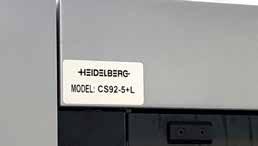
10 minute read
Heidelberg efficiencies for Sain
Heidelberg brings cost and production efficiencies for Sain Packaging
The brand new Heidelberg CS 92 brings savings, quality improvements and capacity expansion for this Pharma printer and converter of Rai, Sonepat.
Advertisement
Mr. Sachin Gupta, founder of Sain Packaging started with Printing after an over a decade long career as government contractor from 1992 to 2004. His father too, who worked in the Delhi Municipal Corporation, had little association with the Printing industry. According to Sachin, it was mostly due to his ambition, hard work and blessings of the Almighty, that he has written his own success story though starting from rather humble resources.
Adding Heidelberg CS92 to the line-up was particularly beneficial as over 80 percent of Sain’s jobs fitted into this size. Moreover, the machine brought a lot of economies in terms of substantial savings on board and plates. “The savings were huge. I would call ‘they’ contributed to the ROI actually,” says Sachin.
Starting his Pharma Packaging business which began at Burari in Delhi, Sachin moved Sain Packaging operations to Rai (Sonepat in Haryana) as the business expanded and the need for a bigger facility arose. “Within 6 months of our starting the unit at Burari with a single colour Adast Dominant Offset printing machine, we installed a 2 colour Heidelberg,” recalls Sachin. Today the company houses only Heidelberg brand printing machines and that is one of the reasons for Sachin to get his latest machine a Heidelberg as well – the new Heidelberg CS 92 press. “Though we have been in touch with a number of other manufacturers too, we went for our time tested favourite brand finally,” cheers Sachin.
Sain Packaging, for the most part, even when it needs printing 100 cartons, does its printing on Offset. “As the proof needs to match with the actual product or else there are chances of rejection which we always try to avoid, we go for Offset,” reasons Sachin. “We have learnt the hard way to do the proofing on Offset itself,” he adds.
Sachin believes that in order to cater to the Pharma market, one needs to have both long and short runs in one’s kitty. Adding Heidelberg CS92 to their line-up was particularly beneficial as over 80 percent of their jobs fitted into the CS92 size. “The main reason for us to opt for the Heidelberg CS92 machine was the efforts of the Heidelberg staff mainly Mr. Deepak Walia,” admires Sachin. Moreover, the machine brought a lot of economies in terms of substantial savings on board and plates. “The savings were huge. I would call ‘they’ contributed to the ROI actually,” avows Sachin. Apart from its size advantages in terms of board and plates costs, the machine brought significant economy in power and labour costs too.
Key Notes :
> Houses a complete
line-up of Heidelberg machines. > Uses Heidelberg Offset quality for Proofing needs. > Aims to double
turnover enabled by new Heidelberg CS 92 capabilities.

Presently the company has three 5 colour machines all with coater, a 4 colour machine and four double colour machines with all allied post press machines required to cater to the Indian pharma industry. Sachin’s purpose of putting up the brand new Heidelberg CS92 was not to increase production capacity but it was rather to bring quality improvements. “The CS92 was chiefly for increasing the quality of our production but then productivity will surely increase all by itself with the apparent production capabilities of this acquisition,” he reckons. In fact, the whole production of the present unit with the available machine is equivalent to half of the production capacity of the new machine and so in addition to quality, they surely have significantly shot up their production capacity as well.
The annual turnover of the company presently is about 50 crores a year with board consumption to the tune of 400-450 tons while operating on a round-the-clock model. “I expect to have a turnover of over 100 crores in the coming financial year with the addition of the new machine,” claims a confident looking Sachin.
Speaking about the Pharma Industry today, Sachin recalls changes that have occurred over the one-and-a-half decade since he started operation, “While in the earlier days
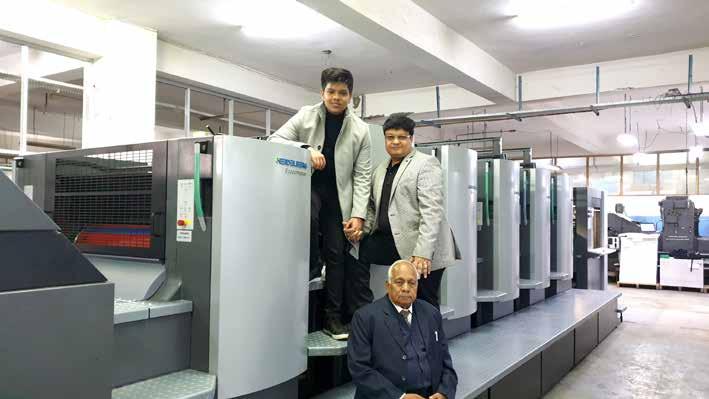
the industry wasn’t very serious about board quality or printing. Today, our customers need only the best quality boards with the best of the printing and add-ons that too at the best prices.”
The post press infrastructure at Sain Packaging includes two Bobst Die Cutters (one new and two second hand machines), three Maxima Die Cutters, three Folder Gluer (one Bobst and two from Cartonal), five UV Texture Machine, seven manual Die Cutters. Sachin is planning to acquire Braille enable machines; their customers in pharma exports have a fixed requirement for that. Moreover, he sees its demand to rise in India as well with it becoming a mandatory requirement in due course.
Sain Packaging as on today, caters to the export market through their principals to the extent of almost 40% of their production. Their clients are mainly from the nearby regions like Baddi, Roorkie, Paonta Sahib, Amritsar, Haridwar etc.
The company presently operates from an industrial plot in the Rai Industrial Area with a covered area of 65000 square feet which includes a basement, ground, plus 2 floors. “We have an in-house corrugation unit too – catering mostly to the in-house requirements only,” informs Sachin. About 250 people work

in his 2025 square meter plant. The company expects to double the turnover in the coming year with the addition of the new Heidelberg. Sain Packaging’s sister concerns are also active into Lamitubes and aluminium tube for containers for pesticides etc.
World’s 1st serial drupa specification SM XL 106

Technology driven Elle Media Group to take delivery of world’s first serial drupa specification Speedmaster XL 106-5+L.
The Elle Media Group in Essex, England, is a leading publisher of charity greeting cards and is renowned for its high-quality commercial printing.
Key Notes :
> Speedmaster XL 106 five-colour press with coating unit to be installed in England in spring. > High-productivity
printer expects over 300 hours more print capacity per year compared to previous model. > With Prinect and Push to Stop concept going for the Smart Print Shop.
Heidelberg recently announced its new Speedmaster drupa 2020 generation. Elle Media Group have concluded the purchase of the very first serial 2020 drupa specification XL106-5+L in the world from Heidelberg UK. This will replace a three-year-old machine which has produced an incredible 210 million impressions since its installation in March 2017.
Elle Media Group continues to be Heidelberg’s most productive operation in Europe on a straight configuration press. The business regularly produces over 7 million impressions on one press, per month with an average run length of circa 4,000 and an average a makeready time of just over 3.2 minute. The new industry benchmark press will be delivered to the Essex based company in March and will continue with the businesses ethos of deploying the latest technology to ensure the lowest operating cost per sheet and to ensure the right capacity is available for its ever growing greeting card publishing division and commercial print customers.
With this investment the company continues to adapt its service structure to ensure technology enhances its customers experience at all times through its journey with Elle Media Group. With a full suite of Prinect products, its transition into a fully working Smart Print Shop and Push to Stop producer has been accelerated through the continued drive and

delivery of its fantastic team. The numbers from Prinect Smart BI both in terms of output and quality showed this investment would deliver the required ROI in what remains one of the most competitive market spaces in worldwide print.
“We had been evaluating this investment for over 12 months as we knew with the output levels we were producing and the fixed operating costs in place that our investment cycle would need to be decreased to ensure we sustained our operating cost per sheet. This was the primary driver for the investment combined with the increase in capacity for the same overhead due to Intellistart 3 ensuring one minute improvement on current performance which will give us another 320 hrs of available press time per year to ensure we maximise the opportunities being presented to us,” says James Cuthbert, Managing Director at Elle Media Group.
Founded in 1982 as Falder Printing, Elle Media Group is based in Seax WAY, Essex. The company boasts an in-house creative studio, the leading charity greeting card publishing house, and a print company equipped with the very best of modern technology. The acquisition of the new drupa specification XL106- 5+L press is intended to ensure that Elle Media Group remains at the cutting-edge of technology in the industry in the years to come.

Highly personalized diaries in runs of one
NINO Druck GmbH enabled by MECCANOTECNICA Universe, folding and book sewing machine.

Examples of highly personalized diaries produced by Nino Druck.
NINO Druck GmbH is a forefront German commercial printer that operates in 4 divisions: Offset, Digital, Web-to-print, and Crossmedia. Based in the RhinelandPalatinate State, NINO Druck employs more than 160 people, and thanks to digital printing, is exploiting new possibilities offering its customers significant benefits in terms of speed, lead time and efficiency.
The company, established in 1988, operates several sheet-fed digital printing machines, with toner technology and produces among other products: photo books, personalized diaries and notebooks in short runs down to one book.
Print-on-demand and web-to-print services are also a core business enabling B2B customers such as publishers and print shops to take advantage of new publishing models and print only when needed.
Challenge “One of our customers had to produce personalized diaries and notebooks in ultra-short runs. Its main request was that the books had to withstand at least one year of daily use and wear. With the existing adhesive binding machine we could not guarantee such durability,” says Michael Schmid, Head of Digital Printing.
SOLUTION “The automatic book sewing machine for digital printing Universe was the right solution for our problem.”
Thread sewing has no rivals in terms of resistance and longevity. It is a purely mechanical process not affected by inks, papers or environmental conditions. Moreover, thread sewing is ideal for digital printers with a very short time-to-market. Books can be opened and validated as soon as they are produced and are immediately ready for delivery.
RESULTS “Thanks to Universe, we are now producing personalized diaries in runs down to one book. These books contain highly personalized details such as birthdays, important events, notes and anniversaries already printed on the pages. Such information is collected through online portals, we receive the order and deliver to the final customer. The hardcover is also personalized with initials and inscriptions.
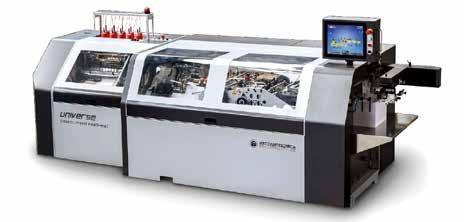
These are truly unique books. Moreover, the new solution has demonstrated its value also for other applications. We now produce with the Universe, photobooks with a high number of pages; this ensures once again durability and excellent haptic user experience,” says Michael Schmid, “We are very satisfied with the Universe. Production quality is consistent, the machine is reliable and change over time is highly automated and quick.”
Universe, automatic folding and book sewing machine, is the sheet-fed solution for fast and versatile digital book production. The solution allows cost-effective binding of short runs and guarantees the production of highquality books.
