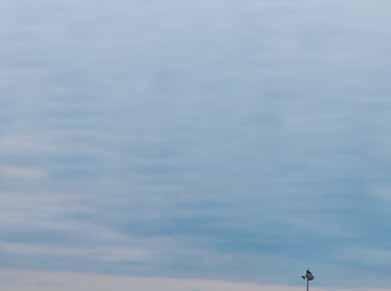
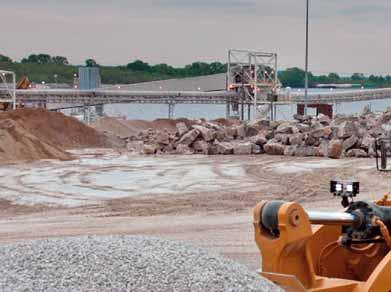
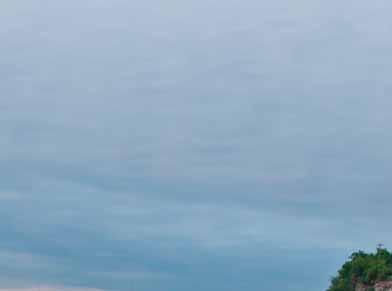
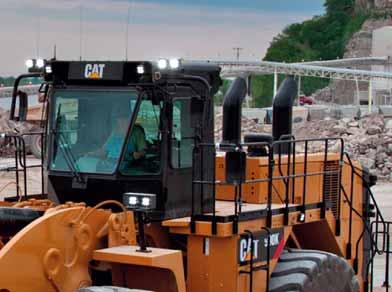
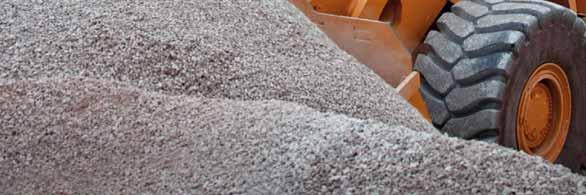
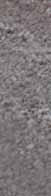
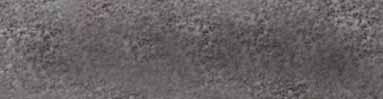
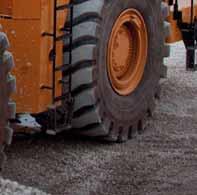
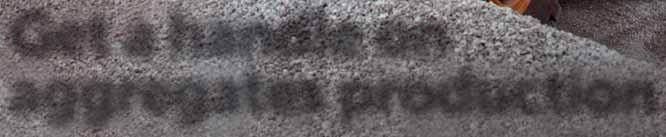

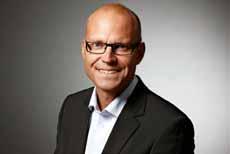
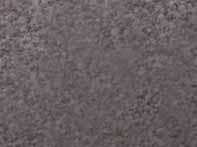
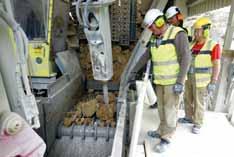
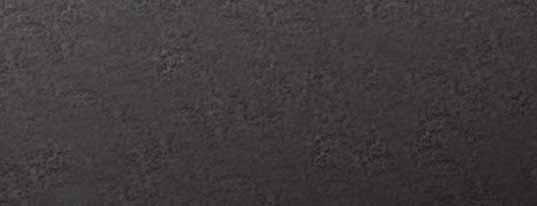
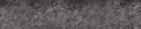

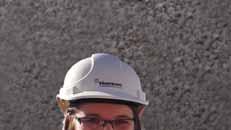
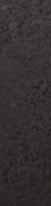
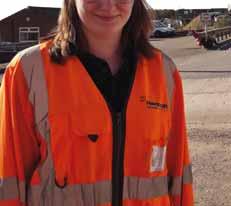
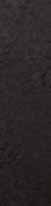
Experience Hitachi’s vision for the future through our unrivalled range of innovations at Bauma 2019. And discover tomorrow’s job site with the efficiency of our ConSite remote monitoring solutions, the accuracy of the ZX210X-6 ICT hydraulic excavator and Hitachi’s advanced technologies.
first turnkey stationary plant in the UK is now fully operational p19
The bigger aggregates picture
Volvo Trucks’ first commercial autonomous haulers; McLanahan to acquire Anaconda
In 2019, UEPG will continue calling for an EU Industrial Strategy and sustainable access to resources, promoting a circular economy workable in the aggregates sector 14 LEGAL UPDATE
Employee ownership is increasing in popularity, particularly in the UK and USA
16 MARKET REPORT
Equipment sales were healthy in 2018, but uncertainty over the policies of the new Italian government is leading to caution over new investment in aggregates and construction plant 43
CEMEX is being supplied with 100% renewable electricity at more than 150 of its UK sites 55 EQUIPMENT
Global quarrying equipment manufacturers’ new model launches and applications 58 EVENTS
All the key events in the quarrying & aggregates world
An eye-catching turnkey stationary plant
first and a leading global aggregates processing brand’s big investment in production facilities
23 LOADING
SDLG’s new Indian market wheeled loader; Volvo CE’s Indonesian and UK quarry customer orders
26 HAULING
With Germany currently a hotbed for infrastructure projects, Terex Trucks plans to capitalise with a new dealer for its ADTs and customer support in the north of the country
29 TYRES – PART 1
A leading global off-highway equipment tyre manufacturer has big plans for its recently inaugurated cutting-edge research laboratory
32 ATTACHMENTS
An MB attachment is helping to facilitate a complicated renovation scheme in Munich, Germany
34 CONVEYORS
A leading conveyor manufacturer has completed two giant projects for a Chinese cement firm, while others have been busy launching new models and opening new production sites
41 CONCRETE PLANT
A top European manufacturer has helped contractors tackle logistical and on-site challenges of concrete supply to a major Alps cable car scheme
08 INTERVIEW
Hans Karlander believes organic growth and a firm focus on environmentally friendly products will ensure the Swedenheadquartered Thomas Concrete Group’s long-term success
45 QUARRY PROFILE
A prominent German aggregates producer is in the frame to capitalise on rising local demand for building materials after a major primary crusher station upgrade
COVER STORY: Caterpillar has launched the 990K Aggregate Handler wheeled loader, designed to handle greater payloads in aggregates yard applications
48 GAIN
Jim O’Brien looks at the history and impressive growth of GAIN (the Global Aggregates Information Network) experiences and ambitions within the building materials production industry
49 HANSON UK LEAD
Four Hanson UK LEAD programme apprentices talk about their learning experiences and ambitions within the building materials production industry
52 ELECTRIC QUARRY PROJECT
Volvo CE and Skanska say the initial pilot of the Vikan Kross Electric Quarry has shown its huge potential environmental, efficiency, safety and cost benefits
Make your fleet management easier and processes more efficient with the renewed Rammer Excellence Line. All of the Excellence Line products are now integrated with RD3 technology – the first ever monitoring system for hydraulic hammers. You can access operating hours and location tracking easily in the My Fleet platform. In addition, the hammers are improved with maintenance features to increase operating costs and reflective stickers to enhance safety and visibility.
Go to rammer.com/excellence for more information and contact your local dealer.
Sandvik Mining and Construction Oy / Lahti, Finland / rammer@sandvik.com / www.rammer.com @rammerhammer @rammerhammer
HEAD OFFICE
EDITOR: Guy Woodford
ASSISTANT EDITOR: Liam McLoughlin
CONTRIBUTING EDITORS: Patrick Smith, Dan Gilkes
EQUIPMENT EDITOR: Mike Woof
DESIGNERS: Simon Ward, Andy Taylder, Stephen Poulton
PRODUCTION MANAGER: Nick Bond
OFFICE MANAGER: Kelly Thompson
CIRCULATION & DATABASE MANAGER: Charmaine Douglas
INTERNET, IT & DATA
SERVICES DIRECTOR: James Howard
WEB ADMINISTRATORS: Sarah Biswell, Tatyana Mechkarova
MANAGING DIRECTOR: Andrew Barriball
PUBLISHER: Geoff Hadwick
CHAIRMAN: Roger Adshead
ADDRESS
Route One Publishing Ltd, Waterbridge Court, 50 Spital Street, Dartford, Kent DA1 2DT, UK
TEL: +44 (0) 1322 612055
FAX: +44 (0) 1322 788063
EMAIL: [initialsurname]@ropl.com (psmith@ropl.com)
ADVERTISEMENT SALES
SALES DIRECTOR:
Philip Woodgate TEL: +44 1322 612067
EMAIL: pwoodgate@ropl.com
Dan Emmerson TEL: +44 1322 612068
EMAIL: demmerson@ropl.com
Graeme McQueen TEL: +44 1322 612069
EMAIL: gmcqueen@ropl.com
SUBSCRIPTION / READER ENQUIRY SERVICE
Aggregates Business Europe is available on subscription. Email subs@ropl.com for further details. Subscription records are maintained at Route One Publishing Ltd.
SUBSCRIPTION / READER ENQUIRIES TO: Data, Route One Publishing Ltd, Waterbridge Court, 50 Spital Street, Dartford, Kent DA1 2DT, UK
TEL: +44 (0) 1322 612079 FAX: +44 (0) 1322 788063
EMAIL: data@ropl.com
No part of this publication may be reproduced in any form whatsoever without the express written permission of the publisher. Contributors are encouraged to express their personal and professional opinions in this publication, and accordingly views expressed herein are not necessarily the views of Route One Publishing Ltd. From time to time statements and claims are made by the manufacturers and their representatives in respect of their products and services. Whilst reasonable steps are taken to check their accuracy at the time of going to press, the publisher cannot be held liable for their validity and accuracy.
PUBLISHED BY © Route One Publishing Ltd 2019
AGGREGATES BUSINESS EUROPE USPS: is published six times a year. Airfreight and mailing in the USA by Agent named Air Business, C/O WorldNet Shipping USA Inc., 156-15 146th Avenue, Jamaica, NY, NY11434. PERIODICALS POSTAGE PAID AT / US POSTMASTER
ADDRESS CHANGES TO: Aggregates Business Europe, Air Business Ltd, C/O WorldNet Shipping USA Inc., 156-15 146th Avenue, Jamaica, New York, NY11434
PRINT: ISSN 1754-2499
ONLINE: ISSN 2057-3413
PRINTED BY: William Gibbons
Kleemann’s HQ near Göppingen, southern Germany
ick and Sharon are a lovely couple. I got talking to them on the Nottingham to London St Pancras train on route to London Heathrow for my flight out to Shanghai for the bauma China 2018 exhibition.
Nick told me how he had come to England from southern Italy aged two with his parents after his dad landed an engineering job in Nottingham in the 1950s. Making their home in the city’s mainly working-class Carlton suburb, Nick described how he and his family strived to make their move to England pay off. He later followed his father into engineering as an electronic design engineer, starting his own business, Voc Rock Amp Valves, selling premium tested amp valves and full re-valve kits for music and hi-fi amplifiers. Now one of the UK’s leading amp valve specialists, Nick’s tone-perfect valves are highly prized by his large number of guitarplaying and other music-based clients.
Nick had discovered a gap in the market and his thriving business, coupled with Sharon’s own successful career, enabled the pair to buy a nice house in the popular north-east Nottinghamshire village of Bleasby, where they brought up their two sons. As our train passed through Market Harborough in Leicestershire, Nick and Sharon said they were on their way to visit one of their now-adult sons who lives with his wife in Woking, Surrey. They also hoped to see their other son, who works as a London-based train driver, that weekend.
Just under an hour later we were saying our goodbyes at London St Pancras, and it wasn’t until I reached London Heathrow and had a bit of time to think while awaiting my flight to Shanghai that I thought how Nick and his family’s self-made success story would strike a chord with many of the readers of this magazine: small to medium-sized quarry owners who have built their aggregates processing businesses
from scratch over several decades.
Indeed, when you add all those small to mid-sized Europe-based aggregates firms together, you have a pretty good idea of what makes up a sizeable part of the bigger European aggregates industry picture. It would be fair to say a decent chunk of the estimated near four billion tonnes of aggregates produced in Europe in 2016, using the latest available UEPG (European Aggregates Association) figures, would come from savvy and hardworking small to mid-sized businesses.
I enjoyed a great 2018 travelling around Europe, Asia and Africa, reporting on the global aggregates sector for Aggregates Business Europe and sister title, Aggregates Business International. Taking in trips across Europe, to countries including France, Turkey, Belgium, the Netherlands and Northern Ireland, and further afield, to China, South Korea and South Africa, I’ve detected far more optimism about the health of the European and wider-world aggregates industry.
I started 2019 with a couple of January trips to Germany. The first took in Kleemann’s impressive headquarters near Göppingen, southern Germany. During the same trip, I visited fellow Wirtgen Group company and asphalt plant maker Benninghoven, at the firm’s state-of-the-art headquarters in Wittlich, south-west Germany. In the final week of January, I was among hundreds of global trade media representatives at the bauma 2019 media dialogue event in Munich, ahead of bauma Munich in April, the world’s biggest construction, quarrying and mining equipment exhibition.
I didn’t bump into Nick and Sharon again on my way to the airport for either trip. But it’s a small world, and it would be a pleasure to chat with them again on my way to another Aggregates Business assignment. GW gwoodford@ropl.com
Guy Edwards has become the new chief executive officer of UK building materials heavyweight Aggregate Industries, a member of LafargeHolcim. The former CEO of U.S.-based Aggregates & Construction Materials (ACM), LafargeHolcim’s subsidiary in the U.S., Edwards replaced François Petry, who was recently appointed country CEO of Lafarge France and market head for France and Belgium.
With more than 30 years of experience in the construction industry (of which 25 has been spent in the UK market), Edwards has held a variety of senior roles within Aggregate
Volvo Trucks is supplying its first commercial autonomous transport solution for real day-to-day operation to Norwegian mining company Brønnøy Kalk AS.
Six autonomous Volvo FH trucks will transport limestone over a five-kilometre stretch from an open pit mine to a nearby port. The solution is said to offer companies working in many industries such as aggregates production and mining greater flexibility and efficiency, as well as increased productivity.
“This is an important step for us,” says Raymond Langfjord, managing director of the mine.
Industries, both in the UK and US. In 2013, he served as a UK executive committee member responsible for European operations and, in 2014, was named chief operating officer for ACM.
Speaking about his new role, Edwards said: “I am excited to be coming home to Aggregate Industries UK as the country CEO. Over the last five years I’ve been part of LafargeHolcim’s growth in the U.S. market - today a $2 billion company delivering aggregates, concrete and asphalt/contracting products and solutions. I understand the business, the opportunities and the challenges, and I know that we have here all that is needed to continue on the same successful path: the highest quality product portfolio, and talented, passionate people devoted to making things easier for our customers.”
“The competition in the industry is tough. We are continuously looking to increase our efficiency and productivity long term, and we have a clear vision of taking advantage of new opportunities in technology and digital solutions. We were searching for a reliable and innovative partner that shares our focus on sustainability and safety. Going autonomous will greatly increase our competitiveness in a tough global
market.”
“We are proud to be able to present an autonomous solution which will meet the challenges of our customers both in terms of safety, reliability and profitability,” says Claes Nilsson, president of Volvo Trucks, adding: “The global transport needs are continuously changing at a very high pace and the industry is demanding new and advanced solutions to stay ahead. Our aim is to be the leader of the development of products and services to respond to these demands.”
Sasko Cuklev, director Autonomous Solutions at Volvo Trucks, said: “By working in a confined area on a predetermined route, we can find out how to get the best out of the solution and tailor it according to specific customer needs. This is all about collaborating to develop new solutions, providing greater flexibility and efficiency as well as increased productivity.”
The agreement involves a deal whereby the customer buys a total transport service and pays per tonne delivered.
Northern Ireland-based CDE says it is on course to move into its new Centre of Excellence in the first half of 2019 after the developer handed over the new campus to the company.
The wet materials processing equipment firm adds that the new offices in Cookstown will enable it to continue to expand its team, providing space for over 400 staff across several areas including
engineering, product development and business services.
CDE claims its new HQ will be the world’s largest campus dedicated to the wet processing of materials in the sand and aggregates, mining, construction and demolition waste recycling, industrial sands and environmental sectors.
The company reports significant growth in its business during recent years, driven by an increase in demand within export markets.
Speaking during the campus handover, CDE chairman Tony Convery said: “Today marks an important milestone in this significant project for the company. I want to pay tribute to the team involved, including our own team, as well as the architects, Teague and Sally, and the building contractor, Felix O’Hare. We very much look forward to moving into the new offices in the first half of 2019.”
Górażdże Cement president Ernest Jelito has been elected as the new chairman of the Polish Association of Cement Producers (SPC).
US aggregate equipment manufacturer McLanahan says it will complete the acquisition of Northern Irelandbased Anaconda within the next two months upon legal closing.
Anaconda specialises in the design and manufacture of mobile tracked compact screening, recycling, loading and conveying equipment for the aggregate, organics and recycling industries.
In the past 10 years, Anaconda has sold over 1,200 units into more than 50 countries across six continents. The company, which was founded in 2008 by Alistair Forsyth
and Martin Quinn, has also expanded its operations to include a sales and distribution office in Massachusetts in the northeastern part of the United States.
In 2017, McLanahan Corporation began a partnership with Anaconda to distribute and sell Anaconda’s line of mobile track equipment.
In a statement McLanahan said that, as the relationship between the two companies progressed, it became clear that their values and business styles were closely aligned.
It added that creating a more official partnership was “a clear step that would provide mutually beneficial
opportunities to both companies.”
McLanahan Corporation CEO Sean McLanahan said: “We looked into growing our line of track equipment in several different ways.
“When it came down to it, we saw in Anaconda a company that was well established, had great employees and dealers, and had many of the same values and business principles as we do. Adding them to our family of companies seemed like a clear fit.”
While Anaconda is joining the McLanahan group of companies, it will continue to operate in the marketplace as an independent brand.
His election was confirmed during a meeting of the SPC board in Krakow in December 2018.
He replaces Andrzej Ptak, president of the Ożarów SA Group, who retired from the role with effect from 1 January 2019.
Jelito was born in 1958 and is a graduate of the AGH University of Science and Technology in Kraków. He started his career in
The Mineral Products Association (MPA) has welcomed the National Infrastructure Commission’s (NIC) Interim Report, the ‘Future of Freight’, notably the highlighting of how the operation of the UK planning system can restrict the operation of key aggregates facilities such as wharves and rail depots.
MPA evidence to the NIC had indicated that the significant use of rail and water transport by the aggregates industry could be constrained by inappropriate
development adjacent to wharves and depots, for example poorly planned and designed housing, which can have the effect of constraining the operating hours of wharves and depots. The NIC concludes that it will “investigate the best way of balancing the need for housing with the need for wharf and rail capacity in its next phase of work.”
MPA chief executive Nigel Jackson said: “It is essential that key industry operations are safeguarded effectively in
the planning system so that the industry can continue to use the most sustainable means of delivering aggregates, cement and other mineral products to customers. Competing land-use pressures in urban areas has led and continues to lead to planning applications and developments close to industry operations which can constrain the operation of industry sites due to complaints from ‘new neighbours.’
1982, and from 2001 to 2005 he was the general director of the Górażdże Group. For the next 11 years he was technical director of HeidelbergCement and managed strategic projects regarding investment, technology, R&D and innovation in all company activities around the world. Since 2015 he has been president of the board of Górażdże Cement and the general director of the Górażdże Group.
“Planning policy and policy implementation must provide effective long-term safeguarding for key industry operations such as wharves and depots. The fact that the NIC has identified “the forgotten element of spatial planning” as one of three critical issues which need to be addressed to enable the UK’s freight system to continue to provide cost-effective services and contribute to sustainability improvements, is a significant moment in addressing this problem.”
The SPC was founded in 1990 and its main goal is the development of the cement industry. It serves as an industry spokesperson in dealings with state administration bodies, local government administration, non-governmental organisations, and European and other institutions. The SPC is a member of the European Cement Association, Cembureau.
The Thomas Concrete Group is a Swedish family-owned company operating in Sweden, Norway, Germany, Poland and the U.S., which in 2018 produced and distributed 5.3 million m³ of high-quality concrete for cast in pace construction. ABE editor Guy Woodford spoke to the company’s chief executive and president, Hans Karlander, who believes organic growth and a firm focus on environmentally friendly products are key to boosting the group’s current SEK 6.5 billion (€635mn) annual turnover.
What have the Romans ever done for us?” – John Cleese’s character Reg famously demanded to know during Monty Python’s brilliant film, Life of Brian. As well as sanitation, medicine, roads, aqueducts, wine and peace - all quoted by members of The People’s Front of Judea (PFJ) in response to a perturbed Reg’s question - they gave us Roman concrete, for which Hans Karlander is truly thankful.
“I’ve always been fascinated by concrete. It has been used in various ways for 2,000 years; the buildings built with it in Rome are still there, and concrete buildings in other cities are still there despite being the scene of devastating happenings. It is a lasting material,” enthuses the Thomas Concrete Group CEO and president. ““It would be strange if concrete was not part of our future. What is more sustainable than it? It is the very definition of ‘sustainability’ as it also absorbs CO2 and is 100% recyclable.”
Based on a hydraulic-setting cement, Roman concrete, opus caementicium in Latin, was used in construction during the late Roman Republic until the fading of the Roman Empire. It differs materially in several ways from modern concrete, based on Portland cement, which is going through something of a green revolution in its production.
Many of Thomas Concrete Group’s own Thomas-branded concrete product range offers a lower CO2 footprint, such as Thomagreen and Thomagarage, while the company’s Thomaplatta pre-cast concrete using recycled aggregates is available to customers in Sweden and Norway.
“Environmentally friendly products are a very important part of our offer, as is communicating their benefits to customers. We have come a long way in Germany with our recycled products, and we aim to roll
out more and more recycled products in all our trading markets. We have a very big responsibility to our planet and how we use its resources; that is true of the aggregates industry as well as the concrete industry.”
Established in 1955 in Karlstad, Sweden, by Martin Thomas, with its headquarters in Gothenburg, Sweden, Thomas Concrete Group has a footprint of 152 ready-mixed concrete plants in its five trading countries – 79 across Sweden, Norway, Germany and Poland, and 73 in USA.
Thomas Concrete Group’s subsidiary in Sweden is Thomas Betong AB. Thomas Cement, another group subsidiary, is a trading and distribution company for among other things, alternative binding material for the Swedish market. The company is also responsible for securing and developing the group’s long-term supply of independently sourced alternative binders, and other raw materials. Thomas Cement currently has three terminals, in Landskrona, Oxelösund and Uddevalla, with an annual capacity of 160,000 tonnes.
“When Martin Thomas founded the business in Sweden, there was a natural geographic tie to Norway, and he had close family ties with Germany,” explains Karlander. “Germany is an important market to be in if you are a European company. It’s the locomotive of European industry, and business culture-wise. Germany and Sweden are also close in that aspect. It was a natural step to go further east when the Eastern Bloc countries of Central and Eastern Europe opened up to Western Bloc business [late 1980s-early 1990s], and we started operating in Poland in 1997.
“We always saw the importance of having a balance between our trading in Europe and the U.S. We want to share the risks and the opportunities and be a very long-term player [in the concrete sector].”
Talking about Thomas Concrete Group’s current and likely 2019 trading environment,
the Thomas Concrete Group CEO says: “We have had pretty strong years in 2017 and 2018. At the same time, we all know that the global economy is at its peak, with several uncertain factors around us: how China develops, Brexit and the European Community, what is happening in the U.S., and how these factors come together.
“For us, 2019 is looking a bit more uncertain. Raw material prices are increasing, and our customers are reluctant to pay more.
“We have during the last few years looked for organic as well as structural growth. We are looking to grow in the U.S. as well as in Europe. We are a family-owned company and everything we do, we do stepby-step with a very long-term perspective in mind.
“Developing our sales network is important. We have plans to expand our U.S operations. We have a fair share of the market but would like to make our geographical footprint larger. Our headquarters is in Atlanta, and we are already well established in Georgia, North Carolina and South Carolina.”
Karlander says Thomas Concrete Group is looking to introduce more “climatefriendly” concrete products in the U.S., as well as in Europe, in the next 12-18 months. In September 2018, the group surpassed 20 million pounds of cumulative CO2 savings in the U.S. using CarbonCure bolt-on technology [technology for existing concrete plants that allows producers to sequester CO2 into their concrete products]. After initially
Since its establishment in the United States in 1985, Thomas has gradually built up a strong position, and now operates a total of 73 concrete ready-mixed plants in the states of Georgia, South Carolina and North Carolina pic: Jordan Blyden
installing the CarbonCure bolt-on technology on a single plant in Atlanta in February 2016, Thomas Concrete Group has been rolling out installations of the innovative CO2-recycling solution. Currently, 25 U.S. group plants have been equipped with CarbonCure bolt-on technology.
“At the same time as creating a more environmentally friendly product, the use of CarbonCure bolt-on technology enables us to produce concrete more efficiently, such as by reducing a product’s cement content,” summarises Karlander.
Karlander, 52, who is six-and-a-halfyears into his dual role of Thomas Concrete Group CEO and president, says demand for the company’s tailor-made and specialpurpose concrete products has increased “substantially” in recent years.
“They are always up for discussion and evaluation if there are special projects, or certain circumstances around projects; such as a specific bridge or skyscraper. I think most concrete suppliers have seen demand for these kinds of products rise in the last few years.”
Karlander says Thomas Concrete Group is looking to take advantage of Industry 4.0, a name given to the current trend of automation and data exchange in manufacturing technologies, to help enhance its product research and development.
“New and complementing binding materials are of great interest to us, as are new admixtures. It will be interesting to see how these can change what we can offer to customers, in terms of better products. If you top that up with the digital movement that is around us right now, this will help us serve customers in a better way, by reducing lead times, and allow us to better control quality and be more efficient in general.”
A mechanical engineering graduate, Karlander worked for 14 years in the automotive engineering sector followed by executive roles in the paper and forestry industries, before becoming Thomas Concrete Group CEO and president in 2012.
Asked how he describes his leadership style, the personable Karlander, who grew up in Sjuntorp, a village on Sweden’s west coast, around an hour’s drive north-east
of Gothenburg, is quick to emphasise the importance of good relationships between employees. “I’m a firm believer in a company being about people. It’s about how we relate to other people. I’m very team orientated but also very results orientated. I like being part of the detail and the numbers.”
Married and a proud dad of two daughters and a son, aged 16 to 21, Karlander enjoys being a key part of what has always been a Swedish family-owned company.
“Martin Thomas had three children and after his time running the firm, his son became CEO and president for 25 years. I’m only the Thomas Concrete Group’s third CEO and president.
“Concrete is natural, creative and recyclable. It is nice to work for a company and within an industry that is helping customers build a society around us.”
As with any senior management role, Karlander is left with little time to enjoy interests and hobbies outside work. However, he still finds time to play sports such as tennis and floorball. “Floorball is a Swedish game like hockey and is played indoors by teams carrying sticks used to hit a small plastic ball. It’s a great high-energy sport that is very popular in Sweden and in other parts of Scandinavia. It’s also big in Switzerland and Asia.”
Floorball. That’s one thing the Romans never invented for us, hey Reg! AB
“I’m a firm believer in a company being about people. It’s about how we relate to other people. I’m very team orientated but also very results orientated. I like being part of the detail and the numbers.”
8. - 14. April
Komatsu in Hall C6 and Demo Area
A versatile workhorse
The new Komatsu WA480-8 wheel loader offers an outstanding combination of stability, breakout power and tractive effort. Very
The European Aggregates Association (UEPG) is set for a busy 2019, with the outcome of the European Parliament election in May and a new European Commission in November expected to have significant implications for all industries, including the aggregates industry.
In January 2019 Romania took over the six-month presidency of the EU Council for the first time.
During the first meeting of the year of the General Affairs Council, the Romanian EU presidency presented the EU Council’s 2019 highlights, including the European Parliament election, the creation of a Multiannual Financial Framework, overseeing Brexit and the promotion of European unity. Watch the YouTube Council Video https://lnkd.in/gjV4iUv
According to its priorities, the Romanian presidency will contribute to ensuring convergence and cohesion in Europe, in order to achieve sustainable and equal development opportunities for all citizens and member states. Its efforts will focus on increasing competitiveness and reducing development gaps, promoting connectivity and digitalisation, stimulating entrepreneurship and consolidating the European industrial policy. Find all priorities and events of the Romanian EU Presidency at www.romania2019.eu
This echoes the 2019 Work Programme
of the European Commission, in particular the new emphasis on jobs, growth and investment, a connected digital single market, and a deeper and fairer internal market with a strengthened industrial base.
The European Aggregates Association (UEPG) will guide its members throughout 2019 on what is relevant for aggregates producers.
Initially, UEPG is focusing on the European Parliament election and its outcome, communicating the UEPG manifesto to election candidates, and subsequently discussing with newly elected MEPs issues affecting the European aggregates industry. UEPG will continue calling for an EU Industrial Strategy and sustainable access to resources, promoting a circular economy workable in the aggregates sector. UEPG is an active partner of the Industry4Europe Coalition, a co-rapporteur of its publications and will continue promoting the activities of the coalition via joint calls to future candidates and heads of state for an ambitious European Industrial Strategy. UEPG is a recognised and trusted partner
of EU institutions and will contribute to the fitness check on the Water Framework Directive. The association will also actively monitor the review of the EU Biodiversity Strategy, while promoting the concept of ‘Temporary Nature’ across European industry.
As an active partner of NEPSI, the Sectorial Social Dialogue Agreement on Silica, UEPG will support the implementation of the 2019-2020 Road Map, with its specific EU co-funded actions from strategy to communications, a review of the NEPSI task sheets, and a simplified protocol.
Technical aspects are essential for the aggregates sector; therefore, UEPG will closely monitor the shaping of the future of the Construction Products Regulation and the standardisation process.
Finally, a must in 2019 is the UEPG Sustainable Development Awards Ceremony on 20 November 2019 in La Madeleine in Brussels. Members are cordially invited to take part in the most prestigious event of the year.
Employee ownership is increasing in popularity, particularly in the UK and USA. Christian Wilson, partner and head of corporate at employee-owned law firm Stephens Scown LLP, considers the benefits for businesses in the aggregates sector.
Arguably the most famous employee-owned business in the UK is John Lewis. On the face of it, aggregates businesses have little in common with the retailer. However, a closer look at the membership of the UK’s Employee Ownership Association reveals that many sectors from engineering and manufacturing to energy are reaping the benefits of becoming employee owned.
In the aggregates and mining sectors, rewarding employees through Employee Share Ownership Plans (ESOPs) is on the increase. One example is Vedanta Zinc International’s Black Mountain Mining. The Employee Share Ownership Plan was launched in 2017 and qualifying employees received their first cash payment a year later, and will receive a guaranteed cash payment of R3,500 (after tax) every year for the next five years. The employees will also benefit from the value of the shares held in the trust, when they will vest to employees in 2022 and 2024. In total, 6% of Black Mountain shares have been placed in the trust. This scheme means that employees can share in the growth and future prosperity of the company.
As well as motivating and rewarding employees, ESOPs can provide owners with tax savings. However, the schemes can be expensive to run, particularly for larger organisations. Does employee ownership, which is much easier (and can be less expensive) to administer, present an alternative opportunity to aggregates and mining businesses?
Canadian mining business Barrick Gold is taking the plunge, with the news that it is moving forward with its global employee share plan, which aims to make every staff member an owner of the company. Last year Barrick’s executive chairman, John Thorner, was quoted as saying: “Just like that first generation of leaders, we want our people today to have the emotional and financial investment of an owner.”
Should other mining and aggregates businesses follow suit?
Employee ownership goes a step further than an employee share ownership plan and according to the Employee Ownership Association in the UK, the sector is growing because: “co-owned companies tend to be more successful, competitive, profitable and sustainable.”
Independent research shows that the combination of employee participation and employee ownership drives business performance.
In the UK the employee-owned sector has seen 60% of its growth in the past seven years and continues to grow at more than 10% a year, contributing between £30bn and £40bn to the UK.
Moving to employee ownership is a big change for any business, but there are times when taking the plunge makes more sense. Alongside company start-up, the next most practical time is likely to be when owners are looking towards succession or exit.
So why should you consider employee ownership?
• A trade sale to an unknown third party is unappealing.
• Your employees are valued and you wish for them to share in success.
• You don’t wish to disappear off into the sunset just yet.
• The business’s legacy is important and you wish to ensure that certain values are continued.
Employee ownership doesn’t necessarily mean handing over 100% of a business to its employees. It can be a percentage and phased over time.
Many companies are reaping the rewards of employee ownerships by giving much smaller percentages to their employees. Just one example is Lush, the cosmetics giant which employs over 13,000 people globally. It has given 10% of the business to its employees through a trust.
An added incentive is that employee ownership can bring tax benefits. In the UK capital gains tax on the business may be zero rated (even better than the entrepreneur’s relief rate of 10%) and employees may be able to take a profit share in the business of up to £3,600 free of income tax.
Employee ownership is not for every business, but any well-advised business owner should at least be aware of it and what it might achieve for their company AB
Christian Wilson is a partner and head of corporate at Stephens Scown LLP. He was instrumental in the introduction of employee ownership at the firm, which was the first large law firm in the UK to become employee owned. If you have any questions about employee ownership, Christian can be contacted on 01872 265100 or email solicitors@stephens-scown.co.uk. For more information visit www.stephens-scown.co.uk
Unrivalled control of sand
Customer-focused solution with unmatched maintenance access
providing industry-leading sand
Truly modular design with unparalleled
Up to 90% of process water recycled for immediate re-use in the system 90%
Rapid installation with industry-leading compact footprint
This is not a machine. This is patented modular technology with the ability to change the wet processing industry as we know it. The expert engineers at CDE have created a solution that can transform raw materials into high value products. This is the shape of things to come.
Outdoor Exhibition Area North/East – Stand FN 1022/1
Together we’re unlocking A New World of Resource 8 –- 14 April, 2019
Construction equipment sales were healthy in 2018, but uncertainty over the policies of the new Italian government is leading to caution over further investments in aggregates and construction equipment. Liam McLoughlin reports.
Construction equipment sales in Italy jumped 22% year on year to reach 9,615 units for the first nine months of 2018.
The figures reflect the continuing recovery of construction equipment sales in recent years, following one of the most serious recessions in Italian history.
Sales of earthmoving machines were up 23% to 9,281 units compared with 7,551 units during the same period in 2017, according to Italian construction equipment trade association Unacea.
The biggest percentage increase in sales was for wheeled excavators which rose by 65% from 111 in January-September 2017 to 183 for the corresponding period in 2018. Articulated dump truck (ADT) sales increased from 34 in January-September 2017 to 51 for the same period in 2018, up by 59%.
“The positive sales trend in the Italian market continued during the third quarter,” said Antonio Strati, Unacea councillor in charge of statistics activities.
“However, it should be remembered that in terms of units, 2018 sales stood at
the same levels of the early nineties. The recovery exists, but the persisting uncertainty in national economic policies and the international financial situation could put a strain on it,” he said.
The Italian Institute for Statistics – ISTAT - reported an increase of 0.6% in construction investments in August. According to the Construction Monitor of the SaMoTer Outlook, this trend was likely to continue until the end of the year.
The restrained development in the sector can predominantly be attributed to suspension of work in numerous infrastructure projects, with difficulties related to the new public procurement legislation and to the implementation of local government budgets.
While Italy´s construction sector continued to grow in recent years, the industry is still far away from a real rebound, according to Italian construction association ANCE, which says that construction investments in the country fell by more than 35% between 2007 and 2016. ANCE adds that construction investment increased by only 0.2% in 2017, driven by restorations (up
0.5%) and non-residential building activity (up 0.6%), while the new residential building segment continued to decline (falling by 1.5%).
A significant number of plant and machines are standing still, i.e. not working at all and/or working very few hours per year (0-500 hours), according to Ángel Luis García del Val, distribution business manager for Italy in the aggregates area at OEM (original equipment manufacturer) Metso.
“In addition, some new machines sold between 2015-2018 in the Italian market are not installed yet,” he adds.
Construction equipment sales were partly inflated in 2017 and 2018 by the tax benefits provided in two recent pieces of fiscal legislation. The Super Ammortamento and the Iper Ammortamento were introduced in the last two governments’ financial laws. These fiscal incentives now appear to have been cancelled, however, with neither at the moment being included in the draft of the 2019 Italian government financial law.
The current political situation in Italy and the low volume of civil work do not help the trust of customers for making investments in quarrying equipment, according to García del Val. “On the other hand, the quarrying machinery installed base is getting older and customers clearly know they must upgrade the plants to keep production costs at a low level,” he adds. For the moment,
Munich, April 8–14, 2019
he says that large construction projects in Italy are proceeding very slowly and some of them could be in doubt after the new Italian government raised doubts over their current economic viability.
“Some of them will probably be postponed due to the lack of money and their cost,” he says. “We believe clearer details will be available in the first quarter of 2019 after the approval of the 2019 Government Financial Law, currently being discussed with EU in Brussels.
“In the short term, we don’t expect a huge increase in the demand for aggregates because the majority of these projects are still to be defined. They may impact the future re-start of some of the stopped plants and the need for more spares.”
Commenting on the prospects for the Italian quarrying and aggregates sector over the next 18 months, Stefano Tacchinardi, MD of the Volvo CE Italia dealership, said: “We expect a stable situation unless exports are affected by economic or political turbulence in specific markets.”
In terms of the type of equipment that
Italian quarry operating customers are currently looking for, Tacchinardi commented: “Machines that further develop efficiency in order to reduce customer operating costs.”
García del Val says: “In the areas of hard stone, cone crushers and jaw crushers are the most popular machines due to the abrasiveness and hardness of the rock deposits [in Italy].”
The value of Italian construction machinery exports totalled €2.18bn in the first nine months of 2018, an increase of 6.2% compared to the same period in 2017, according to the latest surveys made available by the organisers of Italian construction exhibition SaMoTer.
March 2020.
SaMoTer predicted that construction vehicle and machinery imports for full-year 2018 were likely to total €140.5bn, up by 1.9% on the previous year. Residential construction (2.6%) was once again the driving force for the industry in 2018, thanks to renovations and energy requalification projects; the non-residential sector also performed well (+1.7%), while public works are still struggling to take off (+0.3%).
Wheeled excavators 111 183 65%
Wheeled loaders 699 785 12%
AWS backhoe loaders
Rigid backhoe loaders
Skid steer loaders 396 568 43%
Compact track loaders 346 456 32%
Articulated
Source: survey conducted by Unacea on the Italian sales of national and international manufacturers and Italian importers of construction equipment
Italian-built earthmoving machinery and equipment took the largest share of orders from abroad, worth more than €1bn (+13%). Then came machinery for preparing aggregates (€382mn / +0.9%), drilling (€276mn / -0.9%) and concrete (€211mn / -3%). Exports of tower cranes also performed well (€196mn / +10.7%), while road-building machinery came to €93mn, down by 3.6%.
In terms of destination markets, Western Europe confirmed its status as the predominant area in the third quarter of 2018 (€915mn, +6.9%); North America took second place (€287mn, +19.6%) and Central-Eastern Europe plus Turkey ranked third (€275.8mn, +14%). Exports increased to the Middle East (€108mn, +4.4%) and to India (€42mn, +6.8%). Downturns were posted by Central and South America (€99.7mn, -17.75%), North African countries (€75mn, -12.9%), Russia (€56mn, -0.2%) and China (€46mn, -1.4%).
In the Italian domestic market, imports of construction and site machinery and equipment between January and September came to €710.5mn, up by 14.4% over the first nine months in 2017.
The ongoing recovery in the Italian construction sector contributed to results for vehicle and machinery imports, according to data analysed by the SaMoTer - Prometeia Outlook which indicated a growth in investments of 0.5% in the third quarter of the year. SaMoTer is the Italian construction exhibition held every three years in Verona. The next edition is scheduled to take place in
For the next two years, the Prometeia Outlook estimates further expansion by 2.1% per year on average, mainly due to the strong impact of public funding in civil engineering, with a 2.5% increase in total infrastructure investments expected in 2019, followed by a further 6% increase in 2020.
The organisers of SaMoTer commented: “These are encouraging signals during the run-up to the 31st edition of SaMoTer, the only event in Italy dedicated to all construction equipment sectors scheduled at Veronafiere 21-25 March 2020 with a thematic focus on innovation and efficiency improvements of technologies.”
Italy is among the world leaders in the natural stone, and particularly marble, quarrying sector which is mainly located in the Carrara area of Tuscany. The sector is important for both domestic and export sales and one of its main showcases is the Marmomac trade fair, the latest edition of which was held at Veronafiere in September 2018.
“Natural stone, and the technology and machinery industry associated with it, is synonymous with quality and Italy is the acknowledged leader in this context,” said Giovanni Mantovani, director general of Veronafiere.
He added that Italy ranks second in the world in terms of natural stone sales with a positive balance of €2.8bn a year.
“The processed [natural stone] products sector, which is often affected by geopolitical situations, includes among its main customers the United States, Germany, Switzerland, United Kingdom, France, as well as the United Arab Emirates and China,” Mantovani added. AB
Leading global building materials supplier CEMEX will be supplied with 100% renewable electricity at more than 150 of its UK sites.
A renewed partnership with energy supplier ENGIE means that, going forward, all electricity supplied to the sites will be from 100% renewable energy sources such as wind energy.
ENGIE has been providing electricity to over 150 CEMEX UK sites for more than 10 years, and also supplying gas to 33 of these sites. The current contract is to be extended for a further 12 months.
Renewable energy sources produce zero carbon emissions, and CEMEX UK says this makes a significant contribution to reducing its carbon footprint. ENGIE’s renewable electricity supply is underpinned by Renewable Energy Guarantees of Origin (REGOs).
In the 2017/2018 financial year, renewable energy made up 34% of ENGIE’s fuel supply mix, compared to 29% nationally.
Martin Hills, head of energy and carbon at CEMEX in the UK, said: “Cement manufacture is inherently energy-intensive, and we work hard to minimise energy consumption within the process constraints. The switch to electricity from renewable sources is playing a key role in our carbon reduction strategy.”
CEMEX says it is also utilising ENGIE’s demand-side services, such as load management to avoid peak tariffs and rapid
frequency response, which generates extra revenue for CEMEX UK. ENGIE also manages all contractual requirements with National Grid on CEMEX UK’s behalf.
Nicola Lovett, divisional CEO of business energy & services at ENGIE, said: “Our 10-year partnership with CEMEX UK has
delivered major cost and environmental benefits, while also generating additional revenue for the company. Our ability to provide 100% renewable electricity represents another important step forward in addressing CEMEX UK’s sustainability commitments.” AB
McLanahan UltraWASH Modular Washing Systems offer the same world-class washing technology we’ve been supplying since 1835, but in containerized modules for shorter lead times, quick setup and ease of transport if producing at multiple locations or one very large site. Produce up to five products – three clean aggregate and two washed sand products. Additional modules for crushing, screening scrubbing, thickening, and tailings management are also available.
Tice’s Meadow Nature Reserve in Farnham, Surrey, south-east England, formerly a Hanson UK sand and gravel quarry, has been named as an international winner in the Quarry Life Award 2018.
The Biodiversity Trail project, submitted by the Tice’s Meadow Bird Group, won the Connecting Quarries and Communities category and claimed the €10,000 (over £9,000) prize. The project has created a 1.5 mile-long, fully accessible, self-guided circular walk around the nature reserve to enhance and promote biodiversity to visitors.
The scheme, which also won second prize and an award of £2,200 (€2,460) in the UK Community section of the competition, was recognised as one of the top seven international performers out of 100 project groups that entered from 25 countries.
Now in its fourth edition, the biennial Quarry Life Award competition – organised by Hanson’s parent company HeidelbergCement Group – aims to raise the understanding of the
after extraction.
“The Tice’s Meadow biodiversity trail makes it possible for anyone to learn about nature and get closer to wildlife while going for a walk around one of our former quarries,” said Martin Crow, national sustainability manager at Hanson UK, who attended the awards ceremony in Brussels.
“It hosts an abundance of habitats and is considered to be one of the best inland sites to watch birds in south-east England. It is testament to what quarry restoration can achieve in terms of connecting with localcommunities as well as educatingand raising awareness about wildlife and ecology.”
Tice’s Meadow Bird Group chairman Richard Horton said: “We’re both excited and delighted that our community project has been regarded so highly at this international conservation competition. It has inspired us to do more and the prize money will go some way towards our next ambition – to build a purposemade bank for sand martins to nest in within
ABOVE: Tice’s Meadow Bird Group representatives Richard Horton and Richard Sergeant were delighted to collect the €10,000 prize after their project won the Connecting Quarries and Communities category. Pictured from left: Carolyn Jewell, senior expert – Biodiversity, HeidelbergCement; Peter Lukas, director of Global Environmental Sustainability, HeidelbergCement; Richard Grimmett, director of Conservation, Birdlife International; Richard Horton, Tice’s Meadow Bird Group, chair; Richard Sergeant, Tice’s Meadow Bird Group, treasurer; Dr. Scheuer, member of the managing board, HeidelbergCement and Martin Crow, National Sustainability manager, Hanson UK
BELOW: The former Hanson UK sand and gravel quarry, now Tice’s Meadow Nature Reserve
A prominent German aggregates producer is in the frame to capitalise on rising local demand for building materials after a major primary crusher station upgrade. Guy Woodford reports.
Jakob Bauer Söhne GmbH & Co. KG (Jakob Bauer Söhne) based in Erkenbrechtsweiler, near Stuttgart, southern Germany, has been processing White Jura rock from the Swabian Alb since the 1920s.
The company’s gravel plant produces chippings and gravel for road construction and maintenance, with the same site also renowned for its concrete chips for tunnel construction. Jakob Bauer Söhne’s most common gravel product sizes are on average 2-8mm, 8-16mm and 16-22mm.
BELOW: Encapsulated belts, silos and treatment plant at the
As large construction sites are practically on the company’s doorstep, current local demand for quality aggregates is very high.
“Stuttgart 21, the Stuttgart-Ulm rapidtransit railway and the Bossler tunnel are just a few projects in which our concrete aggregates are used,” explains plant manager Siegfried Militsch.
The Jakob Bauer Söhne product sales team work together with Alfred Moeck KG, Steinbruch und Schotterwerk, via the jointly founded Schottervertrieb Vordere Alb GmbH & Co. KG (SVA ).
In late 2017, the Erkenbrechtsweiler plant’s management decided to improve the pre-crushing process within the primary crusher station, replacing a stationary integrated excavator with a more flexible mobile mini excavator equipped with a hydraulic hammer. A new monitoring cage was also installed.
During this period, it was also noticeable that the plant’s old jaw crusher had cracks around its inlet. This initially did not surprise Siegfried Militsch and his colleague Uwe Laderer, as millions of tonnes of rock had already been fed to the
BELOW: Mini excavator with hammer attachment working in the primary crusher station at Jakob Bauer Söhne, Erkenbrechtsweiler
crusher over several decades. However, closer inspection also revealed cracks below the inlet opening. This level of damage had not been expected.
The former manufacturer of the stationary primary crusher explained that a repair would only be possible if the crusher was removed from its steel housing within the primary crusher station and brought to the factory for the necessary welding work. This, however, provided the impetus for further reflection.
It was decided to optimally design the inlet width of the new jaw crusher in relation to the outlet width of the roller grate for the feed material. A crusher with 120-125cm inlet width was agreed on. Prior to this, however, it was necessary
steel housing would be possible under the given circumstances. When it was finally determined that the outer girders of the steel housing still provided “air” for positioning and thus room for a wider stationary crusher, the decisions could be made accordingly.
The favoured option was a Metso modularly designed Nordberg C125 jaw crusher. Fortunately, it was available as a new model that could easily be integrated into the old crusher’s steel housing.
Just a week after agreeing to its installation, the C125 jaw crusher was lifted into the primary crusher station with a large crane and placed into the existing steel housing.
The subsequent commissioning of
and highly efficiently, relieving pressure on the impact crusher used in the latter stage of production. Overall, plant parts wear has also been significantly lower since the Nordberg C125 unit’s installation.
With minerals cultivation areas still available to Jakob Bauer Söhne GmbH & Co. KG for the next 20 years, the company’s investment in Metso technology has left it well set to explore new commercial opportunities. AB
LEFT: The new Nordberg C125 primary crusher fitted comfortably into existing steel housing within Erkenbrechtsweiler quarry’s primary crusher station
BELOW: The new mobile mini excavator with hydraulic breaker and the wider feed opening of the new jaw crusher. This point was previously the production’s bottleneck
Launched in 2010, GAIN (the Global Aggregates Information Network) is a voluntary network of the major regional aggregates associations of the world. Its mission is to openly share experiences and industry best practices, while also promoting greater sustainability and performance within the global aggregates industry. Below, Jim O’Brien, former UEPG president, now honorary UEPG president, and the founder and convenor of GAIN, discusses the association’s impressive growth.
During my time as UEPG president I had a vision that the aggregates industry, despite being an essentially local industry, could share its hard-won experiences internationally and thereby enhance its performance globally. Deliberating with international colleagues, it was decided to give this new network the title of the Global Aggregates Information Network, which also gave the very appropriate acronym of GAIN.
The first GAIN meeting in 2010 in Brussels, Belgium, hosted by UEPG, comprised only five regions, Australia, Brazil, Colombia, USA and Europe, but it opened the doors for an unprecedented level of friendly international exchanges. By the next meeting in Charlotte, North Carolina, hosted by NSSGA, the enthusiastic participation grew to include Canada, China and New Zealand. The enthusiasm continued to grow through the third meeting in Brussels and fourth in Cape Town, hosted by UEPG and ASPASA respectively, by then adding South Africa.
The Fifth GAIN Meeting in 2018 made a new record by including participation from Argentina, Australia, Brazil, Canada, China, Colombia, Japan, Latin America, New Zealand, South Africa, USA and Europe. It is hoped to encompass even more new GAIN members in the next meeting scheduled to take place in Argentina in 2020.
Within GAIN, UEPG represents all of Europe, essentially EU and EFTA countries, where the association started.
From North America, NSSGA represents the United States, while Canada is currently represented by three provincial associations, OSSGA, ASGA and BCSSGA, from Ontario, Alberta and British Columbia respectively. Mexico, represented by ASEC, has just joined GAIN.
In South America, Argentina is
represented by two state associations, namely CEMINCOR and Cámara de la Piedra, which are united under the national association of Federación Argentina de la Piedra. Brazil is represented by ANEPAC, while Colombia is represented by ASOGRAVAS. Chile is represented by the company ARENEX, pending the formation of an association.
From the Middle East, the United Arab Emirates is represented by Stevin Rock (as no national association exists there), which has just recently joined GAIN. From Africa, the only GAIN member so far is ASPASA, representing South Africa.
From Asia, the China Aggregates Association (CAA) strongly represents the largest and rapidly modernising aggregates industry globally. India has just recently joined GAIN, represented both by the Aggregates Manufacturers’ Association (AMA) and the Mining Engineers’ Association of India (MEAI). Japan is represented by its Crushed Stone Association (JCSA). Malaysia has recently joined GAIN, represented by the Malaysia Quarries Association.
From Oceania, Australia is represented by the CCAA, and New Zealand is represented by its AQA.
All these GAIN member countries
together represent 70% of the global aggregates production of 50 billion tonnes, produced in around 500,000 quarries and pits worldwide, estimated to employ up to four million people. The aggregates sector is by far the largest extractive industry globally in terms of its numbers of sites, production tonnages and people employed. Aggregates are the most consumed bulk product on the planet – over six tonnes/person/year.
The key characteristic of GAIN is the palpable enthusiasm in sharing experiences and best practices between all its members. For that reason, a GAIN website has been set up at www.GAIN.ie and every six months or so a newsletter is prepared to promote ongoing GAIN communications, the latest being downloadable from the website. Several major national conferences are held each year, the most recent by the CAA in Shanghai, which several GAIN members attended. It is planned that GAIN membership and best-practice exchange activities will further develop in 2019.
In future editions of Aggregates Business magazine, I will be looking at how GAIN and its members are having a positive impact on the sustainability of aggregates production, while also helping to tackle key challenges and strategically shape the future global aggregates industry. AB
“Although I’ve had a taste for all parts of the business, most of my time has been spent in technical concrete work”
Designed for enthusiastic school leavers, Hanson UK’s Leadership, Education and Development (LEAD) higher management apprenticeship programme allows individuals to learn and develop supervisory skills in a hands-on building materials production environment. It offers the best of both worlds – earning while learning to be a future supervisor or manager. Guy Woodford spoke to four LEAD programme apprentices about their learning experiences.
As business deals go, Hanson UK’s LEAD programme is a pretty good one. Participating apprentices have all their studies funded while Hanson UK pays a competitive salary and benefits package. To be eligible you need 5 GCSEs at grade C or above including Maths, Science and English; 2 A levels at grade C or above; a full clean driving licence; and be willing and able to relocate at any stage before, during and after the three-year programme.
In the first three years of the LEAD programme apprentices gain hands-on experience and relevant qualifications in operational aspects of Hanson UK’s business, while completing a distance learning foundation degree at the University of Derby, which will eventually lead to an honours degree in mineral extractives management. Programme followers could become a trainee manager or plant supervisor by year four. LEAD apprentices will be allowed time for studies within normal working hours but must also study in their own time. They are supported throughout the programme by both a manager and mentor.
Hanson UK’s LEAD programme was
established in 2011. As of December 2018, 39 LEAD trainees had either graduated or were on the programme. Recruitment for LEAD apprenticeships is managed by Cohesion, the early talent specialists.
Emily Burridge, 22, from Shepton Mallet, Somerset, is a concrete technical production manager who covers 25 concrete plants in the West Midlands region of England from her base at Weeford quarry, near Sutton Coldfield.
“I joined the Hanson LEAD programme three years ago and have spent time in all different parts of the business including human resources, finance, customer contact centre and within its cement, asphalt, aggregates and concrete divisions. I also spent two weeks at Whatley quarry near to where I grew up in Somerset. It is one of Europe’s largest limestone quarries and I got to load explosives for a blast and fly a drone to monitor stockpile levels.
“Although I’ve had a taste for all parts of the business, most of my time has been spent in technical concrete work. I’ve helped create Tremiecrete, a new concrete mix for Hanson UK, which was launched in early 2018. I conducted all the trials and it was exciting to be
involved in every aspect of its development.”
With an F6 consistency and featuring a bespoke range of admixtures, Tremiecrete is designed for use in very difficult piling applications and with Tremie pipes. “We’ve had some clients using it in different jobs right across the UK,” explains Emily, who is spending the next two years juggling her Hanson UK management role with building on her July 2018-gained FSc (foundation degree) in Minerals Management from the University of Derby Mineral Products Centre to gain a BSc (honours degree) in Minerals Management.
So why did Emily want to pursue a career in the mineral products sector? “My family were very hands-on in their own careers. My dad was a mechanic and my grandparents were farmers. I always liked to be doing things rather than being sat behind a computer. I also wanted to be a manager, so with my current role at Hanson UK, I’ve got the best of both worlds.”
Elliot Wellbelove, 25, from Sleaford, Lincolnshire, is quarry environment manager at Hanson Cement’s Padeswood Works, near Mold, North Wales. He was part of the firstever Hanson LEAD programme cohort that graduated in June 2018 with a BSc in Minerals Management from the University of Derby.
“I gained A-Levels in Maths, Physics and Engineering and wanted to go to university to study mechanical engineering until I saw an advert for the Hanson LEAD programme. I visited Hanson Cement’s Ketton Works in
Rutland during my LEAD interview and was impressed with the scale of the production site. I thought it was an industry I wanted to work in after university and I liked the idea of learning while getting paid. I was offered a LEAD place and have never regretted it.
“The longer I’ve worked with Hanson, I’ve realised that experience is invaluable. I’ve a lot more than a university graduate looking to enter the industry, and no student debt. I’ve been lucky to have some experience abroad during my time on HeidelbergCement’s engineering training programme. As part of that I’ve been involved in a £25 million project to install a latest technology-equipped cement mill at Padeswood Cement Works. I spent ten weeks in Morocco analysing a similar set-up to the one we would like at Padeswood. The previous year I was involved in a renewable energy project and spent 12 weeks in Slite, Sweden, examining how a solar farm there might be replicated to power Padeswood and other Hanson sites.
“I’m also involved in the recruitment of the next Hanson LEAD programme cohort and visiting local schools in North Wales to discuss careers in the mineral products sector.”
Speaking about his role at Padeswood Works and future ambitions in the mineral products sector, Elliott said: “I was a process engineer and have been seconded to my current role as quarry environment manager.
I’m responsible for the quality of all products and complying with environmental permit regulations around our handling waste fuels. I also monitor the site’s stack emissions online.”
James Kidd, 25, a kiln engineer at Hanson Cement’s Padeswood Works, got on to the LEAD programme after coming out of sixth form and securing a job at Hanson Cement’s Ribblesdale Works in Clitheroe, Lancashire, in September 2012.
“I was never driven at school by an ambition to get into engineering. I went with my secondary school to an open day at Ribblesdale Works and I thought it would be good to work there. “On the Hanson LEAD programme you do the academic as well as the practical side. There are opportunities to go to different sites. The programme encouraged me to mature and become self-sufficient as I had to leave home at 19. I compared myself to some of my friends that went to universities and I thought I was getting a far better experience of life. I don’t think I’ve missed out. When I started at Ribblesdale Works I was offered a decent wage for my age.
“Next year and the year after I will spend six months of each year at different sites to gain more experience. Eventually I would like to work in a senior operational or managerial role. I wouldn’t be averse to going abroad with my work.”
Daniel James, 26, is manager of Hanson Aggregates’ Penderyn quarry, near Aberdare, South Wales. “I finished my A levels and wanted to go into the RAF once I had finished at Sixth Form. Unfortunately, I was diagnosed with Type 1 Diabetes and the RAF was no longer an option for me. Soon after, I was discharged from hospital and bumped into someone I knew who recommended that I apply for the Hanson apprenticeship.
“I was in the first cohort of apprentices into the scheme and was very interested in the ‘earn while you learn’ side of an apprenticeship. I did the three-year [Minerals Management] foundation degree course at the University of Derby’s Mineral Products Centre and earned [from Hanson Aggregates work] £15,000 per year in the first year, £17,000 in the second and £19,000 in the third year. After the foundation year, I went on to do a further two-year course to get me my [BSc] honours degree [in Minerals Management]. This was a similar course to the foundation level and I was already working a full-time role, so I had to manage my studies and work.
“Two-and-a-half years into the course I became a general foreman [at a Hanson Aggregates site] in Oxford, and that was a role I stayed in for 18 months. I have recently started as a quarry manager and moved back to Wales. My day-to-day role includes ensuring the site is running, health and safety at the site, overseeing the direction the quarry is going in.
“Thanks to the LEAD programme I knew that I was going to get a senior management role as they had invested money into training us. The training has been fantastic and has allowed amazing development within the company. I want to go as high as I can within Hanson.” AB
Partners Volvo CE and Skanska say the initial pilot of the Vikan Kross Electric Quarry has shown its huge potential environmental, efficiency, safety and cost benefits. Liam McLoughlin reports.
Volvo Construction Equipment and its customer Skanska have recorded claimed ground-breaking results from their Electric Site research project.
The duo tested the viability of the Electric Site research project in a 10-week trial at Skanska’s Vikan Kross quarry, near Gothenburg, Sweden, from September to November last year. The tests are said to have shown a 98% reduction in carbon emissions, a 70% reduction in energy cost and a 40% reduction in operator cost. The
quarry is the second biggest in Sweden.
Volvo CE says the results indicate that the Electric Site project is taking a big step towards helping the Swedish global quarrying, construction and mining equipment market manufacturer achieve its future vision where work sites are ten times more efficient, with zero accidents, zero unplanned stops and zero emissions. Together, Volvo CE says that the results support the potential for a 25% reduction in total cost of operations. However, at this stage, the reduction in total cost of
operations is just a prediction. As the prototype machines are part of a research project and are not commercially available, it is impossible to give a guaranteed figure.
“Over the last ten weeks, we’ve made incredible progress, learnt a lot and seen huge potential in the Electric Site solution’s environmental, efficiency, safety and cost benefits,” said Uwe Müller, chief project manager for the Electric Site at Volvo CE, after the initial phase of the trial completed in November. He added that the trial was being extended until the end of 2018 to carry out more tests.
“The results we have seen so far confirm that this research project is a step towards transforming the quarry and aggregates industry and creating emission-free quarries,” said Müller.
The Electric Site project aims to electrify each transport stage in a quarry – from excavation to primary crushing, and transport to secondary crushing. It incorporates electric and autonomous prototype Volvo CE machines, new work methods, and site management systems, which together form a complete site solution. New technology encompasses machine and fleet control systems and logistic solutions for electric machines in quarries.
The Electric Site project involves eight HX-02 autonomous, battery-electric load carriers which transport the material from the primary mobile crusher up to the secondary static crusher. When it came to energy use per tonne, the HX-02s proved that they could help Volvo CE take a big step towards achieving its future vision where
work sites are ten times more efficient. The second-generation prototypes incorporate shared technologies and components from the Volvo Group. They use a lithium ion battery to power two electric motors which drive the machine; the hydraulics are driven by an additional electric motor. The HX2 is fitted with a vision system which allows it to detect humans and obstacles in its vicinity. It can follow an adjustable, preprogrammed GPS path.
The LX1 prototype electric hybrid wheeled loader was claimed to deliver more than a 50% improvement in fuel efficiency at the quarry, as well as significant reductions in emissions and noise pollution, compared to its conventional counterparts. Its job was to organise the piles of material at the site. The LX1 is a series hybrid that incorporates a driveline that consists of electric drive motors mounted at the wheels, electric-driven hydraulics, an energy storage system, a significantly smaller diesel engine and new machine architecture, including a new design of the lifting unit. It’s this combination that enables the substantial gain in fuel efficiency.
Jernberg, president of Volvo CE.
At an open day held at the Vikan Kross quarry in November, Jernberg was asked when the technology could actually become available to quarry operators as an “off-theshelf” solution.
The EX1 70-tonne, dual-powered, cable-connected excavator prototype loaded the primary crusher at the quarry. The base machine for the EX1 is a Volvo EC750 crawler excavator that has been upgraded to incorporate an electric motor in addition to the diesel engine. At the quarry, the machine was plugged into the grid, so zero emissions were emitted. If the cable is connected, the EX1 will automatically start in electric mode. If it’s not, it will start in diesel mode. The EX1 is operated in exactly the same way as a conventional Volvo excavator.
“With this research project we are combining intelligent machines, automation and electromobility to challenge traditional ways of working in the quarrying industry and explore new alternatives,” said Melker
“This is the big challenge,” Jernberg responded. “I think the confidence now in our organisation is to do it much quicker than we thought ten weeks ago. You won’t be able to buy it tomorrow, but it will be quite soon.”
In terms of aims in trial’s the second phase, Skanska Industrial Solutions head of Nordics Gustaf Werner said: “We met targets on CO2 emissions, but we also need to see the productivity levels.”
Per-Erik Lindstrom, VP global key accounts at Volvo CE, said the second stage would push the boundaries of the technology to test its resilience and toughness. “We are really on the front line with system complexity such as wi-fi,” he added. “We need to improve the reliability of the technology as we are not quite there yet.” AB
Volvo showcases electric machines at bauma 2019
Volvo CE will be highlighting its electric vehicle and integrated services plans at this year’s bauma construction equipment show in Munich (8-14 April).
The company plans to go electric on its vehicles, starting with compact excavators and compact wheeled loaders in 2020, and then migrating its higher tonnage vehicles to electricity. The first two hydraulic-electric machines will be unveiled at bauma, followed
Demonstrating the breadth of the Volvo Group, Volvo CE will be joined at bauma 2019 by sister companies Volvo Penta, Volvo Trucks and Volvo Financial Services. Under the theme of Building Tomorrow, Volvo’s 2,293m2 indoor stand in Hall C6 and 5,870m2 outdoor stand at FM714 are billed as presenting “a non-stop interactive performance featuring the complete product and service portfolio, for today, tomorrow and well into the future”.
For the first time there will also be an Innovation Area. Exact details have not been revealed, but it will feature Volvo’s automation, connectivity and electromobility technologies.
Volvo CE will also be launching the EC300E Hybrid hydraulic-hybrid excavator and an EC220E excavator that features Volvo Active Control automated boom and bucket movements for a more efficient digging process.
Dustcontrol UK recently exhibited its range of highly effective construction equipment at the Executive Hire Show 2019.
During the 6-7 February event at the Ricoh Arena in Coventry, England, the Dustcontrol UK team showcased the firm’s new quarry application-suited DC Storm LPG propane-powered vacuum (pictured), alongside its powerful Tromb 400 extractors, the DC 2900 and DC 1800 eco vacuums and its DC Aircube cleaners at
d it s Ai rcu b e c l eaners a t stand K3 0.
propane-powered vacuum
The DC Storm LPG has a 15kW motor with the capacity to manage dust extraction in conjunction with work involving large floor grinders, hammer drills, scarifier/shaver or cutting machines for surface preparation, as well as heavy-duty cleaning with long hoses.
As with all of Dustcontrol UK’s mobile equipment, the Storm LPG is fitted with Hepa 13 filters and built to Application Class H as standard for a no compromise approach.
Based in Milton Keynes, Buckinghamshire, England, Dustcontrol UK has over 45 years of experience in developing dust extraction solutions and centralised vacuum systems to fit client requirements in the construction and quarrying industry. www.dustcontroluk.co.uk
Caterpillar has launched its first mobile app designed to allow customers who spend their time in a truck, at the job site and on the go to take advantage of equipment telematics data. The new Cat App delivers simplified, streamlined data directly to mobile devices, helping customers monitor machine location and health, react faster to fault codes and maximise uptime.
This new Caterpillar mobile equipment management tool also gives customers an easy way to monitor their entire fleet, request parts and service, and connect with their Cat dealer from the
work site. The exact location of all equipment tracked by the app is displayed on the mobile device, along with the machine’s operating hours, health and utilisation data. It enables operations to get the most from their equipment by moving an under-utilized asset to precisely where it is needed most.
Customisable push notifications alert Cat App users of machine operating conditions, even if they don’t check into the app every day. Upcoming planned service indicators, based on machine operating hours, are sent to the user, so service can be scheduled
Rammer celebrated 40 years of excellence during 2018. To reflect the landmark, and changing customer requirements, it has renewed both its outlook and its product offering. This has led to the updating and upgrading of its Excellence line of hydraulic hammers.
One of the major features of the Excellence line is Rammer’s purpose-developed RD3 remote monitoring device - the first of its kind on hammers. RD3 uses the Sandvik MyFleet telematics service to track and monitor fleet equipment usage without needing to go to the site to collect the data - ideal for dealers, rental companies and operators. This cloud-based system enables the hammers to be viewed and monitored via Google maps.
The main benefits of the system are that it enables fleet owners/managers to know exactly where their equipment is, and how it is being used. This supports better business decisionmaking - providing improved security and optimised fleet location, whilst enabling enhanced application knowledge and operator education (all accomplished via GPS data) - and contributing to the overall profitability of the business.
As well as RD3, the Excellence line’s onsite lower tool bushing rotation and replacement increases lifetime, which helps to reduce operating costs. This is further supported by two tool retaining pins that increase the lifetime of the
for when it doesn’t impact production. Fault codes, such as engine alerts, provide warnings of critical service issues that need to be addressed before a downtime event occurs. The flexible app allows users to establish different thresholds for when an event notification is sent.
Designed for machine owners worldwide, Cat App users can choose from 35 different languages. It is available on both iOS and Android operating systems and can be downloaded from Apple iTunes or Google Play store. www.cat.com
tool, retaining pins and tool bushings. An IBP on/ off selector is fitted to the valve body, enabling easy field adjustments (2577E and up). Separate greasing channels from the valve body to the upper and lower tool bushing further increase the lifetime of the tool and tool bushings.
www.rammer.com
To help mark Rammer’s 40th birthday, the hydraulic hammer brand has renewed both its outlook and its product offering.
Northern Ireland-based mobile crushing and screening firm EvoQuip showcased its Cobra 230 impact crusher at World of Concrete 2019 in Las Vegas, USA.
Speaking prior to what was EvoQuip’s second appearance at the annual exhibition, this year staged 22-25 January at the Las Vegas Convention Center, Matt Dickson, product line director at Terex-owned EvoQuip, said: “The Cobra 230 impact crusher is a machine that provides classleading productivity, unmatched versatility and excellent fuel efficiency. The quick set-up times, simple intuitive operation and ease of transport make this machine an ideal solution for all applications.”
A number of design features in the Cobra 230
are intended to ensure an optimal material flow through the crushing process. As material moves from the feeder through the impactor onto the product belt, each section becomes wider ensuring an unrestricted flow. EvoQuip says that the undercrusher clearance, the short distance from the crusher discharge to the magnet and the ability to lower the product conveyor while running make the Cobra 230 an ideal machine in all applications.
The Cobra 230 uses a direct drive system to power the impact crusher. EvoQuip says that this, along with two independent hydraulic-controlled aprons, allows the operator to optimise the material throughput and reduction whilst ensuring the best fuel efficiency.
www.terex.com/evoquip
Sandvik Mining and Rock Technology is expanding its Ranger DX series of surface top hammer drill rigs with two non-cabin Ranger DXR versions for improved safety in the toughest quarry and construction applications.
The two new-version models are based on the Ranger DX600 and DX800 drill rigs and, as such, named Ranger DX600R and DX800R, respectively.
Sandvik says the new Ranger
DXR drill rigs can reach places that are off-limits to operators and other drills. They offer the characteristics of conventional Ranger DX series drill rigs, including reliability and a large drilling coverage area, from the standard 17.6m² to an optional 26.4m², in a lighter and more mobile package (a superior solution for hazardous conditions where safe and productive drilling requires advanced radio remote control capabilities).
McCloskey’s big NI demo McCloskey has staged its first multi-spread demonstration event at King Bros. Quarry in Co. Armagh, Northern Ireland.
The demonstrations were an integral part of events tailored to familiarise both new and established dealers with the versatility and productivity of McCloskey’s latest products.
Over two days, more than 70 representatives from over 27 McCloskey dealerships across 21 countries enjoyed guided tours to inspect and watch the spreads at work and have the opportunity for questions and answers with McCloskey experts. The event also featured factory tours of the Granville and Killyman facilities, and a dealer forum at Clonoe.
The Ranger DX600R’s and DX800R’s revolving superstructure offers an innovative counterweight solution, providing a solid foundation for drilling even on extreme terrain. In terms of productivity, the revolving superstructure turns Ranger DXR truly to a powerhouse enabling, Sandvik says, up to 60% more holes to be drilled per set-up compared to conventional top hammer drill rigs. Together with powerful rock drills and Rock Pilot+ drilling control system, the Ranger DXR series is said by Sandvik to represent the highest productivity in non-cabin drill rigs.
Ranger DXR series drill rigs are designed for a 64mm-127mm hole size range, with drill rod sizes between 38mm and 51mm. The standard configuration of the machine can be further boosted with more than 30 useful options, such as extended superstructure turning radius, advanced measurement systems and upgraded dust control. www.rocktechnology.sandvik
McCloskey crushers feed a 100ft stacker to mount the quarry face to the S190 triple-deck screen
For the demonstrations, the equipment was arranged in productive combinations of crushing, screening, and stacking, with one dedicated to showcase the newest compact crushers on the market. Material varied over the three spreads, showing a superior end product from demolition material and crushing blasted rock.
Demonstrated machines included a J44 jaw crusher, C38 cone crusher, a 100ft stacker and an S190 triple-deck screener. McCloskey’s powerful new compact crushers, the 134R recirculating impact crusher and the J35 jaw crusher, were also put to the test.
Steve Walls, McCloskey International sales director, said: “The demonstrations, coupled with the dealer forum, have set a new model for us to assist dealers in developing and delivering high productivity solutions for customers.” www.mccloskey international.com
Astec storage syst ems give operators the option to expand into locations that do not yet justify a plant
Volvo Penta solution for Indian emission regulations
US-based portable and stationary asphalt plant manufacturer Astec is offering satellite silo storage systems.
The stand-alone mix storage systems allow operators to establish a retail location within a transportation radius of the
parent plant.
The company says the storage systems enable users to expand into a location that does not yet justify a plant, while the smaller footprint of the silo system can accommodate installation at small sites that
cannot support a full plant. Features of the systems include a truck unloading hopper to receive mix from the trucks in order to fill the silos. There are also traverse conveyors to deliver mix into the selected silo. www.astecinc.com
BossTek has updated its family of self-powered dust suppression equipment to comply with the US Tier 4 emission regulations.
The company announced the move at the same time as it unveiled the new DustBoss DB-60 Fusion, a suppression system driven by a 25 HP electric motor and paired with a genset powered by a 4-cycle indirect injection diesel engine. The generator features a dualcontainment fuel cell, heavy gauge lockable enclosure and oversized brushless alternator for easy starting.
Permanently mounted on a trailer, BossTek says its Fusion line-up delivers versatile, mobile dust suppression technology to
sites that lack a readily available power source. The company plans to unveil two other Fusion models in early 2019, giving customers the ability to select the size and coverage range needed to best suit their operations
The new generator series is designed with sound attenuation for noise reduction and a multi-voltage switch with utility power outlet in all voltage modes. The digital engine/ generator controller is equipped with single button stop/start and a 364 litre (80 gallon) fuel capacity, giving the units a run time of more than 24 hours at a prime rating of 45 kVa. Like its previous Fusion systems,
BossTek warrantees the DB-60 Fusion for three years/3,000 hours, with 5-year/5,000hour coverage on the electric motor and a 2-year/2,000-hour warranty on the generator.
Tier 4 is the latest emission milestone established by the US Environmental Protection Agency (EPA) and the California Air Resources Board (CARB). The regulations apply to new engines found in off-road equipment, including construction, mining and agricultural equipment, as well as marine vessels, locomotives and stationary engines used in industrial and power generation applications. www.bosstek.com
Industrial engine supplier Volvo Penta is using its existing selective catalytic reduction (SCR) technology for Indian original equipment manufacturers (OEMs) when the stringent BS (CEV/Trem) IV emission regulations come into effect in October 2020.
SCR technology was first developed by Volvo Group in 2006. Volvo Penta introduced the system for industrial off-road customers in 2011, further developing it in 2014.
Volvo Penta says that using the existing SCR technology means no re-generation, easy installation, continuous optimised fuel consumption and low operating costs for OEMs.
For the Indian market, the current emission legislation applicable for off-road vehicles is BS (CEV) III from 2014, covering limited applications. Now, as announced by regulatory authorities, BS (CEV/Trem) IV will cover most of the off-road applications from October 2020.
The SCR system is based on high-efficiency combustion, which reduces the fuel consumption and results in extremely low levels of particulate matter (PM), but also in high levels of nitrogen oxides (NOx). The exhaust NOx is converted into harmless nitrogen gas and water vapour.
“We have extensive experience of SCR technology in the Volvo Group and we firmly believe that our BS (CEV/Trem) IV-compliant product range is industry-leading,” said Miron Thoms, VP and head of Volvo Penta India. “We have been supplying BS (CEV/Trem) IV equivalent Stage IV/ Tier 4 Final engines globally since 2014 and have more than 200 OEM customers.”
www.volvopenta.com
12-14 Agg1 2019
Indiana Convention Center, Indianapolis
Organiser: NSSGA
Tel: 1(800) 342-1415 www.nssga.org/major-event/agg1
12-14 World of Asphalt 2019
Indiana Convention Center, Indianapolis Organisers: NAPA, AEM and NSSGA
Tel: +1 414-274-0644
Email: WorldOfAsphalt-AGG1@itnint.com www.worldofasphalt.com
6-7 Argus Africa Roads 2019 Nairobi, Kenya
Organiser: Argus Media
Tel: +971 4568 3946
Email: me.events@argusmedia.com https://www.argusmedia.com/ conferences-events-listing/africa-roads
8-14 bauma 2019
Munich, Germany
Organiser: Messe München GmbH Tel: +49 89 949-11348
Email: exhibiting@bauma.de www.bauma.de/index-2.html
17-19 Marrakesh Mining Convention 2019 Morroco
Organiser: MMC
Tel: +44 (0)208 242 6566
Email: shariq.abdul@valiantbmedia.com http://marrakeshminingconvention.com/
15-18 CICEE 2019
Beijing, China
Organiser: China Machinery Industry Federation, China Construction Machinery Society and Changsha City Government
Tel: 0731-86969961
www.chinacicee.com
11-13 Plantworx 2019
East of England Arena, Peterborough Organiser: Rail Media & CEA
Tel: 020 8253 4517
Email: simon.frerecook@plantworx.co.uk www.plantworx.co.uk
21-22 CQMS 2019
Punchestown Event Centre, Co. Kildare Organiser: Machinery Movers Magazine
Tel: +353 83 433 5968 www.machinerymovers.ie/cqms/
5-7 RecyclingAKTIV and TiefbauLIVE 2019
Karlsruhe Trade Fair Centre, Germany
Organiser: Karlsruher Messe-und Kongress GmbH
Tel: 0049-721-3720-2300
Email: verena.schneider@messe-karlsruhe.de www.recycling-aktiv.com
MEET THE TEAM
Throughout the year Aggregates Business travels the globe attending conferences, events and equipment shows, keeping you informed of the latest offerings. Why not come and join us for a chat at any of the events below?
APRIL 2019
8-14 bauma 2019
www.bauma.de
Beumer p37 www.beumergroup.com
BKT Tires p28 www.bkt-tires.com
CCCME p47 www.cccme.org
CDE p15 www.cdeglobal.com
CICEE p40 www.chinacicee.com
CMS Cepcor p38 www.cmscepcor.com
ConExpo p54 www.conexpoconagg.com
Hitachi IFC www.hitachicm.eu
OBC www.metso.com
p4 www.rammer.com
Smiley Monroe p51 www.smileymonroe.com
Superior Industries Inc. p13 www.superior-ind.com
Telestack p39 www.telestack.com
Terex Trucks p25 www.terextrucks.com
Trimble p51 http://aggregates.trimble.com
Extended warranty, on-site machine inspections, and performance metrics under a single plan.
In the field, anything can happen. Managing and maintaining a mobile fleet can be risky, especially when unexpected failures occur beyond the standard warranty period.
The Equipment Protection Services plan offers three key solutions. It covers key parts under an extended warranty period, offers inspections and recommendations, and provides insight on fleet performance through a remote data monitoring system, Metso Metrics Services.
By securing asset value and performance, your costs become predictable with fewer surprises and less downtime. To learn more, visit us at booth FS.1111/2 at Bauma April 8-14, 2019.
Metso.com/EquipmentProtectionServices
#TheMetsoWay