
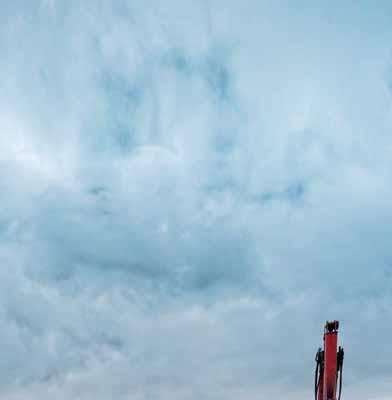
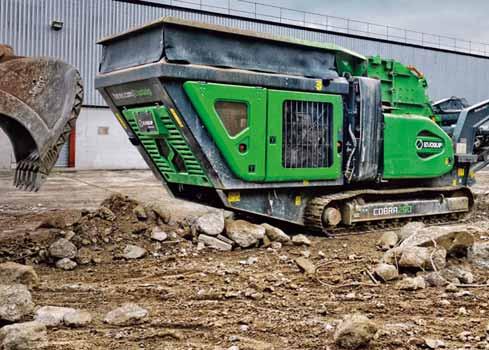


The Sheehan Group, UK
•Producing 6 in spec products
•Over 1m tonnes diverted from landfill
•100% diversion from landfill
For over 25 years, our innovative solutions have enabled customers all over the world to reuse 80-100% of materials from construction, demolition and excavation waste.
Our advanced processing systems are tailor-made to maximise material recovery, and transform it into in-specification sand and aggregates for reuse in the construction industry. These are then used in high-value construction applications such as concrete and asphalt production.
At CDE, we know that one solution does not fit all. That’s why our expertise spans across C&D fines, earth and excavation waste, crushed concrete and railway ballast. Our solutions optimise material recovery by removing contaminants, converting waste into valuable resources and speeding up your return on investment. Want
Using accurate weighing solutions in aggregates production can lead to big efficiency gains 33
New Stage V engines get global lift-off, while the future of diesel power may be clean, mean and green 37 RECYCLING – PART 1
Recycled aggregates are big business in 2019
French aggregates demand is increasing as the country invests
08 INTERVIEW
New Metso CEO and president Pekka Vauramo is excited by the sales and R&D growth potential of the global quarrying equipment heavyweight
40 KLEEMANN GROWTH
German track-mounted mobile crushing & screening plant manufacturer Kleemann has ambitious global growth plans after a period of significant inward investment
43 QUARRY PROFILE
Maptek’s Vulcan software is helping one savvy Greek quarries manager accurately plan and manage his marble reserves
Metso
New standout hybrid excavator from a leading
The bauma 2019 exhibition in Munich, Germany, saw many new hauling stars get their worldwide unveiling
This upgraded 2-Series model features the newly developed CI621 Prisec technology which comes with a host of innovations
HEAD OFFICE
EDITOR: Guy Woodford
ASSISTANT EDITOR: Liam McLoughlin
CONTRIBUTING
EDITORS: Patrick Smith, Dan Gilkes
EQUIPMENT EDITOR: Mike Woof
DESIGNERS: Simon Ward, Andy Taylder, Stephen Poulton
PRODUCTION MANAGER: Nick Bond
OFFICE MANAGER: Kelly Thompson
CIRCULATION & DATABASE MANAGER: Charmaine Douglas
INTERNET, IT & DATA SERVICES DIRECTOR: James Howard
WEB ADMINISTRATORS: Sarah Biswell, Tatyana Mechkarova
MANAGING DIRECTOR: Andrew Barriball
PUBLISHER: Geoff Hadwick
CHAIRMAN: Roger Adshead
ADDRESS
Route One Publishing Ltd, Waterbridge Court, 50 Spital Street, Dartford, Kent DA1 2DT, UK
TEL: +44 (0) 1322 612055
FAX: +44 (0) 1322 788063
EMAIL: [initialsurname]@ropl.com (psmith@ropl.com)
ADVERTISEMENT SALES
SALES DIRECTOR:
Philip Woodgate TEL: +44 1322 612067
EMAIL: pwoodgate@ropl.com
Dan Emmerson TEL: +44 1322 612068
EMAIL: demmerson@ropl.com
Graeme McQueen TEL: +44 1322 612069
EMAIL: gmcqueen@ropl.com
SUBSCRIPTION / READER ENQUIRY SERVICE
Aggregates Business Europe is available on subscription. Email subs@ropl.com for further details. Subscription records are maintained at Route One Publishing Ltd.
SUBSCRIPTION / READER ENQUIRIES TO:
Data, Route One Publishing Ltd, Waterbridge Court, 50 Spital Street, Dartford, Kent DA1 2DT, UK
TEL: +44 (0) 1322 612079 FAX: +44 (0) 1322 788063
EMAIL: data@ropl.com
No part of this publication may be reproduced in any form whatsoever without the express written permission of the publisher. Contributors are encouraged to express their personal and professional opinions in this publication, and accordingly views expressed herein are not necessarily the views of Route One Publishing Ltd. From time to time statements and claims are made by the manufacturers and their representatives in respect of their products and services. Whilst reasonable steps are taken to check their accuracy at the time of going to press, the publisher cannot be held liable for their validity and accuracy.
PUBLISHED BY © Route One Publishing Ltd 2019
AGGREGATES BUSINESS EUROPE USPS: is published six times a year. Airfreight and mailing in the USA by Agent named Air Business, C/O WorldNet Shipping USA Inc., 156-15 146th Avenue, Jamaica, NY, NY11434. PERIODICALS POSTAGE PAID AT / US POSTMASTER ADDRESS CHANGES TO: Aggregates Business Europe, Air Business Ltd, C/O WorldNet Shipping USA Inc., 156-15 146th Avenue, Jamaica, New York, NY11434
PRINT: ISSN 1754-2499 ONLINE: ISSN 2057-3413
PRINTED BY: William Gibbons
on’t know about you, but my work trips with Aggregates Business are very much like the London buses analogy: ‘You wait ages for one and then two or three come along at once’. You can’t be out and about all the time, as you need a reasonable amount of writing and editing time for each issue of this magazine. Consequently, it had felt like a while since my early January 2019 trip to southwest and western Germany with the Wirtgen Group to report on the big growth plans for Benninghoven and Kleemann, the latter of which you can read more about in this issue, and my 28-29 January attendance at the pre-bauma 2019 Media Dialog in Munich, Germany.
Now, as I write this column, I’m looking back on three diverse and productive trips. The first was a 21-22 March trip to Copenhagen for the latest EMSAGG (European Marine Sand & Gravel Group) – Knowledge Sharing Workshop. This highly interesting and thought-provoking event illustrated both the importance of marine aggregates to the overall global aggregates sector, the varied regulation across Europe when it comes to sand and gravel extraction, the difference in product pricing between nations, and the marine aggregates paradox: between marine aggregates suppliers wanting larger areas from which to source material, leading to greater material volume and lower product prices; and the general public and local authorities tending towards the restriction of marine aggregates cultivation, thus limiting supply and raising prices.
On 5-6 April I flew to Milan for the opening of innovative global off-highway machine tyre maker BKT’s new European headquarters, in the attractive town of Seregno in Monza province, near Milan. The highly ambitious Indian manufacturer, whose eye-catching research and development work includes a joint agreement with Kultevat, a leading US bio-tech company specialising in the cultivation and processing of TKS dandelion as a renewable and sustainable alternative to natural rubber, sees Europe as a
key regional market for its wide off-highway tyre range. The firm’s new state-of-the-art HQ is an important part of their global growth strategy.
From the BKT event I was straight on a plane to Munich to join Route One Publishing’s Daily News team covering the bauma 2019 exhibition (8-13 April), the world’s largest construction and quarrying equipment showcase. It was an action-packed week full of new machine and technology launches. Highlights from an aggregates processing perspective included Metso’s debut in the hauling market, with a new haul truck body solution allowing trucks to haul more material than with a standard truck body. Terex Materials Processing’s OMNI solution, a tablet-based system fitted within the cab of a material feed excavator providing centralised remote access to multiple machine control systems within a crushing and screening train, also caught the eye. Meanwhile, leading aggregates wash plant manufacturer CDE showcased CDE COMBO, the world’s first all-inone wet processing and water recycling system, and the firm’s CORE smart technology suite, featuring an easy-to-use monitoring system, a digital tool to manage and simplify operator workflows, and a bespoke 3D catalogue of parts which is tailored for each customer’s individual equipment.
Looking back on the bauma 2019 exhibition, for me the volume of new software solutions linked to the digitalisation of the construction and aggregates processing equipment sectors was the highlight of the week. The fact that quarry operators can, with these solutions, achieve greater production volume and efficiency, thus generating and saving money in equal measure, represents exciting progress for our industry. You will be reading a lot more within this magazine about how technology is becoming a trusted friend to global aggregates production, with new quarrying tech-linked features, like predictive plant maintenance, appearing more frequently. GW gwoodford@ropl.com
Volvo CE’s new Uptime Center will assist the entire Volvo dealer network in Europe, the Middle East and Africa in keeping customers’ machines up and running.
In a bid to become customers’ number one choice for uptime in Europe, the Middle East and Africa, Volvo Construction Equipment (Volvo CE) has assembled a dedicated team to proactively support Volvo dealers in providing solutions to problems that can lead to reduced uptime.
Located in Volvo CE’s EMEA regional headquarters in Eskilstuna, Sweden, the new Uptime Center will assist the entire Volvo dealer network in Europe, the Middle East and Africa in keeping customers’ machines up and running.
It will serve as an IT nerve centre, monitoring data transmitted by connected machines through CareTrack and identifying areas where uptime and efficiency can be increased.
The Terex Materials Processing (MP) segment of Terex Corporation posted sales of US$346m in the first quarter of 2019, an increase of 10% on Q1 2018.
It says the increase was driven by continued strong global demand for crushing and screening products, material handlers and pick and carry equipment.
Terex MP adds that its backlog also continued to grow in Q1 this year, up 11% on the first quarter of 2018 to US$499m. The brand says it is well positioned across its portfolio of businesses to deliver excellent results again in 2019.
“We had a great start to 2019 thanks to strong global demand driven by construction activity, aggregate consumption and robust
CEMEX has signed the final agreement to sell its aggregates and ready-mixed concrete assets in the North and NorthWest regions of Germany to GP Günter Papenburg AG for approximately €87 million.
The Mexican global building materials market giant currently expects to close the sale during the second quarter of 2019.
The CEMEX assets in
Germany being divested consist of four aggregates quarries and four ready-mixed concrete facilities in North Germany, and nine aggregates quarries and 14 ready-mixed concrete facilities in North-West Germany.
The proceeds expected to be obtained from the sale will be used mainly for debt reduction and for general corporate purposes.
demand for scrap steel,” said Kieran Hegarty, president Terex MP. “We expect strong results to continue fuelled by innovations that will excite our existing customers and geographic expansion that will enable us to serve more customers globally.”
At the bauma 2019 exhibition in Munich, Germany, Terex MP showcased its new ‘OMNI by Terex’ tablet-based control system that uses internet of things technology to improve safety and productivity at crushing and screening jobsites.
The Terex MP portfolio covers the Powerscreen, Terex Minerals Processing Systems, Terex Finlay, EvoQuip, Terex Washing Systems, Fuchs, CBI, Terex Ecotec, and Terex Concrete Products brands.
Jan Jenisch, CEO of LafargeHolcim, has welcomed the group’s encouraging Q1 2019 trading performance
LafargeHolcim, the French-Swiss building materials heavyweight, posted a 6.4% yearon-year sales rise to €5.959 billion in the first quarter of 2019. Profitability increased in all business segments, while there was a 20.6% increase in EBITDA (earnings before interest, tax, depreciation and amortisation). The group also achieved a significant reduction in
Looking ahead, LafargeHolcim sees its positive momentum in Q1 continuing throughout the rest of 2019. This is expected to include continued market growth in North America, softer but stabilising cement demand in Latin America, continued demand growth across most countries in Europe, challenging but stabilising market conditions in the Middle East and Africa, and continued demand
growth in Asia Pacific.
Jan Jenisch, CEO of LafargeHolcim, said: “We had a very strong start of the year and I am especially pleased to see our strong sales growth and an over-proportional increase in profitability.
“Our strategic decision to divest South East Asia was executed with very attractive valuations allowing us to achieve a new level of financial strength. We have delivered on the promised strengthening of our balance sheet and we are on track to accelerate the execution of our Strategy 2022 – ‘Building for Growth’.”
“Our momentum in the past three quarters, a solid global market demand and the ambitions of our teams give us great confidence for reaching our targets for the full year.”
Since becoming Metso chief executive officer and president on 1 November 2018, Pekka Vauramo has enjoyed something of a honeymoon period with the global aggregates processing plant giant posting healthy trading performance updates, while fully transitioning into its new business division structure devised by Vauramo’s predecessor, Nico Delvaux. So, what next for Metso and its new boss? Guy Woodford reports.
Pekka Vauramo was in good spirits when we met at St James’s Hotel & Club in Mayfair, central London. He was in England’s capital city for a series of meetings with Metso investors, making the release of the company’s encouraging full-year 2018 and Q4-2018 trading summaries very well timed indeed. They showed how the Helsinki, Finland-headquartered global quarrying equipment market manufacturer increased its sales by 32% in constant currencies from the previous year. Metso Q4-2018 sales were also up 23% in constant currencies compared to the same three months of 2017. Further figures revealed that orders received were up by 17% in 2018 to €3.499bn (€2.982bn in 2017). Meanwhile, company operating profit (EBIT) for 2018 totalled €351mn, or 11.1% of sales (€218mn, or 8.1% of sales in 2017).
What made Metso’s full-year 2018 and Q4-2018 performance even more impressive was that it came during a period of big upheaval in how the company operates.
After just five months in his dual post, Nico Delvaux, a Belgian national, departed as Metso president and CEO on 2 February 2018 to take over as CEO of the world’s biggest lock maker, Assa Abloy. His departure to the Swedish firm came after he had reconfigured Metso to operate under seven dedicated business areas, instead of three, from 1 January last year. The business areas - covering Mining Equipment, Aggregates Equipment, Minerals Services, Minerals Consumables, Recycling, Pumps and Valves - were each given their own dedicated leadership and management teams, with their heads reporting to the CEO and president and becoming members of the company’s executive team.
Speaking to Aggregates Business magazines in November 2017, Delvaux, a former senior executive at Atlas Copco, said the changes would ensure more “focus, dedication, accountability and agility” within each of the business areas, adding that they were businesses that Metso wanted to be in “for the long term”, with more inward investment guaranteed.
After Delvaux’s surprise departure,
Metso’s chief financial officer, Eeva Sipilä, became interim president and CEO, a position she maintained until Vauramo’s arrival late last year, from Finnair, where he had served as CEO and president since 2013.
“Eeva Sipilä did a great job pulling things together and making sure the changes Nico introduced were implemented. As the chairman of our board said, in a good way, ‘She has an iron hand in a silk glove!’”
Vauramo has been impressed by how quickly Metso’s new business areas and management team reporting structures have taken effect. “We grew our sales by a big number last year. If there is a need to finetune things, we will do so. But I’m not going to change things just because I want to put my stamp on Metso. When I arrived, I saw no-one internally fighting back against these changes. Quite rapidly, we have gained a much better control of business and greater understanding of issues, such as those linked to supply chains.”
No stranger to the quarrying and mining industries, Finnish national Vauramo’s career path prior to his years at Finnair had seen him hold several leading positions at Cargotec Corporation (2007-2013), Sandvik (1995-2007), and Tamrock Corporation (19851995), and work as a mine design engineer (1983-1985) for Outokumpu Corporation. Having made a success of heading up a major airline, I was intrigued about what made him want to return to familiar territory with Metso? “I’m a mining engineer by profession and had always admired Metso while working for Sandvik and in roles at other companies. I felt that I’d contributed a lot to Finnair and put a lot of things in place which could allow me to leave and take up Metso’s offer.”
Switching to his first full-year priorities as Metso CEO and president, he says: “There are lots of capable people at Metso. What I want to emphasise is the importance of technology and R&D [research & development] in our business. Our customers expect us to deliver reliable technologies that will enhance their businesses. We need to deeply imbed this in what we do. This could partly come from looking outside Metso to see if there are other technologies we can acquire that will
improve what we do.
“The mining industry is talking a lot about automation, and everyone in ours is talking about data analytics and digitisation. The quarrying and aggregates industry can also contribute to this discussion with telematics that produce more value-adding information for customers. Consumables and wear parts replacement are key areas within crushing and screening and we want to focus on creating a higher level of predictive maintenance technology to use with our machines.”
Vauramo describes his leadership style as “being involved in a business”. He is also keen to stress the importance of strategic internal investment. “Companies need to spend money to create better futures for themselves. We need to make people excited about what we do. At Finnair, I learned so much about people and where you can get to if you have people behind you, who understand their roles within an organisation. With Metso, I know a lot more on the technical side of its business than the equivalent at Finnair.”
At the recent bauma 2019 exhibition in Munich, Germany, the world’s largest construction and quarrying equipment showcase event, Metso staged the global launch of a claimed ground-breaking truck body innovation for off-highway trucks. Combining the benefits of rubber and high structural strength steel, the Metso Truck Body is said to enable mines and quarries to haul more while lowering their operating costs. The launch expands Metso’s product offering into completely new territory.
Metso also gave an exclusive preview at bauma 2019 of the Urban LT96, the latest addition to the company’s Lokotrack Urban plant range. Urban models are designed for crushing in densely populated environments, such as city centres. The units are said to enable up to 60% better noise protection and cut dust emissions.
Another bauma 2019-launched Metso model was the Metso MX3 cone crusher with patented Multi-Action crushing technology. The ‘little brother’ of the CONEXPO/ CON-AGG 2017 Las Vegas, USA-exhibition launched MX4, the MX3 is designed to cut the operational costs of crushers and to provide more uptime compared to traditional cone crushers.
Metso also unveiled at the Munich showpiece event the compact Lokotrack ST2.3 mobile multi-use screen, said to be ideal for secondary and tertiary crushing applications, such as producing aggregates for railway ballast, road construction, asphalt and concrete fractions.
After bauma 2019 Metso reported double-digit growth in both its sales and received orders in the first three months of 2019, Vauramo’s first full quarter as Metso CEO and president. The company’s sales rose 17% to €836 million (compared to €714mn in
LEFT: Pekka Vauramo at the recently expanded Metso Park site in Alwar, India
Q1 2018). Metso recorded an 18% increase in its received orders which totalled €1.013bn (€859mn in Q1 2018), while EBITA (earnings before interest, taxes and amortisation) for the quarter stood at €104 million, or 12.4% of sales (€85mn, or 11.9% in Q1 2018).
Vauramo says he is pleased with the “rapid growth” of Metso’s aggregates business in recent years, both in terms of product development and sales. “We have very solid products that have a nice heritage – such as the Lokotrack plant that come out of our Tampere [Finland], former Lokomo, production facility.
manufacturer’s joint venture businesses based in the south of the vast country - with LiuGong in Liuzhou, Guangxi province, and with Shaorui Heavy Industries near Hong Kong in Guangdong province. “Both these joint venture companies are in the black and in a growth phase. It’s a good position to be in when things are looking prosperous in China, as they are in India.
“We have a good opportunity to grow our plant sales in China. The government ban on using river sand in construction means more aggregates suppliers are looking to produce manufactured sand, which our plant is well
“Our continuing investment in our infrastructure in India is a sign of our belief in that market.”
“We are expanding into growing markets. There are interesting developments in China and, especially, India. I was very positively surprised by Metso’s success there, as it has been a very challenging place for many companies to do business in.”
Metso recently completed the expansion of its Metso Park production facility in Alwar, India. With this expansion Metso is addressing the growing demand for crushing and screening solutions in the Indian market, as well as improving the availability of products for export operations to Asia.
Metso launched operations in India in 1992 and has since been developing a strong footprint in the market. In 2018, the company announced a new foundry project in Vadodara to increase metallic wear castings capacity, and it acquired a valve automation division of Rotex Manufacturers and Engineers Private Ltd. Today Metso is present in India with over 1200 employees in seven regional offices, five production units and foundries, and an extensive service and distribution centre network across the country.
Since our interview in London, Vauramo has visited Metso Park in Alwar as part of a comprehensive tour of Metso’s key worldregion operations.
“Our continuing investment in our infrastructure in India is a sign of our belief in that market,” he stresses.
Focusing on Metso’s trading in China, Vauramo highlights the success of the
suited to. The Chinese have also decided to convert their concrete highways into asphalt highways, and new regulations state that all the construction materials for this need to be reused. Small quarries are also being consolidated due to new safety rules and regulations, so many won’t get operating licences. This creates bigger industrial set-ups.”
Metso has well over 100 official aggregates business distributors globally, with many also selling yellow iron machines from a variety of leading OEMs, such as Caterpillar. “The aggregates business needs dealers and distributors as it’s very much a local business,” explains Vauramo. “We might
somewhere sell directly, but in all major markets we need dealers and distributors. In the U.S. alone, someone told me there are 10,000 quarries. We cannot afford to recruit our own sales force to cover this.
“It’s important that we understand our dealers’ and distributors’ businesses, as well as the businesses of our customers. What is good business for them? If it’s not good for them, it won’t be good for us. When I recall some of the successful plant manufacturerdistributor relationships in my previous roles at other companies in this sector, there was a lot of planning and collaboration on how both parties could benefit from a specific working relationship. For example, very often there are trade-ins and the right distributor might take a wheeled loader and excavator in exchange for a customer taking a Lokotrack crusher.”
Asked about how the global aggregates processing industry is likely to look in ten years’ time, Vauramo says: “I think technology will be playing a big part in it, some of which we are currently not yet aware of. I also hope Metso is the equipment market leader and is very much seen as that by our peers.”
After growing up in Lahti, a city around one hour’s drive north-east of Helsinki, and obtaining a Master of Science MSc (Tech) degree in Mining Engineering, Vauramo, now in his early 60s, has been used to juggling a busy and successful career with family life. “I’m married, and my wife and I have two daughters, a son and two granddaughters. My work week starts Sunday evening and ends Friday night. If I’m not travelling I dedicate my weekend to family. It’s been like that the last 20 years. Having the weekends for family helps to calibrate the mind.
“Like many Finns, I love ice hockey. It’s such a high-tempo sport. Last time I played was three years ago. If my working schedule and health permits, I hope to play again one day.”
Putting on ice skates, picking up an ice hockey stick and dispatching a puck at great speed into the back of a net sounds like a pretty good way to unwind after a hectic, travel-heavy working week. Perhaps I should try it! AB
FOR QUALITY SHAPED PRODUCTS, ESPECIALLY IN HARD ROCK. MOBICONE mobile cone crushers are used in medium-hard to hard applications as well in abrasive natural stone operations. They cover a wide range of applications: from small to medium-sized batches for short-term contractor operations, all the way through to large quantities in tough quarrying operations. The MOBICONE crushers are the perfect match for mobile KLEEMANN jaw crushers and/or screening plants. MOBICONE mobile cone crusher: efficient and strong.
www.kleemann.info
An event not to be missed later this year is the UEPG (European Aggregates Association) Sustainable Development Awards ceremony 2019.
The UEPG’s Sustainable Development Awards 2019 (SDA 2019) is a record-breaker! Europe’s aggregates sector association has this year received an all-time high 53 entries from 13 countries, including Austria, Belgium, Cyprus, Finland, France, Germany, Ireland, Italy, the Netherlands, Spain, Sweden, Switzerland and the UK.
What are the UEPG Sustainable Development Awards?
Sustainable development, as much as it is a buzzword widely used in politics, has real meaning for European aggregates producers and UEPG.
The Sustainable Development Awards (SDA) ceremony is a great opportunity to reward aggregates companies that have successfully integrated the social, economic and environmental dimensions of sustainable development into their daily
operations by achievements which go beyond what is required by legal regulations. This allows a more positive understanding and
Three SDA sustainable development pillars contain a combined seven award categories. There is an additional special award given for Biodiversity and another for Communication.
The Environment Pillar contains two categories:
• Restoration;
• Environmental best practice.
The Social Pillar embraces two categories:
• Local community partnership;
• Health & safety best practice.
The Economic Pillar comprises three categories:
• Economic contribution/added value to society;
• Operational best practice, process or product innovation;
• Best practice or innovation in recycling, marine or manufactured aggregates
For the 2019 edition, the independent jury will be composed of experts in their field.
• Ester Asin director at WWF European Policy Office
• Brenda O’Brien manager at Brussels Liaison Office, European Agency for Safety and Health at Work
• Anna Ostrega professor at AGH University of Science and Technology, Faculty of Mining and Geoengineering
• Slavko Šolar secretary general of EuroGeoSurveys (The Geological Surveys of Europe)
• Guy Woodford editor, Aggregates Business Europe/International
This year, the UEPG SDA ceremony will take place on 20th November 2019 in the magnificent concert hall La Madeleine, Rue Duquesnoy 14,
Built in the 19th century, La Madeleine was originally a covered market. Then, in the fifties, following the Expo 58, the building was turned into one of the most iconic concert halls of
Located at the very heart of the city, only a few steps from the famous ‘Grand Place’, La Madeleine of today remains one of the most renowned attractions of the Belgian capital. With its characteristic facade, the building has kept its charm and UEPG is proud to organise this key
The SDA 2019 ceremony will be moderated by Tory Batten, an experienced independent professional moderator. Batten specialises in assignments on all aspects of the sustainable
You can learn more about the applications received and the SDA in general via the
The new EC200E has extended the Volvo excavator range with a true 20-tonne machine which combines Volvo quality with exceptional value, to deliver performance and profitability in medium duty applications. This machine can be factory fitted with breaker and shear piping, as well as rotator piping. Special attachments such as mowers, grinders, shears, crushers and tilt rotators boosts the versatility and productivity to a maximum. Talk to your local Volvo dealership today. Volvo EC200E: a purpose built
“Innovative use of data has the potential to improve efficiency, productivity and safety”
More and more aggregates producers are considering how data can improve their business thanks to advances in technology and a need to remain competitive in the face of rising production costs. Ben Travers, partner and head of intellectual property and IT at Stephens Scown LLP, explores the legal issues that surround big data and data analytics.
Referred to as the ‘Fourth Industrial Revolution’ or the industrial internet of things, we are experiencing a rapid evolution where intelligent products, processes and technologies are converging and are able to communicate with each other. The scale is huge, with Accenture estimating that the industrial internet of things could add US$14.2 trillion to the world economy over the next 15 years.
For the aggregates sector this has the potential to transform the way operations are run with a more connected aggregates production process and real-time data sharing. By connecting data between production equipment and systems, it will be possible to get a more holistic view of operations.
Innovative use of data has the potential to improve efficiency, productivity and safety and whilst the impact on margins and the bottom line will be of interest to operators, the legal issues arising from data must not be forgotten.
This is no longer the preserve of the sector’s biggest operators. Technology is getting simpler, easier to use and less costly, opening it up to smaller aggregates operators.
This means that most aggregates businesses will find that they have access to all sorts of data, which they may want to analyse and interrogate. Before launching into a data analytics project however, from a legal point of view it is important to know where your data comes from.
If you do not own the data, you will need to check what permissions you have to use
it. For example, a supplier may have provided you with data which you are allowed to use for a particular purpose only. If you would like to use the data for a different or additional purpose you will have to seek express permission from your supplier for this.
The data and information your business holds may end up being one of your most valuable assets. That is why database rights are important and will help you to protect and exploit this asset.
Many people do not realise that the organisation that creates a database retains a legal right to its use. Rights like copyright arise through the creation of something new, but with database rights, your right is due to the hard work in collecting and presenting the data. This could include sales records, extracts from research reports and customer lists.
Database rights will provide you with protection from misuse of the data, but it may also be possible to license your data to maximise its potential to generate revenue for you. For this reason, it is something that you should not overlook.
The General Data Protection Regulations (GDPR) heralded a seismic shift in the way organisations can process data. If your data has the potential to identify individuals, you must handle it in a way that is compliant with GDPR. This includes considerations such as where and how the data is stored, how it is analysed and ensuring that you have permission to use the data in the way you wish.
There is no automatic right that arises to protect information that is confidential or commercially sensitive. If the data you are handling falls into this category, it is imperative to put carefully worded legal agreements in place to preserve its confidentiality. An exception is in an employee/employer relationship where there is an automatic duty of confidentiality.
It may take a number of years for the full potential of big data and data analytics to be felt in the aggregates sector. The businesses which will benefit most from this revolution will understand how it can improve their operation, while not forgetting the legal implications. AB
Ben Travers is a partner and head of intellectual property and IT at Stephens Scown LLP. The firm has more than 70 years’ experience representing mining and minerals clients and its specialist team is recognised by independent guides to the law Legal 500 and Chambers. If you have any questions about how your business uses data, Ben Travers can be contacted on 01392 210700 or email solicitors@stephens-scown.co.uk. For more information visit www.stephens-scown.co.uk
French aggregates demandhasgrownsignificantlyinthelasttwoyears
French aggregates demand has grown significantly in the last two years, fuelled partly by high-profile infrastructure projects.
Guy Woodford reports
The Grand Paris Express (GPE) project is the largest transport infrastructure project in Europe and represents a total investment of about €38.5bn. It is designed to meet the growing city’s needs for an improved transport infrastructure and prepare Paris for the 2024 Olympic Games.
LafargeHolcim has been awarded longterm contracts worth €110 million to deliver aggregates and cement for the GPE works. To help realise the project’s anticipated 200km of new railway and 68 new rail stations, the French-Swiss global building materials market giant will deliver 600,000 tonnes of aggregates and 260,000 tonnes of cement to produce 650,000m³ of ready-mixed concrete.
LafargeHolcim says it will be using barges on the Seine to sustainably manage
excavated earth equal to six times the weight of the Burj Khalifa in Dubai, the tallest building in the world. The company plans to work on the GPE project over the next 15 years.
To meet the project’s challenging schedule, LafargeHolcim has added mobile ready-mixed concrete plants to its existing Parisian ready-mix concrete network, enabling an average production of 300m³/ hour for the GPE. In addition, the company will remove and treat at least three million tonnes of earth from the construction site, then use the excavated material to re-landscape its nearby quarries.
For the transport of both aggregates coming from nearby quarries situated in the Seine valley and the excavated earth, LafargeHolcim will use barges on the Seine
involves an anticipated
river. The company says this solution is more efficient and sustainable than road transportation as two barges can handle the load of 220 trucks. It adds that the solution will also meet the challenge of transporting large amounts of material through an urban area with over seven million inhabitants.
The GPE is one of several infrastructure megaprojects aiding recovery of French aggregates demand. Others include EuropaCity, a €3.03bn 800,000m² cultural, recreational and retail development in the Triangle de Gonesse in Ile-de-France, north of Paris, due to be completed in 2024, and the latest €893mn works in La Défense, Paris’s central business district, which includes modernisation, refurbishment and greener landscaping schemes.
Nouredine Arkhouch, Hitachi Construction
Machinery (Europe) (HCME) key account manager, says that as well as GPE, there are many other French rail and highway projects helping to increase aggregates demand. These include rail works such as the Paris-Normandy, Marseille-Nice, RoissyPicardie, Montpellier-Perpignan, and the LGV Bordeaux-Toulouse projects. Highway projects include the reconstruction of the A79, N70, N79 and N80 routes, the Rouen ring way, and the A31 Toul-Nancy-MetzLuxembourg motorway.
According to the latest available UEPG (European Aggregates Association) figures, aggregates production in France stood at 463 million tonnes in 2017 compared to 331 million tonnes in 2016 and 323 million in 2015. UEPG figures show that in 2017 there were 1,810 company producers of aggregates in France, working across 2,822 extraction sites (quarries & pits). Of the 463mn tonnes of aggregates produced in France that year, crushed rock accounted for 186mn tonnes; sand and gravel for 120mn tonnes; re-used onsite aggregates for over 80mn tonnes and recycled aggregates for more than 65mn tonnes. A further six million tonnes of marine aggregates and four million tonnes of manufactured aggregates were produced.
François Wintergerst, director, Sales and Service operations for Metso France, believes French aggregates demand will continue to grow for the next three years. “The Grand Paris Express is definitely fuelling aggregates demand. There are also other projects like increasing the size of Paris airports, and building new railway stations. A continuous population increase in the western arc of France is also increasing aggregates demand in all western parts of the country.”
Like aggregates demand, cement consumption in France is also rising. It rose 2.5% in 2018 to 18.6 million tonnes, despite just 0.2% growth in the first half and a fall in the housing construction market. This does represent a slowdown from 2017, which recorded a 4.5% increase in cement consumption. Cement imports in 2018 remained stable at 15% of sales. In 2019, cement consumption is expected to remain stable due to the growth in public works and the tertiary real estate market. There are 29 cement works in France with 5,000 employees and LafargeHolcim leads the
best year since the market crash of 2008. Heavy earthmoving equipment is up 8.6% to 5,100 machines, according to data compiled by CISMA, a member of France’s Federation of Mechanical Engineering Industries (FIM).
However, the increase is much lower for compact equipment, just 2% over the 2017 figure in 2018. Sales reached 17,250 machines in France, Europe’s third-largest market for such equipment.
For crawler excavators, the market remained stable in 2018 compared to 2017.
ABOVE: French aggregates demand is predicted to continue rising over the next few years pic: Metso BELOW: Sotravi Group has been using a Hitachi
ZX530LCH-6 excavator at its Guena granite quarry in Saint-Renan, Brittany
Mini excavators, which account for 73% of the total crawler excavator market, posted a slight decline of 2%. The decrease is explained by a 15% decline in sales to renters. Nonetheless, the mini excavator market is close to historical record levels.
The market for excavators of more than six tonnes operating weight continued to improve, with a rise of 4%. Meanwhile, sales of six-12tonne excavators dipped by 1% but sales of crawler excavators over 12tonnes jumped 7% to 2,377 units.
Several yellow iron and crushing and screening plant manufacturers have been investing significantly in their French production sites in recent years. For example, Liebherr-France SAS has invested €5mn in a new state-of-the-art assembly line in Colmar. Based on the principles of lean management, the main task of the new line is to produce the latest generation of Liebherr crawler excavators, which launched on the market worldwide earlier this year as the ‘Generation
Komatsu Hybrid - It makes a difference Reduce your carbon footprint and fuel consumption by up to 40%. Unrivalled on the market, thousands of Komatsu Hybrid excavators work around the world today and have logged millions of fuel-saving hours for our customers. With Komatsu Hybrid equipment, you enjoy a new experience, and the most reliable and advanced technology in the industry today.
8’. The product line consists of the R 922, R 924, R 926, R 930, R 934, R 938 and R 945 models.
With logistical means that are said to be optimally geared to production, the new assembly line achieves average cycle times of 155 minutes per station with an output of five excavators each day. Altogether, the ‘R3’ assembly line has 26 work stations and nine preassembly stations synchronised with the main line.
With a workforce of over 1500 employees and annual production of 2000 machines, Liebherr-France SAS in Colmar is the main production location for earthmoving crawler excavators in the Liebherr Group. The standard production range comprises around 30 crawler excavator models, from the R 914 Compact to the R 980 SME for earthmoving work and for use in mining.
German tracked mobile crushing and screening plant manufacturer Kleemann has a strong presence in France. Among its many customers is SMBP, whose aggregates processing sites include the Prasville limestone quarry at Berchères-les-Pierres, near Chartres in northern France. There, a Kleemann Mobicat MC 162 RRP mobile crushing and screening plant is processing up to 1,000 tonnes of aggregates every hour.
Other major global quarrying plant makers have recently made changes to their French distributor network.
Since 1 April 2019, Bergerat Monnoyeur (BM) has operated as Sandvik Mining & Rock Technology’s (Sandvik MRT) new sole distributor for mobile crushers and screens in mainland France.
BM is not only supplying a comprehensive range of Sandvik mobile crushing and screening equipment but will also be providing spare parts and full aftermarket
service. This move, says Sandvik MRT, will benefit customers in France by offering consolidated, more localised and customerfocused support in their area.
With over 100 years’ experience in the industry, BM is an established and reputable name with a strong footprint for the supply of heavy equipment in France. With its headquarters in Saint-Denis, BM has six branches and 38 workshops altogether throughout France.
SAMI TP is Metso’s new distributor of mobile crushing and screening products and related wear and spare parts and services for the aggregates market in northern and western France, including Brittany, Normandy and Aquitaine, as well as the Paris area and Grand Est.
A subsidiary of BPM Group, SAMI TP specialises in the sale, rental, financing and repair of construction equipment. With eight main locations and a turnover of €52mn in 2018, SAMI TP is mainly active in the excavation and earthworks industries.
Meanwhile, Terex Materials Processing, a business segment of Terex Corporation, has appointed Tipmat as the authorised northwest France region distributor of EvoQuip compact crushing and screening plant.
Eric Gueguen, Tipmat president, met with Terex president and CEO, John Garrison, at the bauma 2019 exhibition in Munich, Germany (8-14 April) to formerly sign their distribution contract.
French demand for recycled aggregates is also rising, according to Metso France’s Wintergerst, with much of it being channelled into the Grand Paris Express project.
“Buildings will need to be demolished before new infrastructure can be installed. Metso is participating in this with its powerful impact crusher installations. able to crush old
concrete and separate it to recover the most valuable fractions.”
HCME’s Arkhouch says other projects increasing the use of recycled aggregates include the Mure, Improvmure, Recybeton, and Ecoreb projects. Currently, Arkhouch says annual French recycled aggregates demand is just over 120 million tonnes.
“Road construction majors like Colas and Eiffage sort extracted material on site with mobile equipment and use it for the same project.”
Speaking about the growing environment protection-focused working regulations within the French aggregates sector, Metso’s Wintergerst says: “The rules for the working conditions, including noise, dust and safety, in quarry installations are strict and getting stricter. Metso’s equipment and installations are designed based on the best standards. Metso participates and follows closely the work done by the various environmental committees at a French and wider European level. This means we can bring our knowledge to the committees and apply the latest regulations to our own plant designs.”
On the same subject, Davy Guillemard, president of Volvo CE France, adds: “French quarry regulations are becoming increasingly restrictive. For each quarry, the environmental impact is analysed by the French authorities. Lots of things fall within the scope of the environmental quarries’ impact like flora and fauna protection, water protection, water recycling, noise and vibrations reduction, dust, sludge recycling etc. Similarly, the end of quarrying must be integrated from the beginning to anticipate the redevelopment of the site. In France, the average time to obtain the licence to open or extend a quarry is between five and 10 years.” AB
Jim O’Brien on a recent visit to Stevin Rock’s Khor Khuwair 60 million tonnes/year quarry in the United Arab Emirates, the largest limestone quarry in the world
Aggregates demand is growing globally. Jim O’Brien, convenor of GAINTM (Global Aggregates Information Network) and honorary president of UEPG (European Aggregates Association) examines the key facts and figures behind this welcome trend.
In the February/March issue of Aggregates Business, I outlined the membership of the Global Aggregates Information Network (GAIN, www.GAIN.ie) across six continents. In this article, I will summarise the best available data on aggregates production in each region, demonstrating a positive overall global growth.
Regional trends
European aggregates production fell by 30% between 2007 and 2013 due to the economic crisis. It has recovered by some 16% since 2013, bringing the 2017 total EU28, plus EFTA, consumption back to the 3 billion tonnes level of a decade earlier. Growth has continued in 2018. The UEPG data (www.UEPG.eu) exhibits variety in the national production per capita, the EU average consumption being 5.8tonnes/ capita (t/c).
Looking to North America, in the USA pre-crisis production was over 3 billion tonnes, but this declined by 35% to under 2 billion tonnes in 2010; it has since recovered by some 12% to 2.4 billion tonnes, equivalent to 7.5t/c. Consumption continues to grow, with significant pent-up demand in the upgrading of road, airport and harbour infrastructures, making for a positive US industry outlook.
In Canada, production is estimated at 400 million tonnes, equating to some 11.4t/c, driven by its strong economy, varied topography and harsh climate. The Mexican production is estimated at around 500 million tonnes, equivalent to some 5t/c. While the market varies by region, there is significant
national growth potential.
Looking to South America, the Brazilian demand for aggregates had grown by 6.2% annually from 340 million tonnes in 2000 to 745 million tonnes in 2013, before suffering a 33% decline to 497 million tonnes in 2017, due to its financial crisis. This is equivalent to only 2.7t/c, but there is significant growth potential through population increase and infrastructure deficit, so growth in demand of 3-5%/year is expected in the coming years.
Next biggest is Colombia, with a current production level of 147 million tonnes, equivalent to just on 3t/c. Its main challenge is that 50% of the national demand is illegally produced, this challenge being proactively addressed by ASOGRAVAS. Next is Argentina, with a national production of some 140 million tonnes, equivalent to 3.2t/c; although this had grown strongly in recent years, it has recently been affected by economic turbulence.
Beyond the figures mentioned above, very little data is available for the rest of Central and South America, but the total regional demand is estimated at about 2 billion tonnes, which equates to just over 3t/c. The region has very significant growth potential in the next decade, derived from economic growth, expanding populations with low median age, plus major housing and infrastructural deficits.
Looking to Asia, the Chinese national production is reported at 20 billion tonnes, which equates to a remarkable 14t/c. The government is strongly rationalizing the industry, closing down smaller quarries in favour of new super-quarries with production in the range of 5-10 million tonnes or larger. The industry is undergoing an unprecedented
modernization with state-of-the-art environmental controls and rapid evolution in machinery technology.
India probably now has the fastest aggregates market growth in absolute terms at a global level. Its market is now estimated at 5 billion tonnes, equivalent to 3.7t/c, with double-digit growth expected in the years ahead. One of the industry’s main challenges, being actively addressed, is the phasing-out of natural sand extraction from rivers, replacing this with manufactured sands.
Japanese aggregates production is 350 million tonnes, equivalent to only 2.8t/c, a result of its rather stagnant economy. However, reconstruction after recent weather events and the 2020 Olympics are driving current demand. Demand in Malaysia is estimated at 100 million tonnes, equivalent to 3t/c, but with solid growth prospects driven by infrastructural megaprojects. Little data on aggregates demand is available for the other major countries of the region, these including Indonesia, the Philippines, Vietnam, Thailand, Cambodia, Myanmar and the Koreas.
The total regional estimate for Asia outside of China and India is estimated at some 8 billion tonnes, equivalent to some 6.2t/c because of generally strong economic and construction growth in the region.
Another salient feature of this region is the international ship-trading of aggregates, in contrast to the more usual internal supply in developed regions.
Australia has enjoyed 27 years of continuous economic growth, with recent weakness in residential construction offset by strong infrastructural and commercial
Table 1. Best estimates of 2017 global aggregates production and usage in t/c. activity; its production of 200 million tonnes corresponds to 8.3t/c. New Zealand demand of 41 million tonnes represents a healthy consumption of 8.9t/c. For the whole of Oceania, overall consumption is estimated at about 400 million tonnes, equivalent to some 8t/c.
Looking at the continent of Africa, South African production of 150 million tonnes represents about 3t/c. No production data is available for the rest of the continent, but it is estimated at around 4 billion tonnes, equivalent to around 3t/c, a typical figure for the early stages of economic development, with significant growth potential in the years ahead.
In the Middle East, the United Arab Emirates has a total national production of 135 million tonnes from 92 quarries, equivalent to 14.4t/c. The biggest company, Stevin Rock, produces 80 million tonnes from three major sites, including more than 60 million tonnes from Khor Khuwair, the largest limestone quarry in the world. Little production data is available for the rest of the
Middle East region, but is estimated at 2.8 billion tonnes, equivalent to 7.2t/c, due to the ongoing buoyant construction in the region. Russian aggregates production continues to grow strongly, now at 700 million tonnes, equivalent to 5t/c. As the main aggregate resources are remote from Moscow, aggregates are shipped in by train. Little reliable data is available on the rest of the former CIS countries, but the regional production is estimated at 1.5 billion tonnes, equivalent to 5t/c. Production in Turkey, having risen strongly over several years, has declined to 480 million tonnes, still representing a solid 6.3t/c, with renewed growth anticipated in the coming years.
The best-estimated global production figure comes to 50 billion tonnes, which for a world population of 7.7 billion, equates to 6.5t/c (Table 1); the breakdown by region illustrates that a remarkable 66% of global production is in Asia.
The global outlook to 2030 looks positive,
with aggregates production driven forward by three key factors, namely, increasing global population (reaching 8.5 billion by 2030), continued economic development and increasing global urbanisation (reaching 60% by 2030). Accordingly, it is estimated that global aggregates production will increase to some 60 billion tonnes by 2030. Regionally, the strongest growth will be in Asia, particularly in India, with lower but positive growth in Africa and Latin America.
It is quite remarkable that the aggregates industry is still highly fragmented, with the identifiable top 20 players combined producing less than 5% of global production, hence future industry consolidation is likely. The other 95% consists of small and medium-sized enterprises (SMEs), for which accurate data collection is very challenging. Only the top nine players produce more than 50 million tonnes each, the top three leaders being HeidelbergCement, CRH and LafargeHolcim (Figure 1). AB
Liam McLoughlin reports on a key crushing and screening plant optimisation solution designed to enable quarry operators to improve productivity and safety by adjusting their existing plant assets.
Metso is looking to expand its SiteBooster crushing and screening plant optimisation solution from the existing core market in France to the rest of Europe. SiteBooster plant optimisation solutions have been applied to aggregates plants since 2005, but are not yet widely used outside of France, apart from a few deployments in Germany, Norway and Morocco.
The SiteBooster team is located at Metso’s French base of Mâcon and the solution involves a three-stage process for optimising the performance of crushing and screening plant at quarries: comprehensive audit, optimised redesign and professional implementation.
The solution has a variety of use cases. These can include a customer that wants to replace an obsolete machine which is acting as a bottleneck for the plant, to change material or end product, to reduce downtime, or to meet new regulations requiring a reduction in energy consumption or improvements to the safety of staff.
“Instead of investing in a new plant, customers can spend much less money to adjust their existing assets, with the minimum of disruption to production,” according to Bruno Peix, VP systems, aggregates equipment business area at Metso.
He adds that Europe is a suitable region to start with for the expansion as Metso has more local resources able to cover this plant optimisation market.
“We have built a dedicated, fully integrated team [at Mâcon] with process experience and people able to do process layout, quotations and project management,” says Peix. “These people are able to audit the site and take measurements of what customers have in the existing quarries. We do the redesign of what could be better for them.
“There are plenty of quarries that want to invest in new plants. If we can show them
that they can have better productivity or product quality with their existing assets, with just a small amount of money to replace or add one machine, they will buy it.”
Metso sells between 40 and 60 SiteBooster projects a year of different sizes in France, encompassing anything from one machine through to three or four.
Peix says that productivity can be increased with better automation, which can also help crushing and screening plant operators to reduce electricity consumption.
“If the operator wants to increase the tonnes per hour capacity of their crushing and screening plant, we start with an audit and provide a list of recommendations,” he adds. “It can be new crushers or new parts, a conveyor issue being a bottleneck, automation which is not done properly, or how you feed a crusher. Some customers tell us that average capacity is not good, and then when we visit the site we realise that
the crusher runs empty for 30% of the day.”
This under-utilisation of plant can be due to a number of issues, such as poor management of hoppers. When these hoppers fill up to capacity, the upstream conveyors have to stop until the level of the hopper decreases. Conversely, when the hopper is empty too quickly, the crusher downstream has to run empty. All should be well balanced thanks to sensors, automation settings and regulation.
“All this stop and start harms efficiency,” says Peix.
“Once the audit and measurements of the existing site have been done, we deliver everything to the site,” he adds. “The shutdown can be anything from two days to a month, depending on the size of the change. We try to optimise the downtime for the customer for them not to lose too much running time and production.”
An example of a SiteBooster deployment is by Durance Granulats at its Peyrolles
RIGHT: Bruno Peix, VP systems, aggregates equipment business area at Metso
BELOW: A Powerscreen Premiertrak 400X jaw crusher at Whitehall Quarry, the first customer to deploy the new OMNI by Terex crusher plant fleet control system
quarry in southern France. The company produces aggregates used in road and highway surfacing and concrete, and its customers include asphalt plants and concrete manufacturers. The aggregate production at Peyrolles has four crushing stages, and with its 30 staff members the quarry can handle 1.2 million tonnes annually.
Durance Granulats wanted to improve the aggregates production capacity and crushing power consumption at the quarry and achieved its goals by replacing obsolete machinery with Metso MX4 cone crushers. Peix says the end result has been better crushing capacity and easier maintenance access.
“At Durance, like in most of the cases, we try to keep as much as we can and only replace what needs to be replaced to limit investments,” he adds.
The main selection criterion for the MX4 was the maximum feed size. The Durance Granulats team worked alongside Metso to develop the latest addition to the MX cone crusher series, the MX3.
“The MX4 has met our expectations and delivered instantaneous flow rate as well as improved crushing energy efficiency of about 12%,” said Mathieu Kasprzak, director of operations at Durance Granulats. “We have also been piloting the MX3 cone crusher on quaternary stage since April 2018 and we are fully satisfied with its performance and plan to continue with it.”
Another deployment of SiteBooster was in a plant relocation project for a quarry operator in France. Metso helped to move an existing plant the operator had in the west of France to a new quarry site that produces hard rock in the north of the country.
“We supplied brand new primary units and relocated all the secondary/tertiary
plant they had in western France to the new quarry,” says Peix. “We moved three screens with all related steel structures and conveyors dismantled and reassembled at the new site. There were very few additions to the existing plant. There were some small screens to wash the final product that they didn’t have on the previous site.”
He adds that the biggest benefits that SiteBooster can provide for quarry customers are better quality of final product (shape of aggregate) and better capacity.
The first customer deployment has taken place of the new OMNI by Terex crusher plant jobsite control system.
The tablet-based system has been launched by Terex Materials Processing (MP) and is available on equipment from Terex MP’s Powerscreen, Terex Finlay and EvoQuip crushing and screening brands in response to the changing needs of the industry.
The OMNI system is fitted inside the cab of a material feed excavator and provides operators with centralised remote access to multiple machine control systems within a crushing and screening train.
The system is designed to improve jobsite safety and efficiency in the operation of crushing and screening equipment. It features a simple graphic control interface
that is designed for ease of use, and livecamera views from critical vantage points. Each crushing and screening machine in the train can be fitted with up to two cameras, from vantage points such as material transition points, chamber inlets, and material choke level on cones.
The excavator operator can view information from each machine that is connected to the system, make informed decisions about the machine’s operation, and remotely manage the entire machine train with global functions. Powerscreen says that this helps maintain high efficiency and produce the required material specification.
The operator can adjust individual machine metrics or use global features, such as pausing the entire material flow across the train with one action, which Powerscreen says allows unprecedented levels of control from the comfort and safety of the excavator cab.
OMNI also provides alerts that indicate when someone on the ground is making process adjustments.
“We have tested OMNI on up to six mobile crushing and screening units in a train,” says Michael McGlinchey, Terex MP Group Electrical Systems Manager, who leads the OMNI project. “The main advantage is health and safety – everything is centrally controlled.”
By enabling multiple linked plant to be controlled from within the cab, it removes the need for operators to leave the cab and manually intervene when they occur.
“There are a lot of blindspots [for operators] in the junctions from one machine to another, such as the transfer of material from the conveyor to the feeder of the first crusher,” McGlinchey adds.
The primary tablet used in the system is a heavy-duty device equipped with a dust screen. The tablet is read/write enabled and is usually used by the excavator operator, who is the person with overall control of the system. One button on the primary tablet can immediately stop all the feeders if a problem is detected or material flow needs to be interrupted.
OMNI also features the facility for a
Amdurit ® from Ammann protects valuable parts and components up to three times longer than wear-resistant steel. The extended life provides significant cost savings at asphalt, concrete and gravel plants.
• Extended life means fewer purchases of replacement parts and components.
• Fewer replacements greatly reduce labor costs.
• Plant uptime and production are improved.
Protecting your plant with Amdurit is easy. Fastening methods – including welding, clamping and bolting – enable quick installation.
Amdurit is a simple change that can lead to real savings at your plant. For more information on Amdurit and asphalt mixing plants, compactors and pavers please visit www.ammann.com
The tablet-based OMNI by Terex system enables multiple linked plant to be controlled from within the cab of one of the machines
secondary read-only tablet that can be operated by a wheeled loader driver or supervisor to monitor the machines.
On the fleet status page for all machines in the train, the tablet displays the serial number of each machine. This can be changed by the primary tablet operator to any name they choose. The fleet status page also features the fuel level, engine RPM, engine load and hydraulic oil temperature of each machine, amongst other information.
Further data can be accessed by clicking on the icon of a particular machine, including the two camera views. The machine settings for crushing and screening can also be changed to tune the machine to the application and manage the effect of material variability.
If the alarm on a particular machine is activated, the machine’s icon on the fleet status page starts to flash.
Whitewall Quarry near Malton in North Yorkshire is the first customer to deploy the
OMNI system, which is being used to control a newly-purchased Powerscreen Premiertrak 400X jaw crusher that can handle 400 tonnes of material per hour.
Kevin Calvert, quarry manager at Whitewall Quarry said, “We have been testing Powerscreen’s OMNI system and we’re impressed at how we’re able to view working information from live cameras as well as the level of control we have—all from the comfort and safety of the excavator cab.”
The OMNI system is also currently being tested by prospective customers in Scotland, the Republic of Ireland and at another quarry in Yorkshire.
The Scottish site is using OMNI to control a train with a cone and a jaw crusher. “With cone crushers the chamber can often get clogged, requiring the operator to get out of the machine,” says McGlinchey. “Now they can handle the problem by making adjustments while staying in the cab.”
OMNI is now being offered as an option on all Powerscreen crushing and screening machines.
E-Mak’s latest invention is an aggregate factory which takes rock from a quarry, crushes it, sorts the aggregates into sizes and delivers them in the proportions required. Called Megaton, it can be used for aggregate production, concrete production and cold mix production.
Megaton has been designed to operate in major materials production facilities, close to large conurbations. It can be built to serve all or any combination of the applications mentioned above.
“The inspiration actually came from Istanbul, where there is a huge quarry, used by multiple construction companies, which is now surrounded by houses due
to the increasing population of the city. In situations like that Megaton would be ideal,” said Onur Recepgil, brand and marketing manager for E-Mak.
As well as limiting dust, Megaton prevents aggregates from taking on moisture, reducing the energy needed for asphalt production. Due to the controlled environment in which the aggregates are stored, it can also lead to higher-quality materials, according to E-Mak.
The first version of the Megaton will be erected at a quarry and materials production facility in Bursa, Turkey, which is owned by E-Mak sister company Singemat, having made a show-stopping appearance at bauma 2019 in Munich.
The Megaton process sees pieces of rock from a quarry fed through a vertical shaft impactor (VSI) crusher with a capacity of 450 tonnes per hour. The aggregate is then lifted by a vertical elevator into the sieving units to grade the aggregate which is then stored according to its size within the 3,000 tonne-capacity silo. The right combination of aggregate grades can then be delivered directly to an aggregate or concrete plant.
“At the quarry in Bursa we will have two sieving units, one to serve the concrete production and the other for the asphalt production because they require different gradings,” explained E-Mak international sales manager Muhammed Elhatip.
As well as the benefits to the air quality and energy savings due to having dry aggregates, the Megaton could also make production more efficient, said Elhatip. “The machine could run all night, for example, so that you have 3,000 tonnes of clean aggregate ready for production in the morning.” AB
Guy Woodford reports on a new standout hybrid excavator from a leading off-highway machine manufacturer and how some proven rock-loading stars are earning their worth at the quarry face.
The best ideas are said to be the simplest. Volvo Construction Equipment (Volvo CE) has taken this idea to heart with its ingenious new EC300E Hybrid excavator. Unlike other systems that capture the swing energy of an excavator’s superstructure to electrically assist the engine, Volvo CE’s novel hybrid machine harvests ‘free’ energy generated by the down motion of the excavator’s boom and uses it to supercharge the hydraulic system.
The EC300E Hybrid’s powerful and regular boom-down motions charge 20-litre hydraulic accumulators, which then deliver energy to drive hydraulic assist motors that help power the hydraulic pump. The new model offers the same levels of controllability and performance as the standard 30-tonne class EC300E, including the ability to work in ECO mode and Hybrid mode simultaneously.
All this simple and uncomplicated cleverness takes load off the engine, and in the process delivers between 10-12% lower fuel consumption, up to 12% lower CO² emissions – and all with no loss of performance. When used in production ‘dig and dump’ applications (esp. those with a 90° swing), Volvo CE says the payback of this simple approach can be a little more than a year. The machine provides the same levels of controllability and performance you would expect from the equivalent conventional machine and, Volvo CE claims, up to 17% fuel efficiency improvement dependent on application.
Not only is the idea simple – the componentry is too – consisting of just a few add-on components that are simple to maintain.
While not commercially available yet, EC300E Hybrids are currently undergoing field tests at customer sites in order to validate the technology in real-world applications.
With a new Stage V engine, LiuGong’s bauma 2019-showcased 856H wheeled loader brings the Chinese off-highway machine manufacturer’s high-performance model capability to more customers in material handling and aggregate preparation.
A Stage V emissions-compliant machine said to move more for less, the 856H’s carrying and V cycle speeds are said to be consistently high thanks to the machine’s 186kW engine, wet axle, 5-speed transmission and standard lock-up clutch torque converter.
An ergonomically designed joystick further enhances the 21tonne operating capacity, 2.5m³ bucket loader’s operator comfort, while also increasing its overall productivity. Silicone oil shock absorbers improve the ride quality over the roughest terrain and help
prevent material spillage.
LiuGong also highlighted at bauma 2019 its new 890H wheeled loader for the European market. For customer applications which require heavy lifting, the 30.8tonne operating weight, 9m³ bucket capacity loader is said to deliver more power (276kW) for lower consumption.
The 890H’s Cummins Stage 4 engine is designed to develop more power at low speed, maximising torque output. The power shift transmission and advanced load-sensing hydraulics combine to deliver superior breakout force with speed and agility. Efficiency is improved further by the Intelligent Power Cut Off function, which
improves braking and supports the hydraulics in reducing fuel consumption. The 890H also features driver safety and comfort improvements including enhanced dust filtration which significantly improves the cab environment.
Great Tew ironstone quarry in north Oxfordshire, England, has purchased a new top-of-the-range Doosan DL580-5 wheeled loader to help the quarry increase its limestone product output. The DL580-5 carries huge 14-16 tonne blocks of ironstone from the quarry face to a new £1 million stone processing plant that has recently begun production at the top of the quarry.
Great Tew ironstone has a striking brown and blue vein and is only available from this Oxfordshire quarry. Quarried blocks can be used for building and walling stone, architectural details, mullion windows, copings, quoins and flooring. Smaller quarried block is suitable for rockery stone and one-off garden features. The quarry lies on the historic Great Tew Estate, which always quarried block for its own use and in 2000, the quarry was opened further to satisfy a wider demand for this novel product.
Great Tew is part of Johnston Quarry Group, the largest supplier of quarried and mined block stone in southern England. As well as Great Tew, the group owns and operates Sarsden quarry in Oxfordshire, Creeton quarry and Ropsley quarry, both in Lincolnshire, and Oathill quarry in Gloucestershire. The group also runs three stones mines in Bath, Somerset. With the wide choice of building stone and masonry products available, the group supplies over 60,000 tonnes of stone block and 300,000 tonnes of aggregates per year.
Paul Keyte, operations director at Johnston Quarry Group, who is responsible for overseeing the Great Tew, Sarsden and Oathill sites, said: “We are delighted with the boost in productivity provided by the new DL580-5 and the processing plant, which allows us to process up to 100 tonne of stone a day. The arrival of the DL580-5 and the opening of the new plant are both timely and are enabling us to meet a significant increase in demand for our Ironstone products in the UK.”
Equipped with specially matched pallet tines, the DL580-5 brings the large blocks from the base of the quarry to the top and along a short road, at the end of which it loads them on to the sawing machines in the processing plant. Previously, the quarry was only able to move blocks weighing up to a maximum of 10 tonnes, so the arrival of the DL580-5 has made this a much more efficient process.
To take on heavy material handling jobs like this, the DL580-5 features robust structural components and an advanced double circuit axle cooling system to provide an ideal solution for heavier work. This ensures the DL580-5 is ideal not only for block lifting in quarries and mines, but also heavy-duty applications in industrial, construction and recycling operations.
The overall size of the DL580-5 is almost
the same as the DL550-5, the next model down in the Doosan range, but it has an operating weight of 36030 kg and higher static tipping loads (straight/full turn 40°) of 29.7tonnes and 26.2tonnes, respectively.
In addition, the new model is equipped with a series of features that make the machine extremely reliable and durable. For example, the front structure is more rugged, with greater rigidity and strength. The DL580-5 has reinforced Z-bar kinematics for heavier lifting with few moving parts. This design also helps stabilise the loader, enables rapid bucket movements and keeps the bucket at the right-angle position at all times.
The DL580-5 at Great Tew quarry was supplied by Doosan dealer, Filtermech Plant Sales Ltd, based in Wakefield, West Yorkshire, England.
On a 40-hectare quarry in East Java, Indonesia, an SDLG L956F wheeled loader is hard at work moving large quantities of material for road contractor PT Gorip Nanda Guna. The reliable and fuel-efficient wheeled loader is helping reduce operating costs at the quarry.
“We have a huge quarry and our project will take at least 10 years to complete. Therefore, it is very important for us to choose the best and most efficient machines to work on site which is why we chose SDLG’s L956F wheeled loader,” said Gorip, owner of PT Gorip Nanda Guna, which also owns the quarry. “The heavy-duty L956F is powerful and features a large bucket that makes moving materials easy.”
At the quarry in Cukurguling, East Java, the L956F works about eight hours per day and loads 150-200 tonnes of material hourly, with average cycle times of about two to three minutes.
The 5 tonne-rated L956F has a 3m³ bucket capacity and is the smallest of the three F-series wheeled loaders. Powered by six-cylinder Weichai engines, the L956F is one of the newest wheeled loaders in SDLG’s F-series and features an updated frame, chassis, transmission, cabin, engine hood and counterweight.
Onsite since October 2017, PT Gorip Nanda Guna, a Surabaya-based road building contractor, purchased the wheeled loader from PT Indotruck Utama, SDLG’s distribution partner in Indonesia. In addition to the L956F, PT Gorip Nanda Guna also owns a SDLG LG938L wheeled loader. The 3tonne LG938L features a 1.8m³ bucket capacity and maximum breakout force of 73kN.
“The SDLG L956F is a heavy-duty machine that is powerful. The machine has proven to be very tough and reliable and certainly value for money. Its low fuel consumption has greatly helped us to reduce costs,” said Gorip, who, like many Indonesians, uses only one name. AB
At a quarry in East Java, Indonesia, an SDLG L956F wheeled loader is hard at work moving large quantities of material for road contractor PT
The Metso Truck Body is said to be a “groundbreaking” innovation that combines the benefits of rubber and highstrength structural steel
The recent bauma 2019 exhibition in Munich, Germany, saw many new hauling stars get their worldwide unveiling. Guy Woodford reports
The new Metso Truck Body is said to be a “groundbreaking” innovation that combines the benefits of rubber and highstrength structural strength steel, enabling mines and quarries to haul more with less.
Lars Skoog, vice president, Mining Wear Lining & Screening, Metso, said: “Hauling is one of the most cost-intensive components of a typical mining or quarrying operation. In addition to fuel and labour, there’s plenty of maintenance involved too. To ensure cost efficiency, a haul truck should carry as much payload as possible on every round. At Metso, we set out to tackle this challenge and designed a truck body that requires minimal maintenance while maximising payload. The result is a lower operating cost per hauled tonne.”
The bauma 2019 exhibition-unveiled Metso Truck Body is a lightweight, rubber-lined tray designed for off-highway trucks. The elastic rubber absorbs the energy of every impact, preventing it from reaching the frame and thus allowing for a lighter-than-usual, high-strength structural steel frame beneath the rubber. Thanks to this, the body can absorb maximum shock at the lowest possible weight.
Metso has been supplying its tried-andtested rubber lining for haul trucks for several decades with eye-catching results, both in reducing the need for maintenance and
every one or two years, or repaired, which gets expensive,” Skoog explains.
“The Metso Truck Body provides an unprecedented solution that is both light and durable. The rubber lining and high structural strength steel frame have been engineered in a seamless process, utilising the best qualities of both materials,” he continues.
A typical Metso Truck Body is said to weigh 20-30% less than a traditional steel-lined truck body. Depending on the application, this translates into a payload increase of several tonnes.
The Metso Truck Body is available globally for all major off-highway truck models used in mining and quarrying. Several lining options ensure application-specific fit, even in operations that struggle with problems such as carry-back.
Terex Trucks launched its updated TA300 articulated hauler at bauma 2019. The TA300
to traditional steel lining, half the noise, and 97% less vibration. The new Metso Truck Body innovation is said to take this concept to another level by combining the wear protection and working environment benefits of rubber with the payload-maximising abilities of a lightweight body.
“Many mines or quarries prefer lightweight truck bodies because they enable the carrying of more payload. However, the problem with these traditional lightweight bodies is their lack of durability - they often need to be replaced in
which comes with two additional forward gears – eight in total – as well as four reverse gears. This helps to ensure smoother gear shifting and thereby superior operator comfort.
In addition to this, the TA300 now delivers a claimed 5% improvement in fuel efficiency, as well as enhanced performance, productivity and operator comfort. It also now comes with long-life transmission fluid, which has helped to increase the length of time between oil maintenance intervals from 1,000 to 4,000
The hauler’s maximum speed has also increased to 55km/h, up from 50km/h. Terex Trucks says that ultimately this means customers can achieve faster cycle times, reduce the cost of operation per tonne and minimise their fuel consumption.
“The TA300 is one of our staple products, hence why we worked long and hard to make it even better for our customers,” said Terex Trucks MD Paul Douglas. “The upgraded TA300 was rigorously tested for nearly two years internally and by operators on real job sites, working in a variety of conditions.”
The new Map feature on Volvo’s updated Haul Assist application now allows operators to monitor the hauler traffic around a quarry or mine site and proactively adjust their driving according to traffic conditions, especially around load and dump zones.
Operated via Volvo Co-Pilot — the award-winning in-cab interface with a 25.5cm-high-resolution touch screen — Haul Assist’s Map functionality allows operators to not only identify their position but also the position of other haulers fitted with the technology. This knowledge comes into its own on sites with restricted visibility, allowing operators to see where the other haulers are, a feature that should reduce potentially dangerous situations. In all circumstances, being able to monitor traffic flow helps operators anticipate the optimum arrival time at load or dump areas and avoid congestion and waiting times … the best way to improve overall site efficiency.
The application works by using the hauler’s in-built GPS function for positioning purposes and combines it with a digital connection via Volvo Co-Pilot to communicate with other machines. The system can also record how fast the hauler is travelling and emit an alert to remind operators to maintain a safe working speed.
The Map function can plot out haul roads and preferred routes to help operators navigate their way around the site. It can highlight when the hauler is approaching a pre-defined
section of narrow or single lane road, and even visualise meeting/passing areas. The map can also highlight any reference points or notable areas of the site.
Load and dump zones can not only be visualised on the map, but can also trigger certain sub-functions, such as activating on-board weighing information. On-board weighing helps to optimise the haul cycle by ensuring every hauler journey moves the correct payload. The highly accurate system eliminates under-loading for good productivity and overloading that increases machine wear and fuel consumption.
LEFT: A screen shot of what is recorded by Command Alkon’s Scale Watcher BELOW: A truck hooked up to Scale Watcher
Weighing technology solutions can supply big efficiency gains for shrewd quarry operators. Guy Woodford reports.
Assets and equipment are the backbones of any quarry business. The ability to account for them is crucial to productivity, efficiency, and cost control. Efficiency is a critical competitive advantage for a small profit industry like aggregates processing, and accounting for assets saves time and makes many processes more streamlined and faster. It also helps to reduce instances of stolen materials and other problems that lead to higher costs. Another key value point is customer service. Customers are able to understand the location of the materials that they have purchased and the approximate time of when those materials will be on the road.
Command Alkon’s Scale Watcher is the next generation of hardware and software to provide photo and video verification of a quarry truck’s weighing process. Scale Watcher is an integrated photo verification tool that overlays ticket information onto a photo of a truck on the scale. This image is then saved in a PDF, HTML or other imagefriendly format by ticket number. The ticket number provides easy retrieval of image to email to customers. Scale Watcher provides you and your customers proof of vehicle pick-up without signatures.
Quarry sites house many extremely valuable and expensive assets. Criminals see these materials as prime targets to take and resell. Not only does theft cost you money and take a huge chunk out of your bottom line, but it also halts production for significant periods of time. With Scale Watcher, an optional Gate/Valve anti-theft module alerts authorised personnel of potential theft of
materials. The anti-theft module sends an email alert to one or more designated addresses whenever the gate/valve is opened and closed on a loading system and a ticket is not printed. The gate/valve antitheft module is not reliant upon the scale or software to function and will work after hours when the plant is shut down.
The Scale Sensing feature will send an alert if a truck has left the scale, but no ticket was generated; the tare weight is above the set threshold; the gross weight from the scale does not match that printed on the ticket; the weight on the scale exceeds the truck GVW (gross vehicle weight); or the ticketing system loses connection with the scale indicator.
Scale Watcher in action
Each vehicle is issued a hand-held RFID (radio frequency identification) badge. The Apex system stores all of the information required to load each vehicle, including configuration (single or double trailer), target weights for each trailer, maximum GVW, billing information, etc.
When a truck pulls into a loadout lane, the driver presents the badge to the RFID terminal mounted at cab height. The driver will confirm his assignment on the terminal or contact the loadout operator if his assignment information needs to change. Once confirmed, Apex will capture the tare weight and communicate the lane ID and target weights for this vehicle to the loadout PLC (programmable logic control).
The operator will lower the spouts and initiate the loading. The scale configuration allows the PLC to load a front and back trailer simultaneously with independent target
weights. Once the loading is complete and the spouts have been raised, the PLC will set the appropriate status and Apex application will capture the final gross weight and print a delivery ticket at the appropriate remote printer.
At the time the ticket is printed, the Scale Watcher module will store the video capture from two cameras, with an overlay of key ticket data values, as a PDF image that is indexed by ticket number for easy retrieval in the Apex application. An additional image of the printed ticket is stored in the ECM (enterprise content management) system.
The ability to deliver proof of pick-up to customers gives them peace of mind to know that the amount of materials they have ordered has made it through the first step of the delivery process. Site-automation technologies, such as Scale Watcher, deliver impressive improvements in the speed and efficiency of operations and help to control costs.
Like any industry, the aggregates world has its own set of specific requirements. Avery Weigh-Tronix’s Mark Wilcox tells Aggregates Business there are 10 key considerations you should bear in mind when choosing a weighbridge supplier.
Think about the way you plan to use your weighbridge both now and in the future. The right supplier should be able to help you maximise your investment by specifying a solution that completely fits your business and its growth plans. This may include optimising or modifying your existing weighbridge operations before even having to make a purchase.
How many years do you expect to use your weighbridge for? Most quarries are looking for 20 years of use to maximise their investment. However, if this is your expectation the weighbridge must be built to cope with a constant flow of heavy goods vehicles carrying up to 40 tonnes at a time. With potentially millions of tonnes passing over a weighbridge during its lifetime, a concrete deck plate can easily cope with heavy loads and build features such as fully welded bottom plates increase weighbridge durability.
Customisation options are important elements of the decision-making process and are vital to ensuring your weighbridge fits your business needs. Weighbridge size, capacity, load cells and even paint finish can all be customised to suit your operations. Dust residue is a common problem for weighbridges situated in quarries. Customisation options like T-rubbers close the gaps around the weighbridge deck to stop dust ingress and prevent dust build-up from giving inaccurate weight readings.
In the event of your weighbridge not working, how much time can you afford to lose? Look for a supplier who can offer service plans which maximise uptime and guarantee your weighbridge is in full working order and legal for trade again as soon as possible. Your weighbridge supplier should offer
An Avery Weigh-Tronix technology-incorporating weighbridge at Hanson’s Whatley Quarry in Frome, Somerset, England
preventative service and maintenance from qualified engineers to minimise your risk of downtime. When introducing external workers onto site, it’s imperative they know the dangers of working with aggregates and have experience and training of how to work safely in this environment.
Common problems from badly designed weighbridges include load-cell failure, or inaccurate weight readings due to lack of drainage or a build-up of spoils around the load cells. Although it’s always advisable to regularly clean your weighbridge and have regular maintenance, the right design for your usage and environment can go a long way to minimising the risks of downtime. Design features such as load-cell inspection covers keep load cells safe from harm including dust ingress. While restraining systems prevent excessive rocking when heavy wagons drive onto the weighbridge.
Reputable weighbridge manufacturers should be able to demonstrate the quality of the key components and materials used in their weighbridges. Weighbridges should be manufactured in line with recognised ISO standards, covering the full traceability and quality of the steel, as well as the competence of in-house automated welding. Another consideration is the manufacturing country as this could impact on stock availability, lead times and shipping costs, especially post-Brexit.
Customer testimonials
Nothing says ‘you’re doing a good job’ more than a customer willing to say how
much they value your product. Look for a weighbridge provider who has customer case studies and reviews on their website from other aggregates producers or can point you in the direction of some previous happy customers who are willing to share their experiences.
Total cost of ownership
A weighbridge is a big investment and cost can often be a deciding factor when choosing a supplier. However, a lower initial price can often lead to a higher overall cost when looking at the lifetime of the weighbridge. Instead, choose a supplier who can help you unlock the value in your weighbridge, through future-proofed plans and configurable options.
Weighbridges can come with a long list of peripheral equipment, including unmanned terminals, traffic management systems and automatic number plate recognition (ANPR). Ensuring all these different components work seamlessly together can be difficult, so choosing a supplier who can provide the full weighing solution makes the process simpler and means one point of contact if anything goes wrong.
Investing in the right supplier can see your weighbridge last years and grow with the changing needs of your business. Look for a recognised name in weighbridge production who has a proven history and strong track record when it comes to delivering quality products and service. It is important that whoever you choose will be around to support your business over the lifetime of your weighbridge. AB
Trimble showcased its state-of-the-art Connected Quarry solution at the recent bauma 2019 exhibition in Munich, Germany (8-14 April). A key element of the solution is the company’s LOADRITE LR360 connected loader scales for quarry loadout.
Speaking to Aggregates Business during bauma 2019, Jérome Thomas, Trimble’s regional LOADRITE sales manager for France and the UK, explained how the LR360 reduces quarry rework and miscommunication by wirelessly synchronising data between the loader and the scale house. As the empty truck arrives its weight is recorded as material request data is being entered in to the POS (point of sale) system. The job details are wirelessly transmitted to the loader and displayed in the cab in a prioritised list. When the job reaches the top of the list, the loader operator can go to stockpiled aggregates material, identify the truck from the ID and load accurately against the target weight. On completion of the job, the data is returned to the scale house and billing is automatically adjusted before the truck arrives to tare out. The quarry manager can see loadout operations in real time with a clear view of workload, productivity and performance.
“As well as the loader, the LR360 system
can also be added on to a dump truck – for further payload weighing analysis,” said Thomas. “We can also create a geofencing capability at the quarry, so users can find out how many tonnes of a particular pit material source has been loaded and how much of it has been taken to a stockpile or the primary crusher. It can track all a truck’s movements, including how much time a truck is spending in a loading area, how much time it is taking to load, how much time it is travelling. This helps operation teams find out whether they have any machine efficiency issues.”
Thomas said that he was working with a customer who had installed Trimble’s complete Connected Quarry system on their site. “They had been using an old 45-tonne excavator and were thinking about purchasing a 75-tonne excavator. We’ve managed to show them through Connected Quarry that their excavator is loading 60% of its work time. When it’s loading, it’s loading an average of 370 tonnes of material an hour. So, we said ‘Is it worth investing in a
going to invest in a new 50-tonne machine which will perform better for them. This shows how our solutions can help with identifying both the correct loader or truck sizing for a job site and how a customer can go about maximising productivity.”
Despite being long-established in the mining sector in South Africa and other countries, the LR360 system is said by Thomas to have been adopted by aggregates quarry operators over the past two years. “We are attracting a lot of customers in Europe. In France, for example, we have 12 quarries using it. For a small site, you can do away with the gate house and the weighbridge as the LR360 scale can be legal
for trade. It also helps on big quarry sites which have 500 to 600 truck loads a day and you don’t want trucks idling while they wait to receive material from a stockpile. The LR360 gives you faster turnaround of trucks by offering a clear visibility of what’s happening.”
Another key part of Trimble’s Connected Quarry offer is its InsightHQ quarry management portal for web browsers and mobile devices. It shows near real-time productivity, availability and performance dashboards and reports for extraction, processing and load-out. To view changes over time, users can adjust reports to suit either the shift, day, week, month or year.
Thomas said the fastest adopters of the Connected Quarry offer have tended to be mid-sized quarry operators, due to their ability to make quicker investment decisions than larger businesses containing a bigger executive management structure.
Trimble is also looking to increase the number of quarry operators using its Groundworks drilling system. The system is said to pay for itself in just four months by drilling to exactly the depth you need, reducing overdrilling and prolonging the life of drill bits and hammers. Groundworks is also said to drill evenly spaced holes and angles, creating an even blasting pattern that delivers better surfaces and improved rock fragmentation, leading to reduced hauling costs.
Trimble Groundworks is also said to increase site safety as users can see machine blind spots and warn the operator when he’s working where he shouldn’t be. The system also reduces time and money spent on site surveying.
“We are looking closely about who we
need to be targeting for this system as quite a few quarries sub-contract their drilling and blasting work,” explained Thomas.
Already proving a hit with many civil engineering contractors and construction companies globally, Trimble Stratus is Trimble’s drone data processing system that Thomas believes can also benefit quarry operators. Its software can help quarry managers use drones to map, measure and share accurate information about their worksites and machine assets. This may include calculations of aggregates stockpile inventory, proof-of-site topography changes, haul-road berm monitoring and quarry mineral reserves assessment. With Stratus, Thomas explains, users can make quicker decisions, avoid mistakes and grow profits by always having the right information to hand.
“To create Trimble Stratus, we have partnered with an Australian [drone data and analytics technology] company called Propeller,” explained Thomas. “It’s having a phased introduction and our distributors are currently being trained in its capabilities. It has huge potential for quarry operators. A good sales guy calls in with a big new aggregates order and can accurately be told the timescale with which it can be met, and which sites can provide the material. If the new big order is going to become a regular order, Trimble Stratus can help the firm in question properly plan how it can be met.” AB
OEMs have been pushing off-highway electric power with the unveiling of exciting new plant. Smaller machines, such as miniexcavators, smaller rollers and compact wheeled loaders, seem more suitable for electrification, particularly when working in urban environments. They are not only emission-free at source but are also extremely quiet. The current battery technology can meet their relatively modest demands for power along with adequate access to charging capacity.
“Diesel will remain a significant power source for the aggregates industry for some time yet,” says Steve Nendick of Cummins
This year’s bauma expo in Munich saw the launches of a host of fully electric machines including dumpers and excavators, but what does this mean for the future of diesel?
Steve Nendick, marketing communications director at engine manufacturer Cummins, assesses the future of diesel power in an increasingly electrified off-highway sector.
Looking at the off-highway sector you would be forgiven for thinking that the age of full-electrified plant machinery is upon us. This year’s bauma show saw the world’s leading original equipment manufacturers (OEMs) unveiling a diverse range of fully electric machines from dumpers to excavators. Indeed, Cummins, synonymous with diesel power, celebrated its 100th birthday at the show with a fully electric mini-excavator prototype showcased on our stand.
So, what does this mean for diesel and does it remain as the go-to power solution for the aggregates sector?
Emission legislation has become progressively stricter, as seen with the introduction of Stage V at the start of the year. There are also the tough new ultra-low emission zones in major cities like London, part of a wider, radical anti-pollution policy. Engine manufacturers have met this challenge by refining diesel engine technology, to give a total reduction in NOx of 96% and particulate matter (PM ) of 97% since regulations began. In real-world operation, the emissions are so low it is a challenge to actually measure them.
But it’s not just about meeting emissions, we are pushing the diesel engine onto the next rung of its evolutionary ladder, and not compromising on performance. Cummins’ new Stage V suite of engines, ranging from 3.8-9 litres (75-321 kW), has reduced weight, size and complexity, yet they deliver on average 10% more power and 20% more torque than their Stage IV counterparts. OEMs and end users benefit as they have an opportunity to increase the capability of their existing machines or select a smaller engine with higher performance – saving weight and money. This makes a compelling case for operators to retain ultra-clean diesel power as their go-to power source.
Cummins is investing in a diverse range of power solutions including clean diesel, hybrid, electric, natural gas and fuel cells. We recognise that it is not ‘one-size-fits-all’, and we will need to work with customers to define the best solution for their equipment. The optimum solution is largely dependent on the duty cycle of the machine. Whichever solution is applicable, we will bring it to market in a dependable way, just as we have done with diesel for 100 years.
For larger, more remote-working, more power-hungry machines, as used in the aggregates industry, then only diesel engines can realistically match the performance - for the foreseeable future at least. A 20-tonne excavator can use 480 kWh in an average working day in a quarry and even the most advanced lithium-ion batteries don’t deliver nearly enough power density required to both power the machine and be effectively installed within its body. Similarly, diesel-powered applications can run continuously up to 20 hours, with multiple intervals of peak power, before being refuelled in-situ via a bowser.
The happy medium for larger plant could be diesel-electric hybridisation, especially for applications working in urban environments
with low emission zones. This marriage of battery power and compact engine-generator gives operators much more flexibility where charging infrastructure is not easily accessible during a working shift. It delivers a good balance of lower emissions, lower fuel consumption and lower noise without impacting operational efficiency.
The expectation is that battery technology will increase in capability while reducing in price. This is why Cummins has invested in battery companies (Brammo and JMBS) to be ahead of the curve. Until this happens though, the business case for electric doesn’t quite stack up, and diesel will remain a significant power source for the aggregates industry for some time yet. AB
Volvo Penta had much to get revved up about at the recent bauma 2019 exhibition in Munich, Germany. Aggregates Business editor Guy Woodford caught up with Björn Ingemanson, Volvo Penta president, and Andreas Viktorsson, Volvo Penta chief project manager, at the show to get the inside track on what lies behind the ambitious Volvo Group company’s rapid growth in its off-highway engine sales.
Volvo Penta has increased its annual off-highway equipment engine sales by a highly impressive average of 45% in the last three years. There is a significant factor behind this, as Björn Ingemanson, Volvo Penta president & CEO, explains, “The majority of our annual sales were traditionally on the marine side of the business - around 70% marine to 30% industrial (including off-highway equipment). Then, around eight years ago, we took a decision to really invest a lot in our planning for Stage IV Final emissions-compliant engines and focus on the industrial side of our business. We acquired more than 100 new OEM [original equipment manufacturer] relationships. In a short time just before Stage IV was going to be launched [in 2014], we gathered them all and showed them a lot of our engine prototypes. Soon after, our off-highway equipment orders exploded
into life. We’ve kept all but one or two of these OEMs with us and acquired new ones with the launch of our Stage V emissionscompliant engines range.”
Volvo Penta’s Stage V emissionscompliant engines are said to have proven extremely promising in field tests, boasting fuel consumption reductions of up to 5%, compared to their Stage IV predecessors. This not only reduces CO² output but also the total cost of ownership.
With a power range from 105 to 585kW, Volvo Penta Stage V engines (D5, D8, D11, D13 and D16) are said to be specifically engineered to give customers optimum productivity, uptime and total cost of ownership, and are developed to offer ease of installation, operation and maintenance.
The Volvo Penta Stage V range provides improved productivity through an engine and exhaust aftertreatment system that has been designed to work seamlessly. Among other
claimed benefits, this maximises passive regeneration during normal operation and, therefore, removes the need for stand-still regeneration. Uptime has also been boosted by improved oil change service intervals, which have been doubled from 500 to 1,000 hours. In addition, Volvo Penta has championed ease-of-installation by ensuring commonality between different emission levels.
Ingemanson said, “I think customers see us as a premium brand offering high quality and a reliable engine. With regards to Stage IV Final, customers liked our compact solution which uses SCR [selective catalytic reduction] technology without the need for a DPF [diesel particulate filter].
“It was good that we didn’t just look for add-ons with our Stage V solution, and really developed the aftertreatment system in sync with the engine. It meant we got something that really gave us something good in terms
“I think customers see us as a premium brand offering high quality and a reliable engine”
“There will be continued tougher emissions legislation and alternative cleaner fuel development. There is also the ongoing focus on the electrification of construction and quarrying equipment, which is a topic being discussed more and more by our customer OEMs.”
In addition to its new Stage V off-road engine solutions, Volvo Penta has also recently unveiled its first Stage V engine for mobile gensets: the D16. The D16 is a neat and compact engine with lower maintenance requirements. It is said to deliver around 3% better fuel economy (versus Stage IIIA), providing improved total cost of ownership.
Gothenburg’s first all-electric ferry and is a significant step in the company’s plans to offer electrified power solutions to both the industrial and marine segments by 2021.
“We look what is done around engines for the trucks side and the bus side of the Volvo Group business and see what would fit our industrial and marine OEM customers,” said Ingemanson. “The implementation will happen step-wise on the basis that the business case for switching to electric will differ across our many customer segments and applications.
of lower fuel consumption. Our Stage V offer also stands up very well, from early analyses, against competition.”
“I think customers like the fact that we are a smaller company within a bigger group. They like the benefits of group experience and, from the other end, our agility,” said Andreas Viktorsson, Volvo Penta’s chief project manager.
“We started our Stage V engines project four-and-a-half years ago, but the journey to develop the off-highway engine side of our business, as Bjorn said, started much earlier than that, with the development of engines without DPF.
“Customer focus has also been key in enabling us to cope with growing demand for our off-highway engines.”
Ingemanson believes that Volvo Penta has a firm base from which to pursue further
Running parallel with the evolution of its diesel-powered engine solutions is Volvo Penta’s leveraging of the strength of the Volvo Group to bring innovative technology to land and sea. The company has embarked on its first industrial OEM electromobility partnership by signing an agreement to design and deliver an electric driveline for Rosenbauer, a world-class fire-service vehicle manufacturer to which Volvo Penta already supplies Stage IV/Tier 4 Final and Euro VI diesel engines. In a system delivery approach, Volvo Penta will develop the electric driveline in Rosenbauer’s first electric truck due for launch in 2021.
This strategic partnership follows
“We are looking at a couple more projects on the off-road engines side of Volvo Penta, but it’s hard to say when they will reach the stage of being commercially viable.”
Ingemanson admits that top global off-highway engine market manufacturers are likely to have to invest more funds into their research and development (R&D) to achieve all goals within their growing project portfolios. “I think all players will have to invest more to meet all their competing project commitments. It’s a big challenge for everyone.
“R&D is the biggest department of Volvo Penta today. We have doubled our R&D investments in five years. We need to continue to grow and it’s very pleasing, looking back, that our strategy to focus
Caterpillar, Kohler and Deutz showcased their latest off-highway engine solutions at April’s bauma expo in Munich. Liam McLoughlin reports.
Caterpillar unveiled its reconfigured C13B engine at April’s bauma expo in Munich. Previously announced for the agricultural sector, it has now been adapted for the aggregates and construction industries with an engine-mounted after-treatment package.
Compared to its predecessor in the category, Caterpillar said that it has increased the C13B’s power output by 20% and torque by 19%. These improvements make it the equivalent of a 15-litre powerplant, according to the company.
Additionally, the after-treatment package is 65% smaller and 63% lighter than its predecessors. Caterpillar has also reduced the number of interface connections between the engine and after-treatment package by around 50%. The C13B is “excellent for a range of applications, including rockcrushers, screeners, rock drills, piledrivers,
chippers and grinders,” said product marketing manager for the nine- to 13-litre market, James Schnuriger.
A variety of energy sources are available on the market. Rather than investigate their different applications and individual characteristics in order to set them up in competition with each other, US manufacturer Kohler says it has chosen to
Kohler’s K-HEM unit features a KDW 1003 18kW diesel engine and a 48-volt electric engine
integrate them, to pair them with each other, so as to reap all of their potential value.
The company says this is the philosophy behind its K-HEM unit that generates power using a combination of a KDW 1003 18kW diesel engine, compliant with Stage V standards and without a DPF, and a 48-volt electric engine that guarantees 15kW of peak power and 9 kW of continuous power. This means that the unit is capable of providing over 30kW without the need for exhaust gas after-treatment systems.
Also at bauma, German engine maker Deutz exhibited its advanced configurator, a new modular product system that offers flexible combinations of alternative drive solutions. The advanced configurator gives customers the optimum combination of conventional and electric drives, according to Dr Frank Hiller, chairman of the Deutz board of management. AB
attractive business opportunities for
In March 2019, Terex Corporation announced a new £12 million (US$15.38mn) manufacturing facility located in Derry, Northern Ireland.
The new 9,755m² facility will focus on the design, manufacture and development of product lines for Terex Ecotec (waste management and recycling) and Terex Conveying Systems (TCS) mobile conveying.
The site purchased for the new facility, which will be operational later this year, consisted of an existing building and ground area that needed redeveloping to meet Terex’s operational and manufacturing requirements. This included the processing of construction and demolition waste which resulted from site clearance of old blockwork and building rubble from internal walls, and concrete and plinths from the yard.
This waste material provided EvoQuip’s Cobra 290 impact crusher with the perfect opportunity to demonstrate its capabilities by crushing the material to be reused instead of sending it to landfill—saving money and reducing the environmental impact.
The material was initially broken up by an excavator and rock hammer and then processed through the Cobra 290 to create a usable product, which was then used as a base layer on the site for new concrete roads that are strong enough to handle the expected number of trucks.
Kieran Devlin, operations manager at Terex Campsie, said: “The Cobra eliminated the need to purchase new material for the road base layer and also meant we did not have to pay to send material to landfill, resulting in great financial savings for us and reduced the environmental impact.”
The Terex Campsie site clearance generated over 650m³ of inert waste material—material that would have ended up in landfill if it had not been processed by the Cobra 290.
The environmental impact as a result of processing on site was greatly reduced, as it eliminated the need for virgin raw materials, significantly reduced the number of lorry movements, and avoided the need to dispose of it in landfill, causing land pollution.
Compared to the cost of disposing unwanted material in landfill, including the landfill tax that would generate, lorry hire and importing stones for blinding, hiring a Cobra 290, stockpiling rubble, loading the crusher, depositing material on site, separating out rebar, salvaging rebar, removing non-crushed concrete for disposal, and reusing surplus, generated financial savings of around £9,000 (US$11,440).
Alongside being better for the environment, this short project proved to be better on the pocket.
Successful recycling requires both process efficiency and fuel economy to become a profitable operation. German recycler H. Scheer boosted its competitiveness by changing an old, portable plant to a modern combination of Metso Lokotrack jaw plant and a mobile screen.
“Both fuel economy and crushing efficiency have taken giant steps ahead during the past 20 years. Our NW100 portable plant consumed more fuel than our new units, LT106 jaw plant and ST3.5 mobile screen together,” comments Markus Scheer, machine operator at the German recycler H. Scheer.
“We are happy to run the new Metso Lokotracks that seem to function well. As a bonus, we are reaching now 20-30% more capacity using modern, track-mounted Metso equipment,” he adds.
H. Scheer, based in the picturesque village of Spenge in North Rhine-Westphalia, can be described as a full-blooded family company. Founded in 1979 by Harald Scheer, the company has been expanding its activities from transporting of materials and container service to a complete offering for recycling.
Today, the company is steered by three women. Christel Scheer has the managerial position, and her daughters Bianca Scheer works as accountant and Christina Eckel as operations manager.
In addition, the family’s two brothers Markus and Volker Scheer work as machine operator and truck driver within the company.
H. Scheer used a Nordberg NW100 portable jaw unit for almost 20 years. as their main crusher for recycling. During the time, over 18,000 crushing hours were accumulated.
In April 2017, the swift changeover from the old, portable plant to new, tracked units was made. To carry on the recycle crushing and screening process, a LT106 jaw plant and ST3.5 mobile screen were selected. Both units were sold by Fischer-Jung Aufbereitungstechnik, Metso’s distributor in Germany.
In the recycle process, the feed material including concrete blocks and bricks, is fed to the LT’s C106 jaw crusher. A closed side setting of 30mm is used. After crushing, a steel wire mesh-equipped ST3.5 unit screens
German recycler H. Scheer improved the firm’s competitiveness by changing an old, portable plant to a modern combination of Metso Lokotrack jaw plant and a mobile screen
the material. A second mobile screen is used for fine screening when needed.
The end product range of H. Scheer includes 0-8mm, 3-7mm, 8-16mm, 0-45mm and 40-80mm grades. The clean, recycled products are used as different kind of base materials for building purposes.
The combination of LT106 and ST3.5 only consumes about 28 litres of fuel/hour while the NW100 alone took over 30 litres. Average capacity has grown 20-30% up to 150 tonnes/hour, respectively.
“In addition to the good fuel economy, we are very pleased with the Metso IC700
received a major boost in its operational productivity and efficiency after acquiring a QJ341 tracked jaw crusher from Sandvik. The plant has impressed all at the company with its reliability, effectiveness and ability to crush asphalt and tarmac even in warm weather.
“We’ve used various crusher brands over the years, but from the initial demonstration the QJ341 was very good. It did more than I was expecting it to do, and we got a lot greater output with it,” says SJ Walchester managing director Steve Walchester. “The different functions on the crusher are very
wages and revenue. That is not to mention the damage to our reputation which is based on supplying customers with a high-quality product, when they need it, at a fair price.”
With that in mind, Walchester decided to take the Sandvik Security+ Gold service agreement when he purchased the machine. This is Sandvik’s extended warranty programme offered through a service agreement which lasts for a duration of two years with the Gold+ package. Through four inspections throughout the year, preventative maintenance and inspections are carried out by a qualified engineer to ensure the unit is
To meet rising customer rock,
and asphalt product demand,
““My service and support experience are that Sandvik is second to none. We had a problem the other week; I phoned Sandvik and within three hours Sandvik was on site and had fixed the problem.”
variety of sources. The arisings mainly come from demolition work, with the materials consisting of demolition waste, reinforced concrete, bricks and 300mm lumps of asphalt. Much to Steve’s and his teams delight, even the latter has proved not to be a problem for the QJ341.
“I’ve used crushers from other manufacturers on asphalt and tarmac, and the QJ341 is the only jaw crusher I’ve experienced which will process it without problems. This is by its very nature sticky –especially when it melts in summer – with the hot conditions we experienced last summer being a case in point. Our previous crusher wouldn’t touch it and kept jumping the jaws. The QJ341 is simply able to be put into reverse and crushes as well as it does when set ‘forward’.
“We are the only company in the city (Stoke-on-Trent) with a crusher that is able to deal with asphalt and tarmac. This has meant other demolition and road maintenance companies bringing their asphalt and tarmac to us for recycling. The Highways Agency is one of our regulars!”
Austrian compact mobile crushing plant manufacturer RUBBLE MASTER has built up
a strong global recycled aggregates customer business. Gerald Hanisch, the company’s chief executive officer, believes the next few years will see a worldwide increase in onsite aggregates recycling. “There are smaller sites and especially remote sites where it pays to recycle onsite. Laws and legislation also influence recycling substantially. Regulations will support aggregate recycling and establish a stable market which will lead to further growth.”
To crush increasing amounts of asphalt, concrete and natural rock to meet rising customer material demand, Swedish company Tommy Nordbergh Maskin & Transport AB (TNMT) has switched from using RUBBLE MASTER’s RM 80GO! impact crusher to the larger RM 120GO! fitted with an RM MS125GO! screen.
The company’s new RM 120GO! with RM MS125GO! is also fitted with the RM GO! SMART digital solution, an optional hydraulic hammer changing system and a steep conveyor belt.
The RM MS125GO! is a mesh deck screen featuring a hydraulically pivoting refeeding belt, giving customers greater flexibility in daily operation. This allows TNMT’s RM
120GO! with RM MS125GO! to crush and screen in a single pass. RUBBLE MASTER says the RM MS125GO! guarantees precise screening of any required size material from 0-65mm.
The RM MS125GO! model’s hydraulically pivoting refeeding belt transports oversize grain either to the stockpile or back to the crusher in a closed circuit. With the aid of a handling frame, RUBBLE MASTER says the screen can be fitted to the machine in less than 15 minutes. The added presence of an RM screen tensioner allows rapid changing of the screen when other grain sizes are required. Owing to the frequent changes between types of feed material, the use of a hydraulic hammer changing system is also said to be proving a worthwhile option for TNMT.
The RM GO! SMART digital used by TNMT while operating its RM 120GO! is making the firm’s performance analysis, crusher maintenance and spare parts management even easier. This intuitive tool provides live data at any time on the machine’s status, daily reports and, in the event of problems, instructions on remedying the fault direct to a smartphone or tablet.
Around 40% of the material crushed and screened by TNMT’s RM 120GO! is concrete and 40% is asphalt, while natural rock accounts for the remaining 20%. Since recycling asphalt and concrete is the company’s main business, TNMT’s choice of an optional even more wear-resistant crusher lining and a steep conveyor belt for the RM 120GO! is said to be paying off. The steep conveyor belt improves the separation of steel from the feed material and the lower wear extends the service life of the belt.
TNMT’s vision and business concept are very similar to those of RUBBLE MASTER. Both aim to always be first choice when orders are placed and to always exceed customers’ expectations. To deliver on this in Sweden, RUBBLE MASTER relies on its sales partner, OP System. AB
German track-mounted mobile crushing and screening plant manufacturer Kleemann has ambitious global growth plans after a period of significant inward investment. Guy Woodford visited the company’s HQ to learn more.
Innovation, operator safety, simple handling and optimal performance are said by Kleemann to be the four key pillars on which the company designs and manufactures its plant range. Elements of all four can be seen in the MOBICONE MCO 9 S EVO plant I am looking at during my tour of Kleemann’s state-of-theart manufacturing and assembly facility at the company’s HQ in Göppingen, a town around 30 minutes’ drive north-east of Stuttgart in south-west Germany.
Kleemann moved to its new HQ in 2009, three years after being acquired by the Wirtgen Group. A major site expansion project in 2016-17 increased plant assembly capacity by 50%, warehousing capacity by 100%, and created additional outside parts storage space. The same project included a big additional parking lot for the rapidly growing 500-plus HQ workforce. The whole HQ site now covers 150,000m² and includes the 45,000m² manufacturing and assembly facility (10,000m² of which is under a roofed area), and the 4,000m² office building. It has allowed the company’s development, construction and distribution capabilities to be housed efficiently under one roof.
An entirely track-mounted mobile crushing and screening plant manufacturer since 2012, KIeemann’s current direct-drive range of diesel or diesel-electric powered models comprises seven 220-1,200tonnes/ hour MOBICAT mobile jaw crushers, five 350-700tonnes/hour MOBIREX mobile
impact crushers, two 300-400tonnes/hour MOBIFOX secondary impact crushers, six 270-650tonnes/hour MOBICONE mobile cone crushers, and 10 200-800tonnes/hour MOBISCREEN mobile screening machines.
All Kleemann crusher plant is manufactured, assembled, tested and qualityinspected at the company’s Göppingen HQ, while the company’s EVO screening plant are manufactured at Kleemann’s Pune, western India facility.
After my tour of the Kleemann production facility, I sat down with Dr Volker Nilles, Kleemann managing director, Mark Hezinger, Kleemann head of marketing, and Paul Holmes, managing director of Wirtgen Group UK & Ireland.
“We have spent some €50 million over the past three years on buildings and property, and this gives us growth possibilities for the long-term future” says Nilles. “The first big step was in the extension of warehousing and investment in increasing our model assembly capacity. It means for the next three to four years we are on course with our growth plan. Depending on how fast we progress, we have opportunities to add additional assembly, warehousing and office facilities. We also have an old hanger we are using for exhibitions, customer events, and facilities for sales and services training for customers, dealers and subsidiaries.”
Nilles says Kleemann has seen a clear trend in recent years of customers converting from stationary to mobile plant, not only in
Europe but globally. As the company is now an entirely mobile plant manufacturer, this presents Kleemann with “exciting” growth opportunities.
Hezinger explains that although Kleemann now exists within the construction & forestry division of John Deere, the company has undergone no organisational change since John Deere acquired the €3 billion-plus annual turnover Wirtgen Group in December 2017. “Our business is a perfect fit within John Deere’s construction and forestry portfolio. Deere is very experienced in telematics and the use of augmented reality, and we can draw on that, and there are some synergies to be had around components, but other than that it is business as usual. That is very good for our customers and for us.”
At the bauma 2019 exhibition (8-14 April) in Munich, Germany, Kleemann appeared besides fellow Wirtgen Group companies Wirtgen (milling machines), Vögele (pavers), Hamm (compactors) and Benninghoven (asphalt plants), presenting a seven-mobile crushing and screening plant line-up. The models highlighted how the manufacturer’s design and engineering expertise are geared towards supplying customers with plant offering the best ‘stone-to-money’ ratio.
From the PRO series, the up to 650tonnes/ hour capacity MOBICAT MC 120 Z PRO is said to impress in natural stone applications. The powerful plant has a 1,200mm x 800mm feed opening and is equipped with an extra long articulated crusher jaw. To guarantee the best
possible material flow, Kleemann’s Continuous Feed System (CFS) adjusts the conveying speed to the crusher’s fill level. The model can rapidly clear material blockages by reversing production with the help of its electric crusher drive.
The bauma 2019-showcased MOBICONE MC0 11 PRO mobile cone crusher is a highperforming secondary crushing plant in combination with the MC 120 Z PRO. The MCO 11 PRO impresses with a maximum 470tonne hourly output.
Meanwhile, from the EVO series, Kleemann’s two packages for the MOBIREX MR 130 Z EVO2 impact crusher are said to guarantee environmentally sound operation. The newly developed solutions provide considerable improvements in noise reduction and dust containment. Operation of the plant is by means of Kleemann’s intuitive control concept, SPECTIVE.
The tried-and-tested MOBICAT MC 110 Z EVO jaw crusher and MOBICONE MCO 9 S EVO cone crusher are compact and powerful and can be combined perfectly. The MCO 9 S EVO also has a secondary screening unit with oversize grain returning.
The bauma 2019-highlighted triple-deck MOBISCREEN MS 953 EVO has a screening surface of 9.5m² in the upper deck. Just like the crushers, the screening plant in the EVO line can be used flexibly thanks to favourable transport dimensions and short set-up times.
500tonnes/hour output is said to be possible thanks to a good material stream through the plant. This starts with the infeed which, thanks to the generously sized feed hopper, is supplied via a wheeled loader or an upstream crushing plant. The material is conveyed to the screen casing on an extra-wide 1,200mm feeding conveyor.
A coarse screening plant for larger feed sizes, the bauma 2019-displayed MOBISCREEN MS 15 Z is a mobile doubledeck screen capable of an hourly output of up to 400tonnes. Well suited to both natural rock and recycling applications, the robustly built screening plant can process up to 400mm-sized initial feed material.
Focusing on the evolution of Kleemann’s plant range, Nilles says: “After 2010 we developed the EVO line of jaw, cone, impactor
and screen plant aimed at the contractor market. We are not trying to develop only a product, but also a total solution for our customer.
“We differentiate our EVO lines from other manufacturers through their performance. They offer higher tonnes per hour with technological features such as our CFS system and material flow concept. This lowers total cost of ownership for our customers. The EVO range is also all about efficiency. The main topic within that is offering lower fuel consumption than our competitors, which we do with our direct-drive concept and our diesel-electric powered option.
“Finally, we focus on design. We think we have very nice machines and we’ve won a lot of design prizes. But for us the design is not only about the plant looking nice, but about being easy to operate and maintain. If you look at our plant you can find the SPECTIVE operating system which can more or less guide you through the whole plant operation process, while also offering solutions to fix any problems. We also think we have the safest machines on the market and have won a couple of safety prizes with our EVO machines.”
Kleemann trades through its 55 subsidiaries and 100 dealers globally. In North America the company sells its products through dealership partners, with its trading in China managed by its subsidiary overseeing a dealer partner network.
“The subsidiary approach is quite different to our competitors and gives us direct access to most markets globally,” explains Nilles. “Our position in Europe and South America is stronger than in some other areas, and we are also market leader [for track-mounted mobile plant sales] in China. Nevertheless, everywhere has growth potential for us. Our target is one third sales in Europe, one third in North and South America, and one third of sales from the rest of the world.”
Of Kleemann’s home market of Germany, Nilles says: “The German equipment market is still very strong. We have a number one position here and are still growing.”
Nilles stresses how Kleemann has been continuously updating its products and “taking them to the next level”. This will include, he says, the launch of additional all-electric Kleemann electric crushers and screeners “within the near future”.
“We are also continuously increasing our
plant portfolio. We did this initially within the EVO line and then introduced the PRO line, which are especially for the quarrying and mining business. Those crushers are very robust but remain quite mobile. The MCO 11 PRO and MC 120 Z PRO have been introduced to the market, and there are more to come.”
As well as having recently showcased its SPECTIVE machine control solution and the MOBICAT MC 120 Z PRO jaw crusher for the first time at the bauma Munich exhibition, Nilles says Kleemann was also keen to highlight the MOBIREX MR 130 Z EVO2 impact crusher’s new features for reducing plant dust and noise levels, which he describes as “a very critical issue in a lot of countries”.
Emphasising Kleemann’s consistent approach to brand quality, Paul Holmes says: “If you walk round the Indian factory where we produce our EVO screening plant, you would find no difference from our factory here in Germany – from a quality perspective, an engineering perspective, and a control perspective. That’s the Kleemann brand.”
Nilles says there are plans for Kleemann’s scalpers to be manufactured in India. “There are cost advantages to manufacturing there. For example, the percentage of steel cost in producing a screener is much higher than in producing a crusher. Also, a one-production facility strategy is very risky in the long term.
“There are markets we are closely following, such as China, which is the largest aggregates market in the world. So far it remains a mainly stationary plant market. If it gets to the stage that mobile plant becomes more established, we will have discussions about a Chinese production presence.”
“With our Indian factory, we have a proven overseas production facility. This stands us
in good stead for other potential overseas production sites,” adds Holmes.
Nilles notes that annual Chinese crusher demand is around 15,000 units/year – with around 95% of those being stationary plant purchases. He adds: “There’s a lot going on in China. New government environment legislation and market consolidation is leading to the closure of a lot of small quarries. There are new projects on both the recycling and aggregates quarrying side of the business. This has opened up discussions about the benefits of mobile plant for these projects, creating good potential for both our EVO and PRO plant lines.”
On this topic, Holmes adds: “It’s not just about introducing more mobile plant to China, it’s about having the capability of supporting customers’ use of the plant.”
Kleemann has invested heavily in its subsidiaries’ regional sales and services outlets. Centre for Training & Technology (CTT) teams offer expert maintenance and repair of customer plant, preventative maintenance through service contracts, and application advice and training.
“We want to deliver a solution that allows our customer to earn money by lowering their cost per [production] tonne. Lowering this cost involves quality plan maintenance and operation that ensures high plant availability. We offer application engineering support to achieve this. You can buy a machine, but if you do not set up properly you cannot achieve best results.
“We offer everything from standard to fullservice and maintenance contracts, depending on regions. For example, we have a lot of full-maintenance contracts in India. It is part of the business we are developing with our
subsidiaries, with contracts tailored to market specifics.”
Focusing on Kleemann’s customer plant replacement parts business, Holmes says: “The crushing and screening plant market has traditionally included a lot of third parties working out of forges all over the world who are producing replacement parts of varying quality and price. A lot of other crushing and screening equipment manufacturers have been happy to let these localised thirdparty suppliers supply their customers with replacement parts. We say an OEM- (original equipment manufacturer) produced part does not mean expensive; it means value.
“For the UK market, certainly, we’ve been very conscious to ensure we’re pricecompetitive against third parties, that we match or exceed quality, ensuring longer wear life, and importantly that we have the availability of the ordered replacement part. This prevents downtime which costs money. I think we have been helped in this area by John Deere, and their agricultural side, in upping replacement parts availability. This means upping warehouse space, like we have done in the UK, so we can supply the customer immediately or next day with at least 90% of what they need, to get them back up and running.”
‘Up and running’ is also a good way to describe Kleemann’s global growth plan. It will be fascinating to witness its full delivery over the coming years. AB
Maptek’s Vulcan software is helping one savvy Greek quarries manager accurately plan and manage his marble reserves. Guy Woodford reports.
The English idiom ‘It’s all Greek to me’ refers to something that is difficult to understand. How best to secure accurate mineral reserves data and find the right platform to clearly interpret it can fit such a turn of phrase, but one Greek quarrying company believes it has found the answer in the form of Maptek’s Vulcan software.
Iktinos Hellas SA and its quarries manager Charalambos Almbanopoulos is using Vulcan at the company’s Platanotopos marble quarry in north-eastern Greece for resource and reserve estimation using quality indicators.
The use of standard estimation and modelling software tools in estimating marble quarry reserves poses several challenges. Reserves are based on marble quality categories which are unique for each deposit. These categories represent visual and physical aspects such as colour, texture and fractures.
Classification is performed by experienced personnel and is based on much smaller samples than the slabs of marble produced. Furthermore, the available information is mostly qualitative, leading to further complications in the application of geomathematical estimation methods.
Almbanopoulos and Iktinos Hellas SA use Maptek Vulcan in the estimation of Platanotopos quarry’s marble reserves based on interpolating quality indicator values from drill hole and quarry face samples to 3D blocks.
Located in public forest land and at an elevation of 380m–540m above sea level, Platanotopos quarry contains calcitic marbles, gneiss and gneissic schists which have no commercial value and are not exploited. Interest is focused on dolomitic marbles, which occur as lenses enclosed by alternating gneissic schist layers and calcitic marbles.
The marble-bearing horizon has a regular strike, with dips between 25° and
30°. The lensoid dolomitic microcrystalline marbles are massive, white, fine-grained and traversed by red-yellow ‘spider-web’ fractures filled with secondary iron oxides and hydroxides. Because the marbles are massive, large slabs can be recovered with minimal production of waste material. The weathered top 1–2 m of the deposit has a low recovery factor for marketable marble.
Quarry production is scheduled for 7,000–10,000m³/year, with an estimated operation life of 15 years. The marble, known as ‘Golden Spider’, has very good physical and mechanical properties and can take a very high polish.
The blocks from the Platanotopos quarry are 6 × 2.8 × 7 m. Quality grading is initially based on colour: gold, yellow or red. Further grading categorises the different spider-web textures. Each block is then classified based on defects such as fractures, dendrite zones, brown lines, discolourings or marks, and a final quality is assigned according to a combination of grading types.
Data used in the resources and reserves estimation includes the original and current topography, as well as diamond drill hole samples and sections on quarry faces which are analysed every metre as to the marble quality.
A total of 1684 one-metre samples, from 47 sections and 45 drill holes, were used in reserve estimation. The data covered the extent of the estimated final pit and was validated in Vulcan for collar location and overlapping intervals.
The estimated volume of the final excavation was designed per bench (level) starting from the existing quarry morphology. The design of each of the 16 benches was modelled as a solid triangulation. These solids were visually checked and validated using triangulation topology checks (selfcrossing, opening, inconsistencies) to ensure suitability for volumetric calculations.
The drill hole and section sample
ABOVE LEFT, VULCAN 1: Iktinos Hellas SA uses Maptek Vulcan in the estimation of marble reserves based on interpolating quality indicator values from drill hole and quarry face samples to 3D blocks
ABOVE RIGHT, VULCAN 2: Maptek Vulcan analyses more than a thousand one-metre samples from numerous section and drill holes prior to estimating resource and reserve levels at Platanotopos marble quarry
database was configured with extra fields (indicators) to allow the interpolation of arithmetic values. Specifically, fields were added representing the different marble qualities based on original colour, texture, fracture and tectonism.
Tectonism is handled separately because the different orientations of largescale tectonism require a different search ellipsoid orientation. This is combined with initial qualities to derive the final quality classifications, with downgrading as necessary based on the estimated value of this field.
After calculation of initial quality and tectonism categories, the location of each sample is calculated, and a weighting factor is assigned. More weight is given to face sections as quality assessment is performed on a surface larger than the drill core and therefore better approaches the actual quality in that location. Weighting factors are used to further assess samples during interpolation.
Quality-class field values were interpolated using the inverse distancesquared method as implemented in a Vulcan block model. The estimated volume is divided into blocks of the same size. Block dimensions were configured based on the marble volumes extracted separately at the Platanotopos quarry.
In each block, the percentage of each marble quality was estimated using neighbouring samples. These samples are selected around each block using search ellipsoids oriented according to the geological features of the deposit. A special Vulcan function was used to calculate the appropriate ellipsoid orientation for each block, taking into account reference surfaces that define folding.
Generalisation of qualities was considered necessary as the limited sampling does not allow for a more detailed analysis of reserves to the original quality categories produced by the quarry. Reported waste quantities are the remaining bench volumes, which cannot be estimated using the available sampling and the limitations set by the reserve categories.
A considerable part of the waste and
the inferred resources can potentially be upgraded in the future with additional drilling, which will provide a clearer and more detailed picture in areas where there are currently no samples.
This method gives Iktinos Hellas SA reliable results according to international standards of resources/reserves reporting. Future work will include integration of historical production data with the quality estimation process and implementation of an appropriate production quality-control system that will produce the necessary data to improve the current quality models and reserve classification.
Speaking about the benefits of Maptek’s Vulcan software, Charalambos Almbanopoulos says: “Having a systematic procedure for reserves calculation and the ability to visualise quarry plans and estimated qualities in three dimensions are the main benefits of using Maptek Vulcan QuarryModeller.”
Speaking about what specific features he most likes about the Maptek software solution, he adds: “The ability of the software to configure and adjust sample database structures and standard estimation procedures so that they can be used to estimate categorical marble qualities.” AB
McLanahan UltraWASH Modular Washing Systems offer the same world-class washing technology we’ve been supplying since 1835, but in containerized modules for shorter lead times, quick setup and ease of transport if producing at multiple locations or one very large site. Produce up to five products – three clean aggregate and two washed sand products. Additional modules for crushing, screening scrubbing, thickening, and tailings management are also available.
Top American companies are looking to increase supply of their proven high-quality equipment solutions to European aggregates sector customers.
Through their product diversity and quality, and their employees’ market expertise and premium customer service, leading American companies Philippi-Hagenbuch, Rice Lake Weighing Systems and Eagle Iron Works have built up a large and loyal client base across North America and other key global aggregates sector markets. Now the ambitious U.S. firms are looking to increase their presence in Europe by partnering with new dealers and distributors.
A McLanahan company, Iowa-based Eagle Iron Works has nearly 150 years’ experience of supplying bespoke high-quality washing and beneficiation equipment to the global aggregates industry. Wisconsin-headquartered Rice Lake Weighing Systems offers a wide range of state-of-theart weighing solutions for aggregates business operators. The firm, founded in 1946, is looking to add to its existing European distribution office in Heteren, Netherlands. Philippi-Hagenbuch, based in Peoria, Illinois, is this year celebrating 50 years of supplying custom-engineered haul truck solutions, lowering customers cost per tonne by improving the efficiency of their day-to-day aggregates hauling operations.
Further details about Philippi-Hagenbuch’s, Rice Lake Weighing Systems’ and Eagle Iron Works’ wide range of products and services for aggregates sector customers can be found at www.aggbusiness.com and clicking on the ‘US companies seeking European dealers’ banner.
Eagle Iron Works
129 E Holcomb Ave
Des Moines, IA 50313
USA
Tel: +1 515 243 1123
Email: info@eiwllc.com www.eagleironworks.com
Eagle Iron Works serves the aggregate industry and its producers with strong and reliable equipment.
TARGET CUSTOMERS
Anyone who is looking for piece of aggregate equipment backed with years of experience and an unmatched customer service team.
EIW, LLC., offers a number of different aggregate processing equipment options, such as attrition mills, coarse and fine material screw washers, classifying tanks, log washers, sol clay washers and stabilized base mixers.
Eagle Iron Works was founded in 1872 to serve the aggregate industry by providing washing and beneficiation equipment.
At EIW, the company begins by engineering a design to best fit the needs of each customer. They continually provide support from the point of sale throughout the life of the machine and offer readily available replacement parts. Engineers, application specialists and service technicians all have the experience necessary to solve the most difficult aggregate processing needs.
For more information on available products and services, you can visit EIW’s website or contact a sales representative directly.
Rice Lake Weighing Systems
Weiland 11 NL-6666 MH
Heteren, Netherlands
Tel: +31 (0)26 4721319
Email: europe@ricelake.com www.ricelake.com
No matter how unique or challenging the industry, Rice Lake has a solution for it. Rice Lake equipment supports all aspects of the aggregate, construction, energy and all types of manufacturing industries.
Master Belt Scales
Belt scale systems are a fast, efficient method of monitoring material flow rate. Rice Lake’s Master belt scales ensure consistent, accurate weight output and are ideal for mining, quarries, bulk material blending, process control, and truck, barge or rail load-out applications.
Weighing Terminals/ Controllers
Rice Lake Weighing Systems products are supported and distributed by a network of authorized dealers. If you are interested in representing Rice Lake products, we encourage you to contact us.
We also partner with OEMs (original equipment manufacturers) and system integrators. Rice Lake products can be integrated with existing systems to provided fully automated solutions in a variety of industries.
Weighing Done Right
Rice Lake Weighing Systems, an ISO 9001-certified corporation, has been a leader in the manufacture and distribution of weight-related products since 1946. We strive to design, manufacture and support quality products to suit every weighing need and unique application. With unmatched customer service and over 40,000 items in stock, Rice Lake is a global trailblazer. Our expansive distribution and service network is made up of over 2,500 distributors in 130 countries, backed by trained technicians and the finest factory support available.
Rice Lake weighing terminals/controllers offer powerful process control and programmability options and can be used in a wide range of applications. With a Rice Lake weighing terminal/ controller, entire systems can be automated by dictated batch formulation, inventory management or traceability. pp
7424 W. Plank Road
Peoria, IL 61604
USA
Tel: +1 (309) 697 9200
Email: sales@philsystems.com www.philsystems.com
Philippi-Hagenbuch is located in Peoria, IL USA and can be reached at +1 (309) 697-9200, found on the web at www.philsystems.com or emailed at sales@ philsystems.com
MARKETS SERVED
Over the past 50 years, PHIL has enjoyed serving North America, Central America, South America, Australasia, Europe, Asia and Africa. To stay up to date on PHIL’s equipment, solutions and offerings, follow us on Facebook and Twitter.
Philippi-Hagenbuch, Inc. was founded in 1969 to bring custom engineered solutions to haul trucks to upgrade them from “standard off-the-shelf” design to achieve client and industry specific needs.
From our original product, the Autogate® Tailgate to our complete line of customengineered HiVol® Bodies that can be designed for every construction and mining operation from coal to copper, gold and aggregates.
Celebrating our 50th Anniversary this year, PHIL is proud that over the years, our product line has grown to include world-class Water Tanks, Bottom Dump Trailers, Rear Eject Bodies, J-Hook Lift Systems, Sideboards, Push Blocks and other custom products for niche applications.
Among the Caterpillar wheeled loaders
benefitting from a 2019 product update package is the 966M wheeled loader
The 2019 product update package for Cat M Series medium wheeled loaders (950M – 982M) includes technology advances that provide lower operating costs via extended service intervals; enhanced operator comfort with new seats and suspensions; emissions control strategies to meet EU Stage V standards (EU only); added machine configurations (982M Forestry Machine and 982M High Lift); expanded productivity measurement tools; remote software update capability; and refinements in ground engaging tool and coupler
Sandvik Mining & Rock Technology has introduced connectivity between the SanRemo remote monitoring system for Sandvik surface drilling equipment and Infrakit Cloud, a solution for connecting work machinery, field equipment and personnel on a single platform for more efficient construction, better quality, realtime accessibility of project data and cost savings.
The new solution creates a flow of communication between Sandvik drilling equipment, the SanRemo information management system and Infrakit Cloud. This way the process data generated by onboard automation and TIM3D drill navigation systems can be easily shared with contractors’ and civil engineering companies’ other systems. Thanks to this new solution, data only needs to be uploaded once from the rig, after which it is automatically shared into the Infrakit Cloud. This allows the data to be shared with as many other systems and users as necessary, eliminating the need for multiple uploads or
systems. Periodic updates allow Caterpillar to bring new and improved features to market more quickly and more frequently than do conventional new product introduction (NPI) cycles.
U.S. EPA Tier 4 Final and EU Stage V emissions-compliant models save maintenance costs by extending engine oil, engine oil filter and hydraulic oil filter change intervals from 500 hours up to 1,000 hours. Based on estimated comparisons of total engine and hydraulic fluids, filters, and sampling costs
manual transfers of data.
A major benefit is the ability to share project data with all the relevant systems and parties: design engineers, drill planners, drill operators, production managers, clients’ supervisors, to name a few. Everyone can also easily access the information they need on-site, eliminating the use of USB drives and issues with multiple file versions. All the necessary data is available in the cloud, everywhere and at all times. The cloud storage also serves as a permanent archive for any future use.
Data generation on the drill rig is built on the Sandvik TIM3D drill navigation system. TIM3D allows pre-designed drill plans and surface models to be uploaded onto the drill rig, and even to be created or edited on the rig (TIM3D availability and features depend on the rig model). During and after drilling, the rig stores as-drilled information, driller’s notes, and measurement while drilling (MWD) data for reporting, quality control and downstream process planning. www.sandvik.com
during a 6,000-hour period, costs can be potentially reduced by 16 to 23%. (For Tier 3 equivalent models, extended intervals apply only to hydraulic filters.)
In addition, several fuel and engine oil filters are being converted from spin-on to cartridge-type. Benefits of cartridge-type filters include fewer parts to replace at servicing (housing is retained), easier disposal of used elements, and less costly replacement parts.
The ‘next generation’ of seats and suspensions offers three trim levels—comfort, deluxe, and premium plus—and features high-visibility, seat-adjustment controls, as well as ride stiffness adjustments. A new ‘breakthrough’ suspension for deluxe and premium plus trim levels increases dampening at the top and bottom of seat travel, providing additional suspension stability and avoiding hard stops at travel limits.
The ride stiffness of the seat suspension is adjustable to different settings, allowing operators to tailor seat dampening to individual preferences and to the application. This feature was previously included only with EH steering (joystick and wheel), but with the 2019 product update, it is now included with HMU steering wheel units with deluxe and premium plus seats.
Among the package of updates for medium wheeled loaders is a new universal coupler for 966M – 972M models. The new coupler eliminates width interference with multiple tools and a reduced offset increases breakout force by 4%.
www.cat.com
21-22 CQMS 2019
Punchestown Event Centre, Co. Kildare
Organiser: Machinery Movers
Magazine
Tel: +353 83 433 5968
www.machinerymovers.ie/ cqms/
20-22 6th China International Aggregates Technology Conference
Shenyang, Liaoning, China
Tel: +86 18735986973 +86 010 57811370
Email: jiaxixi@zgss.org.cn
Organiser: China Aggregates Association/North Heavy Industry Group Co https://www.linkedin. com/company/ chinaaggregatesassociation
AUGUST
1-3 Conmart Expo 2019 Guangzhou, China
Organiser: CMEPCA, GZCMIA, CMIA
Tel: +86 0755 82598142 www.conmart.com.cn/index_ en.aspx
5-7 RecyclingAKTIV and TiefbauLIVE 2019
Karlsruhe Trade Fair Centre, Germany
Organiser: Karlsruher Messe-und Kongress GmbH
Tel: +49 721 3720 2300
Email: verena.schneider@messekarlsruhe.de www.recycling-aktiv.com
23-25 Aggregates China 2019 China Import and Export Fair
Organiser: Trista Chan Tel: +86 20 28945347
Email: grand.zh@grahw.com www.cctee.net
2-5 CONEXPO Latin America 2019 Santiago, Chile
Organiser: CONEXPO Latin America Tel: +1 800 867 6060
Email: customerservice@conexpolatinamerica.com www.conexpolatinamerica.com
10-14 Excon 2019
Bengaluru, India
Organiser: Confederation of Indian Industry
Tel: +91 44 42444564
Email: excon@cii.in https://excon.in/exconpub.php
10-14 CONEXPO-CON/AGG 2020
Las Vegas, NV
Organiser: AEM Tel: +1 414 274 0644
Email: customerservice@conexpoconagg.com www.conexpoconagg.com
21-25 SaMoTer 2020 Verona, Italy
Organiser: Veronafiere S.p.A. Tel: +39 045 8298561
Email: customercare@samoter.com http://www.samoter.it/en
MEET THE TEAM
Throughout the year Aggregates Business travels the globe attending conferences, events and equipment shows, keeping you informed of the latest offerings. Why not come and join us for a chat at any of the events below?
JULY 2019 20-22 6th China
International Aggregates Technology Conference
MARCH 2020 10-14 CONEXPO-CON/ AGG 2020
MARCH 2020 21-25 SaMoTer 2020 Verona, Italy
in AGGREGATES BUSINESS INTERNATIONAL can now be contacted via their websites - for instant links to all the websites listed below, by category, go to: www.AggBusiness.com
Ammann p23 www.ammann.com
BKT Tires p32 www.bkt-tires.com CDE IFC www.cdeglobal.com
Cepcor p36 www.cmscepcor.com ConExpo IBC www.conexpoconagg.com
Evoquip p44 www.terex.com/evoquip
Hitachi p7 www.hitachicm.eu
Kleemann p11 www.kleemann.info Komatsu p17 www.komatsu.eu
p45 www.mclanahan.com Metso OBC www.metso.com/urban Sandvik p4 www.rocktechnology.sandvik
Terex Trucks p28 www.terextrucks.com
Tsurumi p46 www.tsurumi.eu
Verona Fiere p46 www.veronafiere.it Volvo CE p13 www.volvoce.com
Metso Lokotrack® Urban™ Series
Running crushing operations and producing aggregates on-site in urban areas brings new business opportunities, as well as significant savings. However, meeting the strict dust and noise requirements can be challenging. Metso’s Lokotrack® UrbanTM Series makes on-site crushing in densely populated and heavily regulated areas possible. With very low crushing noise emissions and advanced dust suppression, it’s clean, quiet and cost effective, and it makes obtaining crushing permits easier. The Lokotrack Urban Series lets you take your business to a new level while reducing transporting, emissions and costs.
Find out more about the Lokotrack Urban Series at www.metso.com/urban
Cost-efficient on-site crushing
Easier to get crushing permits
Easy and safe to transport and operate