PONSSE NEWS
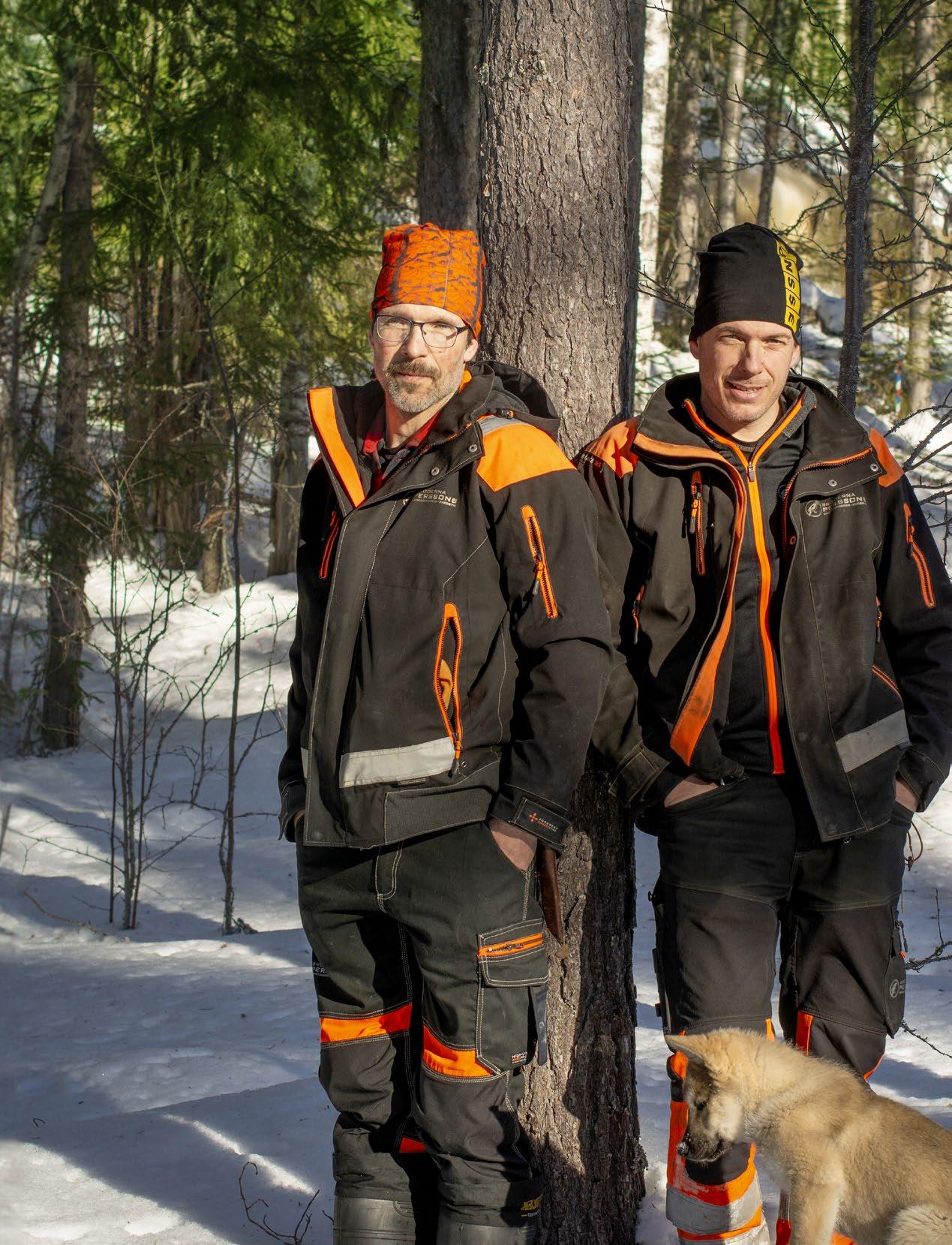
EPEC OPENS A SMART AND SUSTAINABLE FACTORY
EFFECTIVE FIREFIGHTING IN URUGUAY
THE ESW QUIDELINES DEVELOPS THE QUALITY AND SAFETY OF SERVICES
BRÖDERNA PERSSONS SKOGSMASKINER AB
EPEC OPENS A SMART AND SUSTAINABLE FACTORY
EFFECTIVE FIREFIGHTING IN URUGUAY
THE ESW QUIDELINES DEVELOPS THE QUALITY AND SAFETY OF SERVICES
BRÖDERNA PERSSONS SKOGSMASKINER AB
CUSTOMER AND STAKEHOLDER MAGAZINE 1/2024
PUBLISHER
Ponsse Oyj, Ponssentie 22, FI-74200 Vieremä, Finland
EDITOR-IN-CHIEF
Hanna Lehtonen
EDITORS & CONTENT
Ponsse Plc
ISSN 2489-9488 (print)
ISSN 2489-9496 (online publication)
EDITORIAL STAFF
Juho Nummela, Hanna Lehtonen, Mari Komulainen, Marika Ryytty, Jarmo Vidgren, Marko Mattila ja Jussi Hentunen
LAYOUT
Luova Työmaa
COVER PHOTO
Ponsse Plc
ILLUSTRATIONS (PONSSE KIDS)
Ponsse Plc
Painotalo Seiska
PAPER
Cover: G-Silk 150 g/m2 and pages G-Print 100 g/m2
ADDRESS SOURCE
Mailing list of Ponsse News and Ponsse customer register
4 BRÖDERNA PERSSONS SKOGSMASKINER AB Expectional teamwork
8 GROWTH IN SWEDEN, NORWAY AND DENMARK FOR DECADES
10 RENEWED PONSSE VALUES
12 DIGITAL SOLUTIONS
15 AUTHORIZED DEALER IN BULGARIA Progress Technik
Ponsse PLC customer and stakeholder magazine.
Ponsse News is published twice a year.
Please send feedback, subscriptions and changes of address by email to ponssenews@ponsse.com. The magazine is free of charge.
FOLLOW US:
16 EPEC OPENS A SMART AND SUSTAINABLE FACTORY
The Seinäjoki factory aims for carbon neutrality in its operations
18 PONSSE MOMENTS
20 EFFECTIVE FIREFIGHTING IN URUGUAY
Ponsse’s firefighting equipment has already been sold to more than ten countries
22 PONSSE LADIES CELEBRATES IN FINLAND AND THE UNITED STATES
I’ve had the pleasure of working at Ponsse for a little over a year now. My recruitment process is still fresh in my mind – it felt like I wanted to be part of this team and story.
Ponsse has a strong culture that has been developed over several years. The company has seen that a strong culture both carries the strategy forwards and brings business results. The most recent years have been challenging in more way than one due to the coronavirus pandemic, the war in Ukraine, and many other factors that have affected business and people. All of them have also had an impact on the company culture. Last year, we wanted to identify where Ponsse’s company culture was, and what needed to be developed in it. We engaged our entire personnel in this process and allowed everyone to have their voice heard through the personnel survey. More than 450 Ponsse employees from different parts of the world were also interviewed. We had good conversations and received excellent feedback on our strengths and the areas that still have room for improvement.
We are a value-driven company, and our renewed values reflect this.
34
Our updated values published in January marked the first visible step on our journey towards the development of our culture. We are a value-driven company, and this can be seen in our updated values. We wanted to maintain most of our values, but we also fine-tuned them to make them easier to understand.
Our updated values are: We truly care; We work for customers; We are honest; and We are open for renewal.
Everyone at Ponsse can develop our corporate culture through these values, and they also guide our daily activities and conduct. Our employees make the values visible to our customers. The Ponsse spirit is built through our values, and it offers a positive atmosphere and a sense of community while considering what’s best for our customers.
The Ponsse spirit is also materialised in our determination to manufacture the world’s best forest machines, find common solutions, and keep our promises. Ultimately, this also helps our customers succeed with us.
During the spring, Ponsse moved forward with the reform of the global operating model. Our plans to change our ways of working in relation to our renewed operating model and our values also guide this change: we want to further develop Ponsse because we care about Ponsse, and as a company, we also want to ensure a good workplace for our personnel and the best solutions for our customers in the future.
We are taking this work, the development of the culture and the change in working methods related to the operating model, forward with our personnel – caring and looking forward.
TIINA KAUTONEN Chief Human Resources Officer, Ponsse PlcIt’s an amazing feeling when everything goes your way – everyone feels well, and machines do not present any surprises. Now that the sun’s coming out, it’s hard to beat the feel of early spring. These are the thoughts of brothers Mattias and Markus Persson who work as forest contractors in Bredbyn.
During Ponsse’s visit, the temperature is just below zero, but machines are colder after the night and early morning. However, it doesn’t take long when snow starts to melt and fall from the machine loaded and mounted for transport. Early spring, which is sometimes also called the fifth season, has been long-awaited.
“Oh yes, it’s a wonderful time of the year. While the days grow longer and warm-
er, there’s still enough snow for skis and snowmobiles,” says Markus Persson.
Bröderna Perssons Skogsmaskiner Ab has three machine chains: one for thinning and two for regeneration felling. Soon the company will also have a forwarder for logging residues. Most contracts are within a radius of 50 kilometres. The brothers Persson have had a long-standing partnership with Holmen Group. Their customer relationship already started when the company
was established in 1961.
The machine fleet has grown along with the growing number of contracts, stabilising at the current level after the mid-2010s. Machines are traded frequently.
“Machines tie up a significant amount of capital. While the fleet raises a lot of respect, it’s important that machines are of a high level of quality, operate reliably and keep productivity high.”
“Of course, technology is attractive in
itself. We are keeping a close eye on technological development, and our opinions and ideas also seem to be important for machine manufacturers,” Markus Persson says.
The company’s first PONSSE was the Bear harvester, which was purchased in 2020 for regeneration felling. It was followed by the Scorpion harvester to join the group of other thinning machines.
“The Bear is unbeatable when trees are large, but we are not expecting many contracts where it will be needed,” Markus Persson says.
The company will soon have three PONSSE machines. In addition to the harvester in the group of thinning machines, two forwarders are on their way: the Elephant King for regeneration felling and the Buffalo.
• Owners: Markus and Mattias Persson.
• Domicile: Bredbyn, Ångermanland, Västerbotten County.
• Personnel: 14 people.
• Machinery: One thinning machine group and two regeneration felling machine groups, plus a lowbed for machine transportation, a forwarder for logging residues, a trackbased excavator and a wheel loader.
• PONSSE machines: One Scorpion harvester, one Elephant King forwarder and one Buffalo forwarder for logging residues (the latter two are expected soon).
• History: Brothers Rolf and Mats Persson founded the company in 1961. The current owners are Mats’s sons.
The latter machine will, above all, be used to carry logging residues.
“Ponsse’s forwarders will soon make their debut here,” Markus Persson says.
He points out that the effectiveness of the machine supplier’s aftersales services is key.
“Every machine requires maintenance every now and then, and when it does, downtime has to be minimised. Machines must remain in operation. This is what we and also our clients require.”
The closeness of maintenance services was a decisive factor for the brothers Persson to choose Ponsse. The nearest Ponsse location is 45 kilometres away in Örnsköldsvik, and the repair shop in Åsele is also fairly close. This enables the quick availability of both spare parts and maintenance employees.
“We’re in an even more privileged position, as a couple of Ponsse’s employees live near here. This means that help and spare parts are very easy to come by.
The company having a lowbed for machine transportation is a significant advantage.
“It increases our independence, as we can transport our machines on our own,” says Markus Persson.
Recently, the company also provided soil preparation services, and it needed to transport machines even more frequently than at present.
Two years ago, the brothers Persson built a large industrial hall for machines.
“It’s quite an advantage to be able to drive machines and maintenance vehicles inside
the hall. We should’ve made the investment even earlier,” Markus says with a smile on his face.
The company’s history dates back to 1961. At the time, the company was also run by two brothers Persson: Rolf and Mats (father of Mattias and Markus). As the young brothers had grown up on a farm, the idea of working in a forest felt natural. Rolf had even worked at logging sites at the time when loads were still driven by horses.
Mechanisation was still taking baby steps in the early 1960s. The brothers Persson started their career by installing half-tracks in their father Ernfrid’s farm tractor – a Volvo BM 320 Buster – that significantly improved handling in forests. Trees were felled with chainsaws and loaded by hand. The next tractor, which was a little newer, larger and stronger, was equipped with a crane.
Forwarders slowly started to come along: a smaller one for thinning and a larger one for regeneration felling. Soon the company started soil preparation services, which
were initially provided using a towed tiller. The brothers invested in their first harvester in the middle of the 1990s. That was also when Mattias started in the company.
The fleet has for long consisted of harvesters and forwarders. Soil preparation services have also been provided for years. In 2004, the company purchased its first dual machine with Holmen to test the opportunities the technology had to offer. It was later replaced by a forwarder designed to carry logging residues, and the company also invested in a chipper.
“The bioenergy market has gone up and down. Still 15 years ago, we had a machine group consisting of a chipper and two forwarders for logging residues. When the bioenergy market was in a slump, we had to let the chipper go and replaced it with another harvester. We will return to the market with the Buffalo forwarder.”
In addition, the company has provided soil preparation services sometimes, and sometimes not. In 2014, the
Reliable service is the most important. The machines must work, and downtimes must be kept as short as possible.
services resumed after a break of 20 years. Outside the season, the machine offers additional resources in transport services.
“To have more to carry outside the soil preparation season, we purchased yet another harvester. The machine was unemployed during the soil preparation season, and its two operators worked in planning.”
It’s quite a puzzle to have all contracts running optimally day in, day out, and also in the long term. Markus is mainly responsible for resource planning and the company’s administration, as well as machine transport, whereas Mattias plans the company’s operations when the ground is thawed and operates a harvester during other seasons.
Effective teamwork comes first for Markus and Mattias. They also want to give everyone the opportunity to participate and keep an open mind to do things a little better.
“The better everything works, the better we can handle any unexpected challenges whenever they turn up.”
Mattias and Markus share an interest in technology and machinery. After secondary school, Mattias studied mechanical and production engineering, while Markus focused on the transport industry. Mattias started in the family-owned company right after graduating, whereas Markus drove a timber lorry before joining the ranks.
What would you have become if you weren’t forest machine contractors?
“Ha, that’s a tricky one! Here, life largely revolves around forests, and they offer various job opportunities. I probably would’ve ended up doing something with machines or lorries,” Markus says.
Mattias is along the same lines.
“I really enjoy staying in the forest. That’s where I live, work and spend my free time.”
Mattias has a wife and two children. Everyone in the family is into hunting: elks above all, but also bears. They have five dogs, four of which are grey Norwegian Elkhounds and the most recent one is East
Siberian Laika. They also share their owner’s passion for forests and hunting. Mattias is also a forest owner.
Markus and his co-marital spouse have two children who are enthusiastic about skiing, riding, dancing and ice hockey. Markus’s spouse is a skiing coach, while Markus himself coaches an ice hockey
team. Flying is another passion for Markus. He has a two-seated ultralight seaplane with push propellers. Snowmobiles are among his hobbies on firm ground.
“I have nowhere enough time for everything, but I enjoy my hobbies and have fun. That’s what is important,” Markus says.
The committed staff and comprehensive service network in Sweden, Norway and Denmark have developed over the years to respond to customers’ needs. Anniversaries in Sweden and Norway are celebrated according to the Ponsse way – with customers!
This year, Ponsse’s subsidiary in Sweden will celebrate its 30th anniversary on the forest machine market. Managing Director Carl-Henrik Hammar has held the reins of Ponsse’s operations in Sweden for the last nine years. He says that the forest machine market and industry have changed along the years.
“There were not many PONSSE forest machines in Sweden when the company was established in 1994. Our market share has grown steadily ever since. For the last three decades, we have slowly but surely built and strengthened the Ponsse brand,” Hammar says.
During the last decade, the company has focused on its service network and the
smooth delivery of spare parts.
“When I started here at Ponsse AB, we only had two service centers. Now we have eight, and we also work with 17 service dealers across the country. Our head office is in Surahammar, and we already have 73 Ponsse employees in Sweden. Improving our service network has been one of our priorities, along with spare parts logistics.”
Hammar adds that, alongside our service offering, products are still at the core of Ponsse’s operations.
“We should not forget the importance of excellent products. Our machines undergo continuous development to ensure their reliability and technical performance.”
There are roughly a thousand PONSSE forest machines in Sweden, and significant growth is expected, as it is the world’s largest market for cut-to-length forest machines.
“Sweden’s forest industry is fairly stable, and we expect the forest machine market to grow. We also aim to improve our service network further. The network’s coverage has been improved during the last ten years, and now we seek to provide the best service in the industry for our customers,” Hammar says.
“Developing services in Sweden, Norway and Denmark is important to us. We also have a large machine stock in Denmark, and our service dealers keep customers’ machines up and running,” Hammar says in summary.
We want to celebrate our 30-year journey with the people who have made it possible – our customers. In celebration of our anniversary, we will host the two-day Ponsse Show Sweden event on 14 and 15 June. The event will feature forest machine demonstrations, evening activities and possibly a few surprises.
“It will be great to celebrate our joint accomplishments with our customers. It is important to gather together to celebrate this milestone,” Hammar says.
“It will be great to celebrate our joint accomplishments with our customers. It is important to gather together to celebrate this milestone,” Hammar says.
Ponsse’s Norwegian subsidiary was established in 1998. Its head office in Kongsvinger in Southern Norway is home to 14 employees who serve customers in cooperation with seven service dealers across the country.
The 20,000th PONSSE forest machine completed at the Vieremä factory at the end of last year was delivered to Lågen Skogsdrift AS in Norway. The PONSSE Bear machine equipped with the PONSSE H8 harvester head was received by brothers Harald and Gunnar Evju, owners of Lågen Skogsdrift AS. The company is based in Svarstad in the south of Norway.
Ponsse Norway’s anniversary was celebrated with Lågen Skogsdfrift and Ponsse’s people in Vieremä.
“We have served customers in Norway for 25 years now. We have grown with our customers and gained a fairly large market share. Our service dealers are close to customers, and we have incredibly committed staff,” says Carl-Henrik Hammar, Managing Director of Ponsse AB and Ponsse AS.
THE COMPANY’S SENSE OF COMMUNITY AND FOREST MACHINES INSPIRED JAN ERLING YRI TO START AS COUNTRY MANAGER
“I have always found forest machines interesting and considered Ponsse an innovative and advanced company. When I saw that Ponsse was looking for a Country Manager in Norway, I thought that I could be the right choice. As I have understood thus far, the company’s communal, customer-driven and down-to-earth approach is at the core of daily activities,” says Jan Erling Yri, Country Manager of Ponsse AS.
Currently, there are some 350 PONSSE machines in Norway, Scorpion Giant and Elephant King representing the majority. According to Yri, the popularity of Scorpion Giant in Norway is based on its ability to operate on steep slopes and its versatility in challenging terrain conditions. When it comes to the properties of Elephant King, Norwegian customers think highly of the machine’s operations in difficult and steep terrain, as well as its excellent performance.
Norwegian customers appreciate, above all, the performance, reliability and flexibility of PONSSE machines.
“Norwegian customers appreciate, above all, the performance, reliability and flexibility of PONSSE machines. According to feedback given by contractors, Ponsse’s machines are also economical,” Yri says.
Yri will learn more about the forest industry and pave the way for the company towards even better growth.
“We expect to maintain and strengthen our position in Norway and increase our presence in new regions that we believe to have sales potential.”
However, Yri’s primary goal is to make Ponsse the leading forest machine company in Norway.
“Even though I cannot wait to learn more about the forest machine industry, my key objective is to make Ponsse – with the excellent employees of Ponsse AS – the preferred partner of forest machine contractors in Norway.”
Ponsse has a strong and unique culture. The people of Ponsse, everywhere in our Ponsse network, are the company’s main and most important asset throughout its history. We started out to explore Ponsse’s culture, because we wanted to understand what our culture is made of and how we could develop it further as our operating environment continues to change. Our strategic goal is to build a strong culture, and we want to invest in it. Throughout our history, Ponsse’s culture has been one of our strengths and it has allowed us to stand out from our competitors and other employers.
By exploring our culture, we gained valuable feedback and more specific insights into what we want to develop in our culture and how we can work together to continue to be successful in the future. One of the first development steps is related to Ponsse’s values.
We renewed Ponsse’s values respecting our strong culture, while also addressing the requirements of modern working life, future development needs and our personnel’s feedback on our culture and values.
PONSSE SPIRIT is about doing things together. It means that “we” is always more important than “I”, even though we also take care of the individual. It also means doing the best for the customer with great professional pride and a twinkle in your
• We enable the continuous development of Ponsse and Ponsse employees
• We develop our operations with customerorientation and environmental focus
• We are excited and curious about new things
• We see change as an opportunity to learn
• We are resilient and endure uncertainty
eye. Ponsse spirit comes to reality through the everyday work of every Ponsse employee. That’s why we call Ponsse’s values the Ponsse Spirit. This Ponsse Spirit is conveyed in our daily work to the customer, because they are the reason we exist.
• We care about our customers and each other
• We work together
• We care about winning
• We appreciate feedback from each other and customers
• We treat everyone with respect and inclusion
• We are present and support each other’s success
• We ask for and give support
• We act with everyone’s safety in mind
• We keep our promises
• We communicate openly and constructively, even in challenging situations
• We take responsibility together and as individuals
• We base our decisions on facts, we are realistic and effective
• We act ethically and build our future together
• We know our customers and their business
• We know how our work affects the customer
• We make decisions boldly, understanding their meaning
• We do our best - every day
“THE PONSSE SPIRIT BECOMES REALITY WHEN WE OPERATE IN LINE WITH OUR VALUES”
Our values guide our daily activities and allow everyone at Ponsse to have a say in the future direction of our culture. When we act according to our values, we have a positive impact on job satisfaction
and cooperation within our Ponsse network, and thus on the customer experience.
Vast amounts of data are processed every day in our rapidly changing world. For Ponsse, digital solutions and their development are an important step towards sustainable harvesting.
Ponsse prioritises developing these services in ways that allow contractors to easily and cost-effectively extract data from their forest machines for reporting and ERP systems to develop their own business. Easily usable data also ensures systematic and streamlined operations and makes daily tasks easier for harvesting personnel. Precisely measured data helps businesses to bring transparency to their operations. Ponsse’s development of digital services is strongly guided by customer feedback and sustainability goals.
PONSSE MANAGER 2.0 COMBINES DIGITAL SOLUTIONS ON A SINGLE PLATFORM
PONSSE Manager 2.0 is both a platform for next-generation digital services and a forest machine management system. The system allows customers to track the location, productivity, and fuel consumption of their machines. The system can be used to track machine productivity by assortment and delivery, and it can print measuring and loading reports. The PONSSE Manager 2.0 platform supports both field personnel and the professionals in charge of flexible and effective fleet management.
The digital platform allows users to create a custom landing page or dashboard, with immediate access to vital data. Important information can be read quickly and changes are easy to spot. This helps the users take corrective actions immediately. Once logged in, users have access to all the digital solutions for improving their operational efficiency and productivity – all in a single online location.
Users of the PONSSE Manager 2.0 platform gain real-time data on the factors affecting the productivity of their machines, allowing the users to optimise their operations.
PONSSE Manager 2.0 features a comprehensive reporting function that allows users to analyse production volumes, working hours and fuel consumption by logging method, forest company, machine and operator, over a given period of time. The logging method, average tree diameter and forwarder driving distances for a site can be compared with productivity and fuel consumption figures.
One of the new key functions enables uploading all reports into a spreadsheet, for example, where the data can be combined with other data to produce useful operational analyses. Free mobile applications are also available for download from app stores.
The PONSSE Manager 2.0 platform provides customers with a maintenance history for machines maintained by Ponsse’s maintenance services. Up-to-date records help machine owners keep track of the completion and content of each machine’s scheduled maintenance.
Listen to the Ponsse Studio recording from the PONSSE Manager 2.0 platform’s launch event: QR code to the Studio page
Multifleet by Ponsse is a digital solution designed to help companies in full fleet management. It is irrelevant whether the fleet consists of forest or agricultural machines or road vehicles, what their make is, or whether the fleet is large or small. An antenna and electronics module installed onto a vehicle send valuable real-time data on machines and their operations to the cloud over a mobile network or satellite connection. Ponsse’s Multifleet solution then converts this data into reports that support customers’ business. Users only need a network connection to use the data anywhere and at any time, speeding up decisions and maximising their company’s productivity. Users can access company-specific data on their mobile phone, tablet or computer via a link or an app using their credentials. Currently Multifleet is available in Latin America. More information: rafael.paes@ponsse.com or petteri.tuomisto@ponsse.com
PONSSE Service Application is a mobile app that allows customers to browse Ponsse’s maintenance service products such as forest machine accessories. The app is available for Android and IOS, from the Google Play Store and the Apple App Store respectively. The app also works in offline mode.
SPARE PARTS AVAILABLE 24/7
Ponsse’s highly popular online shop for spare parts allows customers to order parts for their PONSSE machine at any time. The system also displays real-time availability and pricing information for parts. In addition, the service includes useful information such as spare parts catalogues and owner’s manuals, and users can add notes for each machine.
Currently, PONSSE Parts Online is available in Finland, Sweden, Norway, Denmark, the UK, Ireland, France, Germany
At Ponsse, the development of digital services is strongly driven by customer feedback and sustainability objectives.
PICKING UP KEY OPERATIONAL MACHINE DATA FROM ALL LOGGING SITES
The PONSSE Manager Satellite service is an upgrade to machine connectivity. The service sends data on work area productivity, machine location, operating hours and fuel consumption to a server, ensuring effective reporting. Data is transferred using the machine’s Opti information system, a satellite connection and the Connectivity Unit telemetry module. With the Satellite service, the machine can communi cate via a satellite connection in areas without any mobile coverage. The Connectivity Unit, developed by Ponsse’s technology company Epec Oy, and the PONSSE Opti information system operate fully automatically without any separate measures.
The PONSSE Manager Satellite reporting tool lists the produced assortment volumes by machine, operator and work area. Customers can use the reporting tool to view machine operating hours and cumulative fuel consump tion from anywhere on the globe. This data is collected and transmitted once a day as part of the comprehensive report produced by the PONSSE Manager service. Using the PONSSE Manager Satellite reporting tool, machine data can be transferred in areas without any mobile coverage.
With the PONSSE Data API service, forest machine data can be retrieved directly from the cloud. The service can be used in the invoicing of harvesting operations or the payment of wages, for example, based on harvesting production data. The service also produces benefits in logistics, as operations can be planned in real time during harvesting. The data can also be used as a source for various applications, even allowing customers to build their own applications based on the data.
The service makes the use of forest machine data significantly easier and more affordable, and it brings knowledge-based management available to more contractors than before. The PONSSE Data API service is available as part of the PONSSE Manager system.
The PONSSE Active Manual service hosts operating and maintenance instructions, including videos, to support the daily work of forest machine operators. The highly visual service includes a mobile app that supplements the conventional owner’s manual with videos of operating and maintenance instructions. The PONSSE Active
The long-term development was finally signed with an official dealer contract. Jussi Hentunen, Director, Dealer Development; Ivan Laskov, Commercial Director; Bojidar Petkov, CEO; and Antti Räsänen, Area Director
PROGRESS
Progress-Technik has developed its operations in Bulgarian markets for several years now and is finally Ponsse’s official dealer. Established in 2014, Progress-Techik Ltd sells and maintains forest and wood processing industry products.
“Our partnership started four years ago, and Progress-Tech-
nik’s personnel have truly shown that they are an excellent partner for us in Bulgarian markets. We are also very impressed with Progress-Technik’s new facilities in Pazardzhik in Central Bulgaria,” says Antti Räsänen, Area Director at Ponsse.
Progress-Technik held the grand opening of its new facilities and a harvesting demonstration, attracting a large group of visitors interested in forest machines and the forest industry.
Forests consist of oak-dominated stands in lowlands, beech-dominated and mixed beech and softwood forests, and softwood stands in mountain areas. The total forest area is little under four million hectares, accounting for more than 35% of the country’s total area. Most forests in Bulgaria are young or middle-aged.
Opened in Seinäjoki in Finland, the electronics factory uses sustainable manufacturing processes and seeks carbon neutrality in its operations. The new modern factory provides with even better working conditions for employees and more streamlined processes.
Ponsse’s subsidiary, the Finnish technology company Epec, opened a new smart and environmentally friendly factory in Seinäjoki. Named Epec Smart Factory 1, the new factory is home to the manufacture of control units, displays, sensors, power distribution units and telematics units, among other components, for various mobile machines and utility vehicles.
In addition, various systems and software are designed and developed for international machine manufacturers at the new factory, and it is equipped to respond to customer needs and strict quality requirements even better. The expanded modern production facilities improve the management of manufacturing process optimisation and material flows. All in all, the new factory features top-of-the-line testing and production technologies.
The factory is 8,500 m2 in size, and its energy-efficient solutions include electricity
generated by more than 600 solar panels (210 MWh per year) and a geothermal heating system. Heat recovery is based on effective needle tube heat exchangers, while the aluminium grating on the office wall significantly reduces the need for cooling energy. All electricity and heating energy come from renewable sources.
The high-technology factory marks a significant investment for Epec and is in line with the company’s growth goals and sustainability commitments.
According to Jyri Kylä-Kaila, Managing Director of Epec, sustainability goals also guide technological changes in the heavy-duty machine and utility vehicle sector, and the transition accelerates digitalisation and electrification.
“Epec’s products play a key role in enabling the development of more sustainable
machines and utility vehicles. They offer solutions for the integration of electrical and control systems, optimise machine efficiency and improve productivity, while reducing emissions,” says Kylä-Kaila.
“Our products lead the way towards zero-emission machines. The factory gives us significant opportunities for growth and supports our customers’ success, also in the future,” he says.
According to Juho Nummela, President and CEO of Ponsse, rapid technological development and increasing sustainability requirements place Epec in an excellent position to enable zero-emission technologies. Ponsse’s vision is to be the preferred partner in sustainable forestry which calls for determined development, also considering the environment.
“We are very excited about the new Epec factory. In its product and service development, Ponsse seeks climate-friendlier and more ecological solutions. The new factory
built in Seinäjoki is a concrete step towards this goal, both in terms of the product range and daily activities. Epec supports Ponsse’s technological development and enables our future growth,” says Juho Nummela.
Aatu Ala-Mattinen, who has worked as a production testing engineer for two years, is enjoying his work much more than before. Working is significantly easier now that operating methods have been clarified and streamlined. For example, production workstations have more room for equipment to make working easier. In addition, working methods have been rationalised in production. End products are now assembled directly according to new orders to avoid any unnecessary work stages.
“What is more, the new facilities are clean and spacious, with colours that are pleasing to the eye. They feel simply excellent,” says Aatu.
“The general level of cleanliness has a significant impact on my wellbeing at work. As my workstation is close to production, I can quickly solve daily production challenges, but I can also go to my workstation when I need to
concentrate on my office work,” he continues.
The new facilities also enable flexible remote working. In addition to production facilities and personal workstations, the factory features various jointly used spaces with a modern and ergonomic interior design. Employees feel that the facilities have been designed specifically with their wellbeing in mind. For example, there are several quiet workspaces and ergonomic furniture and fixtures.
“The facilities are simply amazing, and the working conditions are excellent. Everything here is new and all spaces are effective. What is more, personal workstations offer enough room for working. All technical systems are top-of-the-line which also makes daily working easier,” says Nina Kristola who works as an HSEQ specialist.
“The nice interior design builds a relaxed atmosphere, in which it is easy to stop to chat with colleagues without having to officially book any conference rooms. The small and easily available quiet spaces are ideal for urgent informal meetings. In addition, the new facilities have half the number of floors compared with our previous head office. This makes interaction easier,” says Kristola.
The new facilities are clean and spacious, with colours that are pleasing to the eye. They feel simply excellent,
– Aatu Ala-Mattinen, Production Testing Engineer
• Established in 1978
• Head office in Seinäjoki in Finland.
• Locations also in Tampere, Turku and Kuopio in Finland, and in the United States, China and the Netherlands.
• More than 200 employees in total
• Epec manufactures control units, displays, sensors and power distribution and telematics units for various mobile machines and utility vehicles.
The nice interior design builds a relaxed atmosphere, in which it is easy to stop to chat with colleagues without having to officially book any conference rooms.
– Nina Kristola, HSEQ specialist
PONSSE FIREFIGHTING EQUIPMENT
Firefighting equipment has already been sold to almost ten countries. The advantages of the equipment in difficult terrains have also been noticed in Uruguay.
In the summers of 2021 and 2022, Uruguay was hit by major forest fires. A long-time Ponsse customer, Montes del Plata, learned first-hand how difficult it was to access certain fire areas. Water and firefighting trucks could not reach areas with uneven or rocky terrain or areas where trees had recently been felled.
At the same time, Ponsse had just presented an innovative firefighting solution, and Montes del Plata wanted to examine the equipment.
“Ponsse offered us a new fire protection system to try. After examining the system, we found that it was ideal for firefighting in Uruguay, especially for our own use.”
“Safety is one of our most important values, and Ponsse equipment is extremely safe. Not only does the agile equipment travel and operate off-road, but it is also reliable. This
Juan
is very important. We ended up buying three pieces of equipment immediately,” says Juan Bide.
The firefighting equipment has ability to carry a large volume of water, with a water tank capacity of 10,000 litres. It is easy for the driver to learn how to operate the equipment. The equipment can be operated by the driver of the tractor and the operator in the
field via remote control. The equipment’s water cannon reaches a distance of almost 50 metres, so that there is no need to drive close to the flames when working in front of the fire.
“The results were excellent. We were very pleased with the equipment – so pleased, in fact, that we purchased a fourth unit for the next fire season, 2022–2023,” says Juan.
“Today, we have four Ponsse firefighting systems in operation. If I had to choose the best feature, I think it’s reliability. It is very agile, safe and also effective. It can travel over all types of terrain, so you can fill the water tank wherever you want, which hasn’t always been possible if you’ve had difficulty getting to water. The equipment has greatly improved and enhanced our firefighting,” Juan continues.
Due to its versatility, the firefighting
equipment can be connected to any forklift truck. It is also compatible with other machine brands. Montes del Plata has its own machines for fire extinguishing use but, if necessary, the equipment can be easily moved from one tractor to another in half an hour. If the fire lasts for several days, the basic machine itself can be damaged. In this case it is easy to replace the equipment with another machine. A smaller diameter hose is also available, of which there can be several attached in the same equipment.
In addition to firefighting equipment, Montes del Plata has been working with Ponsse for more than ten years and has been a Ponsse Full-Service customer since 2013.
“We feel we’re more of a partner than a customer, and we’ve developed many improvements to the firefighting equipment together. Partnership is one of the values on
• Compatible with PONSSE Buffalo, Buffalo King, Elephant and Elephant King.
• 10,000-litre water tank with pump and water cannons.
• Water cannon rotates 360 degrees.
• The wireless remote control has an operating range of approx. 100 m. The spray direction, angle and pattern, ranging from water mist to a solid stream, can be adjusted using remote control.
• The solid stream reaches up to almost 50 metres.
• The water tank can be filled from a natural water source in about seven minutes.
• Company established in 2009
• Full Service customer since 2013
• 28 Ponsse machines, firefighting equipment installed on Buffalo King forwarders
• 1.4 million tonnes of pulp per year
• 7.5% of Uruguay’s exports
• 6,500 employees (direct and indirect workers throughout the production chain).
which we base our choice of companies to work with. We share the same values, which helps greatly in finding a common vision of efficiency and sharing experiences. Ponsse has always been open and honest with us.
“These strengths have helped us grow
together. We greatly value the service and maintenance of our machines, the availability of spare parts, the training of our staff, and the rapid response to urgent incidents. These things are very important to us, and Ponsse has been very successful in them.”
Ponsse Ladies’ activities are full of positive thoughts, nice people, team spirit and enthusiasm.
The idea of the Ponsse Ladies club is to bring together the spouses of contractors using PONSSE forest machines, as well as female forest machine contractors, and offer them opportunities to build networks through joint activities. All the club members have some kind of connection to forests and forest-related business operations. Contractors’ spouses are often also actively involved in the day-to-day operations of the harvesting company.
The club came into existence at the FinnMetko trade fair in 2004 and is therefore celebrating its 20th anniversary this year. Almost 270 people are involved in the club in Finland, and the actions has expanded to several different countries.
Ponsse Ladies are united by a desire to share experiences and thoughts related to both work and leisure. Joint training and shared experiences have strengthened their professional skills and networks.
In Finland, Ponsse Ladies’ activities are led by Pia Kainulainen and Piia Vidgren, as well as Eveliina Virkkunen, who has been involved for almost a year.
Close friendships built over the years are also what Ponsse Ladies are all about.
“The members meet 1–3 times a year and also keep in touch between meetings and events. In this group, if anywhere, the
everyday life of forest machine entrepreneurs is understood. When they meet, the laughter and lively discussion can be heard far away,” Piia Vidgren says.
Pia and Piia have been in the club from the very beginning and have fond memories of the ladies’ trips abroad.
“The high points include culinary experiences around the world. For example, in Pärnu in Estonia, we enjoyed Mulgi porridge at a blacksmith’s shop. Yxtaholm Castle in Sweden was majestic, and Rondele Ranch hosted by Ponsse Ladies in the United States was a wonderfully unique experience! Glass-blowing in Norway, bagpipes in Scotland, Charles Bridge in Prague, the green moors of Ireland, two visits to Germany, Ponsse Ladies International Meeting in Évora, Portugal together with the USA, Sweden and Germany Ladies, world-famous sites: the Great Wall of China, Tiananmen Square, Hermitage and the Eiffel Tower. We have walked along the Champs-Élysées to the Arc de Triomphe and cruised on the Seine. In the United States, we saw the Statue of Liberty and experienced the never-ending beat of Manhattan and the flashing lights of Times Square. The ruins of the Twin Towers left us silent with a heavy heart. We also had the opportunity to have lunch at the Consul General’s residence by Central Park in New York. In addition to all this, we have learned about harvesting and forest management activities in
each country when he have visited the local subsidiary or dealer.
In Finnish destinations, we always have some sort of organised activity, from colour analysis and winter driving training to zumba and fitness boxing. In February, during our visit to Vieremä, we got to try yet another new type of exercise: mat Pilates.”
The encounters in Finnish destinations have been memorable: our visits e.g. to the Järvisydän, Epec, Punkaharju and Luppolinna resorts, driving a Bentley in Mäkelä, the Little Bear’s Trail in Ruka, and a Northern
Lights trip in Ylläs, where reindeer came to the yard of our cottage to see what was going on.
“The pandemic interrupted our activities, but in 2023, we were able to travel again and visited Kraków in Poland, where we visited a museum in the Historic Centre of Kraków, which is one of the UNESCO World Heritage Sites, and saw Oscar Schindler’s factory and the Wieliczka salt mine. We invited the local Ponsse Ladies to visit the Vieremä Day event and the Runni Spa,” says Pia Kainulainen.
In Finland, Ponsse Ladies’ activities are led by Pia Kainulainen, Eveliina Virkkunen and Piia Vidgren.
Diana Olkowski and Demi Litke take a look at Ponsse Ladies’ journey in the United States.
Ponsse Ladies was founded in the United States in August of 2014. The first ever event took place in connection with the launch of the Scorpion King harvester. Day one was a live demo with the harvester and day two was a boat trip down the Wisconsin River, and that was the beginning of our journey together. We heard that there was a Ponsse Ladies Club in Finland that brings together women working in the forest machine industry, so we decided to start our own.
We noticed at the forestry shows that women would stay in their own group of family and friends, and we wanted to bring them all together. Not in our wildest dreams could we have been able to imagine what kind of friendships were created and what wonderful moments we would experience together.
Ponsse Ladies meets once per year, and every event is well planned. We always keep in mind that when it comes to club meetings, we should either learn something new or donate our time to help others. For example, we have raised money for the American Cancer Society, helped clean up the ocean beaches, operated Ponsse machines, and learned about the activities of our network. As people often say, “It doesn’t matter where we go or what we do. It’s about the time we spend together.” Our Ponsse Ladies members are the best, and we wouldn’t have this group without them.
We have travelled to many places such as Finland, Spain and Portugal. In the United States, we have visited Florida, Wisconsin, Illinois, New York, Maryland, and Montana. In addition, we have visited the Ponsse North American Headquarters in Rhinelander, Wisconsin and New York City with the Finnish Ponsse Ladies.
In 2024, the ladies will meet in August, which will be exactly ten years since we first met in August 2014. The event will be held in Gaylord, Michigan, where we will spend a few days together. We will play golf, enjoy one another’s company, and participate in and support the first-ever Michigan Timbermen Forest Products Show. We are happy to be able to celebrate the years of friendship!
Whatever the future brings, we are excited about where it will take us!
“We have learned so much over the last 10 years from each other. We have a great
group of ladies that have so many of the same interests and hobbies. It’s amazing how an industry and a company can bring us all together.” Diana Olkowski, Leader of Ponsse Ladies and Marketing.
“Ponsse Ladies’ activities have been a very fun and rewarding time. All the moments and stories we can share together give meaning to our work. We Ponsse Ladies always say we’re a family, and these experiences make it real.” Demi Litke, Leader of Ponsse Ladies and IT/ Product Support Specialist.
“It has been amazing to be a Ponsse Lady and be able to travel with the group. I love new places, and it has been really great to get to know the environments in which Ponsse forest machines work. It has been refreshing to meet women who understand what it’s like to be the wife or daughter of a forestry machine operator.”
An effective and safe service centre provides the best possible maintenance services for customers. ESW helps identify any areas that require development and enables the continuous improvement of maintenance services. More than 600 conducted ESW audits mark an example of Ponsse’s commitment to high quality and customer satisfaction.
The audit was performed at the Kuopio service center in March 2022. It was found that the development of the service center meets the five-star criteria. Full service service center operates in Kuopio with a force of ten people.
”We moved to new premises on Sahakatu at the beginning of 2020. The premises were built according to the requirements of the modern forest machines.
“I am pleased that we have developed our service center to this point and have earned five star”, says the service supervisor of the Kuopio service center Marko Luodes.
There are 14 Ponsse’s own service centers in Finland, 11 of them have passed ESW auditing. Six audited service centers has earned five stars and five service centers four stars.
An effective and safe service centre provides customers with the best possible after-sales service.
ESW is short for Effective and Safe Workshop. It is a comprehensive set of guidelines for Ponsse’s authorised maintenance organisations, covering the activities and services of service centres.
The ESW guidelines help provide customers with services of as high and even quality as possible, regardless of where they operate and whether they acquire services from Ponsse’s service centre, retailer or contractual service partner.
“ESW is also a continuous improvement tool to develop the maintenance network globally and improve maintenance services locally,” says Harri Perätalo who is responsible for the development of Ponsse’s field maintenance and service centre operations.
What started as auditing has been developed into guidelines. The guidelines make information better available, responding to
changing needs. Currently, auditing is part of a larger set of guidelines.
A small development team conducted the first three audits at Ponsse in 2011. Strengthening Ponsse’s quality image in the maintenance network was one of the starting points.
“We also needed to add visibility to local operations and regular two-way communication to our global network.”
ESW covers 28 different areas, ranging from the arrangement of the customer space and branding to the effectiveness and expertise of maintenance and spare parts processes. Key metrics include occupational safety, the environment and training.
“When it comes to ESW, we seek to identify how service centres and field maintenance operations have prepared for various
factors, many of which are related to sustainability. Training is also part of sustainability and safety.”
Currently, Ponsse has 11 factory auditors, mainly maintenance professionals with various specialisations. In addition, local auditors are used in North America, Uruguay, Brazil and Sweden – in markets distant from the factory or with a large contractual service partner network.
The audit process is cooperation in which auditors and service centres work together to identify any areas for improvement.
“It is important that auditing is regarded specifically as a development tool. We want to support our service centres, not rank them. By identifying and making improvements, we can increase the quality of our services which produces the most benefits for our customers and local maintenance services,” Harri says.
According to Harri Perätalo, the leading idea behind the ESW tool is that what can be measured can be improved. If it were not for measurements, it would be difficult to know exactly what should be developed. Once a score has been given for each area, a star rating is determined based on the results.
“For example, the lower limit for three stars is 49% of the maximum score, whereas the limit for five stars, the highest score, is 89%. A onceearned high score does not automatically stay the same forever. Continuous development is required, and the criteria may also change according to needs.”
The rating also creates motivation and positive competition. Maintenance professionals want to show what they can do.
Having worked years across the world for Ponsse, Harri has seen that customers appreciate it when a local authorised Ponsse service partner develops and improves its operations and invests in them in the long term.
“This also gives customers courage to make investments and buy machines. They can rely on Ponsse doing its best and keeping machines up and running.”
Established in 2014, Progress Technik Ltd. provides services for its wood and forest industry customers. Its partnership with Ponsse started in 2018.
“In less than six years, we have become the market leader and are already providing services for roughly a hundred PONSSE machines on the Bulgarian market,” says commercial director Ivan Laskov.
“It is safe to say that our success comes from our close relationship with Ponsse’s sales and marketing, as well as maintenance and spare parts services,” he says.
Progress Technik has used the ESW manual and aimed to follow it as precisely as possible. Intended for Ponsse’s authorised service centres, the ESW manual is a summary of best practices and the result of Ponsse’s long-term experience in forest machine maintenance and customer service.
“To provide the best possible service for our customers, we need to be as prepared as we can, and the ESW guidelines offer the best tool for this purpose. ESW also helps us prepare for situations we have never experienced before,” Laskov says.
According to Ivan, the deployment of the ESW guidelines was a long and demanding process which brought along many useful experiences. The process also brought the team members closer together and motivated them, as they all sought to make it a success.
“Our service centre was given four stars. Our goal is to combine our efforts during the next three years to become a five-star Ponsse partner. We will follow the ESW guidelines as closely as possible,” Ivan Laskov says.
Excellent Swedish service expertise in Örnsköldsvik service center, which received in the audit four stars in 2022.
Ponsse’s service centre team in Mikkeli has developed its activities with great leaps forward in accordance with improvements and instructions created based on ESW audit reports. While the first ESW audit conducted eight years ago produced the result of 76% of the maximum score, the team’s performance in 2023 was excellent at 96%.
“We started from easy and affordable improvements and decided to put them into practice. Each year after that, we have also sought to complete a few more demanding projects,” says Regional Service Manager Marko Iivanainen.
During the first ESW audit, the Mikkeli service centre was still based in its former and smaller facilities.
“Even though the repair shop was cramped, we reorganised it together to make working smoother. We learned valuable lessons trying to find the right place for everything. Despite the limited space, we were able to make our operations more effective,” Marko says.
In 2019, a new building was completed for the service centre, with the repair shop being based on the ESW guidelines. The experiences gained from the previous facilities helped organise the new repair shop like no other before work was started. Working in the modern facilities is effective and safe which is also reflected in high customer satisfaction.
“When customers step in the repair shop, they can see that the space is tidy and everything has been carefully considered. The first impression is systematic, and I believe that customers can see that we have everything under control.”
Ponsse’s maintenance services are customer-driven, with customers given priority in all operations. Marko Iivanainen knows that this is why the development of operations can sometimes be forgotten in all the rush and customer activities.
“The correct moment may never come – we simply have to make time and decide to make everything right. Every hour spent will eventually repay itself through improved efficiency and smoother processes.”
The Scorpion harvester quickly became one of Ponsse’s greatest hits after its introduction in 2013 lmmediately af ter its launch, the Scorpion became an international bestseller and a symbol of sustainable forestry. More than 1,900 Scorpions have already been made so far
The PONSSE Scorpion became a highly popular harvester immediately af ter its launch. With its several strong properties, the Scorpion has also earned its place as a popular used machine. ln Ponsse’s extensive used machine range, the excellent properties of the Scorpion are also available at a lower price.
The PONSSE Scorpion’s unprecedented properties were already introduced in the very first machine which is why the over ten-year-old Scorpion is still a reliable tool. Based on years of experience, we have seen that all of the Scorpion’s key properties are highly durable and optimal considering the whole machine lifecycle.
The powerful engine and strong hydraulics produce more than enough power, both in harvesting and transmission. The Scorpion is available equipped with single-circuit hydraulics for changing harvesting purposes or as the Scorpion King version with double-circuit hydraulics, in particular, for clear cutting. The advanced transmission offers excellent handling and machine control - especially in demanding conditions and uneven terrain.
The unique fork boom moving over the cabin guarantees excellent visibility in every direction. Good visibility, also on both sides of the cabin, enables efficiency without any limits. The operator can select trees and felling directions and place trees into piles efficiently, producing the best harvesting quality. The structure has proven very durable in operations.
ln the PONSSE Scorpion, the machine operator is at the core of all operations. The cabin is located in the middle of the machine, making it easier to see its extremities when working at dense thinning sites. What is more, the operator is situated in the middle of the cabin’s turning radius: when the cabin turns, the operator does not feel like being on a carousel. This has a significant impact on comfort and wellbeing at work.
The most durable and efficient harvester heads on the market are available for the Scorpion. The Scorpion is always the right choice at thinning or energy wood sites where not only efficiency but also excellent harvesting quality is required.
Cabin levelling balances the cabin, also in difficult terrain. The frame of the machine consists of three parts linked by rotating joints. The cabin is located in the middle frame, which is kept hydraulically balanced, while the front and rear frames tilt according to the terrain. The pivot point of lateral levelling is very low, which not only keeps the cabin straight but also minimises any lateral swaying and keeps the centre of mass at the machine’s centre line.
With Ponsse, used machine trading is a smoothly flowing process. Years of experience have given us valuable information about the maintenance measures and spare parts required for machines - we know what parts of machines need to be inspected before delivery to a new customer. We offer help to acquire funding for machine purchases with our financial partners. We deliver machines directly to customers’ logging sites at request, and provide machine training if required. Whether the choice is the Scorpion or the Scorpion King, regardless of the machine age - we can ensure that machine operators, contractors and forest owners are satisfied.
A diverse forest provides a home for animals and plants. Color the picture and think about what your own nearby forest is like.
Draw a picture of your nearby forest and send it to us!
Ponsse Plc, Ponssentie 22, FI-74200 Vieremä, Finland. You can also take a photo of the picture and send it to ponssenews@ponsse.com. Remember to add your name and address and you can win prizes.
The first stages in Ponsse’s history date back to the late 1960s when Dino, the first prototype, was completed. At the time, Einari Vidgren partnered with Erkki Tarvainen and Lauri Uuksunen, two men he trusted. Together, they started Ponsse’s story. Unfortunately, they are no longer with us after Erkki and Lauri left this world’s logging sites at the beginning of 2024. However, their legacy lives on in our history, and we will cherish their memory as we carry Ponsse’s story forward.
Throughout his career, Lassi was known as a meticulous and punctual worker. With the precision he demanded, he set the benchmark for quality in production – every welded seam had to be just right.
Village blacksmith Kauko Väisänen’s workshop was bustling in late winter 1969. Young welder Lauri “Lassi” Uuksunen was welding a forwarder which forest machine entrepreneur Einari Vidgren had designed in his mind. There were no drawings, and Einari simply drew lines in the air to depict how the machine should be built from a bucket loader’s front frame. That moment marked the beginning of PONSSE Dino’s journey to becoming one of the best load-carrying forest machines of its time and also of Lassi’s career as Ponsse’s first welder. Lassi also took part in Ponsse’s first and most notable forest machine exhibition in Myllypuro in Helsinki in 1972, which was a success and highlight for the personnel at the time.
Throughout his career, Lassi was known as a meticulous and punctual worker. With the precision he demanded, he set the benchmark for quality in production – every welded seam had to be just right.
Lassi had a colourful childhood – he was born in the village of Sortavala in the Republic of Karelia and lost his father in the first battles of the Continuation War. After the war, he moved to Vieremä with his mother and stepfather which marked the beginning of his new life. Lassi’s stepfather worked as a tailor in the village, his stepsister Leena was born, and life found its course by the Sotku pond, right next to Rientola. Lassi went from Vieremä to war orphans’ vocational school in Mynämäki. Work and what it requires were learned already in childhood – Lassi maintained his work ethic throughout his life.
He spent his retirement in Iisalmi where he lived in an apartment in a residential building. His last years were shadowed by illnesses which also ended his life in late winter 2024. Lassi’s memory lives strong at Ponsse’s factory and in the history room where stories of his life’s work are passed on to visitors and new employees.
Thank you Lassi.
Erkki played a significant role because, if it had not been for the countless maintenance visits across Lapland and to various logging sites in Kainuu and Savonia, Einari and Ponsse would have never been able to grow and gain their customers’ trust.
Asmall and narrow cart track separated from Kaarakkalantie and meandered to Härkäaho through lush Kytölehto.
That was where Erkki and his parents Viljo and Hilja Tarvainen had their home, a small farm, where he spent his early and late childhood years in the 1940s and 1950s. There was always work to be done on the farm which, combined with living with his siblings, made Erkki a balanced and considerate man who was easy to trust.
Like other members of the post-war generation, Erkki completed a reduced primary school curriculum at Nieminen village school. As there were so many students and so few teachers in remoter regions, only half of the school term could be organised both in autumn and spring. This brought along more work on the farm but also took Erkki to nature, either to go hunting or fishing, or simply to enjoy the beauty of the Savonian countryside. Forest work was an annual undertaking for small farmers, and that was also Erkki’s calling in his younger years and throughout his career.
Härkäaho neighboured with the Mäkelä estate, the home of classmate Einari Vidgren, with whom forests started to attract more attention after the role of agricultural work decreased in the middle of the 1960s. The young men were eager to work, but also found time to go dancing, which was the favourite pastime of young people at the time. Being skilled dancers and non-drinkers, they stood up from the crowd at various dance venues in Northern Savonia over the
years.
Erkki soon dove into the interesting world of agricultural machines, learning how to fix them and make them even better. There were many skilled blacksmiths in the Nieminen village who had built windmills, sawing lines and shingle mills, and knew how to mend tractors, cars and lorries, provided that they had the necessary parts.
The skills of Erkki and the village blacksmiths were soon in demand when Einari from next door started to develop Mehu-Maija, the first load-carrying forest machine. However, the machine was not durable enough and its use in forests was quickly stopped, but it taught valuable information. Einari continued his experiments and the next attempt followed in 1969, on which Erkki had a significant impact – the PONSSE Dino forest machine became a success. It resulted in the establishment of Ponsse Oy, a company which started to build forest machines in Vieremä in 1970, in the middle of the worst depression and the largest structural changes in agriculture.
Einari hired Erkki as Ponsse’s first employee. He needed a skilled maintenance man and, above all, a dependable and hard-working friend to support the company during its early stages. Erkki played a significant role because, if it had not been for the countless maintenance visits across Lapland and to various logging sites in Kainuu and Savonia, Einari and Ponsse would have never been able to grow and gain their customers’ trust. Work was hard and hours were long – Erkki’s work helped build
the good reputation of Ponsse’s customer service and maintenance.
Hard work was balanced by his family – Erkki’s wife Annukka and his children Hannu and Anne added colour and meaning to his life. The family’s home was built in the Vieremä village in the 1970s, including a separate room for Erkki’s disabled brother Esko. Taking care of his brother was another good example of Erkki’s lifelong characteristic of caring for other people. He and Annukka volunteered in various events, carrying firewood, making coffee or heating up a griddle to have a taste of Annukka’s delicious pancakes.
Erkki enjoyed hunting, fishing and going to the family’s cottage in the Suomussalmi wilderness with Annukka. He also taught nature skills and how to hunt wild animals for nutrition to his grandchildren. In the Vieremä village, Erkki was also known for his passion for volleyball – it was the most popular sport in the village during his younger years which he still continued when he was in his 80s, and he sure knew how to play. When Erkki played, he always had a smile on his face and a spark in his eyes, planning who to fool next with a roll shot – that was the most anticipated moment of every game.
Erkki passed away unexpectedly, leaving great sadness behind. A beautiful memory of Erkki and his way of facing various challenges and other people lives on to give us comfort. Honestly and with respect.
Thank you Erkki.
Jerry Koski, Service Manager at Ponsse North America, celebrated his 25th anniversary with Ponsse on 22 February 2024. Jerry, who has Finnish ancestry, graduated as a maintenance mechanic for heavy machinery in 1987. He began his career at a transport company and soon moved to Bark River Culvert & Equipment, a company selling four-wheeled forwarders. He became familiar with Valmet’s forest machines when the company was acquired by the Swedish Valmet Forestry. Jerry met Einari and Janne Vidgren at a common acquaintance’s hunting lodge. Einari was looking for a mechanic for the Gladstone area in Michigan. Jerry was impressed with Einari’s down-to-earth demeanour and joined Ponsse in February 1999.
Of Ponsse’s values, integrity (We are honest) is the core value for Jerry, both in his work with customers and his personal life. “Without honesty and humility, nothing has meaning,” says Jerry.
Over the years, Ponsse has grown tremendously. With growth, the company and its employees have developed, and their safety, wellbeing and opportunities for personal development have improved through successful personnel management, for example.
In his free time, Jerry spends time with his wife and family. Hiking, camping, travel, hunting, and gardening are close to his heart.
Ponsse’s annual report and sustainability report for 2023 have been published Ponsse Plc’s annual report and sustainability report for 2023 are available on our website. The annual report and sustainability report are now published for the first time only in digital format (PDF). You will find the reports at www.ponsse.com.
The Ponsse News online magazine features stories from around the world. The magazine is available at news.ponsse.com in Finnish and English. You can also send us story ideas at ponssenews@ponsse.com.
Janne Loponen has been appointed as the CEO of Ponsse Latin America Ltda, Ponsse’s Brazilian subsidiary, as of 1 February 2024.
Loponen has served in international positions in the Ponsse Group since 2002, including in various aftersales roles in Finland, France, China, the United States and Brazil. Since 2016, he has served as the Product Manager for harvester heads and forwarders in Brazil.
Ponsse provides young people with a wide range of opportunities to gain work experience.
Jakub Šitina from the Czech Republic started a five-month training period related to his studies at the beginning of the year. Jakub works in research and development as part of the cabin design team as a trainee.
He became familiar with Ponsse’s machines as a child. His father, Tomáš, has worked with Ponsse machines for more than 20 years and cur rently works as a service manager at Ponsse in the Czech Republic. Jakub became interested in Ponsse’s forest machines through his father’s work.
Martta Kuhmonen, a ninth grader from Vesanto, completed her work experience period (TET) in the warehouse at the Vieremä factory. She worked in the collection process. Her tasks included packing incoming goods into boxes and storing them in the automated warehouse, as well as collecting parts for production lines, for example.
Martta learned quickly in a supportive working environment. She has narrowed down her career interests to two options: a forest machine operator or a forest machine mechanic.
Joensuu has been chosen as Ponsse’s Finnish Service Centre of the Year 2023. The evaluation is based on customer feedback, operational and safety performance, and profitability. In addition, the development of the service centres is evaluated by a panel of experts from Ponsse.
“Joensuu has improved its performance a lot. Our service personnel consist of relatively new recruits as a whole, but they’ve done a great job and learned quickly, without compromising safety,” says Marko Iivanainen, Regional Service Manager.
Congratulations to the whole Joensuu team!