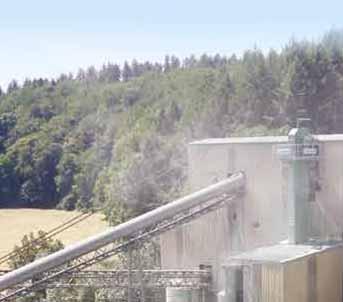
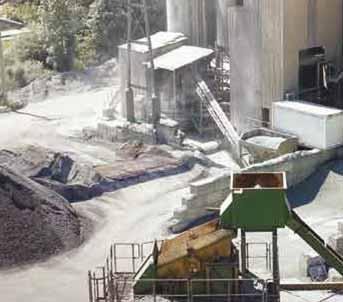
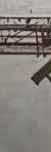
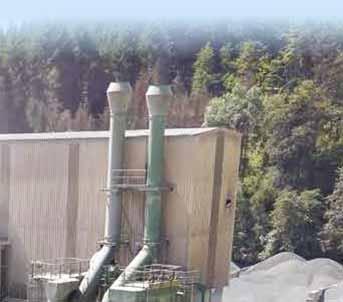
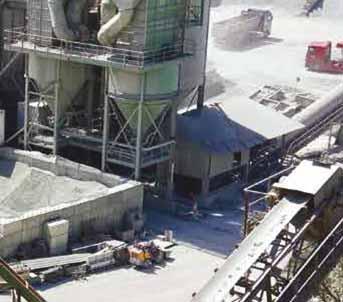

INTERVIEW – KOEN COPPENHOLLE, CEO OF CEMBUREAU
“We
cannot imagine an environment without concrete that keeps our families safe through its durability and fire resistance, that lets us travel through underwater tunnels and bridges linking up communities, and provides our electricity from windmills or water dams”
” p08
05 COMMENT
Rock-steady resolve in the face of the COVID-19 crisis
06 NEWS
LafargeHolcim expands partnership to capture CO₂ in building materials; Hitachi European production to focus on Amsterdam facility
12 ASSOCIATION NEWS
UEPG support for the European aggregates industry during the COVID-19 crisis
14 LEGAL UPDATE
As countries across the EU start to ease coronavirus lockdown measures, what are the legal implications for aggregates businesses as their employees return to work?
50 EQUIPMENT UPDATE
Global OEMs’ new equipment launches and applications
52 EVENTS
All the key events in the quarrying & aggregates world Features
19 CRUSHING & SCREENING
New and proven premium crushing and screening plant have been very much to the fore in the first half of 2020
24 LOADING
Two new loading machine buys are helping a Scottish quarrying and construction company to maximise its recycling efficiency and reduce the amount of materials it sends to landfill
Key construction projects give hauling OEMs cause for optimism
30 ENGINES - PART 1
Start your off-highway machine engines for the return of COVID-19-disrupted market demand
33 RECYCLING - PART 1
Mineral product producers keen to widen their income streams can find big commercial opportunities in recycled aggregate and concrete products
36 PORTABLE POWER – PART 1
Portable power solutions for quarrying industry customers are getting greener and embracing new technology
39 WEAR PARTS
Being able to quickly access and install high-performing replacement wear parts on quarrying plant reduces downtime, leading to enhanced worksite efficiency
08 INTERVIEW
CEMBUREAU CEO Koen Coppenholle on the European cement industry association’s efforts to cement a bright future for a vital building material
15 MARKET REPORT
The UK and Irish aggregates and manufactured mineral products industries are enduring significant disruption due to the global COVID-19 pandemic, but demand is there once things return to relative normality
43 UKRAINIAN AGGREGATES
Aggregates demand and production in Ukraine is in robust health despite the disruption caused by the COVID-19 pandemic
46 QUARRY PROFILE
The modernisation of a German quarry’s high-grade chippings operation was a typical Metso SiteBooster plantoptimisation project
This upgraded 2-Series model features the newly developed CI621 Prisec™ technology which comes with a host of innovations
HEAD OFFICE
EDITOR: Guy Woodford
ASSISTANT EDITOR: Liam McLoughlin
CONTRIBUTING
EDITORS: Patrick Smith, Dan Gilkes
EQUIPMENT EDITOR: Mike Woof
DESIGNERS: Simon Ward, Andy Taylder, Stephen Poulton
PRODUCTION MANAGER: Nick Bond
OFFICE MANAGER: Kelly Thompson
CIRCULATION & DATABASE MANAGER: Charmaine Douglas
INTERNET, IT & DATA SERVICES DIRECTOR: James Howard
WEB ADMINISTRATORS: Sarah Biswell, Tatyana Mechkarova
MANAGING DIRECTOR: Andrew Barriball
PUBLISHER: Geoff Hadwick
CHAIRMAN: Roger Adshead
ADDRESS
Route One Publishing Ltd, Waterbridge Court, 50 Spital Street, Dartford, Kent DA1 2DT, UK
TEL: +44 (0) 1322 612055 FAX: +44 (0) 1322 788063
EMAIL: [initialsurname]@ropl.com (psmith@ropl.com)
ADVERTISEMENT SALES
SALES DIRECTOR:
Philip Woodgate TEL: +44 (0) 1322 612067
EMAIL: pwoodgate@ropl.com
Dan Emmerson TEL: +44 (0) 1322 612068
EMAIL: demmerson@ropl.com
Graeme McQueen TEL: +44 (0) 1322 612069
EMAIL: gmcqueen@ropl.com
SUBSCRIPTION / READER ENQUIRY SERVICE
Aggregates Business International is available on subscription. Email subs@ropl.com for further details. Subscription records are maintained at Route One Publishing Ltd.
SUBSCRIPTION / READER ENQUIRIES TO: Data, Route One Publishing Ltd, Waterbridge Court, 50 Spital Street, Dartford, Kent DA1 2DT, UK
TEL: +44 (0) 1322 612079
FAX: +44 (0) 1322 788063
EMAIL: data@ropl.com
No part of this publication may be reproduced in any form whatsoever without the express written permission of the publisher. Contributors are encouraged to express their personal and professional opinions in this publication, and accordingly views expressed herein are not necessarily the views of Route One Publishing Ltd. From time to time statements and claims are made by the manufacturers and their representatives in respect of their products and services. Whilst reasonable steps are taken to check their accuracy at the time of going to press, the publisher cannot be held liable for their validity and accuracy.
PUBLISHED BY © Route One Publishing Ltd 2020
AGGREGATES BUSINESS EUROPE USPS: is published six times a year. Airfreight and mailing in the USA by agent named WN Shipping USA, 156-15, 146th Avenue, 2nd Floor, Jamaica, NY 11434, USA.
PERIODICALS POSTAGE PAID AT BROOKLYN, NY 11256
US POSTMASTER: Send address changes to Aggregates Business Europe, WN Shipping USA, 156-15, 146th Avenue, 2nd Floor, Jamaica, NY 11434, USA
Air Business Ltd is acting as our mailing agent
PRINT: ISSN 2051-5766
ONLINE: ISSN 2057-3405
PRINTED BY: Warners (Midlands) PLC
’m writing this column on 18 May 2020 amid the COVID-19 pandemic. According to the European Centre for Disease Prevention and Control, between 31 December 2019 and 17 May 2020 coronavirus was wholly or partly responsible for 311,588 deaths globally. More than half (161,420) of those recorded deaths were in Europe.
Given the above harrowing figures, it will come as no surprise that the pandemic has had a significant impact on the European aggregates production industry over recent months. After most of the continent’s governments imposed strict lockdown measures, including an up to two-metre social distancing rule, in a bid to reduce the deadly impact of the virus, work at the vast majority of Europe’s 29,000-plus minerals extraction sites was suspended until further notice. At the same time, aggregates processing equipment makers also halted the production lines in their manufacturing facilities. In the UK, many businesses have accessed the British government’s Coronavirus Job Retention Scheme, which, until 31 July 2020, covers 80% of an employee’s regular wages, up to a monthly cap of £2,500.
The COVID-19 pandemic has also led to the postponement of Hillhead in the UK (22-24 June) and steinexpo in Germany (26-29 August), the European quarrying sector’s two biggest showpiece exhibitions of 2020. Both are now due to take place next year.
Encouragingly, the European aggregates and broader building materials industries and aggregates production plant manufacturers have shown rock-steady resolve during a period of widespread disruption. At the time of writing, Terex had just resumed production at a reduced capacity at all its sites in Northern Ireland (Omagh, Dungannon, Campsie and Ballymoney). Meanwhile, Breedon, a major independent building materials group in the UK and Ireland, has restarted clinker production at its two cement plants and is “progressively” reopening some of its other sites.
The European cement sector has also been showing its resolve. In this edition’s main interview feature, CEMBUREAU CEO Koen Coppenholle discusses how the European cement industry’s association is working with its members and the European Commission to overcome issues linked to the COVID-19 pandemic.
As I write in this issue’s Market Report on the UK and Irish aggregates sectors, demand for aggregates and other building materials remains strong. From a UK perspective, product sales should rise thanks to the British government’s spring budgetannounced £27.4bn revamping of the national roads network. They will also continue to benefit from the long-term implementation of the government’s ‘Levelling Up’ agenda - improving Northern England transport and other infrastructure so that it more closely resembles the south of the country. Furthermore, sales momentum will come from the continuation of the HS2 and the Hinckley Point Nuclear Power Station megaprojects, and the resumption of residential and commercial construction.
In Ireland, Project Ireland 2040 – an overarching policy and planning framework for the social, economic and cultural development of the country for the next 20 years and beyond - includes the National Development Plan - a 10-year strategy for public capital investment of almost €116 billion to 2027. A lot of building materials will be required if the Emerald Isle is to realise its ambitious plans.
Crucially, the positive post-lockdown aggregates and other building materials demand picture in the UK and Ireland is mirrored across Europe, whether it be via highprofile transport or other infrastructure projects or residential and commercial building work.
To shamelessly distort a lyric from English band Chumbawamba’s famous hit ‘Tubthumping’, ‘The European aggregates sector got knocked down, but is well and truly getting back up again’. GW gwoodford@ropl.com
LafargeHolcim is ramping up its cooperation with Solidia Technologies to reduce CO2 across its value chain. With this announcement, the FrenchSwiss building materials giant’s collaboration with the US-based cement and concrete technology company, which began in 2013, is formally agreed until 2025, with an option to extend.
Together, the two companies’ solutions emit up to 30% less CO2 during cement production. They also capture and store CO2, leading to a 70% carbonreduced concrete. With Solidia, LafargeHolcim will continue to develop new innovative solutions focused on non-reinforced concrete structures and paving
while also aiming to make it increasingly applicable for structural applications.
Key US customers have already placed orders for Solidia Cement to produce concrete paving blocks using Solidia
technology. In addition to deliv ering a low CO2 product from a low CO2 cement and permanent CO2 sequestration in concrete materials, Solidia cement can also increase precast production output from full product strength
in under 24 hours (compared to 28 days for traditional concrete) and ensure less equipment downtime for cleaning. Solidia Concrete products are more durable and have a wider colour palette and no efflorescence.
Industrial pilots are currently also ongoing in Canada, Germany, France and the UK, with further pilots being prepared.
Initially, the required CO2 will be supplied by third parties while Solidia supplies the required curing chambers in which the CO2 is injected into the concrete. Over the long term, LafargeHolcim aims to utilise CO2 captured from cement kilns in North America and Europe.
Hitachi Construction Machinery Europe (HCME) plans to move its production and assembly activities, currently taking place in Oosterhout, the Netherlands, to the company’s existing production site in Amsterdam.
HCME says this will enable the firm to focus on producing customised machines that are increasingly in demand among its dealers across Europe. Meanwhile, the production and assembly of standard machines will be left to the factories in Japan.
The consultation process with the Works Council and discussions with the trade unions
on the proposed production relocation have now started. HCME expects to complete these discussions after the summer, with the company aiming to complete the Amsterdam production transition in December 2021.
HCME says that while it is keen to safeguard jobs and ‘guarantee the continuity of the company’ via the new business model, up to 115 jobs may be cut in the course of 2021.
The company says the new business model will also see additional investment in innovations in areas including service, parts, training and lease/rental.
German building materials
heavyweight HeidelbergCement has made an encouraging start to 2020 – with its operating result up 4% and COVID-19triggered expense reductions of €1bn targeted via the company’s COPE action plan.
Compared with a strong January and February 2019, HeidelbergCement sales volumes increased in all business lines in the first two months of 2020. From midMarch, however, company sales volumes were significantly impaired by the effects of the coronavirus pandemic, such as state-imposed production downtimes and construction
stoppages on significant infrastructure projects.
During the first quarter of 2020, HeidelbergCement’s total cement and clinker sales volumes decreased by 3% to 27.7mn tonnes (2019: 28.6mn). Deliveries of aggregates declined by 4% to 60.1mn tonnes (last year: 62.9mn), and ready-mixed concrete sales volumes fell by 6% to 10.7mn m³ (previous year: 11.3mn m³). At 1.8mn tonnes (2019: 1.8mn tonnes), asphalt sales volumes were 4% below last year’s level.
Group revenue decreased by 7% in comparison with the previous year to €3.93bn (last year: €4.23bn). The decline from
the trading activities contributed significantly to this development. Excluding consolidation and exchange rate effects, the decline amounted to 8%.
Changes to the scope of consolidation of €6mn harmed revenue; exchange rate effects, on the
other hand, increased revenue by €23mn. The overall positive price development only partially offset the decline in sales volumes and trading activities.
Dr Dominik von Achten, chairman of the Managing Board of HeidelbergCement, said: “The positive start to the year demonstrates that HeidelbergCement is very well positioned even in difficult times. When the economy picks up again, and construction activity in our markets returns to normal, we will still have good, perhaps even better prospects for sustainable and profitable growth. We see the crisis as a clear opportunity.”
CEMBUREAU represents, promotes and defends the interests of the European cement industry in its work with policymakers at EU and national level. Aggregates Business editor Guy Woodford spoke to the association’s CEO, Koen Coppenholle, to learn more about its work, its priorities and the likely long-term future for the essential building material
Mid-April 2020. Koen Coppenholle is outlining how Brussels, Belgiumbased CEMBUREAU and its members are working to overcome issues linked to the COVID-19 pandemic.
“We have regular contact with our board members and weekly calls with the national associations to collect information on the situation in different countries and companies. We have an open line with the European Commission through regular calls, and we fill in a questionnaire every week with urgent requests to the Commission. We raise the need for liquidity support, especially for downstream SMEs [small and medium enterprises]. We also raise the need for free movement of building materials, for the recognition, by individual countries, of the construction sector as an essential sector and workers as essential workers and for a more uniform interpretation of when a construction site is considered safe.”
Coppenholle says it is difficult to predict the long-term impact of COVID-19 on the European cement industry as the crisis is still unfolding. The situation, he notes, also differs markedly from country to country. “COVID19 and the swiftness of measures taken by national authorities have left the cement sector and many other industries in shock. We have pleaded with European and national authorities to ensure that construction sites can remain open, of course, while showing proper respect for the health and safety rules. These sites tend to be run by small- and medium-sized enterprises (SMEs) that are more susceptible to liquidity problems. If they get into difficulties, this can affect the whole supply chain.
“As the EU’s focus is now switching to recovery and business restarting, CEMBUREAU is fully engaged in ensuring maximum adherence to health and safety rules by sharing best practice among its members.”
CEMBUREAU’s membership consists of national cement associations and, in countries without an association, companies covering 29 countries. The group includes 25 EU countries as well as Norway, Turkey, the UK and Switzerland as non-EU countries. The association works with its members to analyse policy proposals, assess business impact and define opportunities for the cement sector and contributes to the policy debate through position papers and studies on a wide range of topics.
While membership has remained stable over recent years, the association recently finalised cooperation agreements with the Ukraine Cement Association and Cypriot firm Vassiliko Cement.
“The cement industry has suffered greatly from the economic and [2007-8] financial crisis with an average 40% drop in production over the 2007-2013 period,” notes Coppenholle. “It is slowly but gradually recovering from that crisis with production reaching 175 million tonnes in 2018, still far
from the 267 million tonnes seen in pre-crisis levels and representing around 4% of global production. The COVID-19 crisis has thrown some uncertainty in the current market and certainly in the forecast for future demand and output.
“If we put aside for a moment the impact of the COVID-19 crisis, which requires the immediate and urgent attention of our members, the sector is very much focused on how to transition towards a carbon-neutral industry. Following the publication of the Green Deal by the European Commission, CEMBUREAU has set out its ambition to strive for carbon neutrality along the cement and concrete value chain by 2050.”
Coppenholle says that in the first quarter of 2020, CEMBUREAU engaged with experts in companies and national associations to revise its 2013 Roadmap and assess how carbon neutrality can be secured. Based on its ‘5C Approach’, developed in 2018, the experts have looked at CO2 reduction potential in each of the 5Cs – clinker, cement, concrete, construction, and (re)carbonation. They have identified the technologies, innovation and investment required to achieve the reductions, and formulated vital messages to convey to policymakers.
Coppenholle stresses that if the European cement industry is fully supported in its efforts to use alternative fuels and alternative raw materials to heat up kilns, able to count
on public funding and the guarantee of a proper pipeline and infrastructure technology for carbon capture and storage, and given sufficient access to clinker-substituting materials, it can significantly reduce its CO2 footprint.
He continues: “As most of cement is used in concrete, which is an essential enabling material for sustainable housing, renewable energy infrastructure and society’s transition to a low-carbon economy, it is crucial for the cement sector to highlight the recyclability of concrete which, together with the sourcing of alternative fuels and raw materials from waste streams, puts the cement industry at the heart of the circular economy. The recarbonation potential of concrete, whereby CO2 gets reabsorbed during its lifetime and at end-of-life, can turn whole cities into carbon sinks. However, for that to be recognised, we need to advocate for a lifecycle assessment at building instead of product level.
“If the industry can pull off these innovations and CO2 reductions in Europe, it will lead the way globally on innovation and in addressing the climate change challenge. It is important, however, that the industry is helped in its endeavours by a facilitating regulatory framework which guarantees the level of competitiveness needed to engage in the substantial investments required by the low-carbon transition.”
Asked about the importance of the European cement industry to life on the continent, Coppenholle, a Belgian national, replies: “The cement plants are located near to their raw material source, which is limestone quarries. With quarries widely dispersed across Europe, cement plants provide jobs to local communities and are the beating heart of the social and economic fabric. As the end product, concrete does not travel large distances. The full cementconcrete supply chain provides jobs for a large amount of small- and medium-sized concrete manufacturing enterprises.
“Cement and concrete are ubiquitous in everyday life. We cannot imagine an environment without concrete that keeps
trends in cement chemistry
our families safe through its durability and fire resistance, that lets us travel through underwater tunnels and bridges linking up communities, and provides our electricity from windmills or water dams.”
Coppenholle’s CV before taking up his senior role at CEMBUREAU makes for impressive reading. A passion for European law and international politics has driven his career, starting with a firm focus on EU institutional law as a research and teaching assistant at the Katholieke Universiteit Leuven. A year abroad for a Master of Laws at Harvard Law School allowed him to study US federalism as a possible blueprint for the further development of the European Union. A three-year stint at the European Court of Justice in Judge P.J.G. Kapteyn’s cabinet allowed Coppenholle to deal with a wide array of cases in all areas of EU law. It was the ideal preparation for his career as an attorney with Linklaters De Bandt where the focus was also on EU competition law and state aid. In 2000, Coppenholle entered the world of government relations, gaining experience in contributing to the EU legislative process, first with General Electric and then for ArcelorMittal, a leading global steel company. As an energy-intensive industry, the steel industry’s challenges and opportunities are similar to those of the cement industry. As a result, Coppenholle says he saw CEMBUREAU as an obvious next step which allowed him to add management skills to his legal and policy expertise.
“I wanted the freedom to take the initiative and drive an organisation in a direction that responds efficiently to the needs of its customers, who are our members. I have been active in European law and policy for 32 years now. I have tried, at each stage of my career, to add a skill starting from an academic position to go on and represent companies as a lawyer and then moving in-house to get to know the processes at work in the legislative phase leading up to the law as adopted. Adding
“Adding management, human resources and finance skills is enriching my current role”
management, human resources and finance skills is enriching my current role.”
I’m keen to find out more about CEMBUREAU’s relationship with EU decisionmakers. How receptive are they to the needs of the European cement industry? Does Coppenholle’s career background in EU law and working practices help him in his dealings with EU powerbrokers?
“My career background certainly helps me in many ways: the legal expertise helps me to quickly assess where we should focus our efforts, and facilitates reading and analysing policy documents and drafting the necessary briefs. My company background makes me better understand why some decisions are taken and allows me to preempt situations and seek early compromises. This asset should not be underestimated in managing an association where interests are not always aligned.
“I can also confidently say that our relationship with policymakers has strengthened and deepened, helped by the pro-active approach of our industry leaders and a strong public affairs team. We have a network of very useful contacts across a wide range of European Commission departments, in the European Parliament and, with the help of national associations, in member states.”
CEMBUREAU’s CEO is keen to get out of the office as much as possible to get a firsthand take on the European cement sector.
“I travel quite often, less in current COVID19 times, to national associations for either a work visit or to participate as a speaker in one of their events. I always look forward to
plant visits hosted by companies. If I had to choose a standout one it would be a two-day tour organised by Peter Hoddinott, one of CEMBUREAU’s former presidents, during which I visited the LafargeHolcim research centre in Lyon and a cement and a concrete plant in the region. I was welcomed at each of the sites by very expert and knowledgeable people.”
I wonder what Coppenholle sees as being the association’s and his own most significant achievements during his time as CEO?
“As an association, we have been able to provide the correct technical expertise to policymakers in key policy files, and we have done so based on data and accurate information. We always take a proper and data-driven approach to policymakers, and the essence of the relationship must be trust. Looking at the way policymakers approach CEMBUREAU, I think we have now earned that stamp of a respected organisation, and I want to keep it like this. Good communication is essential for clearly conveying our views, but it is a tool that needs thoroughness in thinking and analysis and not hollow words.
“In my role of CEO, I am most proud of having earned respect for the sector with policymakers and support from the members. This drives me forward and ensures that I get out of bed every day feeling the passion and enthusiasm for this job.”
Speaking about goals he’d still like to achieve in his CEO role, Coppenholle says: “Starting from the previously mentioned support and respect, I would like to see that broadened going forward. We have intensified our outreach to policymakers, but it is now our task to deepen relationships with more stakeholders, including NGO’s [non-governmental organisations], trade unions, think tanks and the public at large. We have put our foot in the water for all of these, but we now need to start swimming.”
Away from work, Coppenholle, who grew up in the Belgian port city of Ghent, enjoys spending time with his wife, 24-year-old son and nearly four-year-old daughter. “I love to travel with my family, watch a good movie and enjoy long conversations with friends over a good meal and glass of wine.
“I have been based in Brussels for 25 years. I love the compact size of the city, which allows strolling around, meeting the whole world on a pretty small surface and enjoying a wide choice of excellent food in some unique settings.”
Finally, I’m keen to know how Coppenholle sees the long-term future of the European cement industry given, among other factors, the rise of automation and greater diversity of building materials available to customers.
“Cement will remain an essential building material for the future and is essential for the sustainable built environment of tomorrow. We will need to think of different and more efficient ways of using cement and concrete, and this will be partly driven by digitisation. However, wisely used, cement and concrete will be here to stay.” AB
WHEN FLEXIBILITY AND HIGH PERFORMANCE ARE PARAMOUNT. The MOBICAT MC 120 Z PRO mobile jaw crusher and the MOBICONE MCO 11 PRO mobile cone crusher are exactly what you need – perfectly combined with the mobile screening plants from KLEEMANN. Their high production output and low-maintenance operation make them a real alternative to stationary solutions. The PRO-Line from KLEEMANN: Power packs for the quarry.
www.kleemann.info/pro
COVID-19 is the primary concern throughout the European and wider world economy as everyone is trying to understand the impact and identifying the best response to this unexpected crisis. UEPG, the European Aggregates Association, is at the forefront in monitoring and supporting the aggregates industry in Europe to fight the spread of the new coronavirus, ensure the health and safety of its workforce and to ensure operations can continue or resume.
To help the aggregates industry to effectively tackle challenges related to the management of the new coronavirus in extraction sites, UEPG launched a UEPG Health & Safety Guidance on COVID-19 management. This guidance document gives general, as well as particular information for every type of work done in an extraction site. In the flow of often too general information arising from all levels of governance, it may be difficult for companies to identify the specific measures required for extraction sites. Therefore, UEPG is helping to support them with a document that draws upon best practices in some European countries, as well as EU protocols, like the ones proposed by the European Agency for Safety and Health at Work (EU-OSHA). The added value of having such a document is that national associations and companies have all information in one place, readily available for translation into their national languages and easily implementable. Several UEPG members have published guidance documents which communicate in practical ways basic hygiene rules that should be followed in the workplace.
Furthermore, UEPG collects information from its members to provide an overview of
is looking into practical, easy-to-apply solutions developed by companies facing the COVID-19 crisis. Then, appropriate choices of the central EU institutions, i.e. the European Commission, Parliament and Council, are also continuously monitored. For a more detailed update on the economic impact of the COVID-19 crisis, UEPG members have started to provide best estimates on the loss of production in 2020 and the potential for recovery in 2021. Visit our COVID-19 website: http://www.uepg. eu/covid-19.
At the request of the European Commission, UEPG is providing a weekly update on the social and economic
BELOW: COVID-19 pandemic disruption - the estimated percentage fall in aggregates production in the 27 EU member countries plus EFTA nations (Iceland, Norway, Switzerland) and the UK for the full year 2020 compared to 2019. Source: UEPG
appropriate response to the COVID-19 crisis, which is partly reflected in the €750 billion Recovery Plan presented by the European Commission on 27 May 2020. AB
• The UEPG (European Aggregates Association) has members in 27 countries. The aggregates sector is by far the largest amongst the non-energy extractive industries. European (EU28 + EFTA, 2013) aggregates production is 2.6bn tonnes/year representing an estimated annual turnover of €15bn. The continent’s aggregates industry comprises around 15,000 companies which employ 200,000 people (including contractors) working across 25,000 sites.
ABOVE: Coarse aggregates covered with cement and dust BELOW: A quarry site visit during the UEPG General Assembly 2018 in Barcelona, Spain
A world with less noise is a better world. So now we proudly present our new compact electric construction machines, L25 & ECR25. They are here to Add Silence. For more information and prebooking: www.volvoce.com/electromobility
As countries across the EU start to ease coronavirus lockdown measures, what are the legal implications for aggregates businesses as their employees return to work?
Terry Falcao, head of employment at specialist mining and minerals law firm Stephens Scown LLP outlines the issues.
European countries dealt with coronavirus in slightly different ways, and are coming out of the lockdown slightly differently too. Although this article focusses on the issues in England, many of the themes will be common to other jurisdictions.
Social distancing and hygiene guidelines have been widely documented, so instead, I will focus on other considerations and legal issues employers face as we come out of lockdown.
As an employer, most businesses will be well aware that they have legal responsibility for the health and safety of staff at work. But what about mental health? What sort of support will your staff need upon returning to work?
At the very least, the law and best practice would expect employers to initiate discussions about how staff coped with being at home and away from others, the loss of income or in some cases the loss of partners’ employment.
Whether internal HR, counselling services or external employee assistance programmes are involved will be a matter of what resources you are able to put into this area of hitherto unappreciated risk. It is foreseeable that employees operating away from the workplace or returning from furlough will have different needs from when they simply worked at the business premises. Their fears and anxieties may arise from a number of factors, and offering support and reassurance will be key to retaining them, meeting the business needs and getting them to being productive.
Employment contracts have express and implied terms (i.e. some terms are not written down, but are assumed to be in every contract). Failure to pay employees correctly and changes in the most important terms and conditions are usually actionable breaches of employment contracts and may well mean the contract is at an end, and the employee considers themselves as being dismissed.
In England, many businesses will have used furlough leave and the government’s business support measures as well as voluntary reductions in pay and hours. These are changes to contracts. Employers need to consider whether these were agreed as temporary or permanent. If agreed to be temporary, what
“The economic turbulence from lockdown will certainly persist for a period of time”
were the time limits imposed? If breached, this is a breach of contract which could lead to a claim. Review any such agreements and be prepared to engage in consultation if they need to be extended.
Will your business requirements be the same?
The economic turbulence from lockdown will certainly persist for a period of time. That being the case, you may use this time as an opportunity to keep your best staff, reduce staffing in areas where performance or production has not been successful and invest in areas where there is evidence of high demand.
The law expects lawful processes and decision-making arising from a proper assessment of the needs of the business. Start the process early. Assess your business needs, the demand for your goods or services, current supply logistics and staffing requirements and record this in management minutes or reports. This audit trail may well save you tens of thousands of pounds in the event of litigation and rebuts allegations of targeting an individual for unlawful reasons.
Employers may need to be bold and consider restructures to save costs, reduce bureaucracy and become more responsive to the market. This may entail redundancies. Early
consultation with staff is essential to minimise the additional risks from tribunal claims.
Employers who act commercially and following processes in pursuit of business needs should have no difficulty in being transparent about the business needs and where possible sharing an audit trail with employees. It is so much harder to argue with facts and figures gathered in the course of rigorous business planning.
Our economy has suffered because of the virus. To thrive once again, business will need to be determined and ambitious, compassionate and wise and most importantly prepared for the long haul to normality, but probably not as we have known it. AB
Terry Falcao is partner and head of employment at Stephens Scown LLP. The firm has over 70 years of experience in the mining and minerals sector, and its specialist team is recognised by independent legal guides Legal 500 and Chambers.
To contact Terry, please call 01392 210700 or email solicitors@stephensscown.co.uk. For more information visit www.stephens-scown.co.uk
The UK and Irish aggregates and manufactured mineral products industries are enduring significant disruption due to the global COVID-19 pandemic, but demand is there once things return to relative normality. Guy Woodford reports
Few parts of the world have not been affected in a significant way by the COVID-19 pandemic. In the UK, the British government ordered a lockdown of public life, including a two-metre social-distancing-in-public guideline, on 23 March 2020. The lockdown has hit the national aggregates sector hard, with quarries and mineral production plants forced to close. Many large and small- to medium-sized mineral product suppliers have also accessed the government’s furlough scheme, whereby the state pays 80% of an employee’s wages up to £2,500 per month to 31 July 2020, and a varying lesser percentage from 1 August to 31 October, to avoid immediate redundancies.
Meanwhile, the Hillhead exhibition, the UK’s bi-annual showcase of the latest premium quarrying, construction and recycling equipment, has been postponed. Staged in the former Tarmac Hillhead Quarry near Buxton, Derbyshire, central England, the event, which had been due to take place 23-25 June 2020, will now take place 22-24 June 2021. To avoid a clash with a rescheduled Hillhead, which attracted nearly 20,000 visitors in 2018, Plantworx 2021, another popular exhibition for the UK construction, quarrying and recycling equipment industries, held at the East of England Arena in Peterborough, has been put back until June 2022.
Employing 74,000 people, the UK aggregates and manufactured mineral products industry is one of the biggest in Europe. Putting the current COVID-19 disruption in context are statistics published by the Mineral Products Association, the
trade body for the UK’s aggregates, cement and concrete industries, in its Profile of the UK Mineral Products Industry - 2018 Edition The influential report notes that 390 million tonnes of aggregates and manufactured mineral products are produced in Great Britain every year. That output is four times the volume of energy minerals produced in the UK per annum, including oil, gas and coal. The aggregates and manufactured mineral products industry has an £18bn annual turnover, with £6.8bn of gross value added generated by the industry. The industries supplied by the aggregates and manufactured mineral products industry have a yearly turnover of £513bn. The construction industry, the aggregates and manufactured mineral products industry’s primary customer has an output value of £152bn. Furthermore, 3.5 million jobs are supported by the aggregates and manufactured mineral products industry’s supply chain.
The latest sales figures for the UK mineral products sector show the extent of the COVID-19 effect. Construction market demand for heavy-side building materials in Great Britain, including aggregates, asphalt, ready-mixed concrete and mortar, declined significantly at the start of 2020.
The MPA noted that the fall reflected a “double-whammy” of flooding and adverse weather affecting work on-site in February and the early impact of the COVID-19 lockdown at the end of March. “These two factors brought any early signs of market sales improvements recorded in the second half of last year to a halt,” said an association spokesperson.
Sales volume of ready-mixed concrete and aggregates (crushed rock and sand & gravel), two materials used across most types of construction work, declined by 5.7% and 4.0% respectively over the quarter. For ready-mixed concrete, this follows three consecutive years of market declines since 2017, as Brexit-related uncertainties put a brake on commercial construction work, notably for offices, while housebuilding slowed in the capital. The housing and commercial property sectors have also been significantly impacted by the COVID-19 lockdown, with most significant housebuilders having closed sites throughout the last week of March and April, and office construction affected by the collapse in business and consumer confidence.
Simultaneously, sales of mortar, primarily used in housebuilding, fell by a further 1.6% in the first quarter of 2020, after a 7.9% fall at the end of last year. The MPA says subdued mortar sales volume over the past 18 months is a clear indication of the underlying weaknesses in housebuilding, even before accounting for the impact of the COVID-19 lockdown.
Weak demand for asphalt led to a 9.4% fall in sales volume in the first quarter of 2020 compared to the previous quarter, the biggest quarterly fall since mid-2012. Demand in Scotland and the South West of England was particularly affected. In Scotland, the market has been depressed since the highs recorded in 2016, when sales were boosted by large infrastructure projects, including the Forth Replacement Crossing and the Aberdeen Western Peripheral Route. In South West England, surfacing works were particularly hit by exceptional rainfall throughout February.
“Weak underlying market demand for heavy-side building materials at the start of the year, combined with construction sites closures, are having a significant impact on mineral products businesses. There is an even weaker and more uncertain outlook for the rest of 2020,” explains Aurelie Delannoy, MPA director Economic Affairs. “Since March, demand for ready-mixed concrete declined significantly as a result of widespread closures of housebuilding and commercial construction sites, as well as some early hiatus in major infrastructure projects, including Thames Tideway. By contrast, asphalt demand was somewhat supported by Highways England to supply the critical road network.
“Inevitably, large mineral products producers and SMEs (small- to medium-sized enterprises) alike have had to temporarily close operational sites throughout April, leading to an estimated 80-90% capacity shutdown across the industry due to construction and manufacturing customers closing down. Inevitably there are high levels of furloughing throughout the supply chain, and mineral products are no exception. However, with the prospects of construction and other sites gradually resuming work, mineral products producers are now
“It has been as torrid a time as any of us can remember”
Nigel Jackson MPA chief executive
focussing efforts on reopening their sites safely, bringing back staff and managing operations and work under strict safety guidance. The industry stands ready, able and willing to supply the materials needed for construction work to restart wherever it is safe to do so.”
MPA CEO Nigel Jackson said: “It has been as torrid a time as any of us can remember. Just as optimism was increasing with Brexit uncertainty lifting, the combination of flooding and COVID-19 has knocked the economy for six. We are down to around 10 to 20% of normal capacity but still supplying strategic and essential sites as well as agriculture, utilities and local road maintenance. The industry has the material to supply as and when construction and manufacturing customers reopen knowing it can extract, process, manufacture and deliver safely if customers have new and safer working systems in place.
“We were pleased to be recognised as essential by the government, and our members are ready to support the recovery and kick-start the economy. We hope that government will maintain a ‘can-do’ approach to investment and invest in much needed and overdue infrastructure and that HS2 [the UK’s planned high-speed rail network] having been given the green light will not be frustrated by mischievous legal interventions at this critical time for our country. Government has to recognise the risks all future infrastructure projects could now face from legal action and pull harder on the national need lever to protect a return to growth and to protect jobs.”
The MPA has written to the Chancellor of
the Exchequer, Rishi Sunak, having published a policy paper setting out the impact of coronavirus on the sector proposing some key policy steps to help get the industry through the crisis and be ready to support the recovery. It also warns of an anticipated credit squeeze as the economy reopens, a significant risk for those that survive the current shutdown.
With cash retention being the number one aim after the safety of employees and customers, the paper calls for several tax reliefs to help businesses hold on to cash. These include a further deferral of VAT, deferral of employers National Insurance, Corporation Tax and Business Rates. It also lists some additional charges and costs that should be able to be deferred. Greater flexibility and tapering of furloughing will, the paper states, soon need to be evaluated to avoid a ‘cliff-edge’ at the end of June that may trigger avoidable redundancies.
The MPA paper also calls for ‘Time to Pay’ arrangements with HMRC for the Aggregates Levy to be more readily available. This tax is falling due now as businesses face a very challenging cash environment and making deferment more easily accessible would be invaluable.
Paul McManus, chairman of the British Aggregates Association (BAA) and owner of Cloburn Quarry Company, in Lanark, Scotland, has stressed to BAA members that both he and the association’s officers were making every effort to support the membership throughout the COVID-19 pandemic.
In a statement sent to members, McManus said that despite the good relationship built up between the industry and HM Treasury following the recent Aggregates Levy review process held nationwide, it was “unfortunate” that the UK Chancellor had not so far chosen to suspend Aggregates Levy payments. McManus said this was despite HM Treasury putting forward many other beneficial measures to help the industry.
BAA’s chairman informed association members that he has sent a letter to the Chancellor asking him to clarify and put right the anomaly of Aggregates Levy payments at this time. The question of loans provided by banks is always a contentious one even when they are under a scheme supported by the government. And, in his statement to members, McManus stressed that those companies with healthy balance sheets need to be aware that banks may interpret the rules differently to how the government intended. He emphasised that members can seek the advice of the association which is supported by organisations in the legal profession along with the CBI.
Meanwhile, the UK construction industry bodies the Builders Merchants Federation (BMF) and the Construction Products Association (CPA) have joined forces to identify materials likely to be in short supply in the reopening period following the COVID19 pandemic.
The BMF and CPA stated that they are monitoring the manufacturing and distribution of their respective members, adding that their collaboration will help meet the needs of housebuilders, contractors and SME builders. The two bodies are heading up the Product Availability Group, set up by the Construction Leadership Council (CLC), which is coordinating the industry’s response to the COVID-19 crisis.
The BMF says it is gaining information from across its membership – comprising 710 members with combined sales of £32bn – to identify items likely to be in short supply and take steps to address them.
According to the BMF, early shortfalls in plaster and plasterboard supply were flagged up under the monitoring system, but steps are being taken to resolve that shortfall.
Speaking in late April 2020, John Newcomb, chief executive of the BMF, said: “Currently we are seeing no major issues, apart from plaster and plasterboard, but manufacturing is now scheduled to increase to address this problem.
“As a group, we are meeting every two weeks to keep a watching brief on the situation across the entire construction industry supply chain.
“We want to deal with potential issues proactively, to ensure demand is met across the construction sector.
“Nothing like this has happened before, and the work we are doing is unprecedented.”
Peter Caplehorn, CPA chief executive, added: “The CPA has been closely monitoring the operational status of its members. They are looking for sustainable demand for their products before starting to phase in more factory production, while at the same time ensuring the health and well-being of their workforce.
“With the BMF, we are discussing with government and the wider industry the need to encourage builders and merchants to safely reopen more sites and branches, in addition to continuing support for ‘essential’
activity such as key NHS and infrastructure projects, repair and maintenance.”
UK demand for aggregates and other manufactured mineral products will be healthy once again when the current COVID19 pandemic storm subsides. The British government’s spring budget announcement of a £27.4bn revamping of the UK’s roads network and the implementation of its
Group has resumed clinker production at its two cement plants and is “progressively” reopening some of its other sites.
Further sales momentum will come from the continuation of the HS2 and the Hinckley Point Nuclear Power Station megaprojects, and the resumption of what had been, up until the late March 2020-imposed lockdown, healthy levels of residential and commercial construction.
Heartening evidence of the coronavirus storm subsiding comes from some major UK and Ireland building materials producers partially reopening many of their big production sites.
Breedon Group, a major independent UK and Ireland construction materials business, has resumed clinker production at its two cement plants and is “progressively” reopening some of its other sites.
In total, over 80% of the company’s UK staff has been furloughed or temporarily laid off in the Republic of Ireland on full pay.
In a group statement released in late April 2020, Breedon said it had been “encouraged” by announcements from several companies in the broader construction sector confirming their intention gradually to reopen their operations in several regions of the UK and Ireland.
Ireland’s quarrying and concrete production industries have also been adversely affected by the COVID-19 pandemic.
“We have seen only around 10% of normal industry activity since the [full] lockdown in Ireland started on 27 March,” said Gerry Farrell, chief executive officer of the Irish Concrete Federation (ICF), during a telephone
interview with Aggregates Business on 7 May 2020. “While there was a certain amount of panic buying and building up of stocks in the two weeks before the lockdown, the trade completely died in April. The only work happening here is essential services – such as supplying building materials to COVID19-related health projects, and specific agriculture works. All the main construction sites are closed.”
In its recently published Essential Aggregates - Providing For Ireland’s needs to 2040 report, the ICF heartily welcomes the Irish government’s statement in the National Planning Framework 2018 acknowledging the essential role of aggregates in Ireland’s future development.
The ICF report succinctly highlights the national importance of aggregates, stating: “Ireland has abundant natural reserves of high-quality aggregates (stone, sand and gravel). These aggregates are the essential raw materials from which Ireland’s future infrastructure will be built, including our homes, offices, schools, hospitals and transport network.”
Figures contained in the highly detailed document show that as of 2018, the Irish quarrying and concrete production industries directly employed over 5,000 people and pay out more than €300mn a year in wages and salaries. Ireland has more than 500 large commercial quarries extracting aggregates. Around 36mn tonnes of aggregates product was produced in the country in 2018, excluding aggregates used to manufacture downstream products, while overall aggregates demand is 12 tonnes per capita – double the average of the EU28. Ireland is home to over 200 concrete manufacturing plants. In 2018, the Irish quarrying and concrete production industries
produced 4.8mn m³ of ready-mixed concrete, 125mn concrete blocks, 2mn tonnes of road surfacing materials, 1mn tonnes of agricultural lime, and exported €125mn worth of precast concrete.
The October 2019 publication of the ICF report followed the Irish government’s announcement the previous year of Project Ireland 2040 – an overarching policy and planning framework for the social, economic and cultural development of the country for the next 20 years and beyond. It includes the National Development Plan – a 10-year strategy for public capital investment of almost €116 billion to 2027 and the 20-year National Planning Framework.
Farrell said Irish construction sites were due to reopen on 18 May, but the impact of COVID-19 on the delivery of the Irish government’s national investment plan is uncertain. He continued: “Capital spending in Ireland was budgeted to go up by more than 10% this year. But as a result of the government’s spending on the COVID-19 pandemic, including a temporary wage subsidy scheme for workers and the pandemic unemployment payment for workers who have been laid off, the budget has been completely blown. We will need to wait and see how this affects public investment.
“We had a general election in the first week of February, but we still have no government. That creates its own uncertainty. What should give confidence to the construction industry and industry which supplies the construction sector is that the big issue in the general election was homelessness and the shortage of housing. There is an underlying demand for more housing and schools as the population is going up. There’s going to be another million people living here by 2040. The government will have to invest in the infrastructure and services to meet new societal demands. This will not be achieved without the products produced by our members, so it is important to ensure that there is a long-term plan to preserve access to raw materials.”
On 25 February 2020, the ICF held a major quarry planning conference in Newbridge. The event was held as a follow-up to the publication of the ICF’s Essential Aggregates – Providing for Ireland’s Future to 2040 report,
which was launched by Minister for Natural Resources Sean Canney in October 2019.
The conference was attended by ICF members, local authority planners, environmental NGOs (non- government organisations), regulatory bodies and other stakeholder organisations. Those in attendance listened to presentations from national and European experts, including leading environmental NGOs, industry representatives and legal and industry planning experts.
Some of the themes and issues which arose on the day included the role of aggregates in the circular economy, the essential nature of aggregates for Ireland’s future development, and the effective regulation of quarries. Further discussion topics included the need for legislative change concerning quarries, the importance of effective action against unauthorised quarry operations and national procurement policy.
The ICF says it will continue to support its members to ensure that they are fully briefed on national developments as Ireland responds to the threat of COVID-19. The ICF has also issued ongoing guidance to members on COVID-19 and says it will continue to update this guidance as the situation evolves.
According to CRH chief executive Albert Manifold, the Irish building materials giant’s financial strength and experienced leadership teams have left him in “no doubt” that the group will emerge in good health as COVID-19 pandemic disruption eases.
Manifold’s reassuring comments came as the company revealed its Q1 2020 like-forlike sales were up 3% compared to the same period of last year.
“We have had a good start to the year. Although the global spread of COVID-19 brings challenges for us all”
COVID-19 mitigating actions implemented across CRH include a 25% salary reduction for all leadership teams and board members; temporary lay-offs and a furloughing arrangement in affected areas; and reducing working capital in line with lower activity levels.
Speaking on 22 April 2020, Manifold said: “We have had a good start to the year. Although the global spread of COVID-19 brings challenges for us all, I have no doubt that with the financial strength of CRH and the experience of our leadership teams, we will endure through these unprecedented and uncertain times.
“All necessary actions are being taken to protect our employees and businesses and ensure that we are well-positioned for the recovery in our markets.”
A CRH statement released with the Q1 2020 trading figures says the group is in a strong financial position, holding over US$6bn of cash and cash equivalents.
While the UK and Irish government’s responses to the COVID-19 pandemic remain fluid, the respective aggregates and manufactured mineral products industries are in good shape to bounce back quickly following the peak of the coronavirus crisis. AB
New and proven premium crushing and screening plant have been very much to the fore in the first half of 2020. Guy Woodford reports
Pärhä Oy, located in Orimattila, Finland, is famous for high-quality concrete gravel, delivered directly to production facilities. Metso’s diesel-powered/electrical Lokotrack double-stage plant ensures that different types of crushed rock are produced effectively and economically. As a bonus, the new Lokotrack ST4.10 screen operates carbon neutrally, using electricity generated by the tertiary crusher.
“Last year, we crushed more than 600,000 tonnes, of which some 250,000 tonnes were processed into different types of concrete gravel. The majority of the concrete gravel is delivered to five companies operating in the concrete industry in the Päijät-Häme region,” says Jari Pärhä, who is in charge of the crushing operations and production at Pärhä Oy.
“When such volumes are being produced by a single crushing plant, the machinery needs to be reliable. Metso is known as a dependable Finnish company that also provides well-functioning maintenance services.”
The family-owned company, established by Tuomo Pärhä in 1980, shifted from forestry to the gravel business at the beginning of the 2000s. Currently, the company specialises in crushing and transport services. Since the beginning of this year, the company has three partners: Petri Pärhä is managing director, Jari is in charge of the crushing operations, and Tommi Pärhä is taking care of the transport arrangements.
The company acquired its first Lokotrack LT106 jaw crusher in 2013, followed by a Lokotrack ST2.8 mobile screen. When the company decided to focus more on crushing operations, Pärhä Oy asked Metso for a new tertiary crushing plant. It turned out that the existing Lokotrack range did not have the right solution for the company.
“A few weeks later, Mikko Takaniemi from Metso came to demonstrate a raw version of the plant we were looking for. The cone crusher and screen plant included the pre-screen we had requested,” Jari says.
In 2017, a unique diesel-powered/ electrical plant, called Lokotrack LT330GPSE, started operating at Pärhä’s quarry in Nastola. The LT120E jaw crusher replaced the primary crusher, and last autumn, the screen was replaced by ST4.10, a new Metso model, equipped with a 1.5m × 6m three-
When different types of gravel for concrete and gritting are being produced, primary crusher feed enters first the LT330GPSE pre-screen, which removes the fine materials before going to the cone crusher.
“The pre-screen helps us to only feed pure rock material into the crusher, especially in wet conditions. This makes the production more effective and improves the quality of end products. Metso’s pre-screen works just as we planned,” Jari notes.
The double-stage plant and mobile screen produce gravel of 6–12 mm and 12–16 mm at an hourly rate of roughly 200 tonnes. At the same time, the process produces gritting gravel of 3–6 mm and fine rock dust of 0–3 mm. When coarser material is being produced, the capacity increases to 350–400 tonnes.
Pärhä Oy’s vehicles are used to deliver
operating in the concrete industry, for infrastructure construction and to private customers.
“Quality and documentation are important to us. For example, we check the quality of concrete gravel after every 500 tonnes,” Petri says.
This year, Pärhä will expand its production to asphalt and railway ballast. The company has, therefore, acquired a quarry from Mäntsälä to produce high-quality aggregates.
Sandvik is introducing Peak Screening – said by the Swedish quarrying equipment giant to be an innovative screening solution that helps customers reach their full productivity potential.
A company spokesperson says: “Peak Screening is a complete package offer and performance concept designed to ensure every square metre of a customer’s screening is as productive as it can be for their unique operation.
“Most screening operations, even when they look fine, are capable of more. Often much more. Peak Screening is our term for a complete screening solution, including the right screen, screening media and warranty/ service program for any customer budget or need, all working together towards one goal – maximising the full potential of the customer’s screening operation.”
Sandvik says its screening equipment, screening media and services are designed to work optimally with each other and ensure the screening operation is as productive as it can possibly be. The company says that its customers will also benefit from having ongoing access to experienced Sandvik specialists who can help with the right configuration, optimisation, troubleshooting, and much more.
“Most screening operations, even when they look fine, are capable of more”
Sandvik now has three new ranges of maintenance-friendly, high-performing modular screens that are said to be more versatile, more reliable, faster to get on-site and safer to operate.
All Sandvik screens come with highquality Sandvik screening media as standard, unless otherwise specified. Sandvik says it works closely with customers to determine the right solution for their applications. This includes offering exclusive options such as Sandvik’s WX6500 tensioned rubber screening media with up to a claimed 15x
ABOVE: Sandvik Peak Screening is said to be an innovative screening solution that helps customers reach their full productivity potential
BELOW: As part of its new Peak Screening solution, Sandvik has three new ranges of maintenance-friendly, high-performing modular screens that are said to be more versatile, more reliable, faster to get on-site and safer to operate
Ammann ARX Light Tandem Rollers excel in the open, where covering ground quickly is the goal. But other jobsites call for a compactor that can work tight against obstructions, such as curbs, without losing productivity.
Other key features
Ammann ARX series of light tandem rollers deliver in both worlds. They feature industry-leading compaction output to quickly reach targets when working in open spaces. When obstructions are a factor, the rollers can quickly switch from in-line to offset compaction, providing operators with improved vision and precision.
• Latest EU Stage V / U.S. EPA Tier 4f engine from Kubota
• Spacious operator platform with sliding seat
• Electronic drive lever for smooth starts and stops, especially important on asphalt jobs
• Optional ACEforce, the Intelligent Compaction tool for optimal efficiency
• Simple and reliable dashboard with intuitive machine control
• Perfect all-around machine visibility and LED lights for safety on the jobsite
Looking for even more productivity? When the workday is done, maintenance points can be easily accessed from the ground to ensure quick completion of service work.
longer wear life than standard wire mesh, but with the same screening accuracy for better productivity and uptime.
Sandvik’s novel Reliability & Performance (R&P) package is said to protect customer investment. R&P includes two years extended equipment warranty, regular inspections, maintenance recommendations, troubleshooting and performance analyses that can help optimise service intervals and avoid costly breakdowns.
Screening solutions from Sandvik also come with a performance guarantee where Sandvik guarantees that the solution achieves the performance that has been agreed on together with the customer — or Sandvik will work with the solution until it does.
“Peak Screening shows our understanding of customers’ productivity needs, and commitment to solving their challenges in unconventional, industry-first ways. We want to help customers benefit from the competitive advantage Peak Screening can provide, while establishing it as the defining screening performance standard of our industry,” says Mats Dahlberg, vice president Lifecycle Service Stationary Crushing & Screening.
Terex Finlay is expanding its mobile crusher line with the introduction of its IC-Range of compact impactors. The IC-Range of small impact crushers has been designed explicitly for quarrying, construction and demolition debris, reinforced concrete
and asphalt recycling applications.
The new IC-range comprises four models: IC-100, IC-100RS, IC-110 and IC-110RS.
“The addition of these four new models complements our existing range of mobile impact crushers and opens up new opportunities at the smaller machine sector of the market. Each of these models has been rigorously tested and proven in a diverse range of applications. The compact size, ease of transport, quick set-up times and intuitive operation make each of these machines ideal for contract crushers, independent rental houses and small-scale operators,” says Alan Witherow, Terex Finlay lead technical support and product manager.
The IC-100 features an 860mm x 860mm direct-drive horizontal impact chamber with variable rotor speed. The advanced electronic control system monitors, controls and regulates the speed of the VGF (vibrating grizzly feeder) to maintain a consistent feed of material into the impact chamber to maintain optimal crushing capacity. The IC-100 provides operators with a compact and versatile machine that gives high material reduction ratios and produces a consistent product grading.
Based upon the IC-100, the IC-100RS features an onboard recirculating system and detachable sizing screen to provide the versatility of a compact crushing and screening plant on one mobile. If recirculating and sizing materials is not
required, the sizing screen can be removed quickly from the machine without the need for secondary lifting equipment. The recirculating conveyor can also be utilised for stockpiling an oversize product.
The IC-110 features a 1034 x 1000mm direct-drive impact chamber with variable rotor speed and hydraulic apron-setting assist in providing convenient and efficient adjustment of the chamber aprons. The chamber is also fitted with a hydraulic overload protection system as standard. For operators in recycling and demolition applications, an underpan feeder is also available as an option.
The IC-110RS impact crusher provides the versatility of a compact crushing and screening plant on one mobile platform for quarrying, construction and demolition debris, reinforced concrete and asphalt recycling applications.
The machine features a direct-drive 1034mm x 1000mm horizontal impact crusher with variable speed control to give operators unprecedented levels of fuel efficiency and productivity. A vital feature of the machine is the onboard 2.74m x 1.5m single-deck screen. For applications not requiring recirculation of oversize material back to the crushing chamber or the stockpiling of an oversize product, the complete screening and recirculating system can be quickly detached from the machine.
In other Terex Finlay news, the company’s
o matter how challenging your needs, EARTHMAX No 41 is your best ally when it comes to operations SR at require extraordinary traction. Thanks to its All th eel radial structure and the special block pattern, St ARTHMAX SR 41 provides excellent resistance EA ainst punctures and an extended service life. In aga dition to long working hours without downtime, add e tyre ensures extraordinary comfort. th ARTHMAX SR 41 is BKT’s response to withstand EA e toughest operating conditions in haulage, th ading and dozing applications. loa
standard subscription for its T-Link plant monitoring and performance optimisation system is now available for seven years.
Introduced in January 2016 the T-Link hardware and software can be used on any Terex Finlay crusher or screener with an electric engine.
It allows operators at any given time to see the exact location and status of their Terex Finlay plant fleet.
Furthermore, T-Link shows what areas to improve upon to optimise profitability.
Now, all Terex Finlay machines that are already in the field and fitted with T-Link hardware and software will automatically roll over to the extended seven-year data subscription.
Alan Witherow says: “T-Link takes the guesswork out of machine monitoring and performance optimisation. Our sevenyear standard data subscription places us at the technological forefront of our industry.”
The Terex Finlay T-Link package provides operators with a userfriendly, unlimited portal to access all the firm’s machines in one place at one time. It also gives them key figures and performance metrics of their connected assets in the form of ‘Actionable Reports’ that they receive automatically weekly.
Superior Industries, a US-based manufacturer and global supplier of bulk material processing and handling systems, has unveiled a new series of modular plant for aggregates crushing, sorting, sizing and washing applications. Known as Fusion Modular Platforms, these pre-engineered, ready-to-build systems still allow customisation to achieve the best performance at each job site.
“Our plant designs are scalable and easily expand with a developing customer site,” says Mark Crooks, product manager at Superior Industries. “Producers can quickly expand capabilities as finances allow, the application needs change and as their market develops.”
Today, Superior has pre-engineered a series of plant packages and is working on designing more for its catalogue. Some examples include jaw, cone and impact crushing platforms, horizontal screening platforms with two-, three- and four-deck models, plus a group of traditional washing and modern low-water washing platforms.
“Overwhelmingly, our customers said they want scalability and flexibility in these modular offerings,” says Crooks. “Therefore, as we developed our strategy, we ensured flexibility from top to bottom, convenient installation or dismantling and seamless integration with Superior crushing, screening, washing and conveying machinery.”
Fusion Modular Platform systems are pre-engineered for earlier commissioning, are more cost-effective than a design-build plant, incorporate well into existing plants and utilise creative packaging to limit the number of flatbeds or shipping containers needed for transportation. AB
BELOW: Superior Industries has launched Fusion Modular Platforms, a new series of modular plant for aggregates crushing, sorting, sizing and washing applications
Two new vehicle purchases are helping a Scottish quarrying and construction company to maximise the efficiency of recycling and reduce the amount of materials it sends to landfill
Tayside Contracts has purchased a new wheeled loader and excavator as part of a fleet of machines used in its quarrying, recycling and construction operations.
The Dundee, Scotland-based company bought a Doosan DL350-5 wheeled loader and DX255LC-5 crawler excavator from Balgownie, the local authorised Doosan dealer headquartered in Inverurie, Aberdeenshire.
The two machines can be moved around the various facilities run by Tayson Contracts, including both the quarries and the four recycling centres located in Arbroath, Forfar, Dundee and Collace.
The construction division of Tayside Contracts is a major civil engineering construction organisation in the Tayside area, employing over 400 people with a turnover of over £34mn. The new Doosan machines work mainly in its two quarries – Boysack Quarry near Friockheim in Angus and Collace Quarry in Perthshire.
A key objective of the construction division is to maximise the use of recycled material and minimise waste to landfill. As a result, all the recycling centres accept construction waste to produce a recycled sub-base and a recycled crusher run for further use.
Boysack Quarry produces Type 1 materials which are used internally and are also available for sale to external customers. Much of the product from Boysack Quarry goes to Collace Quarry, which manufactures a range of asphalt mixes including hot rolled asphalt, asphalt concretes, stone mastic asphalt, pre-coated chips and cold-mix for base/binders.
The Doosan DL350-5 wheeled loader has a bucket capacity of 3.5m³. It is made to meet a wide range of material-handling needs from loading and transporting
granular material (such as sand and gravel) to industrial and quarrying applications. Powering the DL350-5 wheeled loader is a Doosan DL08 diesel engine, with an output of 202kW at 1800rpm. The DL350-5 at Tayside Contracts has a five-speed ZF transmission with lock-up and a hydraulic differentiallock front axle for low fuel consumption and excellent productivity in all conditions.
The Doosan DX255LC5 excavator is said to offer comfort and controllability with a focus on increased power, robustness and agility. While overall dimensions are similar to the previous DX255LC3 model, Doosan says the DX255LC5 combines higher power with a 500kg increase in operating weight. This results in up to 17% more lifting capacity over both the front and side and a one dBA sound level reduction.
Volvo Construction Equipment (Volvo CE) has unveiled new enhancements to its H-Series wheeled loaders that it says will help reduce total cost of ownership.
The rimpull control system now comes as standard on all H-Series models. This function allows operators to minimise wheel spin and optimise the balance between rimpull and hydraulic functions. In turn, this helps reduce tyre wear and fuel consumption for more efficient bucket filling.
The L60H-L220H wheeled loaders were launched in 2014, with the larger L260H and L350H models following in 2017.
“Over the years we have built on experience and worked closely with customers to improve these machines,” said Volvo CE product manager Lars Eriksson. “Now, in 2020, we have introduced new features that take these machines to a new level of efficiency.”
The Volvo Co-Pilot monitor is now available on a broader range of machines from the L60H up to the L350H. The 25.4cm in-cab touchscreen provides access to several Load Assist applications (depending on machine model) aimed at optimising operator performance and site efficiency.
Firstly, there is a tyre pressure monitoring system that gives operators real-time information on the conditions of machine tyres.
A map application allows operators to get better visibility and understanding of the site layout and real-time site traffic situation, allowing them to adjust their driving behaviour accordingly. Weather, Calculator and Notes apps are also new, and these functions work similarly to those found on a smartphone and are pre-installed in the Volvo Co-Pilot.
of machines, providing access to several Load Assist applications
Designed to help load the optimum amount of material, the on-board weighing app is upgraded to include two new task modes – stockpiling and processing – adapting the on-screen layout and information displayed according to the task at hand.
For increased convenience and safety, both the rear-view camera and radar detector system feature on the Volvo Co-Pilot display. Volvo CE has also introduced an operator coaching application. This tool is designed to enhance operator performance, helping them get the most out of Volvo wheeled loaders and thereby reducing operating costs.
Additional new updates are designed to optimise maintenance procedures, thereby minimising downtime and service costs. Firstly, there is the extended engine oil change interval, which will be 1,000 hours as standard for H-Series models equipped with Stage V engines from April 2020. A quick-fit connector on the hydraulic tank is standard on all H-Series models. This feature is said to result in quicker and easier hydraulic oil filling.
On the L150H up to L260H models, a new quick-fit option enables cleaner and rapid engine oil changes – in as little as 15 minutes – helping eliminate oil spillage and contamination.
Volvo CE has also added five new applications to the Load Assist system for its H-series wheeled loaders.
The five new apps are aimed at enhancing the ease of operation, safety and overall site efficiency. Tasks that had to be done manually or required operators to step out of the cab can now be automated from the cab.
The tyre pressure monitoring system app enables the Volvo Co-Pilot touchscreen to display tyre pressure and temperature in real time. Each tyre is monitored independently, and pressure limits (low/high) are set per axle. If any of the individual tyres go outside of the set parameters, the operator will be alerted – alarm limits are displayed as nominal values and percentages.
The map app uses the loader’s built-in GPS for positioning and the telecom connection on the Volvo Co-Pilot to communicate between machines. The new map feature allows operators to monitor on-site traffic in real time and proactively adjust their driving according to traffic
conditions, especially in areas where multiple machines are operating close to each other.
The calculator app comes complete with basic calculation (addition, subtraction, multiplication and division) functions.
The calculator can also be used as a unit converter, quickly and easily converting six-unit types – length, mass, angle, time, temperature and speed.
The notes app is designed to remove the need for a pad and pen with a digital notepad, which can be used to write and save notes while in the cab.
The weather app informs the operator of current and upcoming climatic conditions so that they can adapt more efficiently and keep operations on track, whatever the weather conditions.
Several other existing features have also been upgraded. When the Radar Detect System is ordered, it is now integrated into the Volvo Co-Pilot, allowing operators to benefit from a rear-view camera and load information, which is all displayed on a single screen for increased convenience and safety when reversing.
The final update is the addition of two new task modes on the on-board weighing app. Operators can now choose from the trip meter, truck loading, stockpiling or processing mode. Each mode will adapt the Volvo Co-Pilot screen layout and provide relevant information for the operator to be efficient in the different applications.
Hyundai Construction Equipment Europe (HCEE) is continuing the rollout of the A-series with the HX300AL, a 30-tonne Stage V-compliant crawler excavator.
The HX300AL is suitable for infrastructure works and general construction. It features a new engine platform (Stage V), a new hydraulic flow regulation, improved operator controls with 2D/3D machine guidance and new safety features.
HCEE says the new machine offers improved uptime and productivity and incorporates some of its new technologies, including EPIC (Electric Pump Independent Control). By controlling the pump’s regulation independently, the machine is designed to offer improved fuel efficiency and controllability.
Other features include Auto Safety Lock, which prevents unintended operation/start of the excavator, which improves safety for the operator and on the job site.
Eco guidance indicates ‘inefficient operation’ status to prevent energy losses (fuel consumption, hydraulic power) by inadequate working habits which is displayed on the machine cluster.
MG/MC or Machine Guidance/Machine Control indicates the work status and automatically controls the attachment to assist the driver.
MG displays the position of the bucket tip and assists the operator with the use of positioning guidance. MC will automatically take over the grading with the bucket tip or face and has an automatic stop control: up, down, forward, and cabin protection.
“The new Electric Pump Independent Control is an energy-saving technology that reduces the pump flow rate during levelling and truck loading operation by controlling the pump’s displacement individually,” said Peter Sebold, product specialist at HCEE.
“Think next-level load sensing, a fuel saving of up to 8% daily average and general all-round operator and owner satisfaction, that’s just another win for this highly anticipated machine.” AB
The COVID-19 pandemic has affected almost all markets and industries, with many countries going into lockdown. The MD of hauler manufacturer Terex Trucks predicts that the global construction industry – with help from government investment in key infrastructure projects – will be extremely important to economic recovery
The COVID-19 pandemic has forced most construction equipment manufacturers worldwide to reduce or suspend production at their factories over the last few months.
Around the end of March, in line with its parent company the Volvo Group, articulated hauler manufacturer Terex Trucks decided to temporarily suspend production at its facility in Motherwell, Scotland. The company says this was to ensure the health, safety and wellbeing of its employees, customers and the general public.
Speaking at the end of May 2020, Terex Trucks MD Paul Douglas said that the company is continuing to operate with a small team of dedicated employees who are working to support customers and maintain vital spare parts distribution.
Terex Trucks has recently started to see some OEMs (original equipment manufacturers) gradually bring teams back to work and begin a ‘new normality’ and Douglas adds that building sites are expected to gradually re-open over the next few months.
“Right now, it’s hard to predict exactly what’s going to happen in the global construction sector over the next few months, but we do see cause for optimism,” said Douglas. “The construction industry will be vital to global economic recovery. To kickstart economies, we expect that governments will invest in construction and infrastructure projects as an effective way to create jobs and boost their economies – and there are some key projects on the horizon.”
of Britain’s ten largest cities, this high-speed railway linking up London, the Midlands and the North is one of the most important economic regeneration projects in Britain for decades, which Douglas says is expected to kick-start not just the construction industry but the wider economy.
Douglas predicts that, due to this project alone, the UK could see demand for articulated dump trucks rise by an additional 1,000 machines over the next few years.
“In the first stages of the project, articulated haulers such as our Terex Trucks TA300 and TA400 will be used for preparatory tasks and transporting materials before the main construction work can begin,” he adds. “This includes jobs like vegetation clearance and earthwork for tunnel portals and compound facilities.”
In France, where Terex Trucks is expanding its distribution network and currently has four dealers – The Manu Lorraine Group, Framateq, Promatex and Griset Material – the population has slowly been returning to work during the last of weeks of May and Terex dealers have started up their sales activities again.
Looking ahead, Douglas highlights the Seine-Nord Europe Canal project, an important initiative that is expected to boost the French construction sector as well as the wider economy. This will involve the construction of a 107km inland waterway link extending from France to Belgium, connecting the Seine basin north of Paris to the Rhine basin and the northern European waterway network. For the construction, 55 of earth will have to be excavated and transported. Douglas says that robust and reliable dump trucks such as Terex Trucks’ own TA300 and TA400 models are a natural choice for this task.
In the UK OEMs are getting ready for the start of the major High Speed 2 (HS2) infrastructure project, which the government has approved work to start on. Serving eight
“The construction industry will be vital to global economic recovery” Paul Douglas
“While I do believe there is cause for optimism, the last few months have, of course, not been easy for OEMs,” he adds. “In the UK, which is the biggest market for articulated trucks in Europe followed by France and Germany, sales of construction and earthmoving equipment fell by 36% in the first four months of the year, compared with the same period in 2019.”
In April, the Construction Equipment
Association reported that sales fell by 74% compared to the same month last year.
As the lockdown in the UK came into effect at the end of March, Douglas says it is unfortunately the case that the industry’s sales will take a further dive in the second quarter of the year.
“As construction activity has slowed down throughout Europe during the last few months, the demand for machine rentals has also decreased,” he says. “This has had a significant impact on German rental companies – where renting accounts for 70% of the market activity – as well as the Italian market. In Italy, the rental trade association Assodimi-Assonolo reported that in March, 80% of rental companies experienced a downturn in orders.”
In Asia, which was amongst the places initially hit by the COVID-19 pandemic, the region has been one of the first to reopen its factories. In Korea and China, some construction equipment plants are already back up to full capacity and Douglas says there is a good level of demand. However, it still remains to be seen how this will develop over the next few months.
In Indonesia, for instance, the numbers of registrations for articulated haulers indicate a significant drop in demand. Last year, 177 machines were registered in the first quarter, whereas this year there were only four registrations in the same period. This is a completely different situation to Africa, where Douglas says that the number of registrations has been relatively stable so far.
“In other parts of the world, we are hearing that there won’t be any big projects starting over the next few months,” he adds. “In the Middle East, where many countries have oil-dependent economies, a lot of construction and infrastructure projects have been put on hold. This is due to low oil prices as the financing of construction and infrastructure projects in many Middle Eastern countries is often backed by oil revenues.”
The first two Komatsu HD605-8 dump trucks equipped with Metso Truck Bodies have been delivered to a porphyry quarry in Brabant Wallon, Belgium.
The deliveries by Metso distributor BIA Group are the first to be made in Central Europe and come exactly one year after the launch of the Metso Truck Body at the bauma 2019 fair.
The tough and abrasive rock handled by the Brabant Wallon quarry had a significant impact on the previous conventional truck boxes. On a traditional box, the maximum payload is limited by the high weight of the lining and the box itself. Metso says its Truck Body differs from a standard box by its lighter, but resistant, rounded design in ultra-high-strength steel combined with the Trellex rubber lining. The Finnish quarrying equipment maker says this makes it possible to obtain a 20% to 30% lighter body without sacrificing rigidity.
The Metso Truck Body designed for the Komatsu HD605-8 truck weighs 6 tonnes less than a standard version fitted with a steel liner. According to Metso this weight reduction translates into a 10% additional payload and therefore offers greater efficiency from the first run. Likewise, during empty bucket journeys, the dumper will consume less fuel simply because it is lighter. Due to its rounded shape, less carry-back remains in the body, avoiding the transportation of unnecessary weight.
Off-highway truck customisation company Philippi-Hagenbuch has started using new SSAB Hardox HiTemp steel in its Hot Slag truck bodies.
The new steel is purposely designed to withstand extreme temperature environments and Philippi-Hagenbuch says
that it reduces necessary plate thickness while maintaining the product’s service life for increased productivity in processing applications.
“As a true custom manufacturer, every PHIL product is designed to excel in a specific application,” said Josh Swank, vice president of sales and marketing for PhilippiHagenbuch (PHIL). “In the past, steel mill clients requested a unique HiVol truck body to haul hot slag. Our engineers responded with the Hot Slag Body. Now, with the new HiTemp steel from SSAB, we can provide the same strength and durability with less steel, maximizing payload potential and providing our clients with a better product.”
The Hot Slag Body is comprised of two components — an exoskeleton superstructure, which does not come in contact with molten material, and loadcontaining pieces that do.
These pieces form an overlapping structure that is loosely strapped around the body of the exoskeleton to contain the hot slag during operation. This is designed to allow for differential expansion and contraction, where a traditional body would buckle under such extreme heat. When transporting molten material, the pieces expand and contract without breaking welds, binding up or warping. When a piece is damaged or worn out, it can simply be replaced without any structural welding requirements.
Following its acquisition of fellow Italian company Perlini in 2018, Cangialeoni Group has “rebirthed” the brand (now called Perlini Dumpers) from the start of 2020 with the expressed aim of returning it to the elite group of rigid dump truck (RDT) manufacturers.
This strategy has led to the company moving from the exclusively internal production of all components to a partnership with a group of twenty-three local suppliers and to the development of a new truck designed for the most advanced customer needs.
Perlini Dumpers will continue to produce dump trucks at the historic Perlini headquarters in Gambellara, Vicenza. The current range consists of three models, with 40, 65 and 95 tonnes of loading capacity and powered by two types of engines: for European Union users and for users in countries outside the EU.
The just-launched Perlini RDT features a new Scania Stage V engine and a new Avtec transmission.
The 65-tonne model is due to be officially presented at the next SAMOTER exhibition, scheduled to take place in Verona from 21-25 October 2020.
The RDT hauler is designed to comply with recently introduced regulations on exhaust emissions; the new Scania Stage V engine is designed to meet the most severe requirements in this area, providing low fuel consumption and a high torque.
The haulers also feature an electronic weighing system, GPS locator, control of machine parameters and production monitoring in real time, allowing total control of the truck to provide a significant increase in production efficiency.
Cangialeoni Group says that the systems available on the new Perlini trucks mean it is possible to monitor the vehicle and its load at any time. The new electronic transmission control allows the operator to access data in a more comfortable and intuitive way. The selector display provides information on the transmission, allowing the operator to recognise any alarms and codes and integrates some diagnostic tools.
The GPS system collects a range of vehicle data. This information includes location, distance travelled, switchboard status (on or off), body activation (lifted or low), voltage in volts of the internal battery, primary power (on-off), GPS status (on-off), detection of CAN BUS data (non-invasive connection), environment temperature, detection of aggressive driving (acceleration, braking and sharp curves), remote commands (engine block), alert (alarm setting with notification via web and/or email), alarms (including area entry and exit, power failure, GPS/GPRS signal absence) and maintenance (checking of scheduled deadlines with reminder reception on a km/hour basis).
Komatsu Europe has launched its new HD785-8 Rigid Dump Truck. Built for mining and quarrying applications, the HD785-8 has
a Stage V Komatsu SAA12V140E-7 engine (849kW/1,140hp) and a payload capacity of 92.2 tonnes.
The EU Stage V after-treatment solutions use dual Komatsu diesel particulate filters (KDPF) – most regeneration is performed passively, with no action required from the operator and no interference to machine operation. There is no selective catalytic reduction (SCR), and diesel exhaust fluid (DEF), or AdBlue, is not required.
“The new HD785-8 proposes excellent operator comfort, great travel performance and the well-known Komatsu reliability of the previous model,” said Juuso Ahola, product manager at Komatsu Europe.
Key machine metrics for utilisation, production and machine health can be accessed remotely via the KOMTRAX telematics system or on the machine through the upgraded machine monitor.
The HD785-8 has a seven-speed, fully automatic transmission with two selectable reverse speeds. The Komatsu Advanced Transmission with Optimum Modulation Control System (K-ATOMiCS) is designed to ensure smooth clutch engagement for a comfortable ride and reduced material spillage.
The HD785-8 delivers fast acceleration out of the pit and has excellent travel performance on grade. Wet multiple disc brakes on all wheels provide great downhill brake-retarding performance. With a tight turning radius of 10.1 m the HD785-8 provides exceptional manoeuvrability when waiting to be loaded and positioning to dump. The Komatsu Traction Control System (KTCS) is standard on the HD785-
8. KTCS automatically applies pressure to independent brake assemblies for optimum traction in various ground conditions. Caterpillar has introduced the 725 articulated truck whose features include a ‘nextgeneration’ cab, a powerful engine meeting current emissions standards and automatic features to increase productivity.
The new 24-tonne payload truck is designed to build on the reliability and durability of the 725C2, offering increased performance for customers engaging in heavy and general construction, mining, quarry and aggregates, landfill, waste and industrial applications.
The articulated truck is the first to display the new Cat trade dress and offers improved lighting for easier night work with optional high-level LED, high-intensity lights, LED machine-width position marking lights and access lights on both machine sides.
The 20% larger cab features infrared blocking glass to reduce solar heating inside, while sliding windows increase ventilation and enable communication with the loading tool and workers on the ground. More vents positioned toward the operator with the new automatic climate control (HVAC) system deliver improved heating or cooling efficiency inside the cab.
The new 725 powertrain includes the Cat CX31 six-speed transmission with advanced features designed to deliver smoother shifting, up to 8% greater acceleration and increased speed on grade of as much as 9%. Advanced Automatic Traction Control removes all manual traction control decisions from the operator and automatically changes the differential lock engagement level on-the-go to continuously maintain traction, resulting in improved cycle times, increased productivity and reduced tyre wear. AB
The off-highway machine engines industry is full of innovation, with manufacturers keen to get back to full production following the peak of the COVID-19 pandemic.
Guy Woodford
reports
Cummins is among major off-highway engine manufacturers looking for quarrying and heavy construction equipment demand to return to a healthy level as large parts of the world begin to emerge from COVID-19-triggered lockdown.
The US-headquartered company has continued to produce its wide engine range at a reduced capacity since the near total global introduction of lockdowns in the first quarter of 2020. It includes the production of its quarrying-suited 3.8-12-litre, 75-382kW, EGR- (exhaust gas recirculation) free EU Stage V Performance Series power units.
“In the UK, our Darlington and Daventry factories were producing at around 50% when social distancing and lockdown came in. The plant management teams have done a fantastic job in working out how we can keep employees safe, working at a 2m distance from each other, and keep engines moving through the production line. They also modified shift times, so we didn’t have lots of people entering and leaving site at the same time,” said Steve Nendick, Cummins marketing communications director. Certain customers like Komatsu, DAF Trucks and JCB closed down temporarily, so the number of engines needed was reduced, and we were able to keep other OEMs (original equipment manufacturers) up and running through this tough time.”
Speaking to Aggregates Business in late May 2020, Nendick says the Darlington and Daventry sites are now back up to at least 80% production capacity. “Things are going well in the UK, and our production in China is pretty much at 100%. The Dongfeng Cummins (Xiangyang City, Hubei Province) plant achieved record monthly production in April. In India, everything was shut down by the government, and is now restarting. In the US, most of our plants are back up and running now.
“Now that production is building back up, the next challenge for the industry is around
“They have the ability to efficiently drive more from the engine without the need for additional aftermarket systems”
Steve Nendick
supply chain. Suppliers are struggling or have shut down because of the crisis, and our team are working through the best ways to manage them.”
Cummins says its B6.7 and L9 Performance Series power units will now feature new engine power take-off (PTO) capabilities to support key applications such as crushers, screeners and cranes.
Launched at Hillhead 2018, Cummins’ power units are available from 75–503kW, delivered as a complete and ready-made package. This comprises an engine, exhaust after-treatment system, radiator and cooling system, plus auxiliaries such as mounting feet, hoses and an air cleaner. Crucially, Nendick notes that more than 60% of the content is pre-approved, making the machine integration process simpler and quicker.
“Our Performance Series power units offer a flexible drop-in solution for manufacturers. Because we were able to remove the EGR and push up the power, we’ve got excellent power density, particularly on the 3.8, 4.5 and 6.7-litre models.”
Such high machine capability, stresses Nendick, makes the Performance Series power units well suited to hard-working applications such as crushing, screening and pumping.
Examples of installations to date include the L9 power units powering Anaconda’s new J12 tracked jaw crusher, and I12 tracked
impact crusher. The B6.7 version is available with Bandit in their Intimidator 20XP tree chipper plus NLB Corp’s water-jetting systems.
“When we developed the Stage V Performance Series engines, we dualcertified them to Tier 4 Final for the US. That was one of the real benefits that Anaconda saw. It meant they could take the engine and package and build the same machine, whichever region it was destined for. From a production flexibility and capability perspective, they got a really good solution.”
Nendick explains that to increase the flexibility and capability of the Performance Series power units even further, Cummins is integrating new single and dual rear-engine power take-offs (REPTO). These complement its standard PTO capability used for items such as hydraulic pumps. Cummins is also making these available on the base engines without the pack.
As an example, fitted with the dual REPTO, the L9 will have a total drive capability of 560Nm. This will make the engine capable of driving additional pumping capability through SAE B two and four bolt mounts. Integrated into the flywheel housing, the dual REPTO is compact and has a minimal impact on engine packaging. The added weight is approximately 100kg.
“For equipment manufacturers, they have the ability to efficiently drive more from the engine without the need for additional aftermarket systems. This would support the driving of hydraulic pumps for all sorts of machine functions from steering systems to fans, etc. It will reduce installation costs and complexity for a more integrated solution,” says Nendick. “I think the Performance Series power units plus the addition of REPTO, puts us in the driving seat to increase our business in the crushing and screening sector.”
John Deere Power Systems (JDPS) will begin full production later this year of its new CONEXPO/CON-AGG 2020 exhibitionshowcased JDPS 13.6-litre diesel engine (300kW to 510kW). The engine is said by Martin Ryley, JDPS worldwide business development manager, to be well suited to large crushers involved in quarrying applications.
Peak torque for the new 13.6-litre unit is 3050Nm with a series turbocharger, an 11% increase over previous models. With a single turbo, the peak torque rating is 2510Nm. The new diesel has up to a 6% fluid economy advantage, while heat rejection reduction is over 20%.
The JDPS 13.6-litre engine was built with a “clean-sheet” design, offering new levels of performance, serviceability and integration — all key characteristics for OEM customers. This design process — which now includes a DPF- (diesel particulate filter) free solution for Tier 4 Final variable and constant speed markets, in addition to the dual-certified solution for Tier 4 Final/EU Stage 5 markets — was driven specifically by customer requirements.
“We leveraged and optimised our proven
“If one piece of equipment goes down, the whole production chain goes down, and it becomes very expensive” Martin Ryley
technologies developed over the years to best address market and customer needs in heavy-duty applications. This ensured the final product would deliver increased performance and overall value to our OEM customers and end users,” says David Hoffman, director of worldwide marketing, sales and customer support at JDPS.
JDPS and its distributors are now accepting orders for the 13.6-litre engine.
Speaking to Aggregates Business, Ryley said JDPS is also developing an 18-litre, 500kW-plus engine for large quarry plant. The engine is earmarked to be available at some stage in 2022.
The new 18-litre model will move the top end of the JDPS power range to over 650kW. The engine, which will be JDPS’s biggest ever, will be built at the company’s Engine Works facility in Waterloo, Iowa, US. The launch of the unit will be timed, says Ryley, to coincide with construction and quarrying equipment makers’ product development plans.
Ryley says JDPS engines are ideal for quarrying applications due to their robustness and John Deere-proven high performance and reliability. The company has a wide range of engines for quarry plant, and Ryley stresses that this is an important part of the company’s business. JDPS engines are used in quarrying plant manufactured by a number of major global players such as Terex and Rubble Master. Both variable speed engines for industrial applications such as quarrying crushers and screeners, and constant speed engines for generator driven screeners, are available from JDPS.
Ryley notes that JDPS has consistently used high-quality diesel particulate filters (DPF) to meet off-highway engine emissions regulations as they’ve evolved over the years. The company, he says, is very proud of its record in this area. “We started with DPF in 2011. Not many of our competitors did. We have used that experience in hundreds of applications to make it work in even the most challenging of conditions. We’re very confident in our DPF solutions.
“We also have a strong focus on fluid consumption – optimising the mix of diesel exhaust fluid (DEF/AdBlue) and diesel to get the lowest machine running cost for operators.”
Ryley says that JDPS is looking to bring out an engine predictive maintenance solution/s in the next couple of years. “It’s what’s next – putting more engine data and control over maintenance into customers’ hands. John Deere is already developing predictive maintenance solutions for its machines, and we’ll apply that to our engines.
“Preventing machine breakdown is absolutely vital when it comes to quarrying. If one piece of equipment goes down, the whole production chain goes down, and it becomes very expensive.”
Ryley adds that the firm was also investing heavily in electrification - to meet the growing demand for fully electric and diesel electric drives for quarry and general construction plant and vehicles. “The benefits of electrification are enormous: it creates opportunities for much higher operation efficiency, much higher productivity, lower fuel consumption, and to downsize engines required on some machines.
“For a number of years now, John Deere has had a diesel-electric hybrid wheeled loader [the 944K] on the market. It’s an indication of where we see the market going.”
FPT Industrial, the global powertrain brand of CNH Industrial, has acquired Potenza Technology, a company specialising in the design and development of electric and hybrid powertrain systems.
The March 2020-announced acquisition represents another step in FPT Industrial’s path towards electrification, one of the pillars of its multi-power strategy.
“Sustainable powertrain technology is of increasing global focus and concern. Here at CNH Industrial we are committed to delivering solutions, which not only reduce emissions and enhance productivity but which deliver future-proof technology for the long term,” said Hubertus Mühlhäuser, chief executive officer, CNH Industrial. “This, our latest acquisition, is further testament to this.”
“FPT Industrial is acknowledged as a leader in alternative propulsion systems. The acquisition of Potenza Technology will further enhance our brand’s accelerating development of sustainable electric powertrains across a range of operating segments,” said Annalisa Stupenengo, president Powertrain, CNH Industrial.
Potenza Technology, based in Coventry, England, has been at the forefront of electric powertrain technology since 1999. The company has specific expertise in functional safety, battery management systems for traction battery packs, and electrical and electronic systems design and development.
Major global off-highway machine engines player Perkins has appointed Onnyx as its authorised distributor for Algeria.
A family-owned business, Onnyx has 18
years of experience with Perkins engines as a second-level dealer (DPA) since 2002.
Headquartered in the UK with an operations branch in Algiers, Onnyx has already established a strong 21-person team focused on engine and parts sales and the delivery of 24/7 technical service support to Perkins-powered customers.
“I’m excited to be working with Onnyx, which, through its former role as a secondlevel dealer, has a proven reputation for delivering customer service and quality,” said Jaz Gill, vice president of global sales, marketing, service and parts at Perkins. “I’m
confident this highly experienced team will provide the consistent service our customers in Algeria expect and deserve.”
“This is more than a collaboration,” noted Khaled Terai, country manager at Onnyx. “Becoming a Perkins distributor opens many more opportunities for us. With the best-inclass range of engines, the largest genuine spare parts stock in Algeria, premium product support and the best service team in territory provided by Perkins-certified engineers, we always target excellence to deliver the best customer experience. This is our commitment and promise.” AB
We’re meticulous creators of power components that integrate easily and perform reliably. From inspiration to application, we celebrate the process of bringing your equipment to life. We truly understand the needs of the OEM because we are one. We’ll put our insight and expertise to work to provide a seamless solution for your machine — from the engine and electrification to the drivetrain.
We’re John Deere Power Systems. We’re proud to power you.
Campbell Contracts’ new 120 tonnes per hour CDE wet processing plant
Mineral product producers keen to widen their income streams can find attractive commercial opportunities in recycled aggregate and concrete products. Guy Woodford reports
Campbell Contracts, a familyowned and managed business headquartered in Tempo, a small village on the outskirts of Enniskillen in County Fermanagh, Northern Ireland, claims to have doubled its materials processing ability since commissioning a new CDE wet processing plant. Operating from its Letterbailey Quarry, Campbell Contracts has been extracting sand and gravel for over three decades. In recent years it commenced controlled blasting activities and now counts sand, gravel, crushed rock, rock fill and screened topsoil among its growing product range.
In 2019, the Campbell family partnered with CDE, a leading global market manufacturer of wet processing technologies, to help it grow the business and diversify its portfolio of high-quality quarried aggregates.
For decades Campbell Contracts had utilised a traditional barrel washer, as company director Brendan Campbell explains.
“It was suitable for our business needs at the time it was installed, and it has served us well over its 30 years of service.
“Increasingly, we need to ensure we can recycle and reclaim as much primary aggregate as possible during the quarrying process and the barrel washer had its limitations.”
One of the earliest processes for washing aggregates, the Campbell Contracts barrel washer was efficient when processing cleaner virgin material. Its limitations became evident in its inability to wash heavier, claybound materials, rendering them as waste.
“This material was then backfilled into the pits and buried,” Campbell says. “Similarly, the unwashed primary scalpings we generated were inevitably stockpiled as we didn’t have the technology to efficiently process the material.”
Each stage of the quarrying process produces by-products in the form of overburden, scalpings and crushed rock fines. Often, quarry operators classify these as waste materials without commercial market value.
David Kinloch, regional manager for CDE in the UK & Ireland, says: “CDE engineers state-of-the-art wet processing technologies that offer quarry operators the solutions to enhance the quality of products they currently produce, while simultaneously supporting them to add huge commercial value to their enterprises by ensuring value is extracted from all available material, including those which are too often perceived as quarry waste by-products.”
CDE completed tests at Creagh Concrete on material extracted from the Letterbailey Quarry. Material was analysed, and results used to develop a bespoke wet processing system that responds to the needs of Campbell Contracts and would support the family business to stimulate growth.
“This was an important consideration for us,” emphasises Campbell. “CDE understood our operation and what we wanted to achieve with a new wet processing plant. It’s very much a journey and a partnership with CDE that extends beyond the commissioning phase, with first-class proactive and preventative measures to ensure the plant is operating at maximum efficiency.”
Campbell Contracts’ new 120 tonnes per hour (tph) wet processing plant includes the L35 Feed Hopper, M2500 incorporating the twin-deck P2-75 Infinity Screen and EvoWash, and CDE’s AggMax83, integrating the RotoMax RX80 logwasher and H2-60 Infinity Screen.
The fully integrated, modular plant combines feeding, screening, washing and stockpiling onto one compact and mobile chassis.
With the support of its new CDE plant, Campbell Contracts is successfully processing
LEFT: Campbell Contracts claims to have doubled its materials processing ability since commissioning a new CDE wet processing plant
three materials it previously categorised as waste from its quarrying operations: claybound sand and gravel, primary scalpings and crushed rock fines.
Campbell says it has had a transformative impact on the business.
“We’re recovering high-quality materials and value that we had effectively written off as waste. In retrospect, we should have partnered with CDE to commission the plant sooner.”
Virgin sand and gravel feed material is being processed at a rate of 120 tph producing 0-3mm and 0-6mm sand; 6-12mm, 12-25mm and 25-50mm aggregate; and +50mm oversize aggregate for a wide range of applications in the construction industry.
Kinloch adds: “Campbell Contracts is now processing three grades of material that it historically stockpiled or backfilled. CDE wet processing technology has demonstrated that all quarry by-products have the potential to be processed into marketable products that add significant value to a business.”
Savonlinna is the home of one of Finland’s leading bridge demolition companies, Savonlinnan PR-Urakointi (PR-Urakointi). The firm’s processing of demolition concrete is said to be much more efficient thanks to a recently purchased noise- and dust-proof Metso Lokotrack Urban LT96 jaw crusher.
“The Lokotrack is at least five times more cost-effective than the crushing bucket we previously used. Depending on the feed, the LT96 can crush up to 150–250 tonnes per hour,” says Marko Blinnikka, managing director of PR-Urakointi.
“I must say that the Urban is truly quiet. The sound of crushing does not exceed the sound of the engine, and you can talk right next to the machine without raising your voice. Spraying water at high pressure into the crusher’s cavity and main conveyor prevents dust generation.
“As an additional benefit, the Lokotrack’s magnetic separator removes reinforcing bars from the crushed concrete, so that we can use the clean, crushed concrete for landfilling, often at the same site,” Blinnikka continues.
PR-Urakointi used its new Lokotrack Urban LT96 for the first time at Aholahti in Savonlinna. Approximately 20,000 tonnes of concrete from demolished buildings were piled up in an industrial area. The stockpile contained reinforcing steel bars, some of them only as thick as your little finger.
After a couple of days’ practice, crushing with the new tool was said to be effortless. Tomi Inkinen fed the concrete into the jaw crusher, Aulo Nemevalts immediately levelled out the crushed concrete artificial fill, and Jori Kettunen monitored the machine in operation.
Metso’s IC process control is said to have proven to be an excellent tool when getting to grips with the crushing process. The team was already well familiar with the different on-screen buttons after just a couple of days.
Consisting of pieces of concrete, bricks and fines, the feed was crushed in the jaws of the C96 jaw crusher at a setting of 90mm. The mountains of iron waiting to be recycled were an indication of the vast number of
reinforcing bars contained in the concrete.
The processing of concrete does not require high crusher or diesel engine capacity. Consumption during crushing was around 13 litres of fuel per hour.
Every year, PR-Urakointi performs a large share of all the demolition contracts available in Finland. These also include demolishing buildings.
“It will be interesting to see how the Lokotrack can handle the concrete used in bridges, which is much harder than the concrete used in buildings. In addition to more reinforcing bars, bridge concrete can contain up to 50% natural stone,” says Inkinen from PR-Urakointi.
One bridge may easily contain up to 5,000 tonnes of concrete to be demolished. The Lokotrack enables crushing on-site, which results in savings in transport costs.
“When you’re demolishing a bridge, you must always know what you’re doing. Each bridge is a different story. Sometimes you have to perform the demolition work while cars are using one of the lanes, which is a whole new challenge,” Inkinen says.
PR-Urakointi has also been an industry pioneer in the development of demolition equipment. The company has developed an excavator attachment called the Power Dropper, which can easily crush even the most substantial concrete slabs in bridges without disturbing the environment.
Furthermore, the year before last PR-Urakointi expanded its operations to include the more demanding asbestos stripping.
Based in the northern Italian region of Trentino-Alto Adige, Martintoni has been a Rammit Spa (Rammit) customer for around 20 years. During this time the firm has bought breakers and other equipment from the Italian Rammer hydraulic hammer dealer. In recent years, however, Martintoni is said to have also transformed its material processing and handling operations with an Allu attachment for the screening and processing of soils and recycled materials.
A meeting at the Ecomondo exhibition in Rimini, Italy, in 2018 led directly to Rammit supplying a new Allu Transformer with the revolutionary TS blade structure, with the Allu attachment being fitted to Martintoni’s new Liebherr 556 Xpower wheeled loader. The proposed DS 4-23 TS16-32 model with screening blades was demonstrated working on topsoil and other materials that would usually be sent directly to landfill. However, to provide a more difficult proposition, a demonstration was arranged at Allu’s headquarters in Finland on particularly sticky and ‘difficult’ soil.
The demonstration in Finland went very well, with the representatives from Martintoni also taking the opportunity to visit the Allu factory, and inspect the production process, spare parts facility and inspect the quality of the components used in manufacture. Following a reappraisal of Martintoni’s requirements, it was decided to use an OilQuick hydraulic quick coupler (OQL 310) to hook/unhook the Allu attachment rapidly when the need arose.
Since its delivery and fitting to the loader, the Allu Transformer DS 4-23 TS16-32 is said to have performed well above expectations. It was commissioned for the customer by Allu-trained Rammit technicians and has been used regularly for screening soil from excavations carried out by Martintoni or by third parties.
Most of the excavated material contains a high percentage of roots and branches and other contaminants which the bucket, set with a spacing of 16mm, can screen very effectively. The Allu Transformer tends to work at its maximum capacity of 3.5m³. It is said to be able to achieve the desired daily production of over 1,000m³, processing the sticky material in 20-30 seconds.
Martintoni acquired 15,000m² of land, subsequently used to build a new fixed sand and gravel processing plant to enable the company to supply a broader range of aggregates for general structural construction. In addition to the processing
of aggregates, the company now receives and processes materials emanating from excavations, earthmoving, remediation, pipeline, roads, building construction and landscaping. To work with these materials, the company uses a fleet of trucks, excavators, rollers, wheeled loaders, as well as a new Allu TM Transformer DS 4-23 TS25 to help transform its operation.
Kiverco has bolstered its team with several key appointments to support business growth in the UK and increasing demand for its recycling solutions in Europe and around the world.
Combining more than a quarter of a century of engineering know-how with its popular technology brands, Kiverco designs, manufactures and delivers lasting recycling solutions for any waste stream anywhere - with more than 300 installations in the UK alone.
In recent years, the Northern Irelandheadquartered company has grown significantly as a result of increased demand for its recycling solutions in the UK, combined with considerable international expansion in Europe, the Middle East, North America and Australasia.
New staffers include Con Gallagher, who has become the company’s global head of sales, André Matula, the new key account manager/business development, and
Angela Madden, who has taken up the newly created role of head of marketing & PR.
The company, renowned for its robust static recycling solutions, has also brought to market its modular plant range which is sold through its growing dealer network to meet demand. This range of products can run as single units or when combined, provide an alternative to traditional ways of processing waste. Product benefits include simple set-up within hours, reduced footprints and rapid relocation without the need for cranes, with all the benefits of a high-performance static plant.
Kiverco’s modular range can process municipal solid waste (MSW) as well as construction and demolition (C&D), commercial and industrial (C&I) or dry mixed recyclables (DMR) waste and includes material feed, screening, air, magnetic and manual sorting equipment. AB
BELOW LEFT: A materials recycling plant designed, manufactured and installed by Kiverco for Remondis BELOW RIGHT: Con Gallagher is Kiverco’s new global head of sales
Portable power solutions for quarrying industry customers are getting greener and embracing new technology. Guy Woodford reports
European legislatures began implementing emissions regulations for non-road mobile machinery in late 1997. These regulations apply to prime or standby power used in mobile applications such as drill rigs, wheeled loaders, bulldozers, highway excavators, forklift trucks, aerial lifts, mobile cranes and other non-road equipment including mobile generator sets.
Over time, the regulations have become progressively stricter to reduce further harmful engine exhaust substances, including carbon monoxide, hydrocarbons, particulate matter (PM) and nitrogen oxides. The standards have advanced from the initial Stage I to today’s Stage V, which is also known as EU Regulation 2016/1628.
As the mobile generator set market transitions from EU Stage IIIa to EU Stage V, customers will be challenged to adjust to the new product complexity and increased cost. The additional hardware needed to meet the updated Stage V requirements presents new challenges to the power rental market in Europe. Since the legislation for mobile generator sets skipped Stage IIIb and IV, a big jump in technology is required, including both engine modifications as well as off-engine aftertreatment.
For example, a diesel oxidisation catalyst (DOC) and diesel particulate filter (DPF) are required for all high-pressure fuel system units over 19kW, while selective catalytic reduction (SCR) will be required for all units above 56kW. SCR requires diesel emission fluid (DEF)/Ad-Blue to convert oxides of nitrogen (NOx) to harmless compounds. While AdBlue is a common fluid in
automotive and machine applications, it is an additional item to consider for a power rental operator who may be operating in a remote location.
EU Stage V also extends the scope to a broader range of engine types and sizes, regulating engine outputs higher than 560kW for the first time. This presents engine availability challenges for the large mobile power generation market. In addition to technical issues, commercial challenges exist as rental operators must work to increase rental rates to offset the significant increase in product acquisition costs, and maintain acceptable financial returns. As a result, in the years to come, rental rates will need to increase if rental companies are to maintain their return on investment.
The changes occurring because of EU Stage V, along with newly proposed particle number (PN) limits, effectively require the use of DPF to reduce emissions to compliance levels for engines within the scope of EU Stage V.
“The need for this additional hardware, combined with a significantly greater level of complexity in the engine design, requires a fully integrated solution tested for optimal performance and usability,” said Gareth Osborne, Caterpillar product definition manager for mobile generator sets. “Caterpillar is well-versed in the evolving European emission standards, and we have guided our mobile generator set customers through every phase of these regulations.”
At very high pressures, electric commonrail applications deliver fuel to electronically controlled fuel injectors. This process produces a very fine diesel spray resulting
in minuscule soot particulates which pose potential health risks. While this type of system enables complete control over the combustion process and allows for thermal management of aftertreatment systems, the particulates must be managed to meet emissions regulations. A DPF filtration system is designed to reduce PM, including soot from the exhaust of a diesel engine. A series of alternately blocked channels forces the exhaust gas to flow through the channel walls, where the particulates are captured in the filter.
Many rental generator applications have low load factors or utilise oversized equipment because of limited information on the customer’s load profile, or large starting loads with relatively small running loads. During a low load operation, a DPF will accumulate PM due to low exhaust temperatures if the soot deposit rate is greater than the passive regeneration rate from the hot exhaust gas. The result is increased back pressure on the engine. As back pressure increases, eventually, the particulates must be removed from the DPF through a process known as regeneration.
By handling the regeneration processes internally with intelligent measurement of DPF soot level and on-package thermal management, Caterpillar’s high-speed system works without any interaction from the operator. This allows all rental generator sets fitted with DPF systems to have the flexibility to be used in any application and any environment.
“Caterpillar generator sets achieve this process transparently to the operator, without the need to take the generator
set offline or add load banks and other equipment that increases complexity, cost and weight,” said Osborne. “Through our unique position as both the engine supplier and generator set packager, we can ensure all EU Stage V packages our customers receive are fully integrated and tested for optimal performance and usability.”
To ease that change, however, Caterpillar is following the regulation’s built-in transition structure. This allows companies like Caterpillar to continue to manufacture equipment using the previous emission tier for 18 months after Stage V becomes effective. There is also a six-month allowance for generators to be sold after the 18th month of manufacture. Stage V became effective 1 January 2019 for all engines below 56kW and above 130kW.
For engines in the 56kW to 130kW range, the effective date is 1 January 2020. By increasing their EU Stage IIIA fleet before the legislation takes effect, fleets can maintain lower rental rates for their customers and reduce overheads. In contrast, early adopters of EU Stage V-compliant machines will benefit from a rental business in highly regulated spaces such as large cities. Whichever avenue a fleet chooses, Caterpillar says it can help navigate a strategy to reduce cost and complexities.
Cat Connect technology is available to remotely track and manage generator sets, integrating telematics information into business systems and improving operational efficiency. This technology collects data and reports on asset performance, run hours, fuel consumption, maintenance needs and other statistics. Timely information allows
“We see positive opportunities and growth in this segment”
Jan Moravec
customers to control costs better, improve performance and reduce risks.
Cat Connect technology can be used on generator sets and machines built by Caterpillar as well as equipment that is connected to the generator set, such as external fuel tanks for extended running, transformers or temperature control equipment.
Rental customers have access to remotemonitoring information that ensures generator sets are being utilised correctly and are ready to run when needed. Telematics can send real-time information on fuel level, DEF/ (Ad-Blue) level, battery voltage and status (Run/Stop/Auto). This information can be actioned quickly, before the generator set is called to start, ensuring no issues occur when power is needed. Connected assets are said to ensure peak operation of any emission tier of a generator set but are deemed especially valuable with EU Stage V product.
Speaking to Aggregates Business magazines, Jan Moravec, director of Product Management & Engineering for Doosan Portable Power EMEA (Europe, Middle East, Africa), spoke of where he saw growth opportunities in the global portable power market for quarrying customers. “Despite the existing, and we hope short-term, [COVID19] slowdown of the global economy, and shocks to the oil market, our customers in this segment still have to satisfy continuously increasing demand to support construction projects and higher consumption of minerals needed for new technologies such as battery power. So, we see positive opportunities and growth in this segment as the power provided by our products is required to produce these
materials. Though our machines are rather more ‘back-stage’ units than ‘frontliners’ - compressed air and generator power are still key. And the trend of several quarry and mining equipment OEMs (original equipment manufacturers) to move towards electrification for quarry and mining sites will further increase the demand for reliable sources of electric power.”
Commenting on Doosan Portable Power business priorities for 2020 and the first half of 2021, Moravec said: “We have two main strategic streams – the first is the Stage V transition for the EU market. We
are using this as an opportunity to offer a completely new range of products with proven reliability and durability to serve any tough applications, with a focus on easy operation, serviceability and environmental protection. The second priority is to continuously increase our strong position in emerging markets, utilising the strength of our brand and the global organisation capability we have.”
“All our new products have sealed bunded frames to protect the environment from fluid leaks together with centralised, easily accessible fluid drains which together with easily accessible filters significantly reduce maintenance time and make it an easier task.
“Another of our features is ECOmizer, an automatic intelligent system, reducing fuel consumption by up to 70% during non-productive periods in applications.”
Moravec highlighted how in 2019 Doosan Portable Power introduced several new Stage V products including the company’s smallest 7/20 compressor, new medium- and large-size compressor platforms, the G20 generator and the LS9V lighting tower. He continued: “In the near future we plan to complete our Stage V compressor range, the first being the new 7/125-10/115 medium-size compressor platform which will be followed by a completely redesigned small compressor range. We are also working on new Stage V generators and new products for emerging markets.”
Asked by Aggregates Business how he saw the provision of portable power/ power generation solutions for quarrying customers evolving over the next five to 10 years, Moravec replied: “The business will grow as the development of infrastructure and new technology grows. The power sources need to complete work will still be required, especially the availability of electrical power when it is needed.
“As emissions will continue to be a very important topic, I believe there will be continued alignment between emission regulations in the different markets we deal with. This will drive more new technologies and new product development as the markets continue to grow, with the focus on lower emissions, new energy sources and digitalisation.” AB
Being able to quickly access and install high-performing replacement wear parts on quarrying plant minimises downtime leading to enhanced worksite efficiency.
Guy Woodford reports on some of the latest premium wear part options
Aproducer of high-quality crushers since 1896, Swedish quarrying plant manufacturer Sandvik says it has always taken great pride in its innovation and developing products which will improve its customers’ bottom line.
The company’s crushing chambers are based on quality products said to be built with superior finish and supported by in-depth knowledge of every aspect of the crushing process. “It is through this knowledge and expertise that we are able to understand the demands of our customers and develop high-performance wear parts, to ensure the reliable and smooth operation of Sandvik equipment throughout its entire lifecycle,” says Andrew Bolton, product line manager Tracked Mobiles, Sandvik Mobile Crushers and Screens.
for Sandvik mobile jaw crushers. These have been designed to simplify customer service and increase maintenance efficiency. The tailor-made Optitooth kits are designed around the natural usage of the wear parts and offer all components a customer needs with just a single part number.
Following the successful launch of Sandvik Optitooth jaw plates, Sandvik Mobile Crushers and Screens has now created a number of ready-to-order maintenance kits
Key customer benefits are said to include easier and faster means of ordering replacement parts in one simple transaction; greater parts availability – so customers avoid delays or parts shortages with the delivery of all components in one shipment; less downtime - with wear parts replaced in just one service interval; and improved profitability - as enhanced maintenance
efficiency will, ultimately, boost customers’ bottom lines.
Sandvik Optitooth kits come in three different offerings. Optitooth Fixed Kit includes a fixed Optitooth jaw plate and lower cheek plates. Optitooth Swing Kit features a swing Optitooth jaw plate and lower cheek plates. And Optitooth Kit comprises one fixed and one swing Optitooth jaw plate along with upper and lower cheek plates.
All the necessary components are supplied with the kit to keep a customer’s crushing chamber operating at optimal performance.
“The new profile of jaw plate was designed for a higher percentage of the jaw to be utilised resulting in longer wear life and less manganese waste,” says Bolton. “The backing plate was redesigned to make it easier for removal, thereby reducing maintenance time and ultimately downtime, saving time as well as money.
“The improved profile also brings with it a number of additional benefits which all contribute to improved product shape. The unique profile was designed around the production of a more cubical material and reduction of elongated slab material which can cause blocking issues for secondary cone crushers.”
Sandvik says customer feedback on the Optitooth kits has been extremely positive. Average jaw crusher output is said to have increased from 200 to 250 tonnes per hour and wear rates increased upwards of 30% (the test results should not be treated as specifications and Sandvik does not guarantee, warrant or represent the outcome of test results in any or all circumstances).
LEFT: Metso’s Rotable Top Shells for Superior gyratory crushers are complete shell segments relined in advance (either on- or off-site) and ready to be installed
In addition to the increased wear performance, customers are also said to have seen benefits in relation to fuel economy — the improved transfer of material results in lower engine loading with faster material passage through the crushing chamber. Sandvik says results have proven savings of up to 15% less fuel (see above Sandvik comment on test results).
The improved design of the Optitooth jaw plate is said to allow for better breakage and improved material flow, resulting in a more cubical and higher quality product shape. The design is also said to make the plates easier to turn over or replace, saving customers time and money.
All of the above, says Sandvik, results in increased jaw crusher efficiency and higher productivity by up to 20% (see above Sandvik comment on test results).
Scottish quarrying customer G.F. Job is among those benefiting from the use of Sandvik Optitooth jaw plates. “They benefit us all round: we are crushing far more, getting better fuel economy, producing a better product and they last an awful lot longer,” says Graeme Watt, the company’s operations manager.
The Optitooth jaw plate has proved suitable for a wide range of applications, particularly abrasive quarry rock. It is fitted to all Sandvik Q-Range mobile jaw crushers as standard.
Sandvik always recommends using genuine spares and wear parts to ensure reliability and optimal performance of customers’ mobile equipment.
Metso’s Rotable Top Shell for all sizes of the company’s Superior primary gyratory crusher reduces crusher downtime thanks to speedier change-outs while, at the same time, increasing safety.
Most Rotable Top Shell-related work is completed out of the line of fire. There is a large reduction in risk as more tasks are done in a controlled environment, and the actual relining process can even take place off-site. During the time-sensitive changeout period, there are fewer parts to lift and manipulate. The solution includes hydraulic shell separators which also help to minimise human intervention.
By using the Rotable Top Shell’s additional shell segment(s), which are already inspected and lined prior to a shutdown, Metso claims a customer can save up to 45% in downtime for their primary gyratory crusher. This is exceptionally relevant to larger aggregates plant which are operating close to 24/7. However, this is also beneficial for plant which are not operating around the clock. As with this shorter window needed for shutdowns, most aggregates producers can fit the change-out in fewer shifts. Downtime can also be more easily scheduled either off-shift or during the off-season.
In addition to shorter shutdown, less manpower is needed for the complete Rotable Top Shell change-out process. This is said to provide added flexibility for operators who now have multiple options
for relining which won’t affect operations. Producers have the choice to do the reline work themselves, on- or off-site, or with a 3rd party, again on- or off-site.
With a streamlined process, being mostly implemented outside of the critical shutdown path, costs are more predictable, making it easier to plan and manage budgets. Additionally, some traditional cost elements can be minimised further, such as crane rentals, which are typically rented/brought in specifically for relines.
The Metso Rotable Top Shell is a new concept/solution which has been introduced slowly over the last few years as a “complete” customer solution. Four mine sites are currently operating with it now, and a handful is said to be in the final consideration steps.
“This has not yet been formally introduced to the aggregates industry; however, the benefits and process are nearly identical to mining” Terry Galvin
BELOW: A Metso Rotable Top Shell in action – ready to be installed during a planned shutdown at a Boral Australia gold and copper mine.
“This has not yet been formally introduced to the aggregates industry; however, the benefits and process are nearly identical to mining. With hundreds of Superior primary gyratory crushers currently in operation in aggregates industries around the world, this solution has great potential,” says Terry Galvin, Metso business development manager.
The Rotable Top Shell offers the most benefits to producers with a high wear rate on their primary gyratory crusher, where change-outs are happening regularly, i.e., hard and abrasive material, such as granite. Producers who operate a site close to an around-the-clock operation, have a lean maintenance staff, and have an older machine that they are currently considering for shell repairs will also, says Galvin, benefit greatly from using the Rotable Top Shell.
Additionally, given the smaller sized primary gyratory crushers present in the aggregates industry, the Rotable Top Shell can be a very affordable solution for sustaining capital.
“While there may be some suppliers offering additional shell segments in certain markets – as of today, we are the only OEM [original equipment manufacturer] with a complete solution for this – that we know of. We can offer end-to-end solutions (liners, installation, inspection programs, financing, online monitoring, etc.) – technical and commercial to fit individual producer’s operating budget,” Galvin added.
“We are currently evaluating and developing multiple complementary solutions. This includes applying our technology to other OEM primary gyratories, as part of our Metso Contender Series. This series of premium parts and solutions is specifically designed for non-Metso equipment in order to simplify the buying process for our customers.
“We are looking at supplying complementary products to make primary gyratory crusher shutdowns even safer and more efficient. This includes products such as fastening techniques, rigging techniques, and auxiliary components. We are also considering formalising similar concepts for our other crushing products, such as GP cone crushers.”
Inspired by key pain points Weir Minerals’ field staff observed across a range of mines and quarries, the company’s expert engineers have developed Linard modular anti-abrasion panels. The panels are said to provide a cost-effective and convenient solution for reducing downtime caused by high impact and abrasive wear in chutes and other applications in quarries and mines.
Available in 30mm and 50mm thickness, Linard modular anti-abrasion panels are ideally suited to minimising wear and maintenance in localised impact and wear points. The outstanding wear life is due to the wear material: Linard HD60 rubber in a rigid self-sealing construction with steel backing. The optional composite ceramic (92% alumina) or high-chromium white iron
inserts add to the claimed extraordinary wear life of the panels.
“Our new Linard panels have been designed from the ground up to last in some of the most arduous wear applications. Depending on the customer’s needs, we offer composite panels with either ceramic or high chromium white iron inserts. They combine with our Linard HD60 rubber compound to deliver world-class impact and abrasion resistance in chutes, hoppers and under-pans,” says Mark Doyle, global product manager – Rubber, Spool and Hose for Weir Minerals.
Linard modular anti-abrasion panels are said by Weir Minerals to have improved wear life by ten times after replacing a competitor’s teflon wear panels in chutes across two quarries run by Boral Australia. This is said to have saved more than AU$12,000 per annum (US$7,950) in direct costs and led to a significant uptime increase due to a 90% reduction in shutdowns.
The 300mm² panels interlock to facilitate quick and easy installation and replacement while reducing the potential for fine material to ingress between the panels. Linard modular anti-abrasion panels are supplied in a convenient kit including a range of holddown plugs. They can supply drawn arc studs which were needed to provide a convenient off-the-shelf but customisable solution to the application.
“Our engineers can replace these panels in minutes, reducing the amount of time they need to spend in chutes and other confined spaces. They are a bolt-in/bolt out solution and being modular they’re easy to fit onto any flat surface that requires extra protection. This also makes it easy to swap around composite and standard panels to ensure the highest wear areas are the best protected,” says Paul Duthy, Wear Solutions product manager, Weir Minerals.
Haver & Boecker Niagara is guaranteeing customers’ inventory through Make & Hold and Stocking Agreement programmes for screen media and wear parts. The programmes help mineral processing
customers plan ahead and minimise downtime from long lead times while also providing options for pricing stability and simplified inventory management.
“We want to help ensure our customers have the screen media and parts they need to keep their equipment running and maximise production,” said Karen Thompson, president of Haver & Boecker Niagara’s North American and Australian operations. “That is why we provide Make & Hold and Stocking Agreements to help operations with inventory management and provide peace of mind.”
The Make & Hold programme guarantees customers the screen media and/or wear parts they require, and pricing is agreed upon at the beginning of the programme. Items are reviewed annually, and adjustments are made as needed. The manufacturer produces and packages the product in pre-determined quantities so it can be shipped the same day the order is placed. Stock is automatically replenished after shipment in preparation for the next time the customer requires it. The programme gives customers immediate access to items that would normally require longer lead times. Pricing is locked in, and the customer is only invoiced when the product ships.
Haver & Boecker Niagara also offers Stocking Agreements — or blanket orders — for customers interested in a one-time annual agreement. The pricing is locked in for the calendar year upon agreement for a pre-determined quantity of product. Customers pay per shipment as they draw from their stock as needed throughout the year. The product is shipped the same day the order is placed.
Both programmes are said to be an opportunity for operations to ensure product availability and price stability throughout the year and are particularly beneficial for products that may otherwise have extended lead times. AB
Aggregates demand and production in Ukraine is in robust health despite the disruption caused by the COVID-19 pandemic. Eugene Gerden reports
The volume of aggregates production in Ukraine is steadily growing despite the ongoing spread of the coronavirus (COVID-19) in the country harming the national economy, according to recent statements by representatives of local producers and industry analysts.
As in the past, the most significant growth in production is in crushed stone –the industry’s main export and traditionally highest output product.
The majority of Ukraine’s crushed stone output has historically been for export customers. However, in recent years, Russia, which takes 90% of all Ukraine’s exported crushed stone, has introduced a licensing process for all crushed stone supplied from the country. This has led to a dramatic reduction in exports of Ukrainian crushed stone - from 20.2 million tonnes in 2014 to 2-3 million tonnes annually in the last few years.
In December 2020, due to ongoing tensions between Ukraine and Russia, the Russian authorities imposed a package of sanctions against Ukrainian goods. However, they made an exception for some crushed hard rock stone from Ukraine. As a result, last year permission was granted by the Russian government for Ukraine to supply 1.7 million tonnes of this aggregates material to Russian customers.
crushed stone exports to Russia, the Ukrainian aggregates sector has not stagnated, as the volume of domestic demand and production continues to grow.
According to data collated by Pro-Consulting, one of Ukraine’s leading aggregates business market analysts, the production of Ukrainian aggregates has been steadily growing since 2015. Pro-Consulting
says this is mainly due to the recovery of the country’s national economy following the crisis and its consequences and the growth of demand for crushed stone from prominent local consuming industries.
According to Pro-Consulting data, in 2020 the production of crushed stone in Ukraine amounted to 81.9 million tonnes, which is 9.2% more than in 2014. While official results for 2019 are still to be published, Ukrainian analysts believe aggregates production levels will be akin to recent year volumes.
Despite the significant reduction of
Analysts also predict the end of the coronavirus pandemic will act as a catalyst for the rapid development of the Ukrainian aggregates industry. Swift aggregates sector growth will lead to an increase in the number of companies operating in the marketplace, continuing an already notable trend over
In contrast to the past, when the bulk of aggregates businesses were small- to medium-sized enterprises, large Ukrainian firms are now focusing on the industry’s commercial potential. For example, TAS Group, one of Ukraine’s most significant financial groups, owned by billionaire Sergey Tigipko, plans to accelerate the development of its dimensional stone quarry, located in the Zhytomyr region in western Ukraine, a traditional hotbed of national aggregates production. In addition to Zhytomyr, large aggregates quarries can also be found in Vinnytsia and Volyn.
Existing aggregates producers have also announced plans for the modernisation of their business, mainly via the installation of new latest technology-based equipment at their production sites. This will allow producers to improve the quality of their final products.
Pro-Consulting notes that Ukrainian aggregates sector development will also benefit from the growth of the domestic construction industry. In recent years, there has been a notable increase in the amount of new residential housing built in some of Ukraine’s largest regions, including Kiev, Lviv and Odessa.
Pro-Consulting also offers an element of caution by stating that much of Ukraine’s aggregates sector growth hinges on the delivery of large infrastructure projects in and around Kiev and the western regions of Zhytomyr, Poltava and Rivne. At the time of writing, these projects were facing considerable disruption due to the COVID-19 pandemic.
Due to sufficient reserves, Ukraine has been able to export its aggregates and sell them at very competitive prices (from UAH 120 to UAH 220 (€4.03-€7.40) per tonne). The national government plans to increase exports of aggregates, to countries including Poland, in the years to come.
Belarus will continue to be used by Ukrainian crushed stone exporters as a transit point for the supplies of their products further east, to Russia.
In recent years, Ukrainian producers have significantly increased exports of their aggregates to Russia via Belarus, allowing them to avoid existing licensing barriers imposed against them by the Russian government. Belarus is a member of the Customs Union of Russia, Kazakhstan, Armenia and Kyrgystan.
According to various sources, supplying their aggregates to Russia through Belarus
has allowed Ukrainian crushed stone exporters to increase their supplies to the Russian market by up to 10 million tonnes per year. Ukrainian crushed stone supplied to Russia via Belarus has been used in largescale Russian infrastructure projects, such as the building of the 19km-long Crimean road and rail bridge.
Worryingly, the Russian state is looking to restrict the import of Ukrainian aggregates via Belarus and is considering, among several options, the introduction of quotas on the further supplies of crushed stone from Belarus. The Russian Federal Customs Service is advising the Russian government that the future volume of aggregates supplied
via Belarus should be based only on Russian aggregate need.
Analysts believe Ukraine’s roadbuilding sector will be another growth driver for the Ukrainian aggregates industry. The recently created State Road Fund has already begun allocating funds for the construction and reconstruction of roads throughout Ukraine.
According to recent statements by the Ukrainian Ministry of Infrastructure, a state agency responsible for roadbuilding development, UAH 70bn (€2.361bn) will be accumulated annually in the road fund between 2020 and 2022. Such a figure is welcome news to Ukraine’s growth-hungry aggregates sector. AB
Our new Excellence Line hammers are now equipped with the first ever monitoring system for hydraulic hammers – RD3. This system gives you detailed information about the operating hours, service intervals and GPS location of your product. You can see all the data you need by logging into the My Fleet platform. RD3 improves your fleet management, makes your processes more efficient and improves your profitability. For more information visit rammer.com/excellence or contact your local Rammer dealer. @rammerhammer @rammerhammer
Sandvik Mining and Construction Oy / Lahti, Finland / rammer@sandvik.com / www.rammer.com
A production bottleneck has been eliminated at Wilhelm Jost’s diabase quarry in Altenkirchen, Germany, through Metso’s SiteBooster solution
The modernisation of a German quarry’s high-grade chippings operation was a typical Metso SiteBooster plant optimisation project. Guy Woodford reports
Wilhelm Jost GmbH & Co. KG’s (Wilhelm Jost) diabase quarry in Altenkirchen, Germany, wanted to increase the percentage of high-grade chippings that the quarry produced. The aim was to expand the capacity to produce the more popular and higher demand fractions while remaining flexible to meet future requirements. With this in mind, the business turned to Metso Germany, which recommended Metso’s SiteBooster plant optimisation solution. Although the existing plant needed significant modifications, the planning and installation phase of the Metso SiteBooster project went smoothly. The conversion completed within the prescribed time frame of eight weeks, including commissioning.
Wilhelm Jost can look back on a long history. Everything started with a paving operation, more than a century ago. Today, Werner and Bernd Jost operate a well-run road construction company that has been in the family for multiple generations. Their diabase quarry, which Wilhelm Jost acquired in the 1970s, is based in Altenkirchen, a town in Rhineland-Palatinate, 40km east of Bonn. They have also run an asphalt mixing plant a few kilometres away, in BraunfelsPhilippstein, since the 1960s.
The Altenkirchen-based quarry
(Diabaswerk Altenkirchen) primarily supplies three asphalt mixing plants (including its own) and three concrete mixing plants with the production of high-grade aggregates. Other materials are sold as a mixture to nearby clients, with some also serving their internal demand. Metso is a turnkey supplier for the quarry, supplying the screening solution as well as the crushing equipment (LC145, Nordberg HP3 cone crusher, Nordberg HP100 cone crusher Modular and Lokotrack LT1213S) and related wear and spare parts.
Renewing the existing plant and solving a production bottleneck
As early as 2016, Wilhelm Jost’s management was considering two options: construct an entirely new building or gradually renew the existing production plant at the Diabaswerk Altenkirchen over time. Large parts of the plant had been in operation since 1994 and were at the end of their economic life. Because of an impending loss of production and the limited space available, a gradual and partial renewal of the old plant was
considered the best option. So, in 2018, together with Metso Germany, project planning got underway.
In addition to renewing machines, another goal was to eliminate a problematic bottleneck in Diabaswerk Altenkirchen’s high-grade chippings production to be able to expand the capacity of the high-demand 5-8, 8-11, 11-16 and 16-22mm fractions.
“We are convinced that in the future the market will require even greater quantities
of high-quality aggregates,” explains managing director Bernd Jost.
In 2018, Metso won the contract for the detailed planning and realisation of the project to convert and modernise the quarry’s fine-chippings production. The contract included the planning, delivery and assembly of three screening machines, the supply of media and a vertical impact crusher (VSI).
The existing steel construction for the
high-grade chippings plant had to remain untouched as much as possible. The project kicked off with the installation of two new bucket elevators, which were renewed by Wilhelm Jost on its initiative. Metso supplied a new chute and the steelwork reinforcements needed for the conversion.
With limited space available, the capacity expansion of the high-grade chippings plant could only be achieved with machines from the broad Metso portfolio, which
"THE SUPPORT FROM RAPID HAS BEEN EXCELLENT, INCLUDING SETUP AND OPERATOR TRAINING.”
CUSTOMER TESTIMONIAL
“We are convinced that in the future the market will require even greater quantities of high-quality aggregates”
Bernd Jost, managing director
corresponded exactly to the required dimensions. Also, the statics for all system components had to be recalculated and partially revised.
secondary
The first replacement machine was a single-deck screening plant, which mainly screens antifreeze material from the 0-150 mm feed material. The underflow from this screening stage goes to stock for sales or passes through a Metso HP100 secondary crusher into the high-grade chippings production. The oversize passes through the third and fourth crushing step into the Edelsplitt screening. The Metso ES203, a three-deck elliptical screen, was installed as the replacement machine for the processing of the material in the Edelsplitt screening.
The screen divides the material into three fractions (8, 22 and 32mm) over the 9m² of screen decks. Wire cloth is used in the lower deck, and the upper decks utilise Trellex LS RU rubber screen panels. The time spent on maintenance has decreased with the Trellex rubber screen panels because replacements are quick to do.
Like the other screening machines, the more than 10-tonne ES203 had to be lifted through the roof at a 25-metre height
and positioned precisely. Wilhelm Jost chose the new ES screen because, at the given throughput, it manages the job with the smallest screening surface and thus works most effectively.
In the tertiary screening stage, a Metso CVB202 screen classifies the 8-11, 11-16 and 16-22mm chippings fractions. This two-deck screening machine has a screening surface similar to the ES203 and is also equipped with the Trellex LS RU rubber screen panels as well as with wire mesh on the last metre.
More powerful Barmac vertical impact crusher solves production bottleneck
To achieve the planned increase in high-grade chippings production capacity at Diabaswerk Altenkirchen, Wilhelm Jost needed to find a more powerful vertical impact crusher –in addition to the use of more productive screening machines. The choice fell to the Barmac B7150SE vertical shaft impact crusher, which can process up to 545 tonnes/hour, depending on settings and feed material.
The Barmac now takes over in the quaternary crushing stage and with its high performance eliminates the bottleneck that previously existed. Using the Metso HP3 cone crusher in the tertiary stage, the over 45mm material is first broken down to 0-32mm and then processed further in the new Barmac.
Another major challenge was the adaptation of the new material drains, chutes and screen trays to the existing chutes and conveyor belts. The engineering and assembly team also solved this task.
The more powerful machines are transferring much higher loads onto the current steel construction. The new Metso ES203 elliptical screening machine could, therefore, only be commissioned after the installation of structural reinforcements. The weight of this screening machine alone is already double that of its predecessor.
Professional preparation and flawless static calculations allowed all of the machines to be installed correctly from the start.
During the renewal phase of the project and to keep production running smoothly, the company used another LT1213S mobile impact crusher and two mobile screening plants rented from Metso’s distributor Fischer-Jung, in addition to its machines.
Appraising the overall project, Bernd Jost said: “Apart from the adaptation of individual screen panels and settings of the material flows in the Barmac, which is completely normal, there were no unpleasant surprises.” AB
The Sparcric G solution is designed to make conveyor maintenance quicker and safer
New hydraulic breaker range from Hitachi Hitachi has introduced a range of new high-performance hydraulic breakers for use with its full line-up of ZX excavators from ZX10 up to ZX890.
The company says the new breakers are lightweight but very durable, with increased impact energy due to a nitrogen-charged back head that enables energy transfer to where it is most required.
The slim design of the breaker is intended to enable easy accessibility in demolition and trench work while providing high levels of efficiency and productivity in quarrying applications. The top damper is designed to reduce noise and vibration, leading to a less intrusive and more environmentally friendly job site while reducing operator fatigue and machine wear and tear.
The serviceable floating rod seal minimises dust intake, which Hitachi says results in an extended lifetime.
The mono-block cylinder with a replaceable cylinder liner has been developed to reduce the number of parts in the attachment. The front head design includes a replaceable thrust bushing for extended service life, and auto lube is fitted as standard on model FXJ125 onwards.
www.hitachicm.eu
R Brunone has developed the new Sparcric G maintenance solution for replacing conveyor belt rollers.
The French bulk handling solutions company says the device can be installed on any conveyor and enables replacement to be safely carried out by one operator rather than the two that are normally required.
The operator uses a hand pump to operate the tool lifting the conveyor belt. Once the Sparcric device has been fitted, both their hands are completely free, allowing the rollers to be replaced.
R Brunone says that operators often use tools that are not suitable for replacing conveyor rollers such as bars, forklifts or hoists. It adds that this increases the risk of injuries from a sliding bar or falling rollers.
The company claims that using the Sparcric G solution can reduce the average time spent on
maintenance operations by 50% and is less physically onerous for operators. It is now available worldwide.
It is available for four belt widths: 500-800mm, 1,000-1,200mm, 1,400-1,600mm and 1,8002,000mm. It can be operated with a manual pump delivered with the solution, with an electrical pump as an option or with compressed air if available on the site.
“This patented innovation is the result of 25 years of experience and development of innovative solutions in the bulk handling industry in close collaboration with customers,” the company states. It adds that its goal is to improve safety and performance in bulk handling in quarries, mines and ports in addition to industries such as steel, paper mills and power plants.
www.brunone.fr
Equipment manufacturer Liebherr and electric mobility company Designwerk have combined to develop fully electric truck concrete mixers with 10m³ and 12m³ drums on a 5-axle chassis.
The companies say the move is designed to reduce the carbon footprint of the global concrete supply sector.
Liebherr adds that the ETM 1005 and 1205 truck mixers transport large quantities of concrete to the construction site quietly and reliably without exhaust emissions. Charging is normally only necessary at night due to the large accumulator capacities.
According to Liebherr, the Futuricum chassis can cope with the weight of the concrete quite easily, and there is an energy recovery system in place so that braking further increases the
range of the truck and reduces operating and maintenance costs.
Liebherr and ZF developed a drum drive consisting of a lowmaintenance unit and efficient unit of electric motor and gearbox. The truck and the truck mixer body are powered jointly by the traction battery, which helps to remove the need for power electronics components.
The compact electric drive for the mixing drum is flanged directly to the drum and is designed to ensure that power
consumption for relieving the traction battery of the Futuricum truck remains low.
Liebherr claims it also eliminates the need for hydraulic components such as hose connections and pumps.
The first units to go into operation will work for Liebherr customers Holcim and KIBAG in Switzerland.
www.liebherr.com
INMALO,
dberg HP900 egates and mining
Metso is rolling out the new Nordberg HP900 Series cone crusher for the aggregates and mining markets.
The Finnish quarrying plant maker, which has installed more than 10,000 HP cone crushers world wide since 1989, says the HP900 is built to enable increased performance and reduced CAPEX (capital expenditure).
maker, which has one crushers worldis built to enable ced CAPEX
The HP900 is an upgrade on Metso’s HP800 cone crusher
he HP800 cone nstallations, with
The HP900 is an upgrade to the HP800 cone crusher that has more than 175 installations, with approximately 80% of the parts being compatible between the two technologies.
The HP900 features improved kinematics, a raised pivot point and a power increase which provides 15% more capacity. A new lubrication system is included to help support the improved performance level.
“With the HP900 we go straight to the point, with increased performance and reduced CAPEX,” said Jim Bathie, VP, mining crushers at Metso.
d kinematics, a ncrease which ew lubrication rt the improved ht cedCAPEX ” said minimisingproductionstoppagesandprotecting
The HP900 is delivered pre-assembled, prewired and factory tested. The equipment is packaged with a rubber-pad mounted subframe and guards allowing quick and safe set-up with a compact footprint. These factors result in reducing installation time by 50%.
Metso says that the tramp-release system means that the new crusher allows passage of tramp iron,
R700S
minimising production stoppages and protecting internal components.
Top service access to the head, shaft, eccentric and other major components are intended to make disassembly safe and easy.
The crusher is equipped with Metso’s IC70C automation system, which is designed to ensure optimum operating parameters enabling full potential.
www.metso.com
Following Rockster’s move to a larger facility in mid-2019, the Austrian manufacturer has now begun serial production of its R700S impact crusher at the new location. The company says that the move from the previous Ennsdorf site to Neumarkt im Mühlkreis has enabled consistent quality control, better control of delivery times and expansion of production capacity. The R1000S impact crusher is already being produced at the new location.
With a total weight of 19.6 tonnes and a length of 9 metres, the R700S is the most compact system in the Rockster portfolio. In the course of the new production, the control system for the R700S crusher has been revised, and a quick start function has been introduced, said Rockster CEO Wolfgang Kormann. “This enables the system to be engaged and running by pressing just two buttons on the remote control,” he added.
The new material feedmonitoring system guarantees the best possible utilisation of the crusher and contributes to an increase in performance of up to 25%. The overload protection in the crushing chamber also ensures safety against blockages and thus reduces downtime. The new R700S is also equipped with the latest Stage V engine generation from Volvo Penta with 220PS. www.rockster.at
INMALO, a supplier of hydraulic excavator attachments in the United Kingdom, has signed a cooperation agreement with Steelwrist for the supply of fully automatic couplers and attachment interfaces.
agreemen of attac
The two companies say that the demand for fully automatic coupler systems has experienced significant growth for some time, especially within the UK demolition industry.
INMALO has many years’ experience supplying hydraulic demolition equipment and will now be offering the range of quick couplers and attachment adaptors from the Steelwrist SQ product line.
The tw demand f systems h fo within the INMA experienc demolitio now be off a from the S
INMALO is now offering Steelwrist’s automatic coupler systems for excavators
The Steelwrist SQ system is suitable for all types of excavators. The company’s quick couplers incorporate safety features such as Front Pin Lock and a robust steel cast design.
“INMALO’s focus on high-quality demolition attachments, fast support and service to the customers is a good platform for success,” said Steelwrist CEO Stefan Stockhaus. “We see rapid growth for our fully automatic coupler systems on all our markets and have for some time been working within ECY Haulmark.”
The agreement includes the possibility for INMALO to offer the SQ fully automatic interface for demolition tools and Steelwrist SQ quick couplers for the excavators.
www.steelwrist.com
8-11 bauma CTT Russia
Moscow, Russia
Organiser: Messe Muenchen Rus Tel: +49 (0)89 949 20251 info@bauma-ctt.ru https://bauma-ctt.ru/
16-18 Construction Indonesia
Jakarta, Indonesia
Organiser: PT. Pamerindo Indonesia
Tel: +49 3999905 0 contact@merebo.com https://ci.merebo.com/
16-18 Concrete Show South East Asia
Jakarta, Indonesia
Organiser: PT. Pamerindo Indonesia
Tel: +49 3999905 0 contact@merebo.com https://cssea.merebo.com/
21-25 SaMoTer 2020
Verona, Italy
Organiser: Veronafiere S.p.A. Tel: +39 045 8298561 customercare@samoter.com http://www.samoter.it/
03-06 bauma Conexpo
India 2020
Gurugram/ New Delhi, India
Organiser: AEM and Messe München
Tel: +49 89 949 20251 info@bcindia.com https://www.bcindia.com/en/
24-27 bauma China 2020 Shanghai, China
Organiser: Messe München Tel: +49 89 949 20252 info@bauma-china.com https://www.bauma-china.com/
14-17 steinexpo 2021 Homberg/Nieder-Ofleiden, Germany
Organiser: GEOPLAN GMBH
Tel: +49 7229 606 30 info@geoplangmbh.de https://www.steinexpo.eu/
22-24 Hillhead
Hillhead Quarry, Buxton, Derbyshire, England
Organiser: The QMJ Group
Tel: +44 (0)115 945 4377
Email: Harvey.sugden@qmj.co.uk https://www.hillhead.com/
07-10 EIG 2021
Exeter, UK
Organiser: EIG Conferences marcus.dorey@hanson.biz https://www.eigconferences.com/ future-conference-2020
13-16 bauma CONEXPO AFRICA 2021
Johannesburg, South Africa
Organiser: AEM and Messe München GmbH
Tel: +49 89 949 21480 johannes.manger@messemuenchen.de https://www.bcafrica.com/
MEET THE TEAM
Aggregates Business travels the globe attending conferences, events and equipment shows, keeping you informed of the latest offerings. Come and join us for a chat at any of the events below.
JUNE 2021
22-24 Hillhead 2020
Hillhead Quarry, Buxton, Derbyshire, England
JULY 2021
07-10 EIG 2021 Exeter, UK
These dates were correct at the time of going to press, but please note that the COVID-19 pandemic means some events may be rescheduled with little advance notice
Every minute your primary gyratory is shut down, your bottom line is impacted. Relining a crusher can be a lengthy and complex process, which must be closely managed. Metso Rotable Top Shell enables you to save both time and money - when it matters most.
A simple solution with major impact - using additional shell segment(s), which are already inspected and lined prior to your shutdown, makes for faster, safer, and more economical wear parts replacement.
• Reduce downtime by up to 45%
• Minimize high risk maintenance work
• Optimize shutdown tasks Learn more at