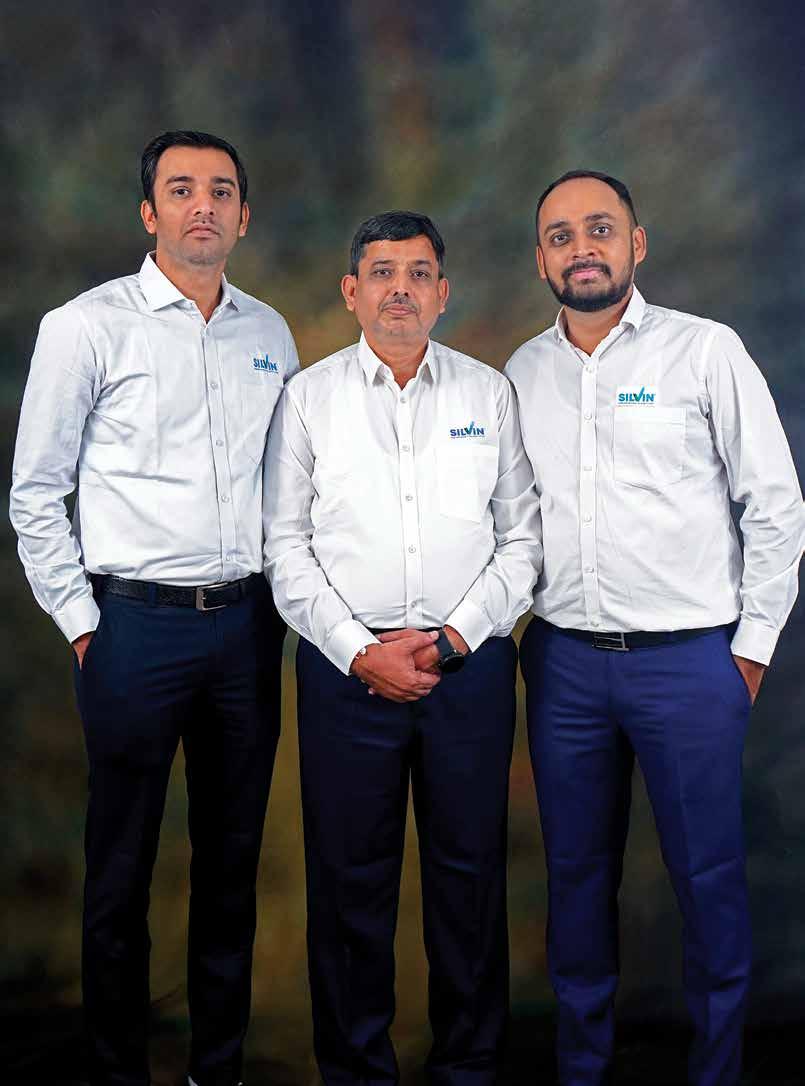
8 minute read
Sustainability Through Recycling of Materials and Waste as Feedstock - Part III: Battery Recycling
Self-compounding
A Futile Struggle
Advertisement
“In the current market, a lot of PVC manufacturers opt for selfcompounding - a process that involves sourcing all the essential components of additives and measuring them separately. Several risks and uncertainties meander around this process. Generally, in self-compounding, chemical proportions differ and the final products eventually get affected. However, manufacturers realise this fact after they are done with producing and testing their products,” shares the Basil Prompt Vinyl team, in dialogue with POLYMERS Communiqué.
Q. A first from Silvin in India is the SUPER1Pack, what prompted this initiative?
It all began when we visited our customers and observed that they were initially buying ready-touse compounds. However, when they switched to self-compounding, it was a struggle for them to adjust the formulation, which was mainly due to insufficient in-and-out knowledge of the additives. Also, due to the lack of necessary understanding, there was a lot of chemical wastage. These observations helped us to come up with this unique concept of Super1Pack.
At Silvin, we believe in providing customised solutions with a detailed understanding of the customers’ requirements to produce PVC and CPVC pipes and pipe fittings. Identifying market trends and developing these solutions has been one of our core values. For instance, our Super1Pack is an all-in-one additive containing stabilisers, internal and external lubricants, impact modifiers and other essential chemicals or additives other than PVC resin, CaCo3 (filler) and pigments. This is a universal, unique, free-flowing powder formulation, particularly for the PVC and CPVC piping industry. Therefore, this additive simplifies the manufacturing process and helps bring more uniformity to production. This ensures that we leave no room for error in the PVC and CPVC manufacturing process. In recent times, with the introduction of a new guideline that restricts the usage of lead-based additives, Silvin has become an even more relevant and indispensable factor in PVC and CPVC manufacturing.
Q. Since the waning of the pandemic, real estate and construction activities are on the upswing; what is your business growth that you anticipate over the next 2 - 3 years?
In the overall market scenario, there is an evident chance of 40 - 50% growth. As we look inwards, our inventory management system, on-time deliveries and no price fluctuation are also some of the reasons for envisioning our progress. That’s why we believe that we too will witness huge growth in the coming 2 - 3 years. We are constantly solving the challenges of procurement and supply chain, and bringing convenience to the customers successfully.
L to R:
Jagat Chokshi, Director, Pradip Chokshi, Managing Director, Mirang Chokshi, Director,
Basil Prompt Vinyl Pvt. Ltd., Ahmedabad
Q. What are the perils of selfcompounding and how does Silvin plan to combat that?
PVC additives are a very important part of PVC manufacturing. However, their combination matters a lot. Anything more or less can affect the process immensely, ultimately impacting the final product. In the current market, a lot of PVC manufacturers opt for self-compounding - a process that involves sourcing all the essential components of additives and measuring them separately. Several risks and uncertainties meander around this process. Generally, in self-compounding, chemical proportions differ and the final products eventually get affected. However, manufacturers realise this fact after they are done with producing and testing their products. Apart from the risk of getting the combination incorrect, there are uncertainties like a sudden price hike by the dealers, variation in quality, delay by suppliers, availability of key ingredients etc.
Salesforce, a CRM software, and SAP, an ERP solution, ensure that the end-toend process stays wellcontrolled. By integrating them, we have developed our ecosystem so we can maintain timely delivery, the right purchase at the right price as well as keep the supply chain management intact and efficient. One of the major benefits is that it helps improve the bottom line. Mainly 80 - 85% is the raw material cost.
As the rejection percentage increases, processors constantly change their formulations. To make things right, they always need an expert for the right combination. And their biggest challenge is to fix the formulations by trial and error.
Our greater goal is to completely eliminate this process with our Super1Pack formula. Over the years, we have been successful in coming up with a device that challenges this practice, and we are constantly innovating to achieve this goal.
We guarantee the best quality, timely material delivery and consistent availability of our products. We always buy in bulk and maintain 2 - 3 months of inventory at any given point in time. Additionally, we have a professional purchase team in place that monitors international prices. This is why our customers never have to face the impact of sudden price fluctuation as compared to the ones who prefer self-compounding.
Q. You have invested significantly in IT infrastructure. How do you see its impact on business? Your message to other business owners...
Salesforce, a CRM software, and SAP, an ERP solution, ensure that the end-toend process stays well-controlled. By integrating them, we have developed our ecosystem so we can maintain timely delivery, the right purchase at the right price as well as keep the supply chain management intact and efficient. One of the major benefits is that it helps improve the bottom line. Mainly 80 - 85% is the raw material cost. So, processing margins are narrow, and if there is even a slight difference of 5 - 7%, there will be a chance of loss. If anyone wants to make their business scalable, it is necessary to implement modern software like inventory and customer-relationship management in their system. Q. As one of the world’s leading additive suppliers, one message that you would wish to convey to the processors would be...
We feel that processors should really invest in making products that are ecofriendly and cause no harm to humans or the environment. Thus, in future, the approach should be on manufacturing ‘harmless’ products, rather than just the R&D or, for that matter, simply replacing hazardous additives.
Q. You are a strong believer in branding. Share with us the kind of impact it has had on your growth.
Collectively, we believe that branding is necessary along with following highquality standards. We have ensured that our processes give us an identity that matches up to the kind of innovation we bring to the table. For the past few years, we have been able to create a product that is unique and has helped the industry immensely. Thus, we call it magic. That’s what we say whenever there’s a mention of our brand. That’s why Silvin, as a brand, believes in adding magic to additives.
We have been dominating the market for quite a long time now. Earlier, we lacked brand recognition and even those who admired our formula didn’t know of us. But as we started building an identity and an effective way of communication, the recall value has increased multifold.
In the past, it took hours to make people understand the USPs of our brand. Now, it takes a few seconds to tell and remind people of the benefits or the rewards of using Silvin. This has only been possible because of our thoughtful communication and identity design.
To know more, please subscribe to PolYmERS Communiqué at subscriptions@polymerscommunique.com
Sustainability Through Recycling of Materials and Waste as Feedstock
Part III: Battery Recycling
During the period 2019 - 2030, 1,000 GWh of remanufactured and second-life batteries will be in the market. The highly recyclable nature of the battery product is still often overlooked, as well as its suitability for second-life repurposing, making it an important technology for sustainability and climate change mitigation. Comprehensive recycling, including recovery and reuse is the potential option to obtain the maximum utilisation of spent power LIBs.
Prof. (Dr.) G. D. Yadav
National Science Chair (SERB/DST/GoI), Emeritus Professor of Eminence, Former Vice Chancellor & R.T. Mody Distinguished Professor, Tata Chemicals Darbari Seth Distinguished Professor of Leadership and Innovation, Institute of Chemical Technology, Mumbai
The Big Surge Begins
We are talking a lot about electric mobility in India in order to meet the demands of the Paris Agreement 2015 and the net zero goal. The high demand for electric vehicles (EVs) has led to a rapid increase in power lithium-ion battery (LIB) production, which has consequently led to an explosive increase in the number of spent power LIBs. Spent battery management consists of comprehensive recycling, including recovery and reuse to obtain the maximum utilisation of spent power LIBs which were introduced by Sony in 1991. LIBs are excellent for energy storage due to their high specific energy, high voltage and high reversibility compared to conventional lead-acid batteries. Because LIBs are an important component in EV, the current increase in demand for green transport has led to an increase in the production of LIBs, which in turn means massive production of minerals, such as Li mines.
The International Energy Agency (IEA) predicts an annual average growth rate of close to 30%; that is, the global EV stock (excluding two / three-wheelers) will continue to increase, expanding from ~8 million in 2019 to 50 million by 2025 and close to 140 million by 2030, in which China will be the major player.
Waste Management of Spent Power LIBs
Obviously, there will be a huge challenge in how to manage the waste of spent power LIBs. LIB failure typically happens after 3 - 10 years of service which will lead to large number of heavy metals and hazardous waste. Spent power LIBs can be viewed as ‘artificial minerals’ which calls for a reasonable recovery process to reduce the associated concerns and
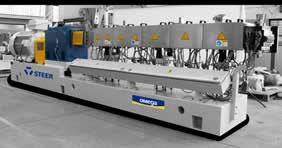
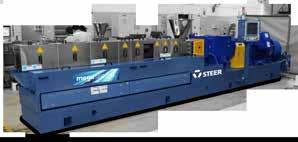