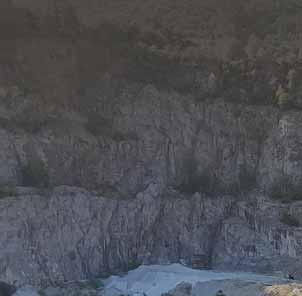
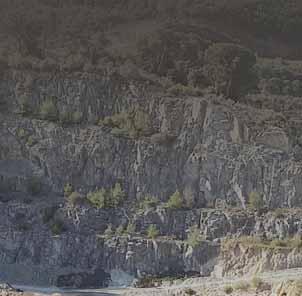


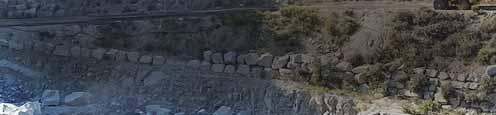
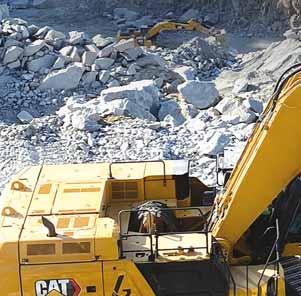
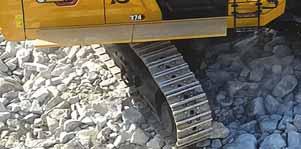


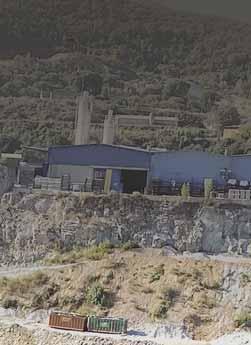
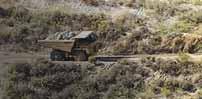
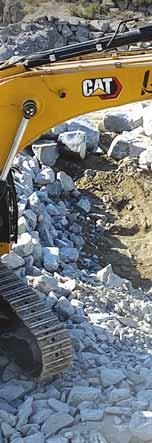
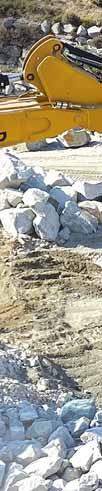
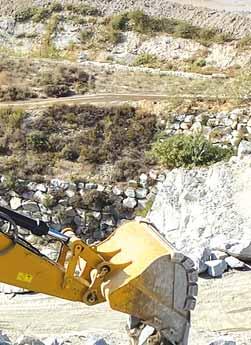
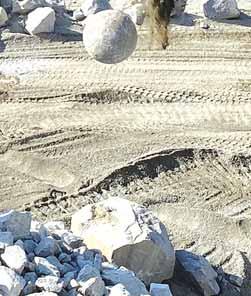
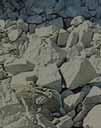

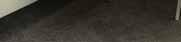

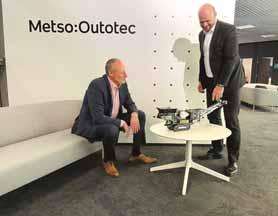
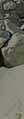

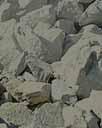
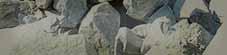
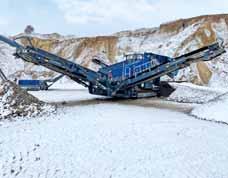
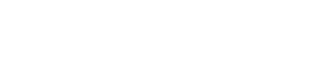
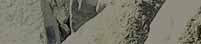
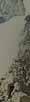
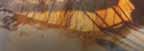
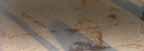
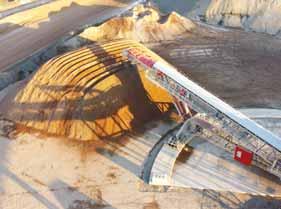
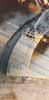
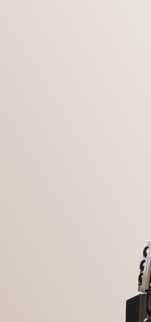

“Conveying equipment manufacturers report healthy order books for 2023 and are responding to the market challenges with innovative new products”
05 COMMENT
When the going gets tough, ‘big data’ gets going
06 NEWS
Volvo CE boosts electric wheeled loader production; EU to fund Holcim decarbonisation projects; Cementa wins right to continue quarrying in Gotland
19
The importance of versatile equipment that can deal with a range of demanding applications is being demonstrated by recent crushing and screening machinery
22
A family-owned Portuguese marble quarry business has a new Cat star of the show, while Doosan, which recently became Develon, believes its eye-catching technology and loading machines can be big assets for quarrying customers
The Turin–Lyon high-speed railway is one of the projects providing major opportunities for hauler manufacturers in Europe, involving extensive earth-moving and construction
Despite ongoing issues with costs and supply of components post-COVID, conveying equipment manufacturers report healthy order books for 2023 and are responding to the market challenges with innovative new products
30
Two of the world’s leading off-the-road (OTR) tyre manufacturers are highlighting the benefits of two products from their latest quarryingsuited ranges
Screening buckets can offer huge productivity and efficiency gains for quarry operators
Demand for concrete plant remains strong, creating a wealth of commercial opportunities for leading manufacturers
Markku Simula and Sami Takaluoma give Aggregates Business the lowdown on Metso Outotec’s exciting plans to build on its leading aggregates processing plant market position
38 SUSTAINABILITY ROUNDTABLE
World Highways and Aggregates Business spoke with a trio of experts from leading construction and quarrying equipment and linked-technology-sector manufacturers to hear their takes on helping to address customers’ current and future sustainability needs
The Àrids Garcia quarry has been at the centre of its community in north Catalonia for over 60 years, providing essential materials for infrastructure in the region
Leading OEMs will be showcasing a wealth of new products and innovations at
In a world where environmental standards are constantly changing, asphalt producers can survive – and even thrive – with the help of a plant retrofit.
A retrofit upgrades an old plant, so it meets new environmental standards – at a fraction of the cost of a new purchase. All projects are managed by the Ammann Retrofit Centre, which relies on proven processes and experienced technicians to troubleshoot any issues and ensure superior results.
What can you get with a retrofit from Ammann
• Increased RAP utilisation
• An electrically heated bitumen tank system that is so cost effective it pays for itself in a few years
• Noise levels that are reduced up to 20 dB without an impact on daily production
• An ability to use low-temperature mixes that reduce fuel usage and emissions
Contact us to arrange a free analysis to learn the best opportunities for cost-effective, environmental improvements at your plant.
HEAD OFFICE
EDITOR: Guy Woodford
ASSISTANT EDITOR: Liam McLoughlin
CONTRIBUTING
EDITORS: Patrick Smith, Dan Gilkes
EQUIPMENT EDITOR: Mike Woof
DESIGNERS: Simon Ward, Andy Taylder
PRODUCTION MANAGER: Nick Bond
OFFICE MANAGER: Kelly Thompson
CIRCULATION & DATABASE MANAGER: Charmaine Douglas
INTERNET, IT & DATA SERVICES DIRECTOR: James Howard
WEB ADMINISTRATORS: Sarah Biswell, Tatyana Mechkarova
MANAGING DIRECTOR: Andrew Barriball
PUBLISHER: Geoff Hadwick
CHAIRMAN: Roger Adshead
ADDRESS
Route One Publishing Ltd, Waterbridge Court, 50 Spital Street, Dartford, Kent DA1 2DT, UK
TEL: +44 (0) 1322 612055 FAX: +44 (0) 1322 788063
EMAIL: [initialsurname]@ropl.com (psmith@ropl.com)
ADVERTISEMENT SALES
SALES DIRECTOR:
Philip Woodgate TEL: +44 (0) 1322 612067
EMAIL: pwoodgate@ropl.com
Dan Emmerson TEL: +44 (0) 1322 612068
EMAIL: demmerson@ropl.com
Graeme McQueen TEL: +44 (0) 1322 612069
EMAIL: gmcqueen@ropl.com
SUBSCRIPTION / READER ENQUIRY SERVICE
Aggregates Business is available on subscription at the rate of: £85 / US$145 / €111 per annum. Single copies £20 / US$35 / €26 Email subs@ropl.com for further details. Subscription records are maintained at Route One Publishing Ltd.
SUBSCRIPTION / READER ENQUIRIES TO: Data, Route One Publishing Ltd, Waterbridge Court, 50 Spital Street, Dartford, Kent DA1 2DT, UK
TEL: +44 (0) 1322 612061
FAX: +44 (0) 1322 788063
EMAIL: data@ropl.com
No part of this publication may be reproduced in any form whatsoever without the express written permission of the publisher. Contributors are encouraged to express their personal and professional opinions in this publication, and accordingly views expressed herein are not necessarily the views of Route One Publishing Ltd. From time to time statements and claims are made by the manufacturers and their representatives in respect of their products and services. Whilst reasonable steps are taken to check their accuracy at the time of going to press, the publisher cannot be held liable for their validity and accuracy.
PUBLISHED BY © Route One Publishing Ltd 202
AGGREGATES BUSINESS USPS: is published six times a year. Airfreight and mailing in the USA by agent named World Container Inc, 150-15, 183rd Street, Jamaica, NY 11413, USA.
PERIODICALS POSTAGE PAID AT BROOKLYN, NY 11256
US POSTMASTER: Send address changes to Aggregates Business, World Container Inc, 150-15, 183rd Street, Jamaica, NY 11413, USA. Air Business Ltd is acting as our mailing agent
PRINT: ISSN 2051-5766
ONLINE: ISSN 2057-3405
PRINTED BY: Warners (Midlands) PLC
When the going gets tough, ‘big data’ gets going
There is no hiding the fact that the European mineral products industry is operating in extremely challenging times. The continent’s construction sector is a key customer, with any drop in its materials demand reflected in mineral products suppliers’ reduced bottom lines. Given this context, a recent webinar hosted by GlobalData, a leading business market intelligence consultancy, featuring its 2023 predictions for the global construction industry, with a specific focus on the industry’s performance across major European markets, made for tough listening.
“The outlook for construction in Western Europe is gloomy, with activity being hit by a decline in investor confidence amid a looming economic recession and high inflation,” said Danny Richards, lead economist on construction at GlobalData, adding, “Output will be severely hampered by weak investment growth and high prices for key construction materials and energy costs, a trend that has been exacerbated by the impact of the Ukraine war given the importance of commodity supplies from Russia and Ukraine.”
Difficult trading conditions tend to make companies across all industries look internally for greater efficiencies without weakening their commercial offer. There are increasing calls for greater and more savvy use of ‘big data’ to enhance business operations, with Jon Prichard, CEO of the Mineral Products Association (MPA), recently urging MPA member firms and the wider industry to lose what he sensed was its feeling of being “behind the curve” on big data and tap into its immense potential.
“Understanding what big data can do for the industry is a step we are only just beginning to take. With the right focus, it can inform decision-making, giving us greater capability to predict rather than simply react. It will enable us to work smarter and set out more compelling evidence-based arguments about the importance of mineral products,”
said Prichard, a chartered civil engineer who left his post as chief executive at the Institution of Chemical Engineers in October 2022 to take over from longstanding MPA CEO Nigel Jackson.
Prichard added: “Big data could even influence how the sector is perceived and give rise to new approaches to policy and regulation. So we need to balance the protection of intellectual property with the need to share good practice, and it’s a journey that will require investment of time and money. But I believe that it’s the route to deliver better outcomes for the mineral products sector and society as a whole.”
Prichard’s ‘big data’ advocacy formed part of his wide-ranging and thought-provoking column in the winter 22/23 issue of mineral products today, a quarterly magazine for MPA members.
He also used the platform to criticise a “persistent lack of awareness and appreciation” of the strategic nature of the UK’s mineral resources, hailed UK mineral products producers’ huge sustainability efforts, and praised the commitment and positive spirit of people working within the mineral products industry.
Having twice been part of the judging panel for the UEPG Sustainable Development Awards, I fully agreed with Prichard’s take on the mineral products sector’s record on quarry restoration and wildlife conservation.
“One of the biggest and best surprises coming into this industry is the incredible work on quarry restoration and wildlife conservation, not just returning quarries back to nature but enhancing the land as we go,” he noted. “Borrowing the land to supply essential minerals and then returning it to a state that’s better than it was before – and repeating that approach nationwide at hundreds of locations –is phenomenal.”
Yes, the European mineral products industry is working in very demanding times. But it has a hell of a lot to take heart from. GW
Heidelberg Materials’ Swedish subsidiary Cementa is allowed to continue quarrying material at its Slite limestone quarries on the island of Gotland, the country’s Land and Environmental Court has announced.
The court decided that Cementa may continue quarrying for another four years, which was the time period the company had applied for. Swedish broadcaster SVT said that, during these years, Cementa must prepare an application for a longer permit that lasts for 20-30 years.
As previously reported by Aggregates Business, a legal decision delivered in the summer of 2021 had provided a potential threat to the future of the Slite quarrying and cement production site that produces three-quarters of Sweden’s cement.
The Land and Environmental Court’s judgment said that the limestone mining carried out in Slite is needed “to satisfy a public interest of greater importance” and that it is, therefore, possible to grant exemptions from the provisions on environmental quality standards for groundwater.
The court has also granted a ‘Natura 2000’ permit because it judged that the nearby Natura 2000 areas will not be damaged by the logging operations.
“Cementa has presented a sufficient basis for the examination that the land and environmental court must make, and that basis shows that continued groundwater diversion for four years will not damage the habitats in the Natura 2000 areas nor endanger the drinking water supply,” the court’s chairman Karin Smoked said in a statement.
The court has also granted an exemption from the prohibitions in the species protection ordinance.
As part of its sustainable solutions strategy, Volvo Construction Equipment (Volvo CE) has made a SEK 65mn (€5.71mn) investment in the production of electric wheeled loaders at its plant in Arvika, Sweden.
The Arvika factory special ises in the production of medium and large wheeled loaders, and the manufac turer says it has already been successful in driving down its carbon emissions.
Thanks to the investment, Arvika will gain a new 1,500m² building, which will allow the facility to free up areas inside its assembly factory to be able to build electric wheeled loaders. While it has not yet been announced which models will begin their electric transformation and when that will start, production of electric wheeled loaders and more traditional wheeled loaders fitted with combustion engines will continue for now on the same
production line.
Volvo CE says the new investment is a milestone in its ambition to be entirely fossil-free by 2040 and will also go a long way to fulfilling the company’s aim for 35% of machines sold to be electric by 2030.
Coming soon after an announcement to invest in electric haulers from the company’s production facility in Braås, Sweden, Volvo CE says it is also a signpost that it is committed to achieving more sustainable solutions for customers across all its product lines.
The European Union (EU) Innovation Fund has announced an investment of €328mn in two Holcim decarbonisation projects at the Financing Innovative Clean Tech Conference in Brussels.
The grants will accelerate the development of Holcim’s breakthrough carbon capture utilisation and storage (CCUS) projects in Germany and Poland. These projects are part of Holcim’s net-zero roadmap, including over 50 CCUS projects worldwide to decarbonise its business. They contribute to the EU’s Green Deal, putting clean technologies to work for a climate-neutral economy by 2050.
is on a mission to decarbonise the building industry. We are encouraged by these EU Clean Tech investments in our next-
Miljan Gutovic, Holcim region head- Europe and global head of operational excellence, said: “As a global leader in building solutions, Holcim
generation technologies. They contribute to making our CCUS projects more viable and scalable, which can fundamentally change our industry for a netzero future.”
The European Union Innovation Fund is one of the world’s largest funding programmes for innovative lowcarbon technologies. In 2022, the Fund granted more than €1.8bn to 17 large-scale cleantech projects out of a pool of 138 submissions.
These investments contribute to advancing Holcim’s net-zero roadmap, with 2030 and 2050 targets validated by the Science Based Target initiative (SBTi). Decarbonising building across its lifecycle, Holcim is greening its operations while deploying innovative solutions from ECOPact green concrete to Elevate roofing systems.
With the Kodiak ® and Titan® cone crusher lines, Astec has rounded out one of the most comprehensive cone crusher offerings on the market. With innovative technology and industry-leading capabilities on both roller bearing and bushing cones, our line is unmatched and unstoppable.
View our Kodiak and Titan cones.
Metso Outotec is a global aggregates plant major with exciting plans to build on its leading market position. Guy Woodford caught up with Markku Simula, the company’s Aggregates business president, and Sami Takaluoma, Metso Outotec’s president of Services, to get the full lowdown on what aggregates customers can expect next
The numbers stack up when it comes to Metso Outotec’s aggregates business. Its eye-catching €1.2bn sales in 2021 came off the back of 12% average annual sales growth since 2016, with the business division representing 27% of the Helsinki, Finland-headquartered quarrying, mining, metals and construction materials processing solutions company’s total annual sales. By far the biggest-selling original equipment manufacturer across its customer industries globally, Metso Outotec has a 36% aggregates business brand market share in North America alone.
Aggregates Business is sitting down with Markku Simula and Sami Takaluoma in November 2022 at Metso Outotec’s HQ as the company prepares for a big 2023 following its highly eventful first two-and-a-half years. Created on 1 July 2020, after Metso’s global Minerals business was combined with Outotec, a Finland-headquartered global provider of process technologies and services for the world’s metals and mining, industrial water treatment, alternative energy, and chemical industries, Metso Outotec’s launch followed Metso’s late2019-completed acquisition of crushing and screening equipment manufacturer McCloskey International (McCloskey). This included McCloskey’s Lippmann-Milwaukeebranded crushing and screening plants. Metso Outotec increased its aggregates product portfolio further in May 2022 by acquiring Tesab Engineering, a Northern Ireland-based company specialising mostly in mobile crushing equipment for aggregates applications, including quarrying, recycling, asphalt, and concrete.
A global business staffed by more than 15,000 employees of more than 80 nationalities, Metso Outotec’s ability to successfully integrate a growing brand portfolio while continuing to grow its sales (Q3 2022 +37% to €1.402bn (€1.023bn in Q3 2021) and 1 Jan-30 Sep 2022 +31% to €3.861bn (€2.958bn 1 Jan-30 Sep 2021) and maintain operating profit (€319mn/8.3% of sales 1 Jan-30 Sep 2022) is even more impressive given how the COVID-19
pandemic, and, since February 2022, Russia’s war in Ukraine have impacted supply chains and other trading norms.
“The pandemic greatly influenced our business, but in some ways positively. The integration of Metso and Outotec to create Metso Outotec went smoother than I would have expected. We were able to reach many people in a short period of time via [Microsoft] Teams. In a day, we could cover the whole world,” says Simula.
“While the pandemic was not good for building personal relationships within new teams, we achieved everything we needed to do in two months during the integration period, rather than what would usually take eight to ten months,” adds Takaluoma.
Simula says Metso Outotec achieved total merger synergies of €142mn by the end of 2021. “That is €22 million more than our €120 million target, and we achieved those synergies far earlier than we anticipated,” he emphasises, adding: “We had two simultaneous integrations really, as our acquisition of McCloskey [International] was completed only a few months before the merger with Outotec.”
Simula says that while acquisitions have helped boost Metso Outotec’s annual aggregates sales revenues, half of the growth has come from expanding the company’s product range and market coverage while also winning market share from competitors. “I think our growth was initially more products driven, and now it is more services driven, growing installed base out in the field and then in servicing those plants. We have a very, very strong services side of our business with a great presence all over the world.
“The market is good in North America right now, so that is good for our aggregates business given our multi-brand presence there.”
“I think our growth was initially more products driven, and now it is more services driven”
business president,
“From an R&D side, everything we do has to have a sustainability improvement aspect to it”
Takaluoma believes that McCloskey International customers in North America could benefit greatly from the premium plant-servicing packages available following the company’s 2019 acquisition by Metso Outotec. “The plant-servicing potential was one of several good reasons McCloskey was such a good fit within Metso Outotec. We knew we could leverage enhanced servicing options while allowing McCloskey to continue its strong relationship with customers.”
Globally, Takaluoma says Metso Outotec’s Life Cycle Services (LCS) contracts take-up is growing among aggregates customers, particularly in India. In 2022, Metso Outotec was rewarded with more than 130 new LCS agreements. Aggregates customers make up a third of the around 560 active LCS contracts globally, with mining customers comprising the other two-thirds.
Simula says that Metso Outotec’s aggregates business trading in the European market has been tougher since 24 February 2022, when Russian president Vladimir Putin announced the country’s military operation in Ukraine. Metso Outotec stopped taking orders from Russia in early March 2022 and, in July 2022, announced it would be booking a non-recurring charge of €150mn related to winding down its business in Russia.
“European demand is clearly going down, which is directly linked to the Russia-Ukraine war, inflation and rising energy prices,” explains Simula. “Some of our customers have fixed contracts with their customers and are struggling to make money due to their rising costs. It is not easy for them. Everyone in Europe is concerned about whether an economic downturn is coming and, if it is bad, will it be really bad? This uncertainty impacts our business.”
Takaluoma says that Metso Outotec infrastructure contractor customers in Finland and other parts of Europe have been saying that while COVID recovery money has been spent by national governments and will be coming via the rollout of the €800bn NextGenerationEU coronavirus pandemic recovery fund, it is not stretching as far as pre-pandemic times. “Two years ago, you could build 1,000 kilometres of highway. But now the same amount of money will only give you 700 kilometres. A 1,000-kilometre highway project means you need ten full-time
employed contractors, but a 700-kilometre project means you may only need six.
“You could use the same 1,000-kilometre highway example to show the impact of rising inflation on the services side of our business. Four out of ten customers do not place an order for a new processing plant as they don’t see the future as too bright, with the other six placing an order as usual, which includes servicing and wear part support. The four customers not investing in a new plant are planning for a longer shutdown period to avoid the high energy costs. They are also using this time to refurbish or upgrade their existing equipment to be ready for 2023.
“We are seeing increased requests from aggregates and mining customers for retrofitting and upgrading mobile crushers, with part of that tied in with customers and our sustainability goals. For example, some customers want to do the same amount of crushing while using less energy and leaving less waste. It is about us helping customers meet their aims and ambitions rather than something new we need to invent.”
“The upgrading of some of our existing Metso Outotec plants and the wider sustainability agenda is a big part of our global growth strategy,” adds Simula.
Asked whom Metso Outotec sees as its biggest global aggregates equipment market competitors, Simula replies: “In China, I would say that the Chinese plant manufacturers are tough competition for us. It is the same in India with the Indian manufacturers on their home turf. In the Western World, Terex, especially Powerscreen, are big competitors.”
Simula says that disruption to Metso Outotec’s supply chain due to the pandemic and other factors was “as bad as it could be” towards the end of 2021. “At the same time, demand from our distributors was going sky-high. So, and this is different, I think,
from most of our competitors, we would not book the orders until we knew we had the availability of components. Diesel engines were, for instance, very difficult to acquire a year ago. Our distributors were surprised at first but quite soon realised that they could deliver on what they promised.”
Focusing on Metso Outotec’s plant range, Simula says there is a growing demand for diesel-electric hybrid-powered mobile crushers and screeners. “If you look at our plant portfolio, the stationary plants are, by nature, all-electric powered; the wheelmounted plants are also run by electricity. All our track-mounted machines were diesel-hydraulic years ago, but some are now diesel-electric hybrids. If you look at what research and development we are doing, by far the biggest investment is in dieselelectric hybrid plants. Around 90% of our track-mounted mobile crushers and screeners range are diesel-electric hybrid-powercompatible. We also have some experimental research being done on fully electric plants.”
Widening his plant-portfolio appraisal to include McCloskey International, Lippmann, and Tesab crushers and screeners, Simula continues: “I think we still have gaps regarding certain types of crushers and a certain size of screeners. Some of the other gaps we had have been filled through utilising some plants and technology from our acquired brands, and vice versa for them in being able to draw on Metso Outotec-branded solutions.”
Simula says he has been keenly watching prototype development of hydrogen-powered excavators and articulated haulers for aggregates and construction customers, led by JCB and Volvo Construction Equipment. “If you look at the excavator or wheeled loader side of the [off-highway equipment] market, manufacturers are making tens of thousands
a year; we [crusher and screener makers] are making thousands. They have scale to develop hydrogen-powered machines. Once a commercial hydrogen engine solution is available, they can take it and put it in our plants.”
“From an R&D side, everything we do has to have a sustainability improvement aspect to it,” adds Takaluoma, pointing to Metso Outotec’s all-encompassing Planet Positive approach to sustainability. The company is firmly committed to helping limit global warming to 1.5°C, with targets validated by the Science Based Targets initiative (SBTi).
I bring up the topic of materials-processing plant automation and advanced plant dataanalytics tools and am eager to hear what customers can expect to benefit from next via Metso Outotec Metrics (Metrics). The company has long highlighted how online digital monitoring can play a key role in every customer business and be a valuable tool for optimising safety standards, maximising operational efficiency, and enhancing profitability. With remote access to your equipment data, the Metrics solution is, says Metso Outotec, like having a production expert alongside you, even though they are hundreds of miles away, providing a proactive way of identifying problems before they cause costly equipment failure, unplanned downtime and productivity losses.
“For us, this is critical. There are thousands of customers using our equipment, and connectivity is part of every new machine that leaves our factory. We have a good solution to remotely support our customers with their troubleshooting, getting their equipment up and running after an event much quicker. It also helps with sustainability, as we do not need someone driving a diesel car to see them,” says Takaluoma. “Digital tools also have big potential around safety, for example, by enabling our crushers and screeners to
be controlled remotely from an excavator cab. The next step is improving the end-user experience with our digital tools. Our distributors have a big part to play in helping our customers with that.”
I ask about what role AI (artificial intelligence) is playing in Metso Outotec’s plant automation and digital plant analytics tools development. “We are working with a particular Finnish company and universities worldwide as part of our AI journey. It is initially being used to help us serve our customers better from a supply chain visibility point of view.
“We want to get to the stage where customers get almost minute-by-minute
updates of where a machine or replacement part is, considering the weather and other factors,” highlights Takaluoma.
Simula says Metso Outotec is expanding its manufacturing and assembly capabilities at its state-of-the-art site in Alwar, Rajasthan, north India. In November 2021, the company announced plans to grow its Alwar production value by 30% from its current level and global track-mounted mobile machine capacity by 15%.
The increased capacity in India will be used for the manufacturing of McCloskey, Tesab mobile and Lokotrack equipment, creating around 200 new jobs. After the extension is completed in Q1 2023, the Alwar
An impressive 90% of Metso Outotec’s track-mounted mobile crushers and screeners are diesel-electric hybrid-power compatible
factory will be one of Metso Outotec’s biggest manufacturing sites globally, employing about 800 people. Most of the machines manufactured and assembled in Alwar are shipped to customers in Southeast Asia and Africa.
“In each of the past three years, we have also doubled our engineering personnel in Alwar. We will be looking to increase our numbers again in 2023,” stresses Simula. “The commercial potential for us in the Indian aggregates market is huge given the way the country’s infrastructure is being developed.”
“What is very interesting already for us is that we have more than 100 Indian aggregates customers with Life Cycle Services contracts,” says Takaluoma. “They truly see the value of being more connected to OEMs [original equipment manufacturers] with their plant maintenance, wear parts replacement and wider services provision.”
“Our LCS contracts are also helping our Indian customers with their sustainability targets and creating more of a circular economy,” adds Simula, showing me a presentation slide illustrating how Metso Outotec electric NW plants used by smallto medium-sized quarry and contractor customers in India are lowering their operational costs while enabling the use of renewable energy. Another slide highlights how the company’s wears return programme within Indian LCS customer contracts is lowering customer CO2 emissions by 58%, air pollution by 86%, water use by 40%, and water pollution by 76%.
I steer the conversation to Metso Outotec’s worldwide distributor network and its effectiveness at retaining existing and gaining new aggregates customers. “We have more than 250 dealer distributors globally and have been developing several networks: a global one for Metso Outotec, a McCloskey International network which is almost global, and Lippmann, which has a multi-regional distributor network,” explains Simula. “We have also revamped Tesab’s distributor network, having identified during the acquisition who we thought would be good new professional distributors for their machines. We are continuously developing our distributor networks across our brands. We have an excellent name within our industry, and people come to us looking to form dealer-distributor partnerships. Our global distributor networks are a key part of our success. I value them very highly.”
I end what has been an enjoyable 90-minute conversation asking Simula and Takaluoma how the world’s 45-billion-tonnesa-year demand for aggregates will be met by producers a decade from now. “There will remain a great need for crushed stone aggregate, but there will be more digitalised, automated, and AI-inclusive production, requiring fewer people on-site,” notes Takaluoma.
“At those future aggregates-processing sites, there will not be too many dieselpowered plants. There will be a lot of hydrogen, electric and other alternative-
fuel-powered machines,” Simula predicts. “I don’t think there will be a power monopoly; customers will choose from many suppliers. There will be more and more solar panels and wind turbines around us, and betterconnected electric grids featuring more and heavier cables.”
Takaluoma concludes: “It might be in ten years’ time that some quarrying companies have their own mini nuclear plants or other low-emission-power-supply factories nearby. Wireless electricity supply is already being tested on roads and may become an option for aggregates producers.” AB
The Àrids Garcia quarry has been at the centre of its community in north Catalonia for over 60 years, providing essential materials for infrastructure in the region. It is now also a site for the nesting and conservation of rock birds in addition to housing a restored Roman ruin that is open to the public. Liam McLoughlin reports
Situated near Barcelona in north-east Spain, the Àrids Garcia granite quarry has been in operation for more than six decades, and throughout this time has been one of Catalonia’s most modern granite aggregates extraction businesses.
The 30-hectare quarry site is located in Llinars del Vallès and produces a particularly hard form of granite, which requires the
use of blasting explosives to remove the materials. Usually two to three blasts are carried out each month.
Francesc Garcia Alonso, the father of current company owners Jordi and Carlos Garcia, founded the Àrids Garcia business in 1962 together with his brothers. The father had been involved in materials-processing activity in the area since 1940 when he and his brothers started extracting sand by hand from the Besòs river, near what is now the
Since the quarry was established it has continued to innovate and improve its equipment to supply major players in the surrounding North Catalonia region. It provides aggregates to large companies involved in the asphalt, concrete, prefabricated, and building sectors, which are a fundamental component of major works and projects in Catalonia.
The company says its belief is that it is characterised by its impeccable service, the quality of its products, its high manufacturing capacity and the constant innovation and automation of its equipment and processes, adding that it always strives for excellence.
The quarry produces about 500,000 tonnes per year, with a maximum production capacity of 6,000 tonnes per day, of which 3,000 tonnes can be aggregates processed in the crushing and screening plant. It produces granite and its various sub-products such as sand.
The produced aggregates are suitable for use in the manufacture of asphalt agglomerates, to make concrete, for bases, and other building and gardening applications. In addition to construction companies, the quarry’s other two main
customer segments are paving companies for its granite products, in addition to cement and concrete manufacturing plants. Blocks are also extracted for the building of land and sea breakwaters at ports, and some quarry products are used in railways for track ballast.
In terms of the end-to-end process of quarrying at the site, initially the area to be quarried is prepared and the mixed over-burden material is removed, with the vegetable component being sold off for use in gardens and the rock element sold to construction companies.
The main quarry face is 15-16m high. An outside company is used for the blasting process to break up the rocks, and is followed by a Metso primary crusher that produces products of between 30cm3 and 1m3 in size. The crusher can handle rocks of up to 1.3m3 or two tonnes in weight and produces from 400 to 600 tones per hour. The material is then moved by an automated conveying process via a tunnel to the secondary Metso crusher, which provides products of up to 250mm3. The site also has a tertiary crusher provided by Swiss manufacturer Gipo. The crushing and screening process at the site is fully automated.
“All our customers require different types of sand products and we supply the specific ones they need”
Jordi Garcia, Àrids Garcia general manager
“We produce eight different product types, both standard and special ones,” says Jordi Garcia, Àrids Garcia general manager. “All our customers require different types of sand products and we supply the specific ones they need.”
The premium materials, which have resistance to abrasion, are extracted from a specific area of the quarry.
The quarry has traditionally supplied customers within a 25km radius of the site, but was then contacted by a German company that required a specific type of material for a supermarket they were building nearly 600km away in the Alicante area in south-east Spain.
Another customer is the building company responsible for the nearby Circuit de Barcelona-Catalunya motorsport race track, home to events including the Formula One Spanish Grand Prix. Àrids Garcia supplies them with a specific white rock for the track which Jordi Garcia says has a strong visual appeal and also helps with the cooling process. He adds that technicians from the building company laid down very specific instructions that the material supplied for the track had to be exactly 85mm3 in size, which required a lot of work for Arids Garcia to achieve.
“These kind of projects are a challenge to deliver this level of product, but also very interesting as they are a change from our usual work,” says Jordi Garcia.
The company also supplies materials for asphalting to other race tracks in the region.
Twenty people work at the quarry site in Llinars del Vallès, with a further four working at a nearby office in the city of Granollers, all of whom are employed by Àrids Garcia.
The aggregates produced at the quarry are
bituminous mixtures, materials for gardening, or large blocks for the construction of walls, breakwaters and maritime dykes, as well as in projects to protect river pipelines and for railway infrastructure.
The quarry still has a potentially lengthy lifespan with permissions of around 40 years to continue quarrying and 20 million tonnes of material remaining to be extracted.
The site operates for 225 days a year on Monday to Friday from 7am to 6pm. Saturday and Sunday work is also undertaken when extra production is required.
Àrids Garcia purchased a Cat 950 wheeled loader in 1972, and since then nearly all the excavating, loading and hauling operations at the quarry have been carried out with equipment from the same brand.
Caterpillar currently supplies all except one – a Komatsu hauler - of the loading, hauling and excavating machines operating on the site
The quarry has four Cat 30 to 80-tonne track excavators for loading the material after blasting. These include a 35-tonne 330C machine, a 40-tonne 340F, a new 71.7-tonne 374, and a venerable 329C which is used with the site’s rock-breaking hammer. Four Cat rigid dumper trucks (two Cat 769s and two Cat 771s) transport the material from the quarry face to the reception hopper at the crushing plant.
“This site is one of the most modern in the Catalonia region. We are always focused on plant automation and are moving towards a point where the whole process –extraction, hauling and processing – will be automatic”
Jordi Garcia, Àrids Garcia general manager
The new Cat 374 produces 361kW of net power and is the largest excavator operating at the quarry. The new machine’s duties include dropping a 7-tonne iron ball to break up rocks instead of the usual process of blasting them.
In addition to the previous Cat 374, the quarry also operated a Cat 385 until fairly recently which consumed 85 litres of fuel per hour. In comparison the new 374 model, which is a smaller machine than the 385, is able to achieve 32 litres per hour in providing
All the Cat equipment at the quarry is supplied by Finanzauto, which is the Cat dealer for Spain and Portugal. Its full line of quarry products includes wheeled loaders, tracked excavators, rigid dump trucks, articulated dump trucks, attachments, as well as generators and other auxiliary machines. It has around 4,400 quarry customers in the Catalonia region, mostly small, family-owned companies.
In terms of what levels of production are likely going forward, Jordi Garcia says this is
difficult to predict given uncertainties caused by developments such as the invasion of Ukraine and the state of the domestic market.
“In Spain we are still below the average European levels for buildings and road construction,” he adds. “We are at a low point in the market at present although of course it may increase in future. We are focusing on finding new applications for our products. We look for projects where we can provide specific types of products.”
As part of its sustainability efforts, Àrids Garcia is increasing its activity in the recycling of aggregates.
Jordi Garcia says: “This site is one of the most modern in the Catalonia region. We are always focused on plant automation and are moving towards a point where the whole process – extraction, hauling and processing – will be automatic.”
The company also plans to migrate all the diesel-powered equipment at the quarry to electric power. It aims to install solar panels capable of powering 1,000kW electric vehicles in the first half of 2023, and has the appropriate permits in place to deploy this. The panels will be located in an older part of the quarry that has been prepared for them.
In addition to advanced technology the quarry site also has historical interest, being home to a more than 2,000-year-old Roman observation tower, that is owned by the company and dates from the year 2BC. The building has been restored and can be visited by the public, with the land surrounding it at the back of the quarry being open for cycling and walking. “We try to give something back to the community,” Jordi Garcia says.
Recently the quarry material has been utilised in the construction, repair and
expansion of different seaports and in the construction and maintenance of roads and highways. It has also been used in the asphalting of several motor-sport race tracks, including the Circuit de BarcelonaCatalunya – home to the Spanish Grand Prix and Superbike events. Arids Garcia says the results have been highly satisfactory and appreciated by the best drivers at the highest levels of the sport.
Jordi Garcia says the company is characterised by its corporate values, and is “a social enterprise, collaborating with different NGOs and local entities, sensitive to the protection of the environment and the development of equality policies, the promotion of health as well as a good working environment.”
He adds that this environmental commitment, respect for the environment and the biodiversity of the environment has led Àrids Garcia to carry out a range of actions during these years.
“The company has constantly launched environmental initiatives,” he says. “One of the most important solutions adopted to minimise the impact of the quarry activities is the closure of the production plant, reducing dust emissions and noise pollution. Àrids Garcia has promoted the biodiversity development project ‘Si Hay Cantera, Hay Vida’ [If There is a Quarry, There is Life] which stands out.”
The project has focused on the nesting, protection and conservation of rock birds in the quarry extraction area. A quarry landscape is the natural habitat of rock birds which thrive on rocky cuts and cliffs. The air currents caused by the walls of excavated rock facilitate the upward flight of birds of prey as they go for a straight glide in the direction of migration.
“In 2008, we discovered a pair of nesting Eurasian eagle-owls,” Jordi Garcia says. “It made us realise the importance of protecting the native fauna and we adopted a firm commitment to protect their temporary habitat during the quarry operations. Over
the last 15 years we installed different nesting areas to facilitate the right habitat for their reproduction. We installed seven devices to record images, 18 nest boxes and built 5 nests on rocky walls. We saw the birth and growth of 23 Eurasian eagle-owl chicks, 39 common kestrel chicks, 35 blue rock thrush chicks and about 300 Eurasian crag martin chicks as well as a multitude of more common species.”
This ‘Si Hay Cantera, Hay Vida’ project has been recognised in Spain with the first National Prize for Sustainable Development in 2022 and has also been a candidate in European quarrying association UEPG’s awards.
Àrids Garcia says this demonstrates that the extractive industry and nature can perfectly coexist. “Over the last 14 years, biodiversity has been intensively promoted in our quarry,” it adds. “Water points have been built and maintained as drinking troughs for the mammals and to encourage the development of aquatic animals and insects.”
Blasting and activities which could be likely to alter the lifecycle of existing biodiversity have been postponed, and Àrids Garcia has modified the vegetation in the area in order to make it easier for birds of prey to hunt.
The company says it is strongly committed to renewable energies to support the fight against climate change. Àrids Garcia anticipates that its new photovoltaic solar panels will contribute 60% of the total electricity energy necessary for the operation of the treatment plant, and the intention is to grow it in the future to supply 100%.
Additionally, the company’s innovation department is working on equipment automation, emission reduction and recycling. These are key objectives to face the future.
The company used the celebration of its 60th anniversary to renew its corporate image. A modern image has evolved and is focused on the afore-mentioned objectives.
“We are a company with an environmental, social and innovation commitment without forgetting our leitmotiv: ‘Hallmark of quality’,” says Jordi Garcia. AB
The importance of versatile equipment that can deal with a range of demanding applications is being demonstrated by recent crushing and screening machinery deployments. Liam McLoughlin reports
From rock-face gravel through railway ballast and on to building rubble: when such a wide variety of materials are loaded on the machines, multi-talents are required from the crushing and screening equipment that is being used.
These requirements provided a highly suitable environment for the new Kleemann screen for coarse elements Mobiscreen MSS 802i EVO. In Germany, the first machine of the new design has been put to work at a quarry operated by Ernst Krebs at Neumünster in central Schleswig-Holstein. Ernst Krebs, located in the far north between Hamburg and Kiel, is a very diversified company. Owner Caren Krebs and her son André operate several gravel quarries and their portfolio includes demolition and recycling work, earthwork, road-building and also a transport and logistics section.
The company's machinery was to be extended in 2021 by a new screening plant. The plant had to be flexible and perform in the gravel quarry just as well as on the recycling site – which is not an easy task. Whereas sand and fine-grained material are processed in the gravel quarry, in the recycling of rubble and railway ballast Krebs processes almost everything. This includes, for example, topsoil which is often
particularly cohesive. The screening plant therefore has to deal with stone material ranging from very fine to very coarse as well as with all degrees of contamination.
André Krebs took his request to his longtime contact partner at Wirtgen Germany, Henning Lüdtke. After hearing the task description, Lüdtke believed that this was an ideal application area for the new Kleemann Mobiscreen MSS 802i EVO screen for coarse elements whose strength is its high flexibility and productivity.
Kleemann’s MSS 802i EVO mobile screen is designed for changing challenges in different application areas
loading from different heights, from both sides and from the rear can proceed in an optimum manner. The screen surface change is comparatively easy even in the lower deck because the screen casing can be placed completely in a horizontal position. The screening parameters can be adjusted precisely and even conversion, for example from three to two final grain sizes, is uncomplicated.
Transport from one work site to another is also swift: the discharge conveyors can be folded in – without the disassembly of parts. Thanks to the stepless driving control, the plant can also be moved precisely into position.
Krebs says that one of the real challenges for the company is the gravel extraction process, with the side discharge conveyor for fine grain having a very tough job. “This is no problem for the new plant!" he adds.
The problem: at the time, the machine was not yet available on the German market. But Lüdtke found an unconventional solution, offering André Krebs a pilot series model of the plant for coarse materials. An offer that Krebs accepted, stating: "Even though it was bit like buying a pig in a poke. There were hardly any documents on the product.
“In our gravel quarries and in recycling we have been using Kleemann machines for a long time with real conviction. I was therefore fully confident that this machine would also do a good job.”
Krebs adds that he was not disappointed. "Everything is so much quicker; set-up times are shorter and output is higher. All in all, it pays off.”
The flexibility begins with the large feed hopper. The hopper rear wall and the filling aids can be folded variably so that
After a few months of practical testing, the screen for coarse elements was able to demonstrate its qualities. "One of the real challenges for us is, for example, gravel extraction. We have to deal with a lot of sand with a relatively small proportion of stone. This means that the side discharge conveyor for fine grain has a real tough job. This is no problem for the new plant," says Krebs, adding that the company has already ordered a further plant.
Another advantage of the new plant is that the screen casing can be set more than 20% steeper than many other screens for coarse elements on the market. This guarantees a great cutting effect for the separation of fine material such as sand and a significantly higher output.
Also in Germany, a Kleemann cone crusher is proving itself in the production of railway ballast and high-grade chippings.
A company near Berlin is using the Mobicone MCO 90i EVO2 cone crusher for recycling and the production of crushed rock and high-grade chippings. Since summer 2021, the plant - the first of this type worldwide - has been recycling mainly railway ballast. A Mobiscreen MS 953 EVO
screening plant operates downstream of the cone crusher.
High demands are placed on railway ballast because, in a high-quality ballast bed, the stones dig into one another with their sharp edges to form a stable base. The sharpness of the edges is therefore an essential quality criterion of the crushing procedure. Furthermore, only suitable material gives the track system the required elasticity and ensures the unrestricted downward flow of rainwater.
At the work site near Berlin, the two Kleemann plants mainly process pre-crushed and screen material. This includes large amounts of crushed rock, which is processed for reuse or is crushed to produce high-grade chippings. The tolerances for the grain sizes in railway ballast production are very tight. An important quality criterion is to observe these values, which is why the cone crusher is fitted with an oversize grain returning system. From the single-deck, post-screening unit of the Mobicone MCO 90i EVO2, the oversize grain can be transported via a return conveyor back to the feed hopper and therefore processed in a closed material loop. The large screening surface with optimised screen utilisation makes effective screening possible even for grain sizes below 20mm.
For separating other grain sizes, a screening plant Mobiscreen MS 953 EVO is positioned downstream of the cone crusher. The classifying screen has large screening surfaces, which guarantee a high throughput even with small final grain sizes. Thanks to the plant design and overall concept, these screening plants are ideal for coupling with the Kleemann crushers.
The complete process is optimised by line coupling of the machines: the interaction of crusher and screening plant is stabilised via an automatic control system. Although both machines work independently of one another, in case of malfunctions or overfilling they send signals to the upstream or downstream machine. The plant train is then switched off quickly and reliably. Among other things, this saves fuel and relieves the burden on personnel: there are no emissions at the upstream or downstream unit and, furthermore, a single person can operate the
deployment. Due to the unique properties of the local basalt and an increase in demand, RF Sand needed a powerful mobile primary crusher that can take on a challenge. To increase throughput and enable the feeding of large quantities of abrasive natural stone at once, they decided to go with a Metso Outotec Lokotrack LT120 mobile jaw crusher.
RF Sand is part of the Reinhard Group which dates back to 1927, when it was founded by the great-grandfather of today's managing directors Marco and Ralf Reinhard.
The basalt extracted from the Balduinstein open-cast mine has an extremely high bulk density, which is why it is suitable, among other things, for applications on the Rhine, Main and Moselle rivers for bank or slope stabilisation. Armourstones from the traditional plant are also supplied as wave breakers to the Dutch coast or to more distant regions.
Due to the unique properties of the local basalt, such as its high abrasion resistance, resilience and acid resistance, and the resulting increase in demand, it was decided
decision was taken in favour of a Metso Outotec LT120, which has been produced almost 1,000 times worldwide and has already proven itself in a wide range of applications.
Ralph Phlippen, MD at authorised Metso Outotec dealer Fischer-Jung Aufbereitungstechnik, commented: "To meet the desire for a significant increase in throughput and to enable the feeding of large quantities of abrasive natural stone at once, our recommendation clearly leaned toward the Lokotrack LT120 mobile jaw crusher.”
Fischer-Jung initially provided the jaw crusher to the open-cast basalt mine for testing purposes for a period of two months. This gave Marco Reinhard and his team, who rely exclusively on mobile processing plants within the site, the opportunity to test the LT120 in interaction with existing units such as the fine crusher and screening plant.
JCB Power Systems has won a contract to supply Stage V IPU engines to leading crushing and screening equipment manufacturer Powerscreen.
The partnership will see bespoke specification JCB 81kW and 97kW Stage V IPU engines power the latest models in Powerscreen’s Warrior and Chieftain screening ranges. Production of the new JCB-powered equipment began in August 2022, with the first models now in the market. This includes the Chieftain 1400, Warrior 1400X and Chieftain 2100X models, which have been flagships of the Powerscreen brand for over 20 years.
JCB Power Systems OEM engines sales and applications manager Jon McNulty said: “To be selected by a market-leading screener manufacturer such as Powerscreen is a fantastic achievement for JCB engines, and it is a testament to the capability and durability of our IPU models that they can excel in the arduous crushing and screening environment. Their proven performance in this type of application is seeing JCB Power Systems gain significant traction in this huge market.” AB
MOBISCREEN MSS 802 EVO
Visit us at: Silver Lot S5020 March 14 – 18, 2023 . Las Vegas www.wirtgen-group.com/conexpo
IMPRESSIVE FROM A TO Z. Thanks to its robust design and extensive range of screen linings, the MSS 802 EVO can easily adapt to changing locations and new operating conditions – making it ideal for a wide variety of applications. The coarse screening plant features an intuitive system control that reduces the risk of operating error. And all relevant functions can be operated from a safe distance for increased work safety. The MOBISCREEN MSS 802 EVO –the heavy-duty, versatile solution in natural stone and recycling.
www.wirtgen-group.com/kleemann
Anext-generation Cat 980BH (Block Handler) is the new star of the show at one of António Galego & Filhos Mármores’s (AGF) two Portuguese Estremoz marble quarries, just two kilometres from each other in Bencatel, around 14km south-west of Vila Viçosa in southern Portugal.
The state-of-the-art machine removes unwanted waste material in combination with two Cat 730C articulated dump trucks (ADTs), spreads waste material for haul-road maintenance, and creates gravel material ‘beds’ to allow primary marble blocks to fall softly after being diamond-wire-saw cut and excavator-nudged away from the quarry face. The Cat 980BH also removes secondary marble blocks up and out of the quarry to the company’s processing plant, where further cutting and polishing work is done. Additionally, the versatile machine is used to lift raw marble blocks from the yard onto on-highway trucks for export to Indian and Chinese customers.
Fitted with a powerful Cat C13 313kW EU Stage V emissions standard engine, the 30-tonne class Cat 980BH can be fitted with a Performance Series bucket to offer improved material retention while reducing dig times. The robust next-generation 980BH is built for premium efficiency and productivity, with its easy-to-use technologies a standard offering.
“We can move a 30-tonne marble block easily with the 980BH as it has got even greater lifting capacity than our 980MBH. Our operators tell me that the 980BH operates smoothly, with all four of its tyres always remaining on the ground,” says Marco Galego, co-general manager of AGF with António Galego, his father and co-founder of the third-generation family-owned business.
Since 1996, AGF has purchased 20 Caterpillar machines, with a Cat 980G
A family-owned Portuguese marble quarry business has a new Cat star of the show, while Doosan, which recently became Develon, believes its eye-catching technology and loading machines can be big assets for quarrying customers.
Guy Woodford reports
wheeled loader and Cat 325B crawler excavator, the first two bought models. As well as the 980BH and 980MBH, AGF has a 980KBH in its current machine fleet.
“We are longtime Caterpillar customers,” continues Marco. “We traded in our Cat 980G in 2009 for the next-generation Cat wheeled loader after it had worked 18,000 hours on the same tyres. We trade all our wheeled loaders in after 18,000 hours, and they are always in great resale condition.
“Our Cat 345D [large hydraulic] crawler excavator, bought in 2009 along with a Cat 330D, was my favourite machine - the best Cat machine ever!” says Marco. “It never had a problem, was very powerful and worked really well.”
When asked to describe Cat machines in a word, António says: “Strong,” adding that the servicing of all AGF’s Cat machines has been very good, helped by a strong relationship he and Marco have built up with Caterpillar’s longstanding Portuguese dealer, STET.
Marco explains that he and his father have used Product Link and VisionLink since 2014 to better assess their Cat machine fleet’s performance, with the pair estimating it has halved the fleet’s running
cost. They use the technology to identify points in the production cycle where they can reduce machine fuel consumption. They also proactively handle fleet maintenance by getting fault-code information sent directly to their smartphones. Fault-code monitoring is an essential part of machinecondition monitoring and repair, significantly increasing fleet uptime.
Marco and António stress that due to increasing energy and fuel prices, Cat Product Link and VisionLink have become even more invaluable to AGF. The father-and-son team is looking into expanding its data and fleet-monitoring capability by investing in a state-of-the-art Cat Productivity solution.
A €9mn-a-year-turnover business, AGF extracts around 150,000t of marble a year across its two Vila Viçosa quarry sites (Tex - where the Cat 980BH is deployed - and MSB), with 30,000t resulting in final product for sale, leaving an 80% waste ratio. Site operating hours are Monday-Friday 8am-5pm and Saturday 9am-1pm. Tex and MSB are running at capacity, with a further increase in production not feasible.
Marco and António decide which marble blocks are selected for final sale,
“Domestic customers are mainly wholesalers who sell to export customers”
Despite a difficult global economic climate, Marco and António say the size of the world’s wealthy marble-block client market is growing, which, along with reduced regional competition, is good for AGF’s long-term future. Marco says that AGF has another 50 years of marble reserves to extract, with the business’s Cat’s 980BH and other Cat loading and hauling machines sure to play a key part in the company’s continued success.
Doosan Infracore, which became Develon on 18th January 2023, has invested significantly in its quarrying-suited medium and heavy excavator and wheeled loader model research and development in recent years. Speaking to Aggregates Business at the bauma exhibition in Munich (24-30 October 2022), Chris Jeong, CEO of formerly Doosan Infracore’s European subsidiary, said: “The last three years have seen us improve our market position across the heavy equipment lines, including medium-to-large excavators where we are now at a 9% market share. We think we can grow further in this area.”
Visitors to bauma 2022 saw the latest developments in Doosan Infracore’s XiteCloud system as the company further expands its business portfolio into the field of construction-site management to complement its existing operations in manufacturing and sales of construction equipment.
with the process drawing on their vast industry experience. “No two marble blocks are the same. The way the veins move throughout the block, their brightness, and the background behind them. All this goes into setting the price for what is a unique product,” explains António.
“We have a lot of repeat business and customer relationships going back a long time,” says Marco, who lists the United Arab Emirates, Saudi Arabia, India, the US, China and North Africa among key export markets for AGF’s premium marble products.
“Domestic customers are mainly wholesalers who sell to export customers. We are getting big orders connected to the Line-Neom project, a new city being built
“Our quarrying and construction customers are very keen on XiteCloud and the big fleet management capability it gives them, and we are keen to give them the best machines to support it.”
Asked how he sees European construction and quarrying equipment customers' expectations differing from what he saw in his extensive experience working in emerging markets, Jeong replied: "Customers in Europe are very diverse and very specific in their requirements. We always look to be well prepared when we launch new products so that we can meet what customers in Germany require, for example, and the differing requirements of, say, those in the UK and so on."
So how does Jeong see the construction and quarrying equipment in a decade’s time?
in [Tabuk Province, northwestern] Saudi Arabia. It will be five times bigger than New York,” stresses Marco in highlighting the US$5trn, 170km-long city megaproject. “India is another big market for us. Its population is growing fast, and even if just a small percentage of the larger population can afford to buy marble blocks, that’s a lot of people.”
While AGF’s trading remains strong, the number of marble quarry sites in the Portuguese Estremoz marble region has reduced from 120 sites down to around 25 following a market consolidation process which began in 2015. Some of the reduction in marble quarry firms is also linked to tightening health and safety regulations.
"I read an article some time ago which said that the construction industry is one of the most conservative industries in the world, but the COVID-19 pandemic brought forward the desire for autonomous machines and technology. Also, to make the [construction or quarry] job site more efficient, connectivity will be key. No single job site has one branded equipment fleet, and customers want full visibility of their job site and its running costs. As not just a manufacturer but also a solution provider, this is something we are very keen on giving to our customers now and in the technology we are working on for the future."
Featuring powerful digging force and strong swing torque, the new fixed-gauge Cat 350 excavator can be equipped with large buckets up to 3.2m³ for claimed classleading productivity. While productive, the 350 consumes up to 13% less fuel than the Cat 349 to lower costs, reduce CO2 emissions, and
operate more sustainably. Three power mode options – Smart, Power, and Eco – match the excavator to the job to further reduce fuel consumption.
“Caterpillar is committed to reducing greenhouse gas emissions while helping our customers meet their climate-related objectives,” said Brian Abbott, Caterpillar’s global product manager for large hydraulic excavators. “The 350 is our latest example of delivering on that commitment.”
The new 350 excavator’s standard Cat 2D Grade system indicates depth and slope on the monitor with alerts to increase operating efficiency. Grade Assist helps the operator to
effortlessly stay on grade with single-lever digging. For truck loading and trenching applications, Swing Assist automatically stops excavator swing at operator-defined set points to consume less fuel. Lift Assist
helps to avoid machine tipping by letting the operator know the load is within safeworking-range limits. To safely work around obstructions, 2D E-Fence prevents the excavator from moving outside operatordefined set points.
Cat Payload onboard weighing gives real-time weight estimates to achieve precise load targets and improve efficiency. When combined with VisionLink, Payload offers remote managing of production targets. Alternatively, the monitor’s USB port allows fleet managers to download up to 30 days of work for progress management without an internet connection or VisionLink subscription.
Available in-cab technology upgrades include Cat Grade with Advanced 2D for creating and editing grade designs via a second high-resolution touchscreen monitor and Cat Grade with 3D to create and edit designs on that second monitor plus the ability to see the front linkage’s full range of motion. All Cat Grade systems are compatible with radios and base stations from top thirdparty technology suppliers.
The Cat C9.3B engine has more than 14 million hours of service to attest to its long-term reliability. Synchronized 1,000hour oil- and fuel-filter service intervals reduce downtime. The hydraulic oil filter offers a 3,000-hour replacement interval – an increase of 50% over the previous design –and provides improved filtration performance.
The 350 can work up to 4,500m above sea level. It features a standard highambient temperature capability of 52˚C (126˚F), cold-start capability at -18˚C (0˚F) with optional cold-start capability at -32C (-25˚F). Automatic hydraulic warm-up in cold temperatures gets the machine to work faster and prolongs the life of machine components. A double-element air intake filter with pre-cleaner features high dust capacity, and the machine’s high-efficiency hydraulic fan offers an optional automatic reverse function to keep cores free from debris.
Product Link collects data automatically and gives fleet managers critical operating information like location, hours, fuel usage, idle time, maintenance alerts, diagnostic codes, and machine health online through web and mobile applications. Maximising machine uptime, remote troubleshoot and remote flash allow dealers to remotely connect with the machine to diagnose fault codes and update operating software. Operators can easily track filter life and maintenance intervals through the touchscreen monitor. AB
The Turin–Lyon high-speed railway is one of the projects providing major opportunities for hauler manufacturers in Europe, involving extensive earth-moving and construction. Liam McLoughlin reports
Having recently marked one year since its rebrand in September 2021, articulated hauler manufacturer Rokbak is looking to expand its operations in key territories including France and Germany.
The Scotland-based, Volvo CE-owned manufacturer says there are major opportunities in the hauling machines sector from major current infrastructure initiatives in Europe.
One of the prominent projects on the radar in Western Europe is the rail connection between France and Italy, a collaboration partly financed by the European Union. The Turin–Lyon high-speed railway is a rail line under construction between the cities of Turin and Lyon. It is intended to link the Italian and French high-speed rail networks and will be 270km (170 miles) long.
with around 200 new employees joining the company in the last year, one of whom is Culliford.
German dealers, Klarmann-Lembach.
One of Rokbak’s French dealers, Framateq, which covers the south east of the country, recently inaugurated a new site in Perpignan. And the Manu Lorraine Group, which covers the north east, held an open day at Walygator Park in Maizières-les-Metz. Culliford also attended the French Mineral Industries Society (SIM) exhibition together with Framateq in October.
The core of the project is its international section, which will cross the Alps through the Mont d’Ambin Base Tunnel between the Susa Valley in Piedmont and Maurienne in Savoie, and at 57.5 kilometres (35.7 miles), it will be the longest rail tunnel in the world. The estimated total cost of the line is €25bn and it will involve extensive earth-moving and construction.
“This is exactly the type of project Rokbak’s RA30 and RA40 are designed for,” says Rokbak regional sales manager EMEA Paul Culliford. “Large infrastructure projects require robust and reliable equipment that delivers high productivity and low total cost of ownership in tough conditions.”
Rokbak has been strengthening its team
“France and Germany are historically strong markets for us,” Culliford explains. “We are seeing an increase in demand and we are currently looking to expand our dealer network in France and Germany to support our customers and strengthen our presence in these important hauler markets.”
Rokbak says the numbers reflect this move. In 2020 there were around 200 units sold – across all brands – within the articulated hauler market in France. In 2021, that increased to in excess of 300 and it looks to be a similar number in 2022. In Germany the numbers were around 150 in 2020 and 2021, heading towards 200 in 2022.
Rokbak already has machines working on French and German job sites. In Germany, an RA30 is working at a gravel pit for earthworks specialist Erdbau Schrader. The machine was sold through one of Rokbak’s
“Rokbak’s articulated haulers are reliable, simple to operate and easy to maintain,” says Mathieu Godard, president of Framateq. “They are fuel-efficient and deliver low total cost of ownership, which is what our customers want. We have a strong articulated hauler market in France and we have recently opened a new site to better support our customers and expand our operations, so it’s great that Rokbak is prioritising our market and sees the same potential as we do for growth.”
Working closely with existing and new dealers and customers is Culliford’s priority. With close to two decades of experience in the articulated hauler industry – including a previous tenure with Rokbak before the company rebranded – and possessing fluency in English, French, German and Spanish, Culliford is able to work with a multitude of targeted territories as the company looks to expand its operations.
“It’s a great opportunity and an exciting time to come back to Rokbak,” he says.
“Since relaunching the brand, we’ve found that there are a lot of dealers and customers interested to learn more about our articulated haulers, and I’m looking forward to working with them.” AB
Despite ongoing issues with costs and supply of components post-COVID, conveying equipment manufacturers report healthy order books for 2023 and are responding to the market challenges with innovative new products. Liam McLoughlin reports
2022 has been another challenging year for manufacturers of conveying equipment, with cost increases coupled with component supply issues have been the biggest issues being the biggest problems.
That is the view of Darragh Cullen, MD of Northern Ireland-based conveyor and materials-handling equipment manufacturer EDGE Innovate, who adds that the challenges brought forward by availability of components have eased but only slightly.
“We have had to constantly adjust our production schedule to meet this everchanging scenario,” says Cullen. “Ultimately, we have surpassed our output goals and targets, but the order in which equipment has been shipped to customers has had to be realigned. Issues at ports have been exacerbated by huge demand and strike action, which has placed further stress on delivery times.”
invested heavily in product development and innovation. 2023 will see the launch of more new world-class, innovative products.
“Our order book has never been as healthy. We continue to challenge everything we do to improve efficiencies, machines design and customer support.”
He says that the good news is that the challenges brought forward by COVID seem to be over, and life has more or less returned to normal: “The size and quality of our team have increased, and we have again
Cullen says EDGE Innovate is looking to 2023 with excitement and determination.
“We are building relationships with new partners and new markets but are more than thankful for the long-standing relationships and partnerships that we already have,” he adds.
Northern Ireland-based dry bulk materials-handling solutions manufacturer says that the needs of its customers have led to improvements across its quarrying operations. One example of this is the introduction of the ‘Self-Driving’ smart stockpiling solution found on Telestack’s radial telescopic conveying range. By deploying technology and experience, this advanced autonomous stockpiling solution aims to maximise returns within any operation, ensuring operational efficiency, improved site safety, reduced operational overheads and complexity, as well as a quality in-spec 'blended' product.
The Telestack radial
telescopic conveyor range has a proven record of performance and reliability operating in a range of aggregates applications around the globe. The mobility options of the unit allow the operator to utilise this technology anywhere on site, ensuring a high production capacity and a 30% greater stockpile capacity on the same footprint when compared to fixed length/ height conveyors. The smart system, once set up, can be operated locally by an operator or operated remotely using the smart onboard PLC (programmable logical controller) to feed information back to the remote central control station. Once the unit’s physical constraints are established, the unit can work independently using the pre-programmed parameters determined in the set-up.
The smart stockpiling system starts at a low working angle, such as 8°, maintaining its lowest workable drop height throughout the operation as the stockpile increases in increments. This is in comparison to a fixed length unit, for example, that would start at an 18° angle, thus wasting more energy to discharge the product at a greater height. In addition, this also results in a greater potential to compromise the
quality of the product due to fracture and degradation of the product caused by material dropping from the elevated operating height. The reduced power usage required for the radial telescopic conveyor ensures less energy/fuel is used in the daily operation, and fuel consumption can be further enhanced with the introduction of an optional VSD (variable speed drive) by allowing the operator (remotely or locally) to increase or decrease the speed accordingly, depending on the needs of the operation.
Telestack says that the continuous autonomous stockpiling ensures that the blend of the product is maintained throughout the stockpile and a higher quality product is achievable, ensuring the product is evenly mixed over a wide area. This helps to eliminate segregation, degradation, contamination and compaction, providing not only a higher-grade product for a lower stockpiling cost per tonne but also reduced labour dependency and reduced labour costs as well as the environmental impact of reduced traffic, dust and noise. The smart system also hosts a range of automatic sensors that guide the independent unit as determined in the set-up. These sensors, as well as safeguarding the drop height of the product, also ensure that the unit will pause when the material has stopped flowing. This ensures the integrity of the continuous stockpile structure, producing an “in-spec” blended product. This would be a significant factor for many in the aggregates sector, for example, where product integrity is critical.
The Telestack range of radial telescopic stackers is available in lengths of 32m (110ft), 42m (140ft), 46m (150ft), 52m (170ft) and 58m (190ft) with possible stockpile capacities up to 200,000 tonnes at 270°. Stockpiling rates range from 100-3,000tph, and stockpile heights up to 20m (65ft) are easily achieved.
In addition, the option of several PLC automatic stockpiling programmes provides the operator with a versatile, economic and reliable stockpiling system that offers the ability for a radial window, incline window and radial
conical stockpile formations, which, in all, offer a larger stockpiling potential and a radial stockpiling potential of up to 270° for maximum stockpiling. The smart stockpiling system controls the operation of the unit and gathers information, and sends it back to the central control station/ remote location. This helps to troubleshoot when issues arise, giving the controller operational information and specific status updates. In addition, the optional Telestack telematic system Telecore, offers remote monitoring and support from the factory to enhance performance. This has proven critical not only in the operational performance but also relating to the general maintenance of the unit. Particularly when labour was restricted, for example, during the recent COVID restrictions, the support from the factory was vital in supporting operations through challenging times.
The Telestack team will be in attendance at the forthcoming CONEXPO-CON/AGG 2023 in Vegas (14-18 March) on the Astec Industries Stand in Central Hall (Booth #C30235).
Mike Schroeder, technical consultant with ContiTech conveying solutions at US specialty belting manufacturer WCCO Belting, is sharing his two decades of experience at the company to set out the factors to consider when selecting a cleated conveyor belt and how a strategic approach to belt design can have drastic impacts to output and uptime.
Schroeder says the height of the cleat will be determined by the conveying angle and the size of the material being conveyed. Typically, conveying angles higher than 15° would benefit from a 0.50” (12.7mm)-tall cleat pattern (or more) to prevent spillback. Spillback creates unnecessary abrasion to the top cover of the belt in addition to decreasing capacity.
A cleat’s profile needs to have an adequate radius and chamfer features to prevent cleat cracking and tearing from the belt carcass. Most profiles will be drafted from the base to the top of the profile to help release it from the moulds post-vulcanisation. Fabricated cleated belts made via skiving and glueing have a higher tendency to delaminate and
Telestack’s smart stockpiling system with onboard sensors negates the need for human intervention
fail compared to single-step vulcanized manufacturing. Cleat ends, in most cases, are angled to prevent stress build-up around rollers and pulleys that can also lead to cleat failure, reduced capacity, and downtime.
“Aggregate material has an abrasive texture. However, almost all industry ‘V’ or ‘U’ cleat profiles are encouraging material movement directing it to the centre of the belt,” says Schroeder. “This results in unnecessary wear and tear on the belt cover, such as high wear points, plus stress on the cleats. Spillage is one symptom of the cleat’s inability to capture and hold product effectively.”
He adds that the angle of the cleat in relation to the drive and tail pulleys is critical. Too little angle (parallel to the roller) and cleat chatter develops from a lack of continuous contact between the rollers and cleat profile, bringing excessive vibration, noise, and eventually, cleat failure. If the cleat angle to the rollers is too large (perpendicular to the roller), cleat cracking can ensue, followed by cleat tear and separation from the belt carcass. Furthermore, cleat height in conjunction with angle will determine the minimum pulley diameter the belt requires to operate. Taller cleats with large angles to the rollers will experience higher bending stress and are at greater risk of cracking and tearing.
The individual cleats will be laid out across the width of the belt. Cleat frequency refers to the repeated pattern down the length of the belt. The frequency by which the cleats repeat is critical in creating a fully nested pattern. A nested cleat pattern allows for a smooth transition over rollers and pulleys, thereby reducing premature cleat wear and belt failure.
In terms of other considerations, Schroeder says the belt construction itself with the cleat pattern must be able to trough appropriately given application requirements.
The flexibility prevents mis-tracking, premature wear, and belt failure. In troughed systems, the belt must be able to make correct contact with the guide rollers when operating under load or empty.
“Cleat profile design is tied to the conveyor system’s discharge,” he adds. “If the discharge stream needs to be small or targeted, the pattern can support material movement to the centre of the belt. Another consideration is if moisture build-up would prevent the success of the operation. An open-type pattern can allow for drainage through the cleat pattern.”
In summary, Schroeder says the ideal cleated conveyor belt will have the cleat height needed based on the material size and conveying angle. The cleat profile should be designed with optimum features to ensure the longevity and performance of the cleats, which impacts operational capacity and uptime. The cleat pattern should be nested and make continuous contact with return rollers to allow the system to operate with limited noise and vibration for a smooth operation. The more continuous contact points on the return rollers, the better the belt and the system will operate.
“If price remains the decision-driver to purchase a conveyor belt and belt design isn’t approached as a strategy, equipment owners and operators will continue to leave a lot on the table,” says Schroeder. “Working with a belting expert on your unique operating requirements can help you learn how your cleated belt is working for you and, more importantly, how it’s not.”
Martin Engineering is highlighting the importance of proper conveyor cleaner blade tensioning, the types of tensioners, and some of the best uses for each. The US bulk materials-handling company says that there are many issues to consider when specifying the most appropriate conveyor belt cleaner, not the least of which is maintaining proper tension to achieve optimum cleaning
performance without introducing related problems. Inadequate tensioning causes carryback to cling to the belt and spill along its path, piling up under the conveyor and emitting excessive dust. This requires extra labour for clean-up and can affect air quality. Over-tensioning leads to friction damage to the carrying side of the belt, premature blade wear and potential splice damage. Both scenarios contribute to unsafe work conditions and raise the cost of operation.
“There are two basic approaches to applying tension to the belt cleaner: linear and rotary,” said Dave Mueller, product manager, Martin Engineering. “The blade’s cleaning position and angle of approach to the belt often dictate whether a linear or rotary tensioner is used.”
The Conveyor Equipment Manufacturers Association (CEMA) defines the cleaning positions as primary, secondary, or tertiary. Primary cleaners typically function with a “peeling” action, while secondary and tertiary cleaners are usually scrapers. Belt cleaners mounted in the primary position generally employ a rotary style tensioner, while most units mounted in the secondary or tertiary positions use linear style tensioners.
In most cases, belt tensioners have to be monitored and adjusted manually so they can maintain optimum pressure and carryback removal. Estimating when blades need changing is often a guessing game that, if left too long, could lead to unnecessary complications.
“Linear tensioners are most often applied where the compensation for wear is required in small increments, such as with hard metaltipped cleaners located in the secondary cleaning position or with brush cleaners,” Mueller said.
The simple design of linear tensioners often allows just one setting for full blade wear. Further, these tensioners can accommodate actuator deflection for accurate adjustment of cleaning pressure, delivering the ability to accommodate uneven mounting positions or asymmetrical blade wear.
Smart stockpiling system with onboard sensors negating the need for human intervention
BENEFITS
•Information feedback to control station to help monitor operation
•30% more stockpile capacity on the same footprint when compared to fixed length conveyors
•Maintains its lowest possible drop height ensuring less energy use and less product fracture
•Eliminates segregation, degradation, contamination and compaction of product
•Continuous autonomous stockpiling ensures that the blend of the product is maintained throughout the stockpile
•Wide range of dust containment and suppression options available
www.telestack.com sales@telestack.com
The required tensioning forces can be applied by springs, hydraulic or pneumatic cylinders, electric actuators or from torque stored in an elastomeric element. Rotary tensioners like the Martin Twist Tensioner are often used with urethane blades, where the change in blade height and thickness as it wears is significant. Rotary designs tend to be compact and, in most cases, the actuator(s) can be mounted at any orientation, which provides options for installing the belt cleaner in the optimum position.
Air tensioners use the resilience of a pneumatic cylinder to cushion impact. The tensioners can use Martin’s Air Connection Kit to plug them directly into an existing air system, allowing for a more streamlined installation process.
Spring tensioners maintain efficient belt cleaning with a rugged coil spring. The Martin XHD Spring Tensioners deliver effective cleaning while cushioning splice shock to prevent damage, well suited for tensioning heavy duty belt cleaners while standing up to tough conditions. Dual tensioning is recommended for belt cleaners installed on belts wider than 1,200mm.
TYRES – PART 1
However, dual tensioning does not change the fact that regular adjustment is required to maintain suitable cleaning pressure on the belt, which is where Martin’s N2® Smart Technology comes into play.
Martin Engineering’s smart technology platform includes the company’s patented N2
Position Indicator to monitor primary cleaner blade wear and inform operators when the blade needs changing. The system uses a cellular gateway that relays data to the cloud and then to the user, delivering actionable information in real-time.
The N2 PI and Smart Device Manager App are designed to ease the burden on managers and workers so they can focus their attention on other critical details of the operation. Precise tensioning and improved belt cleaning reduce the volume of dust and spillage from carryback, improving workplace conditions and decreasing the labour needed to maintain and clean around the discharge zone.
While manufacturers continue to improve belt cleaner effectiveness, it has become clear that there is no single or ideal solution for belt cleaning and tensioner selection. The safety of personnel and the belt itself is the primary consideration when selecting a tensioner. Ease of inspection and maintenance is critical for belt cleaner effectiveness, so the tensioner must allow quick and safe service. Martin Engineering offers the services and tensioning products that are necessary to meet the multifaceted demands of belt cleaning. AB
Two of the world’s leading off-the-road (OTR) tyre manufacturers are highlighting the benefits of two products from their latest quarrying-suited ranges. Guy Woodford reports
Premium OTR tyres from BKT (Balkrishna Industries Limited) are proving their worth on rigid dump trucks (RDTs) operating at a quarry in northwest Spain.
Cufica, a Spanish company founded in 1980 in Valdeorras, Galicia, which also has a notable presence in Bierzo, Castilla y León, specialises in the extraction and sale of slate, a waterresistant stone commonly used in the roofs of buildings.
An employer of around 100 people, Cufica sells much of its premium slate products to customers in France and the UK.
Juan Antonio Illescas Mateo, the Spanish company’s financial director, says Cufica relies on a large equipment fleet to extract, load and transport slate from the company’s quarry to its processing factory. To improve their efficiency, he decided to equip the site’s five RDTs with BKT Earthmax SR 45 M tyres sized 24.00 R 35.
“In such difficult operating conditions, the required main features of a tyre are robustness, grip and traction, and of course, resistance and a long tyre lifecycle,” says Fernando Buelta Gonzalez, foreman of Cufica’s mineral operations. “At our quarry,
No matter how challenging your needs, EARTHMAX SR 41 is your best ally when it comes to operations that require extraordinary traction. Thanks to its All Steel radial structure and the special block pattern, EARTHMAX SR 41 provides excellent resistance against punctures and an extended service life. In addition to long working hours without downtime, the tyre ensures extraordinary comfort.
EARTHMAX SR 41 is BKT’s response to withstand the toughest operating conditions in haulage, loading and dozing applications.
there are paths with a 10% slope. So, above all, in adverse climatic weather conditions such as rain and snow, excellent traction and grip are required. Cufica’s experience with BKT tyres is extraordinary since they fully correspond to our needs, and our operators can work safely.”
The Earthmax SR 45 M is an all-steel radial tyre available in three different compound types: normal, heatresistant, and cut-resistant. Thanks to its distinctive feature, an E-4-deep tread, the tyre is able to withstand cuts and punctures. BKT says this means it is able to deal with operating sites like extraction quarries with very demanding usage conditions. It adds that excellent traction and great resistance for transport conditions on long hauls are guaranteed for all available versions.
“The LD-Master L5 Traction also gives high productivity and ensures vehicle uptime,” he noted.
Headquartered in Mumbai, India, BKT says that one of its priorities is catering for varied user needs by developing increasingly effective and specific products for different operating conditions. "This is exactly why BKT considers important the direct testimonials of those who actually use their tyres on a daily basis, like Cufica," a company spokesperson said.
Continental is another OTR tyre maker with a major global quarrying and construction sector presence. Speaking during the German company’s bauma
Initially offered in size 35/65 R33, the LD-Master L5 Traction radial tyre expands the ContiEarth range and is fitted with integrated tyre sensors. “This enhanced intelligence allows us to monitor tyre air pressure and temperature in real time. With this, we can ensure the most efficient operation,” said Thomale, Continental’s head of speciality tyres. He continued: “Digitalisation of all our radial tyres is an essential element for their operation today and into our future. It also supports sustainability in our customer operations.
“If tyre pressure is optimised, it can save 15 minutes of [daily rigid haul truck eet] vehicle inspection time which can add up to almost 200 hours a year. It also saves about 1% fuel in an [rigid haul truck fleet] operation and can add 15% to the life of a tyre compared to the same tyre underinflated by 10%. This adds up to a significant improvement in operation.”
Munich (24-30 October 2022) exhibition press conference, Wolfgang Thomale said Continental’s new LD-Master L5 Traction radial tyre offers durability and high traction in very big vehicle-carrying load environments such as quarries, which often encounter severe working conditions.
Thomale said the sensors fitted to Continental’s off-the-road radial tyres feed information to the company’s ContiConnect tyre-management system. As showcased at bauma 2022, Version 2.0 of the system is said to put in place the necessary infrastructure for the all-encompassing digital tyre management of the future. “By using big data and digital solutions, we enable fleet managers to avoid vehicle downtime, ensure serviceability and maximise [tyre] productivity,” Thomale concluded. AB
The LD-Master L5 Traction offers durability and high traction in heavyvehicle-carrying load environments
Screening buckets can offer huge productivity and efficiency gains for quarry operators. Guy Woodford looks at the latest products and on-site success stories from some of the major global market suppliers
Finnish premium hydraulic screener crusher and crusher bucket attachment manufacturer ALLU is targeting big growth in the US and China as it looks to step up its already impressive trading in the global construction, quarrying, mining, and recycling sectors. Last year, ALLU opened its new Chinese manufacturing and operating facility in Kunshan, near Shanghai in eastern China, giving the company a firm platform to grow its commercial offer in the world’s biggest off-highway equipment and building materials market.
ALLU’s big trading push in the US is being made from its base in New Brunswick, New Jersey state. The company will have a strong presence at CONEXPO/CON-AGG 2023 in Las Vegas (14-18 March), including launching a new screener bucket well suited to quarrying applications.
A busy 2023 exhibition showcase schedule will also see ALLU making its steinexpo debut during the 11th staging of the major construction materials industry exhibition in Homberg/Nieder-Ofleiden, Germany (23-26 August). The company will also showcase its product range at SIM 2023 in Bordeaux, France (4-6 October).
Offering a diverse range of hydraulic screener crusher and crusher bucket attachments for 1-200-tonne excavators, ALLU has long been renowned among quarrying, mining, construction and recycling customers for its Transformer hydraulic screener crusher bucket attachment range. This includes the now fourth-generation Transformer D Series, well suited to small- to medium-sized quarrying, construction and recycling applications, and the Transformer M Series for 50+ tonne excavators, popular
among large quarry and mining customers. At its new Kunshan facility, ALLU recently started production of Transformer DC Series hydraulic screener crusher bucket attachments for Chinese customers. Meanwhile, ALLU’s crusher hydraulic bucket attachment, suited to various applications in industries including quarrying and construction, also continues to sell well.
After a November 2022 tour of ALLU’s state-of-the-art product assembly and testing centre at the company’s HQ site near Lahti, led by factory manager Tero Saarikangas and head of ALLU projects, Frederick Dromberg, Aggregates Business heard how
ALLU is investing heavily in a 2022-launched global dealer management programme. The programme is being significantly ramped up in 2023 as a key part of the company’s global growth plan.
Jeroen Hinnen, ALLU’s global vice president of sales since January 2018, says that while ALLU sees its biggest sales growth coming from the US and China, Europe remains a vital market for the company, accounting for over half of its sales (including 5% direct sales to Finnish customers). The US currently represents around 20% of ALLU sales, with China and the rest of the world generating the remaining 20%.
ALLU has dealer sales teams in Finland, Sweden, France, Germany, China, the US, Indonesia, and Australia, who all report to Hinnen. While he notes that 80% of ALLU’s Germany sales in 2022 were secured by major national equipment dealerships, Hinnen says dealers generally account for two-thirds of ALLU’s annual product sales. He stresses that ALLU tends to directly supply key account customers.
Stepping up ALLU’s global dealer management programme this year will, says Hinnen, lead to an even better understanding of frontline customer and dealer needs, further increase sales, and, effectively, “shut the door to the competition” in their attempts to partner with the best dealers.
“Every geographical area has its high runners on sales, so we need to be able to adapt to that,” explains Hinnen. “In Germany, we sell many more of our mediumsized bucket attachments. In the US, it was mainly large, and now it’s also more small and medium buckets because of the change in the project pipeline business. The Transformer DC Series buckets for China are Transformer D Series models adapted to the Chinese market. They have been very well received. We have hired two new China salespeople to further cover the vast part of the country. Understanding the differentiation in the various geographical locations in a market is key. Our Kunshan facility handles final bucket attachment assembly as we do in Finland, with the buckets for Chinese customers all manufactured in China.”
Hinnen says ALLU has seen big growth over the last two to three years in its sales linked to material-recycling applications, with material-recycling-based business expected to grow “much more” in the coming years. ALLU remains a family-run company whose owners are, says Hinnen, very sustainabilityminded. ALLU’s building management system is regularly updated to accommodate new green goals, and the bulk of the firm’s product-linked suppliers are also within near range of the company’s HQ, lowering ALLU’s production carbon footprint.
Focusing on ALLU’s approach to product research and development, Hinnen says: “We have a strategy that says we need to come up with new features or new products every year. It has been like that for years and is part of our ethos of being ‘One Step Ahead’. We achieved that in 2022 and will do it again in 2023.”
Before Aggregates Business left ALLU, we spoke to Ilpo Ellonen, the company’s longtime Finland area sales manager, to get the lowdown on home-market trends. Ellonen says ALLU has seen growth in its Finnish rental market business, with screener crusher and crusher buckets suiting 20-30tonne excavators proving the most popular among customers involved in quarrying and gravel screening work, domestically.
“We have sold more than 1,500 buckets to Finnish customers since the company started [in 1985],” says Ellonen. “We have many old and new customers, and our products are used in many big roadbuilding and maintenance works in Finland. The unit rental market here is also increasing rapidly.”
At the bauma exhibition in Munich, Germany (24-30 October 2022), MB Crusher launched its new mid-sized MB-HDS220 shafts screener shovel bucket.
The Italy-based manufacturer says the bucket is suitable for loaders and excavators for groundworks and agricultural applications.
Alessia Valerio, responsible for product growth & content at MB Crusher, said that the MB-HDS220 fills a gap in its MB-HDS shafts screener range, bringing the product line-up to six sizes.
The MB-HDS523 bucket, the biggest in the range, is suitable for quarrying applications.
Valerio said the company is seeing much demand for its smaller buckets in Italy and the rest of Europe, while many customers in Asia and the US are moving towards the larger models.
In Mallorca, Spain, Trans Pep Soler (TPS) has invested in MB Crusher’s MB-LS170 screening bucket to work with the company’s eight-tonne Komatsu WB 97 S5 backhoe loader. The screening bucket allows TPS to recover clean sandstone from cement and demolition debris rather than spending money taking the mixed material to a recycling plant. The MB Crusher bucketscreened sandstone is used for a variety of construction tasks.
At Monrupino quarry in Trieste, northeast Italy, Marmi Repen is said to have achieved great results with a Simex VSE 20 screening
bucket mounted on a CAT M314 wheeled excavator.
The customer needed to screen quarry waste material at different particle sizes for subsequent reuse and resale as stabilised aggregate, useful in the building and construction sector and for road bases. The material to be screened derives from the processing of marble, specifically from the cutting and extraction of the blocks. Given the composition of the material, with the presence of gravel and mixed rock, it was decided to equip the bucket with mixed tools (with lateral blades), which are well suited both for the selection of humid soils and for screening stony materials, as they also guarantee a light crushing during the screening process.
Simex’s patented FIT tool system, which is modular and customisable, allows multiple configurations depending on the materials to be screened. Tools are easily and quickly replaceable, thanks to interlocking elements with no welding, which means saving up to 75% in maintenance costs compared to its predecessor. All models in the VSE range (with the exception of VSE 2) benefit from the FIT screening tools, which allow the operator to get the best bucket configuration for the intended use and the material to be screened.
The customer, who was supplied with the Simex solution by Udine-based off-highway equipment dealer Edilmeccanica, is delighted with the instant adjustment of the output
size and added value of its Simex VSE screening bucket. All Simex VSE products allow customers to obtain different particle sizes in a few seconds via a simple control activated from the cab. The rapid variation system guarantees speed of execution,
versatility (being able to work on different materials) and a considerable saving of time. In fact, Simex says there is no downtime due to the spacing operations of the shafts for the particle size change, as happens in traditional technologies. AB
Thomas Beton, Lürschau, Germany’s Ammann Elba
With careful planning, Thomas Beton's concrete plant, based in Lurshchau, Germany, was successfully modernised during ongoing operations. An Ammann Elba CBS 120 SB concrete mixing plant was connected to an on-site aggregate linear bin as the new heart of the plant.
When the first 300m³ of concrete was mixed during the commissioning of the new plant, Rainer Brings, managing director of Thomas Beton, was impressed by the speed of the plant. With the acquisition, he can significantly increase his hourly output compared to that of the old one - up to 120m³/h is now possible.
This increase in output was urgently needed as demand for fresh concrete had
increased significantly due to the need for large foundations for regional wind power plants and a nearby precast plant. The old plant had reached the limits of its capacity.
Two challenges had to be mastered during this modernisation. On the one hand, the existing dosing construction had to be technically integrated into the new construction across the height difference of an escarpment. On the other hand, the plant had to continue production during the modification in order to be able to serve the current orders.
After the stock had been checked, it was determined in detail which components could be replaced and which could continue to be used. “We now operate 12 Ammann Elba ready-mixed concrete plants of this type in our factories in northern Germany,” says Brings. “When planning the new plant
together with Ammann Elba, we were able to make perfect use of the flexibility of the assemblies.”
The modernisation of the site during ongoing operations took only eight weeks. While the old mixing tower continued to do its job, the new ready-mixed concrete mixing plant CBS 120 SB with single-shaft mixer CEM 2660 S was connected to the existing aggregate linear bin as a belt conveyor plant.
The complete locking and dosing technology of the on-site linear bin itself was renewed. A technical masterpiece was the threading of the new 35-metre-long weighing belt into the concrete linear bin. This challenge was successfully solved thanks to the many years of experience of the Ammann Elba dealer Proschwitz GmbH, Trittau, which was also responsible for the overall assembly.
The discharge gates are actuated via
compressed air by an integrated screw compressor. The weighed aggregates are finally conveyed directly into the pre-hopper of the mixing plant via a conveyor belt. A sand-moisture measuring device below the dosing gate continuously measures the material moisture.
The cement is stored in six cement silos, each with a capacity of 100 tonnes. Highperformance cement screws EZL 80/100 are used for dosing in the generously dimensioned cement weigher.
Brings says he is “completely satisfied” with the result and impressed with the uniformity, stability and high quality of the concrete produced by the Ammann plant. A dedusting filter and a mixer cleaning system are integrated into the CBS 120 SB, preventing contamination. The winter cladding LL 60, which encases the entire mixing plant, also protects against temperature fluctuations caused by the weather.
“From planning to transport and installation, Ammann Elba demonstrated a high level of detailed work,” says Brings. “And since our team knows the Ammann Elba plants very well, we were also able to continue production seamlessly.”
Sakthi Ramamoorthy, CEO of Lintec & Linnhoff Concrete, knows more than most about the concrete industry, having dedicated decades of his career to it. He says spotting the potential for high-quality manufacturing in Asia and harnessing the benefits of automation have helped establish the Eurotec concrete batching plant brand in the global market.
Commenting in a company Q&A session on the most interesting change he’s observed in the industry over his time in the business, Ramamoorthy says: “When I joined the industry back in 1992, automation was just starting. Before that, all the modules had a lever attached to them, and only by moving the lever would you be able to dispense the concrete, but we have come a long way since then. Most plants now are completely
automated and increasingly focused on more sustainable operations.”
Ramamoorthy says that Lintec & Linnhoff Concrete recognised these trends early, enabling the company to create product lines that appeal to customers. He adds: “Also, our Lintec containerised designs have been a real advancement for the industry. Ever since the early designs, it’s been something popular with clients. The new plants are sleek, powerful, and eco-friendly.”
Responding to a question about the success of the Eurotec brand and its future development, Ramamoorthy says: “The cost of importing plants to Asia from Europe has always been high. There was a gap in the market for high-quality plants that could be sourced at economical prices. That’s when we launched the Eurotec brand to fill that gap. Keeping the European design, we manufactured the plants in Asia and achieved high-level cost efficiencies without compromising quality. We launched Eurotec in 2003 and have sold over 400 plants across
“The new plants are sleek, powerful, and eco-friendly”
Sakthi Ramamoorthy, Lintec & Linnhoff Concrete CEO
Southeast Asia, South Asia, the Middle East and Africa.
“I believe we’ll see some interesting innovations in the sector over the next five years. Large concrete batching plants will only be seen on megaprojects, requiring high-level concrete production at the job site. For other applications, we’ll see plants become increasingly mobile and shift to fully electric-powered. This will help the industry boost its sustainability and efficiency. We’re excited to share further details on these trends with our customers in future.”
An ELKOMIX-60 PL precast concrete batching plant and an ELKON ERCYL-10 concrete-recycling plant are providing vital support to a leading Croatian building materials company. The plants are being put to work on ready-mixed, precast and semi-dry concrete production in Drjne, in Croatia’s Koprivnica region. The customer has more than 1,700 employees and is renowned for its quality cement, concrete, aggregates, and bricks.
The ELKOMIX-60 PL plant has an ELKON 1500/1000 1 planetary mixer equipped with a moisture probe to precisely control water content. The set-up also includes 6x20m³ aggregate storage bins made from galvanised steel which are partially buried underground so that aggregate loading can be done without ramps. AB
Sustainability is a huge topic across the construction and quarrying industry – not just in terms of what can be achieved tomorrow via carbon-free hydrogen fuel cells and hydrogen internal combustion engines of machine fleets, but today, through the use of smart technology to make jobsites more efficient and sustainable by getting work done right first time, every time
World Highways and Aggregates Business spoke with a trio of experts from leading construction and quarrying equipment and linked technology sector manufacturers to hear their takes on helping to address customers’ current and future sustainability needs.
Jeremy is responsible for segment strategy development & execution, digital connectivity leadership for construction, global OEM collaborations, and planning for the future. He describes himself as: “A dedicated off-highway professional who has been at Cummins 14 years, holding various positions in the Off-Highway business." His Cummins career path started in new product service engineering for Tier4 Interim followed by leading the customer care function for Tier4 Final.
Henrik is based at Eskilstuna in Sweden. He describes his role as: “Driving Volvo CE’s powertrain development regarding transmission, axles and electromobility.” In the last 25 years he has held different positions with the Volvo CE Technology and research and development departments. Previously he worked with a deeper focus on engines as the group’s director for Engines & Auxiliaries.
Dietmar is responsible for driving Trimble’s approach to strategic management and Key One Trimble initiatives. Dietmar says that this role “includes commercialising sustainability and carbon through the efficiency and productivity gains delivered by Trimble products across natural resources, construction, transportation and logistics, and related sectors.” Prior to Trimble, Dietmar worked at The Nature Conservancy organisation, responsible for creating distinct, country-specific conservation strategies and regional systems change approaches around the world.
J
eremy Harsin, Cummins global construction market director; Henrik Amann, Volvo Construction Equipment (Volvo CE) head of driveline and electromobility; and Dietmar Grimm, Trimble vice president of corporate strategy and sustainability solutions, agreed with Round table chair Nadira Tudor’s outlining of the classic definition of sustainability as ‘fulfilling the needs of current generations without compromising the needs of future generations’. They also endorsed the need for collaboration between global construction and quarrying original equipment manufacturers (OEMs) to give customers the best chance to fulfil their long-term sustainability goals.
“It’s about how you get there. You have to somehow protect that future but also account for current needs. There’s a [financial] cost to be green and technology limitations that exist today. That has to be balanced as we think things through,” said Harsin, adding: “There are things we can do today from a practical perspective that are pretty easy. A lot of equipment is in the field for 10, 20, maybe 30 years, and the machines that have been released in the last few years are a lot more efficient and more environmentally friendly. There are other things like HVO (hydrotreated vegetable oil) and other alternative fuels that are coming around that are drop-ins and could be done easily today where they’re available.
“There are definitely some scalability challenges. One of the things I’ve been pushing for a while is idle [machine] management. There’s a lot of untapped potential there. We did a random test on a wheeled loader that we fitted with a makeshift stop-start system. Just through its normal day-today operation, we found it was running idle 30-45% of the time. If you work out the wasted fuel and unnecessary emissions, they [its owner] could have gained 15-20% fuel economy by turning the engine off.”
Harsin said that from a Cummins perspective, the US off-highway machine engine giant’s role is converting energy into power and having a portfolio of
solutions. “There are going to be different customers and applications where different things make sense, so we need to make sure we have that portfolio available at the right time and help customers along their [sustainability] journey. Some of our customers are in the slice of the market where they are ready for something new today; others are thinking through what they need to do and are looking for a thought partner.”
Speaking about Volvo Construction Equipment’s approach to sustainability, Amann said: “Our overall purpose is ‘Building the world we want to live in’ – which I think is a great purpose. I think it makes people go to work not only for their salary.”
Grimm added: “Sustainability is indistinct from Trimble as a company. For us, we want to drive productivity and efficiency gains that we want to see in society. As a technology company, we have the opportunity to focus on what Jeremy and Henrik were talking about, like driving productivity and efficiency today and finding innovations to do that even more in the future.
“If you look at how society has evolved in the last few hundred years, it has been through technological innovation. We are just past eight billion people on our planet, and technology has really driven that. What we want to help drive through productivity and efficiency gains is better business and improved profitability that drives a strong economy that helps provide the resources for a successful society with high well-being, improved wealth, health and education. That ties into how we can use those resources efficiently to ensure better biodiversity and improved ecosystems.”
Asked how Volvo CE can play an even more active role in industry sustainability, Amann replied: “We have tried to do our best in this area for many, many years. We have had environmental protection as a core value for 50 years. We have signed up for the Science Based Targets initiative (SBTi) and see the value of having a good [environmental] plan for the future.”
Addressing much in resources Cummins is putting into its sustainability initiatives, Harsin said: “I don’t have a dollar amount, but my generic answer would be a lot. We continue to invest more and more in advanced diesel solutions. We expect there will be more legislative hurdles to overcome in the next five to eight years, depending on which market you’re talking about. There has been quite a lot of media coverage of our fuel-agnostic
OUR OVERALL PURPOSE IS ‘BUILDING THE WORLD WE WANT TO LIVE IN'
IT IS ABOUT TRUST AND WORKING TOGETHER WITH CUSTOMERS AND PARTNERS
strategy as we move towards being greener in an affordable way. One of the big challenges is scalability and how you find scale on some components when the market is only ready to adopt in niches. We think fuel-agnostic [off-highway engines] is a really good bridge product and maybe even a long-term one.”
Harsin said Cummins had invested a lot of money in recent years in acquisitions of companies offering different technologies. “We acquired a battery company, and a year or two later, we acquired a company specialising in electric drivelines. After that, we invested in a hydrogen technology company to get hydrogen fuel cells and hydrogen electrolysers, Most recently, we entered a joint venture with NPROXX, which makes hydrogen storage tanks. We’re making investments to cater for what we think is going to be the long-term future for our industries. The good thing is that most of these solutions are complimentary so that you can share components.”
Highlighting Trimble’s sustainability-based resource allocation, Grimm said: “if you look at how we were founded, sustainability has always been at our core. Our technologies have always been driving productivity and efficiency gains. What’s interesting is that in our sectors, people have often said that they had not recognised that as ‘sustainability’. They see it, say, as just wanting a way to reduce fuel use rather than being what it is, which is a core part of sustainability. As such, much of our investment in improving sustainability is linked to reinforcing our continued product portfolio.”
Grimm said Trimble’s Connect and Scale approach ties in with Harsin’s comments on there not being one solution or specific idea to improve sustainability and that everyone needed to be “all in” on this. He continued: “I think market forces will drive this, and so we want to make sure everyone is thinking about how to drive carbon emissions down. Through our Connect and Scale approach, we are trying to connect the entire construction industry to drive the productivity and efficiency gains from an individual work site to how the whole industry works together.
“Construction [sustainability] overall starts with design. You work with architects to make sure you’re designing things with lower embodied carbon and lower long-term operational carbon. The second piece is having site management optimised, so you’re reducing the amount of emissions from the site and the amount of site rework and waste. Lastly, you need construction fleet operators to push machine manufacturers to ensure we’re making machines that reduce embodied and operational carbon. Fleet operators can also manage their assets longer term by scheduling maintenance and repairs and thinking about replacement rates. The longer you manage an asset, the lower long-term carbon emissions you have.”
Grimm said Trimble had been working with construction companies, including Ecovie in Italy, that has been using a Wirtgen cold recycling system to reuse asphalt in road reconstruction works. He also cited how Cummins and other leading global off-highway engine makers had done a great long-term job of increasing power production with lower fuel use, thus boosting sustainability. “We do that, too, with our technology. It’s in our DNA. What we need to do is to work better collaboratively to drive sustainability as a whole industry.”
Asked whether OEMs were actually working together to find construction and quarrying industry-wide sustainabilityenhancing solutions, Grimm replied: “I think we are. I’ve met with several of Jeremy’s and Henrik’s colleagues at meetings of industry associations, and we’ve all found that the sectors we work in all want to talk about sustainability and work together more to understand the solutions, including helping to drive [governmental and industry] policies that can deliver a more sustainable future. I think we have to get much better as an industry in measuring our carbon emissions and sharing that information. Once you can measure something, you can manage and start to reduce it.”
On the same topic, Amann said: “It is about trust and working together with customers and partners to develop things together. Customers are eager to get new types of equipment that support their targets of being CO2 emissions-free. As well as committing to the SBTi targets, Volvo CE also aims to have 35% of its equipment range electric-powered by 2030. We have a huge commitment to sustainability.”
Commenting on the growth in battery-electric-powered construction and quarrying equipment available to customers globally, Harsin said: “Everybody believes battery-electric equipment will find its place. Where the line gets drawn on any given type of equipment is probably the biggest debate point. You need to think about how much energy you need onboard to get the job done. It’s very different to what we’ve talked about in the past when it comes to how you power a product. For us, in some markets, we’re talking about natural gas and different alternative fuels. But from an off-highway perspective, the talk is diesel, diesel-battery-electric, and hydrogen, either in a combustion engine or fuel cell form. Many OEMs offer hybrid installations, and we participate in that as a components supplier.”
Grimm added: “What we are seeing is customers not wanting to put all their eggs in one basket. Equipment powering choice can be site specific. Certain locations work well for battery-electric-powered equipment as the power grid supply is nearby. Other places are more remote, so require different power options. You need a kind of ‘pointy pencil’ analysis: within the lifespan of these kinds of projects, we need to make a selection of equipment incorporating different powertrain options.”
“It also depends on where in the world you are,” said Amann. “Different countries offer different opportunities when it comes to powering your equipment. It also depends on the type of equipment you’re running. An excavator may be able to be connected to the electric power grid, but that doesn’t suit your articulated haulers that are travelling over longer distances. It also depends on which segment you are working in, such as quarries or road construction.”
Harsin said it was important for construction and quarrying industry customers to think “thoughtfully” and “carefully” about
powertrain choices for their equipment. “Diesel has been a really convenient power source for a long time. It has kind of spoiled us when you think how complicated some of the other power sources are. You spec an engine based on your peak power demand, and it is easy with the fuel onboard to do a day or a couple of days' job. When you look at some of the alternative power technologies, you need to be a lot more thoughtful about what you actually need to do the job. There are a lot of trade-offs that come with that, such as cost, operation, serviceability and environment.
“From an OEM’s perspective, a lot of the conversations we have with customers are like, “Okay, you have an excavator, wheeled loader or another piece of equipment, and it’s so big, and you ask, ‘How much run time do they need?' the first answer, generically, is ‘a full shift’. Then you must consider whether a full shift is eight, ten, or only four hours. From a battery-electric perspective, there will need to be much more power onboard if you want the equipment to work a longer shift. That will also impact cost and charge time. From a hydrogen power perspective, it comes down to how much you can pack onboard that piece of equipment, and the packaging would be more challenging than it is for diesel-powered equipment.”
Long-term answers
Asked about the timescale for the widespread introduction of alternative power solutions for construction and quarrying customers, Harsin said: “I think there are what I call site-centric applications today where you have a [industrial] population that’s lived there its whole life and is big enough to drive some financial sense to introduce charging infrastructure locally. They will be early and faster adopters. Others working in a more nomadic way are going to lag behind that. From our side, I think a lot of the solutions are going to come in the hydrogen space as we tend to work with larger equipment, where the power demands are higher. In many places, hydrogen fuel cell and combustion engine power will be the long-term answer.”
IF YOU PUT THE RIGHT DATA IN PEOPLE’S HANDS, THEY WILL DO A GREAT JOB OPTIMISING IT
“Like Volvo CE, Trimble has signed up to the Science Based Targets initiative, and thousands of other companies worldwide have done the same,” said Grimm. “Our economy overall is now tied into incentives for reducing carbon emissions. Cummins, Volvo CE and Trimble are all technology innovators. I’m an economist by training, and back in the day, economics was labelled the ‘dismal science’ as people thought we’d run out of resources. But technology innovation and the green revolution are proving the likes of Thomas Malthus [English economist - 1766-1834] wrong. We’re just at the beginning of this in terms of quantifying and supplying data to people, connecting the digital and physical worlds. If you put the right data in people’s hands, they will do a great job optimising it. We have a bright future ahead of us, and we all hope to scale up what we do faster.”
Harsin said greater data availability will bring to light many things that construction and quarrying customers were not thinking about before, thus boosting their sustainability. “It will help focus customers on how and when they might bring older equipment up to newer spec, and, as I said earlier, with their idle machine management. Part of the challenge we have had is, how do you convince people of the value of that? In a lot of cases, it’s seen as just another thing to have to deal with.
“If you look at what we’ve [Cummins] done over the course of the last three to four emissions changes, you’re talking 5-8% fuel economy benefits in one, another 5% in the next, 3% in the one after, with more coming down the line. If all of a sudden, I’ve also then got a fleet report for all my equipment, and it shows its vintage and how much fuel I burn, it is probably a short trip from there to see how I can monetise the value of upgrades.”
“You can save a lot of fuel by educating drivers to drive their machines in an efficient way,” said Amann. “We have also started with select customers producing machines using fossilfree steel, which is coming from the other way in protecting the environment.”
In responding to a question about how autonomous equipment operation can benefit the construction and quarrying industry, Amann said: “I don’t think all machines are suited to it. Finding drivers can be tricky in some markets, and different types of automation can support their work. We have solutions like Dig Assist [for excavators - powered by the in-cab Volvo Co-Pilot tablet], Terrain Memory [a feature of the intelligent Volvo drivetrain that identifies and remembers slippery road segments to ensure optimised articulated hauler traction control and off-road mobility], and Cruise Control [also for ADTs]. There are also opportunities we are looking into around 5G connectivity. You can have a driver sitting hundreds of miles away driving a machine in a challenging place, like a mine or a forest.”
From a Trimble perspective, Grimm added: “There are two aspects of automation-linked sustainability that we believe are very important. One is safety. In the long-term future, as we start to see some equipment that is operatorless, you will end up not having a cab. A lot of injuries onsite are from getting in and out of machines. As you remove the need to do this, you’ll have fewer injuries. Then, from a carbon reduction
standpoint, there’s a tremendous opportunity. We did a study over the past year whilst trying to prove how productivity and efficiency gains drive sustainability of three compactors: one with an experienced operator; one with an inexperienced operator; and one with no operator that was auto steering – driving itself. We found a 15-30% efficiency improvement over those operators, which also equates to a 15-30% reduction in carbon emissions. This was largely because when you use auto steering, you can reduce [compaction] overlap.”
Grimm said that Trimble is seeing in the US and other parts of the world construction and quarrying customers having to get “smarter” on understanding their carbon footprint and how to reduce it. “Whomever they’re building for is starting to demand it, like a federal agency or another client who wants to see a report on their carbon emissions and how they intend to reduce it compared to other contractors. Work that used to be quantified and won on price has a carbon emissions equation going into a competitive bid. As we start to quantify carbon emissions through carbon counting, I think a big trend that is going to be seen in this industry is going to be around carbon insets and offsets. How do you work around a building or piece of infrastructure, from its design to long-term operation?
“We will see more and more companies joining the Science Based Targets initiative, and more and more federal agencies in different countries requiring us and our customers to be thinking more about our carbon net zero feature.”
Commenting on green [renewable energy-based] hydrogen power as part of the off-highway equipment carbon emissions reduction mix, Harsin said: “It is something we are investing in and believe it will have a critical role to play in the future of the medium- and heavy-duty equipment market that we serve. My earlier references to our acquisitions in this area put us in a good position.”
“The problem for our industry has been how to store electricity near the work site. There are opportunities around that with hydrogen fuel cell electricity generation to run construction equipment. Green hydrogen can also allow us to produce more fossil-free steel,” said Amann, adding: “It’s been really nice to sit here today with Cummins and Trimble and discuss our common view on making a better world to live in. We have an opportunity to do something good for future generations.”
Welcome to the Aggregates Business magazine preview of the CONEXPO-CON/AGG 2023 exhibition. Over the next 8 pages, we will highlight all the key product launches and North American debuts during what promises to be an action-packed, must-attend event
Cummins is highlighting its new fuel-agnostic 15-litre engine platform with hydrogen, biogas and advanced diesel engines. It offers OEMs the opportunity to accelerate the decarbonisation of heavy-duty, off-highway applications.
This new platform, designed for the next level of emissions, has a significant increase in power density with a more compact installation envelope, enabling OEMs to increase machine capability and productivity with no impact on running costs.
The fuel-agnostic architecture of the 15-litre next-generation
engine utilises a common base engine with cylinder heads and fuel systems specifically tailored for hydrogen, natural gas, diesel and biofuels, including HVO (hydrotreated vegetable oil).
The 15-litre hydrogen engine will be available with ratings from 400 to 530hp and a peak torque of 2600Nm. For applications powered by renewable biogas, this engine will offer ratings from 400 to 510hp with a peak torque of 2500Nm available. The advanced diesel-version features will offer a broad power range of 450 to 650hp, with an impressive 3200Nm peak torque. Cummins www.cummins.com
MATEC INDUSTRIES S.p.A.
Via Aurelia Ovest 383, 54100 Massa (MS), Italy
WhatsApp: +39 335 5687581
Phone: +39 0585 8365
Email: matec@matecindustries.com www.matecindustries.com
CONEXPO CON/AGG is North America’s largest construction fair and the premier event connecting professionals from all major construction industries.
Held every three years, CONEXPO CON/AGG takes the construction industry to a higher level, helping professionals elevate their expertise in the industry by experimenting with the latest equipment and products through demonstrations and training.
Matec has decided to strengthen its presence in the American market, where it has been present since 2012 with a sales office and a warehouse in North Carolina.
We look forward to seeing you on Stand C22929, where, following the bauma exhibition, we are presenting our latest technological innovation in the filtration segment, the Twin Frecciarossa, a 2-in-1 filter press that allows you to achieve unprecedented performance with the reliability and guarantee of a product created to reduce maintenance and downtime.
FPT Industrial S.p.A.
Via Puglia 15 - 10156 Torino
Italy
press@fptindustrial.com www.fptindustrial.com
FPT Industrial is a brand of Iveco Group (IVG: MI) dedicated to the design, production and sale of powertrains and solutions for on- and off-road vehicles, as well as marine and power generation applications.
Over 8,000 people across eleven production sites and eleven R&D centres work for FPT Industrial worldwide.
A dedicated ePowertrain division is accelerating the path towards net zero-emissions mobility with electric drivelines, battery packs and battery management systems.
For more information, visit www.fptindustrial.com
FPT Industrial is exhibiting its full range of Tier 4 Final and Stage V solutions for construction and industrial applications at CONEXPO 2023. Ranging from 2.8 to 16-litres, FPT engines guarantee high levels of performance along with flexibility, reliability and maximised uptime. For compact and medium applications, the F28 is a modular, highly compact engine that offers the performance of a 3.4-litre engine in a 2-litre package. The F28 has a multifuel design that shares common base components for the diesel, natural gas and hybrid versions. At CONEXPO, FPT also introduces the PowerPack version of the F28, completing its portfolio of pre-assembled, ready-to-use solutions.
All FPT Industrial engines feature innovative and patented ATS technologies, delivering best-inclass efficiency and minimising downtime. The aftertreatment systems dedicated to North American Tier 4 Final standards are a non-DPF technology (the patented HI-eSCR system), while for global and cross-regional applications the integrated HI-eSCR2 system complies with the more stringent EU Stage V regulations and is dual-certified for Tier 4 Final.
SBM Mineral Processing will showcase its JAWMAX 400 jaw crusher when the innovative Austrian crushing and screening plant maker makes its fourth appearance at the exhibition.
The JAWMAX 400 on show features one of the most advanced diesel-electric drive concepts on the market. A combination of fuel-efficient onboard diesel and performancetuned generator powers the plant’s materials processing.
SBM’s mobile plant range comprises 12 track-mounted JAWMAX jaw crushers and REMAX impact crushers, capable of 250 – 800tph production. The plant range shares the same innovative drive concept, with fewer hydraulics ensuring less risk of failure, lower maintenance and parts inventory costs, and thus higher availability, says SBM. Overall savings from running the plants can, says the OEM, be 40% to 75%.
SBM will also update
showground attendees about the brand-new REMAX 600. Based on the SBM hybrid concept, the new 600tph impact crusher will soon pave the way for "autonomous crushing", says the manufacturer. Extensive sensor technology, including cameras, records and evaluates the feed material as well as intermediate and end products. In real-time, those values reach centralised digital labs at SBM, where they are further analysed. Necessary adjustments are then made on the ‘digital twin’ of the working machine and re-transmitted directly to the REMAX 600 in the field. The REMAX 600 – known as ‘Crusher 4.0 – developed together with the University of Leoben was presented at the recent bauma 2022 Munich exhibition. Largescale field tests are currently being carried out at selected partner sites.
SBM www.sbm-mp.at
S-83941
Keestrack's new R5e impact crusher is making its Americas debut. The completely newly designed R5e is a fully electric plug-in. It also has a plug-out connection to power additional equipment. The impactor used in aggregates production, recycling, quarrying and mining can be powered via mains connection or any genset unit, in case there is no connection to the grid available.
The R5e can process up to 400 tonnes of material per hour and is very mobile and transportable in one piece. The double-deck pre-screen (7'x3') is said to ensure perfect screening. The material can be stockpiled by side conveyors or via the crusher bypass. The impact crusher with an inlet opening of 31" x 41" (HxW) is driven by a 200kW electric motor and drives the rotor, with a width of 39" (1.000mm) and a diameter of 50", with an extremely high mass
Rokbak
Newhouse Industrial Estate
Motherwell
info@rokbak.com
Rokbak.com
At Rokbak, there’s one thing we value more than anything else: Reliability. We’ve built our whole business on it. From brutal heat to biting cold, our articulated haulers are trusted to perform in the toughest conditions around the world. This reliability comes in two sizes: with payloads of 28 (RA30) and 38 (RA40) metric tonnes.
As a member of the Volvo Group, exceptional quality is at the heart of everything we do. We make machines that will fuel your profits, year after year.
For the first time ever at a North American tradeshow, Rokbak haulers will be on display at CONEXPO at booth F8926, together with Volvo Group. The Scottish articulated hauler manufacturer is displaying both models, the RA30 and RA40, providing attendees with the chance to get up close and personal with the earthmoving machines and demonstrate exactly how they can offer grounded ‘Rok-solid’ performance stateside. With sustainability in mind, the Rokbak event booth materials are all recycled or reusable. Two 40ft customised shipping containers, presented in the recognisable Rokbak livery, will be used for meeting rooms and product information displays.
Product experts will be ready and waiting to discuss the technical capabilities and key aspects of the haulers. This will be the perfect opportunity to hear about Rokbak’s latest innovations, see current options for customisation and learn directly from live demonstrations to get the most from your machine.
Rokbak is set to Rok’ Las Vegas to show exactly how the brand has
moment of inertia, giving high productivity and stability. The two-deck precision screen, 15'7" x 5', can be placed in a closed circuit.
The R5e has a drop-off engine/genset which can go either on the machine's chassis or the machine, connected with a power cable. Placed in a less dusty and vibrant environment, it functions as a backup when no connectivity to the grid is available. Connecting several machines to a single dropoff engine/genset results in huge savings, as there is only one engine/genset to run and maintain. Maintenance is also safer and easier when the engine is placed at ground level.
The R5e uses, on average, 173kW when powered fully electric or around ten gal/hour (40l/h) when driven via the dropoff diesel engine/genset. keestrack www.keestrack.com
Simex Srl
Via Newton, 31-33 - 40017
San Giovanni in Persiceto
BO - Italy
+39 051 6810609
simex@simex.it
sales@simex.it
simex.it
simex-na.com
simex-buckets.com
simex-drumcutters.com
HYDRAULIC ATTACHMENTS FOR EARTHMOVING
Over 120 models to provide solutions to the most challenging application fields: road maintenance, utilities, trenching, construction and infrastructure, tunnelling, profiling works, demolition and recycling.
Simex attachments are designed and engineered to be exceptionally durable and highperforming. Our product range includes: cold planers, screening buckets, wheel saws, drum cutters, crusher buckets, granulator buckets, asphalt floats & compactors - for excavators, loaders and skid steers.
Since 1991, Simex has designed and manufactured hydraulic attachments for the earthmoving industry. With a range of 30 products and over 120 models providing solutions to the most challenging applications: road maintenance and underground utilities; construction and infrastructure; tunnelling and demolition; recycling and waste material recovery; and agriculture and forestry. With continuous investment and a global vision proudly rooted in its history, today the company’s production plant in Italy covers a total area of 54,000m², ensuring increased stock capacity and shorter delivery times. A large amount of space is dedicated to testing equipment so as to ensure the highest quality standards. A vast demo area allows the R&D office to develop new products, simulating the various fields of application.
prompt customer and after-sales service and an extensive sales network covering over 80 countries, with a branch offi from 2021, in the US.
Metso Outotec is showcasing its latest innovations, technologies and offering for the aggregates industry. Special previews include the new HPe range, the next generation of the popular Nordberg HP cone crusher, offering high performance and uptime more sustainably, and a sneak peek at the future vision for the iconic Lokotrack trackmounted crushers and screens.
The latest version of the Lokotrack LT120 – one of the most efficient mobile jaw crushers in the market for demanding quarry and contract crushing applications – will also be displayed. The LT120 features the proven Nordberg C120 jaw crusher and is equipped for optimised performance and extended wear life. It includes the Planet Positive hybrid composite MX jaw dies, a rock breaker, rubber lining in the feeder, a belt cleaning set for the
long main conveyor, the latest intelligent crushing solution, and the new Metrics digital remote monitoring platform.
Metso Outotec’s aftermarket solutions will be a key exhibition theme. The solutions help quarries and contractors reduce cost per tonne and decrease their energy consumption and carbon footprint. With the OEM quality parts and digitally powered services, Metso Outotec can optimise the performance and uptime of aggregates-producing equipment at every phase of the production lifecycle.
Metso Outotec Metrics, enabling a wide range of services targeting improved performance, availability and equipment lifespan for different aggregates applications, will also be highlighted.
Metso Qutotec www.mogroup.com
Rokbak is bringing a pair of its haulers and a strong team to show exactly how the brand has become a major mover in both the US and global markets.
The Scottish articulated hauler manufacturer is making its North American tradeshow debut with its RA30 and RA40 machines.
“We cannot wait to give the RA30 and RA40 pride of place on our stand,” says Paul Douglas, managing director of Rokbak. “We’re looking forward to getting as many attendees interacting with what we’ve got lined up as possible, as well as introducing people to our knowledgeable team who are keen to show off our robust and hardworking haulers.”
“Rokbak is seeing huge demand for its RA30 and RA40 articulated haulers in the US,” says Robert Franklin, Rokbak’s director of sales – Americas. “The US is leading articulated hauler
demand globally with huge infrastructure spend. There is a lot of construction activity at the moment around house and road building, so we are keen to meet with customers and potential customers at CONEXPO and discuss how the RA30 and RA40 can help with these projects.”
Rokbak will be showcasing its haulers and aftermarket offer alongside fellow Volvo Group companies, Volvo Construction Equipment and Volvo Penta.
With sustainability in mind, the Rokbak event booth materials are all recycled or reusable. Two 40ft customised shipping containers, adorned in the recognisable Rokbak aesthetic, will be used for meeting rooms and product information displays. Following the event, these will be shipped back to Motherwell for reuse at future events. Rokbak www.rokbak.com
components and plants for rock processing for over 70 years. All our know-how is in our mobile solutions for aggregates and recycling.
equipment, we are guided standards. This starts with the components used and ends with a high-quality durable finish.
Customer service and support are very important to us – also in worldwide sales. We are expanding our global network and are looking for strong dealers for the Americas, South East Asia and the Oceanic markets.
SBM Mobiles offer you the combination of the most advanced drive concept on the market, highest production performance and intelligent operator guidance. The range includes twelve trackmounted JAWMAX® jaw crushers and REMAX impact crushers between 49,000 and 353,000lbs operating weight (max. output: 250 - 800tph). Their diesel-electric drives enable cost savings of up to 75%, guarantee high availability and improve your environmental footprint. At the booth we will display the JAWMAX 400 jaw crusher.
Come with us into the future and learn more about our brand new impact crusher REMAX 600! With its intelligent technology, it detects feed material and end product quality, compares the values online with thousands of reference data and automatically optimises its production settings.
Best results from any material, most economical operation under all conditions – the “autonomous crusher” for even more productivity.
Keestrack America
15066 US HWY 380 W
Krum
TX 76249
USA
info@keestrack.net www.keestrack.com
Keestrack has a strong reputation for innovative and cost-effective track mobile crushing and screening equipment with a relentless search for the best performance at the lowest cost per produced ton.
Keestrack introduced its hybrid and electric plug-in solutions in mobile processing technology in 2012. At CONEXPO Keestrack are presenting an overview of their extensive product range, introducing sustainable full electric plug-in equipment backed up by a drop-off engine/gen-set.
Keestrack, with its Texas based US Headquarters, will be at Conexpo with their American, Canadian and Latin American dealers.
The fully electric plug-in R5e impact crusher will be introduced to the American market. The impactor can be powered via mains connection for a zero carbon footprint, or via a gen-set unit, in the event of no available connection to the grid.
The R5e has a drop-off engine/ gen-set which can be placed either on the chassis of the machine or besides the machine, connected with a power cable.
Being placed in a less dusty and vibrant environment maintenance is safer and easier when the engine is situated at ground level.
When connecting several machines to a single drop-off engine /gen-set, it results in huge savings as there is only one engine/gen-set to run and maintain.
Also on show: the H4e cone crusher in closed circuit, the award winning R3 impactor, the heavy duty B7 jaw crusher, the most mature and productive scalper on the market, the K6 and the dust suppression cannon W7.
Caterpillar will have its largestever presence at the big offhighway equipment industry exhibition's 2023 staging.
The US company will highlight its latest products, services and technologies on a 6,500m2 outdoor demonstration arena. The Operator Stadium in the Expo's Festival Lot will be central to the massive display.
Visitors will find new and current models and batteryelectric machine prototypes. The extensive Cat equipment display in the Festival Lot includes more than 30 machines, including model unveilings and batteryelectric model prototypes with charging stations. Visitors will see two main equipment demonstrations each day; one focused on the latest Cat Technology and one that will spotlight the company's full equipment lineup.
The new Cat 950 medium wheeled loader on display offers performance and simple-to-use technologies to boost operator efficiency, increase productivity, and extend service intervals. Visitors will be treated to a preview of the Next Generation Cat 926, 930 and 938 small wheeled loaders that feature new technologies, a reimagined operator environment and extended service intervals.
Caterpillar Industrial Power Systems Division will exhibit
in booth S84329 in the South Hall a wide and rapidly growing portfolio of high-efficiency Cat industrial power solutions. The exhibit includes the unveiling of a new high-power internal combustion engine, as well as the leading-edge lithium-ion battery technologies under development. Engines on display, such as the C3.6 IPU, C7.1 and C9.3B, meet Stage V and Tier 4 Final emission standards and are compatible with biodiesel up to B20 and hydrotreated vegetable oil (HVO) to EN15940.
The new Cat Central app is the latest tool for access to genuine Cat parts and support. Another new servicerelated solution is the new Cat SIS2GO app which helps with maintaining, troubleshooting and repairing Cat equipment. Both apps are available on Windows, iOS and Android platforms.
The Caterpillar Technology Hub in the Festival Lot will offer attendees the ability to experience a range of new and existing Cat technologies – VisionLink, Cat Command, VisionLink Productivity, Cat Detect, Cat Grade and Cat Payload. Caterpillar SMEs will be on hand to assist each customer in finding a scalable solution designed to fit the business's needs and budget.
CAT www.cat.com
Matec will have an impressive display showcasing its eyecatching ‘Twin Freccia Rossa’ –the world’s biggest filter press.
A prototype of the striking machine was shown at bauma in Munich, Germany (24-30 October 2022). The first fullproduction, 50m-long, up to 380-plate and 600 t/h machine was subsequently snapped up by a Turkish iron ore mining customer. The Italian company says its innovative machine combines the efficiency of two machines into a single product with exceptional performance, offering faster sludge feeding and cake discharge time.
The patented Twin Freccia Rossa is said to reduce customers’ operating costs and allows production to continue during maintenance times. Featuring a single conveyor belt, feeding point, silo decanter, supporting structure, homogeniser tank, high-pressure
10-16-21-30-bar technology, a protective shell for the oleodynamic unit and piston, and four-point cloth washing, the cutting-edge filter press can be equipped with 25mm to 50mm standard or membrane plates.
“All our customers are asking us for two filter presses in one machine,” said Matec Industries CEO Matteo Goich during bauma 2022. “We started work on Twin Freccia Rossa around a year ago and the customer who will operate the first full-sized version of this new filter press already has one of our washing plants and six of our filter presses.”
Matec plans to open a new office on the US West Coast by the end of 2023, enabling the company to strengthen longstanding dealer relationships and attract new dealers, widening its reach across the North American continent.
Matec Industries www.matecindustries.com
Metso Outotec
2715 Pleasant Valley Road
York PA 17402
USA
Phone +1 (717) 843 8671 www.mogroup.com
The most popular cone crusher in the world is undergoing an evolution. The new Nordberg® HPe range is even more efficient, built to meet the increasing performance needs of the aggregates and mining industries. This offers maximised performance and uptime whilst minimising environmental impact.
Lokotrack® track-mounted crushers and screens are famous for their outstanding performance and dependability. At CONEXPOCON/AGG, we are showcasing the newest version of the Lokotrack® LT120, one of the most efficient mobile jaw crushers in the market.
For every production challenge, there is a solution – when you have the right partner. Metso Outotec has been delivering solutions for demanding aggregate applications worldwide for over 150 years. You can count on our dependable products and industry experts to further enhance your operations.
Our comprehensive portfolio covers crushers, screens, feeders, track-mounted and wheelmounted units, stationary plants and related digital solutions. Metso Outotec equipment and parts are built to last and are backed by reliable service and support, giving us the unique ability to elevate customers’ business to a whole new level.
At CONEXPO-CONAGG 2023, visit the Metso Outotec booth to see a sneak peek at the future vision of the next generation of Lokotracks, which will continue to transform and revolutionise mobile crushing.
Whether you run a large quarry or a construction contracting business, we take your business personally. Get in touch today and learn how to optimise your operation!
Cummins Inc.
301 Jackson Street, Columbus IN 47201
USA
www.cummins.com
Cummins, a global power leader, is a corporation of complementary business segments that design, manufacture, distribute and service a broad portfolio of power solutions.
The company’s products range from diesel, natural gas, hydrogen, electric and hybrid powertrains, and powertrain-related components including filtration, aftertreatment, turbochargers, fuel systems, controls systems, air handling systems, automated transmissions, electric power generation systems, batteries, electrified power systems, hydrogen generation and fuel cell products.
Cummins will showcase its new fuel-agnostic, 15litre engine platform with hydrogen, biogas and advanced diesel engine capabilities at CONEXPO, Stand S84615, south hall upper. This Cummins platform offers OEMs the opportunity to accelerate the decarbonisation of heavy-duty off-highway applications.
The new range from Cummins has significantly increased power density than previous generations and a more compact installation envelope, enabling OEMs to increase machine capability and productivity with no impact on running cost.
The 15litre hydrogen engine will be available with ratings from 400-to-530hp and a peak torque of 2600Nm. For applications powered by renewable biogas, this engine will offer ratings from 400-to-510hp with a peak torque of 2500Nm available. The advanced diesel version features a broad power range of 450-to-650hp, with an impressive 3200Nm peak torque.
Komatsu is showcasing its latest electric equipment alongside brand-new and recently introduced machines.
The Japanese quarrying and construction manufacturer will be in booth W42044 and its theme for the show will be 'Creating value together'. With the right products, latest technologies, actionable data and dealer support, Komatsu says it helps its customers create value to help achieve their visions for productivity, efficiency, sustainability and safety.
A sampling of Komatsu machines that will be on show include: the PC210E (with Smart Construction Retrofit) electric excavator; PC900LC (with Smart Construction Retrofit) excavator; HB365LC-3 (with Smart Construction Retrofit) hybrid excavator; D71PXi-24 intelligent dozer; HD465-8 mechanical haul truck; PC230F-11 processor; PC360iLC-11 intelligent excavator; and the WA600-8 wheeled loader.
optimisation.
Komatsu says it will demonstrate how its machines and solutions can help its customers: optimise fleet capabilities; extend the life/ improve the value of machines; operate with safety as a priority and reduce employee downtime; leverage the latest technology to improve efficiencies and productivity; conserve resources and reduce fuel consumption; upskill and retain employees and use them in the most productive ways through leveraging the right training and latest technologies.
Komatsu will also showcase its smart quarry solutions that are designed to help customers understand, visualise and optimise their job sites. Job site studies provide customers with customised, detailed data that may help them meet or even exceed their production targets.
To showcase tools that support operation optimisation, Komatsu will address a sustainability/electrification roadmap, technology implementation, and workforce
Solutions such as Smart Quarry Site take it a step further with continual production monitoring aimed to help increase efficiency, improve production and maintain a high level of performance.
Komatsu www.komatsu.com
MARCH 14-18 / 2023 / LAS VEGAS / NEVADA
250,000 sqm of Exhibits
130,000 Attendees
1,800 Exhibitors
150 Education Sessions
REGISTER at conexpoconagg.com
Save 20% with promo code SHOW20
With proven reliability and safety, highest versatility, top-of-the line operator comfort, and powered by a low-consumption and environmentally-friendly site worldwide.