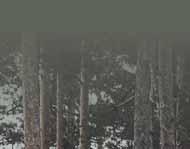
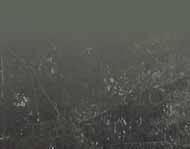
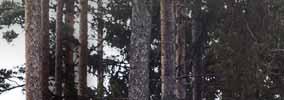
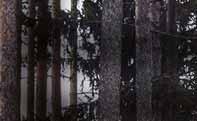
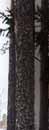
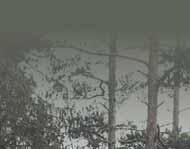
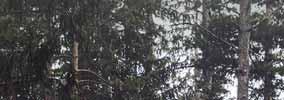
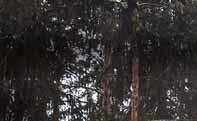

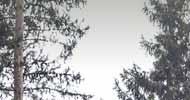
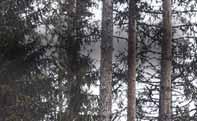
MARCH 14-18 / 2023 / LAS VEGAS / NEVADA
250,000 sqm of Exhibits
130,000 Attendees
1,800 Exhibitors
150 Education Sessions
REGISTER at conexpoconagg.com
Save 20% with promo code SHOW20
EDITOR: Guy Woodford
ASSISTANT EDITOR: Liam McLoughlin
CONTRIBUTING
EDITORS: Patrick Smith, Dan Gilkes
EQUIPMENT EDITOR: Mike Woof
DESIGNERS: Simon Ward, Andy Taylder
PRODUCTION MANAGER: Nick Bond
OFFICE MANAGER: Kelly Thompson
CIRCULATION & DATABASE MANAGER: Charmaine Douglas
INTERNET, IT & DATA SERVICES DIRECTOR: James Howard
WEB ADMINISTRATORS: Sarah Biswell, Tatyana Mechkarova
MANAGING DIRECTOR: Andrew Barriball
PUBLISHER: Geoff Hadwick
CHAIRMAN: Roger Adshead
ADDRESS
Route One Publishing Ltd, Second Floor, West Hill House, West Hill, Dartford, Kent, DA1 2EU, UK TEL: +44 (0) 1322 612055 FAX: +44 (0) 1322 788063
EMAIL: [initialsurname]@ropl.com (psmith@ropl.com)
ADVERTISEMENT SALES
SALES DIRECTOR:
Philip Woodgate TEL: +44 (0) 1322 612067
EMAIL: pwoodgate@ropl.com
Dan Emmerson TEL: +44 (0) 1322 612068
EMAIL: demmerson@ropl.com
Graeme McQueen TEL: +44 (0) 1322 612069
EMAIL: gmcqueen@ropl.com
SUBSCRIPTION / READER ENQUIRY SERVICE
Aggregates Business is available on subscription at the rate of: £85 / US$145 / €111 per annum. Single copies £20 / US$35 / €26 Email subs@ropl.com for further details. Subscription records are maintained at Route One Publishing Ltd.
SUBSCRIPTION / READER ENQUIRIES TO:
Data, Route One Publishing Ltd, Second Floor, West Hill House, West Hill, Dartford, Kent, DA1 2EU, UK
TEL: +44 (0) 1322 612061 FAX: +44 (0) 1322 788063
EMAIL: data@ropl.com
No part of this publication may be reproduced in any form whatsoever without the express written permission of the publisher. Contributors are encouraged to express their personal and professional opinions in this publication, and accordingly views expressed herein are not necessarily the views of Route One Publishing Ltd. From time to time statements and claims are made by the manufacturers and their representatives in respect of their products and services. Whilst reasonable steps are taken to check their accuracy at the time of going to press, the publisher cannot be held liable for their validity and accuracy.
PUBLISHED BY © Route One Publishing Ltd 2022
AGGREGATES BUSINESS USPS: is published six times a year. Airfreight and mailing in the USA by agent named World Container Inc, 150-15, 183rd Street, Jamaica, NY 11413, USA.
PERIODICALS POSTAGE PAID AT BROOKLYN, NY 11256
US POSTMASTER: Send address changes to Aggregates Business, World Container Inc, 150-15, 183rd Street, Jamaica, NY 11413, USA. Air Business Ltd is acting as our mailing agent
PRINT: ISSN 2051-5766 ONLINE: ISSN 2057-3405
PRINTED BY: Warners (Midlands) PLC
UK lime kiln in world-first net-zero hydrogen trial; Epiroc & Skanska partner for world-first battery-electric surface drill rig testing in Swedish quarry; CEMEX optimises supply chain to reduce transport emissions; Tarmac orders UK’s first battery-electric mixer truck.
The building materials and quarrying equipment sustainability-focused headlines on Aggregates Business Europe magazine’s website news stories over recent weeks indicate the huge efforts being undertaken by original quarrying equipment manufacturers and building materials suppliers to lower their carbon footprints and help build a more sustainable Europe and wider world.
A fascinating and illuminating presentation by Dr Miles Watkins, an industry sustainability consultant, at the British Aggregates Association (BAA) annual conference at The Palace Hotel in Buxton, Derbyshire, England, the day before the start of the hugely successful Hillhead 2022 quarrying, construction, and recycling industries’ exhibition, emphasised the need for building materials suppliers to maintain their admirable work to reduce their carbon emissions.
Highlighting the UK building materials sector’s ‘broad terms’ carbon emissions to conference attendees, Watkins, a former Aggregate Industries director of sustainable construction, said that bitumen production generates 450,000 tonnes of CO2 emissions; a further 625,000 tonnes of CO2 emissions come from making asphalt; 1.25 million tonnes of CO2 is emitted during aggregates production; and a whopping 10 million tonnes of CO2 emissions are generated in cement making.
Perhaps unsurprisingly given such figures, Watkins, who is also a former non-executive president and chairman of the Institute of Quarrying (IQ), noted that the building materials sector is responsible for 20% of all UK business CO2 emissions, which to offset at £50 per unit would amount to £616 million (€715.11mn).
He posed a key question: ‘When will we see this liability on balance sheets?’ It also
left me, and I am sure other event attendees, wondering about the kind of numbers a similar analysis of overall European building materials sector’s carbon emissions would produce.
Watkins showed BAA annual conference delegates pictures of Larry Fink, CEO of BlackRock, the giant American multinational investment management corporation, and Mark Carney, an economist and banker who served as the Governor of the Bank of England from 2013 to 2020, to illustrate how the huge sustainability focus of leading major investment bank and finance figures like them had propelled it to the forefront of world commerce.
“Over the past few months, I have spoken to a load of chief executives and CFOs [chief financial officers] from companies all round this [UK building materials] sector who are being pressured beyond belief to make monumental differences to their businesses, particularly around circularity and carbon,” said Watkins. “Investors are now saying, ‘I know it’s been like that forever, but unless you do something on sustainability, we are going to take our money and put it somewhere else’. Especially if you are a CRH which BlackRock already has an around 10% stake in, you are going to start listening to these people.”
Watkins said he had been speaking to management at Forterra, a £380mn annualrevenue-generating concrete building block and brick manufacturing company based in Northampton, England, who told him that the firm’s CEO, Stephen Harrison, spends 50% of his time dealing with sustainability investors. “That would not have happened five years ago,” said Watkins, adding: “Forterra’s CFO now writes the company’s annual sustainability report.”
You can expect to read more about Dr Miles Watkins and his vital work in ABE later this year as I plan to sit down with him and take an in-depth look at sustainability in the building materials industry, including how an ever-growing environmental focus is likely to shape future product demand. GW
Immobile
UK
Hydrogen
New
Aggregates:
Selling
Proven
The
High-quality lime has been manufactured for the first time in the UK using hydrogen technology as part of a world-first net-zero trial.
The trial, led by Tarmac at its Tunstead site near Buxton in Derbyshire, England, was the culmination of a project funded by the Department for Business, Energy and Industrial Strategy (BEIS). It demonstrates the significant potential to use hydrogen as a viable fuel alternative to natural gas for commercial-scale production of lime. Several trials were conducted with differing energy replacements, which culminated in a 100% replacement of the natural gas.
Lime is currently manufactured in high-temperature kilns, heating calcium carbonate from limestone to around
Sandvik has appointed Peter Unelind as president of its Mobile Crushers & Screens business division.
Unelind was formerly vice president, Operations in Sandvik’s Stationary Crushing & Screening division. He joined the Swedish quarrying and mining plant manufacturing giant in 2013. He succeeds outgoing president Andy McCullock.
With a strong background in international business with a particular emphasis on operations, sourcing, technical and quality management, Unelind’s execution capabilities, strong leadership, and focus on collaboration will help deliver Sandvik’s Make the Shift strategy and maximise uptime across the manufacturer’s extensive machinery range.
1,000°C. Using hydrogen as a fuel ensures that there is no CO2 produced from fuel combustion, emitting just water vapour.
Commenting on the innovative trial, Graham Cooper, lime director at Tarmac, said: “Highpurity limes are essential for our way of life and are used in a diverse range of sectors, from wastewater treatment through
to the manufacturing of pharmaceuticals and cosmetics.
“Lime has been manufactured in the Peak District for centuries, and this forwardthinking project aims to ensure the future of this nationally significant industry as the UK transitions to net zero.”
The project builds on the company’s wider long-term
sustainability programme and corporate commitment to deliver net zero by 2050 and cut CO2 by 45% per tonne of product by 2030.
Dr Diana Casey, director of energy and climate change at the Mineral Products Association, which managed the overall project, said: “This trial has shown that lime manufacture can and will be part of a future net-zero society. What is needed now is investment and infrastructure development to enable the rollout of this technology at a commercial scale at sites across the country.”
The project has been funded by BEIS as part of its Industrial Fuel Switching Competition and is part of fuel switching trials managed by the MPA at three sites across the lime and cement sectors.
Astec Industries has announced plans for a US$5 million factory expansion at its Omagh, County Tyrone, Northern Ireland site, to better serve growing market demands in the global mobile crushing and screening industry.
The expansion comes a year after the original facility was built to support the increased demand for mobile material-handling products and was closely followed by the introduction of mobile crushing and screening products.
Tim Averkamp, Astec Group president, said the project would add 44,000 square feet to the facility, bringing the total to nearly 100,000 square feet and investment in the site to nearly US$10 million.
“We opened the original plant a year ago and already have to nearly double it in size, so it’s a real success story and shows the quality and
Artist’s impression of how
demand of our product,” said Martin Dummigan, Astec Group vice president of operations.
“Northern Ireland is where more than half the supply of the global market for mobile crushing and screening equipment originates and establishing a larger footprint here will not only help us grow our business but also
better serve our customers and partners.”
Astec – which expanded into Northern Ireland after acquiring major global bulk materials-handling solution manufacturer Telestack in 2014 - plans to break ground for the expanded facility in late 2022, with expected completion by mid-2023.
Holcim has acquired General Beton Romania, a key national player in ready-mix concrete, with 2022 estimated net sales of €45 million. Since its foundation with a first plant in Timișoara in 1998, General Beton Romania has grown to become Romania’s largest independent readymix concrete player, serving major urban centres such as Bucharest, Arad, Sibiu and Constanta. The transaction will integrate General Beton’s expertise, along with its 160 employees and eight readymix concrete plants. Holcim Romania will now operate 27 ready-mix concrete facilities, advancing the company’s goal to generate 25% of ready-mix net sales from ECOPact green concrete.
Miljan Gutovic, region head Europe Middle East Africa, said: “With this acquisition, we will further expand the footprint of ECOPact green concrete, the first and most comprehensive sustainable concrete range in Romania. General Beton provides an excellent addition to our strong and diversified ready-mix concrete operations. Over more than two decades, General Beton has been a long-standing Holcim partner as well as a growing and highly successful business. I am delighted to welcome them to the Holcim family.”
General Beton Romania was founded in 1998. In addition to the production and sale of concrete, the company also offers logistical and laboratory services. The acquisition is in line with Holcim’s aim to drive profitable growth with innovative building solutions, from ECOPact green concrete to energy-efficient roofing systems.
Hillhead 2022 celebrated the return from a four-year hiatus by recording the busiest opening day in its 40-year history.
A total of 8,283 visitors attended on day one of the UK quarry event for the mineral products, construction, and recycling sectors that was held at Tarmac’s Hillhead quarry near Buxton in Debyshire, central England, from June 21-23.
A total of just under 18,500 visitors was in attendance over the three days and more than 600 major global equipment manufacturers, suppliers and service
providers. The organisers say it was very much back to face-to-face business as exhibitors and visitors took the opportunity to reconnect with their industry peers, take the pulse of what is happening, and see the plethora of live machinery action that took place in the show’s four dedicated demonstration areas.
Following the trials and tribulations of the past 18 months for the events sector, this year’s event was very well received, with every square metre of exhibit space – including a reconfigured
Quarry Face demo area, new-look extended Registration pavilion, and revised layout at the top of the showground – completely sold out before its official opening.
“Despite the supply issues affecting the industry as we emerge from the pandemic, Hillhead 2022 was our largest and most successful edition yet,” commented event director Richard Bradbury.
The bi-annual Hillhead show is next scheduled to take place in 2024 with provisional dates set for 25–27 June.
HeidelbergCement’s newly launched ANRAV CCUS project has been selected for Grant Agreement Preparation by the EU Innovation Fund, meaning that the project’s implementation will be supported.
ANRAV aims to be the first full-chain CCUS (carbon capture, utlisation & storage) project in Eastern Europe. It will link carboncapture facilities at the Bulgarian cement plant of HeidelbergCement’s subsidiary Devnya Cement through a pipeline system with offshore permanent storage under the Black Sea.
“As the EU Innovation Fund is known to focus on technologies that bring on significant emission reductions, we are particularly pleased to have been recognised with our ANRAV CCUS project,” says Dr Dominik von Achten, chairman of the managing board of HeidelbergCement.
He added: “HeidelbergCement is rapidly progressing on a number of
large-scale carbon-capture initiatives globally, covering a range of promising options for both utilisation and storage. ANRAV now has the potential to pave the way for CCUS in Eastern Europe as well.”
“Our vision in the ANRAV consortium is to realise an economically viable CCUS cluster for Bulgaria and the neighbouring regions”, says Mihail Polendakov, HeidelbergCement’s managing director for Bulgaria, Greece and Albania: “It is an integral part of our
HeidelbergCement subsidiary Devnya Cement’s Bulgarian plant. Pic: HeidelbergCement Group
The project is carried out jointly with the oil and gas company Petroceltic. Subject to regulatory and permitting aspects, it could start operation as early as 2028, with a capturing capacity of 800,000 tonnes CO2 a year.
The EU Innovation Fund is one of the world’s largest funding programmes for the commercial demonstration of innovative low-carbon technologies. It aims to bring industrial solutions to the market to decarbonise Europe and
As president of UNICEM, the trade association bringing together the French mineral extraction industries and manufacturers of construction materials, Alain Boisselon is playing a key leadership role as the association’s members attempt to hit ambitious green targets, while remaining profitable in a tough economic climate. Aggregates Business editor Guy Woodford caught up with him to find out more about his crucial work
Being a black belt in judo, Alain Boisselon knows a thing or two about the dedication required to reach a cherished goal.
Having devoted his 35-year working life to date to the French construction sector, the Vicat Group’s French aggregates business director has spent the last two years as president of UNICEM (The National Union of Quarry Industries & Building Materials), heading up a federation encompassing nine unions spanning the rock and mineral extraction industries (aggregates, natural stone), manufacturers of construction materials (ready-mix concrete, additives) and inert waste recovery companies.
To fulfil its diverse missions, UNICEM has a national structure organised around federal services, commissions and working groups, chaired by mandated professionals. Boisselon and his permanent UNICEM staff team represent 1,735 member companies, who, combined, employ hundreds of thousands of people and represent the first link in the French construction and public works chain.
The majority (61%) of UNICEM’s member companies are SMEs (small and mediumsized enterprises) and VSEs (very small enterprises) with a turnover of less than €2 million; 36% of member businesses have a
turnover over €2 million; and a small but influential 3% represent international groups and family-owned ETIs (intermediate-sized companies) which each have a turnover of more than €100 million.
Speaking to Aggregates Business, Boisselon, based in Chambéry, an Alpine town in southeast France, highlights how the French quarrying and building materials industries meet a general interest need by supplying mineral materials that are essential to many sectors, especially building and public works, with local authorities accounting for 70-80% of mineral materials sales.
Commenting on the key challenges facing UNICEM members, he says: “The main issues that concern the profession are access to resources, changes in standards and regulations, which we must address to ensure that companies have legal certainty, and the control of energy costs, a subject that is even more worrying in the wake of the conflict between Russia and Ukraine. On all these subjects, we conduct monitoring and surveys among companies, so that we can then document and enrich our exchanges with the French public authorities. Dialogue is essential to raise the awareness of the authorities and administrations about our sector of activity.
“During this period of health crisis, the industries have shown their resilience in the face of market tensions”
“UNICEM is constantly demonstrating the economic and ecological necessity of producing materials ‘made in France’ and from a local industry. To maintain and support this local industry, which generates jobs that cannot be relocated, we submitted proposals to the candidates in the recent French presidential election to make future executives aware of the importance of maintaining a local and sustainable mineral materials industry.
“The challenge for UNICEM is also to support companies in meeting environmental challenges, such as transition to a circular economy.”
Which of UNICEM’s numerous pro-mineral extraction industries’ initiatives in recent years does Boisselon, who finishes his threeyear term as president in 2023, think has been most successful?
“Among the many battles that UNICEM has waged to defend the collective interests of the profession, I would highlight UNICEM’s proactivity in environmental preservation. This year, we celebrated the 30th anniversary of the profession’s commitment to sustainable development, with a dedicated press conference on April 21. With the Environment Charter for the quarrying industries, it was one of the first industries to adopt an environmental sectoral
approach in 1992. Since 2017, the UNICEM Enterprises Engagements association has also been offering a sectoral CSR [corporate social responsibility] label, assessed by independent third-party organisations to facilitate our companies’ commitment to CSR. To date, some 1,600 sites are involved in these initiatives. More than 500 sites are positioned at the maturity and exemplary levels of the CSR approach. This is a great success that reflects the daily commitment of companies!”
Boisselon says a great strength of mineral extractive industries’ companies is their “agility”. “The latest example of this is as part of the anti-waste law for a circular economy (AGEC), the extended producer responsibility (EPR) system has been extended to construction products and materials in the building sector. To respond to this new orientation, the professional unions (FIB, Routes de France, SFIC and SNBPE, UNPG - both members of UNICEM) have created and participate in the shareholding of an eco-organisation, ECOMINERO, for mineral construction products generating inert waste. ECOMINERO was created by and for manufacturers of mineral construction products or materials, with the aim of simplifying the life of companies, so that they can fulfil their obligations arising from the implementation of EPR, and fully meet the recycling targets set by the AGEC law.”
In its representation of 75% of companies in the French mineral extractive industries and building materials manufacturing sector, which between them generate nearly €7 billion in annual turnover, UNICEM is also a leading economic player.
To support this dynamic, the federation has an economics department whose mission is to carry out studies to give visibility to all the actors involved in the sector and a statistics department which, by delegation from INSEE (National Institute of Statistics and Economic Studies), carries out annual, monthly or specific sector surveys.
I am keen to get Boisselon’s take on the current trading health of the French mineral materials industry, and its growth prospects.
“The results for 2021 show a return to 2019 activity levels, with an estimated increase in production of around +10% at the end of December 2021 (vs. 2020) for aggregates and ready-mix concrete (RMC), bringing volumes to 360 million tonnes for aggregates and 40.7 million m³ for RMC. While the rebound in activity observed in 2021 has almost erased the loss of volumes suffered by materials companies during the confinements, the stigma of the COVID19 pandemic has not disappeared. The global health crisis has caused numerous production tensions – such as supply shortages, recruitment difficulties, and higher production costs. With the war in Ukraine, these tensions are not expected to ease in the coming months, as initially assumed. Indeed, given the current geopolitical context, an energy supply shock, comparable to the oil shock of the early 1970s, cannot be ruled out, with the known consequences for inflation
and growth. For the time being, on the construction side, the latest indicators suggest that activity is holding up well at the start of 2022, even if the single-family home market has lost some of its strength. Conversely, activity is tending to improve in the public works sector, although public order books are still slow to fill up.
“Overall, our scenario for 2022 still favours maintaining a demand for materials that is not far from that observed in 2021 for ready-mix concrete, and even a very slight increase for aggregates (<1%). The constructive dynamics in the building order books will continue to feed the needs in ready-mix concrete, while the aggregates market could benefit from a gradual strengthening of public works activity, via the increase in the stimulus plan and the return of local authority projects (start of the new electoral cycle). However, the surge in production costs linked to the RussianUkrainian conflict and the rise in uncertainties could curtail the momentum and volume of public and private projects. And even if the cash flow situation of local authorities appears solid, the increase in construction costs could lead to some downward adjustments in the budgets devoted to infrastructure investments,
the extent of which is still difficult to estimate at this time.”
Like other industries across Europe, the French mineral extraction industries have had to adjust over the last two-and-a-half years to the myriad challenges linked to the coronavirus pandemic. Does Boisselon think the pandemic will have a lasting impact on the French mineral extraction sector?
“During this period of health crisis, the industries have shown their resilience in the face of market tensions by ensuring the supply chains of its customers on construction sites.
“In concrete terms, the companies and their collaborators mobilised to maintain the activity on the territory by protecting the employees of the sector by respecting the sanitary rules and the protocol of recommendations of the sector with the aim of preserving the supply of the building sites in materials. During this period, UNICEM member companies have chosen to maintain their economic activity, even though many of them were facing a collapse of their orders. Almost no quarry site in France was at a standstill!
“The profession has adapted to the exceptional context but has not changed its mode of operation. On the other hand, this crisis has shown that our companies are an essential link in the production chain, which has made it possible to support the rapid recovery of the construction industry desired by the Government. It has also highlighted our dependence on imported products and consequently the importance of giving priority to local channels whatever the product supplied. This is particularly true for
“The profession has adapted to the exceptional context but has not changed its mode of operation”
Alain Boisselon combines his UNICEM president’s role with his work as the Vicat Group’s French aggregates business director
the mineral industry. We represent a 100% local industry that works through and for the territories. And maintaining the proximity of our sites to the construction sites is a permanent point of attention.
“Indeed, it is this territorial network that allows us to limit transport between extraction sites, production sites and then use sites and therefore the associated CO2 emissions. Natural aggregates are produced within a 30-kilometre radius of their place of consumption; for recycled aggregates, the distances are even shorter due to the necessary optimization between sites, transport, and processing platforms. Similarly, ready-mix concrete, a material now considered essential, travels an average of 17 kilometres, and even less in urban areas (implementation within two hours of its manufacture).”
Turning his attention to the key topic of mineral extraction industries’ sustainability, Boisselon says: “Forerunners at the European level, French aggregate producers have carried out a carbon assessment of the profession, from extraction to the first user, using the ADEME method. The downstream transport of aggregates by road is the main source of GHG [greenhouse gas] emissions (54%), followed by the energy
consumption of quarry machinery (18%). The main lever for action is therefore the type of motorisation of equipment (trucks, machines). It should also be emphasised that the quality of redevelopment can promote CO2 sequestration within the perimeter of quarries.
“To return to the question of engines, companies in the sector and all equipment manufacturers are working to design engines that can use alternative energies: hydrogen, biofuel, and LNG (liquified natural gas). On the business side, groups and SMEs are already using alternative engine technologies. They are mainly developed for the transport of materials. These examples are not yet generalizable or deployed on a large scale, but they reflect the commitment and willingness to act of companies in the sector. In 2017, the first router with zero polluting emissions was put into circulation. The natural gas engine and the electrically operated tank on a lithium battery make it possible to significantly reduce emissions: - 70% NOx, - 92% fine particles, - 96% CO2 emissions.
“In 2018, in Switzerland, the green dumper made its appearance. When it descends loaded with aggregates, the dumper, instead of braking and dissipating energy in the
form of heat, generates electricity thanks to its electric motorization. The 123 tonnes of weight can thus produce a large amount of electricity. Once unloaded, the lightened truck (which weighs 58 tonnes when empty) goes back up the slope thanks to the electricity stored in its batteries (lithiumnickel-manganese-cobalt with a capacity of 600 to 700kWh). With 20 round trips per day, the dumper saves between 50,000 and 100,000 litres of fuel each year, which means a reduction in greenhouse gas emissions of about 130 tonnes/year. In 2020, a company was equipped with a compressed natural gas station that can now recharge three trucks. In the long term, this company’s objective is to be able to run a fleet of 30 trucks on natural gas. The production of gas is partly based on agricultural residues recovered by methanisation, a good example of circular economy.
“The processes are constantly evolving with the aim of promoting energy savings. In a quarry, the use of conveyor belts to transport materials is still preferred to limit the consumption of fossil fuels by the machines. In factories or processing workshops, for example, skylights are installed to reduce electricity consumption. Topographic surveys by drone facilitate and professionalise the work of teams on the sites.”
Boisselon, who is married and has a busy family life with his four children and six grandchildren, sees attracting talent to the mineral extractives industries sector as an “essential” issue.
“The sector’s age pyramid shows that a third of employees are over 50 years old and companies in the “quarries and materials” sector will need to recruit 1,400 employees
every year for 20 years. And we have many assets to attract them.
“Our jobs are close to rural and periurban populations: 58% of employees are employed by establishments located outside of all urban areas. Our jobs are permanent: the authorization period for a quarry is at least 15 years; and it is unlimited for readymix concrete production units... They cannot be relocated. The materials of the sector are produced locally for a local market. Aggregates and ready-mix concrete are produced and used locally within a radius of 30-to-50 kilometres. Our jobs are diversified and accessible to all: We offer a wide range of jobs: from machine driving to engineering, from applied geology to stone cutting. These jobs require a level of qualification from CAP to BAC +5 (engineering degree) through BTS.”
Boisselon says UNICEM and its members reflect a modern industry that responds to societal and environmental issues and is focused on innovation, whether in processes, such as the use of new technologies via topographic survey of quarry sites by drones, in work tools or in research, with a number of companies operating their own product research centres.
He emphasises how the French mineral extraction industries and national
manufacturers of construction materials are also committed to the environment and CSR through UEE (UNICEM’s association of companies committed to implementing sustainable development work), and in their compliance with the French Environment Ministry’s ERC doctrine (avoid-minimisecompensate) fostering biodiversity offsetting for environmentally disruptive works.
Boisselon is also encouraged by figures showing that the employee turnover rate in the sector is five times lower than the French average.
“To highlight these assets and promote the industry, UNICEM participates in numerous job fairs throughout France, and has formed partnerships with the French employment agency (Pôle Emploi) and schools to raise student awareness of the industry. In addition to these ‘field’ actions, we are also adapting our information channels: we are developing the presence of the sector and the presentation of the professions on social networks, including Instagram, and we are working on a new website for next fall.
“We are also working on the place of women in the sector. Today, the employees of the sector are mostly men, but the feminisation is well underway and 17% of the employees are women. We need to tell
women that they have their place in the “quarries and materials” sector. Moreover, on International Women’s Rights Day, we launched a campaign on social networks in which women in the sector talk about their daily lives in the sector.”
As well as holding union mandates at French regional and national levels, Boisselon is a former chairman of the Environment Committee of UEPG (European Aggregates Association).
I am keen to find out about the role UNICEM plays in the wider European mineral materials industry, and how important it is for the association to work with its counterparts in national industry associations.
“As a federation of ‘specialty’ unions, UNICEM does not have a strict equivalent at the European level. However, each UNICEM union works and participates in the work of European unions. The French aggregate producers actively participate in the work of UEPG (European Aggregates Association), the French ready-mix concrete union collaborates with ERMCO (European Ready Mixed Concrete Organisation). These exchanges are essential to prepare and align positions for European debates, to follow the evolution of standards and regulations and to promote the sharing of best practices between members.
“I am personally aware of the importance of the work at this European level, as I have been very involved in UEPG bodies and have led its ‘Environment’ group.”
We end our conversation with Boisselon’s thoughts on the long-term future for the French mineral extraction industries.
“The challenges are numerous. We must accompany sustainability transitions, make better known our actions, and defend the economies of our industries.” AB
“Today, the employees of the sector are mostly men, but the feminisation is well underway and 17% of the employees are women”
Aclimate-resilient infrastructure re-designed and adapted to protect us against and to withstand floods, fires, droughts, heatwaves, and storms. A renovation wave that makes the built environment emitting less CO2 and using less Russian gas (fossil-fuels) contributing to a green energy transition. A transport and military infrastructure that uses more rail and waterways, that provides for modern and partly electrified vehicles and at the same time makes Europe’s ports, airfields and roads ready for defending itself from external threats. All that needs …, right, many more aggregates and other raw materials.
UEPG (the European Aggregates Association) has called for an updated EU Raw Materials Strategy replacing the Initiative published in 2008. Since then, we have had a financial crisis, a pandemic and Russia’s war against Ukraine. The first pillar of the 2008 Initiative addresses critical raw materials and we have seen several editions of the EU list for critical raw materials. For the third pillar we have seen even a legislative package tackling the circular economy. No, we didn’t forget the second pillar: Improving the conditions for access to domestic raw materials, i.e., in Europe, for Europe. The challenge is, that this pillar falls broadly under the subsidiarity principle and is, hence, within the competence of national or regional authorities.
At the same time, environmental legislation including biodiversity, water, air, soil (to some extent) as well as health & safety at the workplace is discussed and ‘Made in Europe’.
I might be cynical, but at times where we see and communicate a clear increased future demand for aggregates – ringing the alarm bell before it’s too late – that’s what we hear from some (though, not all) EU policy makers and stakeholders:
1. Sorry, the focus is on battery and critical raw materials, but we did not forget you.
2. Thank you for the real good work on biodiversity in extraction sites. We need more restoration.
3. No worries, we have the circular economy and can do entirely with recycling.
4. What is aggregates, again?
We have made great progress from a completely unknown industry, and at times mixed up with other sectors, but we have still a long way to go. UEPG President Antonis Antoniou Latouros would add that we must explain better ‘why’ we need our industry before getting into the details of ‘how’ and ‘what’ we do. He is right, the only hope is that this would not be needed for the readers of Aggregates Business Europe
Part of our new campaign on local access to resources is our work within the Construction 2050 Alliance and the
recent event on access to construction raw materials, our Position Paper for a Green and Secure Europe and the new edition of the Leoben Study on improved access to domestic resources providing recommendations for permitting procedures and land-use planning.
For the launch of this new Leoben Study, UEPG invites you to join us for the Late Summer Reception on Wednesday, 7 September 2022 at 17h00 ‘till late in our new Brussels UEPG office. AB
• For registration send us a request to secretariat@uepg.eu. Hope to see you in great numbers to call together for sustainable access to urgently needed strategic and essential raw materials. Aggregates, we are part of the solution!
In this article, Simon Trahair Davies and Jade Kent from Stephens Scown LLP discuss why planning is key if you are thinking of selling your mining business
It is important to consider the below points and acknowledge that the process itself takes time and negotiations do not end until you sign on the dotted line.
Understanding the potential value of your business ahead of any sale provides you with crucial information. The sale of your business needs to meet your personal expectations and fund your next venture (be that retirement or another business venture). In a global market there are a wide range of factors that may determine whether a mine is lucrative. By understanding how you value your business, what adds value and what diminishes value, you may be able to adjust certain things to bring the valuation closer to your expectations before you complete the sale.
The disposal of your business is likely to give rise to tax liability, which will differ depending on what you are selling (trade and assets or shares).
How much tax is payable, and by when, is determined by a wide range of factors. Comprehensive tax planning ahead of any sale will assist in maximising the net proceeds you will receive from the sale, after tax has been paid.
Some of the most common tasks that hold up sales and are often pricier to fix later down the line are:
Inaccurate Statutory Books – Do you know where yours are, and are they up to date reflecting all previous share and director changes?
Companies House filings – Although not all the same details in the Statutory Books are needed at Companies House, the record should also be kept up to date and reflect a true picture of the company’s history.
Share Certificates – Before selling your shares you require evidence of share ownership, so check all current shareholders (and previous owners) have the correct documentation entitling them to the shares they think they own. You will also need evidence that the correct stamp duty was paid on previous transactions.
Disputes – If outstanding disputes with suppliers, customers, adjacent owners or regulatory action cannot be resolved prior to the sale, a prospective buyer is likely to want to ensure that risk in respect of that dispute is appropriately apportioned or mitigated.
Documents – Are your Articles of Association and shareholders’ agreement up to date? Do they do what you need them to? Do you have protection if a minority shareholder wants to block a sale?
Bank charges – It is common for lending to be repaid, but security charges to remain active at Companies House and Land Registry when in fact they don’t need to be. Consent to sell – it is important to ascertain whether you require the prior consent of the bank, a regulator or perhaps a particular shareholder, or if you are selling a lease to a site, the consent of a landlord.
Prospective purchasers will want to understand the rights that the business has to operate from the site. These may include:
• The freehold and leasehold title rights and interests that the business has, or any state mining licences (if applicable) it holds;
• Options, exclusivity agreements, conditional contracts in respect of rights to the surface/ or minerals;
• Planning permissions, environmental permits and other applicable consents.
If you have a trademark, branding, the use of any patents or other IP, do you know whose name it is registered in? On selling your business, would you need to retain any
IP rights and perhaps license them back to the business once it is sold?
Without a formal employment contract in place, employees may be able to give a short notice period before they walk and go and work for a competitor down the road –both of which could affect the value of your business.
Other common issues are:
• Incorrect right to work checks;
• Incorrect calculation of holiday pay. You may face fines of up to £20,000 per illegal worker and claims from employees for unpaid holiday pay.
Outside of employment contracts do you have anything in place with your key customers or suppliers? Are they properly signed and dated?
Mines and quarries bring with them a degree of risk in respect of matters such as statutory, private or public nuisance, trespass, negligence, liability as an occupier under the Occupier’s Liability Act 1957 and 1984, and, in respect of contaminated land, liability under the Environmental Protection Act 1990. Owners looking to sell will need to ensure that such liabilities are appropriately identified and apportioned between the buyer and seller.
Before providing any information to an interested party, speak to your advisor and ensure everyone signs a confidentiality agreement to protect you from disclosing information that either may cause a breach of law and/or be used against you by a competitor. AB
If you would like any information regarding preparing your business for sale, contact Jade Kent or Simon Trahair Davies on 01872 265100 or email enquiries@stephens-scown.co.uk
The Italian aggregates and quarrying plant market is looking far healthier this year, with the brighter sales picture set to continue into 2023, as big Italian government-funded infrastructure works, and other building projects linked to Italy’s earmarked over €200 billion valued share of the European Next Generation EU (NGEU) €750bn coronavirus Recovery and Resilience Facility (RRF) get underway. Guy Woodford reports
The numbers are in, and they are looking pretty good. Sales of construction machinery in Italy rose 30% in 2021 to 25,554 units – with further growth of around 11% to 28,465 units forecast in 2022.
The statistics from the Italian Construction Machinery Union (Unacea) and CER (European Research Centre) were released at the recent SaMoTer Day at Veronafiere in Verona, Italy. The next edition of SaMoTer, the triennial construction machinery exhibition, is scheduled 3-7 May 2023 alongside the Asphaltica exhibition.
Speaking during SaMoTer Day, Federico Bricolo, president of Veronafiere, said: "We are planning for 2023 an edition of the show that will take into account significant expansion, which, in coming years, will see the Italian construction sector receive a sizeable portion of the [NGEU] Recovery and Resilience [RRF] funds. This is why we are also moving at government level to ensure that institutional decision-makers attend SaMoTer and thereby facilitate discussion about these issues with companies and associations."
The data in the Unacea report outlined by
Stefano Fantacone, CER scientific director, indicates that there was a strong acceleration in Italian construction machinery sales in Q4 2021. Data for the first quarter of 2022 indicated only a slight slowdown in the wake of the price of energy and difficulties in procurement of parts. Nevertheless, Fantacone said the construction machinery market trend remains positive, particularly for excavators, wheeled loaders, and wheeled excavators.
Fantacone said 2022 could see an 11.3% rise in construction machinery sales; and an 11.8% increase in earthmoving machinery sales; a 15.1% rise in roadbuilding machinery sales, and a 17.4% uptick in concrete machinery unit sales. Quoting further Unacea report data, Fantacone said Italian construction machinery exports in Q1 2022 were worth €689.5 million - up 7.4% in value on the same period of last year. Meanwhile, construction machinery imports to Italy in the same quarter nearly doubled in value to €529.7 million, up 94.7%.
Summarising the Unacea report, Luca Nutarelli, the association’s secretary-general, said: "The construction machinery market in Italy continues to be dynamic, even if there
is a slowdown for order books arising from uncertainties caused by geopolitical tensions. However, we hope to close the year with two-figure [sales] growth."
Italian hydraulic attachments specialist Simex echoes Unacea and GlobalData’s upbeat Italian market analysis. Alessandro Ferrin, the company’s marketing executive, said: “Global trends indicate a significant increase in Italian demand for machinery, following what happened in 2021, a year that was a turning point after the [height of the] pandemic. The aggregates market is also influenced by large investments in major public works, especially those regarding key infrastructures.”
Commenting on the key issues and challenges facing Italian aggregate producers/ quarry operators, and how Simex is helping to tackle them, Ferrin said: “There are plenty; one of those is related to circular economy and the need to process new types of materials to generate value. This implies a constant effort in research and development of even more versatile and reliable attachments. Recently, we launched a new crushing bucket specifically designed to recover asphalt slabs to generate reclaimed asphalt pavement,
following the updated regulations in terms of end-of-waste and conglomerate recovery. This, therefore, led us to study new equipment for the operators, also beyond the common volumetric reduction or separation of aggregates.”
Asked by Aggregates Business how big a factor sustainability and reducing carbon emissions is to Simex’s Italian quarrying machinery customers, Ferrin said it was “probably the main factor” and “one of the big challenges” for the next decade.
“Electrification, waste reclassification, sustainability of the entire production cycle as well as of the entire quarryaggregates - construction site chain: all this represents huge change stimulated from above [national/regional government, new legislation], but also need to be processed and adopted from below [quarry operators/ aggregates product producers].”
Caterpillar has a big presence in the Italian quarrying and construction equipment market via its CGT dealership. Stefano Giardina, CGT product managerlarge equipment, explains that aggregates production in Italy is traditionally very fragmented and is mostly made up of family-run companies. “Consequently, companies are looking for tailored solutions for equipment and related services. The collaboration between CGT and Caterpillar plays a central role by combining the ability to develop and deliver innovative services together with efficient Cat equipment. For example, the XE range of wheeled loaders helps our customers increase efficiency, lower fuel burn, and reduce CO2 per tonne.”
Like many other countries, Giardina says Italy is suffering from a shortage of qualified operators, and on-board technology in Cat equipment helps operators get better accuracy and hit target payloads. The Cat Operator Coaching feature teaches proper operator technique and Cat Autodig with
Auto Set tyres ensures consistent high bucket-fill factor whilst Cat Payload with Assist provides an accurate weighing of bucket loads.
Commenting on current Italian building materials demand, Giardina says: “The demand for Italian marble remains strong, driven mainly by home construction, especially in markets such as the Middle East and China. The demand for aggregates is also strong and driven by substantial infrastructure projects.
“Under the [Italian] Infrastructure Operational Plan, the government is investing €5.3 billion to develop road, rail, and port infrastructure until 2025. Today, there are over hundred active infrastructure works in the country, both road and rail, such as the Brescia-Padua high-speed rail in northcentral Italy and [the] Palermo-Messina [double-track railways project] in the South, with approved investments of over €100 billion. Such an amount of work requires a high quantity of materials, and that demand will remain high over the next few years.”
Asked about the importance of Italy’s recycled aggregates market, Giardina responds: “Italy is historically poor in raw materials and rich in art and landscapes, which makes natural aggregates extracted from quarries, mines, and riverbeds less and less available to the market and increases the use of recycled and artificial aggregates. Consequently, Italy has become one of the leading countries in Europe for the recovery of material from inert waste, through
construction and demolition activities and other industrial processes. The recovery rate reaches 78% of the produced inert waste.
“The sector is waiting for two important laws to increase the circular rate in the construction industry: The end-of-waste decree for inert waste and the decree for C.A.M. [climate change adaption methodology] infrastructure [planning and implementation]. Its publication could give a strong boost to the market and help solve some issues since the only technical rule currently in force is 24 years old (February 28, 1998) and was written without considering features and differences on the nature of recycled and artificial aggregates and their possible use.
“In addition to the wait for the publication of these two decrees, there is also concern for the text of the inert end-of-waste decree notified to the European Commission by the [Italian] Ministry for Ecological Transition as it contains conceptual errors - for example the exclusion of EER [energy efficiency ratio] codes currently in use in many plants, such as earthquake waste - and imposes limits on the content of some constituent and non-contaminating elements, which risk blocking the entire sector.”
Giardina says the Italian authorities have issued around 1,880 permits for recycling inert waste, most of those are for small quantities. Only a few plants have an authorisation that exceeds 100,000 tonnes a year. “It is thought that there is still a lot to do to encourage an increase of the recycling rate in products and in civil, industrial and above all infrastructure building works,” he adds.
Looking at the Italian aggregates industry’s prospects for the next 18 months, Giardina says: “The demand for material and consequently for machines and equipment should remain at a high level with approved projects and a strong investment drive ensured by Italy’s Recovery and Resilience Plan (RRP) developed within the broader NGEU programme responding to the economic crisis triggered by the 2019 pandemic.
“Within the RRP there are two macro activities that will contribute significantly to the sustenance of the sector: the green revolution and ecological transition, the latter embraces the theme of improving the energy efficiency of public and private real estate assets and that of infrastructures for sustainable mobility. This complex plan benefits from an investment of over €190 billion which will drive the demand for the next few years. There are some variables that may impact negatively in the coming months, including the geopolitical situation in Eastern Europe and the pandemic that still today limits everyday life and work.”
Matec Industries (Matec), a major Italian washing plant solutions manufacturer for industries including quarrying and mining, has been doing strong business in recent years and has ambitious plans to increase its global sales reach.
Speaking about the Italian quarrying plant market to Aggregates Business during the recent Hillhead 2022 exhibition near Buxton, in Derbyshire, England, Matteo Goich, Matec’s founder and CEO, says: “Business in Italy is going much, much better. The Italian Covid Recovery Plan is generating plant demand, as are works associated with Industry 4.0., which come with tax credits
for those who spend on machines linked to the development of new technology infrastructure. Matec is the only Italian manufacturer whose entire machine range is certified as Industry 4.0-approved for the Italian market. It means that our customers can access the tax credits by investing in us –cutting the cost for them by 50% in north and central Italy, and 90% in southern Italy.
“With the [coronavirus] recovery plan, there are a lot of construction projects, such as new highway infrastructure, which increases equipment demand. The Recovery Plan stresses that investment should be made in companies focused on promoting a circular green economy and Matec was born as a producer of wastewater treatment and water recycling plants.”
Speaking about the company’s manufacturing footprint, he says: “We have a 12,000m² wash plants factory in MassaCarrara, and an around 10,000m² factory to produce our pumps and other equipment in Verona. We are opening another factory, a 20,000m² site close to Parma, and staging an open day on this in September. It is a big investment for us and includes a lot of automated production, such as robotic welding. It will manufacture our complete washing plants and our crushing and screening units.”
Goich continues: “Washing plants for C&D [construction and demolition] recycling applications is our biggest growth market within the aggregates industry. It is the
future – and that is good for us as a leader in this area of the market. Another growth area for our complete washing plants will be processing contaminated soil.
“We want to increase the size range of our full washing plants, going from the little size to the big models, which include big log washers.
“I think next year we can achieve turnover of €65-75 million. We are very open to further acquisitions after Alfa Pumps. Our business plan in three years is arriving at €100 million turnover, and in five years, through acquisition and yearly sales growth, to a turnover of €200 million.”
Commenting on the Italian building materials market, Michele Vitulano, commercial & marketing director of Indeco, a Bari, Puglia-based hydraulic hammer manufacturer for industries including quarrying, said: “The market is changing. Italian politicians are pushing for the reuse of concrete and other crushing and demolition waste materials on-site in new building projects.”
To meet rising global hydraulic hammer demand, Vitulano, who was also speaking to Aggregates Business at Hillhead, said Indeco has invested in a new €7 million metal casing fabrication plant in the Bari area.
Speaking about general trading challenges faced by Indeco in Italy and the wider global market, he adds: “The cost of energy and [hammer manufacturing] materials is increasing, which leaves us facing difficulties in managing our production cost. We had not increased our [product] prices since 2007 until small single-digit rises last year. Many companies have made double-digit price increases, including in 2022. We did another single-digit price increase in February this year, but by the end of July, I think I will be forced to do another small increase as there appears no end to the production cost rise.” AB
Digitalisation can drive gains across aggregates-producing assets
Quarry operators can generate a great deal of productivity and efficiency gains through using premium stationary aggregates plants. Roger Murrow reports
Stationary aggregate plants include some of the most advanced crushing and screening equipment available. Many would think that given the development work undertaken by manufacturers of such equipment that product development would have come to a logical conclusion. However, this could not be further from the truth, with some of the leading manufacturers developing new equipment and operating philosophies focused on boosting customer operations.
Some of the leading names in stationary crushing and screening are continuously refining their offering, listening to their customers to produce the next generation of aggregate plants. In this article, we’ve talked to some of the leading manufacturers and outlined their latest developments, along with touching on their development strategies, which look likely to be continuously refined and developed in the coming years.
A long history of product development
Metso Outotec has a long history of developing and introducing some of the most advanced and productive crushing
and screening equipment in the industry.
The company has recently introduced a ‘facelift’ version to its static crusher automation package. The initial release covered the company’s GP cones, with other product lines to be covered later in the year. Alongside this, Metso Outotec has just released its new ‘Metrics’, which provides customers with more data for crushers and screens. With this information, combined with what the company refers to as its expert services, technicians are able to troubleshoot problems and optimise operations, thereby improving performance and availability of quarries.
“The new version [of Metrics] makes it even more user-friendly than before and assists the user to maintain high performance and adapt to changes in feed material and liner wear during the day. With the new Metrics, we can now collect and visualise all data coming from our automation almost in real time,” explains Jason Nelson, global director of marketing, Aftermarket Solutions.
The system further highlights Metso’s commitment to using technology to advance the crushing process, as Nelson
explains: “We provide crusher control packages for all types of static crushers. With these you can automate the crusher level operation and protect equipment. Crusher control packages provide data to the remote-monitoring system Metrics, enabling further digital features. Automated feed rate control keeps the crusher choke fed at all times. Wear compensation and automatic contact calibration help to maintain correct closed side setting. These together assist to maximise yield of desired products. Improved availability and performance of a plant and product quality by using data driven methods, automation, and intelligent sensors.”
Maintaining crushing performance
Another development from the company is in direct response to variability in ore type and changes in liner materials that can impact the wear rates experienced by the liners used to protect the inner walls of crusher transfer and feed chutes. This variability can lead to increased operational costs due to unplanned maintenance which may be required to replace highly worn liners. Alternatively,
high maintenance costs may occur due to the scheduled replacement of plates still in good condition. Regular inspection of the liner condition can reduce these costs but requires the plant to be stopped. This reduces productivity and poses a safety risk for the maintenance personnel who need to enter the chute. In response, Metso Outotec has developed ‘WearSense’ which can safely provide visibility on liner condition with actionable insights to reduce maintenance costs. This is a self-contained wearmanagement system consisting of proprietary IoT sensors that monitor wear and other key parameters, a gateway that connects to cloud-based storage, processing algorithms and a web-based user interface. It is primarily designed to monitor the wear in chute liners and provides near-real time information on remaining material thickness and the ability to estimate the remaining liner life.
Emphasis on ease of replacement
If Metso Outotec has placed its emphasis on recent cone crusher developments, Sandvik has focused on its ubiquitous jaw crushers. Sandvik has now concentrated on what it terms ‘plug and play’ installation, with its jaw crushers being available as a complete crushing solution ready to start crushing in the shortest possible time. “We deliver our jaw crushers with everything a customer needs for plug-and-play primary crushing operations,” says Mats Dahlberg, vice president Lifecycle Service, Stationary Crushing and Screening. “It’s just to choose what extra components they require. There’s also a wide range of jaw plates that can be mixed and reversed to ensure optimal, versatile crushing.”
Sandvik jaw crushers can now be delivered with a complete infrastructure including feed hopper, feed hopper interface, drive and subframe with v-belt guard and motor bracket, a unique guarding retraction arrangement and toggle plate stop. “We now include everything our customers need for a fast start-up and reliable operations. Together with easy and safe maintenance, our jaw crushers increase productivity, offer true reliability and excellent availability,” adds Martin Johansson, product manager Jaw Crushers.
This introduction is part of a focus on ‘circularity’ for the company, which has stressed its commitment to reusing and recycling to offset the use of raw materials and reduce waste. Several initiatives are ongoing to contribute to the Sandvik target of more than 90% circularity by 2030. Material- and resource-efficiency focus within product development and the company’s operations are examples of how
Maintaining equipment availability comes down to combining data with on-site expertise for best results
Sandvik is driving the shift to more circular business models and use of resources, finding ways to close loops and generate new revenue streams from the processes and materials it uses.
The Terex Materials Processing (Terex MP) business division of the Terex Corporation has grown rapidly in recent years, adapting
In April 2019, the Metso Truck Body was officially launched at the BAUMA fair in Munich. It was awarded “Product of the Year” by Mining Magazine and garnered extensive media coverage by some of the most influential mining and aggregate channels. The launch of the truck body has been a great success, and since then, Metso Outotec has seen an ever-growing interest in this innovative solution from the industry.
The Metso Outotec Truck Body was on show on the MSS stand, J6, at the Hillhead exhibition 21-23 JUNE 2022 in Hillhead Quarry, Buxton, UK.
www.hillhead.com www.mss-maintenance.co.uk www.mogroup.com
and adopting high tech and state-of-the-art systems. Terex MP president Kieran Hegarty explains what the company believes are the big issues affecting the industry: “The big trend in our industry is electrification and hybrid power plant. It is accelerating for environmental reasons and for more immediate real-world stuff. I was in India recently, and I was astounded how the electrification of plant there in the last two years is ahead of Europe. China is another major market that is embracing electrification.”
Terex CEO and president John Garrison adds to Hegarty’s comments: “Digitalisation is another huge industry trend: connecting the end-use customer with their dealer and us through telematics platforms. If we are not working via iPads, iPhones, or other digital means, we are also not going to attract young people to our industry.” Terex MP has continued to develop its pioneering work in the industry, recently forming a Digital Solutions Group within Terex MP about six months ago to actively look at digital innovation to help end users and dealers as aggregate crushing and screening plant operators need quality actionable data to improve their operating efficiency. In effect, Terex wishes to help its customers increase their uptime and productivity, producing more tonnes per hour.
Updated cone crusher range
In line with these strategic decisions, Paul Lilley, sales director, Terex MPS ERA, states: “The basic principles of crushing and screening are still the same, but today’s crushing and screening equipment
is designed and built to be more efficient, easier to use, perform consistently, and produce high-quality aggregates at the lowest cost per tonne possible. Terex MPS has renewed the proven Cedarapids MVPX cone crusher range to be more efficient, less costly and to consistently produce quality aggregates.” Lilley adds: “The skills shortage within the quarry industry across the world has meant that skilled operators are in short supply, so Terex has developed the ACE8 control system to ensure quarry operators can easily see how the crusher is performing
and that data can be used to make decisions on the crusher operating parameters.”
The Cedarapids MVP450X’s new ACE8 control system includes a bowl float monitor to ensure users can know the performance limits of their application. It has improved design features, such as stronger head design, without any weight increase, simplified upper assembly and base-frame design. It features a hydraulic clearing function using dual direction ‘Tramp Iron Relief’ (TIR) cylinders, which facilitates faster manganese changes and reduced downtime. The hydraulic anti-spin stops unnecessary wear of manganese.
The new control system helps ensures customers have accurate data immediately, and, importantly, makes it easier for end users to utilize that data and have more control over the final product.
The company states that all MPS equipment is now fully electric, with the most efficient way to power a crushing and screening plant being by mains electricity supply.
Another global, US-headquartered giant, Astec, provides a holistic solution to aggregate operations. The company believes that as the global market consolidates, it expects its customers will take on more construction responsibilities. Astec Industries CEO & president Barry Ruffalo states: “We can help them do it. When you can also give those customers enhanced data and digital analytics, it is an even better offer.”
Ruffalo further explains how the company’s ethos and outlook is further helping customers: “In our ‘OneASTEC’ business model, sustainability is identified as a key driver of our success. When I joined Astec and met with customers, I did not get
many questions on sustainable solutions. Today, eight out of ten customers ask how we can help them with their sustainability goals. Moving forward, all new products will have a sustainable component to them. We’ve used electric generators for over fifty years, so we will continue to roll sustainable power solutions into our product lines.”
Continuing the development of products that fit in with its avowed Rock to Road value chain, Astec has recently launched what the company says is the industry’s first 8ft-wide high-frequency screen. Specifically developed for the processing of fine material, the screen has externally mounted vibrators at the end of the tappets for a more aggressive screening action. This unique design creates a higher G-force and reduces heat load from material to motors when compared to single, centre-mounted vibrators. The design also allows for easier access for maintenance and adjustments and minimizes product contamination in case of leaks. As with other products, the new screen is powered electrically, either as part of a complete electric system or hybrid line power technology.
Another development sees Astec expand its TRAC10 cone control system, used on Titan bushing cone crushers, to its Kodiak roller-bearing cone line. The software expansion provides a new, easy-to-use interface for cone crusher customers, with the stand-alone system monitoring crusher operations, providing automated calibration and setting controls and protecting crushers from overload events. TRAC10 also allows producers to run and control multiple crushers at once, can connect to a laptop or smartphone and can be integrated into existing systems.
Of direct interest to the industry, Astec has recently consolidated its multi-brand offering under the Astec banner. This includes such industry-renowned names
as Kolberg-Pioneer, Osborn Engineering, Telsmith, Johnson Crushers International, Astec Mobile Screens and Telestack.
Astec Industries is also embarking on a major global expansion of its comprehensive product- and linked-services offering across the crushing and screening, material handling, washing and classifying, rock breaker technology, asphalt and concrete sectors.
New modular system provides transferable solution
McLanahan recently added the CMB Cone Crusher to its existing line of crushers. The machine was added as part of McLanahan’s acquisition of CMB International Limited, a manufacturer of crushers, horizontal screens, inclined screens, feeders and conveyors based in Leicestershire, United Kingdom. The CMB Cone Crusher is mounted on a modular chassis as part of McLanahan’s
‘UltraCRUSH’ range to provide a quick setup and an easily transferable solution.
The UltraCRUSh arrives on site in an almost fully assembled state. Once removed from the shipping container it can be set into place, connected to electrical power and is able to start production. Its modular assembly makes it ideal for moving around one site, or to other sites, to fit an operation’s changing needs. As part of an UltraCRUSH system, the CMB Cone Crusher provides producers with a heavy-duty crushing system that requires minimal maintenance, while producing high outputs. The CMB Cone Crusher features a hydraulic adjustment system that enables the operator to rapidly change the discharge setting with little interruption to production. In addition to the adjustment system, the crusher also features hydraulics for a tramp metal release, automatic reset and an unblocking feature that can clear the crushing chamber in a matter of minutes.
Larger units of the CMB Cone Crusher feature a hydraulically tensioned wedge that provides the correct constant crushing pressure for enhanced performance and productivity. Longer, strong rams allow for larger setting and thicker manganese, providing more crushing hours and production, while limiting unwanted downtime. These larger sizes also feature an increased internal clearance for ease of material discharge, which minimises material build up and reduces potential for damage.
More to come soon?
Given that trade shows are once again happening, with the UK’s Hillhead exhibition held in late June, it could be expected that these would be the main developments in stationary crushing and screening in 2022. However, the bauma exhibition in Munich will soon be held, and as the traditional launch pad for new products in the construction industry, it is highly probable that many new products and solutions will be introduced at this behemoth. AB
A new articulated hauler prototype is using hydrogen fuel cells to tackle the issue of how to power heavy quarrying machinery in a sustainable way. Major hauler manufacturers have also been giving details of their latest innovations on show at this year’s rescheduled Hillhead and bauma events. Liam McLoughlin reports
Volvo Construction Equipment (Volvo CE) has started testing the world's first fuel cell articulated hauler prototype, the Volvo HX04.
The eye-catching move follows the global off-highway machine giant's completion of a multi-stakeholder research project aimed at breaking new ground in hydrogen technology. The project's results will provide important insights into the possibilities provided by hydrogen and fuel cells as Volvo CE continues research for its future product development programmes.
Volvo CE has accelerated its work into sustainable power sources by acting on its Science Based Targets initiative (SBTi) commitment of net-zero value-chain greenhouse gas emissions by 2040 and driving industry transformation towards carbon neutrality.
Besides battery-electric solutions, where Volvo CE says it is already offering the largest range of commercial products, the company's efforts also include exploring the potential of electrification through hydrogen fuel cell technology. Now, an important milestone has been reached with the testing of a world-first, emission-free hydrogen fuel cell articulated hauler prototype, the Volvo HX04.
Carolina Diez Ferrer, head of advanced engineering programmes at Volvo CE, says: "Being inventors of the world's first articulated hauler more than 55 years ago, we are happy and proud to again drive change with this fuel cell hauler concept. While an early prototype, this innovation will give valuable insights into the opportunities of hydrogen in the energy transformation alongside battery-electric solutions.
We believe that by exploring multiple technologies and working in partnership, we can create the best path forward to decarbonize the construction industry."
The Volvo HX04 is the result of a research project running between 2018 and 2022, with funding from FFI, a national collaboration between the Swedish Innovation Agency VINNOVA, Swedish Energy Agency, and Swedish Transport Administration, to support sustainable vehicle strategic research, innovation and development. Partners include Volvo CE, RISE Research Institutes of Sweden, who provided specialist competence on driveline development and safety, and PowerCell Sweden, a developer of fuel cell-based hydrogen-electric power solutions.
The development and building of the six-wheel prototype have largely been carried out at Volvo CE's facility in Braås, Sweden – the same location where Gravel Charlie, the world’s first articulated hauler, was born back in 1966, giving the Volvo HX04 the nickname Electric Charlie. Engineers at the technology centre in Eskilstuna, Sweden, have contributed with software development and knowledge gathered through its fuel cell test lab. While not commercially available, valuable insights from the concept will inevitably inform future production.
Infrastructure for hydrogen is still in development, which means refuelling the Volvo HX04 is an important aspect to solve in the project. Shell installed a state-ofthe-art hydrogen refuelling station at the Volvo CE test track in Braås. Both Shell and Volvo Group are founding members of H2Accelerate, a collaboration of companies
working to foster conditions for the mass market roll-out of hydrogen trucks in Europe.
The fuelling process for hydrogen vehicles is fast – the Volvo HX04 is charged with 12kg hydrogen in circa 7.5 minutes, enabling it to operate for approximately four hours.
Fuel cells work by combining hydrogen with oxygen, and the resulting chemical reaction produces electricity which powers the machine. In the process, fuel cells also produce heat that can be used for the cab's heating. Fuel cells only emit one thing –water vapour.
In principle, a fuel cell works much like a battery except that it generates its own electricity from the hydrogen onboard as needed rather than being charged from an external source. Vehicles with fuel cell electric powertrains have an uptime, range, and fuelling time similar to that of combustion engine-powered vehicles.
While battery-electric vehicles and biofuels are commercially available today – as more sustainable alternatives to diesel – commercialisation of hydrogen-powered machines is expected during the second half of this decade.
International articulated dump truck (ADT) specialist Bell Equipment has been giving comprehensive details about its planned programme for the bauma 2022 quarrying, construction and mining equipment show in Munich, Germany (October 24-30).
One of the most interesting ADT innovations that Bell will be exhibiting is its autonomous vehicle operation, which the company says enables interoperability between different control systems and the trucks it produces.
An autonomous haulage system has been fitted on Bell B30E ADTs at a lime quarry in the Alps
An autonomous operation has three elements: machines that can be operated remotely, external sensors that become the eyes and ears of the machine, and sophisticated site control software that manages the operation based on communication with the other two elements. According to Bell Equipment ADT product marketing manager, Brad Castle: “Providing autonomous-ready machines will be a part of our core business in the future but in terms of sensing and guidance systems it makes sense to partner with market leaders
and innovators, as we do with drivetrain, hydraulics and electronics technologies in our trucks.”
At the same time, Bell wants to provide a vehicle that can be fitted and controlled with a guidance system from any number of manufacturers with the easiest integration. Castle adds: “Autonomous applications are industry-specific and require surveying and guidance by an industry expert. We want our customers to be able to choose a guidance solution that they are most comfortable with and that can be fitted to all the machines in
the work cycle. Keeping the guidance system independent of the OEM gives customers the flexibility to run a mixed fleet and benefit from the efficiency and productivity that it provides.”
Adding to the flexibility, Bell provides a standard cab with no extra hardware taking up space to create an environment where manual, remote or autonomous operation is interchangeable.
As economies of scale and technology become more affordable and reliable in the future, Bell expects to see smaller and smaller sites embracing autonomous operations.
“Support vehicles, such as service vehicles and water bowsers, may also form part of autonomous operations,” says Castle. “This would make it even more important that every machine on site, regardless of the OEM, is able to use and respond to the same software. We envisage that there could also be sites where the main earthmoving operations are fully autonomous, but support vehicles that perform a wide variety of functions are remotely operated from a central area. This would allow the site to have no people whatsoever which improves safety.”
Since early 2020, Bell has been working with tech companies indurad and voestalpine on a lime quarry site in the Alps where industrial radar specialist indurad has fitted its iTruck autonomous haulage system (AHS) on Bell B30E ADTs with what are said to be excellent results.
Also on display at bauma will be the new generation of the two-axle ADT Bell B45E 4x4 and a Bell B30E with a vehicle width of less than 3.0 metres. Bell says that both machines offer a compelling advantage to customers with specific requirements.
As a supplement to its range of seven ‘traditional’ 6x6 ADTs, with payloads from 18,000 to 45,400kg, Bell Equipment says it is the only manufacturer of articulated
haulers in the world to offer a parallel range of two-axle ADTs for the past six years. All three models are aimed at different market segments. Bell adds that in the right applications they outperform conventional rigid dump trucks that need good haul roads and the three-axle ADTs designed for extreme off-road mobility.
At the upper end, the Bell B60E 4x4 – with a 55-tonne payload and 35m³ dump body capacity, is designed to be a benchmark for all-weather operations on undulating ground in opencast mines or large quarries. At the bottom of the range, the Bell B30E 4x4 (28t; 18,5m³) is a compact and highly economical solution for sand and gravel pits, material handling or underground operations.
The second-generation Bell B45E 4x4 (41t; 25m³) is aimed at small to medium-sized quarry operations. Here it competes against rigid trucks in the 45- to 55-tonne class or 6x6 ADTs with payloads of 40 tonnes or more. Compared to both types of vehicles, Bell says the 4x4 truck shows its strengths to the full in typical hard-stone quarrying on rough ground with steep climbs and tight bends.
In wet weather, conventional 4x2 rigid tippers quickly reach their limits. Bell says the all-wheel drive and oscillation joint of the B45E 4x4 always ensure high traction, and the retarder and service brakes can be applied in a very controlled manner even under full load thanks to constant ground contact by all tyres. The high power -to-weight ratio keeps cycles times low in difficult weather conditions and extends production times in exposed quarries. In addition, the Bell B45E 4x4 can be also used in overburden or new excavations.
Bell states: “While this machine does not excel in soft underfoot conditions like its 6x6 counterpart, its twin-tyred single rear axle brings substantial advantages over 6x6 ADT tandem axles on hard roads. In tight corners the tandem axle experiences significant tyre wear and wears the road down. In addition, there is greater manoeuvrability thanks to the shorter rear chassis, which, together with the rock bin typical of quarries, results in faster cycles on the quarry faces or at the primary crusher.”
At its first presentation at bauma 2019, Bell says the B45E 4x4 generated a great deal of interest, especially among Central European quarry operators as the 4x4 two-axle vehicle is well suited to their jobsites and productivity requirements.
Bell Equipment's product and application specialists also recognised the potential in a segment that is characterised by a shrinking range of corresponding rigid dump truck solutions. Triggered by the company-wide transition of all Bell ADTs to EU Stage V, it was decided to revise the first generation. In addition to the Stage V improvements, a number of changes were incorporated based on user feedback from practical tests and initial customer placements.
The most significant changes relate to the rear end of the Bell B45E 4x4. The rear axle is
now suspended and the bin has been heavily modified. Despite this, the frame length and wheelbase remained almost identical, making the two-axle articulated truck highly manoeuvrable (max. turning circle: 17.31m).
As with the 60-tonne Bell B60E 4x4, two oil/nitrogen hydro-pneumatic struts now take over the suspension of the rear axle from German manufacturer, Kessler. In combination with the standard adaptive "Comfort-Ride" front suspension, this provides significantly more driving comfort for a vehicle that weighs around 79 tonnes when loaded. In addition to a limited slip differential, the rear axle now also features sensor-supported automatic traction control. The new suspension geometry and kinematics have been designed to allow the 21.00 R35 twin tyres to be fitted with snow chains.
The exhaust-heated rock bin with flat bottom has been completely redesigned. For better matching with the wheeled loaders, often typical in small to mediumsized quarries, the standard bin has been lengthened and given a straight front wall. This gives a longer top edge of the body and better filling speed with wide 3.5 m³ to 6m³ rock shovels (bin height: 3,485mm).
Both the maximum tipping height (6,485mm at 55°) and the large ground clearance of the chute (890mm) remain almost unchanged. This means that the articulated 41-tonne two-axle truck can be fitted into existing infrastructures (e.g., crusher enclosures) much more easily than comparable 6x6 articulated trucks with a long earthmoving body but offers advantages over conventional rigid tippers that have a low tip clearance when unloading quickly on any terrain.
The Bell B45E 4x4 has an almost identical front end to its 6x6 sister model, the B45E. Bell says this means that operators benefit from the company’s continuously developed 6x6 articulated large-series technology in terms of drive, power transmission and
intelligent vehicle control. Under the bonnet is the 390kW in-line six-cylinder OM471LA from Mercedes-Benz.
ADT manufacturer Rokbak's commitment to rock-solid reliability, power and performance was in focus at June's Hillhead quarrying exhibition in Derbyshire, UK, with three of its articulated haulers on display.
The RA40 was on Rokbak's stand, and an RA30 was at the Molson Group's stand. An RA40 was working at the quarry face demonstration area, where visitors could see it doing real-world work in a live quarry environment.
"We're currently seeing huge demand for our articulated haulers, with dealers and customers excited to get hold of the new machines," said Rokbak MD Paul Douglas.
Since becoming part of the Volvo Group almost eight years ago, Rokbak has introduced multiple improvements with the aim of delivering new benchmarks in terms of hauler power, performance and total cost of ownership. For example, for the European market, the RA30 and RA40 feature the latest EU Stage V emissions-compliant engine, boasting up to a 7% improvement in fuel efficiency compared to older EU Stage IV engines.
"The machines we have on the market today are in a different league to what was on offer previously,” Douglas added. “It has been a process of continual evolution. That's why we felt it was right to recognise this evolution with a new brand name [from the previous Terex Trucks] and to launch an exciting new chapter in our history."
Rokbak has also made substantial recent investments and improvements in employees, sustainability, processes, facilities and equipment. Investments at the production site in Motherwell, Scotland, have improved safety, quality and environmental performance. These developments have also improved throughput efficiency and reduced manufacturing costs. AB
Telestack, a major global dry bulk materials-handling solutions manufacturer for industries including quarrying, had a major presence at Hillhead 2022 near Buxton, Derbyshire, England. The Omagh, County Tyrone, Northern Irelandheadquartered, Astec Industries-owned company was promoting its near 30-strong Zero range of track-mounted conveyors, mobile hopper feeders and radial stacking conveyors.
The term Zero relates to units that have no engine fitted. Telestack Zero mobile tracked conveyors and hopper feeders incorporate electric hydraulic power packs to run the tracks in parallel with electric drives to operate the conveyor section. The engine is completely removed from the machine.
The Zero range offers quarrying customers a greener alternative to the sector’s traditional track-mounted dieselhydrualic conveyors and builds on Telestack’s more than three decades global supply of electric-powered conveyors for static applications and the port industry.
Speaking to Aggregates Business at Hillhead 2022 stand, Padraig McDermott, Telestack’s international sales manager, says customers are attracted to the reduced complexity, ease of running and quick set-up times of the Zero range.
Pointing to an on-stand, 500-tonnes-perhour Telestack conveyor, he says: “That is run by two 11kW motors – 22kW, but you do not use all that. Whenever we manufacture a diesel-hydraulic conveyor, we must fit a 37kW engine in it to account for hydraulic losses in pumps, motors and hydraulic lines. Generally speaking, hydraulics is not an efficient technology, because a substantial amount of power is lost in the process of converting energy.
New product lines and a wealth of new technical expert analysis are enriching the conveyors area of the global quarrying equipment market. Guy Woodford reports
“Typically, you are using 30% to 40% less power by going electric. You are not only matching your production volumes, but you’re also likely increasing it, as there is not a lot of maintenance needed. Noise emissions will also be considerably reduced when you compare an engine to quiet electric motors. This is particularly advantageous when working close to built-up residential areas or conservation areas.
“You can power your [Zero range] conveyor from other equipment like the crusher or screener or mains power. If your provider is generating their electricity by renewable technology, then your carbon footprint is drastically reduced.”
Taking the Zero range one step further at Hillhead, Telestack launched its first Zero
‘Battery’ conveyor. McDermott explained the operation. “The Zero battery machine incorporates a battery pack which is used for tracking, relocation and set-up. The battery pack provides power for approximately one to one-and-a-quarter minutes of tracking. This allows the customer to load the machine, transport it to site, offload and bring it to the working area. When in position the conveyor is connected to mains power or a primary power source to run the conveyor section.
“The battery pack we have developed for our conveyors is a modular kit. We can slot it into a bigger machine and increase the module size with extra cells in the battery to gain the required throughput.
“Once you plug in to a mains supply, there
is a trickle supply to the battery, so you can recharge it in four hours.
“With regard to return on investment, typically electric-powered tracked conveyors are more expensive to buy, but your return on investment is quicker.”
McDermott says that “around 90%-95%” of tracked mobile conveyors working in quarries had been diesel-hydraulic powered “until recently”. “It could be that this year we see 25%-30% of our quarry conveyors powered electrically.” That is a significant shift - driven by the cost of fuel and the customer’s desire to become more efficient in their operation
Scandinavia is likely to generate the biggest regional demand for the Telestack Zero range, McDermott believes, followed by well-populated European cities, such as Berlin, Frankfurt and Strasbourg, where there is a big push to reduce carbon emissions and work-site noise levels. He continues:
“After Europe, I think the United States and Australia could be good markets for the range. The sharp rise in the price of diesel fuel is as much as a shock to them as it is to us!”
Cement manufacturers face strict environmental regulations with alternative fuels. This way, they fire calciners and main burners in an efficient and sustainable manner. BEUMER Group develops singlesource solutions to convey, store and feed the differently composed materials. Among other things, the overall systems are made up of specially developed individual components.
Cement is the most used building material worldwide and the usage rate is continuously growing. However, manufacturers must comply with ever stricter environmental regulations in order to get air pollution under control. Depending on the processes used, the emissions from producing cement are at 0.6 to 0.99 t of CO2 per ton of cement. The CO2 emissions from this sector are estimated to account for seven to eight percent of the overall global carbon dioxide emissions. An approach to sustainably reduce greenhouse gas emissions and production costs is to increase the use of alternative fuels.
Fluid materials like waste oil or solvents, but also solids for example, are used instead of coal and gas. The majority is composed of municipal and industrial waste, such as plastic, paper, composite material or textile mixes as well as wood pellets. The use of entire or shredded waste tyres is also welcome. The calorific value of the rubber from waste tyres is comparable to that from hard coal, and the iron from the reinforcement can be incorporated mineralogically into the cement. This minimises the addition of ferrous corrective substances. Alternative fuels are available in large quantities and at low costs and can be disposed of completely in a safe hightemperature process in the rotary kilns at the cement plants. Thus, these materials do not have to be landfilled or otherwise disposed of.
As different materials have different calorific values, the complete household
waste cannot simply be fed into the combustion process in the kiln. Especially in countries where waste separation is not developed like in Europe, the challenge is huge. How the alternative fuels are composed and how they are used often also depends on their availability in a determined region and, in particular, on the economic aspects. In addition, the materials must fulfil determined quality requirements. Some operators for example only use processed waste with a defined minimum calorific value and low heavy-metal content. At this regard, the alternative fuel often may only have a determined particle size and a determined density. The moisture content is also important.
As a system provider, BEUMER Group develops tailor-made solutions for the entire material flow chain from unloading the delivery vehicle to storing, weighing, conveying and control feeding of solid alternative fuels. BEUMER Group also
control feed, singulate and convey large and heavy tyres to the inlet of the rotary kiln. BEUMER Group supports the cement manufacturers with its intralogistic solutions in modernising their plants in sustainable and cost-efficent ways. "Our know-how and tailor-made systems permit us to optimise our customers' processes," says Jan Tuma, chief sales officer (CSO), BEUMER Group, Czech Republic. The user receives everything from one source, thus having a unique contact. In addition to a comprehensive range of reliable systems for handling with alternative fuels, the specialists also focus on planning logistics and customised conveying and storage solutions, including crane halls and steel structures.
"The material flow chain is implemented with the single components of our BG OptiSeries," says Tuma. "We have developed these different systems in our company - a clear unique feature on the market". The systems are designed to meet
performance in daily operation.
The material prepared for combustion in the kiln is usually supplied in movingfloor trailers. The hydraulically controlled moving floor moves the load outwards on the conveying system. "All conveying systems supplied and the accompanying equipment are intertwined like toothed gears to ensure steady fuel feeding," explains Tuma. "At this regard, we can install our unloading station BG OptiBulk at our customers.” This system is suitable for inhomogeneous material that is difficult to handle. Such materials have a low bulk density, high moisture and a large grain size. In addition, this system is suitable for explosive substances. In addition to tippers and moving-floor trailers, which are sometimes in use, trucks can also be unloaded quickly and easily. The system consists of a chain belt conveyor and lateral steel walls.
A further possibility to empty trucks and moving-floor trailers is given by the BG OptiDock. This station is also suitable for inhomogeneous material like alternative fuels or biomass. The BG OptiDock is composed of a receiving box and a screw floor. It guides the raw materials and the alternative fuels coming from the moving-floor trailer and the truck on a feeding system. The receiving box is equipped with a rubber gasket and, if necessary, with a hydraulic pump in case the vehicle is not available. It permits continuous unloading of the semi-trailer.
“The material falls from the unloading station into the BG OptiFeed screw weigh feeder with a connected buffer bin. This screw conveyor with weighing cells is suitable for completely different materials – that means it’s ideal for the continuous feeding of alternative fuels or raw materials," says Tuma. “Since the screw conveyors are positioned on the weighing cells, it can always be seen how much material is extracted. The regulation ratio is max. 1:10 and the maximum feeding accuracy between one and two percent.” In addition, the completely closed screw weigh feeder is protected against dust.
The BG OptiFeed is a screw conveyor with load cells. This allows the material to be fed continuously.
Pic: BEUMER Group
BEUMER Group also offers a BG OptiFeed Duo. This solution has been designed for the continuous feeding of bulk material to two separated feeding points in one process, for example when the preheater tower has two inlets. The material is then stored in a buffer bin and taken off by two single-screw conveyors or one double-screw conveyor.
To transport the alternative fuels to the calciner and to the main burner, BEUMER experts, depending on the application, evaluate different variants of mechanical conveying systems, which for example include the pipe conveyors. "This conveying technology is not only eco-friendly and requires low maintenance", describes Tuma, "its enclosed type of construction also protects the environment safely from material falling down and emissions. Another advantage is the elimination of dust development on the running line". Due to its ability to navigate curves, considerably fewer transfer towers are required compared to other belt conveyors and the system can be customised to the individual routings. "If necessary, we can further equip the conveyor," says Tuma, "for example with a scraper conveyor in order to minimise clean-up, or with a dedusting filter".
A further efficient possibility is the U-shape conveyor. It can be simply integrated and is also suitable for long distances and rough terrain as well as horizontal and vertical curves. Just like in the pipe conveyor, the material conveyed is protected against external influences such as wind, rain or snow and the environment against possible material loss. This conveying solution is
suitable for coarse but also for very fine material.
"At the feeding point, the U-shape conveyor is open like conventional troughed belt conveyors," explains Tuma. "A special idler configuration brings the belt in a U-shape". This way the material conveyed reaches the discharge station. An idler configuration similar to that for the shaping is used for opening the belt.
Conveying elements lead the material to the discharge screw conveyors of the BG OptiLock construction series. The airlock of this system solution protects the pyroprocess from the infiltrated air, i.e. the air that additionally and uncontrollably enters from the outside with the fuel. Also, the BG OptiLock is equipped with load cells and transfers the bulk material continuously to a screw conveyor, which feeds the calciner. The speed of the discharge screw conveyor is controlled so that the shown weight of the entire system and the real material volume in the container is constant. "As the material can catch fire, all systems are carried out according to the ATEX directives," says Jan Tuma.
As a single-source provider, BEUMER Group has substantial competence in handling with alternative fuels and can support the owners of cement plants efficiently - all within a short period of time. All components are complementary and ensure the continuous and economical feeding with alternative fuels.
Martin Engineering CEO Emeritus Todd Swinderman and the company’s process engineer Dan Marshall have spoken to Aggregates Business about mistracking
bulk material-handling conveyor belts and potential remedies.
“On any belt conveyor system that moves bulk materials, the belt must run straight and true to maximise its life, minimise fugitive material and safety hazards, and achieve high system efficiency,” says Swinderman. “There can be many consequences of a mistracking belt, but all result in higher costs and increased maintenance. Even a slight belt misalignment can lead to a variety of issues, from small annoyances to full-blown catastrophes. The most obvious effects include spillage and dust that require personnel to do clean-up, which is unproductive work that introduces risks from activities in close proximity to the moving conveyor.”
Swinderman says spillage from non-centred cargo can often get into idlers and pulleys, reducing bearing life and causing them to seize, leading to friction damage on the belt and potentially starting a fire. He continues: “A misaligned belt can also come in contact with the stringer, causing fraying, shredding or splice damage. Great lengths of valuable belting can be destroyed with surprising speed, and even the support structure itself can be damaged. A compromised bracket or support can cause a catastrophic idler failure, which could damage other components of the system and require extensive downtime to repair. Further, there is potential for injury from a damaged belt or loose idler not to mention the increased exposure to injury from too frequent a need to clean.”
“I’ve been working around conveyors for 20 years, and I’ve seen thousands of belts,” observes Marshall. “I’ve seen just about every problem that can be caused by a mistracking belt, but one thing I’ve never seen is a belt that runs true right out of the box. All conveyors, no matter how well designed and built, have some belt wander.”
Swinderman adds: “A wide variety of circumstances can lead to mistracking, and operators have tried many things to correct the [belt] alignment. Some have elected to place an obstacle such as a block of wood in the belt path, so it won’t travel too far out of line. This occasionally improves the situation, but more often it’s just temporary and the belt will eventually slice through the obstacle.
“Many operators have realised that pivoting an idler is a quicker and more effective way to steer a belt. This common approach is called ‘knocking an idler’, striking it with a hammer to move it slightly and realign the belt.”
Swinderman notes that equipment manufacturers have also designed components to help align a [conveyor] belt, and these solutions can be successful in specific applications. “They include specially shaped rollers, angled idlers and devices that apply pressure to the belt edge to push it back in line,” he explains.
“While these mechanisms can improve a belt that’s consistently off-centre in one direction, they do not react to dynamic belt
movement, meaning that they don’t correct intermittent belt wander,” says Marshall. “To combat such changing conditions, engineers designed the tracking idler. Unlike the edge-correction approach, the device senses belt movement in either direction and pivots the idler slightly to steer the belt back into position. It doesn’t apply a great deal of force to the edges, which can damage a belt and splices. When the belt is running true, it remains centred, and when it senses a misaligned condition, it gently corrects the belt.”
Unfortunately, as Swinderman highlights, to accommodate limited space availability, tracking idlers typically have short sensing arms. This requires a fairly large belt displacement to create a small movement of the idler. “While these designs do tend to improve tracking, there are limits to how much correction they can deliver, and short sensing arms can actually pinch a belt if the idler pivots too far. To combat this, some operators choose to ‘tie off’ a tracking idler to limit its movement. While the practice can help preserve the belt, it doesn’t address significant mistracking.”
To overcome the limitations of existing belt alignment devices, U.S.-headquartered Martin Engineering has invented and patented a multi-pivot belt tracker, the Martin Tracker, which employs sensors, pivoting idlers and geometry to align a wandering
belt. The sensors avoid pinching the belt, and the engineered geometry amplifies any detected misalignment to create a greater pivot.
Swinderman explains how they work: “Multi-pivot belt trackers like the Martin Tracker use longer arms than other designs, positioning the guide rolls further from the pivot roller, as well as closer to the belt edge. The closer proximity allows guide rolls to sense very slight misalignments and make immediate corrections. Rather than waiting for a powerful mistracking force, the longer arms require considerably less pressure to move the pivot roller. The result is better correction with no pinch points and less wear on conveyor and tracking equipment, for a longer and more efficient service life. Specific designs are available for both the loadcarrying belt path and the return run.”
“Installing trackers is the economical solution, but operators should do a full analysis and consider also addressing other causal issues,” says Marshall. “By focusing solely on belt alignment, plant personnel may miss other opportunities to increase production and relieve some of the burden on their system.”
Swinderman stresses that keeping the belt centred and moving quickly is the key to high production, controlled operating cost and a safer workplace. “Misalignment causes downtime and costs money,” adds Marshall.
“But nothing causes more downtime and expense than a destructive belt fire or other catastrophe as a result of inattention to mistracking problems.”
WCCO Belting says it has seen some impressive results from quarrying customer field-testing of its Direct X conveyor belting. Replacing three- and four-ply texture top and back standard industry belting in U.S.-based aggregate crushing applications, WCCO’s two-ply Direct X belting is said to have doubled belt life, reducing belt replacement and production downtime, and achieved claimed energy savings of 15%. Direct X belting is also said to have a 20% lighter carcass than the previously deployed threeand four-ply standard industry belting.
Mike Schroeder, WCCO Belting product specialist, said: “The field tests proved that the Direct X belting delivers on performance, efficiency and longevity. Some people look at conveyor belting and think that it is all about ‘buying on [lower] price.’ That is a misconception. If you buy a thicker [three- or four-ply] belt, for example, that is 20-25% more cost [than a two-ply]. Sometimes, belt replacement can cost just as much as buying a new belt. In the belting world, you get what you pay for when it comes to quality.”
Minnesota-based Ferguson Aggregate and Crushing is among WCCO Belting customers to have trialled the Direct X belt. Adam Wirtjes, the company’s crushing supervisor, said: “We typically run threeply and four-ply conveyor belting because of the aggressiveness of the work – heavy material with rebar sticking out. Belts can take on large punctures and tears within the first season and not last to the next. When I first saw WCCO’s Direct X belt, I was a little sceptical the two-ply construction would hold up. It did take on a couple punctures, but they were smaller and fewer than in the thicker belts we had been using. Not only is the Direct X continuing to run into the next season, but it was also easier to install and had noticeably less drag while running the conveyor.”
The Direct X and all other WCCO Belting’s products are designed and manufactured at WCCO’s North Dakota, USA, facility.
Coveya’s Invader 45 is designed to handle big jobs in tight spaces. At just 4m or 6m long and 450mm wide, the Invader 45 is lightweight, portable and powerful, shifting
up to 50 tonnes of material per hour. Being fitted with a conveyor belt that can handle the pace is imperative to the success of the Invader, which is why Coveya turned to Northern Ireland-based conveyor belt manufacturer Smiley Monroe when choosing the right belt for the job. The Invader, fitted with customised Smiley Monroe cleated conveyor belts, has been used for everything from excavating basements in central London to restoring the floors in the historic Eton College, in Windsor, Berkshire, England. Maximising uptime and long service life are fundamentally important to Coveya, which offers the Invader both to purchase and as part of its hire fleet. When approached to provide suitable belt options, Smiley Monroe engineers worked with Coveya to recommend a customised hot moulded belt that would provide the wear life and performance required for a wide range of applications, while being lightweight enough to allow the Invader to remain easily portable in confined locations.
“Breakdowns are often caused by belt damage or issues caused by a build of carryback material or spillage, so it was important for us as a supplier to safeguard against as many of these issues as possible when choosing the correct conveyor belt,” said John Hancock, Smiley Monroe business development executive.
Smiley Monroe engineers recommended a fabric-backed base belt with reinforced cleats (two per row) to provide the end user with a lightweight belt that runs smoothly at speed while providing adequate protection from carryback and material spillage when used at an incline. Manufactured at Smiley Monroe’s headquarters in Lisburn, near Belfast, the reinforced cleats are hot-moulded to the belt’s carrying surface to ensure superior adhesion and wear life –something which is imperative when dealing with construction and demolition waste and other harsh materials.
“As a company we have built a reputation for supplying reliable conveyors which get the job done. When our machines are out on hire, every hour is costing the customer money and so to suffer a breakdown can have major knock-on effects on their operation and consequently require us to provide a service team. Finding the right conveyor belt for the job was key and having a supplier like Smiley Monroe with so much knowledge, state-of-the-art manufacturing facilities and excellent customer service levels like our own has been instrumental to the success of the Invader,” said Martin Pillar, project manager at Coveya.
With over 40 years’ experience and three global production facilities, Smiley Monroe offers an extensive range of conveyor belt solutions supplying prestigious manufacturers of mobile equipment around the world, covering ten key industries including quarrying, construction and demolition, recycling and waste management, bulk material handling and road construction. The company’s conveyor belts can be customised to suit customer applications with side rail, crosscleats or chevron patterns. Smiley Monroe conveyor belts can be supplied open (ready to splice), endless or as a Zip Clip mechanically fastened belt, said to be perfect for the original equipment manufacturer aftermarket or end users who wish to maximise uptime. AB
Fitted with Smiley Monroe customised cleated conveyor belts, Coveya’s Invader 45 has been used for everything from excavating basements in central London to restoring the floors in the historic Eton College, in Windsor
An MB Crusher excavator bucket is being used in Italy to prepare clean crushed rocks to be laid for new rail tracks, all done reusing available materials
Screening bucket and attachment customers are finding creative and innovative ways of using their equipment to tackle worldwide delays in the supply of materials.
Liam McLoughlin reports
MB Crusher says customers are using its crushing and screening buckets in innovative ways to avoid material wastage in the current climate where infrastructure projects are facing huge delays due to the global shortage of materials.
The Italy-based company says it is noticing how customers are using resources efficiently and producing some “pretty amazing” results.
“They reduced construction costs, avoided waiting for supplies to arrive and used the carrier machine already part of their fleet to do so and one of our attachments,” it adds.
One example is in the maintenance of the railway that connects Warsaw to the nearby Polish regions, which provided an MB Crusher customer with many unused old sleepers. The customer bought one of the company’s BF70.2 mobile jaw crusher buckets for their Atlas 1604 excavator and began to reduce the railway sleepers, obtaining crushed material that can be used as a sub-base for railway ballast.
MB Crusher says that the development of railway infrastructure networks enhances economic development, as a train line is used to transport goods and facilitate commuting and tourism. A huge amount of track ballast is needed to make new rail lines because its layers hold the track in place as the trains roll over. Ballast also facilitates drainage of water and also restrains vegetation growth.
“We saw how in India and Italy our
customers managed to prepare a great pile of clean crushed rocks ready to be laid for the new rail tracks, all done reusing available materials. Cleaning the rocks makes the process cost-efficient,” the company comments.
In India, the customer used a Sany SY220 excavator and an MB-S18 screening bucket during the actual construction, while in Italy the same rotary bucket model was mounted on a Hitachi EX215 to sift at the quarry, salvaging materials and loading the truck in one unique motion.
In the Cerro Negro mine in the Atacama region of Chile, MB Crusher buckets have been used to enable 80km of trenching across the desert to be done without having to purchase and transport the sand needed to fill the trench.
The Chilean customer attached an MB-S18 screening bucket to a Doosan DX225LC excavator to repurpose the excavated material into the filler. MB Crusher says this produced both huge savings and a speedy execution of the job, as well as being environmentally friendly. “On-site processing not only reduces the number of trucks but also avoids contamination of material coming in from outside the region,” says MB Crusher.
Excavator attachment manufacturer engcon will start production of its thirdgeneration tiltrotators during 2022.
The Swedish company says that, to meet future demands, the new tiltrotator
system is taking progressive steps towards sustainability, applying smart technology to reduce energy consumption and is adapted ready for the electrification of excavators.
The new tiltrotator system was presented for the first time at the Norwegian trade fair Vei og Anlegg 11-13 May, with production getting underway in the second half of 2022 with the EC319 models for 14-19 -tonne excavators and the EC314 for 9-14 -tonne excavators. The model programme will then be expanded on an ongoing basis.
The technology is based on a newly developed type of valve in combination with smart software that collaborates with the excavator's load-sensing hydraulic system. This is designed to optimise both the tiltrotator's functions and the excavator's movements, which leads to smoother digging with higher precision. At the same time, the excavator's wear and need for maintenance also decreases.
"To meet increased demands for electrification, digitalisation, security and sustainability, we have developed a solution adapted for the future of digging," says Stig Engström, founder and owner of engcon and the leader of the company's product development. “Our new tiltrotator system shows that engcon is at the forefront of innovative solutions that drive the development forward to reduce dependence on fossil fuels and thus the climate impact of excavators.”
With an app, the third-generation
tiltrotator system also enables a higher degree of individual customisation in the form of improved possibilities for, amongst other things, connected remote diagnostics and mobile support.
In addition to the energy-efficient technology - the new series EC-Oil - the automatic quick-hitch system can easily and smoothly connect the tiltrotator and hydraulic gear automatically without the driver having to leave the cab.
For full compatibility with modern excavator systems, engcon is also building in a newly-developed tilt and rotation sensor as standard in its third-generation product. The sensors contain what is said to be one of the market's first ‘absolute’ sensors and have a plug & play solution for both integrated and third-party machine control systems.
"The third generation will be our premium offering where the excavator operator gets the very latest technology as standard, while at the same time they get an energy-optimised excavator that becomes even smoother to drive," Engström comments.
engcon has also started a listing on the Nasdaq Stockholm Stock Exchange. The company says interest in the listing has been great from institutional investors and private individuals since it began on June 17.
The listing on Nasdaq Stockholm was the result of a year of preparations and the
company adds that it is now taking further steps towards securing future growth.
"We are proud of engcon's position as the world's leading manufacturer of tiltrotators," said engcon CEO Krister Blomgren. "Our innovative products enable a more efficient and sustainable use of resources by effectively turning excavators into tool carriers that replace the need for other machines. The listing on Nasdaq Stockholm will support our journey to change the world of digging and we will work hard to deliver on the trust that our customers and shareholders have placed in us."
engcon says the listing means it will have a broader ownership structure with both large and small shareholders, which will benefit the company's long-term perspective and stability towards the market.
Engström said: "This is a big milestone for me personally. We have come an incredibly long way since I started the company just over 30 years ago. engcon's ambition is to continue to develop future solutions for smarter, safer, and more efficient digging.
“It is gratifying that the interest in our fine company has been so great and that
a strong investor base will be present and support us in the future.”
A quarry operator in the Italian province of Verona is successfully utilising a Simex attachment to extract calcium carbonate.
Monte Bianco, which is based in Stallavena di Grezzana, is using a TF 1100 drum cutter supplied by Simex’s local dealer Mac3, at one of its two quarries.
Simex says low vibrations and seamless milling make the TF drum cutter particularly suitable for quarrying. Firstly, the selective breaking of the rock mass is guaranteed, which ensures the stability of the surrounding structure. In addition, the TF produces crushed material of a suitable particle size, in this specific case for subsequent grinding within the company's specialised plants, for transformation and placing on the market.
Monte Bianco comments: “Calcium carbonate is in fact a natural material with exceptional physical and chemical properties, a fundamental component in many processes and an irreplaceable raw material in many different sectors.” Calcium carbonate has many uses, ranging from the zootechnical field - as an additive in the production of animal feed - to agriculture, being used as an eco-friendly material and absorbent of pollutants in the fertiliser industry.
Simex says that other attempts at crushing in the quarry with the hydraulic
hammer had proved ineffective, as the tip of the equipment tended to get stuck in the material, an elastic and compact limestone. Furthermore, given the sensitivity of the area, the company chose to equip itself with the TF 1100 drum cutter.
Monte Bianco says that the continuous
work, high precision and high productivity of Simex’s cutter heads have enabled extremely satisfying results. With an average production of 50 m³/h, it granted a constant flow of crushed material to the company's processing plants, maintaining a rapid and high-quality production chain. AB
The use of reclaimed asphalt, or recycling, is an absolute necessity of today. Ammann offers you custom-made solutions for using recycled products.
At the forefront of RA use is the Ammann ABP HRT asphalt mixing plant (High Recycling Technology). The HRT concept incorporates a high degree of technology and innovation, in particular the counter-current drying method of the RAH100 recycling drum.
•Indirect heating
•Homogenous heat distribution
•Recycling rates of up to 100% possible
•Recipes are more flexible as there is no need to overheat the minerals
HIGH EFFICIENCY
•Low exhaust gas
temperature
•High RA temperature
•No radiation heat
•Gentle heating of the RA material
Effective dewatering during aggregates production is a vital element of any quarrying business. Guy Woodford hears from industry experts offering invaluable advice on dewatering solution selection, and reports on the latest quality solutions in this area of the market
Weir Minerals’ Multiflo, Warman and GEHO dewatering pumps are used across a wide variety of industries and environments.
Simon Jones, the company’s pumps product manager for Europe, says any analysis of the major factors which will influence a dewatering pump purchasing decision must start with the most important questions: What are you pumping and where does it need to go?
“The available net positive suction head (NPSH) is the static pressure you have available in a system to force the water into the pump and will largely determine which model within a style of pump is right for your application,” he explains.
“NPSH can be affected by several variables, such as the static differentiation between a pump’s suction and the water level, the length of the suction pipeline and the pump’s elevation above sea level. Other factors including temperature and specific gravity play a role.”
Jones notes that every pump has a minimum NPSH requirement to ensure continuous flow, which depends on its operating duty point – so the NPSH available needs to be compared to the NPSH required to select a dewatering pump.
“NPSH available must always be more than NPSH required, typically with a 1-1.5m safety margin to prevent suction cavitation.
“Weir Minerals Europe dewatering specialists can work with you to calculate these values and help determine which pump would be best suited for the application.”
Jones says the demands on a pump transporting clear liquid are substantially different to those moving slurry or tailings, from both an energy and wear perspective.
Multiflo models such as the PB and PJ pumps can, says Jones, handle clear, corrosive liquids efficiently. For slurries with high solids content or corrosive properties, Jones explains that GEHO positive displacement pumps provide reliable, highly efficient long-distance transport. He says the GEHO range also lasts longer than most pumps between maintenance and combines high availability with a low total cost of ownership.
Jones continues: “For higher solids applications requiring a high head, Warman DWU horizontal dewatering pumps offer robust wear life, and have a number of sealing options to reduce the dilution of the slurry and lower the required flow of gland water. When dealing with clear water, low-flow gland seals are an efficient, low-maintenance option for sealing. When dealing with mixed slurry, the Warman Hi-Seal expeller’s large diameter offers excellent performance, while mechanical seals can cope with high-pressure environments.
“When selecting a replacement pump for an existing project, it’s vital to obtain up-todate data on the chemical composition of the liquid to be dewatered. Factors like acidity can change significantly over time as the operation moves into different sections of the ore body, and some seemingly minor pH changes can lead to dramatically reduced
wear life and potentially an unplanned shutdown.”
Jones notes that underground dewatering presents a number of potentially expensive challenges not present on the surface, including the need to lift liquids to significant heights, deal with higher-solids content and contend with strict space limitations.
“One of the key decisions facing any underground application is whether to employ a series of pumps to bring liquid up out of the mine (a multi-stage approach), or just lifting via single pump, such as a GEHO positive displacement pump.
“While the upfront cost of acquiring several smaller pumps for a multi-stage approach is usually less than a larger pump which can perform the entire lift, there are a number of factors which can make single lift a more attractive proposition in certain circumstances.
“Among these is the need for additional space to host each stage of the operation. In some underground mines, the cost of excavating extra room will overshadow the cost savings of the smaller pumps.”
Jones states that a single long-distance pump requires less maintenance than a series of units and is often more energy-efficient, which can translate into a lower total cost of ownership.
For many pump operators, manually priming pumps is the most frustrating part of their job, believes Jones. He explains that manually primed pumps require regular, time-consuming adjustment, and the process is prone to failure and can lead to inefficient
operation if air isn’t correctly removed from the pump.
“While some static dewatering applications can make do with a manually primed pump, more dynamic applications benefit from an automatic vacuum priming system that prevents the pumps from losing prime.
“Multiflo self-priming CF and RF pump models use a ‘ball float’ priming system, which quickly and efficiently lifts water up into the priming tank and ensures it remains primed at all times. It requires no adjustment and operates without a compressor, removing the inefficiencies and hazards of air prime. “
For situations where a feeding sump would be too expensive or physically impractical, Jones notes that Weir Minerals offers submersible dewatering pumps that cater to a variety of sump and pond sizes, throughputs and conditions.
Due to their portability, quick set-up time and high availability, Jones says submersible pumps are frequently used for a number of temporary applications, either for smaller temporary sumps or as stop-gap solutions until a permanent sump-fed solution can be established.
“For submersible applications with high solids content, the all-chrome wet end of Warman SHW pumps provides long wear life in demanding applications, while the Warman SJG offers efficient dewatering for clear liquids.
“In applications where the pump is at risk of pumping itself out (where the motor must run unsubmerged), a cooling jacket ensures smooth operation by pumping water up into the motor of the pump, preventing it from overheating. This is particularly important where the flow rate can vary without someone to actively adjust the pump rate.
“It’s also important to consider the minimum spacing between dewatering pumps, to prevent them from counteracting one another and operating inefficiently. Weir Minerals engineers can provide guidance on
the best way to ensure pumps don’t interfere with each other’s operations.”
For most applications, Jones notes that electric pumps are preferred over diesel, especially in fixed positions, as they’re simpler to operate and cost-effective, as long as the site has reliable power.
Diesel is used mainly in mobile dewatering pumps, Jones explains, such as those operating at the bottom of a mine pit, which require frequent relocation alongside the mine’s sumps as the mine develops.
“In these scenarios, a manually primed centrifugal pump would require a very timeconsuming exercise each time it was moved. This makes a self-priming pump highly valuable, as time and personnel are already at a premium.
“For sites with high electricity costs or limited capacity, our engineering specialists can help you find the most power-efficient pumping options that will help drive down total cost of ownership.
“No two dewatering projects are the same. Whether you need a small, submersible
pump as a stop-gap solution for a high-solids slurry or a comprehensive pumping solution to handle a high quantity of clear water, Weir Minerals Europe dewatering specialists have the experience to guide you to the right dewatering pump.”
Bart Duijvelaar, product marketing manager Submersible Pumps, and Saksham Dube, product marketing manager Surface Pumps at Atlas Copco, Power & Flow, know that one of the most crucial components of any quarrying application is managing water.
“Whether the water accumulates in the quarry from heavy rainfall, groundwater seepage, or both, it must be removed for the quarry site to continue operations. To keep everyone’s feet and equipment dry, dewatering pumps are used in quarries all around the world.
“The fact that many quarries use pumps that are not intended for the task at hand, resulting in low pumping efficiency and, more crucially, higher costs, may not come as a surprise.”
Duijvelaar and Dube outline some of the factors to consider when selecting a dewatering pump and examine the key challenges that must be addressed.
“The first consideration is where the water is being pumped from and where it is going. Apart from overcoming gravity, all pump sizing must consider the amount of friction that needs to be overcome along the entire discharge line length. The so-called head of the pump is the combination of gravity and friction that must be considered for a particular application.
“The sum of gravity and friction, or total head, and the inflow to be dealt with, determine the pump size. We need to apply these concepts to all pump selections, not just in quarries. What can make quarry selection unique is that the distance between the pump and the surface level of the water being pumped might vary over time. A pump that was working efficiently and effectively six months ago might not provide the same performance when the quarry has become
considerably deeper due to the greater vertical elevation difference that needs to be overcome.”
When the water comes in and needs to be removed, Duijvelaar and Dube note that operators will tend to use whatever is available, possibly using the wrong pump for the required flow and pump head. In addition, if the water rises more quickly than is being pumped out, they say there could be a tendency to use more pumps. “Usually, there is no time to change to a bigger pump, so they use what is at hand. Of course, when there is a planned extension to the quarry, they are more likely to select the correct pump from the beginning.”
Duijvelaar and Dube say that while there is a wide variety of pumps that can extract water out of a quarry, dewatering pumps are designed specifically for removing dirty water and are built with more wear-resistant parts. “An ordinary pump, for instance, even if chosen according to the correct flow and pump head requirements, would, after time, pump less and less water out of the quarry. By choosing pumps that resist wear better, quarry operators can reduce their environmental impact while increasing uptime.
“Solids suspended in water can cause an impeller to wear and prematurely fail. Atlas Copco’s PAS - PAC range of surface pumps, for instance, which can handle liquids containing solids of up to 100mm in size, has several design features to ensure it performs reliably for more extended periods. The closed impeller in the PAC H pumps is equipped with deflector vanes that keep the mechanical seal clean and free of detritus, making it last three times longer. Additionally, it eliminates the need to flush the pump with water to keep it clean, saving significant energy and money throughout the pump's operational lifetime.”
Duijvelaar and Dube highlight that Atlas Copco’s PAS - PAC self-priming pumps incorporate many design features to provide reliable, high-performance pumping so operators can improve their efficiency and productivity. For example, mechanical shaft seals are set in an oil bath, enabling dry running without damage.
For electric submersible pumps, the pair also note that Atlas Copco has introduced a new patented Wear Deflector Technology platform for the WEDA D70, an innovative hydraulic design that provides a high pump efficacy. The impellers in this pump are made from high-chrome stainless steel and, as such, have high hardness and exceptional wear resistance. The Wear Deflector Technology will find its way into other WEDA submersible pumps as they receive design updates in the coming years.
“Whether there is excavation or blasting operations within the quarry, dewatering pumps need to be moved, which means they have to be transportable. However, when moving pumps around, there is also rough physical handling to consider,” explain Duijvelaar and Dube.
“Transportability is essential, especially for heavier surface pumps. The PAS pump range, for example, is available with a galvanized undercarriage or skid, which is resistant to corrosion and makes the unit easy to move around on site. This range of mobile dewatering pumps recently added the HardHat canopy, a robust polymer, as an alternative. And the models featuring this technology have a road towing trailer for superior transportability.
“For WEDA submersible pumps, the power-to-weight ratio is far superior to conventional pumps. They weigh up to 40 percent less, which makes them easier to handle and move around a site too. They also feature general robust design decisions in combination with specific solutions, such as shock absorbers, so they are more resistant to rough handling.”
Duijvelaar and Dube stress that routine preventative maintenance may also be delayed when other pressing matters present themselves in the daily course of business. They explain that this is one of the biggest differentiators of the dewatering pumps from Atlas Copco, which, they say, have been designed with ease of maintenance in mind.
“Referring back to the PAC H pump, its semi-cartridge seal design allows changeout without dismantling the pump, reducing downtime and simplifying maintenance.
“Thanks to a novel Atlas Copco hinged door design on the pump itself, the PAS – PAC pumps provide superior serviceability on site. All components are exceptionally easy to access for simple servicing and maintenance. The pumps can be cleaned and restarted in a matter of minutes and serviced in under 60 minutes, making them less of a barrier to routine maintenance.
“The latest WEDA drainage pump additions feature a cartridge-type sealing system with a stainless-steel body that
enables maintenance to be carried out on-site, ensuring that operators achieve minimal downtime. They also feature easily accessible oil inspection plugs, reducing the time needed for routine inspections and maintenance.”
Duijvelaar and Dube say that in Europe, and especially in certain countries where the rental market for dewatering pumps is around 75%, local aftersales support is essential. They highlight that all pumps in the Atlas Copco range come with full aftersales support and ready availability of spare parts via the company’s global network of customer centres. Product training is also available, particularly useful for rental companies with their own maintenance crew.
“Taking advantage of digitalisation, QR codes are also being implemented, meaning that essential information about parts and spares is just a scan away. Rental firms can also take advantage of the Fleet Link telemetry solution by Atlas Copco, a secured and remote-monitoring feature. Hence, operators are always in control of pumping equipment and operations.”
For electric submersible pumps, the WEDA pumps are said by Duijvelaar and Dube to be the most energy-efficient. The surface dewatering pump ranges are now EU Stage V compliant and are certified to work with biodiesel hydrotreated vegetable oil (HVO), which is fossil-free.
“Consider the technical factors and criteria for the best value and efficiencies when selecting a pump. The pump should be flexible enough to meet the needs of various sites and fulfil the flow requirements while accommodating changes in water level. An oversized pump that can handle a far higher flow capacity may be needlessly expensive and might even shorten the pump’s lifetime. On the other hand, an underspecified pump may struggle to move the media and wear out
more quickly, giving it a shorter lifespan.
“With just a few clicks, Atlas Copco has greatly simplified the sizing problem accounting for gravity and friction losses. We have developed a pump-sizing calculator for the submersible WEDA pumps, which will shortly be extended for surface pumps. By simply entering key technical information such as flow, static pump head, hose/pipe length, and diameter, the calculator provides operators with the most appropriate pump for their operation.”
Even the best process design will always create some misplaced product, and the fact of the matter is, process equipment does not recover all potential sand. Deposits change, upset conditions exist and markets evolve. Each one of those areas and changes can have an impact on profitability. When a processing plant isn’t operating at optimal capacity and material goes to the waste stream, it can be profit out the door. That is where the McLanahan UltraFINES recovery plant can be a good option.
UltraFINES recovery plants are a combination of a sump, pump, hydrocyclones and a dewatering screen in a module that is specifically designed to recover fines solids from a wash-plant effluent stream. The recovered material is conveyable and stackable, and is suitable for multiple industries, including sand, iron ore, coal recovery, ash, industrial sands, frac sand and more. UltraFINES recovery plants recover fines solids to produce a standalone product and reduce the volume of solids reporting to the settling pond or downstream equipment.
McLanahan says an UltraFINES recovery plant can capture the good material before it is thrown out with the bad material. The captured material can be sent to a scalping circuit to increase the overall product amount. This becomes an option when the increase in the yield of product outweighs any increase in operating cost.
Additionally, producers will know that a change in the deposit can have significant impact on your final product, especially when it creates more waste. New feed throughput must increase just to make the same amount of product. This means, the system is no longer operating optimally, and equipment may not be performing efficiently.
Plants producing more waste can lead to filling up the tailings area faster than planned. This can lead to a halt in production or significantly modified operations so that producers can dig out ponds more frequently. Undertaking this endeavour is usually timeconsuming and expensive since specialized equipment may be required.
More waste does not just mean more sand in a pond. With a depleted tailings area, water quality can suffer, and additional land permits may be required.
An UltraFINES recovery plant will, says McLanahan, pull a majority of the solids out of the waste stream, keeping them from the downstream water management system, thereby saving a pond from filling up, decreasing a load on a thickener or lowering
operating time on a filter press.
At times, plants may also be faced with an overload condition or an underload condition that keeps the process system from working in its optimum range. This situation will send material in the wrong direction with good product ending up in a waste stream. With a McLanahan UltraFINES recovery plant in place to act as a safeguard, it is said to be possible to blend that material back in or batch it through the process to prevent the loss.
Adding equipment may seem like it is counter-intuitive, but unforeseen operational costs come in all shapes and eat up profitability quickly, notes McLanahan. Proactively handling the issue up front puts you in control, while reacting to the issue can drive up costs and strain resources when it becomes urgent.
However, conditions and markets change, and sometimes, plants need to be updated. When the situation arises, a combination of the points above can drive the placement of a modular unit like the UltraFINES recovery plant. When planned accordingly, a modular UltraFINES recovery solution can be a drop-in improvement to an operation’s capacity that allows it to meet the new demands.
Because the UltraFINES recovery plant is an add-on process, it can fit into most operations fairly quickly and with minimal disruption. An ultra-fines recovery unit does not demand a lot of monitoring and can be set up with remote instruments.
Ultimately, McLanahan notes that an UltraFINES recovery plant is not the answer for every problem, but when it comes to fines, it is a good place to start. When it is the right solution, McLanahan claims an UltraFINES recovery plant will pay for itself in a short time. The major US-headquartered, global quarrying plant market manufacturer has
been working with these types of issues for a long time and knows how an UltraFINES recovery plant can make the difference.
Atlantic Pumps’ key focus is on ‘keeping abrasive fluids moving’, as its strap line goes. With the key pump families of Audex and SlurryPro, plus Gromatex heavy-duty rubberlined products, the company works to provide a comprehensive, efficient pumping solution for all quarry-water-handling needs.
According to Atlantic Pumps managing director, Andy Smith, the most pressing need for quarry operators now, and probably over the next two to three years, is energy supply cost. For commercial and environmental sustainability, many quarries are urgently seeking to optimise their equipment, ahead of the rapidly increasing energy costs expected this winter.
While heavy-plant decisions are often years in the making, “pump operations are an area that can deliver substantial costperformance improvements, fast,” notes Smith.
The daily work of Atlantic Pumps is optimising dewatering operations by reducing downtime, maintenance costs and fuel use by correct specification of newer, more energyefficient pumps. A typical customer story is an independent quarry in the Scottish Lowlands, which recently approached Atlantic Pumps for help with a problematic dewatering pump. The operation’s diesel-powered pump was suffering repeated breakdowns, with multiple (and expensive) trips back to the manufacturer failing to sort the issue.
recommended a solution involving two 37Kwh 6” electric submersibles from the Audex AS range. With these suspended from a pontoon on the lagoon and being managed by a modern control panel, the optimum running efficiency and uptime made for vast operational savings.
Like many established quarries, they had traditionally relied on diesel power so the recommendation of electrically powered pumps may have surprised them somewhat, especially as the location meant mains power was out of the question. Before making the move, the buying team went through all the details in consultation with Atlantic Pumps. Consideration was given to pump wear life, maintenance routines, volume and head variation, sustainability, and lifetime cost plus, of course, return on investment.
Even despite the electrical power being supplied by a generator, this setup is said to have provided more flow capacity than the previous diesel pump – for just 60% of the previous running cost. This level of cost reduction was obviously a huge win for the quarry, aside from solving the original reliability issue that triggered their consultation with Atlantic Pumps.
A frequent phenomenon that Atlantic Pumps’ technicians come across is pumps that have been vastly over-specified (“P is for Plenty”, as the sappers used to say). Whilst this might cover the backs of someone guessing which pump size they need; it always leads to unnecessary fuel wastage for the pump’s entire lifetime. Considering that an average of 80% of a pump’s lifetime
replacing a pump. So, doing some maths and reading the pump flow-curve diagrams, running your needs past a pumping consultant, or at least asking the pump supplier for advice is, in Atlantic’s opinion, a wise approach.
The other major consideration on quarry operators’ minds is water reuse and compliance with Environment Agency discharging permits. Undoubtedly, if it wasn’t for the current energy crisis, the management of water resources is the next most pressing issue. The EnviroHub system featured at Hillhead this year received a lot of orders and interest from firms involved with a variety
of dewatering scenarios. EnviroHub filters, monitors, and treats turbid and out-ofgauge pH wastewater using the latest smart technology and cloud-based communication. It reports (and logs) volume, clarity and pH value data to enable site managers to demonstrate compliance with licensing requirements. It can also be integrated into other dewatering components and control pump switches or valves for extended automatic water control. Examples of its success are found on HS2 sites recycling concrete washout water, to a Gloucestershire project supporting the recovery of salmon breeding by further cleaning ‘clear’ brook water as it enters the river Frome.
One of the most difficult quarry-water types is sand-laden slurry; the heavier-thanwater sand particles are both aggressive on pipe and pump linings and, with their angular facets, prone to ‘lock’ together as a near solid bed wherever they can. Such slurry is often encountered in washplants and quarry runoff. Atlantic Pumps is likely to recommend one of the Audex AW submersible pumps for this turbid slurry, or a surface-mounted pump from SlurryPro.
The Audex AW submersible pumps have an agitator built in to keep the sand/ solids in suspension to prevent clogging and use abrasion-resistant metal alloys for the pump chamber and impellor blades. SlurryPro manufactures powerful centrifugal type pumps which, depending on the circumstances, are fitted with either rubber or high-chrome impellers to resist the abrasive nature of quarry slurries. SlurryPro also makes a sliding base which makes cleaning out and replacing impellor linings on splitcase-type centrifugal pumps much easier, safer and quicker. AB
AMajor asphalt manufacturers are moving from hot mix asphalt (HMA) to warm mix asphalt (WMA) production to cut their CO2 emissions without compromising on performance. They are calling on competitors to do the same. Liam McLoughlin reports
ggregates Industries and Tarmac have both announced a move from traditional hot mix asphalt (HMA) to a lower carbon production method. Aggregate Industries says it has transitioned to warm mix asphalt (WMA) production as standard across its asphalt product portfolio. The UK-based building materials provider says that, as well as boasting a wealth of benefits from carbon savings, reduced build costs and enhanced life expectancy , warm mix asphalt offers the same high quality and performance when compared to its hot mix equivalent.
Mixing at temperatures 20°- 40°C lower, HMA allows for a significant reduction in CO2 emissions by using fewer fossil fuels and resources during the manufacturing process. In addition, Aggregate Industries says nuisance fuming, odour and steam at the project site are minimal, enabling enhanced and safer working conditions at both the plant and site.
WMA also reaches trafficking temperatures quicker than conventional hot asphalt, enabling earlier reopening of carriageways to the travelling public, resulting in less traffic disruption and potential to reduce build costs. This will increase a contractor’s productivity by enabling more material to be laid within a working window, reducing the overall construction timeframe and subsequent delays to motorists.
Lower asphalt production temperatures greatly reduce binder ageing and in
combination with the highly compactable nature of the asphalt, pavement life expectancy is significantly enhanced.
Surfacing contractor, Premier Road Surfacing, has already made the switch to Aggregate Industries' warm mix asphalt. Matt Pursglove of the company said: “Warm mix asphalt is a great product that has many benefits over the standard asphalt mixes. The benefit of using warm mix is that you can multi-layer within the same day if the site conditions allow, thus reducing the time required on site and lowering our carbon footprint. All our road planning produce goes back to Aggregate Industries’ mixing plants or quarries to be recycled back into the warm mix base and binder courses laid on our projects.”
Commenting on the transition to WMA, Vicky Smith, managing director of asphalt at Aggregate Industries, said: “This is an important next step on our carbon reduction journey, and a vital move for the sector. Road networks will continue to be an integral part of society and it is how we produce the raw materials and construct them that must change to incorporate pioneering and advanced technologies, without compromising on performance and quality. We must find ways for roads to last longer and perform better.”
Smith added that if all production in the UK switched to WMA, it would save around 61,000 tonnes of CO2 a year, the equivalent of cutting around 480 million kilometres (300 million miles) of car journeys. Up to £70m a year could also be
saved through increased shift outputs.
Aggregate Industries says that lower temperatures for mixing also means that warm mix asphalt is easier to transport over long distances, saving time and money. When conventional asphalt is transported over long distances the logistical range is often restricted by asphalt temperature loss. Warm mix asphalt offers potentially longer haulage times to transport the product further without compromising workability.
Starting from July 1 this year, Tarmac has also started moving its default asphalt production to warm mix asphalt for all lower layer materials at 40 of its UK plants.
The company says the move to WMA production will help to save 13,500 tonnes of carbon dioxide a year – the equivalent of around 22,000 flights between London and New York.
Tarmac is calling on the UK highways sector to embrace warm mix materials to help decarbonise the nation’s roads. It says warm mix temperature asphalt technology can reduce the embodied carbon of asphalt by up to 15% compared to conventional hot mixes.
Brian Kent, technical director at Tarmac, commented: “While warm mix technology has been widely available to our customers over the past five years, against the backdrop of the climate emergency, we are now proactively switching our plants to offer this low-carbon material as our standard and preferred option.
“This is a significant sustainabilityfocussed improvement on Edgar Hooley’s original process, but it embraces the innovative spirit of our founder which remains at the heart of our business along with our clear commitment to help the UK transition to net zero.”
US-based asphalt equipment company Astec Industries is entering into an agreement to acquire MINDS Automation Group (MINDS), a leader in plant automation control systems and cloud-based data management in the asphalt industry.
Based in British Columbia, Canada, MINDS has locations in the US, UK, France and Belgium. The company develops userfriendly, advanced, customisable plant automation control systems for drum, batch, combo/hybrid hot mix plants, emulsion plants, liquid terminals, silo load-out, ticketing and data management for the asphalt industry.
“MINDS technology complements our existing offerings for asphalt production joining Astec Controls and Grathwol Automation as we build out a digital platform across our Rock to Road value chain of products ,” said Barry Ruffalo, president and CEO Astec Industries. “Our combined business will provide the knowledge and resources to further invest in industry-leading innovations that drive value for customers .”
Pierre Vidaillac, CEO of Minds will stay with Astec, along with the leadership team to support the advancement of its automation and controls technology and its overall ‘rock to road’ digital platform.
Vidaillac said: “We are excited to join Astec. We are a good fit with the company and its products and services. Astec built its business applying state-of-the-art technology to the industry.”
In central China, Henan Guanpu Construction Engineering has become a pioneer in asphalt recycling technology.
Three years ago, the company purchased an Ammann ABP 320 high-recycling
RAP is increasingly being used in Beijing, Shanghai, Tianjin and other locations.
Zhengzhou resides in the middle of China. The Beijing-Hong Kong-Macau Expressway connects north and south, the Lianhuo Expressway connects east to west, and four national and nine provincial highways connect to the surrounding cities. The central city cluster has one of the denser expressway networks in all of China.
The city has attracted 41 Fortune 500 companies and seen a population boom, with more than 12.6 million residents in 2020.
technology (HRT) asphalt mixing plant.
The ABP 320 HRT was selected because of its low emissions, high efficiency, consistency, and ability to produce mix with high ratios of recycled asphalt (RAP).
The plant is supporting the construction of new roads and the renovation of old ones in Zhengzhou, the capital of Henan province. The long-term goal is to help Zhengzhou become the largest city in central China.
After starting production in 2020, the ABP 320 HRT quickly drew attention through its outstanding performance. In around a year it supplied 180,000 tonnes of high-quality asphalt mix for highway and municipal projects in Zhengzhou. The Henan Guanpu ownership group has praised the quality of the finished material and the high stability, reliability and environmental friendliness of the plant.
The plant is fully cladded, and designed to provide pleasing aesthetics in addition to top-quality asphalt.
The standard mix produced contains a high percentage of RAP. Roads created with a proper ratio of RAP meet all performance requirements while re-using old materials.
Traffic on arterial and urban roads has become heavier as the population has climbed. As a result, many roads need to be built, overhauled or upgraded every year. A great deal of resources can be preserved if thousands of tonnes of asphalt are recycled – protecting the environment and reducing construction costs, too.
The parent company of Henan Guanpu is Zhengzhou Jinlu Municipal Engineering. The latter’s project portfolio includes Zhengzhou Shangcheng Road, Xili Road, Jingqi Road, Zheng San Street, Sauling Road and Rainwater Improvement Project, Xinhe Road and many more.
These projects have been praised by provincial and municipal leaders because of the excellent quality and fast completion.
Germany-based asphalt plant manufacturer Lintec & Linnhoff has started making units in India to serve the needs of the local market through its newly appointed licensed manufacturing partner, Gainwell Engineering.
Lintec & Linnhoff launched its locallybuilt TSD1500 MobileMix plant from the Linnhoff brand at the Excon India 2022 infrastructure equipment show at Bengaluru in May.
It also used the event to announce the launch of its new DRX DurableMix asphalt plant series. There will be two models in the new series: the DRX1500DS, with a maximum capacity output of 120 tons per hour; and the DRX2000DS, with a maximum capacity output of 160 tons per hour.
Both units offer productive operation with a batch cycle time of between 45 and 55 seconds and share a range of trademark features familiar to Linnhoff customers. Foremost of these is the double screen drum, which combines the drying and screening of aggregates in a single drum to deliver high levels of operating efficiency. The inclusion of the double screen drum eliminates the need for a hot elevator or vibrating screens, which Linnhoff says translates to lower operating costs and reduced maintenance requirements for its customers.
The locally-built TSD1500 MobileMix units are designed to appeal to Indian customers due to their high mobility , attributed to four fully integrated main mobile modules with built-in chassis.
The TSD1500 is designed to conform to international land transportation
requirements. Lintec & Linnhoff says that, by offering important advantages in terms of enhanced mobility, the unit is ideal for use in remote locations or short-term projects.
All units are equipped with a hydraulicpower pack self-jacking system, which avoids the need for high-capacity cranes during installation and dismantling. As with the new DRX models, they also include doublescreen drum technology for reduced fuel consumption and maintenance.
Despite being a relatively small sector, asphalt manufacturing solutions provider Benninghoven says the asphalt industry can make an important contribution to global decarbonisation efforts because asphalt production offers great potential for reducing emissions such as CO2 and Ctot (total carbon ).
One of the control instruments for owners of mixing plants is the taxation of emitted CO2 and emissions trading, the costs of which will increase worldwide in the years to come. The fewer greenhouse gases are emitted by asphalt mixing plants, the more costs can be saved.
Benninghoven says it supports plant owners with a variety of different solutions, and has decades of experience with recycling reclaimed asphalt. It adds that reusing the material is not only sustainable, but the material removed by milling the asphalt during road resurfacing is also significantly cheaper than virgin mineral from a quarry. In addition, reclaimed asphalt already contains bitumen which is also reused and therefore saves on the most expensive ingredient in asphalt production.
Benninghoven offers different cold and hot recycling feed systems for this, including its hot-gas generator recycling technology. It allows up to 100% recycling material to be added, with low emissions.
The Benninghoven REVOC system is a patented innovation that will be presented at the bauma 2022 exhibition for the first time in October. The new retrofit solution is a supplement for existing asphalt mixing plants equipped with one or more recycling systems and it significantly reduces the total carbon concentrations in the exhaust gas.
Keeping the stored virgin mineral and recycling material as dry as possible is an
important factor for an energy-efficient mixing process – and therefore for lower emissions such as CO2. Germany-based Benninghoven says that 1% more moisture in the starting material corresponds to a litre of additional heating oil or an energy equivalent for each ton of asphaltic mixture. This is one of the reasons why the German TA-Luft regulation now requires covered storage of these materials.
The drying and heating processes for virgin mineral and recycling material are particularly energy-intensive in asphalt production. Fuel and emissions can be saved if authorities and owners use reduced-temperature asphalt types. This refers to asphaltic mixtures with a final temperature of around 120 °C. This equates to a 30% reduction in contrast to conventional mixtures, which usually require a temperature of around 160 °C. The savings potential for energy and CO2 is even greater: 18,000 kWh and 6,000 kg of CO2 are saved during the production of 2,000 tonnes of asphalt every day.
More sustainability in asphalt production means moving away from fossil fuels such as coal and oil. Benninghoven offers the EVO JET burners which use fuels that are made from renewable raw materials and have a neutral CO2 balance. They include biomass-to-liquid fuels (BtL) and wood dust. Even the complex process of burning wood dust results in a smooth flame pattern – the prerequisite for reliable operation of the plant.
Benninghoven’s technology can also be used for modern fossil, gaseous fuels such as liquid gas or natural gas. Changing from coal dust to natural gas or liquid gas already halves CO2 emissions.
In addition to this, Benninghoven says its development engineers continue to work on the sustainable and economical use of other fuel types. It adds that using hydrogen, for example, could be an option for overcoming
The upgraded and versatile Volvo CE L350H wheeled loader is well suited to quarrying, mining and heavyinfrastructure-linked applications
A busy time recently for new quarrying-suited premium wheeled loaders and excavators. Guy Woodford focuses on a trio of standout models
Volvo Construction Equipment’s (Volvo CE) upgraded L350H wheeled loader builds on the Swedish off-highway machine manufacturer’s decades of innovation and is said to further enhance the profitability of customers’ operations.
Complete with a host of upgrades, the L350H is ideal for tackling a range of applications from mining and quarrying to heavy infrastructure – but now with claimed greater productivity and fuel efficiency, all with lower service costs.
The flagship of the Volvo wheeled loader range, the L350H comes prepared for heavyduty applications as standard from the factory, thanks to the proven Z-bar lifting arm with double sealing on each of the pins, and strong frame structure, which is joined by a reinforced upper centre hinge and new Volvo axles. Whether it be log loading, rock loading, rehandling, block handling or slag handling, Volvo CE has the specialised package (of machine features, tyres, and attachments) needed to achieve maximum performance.
This heavy-duty upgrade is built on the success of its forerunners – a proud heritage dating back to the first L320 wheeled loader in 1985 – with a few notable improvements. A more responsive hydraulics system, featuring new lift and tilt cylinders, and an increased hydraulic working pressure allows for claimed 10% faster work cycles and higher productivity.
Meanwhile, the upgraded driveline features new Volvo axles and an all-new Volvo transmission which enables the
third-generation OptiShift to be equipped as standard. Already found on Volvo L150H-L260H wheeled loaders, this proven technology integrates the reverse-bybraking function and the lock-up function in transmission to boost fuel efficiency by a claimed up to 15%. Efficiency is further enhanced by an optimised gear-shifting ratio and the new converter, which delivers higher outputs resulting in a claimed up to 22% more tractive force depending on selected gear and machine speed.
The machine also boasts an even tougher form thanks to a new, more robust upper centre hinge bearing and updated frames to accommodate the new axles and transmission.
Customers can keep working with the updated L350H for longer and reduce costs thanks to extended service intervals –doubled to 4,000 hours for an axle oil change, made possible by an axle oil cooler with filtration fitted as standard.
Operators can configure the machine according to the job with a choice of three hydraulic modes, customisable lock-up engagement and rimpull control, while the bucket-levelling function automatically returns the bucket to level, from both dump and curl positions, helping to reduce operator fatigue.
Whatever application they are in, the heavy-duty powerhouse is ready for action – delivering, says Volvo CE, a lower total cost of ownership for more profitable performance, as the most innovative and refined version of the L350 yet.
Any successful quarry operator will highlight the importance of loading machines offering versatility and long-term durability, and the new Cat 966 GC wheeled loader very much ticks both boxes.
Designed for reliable, high-performing and efficient operation, the Cat 966 GC’s Caterpillar-designed components, on-demand fan, load-sensing hydraulics and intuitive controls are said to keep the model’s fuel consumption and operating costs low, making it a versatile machine that also addresses the needs of rental and municipal markets.
The Cat 966 GC’s 239kW Cat C9.3B engine meets U.S. EPA Tier 4 Final, EU Stage V, Korea Tier 4 Final, China Nonroad Stage IV and Japan 2014 emission standards. The engine’s automatic Cat Clean Emissions Module (CEM), including SCR catalyst and diesel particulate filter (DPF) works in the background without impacting the production schedule. The Cat Engine Idle Management System (EIMS), Auto Engine Idle Shutdown (EIS), variable speed fan and load-sensing hydraulics help result in low fuel consumption and reduced sound levels on this machine. An optional automatic reversing fan assists in cleaning cooling cores to improve performance in high-debris environments.
The new Caterpillar loader features a four-speed forward/reverse electronically controlled, automatic planetary powershift transmission with shift protection and singleclutch gear shifting for efficiency, durability and smooth gear changes. Ensuring excellent
material retention and increasing efficiency, the loader’s optional ride control is said to improve operating smoothness over rough terrain. Optional limited-slip differential axle configurations increase traction in poor underfoot conditions.
Field-proven, Caterpillar’s Z-bar loader linkage with cast crossmember and tilt-lever provides both strong digging capabilities and high breakout forces when the Cat 966 GC is equipped with Cat Performance Series buckets. The load-sensing implement hydraulic system continuously controls flow and pressure to precisely match requirements of the operating situation, reducing both the load on the pump and overall fuel burn.
Using a system-based approach to balance bucket shape with the machine’s lift and tilt capacity, weight, and linkage, the Performance Series Buckets are available for a range of applications including general purpose, flat floor, heavy-duty rock and light material. Design features enable operators of all experience levels to routinely attain 10% higher bucket-fill factors, compared with legacy designs, to improve production and reduce fuel consumption. The 966 GC can also be equipped with the Cat Fusion quick coupler and controls, and combined with optional third-function auxiliary hydraulics, the coupler allows use of a wide selection of Cat work tools.
An optional Cat Payload kit provides on-the-go weighing for precise load targets with proven accuracy, flexible and simple installation, and easy calibration. Bringing payload weighing to the cab, Cat Payload weighs the material while moving to the truck and lifting, so there are no interruptions in the load cycle. It allows the operator to load to exact specification and load more trucks and move more material faster.
Liebherr Generation 8 crawler excavators are successfully penetrating the French market. Corsica’s thriving market for crawler excavators and all other construction machinery is a particularly good sales area. The high versatility and performance as well as the comfort and design are said by Liebherr to be really impressing local customers.
The R 934 crawler excavator for Graziani TP was the first Liebherr Generation 8 excavator delivered to Corsica. Frederick Graziani, the company's managing director, is particularly satisfied with the stability during work and the performance combined with low fuel consumption of just 18 litres per hour (l/h).
In addition, he particularly appreciates the reliability and versatility of the excavator. This allows the company to take on larger jobs, such as demanding earthmoving work or large-scale rock crushing. This in turn enables solid growth for Graziani TP.
Decisive purchase criteria for Frederick Graziani were also the origin of the excavator, which is produced in Europe, and the good reputation of the Liebherr brand.
According to the managing director, Liebherr represents a very good price-performance ratio and efficient customer service.
In Balagne, at the other end of the island, there is also a satisfied customer who specialises in quarrying rock. Valérie Mercuri, managing director of the company Sablière de Calenzana from the town of the same name, particularly appreciates the versatility of the R 945 crawler excavator. On the
one hand, dump trucks can be loaded very quickly, and on the other hand, the flexible changeover from bucket to a hydraulic rock breaker also allows drilling work for easier placement of explosives.
The R 945 replaces an older Liebherr excavator at the customer's site that has already completed enough operating hours to be replaced. The new model is even more manoeuvrable, lighter than its predecessor and at the same time significantly more effective and efficient. Like all Generation 8 excavators, the R 945 is equipped with Liebherr's "Positive Control" hydraulic system, which forms the basis for smooth combined movements and an overall increase in performance.
Valérie Mercuri particularly appreciates these technological advancements, which enable fuel consumption to be reduced by around 20% to just 23 l/h, and this with even better performance data.
The high load-bearing capacity and digging force round off the excavator's performance spectrum. Also noteworthy is the optimal comfort for the operator thanks to the noise reduction in the operator's cab and more safety thanks to the LED lighting and full all-round visibility.
The operator has a spacious and comfortable workspace at their disposal in all working situations. The Generation 8 excavators offer a high level of operator comfort with reduced vibrations and a low noise level. To make daily work easier, the cab is equipped with an air-sprung seat with vertical and longitudinal shock absorption.
Liebherr customer service is also a big plus for all customers and operators. The Liebherr branch in Marseilles, located in the suburb of Rognac, addresses all customers' concerns and ensures a fast and tailored service. AB
The Swerock-owned Vändle quarry in central Sweden is one of the region’s major suppliers of crushed rock and asphalt. Its products are in high demand for infrastructure projects, and site manager Patrick Ericzén says the quarry’s typically Swedish non-hierarchical working structure boosts its productivity and safety. Liam McLoughlin reports
Swerock’s Vändle quarrying site near the city of Västerås in central Sweden opened in 1992 and is the fifth-largest quarry in the country.
The quarry processes around one million tonnes of gravel, crushed stone and asphalt material a year and has a working area of 52 hectares, of which 48 hectares has so far been quarried. It has at least another 30 years of working life as long as suitable quarrying permits can be achieved. Another 300,000 tonnes of material are recycled annually, meaning the site handles a total of 1.3 million tonnes per year.
Swerock is one of Sweden’s largest suppliers of materials and services to the construction industry and the company is part of the Peab Group.
Vändle quarry manager Patrick Ericzén also manages three other Swerock quarry
sites in the area, and visits each one every working day as well as spending time at the company’s office in Västerås.
The Vändle quarry’s products are predominantly used around the Västerås area for road and infrastructure construction projects, with the remainder providing ballast for use on railway track in Sweden.
“Material is moved from this site by truck in a 50km radius only, and for material that is transported by rail for use as rail ballast it is up to a 150km radius,” says Ericzén. “If it’s any further than this there are other quarry sites closer-by and we can’t compete as it’s too expensive. It’s all about logistics.”
There are currently a lot of major construction projects taking place in the Västerås area that are helping drive demand for the quarry’s products. “Västerås has large logistical hubs such as ICA, one of the largest food transporters in Sweden,” says Ericzén. “They are building their main storage
centre for distribution here and need a lot of material.”
Demand for the quarry’s products is also being driven by the current boom in infrastructure and housing projects being carried out across Sweden. “The country has gone from a population of 8.5 million to 10.5 million within the last decade and there is a lot of need for new housing,” Ericzén says.
The quarry boasts the impressive safety record of not having had a significant incident for more than a decade. At the centre of the site’s health and safety measures is a smartphone-based reporting system to log all types of incidents and occurrences.
“We do a lot of preventive work,” says Ericzén. “It’s about the mindset of the operator – if there is some piece of equipment that is broken or defective you take it away and report it, and it is fixed.”
Per Leis, business manager hub north EMEA for Volvo CE which has close business
links with the quarry, says that this effective safety culture is driven by the open and less hierarchical Swedish way of working: “They are all familiar and they are friends. There is a boss and he is still the boss, but they have an open relationship and are not afraid of saying if something is wrong. It’s another way of working in Sweden. Some people say it’s softer, but we say it’s working better.”
Ericzén agrees: “I don’t call myself boss, I’m a working partner, part of the team. If anyone thinks I am doing something wrong I want them to tell me.”
Cameras are extensively used at the site, on the crushing and screening plant as well as being fitted to all vehicles. There are also cameras fitted to the incoming and outgoing sections of the weighing bridge, which is controlled remotely from Swerock’s Västerås office
Thirty-five people work at the Vändle site with only three being employed by Swerock, which Ericzén says is a common set-up in Sweden. Quarries in the Västerås region are generally operated by major players such as Swerock owner Peab, NCC and Skanska with large numbers of sub-contractors working on the sites.
The site foreman and one of the truck drivers at Vändle are Swerock employees, while the other 32 workers also report directly to Ericzén.
He says it is planned in two to three years’ time to go another 22m deeper down into the rock, and to extend over another 29 hectares in area. The lowest point of the quarry that has been drilled down to is currently 15m above sea level.
The quarry operates 20 machines, mostly Volvo CE equipment, as well as some from Caterpillar. The machines include two Volvo L220H and one Volvo L180 wheeled loaders, each weighing between 25 and 30 tonnes, to load material onto trucks. “The loaders travel a total of around 100km each per day,” says Ericzén. “There is a lot of area to cover and we are looking all the time to get an increase in the size of machines.”
Four Volvo CE excavators work on the site : an EC380 used on recycling activity, an EC360 on overburden, an EC380 used with road trucks, and an EC300 working with the site’s crushing and screening plant to process a total of 7,000 tonnes of material each day.
The quarry has one fixed crushing and screening plant which processes 4,000 tonnes of material per day. The plant’s primary crusher is supplied from Metso Outotec, with the other stages provided by Swedish company Svedala Industri.
There used to also be two mobile crushers onsite but this has now been reduced to one which processes 3,000 tonnes per day. The mobile plant is supplied by Jonsson & Söner, and was manufactured in the city of Härnösand.
A Sandvik drill rig works at the quarry all year round. Both the crushing & screening and drilling equipment are operated by sub-contractors. The site carries out both drilling and blasting activity, with drilling
“I don’t call myself boss, I’m a working partner, part of the team. If anyone thinks I am doing something wrong I want them to tell me”
Patrick Ericzén Vändle quarry manager
down and then loading of dynamite and blasting of the material.
A pre-crushing “knocking” crusher is used to reduce the size of the blasted stone so that the main crushing and screening plant can process them. After the blasting process, material is loaded directly onto trucks. It is then unloaded into the primary crusher, which crushes the material down to 300mm. It then goes to the secondary crusher in different sizes, or for the railway ballast that is transported around Sweden.
The site’s mobile crusher produces the highest volume of material from the site, producing 0-16mm and 16-32mm sizes. The fixed crushing plant produces the higherquality material that is required for use in asphalt production.
The quarry has been producing one million tonnes annually for the last five years.
Ericzén says the future production levels of the site are linked to market demand, which Swerock envisages remaining at a high level in the coming years. Swerock is applying for extensions to its current one million tonnes per year production, but these need to be approved by environmental and regional authorities, and such permissions can be hard to obtain in Sweden.
“The latest machines bought for the quarry are a Volvo CE EC180C crawler excavator and a Volvo CE EC220E crawler excavator,” says Ericzén. The machines were bought last year by Nordic construction company NCC and one of the sub-contractors at the quarry.
In addition, there are four haulers used to transport overburden. These include two articulated haulers - a Volvo A25 and a Caterpillar 725; and two 60-tonne Caterpillar rigid haulers.
In terms of the benefits from the quarry’s newer equipment, he adds: “Our excavators and wheeled loaders – both Volvo and other machines - have improved a lot in recent years, particularly in terms of operator environment and ease of operation. They have also improved safety and productivity.
“Fuel consumption with the new Volvo and Cat haulers has been improved by 15-20% compared to the previous machines, which is very important with the recent increases in fuel prices.”
He estimates that the new machines usually take around five to seven years to provide a return on investment. The wheeled loaders usually have a working lifespan of around 10,000 to 15,000 hours and work on average 2,000 hours a year (with a similar figure for the excavators). A lot of material transporting by loaders takes place around the quarry’s large area.
At the end of their working lifespan the machines are then used as back-up at the quarry, replacing the existing back-up machines which are sold off.
The quarry purchases its Volvo CE machines from Swecon, which is the Volvo CE distributor for the Västerås area and is responsible for the servicing contract. “We are very impressed with their service,” says
Ericzén. “There might be some disturbances with parts but they always fix it in due time.”
Under the servicing agreement Swecon performs the oil changes on the quarry’s Volvo CE vehicles, all the 500-hour equipment checks, and the larger service inspections at 1,000 hours.
The quarry does not have a fleet management system providing a complete overview of the equipment, due to the high number of sub-suppliers and contractors working at the site who take care of their equipment in different ways.
Ericzén says: “For the crusher process that is a sub-supplier and there are four guys working on it. They work in rotation and see the workplace with new eyes every time, and if there is something that needs to be fixed, they do it in the evening.”
For the material weighing bridge process there is a card-based system for vehicle drivers to check in and out.
“A fleet management system is sitedependent,” Ericzén explains. “If you have a large quarry with 25 articulated haulers moving around, then it’s effective. We are working with the quality of crushed stone and the tonnage – that is the most important part for us – and we have full control of this without a fleet management system.”
Given its proximity to Volvo CE’s Eskilstuna research & development site, the Vändle quarry’s input has been used in developing Volvo’s excavator buckets and attachments.
Leis, who is shortly to retire after over 25 years at Volvo CE, says: “There is a close cooperation between Volvo CE and the quarry and we do a lot of testing here.”
The quarry is open all year round from 6am to 4pm Monday to Friday, while the onsite crushers operate four longer days a week from Monday to Thursday. “The crusher operators come from further north in Sweden and do four 12-hour shifts from 6am to 6pm,” Ericzén says. “It’s a kind of tradition in Sweden that crusher operators are from the north of the country.”
There are also two asphalt plants operating on the site, which Ericzén says is
very rare. One is operated by NCC and the other by Swerock’s parent company Peab, and each produces around 120,000 tonnes of asphalt per year.
The quarry produces sizes of crushed stone material ranging from 0.4mm, 4-8mm, 8-11mm, 11-16mm, 16-22mm, and 22-32mm for asphalt production. The 32-64mm size is also produced for use on railways. The 32-64mm railway material is washed at an onsite washing plant supplied by Sandvik.
“A lot of concrete and asphalt is recycled on this site,” says Ericzén. “The profitability of recycled material has increased by SEK300 [€28.62] per tonne due to high bitumen prices, partly caused by the war in Ukraine which is a big bitumen producer.”
Sweden is also building a lot of wind turbines in the north of the country to provide clean power, and these require a large amount of concrete.
Peab puts a strong emphasis on reducing its carbon footprint and the Vändle quarry (and all other Swerock sites) only uses machines complying with the latest emissions standards, and aims to electrify as much as it is possible to do. Electrification of quarrying vehicles is still at an early stage but crushing machines and other parts of the production process are electrified as much as possible.
Sweden has been at the forefront of pioneering autonomous and electric quarrying machine technology with initiatives such as the ‘electric quarry’ pilot operated by Volvo CE and Skanska at the latter’s Vikan
Kross quarry near Gothenburg. Ericzén says: “I don’t see it happening here [at the Vändle quarry] for the time being as our operations are too flexible. You probably have to build a site from the beginning and adapt it to these machines.
“We would be interested in deploying electric vehicles but at the moment there is nothing available suitable for quarries such as ours. The loaders do 100km a day so it would need one hell of a battery.”
He adds that, for an excavator, the quarry operator would normally want a 40-tonne machine to provide steady production. Currently the largest electric excavator being piloted is Volvo CE’s 23-tonne model.
As part of its sustainability efforts, the quarry is operating a project where it measures the CO2 output per crushed tonne. “A lot of this kind of activity is due to legislation from the Swedish state,” says Leis. “When a project is started, the carbon footprint has to be declared because the environmental impact is part of the tender. If you don’t have the latest compliant machines, you will not be part of the tender. This is putting pressure on the suppliers as well, including us.”
Despite this range of challenges facing the quarrying sector, Ericzén is positive about the future of the industry in both Sweden and across Europe: “We must have quarrying for infrastructure,” he says. “It’s totally impossible to build if you don’t have the stones.” AB
Sandvik aftermarket product for Optitooth
Metso Outotec is renewing its NW Rapid portable plant solutions in the 250 tonnes per hour (tph) capacity range. The Finnish company says that, to give its customers even better competitive edge, it has renewed the 250tph range crushers with integrated screen.
“The material flow is better, separate the electric cabinet from the chassis for improved ergonomics, and we are introducing a new on-board under -size conveyor for easier transportation of the NW220GPS, NW200HPS and NW7150S Rapid in one piece,” said Jarno Pohja, product manager, portable solutions, aggregates business area at Metso Outotec. He added that two new portable screens are also being added to the range, NW2060S and NW1855S, to provide even more flexibility for customers. As wheel-mounted machines and conveyors designed to be set up without heavy
cranes, the entire NW Rapid plant can be re-located in 1-2 years to a new crushing or construction site. Crushing permits are also easier to get for a portable plant.
”Producing aggregates near a periodical construction site such as highway, airport or a dam project, there are significantly savings compared to transporting the rocks from a stationary quarry,” said Pohja.
The NW Rapid concept provides quarries with capacity, mobility and flexibility and enables short time between job assignment and delivery. The plant consist of primary, secondary and tertiary crushing stations that make the entire plant quick to set up, as the process layout and flow sheets are pre-designed for different capacities and amount of end products.
www.mogroup.com
FPT Industrial has strengthened its position in the construction and quarrying equipment sector, with the company’s Stage V NEF engines powering CASE Construction Equipment’s new E-Series crawler excavators.
Building on a legacy of earthmoving innovation spanning 180 years, CASE now presents the E-Series crawler excavators, ranging from 13- to 30-tonne models: CX130E, CX160E, CX180E, CX210E, CX240E, CX250E, CX300E. Their benefits include offering customers greater controllability, reliability, operator comfort, efficiency, productivity, and lower total cost of ownership (TCO), and all are powered by FPT Industrial’s NEF engines.
FPT Industrial says the choice of its NEF engines will guarantee an improved transient response ensuring high reliability, thus responding to the demanding needs of this specific application. With the E-Series CASE completes its Stage V offering confirming FPT Industrial as a strong partner.
The new E-Series incorporates more powerful and efficient Stage V engines, which offer greater displacement while meeting
stringent emissions requirements. The 13-18-metric ton models feature the N45, the 4.5-litre engine from the renowned NEF series, while the N67 (6.7-litre, 6-cylinder version from the same engine family) powers the 21-30-tonne models.
The NEF engines powering the new CASE E-Series ensure optimal combustion efficiency thanks to their exhaust gas recirculation (EGR)-free architecture, while the FPT-patented HIeSCR2 after-treatment system results in low running costs – this for-life system does not
require mechanical cleaning or replacement parts over its lifecycle. High-capacity fi with clogging sensor deliver best-in-class service intervals of up to 1,000 hours, an outstanding improvement on previous solutions.
To allow the use of renewable fuels, NEF Stage V engines fitted on all E-Series models are compatible with EN15940compliant fuels, such as the increasingly popular HVO (hydrogenated vegetable oils). www.fptindustrial.com
Following the success of its Optitooth jaw plates range, Sandvik is launching its next aftermarket product, Optitooth Premium.
The Swedish quarrying and mining equipment manufacturer says the new product is part of the strategy to increase its sustainability and lower its global carbon footprint.
The new offering is designed to combine the benefits of the original Optitooth with enhanced quality for longer life. It is manufactured with a 70% reduction in CO2 emissions, resulting in a much lower environmental impact.
Sandvik says that initial test results show that Optitooth Premium jaw plates last up to 10% longer than the standard Optitooth offering. A company spokesperson said: “Sandvik Optitooth jaw plates were designed primarily to increase wear life for our customers. We wanted to design a jaw plate that would last longer than your average jaw plate while bringing with it a number of customer benefits to optimise productivity and lower overall operating costs.
“The profile was designed for a higher percentage of the jaw to be utilised, resulting in longer wear and less manganese waste. It was redesigned to make it easier for removal, thereby reducing maintenance time and ultimately downtime, saving time and money.
“The improved profile also brings with it a number of additional benefits which all contribute to improved product shape. The unique profile was designed around the production of a more cubical material and reduction of elongated slab material, which can cause blocking issues for secondary cone crushers.”
www.sandvik.com
30 August
M&T Expo 2022
São Paulo, Brazil
Organiser: Messe Munchen
Tel: +55 11 3868-6340
Email: info@mtexpo.com.br https://www.mtexpo.com.br/en/
19-21: SIM 2022
Marseille, France
Tel: +33 (0)1 60 94 22 21 https://www.expositionsim.com
24-30: bauma
Munich, Germany
Organiser: Messe München
Tel: +49 89 949-11348
Email: info@bauma.de https://www.bauma.de/en/
NOVEMBER
07-09: Trimble Dimensions
Las Vegas, NV
Organiser: Trimble https://dimensions.trimble. com/live
24: ABMEC Conference and Exhibition 2022
Forest Pines, North Lincolnshire
Organiser: ABMEC
Tel: +44 (0)1924 860 258
Email: enquiries@abmec.org.uk https://abmec.org.uk/abmec_ events/abmec-conference-2022/
JANUARY
19-20: CECE Congress 2023
Chamonix, France
Organiser: CECE
Tel: +32 2 706 82 26
Email: info@cece.eu https://www.cece.eu/
31 January-03 February: bauma Conexpo India 2023
Greater Noida, India
Organisers: AEM and Messe München
Tel: +49 89 949-20251
Email: info@bcindia.com https://www.bcindia.com/
MARCH
14-18: CONEXPO-CON/AGG
Las Vegas, NV
Organiser: AEM
Tel: +1 (800) 867 6060 https://www.conexpoconagg.com/
MAY
03-07: SaMoTer 2023
Verona, Italy
Organiser: Veronafiere S.p.A.
Tel: +39 045 8298561
Email: customercare@samoter.com www.samoter.it/en
AUGUST
23-26: steinexpo 2023
Homberg/Nieder-Ofleiden, Germany
Organiser: Geoplan GMBH
Tel: +49 7229 606-30
Email: info@geoplangmbh.de https://www.steinexpo.eu/
MEET THE TEAM
Aggregates Business travels the globe attending conferences, events and equipment shows, keeping you informed of the latest offerings. Come and join us for a chat at any of the events below.
OCTOBER 2022
24-30: bauma Munich, Germany
MARCH 2023
14-18: CONEXPO-CON/ AGG
These dates were correct at the time of going to press, but please note that the COVID-19 pandemic means some events may be rescheduled with little advance notice