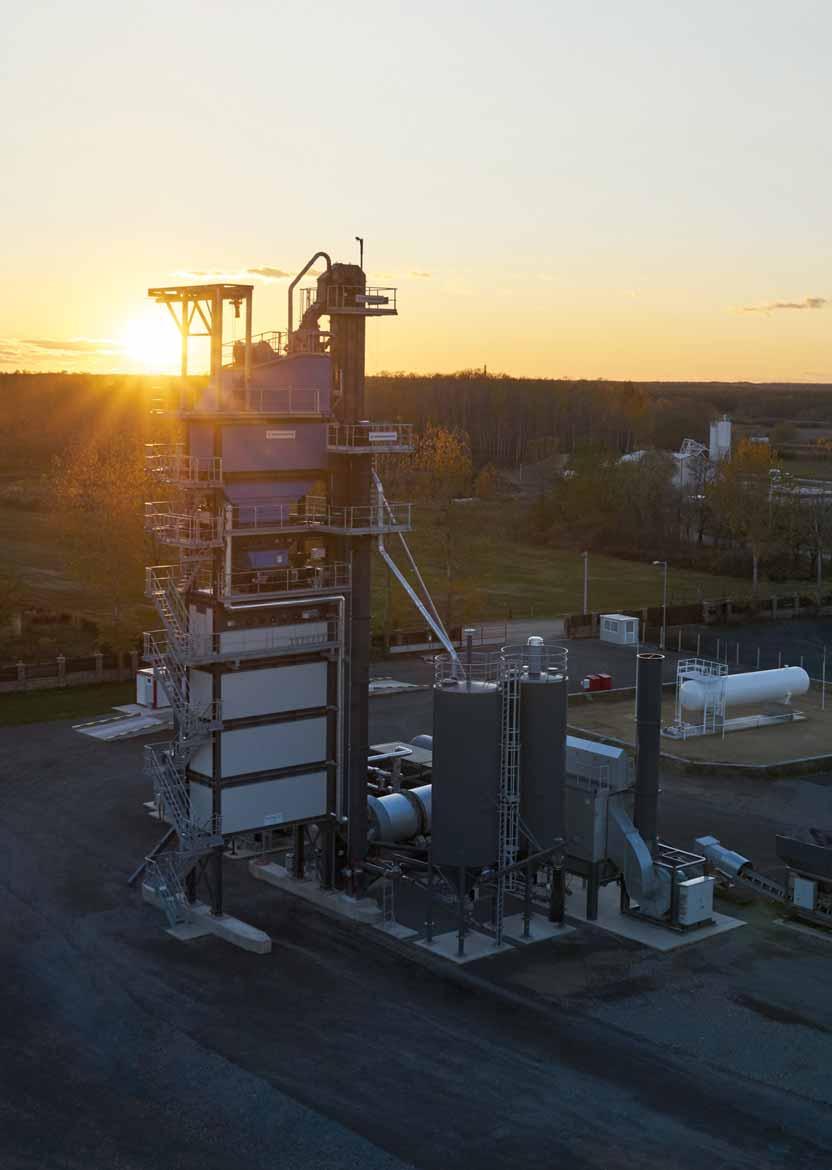
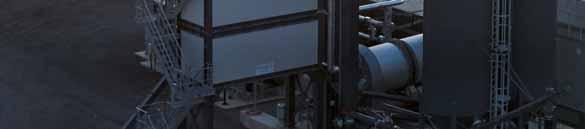
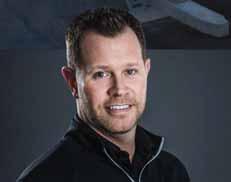
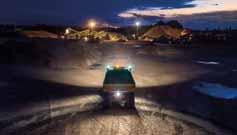
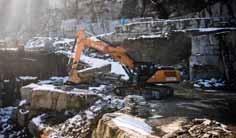
INTRODUCING THE NEW 336 & 336GC.
Our game-changing new machines will work even harder for you. Designed around you and your needs, these Next Generation excavators will totally transform your job sites - with the new 336GC providing lower cost of acquisition and fuel burn, and the new 336 achieving higher levels of productivity. So get ready to witness the revolution of an entire industry from the ground up, and rewrite the rules of operation. Contact your local dealer to find out more. #rewritetherules
Don’t forget the aggregates sector amid populist takeover fears
CRH sales up 6% to €26.8 billion in 2018; LafargeHolcim posts 2018 sales growth 16 ASSOCIATION
UEPG
Big
Global quarrying equipment manufacturers’ new model launches and applications
58 EVENTS
All the key events in the quarrying & aggregates world
Big manufacturing gains for two major aggregates processing equipment makers
Powerful loading options for aggregates producers
Hauler operators are moving away from the one-size-fits-all approach of 25-tonne machines
Reliable & cost-effective drilling & hammering
New facilities and plant showcase demos for major sector players 38 SCREENING
Productivity gains from premium screening media
John Garrison on Superior Industries’ European market focus for its extensive quarrying equipment plant portfolio
After a €130mn Wirtgen Group investment, Benninghoven is well positioned for market growth
A giant Kleemann Mobicat MC 162 RRP mobile crusher and screener at Prasville quarry near Chartres in France is one of only two in the world
With Sandvik My Fleet you can take control of your assets through remote monitoring of your equipment. With access to a wealth of machine data at your
HEAD OFFICE
EDITOR: Guy Woodford
ASSISTANT EDITOR: Liam McLoughlin
CONTRIBUTING EDITORS: Patrick Smith, Dan Gilkes
EQUIPMENT EDITOR: Mike Woof
DESIGNERS: Simon Ward, Andy Taylder, Stephen Poulton
PRODUCTION MANAGER: Nick Bond
OFFICE MANAGER: Kelly Thompson
CIRCULATION & DATABASE MANAGER: Charmaine Douglas
INTERNET, IT & DATA SERVICES DIRECTOR: James Howard
WEB ADMINISTRATORS: Sarah Biswell, Tatyana Mechkarova
MANAGING DIRECTOR: Andrew Barriball
PUBLISHER: Geoff Hadwick
CHAIRMAN: Roger Adshead
ADDRESS
Route One Publishing Ltd, Waterbridge Court, 50 Spital Street, Dartford, Kent DA1 2DT, UK
TEL: +44 (0) 1322 612055
FAX: +44 (0) 1322 788063
EMAIL: [initialsurname]@ropl.com (psmith@ropl.com)
ADVERTISEMENT SALES
SALES DIRECTOR:
Philip Woodgate TEL: +44 1322 612067
EMAIL: pwoodgate@ropl.com
Dan Emmerson TEL: +44 1322 612068
EMAIL: demmerson@ropl.com
Graeme McQueen TEL: +44 1322 612069
EMAIL: gmcqueen@ropl.com
SUBSCRIPTION / READER ENQUIRY SERVICE
Aggregates Business Europe is available on subscription. Email subs@ropl.com for further details. Subscription records are maintained at Route One Publishing Ltd.
SUBSCRIPTION / READER ENQUIRIES TO: Data, Route One Publishing Ltd, Waterbridge Court, 50 Spital Street, Dartford, Kent DA1 2DT, UK
TEL: +44 (0) 1322 612079 FAX: +44 (0) 1322 788063
EMAIL: data@ropl.com
No part of this publication may be reproduced in any form whatsoever without the express written permission of the publisher. Contributors are encouraged to express their personal and professional opinions in this publication, and accordingly views expressed herein are not necessarily the views of Route One Publishing Ltd. From time to time statements and claims are made by the manufacturers and their representatives in respect of their products and services. Whilst reasonable steps are taken to check their accuracy at the time of going to press, the publisher cannot be held liable for their validity and accuracy.
PUBLISHED BY © Route One Publishing Ltd 2019
AGGREGATES BUSINESS EUROPE USPS: is published six times a year. Airfreight and mailing in the USA by Agent named Air Business, C/O WorldNet Shipping USA Inc., 156-15 146th Avenue, Jamaica, NY, NY11434. PERIODICALS POSTAGE PAID AT / US POSTMASTER ADDRESS CHANGES TO: Aggregates Business Europe, Air Business Ltd, C/O WorldNet Shipping USA Inc., 156-15 146th Avenue, Jamaica, New York, NY11434
PRINT: ISSN 1754-2499
ONLINE: ISSN 2057-3413
PRINTED BY: William Gibbons
ou could easily be forgiven in view of the amount of newspaper and current affairs magazine column inches devoted to it, that the European Parliament elections in May this year will result in a populist takeover of the levers of power, with many traditional European parties and political groupings racking up huge member losses after being shunned by an angry electorate.
I am not convinced that the above scenario will play out quite like that, but one thing is for sure: fears of a tidal wave of political populism in Europe and its current manifestations, such as Brexit (the UK’s departure from the European Union) (EU) and the gilets jaunes protests in France, are dominating the minds of the continent’s political movers and shakers. That is dangerous when there are so many other important areas to concentrate on, not least how best to protect and improve European industries, including the continent’s aggregates industry.
In the November-December 2018 issue of Aggregates Business Europe, the UEPG (European Aggregates Association) reported on how it is supporting the Industry4Europe initiative, a coalition involving 137 associations co-ordinated by the European rail manufacturing industry, UNIFE. The initiative is calling for a coherent medium- to long-term industrial strategy that ensures sustainable access for industries to resources and energy at a competitive price.
Industry4Europe also recently issued a joint paper urging the creation of a set of indicators that can accurately assess the industrial performance of the EU and, whenever possible, in comparison to other geographical competitors in the world, such as China, the US, Japan, South Korea and the combined emerging BRICS (Brazil, Russia, India, China and South Africa) economies. Such potent indicators, Industry4Europe argues, will be key to creating a coherent and effective medium- to long-term EU industrial strategy. A further Industry4Europe joint paper on governance calls for an informed and permanent dialogue between the industry and policy decision-makers in association with civil society stakeholders and for a European Commission (EC) vice-president exclusively in charge of industry.
Another well-respected body has joined UEPG and UNIFE in calling for a more joinedup and long-term EU strategy for industry. The Committee for European Construction Equipment (CECE), which represents the European construction equipment manufacturing industry, says the EU must ensure that industry and manufacturing are at the heart of its policy making over the next five-year term for the legislature following the May 2019 elections.
The CECE also echoes UEPG and UNIFE in requesting the appointment of an EC vice-president for industry. It is also seeking a European Parliament intergroup on sustainable industrial competitiveness to accompany the work of the EC and gather stakeholders from across all areas and interests. To me, the calls from the likes of UEPG and CECE are both rational and convincing.
I would perhaps add that it would also help, from a European aggregates sector perspective, if the EU had more sharp-end minerals processing expertise in its law-making ranks. Problems associated with a lack of or a perceived lack of understanding of aggregates producers’ needs is also evident at a national level. Take the UK, for example, and the Mineral Products Association’s (MPA) concern over the lack of any integrated consideration of the supply chain implications of infrastructure ambitions within the draft National Infrastructure Assessment (NIA), or more generally within government. The MPA argues that the implementation and maintenance of British infrastructure projects over the next 20 years is likely to require two billion tonnes of aggregates and mineral products. However, without a strategic approach supporting the future supply of aggregates and mineral products, which is integrated with infrastructure, housing and construction objectives within government and amongst stakeholders, the MPA says there is no guarantee that projects can be delivered in the medium to long term.
Perhaps the overriding message to the Brussels-based EU and national governments such as the UK’s should be it’s good to talk, but it’s even better to listen and act. GW gwoodford@ropl.com
Sandvik has appointed Henrik Ager as president of its Sandvik Mining and Rock Technology business area and a member of Sandvik Group Executive Management.
Currently president of the Swedish-headquartered, global quarrying and mining equipment market heavyweight’s Rock Tools division, Ager will take over his new role, succeeding Lars Engström, from 1 April 2019.
“I’m convinced that Henrik Ager with his experience, already proven leadership skills and excellent performance in Sandvik has the right capabilities to lead Sandvik Mining and Rock Technology going forward. Henrik is committed to further strengthening Sandvik Mining and Rock Technology’s market
Irish global building materials market giant CRH achieved sales of €26.8 billion in 2018, 6% up on the previous year. The group’s earnings before interest, tax, depreciation and amortisation (EBITDA) stood at €3.37 billion, 7% ahead of 2017. Operating profit from continuing operations was also up 4% to €2.177 billion.
Commenting on the full-year 2018 trading performance and CRH’s approach to 2019, Albert Manifold, group chief executive, said: “2018 was another year of record profit delivery for CRH. We benefited from good demand and continued favourable market fundamentals in the Americas coupled with positive underlying momentum in Europe. Both were experienced against a backdrop of energy-related input cost inflation and significant weather disruption throughout the year but with a continued focus on performance improvement and operational delivery, margins were ahead of last year.”
position, reinforcing customer relations, driving aftermarket sales, leveraging further on a decentralised way of working and ensuring our forefront position within automation, electrification and sustainability,” says Sandvik’s president and CEO Björn Rosengren.
Henrik Ager has more than 16 years´ experience in the mining industry, out of which an extensive period has been spent living in South Africa. Additionally, he has worked in Australia, South America, India and other important mining markets.
Henrik Ager’s previous experience from Sandvik includes the role as president for the Global Equipment division and vice president for Strategy within Sandvik Mining and Rock Technology. He has also held leading positions at McKinsey, Ericsson and several high-tech start-ups prior to joining Sandvik in 2014.
The Terex Materials Processing segment of Terex Corporation delivered strong performance across its portfolio of businesses in Q4 2018 with sales of US$340 million (€300mn) - 20% higher than last year.
Full-year 2018 sales of $1.3
Supported by strong cash generation, Manifold said CRH had continued to deliver value through efficient capital management, completing €3.6 billion of acquisitions and €3 billion of disposals, while returning €0.8 billion to shareholders in the year through its share buyback programme.
He continued: “CRH remains well positioned to build upon
the gains made in 2018. With a relentless focus on continuous business improvement, margin expansion, cash generation and returns for shareholders, together with continued strong financial discipline and efficient allocation of capital, we believe 2019 will be a year of progress and further growth for the group.”
billion (€1.14bn) for the segment – which includes Powerscreen, Terex Finlay, Terex Washing Systems, Terex Minerals Processing Systems, EvoQuip and Ecotec brands – represented an increase of 17% on 2017. Growth was driven by global demand
for crushing and screening products, material handlers, and environmental equipment. Terex Materials Processing (Terex MP) entered 2019 with a backlog of US$490 million (€432.1mn), 54% greater than 2018.
Kieran Hegarty, president Terex MP commented, “We’re well positioned to support the strong global demand we see from our customers heading into 2019 and expand our penetration into emerging markets. New product development will continue to differentiate our MP businesseswith new crushing and screening products being launched this year and new Fuchs material handlers that are designed to serve new markets including timber yards, ports and waste processing. To support our growth we will execute our manufacturing strategy which includes expanding capacity in the UK, India and China and utilising the Oklahoma City facility in North America.”
FOR QUALITY SHAPED PRODUCTS, ESPECIALLY IN HARD ROCK. MOBICONE mobile cone crushers are used in medium-hard to hard applications as well in abrasive natural stone operations. They cover a wide range of applications: from small to medium-sized batches for short-term contractor operations, all the way through to large quantities in tough quarrying operations. The MOBICONE crushers are the perfect match for mobile KLEEMANN jaw crushers and/or screening plants. MOBICONE mobile cone crusher: efficient and strong.
www.kleemann.info
LafargeHolcim saw its full-year 2018 sales rise by 1.6% to €24.18 billion (CHF 27.47bn).
The French Swiss global building materials giant also achieved full-year recurring EBITDA profit of €5.3bn (CHF 6.02bn), a modest 0.4% rise.
It was a particularly strong year for LafargeHolcim in Europe, with 2018 full-year sales up 7.8% and worth €6.65bn (CHF 7.55bn). This was said to be assisted by increased public infrastructure spending in Eastern and Central Europe combined with a rebound in construction and residential segments.
On a less encouraging note, LafargeHolcim’s Q4 2018 sales
fell 1.4% to €6.01bn (CHF 6.83bn). Despite a weaker overall Q4, the company’s sales in Europe were up 3.5% to €1.64bn (CHF 1.86bn).
LafargeHolcim confirmed the 2019 outlook it gave in November 2018 when it said it expected sales growth within the 3-5% range, on a like-for-like basis. During 2018 its sales on this measure, which strips out currency and divestments, increased by 5.1%.
Jan Jenisch, LafargeHolcim CEO, said: “Our momentum accelerated in the second half of 2018 during which we exceeded our sales targets while profitability increased over-proportionally.
ABOVE: LafargeHolcim representatives at Mülligen Quarry, northern Switzerland pic: LafargeHolcim
We completed a very successful 2018 with a double-digit EPS (earnings per share) growth and progressed significantly towards our deleveraging target. I am very proud of the fast roll-out of Strategy 2022 – ‘Building for Growth’ and congratulate all employees and teams on the impressive results. We are well positioned and I am expecting a further acceleration of our growth and earnings dynamic in 2019.”
German building materials group
HeidelbergCement says it expects worldwide demand for cement to increase further in 2019.
Announcing its Q4 and fullyear 2018 results, the group said it particularly expects demand to increase in Indonesia, India,
Breedon, a leading UK and Ireland construction materials group, saw its year-on-year revenue rise by more than £200 million in 2018.
Newly published audited figures for the year showed group revenue rose 32% to £862.7 million, compared to £652.4mn in 2017. Breedon’s profit before tax also rose by a healthy 12% to £79.9 million, up from £71.2mn in 2017. Group net debt stood at £310.7mn as of 31 December 2018, up from £109.8mn at 2017 end.
Breedon posted a sizeable increase in its aggregates sales in 2018 to 19.4mn tonnes, compared to 16mn tonnes sold the previous year. The group sold 2.8mn tonnes of asphalt (2017: 1.9 million tonnes), 3.2 million m³ of ready-mixed concrete (2017: 3.3 million m³) and 2mn tonnes of cement.
sub-Saharan Africa and North America.
The manufacturer posted a 5% increase in revenue for full-year 2018 to €18.1bn (€17.3bn in 2017).
HeidelbergCement attributes the rise in revenue to increased sales volume in all business lines and
A HeidelbergCement cement loading site in Germany
successful price increases.
In 2018, the cement and clinker sales volume of the group increased moderately by 3% compared with the previous year to 130 million tonnes. Deliveries of aggregates rose slightly by 1% to 309 million tonnes. Deliveries of ready-mixed concrete increased by 4% to 49 million m³.
In the fourth quarter of 2018 the group increased the sales volume of cement and ready-mixed concrete compared with Q4 2017. Cement and clinker sales volume rose by 2% to 33 million tonnes driven by solid growth in Europe and Asia. Deliveries of aggregates remained stable at 76 million tonnes. The growth in North America and in Western and Southern Europe offset declines in the other group areas. Sales volume of ready-mixed concrete increased by 8% to 13 million tonnes.
In a statement accompanying Breedon’s annual results, Peter Tom CBE, the group’s executive chairman, said the £455mn acquisition of the Northern Ireland-headquartered Lagan Group in April 2018 was transformative. “It took us into an attractive new market with significant growth potential, also helping to offset a muted GB performance in the year under review. In addition, the Tarmac asset swap was important as it enabled us to streamline our concrete network by relinquishing 23 peripheral plants in exchange for 25 million tonnes of reserves in four quarries, together with an asphalt plant, thereby further strengthening our asset base and improving the quality of our earnings.”
Superior Industries (Superior), an ambitious Minnesota, USA-headquartered global bulk handling and processing solutions market manufacturer, is targeting Europe as a major potential growth region for its comprehensive range of new and proven premium equipment. Guy Woodford spoke to John Garrison, Superior’s vice president of sales, to find out more about the company’s business philosophy and long-term ambitions.
Despite hailing from and still living and working in Michigan, John Garrison is something of a Europhile when it comes to discussing Superior Industries’ current global growth strategy. “Today, we’re taking a closer and more aggressive look at Europe. We’ve got a new business development manager in the region, Michael Dunne. He has come to Superior with a
strong history in the industry, first with Terex and most recently with Weir/Trio.
“You certainly have to have reliable products that lower cost per tonne in any bulk processing or handling market you service. But we like to build with the right people first. In his short time with Superior, Michael has established a legal entity in the United Kingdom, collected data and experience reports for new product development and
is developing new relationships with future Superior dealers throughout Europe. Drawing on Michael’s history within the European aggregates industry and feedback from new dealer relationships we are building, we have several European-style models in development.
“Because of our new legal status in the UK, we are building some products there that will allow us to better compete in the global market.”
There are many well-established crushing and screening equipment, conveyor and washing plant manufacturers in the European marketplace – such as Metso, Sandvik, Terex Materials Processing, Kleemann, Beumer, Telestack, CDE and Terex Washing Systems. I ask Garrison, who previously spent a decade as market area director at Terex Mineral Processing Systems (MPS), how he thinks Superior can stand out from its competitors and gain good market share.
“The European aggregates processing market is large and it’s growing, so it’s very important to Superior. While there are a lot of good manufacturers in our sector, Superior’s approach is different. We like to be flexible and adaptable to our customers’ applications. Instead of building a couple of models to serve every customer, we like to customise our offerings by region and even down to each customer application. Certainly, Superior is equipped with standard models, but we also have lots and lots of proven options. We’re excited to share them with the European market.
“We have assembled a huge product development team with lots and lots of industry experience, which includes many individuals, such as Michael Dunne, with backgrounds serving the European markets. They come to Superior from recognisable names and have built solid personal brands in the region.”
Outside its strong trading in its home market of North America, and beyond its efforts to establish itself firmly in Europe, Garrison says that Superior is gaining sales momentum in South America, Russia, Australia and parts of Africa.
“We do business in Africa today especially serving customers in marine material handling or ship loading and mining applications. In both sectors, we offer a unique set of highly mobile conveyors. There are not many other manufacturers of these products in the world, so Africa has accepted the technology well.
“In addition, there are current product development projects in our engineering departments that will serve some of those new sales momentum markets well.”
Turning his attention to the key day-today challenges experienced by aggregates processing businesses and current market trends, Garrison says: “Crusher automation is on the rise. More and more crushers are supported by full automation systems that are monitored from a smart phone or iPad. Operators can track any trend, while gauging throughput volumes and proactively pinpointing maintenance needs. To avoid costly damage and downtime, automated crushers provide protection against tramp events, while also alerting operators to any irregularities in vibration or temperature.
“Attracting new talent to the industry remains a challenge. Producers who scaled back on labour during the recession are seeing further attrition due to today’s ageing workforce. It’s getting harder and harder to find personnel with industry experience. Innovative education and training programmes are imperative.
“To ensure maximum uptime, manufacturers are designing equipment with greater access and ease of maintenance. Alternatively, producers are increasingly partnering with equipment dealers and manufacturers for readily available parts and service support, parts inventory management, and ongoing machine lifecycle management that often includes new full black box diagnostic capabilities and valuable predictive maintenance programs.”
Garrison says Superior divides its wideranging bulk handling and processing solutions offer into four segments: crushing, screening, washing and conveying. “One of our ongoing goals is to generate three to five new products per segment per year,” he explains. “So, there will certainly be some new products coming in each product segment.
“Within the crushing segment, we plan to debut our first horizontal impact crusher. It joins our existing lines of jaws, cones and vertical impactors. Our prototype is nearing completion and field testing begins later this year. It’s designed for primary or secondary crushing in quarry and recycle applications.
“A new bolted frame design for our Liberty Jaw Crusher will also start testing this spring. Designed for portable application, the bolted frame design will be lighter weight than our
“Finally, we reduced the weight of our 500 HP Patriot Cone Crusher by more than 30%. It will have the same internal configuration as our 500HD model but be designed and manufactured with modern mainframe castings.”
Focusing on Superior’s current conveyors and conveyor parts range’s performance in the global marketplace, he says: “Again, there are pockets within certain regions outside of North America where these products have done very well. In other countries or regions, we’re looking for opportunities to partner with distribution. In fact, that is one of our primary goals at bauma 2019 [in Munich, Germany].
If a distributor reading this is interested in meeting with us, we encourage them to visit our website and complete the form.”
Superior has been busy in recent years developing its aggregates washing plant and quarry dewatering product portfolio.
“Of the 100 or so new products we’ve introduced in the last few years, I would say at least half are for our wet processing or washing segment. Some highlights of these
Unrivalled control of sand
Customer-focused solution with unmatched maintenance access
providing industry-leading sand
Truly modular design with unparalleled
Up to 90% of process water recycled for immediate re-use in the system 90%
Rapid installation with industry-leading compact footprint
This is not a machine. This is patented modular technology with the ability to change the wet processing industry as we know it. The expert engineers at CDE have created a solution that can transform raw materials into high value products. This is the shape of things to come.
Outdoor Exhibition Area North/East – Stand FN 1022/1
Together we’re unlocking A New World of Resource 8 –- 14 April, 2019
new products include the Alliance Low Water Washer. It accepts a dry feed within the crushing circuit, which eliminates a costly trip to a separate wash site and creates higher value manufactured sand.
“Our Helix Cyclone is characterised by a uniquely designed inlet. The offset feed eliminates turbulence, which improves classification and reduces component wear.
“Our Spirit Sand Plant is a modular package with cyclones, dewatering screens, sumps and pumps. The unit removes heavy clays from valuable sands, transforming useless material into product that is ready for market.”
Superior’s entry into the crushing, screening and washing sectors of the global aggregates processing market was showcased under the company’s ‘Rock Face to Load Out’ promotional campaign at the CONEXPO-CON/AGG 2017 construction, quarrying and mining equipment exhibition, in Las Vegas, USA.
“We debuted our ‘brand new Superior Industries’ to more than 125,000 visitors. Inside our stand, we showed the world what ‘Rock Face to Load Out’ represents when we unveiled our new crushing, screening and washing equipment. These solutions, all designed and built by Superior, joined our existing product portfolio of conveyors, idlers, pulleys and related accessories.
“In addition, we introduced an expanded group of industry veterans — almost three dozen new sales and service employees — who joined team Superior since the last edition of the trade show.”
I ask Garrison how Superior is investing in automation, including predictive maintenance, solutions for customers.
“Automation development is something we’re equipped to design and build in-house,” he stresses. “We have a team of about a half dozen right now and looking to grow this group. We write our own code and control our own destiny. There is lots of room for new development in this segment. Right now, we have programs for automating radial conveyor stockpiling and crusher operation. We’ve also developed some custom programs for various applications. Our next hurdle will be development of a complete management system.”
Excessive downtime due to a wait for replacement crusher, screener or conveyor parts is a key concern for aggregates processing businesses. Garrison highlights what Superior is doing to meet customer replacement parts needs.
“For any new market we pursue, we like to support the market from within. That means we typically develop strong local support with dealers and distributors. They know the customers best, understand stocking needs and are quicker to respond than most manufacturers.
“One of our goals during the upcoming bauma is to hold meetings with distributors who might be interested in representing our lines throughout EMEA [Europe, Middle East and Africa]. They’re invited to visit www. superior-ind.com/bauma2019 to schedule a meeting with us in Munich.”
I’m curious to know what Garrison, who
ABOVE:
BELOW: Superior’s TeleStacker Conveyor is said by the firm to be the biggest-selling telescopic conveyor in the world. More than 1,400 units have been sold since the telescopic radial stacking conveyor was first designed and manufactured in 1997
joined Superior in 2014 at the start of the firm’s crushing, screening and washing plant product development, enjoys about working in the aggregates processing equipment sector and how he sees the global aggregates processing industry’s long-term future.
“I’m proud to be part of an industry that is foundational to the success of any society. Our customers supply the material to build roads, bridges, schools and hospitals, which create all kinds of new opportunities for the people that use them.
“We see aggregate demand growing for a long, long time. Generally, government policies within each region or market are getting stricter. That means we’ll continue to focus developing products that operate safely and produce at the lowest cost per tonne. Regardless of where our customers are, these are universal goals.” AB
The new EC200E has extended the Volvo excavator range with a true 20-tonne machine which combines Volvo quality with exceptional value, to deliver performance and profitability in medium duty applications. This machine can be factory fitted with breaker and shear piping, as well as rotator piping. Special attachments such as mowers, grinders, shears, crushers and tilt rotators boosts the versatility and productivity to a maximum. Talk to your local Volvo dealership today.
UEPG
The UEPG (European Aggregates Association) is closely following the run-up to the European parliamentary elections in May 2019, as it continues to campaign for a better deal for its members and an effective EU industrial strategy.
The European Parliament elections will take place in all member states from 23-26 May 2019, marking the end of a three-month long period of campaigning following the publication of most manifestos.
The European Parliament is currently made up of 751 members elected in the 28-member states of the European Union. Since 1979 Members of the European Parliament (MEPs) have been elected by direct universal suffrage for a five-year period. It is expected that the number of seats will fall to 705 after Brexit. The new mandate of future MEPs will last from 2019 to 2024.
The current polls indicate a shift towards more populist and Eurosceptic parties in the European Parliament. However, those estimates are variable and change day by day. The EU version of the newspaper Politico dedicated pages to the European elections and set up a projection of what the European Parliament could look like. The current trend across Europe shows an increasing political fragmentation and volatility weakening the established political forces. The European People’s Party (EPP) and the Progressive Alliance of Socialists & Democrats (S&D) will not be able to have the majority anymore and will need the Alliance for Liberals and Democrats for Europe (ALDE). This trend might benefit right-wing nationalist groups with almost 25 % of seats. There are still some remaining questions which might play a part in the final results; first of all, the number of voters in the elections; then, the new alliances which could be formed with current political groups such as ‘En Marche’ in France and the ‘Five Star Movement’ in Italy. The proportion of Eurosceptics is not determined. We do not know yet if the UK will set up European parliamentary elections in May, if Brexit is postponed.
The European Aggregates Association (UEPG) drafted a manifesto which was published on its website and on social media in December 2018. UEPG printed its manifesto and that of Industry4Europe, and widely distributed those to MEPs in February 2019.
The UEPG in its manifesto calls on future European parliamentary candidates to consider how ‘sustainable welfare in Europe needs access to primary and secondary raw materials, which is compatible with environmental management, and provides safe local jobs’. Read more at http://www.uepg.eu/ mediaroom/58/30/EU-Election-2019---UEPGManifesto/
The Industry4Europe Coalition, made up of 139 European associations, among them UEPG, calls on European parliamentary candidates to ‘put industry at the core of the EU’s future”https://www.industry4europe.eu/
Over the coming months, UEPG will carry on commenting on the European elections and disseminating its manifesto. UEPG members were called upon to analyse and use both manifestos and to translate the UEPG manifesto into their native languages and
make it available domestically in the run-up to the European Parliament elections.
The European institutions are keeping EU citizens informed about the European Parliament elections via communication/ social media campaigns and tools. In fact, you might be aware of the campaigns ‘What Europe does for me’, ‘This time I’m voting’, and communications on the European elections from EuroPCOM 2018.
Following the European Parliament elections and the ‘spitzenkandidaten’ process, the European Parliament will recommend the preferred European Commission presidential candidate to be approved by the European Council and confirmed by the European Parliament by July 2019. Jean-Claude Juncker, the current president of the European Commission, was elected for the first time under this process in 2014.
From July to September 2019, under the EU Finnish presidency, each member state government will put forward candidate commissioners. Consequently, the European Commission president-elect will appoint members of the Commission with their portfolios. The list of nominees has to be approved by national leaders in the European Council. Each nominee appears before the European Parliament to explain their vision and answer questions. Parliament then votes on whether to accept the nominees as a team. Finally, they are appointed by the European Council, by a qualified majority.
The process of the appointment of new commissioners and portfolios will be closely monitored by the UEPG and Industry4Europe coalition to make sure that the new European Commission embraces the need to have a new governance structure to ensure an ambitious industrial strategy. With its ‘For an ambitious EU Industrial Strategy: Going further’ joint paper, the Industry4Europe coalition has called for a long-term vision for Europe’s industry which demands a long-term governance structure going beyond the six-month EU presidency cycle and the five-year mandate of the current European Commission. A new joint call to the heads of state and government is to be finalised. On 7 March the coalition is organising, with the support of the European Economic and Social Committee, a conference on ‘EU Industrial Policy: Results and prospects for the next institutional cycle’.
The new European Commission should take office on 1 November 2019. AB
Remote monitoring
Superior accuracy
APRIL 8-14, 2019
Excellent
We invite you to connect with us via our state-of-the-art technology and extensive after-sales support. Using our innovations and expertise, we can share invaluable data and insights with you to maximise the performance of your construction equipment. If knowledge is power, when we share it, we’re stronger.
As we approach the date when the UK is due to leave the EU there are many unanswered questions. Not least is how UK businesses will be able to access the EU labour market. This has potential implications for many businesses in the aggregates sector where EU nationals fulfil some key roles. Lisa Mulholland, a specialist immigration lawyer from Stephens Scown LLP, explores the potential scenarios.
In unprecedented fashion, all EU nationals in the UK will be required to submit applications to the Home Office under the EU Settlement Scheme if they wish to continue living and working here after the UK leaves the EU. People who have been living in the UK for a continuous period of five years will need to apply for settled status. Those who do not yet meet the required period of residence will need to apply for pre-settled status, with a view to applying for settled status later.
A pilot is underway and EU nationals with valid passports can apply under the scheme now. It will be fully open to all applicants on 30 March 2019. Applications must be submitted by 30 June 2021, provided the UK strikes a deal with the EU. In a no-deal scenario all applications must be submitted by 31 December 2020.
Free movement of EU nationals after Brexit
Free movement of EU nationals post-Brexit depends on whether or not there is a deal or
not. If the UK strikes a deal with the EU, free movement of EU nationals will continue during the transition period (30 March 2019 – 31 December 2020). During this time the government will prepare new immigration rules. This will mean that EU nationals can continue to arrive in the UK during this period to work for your business, irrespective of whether they were in the UK at the point of Brexit.
If there is a no-deal Brexit, free movement is likely to end the day after the UK leaves the EU. This means that people from the EU (who are not already in the UK at this point) will not be able to come to the UK long term to work without permission from the Home Office. People who wish to stay in the UK for longer than three months will need to apply for and receive European Temporary Leave to Remain, which will be valid for a further three years. EU nationals who wish to stay for longer than three years will need to make a further application under the new future immigration system, which will begin from 2021.
New immigration system post-Brexit
The long-overdue white paper on immigration, which was published by the government in December 2018, gives an indication of what the UK immigration system may be post-2021. Its key points are:
• All overseas nationals will need permission to work or study in the UK regardless of which country they are from. This will result in one immigration system for EU and non-EU nationals alike. This signals the end of free movement from the EU.
• The government has made it clear that priority will be given to highly skilled migrants, with no specific route for low-skilled workers.
• Transitional and temporary short-term workers’ route until 2025. This route is for low-skilled workers.
• Cap on the number of skilled workers coming to the UK to be abolished.
• Consultation on the minimum salary threshold.
• If an employer wishes to employ a non-EU member of staff, it must currently have a sponsor licence and comply with the Residence Labour Market Test unless the role is on the shortage occupation list. This involves demonstrating that there is no suitable settled worker for the vacant role. The government has confirmed that it will abolish the Resident Labour Market Test from 2021.
What should businesses be doing now?
Despite the uncertainties, which at the time of writing even include the date of Brexit, there are two important things that employers should be doing now. The first is to consider if your workforce will be affected by free movement coming to an end and if you need to apply for a sponsor licence to continue to recruit from overseas. If so, prepare for this ahead of time and seek advice early. The second is to ensure that your workforce is fully aware of the EU Settlement Scheme and that your EU national members of staff submit their applications in time. AB
Lisa Mulholland is a specialist immigration solicitor at Stephens Scown LLP. The firm has more than 70 years’ experience representing mining and minerals clients and its specialist team is recognised by independent guides to the law Legal 500 and Chambers. To contact Lisa, please call 01392 210700, email immigration@ stephens-scown.co.uk or visit www.stephens-scown.co.uk
Northern Ireland’s eminence in the global aggregates production industry has been emphasised by a significant investment by one leading global equipment maker in its Co. Tyrone-based manufacturing and assembly facility. Meanwhile, another leading sector player is to open its own new cutting-edge production site in a different part of the country.
Guy Woodford & Munesu Shoko report
Sandvik Mining & Rock Technology’s (Sandvik) ultra-modern manufacturing and assembly site in Ballygawley, Co. Tyrone, Northern Ireland, has a rich aggregates processing equipment history. The 18-acre plot housing three factory buildings and 300 employees involved in the production of various Sandvik tracked mobile crushing and screening plant, used to be home to a large fabrication factory belonging to John Finlay, the founder and owner of Finlay Hydrascreens, now part of Omaghheadquartered Terex Finlay. John’s widow, Lily, still lives in a house located just above the Sandvik Ballygawley facility, where the couple’s grandson, Jake, works as an inventory planner.
Having moved its manufacturing capabilities from Swadlincote, Derbyshire, England, to Ballygawley in 2014, the last four years have seen Sandvik make huge investments in its Northern Ireland site, creating one of the world’s premier manufacturing facilities for mobile crushers and screens.
In late 2017, Sandvik Ballygawley’s shot blasting area for large components was expanded and upgraded. The enlarged area also reduced the amount of landfill waste linked to the previous operation. The previous shot blast system used a shot material called ‘JBlast’ which could only be used once. This hazardous waste was then collected and sent to landfill. The new shot blast technology has ended the consumption of copper ore,
replacing it with a chilled iron material. This material can be recycled up to 10 times, thereby reducing overall landfill waste by an impressive 96%. The improved shot blasting area is also self-contained under one roof, eradicating any potential quality imperfections caused by parts being exposed to the elements. It also creates a better working environment for employees.
The introduction of an enhanced shot blasting capability followed on from the £1.6 million investment in a state-of-the-art powder coating plant, replacing a traditional wet paint shop. Installed in 2015, the powder coating plant is benefiting customers by improving machine edge protection and increasing a plant’s corrosion resistance. Consisting of a load area, a shot blast, a prime-powder, a green-cure oven, a top-coat powder and a main oven, the powder coating plant uses a high-tech vacuum system so that more than 95% of all unused powder is captured and recycled.
The shot blasting area, powder coating plant and other manufacturing and assembly facility improvements have enabled Sandvik Ballygawley to increase the number of plant models it can supply each year. This is helping the Swedish global market original equipment manufacturer (OEM) cope with challenges associated with meeting greater customer demand for new and proven aggregates processing plant.
Among the models being manufactured and assembled at Sandvik Ballygawley are the Hillhead 2018 UK exhibition-unveiled QH332 DDHS (double-deck hanging screen), said by Sandvik to be the ultimate in tracked, mobile cone crushing technology. Based on
the QH331 mobile cone crusher, the QH332 DDHS Hydrocone crusher comes with the functionality of a double- or single-deck (utilising the top deck as a breaker deck) hanging screen in fully detachable, standalone form. Detachable or attachable without the use of additional lifting equipment, the QH332 DDHS delivers multi-functionality as a one, two or three-way split screener, as well as being an ultra-efficient and productive cone crusher.
During an Aggregates Business magazine tour of Sandvik Ballygawley in late 2018, Austin Walsh, the facility’s manufacturing engineer manager, stresses how employee safety, quality and production scheduling efficiency are, in that order, the top three day-to-day priorities for the Sandvik Ballygawley team. Emphasising the commitment to quality, Walsh explains how each manufactured plant goes through 40-50 quality inspection points during its manufacturing and assembly. Only around 20% of the basic steel fabrication work required on each plant takes place at the Ballygawley facility, with the rest contracted out to local firms. This, says Walsh, frees up critical manufacturing and assembly space.
Staff working in the manufacturing and assembly facility work one of two nine-hour shifts Monday to Thursday, from 7am-4pm
and 4pm to 1am. An extra hour’s overtime on the day or night shift is available during peak production periods. Friday’s two daily shifts are shorter, from 7am-1pm and 1pm-5pm. Further overtime is also offered on Friday evenings and Saturdays during peak production weeks.
Crucially, Sandvik’s significant investment in its Ballygawley site has halved the average time it takes to produce a crushing and screening plant, now 29 days, compared to 57 days three years ago. This has dramatically reduced customer lead times in the very competitive mobile tracked plant section of the global crusher and screener model market.
During our trip, we watched engineering technicians at work on a wide variety of mobile cone crushers and screeners, with a QH332 DDHS Hydrocone crusher and QA451 Mobile Doublescreen among finished models waiting in the yard for dispatch to a customer.
“There’s a culture of change within this company and its very prevalent,” summarises Walsh. “In the last three years we have exceeded all our expectations. But where we are at the minute is not where we want to be in three years’ time.”
Terex Corporation – whose Terex Materials Processing business segment is a major global player in materials processing equipment - is to open a new £12 million
(€13.95mn) manufacturing facility in in Derry, Northern Ireland.
The new 9,755m² manufacturing facility will focus on the design, manufacture and development of Terex Ecotec (waste management and recycling) and Terex Conveying Systems (TCS) (mobile conveying) product lines.
Kieran Hegarty, president of Terex Materials Processing, said: “As part of our growth strategy, we continually review markets to identify potential opportunities. The waste management, recycling and mobile conveying sectors are areas of significant growth and our objective is to be recognised as a leading global manufacturer in these areas. Our Terex Campsie facility will enable us to realise this ambition.”
The Terex Ecotec product line has grown significantly since it was established in 2014 as a strategic response to meet the specialised needs of customers in the growing waste management and recycling sector. The Terex Campsie facility will focus on developing advanced waste management and recycling products and services for Terex Ecotec customers with the goal of becoming a global leader in the industry.
Terex Conveying Systems was established to respond to increasing demand for mobile conveying systems which, as well as being complementary to existing core segment Terex
A new asphalt-mixing plant – and all the efficiencies that go with it – would be a great addition to your business. But the cost of a new plant can be prohibitive.
There is a cost-effective alternative: a retrofit from Ammann. You can rejuvenate your existing plant at a fraction of the cost of an acquisition. All projects are managed by the Ammann Retrofit Centre in Austria, which relies on proven processes and experienced technicians to troubleshoot any issues and ensure superior results.
Among the areas of improvement:
Dryer
A new dryer optimises heat transfer and can incorporate an expanded range of materials.
Mixer
A new mixer improves uptime and reduces maintenance.
Amdurit® Wear Protection
Ammann’s proprietary wear system protects valuable parts and components up to three times longer than wear-resistant steel. It also reduces downtime and cuts maintenance and labor costs.
A retrofit can benefit your plant – whether it was built by Ammann or another manufacturer. Contact us to schedule a free analysis of your plant, and begin the process of revitalising your business.
Materials Processing crushing, screening and shredding equipment, will help enable Terex to enter the port and terminal industry. The mobile conveying range is designed to offer a number of advantages to traditional wheeled conveyor systems, including being cheaper to run, improved efficiency, a reduction in production costs, a reduced environmental impact, improved health and safety and improved product quality. The Terex Campsie facility will manufacture four new products in the conveying range and will facilitate ongoing product development.
Work is already underway at the Terex Campsie facility and is planned to be operational later this year. The facility will initially create approximately 100 new jobs that include production operative roles, management and support roles in HR, operations and finance, as well as a highly skilled engineering team that will be trained to leverage the company’s cuttingedge engineering capabilities and lead the development of Terex Ecotec and Terex Conveying Systems product portfolios.
Hegarty continues: “Our investment of this size in a new facility will support our ongoing growth and development as we seek to build on the momentum of increased demand for our products globally.”
In a pioneering development, Metso and its southern African distributor, Pilot Crushtec International, have rolled out an industry-first, standard five-year/ 10,000-hour warranty on
all Metso crushers and screens.
The move ushers in a new era in the crushing and screening industry where a one-year/2,000-hour warranty is generally the norm on these mission-critical assets. Francois Marais, director – Sales & Marketing at Pilot Crushtec International, says the move is informed by the supplier’s and its principal’s understanding that warranty is a valuable component to any capital equipment purchase, especially mission-critical and big-ticket purchases such as crushers and screens.
Marais says the standard five-year/10,000hour warranty for southern African customers is a true indicator of Metso’s confidence in its product. It is also a sign of service commitment from Pilot Crushtec International as the exclusive distributor of Metso’s aggregates products and services, including static, tracked and wheeled crushers, scalpers and screens in the region.
“We have been offering this warranty for the past six months on a pilot basis to gauge the level of interest and feedback from our customers. Effective the 1st of January this year, we were able to broker a deal with our principal, Metso, to standardise the fiveyear/10,000-hour warranty across the whole
Metso product range we supply,” says Marais.
“The initiative is in the best interests of the consumer. A long product warranty gives customers some extra coverage for their big-ticket purchases, along with a little more peace of mind. From an OEM perspective, it says a lot about the confidence in the brand. From a supplier point of view, it also means that we want to be there for our customers for the long haul and be involved in their businesses with a vested interest,” explains Jorge Abelho, director – Technical and Customer Support at Pilot Crushtec International.
As part of the Metso Life Cycle Services for Aggregates, Metso has previously offered its Equipment Protection Services (EPS) as an optional extra. The comprehensive plan includes extended warranties and scheduled inspections with Metso-certified technicians. EPS is built on three core elements: extended warranty to five years or 10,000 hours; scheduled inspections with Metso-trained and certified technicians, coupled with OEM parts recommendations; and maintenance planning and reporting for mobile equipment through Metso Metrics Services.
In southern Africa, this has since become standard. This gives equipment owners muchneeded confidence in their cost structure by anticipating and minimising unexpected equipment failures. The warranty covers the whole machine, excluding wear parts, for the first 4,000 hours, which is double the industry-wide 2,000 hours standard warranty. From 4,000 to 10,000 hours, the warranty only covers all the critical components.
“It made sense for us to package it as a standard offering. We believe in our quality and know that if customers prescribe to OEM servicing levels, their equipment will last longer and perform better. The extended warranty also assures our customers that the OEM and the supplier are ready to deliver on their promise,” says Marais.
“As part of the warranty, our Metsocertified technicians will undertake field inspections every 1,000 operating hours. During these visits, they will identify preventative and/or correction actions and provide recommendations accordingly,” concludes Abelho. AB
The quarrying of durable Luserna stone requires brute force and nimble machine operation - something a CASE CX370D excavator is helping to provide at a quarry in Italy’s Cuneo province. Liam McLoughlin reports.
In the interwar years, around 90% of the stairs and pavements in Turin were constructed from Luserna stone. The imposing Mole Antonelliana building, which houses Italy’s National Museum of Cinema, uses slabs of this attractive and durable stone to support its looming brick tower.
Turin is also home to the European headquarters of quarrying equipment manufacturer CASE whose CX370D excavator has been used in the quarrying of Luserna stone in Bagnolo Piemonte, Cuneo province, by long-established company Vigilanco Alfredo e Fratelli.
Quarrying Luserna stone requires brute force and nimble machine operation. Once explosives have loosened stone from the quarry face, the CASE CX370D moves in to haul the several-tonne payloads onto safer ground, providing a mix of power, precision and speed. Alessandro Fresia, Italy marketing manager for CASE, commented: “CASE excavators offer the perfect balance between performance, operating costs and productivity, making them ideally suited to heavy earthmoving and quarrying. These are
key markets for CASE, with many of the heavy line machines specifically engineered to cope with the conditions present at these jobsites.”
Accurately moving payloads of this size at such speed requires a high level of operator skill, which the CX370D’s Auto Power Boost function is designed to enhance. The feature increases hydraulic pressure automatically to match operational needs, providing the level of safety and productivity necessary when working in such demanding conditions. Three power modes combine with Auto Power Boost to cater for all aspects of the job: ‘A’ mode allows for precise levelling and lifting; ‘H’ mode strikes a balance between productivity and fuel economy; ‘SP’ mode delivers maximum power, ideal for the hauling of the freshly quarried Luserna stone.
The CASE Intelligent Hydraulic System (CIHS) is designed to ensure force is matched by manoeuvrability, delivering adaptable and smooth control by ensuring that energy is saved in every cycle phase. The operator can precisely control the machine’s huge power and the stone is retrieved from the blast site quickly, efficiently and safely.
Mario Righi from Turin-based CASE
dealership Iveco Orecchia, which supplied the excavator to Vigilanco Alfredo e Fratelli, commented: “This CASE CX370D excavator was exactly what the client needed for the quarry: powerful and large, but not too cumbersome. The client told us they have been able to lift single rocks weighing 20 tonnes, and thanks to its powerful lifting and breakout force offered by the two-piece boom, operators could push the machine to achieve more in each cycle.”
In addition, the CX370D offers rear- and side-view cameras, combined with a wide screen, to provide outstanding visibility, while a soundproof, pressurised cab with plenty of legroom is designed to deliver a smooth ride and quiet work environment.
A Cat 745 ADT, fitted with one of Philippi-Hagenbuch’s PHIL sideboards
Righi added: “The client and the operators gave us really positive feedback on the speed of operation afforded by the hydraulic system, the low fuel consumption and extremely comfortable cab.”
Indonesia is the largest economy in Southeast Asia and is a key node in the Chinese Belt and Road Initiative (BRI).
The country will receive more than US$87bn in infrastructure investment under the BRI, with the Jakarta-Bandung highspeed rail, Manado-Bitung toll road and Sumsel-5 power plant among the most highprofile projects.
The BRI (also known as One Belt, One Road) is a huge Chinese state-run project that aims to strengthen infrastructure, trade, and investment links between China and around 65 other countries.
The steady and reliable supply of raw building materials, such as aggregates, asphalt and concrete plays a vital role in the Indonesian phase of the BRI, according to Aldrin Johar Nurdin, business manager in Indonesia for China-based quarrying vehicle maker SDLG.
“With land acquisition troubles causing delays before some projects can begin, there is pressure to ensure that construction proceeds quickly and efficiently once they are underway,” says Nurdin.
“The production of these building materials as well as their handling and transportation on job sites typically require wheeled loaders.”
Hot-mix asphalt supplier PT Roadmixindo Raya, construction firm PT Hutama Karya, and concrete producer PT Varia Usaha Beton are among the companies that have selected SDLG wheeled loaders to aid in the production of raw building materials, such as concrete and asphalt, at plants across Indonesia.
The loaders handle between 500 m3 and 5,000 m3 of material per day. Transporting these amounts of material involves multiple trips, and a fast cycle time is critical to productivity. Nurdin says that keeping cycle time short involves skilled operation of the wheeled loader, but a responsive transmission and a powerful engine are also essential.
He adds that PT Roadmixindo Raya has praised the performance of the transmission on SDLG’s L958F wheeled loader and credited it with reducing cycle times at its Tangerang site. With an eight-speed transmission, the operator can shift gears to achieve optimal speeds for the 20m to 250m distance between the stockpiles of aggregates and the cold feed bins of the asphalt mix plant. PT Varia Usaha Beton states that the power of the L956F engine enables it to overcome the 15° slopes on the grounds of its crushing plant in Pasuruan, both quickly and effectively.
Beyond the responsive transmission and powerful engine of these machines, reliability and cost-effectiveness are also important considerations for any project, especially when handling highly abrasive minerals, aggregates and rocks.
“A machine’s minimisation of onboard electronics — and therefore its simplicity — is a positive quality, as it makes the machine more reliable and less susceptible to breakdowns,” says Nurdin.
“On megaprojects like those on BRI, this mix of reliability and cost-effectiveness is appealing as upfront costs can be kept low with bulk orders of machines. On the other hand, the reliability of these machines — coupled with responsive after-sales service support when required — help minimise longterm maintenance costs.”
Three Liebherr R 920 crawler excavators that South African mining company KEDASE purchased in 2016 have now completed more than 1,000 operating hours.
KEDASE, based in Boshoek, says that the compact dimensions of the machines and their fuel efficiency were key factors in the decision to buy them.
The three excavators are used for trenching, pipe laying and for the feeding of a screener in a chromium mine. With an operating weight of 21 tonnes and equipped with a Stage IIIA/Tier 3/CHINA III engine with an output of 110kW/150hp, the R 920 crawler excavator was developed specifically for these types of applications. For KEDASE, the machines have been
configured with a 5.7m boom, a 2m stick and a 1.15m3 bucket.
The R 920 concept is based on the standard European models. Launched onto the market at bauma 2016, the R 920 is accompanied by a revamp of the range of 20-to-25 tonne crawler excavators. In addition to the R 920 are the R 922 and R 924. The R 922 weighs 22 tonnes and has an output of 110 kW / 150 HP and the R 924 weighs 24 tonnes and has an output of 125 kW / 170 HP. Liebherr says these machines are aimed at less regulated markets like South Africa, South East Asia, Russia, China and India.
Volvo Construction Equipment (Volvo CE) has launched the EC210D crawler excavator in the African and Middle East markets. Volvo CE says the machine can perform a wide variety of tasks and features a robust frame combined with optimal engine power and hydraulic pressure to provide superior digging forces and fast cycle times for excellent productivity in all operations.
For fast cycle times and optimum fuel consumption, the EC210D is equipped with intelligent work modes, including the new G4 work mode. Operators can choose the best mode to suit the task at hand, selecting from I (Idle), F (Fine), G (General), H (Heavy) and P (Power max) mode. Volvo CE says that choosing the correct mode according to working conditions ensures added versatility and increased productivity.
The EC210D features increased hydraulic flow for responsive, accurate control in grading and combined operations. Operators benefit from smoother, easier movement when traveling and lifting simultaneously as well as better grading quality from the harmonised boom and arm movement.
A new 22-tonne Doosan DX225LC-5 crawler excavator has been converted into an ‘all-terrain’ machine for contracts being carried out in the Wadden Sea in Germany.
The excavator is operated by the Sven
Jacobs Tief-, Garten- und Landschaftsbau company, which is based in Tating, SchleswigHolstein. The excavator was supplied by local Doosan dealer Atlas Hamburg with the conversion being completed by OLKOMaschinentechnik.
The main application area for the new all-terrain excavator is the approximately 11.3km long Hindenburgdamm embankment, which connects the island of Sylt with the mainland in Germany. Around 8.1 km of the Hindenburg embankment runs through the Wadden Sea.
To prevent the standard Doosan 22-tonne crawler excavator from sinking into the water, a particularly low ground pressure was required. Atlas Hamburg therefore contacted OLKO-Maschinentechnik to carry out the conversion needed. OLKO has mounted the superstructure of the Doosan DX225LC-5 on an all-terrain undercarriage, rather than a standard pontoon, to ensure the full manoeuvrability of the excavator has been maintained.
The undercarriage is designed for difficult applications in adverse conditions and on challenging surfaces, such as those found in wetlands, as well as performing environmentally friendly work in sensitive environments. It also makes it possible to carry out work on lakes, rivers and coastal areas.
Caterpillar has introduced a product update package for 2019 to its Cat M Series medium wheeled loaders (the 950M, 962M, 966M, 972M, 966M XE, 972M XE, 980M and 982M models). The update includes technology advances that provide lower operating costs via extended service intervals, enhanced operator comfort with new seats and suspensions, emissions control strategies to meet EU Stage V standards (EU only), added machine configurations (982M Forestry Machine and 982M High Lift), expanded productivity measurement tools, remote software update capability, and refinements in ground engaging tool and coupler systems.
Caterpillar says that periodic updates allow it to bring new and improved features to market more quickly and more frequently than do conventional New Product Introduction (NPI) cycles. AB
Hauler operators are moving away from the one-size-fits-all approach of 25-tonne machines and are also requesting more specialised tyres. Liam McLoughlin reports.
There has been a “decided move” away from 25-tonne machines to the 20- and 30-tonne articulated dump trucks (ADTs) among its customers, according to Bell Equipment UK.
The company says that this may be a demonstration of one size not necessarily fitting all and adds that it has also seen a rise in the number of requests for specialised tyres on its haulers.
“Seventy per cent of our B30Es are now being fitted with wide tyres, whilst 100% of our B20Es are fitted with high flotation tyres, both of which are providing customers with more utilisation over the winter months – keeping them moving for longer,” according to Nic Grout, Bell Equipment UK’s sales, marketing and dealer manager.
He adds that fuel is fast becoming the major consideration for the industry, with more and more customers using the ‘tonnes moved per litre of fuel used’ measurement to determine their effectiveness and profitability.
“Since inception, Bell machines have been designed with an excellent power-to-weight ratio, meaning they use far less fuel per tonne than other like-for-like ADTs,” Grout says. “The introduction of larger 50- and 60- tonne machines is also enabling customers to haul more material in less time, saving both time and money.”
He adds that there is also a noticeable
trend towards the increased use of technology in fleet management. “The ability to monitor a fleet and access information, such as shift results, fuel usage, and tonnes moved, from one central location and at the push of a button, is very attractive to customers,” says Grout. Bell Equipment introduced its off-highway satellite-based management system, Fleetm@tic, in 2003 and the company says it continues to be a major draw for its clients.
The final major trend in hauling that Bell says it has experienced is an increased interest in its 4 x 4 range of ADTs, which is currently available in 30- and 60-tonne units. These are predominantly used for aggregates quarries where good haul roads are in place and they can provide a number of advantages over a rigid truck, including greater manoeuvrability and reduced tyre wear.
Volvo Construction Equipment (CE) has updated its G-Series articulated hauler range with new features including cruise control, downhill speed control and OptiShift.
The Swedish manufacturer says the G-Series already incorporates features to help operators get the most from the machine, such as hill assist, load and dump brake and dynamic Volvo Engine Brake.
These features are now joined by the latest updates including new cruise control and downhill speed control. Operators can
set and adjust the cruise control to maintain a constant travel speed for smoother and more efficient hauling, and when operating downhill the new downhill speed control enables operators to maintain their control and speed. Volvo CE says both these innovations result in enhanced safety, comfort and productivity in all conditions.
The ergonomic cab and intuitive controls are designed to suit all operators. Automatic functions, such as the new OptiShift, are intended to further improve fuel efficiency and productivity via faster cycle times and increased operator comfort, offering greater ease of operation for an unrivalled operator experience.
British quarry operator E & JW Glendinning has taken delivery of a new Volvo R70D rigid hauler.
The vehicle is being used to haul blasted material to the primary crusher at the
company’s Linhay Hill Quarry at Ashburton, Devon.
“We conducted a competitive evaluation of the rigid hauler market and since we have over twenty Volvo branded machines operating here at Linhay and our other facilities, considered the best choice of hauler would be the new Volvo R70D,” said Richard Webb, operations manager of quarry and concrete products for E&JW Glendinning.
“The new Volvo has a long-standing pedigree with its Terex heritage and it carries on the work of our existing eighteen-yearold TR70 which has worked tirelessly here at Linhay. The R70D is well matched to our resident prime loading machine which is a Volvo L350F, dispatching the truck in just four passes. It will be working one single shift, five days a week, delivering approximately 250,000 tonnes of material from the face to the processing plant per annum.”
The R70D is powered by an MTU Detroit Diesel V12 engine developing 695 net hp and achieves a maximum torque of 3323Nm at the relatively low engine speed of 1350 r/min.
Volvo CE British dealer SMT GB says that electronic integration between the engine and transmission allows the hauler to achieve smooth gearshift quality for consistent momentum and acceleration on all hauling applications. Performance and fuel efficiency are enhanced by the integrated shift pattern system, which includes two transmission shift schedules – power and economy – for tailored performance on all hauling conditions. The operator can pre-select the transmission operating mode to adapt to varying haul loads. Meanwhile, the hydraulic systems provide necessary flow for cooling and
actuation systems that provide the required productive performance for quick cycle times and efficiencies.
Established in 1958, E & JW Glendinning produces quarry products, concrete products and asphalt from their facility at Linhay Hill Quarry with satellite outlets strategically located in Plymouth and Exeter. It also produces high polished stone value (PSV) gritstone chippings and asphalt from its Pigsdon Quarry operation located near Bude in North Cornwall. The company also operates a road maintenance division, contracting to private concerns and local authorities in Devon.
SMT GB markets Volvo CE products which include wheeled loaders, articulated haulers, hydraulic excavators, Volvo utility equipment and Volvo road equipment products in Great Britain. There are eight strategically placed customer support centres, a dedicated National Used Equipment Centre and a network of utility equipment dealers.
At the bauma construction expo in Munich (April 8-14), Italian company CASE will be displaying an Astra HD9 truck from sister brand IVECO in the quarrying section of the CASE stand. CASE says the Astra HD9 possesses the dexterity and power required to deal with the demands of quarrying applications.
Terex Trucks will be using bauma to communicate the message that it specialises in robust, reliable articulated haulers.
“The articulated hauler is the only product Terex Trucks manufactures – so therefore we’re able to focus all our attention on this machine,” says Terex Trucks MD Paul Douglas. “We will also be discussing the investments and improvements we’ve made in our product line and our growing dealer network.”
The updated Terex Trucks TA300 articulated hauler will make its first international tradeshow appearance at bauma in Munich. Since August 2018, the machine has incorporated a new transmission that is claimed to lead to a 5% improvement in fuel efficiency.
The largest Terex Trucks hauler, the TA 400, will also be on display. It is designed as a robust machine to excel in delivering cost-effective production at large-scale construction projects, quarries and mines.
Caterpillar articulated trucks will be represented at bauma Munich by the completely redesigned 730, which weighs 22% less than its predecessor the 730C, but retains 98% of the 730C’s capacity. The new truck features automatic control of traction, dumping, and retarding, as well as the Caterpillar Stability Assist system.
Also on display will be the 777G, a 90-tonne hauler with a Cat C32 engine rated at 945 net horsepower (704 kW) with US Tier 2 equivalent emissions. The new truck features a refined cab that positions the operator seat on the left side, along with a new console with an integrated hoist and shift lever.
The revamped 777G provides customers with a choice of bodies. The 60.1m3 dualslope body is designed for maximum material retention on grades and has two side-board configurations available for light material, as well as a rubber liner. The X-body is designed with a flat floor to better meter material into a crusher and is available with either steel or rubber liners.
Doosan Construction Equipment will be launching the new 30-tonne DA30-5 and 40-tonne DA40-5 Stage V compliant articulated dump trucks, replacing the previous DA30-5 and DA40-5 Stage IV models.
Doosan says the designs and developments in the new Stage V ADTs have resulted from intensive market analysis, customer visits, interviews with operators and additional feedback gathered by the company’s ADT product and R&D teams at its ADT plant in Molde, Norway. AB
Quality drill rigs, hammers and breakers are an essential part of any efficient aggregates processing operation. Guy Woodford reports on new models from four leading global market manufacturers.
In order to keep at the forefront of drilling technology, EPC-UK has taken delivery of an Epiroc SmartROC D65 down-the-hole (DTH) hammer drill rig, the first of its kind in the UK.
Incorporating cutting-edge automation and GPS technology, the SmartROC D65 is said to have the intelligence and power to consistently drill accurately located, highquality blast holes. The accurate drilling of blast holes, combined with fully digital blast design and analysis via EPC-UK’s in-house software Expertir, means the blast process can be managed with precision from beginning to end, delivering the desired outcome for the customer.
The rig’s hole navigation system (HNS) enables faster setup at each hole location, whilst the automated drilling process ensures consistent contact with the rock, which controls the compressor and air flow to maximise fuel efficiency. The HNS in conjunction with the built-in GPS removes the need to manually mark and survey hole positions, greatly improving both efficiency and safety.
“EPC-UK is continually investing in the future to ensure its technologies and engineering expertise are industry-leading,” explains Ben Coppock, national operations manager at EPC-UK, “which demonstrates our continued commitment to providing customers with the most up-to-the-minute drilling and blasting technology.
“The Epiroc SmartROC D65 will help us to further optimise the blasting process to produce the best possible fragmentation, as well as reduce fuel consumption due to its intelligent control of compressor load and engine rpm.”
Paul Warren, SED sales manager at Epiroc, explains the importance of EPC-UK’s inaugural UK investment: “The SmartROC D65 is our first ‘down-the-hole’ smart rig to be deployed in the UK. This is a significant step for Epiroc in terms of product development and we are delighted that EPC-UK has decided to introduce this new technology to the industry.
“We have worked with EPC-UK for a number of years and understand its business ethos of constant development and improvement, as it mirrors our own.”
Coppock concludes: “The addition of the new SmartROC D65 drill rig to our portfolio
will put EPC-UK at the forefront of drilling and blasting technology and when combined with our other technologies - drone surveys, fragmentation analysis, digital blast designand our engineering expertise, will enable us to provide our customers with the next level of blasting services.”
In conjunction with these technological developments, EPC-UK is also in the process of constructing a new bulk emulsion facility at its Rough Close Works facility in Derbyshire, England. It will enable the company’s ammonium nitrate blasting intermediate (ANBI) manufacturing process to incorporate some of the latest, safety-enhancing technologies. The plant will provide a safer and more ergonomic working environment for both operations and maintenance personnel and will be the first emulsion plant to comply with BS EN 61511 standard (Functional Safety for the Process Industry). The facility’s construction and installation will meet or exceed a wide variety of British and international standards and provide enhanced protection above the already high EPC Groupe standards.
The new Cat GC S Series top-mount, hydraulic, silenced hammers from
Caterpillar Work Tools—models H115 GC S, H120 GC S, H130 GC S, and H140 GC S - are specifically designed for hydraulic excavators with 13-40 tonne operating weights.
The new GC S Series models are said to combine optimum power-to-weight ratios with design simplicity to ensure reliable performance, versatility, ease of use, convenient maintenance, and cost-effectiveness in a range of applications— including quarrying, mining, municipal and general construction and demolition. As a package solution, Caterpillar-designed hydraulic kits are available to provide an exact hammer-to-machine fit for Cat models, ensuring optimum performance.
The Cat GC S Series hammers provide customers optimum impact power and reduced owning and operating costs. The gas-fired operating cycle delivers a constant reliable performance, maximising hammer efficiency.
The automatic shut-off feature provides blank-firing protection by stopping the piston from cycling internally when no material is under the tool. Eliminating blank firing protects the hammer by reducing internal stress and heat, which results in lower overall owning and operating costs. Additionally, the automatic shut-off helps protect rentalfleet hammers, which typically are used by operators with varied levels of expertise. EPC-UK has
As a standard feature, GC S Series hammers feature a protective, enclosed housing, designed to lower the noise level for the operator, as well as for the overall job site. In addition, the GC S Series incorporates features that buffer the effect of pressure spikes in the carrier’s hydraulic system and reduced shock loads on the carrier’s front linkage also serve to attenuate noise levels.
The most critical maintenance
requirement for hammers is adequate lubrication (hammer paste). To eliminate manual greasing, automatic lubrication systems are available for GC S Series hammers. Customers have the option of installing either a carrier-mounted or hammer-mounted system.
The top-mount design of GC S Series hammers increases impact power by ensuring that hammer force and stick force
are consistently in line. The top-mount style also provides a larger work area and enhances visibility for the operator. A further benefit of the design results from the top-mounted bracket transferring considerably less force into the end of the stick, reducing both potential bending stress and overall impact on carrier structures.
A high-pressure accumulator is standard with GC S Series hammers, factory supplied
likely to find a particularly attractive option in Noise Guard, a simple and rugged cover structure offering a total noise reduction of more than 10dB. It could be a decisive advantage when competing for contracts with strict noise limits.
Like the other Ranger DX series models, the DXR600R and DX800R drill rigs are said to offer reliability and large drilling coverage area - from the standard 17.6m² to an optional 26.4m², the latter via a lighter and more mobile package – a superior solution for hazardous conditions where safe and productive drilling requires advanced radio
and field serviceable. The accumulator helps protect the carrier hydraulic circuit by absorbing pressure spikes created during the firing stroke.
Caterpillar says that hammer speed/ frequency can be easily adjusted to match specific applications and materials to provide optimum productivity.
The design, manufacturing practices, quality inspections, and testing of GC S Series hammers are said to ensure durability in tough applications.
GC S Series hammers are designed with mounting brackets specifically matched to Caterpillar linkages ensuring optimal compatibility with Cat machines.
Full-length side plates on these hammers provide ready access to service points. Also, field-maintenance capability for tools and bushings, plus field-replaceable lower-tool bushings added overall customer value in terms of daily operation and maintenance.
GC S Series hammers are fully supported by Cat dealers. Customers can order parts and service for machines and work tools from a single source. Every Cat work tool is supported with a comprehensive range of pre- and after-sales services, including advice about work-tool selection, operator training, equipment management, and a range of financial and insurance solutions.
As initially reported in the Equipment Update section of Aggregates Business magazine’s January-February 2019 issue, and in response to customer requests, Sandvik Mining and Rock Technology has added to its Ranger DX series of surface top hammer drill rigs with two non-cabin Ranger DXR models, the DX600R and DX800R. The new Ranger DX models are said to offer improved safety in the toughest quarry, open pit mine and construction applications.
Contractors active in urban areas are
remote-control capabilities.
At the bauma 2019 exhibition in Munich, Germany (8-14 April), Furukawa is introducing the FXJ1070 - a new model in its FXJ series of hammers. Replacing the F100XP, the new model will be half a tonne heavier and has much more impact energy than its predecessor. Furukawa says the FXJ1070 offers improved durability and lower lifetime cost. The Japanese company, whose FRD Europe subsidiary is based in the Netherlands, is exhibiting its full range of demolition tools and crawler drills during the week-long bauma showpiece event. AB
HYDRAULIC ATTACHMENTS FOR EARTHMOVING MACHINES SELF-LEVELLING PLANERS • CUTTER HEADS SCREENING BUCKETS • CRUSHING BUCKETS • WHEEL SAWS
OVER 80 INNOVATIVE ATTACHMENTS TO FIND SOLUTIONS TO THE MOST CHALLENGING APPLICATIONS. FIND OUT
CDE says its new global base can develop the company’s position in the aggressively competitive wet processing sector. Liam McLoughlin reports.
Wet processing equipment
provider CDE has officially opened its new global headquarters in Cookstown, County Tyrone, Northern Ireland.
Having grown its team by 65% over the last two years the Northern Irish company, with 2,000 projects around the world, plans to create an additional 150 new jobs by 2020, bringing the total employed globally to almost 800. The new facility can accommodate over 400 people and CDE claims it houses the world’s largest engineering team dedicated to wet processing technologies.
CDE group managing director Brendan McGurgan and chief operating officer Sean Kerr sat down with Aggregates Business to discuss the impact the new facility will have on the company’s business.
“The new base brings everything together under one roof,” said McGurgan. “Over the last 10 years we have grown out of the existing offices in Cookstown, Northern Ireland. Our new HQ is a very open-plan building to encourage increased collaboration and ensure a one team culture to create the best solutions for customers.”
Kerr agreed: “Everything we do is a
bespoke solution for our customers which is quite unique for the industry. The open-plan of the new HQ and collaboration between all departments is critical for our solutions to be world class. That rapid communication, ability to be very agile and do things quickly is greatly enhanced by the environment here.”
As part of its five-year strategic plan, CDE has embarked on a strategy to deal with the end customer directly rather than sell through a distributor network. To that end CDE acquired the extensive Caterpillar NI manufacturing facility located at Monkstown, Belfast, last year to provide for additional considerable manufacturing capacity and further manage every aspect of customer needs.
“We are passionate about maintaining our USP which is about creating bespoke, customised solutions and a partner for life aftercare service,” said McGurgan. “That too is where our new HQ is important. We need the best environment to attract the best talent.
“A strong connection with third level educational institutions such as Queen’s University and the University of Ulster provides CDE a great pipeline of that new talent.”
Once the talent is attracted CDE seems able to keep it, with McGurgan pointing out that the company’s staff retention rate is
extremely high. “Almost half our global board of directors is made up of people who joined the business as a graduate,” he added.
He added that another major benefit of the new HQ is the facilitation of customer visits, and that it is an ideal venue to showcase an innovation ethos. On average, one foreign delegation is present at the new HQ each week with recent visits including groups from Canada, Israel and Argentina.
McGurgan said that, because of the customisable nature of CDE’s equipment, the company innovates in every single project it is involved with - both in terms of product and process. CDE’s innovation ethos appears to be reaping dividends. “Thirty per cent of our revenue, on average, comes from new products released in the last 36 months,” he said.
CDE, which claims to hold more patents than anyone else in the sector, has a specific number of its R&D staff now completely dedicated to ‘blue-sky thinking’ and new product development rather than refinement of existing products. That future thinking team is active in a diversity of areas including alternative materials, 3D printing, technology and software. “This industry is aggressively competitive which is why we focus heavily on new product development, coupled with
a strategy of protecting our design rights and IP [intellectual property] through patents.”
McGurgan also shared that the company had a large pipeline of new products with a significant number of patents pending.
“The main objective of this R&D is to enhance the customer experience and change the direction of the industry with these new and novel ideas, and that’s why we have the reputation as being the industry innovator,” Kerr added.
The internet of things is also set to be an interesting development for the industry as CDE incorporates its smart technology around the operation of plants. “We are moving to a new generation of quarry owners and managers who are brought up with considerable technological skills and therefore expect a certain level of tech sophistication in operating their plants,” McGurgan said. “This is something we have been working on and we will be launching a new innovation at bauma which will change traditional thinking and the manual way plants are typically run.”
This drive for continuous innovation to solve customer challenges means that CDE has plans for expansion beyond its new HQ, with an innovation hub scheduled to open on the same site within the next 12 months.
The new hub will feature a state-of-theart laboratory. “As we develop further into our regions and sectors, customers’ feed materials become increasingly varied,” Kerr said. “There are more surgical requirements on the separation side in terms of size fraction and removing impurities, chemicals and various other things, and this can turn what was typically waste into a valuable product. The new laboratory will enable us to
continue to extract the maximum value from our customers’ feed material streams.”
McGurgan said that recycling is fast becoming a necessity the industry needs to explore and increasingly presents both incredible business opportunities and environmentally sound practice.
“Virgin natural sand is the most used natural resource after water,” he said. “We need to preserve that and ensure we process in a responsible manner as the reserves of natural sand are depleting. We are looking towards material streams that would historically be perceived as wastesuch as highly contaminated soils, earth and excavation waste, over-burden and crusher dust on the sand and aggregates side - and have developed solutions that divert those materials from landfill and bring them back into mainstream construction as an alternative to virgin sand and aggregate.”
Therefore, one key area of CDE’s focus is the construction and demolition waste recycling sector, in which the company has played a central role in the UK over the last two decades. As a relatively small and densely populated island, natural sand availability in the UK was continuously going down. In addition, landfills were becoming filled with construction and demolition waste to the point where they were running out of space.
“People weren’t able to handle this waste or do anything with it,” said Kerr. “But through our R&D at the time we were able to recover up to 90% of the waste into recycled sand and aggregates which was used directly back into the construction trade. As that developed the rest of the regions started following suit and we have quite a number of recycling plants in Europe now, and our first
project in Australia.”
In terms of factors that have driven recycling in the UK he highlights the Aggregates Levy, which is a £2 per tonne tax for extracting natural sand and aggregate. “This really drove the demand towards alternatives,” he added. In addition, the government-supported agency WRAP subsidised the investment in technologies to enable the recycling of construction and demolition waste.
Kerr added that technologies such as CDE’s mean that recycled product is sold for 80-90% of the value that it had in its original, natural state.
“The UK is a global leader in this type of recycling, and on the back of the UK’s success and our experience in this area we have done the first projects of this kind to reclaim from landfill in India, Australia, and North and South America,” he added.
McGurgan believes that there is an increasing need globally to find alternatives to the finite resources used in the construction industry. For example, in the Middle East, Qatar relies on importing natural sand and aggregate for construction purposes. The Gulf state has huge levels of construction and demolition waste, and McGurgan said that ultimately there was potential for technologies such as CDE’s to address a need in such markets.
“There are benefits in recycling across the board,” he said. “In the Middle East water is more expensive than oil and we have the ability to recycle 98% of the water that’s used within the wet processing process. It’s the circular economy in action.” CDE has created what it says is the largest sand washing plant in the world at The Qatar Sands Treatment Plant.
McGurgan added that in some markets, such as Switzerland, the cost of landfill is significantly high which was also driving demand for recycling services.
He concluded: “On top of all that, many countries are facing a shortage of processing capability and raw material resources while at the same time experiencing increasing demand for infrastructure, housing and civil works. Therefore, it is becoming essential for them to explore ways to maximise value from construction, demolition, excavation and various contaminated waste and re-use that valuable resource to meet supply and demand in the face of declining natural resources.”
US-based washing, crushing and screening equipment provider Superior Industries is another company that is heavily involved in sustainable technologies. Its Aggredry Dewatering Washer, a sand washing solution that supports sustainable aggregates processing, has been deployed by Wissota Sand & Gravel, an aggregate supplier based in Wisconsin.
“Our greatest resource is our water,” says Wissota Sand & Gravel president Christopher Larson. As its third-generation owner, Larson is keenly focused on sustainability initiatives, the latest being the installation of new sand washing technology that allows costefficient fines recovery and the conservation of valuable water resources. The operation utilises an innovative system that combines a fines material washer and a dewatering screen in a single machine. “Its advantages are far-reaching. Importantly, we’re realising these benefits at a fraction of the typical costs per tonnes in this application,” said Larson.
When using their prior sand screws, Larson said that the sand was coming out at about 25% moisture content. “Per my calculations, we were losing about 91m3 per hour – and the water was going to a part of the operation where it could not be recovered,” he added. “Replacing that water would require pumping it from a deep well or finding some surface water within the operation that could be recovered.”
It was the latter costly challenge, he stresses, that led to the acquisition of the
Aggredry Dewatering Washer. Larson describes the new system as “making a lot of sense in its unique combination of two triedand-true technologies – sand screws and high-frequency screens.”
The Aggredry Washer at Wissota features twin 1,524mm fines material screws (500 tonnes) combined with twin-high-frequency dewatering screens. “Our sand is coming off the two screens at 8% moisture content and requires no drying time,” said Larson. “Plus, we’re saving about 80m3 per hour.”
In the past, Larson said that his company had to be very selective on what could be run through the wash plant. “If we hit a dirty spot in the pit, we weren’t able to get enough fines out of the sand,” said Larson. “With our new system, we can process dirtier material and still manage the fines on the wash end of the plant. This gives us more throughput without having to be so particular about the material coming from the primary circuit. That’s a big advantage as the face of the pit is always changing.” He added that his operation crushes 1.8-million tonnes per year, with about 90% going through the wash plant.
Terex Washing Systems (TWS) will be presenting live washing demos of its AggWash 60 during the bauma 2019 construction industry show (8-14 April). The AggWash 60 wash plant incorporates screening, scrubbing, sizing and recovery of sand on one modular chassis and produces
up to six grades of saleable sand.
The AggWash is intended to address requirements for recycling customers and quarry owners, particularly in the construction, demolition and excavation waste recycling market. It is designed to maximise yields from feed materials with efficiently designed system processes that keep running costs at a minimum. TWS says the plant’s portable format makes it particularly suitable for green-field applications, contractor use and temporary planning permission sites. The company adds that operators more used to static installations will still appreciate the small footprint and minimal site preparations required.
TWS engineer Paul McWilliams commented on the design: “In all cases, installation time is significantly less than conventional builds thanks to the high level of factory pre-fitting and connections. The no-compromise design ethos ensures maximum serviceability and performance despite numerous innovative features, including easily removed pumps, ready access to screening media and intuitive controls.”
Also at April’s bauma show, McCloskey Washing Systems will present the CSP120 plant. The company says it is designed to deliver superior separation efficiency, produces the driest, drip-free final washed sand product in its class, and produces up to two in-specification sands, to desired grade, at up to 120 (total) tonnes/hour.
The plant has been designed with the machine operator in mind. In addition to the highest level of quality and performance, significant benefits include simple and fast assembly times, ease of operation, low maintenance and an overall reduced footprint.
The CSP range can be tailored to suit any sand application, regardless of desired tonnage, ranging from 40-300tonnes/hour.
McLanahan will be exhibiting its new UltraWASH modular wash plant at bauma, the first time it will have been displayed at a trade show. It can produce up to three aggregate products and two sand products. It features a single process water feed point and a single effluent discharge point.
McLanahan says that, thanks to its recent acquisition of Anaconda Equipment, the UltraWASH feed hopper and conveyor can be upgraded to come with tracks for easier conveyor maintenance. AB
Quality screening media on an aggregates production plant offers big uptime and productivity gains for quarry operators. Guy Woodford talks to one leading global manufacturer’s expert on the topic, and reports on two of another manufacturer’s latest screening media solutions.
Metso is a major player when it comes to state-of-the-art screening media for aggregates processing applications. The Finland-headquartered, global market manufacturer has one of the widest offerings in this business, offering the right screening media product for almost every application.
Claes Larsson, director, Screening Media Products, Metso, spoke to Aggregates Business about some of the most common customer challenges related to aggregates screening today.
“The most typical challenges for stationary plants are related to preventive maintenance and accurate follow-up on wear life of individual components, i.e. making sure every piece of equipment is protected properly for continuous operation. Another issue is health and safety during maintenance: how to minimise interventions to change wear parts and other components. In addition to these, making a variety of sometimes challenging end products according to tight regional specifications for aggregates can be challenging. Difficult
process conditions like blinding and pegging may reduce output.
“For mobile and portable equipment, quick changes of screening media are crucial to meet varying tasks and contractual commitments. These require fast service and prompt deliveries from the screening media supplier.”
Larsson says the main driver for using synthetic screening media is to reduce time-
consuming work related to change-outs, such as wire cloth. “The cost of this labour is important, but even more is the operational time lost when changing media. If screens in the plant are bottlenecks limiting the output, then quick pay-back can be achieved with the use of synthetic screening media.
“Other cases consist of those when customers are experiencing ‘non-performance’, meaning that the screen cannot perform with the existing screening media solution. The problems are often related to blinding of screen surfaces and pegging of rocks in apertures. Changing media will then help and make the unit productive once again.
“Other reasons could be purely health and safety-related. For example, rubber or polyurethane lower noise emissions compared to steel wire or perforated plate. Also, less maintenance needed on the unit equals fewer operator interventions and less risk of injuries. Also, with modular synthetic decks, lifting weights are typically lower when compared to standard steel wire solutions.”
Larsson says poor performance of the screening media can also affect other
equipment such as crushers. Blinding and pegging can result in carry-over of fines into the crushing chamber, resulting in process or wear-related issues.
Highlighting how Metso can solve these challenges, Larsson says: “Metso has been working with screening media solutions for decades and is a pioneer in the development of synthetic screening media. Today, we have a comprehensive range of screening media products and accessories and can select the best solution for almost any customer application.”
Larsson stresses how Metso’s portfolio of polyurethane and rubber screening media products covers applications from heavy primary screening to dewatering, including wire and tension synthetic solutions, as well as modular systems and panels.
He continues: “Metso has screening media solutions to prevent blinding and pegging by using more flexible materials. The Screen Planner software allows you to control and maintain the history and operation of the screens. We also have tools that enable the calculation and identification of hidden added value when planning to change to an optimal screening media solution.”
Larsson says Metso’s recently launched hammerless attachment solution eliminates the use of sledge hammers and crowbars, as the pins are screwed into place and removed by using an impact driver, taking only seconds. This method is safer and is said by Larsson to require less operator force and strain compared to traditional pin and sleeve systems, easing work in confined spaces. Larsson notes that a dramatic decrease in shutdown duration increases the uptime of the screening process and makes a difference in productivity, in addition to improving safety.
During 2019, Larsson says Metso will migrate from “old-style” gravity casting of polyurethane to injection moulding. “This will result in advantages including better availability and better accuracy of openings, leading to more exact production of aggregates. The products will also allow for a higher open area.”
Haver & Boecker, a leading equipment manufacturer and solutions provider in
mining and aggregates applications, has developed Ty-Dura rubber screen media for large tonnages, large top sizes and abrasive material. It is said to work well with crushed dry aggregates and high-tonnage wet applications, such as scrubber or mill discharge, while also being exceptionally durable and offering effective noise reduction.
Ty-Dura was highlighted by Haver & Boecker at the 2019 AGG1 Academy & Expo (12-14 February) in Indianapolis, USA.
“Our Ty-Dura screen media stands up well to the most unforgiving applications,” said Karen Thompson, Haver & Boecker Canada president. “With its high durability and longevity, producers will often be able to spend less time changing worn-out screen media and more time increasing their bottom line.”
Ty-Dura is manufactured in both sidetensioned and modular configurations, and is available in square, round, slotted or specialty opening designs that are all tapered to resist or eliminate pegging.
The side-tensioned hooked sections feature a custom-formulated, compressionmoulded natural rubber, supported by a stainless steel cable substructure allowing for easy tensioning and preventing the stretching often experienced with other types of rubber screen media.
Ty-Dura’s hooked sections also eliminate the need for a deck conversion when switching from woven wire. Retrofitting a machine from a cambered deck to a flat deck can cost as much as US$15,000 per deck. The hooked sections can be used on the cambered deck to eliminate the need for that conversion. This also allows operators to test the media on a vibrating screen with no
additional conversion cost or changes to the machine.
Ty-Dura modular panels are available in pin and sleeve, snap, groove and bolt-down options.
It is said to be a great option for top sizes larger than 15cm and high tonnages. The rubber — up to 10cm thick — also resists abrasive material. Its openings are tapered to prevent blinding and pegging.
Ty-Dura is also ideal for applications where sound is an issue, as the rubber dramatically reduces noise.
Because it handles impact so well, Ty-Dura is highly effective on a vibrating screen’s feed end or in the second position.
Ty-Dura is ideal for all types of vibrating screens except for high-frequency fine screening units.
Haver & Boecker also offers its Tyler brand of hooked engineered screen media, including the Ty-Max and Ty-Wire products, as another solution to the problem of expensive deck conversions.
Tyler engineered screen media was due to be showcased by Haver & Boecker at bauma 2019 in Munich, Germany (8-14 April).
Ty-Max and Ty-Wire can be blended with woven wire or self-cleaning screens on cambered decks. In many applications, operators are looking for more wear life on the feed end of the screen. This can be accomplished by installing a section of Ty-Max at the feed end. Ty-Wire can be used in the middle of the deck, for example, where basic screening takes place to give operators the ideal combination of wear life and open area. Using woven wire or selfcleaning screens at the discharge end will provide maximum open area at the end of the deck.
The screen media is manufactured out of Haver & Boecker’s signature blend of polyurethane. It’s made in one of the only facilities that blends its own material, which is critical for quality control. Chemists developed the media to offer the best combination of open area and wear life for both wet and dry applications. Engineered screen media is poured open cast, resulting in a claimed 1.5 to 2 times longer wear life than injection-moulded products sold at comparable prices. In addition, open-cast polyurethane permanently hardens when cured to maintain its chemical properties, so it resists wear and tear. AB
ABOVE: Benninghoven’s state-of-the-art HQ
Following a €130 million Wirtgen Group investment, asphalt plant maker Benninghoven is primed for growth. Guy Woodford reports.
Benninghoven’s production facility at the Wirtgen Group company’s ultramodern 313,000m², 800-employee headquarters in Wittlich, south-west Germany, is as cavernous as it is well resourced. A tour of the 46,000m², LED-lit facility takes in a raw material storage area, a large laser steel cutting, plasma drilling, component manufacturing and pre-fabrication area, a generously proportioned surface treatment-powder coating hanger, a sizeable final assembly area, a spacious and wellequipped electric production room, and a giant central asphalt plant parts warehouse. All of this is managed via the latest SAP (Systems Applications Product) business management software.
Step outside the central warehouse and you cannot miss a fully assembled asphalt plant used by the company’s senior field engineers, sales teams and apprentices from the Benninghoven training academy, which takes in aspiring engineers from local schools and colleges. Apprentices also have onsite their own large indoor metalworking and
electrical engineering training workshops.
Benninghoven says the health and safety of all employees was a primary concern when designing its new headquarters, which also features an attractive and 12,000m² five floor administration building. This is apparent in the site’s ergonomic, air-conditioned offices and the production facility’s use of powder coating rather than wet paint. This has meant that previously used solvents have been largely eliminated from the production floor. Another big environment-minded advance has been the installation of a system that extracts hot air from the production facility, which is then purified in a filter unit, while the energy generated from the exhaust air is returned to the air circulation.
The new headquarters, which took just over two years to build after groundbreaking in late August 2016, is said by Benninghoven to demonstrate the company’s clear commitment to Germany as a production location. With its emphasis on lean management and the use of Industry 4.0 technologies, the firm, acquired by the Wirtgen Group in 2014, also stresses how the
new production plant, which will eventually rise to a 150 plant/year production, makes it more competitive and able to meet increasing market demand for its asphalt plant and associated products. Overall, you are left with the lasting impression that a lot of thought as well as money has gone into maximising the return on this eye-catching capital project.
Benninghoven produces mobile, transportable and stationary 100-400tonnes/ hour rolled and mastic asphalt mixing plant, capable of handling up to 90% recycled asphalt pavement (RAP). Benninghoven plant is known for its innovative modular system and intelligent connection technology, making assembly easier. The company also produces high-quality, maintenance-friendly components for all its plant.
Benninghoven manufactures four types of asphalt plant – MBA, ECO, TBA, BA (BA RPP), all featuring the company’s BLS 3000 control systems. The company also produces its own asphalt plant combustion (burner) technology, with burners available in five sizes, and carries out full asphalt plant retrofits. During my tour I am told the heat generated by a burner running for just one hour is enough to heat the average family home for a whole year.
MBA 1250, 2000 or 3000 plant are said to
offer high flexibility, easy transport, and short assembly and dismantling times. A gravelled and compacted area is also said to be sufficient for an installation location.
The new concept 1250, 2000, 3000 and 4000 ECO series plant, being showcased at bauma Munich 2019 (8-14 April), offer nearly all mixing tower components in ISO-container dimensions, lowering the logistics cost. Like MBA plant, they can be assembled and dismantled quickly and easily, with modular extension possible. Easily transported, ergonomic and offering simple maintenance access, the ECO plant is capable of 100-320tonnes of asphalt mixing/hour. ECO plant can also accommodate a cold RAP addition of up to 30%.
Benninghoven TBA 2000, 3000 or 4000 plant offer huge hot and ready-mixed asphalt storage capacity. They can handle a cold RAP addition of up to 40%, and a hot RAP addition of 70-90%. An intelligent building block approach is said to allow for quick plant assembly and installation. Like the ECO plant, modular extension is possible with the TBA, which can work off either a transportable or stationary foundation.
Finally, BA 3000, BA/ BA RPP 4000, and BA/ BA RPP 5000 plant have the advantages of the highest capacities and a short project realisation phase and quick assembly and installation. The BA and BA/ BA RPP models are said to offer very good accessibility in all areas, and multiple configurations. BA/ BA RPP plant can handle up to 90% RAP. Their emissions and energy consumption are both said to be low.
A recent development saw Benninghoven install its BA RPP asphalt plant’s proven recycling drum using counterflow action with a hot-gas generator on the firm’s 160-320tonnes/hour semi-mobile and stationary TBA plant range.
Benninghoven’s hot-gas generator is said to be a solution that is environmentally friendly, future-proof and a secure investment. With it, the recycling material –in addition to the virgin mineral – is heated by an EVO JET burner. However, this takes place indirectly in a recycling drum using counterflow action. Depending on the quality of the recycled material used, feed quantities of over 90% are possible.
Unlike conventional parallel drums
used for recycling, these recycling drums use counterflow action for heating the gas indirectly. Here, the material is conveyed in the opposite direction to the heat source. As a result, the discharge temperature of 160 °C is the same as the application temperature, with the exhaust gas temperature approximately 100 °C (though above the dew point). This procedure leads to key advantages for the operators of asphalt mixing plants. In classic recycling systems using the parallel flow principle, the temperature is limited to 130 °C by the resulting exhaust gas emissions. However, the exhaust gas temperatures physically exceed this, which leads to increased energy consumption and a greater load on the dust collection system. To enable the asphalt mixture to reach a temperature of 160 °C, overheated virgin mineral must be conveyed.
The EVO JET burner can be supplied with different fuels as normal and supplies the thermal energy required for drying and heating the recycling materials. The generated hot air is mixed intensively with the circulating air, also using counterflow action. In doing so, the hydrocarbons in the exhaust air are almost eliminated.
After my tour of Benninghoven’s HQ in January this year, I sat down with three senior
Benninghoven figures, Marcio CavalcantiHapple, head of sales, Albert Czerny, sales manager, and Lars Henrich, head of marketing, along with Paul Holmes, managing director of Wirtgen Group UK & Ireland, to discuss how Benninghoven plans to capitalise on its new production facility and headquarters.
Speaking about Benninghoven’s current global market reach and likely growth areas, Lars Henrich says: “We are well established in Europe through our subsidiaries, with a particularly big market in Russia and in Turkey. We are not yet selling into Latin America and Asia, but both offer good growth potential for Benninghoven.”
“The European market is a batch mix plant market. It’s a much more mature market which tends to run asphalt distribution from fixed location plants,” explains Paul Holmes. “In America and developing market countries, they tend to favour continuous mix plant. Wirtgen Group has Ciber, the mobile continuous mix batching plant company in Brazil and there is good cooperation between Ciber and Benninghoven. The new engineering director at Benninghoven did the same role at Ciber. As we look at each market, we need to go into new ones properly. Have we got production capacity? And have we got
localised support from one of our subsidiaries?
“Benninghoven has gone through a big change: two factories to one, a revised product range focusing on the modularity of plant, such as the ECO range, and then bringing everything we do on to SAP business management software. Looking at SAP from an engineering perspective, it means every component on an asphalt plant needs to have its own number, to ensure production line consistency. We now also use Siemens NX software, which is a three-dimensional building block, in our engineering. That’s another big change. The factory is very much the start of our growth strategy. Within the Wirtgen Group, Benninghoven and Kleemann [mobile crusher and screener plant manufacturer] offer two of the biggest growth opportunities.”
Marcio Cavalcanti-Happle adds: “Our focus after this big change period is to
Benninghoven’s state-of-the art production facility has many elements. These include an academy workshop, burner production, steel cutting, electric production, fabrication and an asphalt plant surface treatment powder coating bay
concentrate on our long-time markets while firmly integrating Benninghoven within the Wirtgen Group, in terms of sales network and expertise, to gain the trust of customers. I use the example of one asphalt mixing plant having the same complexity as 19 different paving machines, all with their own options.”
Holmes says there is a growing trend in mature markets such as northern and western Europe to use more RAP in each asphalt mix. This is partly due to increased strict legislation on carbon emissions but also down to other factors such as the rising cost of bitumen, greater knowledge of how to process RAP, and a desire for companies to be ‘seen to be green’. This, he says, creates exciting sales opportunities for Benninghoven.
Cavalcanti-Happle says he has just returned from visiting customers in Finland, Norway and the Netherlands. “They talked
about the market now wanting to achieve a standard target of 100% use of RAP with zero CO2 emissions in asphalt mixes by 2030.”
“I think what will happen in the future is that asphalt production will be more automated, as technology continues to develop,” says Albert Czerny.
“I think off the back of increased automation will be how customers can manage data that our sophisticated [BLS 3000] machine control software and telematics is generating,” says Holmes. “Giving customers the ability to benchmark plants, so they can find out why one of their four plants, say, is performing more efficiently than the others. Why is one plant producing asphalt for £2 a tonne, while the others produce it for £2.05? We want our customers to be able to access all this innovation and, ultimately, make more money.” AB
Volvo Penta’s Stage V solution is designed especially to meet the demands of tough off-road applications, complying with emission standards while ensuring maximum engine efficiency. Optimized productivity, no compromise.
The engine and exhaust aftertreatment system are developed together as a complete, single-supplier package. It’s a solution that makes life easy for OEMs and brings ease of operation, fuel efficiency and uninterrupted productivity to a wide range of construction applications.
And the Volvo Penta global service and support network is always there to back you up. www.volvopenta.com/stagev
WELCOME TO VISIT US AT BAUMA MÜNCHEN 2019, 8–14 APRIL, HALL C6, STAND 203
Demand from both government housing and transport infrastructure projects is predicted to help maintain healthy demand for aggregates in Germany over the next few years. Liam McLoughlin reports.
Demand for aggregates in Germany remained healthy in 2018 due to a strong construction sector, according to MIRO.
The German aggregates industry association adds that prospects for 2019 and the next few years also remain positive with demand from construction projects continuing to rise.
The federal government is working on a housing initiative and the Federal Transport Infrastructure Plan receives €14bn in funding per year. MIRO states that demand for sand, gravel and natural stone products currently amounts to more than 500 million tonnes per year.
“This is good news for the industry and it is expected that demand will remain stable or grow at a high level,” says MIRO president Dr. Gerd Hagenguth.
He adds that there is a strong connection between MIRO’s technical work and the representation of its members’ interests at the federal government and European levels.
“With the office in Duisburg - responsible for technology and standardisation - and the office in Berlin which has operated since 2018 - responsible for politics and communication - we have paved new ways for our work,” says Hagenguth. “Meanwhile, our topics are perceived at the highest political level in terms of the interests of gravel, sand and natural stone companies.”
MIRO has reiterated its warning about the problems of regional supply bottlenecks in gravel, sand and natural stone graining across Germany.
Hagenguth says the situation is acute because, on the one hand, companies are gaining their authorised raw material supplies
faster than originally anticipated due to high demand, while at the same time approval procedures for expansion or reclassification are becoming more complex and long lasting.
Describing the issue as “a dramatic traffic jam”, Hagenguth says politicians at all levels must move to address this issue quickly and consistently.
“We need shorter approval procedures and longer extraction periods so that we can continue to meet demand for aggregates from domestic deposits through short routes,” says Hagenguth. “We need clear decisions and legal certainty for companies.
“Access to domestic mineral resources must be guaranteed. That is, deposits are to be protected from overbuilding or competing uses. What we do not need….are commodity taxes. These do not have a steering effect but, in stark contrast to the creation of affordable
housing, would inevitably make construction more expensive.”
MIRO says its hopes are currently focused on the new edition of the federal government’s raw materials strategy for Germany, the effects of which should be seen by mid-2019.
Stefan Hunger, business regional manager for Europe and Russia at wet global aggregates processing equipment company CDE, says that the German market is facing a shortage of processing capabilities and raw material resources.
“At the same time Germany is experiencing huge demand for infrastructure, housing and civil works and typically around the urban centres such as Munich, Frankfurt and other major cities,” Hunger adds. “Therefore, it will be necessary for Germany to look to ways to maximise value from construction and demolition waste and re-use that waste to meet supply and demand in the face of declining natural resources. That said, it is currently very difficult to secure a permit for construction and demolition waste plants in Germany in a radius from build that makes economic sense.”
However, Hunger says that it is only a matter of time before environmental legislation is introduced similar to that in the UK and Switzerland including landfill levies, which will drive an ever-greater need for washing technology such as that produced by CDE.
“That is why the German market is a significant focus for us given our expertise in recycling waste and providing customers with a high-value end product,” says Hunger.
“Perception has been that recycled waste is of no real benefit. This could not be farther from reality as a substantial amount of construction activities are non-structural and sooner or later the German market will see that as a real solution to its current building challenges.“
With hundreds of billions of euros being spent on German infrastructure projects over the coming years, Terex Trucks has identified the country as a key market. The articulated hauler manufacturer already has three dealers in Germany but it’s keen to sign more – not least because its upgraded TA300 was recently launched there.
Terex Trucks says that many are predicting that the level of infrastructure
investment in the country will continue to grow. Over the coming years, €269.6bn will be spent on modernising and interlinking Germany’s transport infrastructure. This includes €127.1bn that has been put aside to fund the renovation of the country’s road network, which is estimated to take place until 2030. It’s not just the roads that are getting a facelift, though – everything from Germany’s airports to its fibre-optic cable networks are going to be upgraded.
“Germany has the biggest economy in Europe from a manufacturing standpoint,” says Paul Douglas, managing director of Terex Trucks. “Given that we’ve just released an upgraded TA300 articulated hauler, we want to have a strong dealer network in place throughout Germany. The Terex Trucks brand is already well known thanks to our three German dealers, Klarmann-Lembach, Fischer & Schweiger and Baumaschinen Rehnen. However, we are keen to sign more German dealers, particularly in the east and north-east of the country.”
Terex Trucks offers two articulated haulers in Germany: the TA300 and – the biggest hauler in the company’s range – the TA400. These machines are typically used on large-scale construction projects as well as in quarries and on infrastructure developments.
“Looking at the numbers, German customers show a preference for the TA300 because they like its high flotation tyres, mechanical suspension and over-hinged tailgate,” says Douglas. “It’s a relatively maintenance-free machine.” Since August 2018, German customers have been able to get their hands on an upgraded version of the TA300, complete with the new and improved EP320 transmission.”
With the rental market dominating in Germany, Douglas says that Terex Trucks has to ensure that its machines are extremely robust and durable to minimise downtime for the customer.
German construction machinery manufacturers are concerned about a no-deal Brexit – the UK exiting the European Union without a deal - and the possible disintegration of the EU.
Rising global economic challenges can be mastered only with a strong, united Europe, according to the VDMA - Construction Equipment and Building Material Machinery Association. VDMA represents more than 3,200 mostly medium-sized companies in Germany’s mechanical and plant engineering sector.
This was the view by attendees at the VDMA’s construction machinery-specialised group conference held recently in Frankfurt am Main.
The VDMA says that, from an economic point of view, the country’s construction industry is scaling new heights. Total domestic and foreign sales of equipment that was made in Germany (by either German or foreignowned manufacturers) increased by 12% in 2018. Total sales for construction equipment made in Germany were €12.1bn in 2018, of which €4bn were sales on the domestic market and €8.1bn were export sales.
Sales of German-made equipment on the domestic market grew by 9% compared to the
previous year, a greater increase than the previous record annual increase of 8% set in 2007.
Although a moderate decline is anticipated, the VDMA estimates the German market will remain very strong. Representatives of the construction machinery manufacturers expect industry turnover to grow by 3-5% this year in Germany.
“We are at an all-time high, but this time the road that led us here was more stable and sustainable than in 2007,” said FranzJosef Paus, chairman of the VDMA. “This gives us hope that the industry will be able to maintain this good level for longer.”
He believes that only the lack of qualified personnel on the customer side had a dampening effect and that the construction industry in Germany and Europe remains strong and stable overall.
German gravel pit operator Gran has opted to deploy a duty cycle crawler crane from Liebherr’s HS series. Gran has put the new HS 8130 HD in dragline operation at Stauffendorf, near Deggendorf in south-eastern Germany. With a robust steel construction, the duty cycle crawler crane is designed to withstand the high dynamic forces in gravel extraction and dredging.
The machine is not only being used for gravel extraction but also for the development and recultivation of the gravel extraction site.
The HS 8130 HD has a 23-metre boom and is fitted with a Hendrix dragline bucket 7½ HS with a capacity of 5.7 m³. At a digging depth of 8-10 m the duty cycle crawler crane manages 450 m³ of material per hour. Depending on the duration of the shift, this results in a daily performance of 4,500 m3 or 9,000 tonnes. The machine’s two high-performance winches provide a line pull of 2 x 350kN and are designed to mean that a high level of material handling is possible with the duty cycle crawler crane.
Gran has the HS 8130 HD in operation four days a week in single-shift operation. The machine features an eco-silent mode function, which is designed to enable a significant reduction in diesel consumption to be achieved without any impact on operative output. Liebherr says that this results in Gran achieving a fuel consumption of only 40 litres per hour with an engine speed of 1550 rpm. It adds that eco-silent mode also reduces the noise
emission of the duty cycle crawler crane.
The Gran company was founded in 2004 and the new HS 8130 HD is the fourth machine from the HS series in its fleet.
Gran is planning to extend its fleet with four further Liebherr duty cycle crawler cranes (2 x HS 8130 HD and 2 x HS 8100 HD). It says that crucial factors for this decision are the robust steel construction, the economic and quiet diesel engine and the high pull force of the winches, as well as the clear and wellarranged control panel in the operator’s cab. “The complete design of the machine is very well thought out,” says owner Andreas Gran. “We achieve excellent turnovers with an impressively low fuel consumption. That’s why the HS 8130 HD is the perfect machine for extracting gravel.”
Kieswerke Silzen-Peissen (KSP) has purchased three new Doosan machines for operations carrying out gravel extraction both above and below water at the company’s operations in Silzen, in the German state of Schleswig-Holstein. The new machines comprise the Doosan DL420-5 wheeled loader, a custom-made, long-reach 60-tonne DX530LC-5 excavator and the DL420CVT-5 (continuously variable transmission) wheeled loader.
The two KSP plants in Silzen comprise about 70ha of approved mining area, of which approximately 20ha is being developed underwater and is called Plant 1. The materials obtained from the water in Plant 1 are cleaned in the company’s washing systems and then sorted. Plant 1 mainly produces concrete aggregates, screes and special building materials for use on golf courses and riding arenas as well as special sands for playgrounds. The second plant in Silzen – Plant 2 – has been operating for about 15 years and is directly opposite Plant 1. Plant 2 produces materials for applications including road building. The permit for this work covers approximately 40ha.
The two wheeled loaders are used in the above-ground mining and for various loading operations, whilst the DX530LC-5 excavator is responsible for the extraction and earthworks carried out underwater at Plant 1.
The underwater work was previously carried out using a nearly 40-year-old scraper, which had to be replaced at short notice. There were strict requirements that the new excavator had to meet: it had to be able to work in a water depth of up to 9m and be delivered within two months.
Atlas Hamburg was able to offer a solution for this to the Silzen-Peissen gravel works using the Doosan DX530LC-5 with a customised 18m boom. In order to optimise the excavator for underwater work, Atlas Hamburg also made a number of other changes to the machine.
As a result, 900mm-wide tracks have been installed to keep the ground pressure as low as possible. The stability with the long boom was increased by widening the undercarriage and adding an additional three-tonne counterweight. For machine control, Atlas Hamburg also installed a 2D control system
from Zimmermann. This helps the operator to work efficiently and accurately, even without being able to see the attachments at the end of the boom. In addition, the excavator uses a submerged quick coupler, a 1.7 m³ Hardox dumping bucket for underwater construction and a 2,800mm pivoting trough for earthworks above water.
The latest addition to the fleet at KSP is the Doosan DL420CVT-5, the first model in the Doosan wheeled loader range to be equipped with a continuously variable transmission. A CVT transmission is composed of a hydraulic motor combined with a hydraulic pump which
provides a smooth and continuous speed variation.
The CVT design is intended to combine the benefits of a mechanical transmission and a hydrostatic transmission in the same machine. It allows the DL420CVT-5 to automatically transition from hydrostatic power at low speed to the mechanical system to operate at higher speeds.
Jens Rausch, operations manager at KSP, added: “The DL420CVT-5 with continuously variable transmission is the optimum machine for our application in the extraction and loading operations.” AB
Doosan gives you the construction technology of tomorrow – today.
To see all the latest Doosan developments, including our pioneering tele-operation system based on 5G mobile technology, visit us at Bauma 8-14 April 2019, Stand FM.5/517.
The Kleemann Mobicat MC 162 RRP mobile crushing and screening machine was purpose-built for SMBP’s Prasville quarry
The massive Kleemann Mobicat MC 162 RRP mobile crusher and screener at Prasville quarry near Chartres in France is one of only two in the world. Liam McLoughlin reports.
The Prasville limestone quarry near Berchères-les-Pierres in France has a machine that makes it almost unique. The quarry site, which is close to Chartres and one of three in the vicinity operated by construction company SMBP (Société Matériaux Berchères Les Pierres), is home to a giant Kleemann
Mobicat MC 162 RRP mobile crushing and screening machine that can process 1,000 tonnes of material per hour. Only two such machines have been deployed, with the other operating at a quarry in Chile.
The Mobicat MC162 RRP at Prasville, which was purpose-built for the quarry, features a 1.62m jaw crusher that produces
rock in varying sizes up to 300mm at the end of the crushing and screening process. The machine has been in operation since 2000 and has racked up 20,000 hours of production.
In addition to Prasville, SMBP operates two other quarry sites near Berchèresles-Pierres - Viabon and Moulin de Pierre.
Prasville produced 300,000 tonnes of material in 2018 while the other two sites produce 500,000 tonnes each.
The three quarries cover a total area of 150 hectares. All three sites produce limestone that is used to make cement and aggregates for road and transport construction in the Paris area. This includes supplying the giant Grand Paris Express (GPE) project which is designed to meet the growing city’s needs for an improved transport infrastructure and prepare Paris for the 2024 Olympic Games.
The sites operate a three-stage process to quarry the limestone, which involves crushing twice with a jaw crusher and once with an impactor. All the aggregates are then washed and screened for final grain size.
SMBP also operates one other Kleemann machine at the Viabon site, a 160-tonne Mobicat MC 125 RR crushing and screening machine. The single-jaw crushing unit is capable of processing feed material of up to 1,250mm x 1,000mm in size, and of achieving production rates of up to 700 tonnes/hour depending on the feed material to be processed.
The Mobicat MC 125 RR mobile crusher is equipped with a wobbler feeder for thorough pre-screening of adhesive feed material. The machine has operated at the quarry since summer 2016 in the preliminary crushing stage. The limestone with a size of 0-900 mm is fed to the elliptical rollers in the first stage of the wobbler feeder. At the same time, contamination and dust are removed from the stones.
The material is levelled and then conveyed to the second stage of the wobbler feeder for further cleaning and better material distribution. The fines with a size of 0-80 mm fall through the rollers onto a conveyor belt and leave the process via the side discharge conveyor, which reduces jaw crusher wear. A total output of 600 tonnes an hour is achieved. The oversize grain is crushed to 0-300 mm and then further processed by a stationary plant for concrete production.
Kleemann offers its mobile crushers and screeners with diesel-electric power that run from the grid or with dieselhydraulic electric power. “Customers choose electricity as it is cheaper than diesel fuel and they don’t have to do any maintenance,” says Vincent Levesque, area sales manager Kleemann for the Paris area at Wirtgen France (subsidiary of the parent company WIRTGEN GROUP, crushing and screening equipment manufacturer brand of Kleemann). “If the MC 162 operatES with a diesel-electric engine the fuel consumption would be about 1,000 litres a day. Electricity needs less power from the diesel engine than hydraulic.”
Levesque says that the market for large mobile crushers and screeners that can process huge amounts of material is likely to remain a niche one. “You need a very big
quarry to operate these machines,” he adds. He adds that there is a lot of demand in France for Kleemann’s smallest machine, the 39.5-tonne Mobicat MC110 Z EVO mobile jaw crusher and primary screener, as it is easy to move around different job sites.
In addition to the mobile crushing and screening machines, there are more than thirty wheeled haulers, excavators and loaders at the three sites, with the vast majority being Caterpillar vehicles. These include eight excavators, eleven wheeled loaders, two tracked loaders, three haulers and nine articulated dump trucks.
Prasville operates three Caterpillar 771 haulers, which can each carry loads of up to 45 tonnes, in addition to a Cat 980 wheeled loader.
ABOVE: The
Apart from the Cat vehicles, two Volvo A40 articulated dump trucks have been operating at Prasville since 2016.
Prasville quarry manager Franck DésiréLaye said that SMBP is in discussions with Kleemann about another large mobile crushing and screening machine, the MC 160 RR, which would be deployed by 2025.
“We have had a lot of contracts to supply large quantities of materials,” he added. “In the future we will have two machines each producing 1,000 tonnes per hour, which will meet our production needs.”
While the three sites sold a total of 1.3m tonnes of material in 2018, they have
For 100 years, we have defined ourselves by our unwavering values and promise of innovation and dependability. We have led our industry by consistently turning challenges into opportunities. In the next 100 years, we will continue to defy boundaries and unleash our ingenuity in a world hungry for new power solutions.
See how we’re challenging the impossible at Bauma 2019, Hall A4.325.
government authorisation to produce up to 3.4m tonnes per year.
SMBP is a family company, which originally started as an earthmoving business in 1978 before moving into quarrying around 30 years ago. It has four competitors within a 20km radius who also operate limestone quarries.
“Limestone quarry customers want crushers and screeners together,” says Levesque. “There is a lot of sand in limestone, and they have to remove the sand with the screener and then crush the rock. For granite quarries it’s different. There is no sand so you don’t have to screen it and only need a crusher.
SMBP is planning to build a static installation at Viabon for crushing and screening. The machine will involve an investment of around €25m and is due to come into operation by 2024.
“We have our own mechanics and do a lot of preventative maintenance on the machines,” says Désiré-Laye. “We analyse the motor oil all the time. For tyres and oil we order a large amount at a time to get a lower price.”
When asked what specific things he looks for from a quarrying vehicle supplier, he responds: “The design of the machine is important, the after-market service, the parts department, and the cost per hour of production.”
In terms of future plans for the Berchères-les-Pierres quarry sites, DésiréLaye says he would like to see an increased use of telematics.
“We already have telematics on our Caterpillar vehicles,” he says. “This gives us information on fuel costs and hours of use of the engines. At the moment we
don’t have telematics on our crushers and screeners as the lack of wi-fi communications at the quarries makes this difficult.” AB
Astec displays scale-model asphalt plants
Astec will be exhibiting scale models of two of its asphalt plants at April’s bauma construction industry expo in Munich.
The US manufacturer’s stand at the event will feature a 1/8 scale model of a complete Astec M-Pack relocatable asphalt facility and a 1/8 scale model of a complete Astec SixPack portable asphalt facility.
The Astec models have been continuously updated to reflect the latest innovations and best practices in asphalt mix production.
Great Tew Ironstone Quarry in the UK has purchased a new top-of-the-range Doosan DL580-5 wheeled loader to increase production of ironstone products from the quarry.
The DL580-5 carries huge 14-16 tonne blocks of ironstone from the quarry face to a new £1mn stone processing plant that has recently begun production at the top of the North Oxfordshire quarry.
Great Tew Ironstone has a striking brown and blue vein and is only available from this Oxfordshire quarry. The quarried block is often
up to 30 tonnes, which opens up a wide variety of uses, including building and walling stone, architectural details, mullion windows, copings, quoins and flooring. Smaller quarried block is suitable for rockery stone and one-off garden features. The quarry lies on the historic Great Tew Estate, which always quarried block for its own use and in 2000, the quarry was opened further to satisfy a wider demand for the unique product.
The DL580-5 is equipped with specially matched pallet tines. It brings the large blocks of up to 30 tonnes from the base of the quarry to the
Italian manufacturer CASE will be exhibiting its 1121G wheeled loader and CX300D excavator in the quarrying section of its stand at the bauma show held in Munich, Germany, from 8-14 April.
The CASE 1121G wheeled loader features a Stage IV FPT Industrial engine without diesel particulate filters (DPF), which is designed to deliver best-in-class, high-torque
top and, at the end of a short road, loads them on to the sawing machines in the processing plant. Previously, the quarry was only able to move blocks weighing a maximum of 10 tonnes.
Great Tew is part of Johnston Quarry Group which supplies quarried and mined block stone in southern England. The group also owns and operates Sarsden Quarry in Oxfordshire, Creeton Quarry and Ropsley Quarry both in Lincolnshire and Oathill Quarry in Gloucestershire, in addition to three Bath stone mines.
performance at low rpm, without the need for an extra cooling system. The interior of the machine features a one-piece curved windshield and rear-view display, which CASE claims delivers “a breakthrough in operator comfort and visibility”.
The CASE CX300D excavator incorporates an electronically controlled pump, larger main valve and multiple hydraulic sensors
Allu unveils upgraded mobile app
Allu is launching an upgraded mobile app with new functions and internet of things (IoT) capability to provide more information on the attachments it supplies.
The Finnish crushing and screening hydraulic attachment manufacturer says the upgraded app will help improve its customers’ productivity and jobsite safety, whilst also providing enhanced customer service.
The app is part of Allu’s stateof-the-art communications system, which provides an intelligent digital solution for customers and operators to obtain accurate and timely operational information, maximising safe and productive use of ALLU equipment. Through easier and improved contact functionality, customer support is also enhanced through the new features of the app.
which are claimed to result in up to 6% greater breakout force, making it suited to the challenges of a quarry.
The machine also has advanced sensors, which continuously monitor the nature of the work being carried out and then automatically respond with the required amount of hydraulic pressure.
Atlas Copco Power and Flow has completed its portfolio of WEDA electric submersible dewatering pumps.
The comprehensive coverage has been achieved by completing the ranges for drainage and sludge applications and adding a completely new range for slurry applications. The company says that selection from the entire expanded range is simplified as all models are classified by application and type of fluid that they handle.
The range now comprises three families: the expanded WEDA D for dewatering; WEDA S – also expandedfor sludge; and the entirely new WEDA L slurry family.
WEDA D pumps handle either clean or dirty water, even with small solids. The WEDA S range supports dewatering of liquid sludge containing larger solids. The WEDA L products are the toughest and have the largest apertures to enable handling of slurry with the most
The Steelwrist Quick Coupler includes patented Front Pin Lock technology
Steelwrist is launching its SQ65 and SQ70/55 Auto Connection Quick Couplers to meet growing demand in all major markets and in more mature countries in Central Europe.
The couplers follow the symmetrical standard, a wedge locked system according to the ISO13031:2016. In addition to comply with ISO13031:2016, the couplers include the next generation of patented Front Pin Lock technology which ensures increased safety by preventing the operator from dropping work tools by mistake.
Both products will be exhibited at April’s bauma exhibition in Munich and available to order after the show, with deliveries to customers starting from July 2019 and onwards. The different combinations of tiltrotators from Steelwrist with the new SQ couplers will be available at the end of 2019.
Steelwrist is exhibiting its next generation of Front Pin Lock technology, which is a mechanical lock of the front share, at bauma.
challenging solids.
The WEDA D family expansion is marked by the new D80 model for dewatering. S30, and S60, as the new models for the WEDA S sludge family, can handle thick, soft, wet mud or other similarly viscous mixtures of liquids and solids, especially the product of an industrial or refining process.
The new WEDA L family handles semiliquid slurry mixtures, typically of fine particles of manure, cement or coal, and
water.
Atlas Copco says that a lot of focus has been put on making the pumps lighter, enhancing electrical safety, improving the seal design and easing installation. All pumps in the D and S range are available with WEDA+ features, which include phase-failure protection, rotation control, thermal switches and a 20 m cable with phase-shifter plug for all 3 phase pumps. The WEDA+ features are also available as an option on the L range.
McLanahan UltraWASH Modular Washing Systems offer the same world-class washing technology we’ve been supplying since 1835, but in containerized modules for shorter lead times, quick setup and ease of transport if producing at multiple locations or one very large site. Produce up to five products – three clean aggregate and two washed sand products. Additional modules for crushing, screening scrubbing, thickening, and tailings management are also available.
APRIL
8-14 bauma 2019
Munich, Germany
Organiser: Messe München GmbH
Tel: +49 89 949-11348
Email: exhibiting@bauma.de www.bauma.de/index-2.html
17-19 Marrakesh Mining Convention 2019
Morroco
Organiser: MMC
Tel: +44 (0)208 242 6566
Email: shariq.abdul@valiantbmedia.com http://marrakeshminingconvention.com/
MAY
15-18 CICEE 2019
Beijing, China
Organiser: China Machinery Industry Federation, China Construction Machinery Society and Changsha City Government Tel: 0731-86969961 www.chinacicee.com
22-23 Argus European Bitumen and Asphalt 2019
Athens, Greece
Organiser: Argus Media group
Tel: +44 207 780 4341
Email: bitumen@argusmedia.com https://www.argusmedia.com/ conferences-events-listing/europeanbitumen
11-13 Plantworx 2019
East of England Arena, Peterborough
Organiser: Rail Media & CEE
Tel: 020 8253 4517
Email: simon.frerecook@plantworx.co.uk www.plantworx.co.uk
21-22 CQMS 2019
Punchestown Event Centre, Co. Kildare
Organiser: Machinery Movers Magazine Tel: +353 83 433 5968 www.machinerymovers.ie/cqms/
5-7 RecyclingAKTIV and TiefbauLIVE 2019
Karlsruhe Trade Fair Centre, Germany
Organiser: Karlsruher Messe-und Kongress GmbH Tel: 0049-721-3720-2300
Email: verena.schneider@messe-karlsruhe.de www.recycling-aktiv.com
10-14 Excon 2019
Bengaluru, India
Organiser: Confederation of Indian Industry Tel: +91-44-42444564
Email: excon@cii.in https://excon.in/exconpub.php
10-14 CONEXPO-CON/AGG 2020
Las Vegas, NV
Organiser: AEM
Tel: +1 414-274-0644
Email: customerservice@conexpoconagg.com www.conexpoconagg.com
Throughout the year Aggregates Business travels the globe attending conferences, events and equipment shows, keeping you informed of the latest offerings. Why not come and join us for a chat at any of the events below?
APRIL 2019 8-14 bauma 2019
Advertisers in AGGREGATES BUSINESS EUROPE can now be contacted via their websites - for instant links to all the websites listed below, by category, go to: www.AggBusiness.com
Ammann p21 www.ammann.com
Benninghoven IBC www.benninghoven.com
BKT p30 www.bkt-tires.com
Caterpillar IFC www.cat.com
CDE Global p13 www.cdeglobal.com/bauma2019
CMS Cepcor p30 www.cmscepcor.com
ConExpo p55 www.conexpoconagg.com
Cummins p51 www.cummins.com
Doosan p47 www.doosanequipment.eu
Evoquip p53 www.terex.com/evoquip
Hitachi p17 www.hitachicm.eu
Indeco p49 www.indeco.it
Kleeman p7 www.klemann.info
MB Crusher p32 www.mbcrusher.com
McLanahan p57 www.mclanahan.com
Metso OBC www.metso.com
Rockmore p46 www.rockmore-intl.com
Sandvik p4 http://rocktechnology.sandvik
Simex p33 www.simex.it
Superior Industries Inc. p10 www.superior-ind.com
Terex Trucks p29 www.terextrucks.com
Terex Washing p37 www.terex.com/washing
Trimble NZ p56 http://aggregates.trimble.com
Verona Fiere p53 www.veronafiere.it
Volvo CE p15 www.volvoce.com
Volvo Penta p43 www.volvopenta.com/stagev
Weir p8 www.minerals.weir
Wirtgen p25 www.wirtgen-group.com/bauma
Renewed Lokotrack® LT200HP™ crushing plant
The renewed Lokotrack® LT200HP™ mobile crushing plant can save minimum 15% in fuel consumption compared to hydraulic-driven cone crushers thanks to its direct belt drive from gearbox, and is the first Lokotrack to comply with Stage V emission regulations.
In addition to being more efficient, the renewed LT200HP also features several safety and maintenance improvements. These include elevated service platforms to ensure safe, easy access to service and maintenance points and improvements that make daily maintenance quicker and easier.
Scan QR code below to see how it looks!