
9 minute read
PRODUCING SPAWNING
from Quarry Jun 2019
by Prime Group
PRODUCTION OF SPAWNING STONES FOR FRESHWATER TROUT
Amobile screen is proving its versatility by making an unusual contribution to the freshwater environment. For the past three years, Veljekset Kokkonen, a crushing contractor in Lieksa, eastern Finland, has used its Metso Lokotrack ST2.8 mobile scalper to screen various sizes of crushed stone for sand, gravel and soil, and for a highly specialised use – spawning stones to help endangered freshwater trout breed.
These spawning stones aim to restore the extremely threatened freshwater trout in the Naarakoski rapids, on the Lieksanjoki watercourse. The beautiful territory is on the lower course of the famous Ruunaa fishing and nature conservation area.
The freshwater trout wander from the lakes to the upper courses of rivers to breed. For this, they need proper-sized stones. The smaller stones are needed to successfully lay their eggs and the larger stones, about the size of a human head, protect the precious first moments of the trout babies.
Juha-Pekka Kokkonen, the man in charge of crushing and screening at Veljekset Kokkonen, has overseen the operation of the Lokotrack ST2.8 screen at the company’s Pekkilä soil extraction area in Lieksa.
“We screen three sizes of natural stones from the gravel bank,” Kokkonen said. “The sizes of the spawning stones vary between 30-60mm, 20-100mm and 100-250mm. More than 1300m 2 of gravel is being processed. “Working with the screen is fast. We use an eccentric throw of 14mm, and the screen accepts as much feed as the excavator is capable of putting in.
“We use punch plates in three sections on the screen’s upper deck and a steel mesh in one section, as well as on the lower deck.” Veljekset Kokkonen purchased its first mobile crushing equipment from Metso in the early 1980s and then acquired a trackmounted two-stage plant. The Lokotrack ST2.8 screen was delivered in 2016.
“Based on our first experiences, ST2.8 is a screen that gets the job done,” Kokkonen said. “So far, everything has worked well. A Finnish product is a safe choice, because it means that spare parts and maintenance services are locally available when needed.
The Lokotrack ST2.8 screen quickly produces spawning stones of different sizes.
Juha-Pekka Kokkonen. The fry stones, sized 20-100mm, will make it safer for the landlocked trout to reproduce in the rapids.
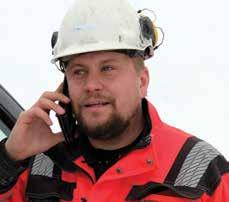
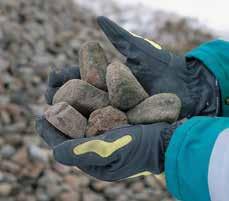
“Good fuel economy is an added bonus for us, enhancing the cost-effectiveness of screening. The efficient screen consumes about 12 litres per hour, which is not much for an hourly screening capacity of more than 200 tonnes.”
Veljekset Kokkonen’s operations are based on three pillars: construction sector transport services, contracting, and crushing and screening.
The family company operates mainly in eastern Finland and employs 20 people. It crushes and screens roughly half a million tonnes of aggregates annually.
As many of Veljekset Kokkonen’s clients are small producers, the equipment is transported from one place to another about 40 times a year.
Veljekset Kokkonen screens the spawning stones for Kuopion Teho-Louhinta, the company in charge of submerging the stones in the Naarakoski rapids, commissioned by the Centre for Economic Development, Transport and the Environment for North Karelia.
The work has provided the landlocked fish with new and better spawning sites.
The spawning stones meet an important need: natural stocks of landlocked trout can be found in only a few headwaters in Finland. In rapids with a stone and gravel bottom, only about one per cent of the fish stock develop into fry.
The Metso Lokotrack ST2.8 scalping screen is available in Australia through national distributor Tutt Bryant Equipment. •
Quality assured alternative wear parts for all crushing equipment
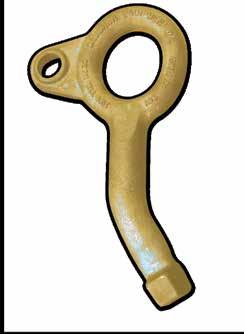

lift jaw & cone liners with
■
Manganese & alloy steel wear parts ■
Bowl, mantle and jaw liners ■
Concave segments ■
Blow bars & hammers ■
Auxiliary wear parts ■
Mining & Quarrying spares ■
Mill liners ■
AUD$5 million manganese in stock
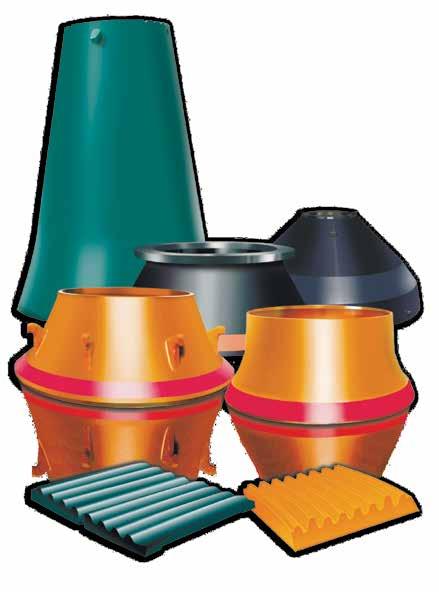
■
Premium grade 12 – 14 % manganese ■
Mn18% HC manganese ■
23% XAlloy manganese ■
Alloy steels
Quality Assurance Standard AS/NZS ISO 9001:2008 covered wear parts for all popular crushers in stock. Assuring you of our careful attention at all times
Unit 2/23-31 Meakin Road Meadowbrook Qld 4131
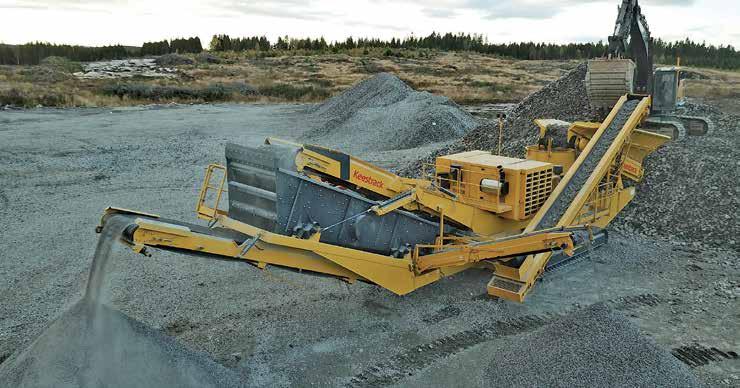
MOBILE PLANT SUPPLIER UNVEILS ITS SUITE OF ELECTRIC INNOVATIONS European mobile plant manufacturer Keestrack recently displayed nine electric-powered processing plants for quarrying and recycling applications at bauma 2019, in Munich, Germany.
The company in particular was keen to show customers its work in the development of cost-effective hybrid and plug-in electrification of plant drives, which it not only implements in new generation models and innovations, but consistently in all of its crushing, screening and handling solutions.
As part of its “e” (for electric) series portfolio in mobile crushers, Keestrack presented diesel-electric full hybrid plug-in models of its track-mounted jaw, impact and cone crushers. According to Keestrack, the new and enhanced models are not only suitable for 60- to 70-tonnes transport weight in terms of size, output, product quality and variety, but are also setting standards for cost-efficient operation with sophisticated drive concepts.
Without restrictions in portability and tracked on-site mobility, the diesel-electric heavy crusher range satisfies the requirements for volume-intensive recycling jobs on construction sites, plus multi-stage production of mineral aggregates in pits and quarries.
For the first time internationally, the 700 tonne per hour (tph) Keestrack B7e jaw crusher was unveiled. Replacing its predecessor, the B6e, the B7e’s core comprises a tried and tested CJ412 single jaw crusher, with a 1200mm x 830mm inlet for feeding sizes up to 700mm and a wide, hydraulically adjustable closed side setting (CSS) range of 75mm to 250mm. In the B7e – only available as plug-in hybrid – the crusher is driven by a 132kW electric motor. Another 55kW electric motor powers the hydraulic system for the tracks, the lifting cylinders, the vibrating feeder with two-deck pre-screening and all conveyors.
The diesel-electric power is delivered by an on-board Volvo diesel engine (optional 273kW EU IIIa or 285 kW EU IV) and on-board 330kVA generator. The engine house is available in a detachable drop-off module, to be positioned away from the crusher, in a dust- and vibrationfree environment.
Thanks to constant and low engine speeds, even under full diesel-electric load, the Keestrack B7e operates with low fuel consumption. According to Keestrack, energy-saving costs of up to 80 per cent can be obtained in emission-free plug-in operation from mains or external gen-sets. The plant, with a total weight of just below 69 tonnes (with options), is highly mobile; by detaching the 6m 3 feeder unit, including pre-screen, the weight drops below 60 tonnes. Complementing the B7e at bauma was the full hybrid Keestrack H6e cone crusher. The H6e offers high production capacities in the secondary and tertiary crushing phases. With a maximum feed size of 215mm, variable crushing chamber configurations and stroke settings (a CSS of 6mm to 44mm), the specially adapted Keestrack KT-H6 crusher, based on proven Sandvik technology, can process up to 400 tph of raw materials. An optional three-deck post-screen module (with a 24.5m 2 surface) with oversize recirculation provides high quality end products, thus guaranteeing high added value. The powerful e-motors for crusher drive, plant hydraulic (220kW/2 x 30kW) and all other directly electric-driven components are powered by a detachable diesel/generator module (345kW) or plug-in via mains or external gen-set. With a total weight of 62 tonnes with all options (51.5 tonnes without the final screen), the large cone can be operated economically at various jobsites. This versatility is also a feature of the compact and highly mobile R6e impact crusher, with double pre-screening and double-deck post-screen modules, including oversize recirculation. Still available as a diesel-hydraulic as well as partially electric model with crusher direct drive (“rotor by diesel”), the R6e is a fully hybrid plug-in version (439kW). Despite its extensive electrification, including the 970mm x 1300mm crusher (250kW), the hydraulic system (2 x 55kW), and almost all conveyor drives and ancillary units, the 62-tonne plant can be flexibly dislocated with the optional dolly system.
The fully hybrid R3e impact crusher and the B3e jaw crusher were examples of Keestrack’s compact range of mobile units. The R3e, which was introduced in 2018, is fitted with a single-deck post-screen and oversize recirculation (total of 32 tonnes).
The 30-tonne B3e jaw crusher features a 1000mm x 600mm feed opening and accepts feed size up to 500mm. It can be fitted with an electric-driven double deck, with new independent pre-screen (1.6m 2 + 1.2m 2 ). The electrical equipment on the predominantly diesel-hydraulic plant includes a 42.5kVA generator for all conveyor drives and ancillaries and a 16A plug-out connection for downstream screens or stackers.
ELECTRIC-DRIVEN SCREENS Compared to conventional diesel-hydraulic units, diesel-electric plants save up to 40 per cent of fuel. While working in production trains, the attributable fuel consumption may even decrease by 70 per cent when the hybrid screens are powered directly via the plug-out
supply of an upstream or downstream diesel-electric crusher. To fully exploit this potential, Keestrack offers six models of its double-deck scalpers (250 tph to 1000 tph) as optional full hybrid plug-in versions. New to the “e” program is the Scalper Keestrack K6e. With an 8m 3 standard feeder and a 4500mm x 1800mm double-deck screenbox (2 x 8.1m 2 ), the 30-tonne plant produces three fractions with 600 tph and can be adapted to a wide range of materials and applications with a variety of screen media and additional equipment.
A full hybrid screen solution with high potential for economical semi-stationary operation from the mains is the Keestrack K5e flipflow screen (of about 29.5 tonnes). The specially adapted BIVITEC technology in the large double-deck screenbox provides a wide range of applications in the economic recycling of residual materials (eg glass, slag) or the processing of difficult materials with high basic moisture.
The flexible screening equipment also allows the efficient and economical production of minimum grain sizes of less than 2mm, handling hot materials (eg slag) or generally the production of large quantities of mineral standard products (up to 450 tph).
SOLAR-POWERED PLANT Positioned close to possible power sources, stackers, with their rather low power requirements, are particularly suitable for economical alternative drives.
That is why Keestrack equipped its tracked stackers with dieselelectric plug-in drives at an early stage.
Brand new emission-free models in stockpile handling were presented in Munich. The semi-mobile electric S1e feeder/stacker is installed on a height-adjustable pedestal with lifting and 180-degree swivel hydraulics. The light 10.2m belt feeder (5.45 tonnes) conveys up to 280 tph of sand or gravel (a maximum size of 200mm) and creates kidney-shaped piles of maximum 2900 tonnes. The S5e “solar” tracked stacker was also premiered at bauma. It is possibly the first directly solar-driven processing plant in the world, with photovoltaic modules mounted above the 23m long conveyor feed, and a 23kWh battery installed in the chassis. The battery powers all electric driving, lifting and conveying functions.
In case of bad weather or intensive continuous operation, the system can be powered or recharged via available external sources, such as upstream diesel-electric crushers and screens, or via mains plug-in.
There are two distributors of Keestrack plant and equipment in Australia: Screenmasters Australia (ACT, New South Wales, Queensland, Victoria and the Northern Territory) and Bost Group (South Australia and Western Australia). •
Source: Keestrack
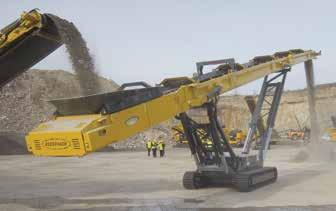