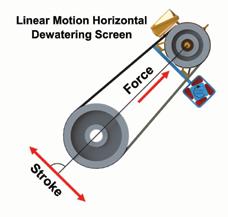
13 minute read
MOTORBASE SOLUTIONS
from Quarry Jun 2019
by Prime Group
MOTORBASE SOLUTIONS FOR VIBRATING SCREEN DRIVES
Almost 30 years ago, I designed some of the first stored-energy motorbases for vibrating screens. These were simplistic in design, using rubber torsion springs that were well known for providing wheel suspension in caravans and trailers for many years.
I have since used and built many motorbases, such as tilt bases, slide bases and other configurations of the same in quarries and extractive industry operations.
In times past, inclined screens dominated the quarrying industry. Today, there is a range of new generation screening machines, including horizontal/variable slope and banana screens. Many new types of screen are driven via lay or jack shafts.
For the purpose of this article, I will focus on those screens and/or feeders directly connected from the screen to the electric motor by vee-belts. These will be referred to as dynamic applications.
LINEAR-ACTION SCREENS More than 25 years ago when visiting a mining operation, the manager showed me a problem he was experiencing with breaking the motor shafts on his linear-action screens.
These were 30kW, D200L four-pole motors, which were fitted with six-groove, B-section belts. They were driving 2400mm x 4800mm horizontal dewatering screens (Figure 1). The motor was adjusted with slide rails. Breaking of motor shafts occurred during resonance (stopping or starting) when a significant percentage of the mass of the screen was transferred to the electric motor shaft. To resolve the problem, I designed a simplistic stored-energy motorbase consisting of a rubber torsion spring, to which a flat plate was welded to carry the electric motor. The spring was pre-positioned to provide sufficient force to tension six vee-belts. There was enough resilience left to allow the electric motor to follow the wild movement of the screen during resonance. No more motor shafts were broken. The client went on to fit up to another 28 screens.
LINEAR-MOTION FEEDER DRIVE A quarry maintenance supervisor contacted us about problems with a 55kW, D280S,
Figure 1. Linear-motion horizontal dewatering screen.
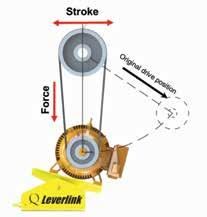
Figure 2. A linear-motion feeder drive.
Figure 3. A circular-motion screen. The correct method of tensioning the drive is to apply sufficient force (tension) to allow the screen to start without the vee-belts slipping.
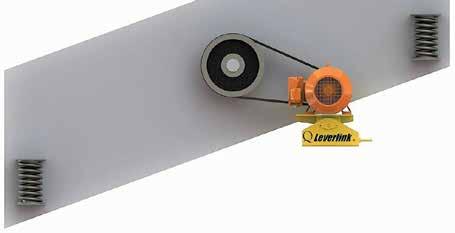
six-pole motor fitted to a linear-motion feeder drive (Figure 2).
A site visit and a check of the stroke angle revealed the vee-belt drive angle was incorrect and that it resulted in energy from the feeder being transmitted via the vee-belts into the supporting structure. This resulted in the cracking of steelwork and welds and an ongoing maintenance problem.
To correct the problem, we relocated the drive position 90 degrees to stroke or line of action and fitted a stored energy motorbase. The mounting position was vertical down. In this position the mass of the electric motor assists in tensioning the vee-belts. The driven pulley now pivots around the drive pulley centre line and minimises the transmission of energy to the supporting structure.
INCLINED SCREENS Inclined screens are most recognised in quarries. Larger screens may have twin shafts (drives). These are circular-motion screens in which gravity is used to assist the screening process (Figure 3). Horizontal screens are becoming more popular and depending on the type of action produced, whether linear or elliptical motion, the positioning of the motorbase can be critical to the vee-belt and pulley life.
A passing conversation with a quarry manager resulted in a site visit to investigate
Figure 4. Correctly tensioned vs over-tensioned screen motor drives.
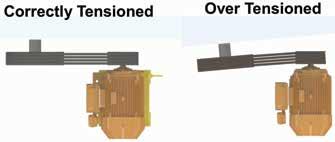
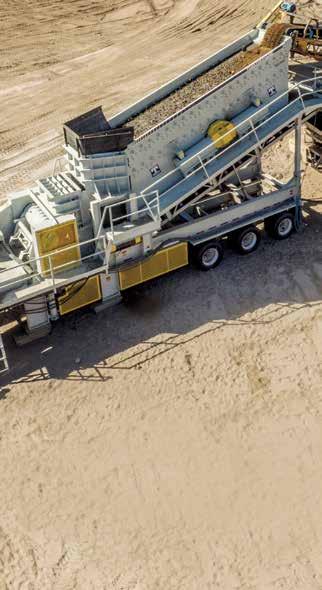
Figure 5. With all screen drives, the most common fault is an incorrect drive angle/motor mounting position.
the high wear of vee-belts and pulleys on an inclined vibrating screen. Upon inspection it was clear the screen was overtensioned (Figure 4), resulting in the screen being skewed on its suspension springs, leading to the drive and driven pulleys becoming misaligned. Maintenance staff had been advised to tension the vee-belts by the deflection method, according to the vee-belt manufacturers’ specifications. This method is incorrect for this type of drive.
The correct method of tensioning the drive is to apply sufficient force (tension) to allow the screen to start without the vee-belts slipping. To ensure they are in good condition, the pulley grooves and vee-belts should be checked beforehand (Figure 5). The OEM would have designed the drive with pulley diameters and vee-belt numbers to start the screen direct online without the belts slipping. Overtensioning may pull the drive and driven pulleys out of line, resulting in extreme belt and pulley wear.
DRIVE ANGLE/MOTOR MOUNTING POSITION With all screen drives, the most common fault is incorrect drive angle/motor mounting position (Figure 5). Inevitably, this may have one or more of the following consequences: • High belt wear. • Reduced drive and driven pulley life. • Belts slippage on start-up. • Belts jumping off. • Energy (vibration) being transmitted to the supporting structure. • Mechanical failure. • Integrity of the supporting structure at risk of failure. • Higher maintenance costs than would be expected. • Unplanned downtime. • Motor failures. •
Henry Derksen, Lonesome Prairie Sand & Gravel operations manager
Lonesome Prairie needed to find a way to sift profits out of mountains of sand. We helped them turn impossible into profitable with our efficient F-Class portable plant.
See the F-Class in action at havercanada.com/f-class.
1-800-325-5993 | www.haverniagara.com
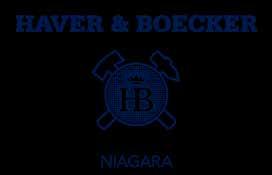
MOBILE SCREENS PROVE THEIR METTLE IN ALLUVIAL DIAMOND MINES
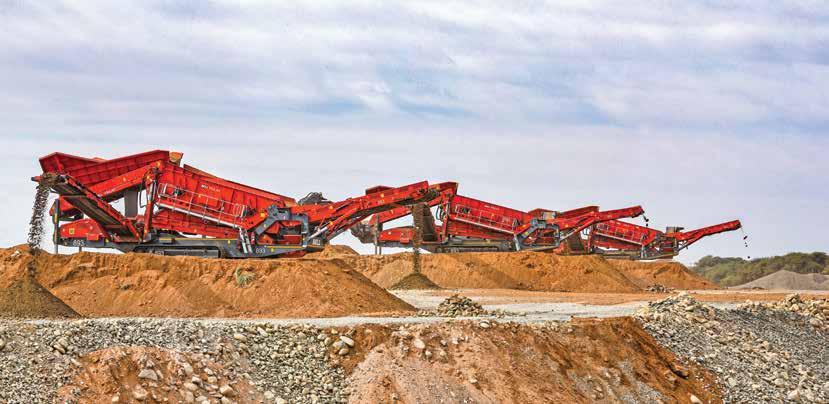
Up to six Terex Finlay mobile screens are “kicking goals” in alluvial diamond mining for two operations on either side of Kimberley, in South Africa’s Northern Cape.
In alluvial diamond mining, as with any other mining or quarrying operation, a lower cost per tonne of pay-dirt produced would find favour with those whose purse is affected.
Therefore, for one operation to save a massive ZAR40,000 ($AUD4000) per week in diesel fuel costs by employing a duo of Finlay screens instead of an electrically driven static screen run off a diesel generator surely makes a lot of sense (not just cents!).
There is fertile ground for alluvial diamond mining near the present run of the Orange River, south of the town of Douglas in the Northern Cape of South Africa.
In 2017 four experienced diamond miners formed a consortium under the name of Nelesco 318 to mine the elusive gemstones in the reddish earth known locally as Rooikoppie. The group mines two pits, at Remhoogte and Saxendrift.
“With the formation of the mining company Nelesco 318, each partner sold some of his equipment, especially articulated dump trucks (ADTs), into the mix and we took over a variety of wheeled loaders and excavators from the mining group which had previously mined this ground,” Remhoogte Mine manager Cobus Botha said.
“We have a fleet of 10 Bell B40D ADTs running here at Remhoogte and 10 Bell B50D ADTs at Saxendrift. All the machines have between 12,000 and 25,000 hours of service, which is testament to their longevity.”
Mining at the Remhoogte site is done in two shifts for 20 hours per day, five days per week. Topsoil is stripped and stockpiled for use in later rehabilitation.
According to Botha, the calcrete gravels and deeper basal gravels are relatively
Remhoogte Mine manager Cobus Botha (left) with Bell Equipment’s Eric van der Merwe and the 694+ (background).
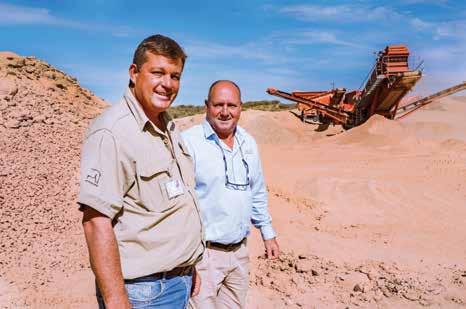
shallow, which means stripping ratios are less critical.
“We load the diamond-bearing gravel with an excavator and this is hauled to a stockpile, from where it is fed into a Finlay 883+ screen,” he said. “We bought the Finlay 883+ screen first, as it is used as a scalping screen and removes the oversized material out of the system at the start of the screening process. This oversized material is fed back into the mining area and forms the base of our later rehabilitation.
“We chose the Finlay 883+ screen for a number of reasons, but most important was that the brand is backed by Bell Equipment. We knew we could count on the technical and parts back-up that would ensure maximum productive uptime for us.”
Botha added some of the Nelesco 318 partners also had Finlay screens in their previous operations, so suggesting the Finlay brand as a first choice was an easy sell. The operators at the Remhoogte mine have found that a high sand content makes processing the gravels difficult. For this reason, the mine recently took possession of a Finlay 694+ inclined screen.
Once through the Finlay 883+ screen, the material is fed directly into the Finlay 694+ inclined screen, where it is split into -34mm, +22mm and +4mm products. The separation protects the bottom deck of the 694+ against potentially too much weight. “The way in which the 694+ separates
out the sand is quite phenomenal, and we can honestly say that its purchase has only added value, as we are assured of feeding our four, 16-foot [5m] pans with diamondbearing gravel of a far better quality,” Botha said. “Another noteworthy feature is the amount of fuel and subsequent money we’re saving. Before we used to feed all the material through a static screen that ran off a generator powered by a diesel motor, and this machine consumed 1000 litres of diesel per day. Running the two Finlay screens, we’re now saving up to ZAR40,000 per week. “The feed to our four pans needs to be approximately 100 tonnes per hour, but our two Finlay screens running in tandem are easily pushing out up to 300 tonnes per hour, which means that we’re always ahead of our processing capacity in the pans.
“This just goes to show that the 883+ and 694+ are the correct tools for our application. With the huge saving in fuel costs, they really do add value to our mining operation by lowering our production costs.”
The 694+ inclined screen splits material into -34mm, +22mm and +4mm products.
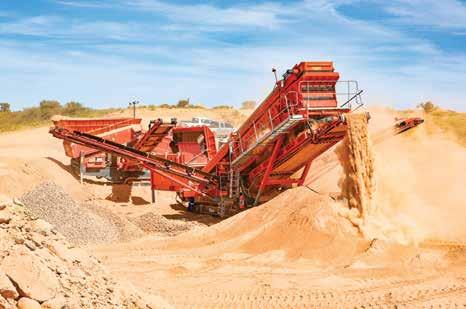
‘FLAWLESS GEMS’ A separate quartet of Finlay screens are also proving to be “flawless gems” for mining giant Steyn Diamante at the Schutsekama diamond mine on the Riet River, near the village of Ritchie, south of Kimberley. It is not a mine where the skyline is dominated by a shaft tower. In fact, the only raised portion shows four large, red mobile Finlay screens processing a constant stream of rock, gravel and sand that is separated onto different moving belts, which spew the material into heaps.
Archaeological data shows the narrow Riet River ran a lot wider some centuries ago.
Mining, quarrying & construction projects done safely and cost-eectively

with our integrated drill & blast services
impactdrillblast.com DRILL & BLAST BLAST HOLE DRILLING
Integrated, safe, tailored drill & blast solutions to optimise outcomes in open cut mining and construction projects around Australia. We own and operate drilling rigs across all areas of Australia. These are fully maintained and serviced to minimise downtime.
COMMERCIAL EXPLOSIVES
Commercial explosives for the mining, quarrying and construction industries - no matter the size or location of your project.
Schutsekama Mine manager Wikus de Winnaar (right) chats to Eric van der Merwe.
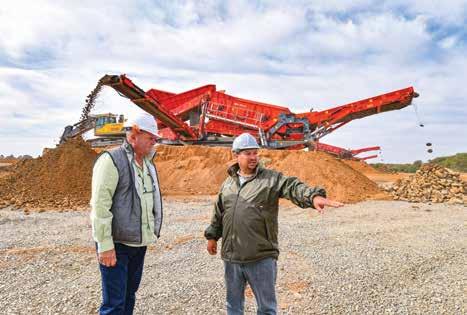
Alluvial diamonds from as far as the presentday Jagersfontein and Koffiefontein were pushed into the surrounding areas as the river flooded the plain en route to joining the Vaal River further downstream.
This is where Schalk Steyn of Steyn Diamante, doyen of alluvial diamond mining in South Africa, established one of his mining operations in 2015.
“Compared to traditional alluvial mining methods, we’ve gone considerably bigger on this site, using a 240-tonne excavator

for loading 100-tonne rigid dump trucks,” Schutsekama Mine manager Wikus de Winnaar said.
“They, in turn, deposit the diamond-bearing gravel onto stockpiles, from where huge 50-tonne excavators feed the material into Finlay 893 screens for separation.
“Anything larger than 125mm is returned to the mining pit to form the basis of rehabilitation, and finer material than that is sent to the processing plant.”
De Winnaar said that in April 2018, almost 160,000 tonnes of run-of-mine material was fed through three of its Finlay 893 screens.
This proved, in de Winnaar’s mind, that “we couldn’t mine so sustainably and on such a large scale if it weren’t for our fleet of Finlay 893 screens. We have four in a row here, but use only three actively, keeping the fourth in reserve for when any of the others need maintenance. Regular rotation also takes place so that the load is spread among the four machines.”
The Schutsekama mine works daytime shifts
Australia’s leading designer and manufacturer of rubber torsion spring motor bases.

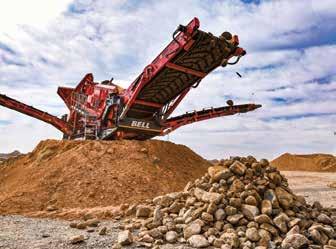
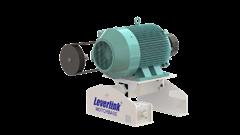
Motorbase -Crushers
Two of Schutsekama Mine’s 893 screens have been involved in the separation of up to nearly 160,000 tonnes of total run of mine materials.
from Monday to Saturday, with month-end long weekends. Machine hours are clocked relentlessly, especially on the Finlay 893 screens. At the time of writing, the newest machine showed 340 hours and the oldest 5477 hours.
The 893 screens are placed as close to the mining areas as possible to shorten the haul distance. This works, as the rigid trucks run full in both directions, bringing mined material to the stockpiles beside the Finlay screens and returning with oversized material for rollover rehabilitation.
“Because of the area where we mine, we come across a lot of wet clay, sand and shale in the diamond-bearing gravels, but we can throw anything at these Finlays and they separate what we don’t want from that which goes to the plant. They are simply amazing,” de Winnaar said.
The four Finlay 893 screens were bought as replacements for four older Finlay machines that were subsequently sold on the preowned market.
“Schalk [Steyn] first used Finlay 883 screens back in 2004 when he started mining alluvial diamonds in South Africa,” de Winnaar said. “He knows the machines’ capabilities and while going on to the larger 893 machines has stayed with Finlay, as he has absolute faith in the brand.”
Fuel is a major cost factor for any miner and this site consumes 8500 litres of diesel per day. The Finlay 893 screens have been recording fuel burn of about 20 litres per hour and, given what they produce, this is considered low.
“What we appreciate, as the mining teams and those working with the Finlay screens daily, is that we have the backing of Bell Equipment in terms of technical support and parts supply,” de Winnaar said.
“Mining equipment always needs attention and can surprise you at any time, but knowing Bell Equipment is close by allows us to do what we do best – mine diamonds and rehabilitate the land afterwards.”
In Australia, Terex Finlay mobile crushers and screens are available through Finlay Crushing & Screening Systems (ACT, NSW, Queensland, SA, Victoria and Tasmania) and OPS Screening & Crushing Equipment (WA and the Northern Territory). •
Motorbase -Screens, Feeders
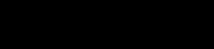
Motorbase -Pumps
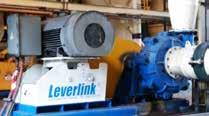
Chain & Belt Tensioners


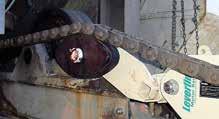