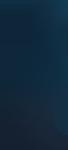
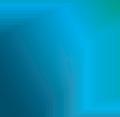


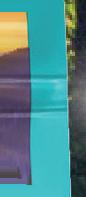
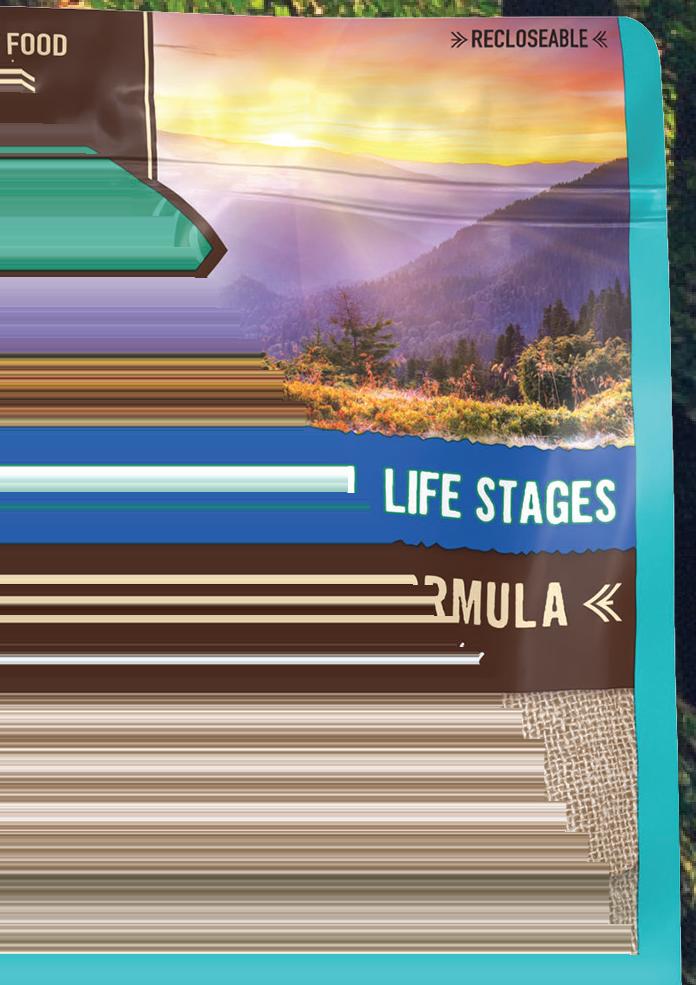

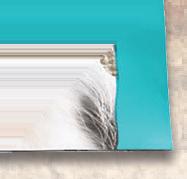
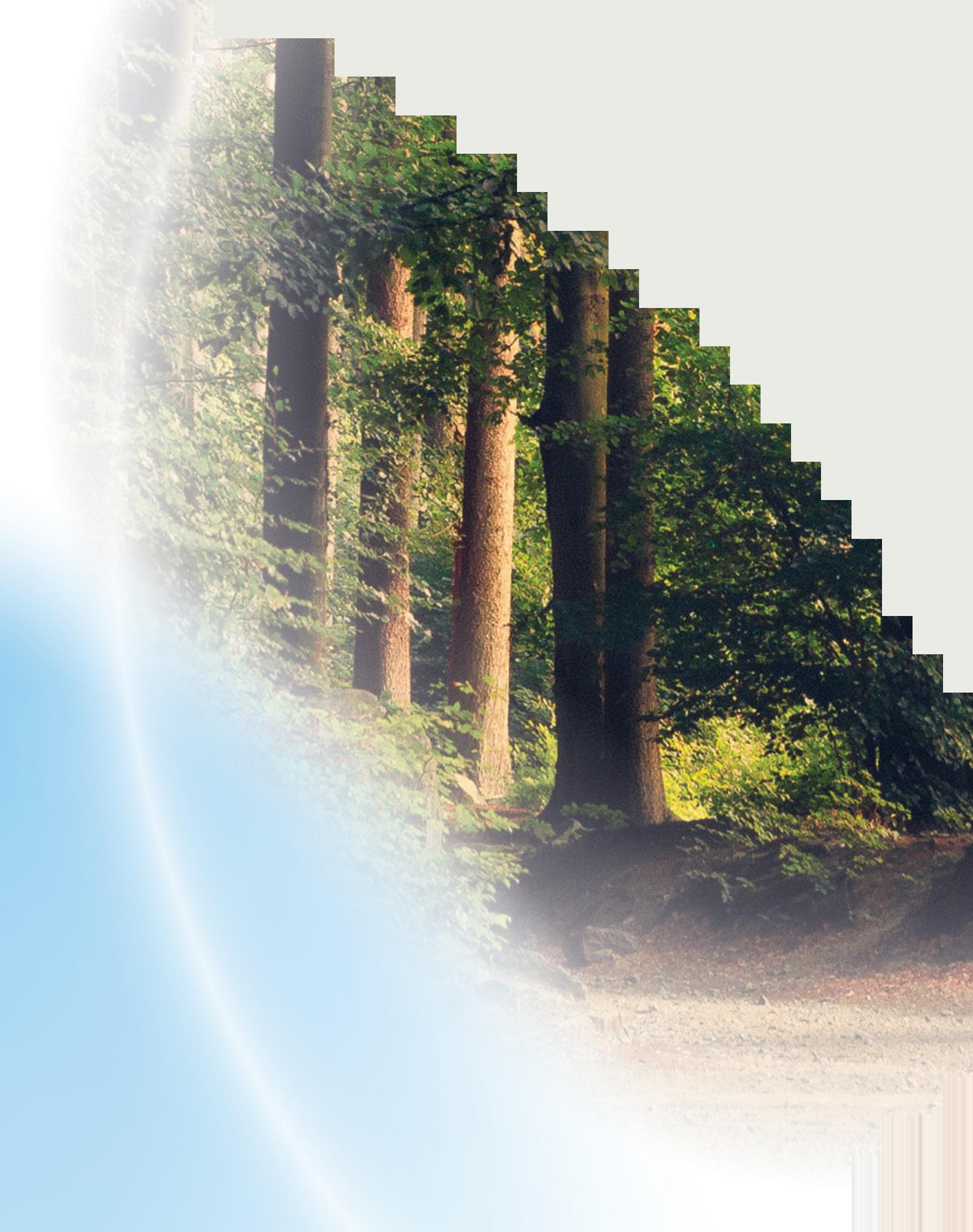
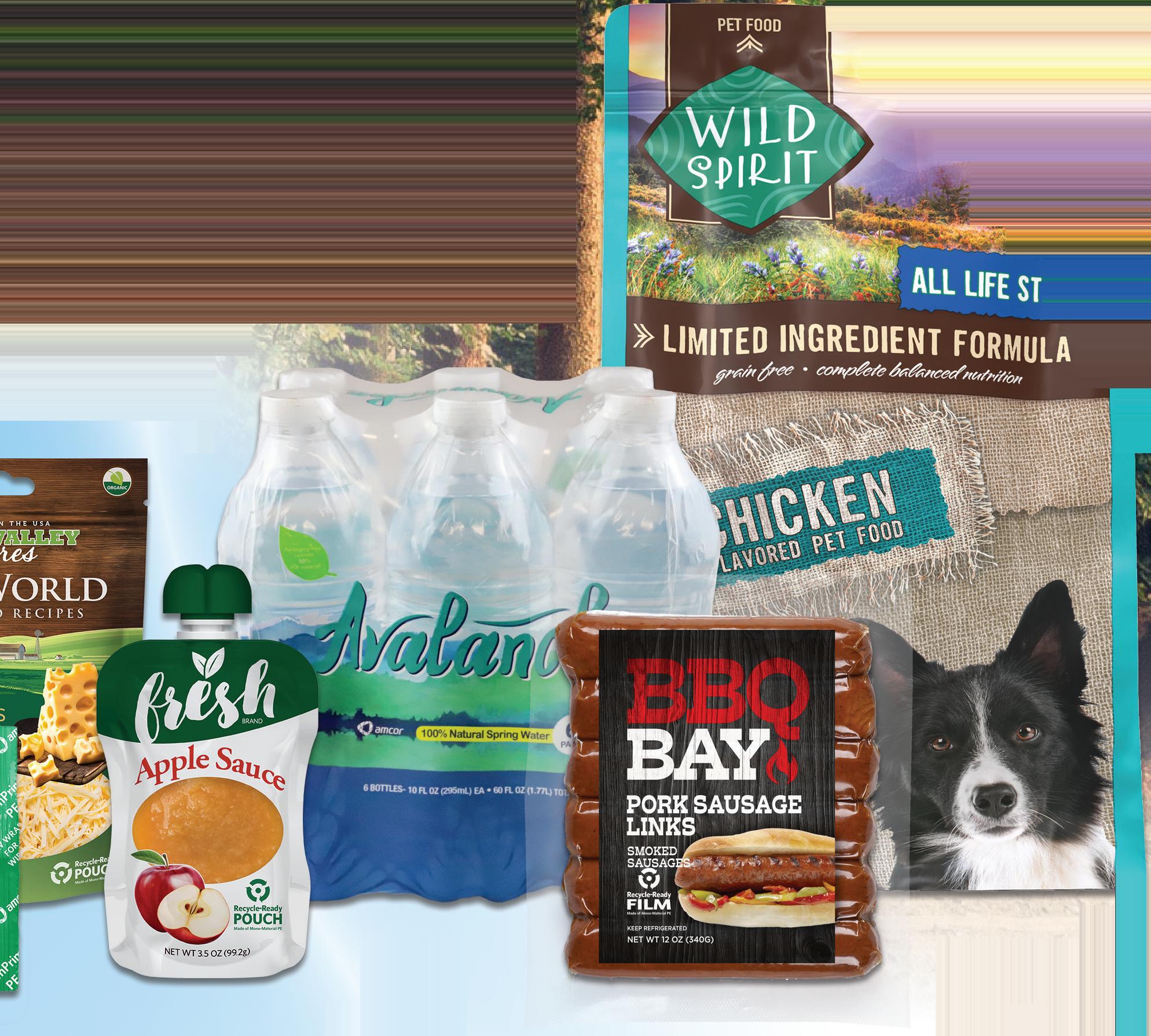
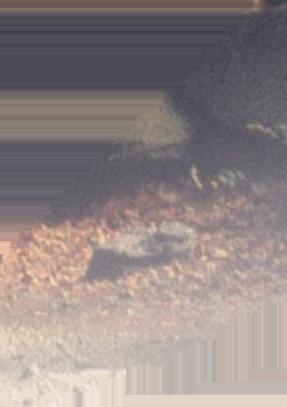

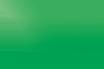



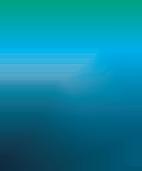
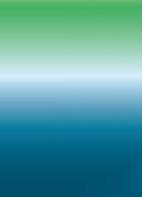
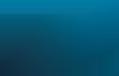
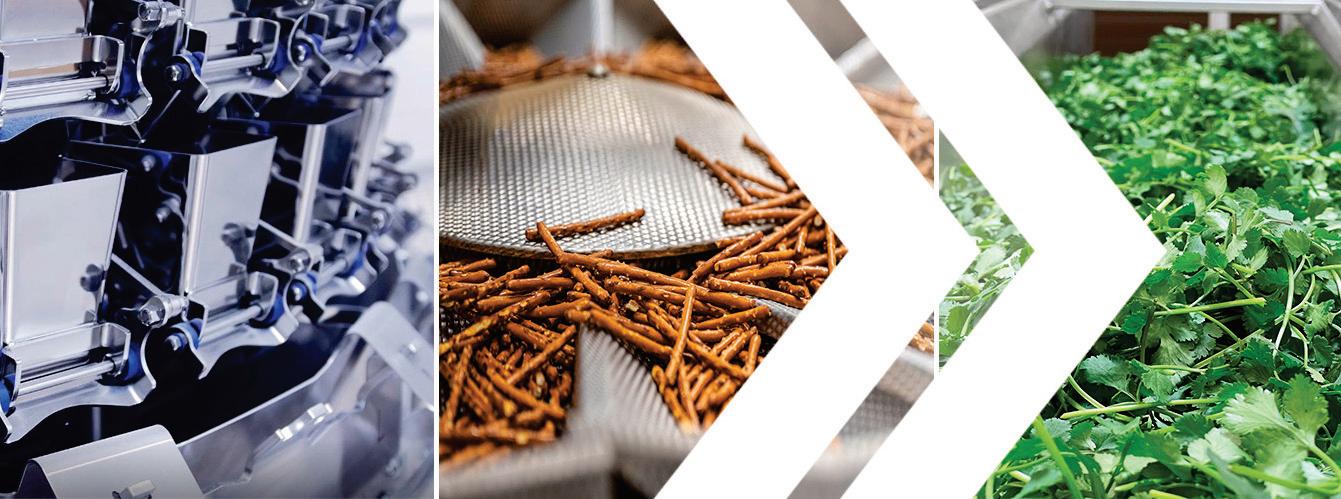

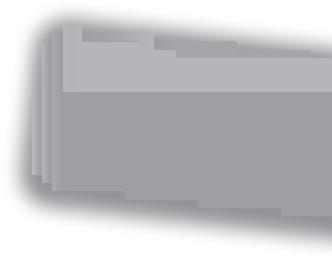
Show Floor Education O ers Insight from Industry Insiders
Session descriptions, times, and locations can be accessed by scanning the QR codes or via the show app sponsored by ProMach (Booth S-3500).
Sustainability Central Unveiled in Chicago
PACK EXPO International’s Sustainability Central is a new show feature debuting in the West Hall. Within Sustainability Central, attendees get di erent takes on sustainability from industry experts and gain insight into making brands more sustainable for the future.
Education session topics in Booth W-21020 include:
• Catalyzing Circularity
• Toward Global Recyclability Design Guidance
• Sustainability in Biopharmaceutical Packaging
• Enabling Circularity with Smart Packaging
• Sustainable Innovation: Collaborations Drive Decarbonization
• Creating a Business Case to Drive Sustainability
• Design E-commerce Packaging to Enhance Customer Experience
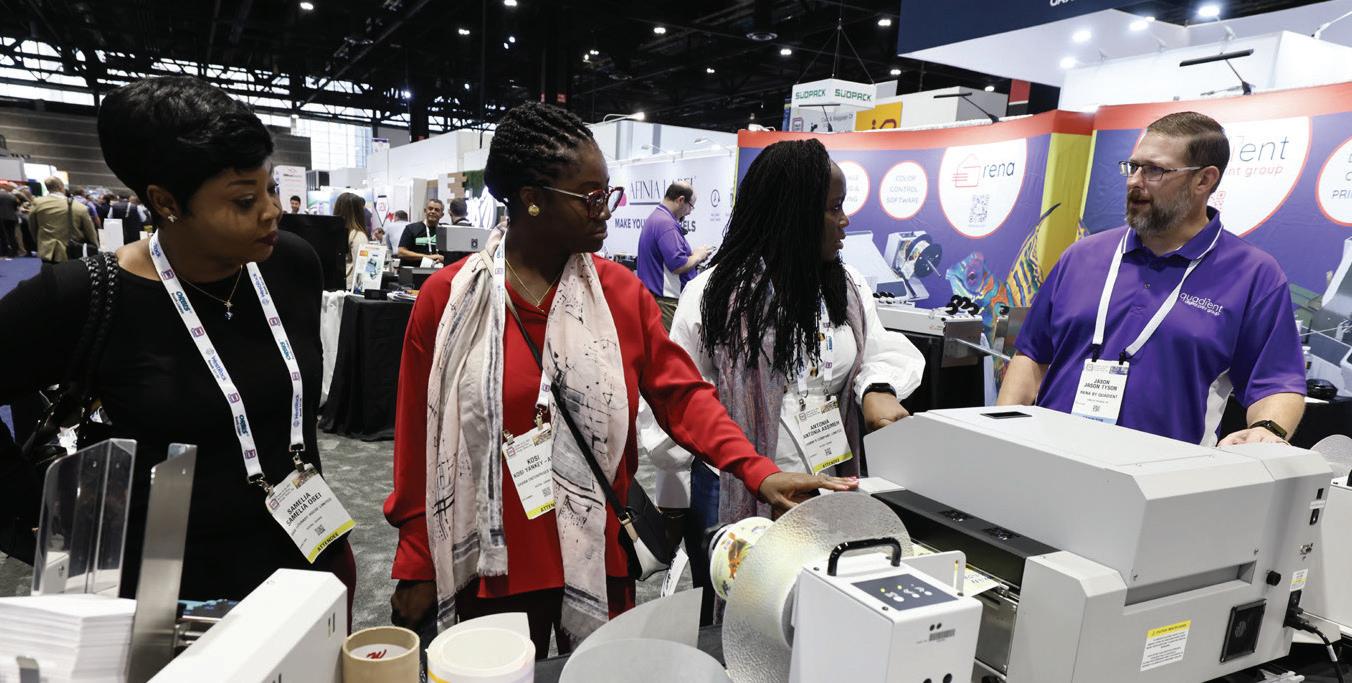
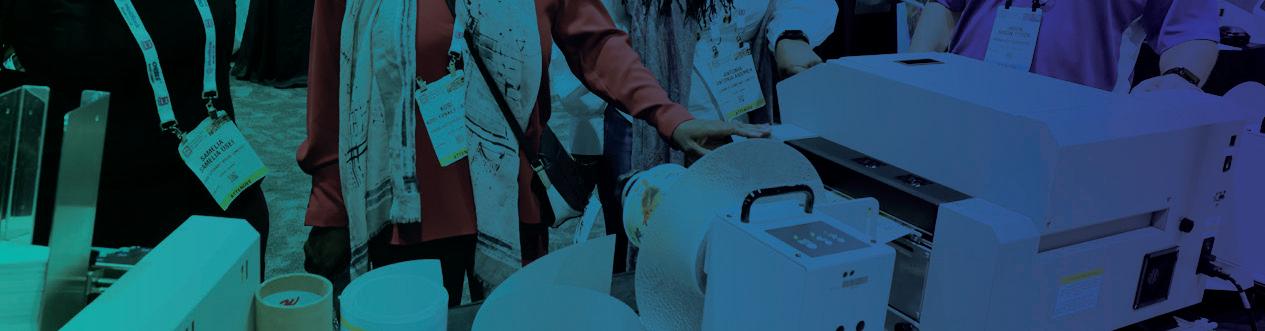

Emerging Brands Central Debuts in Chicago
PACK EXPO International’s Emerging Brands Central is a new show feature debuting in the West Hall. Emerging Brands Central features free educational sessions with industry experts, designed for brands who are scaling their manufacturing operations.
Education session topics in Booth W-20049 include:
• How to E ectively Scale Your Operations rough Methods Like Value Engineering and Incremental Automation
• Responding to Consumer Demand for Product Innovation
• Developing a Smart Growth Strategy for Manageable and Controlled Scalability
Plus, take advantage of our free expert advisors who will be on-site during the show.
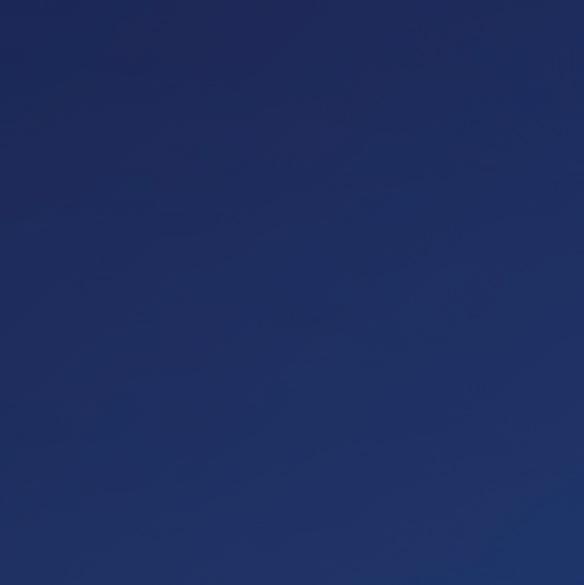
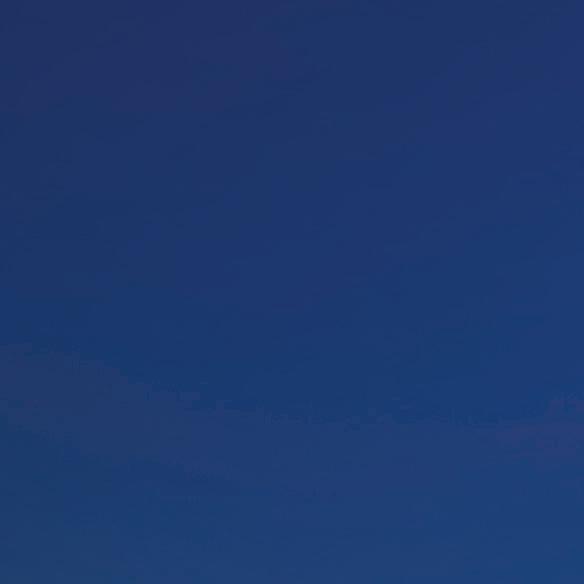
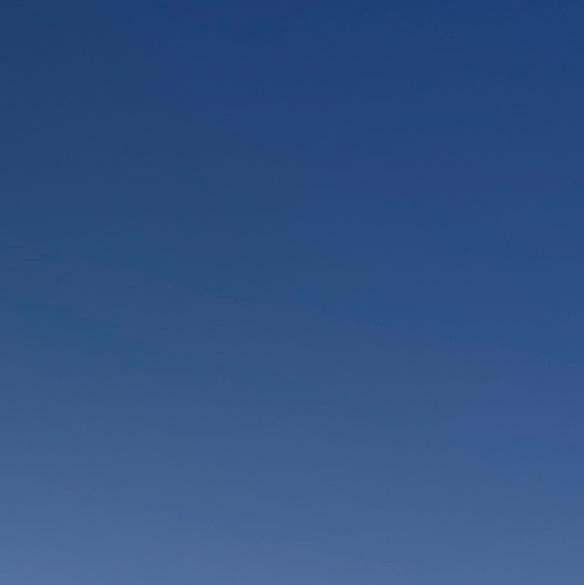
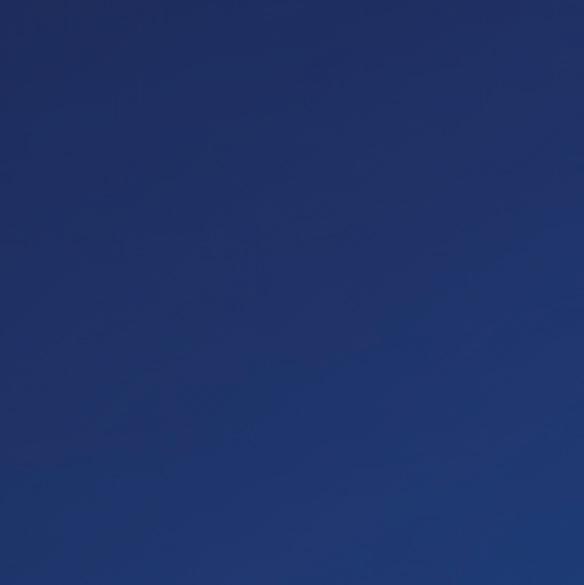
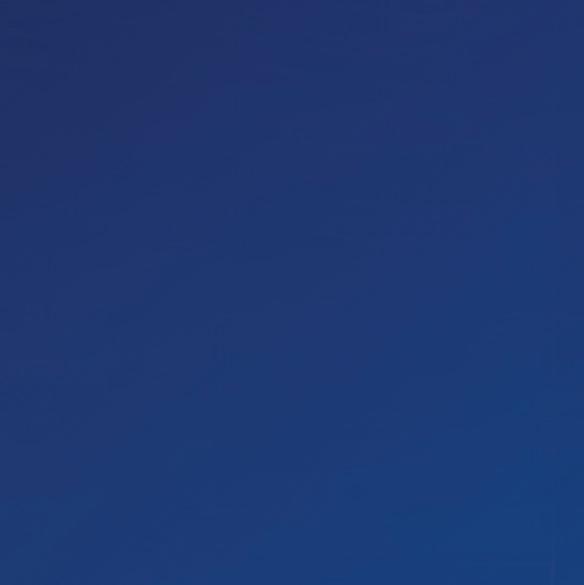
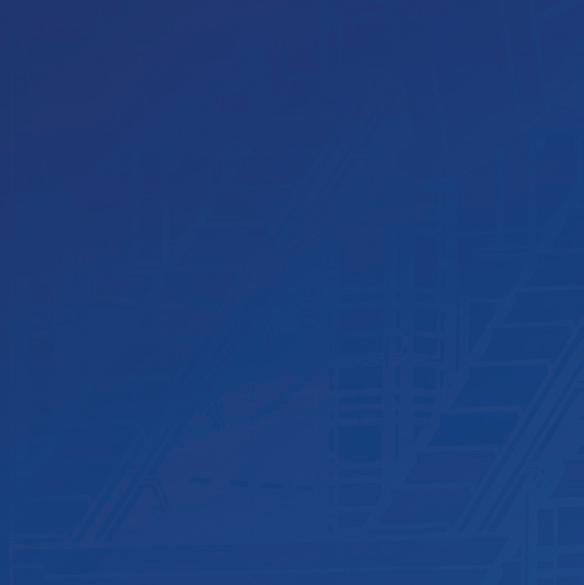
VDG Drum Motors
Maintenance-Free Conveyor Belt Drives
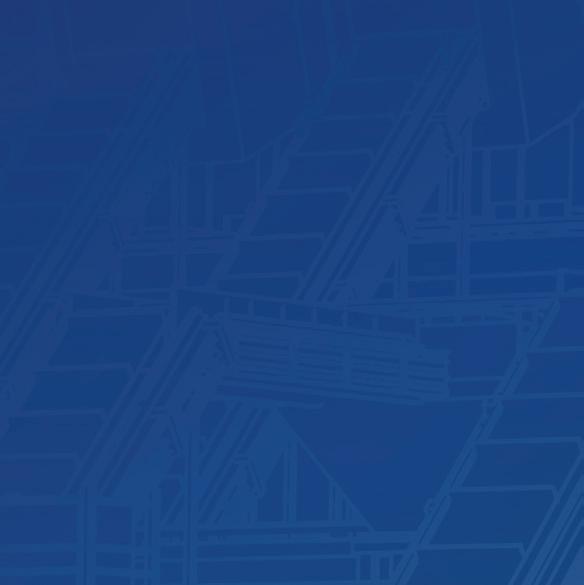
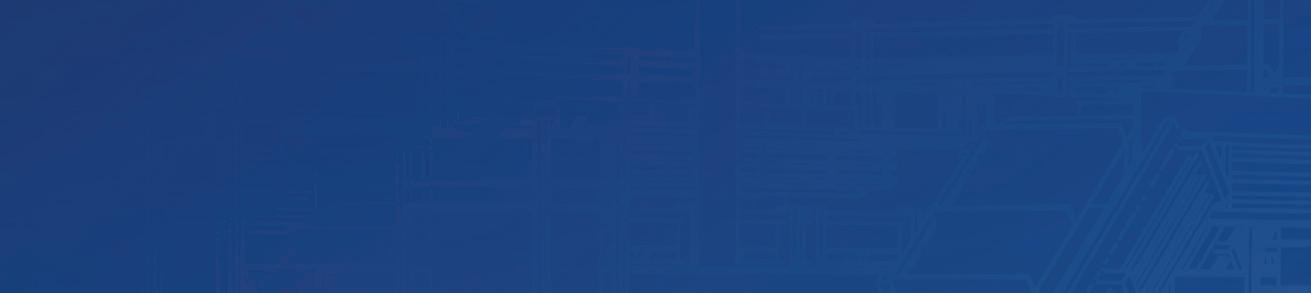
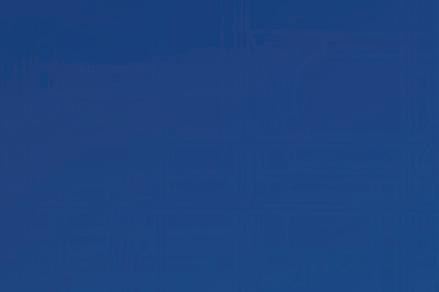
All drive components of the VDG Drum Motor, including the premium-efficiency electric motor, gear reducer, and bearings, are enclosed and protected inside the drive drum and maintenance-free for 80,000 hours of continuous operation, reducing operational and maintenance costs while increasing throughput.
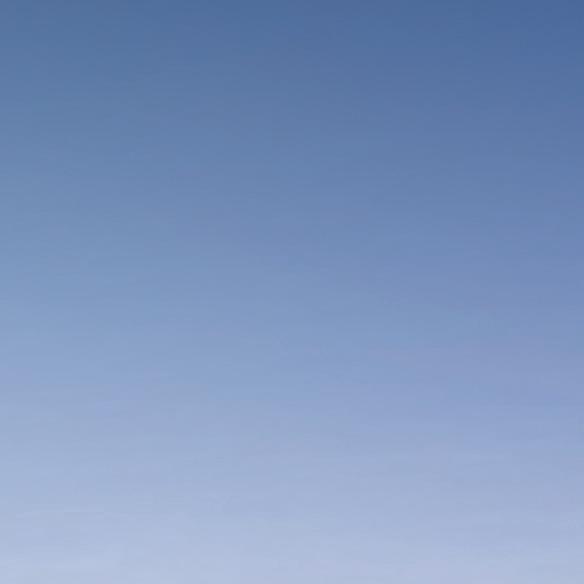

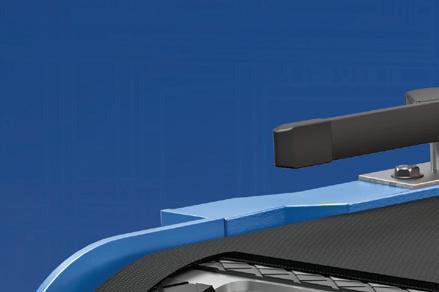

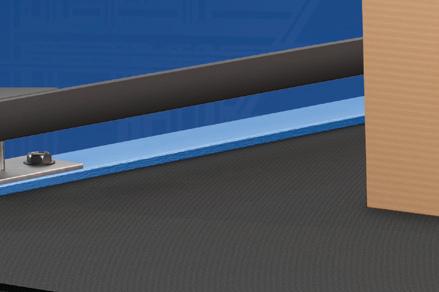
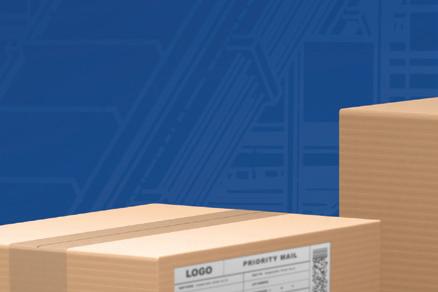
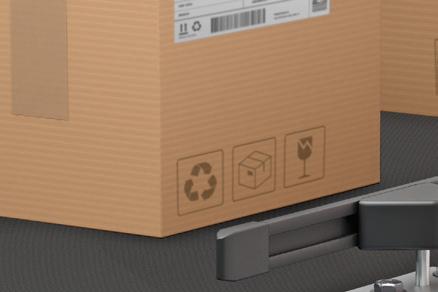
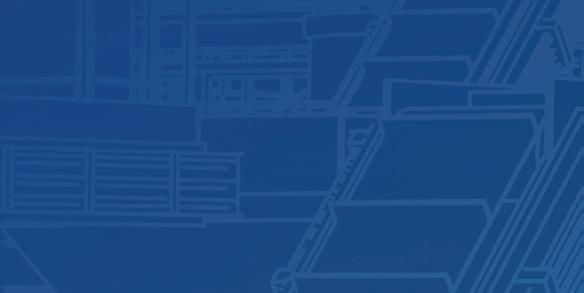
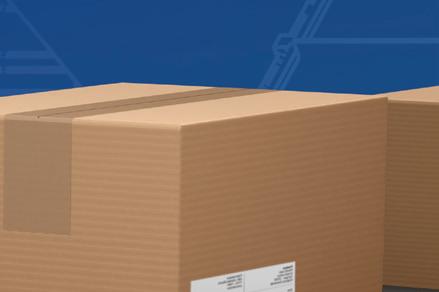
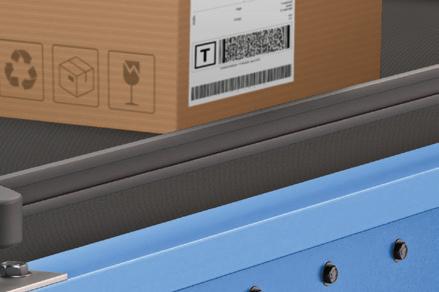
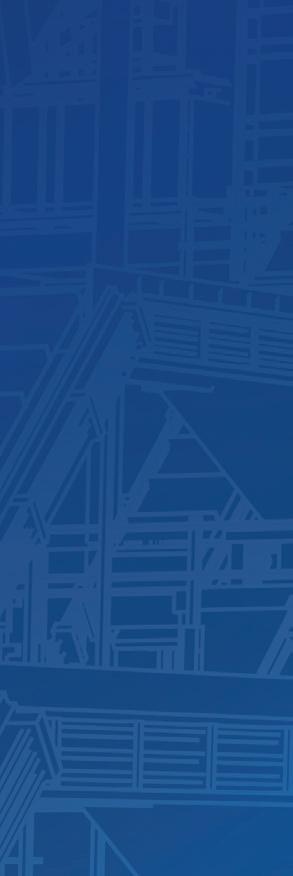
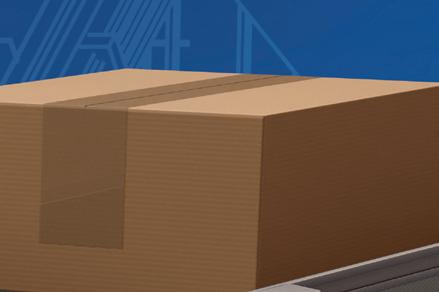
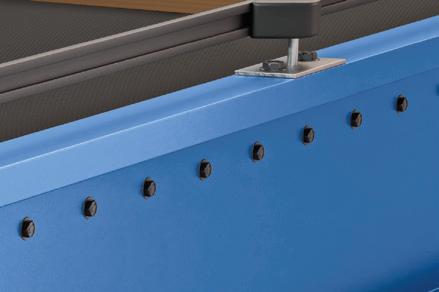
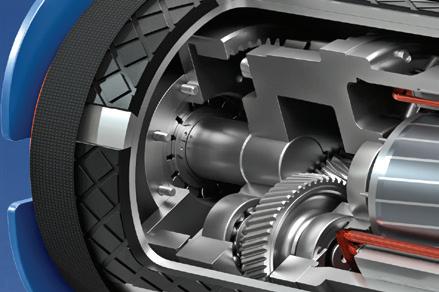
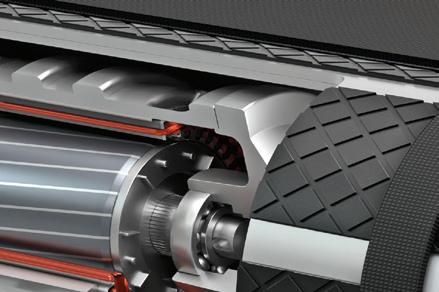
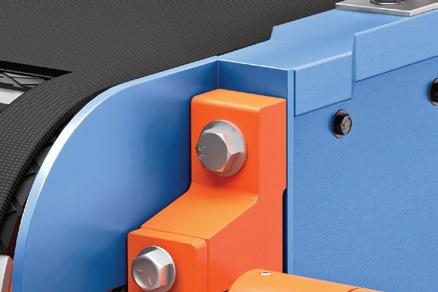
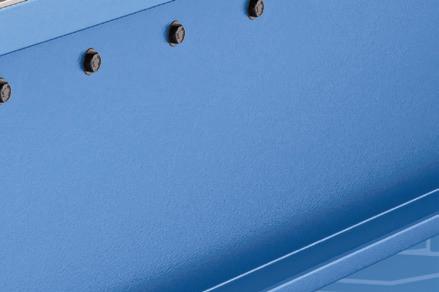
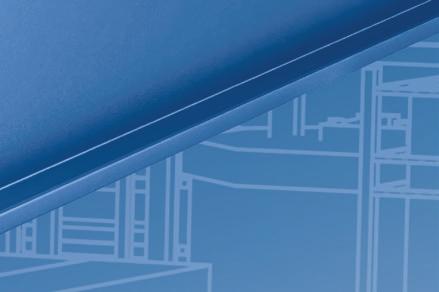
Premium-Efficiency Electric Motor
Eliminate Routine Maintenance
Low Cost of Ownership
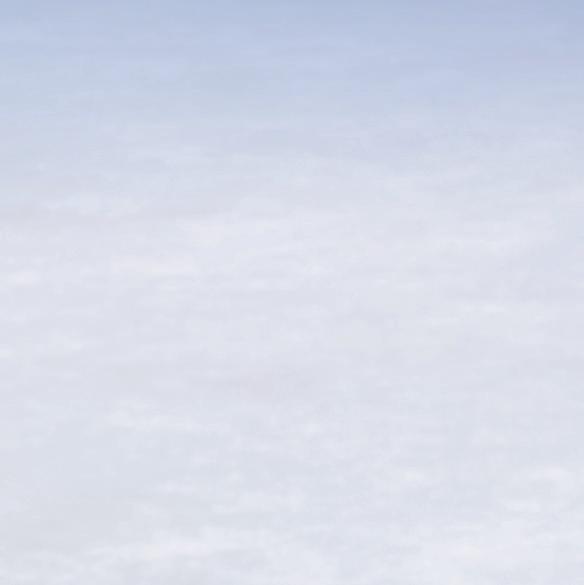
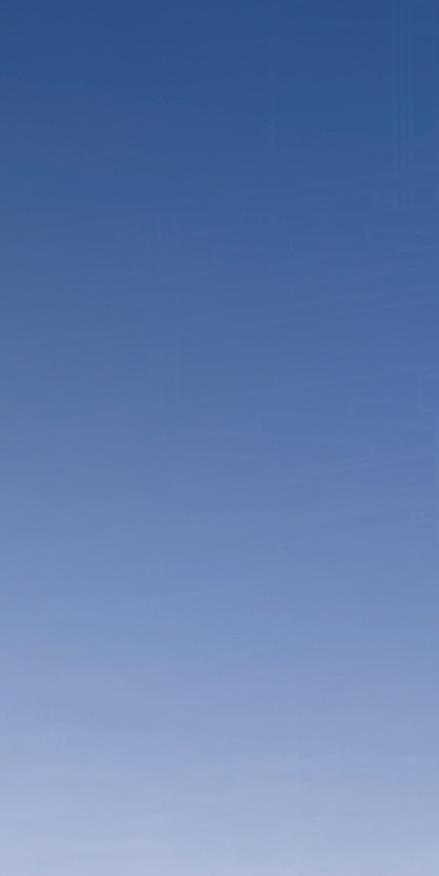


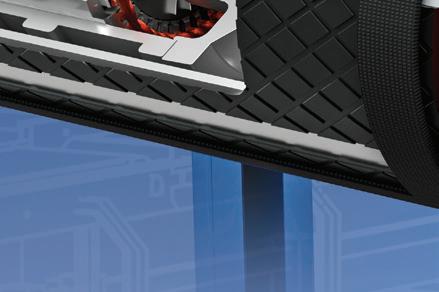
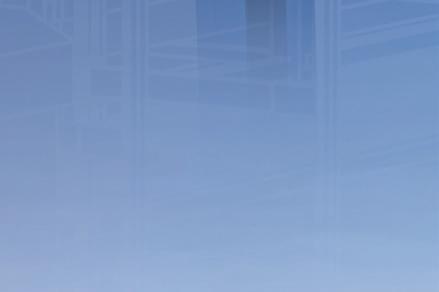
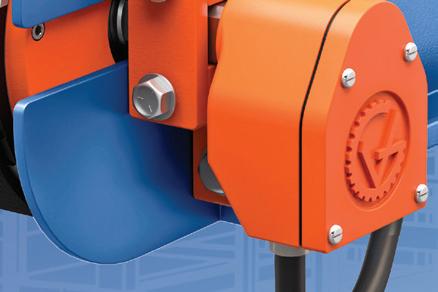
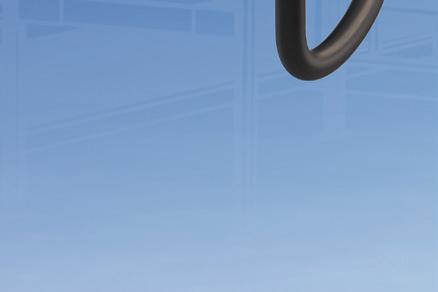


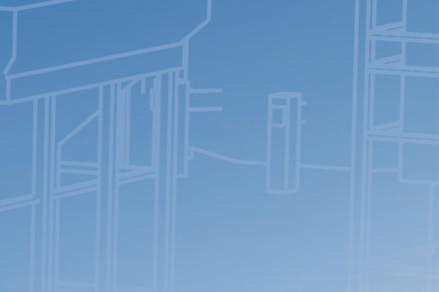
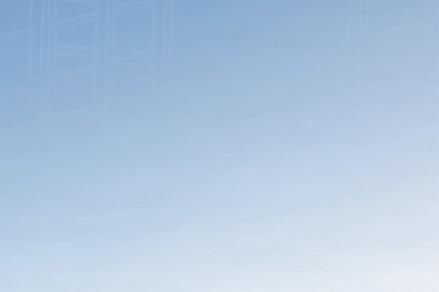

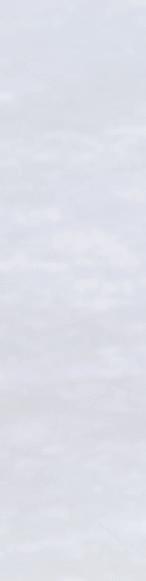
For sanitary applications, SSV Series Drum Motors are manufactured in all-stainless steel, feature an IP69K-rated sealing system, withstand pressure washdown up to 3,000 psi, and drive modular, wire mesh, and monolithic thermoplastic conveyor belts without using sprockets.
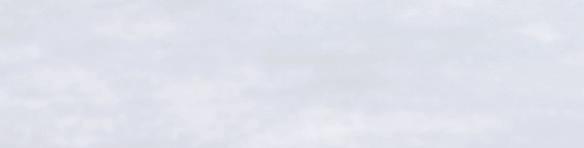
INCREASE ELIMINATE REDUCE
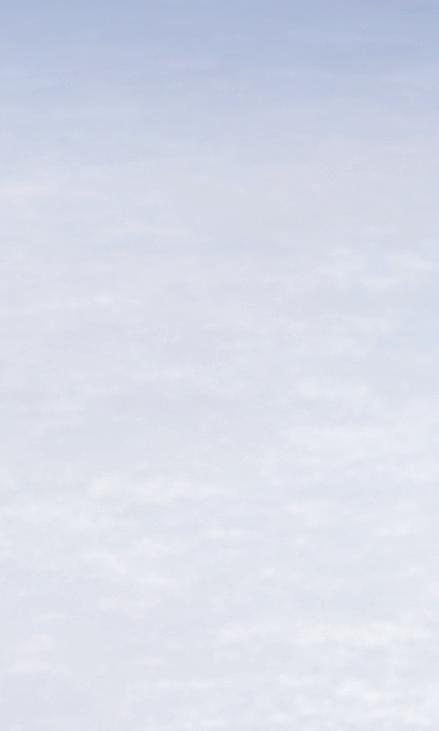
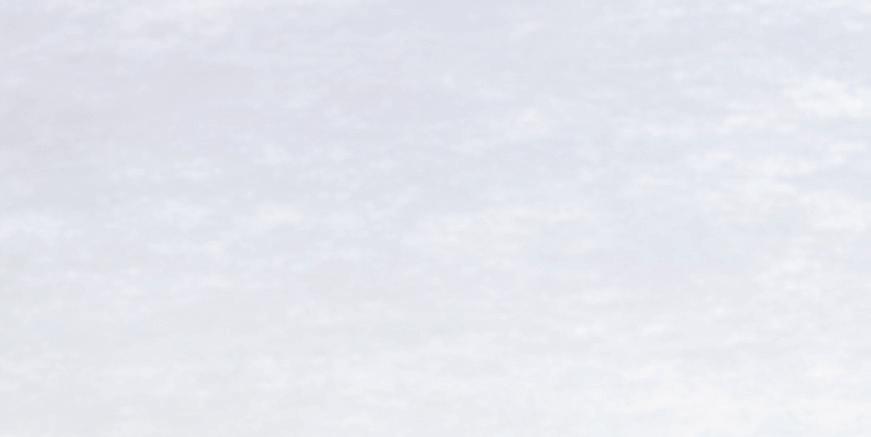
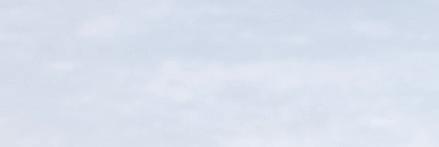

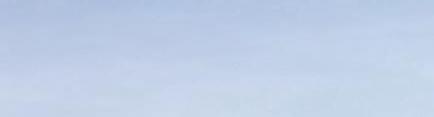
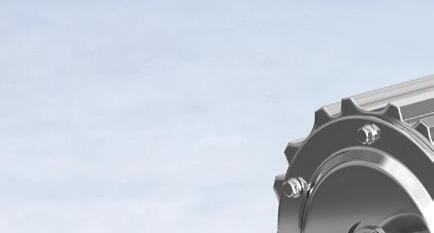

Conveyor Hygiene Drive Sprockets Water Usage & Time for Washdown
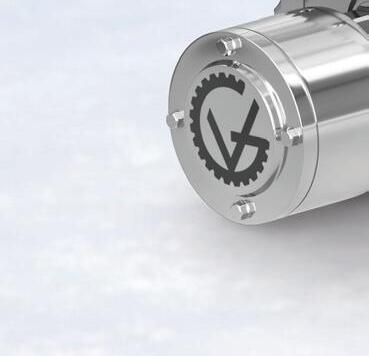


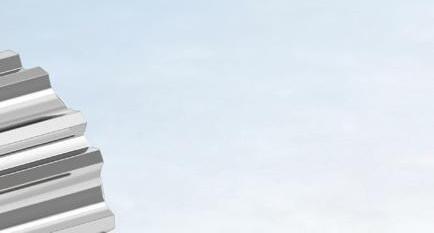
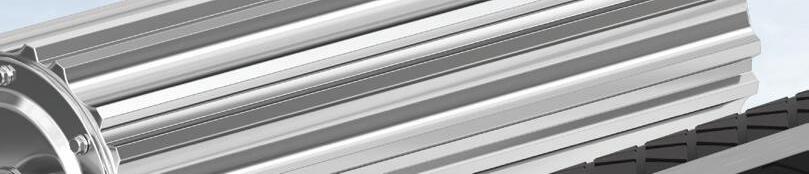

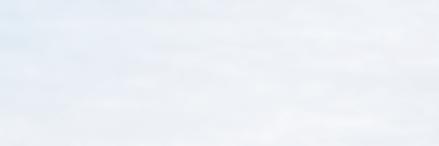
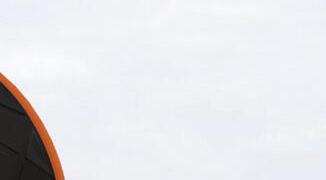

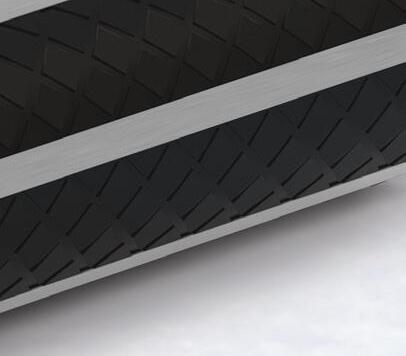
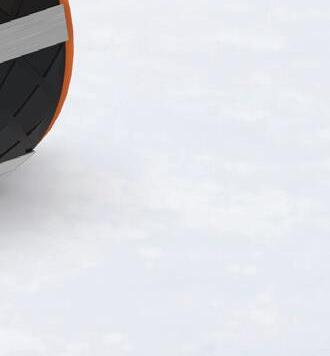
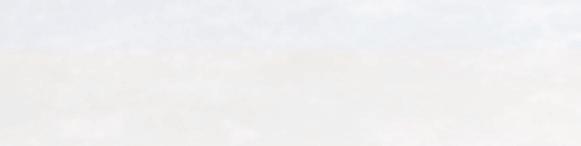
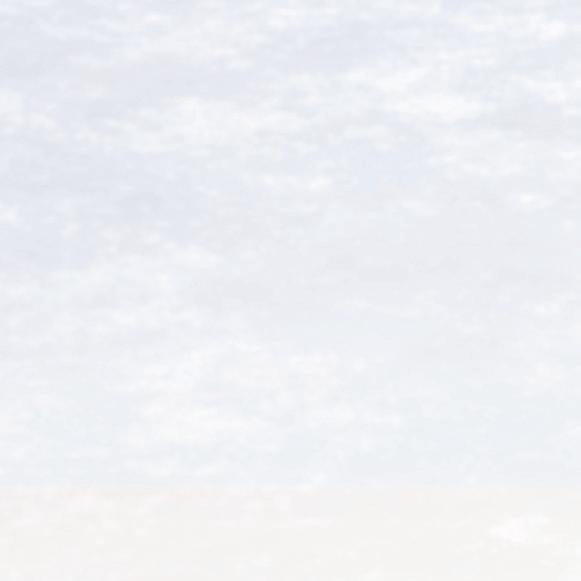

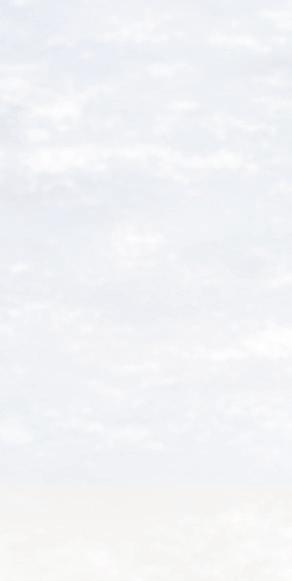
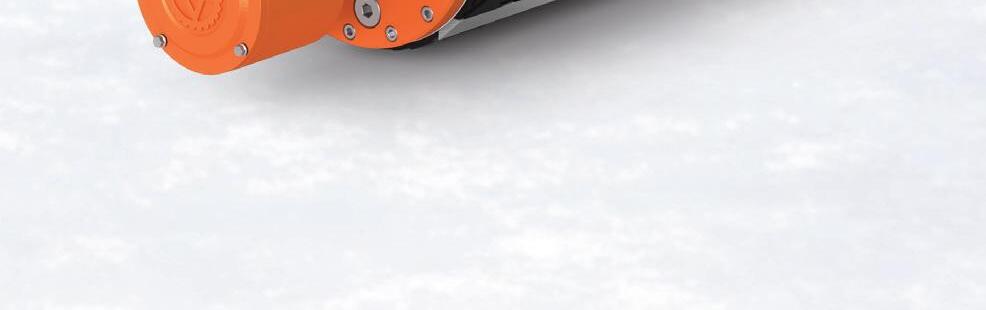
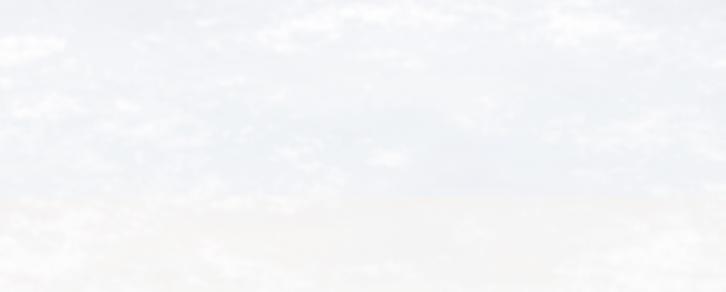
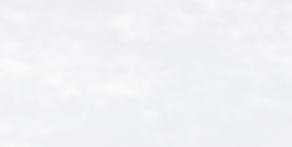
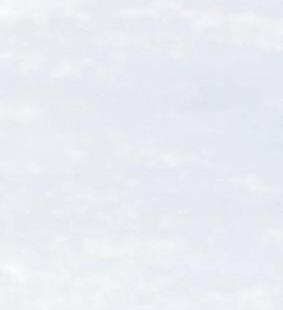
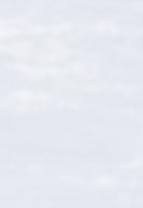
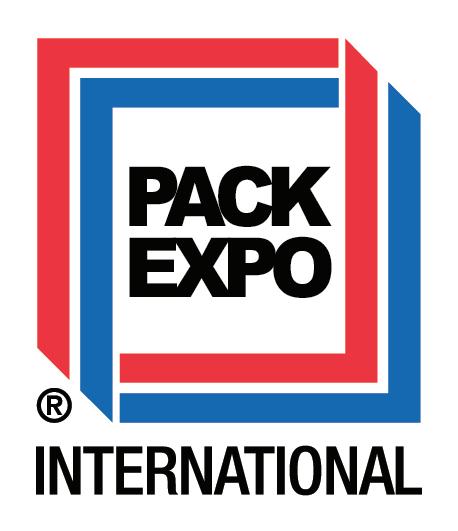
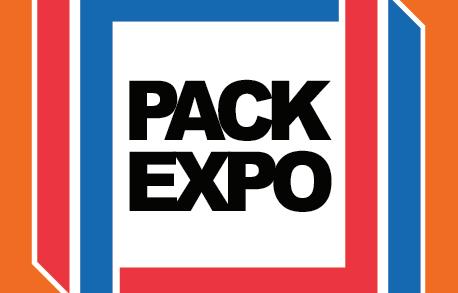
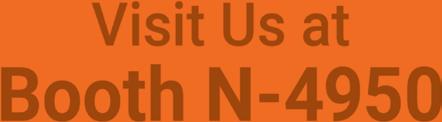

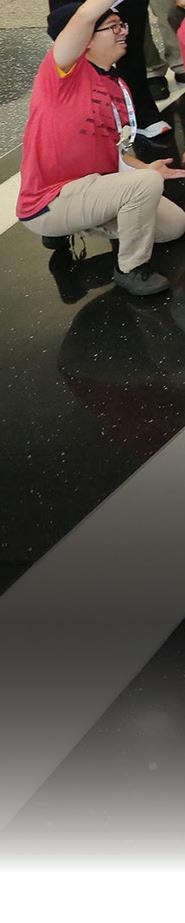


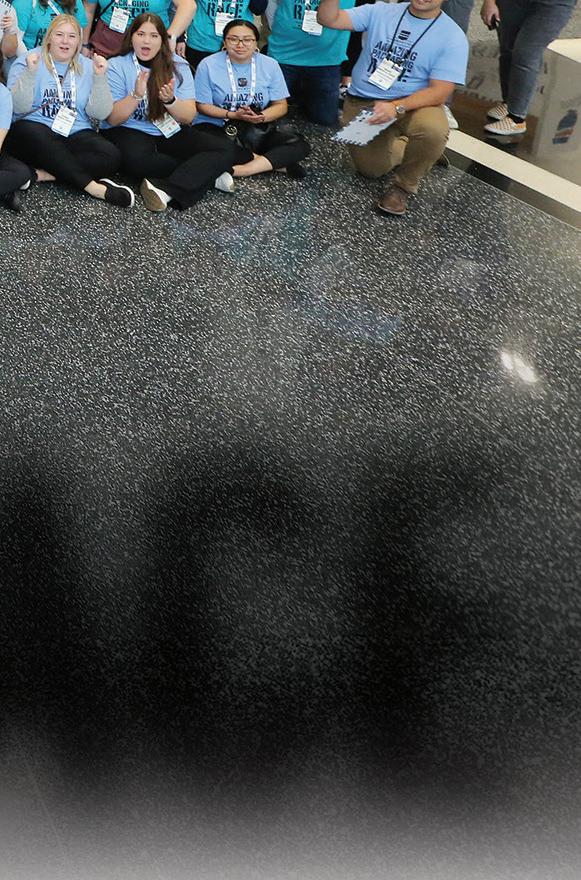

Wednesday, November 6
THE PARTICIPANTS
Packaging and engineering students from across the country.
THE MISSION
Tour the PACK EXPO show floor, visit participating exhibitor booths and complete challenges.
THE GOAL
Learn about new technologies and interact with industry professionals, while earning points for packaging-related challenges. Members of the winning teams will receive cash prizes, courtesy of Emerson. Brought
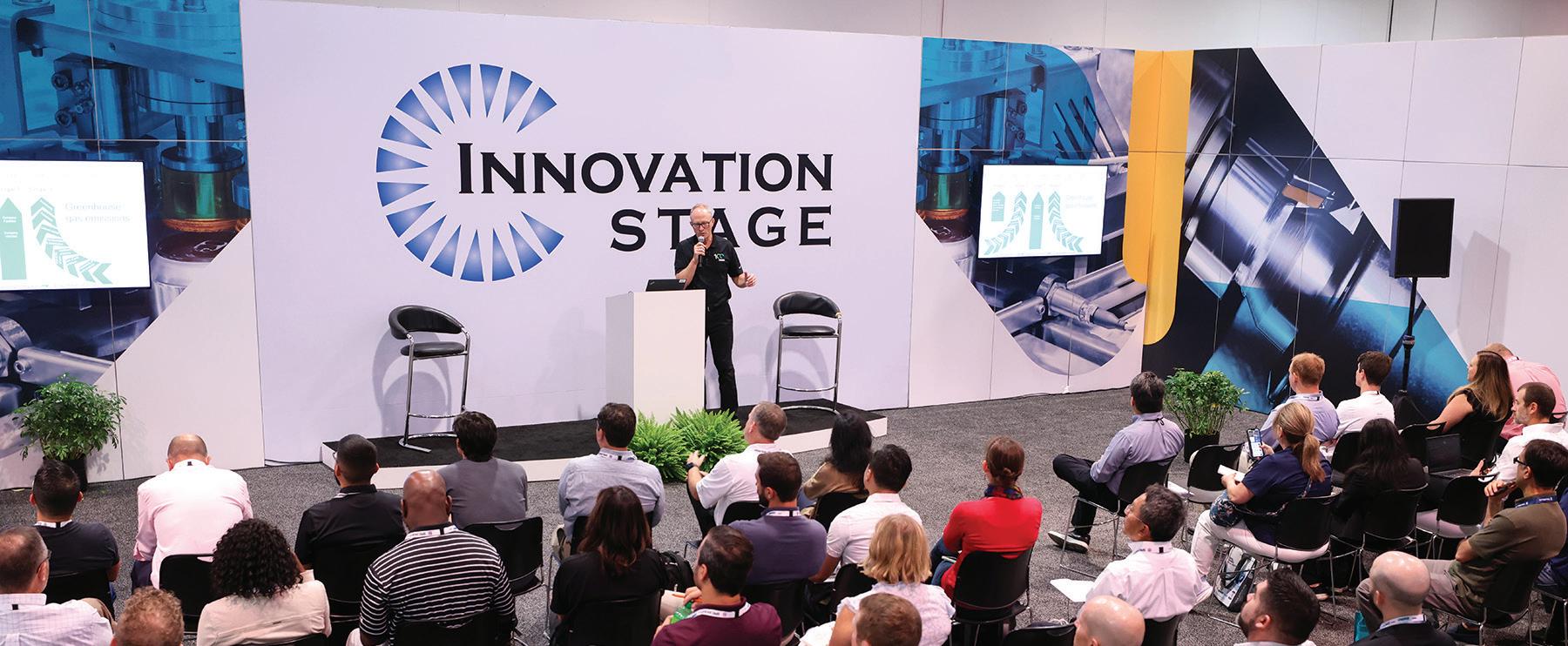
Innovation Stages for Free Cutting-Edge Education Sessions
For up-to-the-minute content, head to the always-popular Innovation Stages (Booths N-4560, N-4580, and N-4585). Exhibitors and subject matter experts present packaging industry breakthroughs, new products, and best practices during fast-paced, 30-minute seminars presented on three stages.
Education session topics include:
• Designing the Future of Packaging
• Ensuring Food Safety
• AI Strategies to Meet Packaging Circularity
• 2024 Maintenance Trends & Challenges
• Accelerating Digitalization
• Leveraging Data for Predictive Maintenance
Education for Improving Food and Beverage Operations
Got 30 minutes? Take a seat at the Processing Innovation Stage (Booth LU7147) to hear about the latest food and beverage processing breakthroughs and improvements to make in operations. Content is targeted to food and beverage manufacturers. Exhibitors and subject matter experts present packaging industry breakthroughs, new products, and best practices during fast-paced seminars.
Education session topics include:
• Advances in HPP
• Transformative Waste Management
• AI-Enabled Vision
• Demystifying Automation
• Next Gen PEF Technology

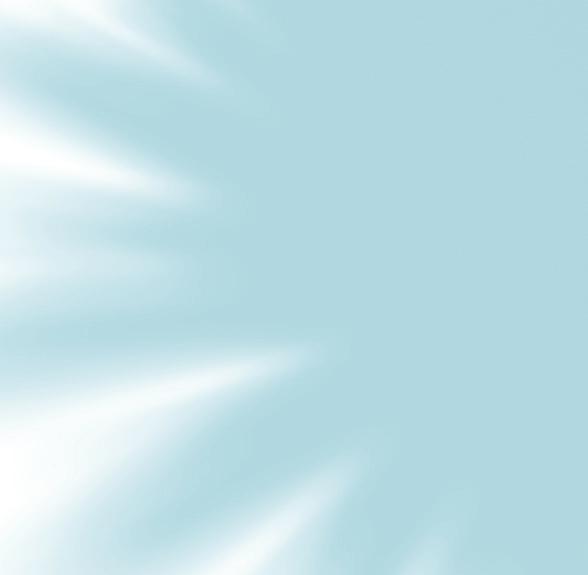
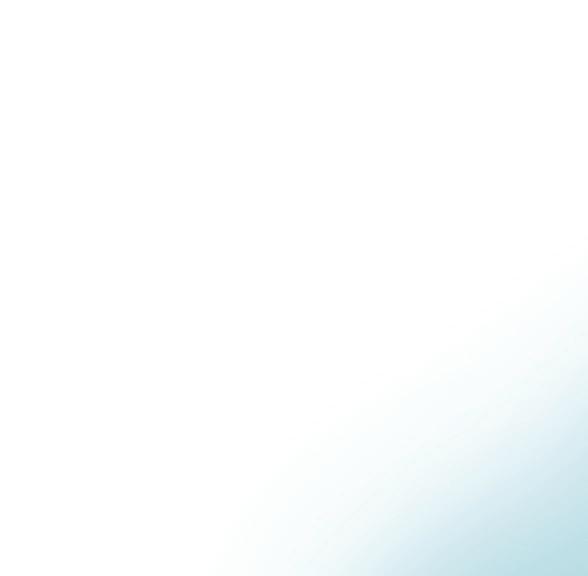

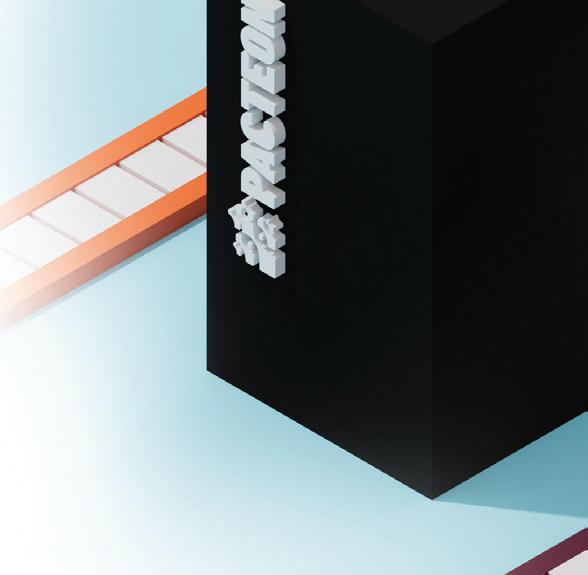
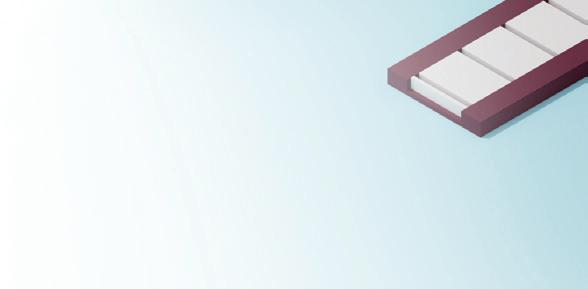
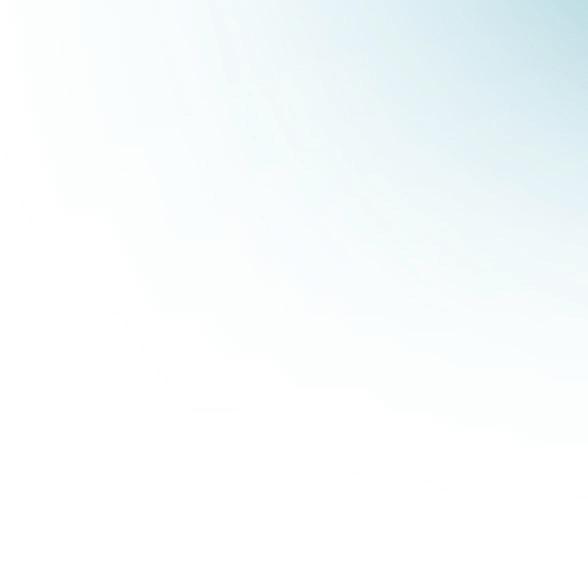
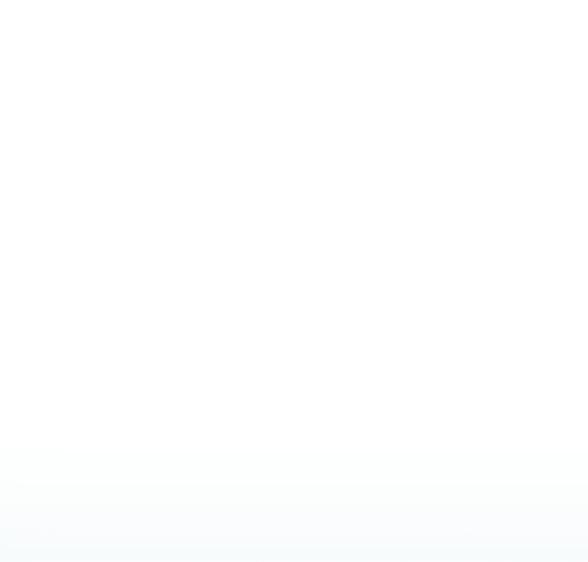
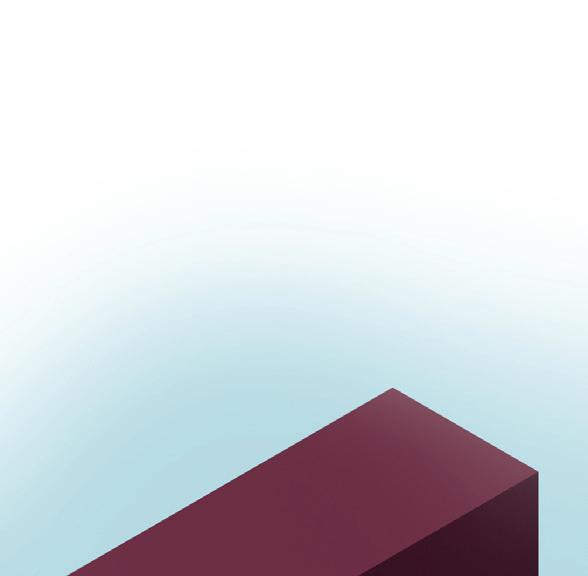

N -O -LIN
IN SOLU IONS
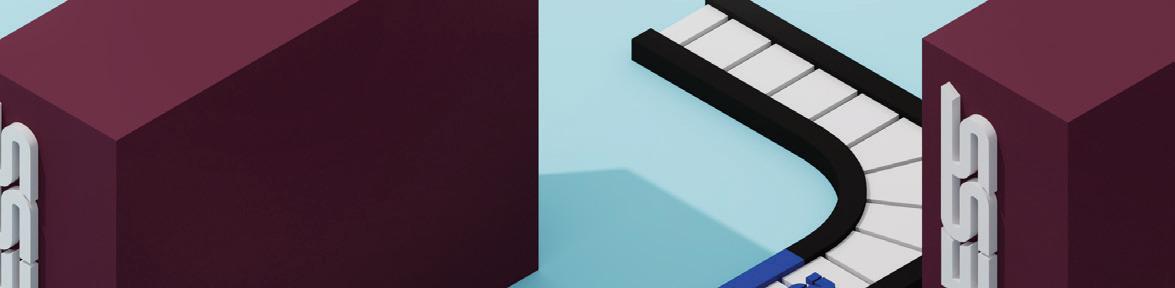

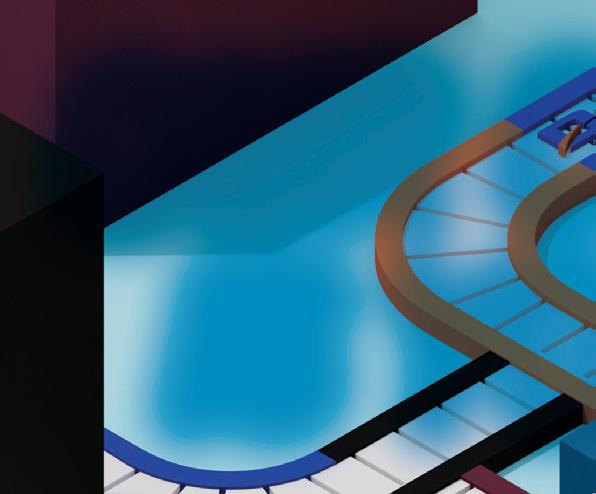
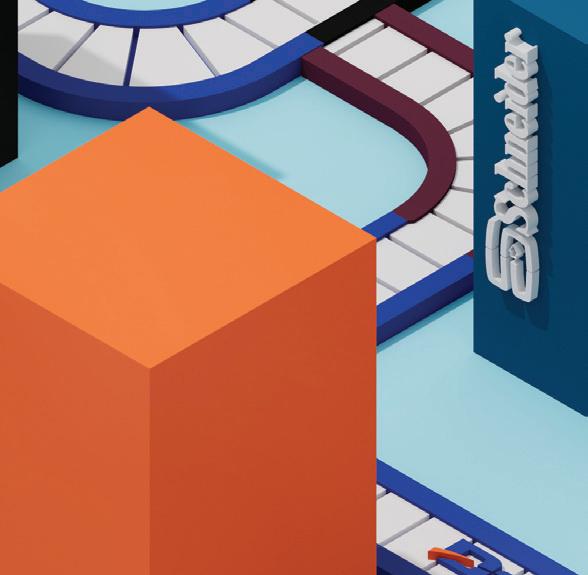
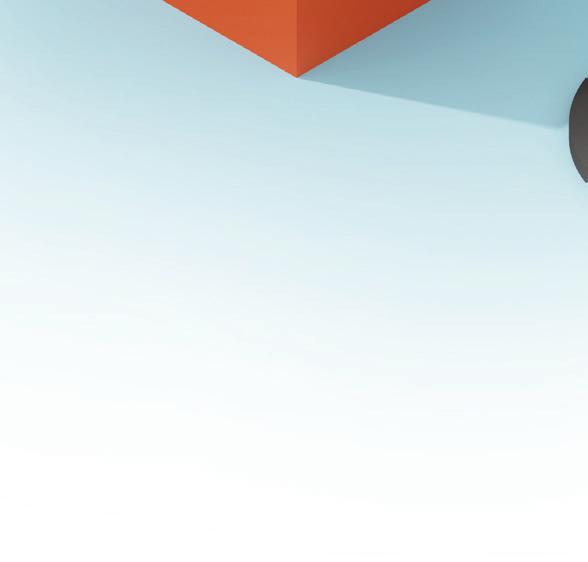
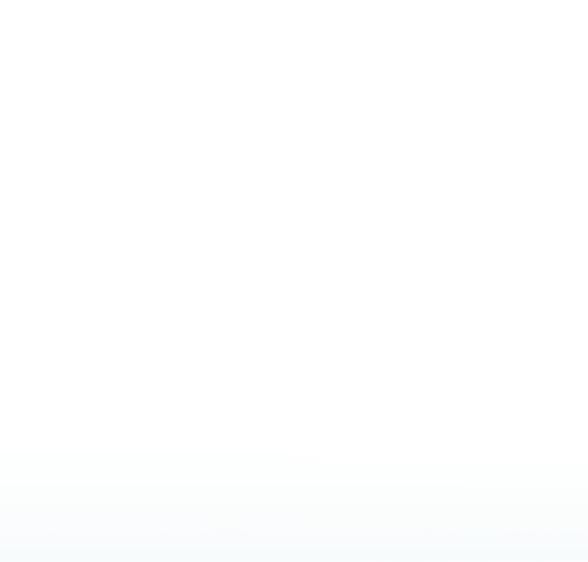
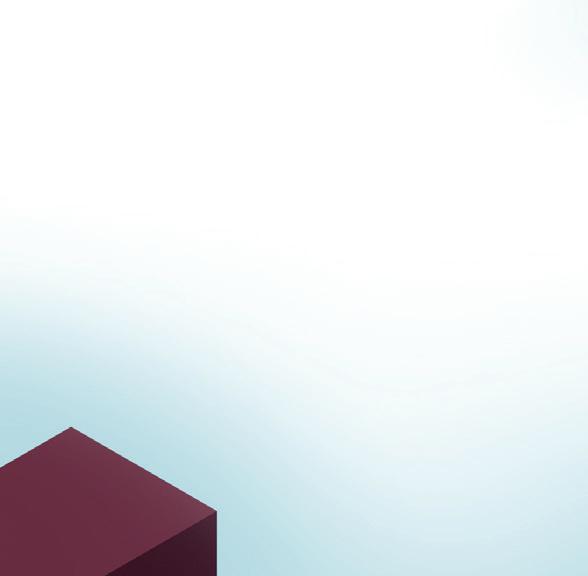

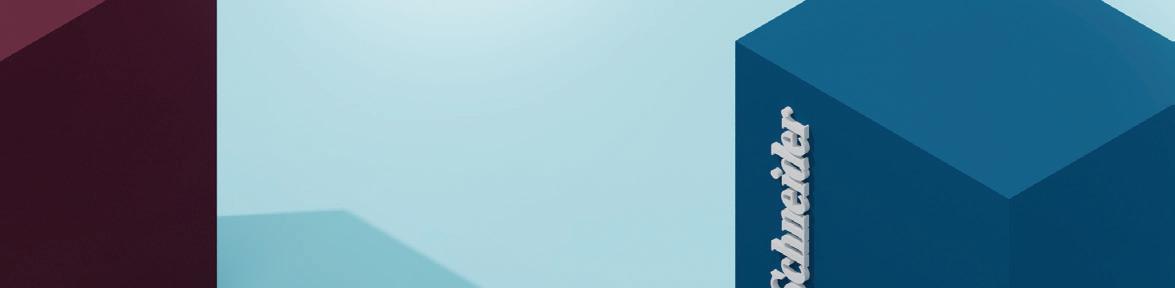


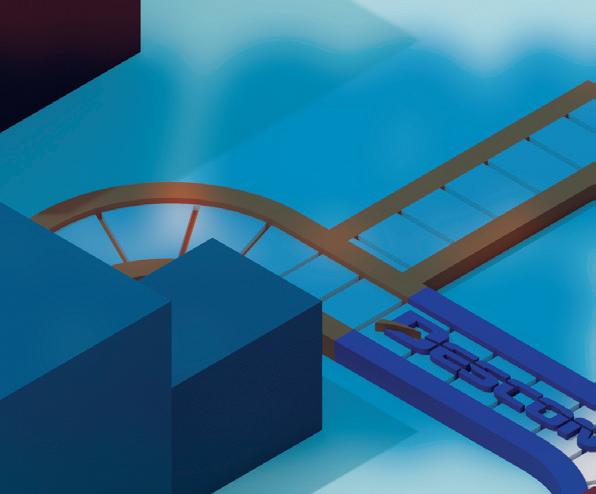
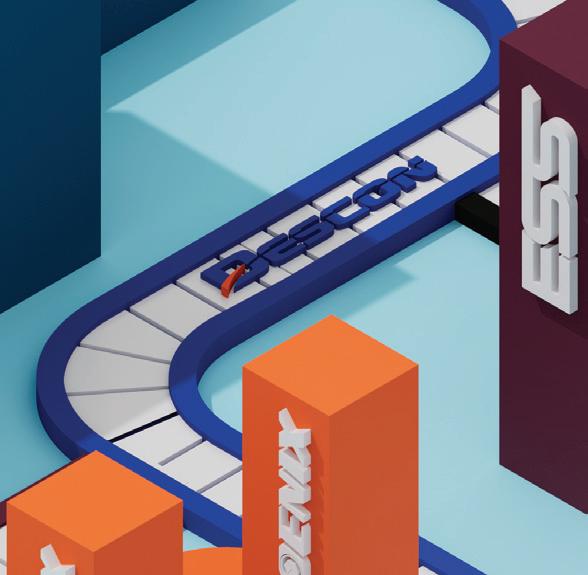
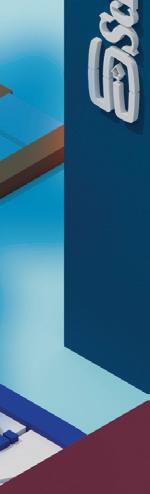
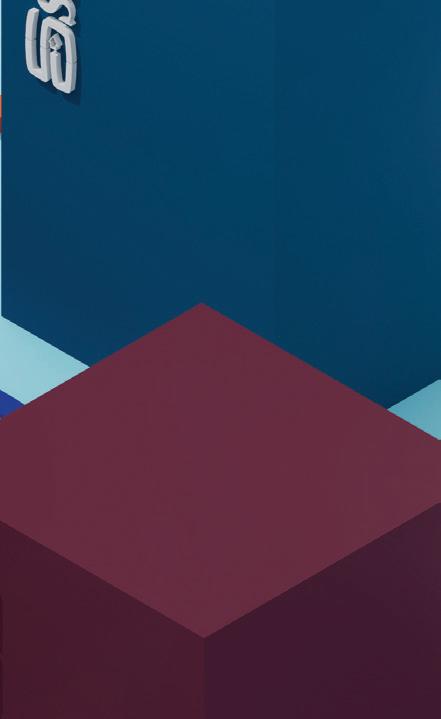
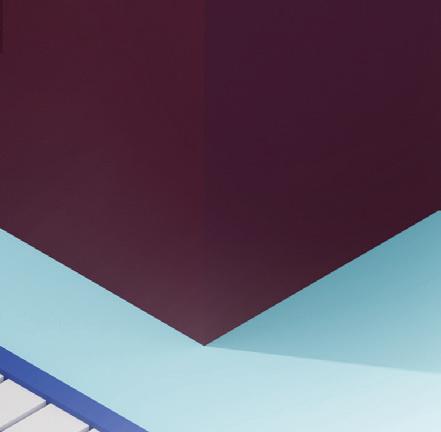
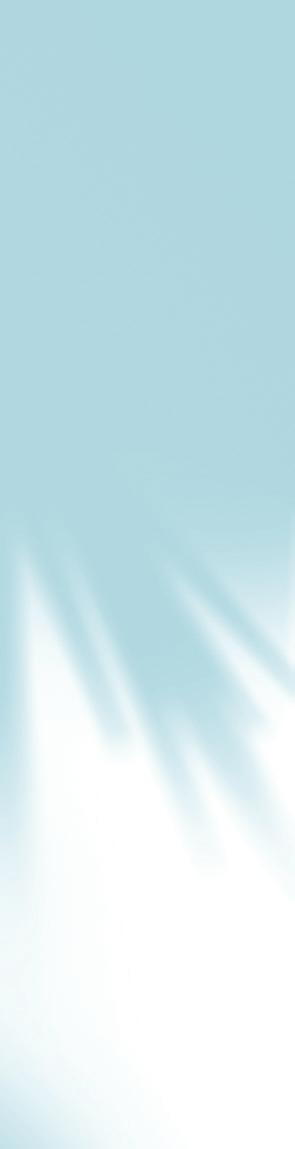
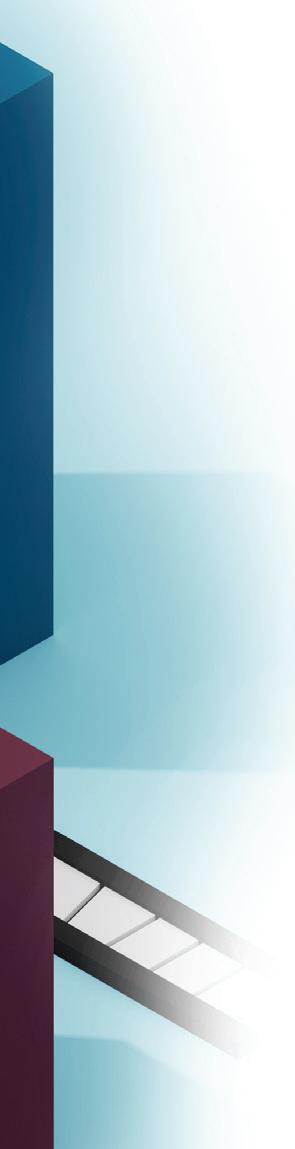
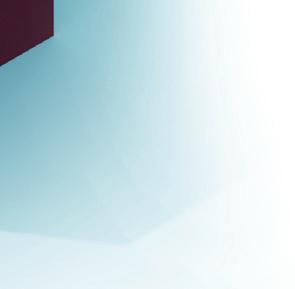

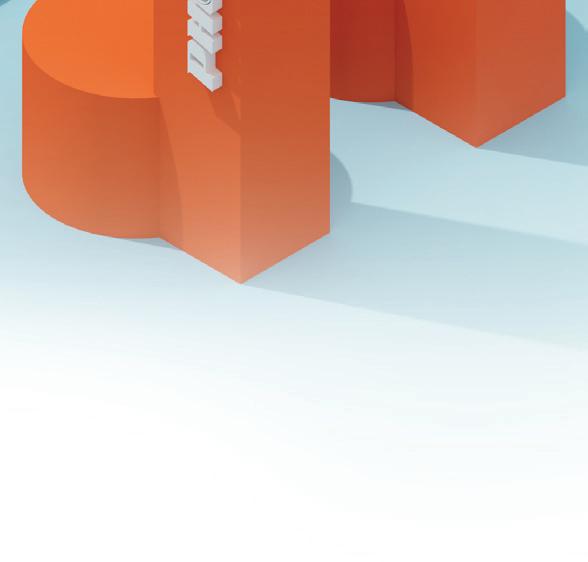
IPacteon works with you and for you as your single source solution to design, integrate, and service your product handling and automation needs. Your success matters.





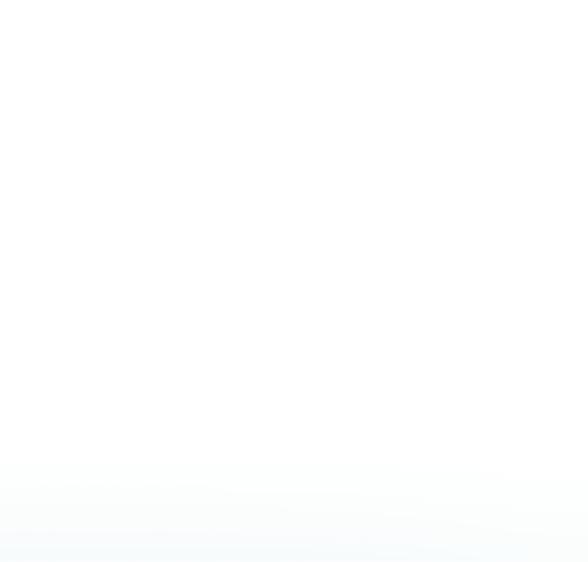
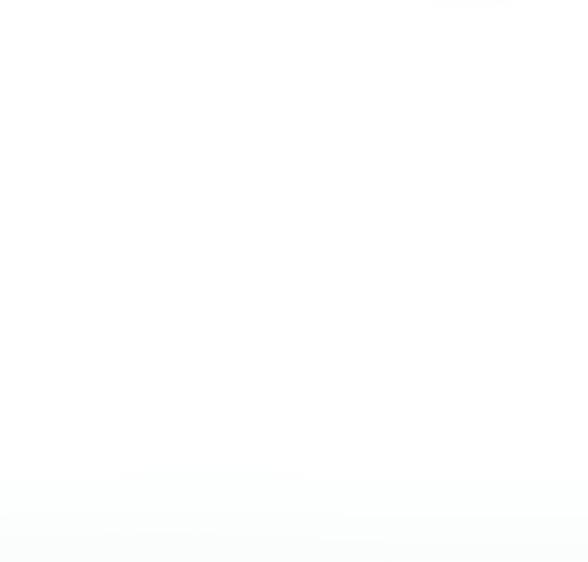




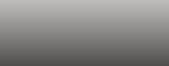















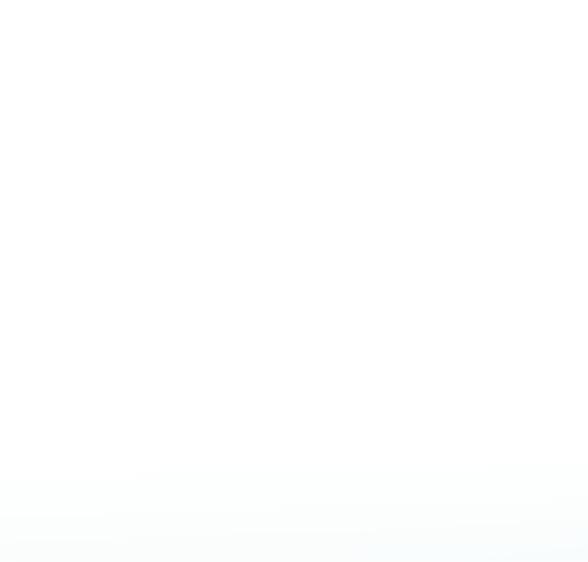

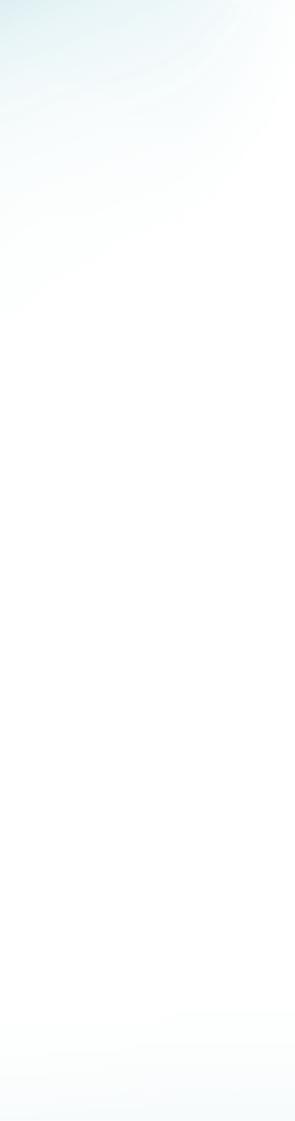

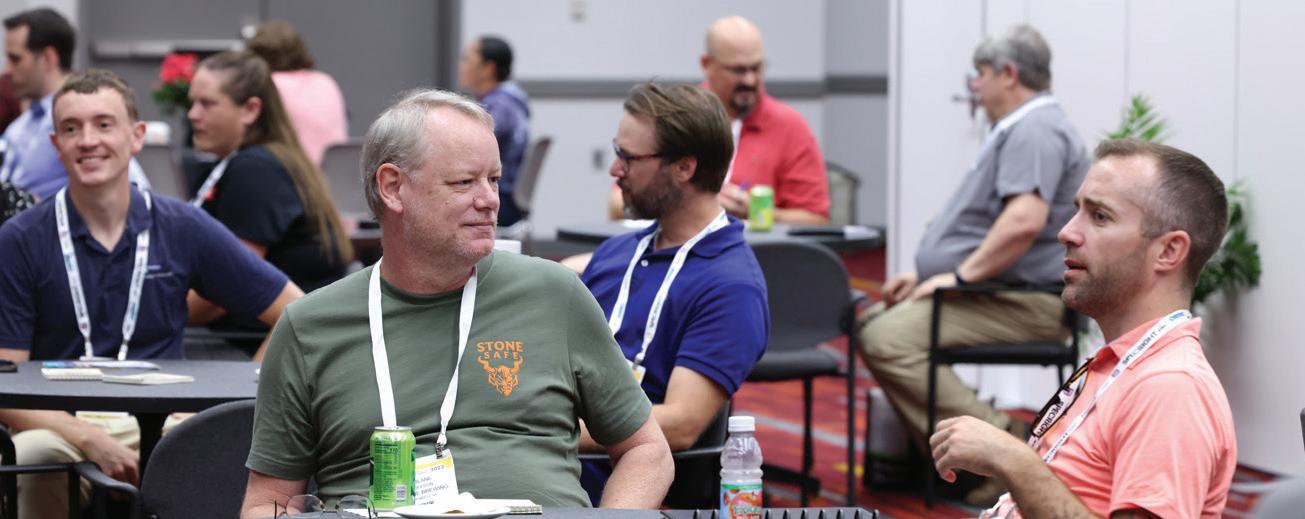
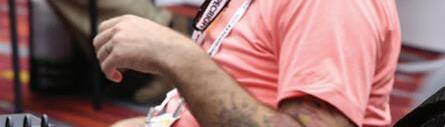


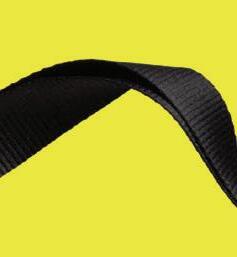
South Building, Room S-102
Lounge Hours:
Sunday – Tuesday:
Wednesday: 8:00 am – 3:00 pm
If your badge says, “First-Time Attendee,” stop by to:
Get expert assistance
Access product locators
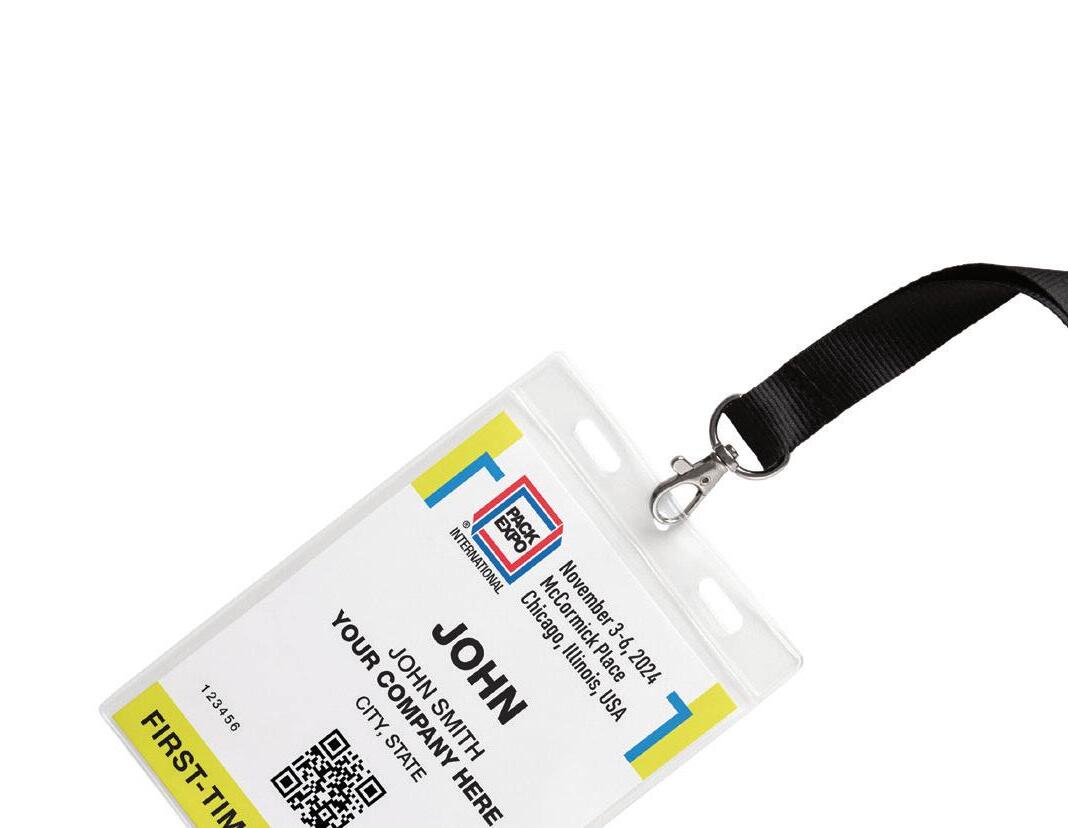

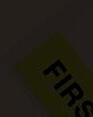

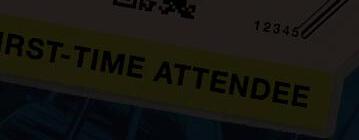
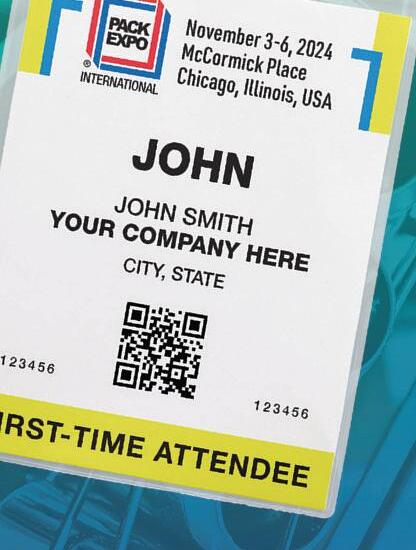
—Continued from page 44
PACK EXPO Partners O er Perspective at Industry Speaks Stage
ought leaders hailing from PACK EXPO International Partner Associations will bring you intriguing views from various vertical industries, address hotbutton topics, and share their thoughts on industry trends at the Industry Speaks Stage (Booth N-4544). Nearly 20 associations are scheduled to speak, including the Cold Pressure Council (Booth N-4512), CPA—Contract Packaging Association (Booth N-4511); IoPP—Institute of Packaging Professionals (Booth N-4513); and F4SS—Foundation for Supply Chain Solutions (Booth N-4510)
e free 30-minute presentations focus on topics including:
• Key Robotic Trends and eir Impact on Industry
• Find Your Perfect Contract Manufacturer
• BEMA Intel: Trending Data that Matters
• State of the Snack Category WEDNESDAY
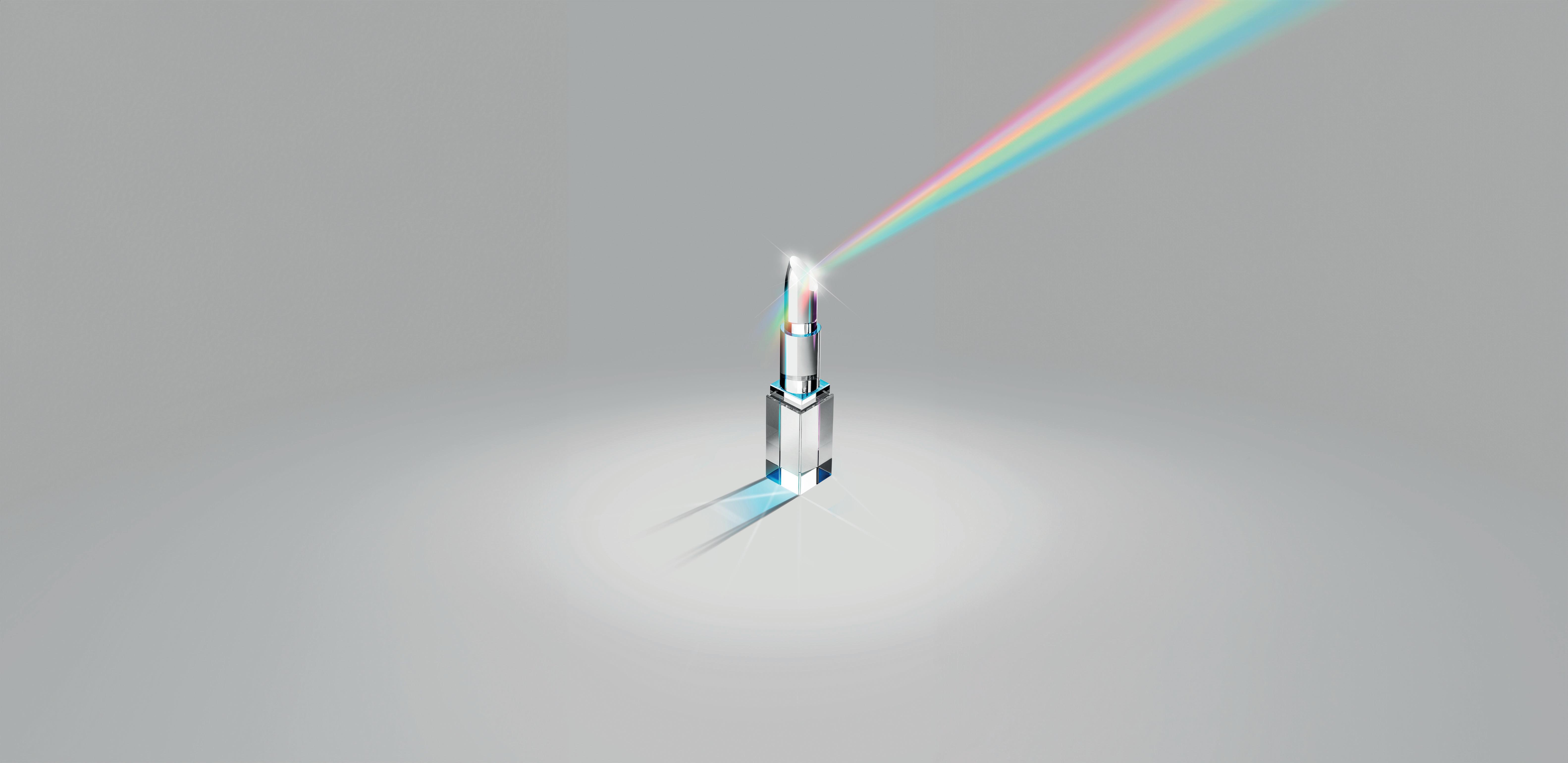
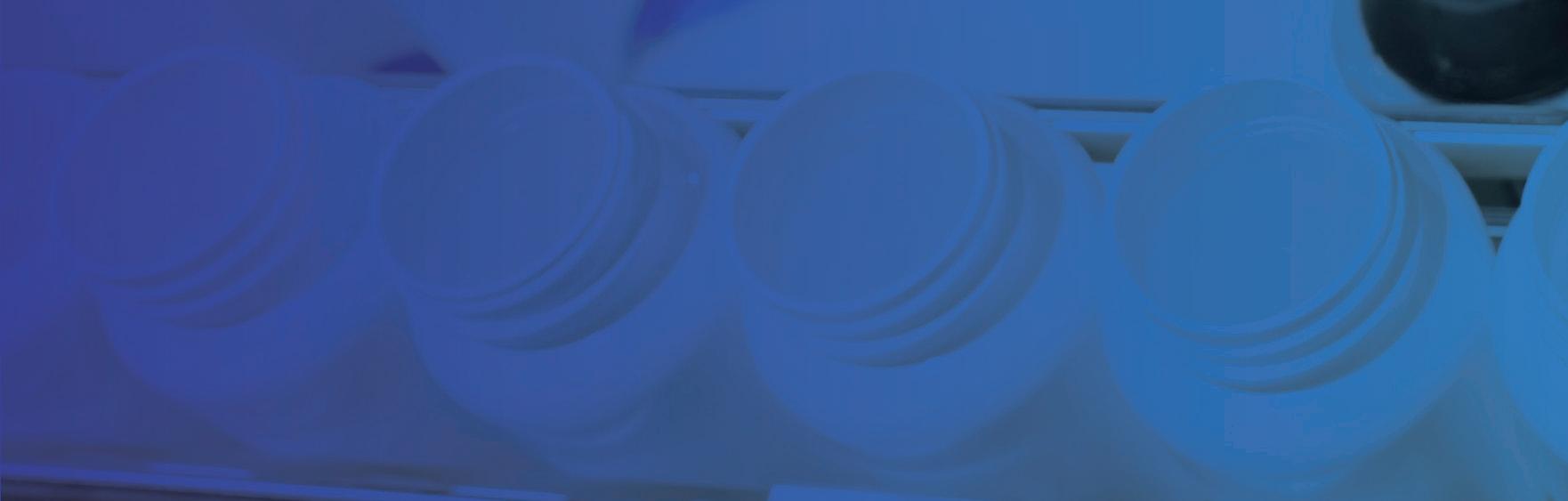
THANK YOU TO OUR SPONSORS!
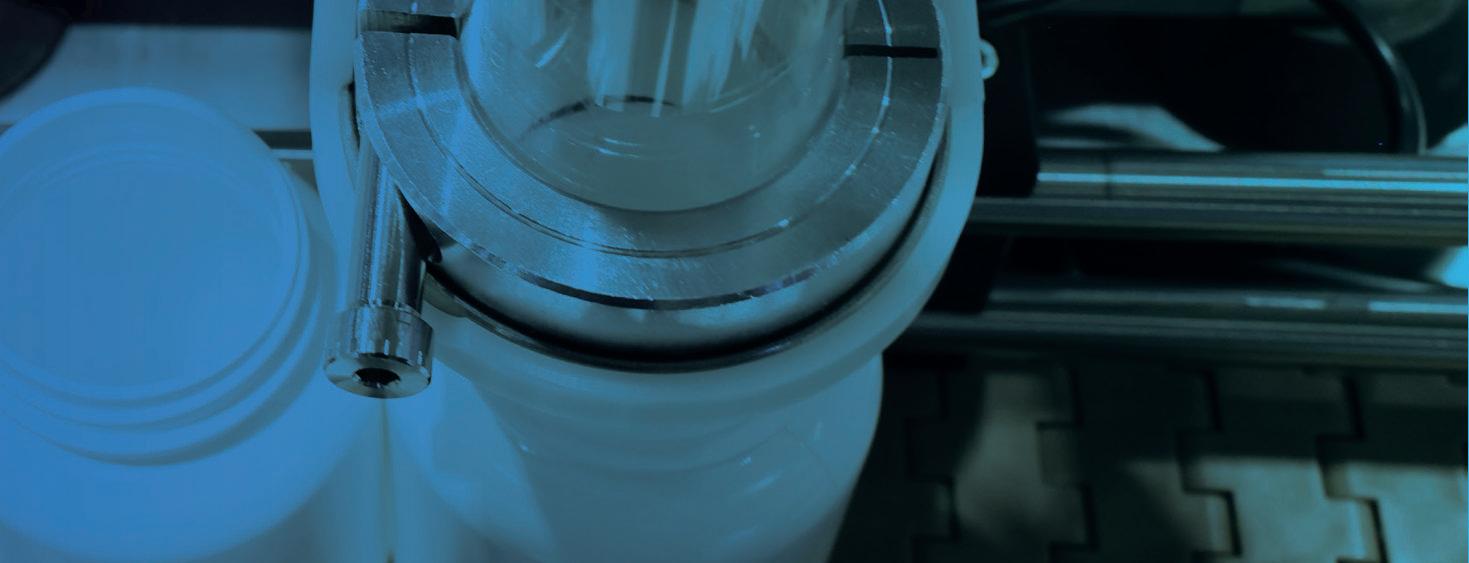
Please join us in expressing our heartfelt thanks to the sponsors of PACK EXPO International 2024 for their generous support.
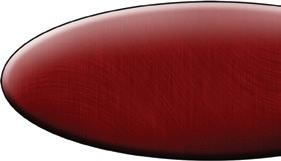
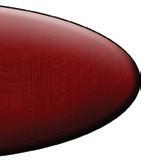
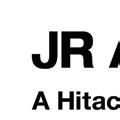
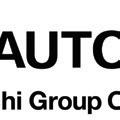
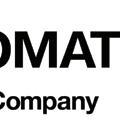
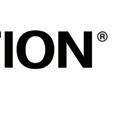

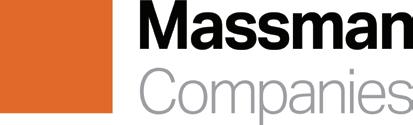
Schubert to Demonstrate Their Pre-configured, Cost-effective Lightline Cartonpacker
Booth N-6151 showcases the packaging of bottles in various sizes with Pine Glo cleaning products.
For Schubert North America (Booths N-6151, W-16095), a trusted name in the automated packaging equipment industry for over 25 years, PACK EXPO is an opportunity to showcase its high-performance machines to a broad audience. Among their innovative offerings is the lightline Cartonpacker, a pre-configured machine that delivers Schubert’s dependable robotassisted technology at a more cost-effective price and quicker delivery time. The Cartonpacker features a compact design that ensures exceptional quality, reliability, and efficiency, helping manufacturers maintain their competitive edge for the future.
“We’re excited to offer our customers two distinct paths to packaging excellence,” says Hartmut Siegel, CEO of Schubert North America. “For those seeking
—Continued on page 50




Protect Your Brand
The
masters standardized packaging tasks with outstanding efficiency and quality—all at an attractive price.

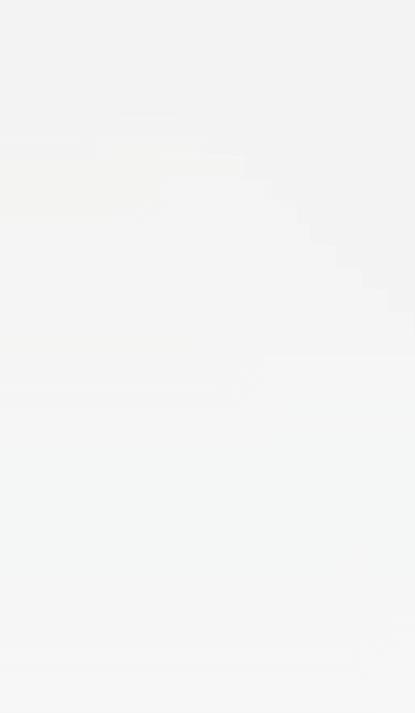
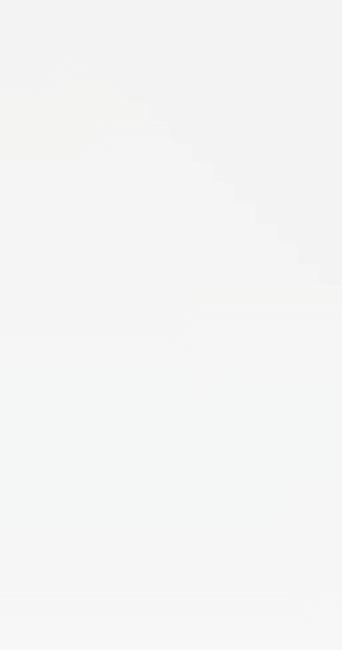

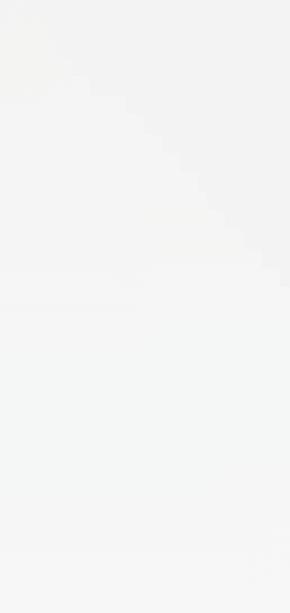
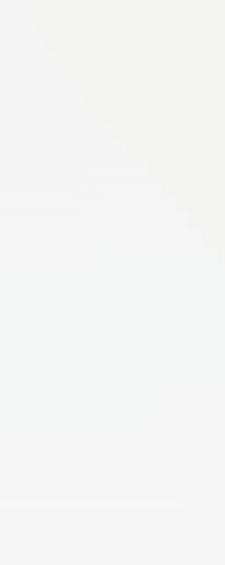

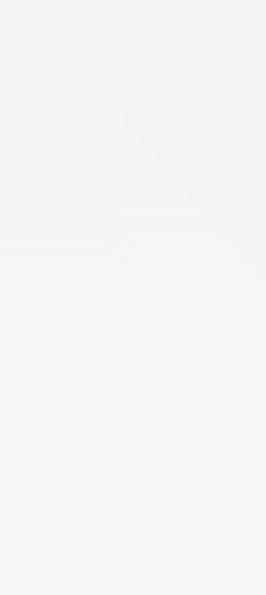
Transform your inspection process with the Raptor BBK Combination System. Engineered for 25kg bags and cases, it delivers unmatched weighing precision and metal detection performance in a streamlined, space-saving design.

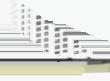
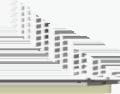

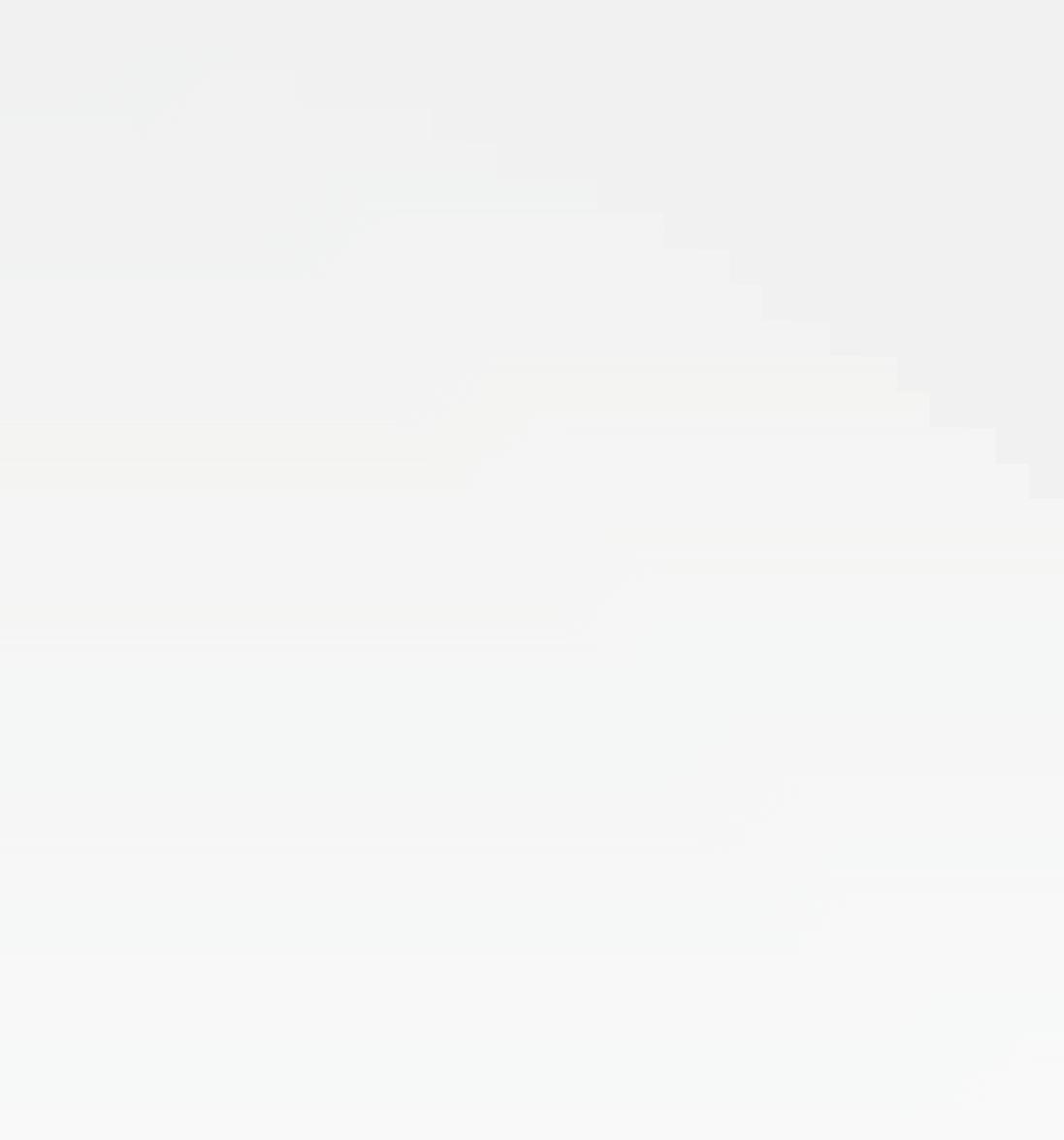
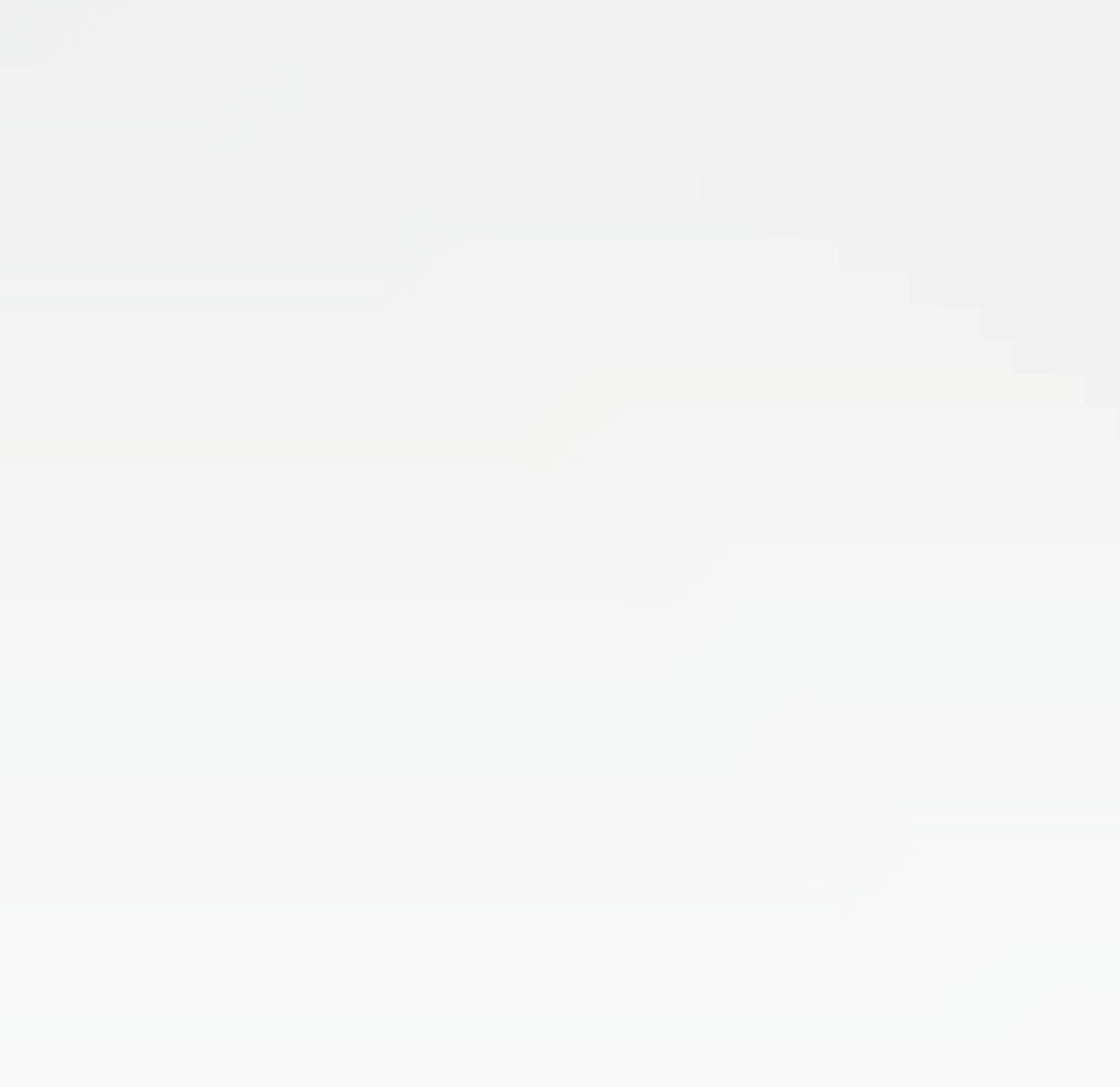
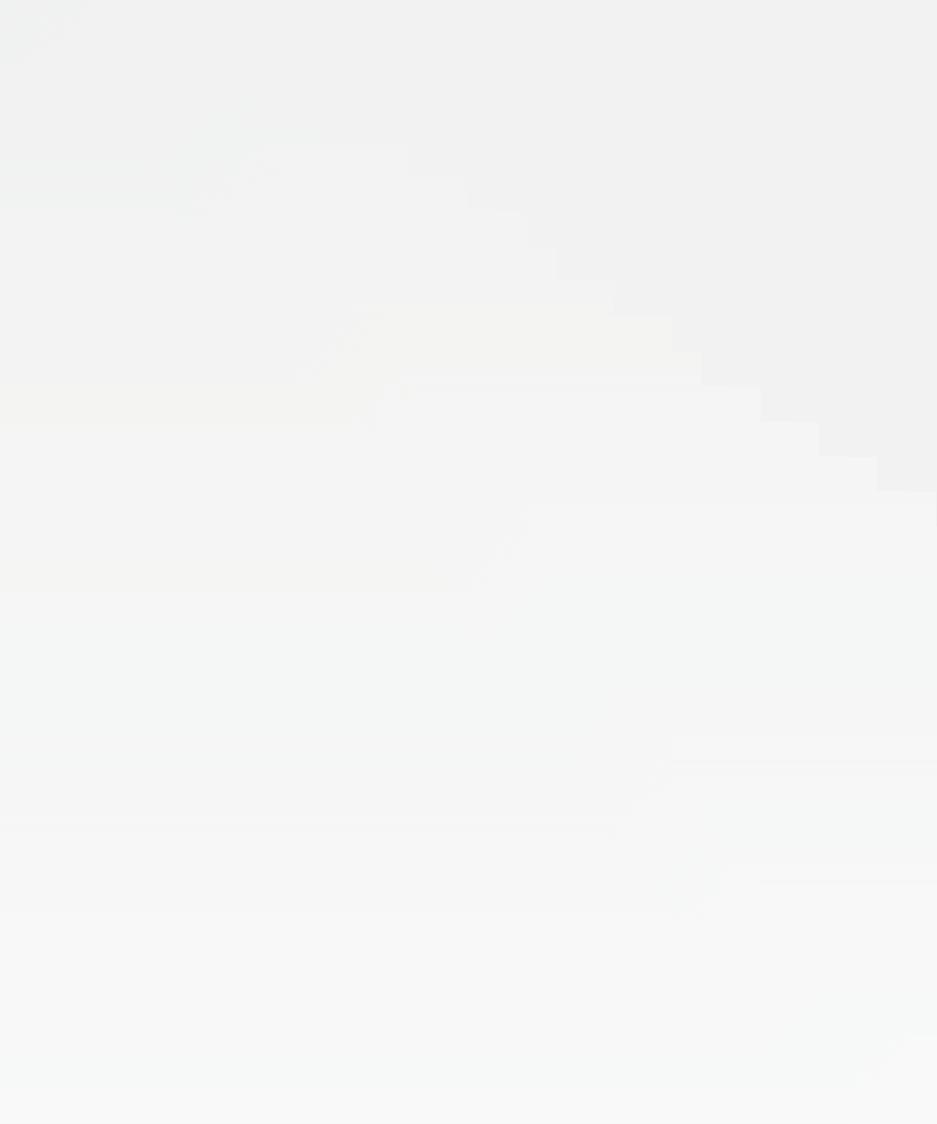
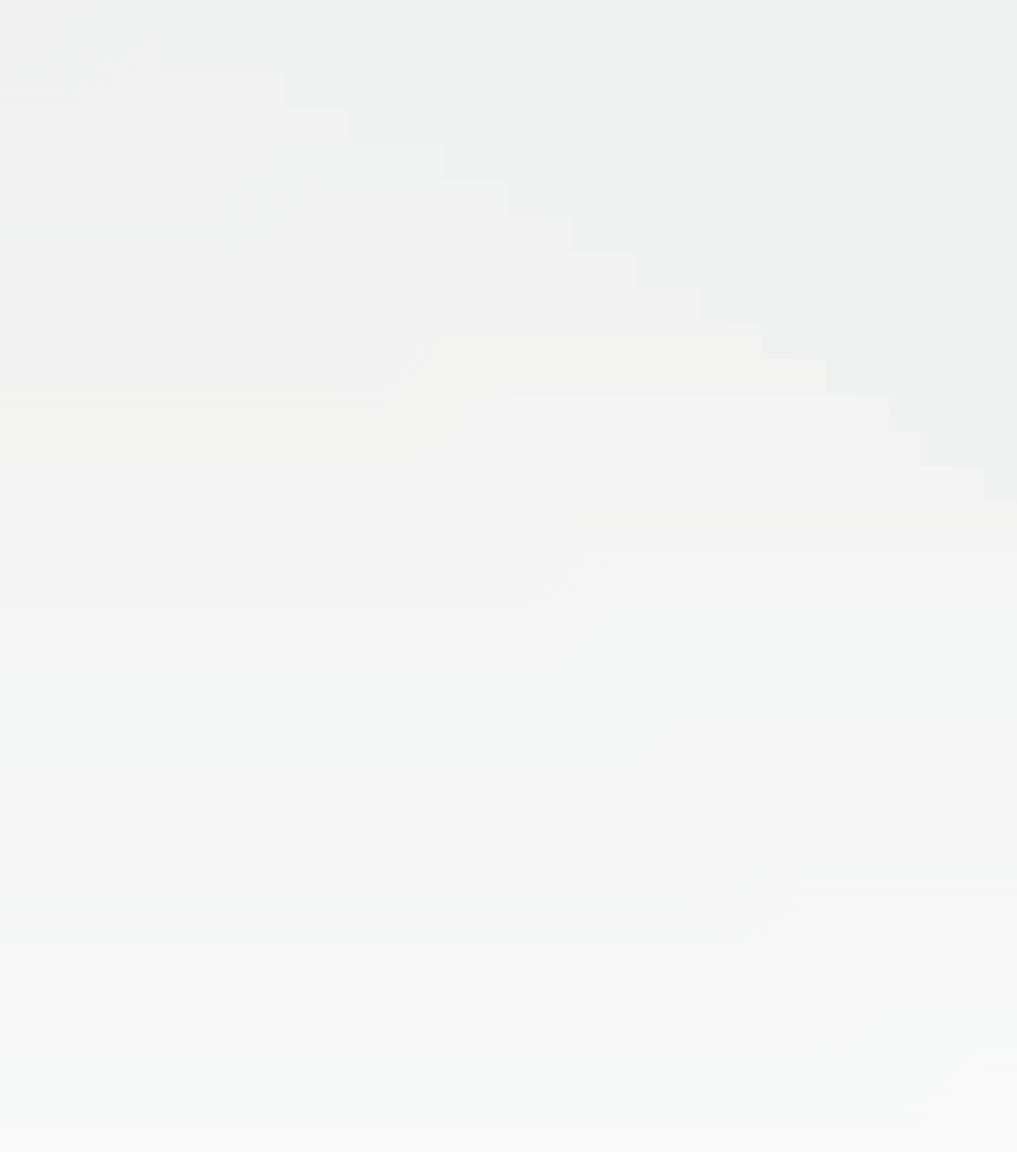
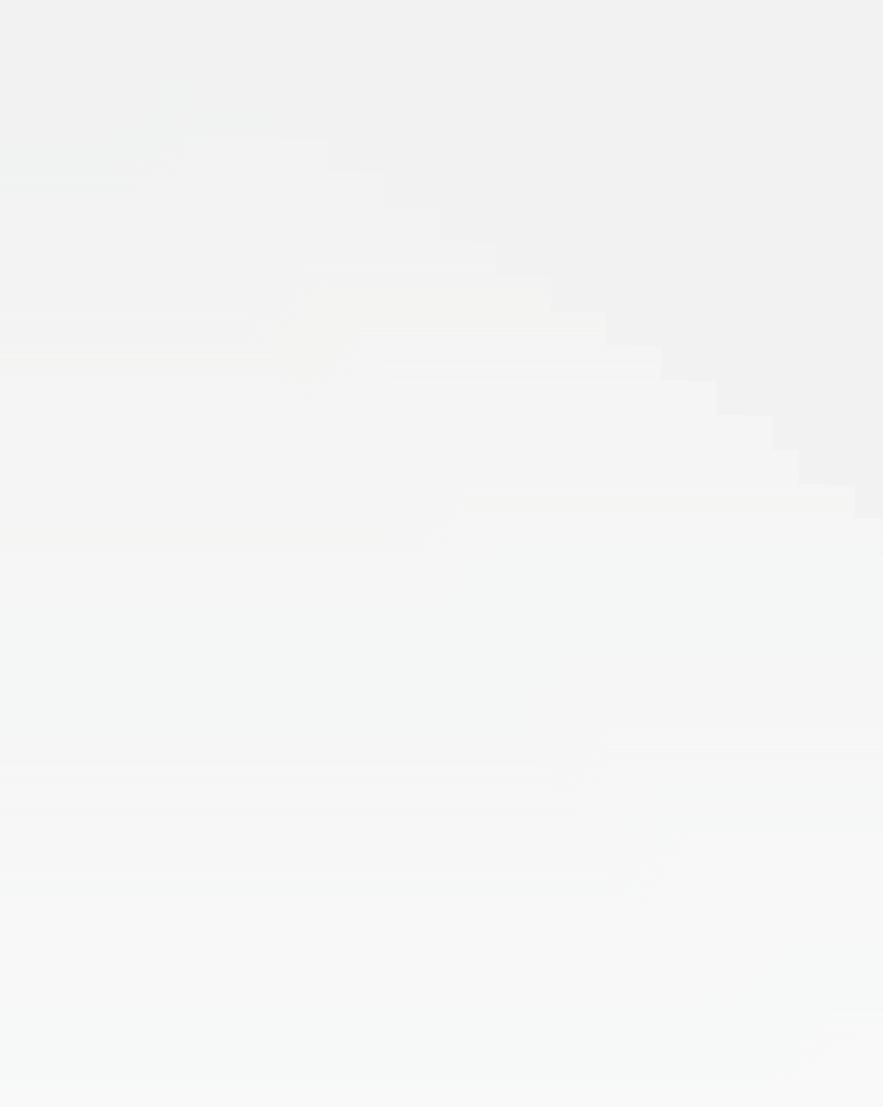
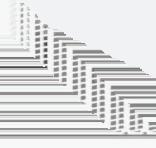
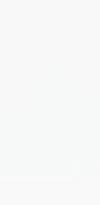
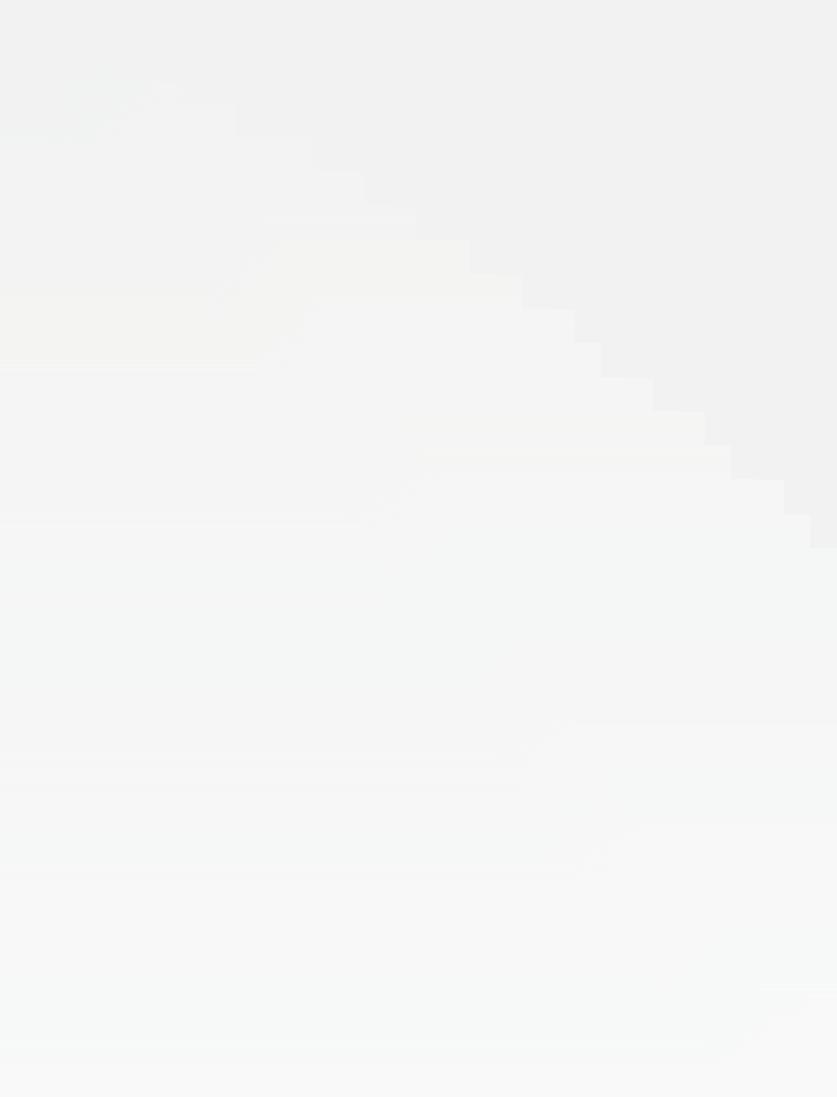


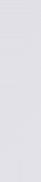

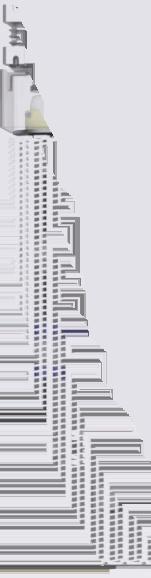
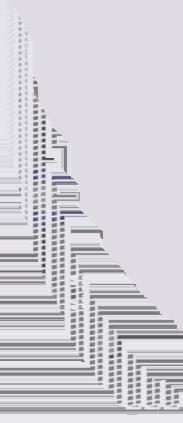

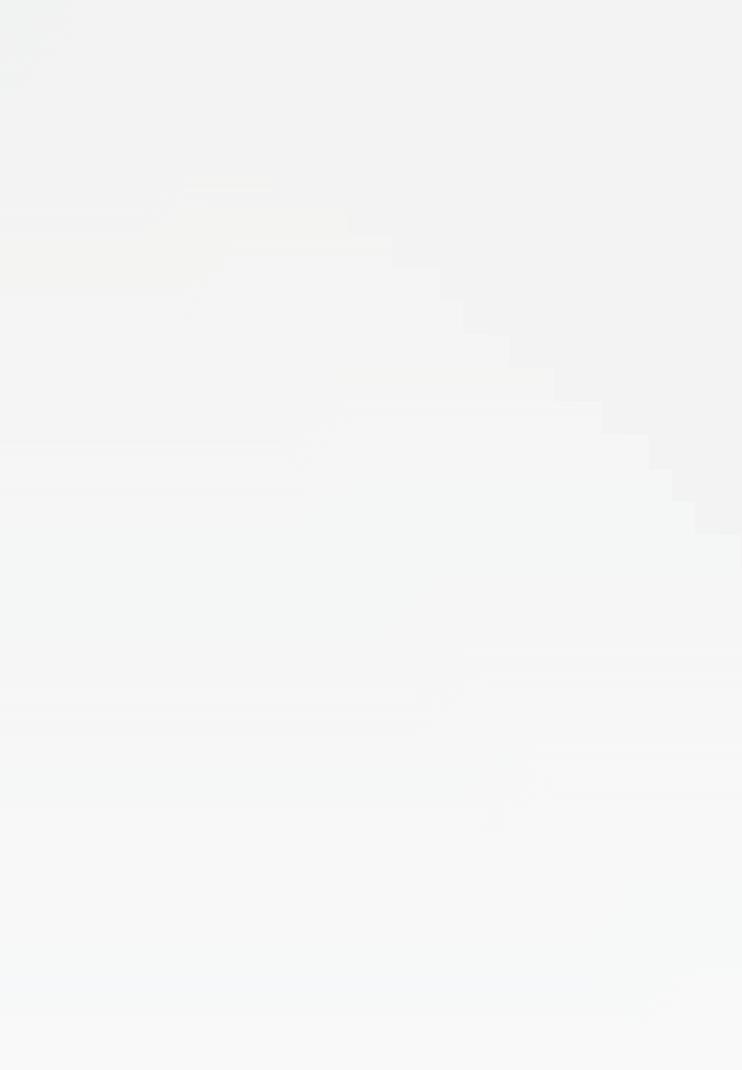







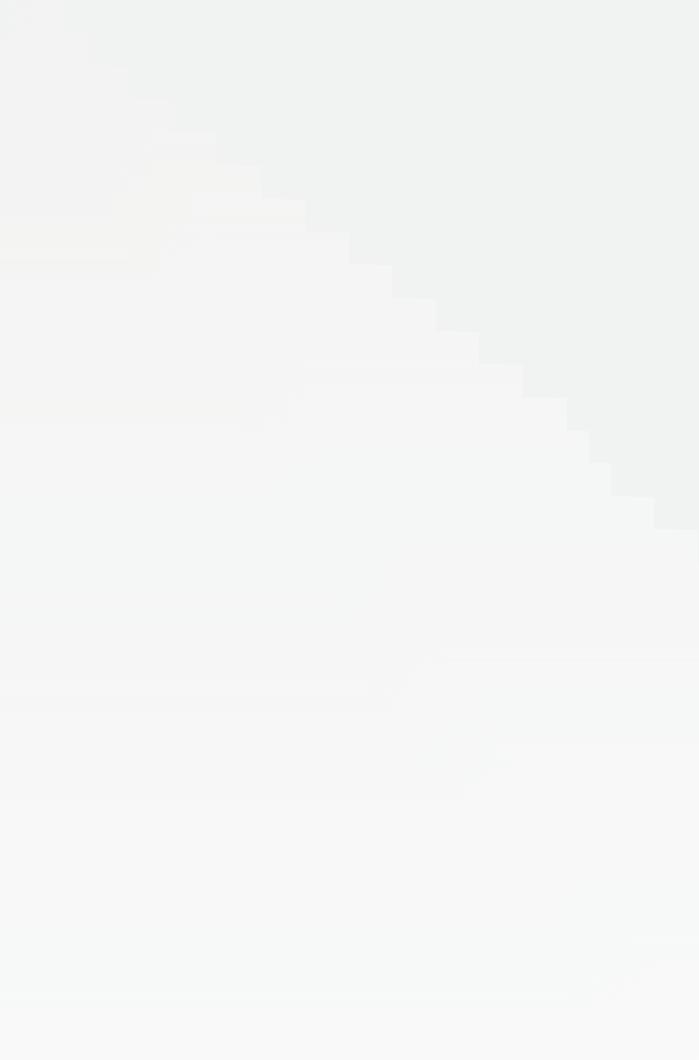







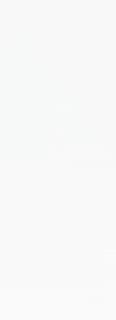
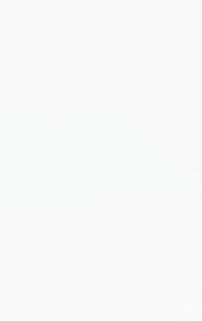
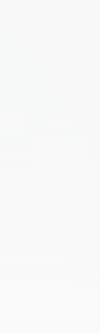

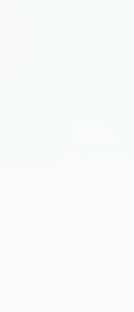
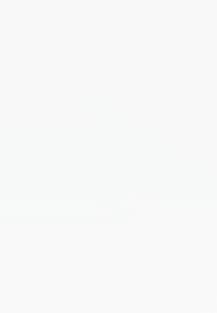
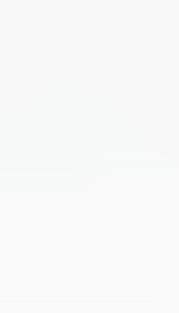
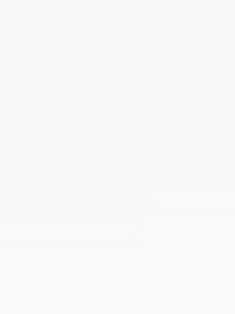
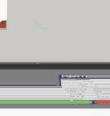
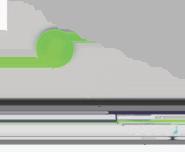
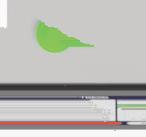
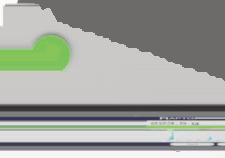


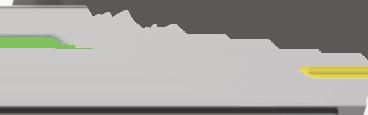
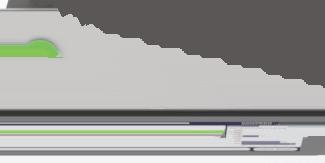

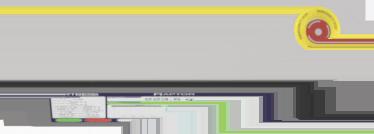

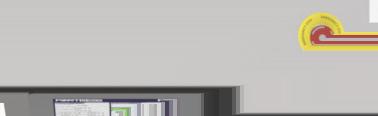
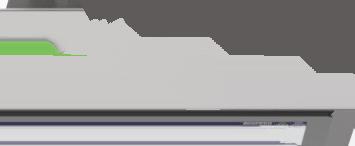
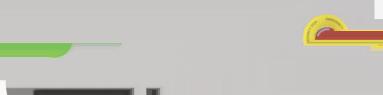

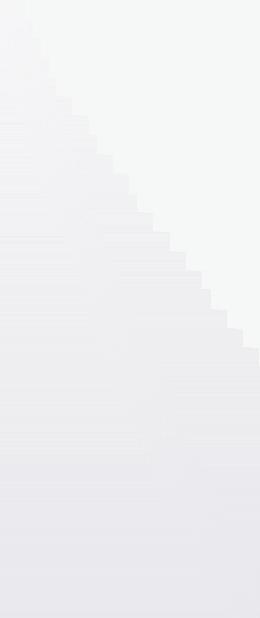
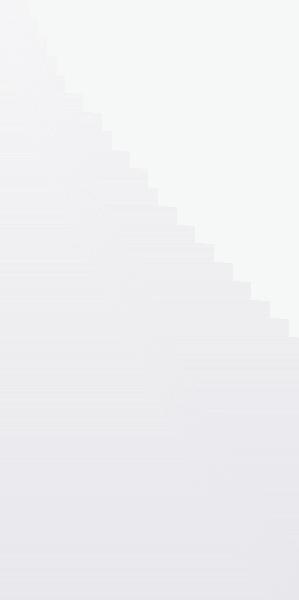
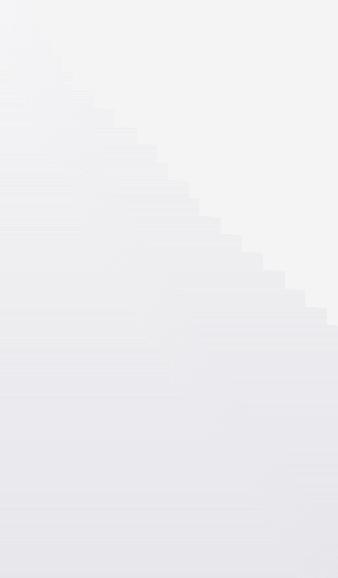
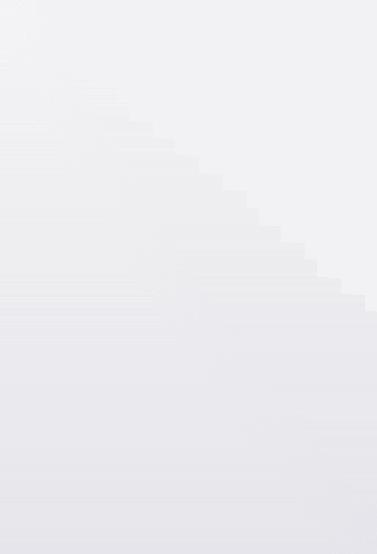
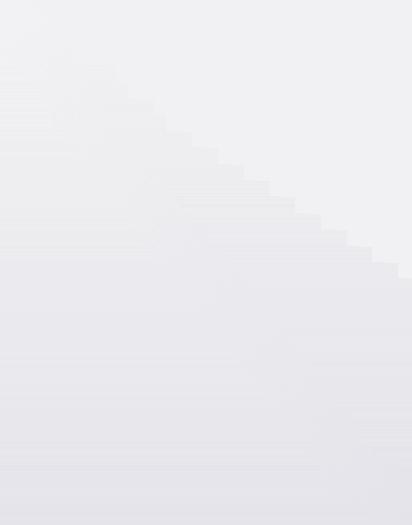
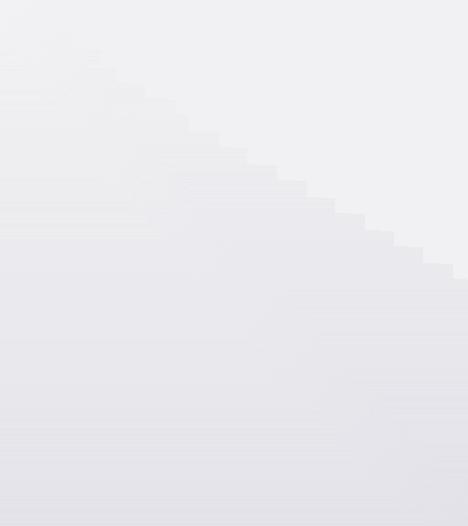
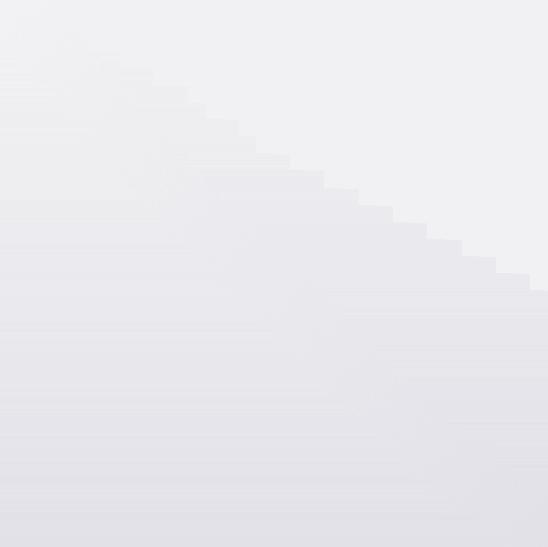

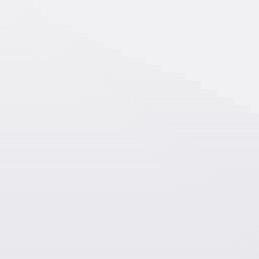
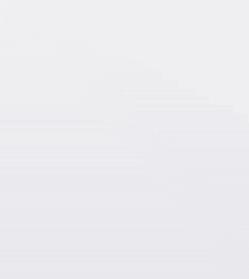


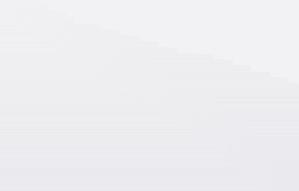
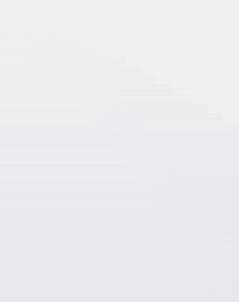

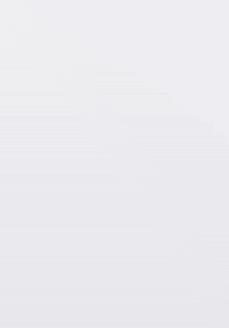

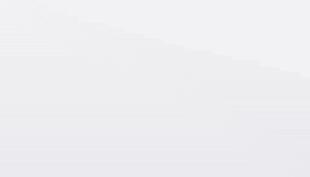
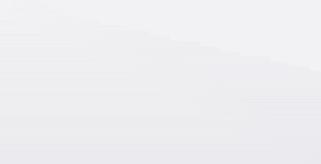
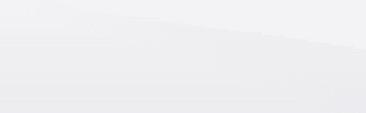
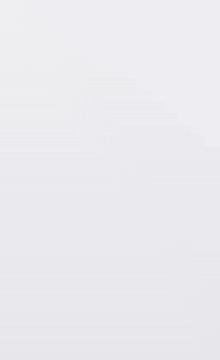
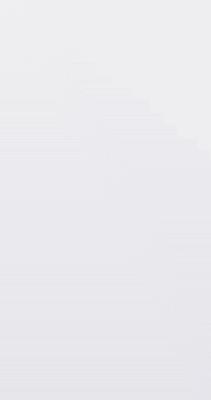

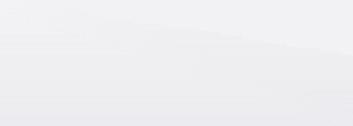
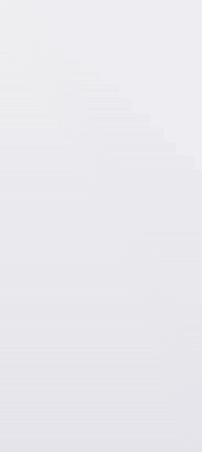
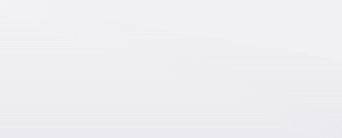
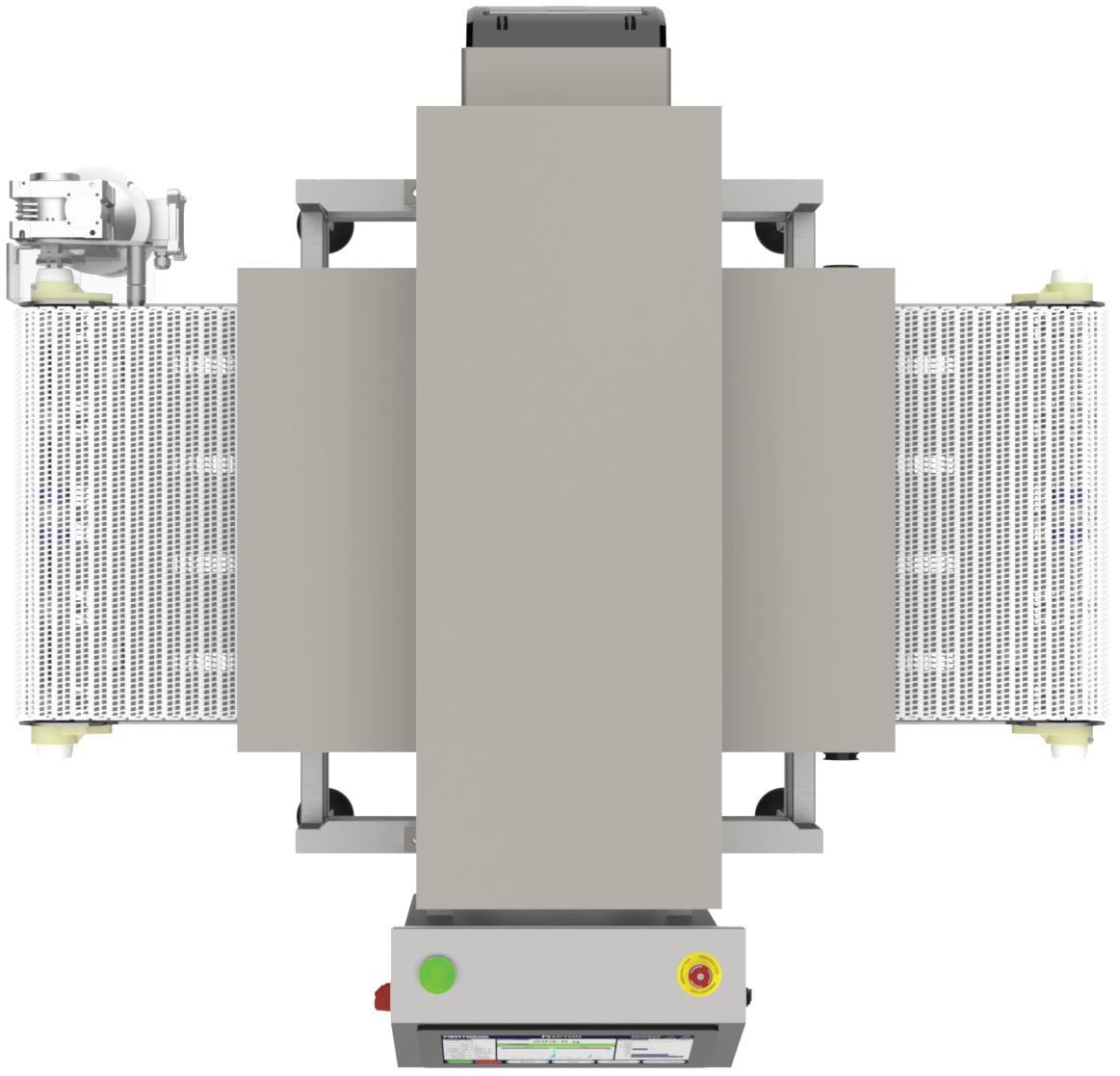

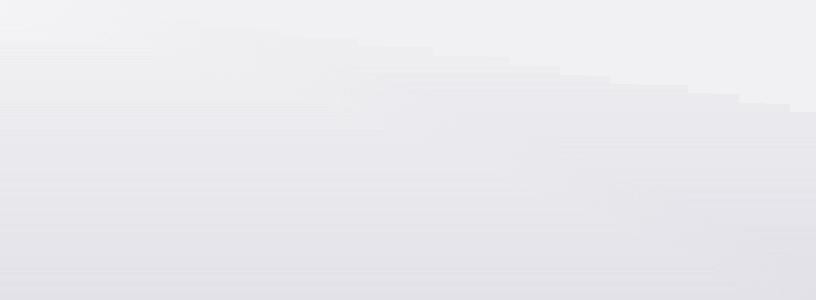
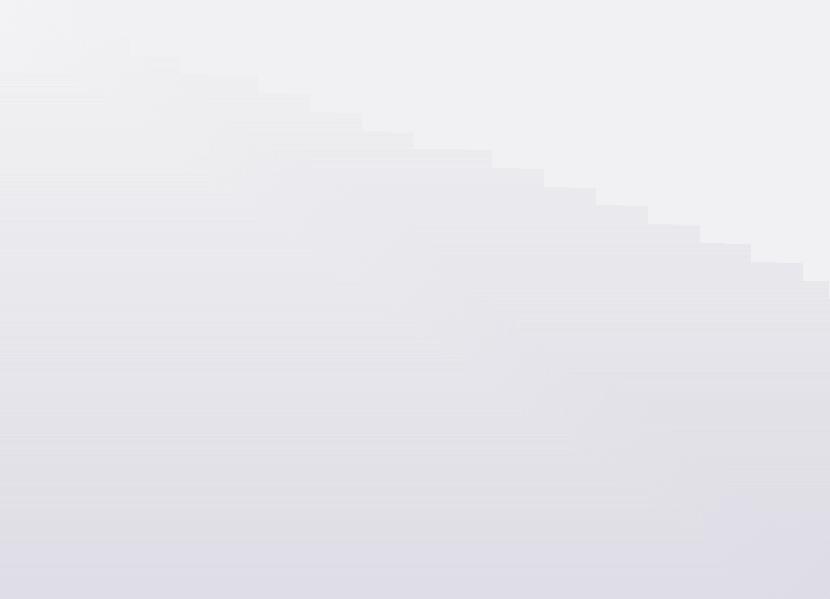
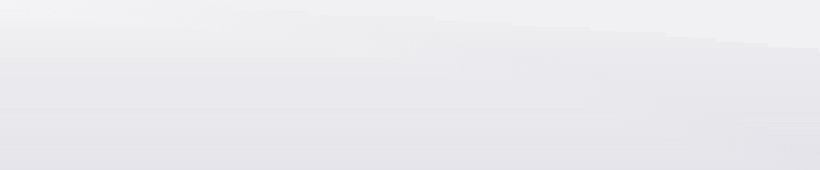
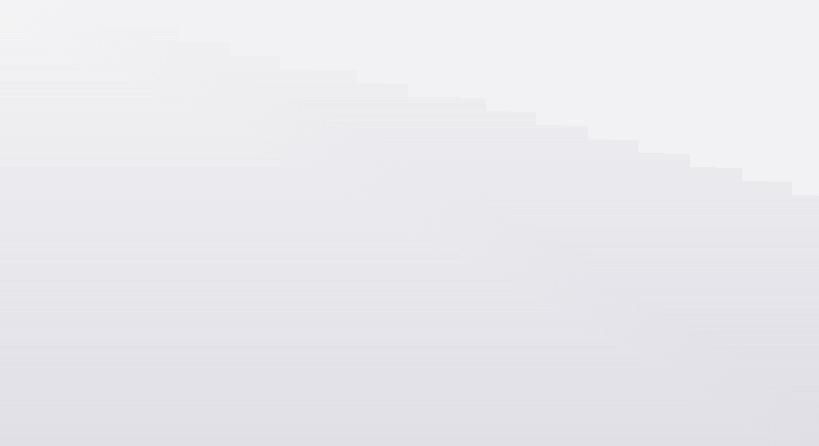
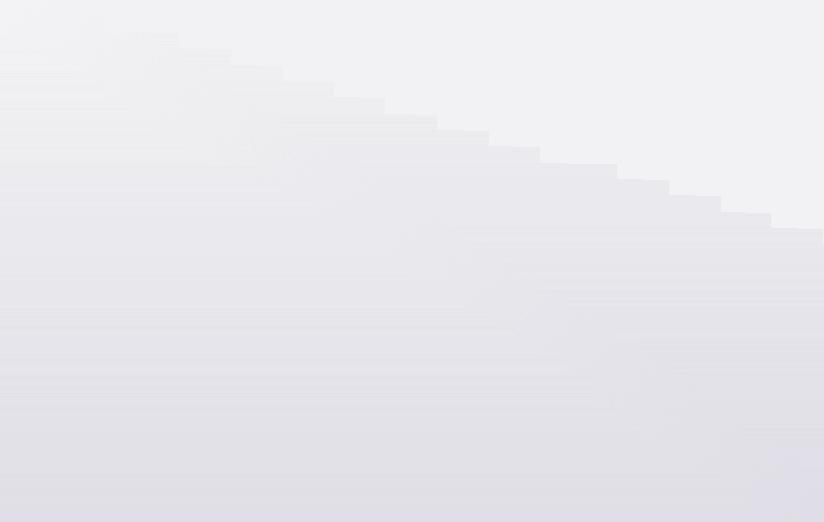

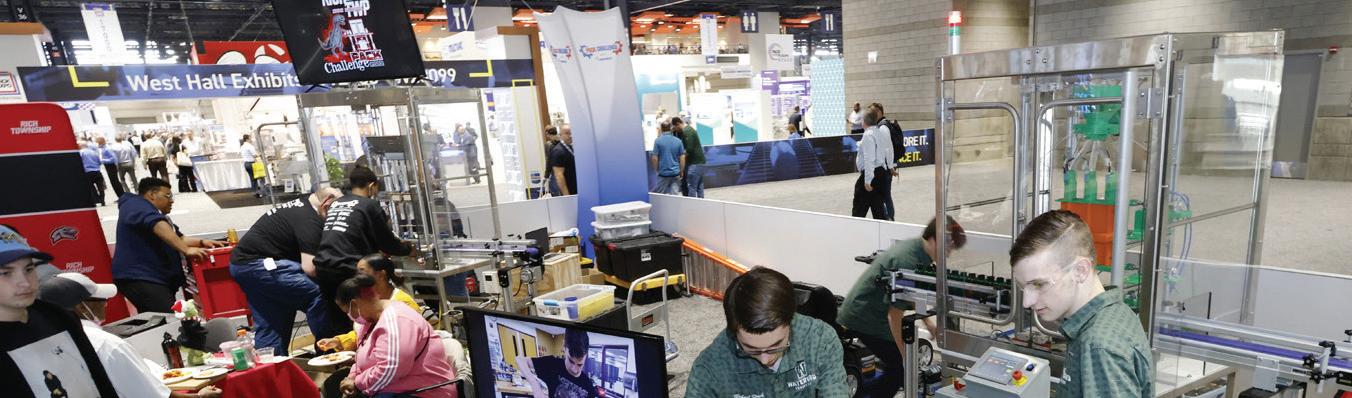
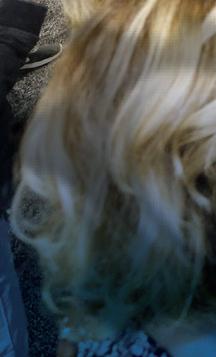
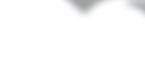
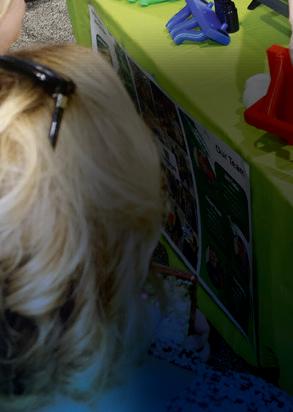
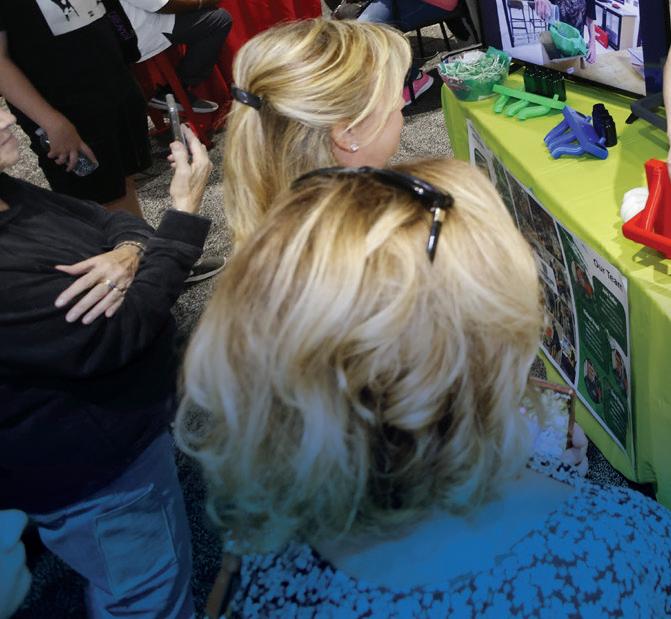

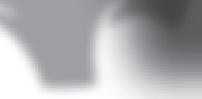
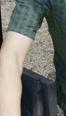

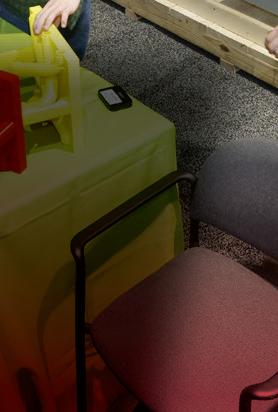
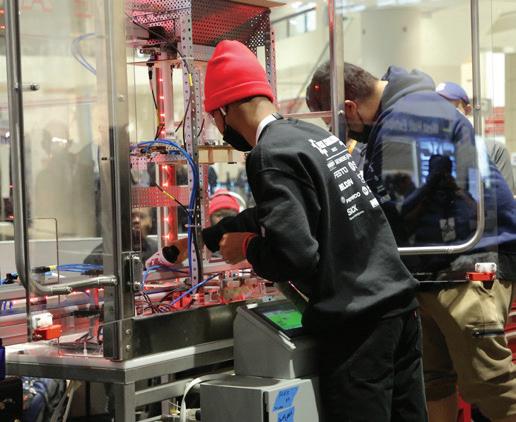
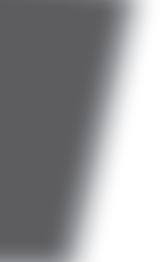
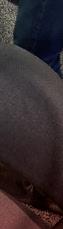

tailored solutions, our highly customizable machines are designed to meet speci c requirements. Alternatively, our new lightline series provides cost-e ective, precon gured options with de ned product and packaging formats. is dual approach ensures we can meet the diverse needs of our clients, whatever their packaging challenges may be,” continues Siegel.
E cient Carton Packaging for Pine Glo Cleaning Products
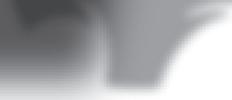
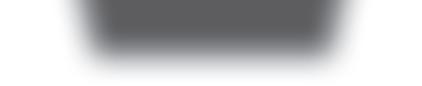
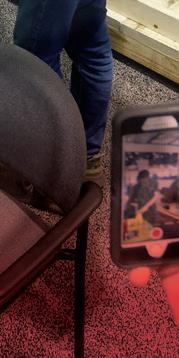
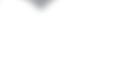
A real-world, end-to-end student competition at PACK EXPO International that requires creativity, conception, design, build, programming, marketing, and field installation knowledge – all put to the test in a competition format!
JOIN US FOR OUR FRIENDS AND FAMILY RECEPTION
Sunday, November 3 • 3 pm – 5 pm PACK Challenge Booth sponsored by Encoder Products Company
CHECK OUT THE COMPETITION IN THE WEST HALL LOBBY W16005
SPONSORS:
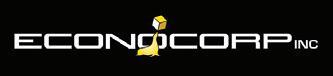
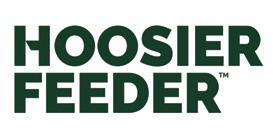
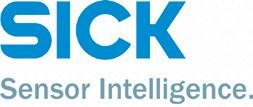
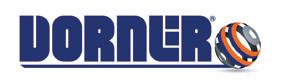
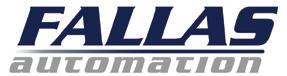

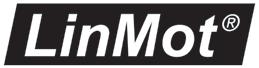

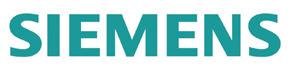
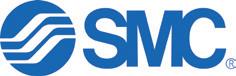
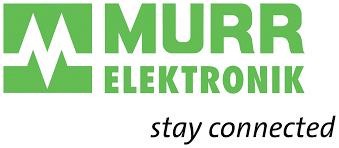
At PACK EXPO, the lightline Cartonpacker demonstrates the packaging of bottles in a variety of sizes with Pine Glo cleaning products. Established in 1979 and based in North Carolina, Pine Glo specializes in the production of liquid household cleaners and antibacterial disinfectants and detergents.
Pine Glo turned to Schubert when they were seeking packaging equipment to reduce labor costs and increase throughput to meet the growing demand for their cleaning products. Additionally, they needed a versatile packaging machine that could be quickly converted to di erent carton formats using easily interchangeable tools, accommodating the wide range of bottle sizes and uniquely shaped spray bottles that are o en di cult to pack due to their shape.
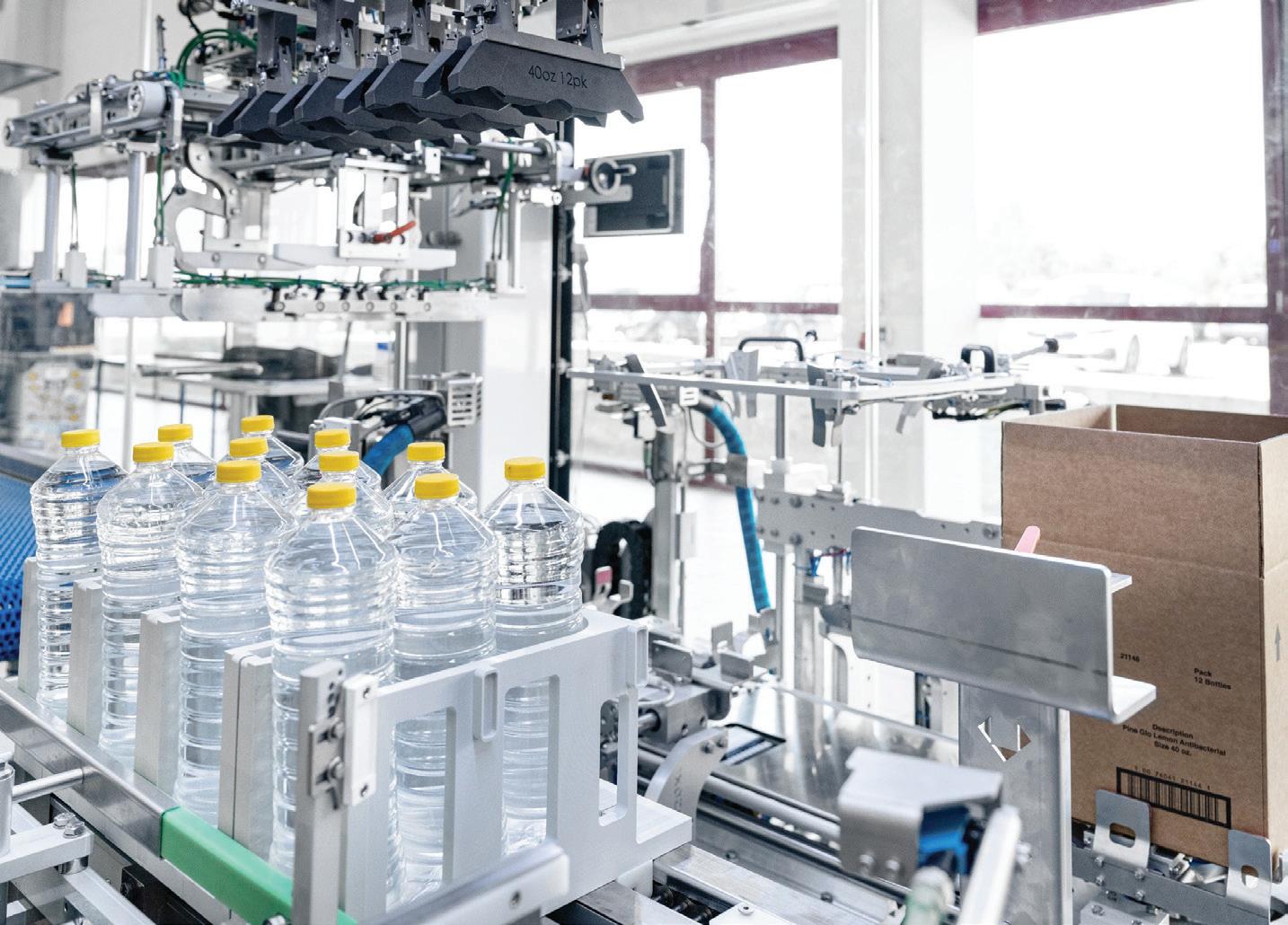
Pine Glo turned to Schubert when they were seeking packaging equipment to reduce labor costs and increase throughput to meet the growing demand for their cleaning products.
“To ensure that our investment in packaging equipment paid o , we were committed to working with a company that manufactures reliable and long-lasting machines, and we found the right partner in Schubert,” says Steve Williams, Operations and Engineering Manager, Pine Glo. “ e lightline Cartonpacker was an ideal choice for us because it is a pre-con gured, easy-to-operate machine with a shorter lead time. We are delighted that Schubert decided to showcase this machine with our products at Pack Expo,” continues Williams.
Additional Products and Services Featured
In addition to live demonstrations of the lightline Cartonpacker, Schubert presents their diverse portfolio of packaging machines. As a market-leading producer of fully automated Top Loading Machines (TLM), Schubert provides their customers with future-proof packaging machine solutions that are easy to operate, adaptable for format changeovers, high-performing, and consistently reliable. e TLM machines pack products of all types and from all sectors – from food, confectionery, beverages, pharmaceuticals, cosmetics, and technical products – into trays, cartons, boxes or into ow-wrap bags.
Beyond their extensive technology portfolio, Schubert o ers comprehensive consulting services, including advice on sustainable packaging, process optimization, and improving machine and line e ciency. ■
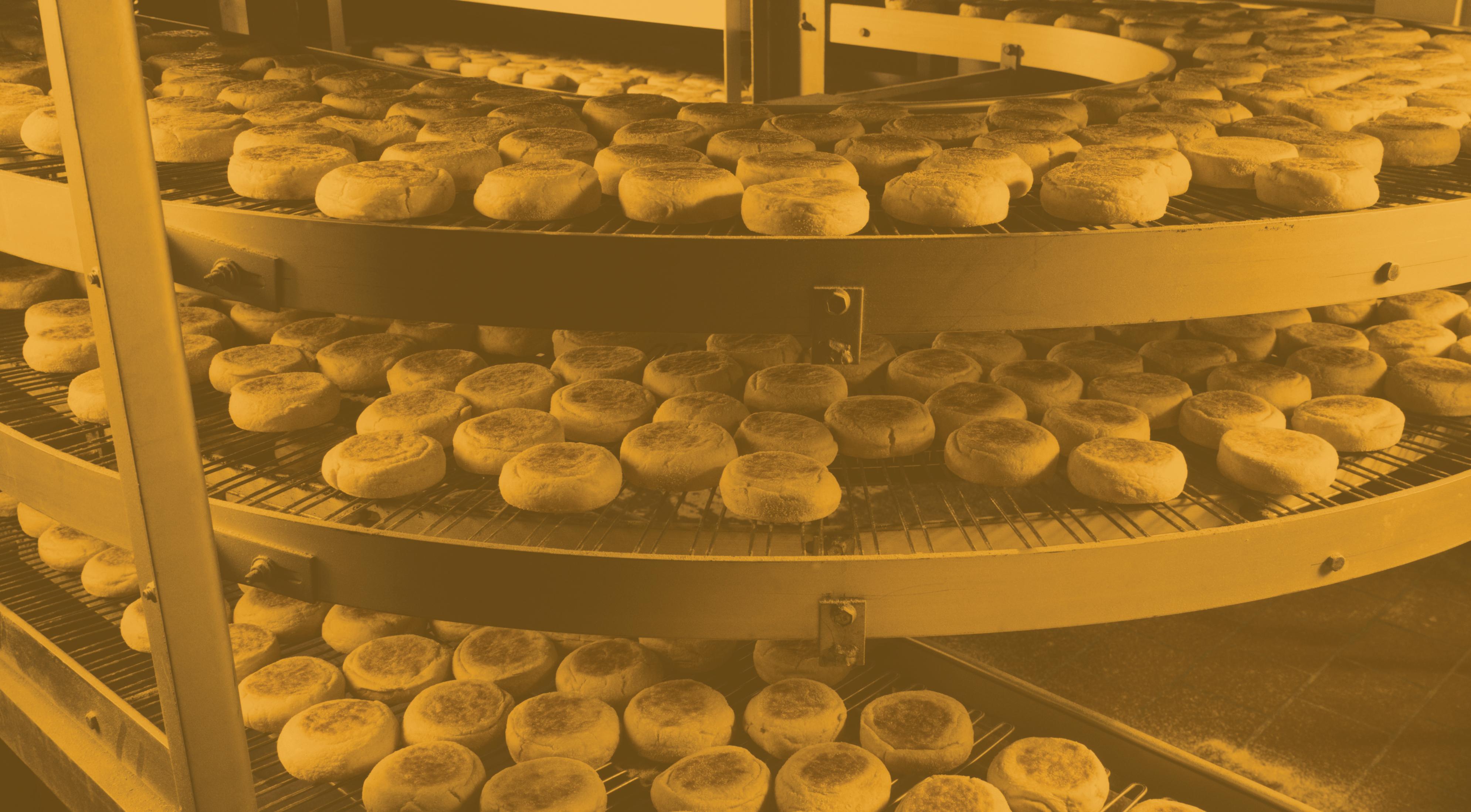
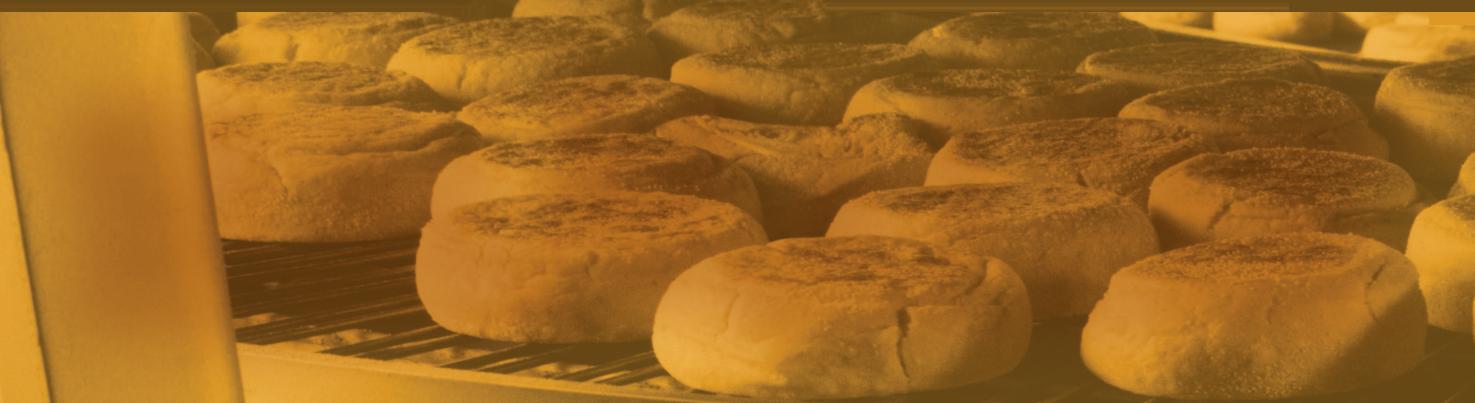
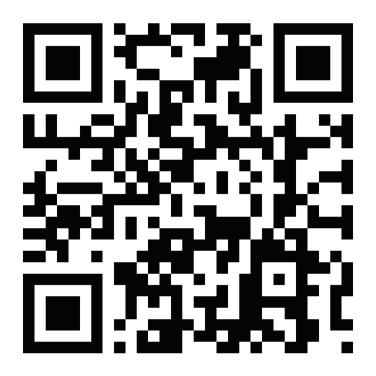
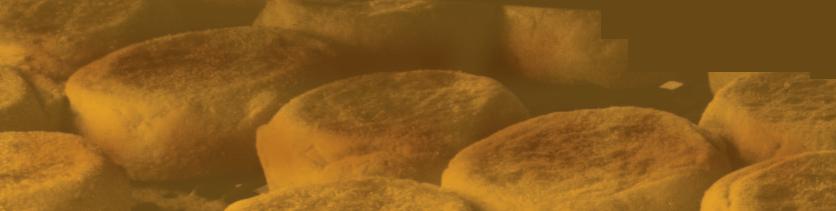
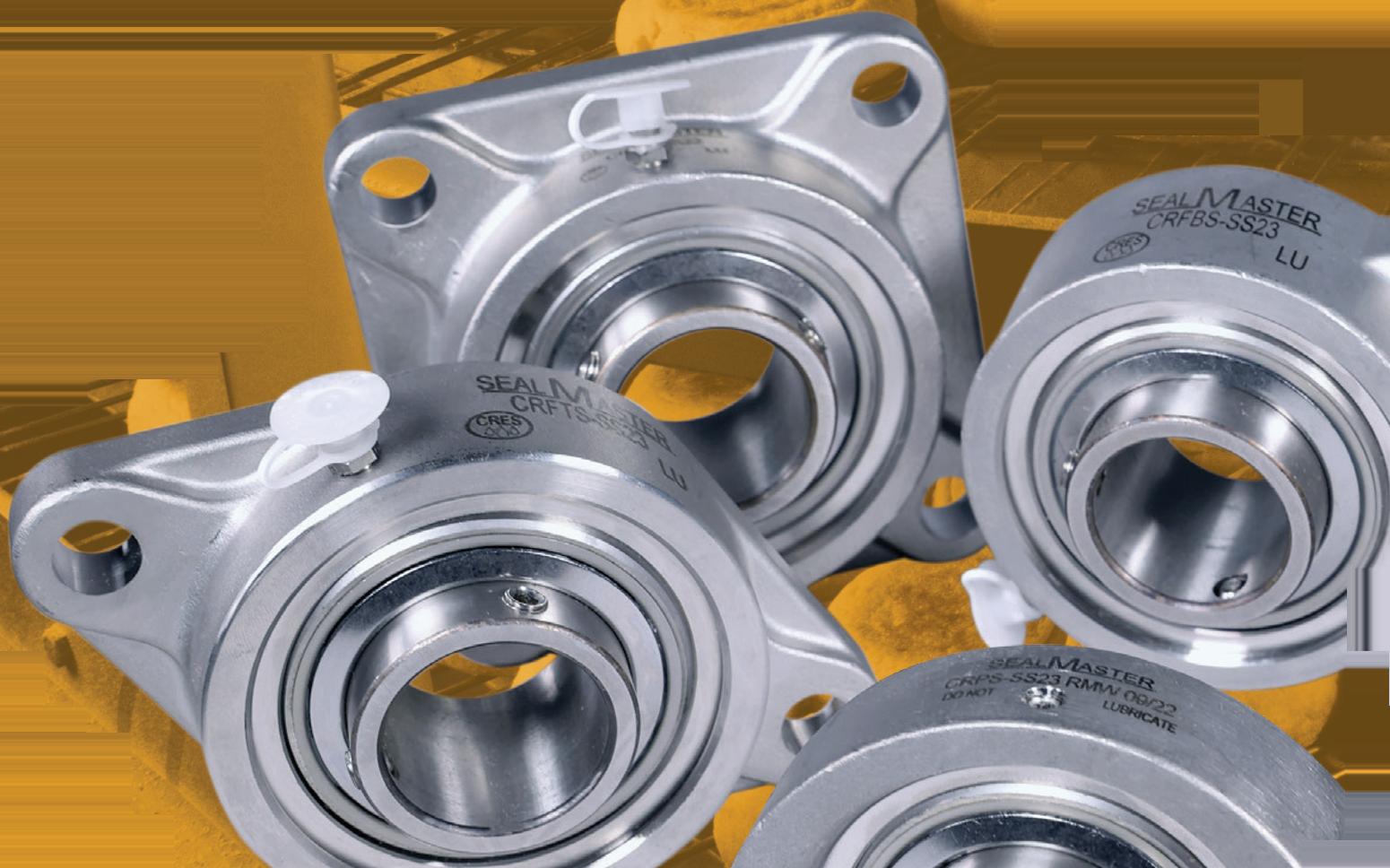

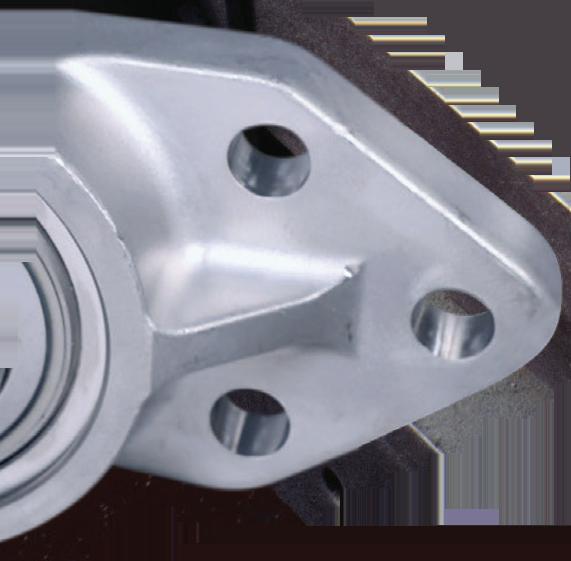
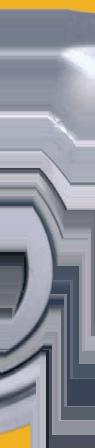

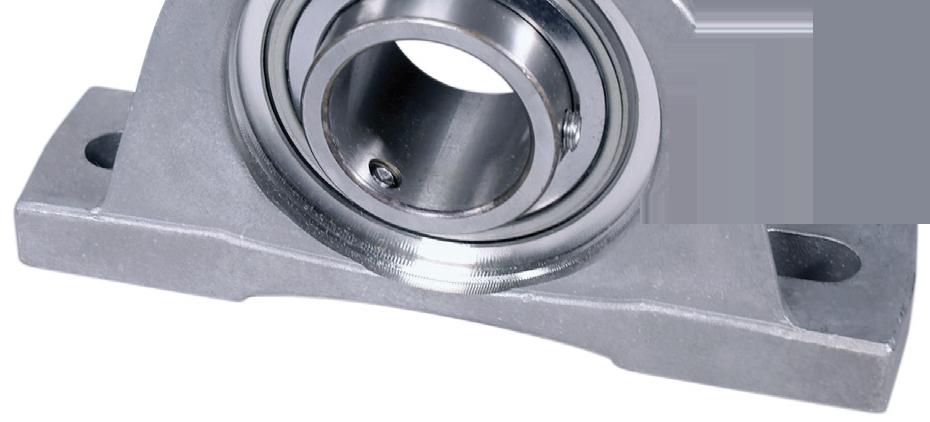
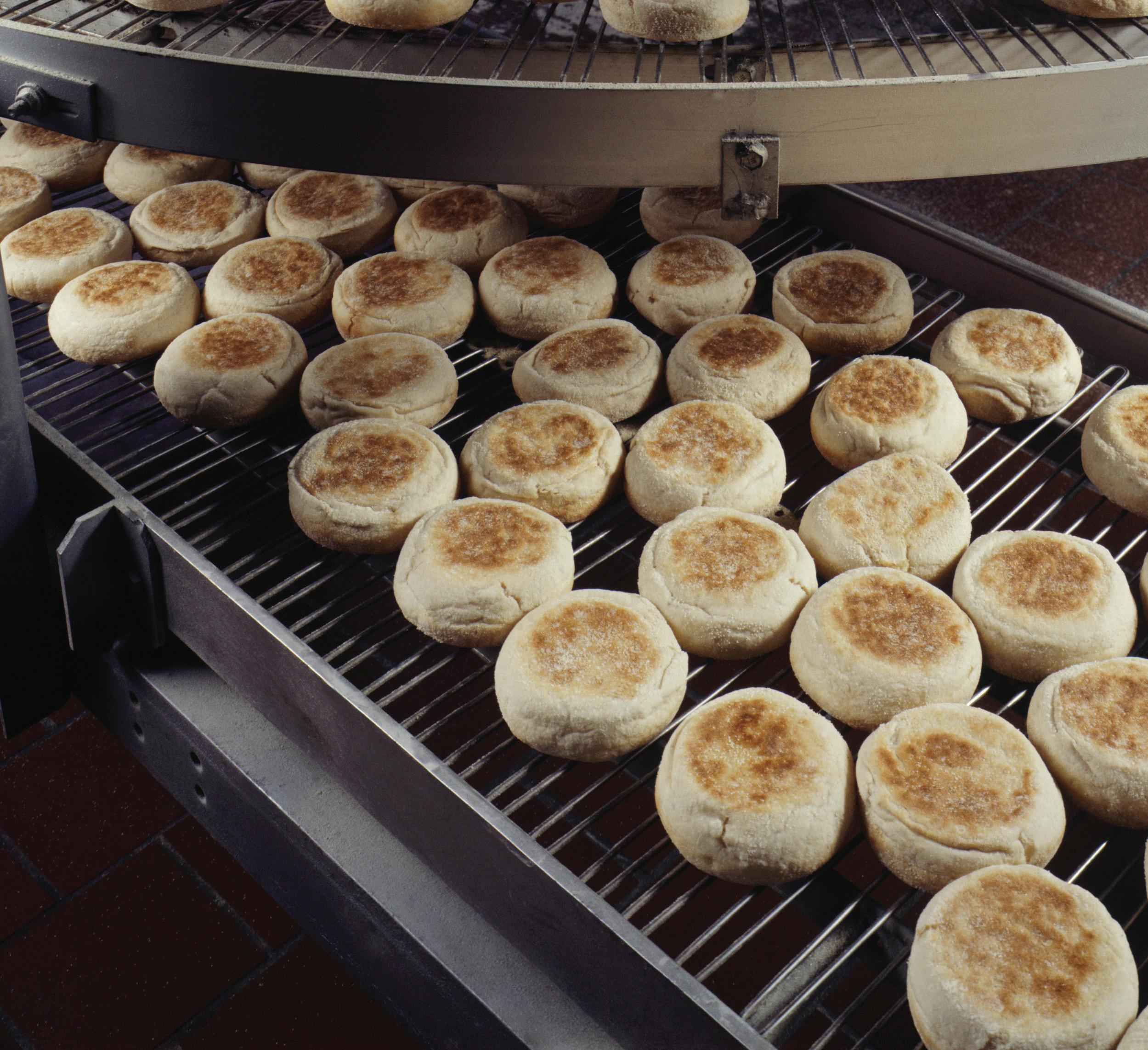
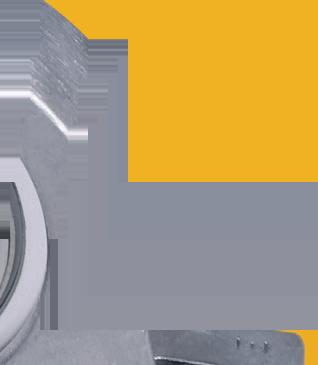
Worn bearings cause erratic movement and slowdowns. The superior durability and advanced technology of Regal Rexnord solutions ensures smooth, consistent performance to alleviate line malfunctions:
• Provides durability, longer life, as well as corrosion and contamination resistance in extreme washdown environments.
• Our suite of stainless steel components are built for high pressure washdowns with less corrosion, which means less frequent replacements.
• Our bearings perform consistently in demanding production environments, minimizing downtime and maintaining high throughput.
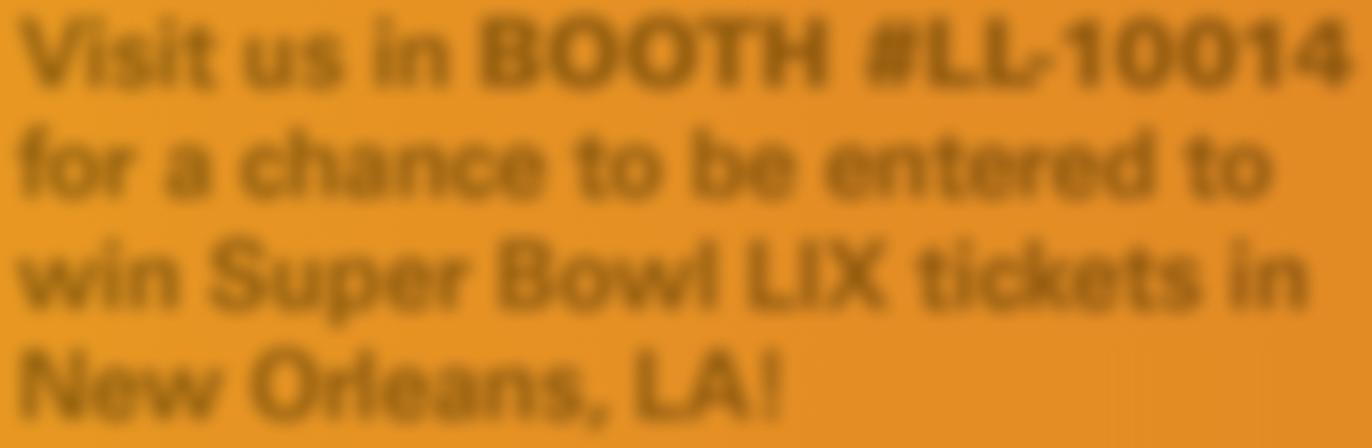
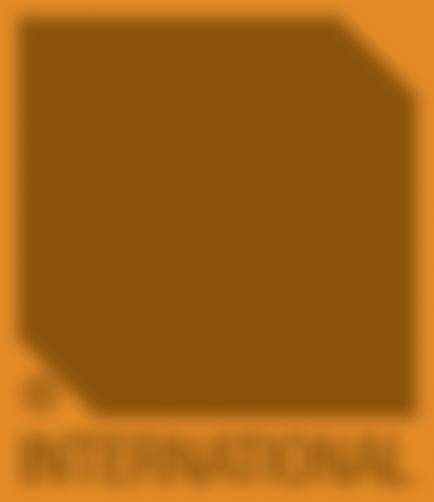
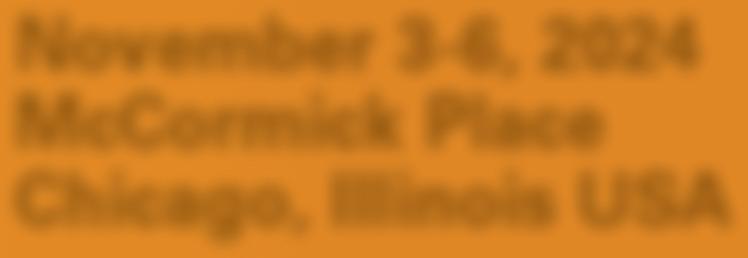
Automate with the best.
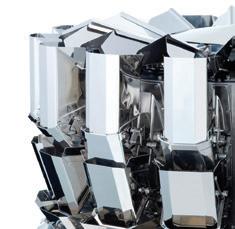

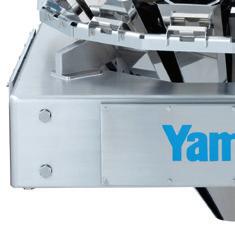
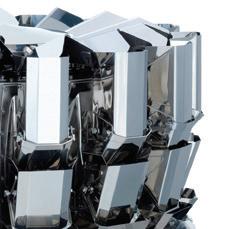
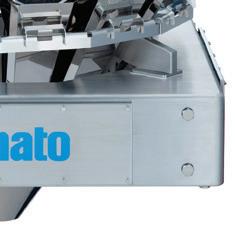
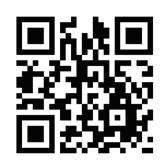
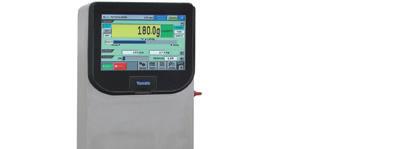
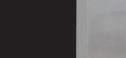
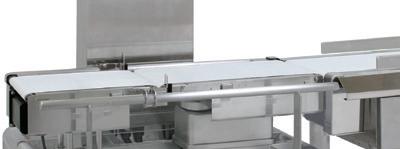



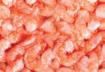

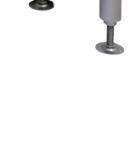

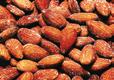
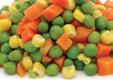

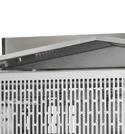
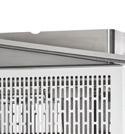
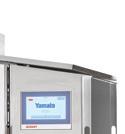
PACK EXPO International 2024 Offers Robust Sustainability Education
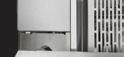
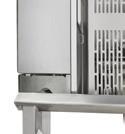
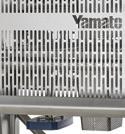
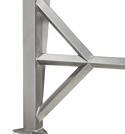
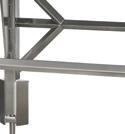
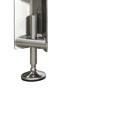

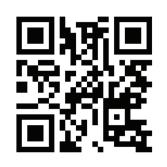

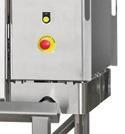
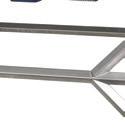
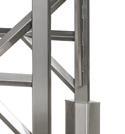
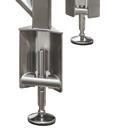
Companies will share best practices in Sustainability Central.
PACK EXPO International 2024 spotlights sustainability with new and expanded show resources to help brands lessen energy consumption, minimize waste, and reduce overall carbon footprint.
Debuting at PACK EXPO International, Sustainability Central (Booth W-21020) is a unique opportunity for attendees to delve into packaging sustainability and its implications. This show floor destination, featuring expert speakers and a showcase of actionable, sustainable solutions in manufacturing, materials, recovery, logistics, analytics, and design, offers over 20 educational sessions. These sessions, led by experts from Amazon, Conagra, Clorox, Dow, Merck, Mars Wrigley, the Consumer Brands Association, and other major industry players, provide insights on a range of topics.
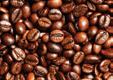
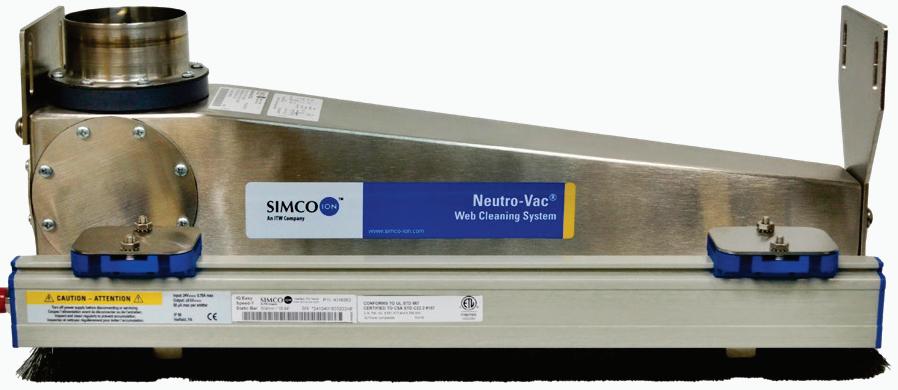
Additionally, Sustainability Central features displays from Virginia Tech, Consortium for Waste Circularity, Clemson University, PMMI Business Intelligence, U.S. Plastics Pact, and AMERIPEN, among others, sharing their latest planet-friendly innovations, research, and best practices.
As a testament to its commitment to a seamless and productive event, show producer PMMI, The Association for Packaging and Processing Technologies, is expanding resources to assist attendees in efficiently navigating the show. This initiative is designed to ensure that attendees can make the most of the show’s exhibition space, where they can witness sustainability-enhancing solutions in action.
• For advanced online planning, attendees can use the Sustainability Solutions Finder, a professionally vetted and searchable tool, to locate exhibitors with environmentally friendly products and machinery. A kiosk is also located in Sustainability Central.
• On-site, attendees can look for the PACK EXPO Green icon to identify sustainable materials and machinery suppliers and educational sessions focused on sustainability. The online exhibitor directory has a complete list of current PACK EXPO Green exhibitors.
“We’ve intentionally partnered with companies, exhibitors, and vendors to integrate sustainability into every component of PACK EXPO International, including educational programming, show features, and how we do business as the largest packaging and processing event this year,” says Laura Thompson, PMMI’s vice president, trade shows.
In addition to the new and expanded education and show navigation resources, attendees can experience the returning features and initiatives that support their ecoconscious efforts:
• Sustainability-focused educational sessions occur at the Innovation Stage, Processing Innovation Stage, and Industry Speaks.
• The Reusable Packaging Pavilion (Upper Lakeside) features Reusable
Packaging Association member companies demonstrating sustainable packaging solutions to help reduce waste, cut costs, and gain supply chain efficiency. Attendees can explore reusable transport packaging products and services and see innovative reuse solutions.
• Sponsored by Smurfit WestRock (Booth S-2830), The Showcase of Packaging Innovations® (Booth W-21030), located within the Containers and Materials Pavilion, displays award-winning packaging from around the world.
Additionally, PMMI worked with Dow (Booth W-21062), the Official Sustainability Partner and the Official Sponsor of Show Floor Recycling at PACK EXPO International, to minimize the event’s environmental impact and divert as much waste as possible from landfills. PMMI is also proud to host PACK EXPO International 2024 at McCormick Place, recognized by independent thirdparty organizations such as LEED, APEX, Green Seal, and the U.S. Environmental Protection Agency for its innovative strategies to reduce its carbon footprint.
Learn more about PACK EXPO International’s Sustainability Commitment at packexpointernational.com. ■

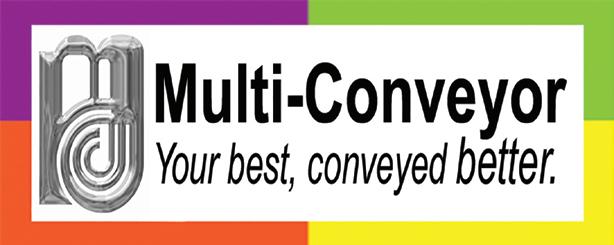
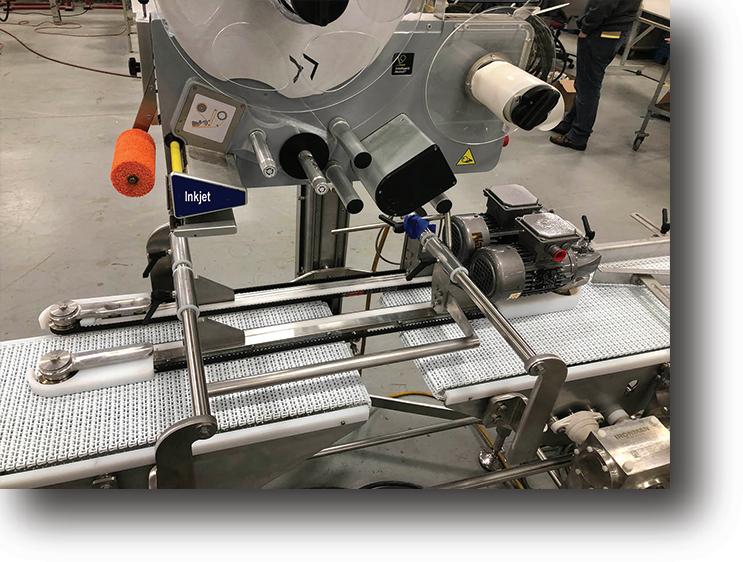
• We connect OEM communications so your equipment “talks” to each other.
• Proven up front technical & electrical support.
• 24/7 workhorse conveyors, standard or custom conveyor designs, integrated, factory tested.
• Engineered for today but built for future expansion.
Accumulate, Rotate, Elevate, Integrate, Lift-gate, Incline, Combine, Decline, Alpine, In-line, Grip, Flip, Split, Invert, Divert, Merge, Twist, Turn, Curves, Transfer, Push, Custom, Stack, Hand pack, Serpentine, Servos, Starwheels ... and more.
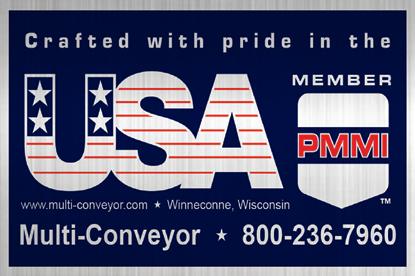
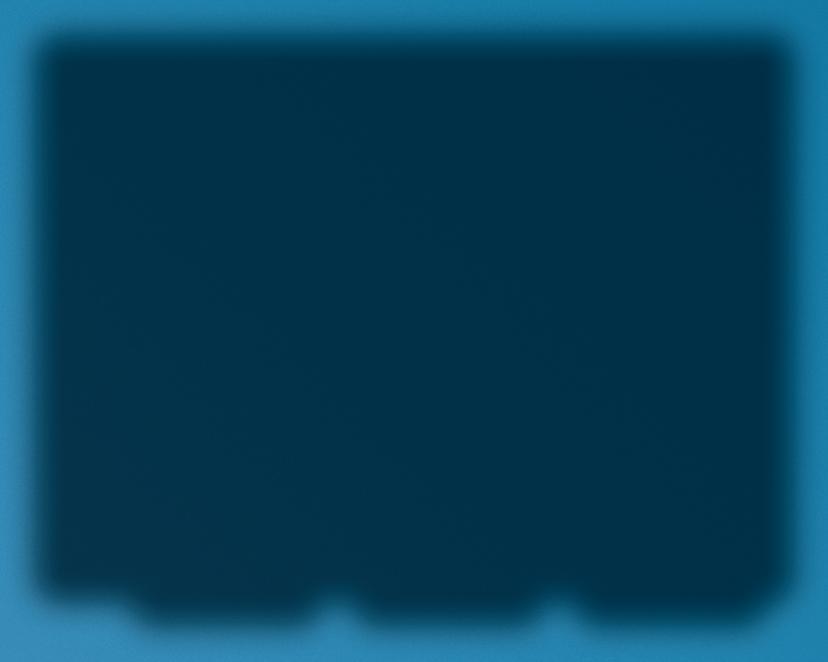
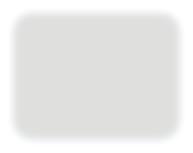

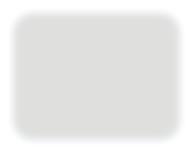
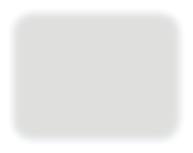

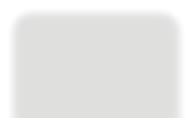
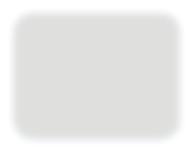
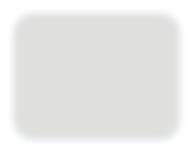
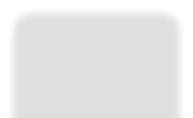
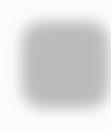

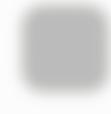

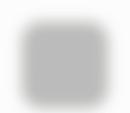
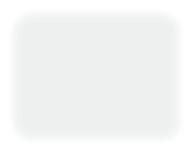

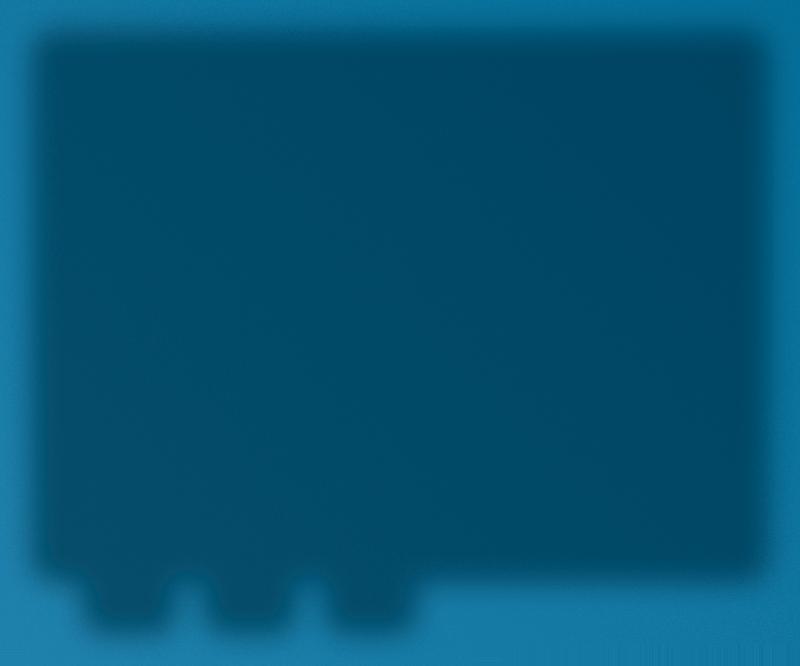

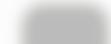

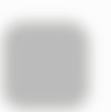
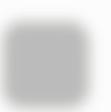



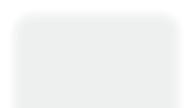
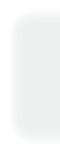

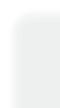
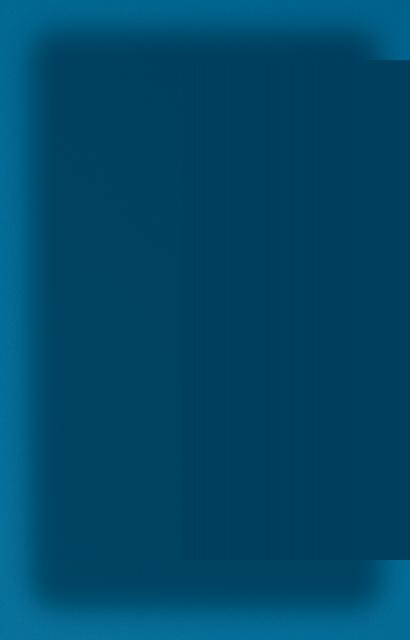


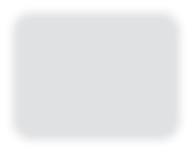
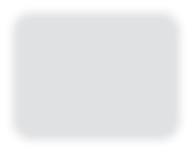
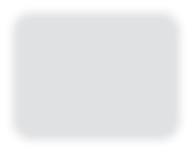



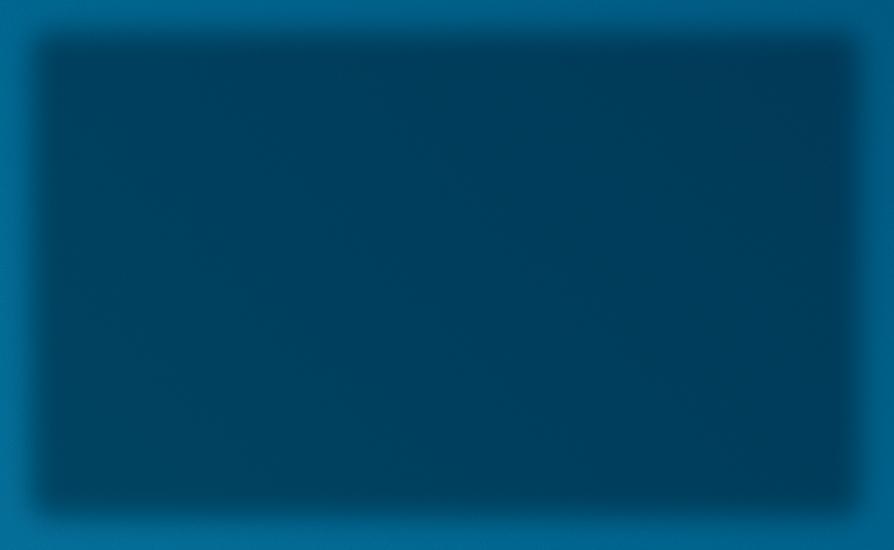
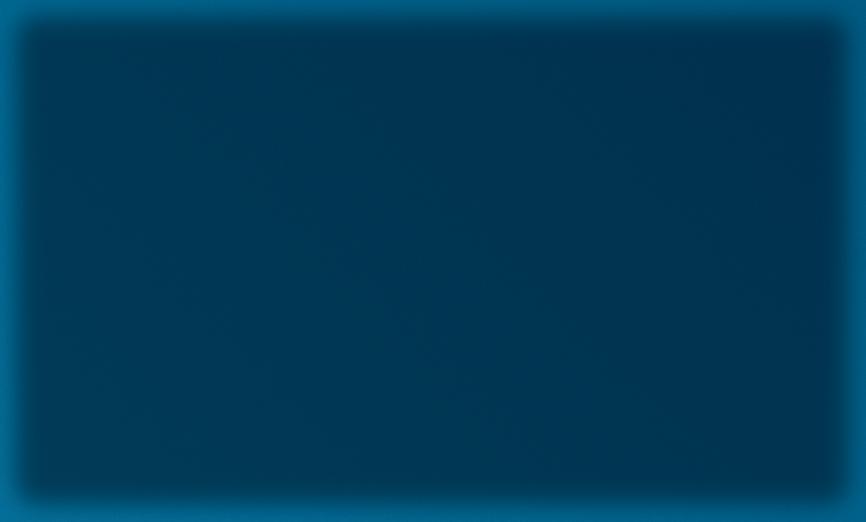
PRODUCTS
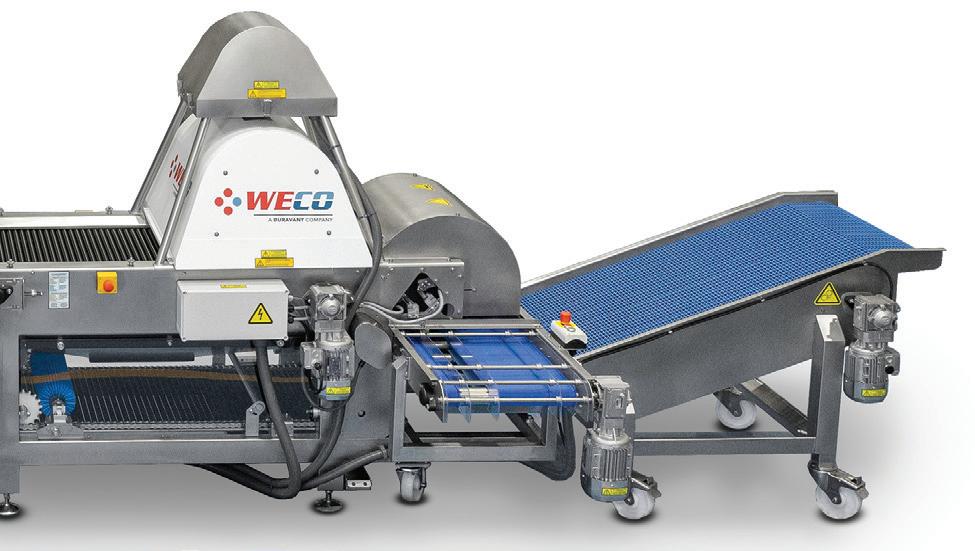
Optical Sorter
WECO, a member of the Duravant Food Sorting and Handling Solutions group, o ers the 360Tek optical sorter for blueberries. Compact, high-capacity sorter can inspect up to 8,000 lb (3,600 kg) of berries per hour. Located at the end of WECO’s modular Sortivator fresh-pack line for blueberry cleaning and sorting, the 360Tek maximizes product quality while reducing labor requirements. e machine removes products with a wide range of defects including scars, splits, and rubs, as well as EVM, like stems and owers. It can also separate large, jumbo berries into a separate stream.
WECO
Booth S-2860
www.wecotek.com
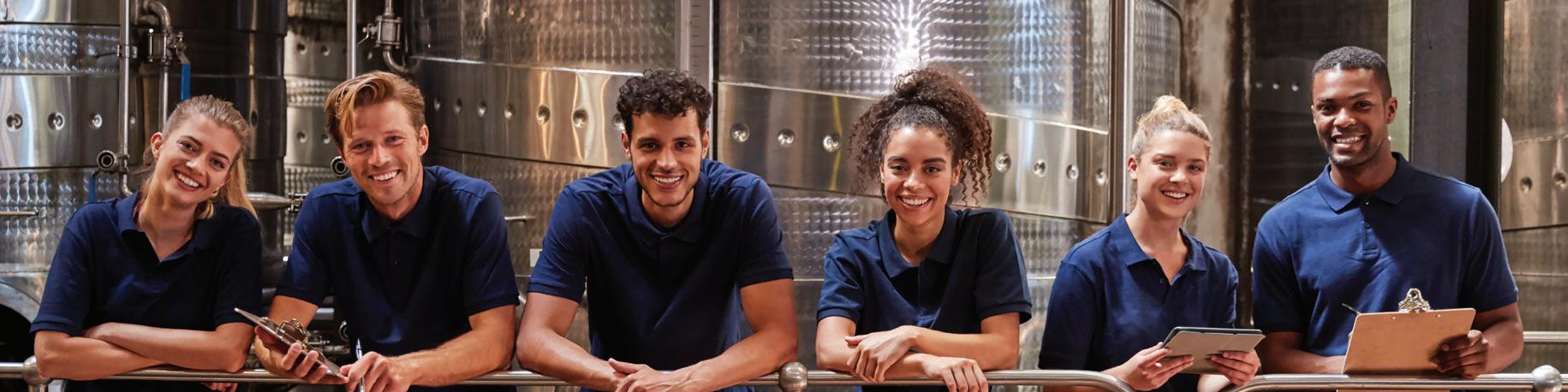
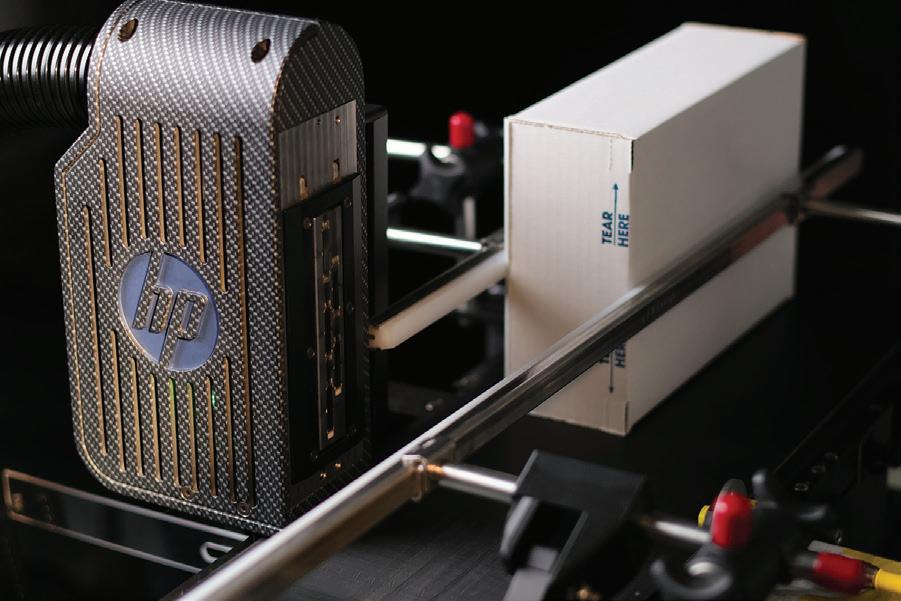
Printhead and Ink Portfolio for Packaging
e HP 23mm printhead and ink portfolio is designed for primary package coding, and when coupled with the enhanced HP 108mm printhead and ink portfolio for secondary and late-stage packaging, demonstrates HP’s commitment to providing comprehensive solution options for the entire package coding and printing process.
HP Inc. Booth W-14105 www.hp.com

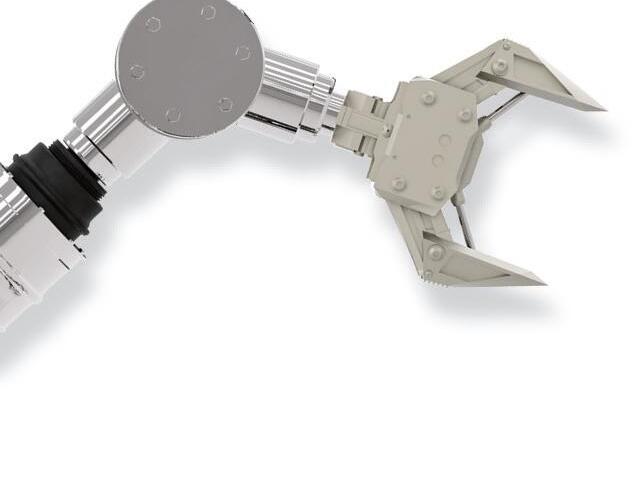
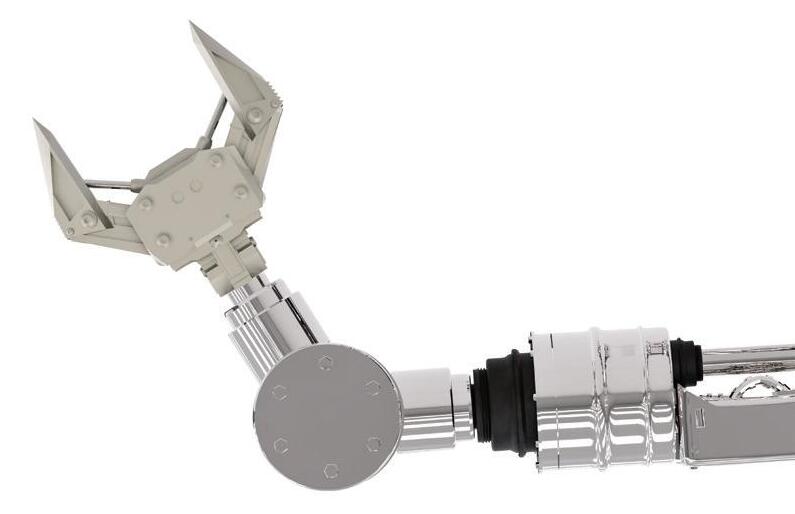
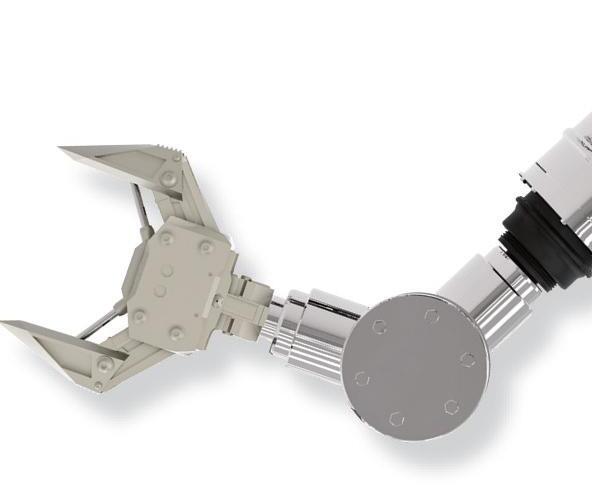
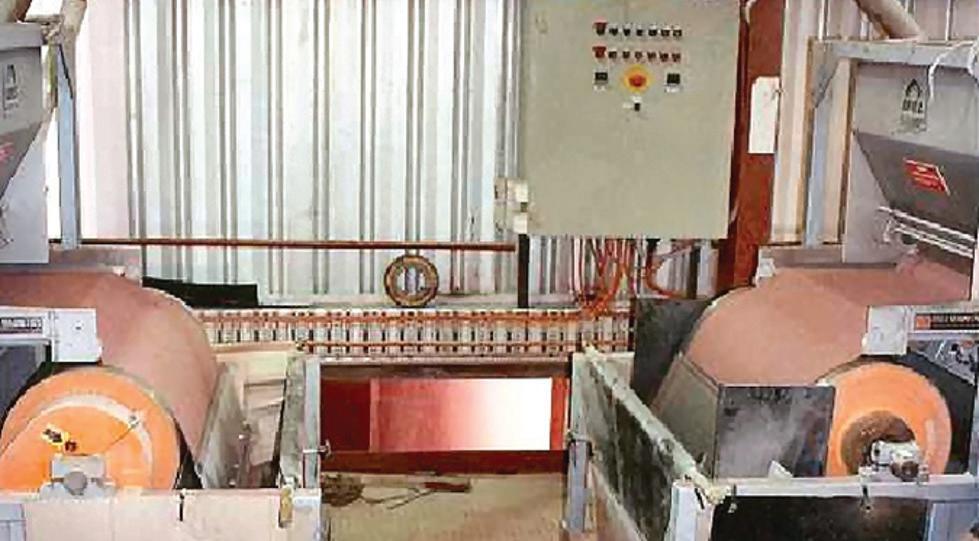
Drum Separators
Eriez expands its Salient Pole Rare Earth (SPRE) drum line to include food processing applications. ey are now optimized to meet the stringent requirements of food processing, ensuring the purity and safety of food products. Drums feature a selfcleaning design and generate a strong magnetic eld of up to 6,000 gauss, allowing the drums to e ectively remove foreign contaminants in even the most challenging food processing applications.
Eriez
Booth N-5121 www.eriez.com
Sustainable Films
Pregis launches AirSpeed® Double Cushion Renew™ PCR, ideal for flexible void-fill applications, providing top, side, and corner protection. Its compact double-cushion design fits tight spaces, delivering reliable protection without compromising durability. AirSpeed® Quilt Renew™ PCR features low-profile air transfer technology and is ideal for wrapping and void-fill, conforming to various shapes and sizes for secure product protection. AirSpeed Double Cushion Renew PCR and AirSpeed Quilt Renew PCR are made from 80% PCR. Pregis LLC
Booth S-3574
www.pregis.com
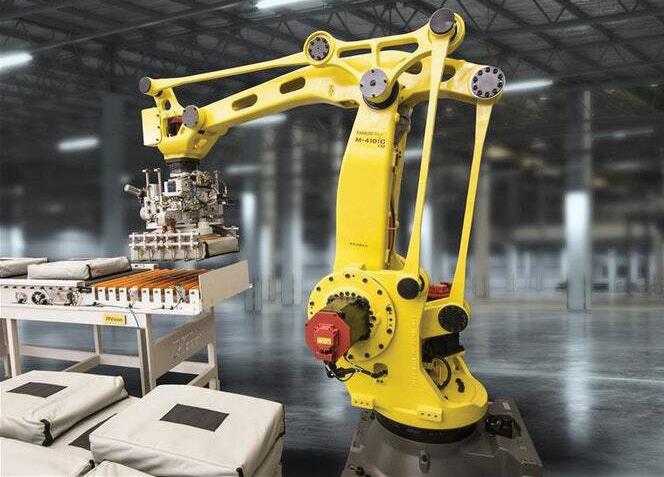
Robotics & Labeling Solutions
Precision Automation’s FANUC CRX collaborative robot features a 45 lb payload, 4.5 ft reach, and simple programming interface.
Precision Automation Company, Inc. Booth N-4920 www.precisionautomationinc.com
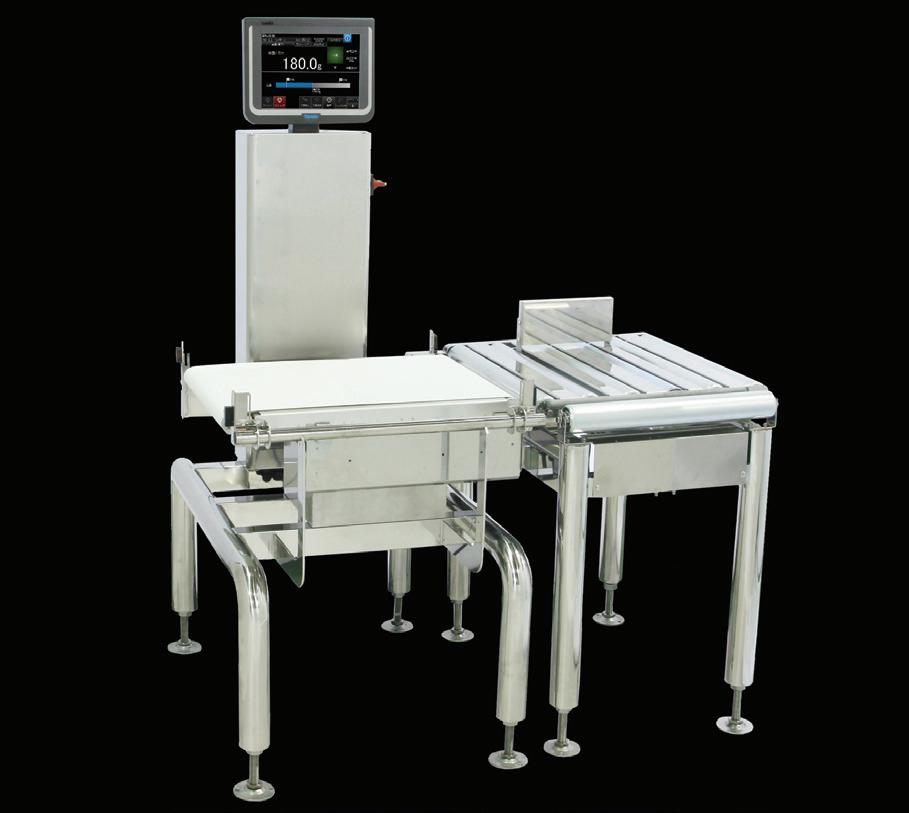
Checkweigher
Yamato checkweighers are designed to ensure the quality and safety of a production line. These advanced inspection systems can check weight and content accuracy or be integrated with components to detect foreign objects using inline metal detection or X-ray. Yamato checkweighers can help manage every aspect of packaging flow.
Yamato Booth S-3195
www.yamatoamericas.com
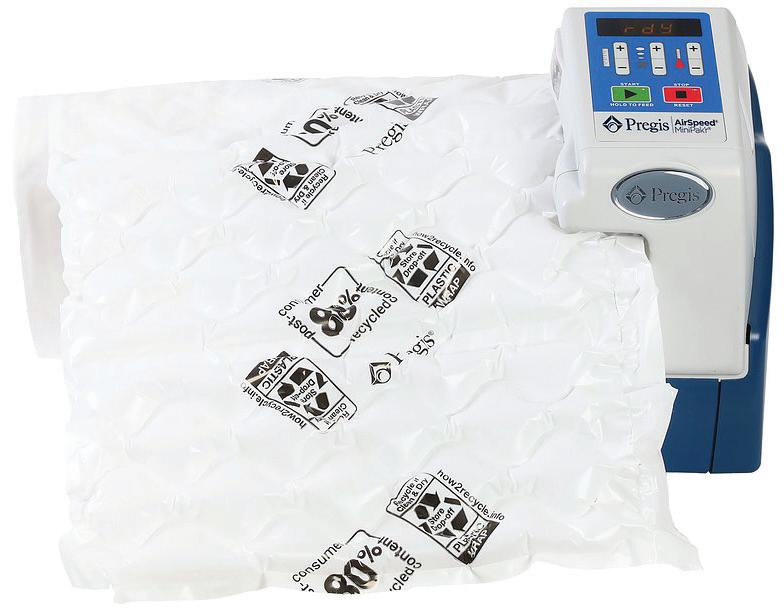
Experience how leading brands are paving the way towards a sustainable future. Expertled sessions and informational displays will help you understand packaging sustainability and what that means for your brand.
Learn From the Best
Hear from companies leading by example. Amazon, Conagra Brands, Dr. Bronners, Merck and more on topics such as:
• How to drive sustainability in your organization
• Innovative collaborations and packaging solutions
• Designing for e-commerce packaging
• Pursuing the circular economy
Get Inspired
See firsthand innovative projects from academic institutions like Clemson University, University of Florida, and Virginia Tech, along with critical research from PMMI Business Intelligence and Ameripen
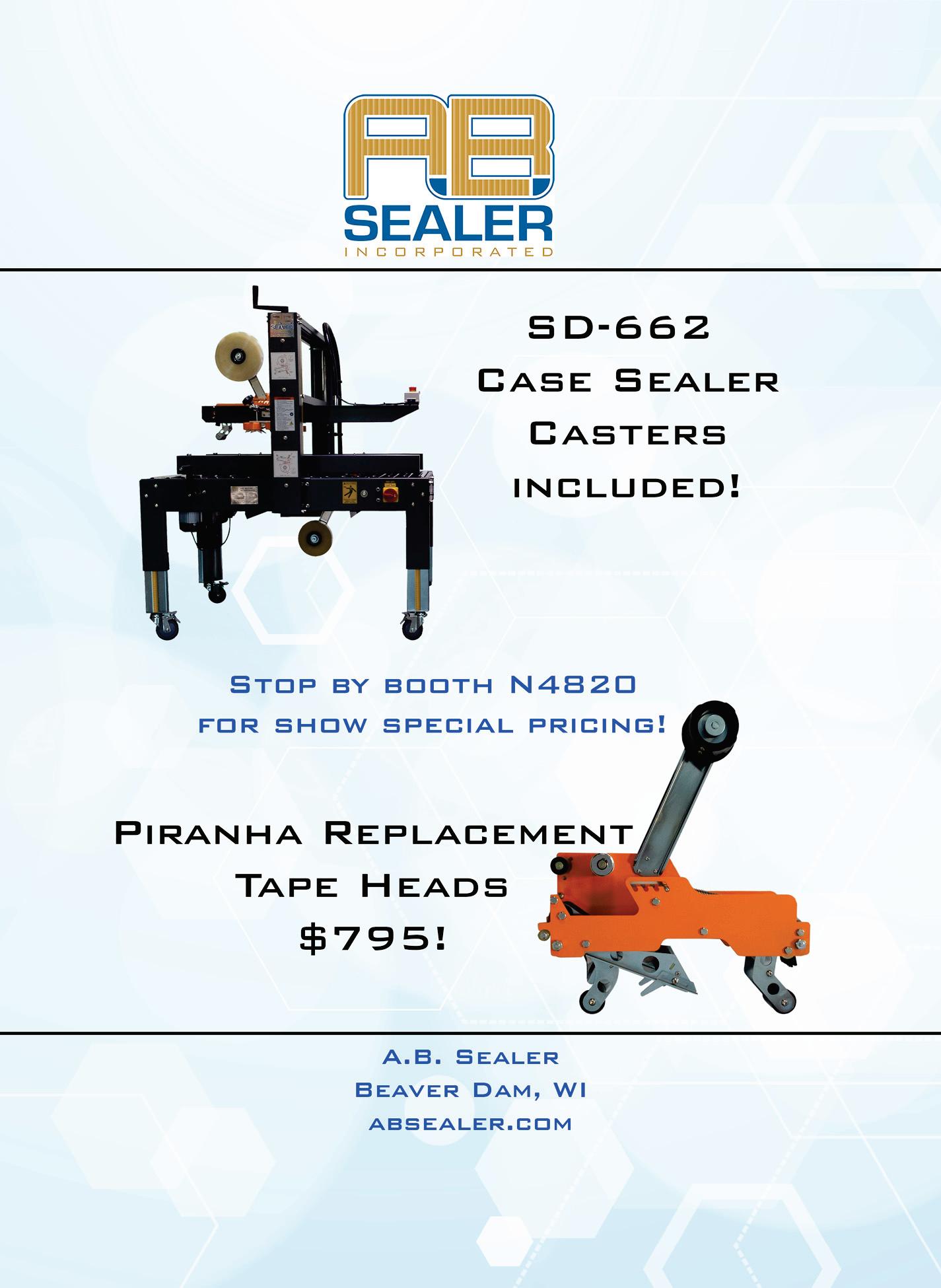

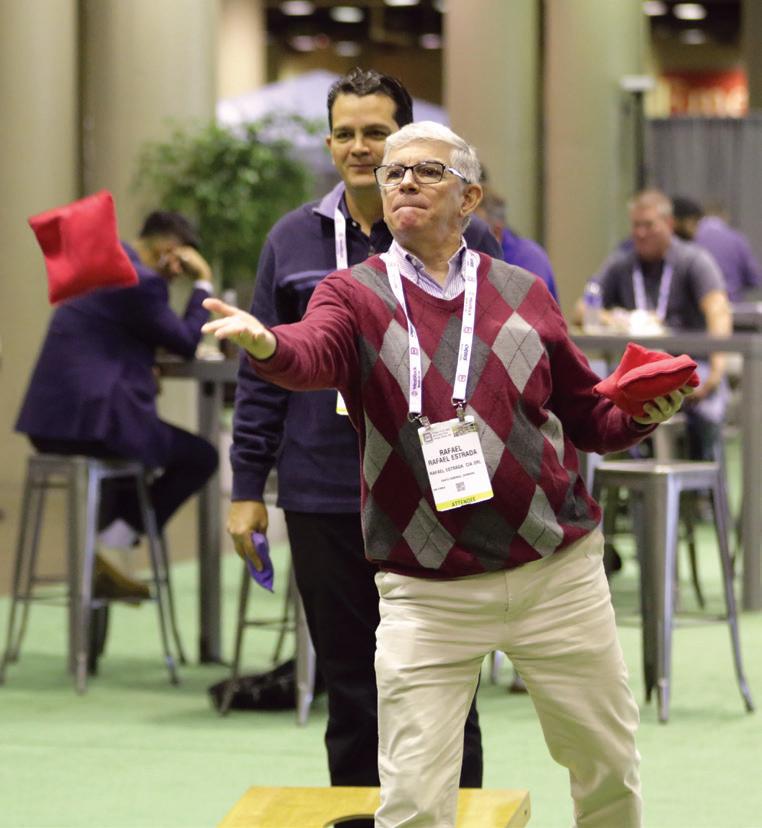
Visit the Lakeside Backyard Bistro, an oasis themed destination with delicious lunch options at discounted rates. Enjoy fun backyard style games and a place to kick back.
Open Daily Open Daily Lakeside Lower Hall back of the show floor
Sunday – Wednesday: 11:00 am – 2:00 pm
Bucket Elevator Conveyor
The Ryson bucket elevator conveyor combines vertical and horizontal transportation of bulk materials in one integral unit. They are designed for gentle handling and transporting a broad range of bulk products in food, pharmaceutical, cosmetic, ceramic, glass, recycling, and more. Units are completely enclosed and have overlapping pivoting buckets that prevent spillage and keep out foreign debris.
Ryson International Booth N-5945 www.ryson.com
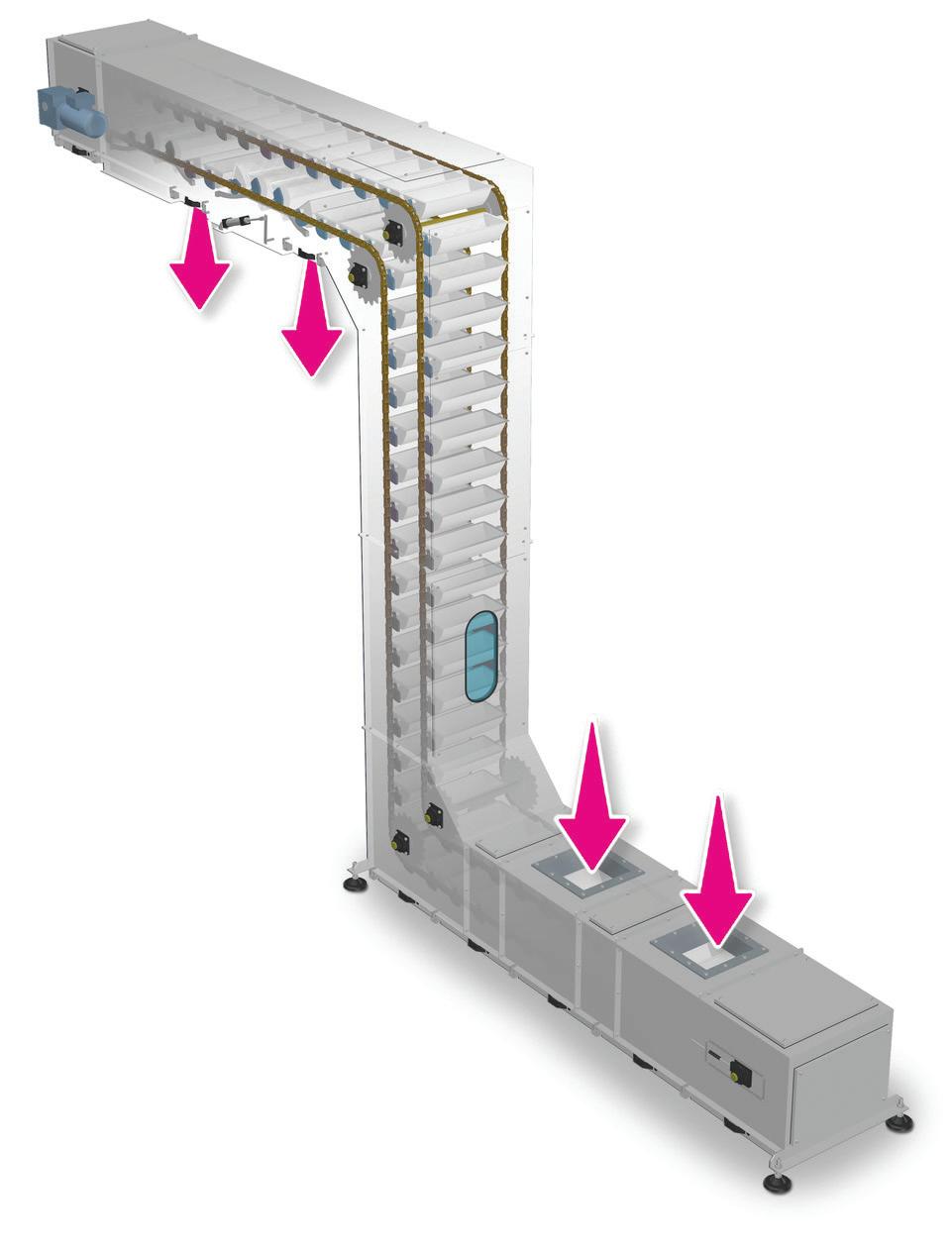
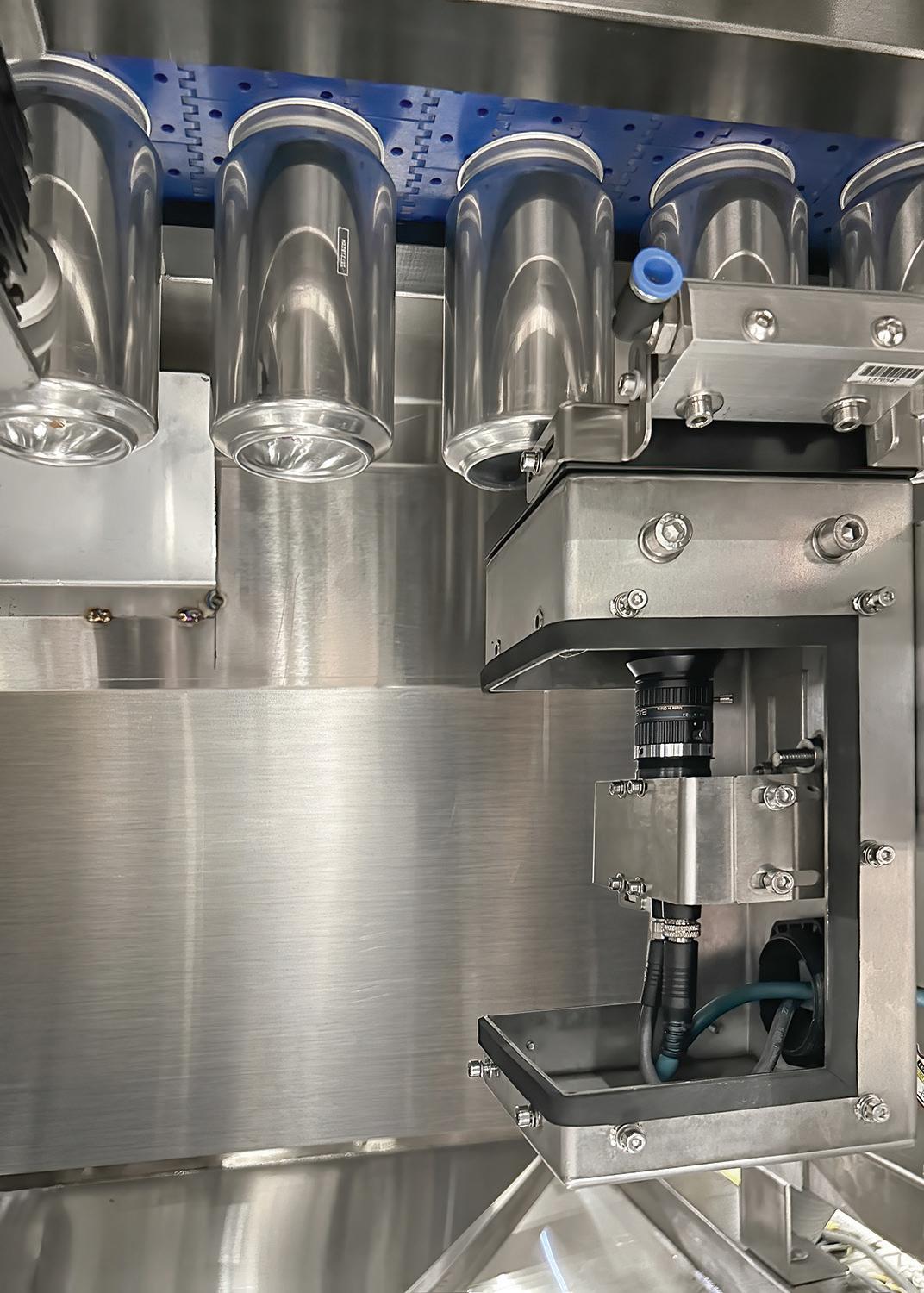
Semi-Automatic Labeling
According to Universal Labeling Systems, labeling machinery manufacturers usually address customers’ needs with high-volume labeling requirements, but what about medium-to-low volume needs? With semi-automatic labeling, the criteria can include labeling volume under 6,000 products/day, product shapes not conducive to automated product handling, and short run volumes under 30,000 products.
Universal Labeling Systems Booth N-6020 www.universal1.com
Empty Can Vacuum Transfer
The single-lane empty can vacuum system from Descon Conveyor Systems, a Pacteon company, features an overhead vacuum conveyor that carries empty cans across laser coding equipment, coding the bottom of the can. A camera detects the code’s accuracy and cans with missing or illegible codes are rejected. A vacuum transfer shifts cans back to a base chain conveyor for secondary inspection with reject.
Descon Conveyor Systems Booths S-3300, W-16041 www.DesconConveyor.com
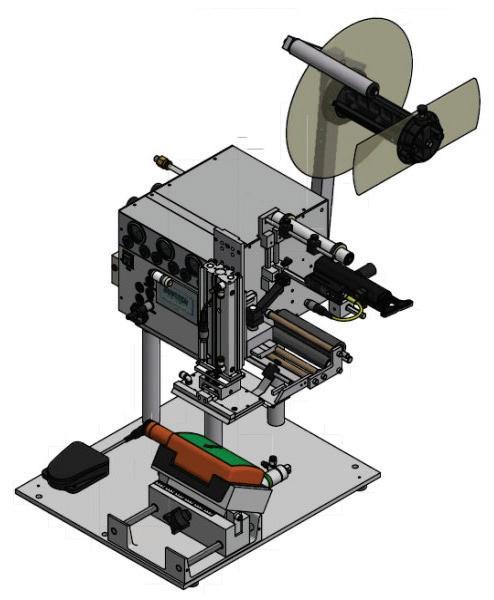
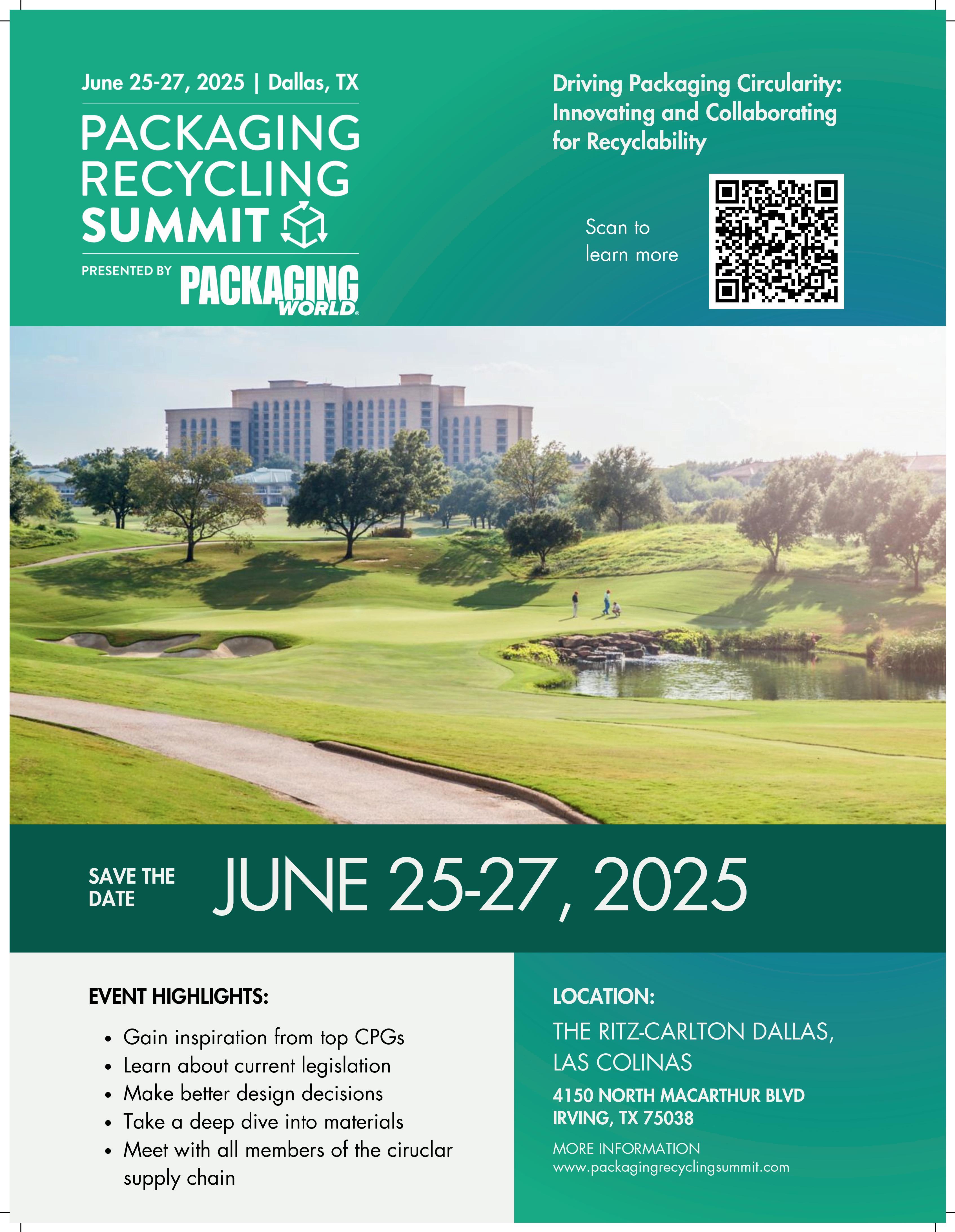
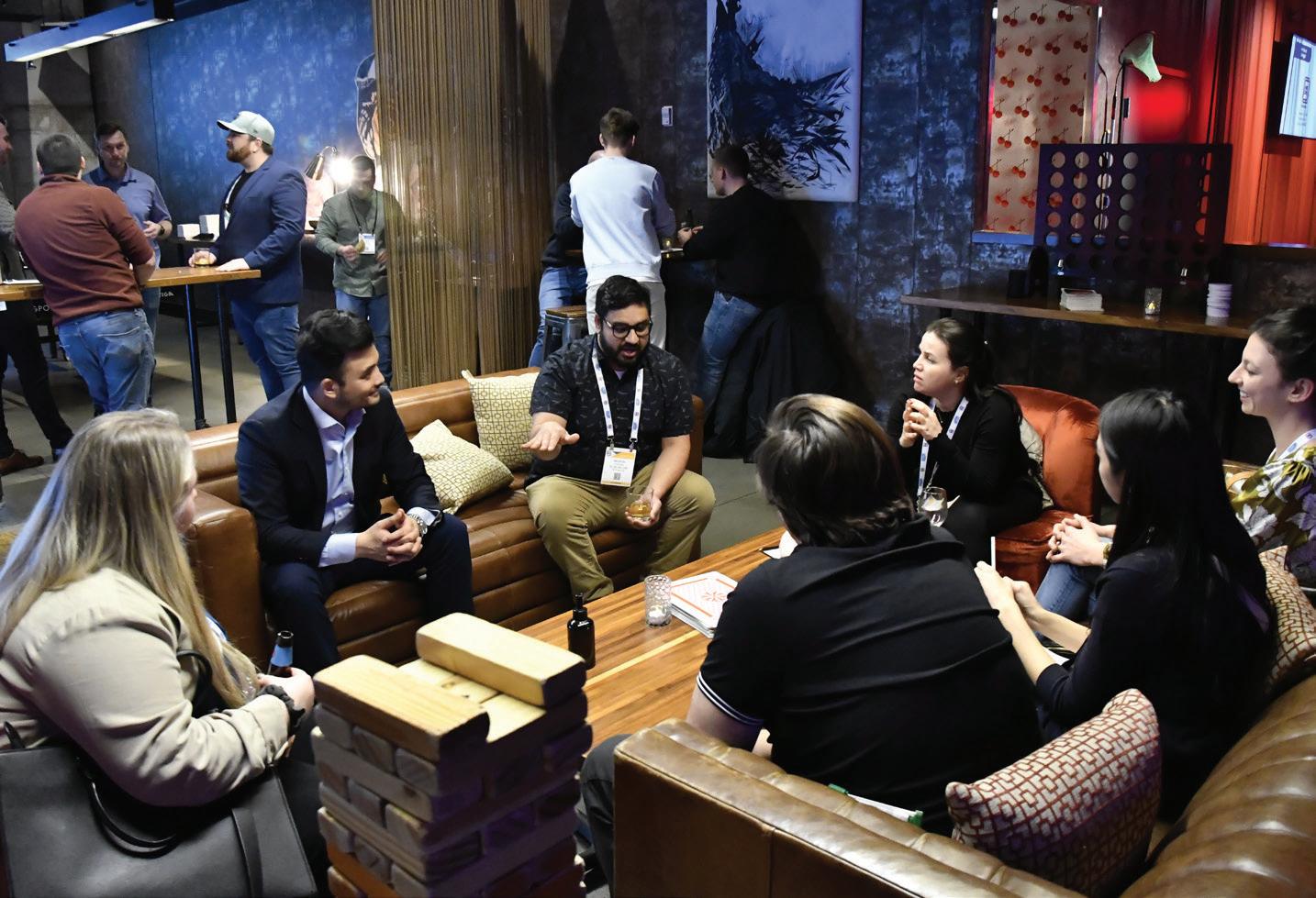
LEVEL UP YOUR CAREER
PRODUCTS
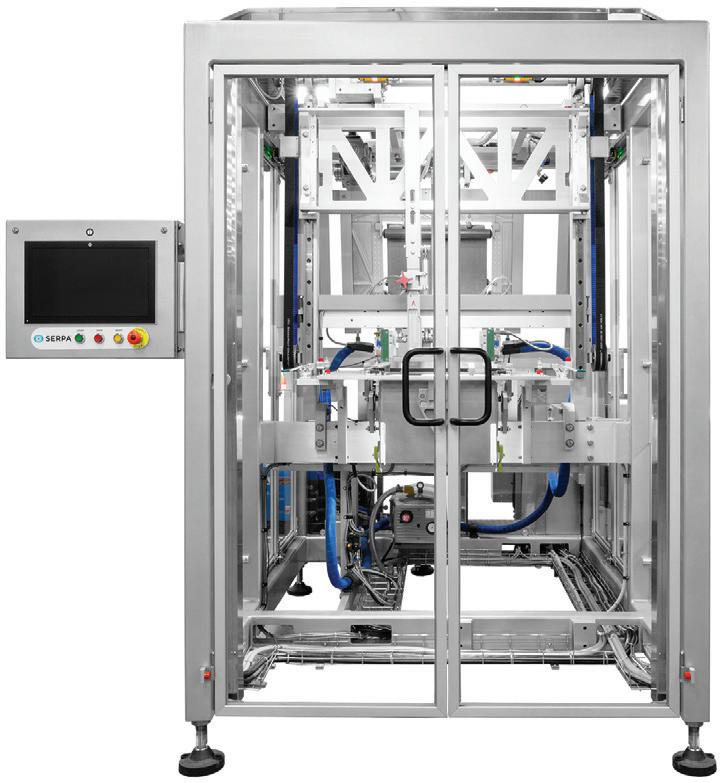
Packaging Solutions
Top Load Carton/Tray/ Case Former
Serpa, a ProMach brand, offers the FG1 top load carton/tray/case former designed to form cartons, cases, or trays using corrugated or chip board materials. It is designed for quick, toolless changeovers in less than 2 min. The machine can be integrated into any existing packaging line and is available in single (up to 75 cartons/min) or dual head (up to 400 carton/min) configurations.
Serpa Packaging Solutions
Booths S-3650, W-16017c www.serpapackaging.com
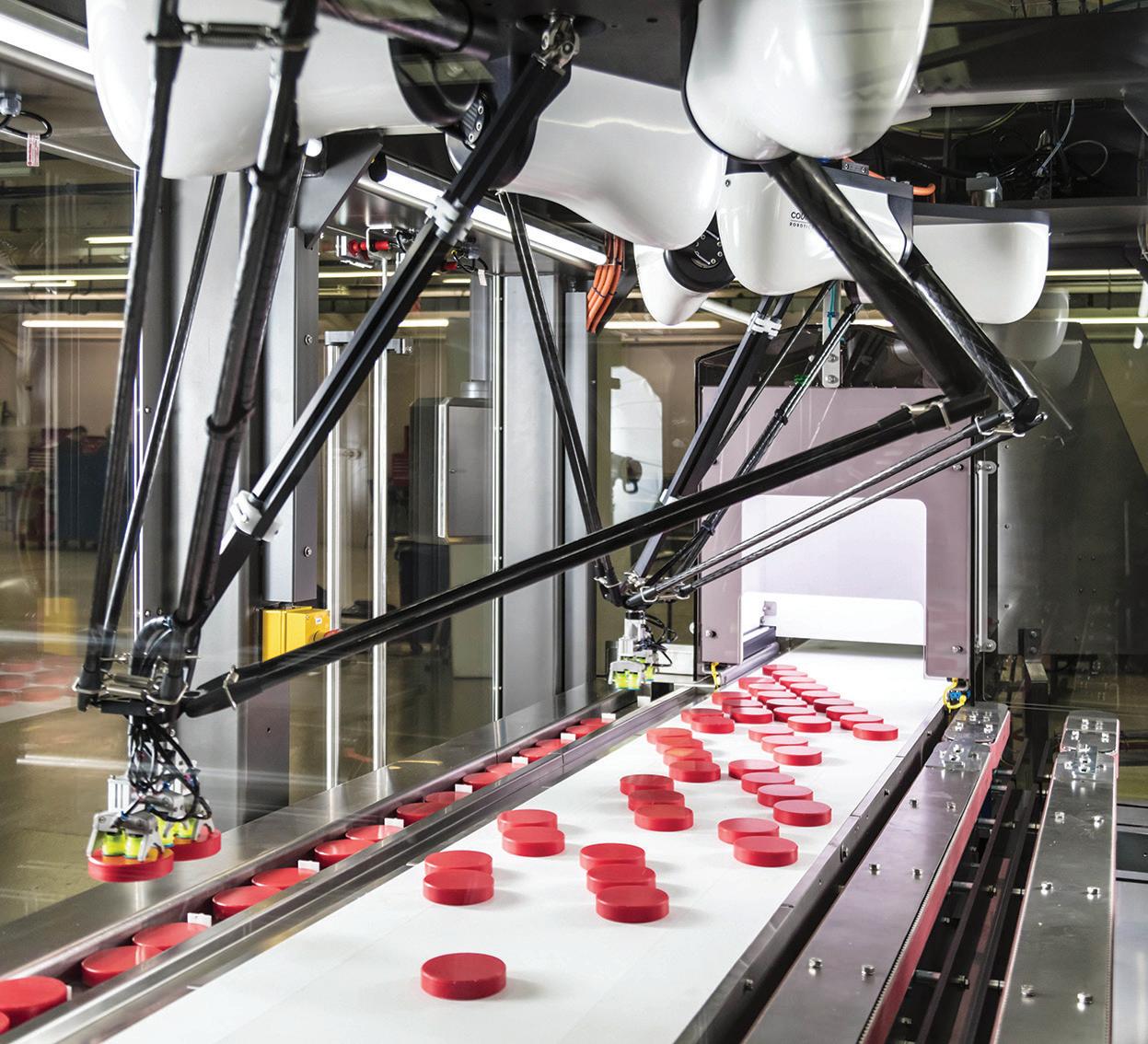
Bradman Lake offers the VGR Vision Guided Robotic Loader, a mini carton and tray former and right-angle carton closer. The VGR is designed to load products into both cartons or the infeed of a multi-pack flow wrapper. The carton and tray former meet fast-changing production requirements, offering quick changeovers and the ability to erect different styles of lock and glue cartons or trays. The carton closer is ideal for running multiple carton sizes, maximizing productivity and minimizing interruptions. Bradman Lake Inc. Booth S-2058 www.bradmanlake.com
Labeler and Capper
NJM, a ProMach product brand, offers an automated adjustments feature available on its BRONCO® 130 labeler and beltorque® capper. This option enables operators to make all critical mechanical adjustments with just a few taps on the HMI when changing to a new package size and/or format. By minimizing manual adjustments, this feature helps pharmaceutical, biotech, and nutraceutical manufacturers and packers speed changeover, simplify operation and achieve reliable system performance.

NJM Booths S-3548, W-16017a www.njmpackaging.com
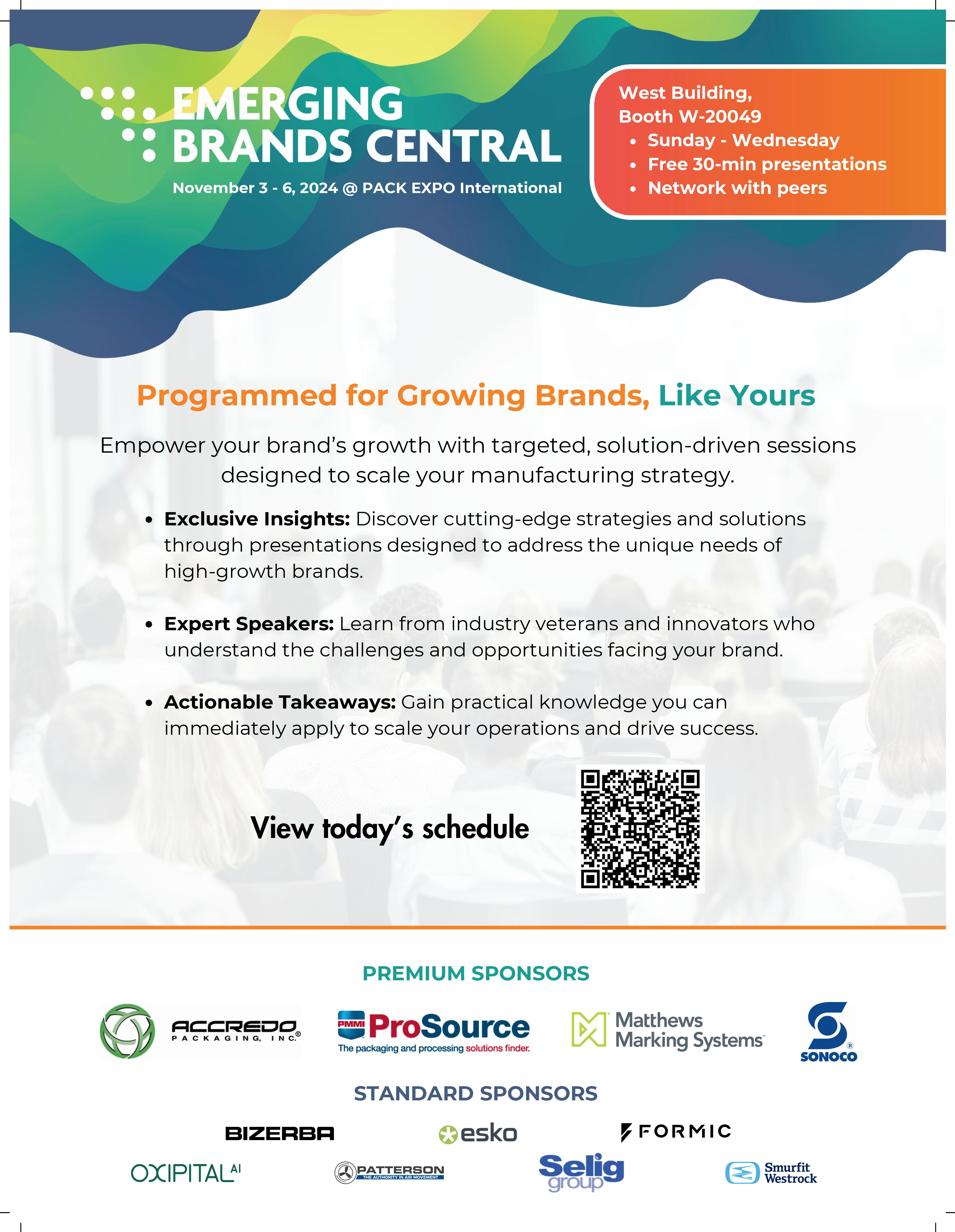
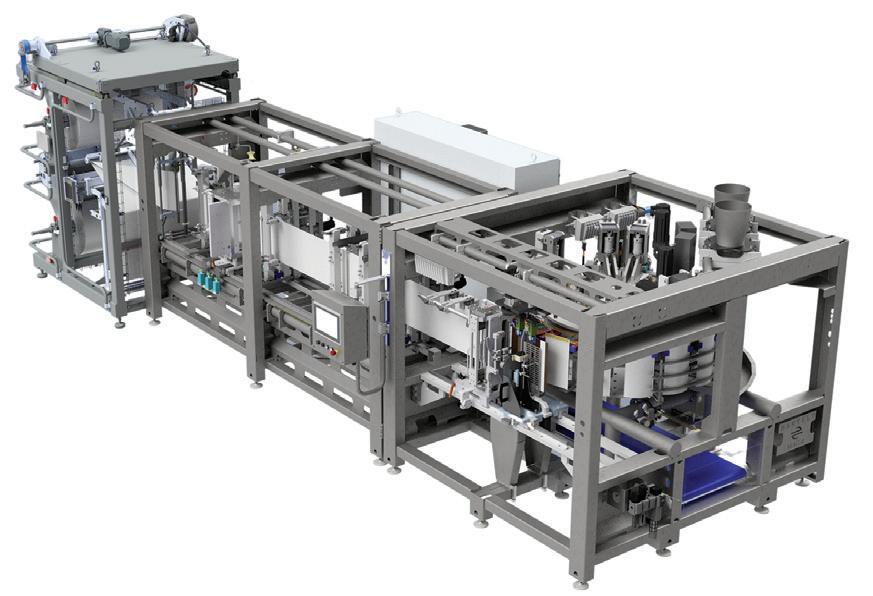
MAG Series FFS-R
Bartelt’s new product lineup includes the MAG Series FFS-R, a rotary hf/f/s machine designed for fast, easy changeovers, reducing downtime and improving productivity. Multiple heat-sealing stations and optional seal-cooling assemblies create high quality, non-leak pouches. Dynamic product settling is accomplished from the XTS track with magnetic linear motion technology, which shakes the pouch from side-to-side during filling. This improves product distribution within the pouch and reduces contamination in the seal area.
Bartelt Booth S-3528 www.barteltpackaging.com
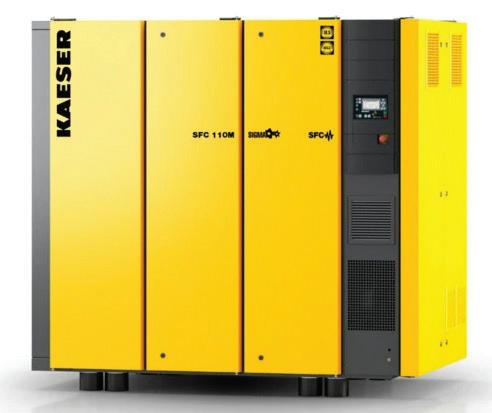
Variable Speed Rotary Screw Air Compressor
Kaeser Compressors’ SFC 110M variable frequency drive compressor features a 110 kW (150 hp) permanent magnet motor and has a flows range of 103 to 742 cfm at 100 psig. The SFC 110M features a new Sigma Profile™ airend driven by a permanent magnet motor. It features improved energy performance with flow increases up to 20% and specific power below 18kW/100 cfm.
Kaeser Compressors Booth LU-7818 www.kaeser.com
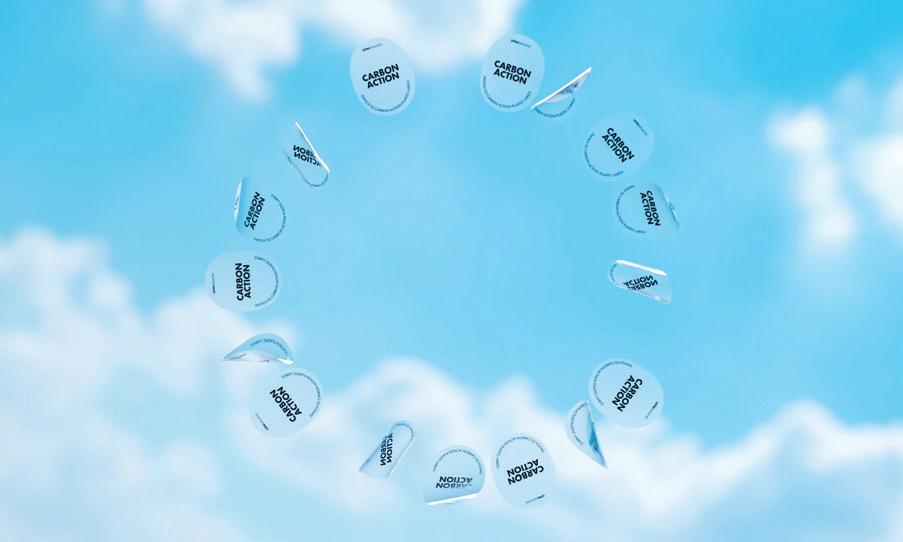
Carbon Action Plastic Labels
UPM Raflatac’s Carbon Action plastic labels offer a sustainable packaging solution by using recycled, renewable, or reduced materials while maintaining performance and quality. Labels made with PP White Biobased face material are ISCC PLUS-certified made with 30% renewable content on a mass-balance basis. Labels made with Forest Film face material are ISCC PLUS-certified bio-circular on a mass-balance basis. The material is derived from UPM BioVerno naphtha, a 100% wood-based solution. The products are made with recycling compatible adhesives to ensure packaging can be recycled in line with APR guidelines.
UPM Raflatac Booth W-15104 www.upmraflatac.com
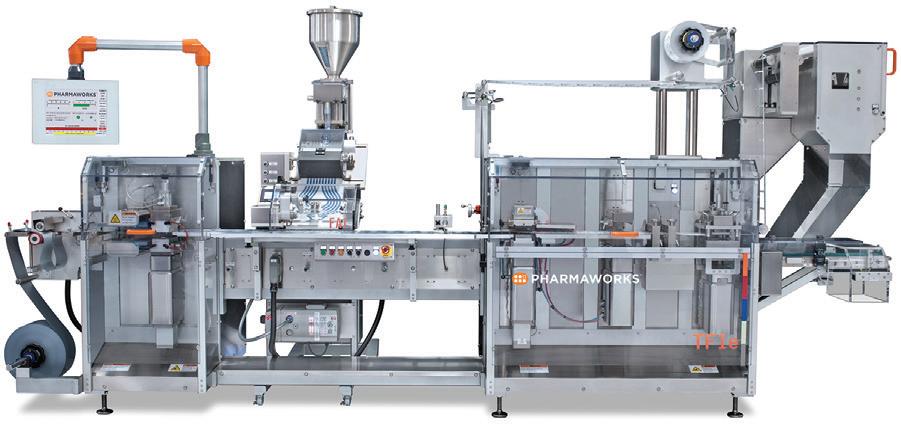
Blister Machine
Pharmaworks, a ProMach product brand, launches its enhanced TF1e blister machine featuring autoadjusting stations utilizing laser feedback, and an extended heater station. The compact machine is designed to handle more challenging packaging films like 100% recyclable mono-materials and can achieve a new thermoforming depth of up to 40 mm. Running up to 90 indexes/min and equipped with cGMP features, the TF1e is ideal for pharmaceutical, biotech, nutraceutical, and consumer goods manufacturers and contract packers. This fully servo-driven, intermittent-motion system supports both thermoforming and cold-forming applications and is compatible with all corresponding materials, including polypropylene.
Pharmaworks Booth W-16017d www.pharmaworks.com
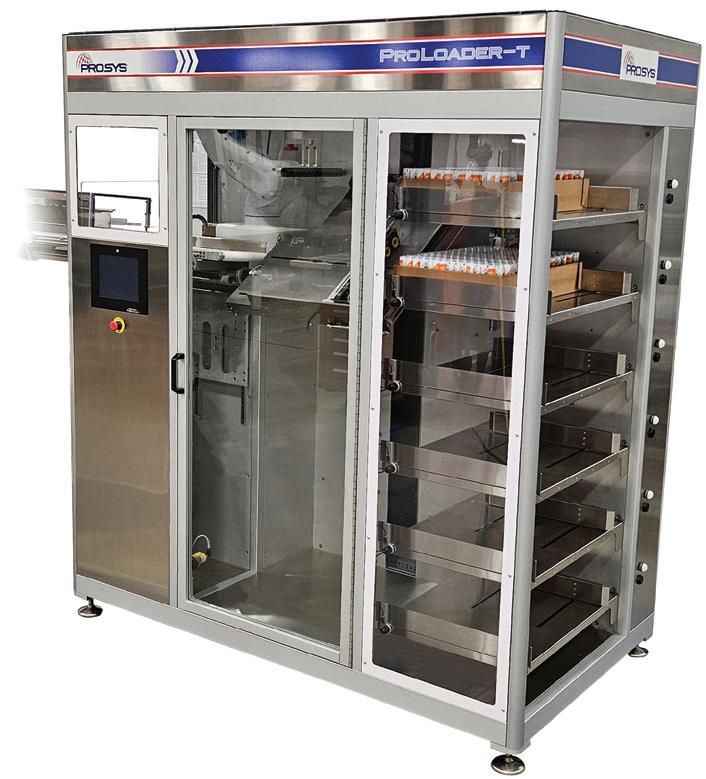
VCF Chub Filler and ProLoader-T Tube Loading System
ProSys Fill, LLC offers the VCF chub filler and ProLoader-T Tube loading system. The VCF offers vertical filling speeds of up to 40/min for self-leveling to highly viscous products. The compact ProLoader-T Tube stores and loads six cartons of tubes and automatically picks cartons, and returns empties for an operator to replace when necessary.
ProSys Fill, LLC Booth C-3656 www.prosysfill.com
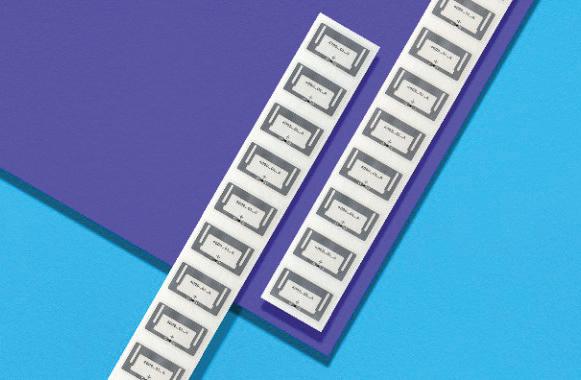
Pharma Memory Inlays, Tags
The AD Minidose U9XM UHF RFID high memory inlays and tags from Avery Dennison are designed to identify small pharmaceutical and healthcare items such as syringes, vials, and as well as a variety of packaging formats. The products’ higher memory enables converters, system integrators, healthcare providers, pharmaceutical, and medical device OEMs to store additional product information such as expiry date and batch/lot on the item. It is also available in several different memory sizes from 96 to 496 bit EPC memory .
Avery Dennison Booth W-20103 www.averydennison.com
Robotic Vial Filling and Capping Machine
Steriline’s RVFCM11-S is an advanced robotic solution designed for the primary packaging of cell and gene therapies. With a compact footprint of 2.25m by 1.65m, the machine operates with nested 2R, 6R, 8R, and 10R vials and can be configured to fill pre-filled syringes (PFS) and cartridges. Equipped with a single filling head connected to an aseptic peristaltic pump, a single stoppering head, and a single capping head, the RVFCM11-S utilizes two Stäubli Stericlean Robots for the handling of primary containers with zero glass-to-glass contact.
Steriline North America Inc.
Booth W-16060
www.steriline.us

Robotic Palletizer
With a modular sortation and layer-forming solution, the RL1000 robotic palletizer from Brenton achieves rates of up to six layers/min. Borrowing innovation from its MP1000, the machine delivers a high-speed layer palletizing solution tailored to RSC, wraparound, lithographic, and display cases, as well as trays and wrapped products. The RL1000 is a modular solution, offering eight standard layouts that can be applied to a customer’s application.
Brenton Booth S-3662
www.brentonengineering.com
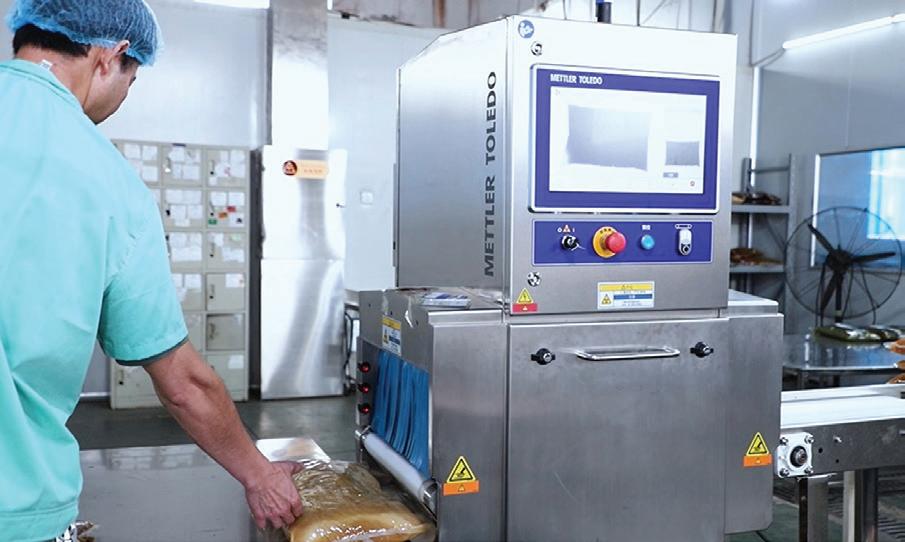
X-ray Inspection System
Mettler Toledo offers the X12 X-ray inspection system designed for small- to medium-sized packaged foods. It detects hard-to-find physical contaminants such as glass, stone, and bone. The system offers an intuitive user interface with easy access for cleaning and maintenance. In addition to foreign material detection and removal, the X12 can perform various product integrity checks to improve overall product quality.
Mettler Toledo Booth S-2939 www.mt.com/pi
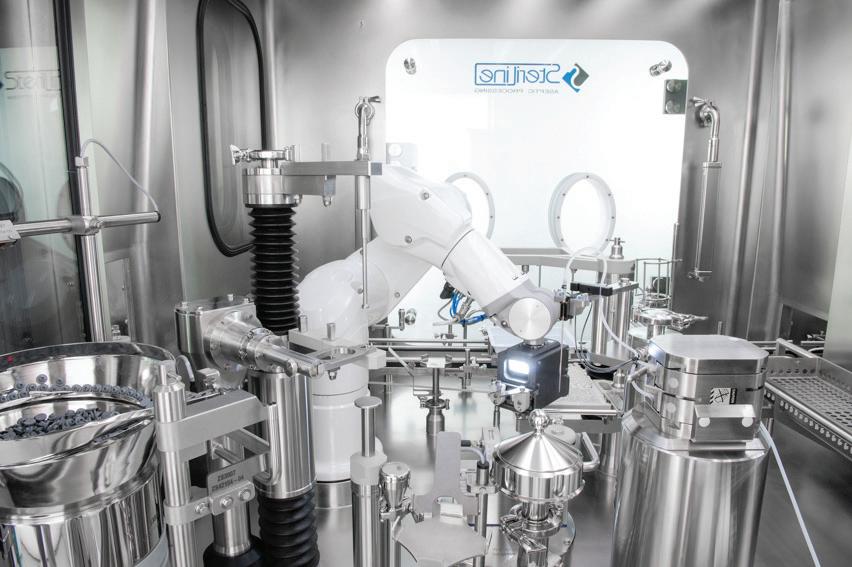

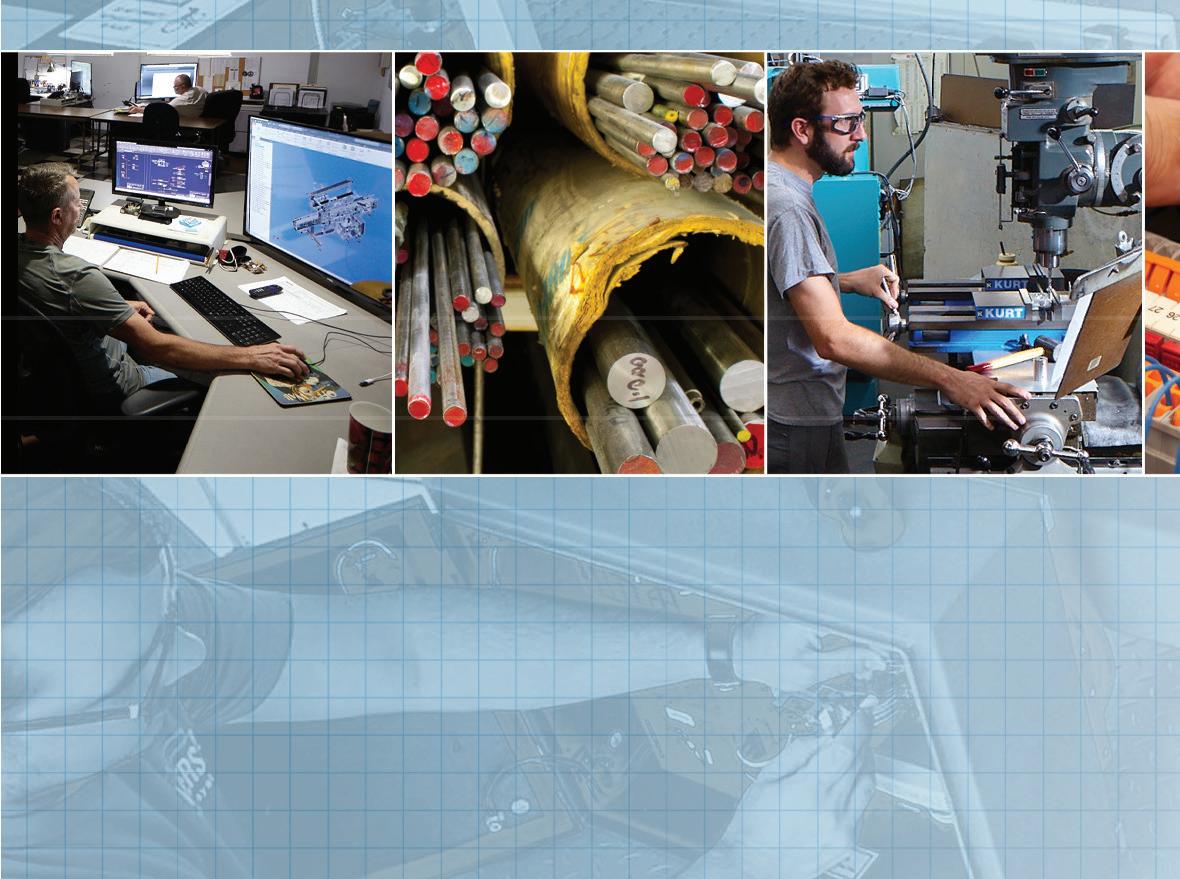
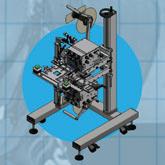
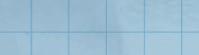

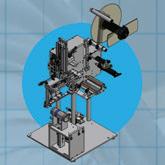
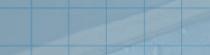
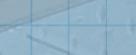
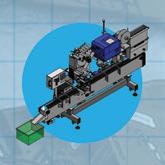
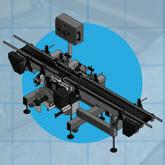
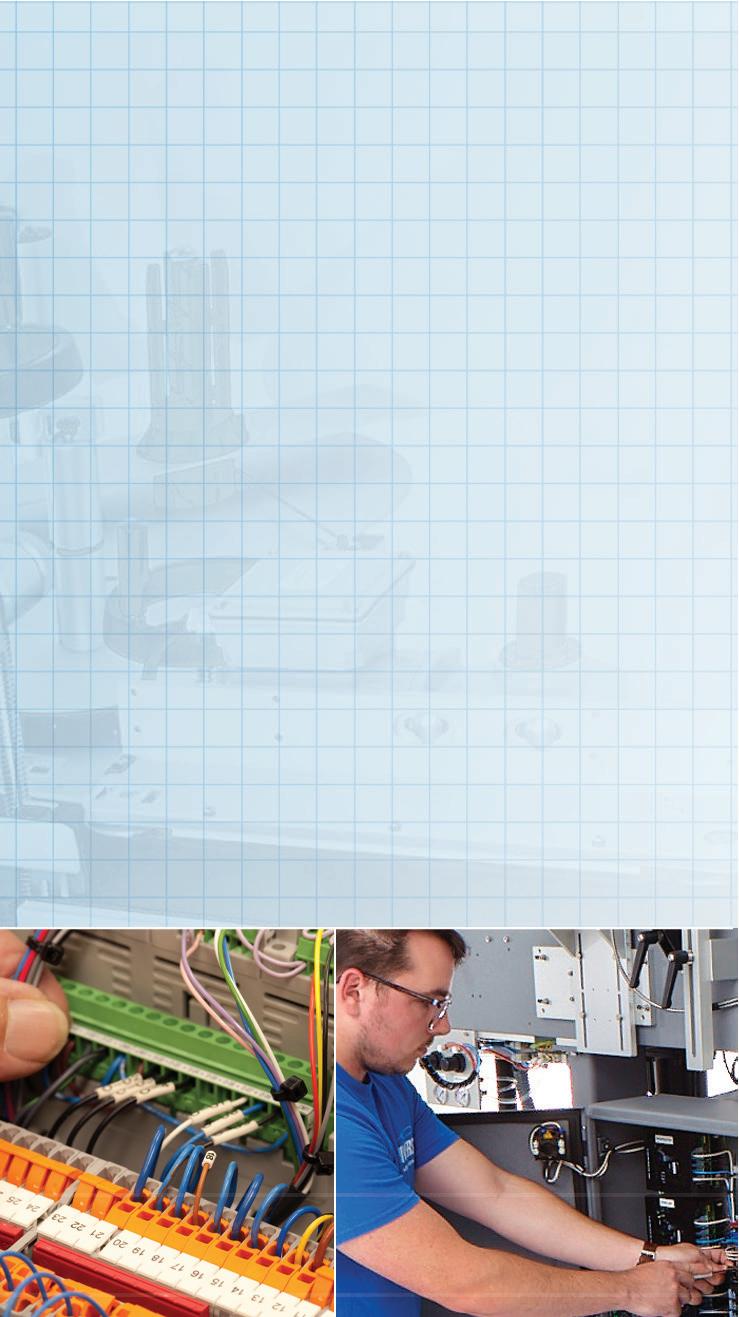
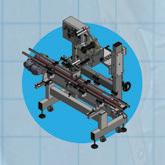
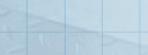
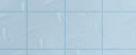
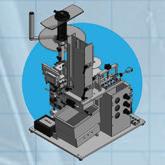


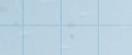

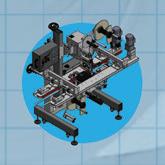
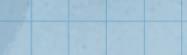
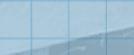
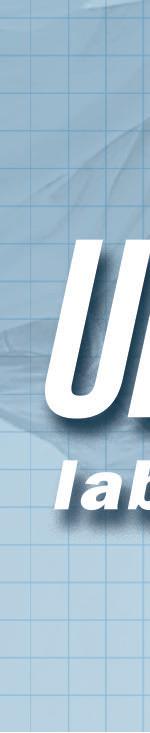
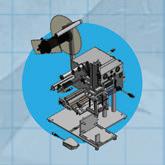
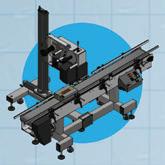
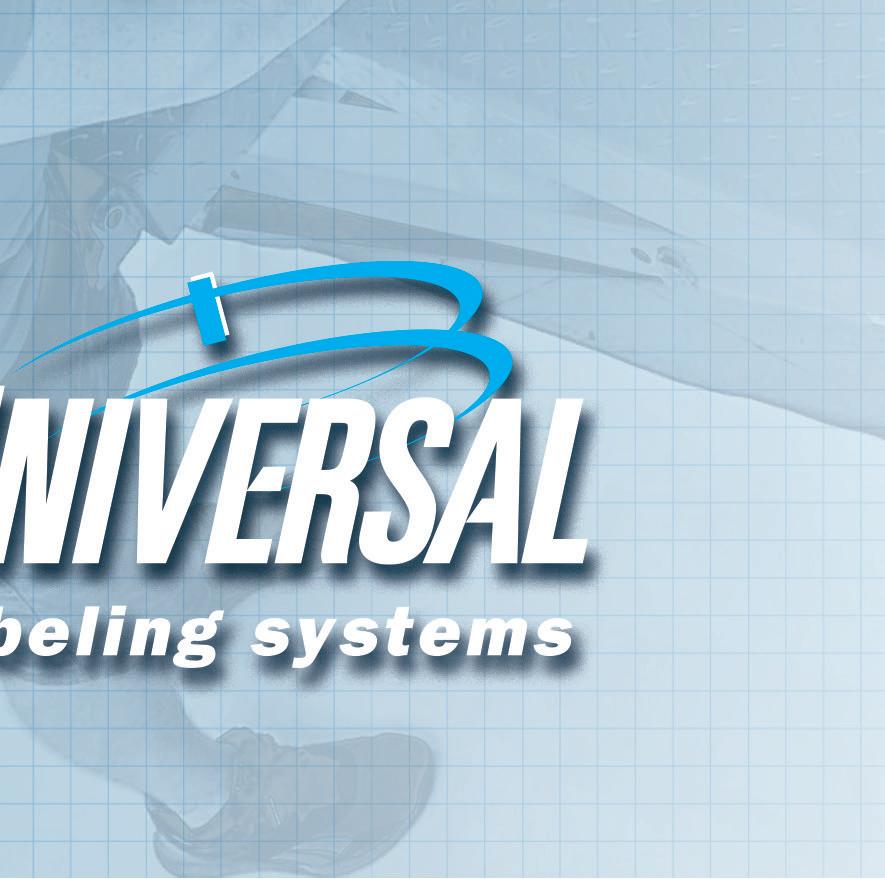
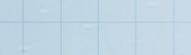
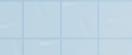
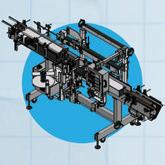
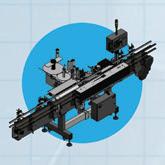
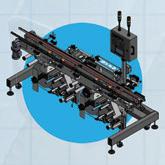


PRODUCTS
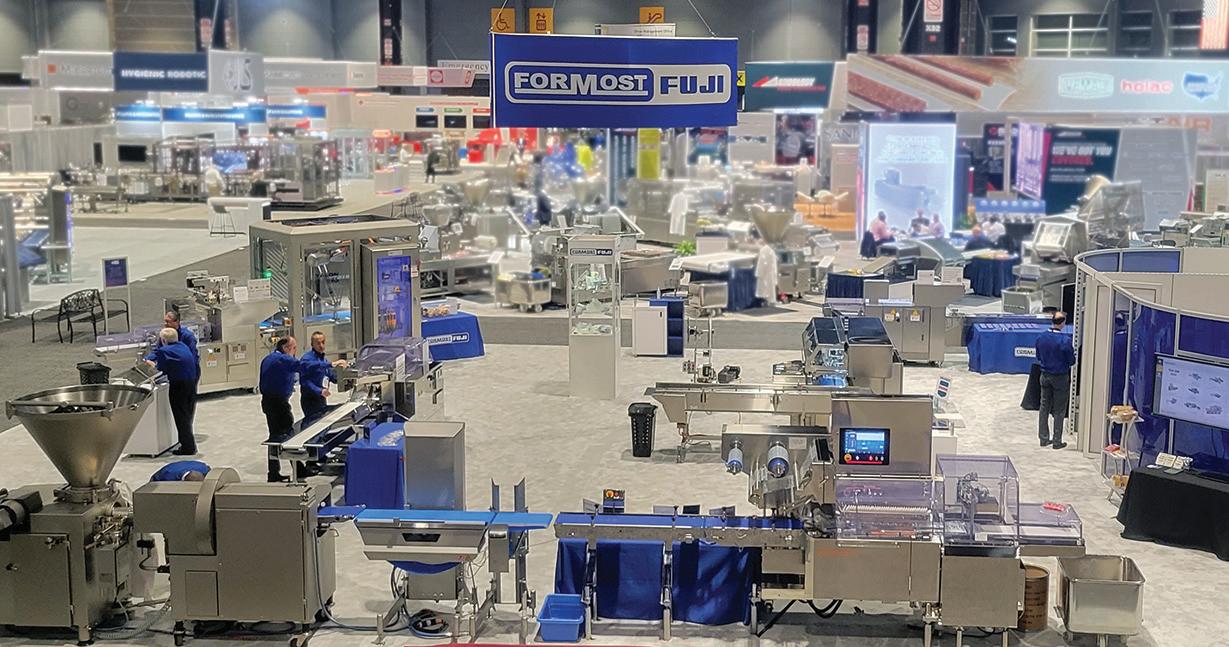
Advanced Packaging Solutions
Formost Fuji Corp. offers horizontal flow wrapping; bagging equipment; and automation solutions that includes a Controlled Speed Indexer (CSI) infeed solution and high-speed swing rotary end seal.
Formost Fuji Corp. Booth S-3566 www.formostfuji.com
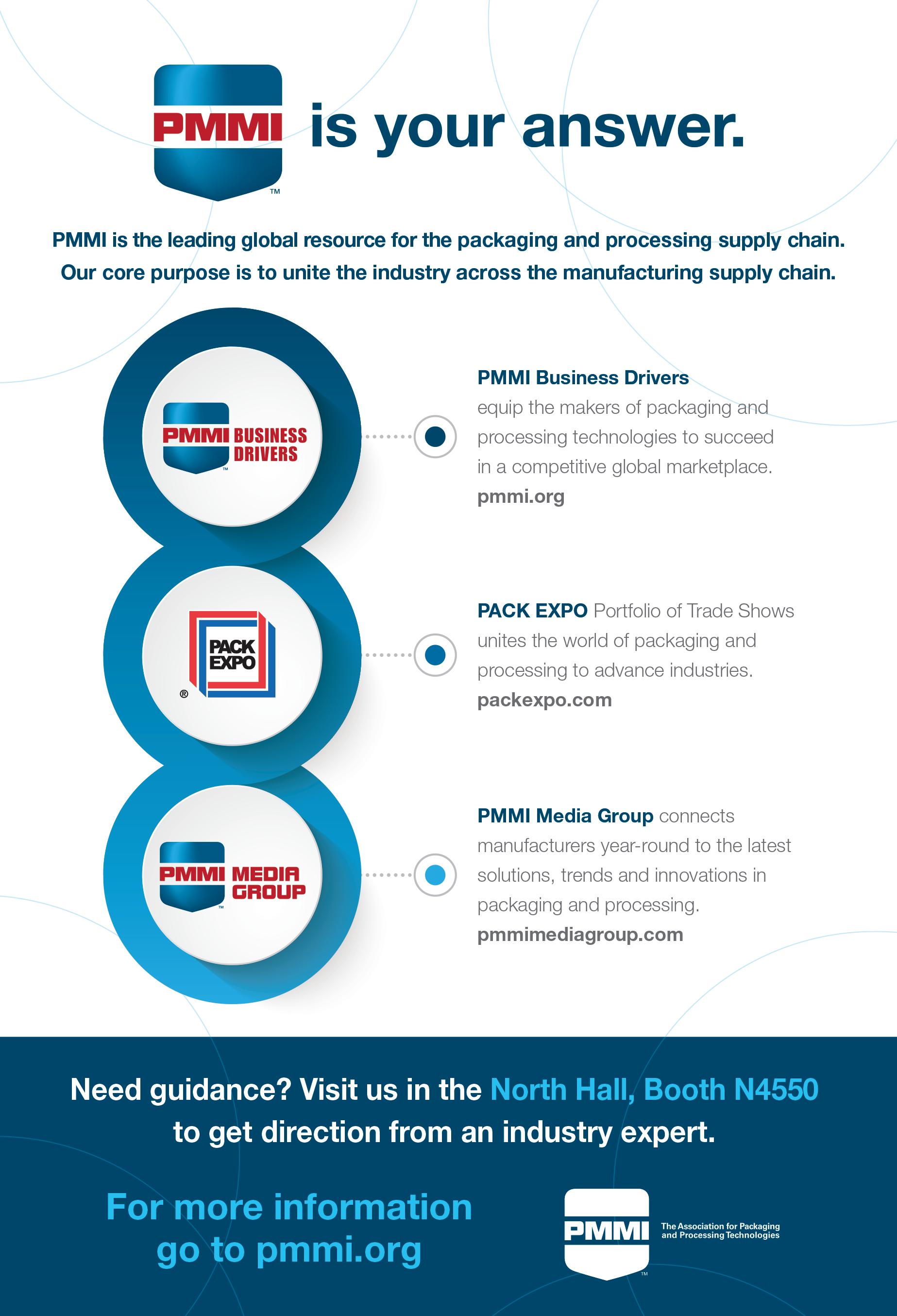
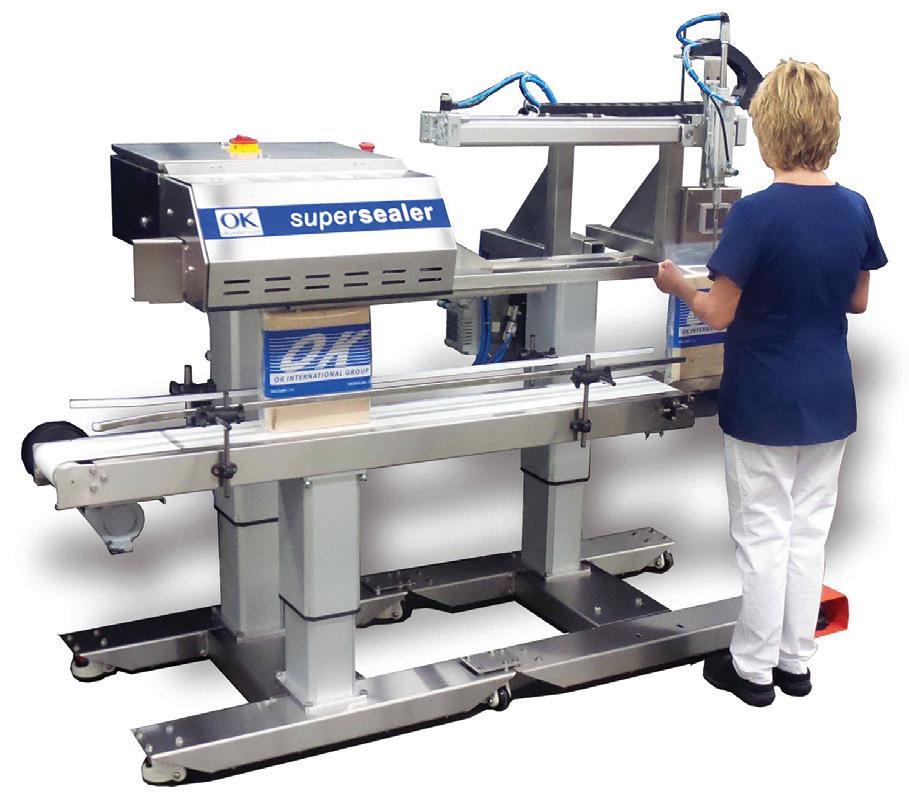
Air Evacuation/Gas Flush Bagging Systems
OK Sealing Systems offers high-speed, customizable air evacuation/gas flushing systems designed to extend product shelf life, reduce package volume, and maintain product integrity. Systems can easily integrate into any packaging operation, including clean room and wet environments. They are available in Stainless Steel, wash down IP69, and wash down IP69K units.
OK International Corp. Booth N-4904 www.okcorp.com

OEE/Data Collection Software
Wintriss Controls Group offers its ShopFloorConnect OEE/Data Collection Software, giving packaging and processing professionals easy-to-use software for increased productivity and reduced machine downtime, even when remote monitoring is required. Software can increase manufacturing capacity and profitability by identifying and quantifying excessive production losses and bottlenecks.
ShopFloorConnect Booth LU-8431 www.shopfloorconnect.com
New Generation Drum Motors
VDG launches a premium-efficiency electric drum motor that provides continuous operation for 80,000 hr before maintenance. All drive components, such as the bearings, gear reducer, and electric motor, are housed inside the drive drum, shielded from the environment and designed for reliability, durability, and maintenance-free operation. Motors are available from 0.25 hp up to 500 hp, in a range of diameter sizes, belt speeds, and industryspecific options to suit various material handling and food processing belt conveyor applications.
VDG (Van der Graaf)
Booth N-4950
www.vandergraaf.com
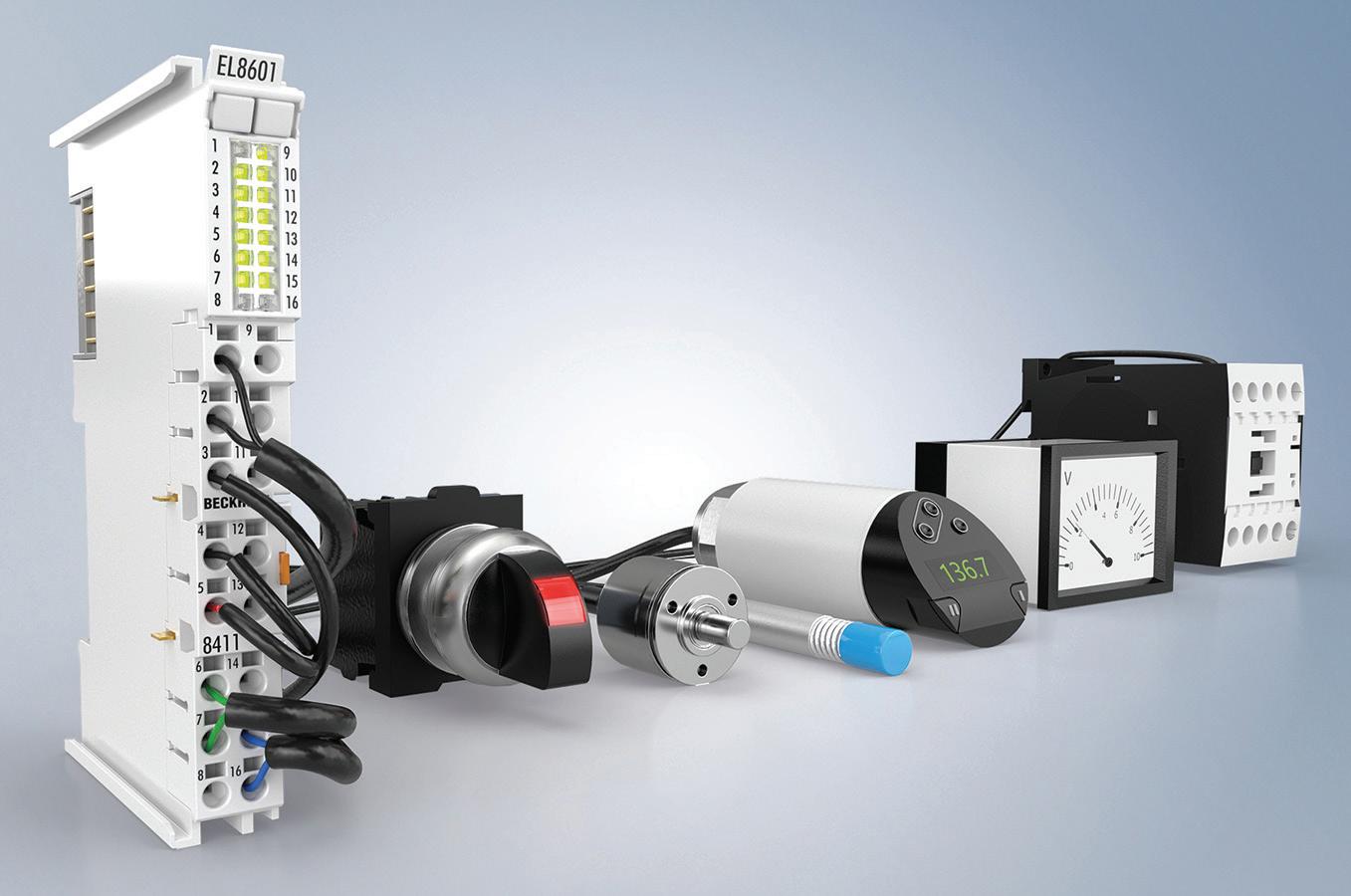
Compact, Multi-I/O Interface
The EL8601-8411 EtherCAT Terminal from Beckhoff is designed to support up to 12 signal interfaces and nine signal types in one multi-purpose I/O module. With up to 12 signal interfaces (8 x DI, 2 x DO, 1 x AI, 1 x AO) and nine signal types in one terminal, the multi-interface is suitable for numerous applications. Beckhoff
Booth N-6136
www.beckhoff.com
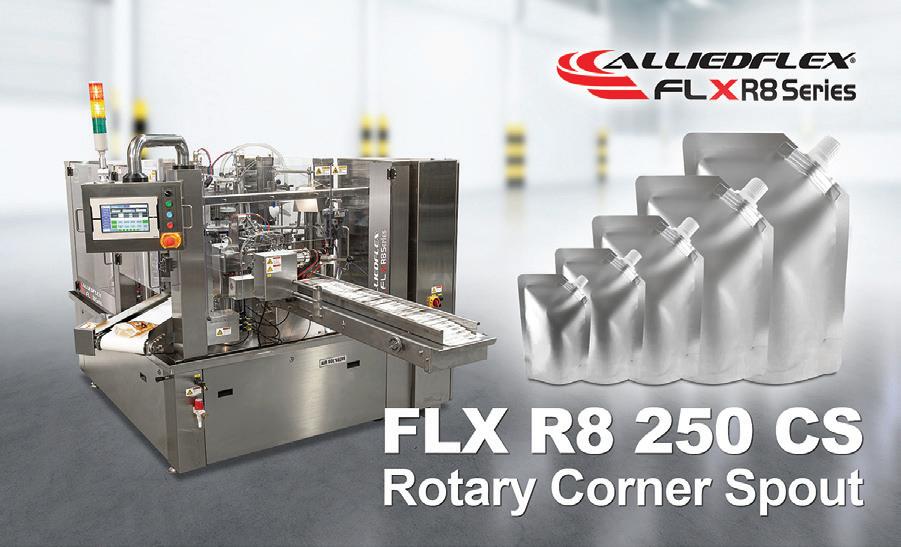
Corner Spout Filling, Sealing System
ALLIEDFLEX’s FLX R8 Rotary 250 CS corner spout pre-made pouch fill/seal system is designed for filling and sealing pre-made corner spouted pouches. It is suited for various liquid food and non-food product applications and is ideal for packaging liquid household cleaners, personal care, and beauty care products. It can accommodate various pouch fill volumes from 300 ml to 1000 ml, including pouches constructed of high-barrier laminated or mono-layer recyclable pouch materials.
ALLIEDFLEX
Booth S-3834
www.alliedflex.com

Carbon footprint reduction
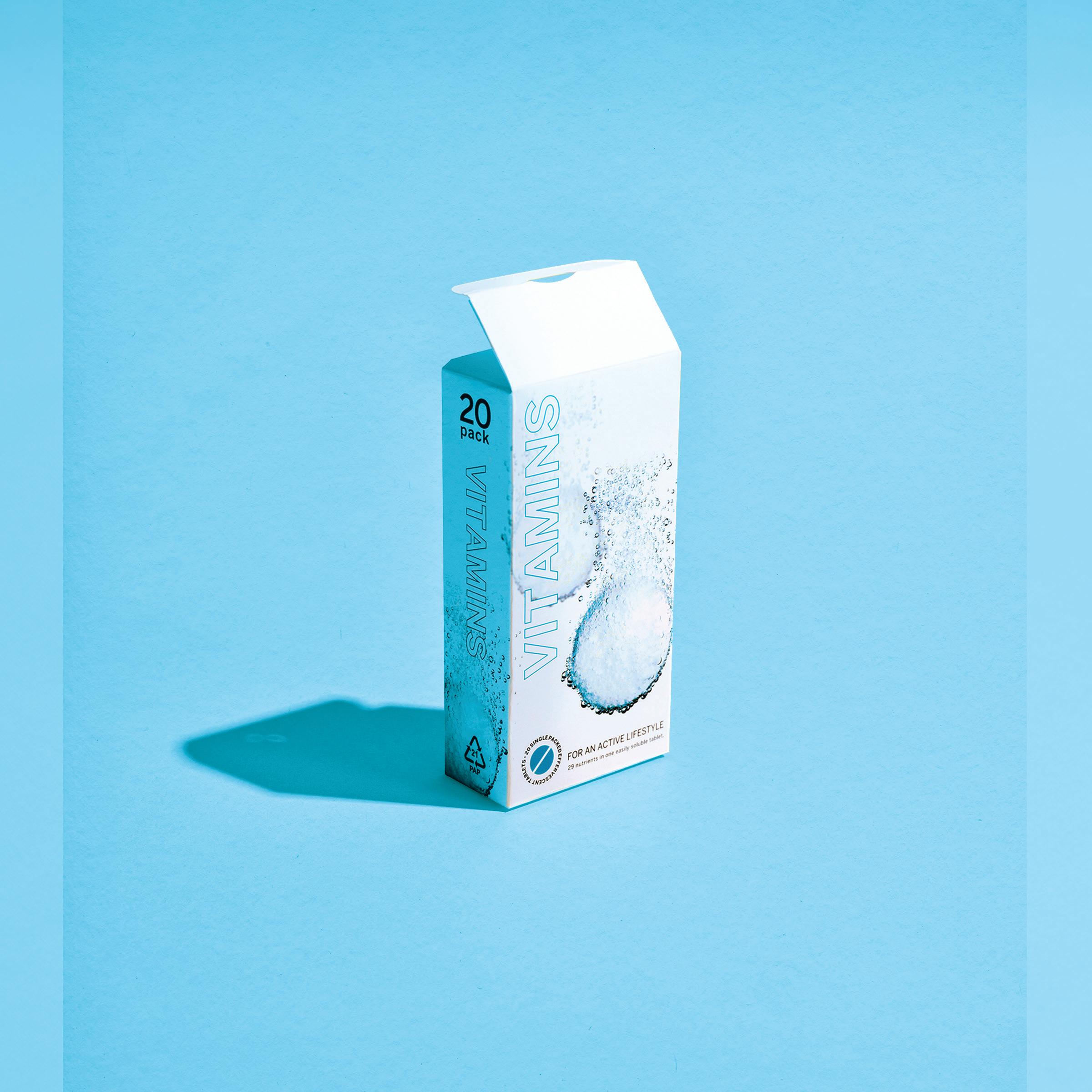
reverse, MetsäBoard Pro FBB Bright provides an ideal base for special finishing effects.



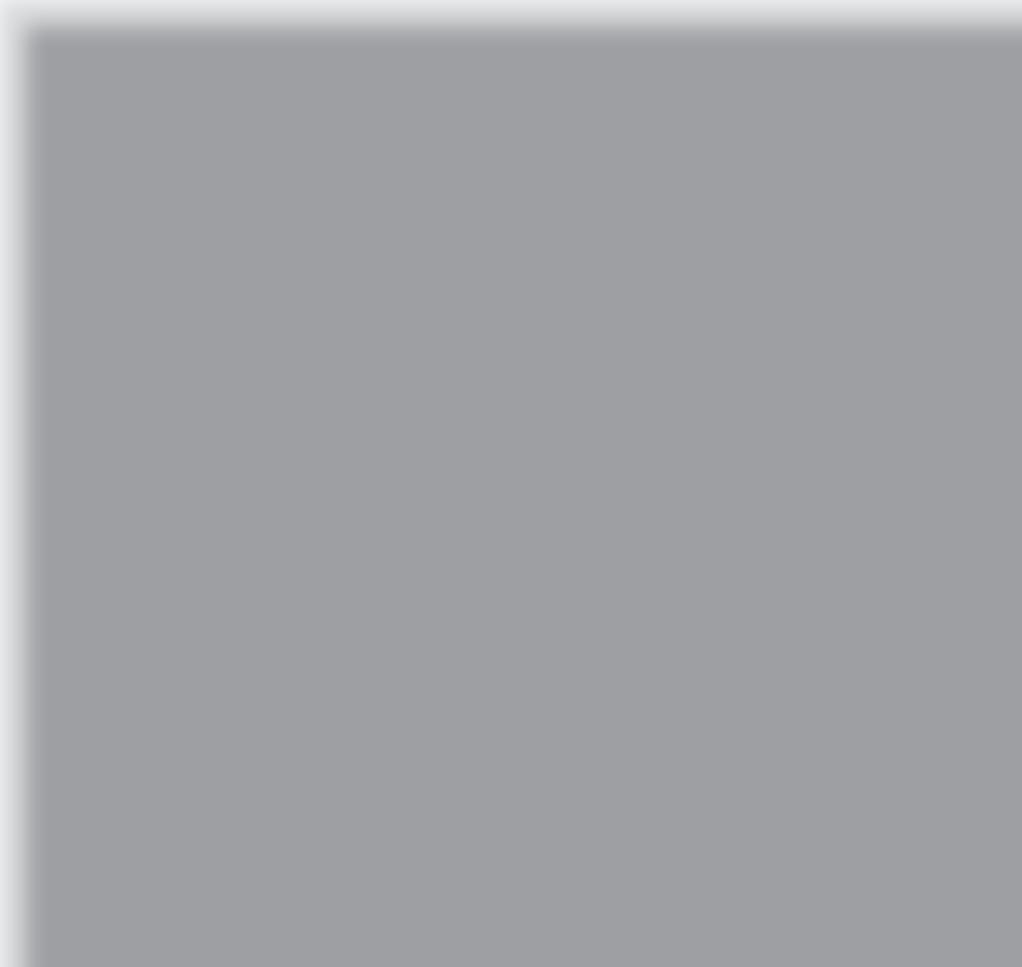


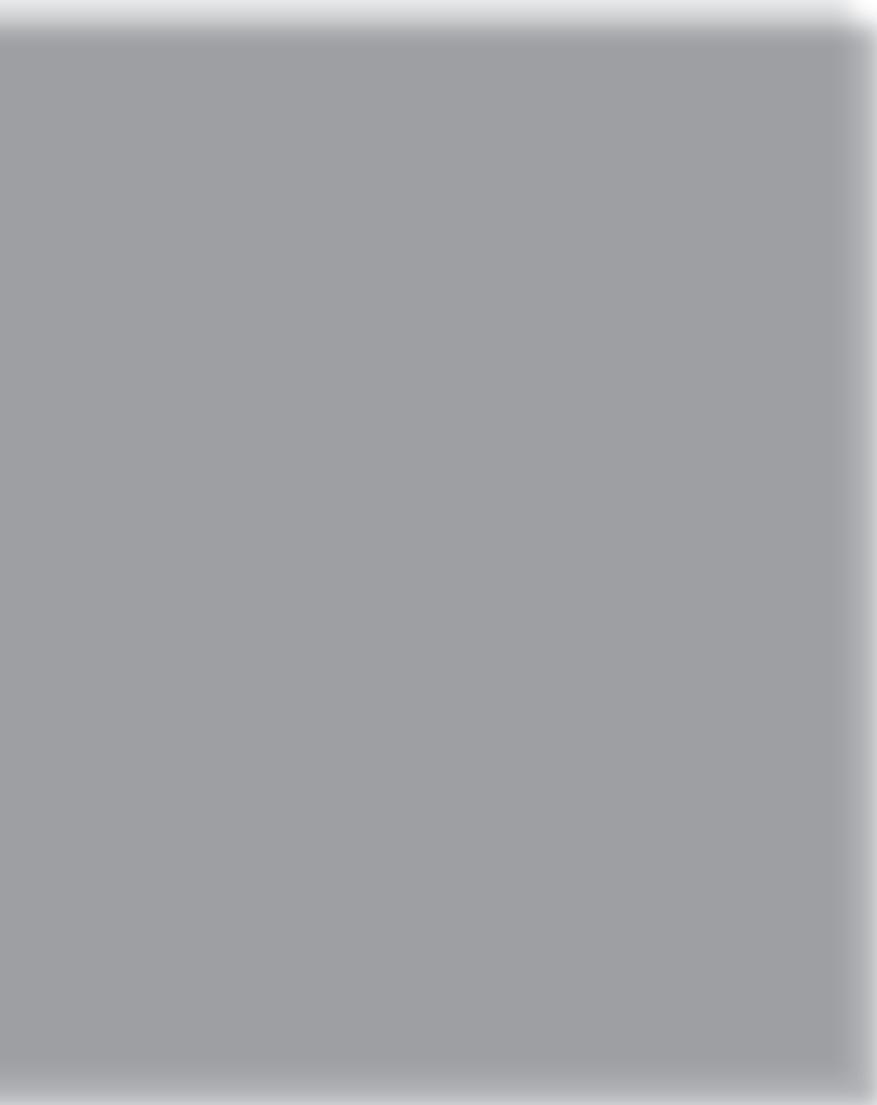




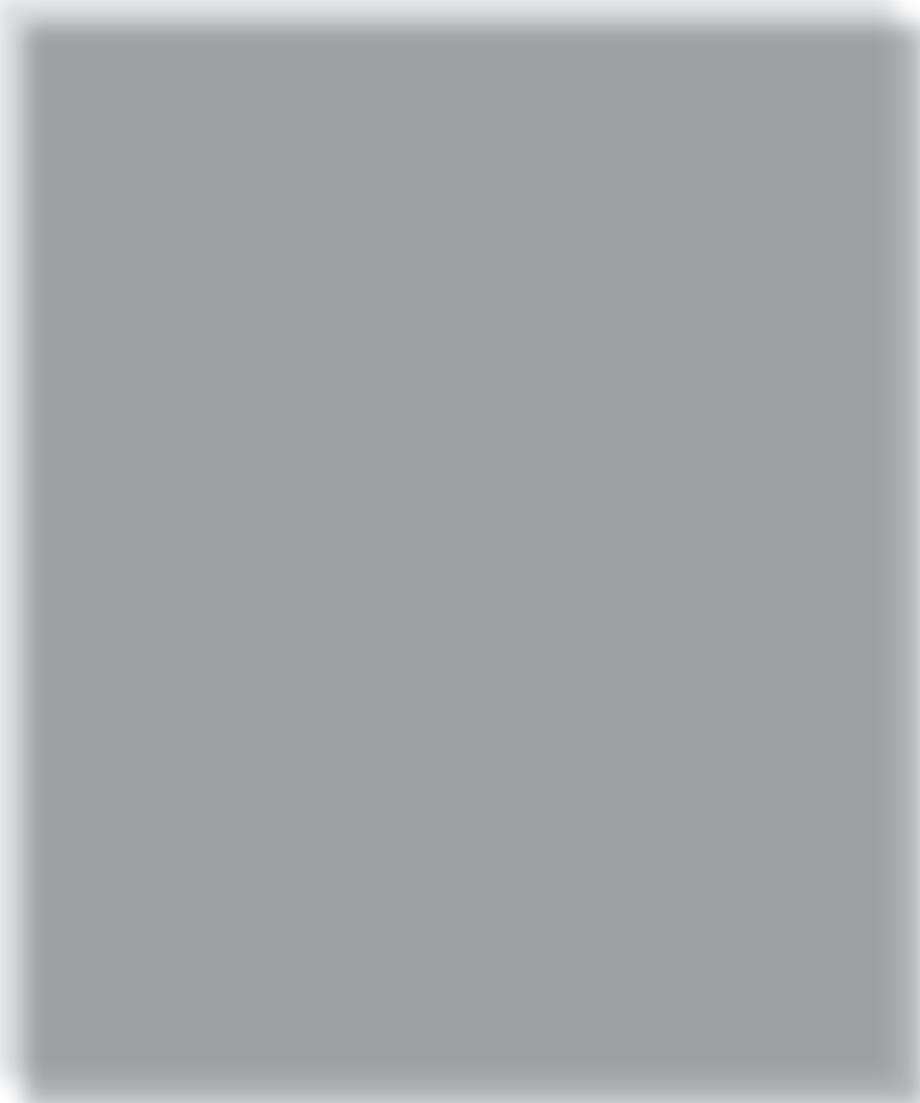




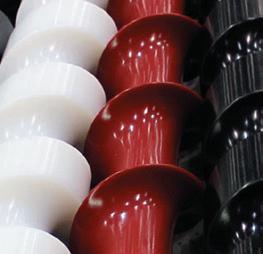
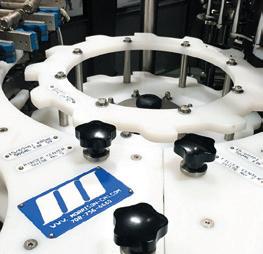
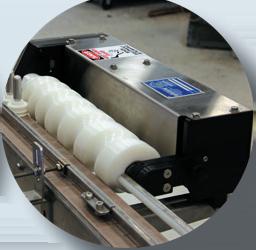
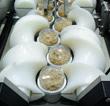
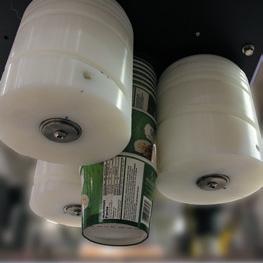
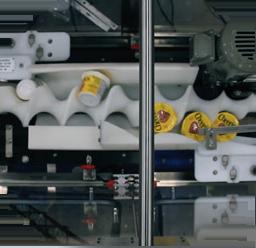
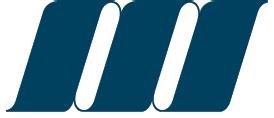
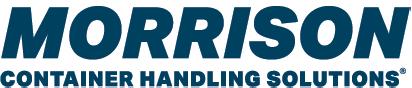


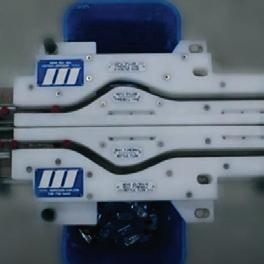

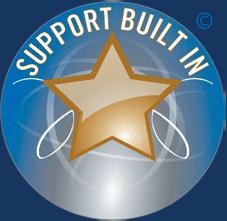



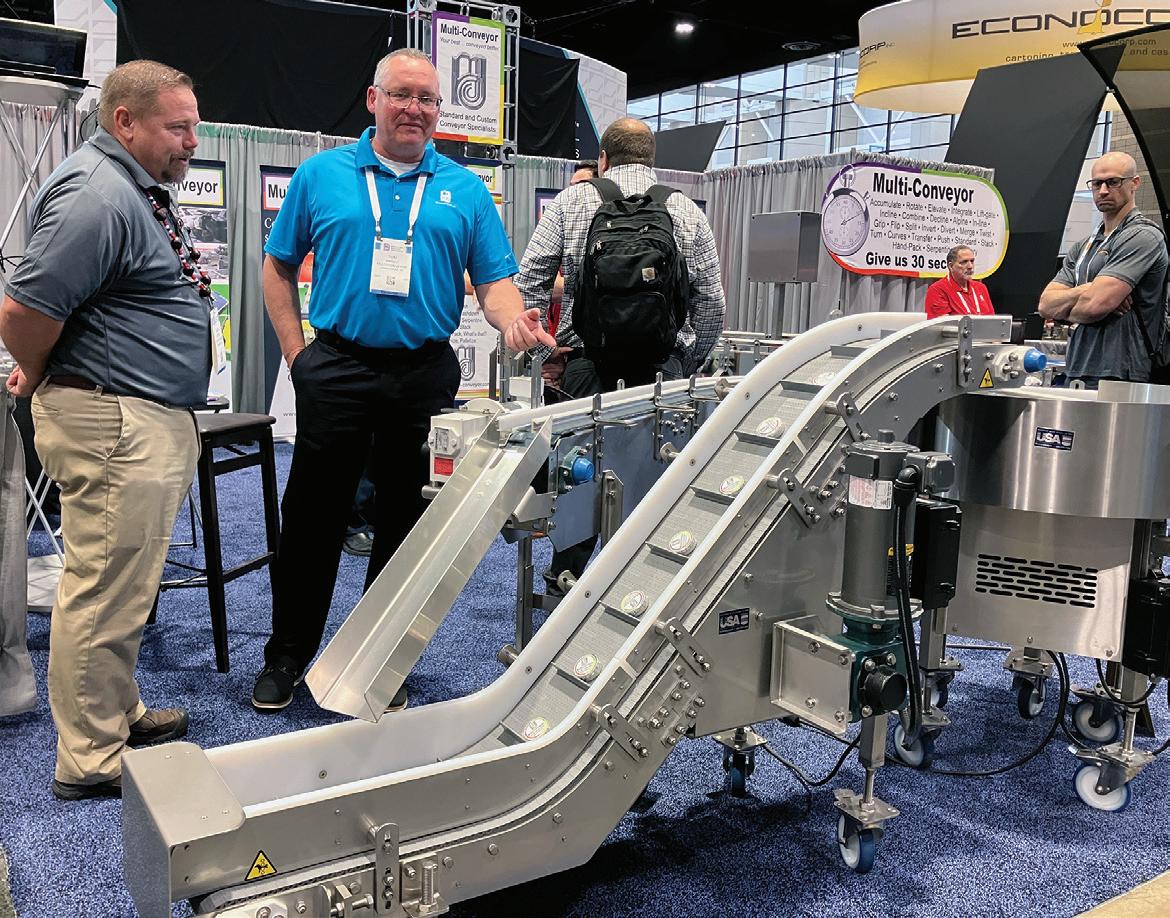
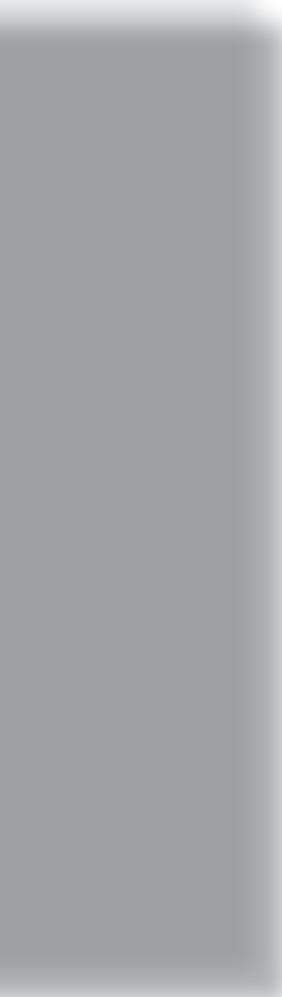

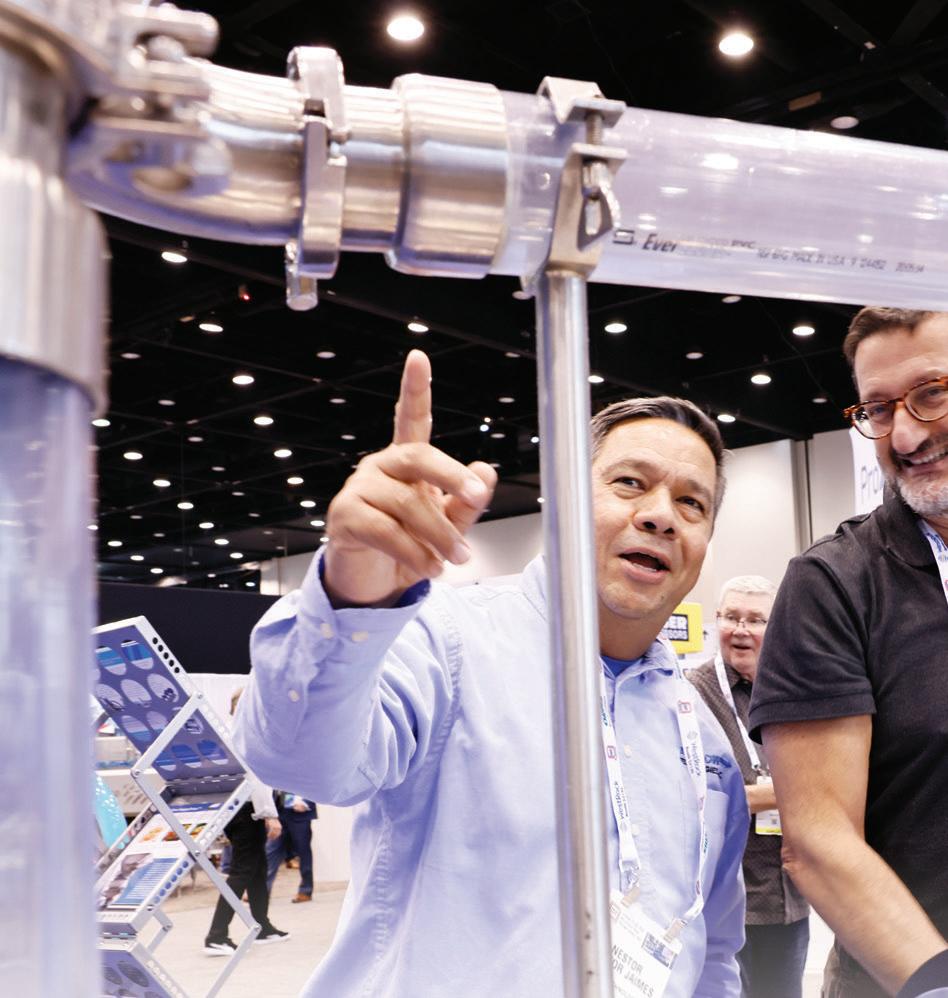
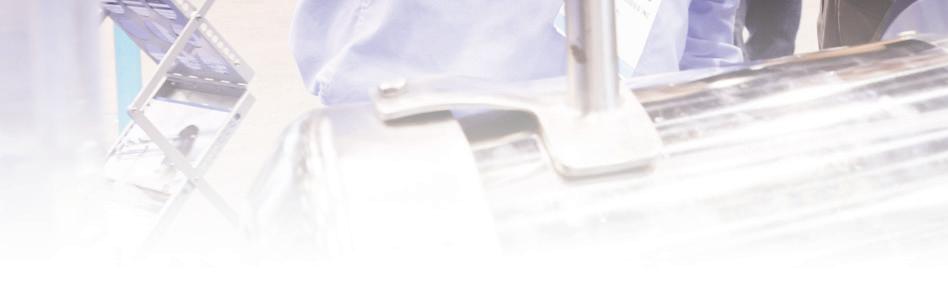
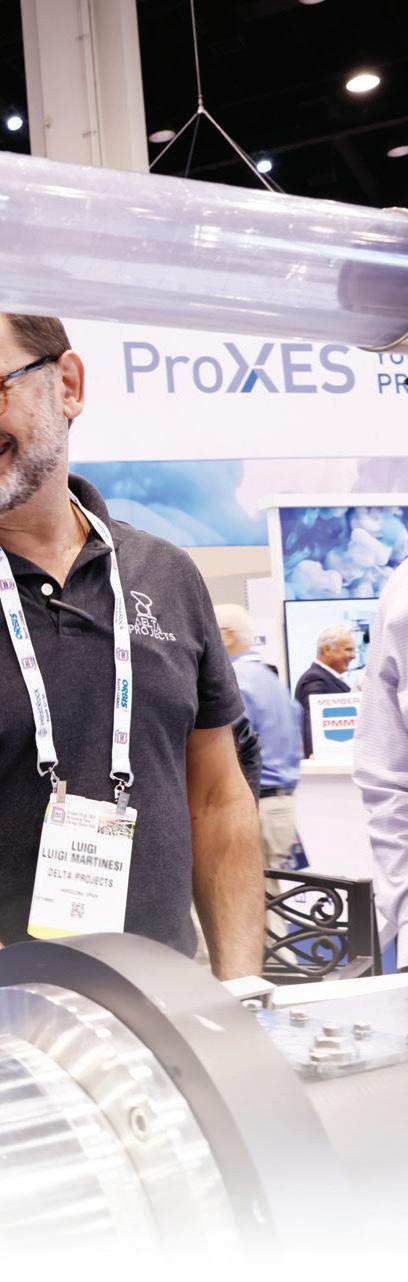




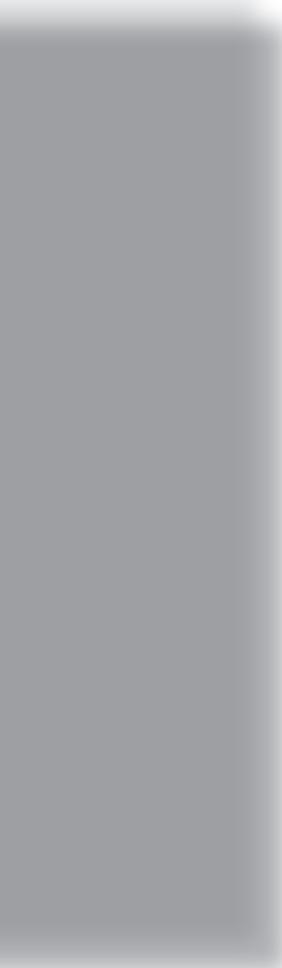



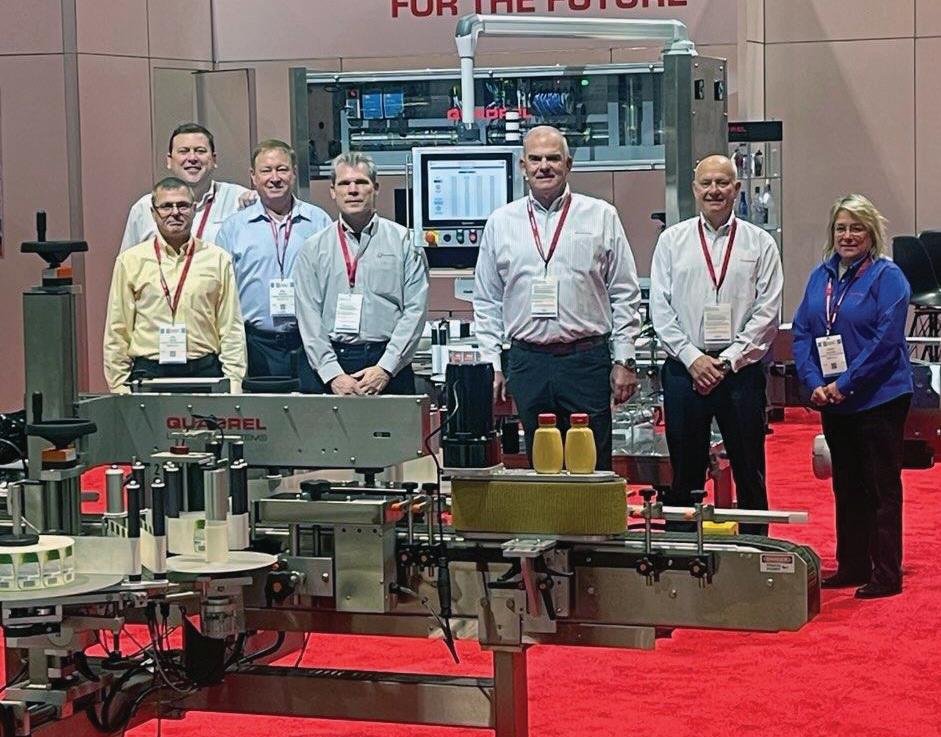

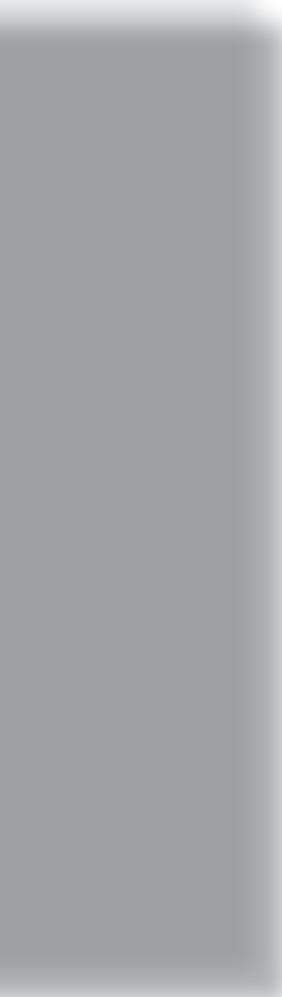


Industry Training

Elevate your talent through PMMI’s convenient training and development opportunities.
Certified Technical Sales Professional (CTSP)
Certification (for PMMI members only)
Be a trusted advisor to your customers.
Certified Trainer Workshops
Develop your team’s training skills.
Field Service Essentials (for PMMI members only)
Give your technicians the non-technical skills they need to provide great customer service.
Mechatronic Certifications
Identify multi-skilled workers to troubleshoot and repair automated equipment on the plant floor.
Risk Assessment Workshops
Improve productivity and ensure worker safety.
SheLeads: Navigating Leadership for Women
Take your leadership skills to the next level.
Successful Selling @ PACK EXPO
Maximize sales from trade shows.
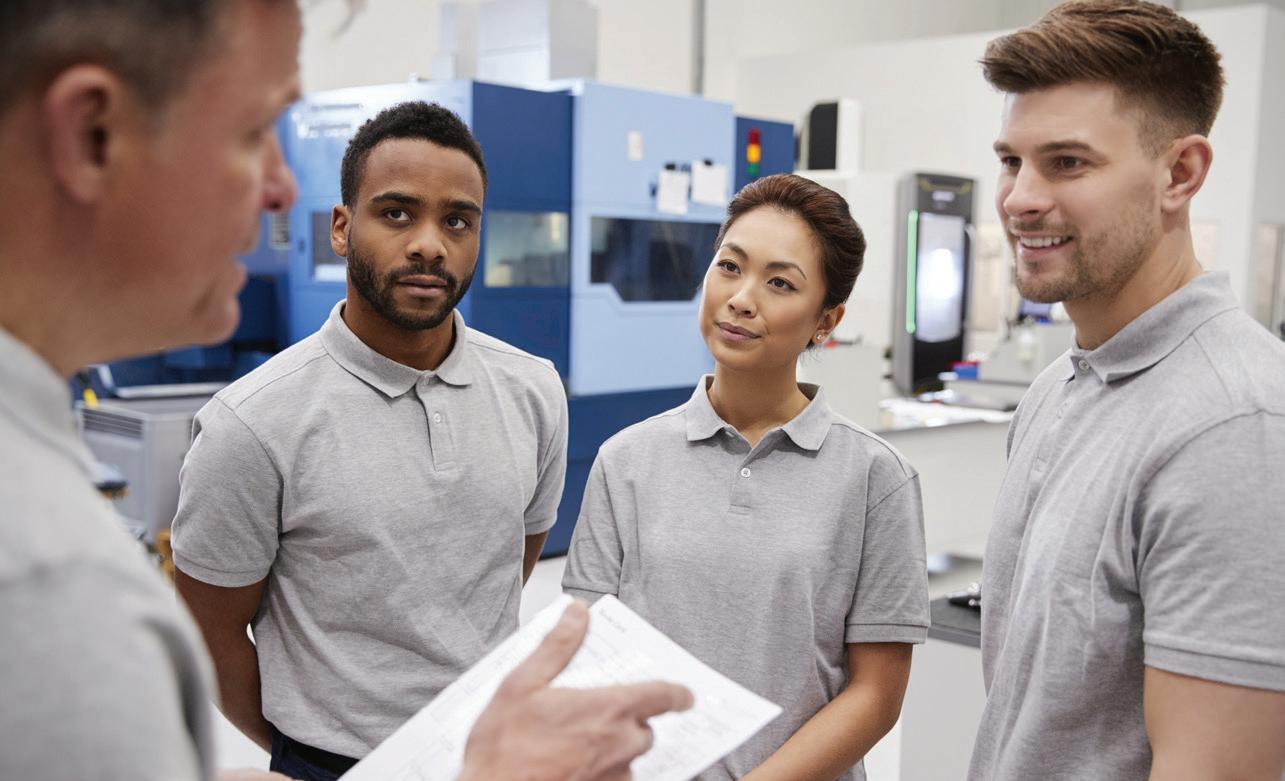

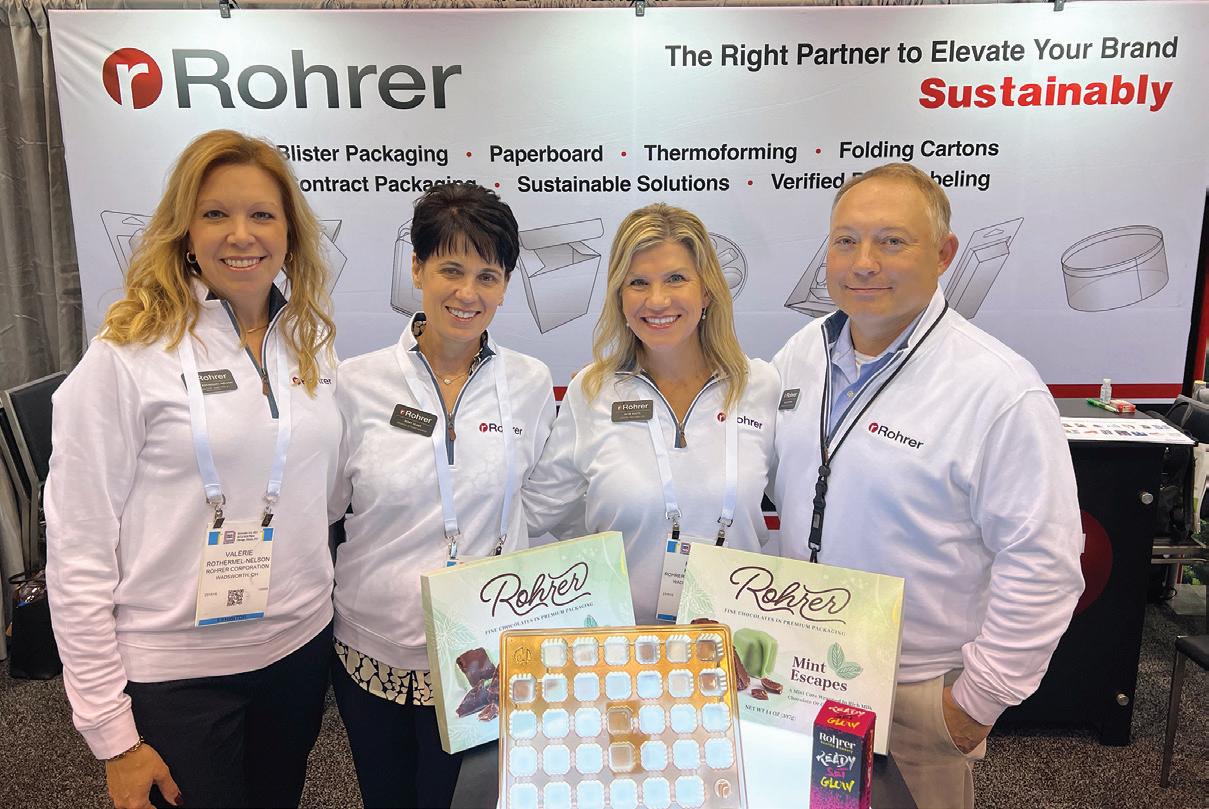
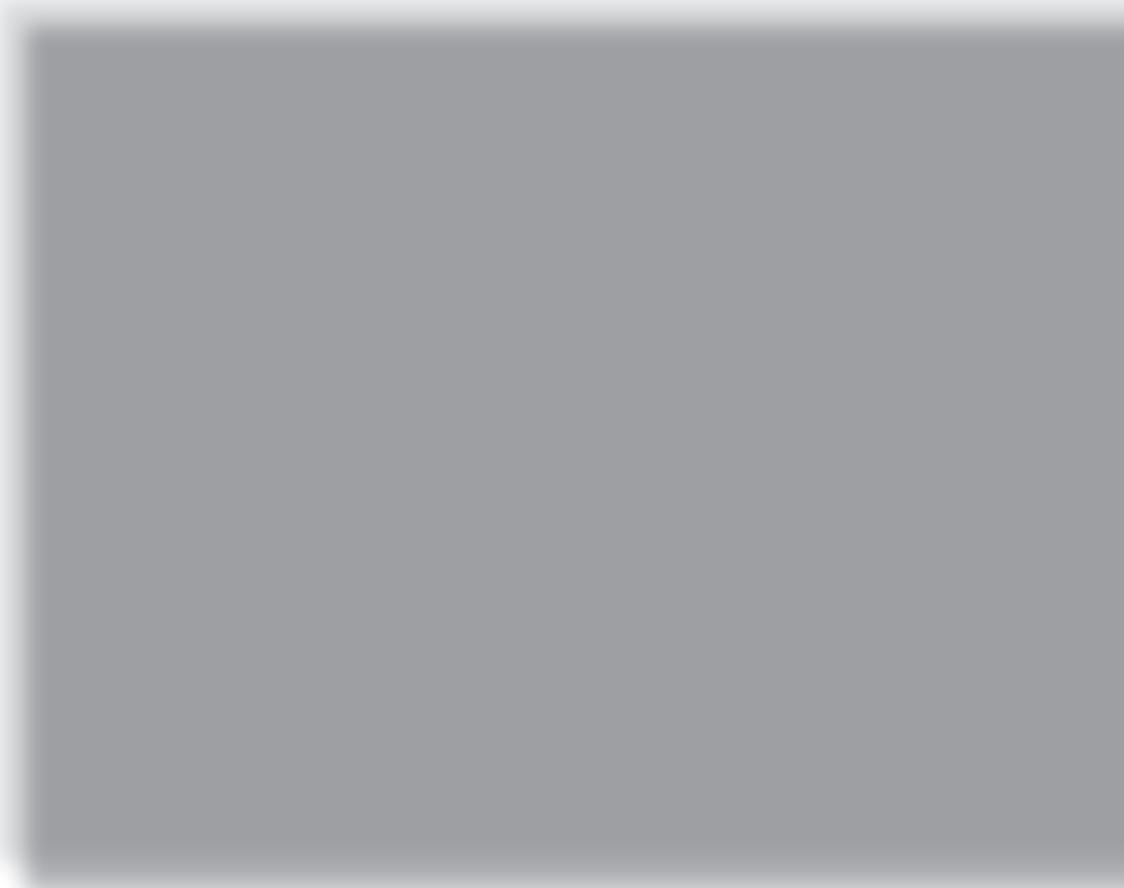



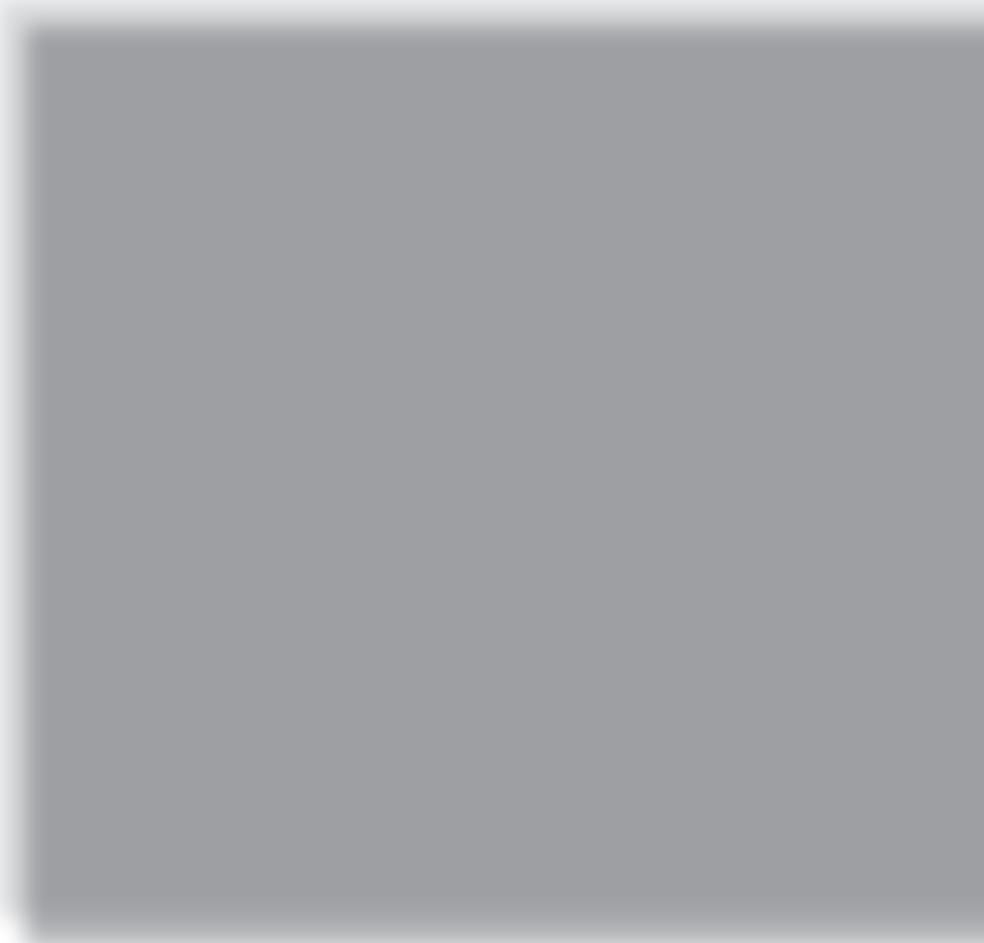
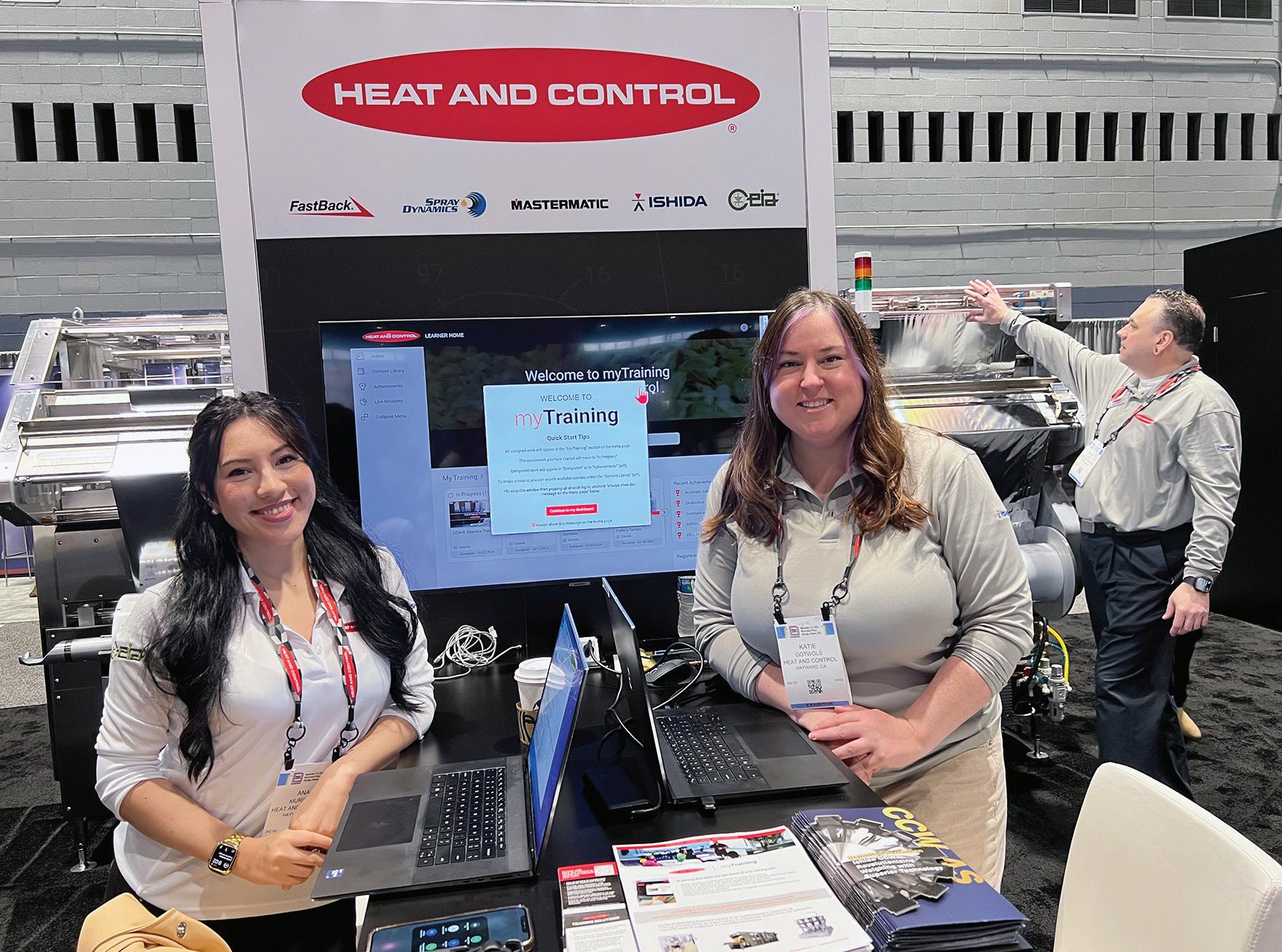
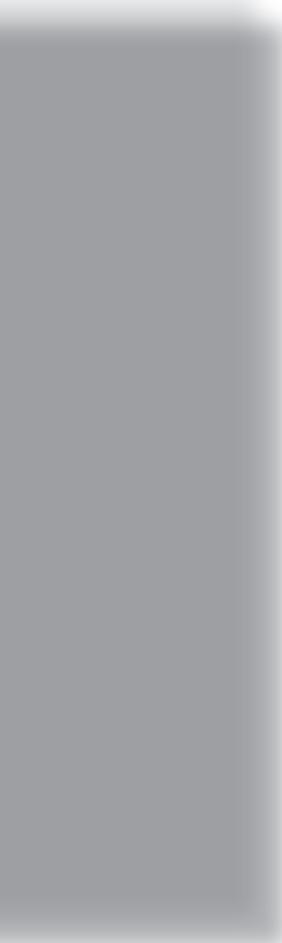



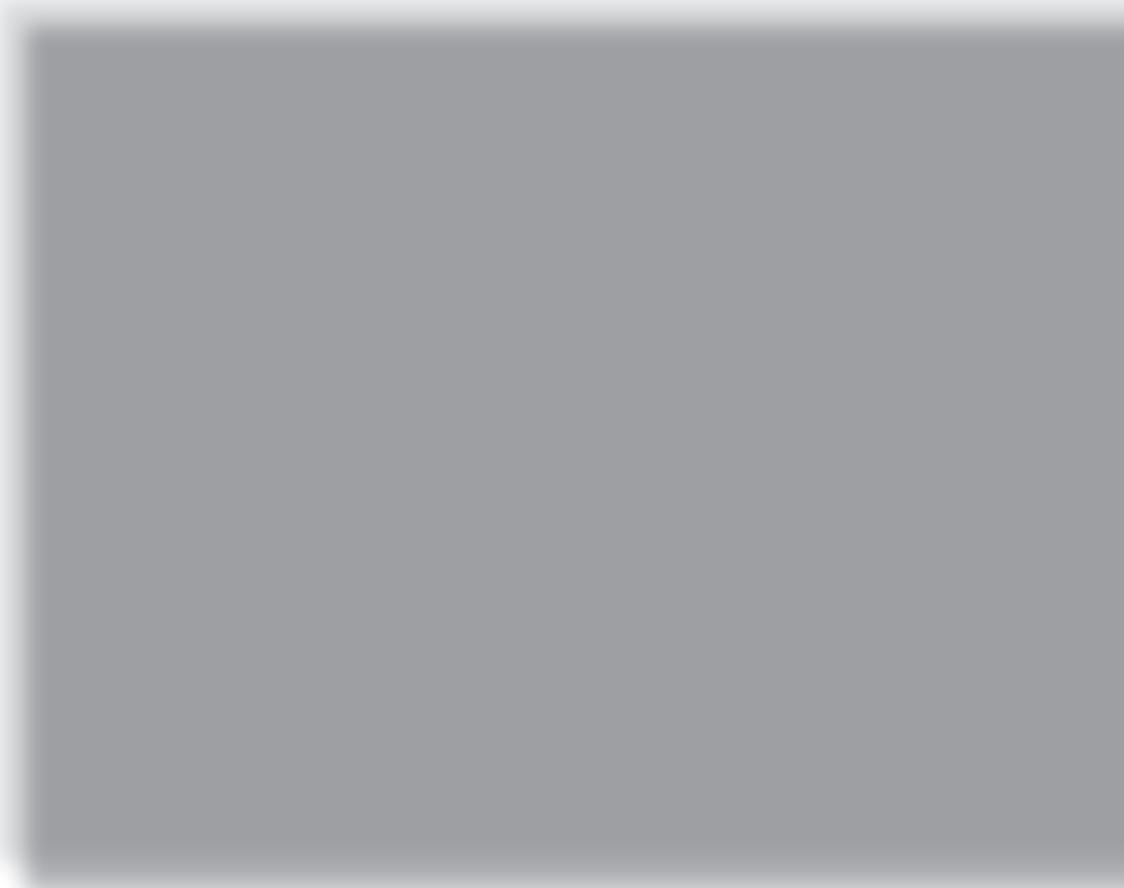



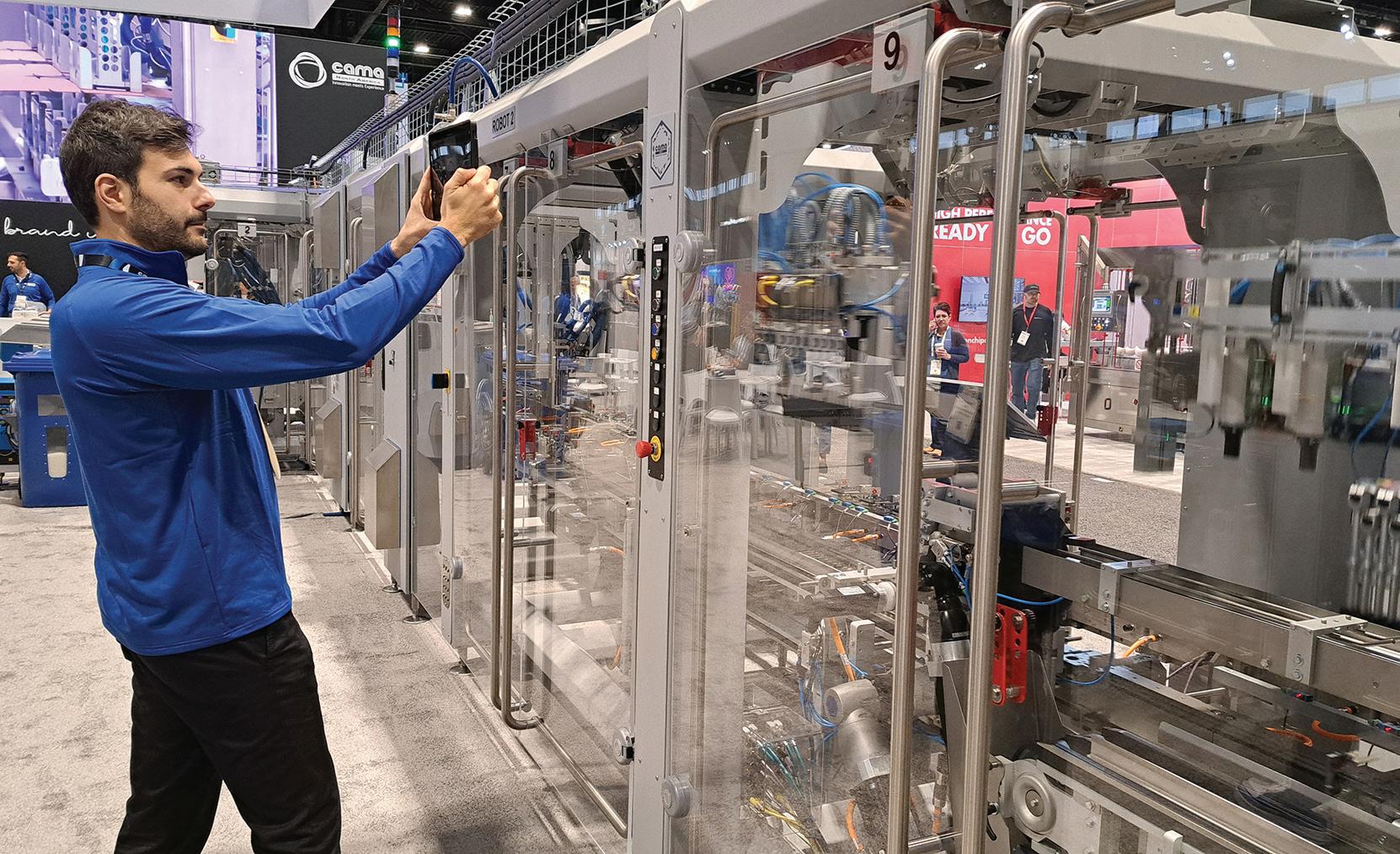
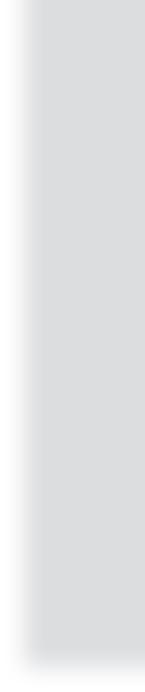

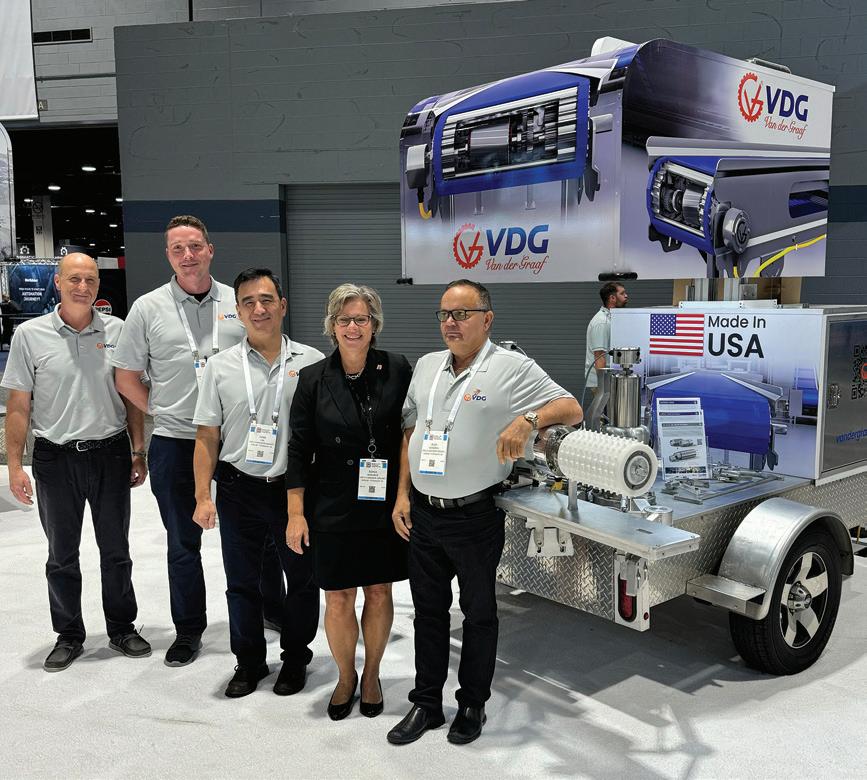
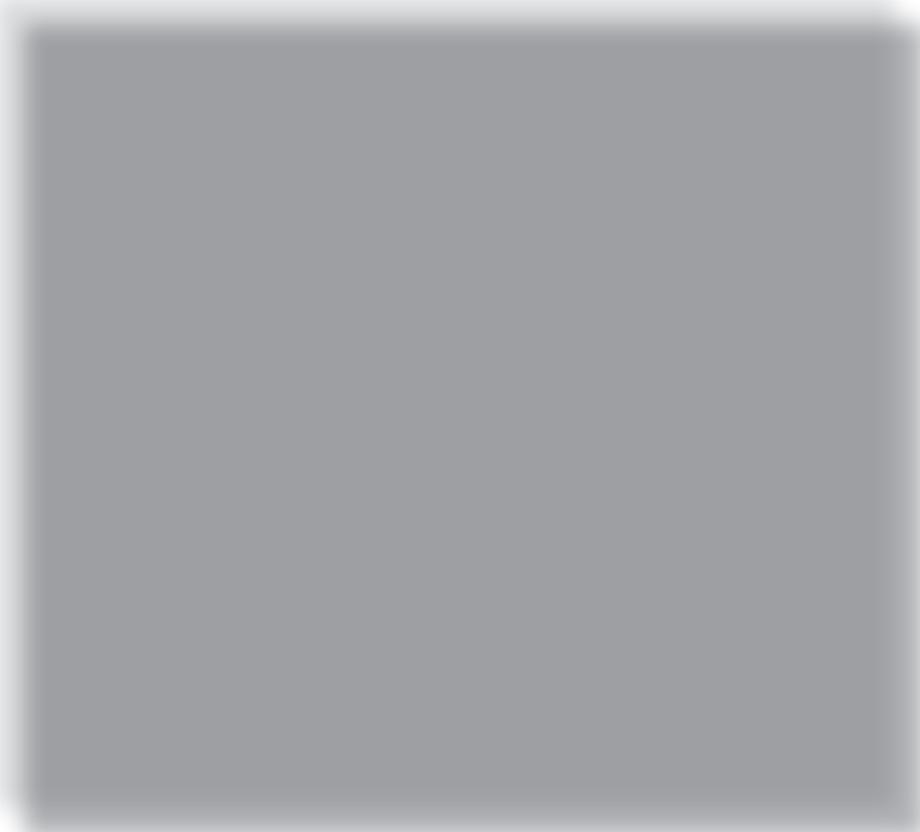
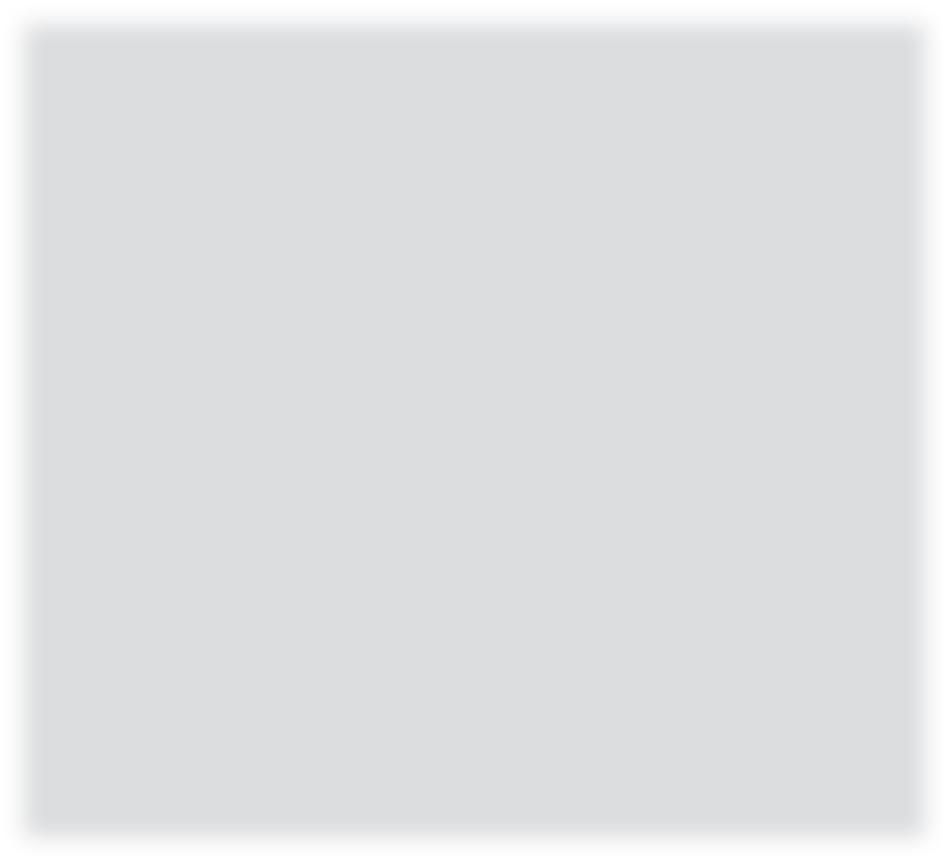
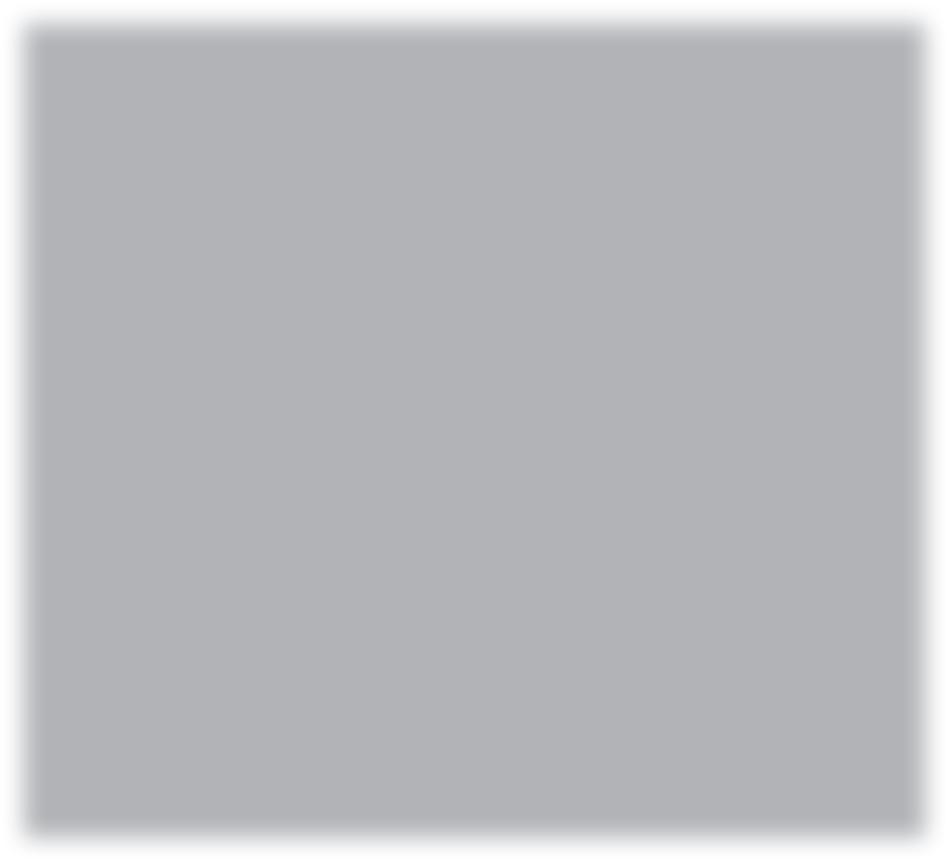
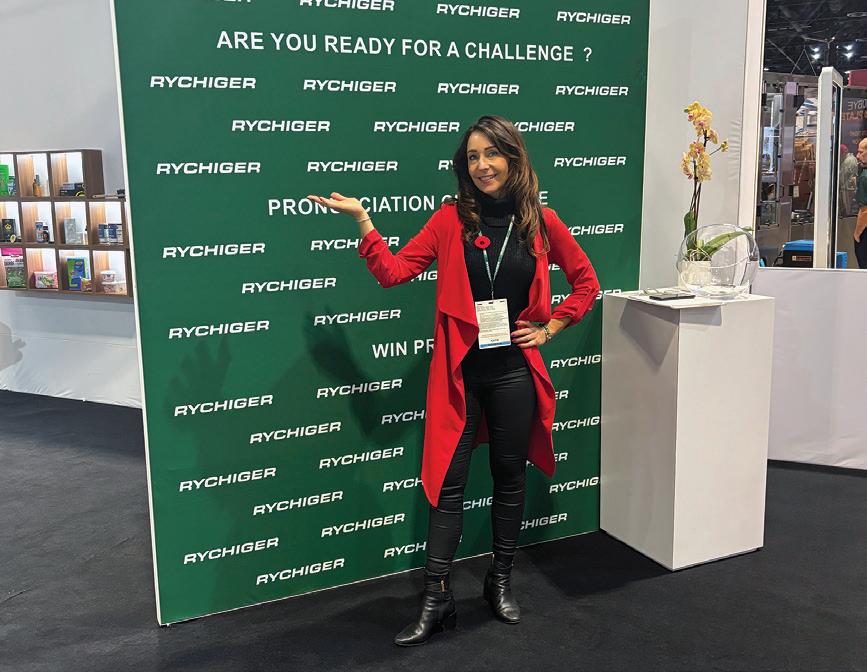
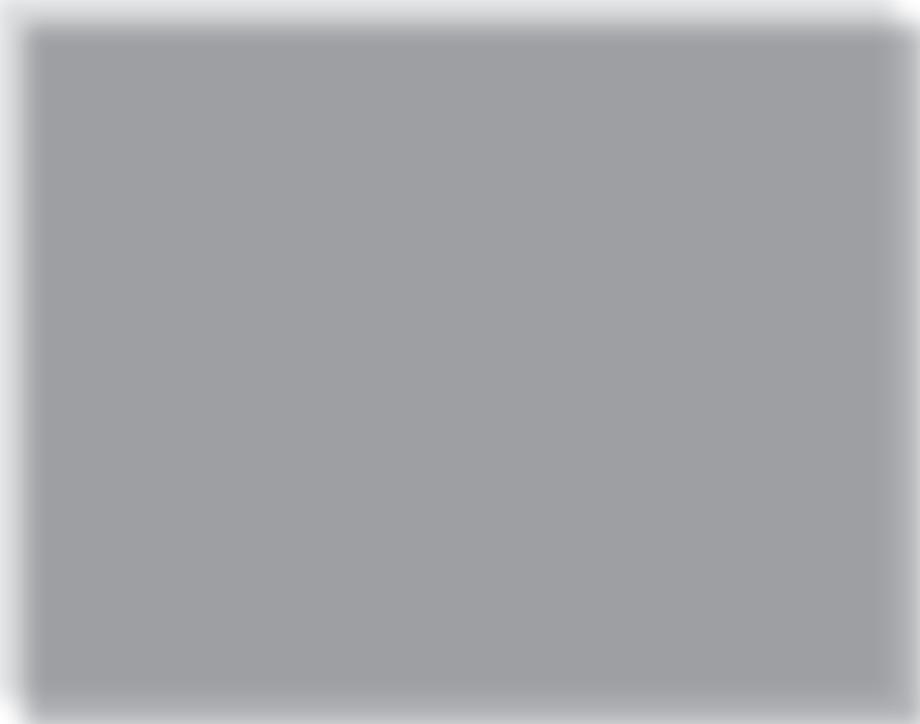

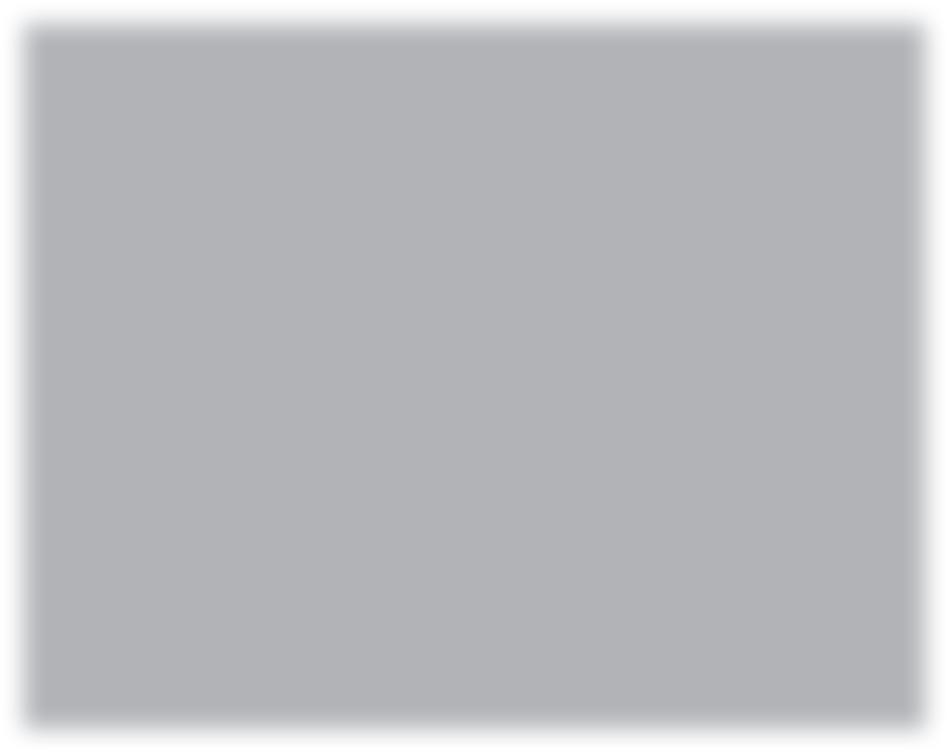
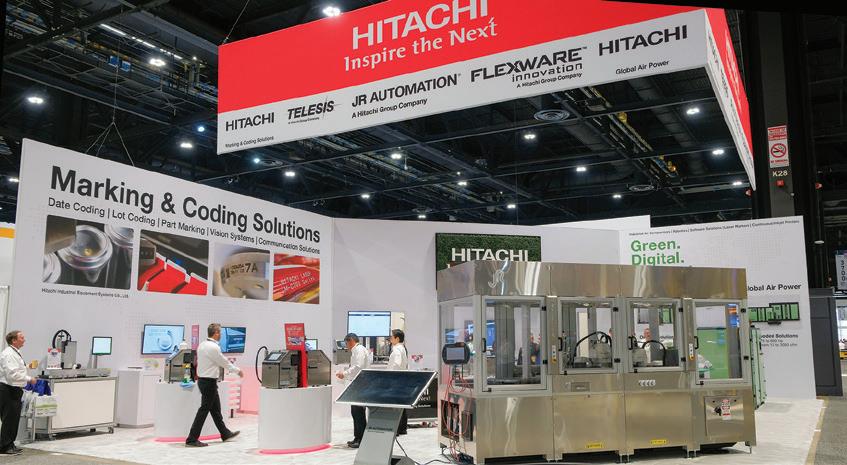




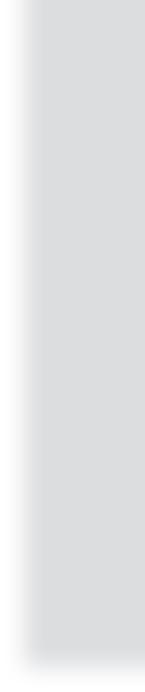
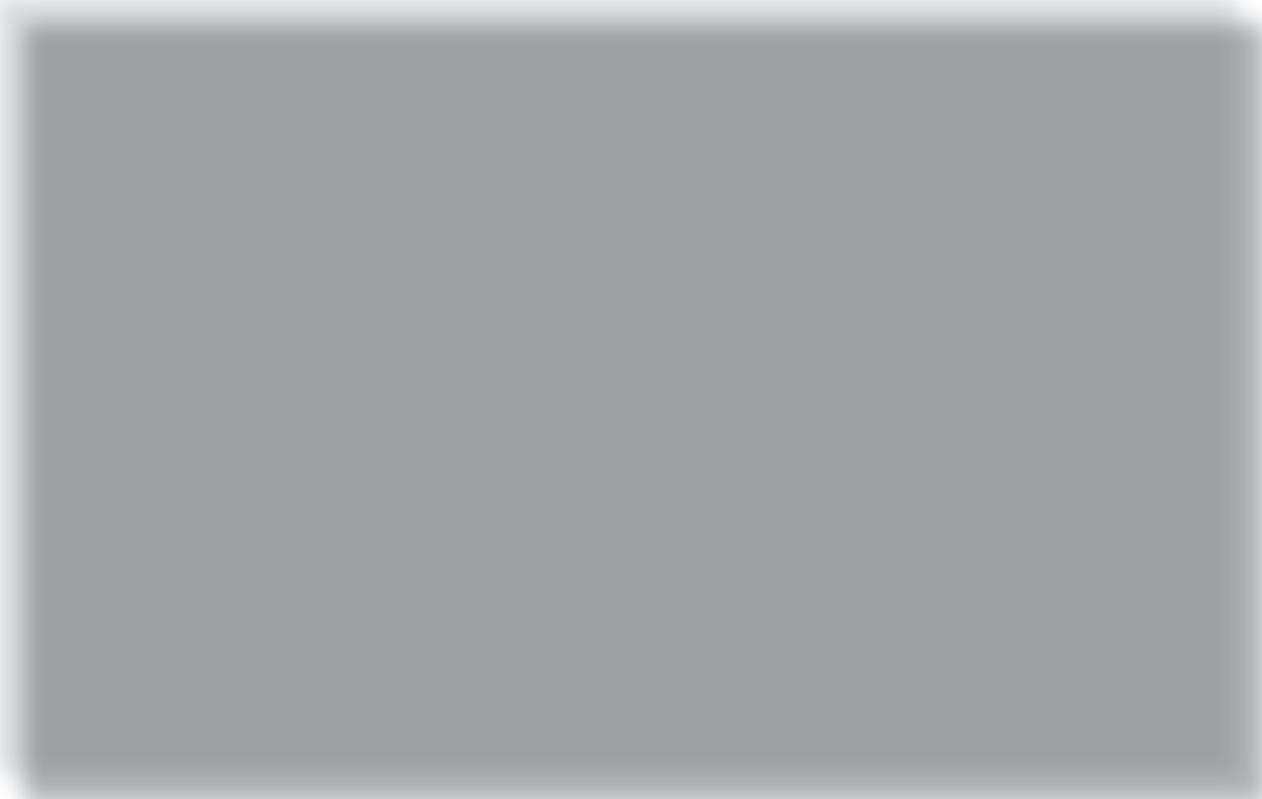
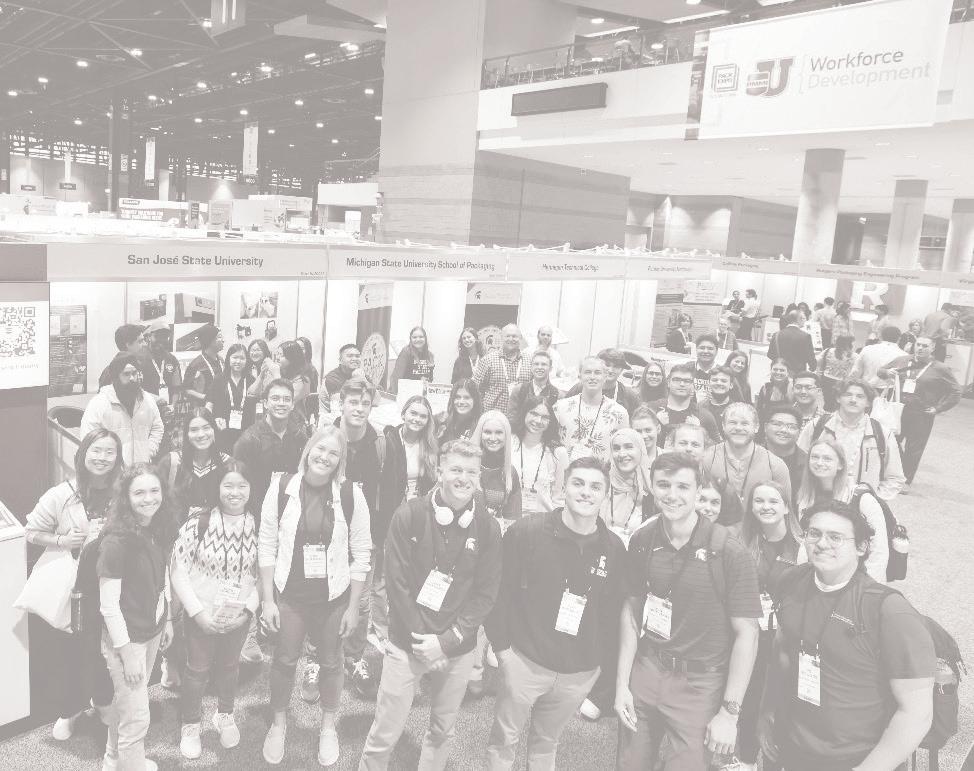
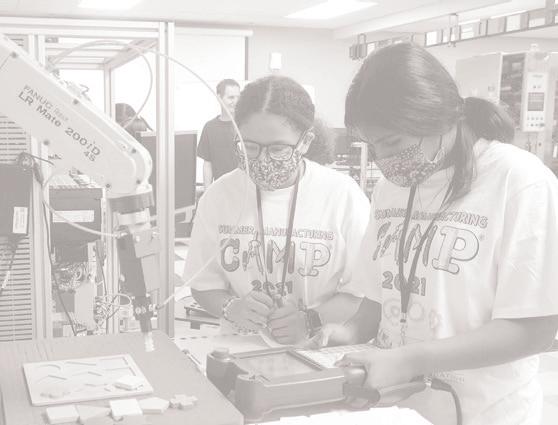
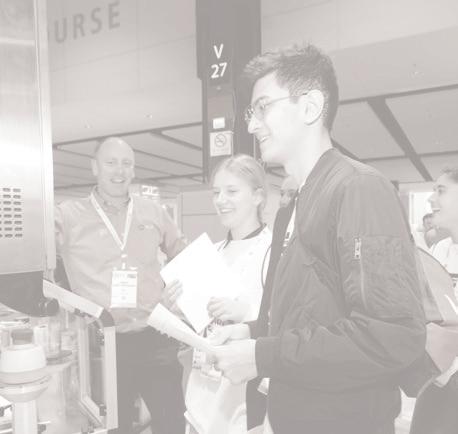
Over $4M contributed to support the next generation of packaging and processing industry leaders
Financial assistance for educational programs such as FIRST robotics teams and curriculum development at local colleges and universities.
Summer Manufacturing Camps to educate and inspire the future manufacturing workforce.
Academic scholarships to students pursuing careers in the industry. and more…
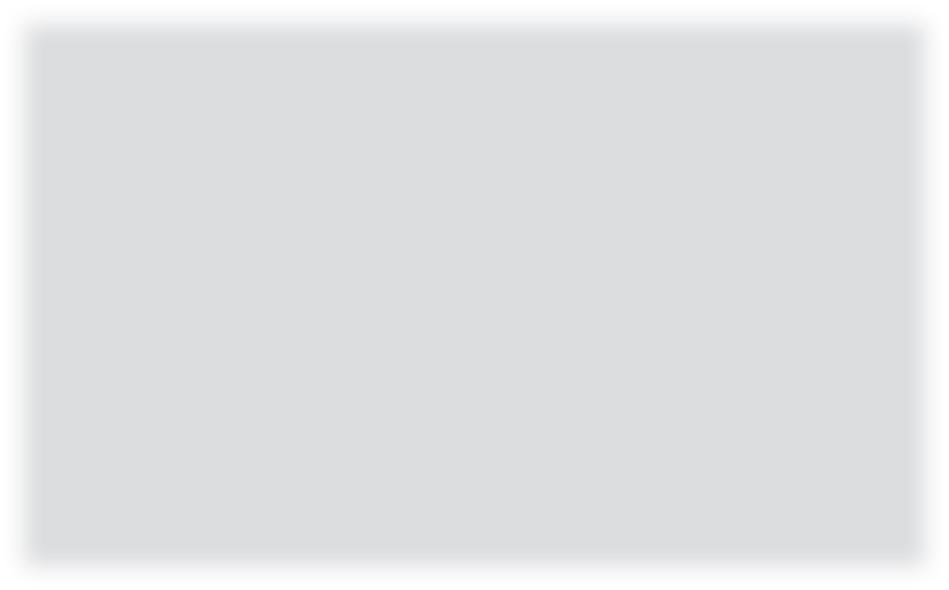
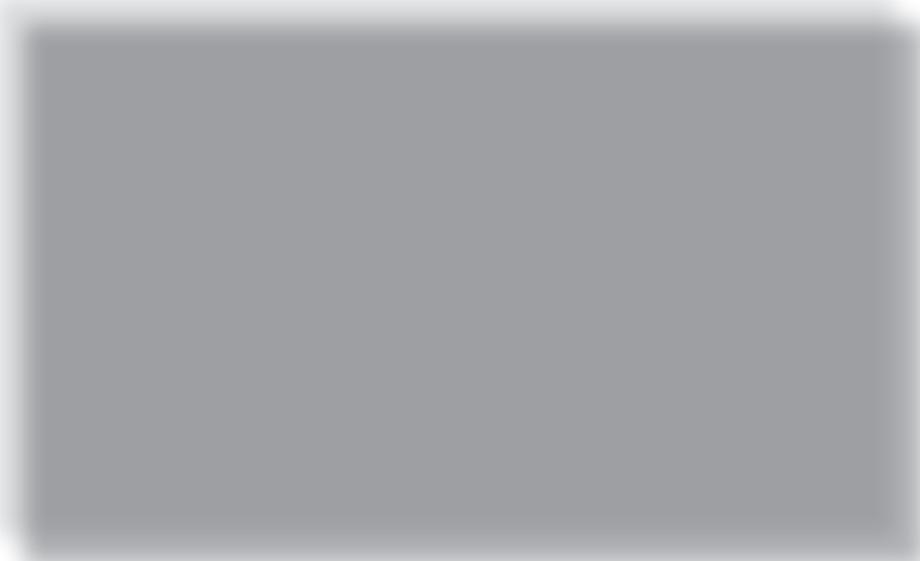
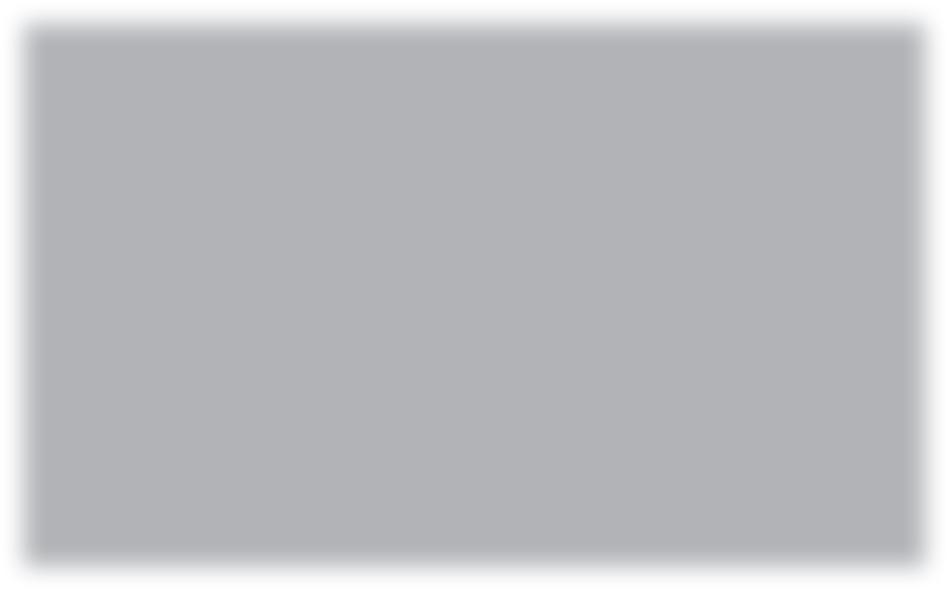
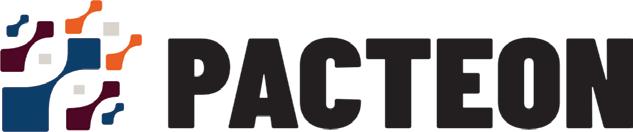


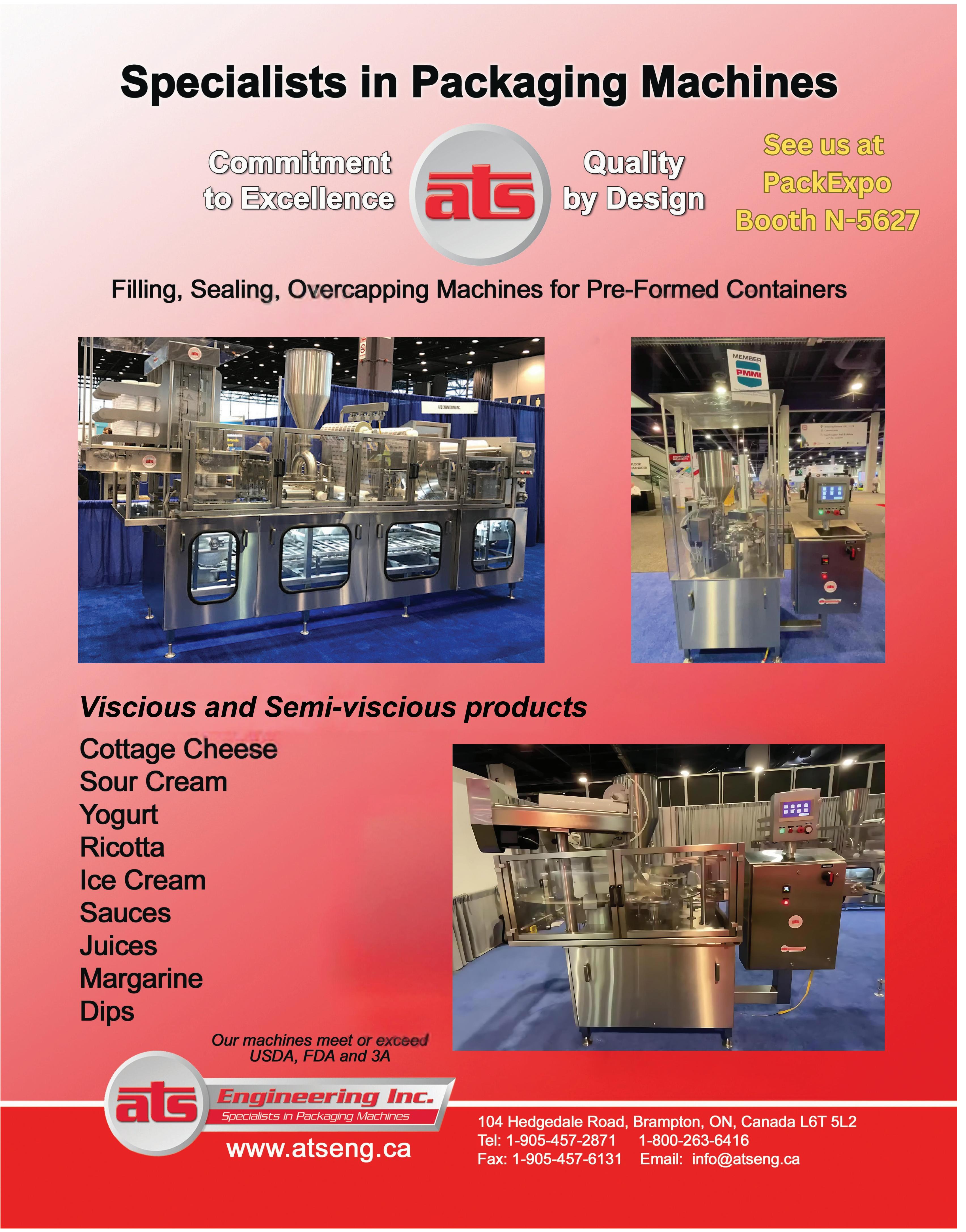

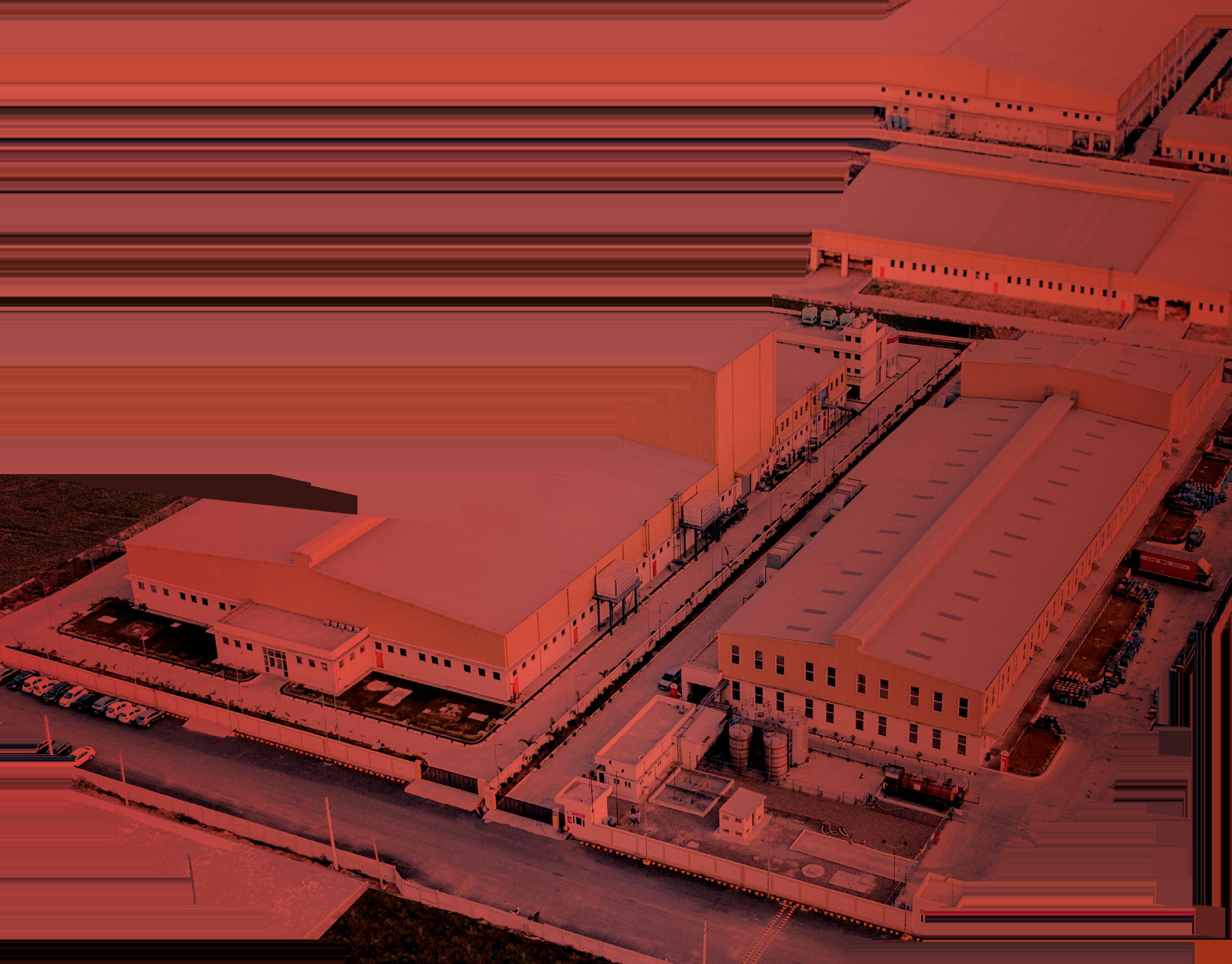


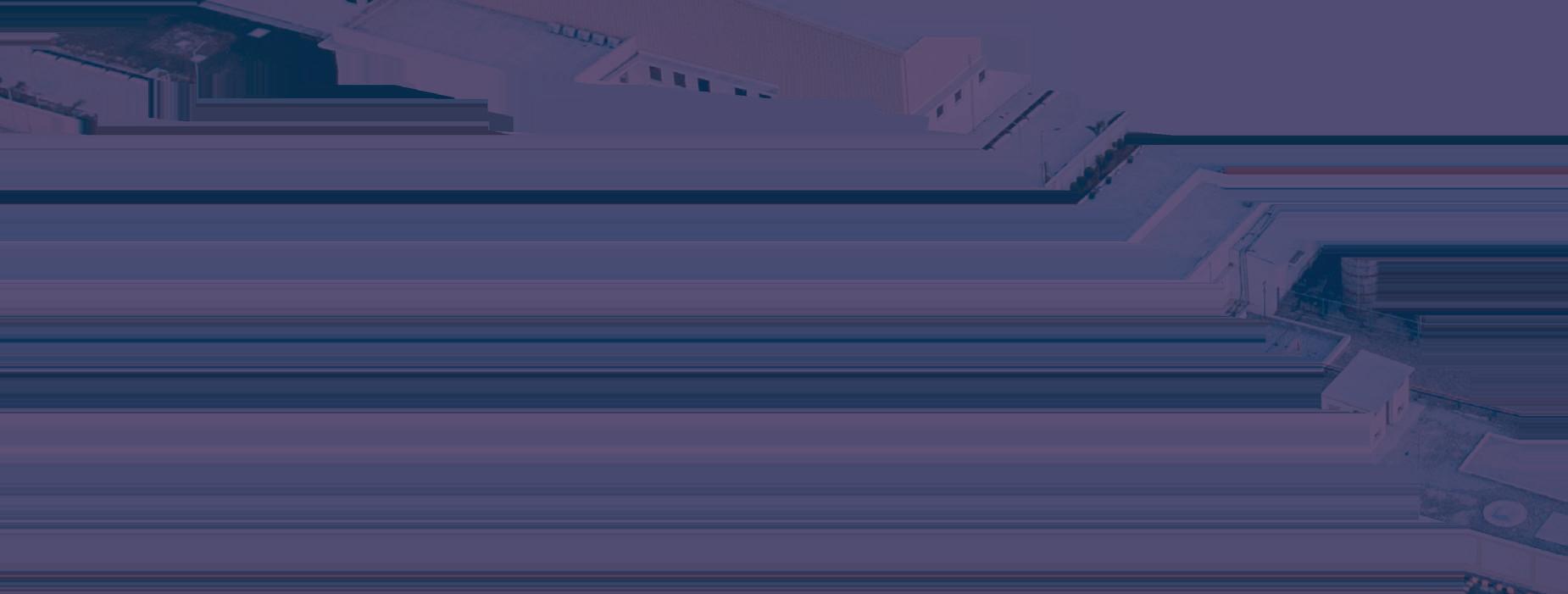
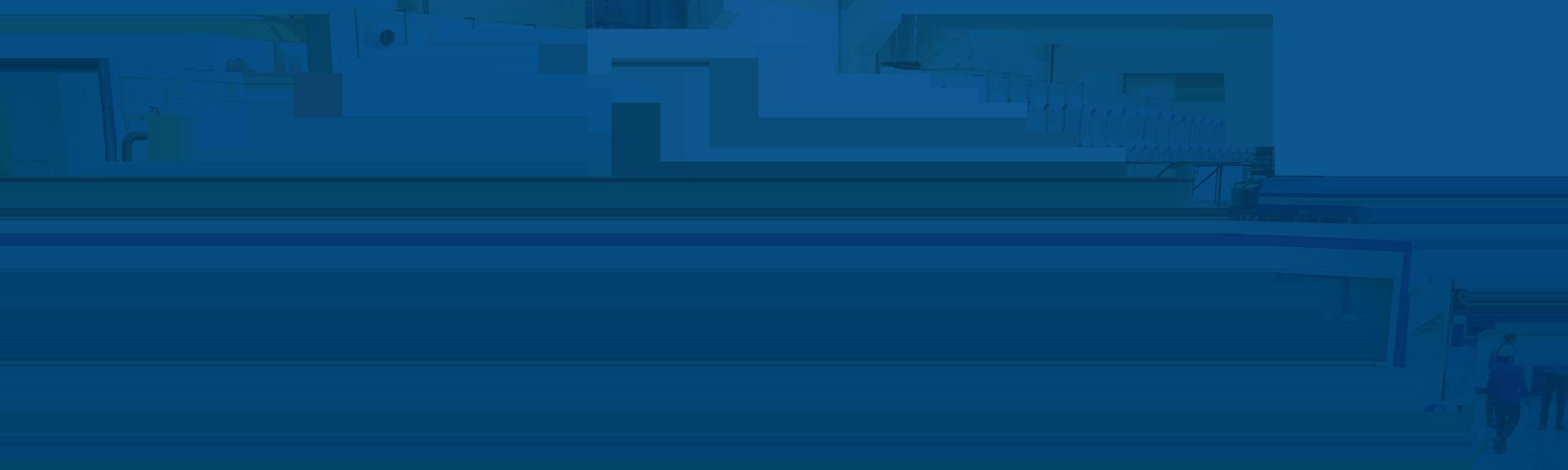
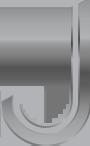
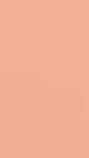
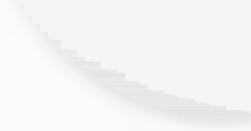
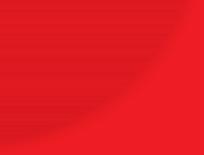
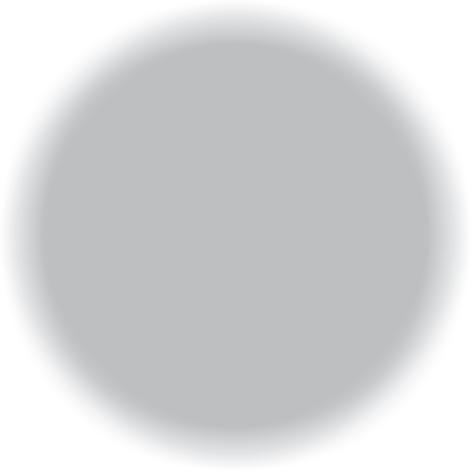

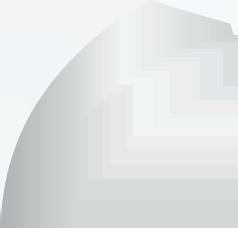


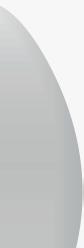
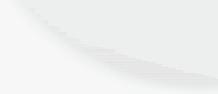
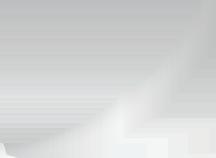
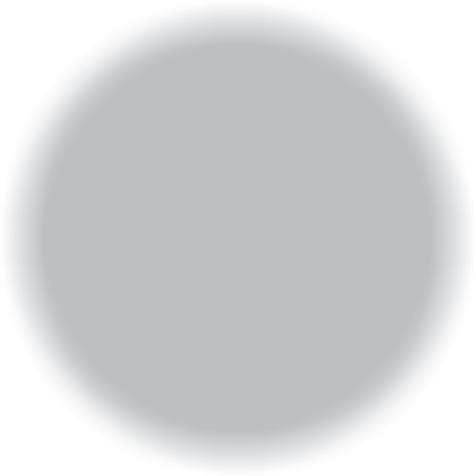
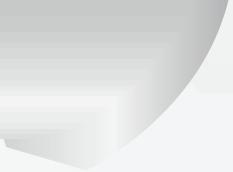
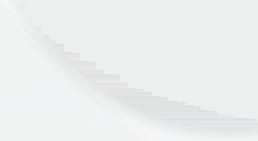
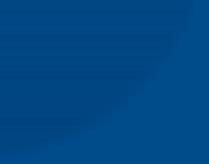
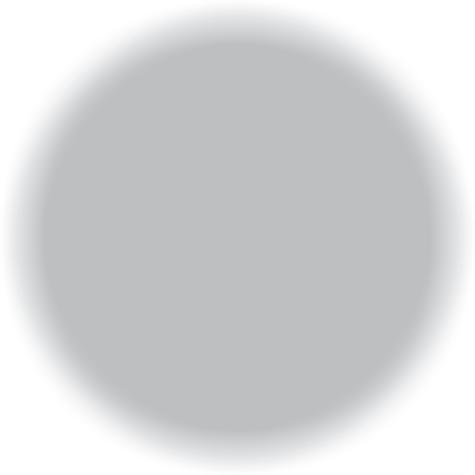
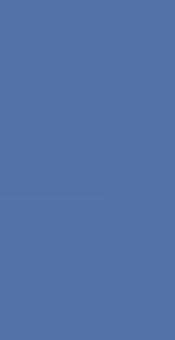
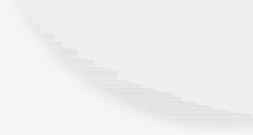

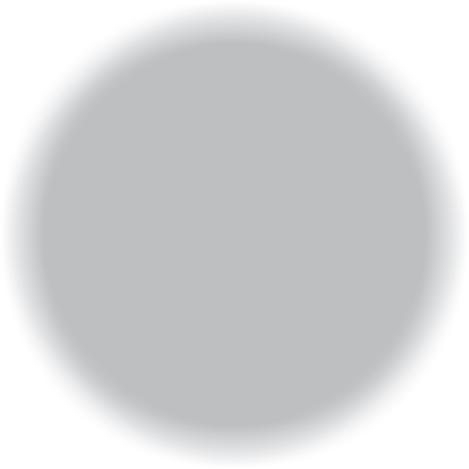
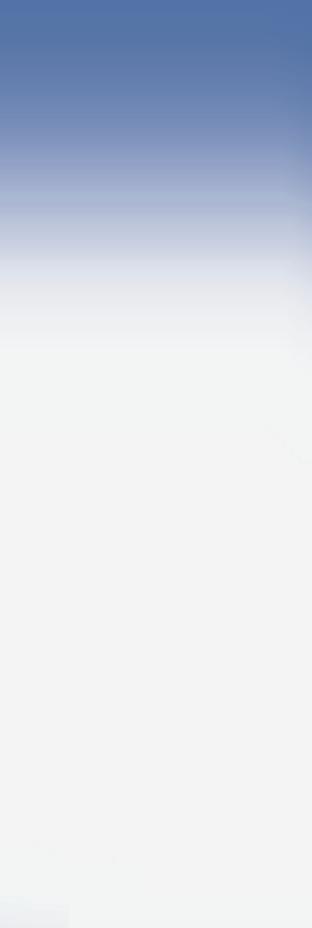
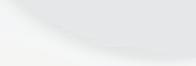












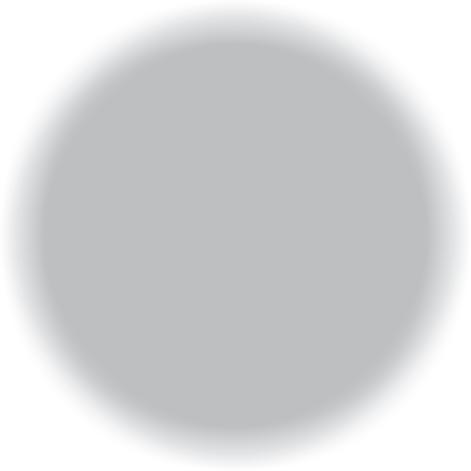

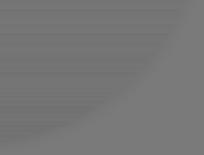
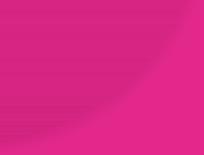
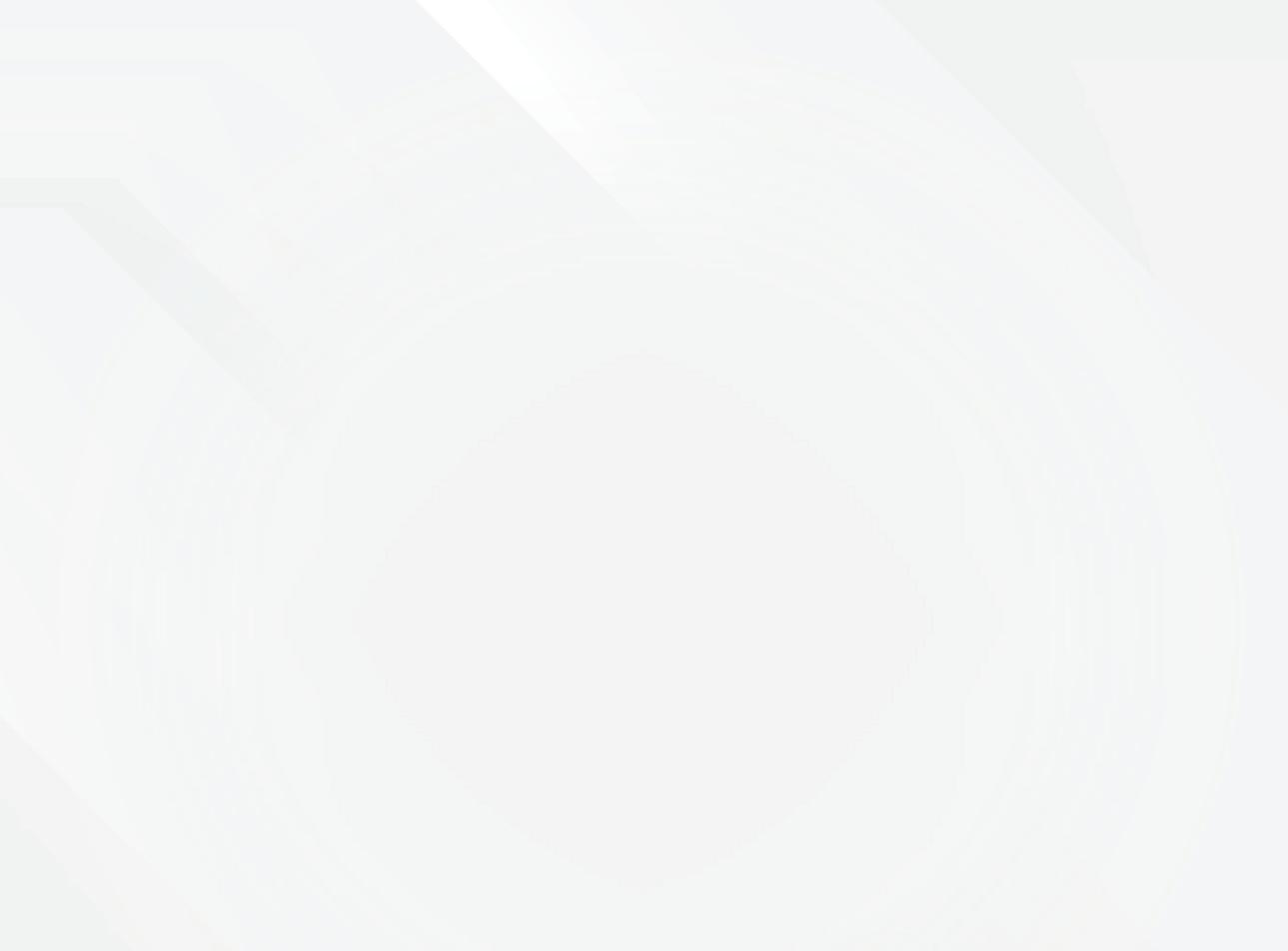
For nearly 40 years...
Trusted Strength
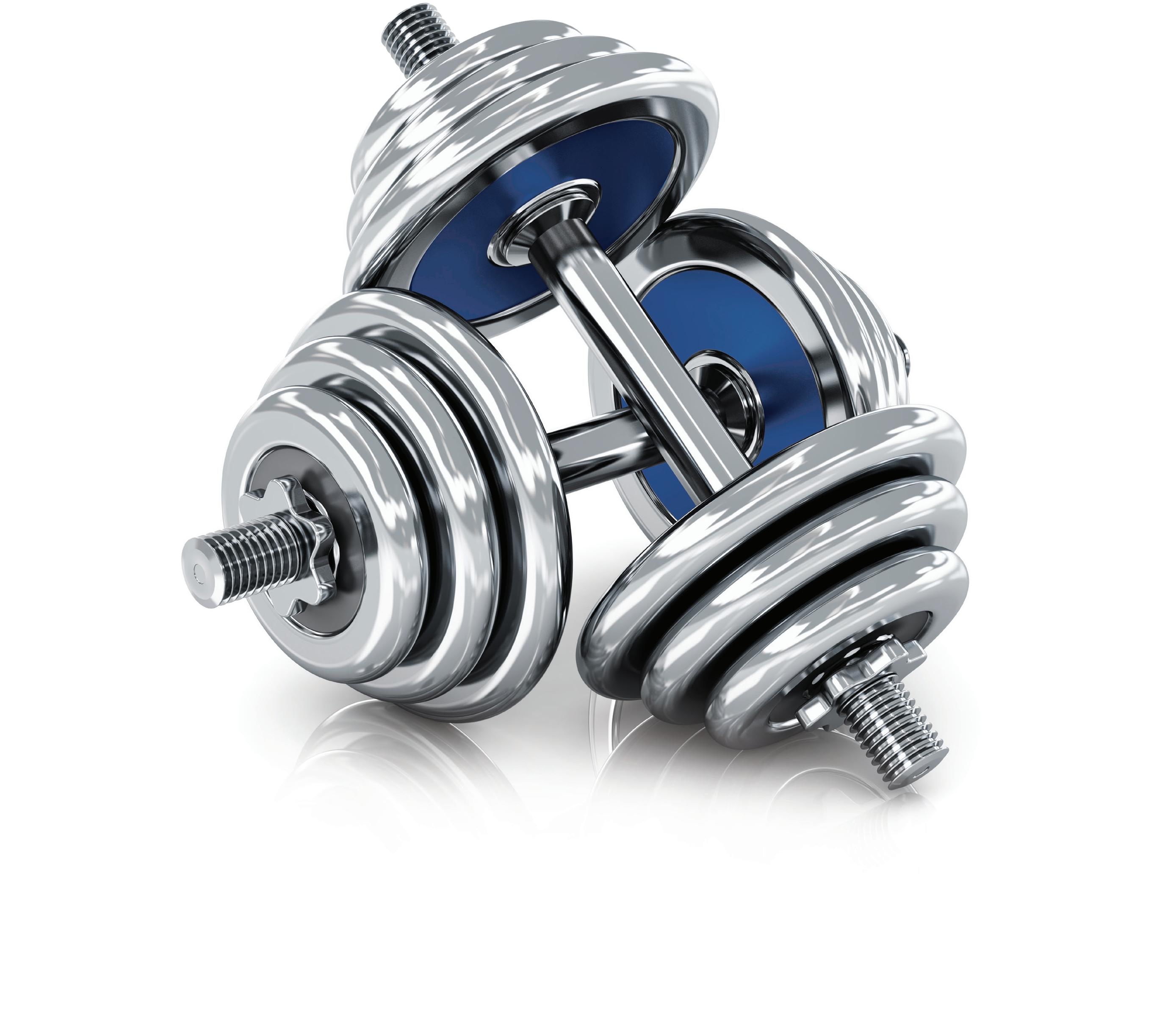
Proven Solutions
Providing a range of today’s finest packaging and processing equipment.
• Capsule fillers
• Capsule check-weighers
• Capsule banding machines
• Pouch fillers
• Cartoners
• Tray formers
• Case packers
• Palletizers
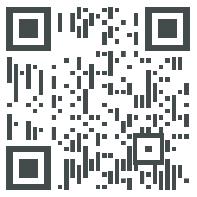
• Packaging line integration
• Metal detectors for capsules
• Bottle unscramblers
• Bottle fillers/cappers
- Tablets/capsules & liquids
• Bottle labelers
• Bottles: Carton coding, verification, serialization
• Bin blending equipment
• Material handling equipment
• Blister machines
• Thermoformers
• Washers
• Sterilizers
• Depyrogenation