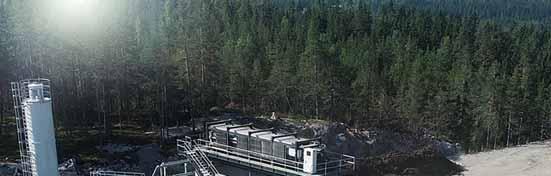
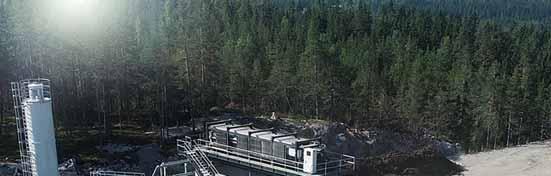
Proud past, fine future
A major washing plant manufacturer builds on its rich history p28






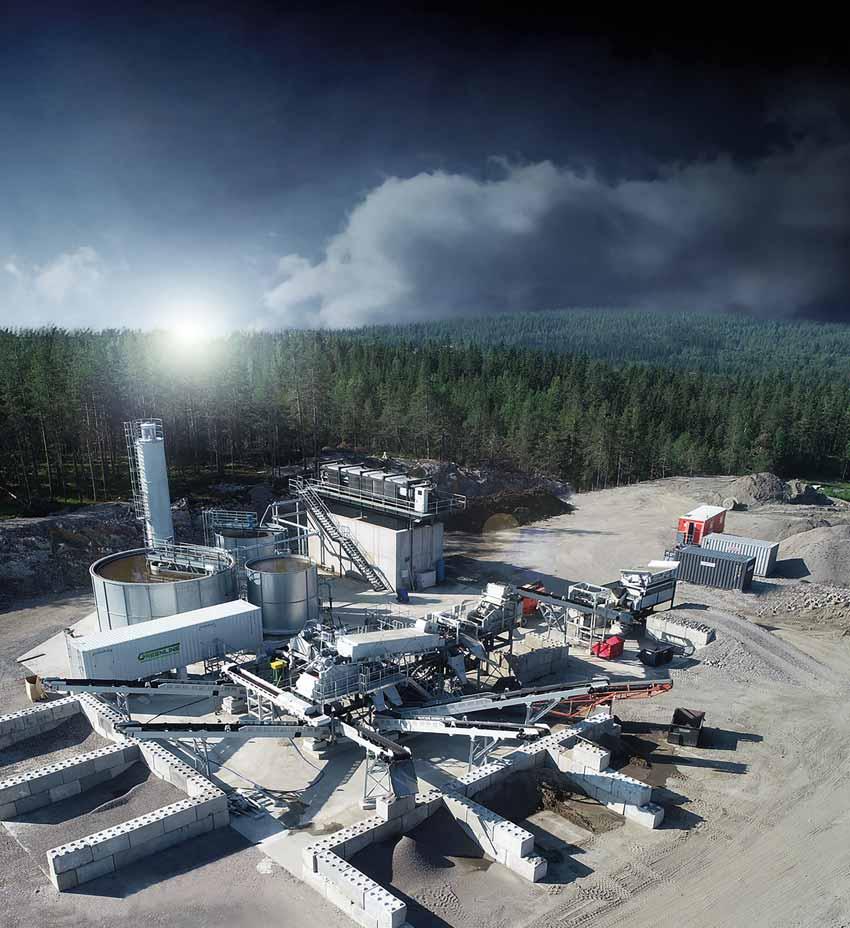






INTERVIEW









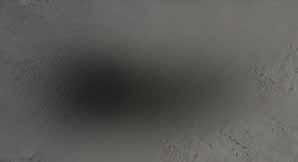






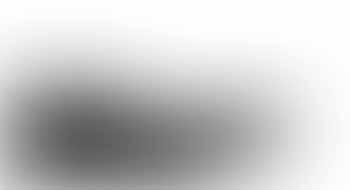



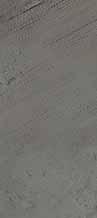
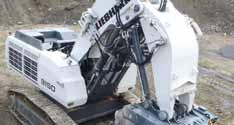

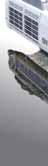


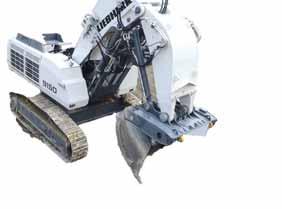
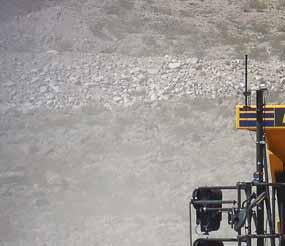

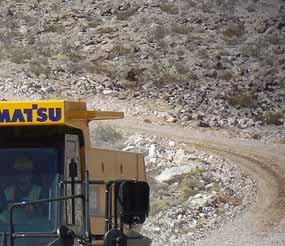

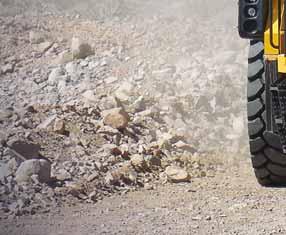
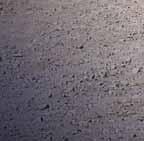
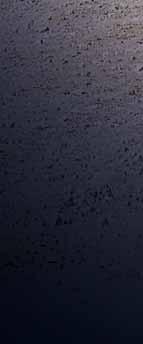
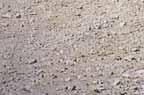
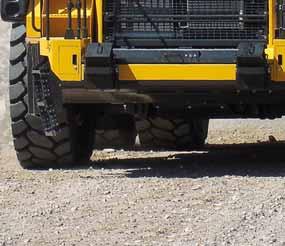




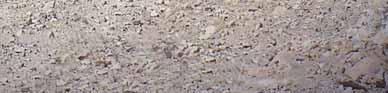





A proven winner
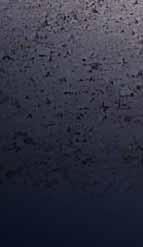

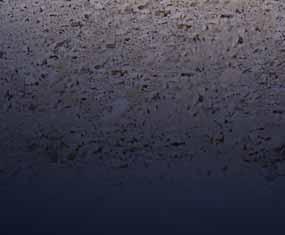

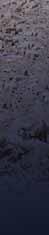
DUMP TRUCK


The HD605-8 integrates the latest Komatsu engine technology, for increased power and reduced fuel consumption. Productivity is maximized and costs are reduced. The hydraulicallycontrolled wet multiple-disc brakes and retarder give the operator great controllability, and a new spacious and ergonomic cab creates a first class work environment.


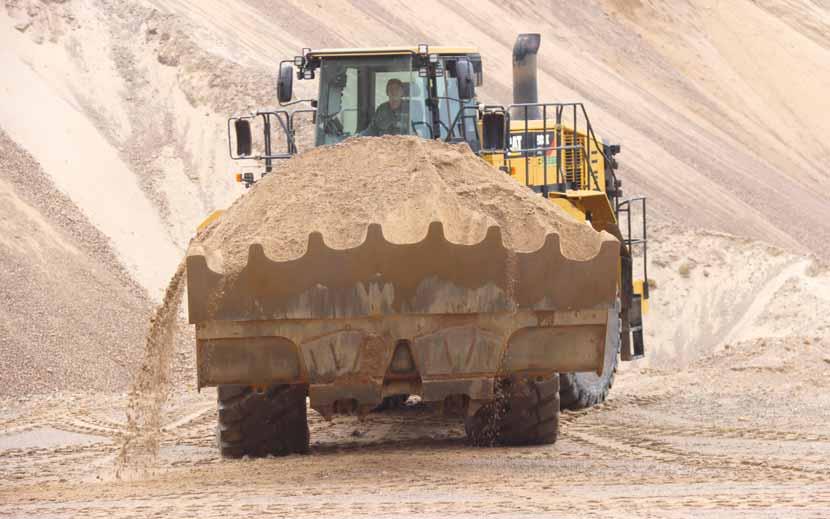
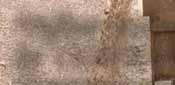
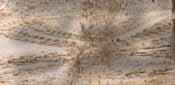
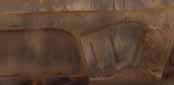


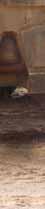
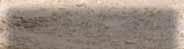





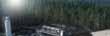





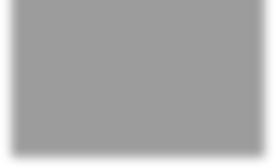

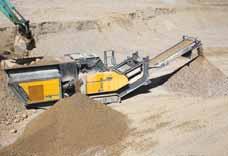
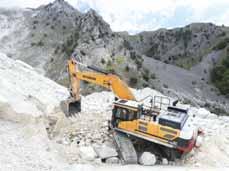













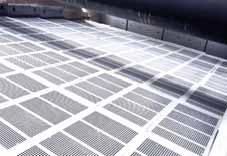
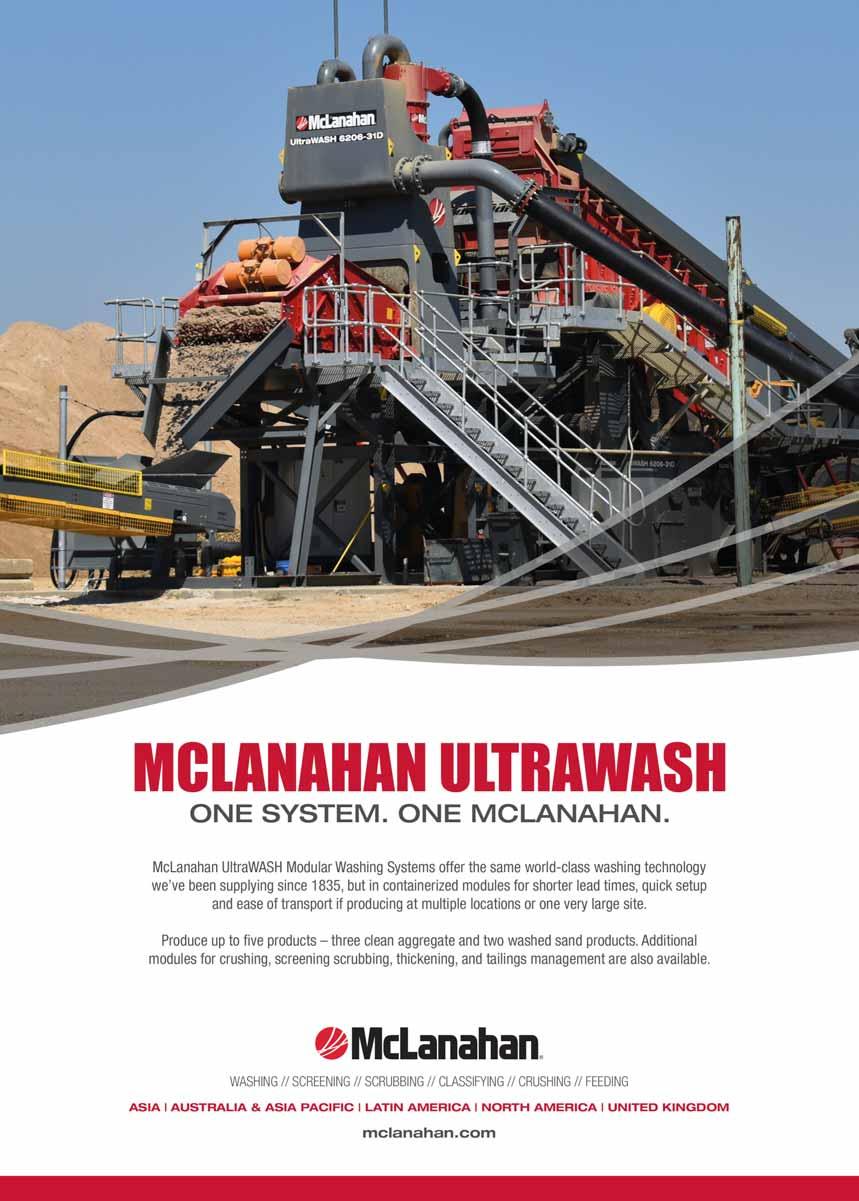
HEAD OFFICE
EDITOR: Guy Woodford
ASSISTANT EDITOR: Liam McLoughlin
CONTRIBUTING
EDITORS: Patrick Smith, Dan Gilkes
EQUIPMENT EDITOR: Mike Woof
DESIGNERS: Simon Ward, Andy Taylder
PRODUCTION MANAGER: Nick Bond
OFFICE MANAGER: Kelly Thompson
CIRCULATION & DATABASE MANAGER: Charmaine Douglas
INTERNET, IT & DATA
SERVICES DIRECTOR: James Howard
WEB ADMINISTRATORS: Sarah Biswell, Tatyana Mechkarova
MANAGING DIRECTOR: Andrew Barriball
PUBLISHER: Geoff Hadwick
CHAIRMAN: Roger Adshead
ADDRESS
Route One Publishing Ltd, Waterbridge Court, 50 Spital Street, Dartford, Kent DA1 2DT, UK
TEL: +44 (0) 1322 612055
FAX: +44 (0) 1322 788063
EMAIL: [initialsurname]@ropl.com (psmith@ropl.com)
ADVERTISEMENT SALES
SALES DIRECTOR:
Philip Woodgate TEL: +44 (0) 1322 612067
EMAIL: pwoodgate@ropl.com
Dan Emmerson TEL: +44 (0) 1322 612068
EMAIL: demmerson@ropl.com
Graeme McQueen TEL: +44 (0) 1322 612069
EMAIL: gmcqueen@ropl.com
SUBSCRIPTION / READER ENQUIRY SERVICE
Aggregates Business is available on subscription at the rate of: £85 / US$145 / €111 per annum. Single copies £20 / US$35 / €26 Email subs@ropl.com for further details. Subscription records are maintained at Route One Publishing Ltd.
SUBSCRIPTION / READER ENQUIRIES TO: Data, Route One Publishing Ltd, Waterbridge Court, 50 Spital Street, Dartford, Kent DA1 2DT, UK
TEL: +44 (0) 1322 612061
FAX: +44 (0) 1322 788063
EMAIL: data@ropl.com


No part of this publication may be reproduced in any form whatsoever without the express written permission of the publisher. Contributors are encouraged to express their personal and professional opinions in this publication, and accordingly views expressed herein are not necessarily the views of Route One Publishing Ltd. From time to time statements and claims are made by the manufacturers and their representatives in respect of their products and services. Whilst reasonable steps are taken to check their accuracy at the time of going to press, the publisher cannot be held liable for their validity and accuracy.



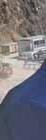

PUBLISHED BY © Route One Publishing Ltd 2021
AGGREGATES BUSINESS USPS: is published six times a year. Airfreight and mailing in the USA by agent named World Container Inc, 150-15, 183rd Street, Jamaica, NY 11413, USA.
PERIODICALS POSTAGE PAID AT BROOKLYN, NY 11256
US POSTMASTER: Send address changes to Aggregates Business, World Container Inc, 150-15, 183rd Street, Jamaica, NY 11413, USA. Air Business Ltd is acting as our mailing agent
PRINT: ISSN 2051-5766
ONLINE: ISSN 2057-3405
PRINTED BY: Warners (Midlands) PLC
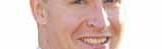
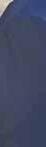
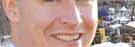
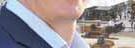
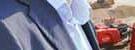
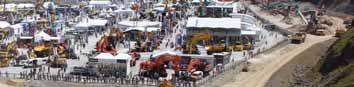
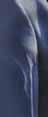
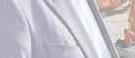




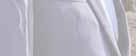




Mirrored demand can be a European mineral products industry gain
When construction equipment demand picks up, so do mineral products sales. Conversely, when construction equipment demand falls it tends to be mirrored by falling demand for mineral products. The European sales landscape in 2020 is a good example of this with the UEPG (European Aggregates Association) reporting a 4.8% fall in annual European aggregates production to around 2.85bn tonnes from 2.99bn tonnes in 2019, coupled with the CECE (Committee for European Construction Equipment) recently confirming a 6.4% drop in the continent’s equipment sales.
I highlight this after digesting all the facts and figures from the CECE’s March 2021 published Annual Economic Report. On an initial glance, the modest drop in construction equipment sales does not sound too dramatic. But on closer inspection it is attributed to the performance of high-volume light and compact equipment, whose sales were almost unaffected at -3%. In contrast, heavy construction machinery suffered a 19% fall in sales, in what emerged as a challenging year due to widespread COVID-19-pandemicinduced disruption, coupled with what the report says was an anticipated cyclical downturn after years of growth.
Presenting the report to the press, CECE president Niklas Nillroth focused on the positive aspects of last year’s results and this year’s expected outcome. “As we all know, 2020 was the most unexpected and unpredictable of years. From an economic point of view, it represented a year of disruptions with certainties and forecasts crumbling before our eyes. However, the construction and industrial sectors in Europe have shown a great amount of resilience and capability to rebound quickly, limiting the damages of the first semester. The foreseeable boost in construction and infrastructure activities from the European Recovery Plan represents another reason to remain optimistic for the near future.”
From a geographical perspective, market sales in most European countries reflected the impact of the pandemic and the lockdowns, but there were a few exceptions. Most notably, the reports highlight that the Italian market reached the same level of sales as 2019, and the Turkish market recovered from its 2019 crash.
While the short-term macroeconomic outlook remains uncertain, with further risks from the spread of COVID-19 variants, the business climate within the European construction equipment industry remains positive. And this can only be good news for building materials suppliers across the continent.
Moreover, after months of improvement, the business climate index in CECE’s Business Barometer survey is significantly higher in March 2021 than at the outbreak of the pandemic in spring 2020.
A significant majority of manufacturers expects business to grow in the first half of the year, and the level of satisfaction with current business has also improved significantly. In addition, the order intake for European manufacturers has been growing year-on-year since December 2020 and sales on the European market are also on a clear growth path. This is consistent with the improvement in equipment sales seen in Q4 2020.
Again, such encouraging news will also be welcomed by mineral products producers, with some now investing in fleet and production plant renewal in their quarries due to the strong likelihood of increased construction contractor customer orders.
A forecast of 5% growth in the European construction equipment market is a realistic assessment of prospects for 2021, says the CECE report. However, the highly respected and benchmark industry document notes that against a background of continued uncertainty and high absolute levels of sales, even a flat market in 2021 would not be a disappointment. GW
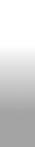
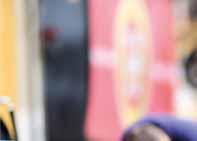
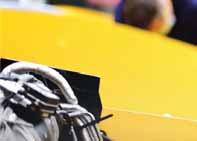
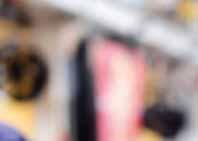

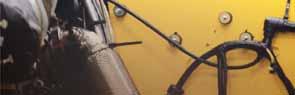

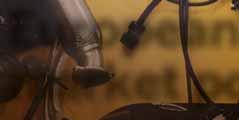
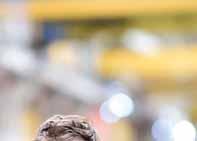
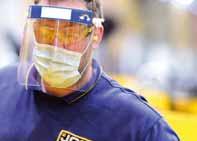
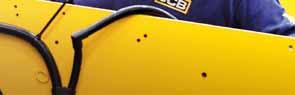
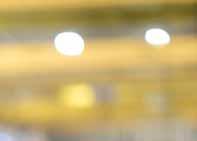
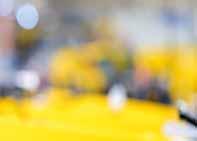
European equipment market positivity
The European construction equipment sector suffered less than expected in 2020, and manufacturers say they are positive about industry prospects for 2021.
European construction equipment association CECE reports that sector sales in the region’s equipment market went down by 6.4% in 2020. It says this seemingly modest drop is due to the performance of high-volume light and compact equipment, whose sales were almost unaffected at -3%. In contrast, heavy construction machinery suffered a 19% fall in sales, in what emerged as a challenging year.
Less expensive machines were sold at almost normal levels during the pandemic, while investment in more capital-intensive equipment suffered from the economic uncertainty. CECE says that these economic figures are the result of a combination of anticipated cyclical downturn after years of growth and a slowdown in business activity due to the COVID pandemic.
Unlike earlier years, concrete equipment, earthmoving equipment, road equipment and the tower cranes business experienced similar market patterns, despite the impact of stronger sales of light equipment.
2020 began in line with expectations, with a 5% market decline in the first quarter – a cyclical downturn that had been anticipated. However, in the second quarter, lockdowns

across Europe began to take their toll and pushed the market to 28% below the levels of the previous year. The decline in sales in Q2 also reflected the impact of the comparison with the quarter in 2019 when the bauma exhibition was held, and the usual short-term boost in sales from it. With relaxation of lockdown measures in Q3, sales reached similar levels to 2019 and were flat year-on-year. The last quarter of the year saw the expected improvement in demand, and sales in Europe went up by 9%. This also reflected the benefit of business postponed in the first half of the year materialising in Q4.
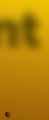

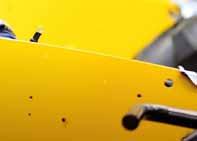

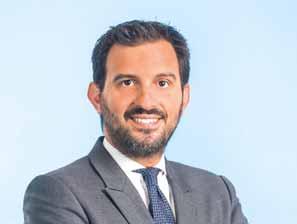
From a geographical perspective, market sales in most countries reflected the impact of the pandemic and the lockdowns, but there were a few exceptions. Most notably, the Italian market reached the same level of sales as in 2019, and the Turkish market recovered from its 2019 crash.
In terms of outlook for 2021 CECE says that, while the shortterm macroeconomic outlook remains uncertain with further risks from the spread of COVID variants, the business climate within the European equipment industry remains positive.
After months of improvement, the business climate index in CECE’s Business Barometer survey was significantly higher in March 2021 than at the outbreak of the pandemic in spring 2020. A clear majority of manufacturers expects business
to grow in the first half of the year, and the level of satisfaction with current business has also improved significantly. In addition, the order intake for European manufacturers has been growing year-on-year since December 2020 and sales on the European market are also on a clear growth path. This is consistent with the improvement in equipment sales seen in Q4 2020.
A forecast of 5% growth in the European equipment market is a realistic assessment of prospects for 2021. However, against a background of continued uncertainty and high absolute levels of sales, even a flat market in 2021 would not be a disappointment. The world market is also likely to show moderate growth in 2021, but the volatility of the Chinese market and its notable influence on the overall outcome means that it is difficult to quote
gures for overall global growth levels. In the medium term, the construction equipment industry faces many substantial risks. One of them is higher debts in many countries that will become a problem, as public infrastructure investments will suffer when austerity measures have to be put in place.
CECE secretary general Riccardo Viaggi said that business expectations are at the highest level for many years among Europe’s construction equipment and component suppliers.
“We expect a 5% increase to be possible from sales in the European market in 2021,” said Viaggi.
He added that CECE members were pleased with the recent move by the Joe Biden administration and the EU for a four-month suspension of the tariff war that had affected construction equipment sales between the US and EU. The multi-trillion-dollar US infrastructure plan that President Biden has approved is further good news for equipment manufacturers.
Viaggi struck a cautionary note in observing that long-terms trends for the construction industry are unstable. The increase in smart and home working following the pandemic means there could be fewer building projects for office spaces, and urbanisation could slow down post-COVID.
Riccardo Viaggi, CECE secretary general
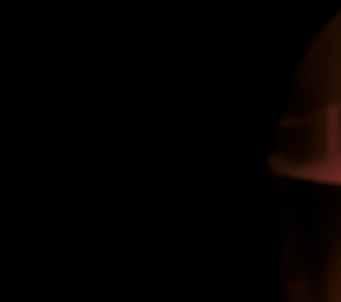
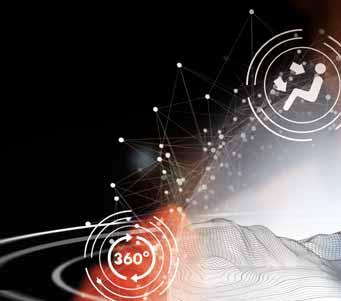

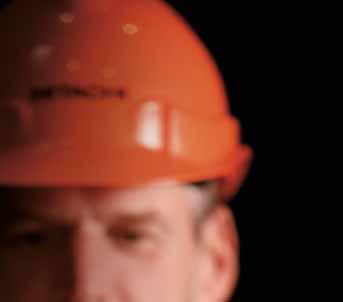


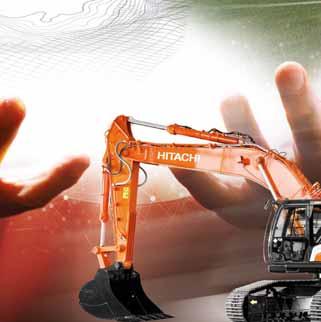

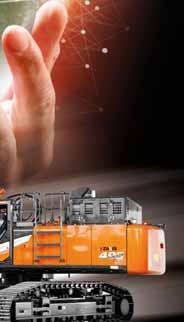

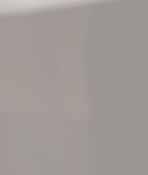
LAFARGEHOLCIM
APPOINTS MAGALI ANDERSON
LafargeHolcim has expanded Magali Anderson’s role to chief sustainability and innovation officer (pictured below), effective March 2021, putting sustainability at the core of its innovation pipeline.
Anderson has been a member of the group executive committee since October 2019, when she was appointed chief sustainability officer. Anderson is taking on the leadership and development of LafargeHolcim’s global R&D strategy and organisation, and external innovation collaborations from academia to start-ups in this expanded position.
Jan Jenisch, LafargeHolcim chief executive officer, said: “I am delighted to appoint Magali as our chief sustainability and innovation officer. Under her leadership, we opened a new chapter in our climate action with our net-zero pledge and growing range of green building solutions, from ECOPact to Ecolabel.
Sustainability is a gamechanger in our industry, and innovation is the most effective catalyst to scale up our impact. By aligning our sustainability and research and development organisations under Magali’s direction, I look forward to stepping up our pace and pipeline of innovation to build a net-zero future.”
Speaking about her new, enlarged role, Anderson said: “I am very proud of how quickly we are advancing on our net-zero journey. We have always taken a rigorous and science-driven approach to sustainability. It’s a natural next step to put innovation and sustainability under one roof to shift from incremental to exponential impact.”
SigmaRoc expands Belgian aggregates operations
AIM-quoted construction materials
group SigmaRoc has entered into an agreement to assume control of LafargeHolcim’s quarrying operations co-located at the group’s Carrières du Hainaut (CDH) Belgian business.
The move provides a platform for the significant expansion of SigmaRoc’s European aggregates business. In October 2019, SigmaRoc established its European heavy side materials platform by acquiring CDH, a major quarry ing and dimension stone company located in Belgium. In addition to an annual production of around 1 million m² of Belgian Blue Stone, a high-value decorative stone, the operations also produce approximately 1.5 million tonnes of standard construction aggregates.
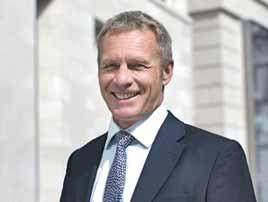
Before entering into the LH Agreement, production and commercialisation of these aggregates were undertaken by LafargeHolcim, under an inefficient royalty deal that was due to end in February 2023.
The LH Agreement gives SigmaRoc full control over CDH’s production assets, putting the group in a far stronger position commercially and operationally to pursue its growth strategy in the Belgian aggregates market as a large-scale supplier.
David Barrett, chairman of SigmaRoc, said: “This agreement is the right next step for Carrières du Hainaut and our partners LafargeHolcim. Over the next four years, we will continue to work together by producing quality material for the Belgian market, improving safety, efficiency, and sustainability on site. Carrières du Hainaut will also welcome nearly two dozen colleagues from Holcim Belgium who will help deliver a good result for both parties.”
HeidelbergCement increased Q4 profit
HeidelbergCement increased its fourth quarter net profit by 3% to €349m, up from €339m in Q4 2019. The German construction materials supply giant’s Q4 revenue declined by 3% to €4.446bn from €4.578bn in the fourth quarter of 2019.
In its main business areas cement volume increased year-onyear by 2% to 31.4 million tonnes during Q4, and aggregates volume was up by 1% to 75 million tonnes. Ready-mixed concrete volume fell by 2% to 12.5 million m³, while asphalt volume remained static at 2.9 million tonnes.
Despite the difficult market environment, HeidelbergCement said the cash inflow from operating activities of the continuing operations increased significantly by €370m to €3,046m (previous year: €2,676m) in the full financial year. The cash inflow was used in particular for the reduction of net debt. It added that the considerable increase in cash inflow from operating activities was based on the good operating business and the consistent spending discipline within the framework of the company’s COPE action plan.
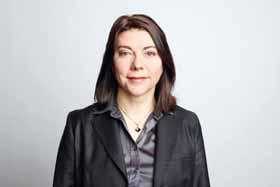
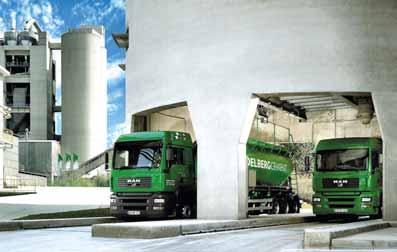
Group revenue decreased by 6.6% to €17,606m in 2020 (previous year: €18,851m). On a like-for-like basis, the decline amounted to 4.6%.
“The entire HeidelbergCement team has demonstrated exceptional flexibility and resilience over the past year,” said Dominik von Achten, chairman of the managing board of HeidelbergCement. “As a result, we were able to achieve top results in key figures despite an unprecedentedly difficult year.”
In terms of outlook for 2021 HeidelbergCement expects demand to develop positively in many markets during the financial year.
“The good start to the year confirms our optimistic outlook for 2021,” said von Achten. “There should be tailwind from the partly massive infrastructure programmes in many countries. The private residential construction sector should also continue to grow.”
HeidelbergCement trucks at work in Germany
David Barrett, SigmaRoc chairman
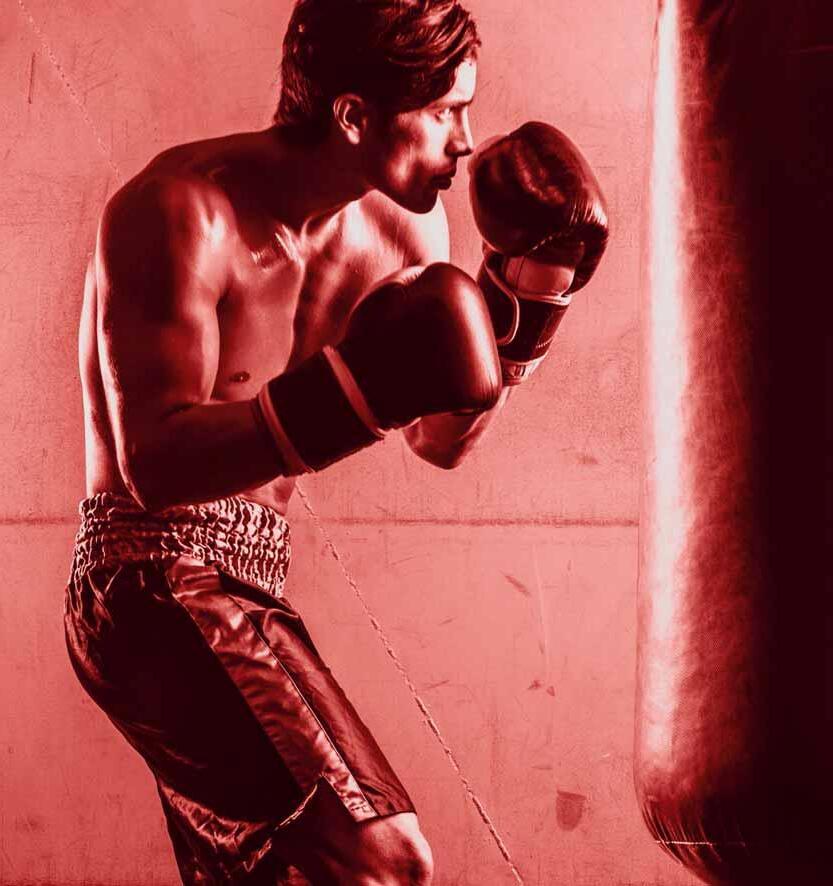
PACK SOME PUNCH ON JOBSITES
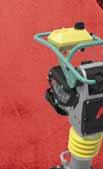

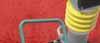

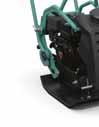







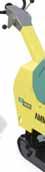
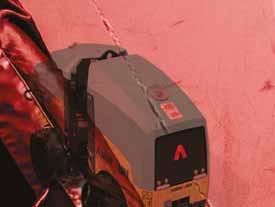

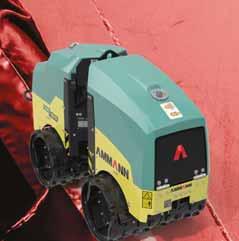


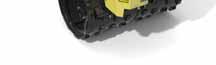



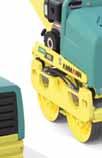
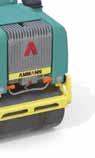
How can you bring compaction punch to your light equipment fleet? Start with a comprehensive product lineup that gives you the ability to choose the optimal weight, dimensions and engine. Then add a powerful vibratory system that puts any material – from wet clays to dry aggregates – in its place.
Last but not least, be sure to use reliable parts and components so you never miss a round. Lightweight machines from Ammann deliver all this –and more. You’ll have a tool to master every challenge.
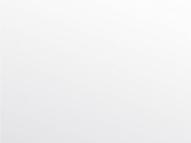
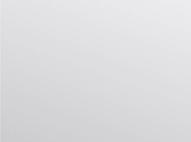
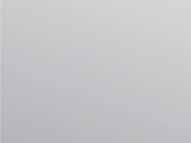
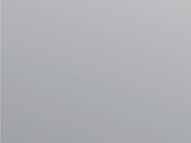


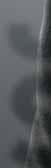
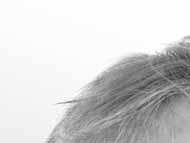

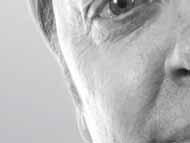

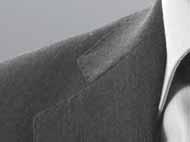
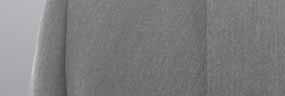
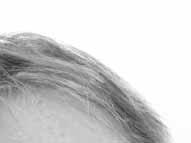
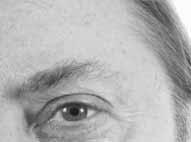
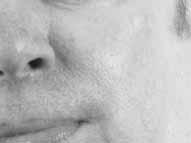


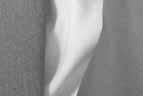

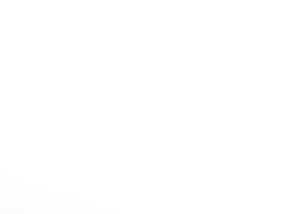
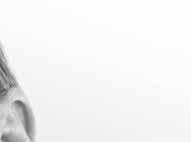
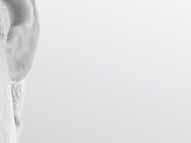
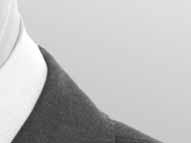
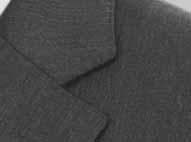

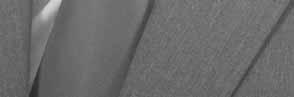
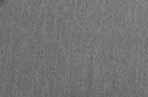
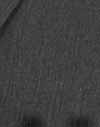

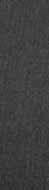
Quarrying’s learned friend
Currently the Institute of Quarrying’s (IQ) head of Education and Standards, Julian Smallshaw’s passion for training and development and his deep love of geology have been the bedrock of his over 40-year career in the quarrying industry. He spoke to Guy Woodford about his vital work and how skills and competencies of current and aspiring future quarry professionals in the UK and overseas are evolving in the digital age

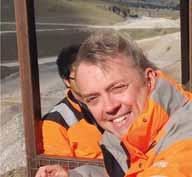
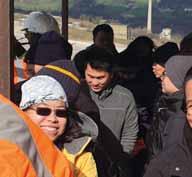
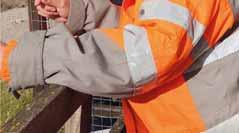
You would struggle to find another individual who fitted their job spec better than Julian Smallshaw fits his. Listening to him outline with such great enthusiasm his many roles and responsibilities as the IQ’s head of Education and Standards, you feel that time has only strengthened rather than weakened what, for him, has been a fascination with quarrying and geology since boyhood.
Before starting his current role in 2019, Smallshaw was the IQ’s head of Educational Development for five years. He also spent five years working as the IQ’s E-Learning manager. As such, the 59-year-old’s years with the globally respected and influential Chilwell, Nottingham, central England-based IQ have been all about “Education, Education, Education”, to coin a phrase made famous in a speech by then Labour Party leader Tony Blair at his party’s 1996 autumn conference.
“I started working in the [quarrying] industry when I was 17. There isn’t much I haven’t done, and I wanted to give a little bit of me back to it. I’ve seen a lot of positive changes over the years, and I was keen to help the industry continue to improve,” explains Smallshaw. “Quarrying faces exciting challenges, not least the advances in technology and how to make the industry sustainable. It’s really important that the workforce has the skills needed to meet these challenges.”
As the IQ’s head of Education and Standards, Smallshaw has a close working relationship with the IQ’s higher education provider, The Centre for Mineral Products Professional Development (C4MP) at the University of Derby. The C4MP draws on what Smallshaw describes as the IQ’s “huge education resource”. The IQ uses the same resource to deliver training to working and aspiring quarrying professionals in the United Arab Emirates, Southeast Asia, and other parts of the world.
“We provide more niche training for equipment manufacturers and suppliers
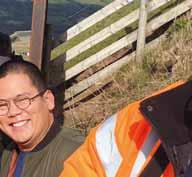
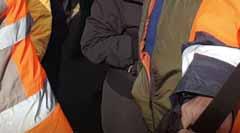
within the quarrying industry, and we have CPD [continuing professional development] courses for mineral planners. We are also an approved assessment centre for the MPQC [Mineral Products Qualifications Council] - the industry body for all vocational quarrying qualifications. We are the sole supplier of the Level 3 SHE [Safety, Health & Environmental] vocational qualification. The IQ is also an ILM [Institute of Leadership & Management] centre.”
Smallshaw stresses that innovative assessment methods are part of all IQ courses. Due to increased demand, the IQ is also looking at quarry recycling training opportunities. “It’s going to be extractive focused: where you have a quarry that brings in materials to recycle and, after recycling them, sells them again.
“We need to encourage a younger generation into what I think is one of the most exciting industries to be in”
“As well as developing courses and qualifications, I assess and train when I can. IQ is also involved in coaching and mentoring, and we have an aspiration to build an industry community. Building strong relationships with industry stakeholders, such as major and SME (small- to medium-sized) quarrying companies, is vital. For example, there is a very good connection between our Level 3 SHE certificates and the small SME operators, like dimension stone firms. It’s an area that we had never really concentrated on before and we’re finding they are coming to us as much as we are going to them with regards to education and training.”


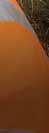
Smallshaw, a member of the IQ’s professional standards committee linking its work on membership, standards and education, says the IQ is also developing its links with UK university and college STEM (science, technology, engineering & mathematics) course providers. He hopes this will help lower the average age, currently 56 years, of British quarrying sector workers. “We need to encourage a younger generation into what I think is one of the most exciting industries to be in.”
A popular speaker at quarrying industry networking events, Smallshaw never misses a chance to further the cause of high-quality quarrying education. But which achievements to date please him the most? “The creation of a BSc (Hons) in Minerals Management at the University of Derby and helping to create the Level 4 Higher Apprenticeship at the Centre have been high points. The BSc started in 2014 and is a bolt-on to the Level 4 Higher Apprenticeships. It created a route to a degree that was not there before. We currently have 21 people on the degree course. I’m also very proud of creating the Level 3 SHE qualification.”
Smallshaw is keen for the IQ to do more overseas to raise standards through the showcasing of quarrying best practice. This, he says, can be done through its affiliates in Australia, New Zealand, Southern Africa, Malaysia, and Hong Kong. The IQ also offers IQ Connect – an app-based membership which Smallshaw sees as a critical driver of developing links with the IQ in countries without an affiliate.
“We also do a lot of work in the United Arab Emirates,” continues Smallshaw. “We started a Gulf meeting group around the time of the global economic downturn in the early 2010s. It was quite successful, but as business gathered momentum again, people’s time was quite limited. People’s working hours in the UAE can be very long. Most of the members that we now have out there are members we first had in the UK.”
Julian Smallshaw (front left) pictured at Hope Cement Works, Hope Valley, Derbyshire, with Dr Mark Pegden (front right), then director of Metso Thailand dealer Uawithya, during a Thai international study tour the IQ organised with Uawithya
Turning his attention to another key area for future IQ education work, Smallshaw says: “There is a realisation among quarrying companies that their people need technical competences to be effective, along with health and safety and environmental knowledge. I am looking to develop softer skills among the workforce; ensuring that site supervisors and managers have the leadership and people management skills to move their businesses and the industry forward. It is the reason we have approved assessment centre status with the ILM.”
Aggregates Business Europe carried an in-depth report on the C4MP at the University of Derby in the July-August 2016 issue. At that time, it had already helped hundreds of students complete prized industry-standard, globally recognised qualifications.
C4MP qualifications run across five focus areas: Mineral Extraction (Quarries); Asphalt and Pavements (Road Construction); Concrete; Cement; and Heavy Clay (Brick & Pipe Manufacturing). In partnership with the IQ, Institute of Asphalt Technology, The Concrete Society, International Clay Technology Association, and the Road Surface Treatments Association, the C4MP currently offers 18 qualifications, ranging from the BSc (Hons) in Minerals Management; Foundation Science degrees (FdSc) in Mineral Extractives Technology; Asphalt and Pavement Technology; Clay Technology; Concrete Technology; and Cement Technology; and a Higher Apprenticeship in Mineral Products Technology to university diplomas in Mineral Extractive Studies; Asphalt and Pavement Studies; Road Surface Treatments; Clay Studies; Concrete Studies; and Cement Studies; a University Certificate in Concrete Technology, and Certificates in Construction

Julian Smallshaw (blue hard hat, second in from the right) on an IQ / University of Derby C4MP study tour in the East Pit of Celtic Energy in Tairgwaith, Ammanford, South Wales. The tour focused on overburden removal in an opencast coal site
Extractives Management; Lean Structures; Quality Management; and Health, Safety and Environment Management. Students undertake a work-based project to apply everything they learn to an issue in their workplace, maximising their learning impact.
“We’re just going through a new validation of courses offered at the [C4MP] University of Derby. It’s a huge project,” says Smallshaw. “We’ve been reviewing and adding content. We’ve got a new HTML format to make courses more interactive and interesting for students to read and learn. New content includes a whole module on sustainability. Quarrying companies outside the UK have also asked the IQ to run sustainability training courses for their staff.
“A great thing about the work being done
course teaching mirrors how the C4MP runs its courses. “Students work their way through assessments with feedback. Then they’ll have a dedicated number of days, usually a Friday and Saturday, when they come into the university. This tends to happen four or five times over an academic year. Of course, this isn’t currently possible due to the coronavirus, so the IQ’s and the C4MP’s learning is done online. The challenge is to make those online experiences really good.
“I think a really interesting feature of the University of Derby courses is the wide age range of the students, outside the higher apprenticeships, which are for younger people coming into quarrying and the wider building materials industry. On any other course, you can be teaching anyone aged 18 to 55. Again,
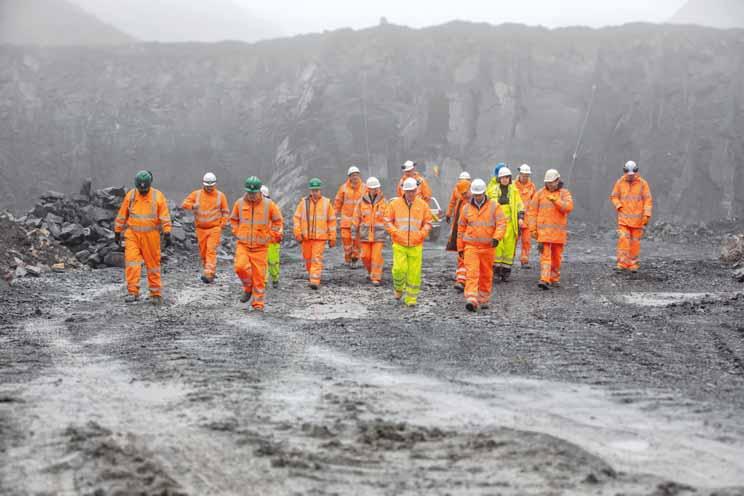
Julian Smallshaw on an IQ study tour with the University of Derby C4MP in March 2019
today’s highly competitive and diverse jobs market.
“It’s not just an issue for the UK quarrying industry. It is an issue for the quarrying industries in a lot of developed countries. One good source of young people has been the Level 4 Higher Apprenticeship. Former IQ president and Hanson corporate director David Sharman was committed to bringing younger people in, and the first six Level 4 Higher Apprenticeship students came from Hanson. That opened the door, and since then we have had a flood of young people coming through.
“The IQ also has links with other institutions. I have a very close link with Leeds University and the Cambourne School of Mines at Exeter University. We appointed a part-time STEM coordinator, Wanda Zablocki, last year. She also works part-time as the IQ’s Benevolent Fund welfare officer. Wanda will spend two days a week helping us develop




























our STEM university and college links.”
There are further quarrying and mining education roles that stand out in Smallshaw’s impressive CV. He was an unpaid board director and chairman of the National Stone Centre (NSC) until 2018 and returned as a board director in September last year. The NSC is an educational institution set in 50 acres of disused limestone quarries in the Derbyshire Peak District, central England. The site reopened in early 2017 after considerable investment, and around 3,500 school children visit every year to enhance their learning. The NSC is a site of special scientific interest and home to the UK’s National Building Stone Collection.
Since November 2019, Smallshaw has also been a board director of Ecton Mine Educational Trust (EMET) based in Ecton, Ashbourne, Derbyshire. The disused Ecton Mine offers a significant educational resource, and the EMET was formed to promote




























education in applied geology, chemistry, mining, and mineral extraction.
After learning so much about his huge contribution to the IQ’s successful education and training work, I am curious to find out about Smallshaw’s experience at the quarry face – including his senior roles at companies including Hanson, Ennstone Johnston, Hills Aggregates and ARC Eastern in the UK.
“I remember my first proper job role running a little 150,000 tonnes a year sand and gravel pit for ARC Eastern near Peterborough. I loved it. I was able to turn it around from a loss to a profit.
“My best time at Hanson was running Clee Hill Quarry in Shropshire. Nobody could hassle you there as you were the furthest away from the regional office. It was an amazing place with absolutely fantastic people. I was there a couple of years.”














Between February 2005 and December 2006, Smallshaw was based in the UAE working as operations manager for Stevin Rock, the largest quarrying company in the Middle East, now capable of producing 75 million tonnes of aggregate a year from three sites. While managing a multinational workforce of 450, Smallshaw was tasked with producing over 12 million tonnes of limestone construction materials a year.
“It was something completely different. I started writing a book about my experiences. I was exposed to things you could only dream of,” Smallshaw says, intriguingly. “My operation was bigger than any UK quarry site. We supplied the most prestigious projects in Dubai, such as Terminal 3 at Dubai International Airport and the Dubai Metro. I was involved in heading up procurement, dealing with customers, and generally being exposed to a unique, challenging, and exciting environment. It has helped me subsequently handle complexity and better understand different workforce cultures.
“When I worked for Stevin Rock, standards were around 20 years behind the UK’s. Now, things have changed. The company is looking to be a global business and is raising standards at all levels. It has been working with the IQ as part of this.
“It’s interesting that the two people I worked very closely with in the UAE have now got the two most senior roles at Stevin Rock. They have built a business going from strength to strength.”
Was Smallshaw’s passion for training and development evident in his frontline quarrying years? “I think when you are younger, you are interested in developing your skills. As you mature, I saw the systems put in place to help quarry managers: like succession planning.
I think you’ve got to have an HR [Human Resources] department that understands operations and can provide good advice to managers. I was always a great believer in ensuring that levels of competence were correct. I like to think that I pushed people that I could see had potential, and I enjoyed mentoring younger people.”
Turning his attention back to the IQ, how does Smallshaw see its role going forward?
Julian Smallshaw on an IQ study tour with University of Derby C4MP students at Taffs Well Quarry, in Heol Goch, Pentyrch, Wales
An IQ study tour with University of Derby C4MP at Taffs Well Quarry in Wales. Julian Smallshaw listening to an explanation of the workings of a processing plant
“The Institute plays an increasingly important role in the quarrying industry. We’ve never been as engaged as we are today. The IQ takes the lead in a lot of initiatives including QNJAC [Quarries National Joint Advisory Committee], the Strategic Safety Forum, and the Education and Skills Board. We also have industry buy-in from the CEOs and other senior people within major building material companies. They know and understand the IQ. We also have senior industry leaders on our board. We also have close working relationships with the HSE [Health & Safety Executive], the MPA [Mineral Products Association], BAA (British Aggregates Association), the Institute for Asphalt Technology, The Concrete Centre, and a lot of previously mentioned education institutions.
“The IQ has always been at the forefront of CPD. That side of our work will grow as we develop our digital offering in that area, such as the IQ Connect app. We’re in a really good place.”
Speaking about the current health of the UK quarrying sector, Smallshaw says: “The industry is tough and resilient. It can recover from trauma, like the coronavirus pandemic. There are many big infrastructure projects either started or due to start –including HS2, Hinkley Point nuclear power station, Heathrow airport expansion, the Lower Thames Crossing, and the [2022] Commonwealth Games [in Birmingham]. Projects like these and other smaller infrastructure projects are more important than ever before as the government looks to kickstart the economy coming out of a downturn. Infrastructure investment also encourages building material companies to invest in new mineral reserves, processing equipment, and developing their people. All this will drive the quarrying business forward over the next decade.”

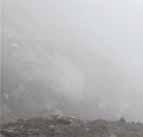
Smallshaw says that the IQ is developing mineral planning expertise in UK county councils to help address long-standing concerns expressed by the MPA and others about a shortage of knowledgeable officials engaging with the mineral products industry. “We run a mineral planning course every year for prospective mineral planners. It sends a message on the importance of mineral resources and the need to have educated officials understand future requirements. Various trade bodies have been doing some great lobbying work in this area.”
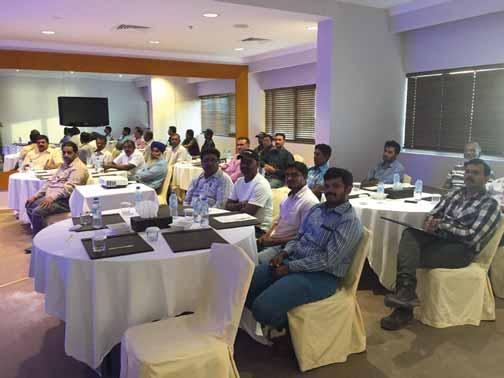
Looking ahead, Smallshaw has some interesting thoughts on how the UK quarrying industry will look and operate by the early 2030s. “I think there will be fewer people working in it, but it will be a safer environment. The automation that we already see in the mining industry will be far more popular in quarrying. Digitalisation will continue to change the way we work. And the green agenda will play an increasingly important role, such as through the need to decarbonise the workplace. Some of these changes will be driven by government legislation.”
After more than an hour’s enjoyable and insightful conversation, I could not let Smallshaw go without mentioning his vast passion for Cornish mining mineralogy.
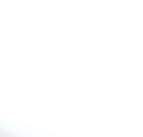
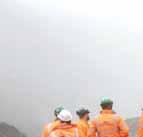
“That originated from holidays in Cornwall. I used to go down with my parents in my early teens. I was interested in industrial archaeology, and the heritage behind the Cornish mines. In the 1800s, it was the biggest mining area in the world – firstly producing copper, and then tin. Consequently, as mines started up, collectors were discovering all kinds of minerals from
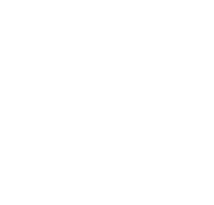
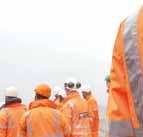

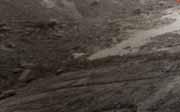
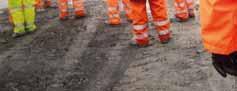
certain mines. Many of those were ‘Type Location’ - where the first mineral of its kind globally was discovered at a particular Cornish mine.
“A lot of 19th-century collectors made a living from their collections. You can see some of them at the Natural History Museum in London. The oldest collected piece I’ve got dates back to the mid-1800s.
“As a child, I was interested in rocks and minerals - where they came from, what they were used for. I also liked the visual aspects of them: the variety of crystal structures and colours. I joined The Russell Society [Britain’s leading society specialising in topographical mineralogy] named after Sir Arthur Russell, a famous collector. That got me access to quarries to look for minerals and rocks. The bug really hit then.”
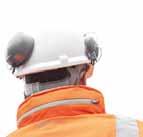


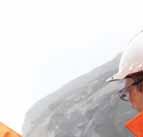
That Julian Smallshaw has never wanted to shake off such a bug has been of huge benefit not just to the IQ, but the wider quarrying world. AB

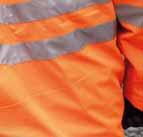
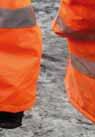
An IQ training event in the United Arab Emirates
As the IQ’s head of Education and Standards, Julian Smallshaw has a close working relationship with the IQ’s higher education provider, The Centre for Mineral Products Professional Development (C4MP) at the University of Derby
READY TO CHANGE YOUR WORLD
HL975A CVT WHEEL LOADER

HL975A CVT
From its robust exterior design to its performance-enhancing smart technologies, the HL975A CVT opens up a world of new
Precise operating systems help you to get the most out of this mighty machine, including optimised power matching for the to 30%, depending on the application, as well as smooth performance in high-load work like digging. Hyundai’s proprietary weighing system technology is integrated as standard.






Powered by a robust Stage combined with a ZF Continuously Variable Transmission (CVT) to harmful emissions to a minimum conditions.
THINKING ABOUT ADDING THE HL975A CVT TO YOUR TEAM? CONTACT YOUR LOCAL DEALER FOR A SMART DISCUSSION! 30% Up to

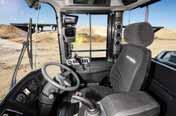
The comfortable and spacious cabin features state-of-the-art
lowest in this machine category. The state-of-the-art ZF CVTpower matching, continually changing the ratios of hydraulic to mechanical energy (depending on load and speed) to keep the engine in a low rpm range acceleration. During deceleration, the CVT acts as a brake, reducing prolonging the life of the axle oil.
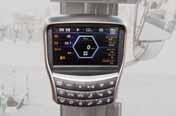
The instrument panel is easy access to machine status information as you inch touchscreen monitor for excellent legibility. You can connect your Android™ mobile
UEPG Webinar: Review of the Construction Products Regulation
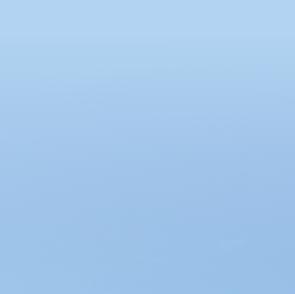
How to bring the legal and technical worlds together? is probably one of the key challenges addressed during the first webinar of the European Aggregates Association (UEPG). With this event, UEPG launched a series of webinars, an initiative that aims to tackle the most important current issues for the aggregates industry and find solutions together with key stakeholders. For the first event of this series, we approached one of the burning issues for our industry: the review of the Construction Products Regulation (CPR) and the related risks and opportunities.
UEPG welcomed Fulvia Raffaelli, a key strategist for the CPR as head of the ‘Construction’ Unit in the European Commission. The unit is in charge of this very important piece of legislation. More than 50 participants from across Europe joined this event. They were eager to find a different and constructive approach to ensure the legal and technical requirements are put on equal footing.
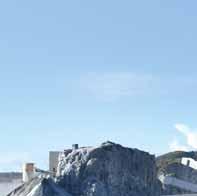

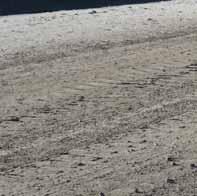

Stefan Janssen, chair of the UEPG Technical Committee, introduced the topic and highlighted the work conducted by industry experts in the standardisation committee for aggregates (CEN/TC 154).
Fulvia Raffaelli presented the Commission’s activity on the CPR and confirmed that there would be a revision of this piece of legislation. Still, the entire revision process will most probably take three to five years. She presented the CPR acquis process which is currently in its early stages. Through this process and CEN, an urgency ranking of products has been created to unblock the update of particular standards. Currently, there are consultations between the European Commission and member states on this list. Ms Raffaelli gave assurances that the industry will soon be involved in the process as well. Aggregates are among the top 10 products on this list. Finally, the Commission confirmed that they continue to review the small number of standards submitted for publication and/or citation.
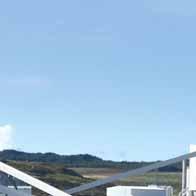
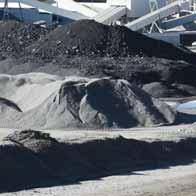
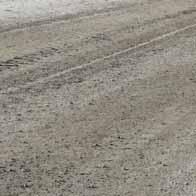
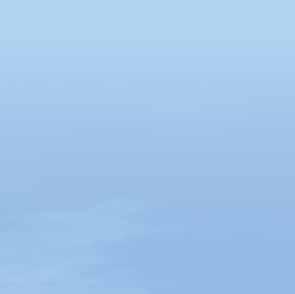
In the second part of the event a fruitful discussion on all the topics mentioned above took place. UEPG experts confirmed that the standards for aggregates have been submitted to the European Commission. UEPG is looking forward to working with the Commission to achieve a positive outcome.
UEPG wishes to take a new approach towards CPR and technical standards through this event, focusing on building trust and links with policymakers and looking for solutions instead of problems. It is readily available to solve difficulties while trying to find common ground and compromise.
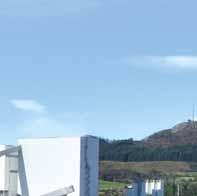
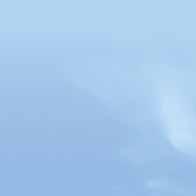
These UEPG seminars are designed as a series of one-hour events, with more than half of the time dedicated to discussions between participants and the invitee. UEPG will soon announce the topic for the next webinar, so stay tuned. AB
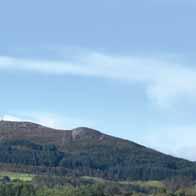
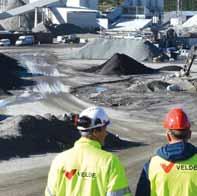
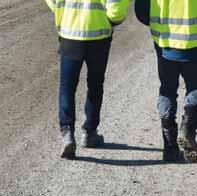
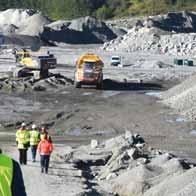

TO
EVENTS ON THE GO
ConstructionTV.TV is dedicated to broadcasting first-class coverage of the world’s leading construction events and the latest industry trends. Combining short, high quality programmes with the latest in digital delivery, ConstructionTV.TV is optimised for mobile devices and can be accessed anywhere, anytime. Individually themed channels provide specific industry information to construction professionals needing to stay ahead in their field of expertise. With expert opinion from only the most experienced editors, ConstructionTV.TV delivers the most reliable and relevant information to the construction industry.
www.constructiontv.tv
Contact: Roger Adshead | radshead@ropl.com
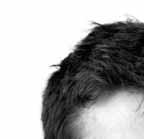
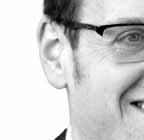
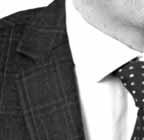





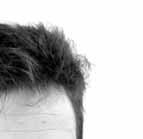
FTOP FIVE INTELLECTUAL PROPERTY MISTAKES WHEN BUYING OR SELLING A BUSINESS





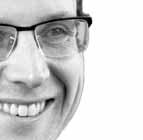
When buying or selling a business, intangible assets such as intellectual property are often overlooked. Ben Travers, head of IP and IT law at Stephens Scown LLP, offers his top five tips on what not to do when buying or selling a business


Goodwill is inherently attached to the business that generates it. It is not possible to separate goodwill from the business which underlies that goodwill. Despite this, we frequently see businesses attempting to value and sell goodwill as if it is a standalone asset.
A transfer of goodwill where a business is not being sold as a going concern will not be effective at law. Only where the whole business is being sold as a going concern will goodwill also be assignable.
4 – Breaking IT contracts

“The new owners have to re-negotiate new contracts or be left high and dry without the IT systems they rely on”
or many businesses, intangible assets have a higher value than their tangible assets. For example, the cost to a capital investment business, such as replacing a key piece of machinery, would be significant for that business. The asset would most likely feature in any business sale. Imagine, however, the fallout if a firm needs to change its name because it failed to obtain a trademark registration. The cost of this re-brand and the impact on future trade would generally be significantly more than the cost of replacing the capital asset.
Despite this, businesses often undervalue intellectual property (IP) assets, but never more than during a sale or acquisition process.
Below are the key mistakes we see in corporate transactions from an IP perspective, many of which are easy to avoid.
1 – Assigning goodwill where there is no trademark registration
In the absence of a trademark registration, a business’s reputation is protected through its goodwill. Goodwill is a way the law recognises and offers limited protection to the effort to develop a reputation (good or bad).
To avoid this risk, businesses should ensure they have trademark registrations in place.
2 – IP licences without quality controls
Businesses often attempt to license IP, such as a trademark registration, across a group of companies. This is a common structure where one company owns the brand name but licenses others to use it, perhaps in a particular territory or market segment.
Businesses often neglect to put in place the necessary control provisions to make this licence sustainable and protect the owner’s interest in the brand.
Make sure that any trademark licences have effective quality control provisions in place.
3 – Ownership of IP assets of the business
When they start doing due diligence for an acquisition or sale, many businesses find that they don’t own the assets they thought they did. Sometimes, the founder registered assets, such as domain names, in their name rather than in the company name. On most occasions, this situation can be resolved by assigning the relevant company’s rights but needs to be done effectively at law. There may also be tax and other considerations.
The second most common area in which this arises is where third parties have been involved in the creation of content, such as a company website. Many businesses do not realise that where they work with thirdparty contractors, those contractors will own the IP they create (unless there is a written agreement to the contrary).
All businesses will have various IT contracts for the software, hardware, and services that make their business work. Many IT contracts will contain change of control provisions, which will enable the IT provider to get out of their obligations under the contract if there is a “change of control” in their client business. This means that a change in shareholding or other structure could result in the IT contracts being invalidated. The new owners have to re-negotiate new contracts or be left high and dry without the IT systems they rely on.
5 – Checking the data
Many businesses are familiar with the requirements of the data protection legislation. However, many are not aware of the impact this has on the sale of assets. For many businesses, a list of current customers will be crucial.
Making sure that effective data protection warranties are in place, and that contracts with third parties such as IT providers who may be storing personal data are compliant, is essential.
Many of these issues can be avoided by making sure the IP elements of a business are considered early during the sale or acquisition process.
Making sure that your brand and other key assets you rely upon are protected, owned by the right people, and managed in a sustainable fashion, will help make sure you maximise the potential when it comes to a business acquisition or sale. AB
CONTACT
Ben Travers is a partner and head of intellectual property and IT at Stephens Scown LLP.
For advice on intellectual property issues, contact Ben on 01392 210700 or email IPandIT@stephens-scown.co.uk
For more information, visit www.stephens-scown.co.uk
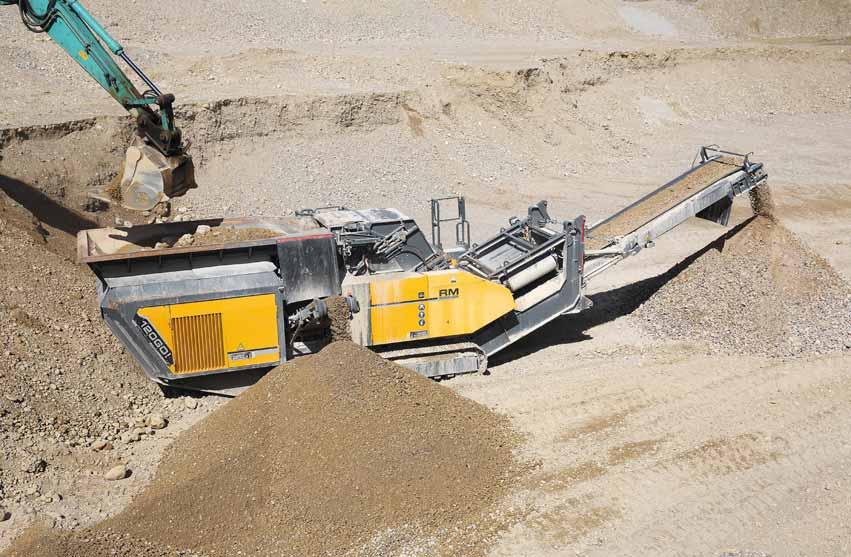
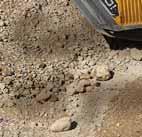
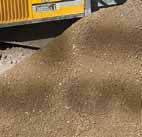
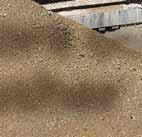
Getting more out of your crusher
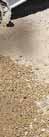
The use of a pre-screen grid can increase crusher output by preventing unnecessary fine material from passing through the crushing process, it is being claimed. Liam McLoughlin reports
Crushers can be used to crush a huge selection of materials thanks to their wide range of applications, from recycling to crushing natural stone. Often the crusher is fed with a high proportion of fine material, which needlessly passes through the crushing process, increasing wear and energy consumption while reducing throughput.
As a remedy, a bar mesh is normally used for pre-screening. However, if the fine material is damp and cohesive, it can quickly clog up the mesh screen and ends up passing through the crusher anyway. Austria-based RUBBLE MASTER (RM) says this is the reason it has launched the patented RM Active Grid, a new pre-screen that is claimed to increase material throughput by up to 30% and reduce wear.
Construction and demolition (C&D) waste, concrete rubble, asphalt, wall gravel and river gravel are just a few examples where a high proportion of fine particles can be found in the feed material. If a pre-screening system is not used, all the material ends up in the crusher, irrespective of particle size, often passing through the whole crushing process.
RM says that, unfortunately, the fine material causes unnecessary wear to the hammers, impact plates and wear plates in the crushing box, as well as higher energy consumption in the form of diesel or electricity because the rotor is subjected to higher stress. The result is higher running costs because the hammers and wear plates need to be replaced more frequently, and maintenance cycles are shorter. This not only reduces the efficiency of the crusher, but also
reduces profit, because material throughput is lower, but running costs are higher.
For this reason, in many cases a bar mesh is used for pre-screening the fine material and small particles. So far so good, says RM, except that the bar mesh has the disadvantage that due to its rigid construction it clogs up over time, especially with damp, sticky or loamy, cohesive material, reducing its pre-screening efficiency. Even with dry material, the screening rate is often not ideal. This again causes most of the material to enter the crushing box, or block the inlet to the crushing box, slowing down the flow of material. This has the effect of reducing the crusher throughput, increasing wear and requiring the crusher to stop so that the bar mesh can be cleaned.
RUBBLE MASTER says it developed the RM Active Grid to solve these problems. It consists of rigid and movable sections of bar mesh that feature a special configuration. The vibration of the vibro-channel causes the Active Grid to oscillate, so it does not need its own drive system. The active vibration of one section of the bar mesh significantly increases the screening performance and, depending on the material and the type of job, increases the total material throughput by up to 30%. Efficiency is also increased thanks to the self-cleaning effect of the Active Grid, ensuring consistent screening performance. The fine material can then bypass the crushing box onto the main discharge belt, or be discharged on a side discharge belt.
The result is claimed to be more material throughput, less wear, lower costs and longer
maintenance intervals, which ultimately adds up to more productivity and profitability. If pre-screening is not required because the crusher is being used for a different application, the RM Active Grid can also be fitted with a subfloor, which is quickly installed.
The RM Active Grid is available for RM 100GO! and RM 120X crushers.
Because processing requirements vary greatly from one job to another, RUBBLE MASTER naturally offers a range of solutions for pre-screening. In addition to the RM Active Grid and a standard bar mesh, a 2-deck pre-screen integrated into the feed belt is also offered for defined feed material particle sizes. RM also offers the HS series of mobile pre-screens, which is available in a range of sizes.
Terex Finlay has launched the LJ-130 hybrid jaw crusher, the largest mobile jaw crusher in its range which has been developed for large-scale quarry and mining operations. The machine can operate as a standalone primary crusher or integrated into a mobile or static crushing and screening plant.
The machine incorporates a Terex 1300 x 1000mm (51” x 39”) high-performance electrically driven single toggle jaw chamber. The large chamber inlet opening has been engineered to accept the coarsest feed, including large boulders in the feed material, and the chamber cavity depth of 2.3m (7’ 5”) provides high reduction ratios and maintains an efficient material flow through the plant. For ease of transportation the machine has been engineered with a compact
RUBBLE MASTER’s new RM Active Grid is available for its RM 100GO! and RM 120X crushers
operational footprint and can be split down into two transportable components without the need for heavy crane assistance on site for setting up, tearing down and transporting between locations.
The machine features a 13.5m³ (17.64yd³) hopper with an integrated pan feeder and heavy-duty VGF feeder, with automatic power monitoring to regulate and automatically increase or decrease material flow to prevent overload and ensure continuous choke feeding of the jaw chamber for optimum and uninterrupted productivity.
The machine can be powered either by the integrated 500kVA genset powerpack configuration or connected to an external power source. Both power options provide operators with significant power, servicing and maintenance cost savings in direct comparison to a diesel/hydraulic-powered plant.
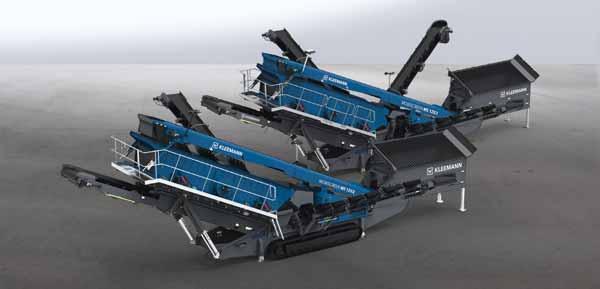
“The LJ-130 hybrid jaw crusher has been developed to provide a robust and powerful mobile solution for operators seeking a highly productive machine for the most demanding and coarsest hard rock and ore applications,” said Alan Witherow, Terex Finlay product manager.
“The Terex 5139 crusher is the largest jaw chamber we put on our tracked plants in terms of depth, width and length. The large cavity volume enables more material to be processed along the full length of the chamber, maximising productivity even with the coarsest unprepared material at the primary crushing stage. The LJ-130 jaw crusher is perfectly complemented by our existing C-1554 cone crusher and large capacity screens such as our 984 horizontal and 696 inclined screeners models for operators looking for large capacity mobile crushing and screening train solutions.”
Key features of the LJ-130, including the plant’s electrically driven power systems,

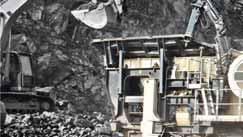
provide significant cost advantages and environmental efficiencies.
The large feed width and gape enables the crusher to accept larger and coarser material reducing the need for hammering of oversized product in the virgin feed material.
Automatic variable speed VGF ensures continuous choke feeding of the crushing chamber for optimal productivity.
High-powered electric drive ensures precise chamber controls and reverse functionality for clearing blockages and assisting in construction demolition, asphalt and recycling applications.
For ease of commissioning and transportation the machine can be dismantled into two separate components without the need for cranes.
T-Link telematics hardware and software along with free seven-year data subscription are fitted and installed as standard.
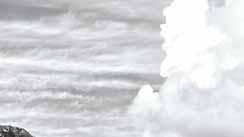
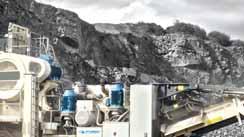
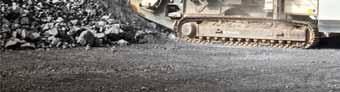
Germany-based Kleemann is offering two new mobile classifying screens with a feed capacity of up to 750 t/h that the Wirtgenowned company says guarantee effective screening of large volumes.
The MOBISCREEN MS 1202 and MS 1203 are available with two or three screen decks and have screening surface areas of 12m² in the upper and middle deck and 11m² in the lower deck. They thus make hourly outputs of up to 750 tonnes possible.
Aiko Fischer, product manager for screening plants at Kleemann, said: “To achieve these high outputs, the material flow must be well designed. Kleemann has thus generously dimensioned the feed hopper with a holding volume of 10m³. This makes feeding both with a crushing plant as well as with a large wheel loader possible. Despite discontinuous feeding by the wheeled loader, the large hopper volume ensures continuous material supply to the screen. Correspondingly wide feeding and discharge conveyors guarantee an unobstructed material flow over the screen. The hightorque diesel engine also ensures that the plant does not ‘run out of steam’.”
Both screens can be combined with both the crushing plants from the Kleemann EVO series and the PRO series. AB

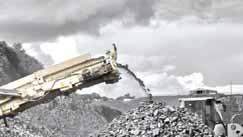


The new LJ-130 is Terex Finlay’s largest hybrid jaw crusher
Kleemann has launched the MOBISCREEN MS 1202 for screening large volumes
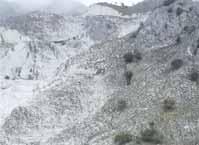
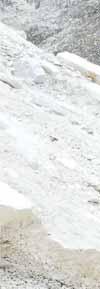
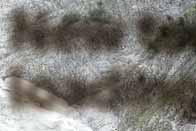
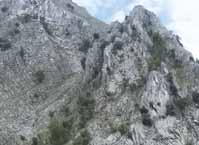
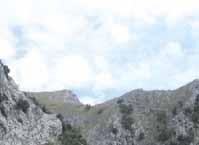

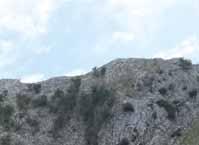
New tech drives improved loading performance
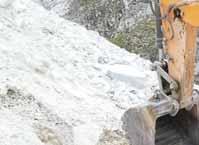
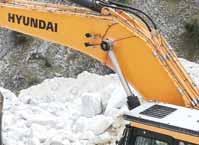
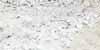

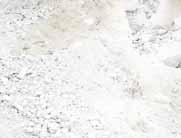
Cutting-edge technologies are helping quarry operators to increase the productivity, fuel efficiency and safety of their loading equipment. Liam McLoughlin reports

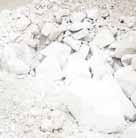

Marble quarrying company Alba Ventura has bought a Hyundai Construction Equipment (HCE) HX520L excavator from Toscomeccanica, the HCE dealer for the Italian region of Tuscany.
The 52-tonne excavator replaces a model of the same capacity and is working flat out at Colonnata quarry in the iconic marble quarrying area of Carrara, where high-quality marble such as White Cattani Marble is extracted.
The HX520L excavator is powered by the Scania DC13 084A 6-cylinder, 12.7-litre, Stage IV engine, which delivers an output of 316 kW, providing energy efficiency combined with high-level performance.
Alba Ventura owner Roberto Vernazza said the HX520L excavator has demonstrated standout attributes such as high power, a high degree of stability and maximum efficiency.
“From the first days of operation in our marble quarry, the Hyundai excavator showed what it was made of – a powerful machine, but also sensitive and precise in its movements; a true champion born to dominate the terrain, whatever the type,” he added.
To optimise performance in the toughest operating conditions, HCE has equipped the excavator with cutting-edge technologies: the Eco Indicator, a system that can give immediate feedback on fuel efficiency while the machine is operating; IPC (Intelligent Power Control), a function that regulates the hydraulic pumps based on the work environment and selects speed mode,
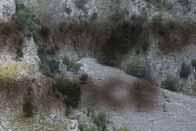

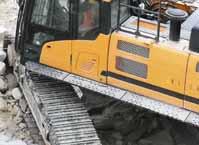

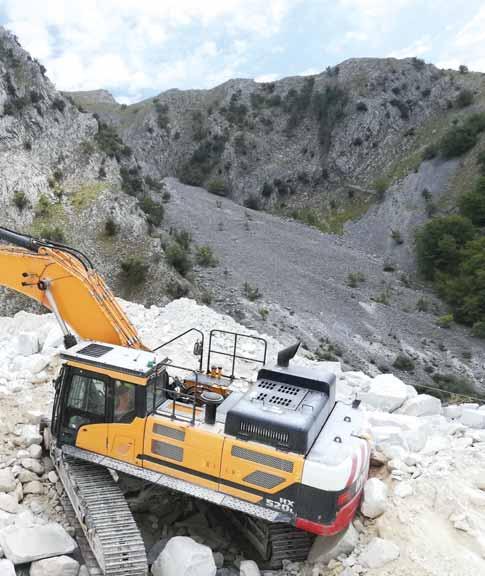
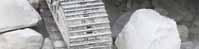
balance mode or higher efficiency to adapt machine performance. In addition, the new variable power control is designed to increase performance, whatever the operating environment.
“In our quarry, we needed a new machine to replace an old model of the same capacity,” said Vernazza. “So, we contacted the dealer in Massarosa, Toscomeccanica, who has provided us with assistance service for years in a professional and timely manner. In this case, too, they supported us by immediately identifying a model which would meet our expectations.”
The HX520L excavator is designed to provide durability and strength. HCE says the solid structure of the model’s upper and lower frame, able to withstand external impact and work with large loads and the performance accessories verified by rigorous testing, are standout advantages of the HX Series.
The manufacturer adds that this is evident in
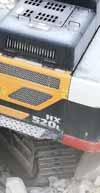
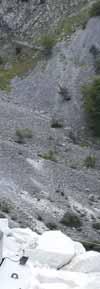
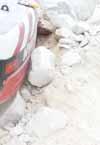
challenging operating environments such as quarries, guaranteeing better productivity. Reduced noise, low vibration and an ergonomic design are intended to make the cabin space more comfortable and pleasant.
The HX520L’s comfort features include a spacious cabin, clear controls, excellent visibility, and high-performance air conditioning. The standard suspension seat, adjustable for height and weight, has a headrest and an armrest, also adjustable. There is an emergency engine stop at the base of the seat. With its focus on operator safety and comfort, the HX520L excavator is designed to allow quick, safe inspection of the instruments, providing its operators with an optimal work environment.
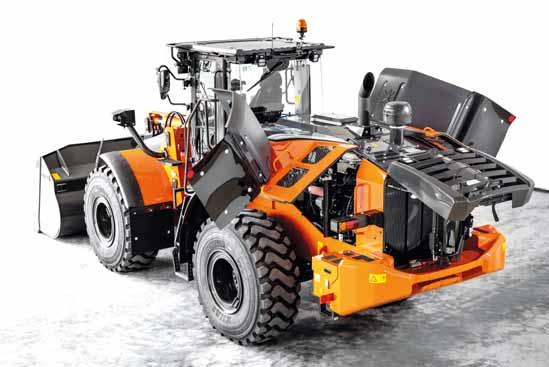
A Hyundai HX520L excavator working at the Colonnata marble quarry in Tuscany
The Hitachi ZW220-7 has a camera system giving operators a bird’s-eye view of jobsites
“In addition to being a robust, powerful machine, the Hyundai HX520L excavator offers longer maintenance intervals and greater ease of maintenance, reducing workshop time to a minimum,” said Toscomeccanica owner Claudio Bacci. “Also, the maintenance areas are easy to access, and the grease points are centralised. Not to mention that the high-performance oil filter extends the change interval to 500 hours. These are surely the key aspects for our customers, who need to keep machine downtime to an absolute minimum.”
Japanese original equipment manufacturer (OEM) Hitachi has introduced the ZW2207, which the company says is its first Stage V-compliant wheeled loader and the first model from its next generation.
The OEM adds that the ZW220-7 has been designed to put operators in control of their workspace, with new safety features and increased comfort in the cab.
The loader features the Aerial Angle camera system, giving operators a 270-degree bird’s-eye view of the jobsite, while the rear obstacle detection and warning system alerts them immediately if anything is close to the rear of the machine.
Hitachi says the ZW220-7 is especially easy to use due to features such as the improved seat with mounted electric pilot control leavers, new monitor controller and convenient side switch panel.
The company adds that owners will be able to increase their profits due to the fuel economy and efficiency of the ZW220-7, in addition to faster and more efficient short loading operations due to the approach speed control feature.
The new ZW-7 model is also designed to load trucks more accurately using the payload monitoring system. In addition, operators can monitor the fuel consumption with the new ECO gauge and performance can be improved with several adjustable functions.
To support owners and operators throughout the life cycle of the new ZW-7 wheeled loaders, Hitachi provides a wide
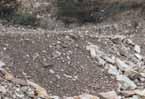
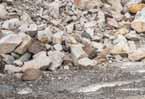
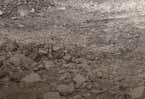
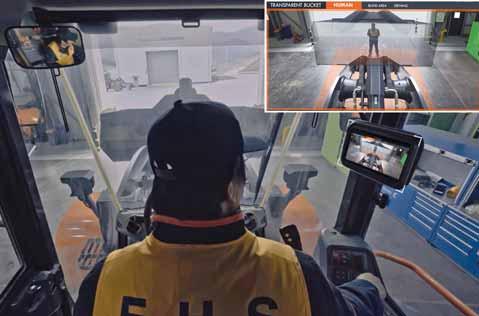
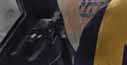

range of after-sales services, and access to vital data and tools so they can manage their machine effectively. These include remote monitoring systems, Owner’s Site and ConSite (part of Global e-Service), and the ConSite Pocket app, which help to monitor performance, track location and plan maintenance.
“Many years of extensive research have contributed to the development of the ZW-7 range to ensure that it meets the specific demands of European customers, from small business owners to large fleet contractors,” said Bill Drougkas, wheeled loader product manager of Hitachi Construction Machinery (Europe).
“As a result, we believe it offers a superior experience in the cab and exceeds expectations in terms of efficiency and performance.”
Doosan Infracore Europe has launched a ‘transparent bucket’ system for wheeled loaders that is designed to allow the loader driver to see blind spots in front of the bucket on the machine via the cab monitor.
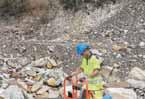
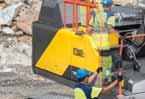
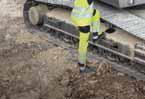
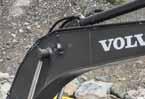
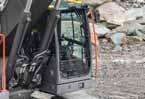
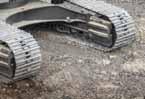

The system records images in front of the wheeled loader with top and bottom frontloaded cameras and shows combined images on the monitor in real time using a curved projection method.
Owing to blind spots caused by the buckets on wheeled loaders, the area in front of the machines has been considered an area of major concern in terms of safety. Doosan says that with its new transparent bucket function the driver can now easily check the blind spots in front of the bucket via the cab monitor, to increase safety and prevent accidents.
Another claimed advantage of the transparent bucket system is that it can significantly improve work efficiency by providing a forward-view perspective for the driver during loading/unloading or when carrying materials such as aggregates, sand and soil.
Doosan Infracore says it is the first company in the world to develop and apply a front projection function with the transparent bucket for construction machines and has applied for patents in Korea, North America, Europe and China.
The manufacturer has also developed further sophisticated safety systems for its machinery range, such as the around view monitor (AVM) system, that can observe the machines’ surroundings, and a rear warning system using ultrasonic sensors, which it says have both received very favourable responses from customers.
A Doosan Infracore spokesperson commented: “As machinery and site safety standards continue to be significantly raised around the world, advanced safety systems have become a key factor in selecting equipment. We plan to continue developing safety features that can protect drivers and other workers on site, and we aim to be at the forefront in creating construction sites that are safer and accident-free.”
Volvo Construction Equipment (CE) has launched updated versions of its EC250E and
Doosan Infracore Europe’s ‘transparent bucket’ system aims to eliminate loader driver blind spots
The new Volvo CE EC300E heavy-duty excavator

EC300E excavators, which are claimed to offer improved fuel efficiency of up to 10%.
The updated heavy-duty machines weigh 26-31.5 tonnes and 30.2-36.8 tonnes for the EC250E and EC300E respectively. They can also come with purpose-built attachmentsincluding buckets and breakers - which Volvo CE says will help operators move more, for less.
The manufacturer says the updated models deliver up to 10% improvements in fuel efficiency, due to a combination of features that includes more intelligent electro-hydraulics, the classic ECO mode and selectable work modes, and finally the new D8M Volvo engine.
This upgraded engine reduces rpm from 1,800 down to 1,600, while delivering a 5% increase in power. The EC300E also has a 700kg heavier counterweight – providing greater stability and a 5% increase in across lifting capacity.
Volvo CE says that operators will benefit from improved response times – thanks to the electric control joystick and full electric travel pedals – and are helped in their task by the optional Dig Assist apps which are powered by the 10-inch (25.4cm) Volvo Co-Pilot in-cab tablet. These include 2D, In-Field Design, 3D software packages and On-Board Weighing. In addition, the Volvo Active Control feature boosts digging accuracy and allows jobs to be completed up to 45% faster, thanks to automated boom and bucket movements. Operators can also set swing fence, height limit, and depth limit to avoid contact with side obstacles, overhead obstacles such as power lines, and underground hazards such as pipes and cables.
For operator comfort, Volvo CE says the excavators include new boom and arm bounce reduction technology – which reduces machine shock – and Comfort Drive Control to help reduce fatigue by enabling operators to steer the machine using the joystick rollers instead of the pedals.
Aggregates-processing solutions company DUO Operations has supplied a fleet of Doosan machines, including two wheeled loaders and a pair of excavators, that is proving central to the smooth running of Carnsew Quarry in Cornwall, south-west England. Carnsew Quarry is one of two
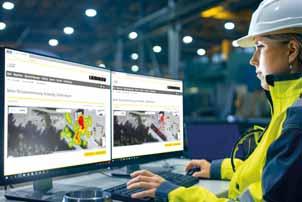
locations in the Colas Cornwall Quarries division, along with the West of England Quarry. Both are hard rock quarries, providing a wide range of quarry products and asphalt to the local market by road, and further afield by road and sea.
Carnsew Quarry is the largest inland quarry in Cornwall and is located in the centre of the developing area lying between the county towns of Redruth, Falmouth and Truro. The quarry produces quality coarse-grained silver-grey granite, meeting demands in different sectors of the construction industry.
The Doosan products at Carnsew Quarry have been supplied to Colas under a longterm hire agreement with DUO Operations to assist in the operation of Carnsew Quarry and to ensure the quarry runs smoothly.
The Doosan equipment supplied by DUO Operations includes two DA40-5 articulated dump trucks (ADTs), which support the haulage between the primary and secondary crushing operations. Working alongside are Doosan DL450-5 and DL550-5 wheeled loaders used to stockpile quarry products, plus load the ADTs and road trucks delivering to sites around the area. The Doosan fleet from DUO is completed by a pair of Doosan DX380LC-5 crawler excavators that load the secondary crusher and assist with breaking.
All the Doosan equipment supplied by DUO Operations comes standard with DoosanCONNECT advanced telematics. Using the data provided by DoosanCONNECT, DUO Operations reports directly to Colas on a monthly basis.
This supplies Colas with information on fuel efficiencies, fuel levels, fault codes, warnings and for the ADTs, it shows load counts. This information enables Colas to plan and maximise the profitability at Carnsew Quarry, and also provides the company with a good indication of the cost per tonne. DUO Operations also provides Colas with details on any operator faults and offers advice and feedback to prevent any future maintenance issues.
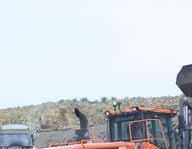

Liebherr has added two new functions to its active personnel detection assistance system for wheeled loaders. The brake assistant and incident map functions have been added to active personnel detection in the system which is used in the Liebherr L 526 to L 586 XPower range of wheeled loaders. The brake assistant automatically slows the speed of the loader to a standstill the moment the active personnel detection issues a warning signal. The incident map displays potential risk zones on the site using GPS data in LiDAT - Liebherr’s in-house transfer and location system.
The manufacturer says that, statistically, accidents with wheeled loaders occur most frequently when the machine operator reverses after a loading process. This reverse travel is particularly risky if people are located in the wheeled loader’s operating area. In these situations, Liebherr says there is a huge responsibility on the machine operator, adding that this is why it is continuing to develop its assistance systems.
Active personnel detection visually alerts the machine operator via the display screen and sounds acoustic signals if there is danger in the wheeled loader’s rear area.
Besides the brake assistant, a second new function for the active personnel detection at the rear is the incident map. Each time the assistance system detects a danger and a warning signal is issued, the system transmits a GPS signal to LiDAT, Liebherr’s in-house transfer and location system. On the basis of this signal, and for each operator of a wheeled loader with active personnel detection, Liebherr provides a Google map in LiDAT showing these GPS points.
The result is an incident map displaying the risk zones and potential sources of danger on the site. The operator can use this to take measures to prevent accidents and therefore increase safety. For example, the operator might reroute footpaths, cordon off areas and alter dangerous work sequences. The head of operations can use the incident map to train employees and make them aware of risky situations. AB
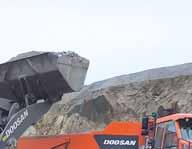
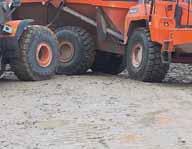

A DL550 wheeled loader and DA40-5 ADT among the Doosan vehicles boosting operations at Carnsew Quarry, UK
The new Liebherr incident map lets loader operators implement measures to avoid on-site accidents




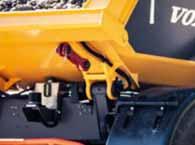
Advancing automated hauling

The intended use of the Volvo TA15 autonomous hauler is to transport material in repetitive flows in quarries and other confined off-road environments


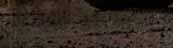
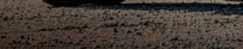

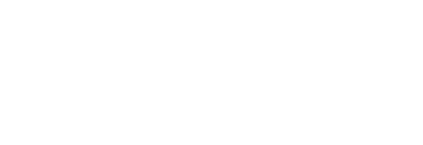
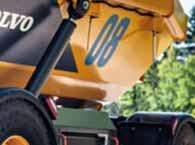
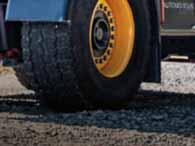
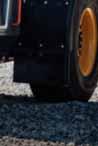
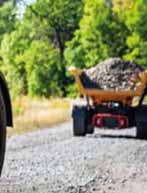
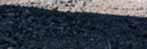
The Volvo Group has been busy developing its TA15 autonomous hauler concept as it looks to rethink how quarries currently operate.
Uwe Müller started his career with Volvo Construction Equipment (Volvo CE) in 2006, where he led several research projects developing new technologies, concept machines and site systems, including the breakthrough study Electric Site. He currently serves as the head of sales and marketing for off-road solutions at Volvo Automated Solutions, specialising in automation and the electrification of construction equipment.
“The TA15 is the result of continuous development of previous concept models. The machine is now part of the TARA autonomous transport solution, which consists of several components — the base vehicles (multiple TA15s), plus required infrastructure such as charging stations, a control tower, connected cloud solutions designed to meet customer operation requirements, maintenance and repair support, and the practical operations set-up which varies site to site,” Müller explains.
“The intended use of the TA15 is to transport material in repetitive flows in confined off-road environments like quarries. The number of machines and respective charging stations will depend heavily on the target production/transport volumes as
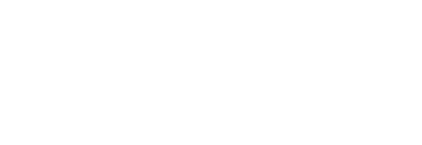
Autonomous hauling is an eye-catching topic within the modern quarrying sector. Here, experts from two major global off-highway haul truck makers give the lowdown on their companies’ latest work in this area
well as the haul cycle. It can start as a small fleet of three to four machines and go up to bigger fleets of 15-20 machines running in a coordinated effort on a site. The fleet of TA15 machines will interact closely with the respective loading equipment at the site (e.g. wheeled loaders or excavators) and be supervised and controlled from a central, onsite control room.”
Müller notes that the TA15 machines are designed for high-power opportunity charging which is a natural part of the haul cycle. This means the machines can, in principle, be charged every cycle with the amount of energy they need to run the next cycle. The charging process is fully autonomous, using a 150kW high-power charger that connects via a pantograph on the ground to a pick-up on the bottom side of the TA15. The charge time will vary from approximately one minute up to three minutes depending on the amount of energy needed.
In his recently published blog on the TA15 concept’s progress, Müller says: “What are the benefits of an autonomous transport solution? The primary benefits customers will experience include increased energy efficiency due to the electric drivetrain and innovative design of the base machine; lower emissions (zero local emissions) due to the battery-powered driveline; increased safety; and an overall increase in process
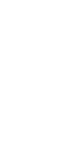
productivity due to the combination of automation, electrification and connectivity.”
Müller highlights that the TA15 concept has performed very well as a prototype during the Electric Site project, clearly validating its benefits and potential. “Our next steps are to improve the stability, uptime and overall performance of the system to reach the needed levels to move the concept from a prototype to a commercially viable solution,” he adds.
“Safety, which is and has always been one of Volvo’s core values, is at the forefront of the TARA solution as well. It starts with having a fenced/confined area for the autonomous operation. There’s also a redundant emergency stop system that can secure a safe stop of the complete system at all times, plus a traffic management system that continuously tracks the position of all machines to secure the right traffic flow. Finally, an obstacle detection system on the TA15 machines consists of a combination of LIDAR and RADAR sensors that helps the machine detect obstacles in the intended drive path.”
Müller states that the biggest change going from conventional transport solutions to the TARA system is the system-thinking approach. “This is not about just exchanging today’s equipment with something new — it’s about changing the way sites work to fully leverage the advantages you can get from
electrification, automation and connectivity.
“We see the TARA solution as an extension of today’s Volvo Group transport solutions offering. It will help transform the transport industry toward more sustainable solutions. The system, however, might not fit into every environment and customer process, so we’ll also see diesel or renewable fuel-powered trucks in parallel for quite some time.”
Müller says the Volvo Group also foresees some changes in the way quarry sites and other customer applications will be operated in the future. This will require different jobs and new competencies going forward, with the group having to work closely with its customers and partners to help make these changes happen.
“In the meantime, our focus and top priorities are to finalise our development, verification and validation process to secure a successful market introduction of the TARA solution for selected customers,” explains Müller. “This will start in the latter part of 2021, with strong ambitions to scale the solution in the coming years. As we work to bring this solution to market, we’ll continue working on many other exciting autonomous solutions that will help make future sites more productive, efficient and safe. Stay tuned — the future promises to be very exciting!”
A focus on improving ease of operation to provide more efficient and safer articulated dump trucks (ADTs) has consistently kept Bell Equipment at the forefront of innovation. The global ADT specialist is now achieving success with autonomous vehicle operation where its forward-thinking approach is enabling interoperability between different control systems and the trucks it produces.
An autonomous operation has three elements: machines that can be operated remotely, external sensors that become the eyes and ears of the machine, and sophisticated site control software that manages the operation based on communication with the other two elements. According to Bell Equipment ADT product
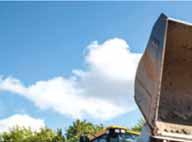
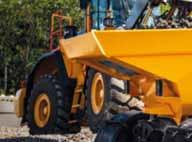


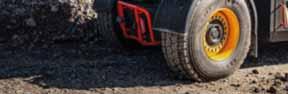
marketing manager, Nick Kyriacos, “providing autonomous-ready machines will be a part of our core business in the future but in terms of sensing and guidance systems it makes sense to partner with market leaders and innovators, as we do with drivetrain, hydraulics and electronics technologies in our trucks.”
At the same time, Bell Equipment (Bell) wants to provide a vehicle that can be fitted and controlled with a guidance system from any number of manufacturers with the easiest integration. “Autonomous applications are industry specific and require surveying and guidance by an industry expert. We want our customers to be able to choose a guidance solution that they are most comfortable with and that can be

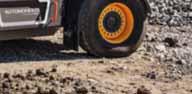
fitted to all the machines in the work cycle. Keeping the guidance system independent of the OEM gives customers the flexibility to run a mixed fleet and benefit from the efficiency and productivity that provides,” says Kyriacos.
Adding to the flexibility, Bell provides a standard cab with no extra hardware taking up space to create an environment where manual, remote, or autonomous operation is interchangeable. Kyriacos continues: “This would be useful for mining contractors, for example. Once their ADTs have finished a contract on an autonomous site, the sensory and control system could easily be removed and the truck either fitted with a new system for another site or be used in a manual operation.”
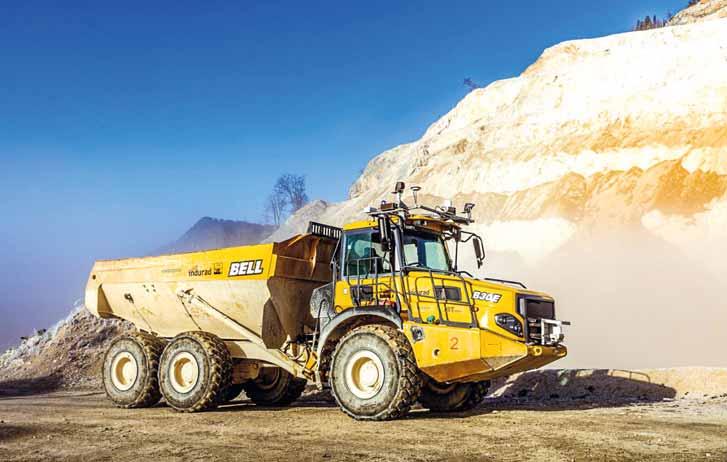
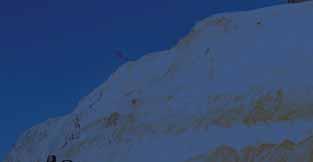
“Support vehicles, such as service vehicles and water bowsers, may also form part of autonomous operations”
Nick Kyriacos
The TA15 autonomous hauler concept is an example of how the Volvo Group is looking to rethink how quarries currently operate
A Bell B30E ADT running in a fully autonomous site in Austria with partners indurad and voestalpine. Image: indurad/voestalpine

As economies of scale and technology become more affordable and reliable in the future, Bell expects to see smaller and smaller sites embracing autonomous operations. Kyriacos summarises: “Support vehicles, such as service vehicles and water bowsers, may also form part of autonomous operations. This would make it even more important that every machine on site, regardless of the OEM, is able to use and respond to the same software. We envisage that there could also be sites where the main earthmoving operations are fully autonomous, but support vehicles that perform a wide variety of functions are remotely operated from a central area. This would allow the site to have no people whatsoever which improves safety.”
Achieving an autonomous-ready platform was a natural progression from the Bell Mark 3 ADT upgrade at the end of 2019 when trucks were made ready to integrate with pedestrian detection systems (PDS) and collision avoidance systems (CAS).
“We’re always looking to add value and stay ahead of the curve,” says Bell’s manager: electrical and software, Eben Lemmer. “We were first to develop our own telematics solution, Fleetm@tic®, and to introduce onboard weighing, which is standard on our ADTs. When we introduced an inclinometer to improve our onboard weighing accuracy, we saw an opportunity to improve the safety of our trucks with our Hill Start and Tip Safe features that prevent rollback on slopes and rollovers due to tipping at unsafe angles. Similarly, by adding further layers on top of the existing PDS ISO standards we have created an autonomous-ready platform that uses an open communication protocol principle to integrate easily with third-party suppliers.”
Bell’s focus is on the execution of instructions from third-party suppliers. Lemmer explains: “In the work environment the guidance software processes all the sensory input, plots a path and sends instructions to the Bell drive-by-wire
interface, which electronically controls the acceleration, braking and steering of the truck. Our communication simulator provides the ability to collaborate with service providers by allowing them to test communication and response in the desktop environment prior to going live in-field. This makes it easier to develop and test new software for controlling the Bell ADT.”
Bell first demonstrated that cost-effective remote control is achievable with the right building blocks when it successfully operated a B45E with a video game controller. Since early 2020 the company has been working with indurad and voestalpine on a lime quarry site in the Alps where the industrial radar specialist has fitted its iTruck autonomous haulage system (AHS) on Bell B30E ADTs with excellent results. “Autonomous control in this application is advancing all the time as technology pushes the boundaries and improves the efficiency of the operation. The project is ongoing, and we are now growing our number of collaborations both locally and abroad.
“Autonomous vehicle operation is an exciting space to be working. Not only is it aligned with the Fourth Industrial Revolution’s objective of achieving higher levels of automation for greater process efficiencies and cost reduction, but we believe it will deliver safer vehicle behaviour by reducing the instances of human error and negate the impact of whole-body vibration on operators in the workplace,” says Lemmer.
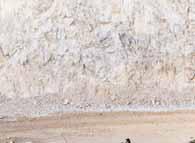
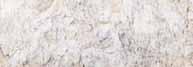
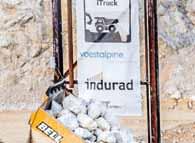
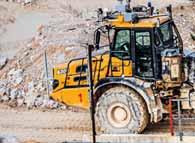
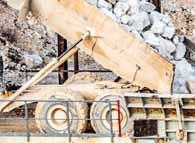
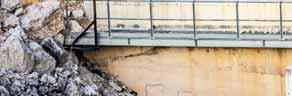
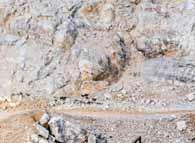
In most cases an autonomous operation will also need the end customer to set up their site to work differently; there may be special traffic control measures, berms or even different roads needed. At this point in time Bell has an autonomous-ready solution available for customers that are interested in doing proof of concept work in their application. “During this phase we are still learning along with our customers, but we expect our offering to stabilise soon. From there, should anyone express a wish for a full-scale commercial solution, we are confident of being able to deliver within a timescale that is consistent with their expectations,” concludes Lemmer. AB
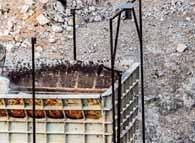
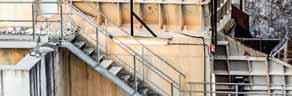
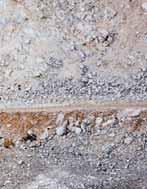
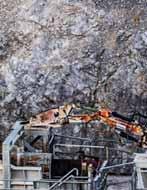
Bell Equipment’s Eben Lemmer
A Bell B30E loading material into a jaw crusher at the autonomous site run by Bell Equipment, induard and voestalpine. Image: indurad/voestalpine
Bespoke washing wins
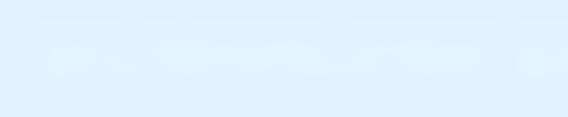
Premium washing solution manufacturers are focused on producing cutting-edge plants that meet more tailored customer needs. Guy Woodford reports
Tunisian quarry operator SOMEVAM has announced plans for its second wet processing solution from Northern Ireland-based CDE.
The new plant will produce highspecification silica sand products.
SOMEVAM is a subsidiary of the Tunisian Sebri Group, which has interests in quarrying, agriculture, and food processing. Sebri Group will work with its wet processing partner CDE to design and engineer the new plant at one of SOMEVAM’s quarries in Oueslatia.
The sand and aggregate materials from Sebri Group’s Oueslatia sand quarries have been supplied to the national construction market for the past two decades.
Its management team identified an opportunity to further diversify the business by expanding into the glass sands market to strengthen its commercial proposition in the region, and in 2019 commissioned its first CDE solution at the site.
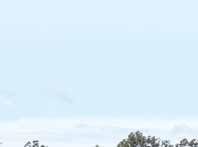

The state-of-the-art silica sand wash plant can treat up to 200 tonnes per hour of sand, producing 100 tonnes per hour of silica glass sand for the glass industry, as well as a range of secondary products including fine silica sand for silica flour production, foundry sand, concrete sand and road base.
Investment in a second silica sand wash plant comes as SOMEVAM says it is recording significant interest in its future
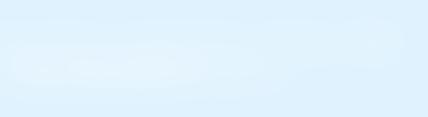
production output. The plant will produce silica sand, which has applications in paints, coatings and inks, adhesives and sealants, pharmaceuticals, lighting and more, and silica for flat glass applications such as windows, mirrors and flat glazing.
The glass industry accounts for more than a third of the total market for silica sand based on end use. The market analysis projects a growth rate of 7.12% in the silica market over the forecast period 2019–2026, reaching US$3bn by 2026. While North America has the largest market share, the Asia-Pacific region is anticipated to display the highest growth rate, according to a report from Bizwit Research & Intelligence.
Commenting on the announcement, CDE’s senior project manager Bassem Idriss said: “We’re very pleased to once again partner with Sebri Group on this exciting project announcement that will significantly expand SOMEVAM’s silica sand processing and production capacity. Its previous investment in CDE technology exemplifies our commitment to engineering excellence and is one of the most advanced plants of its kind.”


SOMEVAM has announced plans to install a second CDE wet processing solution at one of its quarries in Oueslatia, Tunisia. Pictured is its existing CDE plant installation
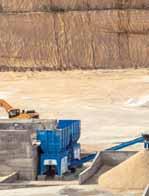

Ruchin Garg, CDE regional manager, MEA (Middle East & Africa), added: “At CDE, every customer is a customer for life. SOMEVAM’s existing silica sand plant, which was commissioned in 2019, receives expert proactive and preventative maintenance and support. It’s this commitment to our

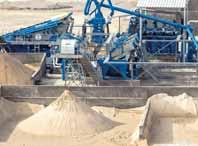
customers, one that ensures their CDE solution is running at optimum efficiency to maximise product throughput, yield and profitability while minimising their environmental footprint, that has formed the foundation from which we can continue to build upon our positive relationship with Sebri Group through this latest announcement.”
Habib Sebri, owner and chairman of Sebri Group, said: “Following a hugely successful venture into the glass sand industry with our first CDE plant, we sought an additional plant to meet the growing demand for our products. We are excited to partner with CDE once again on this new project to maintain the quality and consistency of our offering, and we thank all of those partners who helped secure funding and provided their expertise and resources to help make this ambitious project a reality.”
CDE and Sebri Group said they would share more details about developing the new SOMEVAM silica sand wet processing solution in the Oueslatia region over the coming months.
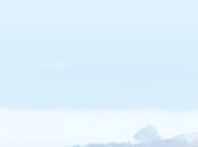
With authorisation from the Central Bank of Tunisia, funding for the new investment was secured with the support of UK Export Finance, AF Capital, Apple Bank, and supported by the British Embassy Tunis.
Tri-Parish Sand and Gravel is a dry mining operation located in Walker, Louisiana, USA.
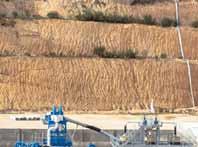
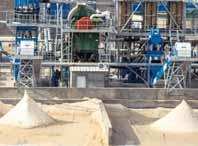

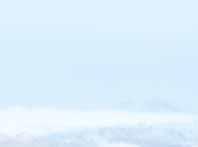
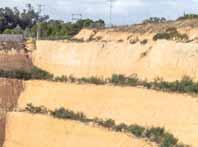

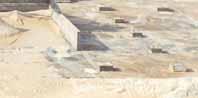

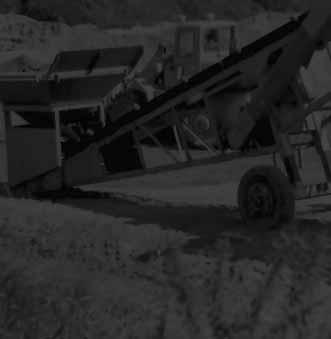
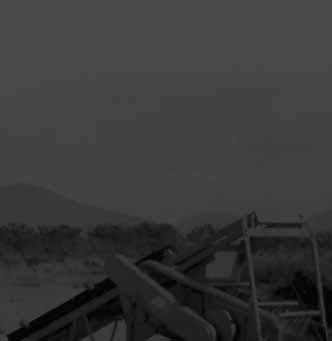
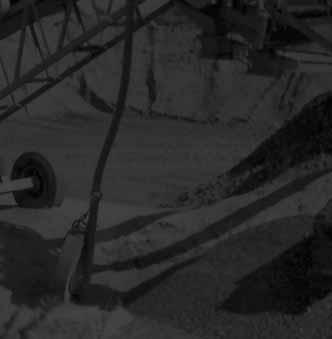
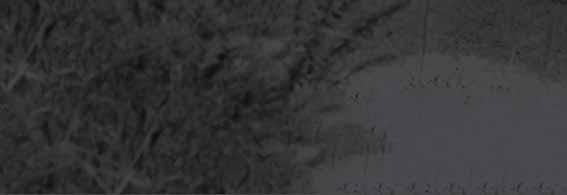


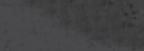

The company produces C-33 concrete sand, pea gravel and #57 concrete gravel for use in their ready-mixed concrete operation, Parish Ready Mix.
James Nolan, who owns Tri-Parish Sand and Gravel with his wife, Gail, has always been concerned about the cleanliness of the products they use in their ready-mixed facility. They strive to deliver quality products on the concrete side of their business, which starts with the material used to make those products.
To better control the quality of their concrete products as well as lower their
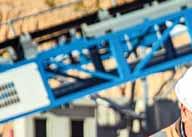
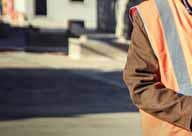

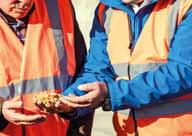
purchased land for dry mining their own sand and gravel. They looked at a few wash plants in different parts of the country for processing the feed and separating it into the various products needed at their readymixed facility.
In 2020, Tri-Parish purchased the McLanahan UltraWASH 6206 modular wash plant that debuted at CONEXPO/ CON-AGG 2020 in Las Vegas. Availability was a key factor in the purchasing decision. Tri-Parish needed a wash plant quickly, and the McLanahan UltraWASH offered an entire wet processing plant in one compact,
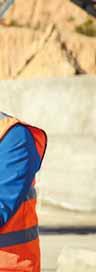
very pleased with it,” said James Nolan. “It definitely does way more than they said it would do.”
The UltraWASH features a McLanahan inclined vibratory screen for sizing up to three aggregate products (the oversize, the pea gravel and the #57 gravel in Tri-Parish’s operation). It also features a sump, two McLanahan Pumps, two McLanahan Hydrocyclones and a McLanahan Dewatering Screen for washing, classifying and drying the sand product. This particular UltraWASH model is a double wash system, which processes the sand twice before discharge for a cleaner end product.
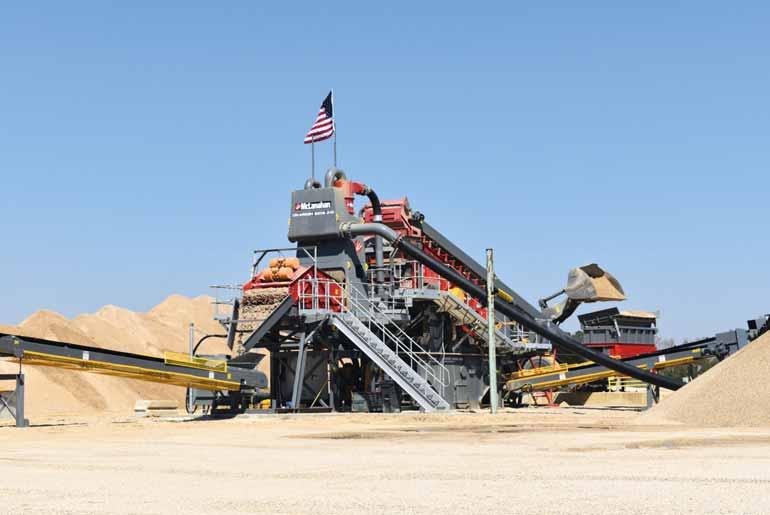
A modular plant, the UltraWASH arrived at Tri-Parish in several partially pre-assembled and pre-wired pieces.
“It went together very easily,” said operations manager Danny Graham. “You could almost do it by pictures alone.”
Graham added that the modularity of the UltraWASH would be beneficial if they need to move the plant closer to the area in which they are mining in the future.
“It could be somewhat portable. You can take it and move it in a matter of a day or two,” he said.
The UltraWASH 6206 unit features a McLanahan inclined vibratory screen for sizing up to three aggregate products
Habib Sebri (left), owner and chairman of Sebri Group, and CDE senior project manager Bassem Idriss inspect sand product at SOMEVAM’s Oueslatia quarry
Sand being conveyed on SOMEVAM’s CDE washing plant at its Oueslatia sand quarry
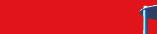
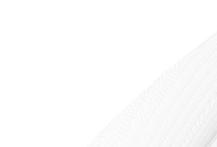
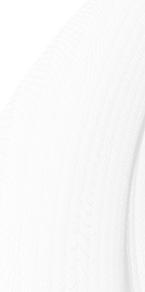
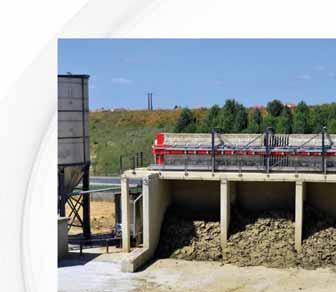
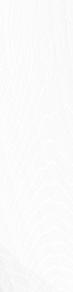



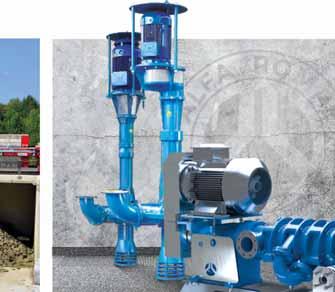
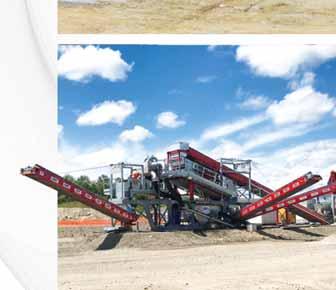
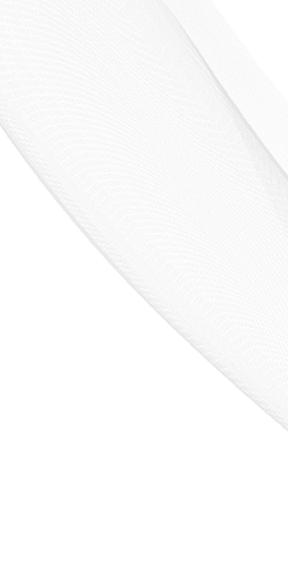

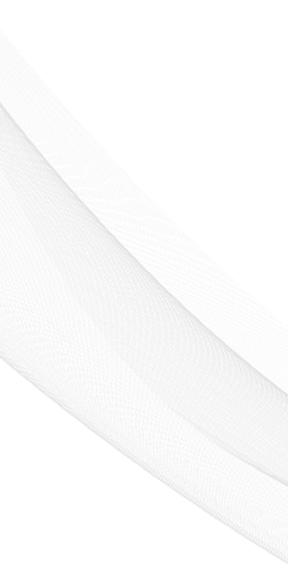
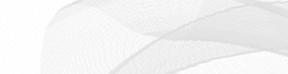


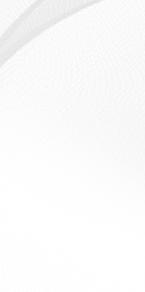
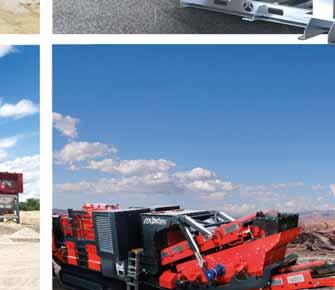

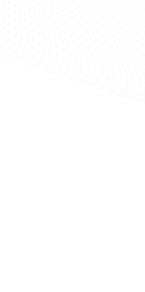


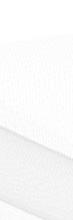
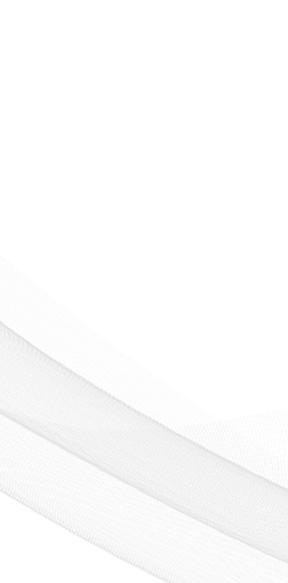
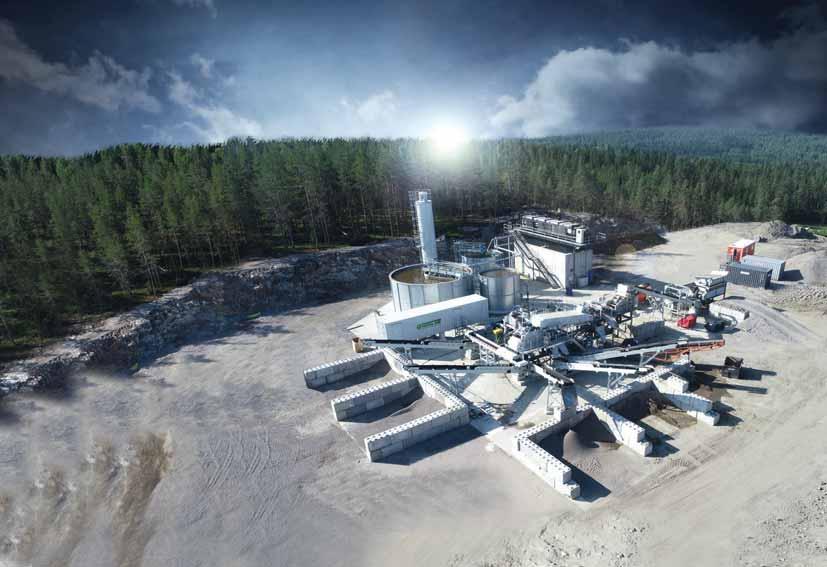
TWS’s Greenline Engineered Recycling Solutions deliver an out-of-the-box approach to processing up to 300 tonnes per hour of diverse materials
Besides availability, one of the aspects that attracted the Nolans to the UltraWASH was the rated tonnage of the machine, but this exceeded their expectations in the field.
“It’s delivering way more than we’ve ever dreamed, so I’m really happy with it,” James Nolan said.
“We’re actually outrunning our guys who are stockpiling raw material,” Graham added. “Production-wise, it’s better than expected. We’re keeping up very easily with this product; it hasn’t been a problem. The UltraWASH is doing a great job.”
Since they started operating the plant, James Nolan said the biggest benefit of the UltraWASH is how quiet it is. The Tri-Parish property borders a housing development, and the neighbours can’t hear the plant when it is running.
Graham likes that the UltraWASH is easy to operate.
“I really like that it’s one central unit,” Graham explained. “Everything’s maintained in one electrical panel. It’s easy to work with; the PLC and everything make it very userfriendly. It’s automated stop/start, so there’s no guesswork and there’s no manually starting different components. You start it, it runs; you stop it, it stops. You can’t beat that.”
In addition to the UltraWASH’s performance, James Nolan is also pleased with the cleanliness of the product coming off the end of the machine.
“I guess I’m bragging on it, but it needs to be bragged on. It turns out a real good material. It’s clean. I’m proud of it,” James Nolan said. “Even the guys at the plant, they realize the change in the material because we have started running out of here now and it’s a whole lot different. We don’t have to be looking for mud balls and sticks and stuff like that because we send out a good product. We’re not going to send it out dirty, but this plant definitely helps us with a lot.”
The UltraWASH allows Tri-Parish to supply the concrete side of their business with a clean, high-quality product.
“Our goal and business is quality, and we’ve achieved it at this point,” James Nolan said.
The Tri-Parish team was also pleased with the support it received from everyone at McLanahan, from sales to project management to field service.
“My experience with McLanahan has been wonderful,” Graham said.
“They were all great in helping us facilitate getting the plant off the ground,” Gail Nolan shared. “They never left us behind. Any time
“The machine is a good machine, but without service, it’s nothing,” James Nolan said. “The McLanahan team helped us out a lot. Without them, we couldn’t have made it.”
With more than half a century of washing experience already under its belt and a proactive research and development team (R&D) that never stands still, Terex Washing Systems (TWS) has a proud and rich history. A division of Terex, TWS was established in 2012, and in this time, it has continued to commit time and resource in developing and investing in R&D and the latest technologies and systems in the wet processing world.
TWS’s product portfolio now offers ‘end to end’ washing solutions, including the more recently introduced AquaClear Water Management Solutions and GreenLine Engineered Recycling Solutions. However, all these solutions’ beginnings can be traced right back to before 1960 within the Finlay and Powerscreen product lines.
The mid-1960s saw the development of the very first washing plants, and the following decade saw the launch of the MK1 and MK11 Rinser range. It wasn’t long before Powerscreen and Finlay realised the crucial need and potential opening in the
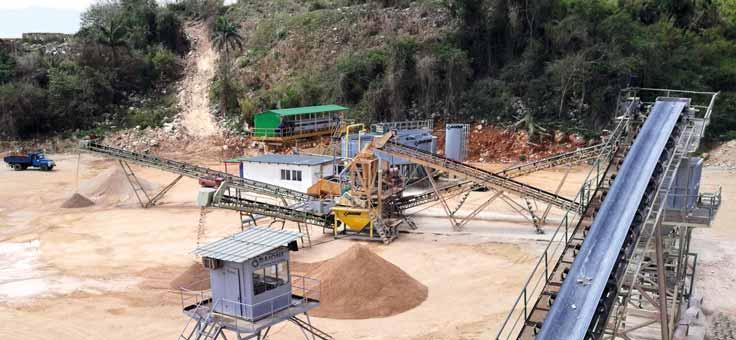
A Baioni washing plant in Cuba
market. They knew that the natural sand and gravel supply would soon be exhausted and foresaw stricter building and construction specifications being written for aggregates usage.
As technology started to advance in the late 1970s, the Sand Saver Dewaterers were soon phased out. They were replaced by the more sophisticated and modernised Screw Recovery Dewaterers, later to be called the Trident range.
The 1990s saw the establishment of a dedicated washing department, set up by Finlay and Powerscreen. By the 2000s the demand for washing was expansive, so TWS was established in 2012 as the sole provider of washing solutions within Terex.
While its roots are firmly established locally in County Tyrone, Northern Ireland, TWS now enjoys a global reach. The business is supported by an over 70-strong global dealer network. While TWS continues to navigate through these unprecedented times, now more than ever, this global dealer network has been fundamental in providing local and regional on-the-ground support to customers worldwide.
Furthermore, the business has significant support from local Terex footprints globally, such as Jacques in Melbourne, Australia, and Louisville in Kentucky, USA. The local support backbone has become increasingly important in allowing TWS customers to continue their operations. It has also allowed

the continuation of plant installations, startups, and commissioning. While also being supported remotely from TWS’s County Tyrone HQ via digital technology, local support is something that TWS says sets them apart from many of its competitors.
To go further, TWS has spent many years developing its portfolio of accompanying AquaClear water management solutions and products. The business has always had a relentless goal to be a single-source partner for complete solutions, perfectly balanced to match the needs of front-end equipment globally.
TWS’s recent launch of GreenLine Engineered Recycling Solutions (Greenline) puts together many years of expertise in easy-to-understand, tailored, packaged solutions designed to deal with varied recycling segment materials, muck-away, trommel fines, and C&D waste across differing capacity levels and at different levels of investment.
Greenline couples TWS’s front-end processing products with the business’s backend AquaClear Water Management Solutions. Several new TWS-patented specialist units will further enhance the Greenline offer, delivering an easily adaptable and potentially bespoke out-of-the-box approach to processing diverse material at a rate of 60-300 tonnes per hour.
Italian washing plant specialist Baioni has a new four-business division set-up
A LONG WAY TOGETHER

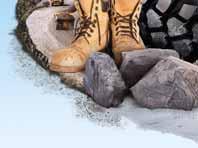
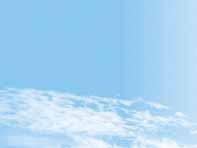
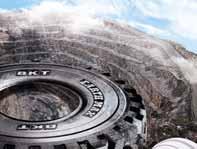
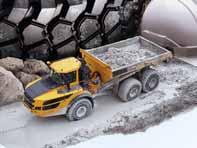

as part of a major strategy and rebranding process, focusing on design, people, and the environment.
The new business divisions – Baioni Crushing, Baioni Environment, Baioni Equipment and Baioni Service – have their own goals and features.
Baioni Crushing focuses on Baioni’s ability to design and build large-sized processing plants. Baioni Equipment incorporates the Italian firm’s comprehensive range of equipment for processing aggregates. Baioni Service handles increasingly important aftersales business, and Baioni Environment is responsible for designing and producing plants to treat contaminated soils and sediments. The business division also offers plants for the treatment of road-sweeping waste and incineration slag.
A Baioni spokesperson said: “In the last few years, the requirement to wash mineral, aggregate and soil has become more frequent as operators tackle more difficult materials. With this upward trend set to continue, Baioni have an important part to play in developing products and solutions that can meet the evolving demands.
“For 2021, our approach in response to the coronavirus challenges is to offer equipment when there is clay or contaminated particles present in the material or high levels of -63 micron material that can ensure production of the highest quality washed sand and aggregates.” AB

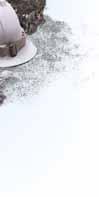
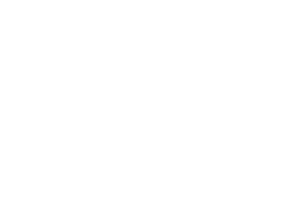



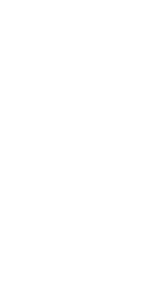


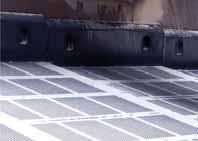

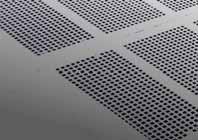
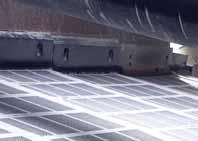
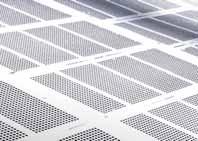
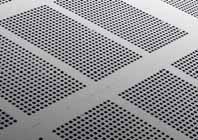
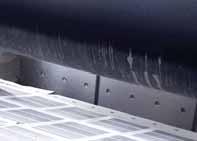
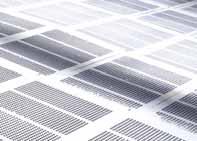
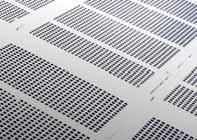

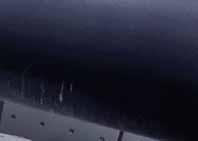
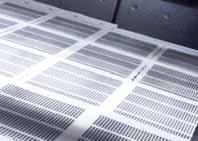
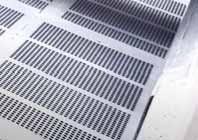
A screening media premium
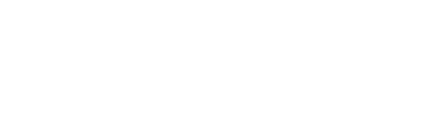

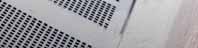
High-quality screening media is vitally important to operational efficiency at any aggregates-processing site. Guy Woodford looks at some of the latest solutions and learns how a partnership approach can be the key to success in this area of the equipment market
Metso Outotec’s high-resilience Trellex 300TS rubber screening media is helping Votorantim Cimentos to nearly eliminate contamination and fines and increase operational efficiency (OEE) by 11% at the group’s Santa Isabel quarry in Brazil. Located in Mogi das Cruzes, in Greater São Paulo, the Santa Isabel site has been in operation since 1959 and serves customers in the metropolitan region of Brazil’s largest city. The quarry provides aggregates for civil construction, major works, and cement block producers.
Despite the quarry’s current success, it was a different story in 2018. At that time, Santa Isabel faced two major challenges. In addition to reduced civil construction works, the plant was having problems due to aggregate contamination and an aboveaverage presence of fines. Both hurt buyers’ perception of the final quality and Santa Isabel’s sales. In the sand and gravel market buyers prefer materials with controlled levels of contaminants and dust. In other words, ‘cleaner’ aggregates.
With the arrival of the new regional manager, Carlos José Barbosa Silva, Santa Isabel began to implement operational changes, including training employees and addressing the main technical problem: the aggregate screening process’s improvements. Specialists from Metso Outotec were invited to assess the operational efficiency of the screens. “We had already faced a similar problem at our Araçariguama site and achieved good results with the solution presented. The screens were retrofitted and the wire media replaced with Metso Outotec’s Trellex 300TS screening media with
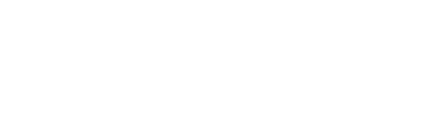
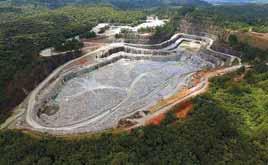
high-resilience self-cleaning panels,” explains Carlos Barbosa, Votorantim’s regional manager.
At Santa Isabel, Metso Outotec replicated the tests conducted at Araçariguama.”In Araçariguama, the tests involved the simultaneous operation of two screens: one with wire media and one with rubber media. When the media change-out was made, an analysis was performed in the site laboratory. We discovered that rubber screening media nearly eliminated the final product contamination and reduced the presence of fines. Even with a smaller open area, the high-resilience Trellex 300TS rubber media is much more efficient than the wire media,” says Metso Outotec’s screening specialist André Rosa. The tests played a decisive role in selecting Metso Outotec as a partner for Araçariguama and, later, for Santa Isabel.
While the screens alone were not the reason for the improved operational performance, the screen adjustments and

the use of Trellex 300TS rubber media were key factors in the increased production quality. An analysis of the end-user feedback supports this: the quarry index of one complaint about every 37,000 tonnes produced (2018) changed to one complaint about every 700,000 tonnes produced, an improvement of 20 times and ten times better than planned. The current assessment parameter is ten times higher than the specified target of one complaint per 67,000 tonnes. “It was a fantastic leap that surprised everyone. We didn’t miscalculate our goal. The results of the changes were significant,” adds Barbosa.
The challenge of the above-average presence of fines was addressed by optimising the screening solution. Furthermore, the main action to address the internal contamination, i.e. the unwanted mixture of different products, was training. Internal contamination was reduced by correcting the loader operators’ improper procedures when moving products in both operating shifts. Mistakes made by thirdparty drivers transporting products from the quarry to customers were also identified and corrected through appropriate guidance. However, the best indicator of success is pricing. In July 2019, for example, the price of stone powder had been increased seven times in a row. The recovery of the price negotiated between local customers and increased production was complemented by bold screening changes that created an intermediary product between fine and medium gravel. This has improved the quality of concrete block production with lower cement consumption and higher mechanical strength and visual quality.
TOP: Metso Outotec’s Trellex 300TS screening media is proving a big hit for Votorantim Cimentos
ABOVE: Votorantim Cimentos’s Santa Isabel quarry in Mogi das Cruzes, Greater São Paulo, Brazil
“There is pent-up demand already being seen, but our production should be able to keep up by making screening adjustments,” says Barbosa. He notes that Santa Isabel has a lean operating approach, increasing productivity by 4,000 tonnes per employee since 2018.
“Some of the buyers of our sand and fine gravel are concrete block producers who have automated machines and demand a high homogeneity standard. They were the first to observe the change in the quality and appearance of our final product,” summarises Barbosa.
Speaking to Aggregates Business, CDE’s Thomas Patterson, senior technical engineer, and Mark Ballantine, senior product development engineer, highlighted that the Cookstown, County Tyrone, Northern Irelandheadquartered washing plant manufacturer had in recent years seen a big increase in demand for plant set-ups focused on C&D (construction & demolition) waste recycling applications.
“We had a more simplistic approach to the recycling market four to five years ago as the needs of the market were very different,” explains Patterson. “Then, our customer was just looking to divert products from landfill, make them saleable, get them out of the door and get a quick return on investment on it.
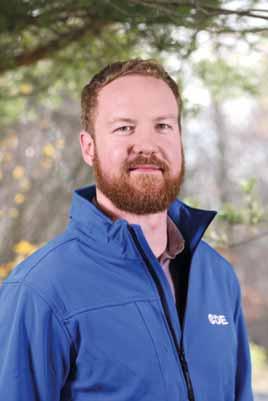

affect your dewatering capacity or fines management. Then next week, you want to get rid of larger sized particles.”
“Now, it’s gone from one sand and one aggregate to two in-spec sands and four aggregates, which are CE certified. That is a drastic change in the range and quality of the final product, which is supported by the level of investment that a customer wishes to make in the complexity and capability of their recycling plant.”
The screening element of the plant
manufacturers of screen media and ancillary products.
“We have a very close relationship with TEMA Isenmann,” says Ballantine. “If there are any problems that arise in the field or anything in our screen media that we think we can improve, be it cut-point efficiency, throughput capacity, or dewatering capacity, we know we can find the right mat for the optimised solution. It’s a continuous feedback loop involving our sales and technical engineer teams and the customer.
CDE has a range of 15 Infinity-branded screens for dewatering and product-sizing classification. “There’s a lot of novel features across that range, like Trilogy side walls and bolted construction, and we’re working on two more screens to add to it,” explains Ballantine. “There is modularity in the Infinity screens design and adaptability, allowing them to accommodate different screen media. The wide breadth of our screens means you need a wide arsenal of screen media to go with them, which we can get through our partnership with TEMA Isenmann.”
Patterson notes that CDE uses its Infinity range of screens on its plants for customers across both material handling divisions, natural processing and waste recycling. “CDE incorporates three main principles of good screening media, that is, plant performance, maximising tonnes per hour; durability, so you have good plant protection and
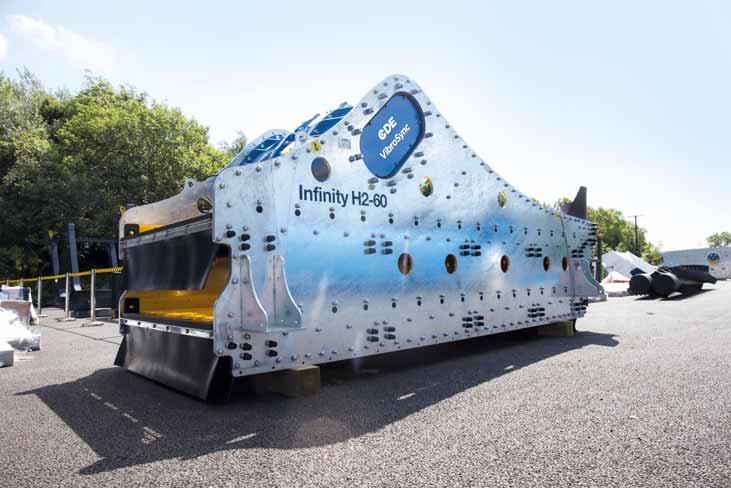
Mark Ballantine, CDE senior product development engineer
Thomas Patterson, CDE senior technical engineer
minimum downtime; and ability to achieve tight product specifications.
“In each material processing solution from CDE, the screening media is tailored to every application. For example working with a crushed manufactured sand is different to working with an alluvial natural occurring sand where the shape and texture of the two particles appear different, and aperture size and shape are very important to retain maximum screen efficiency.
“With a crushed rock application, given crushed rock is very sharp and angular, a slotted mat may be more suitable to gain more screening efficiency. Whereas a naturally occurring product [glass sand] that is rounder and alluvial is going to be more easily screened with a square aperture. Top-cut-point protection and low-cutpoint protection is also much more easily achieved.”
Patterson says around 55% of CDE plant orders in 2020 were repeat customers. “I think the growing relationship we have with these repeat customers helps make each project a success, and that includes the screen media that we supply to them.”
Ballantine highlights how CDE has invested heavily in improving its testing capabilities, especially when dealing with specialist sand applications. “For those kinds of customers, we get a large volume of samples and test them on our screens in our dedicated test rig. You have all the theory and the calculations but being able to thoroughly test out a tailored plant set-up gives us peace of mind that the set-up will be fit for the task in the field. We want to be clear with our performance commitments to every project, and we want to be accountable for the solutions we provide, so it’s important that we get technical certainty around what we’re supplying.”
As well as being the year when CDE opened its new eye-catching, state-of-theart global HQ in Cookstown, 2019 also saw the company move into its first in-house manufacturing facility in Monkstown, County Antrim. “Prior to that, all our manufacturing was sub-contracted out. Moving forward, we envisage a shared approach between in-house and partner suppliers,” says Ballantine. “That brings greater flexibility in how we work while also speeding up product development and ensuring better quality control. It’s been a very positive development.”
Patterson adds: “The big thing for me is the collaboration that the new HQ and manufacturing facility has given us. The new
HQ building also gives us a great opportunity to invite our customers in and complete a technical design workshop where we can transform our customer’s vision or idea into a world-class solution that can be visualised on the same day.”
MAJOR says it has seen encouraging demand for three products launched at the CONEXPO/CON-AGG exhibition in Las Vegas, USA, in March 2020. The product trio is said to maximise the productivity and efficiency of MAJOR’s popular FLEX-MAT range.
The FLEX-MAT ID-Enabled system has been designed to track and store screenmedia data such as panel dimensions and customer-defined details to offer users information at their fingertips for simple reorders.
The FLEX-MAT Sensor is a valuable and easy-to-operate vibration data-measurement tool to review results and fine-tune screen machines without shutting down the equipment.
Meanwhile, MAJOR’s smartphone app gives customers up-to-date information and access to advanced digital tools. The MAJOR App is available for aggregates and mining producers, and MAJOR dealers, with customisations for each. It integrates with the latest MAJOR technologies, including
BELOW: MAJOR says its CONEXPO/CON-AGG 2020 launched FLEX-MAT Sensor has been well received by customers

the company’s FLEX-MAT ID-Enabled and the FLEX-MAT Sensor.
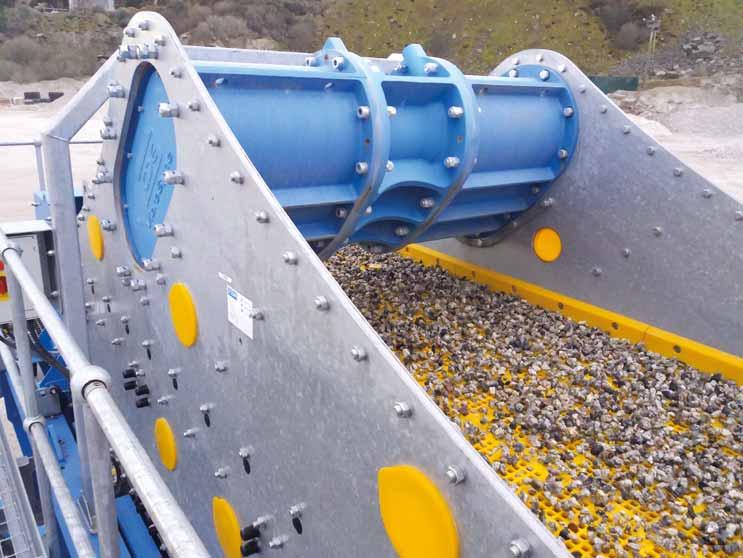
Lars Bräunling, MAJOR director of product technology, said: “2020 wasn’t the launch year we — or anyone — was expecting, but even so, the FLEX-MAT Sensor, MAJOR App and FLEXMAT ID-Enabled have all been well received with varying levels of feedback and utilisation.
“Our dealers say the FLEX-MAT Sensor — our screen box vibration data measurement tool — is an absolute game-changer. Almost every MAJOR dealer now owns the tool, which has made it easier to complete professional assessments and check-ups of customer equipment since it doesn’t require the screen box to shut down to be measured. It’s been eye-opening for quite a few of our customers, especially a couple of operations for whom dealers using the Sensor were able to prevent bearing failures by noticing discrepancies in vibration data and prompting further investigation. The regular use of the Sensor has allowed for tracking of machine development as well as more informed preventative maintenance. Moving forward, we’re continually looking at ways we can expand the information the Sensor collects as well as figure out new and innovative ways to use it as actionable data.
“The MAJOR App is rolled out and is being used by our dealers and customers not only to use the FLEX-MAT Sensor and ID-Enabled but as a resource for newsletters, product details and other MAJOR information. We are continuing to develop the app and its features.
“Our FLEX-MAT ID-Enabled Radio Frequency Identification (RFID) technology will be included on all new FLEX-MAT screens this year. The microchip tracks and stores screen media data such as panel dimensions and customer-defined details to offer users information at their fingertips. It’s a comfort feature available if our customers want to use it, and we expect more and more will realise the benefits of simplified screen media ordering and inventory management.” AB
The screening media on CDE’s Infinity branded screens is based on a longstanding partnership between CDE and TEMA Isenmann
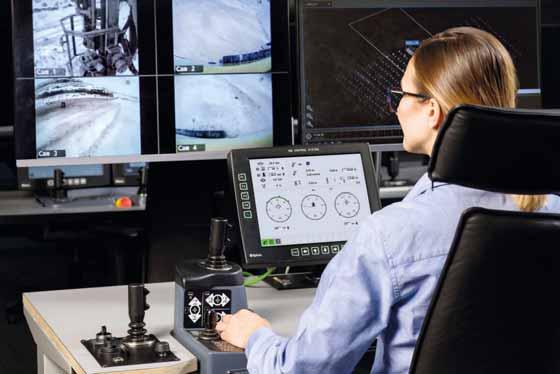
LEFT: Office TeleREMOTE consists of a suitable work desk with adjustable height and ergonomically designed operator controls mounted on it
BELOW: A major benefit of automated drilling is that the operator can run the rig without taking any risks thanks to multiple on-board systems.
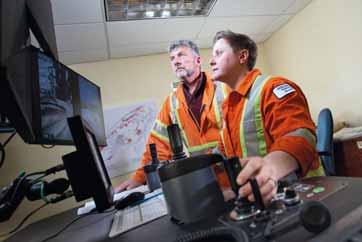
Automated systems changing the face of surface drill & blast
Some of the leading manufacturers of surface drilling rigs have in recent years invested in and developed automated drilling systems to drill more rapidly, and effectively, whilst at the same time improving operational safety. These developments are highly significant in quarries and surface mines, as automated drilling can deliver significant performance improvements to the drill and blast excavation process. Here, Roger Murrow looks at some of the developments and how they are revolutionising global mineral excavations
Increasingly, the challenge for quarries, surface mines and aggregate excavations is gaining access to the rock to produce materials as quickly, accurately and cost-effectively as possible. It is essential that returns are maximised and the reserve deposits are utilised as efficiently as possible. Through automating the drill and blast process, companies are able to significantly reduce costs by improving performance and increasing consistency while simultaneously enhancing rig (and therefore operator) safety. Autonomous drilling technology thus enables operations to be more efficient, achieving the goals of operational cost reduction, improved productivity and zero harm. Developed systems are customerconfigurable, enabling the drill rig’s surface equipment to be controlled in response to data which is prioritised and distributed to appropriate applications as it enters the rig control system.
Automation and remote working enable drillers to remove people from the blasting
and drilling locale, maximising operational safety as well as protecting operators from sound and airborne emissions. Furthermore, efficiency and productivity are enhanced as there is no need to stop drilling for breaks and shift changes. Without having operators on board, the drilling solution can operate through shift changes, lunch breaks and some blasts which increases drill rig utilisation providing greater consistency and accuracy over a long shift.
Operational benefits
By using digital drill plans and navigation, manual drill-hole marking is eliminated which results in improved accuracy and time savings, with the data collected during drilling being used to monitor system behaviour in various rock conditions and to evaluate plan execution. In the long term, autonomous drilling also delivers reduced downtime and increased rig availability due to less damage to the drill and the tooling used. The automated software ensures that the rig is used within its designed operating
parameters which minimises stresses on equipment, with reduced wear and tear on equipment through automated functionality resulting in lower maintenance costs.
As autonomous drill rigs work within the standards established by the manufacturer, longer consumable life is ensured whilst at the same time delivering less unplanned maintenance. As a result, operations can progress more rapidly and improve fragmentation when coupled with an effective blasting programme, delivering lower component costs from reduced machine maintenance repairs.
The benefits translate across the entire mineral excavation value chain with the enhanced blasting and improved fragmentation from autonomous drilling causing less damage on load and haul equipment, which saves maintenance costs for the entire operations fleet. There are also benefits for operations using crushers due to the better fragmentation, a faster feed of the crusher and less energy required to process the material. This latter point highlights that autonomous drilling
also has a positive environmental impact through ensuring that the equipment is consistently operated within specifications, resulting in the amount of energy and fuel burned being reduced, producing a more efficient drilling operation.
Operational benefits often extend to the workforce, as a single worker can operate multiple drill rigs, providing better organisational utilisation of skilled operators. Autonomous drilling reduces the operator to machine contact, making operations safer, with staff (and their expertise) being used more in maintenance of the technical and mechanical systems, solution monitoring and change and process management.
Appropriate system
Generally, drilling automation and the use of drilling IT systems are ideal for almost all quarrying and aggregate-excavation processes that rely on drill and blast in some form. Different levels of autonomy and integration can be achieved depending on requirements, type of application and the IT strategy of the company. However, some operations face many challenges when attempting to progress towards full drilling-fleet automation. One of the biggest is the operation’s readiness for autonomous because this isn’t a feature that comes with a ‘flip of a switch’. Change management processes must be considered and implemented to assist in transitioning
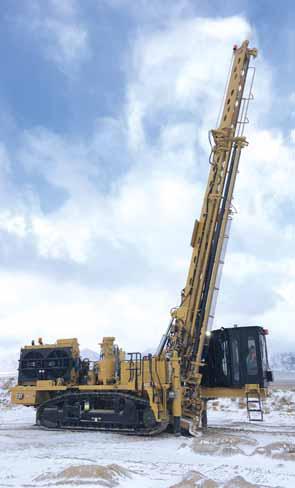
an operation from a manual operation to a fully autonomous operation, with the most important information being that which the drill rig collects about the holes drilled.
In effect, a challenging factor for adopting automated drilling is the ability to manage change. The resulting process changes, with the additional layers of safety that come through the use of automated technology, necessitate a cultural transition with the operator working outside the cab rather than inside, which requires additional personnel training as well as a cultural shift. This means that when it comes to choosing the right automated drilling system, it is important to choose the system that best suits the requirements of the organisation itself. Fortunately, there are now many systems available designed to cater to the requirements of companies large and small, with some of the latest developments set to further aid automated drill and blast.
Caterpillar
Cat has placed increasing emphasis on developing systems for delivering accurate drilling and blasting to ensure a safer and more productive work environment, whilst aiming to reduce even minor deviations from the drilling pattern for more efficient and productive drilling. The company states that with higher precision and more accurate depth tracking, autonomous drills can work far more accurately to plan. That means more accurate blasting and less time

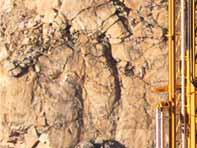

spent removing overburden, resulting in higher productivity.
The newest generation of Cat drills offers all of the benefits of autonomy, starting with the release of the MD6250 and now continued with the MD6200. These come with a number of standard automated functions that help an operator drill more accurately, with simple controls and touchscreen monitors that allow for easy operation. With the addition of Cat Command for drilling, the drill rigs are capable of drilling in autonomous mode with the operator seated at a remote station designed to mimic the drill’s cab. From here, the operator is able to control up to three drills at the same time, programming them to drill single rows autonomously.
Cat Command for drilling ensures that every hole is accurately placed, drilled to the proper depth and angle, and able to stand up until blasting, with a range of capabilities that enables the operator to configure and automate the drilling system based on budget and needs. Semi-autonomous single row drilling automates the entire drilling cycle for one row, including autonomous tramming. Autonomous pattern drilling automates drill cycles and tramming for the entire blast pattern and allows one operator to manage drill operations across the site from a remote operator station.
Epiroc
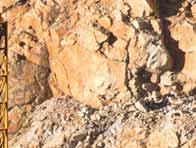
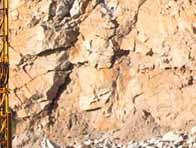
Epiroc’s recently launched TeleREMOTE system is designed to control its SmartROC DTH drill rigs, MK I (based on RCS 4 platform) from a remote location. It enables the operator to access and run multiple rigs from a control centre located away from the blasting area by connecting it to a WLAN network. One of the biggest benefits of the system is its ability to effectively increase the number of productive hours in a day, reducing operator transports and idle time due to shift changes. Remote drilling, together with Epiroc’s AutoDrill and AutoRod Handling System features, boosts productivity as the drill rigs can work almost
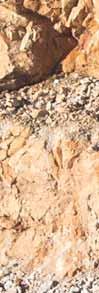
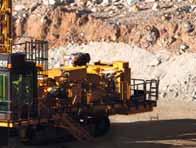

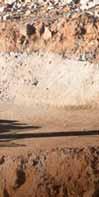
The Cat MD6200 drill comes standard with Drill Assist and is shipped Cat Terrain ready for easy technology installation
Automation allows drilling to be completed without endangering the rig operator
Complemented with the TIM3D drill navigation system and automatic feed alignment option, the Ranger DXi series rigs can perform autonomous movements and position automatically
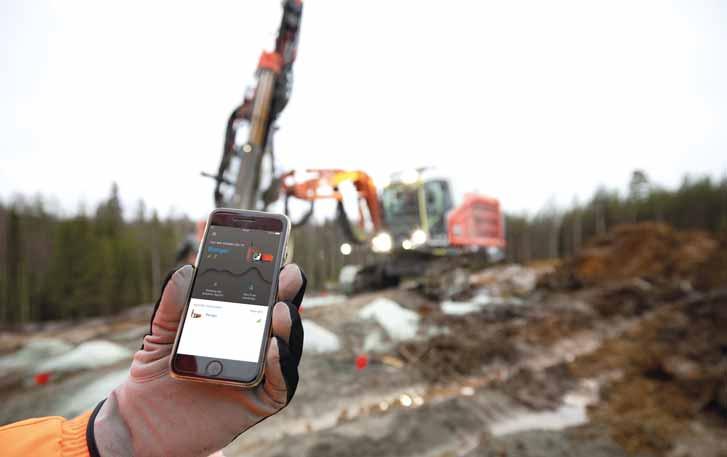
continuously without breaks. The safety aspect is also a major benefit as the operator can run the rig remotely due to its on-board systems.
The operator uses the Hole Navigation System for accurate positioning and a geofence function ensures that the rig stays within the predefined area. The remote rigs are also fitted with multiple cameras which provide the operator with a 360° view all around the machine. Office TeleREMOTE also includes a server rack with Automation Common Machine Server (ACMS), a video system and a safety system capable of handling one remote drill rig, with an option to be extended up to nine drill rigs, in increments of one, if required. Features such as automatic levelling and drill-stop protection are also integrated to maintain precision and safety.
Connectivity and automation have been developed by Epiroc to increase equipment productivity as well as deliver operator benefits through the integration of smart connected machines, programmed to complete a precise drilling sequence. Machine sensors alert the control room if there is an obstacle or the intervention of an operator is required. Without the normal constraints of staff schedules, this allows for extended machine uptime, reducing the wear and tear associated with a manual operation.
Komatsu
Komatsu’s drill automation technology is made up of several key building blocks: an automation controller; situational awareness technologies (cameras, LiDAR and radar); and a GPS receiver. Algorithms convert the
information from the hardware to identify the machine state and execute the appropriate autonomous task. The company offers several levels of drill automation, with the most basic being passive automation which provides on-board blast-hole pattern mapping, additional camera views and uses LiDAR and radar to notify the operator of objects around the drill.
The operator-assist level of automation is effectively an autopilot function. The system executes drilling, levelling and tramming tasks, while the on-board operator manages any exceptions that may occur. The full autonomous level removes the operator from the machine and from most machine operations, only stepping in to remotely manage exceptions. Furthermore, the same information required to autonomously operate a drill can also be leveraged to identify strata to better optimise hole loading and pattern design.
Sandvik
In efforts to continuously improve and automatise its drilling equipment, Sandvik has developed what it terms as ‘full-cycle one-hole drilling automatics’. This enables the drilling of one hole automatically to a specified
Sandivik’s latest app further improves the connectivity of surface drill rigs by allowing mobile devices to be used for data transfer
depth without having to manually interfere in the process. After positioning the feed to the desired hole location and inclination, the operator can select automatic drilling simply by pressing a button on top of the drilling joystick. The rig will drill and add rods/pipes automatically until the selected hole depth is reached.
Automatic drilling ensures continuous high productivity, with less room for human error in the process, with the operator being able to perform other tasks or have a short break when using automatic drilling. Complemented with Sandvik’s TIM3D drill navigation system and automatic feed alignment option, this enables Ranger DXi series rigs to perform autonomous movements for the superstructure and position automatically with only a push of another button. Fullcycle automatic drilling options are available for Sandvik’s Pantera DPi and Ranger DXi series of top hammer drills rigs as well as the Leopard DI650i down-the-hole rig.
Further boosting Sandvik’s offering in automation is its free app, SanRemo Mobile, which makes it easier to connect to a drill rig for transferring drill plans, reports and other fleet management and drilling data in a timely and cost-effective manner. SanRemo Mobile further improves the connectivity of surface drill rigs by allowing mobile devices to be used for data transfer. This eliminates the dependence on USB drives or network coverage at worksites. Reports and MWD (measurement while drilling) data from the Sandvik TIM3D drill navigation system can be uploaded via the SanRemo Mobile app for sharing or storing. The data can be examined using, for example, Sandvik Driller’s Office or other compatible design software. Additionally, production reports from the drill rig are automatically uploaded into the My Sandvik fleet management portal. AB
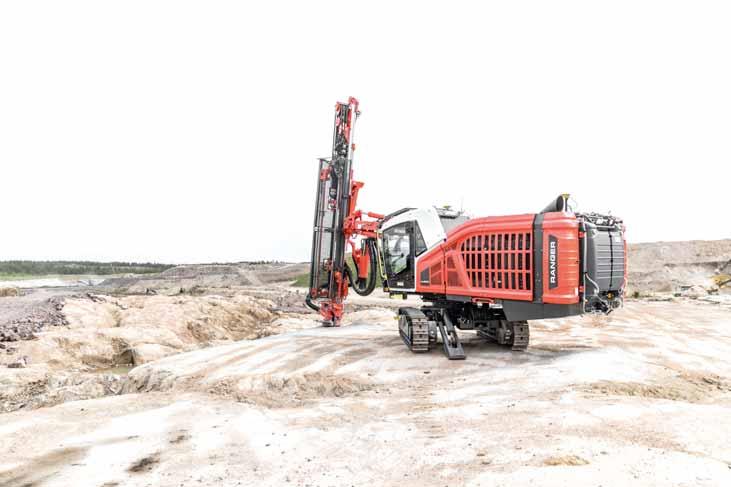
PORTUGUESE QUARRY OPTS FOR RAMMER R45P HAMMER
A quarry in Portugal has recently invested in a new R45P Performance Line hammer. The Rammer is used to break granite before it is crushed and screened into construction aggregate and decorative stone products. The R45P was chosen due to its high productivity, reliability, and durability, all based around features synonymous with the renowned Rammer name.
Portuguese quarrying and aggregates company Britafiel S.A. (Britafiel) is based in Penafiel, a city located in the hills of the north of the country, some 35km from the Atlantic coast. Established in 2006, the company’s quarrying business is focused on the production of aggregates, ornamental blocks and decorative stone products extracted from the granite mineral deposits found in the region. Based around the Pedreira de Vilar and located in Duas Igrejas parish, the granite deposits found in Penafiel have a reputation for being of excellent quality, ideal for the construction and decorative stone products industries.
Using the local mineral deposits to their full potential, it is Britafiel’s intention to be recognised in Portugal and internationally as a major supplier of high-quality aggregates and ornamental decorative stone products. To this end, the company now supplies (following extracting and processing) a wide range of aggregates, sand and gravel, railway ballast and other construction industry products. Also, the

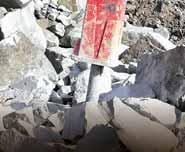

supplies yellow and blue granite blocks and decorative stone for landscaping, including its own granite-based products using ‘STOCONatural Creative Granite Technology’.
To maximise the opportunities provided by the granite deposits found at the quarry and to satisfy ever-growing customer requirements, Britafiel has invested heavily in modern equipment solutions. “All production
equipment must be able to deliver high levels of productivity, even in the most demanding situations, with proven reliability and durability, technologically modern and adapted to the highest quality standards and the requirements of current European legislation,” explained Britafiel’s general manager, Eng. Francisco Guimarães. “Britafiel has the most modern crushing equipment, enabling products with high-quality indexes to be obtained, which is one of the areas with major importance in this type of industry and fundamental to the success of any organisation.”
Before crushing and screening, however, much work has to be done to extract the granite. Hence Britafiel underwent an intensive process in acquiring a new hydraulic excavatormounted hammer. This led to the company choosing a Rammer Performance Line R45P hammer with RD3. “We have used other hammer brands, which were also competing for the supply of a new unit, but we chose the Rammer R45P due to Rammer’s reputation in quarrying and its RD3 monitoring system,” explained Guimarães. “Because of this system, the customer can see online information about the hammer, such as location, working hours, maintenance intervals, and periods of use.” Francisco further noted that working from his office, he can view the performance of the R45P hammer operating on one of the quarry benches without having to leave his office.

quarry
The Rammer R45P hammer was chosen by Britafiel for its high productivity, reliability, and durability
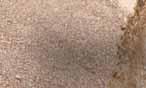
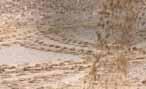
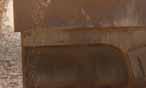
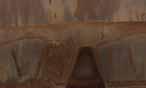
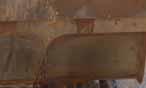
Germany ready to go through growth gears


After robust trading in COVID-19-hit 2020, Germany’s construction and aggregates sectors are primed for growth in 2021 and beyond. Guy Woodford reports
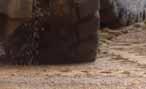
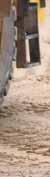
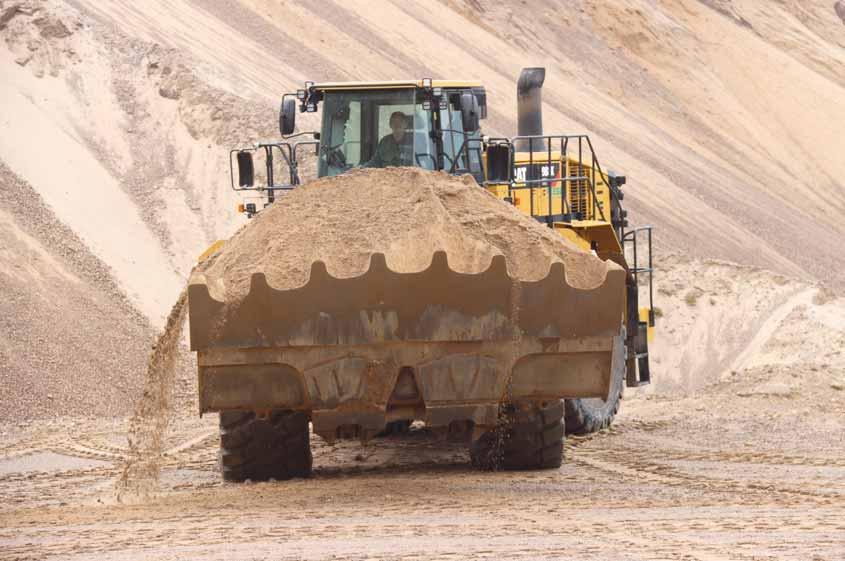
MIRO, Germany’s aggregates federation, states that the construction industry once again proved to be a pillar of the overall German economy in 2020, “excellently” standing up to the myriad challenges associated with COVID-19pandemic disruption.
As the association highlights, Germany’s Federal Statistical Office reported that construction sector companies increased their combined revenues by 6.6% in 2020.
Walter Nelles, vice general secretary of MIRO, said: “Of course, the aggregates industry in Germany also benefited from this situation. Thanks to a strong fourth quarter, while production was predicted to increase by almost 2% in full-year 2020, initial estimates assume an increase in sales of 4%-5%.
“While the prospects for 2021 do not suggest a collapse in construction sector demand, the coronavirus situation and declines in investment mean that no major leaps are expected. Differentiated according to the economic sectors, the order books in the building construction sector seem to be full, while commercial construction suggests a slight decline. This development will also have an impact on the rock industry. Should the decline in public demand for road construction intensify, a slight decrease in total aggregates production is to be expected at the end of the year, with sales remaining the same.”
Discussions around improving the utilisation of recycled German construction waste have intensified, notes Nelles. Although almost all national construction
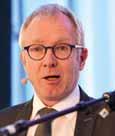
“The
German construction industry and others still need large quantities of primary raw materials such as gravel, sand and natural stone”
Walter Nelles
waste is recycled and reused, the amount of aggregate available from it is limited. “This share has so far only made up 12.5% of the total aggregate demand in Germany,” explains Nelles. “The German construction industry and others still need large quantities of primary raw materials such as gravel, sand and natural stone.”
MIRO president Dr. Gerd Hagenguth explained at the beginning of 2021 that the construction value chain begins with the stone products – gravel, sand, and natural stone. As a result, care must be taken to ensure that the extraction of mineral raw
materials in Germany is not hindered any further and that planning and approval procedures do not remain obstacles. MIRO also states that the backlog of applications for crushed rock, sand and gravel extraction permits that have piled up for years must now be addressed.
In 2021, Germany’s construction industry continues to need, among other things, large quantities of aggregates for a wide variety of major and small- to medium-sized building works. Crucial to this, notes MIRO, is the smooth supply of primary raw materials: gravel/sand and crushed rock - of which 259 million tonnes and 217 million tonnes, respectively, were produced in 2019.
MIRO stresses that import and export quantities must also be considered when analysing German aggregates market buoyancy. In 2019, imports of gravel/sand amounted to around 3.9 million tonnes, and around 6.5 million tonnes of natural stone were also imported. Exports of gravel/sand were around 12.5 million tonnes, with a further 6.5 million tonnes of crushed rock exported.
MIRO notes that in addition to the primary raw materials, there are not inconsiderable amounts of secondary raw materials every year (recycling building materials and industrial by-products), which, taken together, are vital to quantifying German aggregates demand.
The Construction Circular Economic Initiative’s monitoring reports, based on the database of official statistics and enjoying a very high level of acceptance by all stakeholders, show that material cycles were almost completely closed for 2018, the last
A Cat 988K XE large wheeled loader working at a quarry in Germany
survey year. The accumulation of mineral waste from the construction sector and road excavation fractions totalled 74.7 million tonnes in 2018. From this, 59.7 million tonnes of recycled building materials were produced. This corresponds to a recycling rate of almost 80%.
Additionally, a further 13.3 million tonnes of recycled aggregates were generated from processing soil and stones, while another 300,000 tonnes of recycled aggregates came from processing construction site waste. This means a total of 73.3 million tonnes of recycled building materials was produced in Germany in 2018 – equating to a 12.5% share of all national aggregates production that year.
Of the 73.3 million tonnes of recycled building materials made in Germany in 2018, 37.6 million tonnes (51.3%) were used in road construction, 16.3 million tonnes (22.2%) in earthworks and 3.6 million tonnes (4.9%) were utilised in other applications, predominantly in landfill construction. The remaining 15.8 million tonnes (21.6%) were used as aggregates in asphalt and concrete production.
A new report by GlobalData, a leading international business market intelligence consultancy, supports MIRO’s upbeat German market take, stating that the country’s construction industry fared relatively well compared to its peers in Western Europe during COVID-19-hit 2020.
Although the industry’s value-add in real terms contracted by 2.6% year on year (YoY) in Q3 2020, it was preceded by a YoY growth of 2.7% in Q2 and 7% in Q1 2020; this helped the industry to register a cumulative growth
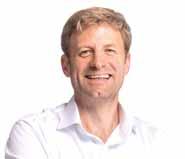
“The demand for aggregates in Germany is trending upwards” Staale Hansen
of 2% YoY during the first nine months of 2020.
Published in February 2021, GlobalData: Construction in Germany – Key Trends and Opportunities to 2025 also notes that German construction activities held up relatively well in the first three quarters of 2020, as the construction sector was exempted from lockdown restrictions imposed that year.
Although the residential sector registered growth during this period, the commercial sector witnessed lower levels of activity. In 2021, the construction industry’s output growth is expected to pick up, driven by the government’s focus on the development of the country’s transport and energy infrastructure.
GlobalData expects the German construction industry to grow by 2.8% in 2021 and rise at a rate of 2.3% between 2022 and 2025. Growth in the industry will, says GlobalData, be supported by the government’s focus on improving regional connectivity by developing the country’s rail and road transport infrastructure, coupled with efforts to boost energy production. The construction of the Fehmarn Belt underwater tunnel between Germany and Denmark, which is worth €7 billion, will underpin activity in the medium term’s transport infrastructure sector. Growth will also be supported by the 10-year plan to invest €86bn in the maintenance and modernisation of the country’s rail network between 2020 and 2030.
Metso Outotec recently stressed the importance of the German aggregates production unit market. Speaking at the 17 March 2021 launch of Nordtrack Liveroom, Metso Outotec’s 360° digital event experience platform, and the unveiling of the new Nordtrack S2.5 mobile screen and the Nordtrack I908 mobile impact crusher, Adrian Wood, Metso Outotec head of Aggregates Equipment Distribution, said: “Germany is a market that is a perfect fit with the Nordtrack range, and its rental business has boomed during the coronavirus pandemic.”
U.S. giant Caterpillar and Zeppelin Baumaschinen, the company’s dealer in Germany, have a long and successful trading history in the German off-highway equipment sector.
“The demand for aggregates in Germany is trending upwards,” says Staale Hansen, manager for Large Machines, Paving and System Solutions at Zeppelin Baumaschinen (Zeppelin). “With state-of-the-art technology, German customers appreciate the choice and reliability of the Cat equipment. The key drivers are the lower costs per tonne of the equipment and the support we offer to keep the machines working longer through preventive maintenance.”
Hansen thinks ecological trends, like the

Cat’s new 395 large excavator

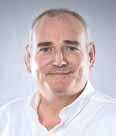
“Over the last few years, we’ve also seen a slow recovery of gravel pits and quarries throughout Germany”
Guy Wilson
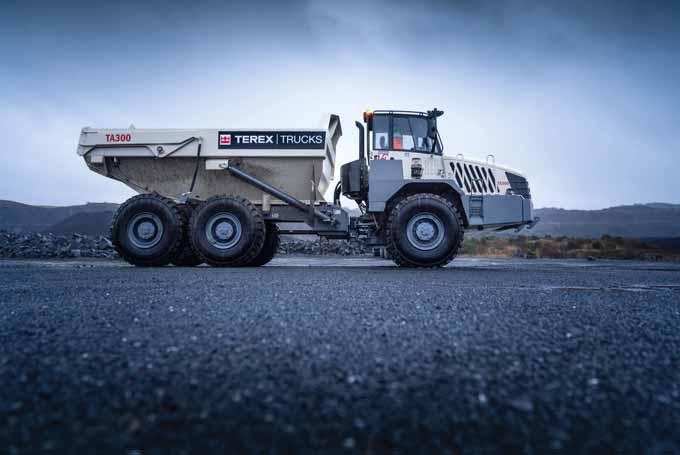
German CO2 tax and the subsidy programme, are great opportunities and offer technology solutions for significant fuel & CO2 savings through the 988K XE large wheeled loader with electric drive transmission. Hansen says the Cat Certified Rebuild programme, which returns an end-of-life machine or component to a like-new condition, also offers a lot of benefits for customers and the environment.
“The trend towards outsourcing includes maintenance and repair work. We are experiencing a growing interest from our customers for service contracts which Zeppelin has been offering for years. Fullservice contracts for prime production equipment are also popular because they offer peace of mind and maximum machine uptime.”
Hansen says that popular quarrying models in Germany include the Cat 775G off-highway truck and the Cat 988K XE large wheeled loader. “Customers like low fuel consumption and high efficiency. The 988K XE offers up to 25% better fuel efficiency than
models with a conventional powertrain,” he explains.
Hansen continues: “There has been an interest in autonomous solutions in the construction industry for some time. Caterpillar has decades of experience with autonomous solutions in the mining business.
“Customers have experienced improved safety, better efficiency, greater productivity, and lower costs. Now, Cat Command is making its way into the construction industry. Cat Command solution is structured as a series of building blocks leading to semiautonomous operation. The solution is scalable and incremental, allowing customers
to enter at whatever level of technology and infrastructure they choose, ranging from lineof-sight (LOS) to non-line-of-sight (NLOS) remote control solutions as well as semiautonomous solutions.
“Currently, we offer Cat Command for loading with the 988K large wheel loader with a line-of-sight console and Cat Command for dozing with line-of-sight console or operation from a remote station.”
Hansen also notes that German construction and quarrying companies are keen to reduce their CO2 footprint while also striving to instil higher efficiency in their operations.
Terex Trucks has a strong presence in the German off-highway articulated dump trump (ADT) market.
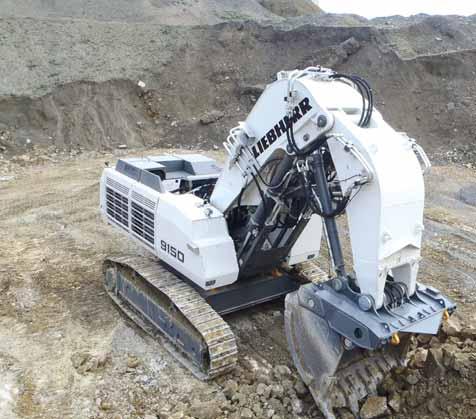
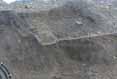
Speaking to Aggregates Business Europe about market demand, Guy Wilson, the Motherwell, Scotland-headquartered company’s global sales director, says: “In 2019, a total of 259 articulated haulers were sold in Germany (from 25- to 60-tonnecapacity ADTs). Due to the pandemic, truck sales dropped to 142 last year. We expect the demand to pick up in 2021, but it’s difficult to predict what the rest of the year will look like exactly.
“We’re seeing opportunities in the German market, even though so far, the government hasn’t committed to any big infrastructure projects to kick-start the economy. This is in contrast to the U.S. and the UK, where the High Speed 2 (HS2) railway project will be one of the most important economic regeneration projects in Britain for the next few years.
“That being said, there are lots of homebuilding projects in northern and central Germany, which is one of the main areas for land development since living space is scarce in many other areas in the country. Deutsche Bahn will also invest several billion euros over the next few years, and an expansion to the existing rail network could drive demand for haulers in the German market.
“Over the last few years, we’ve also seen a slow recovery of gravel pits and quarries throughout Germany. Many quarries in the south had to close down or reduced their production levels to a minimum three to four years ago, but we’re now seeing that demand is slowly increasing again. This could be another good sign for articulated hauler demand in Germany.”
Terex Trucks’ TA300 represents over 80% of the Terex Trucks dump trucks in the German market
A Liebherr R 9150 excavator working at a Schiewe quarry in Ostwestfalen-Lippe, North Rhine-Westphalia
Wilson says that in Germany, machine rental is dominating and accounts for around 70% of the articulated hauler market. Given the pandemic, he believes this trend could further increase, especially if companies remain wary of making big investments in new machinery amid challenging times.
“Very often, contractors simply find it easier to rent haulers for a project in a certain area, and after completion, they move on to their next job in a different region within Germany and rent new equipment.
“This means rented construction machinery needs to be especially durable, which is what our Terex Trucks haulers are renowned for. Our robust and reliable dump trucks are built to excel in the toughest conditions and ensure maximum uptime for customers.”
Wilson highlights that Terex Trucks’ TA300 makes up over 80% of the Terex Trucks dump trucks in the German market. Bringing the 28-tonne TA300 to a new jobsite is easy as the hauler can be transported on German roads without a special permit.
“We’ve recently launched our new Stage V TA300, and TA400 articulated haulers, which means customers in Germany can benefit from a reduction of up to 7% in fuel consumption when compared to the Stage IV engine. The haulers now also deliver an even stronger engine performance and excellent responsive power in all conditions. Equipped with a Variable Geometry Turbo (VGT), the
new Stage V engine allows faster response at all engine speeds and an efficient combustion performance. All of this helps improve operators’ efficiency while keeping the total cost of ownership low.”
German construction, quarrying and mining equipment manufacturer Liebherr is one of the biggest equipment makers globally, with Germany, naturally, a huge market within its European business.
“The German equipment market is a very special one,” says Otmar Wehrle, sales director, Liebherr-Mining Equipment. “An average high-cost level paired with high environmental awareness has led to the abandonment of the big coal mines. The huge bucket wheeled excavators are almost all mothballed, replaced by smaller and more agile 100-tonne class hydraulic excavators.”
Wehrle says that limestone is the biggest quarried material in Germany, with some sites major suppliers of mineral products to the national concrete sector. “Average operation working hours are seldom more than 1,200 hours per year, while in other parts of the world it is rather 6,000 hours per year,” he explains.
“Due to the high hourly cost for personnel in Germany, [quarrying and mining] production must be done in the shortest time possible.
“Machinery and blasting noise and vibration can also become big concerns, giving the customer no other choice than
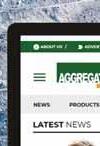

quitting or investing in specialist equipment with noise kit and direct digging capacities. Then bigger machines come into play.”
Focusing on current popular Liebherr models for German quarrying and mining customers, Wehrle says: “The R 9100 and R 9150 excavators are the mining machines for Germany, with their in-face shovel and often with à la carte buckets.
“These machines are the answer to the high-level requests of the German customers when it comes to safety, production and availability. These machines do not yet have the size of the typical mining machines with 250+ tonnes of mass.
“The latest addition is the R 9150 with electric drive, providing the ultimate answer to a high environmental consciousness coupled with extremely low OPEX [operating expense].”
The robustness of German building material and material processing equipment demand during the coronavirus pandemic and the continuing German government commitment to major infrastructure spending are also encouraging signs ahead of the 4-10 April 2022 staging of the bauma, Munich exhibition, the world’s biggest construction, quarrying and mining equipment trade fair.
‘What does the future hold for the construction machinery industry?’ is a key theme of the event. In Germany’s case, at least, the industry’s future will be built on firm foundations. AB
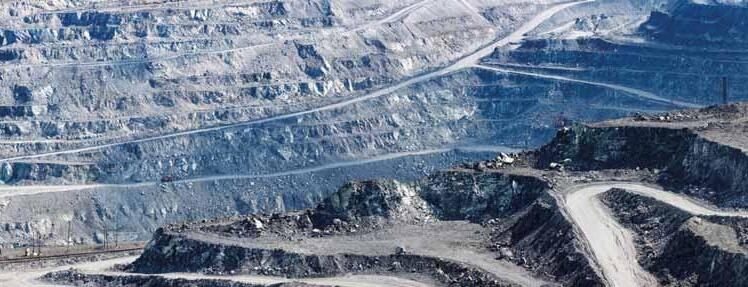
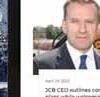
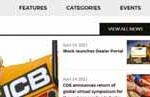
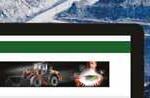
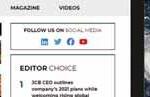


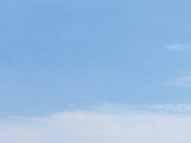
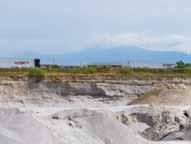

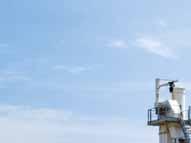
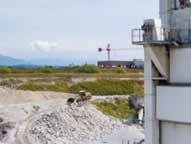
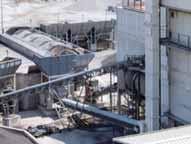


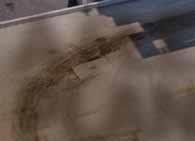
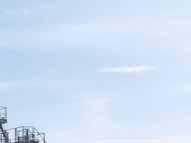
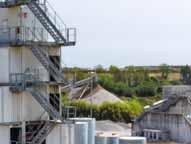
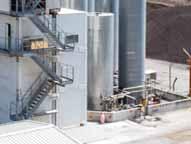
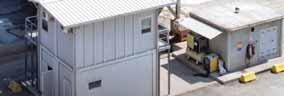
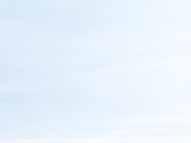
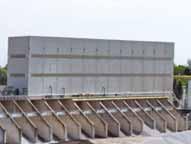
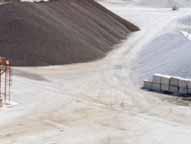
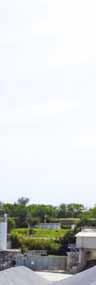
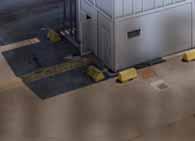
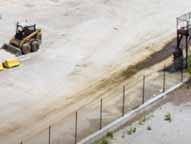
A FLEXIBLE PLANT FRIEND
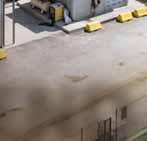
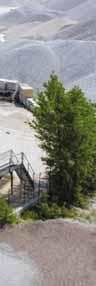

To supply large amounts of materials for the Italian construction industry’s ever-growing and diverse requirements, one company located in the north of the country has arrived at a solution that aims to be as flexible and productive as possible. The need for this solution lies in the Italian construction market’s intricacies, which require a great variety of products to exacting specifications. As Roger Murrow reports, Vezzola believes it has arrived at a system that delivers a flexible response, combining high production volumes with a wide range of products
Vezzola, a family-owned and -operated company, was formed in Desenzano del Garda (Lake Garda) at the end of the 1950s and is still headquartered there. The company began extracting and supplying sand and gravel to local construction companies, subsequently expanding its offering with cement and bituminous conglomerates and earthmoving works. The company operates a vertically integrated business model capable of serving ever-changing and growing customer requirements, including using waste construction material to help make a bituminous and cementitious conglomerate. The company headquarters is just one hour away from Milan and Venice, benefitting from the region’s extensive and efficient
infrastructure system. The central location provides a strategic hub that can serve the complex and diverse northern Italian infrastructure requirements.
Customer-focused supply chain
Vezzola’s production cycle starts with the excavation of material at its quarries or from other quarries, or procured from suppliers, depending on customers’ specific requirements. The company operates three large quarries and sand pits located at Montichiari, Lonato and Manerba, taking advantage of the large mineral deposits in the immediate vicinity, employing 90 people who are purpose-trained at Vezzola’s training facility. Annual production is 1,200,000 tonnes of natural and recycled aggregate in the region, 400,000 tonnes of asphalt and 250,000m³ of concrete.
Fourteen classes of aggregates are produced at the most modern plant in Montichiari. The facility also makes diverse and non-standard concrete and asphalt mixes that are first tested at the company laboratory and then sampled by specialised external laboratories. One such project involves using excavated tunnel material to remove impurities for use as aggregates for producing concrete and asphalt. If not used as construction aggregate, the quarried material is processed at cement, concrete and asphalt plant operations located at Montichiari, Lonato and Manerba.
Adding to its supply of materials, since the 1990s the company has embraced the circular economy (and adopted Italian and EU environmental legislation and specifications), producing an increasing quantity of material recycled from construction works. These
The Montichiari (Brescia) operation is a new high-performance quarry plant that is designed to produce large quantities of high-quality sized aggregate
are processed at Vezzola’s plants located at Montichiari and Lonato, with the material coming from both its construction works and third parties. All Vezzola production plants operate according to a ‘Factory Production Control’ (FPC) in compliance with the Italian Central Technical Service of the Higher Council of Public Works procedures.
In effect, this all means that Vezzola provides, through its multifaceted operations and locations, various services that can cover the entire production chain, from the extraction and processing of natural aggregate to research and development for using recycled materials. Materials are used for producing cement and bituminous conglomerates for use on road and civil construction projects, including airports, viaducts, roads and tunnels.
Flexibility is key
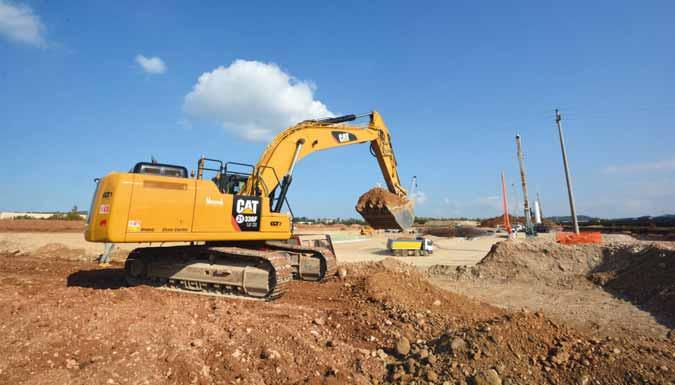
With quarries and plants to operate and diverse customer requirements to satisfy, Vezzola has developed a plant solution that maximises its operations’ efficiency. Thus, all recent plant investment has been for highly mobile solutions. One such operation in Montichiari (Brescia) is a new highperformance quarry designed to produce large quantities of high-quality, sized aggregate whilst emphasising environment and safety. Although the plant is of a considerable size, it has a minimal impact on the surrounding environment as it is wholly contained in the extractive basin. The contour area and escarpment of the basin have been planted and restored, while noise and dust are contained through sophisticated control, suction and humidification systems. The quarry produces sized aggregates, round concrete materials and crushed products for bituminous conglomerates, which are stored and separated into 13 different classes.
The preparation of specific material is undertaken using an automated loading system, managed by PLC (programmable logic controller), which ensures maximum precision and reliability in preparing the mixes and, therefore, the finished product. In addition to the plant’s standard production, Vezzola is also able to provide customised concrete and asphalt mixtures on request, automatically managing up to five hundred different mixtures. The plant can operate up to 400 tonnes per hour, with equipment from Vezzola’s versatile and mobile fleet used if and when required.
New ways of thinking
Vezzola believes that a successful company must be a partner to its customers and form a close relationship with its suppliers. This has proved to be essential as all its operations rely on various crushing, screening, loading, hauling and excavation equipment from one company. “One of Vezzola’s most important operational partners is CGT, a Caterpillar and Sandvik dealer. Caterpillar earthmoving machinery is used to carry out infrastructure works and undertake loading and uploading operations at the company’s operations.
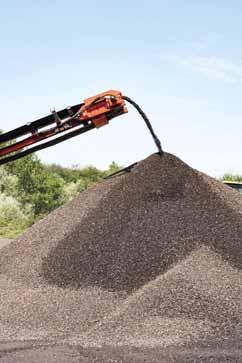
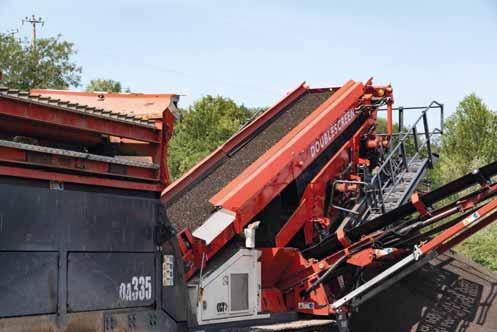
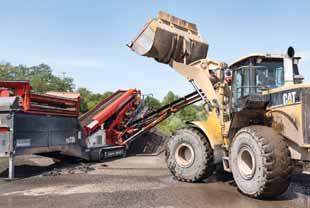
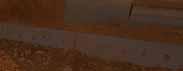

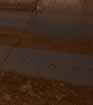
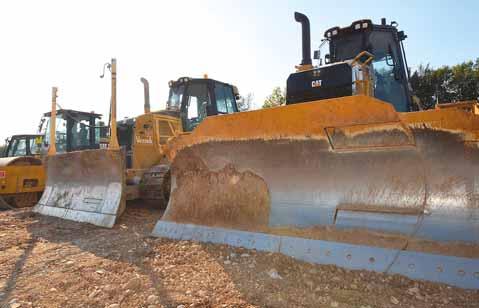
1: A CAT 336 F excavator working at one of Vezzola’s sites
2: Sandvik’s Doublescreen is said by Vezzola to deliver 30% more productivity than screeners of a similar size
3: The QA335 screen produces impressive material stockpiles
4: A CAT wheeled loader feeds the Sandvik screen 5: Some of the CGT-supplied CAT equipment used at quarries and production sites


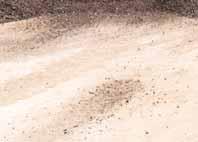
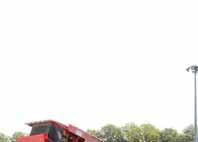

A broad and transparent dialogue has been cultivated over the decades of partnerships between the companies, which are essential for correctly planning the turnover of machinery and always maintaining high efficiency of the machinery,” says Diego Brunello, Vezzola’s production manager.
“In recent years, also thanks to the important stimulus programme of the Italian government for the development of automation systems called ‘Industry 4.0’, the interconnection between earthmoving machinery and the company’s headquarters has increased significantly. These investments have increased onsite machine use safety, scheduled maintenance interventions, the control of the machines’ efficiency, and materials handling data usage. Clients increasingly request the latter to improve the quality of the infrastructural works carried out.
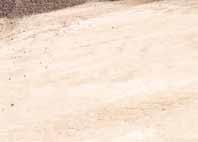

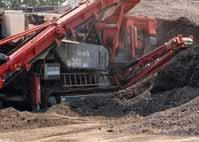
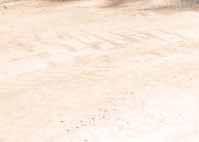

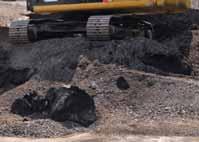
Located throughout northern Italy, Vezzola’s quarry operations consist of sandstone, limestone, sand, and gravel pits. The classes of sand and gravels produced are: 0-2, 0-4, 0-10, 0-20, 0-16, 2-4, 2-8, 4-10, 4-20, 6-14, 10-20, 14-32, 20-80mm. Vezzola’s two main locations’ annual production consists of approximately 1,200,000 tonnes of sand and gravel, 400,000 tonnes of asphalt and 250,000m³ of concrete.

“In partnership with Sandvik, it was decided to renovate part of the mobile systems as the flexibility that the systems could offer was fundamental. The business unit focused on producing building materials processes, not only limestone material but also recycled material. Decades of research and development have led the company (Vezzola) to produce on a large scale these materials from demolition works, milling of road pavements and recovery of steel waste. Large quantities of significantly different products are processed within the waste treatment platforms of Lonato del Garda and Montichiari,” added Brunello. He continued: “It was, therefore, necessary to find extremely flexible mobile systems, which could be easily transported from one plant to another and whose layout could quickly change from one to the other avoiding high costs of maintenance. A change of mentality was made, passing from fixed plants that process the various products to mobile plants transported to the various plants and process the materials directly. This change of mentality leads to lower CO2 consumption since the materials are not moved from one plant to another, but it is the plant that moves.”
Reliability, performance and the environment
Sandvik mobile screen and crusher are used to process very different inert materials. “Sandvik is the most reliable partner that best embodies these three characteristics. Sandvik is close to the customer thanks to a
widespread sales network entrusted to CGT (in Italy). This advantage is irreplaceable as the answers are fast and certain. Reliability as the service is impeccable; maintenance is fast and accurate. Finally, the research that has been done on reduced emissions have made it possible to have machinery with a low environmental impact. In the last two years, the focus on innovation has shifted from product innovation to environmental innovation. We believe that the reliability of a company is also measured in the knowledge accumulated after years of research and development and which will become a new income in subsequent years. The search for the right partner is a very important, indispensable effort, especially in a world where uncertainty reigns supreme. The resilience of companies is today more than ever the minimum requirement to maintain one’s leadership,” explained Brunello.
Maximised plant efficiency
To ensure that its quarries, cement-concrete and asphalt plants operate efficiently (as well as its construction operations), many Caterpillar earthmoving vehicles and trucks
are used, including some of Cat’s latest ‘Next Gen’ developments. Alongside these, the Sandvik equipment consists of a QA335 Doublescreen and a QI341 impact crusher with hanging screen. Vezzola uses them both for recycling (demolition and asphalt) and at its quarries, depending on current requirements. “Vezzola chose Sandvik because its trademark technologies, ‘Doublescreen’ and ‘Prisec’, make the difference. A Doublescreen enables the screener to produce 30% more than another model of the same class. Thanks to Prisec, the impact crusher could work as primary or secondary, having the same production and quality. That gives Vezzola the opportunity to use the machines in different applications,” stated Brunello.
Vezzola purchased its first Sandvik equipment in 2017 and is a CGT customer of long standing. The company acquired its first Cat machine in the 1960s, now owning and operating 10 Cat hydraulic excavators, nine Cat wheeled loaders, two Cat dozers, one Cat motor grader and three Cat skid-steer loaders. Other equipment is hired in from CGT as needed. AB

The recirculating system of the Sandvik QJ341 impactor shown to good effect
The plan picture shows how Vezzola quarries protect the locale through landscaping, planting and using the natural environment
Aquamist by Terex Terex is introducing ‘Aquamist by Terex’— a dust suppression system available across its materials processing brands: EvoQuip, Fuchs, Powerscreen, Terex Ecotec, Terex Finlay, Terex MPS and Terex Washing Systems.
The ‘Aquamist by Terex’ dust suppression system is said to offer an improvement over conventional jets or water-sprays to manage the build-up of dust and better protect workers on job sites. It uses a high capacity misting fan that produces finely divided water droplets of 10-150 micron diameter. At this size, they easily combine themselves with dust particles of similar dimensions and precipitate them out of the air and, because water mists ‘float’ more than a conventional spray, they cover and envelop the dust cloud more effectively.
Paul Kearney, vice-president of Parts and Solutions for Terex Materials Processing, explains: “It is globally accepted that airborne dust that is formed on job sites can significantly contribute to respiratory illnesses. As increased legislation comes into place globally to mitigate this, more effective control of dust is needed. Our Aquamist system will better support worksite operations and strengthen our commitment to making the workplace a safe and healthy environment.” www.terex.com
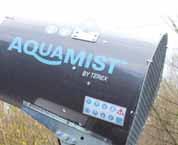
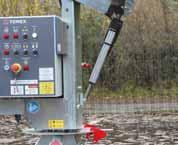
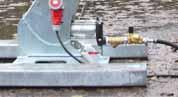
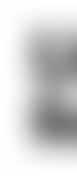
Liebherr loader for Lorban TP
Lorban TP’s Generation 9 Liebherr R 945 crawler excavator at work at a Carrières du Bassin de la Sambre quarry site
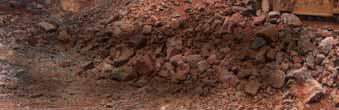


Lorban TP deals with the extraction and loading of limestone at the Carrières du Bassin de la Sambre (C.B.S.) in Saint-Remy-du-Nord, northern France. These quarries produce 600,000 tonnes of limestone granulate annually for industry, construction, and civil engineering.
A near 50-year-old family business, Lorban TP was looking for a high-performance machine with short loading cycle times. The excavator was required to operate a hydraulic hammer to break up the rock and a shovel to load it into the dump trucks. The company chose the new Liebherr Generation 8 R 945 crawler excavator to replace a Generation 6 R 946.
The Generation 8 range of crawler excavator comprises seven models and was launched at bauma Munich in 2019. The R 945 is the replacement model for the Generation 6 R 950 SME. These machines put a new architectural concept into an application that has enabled optimised operating performance, comfort, ergonomics, and safety.
Jean-Pierre Deruelle, the only driver of the R 945, previously worked with an R 946 excavator. When
comparing the old and new generations, he noticed both an increase in performance and an increase in stability. He also appreciates the comfort of the cab and the smoothness of the movements that make the R 945 an ideal work tool. The spacious and airconditioned cab is equipped with an air-sprung seat with vertical and longitudinal shock absorption. The R 945 achieves higher outputs than the old R 946 and has an engine output of 220kW compared to the 200kW of its predecessor. The average fuel consumption is 28.5 litres per hour. The engine efficiency of the Generation 8 excavators meets the European standard of Exhaust Gas Stage V. The transition to idling and the start-up are controlled automatically. The R 945 crawler excavator is equipped with an HDR bucket with a 2.5m³ capacity to load the dump trucks’ granules. It can be easily fitted with a hydraulic hammer for crushing rock. Perfectly adapted to Lorban TP’s requirements, the machine is equipped with a 6.15m-long SME monobloc jib with an SWA 66 hydraulic quick-change system. www.liebherr.com
Screening EDGE with the SM186
EDGE Innovate’s SM186 wheeled mounted screener is the Northern Ireland-headquartered company’s latest recycling applications model.
Ideal for recycling aggregates and demolition waste, the EDGE SM186 incorporates a robust 18’x6’ (5.4mx1.75m) two-deck screen with interchangeable flip flow and conventional scalper bottom decks. This flexibility, combined with numerous screen media options and configurations, allows the machine to process a wide range of materials and tackle screening applications that other conventional screens cannot.
Impressive design features include a low-level feed hopper designed to accept loads from all three sides without construction ramps and a two or three-way splitting configuration. The EDGE SM186 also offers hydraulic
folding discharge conveyors to facilitate the quick transition from operation to transport and a fully integrated power unit with large service access. A user-friendly control system with sequential start/stop functionality provides exceptional operational performance and unit safety.
The EDGE SM186 also comes with a tri-axle bogie with an ultra underslung suspension complete with a fifth-wheel hook-up and air brakes. The wheeled mounted
screener is exceptionally easy to transport between sites, with redeployment taking a matter of minutes.
Operators can choose from various screen boxes, including EDGE Innovate’s award-winning flip flow screen, scalping screen and rinser screen. Optional power sources include diesel/hydraulic, diesel genset, or direct electric. The EDGE SM186 is also available in a static chassis format. www.edgeinnovate.com

EDGE Innovate’s SM186 wheeled mounted screener
The Aquamist by Terex dust suppression system
Fuel-saving Volvo Penta D16 engine
Volvo Penta is starting production of its most powerful versatile engine yet, the new Stage V/Tier 4F D16. The new 16-litre engine delivers a range of industry-leading benefits, including a reduction of up to 10% in fuel consumption compared to its predecessor, the TAD1643VE-B, low to high-end torque and high-altitude performance.
The new D16 unit has been designed to meet the needs of customers working in a range of demanding environments, such as quarrying, mining, and construction applications. It is based on proven technologies that have undergone millions of hours of testing and real-world use.
On top of its low fuel consumption, the D16’s reliable Exhaust Aftertreatment System (EATS) has been designed to use selective catalytic reduction technology only, removing the need for exhaust gas recirculation (EGR) and a diesel particulate
filter (DPF). The optimised EATS design ensures high uptime and low total cost of ownership.
With its dual-stage turbo system, the D16 delivers high performance across the operational range, providing high torque at low and high engine speeds. This enables the engine to meet the requirements of multiple applications without operators having to compromise between performance and torque. For example, in mining customers can benefit from high power and high torque, leading to increased productivity. And in agriculture, where the requirement is often for high torque at low rpm, the D16 is optimised for low fuel consumption.

The D16’s dual turbo system is based on proven technology that has been used in Volvo Penta’s power generation engines for more than a decade. It’s the first of the company’s industrial versatile engines to be equipped with this technology.
The dual turbo technology and efficient combustion system also help the engine to achieve industry-leading performance at high altitude. At an altitude of 2,500m, the D16 delivers the same performance as it does at sea level.
The D16 has been developed to produce smooth operation with low noise levels built on the dependable in-line six-cylinder design. A durable, compact base engine that’s easy to install,
the D16 is built to run. With easily accessible service points, the industrial engine is simple to maintain and now has an extended oil service interval from 500 to 1000 hours.
The 16-litre D16 (TWD1683VE) diesel engine delivers 585kW of power and 3650Nm peak torque at 1900RPM. As well as meeting the Stage V and Tier 4F emission regulations, the new engine also complies with MSHA, CANMET, Reg 120, Reg 96 and RoHS2 requirements.
www.volvopenta.com
Martin Engineering’s N2 Twist Tensioner
Martin Engineering’s N2 Twist Tensioner is an intuitive new smart technology platform that maintains proper blade-to-belt pressure to ensure the best possible conveyor belt cleaning performance. The innovative system also alerts operators via the Martin Smart Device Manager App when the cleaner blade needs changing or if an abnormal condition is detected. The result is efficient cleaning, increased safety, reduced labour and a lower cost of operation.
Located on the head pulley, primary belt cleaners commonly have a twist, ratchet or spring tensioner to ensure the cleaner blade stays in consistent contact with the conveyor belt for proper cleaning and material discharge. Before the new design, belt tensioners had to be monitored and adjusted manually in some applications daily to maintain optimum pressure and carryback removal. Estimating when blades needed changing was often a
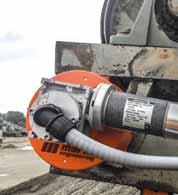
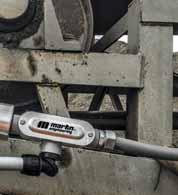

guessing game that, if left too long, could lead to belt damage. Inadequate tensioning causes carryback to cling to the belt and spill along its path, piling up under the conveyor and emitting excessive dust. This requires extra labour for cleanup and can affect air quality. Furthermore, over-tensioning leads to friction
damage to the carrying side of the belt, premature blade wear and potential splice damage. Both scenarios create unsafe work conditions and raise the cost of operation significantly.
The N2 Twist Tensioner automatically maintains precise cleaning pressure throughout the entire life of the blade. The
tensioner applies the proper amount of torque to deliver optimum cleaning pressure at the blade tip, supporting the Constant Angle Radial Pressure (CARP) cleaner design that withstands the force of heavy bulk cargo but retains a consistently tight seal across the belt profile.
Martin Engineering’s smart technology platform monitors blade wear and informs operators when the blade needs changing from control systems housed in a durable weather-resistant NEMA 4 control box. Experts recommend changing blades before there is a chance of detachment or a ‘pull through’ (inversion under the head pulley). In the event of a premature pull through, operators are alerted, and the tensioner’s internal self-relieving coupling rolls over. A blade detachment also triggers an alert allowing operators to shut down the system, avoiding expensive belt damage.
www.martin-eng.com
Volvo Penta’s new D16 engine
Martin Engineering’s N2 Twist Tensioner
2021
MAY
25-28: bauma CTT Russia
Moscow, Russia
Organiser: Messe Muenchen Rus
Tel: +49 (0) 89 949 20251
Email: info@bauma-ctt.ru www.bauma-ctt.ru
SEPTEMBER
02-04: RecyclingAKTIV & TiefbauLIVE
Karlsruhe Trade Fair Centre, Germany
Organiser: Messe Karlsruhe
Tel: +49 (0) 721 3720 2300
Email: verena.schneider@messekarlsruhe.de www.recycling-aktiv.com
08-12: MATEXPO 2021 Kortrijk, Belgium
Organiser: The Fair Experts
Tel: +32 56 98 07 60 Email: info@matexpo.com www.matexpo.com
15-18: Construction Indonesia
Jakarta, Indonesia
Organiser: PT. Pamerindo Indonesia
Tel: +49 3999905 0
Email: contact@merebo.com www.ci.merebo.com
15-18: Geofluid 2021
Piacenza, Italy
Organiser: Piacenza Expo
Tel: +39 (0) 523 602711
Email: alessandra.bottani@ piacenzaexpo.it www.geofluid.it
OCTOBER
21-23: IFAT Eurasia 2021
Istanbul, Turkey
Organiser: Messe Munchen
Tel: +90 212 241 81 71
Email: genc@mmi-eurasia.com www.ifat-eurasia.com/en/
NOVEMBER
03-04: 4th Construction
Equipment Forum Berlin 2021 Estrel Convention Center, Berlin
Organiser: IPM AG Tel: +49 511 473 147 90 www.constructionforum.eu
DECEMBER
07-11: EXCON 2021
Bengaluru, India
Organiser: CII
Tel: +91 44 42444564
Email: excon@cii.in www.excon.in
2022
MARCH
29-31: World of Asphalt 2022
Nashville, Tennessee
Organisers: NAPA, AEM & NSSGA Tel: +1 (414) 274 0644 www.worldofasphalt.com
APRIL
04-10: bauma 2022
Munich, Germany
Organiser: Messe München
Tel: +49 89 949 11348
Email: info@bauma.de www.bauma.de/en
JUNE
21-23: Hillhead 2022
Hillhead Quarry, Buxton, Derbyshire, England
Organiser: The QMJ Group
Tel: +44 (0) 115 945 4377
Email: Harvey.sugden@qmj.co.uk www.hillhead.com
MEET THE TEAM
Aggregates Business travels the globe attending conferences, events and equipment shows, keeping you informed of the latest offerings. Come and join us for a chat at any of the events below.
JUNE 2022
21-23: Hillhead 2022
Hillhead Quarry, Buxton, Derbyshire, England
2022 (DATES TBC)
EIG 2022
Exeter, UK
These dates were correct at the time of going to press, but please note that the COVID-19 pandemic means some events may be rescheduled with little advance notice
ADVERTISERS INDEX
www.constructiontv.tv
Contact: Roger Adshead | radshead@ropl.com | +44 7768 178163


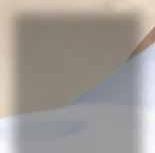

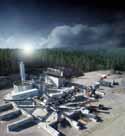
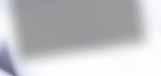
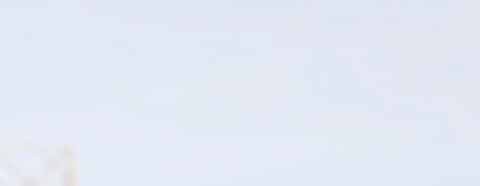


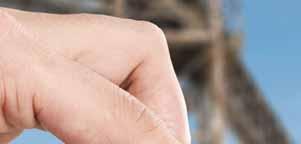
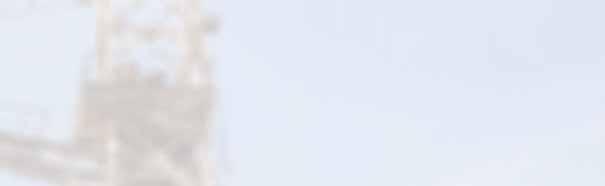


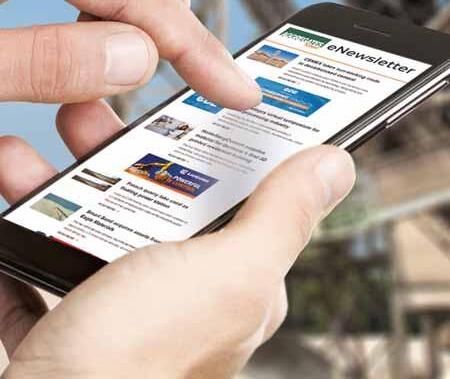




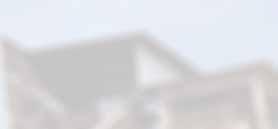




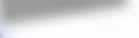
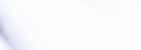



















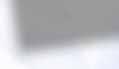

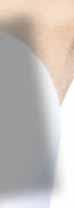
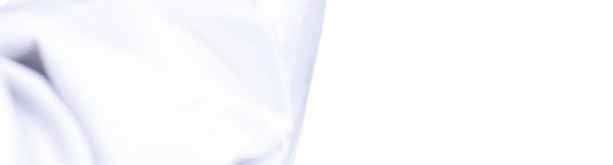
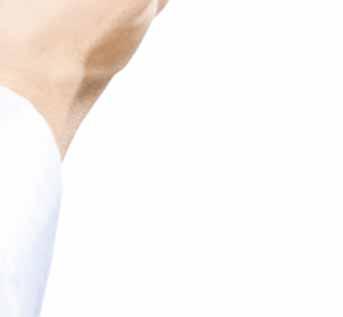
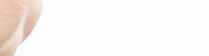
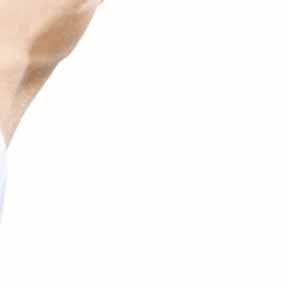

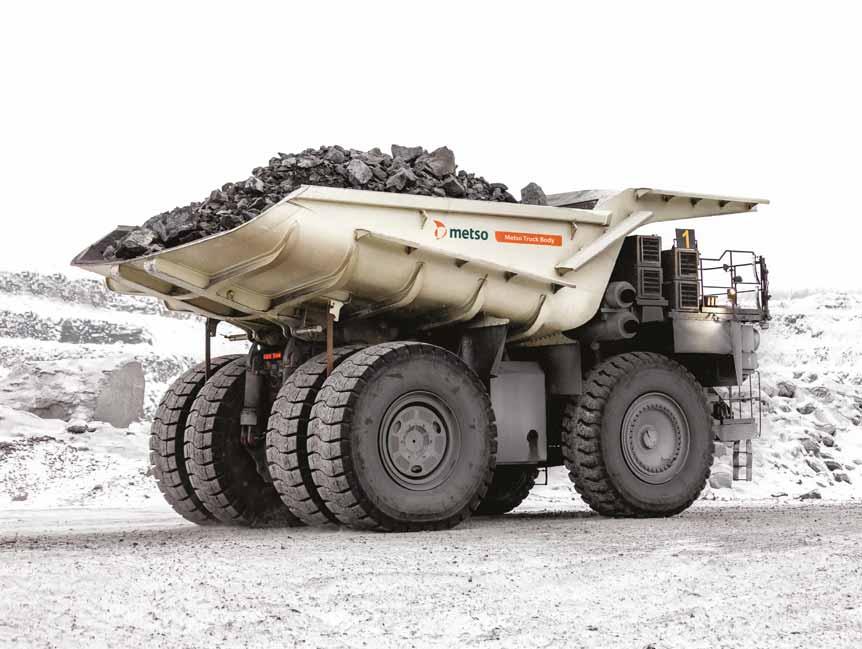