
38 minute read
Inovision embellished with Scodix
Ocean Deep Printers’ embellishes Inovision with Scodix Ultra Pro Foil
Advertisement
Founded in 1995 by Mr. Shripal R. Patel, Ocean Deep Printers carries an ambition to become the world’s top-notch packaging printing services company. In order to offer more innovative prints to their customers, Ocean Deep Printers who is hitting the broadways path launched a new venture name “Inovision” and added Scodix Ultra Pro with Foil to it.
Inovision considers Scodix Ultra Pro as a valuable asset for them as it has given a different dimension to their business after installation in 2017. Inovision understood the value that Scodix and its wide range of applications that bring to any project. The ability to bring those enhancements to an even wider range of projects was what made them be one of the esteemed owners of Scodix Ultra with Foil. With Scodix, Inovision is able to provide a wider range of foil types, on a broader range of substrate options. In addition, the shop will also be able to add foil to pieces printed with a larger range of Coated & Uncoated Substrate as well, opening the door to even more customers and applications.
“The Scodix has proven to be a solid production machine for our business, and we have been benefitted greatly from the investment,” said Mr.Shripal. Scodix Foil adds a touch of prestige to products, whether embossing, using Scodix Sense selective varnishing, adding high gloss or through the remarkable quality delivered by foils. This dynamic system allows us to address a wider range of materials and polymers. As our business has expanded, we’ve gotten requests for all types of projects, produced on all types of substrates. Not only are we now able to deliver these luxury enhancements on personalized and short-run jobs, but with the cost savings made on eradicating the outsourcing of foiling/tooling costs and set-up time, we can make highend finishing available to those even on tight budgets.”
“Following this investment, we also have moved to new markets such as high-end packaging, because even in such an aggressively competitive market, it is clear that we can provide added value for brands in this sector. It’s a testament that demand has grown rapidly as our customers have seen what we can offer with our Scodix,” Mr.Shripal added.
“Our mission is — and always has been — to provide our customers with an innovative and competitive technological and capabilities edge,” said Ajeet Pareek, VP – Scodix Sales,
Monotech Systems. Inovision’s decision to buy the Scodix Ultra to take advantage of the Multi-Material Platform is the perfect example of this philosophy in action. The demand they have created outstripped their original estimates. It is gratifying to not only see such a satisfied customer but one who continues to see the value in the Scodix line of products. We look forward to continuing to serve Inovision as their operations flourish for many years to come.”
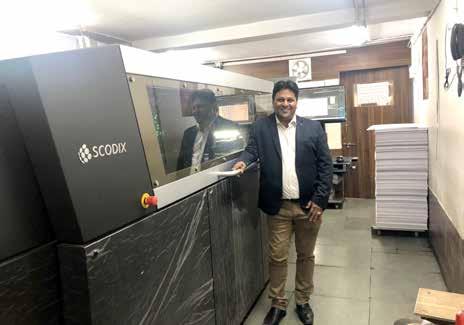
AccurioLabel achieves 500th shipment milestone
Konica Minolta AccurioLabel series hits 500th milestone in total shipments.
Konica Minolta has announced another milestone achieved by its AccurioLabel series: the 500th unit shipped since launched in 2016.
The Konica Minolta AccurioLabel series was designed for small to mid-size label converters by offering affordable entry to high-quality digital printing. It was developed to manage and deliver an increasing number of small to medium print jobs in ever-shorter processing times. Contrary to traditional conventional flexo and offset printing, highly flexible digital presses can process these jobs like variable data printing or numbering printing easily and efficiently.
Toshitaka Uemura, General Manager, Industrial Print Business Unit, Professional Print Business Headquarters, Konica Minolta, Inc. said, “Konica Minolta entered the digital label press market in 2016 and quickly hit the milestone of 500 units sold. We drove the growth of the overall digital label press market by creating a new market of the mid-range digital label press. Last year, we had one of the largest shares of the global market. This has been achieved by widespread support from customers for the AccurioLabel series as a solution to various issues faced by the label printing industry, including the growing demand for small to medium print jobs with fast delivery.”
Uemura added, “Many label converters, which used analogue printing alone, have entered digital printing for the first time using AccurioLabel. We will continue to help customers expand their businesses as their partner in the industrial printing business.”
The AccurioLabel 230 The latest model of AccurioLabel series, AccurioLabel 230 is a highly flexible system for on-demand job needs and runs most
Leo Joseph appointed MD for Xerox India

tack papers and films at speeds of up to 23.4 mpm. The output is high quality and high precision, with the printing resolution of 1,200 × 1,200 dpi and 256 gradations. The touch panel monitor enables intuitive operation and is easy to use for operators, eliminating the need for extensive user training. Tasks that were time-consuming on analogue machines can be performed quickly and accurately.
The AccurioLabel series is also designed to deliver stable printing quality. It is clearly hitting the mark with label converters who want to be able to deliver high quality and consistent results repeatedly.
Xerox has announced the appointment of Leo Joseph as Managing Director for India. In his role as Managing Director, Leo will be responsible for furthering the company’s success and delivering on its business strategy for the India and South Asia market.
Leo comes with over 28 years of extensive leadership experience, an in-depth market understanding. His experience with large enterprises, SMBs, Governments, and B2C consumers across the value chain will help the company strengthen its hold in the existing segments, & charter new growth avenues into the newer markets and segments. Prior to Xerox, Leo was associated with HP, where he held various senior leadership roles in India and APAC. In his last role at HP, Leo was Senior Director, Printing Systems and Solutions – HP Inc. India. In this capacity, he was leading the Printing Hardware, Services, and Consumables business for the country and responsible for the overall revenue, profitability, and market share for the company. Previously, Leo had also worked with IBM India as Vice President - Systems X servers.

Leo holds an Executive MBA degree from the Helsinki School of Economics in Singapore and completed a leadership program from Stanford University, California.”
The future of label printing
– drupa is even more important than you think.
When I think about drupa, I think about it as the World Cup of Printing. The World Cup too happens every four years – but contrary to drupa my own country is usually not a qualifier there. People told me when I first joined the printing industry “don’t go there, it’s too big, you’ll get lost”, or “don’t go there, it’s not focused enough on your business”. Since my first drupa visit, I can’t wait to visit again and I certainly won’t miss it in 2020.
Yes, it’s true that drupa is huge and I did get lost there more than once. Yes, it’s not just focused on labels printing, but to attend the biggest print show in the world gives me an overview of the complete printing market, the latest innovations and the trends that we can expect in future years. The different printing sectors within the industry are related and some trends that occur now in one category will also evolve in another. For example, inkjet technology was first introduced for wide-format applications but it is now playing a major role in label printing. To gain knowledge about competing printing processes at drupa gives me more insight and adds new perspectives to my own business.
So, what can we expect from the next drupa in 2020? First and foremost – innovation! Printing, including packaging, is under intense pressure to transform itself. Brand owners are upping the pace and have
Key Notes :
> The biggest print show in the world gives an overview of the complete printing market. > Latest innovations and trends that we can expect in future years. > The biggest contest is the confrontation between printing techniques: flexo, offset, helio and the new digital rising star.
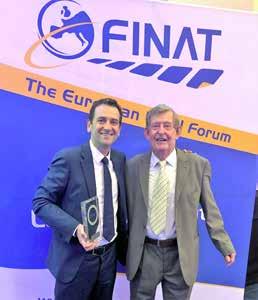

new, different requirements. The industry is more competitive than ever and innovation is what our clients – brand owners – are looking for.
One very important aspect is sustainability. Printing, and especially packaging, is under huge pressure to improve its carbon footprint and to limit waste. Today’s younger generation participates in regular demonstrations to put pressure on governments and brand owners. They don’t know why packaging is important but many think it’s something inherently evil. Most don’t understand the benefits of packaging and look only at the waste generated. Even if today some more sustainable solutions are available, a lot of them are not implemented – simply because they are not yet economically viable. Yes, everyone wants a better, cleaner planet but nobody is prepared to pay for it! Packaging customers are out to cut cost, whatever it takes. Our group has, for example, developed many new solutions and brought them to the market. We are certified PEFC, FSC; Imprim’vert did a carbon footprint analysis. But today our green turnover is still very small. Maybe we are not good enough in promoting or selling our solutions, but the resistance to change is also still very strong – too strong in my view. I really hope to see more
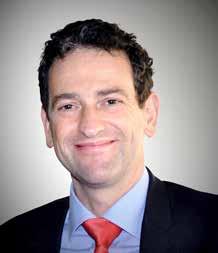
sustainable packaging materials coming through, and more environmentally friendly inks, with print-machines able to print and process substrates in a more environmentally friendly manner.
At the World Cup of print, the biggest contest is the confrontation between printing techniques: flexo, offset, helio and the new digital rising star. In the context of increased demand for more sustainability, quality, shorter delivery times and reduced costs, all printing technologies are improving and innovation can move applications from one printing technology to another. But like at a World Cup, watch out for the hooligans – those who only believe in one printing technology (their own) and don’t appreciate or understand the advantages of others.
Nowhere else can you be as close to the evolution of printing technologies as at drupa. Here an understanding of the advantages and disadvantages is essential in order to better serve your customers’ needs. I expect major changes to come for all printing processes as they need to improve efficiency, waste management, quality and also reduce their environmental impact significantly. Something to have in mind is that traditional print techniques are becoming more and more digital, with sensors all over the machines and taking away time consuming tasks from the operators. For example, digital set-up tools enable printers and converters to be more efficient; cameras and sensors can reduce the set-up time and increases productivity significantly – and all without replacing your current operators.
The digitalization of our world and our lives is everywhere and is rapidly entering into the print and packaging industry. Digital may be a competitor but it can also be part of the solution for printers and converters to be more efficient, to calculate in a more precise way their real costs and to integrate physical products into the digital world using, for example, augmented reality. RFID and printed electronics are also opportunities for the print industry to connect with the digital world. Digital in general, incorporating prepress, printing and converting in one system, is on the rise with the automation of all the steps of the print-workflow, thereby helping to optimize the entire production floor and not only the printing part. And it also links printers and converters better together with their customers and suppliers. In a digital world print can be seamlessly integrated into multichannel communications offering personalization (individualisation).
And what about my expectations for drupa 2020? Well, I don’t usually have specific expectations – most of the time I get surprised by visiting a booth I didn’t intend to visit, which then informs or even inspires me about something unexpected. In the end, you will get a different view on your investments or on the market trends and dynamics. So ‘expect the unexpected’ and be open-minded! As mentioned, drupa is the best place to understand that the printing world is made of numerous applications and that with all the innovation and new technologies being made available, the changes happening are in fact opportunities for printers and converters to reshape their future.
Finally, think beyond the printing-press; it will take more than a new press to be successful. At drupa you need to look at the entire production-chain for print and packaging. Substrate innovations are going to be critical in the coming years. The digitalization and the automation of the entire workflow will change your organization. New technologies will require the hiring of new staff and development of new skills. The way you will engage with your clients will change significantly as they are all soon going to be digital natives. So rather than resist the changes, be ready to embrace them.
Like the World Cup, drupa is an event you really shouldn’t miss – the biggest meeting place for the world’s leaders in printing and packaging, a place where all the latest innovations will be put under the spot light. So, see you at drupa 2020!
drupa cube: eleven days of vision and inspiration To provide participants with the best possible visitor experience, drupa invests in top-class knowledge transfer through its five special forums, the drupa cube being one of them. “educate - engage - entertain” is the slogan of the cube, designed to provide a broad spectrum of highly relevant content that is motivating, very stimulating and interactive for visitors thanks to the various talk formats. World-renowned speakers are set to create a buzz with a visionary range of topics. Amongst others, best-selling author Michael Gale will look at the future of the industry and will offer concrete recommendations for activities that will secure a successful digital management as well as important background information on how to take the plunge into digital management.
- Written by Isidore Leiser – CEO of Stratus Packaging, one of the leading European label converters using both conventional and digital technologies to transform the label industry.

More than 130 visitors attend the Gallus Open Day
Gallus Print Media Center Label hosts Gallus Open Day.
How easy and costefficient the label production is with the Gallus Labelfire with up to 70 m/min was shown during the Gallus Open Day. The hybrid press has a digital heart and an inkjet print unit with seven colours.
Key Notes :
> Live demos of Gallus Labelmaster and Gallus Labelfire. > Focus on low
migration and digital modules. > Insights into Gallus and Heidelberg solutions and innovative applications for a smart label production.

In the Print Media Center visitors could further see how efficient label production is possible, shown on a Gallus Labelmaster Advanced with a production speed up to 200 m/min. Source: Gallus Ferd. Rüesch AG
More than 130 visitors came to Gallus Open Day event, which took place on 6th February 2020 in St. Gallen, Switzerland. The two printing systems Gallus Labelmaster and Labelfire were demonstrated live at the Print Media Center Label. In the Knowledge Forum printing experts talked about the latest developments regarding low migration as well as digital white applications.
The first Gallus Open Day in 2020 in Switzerland was packed with insights into Gallus and Heidelberg solutions and innovative applications for a smart label production. Visitors were able to see efficient state-of-the-art label production as well as the latest Labelexpo highlights: • Gallus Labelfire with Digital Embellishment Unit (DEU) and Digital Metallic Doming • Gallus Labelmaster with new Digital Printbar and the new Rotary Die-Cut Unit Quick
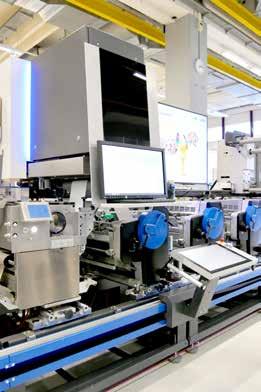
Your partner for digital How easy and cost-efficient the label production is with the Gallus Labelfire with up to 70 m/min (230 ft/min) was shown during the Gallus Open
Thomas Schweizer, Head of Product Management at Gallus, talked about the digital future of label production. Source: Gallus Ferd. Rüesch AG

Day. The hybrid press has a digital heart and an inkjet print unit with seven colours. The Labelfire was demonstrated with the Digital Embellishment Unit (DEU) in order to show the production of highly embellished products. This module can be optionally integrated. Digital foiling effects as well as relief and haptic effects impressed the customers at the event.
Key Topics: Low Migration and Digital Modules Gallus Labelmaster with the new Digital Printbar was explained in detail during the workshop about digital modules. Printing digital white with inkjet can now be included on each Gallus machine system by adding the Digital Printbar. Premiered at Labelexpo Europe 2019 the sales release is planned for the third quarter of 2020.
In the Print Media Center visitors could further see how efficient label production is possible, shown on a Gallus Labelmaster Advanced with a production speed of up to 200 m/min. A further part of the open day event for invited guests were expert talks on low migration requirements, one of the most relevant topics within the label printing market. The next event for customers and interested printers and converters will be in June 2020 during Heidelberg`s “drupa at Wiesloch” at the headquarters of Heidelberger Druckmaschinen AG, taking place from June 18-20 and 22-23, 2020.
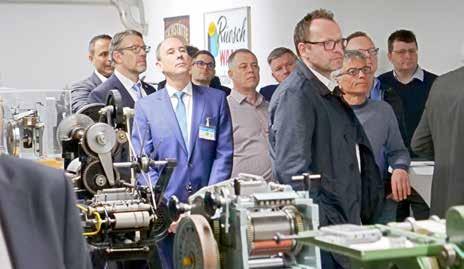
The need to make our manufacturing programs sustainable – leaving a legacy of a cleaner and liveable environment for next generations.
There have been efforts to go linerless in producing labels but the inability to do custom shapes die-cutting and high-speed label dispensing on automatic packaging lines have not produced a lasting solution. Efforts and development in this direction are going on and we hope one day the industry can shift to selfadhesive labels without having release liners to dispose off, becomes a reality.
Key Notes :
Almost forty years ago, when I was just a commercial siliconiser, people at large did not understand what release paper or silicon paper was. I would jokingly explain it was a product, a protective paper behind a sticker, that would eventually go into wastepaper basket. In real terms the release liner, would be disposed-off in landfills or burnt adding smoke and gasses to the environment impacting it adversely. Time has changed; concern for environment is a necessity and cannot be taken lightly as a joke. We are responsible for leaving behind a legacy of a cleaner and liveable environment for generations that follow us. We need to make our manufacturing programs sustainable. Sustainability means giving back to mother earth what we take from it or reduce drawing the resources that we cannot replenish forthwith cut down generation of industrial waste. Unfortunately, 50% of all that self-adhesive label industry produces goes as waste in terms of waste matrix and release liners. While globally many endeavours are being adopted to reduce liner waste yet in India a lot needs to be done. Switching over to liner less labels where-ever possible helps, but not much work has been done in this direction. Using thinner filmic liners does result in reduced tonnage of liners and their recyclability. During this period many a top-end printers have started using clear on clear filmic label materials aiding sustainability to some extent. Global leader in Labelstocks, Avery
> 50% of all that
self-adhesive label industry produces goes as waste in terms of waste matrix and release liners. > Silicone once crosslinked becomes inert and makes paper’s biodegradability in landfills an issue. > The need to design
labels that are a part of recycling process of the package – whole package is mono-material for easy reprocessing and recycling.

Dennison has initiated a program to collect and recycle silicone release liners in India, which is a big step in this direction. But given the size of the country and geographical spread of label units, it is a gigantic task. Other than this, some printers have adopted waste management by shredding waste and compacting it for use as fuel in boilers and other applications; this is only a miniscule portion of the Industry. Largely, the waste is still sent to landfills or is incinerated. In times to come legislation will come to make sustainability and environment safety an imperative. It is time that the label and print fraternity at large must understand that it is the need of the
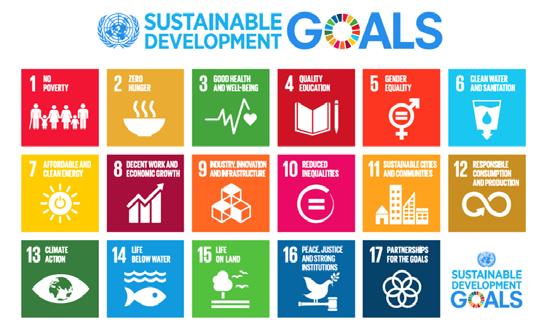
hour and also has larger implications in terms of sustainability, recyclability, circular economy, environmental protection, etc.
The 2030 Agenda for Sustainable Development, adopted by all United Nations Member States in 2015, provides a shared blueprint for peace and prosperity for people and the planet, now and into the future. At its heart are the 17 Sustainable Development Goals (SDGs), which are an urgent call for action by all countries – developed and developing – in a global partnership. They

recognize that ending poverty and other deprivations must go together with strategies that improve health and education, reduce inequality, and spur economic growth – all while tackling climate change and working to preserve our oceans and forests. The Sustainable Development Goal number 12 states; worldwide material consumption has expanded rapidly, as has material footprint per capita, seriously jeopardizing the achievement of Sustainable Development Goals. Urgent action is needed to ensure that current material needs do not lead to

the over extraction of resources or to the degradation of environmental resources, and should include policies that improve resource efficiency, reduce waste and mainstream sustainability practices across all sectors of the economy. In our labels and packaging industry this is an imperative that needs to be attended to because the percentage of waste generated is high, going to landfills. Some companies do incinerate or send the waste generated as matrix or side trim to kilns for use as fuel. This may look good management but in the longer run we are putting gasses into the air from the different materials going into the manufacture of labelstocks viz.; paper, film, primer coats, silicone, adhesive etc. Each component will produce different type of emissions that have in unison no single solution to treat them. Thus, there is a need for reducing the waste generated, use recyclable materials, reduce the energy consumption etc. to become more sustainable.
The label industry globally has been looking at the possibility of recyclability and reusability of the waste matrix or that of the different components of labelstocks. Since release paper is one item that has its usability only until the label is dispensed to be applied on to the product, after that it ends up as waste. Over the years there have been many solutions tried to reduce the impact of this liner waste on the environment. The used liner would either go to landfills or incinerated and in both cases it its impact was adverse. Due to the silicone coating on the paper biodegradability in landfills was an issue as silicone after crosslinking becomes inert. For the same reason paper mills would not buy this waste for re-pulping and making fresh paper. Initial steps taken in reducing the liner waste were replacing the paper liners with thinner filmic liners thereby reducing the tonnage of paper and moreover the waste liner can be remoulded. This was a positive sign, but large-scale shift has not happened in a long time because of additional increased investment in equipment and tooling. There have been efforts to go linerless in producing labels but the inability to do custom shapes die-cutting and high-speed label dispensing on automatic packaging lines have not produced a lasting solution. Efforts and development in this direction are going on and we hope one day the industry can shift to self-adhesive labels without having release liners to dispose off,
becomes a reality. At Labelexpo Europe 2019, four companies Ritrama, Omet, Spilker and ILTI came together to offer their “Core Linerless Solutions”, other companies like Catchpoint are also making strong efforts in this direction, only time will tell how many brand owners move in this direction and prompt their label vendors to offer the linerless label solutions. Some paper mills in Europe have now devised process of de-siliconising release paper and then re-pulping it to make fresh paper but the collection and delivery to the mills from the printing companies widely spread over large geographical locations is a logistic challenge. However still substantial volumes have started to be reprocessed. In India in recent times as mentioned above Avery Dennison has initiated support to a program in which collection of release liners is outsourced to a vendor and then sent to a mill who have devised a process to re-pulp and convert to paperboard. These are positive steps.
The menace of waste is gigantic and it has become an absolute emergency to counter it. Governments have woken up to act against generation of materials going to landfills. It is preferred that whatever waste is generated in industrial process should be gainfully recycled for usability to achieve the benefits as described in circular economy. As per a report published in thehindubusinessline.com of 19th September 2019, leading consumer products companies such as Coca-Cola India, PepsiCo India and Bisleri among others have decided to come together to launch a first-of-its-kind packaging waste management venture in the country. The venture, which is called Karo Sambhav, will focus on creating a formal eco-system for collection of post-consumer packaging and optimising material recycling processes. Commenting on the endeavour, T Krishnakumar, President, Coca-Cola India and South-West Asia added, “Through our vision, World Without Waste, we want to ensure that all our packaging material goes for recycling and not to landfills.” Another report appearing in Live Mint 2nd October 2019 states; The government may soon roll out stringent norms and impose heavy fines on corporates, including hospitality industry, mobile manufacturers and packaging industry, for failing to stop use of plastic. Under the Extended Producer Responsibility (EPR) scheme, which the government plans to implement effectively, manufacturers,
brand owners, and importers of products should realise and bear responsibility for environmental impact of their products through the product life-cycle. Many of the large FMCG companies have started adopting the requirements of EPR. These are other positive steps taken to eradicate waste to landfills to a great extent.
Besides the liner there is the waste matrix which has the adhesive and various kinds of face materials that include uncoated, coated, metallised, coloured, metallised papers, laminates or films with metallisation or topcoats. Side trims are also generated at some label converting units and most labelstock manufacturing units. With increasing prices of real estate besides an environmental issue, the side trims and matrix call for large amount of space to store until disposed off, putting additional pressure on resources. For this reason, larger label companies are shredding and compacting the waste to sell as fuel for boilers, furnaces and cement kilns. There are some innovative entrepreneurs who convert this waste into pallets, floor tiles, wall panelling and some small furniture items. It is interesting to see such endeavours.
Circular economy packaging is another buzzword when we talk of sustainability and environmental protection. A circular economy is an economic system aimed at eliminating waste, continual use and recycling of resources to re-engineer products that are preferably not downgraded. It is contrary to the earlier system “traditional linear economy” according to which the aim was ‘take, make, dispose’ model of production to achieve increased usage of all inputs. Labels are the face of any product and in time of growing organised retail and in view of stringent consumer protection laws labels provide the much-needed statutory information, besides becoming

the marketing tool for any product. In such a scenario we need to design labels in manner that they are able, to be a part of recycling process of the package. For instance, on a PE (polyethylene) container we should have a PE label only so that the whole package is mono-polymer and can be effectively reprocessed and recycled. Multi-polymer plastics are neither recyclable nor biodegradable. It is normal in India that we see ragpickers collect the mono polymer milk pouches but leave behind the fancy multi-layered pouches of instant foods and snacks littered around. This is because the monolayer plastics are resaleable for convenient recycling. Similarly, a paperboard carton should have a paper label.
Sustainability or circular economy must be in the conscience of all manufacturers, it does not advocate compromising safety or user experience of any product. It also does not mean increased cost of inputs. It is a mindset to create products that make life sustainable and do not deplete resources available to humans. There is need to replenish what we extract from our environment and establish a legacy for generations that follow for staying committed to the cause. It is a cause that is impacting humanity across the globe and all efforts to make public of all races and countries aware of the situation and need to contribute towards this issue in unison are necessary.
- Written By Harveer Sahni, Chairman Weldon Celloplast
TSC label printers to help fight Coronavirus outbreak in China
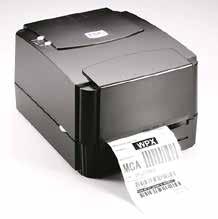
As a part of CSR drive, TSC Auto ID Technology (TSC), innovator in the design and manufacturing of thermal barcode printer technologies, announced that it donated 300 pcs of barcode printers to nearly 20 hospitals among different cities in China to fight Novel Coronavirus (2019-nCoV) outbreak in association with its China partner.
TSC barcode printers will support healthcare frontline for varied application including patients ID tracking, hospital admission, hospital nursery, specimen/ blood labeling, medication tracking, Staff ID & Access Control and healthcare materials management to enhance healthcare workforce’s medical treatment efficiency.
On this occasion, Sam Wang, TSC president said, “We should all join hands to fight this epidemic and help the people in China suffering from this severe outbreak in whatever possible way we can. And we really hope this small gesture of lending a helping hand to the hospitals can help the authorities to facilitate the treatment facilities in a better and efficient way.”
TSC is a global provider of quality Auto-ID solutions for transportation and logistics, manufacturing and healthcare, industry and retail, offering a diversified line of innovative and reliable products with excellent quality. TSC has 3 decades of experience dedicated to barcode and label printers, with more
YesGo opens Branch Office in Noida

than 5 million installed in over 90 countries. Headquartered in Taiwan, the company is among the top 5 manufacturers of thermal label printers in the world.
YesGo inaugurated its first Branch in Noida for Training and Placement on 22nd February 2020. YesGo Noida office will address training and placement requirements for Delhi & NCR Region along with entire Northern Zone. Training classes started from 23rd February 2020. Training includes complete hands on high end prepress and packaging software training along with industry visits. Inauguration on 22nd Feb 2020 witnessed presence of many leading names from the Print and Packaging Industry. The need for training in and high-end technologies based on the current industry trends in print and packaging has seen tremendous escalation lately. “We are continuously receiving enquiries for training from across the globe and most of them are not able to learn online or learn at Chennai Classes,” says Mr. Nizamappas, Founder of YesGo. “Considering these heavy requirements, YesGo office at Noida is a first step to meet the needs of the aspirants at their proximity. Following Noida, we will soon launch other branches at Bangalore and Pondicherry,” he adds.
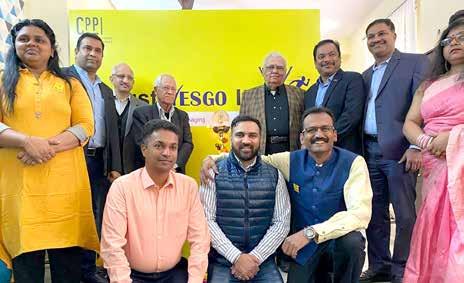
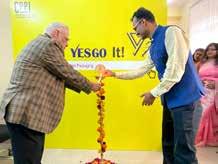
Packaging Innovations in Warsaw
PrintCity Alliance presents a broad range of products and a seminar.
Key Notes :
> Visitors can learn
about new substrates, inks, special effect pigments and coatings. > To feature stamping and digital finishing techniques, and options for using UV and anti-counterfeiting technology. > The focus is on
the environmental aspects of the materials and processes.
The members of the PrintCity Alliance are showcasing a diverse range of products again this year at the Packaging Innovations trade fair in Warsaw.
In a seminar, the Alliance is also highlighting its new Better Human project to show how premium packaging can be reconciled with the demands on environmental protection and sustainability.
Materials, high-quality print finishing, anti-counterfeiting and UV The range of solutions and products exhibited by members and partners of the Alliance is very diverse. Visitors can learn about new substrates, inks, special effect pigments and coatings, stamping and digital finishing techniques, and options for using UV and anti-counterfeiting technology. And here, too, the focus is on the environmental aspects of the materials and processes.
Zeller+Gmelin, a new Alliance member since 1 January, will be participating for the first time. As a specialist for UV-curing printing inks, the company will be providing information on this application and the advantages of UV systems in packaging printing. Its display focuses on its newly developed line of low-migration LED offset printing inks for food packaging. The new line unites the advantages of the low substrate heat exposure resulting from LED technology, with the low-migration and outstanding curing properties of standard UV systems.
Metsä Board, the leading European producer of premium fresh fibre paperboards, will showcase the new ecobarrier board, MetsäBoard Prime FBB EB, which has a medium barrier against moisture and grease, and its comprehensive lightweight folding
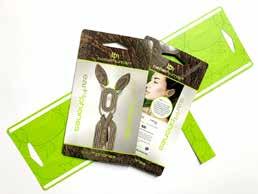

boxboard and white kraft liner (WKL) portfolios and products. “Packaging is a necessity – for product distribution and safety. Paperboard packaging made from renewable materials is a sustainable choice. We will use this opportunity to show visitors how we can provide solutions to any packaging challenge and help customers to evaluate and improve their own packaging goals,” says Stanislaw Moczulski, Sales Director Metsä Board Poland, inviting visitors to the PrintCity pavilion.
WEILBURGER Graphics is introducing not only
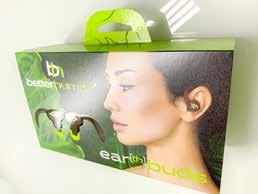

brand-new coatings, flexo inks and adhesives, but also its high-efficiency, resource-saving manufacturing system for premium water-based coatings, which went into production this year and is likely the most modern of its kind in the world.
KURZ will be demonstrating how design and function interact. Its customer-specific TRUSTCONCEPT solutions, for example, deliver effective protection against counterfeiting and promote interaction between a brand and its consumers to strengthen customer ties. With its TTR UNIQUE VEROSPEC solution, products can be marked with hidden authenticity features. hinderer + mühlich is presenting the latest stamping die technology, which lends an irresistible look and feel to print products. KURZ further is displaying examples of its brilliant DIGITAL METAL finishing technique for high-quality individualisation and eyecatching holographic effects.
Seminar on packaging design, print finishing, production and the environment Better Human, the PrintCity Alliance’s new project, combines premium packaging with the demands of environmental protection and sustainability.
The seminar explains the environmental aspects of packaging design.
They start with the structural design of the packaging (monomaterial, elimination of fossil materials), continue with selecting the substrates, inks, coatings and foils, and conclude with options for recycling.
The seminar will be held on 1 April in the Workshop Area of the Green Hall. Attendance is free of charge. No registration required. The trade fair takes place from 1 – 2 April on the exhibition grounds in Warsaw.

Participants at the Alliance’s shared stand D9 in the Blue Hall: Graficus / Epple Druckfarben (offset inks and coatings), KAMA (cutting, stamping and gluing machines), PC Print / LEONHARD KURZ (hot stamping and cold foil applications, holograms), Metsä Board (folding cartonboard, white kraftliner, food service paperboard), Merck (special effect pigments), WEILBURGER Graphics (varnishes, adhesives and water-based flexo inks), Zeller+Gmelin (UV inks and coatings).


ASPA Brand Protection Awareness Seminar
ASPA Anti-counterfeiting, Traceability and Brand Protection Seminar to be held in Kolkata.
Event to cover critical issues such as AntiCounterfeiting & Supply Chain Regulatory requirements including DGFT - Pharmaceutical, EU-FMD, DSSCA, Consumer Protection Bill, Pesticides Bill, E-Commerce, FSSAI – Organic Food & WHO FCTC for Tobacco Packaging.
Celebrating World Consumer Right Day, Authentication Solutions Providers’ Association (ASPA) is conducting a Brand Protection Awareness Seminar on March 13, 2020 at The Park, Kolkata. Fighting counterfeiting is an important aspect in socio-economic development of our country, industry & consumers at large. There is a need to strengthen the authentication eco-systems in the country empowering consumers, industry & regulators at large in fighting counterfeiting. The seminar will bring together industry leaders and government representatives on the same platform to share the insights of Anti-Counterfeiting and Traceability developments and regulations in the country. Shri Atri Bhattacharya, IAS Principal Secretary, Consumer Affairs Department, Government of West Bengal will be the Chief Guest for the brand protection seminar.
As Counterfeit products across various sectors in India are causing losses of over INR 1 trillion every year to the government, the involvement of all stakeholders is extremely crucial in fighting this menace. . The number of counterfeit cases have increased by nearly 15 per cent in the JanuaryOctober period in 2019 as compared to 2018, according to a recent study by ASPA. The top ten
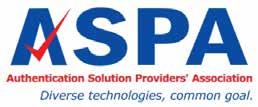
sectors with the highest number of counterfeit cases in 2018 and 2019 were currency, liquor, food and beverages, pharmaceuticals, personal care, documents, tobacco, automotive, construction material and chemicals.
Considering these circumstances, ASPA under its campaign “Make Sure India” is creating an awareness to educate and enable brand owners, consumers, media & stakeholders towards counterfeiting and importance of authentication solutions in fighting this problem. Seminar participants will learn about the latest technologies and good business practice of Authentication providers who are already protecting more than 15,000 brands globally. They will share insights of counterfeiting, anti-counterfeiting landscape and the recent regulations and solutions in fighting the fakes.
Key Notes :
> Overview of AntiCounterfeiting & Traceability Solutions. > Biggest platform to address changing counterfeiting trends in India & West Bengal > Training session on
how to identify fake vs genuine product.

ASPA’s mission is to help the brand owners eradicate the scourge of counterfeiting.
Respected and accomplished business leaders, policy makers and industry experts such as Mr. Manoj Kochar, Chair-Eastern Region, ASPA & Former President, IHMA;; Dr. A. Ramkishan, Deputy Drugs Controller (India), CDSCO, East Zone, Kolkata, Ministry of Health & Family Welfare, Government of India; Mr. Ankur Chaturvedi, Head of International Supply Chain and Projects, Emami Ltd.;, Kolkata; Mr. Shamim Alam, Business Manager - Labels & Packaging, HP; Mr. Harish Agarwal, Partner, Ernst & Young LLP; and Mr. Chander S. Jeena, Secretary, ASAP will be speaking at the event.
The Authentication Solution Providers’ Association (ASPA) Authentication Solution Providers’ Association (ASPA) is a self-regulated, non-profit organization of authentication solution providers. Formed in 1998 with the objective to fight fakes products in various sectors, it is one of its kind association in the world primarily focused on the adoption and advancement of authentication technologies and solutions for Brand, Revenue and Document Protection. ASPA members protect over 15,000 brands worldwide through the identification of genuine products and documents. ASPA is creating awareness to fight fake/duplicate & counterfeit products which are harmful to consumers, industry, economy, and society at large. ASPA works closely with global authorities such as International Hologram Manufacturers Association (IHMA), Counterfeit Intelligence Bureau (CIB - Interpol), FICCI CASCADE, and other industry bodies in India.

Bekum celebrates three anniversaries
– 60 years Bekum in Berlin, 50 years in Austria and 40 years in USA.

The Bekum group celebrated recently three anniversaries – 60 years Bekum in Berlin Germany, 50 years Bekum in Traismauer Austria und 40 years Bekum in Williamston, USA. As part of the celebrations at the American location, the groundbreaking ceremony for the expansion of production capacities was made on November 26, 2019. A new building with a production area of 3,700 m² and almost 700 m² of office space will be added. This increases the site’s operational area to more than 15,000 m².
Michael Mehnert, Managing Partner, who travelled from Germany for this celebration, comments proudly: “My father founded this company sixty years ago. Today I’m standing here and lay the foundation for a new production hall in order to be able to serve the continuously increasing demand in the USA in the future!”
“This is a historic week for Bekum America,” said Steve London, COO and President of Bekum America Corporation. “The groundbreaking on our new facility was a great kick off to our 40th anniversary celebration with our dedicated employees. The Bekum team has continually been providing state of the art products for our clients, and this event is the perfect opportunity to celebrate all the individuals who complete Bekum.” Bekum America was established in 1979 with the mission to introduce top quality blow molding machinery, designed to produce plastic bottles, containers and other large plastic parts in the North American marketplace, via blending German design and technology with American skill and ingenuity. Bekum’s customer base includes large multi-national customers, as well as owner/operator plastic bottle manufacturers.

Book your future…with Meccanotecnica at drupa
From June 16th to the 26th, Meccanotecnica Group will showcase its solutions for book finishing in Hall 16/B42.

In about 100 days Meccanotecnica will be exhibiting in drupa, the biggest trade fair for the graphic art industry. The Meccanotecnica team is getting ready to showcase many improvements, the new generation of several machines together with a new concept proposal. The company aims to better meet the requirements of its traditional customers and potential prospects.
The technical development of Meccanotecnica’s solutions is following a path that is driven by three clear lines: • integration of processes; • increase automation; • better efficiency.
Integration of Processes With this the company aims to reduce the number of critical steps in the production process, avoiding the handling of the paper or of the semi-finished product. The result is a more efficient process and the reduction of production costs. In drupa, this effort will be clearly shown both by the solutions for offset and digital print finishing together with Meccanotecnica’s solutions for print-ondemand book production.
Increase Automation It is no secret that printing runs are getting shorter and the number of job titles, that a binder must process in a day, is increasing. Automation is, therefore, in the top list of the challenges that book manufacturers must face.

In drupa, a specifically designed production workflow will demonstrate the capabilities of our solutions for POD book production. The new generations of Universe Web, Inline and Trimming will demonstrate how to reduce to a minimum the operation required for the setup, saving precious time of the operator and simplify the use of the machines.
Better Efficiency The Full Cycle Technology by Meccanotecnica has increased the efficiency of the asterPRO book sewing machine, by allowing the sewing of books without the blind stitch. In drupa, this innovative sewing system will be presented as a “native” feature in a new “concept proposal” aimed to give a renewed impulse to the production of books in offset.


Discover Meccanotecnica’s latest solutions at Drupa As in the past editions, visitors to drupa will find Meccanotecnica’s solutions in Hall 16/B42. An area of more than 600 sqm will host almost the entire portfolio of their bookbinding and finishing machines. Moreover, this year, Universe Web, the automatic book sewing machine for digital printing will be also showcased in a partner area.

