
5 minute read
EIGHT REASONS TO USE
from Quarry Jun 2019
by Prime Group
EIGHT REASONS TO USE A DEWATERING SCREEN IN YOUR APPLICATION
Dewatering screens have long been considered important instruments in sand processing – and an effective means for producing drier, cleaner end products, particularly in the capture and retention of ultra-fine materials.
The dewatering screen’s origins may be in the coal industry, but it has made a home in the aggregates world. Since appearing in the North American market in the late 1970s, the dewatering screen has become the “go to” piece of equipment for economical removal of water from sand. Here are eight reasons why dewatering screens play such a large role in the production of clean quarry products.
1. A DRIER MATERIAL Several pieces of equipment are used to reduce moisture content in sand. A separator or siphon-assisted hydrocyclone produces an underflow material of 22 to 35 per cent moisture. The material can be stacked on a drainage field or discharged to a dewatering screen for additional moisture removal. Discharging the material directly onto a conveyor belt usually creates a housekeeping issue due to the remaining free water.
A fine material screw washer produces a discharge with a 15 to 30 per cent moisture content. While the product can discharge onto a conveyor directly, material can cling to the belt and create a housekeeping issue. The dewatering screen achieves between eight and 20 per cent moisture, depending on the material’s physical characteristics. Despite the retained moisture range, the dewatering screen discharge is drip-free and can be easily conveyed, loaded into a truck or placed in a bin.
A dewatering screen is a low cost solution when feeding dryers, putting material on conveyors, loading trucks or discharging to other equipment that requires the lowest percentage moisture.
2. HANDLING MULTIPLE PRODUCTS The use of longitudinal dividers allows up to three products to be dewatered on one screen. Many applications feature a twostream process where fine and coarse streams can be kept separate or blended to create specialty products. Utilising one
Dewatering screens are a low cost solution for producing a drier material.
dewatering screen for multiple products reduces the overall footprint of equipment and reduces capital and operating costs.
3. INTEGRATION WITH EQUIPMENT Dewatering screens fit well into many applications to yield a drier product, capture ultra-fine material or allow better control in the process.
The combination of a hydrocyclone or separator with a dewatering screen creates a wash system with a higher efficiency level and a drier product yield. The screen underflow can be recirculated into the hydrocyclone feed for recovery or removed as undesired. to recover ultra-fine material before it goes to a settling pond. Even though some of the fines will pass through the screen media, they will remain in the system. The hydrocyclone overflow is the only exit point for the fine material, and it is operated at a high pressure to retain the material.
Equipment such as attrition scrubbers will not operate at optimal levels when the material is too wet. A dewatering screen will produce a predictable moisture, which will allow better process control. The material can be adjusted to the correct percentage moisture through the addition of water at a controlled rate.
Ultra-fines recovery plant Generally, a screen will make a classification based on the media openings. When trying to capture material that would normally pass through the media, a dewatering screen can be used in combination with a hydrocyclone 4. WIDE RANGE OF SIZE GRADATIONS Since the main purpose of a dewatering screen is to reduce the percentage of moisture in material, it can handle a wide range of particle sizes. From as large as 13mm (0.5”) down to 37 micron (400 mesh)
fines, a dewatering screen can be configured to handle material in the size that is needed. As the dewatering screen is designed to blind off the media openings, material that would normally pass through is retained while the water flows through. When used with a hydrocyclone or separator, a dewatering screen is extremely effective in retaining material and producing a dry product.
5. MEDIA ALIGNMENTS FOR SIZING CUTS A dewatering screen is set up to blind the screen media, to retain material to the overs and allow the water to report to the unders. With this mind, it is still a screen, and the media can be adjusted to perform sharp size classification. The inclined discharge continues to promote the removal of water from the material. The media does not have to be continuous in purpose. One section can be configured for size classification, while others are configured for the dewatering requirement. Spray water can be used to increase the size classification efficiency. 6. ADDITION OF SPRAY WATER While it is preferable to address fines removal upstream, there are situations when fines remain in the product. Adding water to a dewatering screen may seem counterproductive but it can have a significant impact on removing unwanted fines. The media will retain the desired material, while the fines will travel with the water and report to the screen’s underflow. The water amount and the added location will have an impact on the effect but, generally speaking, water is added at the feed end.
7. LOW POWER Fitted with two vibrating motors or a single motor to drive exciters, dewatering screens record significantly lower total power usage (in kilowatts) than similar capacity equipment. With the recommended percentage moisture in the feed of 50 per cent or higher, a dewatering screen can accept a variety of feed sources. Under some circumstances, the feed can go below 50 percentage solids,
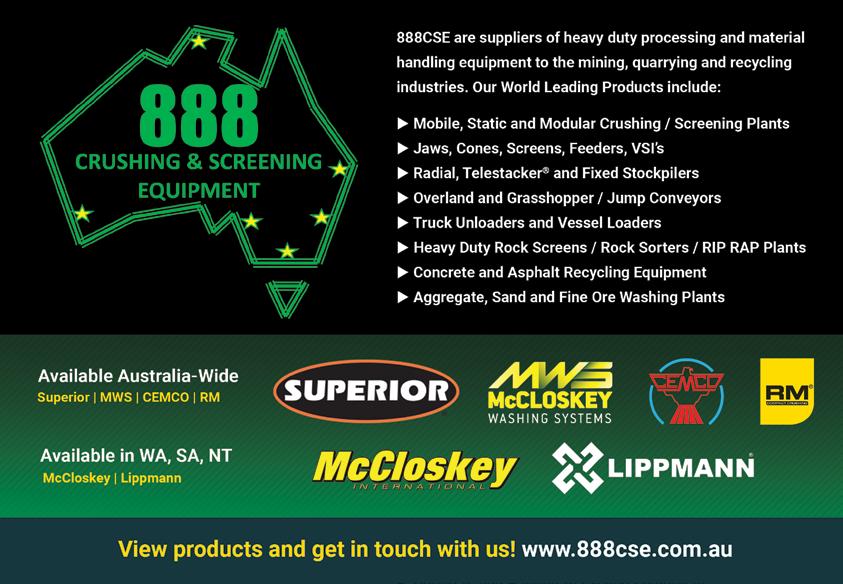
but it can affect the final product dryness or total capacity. When the feed’s water content is too high, it may require more equipment, such as a hydrocyclone, to decrease the moisture percentage prior to introducing the material to the dewatering screen.
8. LOW MAINTENANCE The screen media and springs/buffers are the main items that will need replacing. These items, along with the sideliners and discharge lip, are the only wear parts, and all have a long lifespan. Motors and structural components are designed for heavy-duty applications and have a low rate of failure. For these eight reasons, a dewatering screen can be a welcome addition to a quarry plant when producers are striving to remove moisture and improve productivity.
In Australia, the Lincom Group is the newly appointed national distributor of McLanahan’s sand and aggregates processing range. •
Source: McLanahan Corporation