WEDNESDAY SEPTEMBER 13, 2023
Booth C-2800 SHOW DAILY
NEWS BRIEF
Printing, robotics, pneumatics

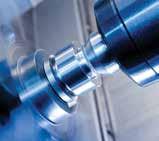

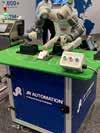
Hitachi (Booth N-9520) displays live printing stations, robotic integration and its new DS45 oil-free air compressor to showcase end-to-end solutions for the industry. Visit JR Automation (Booth N-9163) for a chance to Beat the Bot at blackjack. The robotic dealer integrates the technology of Hitachi’s continuous inkjet printer with a CRX-5iA robot from FANUC America (BoothC-5233). Learn more at hitachifusion.com sustainability. SD
Streamlined automation
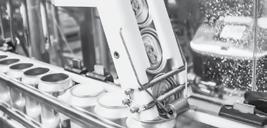
Bosch Rexroth (Booth SL-5964) demonstrates streamlined automation with a ctrlX AUTOMATION-powered, multitech layout consisting of a VarioFlow plus conveyor, which delivers high accuracy with unprecedented speed, and a Kassow collaborative robot. With more than 225 years of engineering expertise, the company’s comprehensive, harmonized factory automation portfolio offers advanced yet easy-to-use components and digital engineering tools. Customized support addresses the most intricate engineering challenges. SD
Integrated vision debuts
Beckhoff Automation (Booth SL-6335) launches fully integrated Beckhoff Vision portfolio in North America. New cameras, lighting and lensing allow engineers to implement robust image processing directly in a standard PLC environment with perfectly paired hardware and complementary TwinCAT 3 software. The integration of vision into control architecture, along with EtherCAT communication, powers real-time reactions and greater data transparency for better quality control, traceability and other functions. SD
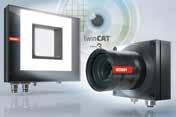
Sustainable tray
Marchesini Group USA (Booth SL-6701) displays a Paperboard Tray Line and its newly designed tray. This innovative tray design generates a saving of around 50% in paperboard and glue and an estimated 30% of space in the final carton/shipper pack configuration, compared to current designs on the market. SD
Build on this year’s success Plan now for PACK EXPOs in Philly, Chicago and Atlanta.
As PACK EXPO Las Vegas draws to a successful close, attention turns to PACK EXPO East (March 18–20, 2024; Pennsylvania Convention Center; Philadelphia) and PACK EXPO International (Nov. 3–6, 2024; McCormick Place; Chicago) and the launch of PACK EXPO Southeast (March 10–12, 2025; Georgia World Congress Center, Atlanta).
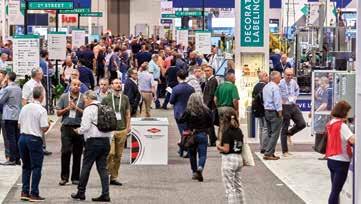
At PACK EXPO shows, attendees:
• See new packaging and processing technology in action for 40 vertical markets
• Get crossover ideas from other industries
• Make new connections via networking events like the Young Professionals Networking Reception and programs sponsored by the Packaging & Processing Women’s Leadership Network

• Participate in free educational programs to gain actionable information to put to use right away
4 win Technology Excellence Awards
Voting closed at noon yesterday for the Technology Excellence Award (TEA) competition, which honors technology never seen before at a PACK EXPO. Voters narrowed the field of 12 finalists down to four winners, one in each category.
FOOD/BEVERAGE WINNER
Designed to quickly empty drums, barrels or jerricans of concentrated liquids, the Aneko Emsys system from Aneko (Booth N-10165) is ideal for syrup preparation rooms with sanitary construction, simple operation and an integrated weighing system. After the operator selects the product, the unit automatically detects the opening and empties the container. Once empty, the container is rinsed, and the system returns to home position for automatic cleaning in place.
(Continued on page 8)
• Move projects forward faster by talking to experts and assessing options side-by-side.
PACK EXPO EAST
As it prepares to present its sixth edition, this well-attended show has grown since its inception
(Continued on page 8)
Manjit Minhas inspires crowd
Manjit Minhas, entrepreneur, beer baroness and television personality, shared insights, experiences and valuable lessons to an audience of 750 at yesterday’s Packaging & Processing Women’s Leadership Network (PPWLN) Breakfast.
In a dialog with Stephanie Neil, PPWLN leader and editor of OEM, Minhas stressed the importance of negotiating skills. “You don’t get what you deserve, you get what you negotiate,” she said, noting everyone who joins her company takes a negotiating course. She also encouraged the audience to set goals and write them down. “This opens the mind to opportunities,” she explained.
At the age of 19, Minhas co-founded the
(Continued on page 16)

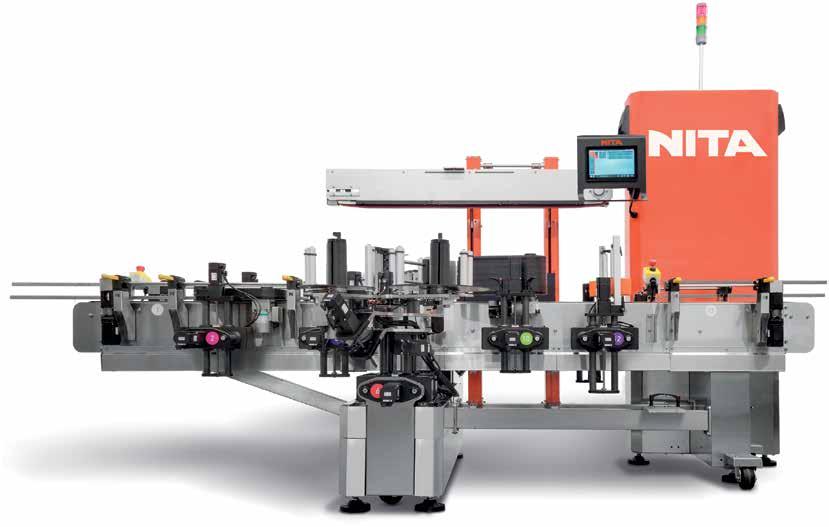
It is time to experience












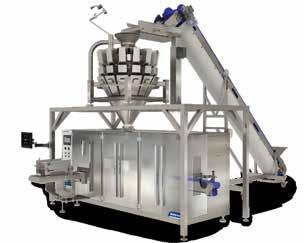
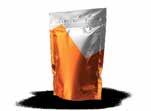

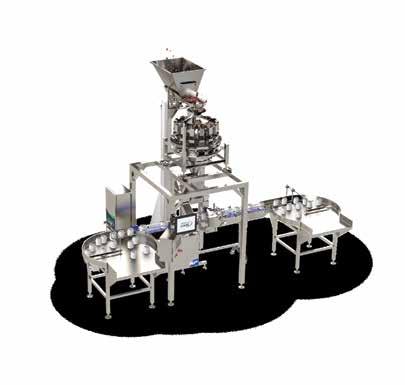
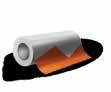
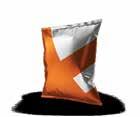
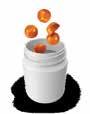
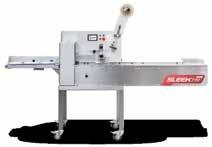

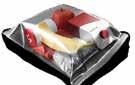
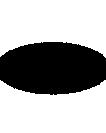

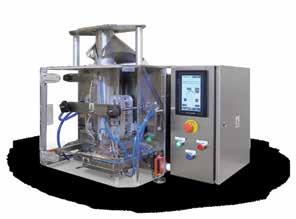
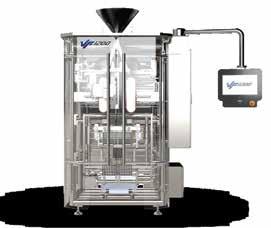
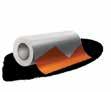
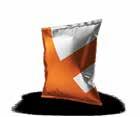
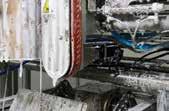
Cartoner handles multiple formats
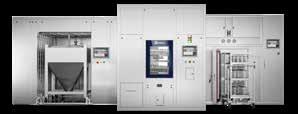
Using manual or automatic feeding, the Cariba C221 intermittent-motion horizontal cartoner from MG America (Booth SL-6534) accommodates most primary pharmaceutical, nutraceutical and cosmetics packaging formats, including blister packs, round/shaped glass and plastic bottles, jars, soft tubes and flow packs at up to 120 cartons/min. SD
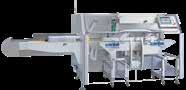
Students compete in show floor tasks
Emerson continues as sponsor of Amazing Packaging Race.
Teams of college students and exhibitors come together this morning in the Amazing Packaging Race, a popular last-day-ofthe-show tradition, sponsored by Emerson Discrete Automation (Booth SL-6107). In this competition, student teams dash around the show floor to take on tasks assigned by participating exhibitors.
NJM reps Steelco
As its exclusive North American representative, NJM, a ProMach product brand (Booth C-3225, SL-6501), is responsible for sales and service of Steelco Group’s cleaning and sterilization systems for the pharmaceutical, biotech, nutraceutical and medical device industries in the U.S. and Canada. “With the addition of Steelco, we’re expanding our portfolio to include related systems that complement the complete, turnkey packaging solutions we’ve been providing for decades,” says Steve Leduc, vice president & GM of NJM. SD
IP rebrands for 125th birthday
To celebrate its 125th year in business, International Paper (Booth N-9305) has unveiled a new visual identity and corporate website that highlight the sustainability of its mission and its commitment to creating what’s next in meeting industry needs for renewable, fiber-based packaging and pulp. SD

Rockwell expands robotics holdings
Rockwell Automation (Booth SL-6127) complements its advanced material handling capabilities with the planned acquisition of Clearpath Robotics and its OTTO Motors Division (Booth SU-8083), a supplier of autonomous mobile robots, fleet management and navigation software. These technologies dramatically increase throughput and reduce costs by eliminating bottlenecks, ensuring product and packaging are in place when needed and transporting finished goods to a truck or warehouse, creating a safer, more productive workplace. SD
The race concludes with the announcement of first, second and third place teams, who win $1,000, $500, and $250, respectively, for each team member.
“We are extremely grateful for Emerson’s support and commitment to offering educational opportunities for students in the packaging industry,” says Jim Pittas, president & CEO, PMMI, The Association for Packaging and Processing Technologies (Central Lobby), organizer of the PACK EXPO family of trade shows. “Throughout the years, Emerson’s consistent sponsorship has played a crucial role in the success of this program, making it possible to provide valuable experiences for students. This is one of our most popular events, and we couldn’t do it without the continued support of Emerson.”
“We are thrilled to be part of this hands-on event that celebrates problem solvers and innovative technology, two principles deeply rooted in Emerson’s heritage,” says Jay Gatz, vice president Commercial Execution & Strategy, Discrete Automation, at Emerson. He concludes, “Our passion and unwavering
support for STEM education is driven by these core values. We’re excited to cheer on this year’s collegiate teams as they solve processing and packaging challenges across the PACK EXPO floor.”
Registration for The Amazing Packaging Race is free for students and $600 for exhibitors. Participating exhibitors include: 3M (Booth C-3243), AllenField (Booth SU-8313), B+R Industrial Automation (Booth C-4343), Baumer HHS (Booth C-5603), Beckhoff Automation (Booth SL-6335), Duravant (Booth C-4230), Econocorp (Booth C-4422), Fallas Automation (Booth C-4214), FOX IV Technologies (Booth SL-6301), Fresh-Lock By Presto Products (Booth C-3003), Hoosier Feeder (Booth SL5925), Institute of Packaging Professionals (Booth C-1154), Lenze Americas (Booth C-4803), LinMot USA (Booth C-5414), Morrison Container Handling Solutions (Booth C-1651), OMAC - The Organization for Machine Automation and Control (Booth C-1255), Paper Machinery (Booth C-1361), Plastipak Packaging (Booth N-9357), Schneider Packaging Equipment/Pacteon (Booth C-2223, SL-6604), Shurtape Technologies (Booth SL-5923), SICK (Booth C-5128), Siemens Digital Industries (Booth SL-6351), Starview Packaging Machinery (Booth C-3600), and WLS, a ProMach product brand (Booth C-3225, SL-6501)
For more info, visit www.packexpolasvegas.com. SD
Hitachi donation supports research Equipment auction raises funds for breast cancer research.
Hitachi Industrial Equipment & Solutions America (Booth N-9520) has donated two UX2 continuous inkjet (CIJ) printers and two WJ200 Series variable frequency drives for an online auction to raise money for the Breast Cancer Research Foundation.
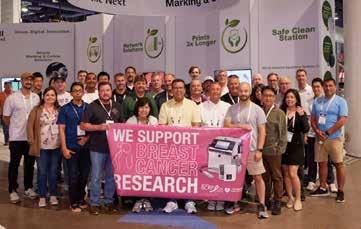
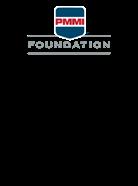
The CIJ printers are equipped with a sealed SafeClean-Station, which cleans and dries in a single operation, consumes less solvent than manual cleaning and reduces downtime caused by a dirty nozzle.
Bids may be placed until 5 p.m. UTC (1 p.m. EDT) on Sept. 30, 2023. Winners will be contacted at the conclusion of the auction.
For more info, visit givebutter.com/c/hitachi, hitachi-iesa.com. SD
Secondary & End of line
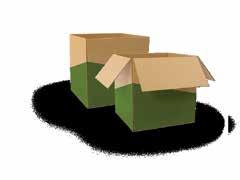





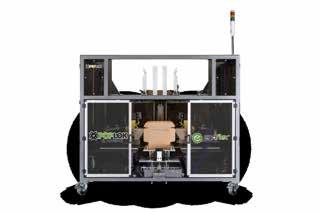








When the choice is yours, why not choose more? A leading provider of primary, secondary, and end-of-line packaging machines, Paxiom has more than 30 years of industry expertise. Operating from seven global facilities, with a passionate and focused staff of professionals with the strongest national service presence, the ability to provide systems integration, and an installed base that included more than 7,000 machines across the world. Paxiom. Get more.

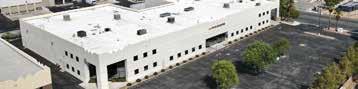
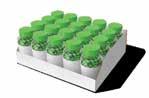


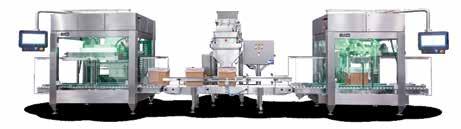
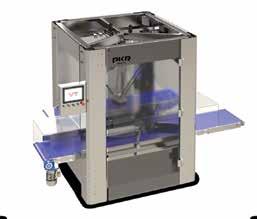




One-button changeover
PLC-controlled, servo-driven, fully automatic labeler from Quadrel Labeling Systems (Booth C-1655) changes over with the press of a button. The new design reduces changeover time to less than 2 min. and is available on ProLine models. SD
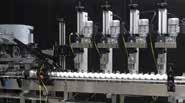
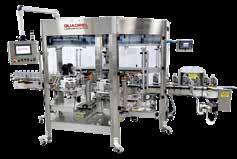
Robotic unscrambler debuts
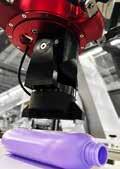
A parallel-kinematic, multi-axis, pick-and-place robot module on the fully automatic robotic unscrambler from Omega Design (Booth C-3836) separates, orients and positions bottles onto a conveyor or into stabilizing pucks. Dual infeed presents two containers at once to the robotic arms from the integrated hopper. Designed with minimal changeover points for applications running complex or multiple bottle shapes, unit handles a broad array of containers, bottles, tottles, jars, vials, jugs and tubes. SD
ROPP capper offers up to 4 heads
An automatic roll-on-pilfer-proof (ROPP) cappers from E-PAK Machinery (Booth C-4614a) accommodate one to four capping heads. Servo feedscrew indexing ensures proper bottle alignment, and a height-adjustment feature accommodates different container sizes. The sorter and capper can handle caps with various diameters, and the cap feed chute has a wide adjustment range to meet specific cap and container combinations with minimal change parts. SD
Weigh cannabis precisely
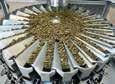
A fully automatic, high-precision cannabis weighing and filling system from MULTIPOND America (Booth SL-6567) combines product protection, easy operation and minimal giveaway with a tamper-proof system. An integrated pre- and post-weighing device continuously checks the weighed weight. SD
Software optimizes
Cloud-enabled PackNet® production and optimization software seamlessly integrates with Packsize’s (Booth SU-7407) On Demand Packaging® machines to manage machine, box production and packaging workflow integrations. Key features include support for multi-tenant environments, reporting, cube optimization and dimensioning. Comprehensive approach provides data to minimize material waste and enhance sustainability practices in real-time. SD
SEPTEMBER 13, 2023
OpX enhances FAT work product
SAT Addendum guides next step in acceptance testing.
An Addendum for site acceptance tests (SATs) will join the One Voice Factory Acceptance Tests (FATs) work product early in the fourth quarter of 2023.
Published by the OpX Leadership Network (Central Lobby) in 2022, the original document, plus a Virtual FAT Addendum, guides consumer packaged goods companies through the FAT process via a playbook and checklist. The SAT Addendum does the same for the SAT process. “Although the FAT and SAT perform many of the same tests, the OpX Leadership Network’s Capital Projects Solutions Group felt a SAT Addendum would be helpful to CPG companies and OEMs,” reports Bryan Griffen, director, Industry Services, PMMI, The Association for Packaging and Processing Technologies (Central Lobby), and convener of the OpX Leadership Network. Machinery buyers rely on FATs to ensure a machine will perform as specified. The tests are performed by the OEM at its facility and typically runs the machine in short bursts to show functionality. The end user may be onsite or observe virtually. At
the end of the FAT, a punch list of what needs to be corrected or reworked is made and completed.
After installation of a machine, the SAT occurs. This involves running the machine at full speed for a specified period to confirm any issues identified at the FAT have been resolved, work out kinks and verify performance is as expected. If the machine will run different formats or sizes, changeovers are made to run each variation. This ensures changeovers go smoothly and that the operators understand how to do them. “If the FAT was done virtually, the SAT also will check physical aspects of the machine like pinch points and sharp edges, which couldn’t be done virtually,” says Griffen.
Once the SAT is completed, the machine is integrated with up- and downstream equipment and a line test is run to synchronize the line and achieve the desired OEE.
The SAT Addendum will be available for free download on the OpX Leadership Network website in a few weeks.
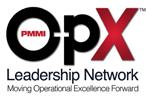
For more info, visit opxleadershipnetwork.org. SD
PACK
Publisher PMMI Media Group

Editorial Director
Hallie Forcinio
Associate Editor
Barbara Rook
Production Manager
Mary Thorne
Art Director
Debi Friedmann
IT/Production Support
Manny Dominguez and Olga Minkevich
Photographers
Miles Boone and Edina Dibusz
Advertising Sales Management
Dave Newcorn, President, PMMI Media Group
John Schrei, Vice President, Sales, PMMI Media Group











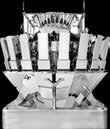
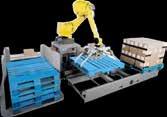
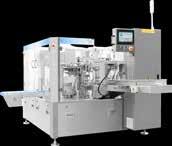
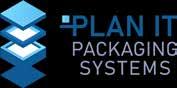
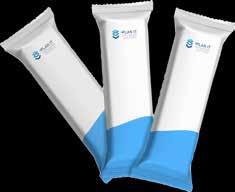
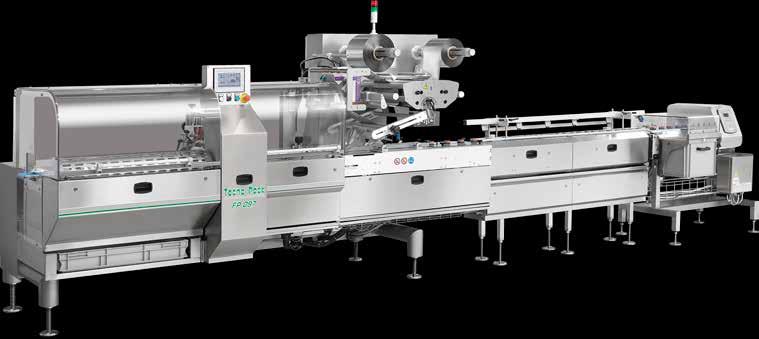











SEPTEMBER 13, 2023
(PACK EXPOs Continued from page 1) DISCOVER THE FUTURE OF
PACKAGING SUSTAINABILITY
but retains an intimate feel with approximately 100,000 net sq. ft. of exhibits, 400 exhibitors and 6,000 attendees. Conveniently located in Philadelphia, the show is a quick trip by train or car from most anywhere on the East Coast.
PACK EXPO INTERNATIONAL
PACK EXPO International will be the biggest packaging and processing show on the planet in 2024. With 45,000 attendees expected and 2,500 exhibitors spread across more than 1 million sq. ft. of floor space, it will connect more packaging and processing end users and suppliers than any other event in 2024.
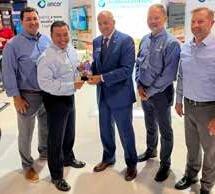
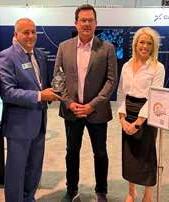
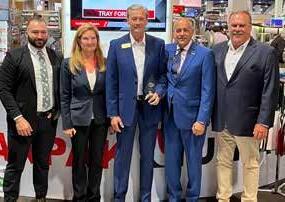
PACK EXPO SOUTHEAST
This show will bring the industry together in a region of the country that is not currently served by a trade show focused on packaging and processing. Atlanta represents an ideal location. Not only is it home to some of the top manufacturing industries in the region, but it’s also located a mere two-hour flight from 80% of the U.S. population.
NORTH HALL, Booth N-9455
Attain a complete understanding of packaging sustainability and what that means for your brand.
Reshape Your Brands Impact
Explore 6 key areas of packaging sustainability encouraging you to think outside the box.
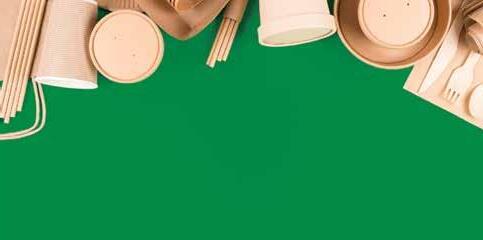
• Manufacturing
• Material
• Design
• Logistics
• Recovery
• Analytics
Find Inspired Ideas
Talk with top universities about their projects centered around sustainability and the circular economy.
• Michigan State University
• Wisconsin Stout
• Indiana State University
Booth: N-9967
Get Insights from Experts
FREE sessions on how to make your brand more sustainable.
PACK EXPO LAS VEGAS 2025
PACK EXPO Las Vegas (Sept. 29–Oct. 1, 2025; Las Vegas Convention Center) returns for its 16th edition.
For more info, visit www.packexpo.com. SD
( TEA Continued from page 1)
GENERAL PACKAGING & PROCESSING WINNER
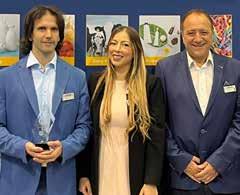
This augmented reality system from Harpak-ULMA Packaging (Booth SL6188, SL-6101) utilizes AI to identify patterns, predict outcomes, optimize decision-making processes and transform packaging operations.
PERSONAL CARE/PHARMA WINNER
The patent-pending Digital LineClearance Assistant™ from Catalyx (Booth SL-6185), formerly CXV Global and Panacea Technologies, deploys a network of fixed-position cameras to ensure coverage of hard-to-reach areas and inspects the entire line in seconds.
SUSTAINABILITY WINNER
Recycle-ready sachet from Amcor Healthcare Packaging (Booth SL-6635) replaces difficult-to-recycle foil laminations with a metallized polyolefin/AmPrima™ film, which is compatible with the polyethylene film recycling stream. For more info, visit www.packexpolasvegas.com. SD
Vertical Conveying. Simplified.






Spiral Conveyors & Bucket Elevators
















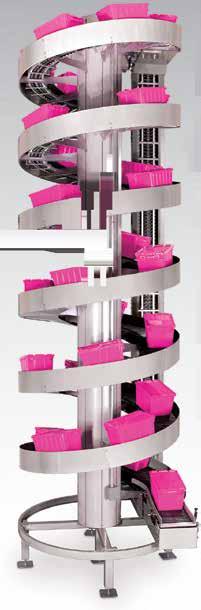
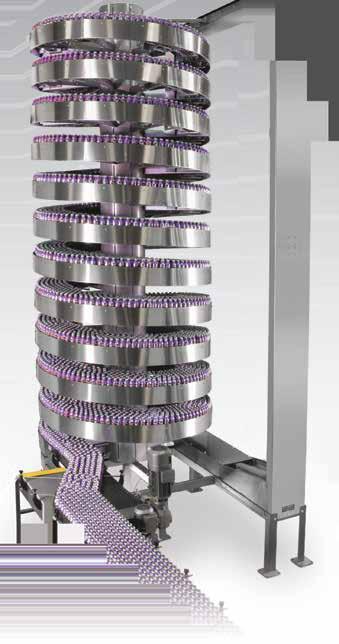
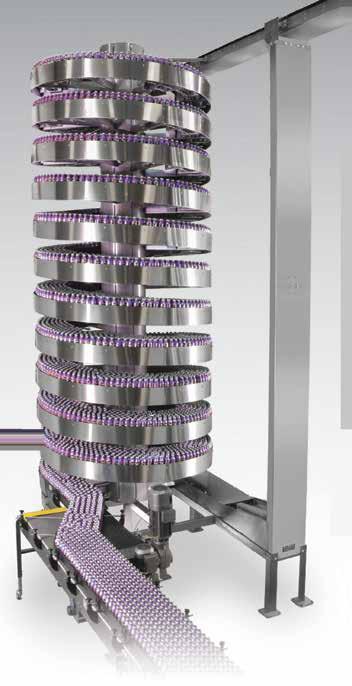



Unit Load Spirals convey cases, totes and packaged goods smoothly on our slat style belts and come in 9 standard slat widths ranging from 6” to 30”. Available in powder coated carbon steel, stainless steel, wet environment and freezer versions.
Mass Flow Spirals handle full and empty bottles, cans and jars in mass up to 2,000 units per minute. Available in 4 different slat widths ranging from 6” to 20”.
Narrow Trak Spirals are super compact and designed to handle smaller loads. Our 6” and 9” wide nesting slats can end-transfer small cartons and packages or side-transfer small bottles and containers in a single file or in mass at speeds in excess of 220 FPM.
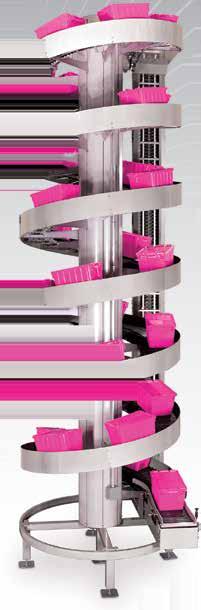
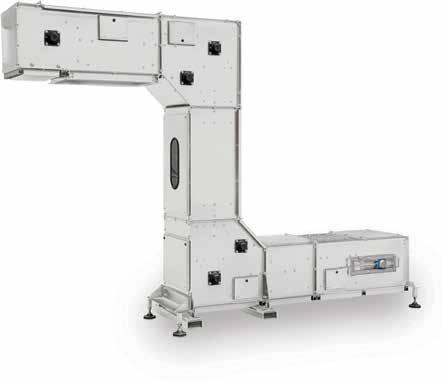
Ryson’s Bucket Elevators combine vertical and horizontal transportation of bulk materials in one integral unit.
Our Bucket Elevators are designed for gentle handling and well-suited to transport a broad range of bulk products. They are completely enclosed with overlapping pivoting buckets, that prevent spillage and helps mitigate foreign debris.
They can be configured with multiple inlets or outlets that can be controlled individually. Available in three standard bucket sizes, yielding capacities up to 300, 700 or 1,800 cubic feet per hour. They can also be delivered in powder-coated carbon-steel, or stainless-steel for wet environments.


All Ryson equipment is modular and built to order. No matter the application, the Ryson team is up to the challenge of finding solutions for your conveying needs. For application assistance or more information, give us a call or visit www.ryson.com
Check out our running equipment at Pack Expo | Booth C-4736








www.ryson.com










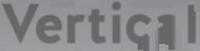


















(757) 898-1530
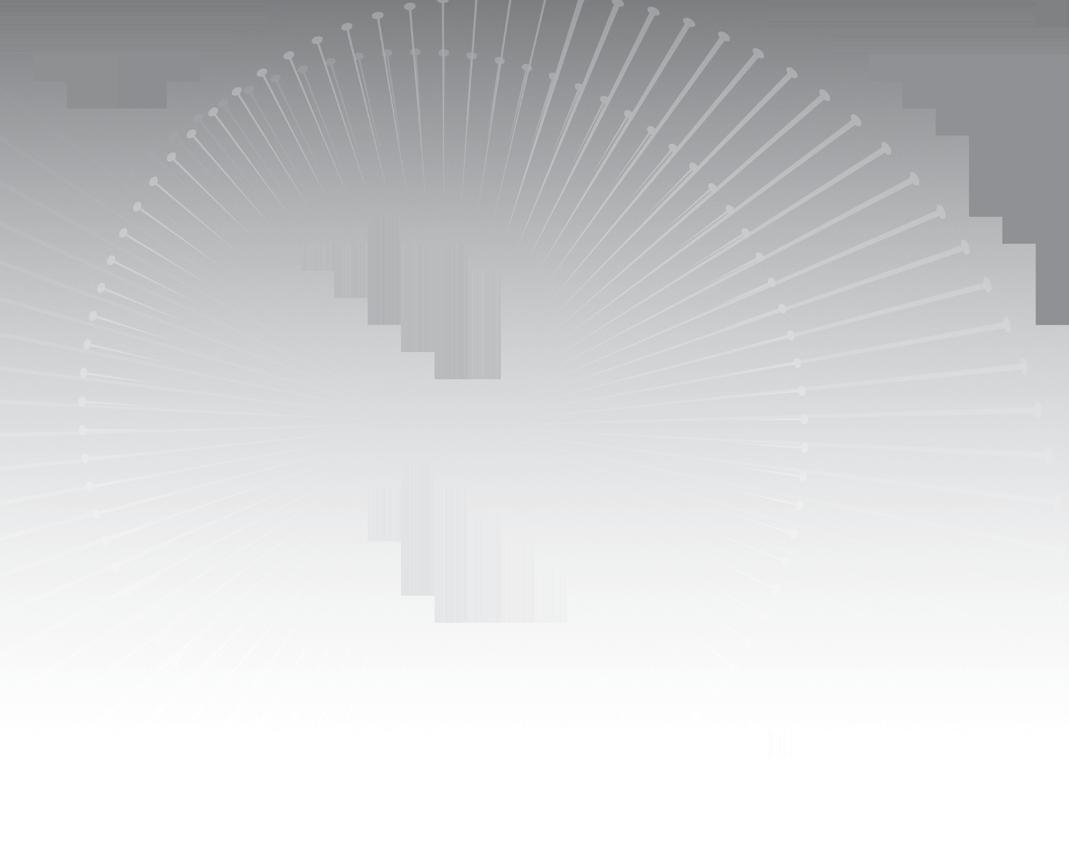
Ryson Spiral Conveyors need less floor space than conventional conveyors and are faster and more reliable than any elevator or lift.
hotspots find targeted solutions
NORTH HALL
The Containers and Materials Pavilion
Find new sustainable materials, flexible packaging, printable films and more. Also see award winning packages at:
PACKage Printing Pavilion
Explore technology that makes customization, promotions, small runs, on-demand production and smart packaging cost effective.
The Logistics Pavilion
Find supply chain solutions including warehousing and dock equipment and systems, inventory management and control, distribution logistics services and transportation.
The Processing Zone
Find front-of-the-line solutions for food and beverage processing and discover ways to increase safety, improve efficiency and achieve total system integration.
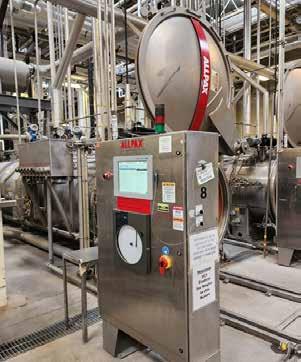

SOUTH
UPPER HALL
The Confectionery Pavilion
Uncover specialized equipment and integrated systems for your candy, chocolate, mints and gum production lines.
Sponsored by:
The Reusable Packaging Pavilion
Discover reusable assets that not only reduce waste but also provide more reliable protection for your production and can be part of a smart supply chain.
Sponsored by:
SOUTH
LOWER HALL
The Healthcare Packaging Pavilion
A one stop shop for solutions targeted to pharmaceuticals, biologics, nutraceuticals, medical devices and more.
Awards honor sustainability efforts Conagra,
Hormel,
Red Mill
Winners in the ninth annual Sustainability Excellence in Manufacturing Awards (SEMA), sponsored by ProFood World, a publication of PMMI Media Group (Central Lobby), a division of PMMI, the Association for Packaging and Processing Technologies, were honored on Monday in a presentation at the Processing Innovation Stage (Booth N-10511)
The award-winning programs and projects were completed and operational between November 2021 and December 2022.
PROGRAM CATEGORY
• First Place: Conagra Brands, Fayetteville, AR, Certified Carbon Neutral Made in a Zero-Waste Facility.
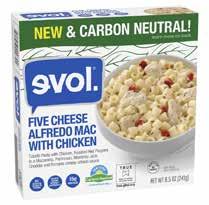
PROJECT CATEGORY
• First Place: Hormel Foods, Dubuque, IA, Reverse Osmosis Concentrate Reuse
• Second Place: Conagra Brands, Imlay City, MI, Steam Trap Optimization
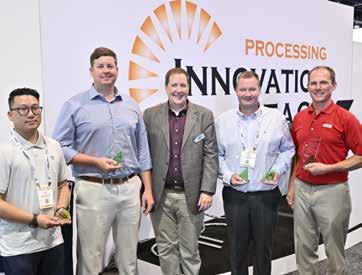
• Third Place: Bob’s Red Mill, Milwaukie, OR, Food Waste Reduction
• Fourth Place: Smithfield Packaged Meats, Kinston, NC, Plastic/Film Waste Reduction. The peer-reviewed awards recognize facilities for
projects or programs that improve sustainability efforts in food and beverage manufacturing operations, focusing on pollution prevention, compliance assurance and environmental protection. Recipients are awarded for reducing water and energy use, waste conservation, pollution prevention and packaging reductions.
“Sustainability is more important than ever for both food and beverage manufacturers and their customers,” says Aaron Hand, editor-in-chief of ProFood World. “As shown by the depth of entries in the Project Category, processors are often chipping away at sustainability efforts on a project-by-project basis, in many cases getting inspiration from their employees who have firsthand knowledge of where waste is occurring and ideas about how operations could be optimized.”
Past award winners include B&G Foods, Pepperidge Farm, Sierra Nevada Brewing, Campbell Soup, McCormick, Hormel, Hiland Dairy and Land O’Lakes.
For more info, visit pfwgo.to/sema. SD
Editor’s Note: Award winners are described in the cover story in the August 2023 issue of ProFood World
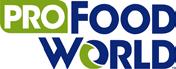
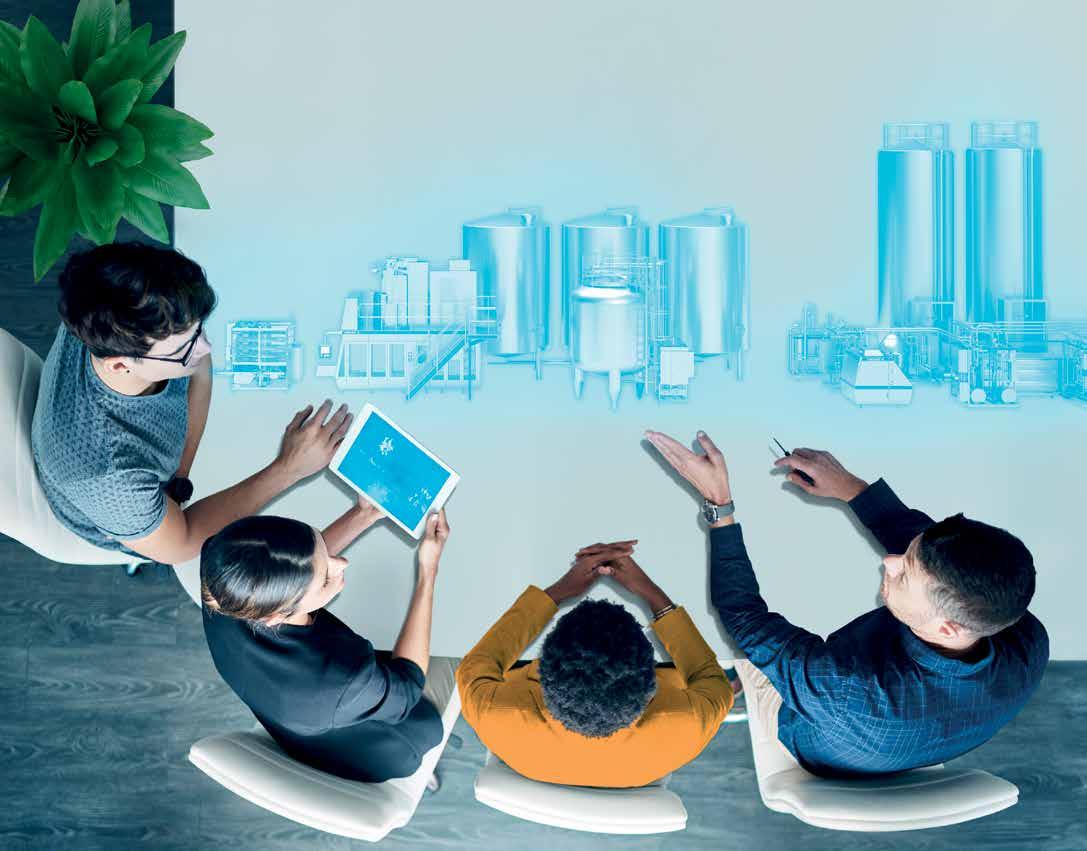
SEPTEMBER 13, 2023
Schubert North America turns 25
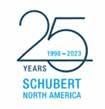
Kick back and dine for leSS!
Kick back and dine for leSS!
Visit the North Hall Backyard Bistro with lunch options at discounted rates
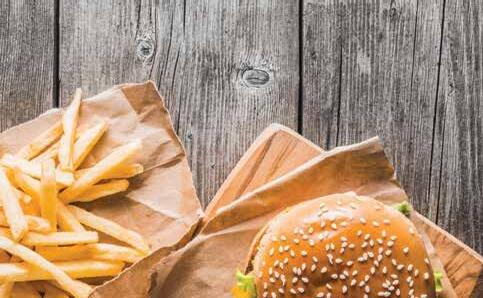
Schubert North America (Booth SL-6820, SU-7654) marked its 25th anniversary with a reception yesterday afternoon, which featured traditional German refreshments in honor of its parent company, Gerhard Schubert, which is headquartered in Crailsheim, Germany, and was founded in 1966.
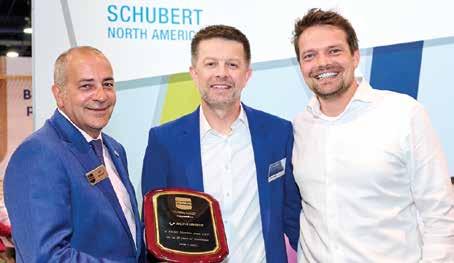
In 1998, the Schubert family set up its first North American location in Dallas, TX, expanding the company’s international presence. A Canadian operation opened a few years later.
Open Daily Open Daily In North Hall
back of the show floor
11:00 AM - 3:00 PM Monday - Wednesday
Refuel Relax Return
FIRST-TIME ATTENDEE LOUNGE
South Upper Hall Room S-220
HOURS OF OPERATION:
Monday – Tuesday: 8:00 am – 5:00 pm
Wednesday: 8:00 am – 3:00 pm
If your badge says “First-Time Attendee” stop by to:

• Ask questions of show staff
• Access product locators
• Enjoy refreshments and comfortable seating
MONDAY, SEPTEMBER 11
8:30 am PACK EXPO 101: Navigate the Show Like a Pro
1:30 pm Bringing Your Products to Market Using Contract Packagers & Manufacturers
TUESDAY, SEPTEMBER 12
8:30 am PACK EXPO 101: Navigate the Show Like a Pro
• Attend special sessions PLUS, an Exclusive Networking Reception on Tuesday 4:30 pm – 5:30 pm. Your First-Time Attendee Badge is your access pass.
In 2015, Schubert established its North American headquarters in Charlotte, NC. Due to continued growth, the company recently acquired seven acres of land in Charlotte to further expand its operations. The new headquarters building, which occupies approximately 45,000 sq. ft., will include sales, engineering, service, final assembly and a customer training center. Today, North American customers also are served from a facility near Toronto in Mississauga, Ontario, Canada.
For more info, visit schubert.group. SD
Automate Floor to Cloud™
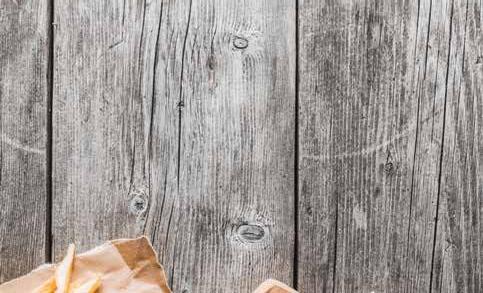
Floor to Cloud™ solutions from Emerson Discrete Automation (Booth SL-6107) empower smarter packaging lines and more efficient processes, enabling continuous improvement of productivity, sustainability and safety. Products on display include AVENTICS Series AF2 flow sensors and multimedia monitoring technology.
By monitoring air consumption in pneumatic systems, AVENTICS Series AF2 flow sensors enable rapid intervention if a leak occurs and help optimize energy consumption, reach net-zero targets, prevent machine downtime and reduce costs. A high-flow model propels compressed air monitoring beyond individual machines to benefit larger air lines and systems.
1:30 pm How to Make Your Product’s Packaging Environmentally Friendly
WEDNESDAY, SEPTEMBER 13
8:30 am PACK EXPO 101: Navigate the Show Like a Pro
Sponsored by: Booth C-3222
Multimedia monitoring, including CoreTigo wireless communication, analyzes water, compressed air, gases, electricity, steam and other utilities. The Edge Analytics Dashboard measures efficiency, optimizes productivity, avoids or reduces downtime and helps meet sustainability goals.
For more info, visit www.emerson.com/en-us/catalog/aventics-af2, Emerson.com/ Sustainable-Automation. SD



PMMI








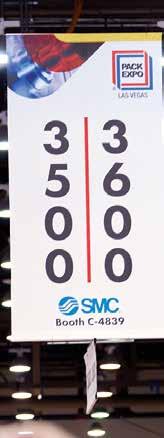
exhibitors can take a break from the show floor in dedicated lounges (Room S-215; S-222 / N-101, N-114), sponsored by Lenze Americas (Booth C-4803), where they will be welcomed by ambassa-



































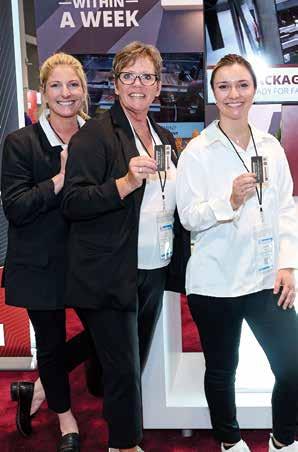
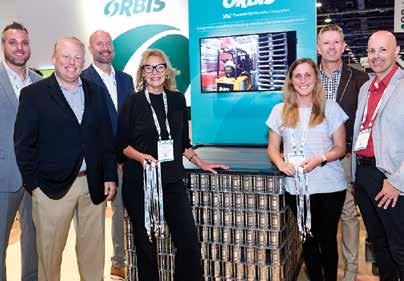

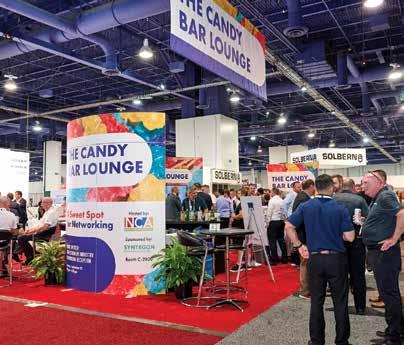
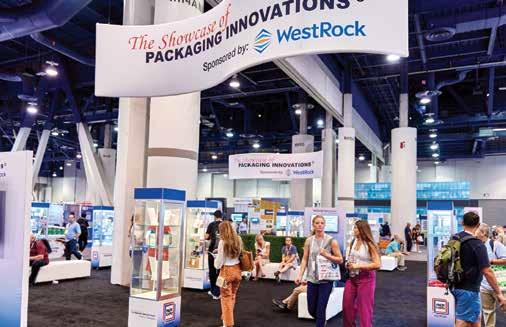
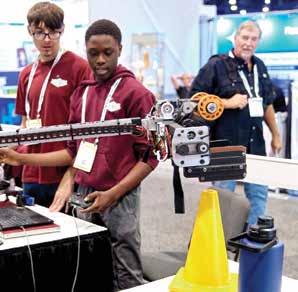
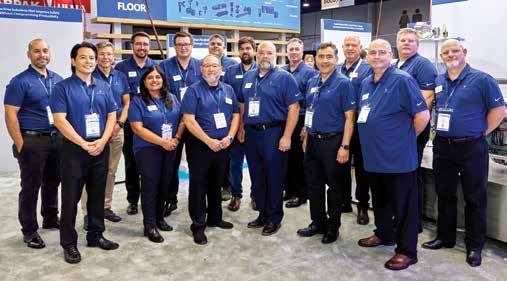
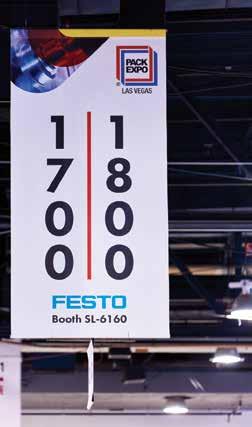
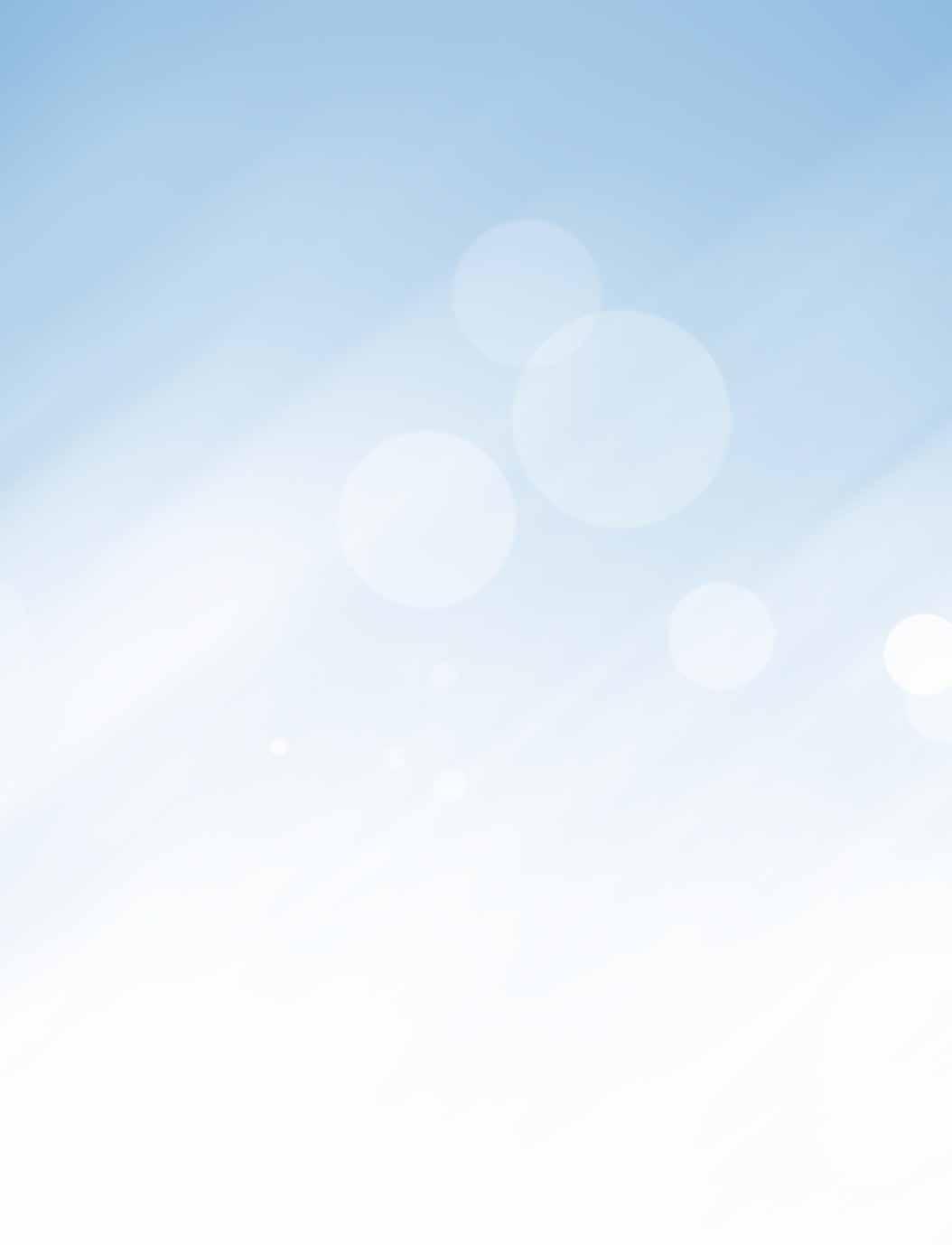
We s et the st a nd a rd fo r susta i nable therm oforme d pac kagin g. Rea c h you r goals quic ke r with ou r SC S Global c ertified 100% pos t- c onsume r re cycled m a ter ia l .
We s et the st and ard fo r susta inable therm oforme d pac kagin g. Rea ch you r goals quic ke r with ou r SC S Global certified 100% pos t- consume r re cycled m ater ial .
Per fec t i n b oth the food and reta i l mar kets , we h ave an in-s toc k o rcus tom solution fo r you r pac kaging needs .
Per fec t i n b oth the food and reta il mar kets , we h ave an in-s toc k o rcus tom solution fo r you r pac kaging needs .
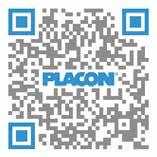
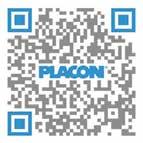
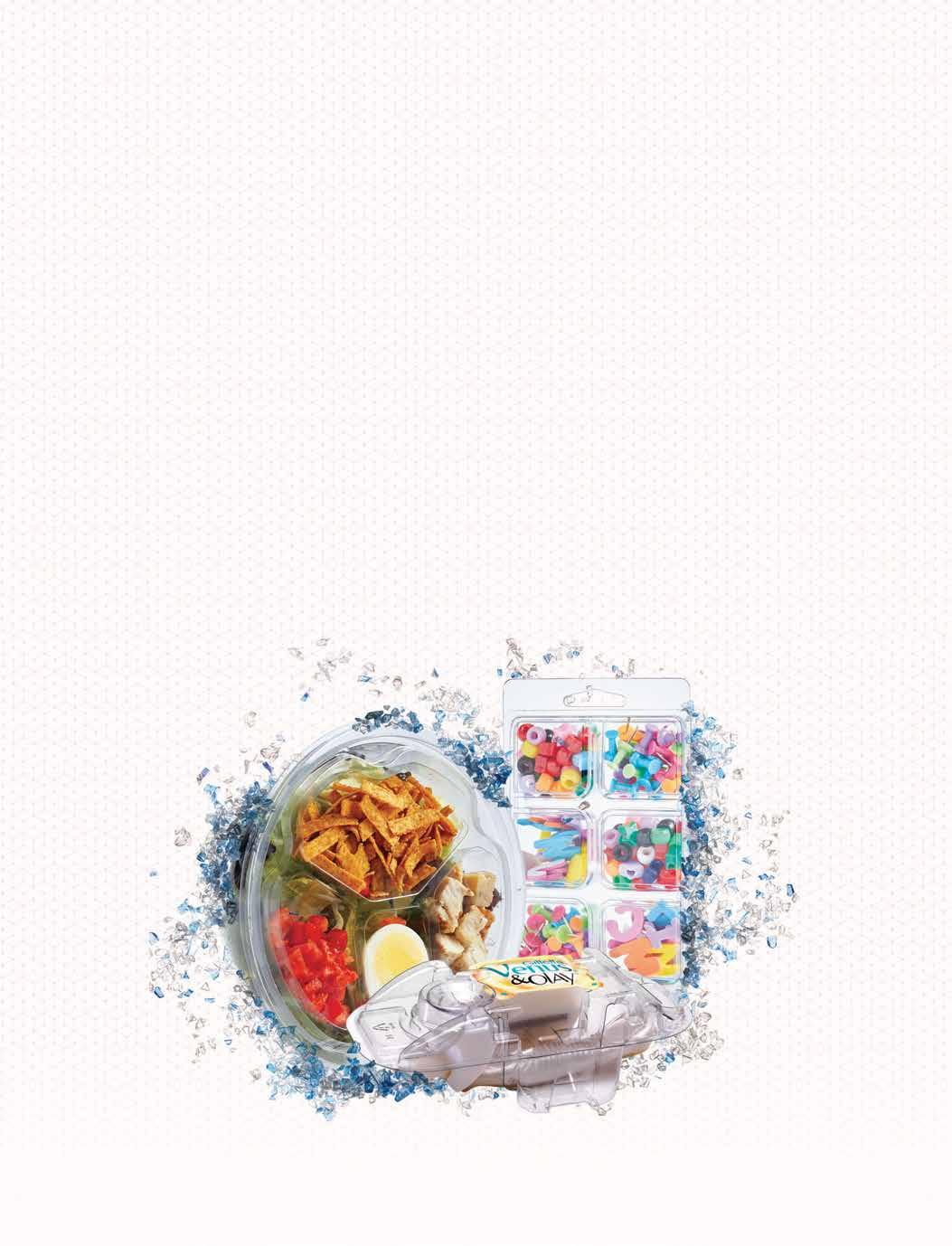
SEPTEMBER 13, 2023
Sustainability Stage debuts
Anew show feature, Sustainability Central in the North Hall, houses the Sustainability Stage (Booth N-9967) where attendees will learn from more than a dozen industry experts about how to improve the environmental profile of their brands.
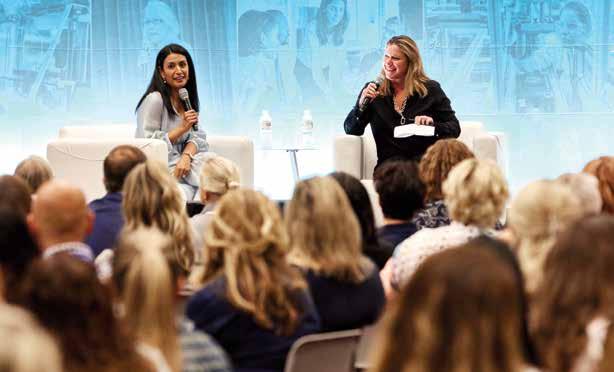
Topics include logistics, labeling, waste reduction, sustainable design and transitioning to more sustainable materials. with an opening presentation on Monday by Daniella Souza Miranda, global business director, Circular & Renewable Solutions at Dow (Room S-116), the show’s official Sustainability Partner. Session descriptions, times and locations are listed below. Updated schedules
LEVERAGING SUSTAINABILITY IN PACKAGING COST OPTIMIZATION: HOW TO CAPTURE SUSTAINABILITY VALUE WHILE SAVING COSTS
10:00-10:30 AM
As the consumer goods and packaging industry faces several headwinds coming out of COVID, including an uncertain economic situation, softening demand, supply chain challenges that haven’t fully been resolved, etc., sustainability often takes a back seat to cost optimization and other performance improvement levers. There are, however, ways to incorporate sustainability into these initiatives to continue to make progress against goals and commitments, as well as not have to sacrifice either objective. Join the Roland Berger team as they discuss how to incorporate sustainability thinking into cost optimization and provide examples of its value creation.
Rebecca MarciniakDilhani de Silva
Roland Berger
(Minhas/PPWLN Continued from page 1)
Minhas Brewery, Distillery, and Winery in Alberta, Canada, alongside her brother Ravinder Minhas. Since then, her companies have evolved into a significant player in the Canadian and US markets with revenues exceeding $220 million and a portfolio of about 120 brands of beers, spirits, liqueurs and wines.
Minhas is committed to sustainability and social responsibility. A special 48-can pack for COSTCO, significantly reduces packaging materials, and she was the first brewer in Canada to add a Management Warning on beer cans, urging against drinking and driving, advising expectant mothers to avoid alcoholic products and promoting responsible consumption.
The PPWLN Breakfast was sponsored by Emerson Discrete Automation (Booth SL-6107), Septimatech Group (Booth C-2836), ID Technology (Booth C-3414), BW Packaging (Booth C-1800), WestRock (Booth C-2023), SMC (Booth C-4839), Morrison Container Handling Solutions (Booth C-1651), Plexpack (Booth C-3036) and POWHER (ProMach Womens Resource Group).
For more info, visit pmmi.org/ppwln. SD
Sustainability STAGE
may be found on the show website or via the show App, sponsored by ProMach (Booth C-3222)
Other free educational opportunities on the show floor include the new Industry Speaks Stage (Booth C-1141) (see schedule, p. 24), the Innovation Stage (Booths C-2051, C-2058, C-2151) and the Processing Innovation Stage (Booth N-10511) (see schedule, p. 30), plus The Forum — An Industry Knowledge Exchange (Booth C-2158) (see schedule, p. 58)
Schedule as of August 23, 2023.
For more info, visit packexpolasvegas.com. SD
WEDNESDAY, SEPTEMBER 13, 2023
ALL TOGETHER NOW: UNLOCKING PACKAGING’S CIRCULAR FUTURE
11:00-11:30 AM
It’s time to go beyond broad recyclability claims and design packaging that is actually being recycled into valuable post-consumer recycled material. But how can brands transform from passive producers of waste to active participants in a circular economy? By embracing a systems approach that engages materials suppliers, reprocessors, materials recovery facilities (MRFs) and machinery makers to shed light on all the links of the circular supply chain. From advanced recycling to reuse and refill and monolayer materials, we’ll explore the ways stakeholders can take their recyclability claims from promise to reality.
Matt Reynolds
Chief Editor, Packaging World
Anne Marie Mohan
Senior Editor, Packaging World
Sean Riley
News Editor, Packaging World PMMI Media Group
INTENTIONAL DESIGN FOR SUSTAINABLE AND RECYCLABLE PACKAGING STRUCTURES
12:00-12:30 PM
To meet the combination of growing consumer demand and an escalating regulatory environment, Michelman helps customers transition to more sustainable solutions for their packaging needs. We will discuss how to transition from film-based substrates to fiber-based substrates that will enable improved end-of-life options for final structures in existing recycling streams – all while maintaining excellent barrier performance!
Talia Collins
Mgr, Global Research & Development
Michelman
Toby Corey
Exec Chairman & COO
Cruz Foam SD
MAKE IT SMARTER AT PACK EXPO 2023
BOOTH C-5033
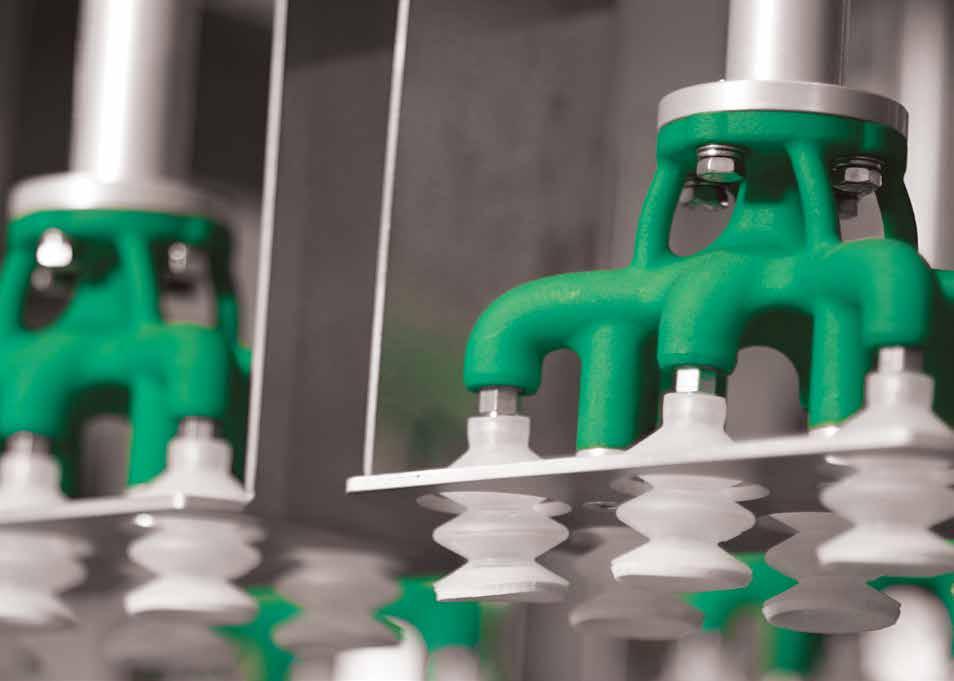
PMMI partners with Festo Didactic
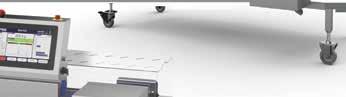
Workforce development effort aims to close STEM skills gap.
Apartnership between PMMI, The Association for Packaging and Processing Technologies (Central Lobby), and Festo Didactic North America, a subsidiary of Festo (Booth SL-6160), seeks to support PMMI members and educators nationwide with advanced technical education, hands-on training and certifications to close the STEM skills gap. Together, the two organizations bring highly customizable training options to packaging and processing companies.
“Packaging and processing is a uniquely innovative industry, with endless career opportunities—but we are seeing the skills gap continue to grow. This collaboration presents a significant opportunity to provide critical resources to PMMI members and educators who need support to meet the technical workforce needs of the industry,” says Stephan Girard, senior director of Workforce Development, PMMI.
MECHATRONICS CERTIFICATIONS
Manufacturing employers need skilled workers who can operate, maintain and troubleshoot equipment. To achieve this, employees must have the right mechatronics skills. The PMMI Mechatronics
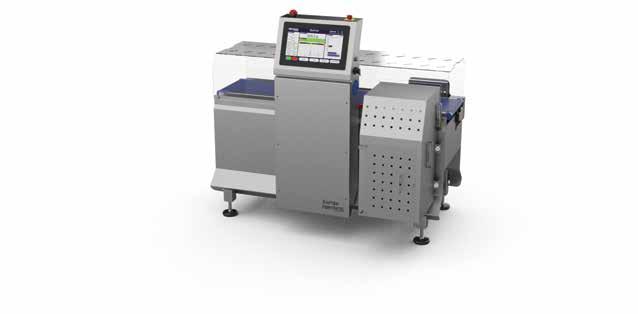
Certification program helps educational institutions create industrial maintenance programs that align with the technical needs of manufacturers and prepare students for careers in advanced manufacturing. Through a series of online tests based on industry-developed skill standards, PMMI’s Mechatronics Certification program helps employers assess the core skills of prospective and current workers.
Festo Didactic, an education company with deep roots in manufacturing automation, offers lab equipment and educational content aligned with PMMI’s Mechatronics Certifications. This provides a turnkey solution for high schools, colleges and universities looking to provide mechatronics training that meets the needs of the industry. Festo’s factory automation learning systems simulate the most technically advanced processing plants, focusing first on individual stations with the option to scale to more complex Industry 4.0 cyber-physical systems.
CUSTOMIZED TRAINING
The customized curriculum and hands-on training offer a wide range of topics and skills related to mechatronics and factory automation such as robotics, CAD/
CAM/CNC and PLC.
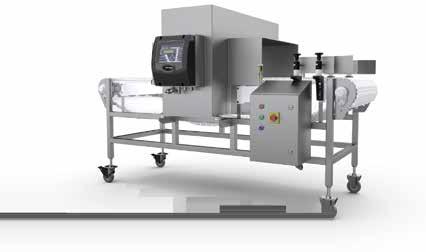
Benefits for industry:
• Improve workforce readiness
• Upskill employees quickly
• Reduce turnover
• Close skills gap with continued learning and professional-development courses
• Highest-quality industry standards.
“As a long-standing member of PMMI, with similar goals and approaches to workforce development, stepping into the role of Preferred Technical Learning Collaborator is a natural fit,” says John Holmes, vice president of Sales for Festo North America. “This partnership was forged in response to the industry’s ongoing hiring and upskilling challenges, and we’re eager to see how our combined expertise and resources positively impact the schools and companies PMMI serves.”
Tony Oran, vice president of Festo Didactic North America, concludes, “We’re committed to setting people up for success in their careers as individuals while looking for smart ways to come together so industry can thrive as a whole.”
For more info, visit PMMI.org, festo.com. SD
Wherever you are and whatever your industry, there’s a PACK EXPO event to provide solutions you need today and the inspiration for tomorrow.
March 18-20, 2024
Philadelphia, USA
June 4-7, 2024
Mexico City, Mex.
Nov. 3-6, 2024
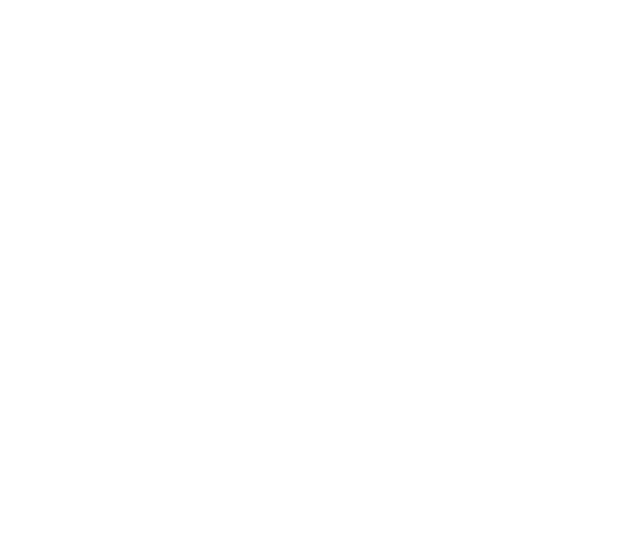

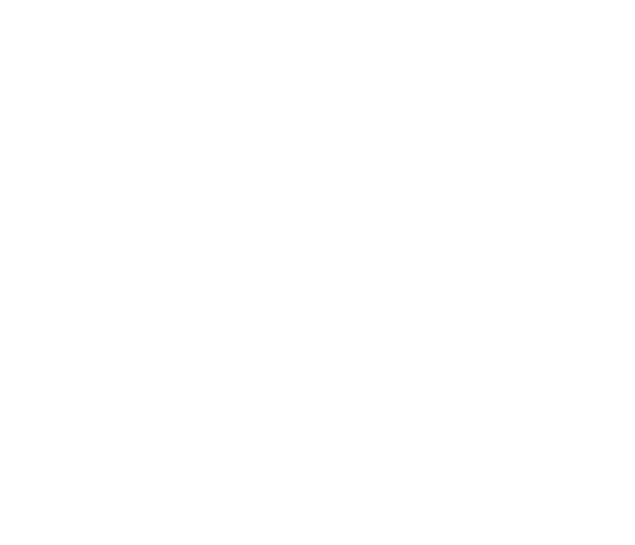
Chicago, USA
March
June
Sept.
Partners bring knowledge to show Partner
Program links attendees to wide array of organizations.
Approximately 30 organizations are partnering with show organizer PMMI, The Association for Packaging and Processing Technologies (Central Lobby), for PACK EXPO Las Vegas, connecting attendees to leading associations from all segments of packaging and processing.
“The Partner Program is one reason why PACK EXPO Las Vegas is the most comprehensive packaging and processing event in North America in 2023,” says Jim Pittas, president & CEO, PMMI. “These organizations bring targeted knowledge to the show floor and give attendees actionable information to improve their operations.”
Participants in the PACK EXPO Partner Program exhibit in the Partner Pavilion or elsewhere on the show floor.
New this year, the PACK EXPO Las Vegas Partner Plus Program gives groups the opportunity to present sessions on the Industry Speaks Stage (Booth C-1141) (see schedule, p. 24) or to co-locate meetings with the show under the banner, Industry Meets. For example, the Cold Pressure Council (Booth C-1153) has scheduled its Annual Conference on Tuesday, Sept. 12, 2023, at the Las Vegas Convention Center and a Board of Directors meeting the next day. Other Industry Meets participants include: the International Bottled Water Association (offsite);
MHI Automation Industry Groups; Composite Can & Tube Institute (Booth C-1350); Contract Packaging Association (Booth C-1256); Institute of Packaging Professionals (Booth C-1154); and OMAC - The Organization for Machine Automation and Control (Booth C-1255). The latter plans a public General Session and a Workgroup meeting at 10:00 a.m. and 11:00 a.m., respectively, on Tuesday, Sept. 12.
The Industry Speaks Stage, another first for PACK EXPO Las Vegas, offers an opportunity to hear experts representing Partner Program participants discuss hot topics and trends including automation, high-pressure pasteurization, digital transformation, contract manufacturing/packaging, flexible packaging, modern warehousing and logistics, machinery standards and sustainability.
“As part of the PACK EXPO Partner Program, we are looking forward to seeing our members and meeting potential members while talking to brand owners, packaging designers, label printers, molders and others who are learning more about the advantages of in-mold labeling and decorating technology,” says Dianna Brodine, managing director at the In-Mold Decorating Association (Booth C-1347). “In addition, we are releasing white papers about the sustainability and recyclability of in-mold labeling/dec-
INDUSTRY MEETS
Cold Pressure Council (Booth C-1153)
Composite Can & Tube Institute (Booth C-1350)
Contract Packaging Association (Booth C-1256)
Institute of Packaging Professionals (Booth C-1154)
International Bottled Water Association
MHI Automation Industry Groups
OMAC - The Organization for Machine Automation and Control (Booth C-1255)
orating processes and presenting an Industry Speaks session on the subject [4:30 p.m., Monday, Sept. 11].”
For up-to-date schedules and Partner Program Pavilion details, check the PACK EXPO Las Vegas mobile App, sponsored by ProMach (Booth C-3222), or the show website.
For more info, visit packexpolasvegas.com, promach.com. SD
PARTNER PROGRAM PARTICIPANTS
3-A Sanitary Standards (Booth C-1353)
AIM (Booth SU-8306)
AMERIPEN (Booth C-1151)
Anuga FoodTec Family (Booth C-1158)
ASD Turkish Packaging Manufacturers (Booth C-1145)
Association for Roll-to-Roll Converters (Booth C-1351)
Association of Plastic Recyclers (Booth C-1157)
Australian Packaging and Processing Machinery Association (Booth C-1150)
CANAINCA
Cold Pressure Council (Booth C-1153)
Composite Can and Tube Institute (Booth C-1350)
Consumer Brands Association (Booth C-1248)
Contract Packaging Association (Booth C-1256)
Flexible Packaging Association* (Booth C-1348)
Foil & Specialty Effects Association* (Booth C-1346)
Foundation for Supply Solutions (Booth C-1152)
International Bottled Water Association
In-Mold Decorating Association* (Booth C-1347)
Institute of Packaging Professionals* (Booth C-1154)
Instituto Argentino del Envase (Booth SU-8135)
International Society of Beverage Technologists (Booth C-1354)
MHI Automation Industry Groups
National Confectioner’s Association (Booth SU-7201)
OMAC – The Organization for Machine Automation and Control (Booth C-1255)
OPC Foundation (Booth C-1250)
PLCopen (Booth C-1253)
Reusable Packaging Association* (Booth SU-8000)
SNAC International (Booth C-1146)
The Tube Council of North America*
UCIMA – Italian Packaging Machinery Manufacturers Association (Booth C-1149)
U.S. Department of Commerce (Booth C-1159)
World Packaging Organisation* (Booth C-1246)



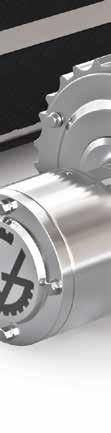
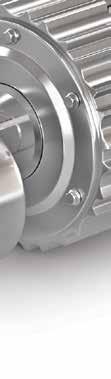
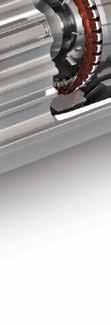

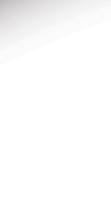
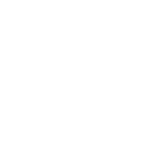

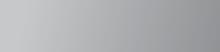

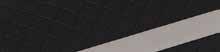





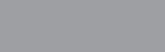


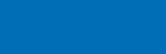

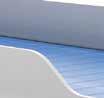

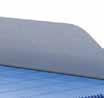
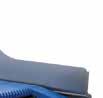
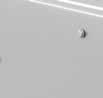
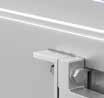

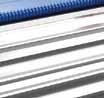
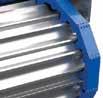
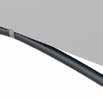
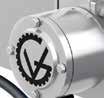
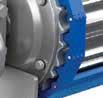

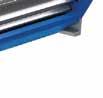


SEPTEMBER 13, 2023
Showcase displays award winners
Visit The Showcase of Packaging Innovations®, sponsored by WestRock.
The Showcase of Packaging Innovations® (Booth N-9550), sponsored exclusively by WestRock (Booth C-2023), features award-winning packages from competitions around the world.
“The Showcase of Packaging Innovations is a traditional and treasured component of PACK EXPO,” says Jim Pittas, president & CEO of PMMI, The Association for Packaging and Processing Technologies (Central Lobby), the show organizer. “We are most grateful to WestRock for sponsoring this facet of the show once again. Being able to view an array of innovative packaging in one place is inspiring and gives attendees ideas to take home and adopt to make their packaging more environmentally-friendly and consumer-friendly.”
Ten organizations are participating in this year‘s
Showcase, which is located in the North Hall straddling the boundary between the Containers and Materials Pavlion and the PACKage Printing Pavilion.
Sustainability plays a role in many of the award winners. A judge for the Flexible Packaging Association competition, Gary Borges, associate professor, University of Wisconsin-Stout, explains, “Sustainability is growing tremendously . . . Post-consumer recycling is a trend that we saw. And we’re seeing an increase in paper structures that . . . we can send to our paper waste streams at home. So, we’re seeing all of these innovations taking place. It is pretty impressive.”
For more info, visit packexpolasvegas.com, westrock. com, dow.com, flexpack.org, fsea.com, imdassociation. com, iopp.org, profoodworld.com, reusables.org, tube.org, worldpackaging.org. SD
At the Flexible Packaging Association, the RESCUE!® Outdoor Disposable Fly Trap earned the Highest Achievement Award. It also won a Packaging Excellence Gold Award, a Technical Innovation Silver Award and an Expanding the Use of Flexible Packaging Award. The flexible packaging, produced by Glenroy for Sterling International, is easy to use: Cut along the dotted line at the top to expose the trap entrance, add water and hang. The pouch construction protects the consumer from the powerful attractant inside. Once the trap is full (collecting up to 20,000 flies), the consumer simply discards it.

In the ninth annual Sustainability Excellence in Manufacturing Awards, organized by ProFood World, a PMMI Media Group (Central Lobby) publication, First Place in the Program Category honors a certified carbon-neutral brand made in a zero-waste Conagra Brands facility in Fayetteville, AR.
PARTICIPANTS
Dow (Room S-116)
Dow Packaging Innovation Awards
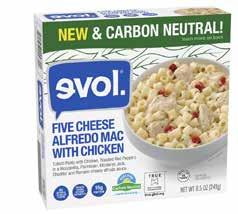
Flexible Packaging Association (Booth C-1348)
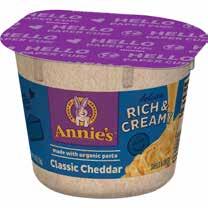
Foil and Specialty Effects Association (Booth C-1346)
In-Mold Decorating Association (Booth C-1347)
Institute of Packaging Professionals (Booth C-1154)

ProFood World (Central Lobby)
Sustainability Excellence in Manufacturing Awards
Reusable Packaging Association (Booth SU-8000)
The Tube Council of North Ameria WestRock (Booth C-2023)
World Packaging Organisation (Booth C-1246)
In a competition sponsored by the In-Mold Decorating Association, label supplier MCC Verstraete and molder Jokey Group were honored with the Best In-Mold Label Award for an interactive in-mold label with a digital watermark. Designed for De Dames van Akkkerlust, a new ice cream brand, the intelligent feature adds value in the packaging journey—from tracking and authenticating products to boosting customer engagement to digitally sorting the package for recycling. The sustainable packaging is designed to reflect the nature of the ice cream, which is made on a sustainable farm from 100% organic milk.
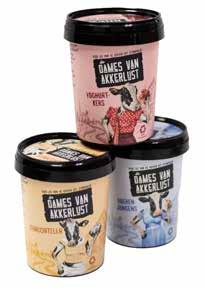
The Best of Show Award in the 2023 AmeriStar competition, sponsored by the Institute of Packaging Professionals, revolutionizes single-use packaging with a focus on sustainability and consumer satisfaction. Annie’s certified industrially-ompostable molded fiber cup offers functionality equal to a plastic thermoform and broadens the use of molded fiber into shelf-stable products. The packaging offers a 45% reduction in carbon footprint and is direct-printed via a flexographic process. A spray coating made from a renewable formula offers grease and water protection. Improved convenience and warmth retention enhance the consumer experience. The package also won an AmeriStar Award in the Sustainable Packaging category.
The top prize in the Dow Packaging Innovation Awards, the Diamond Award, went to Procter & Gamble for its G ECOCLIC® box for liquid laundry capsules. The patent-pending cardboard packaging scores for sustainability and child safety. The carton consists of FSC-certified materials with a minimum of 70% recycled fibers, and its dimensions and design fit 50% more packs per pallet. The certified child-resistant design also is easy to open even for people with dexterity limitations and sight or cognitive impairments. A reassuringly loud ‘one click’ closure signals the pack is closed.
IMA creates eCommerce division
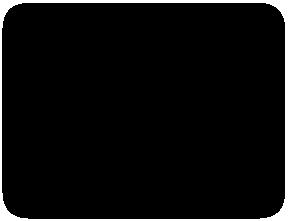
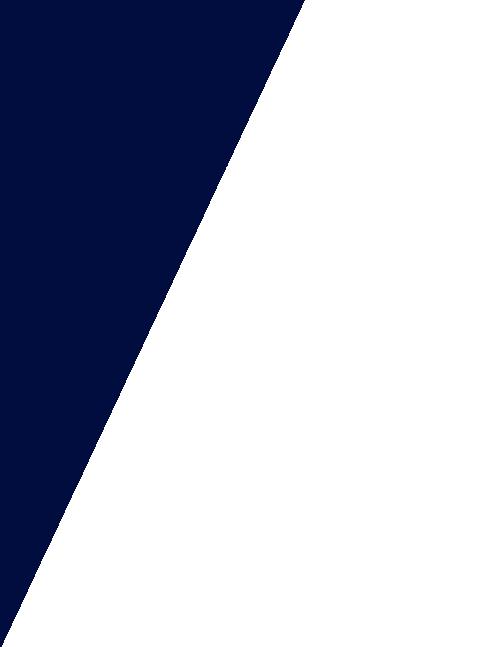





E-CO Flex machine right-sizes boxes, conserves corrugated.
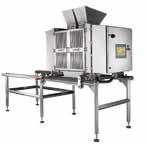


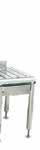









Anew division established by the parent company of IMA NorthAmerica (Booth C-3200, C-3400) serves the increasing demand for online shopping with technologies to automate the packaging process.
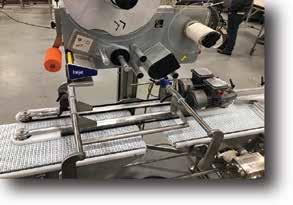
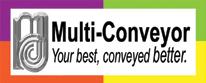





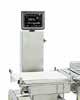

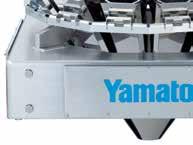
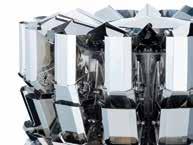




The first model in the IMA E-COMMERCE line, the E-CO Flex machine, simplifies e-fulfillment packaging by connecting to the end user’s warehouse management system and selecting the best fit-to-size box for the products to be packed.
Once the most suitable box is identified, the blank is automatically picked from the magazine, erected and bottom-sealed using water-activated tape. Tape is applied on an integrated, proprietary water-activated tape dispenser from Intertape Polymer Group, which serves as the exclusive distributor of the E-CO Flex machine in the U.S. and Canada.
The pre-assembled container is presented to the operator, who simply inserts the items to be shipped and secures them with the required amount of dunnage. The operator reinserts the open-faced box into the machine where the remaining void is measured. If necessary, the E-CO Flex machine is capable of automatically reducing the height of the box and then closing it, adapting flap-folding to the new box dimensions.
Automated packaging solutions, such as the E-CO Flex machine with right-sizing capabilities, allow e-tailers to combine multiple stations into one unit. By reducing the cubic footage of cases to a minimum, dimensional (DIM) weight pricing can be safely implemented, resulting in reduced material usage. This can reduce corrugate consumption while eliminating the need for void fill in compliance with the latest sustainability policies adopted by IMA Group.
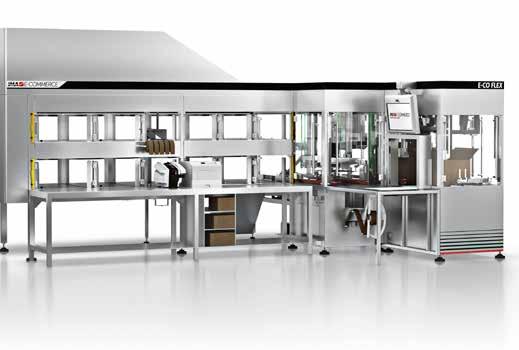
For more info, visit ima.it. SD
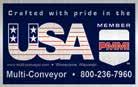
Editor’s Note: The original version of this article was posted on March 20, 2023 by Packaging World.





Industry Speaks Stage features PACK EXPO Partners
Anewcomer to the free educational programming at PACK EXPO, the Industry Speaks Stage (Booth C-1141), located in the Central Hall, draws experts from the PACK EXPO Partner Program, which includes various technical and industry groups.
The 30-min. presentations focus on topics such as automation, standards, developments in high-pressure processing, sustainability, flexible packaging, contract manufacturing/packaging, warehouse automation, in-mold labeling/ decorating, metallic labels/cartons, automatic identification and data capture, beverages and snack food.
THE PACKAGING POLICY PRECIPICE— CHALLENGES
OR OPPORTUNITIES
10:30-11:00 AM
The U.S. remains at a critical precipice on packaging and environment policy with significant new laws continuing to be passed and implemented on packaging producer responsibility, labeling, recycled-content mandates and more. Join a fast-paced discussion about what’s happening and how to engage with the ensuing challenges and opportunities.
Dan Felton Exec Dir AMERIPENSession descriptions, times and locations are listed below. Updated schedules may be found on the show website or via the show App, sponsored by ProMach (Booth C-3222)
Other free educational opportunities on the show floor include the new Sustainability Stage (Booth N-9967) (see schedule, p. 16), the Innovation Stage (Booths C-2051, C-2058, C-2151)/Processing Innovation Stage (Booth N-10511) (see schedule, p. 30), plus The Forum — An Industry Knowledge Exchange (Booth C-2158) (see schedule, p. 58). Schedule as of August 23, 2023.
For more info, visit packexpolasvegas.com. SD
WEDNESDAY, SEPTEMBER 13, 2023
SUSTAINABILITY INTO PACKAGING AND PROCESSING MACHINERY
11:30-12:00 PM
Examine the global and regional perspectives of sustainability and circular design, showcasing initiatives, programs, regulations and roadmaps from Italian packaging machinery manufacturers.
Riccardo Cavanna
Pres
UCIMA - Italian Packaging Machinery Manufacturers’ Association
PMMI adds 47 members
all are exhibiting at PACK EXPO Las Vegas.
PMMI, The Association for Packaging and Processing Technologies (Central Lobby), continues to grow, with the acceptance of 47 new members at its Spring Board of Directors Meeting. The ongoing expansion of PMMI’s membership reflects the trust and confidence that packaging and processing companies have in the association’s resources, networking opportunities and industry expertise.
NEW GENERAL MEMBERS
Advanced Equipment (Booth N-10537)
AGC Heat Transfer (Booth N-10516)
American-Newlong (Booth SU-8046)
CMES Robotics (Booth N-9925)
DCC Automation (Booth SL-6269)
Dispac
Husky Technologies
Kinematics & Controls
Material Transfer and Storage (Booth N-10546)
Matiss (Booth SL-5869)
MXD Process (Booth N-10530)
Pennsylvania Scale (Booth SU-8275)
PSnC/Avanti (Booth SL-6669)
Robotiq (Booth SL-6870)
Silgan
Tronics America (Booth N-9709)
Vecoplan (Booth SU-8281)
WHAT CAN THE ISBT OFFER THE BEVERAGE INDUSTRY PROFESSIONAL?
12:30-1:00 PM
The vision of the International Society of Beverage Technologies (ISBT) is to be the premier global beverage industry technical association, which drives sustainable growth, resolves challenges and leads productivity innovations. ISBT offers the global industry a platform to network and help the industry thrive. Come learn what this 75-year-old society offers its members and their companies in a global format.
Ron PuvakMktg Committee Chair
Int’l Society of Beverage Technologists SD
“We are thrilled to welcome these new members to our community,” says Andrew Dougherty, vice president of Member Services at PMMI. “As the industry continues to evolve and grow rapidly, so does PMMI. And we remain committed to providing the resources our members need to thrive and succeed.” Newcomers include General, Associate, Affiliated Supplier, Component Supplier and Material Supplier members.
NEW ASSOCIATE MEMBERS
American Sleeve Technology (Booth C-5530)
Bairespack USA
Boix Machinery USA (Booth SU-7280)
Canon USA (Booth N-9736)
Elopak (Booth N-9359)
Epson America (Booth SL-6664)
INNOVA GROUP (Booth SL-5903)
Keyence Corporation of America (Booth N-9745)
Sanko Kikai (Booth SL-6550)
Tecma Aries America (Booth SU-7448)
NEW AFFILIATED SUPPLIER MEMBERS
BEXP USA (Booth SL-6529)
Holt Logistics
Mingo (Booth SU-8450)
New Age Industrial (Booth N-9441, SL-6830)
NorthWind Technical Services (Booth N-10733)
POWER Engineers (Booth SU-7236)
SafetyChain Software (Booth N-10451)
Sigma Robotics
Sneed Coding Solutions (Booth N-9530)
NEW COMPONENT SUPPLIER MEMBERS
Bihl + Wiedemann (Booth SL-6029)
nVent - Hoffman
SEW-EURODRIVE (Booth N-10371, N-10453)
VtecUSA (Booth SL-6848)
NEW MATERIAL SUPPLIER MEMBERS
Chicago Tag & Label (Booth N-9817)
ePac Flexibles
Industrias Tuk / HyStik (Booth SL-6463)
Jadex (Booth SL-6835)
Metsä Board (Booth N-9216)
TigerPress (Booth N-9844)
Vibac Americas (Booth N-11231)
For more info, visit pmmi.org. SD
Nearly
NEVER BEEN SO EASY
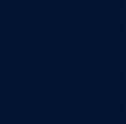

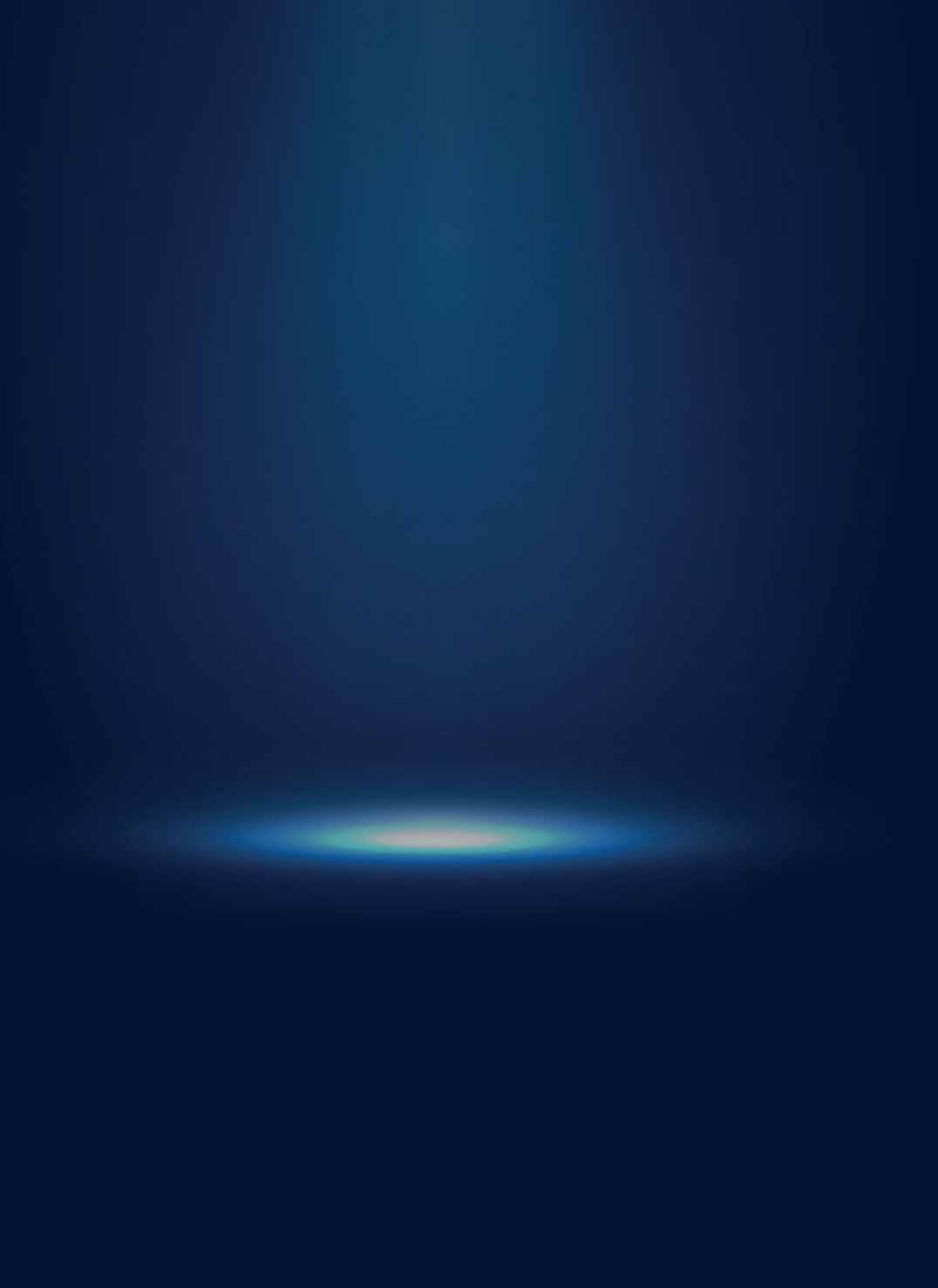
SEE US AT BOOTH SU-7412
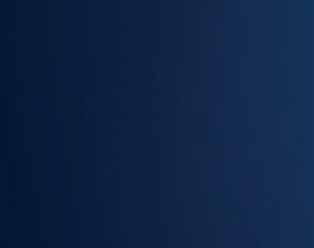

TOTALLY AMERICAN WITH AN ITALIAN HEART
Ronchi America proudly presents the SIRIO/S capper, built in Atlanta, GA. This SIRIO/S capper includes all of the Ronchi features and is FAT ready within 12 weeks or less. The SIRIO/S capper is also capable of being synchronized with the US built Ronchi EXACTA/R 18 filler.
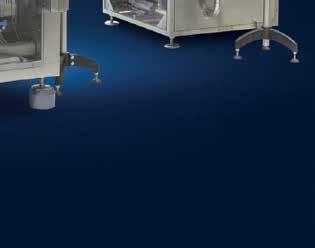
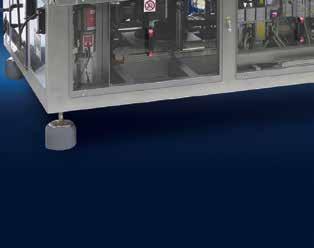




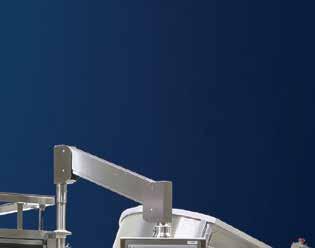

Integrated systems run on show floor
Tabletop vertical form/fill/seal machine debuts.
Demonstrations at Paxiom Automation (Booth C-5006) include integrated systems for filling cannabis flower and edibles, packaging vitamin gummies, and horizontal flow wrapping using equipment from subsidiaries, WeighPack Systems, ValTara and Canapa Solutions. Attendees also may view WeighPack’s newest VersaPak™ vertical form/fill/seal (V/F/F/S) machine.
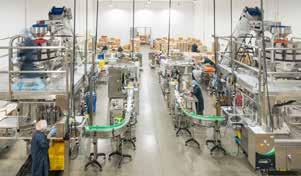
The line from Canapa by Paxiom, a specialist in cannabis packaging systems, fills flowers or edibles into jars. This turnkey operation includes the NTEP-certified PrimoCombi weigh filler, NTEP-certified Pre-CheQ weight analyzer, jar filling conveyor, KAPR rotary chuck style capper, LBLR adhesive label applicator and automatic unscrambling and accumulation rotary tables.
third party traceability software. Simple, compact and easy to use with intuitive controls and a streamlined interface, operators quickly become proficient, reducing training time and maximizing productivity.
Vitamin gummies are being packaged on a PrimoCombi® count-by-weight filler from WeighPack integrated with a high speed SpinDexer® rotary bottle filler. The integrated system can accommodate gelatin or pectin gummies as well as sanded, sugared, oiled and waxed formats. The filler design allows for sticky gummies to be filled into narrow-neck containers by eliminating bridging and ensuring optimal bottle transfer from each traveling funnel.
The SpinDexer rotary bottle filler is available in several models including its base model, rated at up to 60 bottles/min., its HS model for high-speed applications up to 150 bottles/min. and its XL model for large-format club sizes.
In the PKR™-Scara robot demo, the robot picks and places products directly onto the SleekWrapper F65 horizontal flow wrapper. Offering an immediate ROI, this pick-and-place system replaces up to three people hand loading.
The PKR-Scara robot can be integrated into any new SleekWrapper from ValTara or any third-party flow-wrapping machine in the field or in-house. Standard features include integrated infeed and out-
feed conveyors, robust stainless-steel frame and easyto-program parameters with recipe recall. The robot, vision guidance and PLC controls with color touchscreen are based on technology from OMRON.
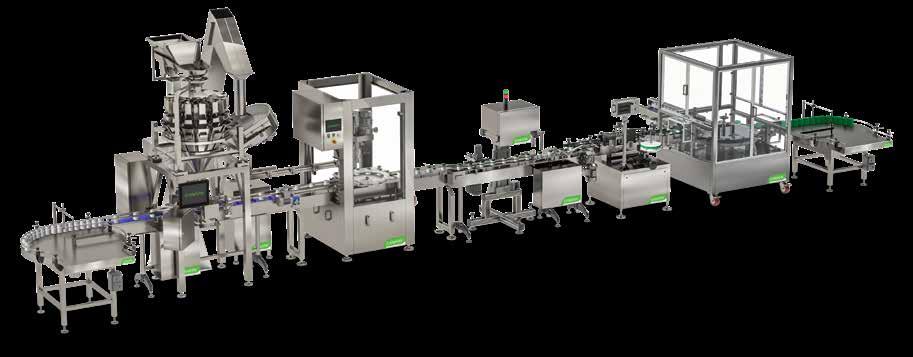
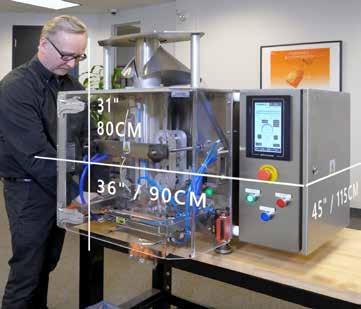
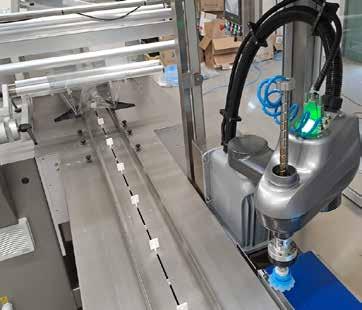
Engineered to fill grams, eighths and ounces, this system features complete stainless-steel construction, includes free online support via digital cameras and a full production suite of reporting that integrates with
An OMRON PLC also controls WeighPack’s newest and most compact VersaPak™ V/F/F/S machine. With its small footprint, the unit can sit on a tabletop or floor stand and is well-suited for businesses with limited space as well as schools, hospitals, kitchens and homes. Easily integrated into existing packaging processes, the automatic bagging system uses non-proprietary rollstock. Producing up to 20 packages/min., the VersaPak machine can fill pouches from 2–8 in. (50–200mm) wide. Standard features include large color touchscreen, bag-forming collar with tube, recipe recall and automatic bag length adjustment. Applications include eCommerce, hardware, food and home goods.
For more info, visit paxiom.com, canapasolutions.com, valtaratec.com, weighpack.com. SD
ATS serves dairy and food industries
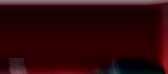
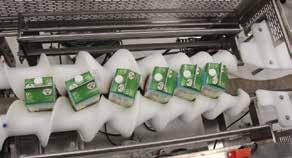
Anthony Subryan, general manager and CEO at Brampton, Ontario-based ATS Engineering (Booth SL-6238), talks with the PACK EXPO Show Daily (SD) about the state of the industry and what drives his company to excel at designing and manufacturing packaging machinery.
SD: What is impacting the industry today?
Subryan: The pace of packaging and product development has increased to a level never seen before in the food and dairy industry. New filling technology is being driven by the variety of new styles of containers that our customers are bringing to market. To be more competitive and stand out on the shelf, the variation of container shapes being produced keeps changing. This drives us to continuously innovate in order to fill, seal and overcap these unique container geometries in the most efficient manner possible. ATS Engineering has a long history of innovation in building filling machines for our dairy customers.
SD: How important is flexibility?
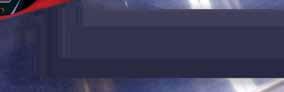
Subryan: In addition to designing for innovative new packaging, the machinery we build needs to be flexible. When a customer runs an assortment of containers, the machinery needs to have a fast and efficient changeover system. ATS has always designed this into every machine. Uptime is critical, so
less time spent swapping parts and preparing for the next product is extremely valuable.
The speed and efficiency of our fillers is paramount. By keeping downtime to an absolute minimum, our customers get maximum throughput. Speed is not the only thing that maximizes production. Customers are always aiming for the greatest efficiencies on their plant floors, so having a machine that is adaptable to a number of container styles and/ or product variations is the best investment for them.
SD: How does ATS address the need for hygienic equipment?
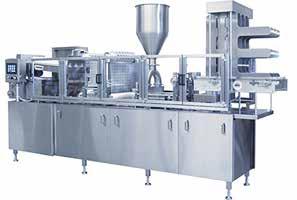


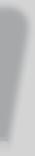
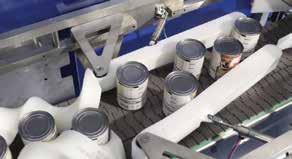
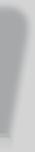
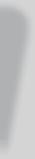
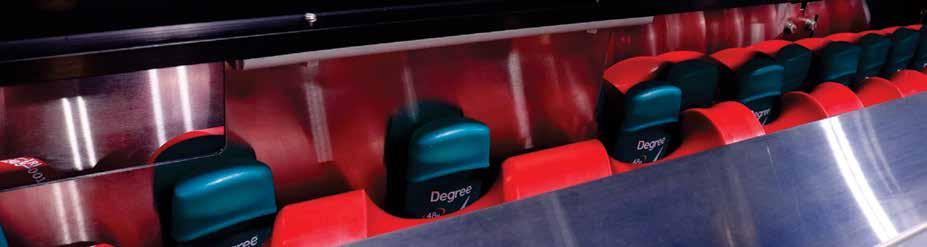
Subryan: One of ATS’ key goals as a machinery manufacturer is to design fillers that have no place for bacteria to hide when the machines are properly washed down and sanitized. This is achieved with the highest-quality grades of stainless steel, as well as all electrical and electronic components, to ensure that everything mechanical and electrical on our machines can operate without failure in these kinds of harsh sanitizing conditions.
Every ATS machine exceeds USDA, FDA and 3-A Sanitary Standards.
Flexible Automation TO IMPROVE YOUR THROUGHPUT SOLUTIONS




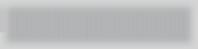

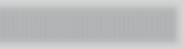
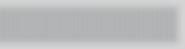
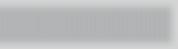

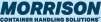
SD: How does ATS collaborate with customers?
Subryan: Working closely with customers from the start of each machine’s design has helped ATS design the optimal systems for clients’ facilities and budgets. No matter what the next development in dairy packaging is, ATS will be there, developing high-speed, flexible machinery that delivers superb results for our customers.
For more info, visit atseng.ca. SD
Product portfolio includes fillers, sealers and overcappers.Hygienic rotary and straight-line machines fill liquid or viscous food products, seal containers and then apply overcaps.
Tetra Pak works toward circularity
Recycling efforts send fewer cartons to
Prior to Earth Day 2023, Tetra Pak (Booth C-4340) unveiled recycling initiatives that are helping to turn all components of a used carton package into quality materials and goods. These initiatives are part of the investments the
landfill.
company has been making for decades to support collection and recycling infrastructure across the world and grow the number of recycling operations handling cartons worldwide from 40 in 2010 to more than 200 today.
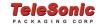

According to the World Bank, global waste will increase 70% by 2050, unless immediate and significant action is taken. Despite its essential role in feeding a growing global population, food packaging can add to the issue if not properly collected and recycled. Tetra Pak’s recent collaborations are focused on creating recycling capacity, increasing collection rates and ensuring that materials from post-consumer beverage cartons can re-enter the economy.
Markus Pfanner, vice president Sustainability Operations at Tetra Pak, emphasizes that building a circular economy requires system-wide action and cooperation, supported by a regulatory framework that creates the conditions to turn challenges into opportunities. “We need to move away from a linear ‘take-make-waste’ model toward a more connected circular economy,” Pfanner comments. “But being part of a circular solution can’t be driven single-handedly by one individual or entity. Scientists, policy makers, recyclers and industry players and citizens must work together.”
Thank
Academic scholarships to students pursuing careers in the industry.

Summer Manufacturing Camps
To educate and inspire the future manufacturing workforce.
Financial assistance for educational programs
such as FIRST robotics teams and curriculum development at local colleges and universities.
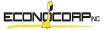

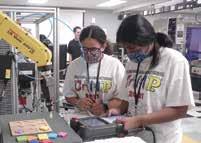

and more…
In 2022, Tetra Pak invested nearly €30 million ($33.3 million) into projects worldwide, with plans to invest up to €40 million ($44.5 million) annually in coming years. As part of the Alliance for Beverage Cartons and the Environment, the company supports the industry ambition to increase the collection of beverage cartons for recycling to 90% and the recycling rate to 70% in the E.U. by 2030.
The company’s goals also include realizing the national recyclability criteria for its packages in all countries where it operates and fulfilling the Ellen MacArthur Foundation’s Global Commitment, a common vision of a circular economy for plastics.


“Three principles are guiding our circularity agenda: designing out waste and pollution; keeping products and materials in use; and regenerating natural systems,” adds Christine Levêque, vice president Collection and Recycling at Tetra Pak. “These initiatives showcase how innovation and a clear drive to change the status quo are key to keeping quality materials in circulation and minimizing the use of new ones. None of these developments could be realized without our 70 experts around the globe, who are collaborating every day with recyclers, local authorities and food and beverage manufacturers to drive the transformation needed to scale up collection and recycling.”
For more info, visit tetrapak.com. SD
Editor’s Note: The original version of this article was posted by Packaging World on April 5, 2023.
According to the World Bank, global waste will increase 70% by 2050, unless immediate and significant action is taken.
Lenze sponsors lounges
Once again, Lenze Americas (Booth C-4803) is sponsoring lounges for exhibitors and PMMI members at PACK EXPO Las Vegas. The lounges provide meeting space, seating, refreshments and a chance to take a break away from the busy show floor.
The Exhibitor Lounges are located in rooms S-215 and N-114. The two PMMI Member Lounges are located in rooms S-222 and N-101.
“Lenze Americas understands the significance of providing members and exhibitors with a dedicated space to rejuvenate amidst networking with attend ees at their booths. We take pride in our continued sponsorship of these lounges this year,” says Paul O’Connor, Lenze Americas.
“We are grateful to Lenze Americas for support ing this resource again,” says Jim Pittas, president & CEO, Processing Technologies (Central Lobby) nizer of the PACK EXPO family of trade shows.
Future Innovators
SHOWCASE
Students demo self-built robots
Robotics teams from Las Vegas-area high schools are demonstrating the robots they have built along with design, engineering, assembly and troubleshooting skills at The Future Innovators - Robotics Showcase (Booth N-9769), sponsored by Bastian Solutions (Booth N-10343)
Come see Vegas-area high school students showcase their “bot skills”. Interact with the bright minds of the future and ask questions about their innovative robot designs.
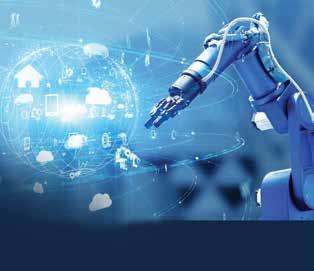
He explains, “This year’s industry growth and numerous new features at PACK EXPO Las Vegas will make the show floor incredibly busy. As a result, these lounges will be highly sought after by exhibitors and PMMI members as a valuable space to relax and network.”
The respite space will be especially welcome this year as the PACK EXPO Las Vegas show floor is expected to be extra busy with 30,000 attendees touring nearly 1 million sq. ft. of floor space to visit more than 2,300 exhibitors.
For more info, visit packexpolasvegas.com, lenze.com. SD
MetsäBoard Pro FBB Bright is up to 35% lighter than conventional paperboards, while retaining the same quality and rigidity.
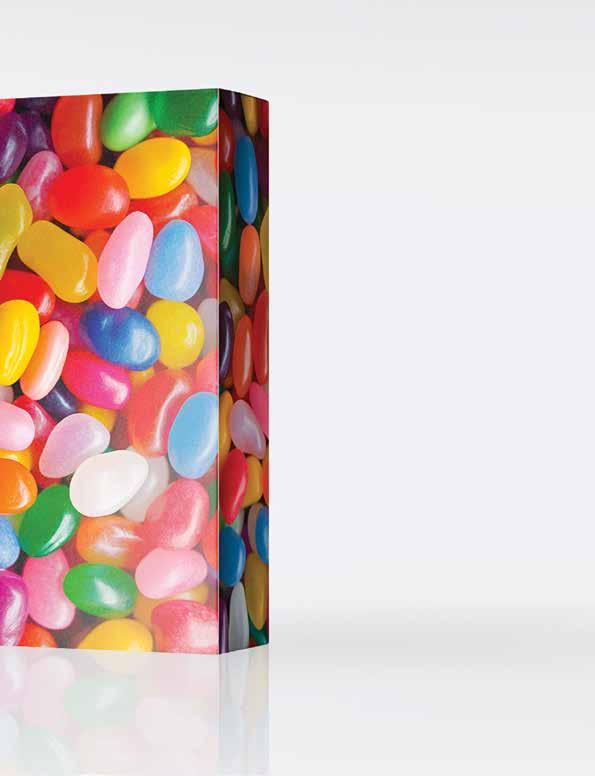
Located in the North Hall in Booth N-9769
Monday - Tuesday | 9:00 am - 5:00 pm
Wednesday | 9:00 am - 3:00 pm
Demos are scheduled throughout each day of the show. Stop by to see what these teams have built, watch their robot in action, ask questions and tell the students about career opportunities in manufacturing and engineering.
This annual event is designed to open doors for a new generation of packaging professionals and encourage participation in STEM studies. It’s one of many student-based activities at PACK EXPO Las Vegas, which also includes the winners of the 2022 PACK Challenge (Booth N-9026) from Waterford Union High School and the Amazing Packaging Race, which is sponsored by Emerson Discrete Automation (Booth SL-6107) and occurs on the final day of the show.
For more information about supporting student programs, visit the PMMI U booth at N-9000.
Produced by:
For more info, visit packexpolasvegas.com, bastiansolutions.com, emerson.com/en-us/industries/automation/ food-beverage. SD
THE ‘BOTS ARE TAKING OVER PACK EXPO Las Vegas!
Innovation Stages offer free educational sessions
The always-popular Innovation Stage program returns to PACK EXPO Las Vegas with four platforms: the Processing Innovation Stage (Booth N-10511) in the North Hall, plus three Innovation Stages (Booth C-2051, C-2058, C-2151) in the Central Hall. Exhibitors and subject matter experts will present more than 60, 30-min. sessions about the latest technology breakthroughs and best practices.
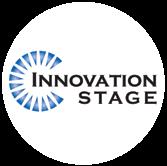
Topics range from automation, digitalization, artificial intelligence (AI) and cybersecurity to food
LEVERAGING DATA TO ENABLE CRITICAL SUPPORT FROM YOUR OEM
10:00–10:30 AM
Innovation Stage 2 | C-2151
In today’s challenging environment, it is becoming critical to leverage your OEMs for your operational success. How do we capture, organize and make data available outside manufacturing equipment to enable this much-needed support from machine builders? Let’s start with the basics: data-ready machines supporting performance management.
Steve MulderAmericas OEM Mgr
Rockwell Automation
HIGH-BARRIER RETORTABLE POLYPROPYLENE SOLUTIONS
10:00–10:30 AM
Innovation Stage 3 | C-2058
“Monomaterial packaging” is one of the buzzwords in the flexible packaging industry, since current multi-material packaging is not easy to recycle. PP GL Barrier film is a key component to make recyclable retort pouches.
Chris WardVP, Toppan Packaging Innovation Ctr


Toppan Group
THE JOURNEY TOWARD SUSTAINABLE PACKAGING WITH ONEBARRIER
10:00–10:30 AM
Processing Innovation Stage | N-10511
The journey toward sustainable packaging progresses with oneBARRIER monomaterials, a family of recyclable polymer- or paper-based substrates.
Chris Marshall Area Sales Mgr BOBSTsafety, workforce challenges, sustainability and technology innovations. Highlights include sessions by WestRock (Booth C-2023) (sustainability), Syntegon Packaging Technology (Booth C-2800) (gloveless fill/finish), Siemens Digital Industries (Booth SL-6351) (digital twins), Delkor Systems (Booth C-3840) (robots), Soft Robotics (Booth N-10311) (AI-enabled food picking) and Metsä Board (Booth N-9216) (zero-waste packaging). Session descriptions, times and locations are listed on the following pages. Updated schedules may be
WEDNESDAY, SEPTEMBER 13, 2023
AI IS TRENDING, BUT FIRST YOU NEED GOOD DATA
10:30–11:00 AM
Innovation Stage 1 | C-2051
Before packaging operators look to artificial intelligence or machine learning to solve their most pressing problems, they need a strong product and packaging data foundation through digitized specifications.
Matthew Wright CEO & Founder Specright PACKAGING SUSTAINABILITY INTO YOUR LINE EFFICIENCY
11:00–11:30 AM
Innovation Stage 2 | C-2151
Industrial digital transformation enables new approaches to efficiency. Whereas traditional approaches break out production efficiency (measured in OEE) from energy management key performance indicators, a sustainability-oriented OEE integrates the two. Currently being tested, this approach offers significant promise in driving decarbonization.
Miguel Najerafound on the show website or via the show App, sponsored by ProMach (Booth C-3222).
Other free educational opportunities on the show floor include the new Sustainability Stage (Booth N-9967) (see schedule, p. 16), the new Industry Speaks Stage (Booth C-1141) (see schedule, p. 24) and another popular standby, The Forum—An Industry Knowledge Exchange (Booth C-2158) (see schedule, p. 58).
Schedule as of August 23, 2023.
For more info, visit packexpolasvegas.com. SD
WAREHOUSE AUTOMATION 2024 TRENDS AND INNOVATION
11:00–11:30 AM
Processing Innovation Stage | N-10511
2024 will be the year automation comes into its own. Warehouses are ready, the technology is falling into place, and all that’s left is for you to jump in and start benefiting. But, before making any investment, it’s good to know where we are today, and what’s coming.
Sriram Sridhar Chief Revenue OfficerAddverb
SUSTAINABILITY — WHAT DOES IT MEAN IN PACKAGING MATERIALS?
11:30–12:00 PM
Innovation Stage 1 | C-2051
Sustainability continues to be a hot topic. Understanding how materials can affect the sustainability curve is challenging and requires a holistic approach. Hear about new developments and improvements of materials specific to thermoforming and tray-sealed package design for food.
VP,
CPG Schneider ElectricTRANSPORT SYSTEMS EVOLVE, TAKE ON PICK-AND-PLACE FUNCTIONS
11:00–11:30 AM
Innovation Stage 3 | C-2058
An entirely new way to think about robotics relies on intelligent linear transport systems. Wireless movers can be equipped with powered end effectors that result in a low-profile, flat multi-robot system that’s fully embedded into packaging machinery instead of attached as a separate, standalone robot module.
Jeff JohnsonU.S. Mechatronics Product Mgr Beckhoff Automation
Gregg Poffenbarger
Business Unit Dir - Materials
Multivac
PACKAGING DESIGN AND QUALIFICATION FOR A CIRCULAR ECONOMY
12:00–12:30 PM
Innovation Stage 3 | C-2058
Address the impact consumer demand for sustainable products has had on CPG and retail. Get your roadmap to use Virtual Twin technology to accelerate sustainable and profitable packaging models to plan the circular logistical journey to develop and qualify packaging of the future.
Raymond WodarGlobal Dir, Business Consulting, CPG & Retail Industry
Dassault Systèmes

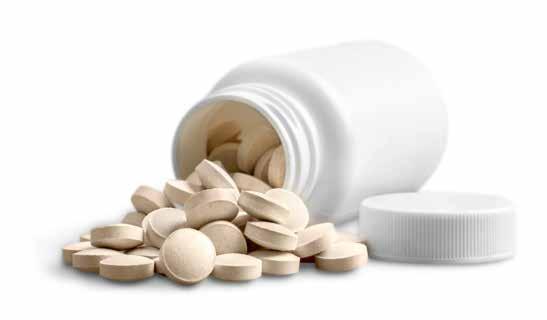
Wednesday, Sept. 13
THE PARTICIPANTS
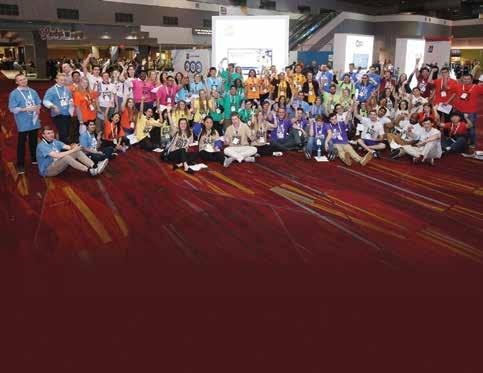
Packaging and engineering students from across the country.
THE MISSION
Tour the PACK EXPO show floor, visit participating exhibitor booths and complete challenges.
THE GOAL
Learn about new technologies and interact with industry professionals, while earning points for packaging-related challenges. Members of the winning teams will receive cash prizes, courtesy of Emerson.
Brought to you by:
Sponsored by:
SEPTEMBER 13, 2023
WEDNESDAY, SEPTEMBER 13, 2023 (CONT’D)
DIGITAL READINESS: HOW TO UTILIZE THE RIGHT TECHNOLOGY
12:00–12:30 PM
Processing Innovation Stage | N-10511

The food and beverage industry has shifted focus to Cloud-based software. This shift has delivered decisive benefits as roughly 75% of food and beverage companies have seen key performance indicator improvements. Digital readiness is essential.
Jack Payne Solution Consulting Dir, Food & BeverageAptean
REDESIGN. REPURPOSE. REVOLUTIONIZE: INNOVATIONS FOR ZERO-WASTE PACKAGING
12:30–1:00 PM
Innovation Stage 1 | C-2051

The circular economy will soon guide all consumption. As the need for packaging grows, we must use design for easy recycling or purposeful re-use. Learn from winners in this year’s Better With Less—Design Challenge.
Nathan Pajka Sustainability Mgr Metsä Board SDBulk printhead prints wider areas
Preview the new high-speed HP 108mm bulk printhead at a demo at HP (Booth N-10054). Built to meet the future needs for coding and marking on secondary and latestage packaging, HP’s continued innovation of thermal inkjet (TIJ) technology is enabling highspeed, high-resolution print on wider swaths without the need for stitching, making production lines run seamlessly, faster and more efficiently.
Booth SL-6107
For more information, visit pmmi.org/pmmiu-packexpo
HP is showcasing its upcoming 108mm bulk printhead with Smart Servicing Solution that mitigates decap for optimal performance and uptime, which is ideal to address labor shortage issues. Bulk systems also significantly lower ink costs.

This innovative technology for TIJ not only allows companies to shift away from having to apply labels on packaging but also reduces cost and streamlines the production line by direct printing the outside of the case.

The HP 108mm bulk printhead also helps companies meet the ever-growing demands from consumers and regulators for greater sustainability by using water-based ink for low environmental impact and improved recyclability.
For HP Partners, the HP enabler kit ensures easy, hassle-free integration of the HP 108mm printhead.
For more info, visit hp.com/thermalinkjet. SD
Heat and Control expands globally
New operations open in South Africa and Mexico.
To support customers in Africa, Mexico and Latin America, trol (Booth C-1623) has set up operations in South Africa and Mexico. With a long-established customer base in Africa, the new office in the Stikland, Bellville area of Cape Town, South Africa, confirms its commitment to the region and its customers in Africa, which include small, local food manufac turers as well as larger multinational companies.
Heat and Control South Africa designs, manufactures and supplies equip ment for a vast range of food-processing operations and represents industry partners such as Ishida, Ceia, Key Technology (Booth C-4225) Laboratories (Booth N-10241) in Africa.
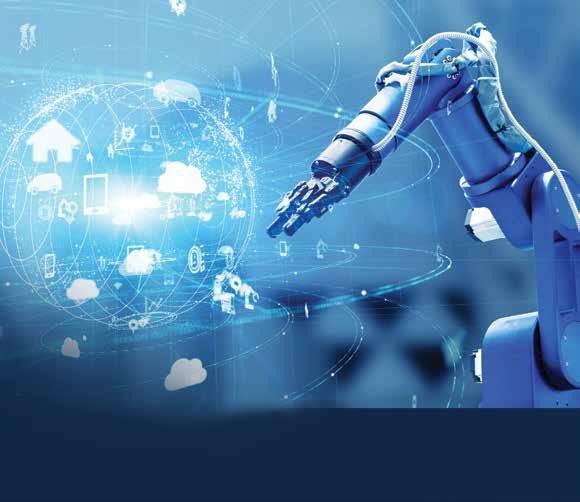
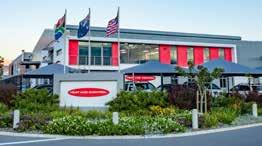
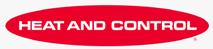
The equipment helps end users achieve higher capacity, lower production costs, greater efficiency and improved product quality. Applications include value-added products such as meat, seafood, poultry, meat-alternative products, ready meals, fruits and vegetables, cereals and pet foods.
“In the last five years, we’ve expanded our personnel in this region by 50%, and we have a direct presence in Nairobi, Kenya, as well,” reports Heat and Control GM (Africa) Jeff Rossouw.
Heat and Control’s new location in Jalisco, Mexico, serves as the headquarters for its operations in Mexico and Latin America and significantly expands the company’s ability to serve new and existing customers.
The total operational size of 356,651 sq. ft. includes offices, a warehouse, manufacturing, R&D and demonstration center. The manufacturing and warehouse (M&W) footprint of 240,896 sq. ft. boosts Heat and Control’s global M&W warehouse capacity to more than 1 million sq. ft.
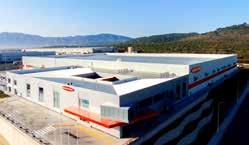
Food companies now can test Heat and Control equipment in a 38,793-sq.ft. demonstration center named in honor of founder Andy Caridis, who has been integral to the growth of the industry and operations in Mexico. The Centro Tecnico Andy Caridis includes access to inspection, packaging and six process production lines including Masa Maker, taco/tostada and other food equipment.
“This new facility will benefit Heat and Control globally, provide additional support to our customers, and further reinforce our commitment to serving the industry,” says Tony Caridis, president of Heat and Control.
The new facility will assist customers in adopting processing technology that helps to reach their environmental goals with proven systems that reduce fuel costs, energy waste and water consumption. The Heat and Control Mexico facility also features new manufacturing technologies, such as the latest material automation machinery with fiber laser for cutting flat and tube material, water jet cutting equipment, deburring machines and an 80-ft. powder coating processing booth.
For more info, visit heatandcontrol.com, key.net, urschel.com. SD
Monday - Tuesday | 9:00 am - 5:00 pm
Wednesday | 9:00 am - 3:00 pm For
Why automate bagging?
Avertical form/fill/seal (V/F/F/S) machine is a popular method to streamline bagging processes, boost efficiency and output and enhance flexibility.
These machines are widely used across various industries for their efficiency and cost-effectiveness. Furthermore, they’re designed to optimize packaging processes and make things work even within limited floor space.
The mechanism of a vertical packing machine is pretty straightforward. A large roll of film is formed into a bag shape. After that, the bag is filled with product and sealed. This is accomplished as the packaged goods move vertically. These machines offer exemplary production speeds, sealing 100+ bags/min.
These versatile machines can accommodate various products too, ranging from candies and crisps to milk, juice, detergent powder, nuts and other foods like oats.
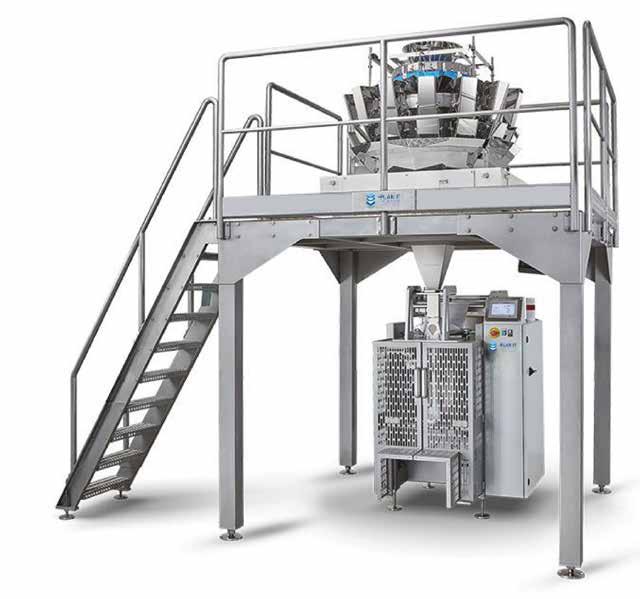
MACHINE CAPABILITIES
According to OEMs, V/F/F/S machines can run a wide range of materials, including:
• Aluminum foil
• Cellophane
• Composite film (laminated)
• Metallized film
• Paper
• Plastic laminate
• Polyethylene
• Polystyrene.
ADVANTAGES OF V/F/F/S
If you’re still unsure whether you need this machine, consider the following advantages:
Versatile Packaging Solutions: One of the most notable benefits of utilizing V/F/F/S machines is having access to a comprehensive packaging solution. This high-powered tool encompasses different processes—filling, sealing and packaging—and streamlines these processes to increase productivity.
With this shift, you save significant packaging time. Aside from that, V/F/F/S machines eliminate the need to purchase supplementary equipment like conveyors. You can use the money you saved from equipment purchases for other, more pressing, needs.
Labor Cost Reduction: V/F/F/S machines reduce manpower expenses. Since they are engineered to be operated by one or two individuals, it’s not necessary to hire multiple people to run your line. With production costs consistently decreasing and productivity increasing, profits will grow.
Improved Efficiency: V/F/F/S machines also contribute to the improvement and efficiency of the entire bagging process. These machines boast highspeed capabilities, enabling more products to be packaged within a shorter timeframe. Over time, an
accelerated packaging rate can be achieved, optimizing productivity and throughput.
Streamlined Manipulation: The user-friendly touchscreen enables swift selection of the desired weight and dimensions for the pouch, ensuring efficient customization within minutes.
Efficient Adaptability: Vertical bagging equipment from Plan IT Packaging (Booth SL-6175) incorporates a modular component, facilitating swift, hassle-free adjustments to accommodate various pouch sizes. Thus, the equipment enables effortless interchangeability between distinct bag sizes, eliminating the need for additional tools or equipment during the changeover process.
A PLETHORA OF APPLICATIONS
Modern V/F/F/S machines exhibit remarkable versatility, enabling effective implementation across diverse industries to meet unique production and packaging requirements.
Manufacturers in the following sectors recognize how V/F/F/S machines can optimize lines, especially when packaging high-volume products:
• Cheese and dairy
• Chemical and liquid
user-friendly operation, specialized models tailored to industry-specific needs and unmatched reliability.
Moreover, these dependable machines are frequently integrated with USB-based data systems, providing convenient storage options and facilitating analytics. It empowers manufacturers to monitor the performance of their machines and accurately assess bagging operations.
Furthermore, today’s V/F/F/S machines are equipped with an extensive array of customizations and specialized equipment, each tailored to meet the distinct requirements of specific industries. Thus, manufacturers with bagging operations can procure a V/F/F/S machine suited to their precise needs.
INVEST IN AUTOMATION
Beat your competitors by providing a seamless solution to your target market’s packaging and bagging needs. You can significantly save on manpower, overhead expenses and equipment purchases with an all-in-one V/F/F/S machine.
For more info, visit planitpackaging.com/. SD
Editor’s Note: The original version of this article appeared as a blog on the Plant IT Packaging web-
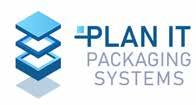
Form/fill/seal machines improve efficiency and flexibility.V/F/F/S machines handle a wide array of products and pack sizes, change over quickly, improve efficiency and lower labor costs.
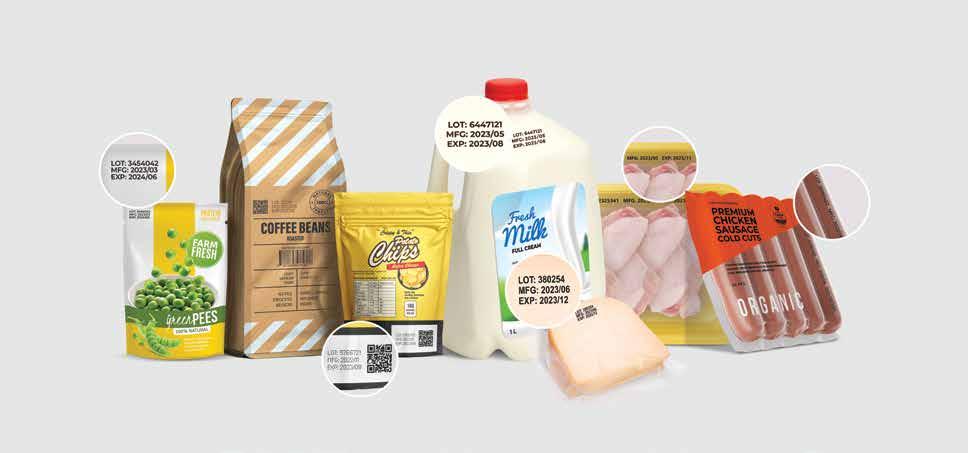

Automation spurs inspection needs
More automated systems raise the risk of contamination.
Food plants are accelerating their use of automation. Processors, seeking to enhance operating efficiencies while compensating for reductions in available labor, are leveraging more innovative technologies for functions ranging from washing, cutting and mixing to robotics and the packaging of final products.
While newer machine designs enable production of higher quality food products faster, this increase in automation also brings operating challenges and requires highly effective detection systems. Not only does the greater use of production technologies increase the probability of having machine components, such as bolts and brackets, fall into food during processing, but also smaller labor forces reduce the chances that workers will spot foreign matter in products or prevent incidents from occurring.
“The recent push for automation is replacing functions that are easy for humans to execute,” states Michael Ahern, national sales manager for Anritsu - Product Inspection and Detection (Booth SL-6163). “When once plant workers had to cut a food product by hand, there are now very sophisticated machines to perform this role.”
While such machines can be expensive, labor shortages are making the technologies more cost-effective. Further, inspection systems are becoming increasingly valuable by enabling detection of smaller objects while having a range of price points and capabilities to support processors of all sizes. That is important, as worker shortages, which were an issue before being exacerbated by the
pandemic, are likely to be ongoing.
“The pandemic will continue to spur the move toward automation because of the reluctance of plant employees to be working close together,” Ahern says. “That means there are fewer hands and eyes examining products. Automation is compensating for the lack of workers and to make sure labor is not the issue for not producing products.”
A SYSTEM FOR EVERY SITUATION
X-ray machines and metal detectors remain the two prevalent inspection technologies. X-ray devices transmit energy in the form of a short wavelength x-ray beam through the product. A detector on the opposing side measures the amount of absorption of the x-ray beam passing through to create a density graph of the product. Elements denser than the product, including metal, glass, calcified bone, stone and cement, show as dark spots. Objects similar in density to the product, such as wood, paper, fabrics and plastics, are difficult to detect.
“Metal is eight times denser than food or proteins, so it is very detectible,” Ahern states. “Glass is three to four times as dense, so it is not as easy to detect. Plastic, wood, hair nets and other low-density materials are not typically detectible.”
Metal detectors, on the other hand, have been used in food plants for decades and operation is based on a magnetic field within a tunnel. Metal objects within the field interfere with the magnetic field, indicating an unwanted inclusion. Performance of the metal detector varies depending on the size of the aperture and the product.
Metal detectors are commonplace within the food industry and offer economic benefits for the operator. While metal detectors do their job effectively, they have limitations on product type and packaging. In addition, operators are looking to find nonmetal contaminants, all of which makes x-ray technology more attractive.
Over the past 10 years there have been significant gains in x-ray technology. The launch of newer designs also is resulting in increasingly cost-efficient inspection systems, and that includes previous generation models that are dropping in price.
Modern x-ray systems can better detect less-dense contaminants, such as bone and glass, as well as plastics impregnated with x-ray-detectable materials. Ahern notes that the top-tier x-ray systems often can detect metals ranging in size between 0.5mm to 0.8mm and that performance level also proves that lower-density contaminants are detected at smaller sizes as well.
Nevertheless, he states that processors will benefit from using both x-ray and metal detectors on their lines, as “there still will be instances in which a metal
detector will find matter that an x-ray system cannot.” Such detection may include clusters of metal particles, which typically are too small for x-ray to locate, and thinner material, including aluminum foil.
There is a school of thought that x-ray devices are most effective when inspecting products that are uniform in size and shape, but evolving technologies are enabling processors to better detect foreign matter in non-uniform products as well.
He notes, for instance, that while it is easier to locate objects in food of consistent sizes lying flat on a conveyor belt, upgrades are enabling better inspection of various-size products that processors might randomly deposit on a line. Today, “We can deal with the natural variations of the production load and still find the contaminants,” reports Ahern.
DEVICE POSITIONING
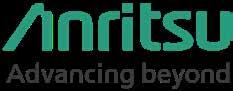
The optimal locations for inspection devices on processing lines, and the technologies that are most effective, can vary in accordance with such factors as: space availability; product temperature, as some devices are more effective on frozen food; and the size of the product undergoing inspection.
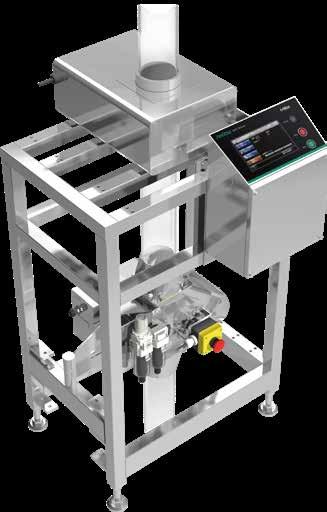
Equipment selection and placement also will differ in accordance with a processor’s inspection objectives and can include the use of multiple technologies in different sections of the processing line to support functions ranging from bulk inspection of raw ingredients to case inspection prior to palletizing. Earlier placement, however, can help prevent damage to processing equipment by enabling operators to detect dense matter before the objects have contact with processing machinery.
In addition, inspecting products at the head of the process can help ensure that larger objects are not reduced into smaller, harder-to-detect pieces, while endof-the-line inspection reduces the chance that foreign matter will elude monitoring.
“Placement becomes more critical when the primary goal is finding low-density contaminants like bones, glass or stones,” Ahern notes. “Often this dictates upstream placement where product thickness is low and consistent and creates more-ideal conditions for detecting the matter.”
X-ray inspection systems can consist of single- or dual-energy technologies. Single-energy x-ray is the traditional technology used by most facilities and excels at detecting metals, stone, glass and bones in
“The recent push for automation is replacing functions that are easy for humans to execute.”
—Michael Ahern Anritsu
certain applications. Dual energy is an upgrade in technology that uses two energy levels to identify the difference between organic and inorganic material and is better able to detect low-density matter such as glass, stone, rubber and bone.
Dual energy also can better “tune out” product effect when detecting foreign matter and is ideal for inspecting products consisting of layers and overlapping pieces. Product effect refers to food characteristics that can alter inspection device readings and cause false rejects.
MINIMIZING FALSE REJECTS
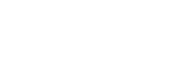
Because false reject readings often result in product waste and mistrust of the detection system, it is critical that processors leverage devices that minimize occurrences. Indeed, frequent false reject readings may cause operators to question whether an accurate positive reading is legitimate. False rejects not only cost money, but the plant’s quality department is more likely to say, “Here we go again” rather than “I have a reject, let me find out what it is,” Ahern explains. “It is important to minimize false rejects because you want everyone in the plant to trust the detection technology.”
Higher false reject rates are more likely to occur if the producer’s inspection goal is too close to the detection device’s performance limit. For instance, metal detectors are subject to performance changes based on product and plant temperatures. So, if the device is tuned to the edge of performance, they are subject to a high reject rate if the product temperature changes. “On the other hand, having performance headroom allows producers to run with much lower false reject rates and that is an advantage with x-ray technology,” says Ahern.
Such headroom is available with x-ray technology that can detect 0.6mm metal where the customer’s specification is 0.8mm. “Having a two-rank margin
against the specification will reduce false reject rates and that can have a dramatic financial upside when there is less interruption of high-speed lines that are processing high-value products,” he notes.
The technology evolution adds ease and efficiencies. Along with greater detection capabilities, x-ray
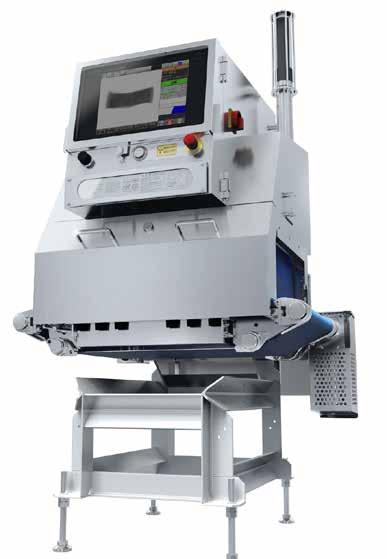
equipment and metal detectors are becoming easier for processors to implement. “The auto setup routine is more intuitive and no longer requires technical skills or the services of an electrician or engineer,” Ahern says. Indeed, operators typically perform simple functions such as inputting product information and the conveyor belt speed before running products through the devices multiple times to set the detection signal.
“Systems can be operating within a couple minutes,” he reports, adding that common user interfaces on equipment from a single supplier can reduce the need to train workers to use different technologies within a plant, including x-ray systems, metal detectors and checkweighers.
The inspection equipment itself is already mostly automatic and requires very little input from operators. The human/machine interfaces are becoming more usable and efficient by simplifying and speeding product setup and easing adjustments.
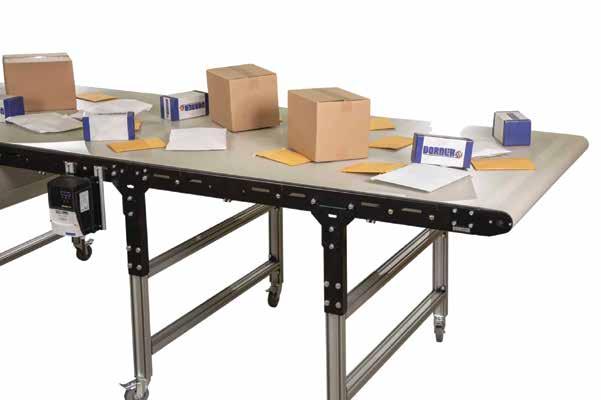
Inspection technologies, meanwhile, continue to evolve with advances to x-ray sensors set to provide even better detection of low-density contaminants, offering higher resolution imaging with more contrast. In addition, improvements to single-energy x-ray equipment are increasing efficiencies and reducing ownership costs.
Inspection technologies also are incorporating deep learning, a subset of machine learning that contains algorithms that are intended to work like the human brain to optimize detection.
“The goal is to find as many contaminants as are reasonable to find with x-ray systems,” concludes Ahern.
For more info, visit anritsu.com/infivis. SD
Editor’s Note: This article was written by Michael Ahern, national sales manager at Anritsu - Product Inspection and Detection.
CLAPS replaces robots
The high-growth intralogistics and packaging markets have developed an interesting overlap that experts in both industries have recognized for years. Once goods have been retrieved and picked to fulfill an order, orders are sorted and conveyed to the last 100 ft. of the warehouse where packaging, weighing and labeling occur before shipping—one of the critical final steps. Serving end users that operate in this crossover area takes knowledgeable equipment suppliers that are experts in both realms. One such supplier, United Sortation Solutions (USS), became a subsidiary of Honeywell Intelligrated (Booth C-1643) in 2016.
“Prior to the acquisition, USS was a preferred supplier to Honeywell Intelligrated’s Warehouse Automation Group, because we’re very agile and not afraid to design something completely new,” explains Eamon Kelly, an advanced mechanical design engineer at USS. “Whenever Honeywell Intelligrated ran into a situation in a distribution center where they needed highly specialized equipment to be delivered very cost-effectively, they would come to USS to collaborate.”

Now, as part of Honeywell’s Safety and Productivity Solutions (SPS) business, USS maintains its role as a solution center for internal and external customers by providing specialized designs for tough or unusual material-handling challenges. While USS typically works in tote-handling applications, often for the largest retailers in the world, the team there considers custom solutions as its core competency. Packaging equipment is just one of the custom solutions they can offer.
“Where many other suppliers have a set catalog and can only deliver the items listed, we are truly a bespoke engineering house,” says Evan Bassett, an advanced software engineer at USS. “That said, we also have a deep catalog of custom-designed equipment, so we sometimes adapt previous designs or create entirely new concepts to meet each customer’s unique requirements.”
MATERIAL HANDLING AND PACKAGING EXPERTISE COMBINED
A large manufacturer in the medical industry approached Honeywell Intelligrated in 2021 to automate its entire distribution center. The facility’s end of line required a highly customized machine to handle complex packaging requirements unique to their application. The customer needed extremely precise product and package handling that assured zero damage after its medical products left the manufacturing area. This part of the project went to USS for a custom machine design.
The application presented USS with a number of engineering challenges. The products are placed in trays, which are then stacked and inserted into plastic bags in a clean room. It’s critical that the bagged trays don’t overlap beyond a set point, which would likely lead to product damage. The customer previously used a six-axis robot cell to complete the process of inserting bagged trays into boxes, but the cell’s speed was too slow to keep up with the high rate of production upstream.
USS rapidly designed and built a custom solution for the application in approximately nine months. The resulting machine is now known as USS’s next-generation Case Loading and Packing System (CLAPS).
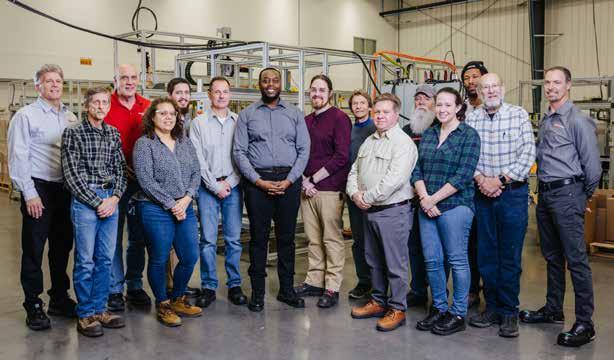
The new CLAPS replaces many functions previously handled by a robot. The machine receives erected and labeled boxes from upstream conveyance equipment as previously packed and tied bags of barcoded product await. CLAPS moves the boxes into position and places cardboard liners at the bottom. The machine then moves the boxes to the next position where bags of product are lifted and placed into the box via a patented gripping mechanism. Then another cardboard liner is inserted on top of the bagged products. While this is happening, barcode scanners simultaneously read box and product barcodes to record which products are packed in each box. After these processes are complete, the filled boxes are sent downstream for taping, final handling and fulfillment in the warehouse execution system (WES).
STANDARD AUTOMATION FOR CUSTOM MACHINES
For years, USS has standardized on a wide range of automation technologies from Beckhoff Automation (Booth SL-6335) for high-speed sortation and tote-handling equipment, especially the scalable CX series embedded PCs for machine control. This includes the high-powered CX2040 with quad-core Intel Core i7 processor, the mid-range CX5130 with dual-core Intel Atom processor and ultra-compact CX8190 embedded PCs. The CX8190 is a microcontroller that also can act as an EtherCAT input/ output (I/O) (or E-bus) gateway to other PLCs over various Ethernet protocols, offering an easy solution with the benefits of EtherCAT on other PLC platforms.
EtherCAT is the common denominator for all USS machines. In the case of the custom CLAPS machine, a CX8190 embedded PC communicates to all EtherCAT devices and uses EtherNet/IP to communicate with traditional PLC hardware for other functionality. EtherCAT I/O in IP20 and IP67 protection is distributed along the entire machine with I/O mounted inside and outside of electrical cabinets. “In our standard machine designs, we try to minimize the amount of wiring that gets home run back to I/O in the main panel,” Bassett says. “On a custom system like this, nearly all of the I/O is mounted directly on the machine to connect with sensors and other field devices. EtherCAT Box I/O lets us connect both input and output channels to a single module.”
Doug Schuchart, global material handling & intralogistics manager at Beckhoff, adds: “Distributed I/O significantly reduces installation time while adding improved equipment uptime with extended diagnostics and simplified maintenance. It also makes the equipment much more flexible for later expansion. ∆
Next-gen
EtherCAT-enabled equipment deploys rapidly.At the USS facility in Owings Mills, MD: Jay McNeil (left) and Doug Schuchart (right) of Beckhoff meet with the machine-building experts at USS. SOURCE: BECKHOFF
Many players, one team. www.syntegon.com
Many players, one team. www.syntegon.com
Many players working hard to ensure the productivity, safety, and sustainability of our machines are always at their best.
Many players working hard to ensure the productivity, safety, and sustainability of our machines are always at their best.
Many players, one team. www.syntegon.com
Many players working hard to ensure the productivity, safety, and sustainability of our machines are always at their best.
Many players working hard to ensure the productivity, safety, and sustainability of our machines are always at their best.
Many players working hard to ensure the productivity, safety, and sustainability of our machines are always at their best.
Many players working hard to ensure the productivity, safety, and sustainability of our machines are always at their best.
One team dedicated to providing exemplary service — every time.
Many players, one team. www.syntegon.com
Many players working hard to ensure the productivity, safety, and sustainability of our machines are always at their best.
See us in Booth C-2800!
See us in Booth C-2800!
See us in Booth C-2800!
See us in Booth C-2800!
See us in Booth C-2800!
See us in Booth C-2800!
See us in Booth C-2800!
One team dedicated to providing exemplary service — every time.
One team dedicated to providing exemplary service — every time.
Many players, one team. www.syntegon.com
One team dedicated to providing exemplary service — every time.
One team dedicated to providing exemplary service — every time.
Many players, one team. www.syntegon.com
One team dedicated to providing exemplary service — every time.
One team dedicated to providing exemplary service — every time.
Many players, one team. www.syntegon.com
(Honeywell Continued from page 38)
Since EtherCAT is not a switch-based protocol, customers like USS can freely design equipment with distributed I/O and not worry about network constraints, such as performance limitations, switch delays, limits on number of devices on the network, limits on the number of connections in the PLC or even in topology branching. This makes EtherCAT uniquely beneficial for intralogistics equipment.”
Previously, scanning and configuring the I/O system with thousands of points was a manual process that could take several days. “That was in addition to several more days of commissioning to check every individual I/O point to make sure that they were all mapped correctly,” Bassett says. “Today, this entire process is easily handled in minutes using the TwinCAT Automation Interface, which enables programming tasks to be automated.”
INNOVATION, EVEN IN THE SMALLEST DETAILS
Even with simple design elements, USS is not afraid to develop a novel approach that results in reliable solutions for end users. One example is applying motor-driven roller (MDR) technology to extend the unique benefits of these brushless DC motors beyond conveyor applications. USS had many challenges with previous MDR controller suppliers with unreliable fieldbus communication and limited-to-no safety integration. “The safety requirements in this application mandate that the MDR controller can cut motor power independent of the overall system power. But most manufacturers do not support this feature without powering down the MDR controller and the entire fieldbus network, which also interrupts the input feedback on the status of all the sensors in the application,” Bassett says.
The engineering team at USS found that establishing reliable communications in this way with MDR controllers was key for their machine to pass new NFPA 79 requirements. “We put a project team together to evaluate different ways to handle the
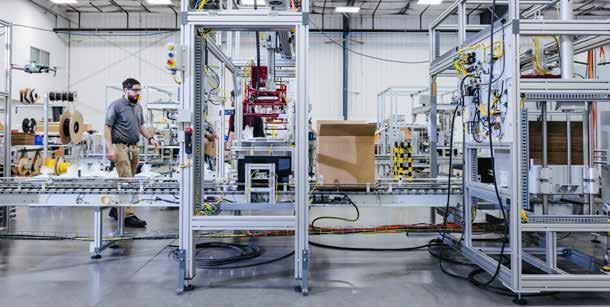
new E-stop category requirements in the 2021 revision of NFPA 79,” says Donna Kiefer, business unit leader and senior engineering manager at USS. “We reviewed a series of vendors’ hardware and standardized on the Beckhoff EP7402 MDR controller boxes with EtherCAT P, which incorporates EtherCAT communication and power in a single cable. The EP7402 is also used on other box- and tote-handling machines from USS and other Honeywell Intelligrated systems.”
The EP7402-0057 MDR controller offers two motor outputs to directly connect 24 V DC conveyor roller motors or other brushless DC (BLDC) motors with a maximum of 3.5 A current. The new EP7402-0167 variant can control a range of MDRs from 24–48V DC. Eight additional digital I/Os enable easy connection of devices such as photoelectric switches and communication between the box modules in operation without a PLC. The EP7402 takes over the complete control of a roller motor or BLDC motor regardless of the manufacturer. It also can be operated without a PLC and provides functions such as zero pressure accumulation (ZPA), sin-
gle or slug mode. Freely available function blocks for TwinCAT automation software also offer ZPA functionality, merge and other important MDR control features. The MDR controller also allows integrated functional safety in the system architecture via TwinSAFE technology from Beckhoff.
USS also uses TwinSAFE in other areas to connect all safety inputs on the system. “We decided on TwinSAFE because of the safety segmentation required for the various zones of the machine,” Bassett adds. “We need the ability to independently disable each subsection to maintain throughput while the operators are reloading liners or clearing jams. We are also able to segment our machine into functional safety areas, so we don’t have to E-stop the whole line for a localized safety event.”
ETHERCAT TIES EVERY APPLICATION TOGETHER

The power of the EtherCAT protocol also proved invaluable to USS when incorporating a customer-specified PLC that did not offer the same networking performance of Beckhoff machine controllers. “With traditional PLCs, we usually get 10- or 20-millisecond scan rates for all of the I/O on the machine,” Kelly says. “But when we add Beckhoff embedded controllers and EtherCAT, we can achieve 1- or 2-millisecond scan rates in the EtherCAT I/O system. This enables us to utilize more I/O with a lower scan rate than what was previously possible with the traditional PLC.”
Smart sensors on sortation machinery often require very fast scan rates that can be difficult for traditional PLCs to meet. “If you’re trying to sense objects passing by a sensor while the machine is running, your pulse time is typically in the tens of milliseconds, so if your scan rate is 15 or 20 milliseconds, you’ll completely miss the trigger,” Bassett explains. “With EtherCAT I/O, we can solidly lock onto the object and get five I/O scans before the trigger goes away. Therefore, we’re guaranteed to track even the fastest-moving objects on the machine, and we can react with millimeter precision on the sortation systems.”
EtherCAT also offers a wealth of diagnostic capabilities and can provide information on exactly where cable breaks are, as well as if individual networked devices are not in an operational state. “In addition to meeting our functional and cost requirements, Beckhoff also went the extra mile for us by providing custom color-coded cables to ensure that the correct connections are made in the field every time,” Kiefer says. “Error-proofing is a major value-add for our customers to reduce their support needs, and it helps reduce calls to our service department.”
For more info, visit honeywell.com, beckhoff.com. SD


Portfolio adds twist block technology
Automated inverting improves productivity.
The container-inverting lineup at Morrison Container Handling Solutions (Morrison CHS) (Booth C-1651) expands with the addition of twist block technology. Twist blocks are mechanical, backlog-fed twists that require no power aside from the movement of the conveyor.
“For years, we’ve seen great success with our power twist timing screw machines, but many of our customers need to simply invert mechanically on a line with backlog present,” says Chris Wilson, president of the container handling specialist.
Unlike traditional twist blocks, which sandwich together dozens of plastic pieces to create the twist, the Morrison Twist Block design consists of only a few pieces of plastic. This minimizes areas that could harbor contaminants and enables quicker disassembly, cleaning and reassembly.
Our customers “ . . . needed a simpler design that was more sanitary and easier to clean,” explains Nancy Wilson, CEO at Morrison CHS. The Morrison Twist Block also occupies a smaller footprint. Standard models range from 12–18 in., and custom sizing is available for retrofit situations.
Featuring simple mounting, the Morrison Twist Block utilizes quick changeover clamps and a builtin handle, making it easier for operators to remove this lightweight block when performing changeovers to different container sizes.
INVERTING CONTAINERS
Inverting containers manually is a labor-intensive process. With many operations shorthanded, adding equipment that automatically performs this action is one way to reduce workforce needs.
Inverting is most often used for:
• Code dating
• Sanitizing caps
• Rinsing
• Laying product down/standing it up on conveyor
• Multipacking/stacking operations.
There are multiple ways to approach inverting. Inverting blocks and power twists are most commonly used. Determining which option is best depends on:
• The shape of the container
• The rigidity of the container
• Backlogged or random-fed conditions
• Container environment (temperature and application).
Twist blocks, also known as inverting blocks, beer can invertors, container invertors, twist assemblies and can invertors, suit areas of high backlog pressure that may have tight line constraints where a longer screw-based system is not applicable or unnecessary.
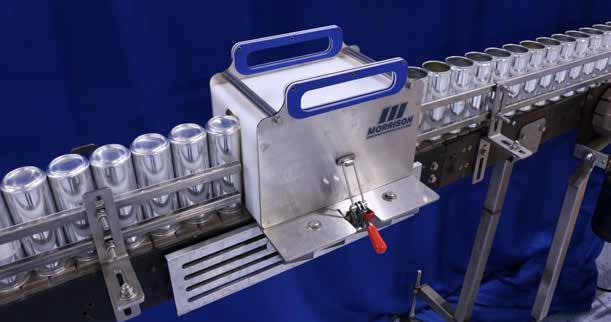
When a line doesn’t have space for a larger inverting method, twist blocks can be the perfect answer. Using backlog, twist blocks are a great way to keep the line flowing correctly. Most twist blocks are compatible with rigid containers such as cans and ice cream pints.
Challenging containers or sanitary applications can be addressed with the stainless steel power twists. These twists are most commonly used for food-contact applications where the containers must be held rigidly in position. This option is preferred when food or consumables are in direct contact with the equip-
ment and when access to the container is needed during inversion, e.g., for code dating the container.
Stainless steel power twists often are seen in multipacking operations such as stacking single-serve applesauce cups lid‐on‐lid in a cardboard sleeve. Using a power twist allows two lanes of containers to be inverted over the timing screw. Since both lanes are being controlled by the same screw, they can be stacked directly on top of each other. Once stacked, the containers would transfer to the grouping screw.
The grouping timing screw would then collate the containers to create the six-pack (three‐over‐three) configuration. If these timing screws were changed out, this could be a four-pack, making the timing screw act as a change part.
Ultra-high molecular weight (UHMW) plastic power twists are best for applications where the product is sealed. This device changes over quickly and is great for repeatability, helping cut down on wait times. They also are utilized in air rinsing.
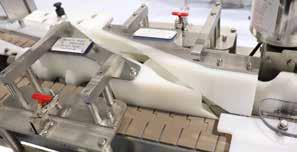
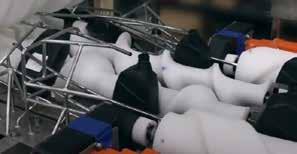
The UHMW plastic power twists are most suitable when containers need to be inverted from a backlog, indexed and inverted again in preparation for the next station on the packaging line. In one application, the UHMW plastic power twists invert the containers and then discharge groups of 12 to be presented to a packaging station downstream. This system allows for proper spacing and a consistent flow as this system required a 1 sec.-dwell time to achieve proper timing and spacing for the downstream application.
Power twist options are great for frequent changeover situations, as multiple twists can be supplied to accommodate running different containers on the same line.
Regardless of the method selected, make sure the twist manufacturer accounts for multiple transition points throughout the twist to ensure the container remains under control during the entire inversion. This will help the entire system blend together and ensure proper container placement on the conveyor.
For more info, visit morrison-chs.com/inverting. SD
Editor’s Note: A portion of this article is based on Automated Inverting Solutions to Improve Productivity in 2023, a blog posted by Morrison CHS on March 20, 2023.
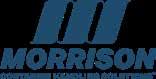
Tips for choosing dairy equipment Success
Selecting the right machinery for your plant is essential to keeping operations running smoothly. Fill/seal and/or form/fill/seal equipment is an essential part of operations for most dairy processors. After all, these pieces of equipment ensure that a product is accurately and seamlessly placed into primary packaging before continuing down the production line.

There is much to consider when selecting such machinery and many potential hurdles to avoid. Max Davis, head of Customer Success at WALDNER North America (Booth C-1841), offers three tips to ensure the perfect purchase.
CUSTOMIZE IT
A common mistake when selecting equipment is the unintentional disregard for the interaction between a product and its packaging on the line. Some dairy processors think packaging is interchangeable and don’t consider this part of the equation when they select a filler.
“We run into problems most often when equipment isn’t properly engineered to the exact package and product you’re looking to run,” notes Davis.
He advises processors to take a “holistic approach” during product development by considering the exact product and packaging specs for manufacturing.
“WALDNER, for example, designs custom equipment, so we take information about specific operational needs and create the filler that would be appropriate for a given product and its packaging,” he explains.
PRIORITIZE FLEXIBILITY
Not all dairy products are created equal in terms of how easily they interact with filling equipment. For example, butter and cream cheese are far more complex to fill than other products. Butter can be difficult because solids separate out very easily, so manufacturers must be careful when dosing.
Conversely, cream cheese is challenging because it’s thick and filled into containers when it is cold, making it difficult to package.
Davis re-emphasizes the importance of understanding a product and its packaging specs, especially when running different types of dairy products on the same equipment.
He says, “It’s crucial to operate flexible machines to ensure the highest levels of efficiency when changing between products and formats.”
VALUE MAINTENANCE SERVICE
Once the appropriate equipment is selected, dairy processors must build an effective preventative maintenance plan. Manufacturers should not wait for something to fail to replace parts.
“It is ultimately much more expensive for companies to replace failed machine parts as opposed to keeping up-to-date on what needs to be changed. Once you’re running to failure, you’re going to have cascading issues
across the machine,” predicts Davis. “A well-considered preventative maintenance plan is essential. It will minimize unplanned downtime and maximize output.”


He recommends that processors choose a machine manufacturer that will help them implement and execute an effective maintenance program tailored to their packages, products and personnel.








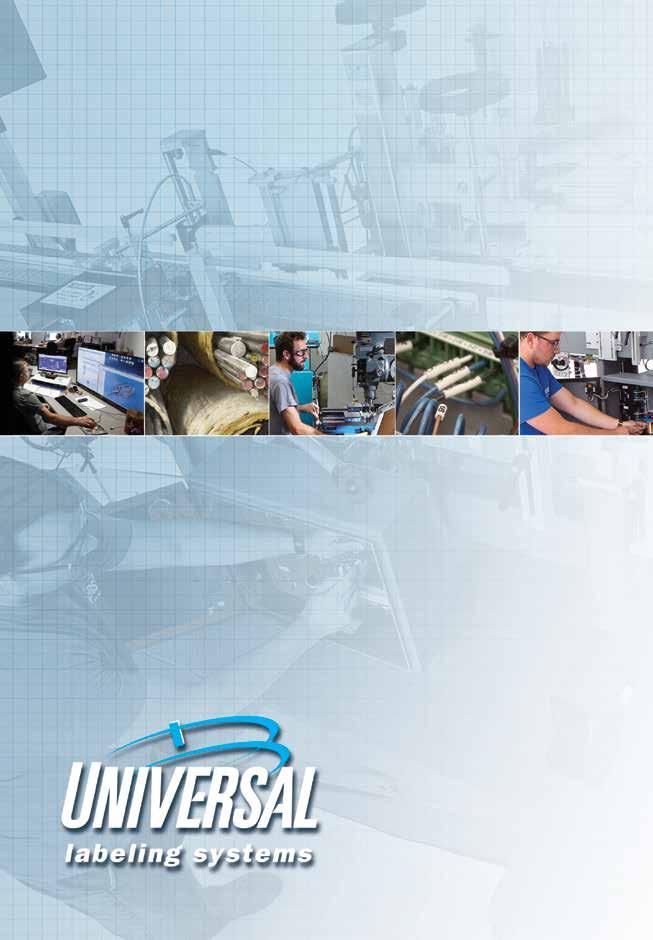
He says, “At WALDNER, we take preventative maintenance very seriously, which is why we created
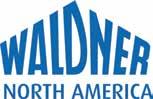

“It’s a customer-care program that offers free Machine Performance Analysis every six to 12 months for every Waldner filling and sealing system installed in North America. Our experts measure performance, identify opportunities for improvement and make recommendations for maintenance and care. Our customers are running at very high levels of efficiency for much longer!”
For more info, visit wnapt.com. SD
Acommon sight at the end of most food and beverage processing lines is an inspection system. Depending on the product being produced, these machines can either be x-ray or metal detection, and in some instances, a combination of both. An x-ray system detects materials like glass, bone, rubber, stone, plastic and some metals depending on density, while a metal detection system is calibrated to identify all types of metal based on their magnetic and conductive properties.
The strategy behind placing a detection system at the end of a processing line is that once an item is packaged, no new contaminants can be introduced, so inspecting after packaging is a final safeguard before distribution to customers.
However, the number of food and beverage product recalls has increased in recent years, which can be partially attributed to an unreliable supply chain for ingredients—resulting in unfamiliar, alternate suppliers being used when materials are scarce—and an influx of inexperienced workers on the lines due to the ongoing labor crisis. As a result, major retailers like Costco are pushing processors to expand their overall detection capabilities farther up the line to catch contaminants before the packaging stage.
Adding inspection upstream can provide additional food-safety protection to consumers. But the cost of adding machinery, coupled with a possible lack of space to install that equipment, are the main reasons this idea hasn’t previously taken root. Now, with retailers feeling pressure from consumers over recalls, that
urgency is being transferred to the processors.
“Many [retail] brands are demanding specific inspection steps be performed prior to product being sent to them by suppliers,” says Marco Azzaretti, director of Marketing for Key Technology (Booth C-4225). “This trend has been growing in conjunction with consumers’ increased attention to the quality and safety of food products, which in turn has made food-safety incidents and recalls more common and more costly for brands to absorb, both in terms of operational costs to correct and the impact on the brand’s reputation.”
For manufacturers who worry about the upfront cost of adding inspection to their existing lines, Geri Foley, product manager, X-ray for Mettler Toledo (Booth C-1814), offers this perspective: “The average cost of a product inspection [system] is somewhere between $25,000 to $135,000, depending on the technology. One product recall can be in the millions.”
HIDDEN SAVINGS
While the food safety benefits of adding inspection equipment farther up the line are numerous, there are also hidden savings that processors might not see immediately.
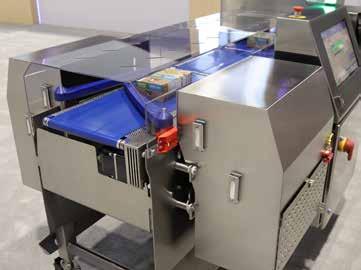
“The cost of a reject [farther upstream] is much lower vs. rejecting finished product or anything farther along in the process,” says Eric Garr, regional sales manager for Fortress Technology (Booth C-4303). “Also, consider that rejecting one larger contaminant upstream may mitigate a much higher quantity of rejects downstream if that contaminant is broken down into smaller fragments. Further, there would likely be some fragments too small to detect with end-of-line inspection.”
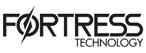
Catching contaminants in the early stages also can save wear and tear on equipment as items are processed down the line. “Larger contaminants, like bigger pieces of metal or stone, if removed at the front end, can protect equipment such as grinders, mixers and fillers that are located farther downstream,” says Lanel Menezes, sales director, USA at Mettler Toledo Product Inspection. “Ultimately, non-conforming product is rejected prior to value being added through packaging.”
Sustainability goals are another benefit of adding inspection upstream. Overall food and packaging waste will be reduced if a contaminant is detected early, rather than at the end when packaged goods would be thrown out. In addition, today’s inspection systems are built with energy savings in mind, so adding this equipment to a line won’t use as much power as in years past. “This is accomplished in a multitude of ways such as deploying energy-efficient x-ray generators, using magnetically driven motors, using LED lights instead of incandescent bulbs, reducing heat dissipation from the machines and more,” Menezes says.
LINE PLACEMENT
An inspection system can go almost anywhere along a processing line, but there are certain areas where processors can maximize the detection capabilities of their equipment, depending on the product being produced.
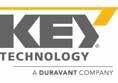
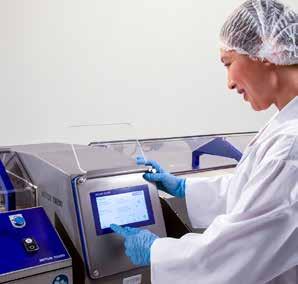
“At every stage throughout the process, inspections can be conducted, starting with raw material receiving,” says Robert Rogers, senior advisor for Food Safety and Regulations at Mettler Toledo. “Liquid products can pass through a metal detector or x-ray pipeline system, and dry goods can pass through metal-detection systems. In the batching area, large
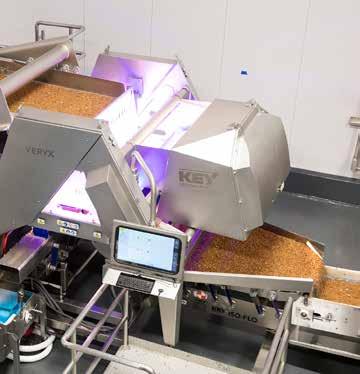
Earlier inspection generates benefits
Recalls, retailer demands prompt inspection farther up the line.In addition to metal detection and x-ray options, digital sorters like this one from Key Technology (Booth C-4225) can also be used when processing raw ingredients at the front of a line. Easy-to-use controls on inspection systems add value for processors with inexperienced staff and the need for a short learning curve. Combination systems merge more than one inspection function into a smaller footprint than two standalone machines, helping processors with limited floorspace in their operations.
container product can pass through inspections as they are dismantled into smaller batch materials, like a 50-lb. bag of flour, through a throat metal detector as it is being weighed into a batch-level item.”
Raw material receiving is a logical place to add an inspection system, since that’s where many contaminants can be introduced from the outside. “Inspecting raw product at receiving allows the input to the line to be profiled, which helps optimize downstream processes,” Azzaretti explains. “Along the production line, placing inspection systems and sensors before and after critical transformative steps such as frying, baking and blanching allows processors to collect valuable data that can be used to control those processes and maximize line performance.” Inspection right before packaging can be another useful area of placement, he adds.
moved from the product stream,” Azzaretti says. “At the same time, these modern inspection systems are designed to be much easier to use and maintain.”
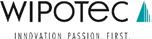
A shorter learning curve to use today’s inspection equipment is a crucial advancement given the ever-dwindling labor pool and the need for new hires to learn as quickly as possible. “Introducing a new piece of equipment into operations will have an impact on your employees, and it is important to ensure that the necessary support is given for them to adopt the technology and trust it,” says Menezes. “This means providing the necessary training, ensuring smooth integration, collecting feedback for improvements, and ensuring ease-of-use and serviceability.”
Simplified operation on today’s inspection equipment can include touchscreens and icon-based use, which helps companies “with high turnover or, in some cases, not enough individuals in the workforce,” Foley says.
INSTALLATION AND INNOVATION
Though it’s possible for a manufacturer to adjust its budget to purchase additional inspection systems, it might be more difficult to find room on the line for these systems. Many processors have limited space, so custom-engineered equipment can be one path to overcoming those challenges.
“It is important for food processors to engage closely with inspection system suppliers and express their specific requirements, because every line in every plant is unique, even when processing the same product type, and the inspection system should be tailored to each instance to maximize value,” observes Azzaretti.
Combination systems are becoming more popular because they reduce the footprint over multiple standalone systems, Garr notes. “Also, specific to metal detection, something to consider is that the aperture size and resulting metal-free area will dictate the minimum overall length for a system,” he says. “So, ensure that metal detection apertures are as small as possible, fitted for the product that is being inspected.”
Not all product inspection equipment will require additional space, according to Foley. “In many applications, the equipment can be inserted into the existing line space, whether using the customer’s existing material-handling solution or replacing a section of their existing line with product inspection equipment,” she says.
to maximize their investment. “First and foremost is the ability to detect varied, ever-tinier contaminants, as well as the capability of defining when contaminants are introduced into the production process,” says Kelvin Binns, food and CPG director for Wipotec-OCS (Booth SU-8027)
“Inspection systems for contaminant detection have become more powerful in terms of what they can detect,” Garr says. “To put it simply, the technology is being doubled up to cover holes and improve performance. Metal detectors operating multiple simultaneous operating frequencies and electromagnetic field orientations are innovations that help improve performance. With x-ray inspection, dual-energy detection is allowing [identification] of less-dense contaminants than was possible in the past.”
Connectivity and data collection also can help processors make sense of target inspection areas farther up their lines. “The ability to pull live data into plant monitoring software and ERP [enterprise resource planning] systems is becoming more of a prerequisite than ever before,” Garr explains. “This makes sense as having live data to make on-the-fly operational decisions can be invaluable.”
Menezes adds, “We live in a connected world that demands transparency. Traceability [of ingredients] and connectivity are becoming vital requirements in the marketplace.”
Combination systems can integrate more than one inspection function into a smaller footprint than two standalone machines, helping processors with limited floor space.
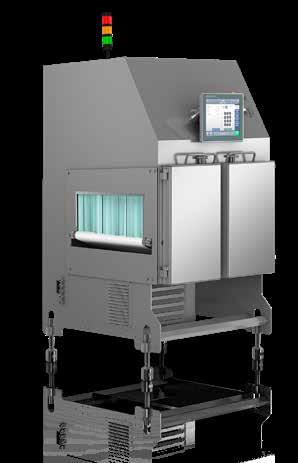
In addition to metal detection and x-ray options, digital sorters can be used when processing raw ingredients at the front of a line. “Today’s optical sorters are more capable in differentiating with consistent accuracy what is good in-spec product, what are product defects that need to be managed, and what are foreign material contaminants that must be re-
Calibration and testing of new inspection systems upstream is also a vital step before finalizing installation, especially since inspection will be new to those parts of the line. “Prior to making a purchase decision, it is essential to validate and measure the performance of the system through application tests that replicate the actual product and production conditions in which the equipment will operate,” says Azzaretti.
Today’s inspection systems feature a variety of innovations, and while not designed specifically for upstream placement, they are helpful for processors
Ultimately, processors will have to weigh their financial and facility footprint options before adding one or more inspection systems upstream to comply with recent retailer demands. Assessing the big picture might help make that decision a bit easier. “Product inspection should play a central role in any manufacturer’s production line upgrades,” Binns says. “Leaving it out of an upgrade budget may leave a food producer out of a retailer’s supplier network.”
For more info, visit fortresstechnology.com, key.net, mt.com/pi, wipotec.com/us/. SD
Editor’s Note: The original version of this article was posted by ProFood World on Jan. 20, 2023.
“ The average cost of a product inspection [system] is somewhere between $25,000 to $135,000 depending on the technology.
One product recall can be in the millions.”
— Geri Foley Mettler Toledo
Amultihead weigher, also known as a combination scale, needs to have product on it in order to record any kind of weight. But how does the product get on the scale? Focusing on how to properly set up and use feed equipment will help you get the best speed and accuracy from your multihead weigher.
There are several different equipment options to consider when looking to feed product to a combination scale. Three of the main ways to feed product onto a multihead weigher include:
• A vibratory feeder (also known as a cross-feeder)
• A bucket elevator
• Belt feeders.
At Yamato (Booth SL-5949), we typically recommend the use of a crosshead feeder, but no matter what type of feed equipment you choose to use, it is important to achieve the correct product flow. The key is to not starve or flood the scale. The goal is to achieve a waterfall-like flow of product onto the top of the scale. The recommendations below will help you accomplish this.
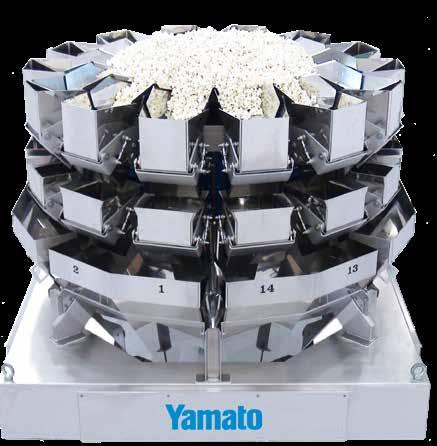
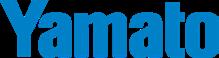
AVOID STARVING
Starving a scale is when the feed equipment is not delivering enough product to the scale, which can leave the top cone void of product, linear feed pans with little to no product and feed/weigh buckets lacking adequate product levels. This will significant-
ly hurt the performance of the combination scale.
A multihead weigher relies on a consistent level of product across all its components. When weigh buckets have limited levels of product inside, finding a good combination of buckets to achieve the pre-programmed target weight will be difficult. On average, the scale is looking for four buckets in combination to reach the desired target weight. If the scale is being starved, it will need to skip cycles as it looks for the best combination of buckets to choose from, reducing the speed of the scale and, in turn, slowing down the entire production line.
AVOID FLOODING
The flipside to starving a scale is when it is flooded with product. Flooding the scale is when the product level on the scale’s top cone, linear feed pans and feed/weigh buckets is too high. Too much product in the weigh buckets will severely limit the number of buckets that can be used in a combination. Again, on average, the scale is looking for about four buckets to make a combination and the total target weight. Flooding weigh buckets will force the scale to potentially choose only one or two buckets in combination. This is not an efficient way to run a Yamato combination scale since each weigh head on a scale increases the accuracy.
A Yamato combination scale’s software contains the ability to force an overfilled bucket into combination after a settable number of cycles, but this is not the ideal way to run a multihead weigher. This should only be a last resort since your product giveaway may increase.
TAKE IT FROM THE TOP (CONE)
The most successful feed equipment delivers product like a waterfall effect onto the top cone, not flooding or starving the scale. To help feed equipment know when to turn on and deliver more product to the scale or turn off when enough has reached the scale, Yamato combination scales come equipped with a load cell below the top cone.
For each recipe/program set, the operator will adjust the high and low limits of this load cell under the top cone of the scale. The high limit refers to how much weight is allowed to be sitting on top of the scale’s top cone. When the load cell below the top cone reaches its set high limit of acceptable product on the scale, it will signal to the feed equipment to stop deliver-
ing product. When the level of product on the top cone begins to be drawn down, the load cell takes a reading to determine if more product needs to be delivered to the top of the scale. Then, a signal will be sent by the scale to the feed equipment to deliver more product.
DETERMINE PROPER PLACEMENT
When setting up your production line, it’s vital to optimize the placement of your feed equipment so it can deliver product to the most central point on the scale’s top cone. Typically, the top 4–6 in. of the top cone is where product should be directed. This allows the top cone to turn on, vibrating the product in a counterclockwise fashion evenly to each of the scale’s linear feed pans. If the feed equipment is not mounted directly above the top cone, there is a high likelihood of product undershooting or overshooting the top cone. This will not allow for the desired waterfall effect and prevent even distribution to each of the linear feed pans.
The mounting height of feed equipment above the top cone also is important. Feed equipment should not be mounted too high or too low to the scale’s top cone. Mounting feed equipment too high above the top cone can cause several problems. First, for fragile products, dropping from an increased height can cause unnecessary damage. Second, dropping product from too great of a height can cause the product to fall away from the uppermost point of the scale’s top cone, defeating the purpose of the top cone’s ability to draw product evenly to each linear feed pan.
Mounting feed equipment too close to the top cone restricts product, preventing it from evenly reaching all the linear feed pans. Feed equipment too close to the top cone also restricts access during the removal of the top cone and linear feed pans on the scale for sanitation and maintenance.
ISOLATE THE FEED EQUIPMENT
Lastly, all feed equipment should be isolated from the structure where the Yamato combination scale is mounted to minimize external vibrations and their transfer to the scale’s sensitive load cells. Isolating this equipment will help deliver the most accurate weighment possible.
CONCLUSION
Regardless of the equipment you choose to feed your combination scale, keep these key points in mind when setting up your product line for maximum performance.
For more info, visit yamatoamericas.com. SD
Editor’s Note: The original version of this article was written by Yamato.
Performance depends on feeding Multihead weighers need optimum product flow.Proper product feeding is critical to precise performance of multihead weighers.
Integration simplifies line design
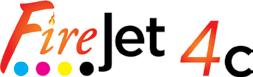
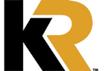
ProMach Pharma brands work together.
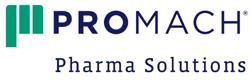
Brands under the umbrella of ProMach Pharma Solutions (Booth C-3225, SL-6501) NJM, Pharmaworks, Serpa and WLS—work together along with partners and other ProMach segments to integrate systems and lines.
“This year, . . . we’re illustrating ‘The Power of ProMach,’” says Tom McDaniel, president of ProMach Pharma. “This allows us to offer deep expertise within a broad range of core competencies, along with advanced technologies, seamless integration and high-level aftermarket support.”
One line integrates Pharmaworks’ TF2 blister machine and Serpa’s P-100 cartoner with their co-developed BTS blister transport system, which seamlessly transfers and collates blisters from virtually any Pharmaworks blister machine to feed most any Serpa cartoner. This synchronized system simplifies line installation, operation and maintenance.
Another integrated system showcases NJM’s beltorque® high-speed capper with the EZ-100 tamper-evident (TE) bander from Axon, another ProMach brand. The capper gently handles up to 300 bottles/min. with precise torque while the versatile bander can be configured for multipacks and twinpacks, partial body sleeves, full-body sleeves and fullbody over-the-cap sleeves as well as TE bands.
Also on exhibit are Steelco Pharma’s new washing
Course helps comply with standards
Standards impact the ability to compete in the marketplace. PMMI, The Association for Packaging and Processing Technologies (Central Lobby), offers a free Introduction to Standards Development course created to benefit business by focusing on the standards development process and participation.
Understanding standards is critical to staying in accordance with regulations related to design, operation and maintenance of machinery. By knowing the fundamentals that are important to any industry, your business will gain awareness and knowledge of U.S. and international standards to support your company’s export business.


For more info, visit pmmi-standardstraining.com. SD
carts, which have been designed specifically to clean product contact parts from a Cremer tablet counter or Dara Pharma liquid filling and closing machine utilizing a Steelco DS Optima PH pharma-grade parts washer, all of which are supplied in North America by NJM.
Other featured products include productivity
software from ZPI, another ProMach brand, NJM’s Courser 230 vial/syringe labeler, the new VR-72 height-adjustable labeler from WLS, a high-speed insert feeder from Serpa, Pharmaworks’ BlisterMate semiautomatic blister machine and the Dara SX310-RDL aseptic vial filling and closing machine.
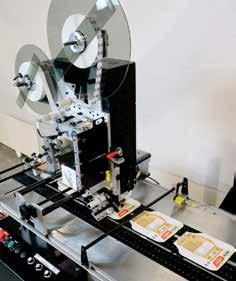
For more info, visit promachpharma.com. SD
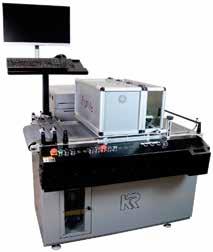
EU updates Machinery Regulation
Technical Services personnel from PMMI, The Association for Packaging and Processing Technologies (Central Lobby) worked with the U.S. Department of Commerce to help address potential unfavorable issues as the new E.U. Machinery Regulation was developed.
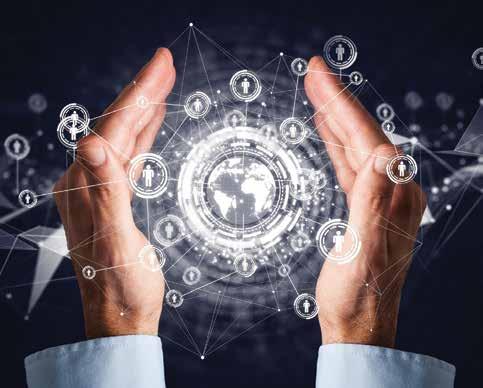
Early drafts of the regulation would have increased requirements, costs and third-party certifications, but these stipulations were removed as the updated regulation evolved due to input from PMMI and the U.S. Department of Commerce. At this point, the new Machinery Regulation provides added benefits to machinery manufacturers with minimal additional requirements. PMMI members can expect an increase in user trust, legal certainty, effective market surveillance and reduction of burdens placed on manufacturers.
The new Machinery Regulation will replace Machinery Directive 2006/42/ EC, which was in effect for more than 15 years. The regulation will apply 42 months after the date of its entry into force, which means full implementation is expected in January 2027.
For more info, visit pmmi.org/standards-and-regulations. SD
In-house CNC router solves supply chain issues
Anew computer numerical control (CNC) router, recently installed at Schneider Packaging Equipment (Booth C-2223, SL-6604), a Pacteon Group company, minimizes the need for outsourcing by allowing its machine shop to manufacture more system components. The sophisticated router increases production volume, accuracy and speed by streamlining processes that previously required multiple-step operations.
“As a technology-focused company, we’re excited to have a state-of-the-art machine that will improve efficiencies and output quality. This will eliminate supply chain issues, and our customers will benefit from improved build times for their machines,” reports Shawn Mason, machine shop manager at Schneider Packaging Equipment.
The company can produce more parts for its case packaging and robotic palletizing equipment, as well as machine components for its sister companies: ESS Technologies (Booth C-2223, SL-6604) and Phoenix Wrappers (Booth C-2223, SL-6604)
Jeff Grinnals, director of Operations at Schneider, concludes: “Expanding the production of in-house parts for all the Pacteon brands provides significant cost savings and alleviates many procurement challenges our industry is experiencing. As we grow, operational investments are a top priority to continue delivering world-class end-of-line machines.”
For more info, visit schneiderequip.com, esstechnologies.com, phoenixwrappers.com. SD
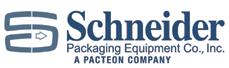
impulse heat sealing
Impulse Temperature Controllers

The PIREG ® heatseal temperature controllers are designed specifically for controlling the heat sealing operations performed in a wide range of applications including: vertical and horizontal form, fill, and seal; pouch filling and sealing; film wrapping, and pouch making. The PIREG ® impulse temperature controllers are cUL Listed and universally adaptable to almost any application, and do not require the use of thermocouples or RTD’s. PIREG ® temperature controllers are designed for “in cabinet” and “panel mount” uses and also available with EtherNet/IP® communication capabilities. TOSS Technology— delivering perfect impulse heat seals every time. www.tossheatseal.com
Here’s WALDO!
Booth SL-6407
Waldo Packaging Machinery is a manufacturer of fully automated vertical form-fill-seal packaging machines for packaging liquids, slurries and high viscosity products. Servicing businesses of all sizes in a range of markets that include food/beverage, cosmetics, and cleaning fluids, their complete line of machines are compact, user friendly and cost efficient. www.waldo.com.mx
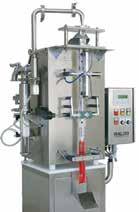
PackworldUSA Medical Sealers
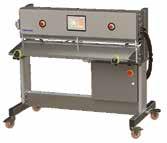
What sets PackworldUSA apart from all the rest is its use of the high response, state of-art, TOSS Technology All PackworldUSA machines come equipped with the advanced PIREG ® temperature controller. Only TOSS uses Variable Resistance Controlled (VRC) heat sealing technology to monitor and adjust temperature precisely over the full length and width of the heat sealing element, accurate up to 500°C. www.packworldusa.com
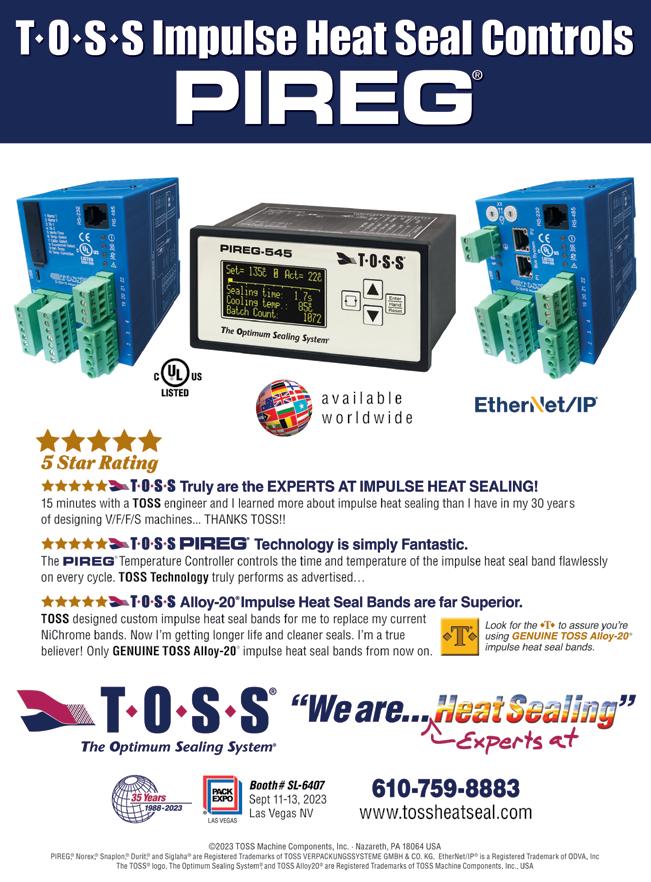
TOSS Alloy-20 ® and Norex® Heatseal Bands are available in over 350 styles, shapes and sizes. Custom designed for any application, new or existing, TOSS Alloy-20 ® Heatseal Band are longer lasting and provide for effective sealing at optimum speeds. When used in conjunction with the PIREG ® Temperature Controllers, the TOSS Alloy-20 ® heatseal bands provide instant thermostatic feedback eliminating the need for thermocouples. This instant feedback assures precise, repeatable results on each and every seal. www.tossheatseal.com
TOSS Heat Seal Cover Materials
In the optimum sealing set up, the heatseal band must be electrically and thermally insulated from the jaw bar. TOSS offers a wide selection of PTFE cover cloths and tapes that are available in standard and custom sizes. Other insulating materials available from TOSS include Silicone Rubber, Snaplon,® Durit,® and Siglaha ® www.tossheatseal.com
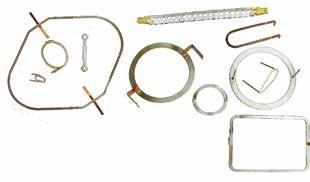
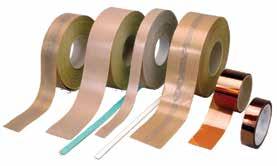
award winning packaging takes center stage
Focused interest areas
narrow search
Check out Sustainability Central, Processing Zone, Logistics and Healthcare Packaging Pavilions, other favorites.
An array of pavilions and other focused interest areas help attendees at PACK EXPO Las Vegas zero in on the products and services they need. New this year is Sustainability Central (Booth N-9455) and the accompanying Sustainability Stage (Booth N-9967) (see schedule p. 16). This interactive destination in the North Hall offers an expansive look into what sustainability means and serves as a resource for sustainable manufacturing, materials, design, recovery, logistics and data.
Another PACK EXPO Las Vegas debut, The Logistics Pavilion in the North Hall, addresses a topic that ranks in the top five searches on the PACK EXPO website. It offers targeted solutions to address the boom in eCommerce. Participating exhibitors include warehousing, fulfillment, distribution logistics and transportation service providers.
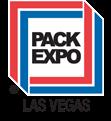
NORTH HALL Booth N–9550
Also new for the Vegas show, The Healthcare Packaging Pavilion targets attendees working in businesses devoted to life sciences. This “show within a show” in the South Lower Hall will house innovations for pharmaceuticals, biopharmaceuticals, nutraceuticals and medical devices.
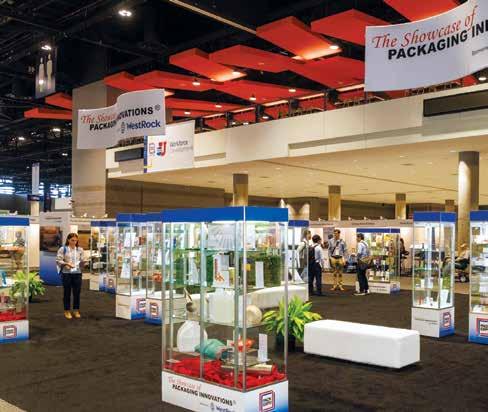
One of the largest special interest areas, The Processing Zone in the North Hall, presents products/services to help increase efficiency, achieve total system integration and ensure employee safety. Roughly 50% bigger than in 2021, this area features front-ofthe-line technologies such as homogenizing, heat treating, forming/sizing and coating. It also hosts the Processing Innovation Stage (Booth N-10511) (see schedule, p. 30).
The Confectionery Pavilion, hosted by the National Confectioners Association (Booth SU-7201), will feature the latest trends relating to aeration, batch refining, shaping, cluster production and other candy-making techniques. Located in the South Upper Hall, this pavilion also provides a spot to take a break and recharge at the Candy Bar Lounge (Booth SU-7201), sponsored by Syntegon Packaging Technology (Booth C-2800)
The Containers and Materials Pavilion will display the latest innovations in paperboard, glass, metal, plastic, flexible and resealable packaging, as well as containers and materials. Located in the North Hall, the pavilion houses The Showcase of Packaging Innovations® (Booth N-9550) (see story, p. 22). Sponsored by WestRock (Booth C-2023), this attendee favorite will display award-nominated packaging.
The PACKage Printing Pavilion in the North Hall focuses on the advantages of digital printing, showcasing the latest in cost-effective solutions for smart, short-run, on-demand, variable data and personalized packaging.
SEPTEMBER
The Reusable Packaging Pavilion, sponsored by the Reusable Packaging Association (Booth SU-8000), presents sustainable packaging concepts to help reduce waste, cut costs and gain supply chain efficiency. This pavilion in the South Upper Hall also houses the Reusable Packaging Learning Center (Booth SU-8000).
The Workforce Development Pavilion (Booths N-9000–N-9026) is a one-stop shop for resources to strengthen the workforce. Learn about PMMI U offerings, including popular training workshops, and meet students interested in careers in the industry.
The Association Partner Pavilion (Booths C-1145–C-1354) ipants in the PACK EXPO Partner Program and connects attendees to leading associations from all segments of packaging and processing. Experts from the PACK EXPO Partner Program address the latest hot topics and industry trends such as sustainability, remote access, supply chain solutions, augmented reality and operational efficiency on the schedule, p. 24)
For more info, visit packexpolasvegas.com.

Economic report helps firms plan
Powerful Research to Move Your Business Forward
Trusted,
The economic forecast carries good news and bad news, according to a new report by ITR Economics for PMMI Business Intelligence, a division of PMMI, The Association for Packaging and Processing Technologies (Central Lobby)
•
•
Spiral conveying. Straight up!
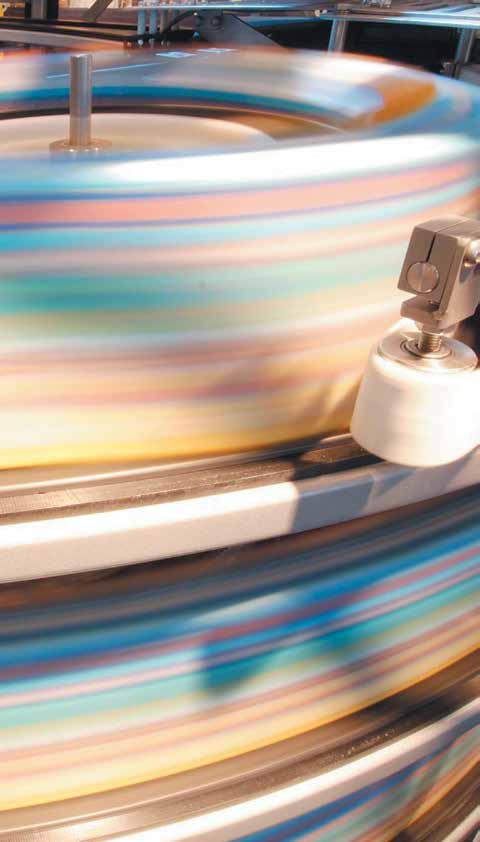
•
The comprehensive study, Guidance in an Uncertain Economy—Gauging the Risks Going Forward 2023-2024, pegs the probability of a recession in manufacturing and industrial production before the end of 2023 at 88% and predicts a “Great Depression” for 2030. The recession is expected to be mild and short, ending by the beginning of 2025. However, the report notes, if the Federal Reserve continues raising interest rates, the recession is likely to be deeper and longer.
Visit
However, companies are in a good position to weather the anticipated recession with healthy order backlogs and supplies of cash. Inflation is waning, and prices for freight, packaging and new material are declining. Consumers are expected to keep spending. Although retail sales will slow, eCommerce will continue to grow, albeit at a slower rate. The report predicts the strongest sectors will be pharmaceutical/medical devices (due to aging baby boomers and reshoring), food and personal care.
With private sector employment at a record high and unemployment at its lowest point in 21 years, the report expects hiring challenges and wage inflation to remain until 2030. However, the weakening economy should have a positive effect on retention since employees are less likely to seek new opportunities in times of uncertainty. To offset workforce challenges, the report suggests now is a good time to invest in automation and efficiency improvements.
In its look at the macroeconomic landscape, the report considers factors such as labor dynamics, interest rates, inflation and global issues; provides predictions for 2024 and beyond; and offers tactics for continued success including use of a Rates of Change Management Tool to help anticipate shifts in business cycles.
For more info, visit pmmi.org/report/guidance-uncertain-economy-gauging-risks-going-forward-2023-2024. SD
As the market leader in spiral conveyors in the packaging industry we think of solutions for elevating and accumulating packed items. It’s what we do. At AmbaFlex it’s not just about building the right equipment, it’s about developing a special solution for you. Here’s to spiral conveying.
Spiral Elevators & Accumulators for primary and secondary packaging handling.
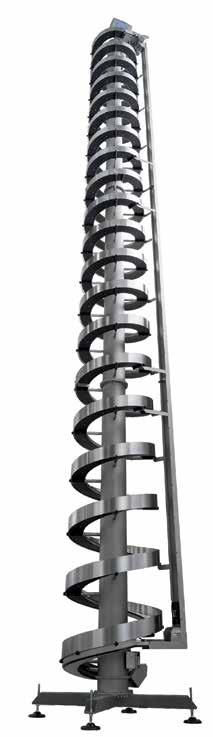
Automated line packs candles
End-to-end flexibility beats complexity.
In Santena, Italy, a short distance from the city of Turin, SER Wax Industry produces and processes waxes for a wide range of sectors, including premium scented candles in jars. For dispatching the jars, a TLM Multipacker from Schubert, parent company of Schubert North America (Booth SL6820, SU-7654), now combines all packaging tasks into a single line. The packaging machine manufacturer also optimized the boxes and cartons for automation—significantly reducing process complexity.
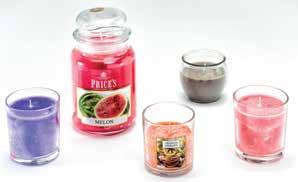
Along with special waxes for the food, cosmetics, construction, packaging and clothing industries, SER Wax is known primarily for its candles. With its Price’s brand, the manufacturer even has the honor of being one of Buckingham Palace’s court purveyors. Candles, however, not only contribute to a feel-good atmosphere at receptions, celebrations and royal ceremonies, they also are popular for more everyday occasions. Candles in glass jars are especially practical and appealing, as they leave no wax on the tablecloth and do not immediately go out in the wind. Until now, the manufacturer had packaged these products painstakingly by hand. Together with Schubert, the customer has now implemented a fully integrated automated line.
In addition to the time-consuming manual work, the various and, at times, double-glued, carton models had resulted in high costs. Schubert used its automation expertise to make these tasks simpler and more efficient. The objectives were clear from the outset: more output, higher packaging quality, reduced costs, quick format changes, no manual packing tasks and secure packaging for the small and large glass containers. The heart of the solution
is a Multipacker, which flexibly integrates different packaging operations into a single line.
PROTECTIVE PAPERBOARD
At the beginning of the project, the Schubert packaging developers revised and optimized the packaging. Instead of diverse paperboard versions, only flat blanks are now used. “This allowed us to implement machine-compatible, secure and cost-effective cardboard packaging with only one system for all formats—from beverage glass formats to the size of preserving jars,” explains Schubert’s Dirk Andrich, who is responsible for the project as area sales manager. The complexity of the packaging process has been considerably reduced by using only one carton system for all formats. This is another reason why format changes take only 10–20 min.
The robot-supported line packs six product formats and 13 carton formats over a length of 11m. It consists of six TLM frames equipped with six F2 robots and three F3 robots. The Transmodul, developed by Schubert, connects the individual packaging processes. For small jars, the line achieves an output of up to 105 jars/min. or 35 packages/min. (three-count cartons) or 17.5 packages/min. (six-count cartons). With the larger candles, an output of 45 jars, or 15 packages/min. (three-count cartons) is achieved.
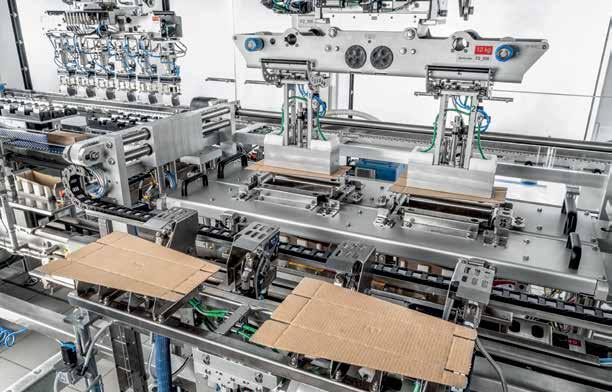

TWO-PART PACKAGING PROCESS
The jars are loaded onto a conveyor and gently grouped at defined intervals by means of a large, horizontal screw conveyor. In the first packaging step, the smaller jars are individually inserted into cardboard sleeves, which protect the jars and provide a market-
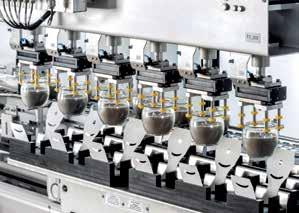
ing platform. The flat blanks are taken from the magazine by an F3 robot, erected and positioned on the Transmodul for precise loading of the jars by the F2 robot. A glue line is then applied to each sleeve, and an F2 robot centers and compresses it to complete the primary packaging. Large jars are not packed into sleeves but are pre-grouped with the aid of a special paperboard separator and further processed.
In the second segment of the line, the robots place three prepared candles into paperboard trays. The trays are then covered individually, or two trays can be combined under one lid and sealed. This creates stable three- or six-count cartons that stack easily. The combination of the newly developed carton packaging and robot-based machine technology makes the SER Wax automation solution exceptionally efficient, powerful and reliable.
For more info, visit schubert.group. SD
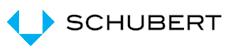
Helping you bring your best products to market.
Delivering Results. With Heat and Control, you have a partner with the scale to support your success, the innovation to advance your operations, and a commitment to quality that will help you offer better products for consumers.
PROCESSING AND PACKAGING SOLUTIONS

• Food processing systems

• On-machine and process area seasoning application
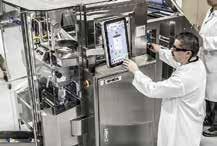
• Conveying and product handling
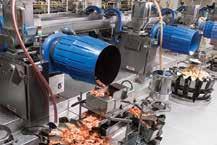
• Multihead/combination scale weighing and filling
• Snack bagmaking and case packing
• Metal detection and x-ray
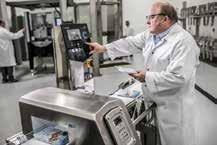
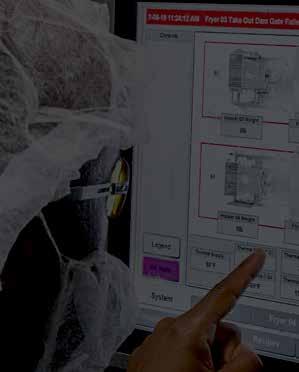
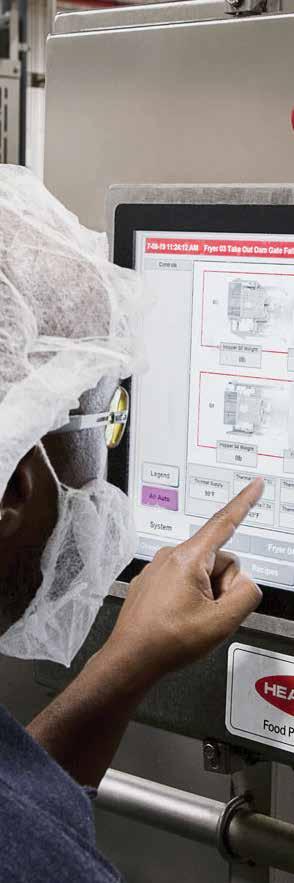
• Check weighing and seal checking
We are successful when you are successful. That’s why we apply creativity, engineering excellence, and determined perseverance to every project to help our customers get the performance their business demands—whether measured by flavor, efficiencies, sustainability, improvement, or innovation.
42 2 ~2~ ~2
107
LOOKING BACK. PRESSING FORWARD. ALWAYS INNOVATING. info@heatandcontrol.com
17 20
36 41 26
|
Brands combine conveyor expertise
Dorner and Garvey introduce AquaGard GT conveyor.
Multiple operating loops showcase material-handling options available from Dorner (Booth C-1455) and Garvey® (Booth C-1555), both Columbus McKinnon brands.
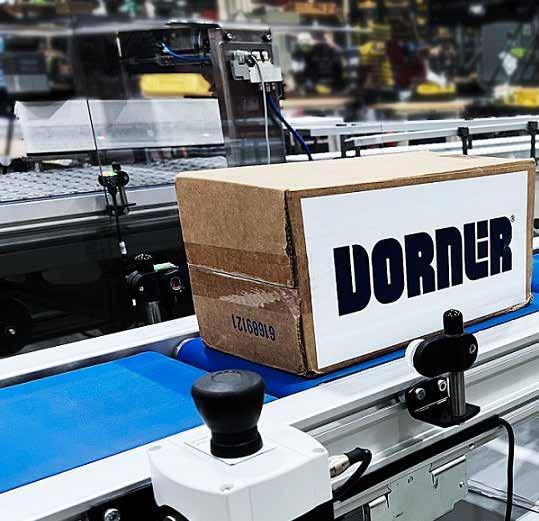
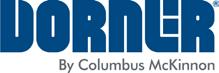
The AquaGard GT conveyor, a joint effort of Dorner and Garvey, combines the strengths of both companies. The meticulously designed infeed and outfeed conveyor prevents bottlenecks during the
accumulation function in packaging, bottling, dry food-processing and part-handling applications
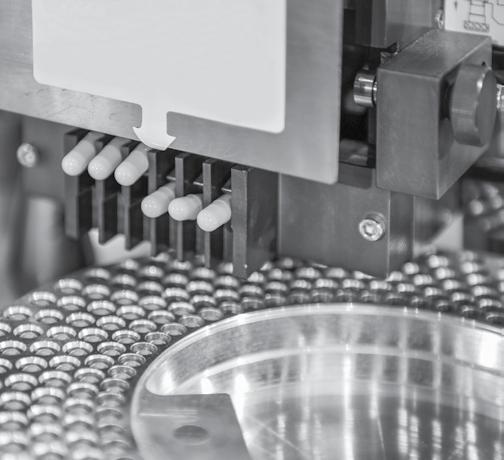
All components (except motors) are stainless steel or FDA-approved plastics, which are ideal for operating in environments that require wipe-down or occasional washdown of the conveyor.
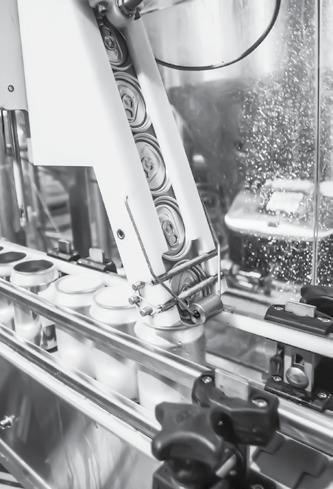
The AquaGard GT system integrates features and benefits such as powered transfer units, flush side tails
and pre-engineered transfer modules, among others, which in-house machine builders cannot match. The conveyor is competitively priced and comes with a short 10-day lead time.
At PACK EXPO Las Vegas, the AquaGard GT system is operating in a fully functional loop with Garvey Infinity™ and Bi-Flow™ accumulation tables. A versatile machine, the Infinity table uses Garvey’s patented technology to accumulate and sort unstable products at high speeds into a single or multi-lane configuration. The Bi-Flow table uses opposing conveyor movement to create a buffer for product accumulation in a small footprint. The loop also includes Dorner’s FlexMove Helix and Wedge conveyors, which enable vertical product movement to accomplish more in less space. This demonstration illustrates the seamless integration Dorner and Garvey can bring to accumulation applications.
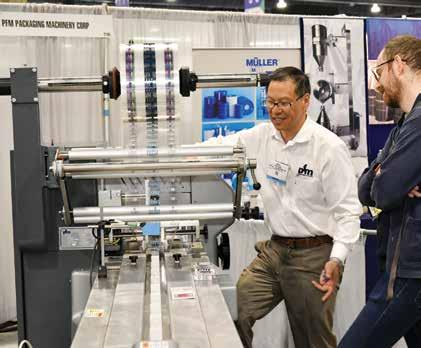
The second operating loop highlights the DCMove belted and the 2700 Medium Duty conveyors. DCMove conveyors provide a streamlined approach needed by more industrial-focused material-handling applications. A painted steel frame combines strength and agility.
The second portion of this loop, the 2700 Medium Duty conveyor, adds an extra boost in load capacity to carry heavier products for industrial automation and packaging applications, including palletizers, multi-lane processing, case and tray handling and end-of-line packaging.
The third operating loop, linking two 3200 Series conveyors with Activated Roller Belt (ARB) technology, belted Edge Roller Technology (ERT), a FlexMove side-acting merge module and a powered side guide, showcases Dorner’s package-handling capabilities.
Conveyors with ARB technology are perfect for moving boxes and packages in merging, diverting and aligning applications. They use low- and
high-friction angled rollers within the belt to help smoothly guide and align items. ERT platforms employ Dorner’s patented Edge Roller gear-drive tech nology to move product smoothly for pacing packag es, bags and boxes. The FlexMove side-acting merge module is a fully mechanical design to easily merge products from two lanes into one on FlexMove con veyors. Finally, Dorner’s powered side guide posi tions a compact 2200 Series belted conveyor on its side to create a simple pneumatic side-plow guide, which can pull or eliminate gaps as needed.
The fourth operating loop highlights Dorner’s sanitary platforms. The AquaPruf VBT (vertical belt technology) conveyor, designed to move bulk products in straight-up 90-degree sanitary applications, features a proprietary staggered sidewall belt designed to increase pocket capacity and improve product release.
The AquaGard LPZ conveyor can be configured with one or two fixed-angle points, which allow the conveyor to accommodate a variety of height and angle requirements.

Lastly, the AquaGard Modular Belt conveyor features a center bearing to eliminate friction. It can carry a heavier load and allows four curves to be driven by a single motor, which saves valuable floor space as the conveyor can make tight turns around existing machinery and equipment without being hindered by extra motors.
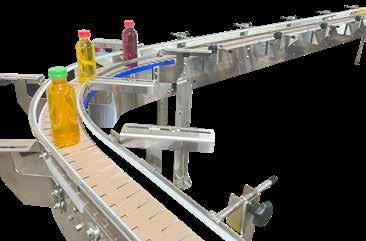
Finally, Dorner will feature the versatility of the low-profile 2200 Series conveyor in its own operating loop. This conveyor features a stronger, single-piece frame design that reduces the overall number of needed stands. The frame is a Universal T-Slot compatible with industry-standard hardware, making attaching accessories and guiding fast and simple. The 2200 Series loop moves product through 90-degree turns as it diverts items quickly and accurately into various lanes
with the use of Precison Move technology.
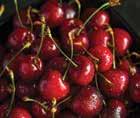

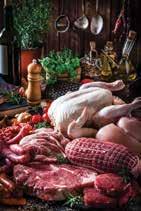
For pallet movement, Dorner is showcasing the Shuttle ERT250 pallet conveyor, which uses rollers to move pallets smoothly with no friction.
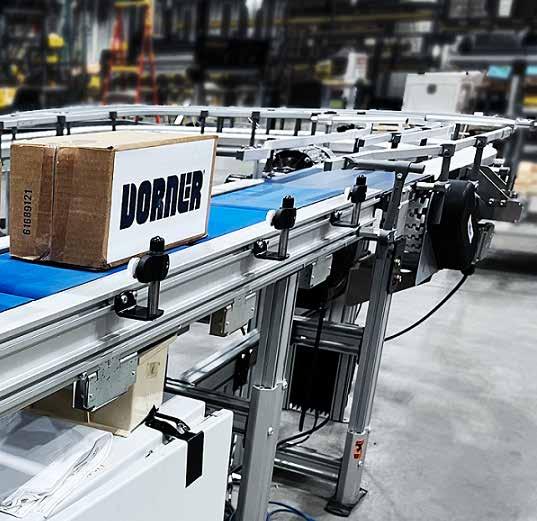
Rounding out the show will be a demo of Columbus McKinnon’s newest acquisition—montratec and its intelligent monorail shuttle system—which will be expanding into more markets soon.
For more info, visit dornerconveyors.com. SD
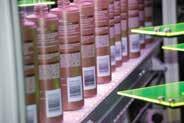
With the Product Inspection Experts
MSU renovates School of Packaging

Investment modernizes and expands the facility.
The newly renovated School of Packaging building at Michigan State University (MSU) (Booth N-9016) has opened following a campaign that raised more than $10 million. “This significant expansion of our facilities, enabled by the generosity of donors and stakeholders, will reinforce MSU’s longstanding leadership in packaging education,” says MSU Interim President Teresa K. Woodruff, PhD. “These improvements anchor our commitment to the excellence of our School of Packaging and will help us prepare the next generation of leaders in packaging science.”
Established in 1952, the MSU School of Packaging was the first school of packaging in the U.S and now is the largest packaging program in the country, with more than 600 undergraduate and graduate students. Housed within the College of Agriculture and Natural Resources, or CANR, the School of Packaging consistently earns top rankings in its field across a wide range of rating platforms. It is the only school that offers a PhD program in packaging and boasts 10,000 alumni worldwide.
Upgrades to the facility, which was last updat-
ed in 1986, will help MSU remain a leader in the packaging field. The renovation helps to modernize teaching and learning by adding flexible classrooms that seamlessly integrate technology. Collaboration-friendly spaces invite industry partners to engage with students, and the modernized facilities will attract faculty by providing the proper space and tools to conduct world-class research.
The renovations were supported by commitments to the project totaling more than $10 million from alumni and donors, including lead gifts from Amcor, parent company of Amcor Flexibles North America/Amcor Rigid Packaging (Booth SU-7244, SU7254) and Amcor Healthcare Packaging (Booth SL-6635), Charles and Jackie Frasier, and Ring Container Technologies.
Amcor made a transformative gift to establish a partnership to create a modern, collaborative environment for students and faculty that will serve as a hub for sustainable packaging thought-leadership across industry, academia, governmental agencies and nongovernmental organizations. The Amcor partnership also established the Amcor Endowed Chair in Packaging Sustainability. Rafael Auras has been named to this endowed chair with a focus on research and teaching in the areas of full life cycle and environmental modeling and analysis, development of novel sustainable materials and solutions, and sustainability through leadership across all stakeholders in the packaging value chain.
Charles and Jackie Frasier of Ft. Lauderdale, FL, made both the first gift to launch the renovation campaign and the last gift needed for the first phase of renovations to begin. The Charles L. and Jacqueline C. Frasier Atrium is a focal point at the building’s entry, and the Charles L. and Jacqueline C. Frasier Sustainability Lab will help advance the school’s research and data-driven approach for finding sustainable solutions and responsible end-of-life packaging innovations. Additionally, the Frasiers committed another $1.5 million to endow a professorship through an estate gift.
Ring Container Technologies provided support to renovate the main corridor, renamed the Ring Container Technologies Innovation Hall, re-imagined with collaboration in mind. The expanded space connects to the Frasier Atrium and welcomes both large and small groups of students, faculty and industry partners. This prominent space will quickly become a preferred gathering location, not only because of its various collaboration spaces, but also because of its comfortable, bright and modern design.
In-kind gifts of equipment also were essential to provide modernized technology to teach students the packaging industry standards of today and to research packaging and sustainability options for the future.
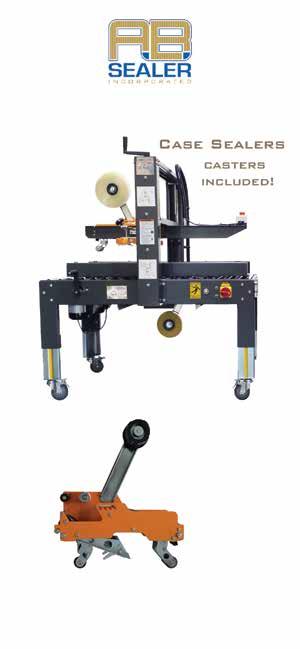
IMV America donated a custom-built, unique multi-axis vibration system for students and researchers to test and study the effects of vibration during product
shipping. A vibration test system simulates the types of vibrations packages endure during handling, transportation and shipping. Traditional vibration tables are limited to a single vertical motion, but the IMV multi-axis system more accurately simulates complex motions such as pitch and roll.
Lansmont, part of the Physical Properties Testers, or PPT, Group, extended its investment in packaging durability testing and research by donating test and measurement technologies for the Lansmont/PPT Group Laboratory. Its in-kind equipment donations will include a TruMotion Acceleration Sled system, updated data acquisition system, vibration table controller and software, shock table and controller, as well as next-generation SAVER units.
A gift from Specright (Booth SU-7670) helped refresh the computer lab so packaging students can prepare for the work world with hands-on technology training. The Specright Computer Lab includes new computers, monitors and furnishings in a remodeled setting. The company also provided the Specright Specification Management software platform on all computers and extended its partnership to help develop an MSU short course for packaging industry professionals to learn how to leverage specification data through analytics and digital tools.
Additional gifts included:
• Greg and Kathleen Hayes Graduate Commons Space to provide exclusive space for graduate student collaboration, meetings and breaks.
• The William J. and Mary Lou Sommerville Conference Room—in memory of former MSU President John Hannah and early influential packaging professors Harold J. Raphael and James Goff. The renovated conference room includes full video conferencing capabilities. For more info, visit packaging.msu.edu, amcor.com, specright.com. SD
Editor’s Note: The original version of this article was posted by Packaging World on April 24, 2023.
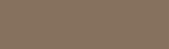
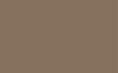
CAPTURE THE WINDS OF CHANGE. QUICKLY, AND WITH GENTLE HANDLING. BROUGHT TO LIFE WITH SCHUBERT.

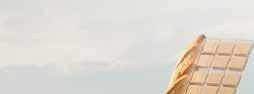
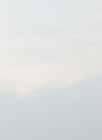
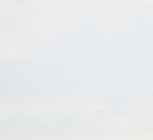
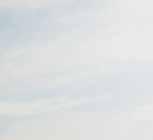

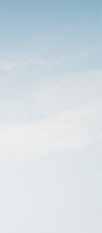
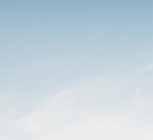
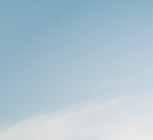
Fresh, crispy baked goods are delicious, But they tend to crumble during packaging. Our solution: gentle robotic hands and a 3D scanner to monitor quality. In a machine that adapts to a wide variety of products in no time at all, Packaging them fully automatically in sustainable materials. In line with our Mission Blue: Only if it’s good for the planet, it’s good enough for our customers. www.schubert.group/en/Confectionary-snacks/
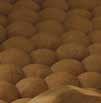
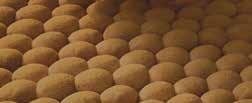
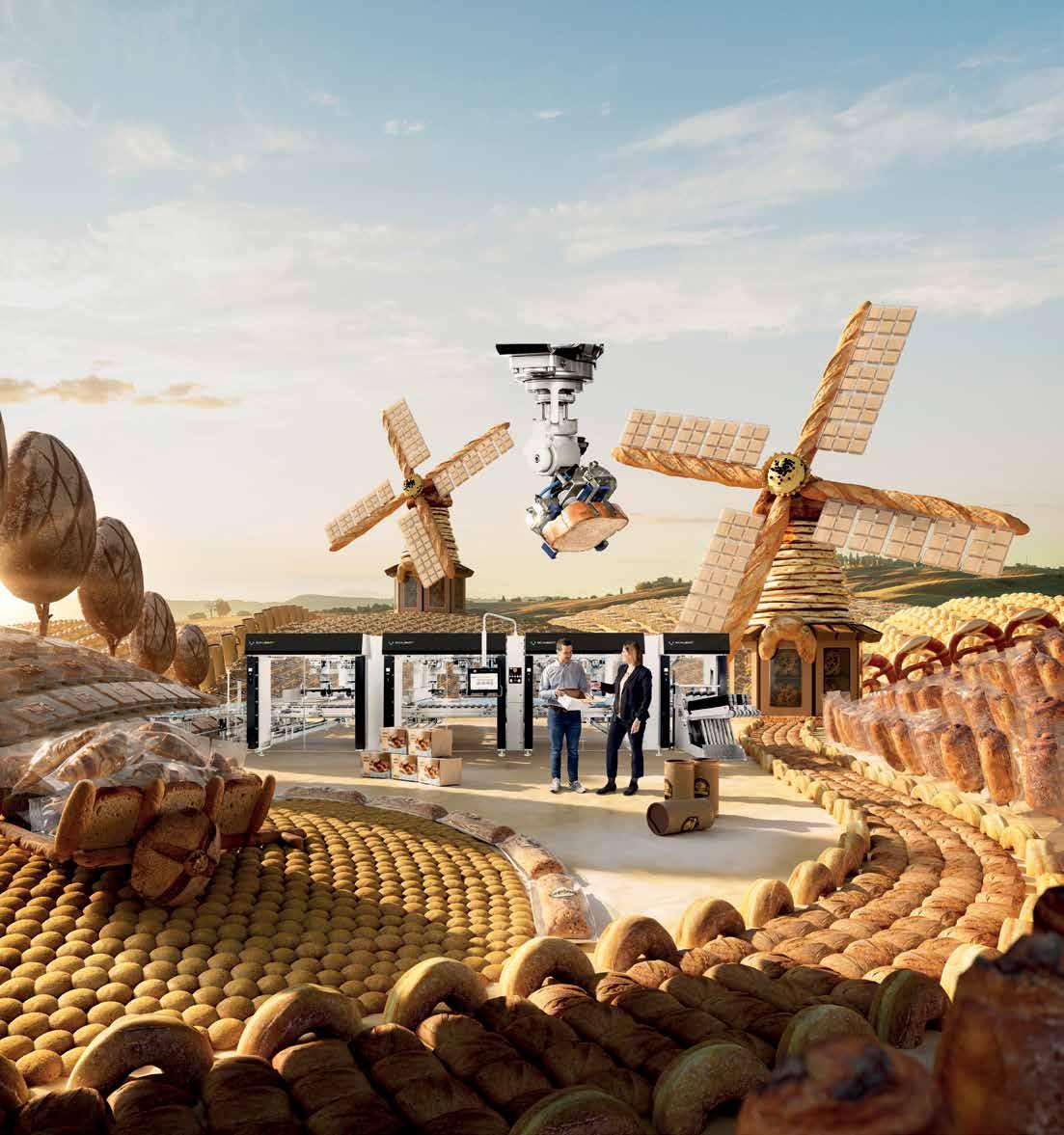
SEPTEMBER 13, 2023
Forum sessions draw crowds
Returning to PACK EXPO Las Vegas, The Forum—An Industry Knowledge Exchange (Booth C-2158) features free, 45-min. workshops and interactive sessions on a variety of trending topics such as digitalization, cybersecurity, emerging brand development, artificial intelligence and Digitial Twins, as well as updates on courses and reports associated with the dairy industry, the cold chain, the circular economy, environmental/social/governance strategies, co-manufacturing/co-packaging trends and sustainability. Session descriptions, times and locations are listed below. Updated schedules

may be found on the show website or via the show App, sponsored by ProMach (Booth C-3222).
Other free educational opportunities on the show floor include the new Sustainability Stage (Booth N-9967) (see schedule, p. 16), the new Industry Speaks Stage (Booth C-1141) (see schedule, p. 24) and the Innovation Stage (Booths C-2051, C-2058, C-2151)/Processing Innovation Stage (Booth N-10511) (see schedule, p. 30). Schedule as of August 23, 2023.
For more info, visit packexpolasvegas.com. SD
WEDNESDAY, SEPTEMBER 13, 2023
BEST PRACTICES OF SUCCESSFUL COMAN/ COPACK RELATIONSHIPS
10:30-11:15 AM
TBD
Ron Puvak
Exec Dir Contract Packaging AssociationDIGITAL TWIN APPLICATIONS: PROCESSING/ SUSTAINABLE PACKAGING
11:30-12:15 PM
Digital Twin technology appears to be the starting point for any operational digitization of industrial processes and the innovation of business models. Learn how Digital Twin supports the interoperability and sustainability of supply chains.
Giuseppe Padula
Regional Branch Organizer
Digital Twin Consortium
Zinet Boz
Asst Professor
University of Florida SD
EXPO PACK shows set for ’24, ’25
PACK EXPO Shows return to Mexico with EXPO PACK México (June 4-7, 2024; Mexico City) followed by the EXPO PACK Guadalajara (June 10-12, 2025; Expo Guadalajara, Guadalajara, Jalisco, Mexico).
The events will build on this year’s record-breaking EXPO PACK Guadalajara (June 13–15, 2023), which brought together nearly 16,000 packaging and processing buyers and 700 exhibitors in more than 15,000 sq. m. of sold-out exhibit space.
Returning after four years as the largest show in its history, “EXPO PACK Guadalajara 2023 surpassed our expectations in terms of innovation, industry engagement and global representation,” says Celia Navarrete, EXPO PACK director. Exhibitors showcased groundbreaking technology that addresses sustainability, efficiency and consumer convenience. Many of these innovations were showcased at standing-room-only Innovation Stage sessions.
In addition to the Innovation Stage, EXPO PACK Guadalajara, in conjunction with Mundo PMMI, offered keynote presentations featuring leading companies such as Walmart, Kraft Heinz Mexico and Casa Herradura (Brown-Forman).
Additionally, the Packaging & Processing Women’s Leadership Network (PPWLN) held its first
keynote address in Guadalajara, sponsored by Polypack (Booth C-1844). “We are thrilled with the overwhelming success of the PPWLN presentation at EXPO PACK Guadalajara,” says Montserrat Cerf, export sales director at Polypack and member of the PPWLN Executive Council. “It was inspiring to see the tremendous support and engagement from attendees, reinforcing the importance of diversity and inclusion in the packaging and processing sectors. We are committed to growing the PPWLN Network in Latin America and continuing our efforts in empowering women and creating opportunities for their professional growth within the industry.”
EXPO PACK Guadalajara welcomed exhibitors and attendees from around the world, providing a truly global platform for knowledge exchange, collaboration and market expansion. International pavilions represented Argentina, Canada, China, France, Italy, Spain, Turkey and the United States.
EXPO PACK Guadalajara 2023 emphasized sustainability as a core theme. As part of the EXPO PACK Verde program, exhibitors showcased eco-friendly packaging alternatives, recyclable materials and sustainable manufacturing practices, highlighting the industry’s commitment to environmental responsibility.
The exhibition served as a meeting point for industry professionals, fostering valuable connections and business opportunities. The Vision 2030 breakfast brought 120 industry leaders together to discuss the robust growth in the investment in packaging equipment in Mexico and Latin America. The event featured a panel discussion of best practices for the procurement, startup and maintenance of equipment.
Leading associations recognized the significance of EXPO PACK Guadalajara with 11 strategic partners supporting the show. AMEE, the Mexican Packaging Association, hosted its member Congress on technologies facing the challenges of circular economy and eCommerce. The group also announced the winners of its Envase Estelar Contest.
“For us it is very important to link the entire value chain and boost the economy,” says Laura Bonilla from Unilever Mexico and president of CANAINCA, National Chamber of Canned and Food Processing Industry.
With its successful conclusion, EXPO PACK Guadalajara 2023 reaffirmed its position as a premier event for the Latin America packaging and processing industries.
For more info, visit expopackmexico.com.mx, expopackguadalajara.com.mx. SD
Exhibitions serve dynamic Latin American market.
Portable conveyor aids flexibility Manual divert gate shunts product to alternate destination.


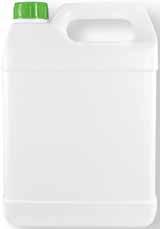
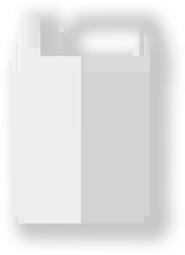
Bagged food products split from one lane into two lanes of travel on a system from Multi-Conveyor (Booth C-1718). The system features a two-position manual divert gate and a single pin-pull interlock release that allows disconnect of a portable conveyor for relocation.
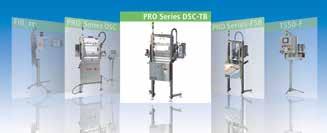
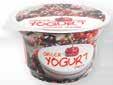
The fixed position 8-in.-wide by 25-ft.-long tabletop conveyor employs two 90-degree curves to shape the system in the end user’s required footprint and feeds a downstream case packer. When required to send product to an alternate packing destination, an adjoining 13ft., straight-running portable conveyor can be wheeled into place and pin-locked to the fixed main line.
Just prior to the first curve, a manual product divert gate was installed to transfer product to the desired packing area.
A video (youtu.be/HQsjZyYQzMk) shows how the manual divert is easily moved into and out of position. Multi-Conveyor 1:2 (one-to-two) diverts divide product into two lanes of travel and include gates, paddles or guides that can be activated manually or automatically using PLCs.
A cost-effective, pin-in-place interlock marries the conveyors. The connecting straight-running section is

on 6-in.-diameter castors for portability. This gives the customer flexibility to move the conveyor out of production, allowing operator access to other critical functions.
The washdown-safe conveyors include slotted
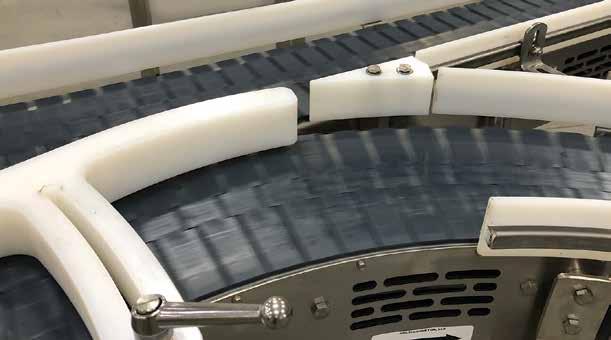
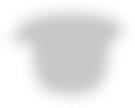
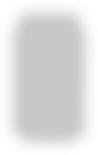
cleanout holes and bolted construction with continuous welds. In this case, the motors and reducers were not required to adhere to washdown specifications.
For more info, visit multi-conveyor.com. SD

Labeler automates changeovers
Servo system reduces operator ‘touch time’ 80%.
Afully automatic changeover system from Nita Labeling Systems (Booth C-5433) boosts labeling efficiency 80% or more. “It’s the first all-servo fully automatic changeover system on a labeler built in North America,” reports Ken Hubscher, vice president Sales and Marketing at Nita Labeling Systems.
He explains the impetus behind the development. The average labeling machine requires the operator to spend time doing changeover. He says, “Most labelers have little to no repeatability so the time factor in changing over from one container to another is significant. Maybe 30 min. Maybe more. Perhaps your labeler has scales, or some dials built in which saves a little bit of time as long as your operators wrote down an accurate recent setting (and that the handwriting is legible!).”
Once all the adjustments are made, particularly the crucial alignment of the labeling head axis, the task of fine-tuning these mechanical adjustments now comes into play. Unfortunately, if any setting is just a few millimeters off, wrinkled or misplaced labels are likely. Hubscher says, “This leads to frustration and downtime on your production line. You also know that your operators (who often are new and inexperienced) rarely understand how to remedy these issues. You are frustrated and your line is suffering.”
According to a study published by PMMI, The Association for Packaging and Processing Technologies (Central Lobby), at the end of the day, up to 13.3% of production downtime across North America is directly related to a labeling, decorating or coding system and that 21.1% of downtime is caused by operator error. (1)
That is unacceptable, so Nita devised a solution: a 100%-servo, fully-automatic changeover system. Full automation generates many benefits.
It can reduce operator touch-time on the machine by 80% or more, so operators can spend more time tending other parts of the line. “This directly influences uptime and overall efficiency,” says Hubscher.
The need to fine-tune the machine is taken out of operator hands. Each servo-run axis is capable of rep-
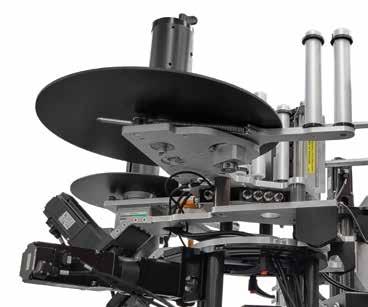
WHY AUTOMATED CHANGEOVERS?
Skilled labor is hard to find
Turnover among trained workers is high
The less operators touch the machine, the less chance of negatively impacting the labeling process and line output

The less operator touch-time on the labeler, the more time to tend other parts of the line
Precise, repeatable adjustments are needed to ensure accurate label placement and product quality
Ultra-precise servo axis adjustments automatically bring the three critical head adjustment points to within 1/256 in. of their position the last time the product ran
Eliminating manual fine-tuning saves time and reduces the level of expertise operators must have Precise label placement ensures product quality and eliminates expensive and time-consuming rework
High product quality is perceived by consumers as higher value
Operator frustration is reduced
Output increases
licating its position to within 1/256 in. of its previous setting. “That is essentially a perfect re-placement of that labeling component . . . as in ‘zero deviancy,’” says Hubscher. “No mechanical system can come close to that! This will save your operators frustration and a ton of time. (Of course, every standard Nita labeler is equipped with an advanced in-screen, step-by-step 3D map of the machine, plus color-coded and numbered
scaled guides and dials on every adjustment point to simplify changeovers and cut typical product changeover times at least 50%.)”
The ultra-precision delivered by the high-tech servo actuators mitigate nearly all label placement issues such
as height, skew and wrinkles. As a result of this perfect replication, precision and quality increase, and re-work essentially disappears. “This saves incredible amounts of time and money on staff required to fix mislabeled products or on the cost of having to discard product that cannot be reworked,” explains Hubscher.
At the end of the day, the unrivaled speed of changeover, ease of operation and application precision due to taking adjustment out of the operator’s hands, make the line more efficient and increase productivity. “As an added bonus,” says Hubscher, “the extremely consistently labeled products will result in a higher value brand perception by the end consumer (not to mention some happy faces from the marketing and branding departments)! Imagine all this at the push of a button.”

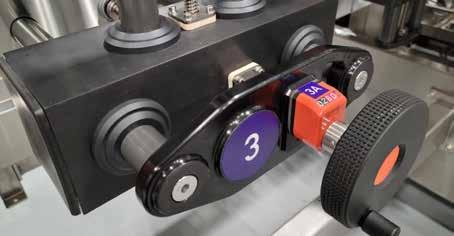
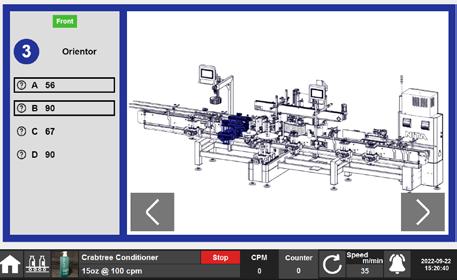
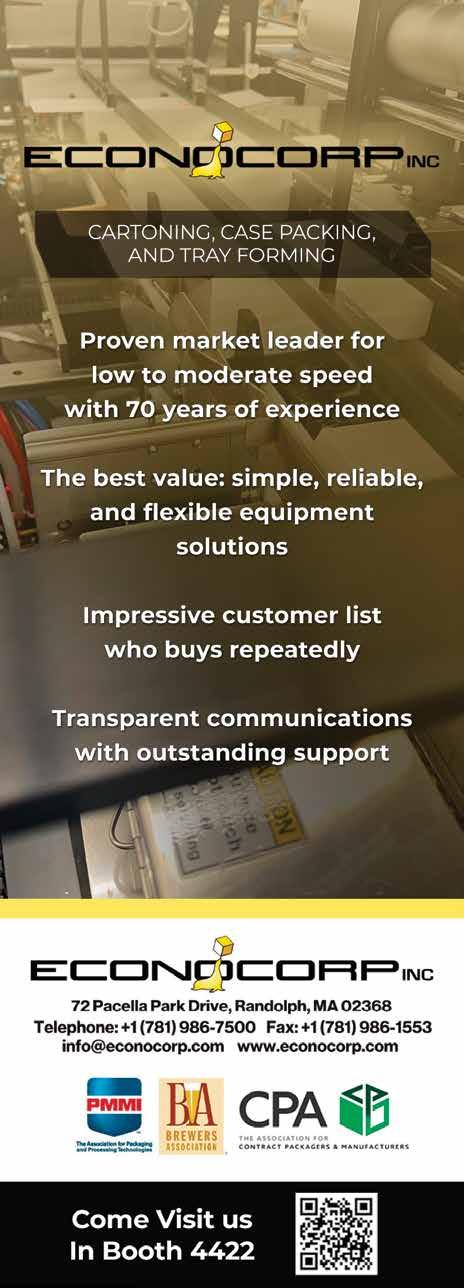
For more info, visit nitalabeling.com. SD
1PMMI Business Intelligence, “Packaging and Predictive Maintenance,” White
2021.
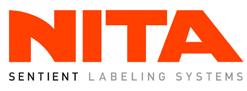
Contest honors sustainable designs
Winners discuss what inspired their submissions.
The third international Better with Less–Design Challenge, organized by Metsä Board (Booth N-9216), invited designers to create zero-waste packaging. The competition drew 124 entries from 27 countries. Six entries received recognition.
The competition jury, which consisted of packaging design experts from around the world, chose two submissions to share First Place: Kid’s Headphones Packaging and the Paperboard Protecting Filler.
“Choosing the winner from such excellent entries was an incredibly difficult decision, so the jury decided to select two first-place winners,” says Ilkka Harju, chairman of the jury and packaging services director at Metsä Board.
The Kid’s Headphones Packaging by Kitty Ching focuses on consumer usability and recyclability. According to the jury, the elegant design engineering provides easy-to-open packaging and excellent protection for the product. It also allows reuse, as the inner part of the packaging provides an option to store the headphones.

The Paperboard Protecting Filler by Marcin Michalski, Monika Klimpel and Adrian Olejnik serves as a transport package for a TV or other electronics. A beam-like structure protects the contents on each side of the package. The lightweight and durable fiber packaging supports the circular economy in terms of easy recycling and source reduction.
THIRD PLACE
Third Place was awarded to David Thiel for RESHAPE, a packaging concept designed to accommodate a wide range of products. The packaging format significantly reduces the number of packaging components that need to be stored. Graphics guide consumers to tailor the packaging to their specific needs.
STUDENT WINNER
The Zero-Waste Medication Blister Pack by Patrick Walby earned an internship at Metsä Board’s Paperboard and Packaging Excellence Centre in Finland. The pharma industry package aims to replace the plastic and aluminum used in medication packaging with paperboard.
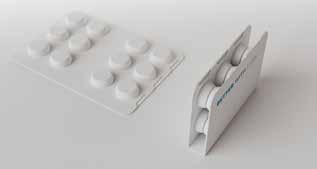
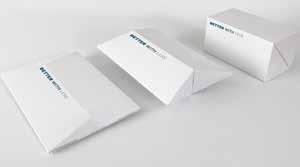
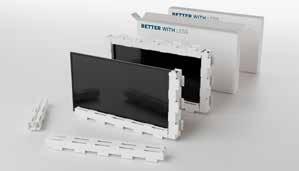
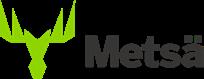
HONORABLE MENTIONS
Two Honorable Mentions also were awarded, one for Totally Bananas packaging, designed by Max Gubbins, and the other to F’lover packaging, designed by Mine Koca.
DESIGNER ROUNDTABLE
After the winners were chosen, Metsä Board convened a roundtable to reveal insights about the motivation and inspiration behind their design concepts and sustainable package design.
Q: What was the initial idea for your Better With Less entry?
Thiel: The core idea of RESHAPE was reduce and reuse—reduce the consumption of raw materials (i.e., water, energy, wood) and reuse the same packaging many times in a variety of ways.
Walby: I began by brainstorming about the variety of packaging that I see and use in my daily life, ranging from food and convenience packaging to consumer packaging. The idea for the Zero-Waste Blister Pack came to me when I was taking medication for a headache. Seeing the empty plastic blister pack end up in the [rubbish] bin made me think there had to be a more sustainable way of packaging medication.
Ching: I noticed that there wasn’t a circular solution for low- to mid-range headphones, especially for junior/kid’s products, the assumption being that most kids would lose the product before they outgrow it.
Koca: A zero-waste experience was one of my main goals. I aimed to find a design solution with the folding method without using extra materials such as plastic, glue or a lot of paperboard. In addition, I wanted a single branch or a small bouquet of flowers to be giftable, to look minimal and stylish, and I thought I could achieve this with a minimal packaging design.
Ching (Kids Headphones Packaging): I wanted the challenge of packaging an irregularly shaped object.
Gubbins: We wanted to create something potentially disruptive and beautiful. Totally Bananas Packaging is a zero-waste packaging alternative because there actually is no packaging. Small and shallow holes are pierced in the skin of the banana which accelerates the bruising of the skin in just that area. This allows graphics and communication of information on the surface of the banana with no ink.
Koca: I thought that the use of plastic and paperboard in the flower packaging sector is unnecessary and that more minimal designs can be created. By making a functional design with less paperboard, F’lover is a package that is easy to produce, transport, store, display and recycle.
Q: Why did you pick this particular category/ packaging design for this product?
Walby: When it came to creating a sustainable blister pack, there was no need to reinvent the wheel but rather reframe it with circularity in mind. The current form of the packaging works and just needs to be redesigned slightly to make it both structurally sound and usable when producing it out of paper. Instead of pushing medication out of the foil seal, the paper can be peeled back and designed so that it can accommodate different size medications.
Michalski: The filler project had earlier appeared in our internal research and development program. The Better with Less competition is the first time we presented this concept to a worldwide audience. We are constantly working on its development and improvement.
Thiel: This solution is directly connected with delivery services/eCommerce and could make a huge impact by minimizing the carbon footprint (through the reduction of empty space in transport). ∆
Leading-edge technology trusted worldwide for superior product inspection and contaminant detection.
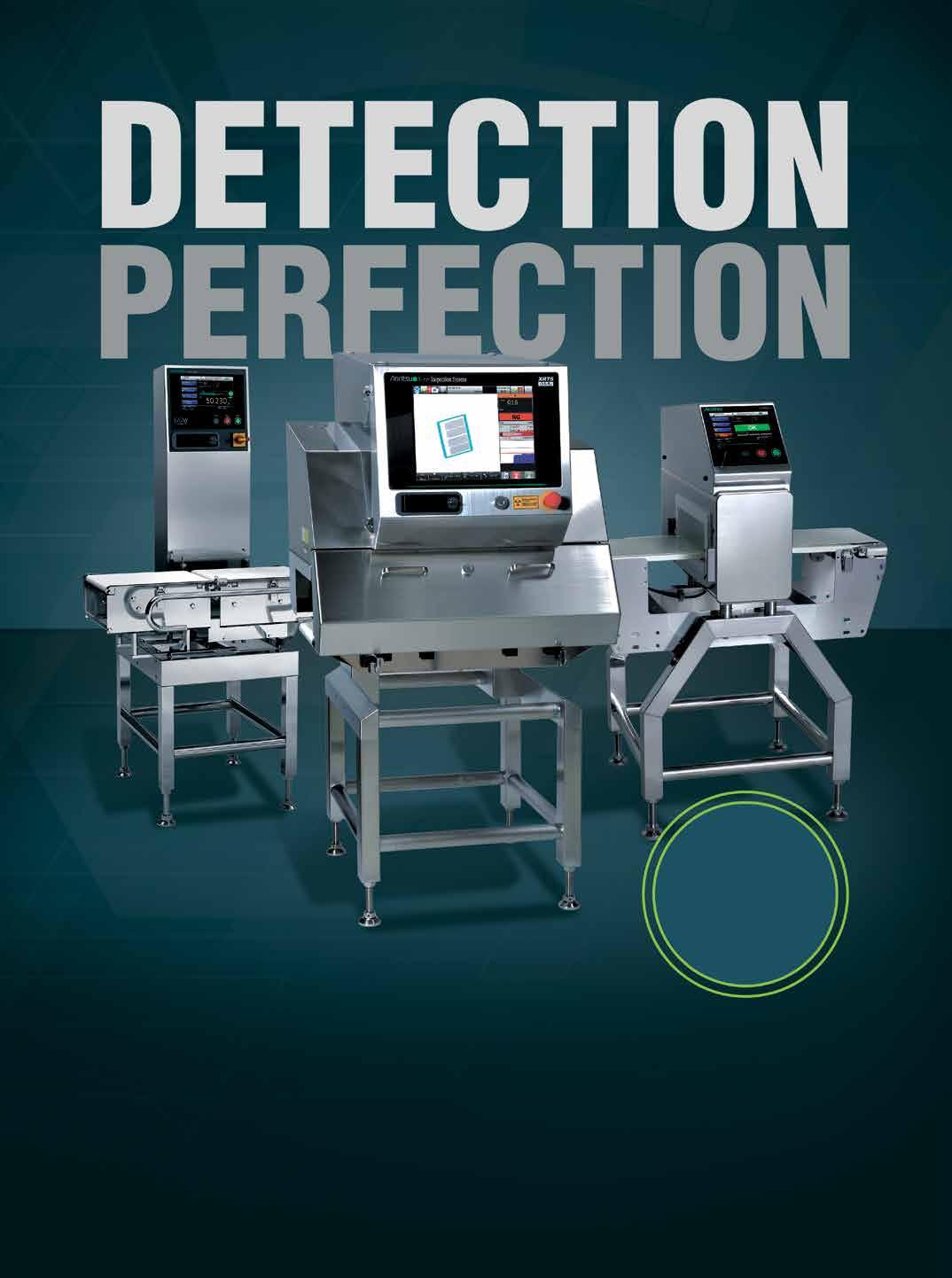
Your brand is on the line, so you need equipment that’s better than good. Anritsu systems deliver performance, reliability and low total cost of ownership Plus, we back our long-lasting equipment with unparalleled service and support.
Discover what you’ve been missing. Learn how to advance your product quality and operational efficiency at anritsu.com/infivis.
VISIT BOOTH SL-6163
M6 METAL DETECTORGubbins: These zero-waste solutions are applicable to nearly everything, it’s just a matter of changing consumer habits and industry mindsets. Manipulating the exterior natural protection of fruits and vegetables to communicate information is certainly possible for much of what we eat. The piercing of the skin like we suggest with bananas is probably limited to bananas and select other fruits.
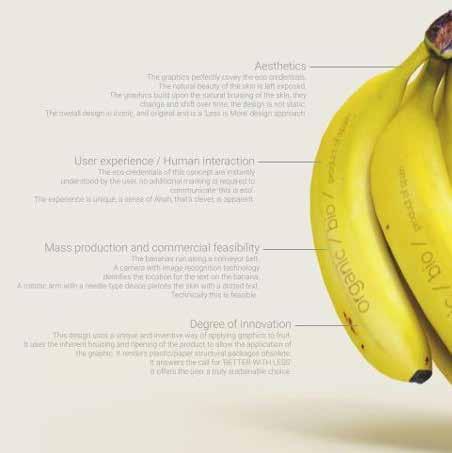
Q: What do you think the future is for your design concept?
Walby: There is no doubt that we need to start
designing for a sustainable future, and I hope this design concept can spark change, particularly in the pharmaceutical industry. Currently, the medical and pharmaceutical industries produce a lot of waste with one-time-use packaging made of both hard and soft plastics. Finding areas that can be moved toward using more sustainable and zero-waste materials such as in the creation of blister packs needs to happen.
Michalski (Paperboard Protecting Filler): We would like our fillers to be widely used as soon as possible. After winning the Better With Less com-

A NEW HUB FOR OPPORTUNITY
petition, we hope to promote our concept to electronics and other manufacturers around the world.
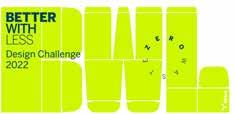
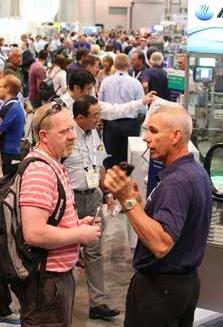
Ching: Ideally, I hope it becomes the standard for headphones, creating uniformity in stores, encouraging all users to care for their belongings because the packaging is for keeps.
Gubbins: We want to collaborate with brands and supermarkets to bring the concept to life. It is these types of solutions that we need if the reduction of waste is the goal.
Koca: I think that more minimal packaging will be made in every field in the future. While not wasting our resources and sustainability issues are at the forefront, it is inevitable that packaging will move in this direction in every sector.

Q: What are the main challenges to creating beautiful and functional packaging that’s also a circular solution?
Thiel: The greatest challenges are the production capabilities and the balance between functionality and consumer-friendly. Most goods and products are packaged in over-engineered and wasteful forms that require an excess of materials. Creating beautiful and functional packaging does not have to be overly complicated but does require thinking outside of the box and exploring how you can get the most out of a packaging concept while reducing the number of materials used.
Michalski: The main challenge was to create a paperboard solution that would meet all the requirements of polystyrene fillers, such as strength, ease of forming, product protection and, of course,
price. The first idea appeared very quickly, but it took quite a lot of time to technically develop a ready-made product that would meet the expectations.
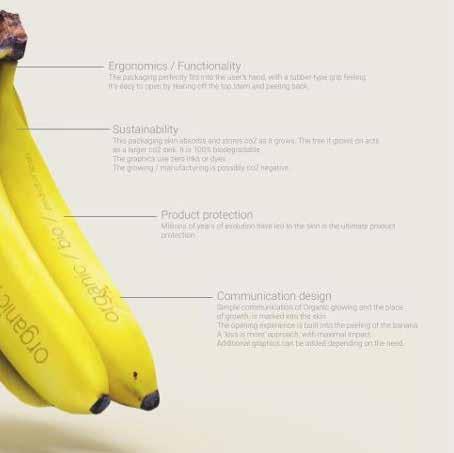
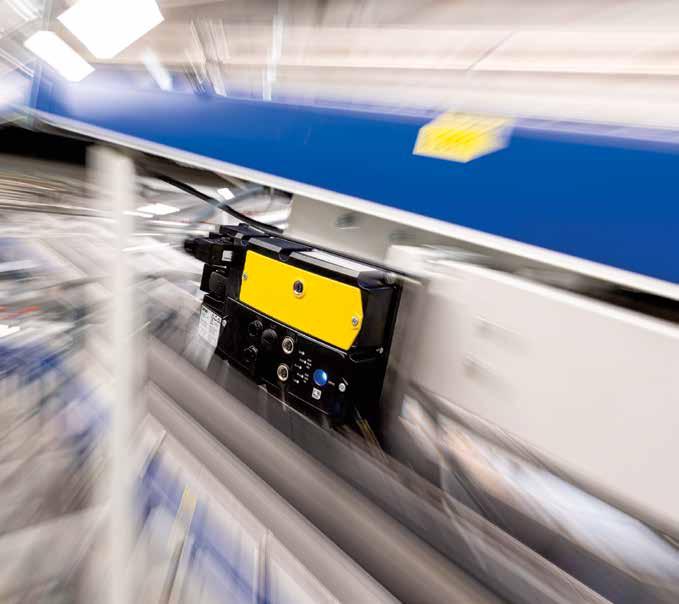
Ching: Main challenges include changing behaviors and education. We must educate others that packaging plays a vital role and shouldn’t be an afterthought so that companies invest in sustainable packaging and design for longevity. In addition, we need to educate the public to recycle and be mindful of their consumption of products/fashion and its impact on the environment.
Koca: The first difficulties that come to my mind are the use of uniform designs, the size of the products and the difficulty of carrying them, and the cost of a design that is both functional and aesthetic.
Gubbins: Circular options are just one potential solution to our waste problem. If circular is the goal, then governments need to provide systems to address the waste stream. Many cities still don’t have comprehensive programs in place. Beyond that, brands need to actually design packaging that can be recycled. Then customers must change their shopping habits and expectations of what packaging is. At Our Way Studio, we believe in reducing the packaging to be minimal, or even better, to nothing. Totally Bananas packaging aims to show how this goal is possible.
Q: What would be your advice for others looking to submit designs for this type of packaging challenge in the future?
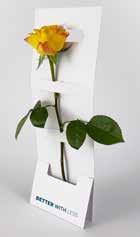
Walby: The best advice I can give is to explore a wide range of avenues that can be taken to package
your chosen product or goods. Beautiful packaging may not be as functional and vice versa—the key is to balance the two. Think about who would be picking up the packaging and using it, and how can I make packaging that meets the needs of my target audience while ensuring zero waste can be achieved.
Thiel: Try to understand real customer needs and the current situation of the market and try to develop your idea with a broad mindset and in line with
sustainability.
Ching: Go for it. Any well-considered design idea should be shared because it encourages others to also make eco-friendly decisions and facilitates conversations on sustainability.
Gubbins: Be brave, not mediocre. For more info, visit metsagroup.com/metsaboard. SD
Editor’s Note: The original version of this article was posted by Packaging World on April 10, 2023.
PET bottles contain sparkling wine

Bottle launched by SIPA and Indorama yields 2-year shelf life.
Polyethylene terephthalate (PET) bottles for sparkling wine move to market, the product of a collaboration between SIPA, parent company of SIPA North America (Booth SL-6662) and Indorama Ventures.
The award-winning PET bottle provides brands with a fully recyclable option that maximizes logistics efficiencies, minimizes handling risks, runs on existing glass-filling lines, offers a lower carbon footprint and costs less than its glass counterpart.
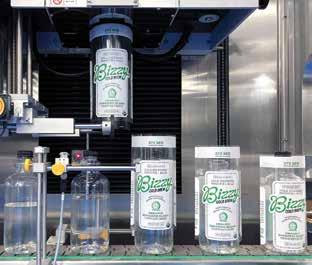
Designed by SIPA’s Packaging Development Team and made from Indorama Ventures’ modified resin and OxyClear® barrier, the patented bottle serves as an alternative to traditional glass bottles and addresses increasing energy prices and costs associated with traditional glass bottles. The PET bottle is designed as a dropin replacement to glass and is helping the European wine industry address a glass shortage due to supply chain, energy and raw material challenges.
Marc Potemans, business head of Specialty Chemicals at Indorama Ventures,
explains, “Indorama Ventures’ advanced barrier resin delivers a monolayer PET sparkling wine bottle with many advantages. The excellent oxygen barrier gives a minimum shelf life of 24 months, and the packaging has glass-like clarity while protecting the sparkling wine’s taste, bouquet and, importantly, effervescence. The new bottle is fully recyclable in the standard clear PET stream. The SIPA and Indorama Ventures teams have developed this solution quickly, and we can now support the full supply chain.”
The PET bottle offers the same look, functionality and feel of a traditional glass sparkling wine bottle and earned the top prize in the 2023 Best Packaging contest at Milan Design Week (April 1723, 2023; Milan, Italy).
The average cost of a glass wine bottle increased 23% between April 2020 and April 2023 and doubled in some European markets. These market con-
New FS2 MKII shrink labeler: Small footprint, Big performance
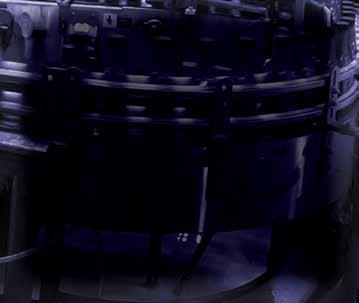
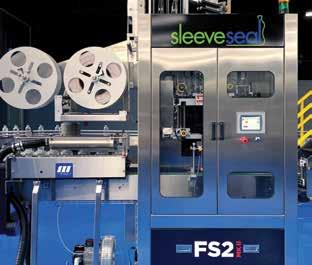
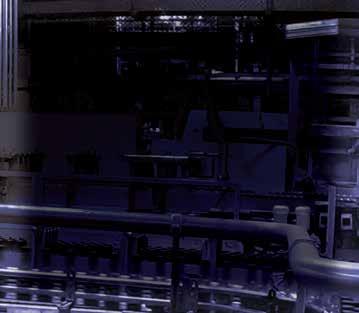
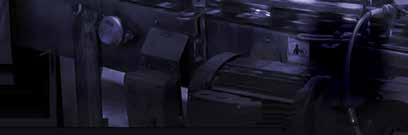
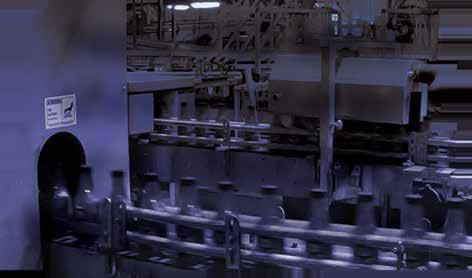

ditions helped expedite this innovation, which went from concept to prototype in less than six months. SIPA began developing the PET alternative to the sparkling wine glass bottle in 2022 and showcased the prototype that September at Drinktec (Sept. 12–16, 2022; Messe München, Munich, Germany). A green version was launched by SIPA and Indorama Ventures in May 2023 at Interpack (May 4–10; Messe Düsseldorf, Düsseldorf, Germany).
Following the launch, the partners proceeded to develop a transparent bottle so consumers can see the color and effervescence of the sparkling wine.
Dr. Patrick Amrhein, managing director, Indorama Ventures Polymers Germany reports, “The latest clear bottle innovation showcases how the partnership between Indorama Ventures and SIPA allowed us to face the challenge of creating a transparent, thick-walled PET sparkling wine bottle, by developing a modified resin that combines a monolayer barrier functionality with excellent glass-like appearance, in a record time of less than six months. This combines the touch and the appearance that results in an appealing PET sparkling wine bottle with a high shelf life.”
Numerous tests of the barrier material conducted

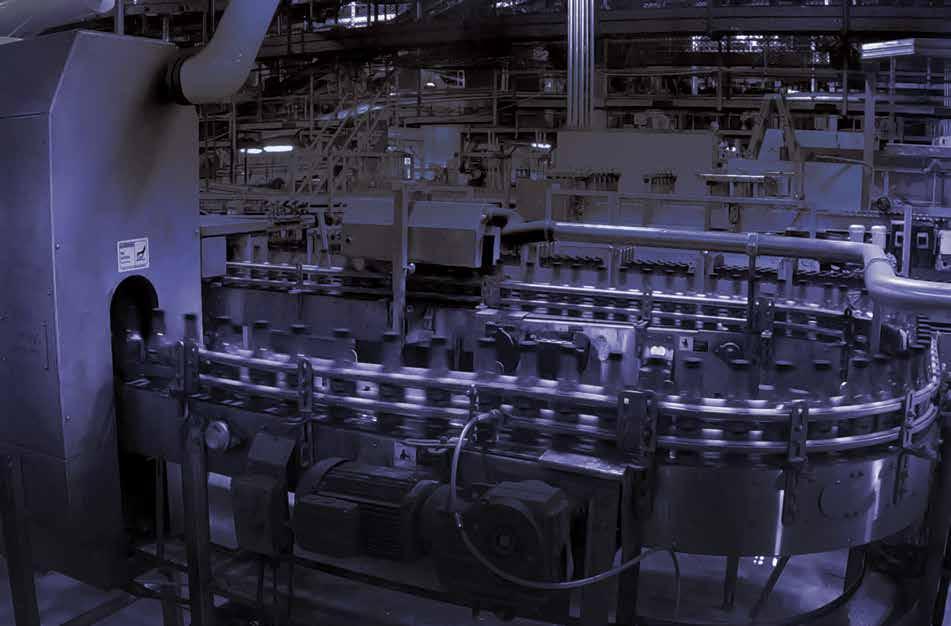
at the German Institute of Geisenheim show that OxyClear® PET wine bottles offer the same benefits and functionality of glass after 24 months in storage at 15 C (59 F).

The PET bottle is designed to run on existing glass lines without any modifications. The neck finish, height and waist circumference are identical to those of the glass version. The filling pressure can be left at 5.5 bar without any problems, and the bottler can retain its existing label and cork.
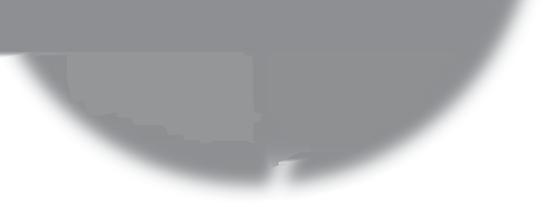
A key SIPA innovation is the design of the bottle neck to resemble the glass version and enable it to accept the classic mushroom-shaped cork with metal cage closure. The base also matches the original glass version, while the bottle has a top-load resistance of 350kg.
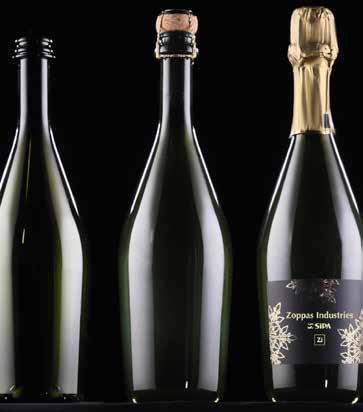
Compared to glass, the carbon footprint of the PET bottle is significantly lower. Glass is processed at 1,400 C vs. 260 C for PET. At just 90g, the new PET sparkling wine bottle is about 80% lighter than a traditional glass bottle and is almost unbreakable. The optimal weight allows up to 33% more bottles per truck, and its shatter-proof properties help improve mobility logistics. These advantages offer wine brands opportunities in new channels like eCommerce and on-board transport as well as new con-

sumption occasions at festivals and events.

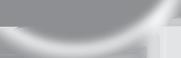


























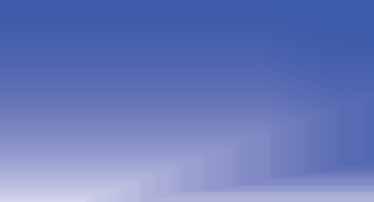
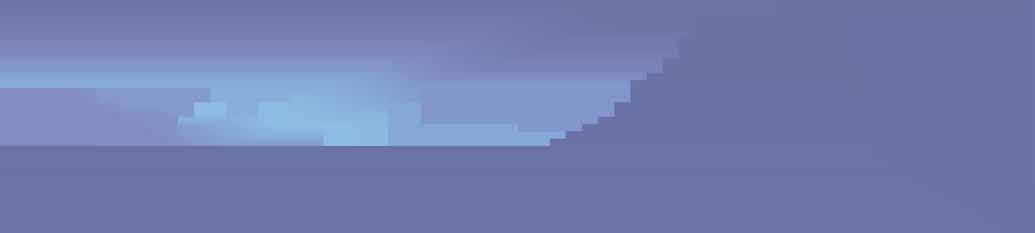
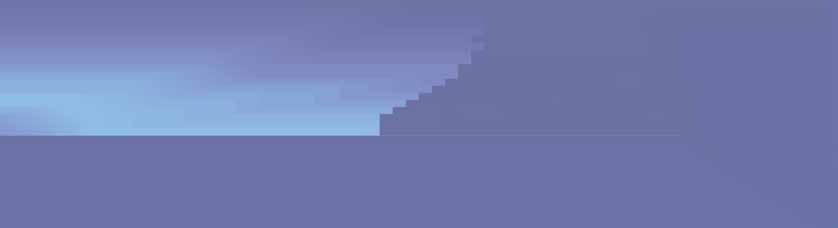
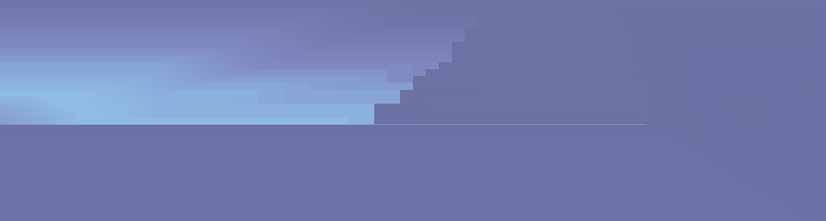
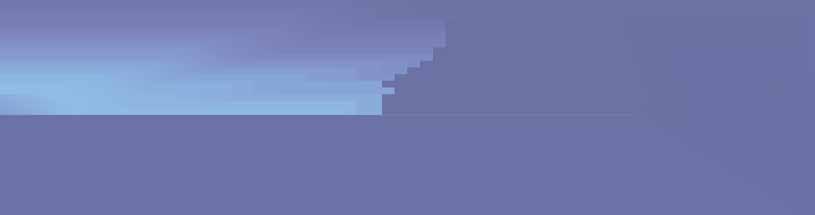
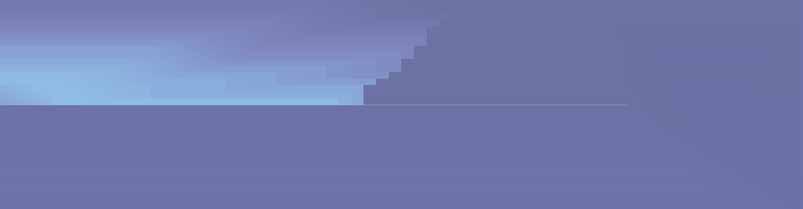
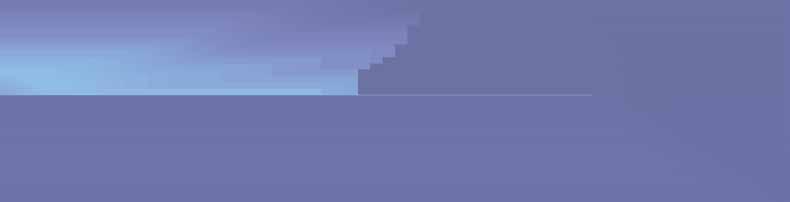
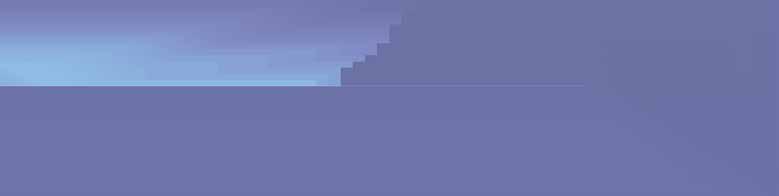

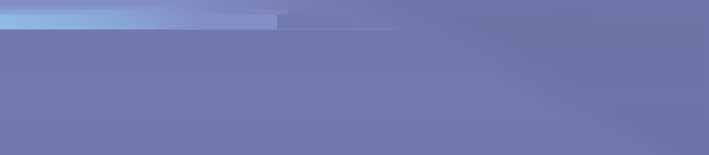

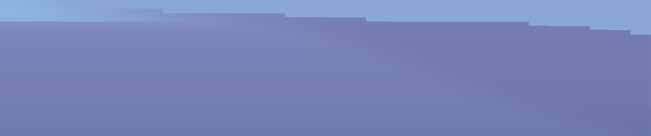

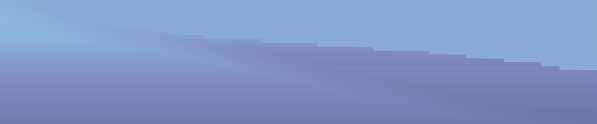
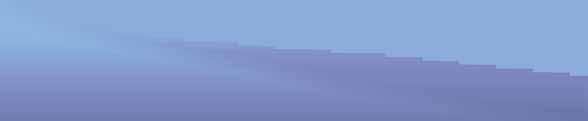
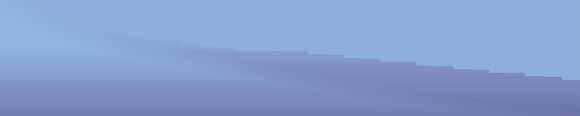



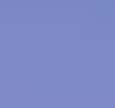


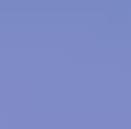
Marco Brusadin, global packaging development director at SIPA, says, “With this proud innovation for the market, our intention is for consumers to enjoy the same celebratory sparkling wine experience— from uncorking to pouring. And second, to support the industry overall as wine companies can make the change at no cost, as extensive tests have proven that PET bottles can run on filling lines designed for glass bottles. The collaboration with Indorama Ventures offers environmentally improved packaging, while allowing brands to stand out by taking a stance on sustainability and differentiating themselves at point of sale, with creative shapes, easy-to-design bottles and improved logistics.”
The new PET bottle comes with strong sustainability credentials to match consumer demands. It is fully recyclable in regular recycling streams, while PET on average emits less than half of the level of greenhouse gases (GHG) of glass bottles. This development is an important demonstration of how PET’s flexible, safe and lightweight properties are driving sustainable growth in packaging as the most recycled plastic in the world.
For more info, visit sipa.it. SD
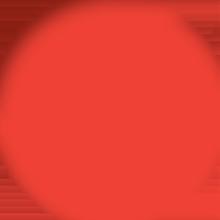

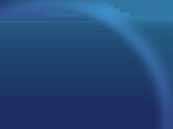
































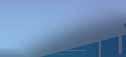
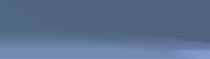







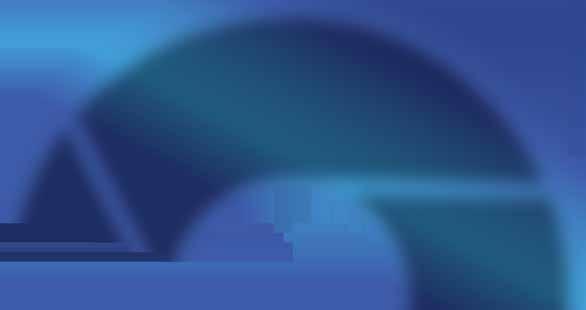
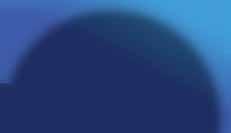


























































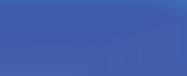

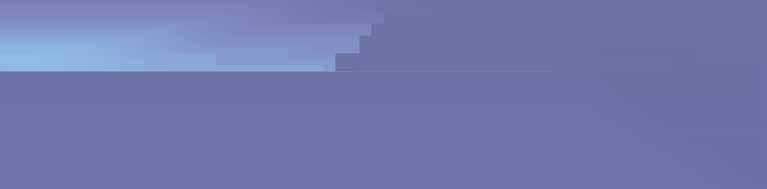
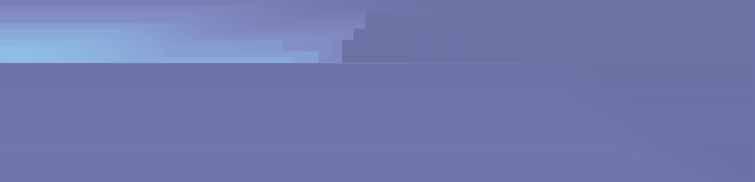


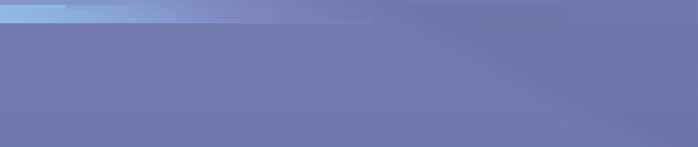

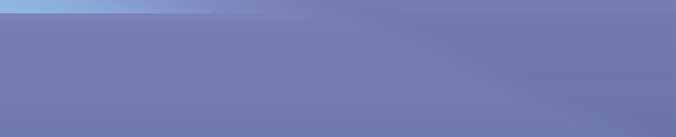
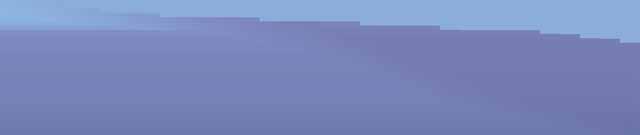
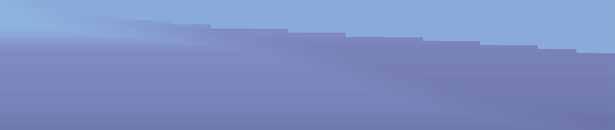
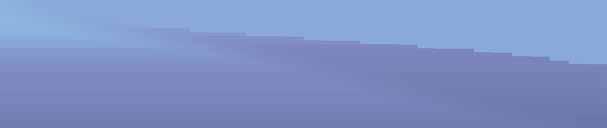




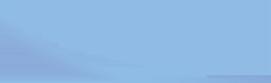
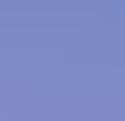
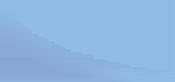
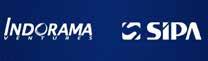
SEPTEMBER 13, 2023
System facilitates in-store pickup
The XpressPickup® (XPP) system from ORBIS (Booth SU-8001) revolutionizes order fulfillment for retail store pickup and delivery operations. Built upon years of market expertise, the XPP system addresses the challenges of buy online/pick up in-store (BOPIS) shopping and is designed to optimize store operations, space and employee safety, while effortlessly moving products from store floor to curbside.
The XPP system combines an innovative tote design and enhanced dolly and cart capabilities. Seamless integration with existing BOPIS operations enables quicker turnaround times, from order placement to in-store fulfillment to curbside pickup.
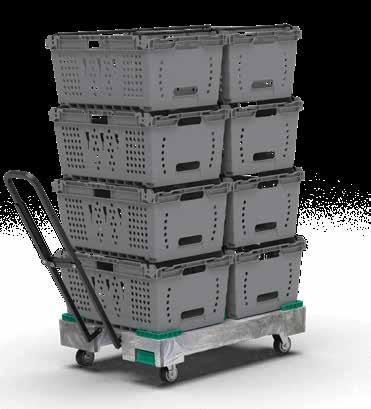
The XPP tote effectively limits spillage of damaged or open products, ensuring the integrity of the items being transported. The compact 24 x 16 x 11in. footprint maximizes picking efficiency and inter-
nal capacity, allowing for optimal space utilization, while built-in bag hooks provide support for efficient picking and curbside delivery, making the process seamless and hassle-free.
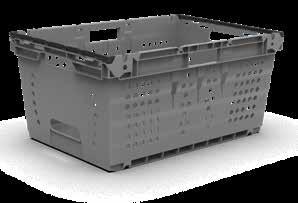
Versatile and adaptable, the XPP tote accommodates all types of merchandise and is also designed for use with standard metal carts, providing retailers with a flexible solution for their in-store order picking and fulfillment needs.
When not in use, the entire XPP system condenses efficiently, optimizing space.
For more info, visit www.orbiscorporation.com. SD


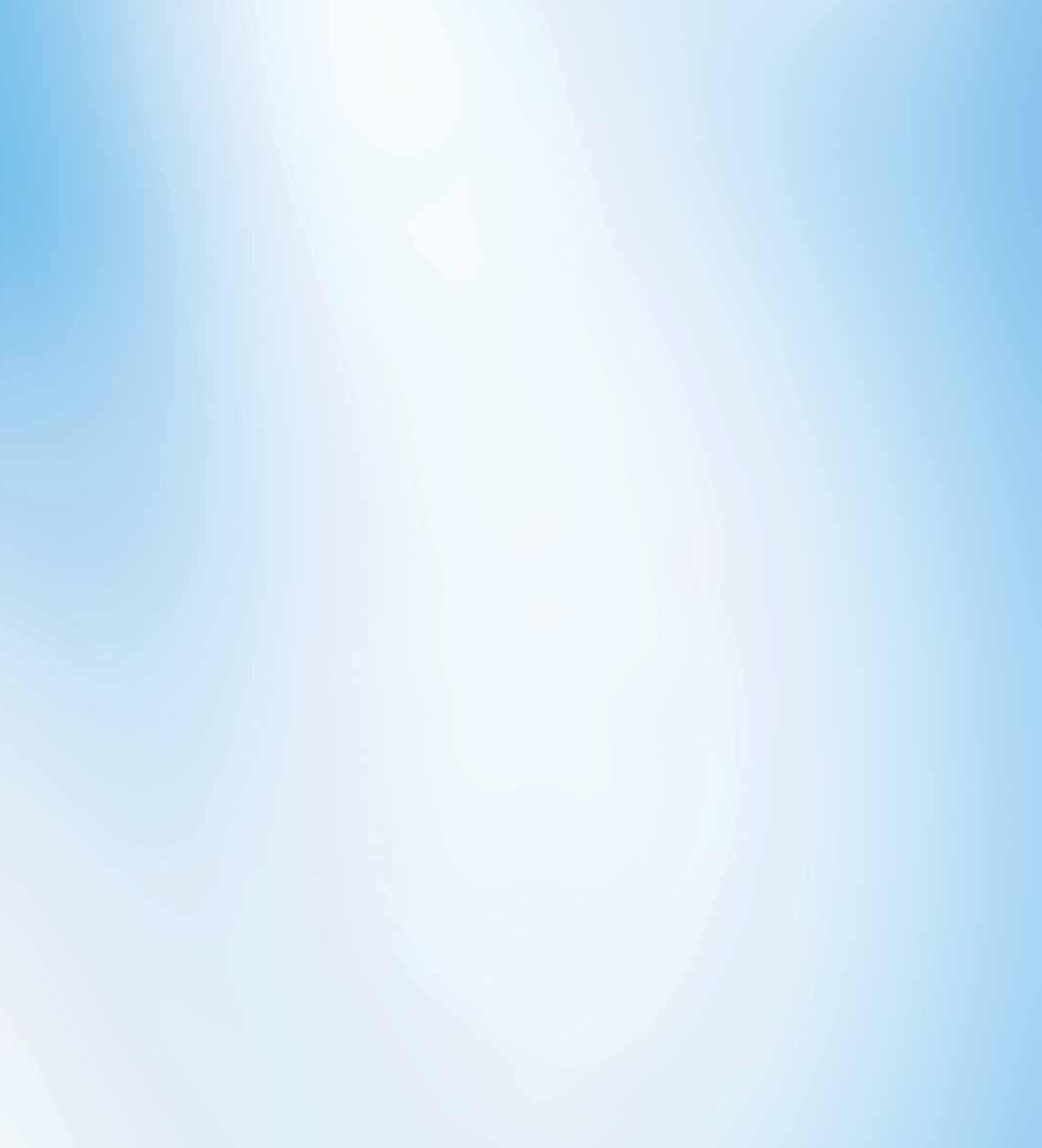

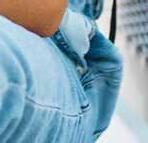
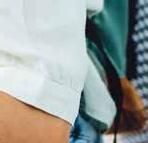
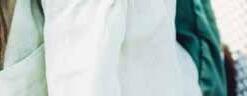

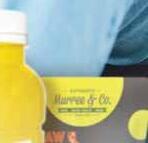
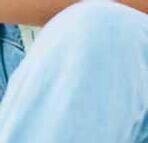
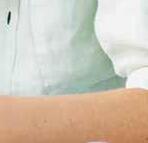
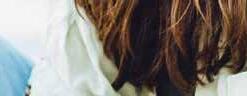
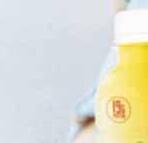
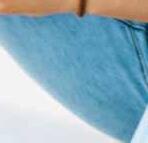
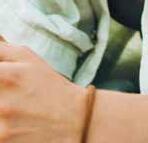
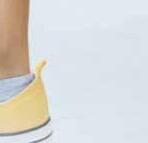
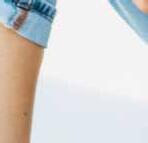

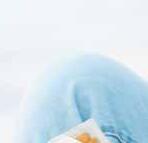


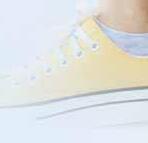
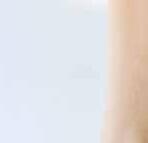
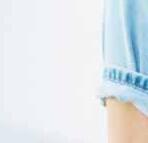
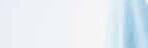










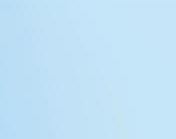
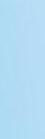


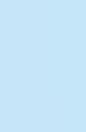



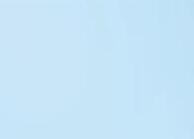

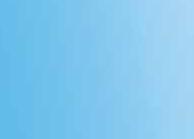

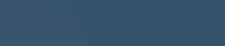

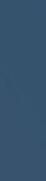
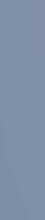


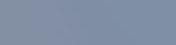
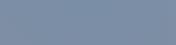



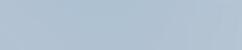
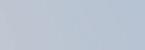


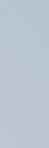


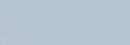



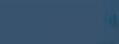
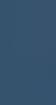


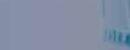



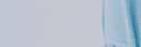

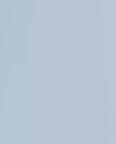
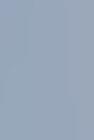

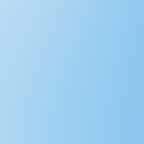
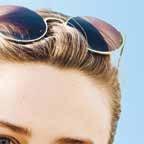
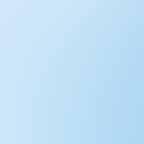

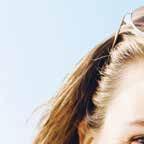
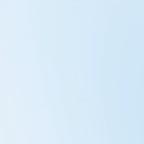
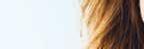

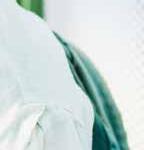
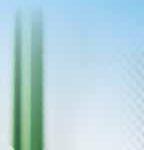
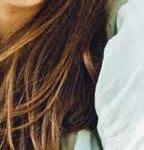
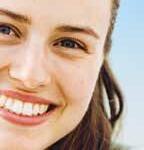

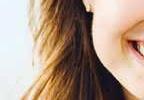

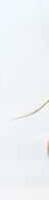



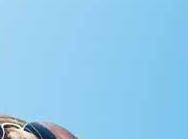

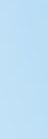

SEPTEMBER 13, 2023
PRODUCTS - PROCESSING ZONE
In the North Hall, the Processing Zone, a fixture of PACK EXPO Las Vegas, occupies 50% more space this year compared to 2021. Exhibitors specialize in the front-of-line technologies shown below. This section of the show floor also houses the Processing Innovation Stage (Booth N-10511) (see schedule, p. 30).
DRUM MOTOR
The VDG SSV-XP drum motor drives modular, wire mesh and monolithic thermoplastic conveyor belts without using sprockets. It features an interchangeable machined profiled sleeve that enables different styles of modular belts to be used with the same drum motor. The all-316-stainless steel motor withstands washdown pressures up to 3,000 psi and comes in a range of diameter sizes, belt speeds, horsepower and industry-specific options for a variety of food processing and packaging belt conveyor applications.
VDG (Van der Graaf)
Booth SU-8025
vandergraaf.com
LABELING TECHNOLOGY FOR THE FUTURE

NEW at Pack Expo ‘23/Las Vegas Quadrel will introduce a system with PLC controlled, fully automatic, one button product changeover. This exciting new design reduces change overs to less than one minute. For a demonstration, stop by Booth #1655
Let Quadrel move your packaging line into the future.
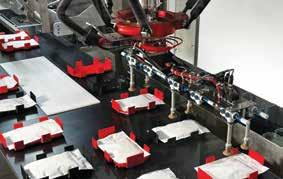
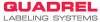
From the harshest environments to the most sophisticated Pharmaceutical applications requiring vision, validation and serialization, Quadrel is ready to partner with you. Our systems arrive Ethernet ready, with secure remote access available for monitoring, editing and trouble shooting.
In addition Quadrel systems feature Internationally compliant guarding, Allen Bradley Compact Logix PLC, Panelview color touchscreen operator interface, full servo control and redundant applicators for zero downtime non-stop operation. These systems are ideal for the most demanding pharmaceutical, food, beverage, automotive and personal care applications.
In addition, we now offer continuous motion labeling technology which dramatically increases production rates.
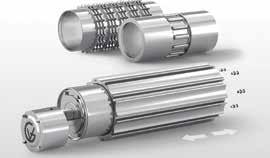
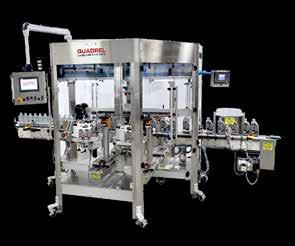
For more info, visit packexpolasvegas.com.
Editor’s Note: Product information and photos are drawn from The Processing Zone Showcase 2023, published by ProFood World
TRANSFER SYSTEM
With customized robotics and tooling, the iFTS flexible transfer system offers pouch size change flexibility. Placed on a magnetic shuttle, the intelligent system automatically substitutes another shuttle as needed. The standard frame mounting, guarding and overhead enclosures can be adapted around other machines on the line, while the lower frame mounting enables the integration of conveyors and other equipment. The system is suitable for a variety of products, including bulk packs and dry foods, such as snacks, cereal and candy.
R.A Jones Booth C-4400 rajones.com
LASER MARKING SYSTEM
The Videojet 3350 Smart Focus 30-watt carbon dioxide laser marking system prints text, barcodes and graphics at speeds up to 2,000 characters/sec. Equipped with a marking head that provides 0- to 90-degree rotation, the unit features an auto-adjustable focal distance, uniform flat field correction, a pilot beam focus finder, a flexible range/ size mode, built-in Wi-Fi and cellular connections and a remote interface control.
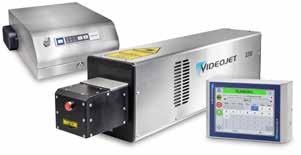
Videojet
Booth C-1935 videojet.com
CHECKWEIGHER
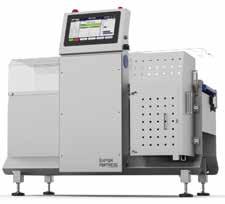
Compliant with global net weight regulations for packaged and premium foods, the Raptor checkweigher comes in 100-, 200-, 300- and 400mm belt widths. The unit verifies the weight of each product up to 17 lb. and rejects non-conforming packs. Defined product application tolerance tables are integrated into the software, while modular electronics facilitate full integration with upstream and downstream equipment. A conveyor-run-only mode provides an override option to run the unit as a conveyor without checkweighing. Optional automated Contact 4.0 data logging and reporting is available to connect machine reporting to back-end reporting software and export in real time.
Fortress Technology
Booth C-4303
fortresstechnology.com
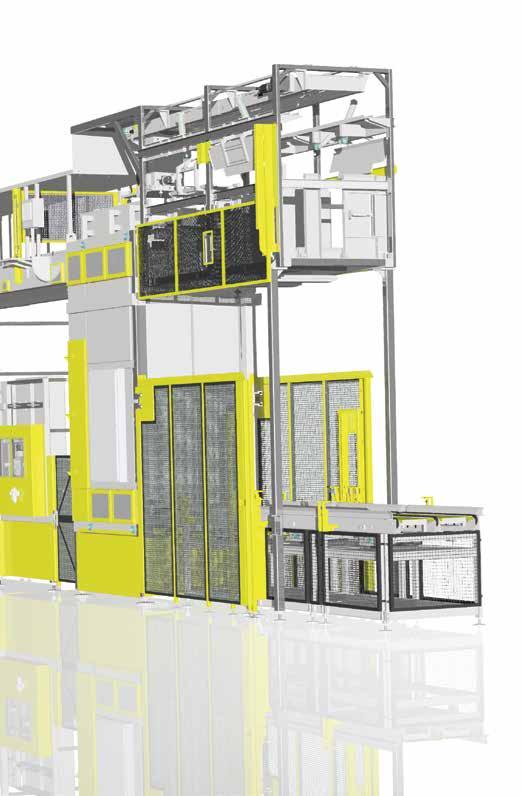
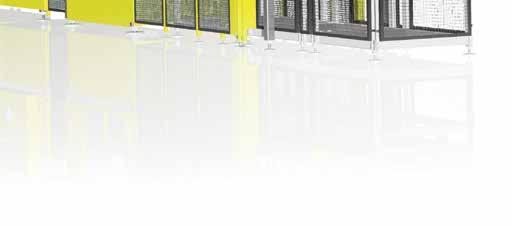

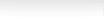
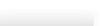




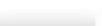







SEPTEMBER 13, 2023
PRODUCTS - PROCESSING ZONE
BULK BAG LOADER
X-RAY INSPECTION MACHINE
Used for boneless poultry processing, the Eagle Maximizer RMI x-ray inspection machine is equipped with an automated reject management system. Dual lanes enable processors to run up to 120 pieces/min./lane. The machine has a small footprint.
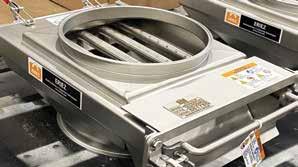
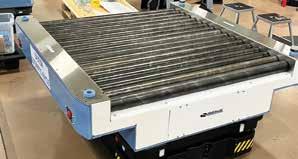
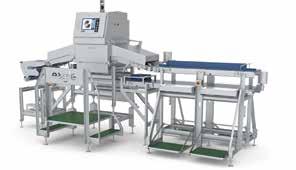
Eagle Product Inspection
Booth N-10813
eaglepi.com
AUTONOMOUS MOBILE ROBOT
The Simplimatic autonomous mobile robot automates full-load and material transportation tasks traditionally performed by forklifts. The unit is made to dock to end-of-line roller or drag-chain transfer conveyors, facilitating the integration of autonomous transfer pallets and gaylords in an existing facility. The robot navigates without the aid of lines or magnetic strips, rerouting to avoid obstructions in its path.
Signode
Booth C-5017 signode.com
CUSTOM PRESSURE VESSELS
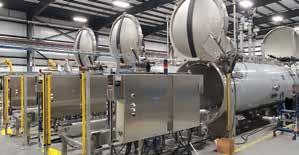
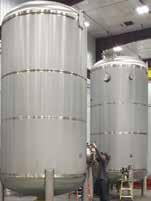
Custom pressure vessels meet or exceed the standards for sanitary and high-purity applications. The stainless-steel and higher-alloy vessels come with diameters from 2 in. to 12 ft. and thicknesses up to ½ in. OEM holds ASME “U” and National Board “R” stamps, and its facility is 3-A certified for sanitary equipment. Atmospheric, noncode tanks; heat-transfer jackets; agitation; membrane filtration; and complete process skids also are available.
Membrane Process & Controls
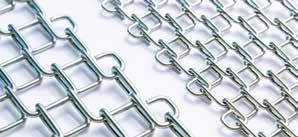
Booth N-10520
membranepc.com
The BFM bulk bag loader prevents material and dust from escaping during filling, preventing contamination of the filling station. The loader consists of a three-layer, inflatable filling head with a stainless-steel core encased in flexible ether-based urethane. Pneumatic air inflates the sleeve in seconds, sealing it tightly on the bag’s neck. After filling, the sleeve deflates to release the bag. The loader can be used with bulk bags with or without a plastic liner. It is USDA (material only), EC and ATEX compliant.
Powder-Solutions
Booth N-10855
powder-solutions.com
ROUND SPOUT SEPARATORS
Round spout magnetic separators feature a lower profile, eliminating the need for square-to-round adapters on the inlet and outlet ports. Available with manual or automatic easy-to-clean functionality, the manual design provides for a push/pull operation to strip accumulated tramp metal from the grates without handling the magnet. On the automatic version, a set of pneumatic cylinders cleans the magnetic grates at the touch of a pushbutton or timer control.
Eriez
Booth SL-5901 eriez.com
RETORT SOFTWARE SUITE
The Allpax retort software suite offers supervisory control, tamper-resistant data capture and retort and retort room automation machine control. Fully compliant with FDA regulations, the next-generation suite was developed in the Microsoft.NET Framework to allow upgrades and future customization. The suite also implements OPC UA for PLC-level communication, enabling the use of encrypted connections. Retrofits are available for older Allpax retorts as well as non-Allpax retorts.
Allpax, a ProMach product brand Booth C-3214 allpax.com
HYGIENIC VALVE
Modular Mixproof CIP hygienic valve manages the flow of cleaning media during cleaning in place (CIP). Double-seat technology with seat lift permits simultaneous routing of two fluids, while keeping them separated to prevent intrusion of harmful microorganisms. The top-loaded valve handles high pressure without the risk of pressure shocks and is certified to FDA, 3-A and other standards.
Alfa Laval
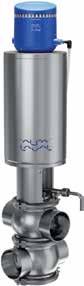
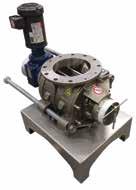
Booth N-10412 alfalaval.com
USDA DAIRYACCEPTED AIRLOCK
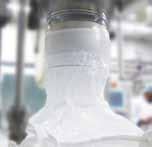
Global USDA dairy-accepted airlock suits applications where dry raw or finished products are handled and where inspection or system clean-out is required. A rail system provides access to the internal valve, cavity, rotor pockets and other product-contact areas. A detection system protects the dismountable airlock from damage and prevents product contamination due to interference between valve rotor and housing.
Schenck Process
Booth SU-8039
schenckprocess.com
CONVEYOR BELT
Compact-Grid CG15 conveyor belt handles difficult conveying challenges. USDA-accepted, the open-mesh, stainless-steel conveyor belt offers a clean-in-place design and simple belt joining. An 0.082-in. wire diameter and 73% open surface area increases flow-through for heating, cooling and coating applications. Thicker, larger 15mm mesh allows the belt to hold more weight per square foot.
Wire Belt Company of America
Booth SU-7164
wirebelt.com
CLEAN-IN-PLACE DRUM UNLOADER
A twin screw pump drum unloader with discharge pressures up to 375 psi and a 50+ gal./min. unloading capability can handle product viscosities in excess of 500,000 centipoise and transfer soft solids up to ¾ in. in size. Variable plate sizes pump out 75-, 55-, 30-, 20- and 16-gal. plastic, metal or fiber drums. Custom plates for pumping out mix kettles and pots, as well as a removable plate for pumping out totes and tanks, are available.
Axiflow Technologies
Booth N-10161
axiflowtechnologies.com
MEAT SUBSTITUTE EXTRUDER
A hybrid solution for meat substitute product manufacturers, the ZSK Mv Plus extruder can be used to produce texturized vegetable protein (TVP) and high-moisture meat analogues (HMMA) with a minimum of retrofitting effort. Using a Coperion adapter, the extruder’s discharge can be changed from the ZGF-centric pelletizer used for TVP to a specialized cooling die for HMMA. The pelletizer cuts product direct at the nozzle plate, while the cooling die produces a solid strand with textures similar to meat.
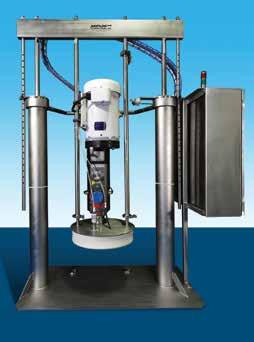
Coperion
Booth SU-7641 coperion.com
VIBRATORY CONVEYORS
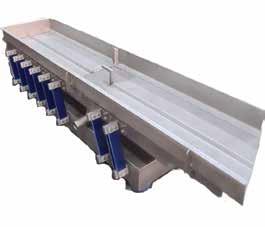
Vibratory conveyors use laminate reaction spring technology, crafted from long-thread fiber that is closely packed and treated with an antimicrobial agent, to move high volumes of product hygienically. They include IP69-rated electromagnetic drive units, an angled edge and internal pan with profiles for easier sanitizing. The custom-built conveyors can be used with fruits, vegetables, poultry, snack foods and pet foods in fresh, frozen, canned, RTE and additional output styles. Typical applications include general conveying, metering, dewatering, grading/sorting and multihead weigher feeding.
Proex Food proexfood.com
Booth SL-6178
BRIXX
BRIXX® is a new, modular, click-and-play solution based on an intuitive software to reduce the manual operations and allow quick transformations for co-packing lines. Based on advanced, mobile conveyors and robots to automate manual repetitive packing and co-packing processes.

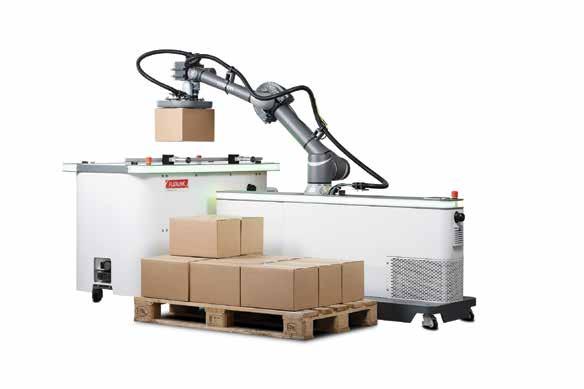
This unique design by FlexLink is a solution to automate currently manual packing operations through a flexible sytem adapting to the variability of products, packs, cartons, or trays. It is scalable according to production capacity needs, affordable and easy-to-use.
Automate product transformations such as:
•Pick-and-place
•Mixing
•Handling
•Re-labeling
•Palletizing
•De-palletizing
Read more at Flexlink.com or contact us at info.us@flexlink.com
SEPTEMBER 13, 2023
PRODUCTS
BOOTH C-3800
Search exhibitors, products and educational sessions




Access Your My Show Planner and add to your personal agenda

Navigate from booth-to-booth using interactive floor plans

Get news and notifications about show happenings, giveaways and more
Vote for the 2023 Technology Excellence Award winners

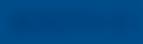
Search “PACK EXPO ” in the App Store or Google Play, or visit
HEAT-SEAL CONTROLLER
Advanced Pireg® temperature controller manages the time and temperature of the impulse heat-seal band and ensures consistent seals. Applications include vertical and horizonal form/fill/seal machines, pouch filler/sealers, flow-wrappers and pouch-converting equipment. Devices are compatible with in-cabinet or panel-mount configurations and available with EtherNet/IP communication. Product line also includes 350 styles, shapes and sizes of TOSS Alloy-20® and Norex® heat-seal bands. When used with the controller, TOSS Alloy-20 heat-seal bands provide instant thermostatic feedback, eliminating the need for thermocouples.
Packworld/TOSS Machine Components

Booth SL-6407
www.packworldusa.com
CASE PACKER
Thousands of pack configurations are no challenge for a variety case packing system. Full cubes of product are received in work-in-progress trays in six depalletizing stations, allowing up to six different flavors—and thousands of flavor combinations—to be processed at a time at rates of 100+ cases/min.
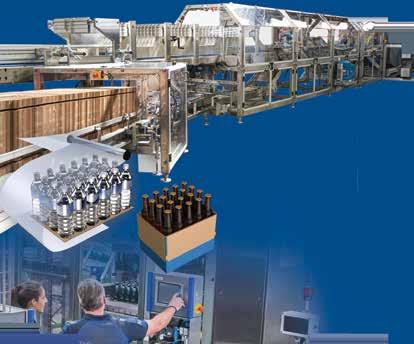

Aagard
Booth SL-5914 aagard.com
VERTICAL F/F/S MACHINES
Custom sealing pressure—thanks to patent-pending cross-seal control—is a key selling point of the SVX Agile vertical form/fill/seal (VFFS) machine. The unit handles 300 bags/min., while its sister machine—the SVX Duplex—doubles that output, via two accessible film lanes, all in a compact footprint.
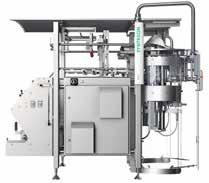
Syntegon
Booth C-2800 syntegon.com
HORIZONTAL FLOW WRAPPER


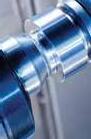
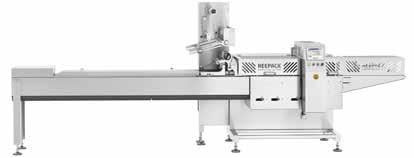
Need to use less film in your wrapping/sealing operations? The ReeFlow 50 horizontal flow wrapper’s no-product/no-bag sensors result in less film waste. Three independent pairs of rollers optimize longitudinal sealing—both bottom and top formats. The unit handles up to 180 packages/min.
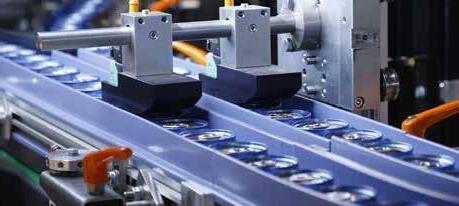
OSSID, a ProMach product brand
Booth C-3033 ossid.com
TUBE FILLER/CARTONER
An integrated tube-filling/cartoning line uses a hot-air tube heating system to fill/close up to 70 metal, plastic or laminated tubes/min. From filling, tubes travel to a vertical, intermittent-motion cartoner. The latter also accommodates bottles, blister packs, jars, pouches and other similar formats. A cam-guided transport system ensures precise positioning.
IWK Packaging Systems
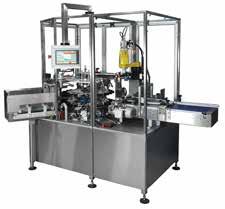
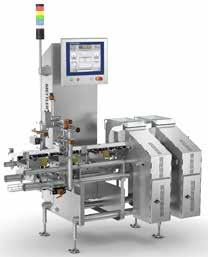
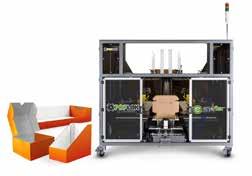
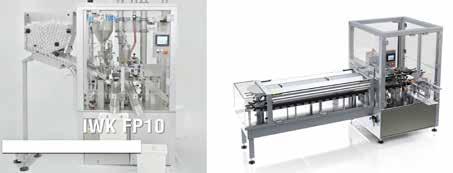
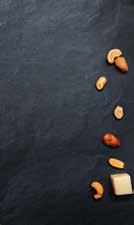
Booth C-5428 iwk.de/en
AUTOMATIC TRAY FORMER
The customizable PopLok® automatic tray-forming machine erects self-locking corrugated or paperboard trays with or without a lid. Capable of forming one-tuck, two-tuck or multituck trays, the machine uses no glue or tape and handles a variety of blank sizes and configurations.

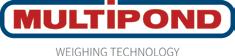
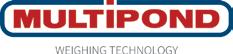
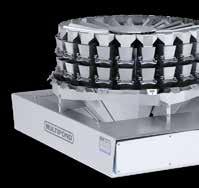
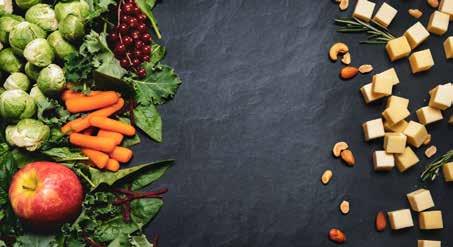
EndFlex/Paxiom
Booth C-5006 endflex.com
AUTOMATED LABEL INSPECTION
Implementing 100% automated label inspection helps minimize misplaced, incorrect, damaged or illegible labels, thereby avoiding risk of recalls and expensive retailer fines. The system, using smart cameras, can work as a standalone unit or can be integrated into related equipment, including checkweighers, metal detectors or x-ray systems.
Mettler Toledo
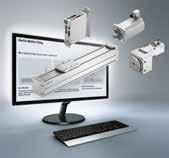
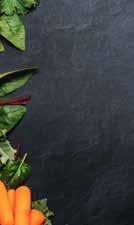
Booth C-1814 mt.com/pi-pr
ELECTRIC MOTION SIZING TOOL
Electric Motion Sizing compresses hours of work down to minutes, reducing engineering time needed to identify and specify harmonized electric motion systems. The free, online productivity tool performs complex mass moment-of-inertia calculations from key input parameters, such as mass, stroke/travel distance and cycle time. The tool outputs up to five optimum solutions and motor curves.
Festo
Booth SL-6160 festo.com
VERTICAL ROTARY CARTONER
The VRC-60 vertical rotary cartoner combines loading, printing, leaflet inserting, coding, inspecting and other functions into one 3 x 3-ft., 12-station machine. Integrated suction cups hold cartons in place throughout the entire arc path, preventing scuffing and scratching of delicate carton surfaces. The cartoner can run up to 60 packs/min., with loading options from single to double to bulk.
Nuspark
Booth C-5033
www.nuspark.com
ROBOT-ASSISTED TOP LOADER
Fully automated end-of-line pharmaceutical packing is facilitated in a single packaging line via a pick-and-place robotic top loader. Robotic handling ensures a controlled process to protect product safety. Plug-and-play tool exchange saves time during format changeovers. Customers can even produce 3D-printed parts themselves.
Schubert North America
Booth SL-6820, SU-7654 schubert.group/en/schubert-north-america
SEPTEMBER 13, 2023
PRODUCTS
COMPACT CASE ERECTOR
Maximum Series case erectors—with glue or tape options— form cases at speeds up to 15 cases/min. The system’s on-demand sensor helps control flow, while the unit’s compact size saves overall floor space.
A.B. Sealer
Booth SL-5805 absealer.com
BUCKET ELEVATOR
Bucket elevators—available in stainless steel or powder coated—transport bulk materials both vertically and horizontally, with a modular design allowing customized configurations. Overlapping pivoting buckets prevent spilling and mitigate foreign debris.
Ryson International
Booth C-4736 ryson.com
CONTINUOUS INKJET PRINTER
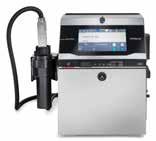
The UX2 continuous inkjet printer brings the next generation of coding to your production lines. It provides added convenience with onboard Safe-Clean-Station, a newly designed printhead, enhanced code quality at high speed and easy-to access troubleshooting videos. The UX Series improves on the existing continuous inkjet products and is versatile enough to provide industry-leading marking on food, beverage and dairy products, health and beauty products, and a variety of containers from lip balm tubes to bag printing and oversized PVC piping.
Hitachi Industrial Equipment & Solutions
America
Booth N-9520
hitachi-iesa.com
SEMIAUTOMATIC SCALE
Accurate weighing is critical for fixedweight food packaging. Semiautomatic combination scales combine manual loading with automatic dispensing. The scales reduce product overweights by dispensing the best weight combination for customer specification.
Yamato Booth SL-5949 yamatoamericas.com
INTEGRATED PACKAGING LINE
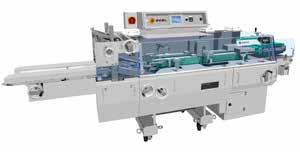
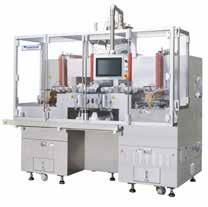
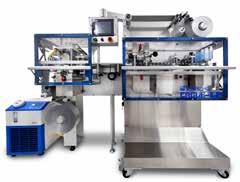

An integrated packaging line fills canisters then tray-packs, overwraps and palletizes them in a multibrand collaboration. A top-load tray former creates trays from corrugated blanks; trays continue to a case packer where a robot orients canisters before shrink wrapping and pick-and-place via an articulated robot. Finally, a robotic palletizer places wrapped trays on a floor-level pallet.
ProMach
Booth C-3222
promachbuilt.com
BLISTER MACHINE
Save cost and floor space with the Eagle-LP blister machine, which accommodates newer, more sustainable blister film substrates, including PVC, PVDC, PET, ACLAR, ALU and PP, which typically are more difficult to form and seal. The unit is particularly well suited for stability testing, clinical trials and small batch runs up to 20 cycles/min.
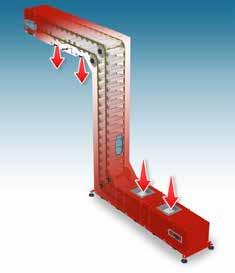
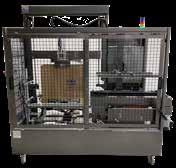
MHI
Booth SL-6808
mhi-innovations.com
SOFTGEL CAPSULE FILLER
A softgel capsule filler, which runs a variety of capsule sizes, is said to increase productivity by more than 35% over previous models. An expanded die roll size increases output, while thermo-chilling technology offers more efficient cooling.
CVC Technologies
Booth SL-6831
cvcusa.com
ROTARY RETORT MACHINE
Rotary retort machines turn cans, jars, pouches and other containers during sterilization and cooling, allowing food content to move while cooking. The process speeds up the internal heat transfer, preventing heat-sensitive food from being discolored or burnt.
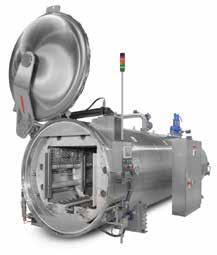
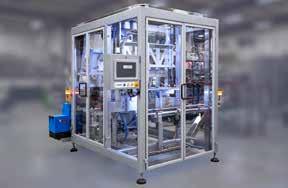
Surdry North America
Booth N-10717 surdry.com
STRETCH OVERWRAPPER
In-line tray stretch wrapping is said to be more streamlined compared to elevator-style machines. The 500Li tuck-and-fold stretch overwrapper produces up to 60 packages/min. Tuck-and-fold film is well suited for produce, low moisture proteins and other food packaging applications.
Ossid, a ProMach product brand
Booth C-3033
ossid.com

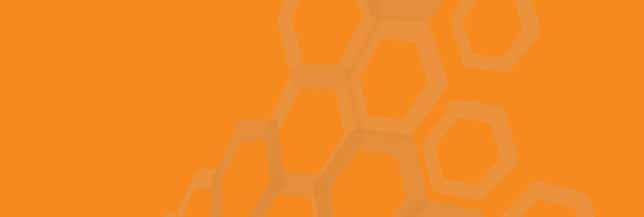


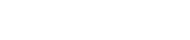
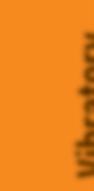
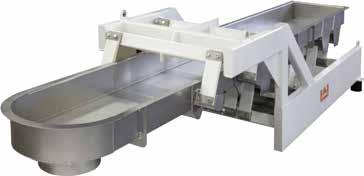
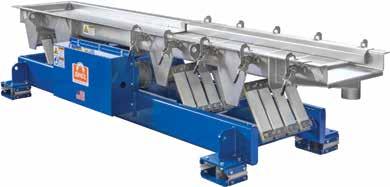
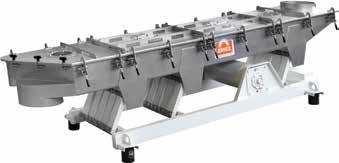
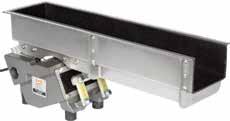
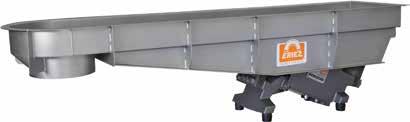
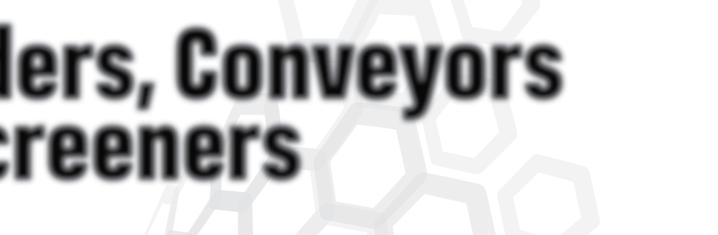
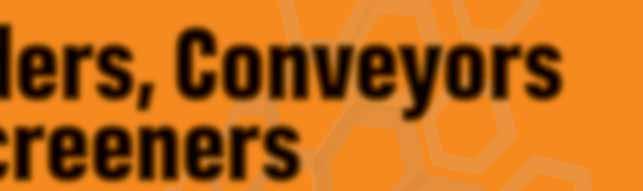
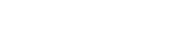



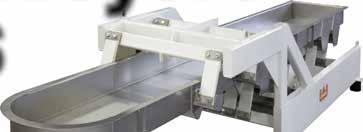
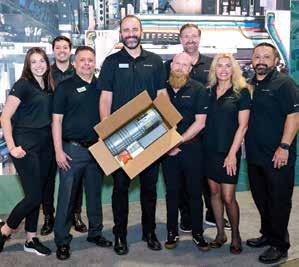
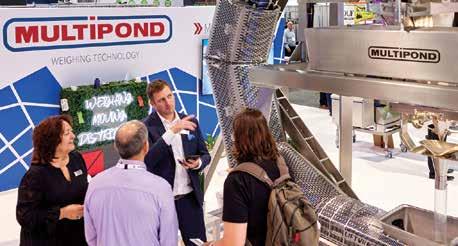
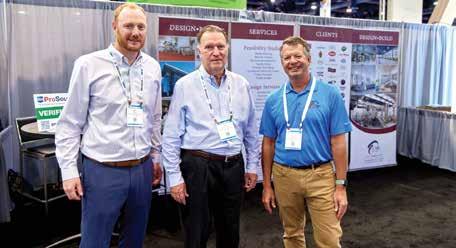
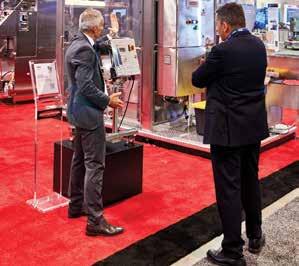
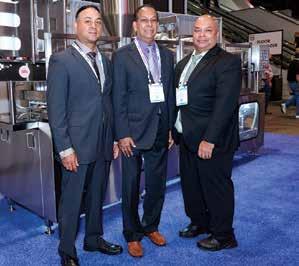
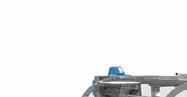
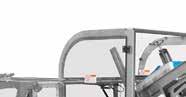
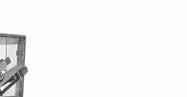
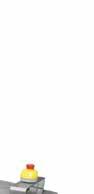
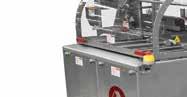
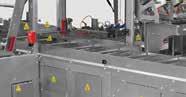
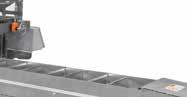

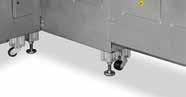
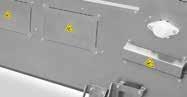
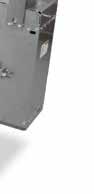
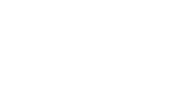

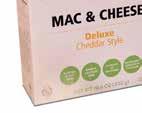
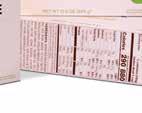
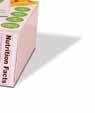
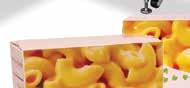
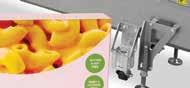
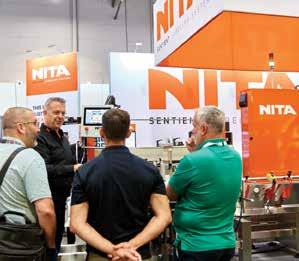
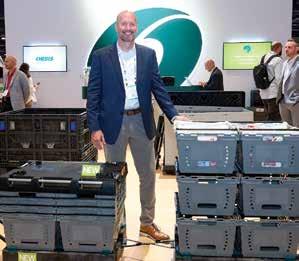
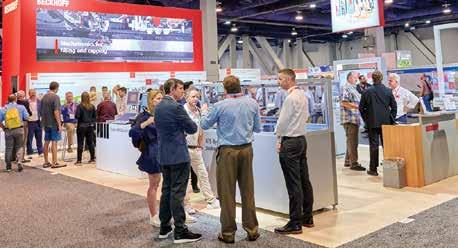

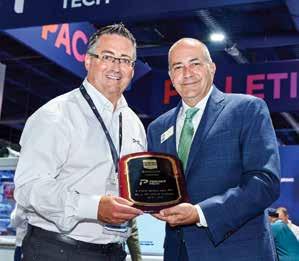
thank you to our partners!


These organizations are an integral part of PACK EXPO Las Vegas 2023 and played a pivotal role in bringing the entire packaging and processing industry together for this event.



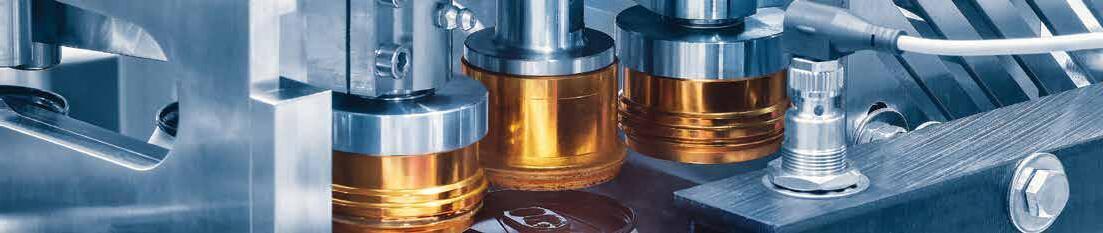
* As of July 6, 2023




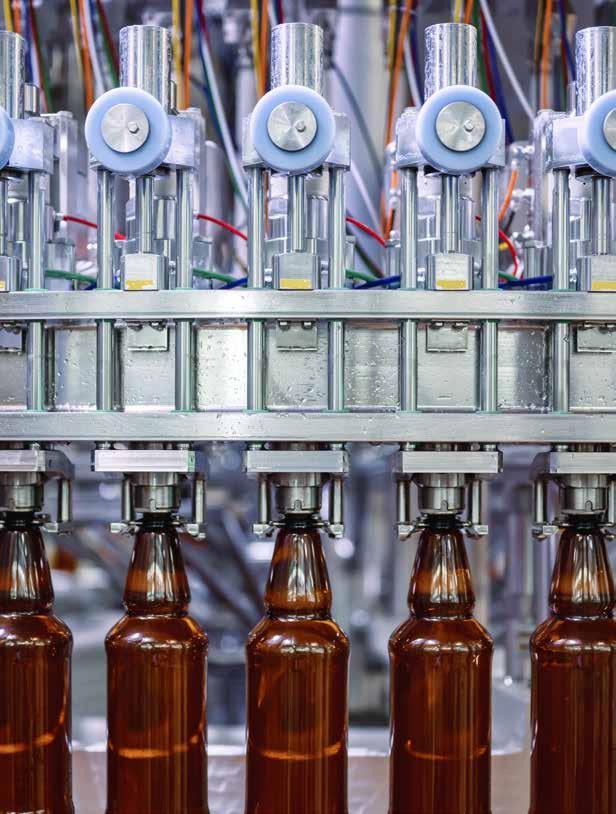
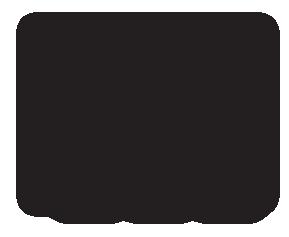









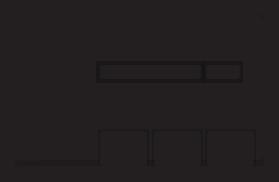


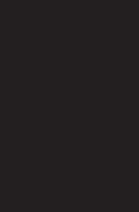




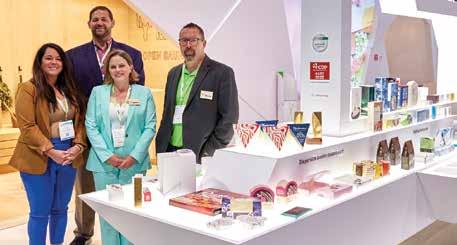
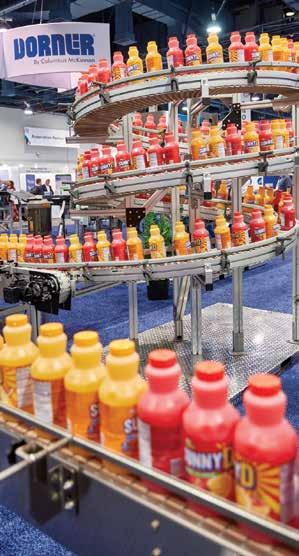
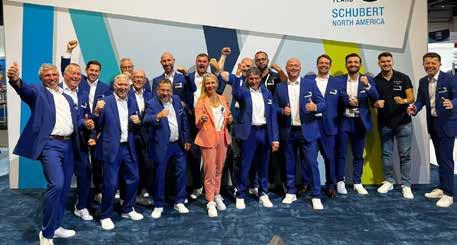
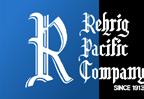
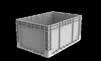

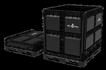
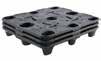
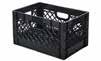
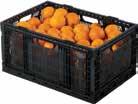
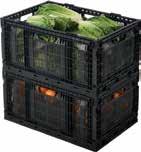

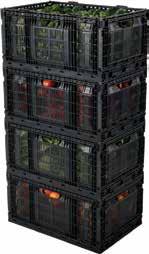
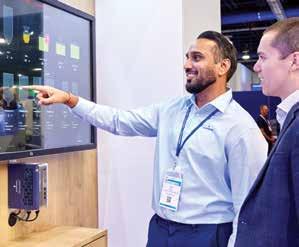

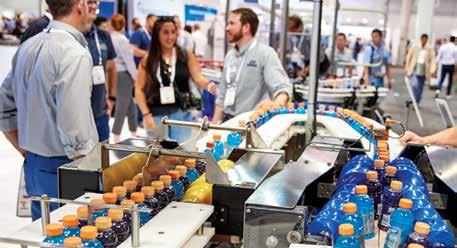
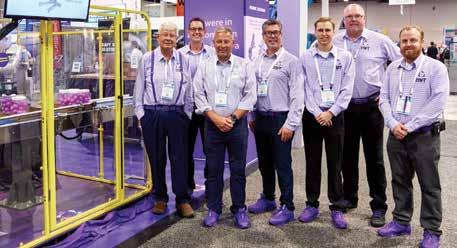
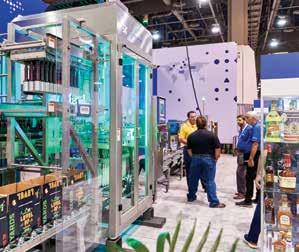
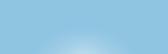
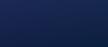
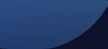
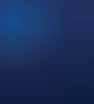


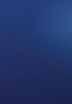
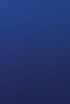
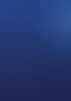




























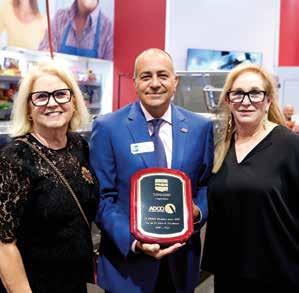
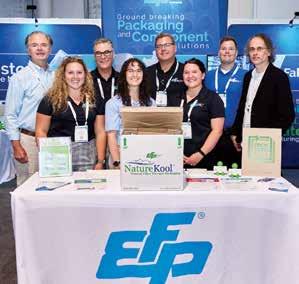

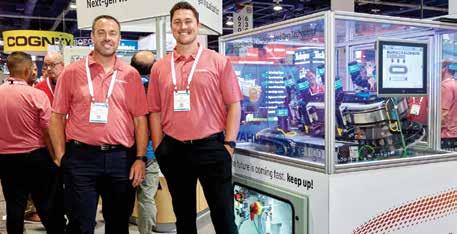
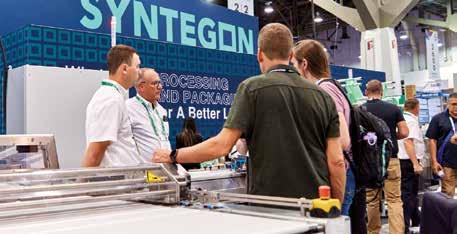


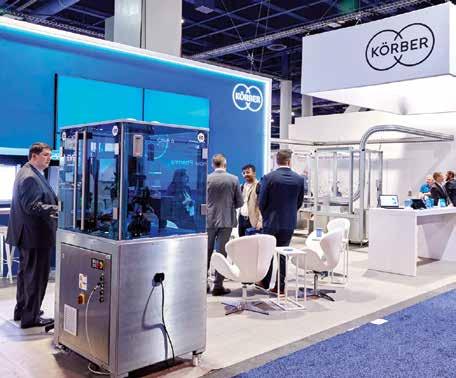
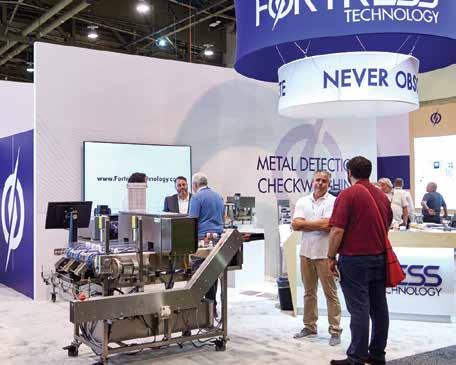
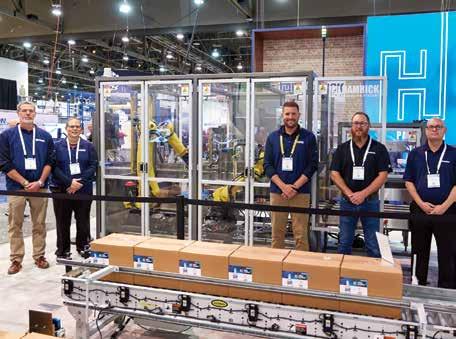
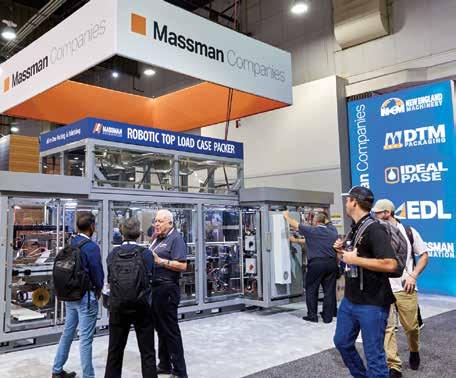
Industry Training
Elevate your talent through PMMI’s convenient training and development opportunities.
Certified Technical Sales Professional (CTSP)
Certification (for PMMI members only)
Be a trusted advisor to your customers.
Certified Trainer Workshops
Develop your team’s training skills.
Fundamentals of
Field Service
(for PMMI members only)
Give your technicians the non-technical skills they need to provide great customer service.
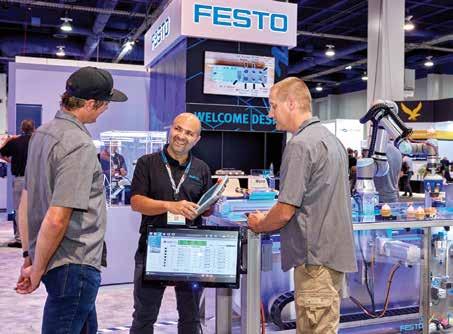

Mechatronic Certifications

Identify multi-skilled workers to troubleshoot and repair automated equipment on the plant floor.
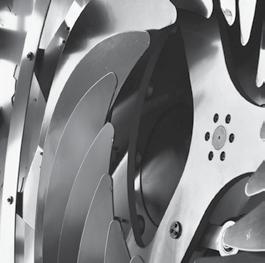

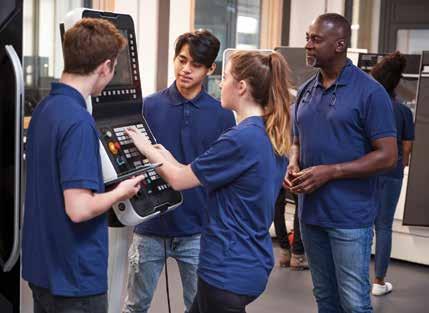
Risk Assessment Workshops
Improve productivity and ensure worker safety.
SEPTEMBER 13, 2023
Learn more at pmmi.org/industry-training
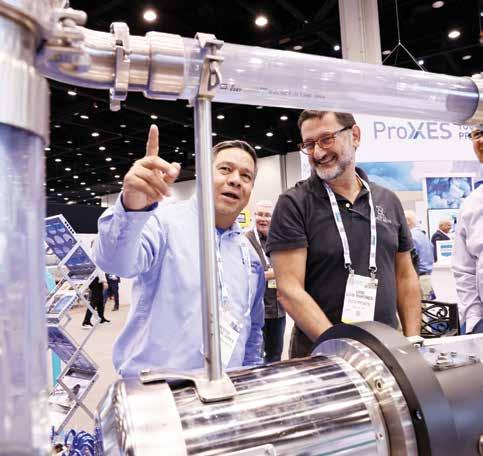

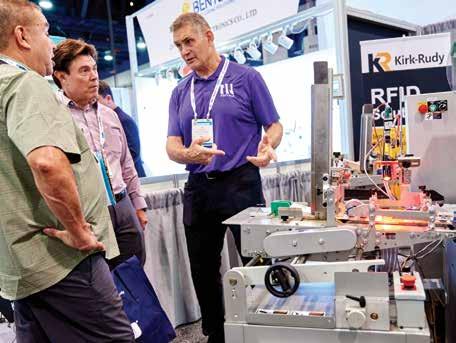
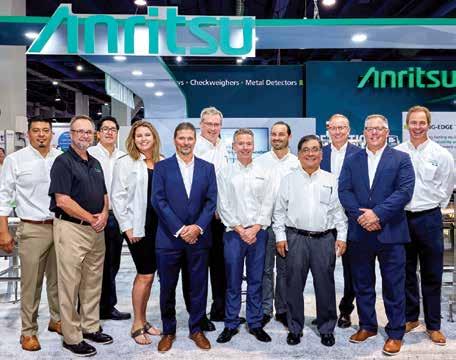
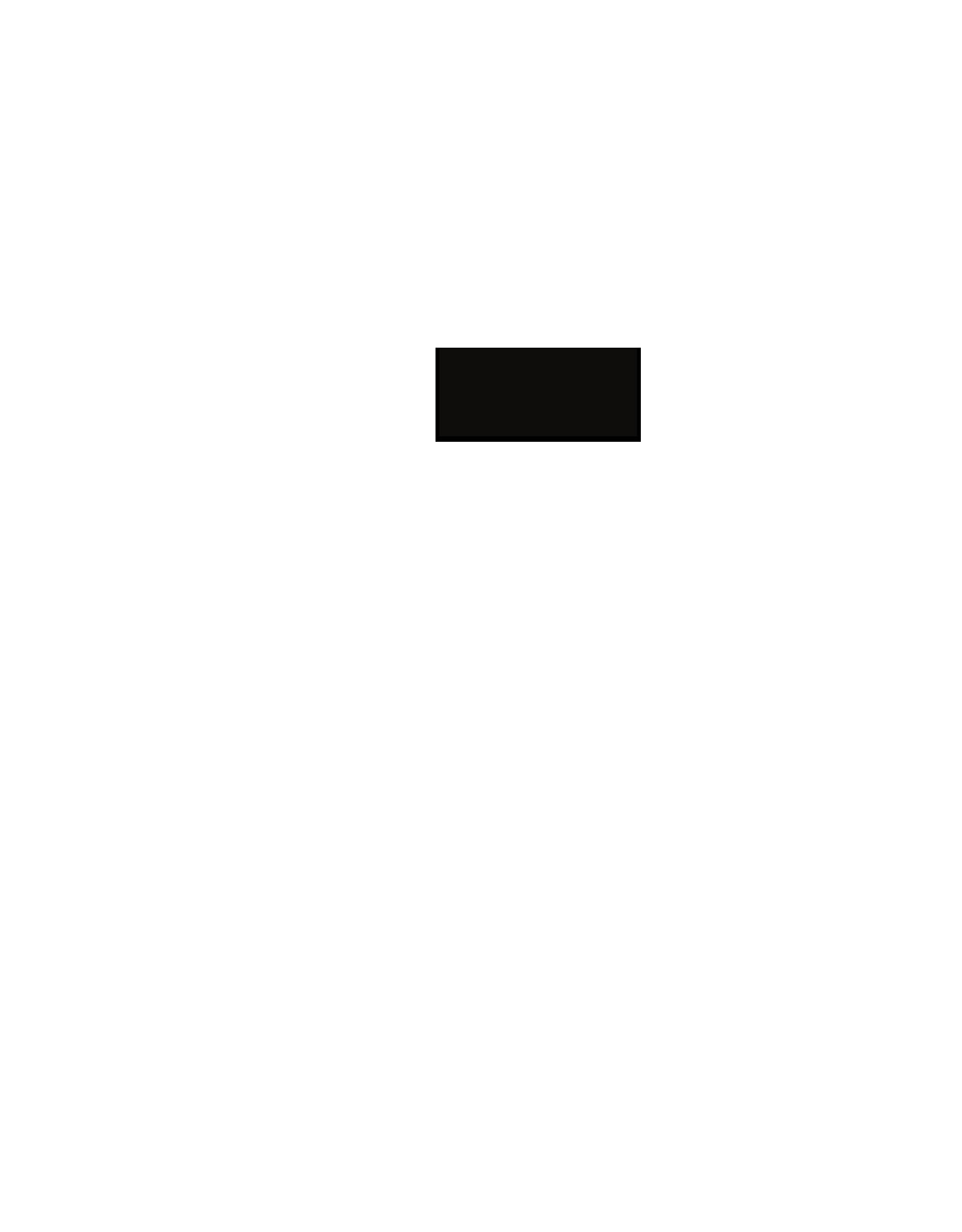
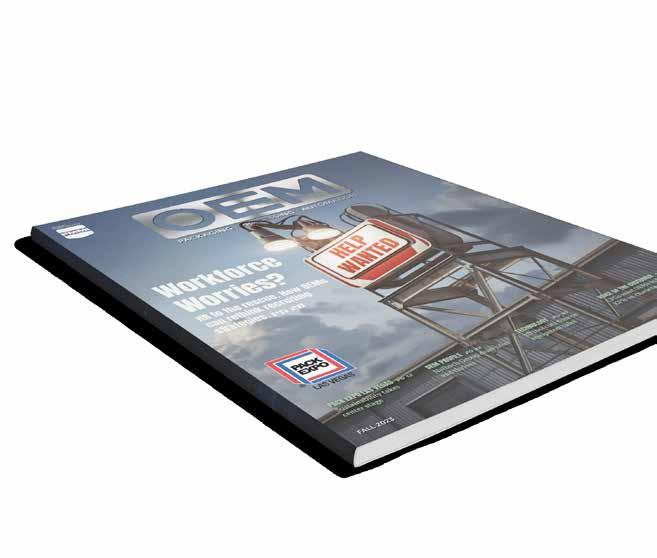
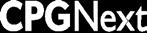
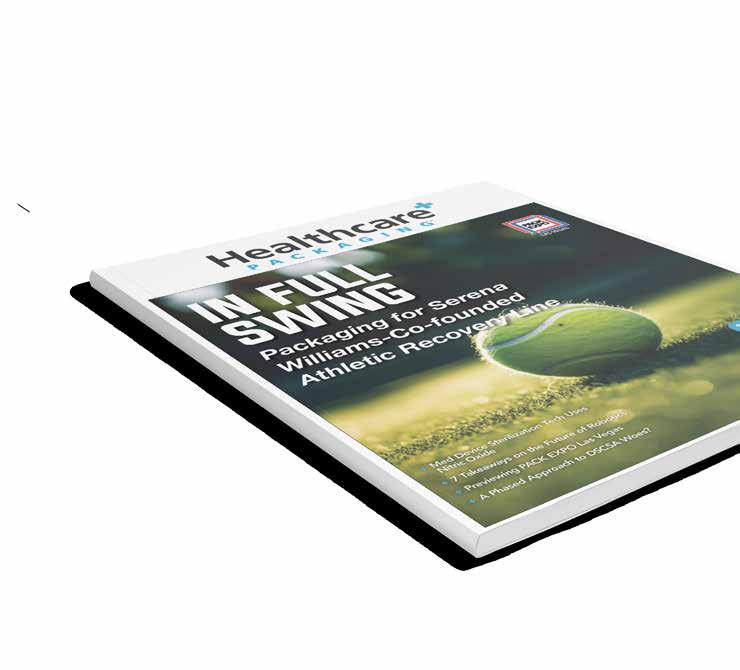

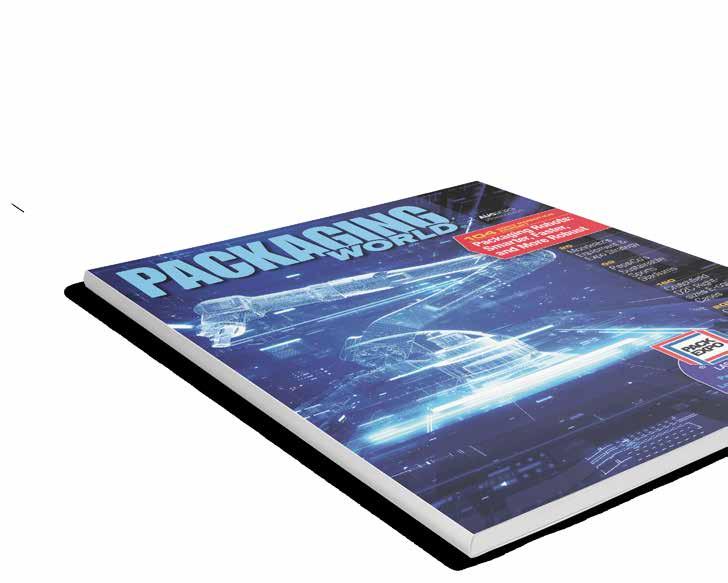

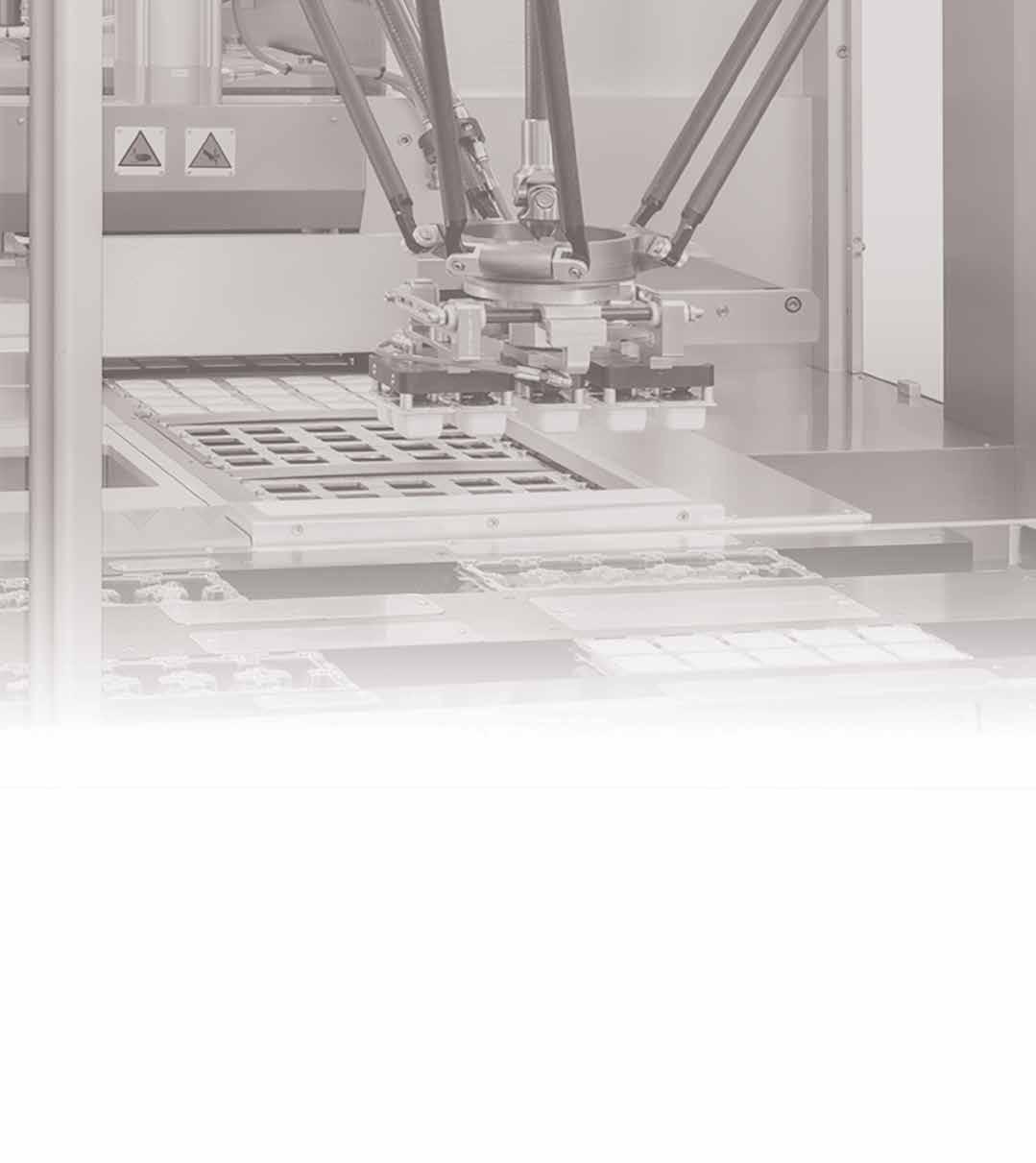
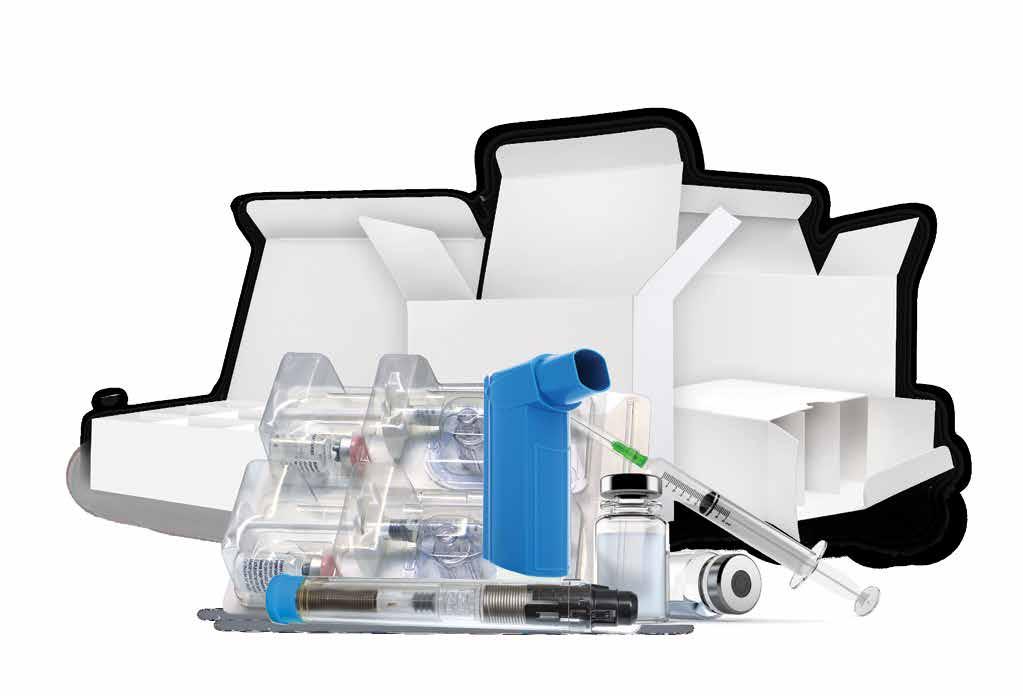

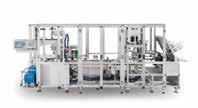
